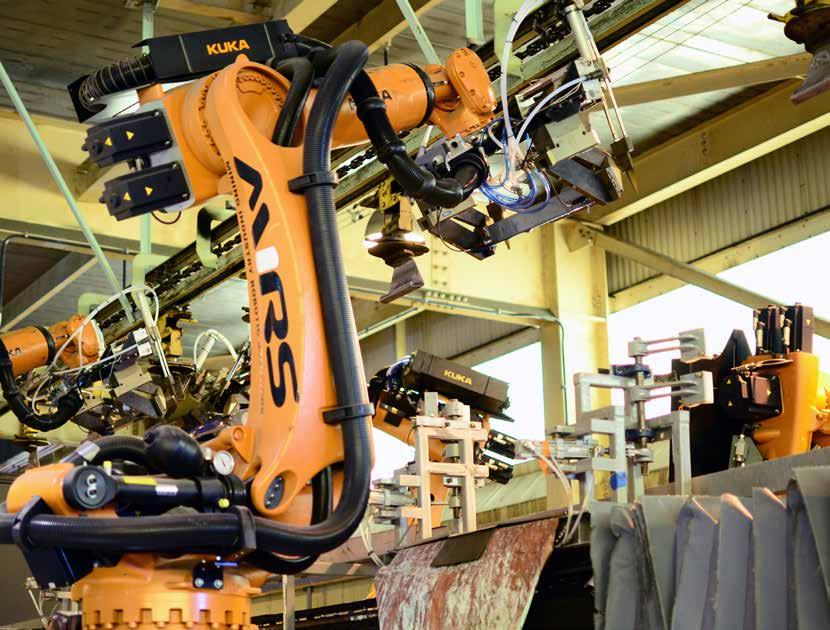
11 minute read
Robótica: para una minería más segura y eficiente
Informe Técnico E vitar que los trabajadores participen en tareas riesgosas, junto con elevar la confiabilidad y competitividad de dichos procesos, son algunos de los atributos que están impulsando la incorporación de soluciones robóticas en minería, un proceso que no está exento de desafíos. En opinión de Luis Baeza, gerente de la Línea Costum de MIRS, “si no hay una visión estratégica como compañía de automatizar procesos e ir a una minería un poco más avanzada -para miradas cortas y que necesito una Tasa Interna de Retorno (TIR) o un Valor Actual Neto (VAN) a un año- la verdad es que la automatización de procesos robóticos le resulta muy difícil competir”. El especialista destaca que la robótica en minería aporta en que, en especial en tiempos del Covid-19 donde se busca el distanciamiento social, “no tener 100 personas en terreno haciendo trabajos que a veces aportan poco”, pero que de todas maneras son necesarias con el fin de que esos procesos no se detengan. Respecto de los nichos donde se ven mayores posibilidades, destaca el área de minas, con procesos como el abastecimiento de combustible y el cambio de neumáticos, cuya ejecución se ve condicionada por las condiciones ambientales, y que involucran un riesgo para los operadores. A ello se suma el ámbito de la concentradora, y el proceso de cambio de revestimiento; junto con las tareas propias del área de refinería y fundición. En ese contexto, menciona que una iniciativa relevante de MIRS es la máquina despegadora de láminas Iniciales, un proyecto que se comenzó a desarrollar hace cinco años aproximadamente, y que tuvo una prueba piloto en Ventanas. Como consecuencia del éxito obtenido, la tecnología se exportó a Estados Unidos, donde se desarrolló una máquina despegadora de cátodos para la refinería Asarco, en En Amarillo, Texas. Baeza subraya que esas mismas máquinas despegadoras se replicaron en Ventanas: “actualmente tenemos ocho robots despegando cátodos en la refinería”. A ello se suma el sistema Robotizado de Apertura y Cierre de Pasajes, una solución que se comenzó a implementar en 2007-2008, en Codelco Chuquicamata, que estuvo en operación
Foto: Gentileza MIRS.
Nuevos usos Robótica: para una minería más segura y eficiente
hasta 2011. Posteriormente, hubo algunas modificaciones operacionales en el horno de Chuquicamata, que hicieron retirar la solución. Sin embargo, se trabaja para implementarla nuevamente en ese lugar. El ejecutivo comenta que “hoy día hemos desarro-
Este tipo de soluciones permiten disminuir la exposición de los trabajadores a condiciones riesgosas, junto con optimizar procesos de mantenimiento y muestreo.
Máquina despegadora de cátodos en la refinería Asarco en Amarillo (Estados Unidos). llado diferentes ingenierías para extrapolar esta tecnología a Australia, Finlandia, Suecia, Estados Unidos, países del primer mundo, porque ellos han hecho una búsqueda tecnológica a nivel mundial de dónde están estos equipos y cuáles son las tecnologías que sirven para estos procesos”. Además, indica que están trabajando en un proyecto de carguío robótico de combustible, junto con una solución de lavado de camiones, que está en construcción, con miras a ser implementado a fines de año en Minera Collahuasi, con el objetivo de darle mayor confiabilidad a dicha tarea, y tener mayor disponibilidad del proceso en general.
Confiabilidad
Considerando la diversidad de ámbitos donde puede aplicarse la robótica en minería, MIRS dispone de tres áreas de negocios fundamentales: Proyectos Especiales, Muestreo y Molienda. Igor Elías, gerente de la Línea Mill de la compañía, explica que “el área de Molienda, a diferencia de Proyectos Especiales -que atiende distintas necesidades particulares- no está enfocada en un solo cliente, sino que en un producto, que se vende a muchos clientes”; consiste en el desarrollo e implementación de sistemas que permitan automatizar y robotizar completamente el cambio de revestimiento en molinos SAG y en molinos de bolas. Es así como desarrollaron tres soluciones complementarias: • Robot de mantenimiento externo del molino (EMMR por sus siglas en inglés)
Fotos: Gentileza MIRS.


• Robot de mantenimiento interno del molino (IMMR) • Manipulador Robótico de Palmetas de Trommel (TMMR) El especialista explica que el Manipulador Robótico de Palmetas de Trommel, como su nombre lo indica, tiene como finalidad realizar en forma automática el cambio, retiro, limpieza e instalación de las palmetas de clasificación de los Drommel de los molinos SAG. Es un sistema que originalmente fue diseñado y construido para Minera Escondida, pero que hoy fue transferido a Minera Spence (ambas de BHP). “En estos momentos la máquina está en nuestras instalaciones para hacerle un upgrade, la modernización, para que Spence la instale en su molino que acaba de iniciar operación”, menciona. Cabe indicar que las soluciones EMMR e IMMR permiten automatizar la tarea de cambio de revestimientos en los molinos SAG y de bolas. Este sistema opera en base a la acción conjunta de robots que trabajan en paralelo a una velocidad que puede alcanzar los dos metros por segundo, reemplazando la labor manual y reduciendo diez veces el tiempo de la operación. Igor Elías añade que el beneficio más evidente que posibilita la robótica es el referido a la seguridad de los trabajadores, debido a que permite que las personas no participen del proceso. Además, “el robot tiene la capacidad de generar todos estos trabajos y emitir un informe electrónico automático al final, garantizando la calidad de la mantención”, acota. Por otra parte, el robot desarrolla la remoción de revestimiento, realizando el corte por oxígeno con la precisión suficiente para poder garantizar que el molino no sea dañado. Respecto de cómo ha sido
De Izq. a Der.: MIRS ha desarrollado soluciones para automatizar el cambio de revestimiento en molinos. Solución para la toma de muestras de concentrado.
la disposición de la industria nacional a incorporar estas tecnologías, el profesional dice que “hoy día hay en Chile hay cinco mineras que están generando sus procesos de compra, no nos han comprado, pero están en etapa de levantar sus presupuestos; y tenemos otra en Canadá, con compromiso también de compra”.
Fotos: Gentileza MIRS.

De Izq. a Der.: Luis Baeza, gerente de la Línea Costum de MIRS. Igor Elías, gerente de la Línea Mill de MIRS. Eric Montiel, gerente de la Línea Sampling de MIRS.
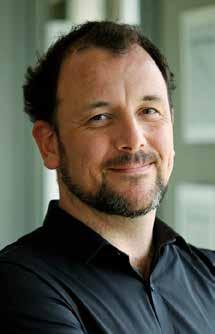
Muestreo eficiente
Otro ámbito en el que la robótica puede contribuir a la competitividad de la industria minera, es el referido a la toma de muestras de concentrado en camiones. El proceso manual considera que un operador se sube a la tolva del vehículo, y realiza el muestreo con una lanza, enterrándola en diferentes puntos. “Esta tolva tiene más menos un metro y medio de profundidad, y a lo más que llega a introducir esta lanza es alrededor de 30 centímetros, dependiendo de cuán compactado esté el material. Por lo tanto, la muestra que saca es poco representativa”, explica Eric Montiel, gerente de la Línea Sampling de MIRS. El especialista puntualiza que durante el traslado del material, luego de un par de horas, “los metales pesados tienden a sedimentarse, se van depositando en el fondo. No poder sacar una muestra representativa, desde la superficie hasta el fondo de la tolva, va a producir probablemente un sesgo en la muestra. Eso significa que no vamos a tener el valor real del material que se está transportando, ya sea que estemos vendiendo o comprando”, lo que implica una pérdida económica para la minera. Además, si las muestras no se obtienen de forma correcta, “podemos tener un impacto gigante en la metalurgia de la planta al procesar, porque no vamos a saber con certeza todos los aditivos que tenemos que emplear, ya que la información disponible no es la correcta”. La utilización de un robot, que se ubica sobre un desplazador lineal que le permite alcanzar toda el área de carga, posibilita que el operador no afronte situaciones

de riesgo, por tener que subirse a la tolva del camión y exponerse al concentrado que es transportado. En esa línea, se trabaja para automatizar el proceso de muestreo e incorporar inteligencia artificial, para poder lograr una completa autonomía del sistema, de tal manera que “el operador pueda estar desde su casa o su oficina controlando todo el sistema, teniendo básicamente todo online, sin que esté presente en la línea de muestreo”. Respecto del interés que genera este tipo de desarrollos, Eric Montiel menciona que en Chile están en conversaciones con las mineras Candelaria y Caserones, y Ecometales. A ello se suman gestiones en los proyectos Antamina, Toromocho y Quellaveco, en Perú, y con compañías mineras de Bélgica y Australia.
FOTO CORTESÍA DE KOMATSU.
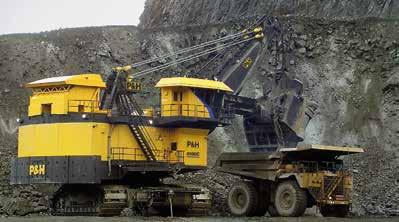
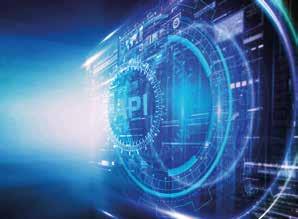
MODULAR MINING AVANZA EN EL CAMINO HACIA LA INTEROPERABILIDAD
LAS APIS FACILITAN LA Amedida que evolucionan las prácticas de la minería también se genera una demanda por operaciones cada vez más rápidas y eficientes. En las últimas décadas, la tecnología ha ayudado a las organizaciones mineras a establecer y cumplir con los objetivos micro, específicos para cada faena, o cualquier otro sistema de terceros que permita monitorear la carga de las palas, para lograr así una integración total del sistema. Al utilizar DISPATCH® (FMS) integrado con ProVision® y los sistemas de medición de carga en palas también se mejoran la CONECTIVIDAD ENTRE UNA SERIE DE SISTEMAS lo cual ha generado grandes cambios en la productividad/ utilización de los activos. exactitud y la eficiencia de la optimización del FMS. Al utilizar los datos del sistema de guía del equipo y el sistema de monitoreo de carga del balde, el FMS y el operador ya no tendrán que INDEPENDIENTES, Para ayudar a que los esfuerzos mineros cumplan sus metas a corto plazo y para generar oportunidades de mejoras conticonfiar en supuestos, ya que las variables reales (ubicación del balde, geología, cálculo de carga dinámica y la cantidad real que ESPECÍFICOS PARA CADA nuas que nos permitan seguir avanzando, los proveedores de tecnología deben recolectar y generar funcionabilidad para una cargan los camiones) son ya factores conocidos. ÁREA DE PRODUCCIÓN inmensa cantidad de datos que provienen de múltiples fuentes. Debido a que Modular Mining entiende que la gestión de la DENTRO DE CADA FAENA, Además, se debe tener la capacidad de compartir estos datos con los sistemas específicos de cada faena, como por ejemplo: carga no es la única forma de realizar mejoras o de refinar la exactitud de las optimizaciones, las APIs incluyen componentes MAYOR INTEGRACIÓN ERP, Gestión de Flotas (FMS) y Planificación Mina, los cuales que abordan las siguientes áreas adicionales de func ionalidad: Y COMUNICACIÓN MEJORADA ENTRE se hacen cada vez más importantes porque permiten generar valor a la industria. Modular Mining lanzó recientemente su programa Public Appli• CONTROL DE SUPERVISIÓN La API Core facilita el intercambio de datos entre los sistemas DISPATCH®, ProVision® y otros sistemas de supervisión/ APLICACIONES DE TERCEROS Y EL cation Programing Interface (API), enfocado en cinco áreas, cada una de las cuales aborda un área distinta de funcionalidad. Las APIs facilitan la conectividad entre una serie de sistemas indecontrol de terceros, incluidos aquellos para ERP. • GESTIÓN DE CHANCADO La API Chancado, que forma parte de la Suite para chancadores, PORTAFOLIO DE pendientes, específicos para cada área de producción dentro de cada faena, mayor integración y comunicación mejorada gestiona el flujo de tráfico en el chancador, al integrar el Control de Supervisión del chancador, la Adquisición de datos (SCADA) TECNOLOGÍAS DE entre aplicaciones de terceros y el portafolio de tecnologías de y los datos del controlador lógico programable (PLC) con el FMS MODULAR MINING. Modular Mining, que incluyen el sistema de gestión de flotas: DISPATCH® y el sistema guía de equipos: ProVision®. La DISPATCH®. Al lograr esto, el sistema DISPATCH® es capaz de incluir los datos del chancador en los algoritmos de toma infraestructura subyacente de las APIs soporta el compartimien- de decisiones en tiempo real de FMS. to bidireccional de los datos entre los sistemas DISPATCH®, • PLANIFICACIÓN MINA ProVision® y otros programas de terceros, lo cual contribuye a La API del sistema de guía de equipos permite a las aplicaciones una mayor productividad, mayor eficiencia operacional y mayor de planificación mina de terceros integrarse con el sistema valor general para las mineras. ProVision®. Al eliminar la brecha existente entre la planificación Un componente clave de las APIs es la gestión de carga. Esta área y la ejecución, las faenas mineras tienen la capacidad de se puede ver especialmente beneficiada con la integración de monitorear el progreso según el plan y responder de forma tecnologías, al entregar datos de carga a los operadores mineros, proactiva a los eventos no planificados. de forma más precisa y rápida, convirtiéndose en una solución • INTEGRACIÓN DE SISTEMAS DE TERCEROS interoperable, la cual permite que las organizaciones mineras La API de integración de sistemas de terceros para equipos aumenten su producción en toneladas, mejoren la eficiencia móviles pesados (HME) facilita la integración entre el FMS y de carga y la confiabilidad de los datos, logrando así una dis- los sistemas de terceros a bordo. Gracias a esta API, la lógica tribución de la carga más precisa. Al existir una vinculación en de toma de decisiones en tiempo real del sistema DISPATCH® desarrollo con MineWare, el componente de carga de las APIs considera estos parámetros específicos entregados por el sistema puede vincular los sistemas existentes de faena ProVision® y de terceros y sus acciones se modifican según reglas definidas DISPATCH® con otros sistemas como Argus PLM de MineWare en el módulo de acciones de DISPATCH®.
Modular Mining Chile
Andrés Bello 2777, Piso 13, Las Condes, Santiago, Chile. • Teléfono: +56 2 2591 3000 • Celular: +56 9 4495 0483 • Email: mundet@mmsi.com • www.modularmining.com/es/