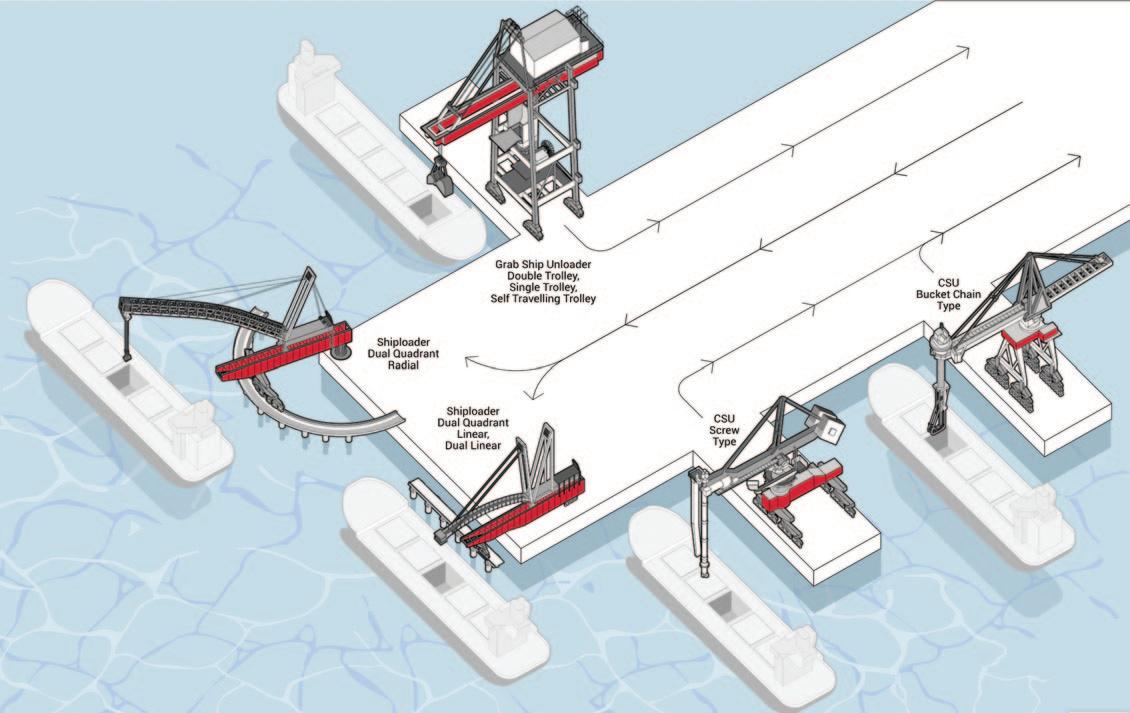
6 minute read
EFFICIENT BULK HANDLING WITH HELP FROM TENOVA’S HIGH-TECH SYSTEMS
Efficient bulk handling
with help from Tenova’s high-tech systems
Tenova is a renowned worldwide partner for sustainable, innovative and reliable solutions in the metals and the mining industries.
From DRI to EAF, reheating furnaces to heat treatment furnaces, cold mills to processing lines and roll grinders, Tenova’s technologies minimize the environmental impact of its customers’ activities, operations and final products.
Tenova is active in a wide range of technologies, including: v iron & steel technologies; v aluminum technologies; v hydrometallurgy; v pyrometallurgy; v grinding & texturing; v port facilities; v green solutions; v digital & process control; and v industrial gas analysers.
Materials handled by Tenova technologies and systems include: v iron & steel; v aluminium; boron;
v v v v v v v v v v v v v copper; ferro-alloys; lithium; manganese; nickel & cobalt; phosphate — PPA; platinum group metals; rare earths; rockwool; silicon metal; titanium; and uranium.
This article focuses on the company’s expertise in the port facilities segment, specifically shiploading and unloading. Follows a brief run-down of the shiploading and unloading technologies available from Tenova.
QUADRANT SHIPLOADERS — RADIAL, LINEAR AND DUAL LINEAR The Tenova quadrant shiploader is a very flexible solution to reach the best compromise between quayside civil works cost and the loading system.
Tenova quadrant shiploaders are suitable for operation on a wide range of vessel sizes, and can handle from very-freeflowing bulk material to complex very abrasive or sticky products.
The shiploaders are specifically designed to the exact requirements of the client, and incorporate various solutions according to their specific application and existing site conditions. There is always a strong focus on minimizing environmental impact.
Tenova quadrant shiploaders can be supplied in three different configurations, depending on the client’s specific needs: radial type (front radial rail and rear pivot), linear type (from linear rail and rear revers bogies) or dual linear (from linear rail and rear perpendicular and linear rail). All of them can perform multiple movements: front travelling (radial or linear) with luffing and shuttling booms. In addition, they can be equipped with a variety of different loading chutes such as cascade type,
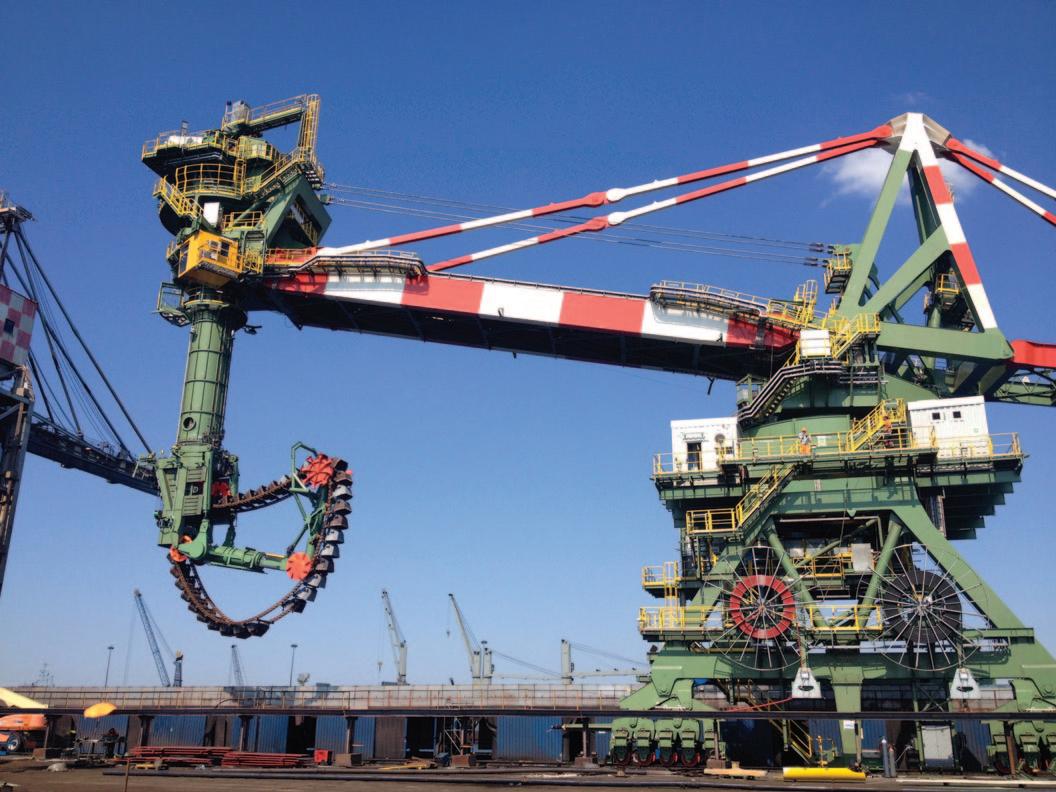
telescopic type or curved type, depending on specific applications, customer special needs and required environmental conditions.
Tenova specializes in fabricating and fully assembling off site and in shipping the shiploader to the final destination in a single unit by heavy lift ship (Lo-Lo) or by flat deck ship or barge (Ro-Ro).
Tenova’s quadrant shiploaders are very versatile machines with: v unloading capacities from 500tph (tonnes per hour) up to 20,000tph; v the ability to unload vessels ranging in size from 30,000dwt up to 400,000dwt;. v an overall efficiency (through complete shiploading process) of ~95% depending of characteristics of unloaded material; v reliability: ~98%; v availability: ~96%; v rail radius and wheel loads based on customer needs: standard value between 60–80m and 35–60 tonne wheel respectively; and v transformer size from 500kVA to 2,000kVA.
BUCKET CHAIN TYPE CSU Bucket chain continuous unloaders (CSUs) are the most advanced technology for highly efficient and environmentally friendly unloading. Tenova’s CSU are suitable to operate on a wide range of vessel sizes, and can handle products ranging from very free flow bulk material to complex very abrasive or sticky products.
Tenova’s CSUs cover a wide-range of capacities and vessel sizes; CSUs are highly efficient, environmentally friendly and capable of unloading large volumes of different material types within a shorter time period compared with traditional systems operated by grabs.
The boom is equipped with a Tenova patented tailor-made bucket-chain to efficiently collect the material from the ship’s hold and transfer it to the jetty/port conveying system. Since unloading operation is continuous, these machines are characterized by very high performances and very low environmental footprint. The fully enclosed and sealed material path means that Tenova’s CSUs significantly reduce the environmental impact, specifically in terms of spillage, dust and noise emissions — they are therefore suitable to operate in particularly sensitive areas.
Tenova specializes in fabricating and fully assembling off site and in shipping to final destination CSUs in a single unit by heavy lift ship (Lo-Lo) or by flat deck ship or barge (Ro-Ro).
Tenova’s CSU are very flexible machines. They offer: v an unloading capacity ranging from 500tph (tonnes per hour) up to 7,200tph; ability to service vessels ranging in size
v
v
v v v
v from small barges up to 400,000dwt ships; overall efficiency (throughout the entire ship-unloading process): ~70–75% depending on the characteristics of the material being unloaded; reliability: ~98%; availability: ~96%; rail spans and wheel loads based on the needs of the customer: standard value between 10–15 m and 25–50 tonne wheel respectively; and transformer size from 630kVA to 2,500kVA.
CSU – SCREW TYPE With the knowledge that it has gained from decades of experience with CSU technology, Tenova is now bringing out a screw-type version. Tenova has developed its own versatile design, which is suitable for handling a good range of products, and which also offers an optimum ratio between machine weight and performance.
GRAB SHIP-UNLOADERS Tenova’s grab ship-unloaders (GSUs) are in many different capacities, and can service a wide range of vessel sizes. They are particularly convenient for ports that unload different types of cargoes, as the grab system can work across various materials.
This consolidated technology has demonstrated good operability and reliability over decades of activities.
Among the available models, Tenova can offer double trolley (with shuttle trolley), single trolley and self-powered trolley.
Tenova specializes in fabricating and fully assembling off site and in shipping the GSU to the final destination in a single unit by heavy lift ship (Lo-Lo) or by flat deck ship or barge (Ro-Ro).
Tenova’s GSUs are very reliable machines and offer: v hoisting capacity from 12.5 tonnes up to 85 tonnes; v unloading capacity: from 350tph to 3,100tph; v the ability to serve vessels ranging in size from barges up to 400,000dwt; v overall efficiency (through complete ship-unloading process): ~55–60% depending of the characteristics of the material being unloaded; v reliability: ~98%; v availability: ~96%; v rail spans and wheel loads based on the needs of the customer: standard value between 15–25 m and 25–50 tonne wheel respectively; v and transformer size: from 630kVA to 3,150kVA.
INNOVATION IS KEY Technological innovation is the foundation of Tenova’s competitiveness with its shiploaders, CSUs and GSUs.
Tenova’s engineering process is the driver of R&D. The company has developed a flexible, individual and effective design concept. In the case of the shiploaders, the shuttling system and the loading chute are the key to finding the ideal solutions for each customer. In the case of the CSU, the digging device and the chain, along with the bucket connections, are key. Tenova’s GSUs are notable for the main control centre of the motors, and the transfer of the material from the main hopper to the wharf conveyor.
By embracing innovation, Tenova is able to offer its customer cutting-edge solutions for both CSUs and GSUs.
SAFETY In all its work, the health and safety of all employees — in addition to environmental protection — are a top priority in the design of Tenova shiploaders, CSUs and GSUs. Its shiploaders and CSUs can be operated also from portable remote control systems, or from a remote on the ground control room.
With the principle of Zero Harm as an integral part of its own business, Tenova is committed to designing shiploaders, CSUs and GSUs for a safe working environment.
AUTOMATION Tenova’s shiploaders, CSUs and GSUs are highly automated machines which implement automatic operation for most of the unloading process.
Tenova is continuing to develop innovations in this field, and it will soon be able to achieve unmanned and remotely supervised operation.
DIGITALIZATION Digitalization is essential to ensure highly automated, safe and reliable machines. Tenova uses the most up-to-date digital technology so that it can offer products that are highly connected and efficiently maintainable.
Soon, on customer request, Tenova will combine its products with: v virtual reality simulator for the training of personnel; v predictive maintenance based on line monitoring of vibrations and temperatures; and v smart anti-collision systems to support remote and unmanned operation. DCi
Grab ship-unloader.
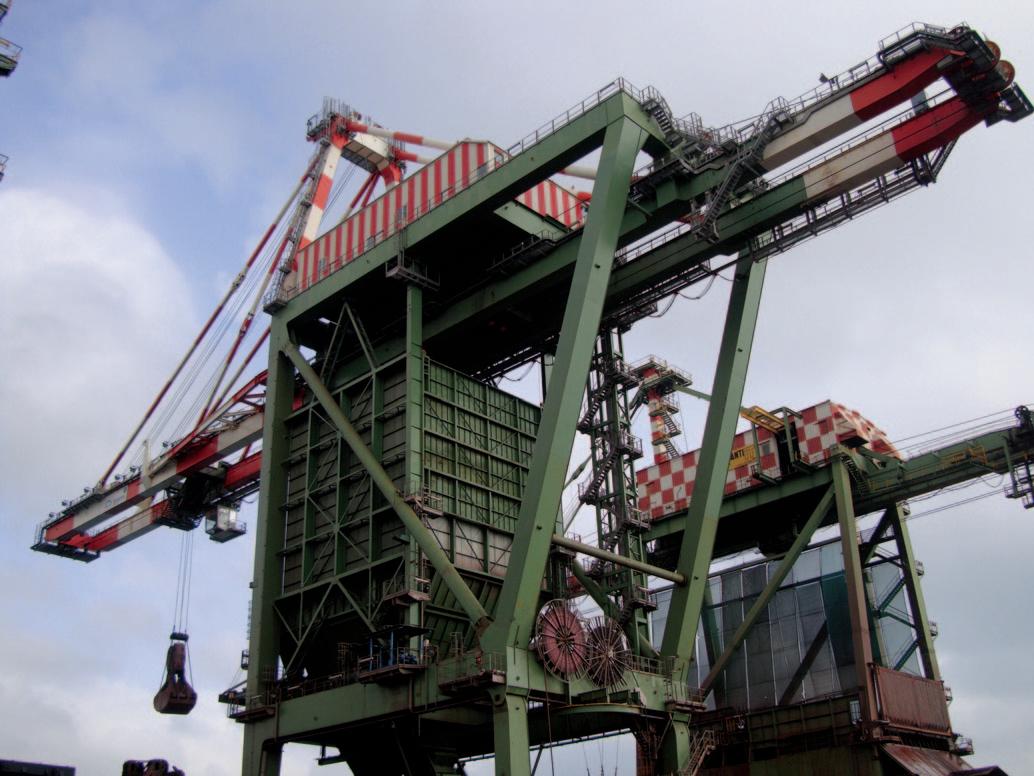