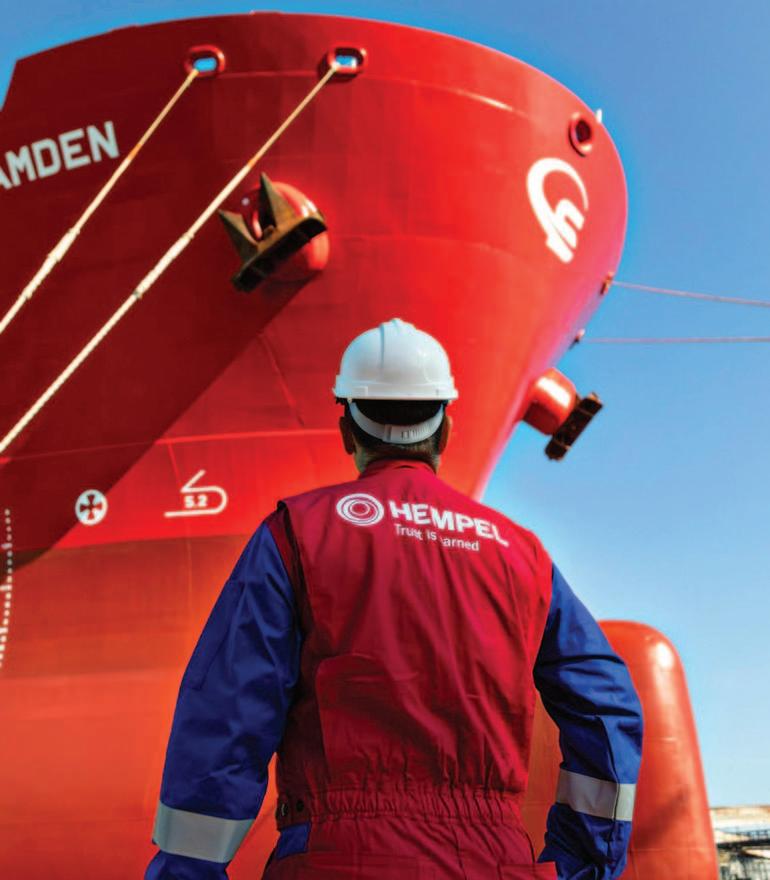
76 minute read
KEEPING THE BOAT AFLOAT: BULKER SERVICES, SAFETY & MAINTENANCE
Keeping the boat afloat
bulker services, safety & maintenance
Jay Venter
Hempel coats 3000 ships with flagship hull coating, Hempaguard
Coatings company, Hempel A/S, has passed a landmark number of ships coated with Hempaguard. Alexander Enström, Executive Vice President of Marine at Hempel, explains why passing this milestone is so impactful. “Our customers are looking for technologies that can support them on their sustainability journey. Three thousand applications of Hempaguard is equal to removing 27 million tonnes of CO2, corresponding with 8.6 million tonnes of fuel saved by having a smoother hull.”
“The adoption of Hempaguard is growing exponentially. This year alone, we have seen sales of Hempaguard systems grow by 82%,” continues Enström. “The antifriction properties of Hempaguard help shipowners and charterers save on fuel usage and thereby emissions, so it’s the obvious choice for our customers.”
With stricter regulations related to decarbonization coming into force in 2023, Hempel is seeing a widening range of clients seeking its advice, including an increasing number of bulker, tanker, containership and cruise operators and owners all keen to keep their vessels in operation come next year.
The new regulations being introduced by the International Maritime Organization are the Carbon Intensity Indicator (CII) and Energy Efficiency Existing Ship Index (EEXI). Hempel’s data suggests that about 80 per cent of the world fleet will be required to take action to secure a good CII rating while reaching the required EEXI. Vessels will be forced out of the market if their owners and operators do not identify and adopt a comprehensive emissions’ reduction pathway.
CALCULATION METHOD The savings related to the 3,000 vessel applications have been calculated by estimating the fuel savings of each Hempaguard application against a market average coating, based on market average numbers from the Fourth IMO GHG Study.
For Hempaguard applications, the consumption, activity, duration until next dry dock and relative savings from the IMO GHG Study are estimated and the impact from the full DD cycle is summarized in the year of Hempaguard application, where the coating choice and thus fuel savings decision is taken.
ABOUT HEMPEL As a supplier of trusted coating solutions, Hempel is a global company with strong values, working with customers in the decorative, marine, infrastructure and energy industries. Hempel factories, R&D centres and stock points are established in every region.
Across the globe, Hempel’s paints and coatings can be found in almost every country of the world. They protect and beautify buildings, infrastructure and other assets, and play an essential role in our customers’ businesses. They help minimize maintenance costs, improve aesthetics and increase energy efficiency.
At Hempel, the company’s purpose is to shape a brighter future with sustainable coating solutions. It firmly believes that it will succeed as a business only if it places sustainability at its heart. Not only is this the right thing to do, it will also strengthen the company’s competitive position, make it more resilient and reduce its risk.
Polish Register of Shipping classification services on the way to assure bulk carriers safety in sea trade
Bulk carriers play a major role in the global economy. Dry bulk cargoes cover a wide range of products, writes Marek Narewski, Rules Development Department, Polish Register of Shipping (PRS).
The most commonly shipped dry bulk materials are for example: coal, cement, grain, sulphur, fertilizers, iron ore and sugar. These products are generally transported in large quantities in bulk in the typical holds arranged in the construction of the specialized ship — bulk carrier. The portfolio of safety-related services for bulk carriers involved in international trade is provided by class societies associated in IACS, and one of its members is the Polish Register of Shipping (PRS).
Currently designed and constructed bulk carriers and implemented survey procedures present high engineering quality necessary to ensure cost-effective, safe and reliable operation. Based on experience gained from the past, the safety of the current world fleet of bulk carriers is much better, as can be seen in EMSA (European Maritime Safety Agency) or IMO statistics. The progress in safety assurance is the result of parallel class societies efforts and flag states activities related to verification of compliance with international and national regulations. This is particularly important in the case of aged ships that require compliance with business standards requested by shipowners and ship operators to keep required level of competitiveness.
IACS class societies play a vital role in and are committed to the safety of existing and future bulk carrier fleet. According to EQUASIS 2019 the fleet of ships over 500 GT is dominated by ships classed by IACS members (56% by number and 78% by tonnage). In the case of bulk carriers, IACS societies are classing over 83% of the total world bulk carrier fleet. We can expect that the number of IACS classed ships will be on a steady increase both in numbers and in GT. The high rate of IACS classed bulk carries means that the majority of the world bulk carrier fleet has a major impact on the safety of commodities trade.
Some studies conducted recently touched subjects of prediction of commercial fleet future structure and certain ship types development as well as the rate of new-buildings and scrapping old ships. One of the studies is forecasting that the number of bulk carriers will remain almost constant within the coming three decades. Considering the maritime safety aspect, EMSA reports contain some statistical data on ship accidents and incidents rates, and these statistics show that the figures for new ships are much better than in the case of old ships.
The ship classification is a special type of business activity where specific and wide expert knowledge and safety consider ations are of utmost importance. The basis for classification societies activities are their rules dedicated mainly to shipping industry as well as to specific parts of the oil & gas industry, energy generation, rail & road transport or aviation. PRS as a classification society offers portfolio of services focused mainly on safety assurance. The set of PRS Rules has been developed based upon the society’s own experience and is continuously amended by inclusion of own R&D work results, e.g. IMO and IACS requirements as well as other applicable international technical and safety standards.
At present, PRS has over 500 seagoing ships classed and bulk carriers constitute about 16% of all classed ships. The substantial number of classed bulk carriers is of the medium age. PRS experience gained when dealing with older ships enabled the society to elaborate effective and high quality survey services. The last two years PRS was on the list of high performance classification societies of the Paris Memorandum of Understanding on Port State Control. Only classification societies that have a low ratio of detentions by PSC can get on the list of recognized organizations with the high performance result, what underlines the quality of their work and at the same time is one of the determinants allowing a vessel to be the Low Risk Ship. Being high on the performance list of Paris MoU shows PRS’ commitment to keeping a high level of services.
Over the years class societies took several steps to enhance the safety of bulk carriers. These have included the introduction of the corrosion protection requirements for ballast spaces, minimum thickness requirements for side shell web frames in cargo areas, tough regime of Enhanced Surveys and most notably the introduction of Common Structural Rules for Bulk Carriers (CSR) in 2005 followed by Common Structural Rules for Bulk Carriers and Oil Tankers (CSR BC & OT) in 2015. PRS implemented CSR Rules into its own activity and developed a set of related PRSCSR software for verification of the bulk carrier strength. The software has been assessed and positively verified according to IACS procedures.
Another important aspect of bulk carriers safety assurance is related to winter navigation in ice-infested waters. Like other class societies, PRS has implemented rules dedicated for seagoing ships that must have a sufficient strength of hull and machinery during navigation where increased risk of damage by brash ice blocks to the propulsion system exists. PRS’ practical experience in that area covers also special surveys and repair of damages caused by ice during ship operation.
An example is a serious ice damage that happened a few months ago when a fully loaded bulk carrier suffered failure to propeller blades. Due to circumstances, the only solution to the problem was to conduct repairs underwater at the nearest harbour. The repair was done after detailed underwater inspection, carried out under supervision of a classifier. Damaged blades were cut and straightened by the professional diving and underwater service provider company. Underwater repairs completed fully underwater has been surveyed by PRS and allowed to release the ship to sail fully loaded across the Atlantic.
PRS provides a specially tailored expert service dedicated to ships involved in commodities trade called Condition Assessment Program (CAP). CAP service is already well established within the tanker industry, but is also implemented as vetting practice in case of bulk carriers as a proved method leading to improvement bulk carriers risk assessment. It is an important voluntary service that provides independent evaluation of the technical condition of a bulk carrier. Based upon CAP process results, third parties can assess the suitability of the ship to be chartered and its current condition in relation to its age.
CAP assessment provides a charterer with a technical evaluation of the condition and maintenance of a vessel above standard requirements for a class. It is applicable to bulk carriers of 15 years of age and above. The CAP programme scope covers a detailed survey of the hull structure including verification of gauging as well as extensive testing of ship
machinery, equipment and cargo systems. Gathered information, combined with a strength and fatigue engineering analysis, is transferred into a numeric rating to be assigned to the verified ship — from 1 (Very Good) to 4 (Unsatisfactory).
A specific class activity is related to evaluation of novel technical solutions for implementation in ship technology. Newly developed designs and equipment prototypes are being verified by class societies to be implemented on board of ships using marine engineering practice. Completion of certification process allows for legal introduction of new solutions on ships and is a proof of the compliance with existing sound marine engineering and new safety and environmental standards as required by law.
Class societies are here to assure that ship technology developments are compliant with the mandatory requirements for technical and operational safety of bulk carriers as well as other ships involved in international trade.
ABOUT PRS
Polish Register of Shipping (PRS) is an independent expert institution acting on the international market, whose business is conducted for the benefit of the community. Through the formulation of the requirements, survey and issue of the appropriate documents, PRS assists State
Progress report: Black Sea Grain Initiative
The Joint Coordination Centre (JCC) was inaugurated in Istanbul on 27 July following the Black Sea Grain Initiative launched by Russian Federation, Türkiye, Ukraine and the United Nations.
From 1 to 15 August, the JCC has authorized a total of 36 movements of vessels (21 outbound and 15 inbound) through the maritime humanitarian corridor in the Black Sea to facilitate the safe exports of grain, foodstuffs and fertilizer, including ammonia, from Ukrainian ports.
During this period, 21 vessels have been authorized to move from the Ukrainian ports of Odesa (11), Chornomorsk (6) and Yuzhny/Pivdennyi (4) under the Initiative. Those vessels are carrying a total of 563,317 metric tonnes of grain and other foodstuffs.
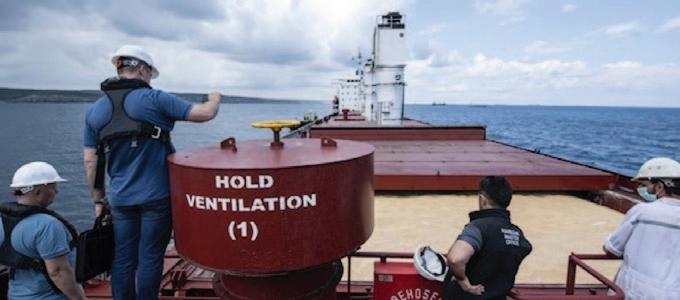
BREAKDOWN: 451,481 tonnes of corn 50,300 tonnes of sunflower meal 41,622 tonnes of wheat 11,000 tonnes of soya beans 6,000 tonnes of sunflower oil 2,914 tonnes of sunflower seed
According to information provided to the JCC, the preliminary destinations of Ukrainian food exports so far include: v Turkey: 26% v Iran: 22% v Republic of Korea: 22% v China: 8% v Ireland: 6% v Italy: 5% v Djibouti: 4% v Romania: 2% v To be determined: 5% ownership are determined through commercial activity and they may change en route. The food en route to Djibouti is 23,000 tonnes of wheat purchased by the World Food Programme (WFP) to contribute to the drought response in Ethiopia as part of the WFP’s humanitarian operations.
From 1–15 August, the JCC has conducted a total of 27 inspections through its joint inspection teams on inbound and outbound vessels. All ships inspected so far were cleared.
As part of its responsibilities, the JCC has been closely monitoring the inbound and outbound movement of vessels through the maritime humanitarian corridor in the Black Sea. It has so far observed on two occasions vessels deviating from the corridor and it has responded appropriately by contacting captains and advising them to follow the co-ordinates.
The JCC is also providing pre-transit briefs to inbound masters during the inspection process in Istanbul. The JCC continues to assess and review the procedures put in place to ensure the safe passage of vessels through the maritime humanitarian corridor. Administrations, Underwriters and the Society’s clients in ensuring the safety of people, floating objects, land undertakings, the safety of carried cargo and that of the natural environment. PRS is IACS member and acts also as RO upon over 40 authorizations of Flag States.
ABOUT THE AUTHOR Marek Narewski is a specialist and expert in PRS R&D Division with wide experience resulting from involvement in number of various marine and offshore R&D projects, novel technologies implementation in ship design and construction including marine application of composites and alternative fuels.
Photo: OCHA / Levent Kulu
The Black Sea Grain Initiative aims to respond to high food price inflation and to global food insecurity which is at record levels with tens of millions of people at risk of famine. According to the UN’s Food and Agriculture Organization, Ukraine contributes about 10.3% and 12.6% of global exports of wheat and maize respectively. Its share for sunflower products (seeds and oil) is 48.2%. Restarting exports will free up storage space in Ukraine and avoid wastage. It will also ensure a supply chain of food for this and subsequent harvests.
The deal aims to improve global food supply and calm markets. Prices across different food commodities are volatile and can be subject to a range of economic and climatic influences that go beyond Ukrainian exports.
Terminology: Outbound: merchant vessels departing the ports of Odesa, Chornomorsk and Yuzhny (Pivdennyi) heading to Istanbul Inbound: merchant vessels departing from Istanbul heading to the ports of Odesa, Chornomorsk and Yuzhny (Pivdennyi)
INTERVIEW: KOSTAS GKONIS, SECRETARY GENERAL INTERCARGO
The time frame required to change the direction of a bulker is frequently quoted in management speak, and many of the issues faced by the dry bulk shipping sector could be said to follow the same pattern. The dry cargo industry is used to making decisions for the long term and dealing with complex issues that have a lengthy lifespan and wide implications.
Today however, dry bulk operators are facing a perfect storm of circumstances to deal with.
Kostas Gkonis, Secretary General of INTERCARGO explains: “Following the turbulent pandemic years, the industry now finds itself dealing with the situation in Ukraine, the legacy of Covid and of course the incorporation of IMO’s greenhouse gas (GHG) reduction targets into everyday operations. Yet these issues are coupled with the safety, security environmental and regulatory challenges that the dry bulk industry has always faced.”
Gkonis explains that progress is being seen in some areas, but other issues are not so transparent.
“Our Association welcomed the Black Sea Grain initiative to resume grain shipments from Ukraine,” he says. “But amid the very public discussions regarding insurance and chartering, it must be stressed that the safety and security of the vessels, and their crews, must be at the heart of the debate.
“Practically, this means that there must be continued assurances at berths and anchorages in Ukrainian ports as to the safety of vessels and their crews, the security of cargoes, and that shipping in the area is free from attack. The creation of a mine-free sea corridor protected by naval escort is essential.”
The issue of Covid is now rarely in the news, but INTERCARGO members have advised of continuing difficulties. “The shipping industry is facing its own version of ‘long Covid’,” says Gkonis. “Seafarers worldwide continue to face major issues with crew change, port entry and changing vaccination requirements. New waves of infection persist at ports, and once again we are seeing local authorities creating their own interpretation of the rules.” He also explains that in a number of ports globally seafarers are finding access to shore leave restricted, and in some cases are finding it difficult to access nonemergency medical assistance.
Liquefaction too remains on the agenda, and industry partners could still do more to ensure the safety of crews, says Gkonis. INTERCARGO recently submitted its latest Bulk Carrier Casualty Report to IMO where it warned that not only were IMSBC Code requirements not being followed, especially in relation to testing and certification of cargo condition, but that there was also lack of adequate assessment and monitoring of the condition of cargoes being loaded in the cargo holds by representatives of all interests.
“Despite high levels of awareness from shipowners themselves of the dangers of improperly loaded cargo, the Report identified that liquefaction continues to be the greatest contributor to loss of life in the bulk sector,” says Gkonis.
“Between the years 2012 to 2021, 27 bulk carriers over 10,000dwt have been identified as total losses and 92 seafarers lost their lives. Liquefaction accounted for about 19% of the total vessel casualties in the past ten years yet was the cause of 76% of the total loss of life, as a result of five related bulk carrier casualties, four carrying nickel ore and one carrying bauxite.”
Ship operators are well aware of the risks to their crews and their vessels caused by carrying cargoes prone to liquefaction and make every effort they can to mitigate those risks, he says. “It is the lack of consolidated effort and commitment from many stakeholders to resolve the problem that is evident. These can include shippers, receivers and port state authorities at loading and discharging ports. We need action from those our industry relies upon for its safety — the IMO, legislators, and suppliers to ensure that the minimum obligations under the IMSBC Code are properly fulfilled. The industry is simply talking to itself if we cannot force action from our other stakeholder groups.”
Of course, all this is taking place against the backdrop of an industry striving to achieve IMO’s target of zero emission shipping by 2050, and facing a confusing array of MARPOL amendments, circulars, resolutions and guidelines, as they work to achieve this ambition. “You cannot place responsibility for meeting IMO’s zero emission shipping targets fully on the shoulders of shipowners,” warns Gkonis. “It must be remembered that the commercial development of these solutions is within the control of a spectrum of stakeholders. Such a target requires a drastic and urgently needed acceleration in the commercial development of the required technologies, fuels, propulsion systems and related infrastructure.
“The net-zero target will only be plausible if governments take the necessary action to achieve this at IMO.”
Returning to the Bulk Carrier Casualty Report, INTERCARGO is pleased to also report good news, with statistics of ship losses and consequential seafarer fatalities suggesting that the safety performance of the bulk carrier industry is showing a clear trend of improvement.
“We note positively that these figures continue to head in the right direction,” says Gkonis. “However, there is no room for complacency and we at INTERCARGO will continue to seek further improvement by re-evaluating and implementing enhanced measures to address cargo safety and safe navigation.”
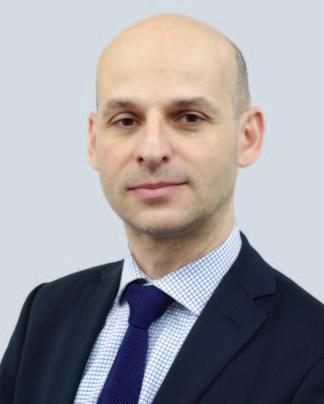
Kostas Gkonis, Secretary General, INTERCARGO.
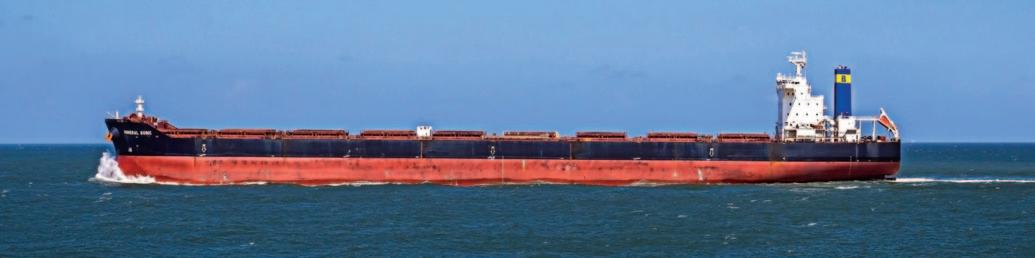
Oldendorff inks a contract with Blue Water for voyage optimization and fleet decarbonization by implementing BOSS after a year-long trial
The largest German bulk carrier company, Oldendorff Carriers, and Indiaheadquartered maritime technology company, Blue Water, announced the official signing of their contract to implement Blue Water’s “BOSS Voyage Optimisation Suite” for Oldendorff’s Cape & Baby Cape fleet of owned and time chartered vessels.
The BOSS Suite will propel Oldendorff’s continuous efforts towards a greener maritime trade by reducing emissions through intelligent voyage optimization, weather routing, vessel performance analysis and efficient fleet management.
Capt. Dexter Jeremiah, Managing Director Operations at Oldendorff, said: “After one year of successful trials, we chose the BOSS Suite for our Cape & Baby Cape Fleet since it met our needs for optimizing voyage operations, whilst enabling us to see real-time CII analytics for the vessels in one platform. The level of customization and development of advance voyage monitoring tools in the BOSS ecosystem with a quick turnaround has been second to none.”
Adding to the announcement, Capt. Kumaresh Gupta, Managing Director at BlueWater, said: “We are elated to have Oldendorff’s Cape & Baby Cape fleet in BOSS. Throughout the trials, we were presented with challenges to develop certain customized solutions for operational excellence and performance analysis, and the BOSS team turned them into opportunities to further showcase the platform’s customizability, scalability, and an eagerness to make significant changes to suit Oldendorff’s needs.”
About Oldendorff Carriers: since its establishment in 1921, Oldendorff Carriers has grown into one of the world’s leading dry bulk owners and operators, operating about 700 vessels around the world.
About Blue Water: the company provides a host of Software as Service for voyage optimization including its pioneer cargo heating management for tankers. Blue Water employs 100+ personnel in its Dehradun office and currently optimizes over 700 vessels of various type for maritime industry leaders, and provides quantifiable savings through a verifiable benchmarking system.
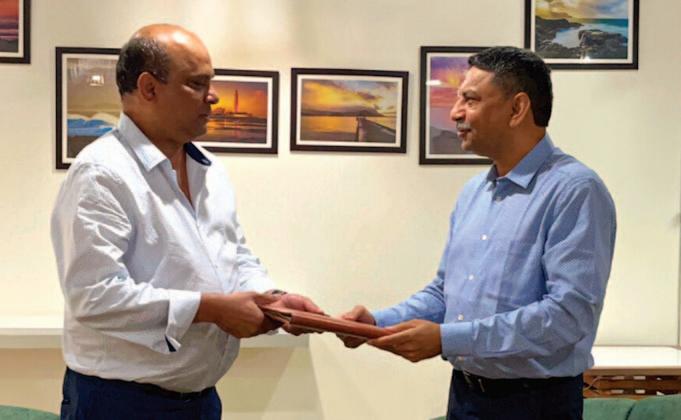
Capt. Dexter Jeremiah (left), Managing Director Operations at Oldendorff and Capt. Kumaresh Gupta (right), Managing Director at BlueWater.
Barnacle-laden bulkers: bad for business, bad for CII ratings
For as long as people, products and raw materials have been traversing the oceans, ship hulls have acted as attractive structures for marine life. Biofouling, whether by shell-forming creatures or soft organisms such as slimes and algae, significantly increase the amount of frictional resistance across a ship’s hull when it moves through the water.
Increased frictional resistance requires a ship to burn more fuel to maintain a set speed, or if operating on fixed shaft power or fuel consumption, then speed losses will occur. A 2007-published study by Michael. P. Schultz proclaimed that a vessel with 10% barnacle coverage would need a 36% shaft power increase to maintain the same speed. Put simply, the greater the barnacle fouling coverage, the greater the fuel demand. These are creatures that you do not want on your ship when profit margins are tight.
In June 2020, the results of a study commissioned by I-Tech AB and carried out by global marine consultants, Safinah revealed the true scale of highly impactful hard biofouling present across the global shipping fleet. A 249-ship sample was surveyed at drydock with their underwater hull condition inspected. The sample spanned all major ship types coated with biocidal and foul release coatings of different grades and generations, covering a wide range of activity and trading routes. Following the analysis of the hull condition inspection data, it was found that every vessel surveyed had some level of hard fouling. Troublingly, 44% of vessels surveyed had more than 10% of underwater hard fouling coverage. When looking at the breakdown of fouling by vessel type, it was found that across vessels with relatively lower activity, the frequency of barnacle fouling was greater. On lower activity vessels it was found that 45% of vessels had barnacle fouling coverage greater than 10% compared to just 27% observed across higher activity vessels.
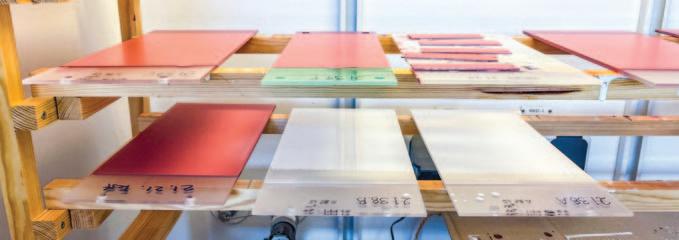

Panel testing of new paint formulations on the west coast of Sweden.
When factoring in data from another Schultz study, published in 2011 that investigated the performance penalty of biofouling, we can assume that levels of barnacle fouling across >10% of the hull surface is present on just under half the global shipping fleet. This means that the global shipping fleet is producing an excess of least 110 million tonnes of carbon emissions per year due to barnacle fouling alone. Furthermore, barnacle fouling on the hulls of ships is estimated to account for an additional US$6 billion spent on fuel per year for the global commercial fleet. The true figure is likely to be even higher, as this is a conservative calculation based fuel prices in 2020 and only assumes a 10% coverage of hard fouling on the fleet.
Since the underwater hull plays a huge role in ship performance, coatings play an equally huge role for a vessel to achieve good Carbon Intensity Indicator (CII) rating. Biofouled hulls, particulary those with any hard fouling, will negate important gains made by installing fuel efficiency enhancing technologies or using cleaner fuels.
The bad news is that the issue of biofouling will only worsen. As we sail further into the future, a greater number of ships will face a higher risk of biofouling creatures and barnacle infestations on the hull and bulk carriers are not immune to this. Any bulk carriers sitting at anchor for a period of a few days, or more are at a great risk of biofouling accumulation. The majority of antifouling coatings rely on a vessel moving through water to function effectively. So, what happens when a vessel stops? Usually that means that barnacles can attach and accumulate at a rate of knots.
The greatest concentration of biofouling creatures are found in the warmer waters of the tropics and subtropics. Since the 1990s, a shift in global trade has resulted in ships visiting ports in tropical and sub-tropical waters. Furthermore, vessels are spending significant periods of idle time in these ports either loading or unloading or queuing in increasingly congested waiting zones. During this time, they face a high risk of picking up hard fouling organisms.
Therefore, an insurance policy against hard fouling is needed. Since idle periods can hinder the efficacy of biocidal and foul release coatings, most coatings can only offer 14–21 idle days performance guarantees. The development of antifouling coatings that better protect vessels which may sit idle or longer than standard idling guarantee offered by coatings manufacturers during a three or five year service period is essential, if not vital.
Yesterday’s solution will not work for tomorrow’s problems. This has catalyzed great innovation in the marine coating sector. An increasing number of ship owners are demanding 30-day plus guarantees and for antifouling coating manufacturers, one way that this can be achieved is through the inclusion of the active agent, Selektope® . Selektope® is an organic, non-metal active paint ingredient that is relatively unique compared to traditional biocides currently found in many marine paints. Through natural receptor stimulation, Selektope® activates hyper-mobile behaviour in barnacle larvae, which prevents them from attaching themselves to the hull and niche areas. The effect is temporary while they are in close proximity to the coated surface and ultimately leaves them unharmed. When used in antifouling paints, all ship types can remain idle or at low speeds for extended periods of time, even in extreme barnacle fouling conditions.
Out of the top six marine coatings manufacturers, three of them have commercialized products containing Selektope® in the past five years: Chugoku Marine Paints, Hempel and Jotun. The technology is also being used in many outfitting coating products following demand from shipyards located in South Korea who were facing the issue of barnacle fouling during long fitting out periods.
The use of Selektope® also presents a significant advantage over a reliance on hull-cleaning technologies for hard fouling removal and reduces the risk of coating damage after cleaning. Also, as opposed to the need to constantly monitor hull condition, antifouling coatings with Selektope® confer relative peace of mind to bulker operators that their ship hulls will remain barnacle-free.
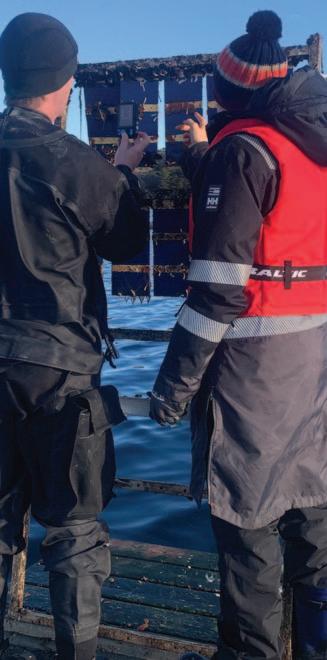
I-Tech R&D Chemists inspecting panel tests.

Blue Water being cognizant of the recent CII developments, has introduced a smart and practical CII Estimator, that allows vessel owners and operators to assess future operational impact on their fleets, and gives them estimates to improve efficiency, optimize CII ratings and help with their decarbonization targets.
Serving as an intrinsic feature of Blue Water’s BOSS Voyage Optimization Suite, the BOSS CII Estimator readily calculates the yearly CII based on multiple parameters using BOSS’ extensive AI & ML assisted vessel digital twins.
HOW BOSS CII ESTIMATOR WORKS The BOSS CII Estimator simulates hundreds of trading patterns at a flick of button to estimate how the operational parameters will impact the vessels’ CII rating. Further, it answers the following most commonly sought questions by vessel owners and operators: v What is the vessel’s current CII rating? v What will be the impact of CO2 emissions on the current CII rating due to the future trade pattern? v How to identify the most suitable trading pattern for better CII ratings? v How to determine the optimum speed instructions for a vessel for a certain trade route?
BOSS CII ESTIMATOR FEATURES v 2,000 Simulations at an Instant:
Considering 100 Cape Vessels in a fleet, simulating all Baltic route combinations for eco and full speed at both laden and ballast conditions would have taken 2000 simulations.
BOSS CII Estimator dramatically cuts this down to one click & one second. v Supports Vessel Specific Baltic
Routes: Computes vessel class specific Baltic Routes at a click of button, and generates the estimated
CO2 emissions and corresponding CII rating. v Estimations basis Vessel’s
Performance: Uses vessel’s past data or sensor data to generate a digital twin and provide realistic estimations. v Estimations basis Vessel’s SnC data v Draft and Load Condition Specific
Simulations v Dynamic Sea Margin: The estimator does not only consider a standard sea margin for simulation, but also provides an option to use historical weather data to calculate sea margin. v Vessel Specific Retardation Factors:
Apart from Sea Margin, the BOSS CII estimator also takes in vessel class specific weather and sea retardation factors to compute speed and emissions details, giving a much v
v
v
v transparent and practical estimates. Determine Optimum Speed & Trading Pattern: On simulating the different trading routes, BOSS CII estimator suggests optimum speed and trading pattern to optimize CII rating of vessels. Fuel Specific Calculations: Calculates CO2 emissions based on fuel type usage. Interactive UI: Removes the need for both tedious excel sheets and evaluating results on multiple routes. Instead, an interactive interface provides a much simpler way to conduct route and speed comparisons. Share Simulation Reports: BOSS CII estimator lets the user easily export and share simulation details with anyone.
ABOUT BLUE WATER The company provides a host of Software as Service for voyage optimization including its pioneer cargo heating management for tankers. Blue Water employs 100+ personnel in its Dehradun office and currently optimizes over 700 vessels of various type for maritime industry leaders, and provides quantifiable savings through a verifiable benchmarking system.
ABB and Wallenius Marine introduce pioneering digital offering driving efficiency gains for ships
ABB and shipping company Wallenius Marine have introduced OVERSEA — the maritime industry’s first digital offering and fleet support center available as a service. The two companies have developed OVERSEA to help ship owners, operators and managers enhance the efficiency and sustainability of vessel operations.
OVERSEA leverages ABB’s extensive expertise in ship technologies and the ABB Ability™ Genix Industrial Analytics and AI suite, combined with fleet management knowledge from Wallenius Marine, to enable measurable performance improvements for vessels, leading to decreased fuel consumption and reduced emissions.
OVERSEA helps address such aspects of vessel performance as hull and machinery, speed and route planning, as well as emissions and carbon intensity reporting. With deeper insights into vessel’s operational data, backed by advanced analytics, OVERSEA centre experts will be able to recommend concrete actions to shipping companies to help them improve energy efficiency, safety and reliability of operations.
OVERSEA is scalable to meet the various and ever-changing needs of shipping companies. With OVERSEA digital solution, shipping companies with in-house fleet support centres can collaborate on the same data with vessels and onshore office to get insights, provide recommendations and manage improve ment actions. In addition, shipping companies in need of further support can rely on the assistance of OVERSEA center experts for daily advice, periodic performance reviews and reporting, and on-demand performance consulting.
“We talk a lot about innovations that will make us more sustainable in the future, and OVERSEA makes a real difference already today. From our experience, we know that the operation of a vessel has a deep impact on released emissions and fuel consumption,” said Johan Mattsson, CEO, Wallenius Marine. “With clear recom mend ations to the crew, based on datadriven analysis, vessel owners and operators are able to significantly reduce both their environmental footprint and fuel cost.
“ABB is committed to driving shipping decarbonization, and OVERSEA has been developed to further support this target,” said Jyri Jusslin, Head of Service, ABB Marine & Ports. “OVERSEA allows turning insights into actions that can significantly improve the efficiency and sustainability of vessel operations. We are confident that this pioneering innovation will serve as a new standard in fleet and vessel performance optimization.”
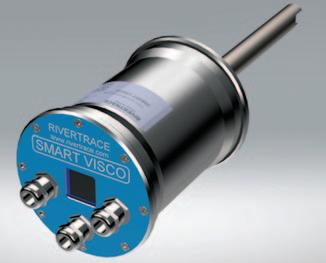
Rivertrace, an ISO9001 Quality-Assured Company and market leader with over 30 years of experience developing environmental monitoring solutions for the marine market, launched its innovative SMART VISCO sensor at the SMM Maritime Fair, which was held in early September in Hamburg, Germany.
The SMART VISCO sensor is designed to measure the viscosity and temperature of fuel oil before injection into the main engines of large ships. The monitor then reports this data via both analogue and digital outputs, with volt-free relay contacts.
The SMART VISCO sensor measures all grades of HFO using ultrasonic guided wave technology. Due to the high frequency and speed of ultrasound, ambient vibration and flow speed have no impact on the measurements. The monitor incorporates an LCD display that visually indicates all parameters. The viscosity and temperature data can also be easily retrieved using RS485 or a USB stick.
The fuel oil’s viscosity provides a direct indication of its impact on engine performance and efficiency. The availability of this information aid in the prevention of engine damage, reduces maintenance costs, and helps to minimize greenhouse gas emissions.
This SMART VISCO, with its digital capabilities can be integrated with the RIVERTRACE CONNECTED service to collect and share the data with ship management to monitor and analyse trends in fuel performance at both a vessel and fleet level.
The RIVERTRACE CONNECTED service initiative provides calibration compliance and equipment performance data. It can either be viewed on a cloud platform or shared through an API to the vessel/fleet management systems. The digital service is designed to support customers seeking simplified, continuous monitoring and efficient operations.
Martin Saunders, Managing Director of Rivertrace, says: “Monitoring environ mental discharge has been at the core of Rivertrace’s ethos for over three decades. However, in recent years we have also embraced digital transformation and provided solutions to automate and analyse the data by making our services smarter, and by connecting into the marine digital ecosystem. The SMART VISCO probe extends our offering to encompass onboard monitoring and expands our environmental solutions to include minimizing greenhouse gas emissions, as well as our oily water pollution prevention system.”
SMART VISCO Sensor.
Stellium and Voyager Portal announce partnership
DIGITAL TRANSFORMATION, PARTNERSHIPS, SUPPLY CHAIN, VOYAGER Stellium and Voyager Portal have announced a first of its kind partnership to bring a fully integrated SAP TM and Bulk shipping operations platform to global markets.
Until now, Transportation Management solutions have struggled to handle the nuances and complexities of global bulk commodity shipping. Instead, TM solutions have been focused on helping businesses manage rail, truck and container freight operations.
“Bulk commodity shipping is a highly complex and fragmented mode of marine transport. Over 90% of ships crossing the ocean will transport bulk commodities such as crude oil, gas, petrochemicals, agricultural products, heavy equipment, and minerals. Given the complexity and variability of each shipment, the operations teams often work exclusively with email and XLS for tracking, planning and execution activities,” says Matthew Costello, CEO of Voyager Portal.
Voyager Portal helps bulk shipping teams digitally manage their operations with their external parties in a shared collaborative environment. Their low-code workflow technology provides customers with the flexibility to design and execute their unique processes, then surface the data for Exceptions Based Management and reporting. The platform allows teams to manage hundreds of common operational workflows such as vessel nominations, survey appointments, terminal clearances, ETA tracking, demurrage and cargo claims.
Working closely with its global customer base of manufacturers, Stellium identified a need in the market for a digitally integrated solution. One that would help customers capture their entire transportation value chain from bulk inbound raw materials, through to outbound finished goods, within a single solution, regardless of mode.
“Our team has extensive first hand experience implementing SAP TM for our customers. Through our many business consulting and system integration engagements we have become acutely aware of both the importance of bulk shipping to our customers, and also the inherent risks that exist with this unique mode. With Voyager and SAP TM, our customers’ planning, production and sales teams can have a true end-to-end picture of their transportation operations in one place,” notes Randeep Nambiar, CEO of Stellium.
“What attracted us to Stellium as a partner was not just their deep domain expertise around SAP, but their extensive reach and global reputation. The Middle East & APAC/India regions are one of the largest importers and exporters of bulk commodities in the world, so we look forward to accelerating growth off the back of the partnership,” says Costello,.
ABOUT VOYAGER Voyager Portal is an operations management platform for bulk commodity shipping. The SaaS application allows Voyager customers to collaboratively manage their operations with internal and external stakeholders in a unified environment. By streamlining operations and data flows across organizations Voyager is able to help teams manage through exception, automate manual processes and deliver real-time insights.
ABOUT STELLIUM INC Stellium is a specialized management consulting firm committed to designing and delivering solutions that improve businesses worldwide. Stellium Inc. is headquartered in Houston, USA and its regional head office resides in Bangalore, India and Toronto, Canada. Stellium has a geographic presence in North America, Asia Pacific and the Middle East region.
By Levent Karacelik, Marvel Consultancy & Shipping Inc. Black Sea was one of the major areas where cargoes, especially for coaster size vessels, were generating and loaded for many years, even close to 100 years.
In normal conditions every year there is around 12 to 16mt (million tonnes) of grain cargo shipped from Black Sea countries and almost 80% of this volume is loaded from Russian and Ukrainian ports in the black sea. Grain cargo ex Kazakhstan/ Kyrgyzstan/Turkmenistan/Azerbaijan are also loaded from Russian Black Sea ports.
Also, those two countries, Ukraine and Russia, are the main coal exporters and coal exports of other countries in the area, such as from Kazakhstan/Kyrgyzstan/ Turkmenistan Belorussia are also loaded from Ukrainian and Russian ports, thus making total coal cargo loaded from the ports of those two countries around 15 to 20mt (million tonnes) minimum per yer.
Fertilizer exports from the Black Sea ports of those two countries is also between 2–4mt per year. When you add steel products, scrap to those cargoes you are talking about yearly around 35 to 45mt of cargo which were loaded from the Black Seaports of Ukraine and Russia.
Once the war started for almost three months there was no cargo movement except the cargoes which were already loaded on the ships just before the war, but even the majority of these ships were blocked at Ukrainian ports, including all Azov Sea ports and navigation in Black Sea was very much limited due to mines left by both sides into open sea.
The biggest negative effect of this situation was on the coasters between 3,000/15,000dwt and sea river type vessels between 3,000/7,000dwt, which were almost 90% depending on the cargoes coming out from Russian Azov Sea ports and Mariupol/Berdyanks and Odessa/ Nikolayev, which were all closed for quite some time.
The number of vessels calling Ukrainian and Russian ports in Black Sea in January 2022 were around 500 and in February 304 and in March that number went down to 99 vessels. There were no alternative cargoes for the vessels to replace the cargoes lost due to the war.
Sometime later the shipments of coal and some grain cargoes started from Russian Azov Sea ports but that did not help the rates to go up as much as they fall. However, some cargoes were moved from Ukraine to ports like Reni/Izmail/Sulina
COAL EXPORTS TO MIDDLE EAST INCLUDING TURKEY
MONTH 2021 2022 % February 1.345 879 -65% March 1.961 1.367 -70% April 1.218 1.089 -10% May 1.442 1.105 -23% June 1.570 2.115 40%
* Numbers are in million tonnes.
Source: Metalexpert
QUANTITY CARRIED LESS DUE TO WAR BETWEEN FEBRUARY – MAY 2022
466 tonnes 594 tonnes 129 tonnes 337 tonnes Total: 1,526,000 tonnes Equals to 305 voyages basis 5,000 tonnes lots.
Source: Metalexpert
canal where due to congestion, vessels were waiting almost 40/50 days to berth and load cargo and freight rates went up almost 300%. Such as a 5,000mt cargo from Reni to Turkish Marmara: Sea freight went up to US$110/120 from US$30/35 levels.
EXPECTATION IN THE FUTURE AND THE EXISTING SITUATION IS THAT The EU’s sanctions do not have any direct implications for Turkish buyers as Turkey is not an EU member. This means Turkish buyers can source Russian coal at steep discounts against API 2 index. Prices for non-Russian coal offered to Europeans buyers — including from Australia, Colombia, South Africa and the US — have risen to record highs. Turkey’s power sector, is expected to continue sourcing most of its needs from Colombia for the remainder of this year, as buyers have term deals in place.
Also China & India who do not follow sanctions are serious buyers of Russian coal. Chinese buyers are now paying in Yuan for coal from several large Russian producers.
Indian companies are also paying for Russian coal cargoes in rupees, although such transactions are made predominantly for trades of thermal coal.
The bulk carriers (Handy/Supramax/ Panamax size), which were coming to eastern-Mediterranean ports and with cargoes were either taking cement or clinker or some minerals from Turkey or Egypt and some from Greece, but majority was ballasting to Ukraine/Russia to load grain/urea/fertilizer/slag/clay/coal/iron ore. The volume of such cargoes decreased almost 70%. Only four major Russian grain traders were shipping almost around 12mt together but since the beginning of the war their export ex black sea ports is not even 30% of this quantity. Turkish coal import from Russia was almost 7mt but that went down to 100,000/150,000 metric tonnes in a period of total 4 months.
Grain carried before war between January 2021 – January 2022 from Ukraine and Russia only to Turkey was around 7mt in total.
From February 2022 until July 2022 it is around 1mt. So 6mt cargo as grain disappeared which is equal to 1,200 voyages of 5,000 metric tonnes each.
Voyage shipments of grain started to increase after Russia, Ukraine & Turkey signed in beginning of August and since then only in August only 2mt grain shipped out of Ukraine and Russia to various destinations.
Thanks to Turkey, who did not follow the sanctions declared by USA/EU countries to Russia, there were still some grain and coal cargos moving, which would otherwise have seen a lot of owners bankrupting.
Besides the decrease in the volume of the cargoes ex Black Sea, there also was sanctions applied to the vessels which were calling Russian ports and that was applied not only to the vessels calling Russian Black Sea port, but all Russian ports. That had affected the export and import of other ex-CIS countries who were only using Russian ports because they do not have any shore on the sea.
Now, as of July 2022, it seems that shipment of grain cargoes and all other agri products and coal is going to be free and there will be no sanction to the ships calling Russian ports.
This will help the freight market to recover and start going firmer.
However, due to the decreasing grain and coal FOB and CFR prices, especially buyers in Turkey are very reluctant to conclude purchase deals and Egypt who’s the biggest grain importer in this area have great difficulties in making the payments. As a result of this now the coaster freight market is very low and depressing as well as the time charter rates of bulk cargoes out from Med to Far East and also to US Gulf destinations are low.
How BSM is supporting to meet new IMO regulations “A win-win situation for owners and charterers”
In BSM’s central Fleet Monitoring Centre, nautical and technical experts monitor 24/7 key performance data in real time, including energy efficiency.
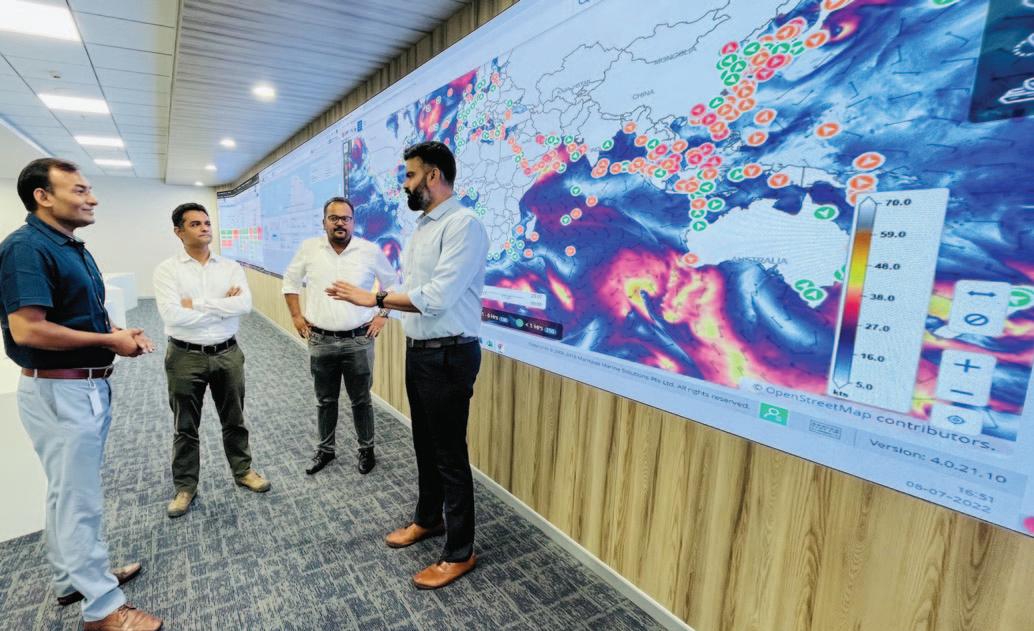
Bernhard Schulte Shipmanagement (BSM) has long been a key player in the dry cargo segment, presently having more than 170 bulkers ranging from handysize to very large ore carriers (VLOC) under management, writes Firoze Mirza, Managing Director BSM Hong Kong.
As part of its technology leadership, BSM has established a Fleet Performance Centre (FPC) and Fleet Monitoring Centre (FMC) to optimize the operations and efficiencies of the managed vessels.
The issue of vessels’ voyage performance, especially in relation to their carbon footprint, has been given greater urgency by the new IMO regulations, with the Energy Efficiency Existing Ship Index (EEXI) and Carbon Intensity Indicator (CII) taking effect in 2023. However, BSM has long recognized the role that enhanced fleet performance plays as part of its service to shipowners, keeping in mind that reducing fuel consumption and thereby emissions automatically saves fuel costs, and thus is a win-win situation for all vessel operators, their customers, and the environment.
Through a holistic process of vessel performance monitoring, decarbonization management, data collection and data analytics managed out of our own Fleet Performance Centre, BSM is helping owners navigate the complexities of the new IMO requirements.
BSM developed an in-house EEXI calculator to compute the required and attained EEXI values of the managed fleet and generate the corresponding EEXI technical files. The data-backed recommendations target technical and operational improvement methods for the ships. Similarly, BSM developed a CII calculator addressing the CII ratings of its entire fleet. This year, BSM’s Fleet Performance Centre will release additional tools for CII performance monitoring services, including predictive algorithms, to assist owners with vessel CII improvement investigations.
The aim of all these initiatives is not merely to ensure compliance with the IMO’s EEXI and CII requirements, but rather utilize these as tools for continuous and ongoing benchmarking and improvement, to reduce carbon emissions and minimize fuel costs.
As part of the FPC, the Fleet Monitoring Centre offers a 24/7 vessel operations and compliance monitoring service. This state-of-the-art facility is supported by nautical and technical experts and fleet performance analysts. The FMC offers decision support to crew, technical staff on shore and continuous improvement of vessel operations. A dedicated fleet performance team models ships and builds a unique digital twin that enables comparison of ships’ actual performance to its ideal performance.
The FMC acts as a central support team for BSM fleets to improve the navigational and commercial aspects of vessels through three key areas: v Increasing energy efficiency and ensuring CII compliance by monitoring major consumption contributors, such as the main engine, auxiliary engines, and boilers as well as compressors. v Operational risk mitigation, assisting fleet teams to prevent any emergencies through weather warnings and routings, emissions area monitoring, canal transits and piracy area monitoring. v Voyage optimization: the FMC can enhance the commercial performance of managed vessels through voyage planning and tracking and post-voyage analysis.
The FPC has developed a benchmark, dubbed vessel performance rating (VPR), which is an aggregate of voyage performance, reporting quality and machinery performance, each of which are themselves a collection of individual
VESSEL PERFORMANCE RATING (VPR) Since measurement of the VPR began, considerable improvement has been noted across the entire BSM Fleet, with the average VPR increasing from 55% in September 2021 to 65% in June 2022.
One challenge we have observed when discussing our performance optimizing services with clients across all shipping sectors, including the bulker industry, is that most benefits (voyage efficiency and fuel savings) achieved through investment are mainly realized by the charterer, as opposed to the shipowner and manager who bear the costs of investing in the improvements.
Due to the archaic charterparty contracts still utilized, there is no mechanism for the owner to share the Vessel Performance Rating (VPR).
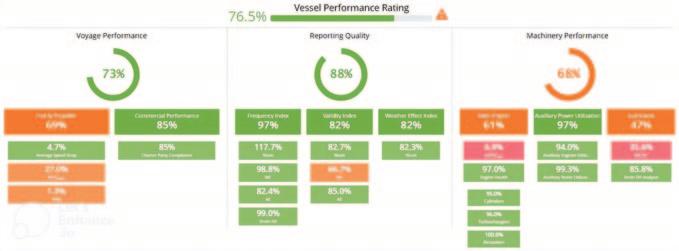
benefits. This results in a less than optimum situation, where owners are unable or unwilling to invest in latest technologies (such as telemetry) which would enhance performance, and charterers lose out on potential fuel savings, and the opportunity of zero cost (or even negative cost) carbon reduction is wasted.
As the industry moves into 2023 and beyond, IMO’s initiatives will result in greater acceptance by ship owners of investment in carbon reduction (and fuel saving) opportunities. At the same time, the end-user charterers will agree to pay a premium for the same, resulting in a winwin situation for all.
Accelleron and Hoppe Marine to partner on data collection for improved vessel performance analytics
Tekomar XPERT marine, Accelleron’s comprehensive digital suite that delivers customers with powerful insights into vessel’s hull and propeller performance. Mauro De Micheli, Head of Sales & Partnerships, Digital Solutions, Accelleron (L), with Hauke Hendricks, Head of Sales, Hoppe Marine GmbH, at Posidonia 2022.
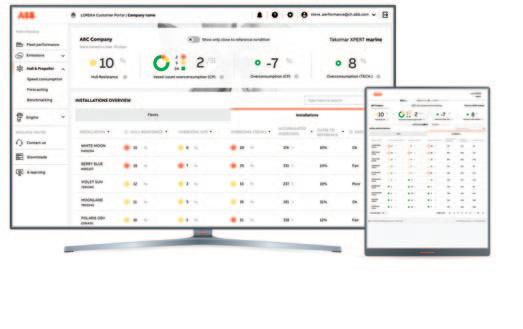

On June the 8th, 2022, Accelleron, the new face of ABB Turbocharging, and Hoppe Marine, the German provider of maritime measurement solutions, have signed a partnership agreement which will facilitate rapid onboard data collection for Accelleron’s digital solutions used in dedicated engine analysis.
In particular, Tekomar XPERT marine, Accelleron’s comprehensive digital suite that delivers customers with powerful insights into vessel’s hull and propeller performance, as well as emissions tracking and forecasting, will be further enhanced with continuous data connectivity.
Hoppe Marine has extensive experience with data generating systems on board, including automation systems and sensors from different suppliers. This data is delivered in a highly structured and standardized way, and will enable Accelleron to pre-populate the input to Tekomar XPERT marine, thereby increasing efficiency and effectiveness.
“Having fast and accurate information is an essential basis for optimizing vessel performance. This agreement will allow us to leverage Hoppe’s established onboard data collection services to serve our customers even better with value-adding analytic support. The data can be transferred swiftly and accurately, eliminating the need for manual data collection by the crew, and is essentially a ready-to-go system,” said Mauro De Micheli, Head of Sales, Marketing and Partnerships for Digital solutions, Accelleron.
Hoppe Marine’s system infrastructure is designed to enable the collection of data from a wide range of onboard systems. This eliminates the need for shipowners to install additional IoT solutions on board to provide data.
This means that high quality data analytics can be carried out continuously, rather than being based on ad-hoc engine readings.
“We are pleased to enter into this important cooperation agreement with Accelleron. Both companies are committed to supporting the maritime sector in its efforts to become carbon neutral. By working together to enable owners and operators to achieve fuel savings, emission reductions, and optimized engine performance, we are delivering concrete evidence of this commitment,” said Hauke Hendricks, Head of Sales at Hoppe Marine.
Customers retain full control over their vessels’ data, and operational signals can be shared via ship-to-shore connectivity. Furthermore, by having enhanced and continuous readings to provide engine and vessel insights, trends become quickly apparent enabling any required actions to be promptly taken. No cabling or wiring onboard ship is required to connect the two systems.
v
v
v What is the vessel’s current CII rating? What will be the impact of CO2 emissions on the current CII rating due to the future trade pattern? How to identify the most suitable trading pattern for better CII ratings? How to determine the optimum speed instructions for a vessel for a certain trade route?
BOSS CII ESTIMATOR FEATURES v 2,000 Simulations at an Instant:
Considering 100 Cape Vessels in a fleet, simulating all Baltic route combinations for eco and full speed at both laden and ballast conditions would have taken 2000 simulations.
BOSS CII Estimator dramatically cuts this down to one click & one second. v Supports Vessel Specific Baltic
Routes: Computes vessel class specific Baltic Routes at a click of button, and generates the estimated
CO2 emissions and corresponding CII rating. v Estimations basis Vessel’s
Performance: Uses vessel’s past data or sensor data to generate a digital twin and provide realistic estimations. v Estimations basis Vessel’s SnC data v Draught and Load Condition Specific
Simulations v Dynamic Sea Margin: The estimator does not only consider a standard sea v
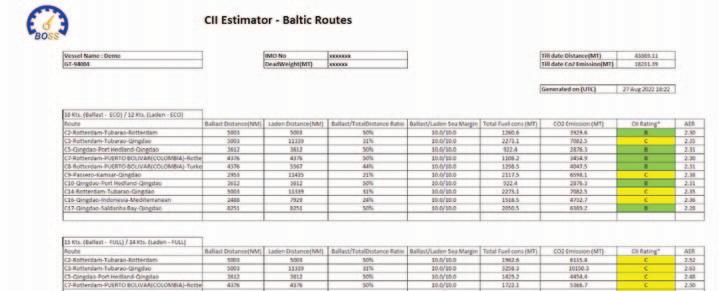
v
v
v margin for simulation, but also provides an option to use historical weather data to calculate sea margin. Vessel Specific Retardation Factors: Apart from Sea Margin, the BOSS CII estimator also takes in vessel class specific weather and sea retardation factors to compute speed and emissions details, giving a much transparent and practical estimates. Determine Optimum Speed & Trading Pattern: On simulating the different trading routes, BOSS CII estimator suggests optimum speed and trading pattern to optimize CII rating of vessels. Fuel Specific Calculations: Calculates CO2 emissions based on fuel type usage. Interactive UI: Removes the need for both tedious excel sheets and evaluating results on multiple routes. Instead, an interactive interface provides a much simpler way to conduct route and speed comparisons. Share Simulation Reports: BOSS CII
v
estimator lets the user easily export and share simulation details with anyone.
ABOUT BLUE WATER The company provides a host of Software as Service for voyage optimization including its pioneer cargo heating management for tankers. Blue Water employs 100+ personnel in its Dehradun office and currently optimizes over 700 vessels of various type for maritime industry leaders, and provides quantifiable savings through a verifiable benchmarking system.
- CUT DELAYS AND COSTS WITH
TRANSFORMATIVE MARITIME ANALYTICS - PREDICT DESTINATIONS WITH UP TO 70% ACCURACY - PREDICT TIME OF ARRIVAL TO PORT
WITHIN +/- 10 HOURS AND TIME TO
BERTH WITHIN 1-2 HOURS Twenty seven per cent of vessels fail to arrive within 24 hours of their published Estimated Time of Arrival. This lack of accurate AIS-based data puts pressure on ports, hampers logistics and pushes up costs. This could soon change, however, thanks to transformative new analytics from Lloyd’s List Intelligence, the maritime data experts, trusted by more than 60,000 professionals across the globe to power their decisions in operations, compliance, and risk management.
Introduced from 8 August 2022, Lloyd’s List Intelligence ‘Seasearcher Predictive Fleet Analytics’ is the first ever ‘air traffic control’ for the world’s commercial shipping fleet. It combines near-real-time data collected from 3,000 sources, resulting in over 327 million AIS vessel positions monthly across the global fleet. Specially designed advanced analytics, AI, and machine learning transform this unique data into accurate estimated times of arrival into port (ETA), arrival times at berth (ETB), and times of departure (ETD) for key active commercial vessels, along with current and future estimates of port congestion.
Lloyd’s List Intelligence are the first to bring ETBs and ETDs to market, and no other provider brings together a broader range of predicted, actionable insight.
INDUSTRY-WIDE PROBLEMS Currently, over a third (36%) of Automatic Identification System (AIS) messages are missing ETA data, while another 27% of vessels fail to arrive within a day of their published ETA. Even destination data is unreliable, with 63% of vessels publishing one port destination but ending up at another (source: Lloyd’s List Intelligence 2020 AIS message analysis).
A POWERFUL SOLUTION, REQUESTED BY CUSTOMERS Destination and ETA data gaps represent one of the most severe business challenges to the supply chain – impacting the ability of businesses to work efficiently, effectively and profitably: v Financial losses: like demurrage charges, additional waiting and handling fees and invalid pricing v Damaged customer relationships: from delivery misjudgements, schedule changes and reassignments v Loss of sales: from a lack of visibility, reactive service delivery which have a negative impact on customer experience Informed by over 100 customer and stakeholder interviews across companies and government organizations, Predictive Fleet Analytics has been built in response
to these widespread industry challenges.
Delivered as API data and integrated into the Seasearcher platform, Predictive Fleet Analytics helps customers gain greater certainty around estimated destination, arrival, berthing, and departure times, along with port congestion status and waiting times. This greater level of insight is key to more efficient voyages and port operations and the optimal use of vessels, fuel, port facilities and services, and the teams that operate them all, resulting in time and cost savings.
With analytics powerhouse partner SAS, a leader in artificial intelligence (AI), data mining, modelling and forecasting, Lloyd’s List Intelligence have developed this pioneering new method of calculating, predicting, and learning from vessel movements and behaviours in ways that were not possible before.
The AI and machine learning models predict destinations with an accuracy of 70%, ETA to port within ±10 hours, and ETB to within 1–2 hours, catering for key vessel types in the commercial fleet operating to both fixed and non-fixed schedules.
“Predictive Fleet Analytics allows our customers to let decisions on scheduling and routes be driven by the best quality data, so that shipping companies can save on resources and costs,” says Parvin Conners, Vice President of Product and Data for Lloyd’s List Intelligence.
“This new level of prediction around destinations and arrivals helps ports to optimize their services and facilities and for maritime servicing businesses to run more smoothly. All of this is possible thanks to the strength of our data and analytics and how we use AI and machine learning.”
Start-up company CleanQuote launches major software update to eliminate hidden vessel cleaning costs
When operation managers tend to their fleet of vessels, their main focus is typically on fuel, food, and crew. But in many cases, the vessels also need extensive cleaning — for instance when a dry bulk vessel changes cargo from coal to grain. Recent findings show that cleaning expenses are taking an increasingly large toll on operation budgets. Often, cleaning supplies are not ordered in time, or cleaning crews are not booked until the very last minute, which leads to longer port time and higher costs. T o avoid this, CleanQuote has digitalized the entire vessel cleaning process and is now introducing a new tool kit enabling operators to gain valuable insights never seen before.
It has been a busy summer for Danish start-up company CleanQuote. While tending to more than 500 existing users of the CleanQuote digital platform, developers have also laid the final touches on a new tool kit that will make a real impact when dealing with vessel cleaning.
“Originally, we set out to make a digital platform that would help maritime operators get their work done faster and easier.” says co-founder Lasse Ekdahl. “Therefore, we built the CleanQuote platform and made it free of charge for our users to send requests for cleaning supplies or cleaning crews. But with the new tool kit, we are really taking things up a notch.”
The new tool kit is called CQ Operator, and it focuses on inventory lists – or ‘ROBs’ as they are called in the industry, which is short for ‘Remaining on Board’.
Via CQ Operator, operators can with a press of a button have captains generate and send ROBs. Furthermore, they can also define stock minimums — for instance if they always wish to carry at least 1,000 litres of a certain cleaning chemical.
The system can automatically setup alerts and notifications when items are removed or missing from the stock, making it a lot easier for the operators to ensure that the necessary cleaning products are available on site as soon as the vessel in question is ready for cleaning.
“The biggest advantage of the new tool kit is that it gathers all communication between operators and their vessels in one user-friendly and manageable solution.” explains Ekdahl. “Until now, many of our customers have had to handle their ROBs as spreadsheets, which are often lost or misplaced making the communication a real struggle. Especially when handing over a vessel from one operator to another. They simply haven’t had a suitable tool to generate the perfect overview of when and how a specific vessel was last cleaned. Now, they can register everything in CQ Operator — including cleaning history and data on chemical consumption.”
Precise inventory of consumed chemicals per vessel cleaning is also valuable information for ship owners and operators committed to reducing their environmental impact. Currently, several global ship owners are seeking to optimize their cleaning processes by cutting down on the use of bleach and other substances. In support of this, CQ Operator can also provide useful insights.
The new module can be accessed via

Remaining on Board flowchart. cleanquote.com and is available to both existing and new customers. Basic use of the CleanQuote platform is free of charge, while use of CQ Operator requires a monthly fee. ABOUT CLEANQUOTE CleanQuote helps simplifying the purchasing process with an easy-to-use platform with a clear focus on cost and time optimization. The continued development of CleanQuote is based on input from numerous operators, ship managers and suppliers involved in hold and tank cleaning all over the world. The company is dedicated to adding value to the carrier cleaning challenge and give its customers the right tools to make optimal decisions.
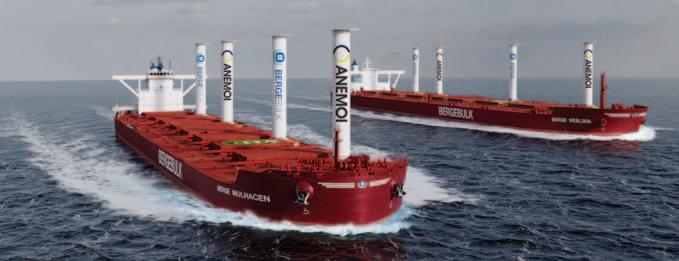
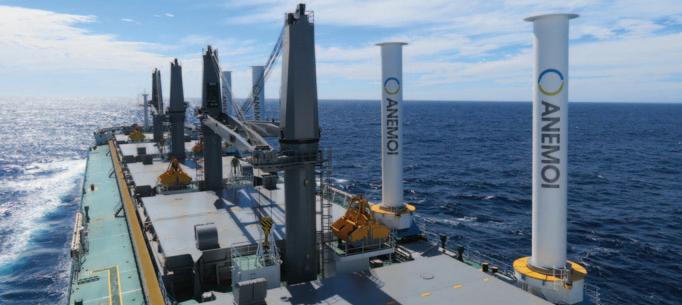
It has been a busy 2022 for Anemoi, a global player in wind-assisted propulsion for commercial vessels, with the company expanding in London and China to meet growing demand for its emission reduction solution.
In July, Singapore-based dry bulk owner Berge Bulk announced that it had signed agreements with Anemoi –– to supply and fit two vessels in its dry bulk fleet with Anemoi Rotor Sails. Berge Bulk is a leading independent shipowner which has put sustainability at the heart of its operations.
The first vessel, Berge Neblina, a 388kdwt Valemax ore carrier built in 2012, was made ‘wind-ready’ earlier this year. This means the structural integration required prior to installing the technology was carried out during a scheduled dry dock.
Four of Anemoi’s large folding (sometimes referred to as tilting) deployment Rotor Sails are set to be installed to improve vessel performance. Folding Rotor Sails can be lowered from the vertical to mitigate the impact on air draught and cargo handling operations.
This flexible ‘wind-ready’ approach has been taken to align with vessel availability and Anemoi’s production slots.
The same approach has been taken with a second vessel, Berge Mulhacen — a 2017built 210,00dwt Newcastlemax bulk carrier — which will also receive four folding Rotor Sails. Plan approval has been obtained for both ships from DNV.
“The agreement with Berge Bulk is a further confirmation that forward-thinking shipowners are turning to wind-assisted propulsion to help them achieve their environmental objectives. It proves, once again, that Rotor Sails are a realistic and workable solution that result in significant carbon savings,” said Kim Diederichsen, CEO of Anemoi.
APPROVAL IN PRINCIPLE In June, classification society Lloyd’s Register granted Approval in Principle (AIP) for an SDARI (Shanghai Merchant Ship Design and Research Institute) designed 210,000dwt Newcastlemax bulk carrier installed with Anemoi Rotor Sails to significantly improve efficiency and reduce environmental impact.
The Newcastlemax AIP is part of a pioneering joint development project (JDP), signed in 2020, with Anemoi, Lloyd’s Register and SDARI.
It brings together the OEM, classification society, ship designer, and ship owner to develop a series of energyefficient vessel designs equipped with Rotor Sails. Oldendorff Carriers is the shipowner partner for this Newcastlemax design.
The AIP covered the structural integration for a ship design with six 5x30m Rotor Sails and Anemoi’s Rail Deployment System, which sees the Rotor Sails move transversely across the deck to avoid inference with cargo handling; and the structural integration for a ship design with four of Anemoi’s folding (tilting) 5x35m Rotor Sails.
Lloyd’s Register assessed the calculation used to estimate the impact the Rotor Sails will have on the Energy Efficiency Design Index (EEDI) and validated that the newbuild would have its EEDI score reduced from 1.92 to 1.37 (29% reduction) by installing six 5x30m Rail Rotor Sails and 1.47 (23% reduction) by installing four 5x35m Folding Rotor Sails.
“We were very pleased with the outcome for the first vessel included in the JDP. EEDI is a significant driver for the installation of Rotor Sail technology and, as we grow closer to the implementation of EEXI and CII, they too become important incentives for Rotor Sails, along with the overarching reductions in fuel consumption and associated emissions,” said Nick Contopoulos, the Chief Operating Officer at Anemoi.
“To have the impact pre-validated by LR has been a key step in continuing to prove the importance of our technology in the context of the decarbonization of shipping. Both design configurations (folding and rail) of Rotor Sails for a Newcastlemax vessel are available to order now.”
Other vessels included in the JDP and to follow are an 85,000dwt bulk carrier, a very large ore carrier (VLOC), a 114,000dwt Aframax tanker, a 50,000dwt MR tanker and a very large crude carrier (VLCC).
TECHNOLOGY REIMAGINED Wind propulsion, which was used to power ships for thousands of years before fossil fuels became readily available, is back in the agenda for shipowners. As a completely renewable resource, wind is an appealing and beneficial option in the race towards decarbonization.
Rotor Sails make use of the aerodynamic phenomenon known as the ‘Magnus Effect’. As the cylinder rotates within an airflow, a forward thrust force perpendicular to the apparent wind direction is created, which delivers additional thrust to the vessel. The thrust generated can either provide additional vessel speed or maintain vessel speed by reducing power from the main engine. The tall cylindrical sails can be installed on the main deck, bow or elsewhere with sufficient space.
Rotor Sails, also known as Flettner Rotors, were first installed on a vessel over 100 years ago. But through research and innovation, Anemoi engineers have reimagined the technology for modern use.
Anemoi rotor sails on Afros. Anemoi rotor sails on Berge bulk vessels.
MoorMaster automated mooring completes one million moorings
Data analytics specialist ioCurrents and ScanReach, a groundbreaking maritime wireless IoT solutions provider, have formed a strategic partnership to help ship operators and the offshore sector become more efficient and sustainable.
ScanReach has spent years researching and testing its systems so that it can confidently offer the industry a robust wireless technology that will collect vessel data from onboard sensors without the need for costly and disruptive equipment installations.
This data will then be analysed by ioCurrents to provide invaluable insights that will improve the safety and performance levels on vessels and offshore installations. ioCurrents specializes in data analysis using AI and machine learning to output real-time fact based insights. This helps improve decision making with the ultimate goal of achieving operational efficiencies and reduced OpEx which will also help contribute to a more sustainable business model and improve crew safety.
“Linking up with ioCurrents was an easy decision to make. I have worked with the team before and know how using the insights from their proprietary platform MarineInsight™ can have a dramatic positive effect on a company’s operations,” said Sven Brooks, ScanReach’s Chief Commercial Officer.
ScanReach’s technology can even be used for onboard personnel tracking and location during emergency situations to aid precision rescue team involvement and automatic mustering count.
Jon Best, Director of Business Development for ioCurrents, said, “Forming a partnership with ScanReach is really exciting as their wireless solution makes data collection so much easier than having to install miles of cabling on a vessel or offshore platform.
“Their tried and tested technology works on even the most complex steel environments and their ‘plug and play’ solution means that clients can do the whole installation themselves with minimal operational disruption. When adding sensors, such as ConnectFuel, ioCurrents can seamlessly ingest the ScanReach data and perform actionable insight to strengthen output with MarineInsight’s analytics.”
Cavotec’s MoorMaster™ automated mooring systems have completed more than one million moorings at bulk, ferry, Ro/Ro, container handling and lock applications all over the world, making ports safer, more efficient and more sustainable.
MoorMaster replaces hazardous conventional mooring lines with remotely operated automated vacuum pads that moor and release vessels in seconds at the push of a button.
The technology dramatically improves safety and operational efficiency, optimizes the ship-toshore interface, and in many cases enables ports to make infrastructure savings.
Passing one million moorings is a major milestone that highlights MoorMaster’s key role in transforming the maritime industry by improving safety, maximizing productivity, and minimizing environmental impact. MoorMaster remains the only widely used automated mooring technology on the market today.
As more and more operators discover the stepchange MoorMaster offers, Cavotec expects to reach two million moorings even faster than it reached one million.
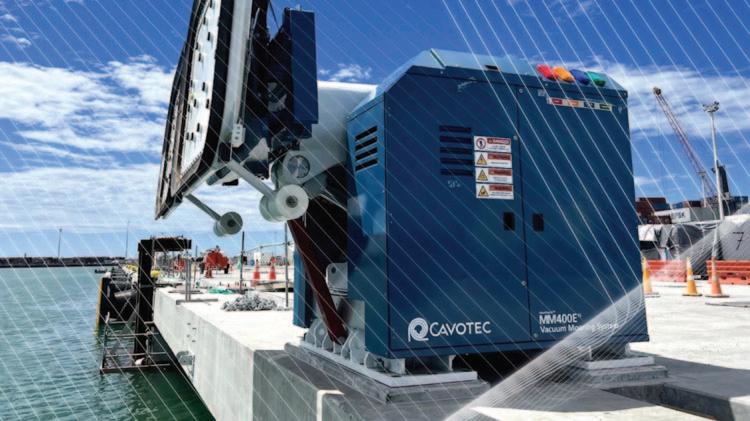
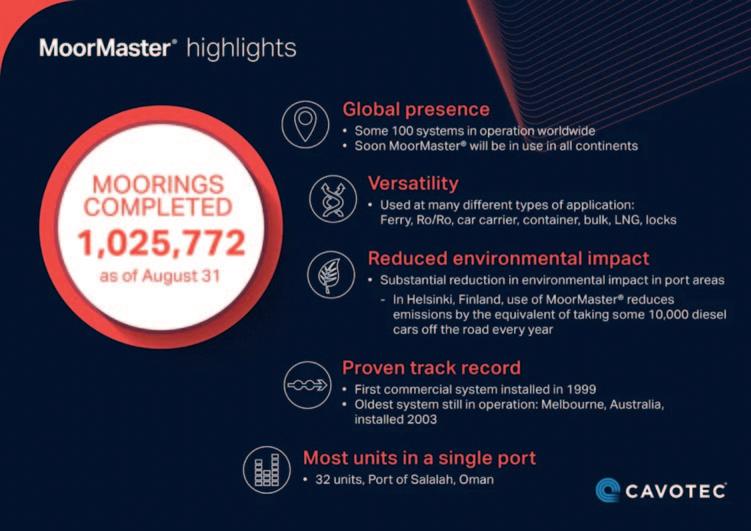
How many times have you heard people asking “When” in a port? Ports are complicated ecosystems where everyone’s actions have an impact on others, writes Anders Berg, Senior Manager Maritime Solutions, Unikie Sweden.
Ports have been the heart of international logistics for centuries. Ports, just like all the other segments of modern society, have been digitized heavily in past decades. Still, in today’s ports, the most frequently asked question is: ‘when?’.
Despite heavy investments to port digitalization, a significant part of daily operations at ports are still managed manually. When something changes, very often the primary communication channel is phone calls. A lot of service and business orders are sent by email and processed manually. Even complex operations are planned and scheduled by using Excel. All these manual processes and one-to-one messages are causing significant inefficiency to ports simply because of the lack of information, data, and communication.
Unikie has during the last three years developed together with ports and authorities a digital solution — based on the open ecosystem platform — that now is in use in 20 different ports in the Nordic countries. Unikie’s Port Activity App (POLO) brings all port call process stakeholders together and enables increased situational awareness and optimized efficiency. The open platform principle emphasizes co-operation and an organically grown ecosystem by taking full advantage of existing systems, better visibility, and utilization of existing data.
All development, both current and future, is created in close cooperation and synchronization directly with ports. POLO provides a new toolset for ports to improve the overall efficiency of port flow, covering the end-to-end chain of actions and operations related to vessel visit. It is a user interface for port digitalization and communication based on open ecosystem and open interfaces, strengthening collaboration both inside the port community and between ports. It creates an ecosystem for awareness, automation and autonomous operations using four layers: v Knowledge: a centralized place of information and common situational awareness; v Communication: a digital toolchain replacing traditional phone calls and emails; v Workflow: enabling a shared workflow for efficient port operations and extended planning horizon; v Intelligence: optimizing business operations with real-time data analytics and AI.
Some recent examples of development are the service order feature and predictive berth planning tool feature. The service order feature enables agents to order any service or permission that a vessel needs in port. The service providers get notifications and also have the possibility to receive automated calls. These processes are clearly visualized in POLO (Fig 1).
And on top of this, it is possible to integrate service orders to external systems via REST API.
Predictive berth planning tool is another new feature that calculates the vessel discharging and loading times based on the cargo commodity and known discharging or loading efficiency. With this information it's possible to get a much better estimated time of departure (ETD) than using any AI or history based data. Improved predictability for ETD leads to higher possibility to achieve Just-In-Time Port Calls.
THIS IS DONE BY: v Reserving needed cranes & forklifts per vessel to have full picture of resource usage v Adding cargo details (commodity, amount, loading & discharging) and operations efficiency to estimate absolute operation duration v Defining work time modes (normal, non-stop, overtime) which is used to calculate actual operation times v Adding & modifying commodities and operational efficiencies v Adding & modifying local holidays and worktimes
These are the new developments that ports in the Nordic countries are starting to implement. There are also numerous features and their implementations that are the outcome of utilizing the open ecosystem in close cooperation directly with ports. One exciting ongoing

Fig 1. Service providers get notifications and also have the possibility to receive automated calls in POLO.
Predictive berth planning tool is another new feature that calculates the vessel discharging and loading times.
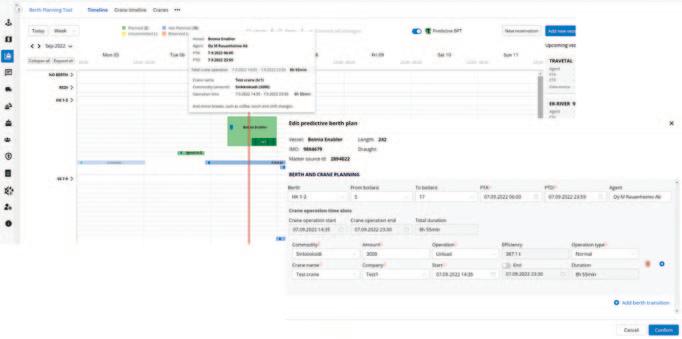
development is the Just-in-Time principle where ports are challenging the “first come, first served” principle with assistance of POLO.
POLO is however merely step one on port digitalization journeys ahead. True value of digitalization is achieved when those using new solutions understand them and, more importantly, use them. POLO offers all information port call stakeholders need at their fingertips in an easy-to-understand way, but to find the benefits and optimize port calls the human element is essential. It’s also good to keep in mind that this is just the beginning. Once data collecting and sharing processes and tools are in place, we are ready to start optimizing port business and gaining a real competitive advantage for ports, shipping and the maritime world.

ABOUT UNIKIE Unikie is a Finnish software technology company that develops technologies for protected real-time processes. Its services concentrate on the crossroads of three global macrotrends — IoE, 5G, and AI — where our technology solutions enable a constant awareness of the surroundings, as well as decision-making and control based on this awareness. Clients include pioneers of real-time data utilization in the automotive industry as well as other industries and telecommunication companies worldwide.
Anders Berg Senior Manager Maritime Solutions, Unikie Sweden.
Cygnus launches a brand new Ex Certified thickness gauge
Visitors to the Cygnus stand at The Materials Testing Exhibition earlier in September 2022, were first to see the much anticipated, new Cygnus Ex-certified product in the flesh. Now, it’s time to reveal what the new Cygnus 1 Ex Ultrasonic Thickness Gauge is all about.
This rugged, IP67-rated, intrinsically-safe instrument is specially designed to take reliable thickness measurements in Zone 0 Explosive Atmospheres, including: v oil and gas; v mines; v chemical plants; v fuel depots; v road tankers; v oil and gas tankers; v explosive atmospheres; and v hazardous storage tanks.
WHAT IS SPECIAL ABOUT THIS LAUNCH? Like its predecessor, the Cygnus 1 Ex is the only one of it’s kind in the world certified to ATEX, IECEx, UKEX for Zone 0 and NRTL for Class 1, Division 1. But the Ex takes a giant leap forward, offering impressive new selectable features including live A-Scan, comprehensive datalogging and manual measurement mode, which brings Cygnus’ Intrinsically Safe offering up to speed with Cygnus’ most advanced gauges.
First of all, the 3 measuring modes that one may be familiar with amongst Cygnus’ surface range, designed for varying levels of corrosion, multiple materials and throughcoat measurement capability, are now built into this new gauge and available to hazardous and explosive environments.
Measurement verification and recording are also far more advanced. The addition of Live A-Scan and B-Scan allows precise measurement verification with on-screen visuals via the large 3.5” outdoor-readable display, and the comprehensive data-logging feature ensures seamless data analysis and report generation.
The entire gauge, from how it sits in one’s hand, to collecting and storing measurements, is entirely geared towards the best user experience, making inspection quick and easy, despite the challenging environment. Four new function keys are purposely integrated to maximize ease and speed of control, four dynamic screen views aimed to suit user requirements, and a user access feature to prevent access to protected features.
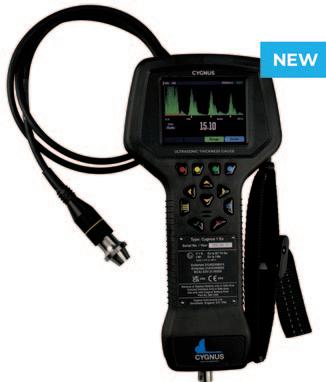
WHY ARE INTRINSIC SAFETY AND EX CERTIFICATION SIGNIFICANT? Carrying out inspections with testing equipment certified to a suitable protection level is vital to ensuring the testing operation does not jeopardize the safety of hazardous environments. It is important to understand which is the correct equipment, and where to use it.
For equipment that contains electronic components including batteries, the intrinsically safe protection concept ensures that under both normal uses and with applied fault conditions, no arc or spark can be generated, and no component can heat up enough to cause an explosion.
SOME INTRINSICALLY SAFE DESIGN CRITERIA: v The output energy at the terminals is limited so a spark cannot ignite an explosive atmosphere. v The equipment must be anti-static and not be able to hold a static electricity charge. v Voltages must be electrically ‘clamped’ to safe levels. The use of redundant safety
The new Cygnus 1 Ex Ultrasonic Thickness Gauge.
v
v components.
If a battery or component fails, it should not produce high temperatures that could be incendiary.
In both IECEx, ATEX and North American NRTL systems, intrinsically safe equipment can be used in any Zone or Division with the correct equipment protection level.
Under the IECEx and ATEX systems, explosion-proof/flame-proof equipment cannot be used in Zone 0 areas, regardless of equipment protection level.
Most importantly, only equipment that has an Ex Certificate (ATEX/IECEx/ UKEX/NRTL) can be considered for use in Zone 0/1/2 areas.
In the USA equipment that only has a MIL-STD-810G, Method 511.5, Procedure I test pass CANNOT be used in Zone 0/1/2 areas.
The Cygnus 1 Ex, like all Cygnus products, is manufactured in the UK and is the only Zone 0 (Ga, Ma) Certified UTG available today (for ATEX/IECEx/ UKEX/NRTL).
Since 1990 Alfa Maritima International AMI, Reliability & Security, has been chartering bulk carriers for dry bulk maritime transportation for grains, minerals, bauxite, iron ore, cement, clinker, and fertilizer, among other dry bulk commodities.
AMI specializes in developing ideas and strategies which lead to achieving the objectives of its commercial allies and suppliers, generating solutions, efficiency, and added value for the grains, minerals & other dry bulk commodities. Its supply chains provide reliable transportation on bulk carrier vessels for North American and Latin American industrial corporate customers such as EMPRESAS POLAR, CEMEX, FERRO ALUMINIO, among others.
In 2020, Luis Urdaneta Eraso established AMI in Cleveland, Ohio, USA.
The company is focused on industrial manufacturers, steel, alum, cement, chemicals, grain, food and beverages, all corporations that require to move, their dry bulk raw materials and recycled commodities located in the United States of America, Canada, and Mexico. Taking into account Mr Urdaneta’s background and his experience of more than 30 years with proven results, AMI is ready to develop synergies with these industrial corporations, offering the following: v Development strategies that lead to generating solutions, efficiency, and added value. Supply of expertise in chartering bulk
v
v v
v
v
v
v
v
v carriers for the transportation of dry bulk commodities. The economy of scale solutions. The Alfa Maritima International strategic vision becomes an added value to its allies. Research & development of reliable business alliances between industrial commodities manufacturers and firstclass ship owners for efficient supply chains. Define the scope and timeline of its service & operations. Charter Parties Administration for charterers to a time charter smooth operation during the hire of the bulk carriers vessels and for the COA executions. Co-ordinate operations of the different supply chain actors, performing between the shipowners and our charterers and other commercial allies to assure the implementation and execution of smooth operations across the supply chain. Develop regular evaluations to assure quality, reliability, and security in its services operations. Keep frequent communications to v
v
v explore new opportunities and develop projects.
Develop expertise in maritime transportation for dry bulk commodities within its charterer's customers.
AMI will present solutions to transportation problems to assure efficiency along the different links of the supply chain.
Reliability and security for maritime transportation.
Currently, AMI is working on mineral projects to ship it from South America to the European Union and other destinations. AMI is attending to different charterers to deliver grains from North America to Latin American countries and transport chemicals between the United States to Latin American customers.
AMI is able to supply added value to its clients’ operations for or from LATAM. AMI is able to assist clients in developing their plans together, by leveraging its direct relationships with the most reliable and best shipowners worldwide.
Despite having 30 years of performance experience in chartering dry bulk commodities, Luis Urdaneta Eraso got the Shipbroking and Chartered Vessel Operations certification from the ASBA New York Shipbrokers Association on 5 October 2020.
How dry bulk can benefit from data standardization
The much-discussed Energy Efficiency Existing Ship Index (EEXI) and Carbon Intensity Indicator (CII) regulations are now just a few short months away from taking effect, writes Tor-Arne Berger, Veson Nautical’s Spokesperson and Q88 Product Manager.
This will have a huge impact on dry bulk carriers. Estimation and analysis from Simpson, Spence and Young suggests more than 75% of the existing tanker and bulker fleet will not attain EEXI baselines and will need to take action to achieve compliance.
Data is a powerful tool for companies in the dry bulk sector that can drive more openness, transparency, and accountability. However, knowing that data can be harnessed to meet ESG regulations, ensure compliance and improve operational efficiency is only part of the puzzle.
In recent years, the amount of data that each vessel generates has increased exponentially. This spans from the information a vessel produces technically (from automation systems etc.), as well as commercial data on where the vessel is, and where it will be, based on the rapid development and sophistication of prediction algorithms. There is so much data noise for companies to sift through –from different sources, stored in disparate locations — that it can be near impossible to make sense of the information, let alone drive actionable insights.
Bulker owners and operators could be using data not only to inform them on vessel compliance, but to manage documentation, handle vessel question naires and enhance commercial communications with charterers, brokers and agents. Keeping data to yourself is no longer viable in today’s shipping market. Strategically sharing information can drive more collaboration, more visibility and means organizations are not making decisions based solely on their single view of the world.
However, being able to share data strategically within the dry bulk sector requires organizations to speak the same data ‘language’. At present, there is no standard way to exchange, interpret information, or effectively speak in a common language across the maritime industry. A lack of common data standards makes it very difficult to exchange information, as data from different sources do not match up or use different formats to describe the same thing.
To maximize data usage and analytics, a normalized language needs to be developed and collaboration across the industry is central to achieving this. Veson’s recent acquisition of Q88 feeds into this vision of working together to define and enable the adoption of a standard that is set to facilitate and drive communication and optimize efficiencies.
The original Questionnaire 88 was built to create standardization around vessel suitability and risk and has long been an established industry standard for
information on tankers for vetting purposes. For the dry bulk industry, the Baltic99 questionnaire is the most common, but it’s not as central as the Q88 is for tankers — yet. As ESG and green initiatives become increasingly more central to doing business, we expect that a standardized questionnaire will become a key method to share vessel data and win business. The questionnaire is a great starting point, but there are many different types of documents and different data points involved. Q88 has evolved to help make fleet certificate management simple for bulk owners and operators, with its Q88Dry solution. Additionally, Q88 Dry enables charterers to programmatically include vessel details into their workflows for greater ease and standardization in maintaining a vessel database.
Having a single source of vessel data can improve efficiency, compliance, and collaboration within the dry bulk sector. Owners and operators could gain full accountability from an audit trail and use that data to maximize fleet utilization, ensure compliance with changing regulation, and respond rapidly to vessel information requests.
The future potential for what can be achieved with data within the maritime industry is exciting. Direct sharing of information between different counter parties will become commonplace within the dry bulk sector, helping to drive more open transactions, better transparency, and compliance.
Willing participation and collaboration are the key to creating the industry-wise protocols and standards that will drive this pace of change, facilitate communication, and optimize efficiencies.
NEOGUARD hold protection reduces routine maintenance for ‘Starnes’
The Nippon Paint Marine NEOGUARD anti-corrosive coating applied to the cargo holds of the 40,000dwt bulker Starnes has been a key factor in ship manager HJH Shipmanagement GmbH being able to extend cargo hold maintenance.
Starnes, delivered from the Chengxi Shipyard in 2020, arrived with a full range of Nippon Paint Marine protective coating and antifouling systems.
“We have not had the chance to physically inspect the tanks ourselves,” says Olaf Riecken, Business Development Manager, Nippon Paint Marine (Germany), “but HJH is very satisfied that the vessel is not expected to require any remedial coating work to the holds until drydock in mid-2025.”
“The bulker carries crushed stones and other aggregates, so the holds needed special attention to mechanical impact, abrasion and corrosion. The owner’s exacting requirements were met with our NEOGUARD range, which was applied to all cargo holds and unloading tunnels,” furthers Riecken.
The 190m-long vessel can self-discharge at a rate of 5,500tph (tonnes per hour). The self-unloading system, which features one of the largest booms ever installed on a self-unloader, can handle lump sizes up to 300mm and free flowing materials with a bulk density in the range of 1.2-3.5t/m3 .
Paying special attention to the cargo holds, Nippon Paint Marine applied its HI-Epoxy 1494 coating, a zinc-rich epoxy primer, to bulkheads and tanktops, prior to two 200μm coats of NEOGUARD 100 GF. For unloading tunnels, two 125μm coats of NEOGUARD TOUGHNESS were applied before a single 50μm finish coating of E-MARINE Finish M.
While Nippon Paint Marine has applied its coatings to existing tonnage operated by the HJH, Starnes was the first newbuilding project with this owner.
Other vessels applied with the same coating include the self-unloading bulkers Bulknes and Sandnes, with the operator noting that extend coating repairs could not be achieved without a NEOGUARD application.
Commenting on the success of the coating, HJH Shipmanagement’s Newbuilding Manager Michael Jäger says: “It is vitally important to choose the right anticorrosive paint for a newbuilding early on in the project. Based on our previous experience of Nippon Paint Marine systems during repair and maintenance projects we wanted the ultimate cargo hold protection for Starnes. We found that with NEOGUARD, which has exceeded our expectations and helped reduce coating maintenance costs.”
NEOGUARD 100 GF is flexible, surface tolerant multipurpose glass-flake epoxy developed to provide unparalleled corrosion and abrasion protection from seawater, chemicals and mechanical impact. And NEOGUARD TOUGHNESS is a heavy-duty epoxy anticorrosive paint newly developed to exhibit resistance against abrasion and impact to provide long-term protection for cargo spaces.
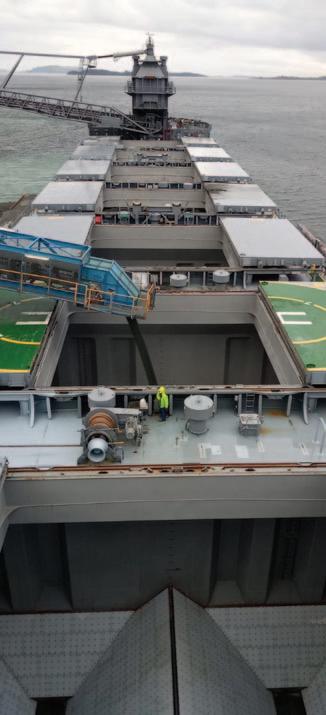


StormGeo Announces Carbon Footprint Dashboard to streamline decarbonization reporting
StormGeo’s Carbon Footprint Dashboard visualizes decarbonization metrics.
StormGeo, a major provider of weather intelligence and decision-support solutions for the shipping industry and part of Alfa Laval, will release a new Carbon Footprint Dashboard to help its customers reduce carbon emissions more effectively. The new dashboard will be the third decarbonization solution released by StormGeo in 2022.
SINGLE SOURCE OF TRUTH Specifically designed for energy efficiency and decarbonization managers but available to all s-Insight users, StormGeo’s Carbon Footprint Dashboard compiles all relevant data in one place to monitor decarbonization metrics, set carbon intensity targets, and streamline regulatory reporting processes.
“The Carbon Footprint Dashboard provides a single source of all CO2 emissions data. It gives access to the analytics necessary to review the impact of implemented measures, identify corrective actions, and report on carbon intensity alignment with industry trajectories to internal and external stakeholders,” says Madeleine Engelhardt, Product Manager, Fleet Compliance and Technical Perfor mance at StormGeo. “The dashboard helps shipping companies focus on the decarbonization metrics that matter.”
With several pre-configured widgets, the dashboard provides numerous graphs and diagrams to visualize the carbon footprint of all shipping activities. The system calculates and displays various CO2 emission indicators for fleets, vessel subgroups, and individual vessels for each leg of the voyage. These insights will be available to all dashboard users, helping to ensure transparency and improve collaboration on decarbonization initiatives across organizational departments.
CARBON FOOTPRINT DASHBOARD TO BE ADOPTED BY STORMGEO CUSTOMERS Many of StormGeo’s customers have already expressed interest in the new Carbon Footprint Dashboard. For example, the German shipping company F.A. VINNEN & CO. will leverage the dashboard to better understand the real operational impact of their actions on carbon emissions.
“StormGeo’s Carbon Footprint Dashboard will help us keep detailed track of how much CO2 our shipping activities emit into the atmosphere and quickly gives us the necessary overview to see whether parts of our fleet aren’t performing as they should,” says Bernd Hein, Managing Director at F.A. VINNEN & CO. “It will enable us to drill down into the data and see how something as small as a single leg of an individual vessel impacts our overall emissions and get the decision-support necessary to correct any issues.”
AVAILABLE SOON StormGeo’s Carbon Footprint Dashboard will be released in October 2022 as part of s-Insight, a world-leading fleet performance management solution that ensures vessel compliance and provides simple, trustworthy data reporting systems. The Carbon Footprint Dashboard will be available for all route advisory and fleet performance management customers.
ABOUT STORMGEO StormGeo is a global provider of weather intelligence and decision-support services, with leading solutions for shipping, oil and gas, renewable energy, onshore industries, and aviation. Offering solutions toward decarbonization, more than 12,000 ships rely on StormGeo software or services for navigational planning, route optimization, weather routing, and fleet performance. The company has 24 offices in 16 countries, including eight 24/7/365 global operations centres.