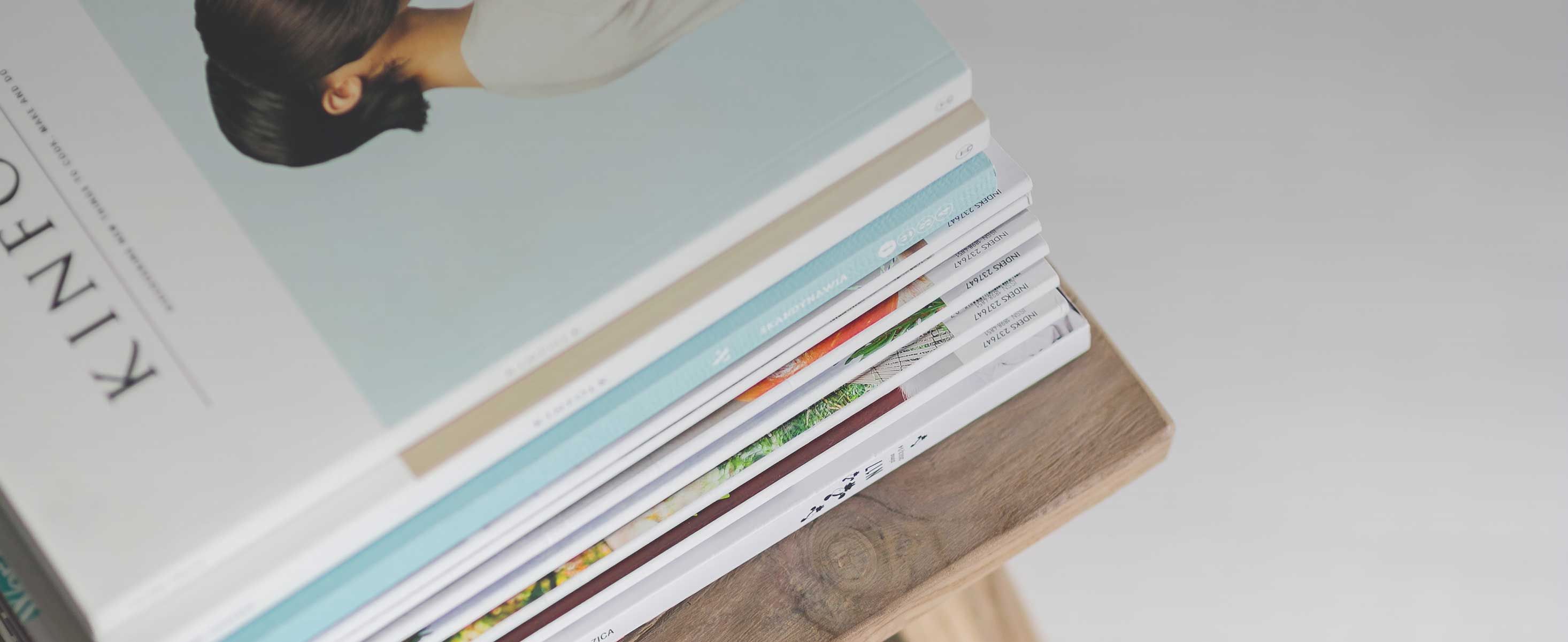
10 minute read
The dawn of the energy code
By David Leonard, P.L.Eng., Eng.L., Associate, Entuitive
The updating and implementation of Building Codes is not a new concept to the construction industry as various provincial and federal codes have been
developed, updated and implemented over the years. As we have now seen the development and later implementation of the National Energy Code of Canada for Buildings (NECB), there has been a fundamental shift in how a new project, addition project or various renovation projects have had to be designed. Previous to October 1, 2016, there were no code minimum requirements for overall building energy requirements within Alberta. We designed buildings following good current practice and improved on methods from previous years and decades incrementally. The NECB was published for the first time in 2011, then 2015 and 2017; it is an objective-based National Model Code that can be adopted by provincial and territorial governments. The principle to develop objective-based codes arose out of the strategic plan adopted by the Canadian Commission on Building and Fire Codes (CCBFC) in 1995.
The NECB does not list acceptable proprietary building products. It establishes the criteria that building materials, products and assemblies must meet. Some criteria are explicitly stated in the NECB while others are incorporated by reference to material or product standards published by standards development organizations. Only those portions of the standards related to the objective of this Code are mandatory parts of the NECB.
Following October 1, 2016, implementation of an energy use minimum standard with NECB 2011 was set using prescriptive envelope requirements which could then be adjusted by making adjustments from the inefficient prescriptive mechanical requirements. It was a simple solution, to use better/more efficient mechanical systems and keep doing what we were doing on the building envelope (IE lower thermal performance targets than what was listed as the prescriptive requirement in NECB). We saw a small improvement with building envelope assemblies to minimize the use of more expensive but extremely efficient mechanical systems.
On December 1, 2019, the NECB 2017 came into effect. This was another baby step in the movement towards more energy-efficient buildings. In the long term, net zero, net positive, minimum carbon emissions, no carbon emissions and retrofit code requirements are anticipated to become part of the language of the Codes, setting even more stringent requirements for how a building is to be designed, constructed and operated. NECB 2015 was skipped in Alberta but is in use in other provinces such as Ontario.
When you’re considering adding to an existing building, the addition will be considered independent of the existing building. It is mandatory that any additions greater than 10 square metres of conditioned floor space must meet the requirements of the NECB. This is a unique definition to the NECB. However, at the discretion of the design team, there may be situations where there are benefits to upgrading elements of the existing building to achieve a more efficient overall building design. If a building was required to meet the NECB at the time of its construction, future renovations must demonstrate that they do not reduce the level of compliance previously achieved. If the building was not required to meet the NECB compliance levels at the time of construction, then the renovations are not required to meet NECB standards.
Generally speaking, if your building falls into occupancy classifications A, B or F1 or it exceeds 600 square metres in a building area or three storeys in height, it is within the scope of the NECB. Additionally, at the applicant’s discretion, any project within the scope of Alberta Building Code 9.36 may choose to use the NECB technical requirements in lieu of ABC 9.36.
Several types of spaces can be unconditioned and thus need to be
treated differently, e.g., mechanical rooms, crawl spaces, garages, loading docks. There is also a need to consider components that separate spaces that are conditioned to substantially different temperatures (e.g., swimming pools, skating rinks). With NECB 2017, we have to mostly consider the Overall Thermal Transmittance (U-value). The overall thermal transmittance, U-value in W/(m2•K), is the inverse of the effective RSI in m2•K/W.
We have three paths to demonstrate compliance with NECB 2017 including the Prescriptive Path, the Trade-off Path and the Performance Path. The first compliance option is to apply the prescriptive requirements of the Code, which generally dictate minimum thermal characteristics for envelope elements and energy efficiency measures that can be stated as specific instructions. The second option affords some degree of flexibility in the application of the prescriptive requirements. For example, the trade-off paths for Part 3 allow Code users to vary the thermal characteristics of one or more components of the building envelope and/or vary the fenestration and door area from that permitted in Section 3.2., provided it can be demonstrated that the resultant building envelope will not transfer more energy than it would if all its components complied with that Section. The trade-off options present an easy way to make small adjustments to the characteristics of the building without having to follow the wholebuilding performance route. The third option is a performance path, if some aspects of the prescriptive and trade-off routes are considered too limiting, the building could, for example, be designed with any thermal characteristics desired (subject to certain limitations), provided that it would not have a calculated energy consumption under standardized conditions that is greater than it would have been had the building been designed in strict conformity with the prescriptive requirements, all other aspects of the building (those that are not the object of a requirement in this Code) remaining the same in both cases. The proof of compliance when using the performance path option is achieved through two energy analyses: one on the building as if it met the prescriptive requirements, which gives the “target” performance of the reference building, and the other on the actual design of the building.
Nearly every project we’ve worked on since NECB came into effect starts with a chicken-before-the-egg conversation. The architect and/ or energy modeller would ask what R-values we need to use on the project. My response was almost always, “you tell me.” We can design any thermal performing assembly we want, that is where the innovation comes in. But really, we need the energy modeller to tell us what inputs they used in their model and whether or not those inputs told us the building would be compliant or not. We would typically make recommendations on what the assemblies could be as a starting point but the reality is that no matter what we come up with we are in a realm where there are too many variables to create a rigid performance requirement for the building envelope. This is where parametric energy modelling can play an efficient role in determining where the greatest energy consuming components in the building are so we can maximize efficiency in those areas and save on other areas which have a minimal impact on the overall building’s energy use.
When practised, the changes to the calculations of Overall Thermal Transmittance may be the most significant changes in the code. The NECB 2017 calculation method considers a host of elements that weren’t previously considered in the analysis when demonstrating compliance with the Code. These elements, when considered into an effective thermal transmittance, have the potential to reduce the demonstrated effective performance by HALF.
There is published data to suggest the derated values for the overall building envelope can range from 30 per cent to 500 per cent, depending on all the variables that can go into the performance of the building from orientation of the building, to WWR, to building geometry, to connections of systems and quantities of those connections.
We note that mechanical penetrations, fasteners and enclosed unconditioned spaces are still not a requirement in our analysis when determining compliance of the proposed building with the reference/prescriptive building.
Analysis for 2011 was actually fairly simple. We didn’t have to “show our work”; generally, as long as the thermal performance values were presented on the architectural assembly page and were described
Analysis for 2011 was actually fairly simple. We didn’t have to “show our work”; generally, as long as the thermal performance values were presented on the architectural assembly page and were described as effective R-values as opposed to nominal R-values, the AHJ was satisfied and we got our building permit. It was unlikely that you were getting held up at BP provided a few of the necessary bits of information were being provided.
as effective R-values as opposed to nominal R-values, the AHJ was satisfied and we got our building permit. It was unlikely that you were getting held up at BP provided a few of the necessary bits of information were being provided.
We need to consider linear interface details; these details are generally expressed in our plan and section details in the architectural drawings. These details can have the biggest impact on the overall thermal transmittance of the building. We then also have the point interface details, minimizing these conditions such as structural penetrations for a canopy or sunshades will help to reduce the overall thermal transmittance of the building envelope.
Under NECB 2017, we must provide a thermal analysis package with every BP submission. It is common that the package is provided by the building envelope consultant, energy modeller or architect. While it wouldn’t be a requirement to provide the thermal calculations to the construction team, there would be benefit to the project so the contractor and their trades and their suppliers can understand the buildings performance requirements.
Incorporating earlier discussions on projects around energy performance and how we are going to meet those targets will establish constructible and more cost effective assemblies as we consider budget and energy use in tandem. Considering a performancedriven design will ultimately result in reduced construction and design costs to meet the energy requirements. Delay of these discussions likely results in potential cost increases.
We have seen cost savings on projects by relying on the accuracy of the model and the recommendations the consultants provide, and then exploring savings that can be found in reduced construction and/or operational costs. Further, looking at more efficient methods of insulating and sealing a building ultimately provides more value both during construction and operation of the building.
Canada has a target of being net zero ready by 2030, and this document outlines the plans for how we’re supposed to get there. We need to consider that 2030 isn’t going to be a monumental year like the fall of 2016 wasn’t by any means a date that will live in infamy. 2030 will come and go like any year and, looking beyond that, we need to consider where the industry will be going, driven by Codes which set the minimum standards, by building owners who want a better buildings to market to their tenants/residents or have reduced operational or maintenance requirements, by designers who take consideration to how their building will perform as much as how it will look, by consultants who can inform the designers and owners on where they can leverage and maximize their designs, and by contractors who can understand the designs and the importance of the materials they’re procuring and installing.
We should consider the next steps, which could involve carbon emissions targets, net positive targets, retrofit requirements. We want to plug in and use more energy than ever, having a building that could not only operate itself but output power to all the electric cars we are going to own in the future.
We also need to be cognizant of the fact that as buildings become more efficient, the risks of creating new problems may exist. We look at all these old masonry buildings that have been around for 100 years as compared to that condo that went up in 2008 that is falling apart. While the newer buildings can use less energy to heat and cool them, the importance of the systems that directly relate to reducing that energy demand become even more critical. n