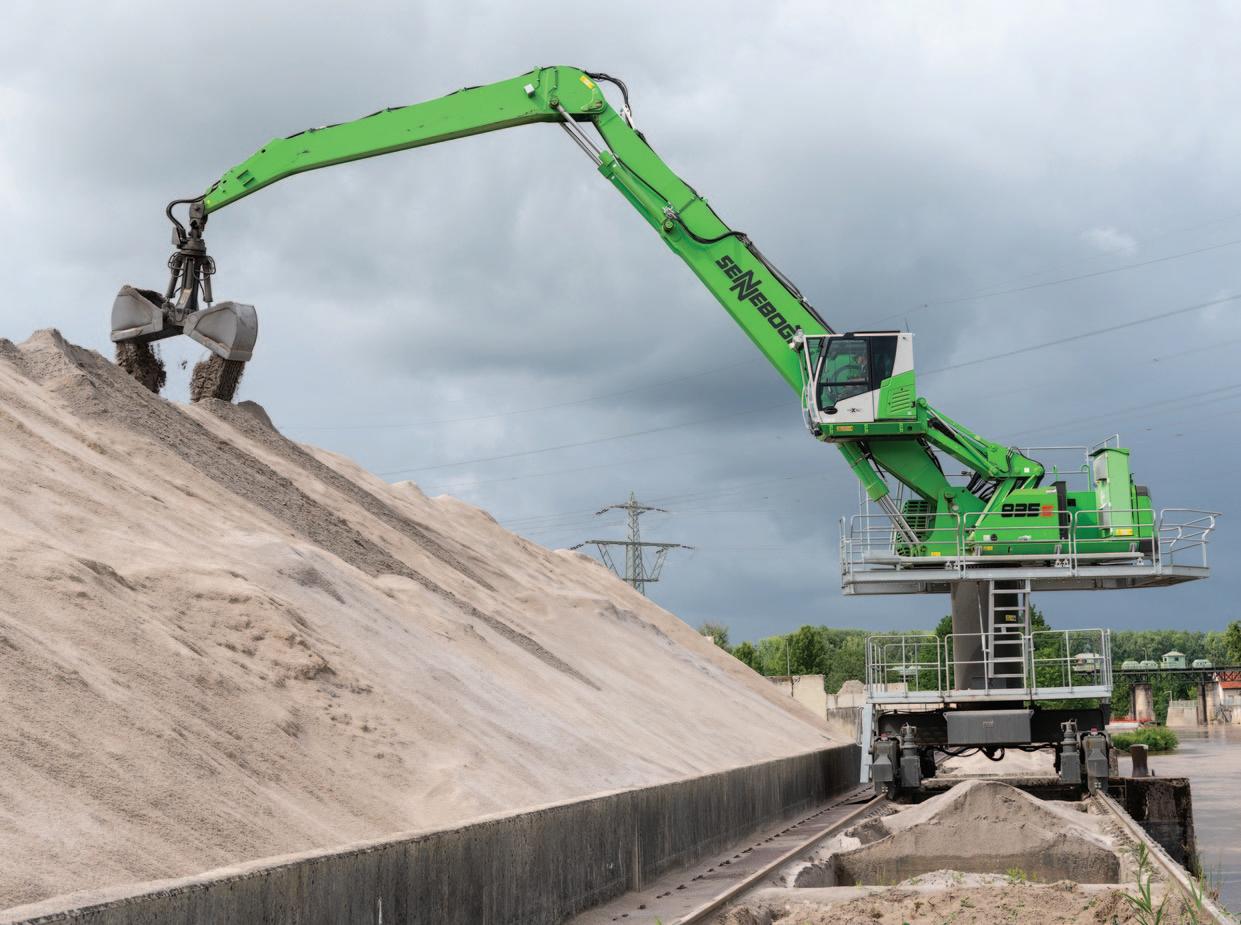
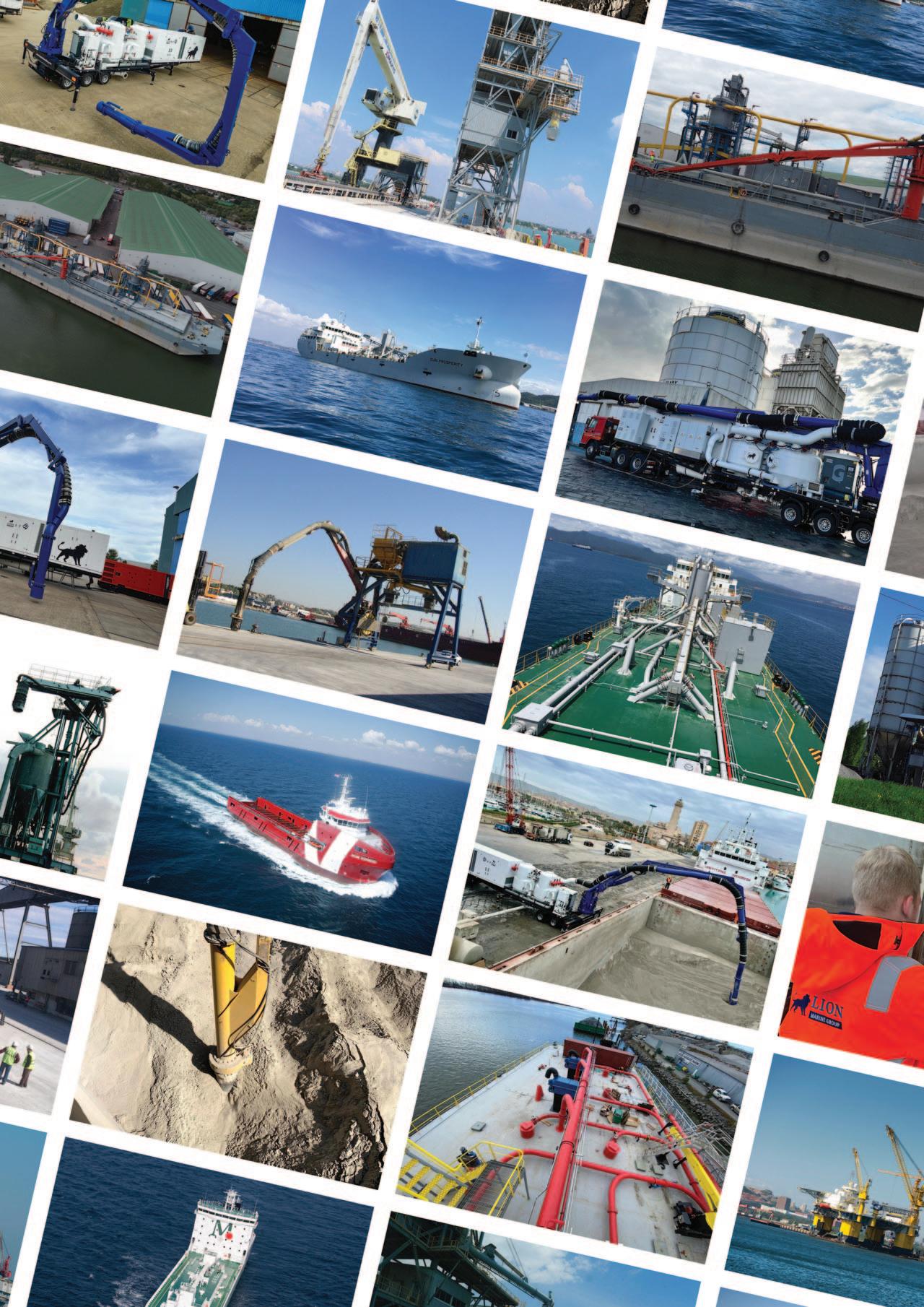
For bulk handling by the tonne in the port, Schlüter für Baumaschinen delivered a new SENNEBOGEN electric material handler to Freiberg to Valet u. Ott GmbH & Co. KG. Thanks to the installed electric drive, the 835 E not only impresses with its low operating costs, but also with its special rail undercarriage, which was specially adapted to the rails already existing in the port at the customer's request.
SENNEBOGEN Maschinenfabrik GmbH
Sennebogenstraße 10 D-94315 Straubing, Germany
T: +49 9421 540-0
E: info@sennebogen.com
W: www.sennebogen.com
PUBLISHERS
Jason Chinnock jason@dc-int.com
Andrew Hucker-Brown andrew@dc-int.com
EDITORIAL
Louise Dodds-Ely Editor louise@dc-int.com
Jay Venter Deputy Editor editorial@dc-int.com
Samantha Smith Directories directories@dc-int.com
Bernice van Wyk Office Manager accounts@dc-int.com
SALES
Matthew Currin Senior Sales sales2@dc-int.com Executive
Zack Venter Advertisement Sales sales@dc-int.com Executive
CORRESPONDENTS
Brazil Patrick Knight
India Kunal Bose
Europe Barry Cross
UK Maria Cappuccio
UK Michael King
UK Richard Scott
ADMINISTRATIVE OFFICE
Business Publishing International Corporate Park, 11 Sinembe Crescent La Lucia Ridge, South Africa, 4051
Tel: +27 31 583 4360
Fax: +27 31 566 4502
Email: info@dc-int.com
Twitter: twitter.com/drycargomag
HEAD OFFICE
Trade Publishing International Limited Clover House, 24 Drury Road, Colchester, Essex CO2 7UX, UK
Tel: +44 (0)1206 562552
Email: info@dc-int.com
Website: www.drycargomag.com
Twitter: twitter.com/drycargomag
ISSN 1466-3643
Insta: www.instagram.com/drycargointernational
Trade Publishing International Ltd does not guarantee the information contained in Dry Cargo International, nor does it accept responsibility for errors or omissions or their consequences. Opinions expressed herein are not necessarily those of Trade Publishing International Ltd
© Trade Publishing Int’l Ltd 2023
During the past twelve months a number of adverse influences affected commodity import demand around the world. Global seaborne dry bulk trade appears to have decreased slightly as a result. Currently signs of a pickup in 2023 are limited.
Among likely restraints on trade expansion in the year ahead, prospects for the world economy are subdued. A revival in China could assist a more positive trend to evolve, but elsewhere prospects are not bright. Inflationary pressures, in particular, and tightening monetary policies accompanying these in many countries, could continue to dampen economic activity for some time. International Monetary Fund economists envisage that a third of the global economy will be in recession during 2023.
GRAIN & SOYA
After a period of strong growth, world trade in grains and soya ceased growing in 2021/22 and looks set to remain flat again in the current 2022/23 trade year ending third quarter 2023. According to US Department of Agriculture estimates published a few weeks ago, trade in wheat, corn and other coarse grains, plus soyabeans and meal could total 664.4mt (million tonnes) in 2022/23, unchanged from the previous year.
While wheat and coarse grains trade is likely to be lower in the current period, soyabeans and meal could increase. One reason for changes in the world market is large variations in China’s purchases. During the past 2021/22
year both grain and soyabeans imports into China declined, reducing the volume by 18mt or 11%, to 142.7mt based on USDA data. But in the current period signs suggest that a recovery in soyabeans buying amid rising consumption could occur.
Global seaborne coal trade was well supported in the past twelve months, following the 2021 partial recovery from the previous year’s steep downturn. What is likely to happen in 2023? Current tightness in the international energy market, which appears set to continue in the months ahead and perhaps through the entire year points to coal trade being firmly underpinned, possibly resulting in a slight rise.
Several forecasts suggest that growth of up to 2% could be seen this year. Revised predictions by analysts at the Australian Government’s industry department, published in late December, show that world steam and coking coal trade (including land movements, but mostly seaborne) may increase by 25mt or 1.9%. After an estimated 1,347mt in 2022, the total is expected to rise to 1,372mt. Although China’s import volume may decline, other countries are likely to more than compensate.
The background envisaged for steel industry activity in many countries, over the year ahead, indicates that constraints on demand for many of the products manufactured by steel users
may remain subdued. In the construction, machinery, vehicles and household appliances sectors and elsewhere business and consumer spending is likely to be restrained by ongoing macro-economic trends.
In Europe, Japan, South Korea and some other producing countries importing iron ore and coking coal signs of strengthening steel output are still awaited and may not appear in the short term.
For China, the biggest raw materials importer, an economic upturn enabled by the relaxation of coronavirus-control restrictions is widely expected to unfold, accompanied by extra government support measures which could benefit steel production, but residential property sector weakness remains a constraint.
Fertilizer movements are an important element of the minor bulks segment. World seaborne trade in potash, phosphate (rock and processed), sulphur and urea evidently was down sharply last year to around 175mt, and may remain weak this year.
Growth in the Handysize (10–39,999 deadweight tonnes) bulk carrier fleet is estimated at about 3% in 2022. Over the next twelve months a deceleration could occur, despite newbuilding deliveries probably remaining steady, if scrapping of old or uneconomic tonnage revives.
Since the initial rebound in global seaborne dry bulk trade emerged after a downturn accompanying the coronavirus pandemic, the trend has weakened. Provisional data suggests that a reduction occurred in the past twelve months, and prospects for the year ahead point to only a minor improvement.
Events during 2022, which greatly constrained import demand for many commodities in countries around the
world, emphasized the potential for unforeseen changes in influences. The intensified range of uncertainties arising and the negative effects of these are mostly still ongoing, casting a shadow over the outlook for dry bulk trade through 2023. Nevertheless there are signs indicating possible limited strengthening, based on a cautiously optimistic view.
Estimates for trade in the past year of 2022 are subject to perhaps sizeable
revision. As shown by table 1, global seaborne dry bulk commodity movements appear to have decreased by 1–2%, following an increase of well over 3% in 2021 when an upturn from the pandemic’s adverse effects occurred. Varying performances among the main elements were seen last year. Coal trade may have increased marginally, while other commodity trades diminished.
Recent clues for 2023 suggest that the
Our bespoke solutions are designed to meet each customer’s specific requirements from a tool kit of proven components, utilising the expertise of a team of specialist in house design engineers.
We lead the loading chute industry & set the standard for dust emissions and environmental pollution control in dry bulk handling.
Our worldwide reputation is built on high quality, well-engineered, robust, high performance chutes, backed up by excellent customer service and global lifetime product support.
outlook is fairly flat, with a possibility of resumed albeit slow growth. Disruptive events restraining import demand for commodities in a number of countries remain prominent, and some or all of these could continue for some time. Yet, assuming that events having such an adverse impact in past months moderate, dry bulk trade may begin to pick up again.
Changing patterns of economic activity in many countries directly affect dry bulk imports, as emphasized by variations in the past few years. Consequences are visible when large changes in the pace of consumer, business or government spending are closely linked to production volumes, in industries using dry bulk
commodities mainly or partly obtained from foreign suppliers.
At the beginning of 2022 predictions focused on the beneficial effects of the global economy’s recovery from the recession caused by the pandemic. Economic activity was expected to grow briskly. But the war in Ukraine, followed by energy shortages, sharply increased inflation and China’s slow progress led to forecasts of global economic growth being revised downwards. World gross domestic product (an overall measure of goods and services output) is estimated to have approximately halved in 2022, from 5.9% growth in the previous year, to 3.1% according to calculations by the OECD organization.
Great uncertainty surrounds assess-
ments of prospects for 2023, amid continuing hostilities in Ukraine, ongoing energy supply shortfalls, an unclear outlook for China’s recovery, and indications of recession in some countries. Forecasts published by the OECD several weeks ago, shown in table 2, reflect a sombre view of unfolding events. World GDP growth could slow further this year, to 2.2%, based on minimal increases or recessions in the USA and Europe, slow improvement in Japan, and an acceleration in China.
In the OECD’s latest report analysts commented that “the global economy is reeling from the largest energy crisis since the 1970s”. According to the authors “global growth has lost momentum amidst high inflation”. Along with weak growth and persistent inflation, elevated risks are
apparent. Recovery may not begin until later this year or in the following twelve months.
Trends in the steel industry affect a large proportion of global dry bulk commodity trade movements. Demand for steel is influenced by consumer, business and government spending patterns in an economy. Changes in steel production volumes result in numerous countries where steel is made, causing in turn consumption and imports of iron ore, coking coal and some other raw materials to vary.
In 2022 steel production changes in major raw materials importing countries were mostly downwards. During the first eleven months of last year, volumes compared with those seen in the same period a year earlier were down by 1% in China, 6% in South Korea, 7% in Japan and 10% in the European Union. The notable exception to this array of reductions was India, which achieved a 6% expansion.
The steel industry raw materials trades, especially iron ore, are dominated by China’s import demand. Over the past twelve months China’s steel production and related consumption and imports of iron ore reflected subdued demand for steel. Two factors especially were apparent. There were adverse effects on overall economic activity from measures imposed to control outbreaks of coronavirus, while weakness in the residential property market which consumes large volumes of steel in housing construction was a more specific influence.
Prospects for global steel production volumes in the next twelve months are not clear because of the prevailing uncertainties about economic activity. A possible outcome is suggested by the recent shortrange steel demand outlook published by the World Steel Association. According to this view, there is limited potential for steel demand in many of the main producing and raw materials importing countries to strengthen in 2023. India, a leading coking coal importer, is the main exception which
could achieve continued robust expansion. Actual steel production volume changes are not forecast by the WSA in this analysis.
Movements of the principal steel industry raw materials, iron ore and coking coal, comprise one-third of all global seaborne dry bulk cargo trade. In 2022 iron ore trade apparently decreased by about 2%, compared with the preceding year, to around 1,490mt (million tonnes) as shown in table 1. Coking coal trade (not shown separately) evidently was roughly flat at about an estimated 260mt.
Iron ore movements are dominated by China’s imports, contributing almost threequarters of world seaborne volume. In 2021 the China imports total (including some overland movements) was 1,126mt. During 2022 the volume received appears to have been about 1% lower. Elsewhere last year, in the other prominent importing countries — the European Union, Japan and South Korea — imported volumes apparently fell by much larger percentages, perhaps exceeding 5%, amid weaker steel output trends.
Within the coking coal segment trade is much smaller than the iron ore volume, while imports are more evenly distributed and not dominated by China. In 2022 China’s quantity, under 15% of the total, evidently declined. In other large importing countries outcomes were mixed. Japan and India may have seen small reductions, while in Korea and Europe advances occurred.
The overall result appears to have been only a minimal change in the volume of world seaborne coking coal trade.
Looking at the year ahead, what is the outlook for global steel industry raw materials trade? Currently potential for expansion seems very limited amid adverse influences affecting world economic activity, which are likely to restrain steel demand and production levels in many countries. This perspective suggests a fairly flat trend evolving. Raw materials imports into the European Union, Japan, South Korea, India and a number of smaller buyers may not increase substantially. In China also it seems unlikely that a stronger imports trend will resume.
Almost four-fifths of seaborne coal trade is comprised of steam — also known as thermal — coal. Consumption and import demand is mostly associated with power station usage in a wide range of countries, and it is also used in cement manufacturing plants and other industrial processes.
Tentative estimates suggest that in 2022 world seaborne steam coal trade may have increased marginally by 1% to reach about 970mt, following the previous year’s upturn. Changes among major importing countries varied greatly in both direction and magnitude.
The year was characterized by a global energy shortage exacerbated by the effects of the Ukraine conflict on European energy supplies in particular. Although the
worldwide shift towards cleaner fuels continued, coal’s contribution to energy security saw a strengthening.
During the past twelve months the post-pandemic global economic recovery’s momentum weakened. Nevertheless energy supplies remained tight, supporting steam coal demand and imports in numerous countries. But the positive effect on trade movements was still restricted by government policies aimed at reducing coal usage. Intensifying environmental pressures to cease or severely curtail coal burning, especially in power stations, were instrumental in preventing a stronger advance in coal trade.
Contrasting large changes in annual steam coal import volumes last year were especially visible in China, where a big fall was seen, and India where a big rise occurred. Among other Asian importers increases were evident. In Europe imports probably increased by around one-third, mainly as a consequence of severe gas shortfalls. Some of the factors strengthening global import demand are set to be sustained through 2023, suggesting that world seaborne steam coal trade could remain well supported and possibly continue rising.
The definition of global seaborne trade in grain and soya usually includes wheat, corn and other coarse grains, and soyabeans, all comprising large quantities. Related
soyameal is usually included in the minor bulks trade segment, together with other oilseeds and meals. In 2022 there was a reduction in grain and soyabeans trade, as shown in table 1, when an estimated 3% decline to about 510mt resulted.
Trade statistics for this commodity group are typically compiled on a ‘split year’ basis, known variously as a ‘crop year’, ‘marketing year’ or ‘trade year’, reflecting the sequence of world harvests and timing of new export seasons. The profound impact of weather variations, often unpredicted, affecting crops harvested by export suppliers as well as domestic crops in importing countries is a notable feature of the annual trade picture. Import demand changes from year to year are often a consequence.
As viewed on the usual crop year basis world trade in wheat and coarse grains during the past 2021/22 year ending June 2022 was marginally lower, by less than 1%, at 424mt. International Grains Council figures show that a large reduction in imports by China and some other Asian countries was almost offset by increases elsewhere around the world. China’s reduction followed a huge expansion in the previous twelve months which improved supplies for the domestic market.
Indications for the current 2022/23 crop year point to a large reduction in global grain trade. The IGC is estimating a 4% decline, mainly reflecting a further large fall in China’s imports from the exceptionally
high volumes seen previously, coupled with other decreases, partly offset by higher imports into the European Union.
Combining statistics for soyabeans and soyameal, data assembled by the US Department of Agriculture shows that global trade declined by 3% in the 2021/22 marketing year ending September 2022, to 222mt. The largest buyer is China, with over two-fifths of the world total. Demand from Chinese importers, mostly consisting of beans, was lower in the past twelve months, while beans and meal imports by other major buyers — Asian countries and the European Union — remained stable.
World soyabeans and meal trade within the present 2022/23 marketing year may recover. The USDA is predicting a 4% increase amid stronger imports into a wide range of countries. A large part of the incremental volume is likely to reflect extra demand for beans from Chinese processing (crushing) mills, rising from 92mt in the past year to reach 98mt, almost returning to the peak annual volume.
Many minor commodity movements are included in this extensive category of seaborne dry bulk trade. Widely varying types of commodities contribute, some of which provide large volumes while others are relatively small. In total the segment is huge, with estimates suggesting that it comprises around two-fifths of all world seaborne dry bulk trade.
Cargoes associated with manufacturing industries and construction activity comprise the biggest part of the minor bulks group. These are the ‘industrial’ bulks.
Agricultural or related cargoes form the remainder. Global seaborne minor bulk trade overall increased by 5% in 2021 to reach about 2,100mt as momentum recovered from the pandemic’s adverse effects. This was followed last year by a weakening pattern in numerous components when economic activity faltered, possibly resulting in the total diminishing by about 3%. Prospects for 2023 show only limited signs of revival.
Among individual commodity components the largest are steel products and forest products, both including many different varieties. Other prominent elements in the ‘industrial’ sub-group are bauxite and alumina, steel scrap, cement, coke and petroleum coke, salt, and nickel and other ores. Agricultural or related bulk cargoes consist of sugar, oilseed meals, rice, plus raw or semi-processed fertilizers.
In the past year negative influences affecting global seaborne minor bulk trade were widespread, exacerbated by slow industrial growth in China — a top importer of minor bulks — and some other countries. Steel products (coil, plate, sheet and other items) and forest products, the two biggest elements of world trade may have declined by 4–7%. Cement trade also apparently was much lower but, by contrast, bauxite/alumina trade was buoyant.
Usually a starting point for assessments of future dry bulk trade volumes is prospects for economic activity and demand for the products of various industries in the countries having the biggest impact on
global commodity import demand. As already discussed many countries may experience slower growth during 2023 or, in some cases, perhaps recession in the early months of the year. Such a pattern could have an unfavourable impact on commodity import movements.
Assumptions about China are particularly relevant to expectations for global seaborne dry bulk commodity trade, because this country’s imports are estimated to comprise well over one-third of the world total. After unusually sluggish economic growth in 2022, a strengthening trend is widely expected, but depends greatly on further progress in controlling the covid pandemic. If this is achieved, dry bulk commodity imports seem likely to increase.
Among wider influences, fairly clear signs suggest that one restraint on future dry bulk trade growth is likely to be obvious over time, although not necessarily in 2023. The outlook for iron ore and coal, two segments contributing half of the total seaborne dry bulk trade volume, is not favourable. Iron ore trade may have reached a plateau, while coal trade is surrounded by longer term downwards pressures even though trade is currently holding up. For grain and soya movements, and some minor bulk elements, prospects seem more positive.
The critical role of the Great Lakes-St. Lawrence Seaway system in the global supply chain has been brought into sharp focus over the last few years. On 24 January, the Canadian St. Lawrence Seaway Management Corporation (SLSMC) and U.S. Great Lakes St. Lawrence Seaway Development Corporation (GLS) jointly announced that more than 36mt (million tonnes) of cargo transited the system during the 2022 navigation season.
US and Canadian producers helped v mitigate global issues affecting fertilizer supplies, which drove significant growth in potash, up over 100% compared to 2021.
Dry bulk commodities, including coke, v salt and potash, contributed over 11mt of the 2022 total.
Petroleum products were up nearly v 28% over last year, due to increased passenger travel.
US grain exports increased, and v although month-over-month Canadian grain performed well, it did not match last year’s results. The effects of the 2021 drought in the Canadian prairies impacted export movements at the beginning of the 2022 season. That said, the improved 2022 grain harvest
2022 End of Navigation Results
is expected to result in a strong start for 2023.
An increase of vessel transits, including v expanded cruise ship activity in the Great Lakes helped contribute to tourism and economic development in Canada and the United States.
“Seaway traffic results show positive trends amongst certain commodities, which demonstrates our system’s ability to quickly adapt to changes in the market,”
said Terence Bowles, President and CEO of the SLSMC. “It’s this agility that enables the Seaway to respond to changes and act on emerging opportunities, such as shifting trade patterns resulting from global events. In addition, we are working closely with partners to develop lands along the Seaway, which will benefit both the economy and local communities.”
“Through decades of investment and reliability, the Great Lakes are uniquely positioned to weather upheavals in the
global supply chain,” said Adam Tindall-Schlicht, Administrator of the GLS. “The Seaway System is a leading example of a worldwide economically-resilient and environmentally sustainable shipping corridor, and optimism is high for expansion of trade on the Great Lakes in 2023.”
The last commercial transit of the 2022 navigation season through the Montreal-Lake Ontario (MLO) section of the Seaway occurred on 1 January. As for the Welland Canal, it closed on 9 January 2023, marking the conclusion of the fourth year of the Welland Canal season extension pilot program.
From now until the opening of the 2023 season, the SLSMC and GLS will carry out maintenance work on critical lock and maritime assets, ensuring the Seaway system continues to deliver safe and reliable service year after year by managing its assets efficiently.
Though there continues to be some uncertainty with regards to economic growth in 2023, the Seaway Corporations will work on key initiatives to further support expanding trade on the Great Lakes. These include facilitating the establishment of green shipping corridors, expanding land development along SLSMC-owned canals, and developing innovative technologies, such as the Vessel Information System.
“It’s this spirit of continuous improvement and agile performance that make the Seaway a relevant transportation system today, and an integral part of future solutions,” added Bowles.
The Great Lakes-St. Lawrence Seaway system is a ‘marine highway’ that extends 3,700km from the Atlantic Ocean to the Great Lakes. Shipping through the Seaway supports over 329,000 jobs and $59 billion in economic activity in Canada and the United States. Binational marketing development efforts, including the ‘HwyH2O’ initiative, aim to enhance Great Lakes-St. Lawrence Seaway System utilization and increase marine cargo shipping.
The St. Lawrence Seaway Management Corporation was established in 1998 as a not-for-profit corporation by the Government of Canada, Seaway users and other key stakeholders. In accordance with provisions of the Canada Marine Act, the Corporation manages and operates the Canadian assets of the St. Lawrence Seaway, which remain the property of the Government of Canada, under a long-term agreement with Transport Canada.
The Great Lakes St. Lawrence Seaway Development Corporation (GLS), an operating administration of the U.S. Department of Transportation, is a wholly owned government corporation created by statute on 13 May 1954, to construct, operate, and maintain that part of the St. Lawrence Seaway between the Port of Montreal and Lake Erie, within the territorial limits of the United States. Formerly the Saint Lawrence Seaway Development Corporation (SLSDC), the GLS was legally renamed as part of the 2021 Consolidated Appropriations Act as signed into US law on 27 December 2020.
CG rendering of the 210,000dwt ammonia fuelled bulk carrier (courtesy of MOL and MITSUI).
ClassNK has issued an Approval in Principle (AiP) for a large ammonia fueled 210,000dwt bulk carrier jointly developed by Mitsui O.S.K. Lines, Ltd. (MOL) and MITSUI & CO., LTD (MITSUI).
Ammonia is expected to be used as a ship fuel for decarbonization since it does not emit CO2 when combusted. Meanwhile, adequate safety measures are imperative as it has been pointed out that ammonia is toxic to humans and corrosive to materials. ClassNK has been involved in projects aiming for zero-emission ships using ammonia fuel in terms of safety assessment, and has issued its ‘Guidelines for Ships Using Alternative Fuels’ as a necessary standard to minimize the risks related to ammonia-fuelled ships for the ships, crews, and environment by stipulating requirements for installation, controls, and safety devices.
MOL and MITSUI have jointly determined the size and specifications for the vessel, and its design has been entrusted to Mitsubishi Shipbuilding Co., Ltd. ClassNK carried out the review of this jointly developed design in line with Part C of its guidelines and issued the AiP on verifying conformity to the prescribed requirements. In addition, risk assessment (HAZID) will be conducted to confirm that no unacceptable risks exist at the basic design stage and to identify items to be considered in the detailed design.
ClassNK will continue to support those companies as the certification body and will strive to provide appropriate standards for ammonia-fueled ships through the expertise gained from the collaboration.
At the initial stage of designing or before the specific target ship to be implemented is decided, the design is examined based on the existing regulations such as international conventions and ship classification rules, and an Approval in Principle is issued as proof of conformity with requirements. It also prevents rework of regulatory aspects in the postprocess, shortens the examination time at the time of class registration, and can be used as a technical basis for external appeal of the design status.
Over the past year it became gradually clearer that broad influences were providing less support for the global bulk carrier market than seen during the preceding twelve months. After a remarkable improvement in the freight rates trend through much of 2021, last year’s performance was inferior. Moreover, current signs for 2023 point to another year when progress may be limited.
Various changes which unfolded in the course of last year, affecting the demand for and supply of cargo carrying capacity in the bulk carrier sector, combined to weaken the demand/supply balance and restrain market freight rate levels. Although changes in the period ahead are likely to differ, the combined effect may be similar albeit perhaps less restricting. This pattern may allow a somewhat more positive freight rates trend than seen in recent months to evolve. However, expectations for many aspects are speculative.
In 2023 a deceleration in the world bulk carrier fleet’s expansion is predictable. An ingredient probably will be greatly increased scrapping, prospects for which are not yet entirely certain. This shift in the
carrying capacity trend amid substantial newbuilding deliveries probably will prove necessary, to accompany the prospective minimal dry bulk trade and tonnage demand growth envisaged, presently seeming quite likely.
Other influences also will be instrumental in shaping how the trend of freight rates evolves over the next twelve months. One of these is changes in trading patterns affecting tonne-miles performed. Another is port congestion and loading or discharging delays, the significance of which has been receding recently, boosting the effective availability of ship capacity in the market.
Bulk carrier fleet growth during the past twelve months was slightly below its annual expansion rate in preceding years. The world bulk carrier fleet’s deadweight tonnage, a measure of carrying capacity, increased in 2022 by an estimated 2.9%. A substantially lower volume of new ships joining the fleet was recorded, while the amount of old or uneconomic ships leaving also diminished. Consequently the net deadweight capacity added decreased, as
One year ago, at the end of 2021, the world fleet of bulk carriers (including all ships with capacity of 10,000 deadweight tonnes and over) consisted of 12,750 vessels totalling 945.9 million dwt, according to data compiled by Clarksons Research. Twelve months later at the end of 2022 this fleet was about 27m dwt larger at 973m dwt, based on estimates which are subject to revision.
A much lower newbuilding deliveries total was a feature of fleet changes in 2022. The newbuildings volume, provisionally calculated at 31m dwt, may be revised upwards when more complete information is available. This figure is almost one-fifth below the 38m dwt seen in the preceding year. Accompanying this rise was decreased scrapping, measured by reported sales for demolition, totalling about 4m dwt, down by about a quarter.
Among the main vessel size groups (Capesize, Panamax, Handymax and Handysize) fleet growth rates last year varied between 2% and 4%. Enlargement was slowest in the Capesize segment, comprising ships of 100,000dwt and over, forming two-fifths of the entire world bulk
By contrast, within the Panamax 70–99,999dwt size group, including Kamsarmax 80–89,999dwt bulk carriers, growth was almost 4%.
Elsewhere expansion rates were in the middle of the range. The Handymax 40–69,999dwt segment (including Ultramax ships exceeding 60,000dwt as well as Supramax bulkers of 50–59.999dwt) grew by 3%. In the Handysize segment of smaller 10–39,999dwt bulk carriers, growth was also 3%.
Actual changes in transport capacity available are not always accurately illustrated by static deadweight capacity figures, however. Changes in world fleet capacity to move cargoes also depend on how productively ships are employed. Large influences on this aspect are ships’ voyage speeds, ballast (empty) voyage patterns, and duration of port visits, data for which involve complex calculations. The advantage of using deadweight tonnage as a measure is that it is simple and available promptly, and is therefore a useful broad indicator of transport capacity for cargoes.
Average voyage speed in the fleet is an important influence. Even a modest change in the bulk carrier fleet’s average speed, resulting in the time taken to complete a voyage increasing or decreasing, substantially affects annual transport capacity available. A declining speed trend has been evident in recent years, resulting in reduced average annual numbers of voyages completed and therefore lower productivity. After an upturn in the average in 2021, a reversal seems to have occurred in 2022, modifying deadweight capacity growth.
Following a recovery in global dry bulk trade in 2021 when the severe adverse effects of the pandemic receded, further brisk growth was widely expected. But unforeseen events around the world resulted in declining trade last year. A
detailed trade overview is contained in another article in this edition of DCI (‘Dry bulk trade growth falters’ — see p4 onwards), so the following comments are a brief overview.
Global seaborne dry bulk trade expanded by well over 3% in 2021, before decreasing last year by an estimated 1–2%. Among the main segments, coal was the strongest performer in 2022, growing by an estimated 1% after a robust performance in the previous twelve months. Elsewhere negative results were prominent. Iron ore appears to have declined by about 2%, while both the grain and soya, and the minor bulk commodities segments apparently saw reductions of around 3%. The 2022 overall dry bulk total is provisionally calculated to have risen by about 95 million tonnes, down to 5.4 billion tonnes.
Lower import demand in China was a feature of last year’s weakness, amid very slow economic growth reflecting the ongoing coronavirus pandemic and property market downturn. The volume of dry bulk imports into China is estimated to have fallen by 4–5% in 2022, including lower coal, grain and soyabeans, and some minor bulk commodities. This outcome is especially significant because China comprises almost two-fifths of global dry bulk commodity import volumes.
From a shipping market perspective, another aspect also determines demand for the services provided by bulk carriers, how much ‘employment’ is created. Trade volumes transported are the usual focus, because these can be measured relatively easily and are a convenient proxy for vessel demand. But voyage distances are influential as well. The distances affect the number of cargo-carrying trips performed annually by a ship. Any significant change in the annual average voyage distance performed by each deadweight tonne of cargo-carrying capacity has an impact on vessel demand.
Incorporating these measurements within a ‘tonne-mile’ unit includes both cargo (trade) volume and voyage distance,
providing a more accurate gauge of demand for transport capacity. However, statistics compiled on this basis are often not as readily available or as timely, because additional information and extensive calculations are required. In 2022, according to preliminary estimates by Clarksons Research, the annual tonne-miles percentage decrease was about one percentage point smaller than the tonnes volume decrease, implying that bulk carrier demand was reduced by less than cargo tonnes.
The balance between demand for, and supply of, carrying capacity in the bulk carrier freight market slackened in the past twelve months, contributing to a weaker freight rates trend. As already discussed dry bulk commodity trade diminished, while the world fleet of ships carrying these cargoes expanded briskly.
For much of the extended period since the global economic depression experienced after the world financial crisis more than a decade ago, together with its adverse impact on trade volumes, surplus capacity was evident in the bulk carrier sector. Over-expansion of the bulk carrier fleet prevailed amid excessive optimism by shipowners and other players about recovery prospects. Consequently the world fleet remained under-utilized.
When the pandemic began, the impact initially was a huge setback for progress towards a sustainable bulk carrier market recovery which could boost freight rates. Vessel employment was weakened, while the fleet of ships available continued to grow. But then, in 2021, strengthening trade volumes and other favourable influences affecting the market balance were a feature. Last year this pattern was not fully maintained, causing a freight market setback.
There is considerable uncertainty about how the freight market trend will evolve in the period ahead. Evaluations must include effects from the direction and trend of the
market demand/supply balance, and the complications of many temporary influences. Estimates suggest that minimal or no growth in dry bulk trade could be exceeded by slower growth in the bulk carrier fleet. Other influences could modify this relationship, but it seems likely that a sustained freight market strengthening is not yet foreseeable.
In 2022 bulk carrier freight rates varied within a wide range. Rates obtained by all the main bulk carrier sizes moved in broadly similar directions although, as often happens, changes tended to be larger in the Capesize segment than elsewhere. Market Capesize freight rates are often especially volatile, reflecting short-term employment fluctuations in the two commodity trades — iron ore particularly, and coal — on which these bulk carriers mostly depend.
Early in 2022 the bulk carrier freight market experienced downwards pressure but strengthened towards mid-year. Capesize charter earnings during this period were frequently exceeded by those secured by the smaller Panamax and Supramax ships. From around mid-year onwards up to the end of the year a weaker trend became established. During this period the unusual pattern of Supramax and Panamax earnings at higher levels than those of Capesize vessels persisted, reflecting subdued iron ore trade employment for the larger vessels.
The evolving bulk carrier market freight rates trend is represented by the Baltic Dry Index (BDI), although this index does not fully illustrate the sector. The BDI,
calculated daily by the Baltic Exchange, is based on a basket of time charter hire rates for various bulk carrier sizes and typical employments on the specific long-distance international routes included. It is an indicator of changes in the cost of transport for dry bulk cargoes.
From around 2,300 at the beginning of 2022, the BDI quickly fell to about 1,400. It then climbed by about 2,000 points over several months to around 3,400 in May. But this recovery proved unsustainable as the demand/supply balance deteriorated. From June onwards a lower market ensued, down to around 1,000 before improving to 2,000 at the beginning of the fourth quarter after which a reduction to the 1,200–1,500 level was seen.
Events around the world during the past twelve months have complicated any assessment of bulk carrier freight market prospects in 2023. The expected pattern of post-pandemic global economic recovery with benefits for seaborne dry bulk trade volumes was not fulfilled last year, and the disruption experienced seems likely to continue, at least partly through the period ahead.
Some optimism has been expressed among market observers about tonnage supply. Bulk carrier fleet growth is widely expected to decelerate markedly, restraining excess capacity. But the tonnage demand side of the balance is not yet showing convincing signs of strengthening much. So it is unclear whether an upturn in dry bulk trade volumes and tonne-miles performed will be
sufficient to match or exceed the lower pace of fleet expansion envisaged. A weakening balance is still a possibility.
Complicating this outlook is the role of ‘disruptions’ in bulk carrier employment patterns which have adversely affected the fleet’s carrying capacity. Recent signs suggest that logistical and operational delays and disruptions are diminishing, enabling the fleet to provide more efficient transportation activity. Port congestion and delays in a number of countries are reported to have eased in past months, enabling bulk carriers to improve productivity, effectively expanding supply and acting as a restraint on freight rates.
Several prominent uncertainties affecting the trade picture are evident. The return of inflation as a major challenge, leading to weaker real incomes, with adverse effects on growth in spending and economic activity, may continue to restrict import demand for dry bulk commodities for some time. This trend has been exacerbated by the war in Ukraine coupled with the sanctions imposed on Russia, directly constraining global energy and food supplies. How long these events will persist is debatable, although economists indicate that inflation rates may improve during 2023.
Another imponderable is when China’s economy will resume a more ‘normal’ rate of growth. The outcome clearly depends greatly on how the ongoing Covid pandemic, and the policies implemented to control it, affects the future pace of economic activity. A successful easing of restrictions during the next few months potentially could provide an economic
boost, which is likely to be reflected in additional bulk commodity import demand. Nevertheless, over two-thirds of the China volume consists of iron ore and coal, two commodities potentially facing downwards pressures in the longer term although not necessarily declining in the next twelve months.
On the supply side of the freight market, one relatively plausible expectation for 2023 is slower growth in the bulk carrier fleet. Newbuilding deliveries are unlikely to contribute to this deceleration because signs point to these increasing from last year’s level, based on interpretations of shipyard orderbook schedules. The scheduled newbuilding deliveries total for
2023 is well above the actual volume delivered in the past twelve months.
But the scrapping volume potentially could increase substantially from the minimal volume seen in the past twelve months. If this occurs, it could result in a diminished annual net deadweight capacity added to the fleet, implying a much slower growth rate. After the past two years when unusually low scrapping totals were seen, an increased level is foreseeable.
Higher scrapping of old or uneconomic vessels may seem predictable. But forecasting recycling volumes more specifically is largely based on guesses. It is a speculative exercise because market sentiment among shipowners — reflecting recent, current and expected future freight market rates, and how secondhand vessel
prices are evolving — is often a major influence on demolition sales decisions which is not predictable.
However, two main influences in 2023 could boost scrapping. The bulk carrier fleet is ageing. The average age is increasing because of low demolition sales in recent years and there is a significant volume which has reached an advanced age. More shipowners may decide not to incur the extra costs of extensive surveys and maintenance involved in older vessels with a limited remaining lifespan. Another influence is that international maritime regulations aimed at cutting greenhouse gas emissions are tightening in 2023. Compliance costs may not be justifiable on some older bulk carriers, resulting in extra sales to the recycling yards.
Investors in middle aged dry bulk tonnage may be cheered by the impact of sustained higher recycled steel values, according to research commissioned by the Baltic Exchange.
Analysis of the dry bulk carrier values undertaken by consultancy Zuoz Industrial looks at the potential impact of longer-term higher ship recycling values on five year old tonnage. With recycled steel an increasingly popular choice, thanks to its lower carbon footprint when compared with virgin steel, the paper discusses whether higher steel recycle values are a longerterm trend. Although down 20% since its April 2022 high, the price of lightweight steel is ~$520/ldt and more than double the historic average since 2009.
“Should the current multi-year higher cycle value turn out to be a fundamental risk trend supported by some of the evolving demand factors, the fundamental risk of investing middle aged dry bulk tonnage, particularly in softer freight markets, will have decreased,” says report author Urs Dür.
The Baltic Exchange publishes a set of investor indices for the major dry bulk sectors which includes the Baltic Residual Risk Index, a ratio of the residual value of the vessel against its recycling value, and the Baltic Residual Value Index, which calculates the value by taking the written down cost
of a five year old vessel by fixing the earnings on the basis of a five year timecharter and adding back the operating costs.
The Baltic Exchange Investor Indices (BII) are an easy to use online analytical dashboard displaying data relevant to vessel investment decisions, residual value, health of earnings, spot and five-year timecharter earnings, purchase & recycling values, and running costs.
They offer a high level of clarity and
transparency for investors in Capesize, Panamax, Supramax and Handysize vessel types. Tanker and gas carrier assets will also be added to the service at a later date.
Subscribers to the Baltic Exchange Investor Indices are offered a health of earnings index which compares spot income with daily running costs; a residual value index which provides an implied write-down value of the vessel over five years; and an implied residual risk assessment which gives the recycling steel value of the vessel as a ratio of its residual value.
The Baltic Exchange is the world’s only independent source of maritime market information for the trading and settlement of physical and derivative contracts. Its international community of over 600 members encompasses the majority of world shipping interests and commits to a code of business conduct overseen by the Baltic.
Baltic Exchange members are responsible for a large proportion of all dry cargo and tanker fixtures as well as the sale and purchase of merchant vessels.
In November 2016, the Baltic Exchange was acquired by Singapore Exchange, bringing together complementary strengths of Singapore and London, two of the world’s most important maritime centres.
The first ship of the year, Cape Alexandros, arrived at 11:00a.m. on 4 January 2023, from Rotterdam in the Netherlands and remained anchored in the bay awaiting loading. On Thursday morning, 12 January, a ceremony was finally held to present Captain Antonios Chatzigeorgiou with the commemorative cane traditionally awarded to mark the first ship’s arrival.
The captain said he was deeply honoured by the gift, adding that it was his second visit to the Port of Sept-Îles in 29 years. He also expressed admiration for the St. Lawrence–Great Lakes and Saguenay maritime corridors, worthy praise from someone who has visited more than 80 countries and spent his career sailing the world’s major shipping routes.
The brief ceremony at IOC Rio Tinto’s port facilities was attended by Marie-Josée Carrier, Senior Advisor, Communications and External Relations; Marie-Noëlle Péloquin, Operations Coordinator, Terminal; Marco Blanchette, Terminal Maintenance Superintendent representing IOC Rio Tinto; and Pierre Gagnon,
President and CEO of the Port of Sept-Îles. Josée Carrier also presented the captain and his crew of 25 with a well-stocked basket of local products.
The 292-metre-long Liberian-registered Cape Alexandros was built in South Korea in 2010 and belongs to the Greek shipowner Golden Union Shipping Co SA. It sailed back to Rotterdam with 170,700 tonnes of concentrate and iron pellets.
The tradition of the cane, now in its 36th year, celebrates the first ship to drop anchor in port waters each year and highlights the impact of port activities in the community.
To be eligible, ships must arrive directly from abroad and be bound for a foreign port.
In 2012, on the 25th anniversary of the cane ceremony, the traditional gold-headed cane got a makeover, with an exclusive new design showcasing the region’s resources. Inspired by a 3D version of the Port of Sept-Îles logo, the polished anodized
aluminium cane is reminiscent of the blue highway. The redesigned pommel contains a fragment of iron ore whose luster is reflected in a hemisphere of acrylic. It also features a distinctive gold element: the seven-star Port of Sept-Îles logo representing the seven islands in the Bay of Sept-Îles has been painstakingly reproduced in 10-karat gold.
Boasting diverse, state-of-the-art facilities, the Port of Sept-Îles is one of North America’s largest ore-handling ports, with a projected volume for 2023 of nearly 40 million metric tonnes. It is also recognized as the largest primary aluminium port terminal in the Americas in terms of operational volume. Sept-Îles port facilities play a vital and strategic role in the economy of Eastern Canada. The Port is also deeply committed to sustainable development and has pioneered the first environmental observatory on the St. Lawrence to monitor the marine ecosystem.
Bothra Shipping Services has placed an order for three Konecranes all-electric Gottwald mobile harbour cranes. These will be deployed at the company’s dry bulk terminals at the Port of Kakinada, which is located on India’s east coast. The cranes are due for delivery in the second quarter of the current year.
Bothra Shipping, which is one of India’s largest port operators, owns and operates
the eight million tonne capacity Kakinada Deep Water Port Coal Terminal as well as a six million tonne fertilizer handling terminal at the Port of Kakinada.
Following the deployment of the new Sixth Generation MHCs, the company aims to increase bulk handling rates whilst at the same time reducing both local carbon emissions and increasing operational performance.
The Konecranes ESP.7B MHCs have a working radius of 51 metres and a lifting capacity of 125 tonnes. They will be able to make use of already existing high-tension electric supplies on the quays where they operate. This is key since none of the units have an onboard diesel generator set. The cranes feature a four-rope hoist system that gives them a 63-tonne grab load curve when handling dry bulk.
Compañía Española de Laminación, which is a subsidiary of Celsa Barcelona, one of the six business units of the Celsa Group, has requested a 13,027m² concession at the Port of Barcelona’s West Quay. It intends to use this area as a hub for the interchange of steel products between maritime and terrestrial transport modes.
In line with existing legislation, the Port of Barcelona is now required to invite within the next month competing proposals from other groups that potentially would like to use the same area.
Compañía Española de Laminación first began trading in 1957. Nowadays, it has an annual 2.5 million tonne production capacity for steel. This is divided among various products, including corrugated and plain bars, wire rods, flat bars, angle squares and structural sections. To make these, it uses two electric furnaces with a capacity of 140 tonnes each and two continuous casters. BC
Maria del Rosario Soto, president of the Port Authority of Almeria, is in the process of identifying possibilities within the port to improve and increase its infrastructure and services for the handling of new dry bulk commodities.
During a visit to the port, Soto noted that “the Port of Carboneras has all the necessary conditions to attract new traffic flows.”
For the half year to end of June 2022, the port authority recorded dry bulk traffic of 1.9mt (million tonnes), which was a decrease of around 14%. By the end
down just 8% on the year. BC
The Port of Liverpool has been ranked as the UK’s top port for port-centric logistics potential in a new industry study.
Property adviser Knight Frank analysed and ranked 41 UK ports based on 13 criteria, assessing their potential for future logistics investment and development, in its latest Future Gazing report.
The Port of Liverpool topped its table, after the port ranked first for forecast export growth and was placed in the top ten percent for access to consumer markets, skilled labour, availability of land, port capacity, import growth potential and size of the existing logistics market.
Peel Ports Group Commercial Director Stephen Carr said: “We’ve long argued that the Port of Liverpool is one of the UK’s best-located ports, and we have built on that with significant investment over many years to create jobs and enable more efficient supply chains. These benefits have been greatly enhanced recently by
confirmation from the Government that the Liverpool City Region has gained final Freeport status approval, meaning the benefits for supply chains locating to the region are even greater than ever.”
Knight Frank researched each port’s potential role in shortening supply chains and mitigating supply disruption. Its report looked into 13 different categories including a port’s capacity, connectivity, as well as the overall investment at the site and import and export growth potential.
The Port of Liverpool received the highest overall score in its rankings.
Peel Ports has made significant investment at the port in recent years, building on the completion of Liverpool2 — a £400 million deep-water container terminal. The report also recognized the importance of the port’s grain terminal to the UK’s agri bulk industry.
The location of the port is of strategic importance to major importers and
exporters of goods as it offers unrivalled connectivity to Ireland and access to a catchment area of over 35 million people.
Peel Ports Group is one the UK’s largest port operators, owning and operating six of the UK’s most important ports (Liverpool, Heysham, Manchester Ship Canal, Medway (Sheerness/Chatham), Clydeport and Great Yarmouth). It also operates a container terminal in Dublin and owns BG Freight Line, which provides short sea container services between the UK, Ireland and mainland Europe and Peel Ports Logistics, one of the UK’s leading shipping and freight forwarders.
Peel Ports handles approximately 70 million tonnes of cargo every year. 14% of the total UK major ports traffic flows through ports operated by the Group. Headquartered in Liverpool, it employs around 2,000 staff.
The Toledo-Lucas County Port Authority has announced a 2.24% increase in tonnage through the Port of Toledo in 2022, when compared to 2021. A total of 11,684,394 short tons travelled through the Port of Toledo last year — the highest tonnage the seaport has seen since 2007. The port set a record for aluminium handled at the General Cargo Dock, operated by Midwest Terminals, and grain had the strongest year-over-year growth with an increase of 14.79% over 2021. The 2022 season was also the first full operating one for the Cleveland-Cliffs’ Toledo Direct Reduction Plant, driving iron ore tonnage up nearly five percent from the
previous year.
The Port Authority invested heavily in infrastructure in 2022. At the General Cargo Dock, over $5 million in repair work has been completed on the dock wall. An additional $10.6 million of work is in progress, which is being funded through the U.S. Maritime Administration’s Port Infrastructure Development Program and the Ohio Department of Transportation’s Maritime Assistance Program.
At the Toledo Shipyard, $640,000 was invested to stabilize a retaining wall and construct pads for the shipyard’s offroad crane to service the dry docks. The port has also received $9 million from the
Ohio Environmental Protection Agency to create additional capacity at the Port Authority’s storage and reuse facility for dredged material. These improvements will provide the Port Authority with 20 years of storage capacity for dredged material.
With 73.6mt (million tonnes) of cargo transshipment from maritime shipping (+7%) and 64.5mt from inland shipping (+7%) in 2022, companies in North Sea Port experienced their best year since the merger in 2018. Dry bulk continues to increase. The US replaced Russia as the biggest trading partner.
Five years ago, Zeeland Sea Ports (Vlissingen and Terneuzen) in the Netherlands and the Flemish/Belgian Port of Ghent merged to form a single port. North Sea Port became the new brand name of the 60km-long cross-border Dutch-Flemish port. It instantly became one of Europe’s top ten ports. “Our aim was to grow in various areas to make sure
we could maintain that position as a newly established port, and indeed to continue our development into a top European port. With a new record year since the merger five years ago, the companies in the port have further cemented that position. That’s pretty remarkable after Brexit, two years of the pandemic, the impact of the Ukraine-Russia war and the energy crisis,” points out North Sea Port CEO Daan Schalck.
In 2022, five years after the merger, North Sea Port posted the best year yet in its still fledgling history in terms of seaborne cargo transshipment: up 7%, a further 3%
up on the previous record year of 2019. Imports increased by 6%, exports by 9%. The import-export ratio was 72–28%.
Schalck says: “With another record year, North Sea Port is cementing its position as the number ten port in Europe. That’s pretty remarkable after Brexit, two years of the pandemic, the impact of the Ukraine-Russia war and the energy crisis.”
North Sea Port has traditionally been a real bulk port. Dry bulk continues to show marked growth, even compared to the preCovid period. Liquid bulk and general cargo remain below their pre-Covid levels. Dry bulk again accounted for more
than half of seaborne cargo transhipment in 2022: 54% (39.9mt +10% compared to 2021). That growth came from commodities including oilseeds, crude iron, fertilizers and coal (+32%), for which additional stocks were built up due to EU sanctions in connection with the Ukraine-Russia war. Grain transshipment declined.
Liquid bulk accounted for 24% of the total in 2022 (17.6mt, +5%). The increase was particularly marked in the transshipment of biodiesel, diesel, liquid fertilizers and kerosene. The share of break bulk was 14% (10mt, +5%). This increase is attributable to growth in the transhipment of steel plates and bananas (shift from containerized transport).
The roll on/roll off (ro/ro) segment grew by 5% (3.7mt +2%). This rise was due to increased transportation of cars. The share of trailers remained the same.
Containers made up 3% of seaborne cargo transshipment (2.6mt, –9%; there was also a fall measured in TEUs, to 230,000 TEUs [–31,000 TEUs]). The reason for the decline was the reduced transportation of bananas in containers (shift to transportation as break bulk).
Broken down by commodity type, there is an increase in solid mineral fuels (including coal), petroleum and petroleum products, metal industry products, raw minerals and construction materials, fertilizers, vehicles and machinery. Agricultural products, food products, ores and metal residues and chemical products remained static.
Schalck says: “In these uncertain times, North Sea Port has posted its best year since the merger five years ago — partly because of the build-up of additional stocks, partly because of the increased supply of raw materials as industry maintains its activity levels.”
Russia is no longer the most important trading partner in terms of seaborne cargo transshipment. With a 15% contraction (–0.9mt, total 5.4mt) as a result of EU sanctions, it fell back to second place, behind the United States, which saw a 27% growth (+1.3mt, total 6.3mt). The United Kingdom took third place (+4%, +0.2mt, total 5.2mt) followed by Brazil, Canada, Sweden, Norway, Spain and Finland, with France completing the top ten.
Trade with Ukraine halved. As a result of companies' search for alternative markets, trade with Canada (+31%), Australia (+123%), Algeria (+42%) and
Germany (+42%) increased sharply. Europe accounted for 57% of trade (–4%), North America for 15% (+3%), South America for 14% (–3%), Africa for 7% (+2%), Asia for 4% (+1%) and Oceania for 3% (+1%).
YEAR FOR SECOND YEAR IN A ROW
Inland navigation transshipment also set a new record in 2022: 64.5mt, up 7% (on top of a 9% increase in 2021). Imports increased by 8%, exports by 7%. The import-export ratio was 41–59%.
Interestingly, ro/ro transport by inland waterway vessels rose sharply to 0.5mt. Inland waterway breakbulk transshipment likewise increased dramatically (+40%, +1mt), while liquid bulk transshipment also grew (+19%, +5.5mt). Dry bulk shrank (–9%; –2.2mt), as did container transport (–9%; –0.2mt).
The record year for inland waterway transshipment does not stand in isolation. No less than 58% of all transport between the port and the European hinterland in all directions is conducted via inland shipping.
With a seaborne transshipment volume of 73.6mt and 64.5mt of cargo transshipped via inland navigation, North Sea Port recorded a total transshipment of 138.1mt in 2022, compared to 129.1mt tons in 2021. Over 9mt more, in other words. 2021 also saw an increase of more than 10mt (compared to 2020).
The expectation was that the pandemic losses of the previous two years would be made up in 2022, and they were. The Ukraine–Russia war and the accompanying energy crisis represent a significant shock to world trade. In these uncertain times, North Sea Port has posted a new record year, its best since the merger five years ago. This is partly because of the build-up of additional stocks, partly because of growth in various types of goods, reflecting the fact that industry is maintaining its activity levels.
North Sea Port expects 2023 to be less of a bumper year, but still a solid one, with seaborne cargo transshipment experiencing similar volumes in the four quarters, well above 70mt. The hope is that energy prices will fall. Investment is expected to continue at a similar level.
As Hudig & Veder Group, we are keen on creating an ultimate logistical plan for our customers by combining different departments and disciplines within our ABC-concept.
Our ABC-concept can therefore be best described as an existing supply chain under control of Hudig & Veder. Agencies, Chartering, Forwarding, Bulk & Projects, we offer the optimal collaboration between our business departments.
DRY CARG
international
– Henry Ford
“A man who stops advertising to save money is like a man who stops a clock to save time”
As of 1 January 2023 Jeroen van der Neut has been appointed as Managing Director of the new Dry Bulk division of the HES International Group. Since 2020, Jeroen van der Neut has been the Managing Director of HES Bulk Terminal Amsterdam. In this new structure, he will be responsible for all dry bulk terminals in the HES International Group which are located in Netherlands, Belgium, Germany, Poland, France and the UK.
Van der Neut joined HES Bulk Terminal Amsterdam (former OBA) as interim Managing Director as from May 2020 and permanently assumed the Managing Director position as from 1 January 2022. During his presence HES Bulk Terminal Amsterdam has redefined its strategic focus, which aims to strengthen its Agri & Minerals activities as well as to develop logistic services solutions in support of bulk production processes at the terminal. As part of that strategy, HES Bulk Terminal Amsterdam acquired IGMA in 2021 and a term sheet was signed in September 2022 for the intended relocation of fertilizer producer ICL to the HES Amsterdam Bulk Terminal for the construction of a brand new and modern plant.
HES International Group has a strong
ambition to further diversify the business portfolio by seizing opportunities from the ongoing energy transition and wants to further strengthen the existing market position in agri, minerals, iron ore and liquids. This will come with a strong focus on proactively generating new, more sustainable business and at the same time delivering on continuous HSSE, operational and commercial improvements. Through the Dry Bulk division a strong commercial focus will be created where available market capacity is used as optimally as possible.
Van der Neut will be at the helm of the Dry Bulk division of the HES International
Group and his team will furthermore consist of Koert Kroon as Finance Director and Perry Thijssen as HR Manager. In close cooperation with the local Management Teams of the terminals they will be responsible for the further expansion and transformation of the Dry Bulk division.
Contributing to the world of tomorrow, is a major focus at HES. With 18 terminals in six countries at strategic located ports in Europe, HES is an important switch in the continuous delivery of essential building blocks for everyday life needed to develop, sustain and improve the world around us. The company’s professional staff ensure that bulk commodities are safely stored, handled and processed 24/7 for customers from all corners of the globe.
HES International has a strong ambition to further broaden its product portfolio and also wants to respond optimally to the opportunities that the energy transition offers for products such as hydrogen, refrigerated gases and chemical recycling. In addition, HES wants to further strengthen its existing market position in agri, minerals and iron ore.
HES International wants to create longterm growth and value for all stakeholders including employees, customers, shareholders and the communities and countries in which it operates. This is underpinned by its focus on safety and its
core values of integrity, respect, accountability, openness and entrepreneurialism.
HES International is headquartered in Rotterdam and has already been carefully handling bulk raw materials since 1908. Macquarie Asset Management, via
Macquarie European Infrastructure Fund 5, and West Street Infrastructure Partners III, managed by the Goldman Sachs Asset Management Infrastructure business, each indirectly control 50% of the shares of HES International B.V.
Deployed
www.dinobulktruckloader.com
YOU ARE RUNNING A TIGHT SHIP
Now let’s tell the world.
The main port served by Maja Stuwadoors
B.V. is Amsterdam. In 2022, Maja rented only one floating crane on a fixed base to a colleague stevedore in Rotterdam.
In 2022, the company handled 360,000 metric tonnes of agribulk and 3.25mt (million tonnes) of minerals. This represents a decrease compared with 2021. There are two main reasons for this fall — the war in Ukraine adversely affected the throughput of agribulk, and problems related to the Covid-19 pandemic and resultant economic issues — especially the soaring energy prices — were behind the drop in minerals.
The main volumes handled by Maja are
scrap and fertilizer; the company is not a major player in the coal market. There was a sharp increase in coal coming to Amsterdam, due to reducing gas supply from Russia. Maja’s colleague stevedores in Amsterdam are much better equipped to handle this volume, so this massive flow was handled by them. Maja offered some assistance with its floating cranes. It is to be expected that this flow will decrease significant in the future when things start to get back to normal. This will, of course, affect Maja’s position in Amsterdam as its fellow stevedores try to find new markets to compensate for this (coming) decrease. The equipment of a bulk stevedore is the
same, it is not so difficult to enter the markets in which Maja specializes.
A recently new development is the arrival of so-called ‘big material handlers’, such as the Sennebogen 885 and Mantsinen 300, which are now installed in the port of Amsterdam; these machines are direct competitors to Maja’s floating cranes. They are easier to operate, offer higher production per hour, have less fuel consumption and maintenance.
In 2023, Maja will start to operate a terminal with a berth of 215m and a draught of 11.1m. On this terminal a Liebherr 550 mobile harbour crane will operate.
Family business and grab specialist Nemag was founded in 1924. The company’s power to innovate leads to increased efficiency in the bulk handling operations of its customers. Its expertise and
experience means is the reason for its stellar reputation among dry bulk handling organizations around the world.
Nemag supplies a full range of four-rope operated mechanical grabs —for loading
and unloading: ores, grains, scrap, minerals, aggregates and other dry bulk goods. Together with its high quality rope connections systems, Nemag always has a productive solution.
Ever since its foundation, Nemag from the Netherlands has believed strongly in the power of innovation to increase the efficiency of customers’ bulk handling operation. This belief has won Nemag countless industry and non-industry awards.
To meet the specific requirements of its customers, Nemag has developed a range of dry bulk grabs. Each grab has its own advantages for specific applications. Increased production, low operational costs, enhanced safety, environmentally friendliness and reduction of the use of trimming equipment have been taken into consideration when developing grab solutions.
In close co-operation with leading bulk terminal operators, crane manufacturers, technical universities and other stakeholders in the industry, Nemag continues to develop new products for the dry bulk industry. The aim is always to reduce handling costs per tonne of dry bulk materials transferred.
The latest software technology like 3D CAD, Multi Body Dynamics (MBD), Discrete Elements Methods (DEM) and Finite Elements Methods (FEM) support
Nemag’s team of designers in optimizing all of its grabs. High tensile steels, wearresistant steels and advanced bearing technology enables the company to design extremely productive, light weight and durable grab mechanisms.
Nemag inventions include the scissor grab, specialized rubber-lined lip sealing systems for handling powdered cargo, the patented Nemag quick-release link and the Nemag rope pear socket for high strength wire ropes, the introduction of a new generation of environmentally friendly clamshell grabs, and last but not least, the patented and awards winning nemaX grab. Nemag is rewarded by the Dutch Chamber of Commerce with the 20th position of most innovative companies (MKB) in the Netherlands.
Alongside innovation, customer support and a very intensive after-sales service are of paramount importance to both Nemag and its customers. A global network of specialized representatives supported by Nemag specialists are ready to assist customers worldwide.
Leading steel plants, bulk handling companies and crane manufacturers in over 60 countries worldwide are part of Nemag’s customer base for decades: companies which, just like Nemag, stand for innovation, quality and reliability.
A Nemag grab lasts longer than average and requires little or no maintenance. Because these grabs have to function optimally for long periods of time and under the toughest possible circumstances, Nemag offers a service and repair team. This team can adequately be of service to you in practically all situations. For Nemag, service and maintenance matters. Nemag always keeps in touch with its customers and offers complete and ongoing after sales support.
Guaranteeing the quality is embedded in the production process. The Nemag system for quality control checks the company’s own products and methods, but also that of its suppliers. Links and sockets are tested by independent laboratories on a regular basis. Newly built grabs, repaired grabs and all links and sockets are tested before they leave the factory.
Nemag has proved to manufacture products with a long life cycle and an extremely low break-down rate. It has at its disposal a great store of knowledge about which grab technique is best suited for the efficient handling of bulk goods. Its highly qualified technicians and engineers apply this technical knowledge and expertise to their designs to optimize its existing products and develop new ones.
When buying a Nemag product, customers also buy a 100% service guarantee that doesn’t end when the warranty period expires.
Whether it is a grab, a Quick Release Link or a Rope Pear Socket, Nemag products are always on the move. Nemag’s employees value direct contact with all its clients and regularly visit customers around the world. It is happy to assist in the long life cycle of its customers’ grabs and is happy to prove that its quality control does not stop after delivery. For international clients, Nemag has an extensive network of selected representatives that take care of the professional after-sales service. Nemag takes service and repairs very seriously. DCi
The downturn in the global economy and the economic impact of the Russian war of aggression against Ukraine meant challenges for the ports of Bremen in 2022. In the third year of the Coronavirus pandemic, the ports again suffered from the disruptions in global supply chains, caused first and foremost by the Chinese ‘zero-Covid policy’.
Moreover, the sanctions against Russia and the effects of the war are also obstructing the global flow of goods and container logistics. “The quays and terminals in Bremen and Bremerhaven are essential for the German economy. This was once again demonstrated very clearly in recent months by the energy crisis as a consequence of the Russian attack on Ukraine and the continuing severe impact of the pandemic,” said Dr Claudia Schilling, Senator for Science and Ports. “But despite all these challenges, the port and logistics industry, just like the employees
on board the vessels and at the docks, ensured supplies to the German and European population during these difficult times. And we, as the Federal Land of Bremen, will continue to satisfy our responsibility for the ports of Bremen by equipping the quays and terminals to cope with future requirements.”
Based on assessments by the Senator for Science and Ports, Bremen and Bremerhaven are expected to report a decline in seaborne freight of 64.5mt (million tonnes) [–7.4%] in 2022. The total throughput forecast for 2022 breaks down into throughput at the port facilities in Bremen-City, which handled 12.2mt (–5.4%), and in Bremerhaven at 52.4mt (–7.9%). The downturn in throughput in Bremerhaven is due to the decline in container throughput, which amounted to
47.3mt (–8.5%). The number of containers, expressed as standard containers (TEU), decreased to 4.6 million TEU, a year-onyear decrease of 8.1%.
Automobile handling in the year 2022 is expected to reach a figure of 1.6 million vehicles (–4.4%). The main reason for this decline is the disruption in supply chains. The impact of the war is particularly apparent in the figures for bulk goods: compared with just under 650,000 tonnes of coal and 914,000 tonnes of refined petroleum products in traffic to and from Russia in 2019, during the first ten months of 2022 these figures dropped to 101,000 tonnes of coal and 311,000 tonnes of refined petroleum products.
The trend for cruise shipping in Bremerhaven was highly satisfactory. A total of 110 vessels called at the terminal, an increase of 190% compared with 2021, a year which suffered very severely from the Coronavirus pandemic.
Despite the downturn in seaborne freight throughput, the railway is again expected to be the strongest transport mode for container hinterland traffic again in 2022.
The Senator for Science and ports welcomes this positive result not only from the point of view of climate protection, but also as one of the tangible successes of the port policies implemented by Bremen’s current government: in addition to the extension of the terminal railway network, the major project ‘Construction of a new Columbus Quay’ (€80 million) is in progress, the western quay at Kaiserhafen III (€32.7 million) and Quay 66 (€17.7 million) have been completed and the Senate has also resolved to refurbish Kalihafen, the former potash port.
Senator Schilling stated, “Since 2019 we have invested unprecedented sums to renew the port infrastructure and thus ensure that the ports of Bremen remain internationally competitive in years to come. Our plan for the future is set out in the new Port Development Concept 2035, which enjoys the support of all major players in the port and logistics business. We will show that we mean business by
investing €50 million a year to equip our port facilities to cope with new challenges. Ports are the driving force of the Germany economy, and that is why we, together with the other German coastal states, are demanding that the federal government assumes more financial responsibility for the German seaports. Moreover, it is vital that the adjustment of the Outer Weser fairway, which is of central importance for the container terminal, is implemented as soon as possible.”
The plans for key future projects, such as the development of Container Terminal
CTI to IIIa, the target of becoming a climate-neutral port location by the year 2035 and of evolving into a hub for the energy transition, are making good progress: amongst other things, the results of the study to assess the potential of the southern part of Fischereihafen and on the subject of hydrogen will be presented within the next few months.
Senator Schilling added, “We will make enormous investments in our ports over the coming decade. The port policies are on the right track to overcome these challenges.”
At the start of December 2022, The Belledune Port Authority (BPA) signed a Memorandum of Understanding (MoU) with Germany’s seaport, the Port of Hamburg, to collaborate on the movement of dry and liquid bulk commodities, and manufactured products, between Canada and Germany, with a focus on clean fuels and green products.
The Port of Hamburg, located on the River Elbe, about 100 kilometres from the river’s mouth on the North Sea, is positioned as Germany’s leading foreign trade hub with up to 450 million consumers in Europe. It has modern handling facilities, communications systems, efficient transport infrastructure and highperformance transport and hinterland connections, serving as a central shipment hub for the entire German energy market.
In August, the Belledune Port Authority (BPA) has also signed a Memorandum of Understanding (MOU) with Niedersachsen Ports, Wilhelmshaven, Germany.
These agreements support the Memorandum of Understanding between the Governments of Canada and Germany to establish an energy partnership aimed at achieving net-zero emissions by 2050 through a transition to safe, secure, reliable, affordable, and sustainable energy. They also support the joint declaration of intent between Canada and Germany to establish a Canada-Germany Hydrogen Alliance signed 23 August 2022, in Stephenville, Newfoundland.
The MoU recognizes that cooperation in transitioning to sustainable energy not only delivers mutual benefits but is also
required for the prosperity of the international community.
The MoU recognizes the importance of the role that the Port operations will play in the production, storage and shipment of clean fuels and green manufactured goods, for both domestic and intercontinental markets. The MoU will assure safe and secure access for the movement of clean fuels, green energy and other products between Canada and Germany.
The Ports will form a relationship that will foster collaboration to support the emerging needs of Canada and Germany’s energy and manufacturing sectors, with a focus on the production, storage and shipment of cleaner fuels such as green ammonia, hydrogen, biomass and renewable natural gas.
The ports will share information on government policy updates, market dynamics, infrastructure developments, technology advancements in the maritime transport sector as it transitions to cleaner fuels and greener energy, best practices on liquid and dry bulk products storage and shipping particularly in the areas of clean fuel and green energy, and actions to support the development of the businessto-business relationships between importers and exporters in Canada and Germany, within the energy and manufacturing sectors.
The Belledune Port Authority (BPA) is a is part of Canada’s Port Authority network. Tasked with managing the infrastructure and assets of the Port of Belledune in
Northern New Brunswick (NB), the BPA’s objectives include not only advancing the growth and prosperity of the economy in both Canada and the province of NB, but also fulfilling public policy objectives. Situated on the Atlantic Ocean, the Port offers some of the shortest sea shipping routes to Europe.
The Port of Hamburg, the third largest container port in Europe, offers state-ofthe-art technology in its handling facilities and data communication systems. The port of Hamburg is a central transhipment location for crude oil, petroleum products, coal and chemical products. The port has excellent rail connections and modern train loading facilities, creating a central coal transshipment hub for the German market. The port makes a key contribution towards ensuring a secure energy supply in Germany.
Import, in million tonnes. Export, in million tonnes.
The goods handled as bulk cargo in maritime transport, such as ore, coal, building materials, grain, fertilizers or mineral oil products, reached a total volume of around 40mt (million tonnes) in the Port of Hamburg in 2021. This makes Hamburg by far the largest port in Germany for the handling of seaborne
goods in bulk.
Bulk cargo handling can in turn be divided into three sub-sectors: at 21.6mt in 2021, grab cargo is the most handled sector in Hamburg. This includes goods such as ore and coal with the largest individual items in terms of volume.
Liquid cargo such as mineral oil
products, biodiesel or chemical products belongs to the second strongest subsegment in bulk cargo handling in the Port of Hamburg with 11.8mt in 2021.
The third sub-segment is the handling of suction cargo or agribulk. In 2021, 6.4mt were registered in Hamburg.
The partners TRANSA Spedition, Rhenus Cuxport and DFDS have repeatedly ensured the smooth supply of a construction site in England with precast concrete parts from the Czech Republic via the RailRo-Cargo network. As a follow-up project to the transports already carried out in the summer of 2021, 120 flatracks with precast concrete parts have again been shipped to England via Cuxhaven since the middle of this year.
The precast concrete parts of the joint customer GOLDBECK were loaded at short intervals onto flats provided by the consignor and transported from the shipping point in Skovice (CZ) to Cuxhaven by rail. In the port of Cuxhaven, the special flats were then reloaded directly from
railway wagons onto Mafi roll trailers. Subsequently, they were shipped from Cuxhaven to Immingham by RoRo. Within the framework of the partnership, particular attention was paid to the issues of import customs clearance, delivery to the construction site in England, as well as the return of the empty flats to the consignor. The overall coordination and monitoring of the supply chain was in the hands of TRANSA-Spedition, which meant that the customer benefited from a complete solution.
Felix Bieling, business economist, GOLDBECK International GmbH: “Our project business is determined by very flexible and timely framework conditions and accordingly requires business partners who can meet these. The top priority is to ensure the safe transport of our material
and on-time delivery to the construction site. With the team consisting of TRANSA Spedition, DFDS and Rhenus Cuxport, we are glad to have found partners who can meet these requirements.”
Kay-Uwe Müller-Gericke, Key Account Manager of TRANSA Spedition: “Once again, we have jointly succeeded in convincing our long-standing customer of the concept of unaccompanied transport by rail and sea and its advantages. In addition to timely delivery to the construction site, delivery reliability also played a key role in the choice of logistics concept.”
Oliver Fuhljahn, Key Account Manager at Rhenus Cuxport: “The smooth and direct handling of high-quality goods and also bulk general cargo fulfils a considerable quality and also productivity requirement, which we implement here on site together with our partners.”
Branch manager of DFDS in Cuxhaven Marcus Braue adds: “With the existing frequency of six weekly departures between Cuxhaven and Immingham, we also offer very good conditions for precise delivery to the construction site in the time-sensitive project business. Meanwhile, we are once again in the bidding stage for new projects and are already looking forward to implementing them as part of the successful partnership with Rhenus Cuxport and TRANSA Spedition.”
A Bedeschi floating terminal which is very similar to the new one the company will supply to the shipyard in Indonesia.
Over the years, Bedeschi has been entrusted by many prestigious clients worldwide to help them overcome various marine infrastructural bottlenecks, both onshore and offshore.
These clients have valued the innovative approach and capability of Bedeschi in understanding their exact requirements and in designing and implementing solutions, which are suited specifically to their projects’ requirements.
Transshippers have a distinct advantage over the shore terminals, because they can be implemented without the need for
dredging the seabed in order to enable the large vessels to come alongside. In addition, the implementation costs of floating terminals is not as high as shore terminals. Moreover, and most importantly, the implementation time of a new floating terminal is much shorter as compared with a shore terminal. Floating solutions are also environmentally safe.
Bedeschi will supply to an important shipyard in Indonesia a new floating terminal with a 2,500 tonnes per hour capacity handling coal from two loaded barges to a big OGV, up to Capesize. The new terminal
is planned to operate in the Far East. The company will supply two receiving hoppers, two belt feeders, one belt conveyor system complete with transfer towers, one slewing and luffing shiploader equipped with a trimming chute, and a full control system.
Bedeschi closed the deal thanks to the support of its new subsidiary Bedeschi Far East, which was able to assist the client with its specific requirements. Bedeschi Far East has a strategic key-role in the support and assistance of clients, and is constantly increasing in that area.
Like the first RopeCon® at the Lenzing plant, the second installation also impresses with high availability, wind stability and its ability to cross high-density plant infrastructure without any problem. As a result, the RopeCon® creates an optimal link between the raw materials storage facility and the digester house.
For the planned expansion of wood chip transport between the storage area and the digester house at its cellulose processing plant, LENZING AG, a major company in the field of the production of fibres made from the raw material wood, contracted a second RopeCon® conveying system to ensure sustainable raw material supply. The system has to cover a length of roughly 630m between wood storage area and digester house, passing right across the existing plant infrastructure. In addition, the system had to guarantee high availability in order to allow optimal integration into the production process and reliably deliver the 350 tonnes an hour to their destination.
The second RopeCon® installation has been built to run alongside the existing RopeCon®, which has been transporting beech wood chips since 2003. In the time since then, the system has proved to be a reliable and efficient solution for supplying the digester house. As the system is raised
off the ground, it makes light work of crossing the existing infrastructure on the premises.
Doppelmayr Transport Technology GmbH is a 100% subsidiary of the international Doppelmayr Group with headquarters in Wolfurt, Austria. Within the group,
Doppelmayr Transport Technology is the point of contact for the transport of goods and materials. Doppelmayr is a technology leader and pioneer in ropeway engineering and is also present in other lines of business. Apart from material transport systems the group also designs, plans, and manufactures passenger ropeways for winter and summer tourism as well as for the urban transit sector, rope-propelled APMs (e.g., the systems currently operating at the airports of Toronto and Mexico City) or fully automatic high-rise warehouses.
Length: 630m
Vertical rise: 33m
Capacity: 350tph
Speed: 2.65m/s
Motor rating, continuous: 60kW
Campostano Anchor, part of the Campostano Group (CG), has ordered a Generation 6 Konecranes Gottwald mobile harbour crane for general cargo and bulk material handling to update its existing fleet at its terminal in Savona, northern Italy. The order was booked in December 2022 and the crane will be delivered in June 2023.
“We have high expectations for our material handling cranes, and Konecranes has fulfilled them all. They’ve offered us an easily adaptable, high-performance hybrid solution that will bring a new level of productivity to our terminal while helping us to cut our carbon emissions and fuel consumption,” says Ettore Campostano, Owner and CEO of CG. “In addition, digital services will give us insights into our crane’s performance and condition data to streamline its operation and maintenance,” he said.
“We’re excited that Campostano Group has chosen to add a Generation 6 Konecranes Gottwald mobile harbour crane to their terminal fleet. We’ve worked with CG for over 30 years, and they trust our ability to meet their changing requirements with high-quality equipment that follows local standards and lifts their business into the future,” says Gino Gherri, Regional Sales Manager, Port Solutions, Konecranes.
The new crane is a Generation 6 Konecranes Gottwald ESP.6 mobile harbour crane, with a working radius of 49m and a lifting capacity of 125 tonnes to serve vessels up to Panamax class. Its strong lifting capacity curves improve cargo handling rates and a high classification ensures a long service life. The crane uses the innovative Konecranes hybrid drive, which comprises an EU Stage V diesel engine paired with an ultracapacitor that can be recharged by energy recovered from lowering and braking motions. This gives the power needed for peak performance, while saving fuel when moving lighter loads.
For a better understanding of how their crane is operating, Campostano Anchor will use TRUCONNECT® remote monitoring. The crane sends its data via a secure mobile connection to the Konecranes cloud service, accessible through the customer web portal yourKONECRANES. Whether its ESP.6 is online or offline, Campostano can get a full overview of the crane, with information such as fuel
consumption and handling performance, as well as a detailed analysis of every load cycle and diagnostic messages. With a combination of remote monitoring and a tailored spare parts package, local technicians will have the resources they need for fast and efficient maintenance. Konecranes digital services align well with Italy’s National Industry 4.0 Plan, a state strategy that encourages industrial innovation.
Established in 1927, Campostano Group has a long and successful history of comprehensive multimodal shipping services. CG consists of 20 companies including Campostano Anchor, which is based in Savona. CG also operates Savona Terminals, with three berths supported by expansive storage facilities as well as rail and road connections inland.
This order is part of Ecolifting™, Konecranes’ continuous work to decrease the carbon footprint of its customers. From eco-optimizing diesel drives to
hybridization and fully electrified fleets, the company will continue to do more with less.
A strong focus on customers and commitment to business growth and continuous improvement put Konecranes at the forefront of the lifting industry. This is underpinned by investments in digitalization and technology, including work to make material flows more efficient with solutions that decarbonize the economy and advance circularity and safety.
Konecranes is a globally respected group of Lifting Businesses, serving a broad range of customers, including manufacturing and process industries, shipyards, ports and terminals. Konecranes provides productivity-enhancing lifting solutions as well as services for lifting equipment of all makes. In 2022, Group sales totalled €3.4 billion. The Group has approximately 16,500 employees in around 50 countries.
Industrial elevator bucket designs have not changed significantly since the 1950s. However, the introduction of NylathaneTM, by 4B Group, brings a new technology to the industry. NylathaneTM is a unique polymer that combines Nylon 6 with an elastomer. It has the durability of nylon with the slick release surfaces associated with polyurethane. This combination makes it ideal for bucket elevators in the cement industry where impact tolerance and discharge efficiency of sticky or powdery products are required to minimize downtime and maintain production efficiency. Prior to its use in elevator buckets, NylathaneTM has been field proven in even more demanding applications such as track pads for tractors.
Iron or steel elevator buckets can be prone to deformation or breakage due to impact from foreign objects or operational issues. Once deformed their capacity and efficiency is diminished. Deformed elevator buckets pose a risk to further damaging the bucket elevator system as they move through the system.
Heavy iron or steel elevator buckets are difficult to manage when being repaired or replaced. Their weight is also a drain on system efficiency due to the amount of energy required to move the heavy bucket assembly. Should a bucket become detached from the elevator belt or chain, it is unforgiving in the collateral damage that it can cause to the system. Some metals in certain applications are prone to become brittle over time. Sticky powders have a tendency to collect in metal elevator buckets, reducing their capacity and clogging vent/drainage holes. NylathaneTM elevator buckets alleviate these problematic issues.
The characteristic advantages of
NylathaneTM buckets are: up to 75% lighter than steel or iron; v outstanding wear resistance; v superior impact strength; v self-cleaning surfaces; v static dissipative (<108 Ohms); and v non-sparking & non-corroding. v
The practical advantages of NylathaneTM buckets are: resists impact and retains original v shape while metal buckets deform and lose efficiency; reduced weight, thereby v reducing overall Amp load; lighter buckets means less wear v and tear on other components; lighter buckets are easier and v safer to install and handle; lighter weight and better v impact absorption means that NylathaneTM buckets are less likely to pull through the belt or chain than heavier steel buckets; compatible with both belt and v chain elevators; ideal for handling wet or sticky v materials; and static dissipative for use v with combustible dust
For bucket elevators conveying sticky products, such as slag, the flexibility and low coefficient of friction of NylathaneTM help prevent product build up and loss in capacity.
In one case study performed by 4B Group in the potash industry, the NylathaneTM buckets exhibited better impact resistance due to their flexibility than solid abrasion resistant (AR) steel buckets. Deposits of salt-based marine evaporate minerals occur naturally
throughout the world. These minerals are high in potassium, calcium and magnesium along with other valuable trace elements. Often deep mined, they are used in the agricultural industry and industrial applications. The mineral is very hard, abrasive and hygroscopic making it difficult to handle efficiently. Once mined the mineral is crushed, graded, blended and stored, often utilizing expensive wear resistant steels in the process. Initially the
user installed solid abrasion resistant (AR) steel elevator buckets which were expensive, and due to their rigidity and the aggressive hygroscopic nature of the mineral, caused loss of production along with frequent and expensive downtime.
Industrial injection moulded nylon elevator buckets were tried and although they improved the discharge of the material from the buckets they wore out in a few months. The NylathaneTM buckets deformed or flexed rather than exhibiting brittle microbreaks in the material.
4B Group also added AR steel wear lips to the NylathaneTM buckets for additional wear resistance, thereby delivering a hybrid elevator bucket with the best characteristics for the application. The 4B engineers devised a best of both worlds scenario by using the unique benefits of NylathaneTM affording better impact resistance due to flexibility (rather than brittle breaks on a micro level) and self cleaning properties due to the low coefficient of friction of buckets.
This in addition to the abrasion resistant steel wearband, originally developed for the glass cullet industry, gave excellent wear and impact resistance.
The results were:
v extended belt life;
improved tonnage through the plant;
v extended bucket life;
v reduction in downtime;
savings on electricity costs; v improved manual handling; and v better health and safety compliance v
In another industrial application, moving glass cullet, the replacement of heavy steel buckets with the lighter NylathaneTM buckets provided a nearly 80% reduction in startup current. Saving both energy and electrical component costs. The installation was also quicker and safer with the lighter NylathaneTM buckets taking just one day to install compared to the usual three days with the steel.
The customer had been using 3mm to 4mm-thick fabricated steel buckets supported by a steel fixing plate fitted with M16 bolts. The total unloaded steel bucket weight was 20kg and they were experiencing belt breakages and long downtime due to the constant repairs and maintenance required on the elevator.
4B replaced the heavy fabricated steel elevator buckets with lighter NylathaneTM elevator buckets weighing just 3kg. The original steel buckets weighed 3.25 tonnes in total whereas the NylathaneTM buckets only weighted 0.48 tonnes. Weighing nearly 2.8 tonnes lighter than the original bucket system was a huge improvement. The system was more reliable with fewer breakages and less downtime.
reduction in downtime; v reduction in planned maintenance; v savings on electricity costs; and v better health and safety compliance. v
NylathaneTM buckets from 4B Group are available in the traditional industrial styles of AA, AC and MF. In AA NylathaneTM centrifugal style elevator buckets, there are now new sizes not previously available in the range allowing designers much more flexibility to achieve the capacities they need.
The AC NylathaneTM slow centrifugal style elevator bucket is a direct replacement for the old BUDD and Cast Nylon versions which are no longer produced. Two new sizes are also now available.
In MF NylathaneTM continuous style elevator buckets there are also two new sizes now available.
Custom sizes and designs are also possible. Any metal bucket design, even complex ones incorporating centre braces, can be produced in NylathaneTM
v
v reduction in planned maintenance;
This new NylathaneTM substitution gave the customer: extended belt life; v
The new NylathaneTM bucket lines from 4B Group offer the opportunity to replace traditional steel and ductile iron elevator buckets with a similarly durable but lighter weight option. The expansion of sizes, along with custom designs, offers bucket elevator designers more options to generate additional capacity which was not available to them in the past.
Mumbai: UltraTech Cement Limited, one of the largest cement producers in the world, has again selected AUMUND India as its partner for a big project.
UltraTech is the leading producer of grey and white cement and ready-mix concrete in India, and is one of AUMUND India’s major and longstanding customers. Dr Pietro de Michieli, CEO AUMUND Group, together with Raju Gupta, Managing Director AUMUND India, led negotiations with UltraTech for the new project.
The AUMUND Group is active worldwide. The conveying and storage specialist has special expertise at its disposal when dealing with bulk materials. With their high degree of individuality, both its technically sophisticated as well as innovative products have contributed to the AUMUND Group today being a market leader in many areas of conveying and storage technology. The manufacturing companies AUMUND Fördertechnik GmbH (Rheinberg, Germany), SCHADE Lagertechnik GmbH (Gelsenkirchen, Germany), SAMSON Materials Handling Ltd (Ely, Great Britain), TILEMANN GmbH Chains & Components (Essen, Germany) as well as AUMUND
Group Field Service GmbH and AUMUND Logistic GmbH (Rheinberg, Germany) are consolidated under the umbrella of the AUMUND Group. The global conveying and storage technology business is spearheaded through a total of 20 locations in Asia, Europe, North and South America and a total of five warehouses in Germany, USA, Brazil, Hong Kong and Saudi Arabia.
It is fair to say that the selling price of an item has the biggest influence on the purchasing decisions that we all make. However, buying something because it is ‘competitively priced’ but which subsequently proves to be unreliable or, at best, a short-term solution, can be a very costly mistake. It is now commonplace to see differences in price of up to 50% or more between one conveyor belt and another, even though they both claim to meet a certain specification. As with just about any product, price ultimately determines the quality. In the case of conveyor belts, this is reflected in the repeated repairs, general lack of resistance to wear and tear and accidental damage and ultimately, much shorter operational lifetimes. Indeed, all the evidence points to top quality European made belts being able to provide up to four or five times longer operational life, especially when compared to their Asian counterparts.
So are you getting the best value for money? And how do you convince the money-men that you want to try a much higher priced belt? The only way to find the answers to these questions is to calculate and compare based on the ‘whole life cost’ of the belt because ultimately, no matter what price you
pay, it is how long your conveyor belts last before they need to be replaced that actually dictates how much they cost.
Managers and engineers who are directly responsible for conveyor operation and maintenance will naturally be very aware of conveyor belts that are prone to damage and the frequency of their repair and replacement. They will also see the prices being offered for replacement conveyor belts. Sadly, in far too many cases, the people at the sharp end have little or no say in the final decision making process. All too often, the decision as to what conveyor belt to buy is made by those who control purchasing and expenditure and almost without exception, they will want to buy at the lowest possible selling price.
Unfortunately, it is extremely rare for those who are responsible for purchasing and capital expenditure to understand the technical differences associated with the performance and longevity of a conveyor belt. They are even less likely to appreciate the substantial additional cost implications caused by conveyor belts that require constant repair and ultimately have to be replaced prematurely. To be fair, they cannot be an expert on every product they are required to source. Trying to convince buyers and accountants can be difficult but it becomes a whole lot easier if you present them with a genuine financial argument that is based on factual, ‘whole life’ cost comparisons.
The principal of ‘whole life cost’ is simply the sum total cost (excluding VAT) of the conveyor belt itself plus the cost of its installation including splicing. Added to this are the labour and material costs incurred in repairing the belt (including the splice joints) during its lifetime plus the estimated costs of lost output while unplanned maintenance and repairs are carried out. These calculations are easier to make if conveyor maintenance and repair is contracted out to a vulcanizing company. However, if these functions are performed ‘in house’ then it is important that accurate maintenance records are kept.
The final step is simply to divide the total. This can either be done by the period of time that the belt has run or, if known, the amount of material conveyed during its operational life. On conveyors that are usually running non-stop during the day then time is usually the best measure. However, if the conveyor only operates intermittently then using tonnage as the basis for the calculation may prove more accurate.
Having calculated the cost of a belt you are using or have finished using, the question then becomes one of comparison. There is little or no point in making a ‘whole life cost’ calculation unless you have something to compare it against. This, of course, means trialling a higher grade of belt or a different type of belt entirely, perhaps both. The most challenging aspect of selecting conveyor belts based on whole life cost is that it can be difficult to accurately predict the lifespan of a belt of a type or supplier that you may never have used before.
Suppliers of conveyor belts, regardless of their reputation for quality or otherwise, can never guarantee how long a belt will last before needing to be replaced. Do not let this put you off. Ask the supplier for a technical datasheet, product reviews, testimonials, case studies and product literature. If you choose a tried and trusted manufacturer, especially one actually manufacturing in Europe, although the buying price may be appreciably higher, the reduction in expenditure and increases in productivity are usually considerable. As the old saying goes, “Price is what you pay but cost is what you spend”.
There is a ‘new kid on the block’ in the bulk handling market — Engineering Services Hamburg. The company offers engineering services for the cement and building material industry.
Engineering Services Hamburg specializes in: Project realization: inland-, import- v and export terminal design, terminal construction and start-up; and Operations: operational management v and maintenance control.
Engineering Services Hamburg can provide engineering and consultancy services on all aspects of cement and clinker handling (including: inland-, import-, export terminal design; terminal construction; and commissioning engineering services) and especially in project realization and operations.
Areas of expertise for example are comprehensive studies for cost-effective solutions for cement import or export terminals for distribution of cement and cementitious material to a satellite market.
Company experts have over 25 years of experience, and over these years have performed many studies for the development of cement distribution
terminals to fit clients’ requirements. The company specializes in pneumatic and mechanical shiploading and unloading.
With extensive expertise in the field of retrofitting and conversions, the goal is always the same: to develop solutions for technically complex tasks that also meet the latest environmental and safety requirements.
The company boasts a wide range of
specific skills in the design of inland-, import- and export terminals. These include: feasibility and technical studies for distribution networks; investigation of potential rail, river or ocean transportation systems; logistical analysis of industrial distribution; technology comparison of equipment tenders; conceptual through detailed design of the cement terminal and equipment; capital cost and operating cost
estimates; logistical cost studies and overall project economics of alternatives; and civil and electric engineering.
Terminal construction is another great strength, with particular expertise in project management and schedule and site work supervision.
When it comes to commissioning, Engineering Services Hamburg can help by training terminal personnel, as well as supervising FAT-, SAT- no loadand load tests. It also offers expert witness service for performance tests.
The company’s engineering office offers sales, design and project management of transshipment terminals, shiploading and unloading facilities for cement and cementitious bulk materials. It is highly competent in the field of designing cement handling terminals. It aims to make this highly specialized knowledge and experience available to organizations wishing to construct cement import, export or domestic transshipment terminals. The basis for this is the company’s 25 years of experience from the planning and design of terminals and equipment to project management and commissioning.
The difference between a well-managed and poorly managed cement terminal can represent a few dollars per tonne, which in a very short period of time can add up to significant sums. Engineering Services Hamburg’s skills in operational management, maintenance improvements and plant optimization mean significant savings for its clients.
In the bulk handling environment, much
depends on the well trained and experienced plant manager. However, operators are always looking for improvements. Areas that can improve are the organization of maintenance, or getting to the bottom of why 1–2% of cement sales always ‘disappear’.
Engineering Services Hamburg’s process engineering service, from on-the-spot advice to assistance during the implementation of technological improvement suggestions, has as its aims the reduction of operating costs, an increase in the production rate, and the improvement of product quality — as well as raising the availability of the plant.
Attention is also paid to the reduction of emissions.
Skills in areas such as the preparation of operation manuals, data collection and investigation of annual cement loss and cement inventory control put the company
at the forefront of operational management.
Working out maintenance routines, schedules and budgets and preparing maintenance manuals help to streamline maintenance operations, leading to a more efficient and cost-effective operation.
Plant optimization is vital. This can be achieved by recording the relevant plant and process data on site; carrying out performance evaluations; suggesting detailed measures that will lead to a technological improvement, and resolution of bottlenecks; and supervising and implementing equipment review measures.
Engineering Services Hamburg’s strength lies in finding superior solutions in terms of technical and planning aspects, not only for simple projects, but especially for more complex situations. It makes its detailed knowledge available in the areas of shiploading and unloading, dome silo systems, flat storage facilities, cylindrical inverted cone silo systems as well as bolted steel silo systems in order to find the optimum solution for the task.
The company’s flexibility enables it to support its customers, from the preparation of feasibility studies and sub-projects to the realization of complete import, export or domestic handling projects. Its expertise includes both cement and cementitious materials such as fly ash, ground blast furnace slag and limestone powder. Its extensive operational experience also enables it to optimize and update existing terminal operations.
A well-recognized name in atomized mist technology for dust control has introduced a new model that suppresses indoor particulate emissions for industries such as demolition and raw material handling. The compact DustBoss® DB-10 is the latest addition to BossTek’s line of atomized mist cannons. Engineered for enclosed working environments, the easily manoeuvrable unit provides excellent suppression in a compact, portable design. The outcome is effective airborne particle control with fewer emissions, less standing water and a safer, more compliant workplace.
“Our customers are well-acquainted with our technology, but before the DB-10, the smallest machine could nearly cover a football field, which is far too powerful for most indoor applications,” said Mike Lewis, Dust Control Specialist at BossTek. “Our first customer to use the DB-10 was a demolition contractor removing dusty drywall, plaster and tile containing potentially hazardous materials. These all produce highly regulated dust emissions. We worked with them to create a unit best suited to their needs and the DB-10 was born. They are extremely happy with the outcome.”
The compact mist cannon is mounted on two wheels with a tall handle. Similar in size to a child stroller, it is light and easy to manoeuvre, while still offering industriallevel dust control. A ¾ HP fan delivers 3,335CFM of airflow, powered by 120-volt current. Mounted on the front of the cannon is a circular manifold with 12 atomizing nozzles that fracture pressurized water into a fine mist. About as loud as a
hand-held hair dryer, the fan forces air through the barrel then pushes millions of tiny droplets in a cone-shaped pattern up to 30 feet (10 metres). Using the 0–50º vertical adjustment, the mist can reach into the rafters of warehouses or be directed at specific emission zones. It is offered with a standard wheeled carriage but can be specified with alternate mounting as needed.
Beyond space constraints, the DB-10 solves several issues associated with dusty indoor operations. During indoor demolition, for example, harmful dust can fill the area and drift across the site line, creating a violation, but atomized droplets stop dust at the point of emission.
Workers are often assigned to use hoses for small-scale dust suppression, which adds to the labour cost, whereas the DB-10 requires no labour to run. Moreover, being in proximity of large machinery and falling material can be hazardous to personnel.
One driver of the new design is the fact that hoses create droplets up to 100x larger than atomized mist, far too large to capture airborne particulates. They can use up to 100gpm of water, causing excessive standing water and runoff, a potential hazard. The DB-10 addresses all these issues.
“The dust emissions from indoor demolition or concrete cutting and breaking can create tiny particles that you can’t see,” Lewis pointed out. “These can get deep into your lungs and cause serious breathing issues, but the mist droplets are small enough to capture individual particles at the moment of emission and drag them to the ground.”
The DB-10 produces droplet sizes of 50–95 microns in size, roughly the same as the cross-section of a single human hair. This is important because regulators test for respirable dust ten microns or less, like those found in indoor demolition. The slipstream created by droplets greater than 200 microns in size can deflect tiny respirable dust particles, rather than absorbing them. That’s why hoses are generally not effective against airborne dust. Using less than a quarter of the water
volume of a handheld one-inch (25.4mm) hose, the DB-10 fills the area with a dusttrapping mist that stops particulates from remaining airborne or migrating away from the area. The wide area of distribution and gentle settling reduces the chance of pooling and runoff.
A demolition contractor was recently performing an indoor demolition and found that disruption to storage piles of recycled material was causing airborne dust
emissions. Although piles could be covered at night, activity during the day was causing particles to drift into neighbouring communities. An onsite demonstration of the DB-10 showed the contractor that the atomized mist pulled the dust out of the air at the point of emission, preventing it from travelling across the site line. The fog cannon effectively controlled both airborne and ground-level particles with no runoff or puddling. This resulted in the contractor purchasing two machines for different projects.
“Watching these units in action under actual working conditions reveals how the dust falls to the ground and stays there,” Lewis concluded. “This approach to particulate control will give operators more flexibility and mobility to respond to dust causing conditions.”
BossTek is a global leader in dust control solutions for wide-area coverage, serving customers involved in demolition, construction, coal, rock, sand, aggregate, landfills, waste handling and many other applications. The firm’s atomized misting equipment has been used to improve air quality during port unloading, recycling and scrap processing, mining, earth moving and demolition activities.
A little over a year ago, Netherlands-based Dunlop Conveyor Belting announced that its Finance, IT and logistics director, Kerstin de Haan, was to become their new Chief Operating Officer. With the knock-on effects of Covid 19 still continuing to cause disruption, the world was then rocked by the Russian invasion of Ukraine in February 2022. To describe her first year in charge as a baptism of fire is something of an understatement so we sent Bob Nelson along to the company’s HQ and production center in Drachten to meet Kerstin and find out more about the challenges and how they are being faced.
Bob Nelson: Even by modern-day standards, the conveyor belt industry and the different industries it supplies such as dry bulk transportation, is very male-dominated. Do you see yourself as being something of a pioneer for women who aspire to be a business leader?
Kerstin de Haan: I do not see myself as a pioneer at all. Perhaps my appointment surprised some people in the industry but
here in Dunlop we really do not see why there should be a fuss. As in everyday life, the role of women in the business world is rapidly changing and expanding. The level of acceptance of women in senior
management roles has progressed enormously, especially in Europe. The time is not far away when it will be commonplace. Of course I welcome that, but this is not just about women in senior
management. When I walk around our offices and workshops and the factory, I feel enormous pride in seeing women fulfilling a whole range of seriously important roles. Times are changing so much and it is great to see.
BN: What have been the biggest obstacles you and your colleagues have had to face during the past year?
KdH: Like almost all businesses, the aftereffects of Covid-19 have created enormous supply chain issues plus huge increases in the costs of our raw materials. We have to compete for premium quality raw materials on the global market and quality raw materials cost a lot more than lower grade, unregulated raw materials.
Naturally, we try to get the best prices possible but because the foundation of our market approach is premium quality, we cannot compromise on the quality of those raw materials. That is how it has always been but now, with the Russia–Ukraine conflict, those challenges have become even bigger, especially the astronomical increases in the cost of gas and electricity. Fortunately, we have a great team here plus the backing of our parent, the Michelin Group, so we remain strong.
BN: In the world of conveyor belts, who do you see as your biggest competitors?
KdH: It depends what you mean by ‘competitor’. We do have competition from other European-based manufacturers such as Contitech and Sempertrans, which is fine and healthy. However, the real threat to European manufacturing as a whole is from South East Asia, primarily China. They are the biggest source of rubber belting imported into Europe. As with the approach they use for virtually every other market, they base their strategy on mass
volume manufacturing at barely acceptable, and often unacceptable, standards of quality at subsidized prices. Much of the European-based conveyor belt manufacturing capacity has disappeared as a result, particularly over the past two decades. Some of the remaining European
competitors now supplement their production with imported belting but we would never go down that road because it would be the beginning of the end.
BN: China is widely described as being ‘the factory of the world’, so how can you
Nobarriers. In Dunlop, women fulfill a wide range of seriously important roles. The after-effects of Covid 19 have created enormous supply chain issues.
compete with them?
KdH: That is an interesting question because the answer is in two, interconnected parts. The first part of the answer is that we have a market strategy of only selling premier quality belts that are exclusively manufactured in our own facilities. This means that we have total control of the quality and safety of the finished product and all of the raw materials that go into that finished product. This has been a principal of our business for over 100 years. The ‘unique selling proposition’ that we use is ‘lowest lifetime cost’. Our belts are so superior to lowgrade imported belt that they can quite easily last for up to four or five times longer, so although the Chinese belts can have a significantly lower retail price, our belts actually cost a lot less in real terms. The hard part is persuading customers to compare the cost rather than the price.
BN: What is the second part of the answer?
KdH: The environment. As a company and as individuals, we have a duty of care. It is widely accepted that urgent action must be taken. If we do not contain global warming by 2030 then the consequences will be catastrophic and irreversible.
KdH: There are many aspects of environmental concern. First of all, China are the world’s biggest source (32%) of carbon emissions. In 2020 for example, they emitted over 10 billion metric tonnes of CO2 into the atmosphere. That is more than twice as much as the USA, who are the world’s second highest CO2 producer. Yet another factor concerning carbon footprint is that imported belt typically has to be transported some 30 times the distance compared to European
manufactured belt. I discovered recently that more than 100 kilos of CO2 is emitted into the atmosphere for every ton of imported conveyor belt. As you would expect, we use this information to try to persuade industry that they should not be using belts that are imported from Asia. Aside from these ethical considerations and ‘lowest lifetime cost’, our belts have many other advantages, all of which are connected directly or indirectly to environment issues.
Manufacturing industrial conveyor belts produces a big carbon footprint so the impact on the environment caused by discarded industrial rubber belting is huge. Because the working lifetime of good quality belts is so much longer, the amount of belting that needs to be manufactured simply to replace worn-out belting could be reduced by up to 50%. That kind of reduction would represent some 75,000 tonnes of conveyor belting that would not
need to be made and transported thousands of kilometers each year. It would also mean that 75,000 tonnes of rubber, polyester, nylon and all the associated chemicals would not have to be disposed of, most of which goes to landfill.
BN: Earlier, you mentioned a threat to human and wildlife safety. What did you mean by that?
KdH: Manufacturers in Asia are not subject to the strict environmental regulations that are applied in Europe such as REACH regulation, which controls the use of potentially hazardous chemicals that pose hazards to human health and the environment. This includes those that may have category 2 carcinogenic classifications. The same applies to EU regulation concerning the use of Persistent Organic Pollutants (POPs). This means that Asian manufacturers are free to use unregulated, unsafe raw materials. They also have an added incentive because unregulated raw materials cost much less than their regulated counterparts.
REACH regulations call for the progressive substitution of “substances of very high concern”(SVHCs) when suitable alternatives have been identified.We believe this is a really positive and progressive thing
Asian manufacturers are not subject to EU regulations concerning the use of dangerous chemicals and pollutants.
because these dangerous substances not only affect the people making the conveyor belts but also those who install them and those who are in contact with them in their day-to-day work.
We are very proud of the fact that Dunlop Conveyor Belting were the first major conveyor belt manufacturer to achieve REACH compliance.
Sadly, many of our European competitors have chosen to ignore the regulations, either completely or at least partially because of the impact on production costs.
What worries me most of all is that because the majority of belt used in Europe nowadays is imported, it is virtually impossible to know how much SVHC and Persistent Organic Pollutants are entering our environment.
BN: You are clearly passionate about environmental impact but at the same time, as chief operating officer, you and your fellow directors also have a responsibility for profitable growth. Do you honestly believe that the two responsibilities are compatible?
KdH: Yes, I sincerely believe that the two responsibilities go hand in hand. Several years before I even joined the company, the Dunlop management team made a conscious decision to pursue environ-
Conductix-Wampfler has one critical mission: To keep your bulk material handling operations running 24 / 7 / 365. You need proven, worryfree energy solutions - and Conductix-Wampfler has them. Our systems provide reliable electric power and water to stacker/reclaimers, barge and ship loaders/unloaders, bulk conveyors, tripper systems, and gantry cranes. Conductix-Wampfler systems are rugged, low maintenance, and timetested in tough, dusty environments. All products are backed by the largest sales and service network worldwide!
www.conductix.com
mentally friendly strategies and achieve sustainable growth. As you would expect, it is essential that the growth is also profitable otherwise we would not survive. The strategy is to focus on three key areas; product life cycle, the environmental impact of our products and our production processes. As I touched on earlier, manufacturing industrial conveyor belts produces a big carbon footprint. However, on the positive side, this also means that the actions we take as a company can make a very big difference.
BN: Can you give me some examples of actual Dunlop solutions in these three areas?
KdH: Well, I must keep coming back to how longer product life cycles mean lowest lifetime cost and how this is hugely beneficial both to the end-user and to the environment. The single most practical and effective solution is for conveyor belts to be engineered so that they can be used for at least twice as long as the low-price ‘throwaway’ belts being imported into Europe from South East Asia. We know from experience that when end-users discover how good quality belts cost much less in the long run and help increase productivity, they come back again and again. For us, it is the best way to achieve sustainable sales growth.
The second key area of focus are the chemicals and ingredients used to create rubber and the lasting environmental impact that they can potentially have on the environment, which I spoke about a few minutes ago. The real problem is a lack of awareness amongst end-users about the
damage they are doing to the environment simply by buying unregulated imported belt. As a company, we do all we can to provide guidance and education on the subject but it is a constant battle to win hearts and minds. I am pleased to say that my colleagues in sales and marketing are telling me that attitudes are starting to change and that a growing number of customers are becoming more environmentally aware, so that fills me with hope.
KdH: The actual production process has not changed fundamentally for a great many years and much of the machinery is often old and not as energy efficient as it might be.
BN: So what has your company been doing to improve energy efficiency?
KdH: Especially during the past ten years or so, we have invested many millions of euros replacing outdated machines and building new, technically advanced production lines. This not only reduces our carbon footprint it also improves the overall efficiency of our business and uses less energy so the truth of the matter is that we win both ways. The fact is that energy saving forms a part of every project plan regarding process efficiency or capex projects. This also includes the constant development work that our engineers are carrying out in the search for new and improved products. The best example of this has been the development of a new type of belt construction that possesses a huge number
of technical and environmental advantages. The most common type of belt has an inner carcass consisting of multiple layers of polyester and nylon fabric with a thick rubber outer coating. What our engineers have done is create a single-ply carcass using an amazingly tough patented fabric that is exclusively made in our sister company’s in-house fabric weaving facility in the USA. The result was Dunlop Ultra X, which is a unique single-ply, super-strength belt that has far greater resistance to ripping, tearing and impact compared to traditional three-ply or even four-ply belting. This increased durability means that Ultra X provides a much longer working lifetime. Very importantly, it is also on average 10% lighter than its multi-ply counterpart so it uses less energy during operation.
BN: But how does this new type of belt contribute to your sustainable growth ambitions?
KdH: Quite simply, having a single-ply construction helps to maximize production efficiency because there are fewer production runs. Another advantage is that not having a rubber skim between the plies results in a thinner, stronger carcass while also reducing the amount of rubber needed. Yet another advantage is that we can make longer production runs at maximum width, which further improves efficiency and, very importantly, minimizes the amount of energy consumed. Sales of Ultra X on both sides of the Atlantic are going very well and we are increasing the range. Having a unique product like this that is also environmentally friendly is already contributing to our sustainable growth ambitions and also the ambitions of our customers.
BN: Thank you Kerstin. Do you have any final comments or messages?
KdH: First of all, thank you for this opportunity. As I hope you can tell, I am passionate about what we are doing here in Dunlop. These really are changing times. I am not alone in this because all of my colleagues in Dunlop’s leadership team and throughout the company share that passion. Every individual and every company has a responsibility to do whatever possible to prevent even more damage being done to our planet. I sincerely hope that enough manufacturers, traders and end-users will wake up and smell the coffee and make a concerted effort to substantially reduce this unhealthy and dangerous reliance on cheap imported belt. The future is in our hands.
A major global innovator of conveyor technologies has announced a factorydirect replacement programme to deliver freshly-moulded polyurethane cleaner blades for conveyor belts. Custom-fitted on-site and installed free of charge, customers pay only for the replacement blades. The programme from Martin Engineering assures customers of accurately sized and professionally installed replacement blades that are matched to their specific application, providing optimum cleaning performance and service life to minimize the cost of ownership.
Manufactured in-house for the highest quality assurance, Martin’s replacement blades are made with specially formulated, color-coded urethane to suit virtually any application. The blades have up to 53% more urethane in the wearable area than competitive designs, extending equipment life and durability. To achieve consistent cleaning throughout all stages of blade life, Martin’s patented Constant Angle Radial Pressure (CARP) technology incorporates a specially engineered curved blade to
maintain optimum cleaning performance and efficiency.
Martin is the only belt cleaner supplier that has designed its own equipment to manufacture moulded blades. This innovative system maximizes quality control and eliminates shipping and labor costs by having the new blades delivered and installed direct from the factory.
The need for conveyor belt cleaning is well established, delivering long-term benefits in both safety and production. Properly maintained belt cleaners reduce the accumulation of carryback under the conveyor and minimize dust build-up on rollers and other components. Excessive dust and spillage can foul rolling components and cause abrasion on the belt, reducing the life of equipment by as much as 30%. Even though a multiplecleaner system can be abrasive when in contact with the belt, it contributes less than 5% to the overall belt wear, delivering
a significant net benefit.
The belt is typically the most expensive piece of equipment on a conveyor, so not removing carryback at the discharge will contribute to premature belt failure. Material build-up on the face of idlers and rollers due to inadequate cleaning is one of the primary reasons a belt will mistrack, causing it to drift toward the stringer and damaging its edges. Fouled idlers and rollers can also erode the covers of the belt through abrasion, leading to premature replacement.
Bulk handlers commonly have several conveyors carrying different types, sizes or grades of materials. Depending on the number of belts, monitoring belt cleaner wear and effectiveness can be labour intensive and require an experienced eye. Beyond carryback, dust and spillage, allowing a cleaner to go too long can lead to pull-through or detachment from the assembly, resulting in belt damage, potential
equipment replacement and unscheduled downtime.
Available technology includes Martin’s N2® remote monitoring system to track tension and wear on all cleaners without having to physically visit the equipment. This technology offers the ability to monitor primary belt cleaner blades in real time and minimizes the need for manual inspections. Customers have immediate access to details on the mounting assembly, tensioner and blade wear, along with total annual cost information for budgeting purposes. The intuitive system notifies technicians and plant operations personnel before re-tensioning or replacement is required and/or when abnormal conditions occur. This critical intelligence reduces the
need to expose personnel to moving conveyors, improving both efficiency and safety while lowering costs. It allows service personnel to deliver and install replacement wear parts during scheduled outages.
Martin offers the components and monitoring service free of charge for qualifying customers. The company also supports the components with factorydirect service and provides customer alerts without cost. The factory-direct replacement program is just one element of the company’s decades-long push to develop new and evolving technologies, improve bulk material handling efficiency and reduce safety hazards.
Martin Engineering has been a global innovator in the bulk material handling industry for more than 75 years, developing new solutions to common problems and
participating in industry organizations to improve safety and productivity. The company’s series of Foundations books is an internationally recognized resource for safety, maintenance and operations training — with more than 22,000 print copies in circulation around the world. The 500+
page reference books are available in several languages and have been downloaded thousands of times as free PDFs from the Martin website. Martin Engineering products, sales, service and training are available from 16 factoryowned facilities worldwide, with wholly owned business units in Australia, Brazil, China, Colombia, France, Germany, India, Indonesia, Italy, Mexico, Peru, Spain, South Africa, Turkey, the USA and UK. The firm employs more than 1,000 people, approximately 400 of whom hold advanced degrees.
For bulk handling by the tonne in the port, Schlüter for construction equipment delivered a new SENNEBOGEN electric material handler to Freiberg to Valet u. Ott GmbH & Co. KG. Thanks to the installed electric drive, the 835 E not only impresses with its low operating costs, but also with its special rail undercarriage, which was specially adapted to the rails already existing in the port at the customer’s request.
In 1926, the company founders August Valet and August Ott laid the foundation for the medium-sized family business Valet and Ott with the first gravel plant in Freiberg am Neckar. The Valet u. Ott Group operates gravel plants in Baden Württemberg, Mecklenburg-Vorpommern and Saxony for the production of highquality concrete aggregates and road construction materials. The focus of production is on the manufacture of highquality gravel, crushed stone and sand products. In addition to its products, the company offers its customers a wide range of services, which include logistics, construction materials monitoring and
structural investigations, civil engineering as a concrete pumping service provider and as a receiving point for uncontaminated excavated material. In total, Valet u. Ott GmbH & Co. KG employs almost 300 people at 38 locations. The headquarters are located in Freiberg am Neckar, where approximately 150,000 tonnes of material are delivered by ship each year — and the trend is rising. The total amount of material handled is about 300,000 tonnes.
The 835 E from SENNEBOGEN is used by Valet u. Ott GmbH & Co. KG in Freiberg, Germany, for loading and unloading ships as well as material handling including truck loading. Thanks to the installed 200kW electric motor, the material handler always works with high performance in combination with low consumption, which ensures fast working cycles during loading and unloading — and that is money-saving and environmentally friendly. Its robust design, due to particularly low-wear and durable machine components, makes the 835 E from SENNEBOGEN a real expert
for continuous operation and protects the machine from longer downtimes. In addition, the electric material handler is particularly easy to maintain. With the E-series installation at the rear of the upper carriage, easy and safe access to the electric components is ensured. A non-slip tread surface also protects the machine operator from accidents during maintenance work.
A major special feature is the rail undercarriage of the SENNEBOGEN 835 E electric material handler at Valet u. Ott GmbH & Co. KG. This was specially designed to meet the needs of the Freiberg-based family business and, together with the electric drive, offers the perfect combination in port handling. To enable the machine to move on the existing grinding rails in the port, a hydraulically driven rail undercarriage of the 835 E series was selected and adapted to the track width of the rails.
In order to be able to accommodate the existing electrical box for controlling the sliding contacts, the undercarriage
Nothing should stand in the way of your productivity – least of all the materials you move. With our compact Hägglunds direct drive systems, you can adapt easily to the job at hand, taking advantage of full torque at an in昀nite range of speeds. And should an overload try to stop you, the drives’ low moment of inertia and quick response will keep your machines protected. We’ll support you too, with an agile global network and smart connectivity to bring you peace of mind. Driven to the core.
Hägglunds is a brand of Rexroth. www.hagglunds.com
of the electric material handler was equipped with cutouts and a bracket. The mechanical connection between the rails and the material handler was carried out by the customer service specialists of Schlüter for construction equipment.
Marco Moradian, operations manager: “One of the main reasons for acquiring the electric material handler was the adapted rail undercarriage. We had massive problems there before and other manufacturers could not offer us a satisfactory solution.”
The SENNEBOGEN 835 E electric material handler has now been in service at the port of Valet u. Ott GmbH & Co. KG. for almost three years. Marco Moradian is very satisfied with the machine: “We looked at several products in the course of the purchase and SENNEBOGEN had the machine that convinced us the most. In addition to the adaptation to our rail portal, we also had a few requirements in terms of outreach and lifting capacity, and that’s where the 835 E
The rail undercarriage was specially adapted to the customer’s needs.
electric material handler from SENNEBOGEN was the machine that fits best.” The SENNEBOGEN 835 E electric material handler was delivered by Schlüter Baumaschinen GmbH in the person of Area Sales Manager Michael Köhnlein. The medium-sized family-owned company sees itself not only as a dealer, but especially as a service provider with first-class customer service. The sustainable satisfaction of the customer is the focus at Schlüter for construction equipment, individual needs and wishes are jointly implemented in market-oriented services.
TAKRAF’s scope of supply includes all structural and mechanical components as well as essential electrical and instrumentation equipment. Commissioning is planned to be completed towards the middle of 2024.
Following an Early Contractor Involvement (ECI) phase, an important contract for engineering and supply of a conveyor system was recently awarded to TAKRAF. The contract also includes technical assistance during construction and commissioning.
The belt conveyor system consists of a
sacrificial conveyor and an overland conveyor. The latter features a negative lift of around 150m, as well as including various horizontal and vertical belt curves along its length.
Furthermore, a new loading module for an existing belt conveyor is also to be supplied.
Marc Hollinger, TAKRAF Project Manager, had this to say recently on his return back from South America: “Many colleagues contributed to this successful project award and there was great interaction between all the TAKRAF offices involved. I would like to personally thank all these colleagues for their commitment and teamwork. This important material handling project only serves to entrench TAKRAF as a leading global provider of high-capacity material handling systems that overcome numerous challenges and we look forward to an ever-expanding base of satisfied clients in South America”
For 55 years now, the company Penkert GmbH has been one a manufacturer of high-quality occupational safety products in Germany.
As reliable partner for its customers’ safety the company is developing practical solutions for different application areas using modern technology. Its expertise, flexibility and trustworthiness are the factors that create the base for a good co-operative partnership.
Penkert is committed to satisfy its customers. For this reason, the basis of the company’s philosophy lies in the quest to gain the partnership and trust of the customer through exemplary quality standards and an acceptable price. It follows the principle of starting work as it intends to go on, carrying it out with competence.
In many cases, Penkert has found feasible solutions itself, where customers could see no solution themselves and where conventional designs did not provide efficient results. The considerable knowledge and experience the company has accumulated over time forms the basis of its expertise. Folded gaiters are manufactured in accordance with detailed specifications.
All of the protective systems are produced in large as well as small quantities. Even with folded gaiters, on account of a process which is developed and patented by Penkert, it is able to inexpensively supply pilot products and prototypes at no additional cost.
THE COMPANY’S MOST IMPORTANT AIMS: satisfied customers v by delivering high-grade products v with the agreed quality characteristics v on a confirmed date v at a competitive price v
Penkert GmbH has been officially ISO 14001:2015 certified since 2022 and is committed to protecting people and the environment.
The certification is the first step towards a sustainable future in which environmental awareness is not only established but also practiced. Sustainable protection that moves the world, protects the environment and protects people.
Thus, it commits itself to the establishment, implementation, maintenance and continuous improvement of its environmental management system.
Just
scan
Konecranes Gottwald Mobile Harbor Cranes are the cranes of choice for precise and safe handling of all types of general cargo. With load capacities of up to 200 t and improved lifting capacity curves, as well as increased operating speeds, our Generation 6 sets new standards. The result: high lifting capacities, a long reach – and more speed.
German manufacturer Achenbach has been producing conveyor belt covers, made of corrugated sheet metal in almost every size, for decades. From small standard hoods in 11 sizes to huge JUMBO hoods for covering also one or two walkways, everything is possible.
The metal covers are produced in four different sections in galvanized, coated or stainless steel or alumnium.
Different opening systems for easy inspection and maintenance, various fixing systems and the sale of plastic made Organit-covers (especially for salt and food industries) complete the Achenbach range.
This means the largest variety of covers in the world and for the user that an optimum, value for money solution is available.
The main reasons for covering conveyor belts are:
Weather protection (year-round use v of the facility).
Environmental protection (no v discharge of the conveyed material).
Accident prevention (no intervention v on the running line).
Economy (protection of the system v and extension of the usage time).
Several of the longest conveyor belts in the world have been covered with Achenbach hoods.
In recent years, bulk/box canopies have
become increasingly important, with widths of up to 6m self-supporting. What’s more, Achenbach is able to offer a statically tested cover tension strip system and is certified in accordance with the DIN EN ISO 9001:2015.
GWS Kraanbedrijf in the Belgian region of Flanders can look back on many years of experience in the provision of bulk and general cargo handling services: constant companions are the now eight SENNEBOGEN material handlers, about which young managing director Stan Goeyvaerts has nothing but praise.
Walter Goeyvaerts once demonstrated entrepreneurial flair when he restructured and modernized his father’s cargo handling company, founded in the 1960s, shortly after the turn of the century: the result today is GWS, a thriving cargo handling service provider specializing in loading and unloading ships.
His son Stan, the third generation, has now taken the wheel. For him, growth means constantly investing in new handling equipment to respond flexibly to increased market demands. The latest acquisition is a SENNEBOGEN 835 E in the mobile version, which was delivered by the sales and service partner SMT in Belgium. “In terms of size and tonnage, this is the most flexible machine you could ask for,” says Stan Goeyvaerts
The reestablishment of the cargo handling company GWS took place in 2012 and builds on the experience of the traditional company, whose material handling activities go back two generations. “Initially, we were mainly active in the Antwerp region, but we are now active throughout Flanders,” Stan Goeyvaerts continues.
This is a success story that can be attributed especially to the personal contact with the customer, to which father and son attach great importance. “I still climb into the cabs of our material handlers myself. That also impresses our customers!
In addition, we always try to stay on the ball technically by having an extensive machine park at our disposal.”
Ship unloading in a double pack: cargo handling service provider GWS Kraanbedrijf in Antwerp has relied on SENNEBOGEN material handlers since the very beginning.
Today, the GWS machine park has grown to twelve material handlers, including eight SENNEBOGEN machines. “We started with three machines at that time. Two of them were used, the third was already a machine from SENNEBOGEN. We really appreciate the mobility of these material handlers, and that was crucial for our first customers, because they were located in close proximity to each other over a distance of 2km. With SENNEBOGEN, we could easily [move] from one customer to the next, without having to leave the cab. But apart from that, these are machines that stand out for their capacity and their handling. They are very easy to operate and at the same time keep productivity high. My employees enjoy working with them,” says Goeyvaerts, summarizing the strengths of the material handlers.
“In terms of size and tonnage, this is the most flexible machine you could ask for,” explains Goeyvaerts, referring to the new, orange 835 E-Series material handler. In addition, this one operates with a reducedemission, fuel-efficient Stage V engine. “As environmental legislation becomes more stringent, we always include this aspect in
our investment decisions.”
Service was also essential for him: “With SMT, we couldn’t have asked for a better partner. They are available to us day and night, if there are ever any problems. As a cargo handling company, we can’t afford any downtime, because a ship has to be able to
leave the port as quickly as possible. Thanks to SMT and the intelligent design of the machines with a focus on mechanical components, we can often easily solve minor problems ourselves. In this way, we can always concentrate fully on our customers.”
Heavy Industry, from Changsha. This is one of the three largest manufacturers of construction machinery worldwide, with a turnover of around US$27 billion in 2021. The company, founded in 1989, offers a wide range of products, with more than 26 product families and over 300 machine models. These are developed, produced and sold by just under 40,000 employees around the world.
SANY's European site is in Bedburg, near Cologne, since 2011. The site employs around 90 staff in sales, service and in adapting products for the European market. In 2021, SANY Europe sold more than 2,000 excavators on the continent. With the help of more than 100 dealers, the turnover across the whole of Europe was more than €100 million in the same year.
SANY Europe's portfolio focuses predominantly on excavators and portmachinery. The SANY site, measuring approximately 140 hectares, provides space for a production hall and warehouse. Proprietary painting facilities, as well as an administration building and the SANY Hotel are also located on the premises.
The internationally recognized brand
SANY Europe’s SMHW48G5 is a versatile material handler that can be deployed wherever large quantities of material need to be moved.
Climate-change and CO2 emission is the number one topic in many industries. Today’s society is interested to learn what CO2-neutral solutions each machine manufacturer can offer, and how this supports the customer on a long-term path towards CO2-neutral operations.
Years ago, SANY started to approve all machines to operate certain grades of Biofuels for current engine models. Currently SANY offers the Hybrid Reach Stacker, this saves 20% diesel per each
container-move. But what about fully electric SANY machines?
As everyone knows, SANY is a Chinese brand and China has an undebatable volume-market for battery electric vehicles and machines. A few years ago, SANY started to bring fully electric Empty Container Handler into the home-market. This has been followed by introducing fully electric SANY-RS into the home market. In the meantime, SANY already operates over 40 battery electric reach stacker and way more than 100 fully electric Empty container handler in customers operations. The company’s R&D teams proudly prepare fully electric product solutions for outside Asia regions.
Dry bulk ports and terminals are in a state of constant change. The materials they handle change and so, too, do the quantities. Operators are constantly having to adapt to new requirements. They want to automate their activities as much as possible while also remaining flexible. They need more space for future expansions, and they are constantly facing the challenge of adapting their facilities to the increasing throughput, while at the same time paying ever more attention to avoiding dust emissions and improving their CO2 footprint. In projects such as these, BEUMER Group works together closely with its customers to develop efficient and new solutions.
The ability to load ships quickly is a decisive productivity factor. It is important to adapt the technology implemented in ports to the local space constraints and the size of the vessels — as well as to take account of the characteristics of the transported material. “Ports are faced with the challenge of increasing their performance,” explains Lukas Paul, Head of Ports & Terminals at BEUMER Group. To
remain competitive, operators must constantly expand their terminals. “That is just one of the challenges. It is necessary to ensure economically viable and environmentally responsible operation and, first and foremost, cost efficiency.” When it comes to dry bulk handling equipment, BEUMER Group is there to help. The system provider supports operators – starting with every aspect of
conveyor technology and through to the loading of the ships.
“When customers come to us, we sit down with them and talk,” explains BEUMER expert Paul. “In most cases, they know their everyday workflows extremely well and are aware of where the weak points and bottlenecks are.” To ensure the efficient handling of dry bulk, they must constantly adapt or expand their terminals.
However, the restricted space available in ports often presents a difficulty. This means that operators face the challenge of integrating new storage areas – and these are not always in the immediate vicinity of the port. To use these areas, environmentally friendly conveyor systems represent an alternative to trucks.
Belt conveyors can be used to transport various bulk materials from and to the port. BEUMER Group supplies a variety of solutions depending on the intended use. Troughed belt conveyors, for example, permit high mass flows. They have an open design and are therefore suitable for coarse materials and very large volumes. Pipe conveyors, by contrast, have other specific advantages. The idlers shape the belt into a closed tube. This protects the transported material against external influences and also protects the environment against emissions such as dust or material loss. Panels with hexagonal cutouts and idler rollers in an offset arrangement keep the tube closed. Pipe conveyors are able to cope with tighter curves and larger angles of inclination than are possible with an open troughed belt conveyor. Their enclosed design also enables them to handle various bulk materials securely without any danger of cross-contamination. They also protect the health of the people who work at the facility or live nearby — for example, when bulk metal concentrates are being transported.
Lukas Paul remembers a project in Peru. To transport zinc, copper or lead concentrates mined by a number of different companies from the store to the terminal, the system provider installed a
pipe conveyor measuring approximately 3,000 metres in length which transported more than 2,000 tonnes of this material per hour. However, there was a problem: The route passed through a military area with barracks for troops. The enclosed conveyor system reliably prevents the concentrates from coming into contact with the environment and conveys them to the ship’s holds without generating dust. The pipe conveyor is also equipped with filters, scrapers, a dust removal mechanism and a control system, making the need for any transfer points superfluous. “Our belt conveyor systems are an economical and environmentally friendly alternative to truck transport,” says Paul. “They allow operators to automate their processes and remove the burden of the manual work from their employees. This solution also reduces energy consumption.”
Sometimes the bottleneck can be a transfer chute. The facilities are already designed to cope with large volumes of bulk materials, but the transfer chutes through which the material moves from one conveyor to the next are not. “That was true of one of our customers,” reports Paul. In this case, the experts at BEUMER were able to perform a DEM analysis which enabled them to adapt the chutes and eliminate the bottleneck.
“When we talk to our customers and analyze the processes, we very soon see whether a technical solution to the problem already exists,” says Paul. An example? BEUMER Group supplied the conveyor technology for an iron ore terminal in Malaysia. “We were making a few small changes to improve plant performance when we discovered a new problem related to conveying iron ore in a
particular condition,” recalls the BEUMER expert: during the rainy season, the material that is to be transported can sometimes become wet and sticky. In this state, material sticks to the conveyor belt and over time is distributed along the complete conveyor route. There was no suitable solution for keeping the belt clean available on the market. “We had tried a number of different belt scrapers but that didn’t really help,” says Paul. BEUMER’s technical experts developed a prototype that cleans the belt using very-highpressure water. “In this way, we were able to remedy a problem for which there had previously been no solution.”
The U-shape conveyor was developed against a similar background. The challenge was to combine the advantages of open troughed and enclosed pipe conveyors: the transported material had to be protected against outside influences such as wind, rain or snow — while the environment had to be protected against potential escaping material and dust.
The solution had to be equally suitable for coarse material as well as very fine material. And all this was made even harder by the sometimes complex routing. “In our U-shape conveyors, a special idler roller configuration forms the belt into a U-shape. This is how the bulk material is transported to the discharge station,” explains Paul. A similar idler roller configuration to that used in troughed conveyors is used to open the belt. In this way, BEUMER Group has extended the possibilities for providing the best bulk material transport solution based on the specific need of the individual project.
BEUMER Group works not only on
greenfield but also on brownfield projects — for example in the case of a fertilizer factory in Malaysia. To meet the growing demand for urea fertilizers, the system provider was commissioned to modernize and improve the performance of the existing system located between the longitudinal stockpile and the shiploading system. The project scope included not only a portal scraper and shiploader but also a fully automatic tripper car which fills the longitudinal stockpile, system monitoring and control equipment, adaptation of the motor control units, a transformer station, a transfer station and a screening station. The schedule was quite tight. However, the particular difficulty lay in finding space to install the new systems. “We had to install a new reclaimer in the warehouse. To do this, we blocked off a small section of the hall in order to construct the new reclaimer, which was approximately 50 metres wide. We had to bring it in part-by-part through the back door and then assemble it during ongoing production,” describes Paul.
“During our discussions, it usually becomes clear to us straight away what the customer needs. As a result, we are often able to propose a solution very quickly.” However, the complex part lies in the actual implementation and identifying precisely where the problems lie. “Thanks to our experience with the pipe conveyor, we were able, for example, to form the belt on the U-shape conveyor into the required shape. However, we still had to find out whether the belt would run stably and whether there were any problems in shaping it,” says Paul. The answers to these problems become clear with time.
It is also important to adapt the systems to the bulk material — for example in the case of fertilizer. Here, it is necessary to make sure that certain components are manufactured from stainless steel. “We have to examine the application very carefully,” stresses Paul. “We can’t simply pick a solution off the shelf and be confident that it will function well in countless other applications.” It is important to have a precise understanding of the materials in order to adapt the design individually using the appropriate technical capabilities. This is the great strength of BEUMER Group.
FAM has been part of the group of companies since May 2022. It plans, designs and manufactures turnkey plant and equipment for extracting,
transporting, loading and storing minerals, raw materials and goods. “This allows us to provide an even more comprehensive
service to port terminal operators, be it very large or also smaller systems,” says Paul.
For over 50 years, our loading systems for bulk materials have been synonymous around the world with long-lasting and reliable technology.
›Bulk loading systems for open and closed loading
›Loading with no segregation e.g. with FLOW-STOP technology
›Dust-free loading
›High quality loading hoses e.g. made in wear-resistant PU-FLEX
›Positioning system LIS-POS
› First-class service: Start-up and installation, Revision and repair services, System maintenance, modernisation and upgrading
More details: www.listenow.com
AUMUND Fördertechnik GmbH in Rheinberg offers reliable and cost-effective transportation and conveying solutions for foundries all over the world. After having supplied a Flat Plate Conveyor to replace a vibratory feeder in the summer of 2021, AUMUND has now developed a special Cleaning and Sorting Conveyor for Hawle Guss GmbH in Fürstenwalde, which was commissioned in August 2022.
Hawle Guss in Fürstenwalde on the Spree is a major manufacturer of products for gas and water distribution systems, such as taps, hydrants and valves. Hawle Guss requires the appropriate conveying technology for its new concept for degating, sorting and cleaning of castings at the foundry.
The function of the Conveyor supplied in 2021 by AUMUND is purely to transport material from the manufacturing plant in the basement on to the next process stage on the ground floor. In August 2022, as part of the next stage of expansion, a Cleaning and Sorting Conveyor was commissioned. This Conveyor had been specially developed for the application, and replaced the previously utilized vibrating conveyor.
The metallurgy specialists at AUMUND Fördertechnik based the project on a particular AUMUND product which had been supplied to foundries decades ago, and of which only a few photos and not a single drawing remained. AUMUND and the customer worked closely together to come up with the concept for a tailormade solution which resulted in the development of a completely new Cleaning and Sorting Conveyor with an overall length of 11.45m and an operational area of 8m.
The previous heavy exposure to noise and vibration was almost completely eliminated. The consequences of this transformation are a considerable improvement in working conditions and at the same time a reduction in energy consumption. The flat surface provides a comfortable working height for sorting and cleaning the castings without danger of obstruction. The design of the conveyor plates was optimized to avoid any cracks at the edges, and to enable the castings to be ejected sideways. At the same time a degree of mechanical stability could be
achieved which is sufficient to enable operation with a manipulator. Because of the high tensile strength of the plates, impact loads of up to approximately 2.5t can be tolerated without causing any deformations. The Conveyor was designed in such a way that all key structural components could be housed internally. With vibratory technology and hydraulic components no longer required, all advantages of a simple and reliable mechanical conveying equipment are at the forefront.
The AUMUND Group is active worldwide. The conveying and storage specialist has special expertise at its disposal when dealing with bulk materials. With their high degree of individuality, both its technically sophisticated as well as innovative
products have contributed to the AUMUND Group today being a market leader in many areas of conveying and storage technology. The manufacturing companies AUMUND Fördertechnik GmbH (Rheinberg, Germany), SCHADE Lagertechnik GmbH (Gelsenkirchen, Germany), SAMSON Materials Handling Ltd (Ely, Great Britain), TILEMANN GmbH Chains & Components (Essen, Germany) as well as AUMUND Group Field Service GmbH and AUMUND Logistic GmbH (Rheinberg, Germany) are consolidated under the umbrella of the AUMUND Group.
The global conveying and storage technology business is spearheaded through a total of 20 locations in Asia, Europe, North and South America and a total of five warehouses in Germany, USA, Brazil, Hong Kong and Saudi Arabia.
After a Liebherr LHM 600 mobile harbour crane could not be delivered due to an incident during transport in the Kiel Canal at the end of last year, Liebherr-MCCtec Rostock GmbH delivered a replacement unit at short notice. With the new LHM 800 High Rise, Port Esbjerg now has two of the strongest mobile harbour cranes in the world.
At the start of January 2023, Liebherr-MCCtec Rostock GmbH delivered a new LHM 800 High Rise mobile harbour crane to its customer Port Esbjerg. The delivery took place only a short time after an incident in the Kiel Canal, in which an LHM 600 ordered by Port Esbjerg was damaged while passing under the Holtenau High Bridge. Liebherr-MCCtec Rostock GmbH sent service engineers and technical specialists to assess the situation on site and to assist with the recovery immediately after the incident. In addition, every effort was made to deliver a replacement unit to Port Esbjerg as quickly as possible.
A PARTNERSHIP BASED ON TRUST
“We have a long and cooperative relationship with the Port of Esbjerg. So it goes without saying that one of our top priorities after the incident was to deliver a new machine as quickly as possible. With a lot of commitment, the trust of our customer and a strong team, we succeeded,” says Roman Chopyk, Area Manager for Liebherr Mobile Harbour Cranes.
With the early delivery of the LHM 800
High Rise, Liebherr is fulfilling its customer promise despite the circumstances and is helping the Port of Esbjerg to achieve its ambitious goals. A new LHM 600 will also be delivered as soon as possible.
“Liebherr’s strength and commitment to solve urgent and complex problems is of real value to Port Esbjerg, albeit it is the robustness and operability of these advanced cranes we treasure most,” says Dennis Jul Pedersen, CEO Port Esbjerg.
Cimbria’s strategic focus on financing solutions support development for customers and create a competitive edge. The collaboration with national Export Credit Agencies (ECAs) enables Cimbria to help customers realize their investment plans for both turnkey solutions and single equipment within industrial processing, handling, and storage, which are becoming more relevant in unsettled times.
Purchasing new equipment and solutions for processing, handling, and storage of grain and seed, as well as coffee, animal feed, foodstuffs and other bulk products is a big investment, and some companies and organizations may require assistance with funding.
With its constant focus on customer needs, Cimbria has developed a new, structured approach to financing solutions that’s tailored to the customer’s specific requirements. Cimbria Financing is a key service offer and an important part of the company’s customer focused sales strategy:
“With an ever-changing market situation, financing big investments can be extra challenging. Investments in projects and equipment to secure food supply are crucial, and the realization of them depends on the possibility of finding suitable financing,” explains Allan Olsen, Trade Finance Manager, Cimbria.
He continues: “Our financing solutions are tailored for the customer’s specific business requirements and often offer lower costs and better conditions than what is locally available from banks and financing institutes. Our down-payment requirements are also attractive. Furthermore, an easy and fast decision process and generally low documentation requirements make up the customer’s most important advantages.”
Cimbria bases its financing solutions on a collaboration with national Export Credit Agencies (ECAs), whose main purpose is to secure and develop national jobs through funding of promising projects and
solutions. As a part of AGCO Corporation, Cimbria also offers financing solutions through AGCO Finance.
“In general, we experience an increasing demand for financial support. In these
unsettled times with high inflation and unstable economic development, customers must be able to achieve low-risk financing that enable investments in new equipment or even in complete plants to grow their business,” explains Thomas Mohr, Sales Director, Cimbria.
One of the projects benefitting from Cimbria Financing includes UMEX, a leading port operator and logistics expert in the Romanian Port of Constanta, which is one of the most important and traffic-heavy transhipment hubs for the Greater Black Sea region. The project consists of two grain and fertilizer terminals. The grain
Cimbria is at the forefront of industrial processing, handling, and storage of cereals and seeds, as well as animal feed, food, and other bulk products. Cimbria works closely with their customers to design, manufacture, install, and service customized solutions, individual machines, and complete turnkey systems. Cimbria is a global brand owned by AGCO Group.
ABOUT AGCO:
AGCO is a major force in the design, manufacture, and distribution of agricultural machinery and precision ag technology.
terminal has 100,000 tonnes of storage capacity across eight separate silos and the fertilizer terminal is a multifunctional warehouse capable of handling and storing up to 66,000 tonnes of bulk fertilizers.
“We identified three main benefits in choosing financing from an ECA via Cimbria compared to other financing solutions. First, we were offered a longer availability and repayment period. Second, we were offered coverage from any commercial and political risks up to 95% of
the loan. And third, the financing solution had reasonable premium costs,” explains Cristian Taranu, General Manager at UMEX.
Currently, Cimbria has approximately 20 ongoing projects within financial support.
“Understanding how and when to contribute with relevant solutions to a customer’s business challenge is crucial to Cimbria, and in some cases the combination of technical expertise and financial support is key,” says Mohr.
AGCO delivers customer value through its differentiated brand portfolio including core brands like Challenger®, Fendt®, GSI®, Massey Ferguson®, Precision Planting®, and Valtra®. Powered by Fuse® smart farming solutions, AGCO’s full line of equipment and services help farmers sustainably feed our world. Founded in 1990 and headquartered in Duluth, Georgia, USA, AGCO had net sales of approximately $11.1 billion in 2021.
Growing demand for grain storage solutions and silos with larger storage capacities is translating into bigger demand for pneumatic unloaders.
Increased capacity and speed are the main reasons why larger-sized equipment is required for unloading increasingly large
vessels. At the same time, minimizing dust emissions, grain spillage and noise pollution are important considerations in the design of the unloaders.
Progress in design is occurring rapidly, giving ports and terminals wider choice for handling free-flowing agribulk cargoes such
as grains and meals, animal food pellets, chemicals and wood pellets.
For other cargoes, both mechanical and pneumatic unloaders can be fitted with optional devices to ‘fluidize’ the cargo before being lifted, such as cutting nozzle or screw accessory equipment.
Mechanical unloaders may have the edge in terms of speed, perhaps 200tph (tonnes per hour) up to 1,200tph, compared to 200tph up to 800tph per pipe for pneumatic unloaders. However, the pneumatic types have versatility — they can work on most quays and handle ship-tobarge transfers etc.
With a ship-unloader’s lifetime of about 30 years, it is essential for the customer to make the right choice of equipment. Vigan’s Commercial Director, Dirk Janssens, confirms progress in pneumatic technology has been so great that ten pneumatics are now sold for every mechanical unit. “This is the case for Vigan, but it must also be true for the whole market — for grain and agribulk at least. It is different for cement, iron ore and coal,” he states.
The three most critically important features to compare pneumatic and mechanical unloaders are efficiency, power consumption and investment cost. Pneumatic unloaders have a higher efficiency which means a higher ratio between the average capacity (which really matters to the operator), divided by the peak or nominal capacity.
Nicolas Dechamps, Managing Director of Vigan explains further: “The main reason for such higher efficiency is that the pneumatic unloader is sucking everything up to the bottom of ship. No grain remains in the suction nozzle. As a result, the total time to discharge the vessel ‘berth in –berth out’ is shorter compared to the same situation with a mechanical unloader of the same capacity.”
He further explains that for any type of mechanical unloader (chain, screw, doublebelt type, or even grab cranes), it is necessary to have the bottom of the vertical leg and its feeder buried in at least one metre of product to keep a high
unloading capacity. “The last layer of cargo in the bottom of the hatch needs much more time to be discharged with a mechanical unloader, making its efficiency lower than the pneumatic unloader.”
In terms of power consumption, he says mechanical unloaders (chain, screw, doublebelt) have a lower nominal energy consumption at full capacity ranging from 0.3kWh/t to 0.8kWh/t.
Pneumatic unloaders have managed to reduce their consumption to lows of about 0.7kWh/t due to reducing the number of elbows in their pneumatic lines, using a multi-stage turbo blower instead of an oldfashioned roots-type blower and the use of inverters for the drive of the turbo blower unit (allowing power consumption to be regulated automatically according to power required).
However, the higher efficiency of the pneumatic unloader outweighs its higher electric consumption by a factor of ten in terms of costs.
With respect to investment cost, Dechamps says the pneumatic unloader is significantly cheaper to buy. “Other factors have to be taken into consideration: extra cost of quay construction or quay refurbishment due to higher weight of mechanical unloader compared to pneumatic unloader. Transport costs are notably high as mechanical unloaders are
usually made in Far-East countries and transported on expensive heavy-lift vessels, with all downstream equipment (conveyors, elevators) having to be sized according to the nominal capacity of the unloaders.”
Financial analysis shows that the pneumatic unloader remains globally the most economical solution and that the extra small power consumption is largely compensated by lower investment costs and its higher efficiency.
Pneumatic unloaders also appeal due to easier maintenance (a pneumatic unloader is an enclosed machine room with pumps and suction pipes and barely any moving parts), machine weight (less need for new quay construction or refurbishment) and simple controls meaning quicker training for operators.
In terms of costs of operation and power consumption, Mr Dechamps says that based on US$0.1/kWh, the difference in power consumption is ±0.2kWh/t which represents approximately US$0.02 or as little as US$1,200 in total for a Panamaxsize vessel.
However, thanks to higher efficiency, a pneumatic unloader of 600tph will unload a Panamax vessel faster than a mechanical of 600tph. Saving one day on average for the discharge of each vessel means a saving of one day of demurrage on each vessel.
Since 1914, NEUERO has been a major manufacturer of mechanical and plant engineering.
NEUERO is the renowned specialist in pneumatic ship-unloading and mechanical shiploading.
Following the ‘Made in Germany’ tradition, NEUERO boasts over 100 years of activity in the production of reliable and individualized conveyor systems.
NEUERO has over 5,000 built references of its systems in over 140 countries, and its shiploading and unloading systems handle several tonnes of grain worldwide every hour.
This article focuses on NEUERO’s shipunloading expertise. All of its machines are characterized by advanced, efficient, reliable and user-friendly design. The systems low maintenance and operating costs and thus ensure a fast return on investment.
NEUERO’s ship-unloaders set standards worldwide. They protect the environment as well as the health and safety of employees through their innovative technologies.
NEUERO is ISO certified and has
guidelines on work safety, health and the environment. More than 300 customers already rely on NEUERO’s expertise. Continuous unloading performance is guaranteed, even during residual cleaning. Lightweight designs make NEUERO’s machines very safe and environmentally friendly for handling.
NEUERO designs pneumatic shipunloaders for grain, feed, biomass, and many other dry bulk materials according to customer requirements. These can be used to unload many types of bulk goods, particularly from the food sector, as well as for products from the power plant and aluminium industry
up the material from the bottom of the hatch, like a vacuum cleaner.
This fact alone results in efficient unloading performance in pneumatic discharges.
The discharge capacity of NEUERO’s pneumatic machines is 75–80% of the bulk material.
A significant advantage of pneumatic shipunloading is the closed flow of product from receipt in the ship to discharge to downstream conveyors, ensuring that adjacent equipment and components are not polluted or contaminated. At the same time, deposits in this closed conveyor strand are hardly possible.
SHIP-UNLOADING OF BULK GOODS
NEUERO’s pneumatic unloaders use the flowing characteristics of bulk goods to feed the ship-unloader.
A key benefit is that NEUERO’s pneumatic ship-unloaders can directly pick
The fact that all areas with maintenance intervals are accessible via stages, the system’s maintenance is possible without any problems and ensures high availability. dust free ship unloading with closed v flow of products; high availability due to easy v maintenance; and laying the boom on the ground. v
L Another advantage of NEUERO’s systems is the low noise emission. NEUERO’s pneumatic unloaders meet extremely high standards.
As a result of this, many clients choose NEUERO shiploaders and unloaders when operating close to residential areas.
In addition to the soundproofed machinery house and corresponding soundproofing on the blower, NEUERO can adjust more silencing measures on other components. low noise emissions; v
<85dB at 1m from the discharge opening; and operation near residential areas. v
SPECIFIC ADVANTAGES OF PNEUMATIC UNLOADING INCLUDE low weight; v the pneumatic conveying of NEUERO v requires relatively little steel to carry the material and thus less weight. As a result, fewer tyres can be used, resulting in leaner foundations and thus lower costs at the quayside;
low acquisition costs; easy handling; v with NEUERO’s pneumatic unloaders, v the residual cleaning in the hull of the ship becomes easy; easy replacement of spare parts is v possible; NEUERO’s pneumatic unloaders can v be flexibly used for different ship sizes; thanks to NEUERO’s pneumatic v unloaders, nearly dust-free work is possible with hardly any grain fracture; high efficiency — due to the efficient v
residual cleaning and continuous unloading, NEUERO’s pneumatic conveyors have a high unloading power.
In summary, the advantages of NEUERO’s pneumatic unloading systems include the following points: Low investment costs, high efficiency, low-noise-emission, nearly dustfree unloading and consistently very good unloading capacity.
NEUERO’s designs are unique and tailored to the customer’s requirements and local conditions. NEUERO distinguishes between three types:
MULTIPORT
unloading capacity up to 800tph v (tonnes per hour), based on wheat; supply via the low or medium voltage; v use of diesel generators possible; v stationary, rail or rubber-tyred v steerable wheels; broad coverage of the ship’s hold by v horizontal and vertical telescopic tube; auxiliary winch for residual cleaning on v the boom for an excavator or front loader; and
if necessary, with explosion protection v concept following ATEX guidelines.
FLEXIPORT
pneumatic ship unloading for non- v free-flowing materials; the vertical tube can be equipped with v a rotating feeder to loosen up the product; and
full coverage of the ship’s hold due to v additional extending and kick-in-kickout movement of the vertical boom.
TOWER
unloading services of up to 1,600tph, v based on wheat; movable on rails; v optional with a loading boom; v integrated auxiliary winch per boom; v two separate suction lines (50% each); v integration of various conveyor v elements, such as container scales, magnetic separators, etc.
The NEUERO suction nozzle is characterized by an automatic electric side air control system, which allows the unloading power to be perfectly adjusted to the conveyed product and operating conditions. In addition, an automatic nozzle lowering can be used. This controls the immersion depth of the nozzle depending on the vacuum and thus ensures continuous suction operation with high average power.
The ability to lower the boom to the ground offers a special advantage in the maintenance and possible replacement of individual parts, e.g. wear plates in the conveying elbow, rope winches, rope rolls, etc. This avoids the need for any potentially dangerous work to take place at large heights. Lowering the boom to the ground also reduces wind loads during typhoons.
With the auxiliary winch on the boom, a small front-end loader or larger track excavators weighing up to 15 tonnes can be lifted into the ship’s hold to support the residual cleaning. The winches operate at
two speeds and are protected by load cells.
Milling head upper swivel device with swivel v bearing and external toothing as well as slewing gear drive, swivel range approximately 300°; kick-in/kick-out using cylindrical joint v and hydraulic cylinders with up to 60 ° deflection;
lower intake area with axial bearings v and cutter, rotary bearings with electric swivel drive and bypass for suction wiring; with speed control of the cutter for better material flow control; and includes a special nozzle for v residual cleaning.
NEUERO also offers an augmented reality (AR) application. Users can select the scale. At 1:1, the view is from underneath, and it is necessary to point the camera upwards to view. The simulator enables users to gain data on subjects including manoeuvrability, and the ability to unload the last grain from the ship’s hold with the use of a bulldozer. With this simulator, users can even explore the inside of the machinery house with NEUERO turbo blowers, NEUERO automatic filter cleaning system, test drive and unload virtual grain using virtual thumb sticks: left for manipulating the boom and right for manipulating the pipes.
NEUERO has been a major manufacturer of mechanical and plant engineering since 1914. NEUERO stands for mechanical engineering, innovation and maximum customer benefit.
Lion Bulk Handling, a division of Lion Marine Group B.V., has recently delivered a pneumatic ship-to-silo unloader to an import terminal in Italy.
This highly technological machine is specially designed to unload dry bulk materials at a rate of 205tph (tonnes per hour). The features of this ship-unloader make it the first of its kind for unloading dry bulk materials such as cement, fly ash, alumina, etc.
v fully electrically driven;
The ship-unloaders features include: Industry 4.0 approved;
v remote access — global remote
v assistance possible;
v Kinematic tested manipulator arm; wireless-controlled manipulator arm;
Finite Element Analysis (FEA)/
v highly advanced PLC control system;
v dock-mobile configuration;
v can be used to unload vessels of up to
operation of its trusted partners.
Lion Bulk Handling offers products for: floating terminals;
v
v 7,600dwt; unloading capacity of 205tph.
Lion was able to engineer, deliver and commission this ship-unloader with the co-
ABOUT LION BULK HANDLING
Lion Bulk Handling is a respected expert in the field of bulk handling equipment. The company designs, manufactures and commissions bulk handling systems for the marine, offshore and onshore industries.
v self-discharging ships;
v offshore rigs;
v offshore vessels;
v shiploading;
v ship-to-truck unloading;
v ship-to-silo unloading;
v conveying;
v storage and reclaim; and
v
v truck loading.
SHIP-TO-SILO UNLOADERS
The ship-to-silo unloaders only require a pipeline connection to handle the entire conveying process from ship to store. All
configurations are available with a manipulator arm for open hatch (option 1) unloading or delivered with a flexible hose connection for closed hatch (option 2) unloading. The closed hatch unloading option can only be used with a fluidized floor vessel and can be operational in any weather condition.
road mobile ship-unloader; v dock mobile ship-unloader; v gantry mobile ship-unloader; v barge-mounted ship-unloader; and v stationary ship-unloader. v
Road mobile ship-unloader
The ship-to-silo road mobile unloader is designed as a road legal unit and can be easily transported to various ports and terminals. One unloader can be used to service multiple ports and terminals for unloading (open hatch) barges and ships up to 7,000dwt. Due to its road mobility, the utilization rate of the road mobile unloader can be very high, driving the investment costs per tonne to a minimum. A permit may be required for movement over public roads, per local law.
The key benefits of the road mobile ship-unloader include that it is a compact unit for easy movement, it can service multiple terminals for unloading operations, it is automated, and it offers continuous material flow. The unit can serve vessels of up to 7,000dwt, with a maximum capacity of 205tph.
Dock mobile ship-unloader
The ship-to-silo unloader dock mobile type only requires a pipeline connection to handle the entire conveying process from ship to storage. This ship unloader configuration can easily move on the dock site or stored when not in use. Tyres are used to move the unloader, so no obstacles are located on the dock. This enables it to work in practically any type of dock environment. The pipeline may run below at or above ground level. The unloader also functions with removable pipeline sections.
The key benefits of the dock mobile ship-unloader include shared dock space, the dock remains free of obstacles such as rails or conveyor belts, it is automated, and
it offers continuous material flow. It can work with vessels of up to 40,000dwt, and offers a maximum capacity of 360tph.
The ship-to-silo unloader gantry mobile type only requires a pipeline connection to handle the entire conveying process from ship to storage. This ship-unloader configuration is ideal for dedicated operations with available shore power. Especially with an existing infrastructure (rails) will save investment costs. The pipeline may run below at or above ground level. The unloader also functions with removable pipeline sections.
Key benefits include a dedicated jetty, existing rails, it is automated, and it offers continuous material flow. The unit works with vessels of up to 40,000dwt, with a maximum capacity of 360tph.
The ship-to-silo unloader barge-mounted type is ideal for unloading locations with large tidal differences, as this requires a minimum required length of the manipulator arm when unloading open
hatch (option 1) ships or barges. When ships cannot reach the dockside, unloading closed hatch (option 2) ships or barges with integrated fluidized floor system through a flexible (floating) hose connection, would be a solution. The closed hatch option can be operational in any weather condition and is advisable for high humidity or monsoons regions. The barge-mounted ship unloader can also be used at multiple terminals, as the complete unit can be towed to another unloading location.
The key benefits of the barge-mounted ship-unloader include the ability to cope with large tidal difference, the ability to be used at multiple unloading terminals, it is automated, and it offers continuous material flow. The unit can be used with vessels of up to 10,000dwt, with a maximum capacity of 200tph.
The stationary ship-to-silo unloader is a cost-effective configuration, as no propulsion system is required. This type of unloader only requires a pipeline connection to handle the entire the conveying process from ship to storage. This enables it to work on a dock with limited space. The key benefits of the stationary ship-unloader include that it is suitable when there is limited space on the dock, barges and ships can easily move alongside the dock, it is automated, and it offers continuous material flow. The unit can be used on vessels of up to 40,000dwt, with a maximum capacity of 360tph.
Bruks Siwertell has secured a new Siwertell ship-unloader contract from cement and ready-mix concrete producer, ARGOS USA. The unit will secure environmentfriendly, dust-free cement and fly ash
handling at the port of Houston, Texas.
“This latest contract continues a longstanding run of Siwertell systems ordered for cement handling operations in the US,” says Magnus Rundqwist, Director Global
Bulk Sales, Bruks Siwertell. “Siwertell screw-type technology has a worldwide reputation for efficient, high-capacity, environment-friendly cement handling and this unit will deliver exactly that.
“Totally enclosed Siwertell unloaders draw material into the vertical screw conveyor using a unique inlet feeder, which operates below the surface of the material, eliminating the risk of spillage and minimizing dust creation. They also have low powerconsumption demands,” Rundqwist notes.
Bruks Siwertell will also supply the
complete screw conveyor system for transporting dry bulk material from the unloader to a storage dome, along with support structures and walkways.
“Our global capabilities mean that we were able to offer a competitive unloading solution, complete with conveyors and storage dome,” he adds. “Once
operational, this state-of-the-art cement terminal will set a new industry standard.”
The Siwertell 490 M-type unloader offers a continuous rated cement handling capacity of 800 tonnes per hour, and is designed to accommodate vessels up to 65,000dwt. It will be assembled on site and is planned for delivery in February 2024.
Bruks Siwertell has received an order from Hallet Capital Pty Ltd for a Siwertell shipunloader. It will secure environmentfriendly cement handling in the South Australian port of Adelaide.
“Hallet Capital is a new customer for us, and part of its decision to choose Siwertell technology was based on Bruks Siwertell’s extensive experience with other cement import terminals,” says Jan Karlsson, Sales Manager, APAC, Bruks Siwertell.
A gantry-mounted Siwertell 490 F-type unit has been ordered along with a jetty screw-conveyor system feeding a dome silo
and individual screw conveyors for installation inside the dome.
“There were two main considerations for this contract,” notes Karlsson. “The first was environmental protection and the second was designing a system that could be moved away from the jetty when not discharging vessels, as the port of Adelaide does not allow any fixed installations to hinder other operations within the port. We were able to meet both.
“The ship-unloader will be fitted with a rubber-tyre wheelbase ensuring in-port
mobility,” he explains. “Furthermore, the jetty conveyor system will be installed in a recess so that the jetty remains clear for other activities. The entire system, from material pick-up in the vessel’s hold to the dome silo, will be totally enclosed, providing a virtually dust-free operation in the port, with no spillage.”
The new Siwertell ship-unloader will be suitable for discharging bulkers up to 40,000dwt at a rated cement handling capacity of 500 tonnes per hour. It is planned for delivery in August 2023 and will be assembled on site.
Bruks Siwertell has delivered a new Siwertell road-mobile ship-unloader for dust-free cement handling operations in Belle Chasse, Louisiana, USA for returning customer, Cemex. The 10 000 S nextgeneration unit adds to a portfolio of Siwertell technology used by the Mexicobased multinational building materials company.
“We are the only company able to offer a mobile ship-unloader around this size,” explains Pedro Alfaro, Project Development Engineer, Bruks Siwertell. “This was a significant driver for the contract, along with our ability to deliver the unit within a short timeframe.
“The road-mobile system also offers a great deal of flexibility, enabling the operator to easily transport ship unloading capabilities between sites,” Alfaro continues. “It is now working hard, and keeping up with significant rises in cement demands.”
Siwertell screw-type technology has totally enclosed conveying lines, which ensure no spillage and keeps fugitive dust to an absolute minimum. “Environmental protection was another key element behind Siwertell technology being selected,” he adds.
The ship-unloader was delivered towards the end of 2022 and offers a continuous rated cement handling capacity of 300 tonnes per hour, and can discharge vessels up to 10,000dwt.
NEUERO produces the most reliable and high-quality bulk ship loaders worldwide. Environmentally friendly with less dust, less noise and more efficiency | neuero.de/en