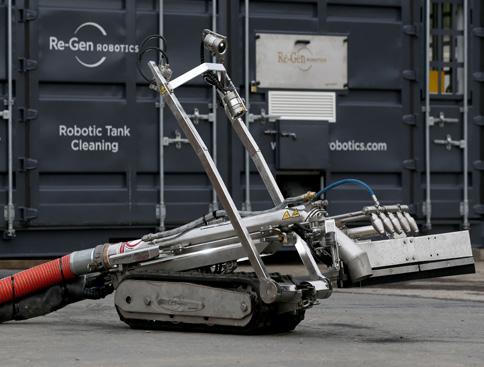
22 minute read
MIDSTREAM & PIPELINES It’s Time to Move on From Dangerous Tank Cleaning Procedures
It’s Time to Move on From Dangerous Tank Cleaning Procedures
OGI sits down with Fintan Duffy, Managing Director of Re-Gen Robotics Ltd, who are revolutionizing the safety of tank cleaning with their ‘No Man Entry’ automated tank cleaning system. Mr Duffy is here to dig deeper with us so we can find out more about this award winning solution and how it will disrupt the tank cleaning industry.
Advertisement
OGI: Could you start by explaining Re-Gen Robotics’ credentials and experience in terms of your products and services for the oil and gas sector? Could you tell our readers the breadth of your experience, how long the company has been active, and its reach? Duffy: Re-Gen Robotics is the first and only Zone 0 EX certified, remote controlled, ‘No Man Entry’ robotic tank cleaning company, in Europe. Launched in Spring 2019, our vision is to become the most efficient, safe and reliable tank cleaning service provider to the petrochemical industry, distinguishing ourselves from competitors through our excellent health and safety performance. Within less than a year of launching, Re-Gen Robotics won the Safety Technology Award at the 2020 Global Tank Storage Awards, in Rotterdam, on 10th of March. Re-Gen Robotic’s technology and service was recognised for revolutionising safety in the tank terminal industry. Over the last year we have worked with some of the benchmark oil majors, who are embracing our state-of-the-art, tank cleaning robots. These industry leaders are committed to enhancing safety and productivity in their operations and will no longer tolerate commissioning manned crews, to clean tanks in environments that are too hazardous to be undertaken by field personnel. Re-Gen Robotics has the solution for nonman entry tank cleaning. The robots are designed to operate in the most inhospitable environments and with specialised access cranes, remote camera systems and engineering expertise, any size or shape of tank can be cleaned. OGI: What are some of the dangers associated with man-entry tank cleaning procedures? Duffy: Tank entry is widely recognised as being one of the most hazardous operations in the tank cleaning business and every year as many as 200 people across Europe, lose their lives working in confined spaces. Traditionally personnel have been required to enter hazardous oil tank environments to implement inspections, desludge and clean for product change. Seven main causes of confined space accidents are listed as asphyxiation, poisoning, engulfment, oxygen deficiency, drowning, explosion, and electrocution. Although safety regulations and industry standards are high, occasionally fatal accidents do occur, owing to human error and failure of safety devices. Fintan Duffy, Managing Director, Re-Gen Robotics Limited.
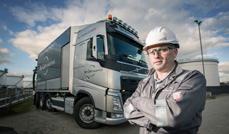
Current Health & Safety legislation stipulates that ‘a person shall not carry out work in confined spaces, if it is reasonably practical that it can be avoided’. Companies can no longer afford to be negligent where human life is concerned and fortunately, there is a very real appetite across the board for new, safer methods of cleaning, inspection and assessment. Almost ALL personnel who die in confined spaces are trying to rescue other workers who fainted due to lack of oxygen or exposure to toxic gases. OGI: Could you explain in detail automated tank cleaning? The processes, what is involved, costs etc? Duffy: By sending our revolutionary robots into dangerous confined spaces, clients are not only eliminating the dangers and liabilities associated with confined space entry but are also saving time, money and reducing operational downtime for their tanks. Re-Gen Robotic’s unique, closed loop cleaning system can reduce cleaning time by up to 45 per cent, significantly decreasing downtime and loss of production whilst oil tanks are not operational. The tank is brought back into operation quicker and reduces the need for additional tank capacity, permit delays and additional support teams. Safety and protection of personnel during tank cleaning services are of the utmost importance. At no time during the ReGen Robotics cleaning process is there a requirement for human presence in the confined storage container. Our technical operator remains a safe distance away in the Zone 1 control unit, where they can monitor activity and progress, through a series of ATEX cameras fixed to the robot, inside the tank being cleaned.
The unique features of the large robot make it ideal for cleaning the storage tanks. A combination of specially designed 3,500 PSI jetting water nozzles, powered by a highpressure low flow pump, play a vital part in the cleaning process. The auger system at the front of the robot breaks down heavy sludge without the requirement to use water, thereby generating less waste. Sludge is then extracted by an ADR certified jet/vac tanker with 4,800 C/ m3 per hour vacuum capacity. The efficiency of the clean is crucial to planning schedules and means that the tanks can be brought back into operation sooner than manual cleaning. Using a fully contained waste removal and a 360-degree cleaning process, the waste material is transported off site using an ADR tanker and safely treated in an authorised, licensed facility. The entire tank cleaning operation is recorded on CCTV from the ATEX cameras and is made available to the client upon completion of the works. All files are date and time stamped to ensure the process is traceable for auditing purposes. A record of gas detection readings is also issued on completion of each vessel cleaning, produced by the onboard gas monitoring equipment. OGI: And a bit of detail of Re-Gen Robotics’ machine? Duffy: Re-Gen Robotics has invested over £3 million in creating three purpose-built, explosion proof robots, designed to operate in the most inhospitable environments. The large robots are designed to fit through a standard 600mm entry hatch via an extending ramp and de-sludge, wash and clean large-scale tanks, including fixed roof and floating roof tanks. The robot has the power to clean the largest oil tanks with no hassle and can handle heavy fuel oil, crude oil, sludge and the like. Once cleaning is complete, the robot safely exits the container via its ramp and is returned to the control unit. The lightweight and highly portable compact unit can move through a 450mm entry hatch and is suitable for use on smaller sites and underground storage tanks and containers, including petrol forecourts, interceptors and process tanks. Our intelligent on-board truck telemetry system track waste gives us the opportunity to collect telemetry data that can then be aggregated and analysed in order to optimise the process. The combination unit provides real time information on all key parameters and is accessible to clients. They can evaluate information including; Waste generation, hours worked per day, water consumption on each project, down to the jetting pressures recorded for the duration of a tank clean. OGI: What different types of tanks can be serviced? And could you talk a bit about your services? Duffy: Our robotic system has power to clean the largest oil tanks with no hassle and can handle heavy fuel oil, crude oil, sludge and the like. Regardless of the nature of the vessels, i.e. vertical, horizontal, over ground or underground, Re-Gen Robotics has the solution for non-man entry tank cleaning. Our robot is designed to fit through a standard 600mm manway using externally fixed hydraulic ramps. For fixed roof tanks, high pressure, low flow jetting systems and vacuum are used to clean and ATEX CCTV and lighting are used for inspection. On floating roof tanks, front and rear ATEX CCTV and lighting are used for internal tank navigation. Camera brackets are adjusted to a fixed height and a 360 degrees jet head is used to wash the roof. The full coverage suction head has the capability to wash the walls and the roof of tanks, affording faster turnaround times by 10% on floating roof tanks, where roof washing is included in the scope of works on tank cleans. Auger systems are available for removal of heavy sludge in Heavy Fuel Oil tanks. Front and rear ATEX CCTV and lighting are used for internal tank navigation and an offset suction head cleans underneath heating coils. Using magnetic or rubber tracks to enable full traction and navigation, our robotic system is capable of cleaning Coned Floor tanks. Front and rear ATEX CCTV and lighting is used for internal tank navigation, our offset suction head and powerful vacuum is used to enable suction to 9m below surface. OGI: Finally, could you enlighten our readers of a case study where you helped a client with your solutions?
Shell UK Oil Products Ltd
Re-Gen Robotics was commissioned by Shell UK Oil Products Ltd to clean two Jet A1 fuel storage tanks. Both tanks have a resin lining applied to the floor and 1m up the tank walls. The ADR tanker was stationed 10m from the tanks and the robotic equipment was craned into position. No scaffolding or bespoke equipment was required as Re-Gen Robotics supplied the complete system to position the robot in the tank. The operator remained in the Zone 1 control unit where they could monitor activity through a series of ATEX cameras and gas monitoring equipment fixed to the robot. A combination of specially designed 3500 psi jetting water nozzles, powered by a highpressure low ow pump, were used in the cleaning process. The efficiency of the clean removed the need for additional tank capacity, permit delays and additional support teams. The waste material was transported from the site using an ADR tanker and safely treated in an authorised, licensed facility. The cleaning operation was recorded on CCTV from the ATEX cameras and was made available to Shell upon completion of the work. All files were date and time stamped to ensure the process was traceable for auditing purposes. A record of gas detection readings was also issued on completion of each vessel cleaning, produced by the onboard gas monitoring equipment. The tank was cleaned without the need to spade the valves. During a manned entry clean this procedure is mandatory as it mitigates an accidental opening of the valve, inhibiting fuel from entering the tank and causing injury. On average it would take two members of staff a full day to spade one tank, so eliminating the necessity to carry out this operation reduced tank cleaning time and tank downtime and was therefore a further cost saving for the terminal operator. Re-Gen Robotics has been commissioned to clean further tanks for Shell, with a floating rooves, navigating approximately 40 legs within each of the tanks.
Conclusion
Robotic cleaning technology is making a monumental difference to safety and is on its way to being adopted as best practice within the tank cleaning sector. There are now realistic and proven alternatives to ‘man entry’ tank cleaning. The health and safety of personnel engaged in tank cleaning is paramount. Using robotic equipment to carry out works in hazardous confined spaces is the most logical and safe way to clean tanks. Terminal and refinery operators can be assured that they have mitigated the risks associated with confined space tank cleaning, as far as is reasonably practicable, when they engage a contractor that has invested in the right equipment to clean their tanks. •
Re-Gen Robotics
tel: +44 28 300 50 800 email: info@regenrobotics.com web: https://www.regenrobotics.com
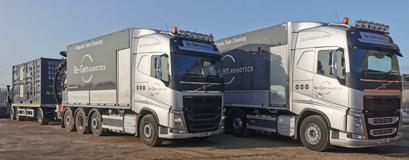

Hauff – Innovative Sealing Solutions for Pipelines
Pipelines form a crucial infrastructure for the transport of liquids and gases – water, waste water, oils, fuels and more. They are the backbones of the exchange network which makes the utilities available where they are required for further processing or for consumption – in industrial complexes, in commercial buildings and in homes. Pipelines traverse huge distances passing through different landscapes and climate zones, crossing roads and rivers and moving in and out of pump stations, storage tanks and buildings . At each section where a pipe passes through a barrier – moves into or leaves a building or a structure – the penetration must be sealed against ingress of water, gas, dust and vermin.
Most penetrations for pipes are circular, made with wall sleeves or core drill holes or formed as a recess while concreting. The ring-like space between a pipe and the circular opening in the wall is called annular space and results from the combination of outer pipe diameter and the inside diameter of the opening, There are different approaches to sealing a certain annular space. Mechanical seals being the most common and trusted choice. The use of elastomers as a sealing material is well known. Among others, elastic properties and resistance to water are the two basic characteristics of rubber which make it suitable for creating a mechanical seal. The pressure plates on both sides of the rubber act as a boundary creating a defined space within which the rubber can flow and the compression is achieved with screws. The rubber when placed in the annular space and compressed mechanically flows in a defined way to fill out the space completely, thus creating a watertight and gas-tight seal. A Modular Seal, as the name suggests, is a chain of same sized modules which can be closed to form a ring. Adjusting the number of modules used allows the same seal to be used over a certain range of annular space. Hence, most applications can be catered to only with a limited number of module sizes on stock. This flexibility makes the modular seal very practical and popular.

Modular Seals have been around for many decades. The GKD is a leap into the next generation of innovative sealing solutions. It stands out because it is the only modular seal with an integrated installation control. For correct installation the seal needs to be tightened till the indication windows turn completely yellow. There is no torque wrench “Hauff-Technik owns the worldwide patent not only for the installation control but also for the caged nuts used in the Modular Seal GKD.”
required. Installation errors related to the incorrect torque application – be it due to missing or incorrect information about the required torque or due to a missing or faulty torque wrench at site – are eliminated. The visual indication is simple, practical and reliable method to ensure correct installation. Hauff-Technik owns the worldwide patent
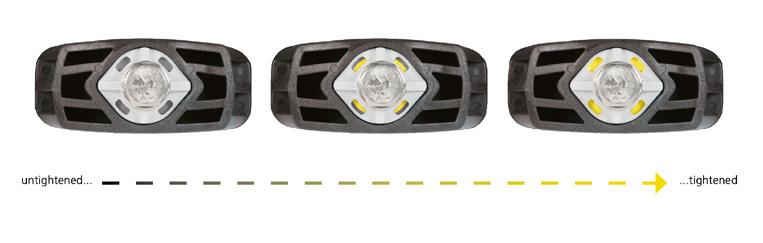
not only for the installation control but also for the caged nuts used in the Modular Seal GKD. Since, the nuts are moulded into the rear pressure plate, there are no loose parts and the nuts cannot fall off or be lost. This makes the installation, which is crucial for the functionality of a seal, easier and error free. Efficiency and cost reduction are further enhanced due to faster installation as the GKD does not require any retightening. In spite of the numerous advantages, a modular seal also has certain limitations. It can only be used to seal one pipe through one penetration. When multiple pipes go through a single penetration, custom seals are the right choice. Likewise, an annular space which is not symmetric calls for a custom-made solution. Choosing the right sealing system calls for a thorough assessment of the prevailing application conditions. Not only the dimensions and the required tightness against gas, water and vermin, but also practical aspects like handling and access must be considered. These factors can be broadly grouped into technical, commercial and handling aspects. Geometry and size of the opening and the pipe will determine whether a modular or a custom seal is required. Environmental conditions – exposure to sunlight, oils/fuels, corrosive environment – require certain type of materials to be used. A seal exposed to oils/ fuels, for example in an airport, should be made of NBR (acrylonitrile butadiene rubber) which has excellent chemical resistance to oils, types of grease and all commercially available fuels. EPDM (ethylene propylene diene monomer rubber) on the other hand has very good chemical resistance to almost all acids and alkaline solutions as well as salt water. A trade-off between conflicting requirements is not uncommon. Custom seals greater than 500 mm in diameter can easily weigh 10 kg and more which makes handling and installation a challenge. Hence, for larger pipe diameters a modular seal is the first choice. But if the pipe is positioned eccentric, a custom seal is the only

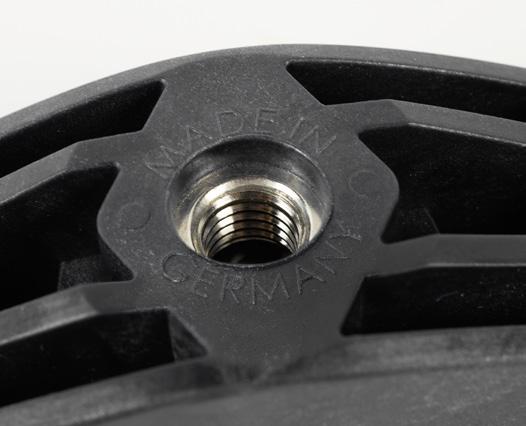
option. In this case proper arrangements for lifting and installation are required. Last but not the least, a sealing solution has to be commercially viable. Features like the installation control of the GKD reduce error, thereby avoiding damage and save the cost of rework. Also, planning the penetration in advance with suitable wall sleeves allows the use of standard seals which are more cost effective than special made to measure solutions. Whatever the need, standard or special, Hauff-Technik, with over 40 years of experience, has a suitable sealing solution. The innovative press seals from Hauff-Technik provide reliable sealing of single or multiple pipes and cables in core drills or wall sleeves.
These range from closed seal inserts for first-time installation to split seal inserts for retrofit sealing of cables and pipes that have already been laid.
Our portfolio of wall sleeve products provides the ideal solution for any type of wall and any load case. Combined with our press seals, these products create the optimum sealing solution between building and supply line. We can provide the ideal solution for every requirement and task, be it tailor-made to the millimetre or suitable for universal use on site, round, oval or even square. Quick and cost-effective. •
If you are interested in any of the solutions discussed in this article, please contact
Hauff-Technik GmbH & Co. KG using the information below to discuss how they can help.
Hauff-Technik GmbH & Co. KG
Tel.: +49 7322 1333-0 office@hauff-technik.de https://www.hauff-technik.com/en
Al-Bader: First Crude Shipment to Reach Refinery August 19
Kuwait Petroleum Corporation (KPC) hosted a press conference in August 3, 2017 to announce the first shipment of crude to the Nghi Son Refinery and Petrochemicals Complex in Vietnam, in preparation for the start of operations. Waleed Al-Bader, Deputy Managing Director for Crude and Derivatives Marketing at KPC, and Ghanim AlOtaibi, Deputy Chief Executive Officer for Asia at Kuwait Petroleum International (KPI) spoke during the press conference. The shipment carries two million barrels and is expected to reach the refinery in August 19th, Al-Bader said, adding that an additional two million barrels are set to be shipped in August 11th. A shipment carrying four million barrels will be sent to the refinery in September, he said, adding that six more shipments carrying 12 million barrels will be sent to Vietnam during the fourth quarter of this year. The refinery has a processing capacity of around 200,000 barrels of Kuwaiti crude a day, he noted. The refinery was established in Nghi Son, which is located around 200 kilometers south of Hanoi, Al-Bader said. It was designed to process Kuwaiti crude by 100%, with a capacity of up to 200,000 barrels a day. The project started in July 2013 and was completed in 43 months, he noted. The refinery targets improving Kuwait’s oil relations with Vietnam and other global partners, Al-Otaibi said, adding that the project is one of the most important oil projects that embody the vision of KPC and its subsidiaries to reach a leading global position in the downstream industry and marketing. The refinery and petrochemical complex project in Vietnam, which is affiliated with KPI, will realize KPC’s strategic goals and provide a safe long-term outlet for the Kuwaiti crude, he added. Meanwhile, Al-Otaibi applauded the role of Kuwaiti young people working in the project, and their contributions which helped push progress forward. He indicated that safe operation for all producing units to achieve maximum capacity and commercial operation as soon as possible is currently the most prominent challenge, noting that KPC started retail marketing inside Vietnam with strategic partners through five stations that were built as part of a retail stations’ network to cover the local market’s demand. Al-Otaibi said that he is looking forward for long-term partnerships with other global companies similar to the Vietnam refinery project. Notably, a joint company was established as the owner of the refinery and petrochemical complex project in Vietnam, where KPI owns a 35.1% share, Japan’s Idemitsu Kosan owns a 35.1% share, PetroVietnam owns a 25.1% share and Japan’s Mitsui owns a 4.7% share. •
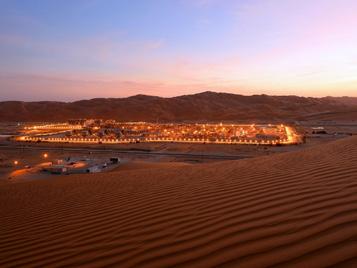
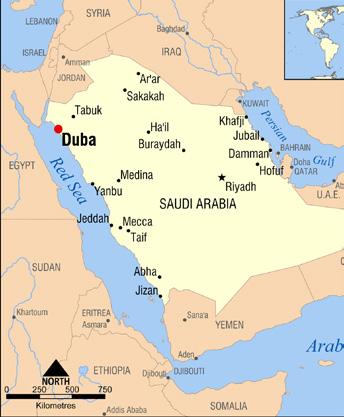
Aramco Announces Downstream Business Reorganization to Enhance Performance and Support
Reorganization designed to enhance Aramco’s competitiveness and support its vision to be the world’s preeminent integrated energy and chemicals company. The Saudi Arabian Oil Company (“Aramco” or “the Company”) today announced the reorganization of its Downstream business to support and enhance integration across the hydrocarbon value chain and better position the Company to drive financial performance, value creation and global growth. The Company’s Downstream operating model will include four commercial business units: Fuels (includes Refining, Trading, Retail and Lubes); Chemicals; Power; and Pipelines, Distribution & Terminals. These business units will be supported by three corporate functions: Manufacturing, Strategy & Marketing and Affiliates Affairs. This reorganization is designed to enhance the effectiveness and efficiency of Aramco’s existing Downstream assets, but does not represent a fundamental change in the overall business structure. Abdulaziz M. Al Gudaimi, Senior Vice President of Aramco Downstream, said: “I am excited that we are launching a new operating model that we believe will help streamline our operations and reinforce our position as a major global energy and petrochemicals player. This reorganization is yet another step in Aramco’s strategy to develop a global integrated Downstream business that enhances our competitiveness by maximizing our value capture across the hydrocarbon value chain.” The reorganization, which is expected to be in place by the end of the year, further strengthens Aramco’s industry leadership in safety, sustainability, efficiency and reliability. Aramco has a large, strategically integrated global Downstream business that leverages the Company’s competitive Upstream position. The Company’s Downstream strategy focuses on creating growth opportunities across the hydrocarbon chain in order to expand the Company’s sources of earnings, providing resilience to oil price volatility and capitalizing on rising demand for petrochemical products. •
OPEC’s World Oil Outlook to Be Launched on 8 October 2020
The 2020 OPEC World Oil Outlook (WOO) will be launched via videoconference in Vienna, Austria, on Thursday, 8 October 2020 at 14:00 (CEST). OPEC’s Secretary General, HE Mohammad Sanusi Barkindo, will present the major findings of the WOO 2020, as well as introduce a video with key messages from the publication’s 14th edition, which coincides with the 60th Anniversary of the Organization. This will be followed by a panel discussion and a Q&A with management and analysts from OPEC’s Research Division. First published in 2007, the WOO provides an in-depth review and analysis of the global oil and energy industries, and offers a thorough assessment of various sensitivities in the medium- and long-term development of the oil industry. The publication provides insights into the upstream and downstream, supply and demand, investments, the potential impact of policies, and the environment and sustainable development. It also provides expert analysis of many of the challenges and opportunities facing the global oil industry. This year’s edition captures an extended horizon of projections up to 2045. HE Barkindo said: “The WOO underscores the Organization’s ongoing commitment to insightful research, data transparency and the enhancement of dialogue and cooperation. We hope it contributes to a better and more enhanced understanding of the global oil and energy markets, and fosters further knowledge-sharing. This is particularly valuable given the unprecedented events of 2020, with the COVID-19 pandemic upending people’s lives, and causing major disruption to economies, industries and businesses.” This year’s publication will again be accompanied by a smart app to give increased access to the WOO’s vital analysis and energy data, as well as a comprehensive interactive version. More details on these will be provided when the publication is launched. •
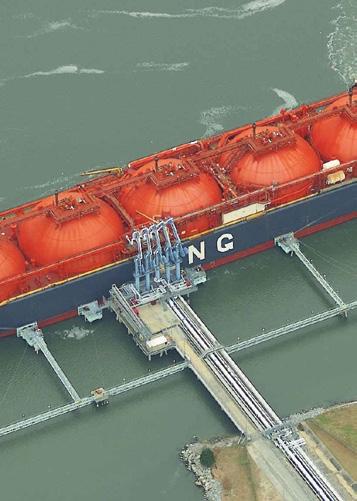
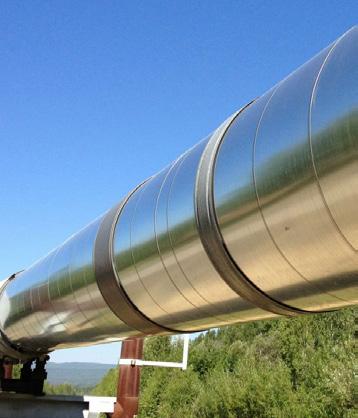
JMMC Focuses on Market Stability and Full Conformity
The 22nd Meeting of the Joint Ministerial Monitoring Committee (JMMC) took place via videoconference on Thursday 17 September 2020, under the Chairmanship of HRH Prince Abdul Aziz Bin Salman, Saudi Arabia’s Minister of Energy, and Co-Chair HE Alexander Novak, Minister of Energy of the Russian Federation. The Committee reviewed the monthly report prepared by its Joint Technical Committee (JTC) and developments in the global oil market since its last meeting on 19 August 2020. The Committee also considered market prospects for the fourth quarter of 2020 and into 2021. The Committee reviewed the crude oil production data for August 2020 and welcomed the positive performance in overall conformity for participating OPEC and non-OPEC countries of the DoC, which was recorded at 102% in August 2020, including Mexico as per the secondary sources. The JMMC reiterated the critical importance of adhering to full conformity and compensating overproduced volumes as soon as possible. The JMMC supported, and recommended, to the OPEC and NonOPEC Ministerial Meeting, the request of several underperforming participating countries in the DoC to extend the compensation period till end of December 2020, after pledging that they will fully compensate for their overproduction. This is vital for the ongoing rebalancing efforts and helping deliver long-term oil market stability. The JMMC observed that the recovery has not been even across the world and an increase in COVID-19 cases has appeared in some countries. In the current environment, the JMMC emphasised the importance of being pro-active and pre-emptive and recommended that participating countries should be willing to take further necessary measures when needed. The Committee thanked the JTC and the OPEC Secretariat for their contributions to the meeting. The next meetings of the JTC and the JMMC are scheduled for 15 and 19 October 2020, respectively. •
2020
IMPORTANT EVENTS CALENDAR
35th International Scientific & Expert Meeting of Gas Professionals 21.10.2020 - 23.10.2020 https://susret.hsup.hr/en/
SPE Virtual Annual Caspian Technical Conference 21.10.2020 - 22.10.2020 Virtual https://www.spe.org/events/en/2020/conference/20ctc/caspian-tech
SPE Virtual Norway Subsurface Conference 02.11.2020 - 03.11.2020 Virtual https://www.spe.org/events/en/2020/conference/20berg/home
SPE Virtual Upstream Finance and Investments Conference 11.11.2020 - 12.11.2020 Virtual http://go.spe.org/_00903-0955l
Future Oil & Gas conference and exhibition 01.12.2020 - 02.12.2020 Aberdeen, UK https://bit.ly/3a7TuAD
35th International Scientific & Expert Meeting of Gas Professionals 21.10.2020 - 23.10.2020 Congress Center of the Grand Hotel Adriatic Ul. Marsala Tita 200, 51410, Croatia https://susret.hsup.hr/en/
Energy from Waste 2020 01.12.2020 - 02.12.2020 Copthorne Tara Hotel, London, UK http://www.efw-event.com/oilgasinnovation
EGYPS - Egypt Petroleum Show 2020
09.02.2021 - 11.02.2021 Egypt International Exhibition Center (EIEC) https://www.egyps.com/
Offshore Technology Conference
4-7 May 2021 Houston, Texas, USA http://2020.otcnet.org/
The 28th World Gas Conference (WGC 2021) 21.06.2021 - 25.06.2021 130 Gongpyeong-dong, Jung-gu, Daegu, South Korea https://www.wgc2021.org/
SIMPLIFY
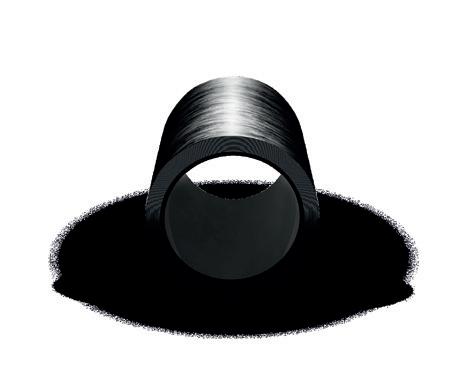
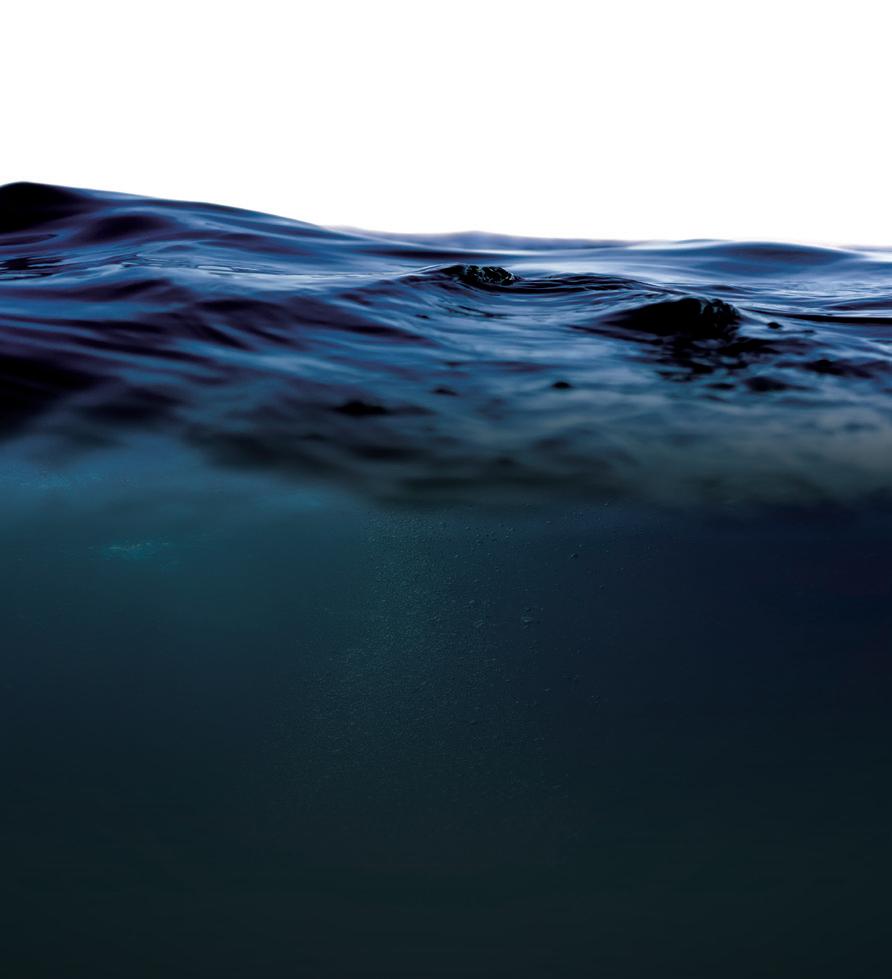