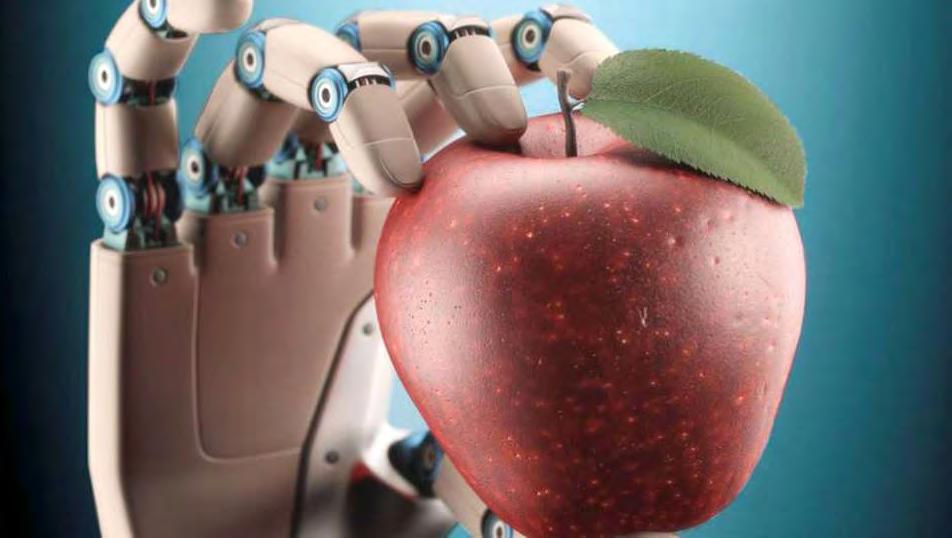
13 minute read
FOOD & BEVERAGE RISPARMIO ENERGETICO MEDIANTE LA RIPARAZIONE DELLE PERDITE D’ARIA NEL SETTORE FOOD/ ENERGY SAVING BY REPAIRING AIR LEAKS IN THE FOOD SECTOR Javier Irazola
RISPARMIO ENERGETICO MEDIANTE LA RIPARAZIONE DELLE PERDITE D’ARIA NEL SETTORE FOOD
L’aria compressa è la “quarta fornitura” pulita e accessibile nel settore alimentare e delle bevande dopo le tre principali di acqua, elettricità e gas naturale. L’affidabilità di questa quarta fornitura dipende dalla prevedibilità della pressione dell’aria, il che significa che anche piccole perdite possono determinare costi elevati.
Advertisement
Javier Irazola*
Secondo la settima edizione del manuale Compressed Air & Gas Handbook (pubblicata dal CAGI (Compressed Air & Gas Institute), “un’unica perdita di circa 10 mm in una conduttura dell’aria compressa può costare a uno stabilimento dai 2.000 agli oltre 7.000 € l’anno. La localizzazione e riparazione delle perdite comporterà un risparmio significativo a seconda dei requisiti di pressione e dei costi energetici.” La tecnologia delle telecamere acustiche industriali portatili aggiunge una componente visiva alle tradizionali best practice di rilevamento delle perdite di aria compressa al fine di semplificare il rilevamento e la riparazione delle perdite d’aria. Ecco una rassegna delle perdite d’aria comunemente riscontrate nel settore alimentare e delle bevande, insieme alle best practice e alle tecnologie per affrontarle.
Applicazioni ad aria compressa negli impianti del settore alimentare e delle bevande I produttori di alimenti e bevande sono particolarmente attenti alle perdite di aria compressa, in quanto la costanza dei prodotti è di importanza cruciale per la reputazione e la conformità del marchio, soprattutto dal momento che
gli impianti e le apparecchiature di produzione sono soggetti a rigidi controlli e normative volti ad evitare la contaminazione. Negli stabilimenti di produzione di alimenti e bevande, molteplici compressori d’aria sono collegati tramite tubi per erogare aria compressa al fine di movimentare i prodotti, azionare utensili pneumatici o pompare liquidi per vari scopi nelle catene di produzione, nelle attività di imballaggio e in quelle di pulizia. Ecco alcuni esempi: • Snack e ammortizzazione con azoto: il flussaggio con azoto viene utilizzato per riempire e ammortizzare le buste di snack delicati per evitare danni. L’ossigeno non viene utilizzato perché reagisce con i prodotti alimentari, soprattutto quelli realizzati con oli. • Alimenti e igiene: l’aria compressa viene purificata e filtrata per garantire la sicurezza alimentare e mantenere il corretto punto di rugiada in pressione necessario per impedire la proliferazione microbica. • Pelatura di frutta e verdura: nella preparazione per l’imballaggio, i getti d’aria pressurizzata pelano frutta e verdura in modo efficiente.
L’aria compressa ad alta pressione viene utilizzata anche per tagliare gli alimenti come alternativa più pulita ai coltelli o alle lame. • Birrifici, fermentazione e imbottigliamento: l’aria compressa aumenta i livelli di ossigeno per completare il processo di fermentazione batterica. I compressori d’aria riducono l’ossigeno residuo durante l’imbottigliamento e le bottiglie vengono lavate con anidride carbonica e riempite di birra utilizzando macchinari ad alimentazione pneumatica. Poiché i birrifici operano in ambienti caldi, i sistemi sono più vulnerabili alle perdite. Le perdite d’aria in qualsiasi punto possono rallentare la produzione, compromettere la qualità del prodotto, creare problemi di sicurezza o contaminazione o tutti e quattro i problemi, con conseguente riduzione dei profitti.
Test pilota un un’azienda di torrefazione del caffè I progettisti di un’azienda di torrefazione del caffè hanno partecipato a uno studio pilota che utilizza la tecnologia delle telecamere acustiche in uno stabilimento le cui condizioni favorisco-
no la generazione di numerose perdite. Dal test è emerso che con il nuovo dispositivo di rilevamento delle perdite, l’azienda potrebbe ottenere un risparmio di oltre il 10% all’anno sul consumo di energia. La struttura, di circa 300.000 piedi quadrati, ospita un’area per la tostatura e l’imballaggio del caffè, un’area per la lavorazione a umido del caffè e un’area per la miscelazione e l’imballaggio del tè. Tutte le operazioni richiedono una corretta pressione dell’aria per completare in modo efficiente i processi, e i metodi di rilevamento delle perdite tradizionali non potrebbero tenere il passo. In media, l’impianto utilizza da 1.000 a 1.600 piedi cubi al minuto (piedi cubi/min) di aria compressa al giorno. L’impianto dell’aria compressa dell’azienda, costituito da cinque compressori d’aria, per un totale di 585 CV, alimenta l’automazione e le tubazioni utilizzate per alimentare l’impianto di generazione dell’azoto dell’attività. L’azoto viene utilizzato per migliorare la qualità del caffè. Inoltre, il gas inerte viene utilizzato per la miscelazione del tè. Grazie alla telecamera acustica, il team ha identificato un potenziale risparmio energetico del 10%, in linea con il suo obiettivo di miglioramento della sostenibilità. Il nuovo approccio ha inoltre dimostrato come il team potesse semplificare il processo di rilevamento delle perdite d’aria,
Fluke ii900 Telecamera Acustica Industriale
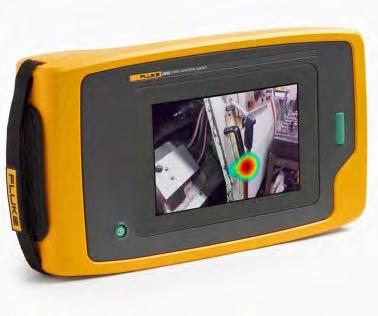
consentendo ai progettisti di continuare a far lavorare il personale sui prodotti anziché fermarsi per lunghi periodi per rilevare e riparare le perdite d’aria. In un test pilota, un’azienda di torrefazione del caffè ha utilizzato una telecamera acustica per identificare e contrassegnare agevolmente fino a 52 perdite d’aria, comprese numerose perdite in punti difficoltosi.
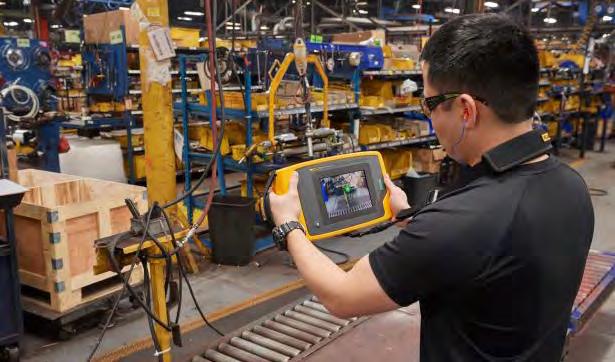
Visualizzazione delle perdite di aria con la tecnologia delle telecamere acustiche portatili Un progresso nella tecnologia di rilevamento delle perdite sotto forma di telecamera acustica industriale portatile sta rendendo più agevole il rilevamento delle perdite ed evitando perdite di profitti. La telecamera acustica introdotta da Fluke Corporation consente agli utenti di individuare e visualizzare le perdite d’aria su uno schermo a LED in tempo reale con un processo “punta e riprendi” che non richiede l’intervento di un tecnico specializzato. La maggior parte degli utenti può tornare a lavorare in circa 10 minuti. Anche i tecnici possono operare rapidamente da una distanza di sicurezza mentre l’apparecchiatura è in funzione. Inoltre, il dispositivo rende più agevole l’individuazione delle perdite nei punti difficili da raggiungere o la distinzione tra più perdite all’interno della stessa area. La telecamera acustica industriale portatile contiene una schiera di microfoni ultrasensibili che rilevano i suoni sia nella gamma dell’udito umano sia nella gamma degli ultrasuoni e li visualizza. Il dispositivo applica quindi algoritmi proprietari ai risultati e produce istantaneamente una mappa visiva della perdita sullo schermo. L’immagine della perdita viene sovrapposta a un’immagine a luce visibile dell’area in modo che gli operatori possano individuare rapidamente la posizione della perdita.
La telecamera acustica Fluke e best practice per ridurre le perdite di aria compressa La telecamera acustica può essere utilizzata anche per verificare che le riparazioni siano state eseguite correttamente. In caso di dubbi, le scansioni acquisite come fermi immagine o video in diretta possono essere condivise e discusse con i colleghi. Le immagini acquisite eliminano la necessità di utilizzare scale o contrassegnare la perdita con la solita etichetta fisica, facilmente danneggiabile. Utilizzando metodi di rilevamento comuni o nuovi, è bene non tardare a eliminare i costi nascosti e gli inutili sprechi dovuti alle perdite d’aria. Ecco alcune best practice da seguire:
• Adottare un approccio basato sui sistemi: spesso, la riparazione di una perdita aumenta la pressione del sistema, ingrandendo le perdite più piccole e compromettendo l’intero sistema. Per un migliore utilizzo dell’energia e sistemi di controllo più robusti, occorre combinare i cambiamenti con le strategie generali. Sebbene possano essere difficili da realizzare, gli investimenti in conto capitale spesso consentono risparmi energetici in grado di ridurre notevolmente i tempi di recupero dell’investimento. • Verifiche frequenti: verifiche frequenti, eseguite più spesso rispetto alle tipiche ispezioni delle perdite annuali o trimestrali, consentono di risparmiare tempo, denaro e risorse nel lungo periodo, anche se richiedono lo spegnimento delle apparecchiature. La nuova tecnologia immaginografica consente di focalizzare le perdite e ripararle su base continuativa senza perdere tempo prezioso di produzione. • Verificare le cause all’origine delle cadute di pressione: la caduta di pressione può essere diagnosticata erroneamente come guasto dell’apparecchiatura. Prima di effettuare spese in conto capitale, i controlli delle perdite e le riparazioni possono far risparmiare migliaia o centinaia di migliaia di dollari e agevolare il recupero immediato della capacità produttiva. • Registrazione, tracciamento e verifica nel tempo: è importante registrare esattamente dove si sono verificate le perdite, poiché in questi punti deboli tendono a verificarsi nuove perdite, e ispezionare tali zone regolarmente. La registrazione online delle informazioni consente di condividere facilmente i dati e di utilizzarli per stabilire le regole del processo di revisione. Subito dopo la riparazione, eseguire un controllo per stabilire se le perdite sono state eliminate o se è necessario intervenire ulteriormente.
Keywords: Food&Beverage, aria compressa, test pilota, telecamera acustica, LED, Fluke Corporation ENERGY SAVING BY REPAIRING AIR LEAKS IN THE FOOD SECTOR
Compressed air is the “fourth clean and affordable supply” in the food and beverage industry after the three main ones of water, electricity and natural gas. The reliability of this fourth supply depends on the predictability of the air pressure, which means that even small leaks can lead to high costs. Javier Irazola*
According to the seventh edition of the Compressed Air & Gas Handbook (published by the CAGI (Compressed Air & Gas Institute), “a single leak of about 10 mm in a compressed air pipeline can cost a plant between 2,000 and over 7,000 € per year. Locating and repairing the leak will result in significant savings depending on pressure requirements and energy costs”. Portable industrial acoustic camera technology adds a visual component to traditional compressed air leakage detection best practices to simplify air leak detection and repair. Here is an overview of air leaks commonly found in the food and beverage industry, along with best practices and technologies to address them.
Compressed air applications in food and beverage plants Food and beverage manufacturers are particularly attentive to compressed air leaks, as product consistency is crucial to reputation and brand compliance, especially since production facilities and equipment are subject to strict controls and regulations to avoid contamination. In food and beverage manufacturing plants, multiple air compressors are connected by hoses to deliver compressed air to move products, operate pneumatic tools or pump liquids for various purposes in production lines, packaging and cleaning activities. Here are some examples: - Snack and cushioning with nitrogen: Nitro-
gen flushing is used to fill and cushion delicate snack bags to prevent damage. Oxygen is not used because it reacts with food products, especially those made with oils. - Food and hygiene: compressed air is purified and filtered to ensure food safety and maintain the correct pressure dew point necessary to prevent microbial proliferation. - Fruit and vegetable peeling: In preparation for packaging, pressurized air jets efficiently peel fruit and vegetables. High pressure compressed air is also used to cut food as a cleaner alternative to knives or blades. - Brewing, fermentation and bottling: Compressed air increases oxygen levels to complete the bacterial fermentation process. Air compressors reduce residual oxygen during bottling and bottles are washed with carbon dioxide and filled with beer using pneumatically powered machinery. Because breweries operate in hot environments, the systems are more vulnerable to leakage. Air leaks at any point can slow production, compromise product quality, create safety or contamination issues or all four problems, resulting in reduced profits.
Pilot test a coffee roasting company The designers of a coffee roasting company participated in a pilot study using acoustic camera technology in a plant whose conditions favor the generation of numerous losses. The test showed that with the new leakage detection device, the company could achieve savings of more than 10% per year in energy consumption. The approximately 300,000 square feet facility houses an area for roasting and packaging coffee, an area for wet coffee processing and an area for blending and packaging tea. All operations require proper air pressure to efficiently complete the processes, and traditional leak detection methods could not keep pace. On average, the plant uses 1,000 to 1,600 cubic feet per minute (cubic feet/min) of compressed air per day. The company’s compressed air plant, consisting of five air compressors, totaling 585 hp, powers the automation and piping used to power the nitrogen generation plant of the business. Nitrogen is used to improve coffee quality. In addition, inert gas is used for blending tea. Thanks to the acoustic camera, the team has identified a potential energy saving of 10%, in line with its goal of improving sustainability. The new approach also demonstrated how the team could simplify the air leak detection process, allowing designers to continue to have staff work on the products instead of stopping for long periods to detect and repair air leaks. In a pilot test, a coffee roasting company used an acoustic camera to easily identify and mark up to 52 air leaks, including numerous leaks in difficult locations.
Displaying air leaks with portable acoustic camera technology An advancement in leak detection technology in the form of a portable industrial acoustic camera is making leak detection easier and avoiding loss of profit. The acoustic camera introduced by Fluke Corporation allows users to detect and display air leaks on an LED screen in real time with a “point and shoot” process that does not require a specialist technician. Most users can get back to work in about 10 minutes. Technicians can also operate quickly from a safe distance while the equipment is in operation. In addition, the device makes it easier to detect leaks in hard-to-reach areas or distinguish between multiple leaks within the same area. The portable industrial acoustic camera contains an array of ultra-sensitive microphones that detect and display sounds in both the human hearing and ultrasound range. The device then applies proprietary algorithms to the results and instantly produces a visual map of the loss on the screen. The image of the loss is superimposed on a visible light image of the area so that operators can quickly locate the location of the loss.
Fluke acoustic camera and best practices for reducing compressed air leakage The acoustic camera can also be used to verify that repairs have been carried out correctly. If in doubt, scans captured as still images or live video can be shared and discussed with colleagues. The captured images eliminate the need to use scales or mark the loss with the usual, easily damaged physical label. Using common or new detection methods, it is best not to delay in eliminating hidden costs and unnecessary waste due to air leakage. Here are some best practices to follow: - Adopt a systems-based approach: Often, repairing a leak increases system pressure, enlarging smaller leaks and compromising the entire system. For better power utilization and more robust control systems, you need to combine changes with overall strategies. Although they can be difficult to achieve, capital investment often results in energy savings that can significantly reduce payback time. - Frequent audits: Frequent audits, performed more often than typical annual or quarterly loss inspections, save time, money and resources in the long run, even if they require equipment shutdown. New imaging technology allows you to focus losses and repair them on an ongoing basis without losing valuable production time. - Verify the causes of pressure drops: Pressure drops can be misdiagnosed as equipment failure. Before capital expenditure, leak checks and repairs can save thousands or hundreds of thousands of dollars and facilitate immediate recovery of production capacity. - Recording, tracking and verifying over time: It is important to record exactly where the leakage occurred, as new leaks tend to occur in these weak spots, and inspect these areas regularly. Online recording of information makes it easy to share data and use it to establish the rules of the review process. Immediately after the repair, perform a check to determine if the leaks have been eliminated or if further action is needed. Keywords: Food&Beverage, compressed air, pilot test, acoustic camera, LED, Fluke Corporation