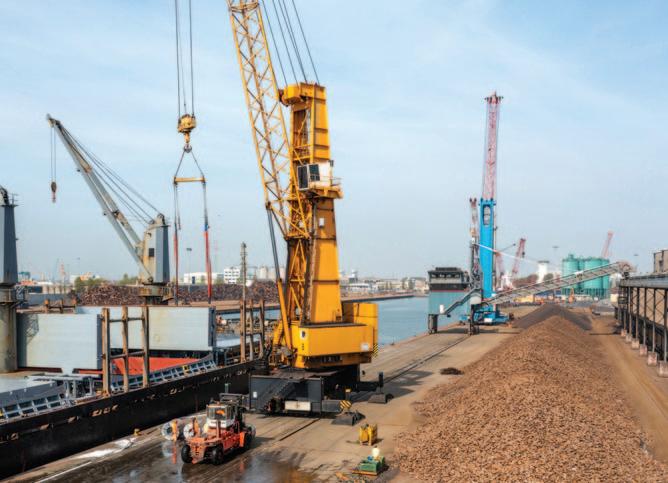
12 minute read
Konecranes Generation 6 mobile harbour crane from Venetian port
Konecranes receives order for Generation 6 mobile harbour crane from Venetian port
The FHP Group has ordered an ecoefficient Generation 6 Konecranes Gottwald mobile harbour crane for its Multi Service Terminal in the Marghera Port near Venice, in northern Italy. The crane will upgrade bulk handling operations by increasing efficiency while reducing local exhaust emissions. The order was booked in April 2022 and the crane will be delivered and commissioned in November.
The FHP Holding Portuale Group manages logistic platforms in Carrara, Livorno, Monfalcone and Venice, creating a strategic link between the Adriatic and Tyrrhenian to support the competitiveness of the Italian industry. FHP manages the Multi Service Terminal (MST) in Venice, which provides a wide range of port handling services including bulk cargo handling. The new crane will provide added capacity for MST’s bulk cargo handling operations.
“We already operate older Konecranes Gottwald mobile harbour cranes at Marghera and other FHP terminals, and they’ve always performed above our expectations. FHP Group continuously works to decrease its carbon footprint. For this reason, we’re very pleased to have a new Generation 6 on order, that is part of Ecolifting Konecranes, from eco-optimizing diesel drives to hybridization and fully electric fleets. With improved performance and additional features, we’re really looking forward to seeing how it handles bulk at the Multi Service Terminal,” says Alessandro Becce, CEO of FHP Group.
The new crane is a Konecranes Gottwald ESP.7B mobile harbour crane, with a working radius of 51m and a capacity of 125t. The crane is equipped for an external power supply, for zero local exhaust emissions and reduced noise when operated via the harbour mains. For unplugged operation, the crane uses an onboard diesel generator set that complies with EU Stage V emission standards. Specially adapted for bulk handling, it features strong lifting capacity curves for improved performance. It also has smart software and digital services in line with Italy’s National Industry 4.0 Plan, a state strategy that encourages industrial innovation.
“Konecranes has been working closely with FHP Group for decades, and we're delighted that they’ve chosen us again for the new bulk crane in their Marghera terminal. This order shows that FHP can really see the potential of the Generation 6 crane with its high productivity, reliability and fuel efficiency,” says Gino Gherri, Regional Sales Manager, Konecranes, Port Solutions.
This is part of Ecolifting, Konecranes’ continuous work to decrease the carbon footprints of our customers. From ecooptimizing diesel drives to hybridization and fully electric fleets, the company will continue to do more with less.
A strong focus on customers and commitment to business growth and continuous improvement put Konecranes at the forefront of the industry. This is underpinned by investments in digitalization and technology, plus its work to make material flows more efficient with solutions that decarbonize the economy and advance circularity and safety.
ABOUT FHP AND F2I SGR FHP Holding Portuale (FHP), part of F2i sgr, Italy’s largest independent infrastructure funds manager, with assets of over €6 billion under management, representing one of the principal Italian port hubs, specializing in the breakbulk and general cargo sector, strategically supplying and servicing some of the largest Italian industries active in the Upper Adriatic and Tyrrhenian Sea. FHP Group is born with the aim of adapting innovation, development, and sustainability in the sector to the changing demands of the market.
ABOUT KONECRANES Konecranes is a globally respected group of Lifting Businesses, serving a broad range of customers, including manufacturing and process industries, shipyards, ports and terminals. Konecranes provides productivity enhancing lifting solutions as well as services for lifting equipment of all makes. In 2021, Group sales totalled €3.2 billion. The Group has approximately 16,600 employees in around 50 countries.
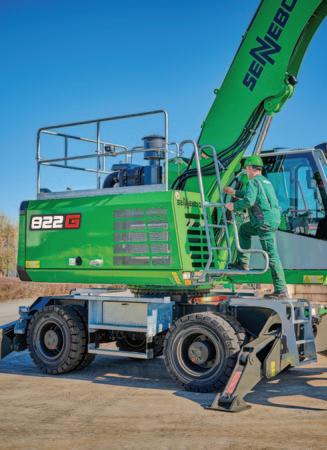
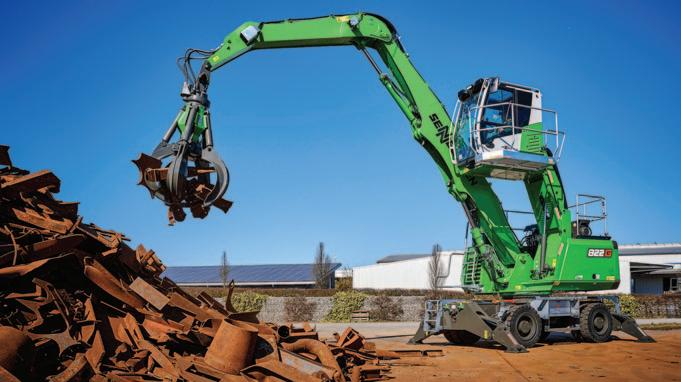
For demanding recycling and scrap applications. The new SENNEBOGEN 822 G can be individually configured and has a range of up to 10m. The redesigned Maxcab impresses with its operator comfort and user-friendliness.
As the next material handler, the popular 22t recycling machine has now also received its update to the latest G series machine generation at SENNEBOGEN and shines with various technological innovations. The completely revamped 822 G features intelligent and resourcesaving machine technology and has everything that could be desired in terms of operator comfort and safety.
The latest generation of material handling technology for use with recycling or scrap. The optimized new edition of the popular 22 t 818 E recycling all-rounder makes it possible to handle and sort material in a particularly environmentally friendly and economical way. The compact material handler's high system performance and outstanding ease of maintenance are impressive, as is the operator's comfort cab, the design and function of which have been reworked.
SUS TAIN ABLE SO LU TION FOR HARSH ENVIRONMENTS With a reach of up to 10m and a comfort cab that can be elevated as standard, the compact 822 G material handler is a true professional when it comes to recycling. Thanks to its tried-and-tested modular system, it can be individually configured and, with its numerous equipment variants, also makes light work of handling scrap. With this machine, it is clear that once again SENNEBOGEN has focused 100% on material handling during development. The 822 G boasts outstanding responsiveness — the hydraulics can be adjusted very precisely by the operator — and fast, overlapping movements with a hydraulic system that is optimized for demanding tasks in recycling and scrap yards.
At the same time, the machine uses Green Efficiency Technology to save resources and work efficiently. Powerful pumps and large-scale hydraulic valves and lines ensure optimum efficiency. Rightsizing was also on the agenda for the engine. The new 822 G now has an economical 110kW Stage V diesel engine with 3.8 l displacement, which is ideally suited in terms of power and consumption to the operating conditions in recycling and scrap. In addition to the low operating costs, the G series is also synonymous with SENNEBOGEN’s sophisticated 6th generation material handling technology based on decades of experience. Durability and reliability are guaranteed thanks to its robust components and intelligent design — a significant advantage for demanding continuous use.
CAB UP DATE: OP ER A TOR COM FORT AND SAFETY FUR THER OP TI MIZED The Maxcab comfort cab has also been redeveloped. All in all, the operator will be even more comfortable going forward. In addition to a fresh design, SENNEBOGEN has also incorporated feedback from customers and dealers with regard to comfort and functionality into the new Maxcab. The backrest has been raised, the seat area has been widened by 3cm and the suspension has been reinforced to give the operator maximum seating comfort. Furthermore, the series standard air conditioning with a total of 12 individually adjustable air nozzles, and the view to the front and side have been optimized.
The full-length windshield, which runs from the roof to the floor, is made of bullet proof glass as standard. All switch elements can be conveniently operated from the seat on a clearly arranged membrane keypad that is in the operator’s direct field of vision.
Customized and stored operator profiles not only increase efficiency in multi-shift operation, but also make the cab a very personal space for each operator — for fatigue-free and focused work with a feel-good guarantee all day long. The infinitely variable cab elevation — 2.80m for the 822G — is and will remain standard for this SENNEBOGEN material handler. Here in particular, the improvements are noticeable in the truest sense of the word, as the new control and particularly torsion-resistant design moves the Maxcab to the desired height even more stably and smoothly.
Features such as the tried-and-tested sliding door, new, colour-coded grab handles and an even stronger LED spotlight on the cab roof also ensure maximum safety when handling the machine.
FO CUS ON EASE OF MAIN TE NANCE Particular focus has been placed on maintenance and service with the G series. The result is a coherent service concept that is characterized by reliability and ease of access. Sophisticated details such as the outward-folding lubrication system and an improved refueling situation make servicing the machine extremely convenient and safe. The technological innovations have also made it possible to extend the overall maintenance intervals once again. Thanks to the large-scale e-box, the central electrical distributors and electronic modules are protected from environmental influences even in extreme conditions and ensure maximum machine availability.

THE NEW 817 ELECTRO BATTERY AS THE FIRST MODEL OF A NEW MACHINE CONCEPT
Useful technology for maximum CO2 savings and flexibility. The 817 Electro Battery battery-powered electric material handler is the first of the freely movable battery-powered models that SENNEBOGEN will be adding to its tried-andtested electric range in the future. Thanks to dual power management, these models continue to offer all the advantages of cablebased electric material handlers, combined with total freedom of movement. Completely safe, comfortable and fully mobile around the clock with zero emissions — a new technological milestone for the industry.
Emission-free electric material handlers have been available in wired form for many years. For over 30 years, SENNEBOGEN has been building electric material handlers, which are used stationary or with limited mobility due to the cable, and provide a solution for a wide range of applications. Pure battery-powered devices already on the market have proven to be disadvantageous so far due to the limited operating time of the batteries. Not so with the new SENNEBOGEN 817 Electro Battery: the new mobile electric material handler with battery technology combines the advantages of both solutions. With the SENNEBOGEN battery-powered material handler, it is possible to continue working even when it is connected to the mains power for charging.
In mains operation, dual power management ensures that the power supply from the mains is used for the work movements, while the excess power fed in also recharges the batteries so that the machine can then work independently again. With an assumed 2,000 operating hours per year and energy generation from renewable energy sources, the batterypowered material handler saves an average of 31,800kg of CO2 per year compared to its diesel-powered counterparts — and with equal freedom of movement. In future, the battery option will be available for the entire electric series of the 817 to 825 models.
With the launch of the new 817 E Electro Battery battery-powered electric material handler, SENNEBOGEN is expanding its electric range with freely movable models that perfectly combine the advantages of stationary electric and battery-powered material handlers.
DUAL POWER MANAGEMENT: ZERO-EMISSIONS MOBILITY WITHOUT LIMITS The battery-powered version of the popular SENNEBOGEN 817 E electric material handler with 9m reach and 18t operating weight thus combines the advantages of two machine concepts: if the material handler is connected to the mains, it uses the wired power supply for the work movements without restricting the freedom of movement of the uppercarriage and equipment. Because the charging power is supplied to the undercarriage, the machine can continue to swivel and work 360°. If more power is supplied to the machine than it consumes, this is used to charge the batteries at the rear. If the mains connection is disconnected, the 817 Electro Battery automatically detects this and works autonomously in battery operation with the same performance data. Depending on the power requirement, the battery pack enables working times of six
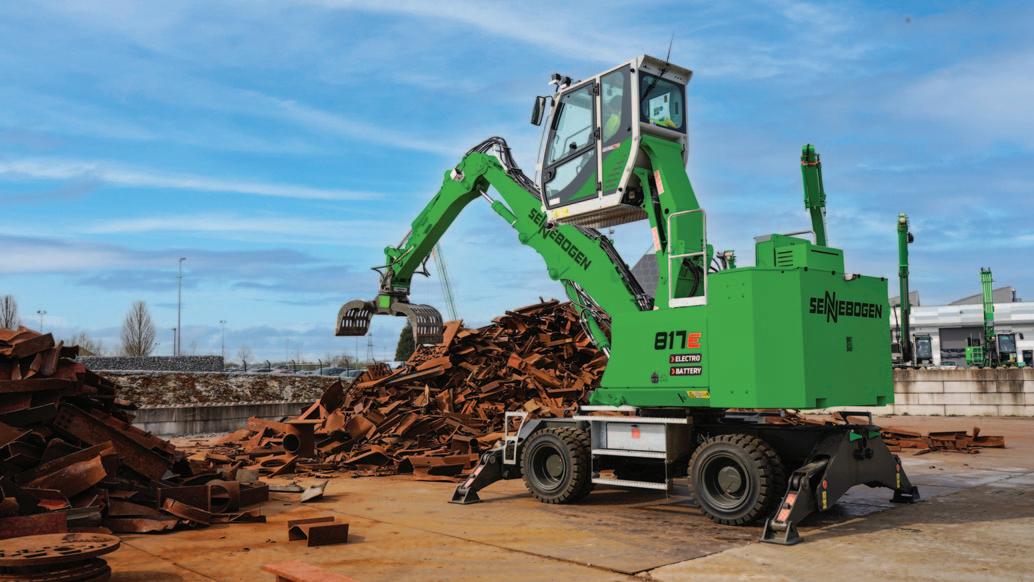
hours without recharging.
The great advantage of dual power management then comes into play once again: if the machine is working in a working position for one hour, for example, it can be conveniently connected to the power supply via a standardized CE plug and charged without having to stop work. The capacities of the battery are easily and flexibly charged so that the machine can be operated continuously over a complete shift and does not need to be switched off for charging.
PRACTICAL BATTERY TECHNOLOGY FOR EVERY OPERATION, COMBINED WITH PROVEN LARGE-SCALE SERIES TECHNOLOGY The machine also impresses with its practical design. Thanks to the CEE 63 A connector system, the 817 Electro Battery can use the existing infrastructure of an industrial company. Investments in expensive charging stations can be avoided thanks to the 44W on-board charger. Charging the batteries at any location is also an option, as a simple industrial socket is sufficient. Another advantage of a battery-powered electric material handler: current peaks when working with the machine can be avoided via peak shaving, i.e. if more power is required, e.g. during combined movements and a full grab, this can be covered by the battery. The connected load is thus reduced to 44kW without further restrictions. The integrated power electronics also ensure a gentle motor start that is particularly gentle on the mains power grid.
With the wealth of innovative drive technology, SENNEBOGEN continues to rely on the proven large-scale series technology that has always characterized the brand’s material handlers. The certified high-voltage battery systems, which were specially developed for off-road applications and are already used in many e-mobility applications, are also used for the batteries themselves: for about 3,000 full charge cycles.
MORE CONVENIENCE, REDUCED SERVICE REQUIREMENTS, MAXIMUM SAFETY The battery model also offers all the advantages of the tried-and-tested SENNEBOGEN electric material handler in terms of operator comfort and service — elevating Multicab comfort cab included. Thanks to this innovative batterysupported electric solution, all applications in the hall will be emission-free in the future and alleviate the burden on employees. At the same time, the machine operates with less vibration and noise, does not need to be refueled and has reduced service requirements, as there is no need to change the engine oil, etc. The operator can conveniently see the charge level indicator via the SENCON control system, does not have to carry out any separate settings even if the power supply is changed and therefore does not come into contact with the high-voltage technology used in normal operation.
The dual power management system automatically detects the energy source and switches to the corresponding working mode automatically. In addition to regular diagnosis, the machine independently detects faults and interventions in the highvoltage system and then switches off in a controlled manner, which guarantees completely safe processes in every situation.

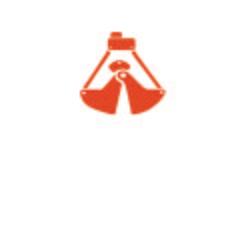



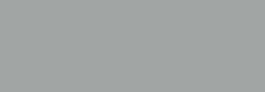
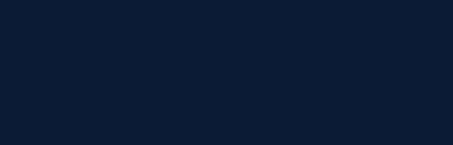