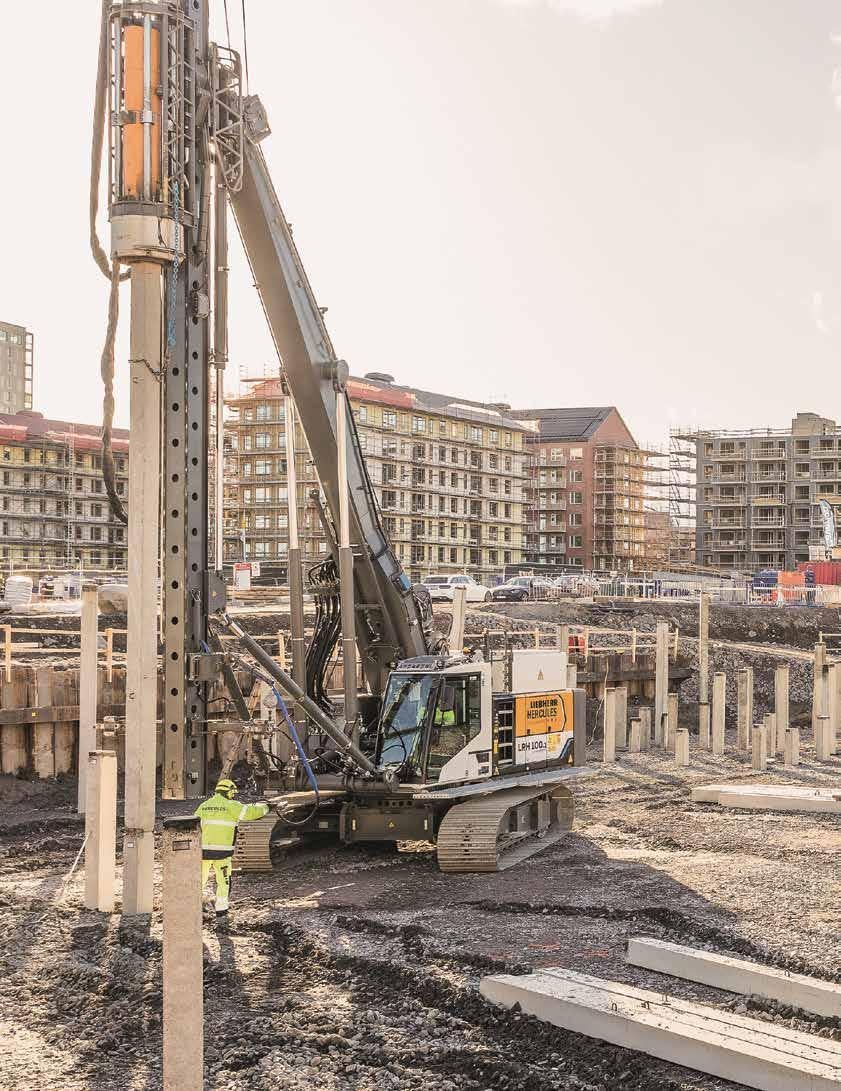
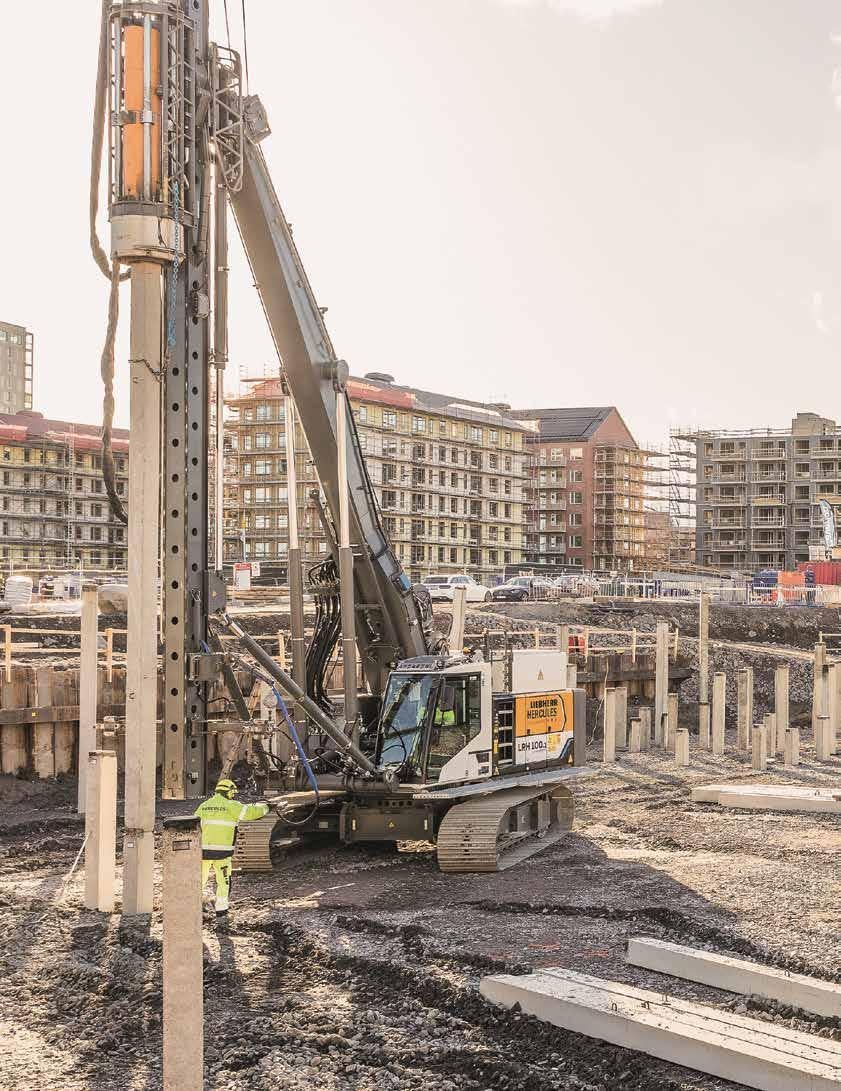
STEEL
n Premier manufacturer of cold formed steel sheet piles with 30+ years of experience

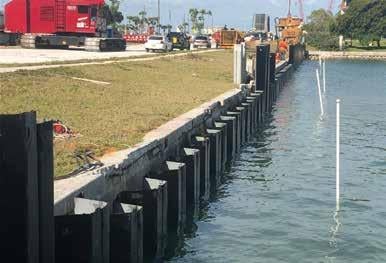

n Wide range of shapes available for all applications
• Elastic Section Modulus: 2.55 in³/ft to 62.32 in³/ft
• Moment of Inertia: 4.5 in⁴/ft to 560.85 in⁴/ft
• Thickness: 0.157 in to 0.55 in
n Available in numerous steel grades including ASTM A572, ASTM A588, and ASTM A690
n Manufactured in custom lengths with industry leading delivery times


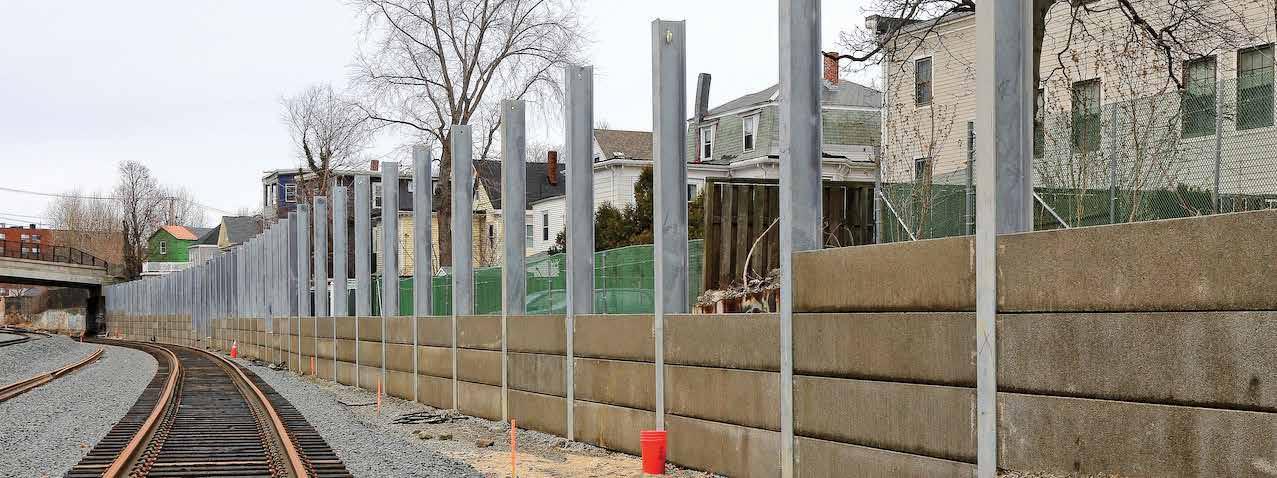
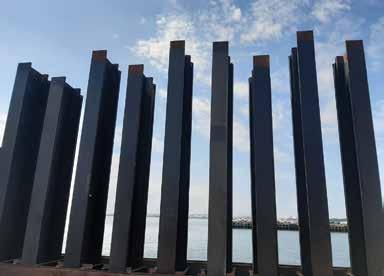
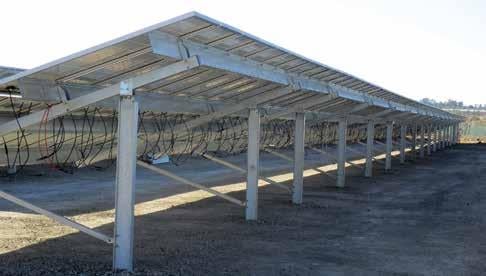
Piling Industr y Canada
PIC magazine
In this issue
Published by DEL Communications Inc.
Suite 300, 6 Roslyn Road, Winnipeg, MB Canada R3L 0G5
President & CEO: David Langstaff
Managing Editor: Lyndon McLean lyndon@delcommunications.com
Sales Manager: Dayna Oulion dayna@delcommunications.com
Advertising Account Executives: Jennifer Hebert | Michelle Raike
Production services provided by: S.G. Bennett Marketing Services
Creative Director / Design: Kathleen Cable
© Copyright 2022.
DEL Communications Inc.
All rights reserved.The contents of this publication may not be reproduced by any means, in whole or in part, without prior written consent of the publisher.
While every effort has been made to ensure the accuracy of the information contained herein and the reliability of the source, the publisher in no way guarantees nor warrants the information and is not responsible for errors, omissions or statements made by advertisers. Opinions and recommendations made by contributors or advertisers are not necessarily those of the publisher, its directors, officers or employees.
Publications mail agreement #40934510
Return undeliverable Canadian addresses to: DEL Communications Inc.
Suite 300, 6 Roslyn Road, Winnipeg, Manitoba, Canada R3L 0G5
Email: david@delcommunications.com
PRINTED IN CANADA | 12/2022
The piling rigs LRH 100.1 unplugged and LRH 200 unplugged expand Liebherr’s battery-powered product portfolio. An outstanding feature of the unplugged models is zero emission. They do not produce any exhaust fumes and are extremely quiet. This strikes the right note especially in noise-sensitive regions and finds favour with construction site personnel and residents.
The battery is charged using a conventional jobsite electric supply. Operation can continue as normal while charging. In order to change to battery operation, you just need to pull out the plug, therefore: unplugged. Whether attached to the electric supply or not, the performance and range of application remains unchanged.
The LRH 200 has been completely newly developed and closes the gap between the proven LRH 100 and LRH 600 in the series of piling rigs. A 200-kWh battery pack ensures that the unplugged models can operate in battery mode for 4 to 5 hours in average pile driving applications. Optionally, it can be upgraded to 400 kWh for 8 to 10 hours of operation.
When equipped with the hydraulic hammer H 6 from Liebherr, the LRH 200 unplugged can lift piles up to 24.5 m long and weighing 16 tonnes. The machine especially excels with its large working range.

A radius of up to 8.7 m has the advantage that the machine does not have to be constantly moved.
The design of the leader enables inclinations of up to 18° in all directions. Furthermore, it is also possible to raise or lower the leader by 6.5 m (e.g., when working in a foundation pit), which makes the machine even more flexible.
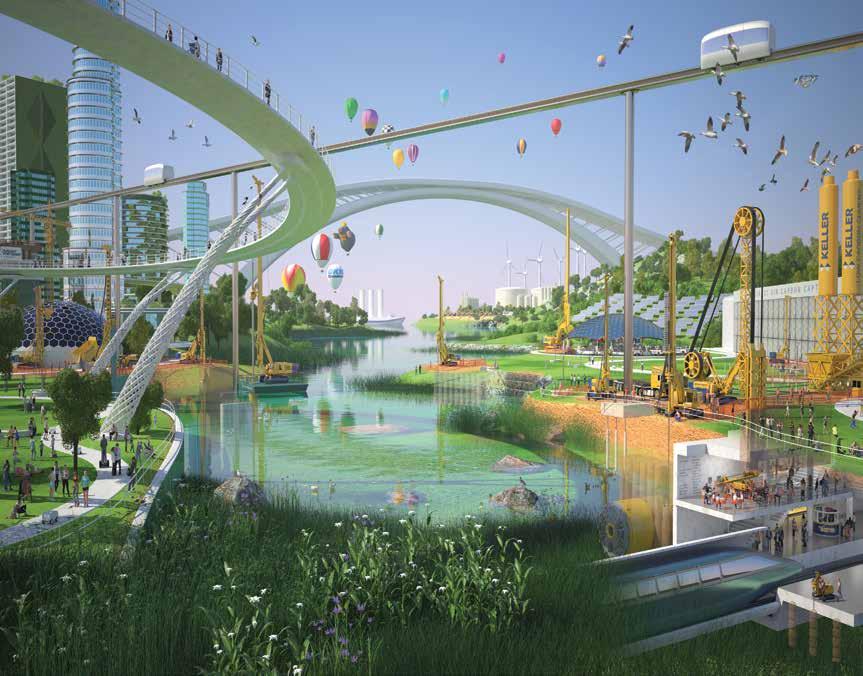

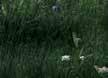
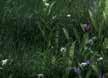
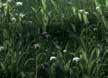
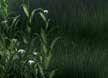
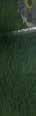




Canada’s construction industry urging all governments to Rebuild Canada’s workforce NOW
By Mary Van Buren, President, Canadian Construction Association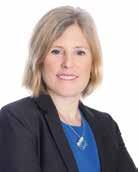
The Canadian Construction Association (CCA) is sounding the alarm about the urgent need for workers in construction through an industry call to action to “Rebuild Canada’s workforce NOW”. “Canada is facing its most severe labour shortage in over 50 years – nearly 1 million jobs are unfilled,” says Mary Van Buren, CCA president. “The situation is especially acute for the construction sector – we have over 81,000 openings now. This also means the essential infrastructure projects that 38 million Canadians rely on every day risk being cancelled or delayed.”
The federal government has an ambitious growth plan – one that includes repairing, maintaining, and retrofitting aging infrastructure while also building for future climate resilience. Retirements and recruitment challenges will be a heavy blow to Canada’ future economic growth if steps aren’t taken to rebuild Canada’s workforce now.
As job vacancy rates grow and competition for talent becomes more fierce, the federal government needs to expand the Temporary Foreign Workers program and facilitate the entry of immigrants interested in working in the construction sector.
Industry representatives met with parliamentarians for CCA’s Hill Day on November 15 to urge the federal government to:
• modernize Canada’s immigration policy and point system to better recognize tradespeople and construction labourers.
• work with the provinces to ensure skills matching is properly funded and supported; and
• update the Temporary Foreign Worker program to allow seamless access for the construction industry. Skilled tradespeople cannot be created overnight. It’s vital that we turn to immigration and temporary foreign labour to help alleviate the choke points created by the workforce shortage.
Help spread the word by visiting https://can.cca-acc. com/cca/rebuild-canadas-workforce-now/.
ABOUT CCA
Across Canada, CCA represents more than 20,000 member firms drawn from 63 local and provincial integrated partner associations. CCA gives voice to the public policy, legal and standards development goals of contractors, suppliers and allied business professionals working in, or with, Canada’s heavy civil, institutional, commercial, and industrial construction industry.
The construction sector is one of Canada’s largest employers and a major contributor to the country’s economic success. The industry – 70 per cent of which is made up of small and medium enterprises – employs more than 1.4 million Canadians and contributes 7.5 per cent of Canada’s Gross Domestic Product. l
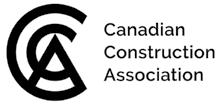

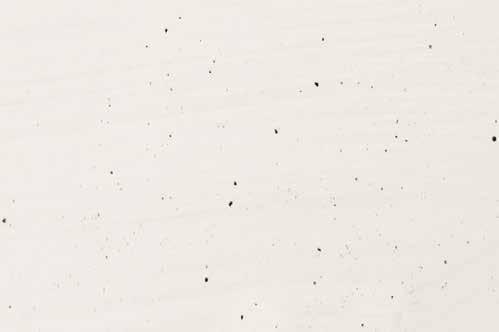
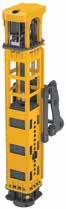
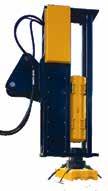

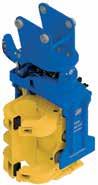
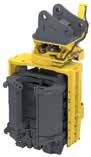
Unleash the full potential with Liebherr Transform
Transforming old into new for a longer service life.
Liebherr Transform, the new upgrade, modification and overhaul service, has a tailor-made solution for all customer needs. It is available for crawler cranes (up to 400 t), deep foundation equipment, and duty cycle crawler cranes.
The new Liebherr Transform provides tailored solutions that respond to the continuously growing demands on today’s businesses. A range of ingenious upgrades, clever retrofits, machine overhauls and service modifications breathe new life into customers’ existing machines. Using the latest technology and years of experience, Liebherr brings you a combination of sustainability, smart technologies, maximum productivity, and cost-effectiveness in one complete solution. This allows existing equipment to reach its full potential.
OVERHAULS, UPGRADES, RETROFITS AND MUCH MORE
It’s inevitable that equipment becomes outdated over time, but that doesn’t mean it has to be replaced. As the name suggests, existing machines are transformed using affordable complete or partial machine overhauls, retrofits, and upgrades. This not only saves the increased capital expenditure of investing in new machines, but also reduces the carbon footprint by avoiding the need for new equipment through the extension of the service
Liebherr Transform includes complete overhauls.


life. Several retrofits and upgrades are available which increase versatility and performance, or ensure compliance with more stringent regulations, and so open up a wider spectrum of opportunities. At the same time, operators don’t have to get used to new machines and can continue to benefit from their vast experience with existing equipment. The Liebherr team of expert engineers takes care of the entire planning and implementation of Transform projects – from consultation through to installation and technical support and service.
STRONGER, FASTER, SMARTER, GREENER
Companies are under pressure to increase volume and performance, widen scopes, or reduce emissions and costs, the list is endless. Liebherr Transform helps to lighten the load through a comprehensive range of structural, electrical, mechanical, ergonomic, or digital modifications. Through the application of new technologies and expertise, Liebherr machines are transformed for the workplace of the future. They are stronger, faster, smarter, greener, and ultimately...better. Further details about Liebherr Transform can be found at https:// www.liebherr.com/en/deu/products/construction-machines/ deep-foundation/customer-service/transform/transform.html
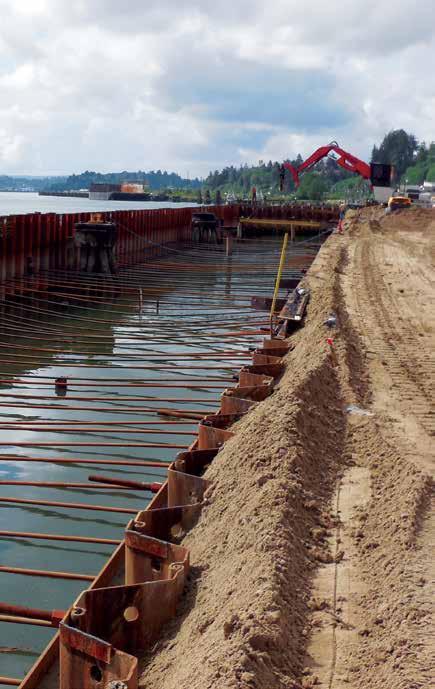
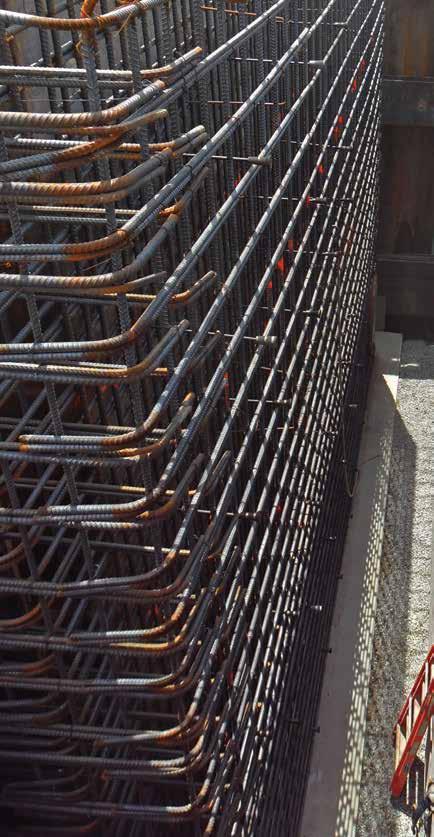
Keller announces new branch and area managers in North America
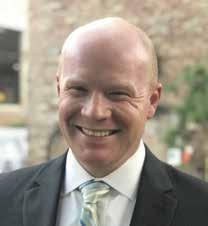
Ray Franz was promoted to Area Manager of Northern California. With over 30 years of experience in geotechnical consulting and specialty construction, Ray has worked with micropiles, auger cast piles, anchors, dynamic compaction, rigid inclusions, vibro compaction, and various types of grouting. Ray started with Keller in 2003 and most recently worked as a Pre-Construction Manager in Chicago, focusing on ground improvement opportunities. He graduated from Worcester Polytechnic Institute with a bachelor’s in civil engineering and Purdue University with a master’s in geotechnical engineering. He is a licensed Professional Engineer in nine states and was elected to the Academy of Geo-Professionals. Ray is a member of the Geo-Institute of ASCE and the Deep Foundations Institute (DFI). He has also served as past Chair of the Illinois Section of ASCE Geotechnical Group. He is a current member of DFI’s Ground Improvement Committee.
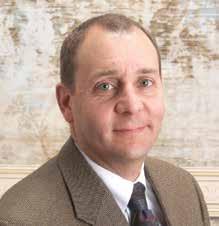
Jose Martinez has been promoted to Branch Manager within Texas. Jose has worked at Keller for over 17 years in various roles from project manager to operations. He has a bachelor’s degree in mechanical engineering from Rensselaer Polytechnic Institute (RPI) and a master’s degree in manufacturing management from the University of Michigan. Before working in the construction industry, Jose worked for General Motors and Dupont, learning about Lean and earning his Six Sigma Green Belt Certification. He is a member of Associated Builders and Contractors, DFI, American Shotcrete Association, and ADSC.
Justin Lewis has been promoted to Branch Manager for the Great Lakes/ Chicago region. Justin started with Keller in 2008 after completing his bachelor’s and master’s in Civil and Environmental Engineering at the University of Illinois Urbana-Champaign. During his time at Keller, Justin has held roles from field engineer to project executive. His work has focused on jet grouting, sheet piling, soldier beams and lagging, tieback anchors, internal bracing, driven piles, and micropiles. l





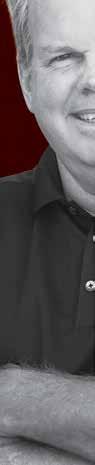

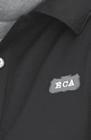
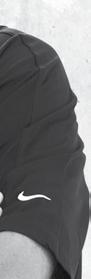
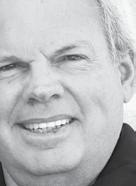
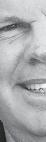
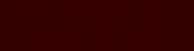



At ECA, we place a premium on giving our people the space to innovate when they see a need. Joe saw the long-term value in developing a certified training program with the aim of producing the industry’s best operators and technicians. Our focus on continuous education, exploration, and collaborative problem-solving translates to innovative solutions that add to our customers’ bottom lines. Together, we are moving the industry forward.
Let us help build your legacy one successful project at a time.


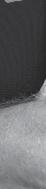


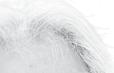
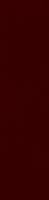

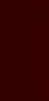

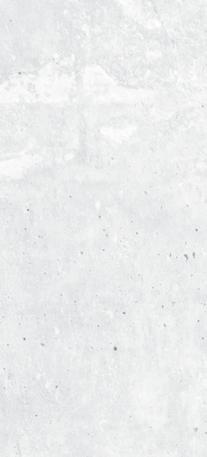



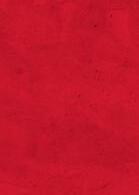

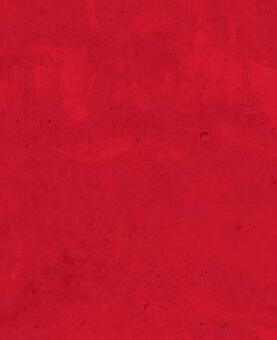
ecanet.com/piling-industry-ca 1 800 PILE USA



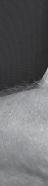
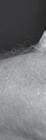





Empowering our customers to safely operate the most advanced equipment in the industry to its fullest capabilities is a no-brainer.JOE
Construction nearly complete on Travers solar project
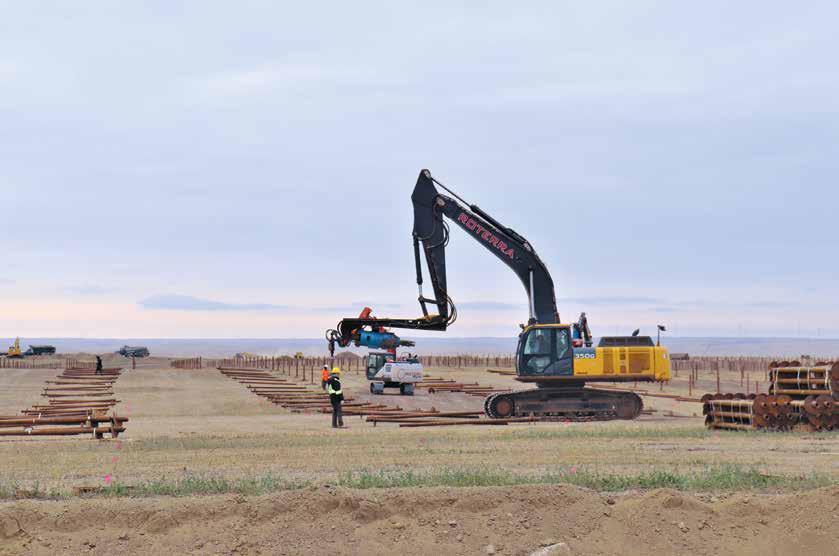
When completed later this year, the Travers solar project—a 465MW photovoltaic power plant in Vulcan County, Alberta, will be the biggest solar power plant in Canada.
Expected to generate power to meet the electricity needs of more than 150,000 homes, it will also offset more than 500,000 tonnes of greenhouse gas emissions annually. Located on approximately 3,330 acres of privatelyowned, cultivated, and grazing land approximately eight kilometres southwest of the Village of Lomond, the area features significant solar resources.
Greengate Power Corporation is a Calgary-based renewable energy
company that developed this project. In April 2019, Greengate Power applied to the Alberta Electric System Operator (AESO) to connect the Travers solar plant to the Alberta Interconnected Electric System (AIES). Operated by AESO, the AIES transmission and distribution system is the main grid in the region and provides approximately 85 per cent of electricity in the province.
(Source: NS Energy magazine)
Financier Copenhagen Infrastructure Partners (CIP) hired PCL Construction Management as the general contractor on this impressive $700 million project that is expected to create more than 200 full-time jobs during the construction
phase, and up to 10 permanent positions during the operation phase.
LARGEST HELICAL PILING PROJECT IN CANADA
Roterra Piling Ltd., a piling solution provider with locations in Edmonton and Houston, Texas, used 50 million pounds of steel to install more than 228,000 helical piles over 3,330 acres, supporting solar PV modules, power conversion stations and an electrical collection system, along with ancillary equipment. This makes this the largest helical piling project in the country.
“We provided fabrication, installation, and remediation (excavation of below
This impressive project is expected to offset more than 470,000 tonnes of greenhouse gas emissions annuallyProduction pile install.
Left: Fields of piles with racking.
Below: Final pile.
ground obstructions impacting pile installation) for this scope, along with a supporting survey, quality and project management team,” explains project manager Laili Abolghasemi.
“This project is entirely helical with piles ranging from 3½ inches in diameter up to 85/8 inches. At peak production, our install fleet had dedicated install units including skidsteers, 100 to 300 series excavators, and drive heads from 20,000 ft.-lbs. to 115,000 ft.-lbs., as well as a full fleet of support equipment including loaders, skidsteers, backhoes, hoe-packs and crew trucks and vans. We installed the first pile on July 20, 2021 and completed all piling activities in early June.”
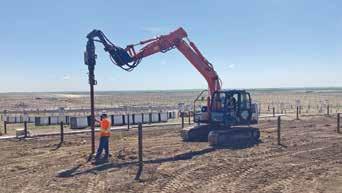
In addition to being the largest solar energy project in Canada with an installed capacity of 465 MWac/691 MWdc., this project is unique in that installed piles per day on this project at times reached over 2,000/day across 28 active install units.
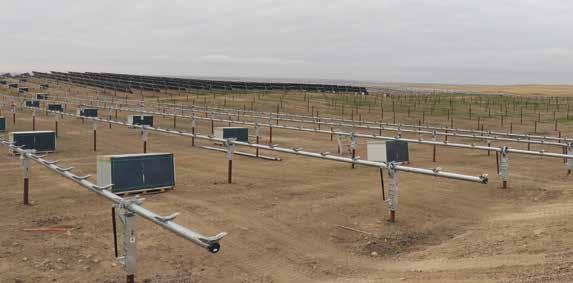
“Amazon has signed a corporate power purchase agreement to offtake up to 400 MWac from the project,” says Abolghasemi. “In total, there are 1.5 million solar panels installed. The project is one-third the size of Manhattan, which
is approximately equivalent to 1,600 CFL fields.”
PROJECT CHALLENGES
Projects of all sizes have their challenges, and this one of such magnitude is certainly no exception.
Abolghasemi says this project necessitated a quick ramp-up, which included sourcing specialized equipment globally and working around multiple trades—often in extreme weather conditions.
“Our team persevered through multiple waves of the global pandemic and two natural disasters – that is, working outdoors under a heat dome in the summer with unprecedented temperatures and mitigating the impacts of massive flooding in British Columbia, which disrupted our supply chain for months. Working 12 hours a day –including an hour-long commute each way from staff accommodations – we maintained a full crew complement seven days a week from July onward, through all these challenges.”
Due to the sheer quantity of pile locations, there was a significant amount of data relating to variable subsurface conditions and the status of individual
piles and related activities. To remain efficient and meet extremely tight tolerances for the project, the operations and project management teams worked closely with PCL, Tulloch Engineering, and Greengate’s representatives to meet these challenges head on.
“As a turn-key helical piling solutions provider, Roterra Piling Ltd. was able to provide technical support for installation challenges, with high-capacity install units with experienced operators to overcome adverse ground conditions, and a dedicated quality team to focus on solutions and detailed tracking as the project covered over a dozen square kilometres with helical piles,” adds Abolghasemi. “We developed new processes and have gained experience that we’ll put into practice in future projects.”
Thirty-five years is the estimated operational life of this project. After this period, it will be either decommissioned or repowered. If decommissioned, the solar modules will be salvaged and recycled, while the remaining infrastructure that is buried 1.5 metres below will be left in placed to prevent further disturbance of the land. (Source: NS Energy magazine.) l
“ This project is entirely helical with piles ranging from 3½ inches in diameter up to 85/8 inches.”
— Laili Abolghasemi, project manager, Roterra Piling Ltd.
Brextor: A quantum leap in pile head processing
By Alois Portmann, BRC Engineering AGDue to increased dense construction
and building in exposed locations, pile foundations continue to gain in importance. Previous pile-heading methods involve risks that can be avoided with the newly developed Brextor method.
BORED PILES AND PREVIOUS PROCESSING METHODS
The world is becoming increasingly crowded. The annual population growth rate is currently two per cent. The necessary building land is becoming increasingly rare, and thus the call for denser construction is becoming stronger. The available building ground is more and more often in exposed locations and of poor bearing capacity. Pile foundations are the solution to ensure a safe foundation in
such conditions. For this reason, pile foundations are becoming increasingly important. The pile head is the connection to the foundation. Highest quality without compromise is required. A foundation failure can end in disaster.
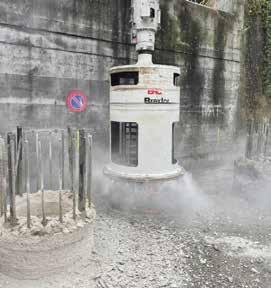
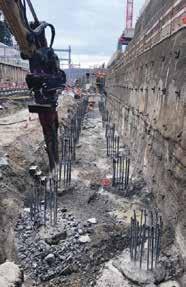
Up to now, bored piles have mainly been processed with air or hydraulic hammers. Air or hydraulic hammers work with a vertical impact energy. This processing energy cannot be controlled. Thus, there is a risk of cracks in the concrete body and spalling on the outer skin of the pile. This can cause corrosion damage in the medium term. Bent or torn reinforcements caused by air or hydraulic hammers additionally reduce the absorption capacity of the tensile load. Due to the design-related mode of operation of these devices, a correspondingly large working space
is required. Furthermore, narrow and long reinforcements are difficult to process, and large obstructions occur with existing spiral reinforcement in the excavation area. In order to ensure quality and to break the surface tension, a cut must also be made to the definitive height. The last 30 to 50 centimetres are only possible with a lot of manual work.
BREXTOR
With Brextor, the working process remains under control. The horizontal force application allows 100 per cent control of the applied processing energy. In addition to the best possible quality, the pile head is handed over to the succeeding gear with precise accuracy (height accuracy +/- one centimetre). Also, the concrete structure and reinforcements remain intact.
The core tension is broken with the Brextor internal cutter. The surface tension is broken with the Brextor external cutter. The remaining concrete border with the reinforcement inside can be broken away with the Brextor crusher without risk of damage. Thus, the finished bored pile head is achieved in four working steps:
1) prepare the pile with the milling disc, 2) mill to level (+/- one centimetre height accuracy), 3) break out the remaining concrete with the BRC pile head crusher, and 4) clean and align the reinforcement.
Brextor is manufactured in Switzerland is a CAD drawn design and incorporates precision CNC machined parts. The process is patented worldwide.
NEW APPLICATIONS
Brextor’s design allows it to be used with very little or even no lateral working space. This means that excavation can be saved. The cut at finished excavation level to break surface tension is made automatically with the external cutter. The clean-up effort is minimized to cleaning work. Brextor is suitable for all pile types/walls. The system uniformity allows easier use by site staff (one system for all uses – bored pile, bored pile wall, earth auger). In addition, the excavated material (80 per cent 0-30 millimetre gravel) can very often be processed directly on site.
FOUR-LANE EXPANSION LIESTAL, SWITZERLAND
Brextor was used for the four-lane expansion at Liestal station, which was carried out by Implenia. The expansion of the northern and southern station entrances to four lanes should ensure significantly fewer crossing conflicts and
more punctual and disruption-free rail traffic for long-distance, regional, and freight traffic.
“With manual removal by hydraulic hammer, there would always be a risk of damaging reinforcements and disturbing the concrete quality at the pile head.
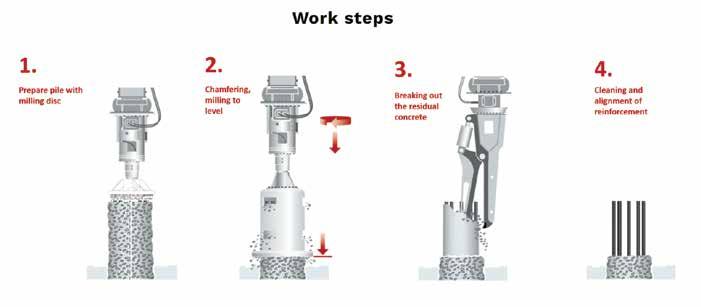
I minimize this risk with Brextor,” confirms Stefan Lang, site manager at Implenia.
TIME AND WORKSPACE SAVING
The client attaches great importance to timely execution of the work; after all, the four-track expansion is being carried out during ongoing rail operations.
“The time pressure on this construction site is huge, as various milestones have to be met,” notes Lang. “We only have a limited time window available and if this cannot be massively extended, such an undertaking would only be possible with a lot of resources and personnel without the Brextor.”
Time as a decisive factor was supplemented by the challenge of very little space.
“We would also need more space, which would be a big challenge here because you don’t have enough room for a pick hammer between the nail wall and the pile head.” For this reason, it would be necessary to move back the wall, which is up to six metres high, over a length of 300 metres, just to create enough space for the pile head to be worked. This would mean a massive increase in costs. Thanks to Brextor, these costs are saved,” says Lang.
In the case of a railroad line extension, 80 centimetres of working space could be dispensed with on the rear side. With an embankment of six metres, over 300 metres, this results in 1,440 m3 excavation (fixed measure) which did not have to be made.
Besides the enormous cost savings for excavation, transport, landfill fee and material replacement, Brextor has made a great contribution to the environment and to the population. At least 280 truck trips of 40 kilometres each could be saved. Thus, the CO2 footprint was reduced and the population benefited from a less polluted road network. l
Junttan showcases sustainable solutions at bauma 2022

Junttan recently showcased its latest sustainable solutions for piling business at bauma 2022, including the world’s first electric pile driving rig, which was officially launched in 2021 by Junttan, on display at an exhibition for the first time.
“Junttan is facing the same demands as other companies in the sector for development toward a safer and more sustainable future. Our history of more than 45 years in the piling business has taught us much, and our products have been ahead of the competition for decades. Our development will not stop there – plenty still needs to be done to reduce our environmental impact.
After 12 months, Junttan customer Aarsleff Ground Engineering Ab is truly pleased with their and the world’s first fully battery-powered pile driving rig, eJunttan PMx2e.
However, one big step forward was taken in 2021 when we launched the world’s first electric pile driving rig, eJunttan PMx2e. The electric rig has been now successfully operating for 12 months. Operator feedback is excellent, and the machine keeps on driving piles without any issues. We are proud to have our PMx2e battery-powered pile driving rig on our stand at bauma exhibition,” says Junttan CEO Tommi Lehtonen.
ELECTRIC PILE DRIVING MACHINE, EJUNTTAN PMX2E
Electric, eco-friendly, energy efficient, epic, evolutionary, economical, emissionfree, exquisite – and more. Just a few
e-words to describe Junttan’s fully battery-powered eJunttan, the PMx2e.
When Junttan set out to design more sustainable innovations, they understood that the new eJunttan model needed to tick all the same boxes from the very beginning as its predecessors. That’s why they decided to combine the best of both worlds: tested and optimized Junttan hydraulics merged with modern batteries and electric motor technology.
The result is the fully battery-powered electric pile driving rig that is ready to meet the same challenges at the work site as its predecessors. Instead of a diesel engine, Junttan is now powering the
hydraulic system with a modern electric motor that generates its power from a battery pack at the rear of the rig where the counterweight was located. In this way, they were able to build a solution that is reliable, easy to operate, and as effective as normal diesel-powered Junttan rigs. To make everyday life at the worksite possible, they chose a solution where the rig is powered by two separate 396 kWh battery packs that can be replaced during the day if needed. By choosing a detachable two-battery system instead of one bigger fixed, charging can be done with a normal 63A mains outlet and both batteries are ready the next morning.
With the state-of-the-art CCS DC-DC quick charging, the battery packs can be charged with up to 250 kW to enable even more flexibility and extended range for future worksites also with a single battery pack.
HHX160 HYDRAULIC IMPACT HAMMER WITH A NEW MODULAR PILE SLEEVE SOLUTION
Junttan also presented a new modular pile sleeve solution for more efficient and flexible operation with quick change inserts for different pile sizes.
Junttan HHx series, the new generation hydraulic hammers for demanding conditions, provides an adjustable stroke with a blow rate of up to 60 to 180 blows per minute. With Junttan intelligent solutions, not only optimized energy and high productivity are gained but also less noise, vibration, and emissions are created. New HHx hammer series combined with intelligent x-series solutions leads to a high level of piling project productivity, flexibility, reliability, and user-friendliness, as well as easy onsite service. The modular structure allows up-grade or down-grade size by changing ram weight. All housing, caps, and sleeves are interchangeable with all Junttan HHxmodels.
The hammers are operated with the new generation Junttan xCU power packs which fulfill the latest environmental requirements. Biodegradable oils and less fuel consumption by hammer automatization with Tier 4Final/Stage V engine help to protect the environment while getting the most out of the hammer.
JUNTTAN LIFE SERVICES
Junttan now offers all new equipment with a selection of service contracts to extend the life cycle of the equipment. LifeCare Service Agreement covers preventative service done every 500 hours to maximize operational safety and maintain machine value and functionality with minimized unplanned downtime. LifeCare+ agreement covers also corrective maintenance once it is due to proper use of the equipment.
Junttan has a strong network of technical specialists to support in acute situations remotely with the newest technology and a considerably faster response time. In Europe, Junttan offers the largest service agreement scope up to six years.
Modernization solutions breathe new life into older Junttan equipment and reduce emissions. For example, Junttan has a solution and references ready to update your Junttan equipment with Tier3 engine into Stage V equivalent level. Also, Rapid Impact Compaction (RIC) – excavator-mounted solutions are now also available from Junttan.
Junttan Rental is an option that offers flexibility to the fleet and a lighter and greener way to utilize Junttan equipment. Junttan’s rental fleet is comprehensive and designed to serve the local market needs. l
Fraser River Pile & Dredge (GP) Inc.
As Canada’s largest �arine Construc�on, �and Founda�ons and Dredging contractor, FRPD is a recognized leader that employs state of the art methods and equipment. FRPD’s versa�le �eet is ready to complete all scope and size �arine Construc�on, Environmental Remedia�on, Dredging and �and Founda�on pro� jects. Established in 1911 as Fraser River Pile Driving Company and incorporated in 2008 as Fraser River Pile & Dredge (GP) Inc., FRPD’s team of highly skilled professionals brings more than 100 years of e�perience and commitment to e�ceeding e�pecta�ons.
1830 River Drive, New Westminster, B.C. V3M 2A8 Phone: 604 522 7971 (24/7) www.frpd.com info@frpd.com
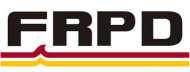
Electrifying: Liebherr launches six new unplugged machines
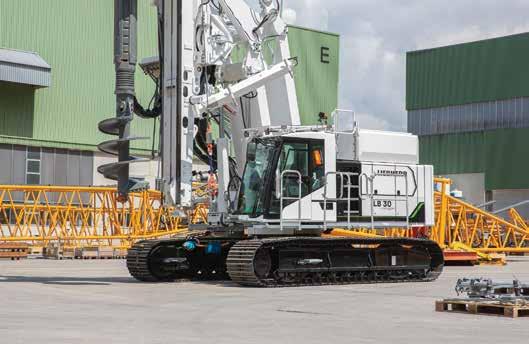
makes if even more versatile in use.
In addition to piling, the machine can be used for continuous flight auger, full displacement and down-the-hole drilling, as well as for soil mixing work. A torque of 250 kNm provides the necessary power.
When equipped with the hydraulic hammer H 6 from Liebherr, the LRH 200 and the LRH 200 unplugged can lift piles up to 24.5 metres long and weighing 16 tonnes. The machine especially excels with its large working range. A radius of up to 8.7 metres has the advantage that the machine doesn’t have to be constantly moved.
Since the alternative drive of the LB 16 unplugged quickly established itself on the market as a gamechanger, the design has been extended to further product areas. Today, the electrified unplugged series comprises crawler cranes as well as piling and drilling rigs.
An outstanding feature of the batterypowered unplugged units is zero emissions: they don’t produce any exhaust fumes and are extremely quiet. This strikes the right note, especially in noise-sensitive regions, and finds favour with construction site personnel and residents. Whether in London, Paris or Oslo, the concept has already been successfully applied.
The battery is charged using a conventional jobsite electric supply. Operation can continue as normal while charging. To change to battery operation, you just need to pull out the plug; therefore: unplugged. Whether
attached to the electric supply or not, the performance and range of application remains unchanged.
All six models are available in both conventional and battery-operated versions and have identical performance specifications.
PILING: LRH 100.1 UNPLUGGED AND LRH 200 UNPLUGGED
The LRH 200 has been completely newly developed and closes the gap between the proven LRH 100 and LRH 600 in the series of piling rigs.
A 200-kWh battery pack ensures that the unplugged models can operate in battery mode for four to five hours in average pile driving applications. Optionally, it can be upgraded to 400 kWh for eight to 10 hours of operation.
The new design of the LRH 200 extends the range of applications and
The design of the leader enables inclinations of up to 18 degrees in all directions. Furthermore, it is also possible to raise or lower the leader by 6.5 metres (e.g., when working in a foundation pit), which makes the machine even more flexible.
The Ground Pressure Visualization of the new LRH model calculates the current ground pressure in real time and compares it with the specified safety limits of the respective construction site. The ground pressure is displayed in the operator’s cabin, meaning the operator is constantly aware of whether the machine is situated in or approaching a critical area.
The operation of the new piling rig LRH 200 is based on the proven concept of the LRH 100 and is therefore very userfriendly. The integrated data recording makes the analysis of the pile data extremely easy and saves a huge amount of time.
DRILLING: LB 25 UNPLUGGED AND LB 30 UNPLUGGED
Over many years, the drilling rigs LB 25 and LB 30 have proven themselves in the conventional version. The new battery-operated unplugged versions are identical with regard to application possibilities, weight, or transport; however, they have the added advantage of zero emissions. The drilling rigs can be used for all common applications in the field of deep foundation.
Thanks to the optional extension of the drilling axis, the machines can be deployed for drilling diameters of up to 3.4 metres. The optional rear support and the new design of the modular rear counterweight ensure higher stability and longer service life.
In addition to the standard design, both machines are available in a Low Head version with a total height of 14.1 metres or as Ultra Low Head with only 7.7 metres.
For battery operation, the charging
Left: Liebherr lr1130 unplugged. Liebherr lrh200 unplugged.
cable only needs to be unplugged and, for unlimited operation, reconnected to the construction site power supply. The battery is designed for a working time of four hours in Kelly operation. Whether in battery or plugged-in operation, the drilling performance remains unchanged.
LIFTING: LR 1130.1 UNPLUGGED AND LR 1160.1 UNPLUGGED
The new machines LR 1130.1 unplugged and LR 1160.1 unplugged extend the range of crawler cranes from LiebherrWerk Nenzing GmbH.
The electro-hydraulic drive of the new cranes has the same performance specifications as the conventional version. Both versions are operated in the same way, which is especially practical if the crane driver must often change between machines in one fleet.
The capacity of the battery is designed for an average lifting operation of eight hours. Alternatively, the main boom with luffing jib can be completely erected. The battery can be recharged within only 2.5 to 4.5 hours. As an option, the
performance can be increased by 20 to 60 per cent using additional batteries.
In idling mode, the sound pressure level of three unplugged cranes is equivalent to that of a normal conversation on the jobsite. This corresponds to a value of only 60 dB(A). If you consider that a crawler crane is in idling mode for 60 per cent of the time on the jobsite, this low noise level is an advantage with great resonance.
The designers of the crane put great emphasis on safety. As with all crawler cranes from Liebherr-Werk Nenzing GmbH, the new battery-operated models are also available with all proven assistance systems.
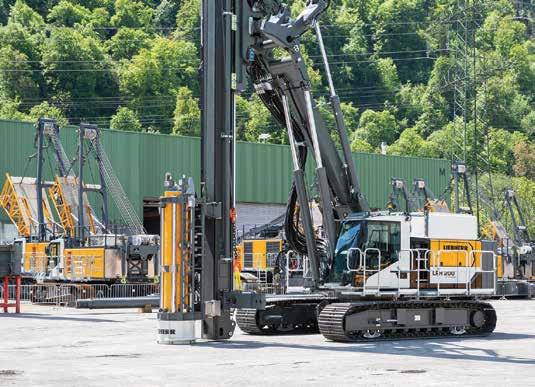
The latest system is the Gradient Travel Aid for the safe negotiation of slopes and inclines. The crane’s control system automatically calculates the centre of gravity and warns the operator before the crane leaves the safe area. While travelling, the operator receives information about the permissible and actual gradient, and the crane’s overall centre of gravity at all times. l

LRB 23 continues the success story of piling and drilling rigs for Liebherr
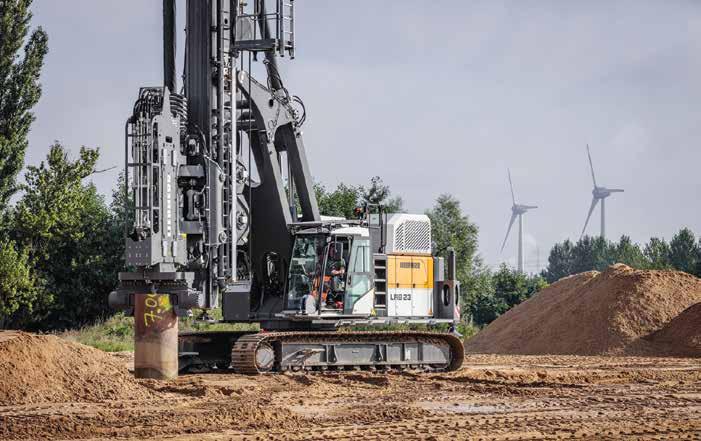
The piling and drilling rig type LRB 23 closes the gap between the LRB 16 and the long-established LRB 355. The compact size makes the machine a perfect all-rounder in the deep foundation sector. Innovative assistance systems simplify operation on the jobsite and ensure a high level of safety.
The new all-rounder for deep foundation work offers an impressive engine output of 600 kW and so delivers the necessary capacity for all common deep foundation operations, such as Kelly drilling, double rotary drilling, full displacement drilling, and continuous flight auger drilling, as well as soil mixing and applications with a vibrator or hydraulic hammer.
The compact design of the LRB 23
allows for transportation in one piece, simplifying mobilization between jobsites and enhancing flexibility. The remote control simplifies the loading process for transportation as well as the assembly of the machine.
The advantages of the rigid leader are proven in operation. As it can withstand high torques, even Kelly drilling is possible – a unique feature for a machine of this size! The rotary drive BAT 300 delivers a maximum torque of 300 kNm.
Highest efficiency and safety through digital assistance systems
Locking of the Kelly bar’s telescopic sections is made significantly easier with the aid of the Kelly visualization system in the LRB 23. Thanks to the real-time
display of the Kelly bar’s locking recesses on the cabin monitor, the operator is constantly updated about the actual distance to the next locking recess. Colour indications inform when the bar can be locked. Furthermore, false positioning of the Kelly bar during the shake-off process is indicated through a warning signal.
During continuous flight auger drilling the concreting process is automated thanks to the drilling assistant. All assistance systems contribute to time savings, higher availability of the machine, and a significant increase in safety during operation. The newly designed piling and drilling rig convinces through precision, high performance, and a long service life. l
As a previous mine pit and tailings pond, the Base Mine Lake near Fort McMurray has residual bitumen forming two mats on the lake floor. Keller designed and installed a shoring solution to create a new dock area for dredging operations for bitumen removal.
THE PROJECT
The mine owner, Syncrude, planned to remove the bitumen using mechanical dredging technology. However, an unloading dock had to be built to unload dredging barges. A shoring solution was required to retain the soils from sloughing into the dredge area and increase the stability of the shoreline for dock construction.
THE CHALLENGE
Shoring solution at Syncrude Base Mine Lake
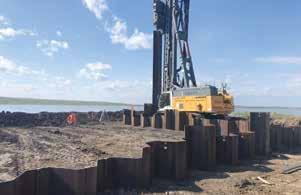
PROJECT FACTS
Owner: Syncrude Canada Ltd. | Keller business unit: Keller
Main contractor: Inner City Diesel | Engineer: Keller Solutions: Support of excavation Markets: Oil, gas and chemical | Techniques: Sheet piles | Email: info@keller-na.com Phone: 1 (800) 456-6548 l
Interpipe Inc. is a steel pipe distributor of new and used structural steel pipe. We have two large stocking locations of Seamless, ERW, Spiralweld and DSAW pipe.
ONTARIO
3320 Miles Road, RR#3 Mount Hope, Ontario L0R 1WO
ONTARIO
Local: (905) 679-6999
THE SOLUTION
3” OD – 48” OD in a variety of wall thicknesses are stocked in both locations.
Heightened safety awareness was required to work on and near water and tight working areas.
Interpipe Inc. is a steel pipe distributor of new and used structural steel pipe. We have two large stocking locations of Seamless, ERW, Spiralweld and DSAW pipe.
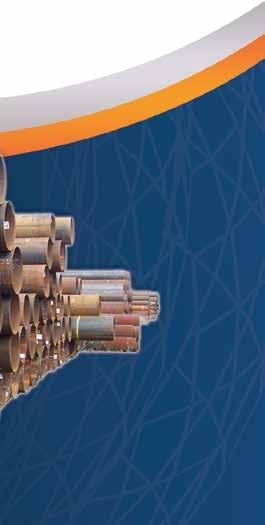

Interpipe Inc. is a steel pipe distributor of new and used str uctural steel pipe. We have several stocking locations of Seamless, ERW, Spiralweld and DSAW pipe.
Piling Pipe 80,000 min yield seamless pipe for Micro Piling.
ONTARIO
3320 Miles Road, RR#3 Mount Hope, Ontario L0R 1WO
Toll Free: (877) 468-7473 Fax: (905) 679-6544
3320 Miles Road, RR#3 Mount Hope, Ontario L0R 1WO
Local: (905) 679-6999
3” OD – 48” OD in a variety of wall thicknesses are stocked in both locations.
3" OD 48" OD in a variety of wall thicknesses are stocked in all three locations.
Piling Pipe 80,000 min yield seamless pipe for Micro Piling.
Seamless and ERW pipe for Driven Piles, Screw Piles and Drill Piles.
Piling Pipe 80,000 min yield seamless pipe for Micro Piling
Seamless and ERW pipe for Driven Piles, Screw Piles and Drill Piles.
Seamless and ERW pipe for Driven Piles, Screw Piles and Drill Piles.
Large Diameter pipe for Driven Pile or Caissons.
The general contractor placed berms around the 50 feet by 75 feet (15 metres by 23 metres) dock area to protect equipment and crews from being able to contact the water. Test pits were dug to assess the potential of constructionrelated soil liquefaction. Once the site was appropriately evaluated, Keller designed and installed a cantilevered sheet pile earth retention system, using sheet piles installed to 40 feet (12 metres) deep from shore level. In several instances predrilling was required to allow for sheet pile penetration through hard soil layers. A continuous cap plate was installed along the top of the sheet piles enabling the boats to tie off onto the wall.
Large Diameter pipe for Driven Pile or Caissons.
Large Diameter pipe for Driven Piles or Caissons.
Local: (905) 679-6999 Toll Free: (877) 468-7473 Fax: (905) 679-6544
Toll Free: (877) 468-7473 Fax: (905) 679-6544
QUEBEC
805 1 ère Avenue
QUEBEC
QUEBEC
805 1 ère Avenue
Ville Ste. Catherine, Quebec J5C 1C5
V ille Ste. Catherine, Quebec J5C
805 1 ère Avenue Ville Ste. Catherine, Quebec J5C 1C5
Local: (450) 638-3320
Local: (450) 638-3320 Toll Free: (888) 514-0040
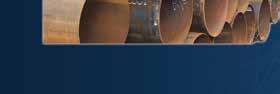
Local: Toll Free: (888) 514-0040 Fax: (450) 638-3340
Toll Free: (888) 514-0040 Fax: (450) 638-3340
This article was originally published in DFI’s bi-monthly member magazine, Deep Foundations, Sept/Oct 2022 issue. DFI is an international technical association of firms and individuals in the deep foundations and related industries. To join DFI and receive the magazine, go to www.dfi.org.
The Santa Fe train station and passenger rail platform were constructed in the downtown district of Fort Madison, Iowa, over a century ago. This landmark building and rail platform were in need of major renovations and rehabilitation in order to restore the site to a functioning railway train station. A multitude of key players from various public and private parties were involved in the design and construction of this project site.
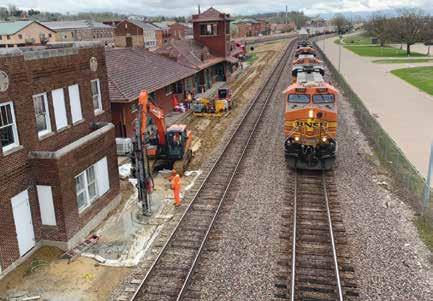
Part of the project consisted of constructing the passenger platform. The original design included helical piles to provide foundational support for the platform. Challenges occurred during construction due to the presence of an obstruction in the form of a poured concrete slab in the immediate area where the helical piles were to be installed. The contractor worked with the engineer of record and other consulting parties to value engineer the helical pile design and utilize self-drilling micropiles as a replacement to the specified helical pile system.
HOLLOW BAR OPTION
The contractor utilized a threaded hollow bar micropile system. The hollow bar simultaneously acts as the drilling rod, grout injection tube and structural reinforcement for the micropile. These systems can be used in most soil types, including unstable soils, without the need for temporary casing. With the use of a sacrificial drill bit, the hollow bar is drilled, with additional bars being added using couplers, until the desired micropile depth is reached. A structural cement grout is then injected through the hollow bar that produces a grout body that encapsulates the structural reinforcement (hollow bar) and bonds with the surrounding soil. The pumping of the grout also further improves the surrounding soils. This provides necessary skin friction for the pile to resist both compressive and tensile forces.
Self-drilling micropiles
By Matt Sotirin, P.E., and Marc Mastrantuono, P.E., Ischebeck USADESIGN
The original helical pile design consisted of 80 locations spanning the length of the platform, requiring a working load capacity of 45 kip (200 kN). The general contractor encountered a concrete obstruction, at approximately five feet (1.5 metres) of depth adjacent to the rail tracks, underneath the ballast rock. The concrete slab was not shown on any of the original construction plans for the rail depot nor was it shown in the soils report. The initial solution was to core a hole through the concrete slab at each of the 80 helical pile locations. However, this solution was going to be a significant added cost to the project. The foundation contractor began looking for alternative options that would be cost-effective while still offering the performance and load carrying characteristics required by the specification.
A piece of the concrete obstruction was exposed and broken up to check for the type of reinforcement. The slab contained a wire mesh reinforcing system. This aided the scenario for a successful hollow bar micropile design, as the drill bits used are capable of drilling through wire mesh.
The next step was to determine structural capacity and geotechnical capacity of a hollow bar system to ensure proper hollow bar selection and micropile length.
Utilizing 45kip (200 kN) as the design load, the calculations for selecting a steel reinforcement yielded a 40 mm (1.6 in) outer diameter, 20 mm (0.79 in) inner diameter hollow bar, which exceeded both the working load (one time the design load) and testing load (two times the design load) requirements.
The geotechnical report indicated loose to very loose mixed soils with single digit Standard Penetration Test blows/ foot. At approximately 25 ft (7.62 m) depth, a harder layer of sandy clay was found. For the geotechnical capacity of the micropile, the first 25 ft (7.62 m) were treated as an unbonded zone that had no contribution to the pile capacity.
Because the boring log was terminated at 31.5 ft (10.5 m), the assumption was that the soil strata below would be representative of the sandy clay material for preliminary design purposes. A pile length of 79 ft (24 m) was estimated.
The hollow bar micropiles were a direct replacement to the helical pier schedule and location. Because there was a lack of soil data below 31 ft (9.5 m), the final micropile design (pile length) would be determined from preproduction load testing to confirm a final micropile design.
LOAD TESTING
Once the location, bar selection and preliminary micropile length were developed and approved, the contractor worked with the engineer of record and the hollow bar manufacturer’s technical consultant to develop a preproduction load testing program to satisfy specification requirements and determine the actual required micropile length.
The load test consisted of three preproduction piles that were installed to varying depths on site just west of the railway on the north end of the existing train depot. The purpose of the test was to verify the load requirements at the respective depths to establish a final production pile installation depth. Even though these micropiles were designed to be loaded in compression, a tension test was selected as it is a more cost-effective test procedure and helps determine the friction resistance of the pile, without the added benefit of end bearing support. The micropiles were loaded to two times the design load of 45 kip (200 kN).
All three tests passed the criteria for the preproduction load testing program. This allowed the contractor to work with the engineer of record to reduce the pile lengths to 40 ft (12 m).
The location for installing the test piles was approximately -10 ft (-3 m) in elevation from where the production piles were to be installed. To account for this additional unbonded zone, the final micropile length selected for use was 50 ft (15 m).
PRODUCTION PILES
After finalizing the micropile design based on load testing results, 80 50-foot (15-metre) hollow bar micropiles were installed per the micropile schedule and layout. The contractor was able to complete the installation of all 80 micropiles on time and meet the required construction schedule. By using hollow bar micropiles, the parties involved were able to provide a solution to the issues posed by the buried slab in a cost-effective manner, all while working next to an active railroad.
CONCLUSION
The Santa Fe Depot Passenger Rail Platform required a unique solution to its foundational support problem. Initially the project was designed and specified with a helical pile system. After obstructive debris in the form of wire mesh reinforced concrete slab was found below grade, a hollow bar micropile system was selected as a cost-effective alternative to provide support for the rail platform.
After successful load testing and revised design considerations, 80 50-foot (15-metre) hollow bar micropiles were used along the rail line where the platform was to be installed. The contractor was able to install the system within the scope of the construction schedule and provide cost savings to the owner when compared to other solutions.
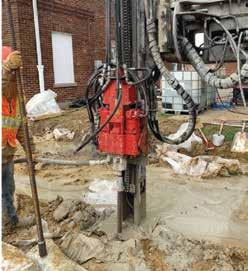
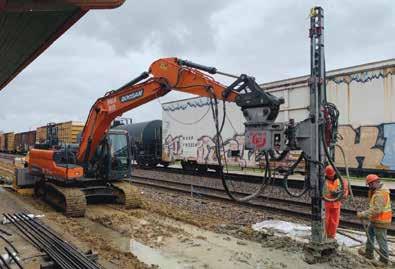
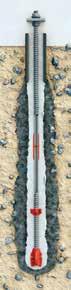
Matt Sotirin, P.E., is a geotechnical specialist at Ischebeck USA. He has extensive experience in the construction industry and works closely with consulting engineers and specialty contractors to provide geotechnical solutions for complex construction projects.
Marc Mastrantuono, P.E., is the geotechnical division manager at Ischebeck USA. He has over a decade of experience in specialty micropile design, installation, and manufacturing. He works with industry professionals to provide the best geotechnical solution and support. l
Liebherr’s HS series has a new all-rounder: HS 8070.1.

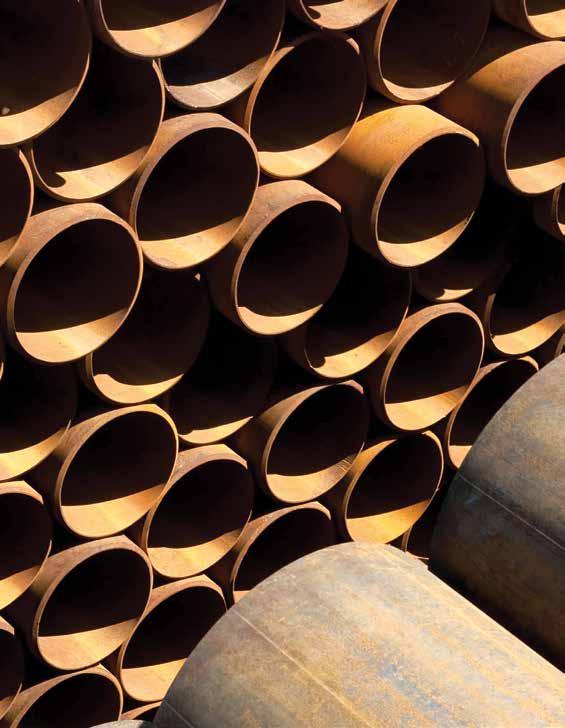
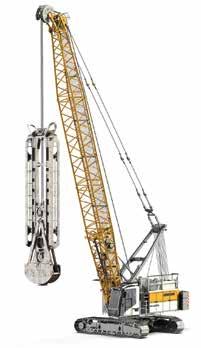
LESS AIR, MORE ENERGY
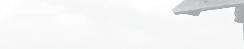

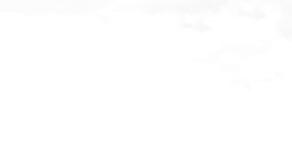
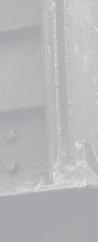
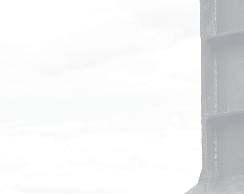

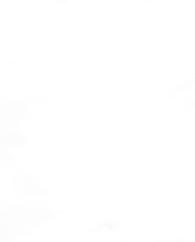





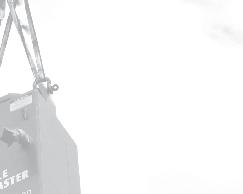
Originally built for the dock building industry, Pile Master® air hammers are designed for driving timber, h-pile, pipe, and prestressed concrete piles. With an optional sheet pile adapter, the Pile Master is also a great choice for driving steel sheet piles in soil conditions where a vibratory hammer cannot drive the sheets to the required depth. Hammers can be guided for use with 21” or 26” pile driving leads or freely suspended with an extended base. Pile Master air hammers are known for their e iciency—producing up to 90% energy transfer into the pile while using an air compressor as small as 185 CFM.

Request more information today. 904 874 6557




pilemasterUS.com/piling-industry-ca

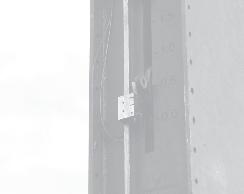
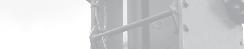
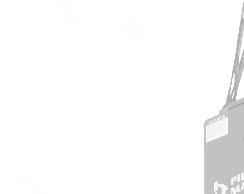
Reuse of foundations in an old school building
By Marcel Bielefeld and Kevin van Velzen, Allnamics Geotechnical Experts, The Hague, the Netherlands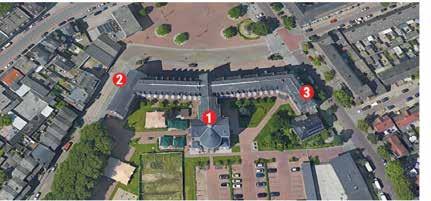
This article was originally published in DFI’s bi-monthly member magazine, Deep Foundations, Sept/Oct 2022 issue. DFI is an international technical association of firms and individuals in the deep foundations and related industries. To join DFI and receive the magazine, go to www.dfi.org.
THE CHALLENGE
A few years ago, an old school building in Breda, a city in the southern part of the Netherlands, was converted into an apartment building. The structure was originally built in 1917 and subsequently expanded: first with the construction of the chapel in 1922, then the west wing extension in 1931 and finally the east wing extension in 1955.

The building is supported by various foundation types. The original structure has a shallow foundation underneath the east wing and the chapel, while a timber-pile foundation was used for the remainder. For the wing extensions, the same type of foundation was used as for the wing itself: a shallow foundation on the east side and a deep foundation with concrete piles on the west side.
THE SOLUTION
In its new function as an apartment building, the design loads are approximately 10 per cent higher than the original design loads, and therefore, the existing foundation had to be reevaluated. The simplest solution would have been to drive some
100 concrete piles to replace the existing deep foundation on the western part of the building. Given the soil conditions, these piles would have been seven-inch (0.18-metre) round piles with a 0.5-inch (12-millimetre) steel casing and approximately 20 feet (six metres) long. Instead, as presented during the DFI SuperPile event in 2021, the contractor inspected the existing foundations and concluded that the foundation could be reused as is. This approach resulted in a reduced project cost, even after the cost incurred to inspect and test the existing deep foundations, and a shorter project schedule.
THE RESULTS
What was not highlighted in the 2021 presentation was the sustainability angle of this approach. Reusing the foundation, rather than installing new piles, eliminated the need for 15.5 tons (14,000 kilograms) of steel and 30.6 tons (28,000 kilograms) of concrete in the piles alone, and the associated emissions of some 31.6 tons of CO2 – equivalent to the electricity generated for six homes in one year. While this may not sound like much, it is a reminder that in concrete foundation, piles every cubic foot of concrete equals the emissions generated by approximately half a day of electricity used in a home. And when it comes to controlling emissions, every little bit helps. l
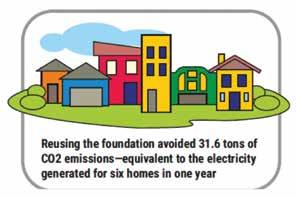
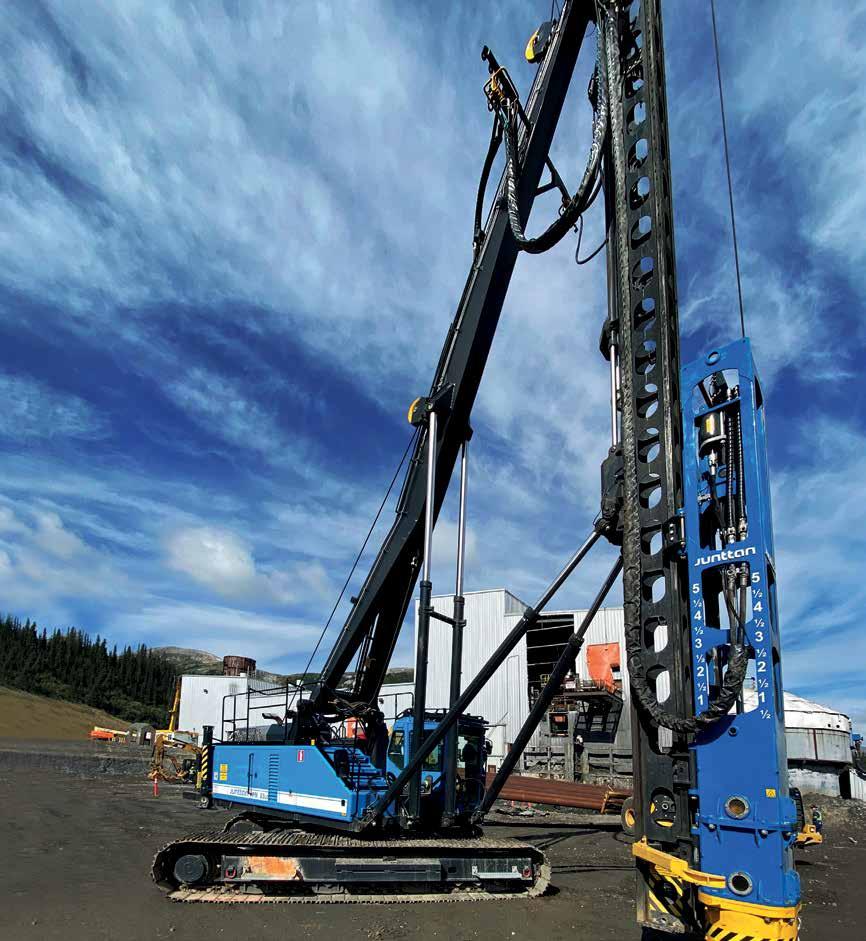

The hammer
For impact driving of steel pipes, beams or sheet piles.
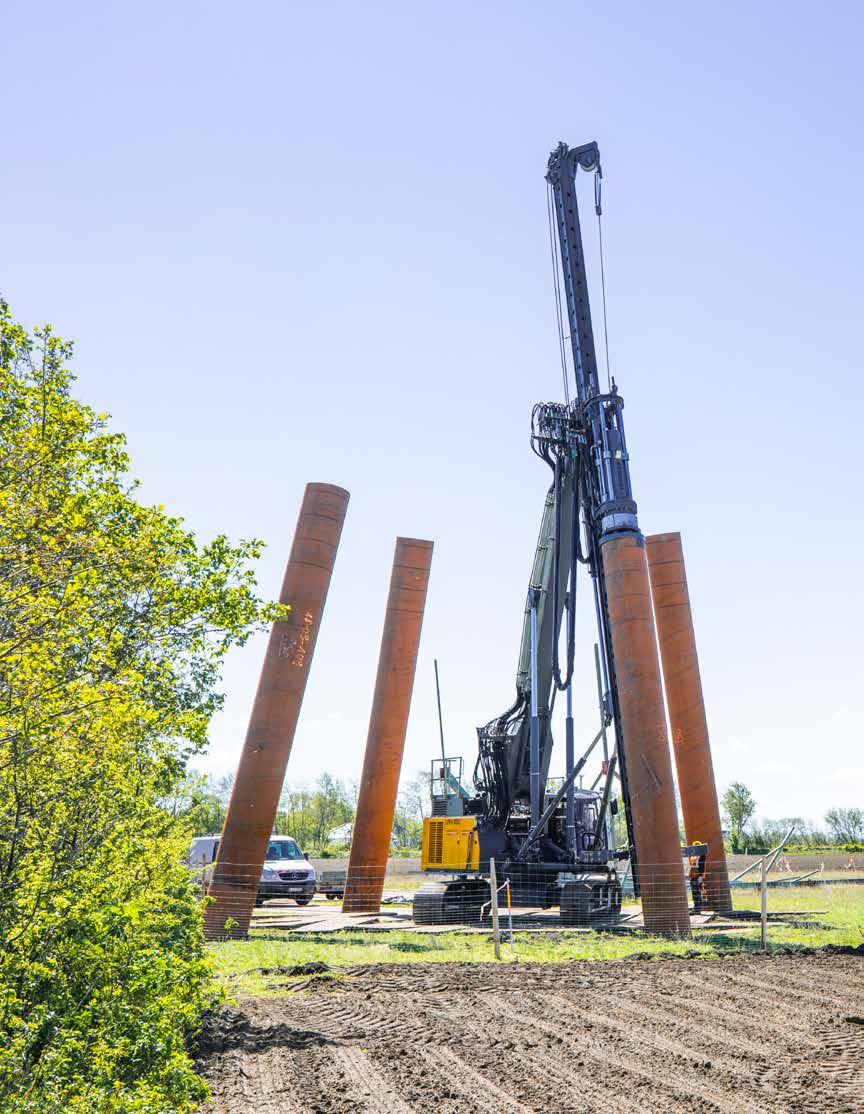
www.liebherr.com
Deep foundation Hammer H 6