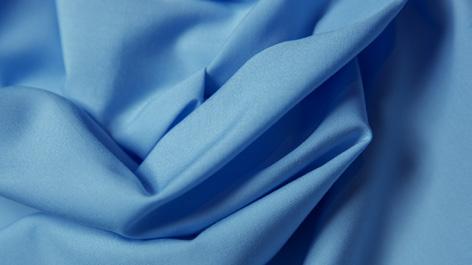
16 minute read
Antiviral Fabrics
ISO Tested Antiviral Fabrics by Carrington Textiles Deliver Outstanding Performance and Launderability
The UK textile manufacturer now produces antiviral fabrics proven to deactivate over 99% of enveloped viruses according to the ISO 18184:2019 standard. Carrington Textiles has successfully tested its new Antiviral and Antibacterial Finish for fabrics under the ISO 18184:2019 ‘Determination of antiviral activity of textile product’ standard, a strategic move of the company’s R&D efforts to respond to the market’s needs in a new COVID-19 world where employees of all sectors including healthcare, construction, hospitality, armed forces and heavy industry need to be more protected than ever.
Advertisement
The textile manufacturer ran trials on its main scrub suit poly-cotton fabric, Alba 2, using the Sanitized® branded treatment that harnesses the natural antiviral and antibacterial properties of silver. After weeks of testing at an independent laboratory in the UK by using an enveloped virus, the results show an effectiveness rating of over 99% of the antiviral properties of the fabric which deactivates viruses in two hours. Even after 50 washes at 60 degrees 98% of viruses have shown to be deactivated, meaning the protective properties of the textile will last the lifetime of the garment. This newly tested finish delivers an antiviral fabric that is not only safe for use on face coverings, medical wear, and a wide range of workwear, but also environmentally friendly garments that -due to its best-in-class launderability and long-lasting properties- will help reduce the amount of disposable PPE that ends up in landfill. How does it work? The porous nature of textiles means that viruses and bacteria can be trapped within the fabric An independent laboratory carried out the ISO 18184:2019 test on Carrington Textiles’ polycotton Alba 2.
structure, which possibly lowers the risk of the viruses being transferred. However, they will still remain viable and bacteria may also replicate within the fabric leading to unpleasant odours, amongst other things. This revolutionary Antiviral and Antibacterial Finish by Carrington Textiles is suitable to use on any woven fabric and works
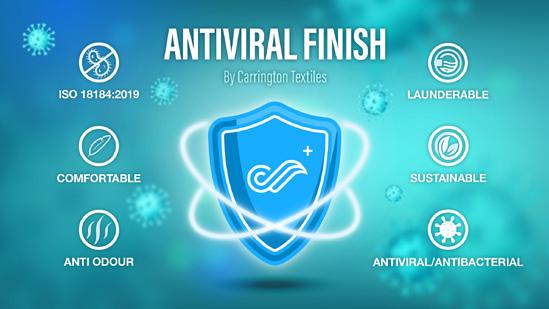
as a coating that is pressed then ‘baked’ into the fabric using specialised machines at the end of the manufacturing process. This Antiviral Finish works as a barrier and any viruses which get trapped in the fabric structure will be deactivated and rendered harmless before they get chance to infect a host cell. This treatment kills bacteria the same way, with the added benefit to working as a ‘built-in deodorant’ as due to its advanced technology protects against unwanted bacteria that causes unpleasant odour. Sales Director Paul Farrell says: “Our R&D efforts to innovate and respond to the market’s needs has allowed us to have a finish available that is able to deactivate enveloped viruses and kill bacteria using technologies that are not only safe and comfortable to wear, but also offer excellent launderability benefits without compromising performance.” •
Carrington Textiles Ltd
+44 (0)1257 476 850
Industrial work wear has historically been designed around male body frames, due to the overwhelming demographic associated with this type of work up until now. With the number of women working in operational roles steadily increasing, Aramco recently took a fresh look at its range of personal protective equipment (PPE) with a view to changing this. “Aramco’s priority has always been the protection of its people, and when the topic of gender and comfort was brought forward, we immediately set about addressing this,” says Loss Prevention Department (LPD) manager Ghassan Abulfaraj. “A one-size-fits-all approach to PPE can undermine a safety program,” said Abulfaraj. “PPE is essential for the protection of our employees, and an important part of this is ensuring that equipment is not only compliant from a safety perspective, but also comfortable to wear.” Safety and gender go hand-in-hand Depending on their role, operational employees and contractors wear a range of PPE, including flame resistant clothing, boots, gloves, hard hats, safety glasses, and hearing protection. With a goal of ensuring the safety and comfort of female personnel, Aramco initiated a project to enhance the company’s line of flame resistant clothing (FRC), including specific designs for the female workforce. Aniela Zarzar Torano and Fatimah Barnawi, both LP engineers who worked as leads on the project, note that effective female PPE is more than simply a smaller or larger size of the male designs, especially in the Middle Eastern region. “A female body frame is often shaped differently and generally smaller than a male frame. Having poorly fitting safety clothing can cause risks such as reduced agility, catching on equipment, and tripping,” said Zarzar Torano. Barnawi adds: “Another unique aspect to this project — besides that of sizing and safety — was cultural requirements. We needed to work on a design that not only covered the areas of safety and comfort, but also one that met our female employees’ requirements for modesty.” It was this recognition that led to a partnership with DuPont, one of the world’s leading companies in terms of science and innovation, to customize an FRC line that improved comfort and met cultural requirements, all while ensuring that all safety guidelines were maintained. Practice makes perfect Over a period of 18 months, LPD and

Du Pont worked tirelessly on a number of design concepts that not only looked to improve design and comfort from a safety perspective, but also ensure that cultural requirements were met. Speaking to the practical aspects of a project such as this, Zarzar Torano adds: “This clothing is the final line of defense that we have in the event of a fire. As such, we had to work through numerous designs, tests and practical trials to ensure that what we were signing off on was absolutely of the highest quality.” Abulfaraj notes that what made this project unique is that it provided an opportunity to not only accommodate the needs of Saudi Aramco’s female workforce, but also lead the way in innovation to further improve FRC safety features for female employees across the industry. “This wasn’t simply a project where we looked to alter the size of clothing; that could be done by anyone,” Abulfaraj says. “We wanted to use this opportunity to challenge the status quo, and to ask ourselves, “How can we do this better?” Work uniforms provide employees with a feeling of belonging and sense of identity, and this project has underlined such an ethos. With many more females taking up roles in traditionally male-dominated industries, the need for adaptation and innovation is increasing. •
HEALTH, SAFETY & ENVIRONMENT Dedication to Air Quality and to Your Bottom Line
OGI sits down with Andrew Balch, Director and Principal Consultant of Air Environment, out of Queensland Australia, to discuss why it is so important for companies to be monitoring their air quality. The obvious reasons are of course, to keep up with legal frameworks and responsibilities within their own communities, but as Mr Balch explains, monitoring ones environment can also be an early detection warning system for failures or leakages in a companies assets as well. Businesses should see environmental management as a potential opportunity and cost saving measure, we learn more below.
OGI: Could you tell us a bit about your credentials and experience in the oil and gas sector? Could you tell our readers the breadth of your experience, how long the company has been active, and its reach? Balch: I have significant experience working on air quality related projects for the oil and gas sector. Over 25 years in air quality consulting, I have worked on many large projects from conventional crude oil and shale oil refining to coal seam gas extraction and processing, gas pipelines and LNG production plants. I have been air quality’s technical lead for the development approval of many of the biggest coal seam gas exploration and processing, and LNG plant projects in Australia. This experience included leading the air assessments for five of the six LNG plants initially proposed for the Gladstone Gas Hub, including the now operating Origin Energy Australia Pacific LNG and QGC’s Queensland Curtis LNG plants on Curtis Island. I also led the air assessments for both project’s upstream CSG extraction, processing and pipeline environmental impact assessments, and several other CSG processing plants including the Origin Energy Ironbark Project. I also led air assessments for gas fired power stations. Since starting Air Environment in 2013, I continued my work in the sector, leading the air quality component of the recently approved Santos Narrabri Gas Project. During this time, Air Environment has also worked overseas on gas and hydrocarbon processing projects for Saudi Aramco in Saudi Arabia. In addition to its air quality consulting and assessment work, Air Environment also distributes a range of tailor-made multipollutant air quality monitors in Australia developed by the innovative Canadian company Scentroid. The range of gas and particulate sensors can be configured in stationary outdoor and indoor monitoring networks or used in portable handheld and drone mountable units. A large range of pollutant-specific sensors can be configured in each instrument for the oil and gas sector including methane, hydrogen sulfide, nitrogen dioxide, sulfur dioxide, volatile organic compounds and carbon dioxide, to name a few. OGI: Why is it so important for companies to be monitoring their air quality? Balch: Businesses have both a legal and social imperative to ensure that their activities do not adversely impact the environment. All industry requires an environmental authority to operate and must comply with the conditions of approval set out by the regulator. Such conditions typically require a business to have a good understanding of their emissions to air and ensure that these emissions do not contribute to poor air quality outcomes in the environment. How well businesses manage emissions and their impact will affect their social license. While not a legal requirement, the perception of how well a business performs in the environmental space can have a significant effect on their financial performance through negative publicity and product boycotts, among others. For the oil and gas sector, a facility’s air emissions can directly affect the health, safety and wellbeing of the local community and their own employees, while greenhouse gas emissions can affect the environment and community more subtly through climate impacts. Additionally, air quality monitoring observations can be directly useful to businesses in the oil and gas industry as they may indicate process failures or leakage where valuable product is escaping to atmosphere. OGI: What are some of the consequences for companies that do not effectively manage their environmental responsibilities? Balch: Environmental management is not seen as a revenue-generating activity and Odour Assessor Conducting an Odour Test.

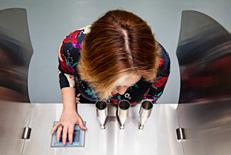
therefore is very easy to neglect. Businesses should see environmental management as part of the cost of doing business and doing it well can provide opportunities and cost savings. We have seen many cases over the years where companies neglect their environmental responsibilities, however this approach always catches up with them eventually. Typically, the permitting officer for the environmental regulatory authority eventually notices the problem and starts pressuring the company to comply. We have often seen three stages play out, known as the “Three D’s”, the denial phase, the delay phase, and the deluge phase. Initially the company denies that there is a problem, or if there is that they are culpable. A lot of energy and bad feeling is expended on all sides to demonstrate that the problem does or doesn’t exist. Eventually the regulatory authority prevails, leading to the delay phase. They admit that there is a problem but they don’t have the resources to address it. This delay phase may last for a while, with environmental impacts stacking up, but eventually the company is forced into action. During the final deluge phase money and resources are rapidly expended. The problem now must be immediately solved and cost becomes a secondary issue. Along the way the company may face a range of options that are available to the regulator, including abatement notices, sanctions, changes to the site permit, or even closure of the facility. The company may also gain a reputation for poor compliance, leading to over-regulation by the regulatory authority and a tarnished public image. In extreme cases we have seen major projects fail due to the lack of social licence as a result of ongoing poor environmental performance.
In the end it is always cheaper and easier to manage your environmental responsibilities well. Ironically good environmental performance, and compliance with licence conditions, may become a point of difference between the company and their competitors, and save money. OGI: What should a client expect with a typical air quality assessment, for example when assessing a gas field collection system and gas processing facility? Balch: There are many steps to follow when assessing air quality impacts for a proposed gas field and processing facility. From the beginning, it is important to clearly define the project area and identify the receptors that will be sensitive to the development, whether these are people in the local community or other environmental receptors. Also, both operational and construction related emissions need to be considered for the assessment. Early in the project baseline ambient air quality and meteorological monitoring should be conducted. It is important to develop a good data set for the existing state of the air environment, including local meteorology. Many proponents ignore this requirement at the start, which can hurt the project later down the track and lead to delays and other important impact assessment issues. Air quality monitoring for gas field developments should focus on the critical operational pollutant, nitrogen dioxide, but also secondary pollutants like ozone, which will be important for assessing nitrogen dioxide impacts in the air quality impact assessment. Particulate matter (PM10) will be the main concern for the construction phase, so it is also a good idea to monitor dust to assess the baseline for the construction air assessment. The third most critical pollutant worth monitoring is not a health concern but an important greenhouse gas emission. Understanding the background methane concentrations in the project area and the natural and anthropogenic sources of these emissions has become an important requirement in coal seam and shale gas developments. CSG developments are often close to coal mines, which have significantly greater methane emissions than CSG production areas. Also, cattle feedlots, wastewater treatment plants and waste management facilities and landfills are also methane sources. Understanding the differences in methane emissions between these local sources and CSG developments has been important in recent projects I have conducted. Estimating the air emissions inventory for the gas development is a critical step, including how the project will be powered and the gas processing approach. I have found that the source with the greatest emissions is not always the greatest contributor to ground level air quality impacts. Consequently, plant layout and stack design are also important considerations along with emission inventory development and emission control technology selection. The main operational emissions sources are gas compressors and power generators, regenerative boilers, pipeline compressor stations, flares and wellhead engines. Other fugitive emission sources can include fugitive emissions from the gas gathering network. While these emissions are primarily methane, other trace hydrocarbons are also present. This information is then used to assess the potential impact to air quality using an atmospheric dispersion model. Care should be taken to select the most appropriate model for this application. Meteorological modelling is also conducted prior to the development of the dispersion model, and this step is greatly enhanced if a year of good quality local meteorological data is available. Gas field projects are geographically large and dispersed, and emission sources and impact areas change throughout the life of the project as gas wells are commissioned and decommissioned. So planning how you will model and assess these impacts is critical. Through our vast experience in assessing these large projects, we have developed a thorough and robust method to assess the air impacts, while covering the entire project and allowing for the flexibility required. OGI: And the work you do with LNG plants? Balch: Assessing the air impact of LNG plants is more in line with typical industrial facilities. While their footprint is large, they are typically confined to a single site and not spread out like gas fields with sensitive receptors situated between various emission sources. As with gas field assessments, an assessment of the baseline air quality is important for LNG plant studies. However, unlike the gas fields, which are geographically spread out in rural areas with few other similar emission sources, many LNG plants are situated in industrial hubs with neighbouring industries emitting similar pollutants. In a similar way to the gas fields, air emissions sources comprise mainly fuel combustion processes so the most important pollutant for the assessment is nitrogen dioxide. A good understanding of the baseline levels of nitrogen dioxide and ozone, and the local meteorology is therefore crucial for a comprehensive air impact assessment. Emission sources comprise routine processes such as gas turbines and power generators and non-routine processes like flares. These have very different uses and operating cycles that need to be considered carefully in the assessment scenarios. While these emissions are typically released from tall stacks, there are critical differences with modelling and assessing air quality impacts from rows of stacks in an LNG train and safety flares. Furthermore, some LNG plants operate with a ground flare, which is very different to the more common stack flare. These are important considerations when modelling and assessing LNG plants and not all atmospheric dispersion models can adequately account for these differences. OGI: How does odour emissions monitoring work? Balch: Developing an odour monitoring plan for any site is inherently more complex than the standard emissions monitoring program for compliance with a site’s environmental license. Compliance monitoring programs are typically focused only on stack emissions, while odour impacts are more commonly, but not always, caused by near ground fugitive emissions and smaller, less obvious stack sources. Odour emissions can also be highly variable across a site and from each source. For instance, fugitive area source emissions from liquid and solid surfaces such as wastewater treatment tanks or compost stockpiles can vary spatially and temporally. These variations need to be measured and understood before developing an emissions inventory for a dispersion model. Industrial processes can also operate continuously or in batch mode, with both producing variable odour emission profiles from stack sources. The point in time at which grab samples are collected for odour analysis from each of these scenarios can dramatically affect the assessment of the odour impact. Odour monitoring requires the collection of air samples from an emission point in sample bags. Samples are then transported to the odour laboratory for analysis within 30 hours of collection. The process of analysing odour is known as dynamic olfactometry and the standard test is to determine the concentration of the odour sample in ‘odour units’. Other odour attributes can also be measured using olfactometry including the intensity of the odour relative to its concentration above detection threshold and its hedonic tone, or pleasantness and unpleasantness. A description of the character of each sample is also provided. Dynamic olfactometry is a process whereby a panel of trained and calibrated (or screened) human assessors are presented an odour to assess at varying amounts of dilution. The dilution of the odour sample is controlled by a device called an olfactometer, which is a sophisticated instrument designed to accurately and precisely mix the odour sample with clean air and present that air to the odour assessors at a series of dilutions. This allows the detection threshold of the odour sample to be determined. Air Environment operates a state-of-the art odour laboratory from its Brisbane offices. We are able to successfully collect and analyse odour samples from sites all over Australia within timeframes mandated by relevant Australian standards. OGI: Thank you for your time. •
Air Environment
T: +61 7 3186 4420 E: andrew@airenvironment.com.au
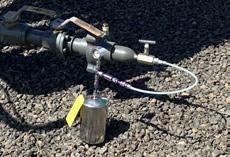