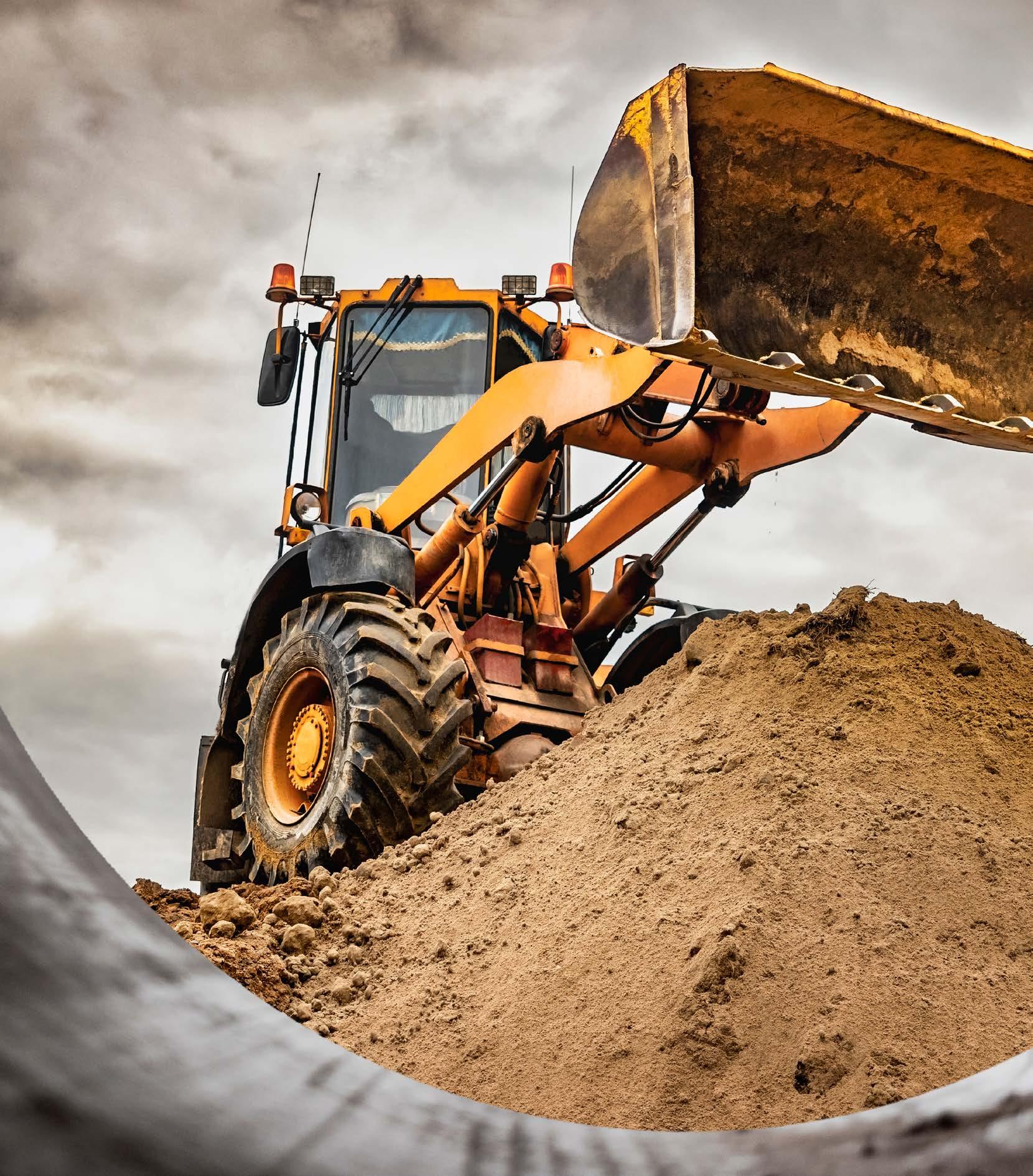
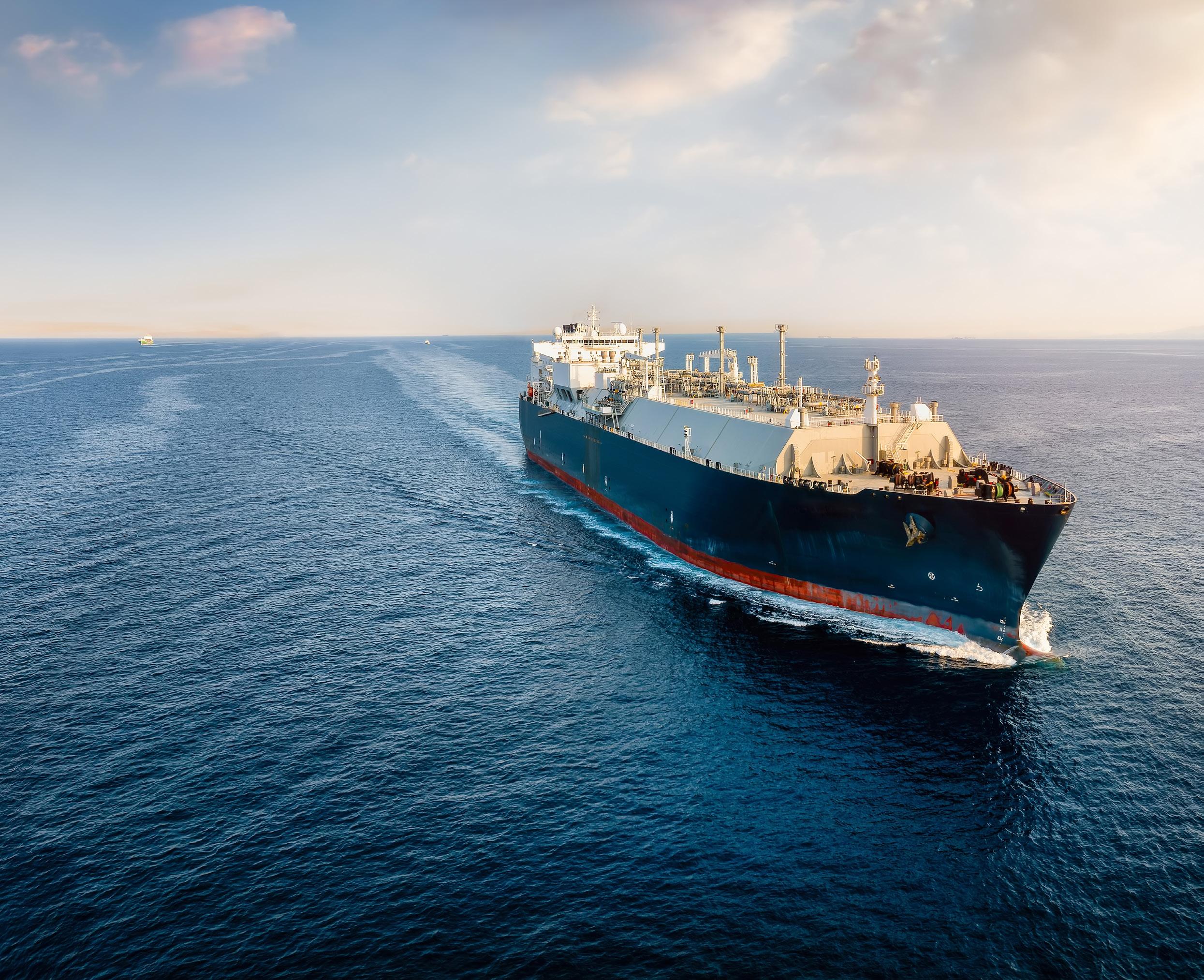
We strive to act as local guides through the unique and varied terrain of shipping and port logistics, always mapping out the best avenues for our clients and walking them through the tricky areas. Showcasing our expertise inspires the trust that remains the primary ingredient in our relationships and the key to our success.
Expert Advisors in Your Camp:
Editor-in-Chief Carley Fallows editor@littlegatepublishing.com
Advert Space Director Emlyn Freeman emlynfreeman@littlegatepublishing.com
Project Director Andrew Richards andrew@littlegatepublishing.com
Commercial Manager James Hamilton james@littlegatepublishing.com
Lead Designer Adam Knights
Research Kristina Palmer-Holt
Editorial Research David Craig
Corporate Director Anthony Letchumaman anthonyl@littlegatepublishing.com
Founder and CEO Stephen Warman stevewarman@littlegatepublishing.com
For enquiries or subscriptions contact info@littlegatepublishing.com
+44 1603 296 100
ENDEAVOUR MAGAZINE is published by Littlegate Publishing LTD which is a Registered Company in the United Kingdom.
Company Registration: 404 2112 62
VAT registration number: 13572767
343 City Road 60 Thorpe Road London 79 Norwich
EC1 V1LR NR1 1RY
Littlegate Publishing Ltd does not accept responsibility for omissions or errors. The points of view expressed in articles by attributing writers and/or in advertisements included in this magazine do not necessarily represent those of the publisher. Any resemblance to real persons, living or dead is purely coincidental. Whilst every effort is made to ensure the accuracy of the information contained within this magazine, no legal responsibility will be accepted by the publishers for loss arising from use of information published. All rights reserved. No part of this publication may be reproduced or stored in a retrievable system or transmitted in any form or by any means without the prior written consent of the publisher.
Copyright© Littlegate Publishing Ltd
back to
Our May edition kicks of with an exciting look into the work of Hitachi Construction Machinery Co. Ltd, to see how the company delivers vital machinery to the construction and mining sectors. The company is committed to providing products that feature the latest technological innovations to make its customers’ operations safer, more efficient, and more sustainable. We are glad to see Edbro Hydraulics Ltd. showing support for this article as a leading hydraulic cylinder manufacturer committed to bringing innovation to every product it creates.
We then turn to Adani Ports and Special Economic Zone Limited (APSEZ) who are supporting India’s commercial port operations spanning across 13 domestic ports and 7 maritime states. The port provides the necessary infrastructure and beneficial economic zones, that allows APEZ to remain competitive in global shipping lines. For this, it is great to see SSR Marine Services Pvt Ltd and Maheshwari Handling Agency Pvt Ltd, providing vital support to APEZ as key maritime and shipping partners helping APSEZ deliver its services across the region.
This month we also return to some vital companies spanning industries from mining with Vale S.A., to tourism with the Department of Culture and Tourism – Abu Dhabi, and even to the medical field with Joint Medical Holdings. All of these companies are focused on delivering vital development for their respective sectors, in a goal to improve life, bring economic growth, and commit to more sustainable future for generations to come.
by Carley Fallows
The World Wide Fund (WWF) for Nature and Lahore University of Management Sciences are working together to develop and artificial intelligence programme which hopes to protect snow leopards across Pakistan. The country is home to the thirdlargest population of snow leopards in the world, with scientist estimating about 300 of the 4,0006,000 left in the wild are within the country. However, more and more leopards are being killed by famers when they attack livestock.
Snow leopards are protected by law, however, their deaths from retaliation from the loss of livestock is thought to have contributed towards a decline in the population in the last 20 years. Therefore, researchers and the WWF have begun working together to set up a system of cameras that alerts to the presence of the snow leopards and warms villagers via text in advance. This text alert it thought to help farmers move their livestock to safety before the big cat arrives, helping to prevent the loss of livestock and the death of the snow leopards as a result of this. However, it has been met with resistance from locals over its effectiveness.
In recent weeks President Donald Trump has imposed tariffs across the world, with many countries getting a base level 10% tariffs on imports to the US. However, Trump imposed larger tariffs on countries he deemed the ‘worst offenders’ and so countries such as China received substantial tariffs. In early April, Trump imposed a 34% tariff on China, which was met with a 54% tariff on US goods by China. Over the last few weeks these tariffs have continued to increase in reaction to the other. Trump currently has imposed taxes of up to 145% on imports from China, with China responding with a 125% tax tariff on products from the US.
Trump introduced the tariffs to encourage US consumers to buy American-made productions, to bring of economic investment into the country. However, some industries in the US rely on products from abroad, such as technology and vehicles with China being big player in these markets. Trump has currently paused proposed higher tariff rates for roughly 60 other countries, as many governments around the world try to work out a trade with between their country and the US.
A young sprinter in Australia is currently breaking sprinting records, and for many has been compared to Usain Bolt for his achievements and speed at such a young age. The sprinter, Gout Gout, of South Sudanese heritage, has taken the Australian school and national-level athletics championships by storm. Gout has led the 100 and 200 metre races in Australia’s age group athletics championships, winning gold in both distances consistently since the age of 15. His speed around the track has been compared to that of Olympic sprinting legend Usain Bolt, having surpasses Bolt’s time of 20.13 seconds in the U16 200m in the Australian All School Championships in late 2024 with a record speed of 20.04 seconds. This makes Gout the second-fastest 200m male athlete ever in the under 18s category. At the same competition he also broke the Australian U18 record for 100m with a time of 10.17 seconds. Whilst Gout is yet to compete in a senior World Athletics champions, it is thought he could make his debut as early as July 2025, should he be picked by the Australian Athletics to go.
50 hippos from the Democratic Republic of Congo have been killed by poisoning in the Virunga National Park. The cause of the poisoning unknown but the presence of anthrax has been shown in tests. Anthrax spores are caused by Bacillus anthracis and are often hidden away in soil for years and are only able to get into the animal through inhalation or via cut or wound. Whilst the spores are not spread easily, it is deadly for the animals.
Recent decades have seen efforts to boost the population of hippos in the national park, especially following the decline in hippo populations in the Democratic Republic of Congo from over 20,000 to just a few hundred caused by poaching and war. Today, Virunga National Park is one of the most biologically diverse parks in Africa, with many different yet deadly species.
A penguin has caused a helicopter to crash in South Africa, after it was unsecured during take-off. The penguin was being transported in a cardboard box sat on the lap of the passenger in the helicopter. However, when the helicopter took off, the box slid off the passenger’s lap and knocked into the pilot’s controls. This caused the helicopter, that was only in 15 metres in the air, to lose control and lead to the main rotor blade hitting the ground and crashing. Thankfully none of the passengers on the plane or the penguin were harmed during the crash.
The helicopter had been part of an aerial survey over Bird Island off the coast of the Eastern Cape. The penguin was being transported to Port Elizabeth on instruction from a specialist, however, the report has not outlined why the penguin was picked up.
As one of the largest gold producers in Africa, and the sixth largest gold producer in the world, Ghana is a vital source of global gold resources. With such a wealth of gold deposits in the country, Ghana has long been home to global mining operations in the region, as well as illegal mining operations. However, in recent years the country has been facing harsh economic times, which has seen the gold mining industry fuelled by rising gold prices and growing youth unemployment. Therefore, the country has established the Ghana Gold Board (GoldBod) that has banned all foreign companies from trading within local gold markets in Ghana. This move is designed to help boost the country’s national revenue and streamline the country’s mining sector. The new law passed by the parliament, has outlined that GoldBod is to be the sole buyer, seller and exporter of all gold produced by the artisanal and small-scale mining (ASM) sector. $279 million has been allocated to the new body to purchase and export at least three tonnes of gold per week. With foreign companies only allowed to apply to buy or off-take gold directly form the GoldBod. However, these companies can no longer operate within the local gold value chain.
A tortoise thought to be about 100 years old from the Philadelphia Zoo in the US, has become a mother. The tortoise, Mommy, laid 4 eggs, with the first to hatch in late February. The father of the four hatchlings is Abrazzo, and the pair are Western Santa Cruz Galapagos tortoises both ages around 100 years. The arrival of the 4 new hatchlings is exciting for the zoo, as the birth is the first of the species at the zoo in the more than 150 years that it’s been in operation. In fact, Mommy, arrived at Philadelphia Zoo in 1932, and is the oldest known first-time mother of her species. The father, Abrazzo, is a newer addition to the zoo’s Reptile and Amphibian House, arriving only in 2020 having previously been located at the Riverbanks Zoo and Garden in South Carolina.
The hatchlings hope to bring a vital population increase of Galapagos tortoises for zoos across the country and may mean visitors can catch a glimpse of the new hatchlings for maybe another 100 years from now like their parents. The baby tortoises are currently being cared for by the Philadelphia Zoo’s care team and will be kept behind the scenes for the time being as they start to eat and grow. The first glimpse of the tortoises is expected in late April in coincide with the 93rd anniversary of the mother’s arrival at the zoo.
To curb child obesity in Mexico, the sale of salty and sweet snacks has been banned in schools. The scheme has been sponsored by the government, to tackle what has been described as one of the worst obesity and diabetes epidemics. It is hoping that this measure will be supported by parents, to phase out food and beverages for kids that contain high levels of salt, sugar, calories or fats.
School are being asked to phase out any food or beverage that displays any of the warnings regarding these 4 groups, and in turn the government is seeking to implement a compulsory front-of-package labelling system for these foods, which it first rolled out in 2020. This system would see black octagons on the front of all packaging for food products that contain excessive amounts of added sugars, saturated or trans-fats, sodium, and calories in processed and non-alcoholic beverages. The system will also have warning about non-caloric sweeteners and caffeine, to advise against their consumption by children.
A nationwide health emergency was declared in April after the deaths of 34 people in Colombia due to yellow fever. The yellow fever virus is transmitted to humans via infected mosquitos, with a vaccine being the leading prevention from the virus. The vaccine in most cases provides lifelong protection, and so the government has encouraged people to get vaccinated before they travelled for Easter.
The number of yellow fever cases has risen in recent years according to figured publishing by the Ministry of Health. Plus, diagnosing yellow fever can be quite difficult, especially when many of its symptoms are the same as that of other diseases or fevers. Whilst most people do recover from yellow fever after the first phase of the infection, which is often linked with fever, muscle and back pain, headaches, shivers, and loss of appetite, as well as nausea and vomiting; some people can develop more severe symptoms in s second phase of the virus, causing high fever, jaundice, bleeding and the deterioration of kidney function. This second phase often has more fatal outcomes for those infected.
The proud guardian of Sudan’s substantial gold resources, Ariab Mining Company Ltd is targeting portfolio diversification in conjunction with international investors.
As the mineral-rich republic’s leading operator in gold exploration and exploitation, the ambitious company is seeking to dig deeper and unlock additional value in several existing mines and highly prospective exploration tenements.
With the goal of achieving long-term value that is strategic, significant, and sustainable, the state-owned firm is on a quest to increase technology acquisition to develop a world-class project pipeline. The forward-thinking enterprise is adopting winning strategies, transforming operational performance and delivering step-change improvements throughout the value chain – from strategy to capital productivity and to developing skills in local communities. With Sudan introducing investment laws that match international standards, now is the ideal time for intelligent investors to bring knowledge and technology to achieve lucrative rewards.
A rare blue diamond went on display at an exhibition in Abu Dhabi in the United Arab Emirates. The diamond, from South Africa, is believed to be one of the rarest blue diamonds to have ever been discovered and was exhibited along with $100 million worth of other rare gemstones. The diamond itself is expected to be auctioned off at around $20 million according to Sotheby’s.
Blue diamonds are rare due to their formation which requires extreme depths, and a very specific chemical composition including the presence of boron. The boron is what gives the diamonds their blue hue, however as their chemical composition is rare to find it makes them super scarce and so can fetch such high price point at auction. The 10-carat blue diamond was exhibited alongside other valuable items such as a 5.05-carat square emerald-cut fancy brown-red diamond and a 303.10 carat par-shaped Fancy Deep Brown-yellow Diamond on a necklace.
A sandstorm in Iraq have led to widespread reports of respiratory issues across the central and southern parts of the country. The region was covered in a thick orange haze, as the dust storm covered the area. The sandstorm caused flights to be suspended, and some localised power cuts were reported by local media. The breathing conditions were very poor, with people wearing facemasks to protect themselves. However, more than 250 people are reported to have been taken into hospital in Najaf province, with a further 530 people reported breathing issues in Dhi Qar and Basra province. It is reported that 1000 people have been left with respiratory problems following the sandstorm.
Sandstorms are not uncommon in Iraq, however with the increase in climate change, it is thought that these sandstorms could become more frequent. In fact, Iraq is listed as one of the five countries that are most vulnerable to climate change by the United Nations, due to its regular sandstorms, extreme heat and water scarcity.
Shark attacks are rare in Israel with the dusky and sandbar sharks that cluster in the area rarely being linked to shark attacks. However, in recent weeks a rare shark attack occurred leaving a swimmer missing off the northern Israel coast. The sharks commonly gather in the waters off the Olga Beach, due to the warm water that is caused by the local power plant at this time of year. However, the sharks are usually harmless with the last fatal shark attack occurring in 1948. People often can get up close with the sharks as they wade in the shallower waters without any attacks occurring.
The scarcity of attacks makes this shark attack a rarity in the region. However, the beach was closed following the attack, as police search for the missing swimmer that is believed to have been caught up in the shark attack. The attack is only the 4th ever recorded in the country’s history according to local media.
Universal has announced plans to build Europe’s first Universal Theme Park, which will be located in the UK. The park, which will be built in Bedford, will span 476 acres and is hoped to bring roughly 8.5 million visitors to the park in its first year alone. The park will bring a massive amount of investment into the local economy, with 28,000 new jobs created. A full planning proposal will be given to the UK government, with construction expected to begin as soon as 2026.
Universal is known for their theme parks in Orlando, Los Angeles, Japan, Singapore and China, which centre around the company’s films. The parks are super popular with people travelling all over the world to attend these parks with Universal’s Orlando Resort in Florida welcoming 9.75 million visitors in 2023. Therefore, in Europe, it will attract new visitors to the UK investing in the country’s tourism sector, and especially in the local economy. Universal Destination and Experience has already outlined that 80% of its employees will be sourced from Bedford, central Bedfordshire, Luton, and Milton Keynes providing vital employment opportunities for those in the local communities.
Following a period of ill-health, the Vatican has announced that Pope Francis died. The Pope, leader of the Roman Catholic Church, had previously spend 5 weeks in hospital dealing with double pneumonia, however, he still led his usual Easter address at St Peter’s Square on Easter Sunday. His death was announced by the Vatican just a day later following a stroke and subsequent heart failure. Services have begun to be held across the world as Catholics mourn his death.
Pope Francis’ funeral will be held on 26th April and will be attended by world leaders, religious figures and thousands of worshippers. Unlike previous Popes, St Francis had requested to be buried in a simple wooden casket lined with zinc, which is much simpler than his predecessors who are typically buried in three nesting coffins made of cypress, lead and oak. Following the death of a Pope, the conclave traditionally goes through a 15day mourning period, after which a new Pope will be elected by the College of Cardinals.
Plans to build a tunnel between Hamburg and Copenhagen have been announced to cut travels time and improve the interconnectivity of Scandinavia with the rest of Europe. The tunnel, proposed to be 11 miles in length, will be the world longest prefabricated road and rail tunnel. The tunnel will require a remarkable feat of engineering which will see 90 segments of the tunnel placed on top of the seafloor and then joined together. Each part of the tunnel will be made with reinforced steel, which is cast with concrete.
The project is expected to cost around €7.4 billion, with the project being largely funded by Denmark, with €1.3 billion from the European Commission. The project will be the region’s largest ever infrastructure project and makes up part of larger plan to enhance the travel links across Europe to help cut down on the need for flying. Once completed, travelling from Southern Denmark in Rødbyhavn to Puttgarten in northern Germany, will only take 10 minutes by car and 7 minutes by train. This is significantly faster than the 45-minute ferry voyage operating between them. Furthermore, travel times between Copenhagen and Hamburg utilising the route, will be cut from around 5 hours to just 2.5 hours. This makes the route a greener alternative helping deliver a more sustainable option for transport between the two cities.
On a mission to deliver innovative products, services and solutions across the construction sector, Hitachi Construction Machinery Co., Ltd. (Hitachi) is a globally expanding construction machinery manufacturer. The construction industry is vital to global infrastructure, with the sector responsible for building roads, houses and laying down waterpipes that are vital for supporting societal development. Therefore, the construction sector relies on innovative and efficient machinery that can help meet these needs across the globe. However, as the world moves towards a more sustainable future, Hitachi is focused on ensuring its products have a longer life cycle and are built with leading technology innovations to contribute towards a more sustainable future for the construction machinery manufacturing sector.
As a subsidiary of the global Hitachi Ltd., Hitachi is focused on bringing a leading worldwide manufacturer of construction equipment. Its role spans across the globe from its head office in Tokyo, to Europe, North America and South America. Today, Hitachi has roughly to 25,000 employees operating across the world who are key to bringing vital development, manufacturing, sales and service operations across the heavy machinery industry. The Hitachi we know today, began over 70 years ago following the start of its mass production of its cable operated shovels in the 1950s. This development was born from a mission to make construction work more efficient across Japan through the mechanisation of its construction machinery, to help rebuild the country and revitalise the economy. Therefore, Hitachi developed and delivered the first capable operated shovel using entirely domestic technology. This innovative spirit remains with the company today, and this is why the Hitachi brand remains a leader across the construction and mining machinery manufacturing sector.
Today, Hitachi’s machinery spans from mini excavators, mini wheel loaders, hydraulic excavators, wheel loads, compaction equipment, large hydraulic excavators, ultra large hydraulic excavators and rigid dump trucks.
Across these products, Hitachi is passionate about delivery top of the line manufacturing supported by leading solutions which maximise the value of its products. These solutions include its Autonomous Haulage System (AHS) which aims to address the challenge of safety across global mining and construction sites. AHS allows machinery to be safer, more productive and reduce costs over time by utilising Hitachi’s 24/7 system and field communication support that is integrated into its product lines. Therefore, Hitachi machinery can provide customers with low risk, staged implementation machinery that can operate efficiently alongside its customers’ existing fleet. AHS is then paired with Hitachi’s Fleet Management System (FMS) which is provided by Wenco International Mining Systems Ltd. under Hitachi. This solution ensures the real-time monitoring of each piece of machinery to enhance fleet management and utilise IoT platforms to optimise mining and construction processes, whilst utilising a wide range of data acquired through the integration of FMS across its product lines.
For construction machinery specifically, Hitachi has a Construction Machinery Solution Linage, which is an ICT/IoT system to help improve the safety and productivity of a product, whilst reducing its costs over its life cycle. It achieves this by bringing together the broad knowledge and advanced technologies from across Hitachi’s expertise, to deliver construction machinery that is designed to deliver results for its customers. Hitachi Construction Machinery ICT Solution is designed to fully support all ICT aspects of construction operations, taking projects from initial construction surveys to as-built data drive operations. A key development for this is the ICT Hydraulic Excavator ZX200X-7 which has been made with safety and construction efficiency in mind, to ensure that no matter the skill level of the operator, it will utilise its ICT system to deliver highly accurate, efficient and productive work every time.
To ensure the operational efficiency of machinery, Hitachi has developed ConSite, a solution which monitors the operational status of machinery and its alarms through operations reports. These reports and notifying alarms, ensure
WE ARE YOUR ONE STOP SOLUTION FOR PRECISION SHEET METAL PARTS AND ASSEMBLIES
Manufacture sheet metal parts and assemblies for Air Compressors, Earth Moving machines, Image and video processing machines, Power Generators, Medical equipment, Architectural signages and furniture, Banking Kiosks and ATM’s and Machine Tool Guardings etc.
that machinery can continue to run optimally and meet it customers needs. The entire ConSite report, is designed to keep customers continually informed about the operational status of a machine, which can then be easily accessed with a smart phone. In fact, ConSite has the ConSite app which helps customers oversee daily inspection and help with both owned and rental machinery.
Then Hitachi operates ConSite Air, which is a remote service helping Hitachi keep an eye on its customers machinery remotely, to more effectively meets customers’ needs and deliver operational support. All of these solutions highlight Hitachi’s goal to deliver machinery products that focused on delivering safety, efficiency, management and optimised performance to keep project sites running smoothly.
As Hitachi moves towards the future, it has set out a Bulidng the Future 2025 plan, which began in April 2023. The plan outlines how Hitachi wants to grow as a true solutions partner, and over the last 2 years this has been the foundation for the company’s machinery and solution development. These developments are outlined in the plan to be innovative and customer-oriented, and through this adding to the expansion of its operations. A key part of this has been in Hitachi’s value chain business which consists of parts and services, remanufacturing of used parts and machinery and the rental of equipment. Plus, with the ever-
Mr. Ashok Punjani – Director +91 9350186940 admin@carrierengineers.com ak.punjani@yahoo.com www.carrierengineers.com
growing issue of climate change, Hitachi has been set on expanding the life cycle of its products and contributing towards a more safe and sustainable society by extending the life of its machinery through remanufacturing, and the ability to rent machinery rather than purchase them. This prevents unnecessary machinery from going to waste, enhancing the performance of mahcinery whilst in operation, and then when parts go wrong, remanufacturing to extend the life of the machinery to reduce over production and in turn help keep its customers costs low.
In April, Hitachi announced that it had launched LANDCROS Connect Insight Solution, which aims to analyse the operational data of mining machinery collected in near-real time to help customers increase the efficiency of their operations. The solutions build on Hitachi’s experience and then utilises real-time data to support further detailed analysis backed by data scientists, mechanical engineers and other consultants in the mining field, to assist customers and dealers in proposals to
help maximise the performance of its machinery. LANDCROS Connect Insight, will allow Hitachi to build a digital platform that is capable of centrally managing and interlinking data with customers, group companies and collaborating business partners to deliver solutions that will continue to optimize its machinery, particularly in the mining sector.
Across Hitachi’s manufacturing developments, there is a real passion for the planet in delivering the vital machinery and tools to make infrastructural developments possible, all whilst achieving these in the most sustainable way possible. With a range of leading solutions under its belt that help to enhance its machinery and almost 70 years of expertise in the construction sector, Hitachi construction is delivering vital machinery that can deliver the future of the construction sector. We look forward to seeing how Hitachi will continue to expand its innovative solutions to optimise its machinery offerings, and deliver products that meet the needs of today without compromising the world of the future.
As India’s largest commercial port operator, Adani Ports and Special Economic Zone Limited’s (APSEZ) operations account for close to 1/4th of the country’s total cargo movements. With such a vast role across India’s cargo sector, it is no surprise that the port operator is present in 13 domestic ports and 7 maritime states, delivering vital cargo and shipping operations to expand India’s role in global shipping markets and deepen its shipping relationship across the country’s hinterland. However, even with such a wide sphere, APSEZ remains committed to being a worldclass business leader that enriches lives and contributes to the country’s infrastructural development for national value creation. APSEZ achieves this by delivering state-ofthe-art port operations supported by leading technology that drives the future of port infrastructure and port automation development.
APSEZ began in 1998 with just two berths at the Mundra Port in the Gulf of Kachchh in Gujarat in India. From these humble beginnings, APSEZ has vastly expanded the Mundra Port, and today, it is India’s largest port, spanning 24 berths and serving as a major economic gateway. From its expansion of Mundra Port, the company has continued to grow, and now it is the largest commercial port operator in the country, with its operations located strategically across 13 ports and terminals in India. These include the Gangavram Port, Karaikal Port, Krishnapatnam Port, Mundra Port, Gopalpur Port, Dahej port, Hazira Port, Vizhinjam Port, Kattupalli Port, Dhamra Port and Dighi Port. Its terminals include the Tuna Terminal in Gujarat, Mormugao Terminal in Goa, and the Enmore Terminal in Tamil Nadu. Across these ports, APSEZ delivers integrated port services focused on 3 areas: ports, logistics and special economic zones. This three-fold focus enables APSEZ to provide integrated services to leading Indian businesses to make its port operations enhance supply chains, making them competitive and cost-effective for these businesses without compromising on safety.
To fully understand the scope of APSEZ’s operations in India, we must look at Mundra Port, which is the largest port in the country and so plays a vital role in supporting the economic development of India and the country’s import and export market. The Mundra Port is a deep-draft, all-weather port encompassing efficient container services for bulk, break-bulk, container, crude oil, and liquid cargo, which APSEZ services with integrated marine and roll-on/rolloff services. The port specialises in cargo from the fertiliser, agri, mine and minerals, and steel and project cargo sectors, which are moved through the port yearround. Across the port, APSEZ utilises state-of-the-art Goliath cranes with attached vacuum lifters to deliver scratch-free handling of items such as steel pipes. In addition to this, the port provides a full mechanised semi-automatic bagging plant for fertilisers and the bagging of food-grade edible cargo. These help the port to remain efficient in serving the direct markets which utilise the port most.
One of the vital benefits of the Mundra Port is that it is strategically located along the Indian coastline in Gujarat, making it easily accessible from Western, Middle East and African markets.
In fact, Mundra provides an ideal location for exports as it provides the shortest logistics route
Set sail with confidence & class! SSR Marine Services delivers top-tier maritime solutions—from expert ship management and technical operations to unforgettable luxury cruise experiences like the iconic Mumbai Maiden. With a legacy built by seasoned mariners, they combine precision, professionalism, and passion to ensure every voyage is smooth and unforgettable. Whether you're navigating business or pleasure, SSR is your anchor in excellence.
Ready to embark on something extraordinary? Visit SSR Marine Services and discover a new wave of maritime brilliance!
Contact Sanjeev K. Agarwal Call +91 9967753807 or Email sanjeev@ssrmarineservices.com ssrmarineservices.com
Our Services: • Technical Management/Manning • Coastal Cargo Operation • Dry Docking/ Ship Building • Cruise/Floatel
connectivity with the North-Western hinterland too, making it ideal for customers across domestic and international markets to access destinations in Delhi, Rajasthan, Gujarat, MP, Haryana, Punjab and HP. Plus, the port is home to the Mundra Manufacturing Zone, which provides a vital gateway for Indian exports by leveraging the port’s robust infrastructure to offer the best investment opportunities for diversified industries across the multi-product Special Economic Zone, Free Trade Warehousing Zone and Domestic Industrial Zone. The zone offers developed industrial clusters for small and medium projects, which utilise the port’s connectivity, power reliability and other utilities. These zones also have access to some fiscal benefits. These fiscal benefits include exemption from custom duty, service tax, VAT, stamp duty and lease tax. Therefore, eligible suppliers gain access to the port’s dynamic infrastructure and special economic zone (SEZ) benefits to help enhance their supply chains, making operations faster and more cost-effective. Therefore, the Mundra Economic Hub is a vital gateway for Indian exports and imports, making the most of the port’s infrastructure, logistics connectivity and economic benefits.
Another vital port under APSEZ is Vizhinjam Port, situated in Vizhinjam. This port is home to India’s first mega transhipment container terminal, developed by APSEZ in recent years. Located near international shipping routes, Vizhinjam Port features largescale automation to ensure quick turnaround times for vessels arriving at the port. This efficiency is made possible by the port’s infrastructure, which is designed to accommodate vessels such as Megamax container ships, with an initial capacity to handle 1 million twenty-foot equivalent units (TEUs), which will expand to 6.3 million TEUs in subsequent phases.
Plot no. 640, 12/C, Lilashah Circle, Gandhidham - Kachchh - 370201
Phone No: (02836) 223228 / 230393
E-Mail : management@mhapl.net
Air freight forwarding, shipping logistics, consolidation, warehousing & distribution, sea logistics
In July 2024, APSEZ announced that the first vessel had arrived at the Vizhinjam Port, marking it as a key milestone event highlighting India’s first step into the global transhipment market. The port, integrated with automation and state-of-the-art infrastructure, is capable of handling large vessels with its modern container handling equipment and IT systems. Therefore, the arrival of the first vessel to the port to utilise these newly developed facilities highlights the future of cargo handling and transhipment for APSEZ in India. The San Fernando vessel, a 300-metre-long container ship operated by global shipping giant Maersk, utilises the port to offload 2,000 containers and has facilitated 400 container movements within the vessel. These giant operations highlight the vital role the port will play in the future of shipping lines traversing India’s coastline.
Karan Adani, Managing Director of APSEZ, outlined in a press release that the arrival of the San Fernando “is a symbol of a new glorious achievement in Indian maritime history. It is a messenger that will tell the world that India’s first transhipment terminal and the largest deepwater port has begun commercial operations”. Adani continues, “No other port in India – including our own highly advanced Mundra Port – has these technologies. What we have already installed here is South Asia’s most advanced container handling technology.
And once we complete the automation and Vessel Traffic Management System, Vizhinjam will be in a class of its own as one of the most technologically sophisticated transhipment ports in the world”. These comments are vital, as currently 25% of India’s container traffic is transhipped enroute to the final destination, and now the port will be able to take on more of a role in the transshipment traffic coming into India via the port to help enhance major routes connecting India with the US, Europe, Africa and the Indian subcontinents. This ultimately highlights the role of Vizhinjam Port and APSEZ in enhancing international trade for India.
In addition to port operations, APSEZ also facilitates vital dredging and reclamation solutions for port and harbour construction. The company has been investing in its dredging fleet for almost 20 years, and this has been vital to the development of the sector in India over the last two decades. Today, APSEZ operates a fleet of 29 dredgers, which help to maintain, develop and enhance the country’s port and waterway development. This focus on waterway expansion is a key part of the current
development by APSEZ over the last year. APSEZ has begun a number of construction projects to expand its port offerings. In September 2024, APSEZ signed a concession agreement with the Deendayal Port Authority to develop Bert No. 13 at Kandla’s Deendayal Port. The berth will handle multi-purpose cargo for the port and is expected to be completed in FY27. The project will see APSEZ consolidate its position across India’s western coast and enhance its existing infrastructure to service customers in Gujarat and North India better.
As experts in providing end-to-end logistics solution, operational excellence, low-cost operation and synergies through acquisitions, APSEZ has spent the last 25 years building its portfolio to deliver greater port services supported by vital infrastructure to keep supply chains moving. With the continued support from its stakeholders, APSEZ continues to go from strength to strength as it expands its role across India’s port sector. With automation, AI, and IT at the forefront of its development, APSEZ are creating ports offerings to meet the needs of today whilst supporting future of Indian ports.
Vale is an international mining company that focuses on producing iron ore, pellets, and nickel. The company works every day to take the natural resources available to us and develop them into prosperous resources; all whilst still working to promote environmental protection. This drive towards sustainable development underpins everything that Vale does, as it believes the safety of people and the planet must always take priority.
As one of the largest mining companies in the world, Vale has operations across roughly 30 countries all over the globe. The company began in 1942 under the name Companhia Vale do Rio Doce, where it first extracted ore in Itabira in Minas Gerais. Over the years, the name was shortened, and the company began to take on a larger role across the country’s mining industry by also providing logistical solutions via the country’s railroads, ports, and terminals. It even began operations within the energy industry to promote sustainable electrical production, and now is responsible for producing 54% of its own energy consumption.
The heart of Vale’s operations centre around iron ore. Iron pellets are vital to the construction and manufacturing industry, as they are used in the production of many products, and across multiple services we use every single day. For this reason, Value knows how valuable iron is for the development of society and human development, especially when these products are used to construct houses and medical facilities, as well as many of the technology product and household appliances that are fundamental to human life today. Brazil is home to a rich deposit of iron and so Vale’s operations centre around the mining and production of these iron products, to deliver vital products for the development of society.
Vale has multiple mine sites across Brazil where it is based, which are involved in the mining, processing, and then logistical movement of the mined products to the steel industries in which it sells the iron. To understand Vale’s valuable role in the mining industry in Brazil, we first must look at the birthplace of the company in Minas Gerais. The state accounts for over 50% of Vale’s iron ore production, with 20 mines currently in operation. Mining in Minas Gerais takes advantage of Vale’s railroad connections between Vitória and Minas. Vale has invested more the 1.3 billion dollars in the acquisition of trains and freight cars, which it primarily uses for transporting iron ore as well as other cargo. The logistics sector of Vale’s operations allows it to play a more well-rounded role in the mining industry and the distribution of its mined products to the ports and steel-making marketplace. Therefore, the mining operations at Minas Gerais highlight how the mining and logistical
operations of Vale work so closely together to deliver the rich ore to end markets for the betterment of a future planet.
In Minas Gerais, Vale is working alongside the city of Itabira to use its efforts within the mining industry to positively impact the city and build a plan for a more sustainable city. The plan, devised in conjunction with the municipal administration, aims to develop the region with projects which concern the environment, education, and security – all of which are developed with innovation in mind. These projects include the Little Seed of Sport Project, Judo Classes and the Bright Minds Chess Project which is bringing key development to kids across the region all thanks to Vale’s commitment to putting people and the environment at the forefront of its operations.
Pará, the largest mining complex in Brazil, is owned by Vale and represents one of the largest private investments in the country in recent years. The S11D mine complex in Pará encompasses the mines, a processing plant, and rail and port logistic services, which have continued to drive the region’s
economic development for many years. The mines are responsible for mining iron, manganese, copper, and nickel across a vast array of mines which span the complex. However, much like in Minas Gerais, Vale also has a vast array of environmental projects in Pará which ensure that the rich biodiversity of the nearby Carajás National Forest is protected.
In Espírito Santo, mining extends back more than 50 years and highlights the vital role the state’s railway and port systems can play in the mining industry. In Espírito Santo, Vale developed a fully integrated strategy for mining logistics which continues to be used every day. Vale’s operations in Espírito Santo highlighted the company for its production of iron pellets, and now the production of pellets by Vale in the region is globally recognised.
Espírito Santo is also home to the largest environmental investment by Vale towards the
development of the Tubarão Environmental Master Plan (PDA). PDA aims to control atmospheric emissions and covers 160 projects which are implementing new equipment, improving the environmental controls of its operations, and researching new technologies to reduce environmental impacts. The vast project which encapsulated Vale’s core values, has been successful in its efforts to make vital developments towards the future, whilst remaining clear in its aim to respect the planet, the local communities and the people who live and work across their sites of operation.
Other key mining sites for Vale include Maranhão and Rio de Janeiro. In Maranhão, Vale works with the state to support the logistical movement of ore production through the Carajás Railway to the Ponta da Madeira Maritime Terminal. The terminal plays a valuable role in distributing the ore to
consumer markets across the globe, including in China which is currently one of the largest buyers of iron ore products. Then, in Rio de Janeiro, Vale operates the Porto Sul Complex in the Costa Verde region. Vale’s headquarters are based in the capital, along with several terminals which are used for the loading of iron ore. The entire site can move more than 75 million tonnes of ore every year through the terminals and towards end markets.
Ultimately, Vale’s existence hinges on a passion for improving life and transforming the future for generations to come. To do this, Vale is carrying out mining operations which are essential to life whilst producing ores, pellets and various metals which help to make this possible. However, it is Vale’s commitment to education, environmental protection and innovative approach to the future that has allowed it to play such a valuable role in Brazil for many years thanks to its constant commitment to developing necessary mining operations whilst putting great investment back into the protection of landscapes to support the rich biodiversity of this part of the world.
TotalEnergies is a global integrated energy company that is present in about 120 countries worldwide, committed to delivering oil, biofuel, natural and green gases, as well as renewables and electricity to customers across the globe. In South Africa, TotalEnergies has long been a key player in the country’s energy sector, mainly active in the renewables, fuel marketing and services, lubricant blending, refining, and exploration and production sectors. With a lucrative business spanning from upstream exploration and production to the downstream sale and marketing of fuel, TotalEnergies’s presence in South Africa’s energy market cannot be understated. However, as TotalEnergies looks towards the future it is set on enhancing the country’s energy sector, whilst also scaling back its presence in some offshore projects.
TotalEnergies has been present in South Africa since 1954, with its first operations focused on distributing petroleum products. Whilst the petroleum division remains a key part of its operations today, TotalEnergies’ role across South Africa is vast spanning from upstream exploration and production to downstream marketing and distribution. With such a widescale operation across the country, it is no surprise that TotalEnergies has been vital to the energy development of South Africa for over 50 years. Today, TotalEnergies has a network of roughly 550 retail sites across the country, with liquified petroleum gas (LPG) distribution nationwide for domestic needs.
However, the company’s exploration and production segment is an exciting venture that sees the company deliver significant offshore oil developments together with fellow industry giants through joint venture agreements. Currently, TotalEnergies EP South Africa, the global company’s exploration and production division in South Africa, holds exploration rights in the Deep Water Orange Basin (DWOB), Orange Basin Deep (OBD), Outeniqua South and in Block 3B/4B to the east of the DWOB block.
The Orange Basin Deep (OBD) sits within the same offshore basin as other major discoveries including the Venus and Graff discoveries. TotalEnergies acquired 77.78% of the OBD Block in 2017 expanding its reach across the Orange Basin and bringing vital technical expertise to the exploration site. However, following this, QatarEnergy farmed-in to the OBD Block, acquiring 29.17% equity, leaving TotalEnergies retaining 48.61%.
In March 2024, TotalEnergies signed an agreement alongside its partner QatarEnergy to acquire participating interest in Block 3B/4B located within the prolific Orange Basin. Following the transaction, TotalEnergies would hold a 33% participating interest in the block and would assume operatorship over it. QatarEnergy, will hold a 24% interest, with the remaining interests held by the existing licence holders, including African Oil South Africa at 17%, Rococure at 19.75% and Azinam at 6.25%. whilst the transaction is subject to final approvals, it would see TotalEnergies take over Block3B/4B to deliver vital exploration of the Orange basin.
The block is located adjacent to the Deep Water Orange Basin Licence, in which TotalEnergies already
has a 50% operating interest, alongside QatarEnergy (30%) and Sezigyn (20%). Kevin McLachlan, Senior Vice President of Exploration at TotalEnergies outlined in the announcement of the acquisition of 3B/4B that “Following the Venus success in Namibia, TotalEnergies is continuing to progress its exploration effort in the Orange Basin, by entering this promising exploration license in South Africa.” Therefore, by acquiring further assets within the Orange Basin, TotalEnergies is expanding its role across South Africa’s offshore exploration and production sector.
The other significant block under TotalEnergies EP South Africa included Block 11B/12B in the Outeniqua Basin. The block, located 175km off the southern coast of South Africa, saw significant gas discoveries in 2019. TotalEnergies entered into the 11B/12B Block in 2013, with the Brulpadda and Luiperd gas discoveries by 2019. However, in July 2024, TotalEnergies announced that it was exiting the offshore Blocks 11B/12B, as well as Block 5/6/7. The press release outlines that following TotalEnergies’ partner in the block withdrawing from 11B/12B, TotalEnergies was also going to withdraw from the block.
TotalEnergies EP South Africa holds a 45% interest in the 11B/12B Block and a 40% interest in the Block 5/6/7. TotalEnergies’ decision to withdraw from the 11B/12B Block comes as the Brulpadda and Luiperd gas discoveries couldn’t be turned into commercial developments because they appeared to be too challenging to economically develop and monetize the gas discoveries for the South African market.
– Includes a benchtop digital density meter, kinematic viscometer + portable density meter (for free)
– Upgrade your analytical capabilities to save time and costs
– Ensure the quality of products in your tank terminal
– Compact and 100 % safe design, meeting international standards
– Rely on the market leader in rheology and density measurement
– Speed up your measurement process with our automation solutions
– Measure different samples with the same instrument setup
– Benefit from more than a century of competence in all petroleum industry segments
Anton Paar’s SVM Series streamlines kinematic viscosity measurements and boasts a 150 % increase in throughput compared to manual techniques, with a minimum of just 1.5 mL of sample and solvent per measurement. With its innovative features, the SVM Series is the ultimate solution for industries requiring fast and reliable results, including petrochemicals and beyond.
The Series stands out with the widest viscosity measuring range in a single cell (0.2 mm²/s to 30,000 mm²/s) and a temperature range from -60 °C to +135 °C (down to -20 °C without external chiller). Users can measure everything from jet fuel to wax, with a single instrument, without changing capillaries. There are no trial-and-error procedures to find the correct capillary – no complex quality management tracking. And the durable metal measuring cell eliminates the risk of broken glass capillaries, ensuring reliability and longevity while reducing consumable costs.
The SVM Series also offers multiparameter capabilities, enabling the measurement of critical properties like viscosity, density, viscosity index, and API gravity, and even allows for advanced tests, including time and temperature scans. This makes it the ideal choice for comprehensive petrochemical product characterization, replacing multiple instruments with a single, efficient device. It operates autonomously and can be equipped with an optional autosampler for up to 71 positions.
Delivering viscosity results in compliance with ASTM D7042 and ASTM D445 (with bias correction), the SVM Series guarantees compatibility with historic measurement data and across test methods. In addition, SVM’s density results are fully compliant with ASTM D4052 or ISO 12185, satisfying the petrochemical industry’s stringent requirements for standardization and comparability.
Packed with industry-leading features, the SVM Series sets a new standard in viscosity measurement. Offering unparalleled speed, precision, and compliance with more than 50 international norms, it is the perfect partner for professionals seeking to optimize workflows and meet the highest industry standards
For further information please contact Serena Govender – Product Manager for Viscosity and
Petroleum Testing; serena.govender@anton-paar. com or +27 76 810 9587
Or find out more visit: https://bit.ly/4jZi2j7
About Anton Paar:
Founded in 1922 in Graz (Austria), Anton Paar is the world market leader in the measurement of density and concentration, the determination of dissolved carbon dioxide, and the fields of rheometry and viscometry. Anton Paar’s customers include most of the major beer and soft drink manufacturers worldwide, companies active in the food, chemicals, petroleum, and pharmaceutical industries, as well as leading academic groups.
For many decades, Anton Paar has combined precise mechanical production with the latest achievements in the fields of research and development. In recent years, the Anton Paar GmbH has invested up to 20 % of its annual turnover in research and development. The company offers analytical solutions that are produced within its nine producing sites (in Europe and the USA).
The Anton Paar Group operates in more than 110 countries and has 35 sales subsidiaries and 11 producing firms in Europe and the USA. More than 4,200 employees in a worldwide network spanning research and development, production, sales, and support are responsible for the quality, reliability, and service of products made by Anton Paar. Since 2003, the Charitable Santner Foundation has been the owner of Anton Paar. It is dedicated exclusively and directly to charitable purposes.
About Anton Paar Southern Africa:
Anton Paar Southern Africa (Pty) Ltd, established in 2013 is a subsidiary of Anton Paar GmbH, comprising of three branches based in Johannesburg (Headquarters), Western Cape and Kwa-Zulu Natal; along with dedicated staff based in Tanzania, Ethiopia and Cameroon. With a total staff compliment of 65, Anton Paar Southern Africa (Pty) provides sales, application and technical support as well as a certified service offering to South African users as well as to Sub Saharan Africa users.
www.anton-paar.com
Whilst, this announcement highlights TotalEnergies’ exit from such offshore development, we look forward to seeing how the Orange Basin continue to provide fruitful in TotalEnergies’ offshore development.
However, we can’t talk about TotalEnergies’ role in South Africa without highlighting its vital role in the downstream petroleum sales and marketing sector. As previously outlined, TotalEnergies operates around 550 petrol stations across South Africa. These are designed to help the people of South Africa with their domestic fuel needs to keep the country’s transportation network moving. The downstream marketing of TotalEnergies’ operations is handled by TotalEnergies Marketing South Africa (PTY) Ltd. which focuses on retail speciality, petroleum and petrochemical products across South Africa. In particular, the marketing subsidiary is focused on the marketing and delivery of fuels, products and related services across its network.
However, in South Africa, TotalEnergies is committed to supporting the local community through its downstream petroleum and petrochemical operations. To ensure that the people
of South Africa can access vital petroleum services, TotalEnergies is committed to introducing service stations in previously disadvantaged areas, to make access to service stations more readily available and bring key employment to local communities through these stations. This highlights just one way that the global energy giant is focused on delivering energy that is more accessible and responsible within the communities in which it operates.
With TotalEnergies Marketing South Africa operating across the company’s downstream operations, and TotalEnergies EP South Africa spanning the company’s upstream exploration, South Africa’s entire energy spectrum is covered and continually enhanced by TotalEnergies’ network, supported by its expertise in global energy development. For this reason, it is clear that TotalEnergies is a major energy player within South Africa, especially with many vital partnerships across its offshore development with other key energy giants such as QatarEnergy. Across every aspect of TotalEnergies’ operations in South Africa, the global company remains focused on delivering energy in a safer, more affordable, cleaner and accessible way. We look forward to seeing how TotalEnergies continues to enhance the Orange Basin and its existing projects across the Southern African coastline, to deliver even greater offshore energy development for South Africa.
As the largest port in the country, the Port of Tema is a leading container hub along the West African coastline. With 85% of the country’s trade passing through the Port of Tema and the Port of Takoradi, the country’s port network remains a vital sector contributing towards the country’s overall economic development. However, it is not just Ghana that benefits from the ports along the country’s coastline; the Port of Tema is invaluable to enhancing trade links and supply chains across the African continent serving landlocked neighbouring countries such as Burkin Faso, Mali and Niger. Therefore, with such a vital role in meeting the local and international trade demands passing through Ghana, the Port of Tema has continued to expand its operations and is now a leading hub of container operations, serving as a beacon of trade for the global shipping industry.
The Port of Tema spans 5.5 million square meters of land located just 3 kilometres from the capital city of Accra. Every year, the ports see more than 1500 vessels calling at the port, which include container vessels, general cargo vessels, tankers, roll-on/roll-off vessels, and cruise liners. All of these vessels are met with leading port services facilitated by the Ghana Ports and Harbours Authority (GPHA), which is responsible for overseeing the port. For GPHA, the port is vital to the continued development of Ghana’s shipping industry and its role in global trade, and so the Authority’s central goal is to provide efficient facilities and services that help the Port of Tema to run smoothly by regulating logistics clusters in the port, which aims to deliver the port as a leading trade and logistics hub in West Africa.
The construction of the Port of Tema began in 1954 by Sir William Halcrow and his partners, who developed two breakwaters covering 500 acres with 12 berths inside. These were divided between 2 quays and were joined by four transit sheds, offices, 2 cocoa sheds and a site for a dry dock, slipway and workshop. Over the last 70 years, the port has rapidly expanded and is now the largest port in Ghana, providing vital shipping and logistics
operations to vessels traversing all corners of the world. Today, the Port spans 21 berths with draughts ranging from 8.2 to 16 metres. Across the port, there is a range of terminals primed to move cargo to and from vessels and across the port’s infrastructure.
The Port of Tema is also home to GPHA’s Golden Jubilee Terminal (GJT) and Transit Terminal. GJT is an inland clearance depot strategically located on the western end of the Port of Tema. The facility includes a container freight station, state warehouse, car park, an open stuffing/unstuffing area, banking services, customs, security, and container storage/ delivery services. This terminal allows vessels travelling into Ghana’s ports to pass through customs clearances efficiently and then on to either storage or delivery methods.
Then, the Transit Terminal is designed to extend the Authority’s services beyond Ghana and into Burkina Faso, Mali, and Niger; providing a one-
stop procedure for clearance so cargo can pass through ports and towards end markets much more quickly. The terminal also supports the port’s Reefer Terminal, which has over 1550 reefer plugging points and caters for the inflow and outflow of cargo which needs temperature regulation, such as fresh produce and frozen foods.
The need for infrastructural development has been vital to GPHA’s work across the Port of Tema and the Port of Takoradi in recent years. GPHA leads the development and management of these ports, with a leading concern being developing the port’s infrastructure to meet the continual demand of cargo and its associated vessels arriving into the port every year. As the demand for cargo moving through the port has risen, so has the size of the vessels arriving at the port, and so major developments have been carried out over the years to help expand the port and meet the size and needs of such vessels.
In response to the growing maritime demands experienced by the port for Ghana and the
surrounding countries, GPHA set out on a mission to upgrade and expand the ports of Ghana with a $115 million investment. This investment has been an ongoing project but has already seen the installation of a 450m long by 50m wide bulk jetty, which is capable of berthing four vessels simultaneously. In addition, the investment has seen the implementation of a new dedicated Reefer Terminal 822, which has a reefer plug-in point and includes offices for regulatory stakeholders within the clearance chains, and a concrete net mending wharf with solar lighting system to facilitate the activities of local artisan fisherman operating from the port.
Investment projects currently under development include the construction of a dedicated 3.5 million TEU container terminal, comprising 4 berths with 16 metres of draught. This development is a vital step in the first phase of the port’s development plans. However, as the Port of Tema looks towards the future, it aims to develop a new cruise passenger terminal, food and fruit
terminal, Ro-Ro Terminal, a new transhipment terminal, break/dry and liquid bulk terminals, and finally, an oil rig ship repair facility. All of these vital expansion plans aim to deliver an enhanced port that is capable of facilitating the growing cargo demand entering and leaving Ghana, making it a vital port for facilitating both local and international trade.
Overall, the Port of Tema is a vital hub for trade and maritime activities, primed with the facilities to meet the global demand for port services along Ghana’s coastline. With the support of the neighbouring Port of Takoradi, the port of Ghana remains vital to enhancing the country’s cargo operations, and with it, bringing valuable economic development to the country and surrounding regions. We look forward to seeing how GPHA’s continued expansion of the port enhances its capacity and grows its reputation as a vital trade hub along the West African coastline.
Since 1966, Point Lisas Industrial Port Development Corporation Limited (PLIPDECO) has been on a mission to be the leading port and estate management company in Trinidad and Tobago. With operations across the Port of Point Lisas and the Point Lisas Industrial Estate, the publicly traded company’s operations bring vital development across Trinidad and Tobago to establish the region as a major international hub for port and shipping operations. Therefore, PLIPDECO is leading the way in providing vital development, marketing and management operations across its ports, logistics and industrial estate infrastructure to deliver vital economic growth for the region.
PLIPDECO has spent almost 60 years providing vital management operations across the Port of Point Lisas and the nearby industrial estate. However, when the company began all those years ago, it was a much different story, with no established port or industrial estate in existence in these locations. Instead, it was PLIPDECO’s role to create the port and industrial estate and then look after them. This development marked one of the most ambitious industrialisation projects for Trinidad and Tobago, and today, PLIPDECO is the owner and landlord of roughly 860,000 hectares across the Point Lisas Industrial Estate and serves both international shipping lines and the petrochemical industry across the region. The company is held in a 51% ownership by the Government of Trinidad and Tobago, with the remaining 49% ownership interest held by various private shareholders. These shareholders include banks, financial institutions, insurance companies, company employees and the general public.
Thanks to the vital location of the PLIPDECO complex on the west coast of Central Trinidad, the company’s operations are primed to access international markets, including those in the US, Europe, the UK, and the Far East. In fact, the Port of Point Lisas is often referred to as the ‘gateway to the Americas’, with a particular focus on the delivery of containerised cargo. The industrial complex spans 103 tenants, with 88 companies active across a range of industries and operations. However, the large majority of tenants’ activities are focused on the petrochemical sector, dealing in methanol, ammonia and urea plants. In addition to these, the industrial site is also home to a steel plant, a power plant, and various smaller light manufacturing and servicing companies that are vital in the development and delivery of natural gas resources across Trinidad and Tobago and American markets. For this reason, a big focus on PLIPDECO’s industrial role has been focused on developing the infrastructure of the industrial estate to help these companies bring vital gas and petrochemicals to
market, which in turn will bring continued economic benefit to Trinidad and Tobago’s energy market.
The Port of Point Lisas spans 6 commercial berths and handles a diverse variety of cargo spanning dry and liquid bulks, containers, general cargo, and break bulk. With such a vast array of cargo operations, the port has gained valuable expertise over the years, which allows it to now be primed for delivering topquality handling across its cargo operations and
Grit
Storage
Equipment Rental
Transport
•
• Scaffolding
•
Fiberglass
the various plants located across the adjacent industrial estate. The Port is the second largest in Trinidad and is located just 32km south of the Port of Spain. Its location on the West coast of Trinidad means that it plays a valuable role in international shipping lines travelling between North and South America, as well as various international shipping lines. Therefore, the Port of Point Lisas is vital to helping move cargo from the region and beyond into both international and local markets.
To aid in its ability to handle cargo travelling from both local and international markets at the Port of Point Lisas, PLIPDECO offers a range of warehousing services to ensure that it can continue to play a valuable role in keeping supply chains running efficiently. Warehousing services under PLIPDECO include the LCL Warehouse which is a customsbonded facility providing housing for trade and non-trade cargo in a covered storage area, LCL Export Services which facilitate intra-regional trade and provides greater market access for small and medium-sized manufacturers, and The Offsite Facility which is designed for clients looking for the temporary storage of dry containers, chassis, and break-bulk cargo. Another key service offered by PLIPDECO is its FCL service, which provides importers with a warehouse facility designed for unstuffing dry containers and short-term storage of the cargo. This service allows PLIPDECO to provide a cost-effective, convenient, and secure stuffing/ unstuffing service to customers using the Point Lisas Port. Through PLIPDECO’s experienced team of specialists, customers can be sure their cargo is in
In order to ensure that the cargo operations at the Point Lisas port remain competitive across both domestic and international markets, PLIPDECO is focused on ensuring that the port’s management
and infrastructure are developed to meet the growing demand for cargo travelling through the port. Therefore, PLIPDECO is committed to strict management and efficient cargo handling operations, which have helped the company to build up its reputation as a leading cargo handling port, supported by first-class customer service. Alongside this customer service, PLIPDECO also benefits from its vital partnerships across the complex and the wider region. These partnerships help PLIPDECO to continue to play a critical role in developing the logistical landscape of Trinidad and Tobago and enhance how cargo is moved through the port and industrial estate before it heads off to end markets. By partnering with local experts in the field, PLIPDECO can provide customers with streamlined end-to-end hauling, packing and warehousing services, which are cost-effective and capitalise on Point Lisas’ strategic location along Trinidad’s coastline.
Across PLIPDECO’s operations, there is a real focus on providing the necessary infrastructure and support to develop the region’s role within international shipping lines. With the port and industrial estate now a thriving hub for shipping and cargo operations, Trinidad and Tobago remain competitive within global markets, and especially within the petrochemical markets as a large portion of its industrial land is used to develop these industries which are then supplied to markets all across the world. We look forward to seeing how PLIPDECO will continue to enhance the Port of Point Lisas and the Point Lisas Industrial Estate as the demand for cargo continues to rise, forming the complex into a competitive hub for international shipping operations.
One of the most significant deposits of platinum group metals (PGM) in Africa is found along the Great Dyke in Zimbabwe, that extends 450km through the centre of the country. Many companies operate across this region, but Zimplats is the leading PGM producer in the Great Dyke region. The company mines and processes highquality metal products safely, efficiently and responsibly across its competitive asset portfolio within the deposit. Zimplats’ vision is to be the most valued and responsible metals producer, and so the company is committed to delivering vital PGMs to market, whilst delivering a better future through sustainable development, and the promotion of economic prosperity and investment into the social development of the regions in which it operates.
Zimplats, is owned by the global Implats Group which is a fully integrated PGM producer with 6 key mining operations across the globe. The company delivers these metals to vast markets across the world including Japan, China, the US, and Europe where the metals are used in developing products such as hard disks, mobile phones, aircrafts, turbine, industrial catalysts and even dental implants. Therefore, Implats’ role across the global PGM sector is vital, and so with Zimplats being a subsidiary of the Implats Group, the company can deliver vital PGM metals to market that can help deliver a better future for the local community and its stakeholders. For Zimplats, its central goal is to deliver the full potential of an asset, whilst establishing sustainable practices. Currently, Zimplats is focused around 5 operating mines, three concentrator plants and a smelter. Today, Implats holds 87% of Zimplats, which began developments in Ngezi in 2003. The Ngezi Platinum Group Metal Mine is located 150km south-west of Harare and is the principal PGM producer in Zimbabwe. The site is 70% owned by Zimbabwe Platinum Mines and 30% by Impala Platinum. However, the development of the deposit at Ngezi extends back way before 2003, when the project replaced the previous Hartley
Geological Complex operations which was developed by BHP and Delta Gold in the mid-1990s. However, after being brought into production in 1997, the Hartley Geological Complex shut down after 2 years, with Delta giving its holdings to Zimplats, who later went on the purchase BHP’s share.
By 2001, Zimplats announced the development of a 2.2Mtpa open pit operation, the Ngezi Platinum Group Metal Mine, which produces PGMs, plus nickel, copper and cobalt. Over the years, the Ngezi PGM Mine has undergone vast development, including a multi-phase expansion project that saw the first $340m phase develop two new underground mines as well as construct of a 1.5Mtpa concentrator, and the second phase boosting the mines capacity to 6.2Mtpa. By 2011, the mine had produced 190,532 ounces of 4E metals, and through Zimplats’ vital mining operations the mine continues to deliver vital PGM materials for Zimbabwe.
Zimbabwe’s leading specialists & suppliers in mineral, water and energy extraction and the civil sectors for over 40 years.
KW Blasting’s expert drillers deliver where others can’t. Specialised borehole and RC drilling services assess mineral deposits and tap into groundwater, even in the most remote and challenging locations.
OUR SERVICES:
• Demolition & Restricted Blasting
• Open Cast Mining
• Dam Excavations
• Road Earthworks
• Lateral Support
• RC/Borehole Drilling
Ore from the Ngezi mine is treated at the Selous Metallurgical Complex, which revived part of the original project at the deposit. The complex consists of a mill, concentrator, smelter and converter, as well as includes onsite laboratories. The mined ore is ground at the facility before flash flotation regrinds and delivers rougher and scavenger flotation. Concentrates that are produced by flotation at the plant are smelted and then converted to give lowiron matte, which contains 44% nickel, 33% copper, 21% sulphur and 1,500g/t of precious metals. These
are sold to Impala Refining Service, part of the Impala Group, for subsequent precious metals recovery.
Another key deposit development for Zimplats in Zimbabwe is the Mupani Mine, which replaced the previous Rukodzi mine. In November last year, Implats and the Zimplats board of directors approved the $264 million development of the Mupani Mine. The mine complex will replace the production from Rukodzi mine and the Ngwarati mine when they reach the end of their mine life. The new development is set to increase Zimplats minerals resources by close to 9 million ounces. The Mupani mine is expected to have a 25-year life of mine, with full production expected to be reached next year in 2026. This development will continue to enhance the potential on the region and continue to delivery significant results from Zimplats and Zimbabwe in the process. Zimplats will oversee the development and upgrade of the Mupani mine, which is currently on schedule and full production is expected to reach 3.6 million tonnes per annum by H1 FY2029. Currently, US$339 million has been spent as of the end of 2024.
In addition to the Mupani mine, Zimplats also completed the construction of the first 35MW
phase of a 185MW solar power project in Zimbabwe, with a grid connection scheduled for the start of this year. Construction to the second phase of the solar development, is schedules for this year and aims to deliver a 45MW solar plant. Finally, the Bimha Mine, a large underground platinum mine that closed in 2014, will undergo a vital development project as part of Zimplats’ strategic plans moving forwards. The development of the Bimha Mine aims to increase its design capacity and partly replace the production from the existing Mupfuti mine. The development project is expected to be completed by 2027, with the design set to increase its capacity to 3.1 million tonnes per annum and so, provide a vital development for Zimplats going forwards.
Across Zimplats’ operations there is keen focus to bring the vital PGM developments of the Great Dyke deposit to market and meet the growing demand for PGMs from industries across the world. For Zimplats, it is on a mission to be the most valued and responsible metals producer, creating a better future for its stakeholders by delivering the vital metals needed for society, whilst achieving this sustainably and efficiently. With so many developments across the complex, we are excited to see how Zimplats continues to develop its mine assets across Zimbabwe to deliver results not only for its stakeholders but for the country too.
Written by Carley Fallows
Death Valley, located in eastern California, United States, is a region known for its scorching temperatures, extremely dry conditions, and sparse plant life, especially during the blazing summers. The valley recorded the highest temperature ever recorded in the National Park in 1913, at a whopping 57°C. Therefore, known as the hottest place on earth, it’s no surprise that there’s little in the way of plants across the valley, located between the Northern Mojave Desert and bordering the Great Basin Desert. However, every so often, following just the right weather conditions in the months prior, the valley’s floor becomes filled with a sea of yellow, blue and red wildflowers in the spring. Whilst this is a rare occurrence, its presence reminds us that even in the most unlikely of environments, beautiful life can bloom.
Superblooms, as they’re often referred to in Death Valley, typically occur once a decade following heavy rainstorms in the autumn and winter months, paired with arid ground. These conditions are what make it possible for flowers to bloom here in the spring, despite the high temperatures. Superbloom flowers typically include red poppies, desert lupines, and sunflowers, which strike a stark contrast against the desert landscape seen for most of the year. Whilst the ‘superblooms’ might suggest a thick, dense flower coverage, the superbloom is instead more of a light scattering of flowers across the valley’s floor – but it is still impressive, especially compared to the very dry landscape typically seen across Death Valley. The last super bloom occurred in 2016 and was brought about by the El Nino phenomenon, which aligns with the surface of the sea rising, leading to more extreme weather patterns occurring across the globe. This particularly looks like an increase in severe weather, including storms across the US, which results in increased rainfall in late 2015 and early 2016. The increase in moisture in the air from such severe weather in the months prior provided ample conditions across Death Valley for a superbloom to occur in the spring of 2016.
One of the main reasons why Death Valley remains such a hot climate is due to its 140-mile valley sitting in the shadow of four major mountain ranges. These ranges include the Sierra Nevada and Panamint Range, which prevent moisture from the Pacific Ocean from moving eastward over the mountains from reaching Death Valley. Therefore, air masses are forced upward by the ranges; this causes cool air and moisture to condense, leading to rain and snow on the western slopes. However, by the time this air reaches the valley, most of the moisture has been lost, and so little is left in the way of precipitation, causing such dry conditions. Therefore, Death Valley has a subtropical hot desert climate, which causes extremely hot and long summers, with warm and short winters and a typical annual rainfall below 2 inches a year. Therefore, such perfect conditions with increased rainfall are needed for the moisture in the air to reach Death Valley, resulting in the rare natural wonder of a superbloom across the valley.
However, the name Death Valley does not actually stem from the extreme heat of summer, as one might expect. Instead, it originates from an incident that occurred during winter in what would later be known as Death Valley. The story behind the
name comes from a group of pioneers who became lost while searching for a shortcut to the gold fields of California in the winter of 1849-1850. The men lost their way in the vast expanse of the valley and were ultimately rescued by two young members of the group who had learned to be scouts. These young men guided the others over the Panamint Mountains and out of the valley. Although only one person died in the valley, it is believed that one member of the group looked back after escaping and said, “Goodbye, Death Valley”. This is thought to be the origin of the name ‘Death Valley’ today, and the lost group, known as the 49ers for the year they were stranded, has become a significant part of Western history in the United States.
With such an interesting history behind the hottest place on earth, Death Valley remains a highly visited place to experience the true heat that the valley has to offer. One of the most interesting natural phenomena occurring in Death Valley is the superbloom, which seemingly brings life against all odds to an extremely dry and hot climate. With global weather patterns continuing to play a vital role in the cause of such superblooms, the chance to visit and see the spectacle of flowers remains an elusive wonder of North America.
Source: https://www.nps.gov/deva/learn/nature/ wildflowers.htm
https://www.nps.gov/deva/faqs. htm#:~:text=Death%20Valley%20was%20given%20 its,valley%20would%20be%20their%20grave
https://www.vogue.com/article/super-bloomdeath-valley-travel
The railway network of Malaysia is vital to the country’s infrastructure, helping both people and materials move across the country and beyond to adjoining networks in neighbouring countries. With this network being vital to Malaysia’s interconnectivity, the need to bring together vital stakeholders and governmental figures has long been essential to maintain the railway network so it can remain efficient, safe and sustainable. Therefore, the Malaysia Rail Industry Corporation (MARIC) was formed in 2017 to contribute to the development of engineering across the Malaysian railway system through the support, unification and network provided by its members.
MARIC began operations in 2017 following the formation of the incorporated association to provide membership to all companies operating across Malaysia’s railway systems engineering and associated works sector. MARIC currently has 60 member companies spanning the country’s railway engineering sector. However, some members also include public transportation companies, communication companies, transitoriented development companies and services, as well as those within the railway infrastructure construction sector. These additional members are vital in helping the core engineering companies to facilitate the development of the country’s railway network. Across the company’s network, there are more than 5,000 personnel who are engaged across all aspects of the railway engineering network from construction, rehabilitation, maintenance, repair and overhaul (MRO), and public-private partnerships (PPP). These members are vital in helping MARIC achieve its goals to deliver a cohesive, developed and comprehensive rail network for the country.
For MARIC, it is particularly focused on engineering clusters, which include Rolling Stone, Signalling Systems, Telecommunication Systems (including SCADA), Power Supply and Distribution Systems (PSDS), Trackwork, Depot Equipment, and Automatic Fare Collection (AFC) systems. These systems are vital to helping MAIRC continue to improve Malaysia’s railway reliability and sustainability. In fact, across these, MAIRC is passionate about developing relationships with local suppliers and vendors to help manage the MRO and construction, rehabilitation, mid-life refurbishments and component supplies for activities in the future pertaining to the rail network.
The central mission of MARIC is to foster collaboration across all levels of the rail supply chain network and, through this collaboration, enhance productivity and deliver great value for the country’s railways. The importance of Malaysia’s
At DK Composites Sdn Bhd, we turn bold visions into reality with cutting-edge technology, advanced engineering, and world-class craftsmanship. Since 1997, we've been at the forefront of highend composite manufacturing, proudly operating from Composites Tech City, Batu Berendam.
From awe-inspiring architectural domes to high-performance marine vessels and next-gen transport solutions, our expertise spans:
• Design, Development & Installation
• Composite Structures – Cladding & Domes
• Marine Composites – Racing Yachts & Power Boats
• Modular Housing
• Rail, Transport & Electric Vehicles
Trusted by clients across Europe, the Middle East, the USA, Asia and Australia, we deliver precision, durability, and innovation — every time.
network and its local supply chains to enhance the system is outlined by Anthony Loke, Minister of Transport in Malaysia, with his message, “Every rail project presents unique opportunities to further the capacity and capabilities of the local rail industry. Whilst the primary goal is to develop infrastructure and systems that enable efficient rail services, these projects must also serve as a catalyst for advancing innovation, developing talent, and empowering local players”.
Loke also outlines in his message on the MARIC website, “implementing a partnership model between local players and like-minded foreign OEMS will ensure a win-win outcome and help create a sustainable rail industry ecosystem that can effectively support the operations and maintenance of these systems throughout their life cycle”. Loke’s message outlines how the rail industry is behind vital development for Malaysia, and through its collaboration with local and international like-minded companies and governmental figures, MAIRC can deliver these projects for the benefit of Malaysia and its supply chains overall.
A key way that MARIC is sharing its mission to enhance and develop Malaysia’s railway engineering network is through education and networking events. To achieve this, MAIRC hosts seminars, symposiums, exhibitions, familiarisation programs, Export Acceleration Missions (EAMs), and business match operations to grow the company’s network and member sphere. This focus on education and networking was highlighted in March with the announcement of MARIC partnering with the University of Kuala Lumpur.
MARIC and the University signed a Memorandum of Agreement (MoA), which will focus on the Peneraju Skil Plus Professional Rolling Stock Maintenance program at the university, which is aligned with the national workforce development initiatives. It is hoped that through the partnership, the University will provide essential academic and technical training in the knowledge and practical skills needed to maintain and develop the railway sector. Thus, the program will promote the future leaders
of the rail network and bridge the gap between academics and the railway industry. Therefore, the partnership shows MARIC’s investment in the next generation of rail engineering to ensure that the railway will remain the mode of transport of choice across Malaysia.
What we have seen across the operations of MARIC is a firm commitment to investing in the development of Malaysia’s rail engineering sector. The railway engineering industry is so vital to keeping the railway network running smoothly, and so MARIC’s work is invaluable in keeping transportation links and supply chains on track. Therefore, by focusing on networking, education, and unification with other vital stakeholders within the industry, MARIC is able to promote the vital work of the sector and help keep Malaysia’s railways safe, reliable and sustainable. We look forward to seeing MARIC continue work with the government, local stakeholders and international OEMS to deliver a more enhanced rail network for Malaysia.
Abu Dhabi is such a popular destination across the United Arab Emirates (UAE) thanks to its rich culture, scenery and shopping facilities available across the capital. For this reason, millions of visitors arrive in Abu Dhabi every year on both business and leisure trips, ready to make the most of the expansive beaches, golf courses and conference centres that the city has to offer. With such a large portion of the city’s economic development focused on tourism, the government established a dedicated Department of Culture and Tourism, which could focus on promoting, protecting and progressing the tourism industry of Abu Dhabi to maintain its role as a leading global hub for tourism across the Emirate.
Led by an accomplished team of executives spanning industry professionals across a wide range of disciplines within the tourism sector, the Department of Culture and Tourism – Abu Dhabi (DCT – Abu Dhabi) is on a mission to drive sustainable growth across Abu Dhabi’s culture and tourism sector, by forming a valuable and diverse ecosystem that works to preserve, promote and embody the Emirate’s heritage, innovative spirit and unparalleled hospitality. By delivering vital development to Abu Dhabi’s culture and tourism sectors, DCT – Abu Dhabi aims to deliver the city as a primed tourism destination, where culture, creativity and discovery are at the forefront of its reputation.
To promote and maintains the popular reputation of Abu Dhabi as a tourism destination in the UAE, DCT – Abu Dhabi sets about coordinating efforts and investments to regulate and use the best tools, policies and systems possible to support Abu Dhabi’s tourism development and deliver it as a leading global destination for both local and international travellers. In turn, it hopes to attract both national and international investment into its tourism sector, to continue to make it an appealing yet distinctive tourism and cultural destination across the Emirate.
Abu Dhabi has long been known as a world-class destination for tourism, with people travelling from all corners of the world to experience the diverse array of leisure, entertainment and cultural attractions on offer across the region. With so much to offer tourists, DCT – Abu Dhabi is passionate about working with industry partners, stakeholders and sponsors to continue to promote Abu Dhabi as a sought-after destination. To achieve this, DCT – Abu Dhabi actively engages with trade partners to convert interest in the city into concrete plans for both leisure and business travel. A key aspect of this is education and familiarisation of the city with international and local tour operations, which helps to encourage a higher uptake of trips to the region. DCT - Abu Dhabi can then work across the region to monitor guest arrivals, occupancy rates and visitor footfall to focus on the areas that need more development with both local and international visitors.
This development can then be carried out across Abu Dhabi’s tourism landscape to analyse trends and, from these, develop innovative programmes to raise Abu Dhabi’s profile as a leading leisure, culture
and business tourism destination. Marketing initiatives are key to this, as so through DCT – Abu Dhabi‘s 10 offices, it carries out vital promotional activities and partnerships to grow tourism numbers from key tourism markets. In addition, DCT – Abu Dhabi is responsible for issuing licenses for hotels, tourism organisations, events and conferences, which ensure that all of these settings are met with the highest international standards. By upholding such strict standards, DCT – Abu Dhabi can continue to support the best possible travel opportunities, contribute towards the growing tourism industry, and improve infrastructure whilst promoting competitiveness for Abu Dhabi as a sought-after destination across the UAE.
One of the vital developments for DCT – Abu Dhabi is business tourism, which sees Abu Dhabi promoted as a great destination for meetings, incentives, conferences and exhibitions (MICE). By focusing on this aspect of business tourism, DCT – Abu Dhabi highlights the vital role the region plays as a meeting point for international business operations at the heart of the Middle East. By delivering popular and dynamic business tourism opportunities, supported by promotion at overseas trade conferences, Abu Dhabi can bring greater business tourism across the region.
For leisure tourism, cruises are a vital division which is at the forefront of developing Abu Dhabi
into a leading winter sun cruise destination. The city is home to the region’s only dedicated cruise stopover beach on Sir Bani Yas Island in the Emirate’s Al Dhafra region. This provides a unique offering to cruise operators traversing the Arabian Gulf. Currently, a range of cruise offerings arrive at the Abu Dhabi port, including those that include the port as a port of call when operating across the regional Arabian Gulf, international cruise lines that arrive on worldwide tours, and those that start and end in Abu Dhabi. With Abu Dhabi being a vital stopping point along many of these cruise itineraries, the cruise line industry remains a vital way that tourism is brought into Abu Dhabi every year. Therefore, DCT – Abu Dhabi works with such cruise line operators to continually enhance its cruise port terminal offerings and establish the region as a valuable stopping place full of culture and tradition in the Emirate.
For many tourists, the rich culture and heritage of Abu Dhabi are a big draw to the capital. Therefore, a key aspect of DCT: Abu Dhabi’s operations is to develop programmes which promote and support the culture of the region with events, exhibitions and museums that celebrate Abu Dhabi. Across Abu Dhabi, there is a range of UNESCO heritage sites, which are protected by DCT: Abu Dhabi, to preserve and promote the significance of the prominent archaeological and historical heritage of the capital, which draws tourists from across the world. This responsibility to promote the dynamic culture of Abu Dhabi is something DCT: Abu Dhabi is very focused on, as these are not only cornerstones of the region’s historical significance, but they also play a vital role in developing the cultural tourism of the region.
With so much on offer across Abu Dhabi, DCT – Abu Dhabi has set out a clear Tourism Strategy 2030, which it aims to bring a new era of expansion and strategic development for the region. The strategy, approved by His Highness Sheikh Khaled bin Mohammed bin Zayed Al Nahyan, Crown Prince of Abu Dhabi and the Chairman of the Abu Dhabi Executive Council, plans to deliver the Emirate as one of the fastest-growing global destinations for international visitors. The plan outlines a boost to visitor numbers, with a goal to reach 39.3 million annually by 2030. With this, the strategy hopes to
see the tourism sector contribute further to the country’s GDP, with its annual GDP contribution totally AED 90 billion by 2030. To achieve this, the sector will undergo fast expansion, and with it, create 178,000 new jobs within the tourism ecosystem.
The Tourism Strategy 2030 is broken down into 4 strategic pillars, which can be utilised to foster sustainable growth. These pillars include offering and city activation, which is set out to enhance visitor experience, whether at a cultural site, hotel, or retail store. The strategy wants to ensure that every visitor across Abu Dhabi is met with only the best offerings. The second pillar covers promotion and marketing, which aims to work closely with partners to double the international reach of Abu Dhabi as a key destination, expanding its current reach from 11 markets to 26. The third pillar is focused on implementing infrastructure and mobility for visitors to the Emirate. This includes increasing room availability, flight seat capacity and the connectivity within the Emirate to make getting to the region easier. The final pillar aims to help all of these goals be achieved quickly, yet to a
high standard, through the enhancement of visas, licensing and regulation processes. This ensures that guests know that they will be met with only the highest standards and regulations across their stay, supported by DCT- Abu Dhabi. All of these pillars really bring into focus the vital role DCT – Abu Dhabi plays in enhancing the region’s tourism and culture sectors to encourage more guests to the city and deliver a reliable future for Abu Dhabi’s tourism.
Ultimately, DCT – Abu Dhabi’s goal is to drive the continued and sustainable growth of Abu Dhabi’s culture and tourism sector in order to fuel economic progress. By focusing on the heritage, culture, and landscapes that the city has to offer, DCT – Abu Dhabi continues to invest in the region by working with vital partners and stakeholders on a local and international scale to position Abu Dhabi as the sought-after location, whether for business or leisure. With innovative strategies, outlined by its Tourism Strategy 2030, Abu Dhabi is set to vastly expand its tourism industry over the coming years and continue to highlight why it remains such a vital destination for all types of tourism, all year long.
In recent years, Kenya’s shipping industry has seen a vast expansion, with many businesses across the world harnessing the competitive location of Kenya as a hub for moving cargo between African and international markets. With the country home to one of the busiest ports along the East African coastline, the ports of Kenya are vital for bringing cargo in and out of the country and across neighbouring landlocked countries. To ensure that this vital industry for Kenya and the African continent continues to operate efficiently, Kenya National Shipping Line Ltd (KNSL) offer a vital and comprehensive shipping service which aims to bring national economic development through the facilitation of cargo on a global scale.
With 35 years of experience across Kenya’s shipping sector, KNSL is a leading provider of reliable shipping and logistics services to the country’s maritime and cargo industries operating within the African continent and across international markets. The company found its origins in 1987 under the Companies Act, which formed KNSL as Kenya’s national carrier through a joint venture between the Kenya Government acting via Kenya Ports Authority and strategic partnerships with Unimar and DEG in Germany. The joint venture set out on a mission to provide a competitive shipping and logistics service that could bolster the national economy and contribute towards enhancing its role across global shipping markets.
Following some restructuring of its shareholders in 2022, KNSL outlined a set of strategic objectives that would lead the company in its role to enhance the shipping industry for Kenya. These objectives include the growth of cargo volume handled by the company to meet the increasing demand for products in Kenya and across Africa, whilst also bringing vital economic development to the region because of this. In addition, KNSL is working to
Powerparts(K) Ltd stands at the forefront of container and industrial material handling, offering an unparalleled range of equipment and services.
As a premier supplier and maintainer of port equipment, we cater to the largest ports in East Africa, including the Kenya Ports Authority, Tanzania Ports Authority, Zanzibar Port Authority, and Société de Gestion du Terminal à Conteneurs de Doraleh (SGTD).
WE PROVIDE SERVICE AND REPAIR FOR ALL BRANDS OF PORT HANDLING EQUIPMENT
Our services cover all operational sections, including: • Container Terminals • Conventional Cargo Equipment • Dockyards • Forklift Sections • Mobile Plant Units
We extend our top-tier services and parts sales across East Africa, ensuring reliable repairs and availability of equipment and spare partsfor all Kalmar equipment.
We deliver comprehensive cargo handling solutions and services to: Ports and Terminals • Intermodal Terminals • Distribution Centers • Metal Industries
CHOOSE POWERPARTS(K) LTD FOR INNOVATIVE, RELIABLE, & EFFICIENT CARGO HANDLING
enhance the efficiency of its logistics value chains, ship management and terminal operations through vital investments, as well as in partnership with local suppliers to bolster its operations across the coast. These objectives hope that with good governance and continual institutional growth, it will enhance its logistics delivery service and be the shipping line of choice for its customers. Therefore, KNSL’s objectives work to enhance the country’s shipping, clearing, forwarding, warehousing, and consolidation of cargo sectors whilst also providing essential recruitment and placement services to seafarers.
In order to deliver efficient shipping to customers, KNSL operates an ocean freight service which works to provide integrated logistics supply chains through its agency network spanning the globe. These services look to ensure that dry bulk, liquid bulk, project and specialised cargo reaches end markets and is moved through bunkering husbandry and protective agency services across the logistics chain to achieve the best operational efficiency possible. The comprehensive role of KNSL is known for providing intermodal solutions
FOCUS CFS is a premier Container Freight Station offering toptier logistics services for cargo through the Port of Mombasa, serving East Africa. As a market leader, we specialize in handling containers, loose cargo, motor vehicles, reefer containers, export cargo, warehousing, and project cargo.
Exceeding customer expectations with our professional, efficient, and reliable services.
for forwarding - specifically designed to provide a one-stop shop for inland shipping requirements which work with local stakeholders to move cargo across the road, rail and inland waterway networks of Kenya with the help of local and international shipping networks.
As we can see, KNSL plays an all-encompassing role in supporting the shipping industry of Kenya so it can continue to function smoothly. Therefore, the shipping line works closely with port authorities as well as with vital logistical services across the country to ensure that the shipping line brings vital cargo to Kenya’s shores and then works with those on the ground to make the movement of this cargo to end markets seamless. This unified operation across the shipping lines, port authorities and local logistics providers allows KNSL to deliver such world-class shipping solutions that support the containerised and conventional cargo sector with efficient, cost-effective and reliable shipping solutions.
A key aspect of KNSL’s operations is in working with the Kenya Port Authority (KPA) across the country’s most vital ports. KNSL and KPA work closely across the Port of Mombasa, an expansive port that continues to deliver vital port operations for Kenya. The Mombasa port was ranked second in the 2023 Africa Ports Productivity report, highlighting its improved efficiency and the increasing number of new shipping lines making maiden voyages to the port each year. Therefore, as a leading shipping line in operation at the port and alongside KPA, KNSL ensures that the shipping and cargo industry of the port is supported by its dynamic shipping network. This then allows KPA and KNSL to work together to deliver vital cargo meeting the growing demand for goods in the country, whilst enhancing Kenya’s role as a profitable and reliable hub for shipping activities along the East African coastline.
Beyond its cargo services, KNSL is committed to delivering vital crew and manning services for international cruise lines and vessel management companies. This division of KNSL utilises the company’s global network to access a thorough and well-updated database of potential crewing
candidates who are ready for employment and deployment. Therefore, KNSL’s reputation across global cargo, cruise and vessel management networks makes it the go-to destination to find skilled employees and employers to continue to develop shipping operations across the globe. This reputation for providing only the best employers and employees further supports Kenya’s reputation as a vital shipping port within global markets.
Across KNSL’s operations, the company is focused on delivering a reliable movement of cargo from overseas and into Kenya and then beyond through the company’s vital shipping network. Across this expansive network, KNSL continues to partner with vital stakeholders spanning local and global supply chains to ensure that Kenya’s shipping and logistics industry maintains its worldclass reputation. We look forward to seeing how KNSL continues to expand the company’s role across Kenya and the neighbouring regions across Africa to ensure the seamless movement of cargo to support both local and international markets.
As one of the largest independent healthcare providers in South Africa, Joint Medical Holdings Group (JMH) prides itself on delivering superior medical care to the community supported by its exceptional clinical team. With 7 hospitals under its operations, JMH is dedicated to offering compassionate and cost-effective patient care services across the province of KwaZulu-Natal. Offering services spanning from emergency services to specialist care units, JMH delivers superior medical care to the community and, in the process, alleviates suffering.
JMH was established almost 40 years ago in the 1980s by a group of doctors passionate about providing accessible healthcare to disadvantaged communities during the apartheid years. After overcoming such obstacles as the Group Areas Act with no roadmap for the future, the group began to grow and established the Isipingo Hospital, set on providing top-quality medical care to the local community. From this base, JMH has vastly expanded and today provides 7 healthcare facilities operating across the KwaZulu-Nata province of South Africa. Across these services, JMH offers the community 24-hour emergency services, 27 operating theatres, cardiac catheterization laboratories, cardiac care, multi-disciplinary specialities, ICU and high care, maternity and NICU care, paediatrics, and renal care services, as well as radiology and pathology services.
The flagship, Isipingo Hospital, is a community hospital facility providing expert medical care for a whole range of conditions. From emergency 24-hour care to wellness services provided by its Mental Health Ward, Isipingo Hospital provides leading medical care across its 171-bed facility, supported by the hospital’s team of multi-disciplinary medical
The Procleix Panther system featuring ART provides enhanced levels of automation for laboratories in a compact footprint without compromising throughput. It combines the proven and reliable performance of the Procleix Panther system with software and hardware improvements. Innovative optional components, such as full track connectivity and remote monitoring, can be installed to optimize variable workflow needs now or in the future.
Optimize variable workflow needs via superior customization with easy, scalable options that help transform the way labs work as lab needs evolve.
Learn more about the Procleix Panther System featuring ART at www.procleix.com
Tel: +27 (0)11 804 4004 | Email: mail@ilex.co.za | sales@ilex.co.za www.ilex.co.za
Standard Bags | Transfer Bags | Bag System with wide bore tubing
Blood bag systems with integrated leukocyte depletion filters
Pediatric storage bags non DEHP
Maximised efficiency and plasma yield | Shortened separation time
Reduced risk of hemolysis | Advanced technological platform
Optimised standardization | Flexibility in processing
Blood Transfusion Products
care experts to treat the people of Isipingo and the surrounding areas. The facility specialises in services to maternity, mental health, NICU, occupational health, travel medicine, paediatrics, pathology and radiology patients, as well as offering 4 operating theatres and a range of medical and surgical wards. To ensure that its patients can receive the best care, the hospital accepts most medical aids, whilst offering competitive private cash rates so each patient can access affordable and quality healthcare services.
In the Durban Central Business District (CBD), JMH has City Hospital, which offers quality and cost-effective healthcare services. The hospital specialises in neurosurgery, cardiac surgery, a cardiac clinic, and dialysis. High-quality dialysis is delivered by Ultra Kidney Care, which offers discounted rates. City Hospital is the largest under JMH with 7 operating theatres and a stateof-the-art cardiac catheterisation laboratory, electrophysiology, a revamped paediatric unit, and a Neonatal Intensive Care Unit. There are 250 beds across the facility, providing patients across the region with vital healthcare services. Much like the rest of JMH’s facilities, the hospital accepts most
medical aids and provides competitive private rates for easy access to necessary healthcare services for those in the local community.
The Durdoc Hospital is also located in Durban CBD, with 139 beds providing 24-hour emergency services and a range of medical services delivered by a dynamic and diverse team of medical specialists. The facility encompasses 5 operating theatres, maternity, medical and surgical wards, medical and surgical ICUs, and a neonatal ICU. Additionally, Durdoc Hospital provides paediatric, pathology, radiology, retail, and pharmacy services. With a well-rounded team ready to treat a range of conditions, those in the local community can easily access the necessary services to alleviate suffering and feel better sooner.
The Ascot Hospital under JMH offers a modern and spacious facility, which overlooks the scenic Greyville racecourse. The facility has a unique and private boutique feel, offering patients topquality medical services across the 87 beds at the hospital. The hospital contains the Ascot Breast Clinic, which is focused on providing much-needed specialist breast care services and occupational medicine to those across the region. In addition
to this, the Ascot Park Hospital, which is the latest hospital under LMH, had introduced a mental health ward offering a wide range of treatment options, including a holistic approach, to tackle a wide range of mental health conditions.
JMH has two state-of-the-art same-day healthcare facilities, which are committed to providing exceptional care to the community. These are the Ribumed Day Hospital in Glenwood, and the Ribumed Medical Care in Ballito. The hospitals believe that everyone is vital, and so it aims to deliver the right procedure, at the right facility supported by the right specialist with the right care. This patientfocused care approach allows each one to provide exceptional care to the communities of Glenwood and Ballito. Both facilities offer 36-day beds and 4 operating theatres in each, with Ribumed Day Hospital providing a dedicated paediatric ward, whilst RIbumed Medical Care focuses on pathology and radiology, with a behavioural centre and a renal unit.
The final hospital under JMH is the Richards Bay Medical Institute, which provides highly advanced Varian Truebeam Linac technology to deliver leading radiation treatments for patients. This
treatment makes it possible to deliver radiation to patients faster, with a higher level of accuracy and precision than other methods. Alongside its leading radiation treatment facility, the hospital is also committed to providing gynaecology, orthopaedics, ophthalmology, pain clinic, general surgery and urology services across its 65-bed capacity.
Across every hospital under the JMH Group, there is a real passion for delivering top-quality care to the local community, supported by its expansive and diverse team of specialists. Each specialist comes with a diverse background to ensure that patients are given the best treatment options possible, supported by care teams that aim to help every patient feel better every day. A key way it achieves this mission to deliver top quality care is through providing affordable and cost-effective treatment options, many of which support Medical Aid schemes, so patients across the KwaZulu-Natal province can access the best care available to them. Therefore, in its mission to provide superior medical care to the community and alleviate suffering, JMH remains successful with its 7 leading hospitals providing the best possible healthcare to its patients across the region.
With Gibraltar being an international hub for maritime operations, the Gibraltar Port Authority plays a vital role in overseeing the country’s vast shipping and tourism industry. With over 2 decades of experience across Gibraltar’s maritime sector, GPA has continued to build on its existing success in the hope of extending its reach across the global maritime sector. Today, the Association oversees all maritime operations serving the country’s port as a vital hub for shipping lines across both the Mediterranean and the Atlantic. For this reason, the port is vital to the country’s economy and receives around 240 million gross tonnes of vessel calls per year. Therefore, as a centre for maritime excellence, GPA is essential to the growing reputation of Gibraltar within international shipping lines.
GPAwas formed in 2005 with the central mission to oversee and maintain control of all vessels traveling throughout the British Gibraltar Territorial Waters (BGTW). GPA has been building on Gibraltar’s strategic location at the heart of international shipping lines by implementing firm and efficient services across the maritime and logistics sector. This includes the navigation, bunkering, and licensing of all port operations. By providing these services, GPA has established a vision for the future which aims to develop more partnerships for the port with a transparent and efficient approach to every aspect of the port industry sector.
GPA monitors and controls the 60,000 vessels that operate along the Strait of Gibraltar every year. An essential part of GPA’s role is in their Vessel Traffic Service (VTS), which GPA utilises to effectively coordinate all vessel movements across the BGTW and into the port. The VTS provides roundthe-clock monitoring from its operations centre in the port’s main office. The system utilises a range of sensors, including radar and automatic
In early 2023, the Company was proud to be selected as a delivery partner by the main contractor appointed by Gibraltar Port Authority for salvaging the OS35 wreck, a 178m LOA Bulk Carrier whic was run aground off the eastern Gibraltar shoreline after a collision with another ship in the area. DMS Gibraltar was approached by the main salvage contractor (KOOLE) and appointed to perform all preliminary diving works, in particular damage assessments and mapping, internal (e.g. cargo holds, engine room, etc) and external UW inspections and general surveys.
Another key milestone for the Company in 2023 was the successful conclusion of the first DMS Gibraltar Training Program. This initiative, supported by the Gibraltar Port Authority, University of Gibraltar, Government of Gibraltar and other partners, provided vocational training opportunities in the maritime and diving sector to several individuals over the course of one year. The idea was to promote and create viable routes to employment in the maritime sector for the younger generations.
We are extremely happy that the 2023 Training Program was a resounding success, leading to a total of 3 fully HSE qualified commercial divers and a total of 8 candidates who achieved one or more accredited qualifications and real-life work-experience in the maritime/diving sector (e.g. STCW 95 Basic Safety Training, Introduction to Shipping Diploma, BSAC Scuba Certificate and working as Able Seamen or deck-hands on locally based serviceboats/dive-boats).
Overall, 2023 was a great year for the Company on all fronts. Going into 2024 and beyond, we strive to further consolidate our reputation for honesty, safety, professionalism and overall efficiency, to the benefit of all clients, partners and industry stakeholders and the community as a whole.
https://dmgroupservices.com
identification systems (AIS), CCTV and night-time thermal imaging to provide a complete picture of movements along the BGTW. Furthermore, GPA works with global partners to update the UK’s Maritime Coastguard Agency (MCA) on all vessel traffic to assist authorities worldwide in monitoring vessel operations across international shores.
The Port of Gibraltar is one of the largest bunkering ports in the Mediterranean, and so one of the central operations across the port is bunkering operations. GPA is committed to providing low-cost bunkering services, which makes the most of the port’s strategic location and allows it to remain competitive within international bunkering markets. In fact, as the island has a tax-free status within the European Union, many shippers utilize the port for the movement and bunkering of goods without additional tax fees, providing the port with yet another competitive edge over others within the same shipping routes.
One of the main advantages of the Port of Gibraltar is that it has a 1-meter tidal variation all year round, which means that vessels can easily port
without having to factor in tidal depths. This means that even large bunkering vessels can easily port at the docks. Once vessels have ported in Gibraltar, each vessel is met with a full ship-to-shore service, helping in the delivery of products whilst at anchor in Gibraltar Bay. However, should a vessel not be able to port, these vital services are also facilitated by GPA alongside the vessel. This complete shipto-shore service is what has continued to support the Island’s cargo movement by providing the port with a reputation for keeping supply chains moving. Therefore, by continuing to provide valuable and efficient services such as bunkering, as well as content quality checks of the cargo throughout its operations, GPA has established Gibraltar as a vital stopping location for shipping lines on an international scale.
Alongside the port’s commercial activities, Gibraltar remains a busy tourism port. Tourism is a vital industry for Gibraltar, especially for the cruise line industry. Under GPA, the port facilitates cruise ships, which can helpfully enter the port at any time of the day due to its one-metre tidal range. Situated only an hour from the Strait of Gibraltar, the port can facilitate these cruise vessels with bunkers of water. The Cruise Terminal is 950 metres long and
INCARGO GIBRALTAR
Our number one
is a quality service for your peace of mind...
Unit 7, 12a North Mole Road, Gibraltar
Tel: (350) 200 41777 :: (350) 200 41778 :: 24 Hr. Tel: (350) 545 05 000
Email: operations@incargogibraltar.com :: www.incargogibraltar.com
allows for four medium-sized cruise vessels or two large-sized cruise vessels to berth alongside each other simultaneously. The terminal includes a range of facilities, including telephones, bars/cafes, art and craft shops, display areas and the Gibraltar Tourism Board Information Office, which provides everything both passengers and staff may require upon docking. GPA monitors the port, along with the Ministry of Defence and the Royal Gibraltar Police Marine Section, to ensure the safety of the port and its customers through its discreet but effective security presence.
As the port continues to build its reputation across international shipping lines, more and more vessels continue to arrive at Gibraltar’s shores for both cargo and tourism. In October, GPA announced the inaugural call from the VS Vista vessel. The MS Vista vessel is a 1,200-passenger cruise ship under the Oceania Cruises umbrella. The vessel made its first visit to the Port of Gibraltar, where it was met by the Minister for Tourism, the Hon. Christian Santo MP. The visit from the cruise liner highlights the continuing role of Gibraltar as a vital stopping point for many global cruise itineraries and highlights GPA’s commitment to delivering the best passenger experiences across the port to ensure the Island
remains a valuable stopping point for vessels and passengers alike.
Overall, it is clear that GPA and the Port of Gibraltar remain a thriving hub focused on delivering vital maritime operations across international shipping lines. With a growing number of vessel calls each year facilitating many sectors from cargo to tourism, Gibraltar is a key stopping point for many travelling across Mediterranean and Atlantic shipping lines. We look forward to seeing how GPA continues to expand its role across the port and as 2025 brings more exciting developments to Gibraltar’s maritime industry.
Written by Carley Fallows
As the seasons change, many of us are looking through our wardrobes for our summer clothes that represent our style whilst keeping us cool during the warmer months. However, with the rise of fast fashion and micro-trends, it’s easy to look back at these clothes and think they are no longer fashionable, resulting in large hauls of new clothing. This seems to be a cycle we are repeating year after year, resulting in millions of items of perfect condition clothing being disposed of and ending up in landfills, causing significant waste and harm to the environment. However, there has been a real shift in recent years with many consumers reevaluating their spending habits and overconsumption, especially in the way of fashion, to examine what they’re spending their money on, where it comes from, and the environmental impact their purchases are having on the world. This is where Love Not Landfill come in, a non-profit campaign group that is passionate about providing a better understanding of the impact of the clothing industry on the world and whilst highlighting the solutions available to us when the clothes we have may no longer serve us.
Aurora can be seen near both the north and south poles, however, in the south, it is called the aurora australis. For millennia, the lights baffled humans as they tried to understand what caused this light spectacle. The answer comes from the sun. Solar storms on the sun’s surface cause large waves of electrically charged particles to travel millions of miles into the solar system. Many of the particles are deflected away from Earth, but sometimes they become captured in the Earth’s magnetic field and quickly are pulled into the atmosphere and towards either of the Earth’s poles.
Love Not Landfill, run by ReLondon, is passionate about encouraging fast fashion fans to buy secondhand, and swap, recycle, and give to charity when clothing is no longer needed. The goal is to help encourage 16–24-year-olds, who are the main target of fast fashion, to never throw away unwanted clothing, resulting in it ending up in a landfill or in incinerators. Instead, the campaign group are providing spaces where recycling and repurposing can take place. It hopes that through its recycling
focus; clothes and other material goods will no longer be wasted in landfills and instead will get a new life with a new owner.
According to Love Not Landfill, £12 billion worth of clothing goes to landfill every year, whilst a further 80 billion new garments are produced in the same time. This creates a vital problem as there are more and more clothes being produced to meet the microtrends that are only ‘fashionable’ for a short period of
time, and then many are disposed of in landfill waste. Often, fast fashion-focused clothing is made with synthetic materials and so requires oil, plants, animal products and a vast amount of water to create.
This creates a two-fold problem: firstly, the garments are already utilising vital resources to create the clothes, often with dyes and chemicals that contaminate waterways. Then, secondly, the clothes are ending up in landfill, causing these resources used to make the clothing to release greenhouse gases as they decompose, contributing to further harm to the planet. Therefore, the whole fashion industry provides a real environmental issue, with the sector producing 10% of the world’s current carbon emissions, contributing towards the ongoing climate crisis. Furthermore, it is expected that by 2050, 25% of the global carbon budget will be used by the fashion industry, making it one of the most aggressively growing sectors in terms of its consumption and waste resources.
So, what are Love Not Landfill doing to help mitigate these problems? Love Not Landfill are not interested in telling people they can’t express themselves through their style, instead they are focused on providing the necessary information to make better and more informed choices when it comes to purchasing clothing. Then, when clothing is no longer needed, Love Not Landfill provide a committed recycling scheme to help stop any
unwanted clothing from ending up in landfill. Across London, Love Not Landfill works with organisations within the fashion and textile industry to help reduce overconsumption, and a big part of this is encouraging young people who are the main market for fast fashion to change their shopping behaviour. The campaign group hopes that by working with charities, launching social media campaigns and educating people on the impact of the fashion industry, it can help encourage people to make better decisions when it comes to purchasing clothing, and when clothes are no longer needed, donate, recycle and repurpose them. It is Love Not Landfill’s goal to stop all garments from ending up in landfills.
A key initiative behind the project is the establishment of clothing banks across London where people can drop off all clean clothes, shoes, bags, jewellery, bedding (sheets, duvet and pillow covers), blankets, and towels. These are then sorted by Love Not Landfill teams, which means that good quality clothes are sent abroad to be worn again, and other materials are recycled and repurposed. The repurposing could include being used as stuffing for things like car seats and house insulation. Some items can also be sent to special textile recycling plants, where they will be used to become new recycled cotton or polyester. The aim is to ensure that clothes neither end up in a landfill nor in incinerators. Both of these waste
routes negatively impact the planet, releasing unnecessary CO2 and greenhouse gases into the environment. Love Not Landfill outlines that recycling, repurposing or swapping clothes can massively help tackle the climate impact of the fashion industry. In fact, by extending the life of a piece of clothing by just 9 extra months, you can reduce the carbon and water footprint of that item of clothing by 20-30%.
Whilst the sustainability of the fast fashion industry is a complex problem, as consumers, we play a valuable role in controlling the impact of the fashion industry on the environment. Consumer choices are vital in showing big corporations that environmental issues are a key concern for their customers, and so, through small actions to buy more sustainably, repurpose and recycle clothes when no longer needed, consumers can show corporations that the future of the fashion industry needs to account for its role in climate change. For many companies, this shift has already begun, with many choosing to pick recycled fabrics and many opting for slower fashion offerings. However, this is just the first step, and Love Not Landfill is passionate
about encouraging this sustainable shift from the consumer to influence these corporations towards the future of the fashion industry.
Overall, Love Not Landfill is a vital non-profit campaign group who are passionate about showing your style and personality through clothes, without the need to buy in excess. For Love Not Landfill, all the clothes we could possibly need have already been made, it is just the consumer’s mission to find them second-hand instead of investing in brand new items that continue to harm the environment. With its clothing banks strategically located all over London, it continues to promote recycling over landfill to save valuable clothing from going to waste, and in the process, helps to reduce the impact of fast fashion on the planet one item at a time.
SOURCE https://www.lovenotlandfill.org/#problem
https://www.bbc.co.uk/future/article/20200310sustainable-fashion-how-to-buy-clothes-good-forthe-climate
The demand for green energy has seen a vital increase over the last few decades, as companies worldwide take on the responsibility to reduce emissions and build infrastructure better suited for a carbon-neutral society. However, many of these vital infrastructural developments, including the development of renewable energy, electric vehicles and sustainable farming, require mined metals and minerals. This a tricky balance to play for companies, who seek to drive the world towards the energy transition whilst also participating in the necessary mining activities required to source such resources like copper, nickel and iron. However, companies like BHP are world leaders in these resources but operate with a key focus on building a better and cleaner future to support the renewable energy industry and the planet.
BHP is a world-leading mining company, which produces iron ore, copper, metallurgical coal and nickel, as well as potash. Its operations span the globe and include a complex portfolio of large, long-life quality assets which are focused on delivering value as well as sustainability. BHP is focused on the need for decarbonisation efforts to take effect immediately, so have established themselves as a responsible body that manages commodities which are vital in the development of a renewable energy future.
To understand the valuable role BHP plays we must understand the role of each of the metals and minerals which they mine and the role they play in energy transition targets. Iron ore and metallurgical steel are vital for the development of global infrastructure, and so are crucial resources needed to support the future implementation of renewable energy on an infrastructural level. Copper and nickel also play a vital role in making renewable energy possible, with copper covering the vast majority of electrical wiring. Nickel is a prominent metal used in the development of rechargeable batteries which are used in electric vehicles worldwide.
A crucial aspect of development for BHP in recent years has been towards potash, which is utilised across the agriculture industry to see higher crop yields which contribute to the production of biofuel on an international scale. Therefore, these metals and minerals are crucial throughout all of BHP’s work to ensure that their mining, processing and transportation services for these products are always working towards the betterment of the future of the planet.
BHP manages some of the world’s most resilient long-term portfolio assets which continue to grow in value thanks to the company’s discovery explorations, development of resources and acquisition of assets. Across its array of assets and mine operations, BHP develops and implements mining operations and then oversees the processing and refinement of ore before it transports these resources to customers. In addition to the mining, processing and logistical movement of the resources, BHP also focuses on waste management to ensure that its environmental impact on the planet remains at a consistent minimum.
www.liebherr.com
MASPRO is a leading provider of cutting-edge engineering solutions for underground and surface operations in the hard rock mining industry. What sets us apart is our unwavering commitment to optimising the parts we produce to increase safety and reliability. Our team works closely with customers to ensure that their machinery performs at its peak, even in the harshest mining conditions. If you’re looking to drill deeper, move more ore, and push your equipment to the limits while maintaining the highest standards of safety and operational reliability, talk to the MASPRO team today!
Having leveraged reverse engineering to fully understand the best way to manufacture high-quality mining products, MASPRO delivers innovative solutions designed to meet the needs of even the most challenging of mining environments.
Established in 2006, MASPRO is a family-owned and operated company based in Condobolin, Australia that is passionate about delivering precision-engineered mining parts to the world. MASPRO, , has spent the last 18 years focused on creating flexible solutions for the mining industry which aim to reduce recurring failures and help to keep its clients’ mobile mining equipment safe, reliable and operating optimally.
This focus on success is what has bred a culture of innovation across the company as it works to utilise its expertise in the underground and surface mobile mining equipment industry to create world-class engineered, manufactured, and tested products which rival OEMs on the market. By investing in cutting-edge technology, digital software design, 3D optical scanning equipment and comprehensive metallurgical knowledge, MASPRO has been able to re-engineer and perfect its mining parts and equipment for the needs of the mining sector. www.maspro.com.au
Whilst the mining and transport of its ore play a vital role, BHP is also heavily involved in the sales, marketing and procurement of assets to bring continued investment and expertise into the mining sector. It achieves this through a close understanding of the markets, customers and suppliers’ needs. By close attention to global mega-trends, BHP can cater its operations and acquisitions to seek out the most vital and profitable assets which will contribute greatly to the renewable energy transition.
Australia is a key site of operations for BHP with assets covering metallurgical and energy coal, iron ore, nickel and copper operations spanning the entire country. In Western Australia, BHP has the West Musgrave Project which covers the Nebo and Babel nickel-copper deposits, as well as the Succoth copper deposit. The project has an expected mine life of 26 years, with a proposed ore production rate of 10-14 Mtpa. Also in western Australia is BHP’s Nickel West operation which is part of its Minerals Australia business. Nickel West covers a variety of locations across traditional lands with a fully integrated mine-to-market operation spanning both open-cut and underground mines, as well as concentrators, a smelter and a refinery all within the complex. The asset is a crucial driver for renewable energy markets for BHP with 85% of its nickel being sold to battery suppliers across the world.
Whilst BHP develops vital metal production at Nickel West, part of the company’s mission is to make its operations just that little bit more sustainable. Therefore, BHP has been implementing a range of sustainable projects aimed at improving the overall impact of the complex’s operations on the region. These projects include the Northern Goldfields Solar Farm and BESS Project with Tansalta, which incorporated two solar farms and a battery energy storage solution. The project aims to support the mine and concentrators needs of the Nickel West complex.
The Goldfield Solar Farm began construction in 2021 and built upon the existing Merredin Solar Farm which was a power purchase for BHP in agreement with western Australia’s largest solar farm. Then
in 2022, BHP announced another power purchase agreement with Enel Green Power for the Flat Rocks Wind Farm which once completed will power the Kalgoorlie Smelter and Kambalda Concentrator on the Nickel West Complex. This investment in utilising renewable energy across BHP’s operations shows the company’s commitment to mitigating its environmental impact on the planet as much as possible.
In Queensland, BHP mines metallurgical coal across 7 assets in the Central Queensland Bowen Basin. The asset is owned in a 50:50 partnership with Mitsubishi Development, and is regarded to be one of Australia’s largest producers and suppliers of seaborne metallurgical coal. The site includes the Hay Point Coal Terminal which can handle more than 55 million tonnes of coal which the mine exports every year. In addition to BHP’s operations in the coal industry in Queensland, BHP also operates the Mt Arthur Coal Mine in New South Wales which produces coal products for an international customer base across the energy sector.
As BHP look towards the future, along with the rest of the world, it is hoping to significantly cut its carbon emissions by 2030, and achieve net zero greenhouse gas emissions (including both scope 1 and scope 2 emissions) across its operated assets by 2050. By working with its partners in the steel and maritime industry, BHP hopes to reduce its emissions across its BHP-chartered shipping operations for BHP products by 40%. To achieve this it is working with key stakeholders, and is backed by US$400 million in investments from its Climate Investment Program to significantly improve the low carbon steel making and low-emission technologies of the future.
With BHP you can feel throughout every operation a need and drive to make real change in the world. Through the acquisition, operations and development of BHP’s long-life assets continue to play a crucial role in developing the world towards a more sustainable future. Therefore, BHP’s goal to bring people and resources together has been largely successful and has built a steady foundation ready to meet the renewable demands of the future.
As part of the SSA Marine and Carrix company, the Tuxpan Port Terminal (TPT) is a privately operated terminal located along the Gulf of Mexico offering a range of services across the cargo and related industries market to the United States. TPT takes advantage of such a vital position, to provide clients from across the worldwide shipping and logistics industry with an alternative cargo handling operation which guarantees a reliable, accessible and high-quality service facilitated through a specialised infrastructure system. Through its team of highly trained personnel, Tuxpan Port Terminal hopes to play a significant role in the development of Mexico’s economy as it expands the country’s foreign trade offerings.
Located 293 kilometres from Mexico City, TPT sits strategically along the Mexico-Tuxpan highway and so provides easy delivery of products from the city into the terminals for distribution across domestic and international markets. The strategic location of TPT utilises the infrastructure links of the region to deliver cargo handling operations that save on freight costs, toll fees and extended transportation times. This reduction in time and distance makes TPT a vital hub that delivers cost-effective benefits for all stakeholders involved in the movement of cargo. By enhancing the operations of stakeholders, TPT hopes to see continued investment into the terminal, which will allow it to maintain its reputation as a reliable and efficient alternative cargo handling service providing vital links to both the Northern and South American markets.
What sets TPT apart from other ports and cargo terminals along the Gulf Coast, is its implementation of cutting-edge technology across its operations. TPT’s operating system has been developed by Tideworks Technology, a subsidiary of the Carrix company, with the aim of providing solutions for the efficient and productive management of the terminal. Tidework Technology’s solutions have already been seen across the world, and in TPT include systems such as Spinnaker which manages yard planning by providing supervision to ship manoeuvres, yard operations, deckhouse activities and the transit of cargo throughout the terminal.
TPT covers a total area of 85.7 hectares (Ha), which is divided into 15. Ha of container storage, CFS and warehousing to handle the high cargo capacities that are travelling through the terminal. In terms of vessels entering the terminal, TPT has a 15-meter (m) depth along its 556m waterfront which has an operational ship capacity of 11,500 twentyequivalent units (TEUs). When vessels reach the terminal, they are met with 2 STS Super Post quay cranes, 30 container trailers, top and side loaders, forklifts, spreaders, 240 refrigeration consoles for containers and the necessary equipment for steel and steel production. All of these facilities, ensure that TPT can seamlessly take cargo from vessels travelling into the Tuxpan port, and move it swiftly off throughout the Terminal complex and then onto
the transportation or shipment companies which will take the goods to their end markets.
To maintain a firm management and standardised system for container merchandise, a Mainsail system has been implemented, which will also enhance the reporting systems across the port. Tideworks Technologies has also implemented traffic control systems which support the effective coordination of cargo across the terminal’s yard. Then, to enhance the connection between the terminal, its customers, shipping lines, transportation companies, and related stakeholders, TPT was installed with a Forecast system to ensure all key players remain updated and in constant communication for the benefit of the smooth flow of cargo throughout TPT.
Typical cargo travelling through TPT includes those in the steel, forestry, project cargo, aluminium and copper industries. All of these industries are global economic heavyweights, and so being the port and terminal of choice for international shipping lines travelling along the Gulf Coast highlights TPT’s
growing role in supply chains for some of the world’s most economically lucrative industries. Therefore, TPT is already highlighting the significant role it has begun to play in the comprehensive economic development of Tuxpan, which in turn will see more importers and exporters utilising the terminals to expand their international distribution network.
Just last year the role of TPT in international markets took a large step forward, with TPT extending its reach across the Gulf of Mexico. TPT announced in June 2023, that it was adding a new multimodal service at TPT, which would connect with Canada, the U.S. and across Mexico. The service will provide exporters and importers with a new strategic channel to enter these markets, supported by TPT’s reputation for efficient and cost-effective cargo handling. This new route will be supported by Crowley, a world-leading shipping and logistics company, which currently provides door-to-door solutions in the U.S., Caribbean, Central American and Mexican markets.
The development of the new multimodal service, will highlight TPT and Crowley’s expertise and professionalism, and provide a competitive advantage for the most modern port terminal complex in Mexico. The General Manager of TPT, John Bressi, outlines in the announcement that “Tuxpan Port Terminal recognises and congratulates both Crowley and CN for the important advantages that the services of both companies will present to foreign trade. Crowley is a premier container line and logistics company that selectively chose TPT for this exceptional service, recognising that this terminal is the best alternative on the Gulf of Mexico coast. This short sea route will offer significant benefits to the BCOs, such as competitive pricing, shorter transit time, reduced CO2 emissions and safer cargo handling. We are delighted to be Crowley’s port terminal partner”.
Bressi’s comments here really solidify the aims of TPT to work with international companies such as Crowley to enhance the shipping and distribution
network for Mexico and bring significant economic benefits to the region. These economic benefits will then provide a wider local and international reputation for cargo handling success, which aims to bring future investment and reliance on TPT for international shipping lines in the future.
Overall, TPT has optimised its strategic location along the Gulf of Mexico to deliver an internationally recognised port terminal which delivers efficient, cost-effective and reliable cargo handling for customers both within Mexico and beyond. With new developments and partnerships, such as with key shipping companies like Crowley, TPT has established itself as the best alternative port terminal serving the Gulf through its specialised systems that ensure every customer’s cargo is delivered with efficiency.
Western Australia is home to some of the largest gold deposits in the world and so the region boasts a range of low-cost, long-life mine sites and operations. One of the most notable gold mine operations in western Australia is the 50:50 joint venture between Gold Road Resources and Gruyere Mining Company (Pty.) Ltd. Gruyere Mining Company is a wholly owned Australian subsidiary of the larger Gold Fields company. The Gruyere Gold Mine Project takes advantage of one of Australia’s largest underdeveloped Archaean orogenic gold deposits to bring continued economic prospects to both the country and the companies for the future.
The Gruyere Gold Mine Project is a Tier 1 lowcost and long-life asset, which has a current expected mine life of 10 years. The mine project has 4.05 million ounces of ore reserves, and 6.69 million mineral resources (both with 100% basis). The deposit was first discovered by Gold Road in 2013 on the southern Dorothy Hills Trend and first poured gold in July 2019. The mine is estimated to produce more than 300,000 ounces of gold per year. Under the joint venture agreement, Gold Fields has been appointed the manager to develop and operate the mine operations, whilst Gold Road has retained its responsibility for the exploration of the joint venture investments.
Just a few years after pouring its first gold, the project has now grown to have 153 million tonnes grading 1.33g per tonne for 6.69 million ounces of contained gold. This makes it one of the largest virgin discoveries in all of Australia. In 2022 the Gruyere Gold Mine Project delivered a record annual gold production of 314,647 ounces of gold, to a total of 918,479 total ounces of gold yielded from the venture as of 31st Dec 2022 (both at 100% basis). Consequently, the project is set to become one of the nation’s deepest open-cut gold mines and announced in April 2023 that the Gruyere Life-ofmine plan set out by Gold Road Resources reaffirms the sustainable production of gold at a rate of approximately 350,00 ounces per annum through to 2030 as further developments of the mine complex continue to be explored.
Operations at the Gruyere Gold Mine currently focus on one main open pit which has been developed in stages to an approximate depth of 500m below the surface. Activities at the mine site currently include loading, hauling, drilling, and blasting. All of this work is carried out by the project’s existing mining contractor, MACA and an expansive workforce of roughly 490 people using largescale mining equipment. MACA carried out the bulk earthworks at the Gruyere mine, the first stage of the run-of-mine pad work and the construction of the tailings storage facility.
Furthermore, due to the remote nature of the mine site, a large majority of the workforce is required to commute to and from the mine every day. This commute includes a 90-minute flight bringing workers from Perth, or a regular bus service to bring
MACA is a trusted contract partner for the Gruyere Gold Mine project. With experience in a wide range of commodities our operating divisions improve your project economics at every stage of the mining cycle.
maca.net.au
those from more local communities. This bus takes roughly two hours and services local communities in Laverton and Cosmo Newberry.
In addition to mining activities, The Gruyere Gold Mine Project also includes a processing plant which has a capacity of 9.75 million tonnes per annum and treats oxide, transitional and fresh ores from the mine. The processing plant consists of a single storage gyratory crushing circuit, 14 MegaWatt (MW) semi-autogenous grinding (SAG) and a 15MW Ball Mill (SABC) grinding circuit, as well as gravity recovery. This processing also includes four 48” Knelson concentrators, a GEKKO In-Line reactor, a Pre-Leach thickener, one Leach and six Carbon-in-Leach (CIL) agitated tanks, split AARL elution circuit and a thickened downstream tailings storage facility.
Following Gold Road Resource’s announcement of the life of mine extension beyond 2030, the company is looking to further develop the mine operation to expand the existing operation into a 7-stage mine design. This development comes alongside the Gold Highway Project which is located roughly 25 kilometres west of the existing Gruyere mine site. The Gold Highway Project currently totals 14 million ounces of gold at 1.44g/t AU for 0.67 million ounces and includes an existing ore reserve of 7 million tonnes at 1.28g/t AU for 0.29 million ounces. The project is currently undergoing feasibility-level studies and is hoped to begin operations by early 2026.
Furthermore, in June 2023, The Gruyere Gold Mine Project announced that mining service provider, MACA, who is the existing mining contractor has secured a contract extension at the mine site. MACA currently provides load, haul, drill and blast, crushing, and screening services to the project, as well as light voltage and high voltage maintenance. The extension of the contract is expected by MACA to generate 850 million Australian dollars of revenue over the 5-year term. MACA are committed to working with the traditional landowners to ensure a collaborative approach to the mine operations which benefits everyone involved.
Overall, the Gruyere Gold Mine Project highlights the rich gold deposits that companies such as Gold Fields and Gold Road Resources are developing towards a future of sustained gold production. The project represents the vast community effort that projects such as these require. With an expansive workforce, pivotal mining contractors and local communities all working together; the mine project is already carving its way to being one of the most significant gold mining operations across western Australia. Furthermore, with developments across the Gold Highway project, we look forward to seeing how the companies continue to develop their joint venture in Australia to bring crucial economic benefits for many years to come.
Operating the world’s largest transhipment hub, PSA Singapore provides unrivalled connectivity in the heart of Southeast Asia. PSA Singapore is a world-leading ports and terminals group which handled 37 million twenty-foot equivalent units (TEU) of containers in 2022. Therefore, as the flagship terminal of PSA International, PSA Singapore leads the industry across the region providing handling, management, depot, and warehousing services to a whole range of container vessels.
PSA Singapore began as the Port of Singapore Authority, which was a statutory board responsible for regulating, operating, and promoting the Port of Singapore in the 1960s. However, in the 1970s its container port and handling facilities were established which over the next few decades saw expansive growth reaching 5 million TEU by 1990. By this point, Singapore was the largest container port in the world, and so in 1996, the regulatory functions of the original company were transferred to Singapore’s new maritime regulator, the Maritime and Port Authority of Singapore (MPA). In 1997, the Port of Singapore Authority converted into an independent commercial company which kept the PSA initials and added Singapore removing the original acronym meaning. Since the container port and handling services began as the central focus for PSA Singapore, it has continued to expand and play a vital role in the overarching multinational PSA International group.
The core business of PSA Singapore is the movement of cargo from one vessel to another whilst in transit to its destination. This vital role is due to its strategic location at the heart of
Southeast Asia, at the crucial crossing point of many major shipping routes. Therefore, the PSA Singapore has become an important hub for global supply chains as feeder vessels bring containers to the Port of Singapore which are then loaded onto larger vessels which are then taken on shipments to their final destinations.
This transhipment method is both costeffective and efficient because it allows vessels to make a single voyage to the port, rather than multiple journeys to each individual destination. Consequently, approximately 85% of the containers that arrive in Singapore are transhipped to another port of call, and so the role that PSA Singapore plays in facilitating and maintaining this system of transhipment can be felt across the local and international cargo industry.
Across PSA Singapore there are 55 berths at the Tanjong Pagar, Keppel, Brani and Pasir Panjang ports. These ports all are equipped with container handling equipment and have a combined capacity of 50 million TEUs. The largest facility is at the Pasir Panjang Terminals (PPT) which has 3 dedicated births and is supported by an open car yard and multi-storey car storage yard which accommodates 20,000 car park lots. In addition, PSA Singapore has its Jurong Island Terminal which is located on the western corner of Jurong Island and has 2 berth terminals with a capacity of 400 TEUs.
A significant part of the development of PSA Singapore is the Tuas Port which is currently under development to consolidate all the company’s container terminals into a single location on the western seaboard of Tuas. The finished port is planned to have an automated and integrated operations system which will be deployed to tackle the next generation of cargo demand. Construction of the first set of berths began in 2021 and is expected to be completed by 2040. The entire project is part of PSA Singapore’s vision to form a holistic ecosystem which will bring goods anywhere in the world faster and more reliably.
For PSA Singapore sustainability is not just an option but a responsibility. It is working constantly to ensure that in order for the business to retain its resilience and continue to grow without compromising the environment it has set out on a mission to reduce greenhouse gas (GHG) emissions for the next generation. It has committed to a range
of targets which are in line with Singapore’s climate ambitions. A crucial step towards these initiatives came in a recent partnership between PSA Singapore and the Pacific International Lines (PIL). As announced this month, the two companies have signed a Memorandum of Understanding (MOU) to jointly develop sustainable solutions to cut carbon emissions and optimise maritime efficiency. This includes the development of a set of low-carbon emission routes for containers shipped by both companies.
PIL is the largest home-grown carrier in southeast Asia with strong shipping links in Asia, Africa, the Middle East, Latin America, and Oceania. As leaders in their respective industries, the partnership signifies a crucial move towards sustainability throughout the shipping industry. Mr Nelson Quek, Regional CEO of Southeast Asia for PSA International
discusses the partnership between its flagship Singapore division and PIL in the company’s recent press release, stating that “PSA is pleased to partner with PIL as we take the bold and essential step towards decarbonising the global supply chains that power our economy. We remain committed to working hand-in-hand with likeminded stakeholders as we spur concerted action towards our transition to a cleaner and sustainable future beyond the areas served by our ports”.
Therefore, this crucial partnership is set to drive change across the industry and allow each company to meet the common goal of achieving net zero carbon emissions by 2050. It is these joint ventures with other respected stakeholders within the shipping and cargo industry, that have allowed PSA Singapore to develop its operations and establish itself as a crucial hub for these industries on a global scale. Through strategic partnerships, PSA Singapore continues to deliver productivity and efficient terminal services.
Overall, PSA Singapore has worked tirelessly over the last 50 years to move from a regulatory board into the world-leading ports and terminal group, which has continued to expand across the globe. PSA Singapore plays a crucial role in an international network of port and container handling services both under PSA International, but also in the shipping industry as a whole. Consequently, through this work to develop its facilities and through strategic partnerships with significant stakeholders across the industry, PSA Singapore continues to foster a leading supply chain which is powered by its innovation, technology, and sustainable practices.
Following DHL Supply Chain’s investment of EUR350 million in Southeast Asia, find out more about how DHL in Singapore is unlocking the future of logistics for our customers.
As the leader in green logistics, we are committed to carbon neutral facilities and a full EV fleet by 2025.
Our investments in digitalization are driving productivity and value for our customers with innovative technologies and services including:
Automated pallet storage and retrieval systems
Goods-to-person picking robots
Automated Guided Vehicles
Warehouse Automation Systems
Connected Control Towers
Whether your business operates in Energy & Chemicals, Engineering & Manufacturing, Life Sciences & Healthcare or Technology, visit our website to find out more about how we can supercharge your Singapore supply chain efficiency.
Contact our supply chain experts today at nazher.khan@dhl.com or xubin.liu@dhl.com.
100 years of excellence in medical and industrial gases, our reliability and commitment to innovation make us the trusted partner of large industries
A century of expertise and leadership
In medical and industrial gas solutions.
Unmatched supply reliability
Always on time, in the right form, and with toptier quality.
Strict safety standards
With internationally recognized certifications.
For a hundred years, the oxygen of Central America and the Caribbean!