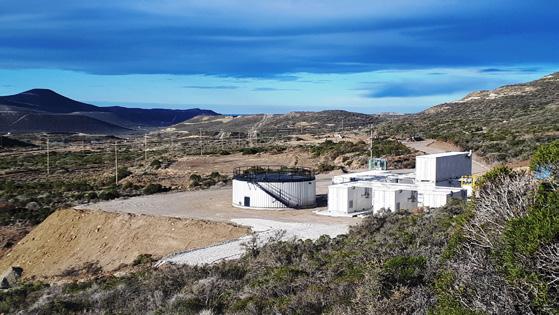
13 minute read
EXPLORATION & PRODUCTION Enhanced Oil Recovery by SNF
eor by EXPLORATION & PRODUCTION
Enhanced Oil Recovery SNF
Advertisement
AUGUST 2020
A COST-EFFECTIVE EOR TECHNIQUE TO REDUCE CARBON INTENSITY WITH POLYMER FLOODING AND MODULAR SKIDS
The COVID-19 crisis has led to an unprecedented situation in the oil industry, with severe oil price depreciation due to sudden demand reduction and failed production cut agreements. Oil companies have been forced to reduce their budgets, and oil exploration has been cut or reduced. Upon return to pre-COVID-19 demand levels, more oil production, and reserves bookings will be required from the existing wells. In this context, quickly and easily maximizing production and proven reserves of existing assets in a cost-efficient way is paramount. Polymer flooding can increase the recovery factor (RF) over waterflooding by up to 20% of the original-oil-in-place (OOIP) at only $3 to $6 per extra barrel of oil.
At the same time, societal pressure is growing and requires immediate action to reach the net-zero production emission target by 2050. Polymer flooding can contribute towards meeting that target by reducing CO2 emissions per barrel by 3–6 times. This reduction is primarily achieved through a more efficient sweep of oil within the reservoir, resulting in water cut reduction and, ultimately, a decrease
BY GUILLAUME DUPUIS AND JAN NIEUWERF EOR@SNF.COM
in required pumping energy at the producers and less taxing on fluid separation equipment and processes. A reduction in produced water can help lower Greenhouse Gas (GHG) emissions1. Operators report significant water
Polymer flooding can contribute towards meeting net-zero production emission target by 2050 by reducing CO2 emissions per barrel by 3–6 times.
cut reduction during polymer EOR operations, with the reversal in fluid cut resulting in increased oil production. It is not uncommon for mature reservoirs to reduce the water-tooil (WOR) ratio by a factor of six2,3. For green or less mature fields, polymer flooding is more efficient in terms of utility factor (UF)4, which is defined as kg of polymer required per barrel of incremental oil. This results in both a recovery and cost efficiency on the EOR process. With
the acceleration in the recovery of oil, several years of water and energy consumption are avoided for the overall
surface facility operations5 , which would include all operational factors (e.g., fuel, travel, utilities, supply, etc.). Thus, the carbon intensity of crude oil can be further reduced.
Currently, 60% of global brownfield production is from water injection, either as pressure support or in flooding operations, delivering recovery factors from 20 to 40%, OOIP.
Polymer flooding is a proven technology with more than 300 projects worldwide. These projects recover more oil, in a shorter timeframe, and at a reduced environmental footprint compared
to water-flooding projects. This EOR technique has been economically and technically successful in full-field projects, such as India (Mangala), Canada (Pelican Lake, Suffield, Medicine Hat), Argentina (Diadema, Grimbeek), China (Daqing, Shengli, Dagang, etc.), the Middle East (Marmul) and Eastern Europe (Patos Marinza, Kazakhstan fields).
In the 1990s, SNF partnered with CNPC in China in the Daqing EOR full-field project. There, SNF built and commissioned the world’s
first captive polymer production plant for polymer EOR. Since then, many EOR projects have been documented. These projects have shown that polymer flooding increases RF by 15 - 20 % of the OOIP6–13 over water-flooding.
Furthermore, these projects report an average UF of 1.7 kg of polymer per incremental barrel of oil, or 80 tons of additional oil per ton of polymer injected.
This UF is attractive, considering today’s polymer costs. Thus, polymer flooding can generate significant short-term production with a low incremental cost compared to exploration.
SNF is the leader for EOR polymer manufacturing, with more than 20 local production plants near oil production areas combined with unique logistics and engineering services to bring the polymer from the plant to the reservoir simply and efficiently.
SNF has also developed surface facilities integrated into sea containers, commissioned before transport to onshore or offshore sites, and connected to existing water pipelines14 .
This “plug and pump” approach accelerates the implementation of polymer injection. In turn, this modular approach offers operators flexibility by enabling incremental deployment from pilot to potential full-field development, as well as simple facility relocation to another part of the field
if needed. Thus, CAPEX is phased with the different project phases, helping to maximize efficiencies and return on investment. Also, rental options are possible. Maintaining combined OPEX and CAPEX at $3 to $6 /bbl allows polymer flooding to be economically attractive, even in a low oil price environment, while adding proven reserves and accelerating oil recovery.
Unquantified additional savings have been observed from the drag reduction effect the polymer has on produced water transport. This drag reduction effect can be seen when the polymer presence exceeds 50 ppm, with up to 70% less friction of the fluid on pipes, elbows, etc. New oil and water separation techniques also enable reducing the fresh polymer consumption by up to 35% after polymer breakthrough by reinjection of the produced polymer. This polymer becomes a high value sustainable recycled material. Furthermore, overall oil field chemical consumption can also be reduced, immediately resulting in proportional cost savings and GHG reduction associated with the production.
Specific to the GHG footprint of the polymer itself, SNF’s manufacturing processes are designed to minimize the environmental impact of our operations. Our primary monomer is produced enzymatically at room temperature under atmospheric pressure. Given the high volumes involved, this biological continuous catalytic process makes SNF a pioneer of soft chemistry. Polyacrylamide is carbon-efficient chemistry since only 3 carbons per repeating unit provide the benefit of the macromolecular structure to the injected water (as opposed to 10 carbons for polyethylene terephthalate and 8 for polystyrene). Challenging times provide an opportunity to innovate. Deployment of polymer
flooding is a cost-effective approach to maximizing the productivity of your current assets while preserving the environment by reducing water use and GHG emissions.
With global sales of about $4B ($1B for the Oil industry), SNF is the leader for EOR
polymer manufacturing, with more than 20 local production plants near oil production areas combined with unique logistics and engineering services to bring the polymer from the plant to the
reservoir simply and efficiently. SNF is uniquely positioned to support polymer EOR technology from FEED to production, including field servicing when necessary.
Our chemists, engineers, and reservoir experts are here to answer your questions and to help you with every step of your project.
www.snf.com eor@snf.com


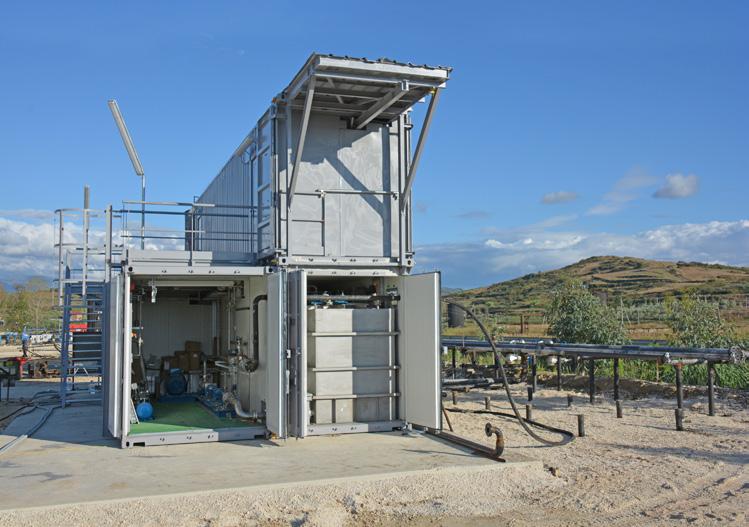
REFERENCES
(1) Farajzadeh, R.; Zaal, C.; van den Hoek, P.; Bruining, J. Life-Cycle Assessment of Water Injection into Hydrocarbon Reservoirs Using Exergy Concept. J. Clean. Prod. 2019, 235, 812–821. https://doi.org/10.1016/j.jclepro.2019.07.034. (2) Dong, H.; Fang, S.; Wang, D.; Wang, J.; Liu, Z. L.; Hou, W. Review of Practical Experience & Management by Polymer Flooding at Daqing; Society of Petroleum Engineers, 2008. https://doi.org/10.2118/114342-MS. (3) Juri, J. E.; Ruiz, A. M.; Pedersen, G.; Pagliero, P.; Blanco, H.; Eguia, V.; Vazquez, P.; Bernhardt, C.; Schein, F.; Villarroel, G.; Tosi, A.; Serrano, V. Grimbeek2: First Successful Application Polymer Flooding in Multilayer Reservoir at YPF. Interpretation of Polymer Flooding Response; Society of Petroleum Engineers, 2017. https://doi.org/10.2118/185487-MS. (4) Delamaide, E. Comparison of Primary, Secondary and Tertiary Polymer Flood in Heavy Oil - Field Results; Society of Petroleum Engineers, 2016. https://doi. org/10.2118/180852-MS. (5) Poulsen, A.; Shook, G. M.; Jackson, A.; Ruby, N.; Charvin, K.; Dwarakanath, V.; Thach, S.; Ellis, M. Results of the UK Captain Field Interwell EOR Pilot; Society of Petroleum Engineers, 2018. https://doi.org/10.2118/190175-MS. (6) Wang, D.; Zhang, J.; Meng, F.; Liu, H.; Li, L.; Han, B.; Qi, L. Commercial Test of Polymer Flooding in Daqing Oil Field Daqing Petroleum Administrative Bureau; Society of Petroleum Engineers, 1995. https://doi.org/10.2118/29902-MS. (7) Wang, D.; Cheng, J.; Wu, J.; Wang, G. Experiences Learned after Production of More than 300 Million Barrels of Oil by Polymer Flooding in Daqing Oil Field; Society of Petroleum Engineers, 2002. https://doi.org/10.2118/77693-MS. (8) Anand, A.; Al Sulaimani, H.; Riyami, O.; AlKindi, A. Success and Challenges in Ongoing Field Scale Polymer Flood in Sultanate of Oman - A Holistic Reservoir Simulation Case Study for Polymer Flood Performance Analysis & Prediction; Society of Petroleum Engineers, 2018. https://doi.org/10.2118/190431-MS. (9) Juri, J.-E.; Ruiz, A.; Serrano, V.; Guillen, P.; Thill, M.; Kichick, L.; Alonso, P.; Lucero, A.; De Miranda, V.; Mac Donald, W.; Figueroa, E.; Robina, N.; Vera, M.; Figueroa, E.; Di Pauly, F.; Rojas, W.; Ojeda, N. A Successful 18%STOOIP 4-Injector Polymer Pilot Expands To 80 New Injectors In 6 Years Adopting A Modular Concept In Grimbeek Fluvial Reservoirs; International Petroleum Technology Conference, 2020. https://doi.org/10.2523/IPTC-20285-MS. (10) Delamaide, E.; Let, K. M. S.; Bhoendie, K.; Paidin, W. R.; Jong-A-Pin, S. Interpretation of the Performance Results of a Polymer Flood Pilot in the Tambaredjo Oil Field, Suriname; Society of Petroleum Engineers, 2016. https://doi.org/10.2118/181499-MS. (11) Sieberer, M.; Clemens, T.; Peisker, J.; Ofori, S. Polymer Flood Field Implementation - Pattern Configuration and Horizontal versus Vertical Wells; Society of Petroleum Engineers, 2018. https://doi.org/10.2118/190233-MS. (12) Batonyi, A.; Thorburn, L.; Molnar, S. A Reservoir Management Case Study of a Polymer Flood Pilot in Medicine Hat Glauconitic C Pool; Society of Petroleum Engineers, 2016. https://doi.org/10.2118/179555-MS. (13) Guo, H.; Dong, J.; Wang, Z.; Liu, H.; Ma, R.; Kong, D.; Wang, F.; Xin, X.; Li, Y.; She, H. 2018 EOR Survey in China-Part 1; Society of Petroleum Engineers, 2018. https://doi. org/10.2118/190286-MS. (14) Juri, J.; Ruiz, A.; Schein, F.; Serrano, V.; Thill, M.; Guillen, P.; Tosi, A.; Pacchy, M.; Soto, L.; Therisod, A.; Paura, M.; Lauro, P.; Alonso, P. Grimbeek Successful Polymer Pilot Extends to 80 Injectors in Factory-Mode Development at CGSJ Basin; European Association of Geoscientists & Engineers, 2019; Vol. 2019, pp 1–14. https://doi.org/10.3997/22144609.201900061.
By Bob Stanton Director of Technology, Omnetics Connector Corp.
Micro Connector and cable systems fit well into electronic tools used in geothermal and petroleum devices used in gravitational detection, magnetometers, and directional sense and controls as well as Measuring While Drilling. (MWD).
The quality of electrical signal connections and information services used in functions such as, directional drilling, electromagnetic signaling and even power routing to sensor systems can make or break the success of a drilling event. Microsized sensors and connectors must be tough enough to offer continuous signal integrity while enduring extreme forces of shock and continuous vibration. Sensor systems are often fitted snuggly deep inside the drill string system to sense and measure data from the drilling fluid being pumped down and back up the annulus of the drill string and the casing. Sensor tools in many drilling events can also experience both high temperature and pressure. Drilling Downhole in North America, temperatures typically run from 150ºC to near 175ºC, and is handled with standard “hightemperature” connector and cable systems. In some cases, such as in Australia and the South Pacific, temperatures in downhole drilling can rise to 200 degrees centigrade and become a serious challenge. Specialty MDW connector and cable connectors must be utilized to competently operate the rig and drill system. Position, direction and measurement data being developed while down-in-the-hole with sensors,
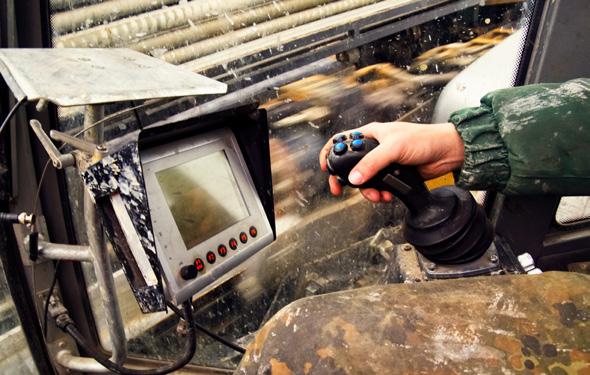
detectors must be processed and routed up to the control center at the surface of the rig. Micro-Connector and cable for petroleum industry electronics often fall into a few specific categories. As noted earlier, focus is on the combination of being small simultaneously with very rugged. Pin and socket elements within the connectors handle the signal integrity and are responsible for
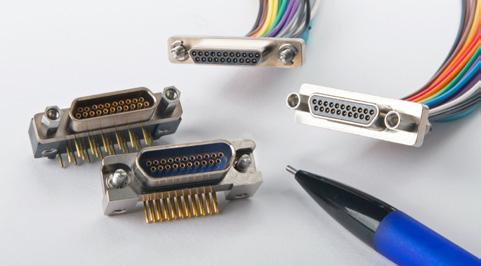
Directional Drilling Controls.
continuous transmission at low resistance. This is solved in micro-connector design using highly tempered BeCu, (beryllium-copper) spring pins tightly interfacing solid cylindrical sockets. These contact elements are fitted into rugged insulator sets that hold their size and shape during temperature and pressure changes. The interconnect system’s electrical current capacity is based on the diameter of pin/sockets as well as the current capacity of the wiring. Micro and, in some cases, Nanosized connectors fit well into the down hole system because new sensor and detectors operate well on quite low voltage and current levels and offer solutions in a number of key areas of the Petroleum system. MWD Controller boards; use a number of sensors for borehole logging and directional drilling and can include high temperature detection sensors that are critical in gas, oil and geothermal drilling applications. The micro-d connector is a small metal shelled connector with proven shock and vibration performance for years in the down-hole steering sector. Current capacity goes to 3 amps per line. Multiple pin/socket counts are available and the designer can specify temperature ranges from 150ºC to 200ºC. When solder attachment
is needed we often use SAC305 which is a high temp lead free solder or what is specified by the down-hole engineer. The smaller Nano-d connector fits very well onto small diameter controller and bit-steering modules. It also passes the shock and vibration rigors and can be used up to 200ºC range while carrying up to 1 amp per wire. Tool Strings: Routing and Installing electronic cable in tool strings can be difficult because of small diameters and flexible connecting sections. Cable are more easily drawn with cable using Micro-Circular and Nano-Circular connectors all along the string. They are more easily pulled with the harness through small openings in the string. Key sensor data is also protected inside the metal connector shells during use from random electrical noise. Special sensor signals can be routed with special high speed digital signal wire when needed. Wireline Tools: Sometimes called dry line tools, will vary greatly based upon the number of conductors needed during steps like geophysical analysis and the well- development data acquisition needed about the geology below the surface, properties of a reservoir and checking for pipeline ruptures. In cased hole and other analysis applications the multiconductor cable system is needed to collect a wider range of analysis info. The cables themselves are fairly small in diameter but often need to be shielded for rugged exposure during insertion and withdrawal. Small and rugged metal connectors, such as the microcircular and micro-d style are a good choice as they offer a number of wire to wire connections and match well with the metal shielding of the overall wireline cable design. When gamma ray tools are used to check for clay volume and any increase in mineral concentration, (which leads to potential fractures), the shielded cable and metal connector can be electrically sealed for additional signal isolation. This insures best data reaching the surface.
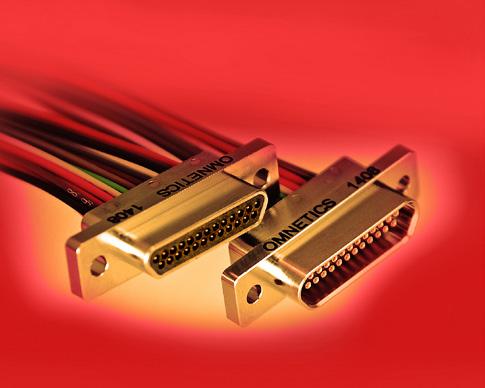
Routing and Installing Electronic Cable.
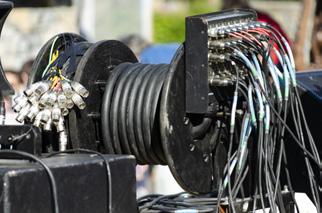
Nano-PZN - Ruggedized.
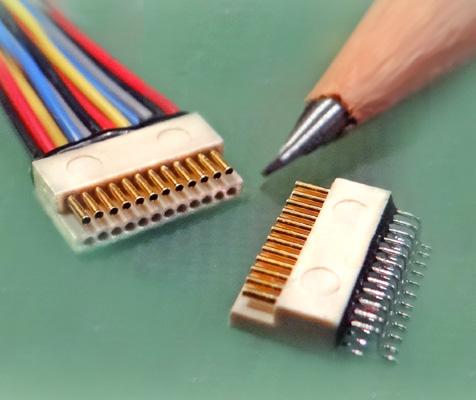
Evolution in power and Portable
geophysical tools: Highly portable geophysical instrumentation devices are being used in research and ground surveillance as well in airborne and marine to analyze a wide range of sciences from petroleum and mineral exploration to measurements of groundwater levels. During transportation as well as in operations, the small, low weight electronics must also withstand shock, vibration and elevated temperatures as see in MWD applications. Changes in today’s active electronics are requiring power supply integrity, but at lower level current and voltages. Similarly, new mud motor design requires lower power and smoothed levels of voltage shift. Hybrid micro-d connectors fit well in many designs and newly models of miniaturized 38999 circular connectors are solving the problem. Conclusion: Rugged Micro and Nano-sized MWD Connector and Cable systems are making life easier for modernized petroleum electronic interconnections. Improved signal acquisition and transmission have increased the reliability of data and the installation and working with new sensor technologies being applied to the industry. Application Specific cable and connectors are readily available and quickly provided for new petroleum device and development. Our leaders in this industry have lead us to Smaller, Rugged, Quickly Adaptable Interconnects. • Omnetics / https://www.omnetics.com +1 763-572-0656 / sales@omnetics.com 35