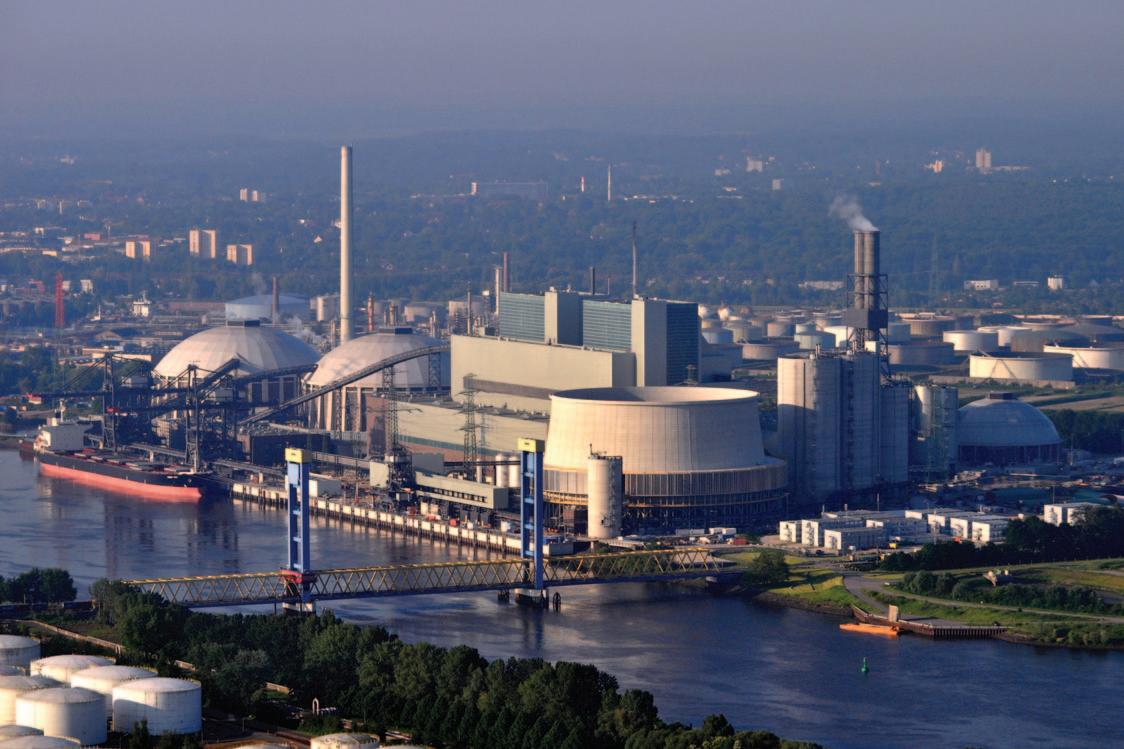
5 minute read
REEL MÖLLER: PNEUMATIC TRANSPORT AND STORAGE SYSTEMS FOR BULK MATERIALS HANDLING
Hamburg-Moorburg plant.
REEL MÖLLER
pneumatic transport and storage systems for bulk materials handling
In 2008, Vattenfall Europe Generation began with the realization of two new units of hard coal-fired power plants at Hamburg-Moorburg in Hamburg port, with a gross output of 820MWel each, write Alen Menzildzic, Solution Sales, REEL Möller GmbH; and Ansgar Stein, Plant engineer, Conveying technology, Vattenfall. Having MÖLLER® conveying and storage solutions successfully in operation in many of its other power plants, Vattenfall decided to implement the same technology for the fly
Pressure vessel conveying system.
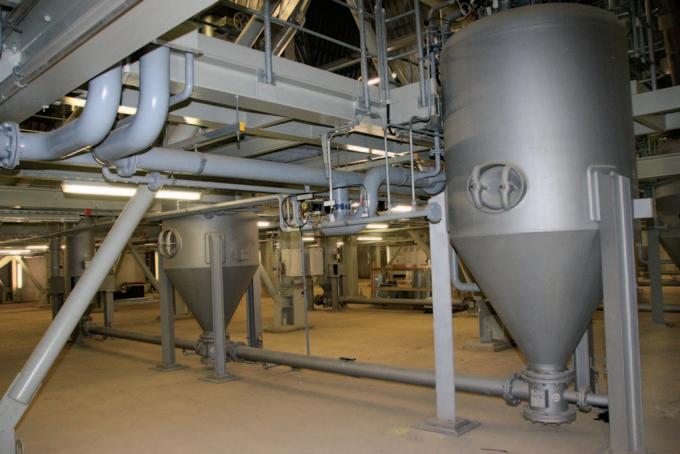
Benefits of the TURBUFLOW system
The TURBUFLOW system is highly cost effective and boasts the following advantages: v very low conveying velocities inside the pipeline, reducing wear; v eliminates blockages; it is possible to restart with a full pipe; v low maintenance and highly reliable; v energy efficient conveying; v minimal air requirement — smaller compressors and exhaust air filters; and v self-regulating; no additional valves are required along the pipe.

ash handling, storage and loading for these two new units.
ASH EXTRACTION/ ELECTROSTATIC PRECIPITATORS (ESP) In 2015 Moorburg started operation. The hard coal fire of each boiler creates up to 25tph (tonnes per hour) of fly ash. The fly ash from flue gas is extracted by ESP.
Usually, TURBUFLOW conveying systems are fed by a single or double pressure vessel system. In this case, however, the chosen solution is a MÖLLER MultiTURBUFLOW system, in which a group of pressure vessels share one common conveying line.
The ESP in each unit is divided in two halves, each with 24 hoppers, arranged in four rows with six fields in gas flow direction. A pressure vessel is installed below each hopper. The six pressure vessels in each row acts as a functional unit that operates like a single pressure vessel. All six pressure vessels in a group are either being filled or conveying at the same time, instead of one after another. Four rows of pressure vessels share one common TURBUFLOW conveying pipeline, which conveys the ash to one of the designated silos.
Filling and discharging of the pressure vessels is controlled by MÖLLER’s Intelligent Cycle Control System (ICC).
REEL MÖLLER two-way diverter valves.

TURBUFLOW® conveying system. ENGINEERING & EQUIPMENT
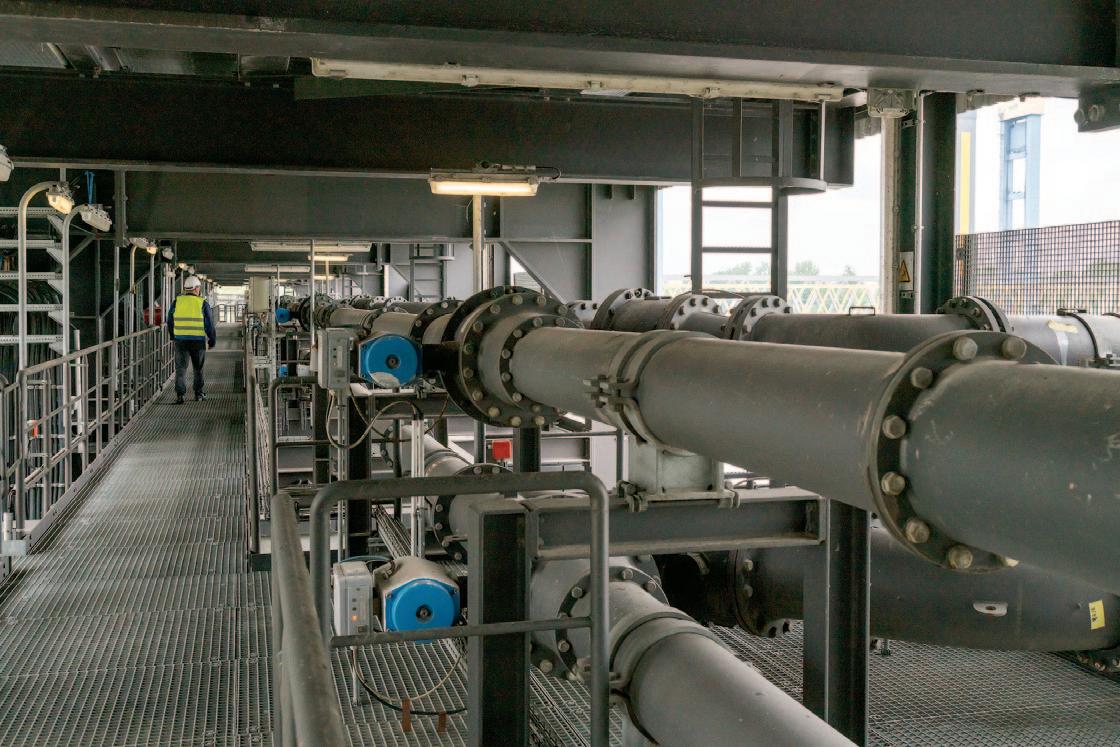
ICC controls conveying time and conveying pressure to determine the quantity of material currently being conveyed, enabling to decide the optimum time intervals for filling pauses, filling regime and conveying cycles, in order to reduce both conveying air and energy consumption especially due to varying boiler loads from 30–100%. In this way, the system is able to convey in every boiler load case maximum amount of fly ash with minimum number of conveying cycles — a highly efficient solution.
The pressure vessels are sized to accommodate the amount of ash produced. The ash amount coming from the rear fields of the ESP is significantly smaller, so that the pressure vessels in these fields are attached directly below the hoppers.
ASH STORAGE The ash quality is analysed while it is still in the ESP to determine if it is suitable for use in the building material industry. When it is, the ash is stored in one of the two 33,000m2 long-term quality ash storage silos. Any ash that does not meet the required standards is deposited in the smaller waste ash silo.
The routing of the conveying lines is designed to enable any conveying pipe to discharge ash into any silo. Discharge is controlled by either MÖLLER two-way diverter valves, or, for conveying pipes with higher pressure MÖLLER dome valves with inflatable sealing are used.
Long-term fly ash storage silos are capable of storing fly ash for several months and still discharge safely and easily. This is thanks, in part, to thoroughly dried conveying air and to the extra-wide silo outlets. Also the ash recirculation system, which pumps the ash from bottom to top of the silo helps to prevent solidification of ash.
In order to protect the silo, as well as the material, MÖLLER designed a special unloading program that extracts ash in areas of the silo where the levels are the highest. This eliminates the danger presented by asymmetric loads.
All silos are equipped with truck loading systems that are designed for loading dry ash (into closed silo trucks) and humidified ash (to be loaded onto open dump trucks).
TO THE HARBOUR Moorburg quality fly ash is used in the cement industry, so it has to be conveyed to the Moorburg pier for shipping out to cement producers facilities. From both quality ash silos, the fly ash is conveyed to the harbour silo via pressure vessels and TURBUFLOW conveying pipe operating at 400tph. The harbour silo then supplies the mobile shiploader’s silo with up to 600tph of fly ash from MÖLLER pressure vessels with two TURBUFLOW conveying pipelines. Both conveying pipes has seven docking points on the pier to give the ship loader the flexibility to reach all hatches without shifting the vessel.
The shiploader is designed to load dry and humidified ash directly onto cement carriers at Moorburg pier with up to 4m tidal range.
The shiploader can load cement carriers either via a loading spout with 400 to 600tph dry ash or via a belt conveyor with up to 300tph humified ash. The same belt conveyor can also be used for loading up to 1,000tph of FGD gypsum.
CONCLUSION “Vattenfall Moorburg is always impressed with the quality of MÖLLER conveying and storage systems. The conveying systems provided for this project are clean, reliable, efficient, and we have since returned to MÖLLER to supply other projects. The after sales performance of REEL MÖLLER can be stated as very satisfying,” says Ansgar Stein, Plant engineer/Conveying technology, Vattenfall.
The Hamburg-Moorburg plant was closed in June 2021 due to the political situation.
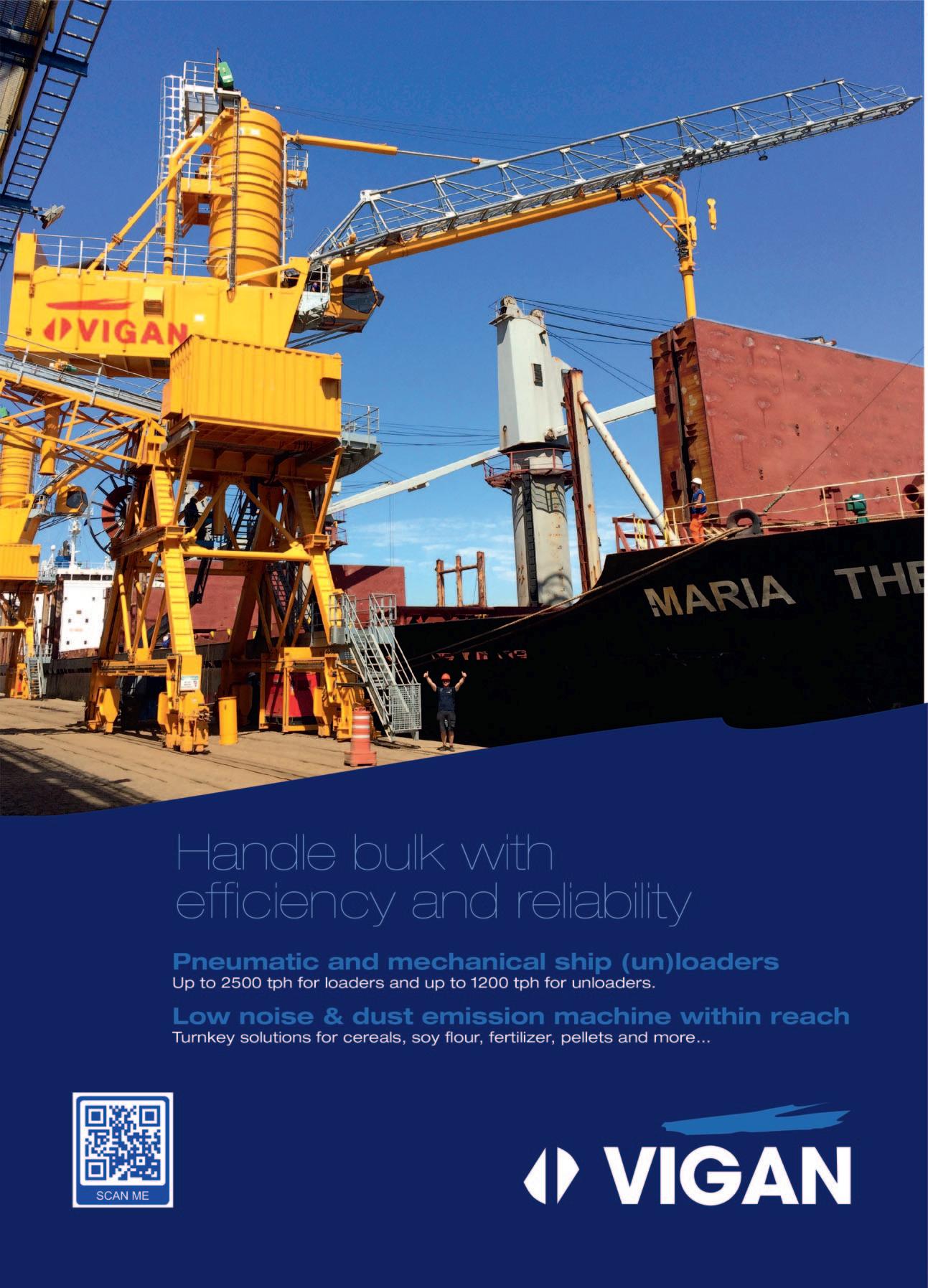