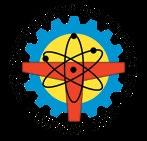
www.ies.org.sg
www.ies.org.sg
STRUCTURAL ENGINEERING: HISTEEL changes the building game
TRANSPORTATION ENGINEERING: Installation of rail systems for the Johor Bahru –Singapore Rapid Transit System Link Project to begin by end-2024
SUSTAINABLE CONSTRUCTION: Total Cost of Ownership will fuel the EV construction industry
The Chartered Engineering Registry aims to provide professional recognition to qualified Engineers, Technologists and Technicians across all sectors.
Being registered as a Chartered Engineering Profession will be an external validation of your experience, expertise and practicing competence; and is a quality mark to differentiate your professional standing in the following sectors of engineering.
04 Closure of the NEWater Visitor Centre and Bedok NEWater Factory
06 Bentley Systems announces the winners of the 2024 Going Digital Awards
07 Shaping the future with record-breaking achievements and new energy trends
08 New and returning exhibitors confirm their participation at bauma 2025
09 New move to boost professional recognition of engineers
14 Projects and project teams receive recognition at HDB Awards 2024
21 HISTEEL changes the building game
24 The digital evolution of Southeast Asia’s construction sector
President Er. Chan Ewe Jin
Chief Editor T Bhaskaran t_b_n8@yahoo.com
Publications Manager Desmond Teo desmond@iesnet.org.sg
Publications Executive Nuraini Ahmad nuraini@iesnet.org.sg
Editorial Panel
Dr Victor Sim
Dr Chandra Segaran
Dr Ang Keng Been
Dr Aaron Sham
Mr Jaime Vega Bautista Jr
Mr Soon Ren Jun
Media Representative Trevor Teh IES@mnc-link.com
Design & layout by 2EZ Asia Pte Ltd
Cover designed by Irin Kuah
Cover image by Darren Soh for Surbana Jurong
by
Institution of Engineers, Singapore
6469 5000 I Fax: 6467 1108
in Singapore
26 Installation of rail systems for the Johor Bahru –Singapore Rapid Transit System Link Project to begin by end-2024
31 Alternative drives can contribute to decarbonising the construction site
32 Total Cost of Ownership will fuel the EV construction industry
34 Singapore’s WSH performance in 1H2024 shows sustained progress from 2023
36 Renovating the interior coatings in the Golovec Tunnel
38 Scaffolding solutions for a residential development in Hungary
39 Enlarging tunnels while trains continue to run
40 The new 440 HC-L from Liebherr
The Singapore Engineer is published monthly by The Institution of Engineers, Singapore (IES). The publication is distributed free-of-charge to IES members and affiliates. Views expressed in this publication do not necessarily reflect those of the Editor or IES. All rights reserved. No part of this magazine shall be reproduced, mechanically or electronically, without the prior consent of IES. Whilst every care is taken to ensure accuracy of the content at press time, IES will not be liable for any discrepancies. Unsolicited contributions are welcome but their inclusion in the magazine is at the discretion of the Editor. www.ies.org.sg
PUB, Singapore’s National Water Agency commemorated the closure of the NEWater Visitor Centre (NVC) and Bedok NEWater Factory (BNF) with a closing ceremony, held recently.
Ms Grace Fu, Minister for Sustainability and the Environment and Minister-in-charge of Trade Relations, was the Guest-of-Honour at the event which was attended by more than 100 guests.
In her opening remarks, Minister Grace Fu paid tribute to the dedication and significant contributions of the pioneers, whose indomitable spirit has been integral in implementing the technology behind NEWater.
Some of these pioneers include PUB’s Senior Consultant Harry Seah, then Project Manager of the NEWater study team, who oversaw the research and development phase of NEWater before it was launched in 2002, and Mr Tan Thai Pin, the study team’s Deputy Project Manager.
Mr Tan played a crucial role in garnering support from industrial partners and convinced them to adopt NEWater in their operations.
Professor Ong Choon Nam, a prominent local expert on water quality, contributed valuable technical knowledge as Chairman of the International Expert Panel on NEWater alongside his fellow panel members.
Although the NVC has officially closed on 31 July, visitors can still head to the Sustainable Singapore Gallery (SSG) at the Marina Barrage to learn more about the Singapore Water Story which features NEWater as one of the key components of Singapore’s water management strategy.
PUB is committed to continuing NEWater education and promoting
water sustainability, and is working on developing a new exhibit on NEWater at SSG and at a learning gallery located at the upcoming Tuas Nexus.
Bolstering NEWater supply
With Singapore’s water demand projected to nearly double by 2065, NEWater’s role as a dependable and weather-resilient National Tap remains vital. To meet the projected increase in water demand from industries, PUB is building a third NEWater Factory in Changi, located within the existing Changi Water Reclamation Plant (WRP).
The upcoming Tuas NEWater Factory (TNF), which will be integrated within the Tuas Water Reclamation Plant, currently under construction, will have a production capacity of 75 million gallons per day (mgd) – the equivalent of 136 Olympic-sized swimming pools.
As progress is made towards a three-node used water management system by 2035, PUB will continue to expand the used water treatment capacity and NEWater infrastructure. Plans are underway to reconstruct Kranji WRP and Kranji NEWater Factory (KNF), while Changi WRP will undergo a third phase of expansion to further increase its used water
treatment capacity.
The three-node system, with the Deep Tunnel Sewerage System at its core, consists of Changi WRP in eastern Singapore, Kranji WRP in the north, and Tuas WRP in the west.
Pursuing research and innovation in NEWater
PUB continues to innovate for greater efficiency of the NEWater production process. Since 2006, PUB has incorporated membrane bioreactor (MBR) technology in the used water treatment process.
This 3-in-1 solution combines conventional bioreactors, secondary sedimentation tanks, and microfiltration and ultrafiltration in one single step. The benefits include increased energy efficiency in used water treatment, reduced land footprint of the water reclamation plants and higher quality effluent for NEWater production.
The development of ceramicbased MBR also further enhanced the used water management. PUB conducted successful demonstration trials to validate the use of ceramic MBR systems as part of the used water treatment process. The ceramic MBR systems proved to be more resilient to chemical damage and able to effectively treat industrial used
water. The upcoming Tuas WRP will be retrofitted with ceramic MBRs for industrial water treatment and will house the world’s largest MBR system.
There is also a continuous effort to enhance energy efficiency in NEWater production. PUB has been collaborating over the last few years with local and overseas partners to develop and scale biomimetic membranes for municipal applications. The
technology uses nature-based protein water channels within a filtration membrane, which facilitates high water flow while minimising energy consumption. Demonstration plant trials at KNF with Aquaporin Asia, which commenced last year, are showing promising results, achieving a 20% reduction in energy consumption.
To improve NEWater recovery rates, PUB explored the incorporation of water technology
company ROTEC’s proprietary FlowReversal technology in the reverse osmosis membranes used during the NEWater production process. Initial trials have successfully demonstrated an improvement in recovery rates, from 85% to as high as 90%, enabling PUB to produce more NEWater from each drop of treated used water effluent. The Flow-Reversal technology will be incorporated into the design of future NEWater plants.
A new report, released recently by Climate Group and Ramboll at Climate Week NYC, reveals close to 50% of global businesses that were surveyed for the research are prepared to pay a premium for lower emission steel and concrete, signalling a powerful and growing demand for more sustainable materials. With steel and concrete emissions responsible for 15% of global emissions, their urgent decarbonisation is critical to meeting the goals outlined in the Paris Agreement.
The report ‘The Steel and Concrete Transformation: 2024 market outlook on lower emission steel and concrete’ comes after over 250 companies from 42 countries and 21 industries were surveyed on their current readiness to use, and willingness to pay for, lower emission steel and concrete. It aims to evaluate business readiness to incorporate lower emission steel and concrete in their operations, their willingness to pay a premium for these materials, and the existing key barriers preventing wider adoption.
Positive market outlook but barriers remain
The research indicates growing momentum, with 45% of respondents saying they would be willing to pay a premium for
emissions reductions of 25% or higher for steel, while 57% would be willing to do so for reductions exceeding 50%. For concrete, these numbers were 40% and 49% respectively. While the ability to pay varies across sectors and geographies, 52% of respondents had a higher willingness to do so, when compared to their stance one year ago, while 34% reported no change in opinion.
The report highlights that businesses expect the transition towards lower emission materials to be inevitable.
Driven by both regulatory pressures and market demand, 78% of respondents answered they expect lower emission steel and concrete will be standard materials for new products or projects within the next decade.
While the outlook is broadly positive, the report also focused on the barriers and solutions to this widescale adoption and transition. Businesses said while progress is accelerating, the greatest barriers to adoption remain cost (84%), industry conservatism (37%), and lack of knowledge (33%).
In terms of solutions, businesses were clear that governments have a significant role to play in supporting them. Financial levers such as tax incentives, credits and subsidies (69%), carbon pricing (50%)
as well as minimum product standards or embodied carbon limits (43%) were identified as crucial policies for governments to prioritise. Without them, the world is unlikely to see the rapid scaling of lower emission steel and concrete in time. Clear and robust policies have to be implemented at all levels of government, now.
“Business leaders are not only calling for change – they are enacting it. This report is a real temperature check of the market. It is hugely encouraging to see the appetite is here, now, for organisations to pay a premium for lower emission steel and concrete,” said Ms Jen Carson, Head of Industry at Climate Group.
“But there is deep work to be done to speed up progress. It is critical that businesses can make the right choices for their operations and the planet, and switch to lower emission steel and concrete. Governments must listen to their concerns, support their ambition, and act quickly to remove barriers,” Ms Carson added.
“The fact that more companies are now willing to pay a premium for lower emission steel and concrete sends a strong signal to the market,” said Mr Michael Simmelsgaard, Chief Operating Officer at Ramboll.
The annual Going Digital Awards honour the work of infrastructure professionals and their innovative use of Bentley software to improve the way infrastructure is designed, built and operated.
This year, 250 projects were nominated by organisations in 36 countries. Winners were selected from among 36 finalists in 12 categories, by a panel of independent judges during Bentley’s Year in Infrastructure event, held on 8 and 9 October 2024, in Vancouver, Canada.
Bridges and Tunnels JMT – Digital Experience for I-95 Rappahannock River Crossing Construction Project USA
Construction Proicere Ltd – SPRS Retreatment (SRP) Sellafield UK
Enterprise Engineering
Mott MacDonald and HDR – Ontario Line Canada
Facilities, Campuses, and Cities
China ENFI Engineering Co Ltd – Digital Construction Project of Comprehensive Waste Management Facilities in Xiong’an New Area China
Process and Power Generation PowerChina Zhongnan Engineering Corporation Limited – Shandong Energy Group Bozhong Offshore Wind Farm Site A Project China
Rail and Transit
SPL Powerlines UK – Midland Main Line Electrification UK
Roads and Highways Department of Public Works and
Highways (DPWH) – Digital Twin Implementation for NLEX-SLEX Connector Road Project Philippines
Structural Engineering
Hyundai Engineering – New Physical Modeling Method for Plant Steel Structures Using STAAD API South Korea
Surveying and Monitoring
Water Supplies Department – Digital Twin of the Ex-Sham Shui Po Service Reservoir Hong Kong SAR, China
Subsurface Modeling and Analysis
Spark and WSP – North East Link Central Package Australia
Transmission and Distribution
Southwest Electric Power Design Institute Co Ltd of China Power Engineering Consulting Group –Butuo ±800-kV Converter Station China
Water and Wastewater Companhia de Saneamento Básico do Estado de São Paulo – Sabesp –Integra 4.0 Brazil
FOUNDERS’ HONORS
Bentley also recognised 16 projects with Founders’ Honors. Chosen by Bentley Systems’ founders, Founders’ Honors are presented to a small number of exemplary projects, individuals and organisations, that reflect the company’s mission of advancing the world’s infrastructure for better quality of life.
2024 Founders’ Honors recipients
• Qk4 Inc – Going Digital Survey with Bridging Kentucky
• Tecne Systra-Sws Advanced Tunneling Srl – Digital Implementation in Tunnel Assessment and Rehabilitation
• Guangdong Airport Authority –
Digital Innovation Application of Guangzhou Baiyun International Airport Phase III Expansion Project
• MCC Capital Engineering & Research Incorporation Limited
– Integrated Application of BIM Technology in the Design, Construction, Operation and Maintenance of the World’s First Hydrogen Metallurgy Engineering Demonstration Project
• Monir Precision Monitoring – 31 Parliament Street Urban Infrastructure and Excavation Shoring Monitoring
• Greenman-Pedersen Inc –Brooklyn Bridge - Montgomery Coastal Resilience
• Arcadis – Cambridge South Infrastructure Enhancements
• Communaute d’Agglomeration
Pau Bearn Pyrenees (CAPBP) – The Multipurpose Urban Digital Twin of Communaute d’Agglomeration de Pau Bearn Pyrenees
• PT Wijaya Karya – Nusantara Road and Highway Connectivity, New Capital City of Indonesia
• PT SMG Consultants Indonesia
– Transformative Innovations in Southeast Sulawesi Nickel-Cobalt Exploration
• University of Canterbury –Incorporating Visible Geology and Leapfrog into undergraduate university courses
• Macquarie Geotechnical –Subsurface reality modelling for enhanced insight
• Exo Inc – Evergy Power Transmission Structure Stabilization
• PUB, Singapore’s National Water Agency – High Fidelity Digital TwinEnabled Anomaly Detection and Localization in Singapore
• Maynilad Water Services Inc. –Network Design using OpenFlows WaterGEMS for Distribution of Direct Potable Reused Water at Parañaque City, Philippines
• Dublin Fire Brigade – Digital Twins for Emergency Response (DTER)
bauma CHINA 2024, held from 26 to 29 November 2024, at the Shanghai New International Expo Centre, represented the triumphant return of bauma China, after a fouryear hiatus and the setting of new records across the board.
Spanning an exhibit area of over 330,000 m2, the trade fair brought together 3,542 exhibitors from 32 countries and regions, representing a 24% increase from 2020. With 281,488 trade visitors from 188 countries and regions, including more than 20% overseas visitors, bauma CHINA consolidated its position as Asia’s premier trade fair for construction machinery, building material machines, mining machines, and construction vehicles, and as a global platform for innovation and industry trends exchange.
Stefan Rummel, CEO of Messe München, organisers of the event, said, “bauma CHINA has made an incredible comeback and impressively confirmed its leading position in the Asia-Pacific region. The density of top players and outstanding technologies was inspiring. For our company, bauma CHINA is a guarantee and cornerstone of our success.”
Su Zimeng, Chairman of China Construction Machinery Association echoed this positive sentiment and said, “bauma CHINA 2024 has once again set a new historical record. Over four days of exhibitions and exchanges, we witnessed impressive achievements by companies serving both domestic and international markets and gained valuable insight into the new opportunities driven by China’s high-quality economic growth.”
Global innovation unveiled bauma CHINA 2024 attracted many international brands, showcasing a wide range of new products customised for the Chinese and
Asian markets. Industry giants such as Ammann, Bomag, Bosch Rexroth, Caterpillar, Haulotte, Herrenknecht, Hidromek, Manitou, Manitowoc, Skyjack, Wirtgen Group and ZF Group were represented, as well as national pavilions from Germany, Italy and Türkiye.
Yang Chengjian, Global Senior Vice President of Caterpillar, said, “bauma CHINA provides an excellent platform for showcasing innovative products, services, and solutions that address the industry’s present and future needs.”
Song Gongcheng, President of Bomag (China) said, “The results exceeded our expectations, with an overwhelming number of visitors. Our booth has been bustling with customers and dealers all along, reflecting the industry’s eagerness to embrace change and innovation. We have signed several agreements during the show.”
Leading Chinese exhibitors such as XCMG, Sany, Zoomlion, SDLG, Longking, Shantui, Dingli, Lovol, NFLG, TZCO and CRCHI showcased cutting-edge technologies in electrification, hydrogen power, automation and digitisation, illustrating China’s progress in smart technologies and new energy transformation, while expanding their international reach.
The Exhibition Manager of XCMG Group said, “Through bauma CHINA as an international platform, we collaborated with global partners to achieve winwin outcomes and drive the high-quality development of the global equipment manufacturing industry.”
bauma CHINA 2024 attracted 281,488 trade visitors, more than 20% of whom were from overseas, representing a significant growth compared to 2018. Besides China, the top 10 countries, in terms of
visitorship, were, Russia, India, Malaysia, South Korea, Thailand, Indonesia, Singapore, Kazakhstan, Brazil and Japan.
The event’s success underscored its role as a key link between international markets and China's fast-growing industry, particularly amidst the ‘Belt and Road’ initiative, Indonesia’s accelerated mining plan and Saudi Arabia’s ‘Vision 2030’ infrastructure investments, which are driving demand for construction machinery products in regions along the Belt and Road, Southeast Asia and the Middle East.
Ma Ji, General Manager of Marketing and Sales of Cummins (China) Investment Co Ltd said, “This year’s bauma CHINA saw the highest number of international visitors I have ever encountered, with foreign attendees crowding the venue. It was truly a grand event for the global construction machinery industry. The entire exhibition was brimming with energy, reinforcing my confidence in the globalisation and future success of China’s construction machinery sector.”
At this year’s bauma CHINA, two new thematic areas were integrated into the exhibition layout, focusing on intelligent management and cutting-edge new energy technologies. The accompanying forums offered in-depth discussions on hot topics and provided insights into pioneering achievements in sustainability, innovative practices in new energy cooperation and intelligent integration solutions within the industry, that are shaping the future of the industry.
The next bauma CHINA will take place from 24 to 27 November 2026, at the Shanghai New International Expo Centre.
bauma 2025, the world’s leading trade fair for construction machinery, building material machines, mining machines, construction vehicles and construction equipment, will be held in Munich, Germany, from 7 to 13 April 2025.
With a total exhibition area of 614,000 m2, bauma is the largest trade fair in the world.
Organised by Messe München, bauma is held every three years.
Exhibitors at bauma 2025, such as Liebherr, Peri and Wirtgen began to set up their booths in October, around six months before the start of the event. Other returning companies include Volvo, Deutz, Liugong, CNH, Skyjack and JLG.
Joining their ranks for the first time are such companies such as Fortescue, DSI/Sandvik, HG - 100% electric dumpers, EXiron AG, Gravis Robotics AG, Metso Oyj, rockrobot oy, Wabtec Corporation and WEICO GmbH. There will be around 150 new exhibitors at bauma 2025.
Key topics at bauma 2025 ‘Digitisation’ and ‘sustainability’ will remain the buzzwords of the industry at bauma 2025. As a result, they are also reflected in the five key topics that bauma will address –climate neutrality, alternative drive concepts, networked construction, sustainable construction, and mining challenge.
From Monday to Friday, the bauma FORUM will focus on one of these key topics. The programme will consist of brief presentations, panel discussions and keynotes. Exhibitors will also present products and innovations from these areas.
New structure for the area of occupational health and safety
As part of changes for 2025, the area devoted to occupational health and safety will be centrally consolidated in Hall B4. This
strategic placement offers visitors a comprehensive overview of developments and technological advances that will improve safety on construction sites.
Focus on research at the Science Hub
Eleven research institutions will present innovative projects at the bauma Science Hub. Among other projects, the Technical University of Munich will present autonomous solutions for bulk goods transportation and a paving robot.
The University of Duisburg-Essen will demonstrate a cable robot for precise use on construction sites, and the Technical University of Dresden will present ways to avoid accidents by using a mobile excavator that can recognise human beings.
Many other exciting projects await visitors directly at the exhibitors’ booths.
Start-ups to showcase innovations bauma 2025 will also offer young, innovative companies the opportunity to present their ideas. Almost 50 start-ups have registered to showcase their innovations and developments related to the main topics at bauma.
These include mobile robot technologies, the development of digital twins of construction sites, alternative drive systems, ultrasonic technology in concrete production, autonomous crane solutions for digital construction sites in rough terrain as well as end-to-end and other software solutions that help companies in the office and on the construction site.
The VR Experience Zone
Another special attraction will be the VR Experience Zone 2025, a partnership between the Construction Future Lab (CFLab) and Messe München. The interactive exhibition will combine a museum-like character with innovative technology and shed light on key future topics in the construction industry.
Interested visitors can experience demonstrations on such topics as construction robotics, alternative drive technologies, additive processes and the digitalisation of machines and interfaces. They are supplemented by expert interviews and multimedia content. This experience will provide visitors with comprehensive and practical insights into innovations in the industry and bring future-relevant developments to life.
Minister for National Development and Minister-in-Charge of Social Services Integration, Mr Desmond Lee unveiled a new chapter in engineering chartership, at the IES 58th Annual Dinner.
The Institution of Engineers, Singapore (IES) celebrated its 58th Annual Dinner on 15 October 2024 by toasting to an illustrious past and announcing a new push for professional accreditation of engineers.
Minister for National Development and Minister-in-Charge of Social Services Integration, Mr Desmond Lee was the Guest-of-Honour at the dinner, themed ‘Empowering Engineers for Sustainable Innovation’ and held at the Shangri-La Hotel in Singapore.
Minister Lee launched the new Chartered Engineering Board –formed through the merger of the Chartered Engineers Board and the Chartered Engineering Technologists and Technicians Board – to strengthen Singapore’s engineering competencies to meet evolving needs. This
integration seeks to accelerate the professional accreditation process for engineers, technologists and technicians, across various sectors of engineering.
This will boost efforts by IES to promote upskilling and career progression of engineering professionals through both academic and non-academic pathways. It is in line with the national SkillsFuture movement.
IES is a Skills Development Partner (SDP) appointed by SkillsFuture Singapore to advance the skills development agenda of engineering professionals and sectors.
“By consolidating our accreditation boards into one single entity – the Chartered Engineering Board – we will streamline the registration process for engineering professionals, enabling faster and more efficient certifications. This will grant applicants quicker access to the training and certification required to not just survive, but thrive, in
their respective sectors. It will also build a robust engineering ecosystem with complementary skillsets to drive Singapore’s growth,” said Er. Chan Ewe Jin, President of IES.
The Chartered Engineering Registry covers 10 engineering sectors – Aerospace, Built Environment, Chemical & Energy, Renewable Energy, Engineering Project Management, Environment & Water, Infrastructure, Railway & Transportation, Sustainability, and Systems.
Minister Lee also unveiled ‘Building the Nation and Beyond’, a commemorative book that chronicles IES’ remarkable evolution and its contributions to Singapore’s development over the past 58 years. From a secretariat size of just two clerical staff, operating from a 9.5 m2 office, IES has grown significantly
in size, stature and partnerships. It has made a lasting impact on the engineering landscape, while advancing towards its vision of being the heart and voice of engineers, and the national body and home for engineers, in Singapore.
During the dinner, IES paid homage to eminent engineering leaders and visionaries, for their extraordinary contributions in engineering that fuelled Singapore’s infrastructure, economic and societal development.
Ms Ho Ching, Chairman of Temasek Trust and Trailblazer Foundation, received the esteemed IES Lifetime Engineering Achievement Award 2024. The award is in honour of her lifelong accomplishments that have made a profound impact on the industry and community, inspiring future generations to do the same.
Senior Minister of State for National Development & Digital Development and Information, Mr Tan Kiat How was conferred the title of IES Honorary Fellow for his steadfast support in advancing the interests of IES and the engineering landscape.
Professor Yeoh Lean Weng, Emeritus President of IES was the recipient of the IES/ IEEE Joint Medal of Excellence Award, recognising his notable contributions to engineering and outstanding leadership in accelerating sustainable development for the benefit of society.
Minister Lee also presented the IES Prestigious Engineering Achievement Awards to recognise projects that demonstrate noteworthy engineering skills and significantly contribute to engineering progress and quality of life in Singapore, as well as the IES Sustainability Awards to honour innovative projects and initiatives that promote sustainability and innovation in Singapore.
Prestigious Engineering Achievement Awards 2024 Emerging out of a rigorous evaluation of 35 submissions, the following projects are the winners of the IES Prestigious Engineering Achievement Awards 2024:
APPLIED RESEARCH AND DEVELOPMENT
Structural Digital Twin of Jack-up Platform – Methodology Verification & Validation by Technology Centre for Offshore and Marine, Singapore; National
University of Singapore (NUS); and Seatrium
The project focuses on developing, verifying and validating a Structural Digital Twin for jack-up platforms, to enhance operational safety and efficiency. It involves designing and testing a novel, large-scale model equipped with a comprehensive sensing system for basin model test purposes and developing a robust, digital twin framework with real-time predictive capabilities for predictive maintenance.
This innovative approach aims to optimise asset life-cycle management and has recently been awarded a Statement of Maturity at the Concept Verified Stage, by the American Bureau of Shipping.
Development and Deployment of Singapore Police Force (SPF) Community Engagement Robot by Ngee Ann Polytechnic
The SPF Community Engagement Robot (also known as CODY) was developed by the Singapore Police Force (SPF) and Ngee Ann Polytechnic (NP), in consultation with the Home Team Science & Technology Agency (HTX). CODY interacts with the public and disseminates crime prevention messages through a wide range of personalised multimedia activities such as videos, games, quizzes and chats. It is able to communicate in local languages.
Having been deployed at numerous SPF community outreach events, CODY enables SPF officers
to reach out to more members of the public, enhancing engagement across Singapore’s diverse, multilingual community.
Aqueous CO2 sequestration and utilisation in ultra-low carbon concrete production by Singapore Institute of Technology (SIT)
The team developed an innovative, cost-effective aqueous carbon sequestration system to produce sustainable, readymixed concrete, addressing environmental and industry needs in Singapore. This system uses CO2-enriched solutions to replace plain water, converting inorganic carbon into nano-sized CaCO3 that is permanently stored in the concrete. The nano-sized CaCO3 enhances cement hydration and reacts with cement components to allow up to 80% replacement with blast furnace slag, reducing embodied carbon by 65%.
Innovative and Sustainable Solution for Seawall Construction in Coastal Development by Housing & Development Board (HDB) & NUS
The project explores the use of geotextile tubes, filled with lightly treated locally excavated soft soil, as coastal protection structures. This innovation aims to re-purpose excavated materials collected from the construction industry for enhanced environmental and financial sustainability. The successfully developed and tested, novel, deep-water installation method can accommodate coastal protection needs in deep waters.
Modification and Flow Diversion to a Live DTSS Segmental Tunnel by PUB, Singapore's National Water Agency
The project involves constructing a temporary and, later, a permanent sewer connection to Singapore’s Deep Tunnel Sewerage System (DTSS), to allow LTA’s construction of the Thomson-East
Coast Line (TEL) to proceed quickly, by diverting impacted sewers to the DTSS.
A temporary Helicoidal Drop Structure was placed in an existing deep shaft of the DTSS in 2016, to facilitate TEL construction without disrupting PUB’s operations. This was later replaced by a permanent sewer connection at a depth of 37 m, in 2022, which required highprecision cutting into a live DTSS tunnel without damaging the tunnel’s composite structure. The connection was completed, safely, while managing high sewage flow and toxic gas levels.
Innovative solutions like a Contingency Flooding System, steel beam stitching of the tunnel segments, water jet cutting and a specially designed safety steel cover were employed to safeguard the tunnel and ensure a safe working environment.
cycleye by cycleye
cycleye is an innovative safety system for cyclists, offering realtime alerts on potential dangers, using advanced ‘Dep-tection’ technology that combines obstacle detection and depth models. cycleye transforms any mobile device into a power data system, allowing cyclists to stay aware of their surroundings with ease and accuracy. Affordable and portable, cycleye is designed for everyday cyclists, ensuring reliable performance in a variety of riding scenarios.
by Institute for Infocomm Research (I²R), Agency for Science, Technology and Research (A*STAR)
I²R’s APM is a prognostics tool that leverages sensor data recorded in aircraft, to predict failure of components and systems, in advance, thus improving engineering operations and averting unplanned flight
delays. I²R’s APM uses a hybrid of human expert-based feature engineering and state-of-theart deep learning technologies to predict failures of critical components / systems in multiple aircraft systems.
By predicting potential failures, this solution enables proactive maintenance, preventing flight disruptions due to engineering faults, thereby significantly reducing Aircraft On-Ground (AOG) incidents.
A total of eight winners clinched the IES Sustainability Awards, from a total of 26 project submissions.
COMPLETED ENGINEERING PROJECTS WITH SUSTAINABILITY FEATURES AND PRACTICES
Sembcorp Cool House at the National Orchid Garden by National Parks Board (NParks)
The Sembcorp Cool House at the National Orchid Garden is a key installation that goes beyond regulatory requirements and building codes, to implement an iconic architecture that is not only fit for purpose but is also a centrepiece of the Gardens’ focus on environmental sustainability.
The completed Cool House is four times larger than the original facility, but consumes 30% less energy. It also increases the Singapore Botanic Gardens’ capacity to curate, conserve and display rare tropical montane plants, raising public awareness of this threatened ecosystem and furthering the Gardens’ mission of plant conservation and outreach.
Super Low Energy Flight Simulator Building by Defence Science and Technology Agency (DSTA)
DSTA developed the first MINDEF/SAF Training Centre to achieve the BCA Green Mark Award (Platinum) (Super Low Energy), cutting annual energy consumption by 40% and water usage by 70%, resulting in utility savings
of up to SGD 340K per year. The design of this specialised training centre prioritises sustainability, modularity, maintainability and user-centricity, while incorporating natural lighting and interaction spaces to create an optimal and conducive environment for both trainers and trainees.
Master planned and developed by JTC, the district is designed by WOHA Architects, and will bring 28,000 jobs, lifestyle and community amenities closer to homes. The district features stateof-the-art infrastructure, green spaces and smart technologies, making it a vibrant environment for digital transformation. With a focus on sustainability and community engagement, Punggol Digital District aims to be a model for future urban developments.
Samwoh Smart Hub – First Positive Energy Building in Singapore by Samwoh Corporation Pte Ltd
Samwoh Smart Hub is the first positive energy building that produces 25% more energy than what it consumes, in Singapore. With the ultra-low Energy Use Intensity and remarkable energy surplus, its operational carbon is kept as low as is practicable. Several sustainable materials, such as green cement, granite fines and sedimentary rocks from Jurong Rock Caverns, have been incorporated into the building construction to reduce its embodied carbon.
SJ Campus by SJ Consultant
The SJ Campus is the global headquarters of Surbana Jurong. Located at the Jurong Innovation District (JID), the campus is a strategic centre for collaboration and learning, and a living lab for innovative solutions for the built environment. JID includes a vibrant ecosystem of enterprises in smart city and urban solutions. SJ Campus adopts regenerative
design practices that contribute to a greener and healthier built environment in the tropical climate context, and demonstrates what a sustainable, maintainable, peoplecentric and future-ready workplace is like. SJ Campus is triple-certified i.e. it has received the GM Platinum SLE, WELL Core Platinum, and GM for healthier workplaces certifications.
Design & Construction of Stormwater Retention Pond at Integrated Bidadari Park by PUB, Singapore’s National Water Agency
Alkaff Lake, situated in the new Bidadari estate, is a first-of-itskind, multi-functional, drainage infrastructure for stormwater management, that enhances the flood protection for Bidadari estate and the surrounding areas.
Alkaff Lake is a 1.8-hectare lake which is around the size of two football fields and can hold up to 40,000 m3 of water.
In dry weather, it looks like a regular lake and forms part of the recreational and aesthetic community space for the public. During heavy rainfall, it plays an important role in regulating the amount of stormwater runoff that flows into the downstream drainage system.
INNOVATIVE SOLUTIONS FOR SUSTAINABILITY
Realising sustainable aviation fuel production from CO2 by the Institute of Sustainability for Chemicals, Energy and Environment (ISCE²) and A*STAR
CO2-based Sustainable Aviation Fuel (SAF) would play a crucial role in achieving 65% of the reduction in aviation emission targets by 2050, as biofuels have feedstock limitations. Combining the expertise of catalysis and process engineering from A*STAR, ISCE2 and IHI, the team developed a breakthrough technology, through innovative catalyst and reactor design, to make SAF directly from CO2 with reduced reactor
footprint and hence lower capital investments as well as greater energy efficiency. The technology has great potential in enabling the decarbonisation of the aviation industry, and IHI and ISCE2 are collaborating on scaling up to validate the technology under industry-relevant conditions.
Singapore Building Carbon Calculator by JTC Corporation, in collaboration with the Building and Construction Authority (BCA), the Singapore Green Building Council (SGBC) and the National University of Singapore – Energy Studies Institute (NUS-ESI)
Accounting for embodied carbon in Singapore remains a challenge, due to the lack of a robust localised material carbon database and limited guidelines, as there was a lack of suitable embodied carbon calculators for local industry use. The emission factors in existing carbon calculators are more suited to other regions in the world.
The team developed a Building Embodied Carbon Calculator (BECC) module and a Mechanical & Electrical Carbon Calculator (MECC) module, with locally contextualised emission factors via a developed classifier structure (innovation).
The calculators account for the upfront carbon of common construction materials and M&E equipment, from cradle (raw material extraction and supply) to its
practical completion (construction and installation) and operation (use stage) to account for operational embodied carbon of M&E equipment (frequent maintenance/ repair, refrigerant top-up etc), that is suitable for local use.
The transportation distances for materials, from their sources, are also built in, considering that Singapore imports most of its building materials from overseas.
The Singapore Building Carbon Calculator (SBCC), with the BECC and MECC modules, has provided the local industry with a unified, free-to-use tool that can be used, during the design stage, to calculate the upfront carbon in their projects and aid in making informed decisions regarding the selection and use of sustainable materials and products.
This will enable the finalisation of the as-built embodied carbon at the end of construction and the ‘during use’ stage calculation of operational embodied carbon associated with the maintenance of M&E equipment.
STUDENT SCHOLARSHIP AWARDS IES also awarded the IES-Yayasan Mendaki Scholarship to Arshof Ahamed S/O Ansar Ahamed, an Electrical and Electronic Engineering student from Nanyang Technological University, in recognition of his exceptional academic performance, and to spur him to pursue an engineering career.
The excellent work of consultants and contractors was honoured, as was, for the first time, the resilience shown by project teams in overcoming the challenges created by COVID-19.
At the HDB Awards ceremony on 22 October 2024, Minister for National Development, Mr Desmond Lee presented a total of 26 HDB Design, Engineering, and Construction Awards, to recognise the excellent work of architectural and engineering consultants, as well as building contractors, in public housing projects.
Among the winners are Rivervale Shores and Kim Keat Beacon. The two projects received both the HDB Design Award and the HDB Construction Award.
HDB also conferred the inaugural Construction Resilience Recognition on the teams for three projects –Marsiling Grove, Waterway Sunrise II, and West Coast Parkview. Amidst the challenging conditions posed by the COVID-19 pandemic, the project teams took over these Build-to-Order (BTO) projects which had been stalled, due to the failure of their previous contractors, and demonstrated resilience in overcoming severe challenges, to support HDB’s efforts in meeting its commitments on delivering homes to flat buyers.
HDB’s Chief Executive Officer, Mr Tan Meng Dui said, “I congratulate all winners of the HDB Awards. Their achievements highlight the excellence that we aspire to, for our public housing projects and affirm the critical partnership between HDB and the industry in delivering quality homes safely to Singaporeans. This year’s HDB Awards is especially significant, as it takes place at a time where HDB is close to completing all the pandemic-delayed BTO projects in the next five months.”
“We are thus delighted to present three of our exemplary builders with the Construction Resilience Recognition, a first-of-its-kind award to recognise the resilience of our BTO contractors in overcoming the severe challenges posed by COVID-19. This recognition demonstrates both the strength and depth of the BTO construction ecosystem, as well as the ingenuity and resilience of our contractors in overcoming adversity and emerging stronger,” he added.
“HDB is proud of the exceptional standard of excellence
demonstrated by our building partners and humbled by their strong commitment to our mission of delivering quality homes to Singaporeans,” Mr Tan continued.
RIVERVALE SHORES – RIVERSIDE LIVING AMIDST LUSH GREENERY Rivervale Shores was awarded both the HDB Design Award and HDB Construction Award. Comprising 2,500 2-room Flexi, 3-, 4-, and 5-room flats, across 16 residential blocks, the 10-hectare development is HDB’s largest BTO project to-date.
Designed by Surbana Jurong (SJ), Rivervale Shores stood out for effectively blending high-rise living with nature, creating a distinctive urban living experience by the river. The project is designed to seamlessly integrate with the Sungei Serangoon’s waterfront. Much of its design is inspired by the rich biodiversity of the area, where Grey Herons, Little Egrets and White-throated Kingfishers are active. For example, the thematic playgrounds in the development are inspired by these bird species.
A key feature of the precinct is the elevated Environmental Deck (e-deck) that connects all 16 residential blocks, creating a vibrant green space with various precinct facilities that encourage outdoor activities and social interactions among residents.
Tucked away beneath the e-deck is the car park. Without the traditional Multi-Storey Car Park (MSCP), there is better spacing between residential blocks – which helps to enhance air circulation and offers residents more privacy. In addition, the residential blocks are strategically orientated and staggered, to optimise residents’ views of the river as well as the lushly landscaped spaces.
Bringing riverine landscapes to the doorsteps of residents
Green spaces make up about 45% of the surface area of Rivervale Shores, offering residents ample opportunities to experience the restorative benefits of nature, right at their doorsteps. Capitalising on the development’s waterfront location, many of these spaces, including sky terraces and sky gardens, have been designed to offer vantage points for scenic views.
Besides softening the urban environment, these green spaces also reduce the heat island effect, by lowering surface and ambient temperatures.
Rivervale Shores features five thematic waterfront gardens, each inspired by a specific aspect of a river’s ecosystem.
For example, the Central Garden is designed to mimic the dynamic activities and green spaces found along a river, while the Zestful Garden captures the essence of river features such as boardwalks and natural habitats.
Boardwalks within the common green provide recreational paths for leisurely strolls and birdwatching, while educational signage along the route informs visitors about the local ecosystem, encouraging a greater appreciation of nature.
Keeping the water clean
The development also features a network of environmentally sustainable Active, Beautiful, Clean (ABC) Waters design features, such as bioretention basins and bioretention lawns. These were designed to capture and treat rainwater from surface runoff collected from the blocks, before discharging the cleansed runoff into Sungei Serangoon.
Collectively, the vast network of ABC Waters design features collects and treats runoff from over five hectares (or over 50%) of the site. For its exceptional standards in integrating environmentally sustainable green features, in
2018, Rivervale Shores clinched the ABC Waters Gold certification, the highest accolade that PUB, Singapore’s National Water Agency, awards to developers. This was the first ever ABC Waters Gold certification received by HDB.
Enhancing the construction process for increased productivity
Given the large size of the Rivervale Shores site, meticulous and detailed planning was essential to ensure that construction could be carried out smoothly. From the outset, LC&T Builder 1971 Pte Ltd (LC&T), the appointed construction firm for the project, identified key challenges and put in place plans
across various aspects, including scheduling, quality control, and environmental health and safety management.
To improve productivity and efficiency on site, LC&T applied new building methods such as using a special steel formwork that stays in place as part of the slab’s base, creating a more effective foundation for double slab construction. It also used a mobile tower formwork for casting the large e-deck. Together, these methods shortened the construction time of the e-deck by at least half.
LC&T also addressed site constraints through innovative solutions. For example, there was limited access to some residential blocks near the centre of the site. To overcome this, LC&T strengthened the site-wide, basement car park ground slab, which increased its capacity and durability to support heavy construction equipment, thereby facilitating the efficient transportation of materials across the large construction area.
With their strong project management capabilities, LC&T and SJ were able to successfully obtain the Temporary Occupation Permit (TOP) for all 16 residential blocks and car park within a 4-month period. This is half the time required for a project of this
size, enabling residents to move into their new homes earlier.
Located along Kim Keat Avenue, Kim Keat Beacon is another project that received both the HDB Design Award and the HDB Construction Award. Designed by Kyoob Architects, the project comprises 542 3- and 4-room flats across three residential blocks. With its distinctive façade, Kim Keat Beacon stands out as a landmark at the edge of Toa Payoh.
Kyoob segmented the façade colours to create striking visual interest and designed the MSCP with cascading terraces stepping down to an adjacent park to reduce the building’s visual mass. Along these steps are pockets of greenery and tranquil spaces for residents to relax and recharge, in addition to park facilities such as playgrounds and fitness corners.
A unique feature of Kim Keat Beacon is the communal balcony located at the lift lobby of every storey of the residential blocks. These are inspired by traditional corridors where residents used to gather, and provide opportunities for neighbours to meet and interact, as they go about their daily activities, thereby fostering
community bonds.
In constructing Kim Keat Beacon, Newcon Builders Pte Ltd (Newcon) employed machinery to increase productivity on site. For example, electric trolleys were utilised so that workers could transport more materials in a single trip, and electric sanders were used during finishing works, allowing workers to complete four units a day, compared to 0.25 units a day with manual sanding. The use of electric sanders also reduced the amount of dust generated.
Newcon also demonstrated resilience during the pandemic by successfully procuring doors and door frames from alternative sources, despite an islandwide shortage. This minimised setbacks and enabled the construction of Kim Keat Beacon to progress smoothly.
This year, HDB conferred the inaugural Construction Resilience Recognition on the project teams for Marsiling Grove, Waterway Sunrise II, and West Coast ParkView. The construction firms for these projects had taken over the projects at various stages of construction, after the failure of their previous contractors.
Amidst the challenging conditions posed by COVID-19, coupled with compressed timelines, the teams displayed strong partnership and dedication as they adapted to the evolving situation, and implemented innovative solutions to resume and accelerate construction activities on site.
Marsiling Grove – new project team resumed works efficiently Marsiling Grove, comprising 1,246 flats across five residential blocks, was one of five projects that was initially awarded to Greatearth Corporate Pte Ltd and Greatearth Construction Pte Ltd (collectively referred to as Greatearth). The project, which was originally expected to be completed in 4Q2022, was delayed, following the liquidation of Greatearth during the pandemic.
To expedite the resumption of work, HDB assisted in sourcing for suitable contractors to take over the project through novation, as the former contractor had ceased operations. CES Engineering & Construction was brought on board as the new main contractor, in
September 2021, about one month after works stopped on site. The project team, consisting of CES Engineering & Construction and SJ as the consultant, took over the project when it was about 50% completed.
Right from the start of taking over the project, the new team resolved to resume works on site, as soon as possible. Within a month, they had assessed the site condition and work status, and developed a comprehensive plan to complete the remaining scope. This included the construction of 10 more storeys of the residential blocks and the MSCP, as well as the installation of extensive underground services.
Their quick planning was complemented by their resourcefulnessin securing building materials so that the project schedule could remain on track, despite global supply chain disruptions.
To ensure that the works could proceed smoothly, the team hired the original sub-contractors and workers, as they were already familiar with the site. With this, CES was able to resume structural works of the residential blocks in
October 2021 – their third week on board. The project team also extended working hours on-site and obtained special permissions for less noisy construction activities to be carried out on Sundays and Public Holidays. These efforts helped to accelerate progress and reduced delays by two to three months.
CES also collaborated closely with SJ, who helped CES resolve issues quickly and keep the project moving forward. A Common Data Environment (CDE) created by SJ enabled the teams to access and share data in real-time, which aided in resolving discrepancies across technical disciplines and improved the overall project delivery schedule.
Their close partnership enabled the project team to complete all five residential blocks at Marsiling Grove within a compressed timeline of less than two years from the time they took over the project. The flats were delivered to flat buyers by March 2023, which was a delay of just one quarter from the scheduled completion date, despite the disruption caused
by the collapse of the previous contractor and the subsequent novation process.
In addition, SJ was also awarded a Certificate of Merit (Engineering) for its adept handling of the engineering and site constraints.
For example, SJ proposed an earth retaining system that ensured soil stability, when past building records showed scant details for an existing retaining wall separating Marsiling Grove from the adjacent Marsiling Secondary School.
This minimised the impact of construction and excavation works on both the school and the retaining wall, while fulfilling the requirements for the earth works.
CONTINUING THE CLOSE COLLABORATION WITH INDUSTRY PARTNERS
As HDB continues with the efforts to complete all the remaining pandemic-delayed projects by early 2025, it is also ramping up the supply of new flats to meet sustained housing demand. HDB continues to work closely with industry partners to explore innovative solutions and deliver well-designed, quality homes to Singaporeans.
WINNERS OF HDB AWARDS 2024
HDB DESIGN AWARD Design Award
Housing
Rejuvenation
To-be-Built
Housing
Surbana Jurong Consultants Pte Ltd
Kyoob Architects Pte Ltd
Building & Research Institute (HDB)
Kyoob Architects Pte Ltd
Rivervale Shores
Kim Keat Beacon
Woodleigh Hillside
Admiralty Place
Building & Research Institute (HDB) Alexandra Peaks
Surbana Jurong Consultants Pte Ltd
Verandah @ Kallang
Certificates of Merit (Design)
Category Consultant
Completed
Housing ADDP Architects LLP
LAUD Architects Pte Ltd
Rejuvenation SA Chua Architects Pte Ltd
To-be-Built
Housing JGP Architecture (S) Pte Ltd
HDB ENGINEERING AWARD
Engineering Award (Design)
Fernvale Dew
Tampines GreenVines
Neighbourhood Renewal Programme at Bedok South Ave 2
Brickland Weave
Building & Research Institute (HDB) Rail Green I & II @ CCK
Category Consultant
Completed
Housing LSW Consulting Engineers Pte Ltd Anchorvale Village
Engineering Award (Construction)
Category Contractor
Completed
Infrastructure Ah Boon Civil Engineering & Building Contractor Pte Ltd
Innovative Engineering Award (Design)
Category Consultant
To-be-Built
Housing
Building & Research Institute (HDB)
Certificate of Merit (Engineering)
Category Consultant
Completed
Housing Surbana Jurong Consultants Pte Ltd
Diversion of Trunk Sewer at Towner Road
Alexandra Peaks - (Bukit Merah C54 & C54A)
Marsiling Grove
HDB CONSTRUCTION AWARD
Construction Award
Category
Completed
Housing
Upgrading
Expand Construction Pte Ltd
Newcon Builders Pte Ltd
LC&T Builder (1971) Pte Ltd
Welltech Construction Pte Ltd
China Construction (South Pacific)
Development Co Pte Ltd
Expand Construction Pte Ltd
SCT Construction Pte Ltd
Certificates of Merit (Construction)
Category
Completed
Housing
Upgrading
Chip Eng Seng (1988) Contractors Pte Ltd
H P Construction & Engineering Pte Ltd
LC&T Builder (1971) Pte Ltd
Shin Khai Construction Pte Ltd
CONSTRUCTION RESILIENCE RECOGNITION (NEW)
Project
Marsiling Grove [Novated]
West Coast Parkview [Novated]
Waterway Sunrise ll [BOW]
CES Engineering & Construction Pte Ltd
Newcon Builders Pte Ltd
Expand Construction Pte Ltd
Fernvale Vines
Kim Keat Beacon
Rivervale Shores
Tampines GreenCourt
Tampines GreenCourt
Design and Build of Upgrading Projects at Simei / Serangoon (G29K)
Design and Build of Upgrading Projects at Bukit Batok / Jurong West (G29E)
Tampines GreenSpring
Teck Whye View
Yishun Glen
Design and Build of Upgrading Projects at Yishun (G29B)
Lead Consultant
Surbana Jurong Consultants Pte Ltd
ADDP Architects
Surbana Jurong Consultants Pte Ltd
A new welding protocol, formulated by two professors from the Singapore Institute of Technology (SIT), is enabling stronger yet lighter steel to be used in construction projects. This achievement clinched the Applied Research Excellence Award at the SIT University Awards 2024.
A new skyscraper is being built in downtown Singapore. When the redeveloped Newport Plaza (once the Fuji Xerox Towers) opens, the 51-storey integrated development will house offices, residential and serviced apartments, and retail spaces. But to those in the construction industry, the most interesting feature of this building is hidden deep within.
At the core of the development lies an engineering breakthrough. Thanks to the work of two professors from the Construction Technology Innovation Laboratory (CTIL) at SIT, the skyscraper’s kingposts, a building’s central supporting posts, are made of S690 structural steel, a material never before used for building construction in Singapore, but which has many advantages.
This innovation has won the research team the Applied Research Excellence Award at the SIT University Awards 2024.
Stronger building blocks
Er. Prof Chiew Sing Ping, Head of CTIL, and Asst Prof Zhao Ming Shan, Principal Investigator at CTIL, have developed a welding protocol that makes it possible to use S690 steel in construction.
S690 steel is almost twice as strong as the S355 steel commonly used today, having undergone quenching and tempering. This process involves rapidly heating and cooling the steel, thereby refining its microstructure to enhance its strength and other properties.
However, S690 steel comes only in long, flat steel plates which are unusable in construction. On the other hand, The S355 comes in I- or H-shaped sections and can be readily used.
Furthermore, the heat generated during welding of the S690 steel creates weakened, compromised heat-affected zones, making it a challenge to shape it into usable structural shapes needed for construction.
The welding protocol, developed by Er. Prof Chiew and Asst Prof Zhao, has managed to overcome these limitations of the S690 steel, without adversely affecting its strength. The result is HISTEEL –high-strength steel sections made of S690 steel in ready-to-use shapes.
“This research demonstrates that high-strength steel plates can be welded and formed into HISTEEL sections, without compromising their integrity. Although the welding process is not codified as a standard, it has gained significant traction. The Building and Construction Authority of Singapore (BCA) has approved numerous projects utilising HISTEEL sections, recognising their potential in modern construction,” Er. Prof Chiew explained.
These steel sections require less material to build and are stronger, yet lighter. Since they use less steel (up to 40% by weight), compared to conventional S355 steel, they are also a more sustainable option.
HISTEEL also addresses the space issue that comes with urbanisation – because they are lighter, smaller cranes can be used to lift them, making them ideal for construction in crowded city areas.
“Weight is a critical factor in urban construction. Lifting lighter materials inherently improves both productivity and safety on the job site,” Er. Prof Chiew said.
The potential of S690 steel has been realised with the use of HISTEEL. Kingposts made of S690 steel have since been used for, apart from the redeveloped Newport Plaza, also the Marina View Residences.
Through a successful partnership between SIT, construction company Woh Hup and steel fabricator TTJ, who are using HISTEEL in both developments, an established welding process for S690 steel has
been successfully developed and significant savings achieved.
TTJ, as the fabricator of S690 steel sections, played a crucial role in producing the components, while Woh Hup deployed them at its construction sites.
Interest in the market extends beyond using S690 steel for kingposts, to using them for sky bridges and other applications. By sharing the research outcome with industry, SIT has paved the way for wider adoption of this high-performance material in the construction industry.
Er. Prof Chiew explains, “We work together with industry partners. We call this ‘Applied Research’. Collaborations with key partners like Woh Hup, as our main contractor, TTJ Design & Engineering, as the steel fabricator, and sometimes with developers, have been instrumental. It is important to have this kind of synergy in partnerships to drive industry transformation.”
The strength of tripartite partnership
Er. Prof Chiew and Asst Prof Zhao started researching S690 steel plates about 15 years ago. When they came to SIT, they were determined to bridge the gap between theoretical research on and practical application of S690 structural steel.
To do this, they needed more than a lab. They needed construction sites as their testbed. But getting industry buy-in was not easy. The professors had to convince major players to try something new. In 2019, the professors went to major construction company Woh Hup with their research. They proved the effectiveness of their welding protocol, which preserved the steel’s mechanical properties, even after it was subjected to the intensive heat generated by the welding.
Woh Hup and the local authorities were convinced. They saw the value in using HISTEEL sections in actual projects. Soon,
all the ‘moving parts’ of the development were on board – the Qualified Person (QP), the design engineers and the developers.
The construction industry is often seen as slow to evolve, with tight regulations and strict safety standards. However, the professors believe the tripartite partnership, between the government, industry, and Institutes of Higher Learning, provides the best chance for innovations to be implemented.
“The success of this project is a testament to the strength of collaboration between academia and industry. By working closely with our partners, we were able to translate our research into a realworld solution that is benefitting the construction sector,” said Asst Prof Zhao.
“As Civil Engineers, we sometimes overlook the personal impact of our
work. While our projects primarily benefit society as a whole, they can also translate into tangible solutions that bring improvements
JTC recently hosted the 2024 Industry Seminar on Innovations in Structural Engineering Systems, bringing together over 250 representatives from 70 companies, agencies and institutions, in the built environment sector.
The seminar showcased groundbreaking innovations in structural engineering systems, developed in collaboration with partners including the Singapore Institute of Technology (SIT), Nanyang Technological University Singapore (NTU Singapore), National University of Singapore (NUS), and SEN Engineering.
As part of the seminar, Er. Prof Chiew Sing Ping, Head of the Construction Technology Innovation Laboratory (CTIL) at SIT, presented a groundbreaking innovation – the Design of HighPerformance Composite Beam (HPCB) using Pre-Engineered S460 Steel Sections. This innovation was developed under the applied research project titled ‘High-Performance Pre-
to people’s daily lives. Seeing our research applied in real-world situations is very rewarding,” said Er. Prof Chiew.
Engineered Steel Concrete Composite Beams for Sustainable Construction’ and funded by JTC.
A highlight of the seminar was the official launch of the book ‘Design of HighPerformance Pre-Engineered Steel Concrete Composite Beams for Sustainable Construction’, authored by Er. Prof Chiew Sing Ping and co-authored by the CTIL research team, JTC and Woh Hup (Private) Limited.
This comprehensive resource
offers practical guidance for industry professionals and explores innovative approaches to sustainable construction.
Focusing on pre-engineered S460 steel sections, the book introduces design equations derived from the Eurocode 4 framework, bridging theoretical knowledge with practical application, to enhance sustainability in heavily loaded and long-spanned industrial buildings.
by Avtandil Mekudishvili, Regional Lead for PlanRadar Singapore + ASEAN
Substantial benefits can be derived.
Southeast Asia’s construction industry is poised for a major transformation, driven by a surge in upcoming projects. The region’s construction market is projected to reach USD 230 billion by 2025, driven by increased infrastructure development and digital adoption.
To address historical challenges such as project delays, high costs and a skilled labour shortage, there is a clear shift towards the adoption of advanced digital technologies, over the past five years – and this is only expected to continue.
The industry is expected to invest USD 7.6 billion in digital transformation technologies by 2025, reflecting a strong shift towards modernisation.
Research from McKinsey & Company indicates that digital technologies, such as Building Information Modelling (BIM), can reduce project costs by up to 20%, by improving design accuracy and streamlining project management, while implementing digital tools like IoT and AI can boost construction productivity by up to 15%, through enhanced project monitoring and predictive maintenance.
Southeast Asia has invested USD 12 billion in green construction technologies, supported by digital tools, for more sustainable development. These digital advancements not only address operational issues but also support the creation of eco-friendly, energyefficient infrastructure, aligning with global sustainability goals.
The role of digital technology in construction
Digital technology is transforming the construction industry, with tools that significantly improve
efficiency, cost-effectiveness and project management. Recent findings from PwC indicate that implementing digital solutions on construction sites can help reduce project delivery times by up to 10%. Digital transformation can also reduce design errors, by 70%, significantly cutting down on costly revisions and delays.
Key innovations include Building Information Modeling (BIM) which offers a detailed digital model, integrating 3D designs, timelines and cost estimates, to enhance coordination, reduce errors and ensure cost efficiency. The Internet of Things (IoT) enables real-time data collection from embedded sensors, improving project monitoring and operational management. Artificial Intelligence (AI) and Machine Learning optimise designs, predict maintenance needs, and enhance safety by analysing data patterns.
Drones and robotics further revolutionise construction by providing high-resolution aerial surveys and detailed inspections, and automating repetitive tasks, thus increasing precision and efficiency.
Augmented Reality (AR) and Virtual Reality (VR) offer immersive design visualisation and realistic training environments.
A primary hurdle, particularly in Southeast Asia, is the initial investment. Adopting advanced digital tools and systems often requires substantial upfront capital for technology acquisition and infrastructure improvements. This financial barrier can be particularly daunting for smaller firms or for projects with limited budgets.
Additionally, integrating these new technologies with existing systems and processes can be complex and resource-intensive. Ensuring seamless compatibility between legacy systems and modern digital tools demands careful planning and execution, to avoid disruptions and inefficiencies. Another critical challenge is the need for comprehensive training and skills development for the workforce. As digital technologies evolve rapidly, construction professionals must acquire new skills and knowledge to effectively utilise these tools. This necessitates ongoing education and training programmes which can be timeconsuming and costly.
Furthermore, data security and privacy concerns are paramount in the digital landscape. With the increased use of interconnected devices and systems, safeguarding sensitive project information from cyber threats and unauthorised access becomes a crucial consideration.
Addressing these challenges requires a strategic approach, balancing the benefits of digital transformation with the practicalities of implementation and security.
Government initiatives and industry collaboration
Government initiatives and industry collaboration are crucial for advancing the digital transformation of Southeast Asia’s construction industry. Key programmes, such as the Singapore Building and Construction Authority’s (BCA) BIM Fund, the Singapore Smart Construction Innovation Programme, Malaysia’s Construction
Industry Transformation Programme (CITP), and the Philippine Construction Industry Roadmap 2020-2030, are increasingly supporting the widespread adoption of ASEAN’s increasing digital transformation.
Digital transformation is expected to bring substantial long-term benefits, including streamlined workflows, reduced errors and
optimised resource use, leading to more sustainable and costeffective construction practices. This modernisation will enhance the quality and speed of project delivery, boost regional competitiveness and align with global sustainability goals.
Research from the World Economic Forum found that digital transformation in the construction industry has the potential to save
Bentley Systems Incorporated, the infrastructure engineering software company, recently announced that it has acquired 3D geospatial company, Cesium.
Cesium is recognised as the foundational open platform for creating powerful 3D geospatial applications and its 3D Tiles open standard has been widely adopted by leading enterprises, governments and application developers, globally. Cesium ion, the company’s SaaS platform, brings 3D geospatial experiences to more than 1 million active devices every month, while Cesium’s opensource offerings have more than 10 million downloads.
Bentley’s iTwin Platform powers digital twin solutions that are used by engineering and construction firms and owner-operators, to design, build and operate infrastructure around the world.
The combination of Cesium and iTwin enables developers to seamlessly align 3D geospatial data with engineering, subsurface, IoT, reality, and enterprise data to create digital twins with user experiences that scale from vast infrastructure networks to the millimetre-accurate details of individual assets – viewed from land, sky and sea, from outer space to deep below the earth’s surface.
The combined power of the two organisations and a shared commitment to openness are expected to provide new opportunities for growth and
up to USD 1.2 trillion annually.
(PlanRadar is a leading platform for digital documentation, communication and reporting in construction, facility management and real estate projects. It enables customers to work more efficiently, enhance quality and achieve full project transparency. Today, PlanRadar serves more than 150,000 users across 75+ countries.)
create greater value for an already flourishing developer ecosystem that ranges from small start-ups to global enterprises.
An example is Komatsu, the largest construction equipment manufacturer in Japan, and the second largest in the world.
The company uses Cesium’s 3D geospatial technology to monitor construction sites globally, track changes over time, compare architectural plans with real-world data, and run precise and near realtime measurements. With Cesium integrated into Bentley, Komatsu gains expanded access to worldleading digital twin technology.
Mr Chikashi Shike, Executive Officer and President, Smart Construction Promotion Division, Komatsu Ltd, said, “Komatsu and Cesium brought novel thinking to the construction industry by leveraging advanced visualisations to deliver more precise insights and enable our customers to make better, more informed
construction decisions. With Cesium as part of Bentley, we can further enrich our Smart Construction digital twins with engineering models, subsurface data, and more, for safer and more efficient construction projects.”
In addition to the widespread adoption of its platform, Cesium is also a leader in promoting open standards, such as 3D Tiles for visualising massive 3D geospatial data. This was adopted as a community standard by the Open Geospatial Consortium (OGC) in 2019.
Mr Peter Rabley, CEO of OGC, said, “As infrastructure sectors become more data-centric, the importance of an open ecosystem will only increase. As the leading voice for open standards and interoperability in the geospatial community, OGC welcomes the ongoing commitment of Bentley and Cesium to solve global challenges through open, interoperable platforms.”
The Viaduct Aesthetic Feature has been completed.
The Johor Bahru – Singapore Rapid Transit System (RTS) Link Project between Singapore and Malaysia is reaching another significant milestone. The Infrastructure Companies (InfraCos) of Malaysia and Singapore will grant RTS Operations Pte Ltd (RTSO) access to the RTS Link civil structures progressively by the end of this year. This will allow RTSO to commence the installation works for the RTS Link rail systems.
The InfraCos, appointed by their respective governments, are responsible for designing, building and maintaining the RTS Link civil infrastructure. RTSO is a jointventure company formed between Prasarana RTS Sdn Bhd and SMRT RTS Pte Ltd, to operate the RTS Link service.
Civil infrastructure progress
On 11 January 2024, then-Prime Minister of Singapore, Mr Lee Hsien Loong and Prime Minister of Malaysia, Dato’ Sri Anwar Ibrahim commemorated the completion of the 17.1 m long connecting span which connects the marine viaduct between Singapore and Malaysia. Both InfraCos have made good progress on the civil structures of the RTS Link, including the stations, tunnels, viaducts and depot.
Works in Singapore are progressing steadily, with more than four-fifths of the overall civil infrastructure works completed to-date. The marine and land viaducts are almost completed, and InfraCo Singapore will be ready to progressively grant RTSO access to the civil infrastructures within Singapore from the end of the year. The remaining works include architectural works, roadworks,
Singapore's infrastructure works.
installation of electrical & maintenance systems, and other key systems such as immigration
gates. These works, which will be carried out in tandem with the rest of the structural works for the RTS
Link, will require close coordination with all relevant parties from Singapore and Malaysia.
In addition, construction works to connect the RTS Link to the existing Thomson-East Coast Line (TEL) Woodlands North station at Basement 1 will begin in 2025. When passenger service commences, this will facilitate seamless connectivity from the RTS Link to the Singapore MRT network.
The railway civil infrastructure works in Malaysia, which encompasses the RTS Link Maintenance Depot, Bukit Chagar Station, terrestrial and marine viaducts, has reached approximately 93% completion. InfraCo Malaysia has granted earlier than scheduled access to RTSO into the RTS Link Maintenance Depot, beginning 30 September 2024, for commencement of trackwork installation and will continue to progressively handover access to the remaining railway infrastructures, from the end of the year.
With that, the focus at the start of next year will be on the fitout and façade installation works for the depot, station and ICQ Complex, as well as the remaining civil, architectural, mechanical and electrical installations, and roadworks.
RTSO is ready to commence installation of the RTS Link rail systems from end-2024 onwards. These include laying the tracks for the RTS Link, as well as the signalling, communications, integrated supervisory control and traction power supply systems.
The railway infrastructure of the RTS Link project is now connected end-to-end from the Wadi Hana Depot in Johor to Woodlands North in Singapore. To commemorate this significant milestone achievement, both the Malaysia and Singapore InfraCos have completed the installation of the Viaduct Aesthetic Feature (VAF), an iconic structure situated near the connecting span along the marine viaduct. It depicts the clasping of hands, which symbolises the close partnership and ties between the two countries.
The RTS Link is a bilateral project between Singapore and Malaysia that involves the close cooperation of multiple agencies on both sides. When completed, the RTS Link will connect Bukit Chagar in Johor Bahru to Woodlands North in Singapore. With a peak capacity of up to 10,000 passengers per hour per direction, it will facilitate the commute between Singapore and Johor Bahru, with a train journey time of about five minutes between the two stations. The RTS Link is targeted to commence passenger service by December 2026.
To facilitate a seamless travelling experience, there will be co-located Customs, Immigration, and Quarantine (CIQ) facilities at both the Bukit Chagar and Woodlands North stations, such that commuters only need to undergo immigration clearance at the point of departure. The RTS Link will improve connectivity, foster people-to-people ties, and generate shared economic and social benefits.
Several solutions are available but they come with challenges and limits.
Construction machinery worldwide emits several hundred million tons of carbon dioxide every year. Since more and more countries, municipalities and companies are aiming for a climate-neutral future, the construction industry is increasingly switching from traditional diesel engines to more environmentally friendly drives. Alternative drives will be one of the main topics at the next edition of bauma.
bauma 2025, the world’s leading trade fair for construction machinery, building material machines, mining machines, construction vehicles and construction equipment, will be held in Munich, Germany, from 7 to 13 April 2025. The event is organised by Messe München GmbH.
Numerous manufacturers and users of construction machinery have already committed to decarbonisation.
The Volvo Group, for example, announced that, from 2040, it will supply only vehicles that are powered entirely without fossil fuels. In the same year, Strabag SE, one of Europe’s largest construction companies, aims to achieve climate neutrality along its entire value chain which includes the operation of its construction machinery.
Electric motors as an established development path
Electric motors can now be considered to be a permanent fixture as a climate-friendly drive for construction vehicles and machines. Whether it was excavators, wheel loaders, rollers, dumpers, or vibratory plates, many exhibitors already presented new solutions from their ever-growing e-portfolio at the previous editions of bauma. This trend looks set to continue. According to a forecast by the analysis and consulting firm,
IDTechEx, the global market for electric construction machinery will be worth USD 105 billion by 2042.
Compact machines with batteries “Battery electric systems are still primarily suitable for compact machines. Their daily energy and power requirements can be covered by an electric motor and a moderately sized lithium-ion battery in conjunction with a welldefined charging strategy,” says Mr Timo Feuerbach, Technical Expert for Construction Machinery and Building Material Machines at the German Mechanical Engineering Industry Association (VDMA).
Current challenges and limits of electrification
“For larger and heavier construction machinery, however, electric drives currently often still reach their technological and, due to the additional costs for electrification, also economic limits,” says Mr Feuerbach.
Added to that are challenges relating to the power supply and the charging infrastructure. For example, the available grid capacity may not be sufficient for the high energy requirements of the e-machines, especially at construction sites in rural or remote areas. Long charging phases, in turn, limit the operating times.
“The industry is currently looking for practicable and affordable solutions to this, for example, by using mobile charging units and fast charging stations, or implementing intelligent energy management systems,” explained Mr Feuerbach.
Hydrogenated vegetable oil as an alternative fuel
It is clear that openness to technology is required for drives that are as climate-neutral as possible, across
the entire spectrum of the construction industry. For example, a life cycle analysis commissioned by the Liebherr Group came to the conclusion that operating mobile cranes with hydrogenated vegetable oil (HVO) promises the greatest potential for reducing greenhouse gases. Other fuel alternatives that can contribute to decarbonising construction sites are biodiesel, biogas and e-fuels.
Hydrogen in combustion engines and fuel cells
Companies and research institutes are also focusing on developing and testing hydrogen-powered construction machinery. The Liebherr Components product segment presented prototypes of two hydrogen combustion engines at bauma 2022, and series production was announced for 2025.
The industry is also exploring potential applications for fuel cells.
For example, General Motors and the construction machinery manufacturer, Komatsu, are working together on a hydrogen fuel cell module for an electric dump truck. Komatsu has also developed a medium-sized hydraulic excavator with a hydrogen fuel cell system, as a concept machine.
Hurdles in extracting and distributing fuel
According to Mr Feuerbach, to really benefit the environment, vegetable oils should, for example, ideally be produced only from plant and food waste, and be widely available. He says that the situation is similar for hydrogen or e-fuels, adding that, alongside producing sufficient quantities from carbon-neutral sources, another prerequisite is also setting up an extensive distribution network.
by Pranav Jaswani, Technology Analyst at IDTechEx
An analysis of various considerations.
There are many facets of electric construction machines, that make them an attractive option for the wider industry. Machines can operate with zero local emissions and can go a long way in assisting a company to reach its decarbonisation goals and create a safer environment for workers. They run with very little noise, which reduces noise complaints and eases communication. In spite of these benefits, IDTechEx’s ‘Electric Vehicles in Construction 2024-2044: Technologies, Players, Forecasts’ report finds that financial savings in the total cost of ownership (TCO) of machines will be the primary benefit that drives the electrification of the industry.
Electric machines run with lower operating costs
Electric construction machines are now sufficiently developed, and achieving performance parity
with diesel is no longer a concern. Instead, potential customers are more engaged with the degree of savings that an electric machine could offer them. These machines can save on two of the biggest components of TCO – fuel and maintenance.
The use of electricity for charging machines instead of diesel fuel can save thousands of dollars per machine per year in operating costs. IDTechEx has calculated that an average 20 tonne excavator will consume 13,000 L of fuel per year – roughly USD 13,000 worth, at global average diesel prices. Charging an electric machine of the same size would cost just over half that, at only USD 6,690 per year (using a global average electricity price of USD 0.15/kWh). This creates huge savings potential for machine operators – as much as USD 75,000 over a full machine service life.
As machines grow in both size and uptime, so do their fuel bills, creating the opportunity for even greater savings through electrification. The regionality of energy prices will make a difference as well. IDTechEx’s estimates for prices in Europe are as much as USD 2/L diesel and USD 0.30/kWh electricity. At these price points, the electric 20 tonne machine will save USD 12,620 a year over the diesel machine. Such considerable benefits should push construction operators in the direction of electric models.
On the maintenance front, electric machines replace mechanical driveline components with electric ones, which have far fewer moving parts and require less general maintenance. This also does away with oil and filter changes, which add cost and downtime to a machine’s schedule. IDTechEx has found that electric
machines can cut maintenance costs by up to 50%, compared to diesel machines. For a 20 tonne excavator, this adds up to nearly USD 15,000 over its lifetime.
Compared to the energy savings from the same machine, maintenance costs will not be the critical factor in the financials of a 20-tonne excavator. However, smaller machines that use less energy (e.g. mini-excavators and compact loaders) do not save as much on fuel, and maintenance will be a more influential source of savings. A 3-tonne electric miniexcavator saves nearly as much in maintenance costs as it does in fuel, compared to an equivalent diesel model.
In areas with emissions charges, often found in city centres, electric machines are not charged for their zero-emission operation, which adds another stream of savings for construction companies to benefit from. For example, London’s Ultra Low Emissions Zone charges GBP 12.50 daily for every high-emitting vehicle.
Many of the emissions charge zones currently in place do not include construction machines in their restrictions, but this is starting to change, and zones that include all emitting equipment are set to become more commonplace. In the future, this will be another significant contribution to machine economics.
With all the savings that they can achieve, why have customers not taken up electric machines en masse? In reality, the industry's relative youth means that electric machines still come at a very high capital cost. This can be quite offputting for many potential buyers, and it must be balanced out by the savings in operating costs, for an EV to be worth the outlay.
The main contributor to high price premiums is the cost of batteries and electric drivetrain components such as motors and power electronics. The relatively
early stage of development of the overall industry means production volumes are quite low, and OEMs are having to spend more on batteries. IDTechEx’s conversations with industry players suggest that battery pricing is now around USD 300/kWh but was as much as USD 500/kWh just a few years ago. OEMs are also looking for a return on their high R&D spending as part of their electric machine development.
As a result, machines come at a high premium, ranging anywhere from 40%-100% added on to the cost of a typical diesel machine, depending on size and machine type. Despite this, the savings generated through operation are great enough to make electric machines cheaper overall on a TCO basis. This applies broadly across all machine types that IDTechEx has analysed, where the electric machine premium can be made up for, within its typical lifetime.
Over the last five years, many machines have been built as retrofits of existing diesel machines. This incurs an additional high cost for retrofitting labour, which shifts the balance of TCO back in favour of diesel machines. IDTechEx estimates roughly USD 60,000 retrofitting cost for a 20 tonne excavator and even more for larger machines. However, the retrofit business model is used far less frequently, as OEMs move production in-house and customers will be able to benefit from the improved TCO.
How will costs and TCO evolve?
As the shift from retrofit to inhouse production continues, OEMs can consolidate their development efforts, which should help bring down costs. At the same time, growing demand for electric machines means OEMs will be able to achieve more significant economies of scale, both in the cost of batteries and other machine components. IDTechEx’s conversation suggests that, with the increased scale of production, OEMs could achieve battery
pricing of USD 200/kWh – still noticeably higher than what is seen in the automotive market, but the lowest that construction machines have seen until now. Battery manufacturers are still working on bringing their own costs down, too, which means the price decline of batteries for construction could continue even beyond this.
In the long run, price premiums of electric machines are expected to drop and incorporate only the cost of its battery pack. This will be achieved when the volumes of production are sufficiently high and OEMs are no longer investing as much into R&D. The additional cost of an electric machine should constitute only that of the relevant electric components – and while motors and power electronics have some associated cost – these are far less expensive than the battery pack which will make up the bulk of the long-term premium.
A drop in upfront cost like this creates even more favourable TCO and should convince more customers to make the switch to electric machines. Many of these potential customers are still more concerned about upfront costs than the overall TCO, so this change may be the one that has the greatest impact on the success of electric construction machines.
The ‘Electric Vehicles in Construction 2024-2044: Technologies, Players, Forecasts’ report, from IDTechEx, presents detailed TCO analysis for a wide range of construction machine types with in-depth scenario analysis.
IDTechEx provides independent research on emerging technologies and their markets. Since 1999, IDTechEx has been helping clients to understand new technologies, their supply chains, market requirements, opportunities and forecasts.
More information can be obtained from www.IDTechEx.com.
Key sectors showed sustained improvement.
Singapore’s Workplace Safety and Health (WSH) performance continued to improve in the first half (1H) of 2024, building on the significant progress achieved in 2023. The annualised fatal injury rate per 100,000 workers held steady at 1.0, maintaining the level first achieved in 2023 (setting aside 2020 when COVID-19 disrupted work). Only four OECD countries – United Kingdom, Netherlands, Sweden, and Germany – have consistently achieved such performance.
The annualised major injury rate for 1H2024 was 16.0 per 100,000 workers, which is consistent with the rate recorded in 2H2023 (16.1) and shows an improvement from 1H2023 (17.4).
Improved safety performance for key sectors
Construction, Manufacturing, and Transportation & Storage remained the top three contributors to fatal and major injuries in 1H2024. However, the total proportion of fatal and major injuries attributed to these three industries decreased from 63% in 1H2023 to 54% in 1H2024, driven by sustained improvements in Construction and Manufacturing.
The Construction sector remained the largest contributor to fatal and major injury incidents (26%), with the number of fatal and major injuries at larger-scale construction sites increasing slightly from 28 in 1H2023 to 31 in 1H2024. Nonetheless, this remains significantly lower than the 43 in 1H2022.
The Multi-Agency Workplace Safety and Health Taskforce (MAST) has further strengthened WSH standards in the Construction sector with additional Safety Accountability,
Focus and Empowerment (SAFE) measures implemented in early to mid-2024. These include enhanced WSH requirements for public sector construction and constructionrelated projects (implemented in April 2024), and mandatory video surveillance systems for construction worksites with contract values of SGD 5 million and above (implemented in June 2024).
The Manufacturing sector also saw a substantial reduction in the number of fatal and major injuries, from 92 in 1H2023 to 60 in 1H2024. This progress was likely due to more rigorous inspections and the Demerit Point System implemented in October 2023.
Enforcement efforts to continue MOM has stated that it will not let up in the enforcement efforts. For the first half of this year, MOM conducted more than 3,000 inspections across various industries, including higher-risk industries such as Construction, Manufacturing and Marine.
Aside from general workplace safety, there were also targeted inspections focusing on priority areas – slips, trips & falls; machinery safety; and falls from height. MOM took enforcement actions for more than 7,000 breaches under the WSH Act and Regulations, which included imposing 673 composition fines amounting to more than SGD 1.3 million and the issuing of 22 Stop Work Orders. These actions were meted out to errant companies found to have contravened rules put in place to protect workers.
Imperative for all employers and workers to remain vigilant
The encouraging WSH performance in the first half of 2024 reflects the collective efforts
of all stakeholders in pursuing a culture of WSH excellence. MOM has called on employers and workers to remain vigilant and prioritise WSH, particularly in light of recent fatal incidents in the Construction and Marine industries. MAST will continue to explore ways to further enhance WSH across all sectors.
Enhanced safety measures for higher-risk machinery and combustible dusts
The Multi-Agency Workplace Safety and Health Taskforce (MAST) will be introducing enhanced measures to strengthen workplace safety and health (WSH) standards for higher-risk machinery and combustible dust. These measures will come into effect on 1 January 2025.
‘Higher risk machinery’ refers to industrial machinery having a higher propensity to cause serious injuries. The identified list of industrial machinery will be added in the Fifth Schedule of the WSH Act.
In 2023, machineryrelated incidents accounted for about 14% of fatal and major injuries, with about 60% of these cases in the Manufacturing sector. Combustible dust hazards also pose a significant risk of fire and explosion. To address these risks, MOM is introducing enhancements aimed at improving compliance and accountability throughout the supply chain.
The upgrading works involved repairing cracks and applying a coating with a high reflectance index.
The almost 600 m long Golovec Tunnel is located on the ring road to the east of Ljubljana, Slovenia, along the stretch of the A1 motorway running between Bizovik and the Malence interchange.
Very little maintenance work was done in the tunnel, after its completion in 1999 until, in 2020, complex renovation work was carried out on both tubes of the tunnel to remediate damage caused by wear, in general, and the penetration of rainwater which was also due to the specific characteristics of the soil.
Mapei d.o.o., the Group’s Slovenian subsidiary, played a part in the project by supplying the company’s solutions and products to renovate the coating on 9,500 m2 of internal concrete surfaces. The new coating, applied at a height of 4 m, extends for the entire length of the two tubes and protects the concrete surfaces from the penetration of aggressive substances and the effects of the weather. The coating also has a high reflectance index, thereby improving visibility and safety.
Preparation of the substrates
To guarantee sufficient adhesion for the new protective layer, the old finish and mortar, applied in the past, had to be completely removed, to make sure that the concrete surfaces were flat and even.
The next step was to blast the surfaces with water at high pressure, using robotic cleaning machines. In the areas where it was not possible to clean the surfaces with this method, they were abraded manually with diamond discs.
All the badly damaged areas of concrete were reintegrated, with MAPEGROUT T60 fibre-reinforced,
shrinkage compensated, sulphateresistant thixotropic mortar, ideal for concrete repairs. Because these areas were small, the mortar was applied by hand, with trowels.
The cracks in the concrete surfaces were sealed with EPOJET LV twocomponent, low viscosity epoxy resin which was injected with IDROSTOP MULTI ST12 metal packers, until the cracks were completely filled.
Levelling and finishing the internal surfaces
Before applying the final finish, all the surfaces were skimmed with TRIBLOCK FINISH three-component, thixotropic epoxy-cementitious mortar to create an even, compact, waterproof layer resistant to abrasion.
After applying two layers of this product, the surfaces in the tunnel were finished off with MAPECOAT W HRI two-component epoxy paint in water dispersion. This type of paint is easy to apply, either by spray, brush or roller. In this case, it was applied in two coats, using a roller.
Thanks to its chemical composition, it guarantees long-lasting protection for concrete surfaces against external agents, a high level of cleanability and a high reflectance index – characteristics that help improve visibility and safety when driving through the tunnel.
The renovation work also included an upgrade of the ventilation, lighting and safety systems. The Golovec Tunnel is the first one on the Slovenian motorway network to have modern LED lighting which guarantees efficient energy savings. It also has an automatic traffic control system which allows any incident to be monitored accurately.
All these features, together with the high quality materials used to renovate the coating inside the tunnel, will help to ensure that high safety standards are maintained in the years to come.
After preparing the substrates, sealing the existing cracks and repairing portions of deteriorated concrete, the internal surfaces were skimmed with TRIBLOCK FINISH mortar and protected with MAPECOAT W HRI epoxy paint.
Project
Golovec tunnel, A1 motorway, Bizovik- Malence, Slovenia
Period of construction 1990s
Owner
DARS d.d.
INTERVENTION BY MAPEI
Period of the intervention 2020-2021
Supervision
DRI Investment Management Ltd
Contractor
Kolektor CPG d.o.o.
Application of Mapei products
Concrete repair – MAPEGROUT T60
Sealing cracks – EPOJET LV, IDROSTOP MULTI ST 12
Smoothing concrete surfaces –TRIBLOCK FINISH
Finishing concrete surfaces –MAPECOAT W HRI
Website for further information www.mapei.com/sg www.mapei.sl
(Some products are available in Singapore. Please contact customer service at Mapei Far East for the available products.)
Doka Singapore is past the halfway point for its work on three stations and a viaduct on the Jurong Region Line (JRL), Singapore’s seventh MRT line. The stations, which include Toh Guan (JE4), Jurong Town Hall and Pandan Reservoir, are part of a wider project that involves the design, site supervision, assembly and installation of Doka’s proposed solution. Once complete, the Jurong Region Line will significantly improve the connectivity and development of the area which is set to become the largest commercial hub outside of the Central Business District. As a result, commuters can expect to be connected to key activity nodes, such as the Jurong Industrial Estate, Jurong Innovation District and the Nanyang Technological University (NTU Singapore).
Working with joint-venture main contractors, DaewooYongnam, and subcontractor, SAE&C, Doka faced numerous logistical challenges, given the project site’s heavily built-up area, live traffic from the fourlane Jurong East Central Road, and its proximity to an existing MRT line.
With the Toh Guan Station requiring 10 cross-heads spanning the highway, Doka’s first challenge was to deliver a solution that allowed the crosshead installation to proceed without interfering with the traffic below. By assembling a Steel Girder Formwork system 3 km away, offsite, the Doka team was able to complete the majority of the work away from the job site, before installing the system in combination with its heavy-duty shoring system, UniKit, via truck and crane,
Following just one night of road closures, Doka’s Steel Girder Formwork and UniKit shoring tower ensured a key stage of the Toh Guan Station was completed on time and on budget. Image: Doka.
resulting in just one overnight road closure.
Serving the dual purpose of truss support and wall formwork, the Steel Girder Formwork also ensured a minimal footprint, as the formwork was supported only at the centre area around the column.
Complete with integrated walkways on both UniKit shoring towers and the Steel Girder Formwork, Doka ensured the safety of site teams throughout the project. Aside from completing the work with minimal disruption, this was also the first time Doka’s Steel Girder Formwork system had been used outside of North America and the first time UniKit had been used in Singapore.
Having started the project in February 2024, Doka’s portion of the project is expected to be handed over by January 2025. Upon completion, the JRL will connect more than 60,000 households in the Jurong area within a 10-minute walk from a train station, while its three interchange stations will enhance connectivity to the existing rail network.
They are innovative and sustainable.
The Metrodom Green project, located in a redeveloped district of Budapest, Hungary, is a residential development known for its premium quality, sustainability and innovative technical solutions.
The 513-apartment complex is being developed in two phases. The first phase, comprising 277 apartments, is currently under construction and will take approximately two and a half years to complete.
The most characteristic feature of the building is the green façade which extends from the 5th to the 10th floor, where pre-planted plants are grown in a nursery and maintained by a watering system in front planters. A 36 m high scaffolding system covering a total of more than 12,000 m2 was required in order to construct the façade.
Due to the unique design of the green wall panels and the challenging anchoring requirements, PERI was chosen to provide compatible scaffolding solutions that met the specific requirements. Due to the complex layout, the PERI UP Scaffolding Kit is being used to facilitate an efficient construction process over a period of 13 months, with a second phase of a similar scope to follow.
Anchoring challenges and compatibility
The project team faced several difficulties, including a complex layout, special anchoring characteristics and metal trusses on almost every vertical surface. The main challenge was the prefabricated structure of the green wall panels on the façade, which limited the number of scaffold anchoring options.
To overcome this difficulty, PERI engineers developed a solution to
anchor the façade scaffold directly to the modular scaffold erected between the balconies, thus providing the required stability and safety. Another challenge was the high demands on the load-bearing capacity of the scaffolding and the height of 36 m to which it has to be erected.
However, the components of the PERI UP Modular Façade Scaffold made it possible to manage this requirement.
Innovative scaffolding technology for a modern complex
PERI engineers provided detailed 3D drawings for the scaffolding plans. These visualisations gave the scaffolding contractor a deeper and more vivid insight into the proposed solutions. Not only the 3D design, but also the on-site training and ongoing site support were key factors in enabling the customer to realise this project successfully.
Versatile scaffolding solution
A total of 19,000 m3 of modular scaffolding is being erected
between the balconies and in the lobbies. The project required flexible scaffolding solutions, which were achieved thanks to the modular design and adaptability to the specific building environment. In this case, a wide range of ledges and decks allowed the direction of the decks to be varied during assembly, to suit the specific geometries.
The Metrodom Green project exemplifies how advanced scaffolding technology can facilitate the implementation of sustainable architectural solutions. Effective use of the PERI UP Scaffolding System not only enables safe and efficient construction, it also plays a pivotal role in creating an environmentally responsible façade. This project exemplifies innovation and sustainability.
Contractor
MTB Industrial Ltd, part of MTB Group, Hungary
Field Service PERI Hungary
A solution has been developed to enable the renewal of old railway tunnels.
Two Tunnel Enlargement Systems (TES) from Herrenknecht have been in use, since January 2024, for the renewal of Deutsche Bahn tunnels near Limburg an der Lahn, in Germany. The 160-year-old tunnels will thus be renovated while rail service continues. The 426 m long Fachingen Tunnel and the 732 m long Cramberg Tunnel are part of the Lahn Valley Railway connecting the cities of Koblenz and Wetzlar.
In Austria, Switzerland and Germany, alone, around 800 tunnels were built between 1850 and 1910. They are now getting on in years. In order to electrify the lines, accommodate larger track gauges and faster trains, comply with current safety standards, or replace the tunnel linings that have aged, it is necessary to enlarge the tunnel profile.
The Tunnel Enlargement System (TES), developed by Herrenknecht, makes it possible to carry out tunnel renewal during ongoing rail operation. First the existing tracks are dismantled and a track is laid in the middle of the existing tube, instead. Rail traffic will continue to run safely on this track throughout the entire construction period.
The TES moves forward, step by step, during excavation for the widening of the tunnel. At the same time, it serves as a protective enclosure and separates the construction work from ongoing rail traffic.
For the two double-track tunnels of the Lahn Valley Railway, the radius of the tunnel cross section will be enlarged by a good 2 m, thus achieving dimensions corresponding to current new tunnels. The approximately 46 m long, 270 tonne TESs with a diameter of around 12 m, for for the Fachingen and Cramberg tunnels, run on foundations and rails specially laid in the tunnel.
The TESs are equipped for conventional excavation and
support work. Depending on the hardness of the rock, excavation is done by chiselling or blasting. First, the old tunnel walls, usually masonry, are broken out. This is followed by excavation of the rock, by chiselling or blasting and removal of the material. The excavated material falls to the side of the machine into the tunnel invert and is removed by separate conveyor and loading equipment.
After each drilling and blasting round, a shotcrete manipulator applies the temporary shotcrete support. The rock is also stabilised with anchors. Reinforcement mesh and steel arches together with the shotcrete and anchors form the initial support. Once tunnelling with the TES has been completed, the final lining of the tunnel, using in-situ concrete, is carried out in a second construction phase.
The TES consists of three parts. The front part of the machine is used for pre-excavation protection. It prevents the existing tunnel from collapsing in the area ahead of the respective excavation work, or rock falling onto the tracks.
The middle section is the carrier for the equipment required for tunnelling – telescopic drill rigs on both sides, and a hydraulic impact hammer on a central boom with a large radius of action, shotcrete system on a ring guide. The machine has large, retractable working platforms that allow the
workers to safely reach the tunnel face and the intrados.
The equipment for operating the TES is located in the rear part of the machine. This includes a hydraulic station to supply the hydraulically driven equipment, a compressor for the supply of compressed air, the electrical system, and material storage equipment.
The design of the TES used on the Lahn Valley Railway incorporated the consortium’s experience from previous projects and that of Herrenknecht from the use of a first TES in Spain.
PROJECT DATA
Fachingen Tunnel and Cramberg Tunnel
Client DB InfraGO AG
Contractors
Consortium comprising:
Porr GmbH & Co KGaA
Feldhaus Bergbau GmbH & Co KG
Heinz Schnorpfeil Bau GmbH
Application
Tunnel renewal, tunnel widening under ongoing rail operation
Drive lengths
Fachingen Tunnel - 426 m
Cramberg Tunnel - 732 m
Geology
Clay schist
Boring technology
Machine type - 2x Herrenknecht TES
Boring diameter - 12,060 mm each
Weight - 270 t each
Liebherr’s new 440 HC-L luffing jib crane is a response to ever faster construction site cycles. This evolution of its successful predecessor, the 357 HC-L, comes with improved performance values and is available in two versions –the 440 HC-L 12/24 and the 18/36. The maximum lifting capacity of the 440 HC-L 18/36 has increased from 32 tonnes to 36 tonnes. It has also been possible to raise the tower height of both crane versions by one tower section, compared to the previous model.
The new 440 HC-L requires very little space for a crane of its size – an out-of-service position of up to 10.7 m or a minimum working radius of less than 4 m is possible. In practical terms, this means that the crane can be set up closer to buildings, property boundaries or another luffing jib crane, which makes site planning easier. Depending on the situation, the out-of-service position makes it possible to accommodate and operate an additional crane on site.
This is the first time aramid fibre guying is being used for a luffing jib crane. The lightweight material reduces the weight on the jib, resulting in a higher lifting capacity. Significant weight is saved compared to the use of steel ropes. Dead load can consequently be transformed into load capacity. An aramid fibre guying system also offers advantages for crane assembly and disassembly, owing to its lighter weight. Aramid fibre
has already proven itself and has become an established material with other Liebherr Group cranes, including crawler and maritime cranes.
The 440 HC-L requires only one central switchgear cabinet. Electronic components are arranged in a plug-and-play setup, which significantly reduces assembly time.
Assemblies are pre-assembled at the factory, prior to the crane being delivered, thereby optimising transport costs and enabling the crane to be unloaded more quickly on site. The counter-jib ballast, which consists of a single block, also contributes to faster assembly and disassembly. Only nine transport units are needed for the slewing section at full jib length, including its counter-ballast.
The 440 HC-L’s maximum radius has increased to 65 m and its jib head lifting capacity has increased by up to 52% . The jib can be extended in 5 m increments. Thanks to Load Plus, performance can be increased by up to 22%, at the touch of a button. With a 50 m jib, for example, the maximum jib head lifting capacity increases from 7.5 tonnes to 9 tonnes. Tower heights have also been significantly improved. The free-standing height has been increased by up to 5.8 m. The maximum assembly height (freestanding) measures in at up to 76.4 m. This makes planning the climbing steps more flexible.
The luffing jib crane is available with Liebherr’s own drives and the latest TC-OS control unit for simple crane operation.