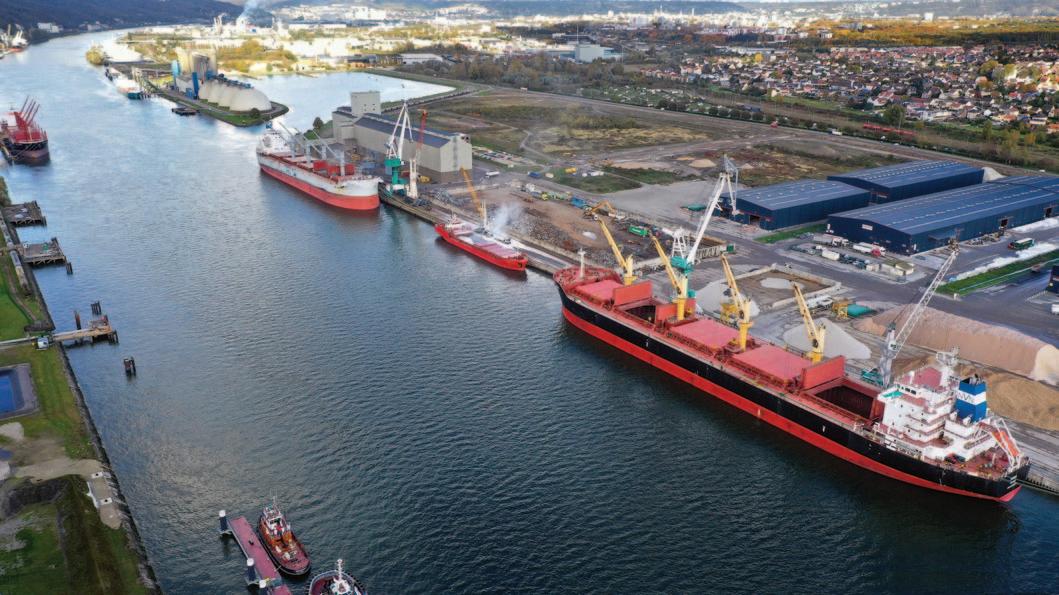
20 minute read
RUSSO–UKRAINIAN WAR CASTS MAJOR SHADOW OVER PORTS IN THE HAMBURG–LE HAVRE RANGE
PORTS & TERMINALS Russo–Ukrainian war
casts major shadow over ports in the Hamburg–Le Havre range
The Port of Rouen.
The 24 February invasion by Russia of Ukraine has had some unexpected consequences for ports across the entire Hamburg–Le Havre range. Clearly, with many grain exports out of Ukraine either delayed or cancelled entirely, importers are having to source grain from other suppliers, with France an obvious starting place in Europe.
Electricity generators have also had to find alternative supplies of energy given that Russian oil and gas are no longer available as embargoes begin to bite. Coal, therefore, has made a surprising important reappearance in some ports.
Haropa Port, which undertakes freight handling operations at the ports of Le Havre, Rouen and Paris reported total maritime traffic of 42.08mt (million tonnes) in the first half of the current year. Despite a 2% upswing in cereals traffic, overall dry bulk traffic dipped by 4.2% for the January–June period.
Aggregates for the construction industry declined by 22% or 260,000 tonnes as of the end of June, but were up 8% overall and remaining generally at historically high levels, underpinned by an positive trend in construction projects. The operator blames the slight downturn on unfavourable weather in the early months of the year, which had an impact on worksites and logistics conditions for materials.
The war in Ukraine, notes the company, has had a substantial impact on trade in agricultural products globally, and specifically on exports of wheat, corn and oilseeds, these being largely carried by sea, which means that stocks have been locked up in Black Sea ports while forthcoming harvests are also heavily compromised by the war.
Nevertheless, because France is a major European producer of wheat and barley, it remains a major exporter to those countries unable to grow sufficient grain of their own. Indeed, the current situation may well open up new market oppor tunities for French grain, believes Haropa.
Slightly further to the south, Port Atlantique La Rochelle remains France’s second-largest exporter of grain, with only Rouen handling more cereals traffic bound for overseas clients.
The difficulties in shipping grain consignments from ports in Ukraine linked to the recent hot and dry summer in Europe has meant that France is exporting more grain than it did last year. So, while some other traffic groups have seen something of a downturn compared to previous years, cereals consignments out of La Rochelle have notably increased.
For the first nine months of the present year, La Rochelle reported total traffic across all traffic types of 7.328mt which is an increase of 10.8%. However, grain traffic, at 3.24mt was up 29.6% from the 2.508mts reported in the corresponding 2021 period. Of this total, the three most important cereals were wheat (2.244mt), barley (577,363 tonnes) and corn (366,113 tonnes).
In contrast, forestry products grew by
Barry Cross
5.1%, from 435,233 tonnes to 457,515 tonnes, while other agricultural products declined by 0.5% from 579,052 tonnes to 576,430 tonnes.
However, figures relating to cereals invariably depend on a number of factors, most notably the weather. The 2020/2021 cereals campaign, for example, was one of the lowest in volume for nearly 20 years, due in part to extreme wet weather. In contrast, the 2021-2022 campaign generated exports of 3,962,066 tonnes, which is an increase of 51%. Indeed, as Vincent Poudevigne, General Manager of the Sica Atlantique Group — which is one of La Rochelle’s main cereals terminal operators — says, “The campaigns follow each other but are not alike!”
La Rochelle has basically two companies that handle the vast majority of export grain. The Sica Atlantique Group, which is a co-operative, and Socomac (Soufflet Group), which is an entirely private company. They benefit from being able to source products from what is France’s third-largest cereal growing region, where soft and hard wheat, corn, barley (for brewing or fodder), sunflower, rape, and alfalfa are all produced. Much of this arrives at the port via a highly developed rail network, which in 2021, for example, was responsible for transporting 88% of the total export grain volume.
The importance of grain at La Rochelle cannot be underestimated. In 2021, for example, the combined volumes of cereals and oilseed amounted to 37% of total traffic at the port, which remarkably was 13% lower than the previous year. The recent increase in export consignments could very well mean that the preeminence of this traffic sector could be reestablished in 2022.
Customers for La Rochelle’s grain include countries in the Maghreb, as well as those in the Middle East and West Africa. In recent years, there has also been an increase in intra-European traffic, particularly to Italy, Portugal and the United Kingdom.
Investment in handling is ongoing. In March 2018, Socomac inaugurated a new €32 million dockside silo that has a storage capacity of 63,000 tonnes. The company now has static storage capacity at its La Pallice terminal of 188,000 tonnes and has the ability to export 2mt annually, up from the previous limit of 1.6mt.
As for the Sica Atlantique Group, it has invested in a new grainoduct, which features two enclosed conveyor belts, aimed at increasing shipping outputs and absorbing logistical jolts. The grainoduct was commissioned in two stages: the first conveyor belt in June 2018 and the second in August 2018.
Between them, the two operators have a combined total of 232 storage cells, enabling them to undertake precise blending to meet the most demanding specifications of their customers.
In part, both operators benefit from the fact that the Port of La Rochelle is the only one on the Atlantic seaboard that offers safe and fast deep-water access for

Port of Antwerp-Bruges.
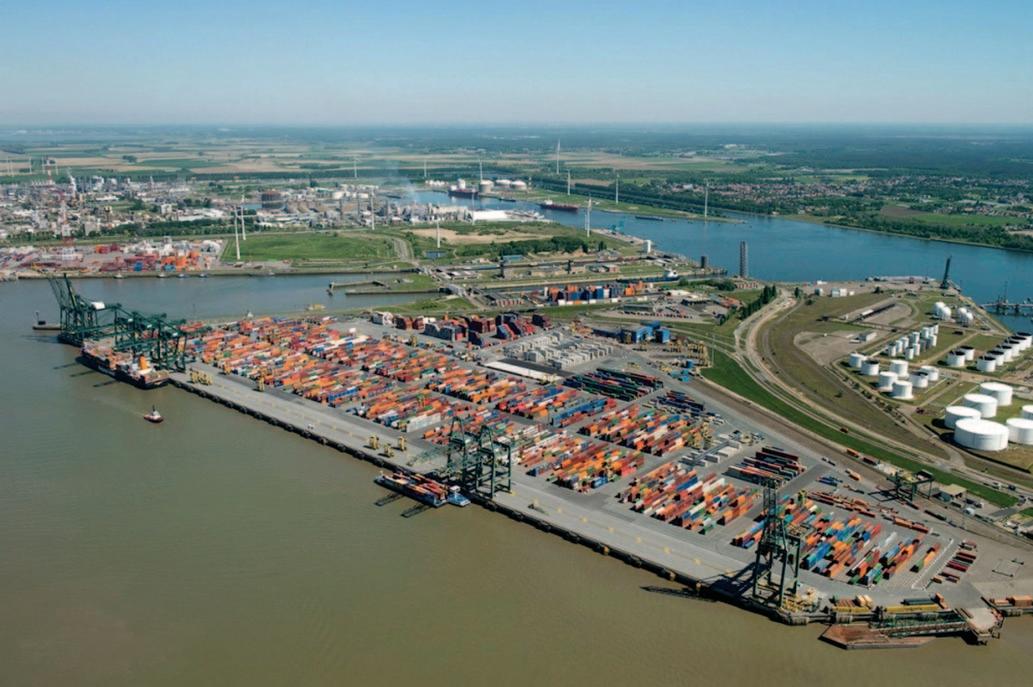
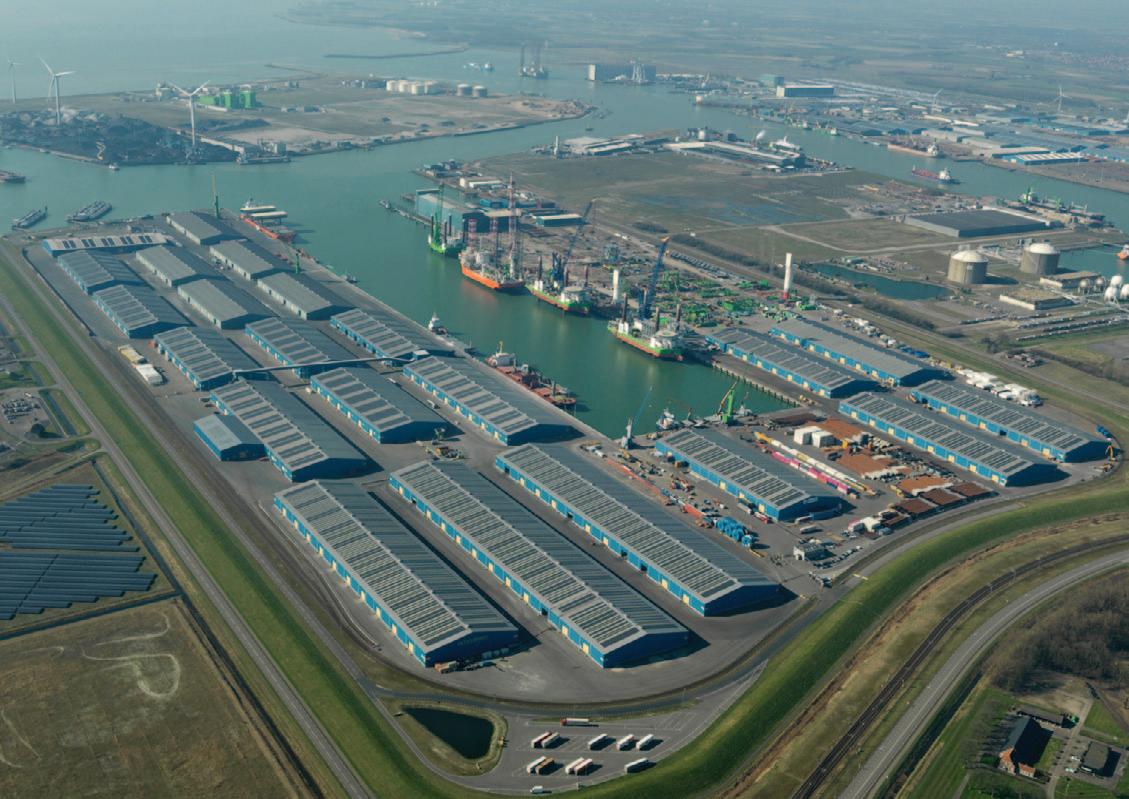
Panamax-type vessels. Loading rates are also extremely productive, with up to 2,500 tonnes/hour per berth achievable with two simultaneous gantry cranes, one loading at 1,000tph (tonnes per hour) and the other at 1,500tph.
Another port that has also unexpectedly benefited from the RussoUkrainian war is that of the Port of Antwerp-Bruges. This maritime facility, which sits at the very heart of the Hamburg–Le Havre range reported total traffic of 217.4mt for the first threequarters of the current year, equivalent to a slight increase of 0.8% compared to the same period last year.
Significantly, with the exception of the container market, all business segments at the port reported growth. In terms of tonnage, box throughput fell by 8.8% in the January–September period, which the port authority candidly attributes to the war in Ukraine, and business is not expected to return to normal until the first quarter of 2023 at the earliest.
In direct contrast, conventional breakbulk grew by 9.7%. Steel exports are holding their own, even while steel supply volumes are showing a downward trend as a result of high inventories and falling demand.
While the throughput of wood and building materials are showing a declining trend, both nevertheless still recorded some growth in the period in question.
As for dry bulk, it has experienced a boom, rising by 21.5% in the first nine months, astonishingly fuelled by growth in the transport of coal. As electricity producers in Europe scramble around for ways to close the gap left by the cut in Russian oil and gas, many have again sourced coal for power generation. The impact at Antwerp is that, while the port handled just 364,000 tonnes of coal in the first three quarters of 2021, in the corresponding 2022 period this has leapt to 2.43mt.
Throughput of iron ore is also showing growth this year, although scrap metal, sand and gravel have declined while other building materials show no change.
With Russian fertilizer now harder to acquire, both imports and exports of this commodity at Antwerp have picked up compared to the second quarter, although there is still an 11.8% decline from the record year of 2021.
Another of the big hitters in the Hamburg–Le Havre range is the crossborder North Sea Port, which encompasses the ports of Vlissingen, in the Netherlands, and Ghent, in Belgium. It reported total traffic of 57mt in the first three quarters of this year, up 9.3%. To put this into perspective, the coronavirus pandemic in the first three quarters of 2020 caused a 13% traffic drop, while growth of 9% was generated in the first three quarters of last year.
In January–September 2022, dry bulk traffic at the port grew by 13% or 3.6mt to 31.4mt. Significantly, as with Antwerp, solid fuels account for almost half of this increase (up 1.6mt). The handling of oilseeds, iron and iron ore also increased.
Non-containerized general cargo additionally showed strong recovery, up 11% growth or 0.8mt to 7.7mt. More than half of this increase was generated by the trade in steel plates.
Daan Schalck, CEO North Sea Port, is in no doubt that there has been something of a negative fall out from the war in Ukraine.
He points out that, during the March to July period this year, immediately following the start of the war in Ukraine, many companies stockpiled large amounts of goods. This was because of limited exports from Ukraine and EU embargoes on goods
from Russia such as coal and wood.
“Uncertainties on the geopolitical stage [...] cause [temporary] spikes in supply streams in certain segments. The drop in trade with Russia will be compensated by additional transshipment from mainly the United States, Canada and Finland. Russia may then cease to be the first trading partner by the end of this year,” he says.
At the same time, Ukraine has also dropped further down the list of trading partners despite the resumption of grain supplies as of early September thanks to the establishment of grain corridors set up by the United Nations. A total of 0.4mt have so far been traded, well below the 1mt in the same period in 2021. The declines are in corn, animal feed and iron ore.
Clearly, the Port of Hamburg has also been affected by sanctions imposed by the European Union on the Russian Federation in response to Russia’s war on Ukraine, since large amounts of Russian trade has long been handled at the north German port hub.
“Russia plays an important role in the Port of Hamburg, particularly for imports of bulk cargo. These goods were not affected by the first sanctions,” notes the port.
However, that situated changed radically with the European Union’s sixth package of sanctions, which was implemented as of 3 June 2022. Mostly, this impacted liquid bulk, since Russian oil was effectively embargoed, with imports of Russian crude oil to be phased out over a period of six months and other refined petroleum products within eight months.
In terms of traffic figures, for the half year, Hamburg reported handling 61.8mt, down 2.7%. Much of this was due to a decline of 8.9% bulk cargo to 17.6mt. Suction cargo, at 3mt, was down by 7.2%. Grab cargo, which amounted to 10.2mt, was also down, by 3.2%. However, it was liquid cargo that suffered the most, falling by 20.5%.
The port concedes that the overall total was partly the result of stiffer EU sanctions
Ukraine has dropped further down the list of trading partners despite the resumption of grain supplies. against Russia, along with changes dictated by the market in the trading and transport of raw materials.
According to Axel Mattern, CEO of Port Hamburg Marketing, it is not only war in Ukraine, but also the repercussions of the global Covid-19 pandemic that will continue to cause transport and supply bottlenecks for trade and industry. On many routes, he says, this is leading to longer transit times and steeply increased freight rates.
Significantly, with a 52.8 share of the modal split, rail freight transport remains the top carrier for the Port of Hamburg’s incoming and departing traffic, he adds, with around 210 freight trains with more than 5,500 wagons using the port railway’s highperformance 300km network daily.
Port of Hamburg (©HHM Hasenpusch).
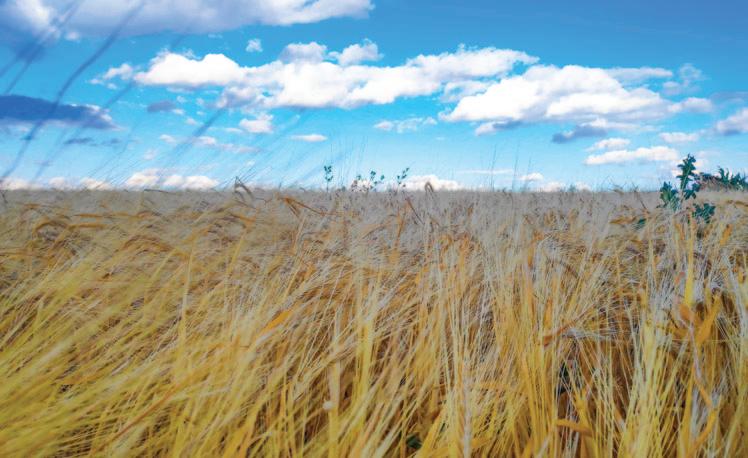

OVET dry bulk terminal is a stevedore company which specializes in storing, transshipping and processing dry bulk. With over 100 employees, the company has been offering very high quality and flexibility in services, since 1957. It can achieve a total unloading capacity of as much as 80,000 tonnes dry bulk per day, using its four floating cranes.
It is not surprising that, since OVET was founded in 1957, a lot has changed. At first, the company operated exMarshall Plan six-tonne floating cranes to discharge coal from seagoing vessels on Terneuzen roads and at the Zevenaarhaven terminal in Terneuzen. This gradually evolved to the 25- and 36tonne units which nowadays handle all kinds of bulk and breakbulk cargoes at its Massagoed and Kaloothaven terminals in Terneuzen and Vlissingen. However, what hasn’t changed is the nature and spirit of OVET. As ever, each project benefits from an all-out effort on behalf of OVET, where all floating cranes are combined to ensure the customer receives swift and quality service.
ABOUT OVET
The history of OVET begins in 1957. This is the year when the French stevedoring company Manufrance decided to establish a local trans shipping company for a major customer: the Association Cooperative Zélandaise de Carbonisa tion, also known as the Cokesfabriek (coke factory).
This factory focused on the production of cokes for the blast furnaces of French steelworks. Terneuzen was a favourable location, because it is well-situated with regard to England and the Ruhr area, which is where the coals came from. The deep waterway was also a major advantage.
The main reason for choosing a location in Zeeuws-Vlaanderen was the substantial price difference between supplying coals via Rotterdam or directly to Terneuzen. On 2 May 1957, the company was established. The managing director at the time, Y.H.M. Simenel, started out with seven other employees and ran the company from the Grand Hotel Rotterdam in Terneuzen.
OVET decided to use floating cranes in order to be able to lighten vessels midstream as well as from the quay. The very first floating crane had a lifting capacity of six tonnes. The company was successful and steadily gained new clients, besides the coke factory.
The lifting capacity of the cranes increased from six to 16 tonnes and later to 25 tonnes. In 2007, the newest crane with a lifting capacity of 36 tonnes came into service.
From an annual 500,000 tonnes of transshipment during the beginning, OVET has grown and today handles as much as 11 million tonnes of transshipment cargoes each year.
The company now has dry bulk terminals in Vlissingen and Terneuzen and over 100 employees ensure services of
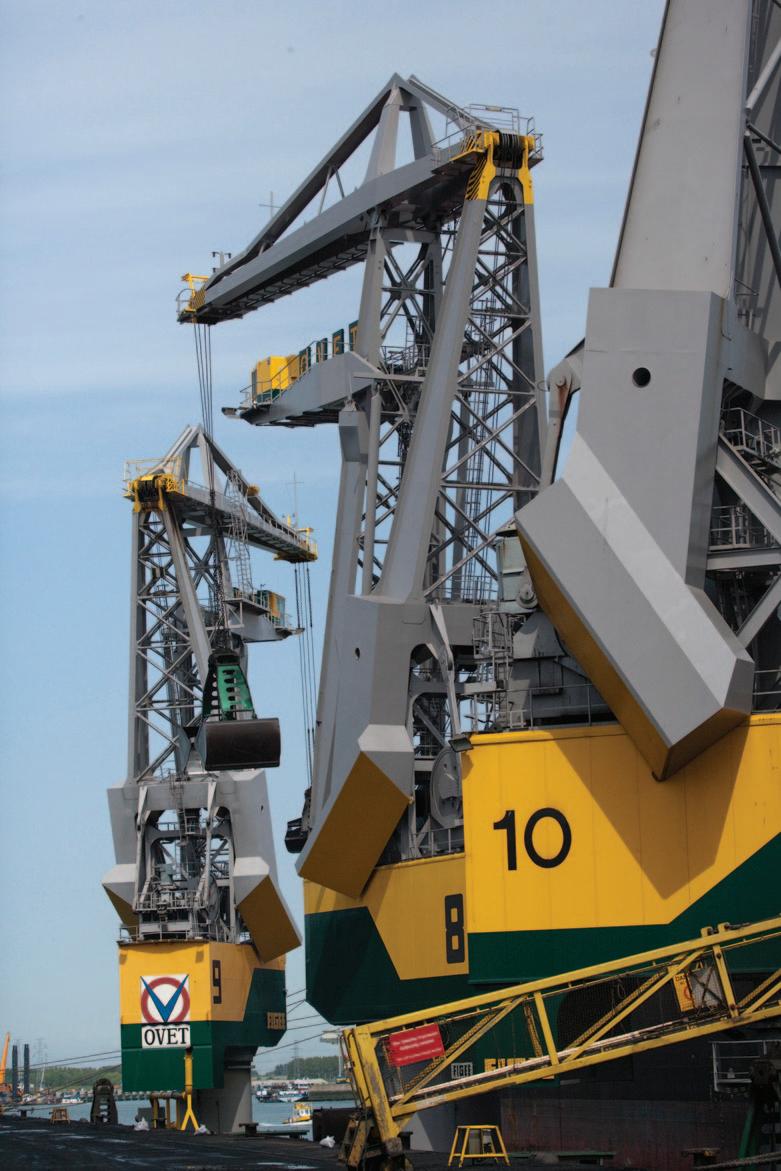
Handling biomass at the Ovet Terminal at Vlissingen.
high quality for the customers.
OVET can achieve a total unloading capacity of as much as 80,000 tonnes dry bulk per day, using its four lemniscate floating cranes.
In addition to creating more capacity, OVET also makes use of mobile SENNEBOGEN material handlers.
OVET high-quality offering comes from its strong focus on the questions and requirements of customers. Every OVET employee knows their daily duty of providing good service and quality; they deliver high quality personal service. This personal touch distinguishes OVET dry bulk terminal as a specialist and leader when it comes to the flexible handling of dry bulk.
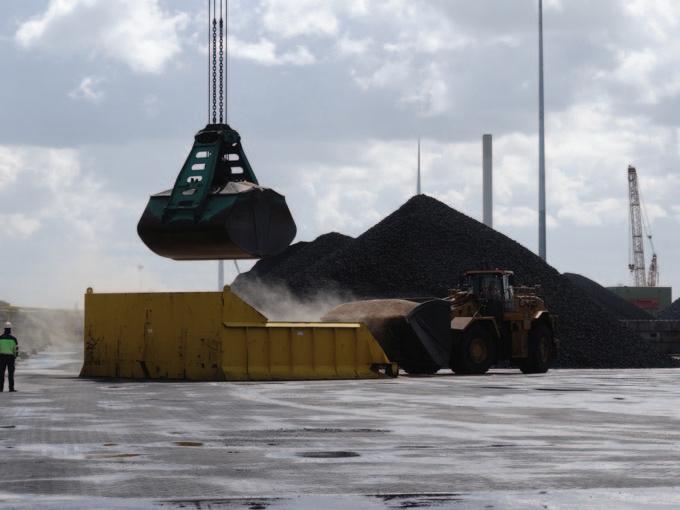
TERMINAL TERNEUZEN (MASSAGOEDHARBOUR) AND TERMINAL VLISSINGEN (KALOOTHARBOUR) With its floating cranes, OVET is active throughout the entire area of the Western Scheldt, in Vlissingen, Terneuzen and Ghent, but also at anchorage berths on the Western Scheldt itself.
TRI-MODAL PLATFORM
WATER TRANSPORT (INLAND NAVIGATION/ MARITIME SHIPPING) The OVET dry bulk terminals are connected to the most important waterways in Europe. Access to the Rhine is gained through modern channel connections. The proximity of the North Sea ensures the OVET dry bulk terminals are very suitable for sea traffic. OVET is able to load and unload all inland navigation (lighters and tug-pushed barges) and maritime shipping (coasters, Handysize, Panamax and Capesize). All possibilities are therefore open for its customers.
ROAD TRANSPORT OVET uses loaders to fill up trucks, which then pass a weighing platform to determine the exact weight.
RAIL TRANSPORT Since July 2013, OVET has had a completely renovated track and a new train loading system at the Vlissingen terminal. This ensures OVET is able to provide an even better hinterland connection for its customers. OVET has successfully proven that a train can travel to and from the German Ruhr area within 24 hours. On top of that, both dry bulk terminals have a good connection to the European railway network with good access to the Betuwelijn and the Corridor C.
FLEXIBILITY With its four floating cranes, OVET is capable of working in the entire ARA (Antwerp–Rotterdam–Amsterdam) range. The floating cranes can be moved between the terminals in the ports of Vlissingen (Flushing) and Terneuzen, in a mere three to four. On top of that, lightering can take place at Terneuzen Rede and Everingen (on the Scheldt). Also, almost all equipment at the terminals is mobile. Flexibility and OVET belong together.
WIDE RANGE OF CARGOES OVET is able to handle many different cargoes, including: v coal/(pet)cokes/anthracite; v minerals; v agricultural products (seeds/grains); v biomass/GMP; v offshore/density stones; and v scrap.
WAREHOUSING In order to meet the needs of its customers, OVET has a large covered storage facility with six compartments, in which products can be stored while staying dry. The large warehouse is mainly used for biomass, but other products can also be stored. DCi
WAREHOUSE STATISTICS
Number of compartments Surface area 6 1,000m2
per compartment Capacity per compartment 7,500m3 Total warehouse capacity 45,000m3
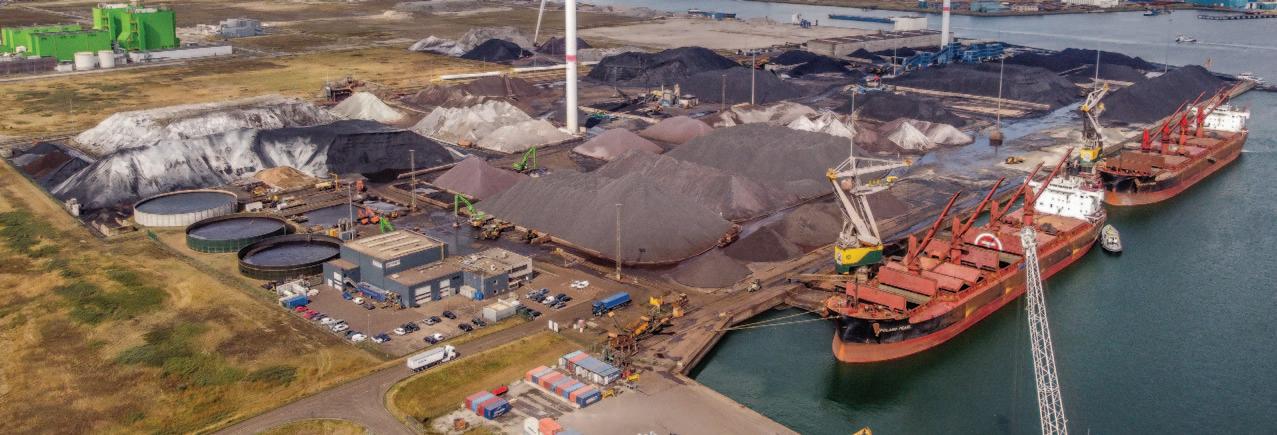
Poor quality rubber — trust your senses
The vast majority of rubber used to manufacture industrial conveyor belts is synthetic. That is because synthetic rubber can be engineered for specific demands and is far more adaptable compared to natural rubber. This is vitally important when you consider the wide variety of working conditions and materials that they have to cope with. It is the quality of the rubber covers, in particular the ability to resist wear and tear, which has the biggest influence on the durability and operational lifetime of a conveyor belt.
Sad to say however, an enormous proportion of conveyor belts fail to provide a cost-efficient working lifetime simply because the rubber used to make them is of insufficient quality. The reason for this is that rubber usually forms at least 70% of the volume mass of a conveyor belt and more than 50% of the cost. With most conveyor belts being sold on the basis of lowest selling price rather than performance and durability, the rubber is therefore the prime target for minimizing costs. The outward appearance may seem perfectly okay but how can you tell if the rubber is poor quality? Fortunately, you do not necessarily need to be a conveyor belt expert to identify some of the tell-tale signs. You just need to use your senses.
SOMETHING SMELLS WRONG One of the first clues is smell. All European manufacturers are legally obliged to comply with REACH (Registration, Evaluation and Authorisation of Chemical substances) regulation EC 1907/2006, which came into force in June 2007. The regulations relate to the use of potentially hazardous chemicals that pose hazards to human health and the environment. This includes those that may have category 2 carcinogenic classifications as well as Persistent Organic Pollutants. Sadly, many European manufacturers have chosen to ignore this legal requirement because of the impact on production costs while manufacturers in Asia, the source of a huge proportion of the conveyor belts sold in Europe, are not subject to the regulations at all. This means that they are free to use unregulated raw materials that cost much less on the global market compared to their regulated
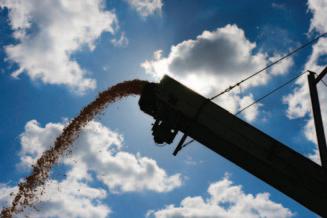
Pouring money down the drain - an enormous proportion of conveyor belts fail to provide a cost-efficient working lifetime.
Asian manufacturers are not subject to EU regulations concerning the use of dangerous chemicals and pollutants.
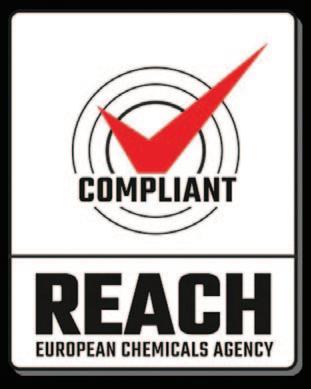
CONVEYING ADVICE
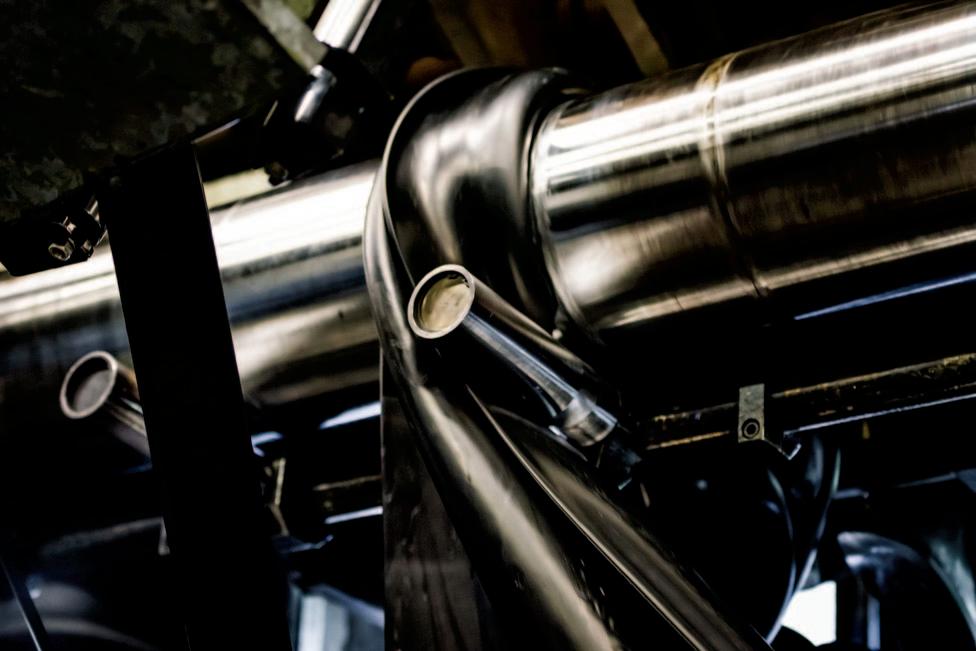
counterparts, even though those materials may be prohibited or have strict usage limitations within Europe.
One of the biggest concerns involves short-chain chlorinated paraffin’s (SCCP’s), which are most commonly used to reduce production costs by accelerating the vulcanization process. REACH regulations stipulate that SCCP’s should either not be used at all or at least only used on a very restricted basis because of their category 2 carcinogenic classifications. The tell-tale sign of their presence is usually recognizable due to an unpleasant pungent odour given off by the rubber whereas good quality rubber usually has very little smell at all.
HEARING THE DIFFERENCE Perhaps an even more surprising way of identifying poor quality rubber is sound. Belts with good quality rubber covers tend to run appreciably quieter than their lower-grade counterparts. A key component contained in every black rubber conveyor belt is carbon black. It makes up around 20% of a typical rubber compound and good quality carbon black is an expensive commodity. Carbon black plays a vital role in prolonging belt life by helping to conduct heat away from the surface area of the belt, thereby reducing thermal damage. It also acts as a reinforcing compound. Belts offered with significantly lower prices are virtually certain to contain carbon black that is of a much lower quality that has been produced much more cheaply such as by burning scrap car tyres for example. Other methods used to minimize rubber costs include the use of recycled rubber of highly questionable origin and cheap ‘bulking’ fillers such as chalk, which are used to replace part of the more expensive rubber polymers. The end result is that the rubber is more rigid and less flexible, causing the belt to emit a constant loud rumble. There is also a tendency to slip, causing loud squealing sounds.
In contrast, higher quality rubber contains much higher proportions of top grade polymers and premium quality carbon black. As a consequence, rather than being rigid, the rubber is much more elastic, which helps to reduce its rolling resistance because it ‘conforms’ more easily. This means that it requires less drive power and makes less noise because the sound is dissipated as the belt surface passes over the rollers. Good quality rubber also has more grip so it is less prone to slipping under tension at the head. A perfect example of this was discovered recently by one operator who, after replacing its low grade imported belting with belts produced by Dunlop Conveyor Belting in the Netherlands, found that the noise level of its conveyors dropped by at least 50%.
COMMON SENSE When trying to differentiate between what is likely to be good quality, more cost-efficient belts and low grade, short lifespan belts, perhaps the best sense of all is good old-fashioned common sense. As I said earlier, rubber usually forms at least 70% of the volume mass of a conveyor belt and more than 50% of the cost. When there is a big difference in the price of one conveyor belt and another, invariably the best tell-tale sign of all is that the price reflects the quality and longevity. Bob Nelson
CONVEYING ADVICE
Authors note: Please be aware that the level of noise emitted by a conveyor can also depend on other factors such as the quality of the infrastructure, maintenance, type and condition of other integral components such as rollers and/or general operating conditions. Consequently, a reduction in noise level cannot be guaranteed simply as a result of changing your belt to a premium quality band such as Dunlop. For more advice on this subject please consult an experienced application engineer.

