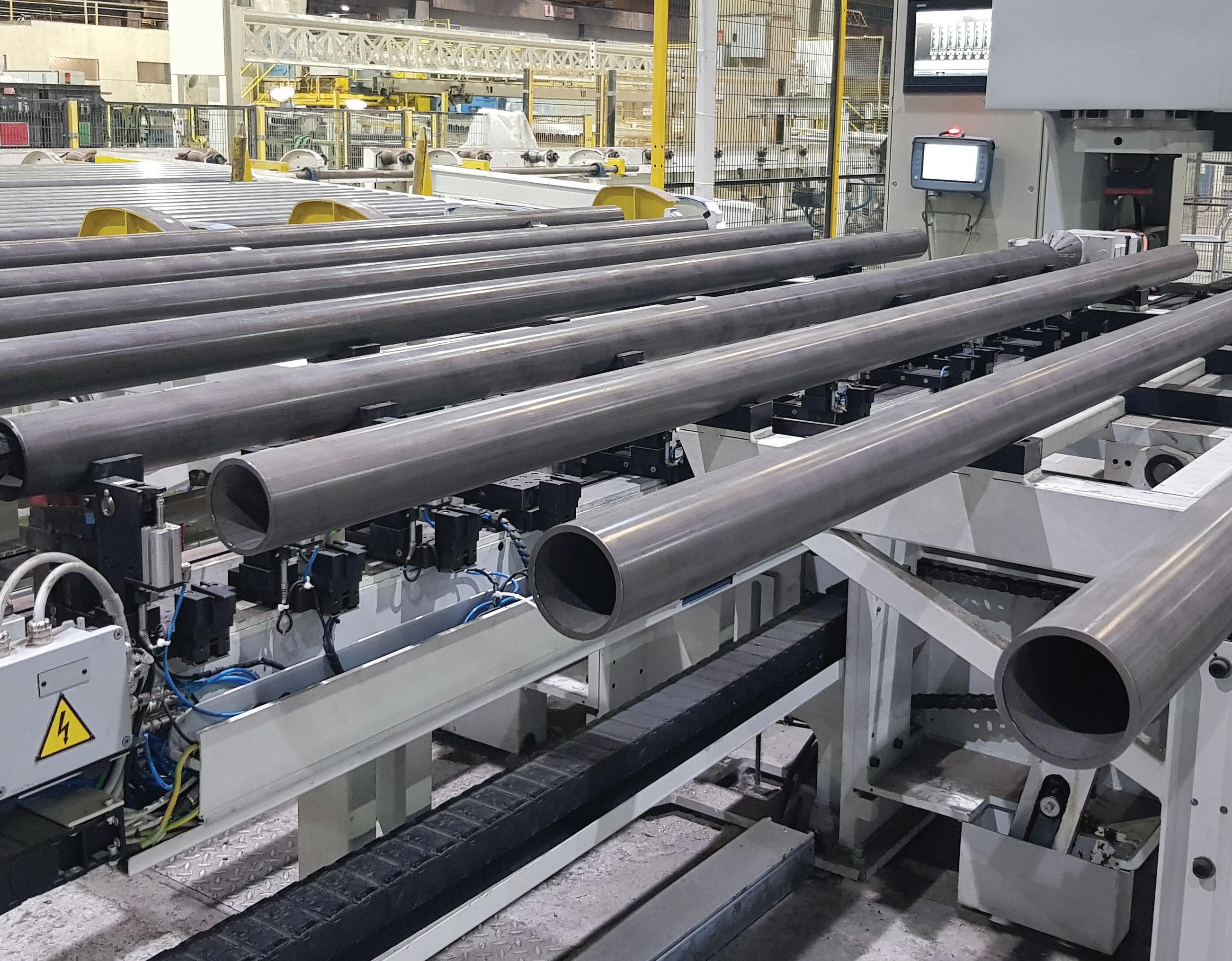
6 minute read
Steel-made precision tubes for drill rods
by Steffen Zimmermann, Head of Technical Sales/Application Engineering; Sebastian Schulze, Application Engineer; Corentin Lorc’h, Quality Manager and Pierre-Jean Marchais, Process Engineer at Mannesmann Precision Tubes
Precision tubes made of steel are widely used for exploration or blasthole drilling. But to keep the drilling process running and the direction of drilling straight, tubes must behave elastically under service loads. This means no plastic deformation is allowed to take place to prevent drill rods from inelastic bending. Especially for long-distance drilling, tubes must withstand severe and harsh conditions. Besides the wear, mainly mechanical loads stress the precision steel tube by a combination of factors like tensile, torsion and bending loads at the same time.
Advertisement
The engineering of drill strings needs to consider the static tensile properties, the tube dimensions and apparent ‘secondary factors’ like residual stresses and corresponding straightness. The manufacturing process of precision steel tubes must balance all these properties by adjusting the cold deformation during the cold drawing parameters, the heat treatment conditions and the tube straightness all along the production process. These production steps and their interactions will define the performance of drill rod characteristics.
As soon as the level of tensile residual stresses exceeds a critical limit, the internal stresses will cause a premature local plastic deformation - the permanent distortion that occurs when a material is subjected to tensile, compressive, bending, or torsion stresses that exceed its yield strength and cause it to elongate, compress, buckle, bend, or twist. This local plastic deformation will lead to a fast and early deviation from the planned drilling direction and, in combination with increased
↑ New straightening machine at Mannesmann plant in Vitry-leFrançois; in the front: measurement to check straightness; in the back: straightening operations
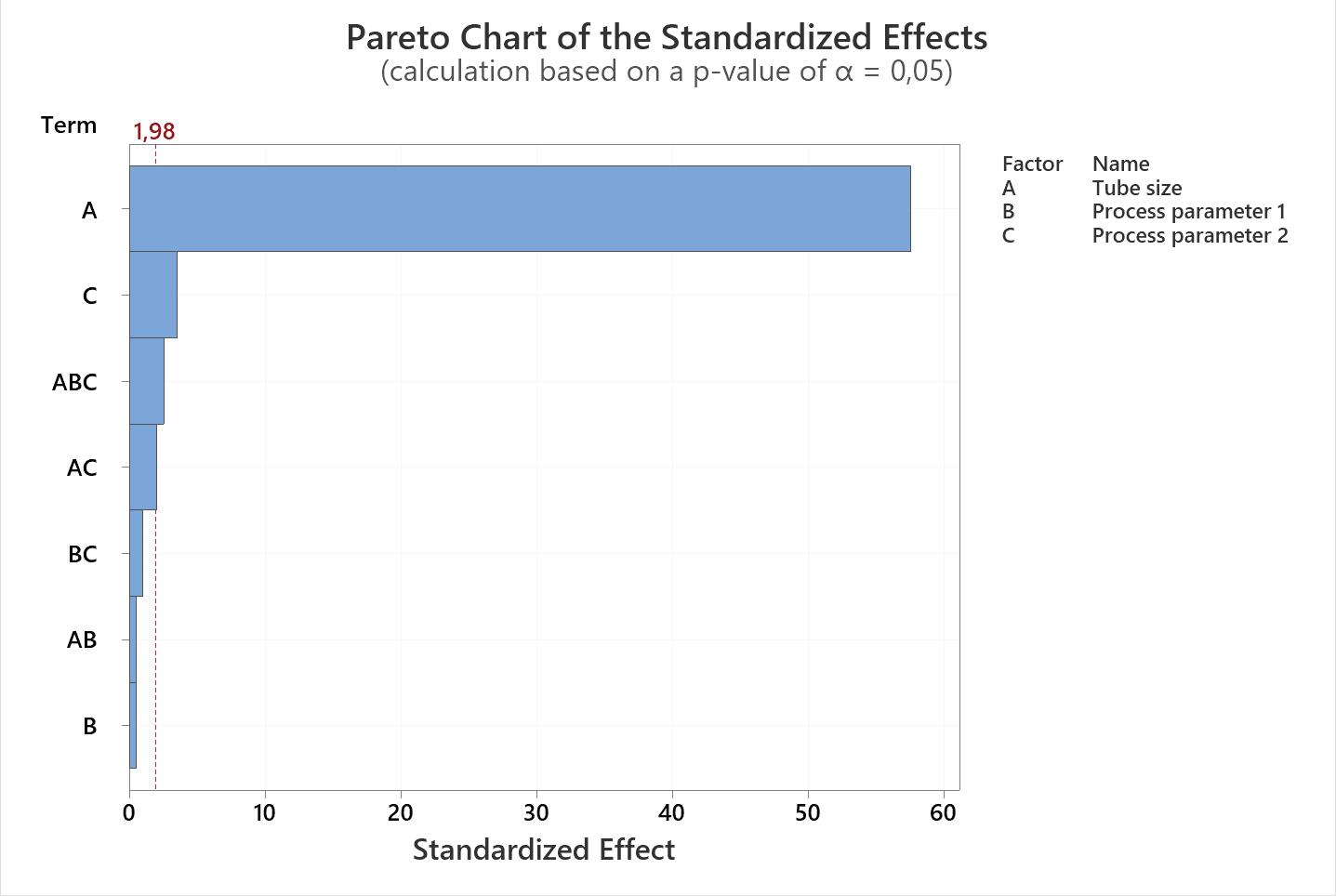
Figure 1 - Pareto diagram to estimate single influences of production parameters
vibration fatigue, would potentially lead to rod failure. Due to the trend towards being lightweight-structured, precision steel tubes have become lighter in recent years or, alternatively, already established tube dimensions have been used for deeper drill holes today. In both cases, tubes act closer to their limits.
Therefore, Mannesmann focused its development activities on the product-process-interactions to ensure a well-balanced combination of straightness while maintaining the lowest level of residual stress and to fulfill all requirements regarding desired mechanical properties.
Precision tube manufacturing process
In principle, precision steel tubes are produced by casting billets from a blast furnace (BF) steel mill, piercing the billets at very high temperatures and the subsequent hot rolling of pierced blocks. Hot rolling of pierced blocks comprises a dedicated stretching of length and a dedicated reduction of the outside diameter. The hot-rolled tubes (hollows) are handed over for a cold drawing process, which tightens the dimensional tolerances of the outside diameter, inside diameter, and thus wall thickness. At the same time, the mechanical properties are settled on a very homogeneous level all over the axial and transverse directions of the rod. This is thanks to the steel grade, the plastic deformation rates and all the parameters applied during the cold drawing process. Specific heat treatments judiciously positioned in the production route guarantee the best properties in terms of both yield and tensile strength. Finally, precision tubes for drill rod application are straightened to reach the best values of straightness. This process step will ensure the lowest deviations from desired drilling directions. Additionally, Mannesmann ensures the smoothest straightening operations to guarantee the lowest residual stress levels on final tubes.
Especially straightening operations and their interactions with applied heat treatments have moved into the engineering focus because residual stress level and straightness are not acting fully independent from each other. In particular, both properties may counteract each other. The global aim of tube production is to minimize residual stresses and to increase straightness.
Mannesmann fulfills that by producing precision steel tubes for drill rod applications in their plant, located in Vitry-leFrançois, France.
Mannesmann Precision Tubes’ process capability: Design of Experiments & statistical analysis
Mannesmann plans its experiments with Design of Experiment - the systematic method to determine the relationship between factors affecting a process and the output of that process - to analyze and lay out process stabilities of productions already at the early stages of the development process. Statistical approaches help to understand why properties may show scatter - the degree to which repeated measurements or observations of a quantity differ - and the significance of every single parameter. Thus, statistics is the key to controlling scatter of mechanical and geometrical properties and, therefore, constitutes the foundation for safe and reliable resistance against fatigue of tube components during drilling service.
Mannesmann has varied the production steps parameters like heat treatment, drawing or straightening. Thus, drill rod precision tubes will release detrimental residual stresses in one way or another depending on operations and production parameters. At the end of the production route, tubes will show excellent straightness and very low residual stress levels at the same time.
To characterize rod performance, Mannesmann has applied a four-point-bending configuration to determine the onset of plastic deformation of the tube’s mid-body. Instead of determining an Rp0,2-level by classical tensile tests, Mannesmann follows the idea of characterization of elastic limits (see Coring Magazine, September 2017 edition, page 16-19).
Figure 1 shows the Pareto diagram of different production parameters. Mainly, the tubes’ dimensions, show the most effect on tube performances. But, the single effect of each parameter should be considered as well as the interactions of different parameters and each must be evaluated in detail.
If the tubes’ dimension (diameter and wall thickness) is defined bigger, stiffness and bending forces will feature higher values. The main reason for this is the moment of inertia of the tubes (compare Figure 1), which grows rapidly with the diameter and wall thickness.
At a first glance, the additionally investigated parameters seem to be less important or of the same importance. But with a closer look, it becomes apparent that straightening operation becomes the most important parameter to steer the desired tube performance.
Conclusions
Mannesmann has adapted its manufacturing process to improve tube performances. By adjusting parameters all along the processes, tubes can be produced with differently balanced values of straightness: • 1 mm/6 m combined with residual stresses < 120 MPa or • 1 mm/2 m combined with residual stresses < 100 MPa.
Mannesmann Precision Tubes invested in the recent years in the technology for heat treatment and straightening to install production means at the edge of available technologies. Therefore, Mannesmann installed a new straightening machine, including the interaction of measurement techniques plus online analysis of data to improve straightening operations.
Now, the designer can choose between two different states depending on the applied drilling technology. Further optimizations are achievable by choosing between different steel grades. Mannesmann offers yield strength levels ranging from 550 MPa up to 950 MPa. They provide a broad variety of design strategies. Additionally, higher strength grades provide excellent resistance against abrasive degradation.
If the tubes must be joined to connectors, perfect weldability for friction-stir welding is given for several grades.
In addition, Mannesmann has developed a wide range of variable thickness tubes: Taylor Drawn Tubes (TDT®) B-/N-/H-/P-sizes and other specific designs on demand. This innovative family of tubes allows a weight reduction of up to 30% compared to the same dimension for the standard tube. These tubes are cold-drawn, and the same level of quality is guaranteed with the same yield strength levels ranging from 550 MPa up to 950 MPa.
With the whole portfolio of strength level, extraordinary straightness, lowest residual stress levels, excellent wear resistance and weldability any application engineer has the freedom to design drill rod products as they prefer. C ↑ Storage of drill rods
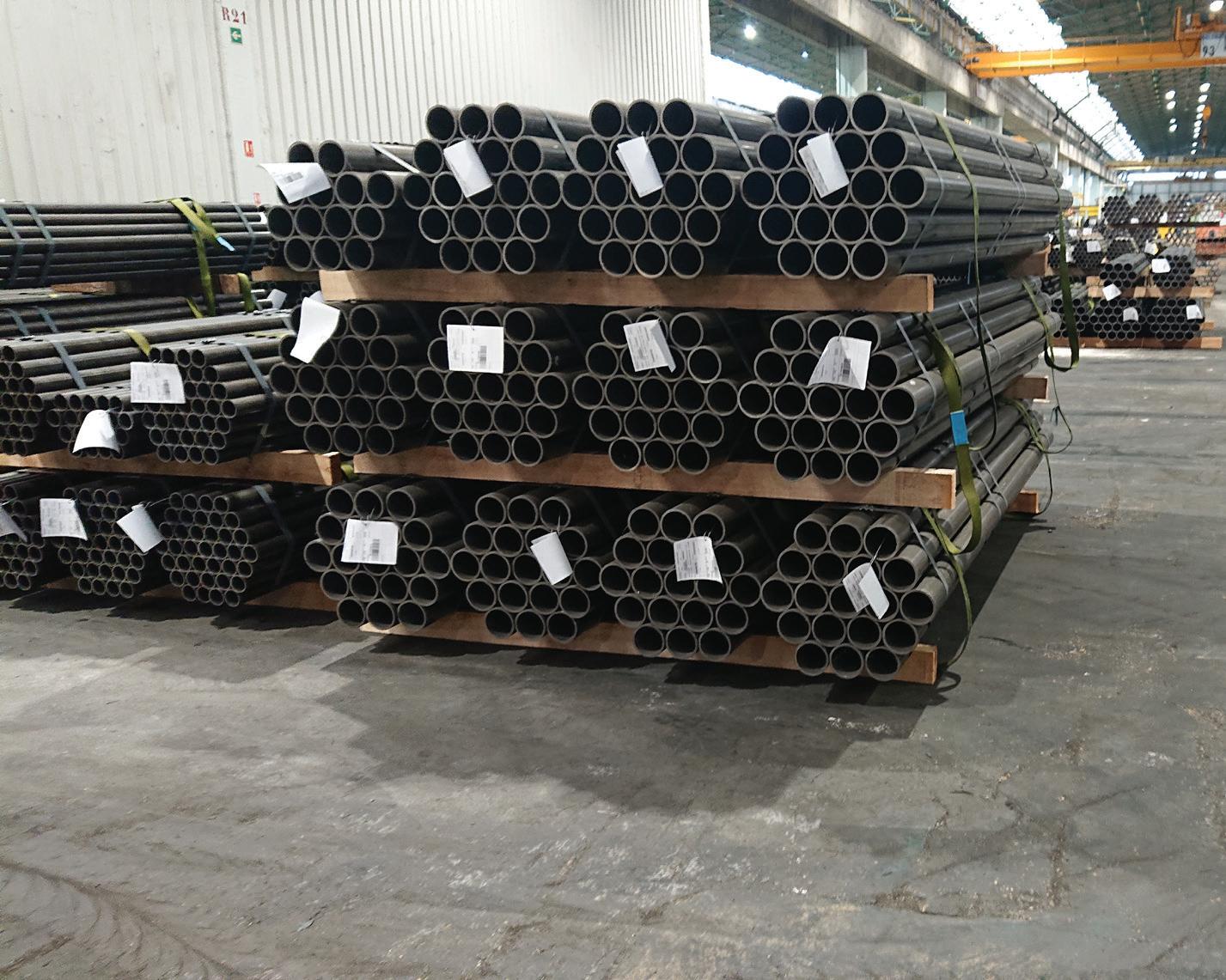

↑ Mannesmann - Taylor Drawn Tubes (TDT®): thick and thin parts of the wall thickness and transition zone
For more information
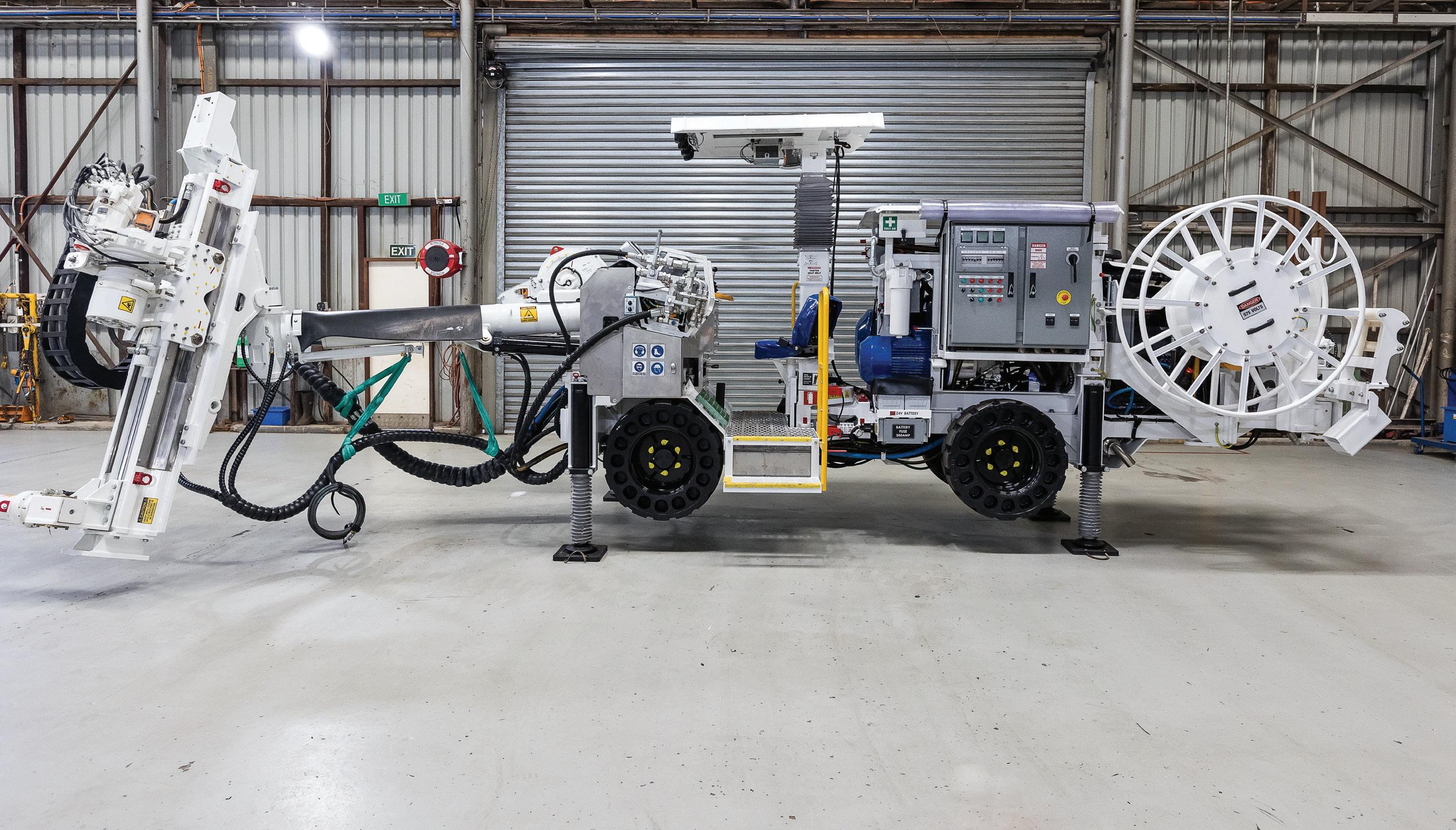
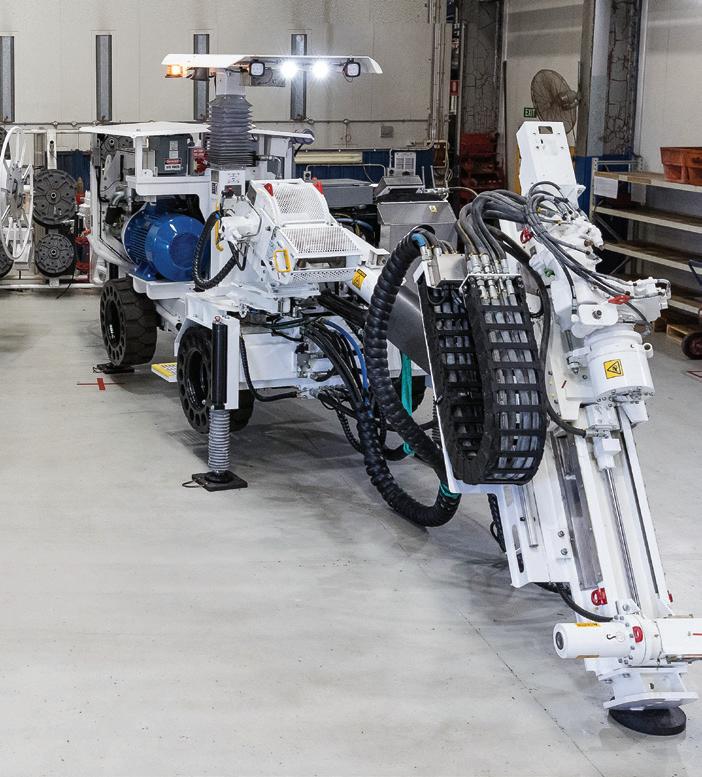