
14 minute read
UNDER COVER — MARINE PAINTS & COATINGS: BEHIND-THE-SCENES PROTECTION
Under cover
Jay Venter
Marine paints & coatings: Behind-the-scenes protection
To help owners and operators improve hull efficiency to reduce emissions, Jotun’s HullKeeper programme offers trusted analytical and technical services, digital capability and ROV inspections.
Jotun’s HullKeeper programme may include some advanced monitoring technology, but it is Jotun’s fouling control expertise, supported by proprietary fouling risk algorithms, that helps shipowners and managers improve their environmental performance.
Biofouling is a major issue in shipping and leads to significant increases in fuel consumption and greenhouse gas (GHG) emissions. And with growing pressure from regulators and consumers on the shipping industry to address sustainability issues, Jotun has worked to develop solutions to help its customers comply with existing and pending regulations, improve performance and lower emissions.
While the quality of Jotun’s antifouling hull coatings remains critical to improve hull efficiency, Jotun has also invested in after sales service and digital technologies to develop new solutions to help owners and operators reduce fuel costs and improve environmental performance. These new digital tools allow Jotun’s customers to track and analyse hull performance over time, providing them with the information they need to track and improve environmental performance.
In other words, what can be measured can be managed.
THE SCIENCE OF FOULING CONTROL Launched for a limited number of customers in 2020, the HullKeeper programme is the latest example of Jotun’s innovative approach to helping customers improve hull efficiency. Designed by Jotun’s team of hull performance experts, the four-part programme optimizes hull performance, allowing customers to take full control of their operations through hull monitoring, fouling risk alerts, inspections, and advisory services.
The HullKeeper programme is grounded in Jotun’s proprietary fouling risk algorithm, supported by data from different sources to make fouling control and efficiency more predictable. By providing insight into issues before they occur, ship operators can take planned corrective actions that help shipping lower fuel costs and corresponding emissions.
Because increased fuel consumption due to biofouling is the cause of around nine per cent of the 919mt (million tonnes) of CO2 and 21mt of other greenhouse gases emitted by shipping annually, proper fouling control has the potential to reduce emissions significantly.
While it is unlikely that the industry will reach its full potential of a reduction of 85mt of GHGs through fouling control, Jotun believes that even a modest contribution would be a genuine achievement.

PPG SIGMAGLIDE 1290 fouling release coating helps Enterprises Shipping & Trading achieve carbon reduction goals
PPG has announced that Enterprises Shipping & Trading SA (EST) has selected PPG SIGMAGLIDE® 1290 biocide-free silicone fouling release coating to improve the energy efficiency and reduce the carbon emissions of its fleet.
EST aims to improve its environmental performance through investments in energy-efficient technologies. The company selected PPG Sigmaglide 1290 coating for its ability to reduce the frictional resistance of the fleet’s hull surfaces, which decreases power demand and related emissions.
PPG performed several studies in cooperation with leading independent marine institutes to measure the power and speed impact on vessels retrofitted with PPG Sigmaglide 1290 fouling release coating. Those tests determined that the coating provides a 20% reduction in power consumed at design level, and up to 35% reduction in carbon dioxide emissions when compared with traditional antifouling coatings.
EST vessels that were retrofitted with energy-efficiency technologies are demonstrating a power reduction of more than 20%. PPG Sigmaglide 1290 coating has been a major contributor to this performance.
“EST is a pioneer in energy-efficient operations and is committed to minimizing its environmental impact,” said George Sarris, President, Enterprises Shipping & Trading SA. “Our investment in PPG Sigmaglide 1290 coating is a major EST selected PPG Sigmaglide 1290 coating for its ability to reduce the frictional resistance of the fleet’s hull surfaces, which decreases power demand and related emissions.

contributor to our goals of achieving the maximum efficiency potential of our fleet and not only meeting but exceeding the carbon reduction goals set by the International Maritime Organization (IMO).”
IMO’s greenhouse gas (GHG) strategy for the shipping industry calls for a reduction in carbon intensity of 40% by 2030 and 70% by 2050 as compared to 2008, as well as a reduction of total GHG emissions from shipping by at least 50% by 2050 compared to 2008. Silicone coatings are included among IMO’s published list of energy-efficiency technologies that can directly shift the power curve.
“PPG Sigmaglide 1290 silicone coating can help shipowners comply with IMO regulations by contributing to a significant speed improvement and increased operational efficiency,” said Ariana Psomas, PPG segment director, newbuilding and drydocking, Protective & Marine Coatings. “The coating’s ultra-smooth surface enables vessel operators to improve their speed and save on power consumption while also resisting even the most difficult fouling conditions.”
Plasmet ZF Aerosol: fast, effective corrosion protection in an instant
Corrocoat, global producer of specialist anti-corrosion coatings, has put one of its most successful materials — Plasmet ZF a corrosion-inhibiting coating — in to a 400ml aerosol can.
Intended for use off-shore and on-shore or where a long lasting minor repair is needed, this coating has exceptional properties. The product is easy to use, requires minimal surface preparation and is ideal for small holding repairs.
The Plasmet ZF aerosol is a tough, durable rust tolerant coating requiring minimal surface preparation. Offering long-term resistance to corrosion attack, Plasmet ZF is ideal for applications ranging from all types of structural steelwork, tanks and pipework in a range of industries including off-shore, refineries, shipping, power generation and many more.
Coating with a Plasmet ZF aerosol takes much less time when compared with brush application; it also ensures that every inch of the surface is covered — even deep and hard to reach areas which might otherwise be missed.
Other key benefits that users can expect are even coverage, minimal preparation; there is no longer a need to mix components on-site from separate containers, and no clean-up requirement afterward. In addition, once opened, the aerosol has a long pot life — at least 24 hours, meaning the user has time to complete a number of jobs across a site or installation.
Plasmet ZF for Tough, durable and tolerant of vehicular traffic, Plasmet ZF can be used for protection in both immersed and atmospheric conditions.
NORSOK APPROVED In 2020 Corrocoat submitted Plasmet ZF for independent testing to NORSOK Standard M-501, by globally renowned inspection and testing organization SGS. NORSOK standards were developed by the Norwegian petroleum industry and describe in detail how to achieve the safest and most cost-effective products in design, engineering, manufacturing and maintenance of structures in the oil and gas industry.
To pass NORSOK Standard M-501 test protocol, a coating system must demonstrate high levels of protection with a minimum need for future maintenance
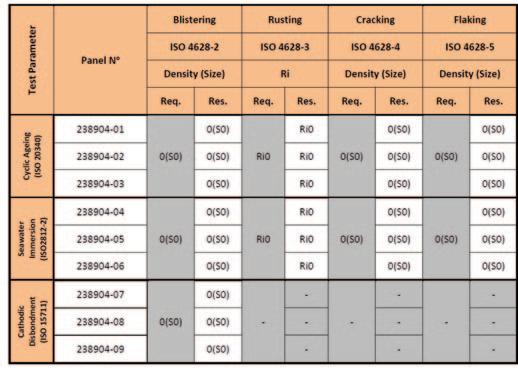
and health, safety and environmental impact.
Plasmet ZF was tested against System 1 — use on carbon steel with a max operating temperature of <120°C — structural steel, equipment exteriors, vessels, pipework and valves including in tidal and splash zones and System B — internal surfaces of carbon steel vessels — ballast water tanks/internal seawater filled compartments.
After six-month long exposure tests for cyclic ageing, seawater immersion and cathodic disbondment, the results demonstrated the coating performed extremely well, passing all tests with flying colours.
As testament to the success of Plasmet ZF, SGS commented that the results on the cathodic disbondment tests were “exceptional” reporting that they could not even get a knife blade between the coating and the steel after 175 days on test.
“Plasmet ZF and many other Corrocoat systems have for years been used in demanding energy applications throughout the world,” says Corrocoat Sales Director, Rob Cole. “The NORSOK test results give us unbiased confirmation of its performance and our customers an added level of confidence that will meet their toughest requirements.”
This chart displays the results achieved by Plasmet ZF after cathodic disbondment, seawater immersion and cyclic ageing tests. Visual inspection of the coated sample plates showed no blistering, rusting, cracking and flaking and no chalking.
Case study: Repairing ballast pump for an FPSO
Damaged ballast pump. Damaged ballast pump. Resin laminate on damaged area.
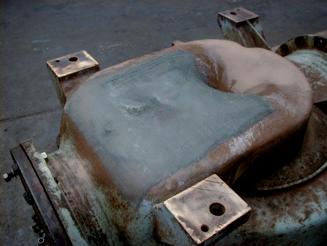
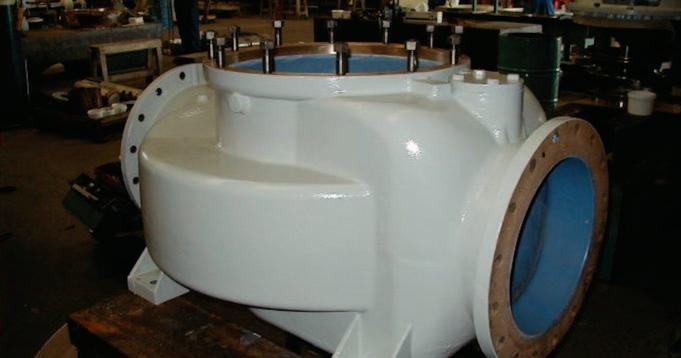

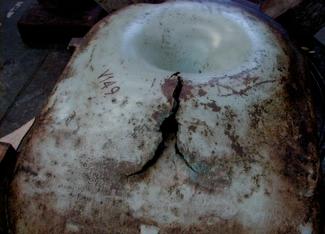
Corroserve was approached by a client; a major commercial shipping company, to repair a badly damaged ballast pump casing. The pump had pulled in a large item that had cracked open the casing at the bottom of the suction chamber.
Following arrival at the Corroserve workshop (based in Leeds), the affected area was cut out and a new bronze plate was welded in its place. The volute casing surface was then abrasive blasted to Sa2 ½ surface finish to provide a minimum surface profile of 50 microns. A two-pack cold cured vinyl ester laminating resin was then applied on the inside and outside of the affected area, to re-profile and add strength to the area.
RESIN LAMINATE ON DAMAGED AREA Finally, the casing was coated with Corroglass 600 series to a DFT of 1.25mm inside and painted to the requested RAL outside. The professional preparation and repairing of the casting before coating and the use of Corroglass 600 will ensure the casting will be in service for many more years. The specialist coating Corroglass 600 series is a two component, high build Glassflake Vinyl Ester lining and repair material. Designed to provide protection against erosion corrosion in immersed environments, the product is outstanding in its performance, and can be used in many areas of application to build thick layers. It can also be moulded and machined.
Corroserve has the experience and expertise to either coat from new or provide remedial coatings to process equipment.
The bespoke coating systems used are designed and manufactured by partner company Corrocoat, and determined by the operating conditions and mediums. The coating systems have provided unrivalled levels of corrosion protection in the harshest environments in over 40 years. Repaired ballast pump.
Across all industries, businesses and households, one of the major challenges in the year(s) ahead is going to be managing the impact of increased energy costs on the ability to live, work and trade profitably, writes Mads Raun Bertelsen, Head of Marine Solutions, Hempel.
This has been the case for some months now, but with the sanctions environment becoming more complex by the day, the situation looks ever-more complicated and costly.
For shipowners, operators and managers, one issue of immediate concern is the cost of keeping vessels moving. At the time of writing, bunker costs are hovering near the US$1000 per tonne mark, having hit unprecedented highs in recent weeks. According to Ship & Bunker, which collates ship fuel prices, the average price of Very Low Sulphur Fuel Oil (VLSFO) at the world’s top 20 bunker ports is up more than 80% year on year.
This represents a significant increase in operating costs for all shipping companies, which will have to look at every possible avenue for reducing fuel use in order to protect profit margins and avoid passing on costs to their customers.
MANAGING FUEL USE TO REDUCE COSTS Smart fuel purchasing of course will be key. Bunker costs are not the same globally and savvy owners can make significant savings through their bunker procurement systems and contracts in many instances. But costs will rise and will likely be sustained at much higher levels than we’ve seen in recent years given the wider energy price volatility caused largely by sanctions on Russian oil and gas exports. Investing in solutions that enable vessels to operate more efficiently — by making their fuel go further — will pay dividends.
The most accessible solution for many will be the application of an eco-efficient hull coating solution which has been formulated to reduce drag, optimize engine and propeller efficiency and, as a result, reduce fuel use. While there is an upfront cost to such an investment, the right solution will directly impact fuel bills in the immediate and longer term. This is why Hempel, the worldwide coatings manufacturer, has focused so much energy on developing hull coating solutions that deliver tangible efficiency gains that directly reduce fuel usage.
The correlation between hull coating and fuel use is, at its most basic, down to frictional resistance below the waterline. The reason for this is simple. Fouling on the hull of a vessel creates frictional resistance as algae, barnacles and invasive species accumulate on the ship’s hull over time. As the ship’s hull is the largest single surface capable of affecting vessel efficiency, the more biofouling that accumulates on a ship’s hull, the more frictional resistance slows the vessel — meaning more fuel is required to maintain a given speed. At its worst, fouling can increase engine power requirements by close to 20% over five years.
A SOLUTION TO OFFSET HIGHER OPERATING COSTS Hull coating solutions such as Hempel’s Mads Raun Bertelsen, Head of Marine Solutions, Hempel.
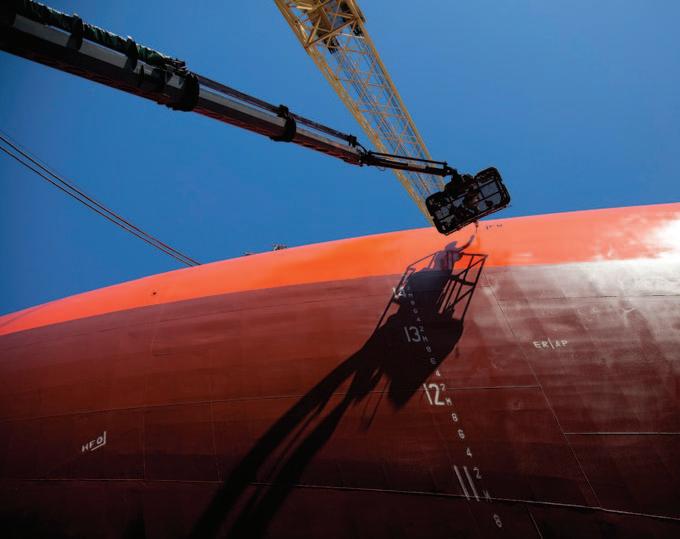
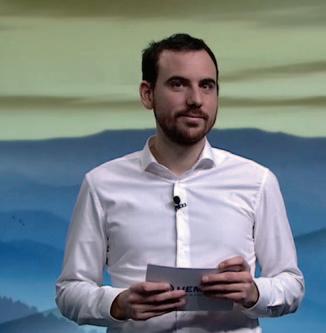
flagship coating Hempaguard X7 is a great example of a hull coating solution that offers significant fuel savings by reducing the build-up of biofouling. This innovative coating delivers 8% in fuel savings (compared with a market average) and a maximum speed loss of 1.4% across a fiveyear docking interval.
Hempaguard X7 is formulated with an activated silicone hydrogel which exhibits superior non-stick properties that repel organisms and effectively maintain a lower frictional resistance to aid the movement of the ship’s hull through the water. A biocide-activated hydrogel is formed on the surface of the silicone coating and as the biocide diffuses out of the film, it is trapped in the hydrogel layer . This increases its surface concentration and prolongs the time the biocide is retained at the surface of the coating – where it is most effective.
This means that considerably less biocide is needed compared with standard hull coatings, yet it is much more effective at preventing the settlement of biofouling organisms.
As a result, the Hempaguard X7 coating delivers unrivalled flexibility as it retains its effectiveness regardless of speed, water temperature and during idle periods (of up to 120 days). This is particularly beneficial for bulkers and tankers that frequently sit stationary at anchor or in port for extended periods, making them more susceptible to the build-up of biofouling. The coating solution is so effective that it has been selected as the coating of choice on more than 2,000 vessels since its launch, collectively reducing fuel consumption by a total 7.6 million tonnes.
That is an investment that will certainly help to alleviate the pressure on shipping supply chains in these most uncertain of times.
SHIPPING & TRANSPORT Lasting protection for scrubbers and outlets


Ecospeed application on scrubber pipe.
Over the last year the Ecospeed coating system was applied on the scrubber pipes, outlets and diffusers of over 30 vessels. This demonstrates that Ecospeed can be used for a wide range of other purposes. The result is a lasting, non-toxic protection against corrosion, cavitation and mechanical damage.
Because of the tight regulations on emissions in the shipping industry, the installation of an exhaust scrubber system has become increasingly widespread. This unfortunately has also led to an increase of corrosion damage on scrubber pipes and outlets which results in water ingress in the engine room, ballast tanks and cargo holds.
Ecospeed however is highly chemically resistant. Using the coating to protect the exterior outlets as well as the interiors of scrubbers will prevent corrosion damage and the resulting consequences.
Ecospeed fits in seamlessly with the environmental idea behind scrubber systems. It is a lasting, chemically resistant coating that will withstand the hazardous pollutants and protect the scrubbers for the lifetime of the vessel.
FIXING CORRODED PIPES If an existing scrubber suffers corrosion damage, it is not too late to fix it. Subsea Industries’ sister company Hydrex regularly replaces scrubber overboard pipes. This is done on-site without the ship needing to go to drydock.
In all cases the new pipes are protected with Ecospeed. If no welding work needs to be carried out in close proximity to the coated area, the new pipes are coated in advance. If this is not an option, Ecospeed is applied after the new pipe is installed.
Pipes can also be replaced preemptively. If a pipe starts to corrode, a leak is just a matter of time. By performing the replacement before the leak occurs, a costly, unscheduled repair can be avoided.
CONCLUSION Several benefits make Ecospeed the
Ecospeed application on scrubber outlet. perfect choice to protect scrubbers.
The coating system is highly chemically resistant. Taking into account the nature of the process taking place inside the scrubber, this is essential for our customers.
Ecospeed lasts the lifetime of a vessel. No repaints will need to be scheduled during future dockings of the ship. This saves time and money.
It is a true biocide-free solution. The coating is 100% toxin-free and there is no negative effect on the water quality or the marine environment at any point of its application or use. DCi