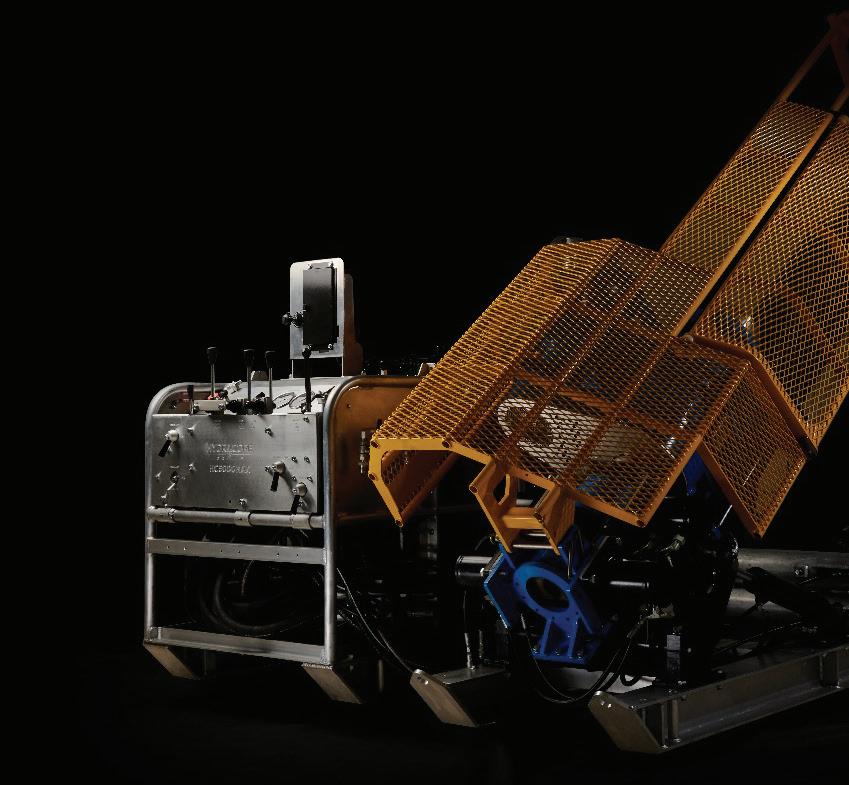
7 minute read
Meet MAX: The 8000 lb beast that drills up to 3100 meters N-size
Meet MAX:
The 8000 lb beast that drills up to 3100 meters N-size
Advertisement
by Rishi Budshah, CMO at Hydracore Drills Ltd.
The story about HC5000max (Max) started when one of our existing customers requested a deep hole core drill that was truly heli-portable, meaning lifts under 2000 lb (907 kg). This request aligned with our market research showing that more holes were being drilled beyond 2000 m (6562 ft) and an increase in projects demanding core in H- and P-size. This highlighted the gap in the portable drill category for purpose-built deep hole drill rigs. Hydracore’s business philosophy is to challenge the status quo and this opportunity was exactly what was needed to make a difference while providing renewed value to our customers. Hydracore returned to the drawing board and embarked on designing a ‘Max’ version of the HC5000.
The design process
Increasing the capacity of the drill was our main objective, however not an easy task. The challenge was to maintain the portability of the drill in terms of the light weight and small footprint; but at the same time achieve never seen before power and pullback force. A thorough analysis of the entire structure and circuits was required.
Hydraulic powerpack
We decided to increase the pressure of the hydraulic system to achieve higher available hydraulic horsepower. To back this up we increased the overall engine horsepower from 206 hp to 260 hp. The hydraulic pumps were changed out for high pressure piston pumps which also increased efficiency.

↑ Hydraulic Powerpack and the Drill Module
Drill head
The increase in system pressure gave us the increase in available torque needed for deep hole drilling. Many drills are advertised with incredible torque numbers, but these are only available in RPM ranges that are inefficient for drilling. Max’s drill design focused on optimizing the torque at drilling speeds of 500-1350 RPM. This directly increases the footage per shift.
The HC5000max drill head follows Hydracore’s proven design and does not require a gearbox. Its large bent axis variable displacement hydraulic motor has sufficient range for all drilling speeds and is controlled by an infinitely variable control knob. The Hydraulic motors last for five to ten years and are easily replaced in the field in one to two hours. This means less downtime and more drilling.
In a chuck type drill head, large diameter bearings are required to accommodate the drill rods to pass through the center of the main spindle. With large bearings comes a great deal of friction and therefore the power you could use for drilling is wasted producing heat.
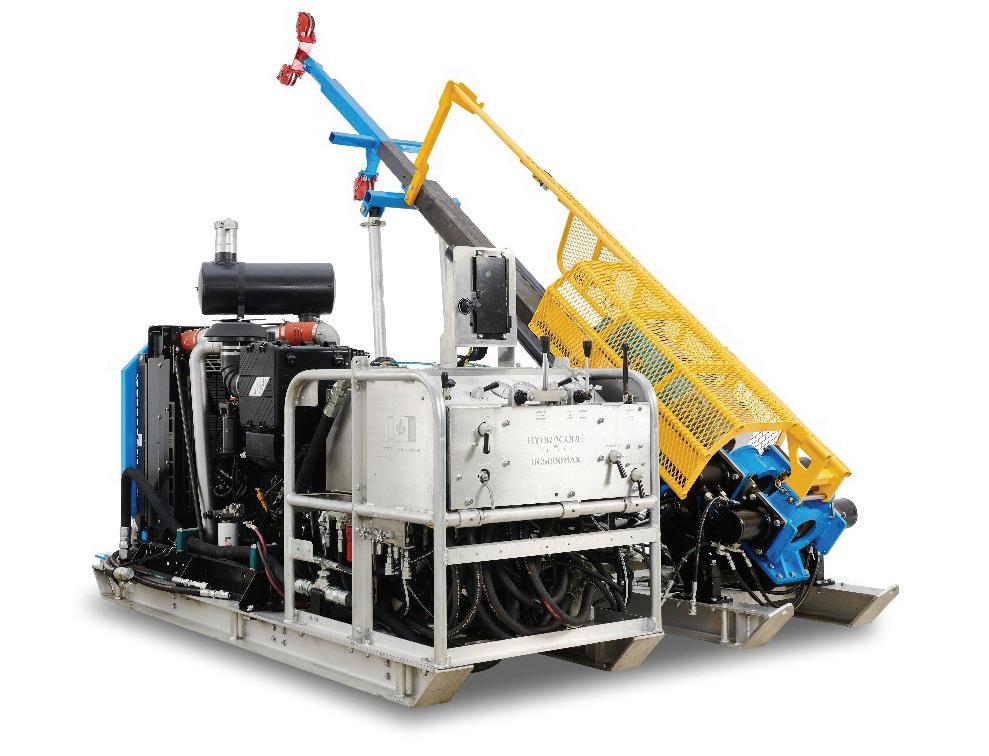
↑ Hydraulic Powerpack and the Drill Module ‘Hydracore’s business philosophy is to challenge the status quo and this opportunity was exactly what was needed to make a difference while providing renewed value to our customers.’
Through a careful design process, we have optimized the bearings on HC5000max to handle both the high speeds and high loads without creating excess heat, there are only three bearings in the entire head. The reduction in heat and lack of gears and chains means we have eliminated the need for oil, lubrication pumps, filters and radiators. A couple of shots of grease daily is all that is required to have a cool running head. This is one way our customers save money on their maintenance costs.
Chuck
A drill’s pullback capacity is only as strong as its weakest link. The chuck holding capacity was reviewed and upgraded to 70 000 lb (31 750 kg). We were able to achieve this with a bolt on design that included a new set of stronger springs. This upgrade kit will fit on all the previous Hydracore P Heads.
Feed frame and pullback force
HC5000max’s feed frame is of simple, strong and compact design. The two side-mounted cylinders combined offer a market-leading 70 000 lb (31 750 kg) of pullback force and have a 72 in (183 cm) stroke. The feed frame looks similar to the design on the HC5000, but the steel is twice as thick, and hand-selected by reviewing mill certifications. Using Finite Element Analysis (FEA) each component of the drill has been optimized in this same manner for strength and weight. A lightweight mast is provided for the wireline cable and allows for pulling 20 ft (6 m) rods.
Mobility
The light weight and small size of the HC5000max allow for mobilizing with a helicopter or a small, tracked carrier. The 8000 lb (3629 kg) total weight is moved in five lifts with an A-Star/Airbus AS350 helicopter. This reduces safety risks, decreases mobilization time and at USD 2500/hr+, it saves considerable money on helicopter rental.
In some areas it is permissible to have small roads with minimal permitting, in this case using the tracked carrier might be best. Equipped with a picker crane, the vehicle makes for safe and efficient moves and the drill can be moved in two trips. The vehicle with a picker crane also doubles up to move other site supplies. The time saved in the permit process and the reduced cost/time in making trails as compared to roads allows you to drill sooner, invest less into infrastructure and has a greatly reduced environmental impact. These abilities sum up to a significant advantage over others in the bidding process.
Foot clamp
While torque and pullback were the parameters under scrutiny, safety must always be a priority in any equipment design. As the drill was going to be used for P-size core, running casing below the drill head would be required. To eliminate the inherent dangers of pipe wrenches on the drill string a ‘Double Breakout’ foot clamp was designed. This foot clamp has two sets of independent jaws with the upper having controls to function as a hydraulic wrench.
Foot clamp jaws on most drills are replaced to accommodate the various sizes of drill rods, e.g., from a B- to P-size. The changeover time to swap the jaws ranges from 15 to 20 minutes. You are then also required to inventory multiple jaw sizes and the spares to back them up. The foot clamp on HC5000max will hold B rod to PW casing with the same standard carbide-tipped jaws, therefore, no jaw changes are required, and parts inventory is kept to a minimum.
It is common in the industry for foot clamp jaws to only move 1/8th of an inch (3.18 mm); this results in the rods rubbing on the jaws and damaging them. In this case a very tight-fitting steady bearing must be used to center the rods; it must be removed whenever the core barrel is pulled.
The foot clamp jaws on the HC5000max can move up to 1 in (25.4 mm); there is sufficient clearance between the rod and the jaws eliminating the chance of rubbing. This clearance also allows the steady bearing to
remain in place during all drilling operations, including when pulling the core barrel. These design features save you both time and wear and tear.
Rather than using steel springs which have a limited life to provide the foot clamp clamping force, HC5000max’s foot clamp is closed by a nitrogen gas accumulator. Using nitrogen gas is much more efficient compared to steel springs. The foot clamp closes automatically when the machine is shut down, ensuring a fail-safe operation and avoiding any loss of drill rods.
The resulting impact
The beast operates at more than 260 hp, depending upon your engine choice, providing a massive 233 hp to the drill head and drills up to 3100 m N-size (10 171 ft). Max comes with an impressive pullback force of 70 000 lb (31 750 kg) and weighs a mere 8000 lb (3629 kg). The final increase in weight was minimal, therefore the mobility and versatile character of the machine were maintained. There is nothing in the core drilling industry that can come even close to it. HC5000max offers the highest power to weight ratio available in the industry, it was designed to be light yet tough, matching and exceeding the specifications of drills four to five times its size. C ↑ Designed for safety, Double Breakout Foot Clamp
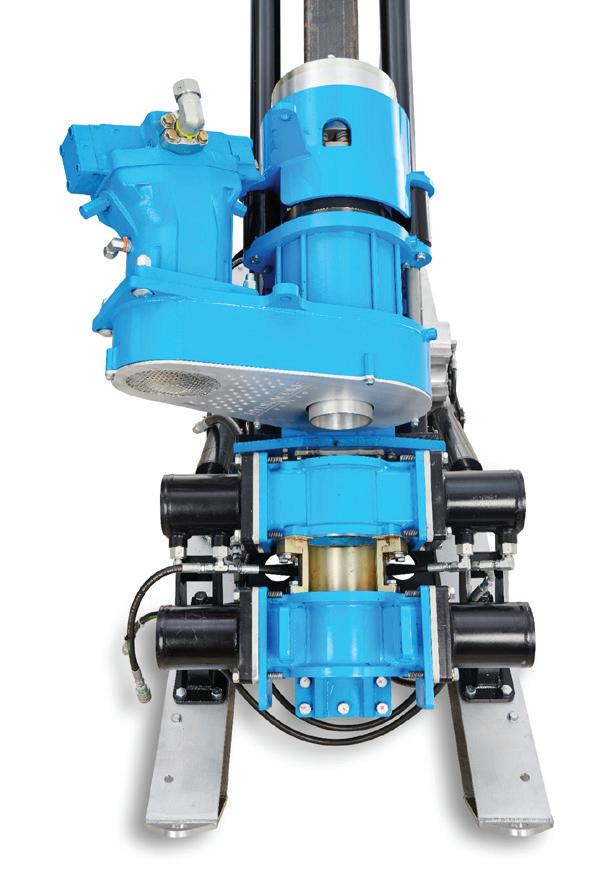
For more information
Visit: www.hydracore.com
GYRO COMPASSING SYSTEM


IT HAS NEVER BEEN EASIER TO CONTROL A LARGE NUMBER OF BOREHOLES
The innovative one man hand-held system works independent of environmental distraction and provides unsurpassed accuracy. You‘re looking for a fast, economical and reliable solution? LiPAD®-100 is the answer. LITEF.COM