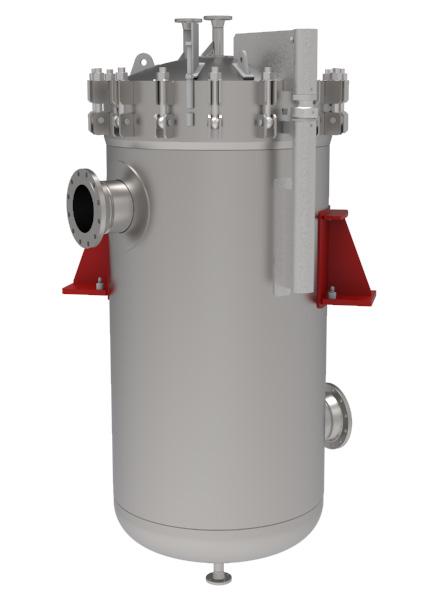
6 minute read
How the Design and Supply of Filtration Technology Protects and Improves Production Processes
PERFORMANCE BOOST: How the Design and Supply of Filtration Technology Protects and Improves Production Processes
Any disruption to business-as-usual processes and operating performance can create major financial headaches for oil and gas producers. That’s acutely true right now in the battle to stay on top of costs given the economic impact of Covid-19. Delivering investment and maintenance projects on time and to budget is key to ensuring essential cost control and a sustainable operating model.
Advertisement
One of the most critical processes in oil and gas production is water filtration and treatment. It is pivotal in protecting both equipment and rock formations while recovering reserves, complying with environmental legislation, and ensuring high uptime of water injection systems. UK manufacturer Amazon Filters, one of the leading suppliers of pleated and depth filters and bespoke pressure vessels, works with a growing list of oil and gas producers and service providers to help them find optimal filtration solutions.
Flexibility in supply is paramount
A focus on cost reduction must be tempered with the need for equipment to perform efficiently and cost effectively over a 20-year operating life. Locally manufactured pressure vessels can be the most appropriate way to minimise capital cost, reduce the carbon footprint of freight and ensure a high percentage of local content to support local economies. While local expertise in vessel fabrication is widely available, expertise in housing design, filter choice, sizing and installation may be limited. Inappropriately designed filter housings can lead to very high year-on-year operating costs that can quickly dwarf any saving made on capital expense. Amazon Filters’ Project Specialist Padrig O’Hara said: “Our dedicated, experienced proposal team works with clients to specify the most appropriate housing and filter design. The complete assembly can then either be manufactured in the UK or the designs can be shared with a third party to manufacture locally. A common approach to mitigate risk with filtration performance has been to manufacture the pressure vessel locally and manufacture the filter internals in the UK. “We have taken exactly this approach on a wide variety of filter installations and applications. We apply our expertise in filter selection and sizing to optimise cartridge lifetime and filtrate quality and guarantee performance on installation. The perceived additional complications with design support documentation and approvals can sometimes put clients off taking this flexible approach but we have the project management expertise to guide customers through this process. We provide partial or complete documentation packs in accordance with the appropriate codes depending on the scope for supply to satisfy project specifications.”
The cost of poor design
With the operational and financial pressures facing the oil and gas industry in recent years, Amazon Filters has seen an increase in examples of poorly designed filter housings coming into service. Padrig said: “We are often approached by operators to try to resolve problems in cases where the original vendors lack the expertise
The filter assembly above was designed by Amazon Filters. The scope of supply involved a diaphragm plate, cartridge support baskets, retaining plate and cartridges. The internals, manufactured in super duplex stainless steel, support and protect 82 off 60” high-flow cartridges for seawater filtration.
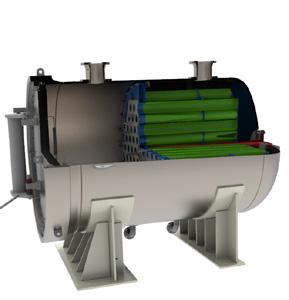
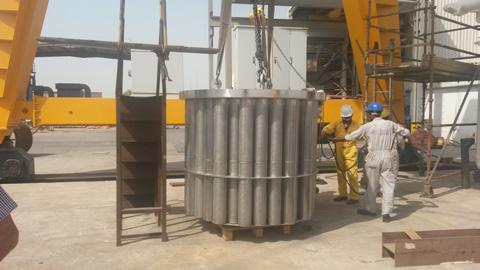
in filtration to diagnose the root cause and propose rectification solutions. Poorly designed vessel internals, either not adequately sealed and located in the vessel, or not offering correct support and location to the cartridges, pose a serious threat to the integrity of the filtration process.” As well as bypass, problems caused by poor design of internals include: • Cartridges bursting or having to be operated to a lower differential pressure than that for which they originally designed. • Cartridges becoming un-seated under even small amounts of back pressure due to inadequate retention. • Excessive clean differential pressure due to poor flow path, which reduces the cartridges’ operational life. • Direct impingement of the flow onto the cartridges, with subsequent erosion and potential gross failure. The design of the pressure vessel is itself critical, not so much to the process, but for operation. Unlike most other vessels which are rarely opened during scheduled maintenance shutdowns, filter housings are frequently opened for replacement of spent cartridges. With regular filter cartridge change-outs, features such as quick-release closure, properly designed davits, easy to access internals and low weight removable internal components are critical, not just to reducing the number of operator hours required for maintenance, but also to ensuring the safety of the operators.
Left: A well-designed filter housing can have its cartridges changed in less than an hour and returned to service so minimising OPEX and downtime. A poorly designed housing can need more than a day to achieve the same task. It is far better to procure housings through a reputable filter company who designs and manufactures both filter media and housings, rather than a vessel fabricator or a supplier who only makes one or the other. The reputable company will understand how the equipment will be used and the critical interaction between the filter cartridge and housing. A properly designed housing may well cost more but the difference in CAPEX is vanishingly small compared to the additional operational expenses, process risk and downtime costs involved in sorting problems associated with poor design. Padrig said: “We’ve seen many examples where the spend on disposable media in the first two years of a filtration system expected to last for 20 years or more has exceeded the costs of the housings. And of course, cartridges are usually protecting something with far higher potential costs of replacement. With a poorly designed housing easily doubling the cartridge usage, the additional 10-20% premium for properly designed housing can easily repay itself in the first year of operation. Operators and package providers must therefore understand these risks and specify housings to the appropriate standard, and satisfy themselves that their supplier truly understands both filtration and filter housing design.”
Coalescing technology
The relationship between housing design and filter is even more critical when it comes to coalescing technology, both liquid/liquid and liquid/gas. A perfectly good coalescer cartridge can be rendered useless if installed in an inappropriate housing where velocities result in entrainment and high operating differential pressures. Amazon Filters has launched a new range of liquid/gas coalescers, the SupaSep LG. These high-performance filters can be supplied complete in a bespoke housing or as consumable retrofits for products such as the Pall Seprasol™ and Parker Peco Dynaceptor™ range. Incorporating a patented process for application of the drainage and anti re-entrainment layers, the filters provide exceptional efficiency and drainage characteristics. Neil Pizzey, Amazon Filters’ Managing Director, said: “We design our solutions to the client’s specific requirements combining empirical data with coalescing theory. We have over 100 years of experience in coalescer design. Our engineers work with academics at the forefront of design research. This ensures we always provide the best combination of performance and cost.”
Conclusion
When selecting a process filtration supplier, it is essential to view the design in terms of OPEX and not just capital. A company that specialises in both housing and cartridge design and manufacture will ensure the solution performs to the customer’s specification in the most cost-effective manner. Neil added: “We have invested substantially in our manufacturing capability to make sure that even in these uncertain times we can provide continuity of supply to all our customers…and some new ones too.” • To find out more about Amazon Filters’ solutions for oil and gas, visit:
Amazon Filters.
https://www.amazonfilters.com/industry/oiland-gas-filtration-solutions Or call: +44 (0) 1276 670 600.