ACÉRICULTURE
CAHIER DE TRANSFERT TECHNOLOGIQUE EN 2e édition

VOLUME 3 : LES INFRASTRUCTURES ET LES ÉQUIPEMENTS DE RÉCOLTE
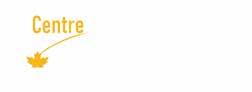
mìÄ=`ai=`ÉåíêÉ=^ÅÉêKéÇÑ===N===OMOQJMOJOU===MVWPT
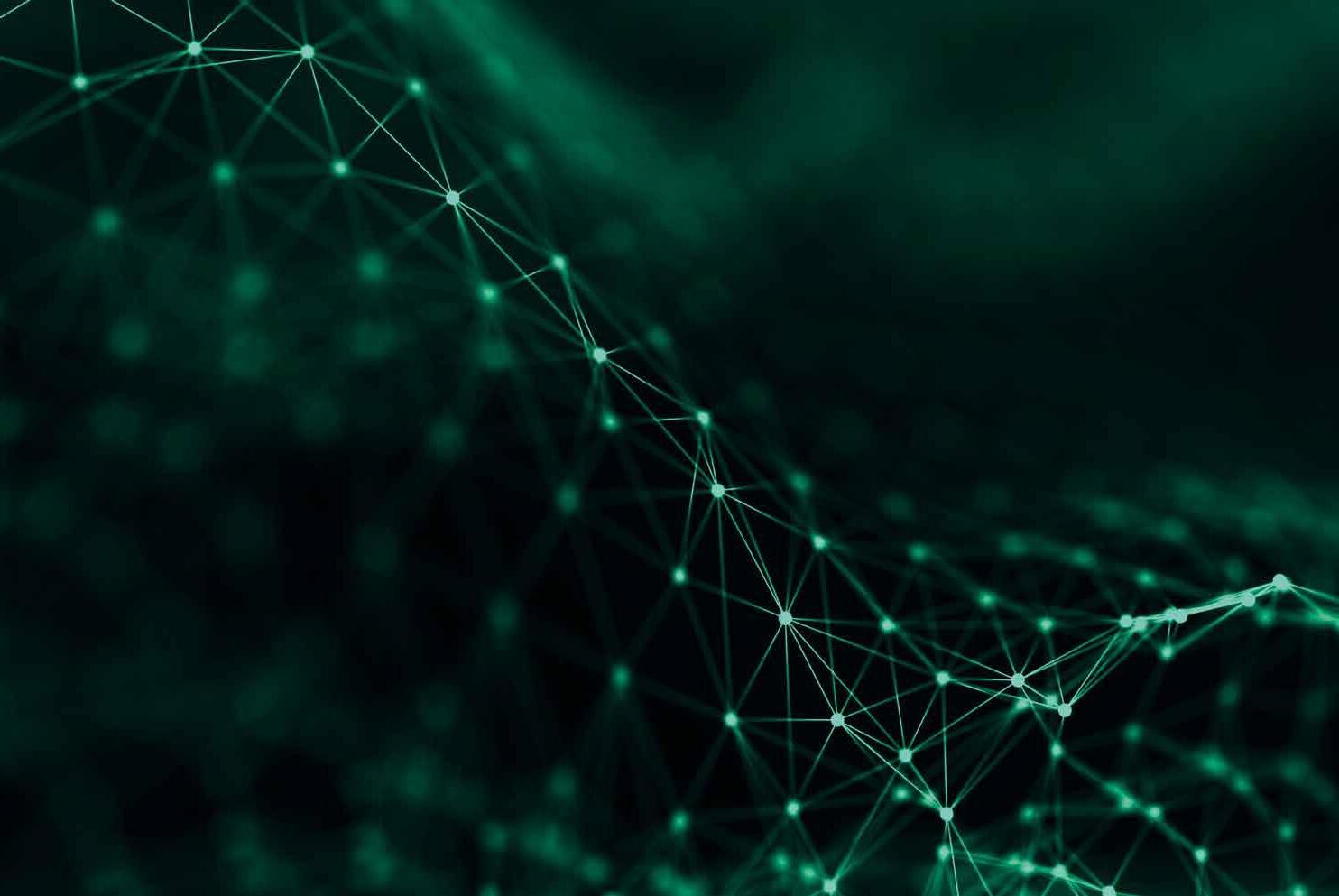

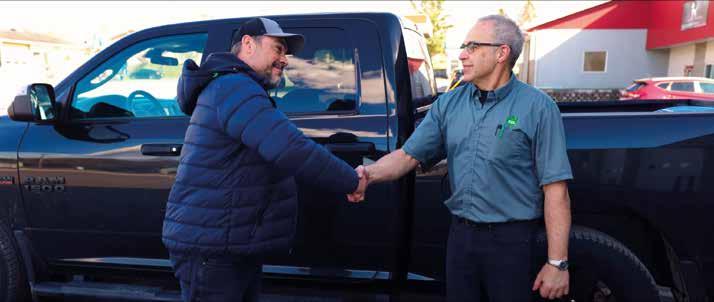
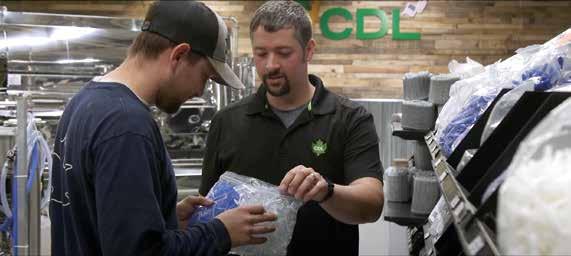
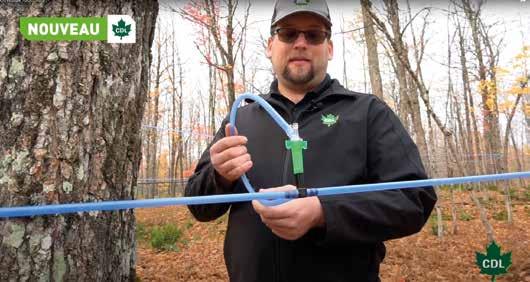
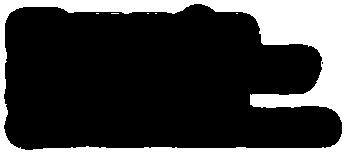
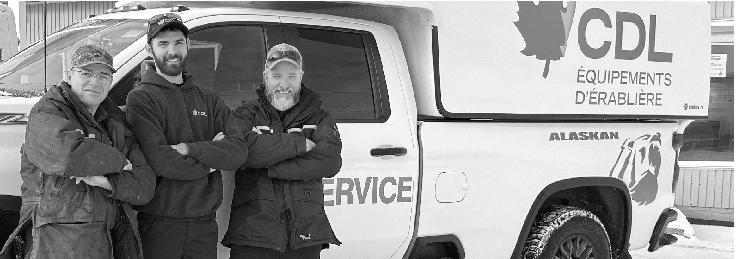
mìÄ=`ai=`ÉåíêÉ=^ÅÉêKéÇÑ===N===OMOQJMOJOU===MVWPT
Centre de recherche, de développement et de transfert technologique acéricole
Sous la direction de Jessica Houde, ing.
Droits d’auteur
Il est interdit de reproduire, de traduire ou d’adapter cet ouvrage en tout ou partie sans l’autorisation écrite du Centre de référence en agriculture et agroalimentaire du Québec (CRAAQ) afin de respecter les droits d’auteur et d’encourager la diffusion de nouvelles connaissances.
Avertissements
Les marques de commerce mentionnées dans ce document le sont à titre indicatif seulement et ne constituent nullement une recommandation de la part des auteurs ou de l’éditeur.
Au moment de sa rédaction, l’information contenue dans le présent cahier était jugée représentative du secteur acéricole au Québec. Son utilisation demeure sous l’entière responsabilité du lecteur. Certains renseignements pouvant avoir évolué de manière significative depuis la rédaction de cet ouvrage, le lecteur est invité à en vérifier l’exactitude avant de les utiliser.
Pour citer cet ouvrage :
Houde, Jessica (sous la dir. de). 2024. Cahier de transfert technologique en acériculture, 2e édition, volume 3 : Les infrastructures et les équipements de récolte. Centre de référence en agriculture et agroalimentaire du Québec. 276 p.
Centre de référence en agriculture et agroalimentaire du Québec 2875, boulevard Laurier, Édifice Delta 1, 9e étage
Québec (Québec) G1V 2M2 418 5235411 | 1 888 5352537 client@craaq.qc.ca | www.craaq.qc.ca
© Centre ACER
PEDI0224
ISBN 9782764907160
ISBN 9782764907177 (PDF)
Dépôt légal
Bibliothèque et Archives Canada, 2024
Bibliothèque et Archives nationales du Québec, 2024
Direction du projet
Jessica Houde, ing., Centre ACER
Rédaction
Jessica Houde, ing., Centre ACER
Stéphane Corriveau, tech., Centre ACER
Raymond Bernier, ingénieur à la retraite
Révision scientifique
Luc Lagacé, Ph. D., Centre ACER
Jack Bauer, Ph. D., Centre ACER
Révision technique
Sylvain Bilodeau, L. S. Bilodeau
Joël Boutin, tech. agricole, Club d’encadrement technique acéricole des Appalaches
Guy Breault, Producteurs et productrices acéricoles du Québec
Philippe Breton, Les Équipements Lapierre
Frédéric Dostie, ing., Les équipements d’érablière CDL inc.
Simon Forest, chimiste, MBA, Producteurs et productrices acéricoles du Québec
David Lapointe, ing.f., géog., M. ATDR, ministère de l’Agriculture, des Pêcheries et de l’Alimentation du Québec
Sylvain Mailloux, conseiller en production acéricole (Montérégie)
Daniel Majeau, Dominion et Grimm
Élodie Nadeau, Producteurs et productrices acéricoles du Québec
Andréanne Ouellet, agr., Club d’encadrement technique en acériculture de l’Est
Rachel Proulx, tech. agricole, ministère de l’Agriculture, des Pêcheries et de l’Alimentation du Québec
Éric Roy, tech. agricole et écologie, ministère de l’Agriculture, des Pêcheries et de l’Alimentation du Québec
Gabriel Weiss, agr., CCS Env., Direction régionale de l’Estrie, MAPAQ
Coordination, édition, mise en page et graphisme
Jacques Leblanc, chargé de projets, Centre de référence en agriculture et agroalimentaire du Québec (CRAAQ)
Nathalie Nadeau, graphiste, CRAAQ
Barbara Vogt, éditrice, chargée de projets aux publications, CRAAQ
Figures
Sauf mention autre, les figures originales de cette édition sont de Jessica Houde, Stéphane Corriveau et Raymond Bernier.
Certaines figures sont reproduites du CTTA 1e édition (2004)
Photos
Jessica Houde et Stéphane Corriveau, Centre ACER; Bernard Lapointe; Joël Boutin ; CDL; Les Équipements Lapierre
Certaines photos et schémas sont reproduites du CTTA 1e édition (2004)
(Certains textes figurant dans ce cahier ont été repris de la 1re édition.)
Recherche et rédaction
Gaston Allard, Centre ACER inc.
Martin Belzile, Centre ACER inc.
Comité Entreprises et producteurs
Onil Beaudoin, SaintPaul d'Abbotsford
Jogues Beaulac, Érablière Beauvan
Enrico Bélanger, Commission scolaire des Fleuves et des Lacs
Gilles Bernard, Équipement Gilles Bernard inc.
Sylvain Bilodeau, L. S. Bilodeau inc.
David Bolduc, Leeds Village
René Cantin, Cantin (HE) inc.
Bruno Carrier, Évaporateur Dallaire inc.
Robert Dupuis, Dominion & Grimm inc.
Jocelyn Faucher, Évaporateur Jean Faucher
Jean Gosselin, Les Plastiques Fusionex inc.
Rock Lavallée, Acériculteurs et Acéricultrices du Québec (ACERQ)
Donald Lapierre, Les Équipements Lapierre inc.
Marcellin Lavoie, Équipement d'érablière CDL
Gérald Lehoux, Entreprises Denis Darveau
Jeannine Lemieux, exploitante d'érablière
Josée Lussier, Les Spécialistes Techniques de Valcourt inc.
Diane Massicotte, Coopérative fédérée de Québec
Jean Marc Mathieu
Yvon Paquette, Équipement Y. Paquette ltée
Yvon Pellerin, Airablo inc.
Vincent Pépin, Dominion & Grimm inc.
François Périnet, Les Sucres Gosford senc
Jean François Plouffe
Louis Rivard, L'érablière de Stanfold
Angelo Trépanier, Érablière Aux Mille Érables
Rolland Urbain, Érablière Lise et Rolland Urbain
Comité scientifique et technique
Donald Beaulieu, MAPAQ BasStLaurent
Mario Beauregard
JeanPierre Bellegarde, Fédération des producteurs acéricoles du Québec
Raymond Bernier, MAPAQ OutaouaisLaurentides
Michel Bilodeau, Direction des laboratoires d'expertises et d'analyses alimentaires, Parc technologique du Québec métropolitain
Alain Boily, MAPAQ Chaudière Appalaches
André Boucher, MAPAQ OutaouaisLaurentides
Joël Boutin, Club d'encadrement technique acéricole des Appalaches
Michel Cartier, Centre ACER inc.
Damien De Halleux, Faculté des sciences de l'agriculture et de l'alimentation, Université Laval
René Desruisseaux, Centre ACER inc.
François Dumas, Groupement acéricole de l'Est
Andrée Gagnon, Club acéricole des Pays d'en haut
François Gagnon, Club Acéricole du Granit
Roméo Gauthier, MAPAQ Québec
Stéphane Guay, Centre ACER inc.
Luc Lagacé, Centre ACER inc.
Patrick Lang, Club d'encadrement technique acéricole de l'Est
Gaétan Lauzier, MAPAQ BasSaintLaurent
Julien Lavoie, Centre ACER inc.
Marie Josée Lepage, MAPAQ Estrie
Nathalie Martin, Centre ACER inc.
Richard Mongrain, Club de qualité en acériculture de la Montérégie
Louis Montambault, MAPAQ Mauricie
Robert Montambault, Citadelle Coopérative de producteurs de sirop d'érable
Sylvain Morasse, Club de qualité en acériculture de Portneuf
Marcel Moreau, MAPAQ Montérégie, secteur Ouest
Raymond Nadeau, Club de qualité en acériculture de Thetford
Alain Pelletier, Club de qualité en acériculture des Appalaches
Richard Pelletier, MAPAQ MontréalLavalLanaudière
Bernard Prince, Les entreprises Bernard Prince
Huguette Robichaud, Agence canadienne d'inspection des aliments
Richard Turmel, MAPAQ Centre du Québec
Les infrastructures et les équipements de récolte iv
Comité de validation
Lyne Beaumont, MAPAQ Direction de la normalisation et de l’appui à l’inspection
Patrice Bertrand, Club de qualité acéricole de Portneuf
Pascale Boivin, Regroupement pour la commercialisation des produits de l’érable du Québec inc.
André Boucher, MAPAQ OutaouaisLaurentides
Sylvie Chagnon, Érablière la coulée d’Abbotsford
JeanMarie Chouinard, Citadelle Coopérative de producteurs de sirop d’érable
Ghislain Jacques, Les produits alimentaires Jacques et fils inc.
Gaétan Lauzier, MAPAQ BasSaintLaurent
Richard Pelletier, MAPAQ MontréalLaval
Lanaudière
Marcel Pépin, Dominion & Grimm
(Les titres et affiliations sont ceux qui étaient valides en 2004, au moment de la rédaction de la 1e édition.)
Nous remercions le ministère de l’Agriculture, des Pêcheries et de l’Alimentation du Québec pour le soutien accordé au projet de mise à jour du Cahier de transfert technologique en acériculture. Nous remercions également le Créneau Acéricole, ainsi que le ministère de l’Économie, de l’Innovation et de l’Énergie pour le support accordé à l’édition et la publication du projet.
Au nom du Centre ACER, nous exprimons nos remerciements envers les membres du groupe de travail qui ont assuré la révision technique de l’ouvrage. Leurs connaissances et leur expérience ont été de précieux atouts pour bonifier le contenu de ce troisième volume du Cahier de transfert technologique en acériculture, 2e édition.
Des remerciements spéciaux vont aux personnes suivantes, qui ont collaboré à la recherche d’information pour permettre la rédaction de l’ouvrage :
• Maxime Cadotte, ing., M. Sc. A., Centre ACER,
• Mélissa Cournoyer, Centre ACER.
De plus, nous souhaitons remercier chaleureusement les personnes et organismes suivants, qui ont accepté de participer à des rencontres d’échange et de partager leurs précieuses connaissances sur les caractéristiques des équipements de récolte de la sève d’érable.
• Patrice Bertrand, ing.f., Club acéricole de Portneuf
• Anne Boutin, ing.f., Association des propriétaires de boisés de la Beauce
• Michael Cliche, ing.f., Association des propriétaires de boisés de la Beauce
• Chantale Francœur, tech. f., Club d’encadrement technique en acériculture de l’Est
• Andrée Gagnon, ing. f., Club acéricole des Pays d’enHaut
• Raymond Nadeau, Club de qualité acéricole de Beauce Appalaches
• Vincent Poisson, ing.f., Club acéricole du Sud du Québec
• Benjamin Roy, agr., Club d’encadrement technique en acériculture de l’Est
• Marie Claude Sirois, agr., M. Sc. f., ministère de l’Agriculture, des Pêcheries et de l’Alimentation du Québec
L'équipe de rédaction
Les infrastructures et les équipements de récolte vi
Ce projet a été financé par l’entremise du Programme services-conseils, mis en œuvre en vertu du Partenariat canadien pour l’agriculture, selon une entente conclue entre les gouvernements du Canada et du Québec, ainsi que par le ministère de l’Économie, de l’Innovation et de l’Énergie (MEIE), via le Programme d’appui aux projets de développement économique (PADS) et le créneau d’excellence Acéricole reconnu au sein de la démarche ACCORD .
Fondé en 1998 dans le cadre d’un partenariat unissant le ministère de l’Agriculture, des Pêcheries et de l’Alimentation du Québec (MAPAQ), le ministère de la Forêt, de la Faune et des Parcs du Québec (MFFPQ) et les différents acteurs de l’industrie acéricole, le Centre de recherche, de développement et de transfert technologique acéricole inc., aussi connu sous le pseudonyme Centre ACER, est un acteur incontournable du développement et du partage de l’information technicoscientifique dans l’industrie acéricole québécoise et mondiale. Principalement axé sur la recherche appliquée et le transfert de technologie, le Centre ACER, en collaboration avec les différents intervenants du milieu, a pour objectif de contribuer au développement de l’acériculture dans les domaines suivants :
• Le développement des techniques de production et de transformation;
• Le contrôle et l’amélioration de la qualité et de l’innocuité des produits de l’érable;
• La valorisation et l’exploitation durable de la ressource.
Depuis sa création, le Centre ACER a contribué à l’avancement de l’acériculture en traitant de différents enjeux de taille. On peut notamment souligner les efforts répétés visant à favoriser l’innocuité et l’intégrité du sirop d’érable par l’innovation et le transfert de connaissances, entre autres en matière :
• De détection de l’adultération du sirop d’érable tant par des analyses non ciblées à grande échelle que par des analyses ciblées utilisant des techniques novatrices;
• D’identification, de caractérisation et de compréhension générale de la saveur du sirop d’érable;
• De contribution à la recherche fondamentale en microbiologie acéricole;
• De soutien à l'amélioration et à la validation des performances de divers équipements employés en production acéricole;
• D’appui au développement d’innovations faisant l’objet d’un brevet;
• De travail sur les produits et les méthodes d’assainissement des équipements de récolte permettant de favoriser les rendements et la qualité du sirop;
• De soutien à l’élaboration de différents règlements et normes ainsi qu’à la mise en œuvre de la politique bioalimentaire du Québec.
Centre ACER
142, rang Lainesse
SaintNorbert d'Arthabaska (Québec)
G0P 1B0
Tél. : 8193694000 www.centreacer.qc.ca
Les infrastructures et les équipements de récolte viii
Le Centre ACER recevait en 1996 le mandat de réaliser la première version du Cahier de transfert technologique en acériculture (CTTA), qui fut publiée en 2004. La nécessité d’un tel document de référence avait été exprimée par tous les membres de la Filière acéricole. Le CTTA a donc été créé pour regrouper l’ensemble des connaissances dans ce domaine, tant les pratiques issues du savoir traditionnel que les techniques plus modernes s’appuyant sur des fondements scientifiques. Il a été écrit en impliquant les gens du milieu, en colligeant l’expérience de nombreux producteurs et productrices et en travaillant dans un esprit de consensus pour arriver à une compréhension commune. Cet ouvrage constitue désormais la référence pour le monde acéricole au Québec.
Le besoin de mettre à jour les connaissances sur les équipements et les technologies en usage a cependant rendu nécessaire la production d’une 2e édition du CTTA. Cette version modernisée est conçue sous la forme de volumes thématiques, qui reprennent certains textes de la 1ère édition, les bonifient et les enrichissent de connaissances nouvelles.
• Le volume 1 traite des appareils de concentration membranaire et des évaporateurs.
• Le volume 2 est consacré à la production d’un sirop d’érable de qualité.
• Le volume 3 décrit les infrastructures de production et le système de récolte de la sève d’érable.
L'équipe de rédaction espère que cet outil actualisé que constitue cette 2e édition du Cahier de transfert technologique en acériculture saura permettre aux acériculteurs, acéricultrices ainsi qu’aux spécialistes du secteur d’ approfondir leurs connaissances et de répondre à leurs questions sur de nombreux points techniques.
À télécharger gratuitement
L'outil ACER DimSys Récolte vous facilite certains calculs présentés dans ce guide. Pour le télécharger, connectezvous à votre compte CRAAQ à partir de la page d’accueil du site www.craaq.qc.ca et récupérez le fichier Excel dans la section « Mes achats ». L'utilisation de ce chiffrier d’aide au dimensionnement du système de récolte est présentée au chapitre 4.
CHAPITRE 1
Tableau 1.1. Composantes et techniques pour unir les tubes de grandes dimensions (union et fusion) ...........................................................................28
Tableau 1.2. Composantes et techniques utilisées pour unir des segments de latéraux ...................30
Tableau 1.3. Facteur à appliquer pour calculer approximativement le débit équivalent d'une pompe à vide dans des conditions de température et de pression normales (TPN) ............................................................................................39
Tableau 1.4. Estimation de la per te de charge typique à travers un accentuateur de pente (pieuvre) en fonction du nombre d'entailles, de la hauteur (H) et du nombre de tubes de l'accentuateur ............................................46
CHAPITRE 2
Tableau 2.1. Actions à réaliser en érablière en concordance avec la règlementation et les bonnes pratiques en vigueur ............................................70
CHAPITRE 3
Tableau 3.1. Caractéristiques des aciers inoxydables utilisés en acériculture ....................................78
Tableau 3.2. Caractéristiques des plastiques utilisés en acériculture...................................................79
Tableau 3.3. Caractéristiques des matériaux en fibre de verre utilisés en acériculture .....................80
Tableau 3.4. Effet de l'augmentation du niveau de vide à l'entaille sur le rendement en sève d’érable et en sirop pour une érablière moyenne .................83
Tableau 4.1. Écar tement moyen (en m) à laisser entre les collecteurs en fonction de la densité relative des entailles, de l’espacement entre les tubes latéraux et du nombre moyen d’entailles par tube latéral (système métrique) ......... 104
Tableau 4.2. Écar tement moyen (en pi) à laisser entre les collecteurs en fonction de la densité relative des entailles, de l’espacement entre les tubes latéraux et du nombre moyen d’entailles par tube latéral (système impérial) 104
Tableau 4.3. Nombre d’entailles maximal théorique pouvant être utilisé pour un tube collecteur, selon le diamètre de tube, la longueur et la pente, basé sur une coulée à l’entaille de 0,166 gal/h/entaille et un espace libre dans le tube de 30 % .............................................................................. 110
Tableau 4.4. Nombre d’entailles maximales théorique pouvant être utilisé selon le diamètre de tube à eau, la longueur et la pente, basé sur une coulée à l’entaille de 0,166 gal/h/entaille et un espace libre dans le tube de 0 % (système air-eau) ................................................. 111
Tableau 4.5. Indications de référence pour le dimensionnement d’un collecteur, basées sur une coulée à l’entaille de 0,166 gal/h/entaille et un espace libre dans le tube de 30 % .............................................................................. 112
Tableau 4.6. Indications de référence pour le dimensionnement d’un collecteur, basées sur une coulée à l’entaille de 0,166 gal/h/entaille et un espace libre dans le tube de 0 % (système air-eau) ................................................. 113
Tableau 4.7. Diamètre nominal et diamètre intérieur des tubes à air ............................................... 119
Tableau 4.8. Diamètre nominal et diamètre intérieur des tubes à air et nombre équivalent de tubes (D1) pour obtenir une surface d’écoulement semblable à celle obtenue en utilisant un tube de diamètre (D2) plus grand (système métrique) ......................................................................................... 119
Tableau 4.9. Débit de fuite équivalent à température et pression normales (TPN) pour différents niveaux de vacuum .................................................................................. 120
Tableau 4.10. Calcul des pertes de charge (po Hg) dans un tube servant au transport de l’air en fonction des fuites dans le système par section de 250 pi (nombre d’entailles < 5 000), pour un vide de 20 po Hg ............................................... 124
Tableau 4.11. Calcul des pertes de charge (po Hg) dans un tube servant au transport de l’air en fonction des fuites dans le système par section de 250 pi (nombre d’entailles < 5 000), pour un vide de 25 po Hg ............................................... 128
Tableau 4.12. Calcul des pertes de charge (po Hg) dans un tube servant au transport de l’air en fonction des fuites dans le système par section de 250 pi (nombre d’entailles < 5 000), pour un vide de 28 po Hg ...............................................
Tableau 4.13. Calcul des pertes de charge (po Hg) dans un tube servant au transport de l’air en fonction des fuites dans le système par section de 250 pi (nombre d’entailles > 5 000), pour un vide de 20 po Hg 136
Tableau 4.14. Calcul des pertes de charge (po Hg) dans un tube servant au transport de l’air en fonction des fuites dans le système par section de 250 pi (nombre d’entailles > 5 000), pour un vide de 25 po Hg ............................................... 140
Tableau 4.15. Calcul des pertes de charge (po Hg) dans un tube servant au transport de l’air en fonction des fuites dans le système par section de 250 pi (nombre d’entailles > 5 000), pour un vide de 28 po Hg ............................................... 144
Tableau 4.16. Distance de tuteurage en fonction de la pente et du diamètre du tube collecteur ........................................................................................ 151
Tableau 4.17. Distance à respecter lors de travaux d’enfouissement par rapport au DHP des arbres à proximité .................................................................... 155
Tableau 4.18. Largeur d’isolant (épaisseur 2 à 4 po) à installer en fonction de la profondeur de la tranchée ....................................................................................... 157
Tableau 4.19. Intervalle de vide maximal moyen atteint par type de pompe ..................................... 158
Tableau 4.20. Évaluation de la puissance de pompe requise en fonction du nombre d’entailles et débit d’air correspondant ....................................................... 161
Tableau 4.21. Pertes de charge exprimées en pi et en psi pour 100 pi de tube à parois lisses (K=0,60) ........................................................................... 174
Tableau 4.22. Puissance théorique du moteur de la pompe (HP) pour élever de l'eau à une élévation (pi) donnée (K=0,60)........................................... 178
Tableau 4.23. Recommandations pour l’entretien sanitaire des éléments du système de récolte 187
Tableau 4.24. Compatibilité des matériaux utilisés en acériculture avec différents types de produits 188
Les infrastructures et les équipements de récolte xii
Tableau 4.25. Dilution d’une solution commerciale à utiliser en fonction de la concentration de la solution commerciale (%) et de la concentration de solution de lavage ou d’assainissement (ppm) ............................ 191
Tableau 4.26. Dilution à réaliser en fonction de la concentration de l’agent actif dans la solution concentrée pour obtenir une solution de lavage ou d’assainissement à 200 ppm...................................................................... 192
Tableau 5.1. Points et fréquence de vérification de l’étanchéité et du niveau de vide des composantes du système de récolte sous vide ........................ 199
Tableau 5.2. Perte de vide maximale (en secondes) aux collecteurs en fonction du niveau de vacuum appliqué .................................................................... 212
Tableau 5.3. Différentiel de vide entre l’extracteur et la tête du collecteur (coulée faible) ........... 219
Tableau 5.4 Caractéristiques de l'eau potable et de l’eau à utiliser pour le lavage, l’assainissement et le rinçage des équipements .................................. 232
Tableau 5.5. Produits couramment utilisés pour l’assainissement des composantes du système de récolte ......................................................................... 233
Tableau 5.6. Volumes de solution de lavage et d’assainissement pour les réservoirs 245
Tableau 5.7. Recommandations pour les volumes de solutions de lavage, d'assainissement et d'eaux de rinçage et le nombre total de rinçage successifs selon la capacité des extracteurs et réservoirs ............................... 246
Tableau 5.8. Volumes de solution de lavage, d’assainissement et d’eau de rinçage et nombre total de rinçages requis pour quelques exemples d’extracteurs et de réservoirs selon leur volume ......................... 246
Figure 1.1. Mécanisme de production de la sève d’érable ..................................................................... 8
Figure 1.2. Description des unités de mesure pour le volume d’air extrait d’un système................10
Figure 1.3. Aménagement du réseau de drainage autour de la cabane à sucre ...............................15
Figure 1.4. Caractéristiques des matériaux utilisés dans le domaine acéricole ................................19
Figure 1.5. Quelques modèles de chalumeaux utilisés en acériculture .............................................21
Figure 1.6. Exemple d’un chalumeau déformé par des traces de dents d’un animal ........................21
Figure 1.7. Bonne installation de la chute avec le raccord des chalumeaux .....................................21
Figure 1.8. Exemple de chute retrouvée en érablière ..........................................................................22
Figure 1.9. Caractéristiques minimales d’un tube latéral de qualité ..................................................22
Figure 1.10. Illustration d’un tube latéral en érablière avec l’outil de raccordement adapté ............23
Figure 1.11. Exemple d’un tube latéral mâchouillé par un animal .......................................................23
Figure 1.12. Longueurs de latéraux et leurs avantages et inconvénients ...........................................24
Figure 1.13. Exemples de fin de course de latéral : (a) utilisation d’un T-bouchon fin de ligne accompagné d’une union crochet fin de ligne; (b) utilisation d’une union coudée crochet fin de ligne ....................................................24
Figure 1.14. Exemples de tubes collecteurs principaux (maîtres-lignes) retrouvés en érablière .....25
Figure 1.15. Exemple de tubes à air installés en érablière et arrivant à la station de pompage ......26
Figure 1.16. Exemple de perçage d’un trou pour installer un T-en-selle .............................................29
Figure 1.17. Exemple d’utilisation d’un T-en-selle (a) et d’un raccord fusionné (b) en combinaison avec une union crochet en érablière .................................................30
Figure 1.18. Emplacement et utilité des valves 32
Figure 1.19. Exemple de positionnement des valves à la tête des collecteurs en érablière .............32
Figure 1.20. Exemple de positionnement des valves aux pieds des sous-collecteurs avant de rejoindre un collecteur principal .....................................33
Figure 1.21. Exemples de positionnement des valves (a) à la sortie des collecteurs et (b) à l’entrée de l’extracteur .................................................................................................33
Figure 1.22. Exemples de valves retrouvées à la sortie de réservoirs ..................................................33
Figure 1.23. Vue en coupe d’une pompe à anneau liquide ....................................................................35
Figure 1.24. Vue en coupe d’une pompe à palettes rotatives ................................................................35
Figure 1.25. Vue en coupe d’une pompe à palettes lubrifiées haut vide ..............................................36
Figure 1.26. Vue en coupe d’une pompe à crochets
Figure 1.27. Vue en coupe d’une pompe à vis à sec ou à bain d’huile ..................................................
36
37
Figure 1.28. Vue en coupe d’une pompe à diaphragme .........................................................................
37
Figure 1.29. Courbe typique illustrant la perte de performance d’une PAL en fonction de l’augmentation de la température du liquide de service ........................38
Les infrastructures et les équipements de récolte xiv
Figure 1.30. Influence de la température et de la pression sur la proportion du volume d’air déplacé par les pompes à vide, à température et pression normales ..................................................38
Figure 1.31. Illustration et fonctionnement d’un extracteur de type mécanique ...............................41
Figure 1.32. Illustration et fonctionnement d’un extracteur de type électrique 41
Figure 1.33. Description des transports par gravité, par pompage et par aspiration (vacuum) ........44
Figure 1.34. Exemple de schéma d’installation d’un accentuateur de pente ......................................45
Figure 1.35. Exemple d’un système d’accentuateur de pente lorsque le latéral est installé sous le tube collecteur..................................................................... 47
Figure 1.36. Exemple d’un monte-eau mécanique utilisé en acériculture ........................................... 47
Figure 1.37. Monte-eau électrique autonome .........................................................................................48
Figure 1.38. Arrangement typique d’un répartiteur de vide ..................................................................49
Figure 1.39. Schéma d’un système en série 51
Figure 1.40. Schéma d’un système en parallèle ......................................................................................51
Figure 1.41. Vue en coupe des collecteurs principaux dans un système air-eau ................................51
Figure 1.42. Principaux types de réservoirs utilisés en acériculture ....................................................52
Figure 1.43. Critères à respecter pour les réservoirs utilisés en acériculture
Figure 1.44. Points critiques de monitorage en entreprise acéricole
Figure 3.1. Schéma montrant la formation d’un bouchon et d’un écoulement à rebours dans un tube rempli de sève .................................................75
Figure 3.2. Effet de différents paramètres sur la perte de charge dans une tuyauterie ..................76
Figure 3.3. Description des évaluations de performance des matériaux ........................................... 77
Figure 3.4 Critères à respecter pour une bonne étanchéité du système de récolte sous vide de la sève .......................................................................84
Figure 3.5. Description des différents types de résidus retrouvés dans les produits de l’érable...............................................................................86
Figure 3.6. Description résumée des étapes d’entretien sanitaire recommandées .......................... 87
Figure 3.7. Actions mécaniques recommandées pour améliorer les étapes d’entretien sanitaire ......................................................................... 87
Figure 3.8. Exigences à respecter lors de la sélection d’un produit d’entretien sanitaire en entreprise acéricole ...............................................88
Figure 3.9. Conditions à respecter pour optimiser l’efficacité des produits d’entretien sanitaire .....................................................................90
Figure 3.10. Représentation de l’échelle des pH ....................................................................................90
xv
Figure 4.1. Méthodes d’installation de la broche de support à l’arbre : utilisation de cales de bois ou de crochet. .........................................................................96
Figure 4.2. Exemples de l’utilisation de cales (a) et de la fixation de broches de support (b)........ 97
Figure 4.3. Exemples d’une broche de support fixée à un arbre en érablière ................................... 97
Figure 4.4. Exemples de dispositifs mécaniques (a) et d’épissures (b, c) utilisés en érablière entre deux points permanents d’ancrage .............................. 97
Figure 4.5. Illustration des bonnes et mauvaises techniques de haubanage ....................................98
Figure 4.6. Exemples de haubans correctement installés en érablière .............................................99
Figure 4.7. Exemple d’installation de la broche de support et des collecteurs dans une courbe prononcée .............................................................. 100
Figure 4.8. Illustration d’une localisation traditionnelle (a) et d’une disposition plus judicieuse (b) de la tête des collecteurs d’un réseau de collecte sous vide de la sève d’érable .................................................... 103
Figure 4.9. Illustration de la répartition du débit dans un collecteur ............................................. 106
Figure 4.10. Illustration d’un scénario pour le dimensionnement des collecteurs sur un système à 3 segments ................................................................. 107
Figure 4.11. Exemple de résultante du chiffrier de calcul pour dimensionner les collecteurs à partir du nombre d’entailles ................................................................ 109
Figure 4.12. Exemple de résultante du chiffrier de calcul pour estimer le nombre d’entailles maximal en fonction du diamètre de tube collecteur .............. 109
Figure 4.13. Technique d’installation des broches d’enroulement galvanisées pour fixer le collecteur ................................................................................. 115
Figure 4.14. Exemples de collecteurs avec broches d’enroulement galvanisées (a) et « lynchés » (b) ........................................................... 115
Figure 4.15. Exemple de la méthode d’installation d’une chute 117
Figure 4.16. (haut) Position du raccord en T de la chute permettant d’ajuster la tension pendant la vie utile du latéral; (bas) position du tube latéral permettant l’installation de plusieurs chutes sur un érable de fort diamètre (plus de 60 cm) .................................................................................... 118
Figure 4.17. Schéma simplifié d’un système de récolte à 600 entailles, section entre le répartiteur de vide et la station de pompage ..................................... 121
Figure 4.18. Exemple de résultante du calcul des pertes de charge pour les tubes à air (20 po Hg) ......................................................................................... 122
Figure 4.19. Exemple de résultante du calcul des pertes de charge pour les tubes à air (25 po Hg) ......................................................................................... 122
Figure 4.20. Exemple de résultante du calcul des pertes de charge pour les tubes à air (28 po Hg) ......................................................................................... 123
Figure 4.21. Si l’accès à des sections du tube est difficile par endroits, certains ont recours à des nacelles .................................................................................. 148
Figure 4.22. Illustration et calcul de la tension s’exerçant dans la broche de support pour soutenir le poids du tube sans déflexion .......................... 150
Les infrastructures et les équipements de récolte xvi
Figure 4.23. Exemples d’utilisation de tuteurs pour diminuer la tension de la broche de support .................................................................................. 151
Figure 4.24. (a) Illustration de la distribution des tuteurs sur le parcours d’un collecteur; (b) illustration de la méthode suggérée pour procéder au tuteurage d’un collecteur ............................................................................. 152
Figure 4.25. Ajuster le nivellement : niveau électronique .................................................................. 152
Figure 4.26. Feuillards utilisés pour ajuster le niveau des collecteurs aux tuteurs 153
Figure 4.27. Graphiques illustrant les débits de pompes à anneau liquide utilisées en acériculture en fonction de leur puissance et du niveau de vacuum appliqué ......................................................................................... 159
Figure 4.28. Graphiques illustrant les débits de pompes à crochets ou à palettes utilisées en acériculture en fonction de leur puissance et du niveau de vacuum appliqué........................................................... 159
Figure 4.29. Graphiques illustrant les débits de pompes à vis utilisées en acériculture en fonction de leur puissance et du niveau de vacuum appliqué ...... 160
Figure 4.30. Particularités à prendre en compte pour la sélection d’un extracteur......................... 162
Figure 4.31. Différents modèles d’extracteurs mécaniques retrouvés dans le marché acéricole ................................................................................. 163
Figure 4.32. Différents modèles d’extracteurs électriques retrouvés dans le marché acéricole ................................................................................. 164
Figure 4.33. Exemple d’ancrage indépendant de la station de pompage ......................................... 165
Figure 4.34. Exemple de résultante du chiffrier de calcul pour le dimensionnement des extracteurs ..................................................................... 167
Figure 4.35. Exemple de la résultante de l’outil de calcul pour la puissance de pompe requise à l’extracteur ........................................................ 169
Figure 4.36. Positionnement de la trappe d’humidité (a), entre l’extracteur (b) et la pompe à vide (c) .................................................................... 170
Figure 4.37. Illustration des paramètres utilisés pour le calcul de dimensionnement d’une pompe de transfert de sève .............................................. 171
Figure 4.38. Exemple de la résultante de l’outil de calcul pour la puissance de pompe de transfert requise ................................................................... 172
Figure 4.39. Exemple d’arrangement des répartiteurs de vide pour répartir le nombre d’entailles et réduire au minimum la course des tubes transportant la sève 173
Figure 4.40. Localisation des différents réservoirs utilisés en acériculture ..................................... 181
Figure 4.41. Modèles de réservoirs utilisés en acériculture (partie 1) .............................................. 182
Figure 4.42. Modèles de réservoirs retrouvés en acériculture (partie 2) .......................................... 183
Figure 4.43. Critères de sélection d’un produit chimique ................................................................... 184
Figure 4.44. Conditions à respecter pour un assainissement à l’eau chaude .................................... 185
Figure 4.45. Catégories de produits de lavage et d’assainissement utilisés en acériculture 186
Figure 5.1. Exemple de montage pour l’utilisation d’un manomètre portable .............................. 197
Figure 5.2. Grandes étapes de vérification des fuites dans l’ensemble du système de collecte ......................................................................... 200
Figure 5.3. (a) Exemple de pinces adaptées pour bloquer un latéral (ici avec ajout d’embouts de protection par-dessus); (b) outil (rouge) d’insertion ou de raccordement des tubes latéraux, et deux pinces adaptées ........... 201
Figure 5.4. Schématisation d’un système de récolte et des valves requises pour procéder à une bonne vérification des fuites ......................................... 202
Figure 5.5. Section à isoler et positionnement des valves pour la procédure 14 .......................... 203
Figure 5.6. Vérification des fuites à la pompe à vide : exemples de composantes à tester .......... 204
Figure 5.7. Section à isoler et positionnement des valves pour la procédure 15 .......................... 205
Figure 5.8. Vérification des fuites entre la pompe à vide et l’extracteur : exemples de composantes à vérifier sur une trappe d’humidité .................................. 206
Figure 5.9. Section à isoler et positionnement des valves pour la procédure 16 (test de l’extracteur 1) .................................................................. 207
Figure 5.10. Vérification des fuites à l’extracteur : composantes à tester......................................... 208
Figure 5.11. Exemple d’un montage avec manomètre à chaque collecteur pour vérifier le niveau de vacuum .................................................... 209
Figure 5.12. Section à isoler et positionnement des valves pour la procédure 17 (test des collecteurs de l’extracteur 1) ................................................ 210
Figure 5.13. Schéma décisionnel pour vérifier les fuites principales aux collecteurs (3 cas) 210
Figure 5.14. Un manomètre sur l’extracteur seulement ...................................................................... 211
Figure 5.15. Manomètre et valve à chacun des collecteurs ................................................................ 212
Figure 5.16. Schéma décisionnel pour vérifier les fuites aux collecteurs problématiques, selon le système de récolte en place ....................... 213
Figure 5.17. Patron d’écoulement et débit des fuites sous un niveau de vacuum de 20 po Hg ..... 214
Figure 5.18. Schéma décisionnel pour vérifier les fuites aux collecteurs d’un système en série - Procédure 18 ................................................... 215
Figure 5.19. Vérification d’un collecteur problématique – Étapes 2 et 3 .......................................... 216
Figure 5.20. Vérification de l'écoulement à la boucle de branchement au collecteur ..................... 216
Figure 5.21. Bloquer l’écoulement vers le collecteur avec une pince pour vérifier la source de la fuite ........................................................... 216
Figure 5.22. Schéma décisionnel pour vérifier les fuites dans les systèmes en parallèle (aux têtes de ligne des sous-collecteurs de systèmes en parallèle ou branchés à un répartiteur de vide) – Procédure 19 .................................................. 218
Figure 5.23. Vérification du niveau de vide à la tête de ligne ............................................................ 218
Figure 5.24. Schéma décisionnel pour vérifier les fuites aux latéraux.............................................. 220
Figure 5.25. Déplacement le long du latéral pour la vérification des fuites - Procédure 20 .......... 220
Figure 5.26. Vérification du patron d’écoulement à chaque chute ..................................................... 221
Figure 5.27. Technique pour appliquer une tension sur le tube et observer le patron d’écoulement .............................................................. 221
Les infrastructures et les équipements de récolte xviii
Figure 5.28. Exemple de positionnement des outils pour réparer une fuite située sur un latéral .................................................................... 221
Figure 5.29. Vérification de l'écoulement à la boucle de branchement au collecteur ..................... 222
Figure 5.30. Exemple d’une fuite observée au niveau d’un raccord chute–latéral .......................... 222
Figure 5.31. Positionnement des pinces pour vérifier la provenant d’une fuite observée entre le chalumeau, un raccord et le latéral ............................... 222
Figure 5.32. Remplacement d’un raccord après détection de la fuite ............................................... 223
Figure 5.33. Informations complémentaires sur le rinçage ................................................................ 230
Figure 5.34. Critères de qualité de l’eau utilisée pour l’entretien des équipements ....................... 231
Figure 5.35. Recommandations de traitement avant la première utilisation des équipements .... 234
Figure 5.36. Conditions à respecter pour l’assainissement des latéraux et collecteurs 235
Figure 5.37. Pompe à vide – vérification du niveau de vide au manomètre ..................................... 236
Figure 5.38. Assainissement des latéraux, étape 2 ............................................................................. 236
Figure 5.39. Assainissement des chalumeaux : (a) injection de la solution d’assainissement avec le doseur; (b) insertion du chalumeau dans le bouchon de remisage en s’assurant d’avoir une forme régulière de la chute, sans torsion ni pliage 237
Figure 5.40. Processus d’assainissement des tubes latéraux : (a) début du déplacement des opérateurs, à partir de la dernière entaille à la tête du collecteur; (b) suite du déplacement le long du collecteur, jusqu’à l’extracteur ........................... 238
Figure 5.41 Assainissement des collecteurs par aspiration, système en série (1er collecteur) 239
Figure 5.42 Assainissement des collecteurs, système en série; (a) éponge imbibée de produit; (b) éponge insérée par la valve; (c) passage d’AIP par aspiration ........................................................................................ 239
Figure 5.43 Assainissement des collecteurs par aspiration, système en série (2e collecteur) ....... 240
Figure 5.44. Assainissement des collecteurs par aspiration, système en série (suite des collecteurs) .......................................................................... 240
Figure 5.45. Ajout des derniers 2 L/305 m d’AIP en tête de collecteur............................................. 240
Figure 5.46. Assainissement des collecteurs, système en parallèle; (a) éponge imbibée de produit; (b) éponge insérée par la valve; (c) passage d’AIP par aspiration ........... 241
Figure 5.47. Ajout des derniers 2 L/305 m d’AIP en tête de collecteur............................................. 241
Figure 5.48. Extracteur à pompe submersible : (a) grillage de récupération; (b) crépine .............. 244
xix
Procédure 1. Localiser une route d’accès et un chemin d’exploitation sur la carte de l’érablière ......12
Procédure 2. Installation des broches de support et des haubans ........................................................96
Procédure 3. Installation des latéraux ................................................................................................... 101
Procédure 4. Installation des collecteurs ............................................................................................... 114
Procédure 5. Préparation et installation des chutes............................................................................. 116
Procédure 6. Dimensionnement et installation des tubes à air .......................................................... 148
Procédure 7. Préparation et installation d’un tuteur ............................................................................ 150
Procédure 8. Ajuster la pente et le nivellement ................................................................................... 151
Procédure 9. Enfouissement des tubes .................................................................................................. 155
Procédure 10. Sélection d’une pompe à vide ........................................................................................... 160
Procédure 11. Sélection des extracteurs .................................................................................................. 165
Procédure 12. Première sélection de puissance d’une pompe de transfert ......................................... 171
Procédure 13. Calcul de la concentration d’une solution de nettoyage ............................................... 189
Procédure 14. Vérification des fuites à la pompe à vide 203
Procédure 15. Vérification des fuites entre la pompe à vide et les extracteurs .................................. 205
Procédure 16. Vérification des fuites à l’extracteur ................................................................................ 207
Procédure 17. Vérification des fuites principales aux collecteurs (tous) .............................................. 209
Procédure 18. Vérification des fuites aux collecteurs à problèmes (système en série) ...................... 214
Procédure 19. Vérification des fuites aux têtes de ligne (sous-collecteurs de systèmes en parallèle ou branchés à un répartiteur de vide) ........................................................ 217
Procédure 20. Vérification des fuites aux latéraux ................................................................................. 219
Procédure 21. Vérification des fuites aux collecteurs (détection de glace) ......................................... 223
Procédure 22. Vérification des fuites des systèmes enfouis (souterrains) ........................................... 225
Procédure 23. Transport de sève ou de concentré .................................................................................. 226
Procédure 24. Nettoyage sanitaire des surfaces et des équipements .................................................. 230
Procédure 25. Assainissement des latéraux par aspiration ................................................................... 236
Procédure 26. Assainissement des collecteurs par aspiration pour les systèmes en série ................ 238
Procédure 27. Assainissement des collecteurs par aspiration pour les systèmes en parallèle ......... 241
Procédure 28. Assainissement des tubes à air par aspiration ............................................................... 242
Procédure 29. Lavage et assainissement des extracteurs et des répartiteurs de vide ....................... 243
Procédure 30. Lavage et assainissement des réservoirs ........................................................................ 245
infrastructures et les équipements de récolte
Cet ouvrage présente le système de récolte de la sève d’érable, ses infrastructures et les bonnes pratiques d’entretien sanitaire de ces équipements. Il fournit les connaissances de base pour bien comprendre les principes de fonctionnement du système de récolte de la sève, savoir sélectionner les équipements voulus et en assurer les opérations selon les méthodes recommandées. Il vise donc à outiller les conseillers et conseillères, tout comme les producteurs et productrices, afin de maîtriser les paramètres permettant d’optimiser l’efficacité du système de récolte ainsi que la qualité de la sève et du sirop qui en résulte.
Ce troisième volume du Cahier de transfert technologique en acériculture, deuxième édition, rassemble les connaissances disponibles sur les différentes étapes et techniques de récolte de la sève et d’entretien sanitaire des équipements. Afin que chacun en tire profit selon ses besoins, l’ouvrage est divisé en plusieurs sections organisées suivant un ordre logique, mais qui peuvent être consultées dans le désordre.
• Chapitre 1 – Notions de base : Ce chapitre décrit sommairement le processus de la récolte de sève et les composantes qui en font partie. Il permettra à tout lecteur de connaître les termes utilisés et de démarrer avec une solide base de compréhension sur le fonctionnement du système.
• Chapitre 2 – Règlementation et bonnes pratiques : Ce chapitre offre un survol des lois et règlements principaux qui s’appliquent aux aménagements de l’érablière et des bâtiments, ainsi qu'aux équipements. Il mentionne aussi des guides de bonnes pratiques à connaître.
• Chapitre 3 – Fondements scientifiques : Ce chapitre présente et explique les bases scientifiques sur lesquelles reposent la conception et l’opération des systèmes de récolte. Il regroupe également des informations non exhaustives sur les propriétés des matériaux utilisés et sur l’importance de l’entretien sanitaire1 en entreprise acéricole. Il s’adresse à un public qui souhaite mieux comprendre la théorie et les notions scientifiques qui soustendent la récolte de sève d’érable et l’entretien sanitaire requis.
• Chapitre 4 – Sélection et conception des systèmes : Ce chapitre rassemble les informations nécessaires pour faire la conception, le dimensionnement et l’installation d’un système de récolte et de ses composantes. Il vise à alimenter une démarche d’ingénierie pour concevoir les systèmes de façon à optimiser les opérations de récolte. L'utilisation de l'outil ACER DimSys Récolte (voir plus bas) y est démontré avec des exemples. Le choix et la gestion des produits d’entretien sanitaire y sont également abordés.
• Chapitre 5 – Opérations : Ce chapitre détaille les étapes nécessaires pour faire fonctionner le système de récolte et procéder adéquatement à son entretien sanitaire. Les procédures décrites permettront à tous de partir sur une même base de fonctionnement des systèmes, une fois que ceux ci sont installés et en fonction.
• Chiffrier ACER d’aide au dimensionnement du système de récolte (ACER Dim-Sys Récolte) : Une feuille de calcul Excel accompagne l’ouvrage. Cet outil sert à simplifier les calculs de conception du système, en automatisant ceuxci plutôt qu’en les réalisant manuellement.
1. Dans cet ouvrage, le terme « entretien sanitaire » sera utilisé pour désigner toute opération de lavage, d’assainissement et de rinçage des équipements acéricoles.
Introduction
1.1.2
1.3.1.
1.3.7.
1.4.
1.4.1.
1.4.2.
1.4.3.
1.4.4.
1.4.5.
1.4.6.
1.4.7.
1.5.
1.5.1.
1.5.2.
1.5.3. SYSTÈME
1.7.
1.7.1.
1.7.2.
1.7.3.
1.7.4.
1.7.5.
1.7.6.
1.7.7.
1.7.8.
1.7.10.
1.8. MAIN-D’ŒUVRE QUALIFIÉE
Le sirop d’érable est un produit d’exception reconnu et apprécié par les consommateurs et consommatrices dans plusieurs régions du monde. Sa production passe par plusieurs étapes, qui doivent toutes être maîtrisées pour obtenir un produit répondant aux plus hautes normes de qualité. La première étape provient de la récolte de la sève à partir des érables. Les systèmes de récolte par tubulure se composent habituellement d’un réseau de tubes (latéraux, collecteurs, tubes à air), d’extracteurs, de réservoirs, de trappes d’humidité et de pompes à vide. Les systèmes de récolte utilisés doivent être bien réfléchis, dimensionnés et installés pour optimiser le rendement ainsi que la qualité de la sève récoltée. De bonnes pratiques d’entretien sanitaire doivent aussi être adoptées pour garantir le fonctionnement adéquat des équipements et la qualité du produit. En optimisant le rendement et la qualité du produit, on s'assure d'une meilleure rentabilité de l’exploitation.
La sève d’érable est la sève brute dont se gorgent les érables au printemps lors du dégel, qui est enrichie en saccharose*2 et de laquelle sont dérivés l’ensemble des produits de l’érable. Elle est récoltée principalement à partir de l’érable à sucre (Acer saccharum Marsh.), mais aussi de l’érable rouge (Acer rubrum L.), de l’érable noir (Acer nigrum Michx.) et de l’érable argenté (Acer saccharinum L.). L’extraction de la sève des érables est rendue possible par les cycles de gel et de dégel qui se produisent
au printemps. Lors du gel des branches à la tête des érables, il se forme une accumulation de glace dans ces dernières. La glace possède une attraction forte pour les molécules d’eau. Cette attraction crée une pression négative dans le tronc. Les petites branches grossissent en diamètre par la formation de glace à l’intérieur de cellesci. Cela se produit durant la période du début du gel où la sève peut encore circuler, sans geler, dans le tronc. Cette accumulation de glace dans les petites branches dépend de la vitesse de diminution de la température de l’air. Si la température baisse rapidement, il y a peu de formation de glace. Si le gel est progressif, il y a plus d’accumulation de glace. Lors du dégel, cette glace prend de l’expansion dans les petites branches et engendre une pression positive dans le tronc. C’est cette pression positive qui repousse la sève vers le sol (Figure 1.1). Pour récolter la sève, il suffit d’une entaille (trou) percée dans l’arbre pour recueillir le liquide avant qu’il ne retourne au sol. La vitesse d’écoulement de la sève d’érable est variable selon la période de la saison. Elle dépend de plusieurs facteurs, dont les caractéristiques physiques et physiologiques des arbres, leur emplacement, les conditions climatiques ainsi que l’installation et la gestion du système de récolte.
La sève produite peut être récoltée naturellement par l’effet de la gravité dans un récipient (chaudière) placé directement sous l’entaille. Ce genre d’installation traditionnelle est souvent en place dans les érablières de plus petite taille (1 000 entailles et moins), puisqu’il représente beaucoup de travail comparativement aux systèmes à tubulure. Pour limiter les risques de contamination de la sève, il faut utiliser des récipients propres et prévoir des tournées de ramassage fréquentes. En effet, l'un des inconvénients de ces systèmes réside dans le risque d’avoir des éléments indésirables dans les récipients, tels que des souris, des insectes et de l’eau de pluie. Les récipients doivent être démontés, lavés, séchés et remisés annuellement.
L’utilisation d’un réseau de tubulures remplace les récipients et permet de centraliser la récolte de sève tout en offrant la possibilité d’accéder à des érables
2. Les mots marqués d’un astérisque (*) sont définis au glossaire en fin de l’ouvrage.
sur une grande superficie. La récolte de sève par un réseau de tubulures est un système d’écoulement en deux phases (biphasique) : une phase est le liquide et l’autre phase est l’air. À l’intérieur des tubes, la sève s’écoule par gravité dans le bas et l’air circule dans la partie haute pour maintenir le niveau de vide dans le réseau de tubulure*. Le système doit également être dimensionné correctement : on s’assure que les pentes sont considérées et que le tuteurage est parfaitement mis en place. Lorsqu’elles fonctionnent uniquement par gravité, ces installations sont réalisées à l’aide de tubes latéraux de diamètre de 3/16 po (6 à 35 entailles maximum) ou de 5/16 po (18 à 100 entailles maximum). L’utilisation de ce genre de système nécessite une pente minimale de 2 % pour que le poids de l’eau combiné à la vitesse gravitationnelle permette à la sève de s’écouler sans trop de difficulté vers un point de récolte unique.
Avec une pente minimale de 5 %, il est possible de créer un vide « naturel » grâce à la descente par gravité de la sève, si le réseau est étanche. Dans ce type d’installation, une pente élevée (5 à 8 %) (dénivelé* minimal environ 15 pi), combinée à une coulée constante, permet que le niveau de vide « naturel » causé par la gravité sur la sève soit plus important. Par exemple, pour obtenir un vide maximum de 26 po Hg, il faudrait un dénivelé vertical d’au moins 50 pi pour contrer la friction dans les tubes, en fonction de la longueur à parcourir selon la pente. De plus, une bonne surveillance des fuites est importante, puisque les systèmes avec tubulure sont sujets à des bris provenant de l’action d’animaux. Les méthodes d’installation dépendent du nombre d’entailles, de la pente du terrain et du budget disponible.
des
Phénomène de vide dans l’arbre : montée de la sève
Phénomène de pression dans l’arbre : coulée de la sève
Les infrastructures et les équipements de récolte
Le rendement des systèmes de récolte par un réseau de tubulure peut être amélioré par l’ajout d’une pompe à vide, qui maintient un gradient de pression quasi constant (ou un vide partiel) au niveau de l’entaille pour créer artificiellement des conditions propices à la coulée. Ces installations sont aujourd’hui le mode d’exploitation privilégié des érablières. Des études réalisées au Centre ACER sur l’effet du haut vide (Allard et coll., 1987) ont permis de démontrer de façon expérimentale que le pourcentage d’augmentation de la coulée par rapport à un système de tubulure fonctionnant seulement par gravité est peu significatif pour des gradients inférieurs à 12 cm de Hg (5 po Hg), alors qu’il s’accroît rapidement selon le niveau de vide. Les systèmes utilisés à l’époque n’étaient pas aussi étanches qu’aujourd’hui, et les résultats obtenus par cette étude étaient relativement peu précis. D’autres études ont ensuite montré que pour un système étanche, chaque pouce de Hg a un effet mesurable sur le rendement du système. L’augmentation du volume de coulée qui en résulte nécessite une meilleure gestion des fuites et une conception judicieuse du système (pentes, diamètres de tubes, infrastructures de récolte). L’emplacement des tubes (tête des collecteurs) et de la station de pompage est un élément important à considérer dans la mise en place des infrastructures, pour faciliter l’accessibilité ainsi que la disponibilité de l’eau pour les opérations de lavage, d’assainissement et de rinçage des équipements qui sont à la station de pompage. Comme le système de récolte par tubulure est le plus communément rencontré de nos jours, il sera exclusivement traité pour la suite de cet ouvrage.
Tous les éléments cités plus hauts et liés à la récolte de la sève font naturellement partie d’un environnement économique particulier. Si on la compare au mode traditionnel d’exploitation de l’érablière, l’acériculture moderne est un secteur économiquement plus contraignant et plus compétitif, dans lequel les notions de productivité du travail, de rendement du capital investi et de qualité du produit fini doivent être considérées
avec beaucoup d’attention. En effet, il est peu probable que les éventuelles hausses du coût de production (main d’œuvre, énergie, etc.) soient totalement absorbées par une augmentation du prix de vente du produit. Une bonne planification et une analyse économique rigoureuse sont donc particulièrement importantes pour obtenir le meilleur équilibre possible entre les immobilisations (infrastructures telles que la route d’accès, l’alimentation électrique et les bâtiments d’exploitation, etc.) et le potentiel réel de l’érablière3.
En physique, le terme « vide » correspond à une absence totale de particules matérielles. Le terme « vacuum » est un mot latin signifiant « le vide ». En acériculture, on désigne par « vide » ou « vacuum », un espace vide, dans lequel l’air a été retiré dans des proportions variables (vide relatif). Les propriétés de l’air ambiant sont affectées par la pression à laquelle il est soumis. L’air est plus dense à pression atmosphérique normale (101,3 kPa ou 29,92 po Hg), et il se raréfie lorsque la pression change avec l’altitude. La pression à laquelle l’air
Vacuum : espace vide d'où l’air a été retiré selon différentes proportions
En acériculture :
• Le niveau de vide est la différence de pression entre la pression atmosphérique et celle du système de récolte sous vide.
• Il est mesuré en po Hg (pouces de mercure).
• Une pompe à vide permet de retirer l’air du système et de maintenir, au niveau de l’entaille, un vide partiel créant ainsi artificiellement des conditions propices à la coulée.
• Pour un niveau de vide élevé, il faut garder le système le plus étanche possible.
3. Se référer par exemple à l’outil de calcul InvestAcer (voir CECPA, 2022 dans les références bibliographiques).
est soumis joue donc un rôle important dans la capacité d’un système à créer le vide. Pour obtenir un vide absolu, il faut que la pression soit égale à 0 (po Hg ou kPa).
En acériculture, ce qu’on mesure est la différence de pression entre la pression atmosphérique et le système de récolte sous vide. Sur un manomètre, le retrait complet de l’air du système correspondrait à la pression absolue (29,92 po Hg). Le but d’appliquer du vide est d’augmenter artificiellement la différence de pression entre l’intérieur de l’arbre et le chalumeau (en contact avec le trou de l’entaille) où la sève circule. Cet effet engendre une hausse du débit de coulée de sève à l’entaille.
Un système de récolte sous vide ne sert donc pas à tirer la sève plus rapidement à travers les tubes, mais bien à retirer l’air présent dans le système de récolte, pour conserver au maximum le vide naturel
déjà produit par l’arbre. Le niveau de vide appliqué dépend donc de la quantité d’air retirée du système. Le rendement du système de récolte en fonction du niveau de vide appliqué sera abordé en détail à la section 3.5. Pour atteindre un niveau de vide élevé (> 25 po Hg) dans un système de récolte, il faut conserver le système le plus étanche possible, en y limitant les entrées d’air (ou fuites). Plus un système étanche est soumis à un niveau élevé de vacuum, plus le rendement en sève est élevé, à condition que les entrées d’air (fuites) soient minimisées. Les fuites empêchent la pompe à vide de maintenir le niveau de vide à l’entaille et dans le système, ce qui se répercute sur le rendement du système de récolte. Il est possible que le niveau de vide à la station de pompage soit celui de la consigne, mais que plusieurs entailles soient à un niveau plus bas du fait de la présence de fuites. Pour mesurer le volume d’air extrait d’un système, on parle généralement de pieds cubes d’air extrait par minute : CFM ou cubic feet per
• Volume d'air extrait d'un système (en pi3 d'air extrait par minute)
• Mesure générale du volume d'air qui sort d'une pompe à vide
• Exprimé en ACFM ou en SCFM
• Débit d'air massique réel d'un système sous vide, mesuré selon les conditions environnantes réelles
• In uencé par les conditions atmosphériques et environnantes au moment où la mesure est réalisée
• Variable d'un endroit à l'autre
• Peut être mesuré à l'aide d'un débitmètre, dans les conditions d'utilisation réelles
• Débit d'air massique d'un système sous vide, mesuré selon des conditions standards
• Mesure réalisée par les fabricants d'équipement
• Pour obtenir une valeur réelle, il faut pouvoir contrôler les paramètres de mesures tous les jours. Des installations spécialisées sont requises.
• Paramètres de mesure à appliquer :
• Pas de norme unique, plusieurs existent, donc celles de l'ASME (American Society of Mechanical Engineers)
• Pression atmosphérique : 14,7 psiA, soit 760 mm Hg ou 29,9 po Hg.
• Humidité relative : 36 %
• Température ambiante : 68 °F ou 19 °C
1.2. Description des unités de mesure pour le volume d’air extrait d’un système
Les infrastructures et les équipements de récolte
minute. Les différentes unités de CFM sont détaillées à la Figure 1.2.
Les SCFM sont un point de référence commun, utilisé pour comparer les performances de différents équipements, alors que les ACFM sont le débit volumétrique réel d’un équipement en fonction des conditions (pression, température et altitude) où la mesure est prise. Puisqu'il n’y a pas de norme unique pour la mesure standardisée en SCFM, les données disponibles actuellement ne sont pas toutes établies selon la même norme. Les données obtenues doivent donc être considérées comme des ACFM. Cellesci sont considérées valables pour une première sélection de pompe à vacuum, bien que les conditions dans lesquelles les mesures ont été réalisées ne sont pas standardisées. Dans tous les cas, il faut comprendre que les performances de la pompe à vacuum sélectionnée seront différentes lorsqu’elles seront en conditions d’utilisation réelles. En l’absence de données plus complètes, le terme CFM sera utilisé pour le reste de cet ouvrage.
Les fuites d’air présentes dans un système de récolte peuvent provenir soit des entailles, soit du système luimême. Cellesci causent aussi du frasil* (cristaux de glace ou lentilles de glace) dans les tubes et cela même audessus du point de congélation. L’air qui entre dans un tube à basse pression se refroidit en prenant de l’expansion. Ce phénomène est basé sur la loi des gaz parfaits (PV=nRT).
Loi des gaz parfaits
PV=nRT
où :
P représente la pression (en kPa)
V représente le volume (en L)
n représente la quantité de gaz (en mol)
R représente la constante des gaz parfaits (en kPa L/mol K)
T représente la température absolue (en K)
C’est d’ailleurs la même chose qui se produit lorsqu’on dégonfle un pneu en pressant sur la valve et que notre doigt devient froid. Si la fuite est
importante, le collecteur peut même s’emplir de glace en fin de journée avant que les érables aient fini de couler et ainsi faire manquer la fin de la coulée quotidienne, puis retarder le départ de la prochaine coulée. Souvent, c’est durant les premières heures de coulée que le débit des entailles est le plus élevé, soit la période où l’arbre est sous sa plus grande pression interne. Ainsi, la présence de glace dans les tubes, en plus de nuire à l’écoulement de la sève vers la station de pompage, gêne le passage de l’air pour maintenir le niveau de vide dans une partie du réseau. Le rendement de ces entailles soumis à une ou plusieurs fuites d’air est donc très diminué. Lorsqu’une entaille qui n’est pas étanche laisse passer de l’air, c’est le même phénomène qui se produit.
La formation de glace due à la fuite à cette entaille bloque le tube de diamètre 5/16 po; toutes les entailles de ce latéral s’en trouvent alors affectées.
Il est à noter que dans des « conditions standards », s'il n’y a pas de perte d’efficacité, les valeurs de SCFM et d’ACFM sont équivalentes. Quand les conditions d’admission d’air diffèrent (altitude, température, humidité), il sera alors pertinent de se questionner sur la capacité de la pompe à vide sélectionnée.
D’EXPLOITATION
Pour exploiter une érablière, il faut permettre un accès facile aux bâtiments et aux équipements de récolte et de transformation. Cet accès doit être possible à toute période de l’année. La planification du chemin d’accès et des chemins d’exploitation doit être réalisée selon une analyse minutieuse de l’ensemble des contraintes et des caractéristiques opérationnelles de l’érablière. Les travaux devraient être confiés à des entrepreneurs spécialisés en la matière, pour s’assurer de respecter les lois et règlements en vigueur.
Notions de base
É R A B L I È R E ?
V ISITEZ N O T R E SIT E W E B
Ce troisième volume du Cahier de transfert technologique en acériculture — 2e édition a pour but de présenter les équipements de récolte de la sève, de l’entaille jusqu’à l’extracteur, pour les érablières qui utilisent des tubulures et non les chaudières traditionnelles.
Abondamment illustré de photos et de schémas, il décrit l’ensemble des composantes de ce type de systèmes, en incluant les infrastructures extérieures et les équipements qui recueillent la sève brute dans la cabane à sucre (pompes, extracteur, trappe à humidité, etc.), ainsi que le monitorage des données de production. Les fondements scienti ques sont expliqués a n d’aider la compréhension des caractéristiques et du fonctionnement des systèmes de récolte de sève. Un chapitre est dédié à l’encadrement règlementaire et à certains ouvrages de référence à connaître pour les opérations d’aménagement et l’entretien de ces systèmes. La conception, le dimensionnement et le choix des équipements sont accompagnés pas à pas et les calculs sont facilités par l’outil ACER Dim-Sys Récolte. En n, ce guide fournit, étape par étape, toute l’information nécessaire à l’installation de ces équipements, à la véri cation de leur bon fonctionnement, à la réparation des fuites de vide, ainsi qu’aux méthodes de nettoyage sanitaire requises.
Cet ouvrage aidera les acériculteurs, acéricultrices et spécialistes du secteur à acquérir une compréhension claire et détaillée des équipements et des procédures de travail qui permettront de récolter la sève de façon e cace et optimale pour conserver sa qualité.