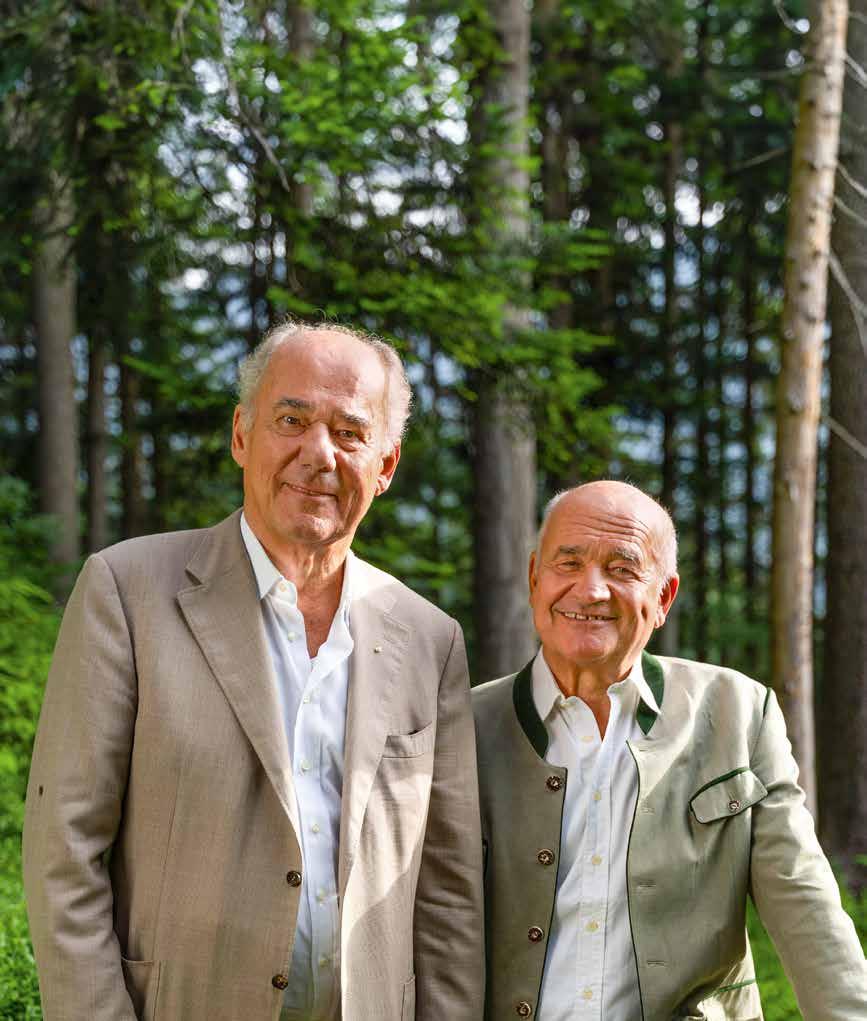
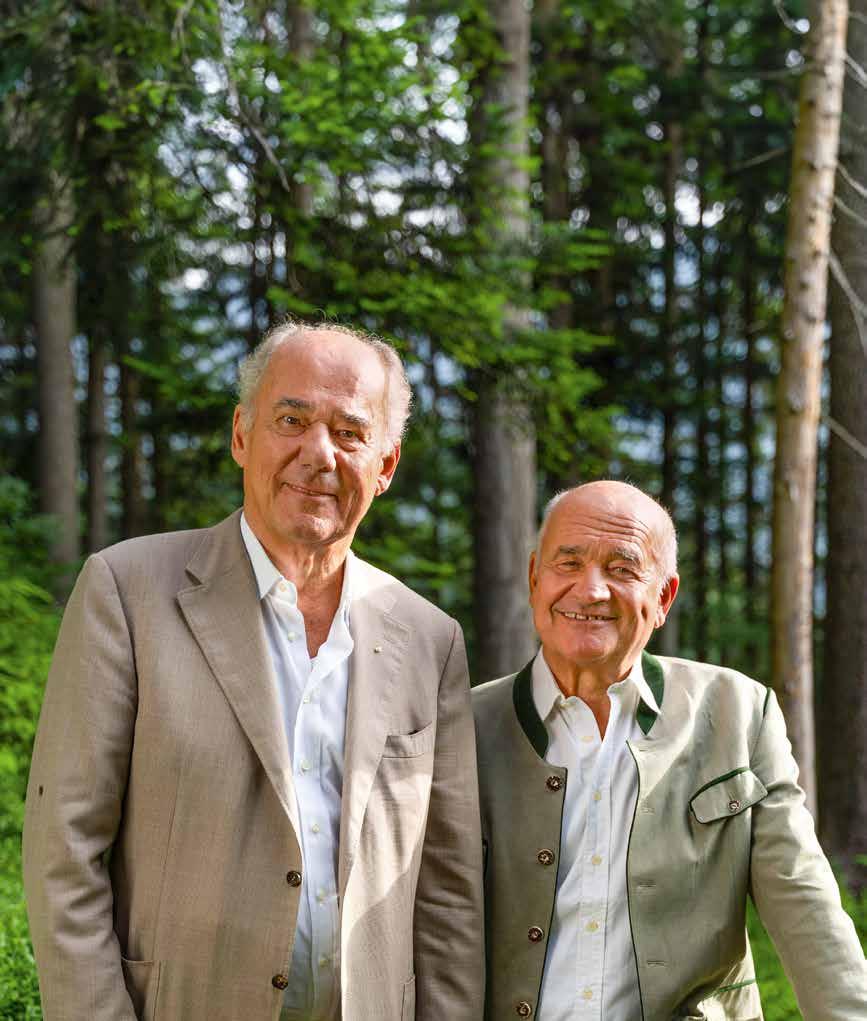
Family values provide strong roots
Stories of togetherness
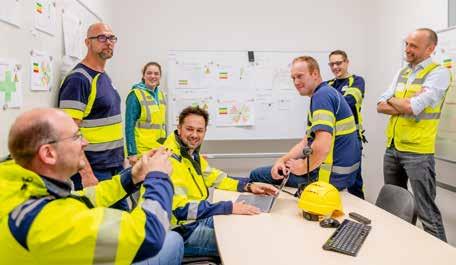
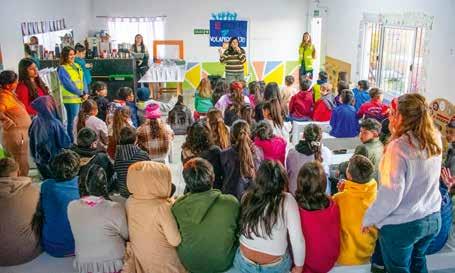
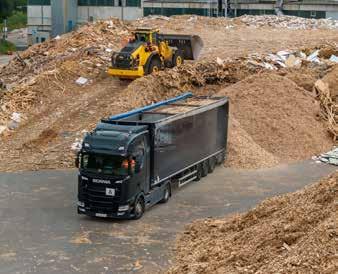
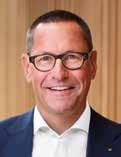
Thomas Leissing Chief Financial Officer EGGER Group
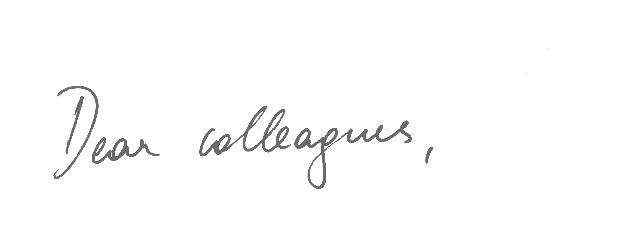
When navigating particularly turbulent and challenging times, it is important that we know exactly where we are going and that we can rely on our strong foundations. As a family business, we are in a fortunate position.
What does it mean to be a family business? For us, it means thinking long-term and being mindful of how the company can evolve over generations. In contrast to maximising profits in the short term and championing the distribution of dividends, we prioritise sustainable development. Our desire to focus on future generations is firmly anchored in our strategy.
Our employees are another key aspect of our family business. They are at the heart of all our successes. We know that each and every one of you makes a valuable contribution and that your engagement is essential for our family business.
The current economic climate is posing us major challenges. Interest rate level over the last two years plus consumers lacking confidence mean that less is being spent on new homes and furniture. This has an impact on demand for our products in almost every market.
Here at EGGER, we also see the market situation as an opportunity.
We have continuously invested in our plants and can proudly say that we have the highest levels of automation, productivity and digitalisation in the industry. Our product range is characterised by innovation and a high degree of refinement. This is why we are able to utilise our plants fully, even during a crisis. We want to expand our position with existing customers, while also acquiring new ones. We are confident that we will emerge stronger from the crisis. As a family business, we have the financial strength to do so.
And every single employee has a crucial role to play. We’d therefore like to ask you all to do your utmost to support us in overcoming these challenges. Together, we are strong –the stories of togetherness in this issue of our employee magazine shine a light on this.
With this in mind, I would like to thank you all for your continued engagement. I would like to wish you and your families a happy holiday season and all the best for 2025.
Kind regards,

Thomas Leissing
Our company culture makes us strong
Michael Egger Jr. and Uli Weihs, the third generation to run the EGGER family business, discuss courageous decisions, trust and having fun at work.
We met on the eve of All Saints’ Day to conduct this interview. Cousins Michael Egger Jr. and Uli Weihs were clearly delighted to see each other again after business trips and meetings. And they are looking forward to the upcoming bank holiday, which they will spend with the whole family as they do every year, remembering loved ones who have passed away and enjoying hearty Leberkäs snacks and a good Egger beer. It therefore seems to be a fitting moment to talk about the
importance of family and working together in the EGGER family business.
You are the third generation to run the Egger family business. Did you know from an early age that you wanted to get involved in the family business and prove your worth?
Michael: No, quite the opposite. It was important for me to be able to strike out on my own. But after finishing school, I made a very conscious decision to join the family business. My holiday jobs in the various production areas were very educational and I was allowed – or should I say – had to do everything. I will never forget cleaning the oil pan on the Conti press in St. Johann as part
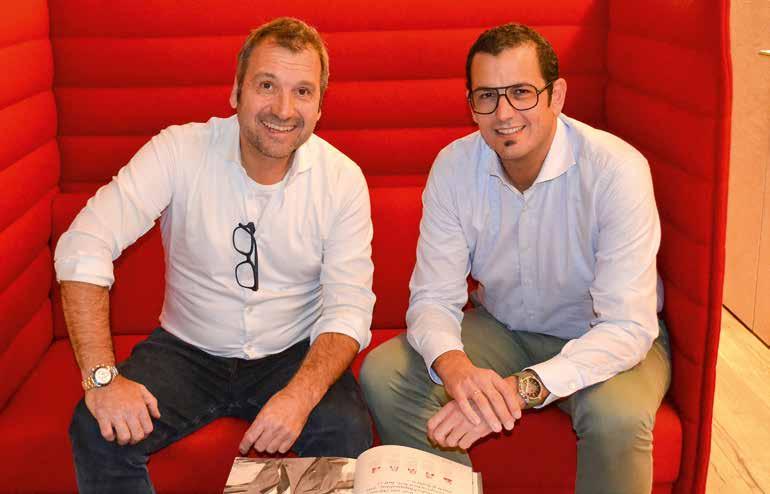
Cousins Uli Weihs and Michael Egger Jr. leaf through the EGGER chronicle featuring a picture of their grandfather.
Matthias
Alexander
Georg Weihs
Birgit
Uli Weihs
Christl Weihs
Dieter
Anna Weihs
Willem
Carl
Anton
Emma
Simone Fritzen
Clemens
Egger family tree
Matilda
Frida
Rosa
Leo Paul
Theresa Schott
Franz
Michael Egger
Susanne
Michael Egger jun.
Tetyana
Gustaf
Kathrin Golger
Fritz Egger jun.
Fritz Egger († 1982)
Rosa († 2001)
of major maintenance works: It was a real challenge because of my height, but it certainly stood me in good stead. As a result, I have developed a great appreciation for everything all our company employees do every day.
Uli: I joined the company in 1996. However, during my first job interview, my uncle Michael warned me that I first needed to fix my hair, which was dyed orange at the time. Eventually, I was allowed to start as deputy head of department in Postforming. I worked the night shift a lot. We made worktops back then, but also early versions of flooring. There was a real pioneering spirit. Little by little, I got the chance to develop further. I always strove to work in the family business, and my grandfather and uncles were my role models.
Uli, you knew your grandfather Fritz Egger Sr., the company’s founder?
Uli: Yes, unfortunately Michael was too young to meet him. But I have many wonderfully vivid memories of our grandfather, especially on his farm. As a little boy, I was in the stables almost day and night, and often up in the Brunnhofer Alm mountain pastures.
I clearly remember that he truly valued family and togetherness.
Louis
Noah
Johanna Egger
Stefan
Fritz Egger
Eva
Omar
Christiane Egger
Edmund Egger († 1996)
Marina
It was important to him that the family got together for a meal on Sundays. Despite working a great deal, he always made time for his family. I was 10 years old when our grandfather suddenly passed away and I still remember the pain very clearly.
That was in 1982, when brothers Michael, Fritz and Edmund Egger took over the company reins and managed it for the next few decades. How did they influence you?
Uli: Through them, we were able to experience what entrepreneurship truly means. Of course, there were also hardships, no evenings off, lots of travelling. But above all, a great deal of spirit and creativity, which we can still feel across the entire workforce today.
Michael: Perhaps it needs to be said that it was a different time back then. The person who arrived at the company the earliest and stayed the latest was the best. Nowadays, the overall speed is better, but that’s also thanks to digitalisation. That’s why it’s important to consider a work-life balance. We are currently undergoing a generational transformation process. We have an incredible amount of company knowledge thanks to employees who have been with us for 30 or even 40 years. But we also have many fantastic young colleagues who will develop and flourish with us.
Family values provide

have a certain willingness to take risks, but we always think long-term. We want to hear ideas from within the company and then implement them. You don’t have to analyse everything in minute detail; you simply have to try it out.
What are you doing to promote this trust and cooperation throughout the organisation?
Michael: Our corporate culture is what makes us so strong. It is important for our corporate culture that we come together. Sharing lunch together or chatting beside the coffee machine –conversations happen here that would otherwise not take place. The most important thing is to talk to each other and be open. Problems must be addressed openly, as this is the only way we can continue to improve.
Uli: Given our level of internationality, it is also important that we do not impose our culture. We have to find a sensible middle ground. Being seen in the plants and talking to employees on site are both very important to me personally. You have to adapt to situations and people, and perhaps put aside your Tyrolean stubbornness from time to time.
Michael: Everyone at EGGER is a role model. We have to constantly work on ourselves. Here’s an example relating to work safety: I am always grateful when an employee points out to me that I have not complied with a safety regulation. This clearly demonstrates that everyone takes responsibility for one another.
strong roots

The Egger family relies on four key values: heart, head, common sense and trustworthiness. They are just as important at home as they are at work, the gentlemen emphasise. We asked why these four specific values are so crucial and what they mean for everyone personally.
Heart
The heart is the most important. It’s about passion. Passion for the product, passion for people, passion to move things forward. We need this passion so that we enjoy working every day and always strive to improve. And we want to pass on this spirit that we have inherited from the previous generation.
Michael Egger Jr.
Head
It is important to learn and to build up knowledge and gain experience. We need to understand processes so we can categorise and evaluate things appropriately. We can use our knowledge to analyse problems pragmatically and adopt different perspectives in order to make decisions. And common sense also comes into play when making decisions.
Uli Weihs
Common sense
We must not make things too complicated. Instead, we must and want to remain clear and simple. Adopting a layman’s view of things helps us to make sensible and practical decisions. By using your common sense, you can navigate life easily, striking the right balance and finding the best way to deal with people.
Michael Egger Sr.
Trustworthiness
Our father set an example of trustworthiness and it still characterises us today. We do as we say. We have a backbone and stand by our word. We don’t always need contracts; we agree what we’ve discussed with a handshake – and then it’s valid. This lays the foundations for trust, which is extremely important.
Fritz Egger
Diversity is the key
At EGGER, we value every single person’s uniqueness and are proud to be a diverse and inclusive family of companies. Regardless of cultural background, gender or age, everyone is welcome at our company. We are convinced that
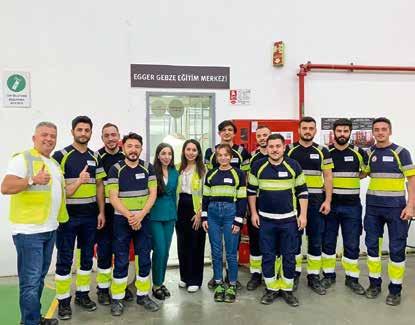
diverse teams work together more creatively and innovatively. On the whole, we all benefit from diversity within the company, which is why we champion it specifically.
New skilled labour brings a breath of fresh air
This summer and autumn, over 180 new apprentices started working at EGGER, providing crucial expertise for our sustainable growth. This talented young bunch are developing their skills in areas such as electrical engineering, wood and metal technology, and are our next generation of experts. With over 550 apprentices, our apprenticeship programme is crucial for our future. Following this year’s launch in Turkey, we are delighted that we will be expanding our training programme to include Italy in 2025. Our training programme is only so successful because our long-standing, experienced colleagues are happy to share their in-depth specialist knowledge, while also embracing the breath of fresh air that our new generation ushers in. We would like to thank everyone who supports our specialist training programme.
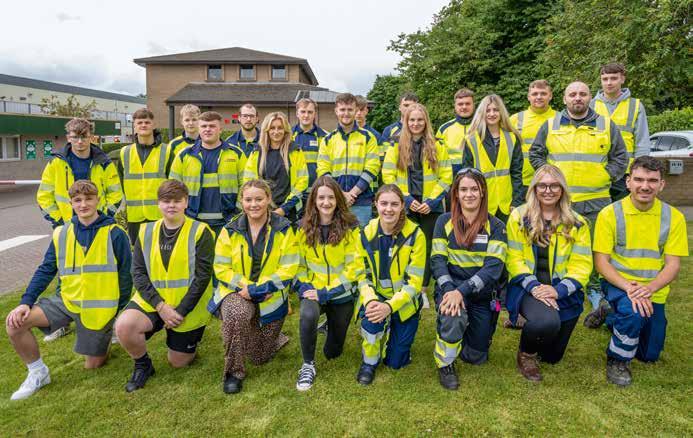
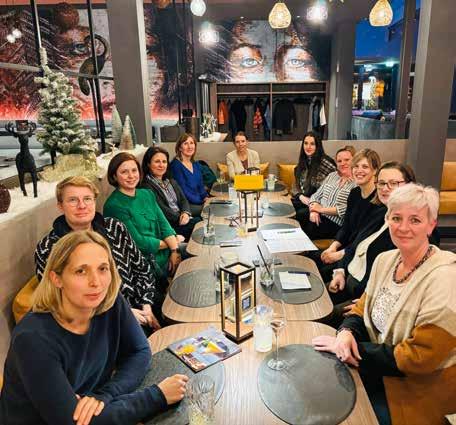
A strong network for women
We signed the United Nations Women’s Empowerment Principles in the spring. With this commitment in mind, we are working even harder to empower women within our company. One key component involves establishing women’s networks in our plants. For the past four years, female line supervisors who work at the plant in St. Johann in Tirol (AT) have been meeting twice a year to share ideas in a structured manner. This group of colleagues has been able to build up a strong network and discuss relevant topics across departmental boundaries. This has been hugely fruitful: The meetings garnered overarching insights for promoting more women to management positions. This successful example is now being extended: Similar meetings have been held in Unterradlberg (AT) in recent months, as shown in the picture, and more plants will follow soon. We have planned numerous other measures to make our commitment to championing women a reality. We will provide further updates in due course.
Intercultural training for global understanding
How do we maintain international partnerships harmoniously and in the long term? How do we take into account the different cultural manners? Our intercultural training courses deal with precisely such issues, such as the “Power seminar” for all local colleagues who are in contact with other cultures or the “Predeparture training”, which specifically prepares employees for secondment to markets such as the USA, China or Thailand. Intercultural preparation has been mandatory for seconded employees since May. The training seeks to avoid misunderstandings. Through realistic simulations, employees experience stereotyping and learn how to overcome this with confidence. The aim is to promote intercultural competence, thereby dealing flexibly with other ways of working and learning from them. This allows us to create successful, sustainable cooperation across cultural boundaries.
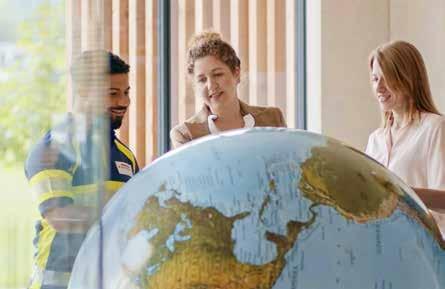
For interested colleagues
To find out more about these offers, talk to your line supervisor or your local Learning & Development contact person.
Working for our fellow human beings
In the areas surrounding our plants, we are not only an employer, but are also committed to supporting the local community. Our support comes in the form of donations, sponsorship and involvement in the areas of health, social issues,
Health
This year, our plant in Biskupiec (PL) was involved in providing emergency assistance to its fellow human beings. As such, defibrillators were donated to a police station, volunteer fire brigades and the town hall. Training was also provided on how to use the device in an emergency.
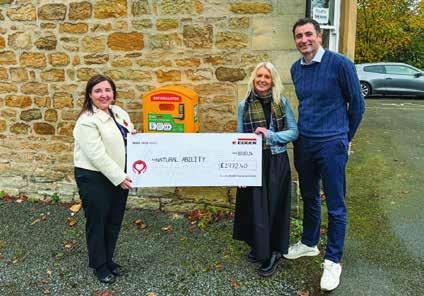
education and environmental protection. We have once again been involved in pioneering projects this year. We’d like to share a few examples with you here. Thank you to everyone who gets involved in this way!

In Barony and Hexham (UK), our colleagues focus on their health while also raising funds for good causes. Recently, our Hexham colleagues completed a physical exercise challenge and raised money for Hexham’s headline charity Natural Ability, which supports local people with learning difficulties. There is a new sporting challenge every month and for every person who completes this “challenge”, EGGER donates £40 to charity.
Environmental protection
In Rambervillers (FR), we recently set up sports trails and hydration stations on our specially designed biodiversity trail, where we have been bringing people and the forest together since 2022. Covering a distance of 3.5 kilometres, it meanders through meadows, forests, wetlands and riverbanks, and is home to a wide range of biodiversity, including frogs, beavers and bats. This allows people from the region – young and old alike – to experience biodiversity and sustainable forestry first hand.
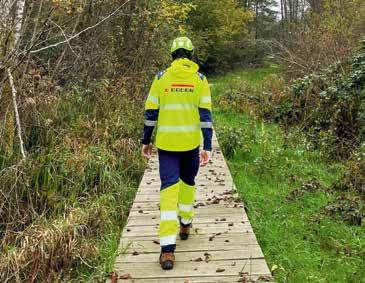
Social issues
Since the “THISABILITY” project was established, our plant in Caorso (IT) has provided valuable support year after year to open up career prospects for people with disabilities. Today, this plant offers 30 people with disabilities the opportunity to actively participate in working life.
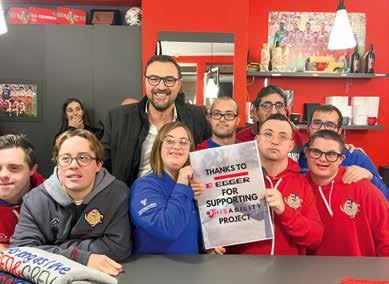
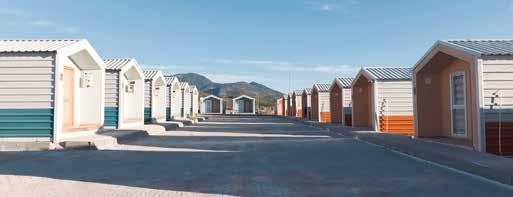
Education
Our plant in Concordia (AR) continuously supports the organisation “Volando Alto”, which opens up opportunities for children. We want to create spaces in which boys and girls have access to the best possible environment so they can enjoy a better future. To this end, we regularly provide wood-based materials. Most recently, we donated tables, benches, blackboards and other equipment so that the children can learn to read in the best possible conditions.
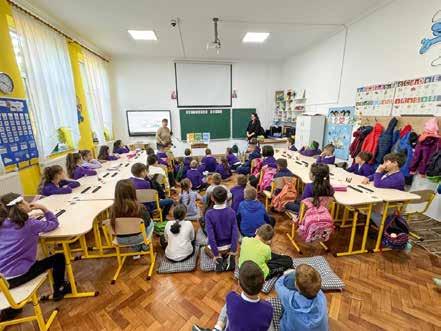
At the beginning of this year, those affected by the devastating earthquake in south-east Turkey and Syria in 2023 were able to move into the temporary houses that were built and furnished with EGGER products. After all the suffering they have endured, people can now at least enjoy a sense of security in a welcoming environment.
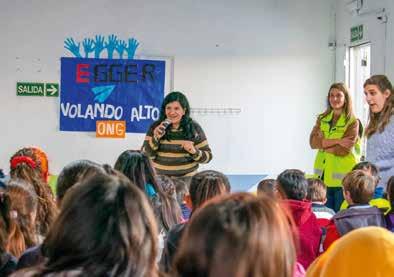
Our plant in Radauti (RO) is particularly dedicated. In 2024, the company donated over one million Euros to charitable causes. A significant percentage of these funds are used to continually equip and renovate schools as part of the “EGGER adopts a school” programme. This allows EGGER to help create a better learning environment for children.
More than just a job: Commitment beyond the workplace
Many of our colleagues volunteer to support the health and safety of others outside of work. They apply this same passion to their role at EGGER. To them, humanitarian activities are not merely a career, but a true vocation. We are very grateful for their extraordinary commitment. On behalf of the many volunteers, we spoke to three of our emergency services personnel about their vocation.
Felix Kickinger, Project Supervisor at the Sustainability Competence Centre in Unterradlberg (formerly at our Health and Safety Competence Centre), is a volunteer paramedic with the Herzogenburg Red Cross.
Did your work as a paramedic influence your choice of career?
The fact that I ended up at the Health and Safety Competence Centre back then was closely related to my background in the emergency services. The practical experience I gained early on in emergency care made it easier for me to get to grips with topics such as safety and accident prevention.
Are there any similarities between your work at EGGER and your voluntary work?
Thanks to my experience in the emergency services, I was able to bring valuable practical knowledge to my professional work, particularly relating to accident analyses and safety measures. My leadership skills have also been strengthened, as I have learnt to provide support in moments of stress.
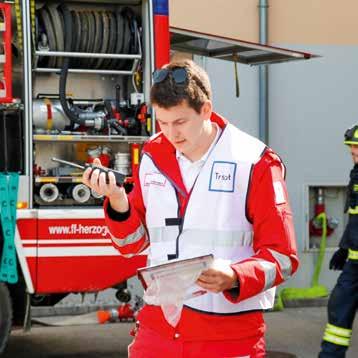
How have you applied your knowledge from the emergency services?
This knowledge helped me to categorise occupational accidents at EGGER, which was one of my previous tasks in the Health and Safety department. My experience in the emergency services meant that I was used to categorising situations clearly. This skill helped me to systematically analyse accidents and precisely assess their severity.
I think I have always had a touch of ‘ helper syndrome’ and a desire to help others who are facing a difficult situation.
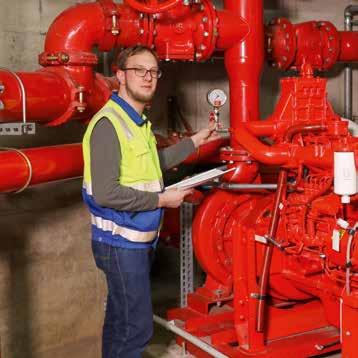
It was a series of lucky coincidences that ultimately led me to work safety. My work in the fire brigade laid the foundations and heightened my desire to help others.
Helge Manzke, work safety specialist and fire protection officer at the Gifhorn plant, gives up his own time to volunteer with the fire brigade.
Why do you volunteer alongside your normal job?
Looking back, I can say that offering support is simply part of who I am. In the village where I grew up, it was customary to join the volunteer fire brigade at 16. Helping people in need has stayed with me and shapes my day-to-day work at EGGER. For me, volunteering also opened the door to work safety and in the end, everything just came together wonderfully.
Are there any similarities between your work at EGGER and voluntary work?
In terms of fire protection, I can apply a lot of my knowledge from the fire brigade directly at EGGER. At the same time, I also share EGGER’s industrial fire protection expertise with the volunteer fire brigade – so both sides benefit from the experience.
Why are you so committed to helping others?
The village fire brigade is simply not questioned as helping each other is something we do for our fellow human beings, and I support our community in my role as a ‘busy bee in the background’. To my mind, human interaction takes centre stage and I benefit a great deal from being part of a community that is there for each other.
Melanie Pierrel, Nurse Health Coordinator in Rambervillers, volunteers as a nurse with the volunteer fire brigade.
Why do you volunteer alongside your normal job?
Helping others has been an important value for me from an early age, which is why I started volunteering at the age of 15. With around a decade of experience under my belt, I then concentrated fully on victim support.
Are there any similarities between your work at EGGER and voluntary work?
My experience as an emergency nurse helped me to establish emergency protocols for the industry that enable action to be taken rapidly in an emergency. The experience I have gained from providing medical care on site also helps me to look after our employees’ health in an industrial context.
Why are you so committed to helping others?
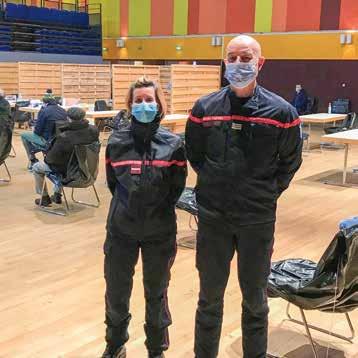
The gratitude shown by the people I help is what drives me every day. I can hardly put into words the feeling that washes over me after receiving a sincere smile and heartfelt words. I’m sure that all my nursing colleagues will recognise this feeling – it connects us and makes our work so valuable.
Being able to help others has always been a key part of me, my principles and values.

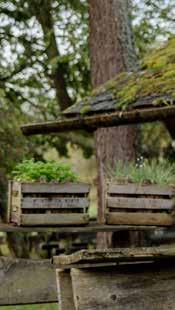
Us and wood
The forest provides us with our most valuable resource: wood. This is precisely why it is crucial for us to work in harmony with it, to value and protect this resource and use it wisely.
We visited Brilon (DE) to take a look at how sustainable forest management and modern industry is perfectly combined in our fully integrated plant. We headed out into the forest with our colleagues from wood purchasing, Christian Witte and Martin Hillebrand, as well as Sebastian Schönnenberg, forester at the Brilon municipal forest.
Forest in balance
“The most important criteria is achieving a balance: we only fell what grows back,” explains Christian Witte, Wood Purchasing Manager at EDP Central, as we walk through the dense forest together. This principle of sustainable forest management is crucial for EGGER to ensure a long-term supply of raw materials and is the basic prerequisite for being able to use wood as a climate-friendly material. We rely on long-term, binding co-operation with local and regional timber suppliers. We seek to purchase materials from within a radius of 150 kilometres of our plants wherever possible. This not only minimises transport emissions, but also strengthens the relationship with our partners. We have a particularly important partnership with the Brilon municipal forest.
Working together for the benefit of all Sebastian Schönnenberg is a forester in Brilon, a large proportion of the wood we use on site comes directly
from the municipal forest in Brilon, which falls under his area of responsibility. Sebastian describes the value cooperation brings to the region: “The fact that EGGER is based directly in Brilon means that the wood arrives at the plant without having travelled great distances. Regional transport companies are hired for this task, this reduces daily congestion on the motorway, saves on diesel and cuts CO2 emissions. EGGER is seen as an important and secure employer in the region, and young people are trained and educated in a wide variety of areas. As a raw material, wood acts as a connecting link; it is at the heart of our daily work together.”
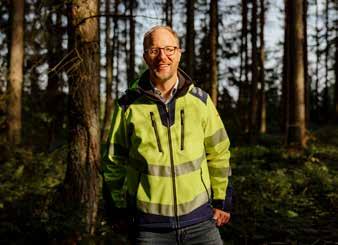
Our wood comes from sustainably managed forests.
Christian Witte is in charge of wood purchasing for EDP Central.
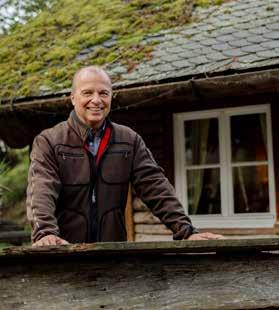
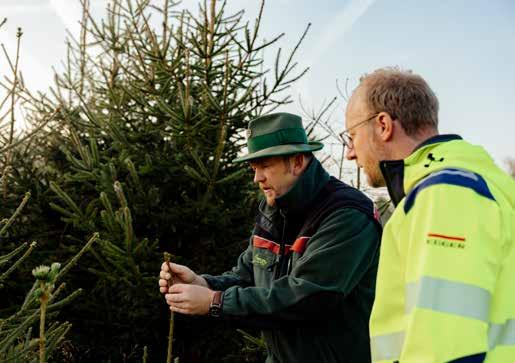
Side by side at difficult times
The significant value afforded by good partnerships is often particularly evident in times of difficulty. Brilon was hit by severe storms in 2007 and 2018. This resulted in major forest damage, which created enormous quantities of damaged timber. It is important to harvest this disaster-relief timber quickly, otherwise bark beetles can spread unhindered, using the lying trunks as their breeding ground. Martin Hillebrand, Wood Purchasing Manager at the plant in Brilon, explains EGGER’s key contribution: “As a wood purchaser, I am proud and very grateful that EGGER has mustered the enormous financial strength to store and preserve a lot of wood after the storms. We were able to support many forest owners and take their damaged timber off their hands.” This wood was then temporarily stored and preserved in specially created wet or dry stores across the region, where it was protected from further decay and could be used in our production as required.
Cascading use: a model of raw material efficiency
At EGGER, we consistently follow the principle of cascading use of wood: At the top of the wood cascade is high-quality round sawn timber, from which timber is produced in sawmills, such as our own sawmill in Brilon. This sawing process creates sawing by-products. This is by no means considered waste, but a valuable resource for producing durable wood-based materials such as chipboard or MDF boards. Industrial roundwood – thin, crooked, knotty trunks, thinning or damaged wood resulting from storms or snow breakage – is also processed into derived timber products. “We can use lower-quality wood to produce wood-based
materials. They are a little too thin for the sawmill, but certainly too good to burn,” explains Christian. If wood is reprocessed and reused after initial use, it is referred to as recycled wood. This gives the valuable resource of wood multiple lives, and the carbon stored in it can continue to be stored over its entire useful life. Wood should only be used to generate energy at the very end of it’s useful life.
Our masterplan to counteract raw material shortages Forests are coming under increasing pressure as a result of climate change. Ideas are needed to use these changing wood qualities in the best way possible. And joint efforts are required to regenerate forests as well as ensuring climatefriendly, sustainable forests. Successful partnerships are the key, as highlighted perfectly in Brilon. There, many hands make light work to ensure forests are managed sustainably –

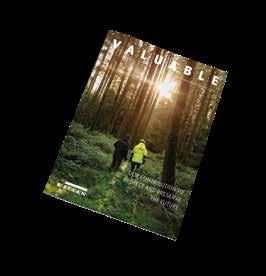
Read the full story from
This story and many available to read in our new sustainability journal, . It’s really worth
Martin Hillebrand has been a wood purchasing manager in Brilon for many years.
Reforestation is a crucial part of sustainable forest management. Sebastian Schönnenberg and Christian Witte inspect young trees.
A circle in all it’s beauty
Closed loops extend our ability to use the valuable resource wood. By consistently using recycled wood, we are clearly committed to the circular economy. This stance is abundantly obvious in the interaction between our international recycling collection centres and our plants. We wanted to take a closer look at this and followed some of our recycled wood from our Timberpak site in Leeds (UK) to our nearby plant in Hexham (UK).
Leeds: a hub for recycled wood
Under the name EGGER Timberpak, we run international recycling collection centres that supply our plants with recycled wood. There is a lot of coming and going at our Timberpak site in the northern English city of Leeds. Approximately 150,000 tonnes of recycled material are processed there annually. The wood comes from a wide variety of sources – from disused pallets to furniture and construction waste. The material is carefully prepared here at Timberpak.
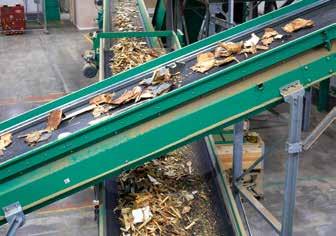
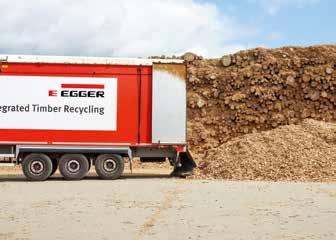
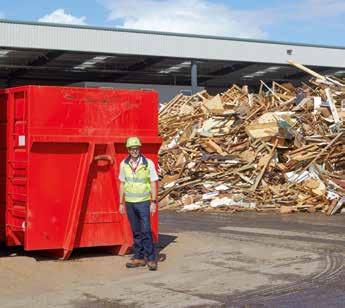
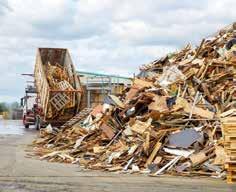
Crucial for further use: the sorting process
“It’s a fascinating process,” explains Mark Hayton, Head of Timberpak UK. “The wood waste is sorted, shredded, cleaned and tested before it makes its way to the EGGER chipboard plants in Hexham and Barony.” The sorting process is one of the biggest challenges: Around 40 percent of the wood we receive comes from household waste sites, where pieces of furniture embellished with fabric or other materials often end up in the wood container. Timberpak’s quality controllers therefore have a key role to play. They ensure that only suitable material is loaded onto the lorries that set off for our chipboard production sites every day.
We then head to Hexham where new products are made from recycled wood
The cleaned and shredded recycled wood arrives at the log yard in Hexham. The final processing step is then completed in our plant. State-of-the-art processing plants ensure that this used wood is turned back into a high-quality material for boards.

Mark Hayton, Head of Timberpak UK, shows us around the site in Leeds.
Our production in a closed cycle
Renewable energy
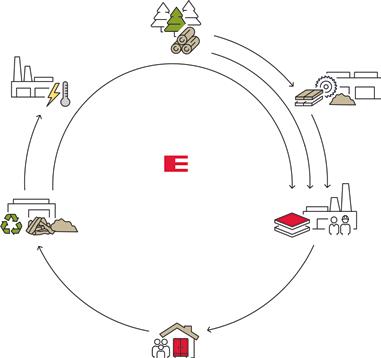
To us, recycling is more than just a process. It is a philosophy that helps us to work towards a sustainable future through the circular economy. However, recycling is only one element of the EGGER Group’s closed-loop production, which forms the basis of our business model. We want to maximise the use of wood as a valuable resource. We achieve this by utilising it in several stages and keeping it in circulation for as long as possible. The equation is quite simple: the longer wood remains in the cycle, the longer the carbon remains bound in it. Even today, 65% of the wood used in our wood-based
Production in a closed cycle
Wood-based material production
Processing and utilisation
materials throughout the Group comes from the circular economy, i.e. from recycling or sawmill by-products. Only when we can no longer utilise the wood as a material do we use it as a source of renewable energy.
Quality and sustainability are two sides of the same coin Recycled material from Leeds is therefore used to produce new chipboard. We then refine the boards to transform them into high-quality design products featuring on-trend surfaces. “Our aim is to create products that are not only sustainable but also aesthetically pleasing,” emphasises our colleague Aimee Fletcher, Product and Design Manager at Hexham. She understands our customers’ needs inside out and knows that our products stand out thanks to their quality and design features.


Have we piqued your
You will soon find this story in full in our new sustainability journal,
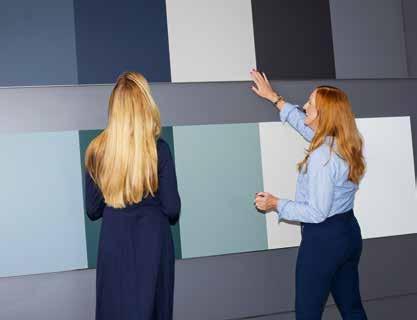
Aimee Fletcher (right), Product and Design Manager at Hexham, knows that sustainability and quality are important to our customers.
Sawmill
Recycling
Have you heard?
#Joethebedsidetable
Do you already know the story of Joe the bedside table? Take a look at our brand new About Us page on egger.com and find out how Joe is transformed into a bedside table thanks to the circular economy.

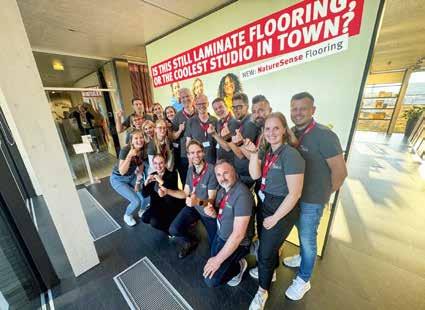
#GermanSustainabilityAward2024
Since 2008, the German Sustainability Award has honoured outstanding achievements in business, local authorities and research and is considered the largest of its kind in Europe. At this year’s award ceremony in Düsseldorf, the EGGER EcoBox secured victory in the ‘Resources’ category and sent a strong signal in favour of sustainable innovations.
#FlooringTrainingFestival
In September, our sales and marketing colleagues discovered the new 25+ flooring collection in a totally new atmosphere. At the Flooringland Festival in Wismar (DE), our new products and campaigns were introduced alongside music, wristbands and presentations on three product, decor and marketing “festival stages”.
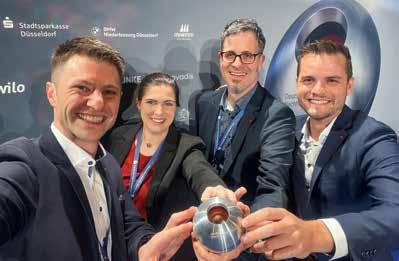
#EGGERzum
This year, EGGERZUM took place for the second time from 18 November to 13 December. Based on the motto “conNEXTion”, new introductions such as the EGGERTrendCast were presented, which provides interactive advice on various surface solutions using specific application examples. In response to customer requests for information about new products to be shared earlier, EGGERzum will be held annually in autumn in future.
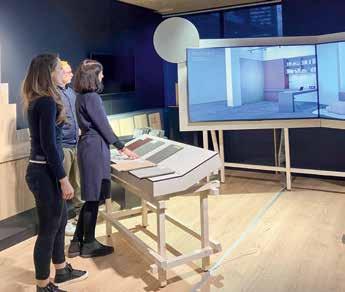
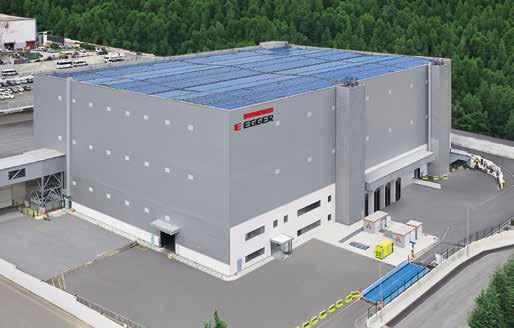
#GEBSolarEnergy
Since the end of last year, our logistics centre in Gebze (TR) has been selfsufficient in terms of energy. This is all thanks to the power of the sun, which supplies our new photovoltaic panels on the 6,500 m² roof area with solar energy.
#FirstLaminatedBoardBarony
A reason to celebrate: Barony (UK) has made a significant step from raw chipboard manufacturer to producer of laminated Eurodekor chipboard. All those present proudly signed the first coated board.
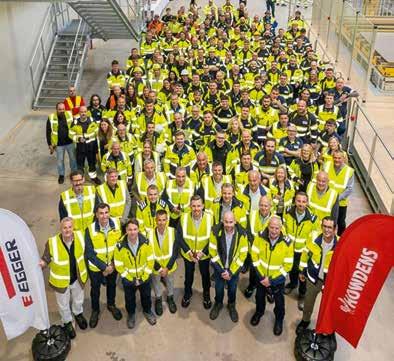
Investments
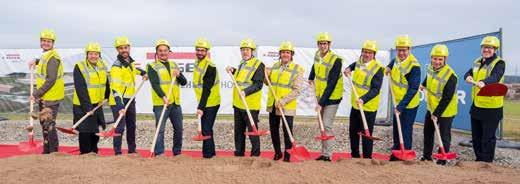
The ground-breaking ceremony for a sustainable future – from left to right in the picture: Thomas Abrell (Division Management), Helmut Bodner (Bodner Group), Manuel Aigner (Project Management representative), Fritz Egger (Owner), Markus Scheran (Plant Management), Hans Herold (Deputy District Administrator), Robert Kelca (ATP Architects), Michael Egger Jr. (Group Management), Klaus Nölp (Mayor of Markt Bibart), Bruno Hülsbusch (Plant Management), Bernhard Vorreiter (Division Management), Gerhard Riedmann (Plant Management)
Markt Bibart combines new construction while modernising existing buildings
The multi-stage investment plans in Markt Bibart have started successfully. Construction of the new recycling wood processing plant began at the end of September. To mark the start of the expansion phases, an official ground-breaking ceremony was held on 24 October. Michael Egger Jr., member of the EGGER Group Management, Fritz Egger and Walter Schiegl, members of the Supervisory Board, and the Markt Bibart plant management welcomed numerous guests, including Deputy District Administrator Hans Herold, Mayor Klaus Nölp and representatives of the companies realising the construction work, to inspect the construction site together.
A strategically far-reaching investment
In total, we are investing over EUR 200 million in Markt Bibart to drive forward our focus areas of sustainable and responsible management, expanding our processing capacities and automating our logistics. It is planned that the investment project will be complete by autumn 2026. In addition to the sub-projects of recycled wood processing, creating lamination capacities and automated storage areas, the agenda also includes optimising existing facilities. All expansion phases have one thing in common: EGGER is using state-of-the-art plant technology. The investment will also create around 50 new jobs.
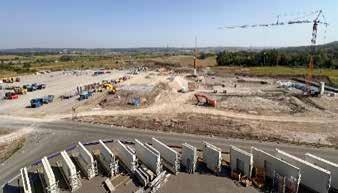
We are convinced of the great potential of the Markt Bibart plant. We have undertaken far-reaching strategic projects that will significantly develop both our use of raw materials and our product portfolio at the site. We are proud that we can start construction work so quickly. This is a great team effort. We would like to thank our employees and partners as well as all political decision-makers for their constructive cooperation. Michael Egger Jr., Chief Sales Officer EGGER Group.
The first expansion phase begins on the greenfield site
A new space is being created in Markt Bibart to process recycled wood so this wood can be used several times in different production cycles. Scheduled to go into operation in summer 2026, the state-of-the-art processing plant will be key for using recycled wood. We will ensure the plant is supplied in the long term, thanks to the new Timberpak Recycling collection centre directly next to the plant premises. This provides access to recycled wood from the metropolitan regions of Würzburg/ Nuremberg. Many congratulations on successfully launching the project and we will continue to report on the expansion in Markt Bibart.
Brilon’s new finger-jointing line
In October, the EGGER sawmill in Brilon (DE) marked the official commissioning of the new finger-jointing line with all of the sawmill’s employees. Together, all those present signed the first finger-jointed timber in celebration. This marks an important milestone for the sawmill in Brilon and the EGGER Building Products division.
An investment in the highest quality standards
The finger-jointing line has an investment volume of around twenty million Euro and has been built on a surface of 5000 m². Four employees per shift monitor the production of fingerjointed timber with an annual production volume of up to 80,000 m³. The line was set up and installed in co-operation with System TM in Brilon.
We are pleased that we were able to keep to our schedule and that production is starting as planned. A big thank you goes to our project team and the system specialists from System TM.
Georg Lingemann, CEO Brilon sawmill
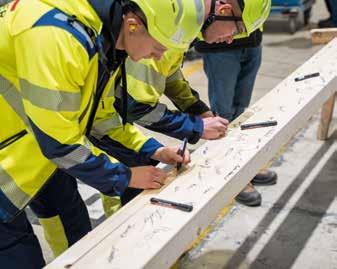
The first finger-jointed timber was ceremoniously signed by all those present.
Finger-jointing creates new possibilities for wood construction
The new, stable method of joining wooden elements makes it possible to produce new, long slats, planks, boards or beams from shorter singular pieces of wood. The wooden parts are given wedge-shaped teeth through milling. These are then glued together, pressed and cured. Previously in wood construction, it was only possible to use roof battens made from a single piece of wood in order to guarantee standardised lengths and qualities. The main advantages of finger-jointing lie in upgrading the timber quality through the targeted cutting out of defects, which significantly reduces the proportion of waste and ensures the resource-efficient production of highquality timber products – true to our motto ‘More from wood’,” explains Arndt Silberg, Plant Manager Technical/Production in the sawmill.
The modern finger-jointing line generates maximum added value
To continue to meet market demands, EGGER is the first producer in Germany to include finger-jointed roof battens in its product portfolio. “Due to calamities, such as drought and beetle infestation, the raw material wood is becoming scarcer. As a result, products and production processes will have to change and adapt. Finger-jointing enables us to achieve maximum added value from the available raw material and provide our customers with the timber products they need,” explains Georg Lingemann about the investment in the fingerjointing line. We would like to congratulate all those involved on successfully launching this ultra-modern line.
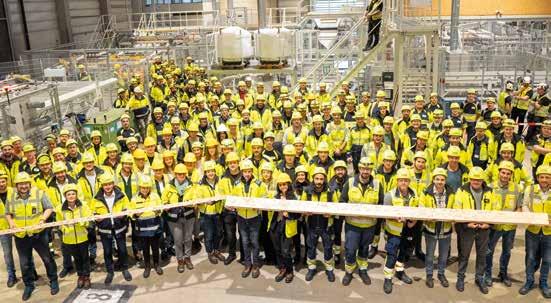
The start of production of the new finger-jointing line in Brilon (DE) was celebrated by all sawmill employees.
What happened...
We have grown considerably throughout our 60+ years of history. Six of our plants are celebrating an anniversary this year. Some of our colleagues have even been involved from the very beginning. We value their loyalty hugely and wanted to know their experiences of the plants developing.
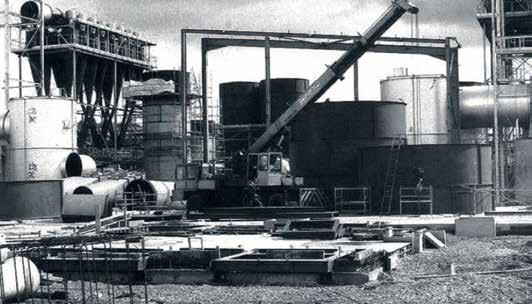
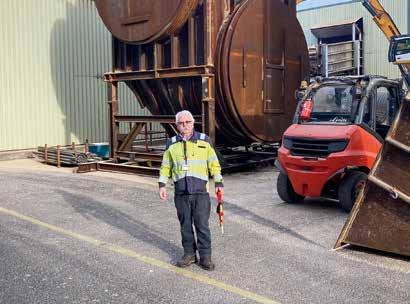
… 40 years ago?
In 1984, we positioned ourselves internationally by acquiring a chipboard manufacturer in Hexham (UK). Since then, we have continuously invested in the plant, which has subsequently been equipped with the most technologically advanced systems. Our colleague Arthur Harvey became part of the EGGER workforce shortly after it was acquired and now coordinates technical projects in Hexham. He’s shared his memories of that time with us.
Arthur Harvey – Specialist Project Engineer, Hexham (UK)
“The company was still young in the mid-1980s, but it had an adventurous vision for expansion – and a grand plan! It became clear to me in the first few days alone that this company thinks long-term and has a great future ahead of it. I've always loved working with machines and learning new skills. I was very impressed by the modern KTs and impregnation processes that were soon established. My time with the company got off to an exciting start and I am grateful for the inspiring people I worked with! Today, I am proud that I was able to contribute to EGGER’s international success alongside the team in Hexham.”
… 30 years ago?
In 1994, EGGER took over a chipboard producer near Bordeaux, in Rion-des-Landes (FR), thus expanding its sales network to include France and Spain. The plant has grown hugely since then. Our colleague Béatrice Montes-Bougès, one of our very first employees, works in Marketing and has taken a very emotional look back on the past 30 years.
“I still remember the company takeover celebration very clearly. This is when I got to know my
Austrian colleagues. I still remember their friendly manner, team spirit, commitment and passion for their work.
Over the past 30 years, our plant has constantly evolved and now looks totally different. Investments were made in production capacity, as well as in logistical processes, the use of recycled wood and much more besides. To my mind, EGGER is family since I’ve grown up with EGGER and have developed with EGGER.”
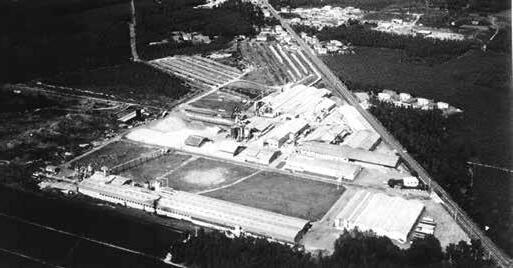
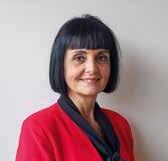
Béatrice Montes-Bougès, Communication Expert, Rion-des-Landes (FR)
… 25 years ago?
We built one of the largest EGGER plants in Wismar (DE) in 1999. It was originally designed for MDF production, but more and more wood-based materials were soon added. Today, the plant on the Baltic coast impressively epitomises our status as a full-range supplier in the furniture industry. Our colleague Dörte Döring, who has been with the company for 25 years and is now a works councillor in Wismar, talks about the early days and what she particularly appreciates about the company.
“The staff team was much smaller in 1999. But it grew rapidly in the years that followed. Just like the plant premises: when you went home in the evening, you would see something new the next day. There are many stories worth telling from this exciting construction phase and I am proud that I was able to witness this huge plant being constructed. These early days also shaped me personally, as I formed valuable friendships with my colleagues.
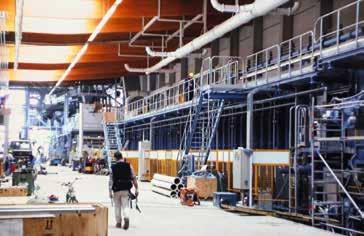
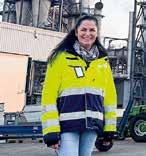
Dörte Döring – Works Council, Wismar (DE)
We are simply a family and I am grateful every day that I work in a place where the employees are the most important thing. Whether through further training opportunities or a great sense of solidarity within the company – you can simply feel that EGGER is a family business.”
Reaching new heights in digital collaboration
Together towards the digital future at EGGER
We aim to be able to collaborate efficiently from anywhere –whether at a desktop/Citrix workstation or on a smartphone – and with any partner, whether internal or external. The improved digital workplace will take our collaboration to the next level. To this end, we are restructuring our tool landscape in order to have fewer systems and achieve greater simplicity and user-friendliness. This change affects us all, and we look forward to working together to create a more modern and flexible digital workplace at EGGER.
Microsoft 365 CoreSetup begins to be rolled out
The first part of the roll-out has already begun. 700 Corporate Services employees received access to the new Microsoft 365 tools in early autumn and are providing valuable feedback for rolling out the Microsoft 365 CoreSetup across the entire workforce.
Over 50 Key Users within Corporate Services
Our Key Users are the pillars of our success. As multipliers, they are not only contact people for their teams and departments, but also driving forces that motivate others and reduce uncertainty. They will receive intensive training to support their teams and drive the change process forward.
In 2025, the Microsoft 365 CoreSetup will be rolled out to all colleagues with a personal email account
The improved Microsoft 365 tools form the basis for a standardised, flexible working environment that makes digital working easier and more effective. Some of these tools are already in use. These will be replaced by modern cloud-based versions, while others will be added and replace existing tools. Throughout 2025, the CoreSetup will be rolled out and Key Users will continue to be trained department by department.
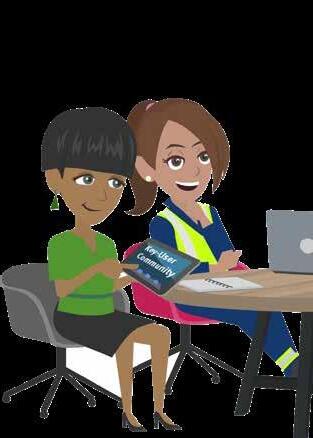
Hi, I’m Bennet!
In future, I will help you to find your way around the training and information that is on offer in relation to the Digital Workplace. You will quickly learn which tools are available on which device for whom and what benefits they bring you in your day-to-day work. In short:
Don’t worry. Since 1 July, the newly created Digital Workplace Team has been working hard to make sure that everyone is empowered to work productively and efficiently with the improvements.
We’re here to support you. We have many experts on hand to help facilitate the switch. The Digital Workplace Team, the IT helpdesk and our Key Users are available to answer any questions you may have and help you make the most of the new tools and the improved digital workplace.
We will keep you updated on this: You will receive regular information so that you know exactly when it is your team’s turn and what support you will get.
And most importantly: It’ll be worth it for you. Even if there are still open questions at the moment, as soon as you learn the tools, you will discover how much easier and more efficient digital working at EGGER will be.
We are starting gradually and look forward to reaching the next level of digital collaboration together.
Digital Workplace EGGER
1. Microsoft 365 CoreSetup
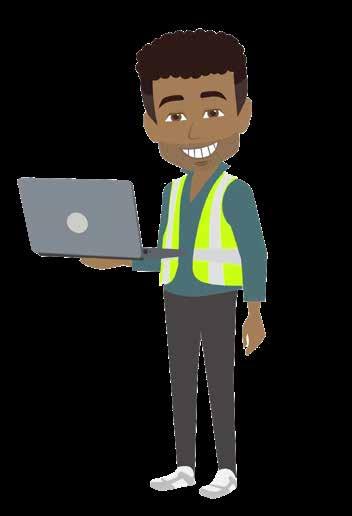

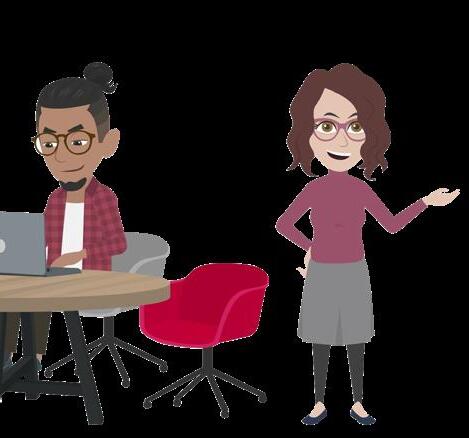

MS Teams for easy communication and collaboration (will replace Jabber and Webex software).
OneDrive for saving and sharing personal files.

OneNote for personal and shared notes.
Planner/ToDo for task organisation.

Whiteboard for creative work in groups.
Curtain call for... Monika Stadler
Monika Stadler has been at EGGER since 1995 –her journey began at the Braustüberl brewery tap-room in Unterradlberg (AT), where she waited on guests with heart and soul. Over the years, she has also worked as a cleaner in Production – anyone who knows her also knows that her passion is infectious.
What does your work look like?
“Nowadays, I am only employed part-time and they simply call me when I am needed. But it’s not a must for me. If the phone rings, I just ask “When can I come to work?”
What motivated you to work at EGGER for so long?
“EGGER is a down-to-earth family business. Here, we rely on trustworthiness, and you can sense that in our daily interactions. It’s just nice to work in an environment where the values hold true and are tangible. From the very beginning, I built up a strong bond with the family and the advisory board, which keeps me going. And whenever I drive past the company on the motorway, I always think proudly that this is my company.”
What do you value most about your direct interactions with customers and colleagues?
“The guests were mostly strangers, especially those on guided tours. But that’s precisely what brought me great joy: Chatting with them, getting to know them and watching their reactions – especially when they try our EGGER beer for the first time – is simply priceless! And the same can be said about my colleagues.
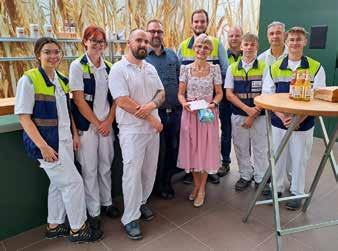

When I come to work now, I get such a warm welcome that it feels like coming home every time.”
You have another passion – running – what motivated you to take this up?
“I’ve been involved since the very first run in 2003. When I heard that we were accumulating kilometres to donate money to families in need, I immediately started running. This inspired me because it makes such a difference. I’ve got to know a lot of people from EGGER during the runs, and sometimes I even get asked: ‘Are you the Monika from EGGER?’ It’s a wonderful feeling to be recognised for something like this. I always wear my EGGER top when running – I wear it with pride at home and when I’m out and about.”
What changes have you witnessed during your time at EGGER?
“It goes without saying that there have been ups and downs over the years, that’s par for the course. But things have always worked out for me. What particularly struck me is that many of the people I got to know as a teenager are now managers – it’s wonderful to go on this journey together with them. We have become more international, and this is also reflected in the diversity of our guests. In the past, our visitors were mostly older, but today they are younger and even more interested. We are constantly evolving, and that is precisely what makes EGGER so unique. I hope things continue to progress so positively!”

Reinhard Grießler, Managing Director of EGGER Getränke and our long-standing employee Monika Stadler.
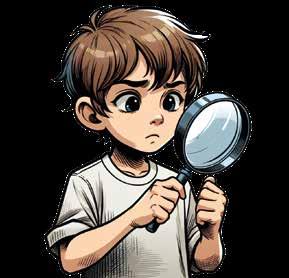
The page for grown-ups and children
Welcome to our forest. But it’s much more than just wood. It is home to many plants and animals, and also a place of leisure for us humans.
Help us to keep the forest clean – find five things that don’t belong in the forest. Someone has carelessly thrown a rubbish bag, a car tyre, a glass bottle, a shoe and a tin can into the forest
Have fun!
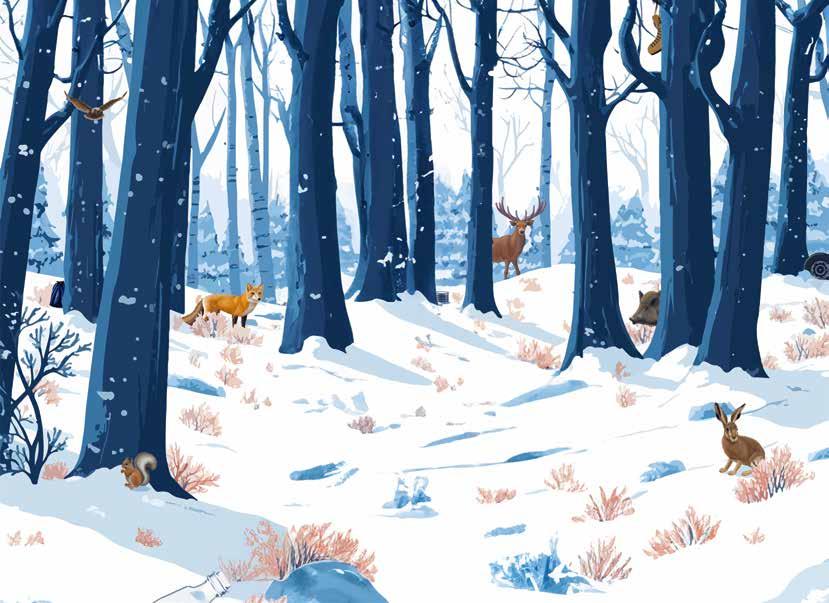
What's next?
Unique exhibition stand at BAU
We will once again have a presence at the BAU exhibition in Munich from 13-17 January. Under the motto “The house –Sustainable.Creative.Innovative.”, we will present the future of construction.
Our flooring collection is launched
Sales of the new 25+ flooring collection have begun. We’re looking forward to launching the campaign “Is that laminate or the coolest dancefloor in the world?”.
Our journey into the future of marketing
Details of workshops that are part of the “Next Level Marketing” series, in which colleagues from different cultures and positions work together, will be finalised in January. The new jointly developed marketing strategy will be presented at the beginning of the year.
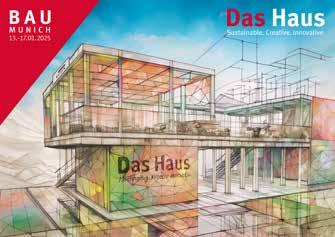

Thank you for your tireless efforts throughout the year. Together we will make another great start in 2025!
Do you have a suggested topic? Please get in touch with: annika.kleber@egger.com
We look forward to your suggestions!
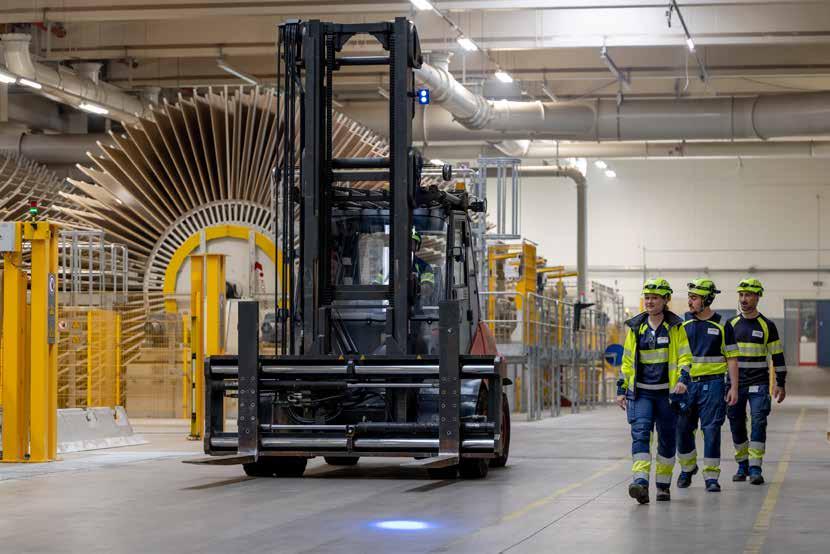