
13 minute read
BASINÇLI KAPLARDA KAYNAK PROSESİ
by Eda
yaklaştırılmıştır.
Kırılma mekaniği kavramlarına göre dizayn için tahribatsız usullerle bulunabilecek hata limitlerini en düşük seviyeye çekebilecek yöntemler araştırılmıştır ve araştırılmaktadır.
Advertisement
Bulunan hatalar için kabul red kriterleri oluşturulmaya çalışılmıştır. Tahribatsız muayenelerin uygulamaları aşağıdaki gibidir;
GörselMuayene(VT): Görsel muayene, tahribatsız muayene yöntemlerinin en hızlı ve ucuz yöntemidir ve diğer tahribatsız muayenelerden önce mutlaka uygulanması gereken bir yöntemdir. Çıplak gözle yapılan bu muayenede, büyüteç, ışık kaynağı, kamera, ayna ve bunun gibi yardımcı ekipmanlar kullanılabilir.
Bu yöntemle malzeme yüzeyine açık çatlak, gözenek, yanma oluğu vb. hatalar tespit edilebilir ve yüzey temizliklerinin iyi yapılması gerekmektedir.
Görsel muayene çok basit bir yöntem olarak görünse de kendine özgü inceleme koşulları vardır ve personel tecrübesi çok önemlidir. Yeterli ışık şartları altında ve uygun bakma açılarında inceleme yapılmalıdır. Tavsiye edilen minimum ışık şiddeti 500 lux, minimum açı 30 Derece ve parçaya olan maksimum uzaklık 300 mm‘dir. Görsel muayeneyi yapacak olan personelin EN 9712 standardına göre Level II sertifikalı olması gerekmektedir.
Metalik veya metalik olmayan bütün malzemelere uygulanabilir.
ManyetikParçacıkTesti(MT): Manyetik Parçacık Testi, yüzeye açık veya yüzeyin hemen altında oluşan hataların tespiti için kullanılan bir muayene yöntemidir. Bu yöntemin temel prensibi; Muayene yüzeyine bir manyetik akı(Magnetic flow techniques) veya akım (Current flow techniques) uygulandıktan sonra herhangi bir süreksizlikle karşılaşılması durumunda manyetik dalgaların malzeme yüzeyde yoğunlaşarak taşmasıdır(Kaçak akı). Fon boyası, demir tozu vb. yardımcı ekipmanlar kullanılarak süreksizlikler görünür hale gelir ve süreksizlik tespit edilmiş olur.

SıvıPenetrantMuayenesi(PT): Penetrant testi yüzey hatalarının tespiti için kullanılan başka bir muayene yöntemidir. Tespit edilmesi istenen hataların yüzeye açık olması gerekir, yüzey altındaki hatalar tespit edilemez. Bu yüzden uygulanacağı malzemenin test yüzeyi düzgün ve temiz olmalıdır. Ön temizliğin yeterli ve uygun olarak yapılmaması durumunda, hataların üzerini kapatmasına ve penetrant sıvısının bu hatanın içine nüfuz edemediği için test sırasında herhangi bir hata belirtisi göstermemesine neden olacaktır.
Sıvı penetrant testini yapacak olan personelin EN 9712 standardına göre Level II sertifikalı olması gerekmektedir.
Bu yöntemin en büyük avantajı malzeme tipi ile sınırlanmamasıdır. Yani çelik, seramik, cam, plastik vb. birçok malzem e üzerinde kullanabilir.

Bu yöntemin uygulanabilmesi için parçanın mutlaka ferromanyetik (mıknatıslanabilir) olması gerekmektedir. Yani paslanmaz, kompozit vb. malzemelere bu yöntemin uygulanması imkânsızdır ve bu durumda süreksizlik tespit etmek için alternatif test yöntemi uygulanmalıdır. Manyetik parçacık testini yapacak olan personelin EN 9712 standardına göre Level II sertifikalı olması gerekmektedir.
Manyetik test yöntemleri aşağıda verilmiştir. Endüstride kaynaklı imalat, döküm vb. sektörlerde en çok kullanılan manyetik test yöntemi ‘’Portable electromagnet (Yoke)’’ ‘dir.

UltrasonikTest(UT): Ultrasonik muayene, yüksek frekanslı ses dalgalarının malzeme içine gönderilmesi ve geri yansıması prensibine dayanır. Ses dalgaları alıcı-verici özelliği olan tek probla ya da verici prob ve alıcı prob kullanarak malzeme içine gönderilir ve alınır. Test edilecek parçanın boyutsal ölçüleri bilindiğinden gönderilen ve alınan ses zayıflamamsın hatasız parça için önceden hesaplanır fakat parça içinde herhangi bir hata(süreksizlik) olması durumunda ses zayıflaması daha fazla olur ve cihazın ekranında hatanın konumu hata yankısı olarak belirir.
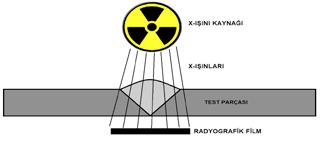


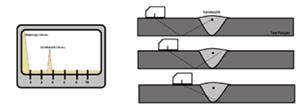
Ultrasonik test ile her türlü parça, kaynak dikişleri, döküm ve dövme parçalar test edilebilmektedir. Endüstride, Petro kimya, enerji, denizcilik, havacılık, otomotiv gibi endüstriyel ortamlarda metal et kalınlığını veya kaynak kalitesini izlemek için kullanılır.
Ultrasonik testi yapacak olan personelin EN 9712 standardına göre Level II sertifikalı olması gerekmektedir. RadyografikTest(RT): Bu yöntem X-ışınları ya da Gama ışınları kullanılarak malzeme görüntüsünün bir film üzerine yansıtılarak oluşturulmasına dayanır. Test edilen parçanın içine nüfuz eden ışınlar, kalın ve ince kısımlarda farklı absorbe edildiği için parçanın arka tarafına konulan filmin üzerindeki görüntüdeki renkler kalınlığa göre farklılık gösterir. Eğer parça içinde bir boşluk (Gözenek) var ise görüntü daha koyu, eğer ana malzemenin yoğunluğundan daha yoğun (Tungsten kalıntısı vb.) bir süreksizlik var ise görüntü daha açık renkli çıkar.
Metalik veya metalik olmayan bütün malzemelerde beklenen hacimsel ve yüzey hatalarının tespiti için kullanılabilir.
Radyografik testi yapacak olan personelin EN 9712 standardına göre Level II sertifikalı olması gerekmektedir.
Endüstride Gama ışınla rı elde etmek için İridyum 192, Selenyum 75 ve Kobalt 60 gibi yapay çekirdekler kullanırken, X–ray ışını elde etmek için X-ray tüpleri kullanılmaktadır.
KAYNAKLI İMALATTA KALİTE YÖNETİM SİSTEMİ Kaynak, üretimde anahtar rol oynayan bir üretim yöntemidir. Basitten karmaşığa tüm ürünlerde bir anlama sahiptir. Örneğin; merdivenler, binalar, vinçler, köprüler, basınçlı kaplar, tasıma ve kaldırma ekipmanları gibi. EN ISO 9000’e göre özel prosestir,
Hataların ortaya çıkmaması için önlemler alınmalıdır: Kalite Güvencesi
• Yetişmiş ve belgeli üretim personeli istihdamı • Kalitesi güvence altına alınmış malzeme kullanımı • Onaylı talimatlarla çalışılması • Yetişmiş ve belgeli denetim personeli istihdamı • Önleyici faaliyetler ve sürekli iyileştirme • Düzeltici faaliyetler
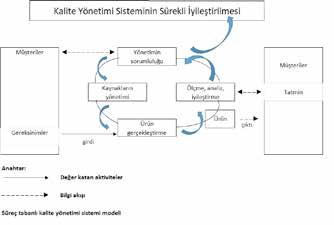
Kaynak işlemi hatalara açık bir uygulamadır. Kaynaklı bileştirmelerde yapılan hataların birleştirilmiş olan malzeme tahrip edilmeden ortaya çıkarılması olasılığı düşüktür. Bu nedenle; • Kaynak işleminin eğitimli ve belgeli personel tarafından uygulanması gereklidir, • Kaynak işleminin çok sıkı denetim altında tutularak uygulanması gereklidir, • Denetimi (kontrolü) yapacak olan personelin uygun nitelikte olması ve gerekli yetkilerle donatılması gereklidir. Bu personelin görev, yetki ve sorumlulukları EN ISO 14731 standardında tanımlanmıştır:
o Kaynak Mühendisleri (IWE) o Kaynak Muayene Personeli (IWIP) o Kaynak Spesiyalisti (Teknikerleri ) (IWS) o Kaynak Teknisyeni ISO 9001 genel bir kalite yönetimi sistemidir. ISO 9001 kalite yönetimi sistemi kaynaklı imalat yapan işletmeler için bazı konularda yüzeysel kalmaktadır.
EN ISO 3834, “Kaynaklı İmalat Yapan İşletmeler için Kalite Yönetimi Sistemi” özel olarak hazırlanmış bir standarttır. KaynaklıİmalattaKaliteYönetimiSistemi; ENISO3834 EN 729: 1995 Kısım 1-4’ün yerine geçmiştir. 5 kısımdan oluşan standart, atölye ve/veya şantiyede yapılan kaynaklı imalat için gerekli kalite şartları ile ilgili yaklaşımları açıklar ve imalatçıların kaynak kalite sistemlerinin değerlendirilmesi için bir temel oluşturur. Kaynaklı imalat yapılan işletmelerde kalite gereklerini tanımlamak amacıyla hazırlanmıştır. EN ISO 3834 serisi, yalnız basına imalatçının kendi üretim sistemi içinde veya ISO 9001 ile birleştirilerek uygulanabilir. Kullanımı; • Sözleşme görüşmelerinde: Kaynak kalite beklentilerinin belirlenmesi • Üretici için: Kaynak tekniği kalite gereklerinin
oluşturulması ve üretim sürecinde bunlara uyulması • Şartname hazırlayan kurullar: Kaynak tekniği kalite beklentilerinin belirlenmesi • Kalite uygulamalarını denetleyen organizasyonlar, örneğin; bağımsız muayene merkezleri, müşteriler veya üretici ENISO3834’ünsağladıkları • Kaynaklı Üretimin daha fazla kontrol altına alınabilmesi, güvenilirliğin sağlanması • Kaynaklı imalatta kalite ve maliyetlerin daha iyi kontrol altına alınması, • Tamir maliyetlerinin azalması, • Bakım Maliyetlerinin azalması, • Çalışanların sağlık ve güvenlik koşullarının iyileştirilmesi.
EN ISO 3834 standartlarının tanımları ve kabul kriterleri aşağıdaki tabloda kısaca tanımlanmıştır.
EN ISO 3834-1 Metalik Malzemelerin Ergime Kaynağı için Kalite Gerekleri EN ISO 3834-2 Metalik Malzemelerin Ergime Kaynağı için Kalite Gerekleri EN ISO 3834-3 Metalik Malzemelerin Ergime Kaynağı için Kalite Gerekleri EN ISO 3834-4 Metalik Malzemelerin Ergime Kaynağı için Kalite Gerekleri EN ISO 3834-5 Metalik Malzemelerin Ergime Kaynağı için Kalite Gerekleri Kalite gerekliliklerinde uygun seviyenin seçilmesi için kriterler
Kapsamlı kalite gerekleri
Standart kalite gerekleri
Temel kalite gerekleri
Uygulanabilir dokümanlar
İşletmelerde sistemin uygulanmasında aşağıdaki hususlara mutlaka yer verilmesi beklenir. • SözleşmeninGözdenGeçirilmesi: İmalatçı, sözleşmedeki kaynakla ilgili bütün gereklilikleri yerine getirebileceğini teyit etmeli ve ilgili kalite faaliyetleri ile ilgili ayrıntılı bir planlama yapabilmelidir. Bu aşamada işletmede görev yapan sorumlu kaynak gözetim personelinin (kaynak koordinatörü) mutlaka yer alması ve isin yapılabilirliği konusunda onay vermelidir. • TasarımınGözdenGeçirilmesi: İmalat hattına verilmeden önce kaynak tekniği uygulamaları ile ilgili tüm tasarım detayları, kaynak gözetim personeli tarafından detaylı bir biçimde incelenmelidir. • KaynakPersoneli: Tüm kaynakçı ve kaynak operatörleri EN 9606-1 veya EN 14732 standartlarının uygun kısımlarına göre test edilmiş ve sertifikalandırılmış olmalıdır. • MuayeneveTestPersoneli: İmalatçı kaynak uygulamaları ile ilgili gerekli planlama ve hazırlıkları yapacak, uygulamada denetim görevini yerine getirecek nitelik ve nicelikte personele sahip olmalıdır. Tahribatsız muayene yaptırılacak personel EN 9712 standardına göre uygun belgeye sahip olmalıdır. • İmalatveTestEkipmanları: İmalatçı gerekli ve yeterli sayıda ekipmana (kaynak akımı üreteci, tasımakaldırma ekipmanlar, takım-aparat-fikstür vb.) sahip olmalıdır. Kullanılan ekipman düzenli aralıklarla (periyodik) kontrollere tabi tutulmalı ve bu kontroller kayıt altına alınmadır. • FaaliyetlerinTanımı: İmalatçı, donanımını bir listesini yapmalı ve bunları izlemelidir. Gerekli donanımın kalibrasyonunu/doğrulamasını periyodik olarak yapmalı be bu işlemi kayıt altına almalıdır. o En büyük vinç kapasitesi, o Atölyenin ekipman alma kapasitesi, o Yarı otomatik veya otomatik kaynak ekipmanları kapasitesi,
o Isıl işlem için fırın ebatları ve maksimum sıcaklık değerleri,
o Bükme, kesme ve doğrultma ekipmanları kapasitesi, • Bakım: Bakım planları, kritik donanım için yapılmalı ve buna bağlı olarak periyodik bakımlar gerçekleştirilmelidir. Yapılan her türlü bakım işlemi kayıt altına alınmalıdır. Bu planlar, kaynak konstrüksiyon kalitesini doğrudan etkileyecek cihazlarla sınırlı kalabilir. Bakım işlemi aşağıdaki uygulamaları kapsayabilir: o Isıyla kesme makinalarının, otomatik kaynak aparatlarının ve benzeri makinaların kılavuzlarının duru mu, o Kaynak makinalarının kullanımı için gerekli olan ampermetre, voltmetre, debi ölçer gibi cihazların durumu, o Kabloların, hortumların ve bağlantıların durumu, o Yarı ve/veya tam otomatik kaynak ekipmanlarının kontrol sistemlerinin durumu,
o Termokupulların ve diğer sıcaklık ölçme cihazlarının durumu,
o Tel besleme ünitelerinin durumu.
• KaynakFaaliyetleri: Kaynaklı imalatın başlamasından önce aşağıdaki aşamaları geçilmiş ve dokümante edilmiş olması gereklidir: o İmalatPlanı; Kaynaklı imalat için ayrıntılı bir imalat planı hazırlanmalıdır ve bu plan şunları içermelidir:
▪ Konstrüksiyonun imalat sırası, ▪ Konstrüksiyonun imal edilmesi için gerekli ön imalatların tamamlanması,
▪ Uygun kaynak yöntemi ve ilgili proseslerin referanslarını,
▪ Mümkünse kaynak pasolarının sırasını, ▪ Ön imalatlar için talimatları, ▪ Yapılacak muayene ve testleri (tarafsız kontrol kurulusu faaliyetleri dahil),
▪ Numuneler ve/veya parçalar yardımıyla tanımlamaları o KaynakTalimatı(WPS); İmalatçı EN ISO 15607 standardının uygun kısmına göre kaynak yöntem spesifikasyonlarını hazırlamalı ve imalatta uygulandığından emin olmalıdır. oYöntemOnayları(WPAR); Uygulanacak kaynak yöntemleri, imalattan önce, EN ISO 15614-1 standardının uygun kısmına göre onaylanmış olmalıdır. oİştalimatları; İmalatçı, talimat amacıyla doğrudan WPS’leri kullanabileceği gibi, WPS’ye atıfta bulunarak da is talimatları da hazırlayabilir. oDokümantasyon; İmalatçı, ilgili kalite dokümanlarının (örn. WPS, WPAR, kaynakçı sertifikaları) kontrolü için prosedürler hazırlamalı ve uygulamalıdır. • KaynakSarfMalzemeleri: Kaynak sarf malzemelerinin kontrolünü içeren prosedürler, imalatçı tarafından hazırlanmalıdır. İmalatçı, sarf malzemelerin depolama, tasıma ve kullanımı için prosedürler hazırlamalı ve uygulamalıdır. Prosedürler, imalatçı firma tavsiyelerine uygun olmalıdır. • AnaMalzemeninDepolanmasıveİzlenebilirlik: Malzemeler, dış etkenlerden korunacak şekilde depolanmalıdır. Depolama sırasında, malzemelerin kalitesi ve boyutları tanımlı olmalıdır, ayrıca malzeme sertifikasına ulaşılabilecek şekilde izlenebilirlik sağlanmış olmalıdır (Markalama ve marka aktarımı). • KaynakSonrasıIsılİşlem: İmalatçı, kaynak sonrası malzeme cinsi ve kalınlığına bağlı olarak uygulanacak ısıl işlemin belirlenmesinden ve uygulanmasından tamamen sorumludur. Isıl işlem yöntemi, ana malzeme, kaynak tipi, konstrüksiyon, vb. ile uyumlu olmalıdır. Kayıtlar gerekli işlem sırasının takip edildiğini göstermelidir. Özel ısıl işlem uygulamaları da izlenebilir olmalıdır. • KaynaklaİlgiliMuayeneveTestler: Muayene ve testlerin yeri ve sıklığı aşağıdakilere bağlıdır: o Sözleşmeye ve/veya standart, o Kaynak prosesi, o Konstrüksiyon tipi, Muayene ve Testler uygulanma zamanlarına göre aşağıdaki gibi sınıflandırılabilir: o Kaynaktan Önce ▪ Kaynakçı sertifikalarının uygunluk ve geçerliliği, ▪ Kaynak talimatı (WPS) uygunluğu, ▪ Ana malzeme uygunluğu, ▪ Sarf malzemelerin uygunluğu, ▪ Kaynak ağzı hazırlığı, ▪ Kaynak için çalışma şartlarının uygunluğu ▪ Vb. o Kaynak işlemi sırasında ▪ Pasolar arası temizlik, ▪ Altlık için arkadan taslama, ▪ Kaynak sırası, ▪ Vb. o Kaynaktan sonra ▪ Uygun EN standardına göre gözle kontrol, ▪ Uygun EN standardına göre tahribatsız muayene, ▪ Uygun EN standardına göre tahribatlı muayene, ▪ Kaynaklı yapının ölçü, biçim ve sekil kontrolü, ▪ Kaynak sonrası işlemlerin sonuç ve kayıtları, taslama, kaynak sonrası ısıl işlem, ▪ Vb. • UygunsuzlukveDüzelticiFaaliyetler: Belirlenen gerekliliklere uymayan parçaların istem dışı kullanımını engellemek için ölçümler yapılmalıdır. Tamir, imalatçı tarafından üstleniliyorsa, uygun yöntem tarifleri (tamir talimatları) tamirin yapıldığı bütün is istasyonlarında mevcut olmalıdır. • Tanımlamaveİzlenebilirlik: Kaynak operasyonlarının tanım ve izlenebilirliğinden emin olmak amacıyla dokümante edilmiş sistem aşağıdakileri içermelidir:
o İmalat planları, o İş sıralama kartları, o İmalattaki kaynak yer kayıtları, o Kaynak markalama, damgalama, etiketleme, vb. o Özel kaynaklar için izlenebilirlik, o Kaynakçı ve yöntem onayları, o Tahribatsız muayene yöntem ve personeli, o Kaynak sarf malzemeleri, tip, döküm no, numune no, o Ana malzeme, tip, numune, o Tamir bölgesi. • KaliteKayıtları: Kalite kayıtları, aksi belirtilmedikçe en az 5 yıl boyunca muhafaza edilmelidir, kabaca aşağıdakileri içermelidir:
o Sözleşme ve tasarımın gözden geçirme kayıtları, o Malzeme sertifikaları, o Sarf malzeme sertifikaları, o Kaynak talimatları (WPS), o Kaynak yöntem onayları (WPAR), o Kaynakçı ve kaynak operatör sertifikaları, o Tahribatsız muayene personel sertifikaları, o Isıl işlem ve yöntem test kayıtları, o Tahribatlı, tahribatsız muayene yöntem ve raporları, o Ölçü raporları, o Tamir, uygunsuzluk rapor ve kayıtları.

Dalgakıran Kompresör'ün gözbebeğinde üretim başladı
Dalgakıran Kompresör, Kocaeli Dilovası’ndaki 50.000 m2’lik kapalı alana sahip yeni fabrikasında seri üretime başladı
Dalgakıran Kompresör Avrupa’nın en büyük kompresör fabrikalarından birisini Kocaeli Dilovası’nda her ünitesiyle bitirmek üzere. Bir yandan fabrika’da inşaat çalışmaları ve çevre düzenlemeleri yoğun bir şekilde devam ederken diğer yandan da tam kapasite üretime yeni fabrikada start verdi. İdari binanında yıl sonuna kadar tamamlanmasıyla 70.000 m2 lik arsanın içerinde yapılan 50.000 m2 lik fabrika yatırımı Türkiye’de alanındaki en büyük, Avrupa’nın ise ilk 3 tesisinden birisi olacak. Dalgakıran Kompresör daha öncede japonya’nın Dünya devi IHI ile ortaklık kurmuş ve Türkiye’nin ilk Turbo Kompresör fabrikasınıda Dilovasında IHI DALGAKIRAN adıyla hizmete açmıştı.
Haus’dan eğitime katkı
HAUS olarak, Aydın Meslek Eğitimine Katılım Sağlama (Aydın MEKAS) Projesi kapsamında meslek lisesi öğ rencilerine burs verdiğimiz ve projede sosyal sorumluluk kapsamında görev aldığımız için şirketimize Aydın Valisi Sayın Yavuz Selim KÖŞGER tarafın dan plaket verilmiştir. Bölgesinde ilk örnek proje HAUS şirket bünyesinde Millî Eğitim Bakanlığı ve Aydın Valiliği iş bir liğiyle meslek lisesi projesi için protokol imzaladı. Böylelikle meslek lisesi öğren cileri HAUS ile güncel teknolojik imkanlarla pratik yapma ve uzmanlık kazanma fırsatı elde edip, gelecekteki meslek hayatlarına şirketin örgüt kültürüyle birlikte hazırlanacaklar. Bölgesinde ilk defa gerçekleştirilen bu proje ile HAUS örnek bir çalışmaya imza atmıştır.
Geçtiğimiz yaz aylarında ülkemizin birçok bölgesinde ve bölgemiz civarında bir çok yangın sebebi ile ülkemizin can damarları olan ormanlarımızı kaybettik. T.C. Tarım ve Orman Bakanlığı Orman Genel Müdürlüğü tarafından düzenlenen Geleceğe Nefes Projesi kapsamında

HAUS Makina Sanayi Ticaret Anonim Şirketi olarak biz de ülkemizin geleceğine nefes olmak adına Aydın Bölgesine çalışanlarımız adına fidan bağışında bulunduk. HAUS Santrifüj Teknolojileri olarak ürettiğimiz ürünler ile çevreye faydalı olmaktan gurur duymanın yanı sıra bakanlığımızın düzenlediği bu projeye katılmanın da mutluluğunu yaşamaktayız.
Vidalı Hava Kompresörlerinde 5 YIL GARANTİ Dönemi Başladı!
TÜRKİYE’DE İLK
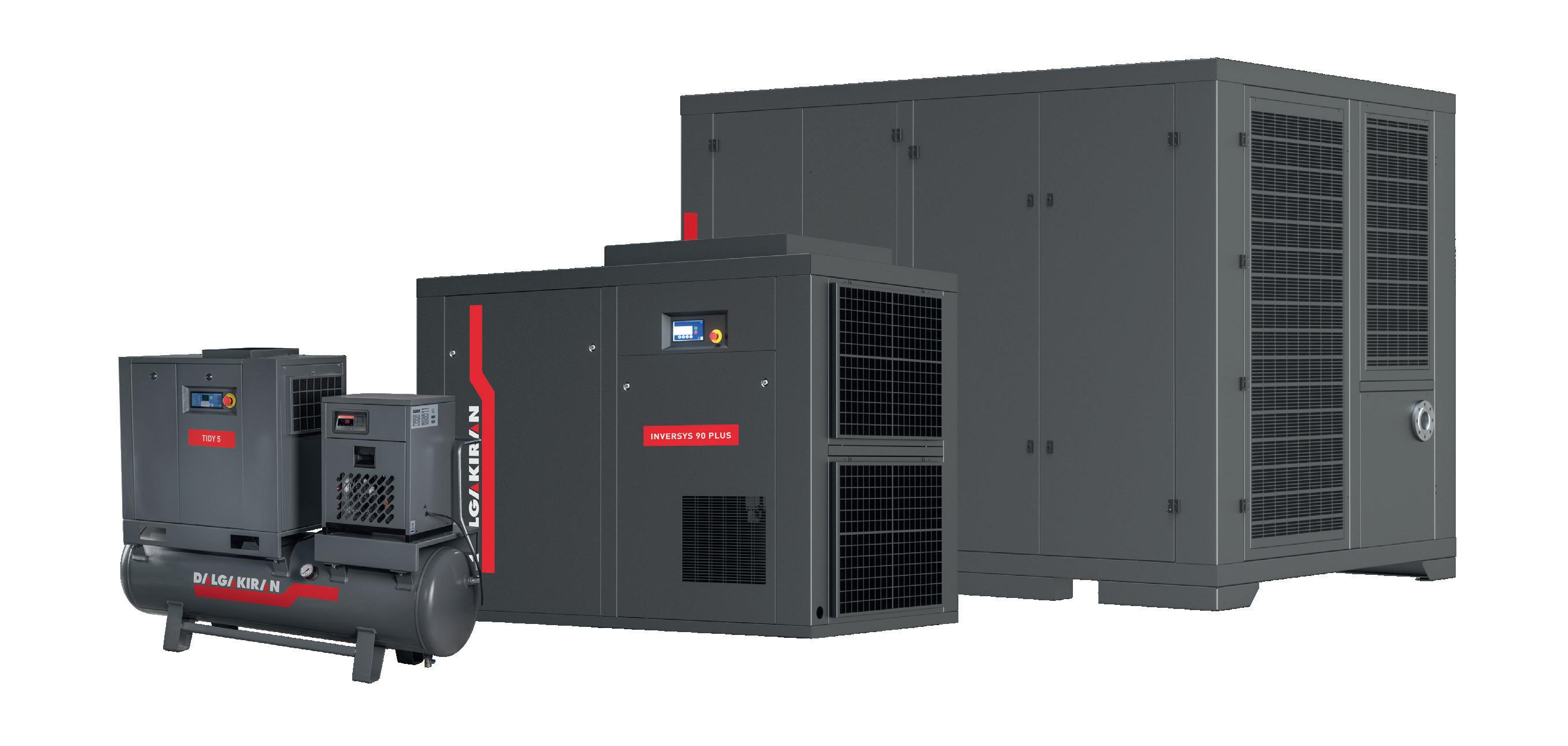
Yeni AR Serisi
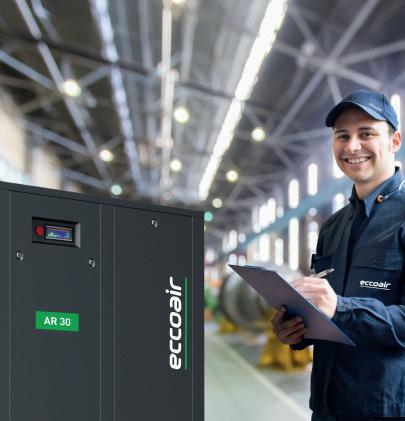
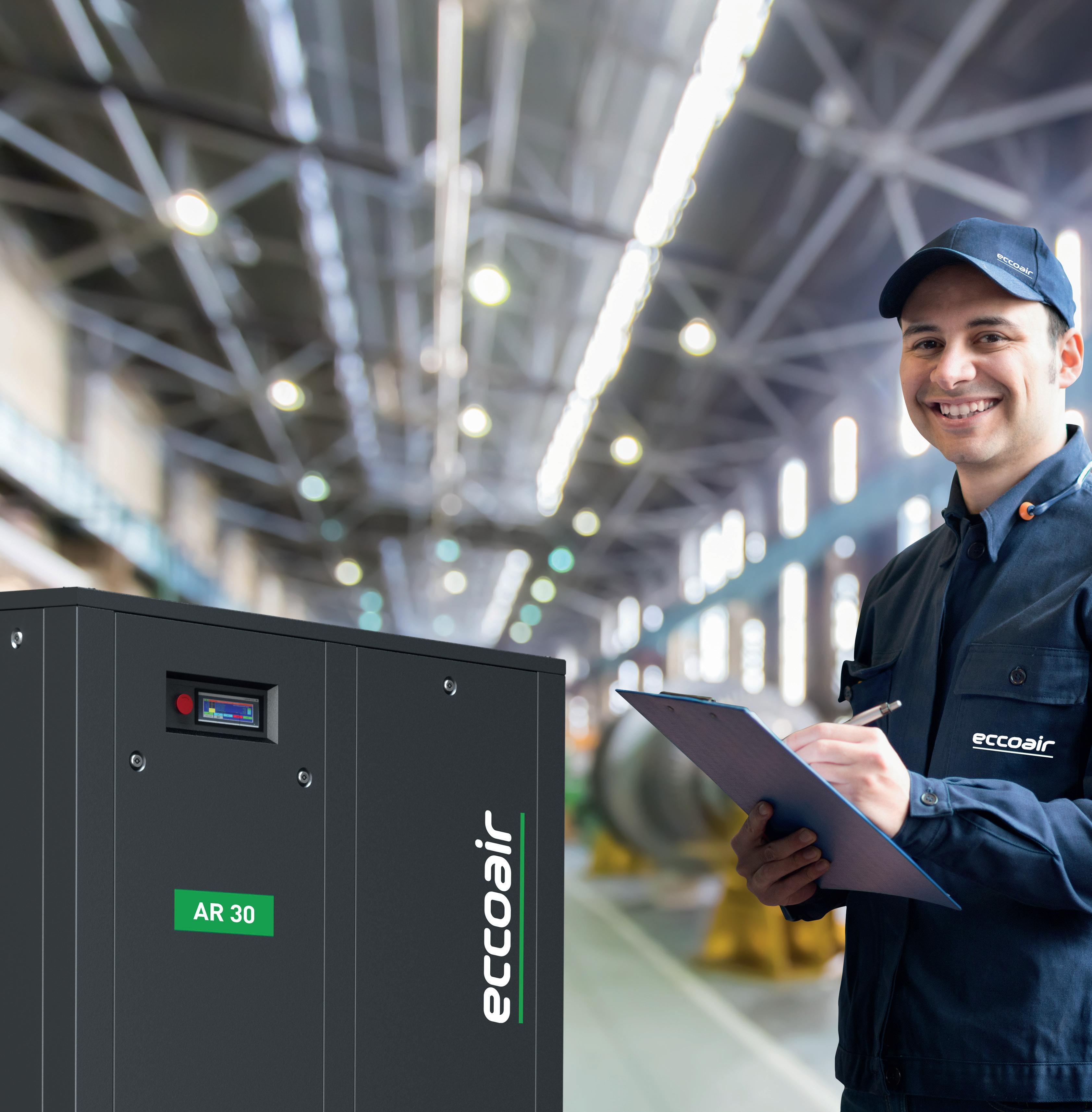
Pistonlu ve vidalı kompresörler olmak üzere geniş bir ürün yelpazesine sahip Eccoair, az yatırımla mümkün olan en yüksek kalite ve performansı sunarak şirketinizin gelişiminde itici güç oluyor. Eccoair bir Dalgakıran Grup markasıdır. Pistonlu ve vidalı kompresörler olmak üzere geniş bir ürün yelpazesine sahip Eccoair, az yatırımla mümkün olan en yüksek kalite ve performansı sunarak şirketinizin gelişiminde itici güç oluyor. Eccoair bir Dalgakıran Grup markasıdır.
1915 Çanakkale Köprüsü Projesi'nde Özen Kompresör Tercih Edildi

Mart 2017'de temeli atılan Çanakkal e'nin Lapseki ilçesine bağlı Şekerkaya mevkisi ile Gelibolu'nun Sütlüce mevkisi arasında yapımı süren 1915 Çanakkale Köprüsü inşaatında; toplam 4 adet olmak üzere, her bir ayağında Özen Kompresör ürünleri kul lanılıyor. Projeye özel olarak hazırlanan kom presör seti; OSC V serisi frekans invertörlü vidalı kompresör, kurutucu ve hava tankından oluşuyor. Ortam koşullarına ve taşımaya uygun olarak tasarlanan sette yer alan OSC V serisi frekans invertörlü vidalı kompresör, motor devrini işletmenin anlık hava ihtiyacına göre ayarlayarak enerji tasarrufu ve düşük maliyetli üretim yapma imkânı sağlıyor. Set üzerinde entegre soğutmalı tip hava kurutucusu basınçlı hava sistemindeki nem ve partikülleri uzaklaştırıyor. Basınçlı hava şartlarına özel olarak tasarlanan hava tankı ile de komple bir çözüm sağlanmış oluyor.
Verimliliği ve dayanıklılığı ile ön plana çıkan Özen Kompresör ürünleri köprü inşaatının kumlama ve boyama işlemleri için kullanılıyor.
Projeye ilişkin olarak Özen Kompresör Yönetim Kurulu Başkanı İbrahim Öze n; “Ülkemiz için önemli olan bu proje bittiğinde Trakya ile Ege Bölgesi’ni bağlayacak ve bölgenin entegrasyonuna büyük katkı sağlayacak. Bu projeye verdiğimiz katkıdan dolayı gururluyuz. Yerli bir
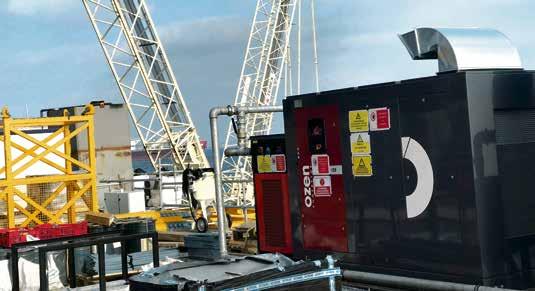
kompresör üreticisi olarak üzerinde hassasiyetle durduğumuz konulardan biri uluslararası rekabette global bir oyuncu haline gelmek için gerekli tüm altyapı çalışmalarını yapmak ve bu yolda kararlılıkla ilerlemek. Yaptığımız tüm çalışmalar ve aldığımız büyük projeler bu yolda ilerlediğimizin bir göstergesi” dedi.