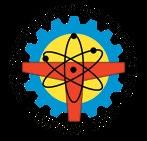
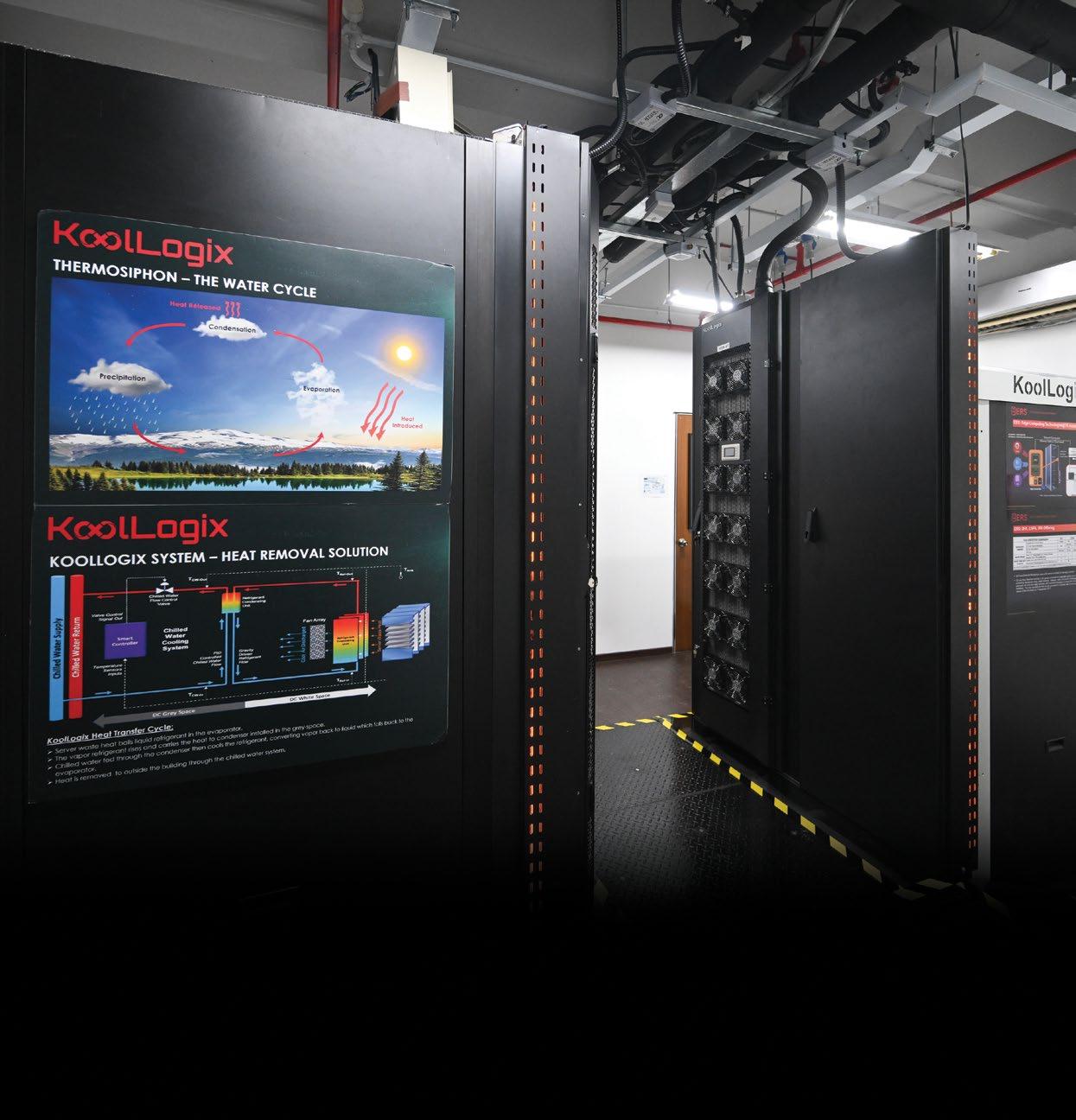
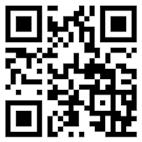
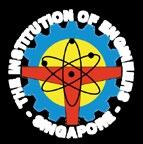
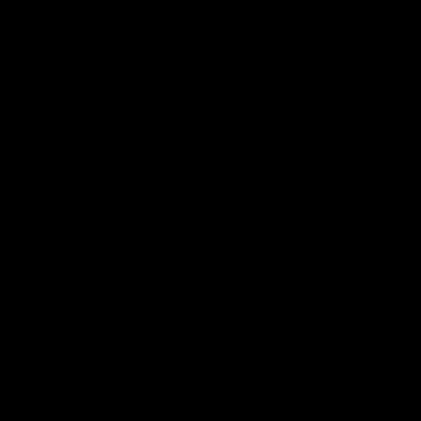
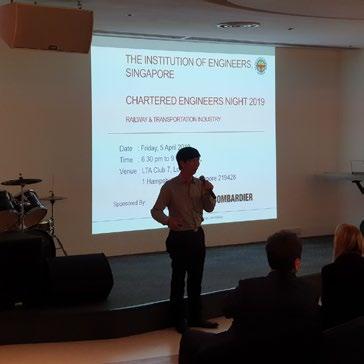
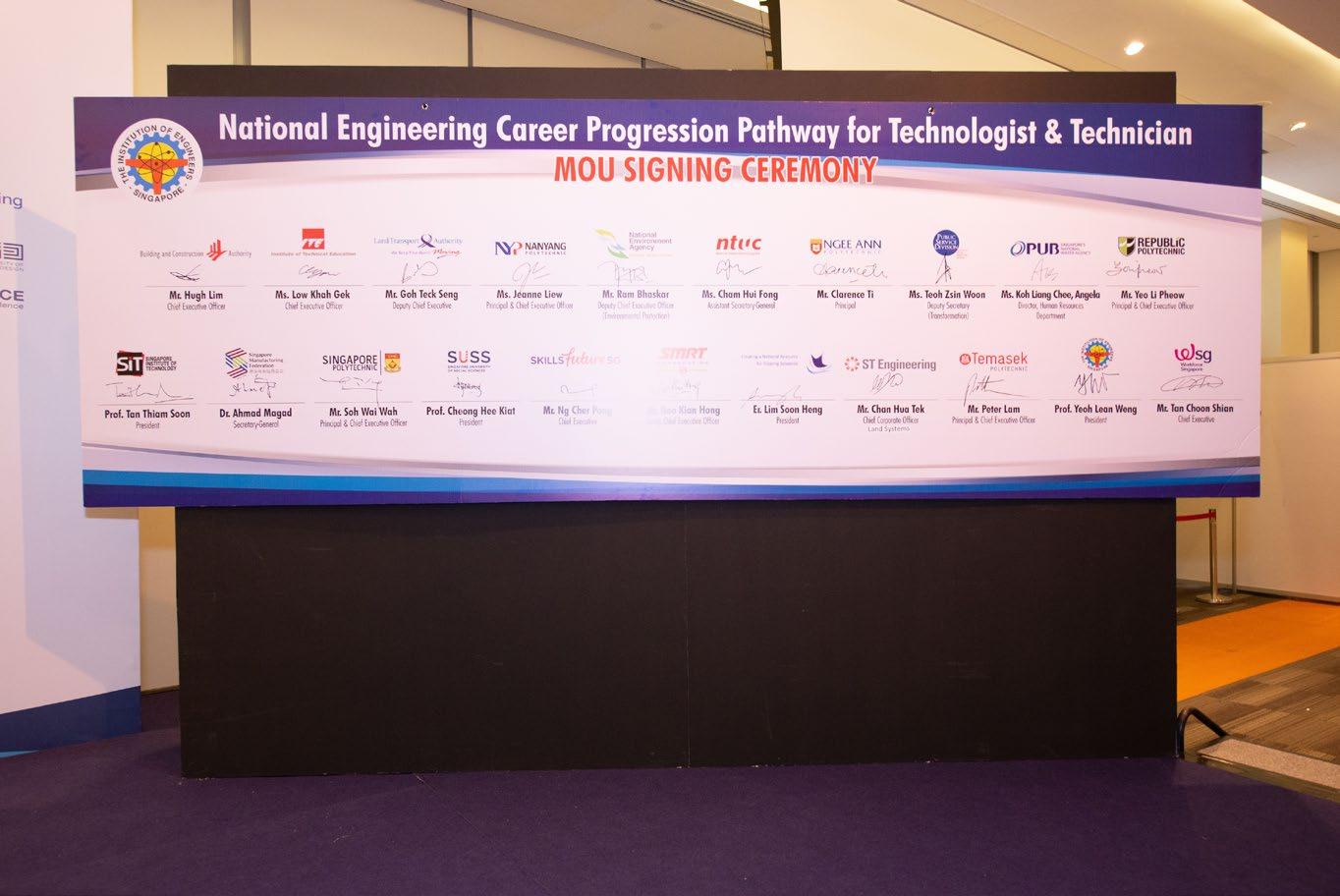

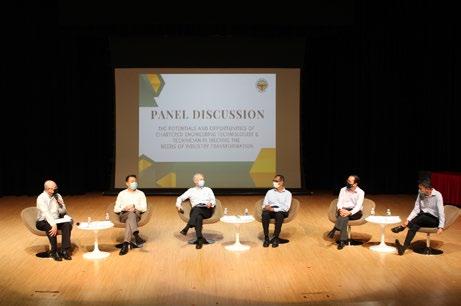

The Chartered Engineering Registry aims to provide professional recognition to qualified Engineers, Technologists and Technicians across all sectors.
Being registered as a Chartered Engineering Professional will be an external validation of your experience, expertise and practising competence; and is a quality mark to differentiate your professional standing in the following sectors of engineering:
06 Bhutan appoints leaders to propel Gelephu Mindfulness City to global prominence
08 SAP announces further investment in its Digital Innovation Accelerator in Singapore
09 Bringing advanced microcontrollers to next generation software-defined vehicles
10 New lab to develop cooling solutions for AI and GPU-driven data centres
12 Vapour compression cycle-based air conditioning/ cooling systems and their energy optimisation
18 Panasonic VRF systems in Singapore
20 The future of HVAC management
CENTRES
21 Innovations in critical digital infrastructure
President Er. Chan Ewe Jin
Chief Editor T Bhaskaran t_b_n8@yahoo.com
Publications Manager Desmond Teo desmond@iesnet.org.sg
Publications Executive Nuraini Ahmad nuraini@iesnet.org.sg
Editorial Panel
Dr Victor Sim
Dr Chandra Segaran
Dr Ang Keng Been
Dr Aaron Sham
Mr Jaime Vega Bautista Jr
Mr Soon Ren Jun
Media Representative Trevor Teh IES@mnc-link.com
Cover designed by Irin Kuah
Cover image by KoolLogix-A*STAR
The Hi-Flo Next Generation bag filters have been developed with performance and sustainability in mind. Performance means long service life, low energy consumption and stable filtration efficiency throughout its lifetime.
Extended operating life with the best Total Cost of Ownership (TCO)
Lowest energy consumption and initial pressure drop
Reduced energy consumption
12% vs old Hi-Flo generation 30% vs industry average
Superior indoor air quality
Particle efficiency meets requirements according to the European Standard EN779 and ISO16890 for indoor air quality (IAQ)
Reduced labour cost
25-50% Longer filter lifetime, compared to synthetic bag filters
Improved air flow
Conical and tapered pocket shape allows better airflow through the filter
Optimised design for high performance Fully incinerable with the plastic frame
Using Camfil Life Cycle Cost (LCC) Analysis software, our experts conduct a comparative analysis of different air filters to provide you with a comprehensive report on potential savings.
Camfil offers a complimentary Life Cycle Cost analysis and supports you in selecting the right air filter solution.
SCAN THE QR CODE to complete the survey. Accuracy is subject to information provided.
24 Automated and digitised production of cylindrical battery cells
28 Machining medical device components
COMPANY PROFILE
29 Yokogawa marks 50 years in Singapore
PROJECT APPLICATION
32 Digital monitoring solution for Finnish hospital’s power supply
33 Technology for data centre in Estonia
34 Lighting solutions for night-time motor racing events
36 The potential of lighting for a better world
39 Apollo Quad Handler launched for semiconductor testing
40 Keysight expands signal generator portfolio with new solutions
The Singapore Engineer is published monthly by The Institution of Engineers, Singapore (IES). The publication is distributed free-of-charge to IES members and affiliates. Views expressed in this publication do not necessarily reflect those of the Editor or IES. All rights reserved. No part of this magazine shall be reproduced, mechanically or electronically, without the prior consent of IES. Whilst every care is taken to ensure accuracy of the content at press time, IES will not be liable for any discrepancies. Unsolicited contributions are welcome but their inclusion in the magazine is at the discretion of the Editor.
The use of Al technology in HVAC systems opens up a new era of thermal comfort. offers a comprehensive answer to the question of how to keep an indoor space comfortable and its occupants as productive as possible.
In a significant move, His Majesty the King of Bhutan has appointed Liew Mun Leong as CEO to lead the groundbreaking Gelephu Mindfulness City (GMC) in the Kingdom’s Special Administrative Region.
His Majesty, Chairman of the Board of Directors (BOD) of the Mindfulness City, concurrently appointed Liew to the BOD, alongside Joichi ‘Joi’ Ito, Pang Yee Ean, Lee Seow Hiang, Arun Kapur and Lauren Chung. Further additions to the Mindfulness City BOD will be announced. His Majesty also named Ito as Chairman of the Gelephu Investment Development Corporation (GIDC).
With decades of global experience in their fields, these leaders will work with Bhutanese peers and
international partners to establish GMC as a beacon of mindful development, blending cuttingedge infrastructure with Bhutanese values, to drive sustainable, transformative growth. Announced by His Majesty in December 2023, Gelephu Mindfulness City is a global economic hub designed to reframe core principles of economic and social development.
Liew Mun Leong will lead the charge, based on his extensive experience at the helm of international investment and development projects. He has a solid track record in urbanisation, airport development and infrastructure, garnered through planning and executing groundbreaking projects across global markets, in leadership roles with CapitaLand, Changi Airport
Group and Surbana Jurong Group. As founding President and CEO of CapitaLand Group, he grew the publicly listed company to USD 12 billion in market capitalisation and expanded its footprint to more than 20 countries, making it Southeast Asia’s largest real estate group. His leadership at Changi Airport Group saw the creation of the globally recognised Jewel Changi Airport, among other developments.
This positions Liew well to steer GMC’s strategic vision, infrastructure projects and global investments. A core focus of his mandate will be capacity building, developing Bhutanese talent in preparation for future leadership succession of the Gelephu Mindfulness City team.
Commenting on his appointment, Liew said, “I am deeply honoured
to be entrusted with this leadership role and thrilled to build the team that will bring Gelephu Mindfulness City to life. This project will redefine sustainable urban living, and I am eager to collaborate with a diverse team of bright, passionate professionals to realise His Majesty’s vision. Together, we will create a truly unique city that embodies Bhutanese values while shaping the future of mindful economic growth.”
Joichi ‘Joi’ Ito has concurrently taken the role of Chairman of the Gelephu Investment Development Corporation (GIDC). Ito will work with Bhutanese and international peers to facilitate investment and economic growth and development for enterprises in Gelephu Mindfulness City SAR, other areas of Bhutan and globally.
This will include working to enhance digital connectivity for the Mindfulness City and the Kingdom and driving investment in green energy sources such as hydropower and solar. At the same time, GIDC will foster the establishment and growth of technology industries to utilise carbon-free power, including data centres and artificial intelligence (AI) companies.
Ito is uniquely qualified for this mandate, based on extensive technology sector experience. His current role as President of Chiba Institute of Technology and previous position as Director of the Media Lab at the Massachusetts Institute of Technology (MIT) puts him at the forefront of research and development, in areas such as green energy, AI, web3 and Blockchain.
Similarly, his work with The Digital Society Council of the Digital Agency of Japan and international organisations, such as The Mozilla Foundation and The Electronic Privacy Information Center (EPIC) means that he brings a broad network of relationships with him. Ito commented on his appointment, saying, “Gelephu Mindfulness City and the Kingdom of Bhutan are trailblazers in environmentally responsible and mindful development, based on abundant green energy sources;
entrepreneurs pushing boundaries in areas such as AI, blockchain and drone development; and commitment to harnessing technology to improve the human condition.”
Pang Yee Ean joins the BOD with a strong investment track record in greenfield and infrastructure development across Asia, with a USD 6 billion portfolio, a significant portion of which is dedicated to renewable energy. He is currently focused on social sustainability investments. As the Founder and Director of Urbina Capital, former CEO of Surbana Jurong Capital and Director General of Operations at the Asian Infrastructure Investment Bank, his expertise will guide Gelephu’s alignment with triple sustainability investment strategies, working to ensure economically, socially and environmentally responsible development.
Lee Seow Hiang, former CEO of Changi Airport Group, brings deep insights into urban development and international connectivity to the BOD. Having overseen the rise of Changi Airport to global prominence – the transportation hub has been named the World’s Best Airport multiple times – his deep understanding of the interplay between government and the private sector in the pursuit of infrastructure development and economic growth will be pivotal in ensuring Gelephu Mindfulness City’s competitiveness as a regional economic hub.
Arun Kapur, who led the establishment of the Druk Gyalpo’s Institute (DGI) at Paro, Bhutan, contributes deep understanding of training and education systems to the BOD. He will play a key role in upskilling Bhutanese talent to take leading roles in private and public institutions in the Mindfulness City. Prior to his work with DGI, Kapur held leadership positions with some of the highest ranked schools across India, including as Principal of The British School and Headmaster of the Vasant Valley School, both in New Delhi, and as Executive Director of Learn Today, headquartered in
New Delhi.
Lauren Chung, Asia Pacific CEO of Teneo, the global CEO advisory firm, brings significant expertise in international relations and communications strategy to the BOD. Lauren is a trusted advisor to corporate boards, CEOs, investors, governments and civil society leaders, helping them achieve strategic goals while navigating high-stakes economic, geostrategic, regulatory, media, social, technological and environmental change. She will provide guidance on the necessary communications infrastructure and skills development to support the Mindfulness City’s global stakeholder engagement.
The new appointees recently attended the opening session of the Bhutan Innovation Forum in Paro, Bhutan, where Bjarke Ingels, Founding Partner & Creative Director of Bjarke Ingels Group (BIG), presented the concept masterplan for GMC.
Together, these development, technology and education pioneers will lay the foundation for Gelephu Mindfulness City to emerge as a global model of economic and social development, in harmony with the human spirit and the environment. As Bhutan embarks on this visionary journey, it continues to seek likeminded, visionary professionals to join this pioneering initiative, driving forward a new era of growth and mindfulness for the Kingdom and beyond.
The Gelephu Mindfulness City (GMC) project is a pioneering initiative, creating an urban environment centred around mindfulness, sustainability and innovation. The city will integrate traditional Bhutanese values with cutting-edge design and technology, harnessing the Kingdom’s abundant green power to serve as a global exemplar of holistic development. The GMC will operate as a Special Administrative Region (SAR) vested with executive, legislative and independent judicial power.
SAP, a global leader in enterprise applications and business AI, recently announced the expansion of its Digital Innovation Accelerator in Singapore.
Supported by the Digital Industry Singapore (DISG), SAP will invest SGD 12 million in the Singapore-based Digital Innovation Accelerator, first launched in 2019. The investment will focus on developing practical applications of artificial intelligence (AI) in industry-specific scenarios, initially focusing on advanced manufacturing, financial services, and travel and logistics services.
Digital Industry Singapore (DISG) is an alliance between the Singapore Economic Development Board (EDB), Enterprise Singapore (EnterpriseSG) and Infocomm Media Development Authority (IMDA), leading tech industry development in Singapore.
Since 2019, SAP has committed almost SGD 300 million to developing Business AI and other deep tech in Singapore. This includes establishing Southeast Asia’s first SAP Labs in 2022, and Asia’s first innovation centre for experience management (XM) in 2023.
SAP Business AI is built into the SAP applications that power critical business processes for customers across Asia Pacific and Japan. It comprises a range of AI innovations developed using extensive industryspecific data and deep process knowledge.
Announcing the expansion, Ms Eileen Chua, SAP Singapore Managing Director, said, “Singapore is significantly investing to futureproof its citizens and businesses through initiatives like the National AI Strategy, workforce development programmes like SkillsFuture, and its Net Zero ambitions. SAP’s vision to boost local research and innovation will only strengthen the ongoing mission to sharpen Singapore
organisations’ competitive advantage on the global stage.”
“Co-innovation initiatives like our Digital Innovation Accelerator are aimed at enabling SAP and our customers to rapidly scale digital transformation by tapping into our global expertise and ecosystems. Over the past five years, we have co-developed solutions with more than 80 Singapore enterprises, achieving tangible impact in their business processes and international growth,” Ms Chua added.
Commenting on the announcement, Mr Philbert Gomez, Executive Director & Head, Digital Industry Singapore (DISG), said, “SAP has been a longstanding partner in developing Singapore’s digital ecosystem. The Digital Industry Singapore (DISG) supports the adoption of AI across industries to increase the competitiveness of businesses. We are delighted to partner with SAP in the expansion of its Digital Innovation Accelerator, which will work with industry leaders to develop, prototype and scale AI solutions to advance their sustainability goals from Singapore.”
The expanded SAP Digital Innovation Accelerator will see industry leaders work with a dedicated team of in-house SAP business architects, data experts and developers, to develop unique AI use cases tailored for their unique business scenarios.
The Accelerator team will also focus on sustainability, aiming to create positive climate action outcomes through the application of AI and SAP’s sustainability solutions for use cases like environmental monitoring and reporting, and optimising supply chains.
Commenting on the decision to work with SAP’s Digital Innovation Accelerator team, Mr Khoo Boo
Hor, CEO and Executive Director of precision plastics manufacturer, Sunningdale Tech, said, “SAP’s new industry-focused AI development initiative comes at a timely moment for Sunningdale, as we continue to drive long-term sustainable growth. We expect AI-driven solutions to help us make predictions and forecasts with greater accuracy and reduce overproduction and machine underutilisation.”
“We also hope to leverage artificial intelligence to enhance our analysis and usage of corrugated boxes as we strive to reduce wastage across our operations,” Mr Khoo added.
“While AI is only just starting to be applied to climate-related scenarios, leading organisations are already demonstrating the promise of AI for climate impact and delivering results. Combined with SAP’s sustainability solutions, these initiatives aim to support Singapore to achieve Net Zero by 2050,” said Ms Chua.
Bolstering talent pipeline with AI courses
Over the past five years, SAP has collaborated closely with the Singapore Government, under the SkillsFuture programme, to support and upskill over 1,000 mid-career professionals to teach practical and hands-on digital skills.
SAP has also invested in and launched eight free AI foundational courses, and plans to introduce certification courses on Business AI.
“These new, on-going and upcoming initiatives are testament of SAP’s continuous commitment to build Singapore’s digital and technology capabilities across all sectors and levels of the economy, from shaping budding talents to transforming mature enterprises. We look forward to extending our long-term partnership with Singapore to build the future of AIenabled enterprises,” said Ms Chua.
Siemens Digital Industries Software has announced an ongoing collaboration with Infineon to combine Siemens’ embedded automotive software platform, based on the AUTOSAR Classic platform R20-11, with Infineon’s AURIX TC4x microcontroller. This helps automotive OEMs achieve production readiness to deliver the next generation of capabilities required by Software-Defined Vehicles (SDV).
In the automotive industry, the growing demand for autonomous driving, ADAS, electrification, passenger comfort and entertainment, requires more computational power, functional safety and cybersecurity. To achieve this, more advanced microcontrollers (such as the AURIX TC4x) along with intelligent software platforms that fit into the system development flow, are becoming mission critical.
Siemens’ embedded software team and Infineon worked with the lead customer, BMW, to achieve production-ready, embedded ECU (Electronic Control Unit) software. In addition, Siemens and the OEM have collaborated to implement a
cloud-based software development process for SDVs, using Siemens’ advanced embedded software development tools.
“Our collaboration with Infineon is long established and highly successful, providing leading automotive customers with advanced microcontrollers running AUTOSAR-based embedded software to help drive the future of the software-defined vehicle industry,” said Ms Frances Evans, Senior Vice President, Lifecycle Collaboration Software, Siemens Digital Industries Software.
“The first production-ready implementation of the AURIX TC4x demonstrates how a more consolidated, holistic approach helps the SDV industry to deliver the advanced features customers demand,” Ms Evans added.
“Infineon has contributed to the AUTOSAR standard since 2004 and provides AUTOSAR solutions for its microcontroller portfolio like the AURIX TC4x. Our collaboration with Siemens Digital Industries Software focuses on delivering advanced microcontrollers equipped with AUTOSAR-based embedded software to empower OEMs in
Epicor, a global leader in industryspecific enterprise software designed to promote business growth, recently announced that it has been positioned by Gartner as a Leader for the second consecutive year in the 2024 Gartner Magic Quadrant for Cloud ERP for ProductCentric Enterprises, based on completeness of vision and ability to execute.
“We are incredibly proud to be recognised once again as a leader for our commitment to empowering essential industries
with cloud ERP solutions,” said Steve Murphy, CEO of Epicor.
“This recognition reaffirms our dedication to innovation and helping businesses across the make, move, and sell industries operate with greater agility and resilience, to drive productivity and growth,” he added.
According to Gartner, “Cloud ERP solutions encompass technologies that support operational and financial business capabilities. Buyers of cloud ERP solutions are focused on replacing legacy capabilities while acquiring
driving the future of the softwaredefined vehicle,” said Mr Thomas Schneid, Senior Director Software, Partnership and Ecosystem Management at Infineon.
Siemens’ advanced Capital Embedded AR Classic software supports the most advanced microcontrollers on the market with an AUTOSAR software platform, enabling the multicore, functional safety and cybersecurity features of the AURIX TC4x, and provides feature-rich software with pre-validated evidence for functional safety and cybersecurity, that simplifies the OEMs’ homologation process.
Microcontrollers like the AURIX TC4x are key components in the automotive industry, controlling and monitoring a wide variety of systems in the automobile, such as electric powertrain, battery management, ADAS, radar and chassis.
The AURIX TC4x microcontrollers from Infineon combine power and performance enhancements with the latest trends in the fields of virtualisation, AI-based modelling, functional safety, cybersecurity and network functions.
innovative capabilities that will contribute to delivery of their mission-critical priorities.”
The recognition underscores the results of Epicor’s continued investment in its Industry ERP Cloud platform which is tailored to meet the specific needs of businesses in the make, move, and sell economy. The platform’s capabilities, such as enhanced data-driven insights and AIpowered tools, allow businesses to navigate complex workflows and stay competitive in their markets.
Achieving higher energy efficiency and lower carbon emissions.
KoolLogix Pte Ltd and the Agency for Science, Technology and Research (A*STAR) have unveiled an SGD 8 million joint lab, located at Toa Payoh, to develop cuttingedge cooling solutions for AI and Graphic Processing Unit (GPU)driven data centres, paving the way for sustainable, energy-efficient innovations that align with global decarbonisation goals.
A collaboration for smarter and greener data centres
Data centres in Singapore are significant energy consumers, accounting for approximately 7% of the nation’s total electricity consumption, as of 2020. The tropical climate of Singapore exacerbates this issue, as cooling systems in data centres can account for up to 40% of their total energy consumption. Artificial intelligence (AI) and graphics processing units (GPUs) have significantly amplified energy demands in data centres, contributing to increased heat generation and carbon emissions.
The KoolLogix-A*STAR Joint Lab will focus on developing and testbedding next-generation energyefficient cooling technologies for future AI and GPU data centres, driving decarbonisation in the data centre cooling industry. These innovative systems will enable remote monitoring and fault prediction for KoolLogix’s heat removal solutions deployed by its clients.
By combining KoolLogix’s expertise in the data centre cooling industry with A*STAR’s advanced research capabilities in predictive maintenance, intelligent control systems, AI, Internet of Things (IoT) technologies, and digital twin solutions, the partnership seeks to enhance KoolLogix’s cooling capacity and heat removal
efficiency. This collaboration aims to deliver smart, adaptive cooling systems that meet the growing demands of AI-driven data centres, while reducing energy consumption, operational costs and environmental impact.
Building on proven success
This collaboration builds on the long-standing partnership between KoolLogix and A*STAR. The firstgeneration KoolLogix Heat Removal Module (HRM) 20 Series, an innovative heat removal system, capable of removing 20 kW of heat per rack, was first developed, in
2019, under A*STAR’s Technology for Enterprise Capability Upgrading (T-Up) programme. This technology has already helped the data centres of KoolLogix’s clients to cut down up to 75% of cooling energy consumption, all without mechanical pumps or compressors – thereby supporting Singapore’s sustainability efforts.
The T-Up programme by A*STAR supports promising local companies in enhancing their business competitiveness through technology upgrading. Senior A*STAR scientists or researchers are seconded to the companies for
up to two years, to advise on the technology upgrading strategy and to impart knowledge in technical areas supporting them in their development of new products, process, and IP development, through the transfer of technical know-how and skills.
The HRM20 Series laid the foundation for KoolLogix’s latest breakthrough, the HRM50 Series, engineered to meet the extreme cooling needs of AI-intensive environments.
The HRM50 Series, the next generation of KoolLogix’s Rear Door Heat Exchanger, capable of removing 45 kW of heat per rack, sets a new benchmark in cooling efficiency. Featuring a pump-free and compressor-free design, the system achieves an industry-leading Coefficient of Performance (COP) of 150, delivering improvements in operational reliability and energy savings of up to 50%, compared to traditional cooling technologies.
Its Zero Water Risk Technology, which does not require chilled water to flow through the data centre white space, ensures infrastructure safety, by eliminating the risk of water damage to expensive computer hardware while supporting decarbonisation and sustainability goals.
This advanced cooling technology has enabled KoolLogix’s clients, including OCBC Bank and the National Supercomputing Centre (NSCC Singapore), to achieve significant environmental and economic benefits, given the reduction of electricity usage.
KoolLogix’s commitment to innovation and sustainability has also been recognised with the Emerging Enterprise Award 2021 and the Sustainability Award, from Business Times and OCBC.
“This decade-long collaboration with A*STAR has been transformative for KoolLogix. By leveraging A*STAR’s expertise in computational fluid
dynamics and advanced modelling, we have been able to pioneer paradigm-shifting sustainable heatremoval solutions that enhance data centre performance while significantly cutting energy costs,” said Mr C K Cheong, Co-founder and CEO of KoolLogix.
Professor Yeo Yee Chia, Deputy Chief Executive (Innovation and Enterprise) at A*STAR, added, “The rapid and widespread deployment of AI requires innovations to improve the power usage efficiency in data centres. One key challenge is efficient heat removal. A*STAR is proud to work with KoolLogix in developing solutions that address key issues, and translating science into technologies that benefit companies and contribute to Singapore’s sustainability goals.”
Through this partnership, KoolLogix and A*STAR continue to demonstrate the power of industryscience collaboration to solve realworld problems, drive economic growth and advance Singapore’s position as a global leader in sustainable technology.
KoolLogix
Founded in 2018, KoolLogix is an award-winning data centre thermal management company with a paradigm-shifting heat removal solution that delivers improved energy efficiency and lower carbon emissions. This is ideal for data centre operators and their clients
in achieving better operational returns and environmental sustainability goals.
With headquarters in Singapore, KoolLogix has successfully deployed its solution to colocation, enterprise, and supercomputer data centres, servicing low to high power density ecosystems.
The Agency for Science, Technology and Research (A*STAR) is Singapore’s lead public sector R&D agency. Through open innovation, A*STAR collaborates with its partners in both the public and private sectors to benefit the economy and society.
As a Science and Technology Organisation, A*STAR bridges the gap between academia and industry. Its research creates economic growth and jobs for Singapore and enhances lives by improving societal outcomes in healthcare, urban living and sustainability.
A*STAR plays a key role in nurturing scientific talent and leaders for the wider research community and industry.
A*STAR’s R&D activities span biomedical sciences to physical sciences and engineering, with research entities primarily located in Biopolis and Fusionopolis.
by Er. Dr Jahangeer K Abdul Halim, Founder & CEO, Energy Conservation Specialists Singapore Pte Ltd
The article covers the basic concepts and working principles, and various strategies for achieving the desired outcomes.
The vapour compression cyclebased cooling system, used both in commercial and industrial space cooling, consumes about 50% of the total building/facility energy requirements.
In an industrial set-up, the cooling systems are used both for space cooling as well as process cooling, consuming significant amounts of energy out of the total energy requirement in the facility. The air conditioning/cooling system used in the industrial sector could also serve sub-zero applications, with the temperature going as low as -20 oC to -30 oC.
The air cooling system used in such applications could utilise a working fluid such as glycol. In Singapore, mechanical engineers, who are also Singapore Certified Energy Managers (SCEMs) are well conversant with the working principle and optimisation techniques of such cooling systems.
However, since the inception of the SCEM programme in 2009, the author who is also an SCEM trainer has come across many non-mechanical engineers enrolling for the SCEM programme without any prior exposure to the basic principles of such cooling systems. In this technical article, an account of vapour compression cycle-based cooling systems, especially their working principle and various potential optimisation strategies, is provided.
This will serve as good reference for engineers taking up the role of
Facility Engineers, and assist them in approaching the maintenance of air conditioning systems, from an energy conservation perspective.
In a tropical country like Singapore, the ambient air is hot and humid, with an average daily annual drybulb temperature of about 30 oC and a Relative Humidity (RH) of about 80% to 90%. Therefore, the air needs to be conditioned, such that both the temperature and humidity are reduced to the level of thermal comfort (the ASHRAE air conditioning design condition for summer air conditioning is 24 oC dry-bulb temperature and 50% RH). The summer air conditioning of air involves the cooling and dehumidification of air (removal of moisture from air).
In layman’s terms, RH is the moisture-holding capacity of air, expressed as a percentage. In terms of the technical definition, RH is the ratio of actual moisture content in air to maximum moisture content, at a particular temperature. It is to be noted that air at a low temperature can hold only a small amount of moisture, while at a higher temperature, it can hold a larger amount of moisture.
Based on the above, an RH of 95% is quite common, after the cooling coil (off-coil) of an air handling unit (AHU), because of the prevailing low off-coil temperature of air. Typically, an RH of about 50% to 60% is required to maintain the thermal comfort level in human-occupied
commercial buildings, by dissipating the heat resulting from metabolism, through moisture migration.
As for process applications in an industrial set-up, conditioned air at various temperatures and values of RH may be required, depending on the type of application. For example, in a pharmaceutical industry set-up, an RH of 35% to 40% may be required for safe storage of certain raw materials. In precision manufacturing industries, such as electronics and semiconductor manufacturing factories, conditioned air is extensively used for cleanroom applications.
TYPES OF AIR CONDITIONING/COOLING SYSTEMS
Air conditioning/cooling systems are classified, based on the cycle of operation, as vapour compression cycle-based and vapour absorption cycle-based.
In the vapour compression cyclebased system, there are two or three working fluids, depending upon whether the system is a directly cooled system, interchangeably known as a direct expansion (DX) system, or an indirectly cooled system.
In a directly cooled system used for small-scale applications, two working fluids are used (refrigerant and air), whereas in the indirectly cooled system used for large scale applications, three working fluids are deployed (e.g. refrigerant, water and air, for normal temperature applications). Vapour
compression-based air conditioning systems are also known as electrically driven air conditioners.
In a vapour absorption cyclebased air conditioner, a pair of liquids, one acting as a refrigerant and the other acting as an absorbent, is used. The commonly used refrigerant-absorbent pair comprises water, which is a refrigerant under vacuum conditions, and lithium bromide (LiBr) which is the absorbent.
The vapour absorption cycle air conditioners use waste heat in the generator to drive off the water vapour from the dilute LiBr-water solution. Hence, vapour absorption-based air conditioners are interchangeably called as heat-driven systems. Despite the extremely poor performance of vapour-absorption air conditioners, they are commonly installed in industrial facilities where waste heat is available as a byproduct which, otherwise, would have to be rejected into the environment.
Figure 1 shows the schematic of a vapour compression cycle-based air conditioner. As can be seen from the figure, there are four main components in the cycle, namely, evaporator, compressor, condenser and expansion device.
In the evaporator of the vapour compression system, either the air is directly cooled and dehumidified or a secondary coolant such as water is cooled to an appropriate temperature suited to the end-use. The air conditioner in which the air is directly cooled and dehumidified is called as a direct expansion (DX) system, whereas the system, in which the secondary coolant is cooled first, is known as an indirect system.
The other three components, as shown in Figure 1, are the compressor, condenser and expansion valve. In the context of a unitary air conditioner, such as a split air conditioner, the three components are collectively known
as the condensing unit and placed outside the space to be cooled. The evaporator and condenser are heat exchangers where heat is exchanged between two working fluids.
The liquid refrigerant-vapour mixture (about 85% liquid and 15% vapour) enters the evaporator cooling coil (point 4, in Figure 1) absorbing heat from the warm air or returning secondary coolant. The cooled and dehumidified air in the case of a DX system is supplied to the room where the air picks up both sensible and latent heat from the people, and sensible heat from the heat emitting sources.
The evaporated refrigerant vapour (point 1, slightly superheated) at moderate pressure and temperature is unable to exchange heat with the ambient air or cooling medium, such as cooling tower water, because of the higher enthalpy (heat content) of the ambient air or cooling tower
water, and therefore needs to be subjected to compression in the compressor.
After the compression, the slightly superheated refrigerant vapour becomes high pressure and temperature refrigerant vapour (highly superheated vapour) with adequate enthalpy potential to exchange/reject heat to the ambient air and changes to a high pressure, moderate temperature liquid refrigerant (point 3). The high pressure, moderate temperature liquid refrigerant is expanded with the help of an expansion device and the state of the refrigerant is restored (point 4). The cycle is repeated.
The processes taking place during the cycle, namely, evaporation, compression, condensation and expansion, are labelled on the Pressure-enthalpy (P-h) diagram, as shown in Figure 2.
The direct expansion system (DX), illustrated in the preceding section, is used for small-scale applications, such as in residential units and small and medium-sized offices. For large scale applications, such as industrial and multi-storey commercial buildings, the use of DX systems is not technically and economically feasible.
Therefore, a larger scale, airconditioning system with water (for normal temperature applications) or glycol (for sub-zero temperature applications), as a secondary coolant, is used. Such a larger scale air conditioner is called a chiller. The chiller produces the secondary coolant (either chilled water or cold glycol) in the chiller plant room. The chilled water and cold glycol is transported to Air Handling Units (AHUs) and process cooling equipment, respectively, to satisfy the end-use requirements. The chillers are further classified as water-cooled or air-cooled chillers, based on the cooling medium used in the condenser of the chiller.
The water used in the condenser of a chiller is conditioned with the help of a cooling tower (CT). For transporting the chilled water, from the chiller plant room to the load, and for transporting condenser water, from the cooling tower to the condenser of the chiller, pumps are used. These pumps are called chilled water pumps and condenser
water pumps, respectively.
Figure 3 shows a water-cooled chiller system comprising chiller, chilled water pump, condenser water pump and cooling tower.
Like in the case of any significant energy consuming system, it is of paramount importance to monitor the performance of the air conditioning or chiller system and compare the actual operating performance with the expected performance, subject to certain operating conditions.
Typically, chiller performance is expressed in terms of the chillerspecific power consumption, traditionally known as chiller efficiency, expressed as the ratio of the power consumed to the unit cooling produced in Refrigeration Tons (kW/RT).
1 RT represents the removal of about 3.517 kJ of heat in 1 sec. Based on the definition of chiller efficiency, the smaller the number expressed in kW/RT, the more efficient is the chiller. A chiller with a chiller efficiency of 0.6 kW/RT is more efficient than a chiller with an efficiency of 0.7 kW/RT. The first chiller consumes 0.6 kW of power to produce 1 RT of cooling, compared to the second chiller which requires 0.7 kW of power to produce the same amount of cooling, under the same operating conditions.
Another way to express air conditioner/chiller performance is in terms of the Coefficient of Performance (COP), defined as the ratio of cooling capacity (kWc) to power consumption (kWe).
In an air conditioning/chiller system, besides the chiller, the auxiliary equipment, such as chilled water pumps, condenser water pumps and cooling tower, also consume energy to transport the chilled water and condenser water, and cool the condenser water, respectively. Therefore, the chiller system/chiller plant efficiency is the ratio of the total chiller plant power (kWe,plant) to the cooling load produced (RT), or (kWe,plant/RT).
All the above performance indicators are expressed mathematically, as follows:
Chiller efficiency (ƞchiller) (1) = Power Consumption (kWe)/ Cooling capacity (RT)
Coefficient of Performance (COP) (2) = Cooling capacity (kWc)/Power input (kWe)
Chiller system efficiency (3) (ƞchiller,system)
= Total Plant Power Consumption (kWe,total)/Cooling capacity (RT)
Total plant power (4)
= Chiller power (Pchiller) + Chilled water pump power (Pchwp) + Condenser water pump power (Pcwp) + Cooling tower power (Pct)
Substituting equation (4) in equation (3), we get:
ƞchiller,system (5)
= (Pchiller + Pchwp + Pcwp + Pct)/ RT
Simplifying, we get:
ƞchiller,system (6)
= (Pchiller/RT) + (Pchwp/RT) + (Pcwp/ RT) + (Pct/ RT)
ƞchiller,system (7)
= ƞchiller + ƞchwp+ ƞcwp+ ƞct
Currently, a chiller efficiency of about 0.47 kW/RT to 0.48 kW/RT, for a normal chilled water supply temperature of about 6.7 oC to 8 oC, is quite achievable. Based on the NEA Minimum Energy Efficiency Standard (MEES), a minimum system efficiency of 0.67 kW/RT needs to be achieved for a water- cooled chiller system with a rated cooling capacity of 300 RT and above.
Another way to classify chillers is based on the type of compressors deployed, such as reciprocating, scroll, screw and centrifugal compressors. Chillers with reciprocating, scroll and screw compressors, are called as positive displacement chillers, whereas centrifugal compressor chillers are called dynamic chillers.
Positive displacement chillers are used for small to medium capacity applications whereas centrifugal chillers are used for bigger capacity applications.
The chiller data sheet for different loading (%) parameters can be obtained from chiller manufacturers, upon providing the required cooling capacity and other relevant operating parameters.
A chiller system includes the chiller as well as the auxiliary equipment, such as chilled water pumps, condenser water pumps and cooling towers (for water-cooled chillers). Before the optimisation of the chiller system, the current performance of the chiller system needs to be established, from quality data either available from the building management system (BMS) or freshly acquired using accurate instrumentation, as stipulated in SS 591:2021 (Code of practice for long term
measurement of central chilled water system energy efficiency).
The typical operating parameters established from the data analysis are the operating efficiencies of chillers, chilled water pumps, condenser water pumps and cooling towers (if applicable).
The performance indicators are compared with available benchmark values or achievable values, based on the engineering expertise looking at the analysed data plots.
Some of the selected optimisation techniques are, as follows:
• Operating the chillers, based on the established cooling load profile and the chiller part-load data, obtained from the chiller manufacturer, to make the chillers perform with their highest efficiency.
• Resetting chilled water supply temperature to a higher value after ensuring the reset chilled
water supply temperature can still meet the end-use requirements. It is recommended that extra caution be exercised, if the enduse application is critical, such as the maintaining of a very low relative humidity (RH) in a highend manufacturing environment. A higher chilled water supply temperature results in lower pressure lift, as shown in Figure 4. It is well established that every 1 oF increase in chilled water supply temperature will result in a 2% to 4% improvement in chiller efficiency.
• Sending low temperature condenser water to the condenser of the chiller will also help to improve the chiller efficiency. A lower temperature condenser water supply results in a lower pressure lift, as shown in Figure 5, resulting in reduced compressor power consumption and better chiller efficiency.
It is to be noted that the effective heat exchange in the condenser of a chiller is of paramount importance, as the heat exchange is between vapour and liquid. Anything that impairs effective heat exchange in the condenser will result in unwanted outcomes, such as building up of condenser pressure, resulting in a drop in chiller performance due to the elevated pressure lift. Over time, elevated pressure lift could even cause the chiller getting tripped, resulting in significant losses in high-end manufacturing environments, e.g. semiconductor and pharmaceuticals industries.
Like in the case of the chilled water temperature reset, it is well established that every 1 oF decrease in condenser water supply temperature will result in a 2% to 4% improvement in chiller efficiency.
• Another way to achieve and maintain the expected chiller efficiency is through periodical cleaning of, especially, the condenser tubes, as they are susceptible to scaling, since they are being operated in an open loop arrangement. The condenser tube cleaning can be performed, using an automatic, brush or ball type, tube cleaning system, commonly available in the market.
• Chiller performance could be improved, through the consolidation of chiller plant rooms, if there is more than one chiller plant room in an industrial or commercial facility. The consolidation of the chiller plant rooms is done such that the chiller loading always remains in the healthy region, for the chillers to provide better performance, based
on their characteristics.
• Chilled water pump and condenser water pump optimisation: Once the chilled water pumps and condenser water-specific power consumptions (kW/RT) are established from the measured data, there could be potential for optimising the performance of the pumping system.
Figure 6 shows a typical chiller pumping system comprising a variable speed drive (VSD), motor, gear and pump. There are two possibilities for pumping system optimisation – it can be achieved either by optimising the components’ efficiencies or by optimising the pumping system output.
For optimising pump efficiency, the current operating pump efficiency needs to be established, through measurement and available name plate information.
For the optimisation of the output required, the pump head and/or flowrate (Q) could be minimised. The pump head for an existing chiller plant room could be minimised, through the opening of partially closed valves or eliminating the redundant valves altogether.
Flow rates can be optimised by increasing the measured chilled water and condenser water temperature differences (in the case of very low ΔT) to design values. Chilled water flow rates should be determined with due diligence, without compromising the minimum chilled water flow through the chillers.
Another potential method for the optimisation of the pumping system is through the selection of low pressure drop (both for the
evaporator and the condenser) chillers, right at the chiller selection stage. 30 kPa pressure drop chillers are currently quite common.
• Cooling tower (CT) fan optimisation: Cooling tower operation can be optimised through the operation of spare cooling towers, at part load, with the help of VSDs. The resulting power savings can be estimated using the power affinity law. For instance, let us consider a facility which has three cooling towers, each consuming 25 kW at full load and, normally, two CTs are in operation at full load and one is on standby mode. If all the three CTs are operated at two thirds of their full capacity, the power consumption could be reduced significantly. In this case, the resulting power savings can be estimated as follows:
Power affinity law: P1/P2 = (N1/N2)3 (8) where P1 = initial power = 25 kW
P2 = final power
N1 = initial speed
N2 = final speed = 2/3 N1 (9) Using equation (8), P2 = P1 x (N2/N1)3 (10)
Substituting equation (9) in equation (10), we get power consumption of one cooling tower at the reduced loading as:
P2 = 25 x ((2/3)N1/N1)3 = 25 x 8/27 = 7.41 kW
Therefore, power consumption for three cooling towers at 2/3 capacity = 3 x 7.41 kW= 22.23 kW
Initial power consumption = 2 x 25 kW = 50 kW
Therefore, power savings = 50 – 22.23 = 27.77 kW
Despite Singapore being located in a tropical environment, free cooling from cooling towers could be achieved without the fans of
the cooling towers being switched on. Experience suggests that free cooling of about 5% can potentially be achieved from a cooling tower without the fan being switched on. For example, for a commercial building with five 600 RT cooling towers:
The total free cooling achievable = 5 x 600 x 0.05 = 150 RT This free cooling from the CTs is adequate to serve the typical nighttime cooling load of about 100 RT to 120 RT, without the CT fans being switched on.
In this technical article, two different types of cooling systems, based on their cycle of operation are presented.
The importance of understanding the basic concepts of the mostly used vapour compression-based cycle, with superior performance, is emphasised. A brief account of the working principle of such an air conditioning system is included for the benefit of engineers who are not familiar with air conditioning operating principles. Vapour
compression-based chiller systems, with auxiliary equipment, and their performance indicators, are discussed. Finally, selected chiller system optimisation systems are highlighted and discussed with some illustrative examples.
[1] Stoecker W F: ‘Refrigeration and Air conditioning’, McGraw-Hill, 1982.
[2] Jahangeer K Abdul Halim, Lecture notes on Air conditioning & Mechanical Ventilation Systems, Nanyang Polytechnic Specialist Diploma Course, 2022.
Johnson Controls, a global leader in smart, healthy and sustainable buildings, will showcase its comprehensive portfolio of innovative HVAC and building technologies at the 2025 AHR Expo, to be held from 10 to 12 February 2025, in Orlando, Florida, USA.
Johnson Controls will also celebrate its 140th anniversary and the 150th anniversary of its iconic YORK brand. The company’s booth will demonstrate how its strategic partnerships with distributors, contractors and business owners – combined with industry-leading technologies and services – deliver optimal outcomes across every stage of a building’s lifecycle.
“From state-of-the-art building automation systems to advanced cold-climate heat pumps, attendees will see how these innovations drive performance and efficiency for our customers,” said Ms Lei Schlitz, Vice President and President, Global Products, Johnson Controls.
Meeting evolving efficiency goals and maximising building performance
As expectations for built environments continue to evolve, distributors, contractors and
building owners are looking for solutions that help drive efficiency and meet decarbonisation targets, while delivering enhanced experiences for occupants and driving long-term value.
The newest iteration of the company’s building automation system, Metasys 14.0 is designed to elevate a commercial building’s overall performance and sustainability while enhancing occupant comfort, health and safety.
It builds on the proven Metasys platform with revolutionary new features that offer an improved user experience; enhanced network efficiency, flexibility and security; simplified administration; and improved energy management.
Another innovation in the HVAC/R controls portfolio is the NSW 8000 Sensors. These sensors are designed to enhance real-time energy tracking, occupancy-based sensing and indoor air quality monitoring, optimising HVAC, lighting and ventilation systems, to deliver up to 30% energy savings while enabling predictive maintenance and performance benchmarking.
In response to the American Innovation and Manufacturing (AIM) Act, Johnson Controls is
helping industry professionals adapt to the low-GWP refrigerant transition with innovative, A2Lready technologies, including refrigerant detection systems (RDS) for leak detection, mitigation and regulatory compliance.
Available within the company’s Ducted Systems Solutions App, the new Refrigerant Detection System (RDS) Calculator is a firstof-its-kind tool. After entering details about a job, such as refrigerant volume, supply air discharge height and total area being conditioned, the calculator provides contractors with an immediate report confirming if an RDS is required for A2L equipment. This ensures an installation is compliant with current regulations without requiring contractors to complete complicated calculations.
The new, plug-and-play PENN System 550 is a user-friendly modular electronic control solution that fulfills temperature, humidity and/or pressure control needs. It is the first of its kind to include A2L refrigerant leak sensing and mitigation functionality and optional twoway cloud connectivity, providing a complete solution to meet A2L refrigerant regulations.
Enhancing comfort and efficiency at Commonwealth Towers and Bartley Residences.
In Singapore’s tropical climate, where heat and humidity are constant, air conditioning is essential for comfort. As the demand for energy-effiicient and sustainable solutions grows, residential and commercial buildings in Singapore can benefit from Panasonic’s Variable Refrigerant Flow (VRF) technology. Commonwealth Towers and Bartley Residences are two prominent examples of buildings in Singapore, that are benefitting from this technology.
Commonwealth Towers: a smart solution for modern living Commonwealth Towers, located in Queenstown, is a high-rise residential complex offering modern living with stunning views and advanced amenities. With 2,000 units across two towers, the development uses a VRF system to provide efficient cooling. Each unit features independent temperature control, ensuring personalised comfort and energy savings. The system adapts to varying needs, delivering cooling only where necessary, making it ideal for large residential complexes. Its compact design also helps maximise space within the building.
Bartley Residences: a focus on sustainability and comfort
Bartley Residences, a luxury condominium, offers residents a high standard of living with modern amenities and a sustainable design. To meet the cooling needs, while promoting energy efficiency, the development uses Panasonic VRF systems. These systems provide independent temperature control for each unit, minimising energy consumption and reducing utility costs. Additionally, the quiet operation of the VRF units enhances the peaceful living environment for residents.
Benefits of Panasonic VRF systems
The benefits of Panasonic VRF systems include the following:
• Energy Efficiency: The systems adjust refrigerant flow, based on demand, thereby reducing energy wastage and lowering electricity costs.
• Personalised Comfort: Each unit can independently control its temperature, enhancing comfort for residents.
• Space-Saving Design: The compact VRF system requires less space than traditional air conditioning systems, making it ideal for space-conscious developments.
• Sustainability: The systems use eco-friendly refrigerants and optimise energy use, supporting sustainable living.
• Improved Indoor Air Quality with nanoe™X: The advanced nanoe™X air purification technology effectively filters and refreshes indoor air, enhancing air quality by inhibiting the growth of harmful substances such as bacteria, viruses and allergens. It also neutralises odours, purifies the air with the help of hydroxyl radicals, and maintains a fresh, healthy indoor environment. This contributes to improved respiratory health and the overall well-being of residents.
Panasonic VRF systems have revolutionised cooling in high-rise residential buildings, in Singapore, providing energy-efficient, flexible and sustainable solutions.
Commonwealth Towers and Bartley Residences are prime examples of how these systems enhance comfort, while reducing energy consumption. As the demand for eco-friendly, smart buildings grows, Panasonic VRF technology will play a key role in the future of air conditioning in Singapore.
Advancements in technology have produced smarter, safer and more efficient systems.
Heating, Ventilation, and Air Conditioning (HVAC) systems are essential to modern living, ensuring comfort and air quality in homes, offices and industrial spaces. With rapid technological advancements, HVAC solutions are becoming smarter and more efficient, addressing the growing demands for reliability and convenience.
One transformative development is the integration of cloud-based systems into HVAC management. These systems connect HVAC units to centralised platforms, offering real-time insights into performance, energy usage and potential issues. This shift enhances operational efficiency and enables a proactive approach to maintenance, reducing downtime and extending the lifespan of equipment.
For example, LG’s BECON cloud represents a sophisticated leap in HVAC technology. It continuously monitors LG system air conditioners and HVAC units, analysing their performance in real-time. By identifying potential issues early, the system ensures that maintenance teams can respond quickly and effectively, minimising disruptions and operational costs.
The accessibility of cloud-based platforms, like LG BECON, allows users to monitor operations anytime, anywhere, without being restricted by time or location. This feature is precious for large-scale operations requiring consistent performance across multiple sites. Additionally, leveraging big data for diagnostics allows these platforms to optimise repair processes, streamline maintenance and ensure smooth operations.
As building management
priorities shift toward sustainability and energy efficiency, cloudbased HVAC systems are poised to become the industry standard. These solutions boost system reliability and align with the global push for environmentally conscious practices.
Integrating intelligent, datadriven platforms marks a pivotal breakthrough for HVAC management, shaping a future that prioritises both performance and efficiency.
‘The Singapore Engineer’ learns more about the advantages and challenges created by the adoption of artificial intelligence (AI), from Danny Wong, Senior Director of Global and Regional Accounts, Asia, at Vertiv.
The Singapore Engineer (TSE): What is the impact of AI on data centres?
Danny Wong (DW): AI has a significant impact on data centres, bringing both advantages and challenges. One of the key advantages is enhanced operational efficiency. AI can optimise data centre management by automating routine tasks, predicting equipment failures and improving energy efficiency. This can lead to reduced costs and carbon emissions, in line with the industry’s growing concerns about sustainability and environmental goals.
The Ministry of Communications and Information (MCI) of Singapore has acknowledged that AI compute power from data centres is a critical enabler of Singapore's national AI strategy to improve the energy efficiency of data centres and drive the development of efficient cooling solutions.
However, it also presents challenges. The data centre industry faces ever-growing power and cooling capacity challenges from AI workloads and increasing requirements to decarbonise operations. To support these changes, data centres must be much more agile, intelligent and integrated. Data centres must be like community assets that support local energy production and help balance grid demands, without causing disruptions. This requires significant infrastructure upgrades and investments which can be a barrier for some organisations.
Furthermore, the reliance on AI also raises concerns about security and data privacy, as the systems must be robust enough to protect sensitive information from
potential threats. Overall, while AI offers transformative potential for data centres, it also requires careful consideration of the associated challenges to ensure successful implementation.
TSE: Are high energy requirements, high heat generation and cybersecurity issues, among the challenges faced by data centres?
DW: The integration of AI in data centres significantly impacts energy consumption, heat generation and cybersecurity. In the Singapore market, where data centres are rapidly expanding to meet the needs of AI and cloud computing, these challenges are particularly pressing. Singapore aims to increase its data centre capacity by more than one-third, adding at least 300 MW in the next few years, to satisfy rising computing demands.
The growth of AI workloads amplifies this, as AI-driven data centres can consume significantly more power. High-density AI servers can demand over 100 kW of power per rack, far exceeding the capacity of many older facilities. This has led Singapore to implement stringent regulations to improve energy efficiency, including a temporary moratorium on new data centres in 2019 and initiatives to promote green data centre development.
The concentrated processing power of AI chips, such as GPUs, generates immense heat. In Singapore’s tropical climate, managing this heat becomes even more critical. Traditional air cooling methods are proving insufficient, leading to the adoption of advanced cooling solutions such
Wong
as liquid cooling.
Some data centres are exploring more sustainable cooling methods, such as rear-door cooling and liquid cooling that directly removes heat from chips. These innovations are necessary to meet both the operational and environmental needs of the country.
Additionally, a crucial aspect is the need for a holistic approach to data centre management, particularly in integrating power and thermal management across the entire system, and not just focusing on liquid cooling.
AI workloads are transforming power requirements in IT, creating new challenges for grid capacity and operational complexity. Even as rack densities increase, data centre power infrastructure and technologies have largely stayed the same. This situation puts pressure on data centre owners and operators to ensure every component in the power chain reliably delivers power from the utility to critical parts of the infrastructure.
The uninterruptible power supply (UPS) plays a critical role in minimising disruptions during power outages and maintaining a continuous and dependable flow of electricity.
As enterprises embrace AI at an unprecedented pace, it is crucial for them to adopt cooling to support accelerated computing with the most complete portfolio of critical digital infrastructure that is capable of managing the unique requirements of AI and other accelerated compute applications.
As stated above, AI increases the complexity and volume of data processed. Also, data centres face
heightened cybersecurity risks since AI-driven operations handle vast amounts of sensitive data, making them prime targets for cyberattacks.
The Cyber Security Agency of Singapore has emphasised the importance of securing AI infrastructure, and many companies are investing in advanced cybersecurity protocols to protect their systems against sophisticated threats.
TSE: What are some of the solutions that Vertiv can offer to address these challenges?
DW: Vertiv provides advanced power management systems to optimise energy usage in data centres. Our UPS solutions help reduce energy waste while ensuring reliable power delivery. Additionally, Vertiv’s energy storage systems, including lithium-ion batteries, provide higher efficiency, lower maintenance and longer lifespans, compared to traditional batteries, thereby helping data centres manage their high-power demands more sustainably.
To tackle the intense heat generated by high-density AI workloads, Vertiv offers cuttingedge cooling technologies. Vertiv’s liquid cooling solutions are designed to handle the heat from advanced AI processors like GPUs, removing heat directly from the chip.
The company also offers reardoor heat exchangers that can neutralise heat before it exits the rack, as well as other precision cooling systems that help data centres maintain optimal temperatures efficiently, especially in tropical climates like Singapore.
Many older data centres lack the infrastructure flexibility to support AI workloads and advanced cooling systems. Vertiv addresses this with scalable, modular data centre solutions that can be tailored to meet the evolving demands of AI and other computational tasks.
For instance, high-density data centre infrastructure solutions by Vertiv (Vertiv 360AI) include
modular solutions that can be deployed, maintaining the existing footprint. A complete portfolio of power, cooling and service solutions helps solve the complex challenges arising from the AI revolution.
The pre-engineered solutions can eliminate complex design work, reducing deployment time by up to 50%. It is designed to accelerate AI deployments of any scale, with designs ranging from rack solutions for test pilots and Edge AI, to full data centres for AI model training.
Partnerships within the industry can also facilitate efforts to address these challenges. Vertiv is collaborating with NVIDIA to offer expertise in critical power and cooling infrastructure with advanced computing capabilities. We plan to combine direct-chip liquid cooling and immersion cooling for a more efficient and cost-effective approach. This can potentially reduce data centre energy consumption and environmental impact. Vertiv’s power and cooling expertise will also contribute to the safe and reliable deployment of AI infrastructure.
Vertiv’s infrastructure management tools provide comprehensive monitoring and control of data centre operations, helping to identify and mitigate potential vulnerabilities. These tools enhance the security of the data centre by ensuring that critical infrastructure is protected from
both physical and cyber threats.
TSE: Could you provide an overview of the new developments in data centre design and operation, and in cooling technologies?
DW: We are witnessing significant advancements in data centre design and operation, primarily driven by the increasing demand for efficiency and sustainability. One of the most notable trends is the shift towards high-density computing environments, which necessitates innovative design strategies to manage the rising power and cooling requirements.
Modular data centres are becoming popular, as they allow organisations to scale their capacity as needed, enabling more flexible and cost-effective growth. Additionally, enhanced monitoring and management systems are being implemented to ensure that critical conditions, such as those relating to temperature and humidity, are maintained, thereby protecting sensitive IT equipment and improving overall reliability.
In terms of cooling technologies, liquid cooling solutions are gaining traction, particularly in high-density environments where traditional air cooling may struggle. Vertiv is leading the charge in this area with innovations specifically designed for these demanding applications.
Other innovative approaches, such as immersion cooling and indirect evaporative cooling, are
also emerging as effective methods for managing heat in data centres. As the industry continues to prioritise sustainability, we are seeing a growing commitment to using environmentally friendly refrigerants, in order to enhance the efficiency and eco-friendliness of modern data centre operations.
TSE: Any other information that you would like to provide?
DW: The world depends on data. As industry experts, Vertiv brings together hardware, software, analytics and ongoing services, to enable customers’ vital applications run continuously, perform optimally and grow with their business
needs. Vertiv’s offerings address AI’s complex demands on data centres, supporting Singapore’s vision for a sustainable, efficient digital infrastructure. Through innovative power, cooling and security solutions, Vertiv is driving the future of AI-ready data centres in Singapore and in the region.
Vertiv, a global provider of critical digital infrastructure and continuity solutions, recently held its Vertiv Masterclass event in Singapore. The event attracted about 200 attendees comprising data centre consultants, contractors, designers and operators, all looking to learn about the latest trends and technologies transforming the industry today.
The Vertiv Masterclass is an annual series of supplementary learning and knowledge refresh sessions on the latest technologies in power protection, thermal management and other key elements of critical infrastructure. It offers continuing education and knowledge transfer to consulting engineers and infrastructure designers by way of interactive discussions and technical presentations.
This year’s masterclass put the spotlight on the impact of AI and the challenges brought by highdensity and high-performance compute deployments.
The session kicked off with welcome remarks from Kwang Chin Chong, Vertiv’s Sales Director for Singapore, followed by keynote presentations from Danny Wong, Senior Director for Global and Regional Accounts, Southeast Asia at Vertiv; and Alvin Cheang, High Density Compute Business Director for Asia at Vertiv.
Both Wong and Cheang highlighted the impact of AI on the critical infrastructure and how
Vertiv can support its customers with its portfolio of solutions, notably the Vertiv 360AI.
Dr Gabriel Noaje, Business Development Lead for Supercomputing and HPC, at NVIDIA APAC, also delivered a presentation on building AI factories and data centres for the next industrial revolution.
Another highlight was the panel discussion with industry experts. With the theme ‘Overcoming the real-world complexities of high-density AI deployments’, the panel was moderated by Hitesh Prajapati, Vertiv’s Vice President for Southeast Asia Sales, and featured meaningful insights and on-the-ground scenarios from panellists, Darryll Howell, Chief Executive Officer of RED Engineering; Er. Joseph Goh, Managing Director, DLM Pte Ltd; and Simon Brady, Product Manager for Vertiv.
Participants were divided into the mechanical and electrical tracks, in the afternoon, where targeted power and cooling sessions were held, focused on the topics of high density power distribution, liquid cooling, as well as the Vertiv AI reference design. “The astounding turnout of the Vertiv Masterclass session in Singapore highlights the growing criticality of AI and its far-reaching impacts on the critical infrastructure and organisations, as a whole. It is great seeing our peers very interested and eager to learn about the technologies and solutions that are available today, to support high-performance deployments. We thank all our partners, attendees and experts for sharing their insights and best practices and we look forward to successful masterclass events in the coming days,” said Danny Wong.
An important part of the system is an innovative winding machine.
Introduction
Battery cells are crucial for energy storage in e-mobility and other applications – and a major cost factor.
In order to reduce reject rates significantly, improve quality and develop innovative cell designs, an automated and digitised production line for cylindrical battery cells has been developed at the Center for Digitized Battery Cell Manufacturing ZDB at Fraunhofer IPA, in Germany.
A core element of this is the fully automated system from machinery and equipment manufacturer, acp systems, for manufacturing jelly rolls in a range of formats and designs, which also includes a variety of testing options.
The traction battery accounts for around 40% of the costs of an electric car. Accounting for up to 80%, battery cells are the most expensive component, with cylindrical cell formats becoming increasingly popular. Their manufacture is extremely complex. It can be roughly divided into the following steps – electrode
production, winding and assembly, and electrolyte filling and forming.
High reject rates are a problem. Conservatively estimated at 10% to 15%, this amounts to between 100 and 150 million cells per year in a gigawatt-hour factory. Consequently, there is enormous scope to cut costs. Another potential cost-saving area is through the development of innovative cell formats and designs for round cells. To fully exploit these possibilities, production processes need to be adapted and further developed, taking into account the economic and ecological aspects.
Improving quality with digitised and networked processes
The Center for Digitized Battery Cell Manufacturing (ZDB), which was founded in 2018, at the Fraunhofer Institute for Manufacturing Engineering and Automation IPA, has the expertise in digitised and networked processes.
“We felt that by automating, digitising and networking the entire value chain in production, individual
processes can be optimised, and rejects can be identified earlier and more effectively, using feedback and sensor information. This improves the quality of the cells and cut costs significantly,” said Prof Kai Peter Birke, Director of Battery and Hydrogen Systems and Storage Technologies at IPA.
To this end, a complete, digitised and networked production line for manufacturing cylindrical cells for lithium-ion and sodium-ion batteries has been developed at ZDB. The line not only enables production processes to be optimised for existing cell formats and adapted for new cell formats up to 46xx, but also allows corresponding prototypes to be manufactured in small series of up to 1,000 units.
The centrepiece of the production line is the versatile winding system for producing jelly rolls in different formats and designs, which was developed together with acp systems.
“We also discussed this task with other equipment manufacturers but found that they were unable to respond to our specific requirements and wishes, and start a joint development,” said Prof Birke.
One of the requirements was that the machine must be able to wind jelly rolls for very small battery cells as well as for very large ones. In addition, the machine had to be able to integrate various solutions for inline contacting/current collection (tabs), with welded tabs as well as tabless notched design (with laser notches) and tabless continuous design (without laser notches).
It was essential that the contacting solutions can be combined as required. The machine also had to include different options for testing the quality of the jelly rolls and have the ability to process all common materials used in the manufacture of high-performance round cells.
Modular system concept for the various process steps
The result was a modular system concept with a total of four stations. The coils holding the anode and cathode sheets are located in the first module and are first unwound in parallel, next to each other, in a specific way.
During each process step, web edge control systems ensure that the sheets are always guided precisely into position. The current collectors are also contacted in the first station. To do this, a robot places tabs on the anode and cathode, which are then joined using an ultrasonic welding head.
The second module includes a laser cutting system for notching, which can be used to notch both the anode and the cathode. It also features an integrated deflecting device that moves the electrode sheets laterally into the winding plane so that they run over each other into the third module without touching.
This module contains two further coils holding the separator films. The actual winding process starts by inserting the separator films
into the core of the roll. After a few turns, the anode sheet is inserted
between the two separator films from above. A gripper then inserts
the cathode sheet into the core. Once this is completed, the winding process starts.
In the last module, the jelly rolls first undergo a high-voltage test, known as the hi-pot test, to rule out any subsequent short circuits in the cell. This is followed by an optical inline inspection. Here, the dimensional accuracy of the cell is checked with regard to the winding geometry and the position of the current collector. Cells that have passed both tests are placed in a workpiece carrier and forwarded to the next production step. Cells that are not up to standard are automatically taken out of the line.
Modularity ensures optimal adaptation to individual requirements
The modular winding system also offers advantages when it comes to the mass production of cylindrical battery cells. It can be used to
manufacture coils with a diameter of up to 60 mm and a maximum length of 110 mm. Winding speeds up to 2.5 m/sec can be achieved. The various contacting solutions and test options can be adapted to any company-specific requirements. Furthermore, an additional dry and residue-free cleaning process
can be integrated in a space-saving manner after the process steps in which particles are generated, such as ultrasonic welding and laser cutting.
In the automotive industry, shot peening is utilised to induce a compressive residual stress in, for example, gear components and, thus, extend the life-span of the material.
For this challenging task, the BMW plant in Dingolfing, Germany, uses satellite table shot blast machines from Rösler, which have been precisely adapted to the customer’s technical requirements.
Now, the adaptable RST 200S15 equipment concept has been implemented in a new manufacturing line producing gear components for E-vehicles.
The rotary table of the compact shot blast machine contains 15 rotating satellite stations equipped with work piece-specific fixtures. Depending on the work piece type, a work piece loading/unloading system supplied by the customer places one or several work pieces on the satellite stations.
Thanks to the machine design,
non-productive idle times are minimal. After they have been loaded, the work pieces pass through multiple stations in the shot blast machine at indexing cycles of 20 seconds. These stations include two blast positions. Special lifting gates prevent spillage of blast media into other stations.
During the peening operation, the satellites rotate at preset speeds, in front of the blast turbines. In combination with the automatic blast pattern adjustment to the respective work piece shape, this ensures that homogeneous peening results are achieved. A compressed air cleaning station placed in front of the loading/ unloading section blows off dust and residual blast media from the finished work pieces.
Selection of the work piecespecific processing programs, including the setting of the turbine position and blast pattern, is
handled by the master computer of the manufacturing line. For this purpose, the controls of the peening machine were integrated into the upper-level computer system at BMW in Dingolfing.
To safely achieve the peening results, defined by predetermined Almen values in the specified cycle times, the machine is equipped with two high-performance blast turbines, model Rutten Gamma 400 with a drive power of 22 kW for each turbine.
The special ‘Y’ design of the throwing blades, with their precisely calculated curvature, guarantees precise media acceleration with maximum throwing speed, producing high operational efficiency.
Compared to conventional turbines this is said to result in lower energy requirements. Another significant benefit of this design is that both sides of the throwing blades can be utilised.
by Annika Langéen, Vice President Offer Management And R&D at Sandvik Coromant
Manufacturing components for medical devices presents unique challenges that demand advanced machining solutions. End-users rely on these devices being manufactured to the highest quality, as any products that do not meet quality standards can cause huge disruption. Entire operations could be paused, products recalled, organisational reputation damaged and patients’ lives could be at risk. Additionally, regulatory requirements are stringent in this field. There are international standards around quality management, such as ISO 13485, and risk management, such as ISO 14971, as well as regional regulations such as 21 CFR and FDA for the US, and EU MDR for the European Union, which all devices must meet. The requirement for such high accuracy means manufacturers cannot risk even a millimetre of differentiation between components, so having a robust machining setup is paramount.
Machining challenges
From a machining perspective, the size and complexity of device components require micron-level precision, so any manufacturing process that is used must offer accurate end products.
The materials used for a wide range of medical device components, typically titanium, stainless steel and special alloys, are selected due to their resistance to corrosion and wear, toughness and biocompatibility. But machining such materials to a high degree of precision does not come without its challenges. In particular, they must address issues around tool wear, heat generation during machining and surface finish on the component.
There is also the issue of productivity. In general, there is an imbalance between the cost
development and what the market is willing to pay for, in any industry. To bridge that gap, manufacturers must continuously increase efficiency and productivity.
Sandvik Coromant estimates that manufacturers waste between 10% to 30% of material in their machining processes, with a typical machining efficiency of below 50%, which includes at the design, planning and cutting phases.
Bone screws are the most common general purpose fixing devices, with many applications. They may be used alone in reconstruction or reparative surgery, or with other hardware devices, such as plates, to fix them to the bones. Typically, bone screw bars are between 4 mm and 12 mm in diameter and are made of titanium or stainless steel.
With such a wide array of applications, bone screws typically are long and thin in shape, and manufactured in many different sizes, to cater to different body parts. They are generally produced in quantities of between 30 and 1,000, using a technique known as thread whirling – a machining process used to create high-quality, precise threads. A cutting tool is mounted on a rotating spindle, which is fed into the workpiece while it rotates. The cutting tool typically has multiple inserts arranged around its circumference.
During thread whirling, the workpiece rotates on its own axis while also being moved longitudinally along its axis. Meanwhile, the cutting tool rotates around the workpiece, cutting the thread profile into it. This simultaneous rotation of the workpiece and the cutting tool allows for the creation of threads with high accuracy and surface finish, and avoids bending and vibrations. However, challenges
include avoiding burr formation in the tip while the thread whirling is underway, and maintaining thread quality when high feeds are used.
Sandvik Coromant machining solutions for sliding head machines use the CoroMill 325 whirling system, a dedicated whirling unit and high-pressure coolant pump with filter. The CoroMill 325 is a thread whirling cutter designed specifically for medical device manufacturing, which produces special thread forms quickly and at high tolerances. With multiple thread whirling inserts and holders available, the machine ensures that bone screws are produced without the risk of bending or burr formation.
Additional benefits of Sandvik Coromant’s cutting tool solution include increased productivity. The machine completes single-pass machining from stock diameter to reduce the cycle time by minutes and is easily set up to reduce downtime. All Sandvik Coromant thread whirling inserts are available in GC1105 (the first-choice grade for medical machining), increasing tool life and reducing operational costs.
Sandvik Coromant offers a large range of advanced tooling and machining solutions for many additional devices, including hip joints, pedicle screws and bone plates.
As the field of medical device manufacturing continues to evolve and become more competitive, driven by advancements in materials, design and manufacturing technologies, precision machining is essential. Partnering with industry leaders like Sandvik Coromant and embracing cutting-edge solutions enable manufacturers to navigate the complex landscape of medical machining, and advance their innovation to improve patient outcomes.
A milestone of growth and expansion with the nation.
This year, Yokogawa is celebrating its 50th anniversary in Singapore and the 20th year of its Singapore Development Centre (SGDC).
The company held the 50th anniversary dinner on 25 April 2024. Dr Tan See Leng, Minister for Manpower and Second Minister for Trade and Industry, was the Guestof-Honour at the event.
Yokogawa started from a small factory, as the first manufacturing venture outside Japan, and has expanded over the years to become the regional headquarters for Southeast Asia, Taiwan and Oceania.
Today, Yokogawa offers more than its manufacturing capabilities and provides advanced solutions that maximise customer value over the entire plant life cycle, from supply chain management, production control, process optimisation, cybersecurity to AI and predictive maintenance.
The company is dedicated to supporting digital transformation
and helping customers transition from industrial automation to industrial autonomy.
Yokogawa‘s commitment to quality
reliability has made
it a trusted partner for industries such as oil & gas, petrochemicals, renewable energy, pharmaceuticals and more.
Founded in Tokyo, Japan,
1915, Yokogawa has, today, more than 17,000 employees in a global network of 126 companies spanning 60 countries. Till date, the office in Singapore hosts more than 800 employees supporting activities, from upstream R&D to product development, engineering, business and sales capability.
The SGDC was established in 2004,
to drive innovation in production control applications. Since then, it has grown in staff strength to over 100 and is the company’s largest R&D centre outside of Japan.
The SGDC develops test-beds and innovative proof-of-concepts, and supports customers in digital transformation and smart manufacturing to accelerate
Yokogawa Engineering Asia launched the Sustainability Incubation Hub (SIH) on 22 November 2024. The SIH is a first-of-its-kind corporate Research and Development (R&D) hub dedicated to driving environmentally sustainable innovations in process manufacturing.
Co-located with the company’s Singapore Development Centre (SGDC) operations, the SIH has been established in partnership with the Singapore Economic Development Board (EDB), and provides a crucial platform for Yokogawa to collaborate with customers and partners in the region and beyond, to develop and deploy frontier technologies
to accelerate their energy transition to a net-zero future.
“We recognise the need to raise the level of climate change action in the region. To support this move, we will invest over SGD 6 million in establishing SIH. Through the new hub, we will apply our expertise to drive sustainable innovations across industries to close the gap between ideation and application,” said Mr Chay Kin Wah, President and CEO of Yokogawa Engineering Asia.
“As we integrate sustainability throughout our operations and business model, we are ramping up efforts to develop new solutions and collaborate with like-minded partners and
their transition to autonomous operations.
Yokogawa in Singapore has also recently launched the new Sustainability Incubation Hub to focus on removing the barriers to adoption of low carbon technologies and enabling innovations from concept to commercialisation.
agencies including the EDB to catalyse positive sustainability impact,” he added.
“Congratulations to Yokogawa on its 50th anniversary in Singapore. The launch of the Sustainability Incubation Hub builds on this longstanding partnership, and is a good example of how Singapore can serve as an innovation hub for green and sustainability solutions. We look forward to the collaborations this hub will foster with our ecosystem, as well as the impactful solutions this hub will develop for the region,” said Mr Lim Tse Yong, Senior Vice President and Head, Mobility and Industrial Solutions, EDB.
“We need to be close to our customers to help them succeed. This means knowing the challenges they are facing intimately, so that we can better address their unique needs on the ground. Our strategic location enables us to gather critical insights and talents in the region for rapid creation and deployment of innovations at scale for our global customers,” said Mr Saurabh Bhandari, Group Leader, Sustainability Incubation Hub, Yokogawa Engineering Asia.
The establishment of SIH reinforces Yokogawa’s commitment towards growth for sustainability, focusing on net zero emissions, a circular economy and well-being, to support the industry transition to a low-carbon economy.
‘The Singapore Engineer’ finds out more about Yokogawa’s growth journey in Singapore and the progression of its R&D operations.
The Singapore Engineer (TSE): What is the significance of crossing the 50th anniversary milestone in Singapore, for Yokogawa and the local industry?
Mr Joseph Lee (JL): Yokogawa’s 50-year presence in Singapore represents a long period of commitment to the country’s industrial development. Since 1974, Yokogawa has been a key player in Singapore’s journey from a developing nation to a global hub for advanced manufacturing and innovation.
This anniversary not only celebrates our past contributions, it also marks our continued dedication to driving technological advancements and supporting Singapore’s vision for a smart, sustainable future.
TSE: How has Yokogawa contributed to Singapore’s digital transformation journey?
JL: Yokogawa has been instrumental in driving digital transformation across various sectors in Singapore. A prime example is our collaboration with Tuas Power on their digitalisation efforts, enhancing operational efficiency and sustainability in the energy sector.
Another example would be from the water industry, where we have partnered PUB, Singapore’s National Water Agency, to implement AI-based predictive monitoring of critical assets, contributing to more efficient and sustainable water management practices.
TSE: What role does Yokogawa see for itself in Singapore’s push towards sustainability and a circular economy?
Mr Saurabh Bhandari (SB): Yokogawa is deeply committed to supporting Singapore’s sustainability goals. Our solutions focus on optimising resource use, reducing waste and improving energy efficiency, across industries. We are actively involved in projects that promote the circular economy
principles, such as the installation of water recycling and energy recovery systems.
Our global sustainability report outlines our commitment towards contributing to the UN Sustainable Development Goals, many of which also align closely with Singapore’s own environmental and social objectives.
TSE: How is Yokogawa addressing the shift towards industrial autonomy and what implications does this have for Singapore’s manufacturing sector?
JL: Our global surveys on industrial autonomy indicate
Building on our 50-year foundation in Singapore, we are focused on further expanding our role in the country’s innovation ecosystem
a significant shift towards autonomous operations, with the Asia-Pacific region showing strong interest. In Singapore, we are working with manufacturers to implement advanced control systems, AI and machine learning technologies, that enable more autonomous operations.
This shift not only improves efficiency and safety but also addresses challenges like labour shortages and the need for more flexible production systems, supporting Singapore’s vision of becoming a leading advanced manufacturing hub.
TSE: Looking ahead, what are Yokogawa’s plans for further innovation and expansion in Singapore over the next decade?
SB: Building on our 50-year foundation in Singapore, we are focused on further expanding our role in the country’s innovation ecosystem. Through the establishment of SIH, we plan to accelerate the development of new technologies in our focus areas of net zero emissions, circular economy and well-being.
We are also committed to nurturing local talent and collaborating with Singapore’s universities and research institutions to drive innovation in sustainable industrial practices and smart manufacturing solutions. Our goal is to contribute significantly to Singapore’s position as a global leader in advanced technologies and sustainable industrial practices.
Benefits include more reliable and sustainable power supply, prolonged component life, early fault detection and improved condition-based maintenance.
In less than an hour, Helsinki University Hospital switched from the time-consuming, physical inspection of its transformers to ABB’s cloud-based digital solution.
Mr Jari-Pekka Korhonen, Operations Manager for the hospital, explained, “We operate both dry and oil transformers, which require regular monitoring and inspection. For the oil transformers, this required a complete shutdown to take samples – a massive challenge in a busy hospital performing 87,000 surgical procedures every year and with many patients on life-support.”
“We have transformers scattered across this massive site. My team cannot physically be everywhere, so we needed to be able to monitor and supervise remotely,” said Mr Korhonen.
Using the recently launched ABB Ability Asset Manager for Transformers – a solution developed in partnership with Danish startup Oktogrid – Mr Korhonen and his team are now able to access key operational performance data and real-time trends for the transformers via the cloud. This has not only reduced the requirement for time-consuming physical inspections and costly shutdowns but also provided the hospital’s management team with a wealth of actionable data around the performance and efficiency of the transformers.
The solution works with any type, make or age of transformer, by measuring sounds and vibrations, the temperature and the magnetic field, to facilitate real-time, remote condition and performance monitoring, with no asset downtime or redundancy.
Helsinki University Hospital (HUS)
is the biggest health care provider in Finland. Responsible for the health of 2.2 million residents of 24 municipalities, HUS treats more or less 700,000 patients every year, while employing 27,500 professionals which makes them the second-largest employer in the country.
HUS consumes electrical energy equal to a small town. Supporting this output is a network of transformers, which requires regular inspection and permits only an occasional shutdown, as the hospital requires 100% uptime to safeguard patients’ lives.
“We are now getting uninterrupted real-time data on the transformers, which was not possible with visual inspections, which could only tell if there was a leak or change in either the temperature of the unit or the sound it is making. We can monitor the transformers 24/7 and are immediately aware of any issues that may require our attention,” said Mr Korhonen.
Mr Sixten Holm, Business Development Manager from ABB Electrification Service said, “We are delighted to have helped HUS solve its inspection challenges with our game-changing transformer
sensing device. We have significantly reduced the number of physical inspections required and limited the need to perform oil analysis. Crucial data regarding the health of the electrical system is now readily accessible, enabling early fault detection and improved conditionbased maintenance.”
“There are many electrical network transformers in the market, which are challenging to monitor without physical intervention and possible shutdown. Some have never been monitored in 15 to 20 years, due to the high costs and complexity. ABB Ability Asset Manager for Transformers overcomes these barriers, as a simple and cost-effective way to modernise the grid,” he added.
Ensuring
Greenergy Data Centers’ top-tier and highly energy-efficient data centre, in Tallin, Estonia, has increased the competitiveness of the Estonian economy and created the necessary infrastructure for digital transformation.
The 14,500 m2 data centre has a smaller ecological footprint, as it runs on renewable energy, and enables even better access to e-services. The total planned capacity of the complex is 31.5 MW – in other words, the centre’s electrical connections could cover the energy needs of a smaller town.
The building that cost nearly 40 million euros is the first of three buildings to be built in the same area, all of which will contribute to the development of the Baltic countries’ e-commerce and digital societies.
Founding the Greenergy Data Centers took more than five years, from inception to its opening, and experts from six countries participated in the process.
As the technology partner of the project, Siemens delivered the solution for the electrification in the medium and low voltage, with busbars to ensure reliable and safe power supply. In addition, the company delivered a modern energy management solution.
An integrated, large-scale and modular system suite optimises energy use, based on artificial intelligence (AI); ensures the right conditions for servers; secures and monitors electricity distribution in terms of operation, quality and reliability; increases efficiency throughout the lifecycle; and minimises the environmental impact of the data centre.
Since the data centre has to be prepared for the unexpected and has to always function, every important support system of the complex is duplicated. In some places, back-up systems have their
own back-up systems.
The Three Seas Initiative Investment Fund provided funding for building the facility.
Deployment of AI
Siemens has deployed integrated data centre management software at the data centre. The building management software (BMS), the energy and power management software (EPMS) and the White Space Cooling Optimization (WSCO) help Greenergy Data Centers to lower energy usage, ensure thermal protection and manage reliable operation of the critical infrastructure.
Providing the operational technology control platform of the new data centre is Desigo CC, an integrated building management platform from Siemens Smart Infrastructure, which connects and controls critical and noncritical building systems.
Desigo CC gives operators at the data centre a single pane of glass from which to visualise, monitor, control and optimise critical building management systems, energy performance and the WSCO.
Siemens building automation technologies also control the data centre’s ability to distribute excess heat to a district heating company, if required.
Thermal optimisation has improved by combining Desigo CC building management with Siemens’
AI-powered WSCO software, increasing the building’s energy efficiency and contributing to its target Power Usage Effectiveness (PUE) value of 1.2, against an industry average of around 1.6.
Crucially, the software also ensures thermal protection of server rooms by automatically adjusting the operation of the cooling systems.
A dense mesh of sensors across the centre’s white spaces provides the WSCO software with detailed temperature data. The system then uses an advanced machine-learning model to analyse the effect of cooling on specific areas, creating an influence map to optimise cooling distribution at rack-level, and limiting energy use to only what is necessary.
The solution responds automatically to events such as temperature fluctuations, minimising the risk of malfunction, mitigating overconsumption issues and ensuring the availability of equipment without interruption. This solution is implemented in both greenfield and brownfield data centres.
To ensure a reliable and safe power supply to the data centre, Siemens provided, from concept to delivery, customised power distribution systems natively integrated into Desigo CC for energy performance monitoring from a single pane of glass.
Innovative technology and project expertise ensure efficiency and sustainability.
DZE Asia was recently awarded an exclusive five-year contract to design, deliver and manage the race Track Lighting System, Race Communications System and Overtrack Signage Lighting System, for the F1 Singapore Grand Prix. In 2024, DZE Asia participated in the project for the revamping of the F1 Pit Building paddock lighting system, with the existing metal halide lights replaced with efficient LED lights, marking a pivotal shift in motorsports lighting, through the reduction of the energy consumption by over 60%.
The successful installation of LED lights for the building facade and paddock area showcases DZE Asia’s expertise in the planning, procurement and installation phases.
Solutions portfolio
As experts in lighting, motorsport, telecommunications and audiovisual systems, DZE Asia has consistently delivered innovative solutions for motorsports events. Among the company’s specialised portfolio of solutions are the following:
• Race Track Lighting Systems: DZE Asia offers infrastructure, designed for night-time motorsport events. Made up of strategically positioned
light projectors, visibility across the track and surrounding areas is ensured with minimal glare for drivers and cameras, and optimal lighting for high-speed racing and live broadcast coverage.
• Race Communication Systems: DZE Asia performs installation, testing, commissioning, operation and removal of critical equipment, offering an all-encompassing seamless communication, safety and operational efficiency throughout events – providing optimal experiences for motorsport professionals.
• Overtrack Signage Lighting Systems: In the provision of bright and clear illumination of advertising signages around the circuit, that enhances visibility and impact, DZE Asia strictly adheres to local standards, laws and regulations, ensuring operational efficiency throughout the event. By prioritising optimal visibility, this creates an engaging and vibrant environment for all attendees.
DZ Engineering, part of the Dino Zoli Group, is well-known in Singapore for its lighting solutions for the F1 Singapore Grand Prix races, since 2008.
In 2024, DZ Engineering shifted the spotlight to its sister company, DZE Asia Pte Ltd, also a subsidiary of the Dino Zoli Group. Established in Singapore, in 2019, DZE Asia covers the entire Southeast Asian market with its offerings in advanced lighting technology and innovative solutions within the motorsports industry.
As the motorsports landscape expands globally, the shift in focus to DZE Asia signifies a natural progression of DZ Engineering to better align itself with the industry’s dynamic changes.
At the forefront of the industry, DZE Asia is committed to meeting the evolving needs of clients with specialised, professional services such as race electronic systems, race track lighting solutions, and overtrack signage lighting systems.
The company is led by Mr Roberto Grilli, Global General Manager and Mr Marco Scaioli, Director of DZE Asia.
Mr Grilli has over 20 years of expertise in both the motorsport and lighting business, with an extensive background spanning integrated solutions for race track circuits, sports venues, museums and architectural lighting in places of worship. Equipped with a deep
understanding of the industry, he drives the company's growth through strategic collaborations and innovative new projects.
Mr Scaioli, as Director of DZE Asia, brings a wealth of experience from the broadcast TV production industry. His team’s deep understanding of high-pressure, fast-paced environments, combined with their technical proficiency and industry knowledge, positions DZE Asia as a leading provider of innovative, reliable solutions in the ever-changing global motorsports industry.
“DZE Asia is committed to driving
impactful change and delivering exceptional value to our clients. We are always pushing boundaries and continuously provide tailored solutions that best fit our clients’ framework. This shift marks a new chapter of growth as we expand our reach globally, while maintaining our commitment to our company vision. We look forward to working towards deepening our partnerships with current clients and exploring exciting opportunities on a global scale,” said Mr Scaioli.
further and higher With the company’s diverse
portfolio of clients and services, DZE Asia is ready to take on a new set of challenges and achieve even more in the years to come. Since 2019, the company has partnered with prominent clients both in Singapore and internationally.
DZE Asia is enthusiastic about advancing its services and reaching a broader clientele, providing top-tier solutions for electrical and telecommunication needs. This shift is a crucial, strategic step for the company towards new market opportunities and driving growth.
Mr Roberto Grilli, Global General Manager of DZE Asia, provides the background to the establishment of DZE Asia in Singapore, and the scope of the company’s activities.
The Singapore Engineer (TSE): Could you provide an overview of DZ Engineering, the company’s expertise and activities, and its international reach?
Mr Roberto Grilli (RG): DZ Engineering, part of the Dino Zoli Group, specialises in designing and constructing integrated systems and solutions across the electrical, lighting, and telecommunications sectors. Serving both public and private clients, the company delivers tailored, high-tech solutions to meet diverse customer needs. With extensive experience at international levels, DZ Engineering excels in system integration across various applications. It holds a prominent position in the market, particularly in the lighting enhancement of historical and artistic landmarks, sports lighting, and safety systems for motor racing circuits.
We have our headquarters in Italy and an international presence, with our subsidiaries in Singapore, Riyadh, London and Las Vegas.
TSE: When was DZE Asia established, and what are its aims and objectives?
RG: We established DZE Asia in 2019 to develop race electronic systems for the Hanoi street circuit in Vietnam, which was set to host the country’s first-ever Formula 1 Grand Prix the following year. Unfortunately, the event was cancelled due to COVID-related reasons.
However, the project’s primary objective remained intact – to create an independent subsidiary in Singapore, capable of managing DZ Engineering’s activities across the Asian region, with a focus on APAC countries.
TSE: Specifically, could you elaborate on the upgrading of the track lighting system for the Singapore Grand Prix to energyefficient LED lighting systems, and the results achieved?
RG: In 2023, the organisers requested an upgrade to the lighting system. Together with our partner Signify (formerly, Philips Lighting), we participated in and
won the tender for the project.
The same year, we collaborated with Signify to develop the lighting system for the Las Vegas Grand Prix.
Today, LED technology is widely adopted, also in sports lighting due to its significant energy savings and enhanced reliability, including improved safety. The results are remarkable – the entire circuit is now illuminated with a light that offers superior uniformity and more realistic colours for spectators.
This advancement is a crucial step in meeting the increasingly demanding requirements of modern television broadcasting, while simultaneously reducing energy consumption and the overall carbon footprint.
TSE: Any other information that you would like to provide?
RG: We have good reason to believe that the number of motor racing circuits hosting night-time events will increase in the coming years. This presents an exciting challenge, allowing us to develop and test new technologies, paving the way for an even brighter future.
Signify is a world leader in lighting for professionals and consumers, and lighting for the Internet of Things. The company leverages over 130 years of leadership in this area.
Signify’s smart connected lighting offerings bring light and the data they collect to devices, places and people – redefining what light can do everywhere, from homes, offices, shops, supermarkets, sports stadiums, cities, greenhouses, factories and more.
Switching to LED and connected LED lighting is one of the quickest, most effective paths to a greener future. Yet, it is also often one of the most overlooked ways to make progress towards attaining sustainability goals.
Switching all the light points in Singapore to LED could annually reduce emissions by 1 million tonnes of CO2, saving SGD 700 million in energy costs.
A commercial building, industrial facility or even a carpark, could significantly improve its operations through a lighting retrofit.
Upgrading to energy-efficient LED lighting will reduce energy consumption and maintenance costs, ensuring optimal productivity and safety.
Financing, funding, and subsidies are available to help businesses and citizens optimise their use of lighting, and reduce their energy and carbon footprints.
Signify has created the Green Switch programme to help organisations and individuals take advantage of these initiatives.
Signify has also unveiled a breakthrough with Philips UltraEfficient LED bulbs. The bulbs can deliver up to 50,000 hours of light, more than three times the lifetime usage, as compared to standard Philips LED bulbs. Consuming 60% less energy than standard LED alternatives, energy
savings of up to 50% can be made. This breakthrough can ensure longterm reliability for cities, business and consumers.
Interact, from Signify, is a portfolio of IoT-enabled software suites that manage connected lighting systems and the data that those systems collect. Interact software manages, monitors, and controls lighting systems that include connected luminaires, sensors, and other connected devices from Signify and third-party manufacturers.
Interact, the connected LED lighting system and management software, enables users to remotely manage, monitor and control all city lighting, from roads and streets, to sidewalks and crossings, and parks and plazas, all from a single dashboard.
It is also compatible with existing lighting infrastructure, allowing it to be integrated with a smart city dashboard and other applications like noise and air quality monitoring, incident detection and more, via open APIs.
Lighting asset management
Automatic fault detection alerts users to issues for quick response and minimal downtime. Data can be used to make informed decisions and optimise lighting performance.
Energy optimisation
Users are able to optimise street lighting performance and accurately measure energy usage in real-time, reducing CO₂ emissions and making trackable progress towards the city’s sustainability goals, whilst lowering energy costs.
Scene management
The city lighting can be adapted remotely to suit the time of night, season or event.
Sensors
Outdoor sensors, which detect motion/presence, street light tilt angle and strong impacts, ambient temperature, noise and other parameters, can be attached to a street light luminaire. The sensing functions can be remotely configured, and data sent to the Interact application via the connected lighting network.
Solar lighting
Solar and hybrid street lighting minimise emissions and scale up the use of renewables. Hybridsolar technology uses clean solar powered electricity when there is sunlight and will switch to the grid. when required.
Color Kinetics
With 16.7 million spectrums of colours, Color Kinetics delivers plug-and-play solutions for interior and exterior applications. From exterior facades and architectural details to interior retail and hospitality environments like clubs and restaurants, Color Kinetics can provide straightforward solutions in dynamic, colour or white light luminaires.
Sports venues
Signify have been lighting major sports venues around the world for
the past 60 years, providing glare-free stadium floodlights that meet the highest broadcasting standards, to dynamic and colourful architectural lighting that can be used to create vibrant and immersive fan experiences. Lighting can be managed across the entire venue, including the pitch, stadium façade and hospitality areas, via an easy-to-use system, enabling the venue to host different types of events, whilst also reducing energy costs and improving operational efficiencies.
In collaboration with DZE Asia, Signify supported the installation of a more energy-efficient track lighting system for the Formula 1 Singapore Grand Prix. The metalhalide projectors that were in place, since 2008, were replaced by LED track lights in 2023 to illuminate the 4.928 km-long racetrack. The upgraded LEDs require less power per fitting and consume around 30% less electricity than the previous bulbs. The new lights also do not require any warmup time to reach their full luminance when switched on, saving time and energy.
Interact Hospitality supports in delivering an enhanced experience for guests and attendees, while improving staff efficiency and energy savings. Connected LED lighting delivers dynamic, moodenhancing lighting scenes in guest
rooms, restaurants, concert halls and elsewhere.
Interact integrates with heating, ventilation, and air conditioning (HVAC), property management systems, and other services in hotels and other hospitality venues, giving real-time visibility on one intuitive dashboard, to streamline operations and improve guest services. Circadian lighting improves guests’ mood, experience and overall well-being.
The Interact Hospitality dashboard allows staff to see real-time guest requests, ensuring quick response and turnaround times, helping to improve productivity and service levels. The system also reduces unnecessary work for staff while minimising guest disruption.
The control panel has proven popular with hotel guests, who appreciate the ability to control air conditioning, temperature and lighting, from a central point.
In some climates, HVAC can account for over half of a hotel’s energy consumption. Linking it to check in/out information via the Property Management System and data from smart occupancy sensors will help optimise energy usage in the guest rooms by turning down systems when rooms
are unoccupied. This enables hotels to keep rooms just as guests want them, while reducing energy usage when they are out of the room.
Interact dashboard and API
Staff efficiencies can be optimised and management teams can be empowered to work more effectively with complete visibility of hotel operations via the Interact Hospitality dashboard.
Signify has successfully completed hundreds of offices and industrial projects. In a smart building, Interact connected lighting systems can host sensors that collect data about the illuminated environment, including motion, light levels, occupancy, people count, temperature, humidity, air quality and more. Positioning and density of sensors depends on ceiling height, configuration of space and other factors.
Connected systems integrate and manage various lighting systems for centralised control and smart functionalities.
Data analytics
Data analytics provides insights and reporting on energy usage, performance, and operational efficiency. The lights can collect data such as occupancy or temperature. Such data can support the sustainability goals of their customers. The data can be shared with other partner systems such as AC systems.
Energy optimisation
Energy optimisation reduces energy consumption and costs of the lighting, through real-time datadriven adjustments and predictive maintenance. Each light has an energy meter that measures how much energy is being consumed.
Customisation
Customisation of lighting offers scalable and tailored solutions for
diverse environments, enhancing user experience and comfort.
Integration of the lighting with other systems, such as building management and smart city infrastructure, facilitates comprehensive management.
Sustainable lighting supports environment-friendly practices by improving energy efficiency and contributing to sustainability goals. The lighting can help to achieve energy savings of up to 80%. Green building adoption accelerates with points granted for green certification of occupancybased lighting and circadian lighting.
NatureConnect by Signify brings the benefits of natural light, indoors.
The NatureConnect lighting innovation is built on proven biophilic design principles. The lighting mimics the natural patterns of daylight, indoors, to create comfortable, engaging and attractive environments.
The benefits of natural light, indoors, include enhanced wellbeing, achieved by supporting the body’s natural day-night rhythm to stay active during the day and rest well at night, boosting performance and creating an inspiring environment.
The NatureConnect lighting solution combines various LED luminaires with intuitive lighting control for a fully immersive natural experience.
esmo group (esmo), a leading global full-service systems integrator, developer and supplier of innovative and advanced automation solutions, has announced the launch of its latest product – the Apollo Quad Handler. Designed to bridge the gap between the engineering and production phases, this advanced handler offers flexibility, reliability and energy efficiency, for final test operations, setting a new standard in semiconductor testing.
“As semiconductor manufacturers continue to face increasing demands for greater throughput and efficiency, our new quad handler responds to industry needs with a state-of-the-art solution. We are excited to introduce a handler that not only delivers superior performance, but also addresses critical issues like energy consumption and cost-effectiveness for applications where ultra-high parallel testing is not required,” said Mr Simon Murnauer, Manager R&D of esmo AG.
The success of esmo’s talos engineering handler sparked demand for a similarly flexible and reliable machine optimised for higher volumes. The Apollo Quad Handler addresses this need, offering an alternative to energyintensive legacy systems. Optimised for testing complex devices like SoCs and AI chips, it is designed for applications requiring up to 50,000 devices per day, delivering precise thermal performance and real-world UPH (units per hour) efficiency.
Key features and benefits
• Universal I/O Interface: Supports tray, tube and tape loading/ unloading with flexible module configurations, AMR/AGV ready.
• Adaptable Device Pitch: Easily configurable for different pitches through conversion kits, minimising costs by reusing existing loadboards and sockets.
• Versatile Device Range: Quad-site supports devices from 2.5 mm x 2.5 mm to 50 mm x 50 mm. Single-site handles larger devices up to 125 mm x 120 mm (JEDEC tray size).
• Energy Efficiency: Uses 200 l/ min CDA and 8 l/h LN2, reducing operating costs.
• Ultimate Thermal Control: Plunger temperature range from -80 °C to +225 °C for precise testing.
• Quick Conversion Kit Changeover: Tool-less and fast, with automatic kit-specific parameter transfer from kit to machine via RFID tags.
• Mixable Media Options: Allows flexible handling, with mixable media configurations (e.g. tray in, tape out), reducing additional inspection steps.
Another key feature of the Apollo Quad Handler is its seamless integration with existing automated test equipment (ATE). It can adapt to legacy handler-specific hardware interfaces, such as loadboards and site pitches, allowing users to upgrade their test cells without having to invest in new hardware. This makes the handler an ideal choice for companies looking to modernise their operations, while minimising capital expenditures.
“Our product meets the evolving demands of the semiconductor industry by delivering similar UPH at significantly lower costs – both in terms of purchase price and ongoing energy consumption. It is a solution that addresses both the needs of low- to mid-volume production and engineering trials,” said Mr Murnauer.
Designed for maximum versatility, the Apollo Quad Handler is a good fit for both small-scale engineering trials and production runs. It supports flexible I/O module configurations, including tray, tube and tape, allowing customers to
transition seamlessly between testing formats, without extensive downtime. With its modular design and tool-less conversion kits, the machine can be configured on-site in less than five minutes.
Additionally, the handler’s real-time monitoring capabilities, continuous data tracking with adjustments implemented immediately and detailed reports generated automatically, simplify the process of maintaining peak operational performance.
A transformative solution for the semiconductor industry
The Apollo Quad Handler is set to transform the final test landscape for chipmakers, foundries, OSAT providers and test houses. By delivering the flexibility of engineering handlers at a scale that matches production needs, it helps manufacturers streamline their processes, reduce energy consumption and lower operating costs. As the first final test handler to offer I/O module flexibility, including vision, bulk and magazine options, the quad handler allows for highly customisable, efficient testing of workflows.
This launch comes at a time when semiconductor companies are looking for ways to boost efficiency without sacrificing quality.
Keysight Technologies Inc has expanded its signal generator portfolio with two new analog signal generators – an RF analog signal generator and a microwave analog signal generator.
These new solutions provide radio frequency (RF) engineers with portable and compact tools for component and device characterisation at frequencies up to 26 GHz.
RF engineers rely on signal generators to develop and test components and devices across consumer electronics, wireless networks, radar systems and more. These tools are essential for producing continuous waveform and analog modulation signals during the design and testing process.
The new Keysight signal generators offer several key advantages:
• Portability: Compact size and lightweight design for easy transport and efficient use of lab space.
• Versatile power range: Accurately levelled output power from -120 dBm up to +23 dBm, suitable for various RF and microwave applications.
• Low phase noise: Oven-controlled crystal oscillator stabilised signal (phase noise -130 dBc/Hz at 1 GHz, 20 kHz offset) with mHz resolution ensures the measurement accuracy.
• Rapid testing: Fast switching speed (down to 20 µs) accelerates testing and boosts throughput.
• Extensive modulation capabilities:
Supports amplitude modulation, frequency modulation, phase modulation, pulse modulation, pulse train and frequency chirps.
• Optimised user interface: Features an LCD touch screen and remote desktop PC software, making it easy to operate.
• Future-ready: All frequencies and options are licence upgradeable.
Keysight Technologies Inc has introduced its new Electronic Design Automation (EDA) software portfolio to transform how engineers address the demands of next-generation technologies.
For 5G/6G and data centre applications, Keysight’s suite of EDA tools leverages AI, machine learning (ML), and Python integrations to dramatically reduce design time for complex RF and chiplet products.
Keysight’s EDA 2025 software addresses critical challenges in the development lifecycle.
ADVERTISERS’ INDEX
AI-enhanced workflows and high-performance computing further reduce the time-to-insight. Core benefits of the EDA 2025 software portfolio include:
• RF Circuit Design: Accelerate RF design cycles through open, automatable workflows featuring Python integration and multidomain simulation. Additionally, the Python toolkit enables engineers to quickly consolidate measured load pull data from various files and formats into a single, cohesive dataset to train fast AI/ML models.
• High-speed Digital Design: Create precise digital twins for complex standard-specific SerDes designs, including Universal Chiplet Interconnect Express (UCIe) chiplets, memory, USB, and PCIe, with the Advanced Design System (ADS) 2025 release.
• Device Modelling and Characterisation: Reduce model re-centring time by 10X through AI/ML capabilities in the IC-CAP 2025 release, while Python integrations streamline and automate the modelling process.