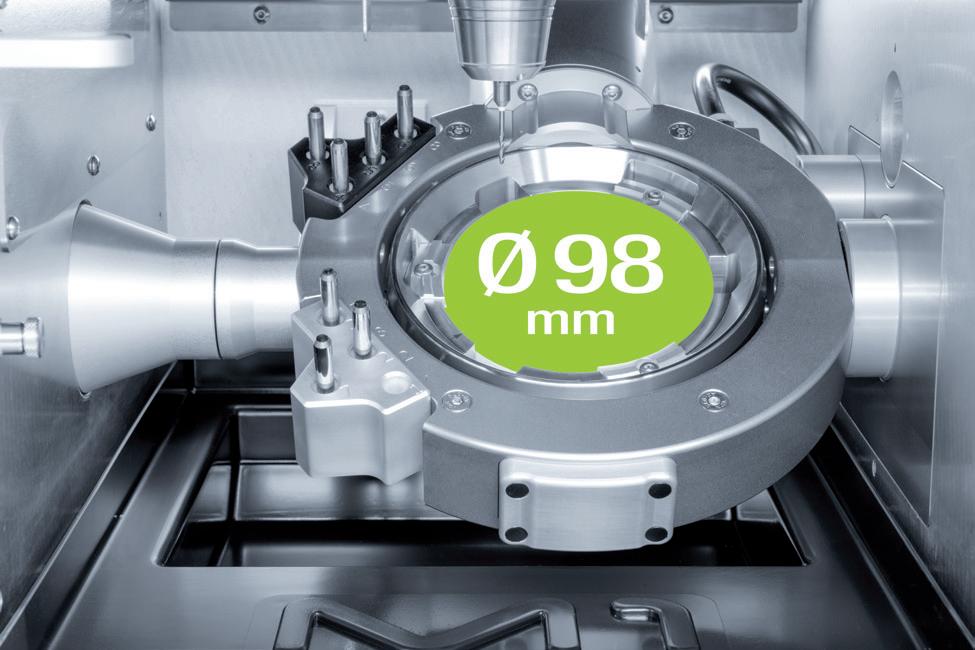
3 minute read
M1 Wet Heavy Metal and Ø 98 mm orbit
from eLABORATE Current
Zirkonzahn M1 Wet Heavy Metal milling unit was developed with a specific mission: to guarantee high precision milling of hard materials in laboratories with limited space. Thanks to the integrated wet processing function, it can namely mill hard metals such as titanium, cobalt-chrome and Raw-Abutments® (prefabricated blanks for individual titanium abutments). The machine is equipped with both wet and dry processing functions, also permitting the milling of glass ceramics and composites. In this way, all types of dental materials can be processed.
In addition, the M1 Wet Heavy Metal milling unit features high stability thanks to its four-bearing orbit with Ø 98 mm and the high-torque spindle. With its extremely compact design (48 x 69 x 63 cm) and a tool magazine for the storage of up to 8 milling burs with automatic tool changer function, this milling unit is a perfect example of versatility, ensuring dental laboratories with limited space can produce all kinds of dental restorations in-house.
Accurate titanium milling: Production of full-arch prosthetics on divergent implants with the new Double Screw Metal technique
The M1, like all other Zirkonzahn milling units, is perfectly compatible with the company’s software, hardware and components, in order to guarantee a smooth workflow from the beginning to the end of the treatment. The case described in this article exemplifies a smooth workflow made for a patient suffering from maxillary edentulism. Threaded channels on the metal structure were milled with the M1 Wet Heavy Metal milling unit, showing the machine’s high-precision milling.
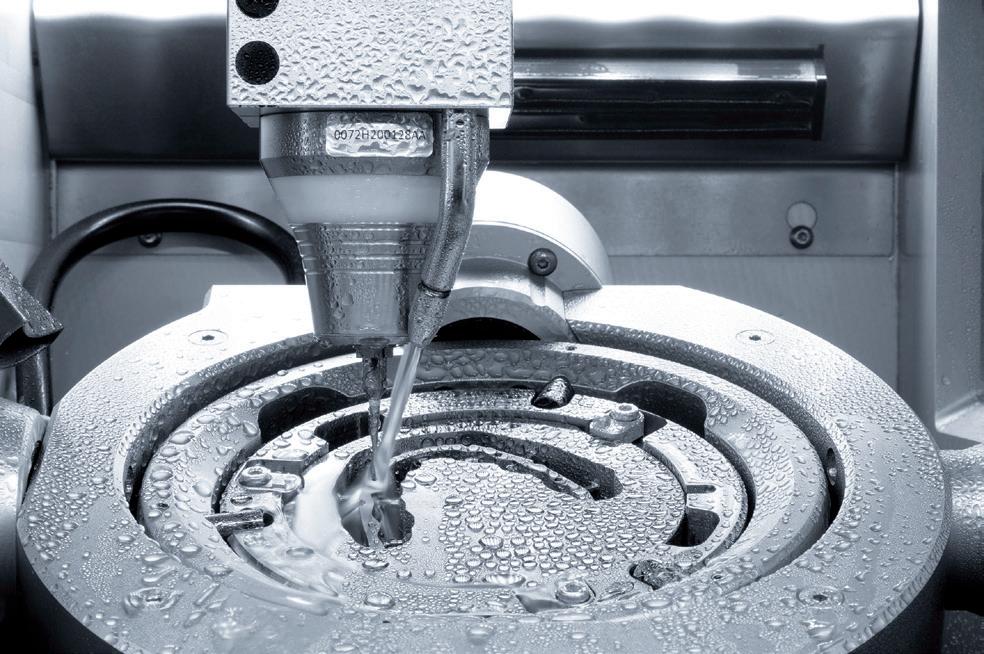
The production of full-arch prosthetics on divergent implants is one of the most challenging jobs for a techno-clinical team. However, the new Double Screw Metal technique avoids unaesthetic vestibular channels, ensuring the production of highly stable, bar-supported rehabilitations even in complex cases without compromising the full arch aesthetics.
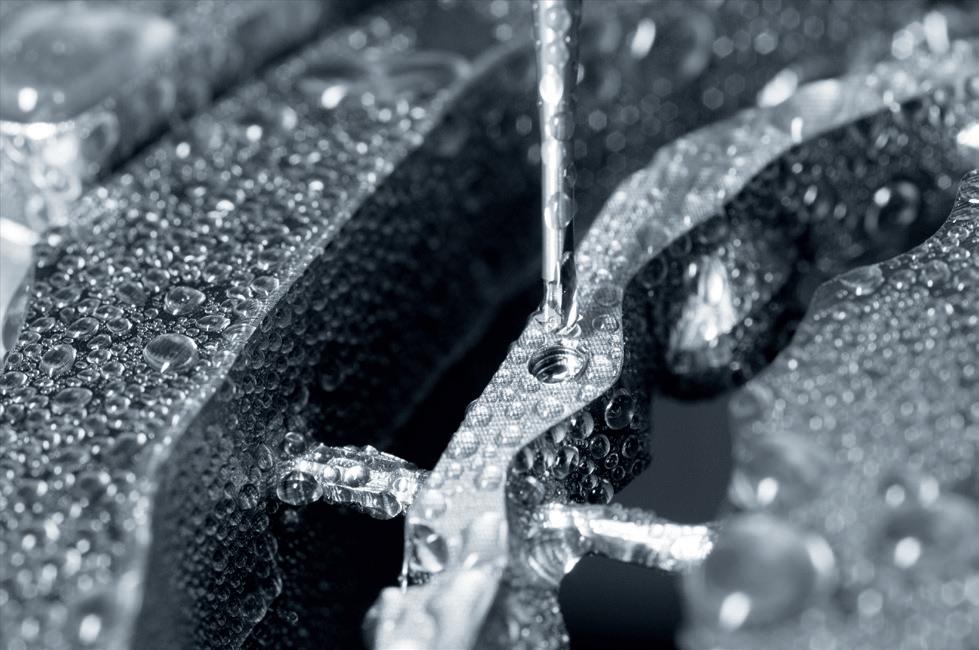
In the current case, the virtual tooth set-up revealed a strong divergence of the implants towards the vestibular tooth area. To strike a balance between function, stability and aesthetics in the final restoration, a primary bar was integrated using the Double Screw Metal technique.
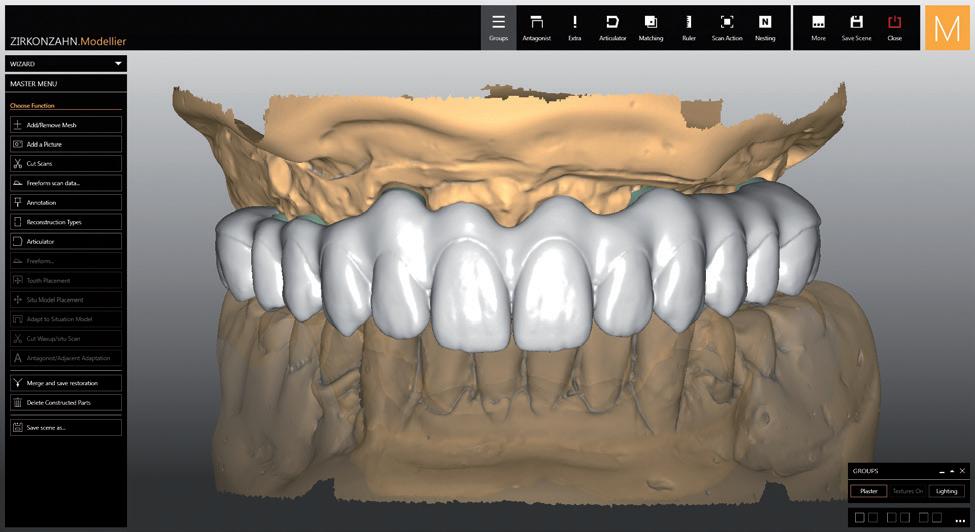
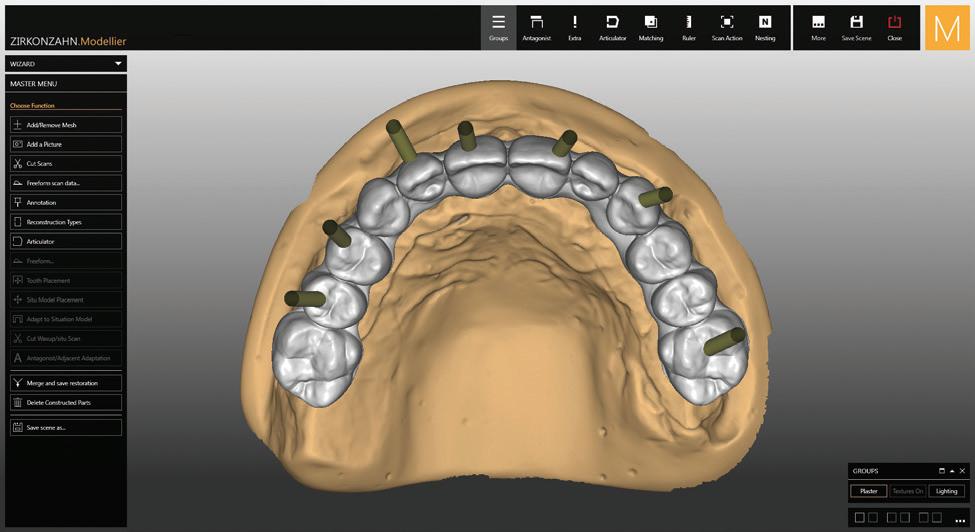
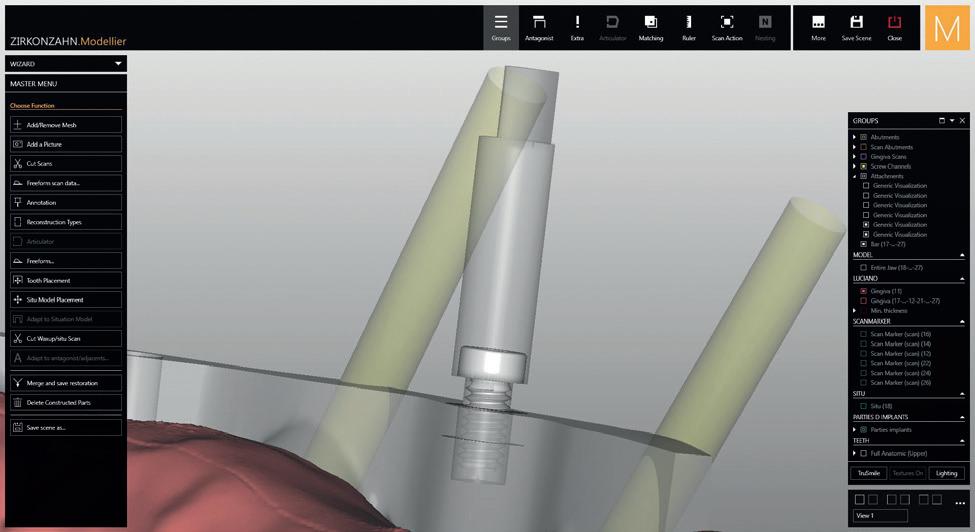

The planned restoration consisted of a titanium bar and a secondary structure in Prettau® 2 Dispersive® zirconia. The design of the primary structure incorporated an innovative CAD/CAM workflow, in which four additional screws were integrated to screw the secondary structure to the bar. The virtual position of the screws was visualised using the new Double Screw Metal function of the Zirkonzahn.Modellier design software (Attachment module), which allows the generation of virtual screw threads within the bar design. The 3D rendering provides the optimal position of the screw channel in the primary structure, as well as the ideal fit of the screw head in the superstructure. The additional threaded screw channels were then milled during the bar milling process. After milling, the final restoration in Prettau® 2 Dispersive® zirconia was characterised with the ICE Stains 3D by Enrico Steger and veneered in the gingival regions with Fresco Ceramics. The
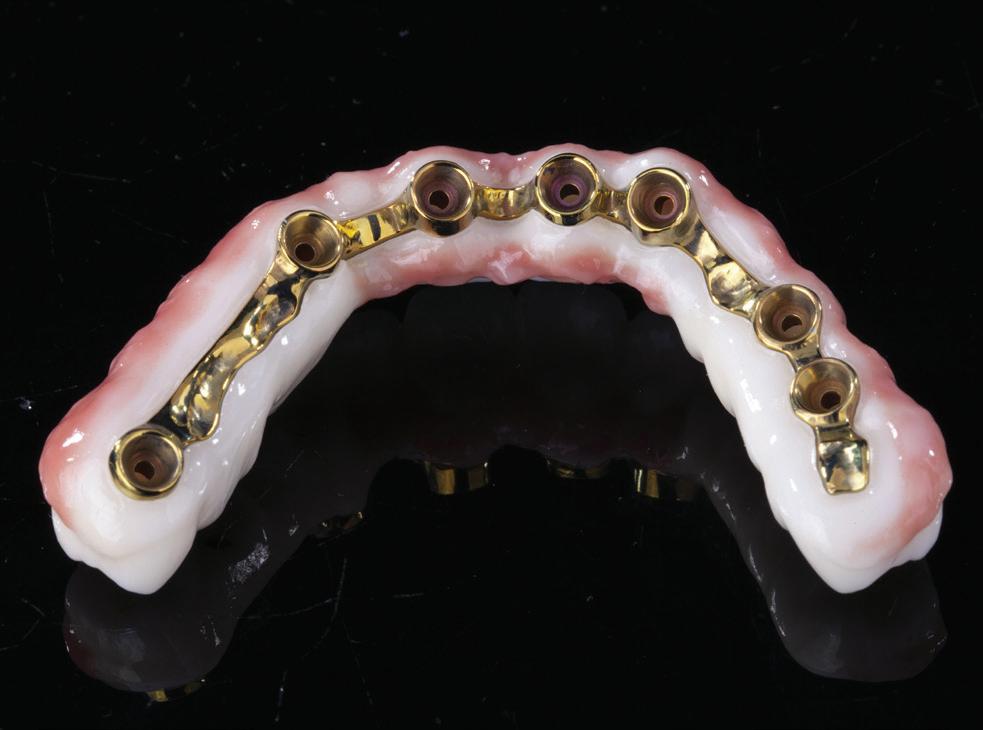
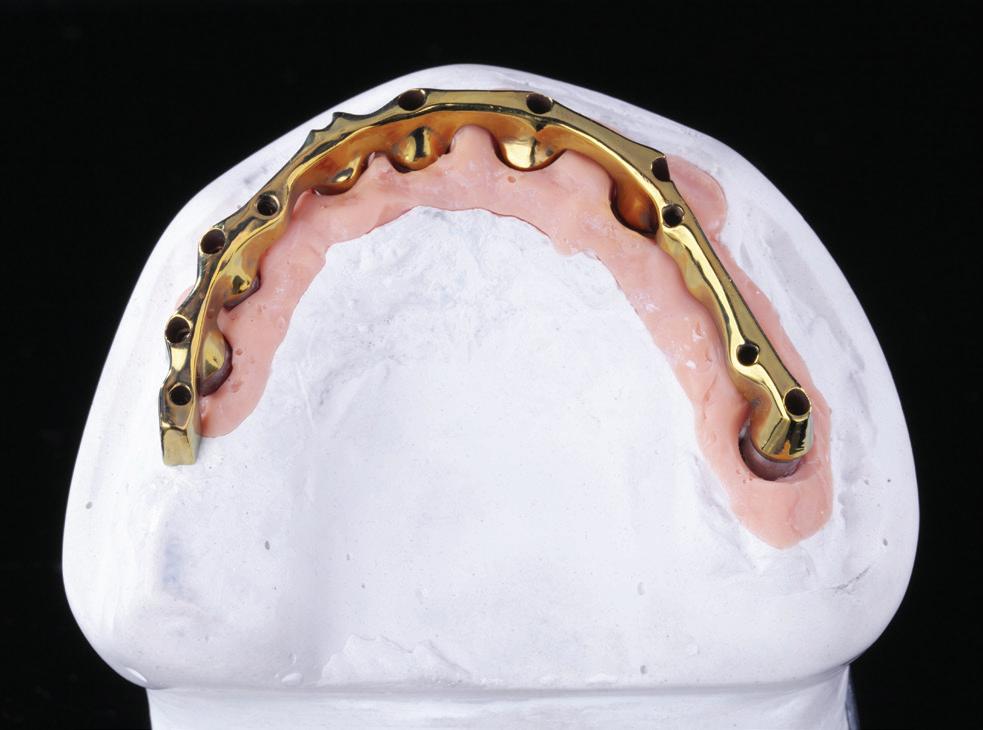
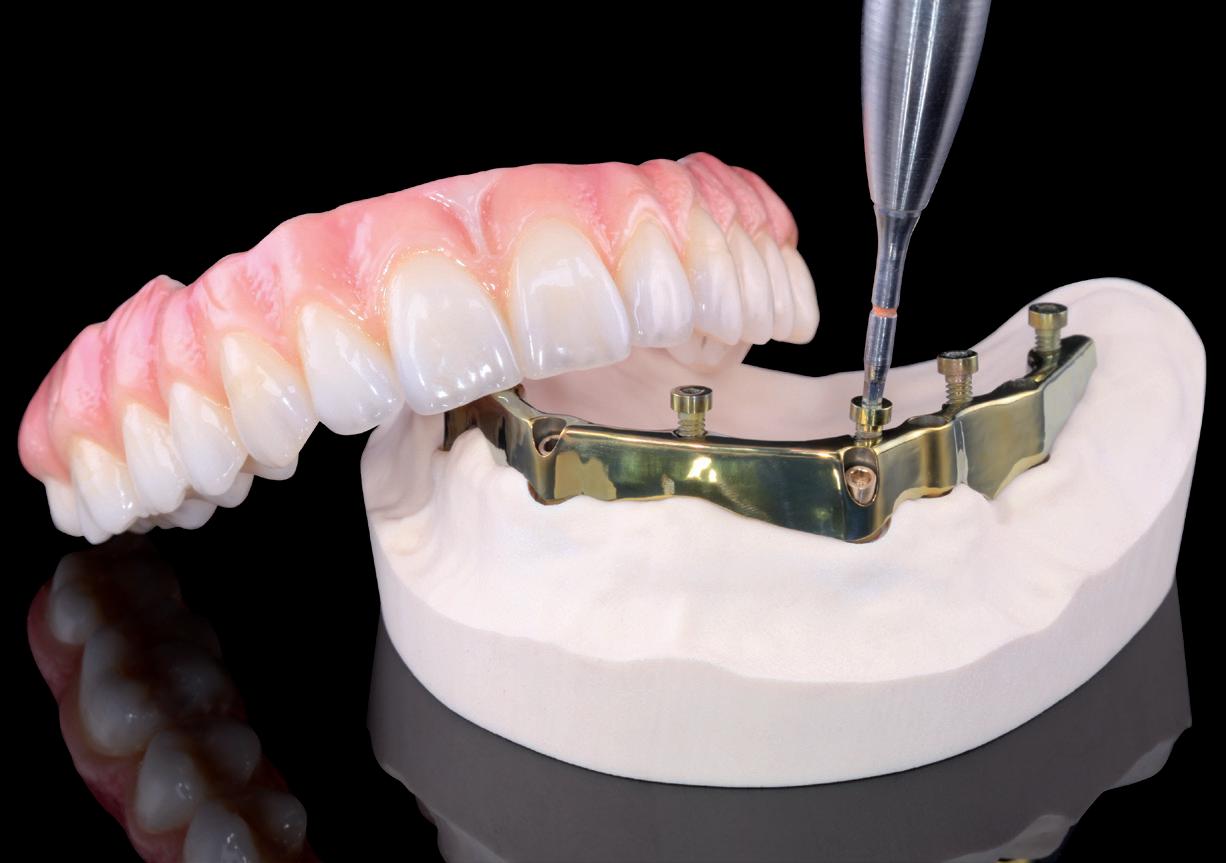
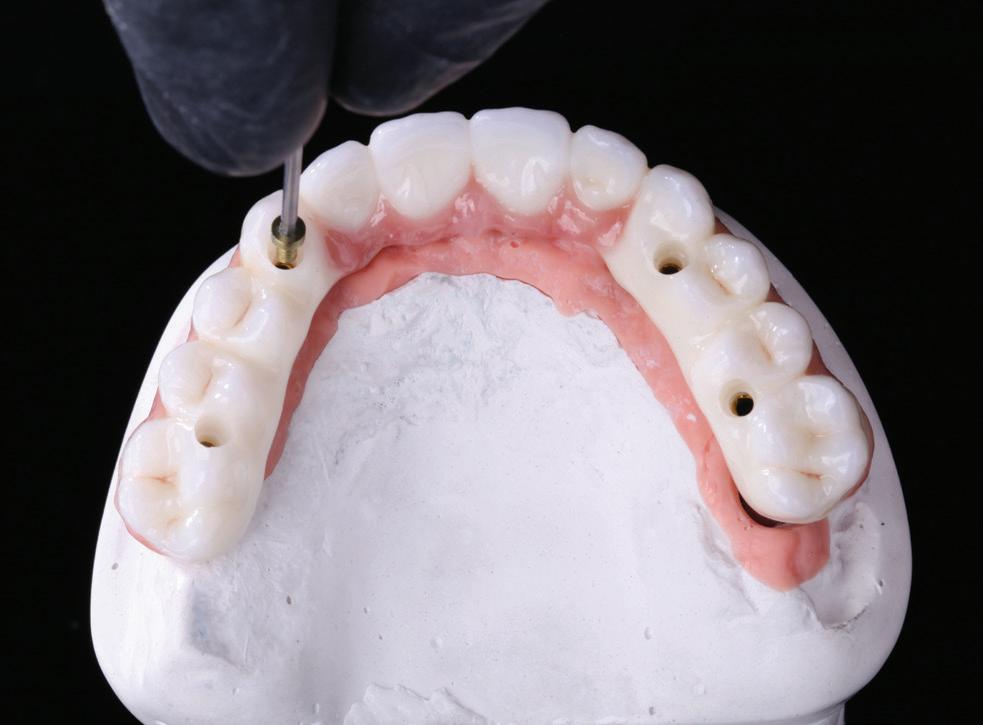
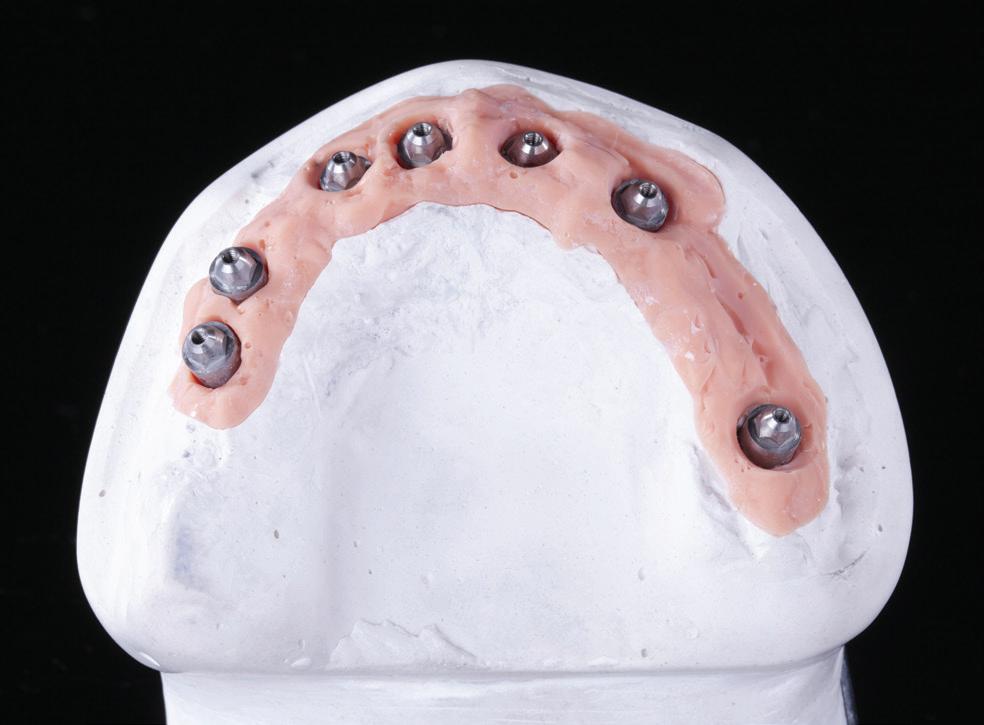
- Computer-controlled milling unit with fully automatic 5+1 axis simultaneous technology
- NEW! Milling of material blanks with Ø 98 mm
- NEW! Milling of material blanks with Ø 98 mm
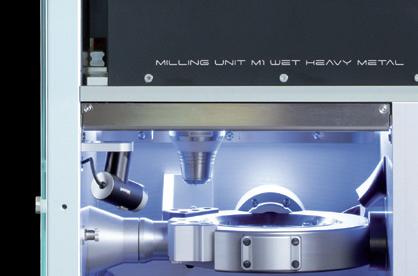
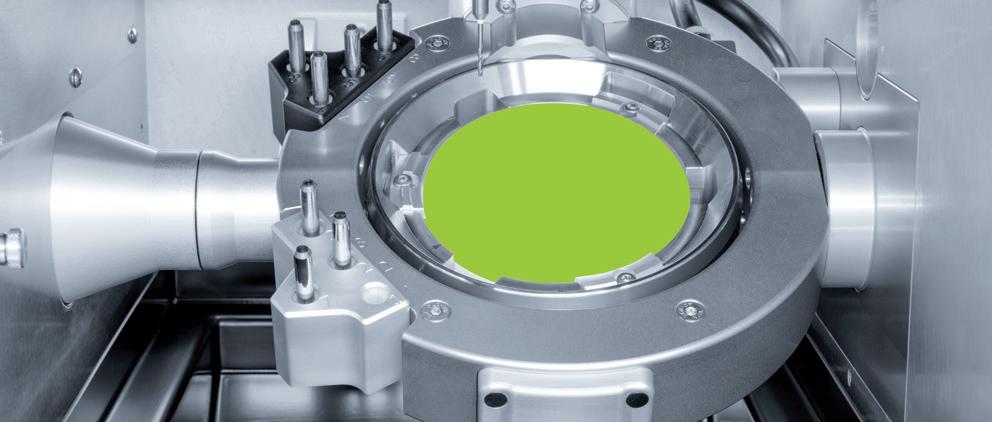
- Wet and dry processing for milling all types of dental materials, even hard metals such as titanium, cobalt-chrome and Raw-Abutments®
- Wet and dry processing for milling all types of dental materials, even hard metals such as titanium, cobalt-chrome and Raw-Abutments®
- Tool magazine for the storage of up to 8 milling burs, with automatic tool changer function
- Tool magazine for the storage of up to 8 milling burs, with automatic tool changer function

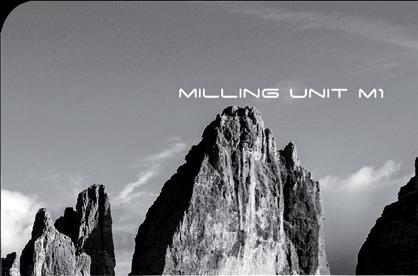

LIMITED
AU$ 39.270
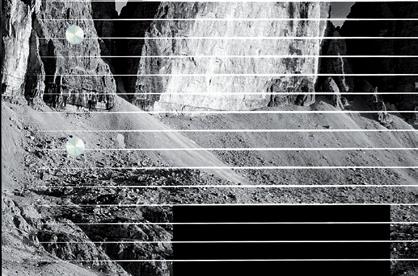
OFFER AU$ 39.270
- Particularly space-saving thanks to the compact design (48 x 69 x 63 cm) OFFER
Fast manufacturing of individual abutments for high precision and fit accuracy
In cases of an edentulous maxilla with divergent implants, the Zirkonzahn. Modellier software permits the generation of a consistent insertion direction for all abutments, designing the abutment geometry individually. In this way, it is possible to prevent the vestibular orientation of the screw channels.

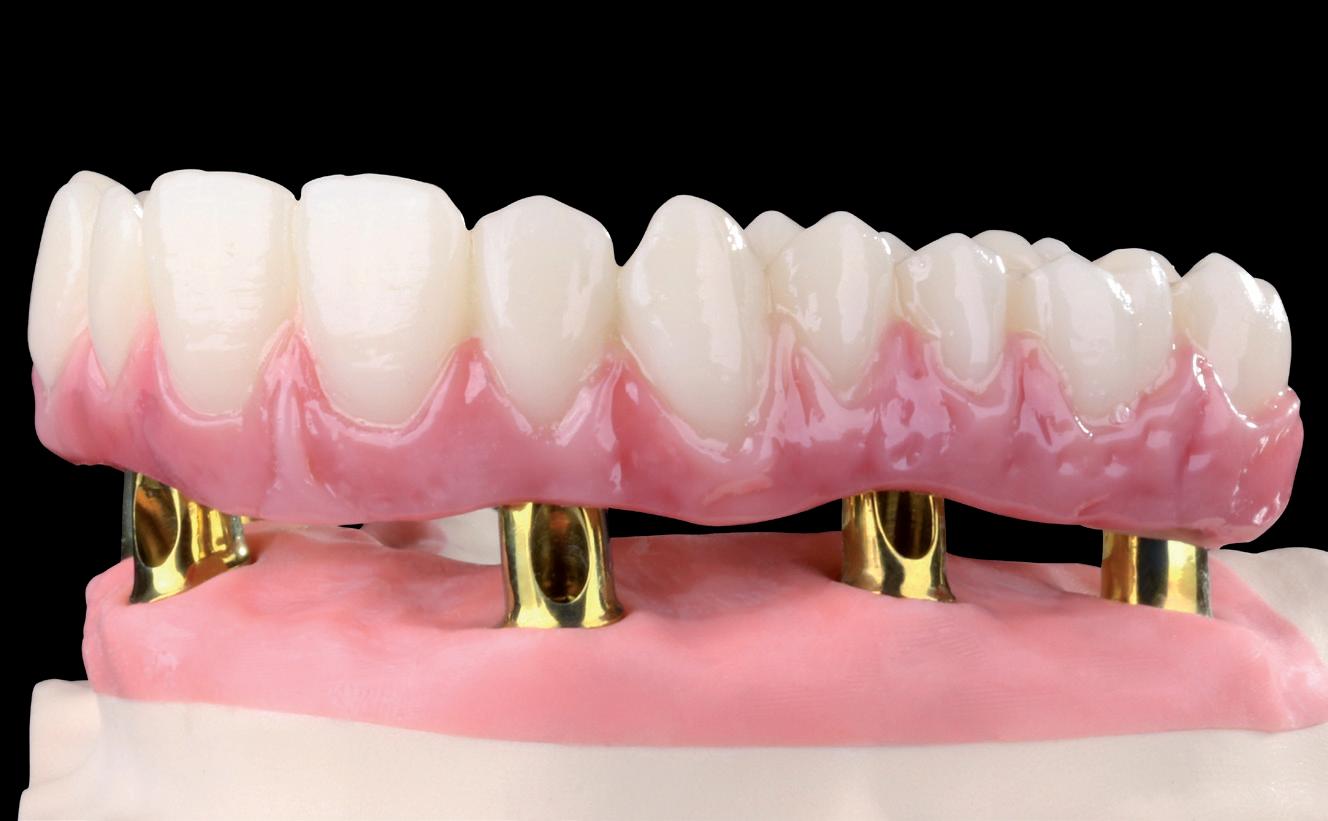
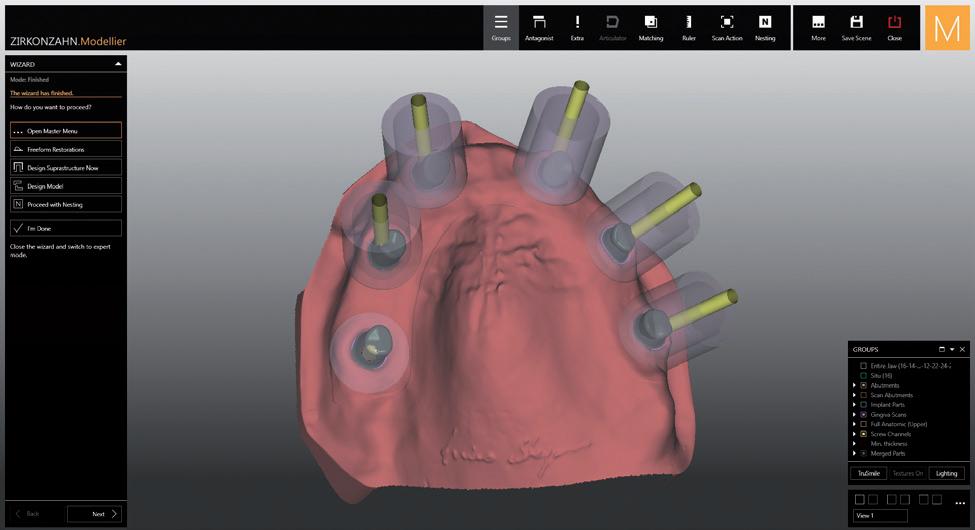
Raw-Abutments ®, made of a highquality medical titanium alloy (Ti-6Al-4V ELI according to ASTM F136 and ISO 5832-3), are prefabricated titanium abutment blanks conceived for the production of individual abutments. Their industrially prefabricated implant connection ensures high precision and fit accuracy. Depending on their application, Raw-Abutments® are available with a diameter of 10 or 14 mm, the latter being particularly suitable for the molar region. During the design phase, the 3D rendering permits the identification of the precise diameter needed. The use of special milling strategies and burs ensure a particularly smooth surface structure and by means of specially conceived holders up to three Raw-Abutments® can be milled with the M1 Wet Heavy Metal in just one milling process.
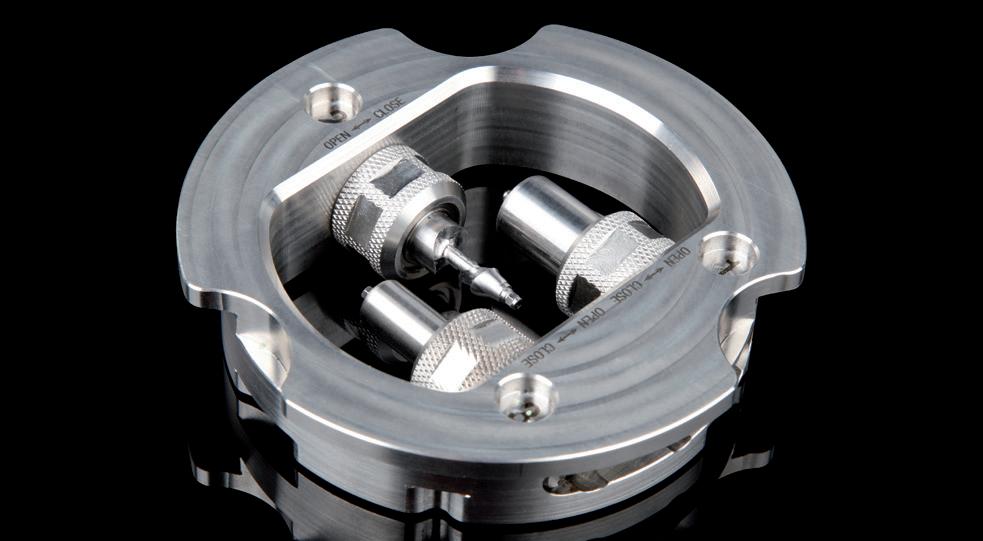
Raw-Abutments® are equipped with an anti-rotation device and are ideal for single-unit as well as multi-unit restorations.
For more info, see www.zirkonzahn.com.
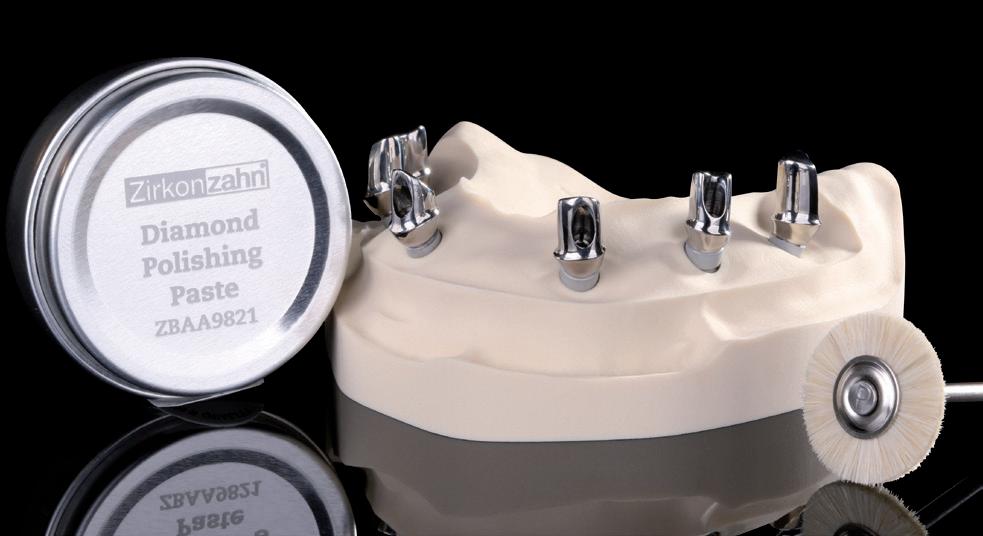
AU$ 39.270
100 % FROM THE DOLOMITES EVERYTHING FOR YOUR
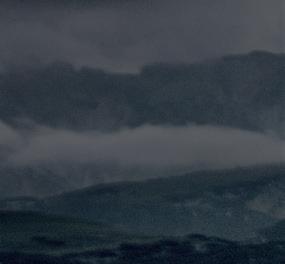
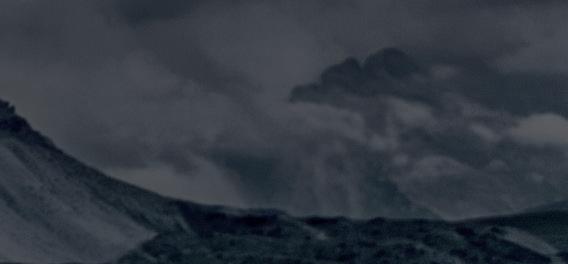

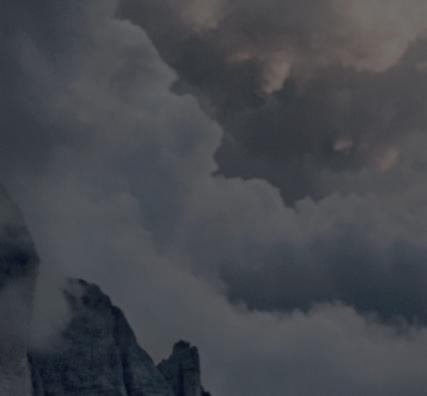
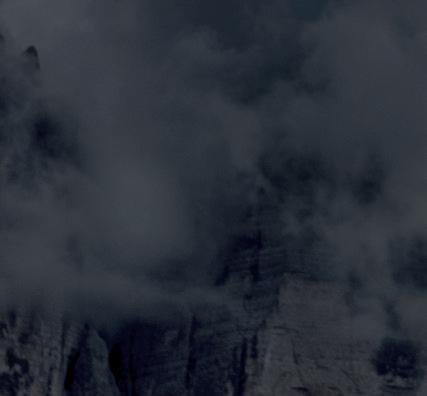
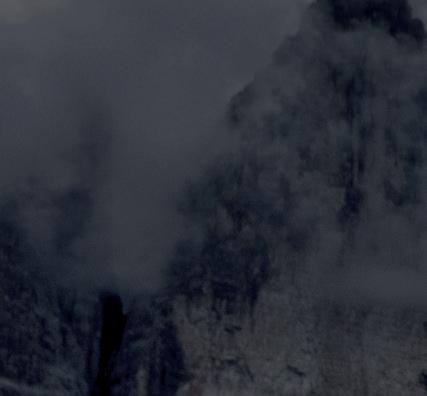
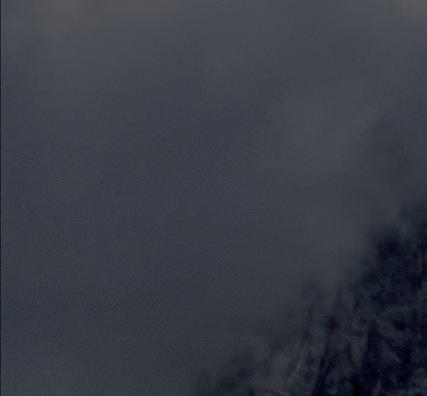
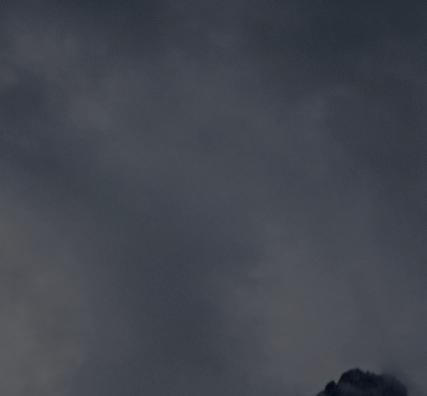
WORKFLOW
In the heart of the Italian Alps, with the fundamental values of discipline, innovation, trust and responsibility, we produce everything on our own. Purchasing raw materials only from specially selected suppliers, we develop new visions, dental materials, tools and technologies all under one roof. We provide dentists and dental technicians with technical support as well as educational trainings, to help them stand out in terms of quality and excellence.
INTRAORAL SCANNER AND 3D PRINTER
A complete package for a smooth digital workflow
ZIRKONZAHN SHADE GUIDES

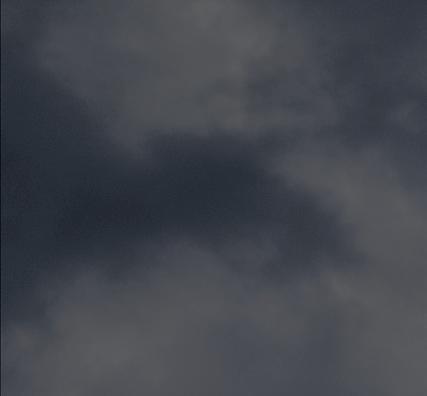
With monolithic Prettau® zirconia sample teeth for optimal material and colour selection
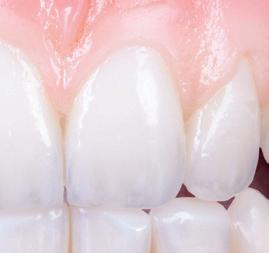

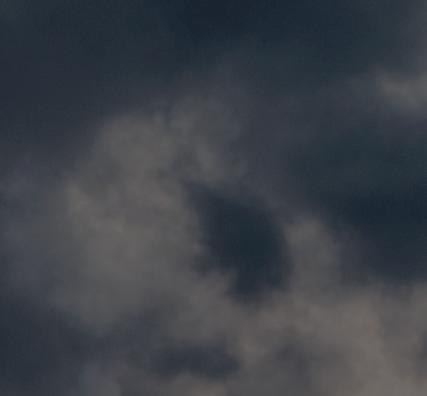