
26 minute read
LOADING UP ON GOOD IDEAS: BULK LOADING SYSTEMS AND TECHNOLOGIES IN THE SPOTLIGHT
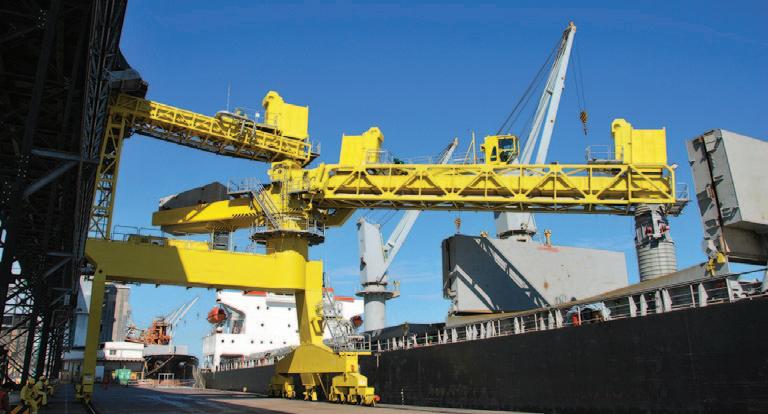
... on good ideas Loading up ...
bulk loading systems and technologies in the spotlight

Clean alumina loading in Brazilian port with the help of Bruks Siwertell
Environmental benefits were key factors in Alunorte’s decision to award the Brazilian contract for a new shiploader to Bruks Siwertell. All Siwertell shiploaders are totally enclosed providing a dust-free operation with no spillage.
Environmental benefits and mechanical efficiency were key factors in Brazilian alumina producer Alunorte’s decision to opt for a Siwertell alumina shiploader.
It is used to load Kamsarmax vessels of up to 80,000dwt at Alunorte’s production plant in northeast Brazil.
Alunorte owns one of the world’s largest alumina production plants. It contracted Bruks Siwertell to replace its existing belt-type shiploader, which needed to be changed because of problems related to its high dust emissions.
Bruks Siwertell’s new shiploader is built to a different design concept. The new design is based on a totally enclosed air slide system and a Cleveland cascade-type vertical telescopic loading spout. The provision of two dust collectors at the transfer points makes this a very efficient loading system in terms of the elimination of dust emissions into the environment. The loader is constructed on a travelling gantry and has one horizontal arm capable of slewing and luffing motions, fitted with a vertically adjustable loading spout.
The operator cabin is located on an arm which extends out over the ship’s hold. This provides the operator with a perfect view of the loading operation.
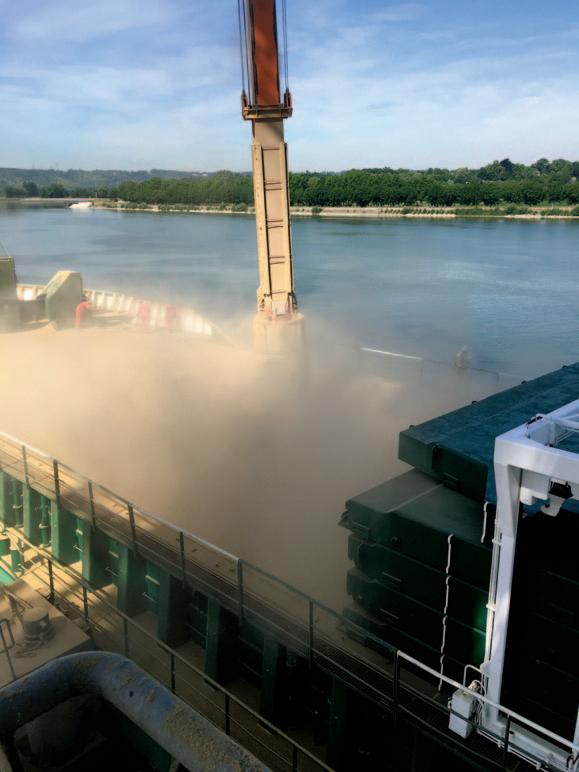
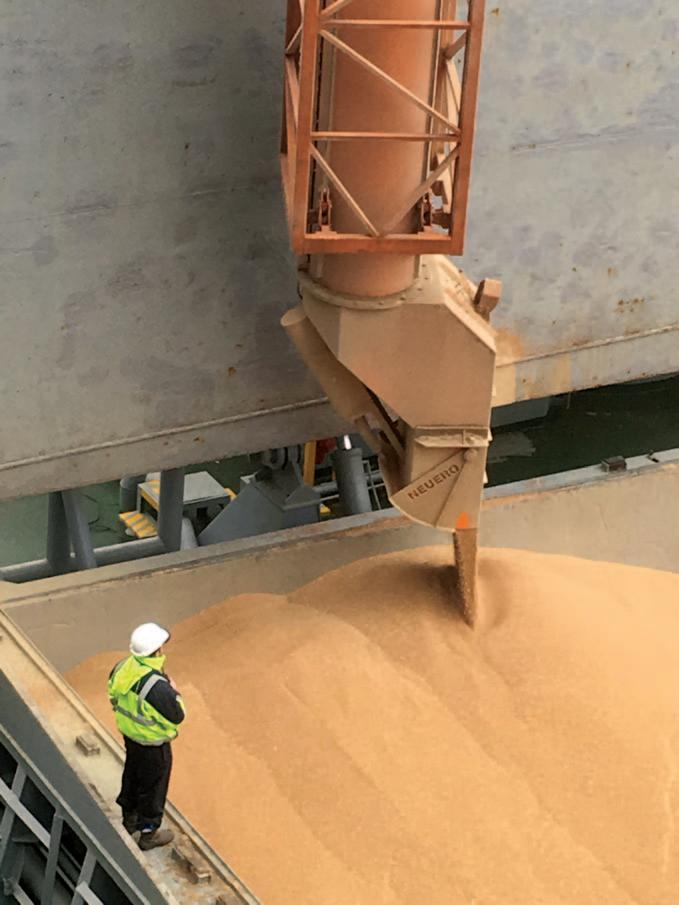
There is an evolution taking place in the field of shiploading — the focus is now increasingly on OPEX (operating expenses) instead of CAPEX (capital expenditures).
It is also widely accepted that a shiploader should not only fill a vessel’s hold efficiently, but that it should also be acceptable to all stakeholders. Neighbours complaining about dust emissions, for example, could, in an extreme case, stop operations. Many ports are located close to cities, which increases the pressure to solve pollution in water, air and noise.
Many shiploaders look similar and also have similar KIKO (kick-in/kick-out) and telescopic movements. As usual, the devil lies in the detail. Telescopic movements should move in both directions, pull and push — not only pull. Filters should be able to capture the air with dust from the pipes with reserve. A system should be able to detect the flow and adjust itself to avoid product to speed up.
Today with technologies like the KIKO DLH system, this problem is solved. The differential is the automation of operations with self-learning software. Intelligent shiploaders provide the best operational conditions at all times. This is much more efficient and facilitates operations. The operator can concentrate on filling all spaces, and does not have to focus on controlling the material flow. This is the next step in automating the operation. Before: three people trying to guide the loading operation.
After: normal operation with Neuero KIKO DLH.
Thirty years ago, a simple shiploader with a telescopic spout and rotating spoon was standard. Some shiploaders included a jet slinger to throw product under the hatch. The problem with this is that in many cases, it is not possible to see where the product is being thrown, making it difficult and unhealthy work.
NEUERO, a renowned specialist in shiploading and unloading, worked with a client that needed to was hundreds of cars every week as its system emitted such high levels of dust. This was expensive, because the operator was regularly fined, and new equipment was required to replace the old, inefficient system.
The same applies with another operator — having bought a simpler system without efficient dust-suppression, the operator now needs to change its equipment. NEUERO hopes to win the contract and supply its KIKO DLH systems, as it has a strong understanding of all factors, and knows that terminals that have already invested in dust control systems would be most unhappy to have a dusty neighbour.
Dust control is often subject to rules that are not entirely clear — but there are fewer excuses made when a neighbour invests in an efficient system.
The KIKO DLH system is a commonly used solution that offers a reduced OPEX.
ENGINEERING & EQUIPMENT Kinder Australia: lining media to ensure smooth loading and unloading
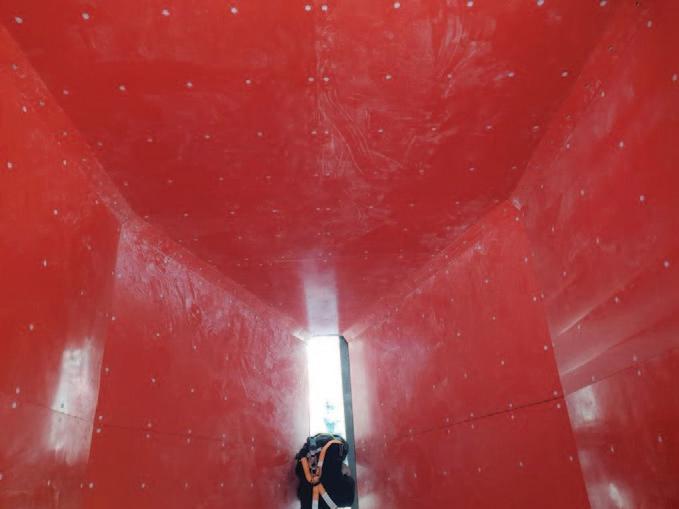
A major issue encountered during loading and unloading operations — as well as handling and storage in general — is blockages, and flow problems. These can be caused by poor chute design and varying moisture content.
Using linings can be an effective solution. However, not all conveyed materials are the same, and therefore not all lining media should be the same. Each lining application must be evaluated properly, taking into consideration all aspects of the material being handled. These factors determine the grade, material and style of the lining media used. Some factors to consider: v material/particle size and concentration; v material moisture content and environmental conditions; v impact strength; v abrasion; and v chute shape & head room restriction.
Kinder Australia can offer lining media to suit a wide range of applications, to stop common issues such as bridging/arching, caking, ratholing and wear.
K-SLIP The K-Slip Rubber Backed UHMWPE Wear Liner is a low co-efficient of friction thin polyethylene lining material, with a synthetic rubber backing (SBR). The thin flexibility of Kinder Australia’s K-Slip Rubber Backed UHMWPE Wear Liner allows almost any complicated shape to be lined including bins, hoppers and chutes, providing a reliable and effective uniform surface and therefore improve the controlled rate of flow. The application to
K-Slide UHMWPE Low Friction Liner.

a metal surface is by normal cold rubber bonding.
The flow of very fine particles, although not a high wear problem, does present a new challenge in the way in which it flows, or importantly, not flows. Fine nonabrasive particles having passed through the crushing and grinding circuit, may be required to flow through complicated shaped chutes where restricted head room limits the advantage of effective chute design. Lining with a conventional low friction material can be difficult to install in these complicated transition and confined points. Round corners and acute angles do not fix well with fasteners; in fact they often provide another point on which the material can bridge.
When handling mineral concentrates especially, these material types tend to hang up on any surface and at any angle. Kinder Australia’s K-Slip Rubber Backed UHMWPE Wear Liner has been used successfully to overcome many of these flow problems. Advantages include: v extra slippery with very low coefficient of friction; v thin and flexible for complicated shape applications; v synthetic rubber backing — adhesive available.
K-SLIDE K-Slide UHMWPE Low Friction Liner features unique properties that deliver a low co-efficient of friction, superior abrasion and corrosion resistance. The UHMWPE low friction liner is light weight and easy to work with. However, they cannot be used in continuous service above 85°C, or where they are subject to large or sharp feed with high energy.
K-Slide UHMWPE Low Friction Liners cover a wide range of grades to suit all applications considering abrasion resistance, impact strength, UV-stabilized or having anti-static properties. K-Slide UHMWPE liner is available in wide varying thickness and sheet sizes.
K-Slide UHMWPE Low Friction Liner products offer a high-performance abrasion resistant solution in difficult bulk material handling applications. Flow problems such as ratholing, bridging and caking may be solved by the use of a low friction lining material.
Blockages and flow problems may be encountered because of poor chute design and varying moisture content. Each lining application must be evaluated properly, taking consideration all aspects of the material being handled. These factors determine the grade of UHMWPE lining media used.
K-Slide UHMWPE Low Friction Liners: v offer easy installation for coated surface applications, standard installations or oversized sheets; v are ideally suited for high velocity, high impact load zone and excessive abrasion applications and where a superior 100% poly surface is a key requirement for attaching poly surfaces onto hardware; v are highly effective in securing UHMW and fasteners parts to achieve a 100% poly on poly surface; v have bolts and all fittings that are all zinc-plated for corrosion resistance; v improve performance of existing hardware and extends the wear life of parts; v
v basic wear protection; offer abrasion and corrosion resistance; are available in a wide range of thickness and sheet sizes.
K-SUPERLINE® K-Superline® Polyurethane Lining System is a unique proprietary Kryptane urethane wear liner, purposely engineered to meet the particular demands of the application specific material.
Whether the wear issue is sliding abrasion, impact damage, sticking material or excessive corrosion, lightweight,
K-Superline® provides these benefits: v 85% lighter compared to steel; v longer lasting anti-wear protection; v reduced material hangup;

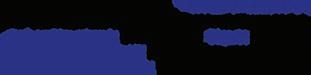
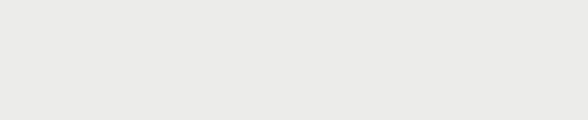
Ship unloaders
Road mobile ship unloaders
Storage & reclaim
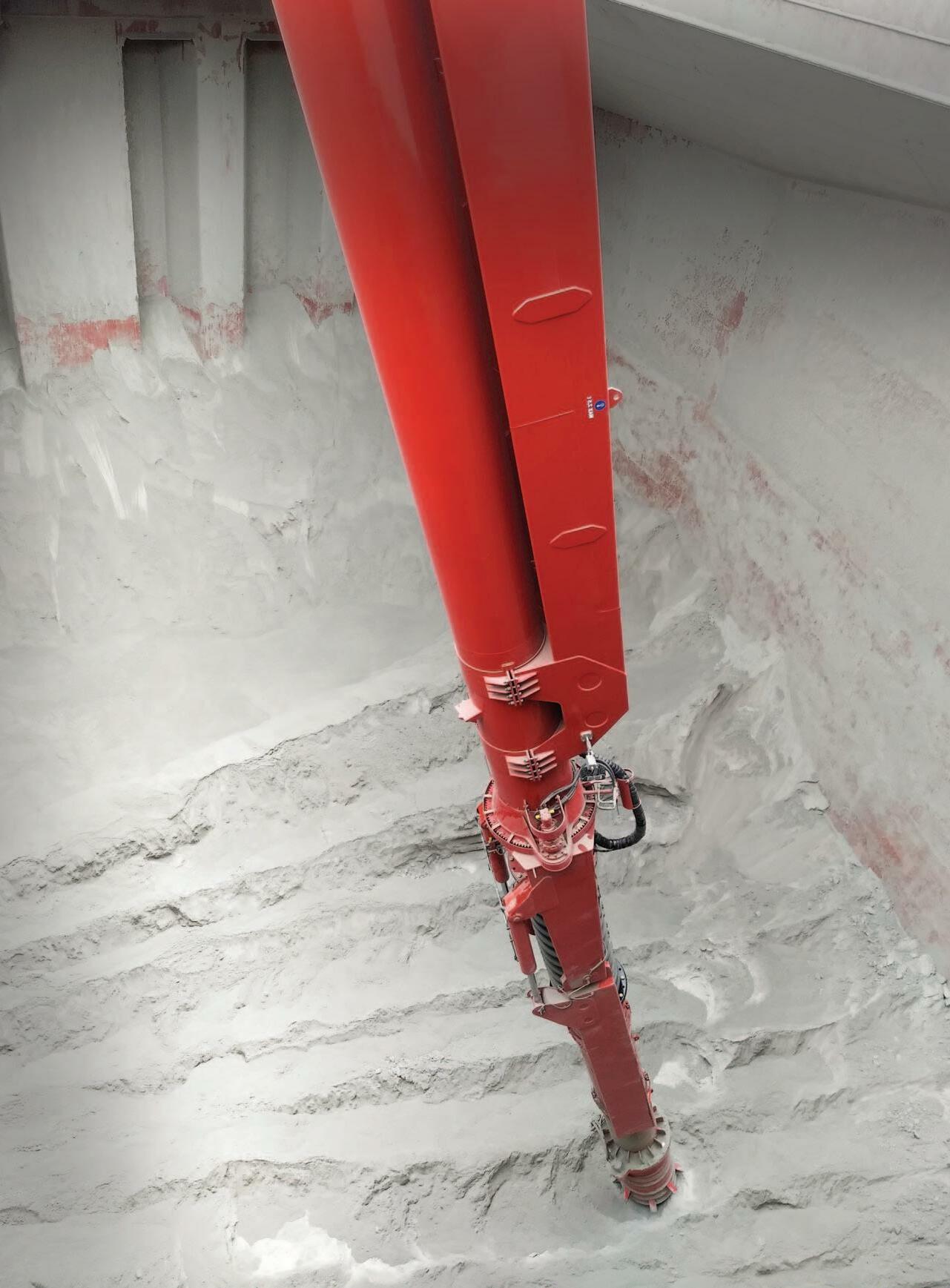
Convey units
Truck loading
Ship loaders
The answer to your bulk handling questions
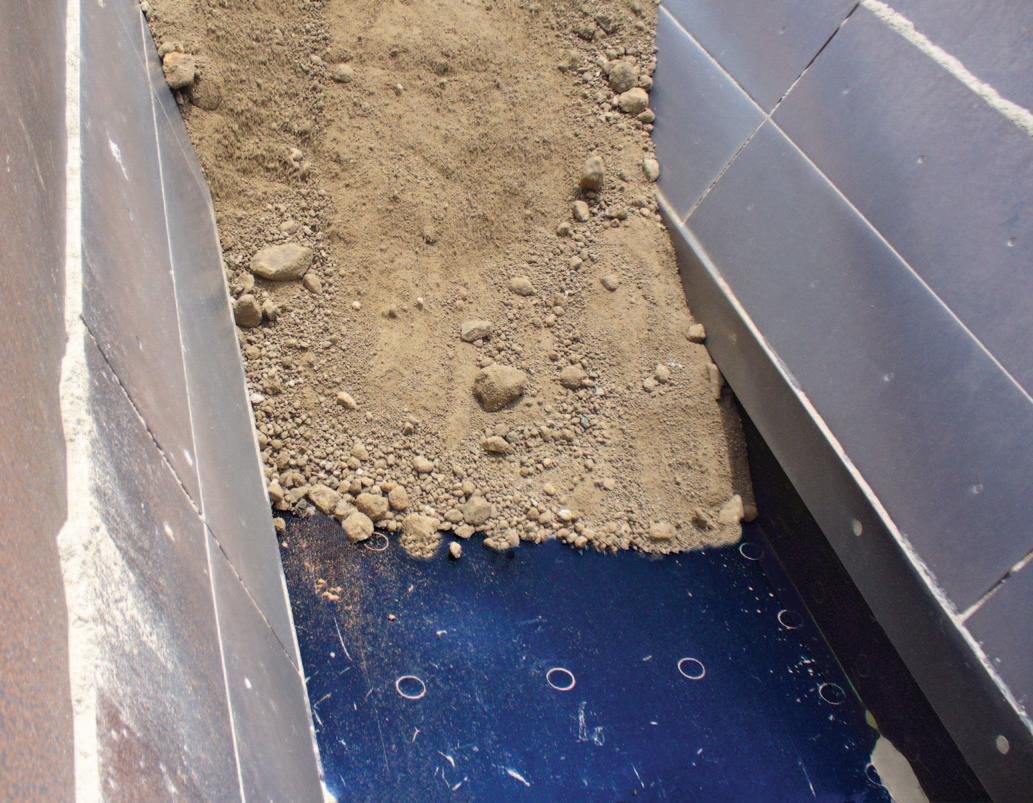
v v v v
greater tear resistance; simplified installation and 80% less noise compared to steel; and low co-efficient of friction PLUS high wear protection. K-Superline® is a stronger and more elastic version than all other outwardly similar polyurethane products. It is based on a patented chemical formula, with a modified molecular structure to alternative polyurethane materials.
By correctly matching the K-Superline® characteristics, the specific product type, the angle of impact and the existing wear liner issue, K-Superline® Polyurethane Lining will provide a genuine improvement as a replacement for polyethylene, rubber, UHMWPE and steel wear liners.
An integrated dual-colour wear indicator option is also available, this provides fast and accurate visual detection of the K-Superline’s wear performance.
This feature reduces the need to access the lining system for inspections, minimizes production downtime and wear “hot spots” can be quickly identified and easily rectified.
K-SUPERLINE® CUSTOM SHAPED WATERCUT CAPABILITIES Key features: v waterjet up to 60,000psi can easily cut through Polyurethane to any specific shape or profile; v accurately placed holes to suit existing chute liners for easy repeatable installation; and bevelled edges available.
v
K-FLOSHIELD K-Floshield Polished High Chrome Liner is an extreme impact and abrasion resistant wear liner solution. Subject to technical advice K-Floshield can be highly effective against blockage and hang up problems within a multitude of heavy-duty applications.
Pre-polished, high strength chromium carbide top layer is fused onto a mild carbon steel base plate. The pre-polished top layer can withstand extreme abrasion and is ideal for applications where material carry back and wet/sticky conveyed material is a major concern.
K-Floshield maintains the efficiency, integrity and performance of processing bins, buckets, chutes, crushers, pugmills and other materials handling equipment.
The combined polishing action delivered by the top layer and the highly abrasive bulk material qualities delivers a low co-efficient of friction and reductions in surface scratching. These unique properties further aid the slipperiness of the wear liner and thereby minimizes the incidences of hang ups and blockages.
Highly versatile, K-Floshield comes in standard 1.2m x 3m plate size (other sizes available) and can be cut, welded, rolled and moulded into a multitude of shapes and sizes.
Key features: v high carbon, chromium-rich (polished chromium carbide) wear plate is five to six times more wear-resistant than heat-treated steel and five times more resistant than stainless steel; v extreme abrasion and impact resistance for ‘violent material’; v customized sized plates to suit most requirements and applications.
Key benefits: v resolves hang up and blockage problems; v minimizes production downtime, cleaning and maintenance costs; v easy installation with studs, welds and bolts; and v extends the wear life of equipment.
Liners can be cut to size complete with studs welded to the back.
Suitable industry/applications: v cement — chute liners, fan blades; v coal — feeding chute liners, hoppers; v energy/power — liners for ash and slag pipes, dust collector inlets, hoppers, separators; v mining — chute liners, crusher parts, wear plates; v steel — hopper liners, bin liners, skip cars; v recycling/glass — pugmills.
K-Superline® Polyurethane Lining System.
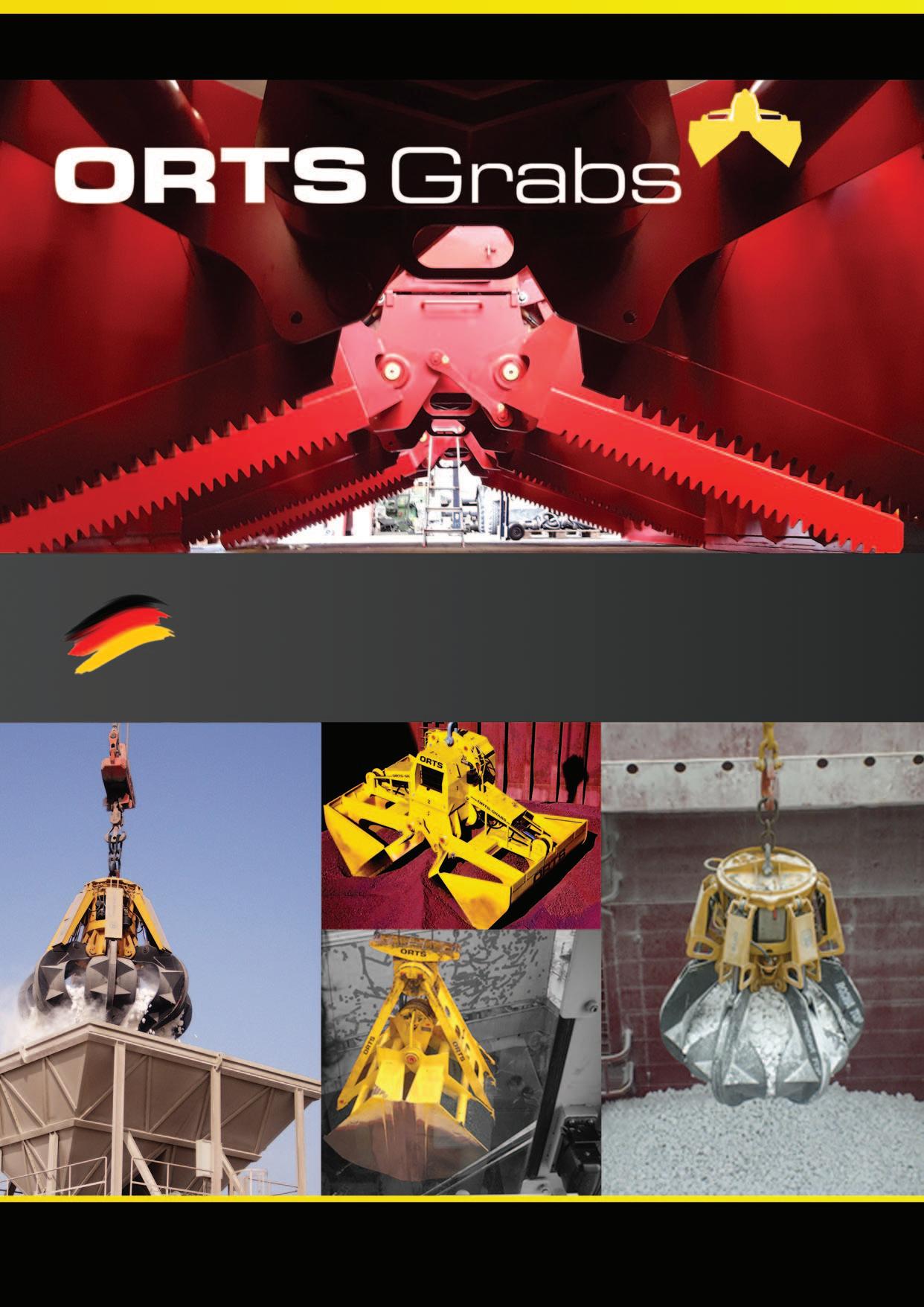

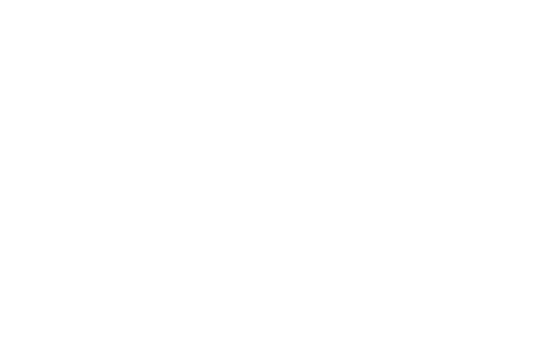
ENGINEERING & EQUIPMENT Shiploader equipment delivered to Port Milwaukee’s future agricultural maritime export facility
Shiploader arriving at Port Milwaukee (all photos: The DeLong Co., Inc.).
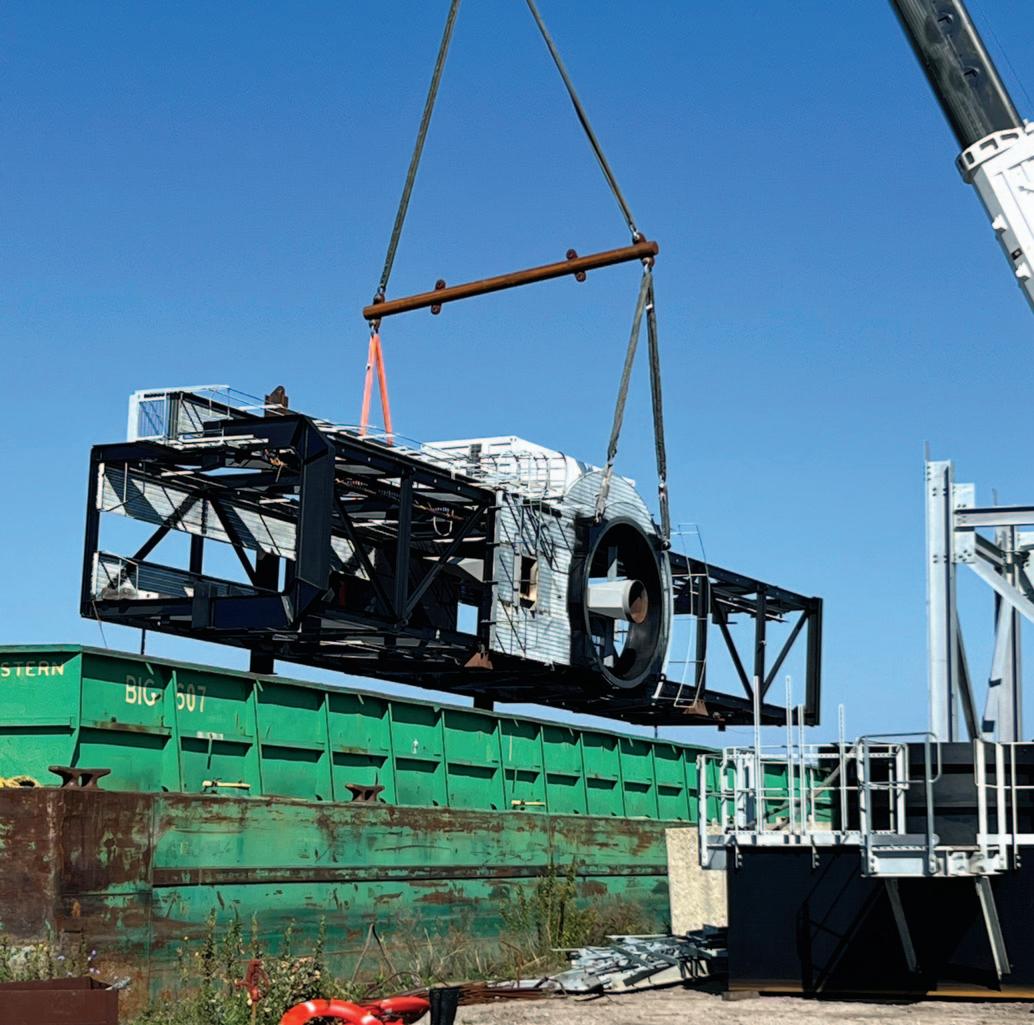
A significant piece of loading equipment was recently delivered to Port Milwaukee, USA, for The DeLong Co., Inc. agricultural maritime export facility.
The made in America shiploader travelled more than 1,500 miles by barge from New Orleans, Louisiana, up the Mississippi and Illinois Rivers to Jones Island. This equipment is capable of loading 40,000 bushel/1,100 tonnes per hour onto both vessels and barges.
The shiploader, which is currently being installed on Jones Island, will serve as the heart of DeLong’s loading operations and represents a major milestone in the development of the agricultural maritime export facility at Port Milwaukee. Construction of the full facility is expected to be complete in 2023, coinciding with the annual start of Port Milwaukee’s international shipping season.
“Milwaukee is an economic catalyst for our state and region, and this addition to the Port’s operations will expand the partnership that includes The DeLong Co., the City of Milwaukee, Wisconsin agriculture and world markets,” said Milwaukee Mayor Cavalier Johnson. “Thank you to DeLong for its continued growth at Port Milwaukee.”
“We at DeLong are excited to see the progression of this project. Our shiploader is currently being installed and we hope to have final project completion by March 2023,” said Bo DeLong, Vice President of Grain at The DeLong Co., Inc.
“Delivery and installation of the shiploader, as part of the future agricultural maritime export facility, is a turning point in our efforts to realize new agricultural opportunities and advance economic activity in the city and throughout the Great Lakes region,” said Port Milwaukee Director Adam Tindall-Schlicht. “The port is looking forward to next year when the terminal comes to life. Wisconsinproduced cargoes handled on Jones Island will be multiplied through new rail and vessel efficiency at the DeLong terminal.”
The new facility, located on the west side of Jones Island, will be one of the first
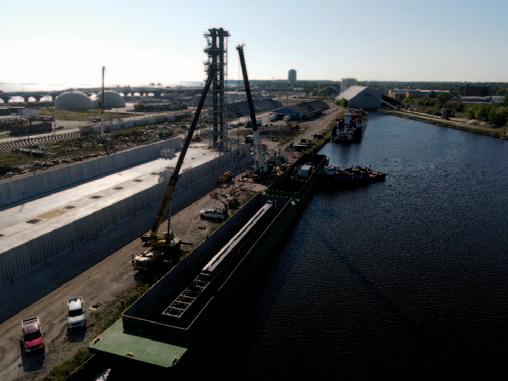
on the Great Lakes – St. Lawrence Seaway (GLSLS) system to handle various agricultural commodities via truck, rail and international vessel, including dried distillers grains with solubles (DDGs). DDGs are an animal feed supplement derived as a byproduct of ethanol high in nutrients. This facility will open Wisconsin’s maritime and agricultural economies to new international markets for this and other products. Future service at the facility may also include the export of Wisconsin-grown soybeans, corn and grain.
The Wisconsin Department of Transportation has estimated the DeLong terminal will alone generate $63 million in new statewide economic impact annually, increasing exports through Port Milwaukee by as much as 400,000 metric tonnes per year.
Thanks to a robust public-private partnership, this development is the largest one-time investment in Port Milwaukee since the 1950s, when the St. Lawrence Seaway was being built. Port Milwaukee was one of the first nationwide grant recipients of the Port Infrastructure Development Program (PIDP) through the U.S. Department of Transportation. Additional facility funding has been provided by the Wisconsin Department of Transportation, Port Milwaukee, and The DeLong Co., Inc. Overall terminal construction costs are currently estimated at approximately $40 million.
ABOUT PORT MILWAUKEE Port Milwaukee is an economic entity of City government governed by the seven-member Board of Harbor Commissioners, a panel appointed by the Mayor and confirmed by the Common Council. It administers operations on the 467 acres that make up the Port. It promotes shipping and commerce throughout the region by providing access to domestic and international ships, rail, and overthe-road transportation.
ABOUT THE DELONG CO., INC. The DeLong Co., Inc. is a sixth-generation, family-owned business that is head quartered in Clinton, WI. The company operates 37 locations around the US and comprises six divisions of agricultural and logistical sales and services: grain, exports, agronomy, seed, transportation and wholesale feed. The DeLong Co., Inc is the largest US exporter of containerized agricultural products.
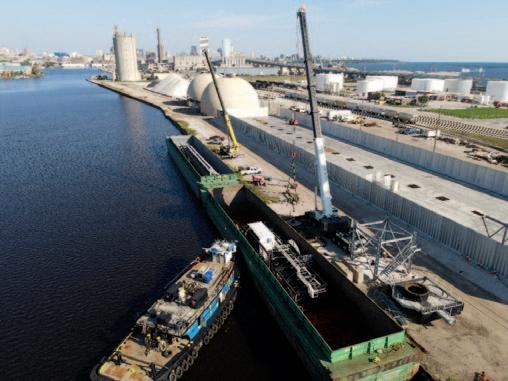
Sandwich belt high angle conveyors in harmony with the environment: integral part of loading and unloading operations
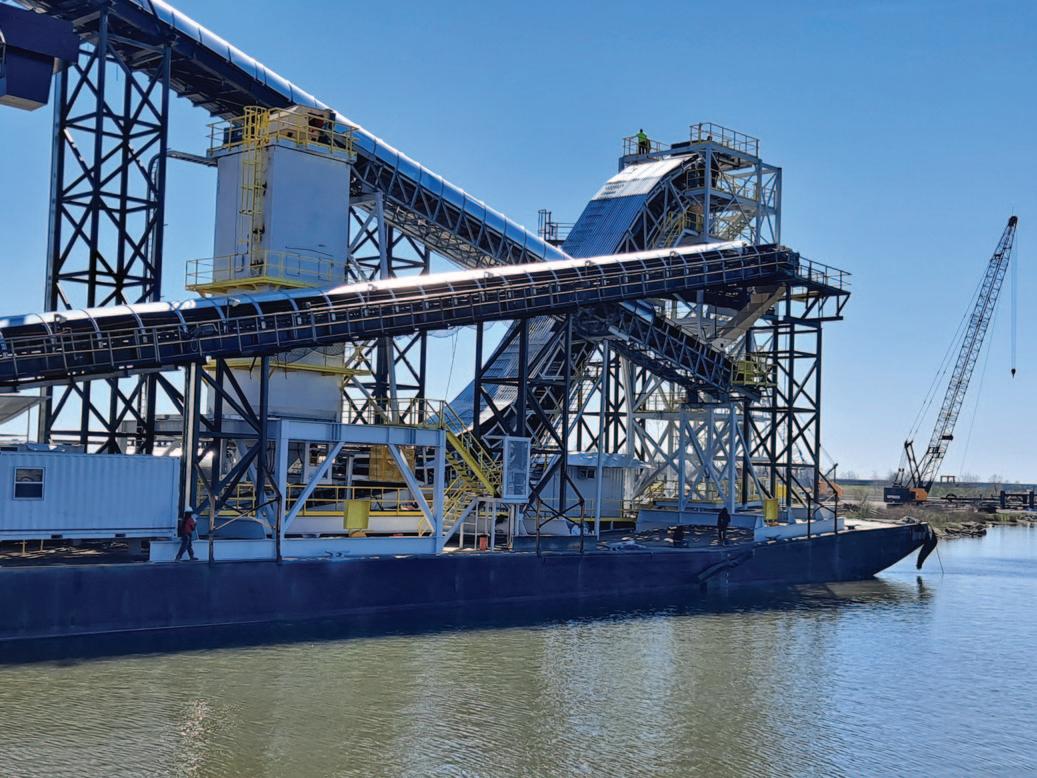
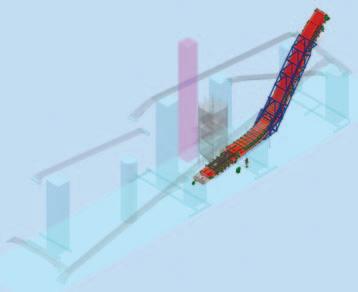
BACKGROUND DSI Sandwich Belt high angle conveyors are proven, versatile systems for elevating or lowering materials continuously at steep angles up to 90°. Widely varying industries have exploited the benefits of Sandwich conveyors. They have found application in coal mining, preparation, power and synfuels, in various minerals and metals mining, in municipal waste treatment, rapid transit projects, pulp and paper mills, cement plants, and transshipment of grain.
Throughput rates for Dos Santos Sandwich Belt high angle conveyors that have been put into operation vary from 0.27 to 4,250tph (tonnes per hour). Conveying profiles vary widely and elevating heights range from 3.66m to 174.8m. These installations are by no means the limit of this versatile technology, however.
THE SANDWICH BELT PRINCIPLE The Sandwich Belt high angle conveyor consists of a carrying conveyor belt which is supported on closely spaced troughing idlers. A floating cover belt is gently pressed onto the conveyed material by closely spaced, fully equalized, pressing rolls. The required material hugging pressure varies according to the conveying angle, material characteristics and the dynamics of the system. The hugging pressure device is, therefore, designed for the specific requirements of the application with provision for field adjustments.
IN HARMONY WITH THE ENVIRONMENT Various industries have utilized Sandwich Belt conveyors. Even before the increased awareness for environmental compliance, Sandwich Belt conveyors provided the following benefits with
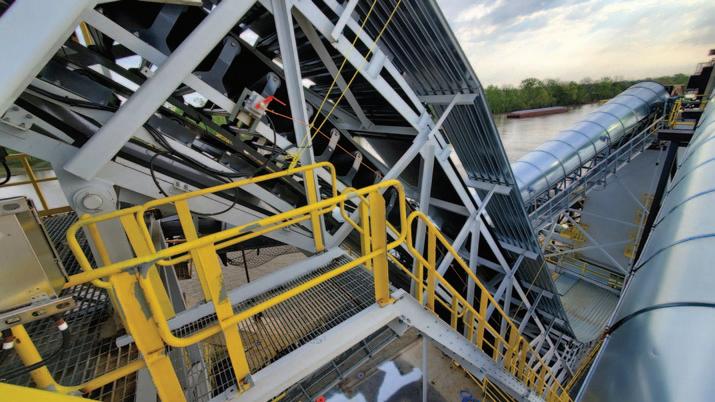
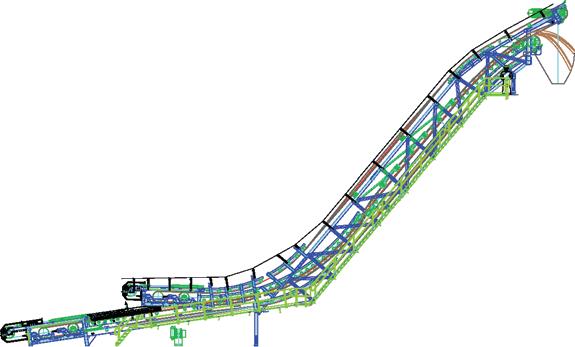
Material for Cooper Consolidated, New Orleans, LA USA
Grains
Density 0.77t/m3 (48 PCF)
Size 101.6mm (4”) minus Conveying rate 2,268tph (2,500 rate STPH) Conveying angle 50° Belt width 2,134mm (84”) Belt speed 4.57m/s (900FPM) Lift 18,474mm (60.6’) Length 36,538mm (119.9’) Drives
Lower Belt 112kW (150HP)
Upper Belt 149kW (200HP)
their natural capabilities: v conformity to landscape: conform to irregular (steep) paths to blend in with the surrounding environment. This feature precludes the need for many transfer points which are a common source of spillage and fugitive dust. v compact arrangements: by virtue of their high capacity, high angle and adaptable profile features, Sandwich conveyors facilitate the most compact arrangements of any materials handling system, minimizing disturbances of the environment.
minimizing excavation disturbance
v
of the sub-surface: Sandwich Belt conveyors allow the most direct haulage path from deep open pit mines v

v and from underground excavation projects eliminating the cost of any additional excavation.
reduction in real estate and spatial
volume: in plants, they use the least real estate and displace the least spatial volume in 3-D space. Because Sandwich conveyors can be housed in a facility, they will require the least amount of wall and roof surface. For heated facilities in cold climates, they offer the least heat escape, thus the lowest heating cost. creating a power source: a downhill Sandwich conveyor system can operate regeneratively, thereby feeding power to the grid, becoming a power source.
Industries that have benefited from these features include sludge and sawdust handling in composting systems, biomass for fuel in the form of RDF (refuse derived fuel to garbage) to power projects, hog fuel at pulp and paper mills and shredded tyres for fuel at cement plants, to name a few.
CONFORMITY TO THE LANDSCAPE Sandwich Belt high angle conveyors’ ability to conform to the irregular profile of the landscape was proven at a Virginia, USA mine. Coal refuse was being hauled from the prep plant to the dump site along a steep mountain path by two aerial tramways. They travelled conspicuously above the mountain slopes and created a black streak of spillage under their respective travel paths. Steep curving ramps for the trucking scarred the landscape, while the trucks polluted the air with fumes, particulates and noise and created the potential for disaster from traffic accidents.
The Sandwich conveyor eliminated these problems while offering a conveying capacity higher than the previous combined
system. High angle, as well as conventional conveyors were considered for this application, however conventional conveyors required considerable elevated structure, were obtrusive on the landscape and with the several additional transfer points, created a potential source of spillage and additional expense.
COMPACT ARRANGEMENTS In some cases, Sandwich Belt high angle conveyors have facilitated materials transfers in very tight spaces at existing sites, while in others they have opened the door for the most compact new materials handling systems. A vertical DSI GPS Sandwich Conveyor for the Paris Metro tunneling project elevated sticky tunnel muck at a design rate of 800tph. This was done without disturbing vehicular or pedestrian traffic.
The particular challenge of this project was the requirement to provide a versatile system that will be reused in future projects. Accordingly, Dos Santos International designed a system with a high degree of versatility — particularly extend-ability. With all the drive and take up equipment located at the head end, DSI designed the vertical portion as a hanging structure which can be extended as necessary for higher lifts at future applications. The two Sandwich conveyors at the two sites in Paris are nearly identical, with only a small difference in the length of the vertical portion. DSI designed both conveyors for the possibility of increasing the lift to 45m. The two conveyors in Paris have vertical lifts of 24.6m and 26.3m respectively and can be used for any intermediate height up to 45m. This makes them very versatile for use at future sites.
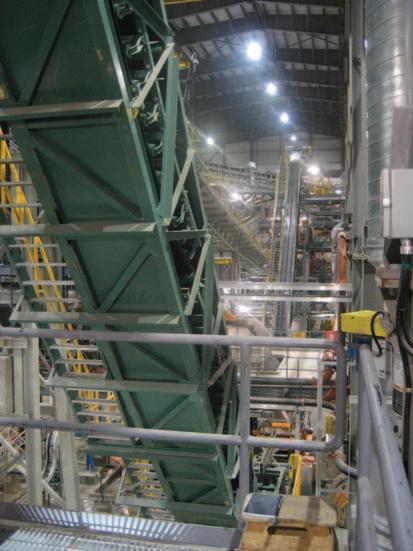
MINIMIZING EXCAVATION, DISTURBANCE OF THE SUB-SURFACE Sandwich Belt conveyors allow the most direct haulage path from deep open pit mines and from underground excavation projects. A high capacity, high lift system can most certainly handle the severe haulage requirements.
One such system conveyed hard primary crushed rock (250mm minus) along the steep mine wall, directly out of the pit. This substantially reduced the truck haulage requirements of that mine, displacing ten 240-tonne trucks from the severest of haulage duties (the slow, high power, continuous climb to the surface).
As important as it is to eliminate the associated pollution and accident potential, minimizing of total excavation for the ore recovered is also important. The Sandwich Belt system requires no additional excavation. Conventional conveyors, though nearly equally efficient to the Sandwich belt conveyor, do require additional excavation and/or additional transfer points because of the limited slope capability.
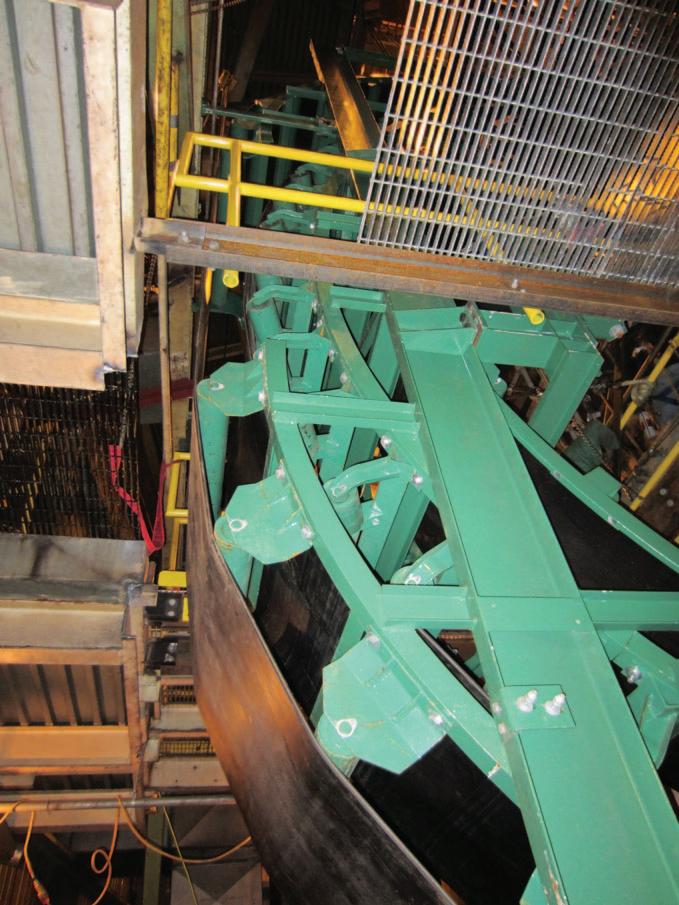
REDUCTION IN REAL ESTATE AND SPATIAL VOLUME The challenge to use the least amount of space possible to process and separate kimberlite at Canadian diamond mines was the motivation for the installation of DSI Sandwich Belt high angle conveyors.
The first project was in the Northwest Territories at Snap Lake. The ore body was a dyke that dipped an average of 12–15° from the northwest shore down under the lake. Kimberlite, the diamond bearing ore was brought to the surface to a processing facility where the diamonds were
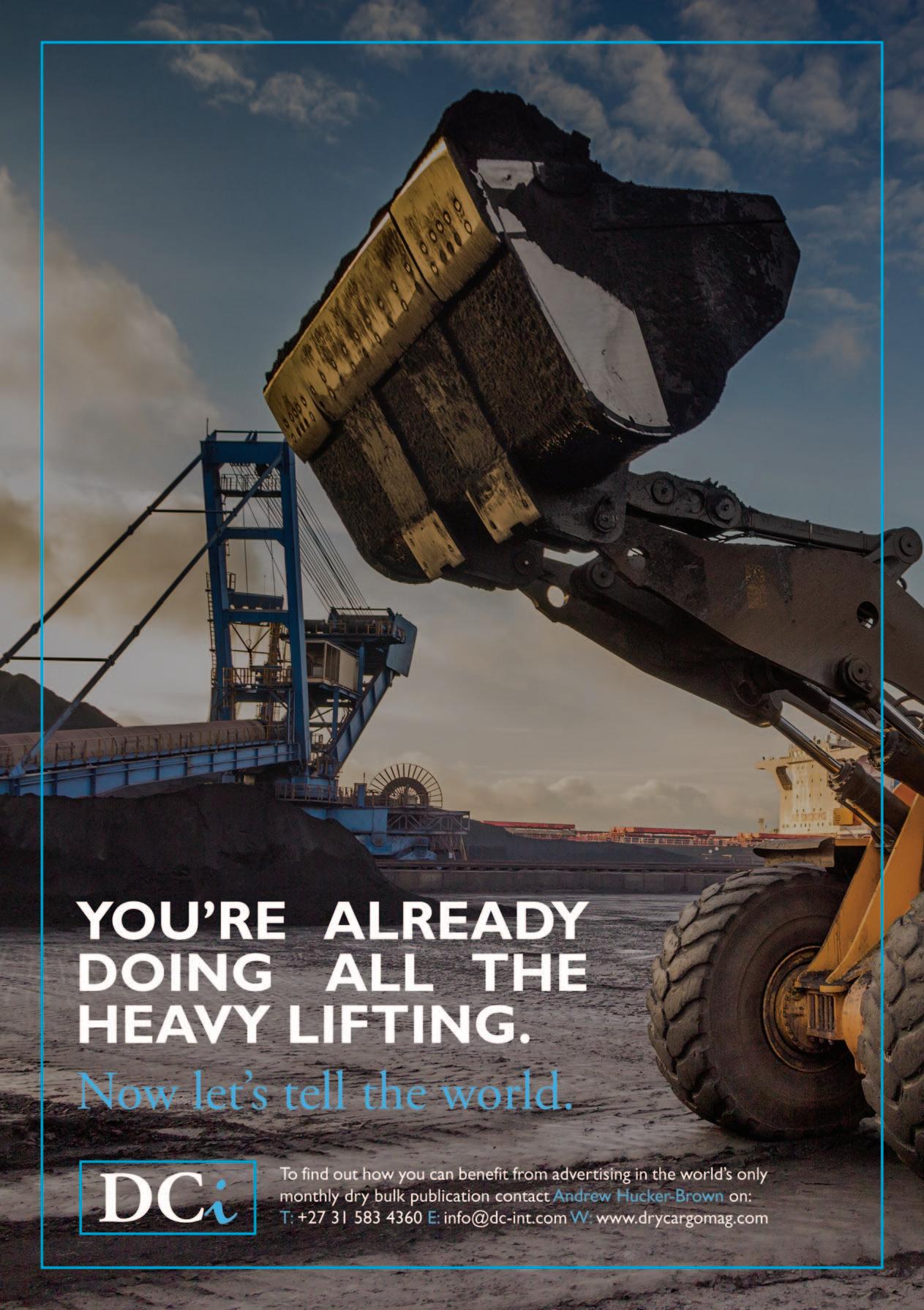
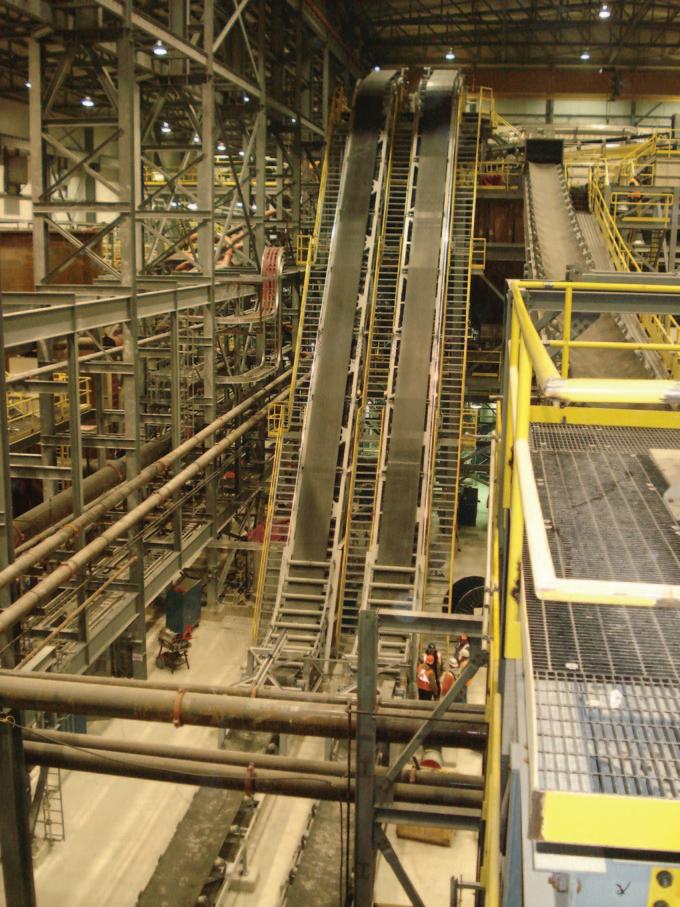
extracted. Because of the hostile environment, the facilities had to be enclosed and heated. A smaller footprint for the plant was determined to be the optimal way to minimize environmental impact and cost.
The original concept was to use a multitude of Sandwich conveyors to minimize the facilities. This was ultimately rationalized to require only two Sandwich conveyors, which defined the facility’s minimal footprint. The ability to convey at any high angle, along with the Sandwich Belt imparting a gentle, yet firm hugging pressure on the material, allowed the precious gems within the kimberlite to be elevated at high angles without damage or spillage. The Snap Lake project incorporated two DSI Sandwich conveyors, each travelling to opposite ends of the building. The units were standardized at 36” belt width to simplify spare parts inventory. Design of the units included provision for future upgrade, from 275tph to 524tph, merely by increasing the belt speed. By operating at the lower speed until the upgrade is required by the Sandwich conveyors, optimal energy efficiency is preserved.
The success of Snap Lake then led to the incorporation of DSI Sandwich Belt conveyors into the Victor Project in Northeastern Ontario. The Victor Project, Ontario’s first diamond mine, had three DSI Sandwich belt units in operation.
Simplification of inventory was further exercised at the Victor Project with all units at 42” belt width. However, tonnage requirements for these units vary from a low of 185tph at unit 11 to a high of 422tph at unit 12. For prolonged equipment life and energy conservation, unit 11 ran at a slower speed than the other units.
The Snap Lake Mine was operated by DeBeers with a commitment to maintain the highest environmental standards. It was the only diamond mine in the Northwest Territories that certified its environmental management systems to the high international standard, ISO 14001 through advanced exploration, construction and pre-operations.
CREATING A POWER SOURCE A downhill Sandwich conveyor at a Venezuelan phosphate mine combined the duties of a gathering conveyor from beneath the storage pile and an overland conveyor. This eliminated a transfer and much elevated structure. An added feature to this system was that as a regenerative lowering system, it produced electricity to become a power source.
Another example of a power producing downhill system is the DSI GPS Sandwich Belt conveyor for the Los Filos gold mine. This system would bring material from the crusher, downhill, to the leach pads. In operation, it would have produced 220kW of power. Unfortunately, this conveyor contract was cancelled due to geological instability on the mountainside. Instead, DSI designed an overland conveyor system that had the same lowering difference, but because of the losses inherent in a multiflight conventional conveyor, it produced only 14.5kW of power.
OTHER INDUSTRIES THAT BENEFIT The versatility of Sandwich Belt conveyors allow for endless profiles that are adaptable to many widely varying configurations, especially beneficial for environmentally friendly projects.
At composting systems, city sludge is mixed with sawdust and composted into a useful material, a soil additive. In biomass to fuel and RDF, garbage to power, a Sandwich Belt conveyor replaced four pocket belts that were in place at a plant in Florida.
In Maine, at a pulp and paper mill, the refuse bark and rejected chips went to a boiler to serve as fuel. This would otherwise be wasted materials.
Finally, DSI designed a hybrid Sandwich Belt high angle conveyor to efficiently transport shredded tyres at a cement plant to create an alternative fuel source for cement production. Instead of disposing of the rejected tyres, they now serve as a power source for the cement plant.
SUMMARY AND CONCLUSIONS The Sandwich Belt high angle conveyor system is used widely throughout the world in various industries. It can conform to the environment by virtue of its sandwiching, high volume, high angle, and conforming profile features. It has furthermore proven reliable and economical. The Sandwich Belt conveyor, when employed, results in minimal material transfers, minimal displacement of space, i.e. minimal intrusion into the environment, and proves to be a positive solution to environmental challenges.
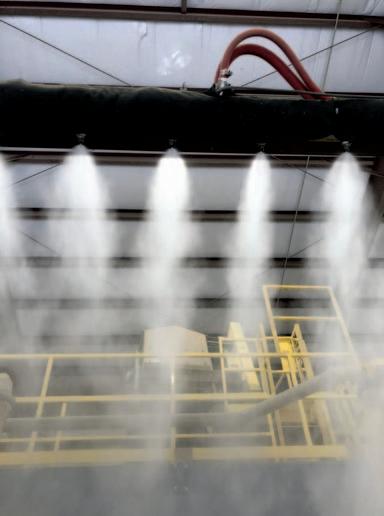
The Raring Corporation (TRC), in conjunction with its exclusive North American Sales & Distribution company, PEBCO Inc, is a company focused on the control of airborne dust in the industrial workplace. Its technology is simple, low cost and natural. TRC uses no chemicals, therefore helping to keep the world clean. The company operates worldwide and has installed over 600 systems around the globe — and it has been doing so for 38 years.
Raring’s manufacturing facility is located in Vancouver WA USA where its unique technology is created to help with reducing dust emissions in many of the different materials associated within the dry bulk materials industry such as sand, coal, copper, iron ore, cement, phosphate rock, limestone. The ADSTM (Atomized Dust Suppression System) technology also applies to many different plant applications including barge unloading, reclaim tunnels, trippers and cascades, transfer points, screens, truck dumps, crushers, bins and silos and limestone handling.
By combining air and water, 1–30 micron water particles are created in the same range as the airborne respirable dust. Fog dust collection systems are highly efficient, patented, fine particle scrubbers that use very little water and do not increase the overall moisture of the flowing material.
Successful application of dry fog technology to industrial dust control requires four design elements: v containment; v an adequate quantity of fog; v retention time; and v collection surface.
Of the four, containment is the most important.
One very interesting integration of a passive and active technology is what TRC created on an unloading hopper at a port facility. By combining a wind fence from WeatherSolve and the ADSTM Dry Fog System, TRC offered a unique way to control the dust at specific points. The wind fences are built to withstand hurricanes and cyclones due to their overload release system. By keeping the dust contained within the wind fence boundary, this allowed the retention time needed for the fog to do its job.
Another example of the ADSTM Dust Suppression Fogging System is integrating the system with another piece of equipment in the barge loading Raring Fog System installed on the discharge of a PEBCO Dustless Loading Spout used to control fugitive dust in an open truck loading application (above and right).
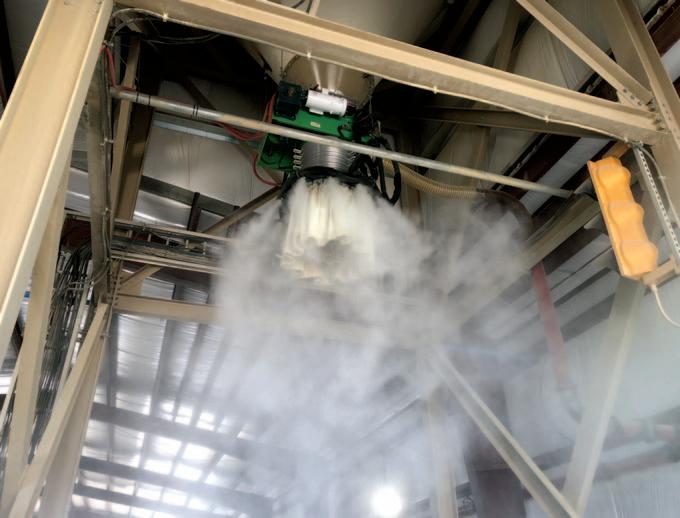
Fog spray screeners.
industry. Barge/shiploading can be a little more difficult and each one presents its own challenges.
The main challenge can be containment and most of the time an operational modification is needed to help minimize the amount of dust generated.
For one such project the Raring Corporation used the PEBCO Telescopic Chute and installed a TRC ADSTM Dry Fog spray ring at the bottom end of the chute, thereby providing the dust control system and the containment required. The

telescopic chute loads the hold from the top of the pile and the spray ring will generate enough fog to fill the hold with a dense cloud of fog to keep the dust inside the ship hold.
When dust is generated and the spray ring is fogging, dust sticks to the fog and the dust particles become heavier and eventually settle down into the hold. Fog spray rings have also been used with a PEBCO Dustless Loading Spout to contain silica dust within an open truck loadout application. Fog spray rings can also be integrated with the PEBCO Cascade Chute® for applications such as stockpiles, ship and barge loading.
In conjunction with its partners, The Raring Corporation continues to develop ways to decrease the effect of dust emissions in industry to pave the way for a cleaner planet. DCi