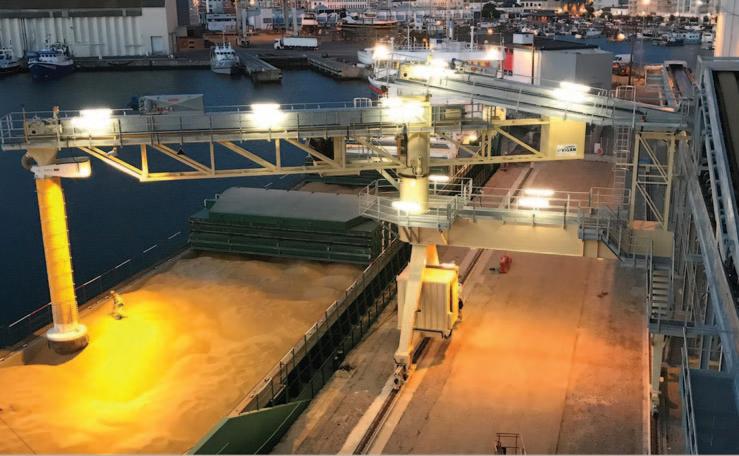
16 minute read
GETTING CHARGED UP WITH BULK LOADING EQUIPMENT
700tph VIGAN loader in operation at Les Sables d’Olonne in France.
Getting charged up
with bulk loading equipment
Combined loader (800tph) and unloader (400tph), at the Port of Rouen in France.
VIGAN’s loaders are all made in-house to ensure quality and longevity
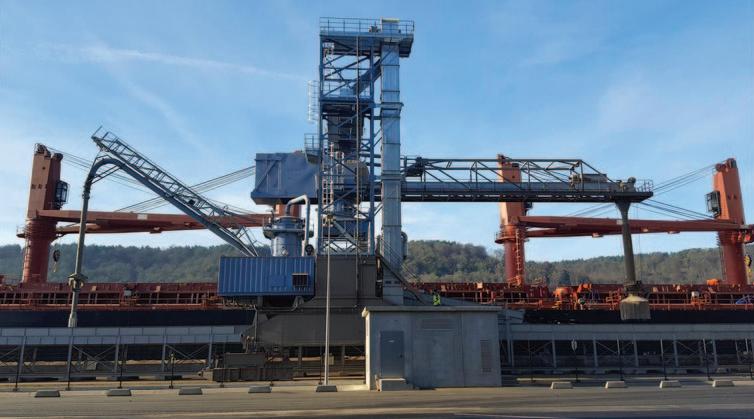
In our professional jargon, it is sometimes said that it is easier to load than to unload a grain vessel. Bearing in mind the physical laws of gravity, that is indisputable. In his day, Isaac Newton would most likely have been able to build a loader much faster than an unloader.
Technically speaking, this is still the case. However, loading has become much more than just getting cargo into vessels of all kinds and sizes. Loading has become a fully integrated activity. Sometimes conveyors have to fulfill unloading and loading tasks, smart systems must designate silos that will take certain cargo or grain qualities steered by in-line NIR (Near Infrared Spectro scopy) systems that screen these different qualities. Therefore loaders (and unloaders) are becoming less stand-alone tools and more a vital part of the whole logistic system. And that makes their design and functioning more complex than ever.
Moreover, exporting countries and exporting facilities are faced with other challenges: they are often close to or embedded in urban areas, which presents new challenges such as the need to reduce air pollution, dust and sound emissions. Other considerations such as aesthetic constraints of integration within the global landscape, and so forth, must be taken into account.
At the end of the day, the equipment must perform according to the specs: v capacity in tonnes per hour; v different types of cargo to load; v dB(A) sound emissions; v dust specs in particles per m³; v optimal coverage of the growing vessel sizes; v breakage-free handling; v operator friendly and easy; v safety and explosion hazard management;
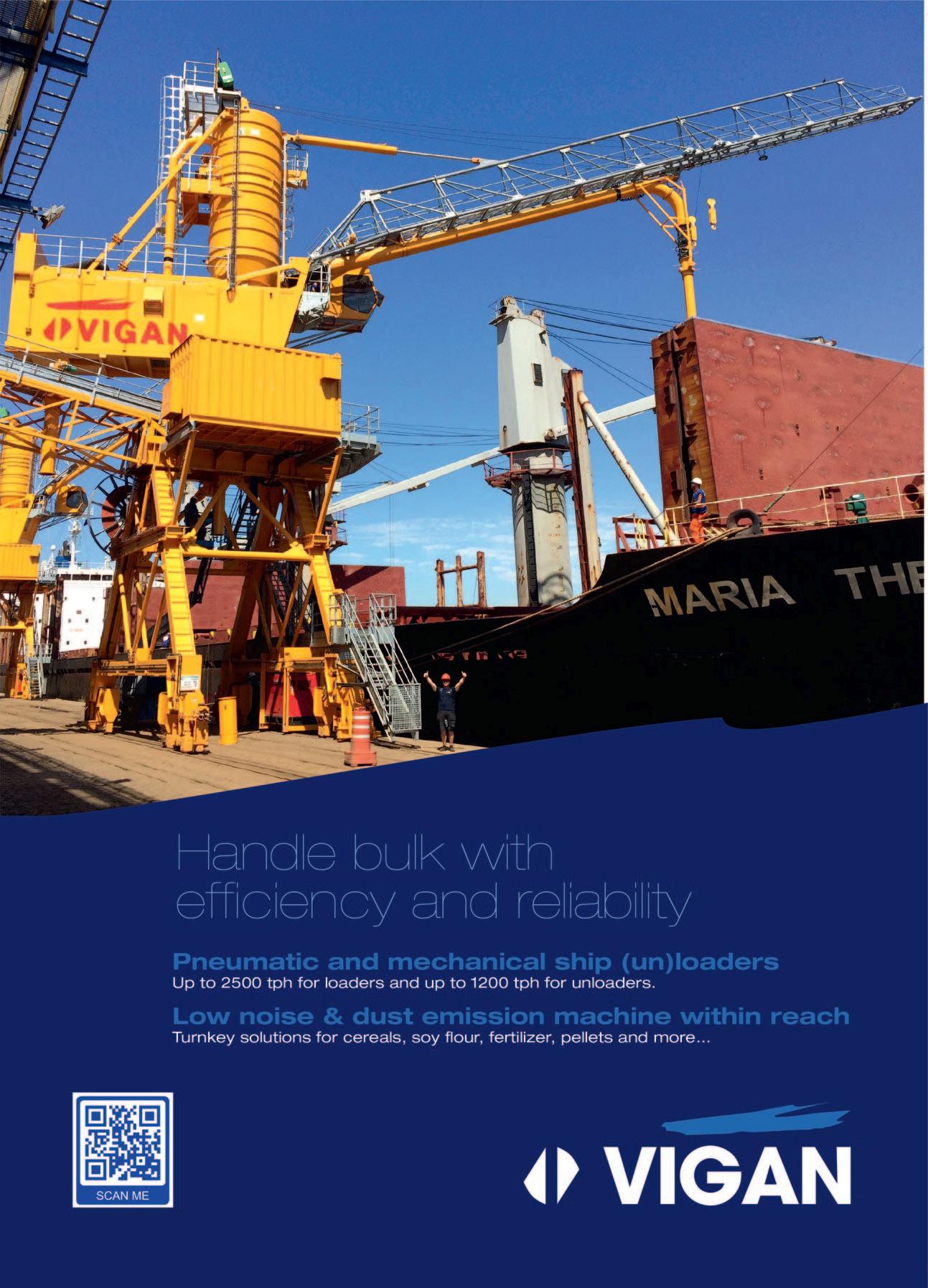
v
v specific products; quality finishing with respect to paintings, coatings, alloys and galvanization; electronic steering and
v
v v v
v monitoring; integration and functioning in the total concept; durability and robustness; energy consumption; spare parts and consumables tendencies; and servicing programmes and time intervals.
VIGAN has a particular opinion and approach on how to fulfill these

typical but important features. At the ground level, VIGAN designs and builds everything under one roof at its facilities in Belgium. It laser cuts its steel plates, folds them, welds them, sandblasts them, paints them, electrifies them and finally pre-assembles them in its large industrial halls. In this way, VIGAN reduces local assembly times to the minimum, and can also avoid any impact from unforeseen events, such as weather forecasts, availability of secondary parts, local specific manpower.
This is a logical and strong USP (unique selling point) for VIGAN. Ever more companies are now outsourcing strategic (and maybe expensive) production sequences out of their factories and even out of their country. VIGAN does not adhere to this philosophy. Its machines have very long expected lifetimes, so it is essential that the company remains fully in control of every little engineering and functioning detail. This is why VIGAN will continue to work in this way. It also helps VIGAN to make sure that, even after many years in operation, machines can still be adapted to fast-moving new standards. The past has proven to VIGAN that this approach is valid and trustworthy. As technology continues to evolve nearly at lightspeed, the company has no doubt that this is the best philosophy. Therefore, any machine that is made by VIGAN is also ‘made in Belgium’ — in its own facilities, and not just a statement on paper. Customers can visit VIGAN’s loaders and other equipment during production or before shipment.

1,000tph loader at the Port of Szczecin in Poland.
300tph loader at Ghent in Belgium. ENGINEERING & EQUIPMENT
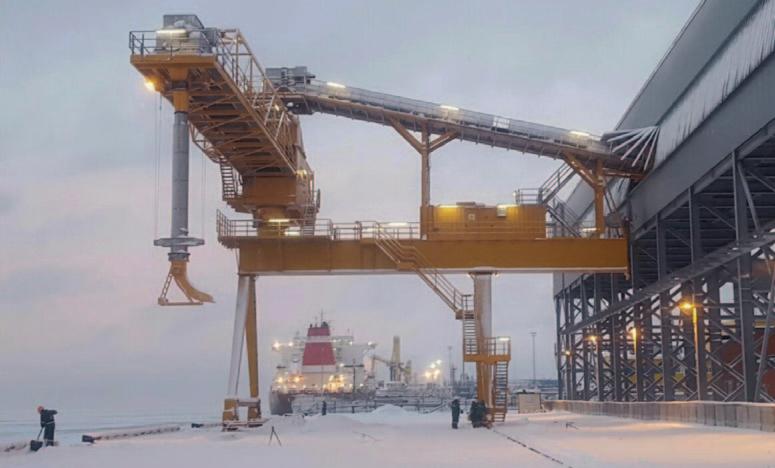
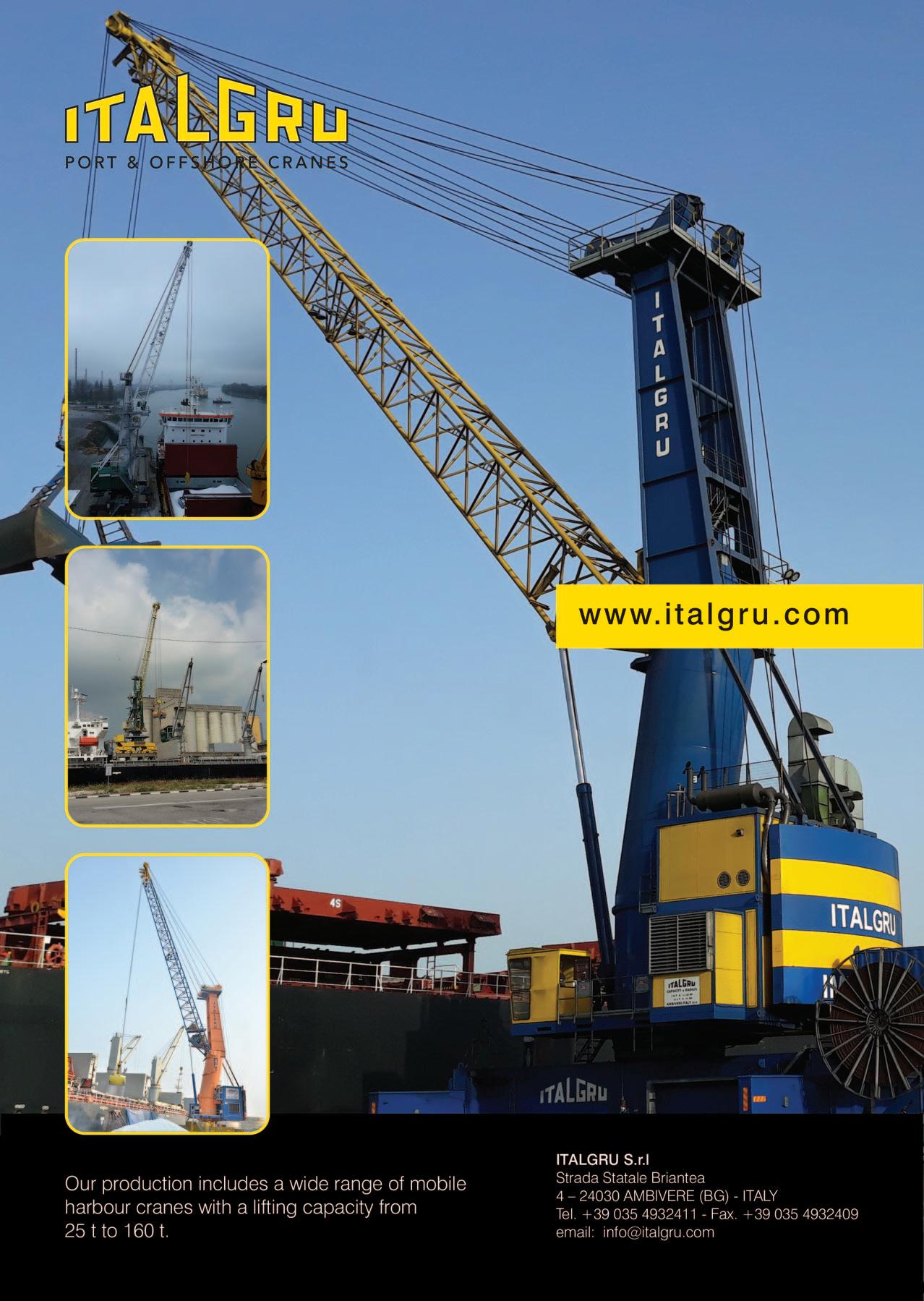
Dry bulk materials such as wheat, cement, limestone, calcium carbonate and many other related bulk solids are transported from one point to another for various purposes. Numerous bulk handling industries including the cement industry necessitate high loading capacities. Bulk trucks are used to transport large amounts of dry bulk solids. Stationary or mobile bulk truck loaders are utilized to load dry bulk solids from bulk bags, stockpiles and other relevant sources into bulk transporter vehicles. Stationary dry bulk loading stations are frequently not sufficient because of logistics challenges within a working plant. Mobile bulk truck loaders are the go-to choice to address such challenges.
WHAT IS A BULK TRUCK LOADER AND WHAT TYPES ARE AVAILABLE? Mobile bulk truck loaders are machines/systems that render an effective and efficient method of loading dry bulk materials into bulk trucks. They are generally used to automatically and dustfree load dry bulk solids from stockpiles, big bags (FIBC) and other places into bulk transporter vehicles such as tanker trucks, tipper trucks etc. Polimak offers three distinct variations of mobile bulk truck loaders. v Mobile big bag discharging and bulk truck loading system: this system is used to effectively discharge dry bulk materials from big bags and load them into silo trucks in a dustless manner. v Mobile truck loading with front end loader hopper system: this bulk truck loader is utilized to effectively dump bulk materials by a wheel loader and fill bulk trucks (e.g., tipper trucks). v Mobile truck loading with vacuum system: this variation of mobile truck loaders is used to efficiently convey dry bulk solids from a specific source like a stockpile to a bulk truck.
THE MOBILE BIG BAG DISCHARGING AND BULK TRUCK LOADING SYSTEM Polimak’s mobile big bag discharging and bulk truck loading system ensures systematic bulk bag discharging and dustless loading of dry bulk materials into tanker trucks. This system eliminates operational challenges by providing better logistic solutions in working plants over stationary loading stations. It may not be possible for huge bulk trucks to easily approach a stationary loading station in a plant but the mobile big bag discharging and bulk truck loading system renders improved manoeuvrability for handling dry bulk solids. The system comprises many components. Some of the main components include the following: v Screw conveyor: this ensures smooth conveyance of dry bulk materials from a bulk bag discharging hopper to a connected loading spout from where the material free falls into the tanker truck. It makes an acute angle (45°) during loading operations. v Screw jack: two screw jacks are installed on the system and are primarily responsible for raising and lowering the screw conveyor. v Hopper: the discharging hopper is used to discharge bulk materials from bulk bags into downstream equipment during material handling. A screw conveyor is a piece of downstream equipment connected to the hopper. The hopper can be designed to have additional features such as a cutting knife and agitators. v Loading spout: a loading spout is connected to a screw conveyor’s outlet port. It allows smooth bulk material deliverance into a silo truck. The loading
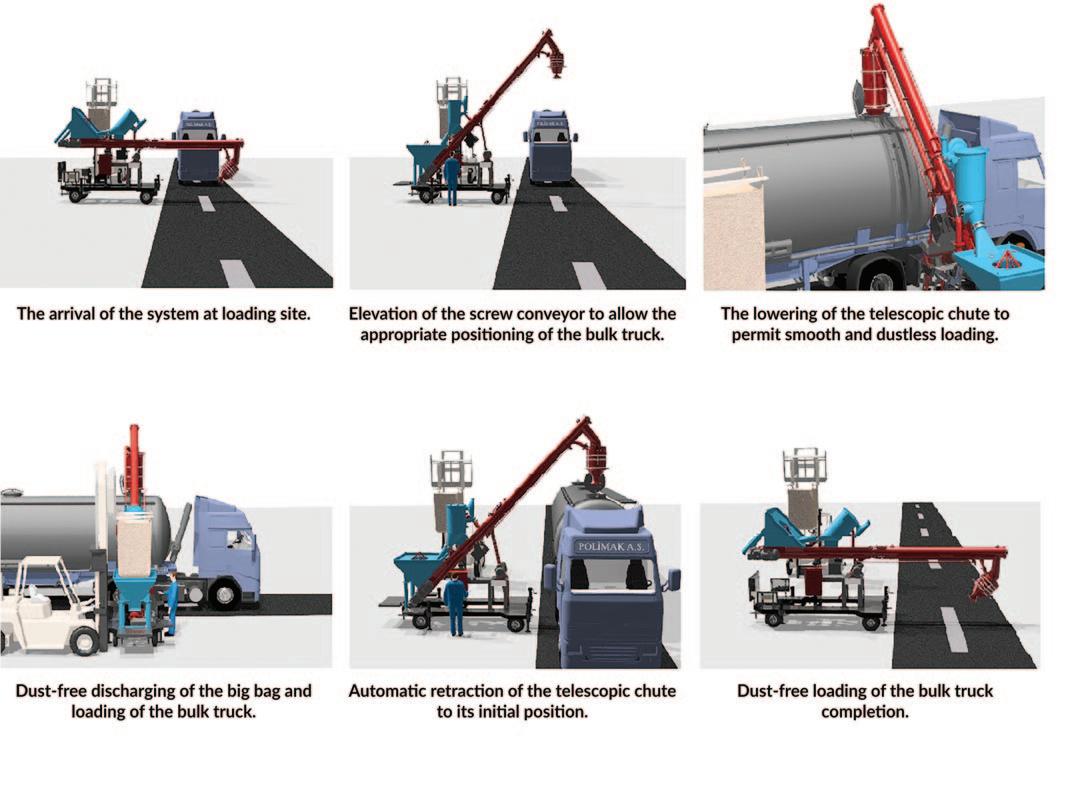

below also aids with dust suction within the system, thereby allowing practically dust free loading. v Chassis: a four-wheeled mobile chassis allows swift and easier manoeuvrability of the entire system. Swivel jacks are installed on the chassis to provide rigidity while loading a bulk truck. v Dust collection system: this system is responsible for creating a clean dustfree operating environment. It makes use of the pressurized air produced by an air compressor to successfully suck dust within the system. The captured dust is fed back to the material flow during loading.
HOW DOES A MOBILE BIG BAG DISCHARGING AND BULK TRUCK LOADING SYSTEM WORK? The system is towed to the site of use during dry bulk material handling. The screw conveyor is elevated by screw jacks and a loading bulk truck is moved into position such that the outlet of a loading spout is right above a bulk truck’s filler neck. The spout is lowered towards a filler neck to create a precise fit. A bulk bag is placed on a hopper to begin the discharging process. A discharging hopper with or without additional features (a cutting knife and agitators) is utilized. The bulk material is discharged through a hopper and supplied to a piece of downstream equipment (screw conveyor), which then conveys the material up to its outlet port. The bulk solids free-fall from a screw conveyor through a loading spout into a bulk truck.
During operation, dust is produced within the system. The dust produced within the system is captured by a dust collection unit connected to the hopper and loading spout. Dust particles trapped on filters inside a dust collection system are fed back into the material flow. With the help of a level sensor installed on the spout, loading is stopped when the tanker gets filled. The loading below retracts to its initial position a few minutes after loading stops. This ensures complete dust suction within the system. Interaction with the machine is achieved via the use of a control panel.
BENEFITS OF A MOBILE BIG BAG DISCHARGING AND BULK TRUCK LOADING SYSTEM Polimak’s mobile big bag discharging and bulk truck loading system guarantees safe working practices and ensures large capacity deliverance of dry bulk materials within a short period. Other benefits which our bulk truck loader offers are: v cost-effective; v low maintenance and easier to clean; v easy manoeuvrability within a plant; v adjustable loading spout for different heights; v environmental friendly as well as operator’s safety; v no dust emission and bulk material loss prevention; and v problem-free which allows it to be used for a long period without maintenance.
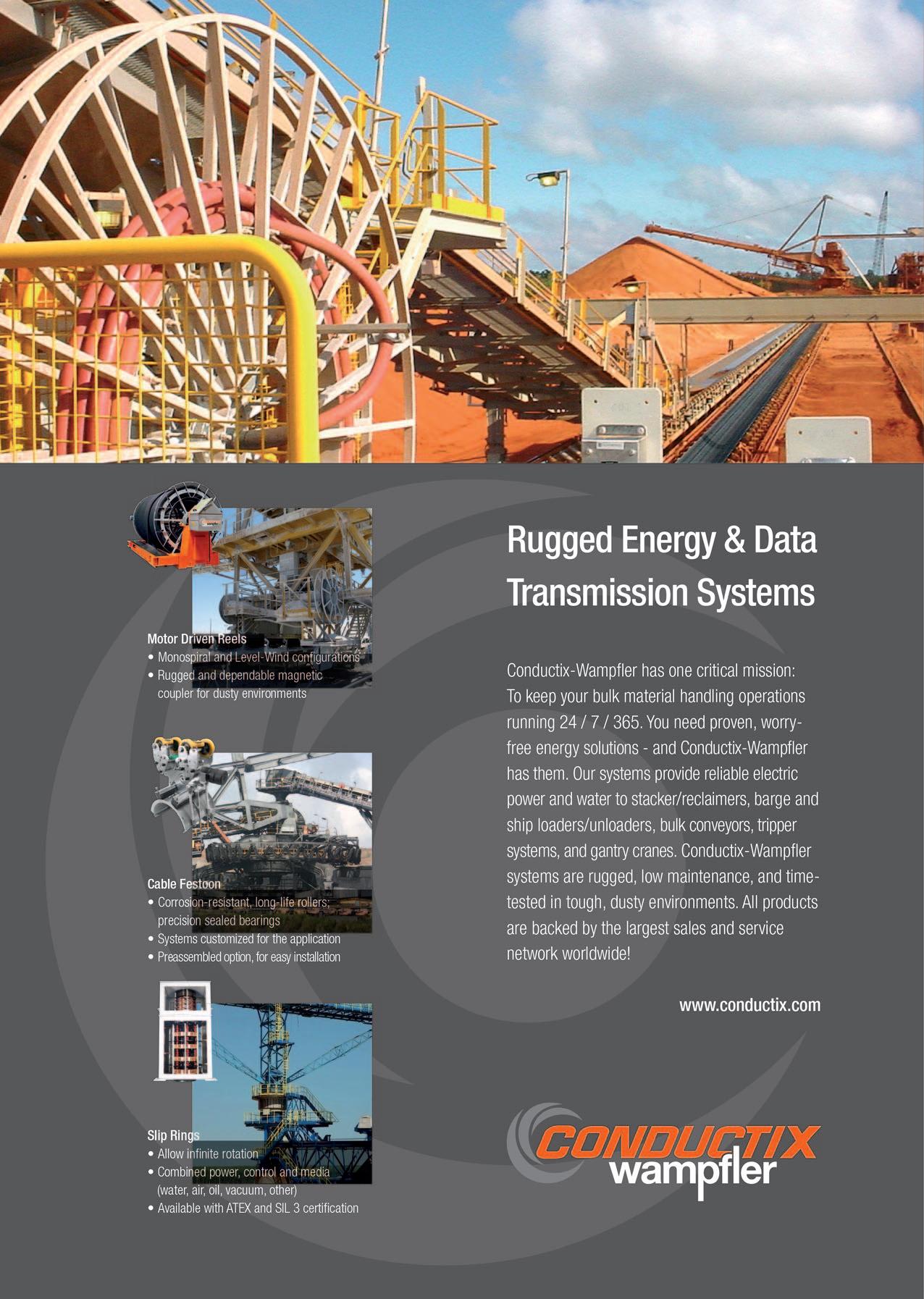
ENGINEERING & EQUIPMENT International reach for Bedeschi shiploaders

Bedeschi shiploader for Cargill Australia in operation.
In an ever-more globalized and competitive world, port infrastructure is changing quickly. There is often the need to handle bulk material far from the quarries by sea with ships that are becoming bigger.
Handling dry bulk is very different to handling containers and many aspects must be addressed: loading rate, weather conditions (wind especially), dropping height, technology used to load/unload the material and its specific characteristics. It seems clear that to guarantee efficiency in the ports in this changed scenario, it is necessary to optimize the land side logistics (storage size and layout), reduce the loading/unloading times and create functional and eco-friendly terminals.
Investments into eco-friendly and innovative equipment are unavoidable for the complete port environment.
Bedeschi’s R&D Department is constantly working to improve the capability of its systems, focusing on environmental protection, energy efficiency and pollution prevention that will become even more important in our industries and this is where Bedeschi is pushing the upcoming technology development efforts.
The solutions Bedeschi is improving in its machines to reduce dust emissions during bulk material loading and unloading operations are wide-ranging: the proper selection of belt speed according to the handled cargo; the positioning of the belt conveyor and tripper in an enclosed gallery; the use of pipe conveyor and enclosed conveyor, where possible; and the use of gas cleaning and water spray for dust suppression.
The use of different conveying systems, like screw conveyors and chain conveyors, might be an interesting alternative to avoid dust pollution.
All these solutions can also be applied to shiploaders. Here, chute selection is one of the aspects that requires close attention to ensure environmental protection.
The choice of the chute depends on the material’s fragility, especially for the pelletized or briquetted types that can be easily broken.
Bedeschi dedicated special attention and in-depth studies to the loading chutes. This includes, for example, the telescopic chute with tiltable hopper to better control the flow with a very low environmental impact, suitable for dusty product, and the spiral chute to allow the loading of the vessel avoiding material falling from too great a height.
Bedeschi’s latest applications to guarantee environmental safeguard inside ports are detailed below:
CARGILL AUSTRALIA One of the best examples of Bedeschi’s engineering and manufacturing capabilities (see above). This shiploader is fully mobile on rubber tyres and can load grains and oilseeds on Panamax ships at a capacity of 1,000tph (tonnes per hour) received from trucks on a two-lane drive-over hopper, fully integrated and mobile with the shiploader itself. The shiploader is engineered according to local standards and loads the material dust-free thanks to a Cleveland Cascades telescopic chute. Moreover, due to the reduced availability of the receiving quay, the machine was delivered at site fully erected and dry tested.
AL SARH The client Al Sarh Trading Co. – Qatar has commissioned to Bedeschi to supply handling equipment to operate in Oman — Khatam Malaha.
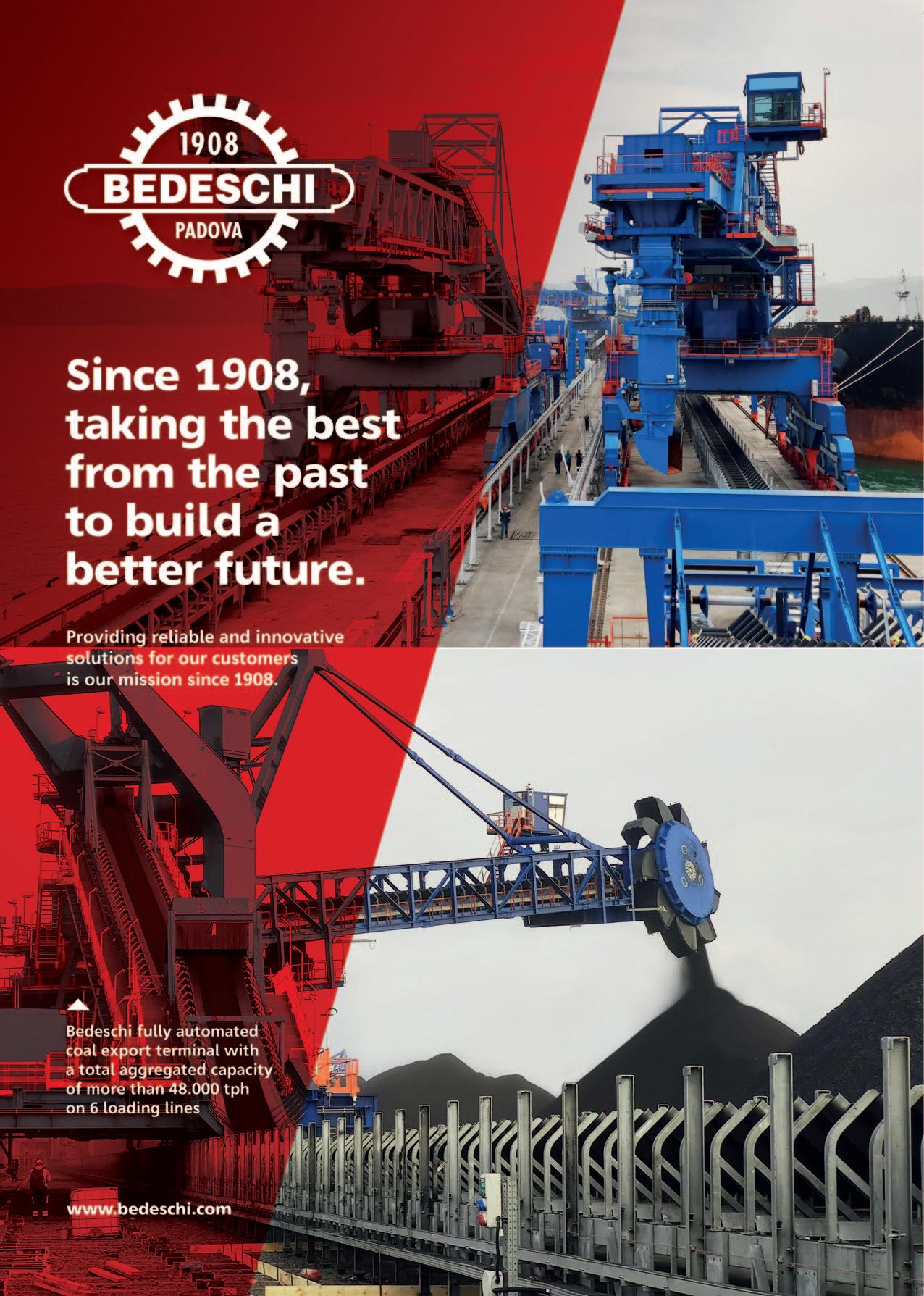
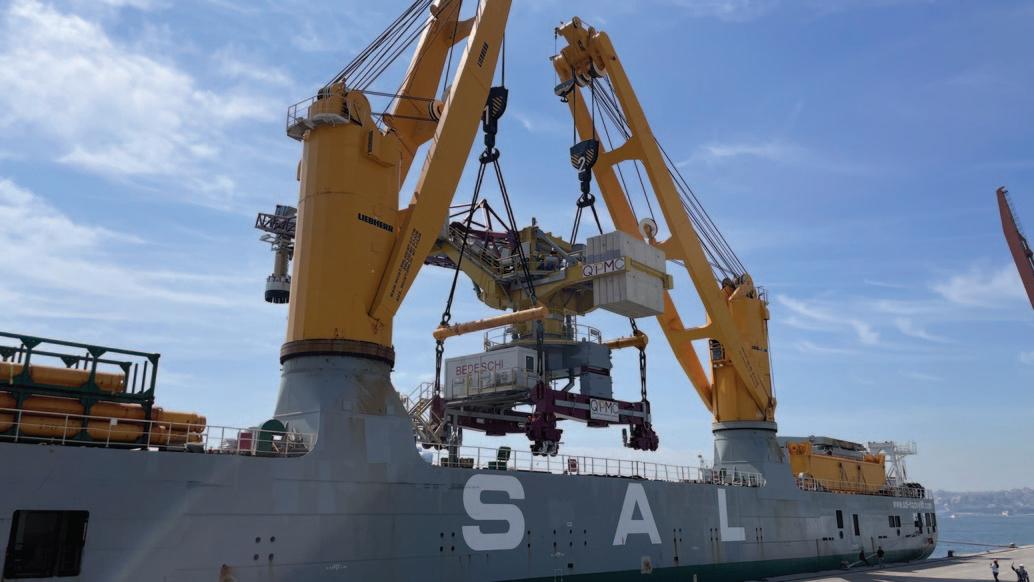
Bedeschi shiploader for Al Sarh delivered fully erected.
The equipment includes three conveyor belts with a total length of 4.3km, with capacity to handle gabbro and other materials at a rate of 2,000tph. The last section of the conveyor is engineered for offshore installation, with self-holding galleries structure installed above pylons.
This last section of the conveyors runs above to the sea, so to reduce the possibility of spillage of the material due to unexpected weather conditions, the belts run inside a gallery completely sealed on all four sides.
Approximately 2km on open sea, there is a luffing and slewing type shiploader. The capacity of the shiploader is 2,000tph to load vessels up to 55,000dwt. It is installed on an off-shore platform and designed to work on both sides of the platform, with a boom length of 30 metres.
WEST WEGO In this case study, Bedeschi supplied a shiploading system for the refurbishment and upgrade of an existing facility operating on the Mississippi River and the most important export terminal of the area.
Bedeschi has engineered, manufactured, installed and commissioned a shuttle type shiploading arm capable of loading grain and oilseeds at 80,000 bushels/hour (2,200tph) on vessels of up to 120,000dwt. Bedeschi undertook the project as well as related mechanical and electrical works on a turnkey basis. The equipment was preassembled in Italy and shipped to the New Orleans area in three main parts. This is a clear example of an eco-friendly solution intended to reduce to the minimum the downtime in port handling operations and maximizing the customer’s benefits.
Bedeschi shiploader operating on the Mississippi River.
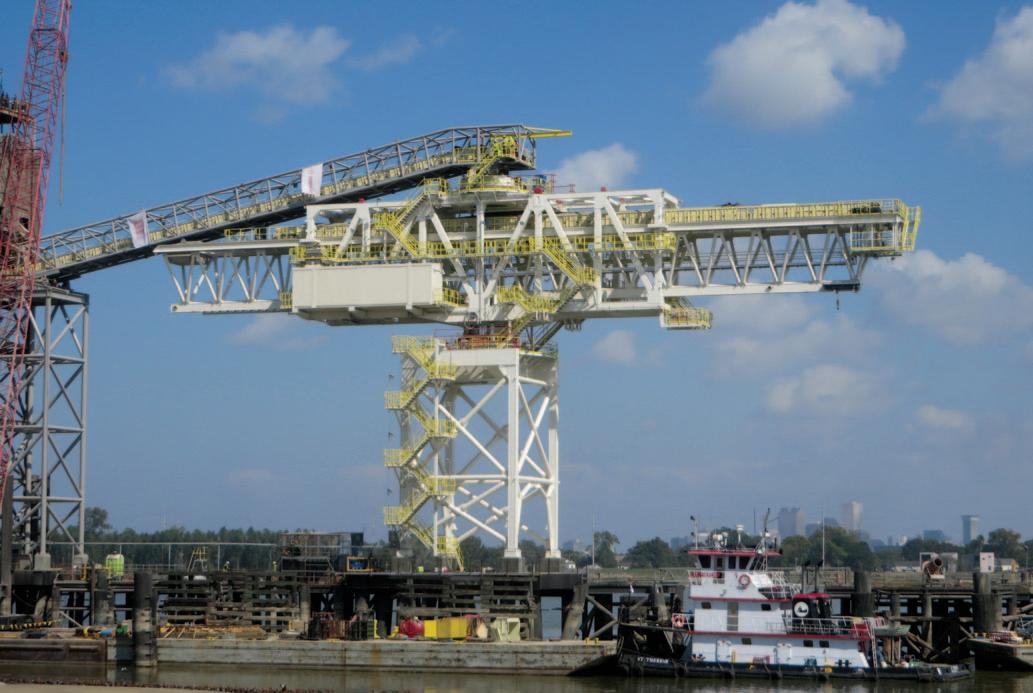
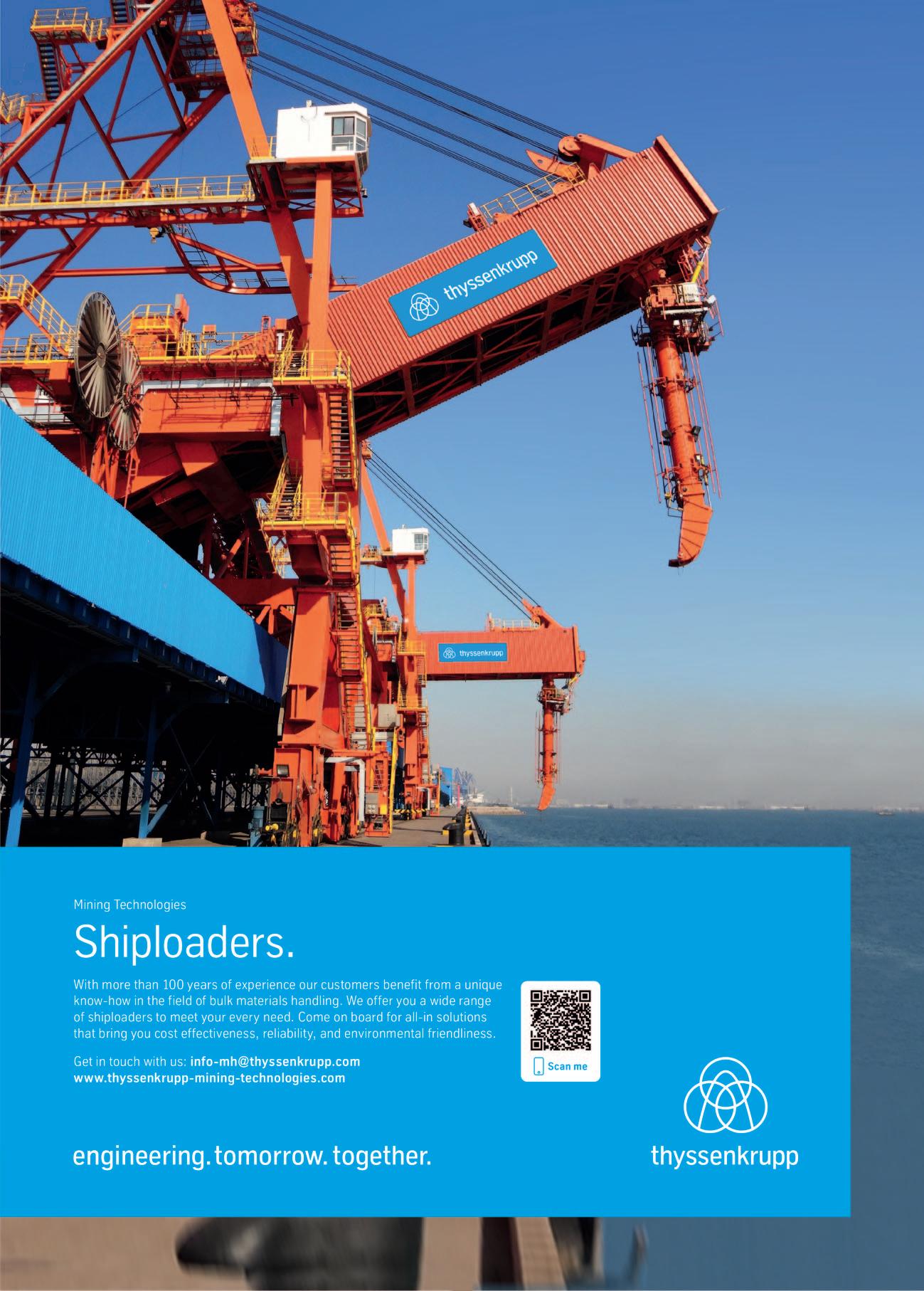
Efficient shiploading: Schrott Wetzel invests in environmentally friendly harbour colossus from SENNEBOGEN
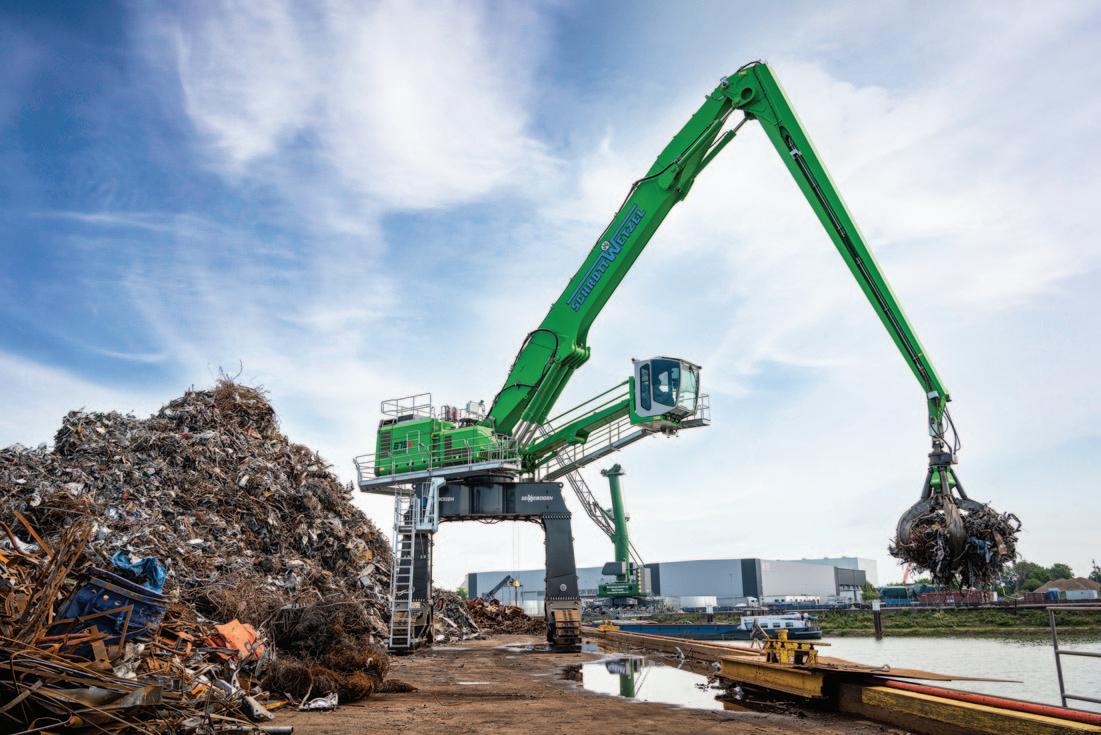
Mannheim-based Schrott Wetzel GmbH has invested in a new 875 E Hybrid material handler from SENNEBOGEN for efficient and fuel-saving scrap handling.
The green port colossus with crawler gantry undercarriage was delivered by Schlüter für Baumaschinen and is intended to help the scrap supplier optimize its scrap and cargo handling under environmentally friendly conditions.
SCHROTT WETZEL GMBH VALUES SUSTAINABLE MANAGEMENT Schrott Wetzel GmbH is a family-run company that has established itself as one of the leading providers in scrap processing and recycling since the early 1950s. Schrott Wetzel GmbH obtains its material from the regions around its own sites, within a radius of 150–200km. After sorting, processing and loading, the scrap is then transported by ship to consumers or to the company's own deep-sea terminal in Ghent. The deepsea orders reach consumers all over the world. For years, Schrott Wetzel GmbH has paid special attention to the environment and has therefore made the responsible use of limited raw material resources an important duty.
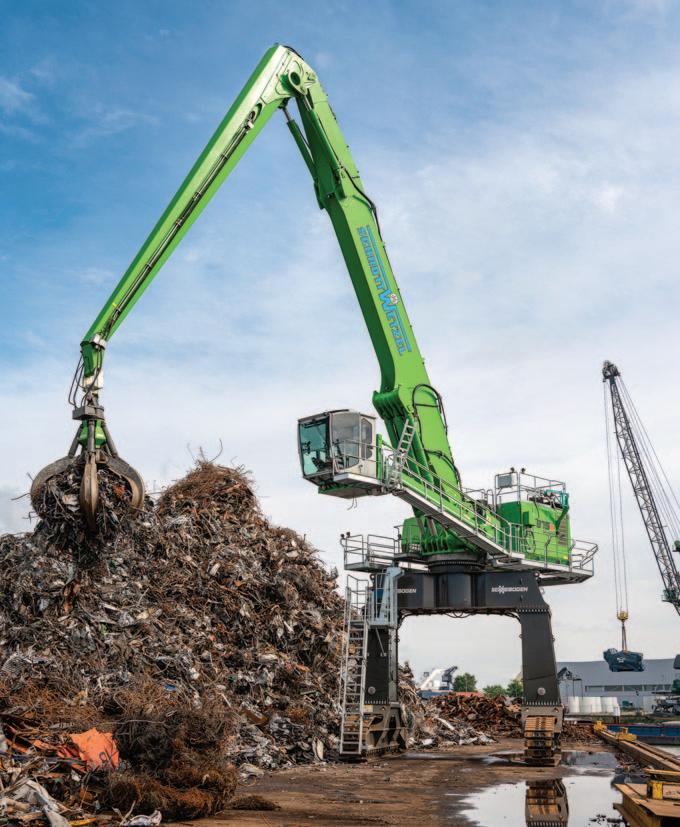
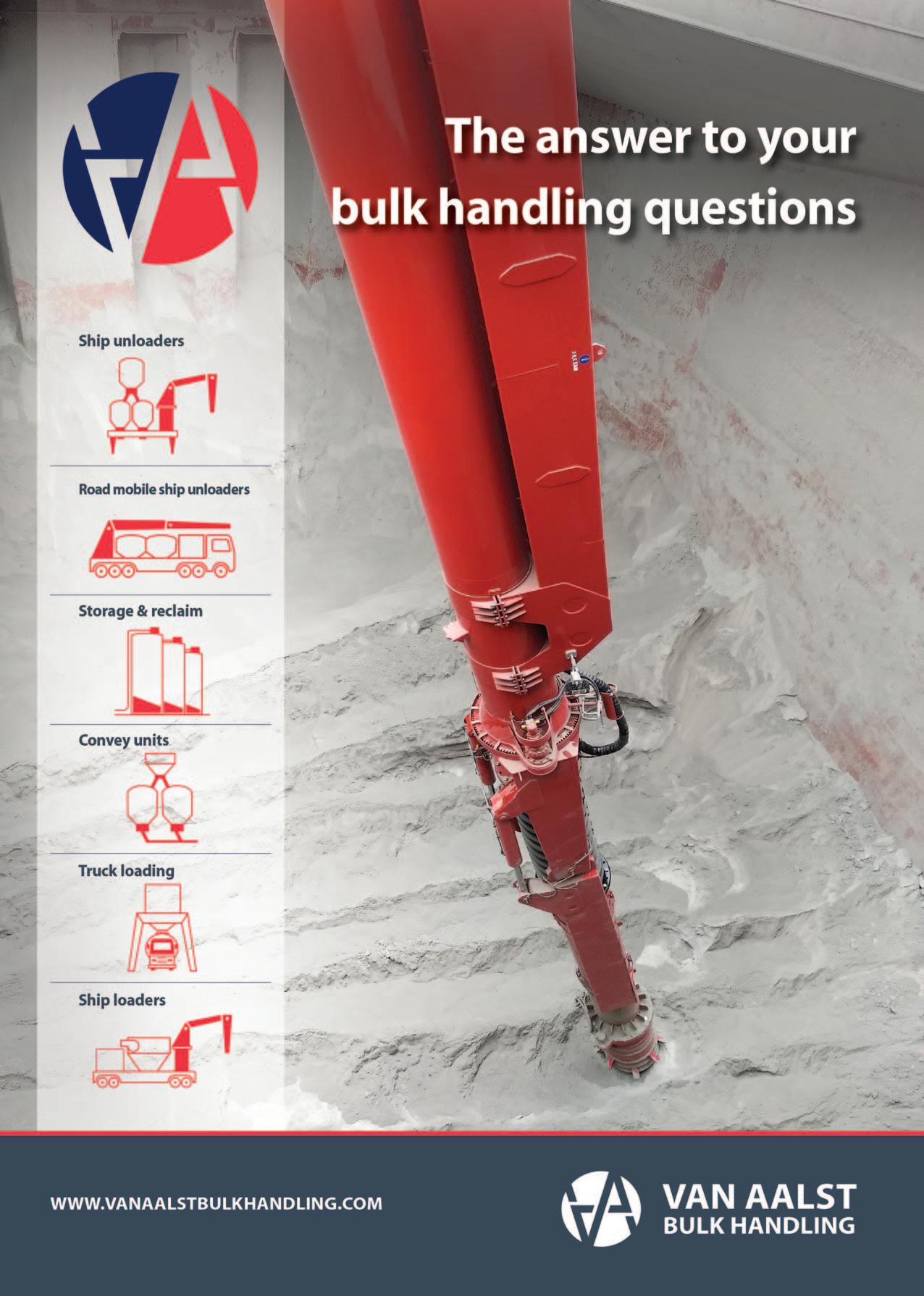
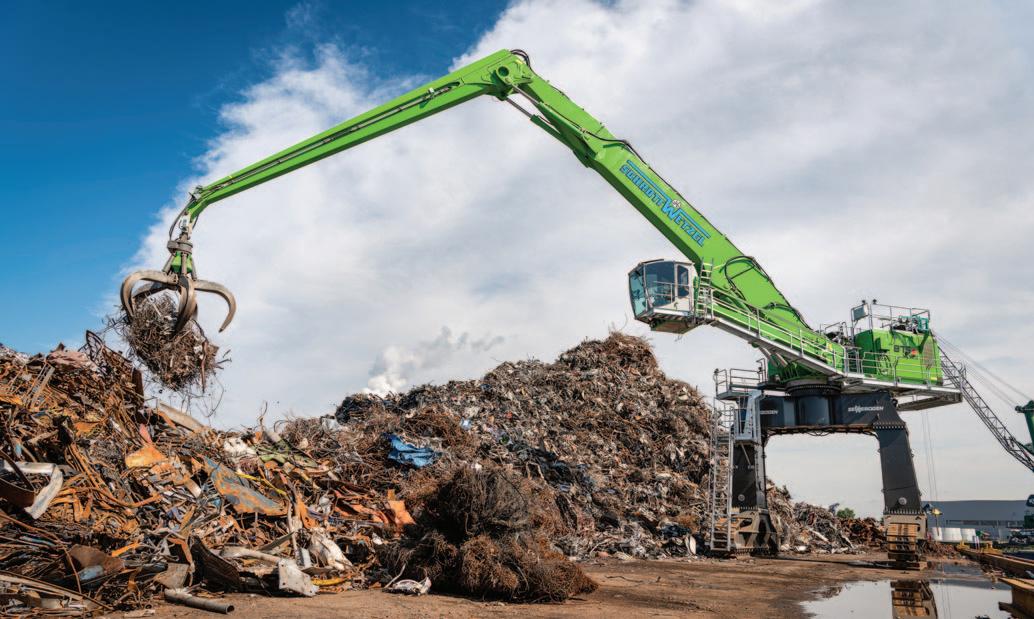
MAKING TWO INTO ONE: 875 E HYBRID REPLACES TWO MATERIAL HANDLERS FOR SHIP LOADING In order to guarantee efficient and raw material-saving work in the scrap yard as well as during ship loading, the warehouse handling must be designed as optimally as possible. In the past, Schrott Wetzel GmbH sometimes loaded ships with two material handlers. However, this method proved to be very inefficient, as the scrap had to be spread over a wide area due to the short reach of the material handlers so that both machines could access the ship. Thus, valuable storage space for ship loading was unnecessarily occupied. Therefore, the company led by Managing Director Dirk Sauter set out to find a machine that would replace both material handlers and at the same time optimize ship loading. With the 875 E Hybrid from SENNEBOGEN, the ideal machine for all requirements was found.
SPECIAL EQUIPMENT OF THE 875 E HYBRID FOR MORE LOAD CAPACITY AND SAFETY The SENNEBOGEN 875 E Hybrid is the ideal machine for challenging port handling. Thanks to a 391kW engine complying with the latest Stage V emission standards and a long reach of up to 29m, ships are loaded or unloaded quickly and efficiently. At the request of Schrott Wetzel GmbH, the ‘Port’ type K29 equipment was installed: this is a port stick built of high-strength steel, which achieves higher load capacity due to its lower deadweight. For best visibility even in bad weather, additional cameras and LED headlights were mounted on the material handler, and an additional ballast of 2.7 t on the counterweight ensures high stability on the dock.
SENNEBOGEN 875 E HYBRID: UP TO
50% ENERGY SAVINGS THANKS TO GREEN HYBRID TECHNOLOGY However, Sauter was most convinced by the Green Hybrid technology installed as standard. With the innovative SENNEBOGEN Green Hybrid energy recovery system, up to 50% energy can be saved compared to conventional concepts. The principle is simple to understand. A third hydraulic cylinder, placed centrally between the two lifting cylinders, stores energy in compressed gas cylinders when the boom is lowered. This stored energy is then available again for the next lift. The concept can be compared to a spring that is compressed and then gives off its energy again when it is released. With the correct system bias, around 50% of the power actually required can be substituted, thus saving energy costs on a large scale — ideal for use in ports.
Sauter is fascinated: “We looked at various options for our port and finally ended up with the 875 E Hybrid from SENNEBOGEN, because in addition to all the requirements needed for cargo handling, it also meets our environmental concerns. Thanks to the installed Green Hybrid energy recovery system, we also save even more fuel and CO2. Our focus is on being CO2-neutral and reducing our fuel consumption, and the machine definitely contributes to that.”
DCi
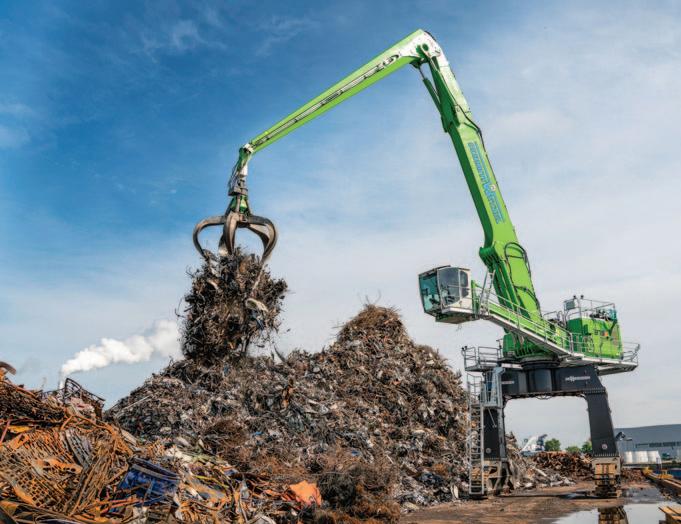
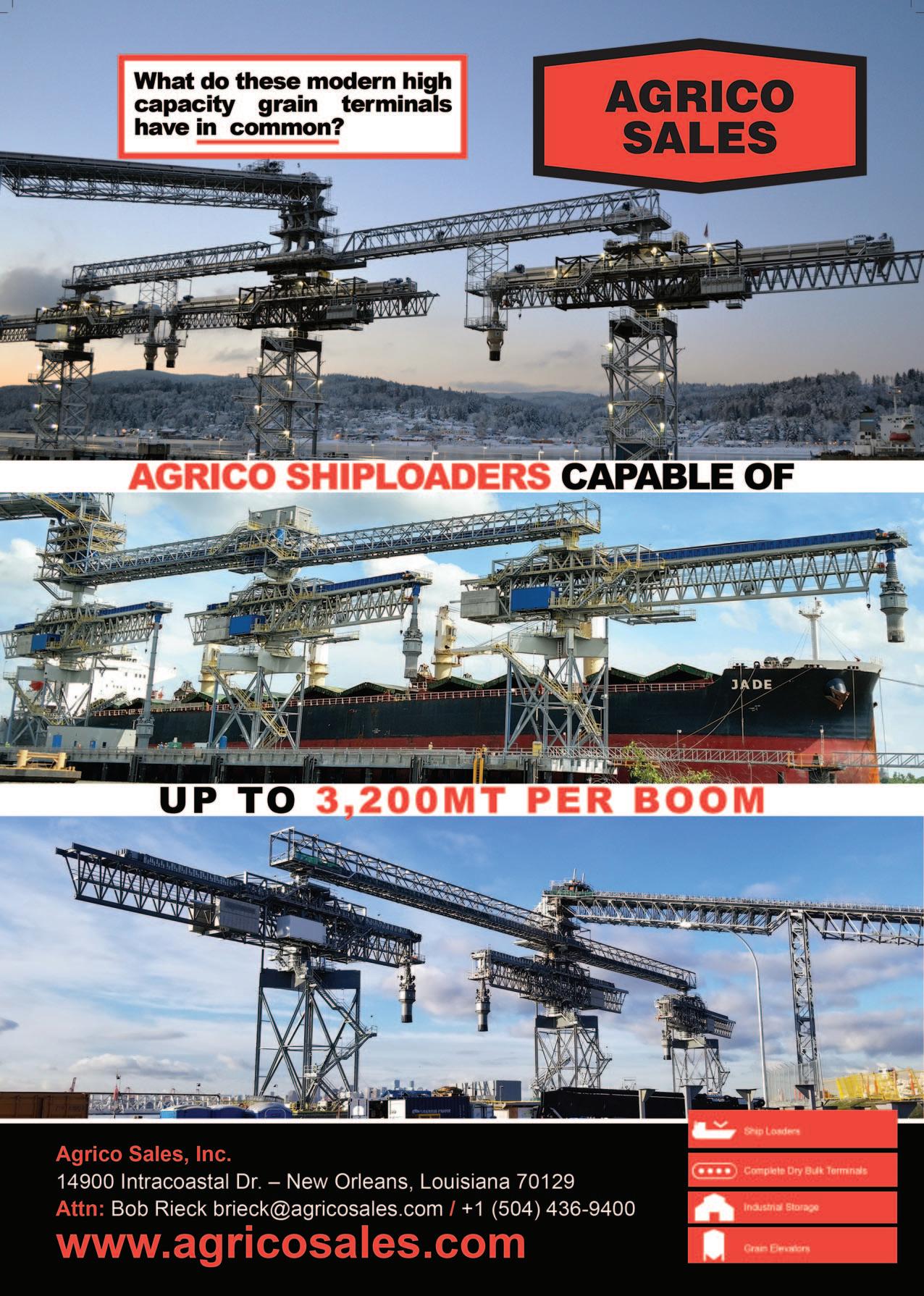
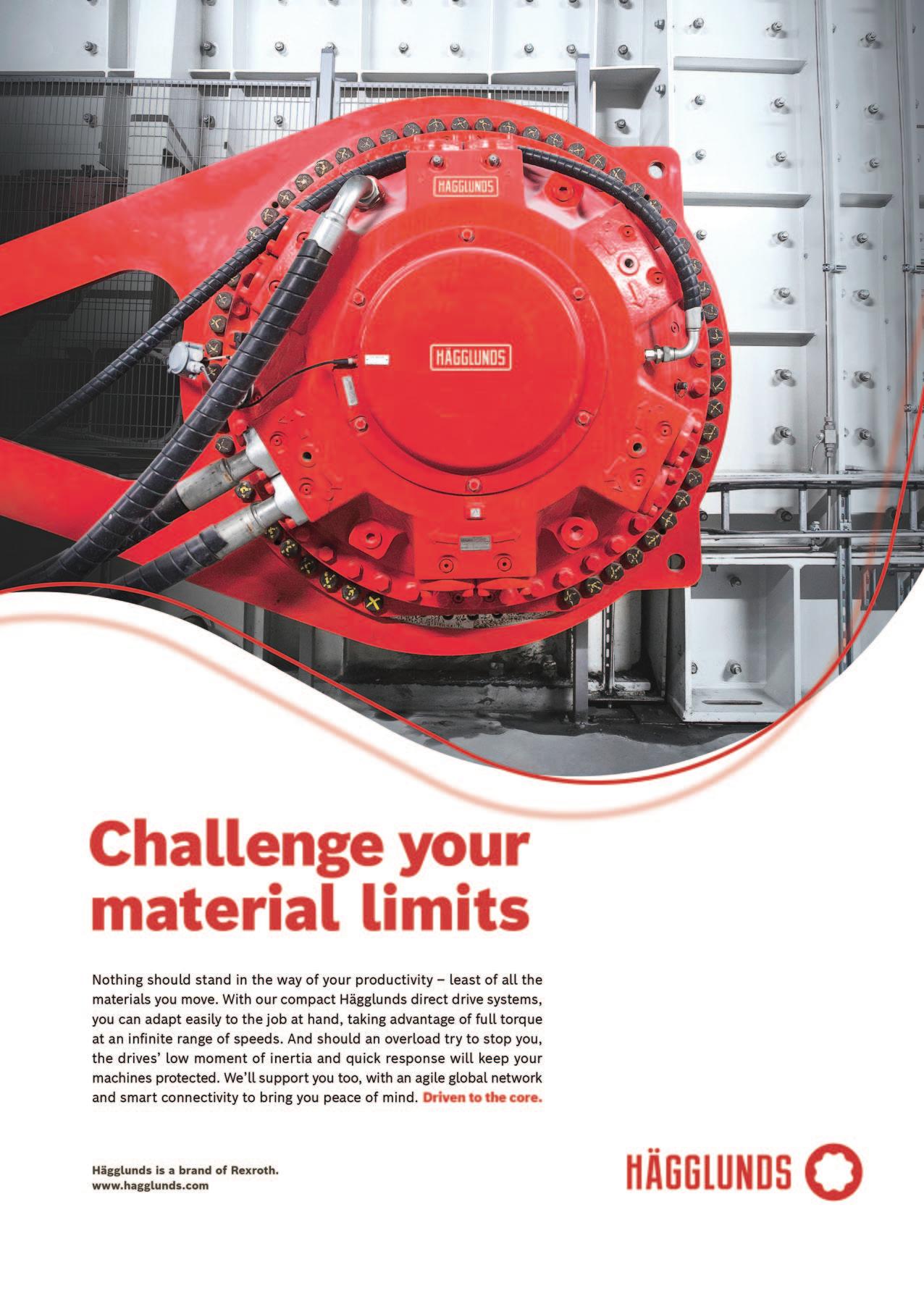