
23 minute read
DEVELOPMENTS IN THE NETHERLANDS: FOCUS ON EUROPE’S MAJOR HUB
Developments in the Netherlands
regional focus on Europe’s major hub
Jay Venter
The Port of Rotterdam Authority accelerates the reduction of its own carbon emissions
The Port of Rotterdam Authority is planning to accelerate the reduction of its own carbon emissions. Today, most of the CO2 of the Port Authority is emitted by the (patrol) vessels. CO2 is also emitted by the use of cars and buildings. The levels of CO2 involved totals 4,000 tonnes per year all told. The Port Authority’s own carbon emissions should be 75% lower in 2025 and 90% lower in 2030 than in 2019. Eventually, the Port Authority wants its operations to be entirely emission-free. “We are going to reduce our own carbon emissions as quickly as possible, while compensating in full what we still emit. So from that perspective, the Port Authority is already carbon neutral as we speak. Because our emissions will be lower and lower in the next few years, the compensation required will also decrease more and more,” says Allard Castelein, CEO Port of Rotterdam Authority.
In the past year, the Port Authority used so-called science-based targeting to calculate the emission reduction amount required to pull its weight to keep global warming below the 1.5°C limit. Sciencebased targeting is a way of translating the Paris Climate Agreement per company into specific targets. With this method, the Port Authority should achieve a reduction of at least 46.2% by 2030 (in comparison with 2019). As this seems to be technically feasible, however, the Port Authority is opting for accelerated reduction of its own emissions by 90% in 2030. To this end, the Port Authority will ensure that all its vessels will switch completely to biofuel in the short term, and it has the ambition that from 2025 new vessels will be emissionfree.
The Port Authority also wants to realize lower carbon emissions in other areas. Emissions caused by its employees’ air travel are to be reduced by 70% in 2025 and by 80% in 2030, as a result of flying less and participation in a biokerosene programme.
Reduction objectives have been formulated for assignments awarded to contractors of the Port Authority as well. In this case, it is about a 45% reduction by 2030 with the use of fuels (especially dredging and earthmoving) and 20% for (construction) materials. Huge amounts of steel are used in the construction of quay walls, for example. Since its production provisionally involves high carbon emissions, 20% in 2030 seems to be the maximum feasible level.
Reasons for tightening the climate targets include the recent climate studies of the Intergovernmental Panel on Climate Change, the ‘Fit for 55’ plans of the European Commission, and the Glasgow Climate Summit at which the target of a maximum temperature increase of 1.5°C was confirmed.
INDUSTRY AND SHIPPING The Port Authority also does its utmost for emission reduction in shipping and industry, although it cannot influence this directly. This approach is based on two studies by the German Wuppertal Institute from 2017 and 2018 respectively into the emissions of industry and shipping and the transition paths for both sectors.
For shipping in the port management area (which reaches as far as 60km off the coast) the emissions should be reduced by 20% in 2030. In order to make this happen, various developments are in progress, like efficiency increase (by optimizing logistics processes), the application of shore power (so that berthed ships can switch off their generators and plug in), and bunkering clean fuels (such as LNG, biofuels, and methanol) by shipping.
This should be made possible by projects on capturing CO2 and storing it beneath the North Sea bed (Porthos), construction of pipes for hydrogen and residual heat, and attracting innovative developments, such as the production of green hydrogen and biofuels.
All these projects together amount to some 23 million tonnes of carbon reduction in the port and outside (by the use of biofuels produced there, for example). This is 35% of the Dutch carbon reduction objective for 2030.
Marcor Stevedoring B.V. to develop and operate dry bulk terminal at Steinweg Hartel Terminal
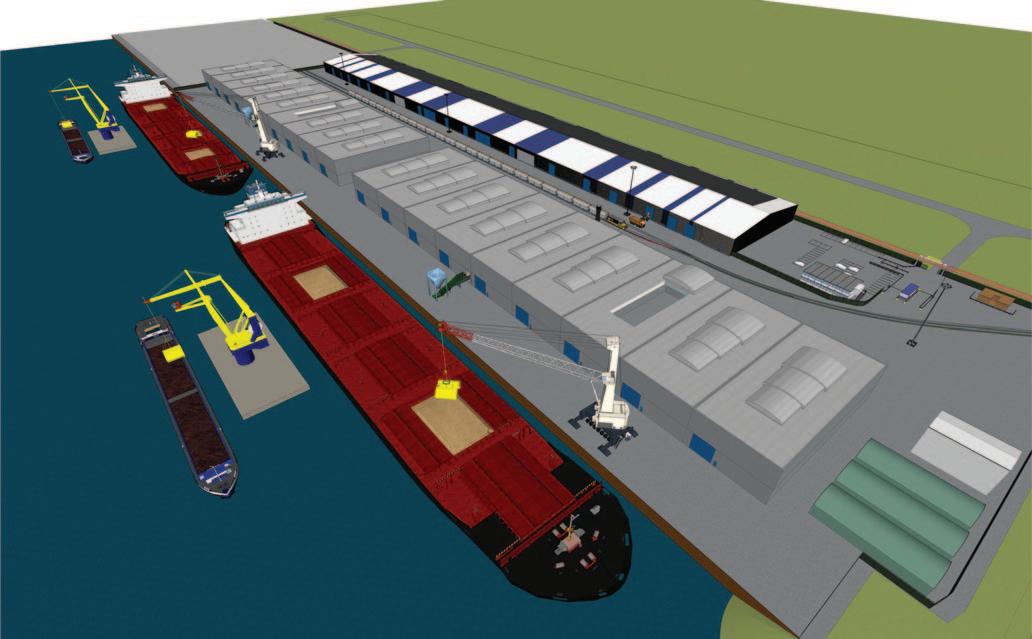
Marcor is planning to expand its floating terminal in Rotterdam with the development of a dry bulk terminal at the Steinweg Hartel Terminal. The terminal is currently operated as a breakbulk terminal by C. Steinweg – Handelsveem B.V. (Steinweg), Marcor’s parent company.
After the redevelopment and construction of state-of-the-art storage facilities, Marcor’s aim is to phase in sustainable and efficient storage and stevedoring operations at the site by the end of 2023.
EXPANDING BUSINESS ONTO SHORE AND OFFERING NEW SOLUTIONS TO CUSTOMERS Marcor is specialized in storage and transshipment of dry bulk and is known in the port of Rotterdam for its floating cranes and storage vessel in Waalhaven.
“Marcor already had the ambition to develop an on-shore terminal for quite a while,” says Danny Swart, Managing Director, Marcor Stevedoring B.V.
“We are witnessing a growing demand for (covered) storage, and multiple cargo flows we (plan to) serve also require a home onshore, with multi-modal delivery flexibility to later receive these, whether on barge, rail, truck or vessel.
“In the last two years, our parent commenced to execute a consolidation plan in Rotterdam, which involved the development of a large new breakbulk and project cargo terminal in Rotterdam in the Waalhaven.
“This plan made the development of a bulk terminal at the Hartel Terminal by Marcor opportune. This terminal was already ranked #1 on our bucket list, as it allows for synergies with our floating terminal operations, has excellent draught to serve a wide range of vessel sizes, and already has the necessary infrastructure available to meet this growing demand for storage and flexible delivery options.
“In the same period, within our group an exciting bulk terminal development in Antwerp was completed, with similar warehouses to those we now plan to construct at the Hartel Terminal.
“The growing demand, our ambitions, a suitable terminal becoming available and the successful Antwerp project which can be timely brought to market, were all important developments which kickstarted our project.’’
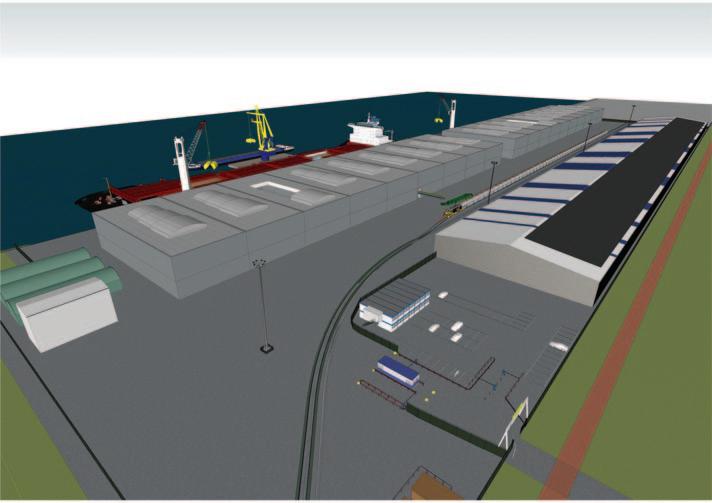
MARCOR’S PLANNED DEVELOPMENT AT THE STEINWEG HARTEL TERMINAL AIMS TO PROVIDE ITS CURRENT
v
v
v
v The expansion of flexible stevedoring and storage capacity; Multi-modal connectivity, beyond its current floating operations, adding truck and rail connectivity; Multiple options to handle bulk, whether loose, in jumbo bags or containerized; The potential to introduce additional value added services; Facilities suitable for the import, export and transshipment of a wide variety of goods, including agri-bulk, biomass, concentrates, fertilizers, (industrial) minerals and ores.
FROM BREAKBULK TO DRY BULK The Hartel Terminal will be the scene of the transition from breakbulk to dry bulk cargo in the next few years.
The 13-hectare terminal has a total quay length of 600 metres and a depth of 16 metres, so that a wide range of vessel types can be served with ship-to-ship and terminal transfer.
Located near the N15 motorway and with a railway connection already in place, the terminal has multimodal transport connections from and to the hinterland.
KEY DETAILS OF THE DEVELOPMENT AND THE STEINWEG HARTEL TERMINAL INCLUDE: v v
v
v 130,000m2 terminal; 600 metre quay with 16 metre draught alongside; Vessel handling options from barges up to 120,000dwt baby-Cape vessels, both for board-to-board trans shipment and discharge to/from terminal; Existing 28,000m2 warehouse will be utilized for the storage of bulk (loose/bagged) and value added v
v
v warehouses with fully (±18) segregated bunkers, directly reachable through a single manipulation crane grab; Located in the near vicinity of the N15 Highway at the beginning of the Maasvlakte; Existing double rail track at the terminal, suitable for ± 2 x 225m train combinations; A sustainable operating model, including electrified shore cranes and conveying equipment, with 11,000m2 solar panels being already installed.
A final investment decision for the development will be made latest end of 2022. The plans for the development of the terminal were made in dialogue with Rotterdam Port Authority and Steinweg.
Royal Bodewes to build cement carrier for Asian Shipping company U-MING Marine Transport Corporation
Digital rendering of the 7,750dwt cement carrier Royal Bodewes will build for U-Ming Marine.

Royal Bodewes announced in April 2022 that it will build a 7,750dwt cement carrier for Taiwanese shipowner and operator U-Ming Marine. It is the first time Royal Bodewes has built for an Asian partner and the shipping company is looking forward to a long-term and wonderful partnership.
The Taipei-based dry bulk shipowner has ordered a cement carrier (NB 778) with a length of 115 metres and a width of 15.8 metres, the design being that of a Bodewes cement trader, based on a previously delivered ship. The vessel has a customer specific loading and unloading system and is designed specifically for sailing along the coast and the islands of Taiwan.
The co-operation has had a long run-up (several years), mainly because of the pandemic. But by maintaining intensive digital contact, the two companies managed to conclude a contract by the end of 2021 (without ever having seen each other in real life). The shipyard will start construction of the ship in 2023. Estimated delivery time of the vessel is Q1 2024.
Both parties see their partnership as a unique opportunity for intercontinental cooperation and look forward to the future with anticipation.
ABOUT ROYAL BODEWES Royal Bodewes is a shipyard in the North of the Netherlands that has been building vessels for over 200 years. The yard is specialized in building multifunctional vessels in a range 1,500 to 15,000 tonnes. Royal Bodewes develops technically advanced vessels, such as hybrid ships, selfdischarging cement carriers and LNG bunker vessels.
ABOUT U-MING MARINE TRANSPORT CORPORATION U-Ming Marine Transport Corporation, formerly named Yue Ming Transportation Co., was established in 1984 to provide marine transportation of cement, dry commodities and industrial raw materials, specializing in the trading of vessels and providing agency services.
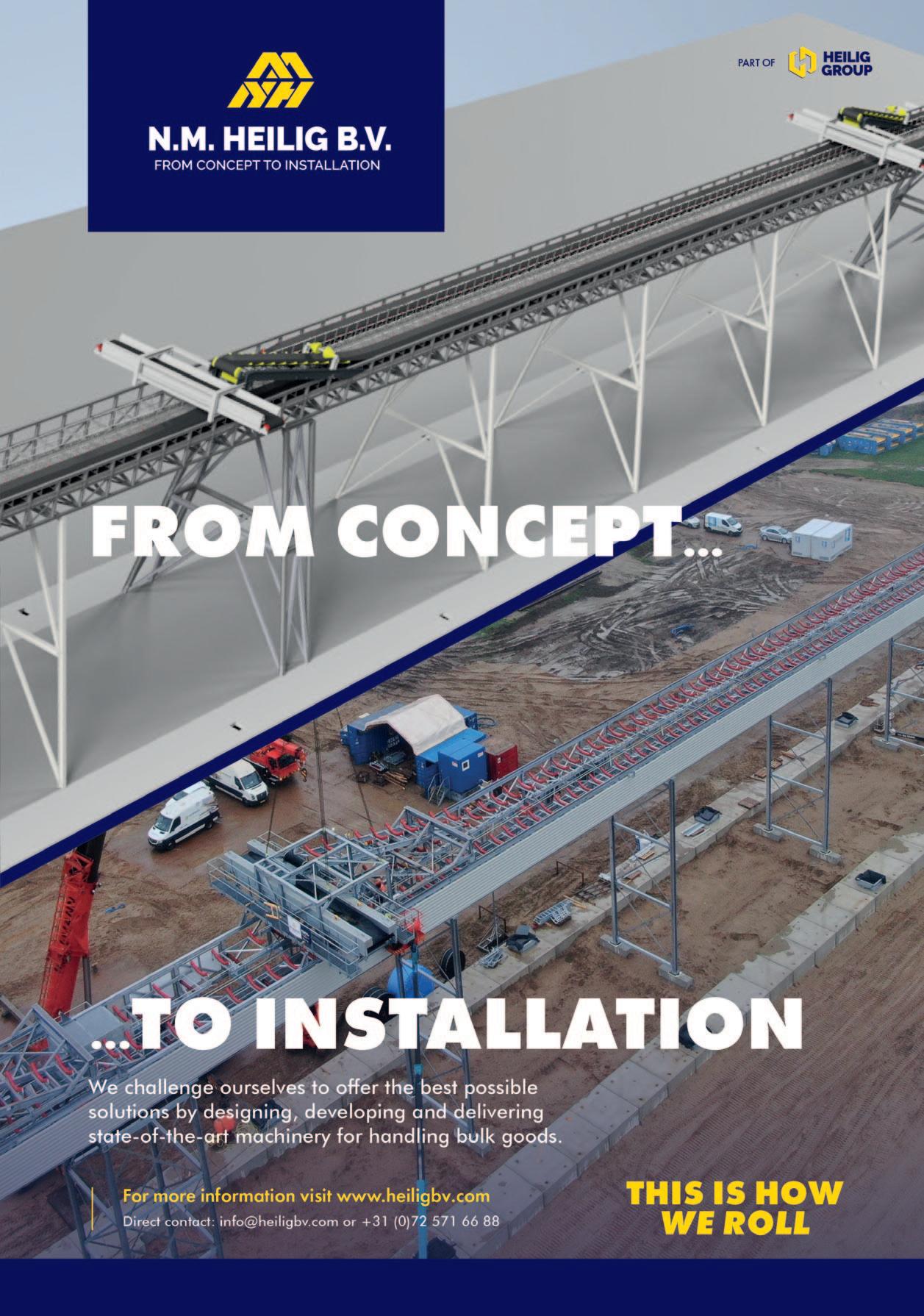


Not surprisingly, since OVET was founded in 1957, a lot has changed. At first, the company operated ex-Marshall Plan six-tonne floating cranes to discharge coal from seagoing vessels on Terneuzen roads and at the Zevenaarhaven terminal in Terneuzen. This gradually evolved to the 25- and 36-tonne units which nowadays are handling all kinds of bulk and breakbulk cargoes at its Massagoed and Kaloothaven terminals in Terneuzen and Vlissingen. However, what hasn’t changed is the nature and spirit of OVET. As ever, each project benefits from an all-out effort on behalf of OVET, where all floating cranes are combined to ensure the customer receives swift and quality service.
ABOUT OVET
The history of OVET begins in 1957. This is the year when the French stevedoring company Manufrance decided to establish a local transshipping company for a major customer: the Association Cooperative Zélandaise de Carbonisa tion, also known as the Cokesfabriek (coke factory).
This factory focused

on the production of cokes for the blast furnaces of French steelworks. Terneuzen was a favourable location, because it is well-situated with regard to England and the Ruhr area, which is where the coals came from. The deep waterway was also a major advantage.
The main reason for choosing a location in Zeeuws-Vlaanderen was the substantial price difference between supplying coals via Rotterdam or directly to Terneuzen. On 2 May 1957, the company was established. The managing director at the time, Y.H.M. Simenel, started out with seven other employees and ran the company from the Grand Hotel Rotterdam in Terneuzen.
OVET decided to use floating cranes in order to be able to lighten vessels midstream as well as from the quay. The very first floating crane had a lifting capacity of six tonnes. The company was successful and steadily gained new clients, besides the coke factory.
The lifting capacity of the cranes increased from six to 16 tonnes and later to 25 tonnes. In 2007, the newest crane with a lifting capacity of 36 tonnes came into service.
From an annual 500,000 tonnes of transshipment during the beginning, OVET has grown and today handles as much as 11 million tonnes of transshipment cargoes each year.
The company now has dry bulk terminals in Vlissingen and Terneuzen and over 100 employees ensure services of high quality for the customers.
OVET can achieve a total unloading capacity of as much as 80,000 tonnes dry bulk per day, using its four lemniscate floating cranes.
In addition to creating more capacity, OVET also makes use of mobile SENNEBOGEN material handlers.
TERMINAL TERNEUZEN (MASSAGOEDHARBOUR) AND TERMINAL VLISSINGEN (KALOOTHARBOUR) With its floating cranes, OVET is active throughout the entire area of the Western Scheldt, in Vlissingen, Terneuzen and Ghent, but also at anchorage berths on the Western Scheldt itself.
TRI-MODAL PLATFORM
WATER TRANSPORT (INLAND NAVIGATION/ MARITIME SHIPPING) The OVET dry bulk terminals are connected to the most important waterways in Europe. Access to the Rhine is gained through modern channel connections. The proximity of the North Sea ensures the OVET dry bulk terminals are very suitable for sea traffic. OVET is able to load and unload all inland navigation (lighters and tug-pushed barges) and maritime shipping (coasters, Handysize, Panamax and Capesize). All possibilities are therefore open for its customers.
ROAD TRANSPORT OVET uses loaders to fill up trucks, which then pass a weighing platform to determine the exact weight.
RAIL TRANSPORT Since July 2013, OVET has had a completely renovated track and a new train loading system at the Vlissingen terminal. This ensures OVET is able to provide an even better hinterland connection for its customers. OVET has successfully proven that a train can travel to and from the German Ruhr area within 24 hours.
On top of that, both dry bulk terminals have a good connection to the European railway network with good access to the Betuwelijn and the Corridor C.
Due to the situation in Ukraine, one of EMO’s largest customers from the steel production sector has purchased iron ore in Australia.
This cargo with a total of approximately 172,000 tonnes was shipped aboard the Schinousa.
Because of the longer transport distance from Australia, there was a risk that this raw material would be delivered too late to its final destination in Germany and that the process of making steel would be disrupted.
In order to save time for this customer, EMO unloaded approximately 60,000 tonnes as a priority, so that this could be delivered as quickly as possible to the final destination.
The remainder of the load was unloaded a week later.
In the meantime, the ship is moored at the quay of the brand new HES Hartel Tank Terminal B.V. on the Maasvlakte.
This a great example of co-operation between EMO and HHTT, both companies of HES International B.V., which is active in both dry bulk and liquid bulk.
The result was a satisfied customer and coincidentally a first ship on the quay in front of the HHTT terminal, a nice exercise prior to putting the terminal into official use.
EMO and HHTT collaboration keeps iron ore flowing
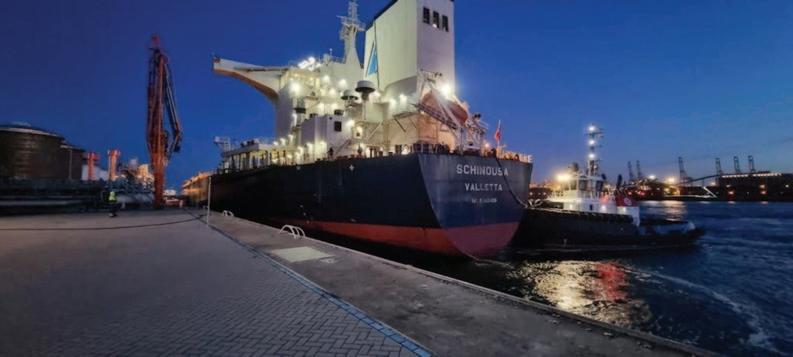
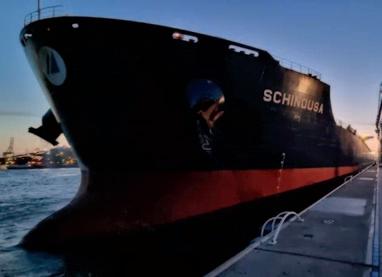
Schinousa moored at the new HES Hartel Tank Terminal B.V. on the Maasvlakte, after unloading iron ore in Germany.
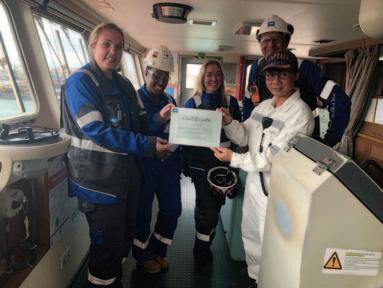
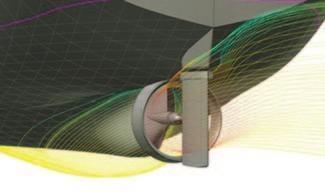
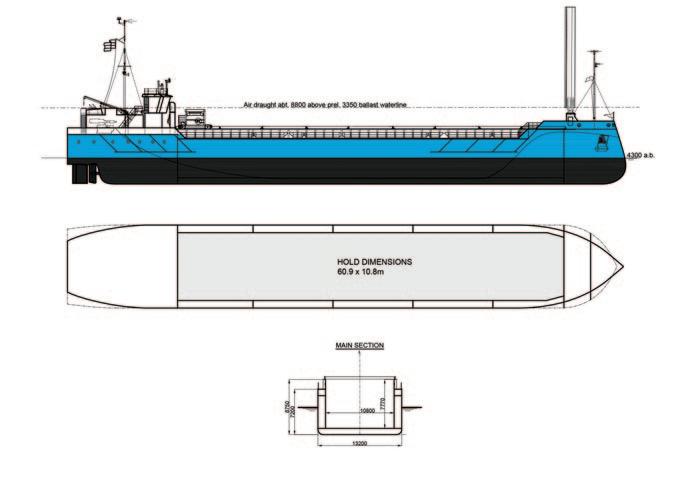
Conoship International develops CIP3600: a future-proof 3,600dwt general cargo vessel
Dutch ship design specialist, Conoship International Projects, recently developed an innovative, future-proof and environmentally friendly 3,600dwt general cargo vessel, suited for sea-river operations. The CIP3600 vessel can be considered the new standard for low-air draught sea-river coasters.
NEW STANDARD SEA-RIVER COASTER With its well-thought-out diesel-electric propulsion system, enlarged propeller in combination with a ConoDuctTail® and optimized hull lines, its fuel consumption will be best in class, especially in wind and waves. To further improve its performance, the design is ready for windassisted propulsion, as it is prepared for the placement of two Econowind VentiFoils® , which would reduce the fuel consumption and CO2 emissions by about 10%, depending on sailing route.
FUTURE-PROOF DESIGN The design is highly future-proof. The EEDI of the vessel as calculated as a diesel-driven vessel is already below the phase 3 requirements. Furthermore, a switch of fuel type to future fuels such as liquid hydrogen or ammonia is facilitated by smart arrangement design, where the requirements of the future fuels have been taken into account from the beginning of the conceptual design process.
MAIN PARTICULARS OF THE CIP3600 VESSEL: Length overall: 88.00m Breadth moulded: 13.20m Draught design: 4.30m Draught maximum: 5.00m Deadweight @ T = 5.00m: 3,640t Hold volume (cubic feet): 180,105ft3 Service Speed 10.00kn Attained EEDI abt. 35% below phase 3 requirements.
HULL FORM AND PROPELLER In all the designs of the CIP series a ConoDuctTail® is incorporated. The ConoDuctTail® is an in-house developed aft ship design with a strong focus on the combination of a low resistance and a high propulsive efficiency, both in calm weather and when sailing in waves.
Optimization based on extensive CFD calculations conducted by Conoship led to 17% reduction of resistance compared to a conventional tunnel shape aft ship.
The differences between the ConoDuctTail® and extreme pram type aft ships are reflected in the propulsive characteristics: the propulsive efficiency of the ConoDuctTail® is substantially higher. This is the result of the larger propeller diameter, nozzle and evenly distributed wakefield. The propeller diameter is up to 25% larger than what is normally seen for this type of vessels of this size.
RETURN TO THE NORTH Due to production-friendly construction principles, optimized logistics and increased series effects, the construction of these vessels can be carried out competitively at a variety of shipyards in North Western Europe.
The project was initiated by Conoship International Projects (CIP) based on extensive market research Conoship International Projects proactively marketed this vessel, looked for clients, and sourced shipyards. Furthermore, CIP actively brokered between finance houses, owner and shipyard.
This environmentally friendly CIP 3,600dwt general cargo vessel attracted a lot of interest from people all over the world. This inspires Conoship to develop slightly bigger vessels based on the same philosophy in a size range from 5,800 to 7,500dwt.
ABOUT CONOSHIP INTERNATIONAL Conoship International is an ambitious and innovative ship design and engineering office. Founded in 1952 as the central design office for a group of Northern Dutch shipyards, Conoship International developed a strikingly wide range of ships, from general cargo vessels, tankers, dredgers, to ferries and offshore vessels. Over 2,000 ships were built based on its designs, operating all around the world.
With its multi-disciplinary team, Conoship International can provide assistance from the early steps of a project, through feasibility studies, concept design, to providing a full engineer and production package, up to financing, yard selection and production support. This interaction and integration of the various disciplines of ship design and engineering enables Conoship International to create and develop the next level in ship design.
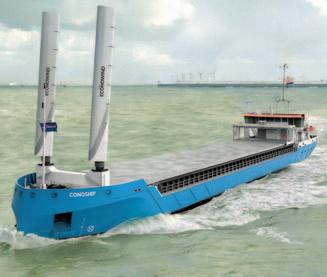
General cargo vessel with diesel-electric propulsion. Copyright Conoship International. Fuel consumption is only 2.5–3.5 tonnes per 24 hours at a service speed of 10 knots. In some cases this equals to a 50% lower fuel consumption compared to conventional general cargo vessel designs. Copyright Conoship International
OBA is a multipurpose terminal, strategically located in the Port of Amsterdam and has excellent sea, river, rail and road connections to the European hinterland, with short communication lines and a flat and dynamic organizational structure.
It specializes in transhipment, storage and processing of dry bulk commodities. Its staff is the foundation of the company. OBA services international customers from a variety of sectors: energy and steel, animal feedstuff, chemical, building and recycling.
With a customer-focused service portfolio which includes handling, indoor & outdoor storage and value-added processing activities, OBA can handle an annual volume of up to 22 million tonnes of various dry bulk commodities.
SAFETY FIRST At OBA, a safe work environment and care for the surroundings is paramount. The company has extensive safety regulations for its staff, visitors and suppliers. Besides complying with legal standards, it often goes the extra mile. By strictly adhering to the safety regulations OBA can create the safest possible working environment. With these standards, it ensures that strict safety regulations are enforced, enabling a safe work environment.
OBA is a logistics service provider for cargo owners and not the final consumer of the cargo. The operational management is aimed at keeping the energy usage and the footprint (emissions) as low as possible, and it continuously monitors that.
OBA is certified for ISO 9001 Quality management (including the BLu (Bulk Loading and Unloading) code), ISO 14001 Environmental management, GMP+ B1 Feed (production, trade and services of feedproducts) and ISPS (International Ship and Port facility Security) Code.
FUTUREPROOF IN THE ENERGY TRANSITION The energy transition — a transition involving the use of fossil fuels and not the transportation thereof — is here to stay, and that is an important and positive reality. OBA adapts its portfolio to meet market demand. For instance, it invests in covered storage capacity in which it focuses on new products and services as well as play a role in the circular economy. OBA has proven as no other, that it’s capable of providing storage and adapting to strong fluctuations in its customers’ storage and transhipment needs. OBA’s customers often operate in volatile markets as well.
VALUE-ADDED SERVICES Modern facilities guarantee fast and efficient unloading and loading of the largest seagoing vessels, as well as barges, trains and trucks. In addition, OBA offers multiple value-added services such as screening, blending and washing.
THE HISTORY OF OBA OBA’s success is partly due to the opening of the Amsterdam-Rijnkanaal in 1952. During the 1950s and 1960s, the West German steel industry’s demand for iron ore was especially high. These products were imported mainly from countries of origin because this was less expensive than importing from European countries. Once the channel was opened, the connection between Amsterdam and the German hinterland greatly improved. Supplying iron ore and other raw materials became easier.
Two years later Overslagbedrijf Amsterdam (OBA) was established. Within three years, OBA’s transshipment doubled and laid this customer-oriented logistical service provider’s foundation. OBA has proven during the past years that it responds well to market developments. It is therefore OBA’s ambition to develop from a leading dry bulk terminal to a leading multipurpose terminal.
HES 100% INTEREST IN OBA GROUP In March 2022 HES International B.V. (HES) acquired the remaining 25% of the shares ultimately held by Oxbow as per 1 March 2022, resulting in a 100% interest in OBA Group (OBA) by HES.
OBA has traditionally been focused on the storage and transshipment of coal and agricultural products. In early 2020, OBA embarked on a transformational journey, which aims to strengthen its Agri & Minerals activities as well as to develop logistic services solutions in support of bulk production processes to be established at the OBA site. The acquisition by HES of the remaining interest in OBA, enables OBA even better to optimize its capacity. As part of that same strategy, OBA already acquired IGMA Bulk Terminal from Cargill in 2021.
The acquisition ties well in with the HES group strategy to strengthen the dry bulk portfolio by investing in state-of-the-art infrastructure for the storage and handling of Agri & Minerals products.
The shared ownership of HES and Oxbow in OBA Group has always been very constructive and highly valued by HES.
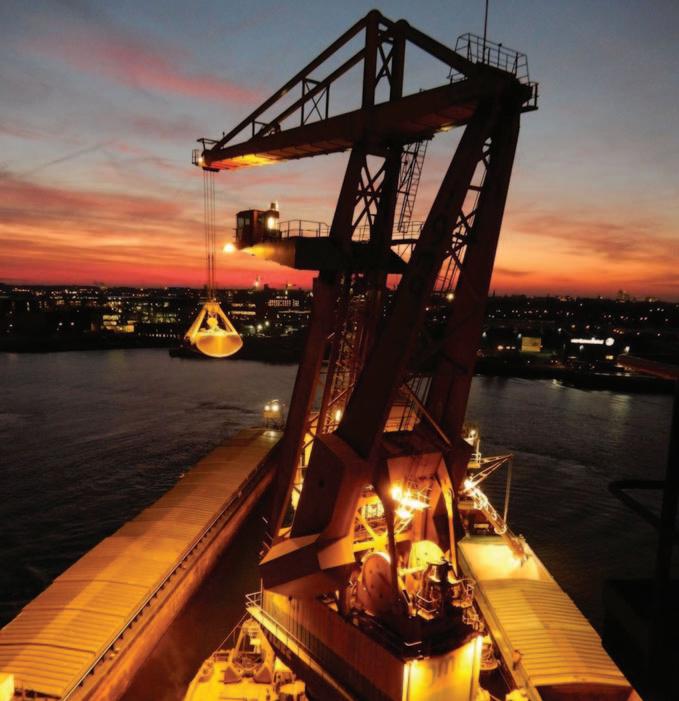
Yes, of course it’s possible! That seems to be the motto of Nils Janbroers, founder of the Dutch company Instral. With a group of bright minds, he solves problems that other companies cannot or do not want to solve. Problems in the oil industry, fertilizer industry, water management, environment, agriculture and mining. Among other things that is, because if a problem arises somewhere else that he can tackle with chemical-technical solutions, then he will not fail to do so. “Anything is solvable,” says Janbroers.
LIMITED IN HIS CREATIVITY As a salaried oil and gas engineer, he felt limited. He wanted to have the freedom to use all of his creativity to solve problems. But companies don’t deal in solutions, they deal in products. And in his industry, companies are not always keen to solve some of the problems at hand. That’s why he started his own business in late 2010 and now the team consists of bright people. “We are small, flexible and independent in all our actions. We take on issues that are of no interest to large chemical companies or others not able to tackle.”
SOLUTION FOR PARTICULAR MATTER In 2014 Instral was challenged to solve a specific dust problem due to particular matter in Romania. Eighteen months of non-stop work produced the solution: a (safe and environmentally friendly) product that combats particular matter: C-Force dust control additives. It can be used in mining and other industries, road building and agriculture. “It’s incredible that there has never been a serious search for a sustainable and practical solution to the dust problem in agriculture, but we have found it.” As a result, Instral received a local award for most innovative company in 2015.
One of the applications of the agricultural dust control agents is in really dry areas, like United Arabic Emirates. Says Janbroers: “The roads are often covered with sand, leading to dangerous situations. The local authorities try to solve this by planting marram grass next to the roads. But often, the newly planted grass gets damaged by sand particles. Our dust control agent can prevent this from happening, giving the plants a chance to root properly and grow.” “Anything is solvable,” says Nils Janbroers, who founded Instral in 2010.
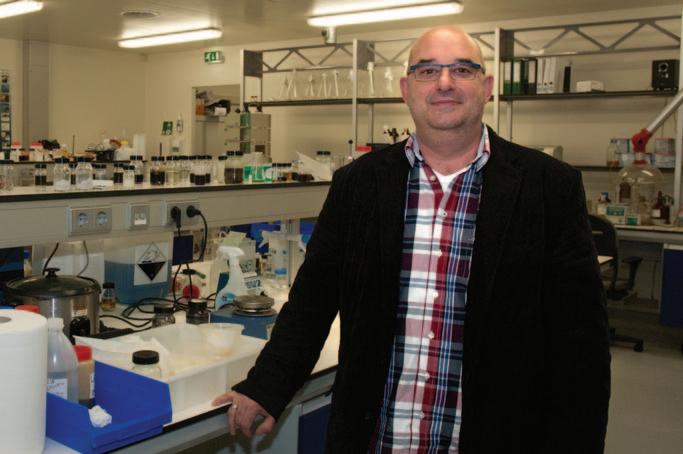
IMPROVING FERTILIZERS In its C-Force line, derived from ChemicalForce, Instral provides solutions for oil treatment, dust control and water treatment. In recent years, Instral has also been working on improving fertilizers. Janbroers states: “Fertilizers possess extraordinary physical properties that may cause problems during production, handling, application chain, storage and transportation. Like caking, dusting and moisture uptake. We developed a line of products than can improve the granulation or prilling process and products that provide excellent coatings for the fertilizer granules.”

BIO-BASED SOLUTIONS Recently Instral’s resolving power was challenged yet again. In the ‘BioVoice’ challenge — a Dutch initiative to help speed up innovations on bio-based products — Cargill challenged companies to develop bio-based coatings for fertilizers. But of course, the out-of-thebox-thinking team of Instral came up with something better. “Coatings are really only patch-work solutions for poorly manufactured granulated fertilizers,” Janbroers explains. “So instead, we focused on bio-based additives that would improve the granulation and prilling process, improving the quality of the product so that it needs no or only a little (bio-based) coating. These bio-based additives are now being tested in the laboratory of a huge fertilizer manufacturer and will hopefully be implemented in the production line soon”.
BRING IT ON Even before the new bio-based products go to market, Instral is already contemplating new problems to solve. “We are always game to tackle new problems the industry or society needs solving. Bring it on!”

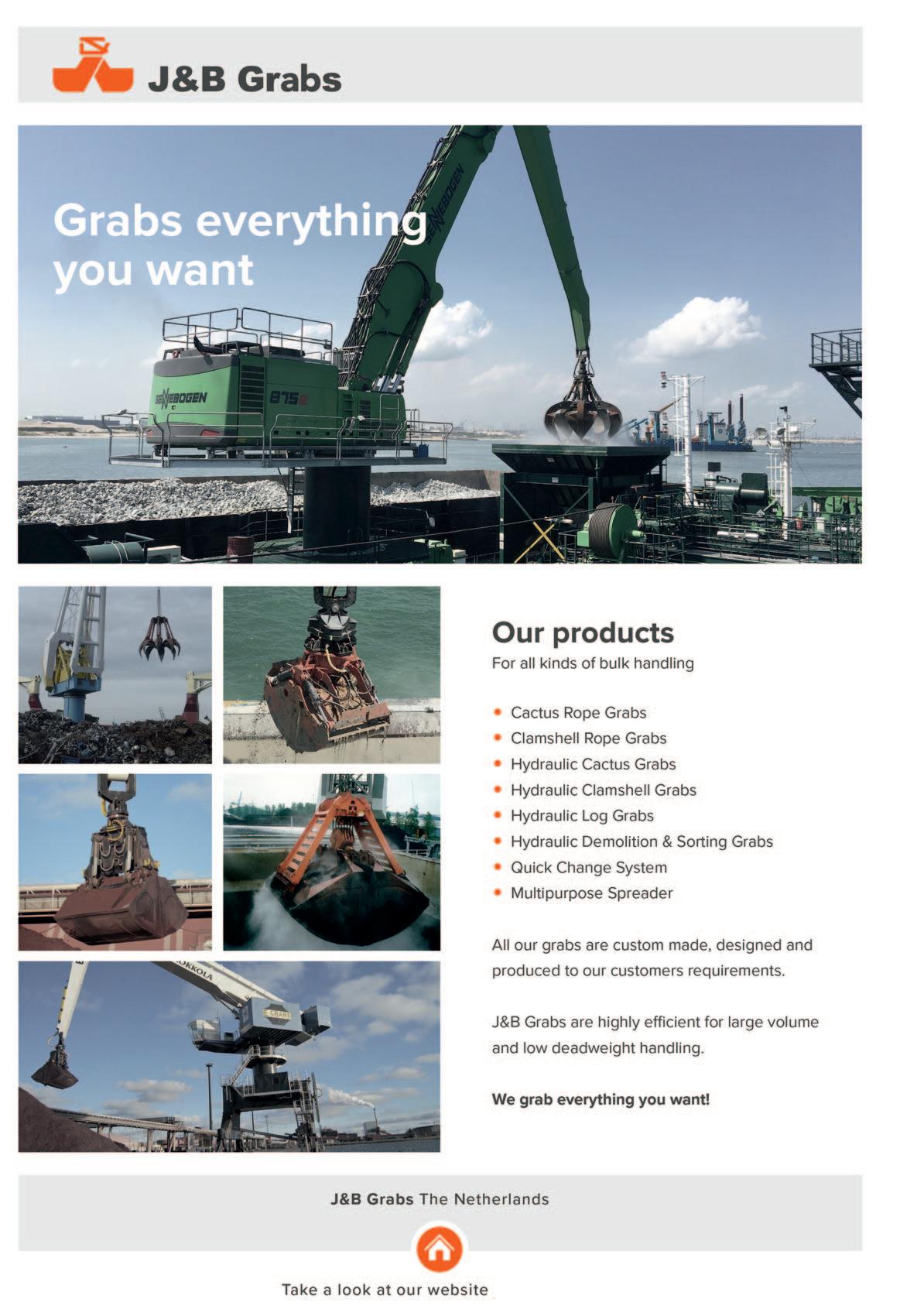