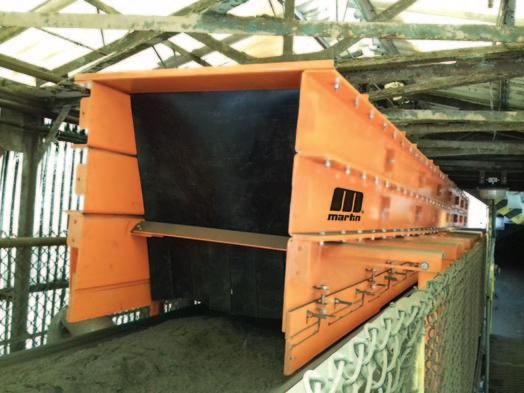
40 minute read
AT THE COAL FACE OF BULK OPERATIONS: COAL HANDLING TECHNOLOGIES CONTINUE TO DEVELOP
Copyright © 2022 Martin Engineering The modular system can be configured to fit the needs of the specific application. Copyright © 2022 Martin Engineering | The Modular Transfer Point Kit can be easily modified to adapt to changes in production.
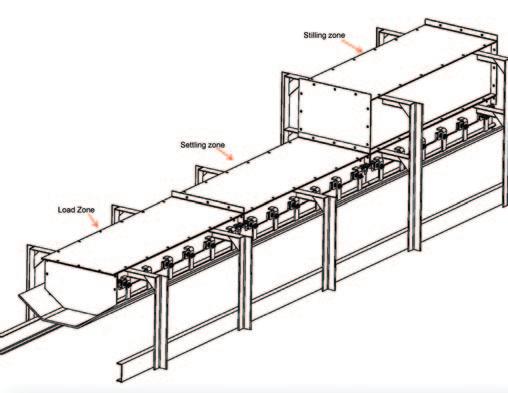
accommodate new belt support equipment or adapt to increases in production, the chute is often raised or lengthened.
The Transfer Point Kit addresses these problems, as chute sections are 1) delivered in a single crate with every component for assembly included, 2) able to be assembled prior to the shutdown and installation, saving time and money, and 3) fully modular, making future changes easy without expensive construction projects.
The transfer point system accommodates belt widths of 18-72 in. (450–1,800mm) and an internal chute width of 9-59 in. (228–1,498mm). Each modular section is either 4 feet (1.21 metres) or 6 ft. (1.82m) long and constructed of mild steel, 304 stainless steel or 316 stainless steel, with a thickness of 0.25in. (6.35mm), 0.5in. (12.7mm), or 0.75in (19.05mm) to accommodate a wide variety of materials and conditions.
The Transfer Point Kit installation is covered under the Absolutely No Excuses Guarantee as long as a Martin Engineering technician is involved in the installation process. Although assembly instructions are clear and easy to follow, another benefit of involving a factory-trained Martin expert is that customers who have ordered the kit have experienced a significant reduction in assembly and installation time. Moreover, once the system is started up and tested, there is a knowledgeable person on hand to offer advice on adjustments to ensure optimum performance.
“After installation, Martin Territory Managers or partner distributors are available to offer support,” Mueller added. “The feedback for the kit has been excellent. Customers get the heavy-duty Martin quality they’ve come to expect in a more convenient, efficient and sustainable package.”
Martin Engineering has been a global innovator in the bulk material handling industry for more than 75 years, developing new solutions to common problems and participating in industry organizations to improve safety and productivity. The company’s series of Foundations books is an internationally recognized resource for safety, maintenance and operations training — with more than 22,000 print copies in circulation around the world. The 500+ page reference books are available in several languages and have been downloaded thousands of times as free PDFs from the Martin website. Martin Engineering products, sales, service and training are available from 17 factoryowned facilities worldwide, with whollyowned business units in Australia, Brazil, China, Colombia, France, Germany, India, Indonesia, Italy, Mexico, Peru, Spain, South Africa, Turkey, the USA and UK. The firm employs more than 1,000 people, approximately 400 of whom hold advanced degrees.
Remote monitoring for conveyor belt cleaners launched in Europe, Middle East, Africa and South Asia
Global leader in bulk handling equipment solutions Martin Engineering has launched its innovative N2® remote monitoring system for conveyor belt cleaners in countries across Europe, Middle East, Africa and South Asia.
Designed for any belt cleaner using a polyurethane blade, the N2 Position Indicator (PI) system tracks belt cleaner performance and tells users when servicing is required via an intuitive cloud-based mobile app or desktop dashboard.
The N2 PI allows maintenance managers to keep on top of belt cleaner performance, eliminating needless Martin’s N2 PI attaches to the belt cleaner mainframe and feeds performance data to the gateway.

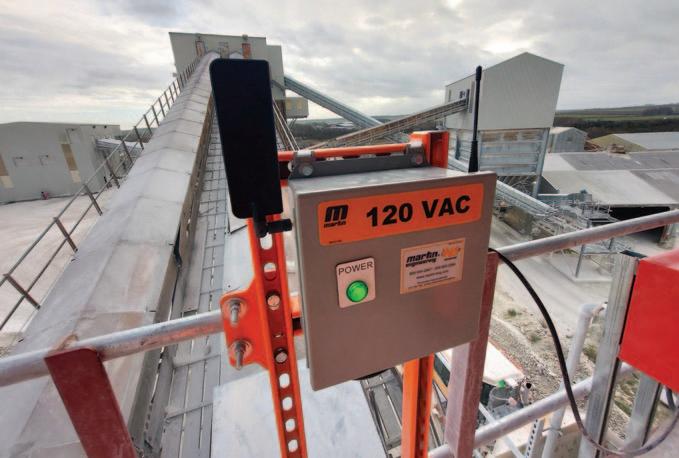
inspection visits, reducing human exposure to moving conveyors and helping to increase production uptime. The N2 PI recently met all the requirements to achieve CE Marking in Europe.
Robert Whetstone, Vice President for Martin Engineering’s EMEAI region, said: “Martin has a long track record for outstanding innovations that keep industrial processing plants running safely and efficiently. Our new N2 system is a game-changer that combines tried and tested technologies into one easy-to-use package so users can monitor their conveyor belt cleaners remotely.
“With this smart yet simple upgrade, the technology does the legwork, providing real-time data on each belt cleaner blade to give an early indication of when servicing is needed. In the meantime, plant managers can be confident that material carryback, spillage and build-up is being controlled by the belt cleaner so they can keep the plant running to maximize productivity.”
By tracking the individual performance and status of each belt cleaner, N2 PI delivers continuous, real-time feedback and eliminates guesswork. The detailed historic data also provides a maintenance log so service dates can be tracked and wear rates calculated. The result is an improved return on belt cleaner investments plus the ability to budget and forecast for essential replacement parts. Replacements can also be scheduled for just-in-time delivery helping users to better manage their inventory.
Development of the N2 PI has involved extensive technical research, as well as long-term customer trials at major material processing facilities in more than 10 countries worldwide. In the UK the system has been delivering results for more than 12 months at the country’s largest lime production plant, operated by Singleton Birch.
Stuart Howden, Engineering Manager at Singleton Birch, who has overseen the UK trials from the start, said: “Martin Engineering’s N2 Position Indicator is a clever system that eliminates the need for repeated visits to each conveyor belt – we will never need to go back to doing regular physical inspections of all our belt cleaners. With more than 90 conveyors across our production site, the ability to monitor our belt cleaner blades remotely is a massive advantage.
“Initial trials on six conveyors showed us that the N2 PI not only cuts inspection time, but it also helps reduce exposure to moving conveyors and associated hazards. The Martin app shows us when belt cleaner servicing is needed, and we can arrange inspections at the end of shifts or during planned stoppages, which decreases unscheduled downtime. The app also allows us to monitor blade performance over time and budget accordingly. We now have PI’s installed on 43 conveyors across our operation.”
The N2 PI can be retro-fitted to most conveyor belt cleaner mainframes that use polyurethane belt cleaner blades, or it can be introduced as part of a new installation. The battery-powered device feeds data about the performance and condition of conveyor belt cleaners to a central cellular ‘gateway’ unit. The gateway then sends the information to a cloud-based server, which delivers it to Martin’s dedicated mobile app and desktop dashboard on a computer.
The Position Indicator itself is a small, robust and self-contained device with a proprietary grade polyurethane housing that stands up to punishing industrial environments. The device can be mounted
The cellular gateway receives data from up to 200 N2 PI’s and sends it to a cloud-based server. up to 1,000 metres from the gateway, which is located on a high part of the plant to achieve the strongest signal. The system does not require a cellular link for each PI – connection is via radio frequency enabling as many as 1,000 PI’s to be monitored through a single gateway. Supporting Martin Engineering on the technology side are two trusted Amazon Web Services (AWS) ‘Internet of Things’ partners. The result is a fully automated, seamlessly integrated and secure cloud-based system that delivers super-reliable connectivity. Operating independently of any plant communications infrastructure, the low power requirements of the PI device give a projected battery life of at least two years. Only the gateway requires a constant power supply and work with a wide range of input voltages to match local standards in any country around the world. The Martin mobile app receives data from the cloud and The PI system works by presents it in a user friendly format. recognising how much rotation of the belt cleaner mainframe is acceptable before tensioner adjustment is required. The mobile app tracks and displays blade status, remaining life, next scheduled tensioning, run time, wear rate, cleaner model, blade type and other details. Alerts are provided automatically when a blade change is required, retensioning is needed or an unusual condition or change is detected. By relying on actual operating conditions instead of human judgement to monitor blade wear and tension for optimal cleaning performance, the PI maximizes the cleaner blade’s usable surface area and reports with certainty when a blade is nearing the end of its useful life.
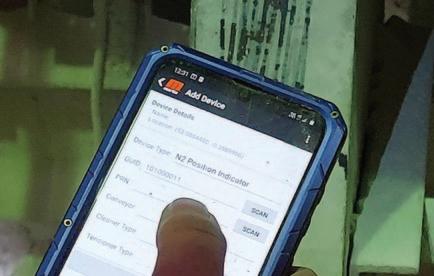
CONVIR is a company located in Kaunas, Lithuania. The company‘s team of professionals has been in the material handling business for a long time, and offers about 17 years of experience in this field. It can help customers with all their bulk handling needs. Here, CONVIR explains why it is important to maintain belt conveyors in bulk handling systems and how to carry out this maintenance.
FROM THE EXTRACTION OF THE RAW MATERIAL TO THE LOADING Reliable conveyor systems assist bulk materials handling from the moment the first stone cracks underground. As a manufacturer and system partner, CONVIR creates full solutions for moving raw materials on their path to being treated further. v Long distance belt conveyor: bulk goods are transported on overland belt conveyors through inaccessible terrain along meandering paths of up to 25 kilometres. The rocks hurtle along the conveyor belts at a fast pace, which corresponds to fast cycling. In addition, the conveyor systems can carry 15,000 tonnes of bulk material each hour. It is about 200 times as heavy as The Space Shuttle. CONVIR is constantly improving its bulk material handling performance, using its many years of experience, data from existing conveyor systems, and internal research and development. v Medium and short-distance

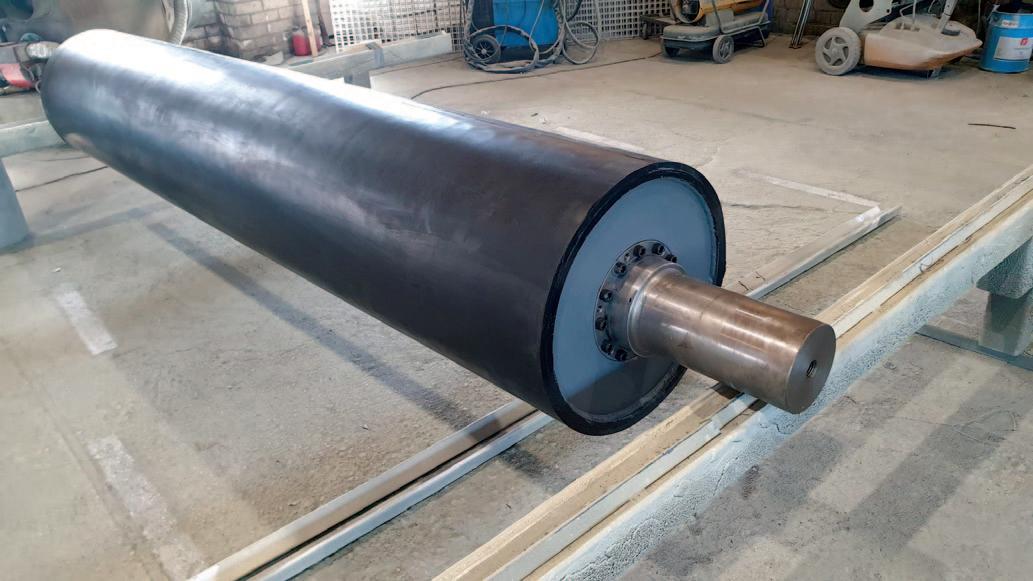
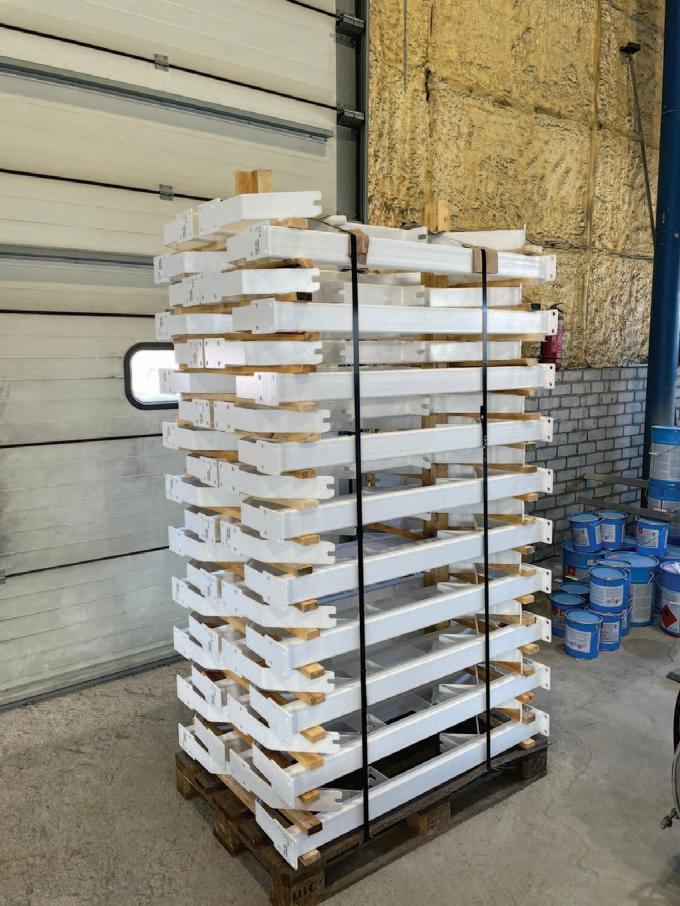
v conveyor systems: mobile belt conveyors, also known as movable belt conveyors, can adapt to the transport distance needs in quarries or other environments at any time by adding or removing them. They are also known as grasshopper conveyors or jump conveyors. Heap and discharge belts, as well as discharge conveyors, are other types of bulk material conveyors. CONVIR creates customized full solutions for its customers’ bulk items. From material receipt through loading, the whole solution can be customized. Other types of conveyors may be used in bulk handling systems, such as telescopic, radial, stacker, truck unloading, shiploading and stockpiling conveyors.
THE ROLE OF THE BELT CONVEYOR IN BULK MATERIAL HANDLING SYSTEMS A belt conveyor is designed for continuous operation and can be utilized in a wide range of capacities and distances, with lengths ranging from a few metres to tens of kilometres. The belt loops around a pulley at each end of the conveyor. This is the most frequent type of belt conveyor. To move the belt and carry the materials, one pulley (often at the conveyor head) is attached to a drive unit. Other designs are available, such as conveyors with three or more pulleys or those with two or more drive pulleys. They are, nevertheless, typically used in specialized applications.
The belt is an essential element of belt conveyors because it serves two functions: it contains transported materials and it transmits force (in the form of tension) to convey the load. The belt is also one of the more expensive components of a belt conveyor. Many considerations, including the materials to be handled, corrosion, impact, tension, strength, and elongation, should be taken into account while making a cautious selection.
CONVIR's equipment offers an efficient and reliable material handling solution. The company produces customized belt, screw and scraper conveyor systems for transporting bulk products and sorted waste. The main industries it works in are: ports & terminals, quarries, recycling, agriculture, wood & paper, mining & metallurgy and more.
BELT CONVEYOR MAINTENANCE FOR BULK MATERIAL HANDLING The primary belt conveyor components, such as idlers, rollers, pulleys, bearings, shafts, and belts, must work under dynamic loads and extreme conditions in order to retain reliability. As a result, if they are badly designed or produced, they can fail frequently. Rolling element bearings are frequently used in various types of equipment and can have a limited life, even as little as a few months, if subjected to dynamic or unexpected stresses that are not acceptable for their design.
Belts can also be damaged or destroyed when subjected to loads that are not adequate for their design; when exposed to corrosion; or when used in situations that are not appropriate for their material. Many other elements must be addressed in conveyor belt design, operation, and reliability. Dust and pollutants, for example, are frequently prevalent in processing areas. This equipment may be harmed and ruined if better seals are not used for bearings and other components. On the other hand, if all of these components are properly designed and selected, they can operate without issue for many years.
To extend the life of several components such as idlers and rollers, appropriate accessories should be used to clean the belt at the feed and discharge points. Belt cleaners play critical roles in the reliability, safety, and overall environmental conditions of a belt conveyor and its associated facilities.
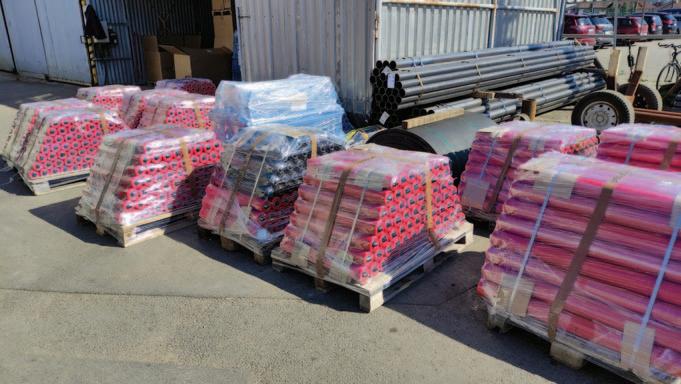
Idlers from Kinder Australia: fundamental to conveyor function
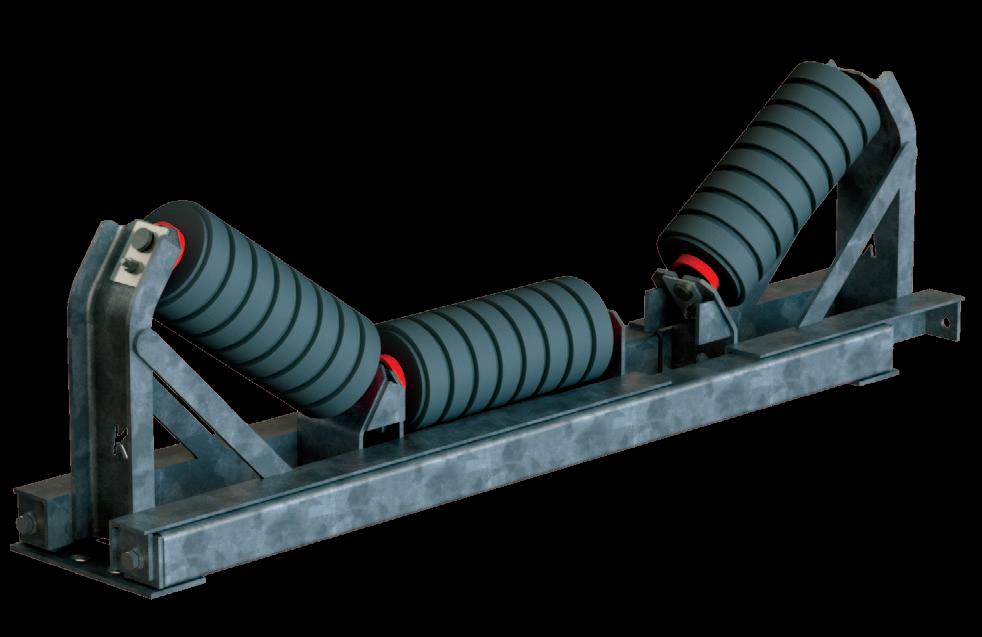
A fundamental component of the conveyor system are the idler frames. These are quite literally the backbone of the conveyor. If they are not well profiled and positioned, the belt is at increased risk of misalignment. Misalignment can lead to uneven wear and damage to the conveyor belt itself, or disastrous material spillage. It’s a costly productivity issue to have — and it often stems from poor frame set-up.
Kinder Australia’s applications and engineering team are able to assist with proactive site analysis and audits. They can check your site’s framework from all angles to ensure that it is level and square, whilst advising whether your conveyor is at risk of misalignment. The team can recommend the ideal idler frame to fit, to providing an optimal and supported conveyor.
The idler frame range at Kinder Australia is as follows: v Adjustable Conveyor Trough Frame (Inline); v Adjustable Conveyor Trough Frame (Offset); v K-Commander Tracking Frame; v K-Ergo Swift Return Idler Frame; K-HD Retractable Impact Frame;
v v v
v K-Retractable Idler/Impact Frame; K-Shield Dynamax Impact Idler Frame; and K-Vee Return Idler Frame.
The expanding selection of idler frames at Kinder Australia covers a wide range of applications depending on what the conveyor requires to operate efficiently.
Adjustable conveyor trough frames can be installed at the head and/or tail transition zones of all types of conveyors. They replace the need to have an already predetermined mounting/feet hole pitch and/or position, whilst using fixed angle transition frames. They are available as both Inline and Offset configuration.
Designed by the engineers at Kinder Australia, the K-Retractable Idler/Impact Frame and K-HD Retractable Impact Frame allows conveyor rollers to be changed under conveyor transfer loading chutes without the idler frames being laid down or removed.
The bottom bracket remains aligned whilst the upper bracket of the base is retracted exiting from the side. The KRetractable Idler/Impact Frames range cover all belt widths and trough angles, inline or offset configurations, and are suitable for all bulk material handling applications.
The K-HD Retractable Impact Frames are applicable for high-capacity bulk materials handling industries, including the toughest quarrying/mining applications.
Kinder’s K-Ergo Swift Return Idler Frame makes roller change outs quick and seamless, with access to only one side of the conveyor required. The specialized flip down design eliminates the need for belt jacks as the belt does not need to be raised out of the way to lower the frame. Safe and easy to use, the K-Ergo Swift Return Idler Frame is ideal for conveyors which have maintenance access from one side and can be custom built to suit a range of belt widths.
Kinder Australia offers a wide variety of idler frames that will continue to provide ample alignment for conveyors, and the specialists at Kinder Australia can determine the best option for any application.

REMA TIP TOP specializes in the consistent optimization of production plant operational readiness. In over 50 years of research and development work, the company has continuously improved production and application possibilities in co-operation with its customers.
The use of specific REMA TIP TOP products lengthens the service life of conveying and processing plant and reduces downtime. Special products optimize operational readiness, increase production capacities and thus increase profit for the plant operator.
REMA TIP TOP offers particular expertise in wear protection, mineral processing, conveying solutions and Dunlop conveyor belts.
CONVEYING SOLUTIONS REMA TIP TOP conveying solutions and technologies ensure smooth production processes and decisively increase the life expectancy and economic efficiency of conveyor belt systems.
They are used to repair and link up conveyor belts used in both cold and hot processes as well as for belt cleaning and the provision of sidewalls and drum and roller coverings. The portfolio is completed by a specific service programme that matches the individual need and makes REMA TIP TOP a global and dependable partner for all questions concerning conveyor belt operation.
HIGH-PERFORMANCE CONVEYOR BELTS With the conveyor belts being produced at DUNLOP Belting Products to the high REMA TIP TOP quality criteria, the company is in the position to supply such belts to any continent in the world.
DUNLOP Belting Products South Africa manufactures innovative high-performance conveyor belts that meet or even exceed all established international standards. The headquarters of the company is located in Benoni (Gauteng), while the company has a second manufacturing facility in Howick, in the heart of Kwa Zulu Natal. In this tradition-rich location, which was already known for its rubber production by 1919, rubber compounds for a wide range of industrial rubber goods are manufactured in addition to conveyor belts, as are industrial hoses, materials for mill cladding and other products for the material processing sector.
360° service from REMA TIP TOP (all pictures ©REMA TIP TOP).
360° SERVICE TO ENSURE RELIABLE CONVEYOR OPERATIONS
REMA TIP TOP INTEGRATES PROJECT & MAINTENANCE FOR BETTER RESULTS In mining, food and any other raw materials processing industry, continuous operations are essential to deliver sustainable performance and avoid financial losses. To ensure reliable operations, the entire lifecycle of transportation systems, from design to continued operation, maintenance and services must be planned and implemented in an integrated manner and ideally delivered by an experienced and quality-assured service provider.
REMA TIP TOP supports its customers with proven experience, know-how and a worldwide service network to successfully manage the entire lifecycle of their conveyor systems.
Mario Delmaestro, R&D and Service Manager REMA TIP TOP Middle East, explains how REMA TIP TOP’s 360° service not only helps its clients to increase the reliability of transport equipment but also to achieve the expected results of their projects, such as higher operational capacity, better maintainability, greater physical availability, etc. Q: Mr. Delmaestro, what are the challenges when planning a conveyor project? A: From many years of experience and countless projects, we know that in many cases the reliability and operation of facilities are not considered sufficiently or at all in the development phase, which can lead to problems later in operation. Regardless of whether a new conveyor system is being built (green field) or an existing system is being modified (brown field), project development and maintenance should be planned and implemented in an integrated way throughout the entire life cycle. If the two areas diverge, for example because the project does not take subsequent maintenance into account, problems can arise and compromise smooth operations. That’s why at REMA TIP TOP we take a more
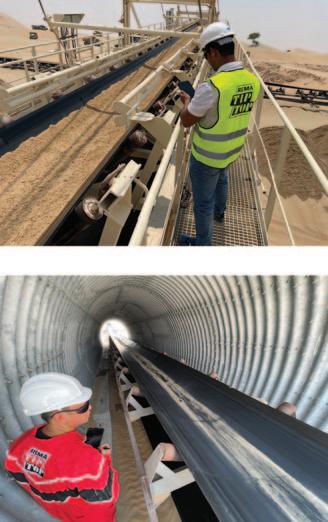
Mario Delmaestro.
holistic approach, analysing all the factors that influence not only the technical development phase, but also the years in which the new equipment will be in operation. Q: What solutions and services does REMA
TIP TOP offer its customers? A: REMA TIP TOP offers services covering all phases, starting with the identification and collection of asset data, establishing a maintenance and failure history, as well as risk and technical analysis, including development calculations, material specifications and their applications, up to training and operational qualification, in order to achieve the results expected by the customer. In this way, REMA
TIPTOP offers a 360° service, ranging from problem analysis and customer requirement to continuous monitoring, using an extensive portfolio of maintenance and monitoring services providing us with reliable data on the equipment and measures to guarantee the best results. All these services are provided by professionals who have many years of experience in these fields and have completed numerous successful projects, guaranteeing the best and most efficient service for our clients. Moreover, at REMA TIPTOP we believe that the best way to make a project successful is to involve the customer at all stages. Through the exchange of knowledge and experience and in-depth discussions, customer involvement becomes the cornerstone for achieving superior results. Mutual partnership with its customers coupled with extensive know-how and experience distinguishes REMA TIPTOP from other suppliers.
Q: What added value does REMA TIP TOP offer its customers? Q: First of all, it should be mentioned that
REMA TIP TOP is a partner that not only provides the engineering, but also has several decades of experience to ensure the best transition and delivery of projects in terms of maintenance, which guarantees a complete delivery from a maintenance and operational point of view. Secondly, with its 360° service concept, REMA TIP TOP is able to provide all the necessary services in terms of design and maintenance of the highest quality and, last but not least, we offer the possibility of continuous monitoring of the equipment, using all the technical data provided by our monitoring systems for an effective strategy to monitor and control the equipment during its operation. The bottom line is that our 360° service is much more than the sum of its parts.
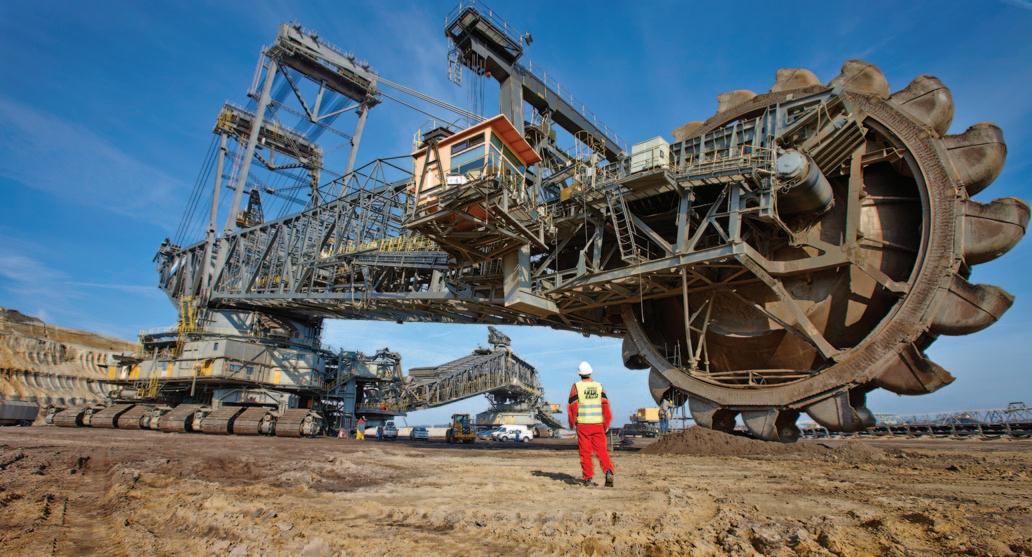
Maintenance of conveying systems.
HOW TO MASTER PLANT MAINTENANCE SHUTDOWNS
REMA TIP TOPS SOLUTIONS AND SERVICES FOR SCHEDULED SHUTDOWNS In construction, mining, and any other industry processing raw materials, seamless operations are essential to deliver sustainable performance and avoid financial losses. Smart systems and services help prevent or detect irregularities and perform efficient maintenance during operation. REMA TIP TOP offers a wide range of wear-resistant products, repair materials, surface protection solutions and services for raw material extraction and processing. Providing a broad range of services, such as inspections, maintenance support, system upgrades, and shutdown and asset management services, REMA TIP TOP also supports its clients with proven experience, know-how and a global service network in planning and managing

scheduled shutdowns for plant maintenance.
Mohamed Saffour, General Manager REMA TIP TOP Middle East, on how to plan and execute scheduled shut-downs successfully. Q: Mr. Saffour, what are the challenges when executing scheduled shutdowns? A: Every day a plant is down for maintenance costs a business time and money. That’s why it is essential to plan scheduled shutdowns in order to keep the downtime as short as possible.
Shutdowns are highly complex and require specialized planning and efficient execution. The duration of a shutdown depends on various variables: what work needs to be done? What parts need to be serviced, which ones need to be sourced and replaced? The challenge is to have a clear idea and action plan of the project beforehand to avoid unexpected events leading to huge costs. Q: What solutions and services does REMA
TIP TOP offer its customers? A: REMA TIP TOP supports its customers along their entire business value chain from planning and implementation to operation and beyond. To ensure smooth operations, we offer our customers services for predictive maintenance and scheduled shutdowns, backed by our know-how and experience from countless service projects worldwide. As supervisors, our experts help properly plan and control maintenance projects and guide serviceteams, but also can manage the shutdown activities with our global service network. Q: What is the added value of involving REMA
TIP TOP in scheduled shutdowns? A: We help our clients to minimize the risk of unforeseen downtime and gain more planning reliability and control through regularly scheduled shutdowns and preventive maintenance plans even during operation. With our experience, expertise and proven methods in planning and project management, as well as tailored technical solutions, we successfully reduce downtime — in one project, we were able to significantly reduce the shutdown by using specialized engineered equipment speeding up the belt replacement drastically. Our customers save significantly more than they invest in our support, and the proven time savings are remarkable. What more could you ask for?
ANCILLARY BELT CONVEYOR SOLUTIONS REMA TIP TOP is renowned for its belt repair service, which offers efficient repair, and fast and reliable results. Its REMAREP ULTRA 10, for example, is marketed as ‘The Industry’s Fastest Belt Repair’. The REMAREP ULTRA 10 in a red version is ideal for minor repairs. The new REMAREP ULTRA 10 ‘Black’ can fix even major damage.
The two-component repair paste REMAREP ULTRA 10 ‘Black’ made of solvent-free PU in the new cartridge size helps to significantly reduce repair time, especially for major damage to conveyor belts as well as to PU, PVC and elastomer components.
With the new product, REMA TIP TOP is responding to the high demand from customers who are already successfully using the red 210ml cartridges and require an equally reliable solution for larger conveyor belt repairs. Accordingly, the new black repair paste is available in larger units of 1,500ml per cartridge. A battery gun is used for easy and efficient application.
Like REMAREP ULTRA 10 for minor repairs, the new repair system for major defects offers exceptionally fast curing: at 24° Celsius, the hardness averages 65 Shore A after 15 minutes, and a repaired conveyor belt can be loaded after 60 minutes.
REMAREP ULTRA 10 ‘Black’ offers similar wear properties as the original belt material and is resistant to UV radiation, oil and diesel fuel. The main applications of the repair compound are in conveyor belt repair, for example in case of damage to cover plates and longitudinal cracks in the conveyor belt, and in sealing punctures on belts.
In addition to the repair of conveyor belts, the REMAREP ULTRA 10 repair material is particularly suitable for filling joints in rubber linings and for cosmetic repairs to PU, PVC and elastomer components. The repair can be done either by trained REMA-TIP-TOP service personnel or by qualified personnel at the plant operator’s site.
REMA TIP TOP also offers a full range of belt bonding systems.
Other conveyor related services include: v REMATRACK: belt tracking systems v REMACLEAN: belt cleaning systems v REMA CCUBE: Cloud-based service management v REMA MCUBE: belt monitoring system v REMA PERFORMANCE: pulley lagging solutions — REMA
PERFORMANCEgrip 70/CN; REMA
PERFORMANCEgrip 70/CN-SL; and
REMA PERFORMANCEline 70/CN v FEEDING SYSTEMS: low-friction impact bars — REMASLIDE and
UNISLIDE v SKIRTING SYSTEMS: skirting rubber —
REMASKIRT and UNISKIRT v CONVEYOR BELTS: DBP conveyor belting and EP fabric conveyor belts.
MCube fixed installation.
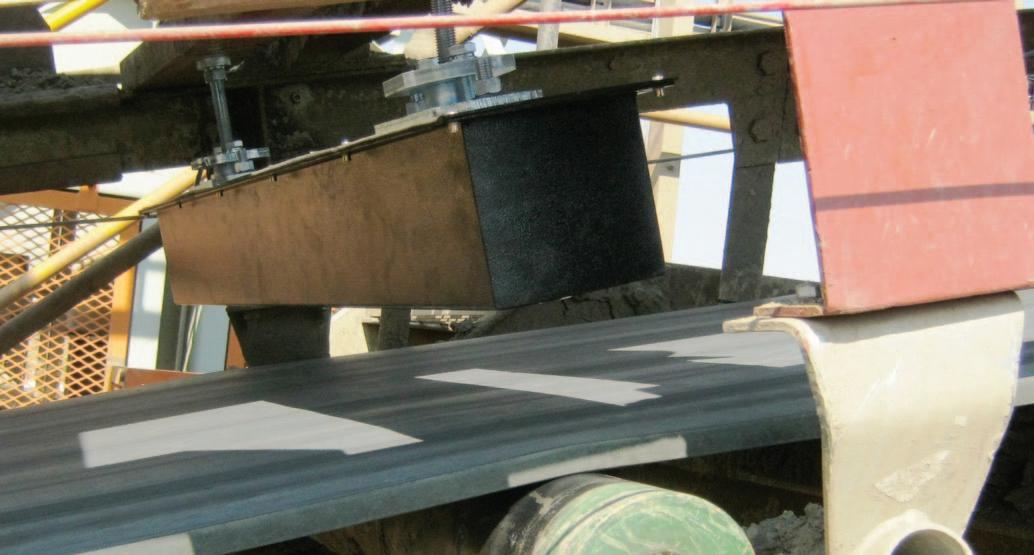
At the coal face of bulk operations
coal handling technologies and systems continue to develop
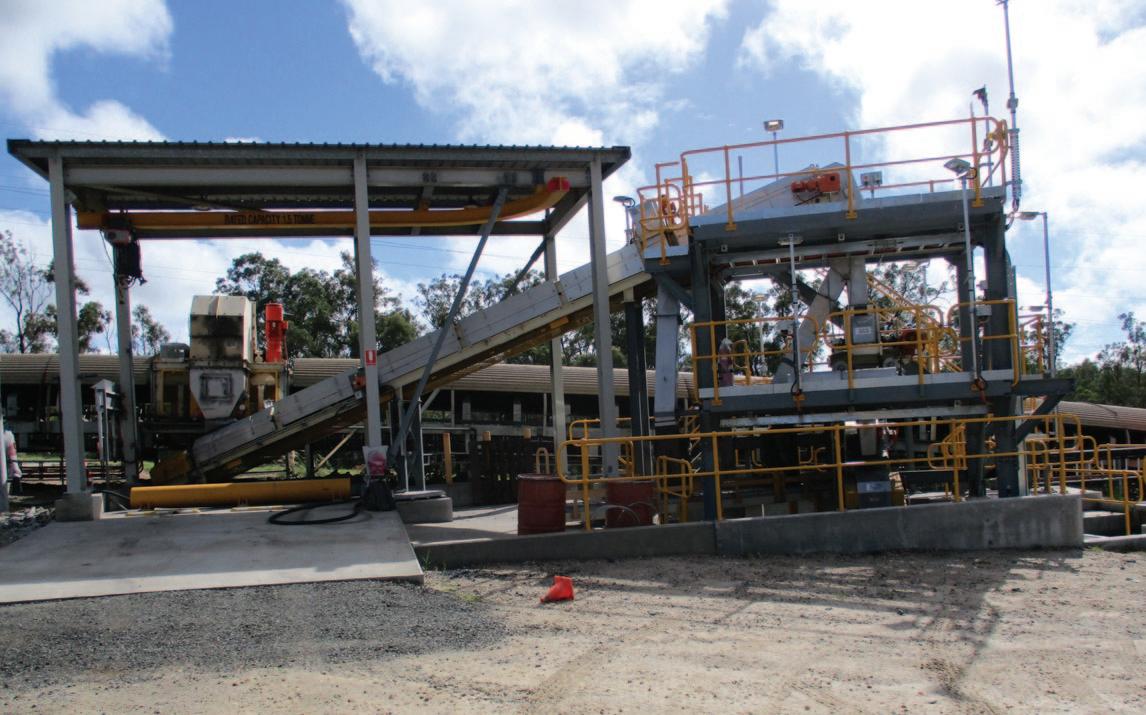
The what, why, and how of coal mechanical sampling systems
Sampling plays a pivotal role when trading coal in bulk, both for the buyer and the seller, write Gangadhar Udnur, Head Mechanical Sampling System at SGS India and Sasho Atanasovski, Business Manager at SGS Australia. It reveals the cargo’s quality, which helps the two parties determine a fair price. By understanding coal quality, buyers and sellers can eliminate penalties and maximize profits — but it’s crucial to get the sampling process right.
It’s commonly accepted among most sampling industry experts that incorrect coal sampling causes 80% of all errors in test results, while mistakes in the analysis and preparation stages are responsible for the remaining 20%. Therefore, organizations must follow the latest sampling best practices and methods. This will ensure they obtain unbiased samples that are representative of the material being sampled. In other words, the samples must provide a realistic picture of the cargo.
COAL SAMPLING: CHALLENGES AND KEY CONSIDERATIONS Coal is a difficult material to sample due to the inherent heterogeneity within its inorganic and organic constituents. It can also be widely variable with respect to size and chemical composition, varying in moisture, ash, sulphur content and its heating value.
The sampling and laboratory analysis processes provide valid estimates of the desired quality parameters. However, there are some uncertainties associated with each such estimate. For example, the minimum mass of the gross sample should be sufficient to ensure that extraneous mineral and coal particles appear in the

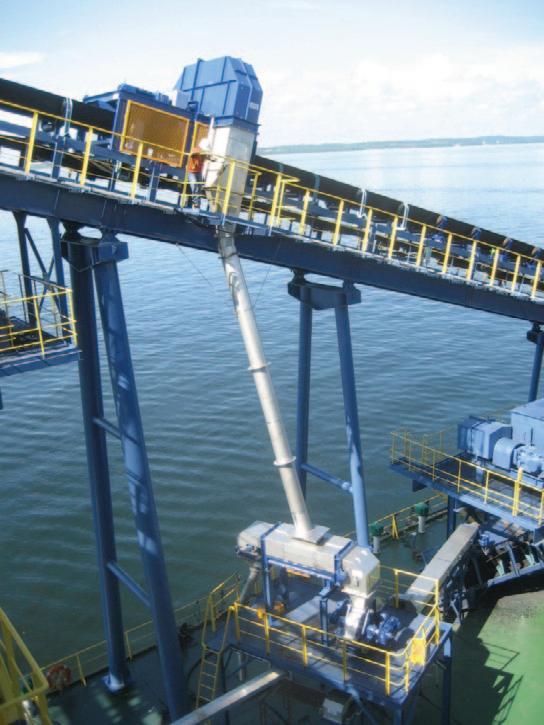
sample in the same proportions as in the lot from which the sample was collected. Attention must also be given to sample flows through the system so as to minimize the potential for sample moisture losses.
WHAT IS A MECHANICAL SAMPLING SYSTEM (MSS)?
Coal samples have traditionally been collected manually, but these methods lead to results that are not representative of the entire lot. What’s more, there is the potential for bias due to regular human intervention at various stages throughout the sampling process.
Biased sampling methods lead to inaccurate valuations of your coal shipment — either overvaluing or undervaluing it. In either of these cases, the transaction will be unfair to one party.
MSS addresses this potential issue. It provides accurate, representative and unbiased sampling to ensure the quality of the bulk cargo, offering a host of advantages over other sampling techniques. These include more efficient operations, minimal risk, reliable results and the possibility of customization according to the site and the material being sampled.
HOW DOES MSS WORK? MSS uses an automated process for collecting representative samples from a conveyor belt, falling stream or fixed point, truck or rail car.
It systematically removes a portion of the material stream for a representative sample, with a well-operated and closely monitored system consistently providing accurate, quality data.
MSS can be expensive to purchase, install and maintain. However, the increased reliability and precision is well worth the cost — especially if organizations handle large quantities of coal cargo. When using MSS, businesses must also establish an ongoing quality assurance program, including monitoring the coal sampling ratio. The system should also be periodically bias-tested to ensure bias-free performance.
MSS can also incorporate online analyzers for moisture, ash and elemental analysis to provide real-time data on the quality of the commodity being sampled. In addition, it may also be used to allow online particle analysis.
WHY MSS IS TOO GOOD TO IGNORE MSS optimizes the coal sampling process, providing a range of tangible benefits.
Consider that employees can operate and supervise MSS remotely. By no longer conducting manual sampling on conveyor belts, organizations will notably reduce the risk of injuries amongst their personnel.
Furthermore, MSS provides effective probability sampling and eliminates bias. Organizations can access all the material being tested and particles won’t be rejected owing to their size.
Sample increments are properly delineated, meaning bias and precision can be measured. In short, MSS is consistent, accurate and error-free.
Last, MSS reduces the risk of penalties and optimizes process plant efficiency. It’s worth noting it also reduces the manpower and time required for sampling and sample preparation, helping to reduce costs.
MSS EXPERTISE FROM SGS With over 35 years’ experience designing, installing and commissioning clientdedicated, site-specific MSS, SGS keeps continually re-engineering its cross-belt samplers, auger samplers, updating and improving the design to supply superior yet cost-effective systems. There are over 500 SGS-designed systems operating in more than 20 countries worldwide.
SGS is synonymous with the highest levels of integrity, independence, impartiality and accuracy. Its services and industrial expertise help its customers improve their operational efficiencies while its global technical leadership helps minimize operational and financial risk. Whether customers need MSS, sampling, inspection or testing services, SGS staff provides outstanding experience and value to help maximize potential.

ENGINEERING & EQUIPMENT Host installs two E-Cranes at United Bulk Terminals, Davant

In 2019, Host acquired United Bulk Terminals on the Mississippi River in Davant, LA. UBT is one of the largest bulk terminals in the US Gulf region, with substantial loading, unloading, and storage abilities. Since Host acquired UBT, it has invested in lots of new technology and equipment to improve the facility. One of the improvements is the arrival of two E-Cranes.
The first E-Crane purchased by Host was a 2000C Series/Model EC13382 with 38.2m (125’) of outreach and 20t (22T) capacity. This E-Crane is equipped with a 16m3 (21yd3) clamshell bucket for handling coal. The E-Crane is barge mounted and has the capability to load and unload both barges and ships.
The E-Crane began successfully operating last November and loads about 10,000 tonnes per day, a 15% increase from previous production.
After the successful operation of its first E-Crane, Host decided to acquire a second machine shortly after. Host recently purchased a refurbished 2000C Series/Model EC15317 E-Crane with 31.7m (104’) of outreach and 24t (26.4T) capacity. This E-Crane is also barge mounted, with the capability to perform midstream transfer barge-to-ship operations. This E-Crane is equipped with a 17.6m3 (23yd3) clamshell bucket. This E-Crane became was commissioned and became fully operational in April 2022.
Both E-Cranes are mounted on floating barges, meaning that they can easily relocate to do different jobs. Both floating terminals are also used at Host’s Avondale shipyard as well as at the Davant facility for various operations.
Host purchased six different attachments for the E-Cranes allowing for the successful transloading of multiple aggregates, coal, coke, and urea.
2000C Series/Model EC13382 barge-mounted E-Crane.
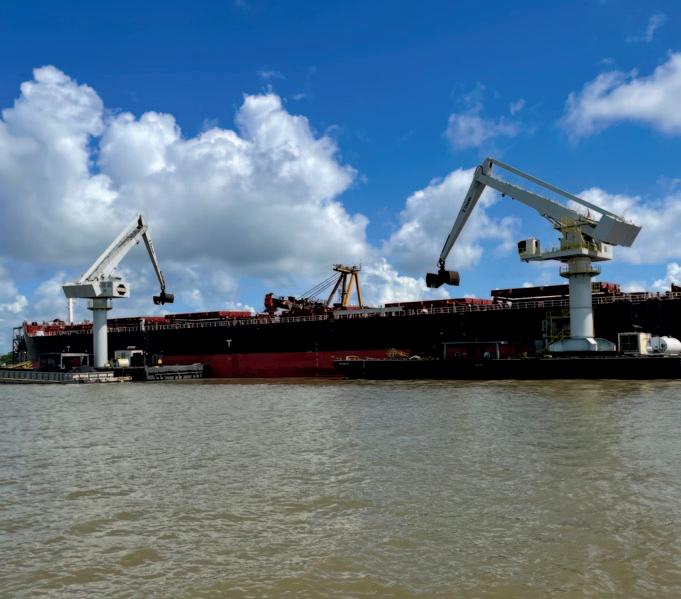
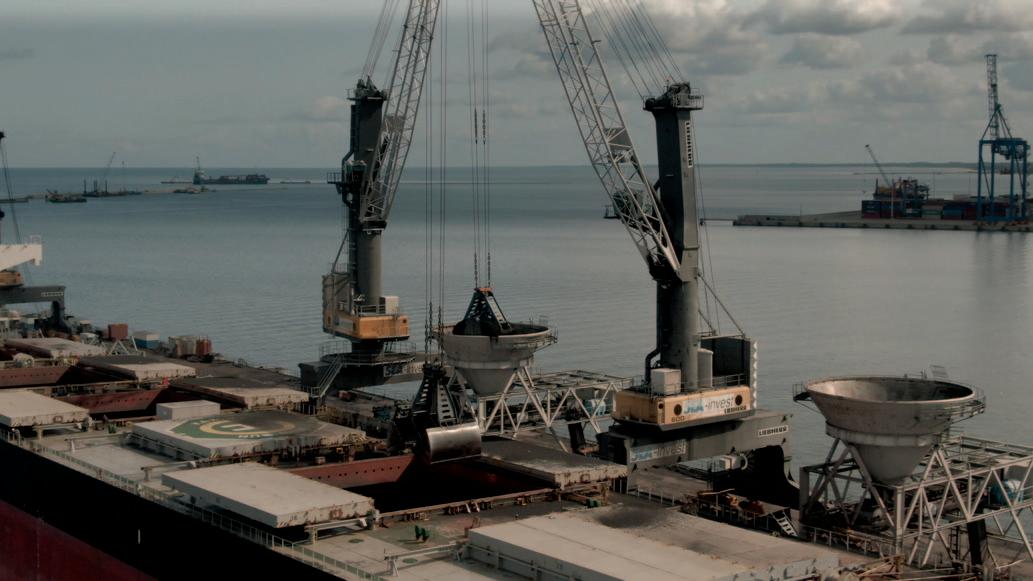
Nemag is a family business from the Netherlands, founded in 1924. It specializes in grabs, as well as its Rope Pear Socket and Quick Release Link.
Ever since its foundation, Nemag has believed strongly in the power of innovation to increase the efficiency of customers’ bulk handling operation. This belief has won the company countless industry and non-industry awards. It also made Nemag the preferred partner of many dry bulk handling organizations around the world.
Nemag helps its partners with a full range of four-rope operated mechanical grabs. Coal is just one of the many cargoes that can be loaded and unloaded by Nemag’s grabs — the others include iron ore, wheat, scrap metals, minerals, clinker, biomass or other dry bulk goods. Together with its high quality rope connections systems, Nemag always has a productive solution to meet its customers’ needs.
To meet the specific requirements of its customers, Nemag has developed a range of dry bulk grabs. Each grab has its own advantages for specific applications. Increased production, low operational costs, enhanced safety, environmentally friendliness and reduction of the use of trimming equipment have been taken into consideration when developing all grab solutions.
For the coal industry, Nemag offers grabs which could be equipped with environmental protections to prevent dust or material falling off the grab whilst travelling.
To stay competitive in the market, Nemag is constantly working on the technological development of its products.
In close co-operation with leading bulk terminal operators, crane manufacturers, technical universities and other stakeholders in the industry, Nemag continues to develop new products for the dry bulk industry. The aim is always to reduce handling costs per tonne of dry bulk materials transferred.
The latest software technology like 3D CAD, Multi Body Dynamics (MBD), Discrete Elements Methods (DEM) and Finite Elements Methods (FEM) support Nemag’s team of designers in optimizing its grabs. High tensile steels, wear-resistant steels and advanced bearing technology enables the company to design extremely productive, light weight and durable grab mechanisms.
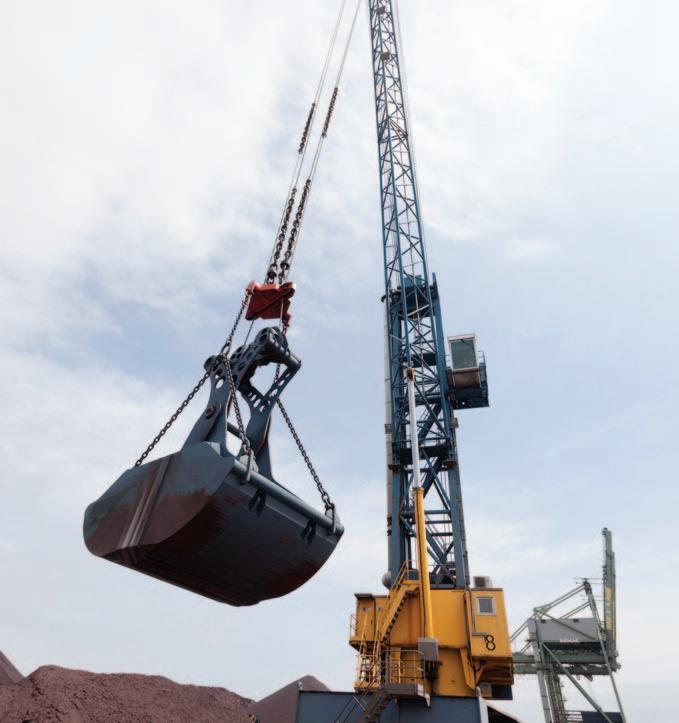
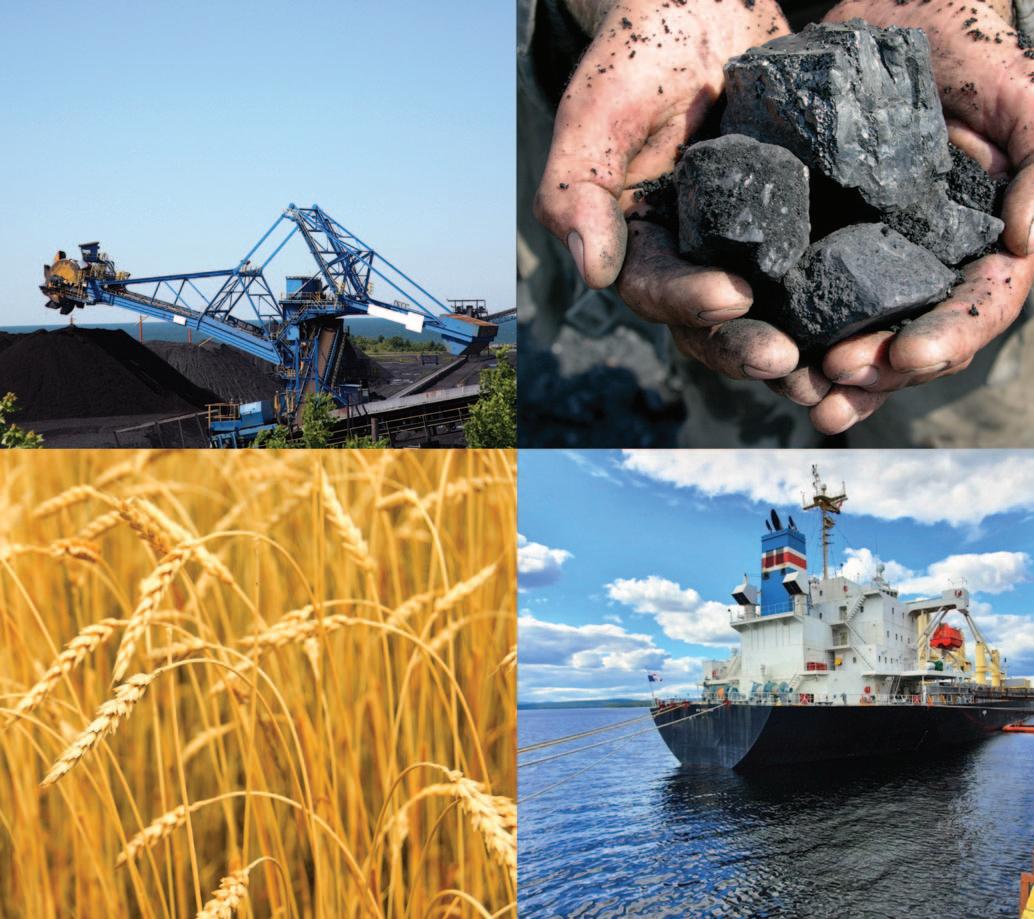
PSB Inspection was established by Peter Bagchus, CEO and owner, in 2017. Since that time, the company has grown organically and is now financially healthy and very successful.
The company operates from its head office in Vlaardingen (Rotterdam port area). It has highly qualified and experienced senior surveyors and an experienced sampling preparation team. PSB Inspection runs its own laboratory with highly qualified and experienced laboratory technicians which is all managed by the operational team in close conjunction with the management team members, who have been active in this type of business for decades.
Currently, PSB Inspection focuses primarily on coal and coal-related products. However, bearing in mind that the world — and the energy market — is changing vastly and rapidly, it is also working hard to expand into markets such as biomass, alternative fuels, minerals, metals, slag, flyash and fertilizer, which are under development in different phases.
This all takes place with a clear eye on high quality services in the field of inspection, sampling, sample preparation, analytical services and weight ascertain ment required by PSB Inspection’s customer base. Recently, the company expanded its service portfolio with gas/toxin measurement (four qualified and certified gas/toxin measure ment experts including high quality, certified equipment (ISO 9001). More expansion is in the planning.
Other than Europe, PSB Inspection can offer its services in various other countries (South Africa, Turkey, UK, Latin America) as well and expanding its country portfolio. All is being coordinated from its head office, obviously under the applicable ISO standards 9001 and 17025. Certifications to 17020 and GAFTA are on the way.
It is not only PSB Inspection’s business — but the whole world — that is affected by the horrific situation in Ukraine/Russia. It is a given that the coal market is being significantly affected. The Russian Federation supplies the market with a high volume of coal; as of mid-August this year, a ban on exporting to the rest of Europe will be in force. As the world wants and needs energy in the widest sense of the word — and because renewables cannot completely replace coal, but remain merely part of the energy mix — finding alternative supplies is at the top of the agenda. For example, South Africa is one of the countries that will take up the slack, as well as Colombia and the USA — regardless of the difference in quality parameters. Diversification is fully under way and a new market structure is becoming ever more visible.
The global market is shifting and changing significantly — and reliable sources suggest that this change may be permanent.
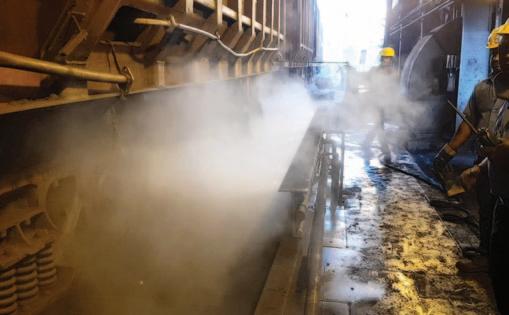
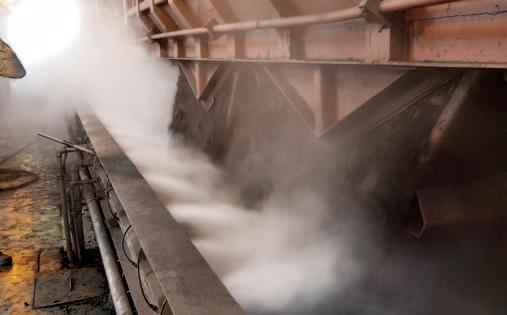
For the last few decades, the world had been trying to reduce greenhouse emissions in order to limit the effects of climate change, writes Gonzalo Campos Canessa, CEO, The Raring Corporation. To achieve that goal, plans on decarbonizing the economy and transportation, moving into cleaner energy sources, and incentivizing renewable energy are just some of the strategies that the Paris Agreement (2015) adopted to limit global warming below 2°C above the preindustrial temperatures. Within this greener world, the energy source that suffered the most was coal; it is seen by most as a dirty fuel, and rich economies understood that stepping away from it will help them meet the environmental targets faster. In the rich world, there has been a consequent steep reduction for coal demand and a decrease in infrastructure investments.
On February 2022, after the Russian invasion of Ukraine, this world scenario dramatically changed. The world’s dependence on Russian oil and gas has forced the developed world, especially the European Union, to find alternatives to reduce their dependence on Russian energy sources. The obvious alternative would have been to replace Russian fossil fuels with oil produced by NATO (North Atlantic Treaty Organization) allies. However, ramping up production to fully replace Russia will take years and require intensive investment in infrastructure. Reviving coal-fired power plants seems to be a way to immediately start reducing dependence on Russian energy resources.
Increasing demand for coal means increasing coal handling procedures, the environmental effects of which can be mitigated using different technologies and strategies.
Let’s start with mining the coal. During the boom of the PRB Coal from the Powder River Basin in the USA in the early2000s, the Raring Corp (TRC) designed, manufactured, installed, commissioned and maintained dust suppression systems at transfer points, truck dumps, crushers, screens and trucks/Rail load-outs. TRC solved dust issues in all those applications. Similar solutions and dust control strategies have been successfully implemented in other industries like hard rock mining. The stockpiles, which are normally exposed to winds, and which are normally located close to rivers and seashores, are a large contributor to fugitive emissions. Stockpiles can be encapsulated using domes, stilling sheds or Weathersolve’s windfences. In addition to that, TRC can offer conditioning systems to keep surfaces humid and dustless.
Then comes the ground transportation from the mine sites to the end users or ports. This part of coal material handling presents a major concern to environ mentalists, and can be solved making sealed wagons and truck beds. Also, humidity and or sealing products can be spread at the top surface to minimize coal spills.
TRC has installed its dust control systems on belly rail dumps and also on rotary rail dumps. These items of unloading equipment then feed power plants or ports, barges (transport the coal to coastal ports) or ships (to then export the coal).
A recent example of where TRC helped its clients to stop working under hazardous conditions was at a belly rail dump on the state of Odisha, India. Here, visibility was restricted by dust, causing maintenance problems, operational delays and pollution. In terms of rotary rail dumps, TRC has several good examples of good dust control in the US Mid-West.
Finally, and probably the most challenging and costly step for coal handling, is tackling the flu gas emissions. Even though the Raring Corp can’t offer a solution for this part of the process, there are dry filtration technologies capable of minimizing the coal’s combustion emissions. On top of those proven and expensive technologies, there is a theory called Carbon Capture and Sequestration. This process captures the carbon dioxide before getting into the atmosphere and storing it underground for centuries. This technology hasn’t been proved in high scales yet, but it could be the right time for investing in R&D to make significant progress in this field.
The material handling for coal has many steps before it is burnt inside a boiler to generate energy, most of which can pollute the environment in different ways. Nevertheless, there are technologies available and others at the early stage of development that can help coal to minimize its environmental issues and contribute to decarbonizing and limiting the climate change effects. Belly rail dump in Odisha, India.
Belly truck dump in Utah, USA.


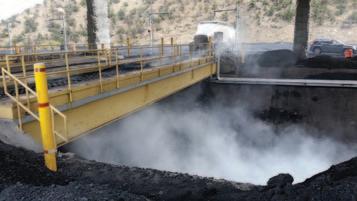
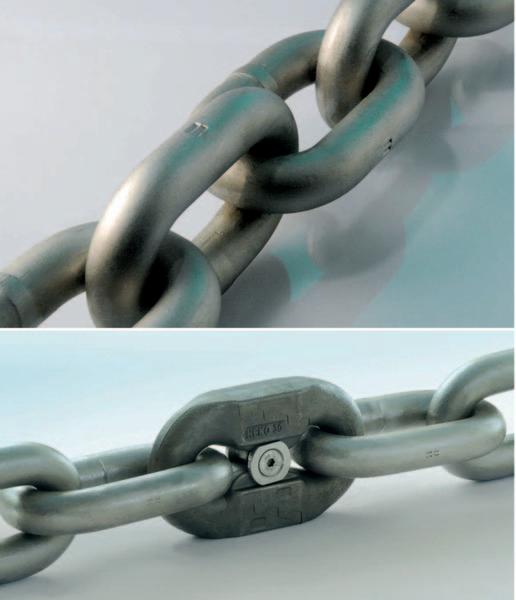
German company HEKO specializes in the production of chains, many of which are a vital part of equipment that is used to handle coal and similar cargoes.
HEKO’s chains are particularly popular in the ash handling market. Scraper reclaimers that are fitted with HEKO chains are installed in many coal power plants worldwide. HEKO’s chains are also used widely in coal feeder conveyors, bucket elevators, and more.
HEKO has 100 years of experience in the field of chain production.
The company is privately owned, and takes special care when it comes to reliability and a fast and competent service.
The fast and competent reply is a reason why customers like to work with HEKO. It does not matter if they have any emergency and need some items urgently — or if they have problems with any existing conveyors or bucket elevators — HEKO strives to find the best solutions.
A recent example of HEKO’s responsiveness is when it was called upon to help out a customer in Malaysia, whose equipment had broken down. HEKO collected items from a German plant, and within two days, the customer was able to re-start operations.
HEKO manufactures: v round link chains with high resistance to wear; v shackles for attaching scrapers and other components; v chain wheels; v central chains; v heat resistance chain for rotary and other kilns; v forge link chains; and v bushed chains. CHAIN MANUFACTURE HEKO's chains are manufactured using the most up-to-date welding machines. Manganese, chrome-nickel and fine grained chrome-nickel-molybdenum alloy steel are used in the chain manufacture. The chains are case hardened in modern, computer controlled heat treatment facilities.
Important characteristics of HEKO chains are: v Heat treatments selected to suit the requirement of the application; v High long-term dynamic strength; v Close length tolerance of
matched chain pairs; and v Long chain strands to suit clients requirements MACHINING HEKO has for many years manufactured chains and chain wheels to different dimensions and arrangements. The many variations virtually make every chain or chain wheel unique. HEKO's flexible manufacturing facilities enable easy adoption of customer's requirements for a particular order.
Modern CNC machining centres and automated lathes are utilized for machining of chain wheels, rollers of all types and shafts. HEAT TREATMENT Heat treatment, considered the key technology in the manufacture of conveyor components, has been given a prominent place in HEKO since the 1930s. Different technologies are applied to achieved optimum wear resistance for particular requirements and material characteristics: v case hardening; v induction hardening; v tempered and quenched; and v nitriding.
HEKO's use of vacuum chamber ovens with helium quenching is the most popular technology for the manufacture of chain. The bespoke heat treatment facilities enable charges of up to 750kg. Through such heat treatment, HEKO's chain and accessories achieve special product characteristics: v highly wear-resistant hardened case with a minimum surface hardness of 800HV; v high long term strength; v high breaking load due to fine-grained, tough core; and v excellent dimensional accuracy.
HEKO round-link chain. ABOUT HEKO
HEKO is one of the world’s foremost producers of chains and other wearresistant parts for the bulk handling industry. Innovation and high quality standards have been quintessential to the family business for over 100 years. Three locations in the state of North Rhine Westphalia, Germany with a production area of approximately 40.000m2, provide for the manufacture of a large variety of chains, chain wheels, chain accessories and unit assembly for conveyors. HEKO is a specialist in heat-resistant kiln chains as well as being a respected manufacturer of hardened round link chains. The extensive know-how in hardening techniques and up-to-date heat treatment technology is also offered as a separate service. HEKO supplies the worldwide bulk solids handling industry in all areas of operation. It not only supplies the cement and lime industry but also has an extensive market share in waste incineration, coal fired power stations, wood and other types of bio-fuel power stations, ore and mineral preparation, fertilizer manufacture, gypsum manufacture and concrete plants. HEKO has a sales organization in India and a sales office in China and has agents in over 50 countries. The efficiency of HEKO's chains is confirmed daily in over 80 countries around the world. All HEKO employees fully accept their responsibility for the quality of their work. HEKO's quality management is actively pursued by all and HEKO is certified to ISO 9001. HEKO also hold the environmental certificates to ISO 14001, health and safety certificates to OHSAS 18001, HEKO chain locks type HF. custom certificate AEO-F and LBA certificate. DCi