

SINOBOOM ON THE RISE!
THE ACCESS POWERHOUSE IS READY TO TAKE ON THE BIGGEST CHALLENGES
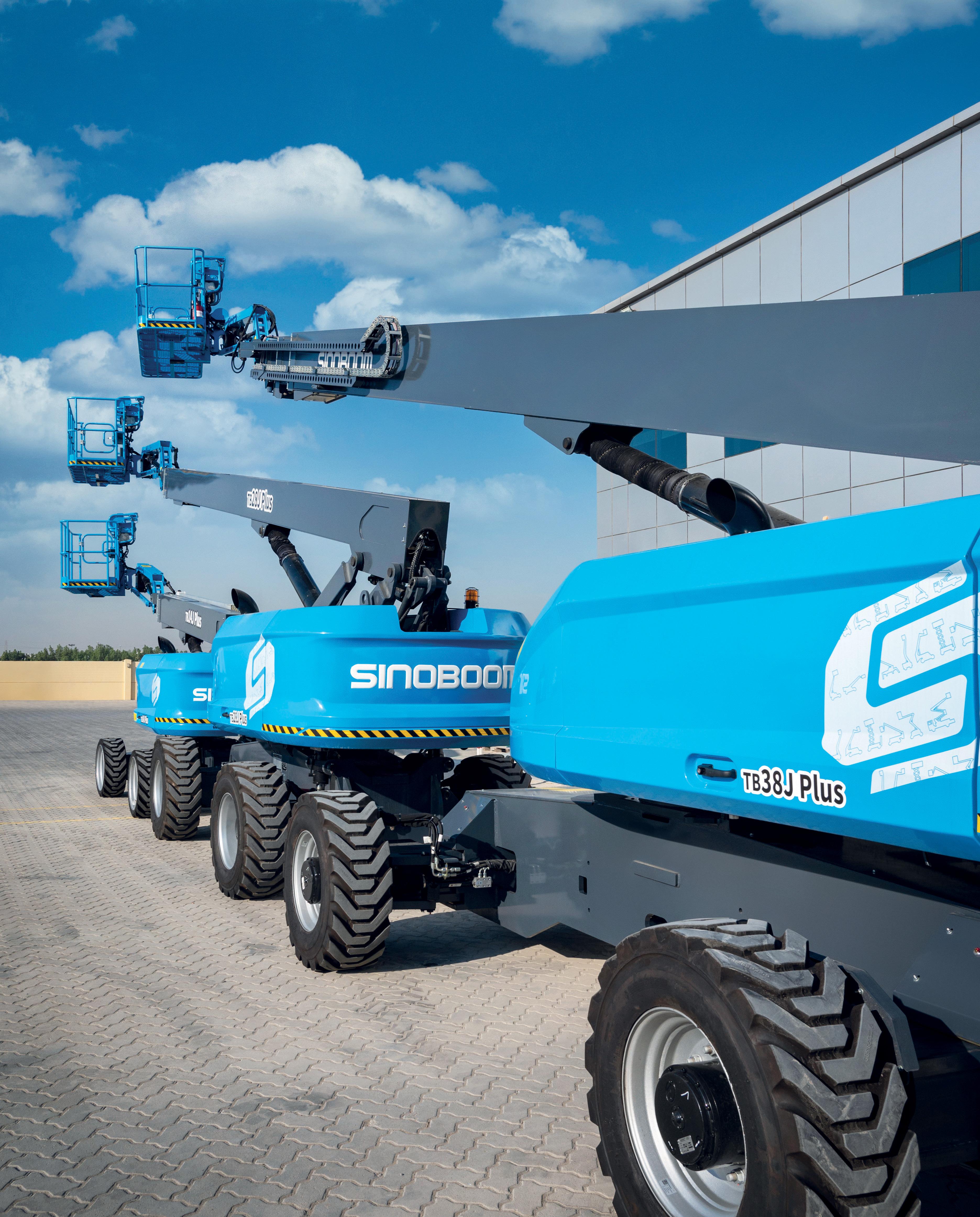
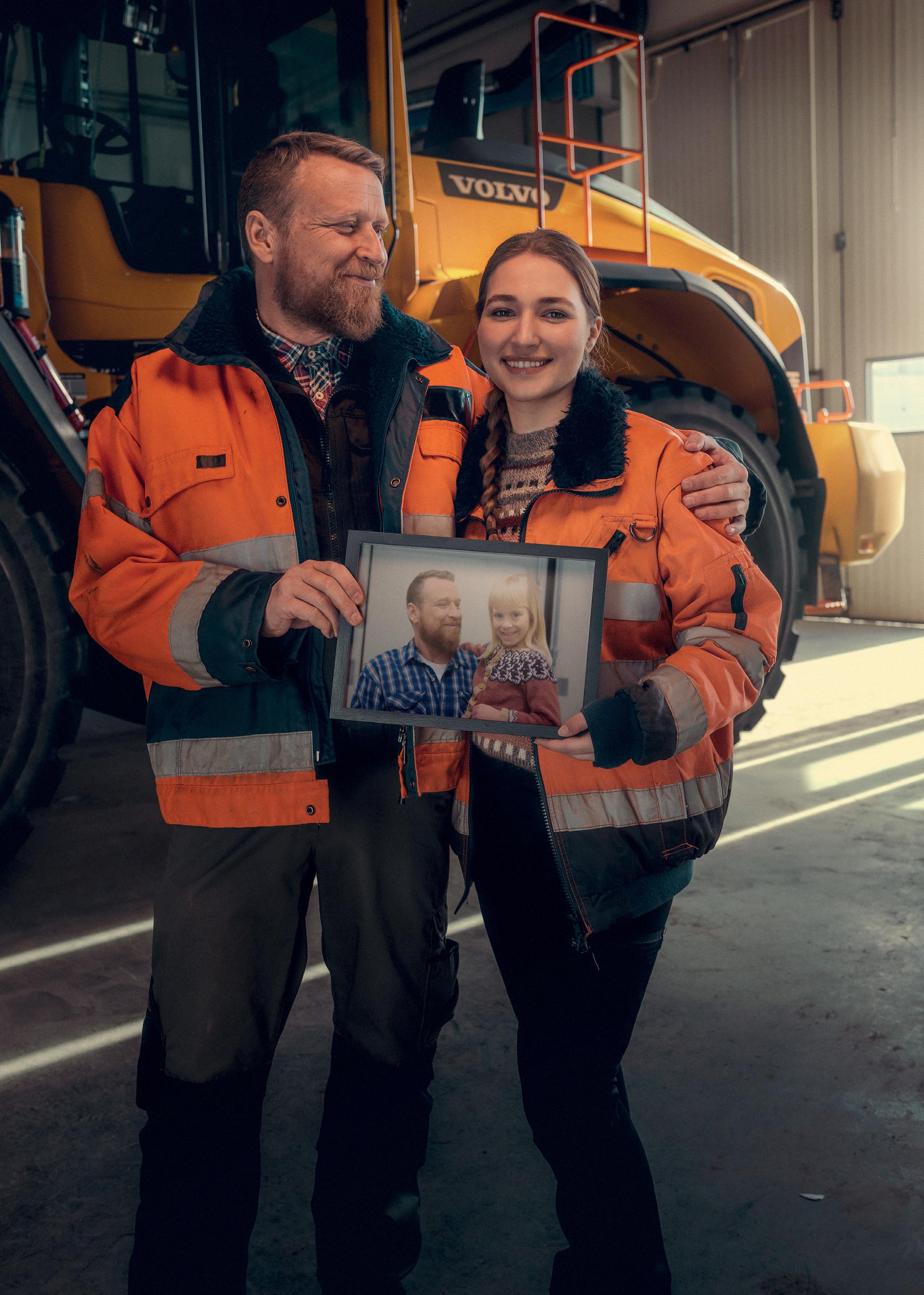
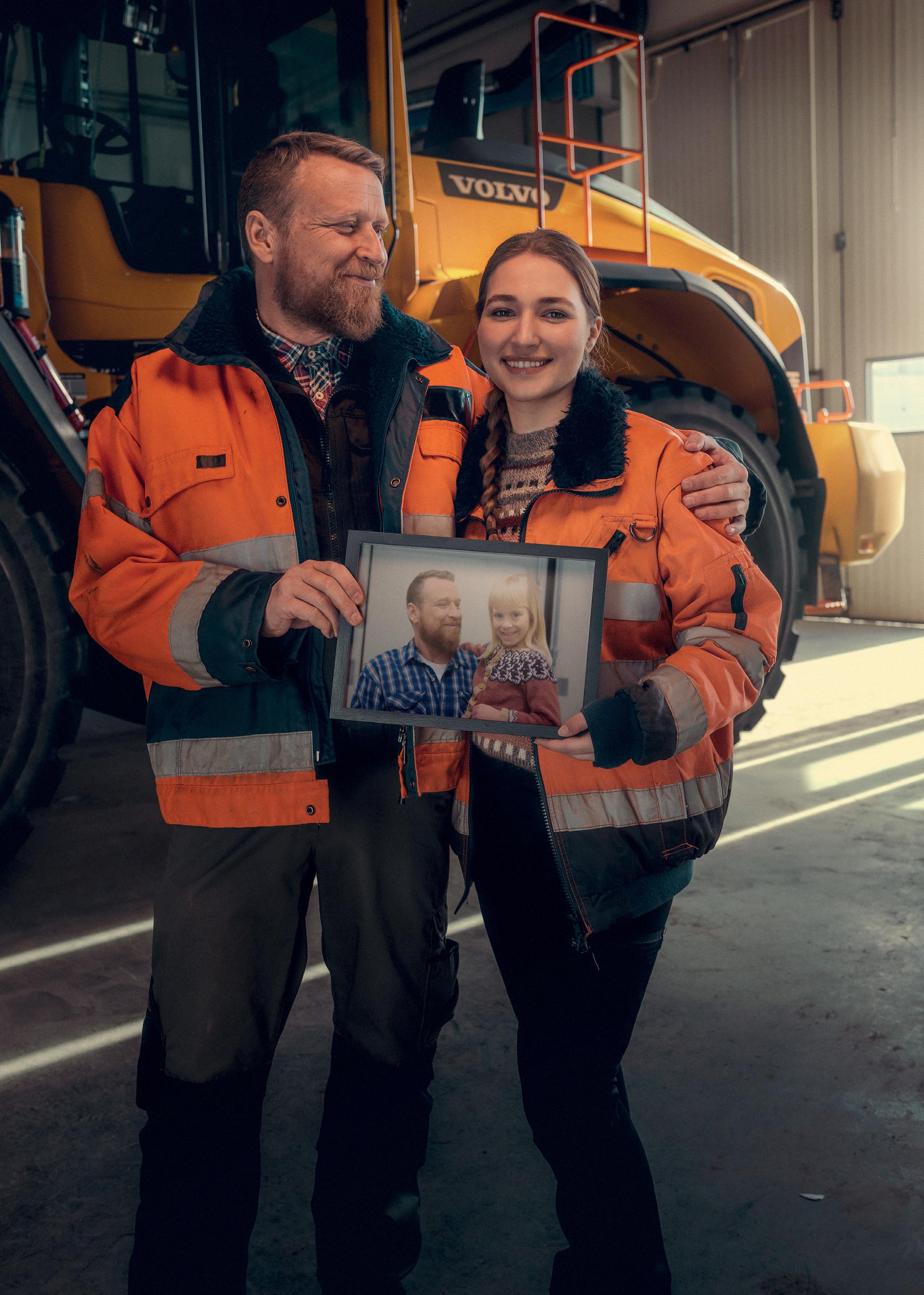
RAW POWER CONTENTS
Meet
Ahmed
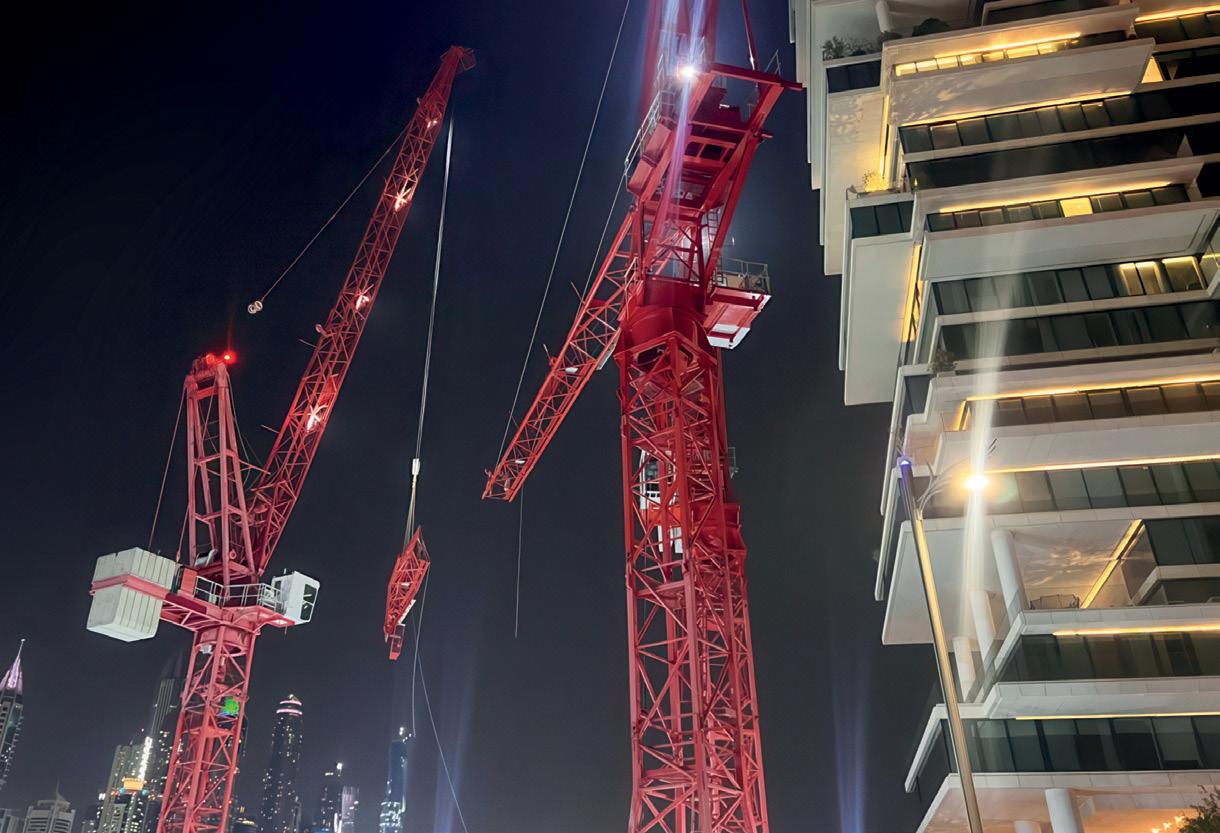
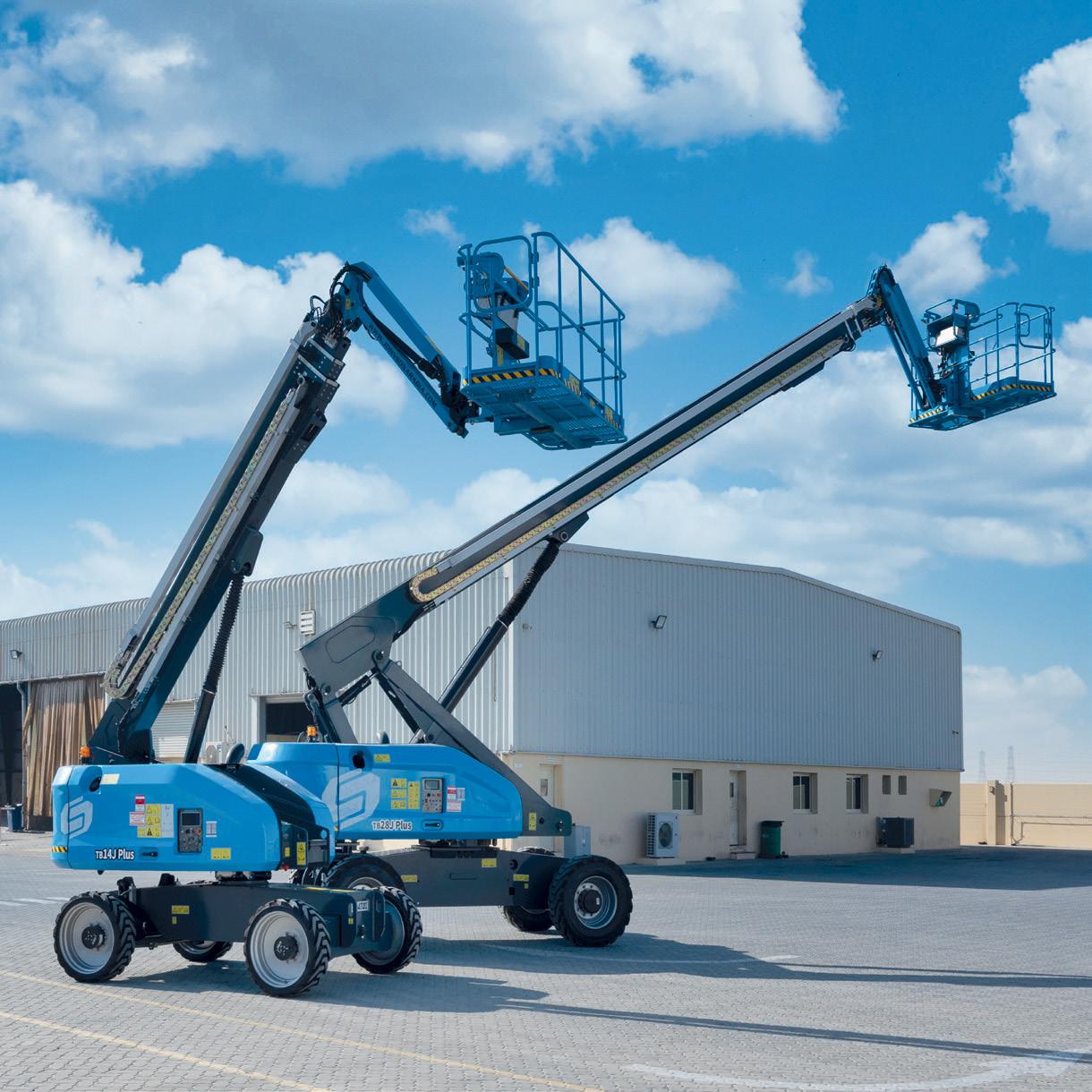

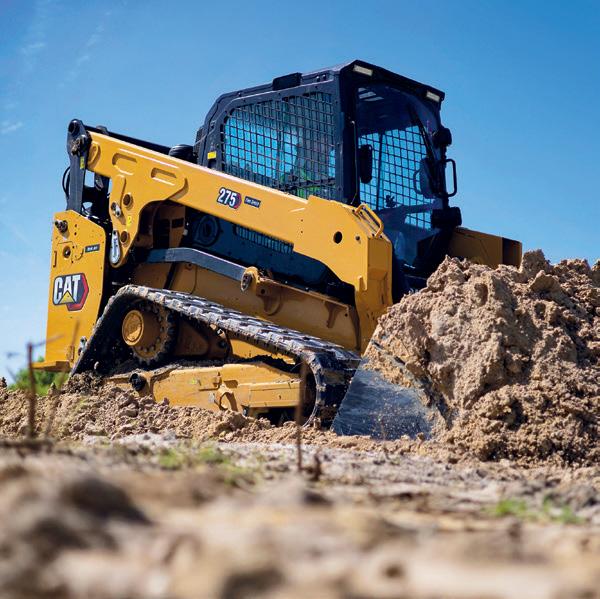
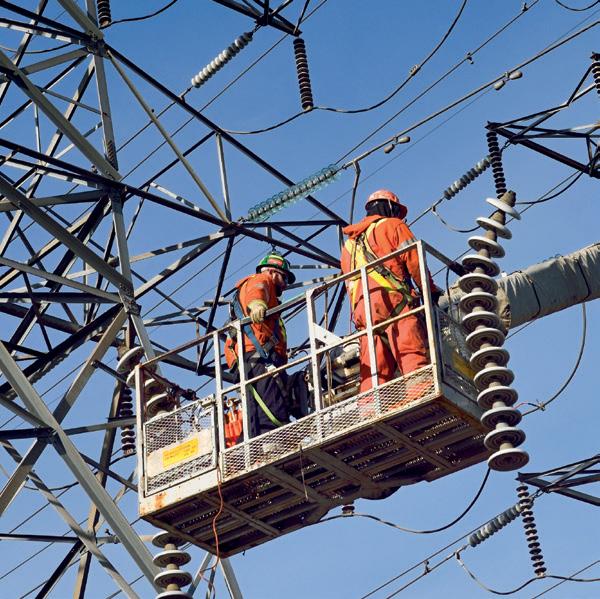
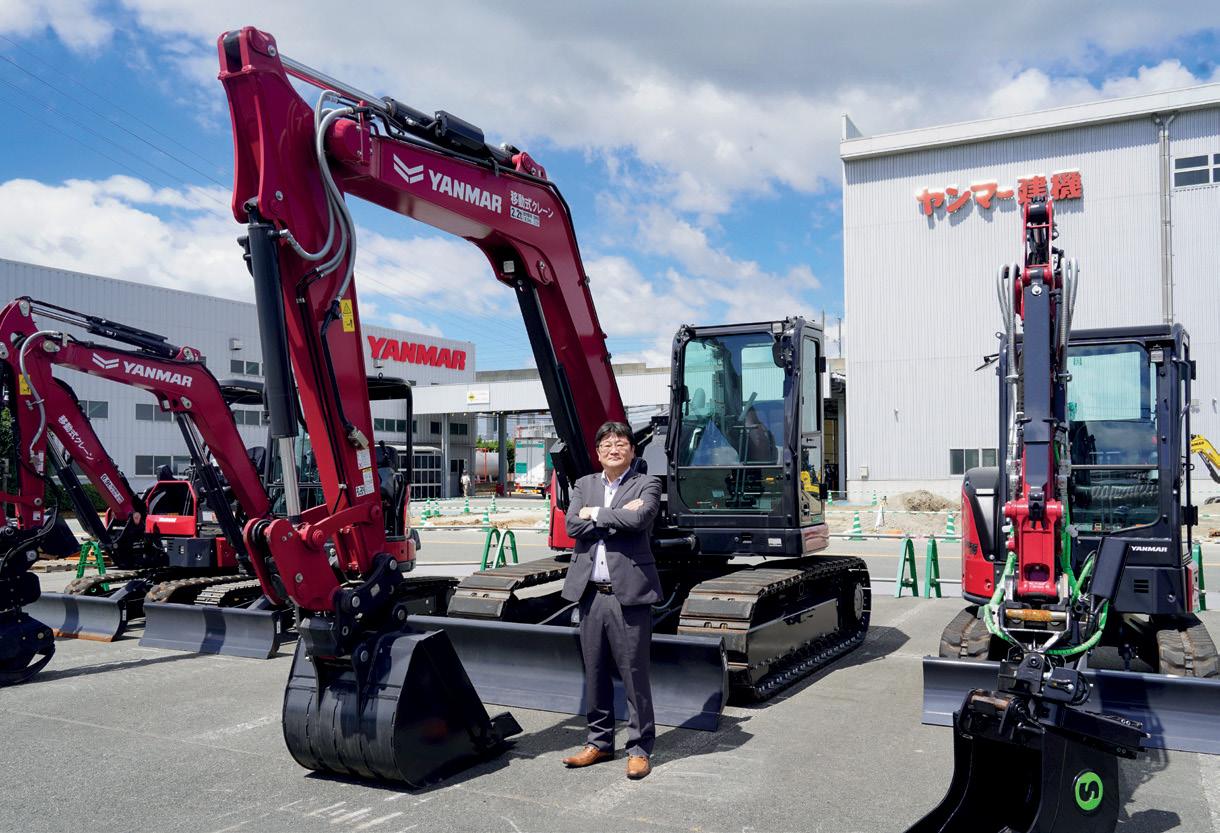

KSA: WHERE AMBITION FIGHTS REALITY
Last month, I had the privilege of witnessing firsthand the vast scale of Saudi Arabia’s ambition by visiting the Western Region where the Kingdom’s initiatives, like NEOM, the Red Sea Project, and other “giga” projects, represent a reimagining of what modern construction and sustainable design can achieve in the region. While there is much to be admired in the scope and forwardthinking nature of these undertakings, they also underscore significant challenges faced by contractors on the ground.
One of the foremost issues facing these mega projects is the challenge of sourcing the right materials and machinery. The demand for specialised construction equipment is immense, and supply chains are struggling to keep pace. This shortage is intensified by a global supply chain that has yet to fully stabilize, making lead times on crucial machinery longer than anticipated. As a result, contractors are sometimes forced to accept equipment that may not perfectly suit the project requirements, then adapt or modify it as best as possible to fit the job. However, while this resourcefulness can be impressive, it presents serious risks. Machinery that isn’t perfectly suited to the job at hand can increase wear and tear on the equipment, amplify operating costs, and create hazards if not rigorously inspected and maintained.
Contractors face unrelenting pace in the Kingdom. Tight deadlines, paired with high expectations from investors and stakeholders, place constant pressure on site teams to keep moving forward, sometimes at the expense of ideal conditions. This race against time means that even as they strive to maintain quality and precision, contractors are expected to deliver extraordinary results within
extraordinary constraints. But here lies the potential for risky trade-offs, where meeting deadlines could inadvertently compromise site safety standards. Cutting corners or pushing machinery and teams to their limits can lead to accidents, breakdowns, and even project setbacks if health and safety protocols aren’t maintained as top priorities. Safety on site must be the bedrock of any project, and nowhere is this truer than on the monumental projects forming the backbone of Saudi Arabia’s future. Maintaining safety isn’t just about following regulations; it’s about protecting the lives of every worker involved, the stability of the project timeline, and the integrity of the final product.
Contractors, suppliers, and stakeholders alike need to collaborate closely to ensure that even under immense pressure, safety protocols are meticulously followed. This means ensuring that all equipment is fit for purpose, conducting regular safety checks, and maintaining a working environment where teams are encouraged to speak up about potential hazards without fear of repercussion.Saudi’s success will depend not only on the completion of its impressive projects but also on how they are achieved. Building a future that is safe, reliable, and sustainably constructed must be the ultimate priority, even with KSAs relentless ambition.

Stephen White Head of Content, CMME stephen.white@cpitrademedia.com
GROUP
MANAGING DIRECTOR
RAZ ISLAM
raz.islam@cpitrademedia.com
+971 4 375 5471
DIRECTOR OF FINANCE & BUSINESS OPERATIONS
SHIYAS KAREEM
shiyas.kareem@cpitrademedia.com
+971 4 375 5474
PUBLISHING DIRECTOR
ANDY PITOIS andy.pitois@cpitrademedia.com
+971 4 375 5473
EDITORIAL
HEAD OF CONTENT
STEPHEN WHITE stephen.white@cpitrademedia.com
+971 58 584 5818
EDITORIAL ASSISTANT
PRIYANKA RAINA priyanka.raina@cpitrademedia.com
+971 4 375 5478
ADVERTISING
SALES MANAGER
BRIAN FERNANDES brian.fernandes@cpitrademedia.com
+971 4 375 5479
STUDIO
ART DIRECTOR SIMON COBON
simon.cobon@cpitrademedia.com
DESIGNER PERCIVAL MANALAYSAY percival.manalaysay@cpitrademedia.com
MARKETING
SOCIAL MEDIA EXECUTIVE
FRANZIL DIAS franzil.dias@cpitrademedia.com
+971 4 433 2856
CIRCULATION & PRODUCTION
DATA & PRODUCTION MANAGER
PHINSON MATHEW GEORGE phinson.george@cpitrademedia.com
+971 4 375 5476
DIGITAL
ABDUL BAEIS
abdul.baeis@cpitrademedia.com
UMAIR KHAN umair.khan@cpitrademedia.com
FOUNDER
DOMINIC DE SOUSA (1959-2015)
PUBLISHED BY
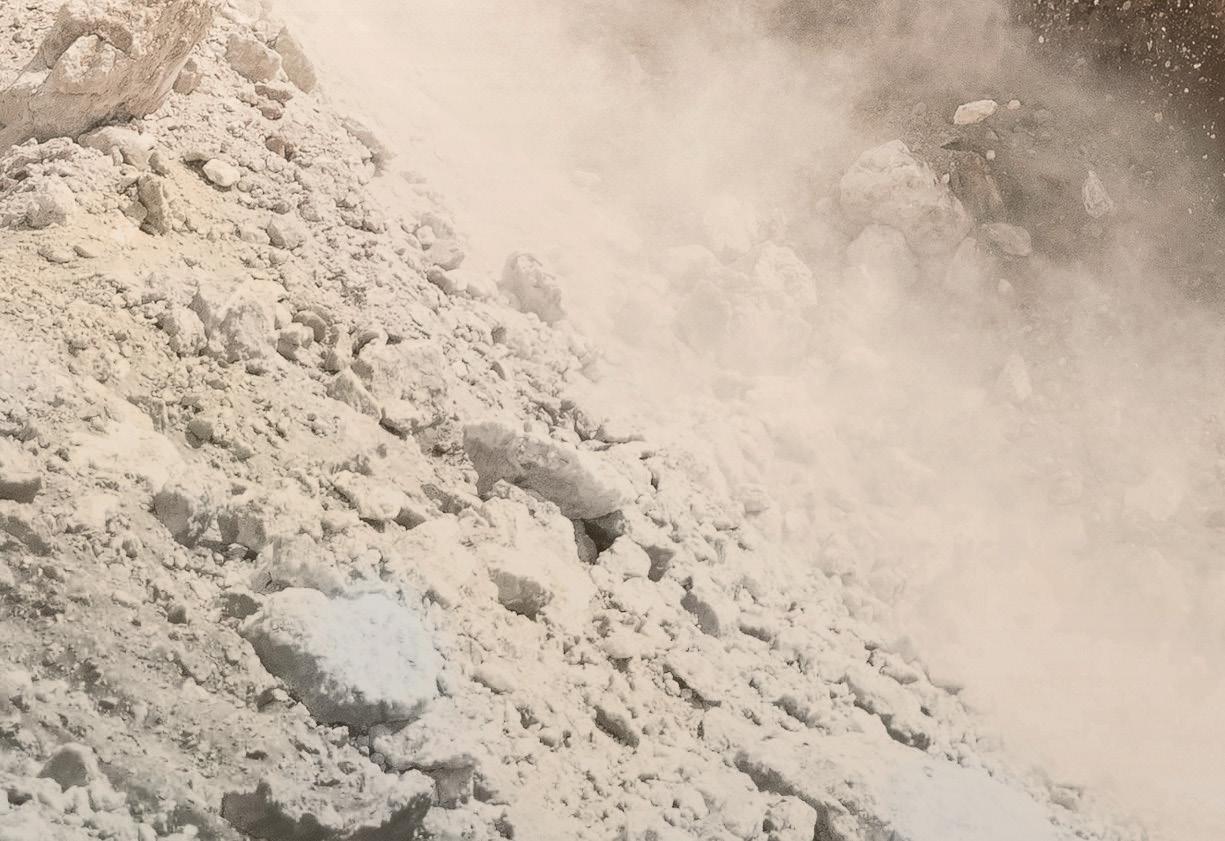
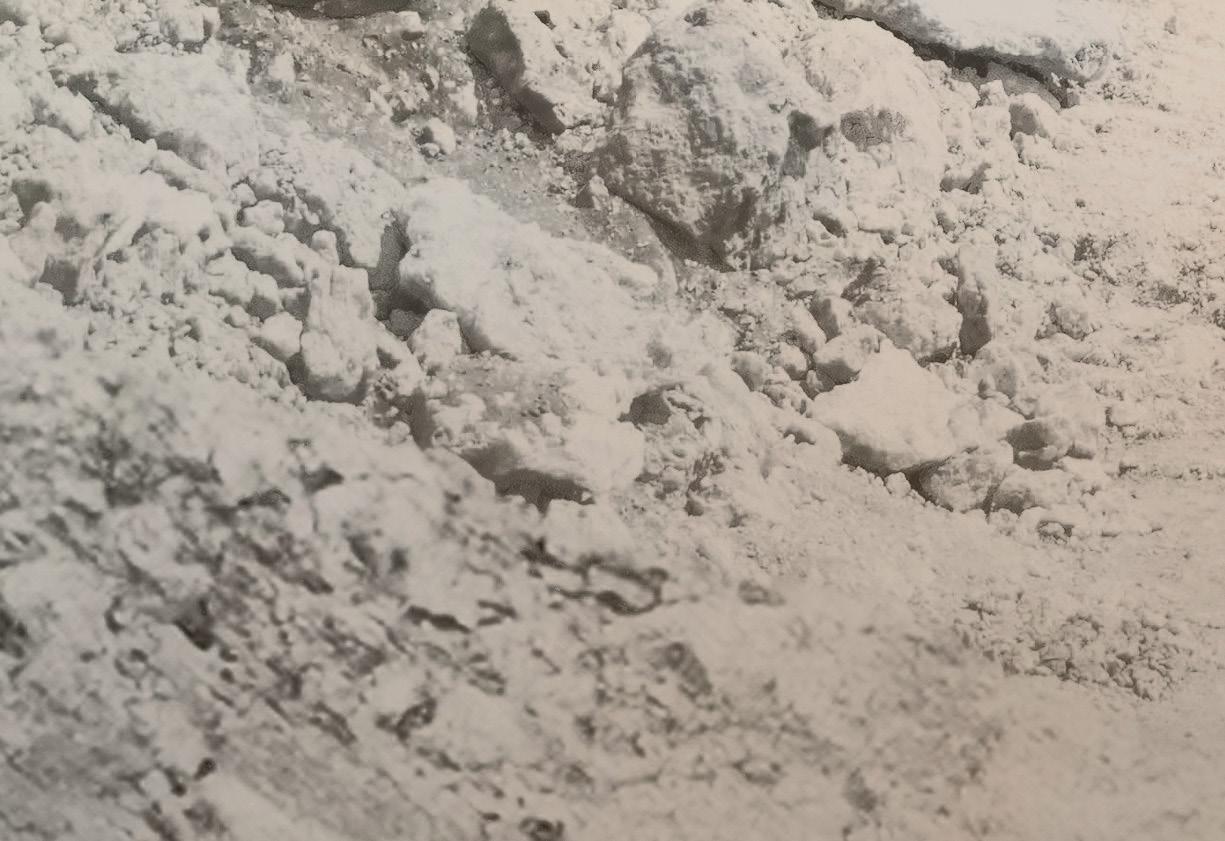
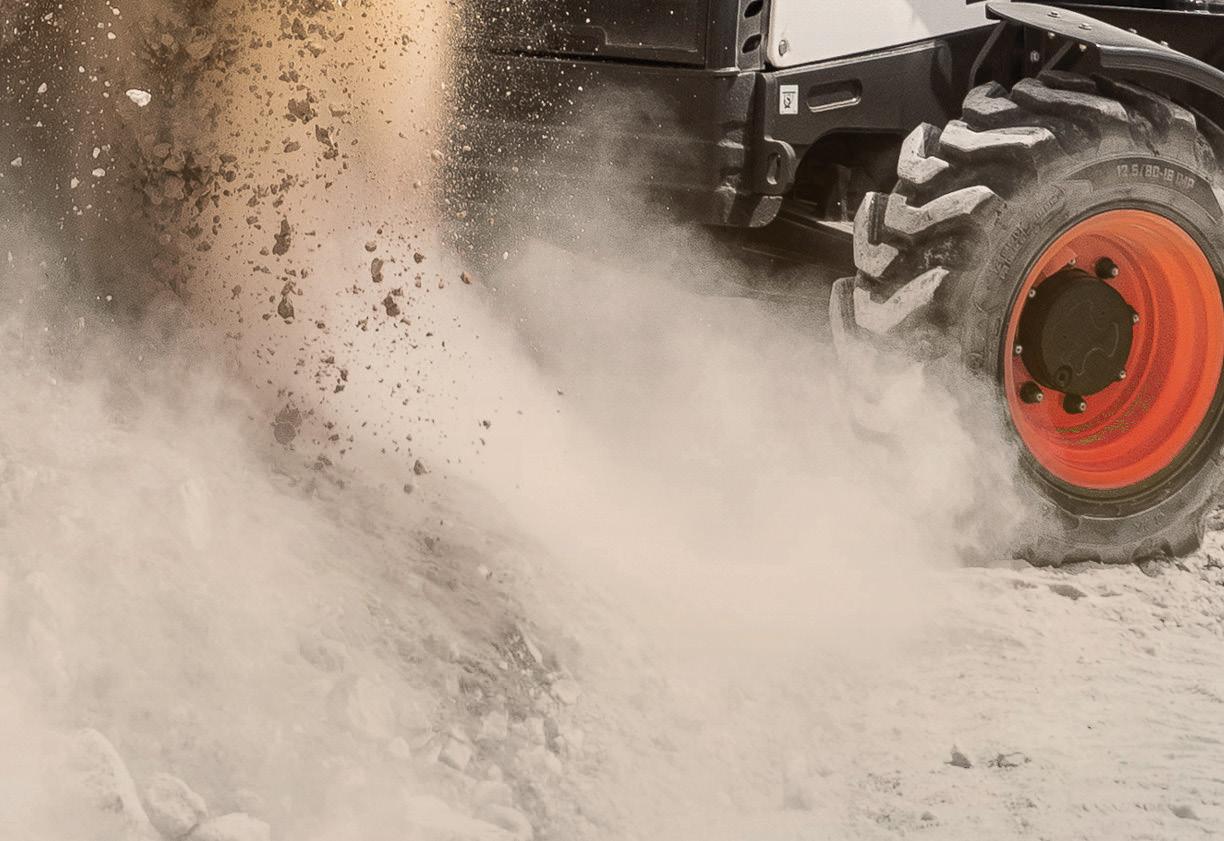
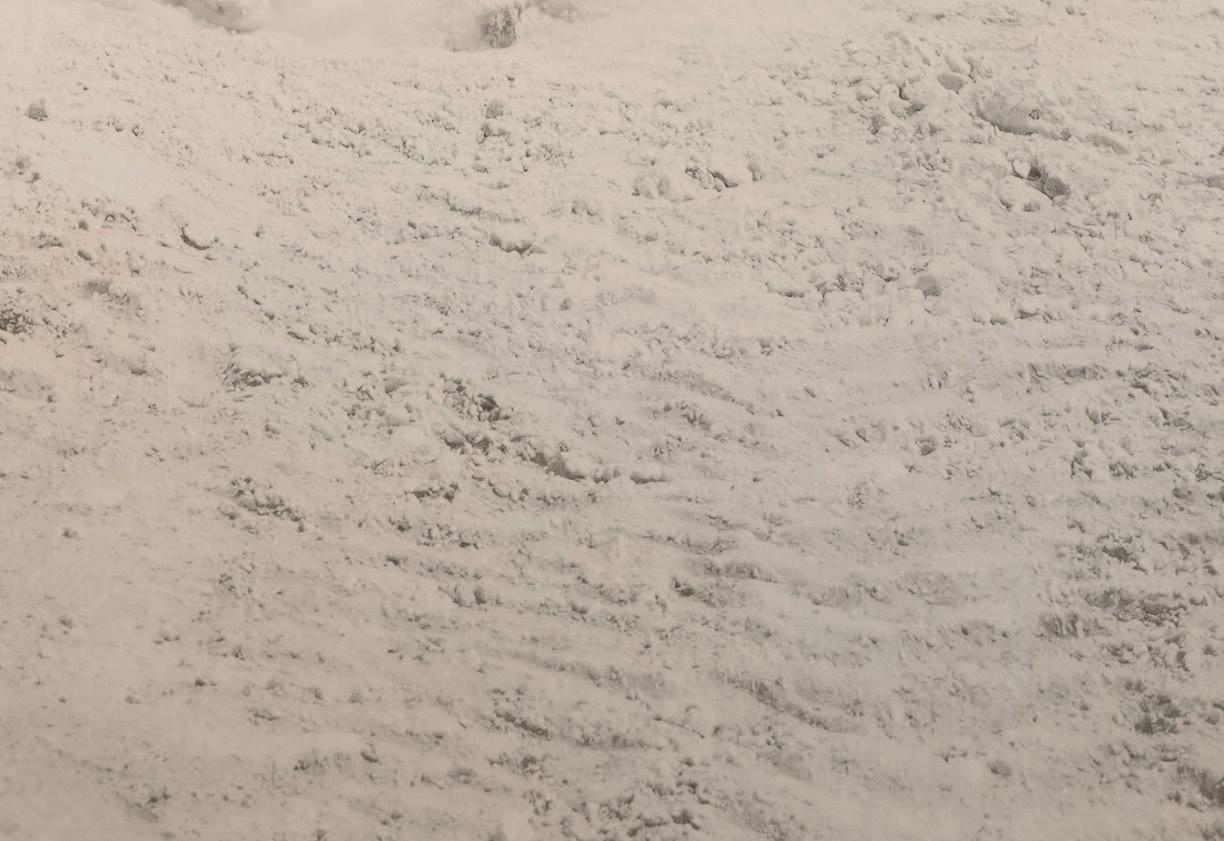

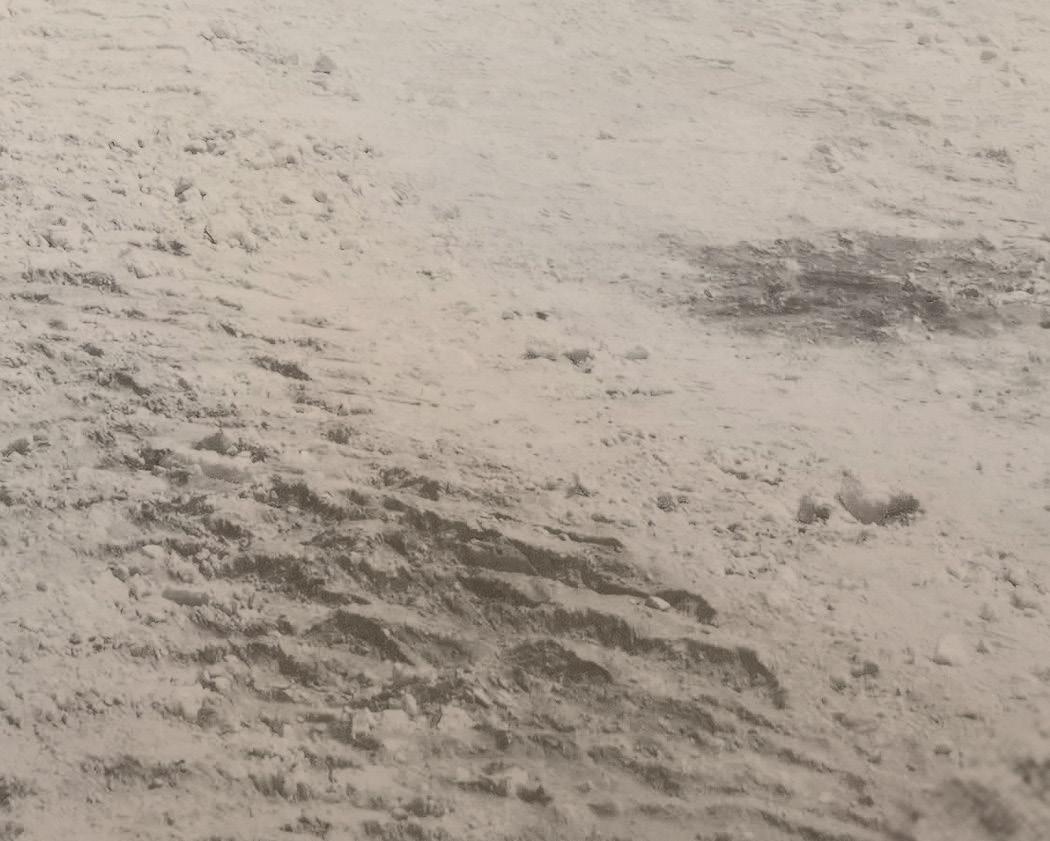
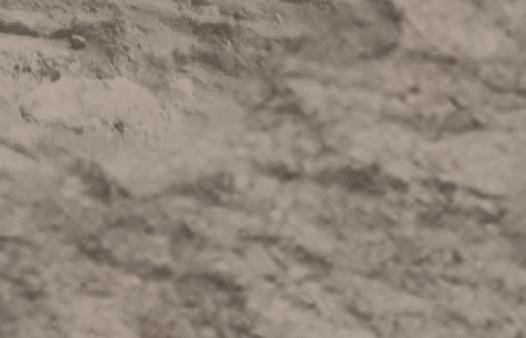
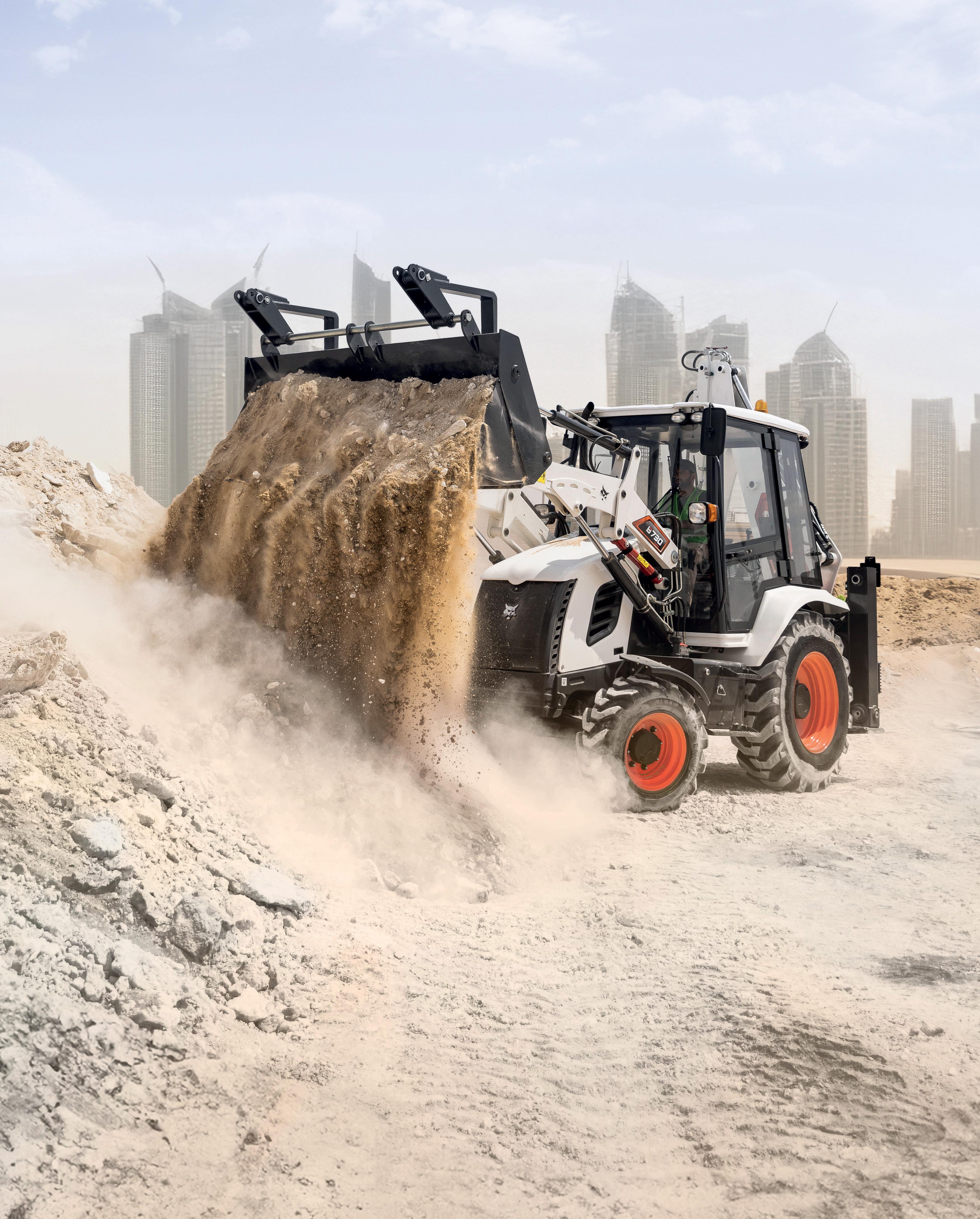
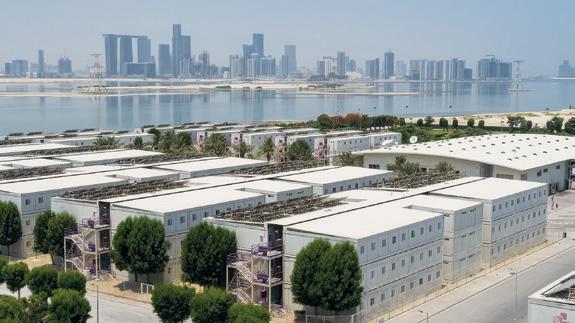
CONSTRUCTION
Azizi Developments to set up 12 factories in KEZAD

PROPERTY
Savills Middle East appoints Toby Hall as Head of Commercial Agency
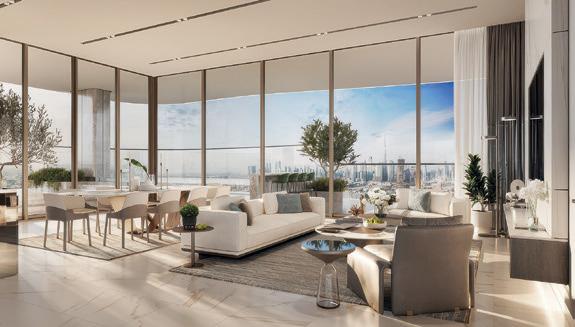
PROPERTY
Amaal launches its first lifestyle residential development, Amaal 8
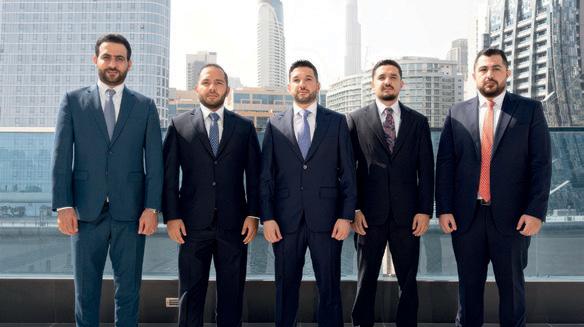
PROPERTY
KASCO Developments launches in the UAE
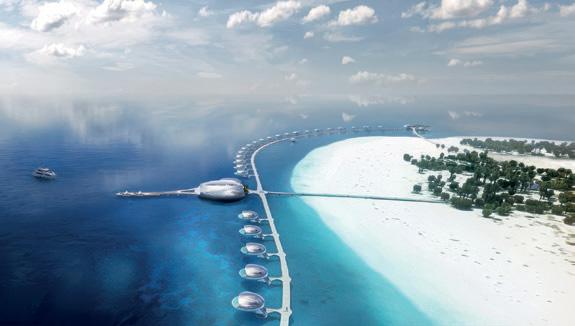
CONSTRUCTION
Red Sea Global and Marriott
International unveil The RitzCarlton, AMAALA
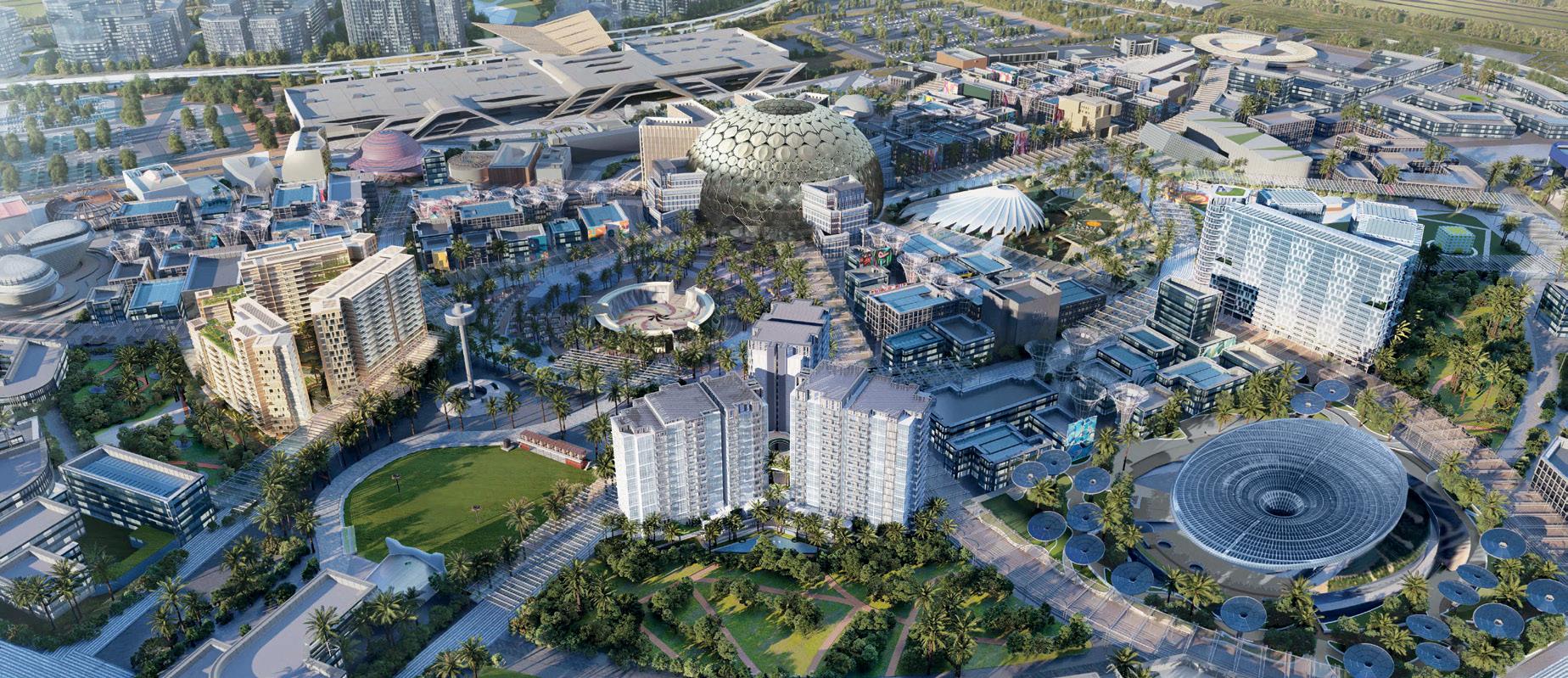
EXPERTS: Embracing the 20-Minute City

INTERVIEW: Climate Positive Concrete
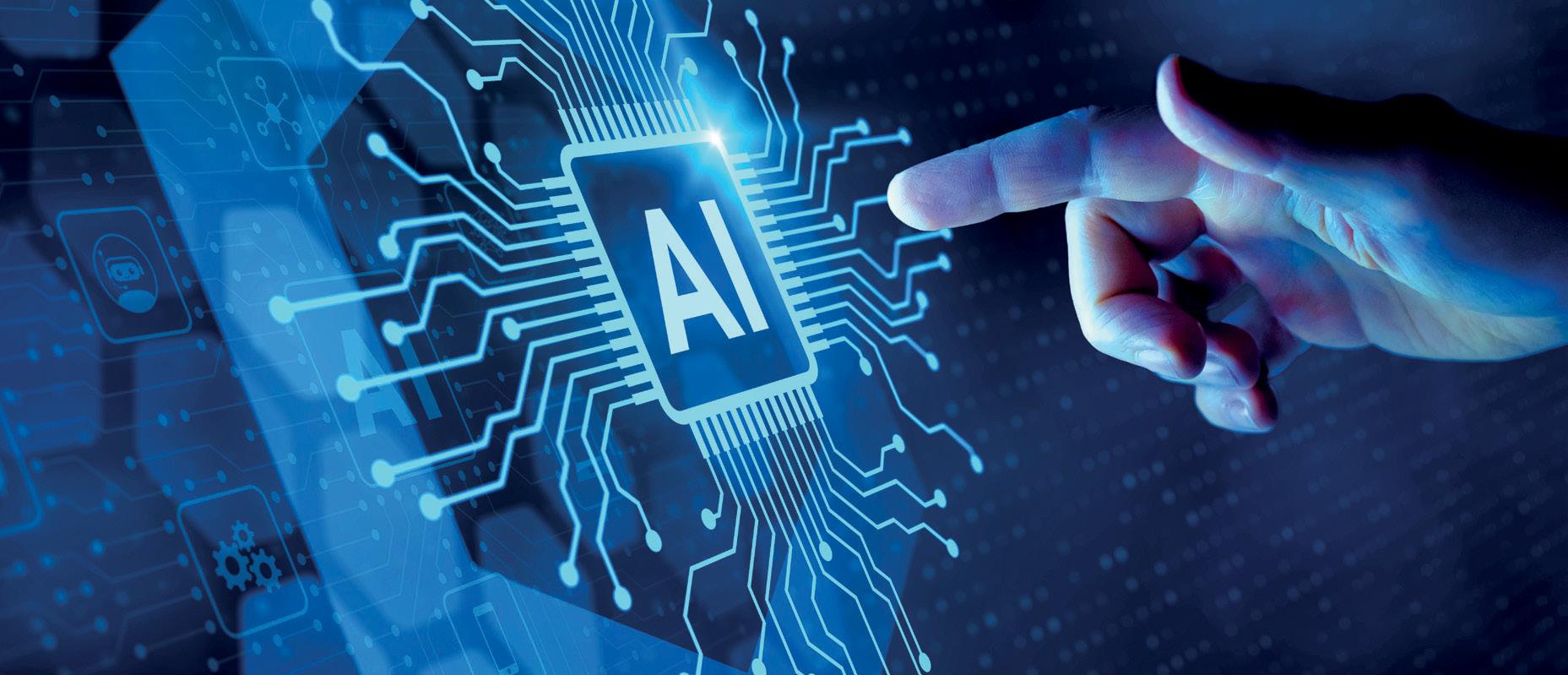
OPINION: Artificial Intelligence for Construction Quality
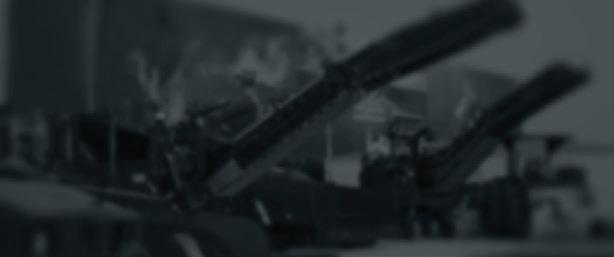
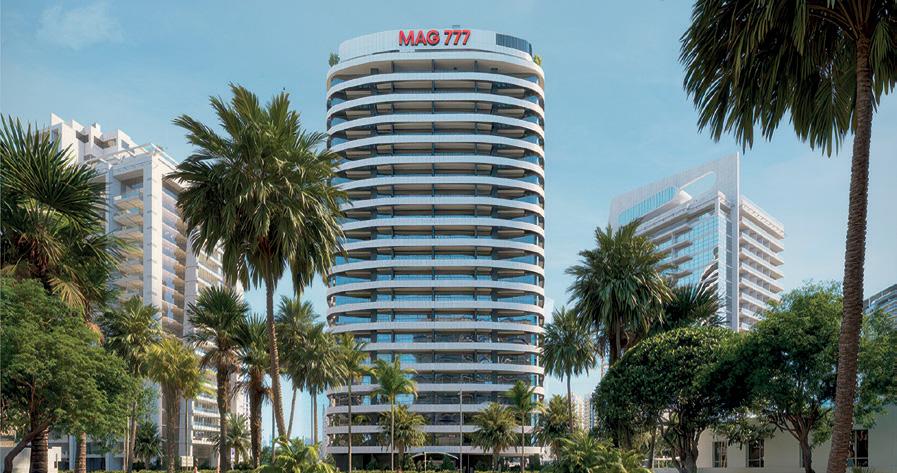
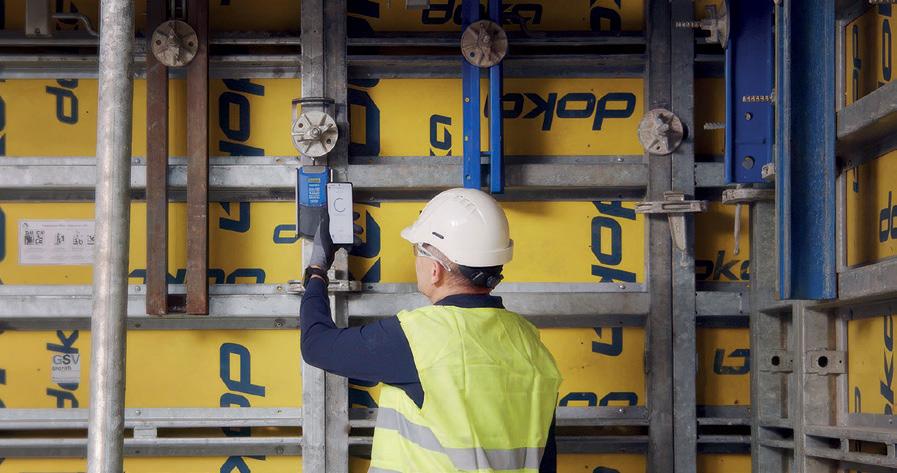

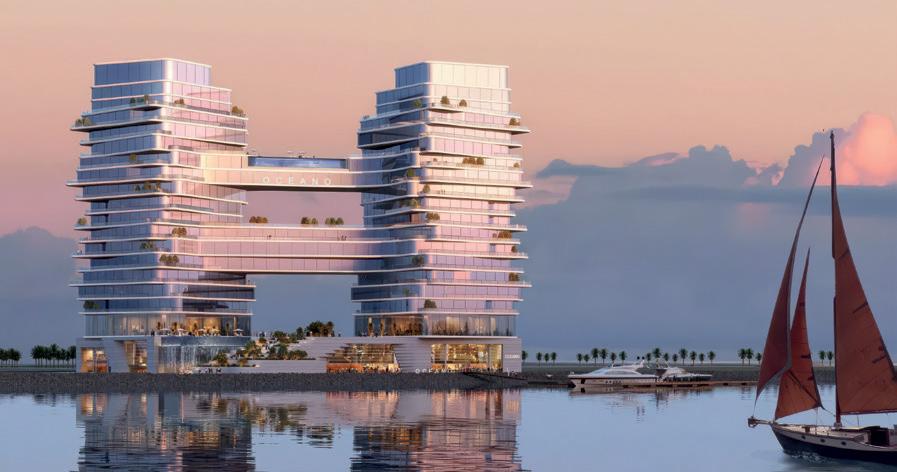

PROPERTY
MAG launches $95mn MAG 777 tower
The 22-storey building will offer 261 fully fitted units, featuring studios, one-bedroom, and twobedroom apartments designed to embody luxury and functionality
CONSTRUCTION
Doka introduces DokaXact Load & Pressure sensor
The real-time data from the new wireless DokaXact sensors ensure that concrete is poured as fast as possible while ensuring safety and quality
CONSULTANT
Egis to lead engineering and architectural consultancy for DEC Expansion
The project will feature sustainable infrastructure, renewable energy systems, and waste management strategies in line with global practices
PROPERTY
The Luxe Developers appoints China State Construction as the main contractor for Oceano Oceano is due for completion in 2026, with 206 units over 18 storeys
PROPERTY
London Gate and Franck Muller announce Franck Muller Vanguard Tower Billed as a luxury development set in the Dubai Marina, the new project aims to offer a luxury lifestyle experience, and has a planned handover by September 2027
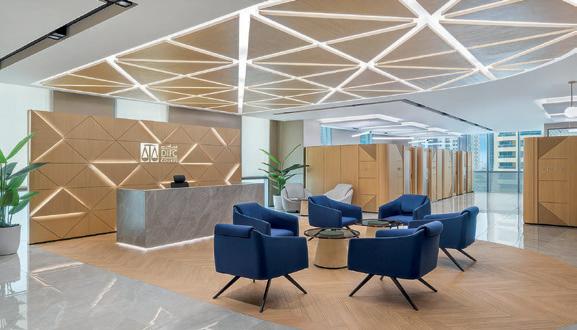
CONSULTANT
Designfit announces major re-brand

INFRASTRUCTURE
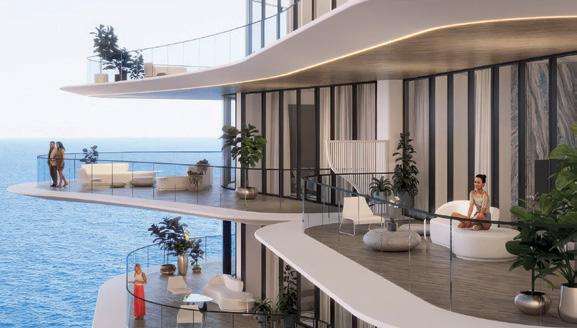
PROPERTY
RAK’s Manta Bay project officially launched
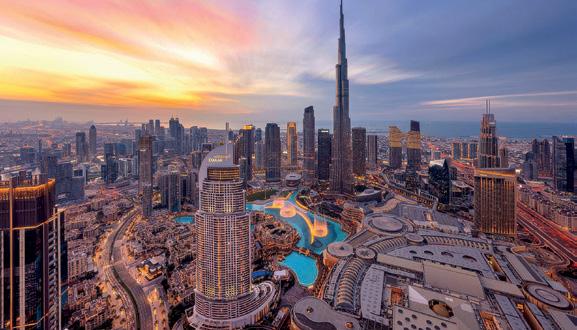
PROPERTY
Dubai real estate market sets US $38bn quarterly sales record
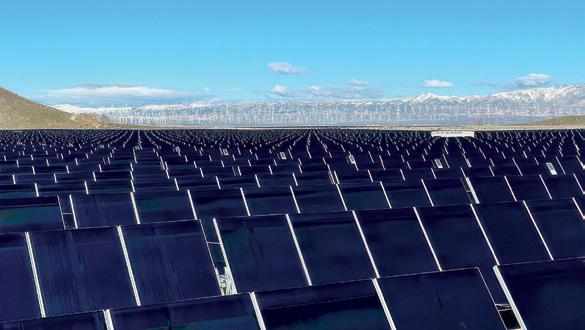
ADIO, ADAFSA and DMT announce tender for animal feed markets FINANCE
Masdar closes acquisition of
Rapid Access deal with Dingli takes boom lift offering to new level NEWS
NEW MACHINES, NEW OFFICES, NEW PROJECTS, NEW INITIATIVES – WE LOOK AROUND THE REGION AT WHAT’S NEW THIS MONTH
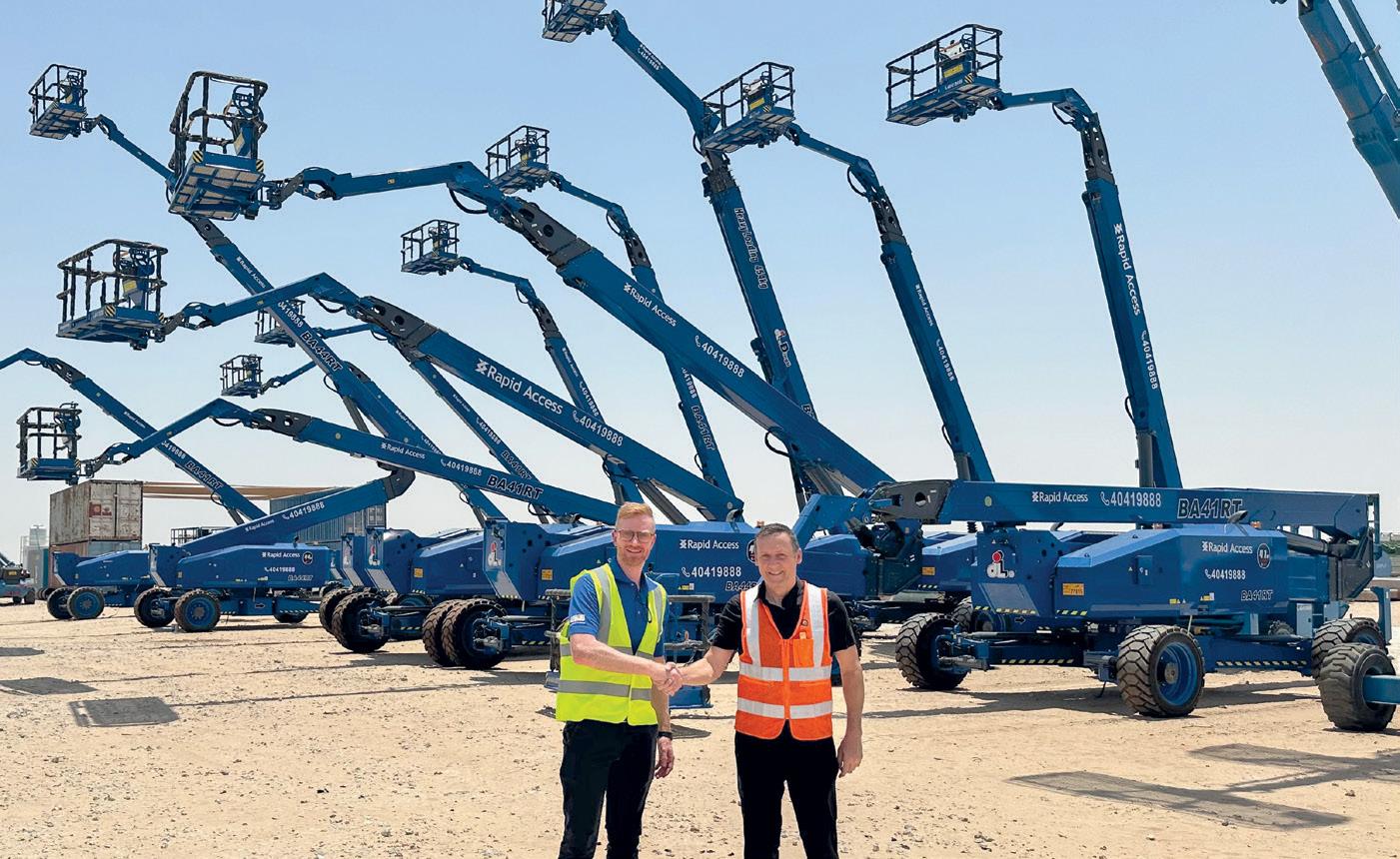
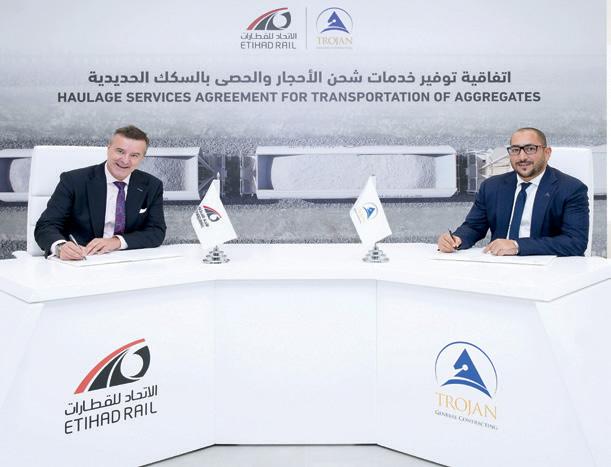
MYCRANE SURPASSES
Rapid Access LLC, the Middle East’s leading powered access rental company, has reinforced its commitment to the Oil & Gas sector in Qatar by expanding its fleet with a series of new diesel boom lifts. The company recently acquired advanced machines from Dingli, with working heights ranging from 28 meters to 44 meters, designed to meet the demanding operational requirements of oil and gas projects in the region. The new additions to the fleet mark a significant step for Rapid Access, as the company continues to prioritise its selection of equipment.
Martin Newton, Regional Operations Director at Rapid Access LLC, highlighted the company’s commitment to excellence, stating: “Our commitment to quality and innovation drives every decision we make when it comes to selecting new equipment for our fleet.
The recent acquisition of diesel booms from Dingli, designed specifically for the demanding conditions of the oil and gas sector, reflects our dedication to providing our clients with the best tools for the job. These machines not only enhance our capabilities but also set a new benchmark for reliability and performance in the industry.”
The expansion reflects Rapid Access’ strategy to stay ahead of market demands by investing in cutting-edge equipment tailored to the needs of the Oil & Gas industry. By offering machines specifically designed for Qatar’s challenging environments, the company aims to provide unparalleled service and support to its clients in this critical sector.
James Davis, Qatar Country Manager at Rapid Access LLC, emphasised the importance of this expansion for the company’s regional operations.
10,000 CRANES FOR FIRST TIME MYCRANE, the world’s first digital platform for crane rental, has achieved a significant milestone, with its inventory of lifting equipment surpassing 10,000 machines following recent supplier registrations. Launched in 2021, the platform aims to assemble the largest global fleet of cranes, a goal now realised. Speaking on the achievement, Andrei Geikalo, founder and CEO of MYCRANE, expressed pride in the company’s rapid growth. “When we launched MYCRANE, our goal of assembling the world’s largest fleet of cranes was rather ambitious, but that’s exactly what we have created,” he said.
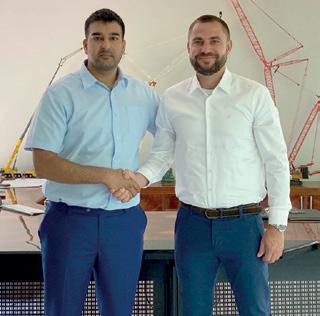
Etihad Rail Freight, a subsidiary of Etihad Rail has signed a Haulage Services Agreement with Trojan General Contracting. The partnership is said to reinforce Etihad Rail Freight’s commitment to enhancing connectivity and providing end-to-end supply chain solutions for efficiency and reliability across the UAE.
The company will provide first and last-mile services to transport aggregates from Trojan’s quarries in Ras Al Khaimah and Fujairah via its Al Ghail Dry Port rail terminal in RAK to the Industrial City of Abu Dhabi (ICAD) and Dubai Industrial City (DIC). Furthermore, Etihad Rail Freight will also offer secure storage services for Trojan General Contracting’s products at its Al Ghail Dry Port terminal in RAK, as well as at its terminals in ICAD and DIC.
Gunther J. Ferk, CEO of Etihad Rail Freight said, “Building on the momentum of our freight operations, we are focused on enhancing our service offerings to clients by integrating seamlessly with existing providers to deliver comprehensive end-toend solutions. This partnership aligns with our commitment to strengthening the UAE’s logistics infrastructure, while prioritising sustainability and safety.”
“By leveraging our National Rail Network and connecting key industrial hubs, we are reducing the reliance on road transport, removing trucks from the roads, and helping in minimising the environmental footprint. In doing so, we provide our clients with streamlined, efficient, and reliable transportation options, reinforcing Etihad Rail Freight’s role as a key facilitator of economic growth and connectivity within the UAE,” Ferk added
Ritchie Bros. latest
Dubai
auction attracts
a total of 1,000 bidders
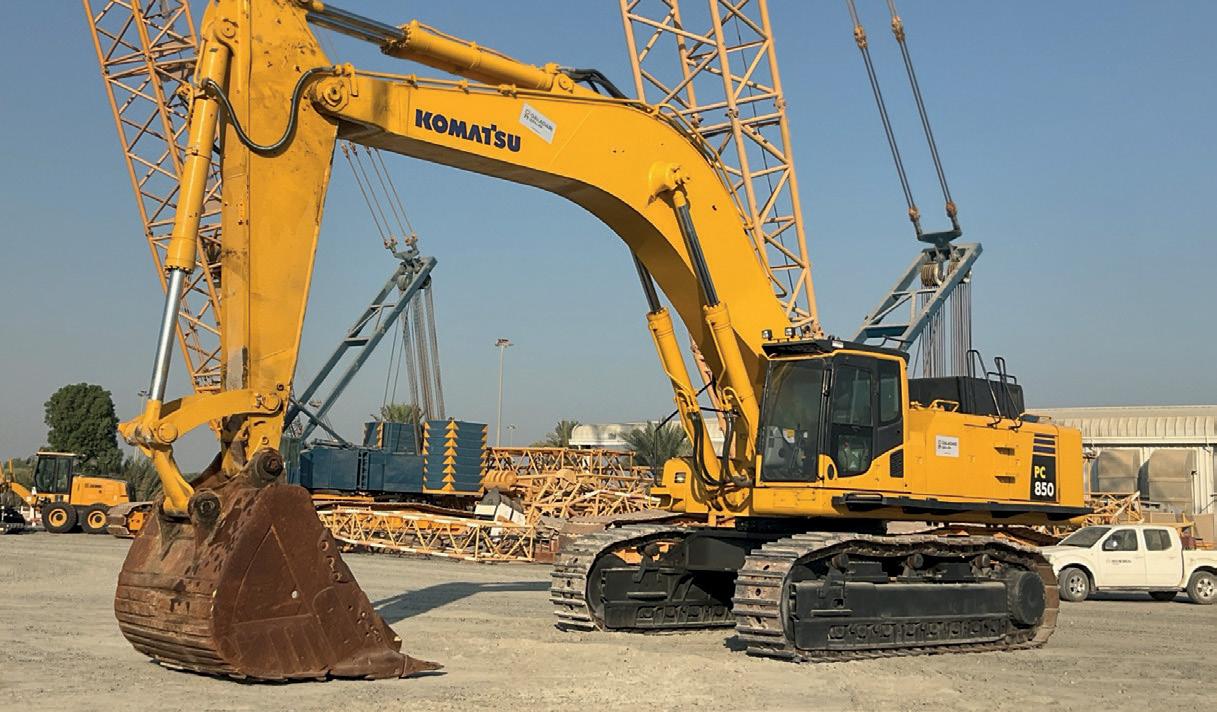
Ritchie Bros. concluded a highly successful online auction in Dubai on September 24-25, 2024, marking the end of a strong third quarter with significant global engagement. The auction drew 1,000 bidders from 69 countries, highlighting Ritchie Bros.’ extensive reach and solidifying its position as a trusted platform for industrial equipment. Of the bidders, 490 were from the UAE, while 510 participated from various international locations, illustrating the global appeal of the event and the platform’s ability to connect buyers across regions.
The auction saw a robust performance with 1,432 lots sold to a total of 384 buyers. Out of
CONTRACTORS
these buyers, 284 were based in the UAE, and 100 were international, showcasing both the wide reach and the trust buyers place in Ritchie Bros. for acquiring high-quality industrial equipment. This blend of local and international buyers reinforces the auction house’s reputation for well-curated sales events, drawing a diverse audience eager to engage in the market.
Leading the bidding numbers was the UAE with 490 participants, followed by the USA with 122, Canada with 90, Saudi Arabia with 34, and the United Kingdom with 21 bidders. Several highvalue equipment sales were recorded during the auction.
DUTCO APPOINTED AS MAIN CONTRACTOR FOR GRAN MELIÁ HOTEL DUBAI JUMEIRAH
ASB Hospitality has appointed Dutco Construction as the main contractor for the Gran Meliá Hotel Dubai Jumeirah. Set to be the first beachfront property under the Gran Meliá brand in the UAE, the resort will be a addition to Dubai’s luxury hospitality sector. Located on the prime headland of Port De La Mer in Jumeirah, the development spans a plot totalling 31,066sqm, and will have a gross floor area (GFA)
of 42,522sqm and built-up area of 88,909 sqm. The resort will offer views of the Arabian Gulf from three sides of the hotel and Dubai skyline.
“The Gran Meliá Hotel – Dubai Jumeirah represents more than just another hotel; it’s a lifestyle destination, born from the strategic partnership between ASB Hospitality and Meliá Hotels International” said Heddo Siebs, CEO of ASB Hospitality.
18th - 21st
Machinery Exchange agrees disti deal for Rokbak

Rokbak has strengthened its presence in Zimbabwe’s growing construction and mining sectors by appointing Machinery Exchange as its official dealer in the country. A subsidiary of the Industrial Exchange Group (IEG), Machinery Exchange will provide full sales and service support for Rokbak’s articulated haulers, catering to the increasing demand driven by infrastructure and mining projects across Zimbabwe. Machinery Exchange, celebrating 70 years of
NEW BRANDS
CELEBRATE UNITED DIESEL’S 50TH
operations in 2024, is wellestablished in Zimbabwe’s earthmoving equipment sector, with its headquarters in the Zimbabwe capital of Harare and additional branches in Bulawayo and Hwange.
Through this partnership, the company will now be able to offer Rokbak’s popular RA30 and RA40 rigid dump trucks, known for their reliability and performance in demanding environments.
Irene Khumalo, IEG’s Head of Marketing and PR, commented on the new partnership: “The
collaboration with Rokbak will help us meet the growing demands of our customers in the mining and construction industries. It further solidifies our position as a leading earthmoving equipment supplier in the region.” Zimbabwe’s construction industry is experiencing significant growth, with major projects underway in areas such as dam construction, road rehabilitation, and urban development.
The country’s mining sector also holds vast potential, with local resources including diamonds, gold, lithium, chrome, and iron ore.
This growth has been bolstered by increased foreign investment, particularly from China and India, which is expected to drive demand for reliable machinery like Rokbak haulers.
“Mining and infrastructure are the backbone of Zimbabwe,” explained Chetan Samji, IEG’s Commercial Manager. “We see strong opportunities for Rokbak trucks in the near future.”
MACHINERY CAT AND TRIMBLE TO CONTINUE ON
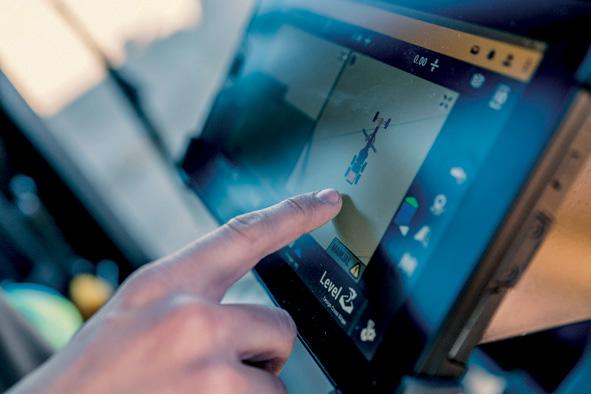
Caterpillar Inc. and Trimble have announced an extension of their longstanding joint venture, Caterpillar Trimble Control Technologies (CTCT), aimed at expanding the distribution of grade control solutions within the construction sector. This renewed agreement focuses on accelerating innovation and increasing the adoption of advanced grade control technologies among customers.
With the updated partnership, Caterpillar and Trimble are set to broaden their industry reach, offering interoperable grade control solutions through a flexible platform accessible to Caterpillar, Trimble, and other technology providers and equipment manufacturers. This collaboration opens up new possibilities for both companies to develop innovative offerings and explore additional geographic and industry markets, ultimately providing customers greater access to grade control technology through a wider range of channels.
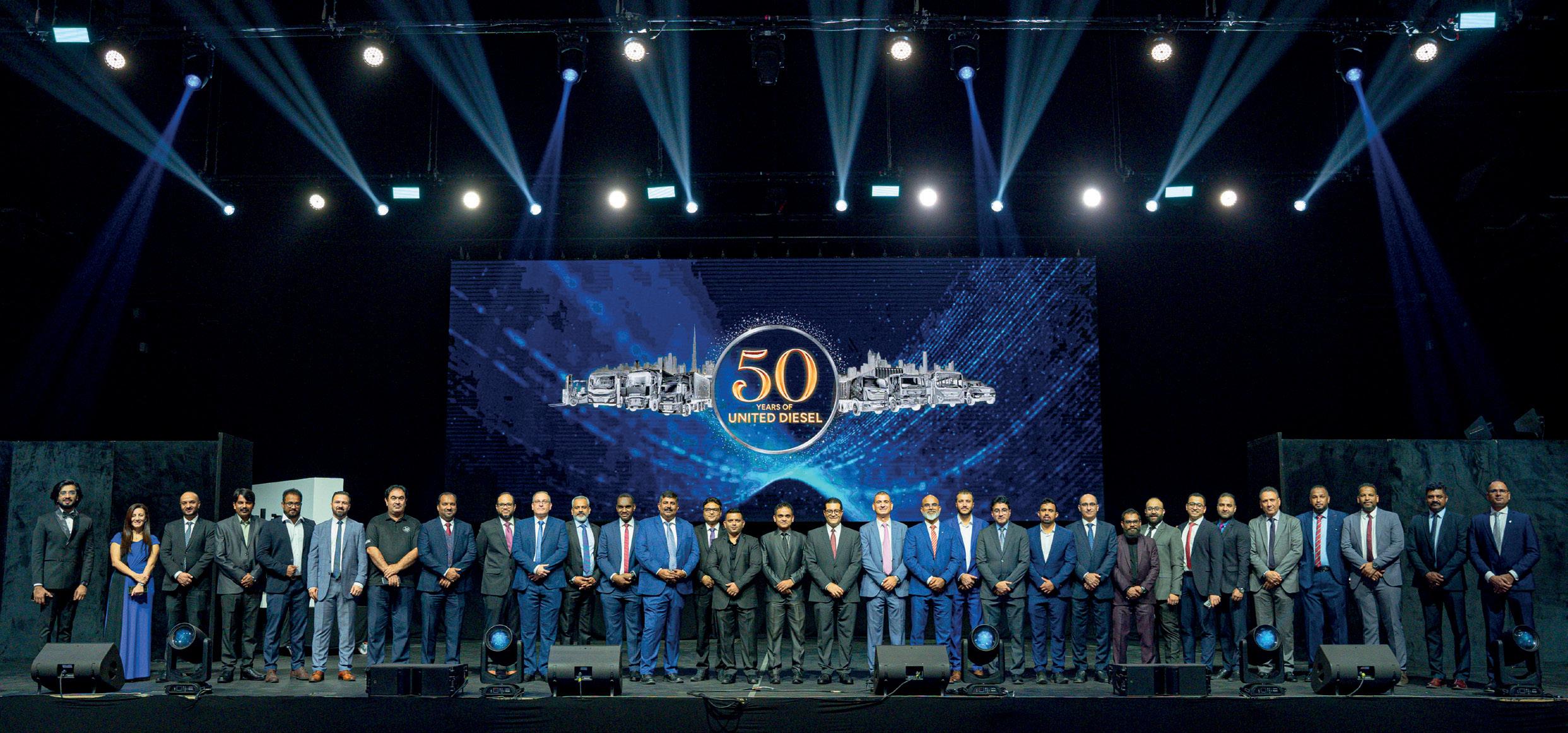
United Diesel celebrated its 50th anniversary with a grand gala dinner last month and announced several new brands will be joining its ranks. The event, highlighted United Diesel’s enduring success and its plans for a smarter and greener future. It unveiled three new brands — Yutong Trucks, Starkgen, and Chinese company CHL.

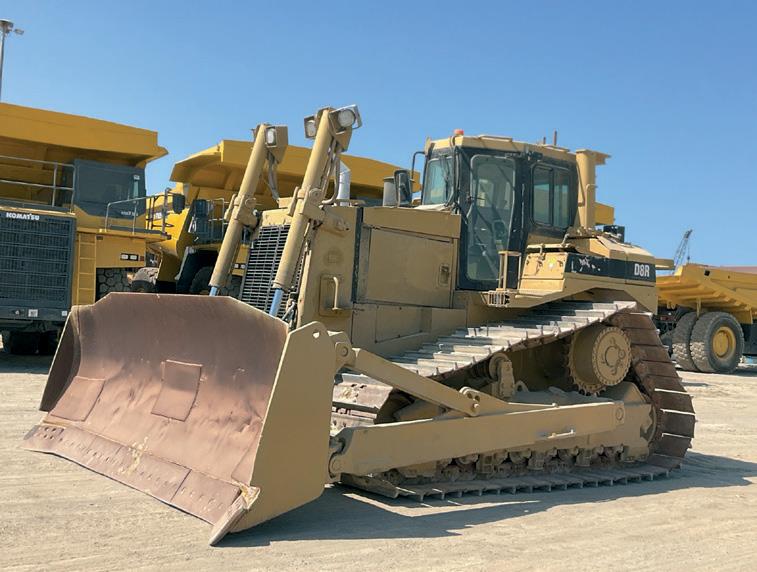
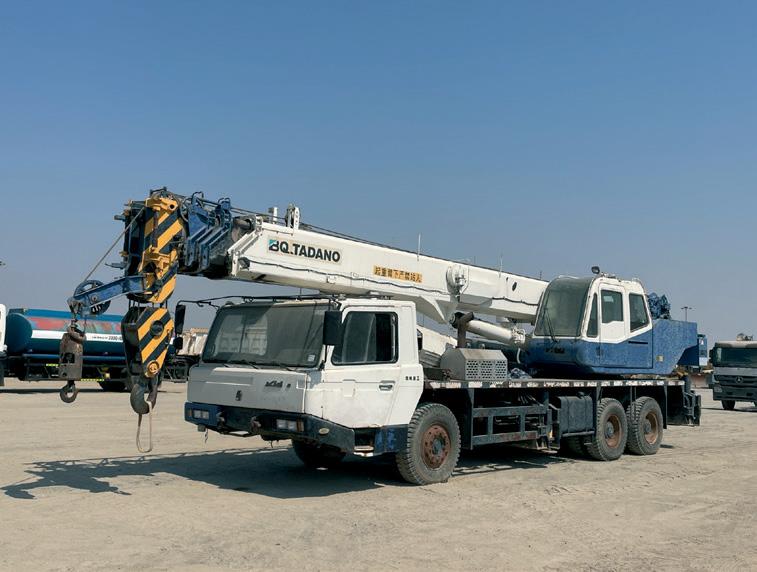

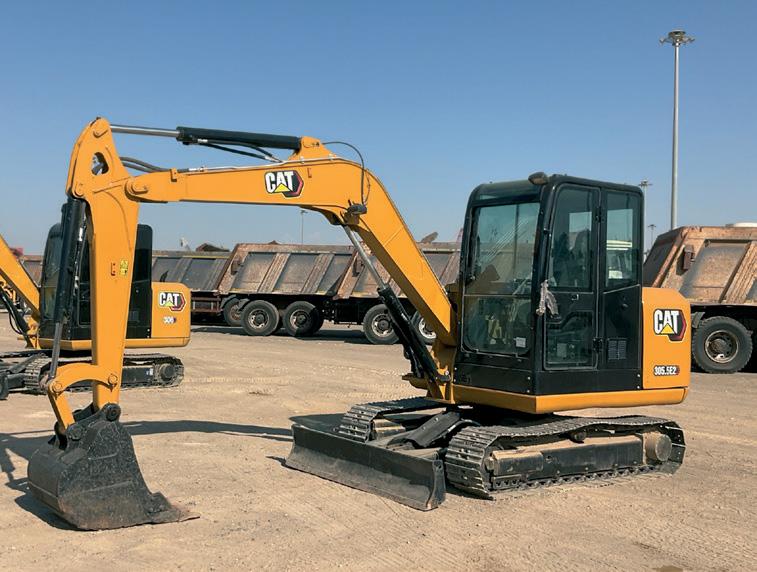


Personal Inspections: December 5-10 Address: Junction 9Gate 8 - Jebel Ali Free zone - Dubai - United Arab Emirates
+971 4 812 0600
rbauction.com/dubai
Gargash unveils LiuGong LD36D Bulldozer
Gargash, in partnership with LiuGong, has launched one of the most powerful bulldozers in the world into the Middle East market, the LiuGong LD36D.
This 40-ton behemoth, inspired by Dressta’s renowned heavy machinery designs, is engineered for demanding projects in construction, mining, quarrying, and infrastructure development, and promises to deliver exceptional performance and durability.
Equipped with a robust Cummins engine, a giant shank ripper, and a Semi-U blade boasting a capacity of 9.6 cubic meters, the LD36D is designed to move large quantities of heavy materials with high tractive power.
Its versatility is underscored by its capability to handle various
CONTRACTORS
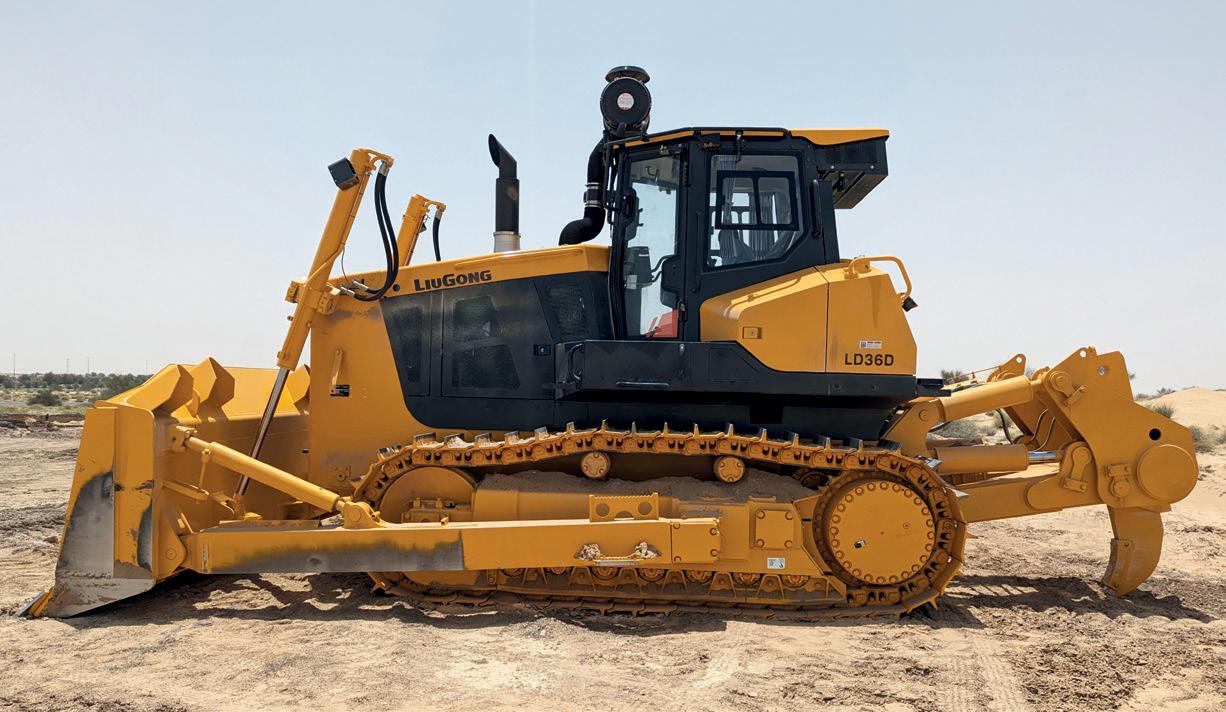
applications, from land clearing and rough grading to towing other heavy equipment and supporting excavation work.
The LiuGong LD36D bulldozer is also ideal for tasks such as spreading soil, shallow digging and
BRIGHT ACCORD AWARDED $108MN CONTRACT

Jubail Island Investment Company (JIIC) has awarded the construction contract for the Jubail Town Centre in Souk Al Jubail. The $108mn contract was awarded to Bright Accord General Contracting Company and comprises four office buildings and two residential buildingsJubail Terraces buildings 7 and 8.
Jubail Town Centre is a familyfriendly destination offering a modern, vibrant environment that includes well-being, connectivity, leisure, retail, and commercial services. With direct access to the E12 Highway, the Town Centre includes commercial properties, low-rise residential buildings, green spaces, walkways, and
seating areas, encapsulating the essence of community life on the island, JIIC said in a statement.
It will feature outdoor spaces and parks, a mosque, medical clinic, nursery, supermarket, fitness centres, over 40 retail outlets, 5-star rated F&B pavilions, campuslike offices, wellness hubs, and a community centre and a beach club.
Jubail Terraces offers apartments including studios, one, two, and three-bedroom units, as well as duplexes. Retail spaces have been designed to create an engaging shopping environment for both the local community and visitors.
“JIIC is committed to delivering high-quality developments,” said the developer.
ditching, dozing rocks, clearing quarry floors, and assisting scrapers in loading operations.
Built for resilience and heavyduty work, the LiuGong LD36D buldozer is engineered to withstand the region’s frequently extreme
and harsh working conditions. Its introduction by Gargash and LiuGong signals an exciting opportunity for Middle Eastern industries and contractors looking for high-performance, reliable equipment to tackle complex and large-scale projects. Whether it’s small- or large-scale construction, foundation laying, or mining and quarrying, the LiuGong LD36D promises to be an invaluable asset for businesses across the region, bringing power, precision, and unparalleled reliability to the field.
“This heavyweight is great for moving heavy materials from one area to another with its high tractive power. Built tough, the Liugong LD36D is made for getting the job done no matter how difficult,” said the two firms in a statement.
Uriquip hails success via its trading platform
Just eight months after its launch, Uriquip, an international equipment trading company founded by industry veteran Uri Toudjarov, has become a multi-milliondollar success. The company’s swift rise is credited not only to Uri’s extensive experience and reputation in the construction sector but also to the cutting-edge technology behind its online sales platform, powered by Krank.
Uriquip’s impressive early success includes landmark deals such as the sale of a reconditioned 650-ton crawler crane and two 500-ton all-terrain cranes to clients in Latin America, as well as the delivery of a new 550-ton all-terrain crane to a customer in Africa. With an inventory of over 200 cranes, including a 2016 Liebherr LR1600 and a 2024 Bullit, Uriquip has become
a major player in the international crane market. The company’s stock, located in Houston, Texas, ranges from 40- to 130-ton cranes, with several RT1100 rough terrain cranes among its offerings.
While Uri’s deep industry knowledge and network are key to the company’s rapid growth, much of the success also comes down to the advanced technology that powers Uriquip’s online trading platform. The platform allows the seamless marketing of used equipment, helping sellers reach buyers.


TMC550: GROVE’S NEW TRUCK CRANES ARRIVE IN DUBAI
Manitowoc recently hosted an exclusive launch event at its regional headquarters in Dubai, debuting a new lineup of Grove truck-mounted cranes tailored for emerging markets. The gathering drew industry leaders and customers from across the Middle East and Africa, marking a significant milestone in Manitowoc’s expansion efforts.
The company showcased the Grove TMC550 and introduced two additional models: the Grove TMC250 and the Grove TMC750. These models, designed specifically
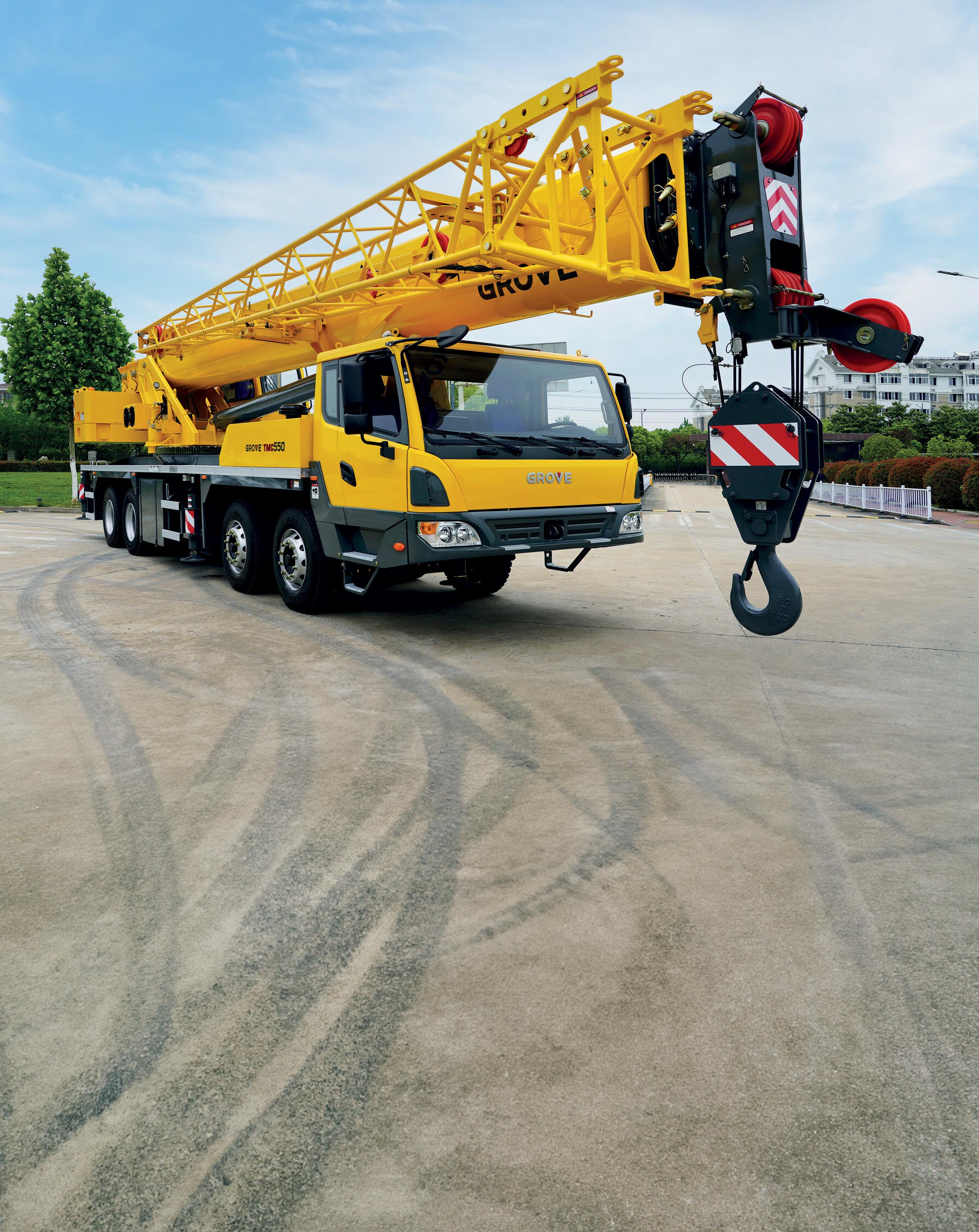
for markets in the Middle East, Africa, and Latin America, highlight Manitowoc’s commitment to offering high-performance, marketspecific solutions.
Each crane in the lineup is equipped with advanced technologies that boost efficiency, productivity, and environmental compliance, reinforcing Manitowoc’s role at the forefront of lifting solutions. Supported by Manitowoc’s extensive regional network, the cranes come with comprehensive aftermarket support that includes parts, service, training, and maintenance.
Andrew Youssef, General
Manager of Manitowoc in the Middle East, Africa, and CIS, remarked, “As we expand across emerging markets, these new truck cranes enhance our existing offerings by adding models that complement our product portfolio. The Grove brand has an excellent reputation, and adding these truck cranes has allowed us to provide a more comprehensive range of solutions to our customers.”
The TMC550, a 55-ton capacity model with a 45-meter telescoping main boom, targets a high-performance market segment demanding reliability and robust support. Meanwhile, the TMC250
and TMC750 offer capacities of 25 tons and 75 tons, respectively, with boom lengths reaching 43 meters on the TMC250 and 48 meters on the TMC750. All models are powered by Cummins engines with ECO Mode for reduced engine speeds and fuel savings, and each comes with optional luffing jibs for additional versatility.
Grove’s distribution network has already facilitated sales of the TMC550 in key markets such as the UAE, Saudi Arabia, Qatar, and Latin America, showcasing strong demand for this latest addition to Manitowoc’s lineup.
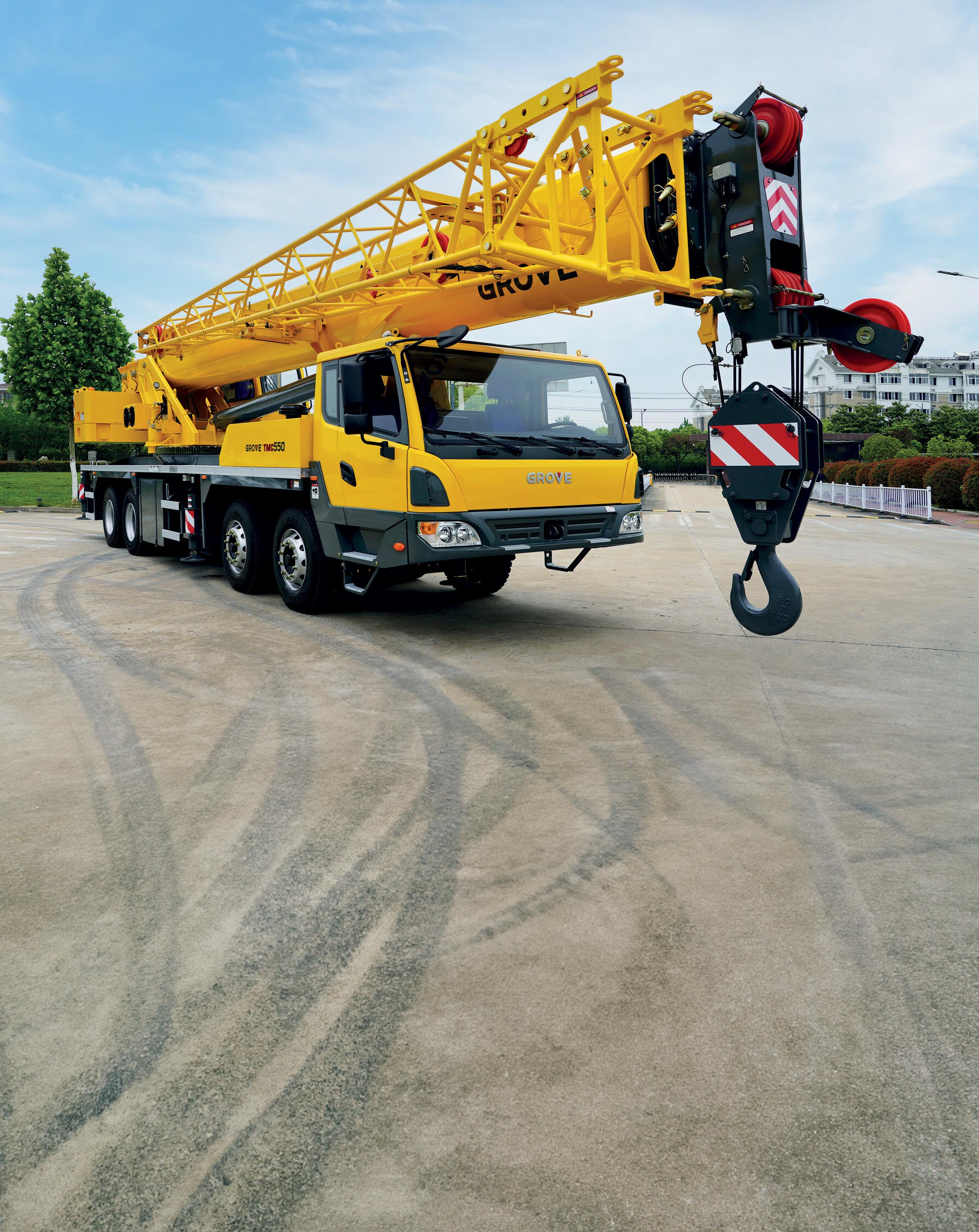
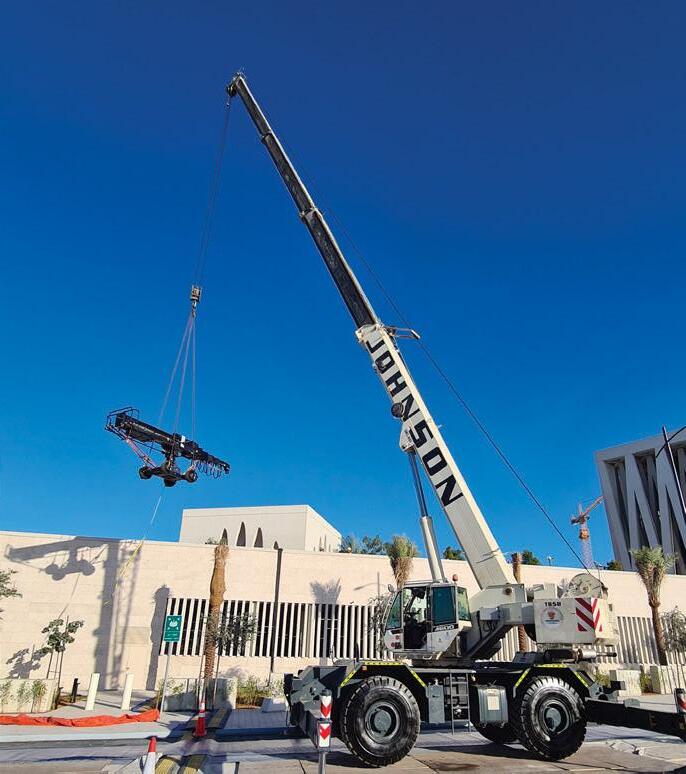
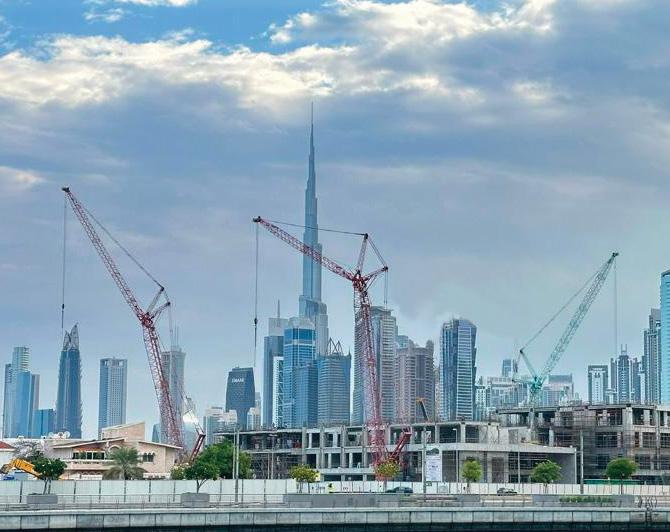
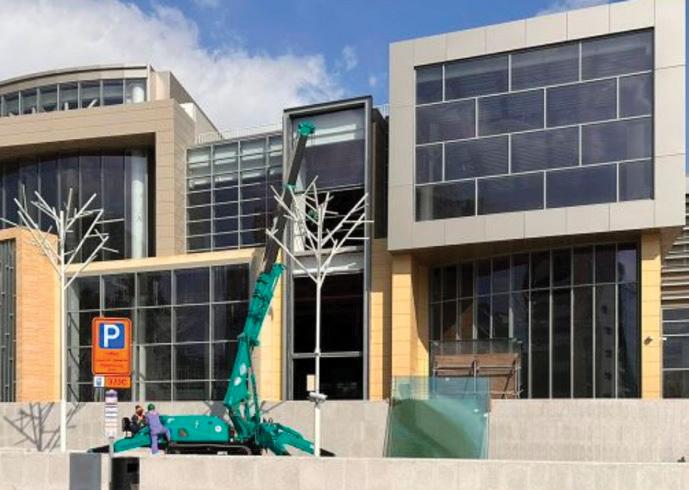
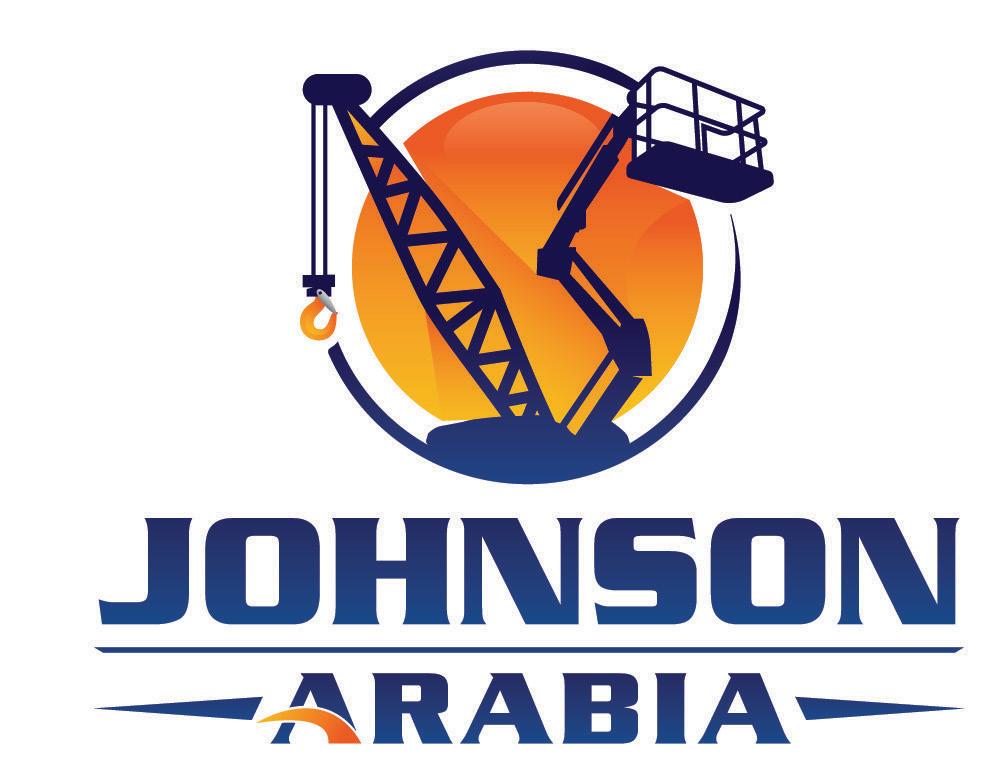
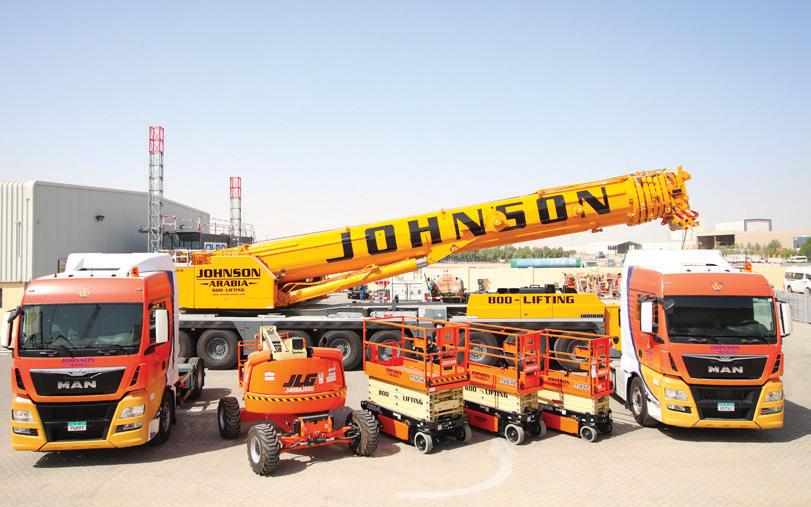

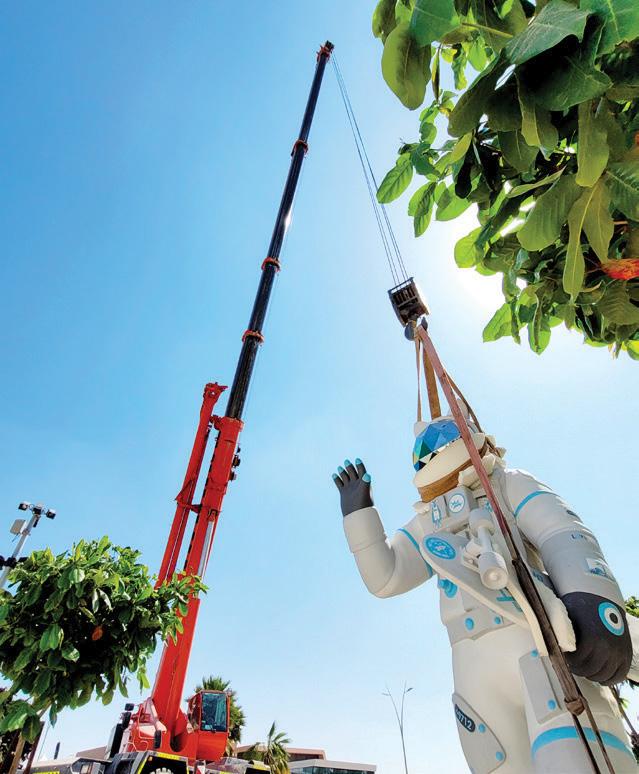
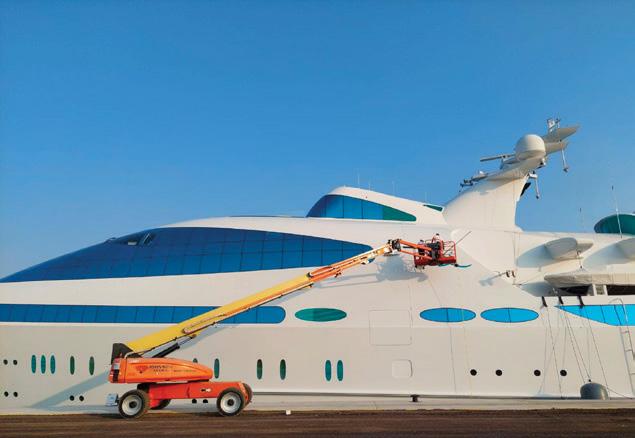



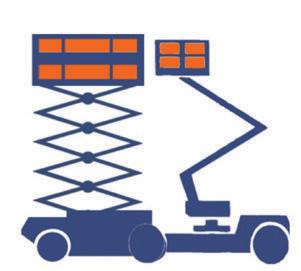
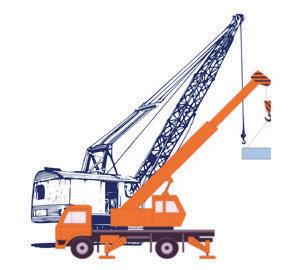
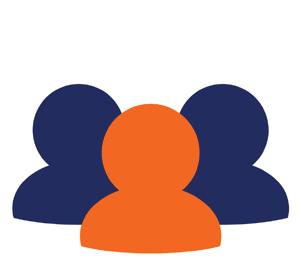






SINOBOOM AND THE GRAND EXPANSION
REGIONAL HEAD ALISTAIR PALACIOGLU TALKS
SINOBOOM’S STRATEGIC EXPANSION AND DEEPENING PARTNERSHIPS IN THE MIDDLE EAST
With an extensive background in the access equipment industry, Alistair
Palacioglu is a wellrecognised figure in the Middle East. His recent appointment at the helm of Sinoboom Middle East FZE marks a significant milestone for both his career and the company as it continues to strengthen its position across the region. Effective from 1st July 2024, Palacioglu’s new role at Sinoboom is designed to drive growth and foster meaningful partnerships. Sitting down with CMME, Palacioglu discusses his plans for Sinoboom, the company’s commitment to customer-focused service, and his multi-faceted approach to building long-term partnerships across the Middle East.
Reflecting on his new role, Palacioglu expresses enthusiasm for the opportunity to guide Sinoboom’s development in the Middle East and Africa.
“I’m honoured to take on this role with Sinoboom, and I’m excited about the opportunity to lead the company’s growth in the MEA region,” he shares. “What attracted me to Sinoboom is their forwardthinking approach and their commitment to product range, innovation, quality, and customer-centricity. Having spent many years within the access industry, I’ve seen how critical these factors are for success in the equipment industry, especially in rapidly
evolving markets like the Middle East and Africa.”
As infrastructure projects drive demand for highperformance, sustainable equipment, Palacioglu recognises the importance of building a robust distribution network that can provide localised support. “My vision for leading Sinoboom’s growth here is to build a strong distribution network and ensure that we offer excellent aftersales support and service, which is key to long-term success,” he says. This approach aligns with his broader strategy to engage closely with local partners and create enduring relationships based on mutual trust.
The Middle East, particularly the countries within the Gulf Cooperation Council (GCC), continues to invest heavily in large-scale infrastructure projects, including smart cities, mega-events, and ongoing ultra-urbanisation. This trend is driving demand for modern access equipment that can support large, complex construction needs, he says.
“Sinoboom already offers some of the largest boom solutions that cater specifically to the region’s demand for high-reach, robust, and versatile access equipment. We will ensure that our product range includes machines capable of working in challenging environments such as high-rise construction, oil and gas facilities, and large infrastructure projects. We are also enhancing local inventory levels and parts availability to meet urgent project needs.”
Drawing on his vast experience, Palacioglu is acutely aware of the evolving trends in the Middle East access equipment market, each presenting unique opportunities for Sinoboom.
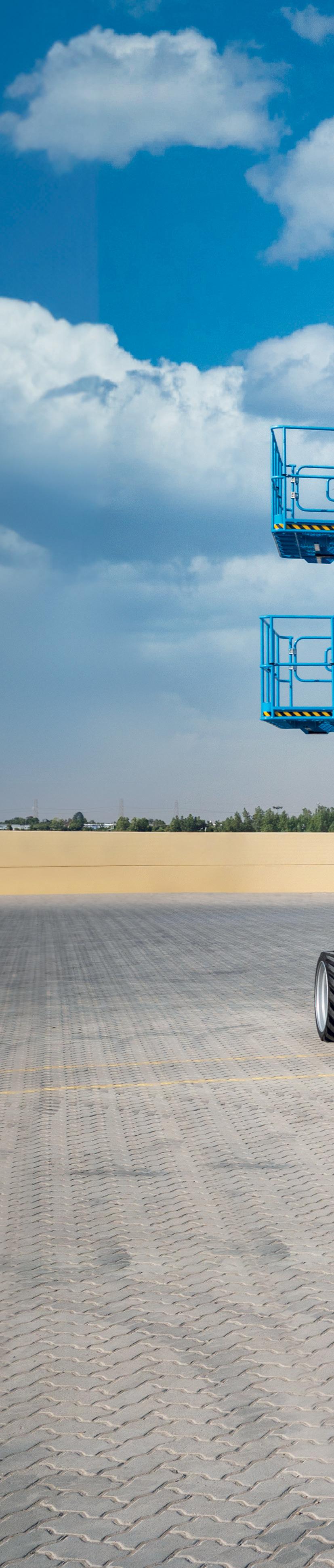
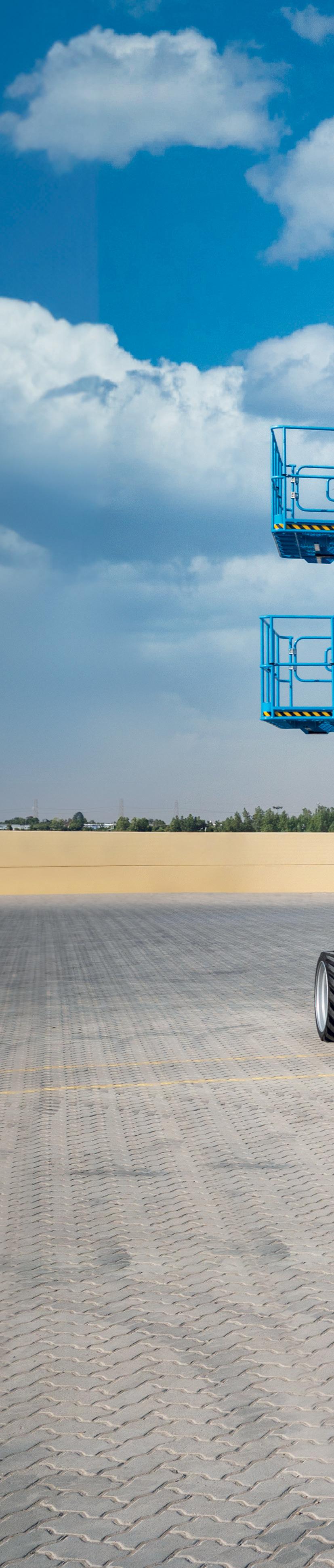
Sinoboom is investing heavily in infrastructure that supports its clients and partners, and has opened a localised service hub, parts depots and a dedicated training centre as part of a longterm commitment to the region.

“ We are not just here to sell equipment; we are dedicated to building strong, lasting relationships founded on trust and mutual success”
“Growth in construction and infrastructure projects across the GCC is a significant trend we’re focusing on,” he explains. “We aim to offer some of the largest booms and rugged terrain scissor lifts specifically designed to support the demands of ultra-modern, high-rise construction and complex projects across oil and gas facilities.” By maintaining substantial local inventory, Sinoboom can quickly deliver machines for time-sensitive projects, demonstrating their commitment to supporting large-scale development in the region.
Increased focus on safety and compliance is another critical trend. As construction standards and safety regulations strengthen, companies need equipment that meets both operational needs and compliance requirements. “Sinoboom is committed to meeting and exceeding international safety standards,” Palacioglu states. “We will continue to provide fully compliant, certified equipment and comprehensive training programs through IPAF-certified training centres.” With features like telematics and real-time monitoring, Sinoboom’s equipment can help clients meet regulatory standards and maintain high safety levels on job sites. The shift toward electrification and sustainability is equally vital as regional governments push for greener construction practices.
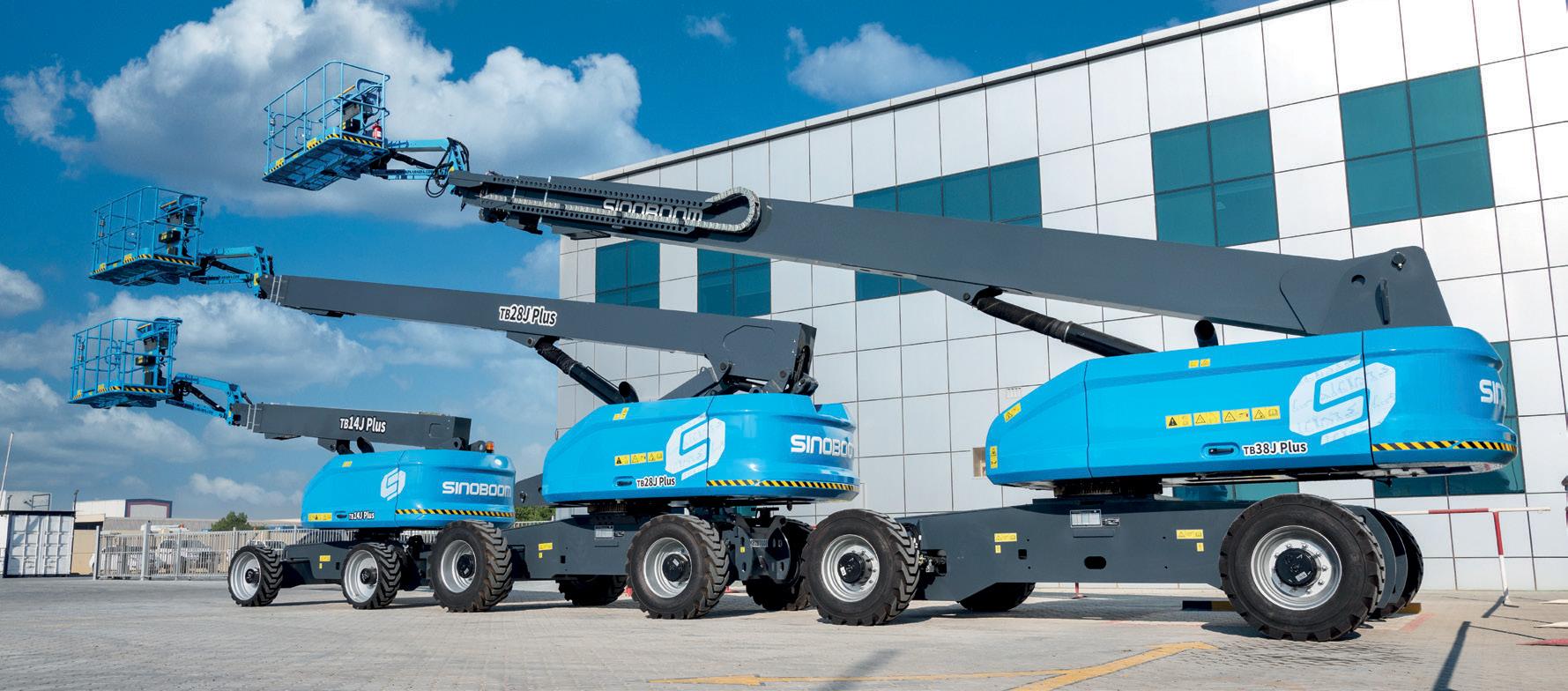
“Our electric and hybrid aerial work platforms align with the region’s growing sustainability goals,” he says. “Sinoboom’s range is designed for reduced environmental impact, offering zero-emission operation and quieter machinery, which is ideal for urban settings and projects that need to meet stricter environmental standards.”
Sinoboom’s R&D department remains focused on increasing both the performance and energy efficiency of its electric products, helping Middle Eastern companies adopt more sustainable equipment solutions without sacrificing functionality.
Digitalisation is another rapidly growing trend, with telematics and IoT integration
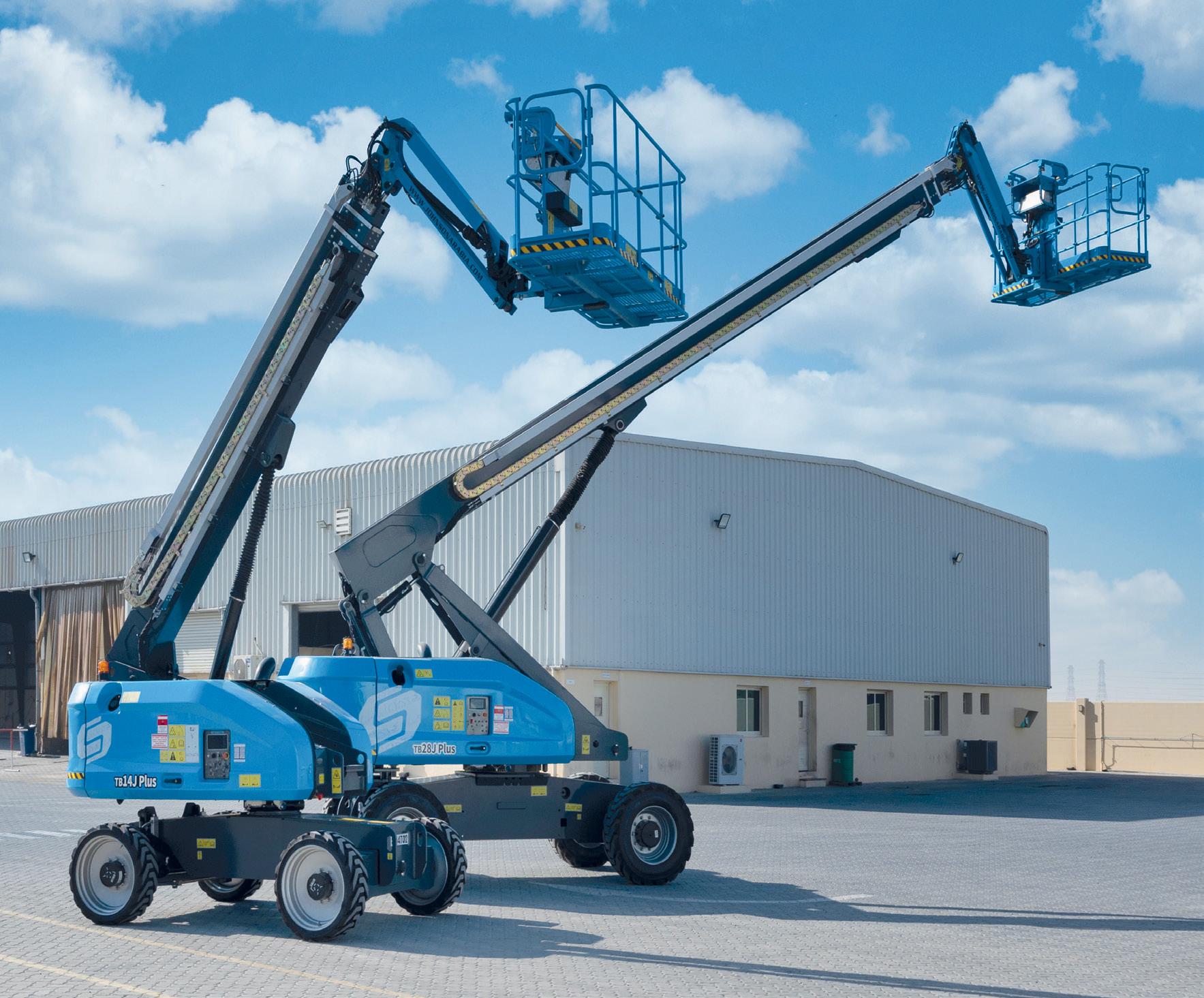
becoming essential for fleet management, predictive maintenance, and cost efficiency.
“Sinoboom is actively integrating telematics and IoT solutions into our product range, providing advanced monitoring systems that allow customers to track performance, location, and maintenance needs in realtime,” Palacioglu explains. By embracing digital tools, Sinoboom supports clients in reducing operational costs and optimising equipment uptime, positioning itself as a forward-thinking partner in the region.
Finally, Palacioglu highlights the market’s need for reliable, localised support to maintain equipment availability and minimise downtime. “To meet this demand, Sinoboom is actively expanding our local team and our distribution and service networks across the Middle East,” he says. Sinoboom’s ongoing investments in regional parts depots, training centres, and support hubs reflect its commitment to swift and comprehensive customer support.
With his deep understanding of the powered access sector and the Middle East and Africa market, the former JCB executive brings a nuanced approach to strengthening Sinoboom’s partnerships with key stakeholders. His strategy begins with a tailored engagement plan, which includes working closely with local dealers, contractors, and distributors to ensure that Sinoboom’s partnership strategy meets the specific needs of each market. “I plan to work closely with existing and potential local partners to ensure that our strategy aligns with their unique market needs,” he explains. By focusing on collaboration and adaptability, Palacioglu believes Sinoboom can create solutions that resonate with the region’s demands.
Another pillar of his strategy is building trust through consistent support. “Stakeholders value reliable partnerships. To build trust, I will focus on providing consistent support in terms of product availability, competitive pricing, and aftersales services,” he shares.
Strengthening Sinoboom’s aftersales network through prompt technical support and comprehensive maintenance agreements is essential, demonstrating Sinoboom’s commitment to delivering long-term value across the region.
For Palacioglu, open communication is the cornerstone of strong relationships. He aims to establish regular touchpoints with key decision-makers to ensure transparency and responsiveness. “I believe in facilitating open communication channels to build strong relationships,” he notes. “Through active listening and regular check-ins, we can better understand their needs and challenges.”
Leveraging local expertise within Sinoboom’s regional teams is another key aspect of Palacioglu’s strategy. By empowering teams with market knowledge and decisionmaking power, Sinoboom can respond more swiftly to diverse customer needs. “This localised approach allows us to be more agile and adaptive, providing stakeholders with quick, relevant responses,” he explains.
Long-Term Commitments
Palacioglu is also focused on deepening Sinoboom’s long-term presence in the Middle East through strategic initiatives, including hosting regional events and workshops. By organising dealer conferences, product showcases, and training workshops, Sinoboom can foster collaboration and strengthen its relationships with local stakeholders. “These events will not only showcase our products but also provide valuable networking and learning opportunities for our partners,” he says.
Sinoboom’s alliances with government authorities and industry bodies further demonstrate its commitment to the region. By engaging with key regulatory entities, Sinoboom ensures compliance with local standards and participates in major infrastructure projects.
“Strategic alliances with government and industry bodies are essential,” says Palacioglu. “They allow us to align with local regulatory requirements and support largescale regional initiatives.”
To solidify its commitment, Sinoboom is investing heavily in infrastructure that supports its clients and partners. Palacioglu highlights recent investments in a localised service hub, parts depots, and a dedicated training centre as a reassurance of Sinoboom’s long-term dedication. “These investments underscore that Sinoboom is fully committed to growing alongside its partners,” he notes. “We’re not just here for the short term; we’re invested in supporting our clients well into the future.”
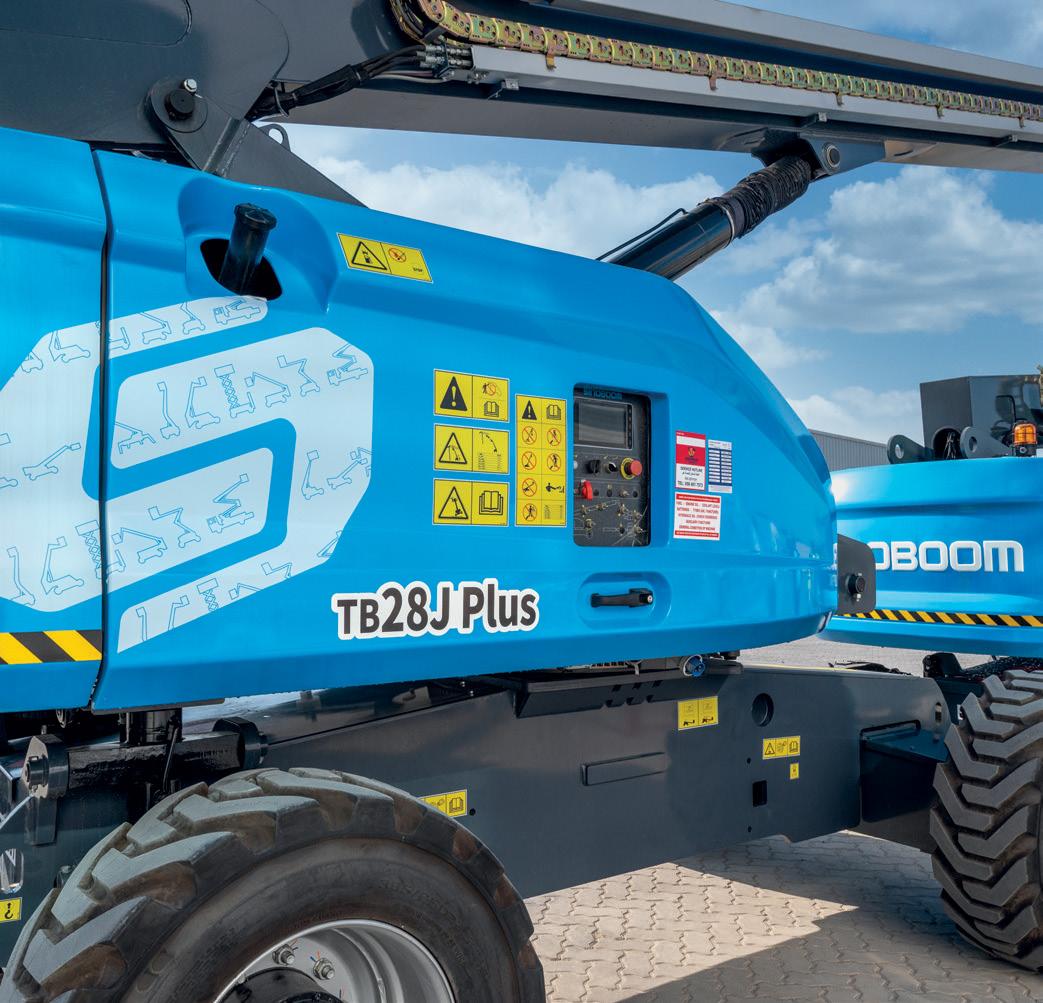
regional demands for sustainability. “Our electric booms and scissor lifts not only meet zero-emission requirements but also offer quieter operation, which is critical in urban and indoor projects,” he adds.
As Palacioglu embarks on this new chapter, his focus remains on building relationships founded on trust and collaboration. “We are not just here to sell equipment; we are dedicated to building strong, lasting relationships founded on trust and mutual success,” he emphasises. Sinoboom’s commitment to understanding customer needs and delivering relevant, efficient solutions is central to its strategy in the Middle East.
Alistair Palacioglu says he is deeply honoured to lead Sinoboom’s efforts in the region, a company he describes as taking a forward thinking and committed approach to the powered access sector.
Palacioglu’s extensive experience in the region is also shaping his approach to positioning Sinoboom’s products effectively in the Middle Eastern market. He highlights Sinoboom’s focus on high-reach booms, rough-terrain scissor lifts, and telehandlers, which are essential for the large-scale projects and challenging environments often encountered in the region. “Our machines are designed to be robust, durable, and capable of handling the harsh environments often found in the Middle East,” he explains.
Sinoboom is also a leader in electrification, with an extensive range of electric and hybrid access platforms that meet growing
Through a multi-faceted approach that includes tailored local engagement, consistent support, transparent communication, and strategic alliances, Palacioglu is confident that Sinoboom will set new standards in the access equipment market. “Our focus is on understanding your needs and delivering solutions that drive efficiency and growth in your operations,” he says. “Together, we will set new benchmarks in the market, ensuring that our customers and partners receive unparalleled support and service.”
With Palacioglu at the helm, Sinoboom is poised to grow its presence in the Middle East by creating a customer-first, long-term approach that resonates with the region’s evolving needs. “I intend to demonstrate Sinoboom’s long-term commitment to the region, and our client stakeholders can be reassured that Sinoboom is fully dedicated to growing alongside them in the long-term.”

“Merlo telehandlers incorporate unique design elements like inhouse manufactured axles with differential lock, ensuring traction on unstable terrain, and a capacitive joystick for seamless control”
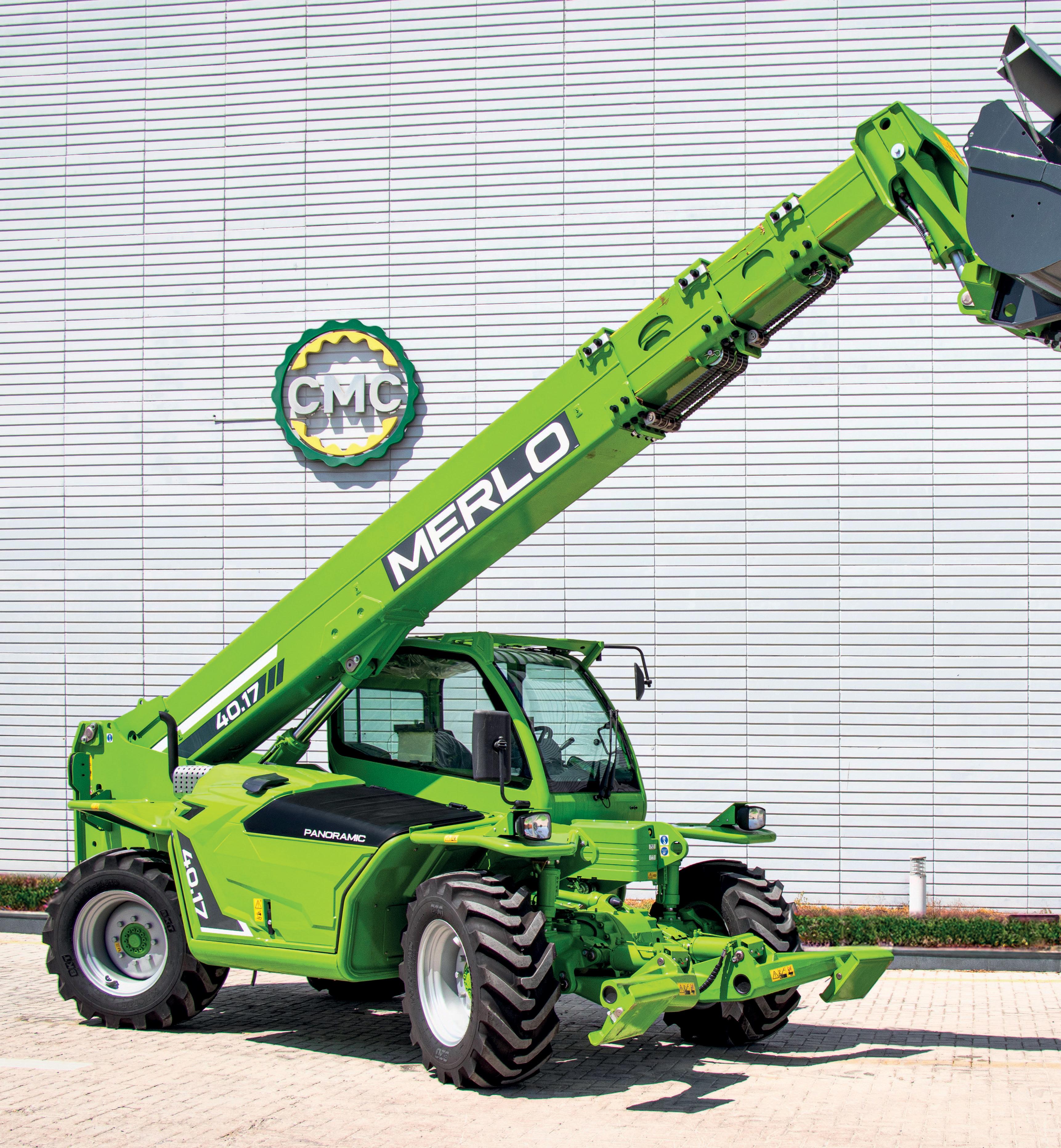
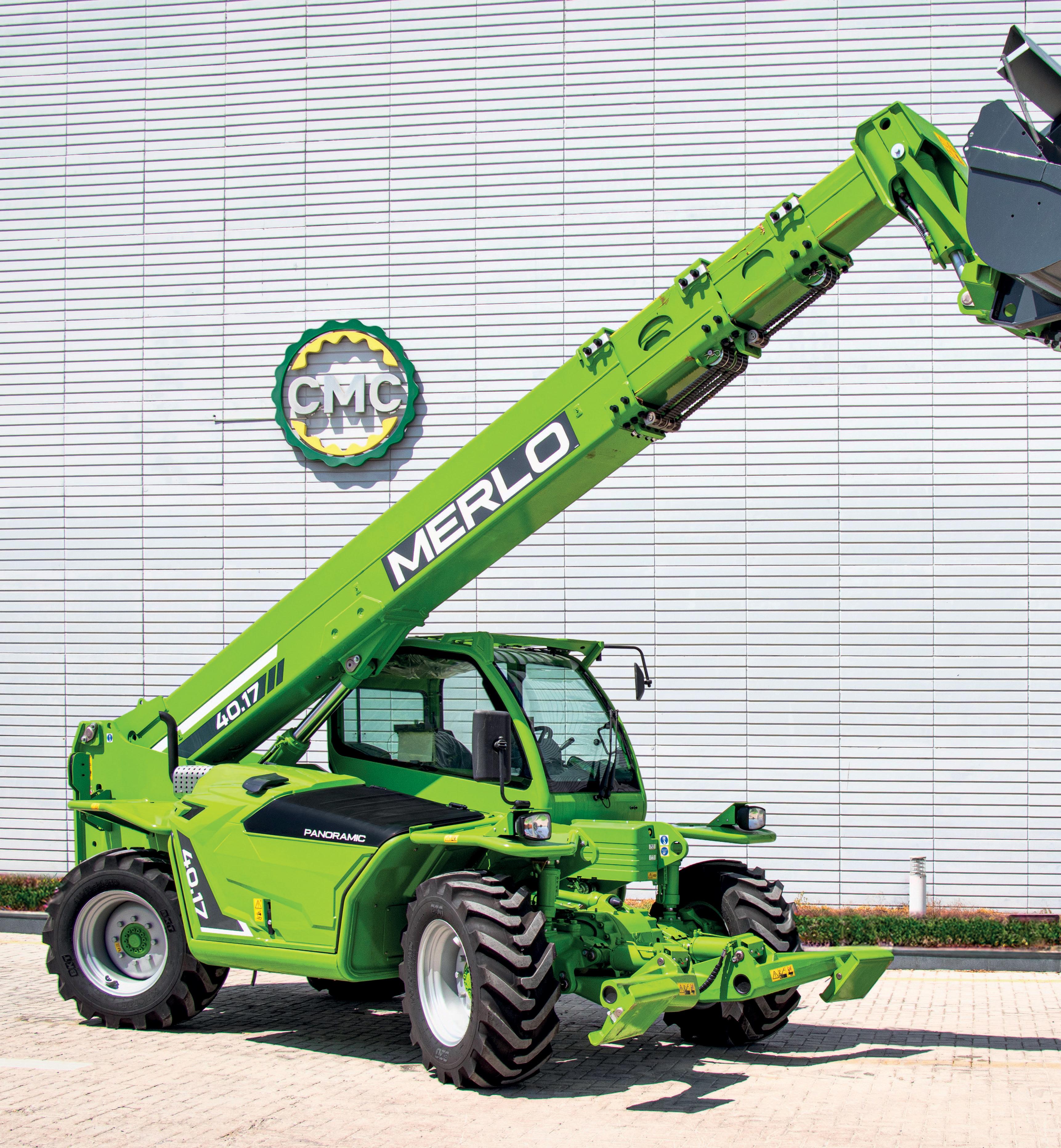
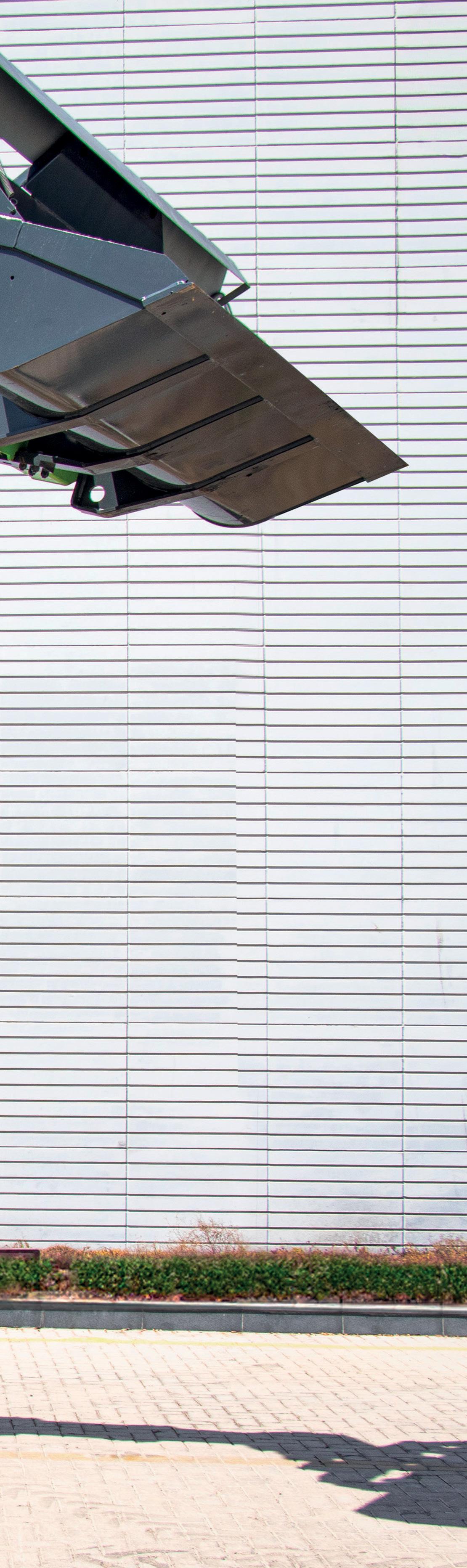
HOT TO HANDLE
CMME LOOKS AT THE TELEHANDLER SCENE IN THE MIDDLE EAST
Deciding whether to rent or buy a telehandler depends on factors such as your project timeline, budget, frequency of use, and longterm business goals. Here’s a breakdown of considerations to help you determine the best approach.
Renting a telehandler can be a costeffective option for companies that need flexibility, especially if you need the telehandler for a short period or a specific project. Renting can save you the upfront costs and long-term maintenance expenses associated with owning the equipment. Companies working on temporary projects often benefit from renting, as it allows access to a telehandler without committing to ownership. Rental companies frequently update their fleet with the latest models, meaning you can access new technology without investing in an upgrade. Rental agreements often include maintenance and repair, which reduces downtime and costs related to servicing. If you need different types or sizes of telehandlers for different projects, renting offers flexibility to select specific models as required.
Owning a telehandler may be more beneficial if you have ongoing or repetitive needs. If you need a telehandler frequently, purchasing can be more cost-effective over time as rental costs add up. Ownership guarantees availability whenever needed, without the risk of rental shortages or scheduling conflicts during peak project
times. While purchasing has a higher upfront cost, long-term ownership can lower overall expenses, especially if you frequently use the machine. Ownership allows you to invest in specific attachments, modifications, or upgrades tailored to your business, adding more value and functionality to your equipment. For companies prioritizing tax benefits, equipment ownership allows for depreciation deductions, which can offset operational costs over time.
Before making a decision, consider budget and cash flow. Buying requires significant upfront capital, while renting spreads out costs. Assessing cash flow can help determine what is feasible. Think about operational flexibility and whether the flexibility of renting outweighs the control and availability of owning the equipment. Owning a telehandler means taking on storage, maintenance, and repair responsibilities, while rental companies handle these for rented equipment. For companies with varied project locations, renting from local providers may reduce transport logistics and costs, as many rental agreements include delivery.
In general, renting is ideal for short-term, project-based use with no long-term storage or maintenance obligations, while buying is suited for companies with frequent, ongoing needs where long-term use justifies the upfront investment. Evaluating your business needs, project requirements, and financial flexibility will guide you toward the option that aligns best with your operational goals.
The telehandler, or telescopic handler, market in the Middle East is stretching out as regional infrastructure projects fuel demand for versatile, high-performance
lifting equipment. Recent months have seen a series of announcements that may help contractors to make the most of the offerings from key players like Bobcat, CMC Gulf in partnership with Merlo, JLG, and Genie with many of them focusing on their technological advancements, safety features, training support, and strategies tailored to meet the unique needs of the Middle Eastern market.
Bobcat has established itself as a full-liner in the Middle Eastern telehandler market with an impressive lineup. Offering 12 models with lifting heights from 6m to 18m, Bobcat also provides a selection of four rotary telehandlers, extending reach up to 26m for applications requiring extra versatility. Recognising the challenging operating conditions in the Middle East, Bobcat has equipped its telehandlers with high-performance cooling systems designed to withstand prolonged usage in high temperatures.
Three years ago, Bobcat introduced a redesigned operator cab for their telehandlers, prioritising comfort and ease of use, which is especially beneficial in a market where telehandlers are often operated by multiple users. “Our goal is to make our machines not only robust and reliable but also accessible and intuitive for different operators,” a Bobcat representative explains to CMME
To enhance safety, Bobcat telehandlers feature a Load Limiting Management (LLM) system, which monitors load limits to prevent tipping and ensure stability. The cab is reinforced with a Roll Over Protection Structure (ROPS) to guard operators from falling debris, and options like rearview cameras provide additional safety in proximity control. Training is an essential aspect of Bobcat’s support for its equipment, with each machine coming equipped with a detailed operator manual, load charts, and access to maintenance videos to ensure proper handling and safety practices are maintained across the region.
Bobcat also offers a wide spectrum of telehandler models to cater to different market needs, from cost-effective standard machines to high-end models with features such as air conditioning, air suspension seats, and advanced attachment capabilities, allowing configurations for platforms, winches, and specialised buckets.
CMC Gulf & Merlo: Precision for Middle Eastern Conditions
CMC Gulf, the sole distributor for Merlo telehandlers in the UAE, brings to the market Merlo’s broad selection, including compact and rotating telehandlers. Popular models in the Middle East include the 17m telehandler, capable of lifting loads of up to
Telehandler manufacturers operating in the Middle East understand the demanding conditions and the importance of safety features tailored to these environments.
4 tons. This model is available for immediate delivery, allowing contractors to meet tight project timelines.
Merlo telehandlers are renowned for technological innovation, winning several awards in this area. Speaking to CMME, Suhail Mustafa, Chief Business Development Officer at CMC Gulf says: “Merlo telehandlers incorporate unique design elements like inhouse manufactured axles with differential lock, ensuring traction on unstable terrain, and a capacitive joystick for seamless control.”
Additional advancements include Merlo’s
“Our goal is to make our machines not only robust and reliable but also accessible and intuitive for different operators”
Engine Power Management (EPD) system, which reduces fuel consumption by up to 18% by electronically managing engine speed and hydraulic power, a feature especially valuable as fleet operators in the Middle East face rising fuel prices.
For navigating confined spaces, Merlo telehandlers are designed with all-wheel steering and compact stabilisers that remain within the machine’s footprint, allowing for efficient stabilisation and precise handling. This design includes a boom side-shift feature, enabling operators to reposition loads
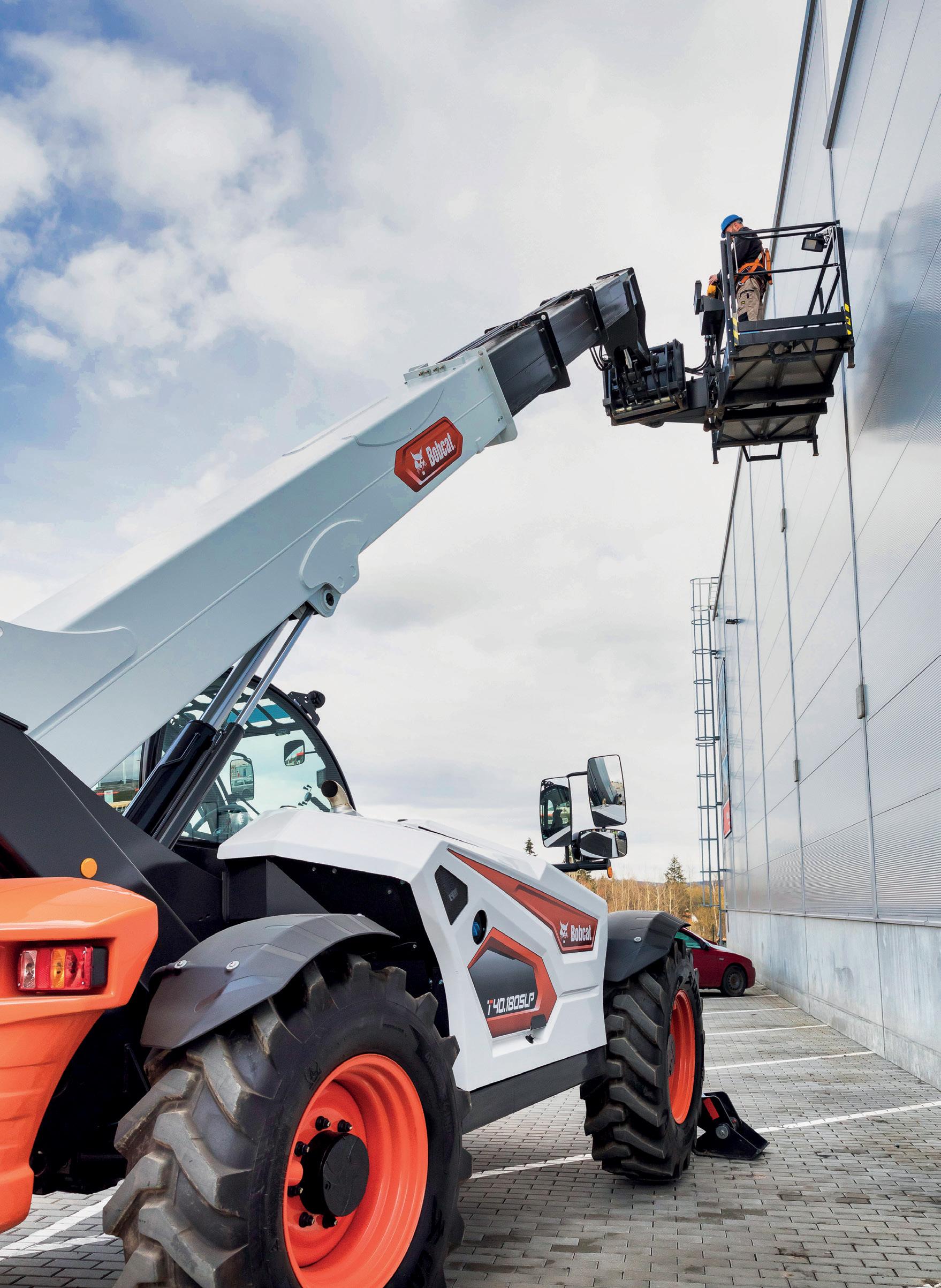
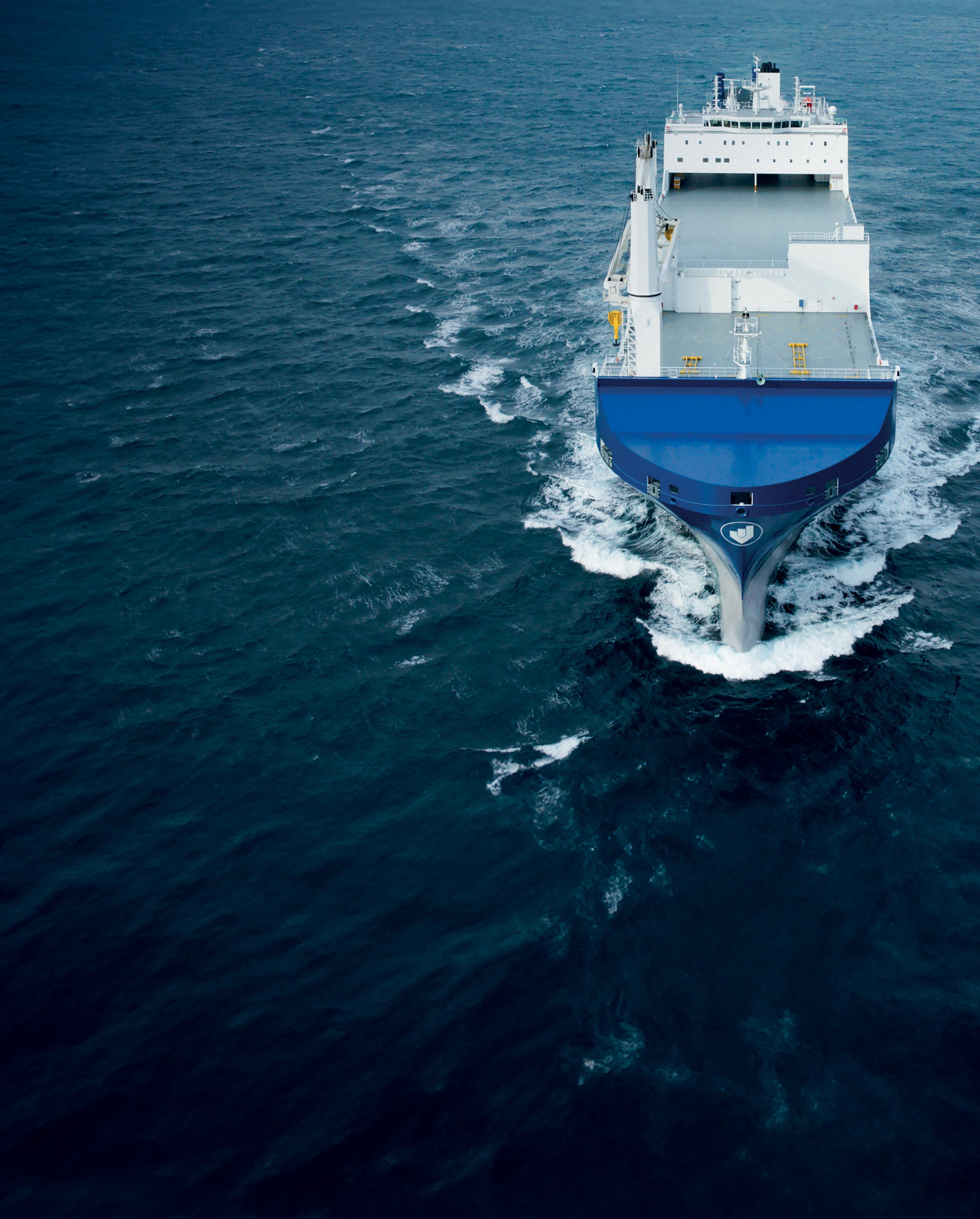
without repositioning the entire machine.
“Operator fatigue is reduced with our 180° cab door design, providing easy access, and we prioritise safety with the highest FOPS Level II protection,” adds Mustafa.
High-Demand JLG Boom Lifts
The telehandler market in the Middle East has also seen increased demand from the rental sector, with companies such as UAEbased Quality Equipment Rental LLC (QER) investing in a fleet of JLG boom lifts. With high-reach capacities, these machines cater to construction, oil and gas, and facilities management, where adaptability, reach, and safety are paramount.
JLG, known for its commitment to advanced technology, equips its machines with features like telematics for fleet management and safety enhancements that meet industry standards, bolstering their reputation as a trusted provider in the Middle East.
Ashfaq Hussain, Managing Director of QER, states that the investment in JLG equipment enhances operational efficiency, “helping us stay competitive in the rental market by providing the best technology to our clients.”
Genie’s recent partnership with Türkiye’s Global Lift Makina expands its footprint in the region, meeting increased demand for electric equipment amid rising environmental regulations. Genie’s lineup includes rough-terrain and electric scissor lifts, telescopic and articulated boom lifts, and vertical mast lifts, with after-sales support and maintenance provided through Global Lift Makina’s established network.
As Serkan Yörenç, General Manager at Global Lift Makina, shares: “With increasing focus on carbon emissions and green initiatives, Genie’s electric models are ideally suited for clients seeking environmentally-friendly alternatives.” Genie machines are equipped with telematics, real-time monitoring, and industry-leading safety features, offering reduced operating costs and longevity—key benefits for companies looking to align with regional sustainability goals.
Telehandler manufacturers operating in the Middle East understand the demanding conditions and the importance of safety features tailored to these environments. To counteract high temperatures, intense usage, and multiple operator requirements, companies like Bobcat and Merlo have engineered telehandlers that stand up to these conditions with enhanced cooling systems, load management features, and robust, operator-friendly cabins.
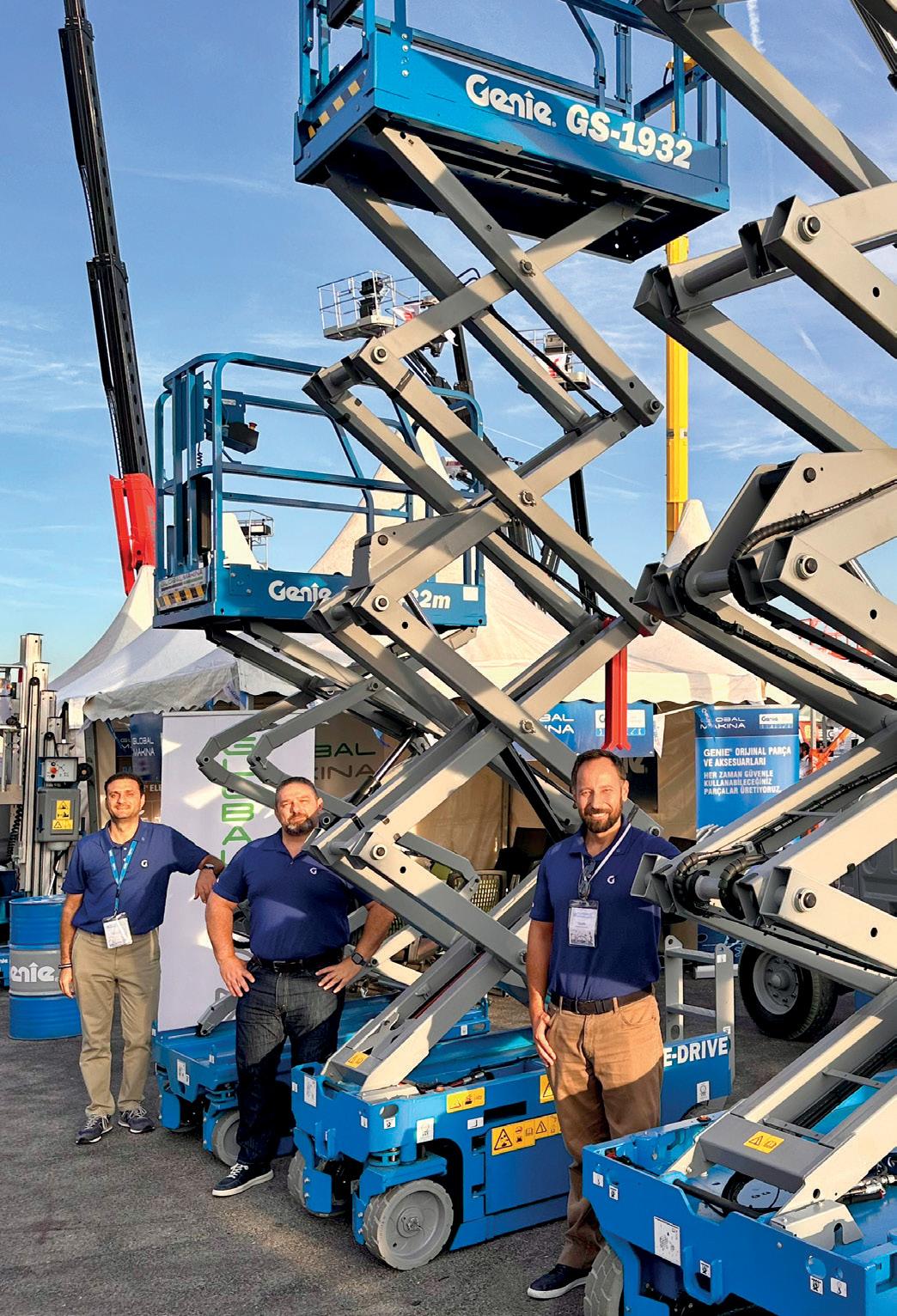
For applications ranging from construction and logistics to agriculture, the demand for versatile telehandlers is growing, and manufacturers are responding with models that support a wide range of attachments.
Safety features have become nonnegotiable, with all major providers incorporating technology that prevents overloading, offers cab protection, and allows for precision handling. For example, Bobcat and Merlo’s LLM and frontal tipping prevention systems, along with FOPScompliant cabins, help operators stay protected even in high-risk construction settings. Furthermore, extensive operator training, including real-time and online resources, supports safe and optimal machine performance across industries.
Versatile Attachments and Customisation
For applications ranging from construction and logistics to agriculture, the demand for versatile telehandlers is growing, and manufacturers are responding with models that support a wide range of attachments. Bobcat telehandlers, for instance, can be fitted with platforms, winches, and specialised buckets, catering to an array of lifting and positioning needs.
Merlo telehandlers offer similar flexibility, with options for aerial work platforms, automatic fork positioners, and crane hooks. Such adaptability allows rental companies and contractors to employ a single machine across multiple tasks, maximising ROI and efficiency.
Additionally, Genie’s partnership with Global Lift Makina provides customers access to a comprehensive selection of attachments and customisation options suited to specific operational requirements.
The Middle Eastern telehandler market continues to evolve, with manufacturers like Bobcat, Merlo, JLG, and Genie setting new benchmarks in performance, safety, and versatility. From heavy-duty builds for the construction sector to sustainable, fuel-efficient options for environmentally conscious buyers, these brands are at the forefront of meeting the region’s dynamic demands. Through localised support, continuous innovation, and partnerships tailored to regional needs, these companies are well-positioned to drive the next wave of growth and development in the Middle Eastern telehandler sector.
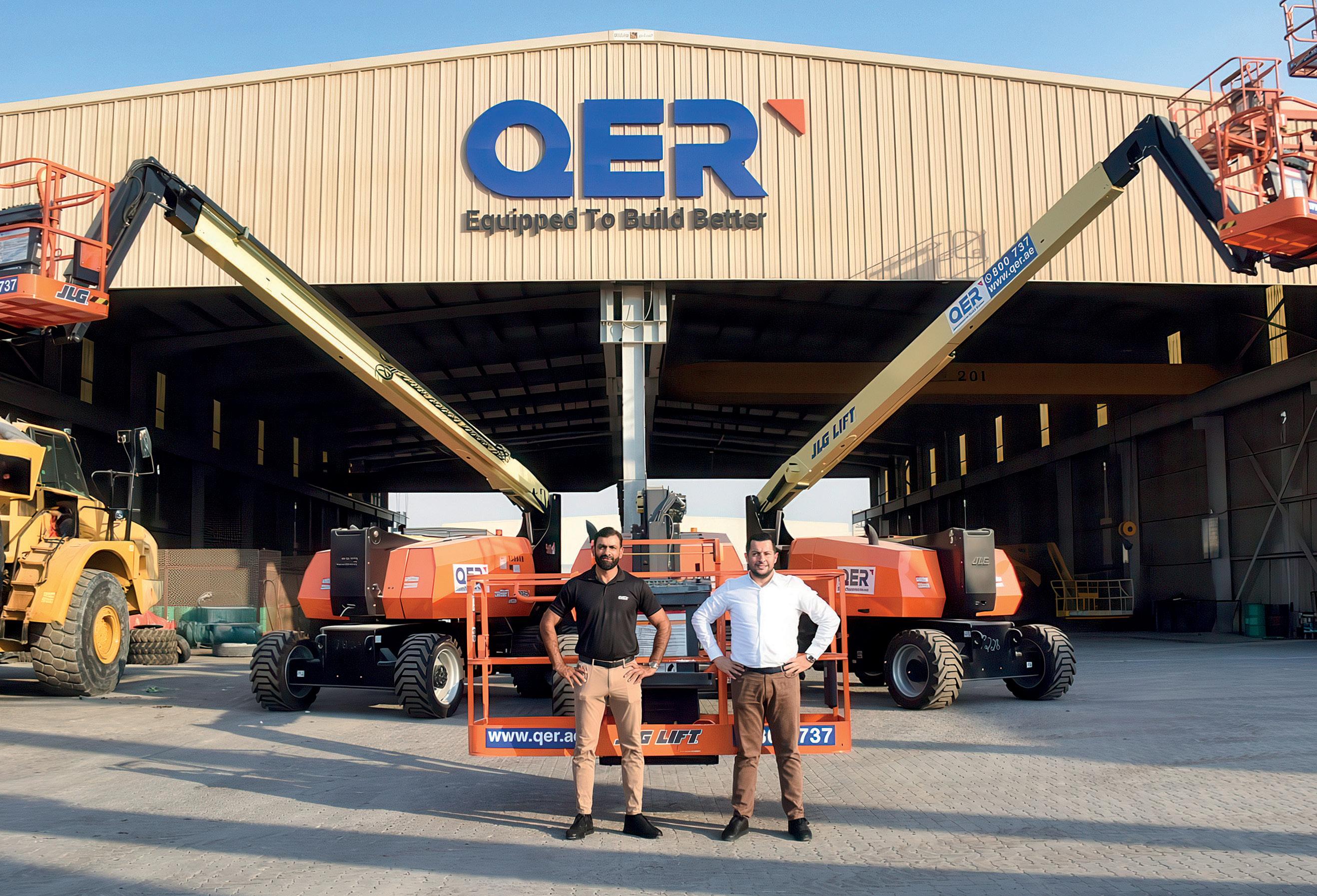

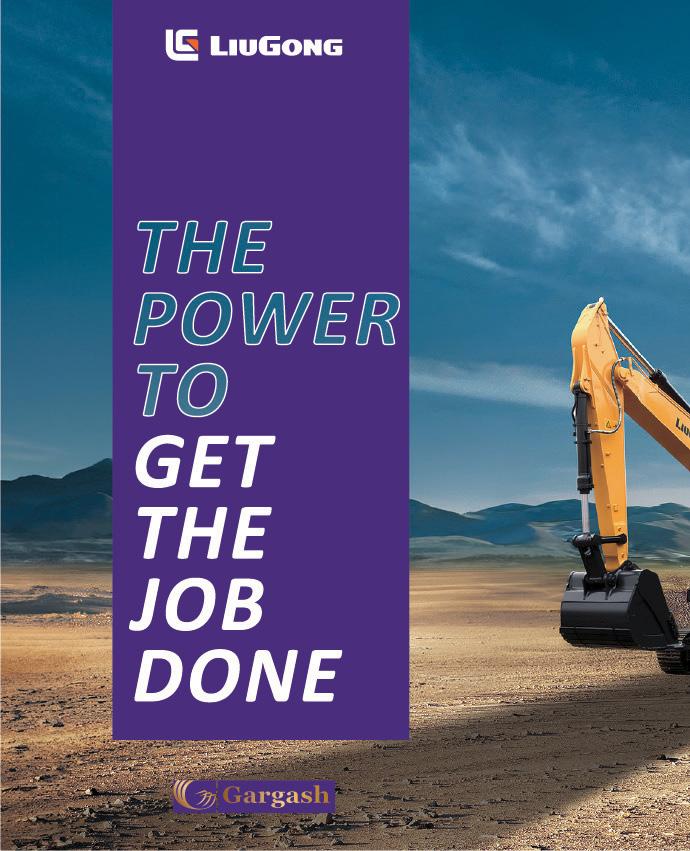
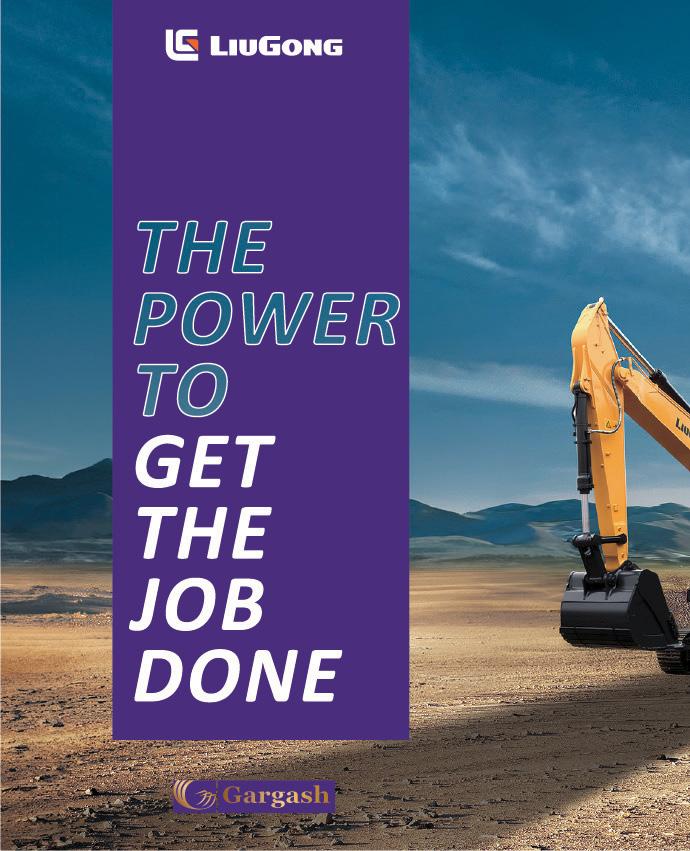
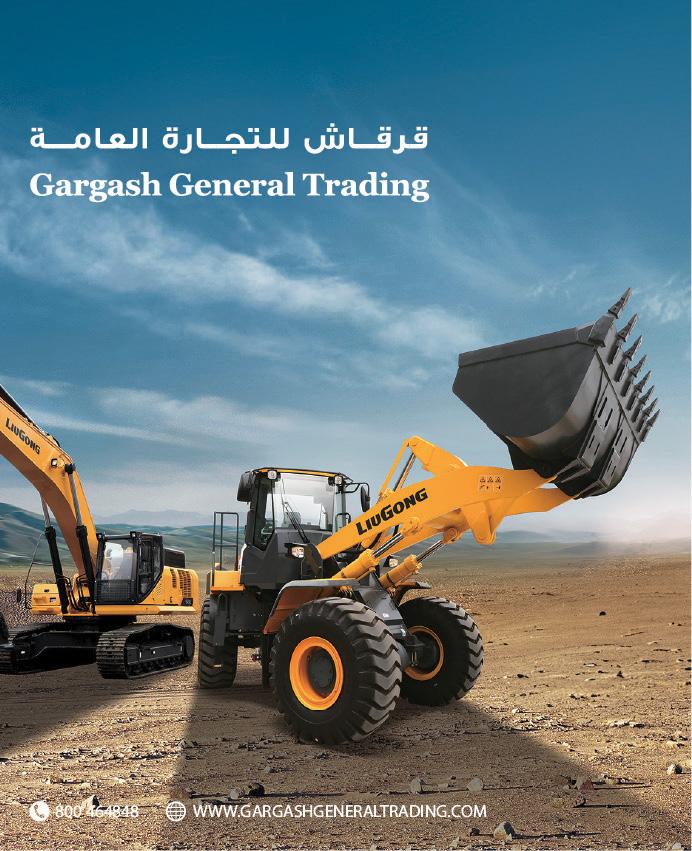


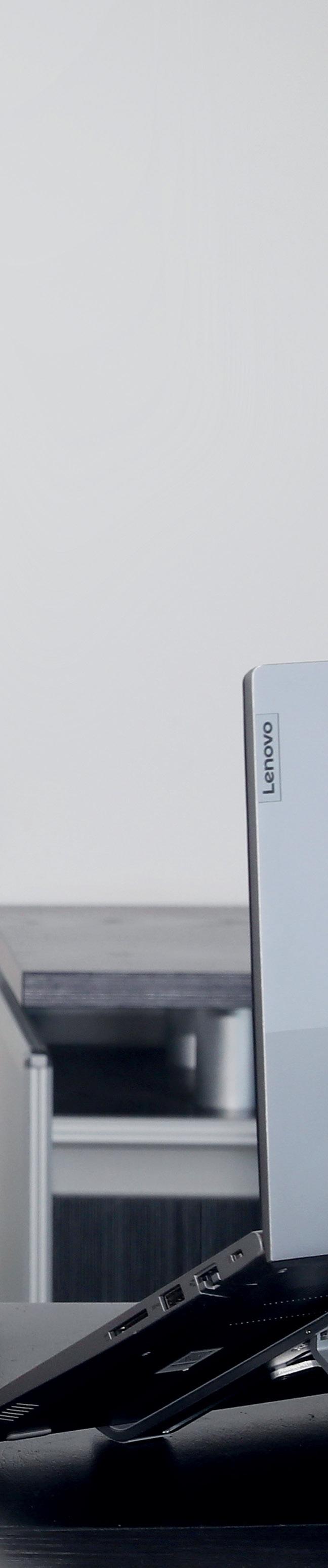
DRIVEN TO SUCCEED
GM AHMAD WRAIKAT TALKS DRIVING
STRATEGIC GROWTH AND INNOVATING AT KANOO CRANES AND WOLFFKRAN ARABIA
With over 15 years of experience in the lifting and logistics industry, Ahmad Wraikat recently took on the role of General Manager for Kanoo Cranes and Wolffkran Arabia. As he steps into this new position, Wraikat brings his expertise to a challenging and competitive market, where his strategic vision is set to guide Kanoo Cranes through a period of growth and transformation.
In an exclusive interview with CMME, Wraikat discusses his new responsibilities, his goals for the company, and the trends shaping the crane industry in the GCC region.
When asked about his new role, Wraikat explained his primary areas of focus: “In my role as General Manager of Kanoo Cranes and Wolffkran Arabia, I am responsible for overseeing operations, ensuring efficiency in our crane rental and sales services, and driving growth within the company,” he says. His leadership spans strategic planning, team management, and fostering customer relationships. “This is an exciting role that allows me to work closely with a talented team while making a positive impact on the industry,” Wraikat adds.
Having joined the lifting and logistics industry in 2007, Wraikat brings a wealth of knowledge to his role, which he intends to put to good use in several key areas. “I plan to leverage my expertise by increasing operational efficiency through best practices in project management and logistics,” he explains. He also emphasises the importance of safety and compliance, noting that his commitment to these standards will drive him to “implement
rigorous training programs and compliance checks to minimise risks.”
Wraikat underscores the importance of customer relationships, a focus he has cultivated over his career. “Having developed solid relationships over the years, I will focus on understanding our clients’ needs better and tailoring our services to exceed them, which is key to retaining and growing clients.” He also plans to bring a forward-looking approach to technology and progress, particularly in integrating advanced crane monitoring systems and data analytics to optimise fleet management. “My experience in mentoring and developing talent will be valuable as I build a strong team culture, ensure continuous learning, and foster collaboration to achieve our goals,” he says.
The role of a General Manager in the crane industry is evolving, especially in the GCC region, Wraikat points out: “As the region increasingly prioritises sustainability, GMs will need to focus on eco-friendly practices and technologies, such as energy-efficient cranes and sustainable logistics solutions,” he says. Workforce development is also a key focus, as Wraikat notes that: “GMs will play a crucial role in fostering a skilled workforce that can adapt to new technologies and practices.”
In a competitive market, he sees an increased emphasis on understanding customer needs, regulatory compliance, and strategic partnerships. “The role will increasingly demand a blend of strategic thinking, technological adaptability, and a focus on sustainability and customer satisfaction,” he explains, highlighting how these elements will shape the future of the GCC crane industry.
As he steps into his new role, Wraikat has set several immediate priorities to build a solid foundation for Kanoo Cranes and Wolffkran Arabia’s future. “Conducting a thorough review of current
operations is essential to identify strengths, weaknesses, and areas for improvement,” he says. In addition, safety remains a cornerstone of his strategy, and he aims to continue reviewing and enhancing safety protocols and training programs.
Wraikat also prioritises team engagement, actively building relationships with his team to understand their insights and challenges. “I plan to focus on team development and morale, ensuring everyone feels valued and motivated,” he shares. On the customer side, he intends to engage with clients to gather feedback on services and identify opportunities for improvement. This, he believes, will help Kanoo Cranes “tailor offerings to better meet client needs.”
The GCC region presents both opportunities and challenges for the crane industry, which Wraikat is determined to navigate strategically. “Ongoing megaprojects such as urban development, transportation networks, and tourism are driving demand for cranes and lifting solutions,” he explains. Additionally, he sees new sectors emerging in response to regional diversification, such as renewable energy and logistics, which could provide fresh opportunities for Kanoo Cranes.
Yet, he acknowledges that challenges such as varying regional regulations,
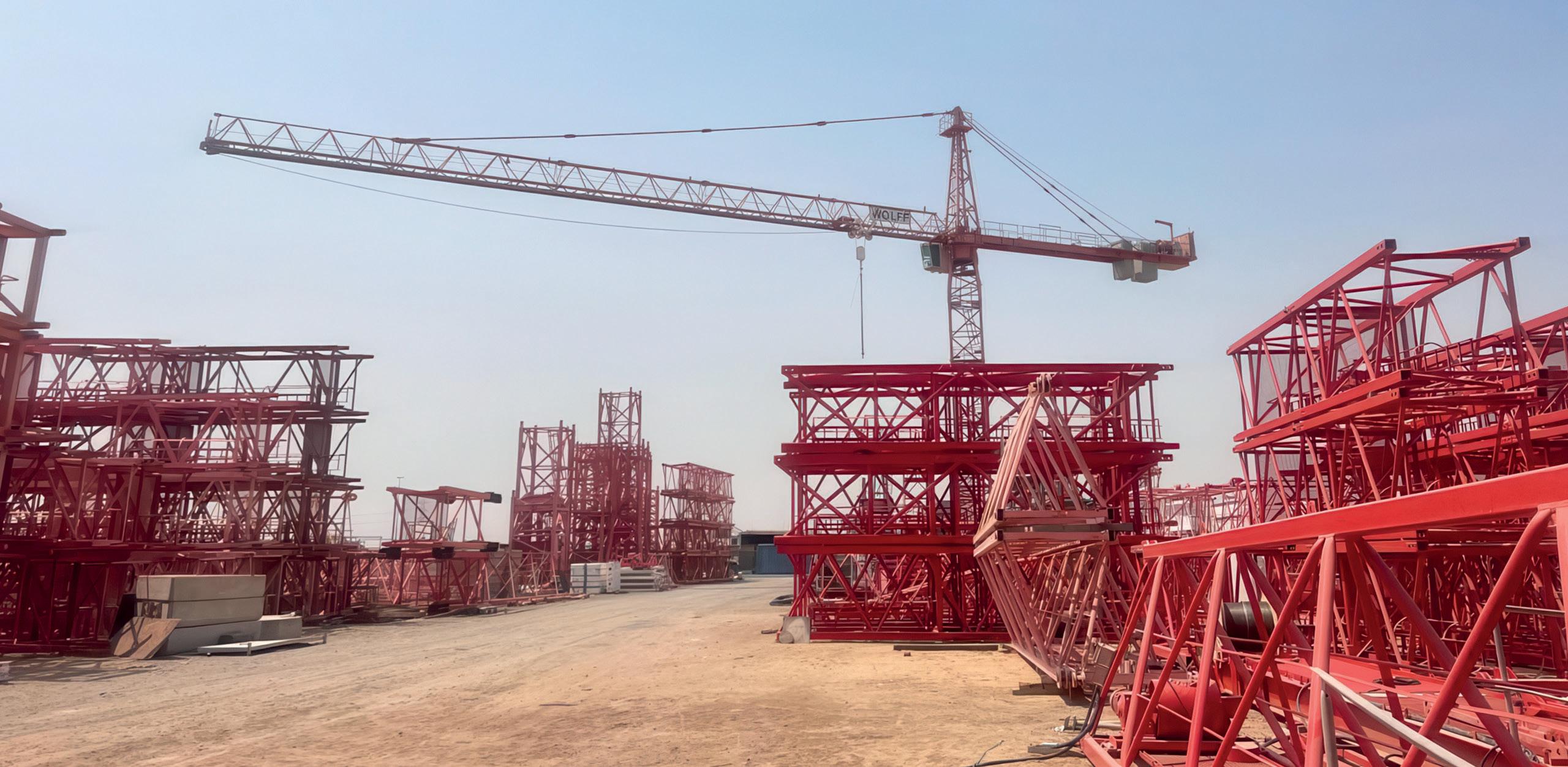
economic volatility, and talent shortages may impact the industry. “Navigating the regulations across different GCC countries may pose compliance and operational challenges,” Wraikat notes, adding that attracting and retaining skilled workers will be critical in this competitive labour market. However, he remains confident that Kanoo Cranes can succeed by strategically addressing these challenges and capitalising on the region’s growth potential.
To meet the growing demand for lifting solutions in the GCC, particularly in
construction and infrastructure projects, Kanoo Cranes is focusing on several core strategies. “We are constantly investing in our fleet by acquiring the latest cranes and lifting equipment, which allows us to meet diverse project requirements and handle large-scale operations with ease,” says Wraikat.
The company is also enhancing its operational efficiency through technology, including telematics and remote monitoring systems. “Real-time data tracking and predictive maintenance minimise downtime and ensure operational efficiency,” he explains. Furthermore, Kanoo Cranes is committed to safety, offering rigorous training programs and safety protocols to protect employees and build client trust.
As Wraikat embarks on this new phase of his career, he’s eager to support the ambitious projects taking shape across the GCC and reinforce Kanoo Cranes’ reputation as a leading provider of lifting solutions. Through his focus on efficiency, safety, and client satisfaction, Wraikat aims to position Kanoo Cranes for sustainable success in the region’s evolving landscape.
“ We are constantly investing in our fleet by acquiring the latest cranes and lifting equipment, which allows us to meet diverse project requirements”
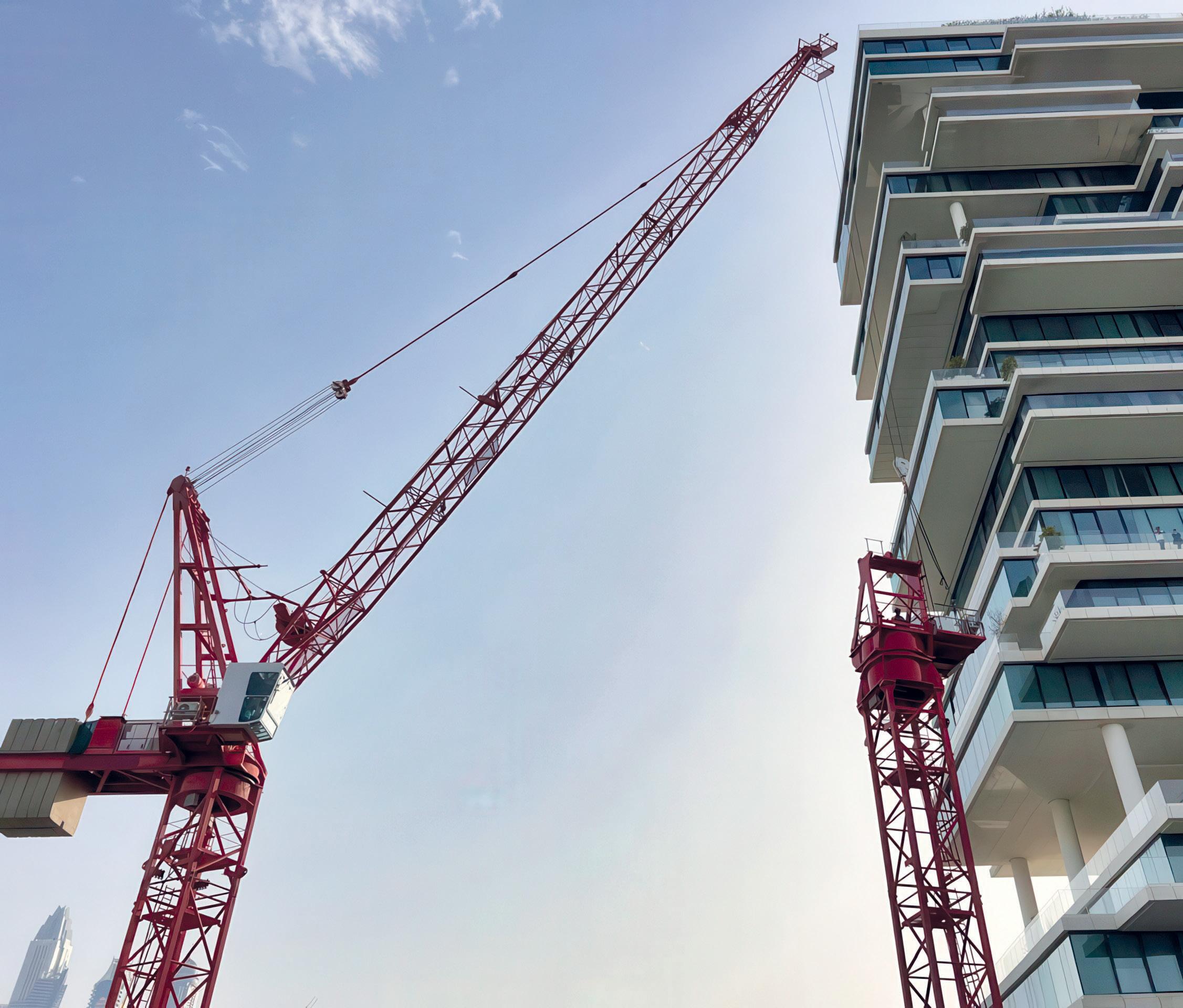
He is also not only focused on operational efficiency and strategic growth but also on advancing in-novation within Kanoo Cranes to meet the evolving demands of the GCC’s dynamic market. He envisions leveraging the latest technology to streamline operations and enhance service offerings.
“Our goal is to integrate advanced technologies that allow us to operate more efficiently, enhance safety, and deliver better outcomes for our clients,” he explains. Key to this approach is the adoption of telematics systems, which provide real-time data on crane performance, usage, and maintenance requirements. “By utilising predictive maintenance through telematics, we can significantly reduce downtime and optimise fleet performance,” he adds, noting that data
analytics will play a crucial role in proactive decision-making and resource allocation.
A Data-Driven Approach
For Wraikat, utilising data to make informed decisions is essential to modern fleet management. He plans to introduce advanced crane monitoring systems that enable precise tracking and data collection, providing insights into operational efficiency and identifying areas for improvement.
“By embracing a data-driven approach, we can continuously monitor our fleet’s performance, optimise fuel consumption, and anticipate maintenance needs before issues arise,” he says. This proactive model not only enhances equipment lifespan but also helps clients avoid costly project delays.
Sustainability is becoming increasingly important across the GCC, and Wraikat is determined to position Kanoo Cranes as a leader in eco-friendly lifting solutions.
“We are committed to investing in energyefficient technologies, such as electric and hybrid cranes, which align with the region’s sustainability goals,” he states. Kanoo Cranes is already exploring options to implement variable frequency drives and regenerative braking systems, which can significantly reduce energy consumption and lower emissions.
Additionally, Wraikat plans to implement sustainable practices across Kanoo Cranes’ operations, from waste reduction and recycling initiatives to eco-friendly maintenance protocols that extend equipment lifespan. “These steps align with both our commitment to the environment and our clients’ increasing expectations for sustainable practices on job sites,” he notes.
One of the most exciting advancements in crane technology is the shift toward automation and remote operation, which Wraikat believes can drastically improve job site safety. “The rise of automated cranes and remote operating capabilities allow us to remove operators from potentially hazardous environments, which is a huge step forward for safety,” he says. By investing in technology that ena-bles remote control of cranes, Wraikat aims to minimise risks while maintaining operational precision. This focus on automation reflects Kanoo Cranes’ broader commitment to safeguarding its workforce and building trust with clients.
Kanoo Cranes is also exploring progressive training methods through AR and VR, which provide immersive, hands-on learning experiences for crane operators and technicians. “With AR and VR, we can simulate real-world scenarios in a controlled environment, allowing operators to gain

critical skills and confidence before stepping onto an actual job site,” explains Wraikat. This technology-driven approach to training not only enhances skill development but also promotes a culture of continuous learning and adaptation, which Wraikat sees as essential in a rapidly changing industry.
Kanoo Cranes’ approach to advancement isn’t limited to its internal operations; the company also focuses on collaborative solutions that can address specific client needs. “We’re developing customised crane solutions and providing expert consultation
to help our clients achieve project efficiency and safety,” says Wraikat. By combining Kanoo’s expertise with technologies such as advanced load monitoring systems, Wraikat envisions tailored solutions that allow clients to navigate the complexities of large-scale projects.
To strengthen these client-focused improvements, Kanoo Cranes is building strategic partnerships with technology providers and industry experts, ensuring that its service offerings are both cuttingedge and adaptable. “We see great potential in forming alliances that can expand our technological capabilities and keep us at the forefront of industry advancements,” he adds.
In Wraikat’s view, Kanoo Cranes’ commitment to progress will not only enhance operational performance but also set a benchmark for sustainable and technologically advanced lifting solutions across the GCC. “As we invest in these new technologies, we’re positioning ourselves as a forward-thinking leader that’s responsive to both client and market demands,” he explains. Looking ahead, Wraikat is confident that Kanoo Cranes will continue to shape the industry by aligning with regional sustainability goals and pushing the boundaries of what’s possible in lifting technology. Through his emphasis on data, automation, sustainability, and client-driven solutions, Wraikat is paving the way for Kanoo Cranes to lead the lifting industry into a future where technology and efficiency go hand in hand.
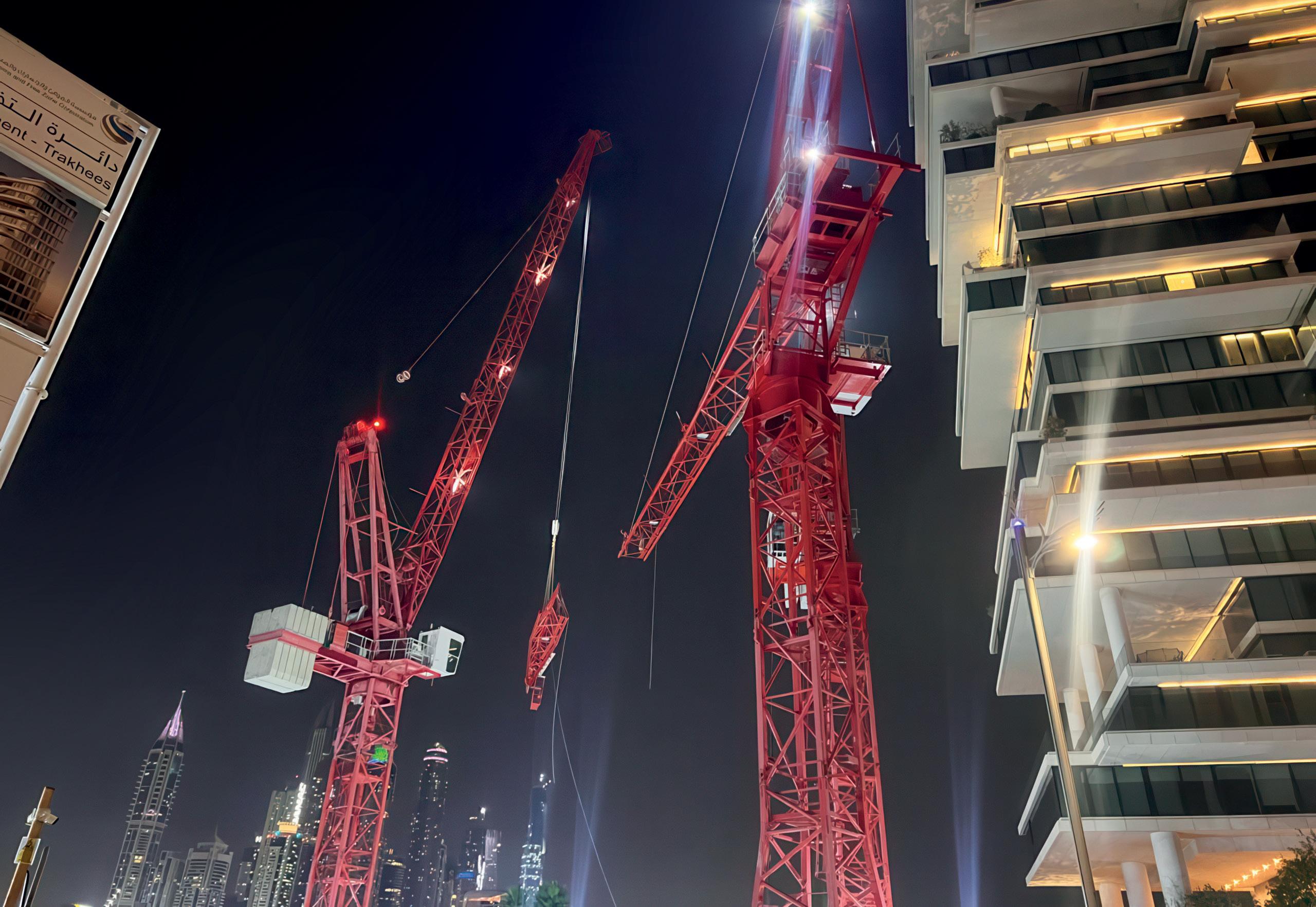

RAW POWER


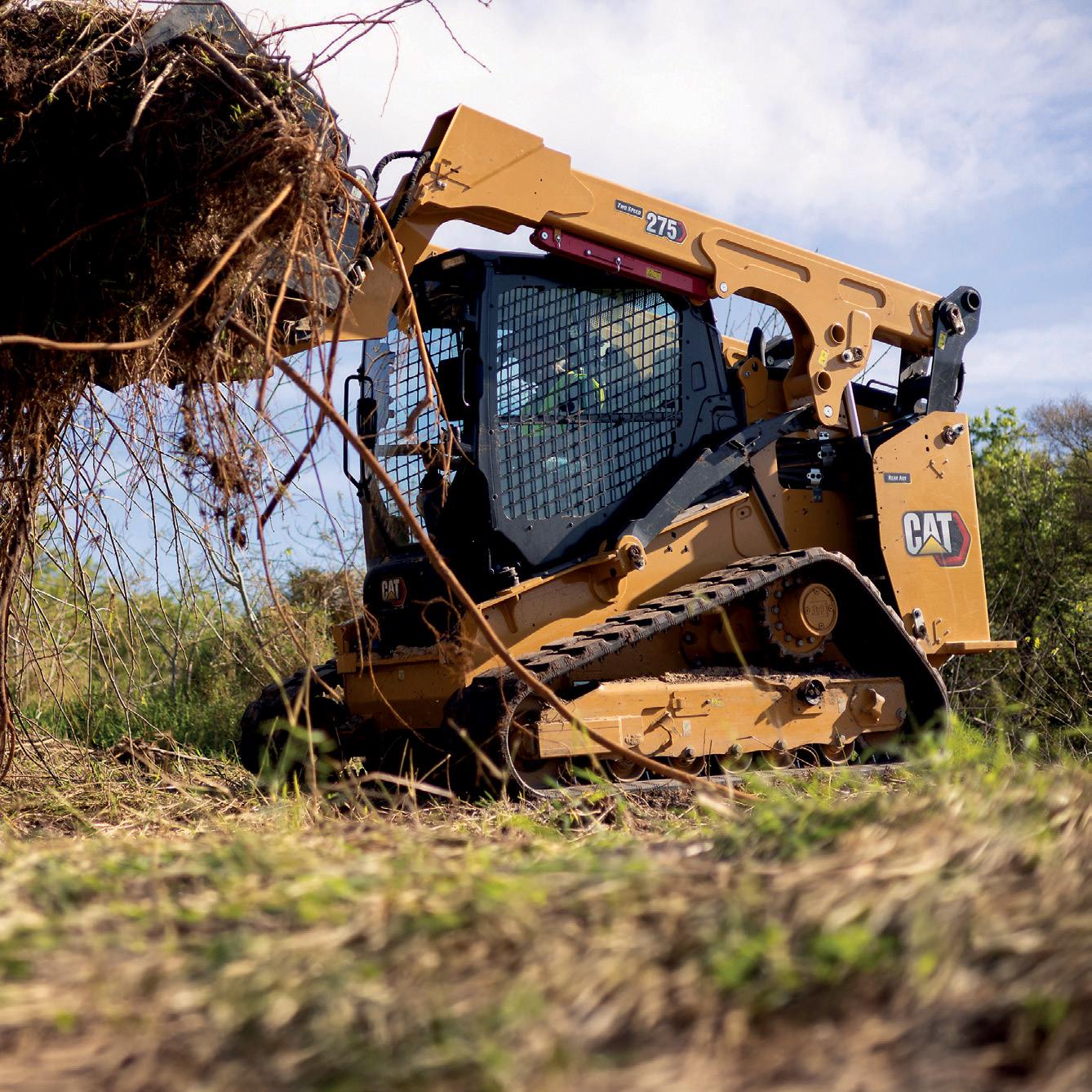
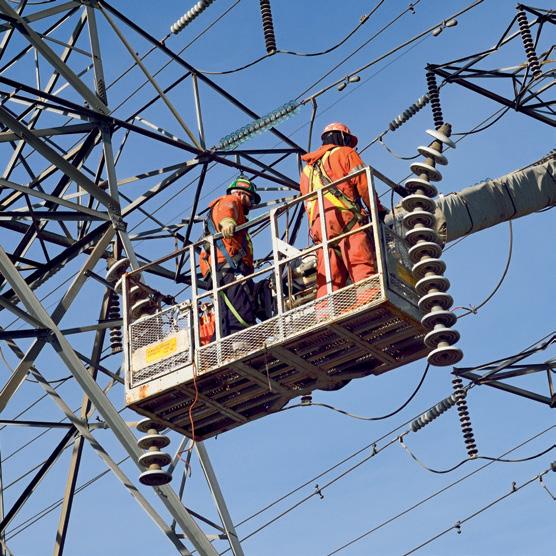

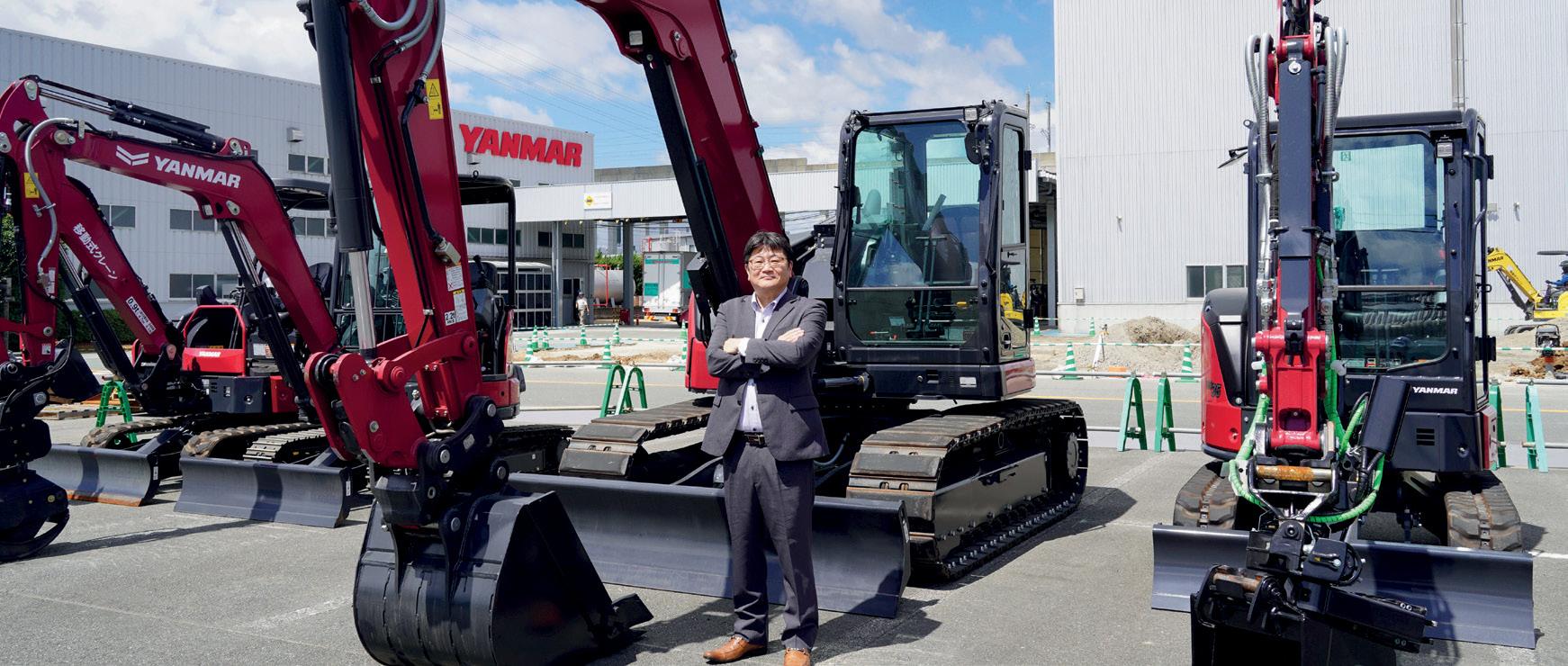
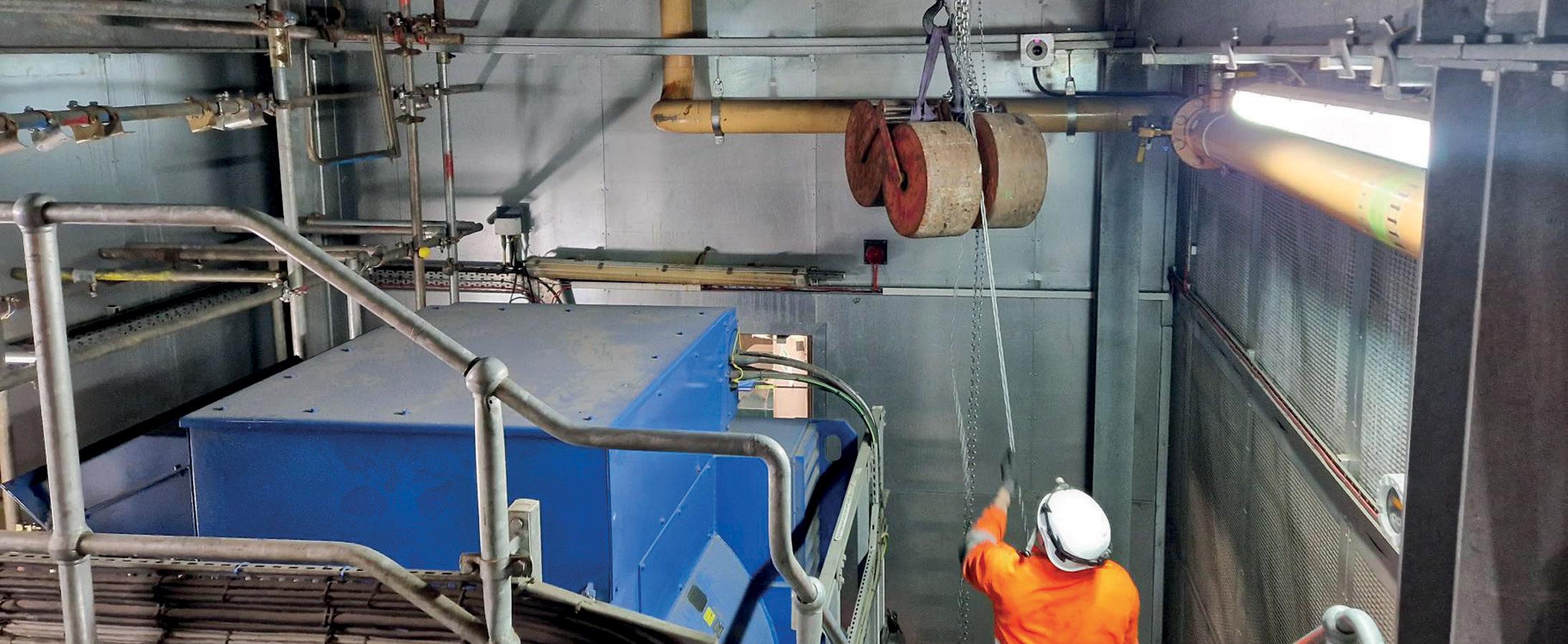


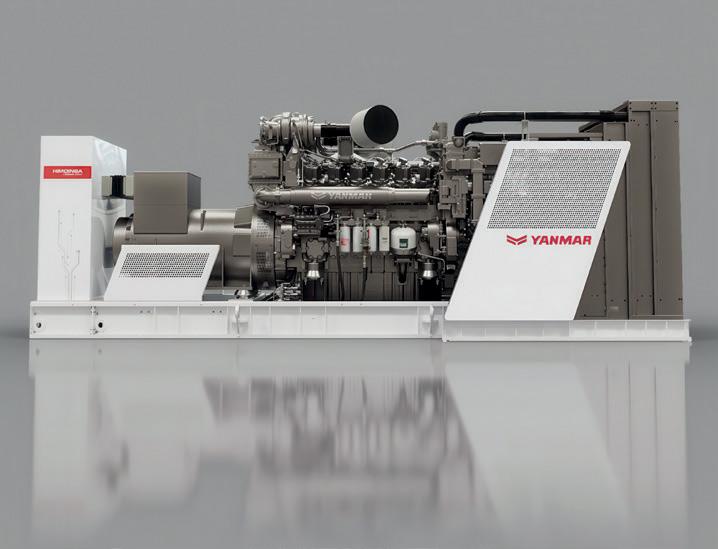
HIMOINSA LAUNCHES HGY SERIES
WHY GET IT?
EASY MAINTENANCE AND ACCESSIBILITY HAVE BEEN INTEGRAL TO THE NEW PRODUCT DEVELOPMENT WITH ALL ENGINE CONSUMABLE PARTS, SUCH AS FUEL AND AIR FILTERS AND THE OIL FILLING POINT, LOCATED ON ONE SIDE.
Developed collaboratively by HIMOINSA and Yanmar Power Technology (YPT), the HGY Series combines HIMOINSA’s expertise in power generation with YPT’s advanced engine technology. The launch event for the new HGY Series generators launch event took place in Madrid, Spain, where around 400 customers and partners enjoyed a breathtaking show in the Metropolitano Stadium.
The HGY Series is powered by Yanmar engines, ranging from 1250kVA to 3500kVA (future plan up to 4000kVA). This includes the GY175L engine family, featuring multiple models with 12 and 16 cylinders and future engine developments with 20 cylinders, all of which are electronically controlled. The HGY Series is configured to support the future adoption of alternative fuels such as HVO, gas and hydrogen.
SPECIFICATIONS
HGY SERIES
Power Output Range: 1250 kVA to 3500 kVA (future extension up to 4000 kVA)
Engine configurations: 12-cylinder, 16-cylinder
Pump Pressure: 2200-bar, providing maximum combustion efficiency and optimized pressure control
Emissions: EPA Tier 2
MAMMOET SPRINGS MEGA JACK 10000
WHY GET IT?
ONE MEGA JACK 10000 TOWER CAN LIFT THIS WEIGHT ON ITS OWN, MEANING THAT LIFTS THAT WOULD FORMERLY REQUIRE STARTER BEAMS OF TWO TOWERS’ WIDTH MAY NOW ONLY NEED ONE.
Mammoet has announced the launch of the Mega Jack 10000, a new addition to its heavy lifting portfolio. The new system provides 10,400t of lifting capacity per tower – upgraded from 5,200t currently – without increasing the footprint of the tower base. This means that less steel is required to support structures as they are lifted, and the heaviest lifts will be able to start meters closer to ground level. Moreover, as the system’s capacity per tower has doubled, fewer towers will be needed to lift larger loads. This means smaller foundations are needed – further enhancing both scheduling and costs.
The Mega Jack 10000 introduces a revolutionary five-meter jacking beam with three connection points, allowing for load distribution across eight Mega Jack base units: four at the corners of the tower, and four at the center of each side.
Large jacking projects require starter beams, which are used to connect these jacking towers together and distribute the load. For example, if two Mega Jack 5200 towers are connected by a starter beam,
they will be able to lift a load of 10,400t. One Mega Jack 10000 tower can lift this weight on its own, meaning that lifts that would formerly require starter beams of two towers’ width may now only need one. So supporting steel can be smaller, thinner and require less engineering to develop. This also reduces the lift’s starting height, making access easier and meaning smaller cranes are needed to complete projects.
Richard Verhoeff, Director Sales Global Special Devices at Mammoet, said: “We noticed that loads were growing beyond the capacity of the Mega Jack 5200 and came up with the idea of the Mega Jack 10000. We designed an early initial concept and now we have upgraded the system to accommodate future projects that require a 10,000t single tower solution. With the introduction of the Mega Jack 10000, Mammoet is setting a new standard in heavy lifting technology. This innovative solution not only increases lifting capacity but also enhances safety and sustainability by optimizing the jacking process.”
TECH TALK BASEMENT JACKS
The Mega Jack 10000 offers a 10,400ton lifting capacity per tower, doubling previous limits without increasing the tower base footprint. Its five-meter jacking beam, with three connection points, distributes load across eight base units, enhancing stability. The singletower system reduces the need for multiple starter beams, enabling smaller, lighter support structures.
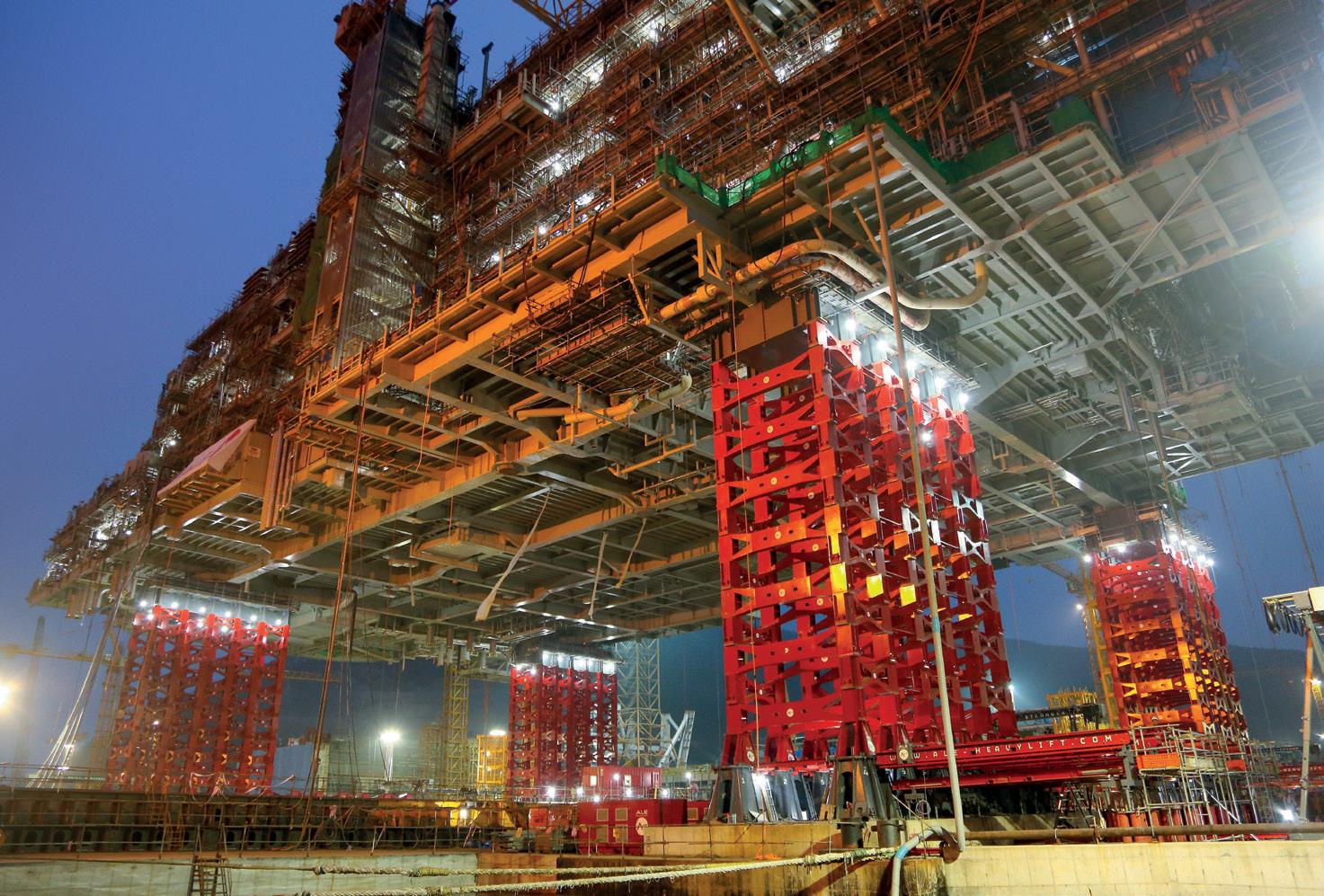
CATERPILLAR LAUNCHES EIGHT NEW NEXT GENERATION SKID STEER AND COMPACT TRACK LOADERS
WHY GET THEM? WITH ENHANCED POWER, FLEXIBILITY, AND OPERATOR COMFORT, CAT’S NEXT GENERATION SSL AND CTL MODELS REPRESENT A SIGNIFICANT UPGRADE FOR COMPACT EQUIPMENT, AIMED AT MEETING THE EVOLVING NEEDS OF THE CONSTRUCTION AND HEAVY MACHINERY INDUSTRIES
Caterpillar has introduced eight next generation Cat Skid Steer Loader (SSL) and Compact Track Loader (CTL) models, designed to enhance power, lift capacity, and operator comfort for demanding job sites. The lineup includes four new skid steer loaders – the Cat 250, 260, 270, and 270 XE – and four compact track loaders – the Cat 275, 275 XE, 285, and 285 XE. The Cat 285 and 285 XE models are the largest CTLs Caterpillar has produced, bringing new lift heights, greater lift and tilt breakout forces, and expanded capabilities to the market. This new generation builds on the strengths of the Cat D3 series but is redesigned from the ground up to enhance performance in key areas such as engine power and torque, lift capacity, and operator comfort. Caterpillar has also
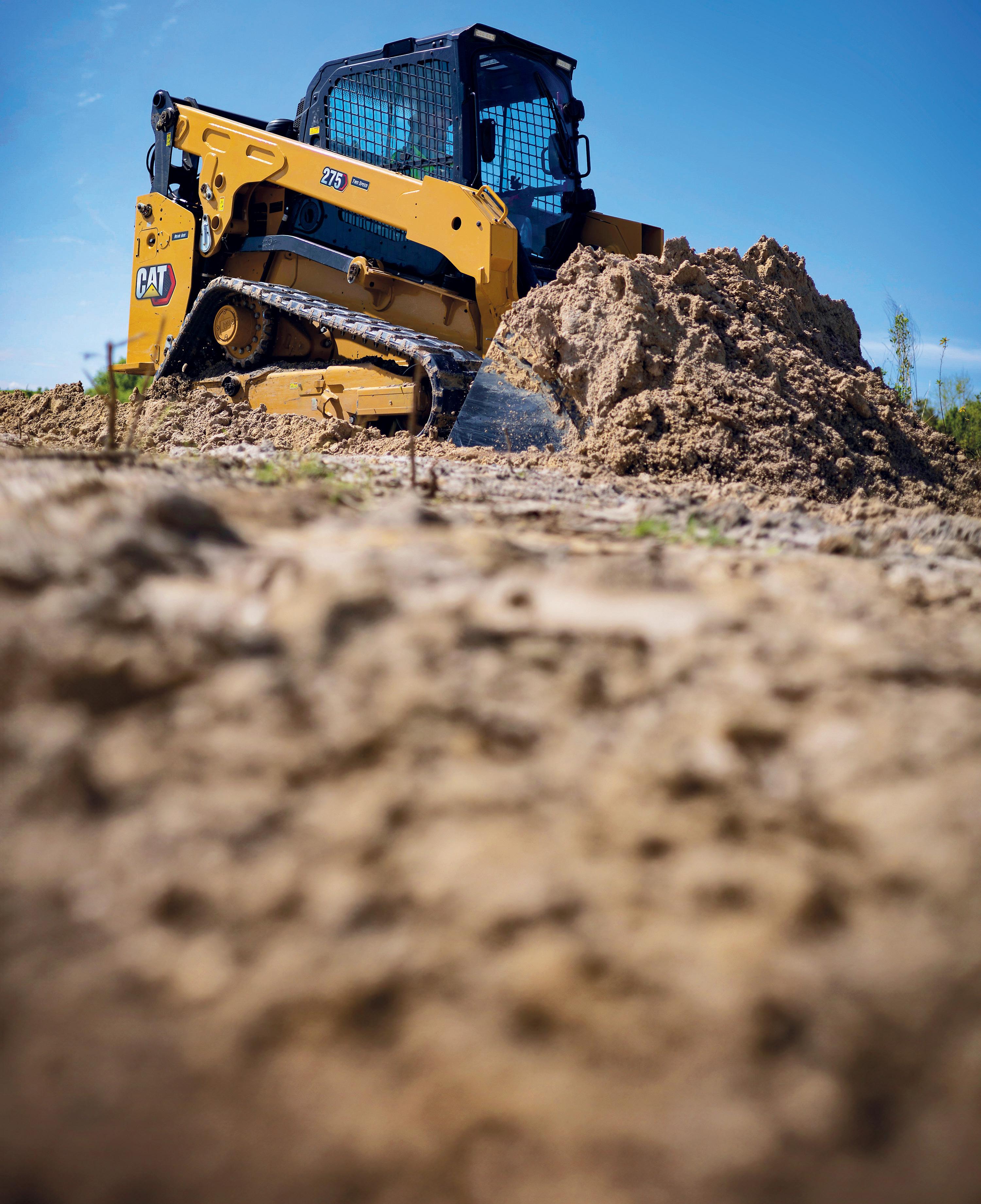
simplified its model nomenclature, with SSL models now ending in “0” and CTLs ending in “5,” making it easier to identify machine sizes and categories. Trevor Chase, senior product consultant at Caterpillar, said: “Their increased power, lift height, breakout forces, rated operating capacity, and multiple high-flow auxiliary hydraulic system options give customers a flexible, high-performance. ,The models feature a redesigned engine compartment that enhances stability by placing the engine and cooling system lower in the frame. The Cat 250 and 260 are powered by the Cat C2.8T engine, while the 270, 270 XE, and all CTL models run on the Cat C3.6TA. These new engines deliver better torque across a wider RPM range, with torque increases of up to 50% in some models, which significantly boosts working performance. Cat’s vertical lift design enables substantial increases in lift height and breakout force across the series. For instance, the Cat 250 now has a lift height of 124 inches and a 36% increase in tilt breakout force compared to previous models, while the new Cat 285 XE provides a lift height of 146 inches and a breakout force of 13,920 pounds. Cat has equipped the SSL and CTL models with
a new closed-center auxiliary hydraulic system, allowing seamless operation of Cat Smart Attachments. High Flow options are available, with pressures reaching up to 4,496 psi and flow rates as high as 40 gallons per minute for enhanced hydraulic performance. In addition, Caterpillar introduced a new E-bar undercarriage for the four CTL models, which combines the stability benefits of rigid undercarriages for lifting heavy loads with the flexibility of an oscillating undercarriage for navigating uneven terrain. Operator comfort has been a priority, with a 22% larger cab, upgraded suspension seating, and new AC vents that quickly cool the interior.
SPECIFICATIONS
MODEL 275
Engine: Cat C3.6T
Power: 82kW
Torque: 501 Nm
Operating Weight: 5.6t
Rated Operating Capacity @ 35%: 4,261 lbs (1933 kg) w/counterweight
Standard Hydraulic Pressure: 3500 psi (24130 kPa)
SCAN THE SITE
Check ground conditions, obstacles, and utilities thoroughly before setup to ensure no hidden risks lie beneath or overhead.

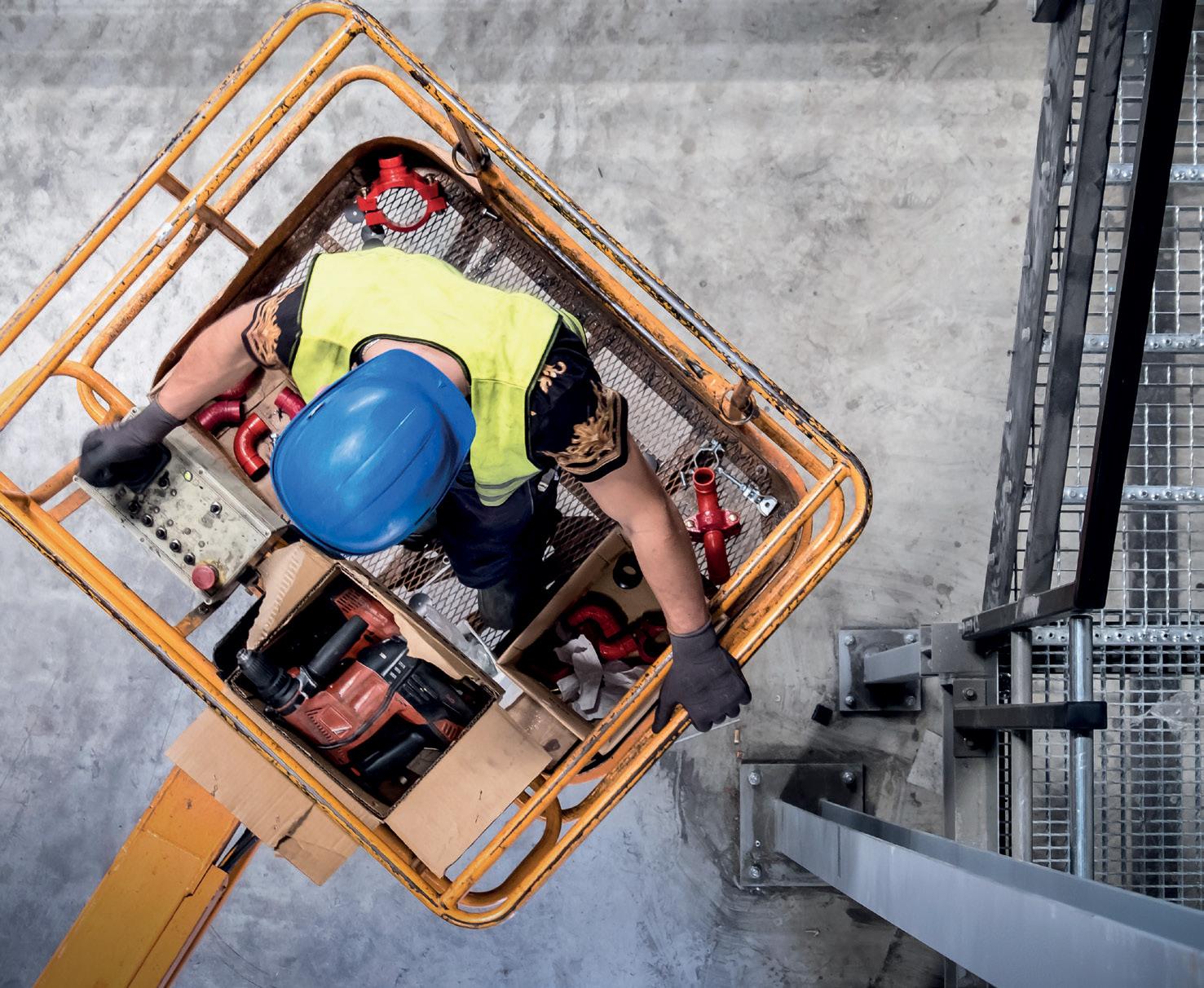
TOP TEN: PLACING POWERED ACCESS EQUIPMENT ON SITE
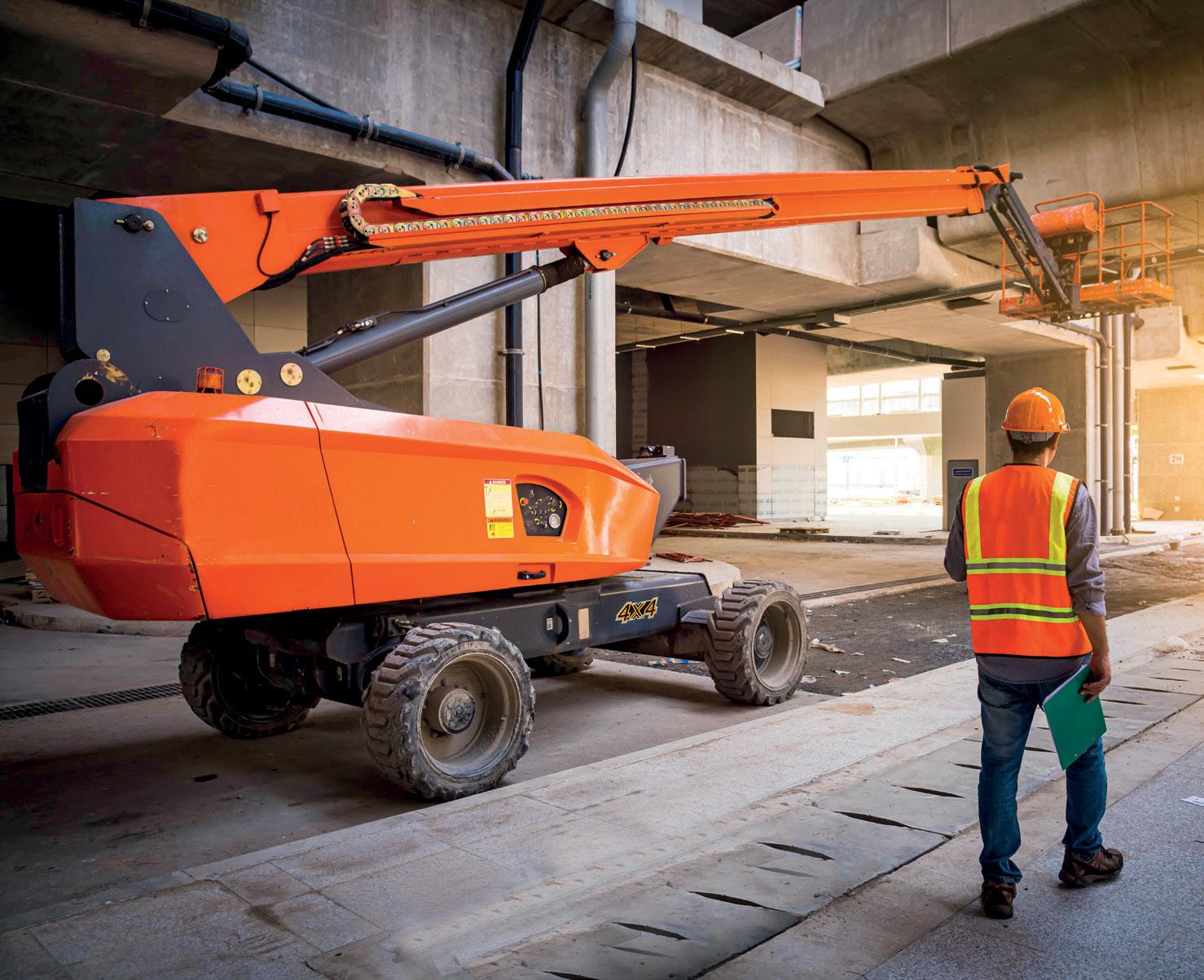
DO A SAFETY CHECK
Inspect all controls, safety features, and stability systems on the equipment. No shortcuts—your safety depends on it.
TRAIN TO GAIN
Operators must be certified and up-todate on equipment use. Keep skills sharp with periodic refresher courses.
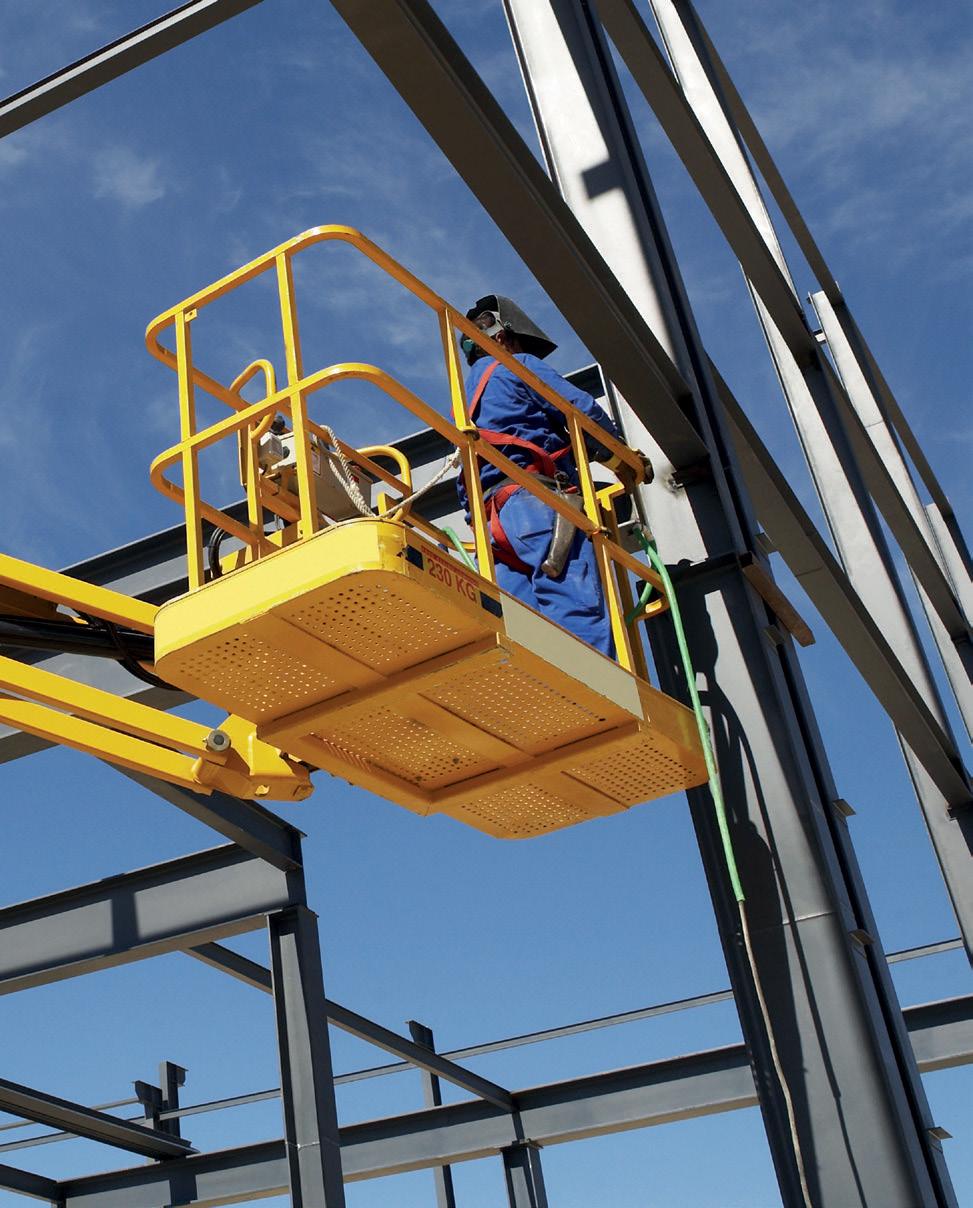

GROUND IT RIGHT
Place equipment on firm, level ground. Use stabilizers or pads on soft surfaces to prevent unwanted tipping or shifting.
KEEP IT SOLID
Remember, even the best equipment needs a firm foundation. Stable ground and clear surroundings make every job safer. Proper planning from the beginning ensures safer setups, fewer accidents, and more efficient operations.
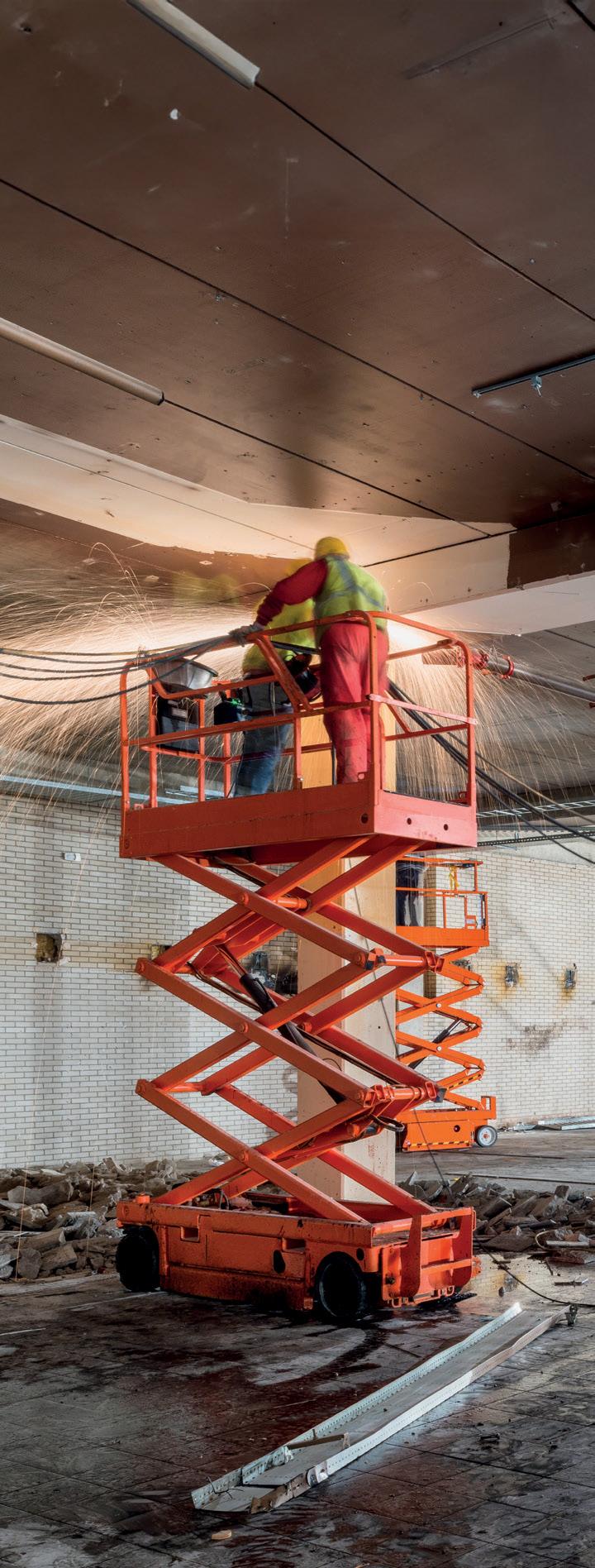
GEAR UP
Safety gear is nonnegotiable: harnesses, helmets, and gloves are a must for operators and nearby personnel.

KNOW YOUR LIMITS
Calculate and respect the equipment’s weight limits for workers, tools, and materials. As CMME has said numerous times, stick to these for structural stability.
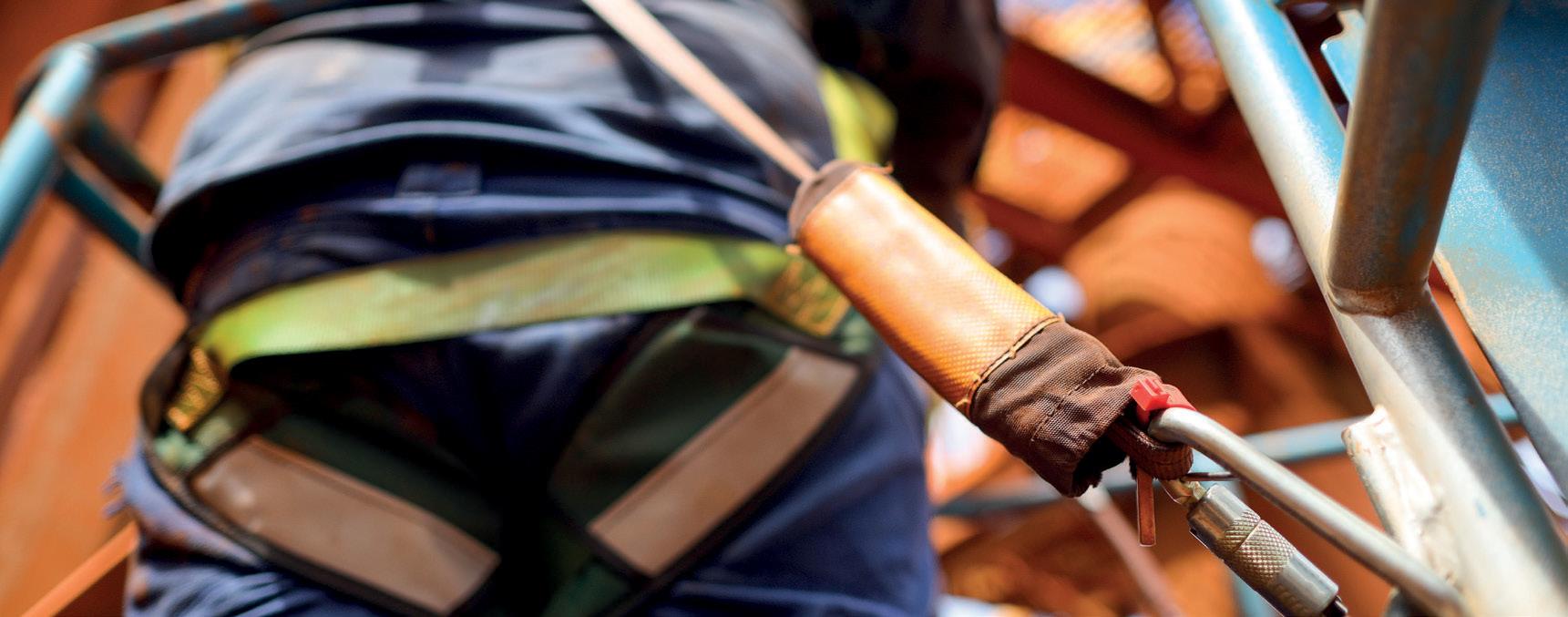

REVIEW AND REACT
Regularly reassess equipment placement as site conditions evolve. Make adjustments to stay safe in changing environments.
07 10 06


“AT A PACE THE CUSTOMER CAN ABSORB”
RYU KUDO, PRESIDENT OF YANMAR COMPACT EQUIPMENT,
TALKS MANAGING THE PACE OF CHANGE IN THE INDUSTRY
For differing social reasons, smaller machines need to become both simpler to use and more autonomous. That’s the verdict of Ryu Kudo, president of Yanmar Compact Equipment’s Japan region.
Question: When it comes to construction equipment, what do advanced societies have in common with developing economies?
Answer: They are both struggling with a lack of skilled machine operators. But the reason for this is very different. In advanced countries like Japan a shrinking-and-ageing population means that the industry struggles to attract and retain operators, while in developing markets the rapid transition from manual labor to the use of compact equipment isn’t keeping up with the training required to produce skilled operators.
“The answer to both challenges is to produce machines that are simple to operate and safe, with clever but not overly costly technology that can
automate key functions, such as digging.” So says Ryu Kudo, the new president of Yanmar Compact Equipment’s Japan region.
Kudo may be new in the role, but he’s been with Yanmar since 2019 – and spent a lifetime in construction. Following a childhood in Hokkaido in Northern Japan watching his parent’s building business prosper, he then studied mechanical engineering at Niigata University. Mr Kudo spent 21 years working for a major US construction equipment manufacturer. His first role was to design a small wheel loader, for which – due to a lack of
resources – he had to do everything himself, from the original market research to the design all major features. At the other end of his time at the company, his last role was as head of customer support for a major dealer, where he often first met customers once their machine had broken down.
“I met with over 200 customers, and I always had to start by apologizing for the machine breaking,” smiles Mr Kudo. “But relationships soon flourished and once we had fixed the problem the customer was happy – and generally bought another machine from us. It was then that I realized that designing a good machine was not enough – we really had to look after the customer from start to finish.”
Easy-to-use – but affordable?
Despite the broad span of customer types in both advanced and developing economies, they often share surprisingly common needs. Mr Kudo is committed to leveraging technology to enhance the Yanmar product offering. He envisions a future where compact equipment is fitted with simple automation systems that facilitate easeof-use, while maintaining affordability. Safety remains a top priority, and obstacleavoidance and anti-collision technology will become standard features in the machines of tomorrow. But as mentioned above, the product is only part of the story.
“Like our tagline ‘Building with You’ suggests, establishing close customer relationships is incredibly important,” says Mr Kudo. “We intend to collaborate closely with customers, develop new service offerings and provide comprehensive training, so operators can get the most out of our machines. We need to be active partners in building our customers’ success.”
The Yanmar brand is in a leading position in its home market of Japan, and – thanks to the ubiquity of small Yanmar engines around the world – starts its entry into developing markets with the brand already considered high quality. But while the company knows how to sell machines in mature markets, it is having to develop a new approach when it comes to rapidly developing, price sensitive – but huge – developing nations.
“Yanmar CE is of course excellent at innovation, but new features need to be introduced at a pace the customer can absorb,” he says. “Fully autonomous operation, for example, is currently possible, but expensive. So, what is needed is simple and affordable automatic systems, where an unexperienced operator can, for example, press a button and the machine will conduct a simple digging operation.
“I’m happy to encourage my team to embrace change and the innovative, pioneering, rulebreaking roots we came from,” says Ryu Kudo.
The features need to be appropriate and affordable for the target markets.”
Channelling a pioneering ethos
Kudo is also fostering a new mindset among his colleagues. “Yanmar may be an old and traditional company, but that doesn’t mean we have to act like one,” he says. “Change is in our DNA – our founder Yamaoka Magokichi, was the ultimate innovator. He saw an unserved customer need and developed a totally new small, practical, diesel engine – an innovation that became
a global benchmark. More than ever before, we need to channel our founder’s innovative spark to serve our customers’ needs.
“Having a mindset that constantly challenges us to answer the question: ‘What does the customer really need?’ is more important now than ever before,” Kudo concludes. “Yanmar CE has grown into a big business – but we must not lose sight of the exciting ‘Let’s-dothings-differently! mentality of our founder. I’m happy to encourage my team to embrace change and the innovative, pioneering, rulebreaking roots we came from.”

VEHICLES
Eleo, a Yanmar company, has launched an innovative range of battery packs specifically engineered for off-highway applications. Designed to meet the demands of low-volume, high-diversity vehicles and equipment, the new battery technology is tailored for rugged environments, tested to withstand dust, shock, vibration, and water exposure commonly encountered by off-highway machinery.
These advanced battery packs address a significant gap in the market, offering seamless integration for offhighway Original Equipment Manufacturers (OEMs) aiming to electrify their product lines. The new Eleo battery packs are versatile, featuring
a modular design that adapts to space constraints with options for both horizontal and vertical placement, making them suitable for a range of equipment types. Their scalable voltage range, from 50V to 720V, coupled with a maximum continuous power output of up to 90 kW, provides robust and adaptable power for diverse applications.
The packs also come with multipack functionality, enabling users to combine multiple packs to increase system capacity and voltage as needed, with flexible integration in two orientations. Utilising industry-standard protocols such as CANOpen and J1939, the packs seamlessly communicate essential data for reliable operation and
safe use. The battery packs also feature a service-friendly interface box, allowing quick part replacement to reduce service turnaround times by eliminating the need to send full batteries back for repair.
“Eleo is dedicated to advancing off-highway electric vehicle technology,” said Bas Verkaik, CEO of Eleo. “Our battery packs provide a practical alternative to internal combustion engines, supporting the global transition toward net-zero emissions.” With Yanmar’s support, Eleo is positioned to offer scalable manufacturing capabilities and secure supply chains to meet the growing demand for electrification in the off-highway sector.

TAKING CARE OF OVERHEADS
HOIST &
WINCH
TAKES CMME THROUGH ITS PAINSTAKING APPROACH TO AN OVERHEAD CRANE REPLACEMENT OP
A
design and installation by Hoist & Winch Ltd of replacement end carriages for two overhead cranes reached its conclusion recently with the end-user expressing complete satisfaction in the outcome.
Previously, the 2-ton swl (safe working load) manual overhead cranes were suffering from potentially dangerous crabbing problems due to the original design of the end carriages. Hoist & Winch thus had a responsibility to work expediently and professionally, with the aim of bringing this
concerning issue to a safe resolution.
Alongside the supply, installation, hire and load testing of hoist units/cranes for all types of industries, Hoist & Winch also offers lifting equipment refurbishment and rectification services. With each project of this type presenting its own set of challenges, the company comes to the fore in tackling work that competitors often prefer to avoid.
For this project, the relatively high-temperature working conditions and access requirements were a factor due to the basement location of the manual cranes in a large, ageing building in central London. The cranes work over two large gas-fired piston engines that provide heat to neighbouring buildings.
The core objective was to design and install
replacement end carriages for the cranes that in the first instance would eliminate the potentially dangerous crabbing issues. Due to this problem, the cranes had not performed correctly since initial installation.
Crabbing occurred because the original end carriage wheelbase was insufficient for the crane span, exacerbated by insufficient tread depth on the crane wheels. During long travel motion, the end carriage wheels would try and ride up (crab) on to the crane rails, a situation that can potentially lead to crane derailment.
With a solution required urgently, Hoist & Winch performed a detailed site dimensional survey to gather important design information and check the alignment of the existing crane rails. The company

then set about designing replacement end carriages with a longer wheelbase and new crane wheels featuring deeper tread. Side-acting crane rail guide rollers at each extent of the end carriages were a further important part of the new design.
Working closely with the customer’s onsite scaffold team, Hoist & Winch carried out a comprehensive installation survey. For the rectification work, the scaffolders agreed to build a temporary tube and board scaffold below each crane, providing both general access and jacking positions to vapiraise and lower the cranes when replacing the end carriages.
Hoist & Winch submitted a Risk Assessment
Method Statement (RAMS) for approval by the customer. The RAMS detailed the installation procedure, the required equipment, and the hazards and risks associated with the various tasks and how appropriate actions would mitigate accordingly.
Following a five-week period to manufacture the replacement end carriages, installation took place over four days for both cranes. The work included dynamic load and 125% proof load testing with a certified roller test load for each crane. A series of lifting beams helped to move the test load into the basement area via the use of temporary manual hoist units.
Hoist & Winch issued a Thorough Examination
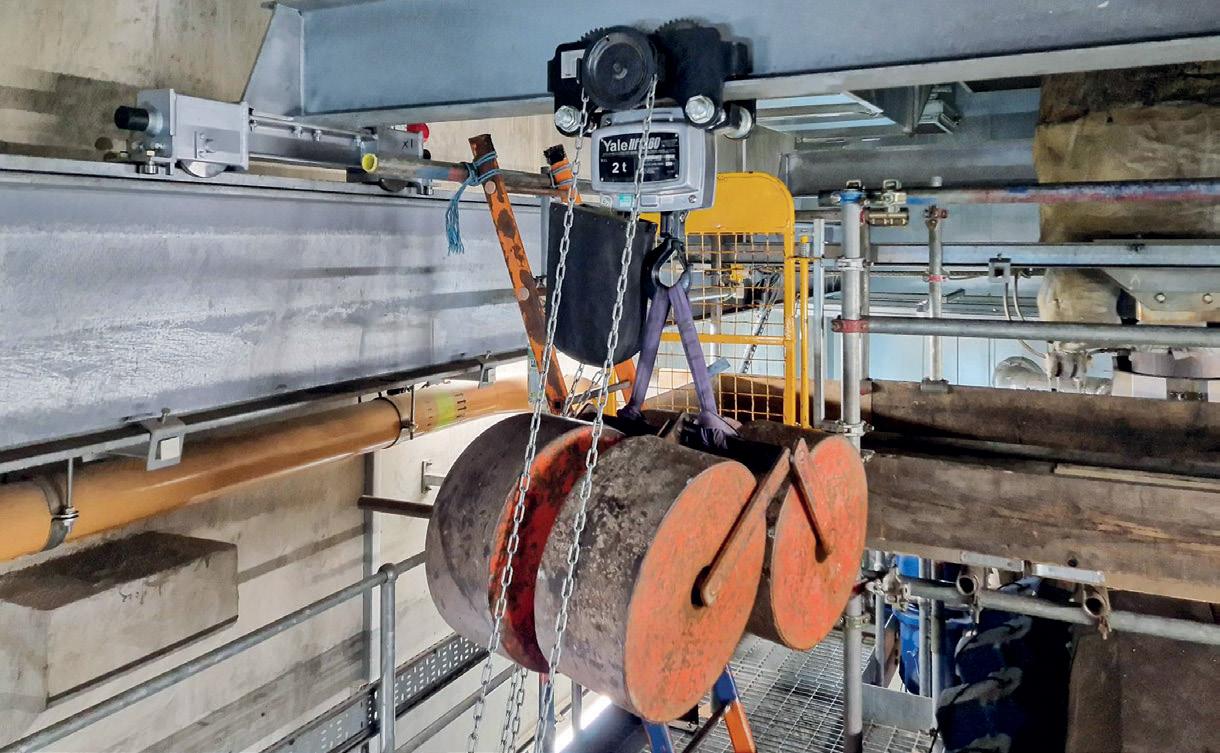
Hoist & Winch
Ltd recently designed and installed replacement end carriages for two overhead cranes that had not performed correctly since initial installation. Previously, the 2-ton swl (safe working load) manual overhead cranes were suffering from potentially dangerous crabbing problems due to the original design of the end carriages.
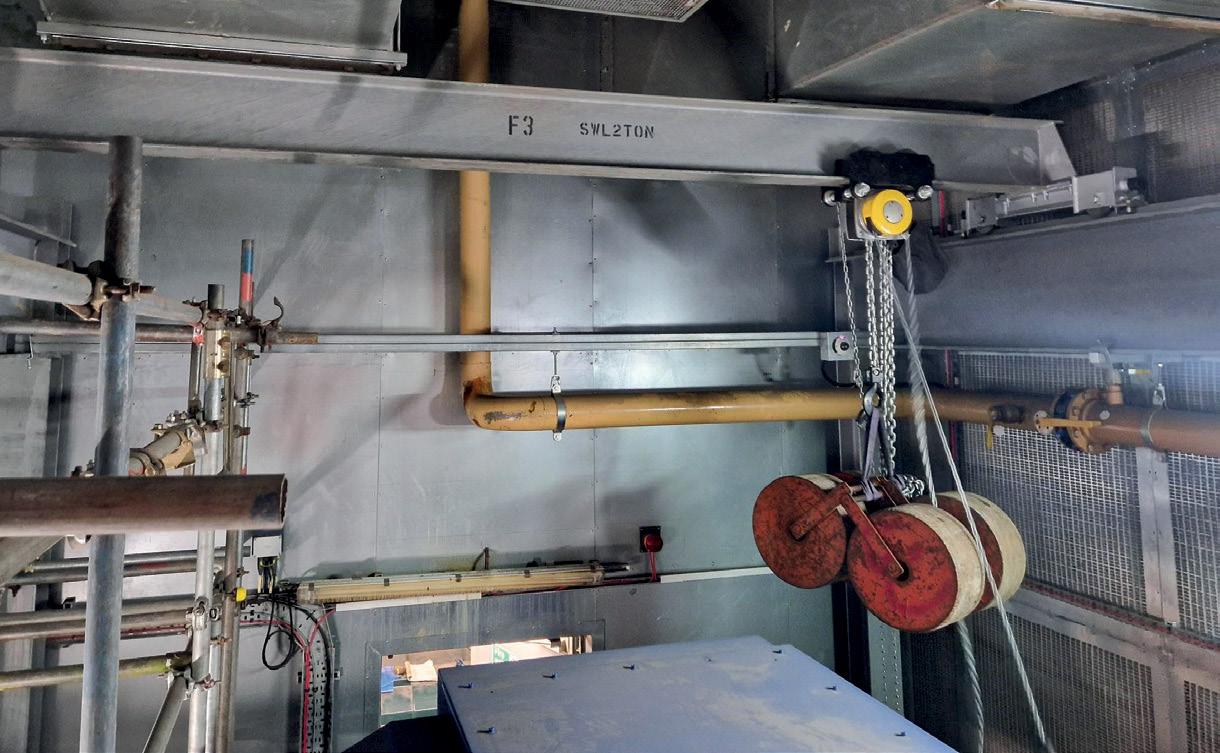

report in accordance with LOLER (Lifting Operations and Lifting Equipment) regulations.
“The new replacement end carriages served to eliminate the crabbing issues exhibited by the original crane design,” confirms Hoist & Winch Director Andy Allen. “Our customer was very satisfied as they could carry out essential maintenance work on the gas-fired piston engines that was previously delayed. The successful conclusion of this task is yet another example of how Hoist & Winch works with its customers in a professional way to overcome challenging issues and bring genuine added-value to lifting projects.”
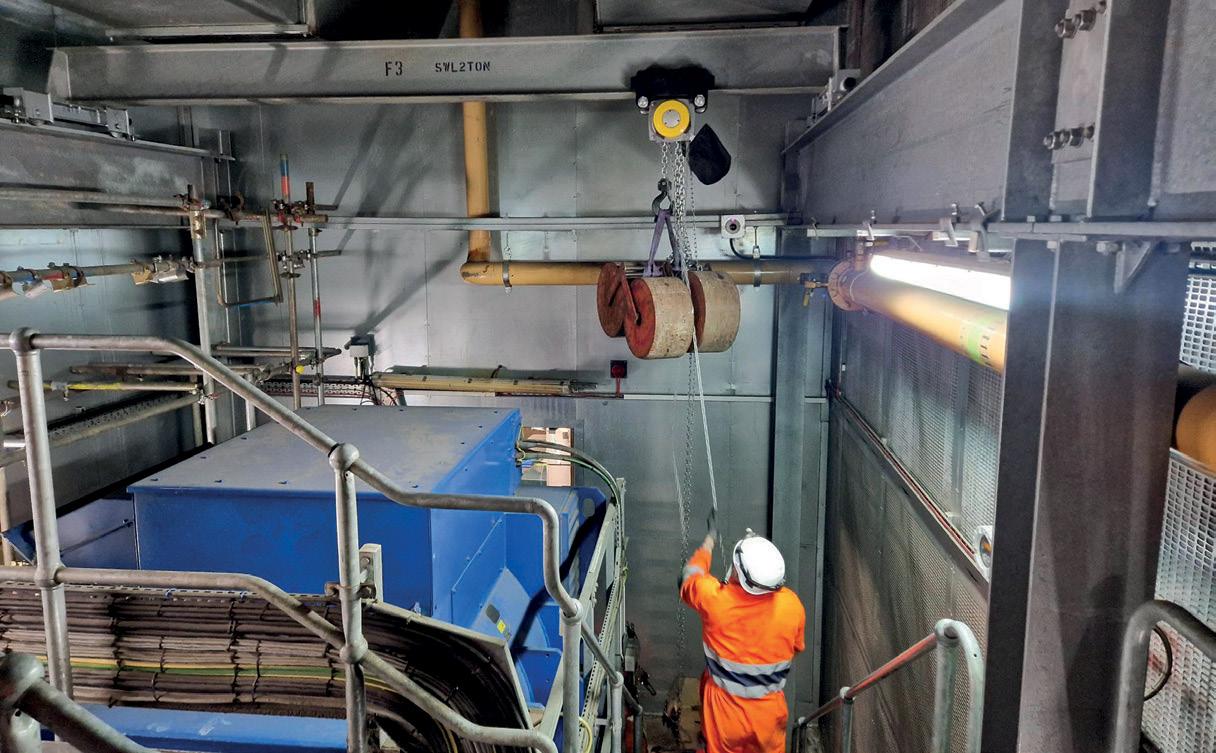
01 02 03 04 05 06
The core objective was to design and install replacement end carriages for the cranes that in the first instance would eliminate the potentially dangerous crabbing issues.
Installation took place over four days for both cranes. The work included dynamic load and 125% proof load testing with a certified roller test load for each crane. The new replacement end carriages served to eliminate the crabbing issues exhibited by the original crane design.
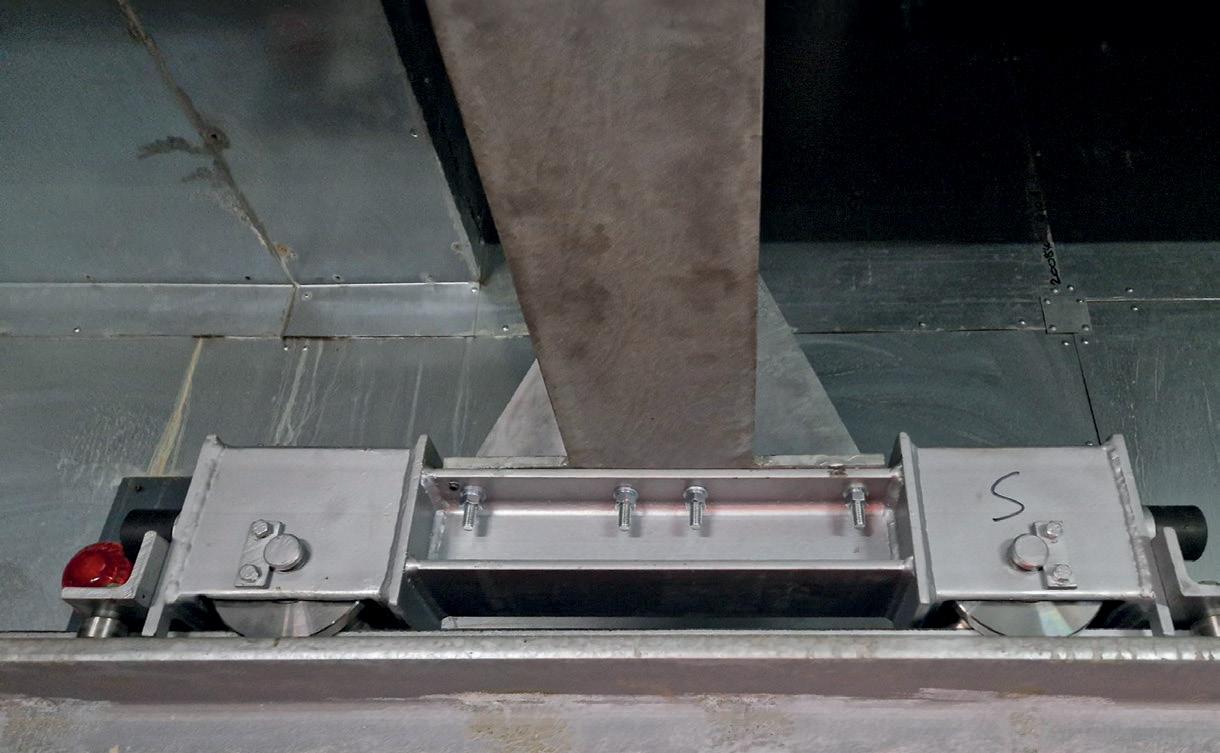
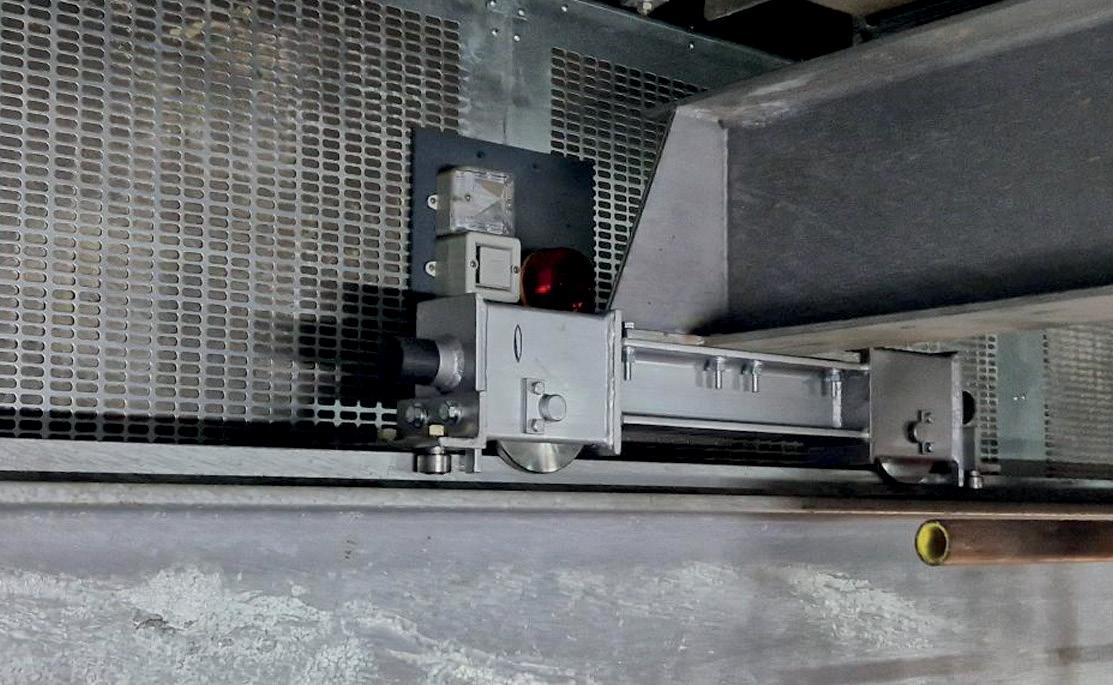
The cranes work over two large gas-fired piston engines that provide heat to neighbouring buildings and the customer can now carry out essential maintenance work that was previously delayed.
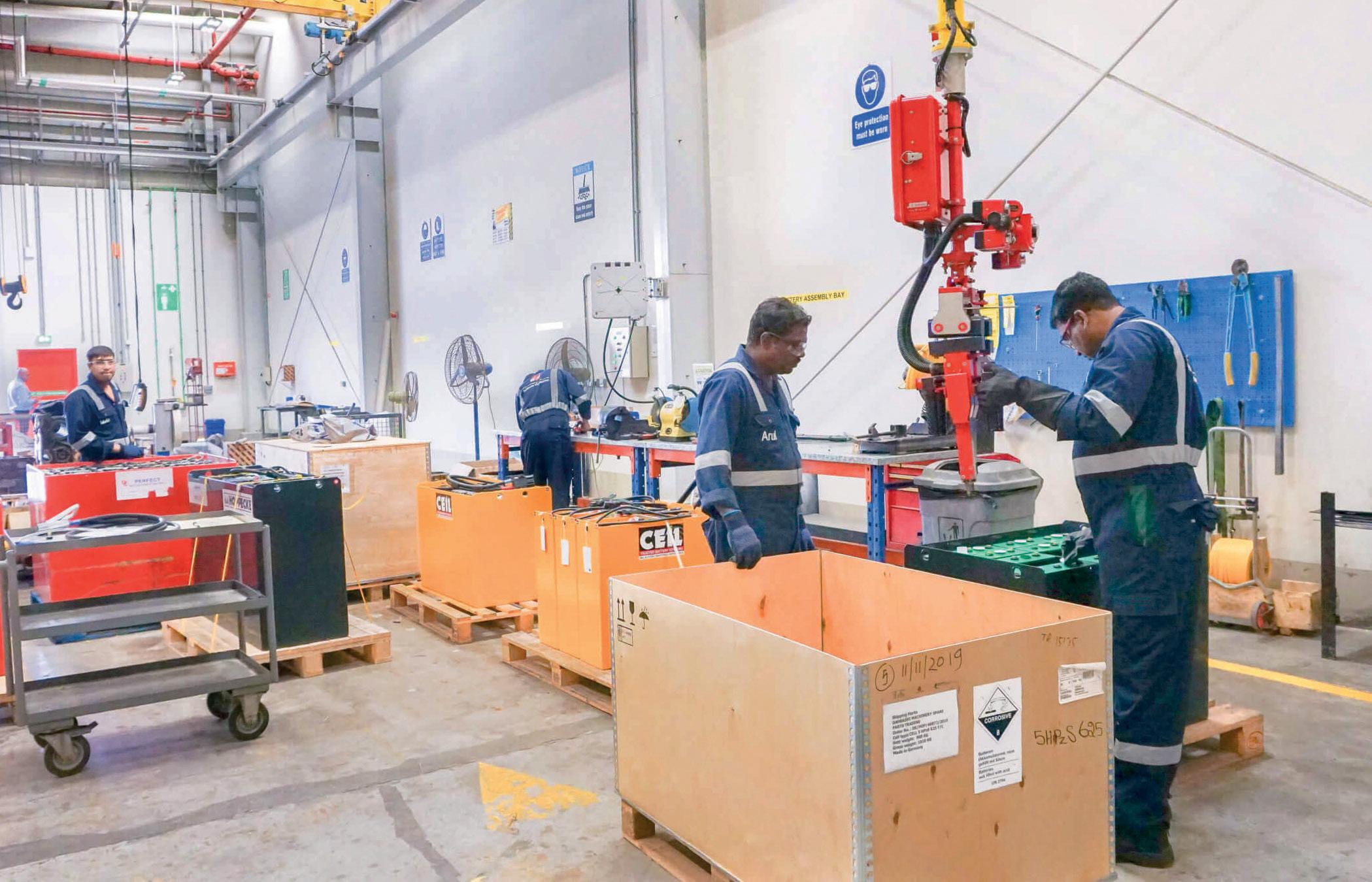
THERE
IS A GROWING
EMPHASIS ONMORE SUSTAINABLE
AND ECONOMICAL MANUFACTURING PRACTICES IN CONSTRUCTION, WRITES SAIFUDDIN DARGAHWALA OF DAHBASHI ENGINEERING
EMBRACING REMANUFACTURING
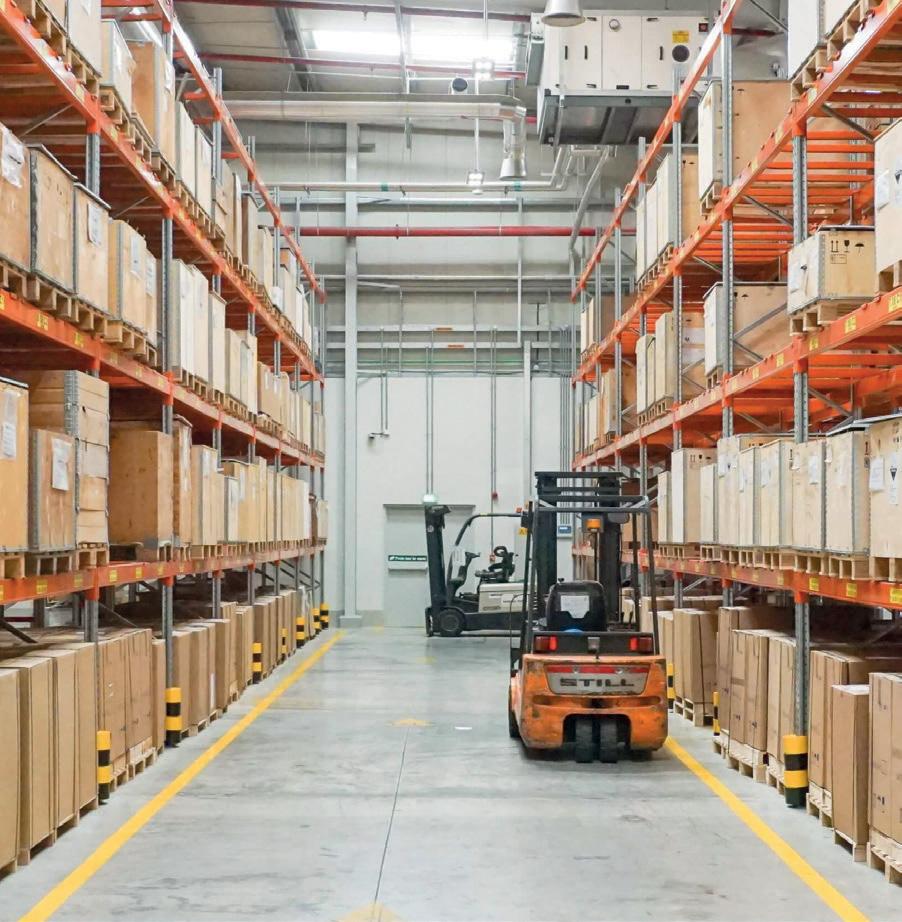
One notable trend is the exploration of unconventional power sources, such as electric solutions, for large heavy earthmoving equipment. While these technologies are being actively tested and developed, their commercial and operational viability for mass production remains uncertain. However, the industry has long embraced other sustainable practices that continue to make a significant impact in reducing the carbon footprint— namely, remanufacturing, refurbishment, and rebuilding. These practices have been instrumental for many years, providing essential benefits by extending the lifecycle of equipment and minimizing environmental impact. By adopting sustainable processes, businesses can maximise the economic and operational value of their machinery throughout its lifecycle. Remanufacturing, in particular, offers a unique opportunity to transform old units, such as engines, transmissions, and powertrain components, into like-new condition. This process breathes new life into aging equipment, often at a fraction of the cost of purchasing new machinery. One of the key advantages of remanufacturing is the significant time savings it offers. With the long delivery periods associated with new equipment, remanufacturing can provide a quicker solution, allowing businesses to maintain their operations without extended downtime. Remanufactured equipment can be
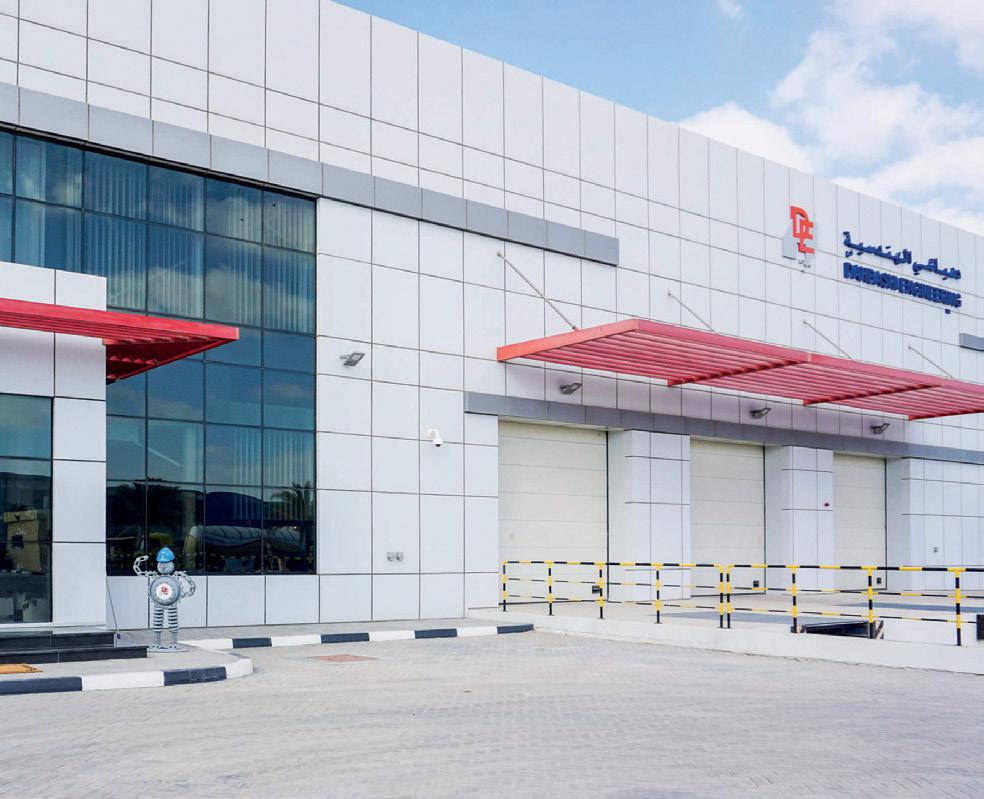
budgeted as an operating expense rather than a capital expenditure, simplifying the approval process and reducing bureaucratic hurdles. The remanufacturing process itself is meticulous and thorough. It involves utilizing previously used units and converting them to like-new condition without compromising performance or quality. Critical to this process is the opportunity to upgrade the units with the latest modifications provided by the original equipment manufacturer (OEM). During remanufacturing, failed, worn, or likely-tofail components are replaced with new ones, while salvageable parts are reclaimed through various machining and rebuilding operations. The result is a reliable, high-performing unit that improves equipment uptime and productivity.
At Dahbashi Engineering, we are committed to sustainable practices through remanufacturing. Our team combines extensive experience in remanufacturing a wide range of equipment, ensuring that each unit meets the highest standards. For instance, we recently remanufactured an engine for a track-type tractor, restoring it to optimal working condition and extending its life. Remanufacturing is not just a cost-effective solution; it is also a crucial step towards a sustainable future. By choosing to remanufacture equipment, firms can reduce waste, lower their carbon footprint, and contribute to the conservation of valuable resources. It can help you renew your aging fleet efficiently and sustainably.
Concrete Technology

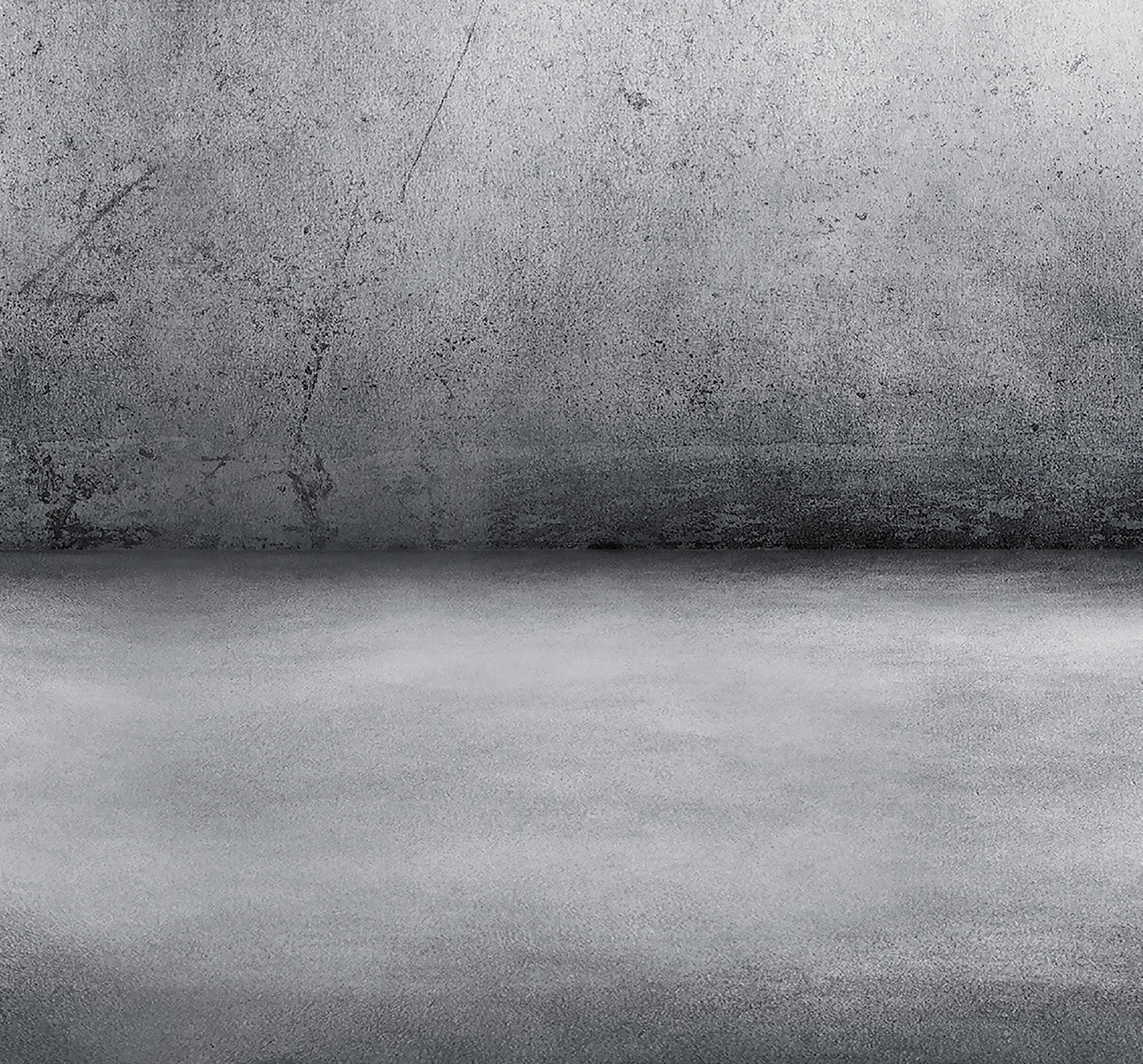


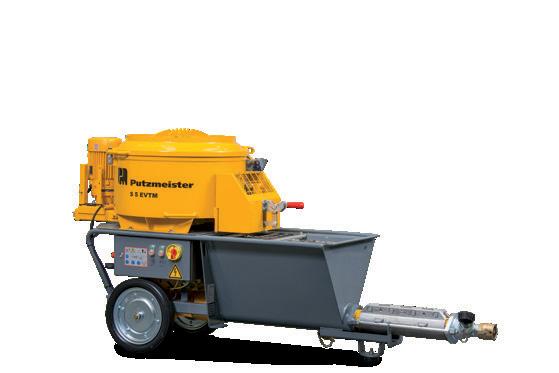
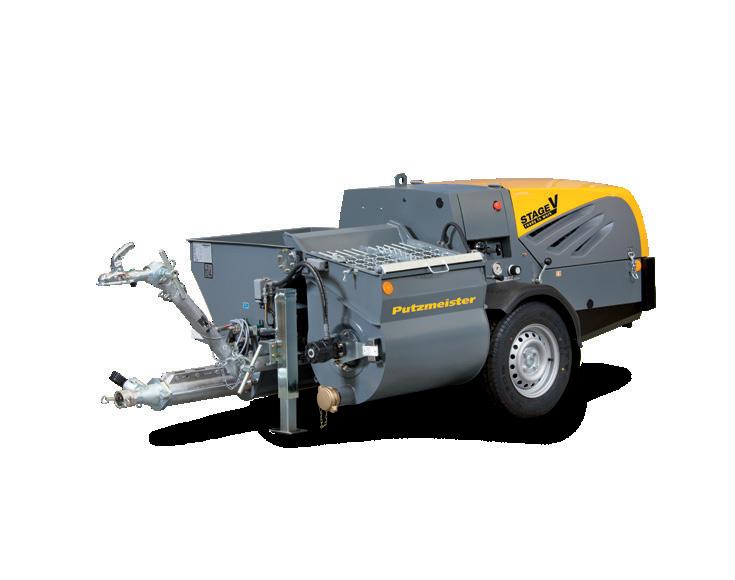

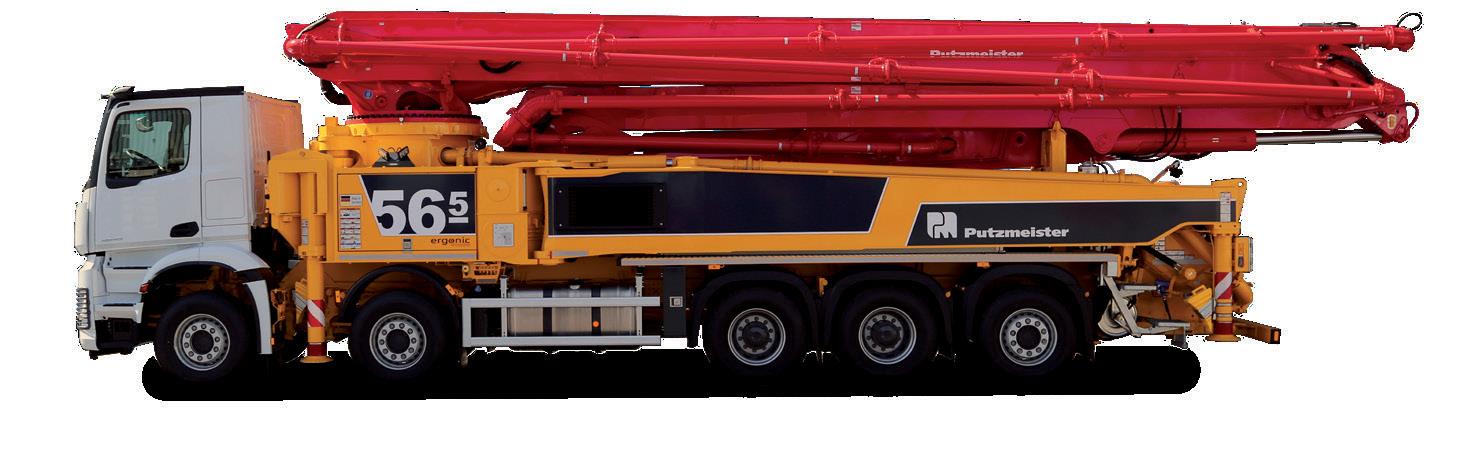
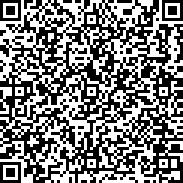

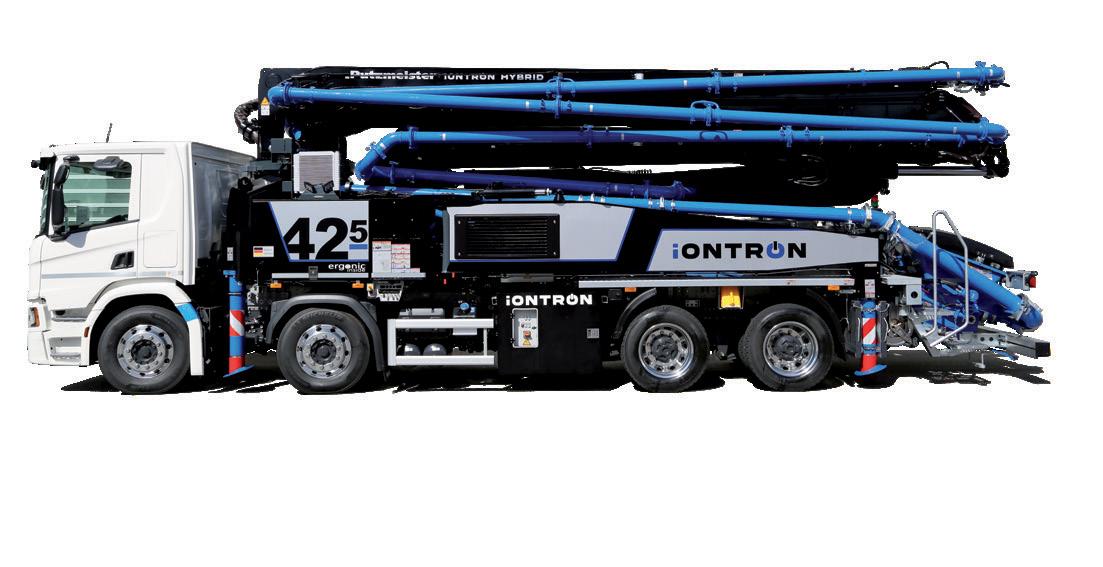
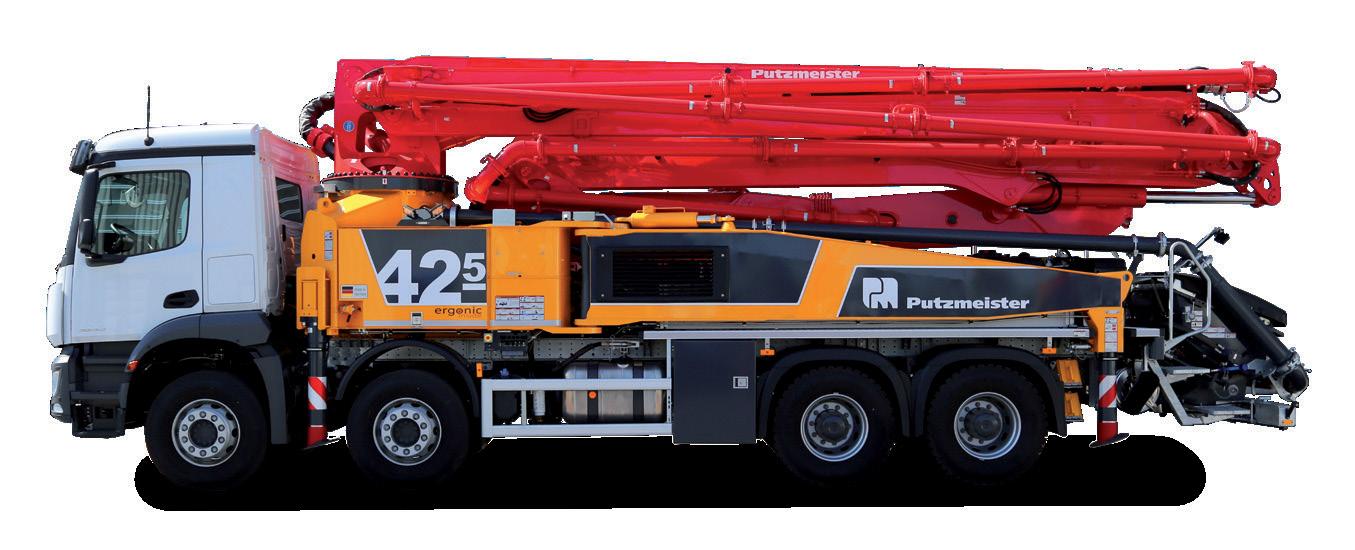
Putzmeister Concrete Pumps GmbH · www.putzmeister.com
Putzmeister Middle East
Jumeirah Lakes Towers (JLT) · 2406 Fortune Tower Cluster C P.O. Box 337508 · Dubai, U.A.E.
Tel: +971 (0) 4 454 27 83 · Fax: +971 (0) 4 454 27 82
Mr. Mohammad Sabah +971 526700057
Mr. Binoj Syamala +971 526700016
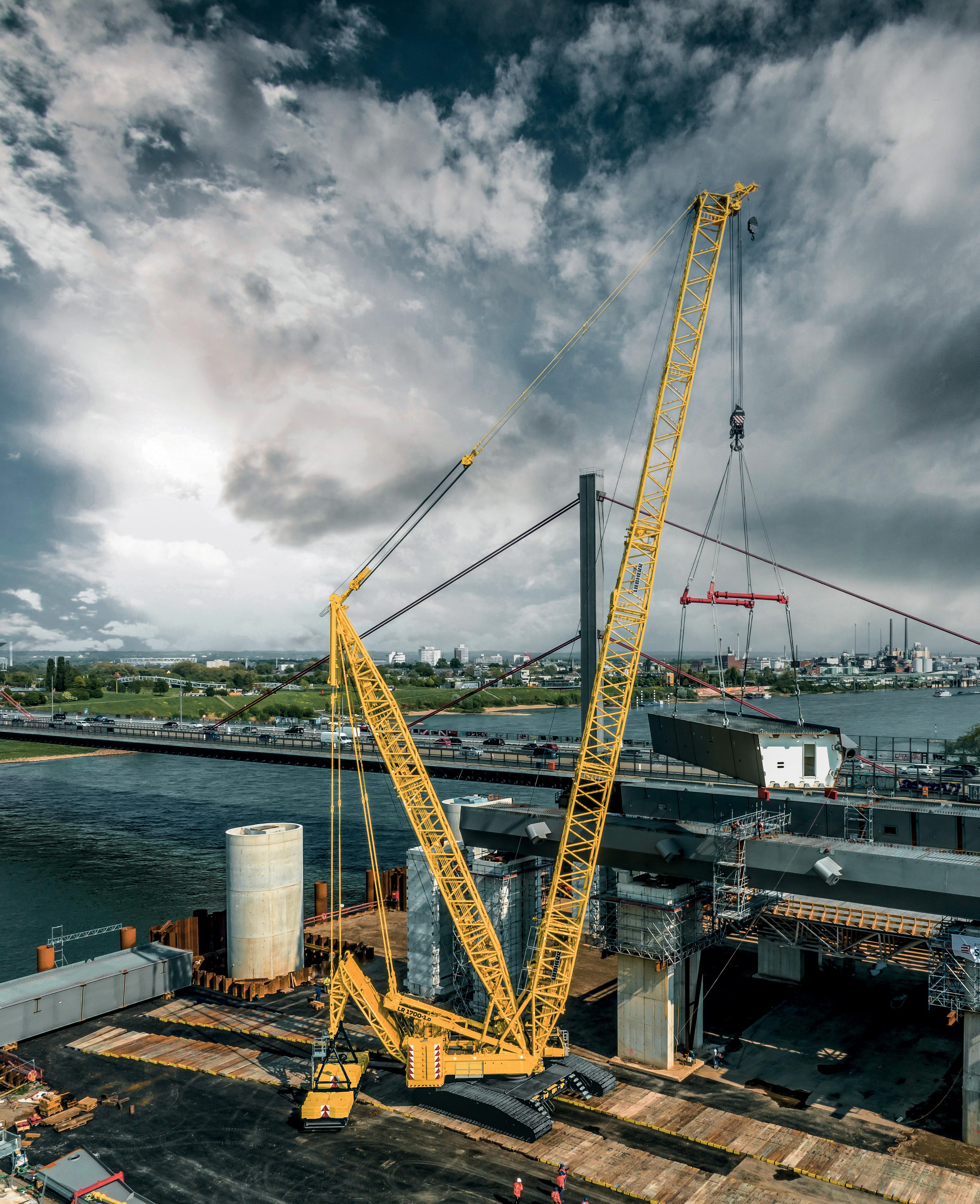
Connects worlds, unifies types
The LR 1700-1.0 combines the transport advantages of the 600-ton crawler crane class with the performance of the 750-ton class. It has the latest innovations of the Liebherr crawler crane portfolio. The high performance level is based on the statically new base machine with up to 15 percent more load capacity. The modern derrick system comes with V-frame, VarioTray and modular M-Wagon ballast trailer. Perfect for wind power, infrastructure and industry. www.liebherr.com