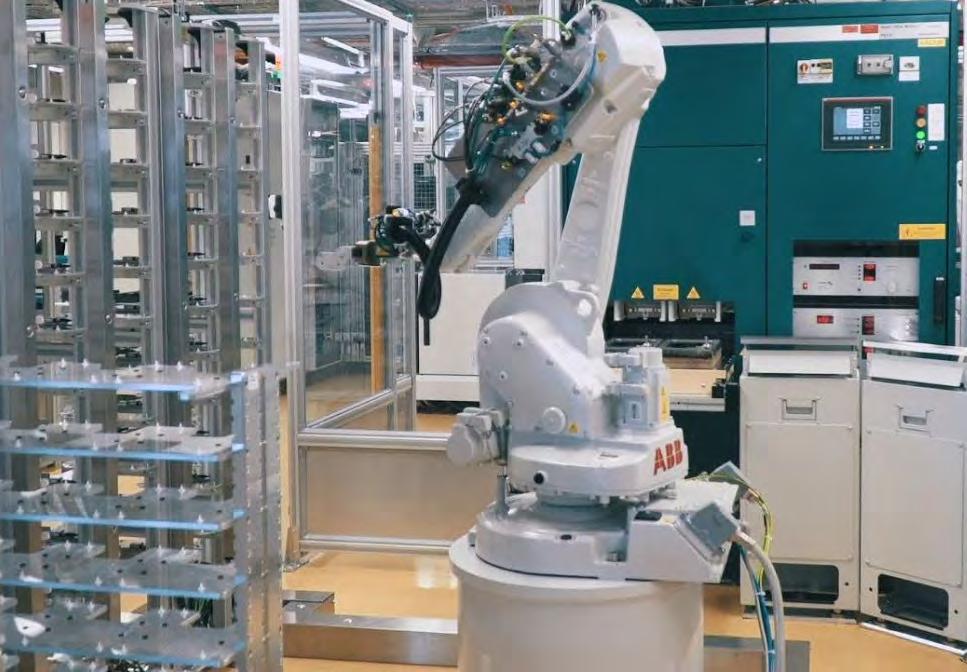
20 minute read
PRIMO PIANO/FOREGROUND HITACHI ABB POWER GRIDS INAUGURA UNA NUOVA ERA PER L’AUTOMAZIONE DI FABBRICA/HITACHI ABB POWER GRIDS OPENS A NEW ERA FOR FACTORY AUTOMATION A cura della Redazione
HITACHI ABB POWER GRIDS INAUGURA UNA NUOVA ERA PER L’AUTOMAZIONE DI FABBRICA
Di fronte alla necessità pressante di aumentare la produttività dello stabilimento di semiconduttori di Hitachi ABB Power Grids a Lenzburg, Svizzera, l’attenzione si è focalizzata verso un progetto di automazione innovativo che ha combinato AGV e robot per ottenere un processo produttivo completamente automatizzato.
Advertisement
A cura della Redazione
Lo stabilimento Hitachi ABB Power Grids produce una gamma di semiconduttori BiMOS per clienti che vanno da linee ferroviarie elettriche a operatori nei settori della trasmissione e distribuzione dell’energia. I semiconduttori di potenza sono commercializzati in tutto il mondo. Per garantire la competitività delle attività in un Paese come la Svizzera, che notoriamente ha costi molto elevati, era fondamentale garantire un aumento della produttività. Questa misura avrebbe inoltre aggiunto un vantaggio ecologico alle operazioni, grazie a un migliore utilizzo dell’energia e delle altre risorse. Come tutte le implementazioni di Industria 4.0, il progetto, avviato sei anni fa, è ancora in evoluzione. Le prime incursioni nell’automazione sono iniziate con due progetti mirati: uno aveva come target il processo “front-end”, ovvero in cui viene realizzato il silicio, mentre l’altro era il processo “back-end”, in cui il prodotto viene assemblato.
Fig.1 Rendering stabilimento di semiconduttori di Hitachi ABB Power Grids a Lenzburg, Svizzera
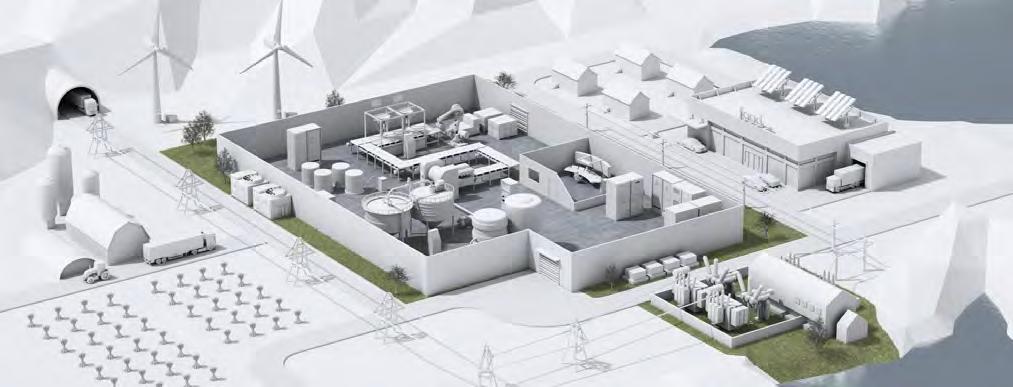
Dall’impianto pilota alla produzione
Il processo “back-end” da solo è stato individuato come particolarmente idoneo per l’automazione, così Hitachi ABB Power Grids ha avviato una completa automazione della produzione. Il programma di trasformazione è stato chiamato “Genesis” ed è iniziato nel 2014. Non era un programma semplice: con oltre 100 progetti, 20 nuove unità produttive, più di 50 robot e inizialmente sei veicoli a guida automatica (Automated Guided Vehicles, AGV), tutti da integrare nel sistema di controllo della produzione (Manufacturing Execution System, MES), l’adozione di tale programma ha richiesto un approccio graduale. È stato deciso di testare la tecnologia su una linea pilota appositamente costruita, utilizzando celle e attrezzature di produzione reali, oltre a quattro AGV e alcuni robot ABB. “Questa linea pilota rappresentava su piccola scala tutto ciò che volevamo realizzare in seguito e ha consentito di testare il funzionamento dell’hardware, del software e delle interfacce”, afferma David Hajas, responsabile del programma Genesis. “Ha testato le comunicazioni tra il sistema MES e i robot, quelle tra il sistema MES e gli AGV nonché il trasferimento meccanico tra gli AGV e l’attrezzatura di produzione. Sono stati necessari due anni di lavoro, dall’avvio dello studio di fattibilità alla piena operatività dell’impianto pilota.” Durante questa fase pilota il team di Lenzburg ha sviluppato, insieme ai diversi fornitori, il proprio standard e scritto le specifiche per le interfacce. “Abbiamo compiuto un passo avanti, abbiamo scoperto dov’erano i problemi, li abbiamo risolti e siamo andati incontro alla sfida successiva; è stato un approccio iterativo. Durante i due anni dello studio di fattibilità abbiamo creato il nostro standard e lo abbiamo applicato al resto dell’attrezzatura. Lo abbiamo inserito in tutte le specifiche di ciascun fornitore con cui stavamo lavorando.”
Fig.2 David Hajas, responsabile progetto Genesis
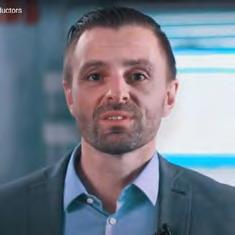
Un processo produttivo automatizzato
Il programma finale ha coinvolto diverse celle produttive, la cui configurazione è stata modificata dai robot ABB. La logistica tra le celle di produzione viene gestita con AGV appositamente sviluppati per il progetto Genesis
e controllati dalla tecnologia di navigazione a guida autonoma (Autonomous Navigation Technology, ANT®) di BlueBotics. Questo sistema impiega le strutture naturali permanenti nell’ambiente come riferimento per la localizzazione dei veicoli e combina le informazioni provenienti da encoder industriali e i laser scanner di sicurezza degli AGV, in grado di raggiungere un’accuratezza di ±1 cm e ±1°. Il sistema ANT® consente agli AGV di arrestarsi autonomamente in caso di situazioni di blocco d’emergenza (strategia del path-following). Non è pertanto necessaria una connessione fissa tra le singole celle di produzione. La produzione risultante è altamente flessibile e conFig3. Modello piattaforma digitale Abb Ability Umili origini Il concetto iniziale di automazione della produzione è stato sviluppato da Hajas mentre lavorava come ingegnere addetto alla linea di produzione, un ruolo da cui ha potuto assistere alle sfide quotidiane poste dall’operatività dello stabilimento. “Conoscevo i problemi”, afferma Hajas. “Sulla base di ciò, ho presentato alla direzione l’idea di una produzione completamente automatizzata da cui è iniziata tutta la storia. Da allora gestisco questo programma. È ancora in corso, si tratta di una trasformazione e durerà molti anni.” Oltre alla necessità di rimanere competitivi, disente di passare da percorsi diversi. L’intero processo è diretto e sincronizzato attraverso il sistema MES e un sistema di controllo, in questo caso il sistema di gestione dei processi produttivi (Manufacturing Operations Management, MOM) Ability™ di ABB, che consente una produzione autonoma e agile. A differenza delle soluzioni di automazione tradizionali, in cui il flusso del materiale è permanentemente programmato nella cella, la logica delle attività per questa applicazione viene trasferita al sistema MES. Ciò consente un adattamento flessibile della logica stessa senza modificare la programmazione delle cel-
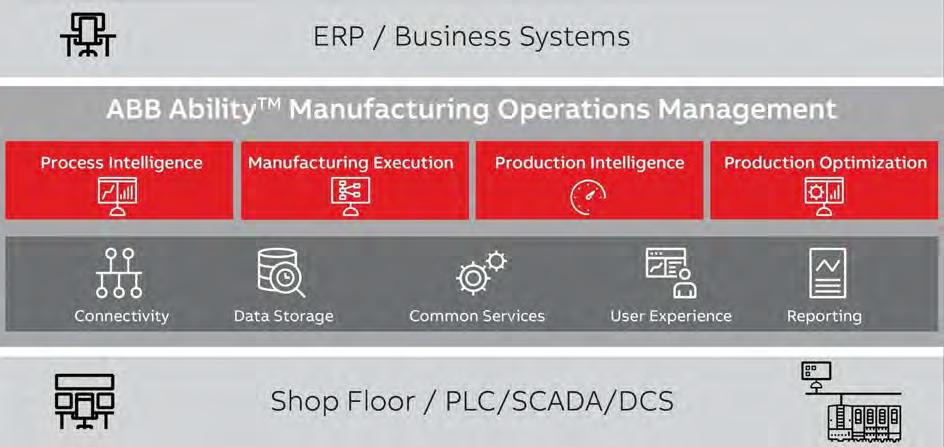
le robotizzate.
La logistica tra le celle di produzione viene gestita con AGV appositamente sviluppati per il progetto Genesis e controllati dalla tecnologia di navigazione a guida autonoma (Autonomous Navigation Technology, ANT®) di BlueBotics.
versi sono stati i fattori alla base del progetto di automazione, per primo l’intento di aumentare la produttività e i profitti migliorando la qualità, aumentando il rendimento e massimizzando il throughput. “I semiconduttori che produciamo a Lenzburg sono high tech e di alta qualità, così ogni pezzo che non scartiamo ci fa risparmiare sui costi”, aggiunge Hajas. Uno degli elementi fondamentali del progetto è il sistema di controllo della produzione. Hajas lo descrive come il cervello che tiene traccia di tutto e coordina tutte le operazioni. La scelta dei robot ABB e di un sistema di controllo era prevista, ma in relazione alla logistica del trasporto dei materiali da una cella all’altra sono state prese in considerazione diverse opzioni. Sono stati prima considerati i nastri trasportatori tradizionali, quindi un nastro trasportatore sopraelevato, ma nessuno rappresentava la soluzione ideale. “Inizialmente non eravamo sicuri di quale tecnologia avremmo usato per trasferire il materiale, perché il nostro schema iniziale prevedeva semplicemente delle scatole che rappresentavano le macchine della nostra linea di produzione”, spiega Hajas. “Poiché si trattava di un’area pre-esistente, abbiamo dovuto adattarci alla disposizione e alle ubicazioni delle attrezzature, che non sempre si trovavano in una posizione ottimale. “Ho valutato diverse tecnologie di nastri trasportatori arrivando ben presto alla conclusione che la soluzione sarebbe risultata troppo disorganizzata, poiché il nostro sistema di produzione non è lineare. La logistica richiesta consisteva in percorsi molto complessi che avrebbero richiesto nastri trasportatori dappertutto, i quali avrebbe reso difficile l’accesso alla linea per la manutenzione. Il secondo problema era che, sebbene esistano nastri trasportatori compatibili con le camere bianche, abbiamo sempre cercato di evitarli perché hanno superfici aggiuntive che, per essere mantenute pulite, richiedono cure speciali. Gli AGV sono stati suggeriti da un fornitore con cui stavamo lavorando e che mi ha aperto un mondo di nuove possibilità. Il piano iniziale consisteva infatti nell’automazione di una sola area, ma la scelta degli AGV ci ha consentito di valutare un’automazione completa.”
Fig.4 Innovativa combinazione di AGV e robot per la produzione flessibile di semiconduttori
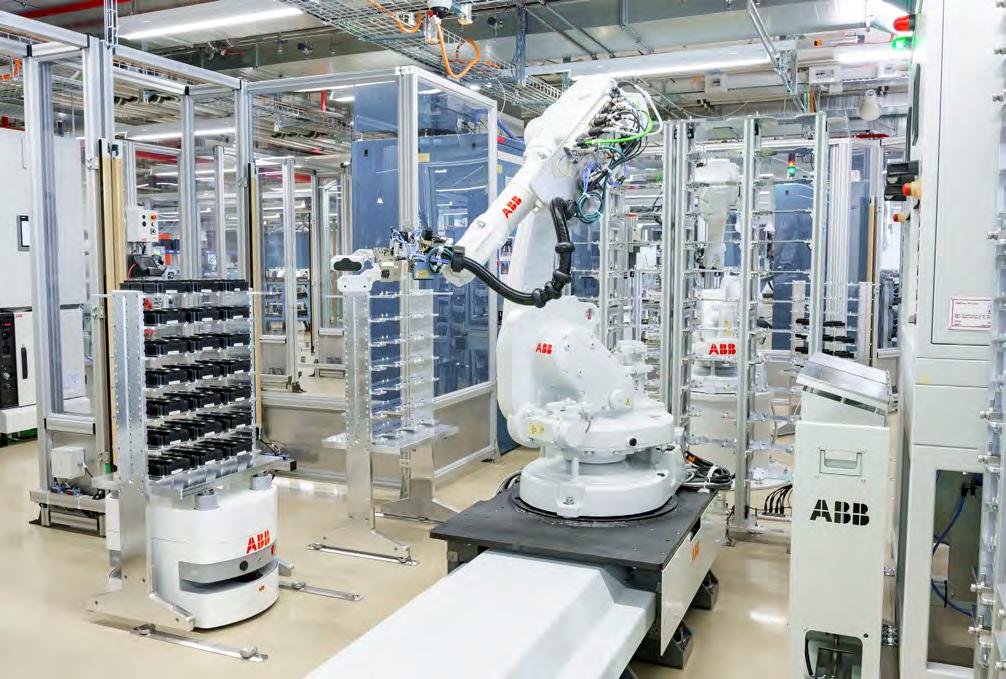
Far funzionare un processo complesso senza soluzione di continuità
La produzione di semiconduttori è un processo estremamente complesso già di per sé, che, inoltre, deve rispettare severi requisiti di tracciabilità. Se qualcosa non funziona, è fondamentale sapere quali macchine e materiali sono coinvolti. “È stato impegnativo integrare tutti gli AGV, poiché la produzione a Lenzburg è un processo complesso con molti passaggi. Il sistema MES doveva conoscerli tutti”, spiega Nicola Tomatis, CEO di BlueBotics. “Non deve solo garantire che gli AGV eseguano perfettamente la loro funzione, ma anche assicurare che tutte le comunicazioni tra l’attrezzatura e i veicoli siano garantite.” “Alla prima riunione a Lenzburg hanno partecipato circa 30 - 40 persone che hanno discusso di cosa fosse necessario durante il progetto. Fin dall’inizio non potevo non pensare che, in termini di progetto, si trattasse di una grande sfida. In passato il lavoro dell’integratore tecnologico era quello di capire le tecnologie complesse e applicarle a processi piuttosto semplici. Ora questo sta cambiando poiché le tecnologie divengono sempre più semplici, mentre gli integratori devono capire processi complessi affinché queste soluzioni possano funzionare.” Il più grande ostacolo per gli AGV è tuttavia rappresentato dall’interazione con la cella di produzione. “Il trasferimento automatizzato dei vassoi contenenti i componenti è stata la parte più difficile, perché richiedeva un’elevata precisione e una certa procedura”, aggiunge Tomatis. “Avevamo bisogno di comunicazione, nonché di coordinamento e di sincronizzazione con le apparecchiature e con il sistema MES. Dovevano tutti comunicare localmente tra loro per essere sicuri di ottenere un corretto handshake. La necessità di implementare i protocolli specifici di handshaking utilizzati in questo mercato per completare il lavoro costituiva una vera e propria sfida per noi.” Le comunicazioni nell’impianto sono gestite tramite Wi-Fi attraverso una rete industriale e ciò non ha creato alcun problema al team. Nemmeno lo spinoso tema della latenza, che spesso viene citato come un problema negli impianti robotizzati industriali. “La latenza non è un problema perché per questa applicazione non sono necessarie comunicazioni in tempo reale”, aggiunge Hajas. “Il bello del nostro concept è che la linea di produzione informa il sistema MES sullo stato di una cella che ha terminato la produzione e su cui è presente materiale da scaricare. Il sistema MES invia una richiesta di trasporto al software del server ANT [gestione della flotta] indicando che l’attrezzatura X è pronta per scaricare, quindi viene inviato un AGV.”
Inizialmente erano previsti 50 passaggi di produzione nell’ambito del programma Genesis. Ad oggi metà di questi è stata implementata. Le parti rimanenti sono ora in fase di installazione e di test presso il sito degli integratori e saranno le prossime a essere installate. Finita questa parte, i chip verranno inseriti all’interno dello strumento nella prima fase del processo e il modulo finito e testato uscirà dalla linea senza che una sola persona abbia toccato il prodotto. Il trasporto e l’invio sono quindi completamente automatizzati, così come la selezione delle formule e diversi router vengono prodotti in parallelo. Lo stabilimento ha già ricevuto un riconoscimento nell’ambito del prestigioso premio “Factory of the Year 2018” per la categoria “‘Excellent Location Safeguarding by Digitalization”. Anche se il premio non è stato assegnato solo per il progetto Genesis, bensì per l’intera strategia di digitalizzazione in sito, l’automazione della linea di processo è stata la componente chiave di questo successo.
Keywords: BiMOS, AGV, MES, MOM, Ant, BlueBotics, Ability, Hitachi ABB Power Grids, Genesis
Hitachi ABB Power Grids Ltd. Hitachi ABB Power Grids è leader tecnologico globale con quasi 250 anni di esperienza combinata e circa 36.000 dipendenti in 90 Paesi. Con sede in Svizzera, l’azienda fornisce servizi ai clienti operanti nei settori delle utility, dell’industria e delle infrastrutture lungo tutta la catena di valore, nonché ad aree emergenti come la mobilità sostenibile, le smart city, l’immagazzinamento dell’energia e i data center. Con una comprovata esperienza, una portata globale e una base di impianti installati ineguagliabile, Hitachi ABB Power Grids bilancia valori sociali, ambientali ed economici. Si impegna per un futuro energetico sostenibile, con tecnologie all’avanguardia e digitali, come partner affidabile per creare una rete più forte, più intelligente e più verde. www.hitachiabb-powergrids.com
BlueBotics BlueBotics punta a diventare il riferimento nella navigazione autonoma, con la mission di consentire la mobilità dei veicoli per l’automazione nel mercato dell’uso professionale. L’azienda ora è attiva in due segmenti: • Automazione industriale – BlueBotics propone ANT®, un’innovativa soluzione di navigazione. • Robotica dei servizi – L’azienda propone servizi ingegneristici basati sulla propria esperienza nella robotica mobile, con piattaforme standard, studi di fattibilità, progetti personalizzati e sviluppi dedicati per abilitare nuove applicazioni per i clienti. www.bluebotics.com HITACHI ABB POWER GRIDS OPENS A NEW ERA FOR FACTORY AUTOMATION
Faced with the pressing need to increase productivity at the Hitachi ABB Power Grids semiconductor plant in Lenzburg, Switzerland, the focus was on an innovative automation project that combined AGVs and robots to achieve a fully automated production process.
By the editorial staff
The Hitachi ABB Power Grids plant produces a range of BiMOS semiconductors for customers ranging from power lines to power transmission and distribution operators. Power semiconductors are sold worldwide. To ensure the competitiveness of activities in a country like Switzerland, which is known to have very high costs, it was essential to ensure an increase in productivity. This measure would also have added an ecological advantage to operations, thanks to better use of energy and other resources. Like all implementations of Industry 4.0, the project, which started six years ago, is still evolving. The first forays into automation began with two targeted projects: one targeted the “front-end” process, where silicon is made, while the other was the “back-end” process, where the product is assembled.
From pilot plant to production The back-end process alone has been identified as particularly suitable for automation, so Hitachi ABB Power Grids has started a complete automation of production. The transformation program was called “Genesis” and started in 2014. It was not a simple program: with over 100 projects, 20 new production units, more than 50 robots and initially six Automated Guided Vehicles (AGVs), all to be integrated into the Manufacturing Execution System (MES), the adoption of this program required a stepby-step approach. It was decided to test the technology on a specially built pilot line, using real production cells and equipment, as well as four AGVs and some ABB robots. “This pilot line represented on a small scale everything we wanted to achieve la-
ter and allowed us to test the operation of the hardware, software and interfaces,” says David Hajas, head of the Genesis program. “It tested the communication between the MES system and the robots, the communication between the MES system and the AGVs as well as the mechanical transfer between the AGVs and the production equipment. It took two years of work, from the start of the feasibility study to full operation of the pilot plant”. During this pilot phase, the Lenzburg team, together with the various suppliers, developed its own standard and wrote the specifications for the interfaces. “We took a step forward, found out where the problems were, solved them and faced the next challenge; it was an iterative approach. During the two years of the feasibility study we created our standard and applied it to the rest of the equipment. We incorporated it into all the specifications of each supplier we were working with.
An automated production process The final program involved several production cells, whose configuration was modified by ABB robots. The logistics between the production cells are managed with AGVs specially developed for the Genesis project and controlled by BlueBotics’ Autonomous Navigation Technology (ANT®). This system uses the permanent natural structures in the environment as a reference for vehicle location and combines information from industrial encoders and safety laser scanners of the AGVs, capable of achieving an accuracy of ±1 cm and ±1°. The ANT® system allows AGVs to stop autonomously in case of emergency lockout situations (path-following strategy). A fixed connection between the individual production cells is therefore not required. The resulting production is highly flexible and allows you to switch between different paths. The entire process is directed and synchronized through the MES system and a control system, in this case ABB’s Manufacturing Operations Management (MOM) Ability™, which enables autonomous and agile production. Unlike traditional automation solutions, where the material flow is permanently programmed in the cell, the task logic for this application is transferred to the MES system. This allows flexible adaptation of the logic itself without changing the proHumble roots The initial concept of production automation was developed by Hajas while working as a production line engineer, a role from which he was able to witness the daily challenges of plant operation. “I knew the problems,” says Hajas. “Based on that, I presented the management with the idea of a fully automated production that started the whole story. I have been running this program ever since. It is still in progress, it is a transformation and will last many years. In addition to the need to remain competitive, there were several factors behind the automation project, the first being the intent to increase productivity and profits by improving quality, increasing yield and maximizing throughput. “The semiconductors we produce in Lenzburg are high tech and high quality, so every part we don’t discard saves us costs,” adds Hajas. One of the key elements of the project is the production control system. Hajas describes it as the brain that keeps track of everything and coordinates all operations. The choice of ABB robots and a control system was planned, but in relation to the logistics of transporting materials from one cell to another, several options were considered. Traditional conveyor belts were first considered, then an overhead conveyor belt, but none was the ideal solution. “Initially we were not sure what technology we would use to transfer the material, because our initial scheme simply involved boxes representing the machines in our production line,” explains Hajas. “Since this was a pre-existing area, we had to adapt to the layout and locations of the equipment, which were not always in an optimal position. “I evaluated several conveyor belt technologies and soon came to the conclusion that the solution would be too disorganized, as our production system is not linear. The logistics required consisted of very complex routes that would have required conveyor belts everywhere, which would have made it difficult to access the line for maintenance. The second problem was that although there are cleanroom compatible conveyor belts, we always tried to avoid them because they have additional surfaces that require special care to be kept clean. The AGVs were suggested by a supplier we were working with
and that opened up a world of new possibilities for me. The initial plan was in fact to automate only one area, but the choice of AGVs allowed us to evaluate a complete automation”.
Making a complex process work seamlessly The production of semiconductors is an extremely complex process in itself, which also has to meet strict traceability requirements. If something does not work, it is essential to know which machines and materials are involved. “It was challenging to integrate all AGVs, because production in Lenzburg is a complex process with many steps. The MES system had to know them all,” explains Nicola Tomatis, CEO of BlueBotics. “Not only must it ensure that the AGVs perform their function perfectly, it must also ensure that all communication between the equipment and the vehicles is guaranteed”. “The first meeting in Lenzburg was attended by about 30 to 40 people who discussed what was needed during the project. From the outset, I couldn’t help but think that this was a major challenge in project terms. In the past, the work of the technology integrator was to understand complex technologies and apply them to rather simple processes. Now this is changing as technologies become simpler and simpler, while integrators must understand complex processes in order for these solutions to work”. The biggest obstacle for AGVs, however, is the interaction with the production cell. “The automated transfer of the trays containing the components was the most difficult part because it required high precision and a certain procedure,” adds Tomatis. “We needed communication as well as coordination and synchronization with the equipment and the MES system. They all had to communicate locally with each other to make sure they got the right handshake. The need to implement the specific handshaking protocols used in this market to complete the work was a real challenge for us. The communications in the plant are managed via Wi-Fi through an industrial network and this has not created any problems for the team. Neither did the thorny issue of latency, which is often cited as a problem in industrial robotic systems. “Latency is not a problem because real-time communications are not required for this application,” adds Hajas. “The beauty of our concept is that the production line informs the MES system about the status of a cell that has finished production and on which there is material to download. The MES system sends a transport request to the ANT server software [fleet management] indicating that the X equipment is ready to download, then an AGV is sent.
At first there were 50 production steps in the Genesis program. To date, half of these have been implemented. The remaining parts are now being installed and tested at the integrator site and will be the next to be installed. Once this part is finished, the chips will be inserted into the instrument in the first step of the process and the finished and tested module will leave the line without a single person touching the product. The transport and sending are then fully automated, as well as the selection of the formulas and several routers are produced in parallel. The plant has already received an award in the prestigious “Factory of the Year 2018” award for the category “’Excellent Location Safeguarding by Digitalization”. Although the award was given not only for the Genesis project, but for the entire on-site digitization strategy, process line automation was the key component of this success.
Keywords: BiMOS, AGV, MES, MOM, Ant, BlueBotics, Ability, Hitachi ABB Power Grids, Genesis
Hitachi ABB Power Grids Ltd. Hitachi ABB Power Grids is a global technology leader with nearly 250 years of combined experience and approximately 36,000 employees in 90 countries. Based in Switzerland, the company provides services to customers in the utility, industry and infrastructure sectors throughout the value chain, as well as emerging areas such as sustainable mobility, smart cities, energy storage and data centers. With proven expertise, global reach and an unrivalled installed base, Hitachi ABB Power Grids balances social, environmental and economic values. It is committed to a sustainable energy future, with cutting-edge, digital technologies, as a reliable partner to create a stronger, smarter and greener network. www.hitachiabb-powergrids.com
BlueBotics BlueBotics aims to become the reference in autonomous navigation, with the mission to enable the mobility of vehicles for automation in the professional use market. The company is ELETTROTECNICA PRATICA Antonio Bossi - Ezio Sesto now active in two segments: • Industrial Automation - BlueBotics offers VOLUME IELETTROTECNICA PRATICA
ANT®, an innovative navigation solution.Il volume offre un quadro completo ed aggiornato delle leggi che regolano l'elettrotecnica, leggi che anche un 1 2 3 4 Service Robotics - The company offers entecnico pratico, quale può essere un installatore, non può esimersi dal conoscere per svolgere razionalmente il proprio lavoro. Ampio spazio è stato riservato anche agli elementi fondamentali dell'elettronica, tenuto conto Elementi fondamentali gineering services based on its experience del notevole sviluppo che i dispositivi a semiconduttori hanno avuto in ogni campo ed in particolare negli N in mobile robotics, with standard platforms, impianti industriali. Lo studio dell'elettrotecnica diventa così interessaste e consente al lettore di apprendere le leggi fondamentali sulle applicazioni e di avere una visione chiara e precisa dello stato attuale del progresso feasibility studies, customized projects and tecnico scientifico. I numerosi esercizi svolti e da svolgere riportati alla fine di ogni capitolo consentono di dedicated developments to enable new apsuperare le piccole difficoltà che sempre si incontrano nello studio della teoria e di verificare il proprio grado di acquisizione dei principi enunciati. S plications for customers. E1 E2 E3 E1
120°
120° E3 120° E2 www.bluebotics.com
Autore: Antonio Bossi - Ezio Sesto Prezzo: 28,00 € Pagine: 364
Editoriale Delfino
PER L'ACQUISTO https://www.editorialedelfi no.it/elettrotecnica-pratica-i-432.html
Editoriale Delfi no Srl • Via Aurelio Saffi 9 • 20123 Milano (MI) • Tel. 02 9578.4238 • info@editorialedelfi no.it
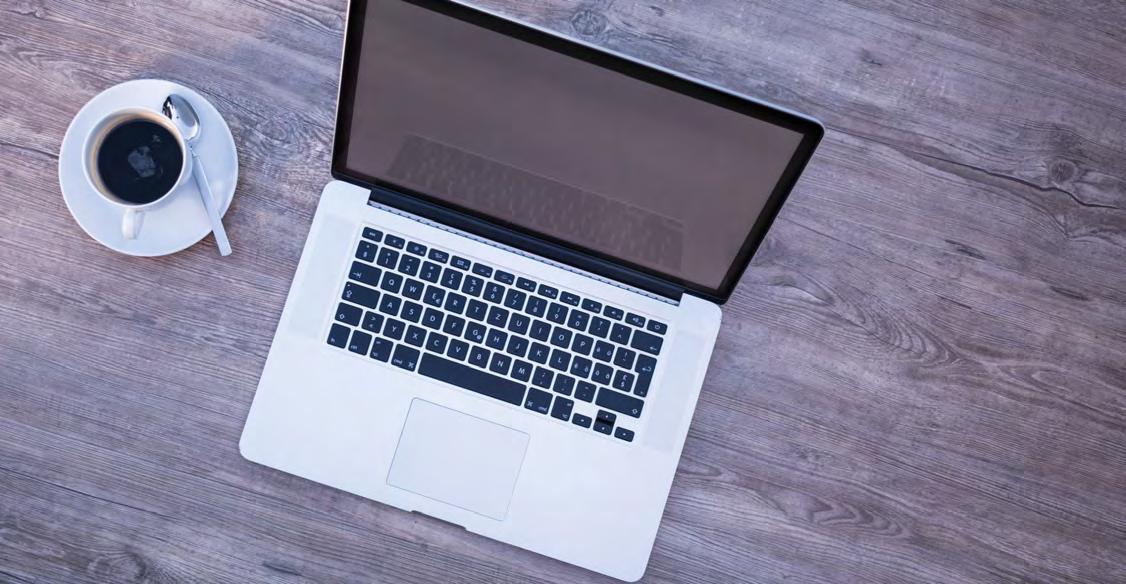
Editoriale Delfino
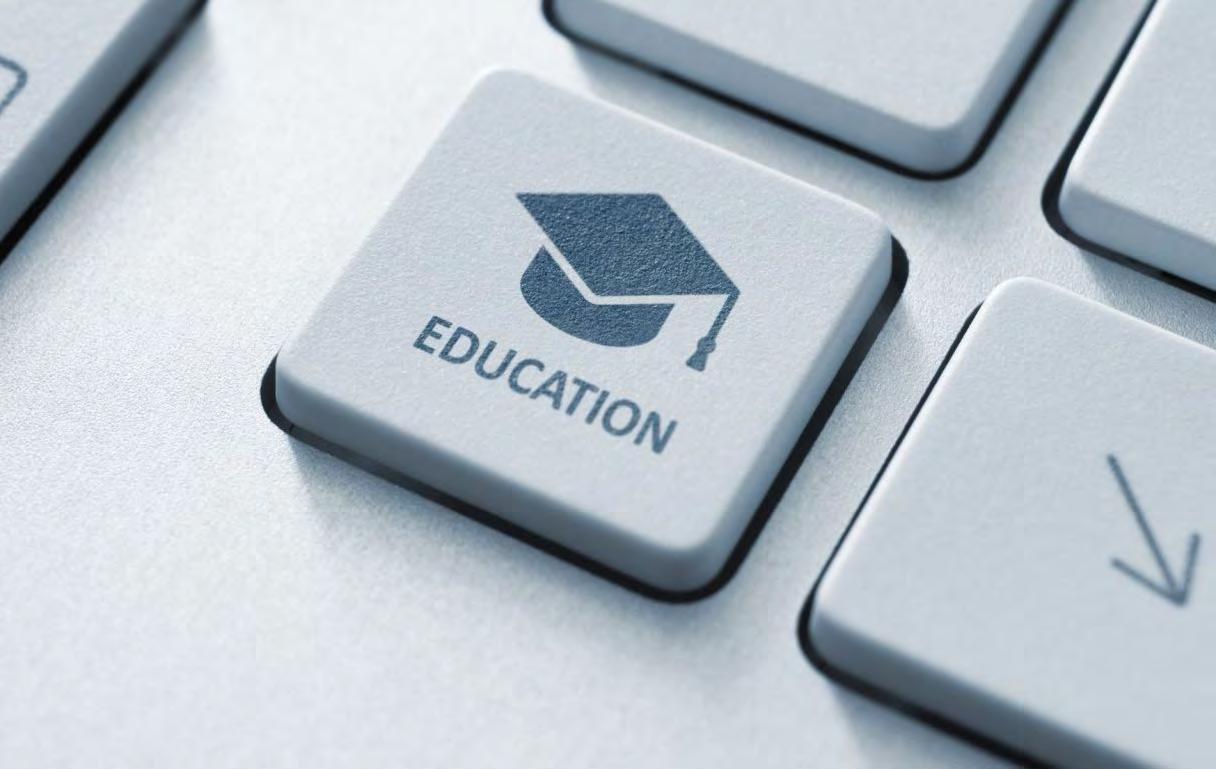
www.editorialedelfino.it www.editorialedelfino.it
Preparati!
Preparati! Stanno arrivando tanti Sono in arrivo numerosi corsi online corsi tecnici online per la tua preparazione tecnico-professionale, curàti dai più autorevoli esperti di settore. Comodamente da casa tua!
Elettrifi cazione 11-12 2020 n. 750 I 57