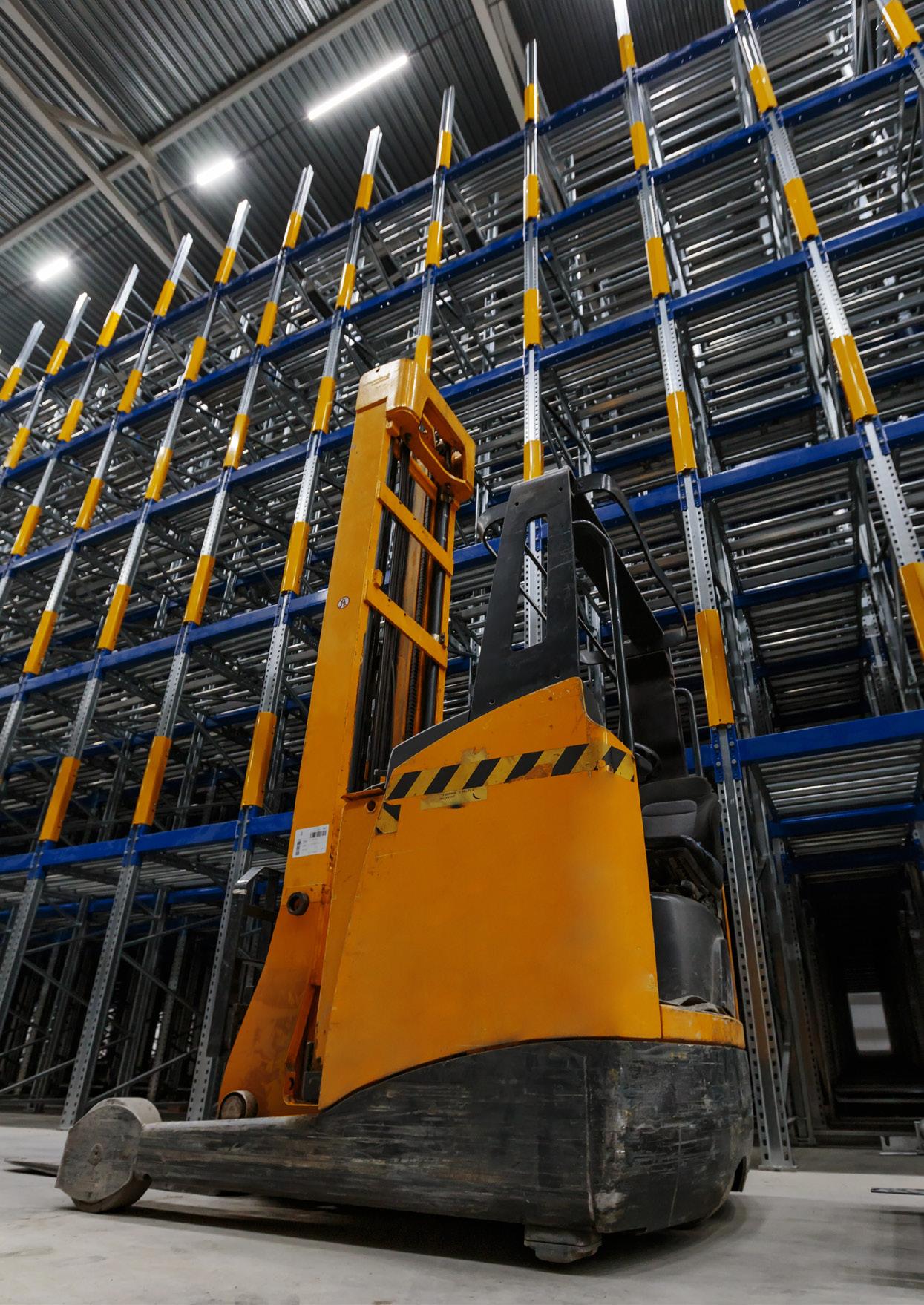
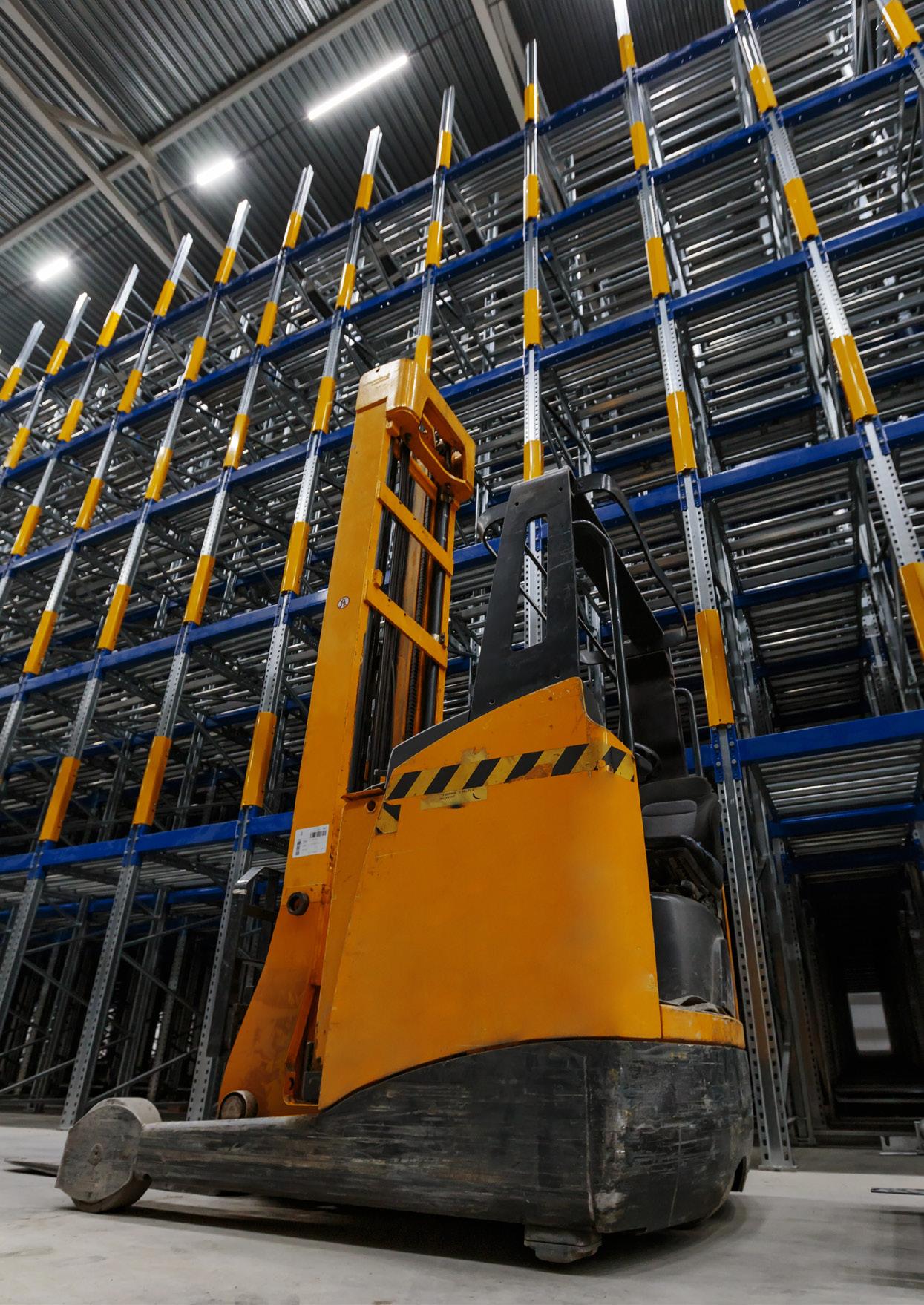
EXCEEDING EXPECTATIONS.
That’s What Continental Hose & Solares Deliver Every Day.
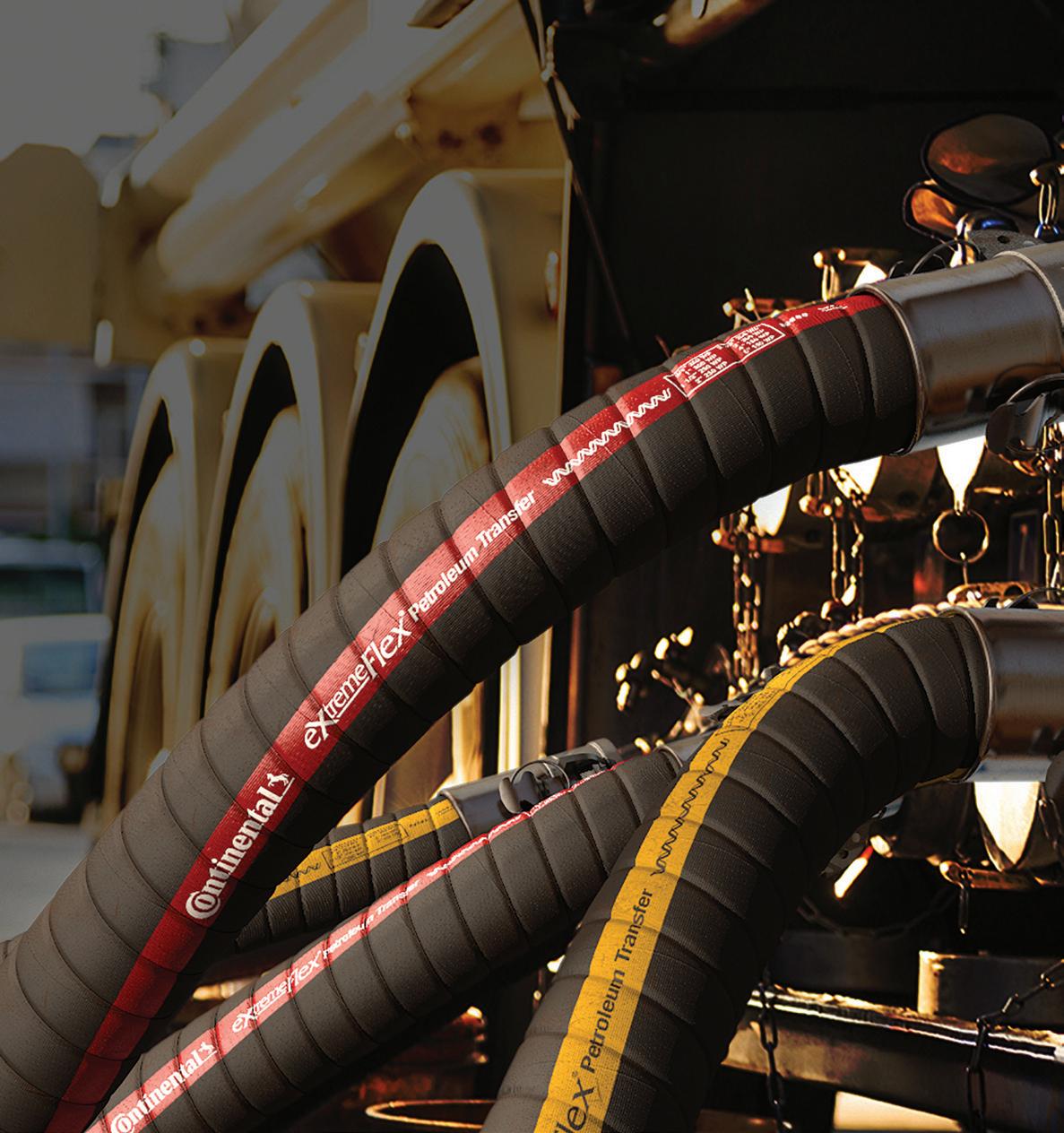
Solares’ STAR Distributor recognition indicates our team meets rigorous fabrication standards when coupling Continental hose assemblies, including Underwriters Laboratories, LLC verification. Our clients trust our premium oil & gas hose assemblies to deliver maximum efficiency, reliability, and safety to their operations. www.solaresflorida.com
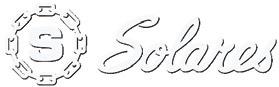
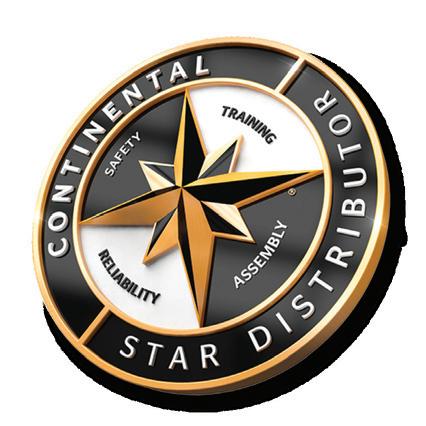
Heads of Departments
Editor-in-Chief Carley Fallows editor@littlegatepublishing.com
Space Management Emlyn Freeman emlynfreeman@littlegatepublishing.com
Media Coordinator Andrew Williams andrew@littlegatepublishing.com
Lead Designer Alina Sandu Research Kristina Palmer-Holt Editorial Research Amber Winterburn
Corporate Director Anthony Letchumaman anthonyl@littlegatepublishing.com
Founder and CEO Stephen Warman stevewarman@littlegatepublishing.com
For enquiries or subscriptions contact info@littlegatepublishing.com
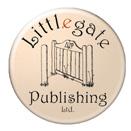
+44 1603 296 100
ENDEAVOUR MAGAZINE is published by Littlegate Publishing LTD which is a Registered Company in the United Kingdom.
Company Registration: 404 2112 62
VAT registration number: 13572767
343 City Road 60 Thorpe Road London 79 Norwich
EC1 V1LR NR1 1RY
Littlegate Publishing Ltd does not accept responsibility for omissions or errors. The points of view expressed in articles by attributing writers and/or in advertisements included in this magazine do not necessarily represent those of the publisher. Any resemblance to real persons, living or dead is purely coincidental. Whilst every effort is made to ensure the accuracy of the information contained within this magazine, no legal responsibility will be accepted by the publishers for loss arising from use of information published. All rights reserved. No part of this publication may be reproduced or stored in a retrievable system or transmitted in any form or by any means without the prior written consent of the publisher.
Copyright© Littlegate Publishing Ltd 2023
We can’t quite believe that summer is almost over, and we will shortly be welcoming in Autumn. After a much colder summer than usual here in the UK - even by our standards - we look forward to the renewed freshness the next month will bring after a chilly but relaxing summer.
This month we jump back in with some giant gas and petroleum companies bringing crucial infrastructure across their respective regions. We look at Sol Guyana Incorporated which is bringing key investments to the downstream energy and petroleum markets of Guyana. Then we see how BP’s Greater Tortue Ahmeyim LNG Project is working to position Mauritiana and Senegal as key players in the global LNG field.
Some personal favourite features from this month include Intercare Group which is bringing accessible and convenient healthcare across South Africa through a range of specialised medical and dental facilities. It is clear that Intercare’s focus is on putting patients’ well-being first, and this is shown across all aspects of its operations. Another favourite is Bay State Milling which is a family-run operation that remains ahead of the food industry by providing a range of ingredients and food products that are created with dietary needs in mind.
Once again, we cover a vast array of businesses that are working towards a more sustainable future whilst establishing their companies as leaders across international markets. Over the next few years, we are excited to see how each continues to strive for success and develop their businesses across the globe.
by Carley Fallows


Asia/Oceania
India’s Chandrayaan-3 Mission lands on the Moon
India’s space agency has confirmed that its Chandrayaan-3’s Vikram lander which is carrying a rover has touched down on the surface of the moon. This mission marks the first to land on the lunar south pole region of the moon. India had previously launched a mission to land on the lunar south pole, which was unsuccessful, so the lander reaching the surface safely is a crucial win.
Inside the lander, named Vikram after the Indian Space Research Organisation (Isro) founder, was the Pragyann rover. Over recent days the Pragyann rover has been providing the space agency with photos and data gathered as it roams the moon’s surface. One of the major goals of the mission is to hunt for water-based ice which may be able to support human habitation in the future, or for use as a propellant for spacecraft heading for other destinations further out into space.
Ancient Amphibian Species Discovered in Australia
A new species of amphibian that is thought to have occupied Australia some 247 million years ago has been discovered in Australia. The discovery was first made by a retired chicken farmer in New South Wales, where he discovered the fossilised remains of an amphibian-like creature. The amphibian was approximately 1.5 metres in length with a salamander-shaped body.
Scientists have said that the carnivorous amphibian is thought to have lived in the freshwater lakes of Sydney and is believed to belong to the Temnospondyli family, which is a species of resilient amphibians that survived at least two of the earth’s mass extinction events. Only three other fossils of this species have been identified in Australia.
Jakarta Named the Most Polluted City on Global Charts
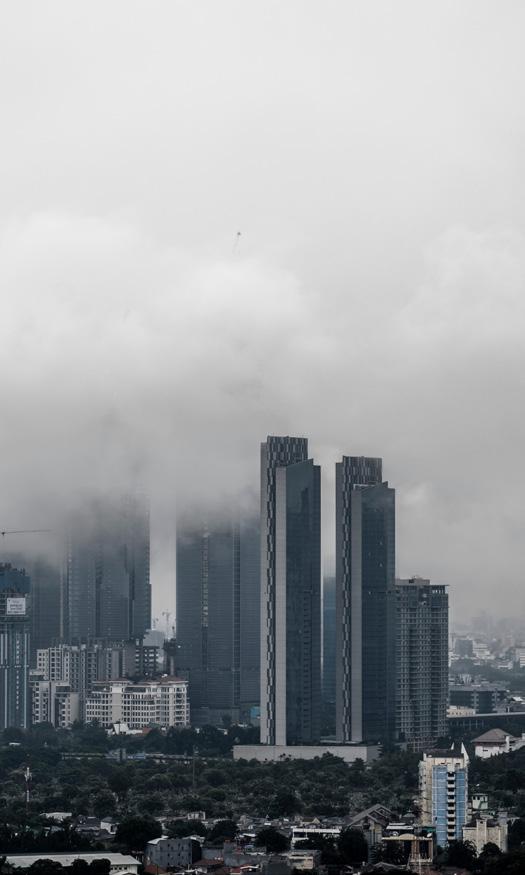
For many years Jakarta has been ranked as one of the top 10 most polluted cities globally, and so with a population close to 30 million, it has caused significant health concerns for those living in the capital and surrounding regions. Local authorities have blamed the recent pollution increase on the dry season which typically means pollutants remain suspended in the air for extended periods and vehicle emissions. As a result of the air quality conditions, many companies have been urged to impose more hybrid working for their employees to reduce vehicle emissions.
However, many blame factories and coalpowered plants for their contribution to the smog in Jakarta. Indonesia has had recent goals to cut carbon emissions, with the goal of phasing out coal for electricity by 2056. However, the coal industry is one of the largest employers across its related industries in Indonesia and so phasing out is expected to be costly.
Africa
Torrential Rains Batter War-Torn Sudan
Sudan has been the site of widespread conflict in recent months, but now torrential rains have damaged more than 500 homes across the country. Aid groups have feared that Sudan’s rainy season would cause further devastation for millions as the country is already facing significant impacts from the war that has destroyed infrastructure and plunged millions into hunger. The rain is feared to increase the already serious cases of malnutrition across the country and may bring with it further displacement and risks of diseases.
Currently, more than 3 million people internationally have been displaced as a result of the conflict with more than 80% of Sudan’s hospitals no longer being in service. Therefore, as outbreaks of cholera and measles have already been reported by the World Health Organisation there are fears that the torrential rains will add to an already difficult position and put the existing health facilities under further strain.
Clothes Repurposed in Ghana to Avoid Landfill

Across Ghana close to 15 million garments arrive in the country, and roughly 40% of these will end up in landfill waste. Therefore, the Or Foundation has been working across Ghana to repurpose the clothes into mop heads to reduce the number of materials going straight to waste. The Or Foundation is a non-profit registered in the US that has been operating across Ghana to tackle the increasing waste problems from textiles.
To prevent waste from ending up in landfills the Of Foundation is remanufacturing garments to make mops from unsold t-shirts. The organisation sorts through retailers’ unsellable clothes that are 100% cotton. The team then works to cut, sew, and assemble mop heads. The process is relatively simple and is designed in the hopes that it can be easily replicated across the country to help people create their own mop businesses which will bring in extra income, whilst stopping significant amounts of textile material from ending up in landfills.
Growing Algae in the Sahara to Tackle Climate Crisis
A London-based startup Brilliant Planet has leased 6,100 hectares of land in southern Morocco which it is using to cultivate algae. Algae absorbs carbon dioxide and emit oxygen through photosynthesis, and so the company has developed a way to grow algae across large pools of sourced seawater. The process mimics natural algae bloom, and so a small amount of algae can multiply to fill 16 12,00 -square-meter pools in just 30 days. The algae is then pumped up a 10-story tower and sprayed into the desert air. The hot air of the Sahara dries the algae as it floats to the ground leaving hypersaline algae flakes that can be collected and shallowly buried, and is supposed to isolate the carbon for thousands of years according to the company.
The algae is meant to provide a nature-based solution to reduce carbon and claims that its solution could permanently remove 30 times more carbon dioxide from the atmosphere per hectare per year than a typical European forest.
Amazon Nations gathered at Summit in Brazil
Eight South American nation leaders met in Belem, Brazil to work together to determine environmental policies that would stop the destruction of the Amazon rainforest. The summit of the Amazon Cooperation Treaty Organisation (ACTO) is working together to save the rainforest which is a crucial global buffer against climate change. However, it has seen vast deforestation over recent years and so leaders from nations across the Amazon came together to protect it.
The nations which include Bolivia, Brazil, Colombia, Ecuador, Guyana, Peru, Suriname, and Venezuela agreed on a plan that asserts Indigenous rights and protection, whilst also establishing a set of water management, health, common negotiating positions at climate summits, and sustainable developments. However, the summit did not establish a set deadline to stop illegal gold mining and deforestation or prevent new oil exploration like many environmentalists had been calling for.
Wildfires Devastate Hawaii
Wildfires have caused widespread devastation across the island of Maui and destroyed homes and businesses across Lahania. Lahaina is one of the most historic towns in Maui and was home to roughly 12,00 people. Hundreds of people fled their homes and have been relocated to emergency shelters, as roughly 2,700 homes are reported to have been destroyed. The fires are believed to have claimed the lives of many with hundreds of people remaining missing in the weeks following the disaster.
The strong winds from Hurricane Dora which was sweeping the south of Hawaii contributed to fanning the flames causing further widespread damage, which also prevented aircrafts from flying over the town during the fires. Furthermore, the abnormally dry conditions across large parts of Hawaii are thought to have also played a significant role in the widespread devastation. Many had to resort to jumping in the harbour to escape the rapidly advancing flames and smoke. Maui now faces a big rebuilding and rescue mission to determine the extent of the damage on the island.
Storm Idalia hits Florida
A Category 3 hurricane crashed its way through Florida, making its way across the west coast before moving inland towards the state of Georgia. The hurricane had winds up to 125mph, which has left more than 225,00 people without power in Florida, and a further 230,00 in Georgia. Idalia was downgraded to a tropical storm as it passed through Georgia however its powerful winds remained lifethreatening.
Following the storm, widespread flooding is expected to be seen across Florida and large parts of Georgia. The storm is the strongest one to hit Florida for more than 100 years, however, luckily there are currently no reported fatalities from the storm.
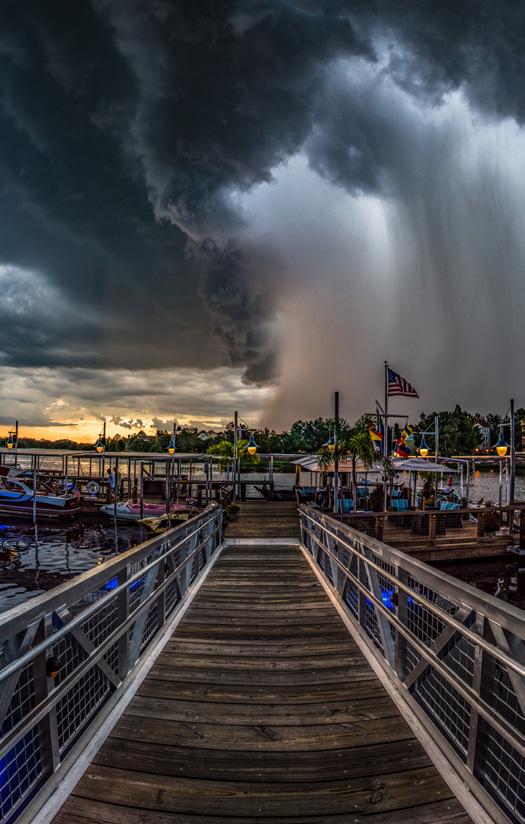
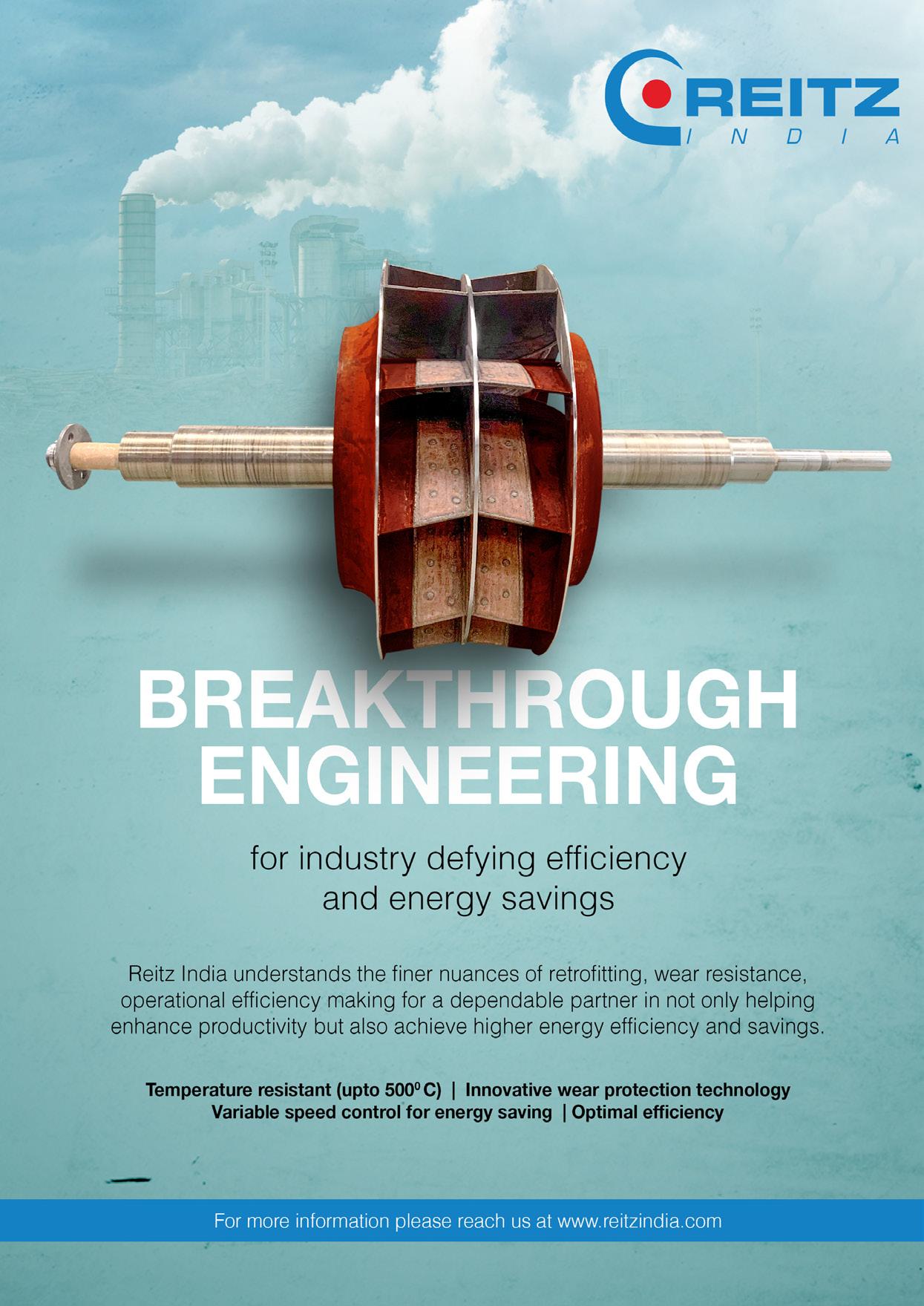
Middle East
UN Successfully Remove All Oil from FSO Safer
For months there has been an ongoing mission by the United Nations to remove all oil from the FSO Safer floating abandoned in the Red Sea off the coast of Yemen. After it was left in 2014 following the outbreak of a civil war, the vessel posed a risk of environmental disaster as it slowly began to decay. The multimillion-dollar operation has now successfully removed all oil from the safer that previously was seen as a disaster waiting to happen.
An oil spill in the Red Sea would cause major issues in the distribution of food and aid to millions, so the operation was a crucial humanitarian and environmental disaster-preventing project. Work is now set to begin the difficult task of decontaminating and scrapping the vessel.
Roberto Mancini Appointed as Saudia Arabia’s National Team Coach
After leading Italy to win the Men’s Euro 2020 title, Mancini has been named as the new coach of the Saudia Arabia national team in a deal reported to be worth more than $25 million a year. His resignation was a shock to the Italian side after being handed the responsibility for the country’s Under-21 and Under-20 teams. Many have criticised the move following reports which stated that he was set to accept a major sum for the move. However, he has denied this being the reason for his resignation.
In a statement confirming Mancini’s appointment, the Saudia Arabian Football Federation stated, “The appointment confirms the new era of growth for the Saudi Arabian national team and marks a new milestone in Mancini’s distinguished career”. His first match with the team is set for early September in an international friendly game against Costa Rica.
Israel to Expand Natural Gas Exports to Egypt
Israel will expand its natural gas exports to Egypt from its offshore Tamar Field. Egypt has recently faced a growing demand for gas, as its production between January and May this year saw a 9% decline compared to its output in 2021. With the decrease in gas supply, the country has grappled with power shortages as heatwaves have driven up the demand for gas used in air conditioning.
However, Israel has seen major gas deposits discovered over the past 15 years off Israel’s coast to bring greater gas production to the country. Previously, Israel’s government had set limits on how much of this gas could be sold abroad but has recently decided to expand its natural gas exports to Egypt which is expected to bring further revenue to Israel and diplomatic ties between the two countries.
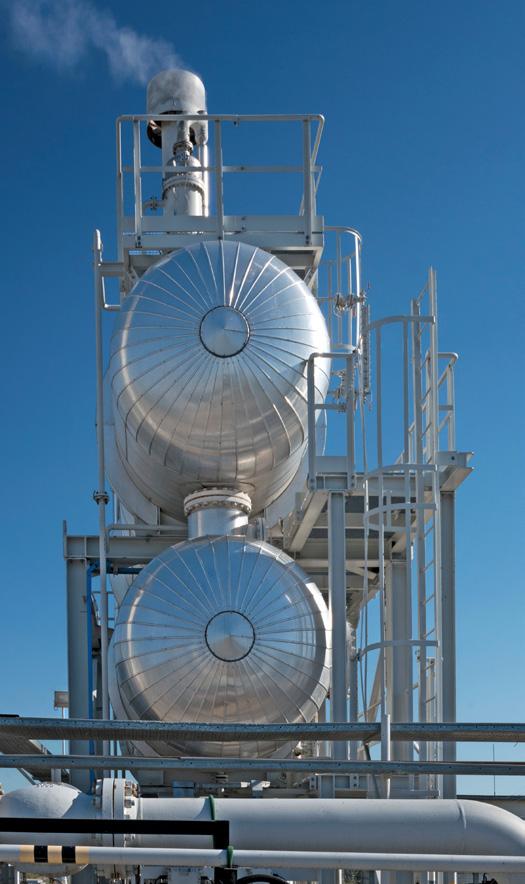
Spain wins the Women’s World Cup
Having beaten out the competition, the Spanish women’s football team has achieved a 1-0 victory over England. After a 64% possession rate in the first half to Spain, they looked the stronger team on the day. However, England didn’t go without a fight and had many close attempts, but ultimately, they were no match for Spain’s Olga Carmona who at the age of 23 scored the winning goal for the team. They became the first European team to win the Women’s World Cup since Germany in 2007.
However, the win for Spain has been shrouded in controversy, as Spain’s team announced they would not play any more games until the president of the country’s football federation stepped down for him kissing a Spanish player following the victory.

Drunk Tourists Found Sleeping in Eiffel Tower
Two men were found by security in the Eiffel Tower on the floor that is normally closed to the public. The areas between the tower’s second and third levels are not usually open to tourists, however, two American tourists were found there after getting stuck while drunk. A specialised firefighting team was required to rescue the men from such a height.
The two men are thought to have visited the landmark late in the evening and after hopping security barriers on their way down, had got themselves stuck in an area of the landmark which is usually closed. The pair were quickly determined to not pose any threat but were questioned by Police and a criminal complaint would be filed.
Wind-Powered Cargo Ship Sets Sail
A vessel from shipping firm Cargill has set sail from China to Brazil with the hope of helping to develop wind-powered vessels for the future. The WindWings sails on the ship are designed by the British company to cut fuel consumption and reduce the ship’s carbon footprint. Using the wings, the vessel can be blown along by wind power, rather than relying solely on the engine which is hoped to reduce the cargo ship’s lifetime emissions by 30%.
The vessel, The Pyxis Ocean, will make its maiden journey to test out the sails which when fully opened stand 37.7 metres tall. The sails are built of the same material as wind turbines and can be folded down when the ship is in port to make docking much easier. The ship will take 6 weeks to reach its destination in Brazil, but it is hoped that it will provide crucial development of the technology to develop something much faster in the future.
CHOCOLONELY FOUNDATION: Dedicated to Supporting Cocoa Supply Chains

I’m sure many of us are very familiar with the iconic Tony’s Chocolonely chocolate bars, which are available to many of us in a variety of incredible flavours. However, behind the company is The Chocolonely Foundation which is doing vital work to establish strong, resilient and prosperous cocoa communities that play a crucial role in creating a chocolate industry where equality is the norm.
Founded in 2008, The Chocolonely Foundation is focused on funding projects across Ghana and Côte d’Ivoire that work to create inclusive cocoa communities and reduce poverty by providing networks to promote prosperity whilst empowering environmental conservation. Whilst the foundation shares its name with the chocolate brand and is funded by 1% of the company’s annual turnover, it is a separate independent organisation with its own board of directors making all the decisions. The foundation has been working for 15 years to support projects and organisations across Ghana and Côte d’Ivoire that contribute to creating decent livelihoods in cocoa-growing communities and facilitate systematic change to challenge the status quo.
The foundation at present has taken part in and funded over 56 projects across the two countries that contribute to the advancement of the foundation’s mission to create a strong and resilient cocoa community and subsequent
chocolate industry. One of the projects currently in operation under The Chocolonely Foundation is the Child Learning and Education Facility in Côte d’Ivoire. The facility brings a strong coalition of philanthropic partners, cocoa companies, and the chocolate industry together with the Government of Côte d’Ivoire to support the combined goal of combatting child labour across the industry.
The project therefore aims to take these children and provide them with access to quality education. Therefore, this project is in direct partnership with CLEF an innovative public-private partnership focused on scaling investments to systematically improve access to quality education across the country.
A further project under The Chocolonely Foundation is the Ghana Food Movement Kitchen which provides a unique meeting and learning space for youth across Ghana. The kitchen space
provides programs to help build on the thriving food and hospitality of the country, with the aim of helping young talent to advance their food careers. By providing key culinary education and skills, the project is boosting new business ideas, and value chains, developing the hospitality sector, embedding cocoa education in the local culture, and providing crucial education to Ghanaians on their food systems and their impacts.
Overall, The Chocolonely Foundation is doing vital work across Ghana and Côte d’Ivoire to develop local communities towards education and promote equality across the cocoa supply chain. Therefore, when we are tucking into those lovely Tony’s Chocolonely chocolate bars we know that behind the scenes the company is putting funding towards The Chocolonely Foundation which is doing great work to promote education and community development with the goals of reshaping the future of the chocolate industry.
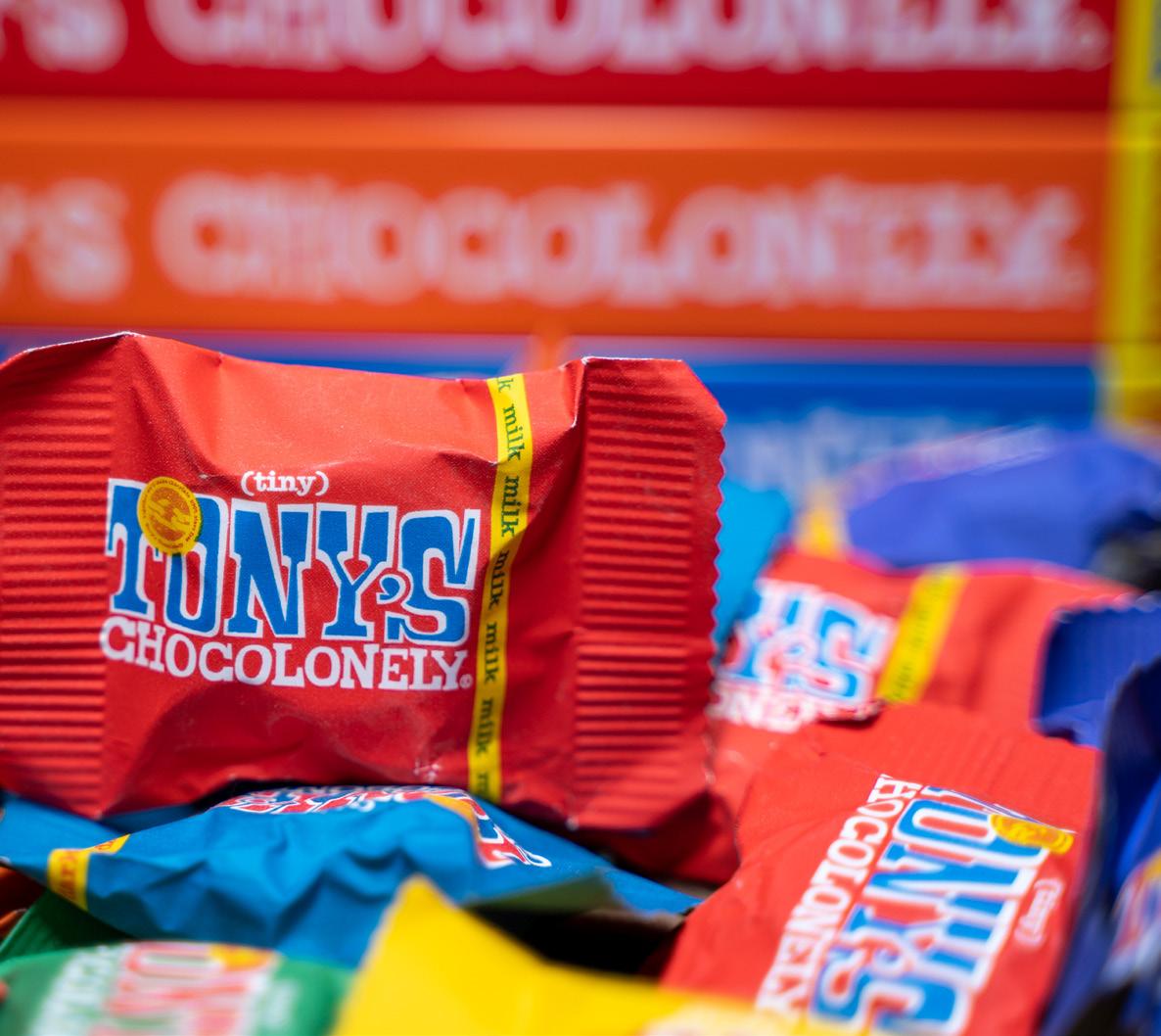

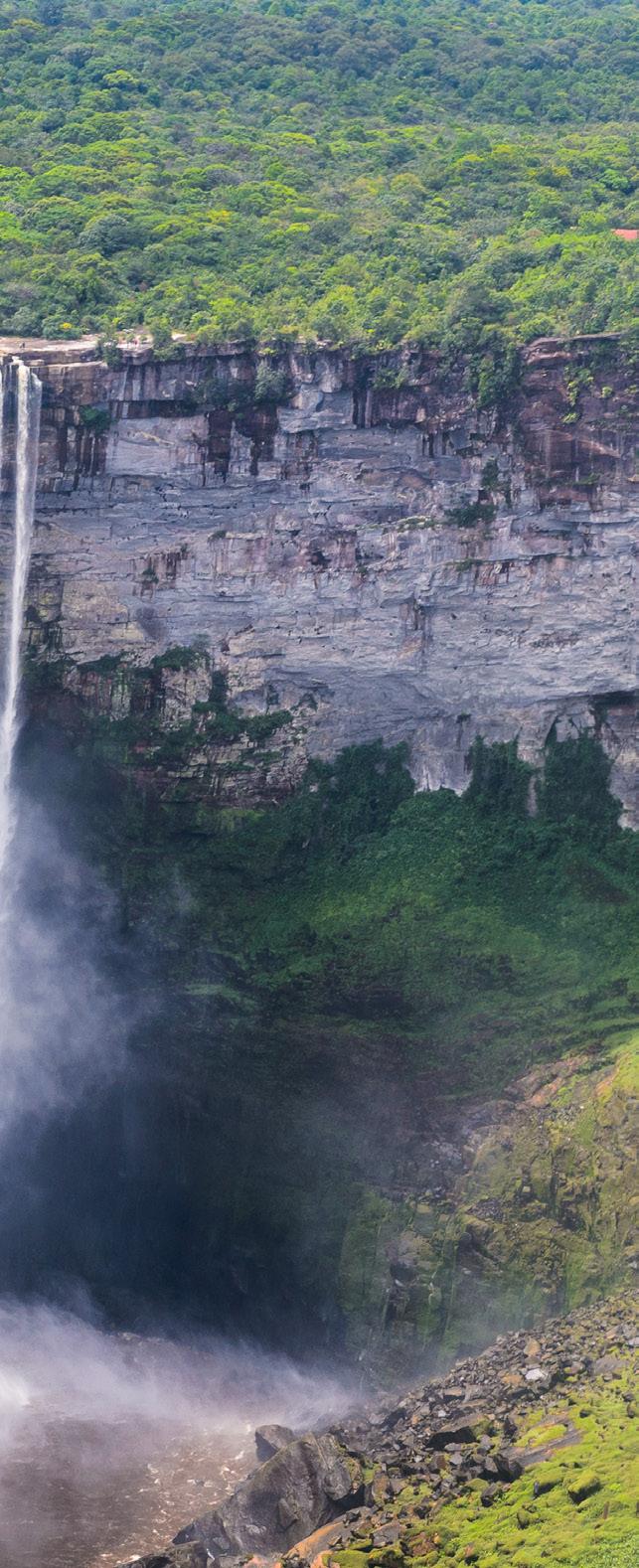
As part of the Sol Group, which is a leading supplier of petroleum-based products and energy solutions across the Caribbean, as well as Central and South America, Sol Guyana Incorporated is focused on bringing key investment and development to the downstream energy and petroleum markets across Guyana. The Sol Group, which is a member of the Parkland Family, operates across 23 territories with a united workforce of engineers, technicians, customer service representatives, and solutionbased innovators who are dedicated to fuelling the Caribbean basin. Therefore, Sol Guyana is expanding the overarching company’s network across the region with a specific focus on developing Guyana’s fuel and energy sector.
The Sol Group provides petroleum and energy solutions to its wide range of commercial customers involved in shipping, luxury boating, aviation, mining, trucking, and fleet operations. It also provides petroleum directly to the individual for fuelling their cars. It is the largest petroleum company serving the region with a key focus on offering quality and convenience with its products and services, whilst being passionate about supporting community activities and events across the region every year. Consequently, Sol Guyana, a division of The Sol Group, has established itself as a responsible partner for the people of Guyana providing a range of fuel services. Sol Guyana provides the country with a range of services including retail fuels, lubricants, liquified petroleum gas (LPG), convenience retailing, marine services, and bitumen services. As announced in February 2023, Sol Guyana plans to invest US$13.8 million in local projects in 2022, including the commissioning of a new jetty facility at Rome on the East Bank of the Demerara.
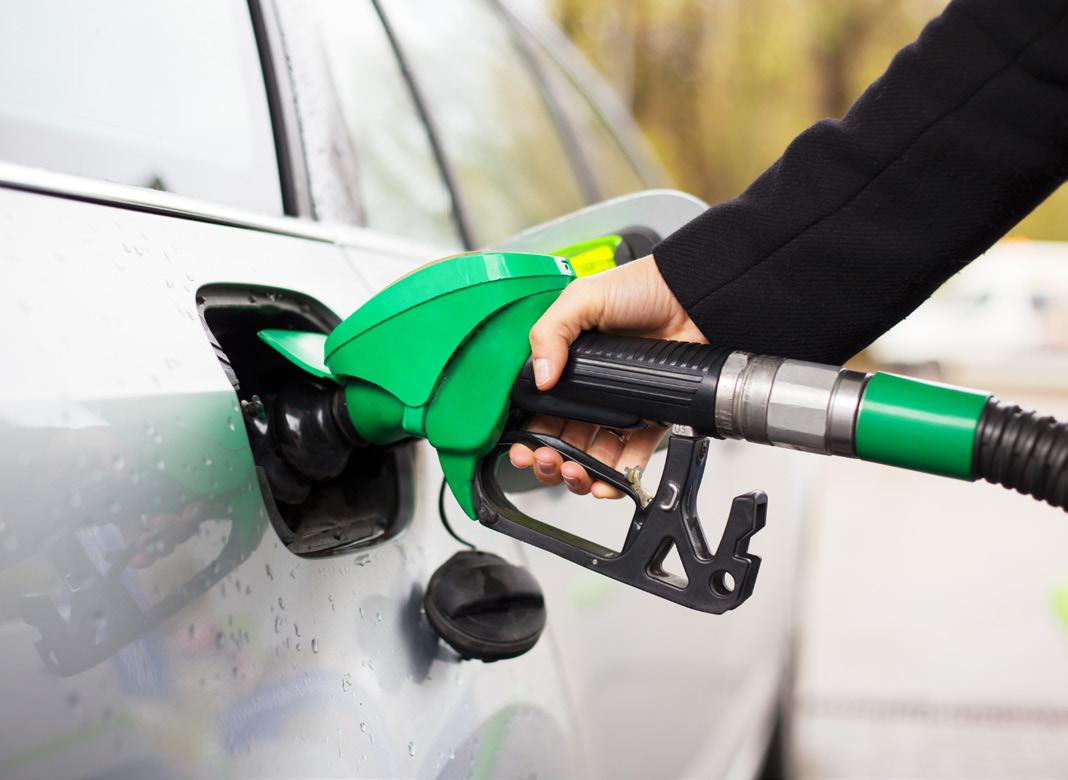
The project is a milestone project and investment for the region which exemplifies the development agenda that Sol Guyana is undertaking across the country in conjunction with Guyana’s government. General manager of Sol Guyana, Earl Carribon said in the press release announcing the jetty that “the future of Guyana is indeed bright, and Sol remains committed to being a dependable and responsible partner to the people of Guyana as we have been over the years”. This investment into the jetty comes as part of a US$50 million over the next 5 years, which is hoping to develop the region towards a more sustainable future.
Furthermore, Sol Guyana opened a US$2.8 million service station facility at Mandela Avenue earlier this year in February, which comes from investments from the Guyana government. The project is facilitated by Sol who is the Shell licensee of the Sol Guyana division. The facility will provide petrol to customers, as well as allow them to purchase

items such as lubricants and Sol Gas cylinders on the forecourt.
Additionally, the station will have a range of convenience products which can be purchased from the Sol shop. It marks one in a series of developments that Sol Guyana are implementing across the country, with the end goal of growing the trajectory of Guyana’s petroleum industry.
The project faced a few challenges after it began construction in 2022 due to weather and material shortage complications, however, Sol Guyana still impressively delivered the completion of the project in February 2023.
The investments from the government exemplify the role that Sol Guyana is playing in developing not only the industry but also the development of Guyana’s infrastructure for the benefit of its citizens as a priority. Consequently, the project represents a key objective of the overarching Sol Group, to develop and expand the fuel and energy industry markets however its focus is on ensuring
that all developments are first and foremost for the benefit of its citizens.
Consequently, Sol Group’s role in the community is crucial. The Sol Group, as by consequence Sol Guyana, are passionate about supporting the Caribbean and the communities in which it operates, and so is involved in various community-focused projects and activities. These activities range from relatively small school projects and local environment groups to large-scale regional community initiatives and major sporting events. The Group has focused most of these initiatives on education, environmental preservation, sport, and community development.
A key example of this is Sol Guyana’s partnership with the Guyana Technical Institute (GTI) to enhance the educational opportunities available to students in GTI’s Motor Vehicle Engine Systems programme. The sponsorship from Sol Guyana will span three years, as announced in September 2022, to invest in the education of Guyana’s youth. The programme
provides students with the opportunity to power their journey and equip them with key skills to achieve high-level jobs in the future. Ultimately, Sol Guyana has been supporting Guyana’s education sector and the wider Caribbean for students at all levels over the past few years as part of its overall goal to develop communities towards a future of sustainable development in every aspect from fuel to education.
Overall, Sol Guyana has developed a sustainable economic journey across Guyana which is being led by its natural resources. The company plays a vital role in the power and fuel development of Guyana through its facilitation of oil and gas. However, Sol Guyana operates across a whole range of sectors outside of the gas industry to bring the people of Guyana support and investment to develop the country and its economic development towards global recognition. Therefore, as part of The Sol Group, Sol Guyana is achieving its mission to be a partner of choice for its customers, suppliers, and the people of Guyana through its focus on safety, integrity, community, and respect in every aspect of its operations.
From the Ship’s Manifold to the Tank Truck.
Solares is an industry leading systems integrator and distributor providing mission-critical technology solutions to the petroleum-based products and energy industry. Applicatiosn include aviation, truck / marine terminals, refinery, bunkering, LPG, and power.
Established in 1919 and based in Miami, Solares is ideally located to support our clients throughout the Caribbean, Central America, and the Guyana’s. Product scope includes hose assemblies, skid-mounted flow measurement systems, tank gauging solutions, and terminal automation.

Solares was established in 1919, is certified to ISO 9001:2008, and is active members in key industry groups and associations. WWW.SOLARESFLORIDA.COM
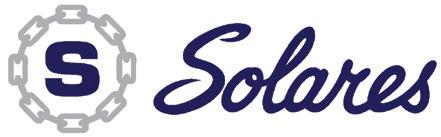
EXCEEDING EXPECTATIONS.
That’s What Continental Hose & Solares Deliver Every Day.
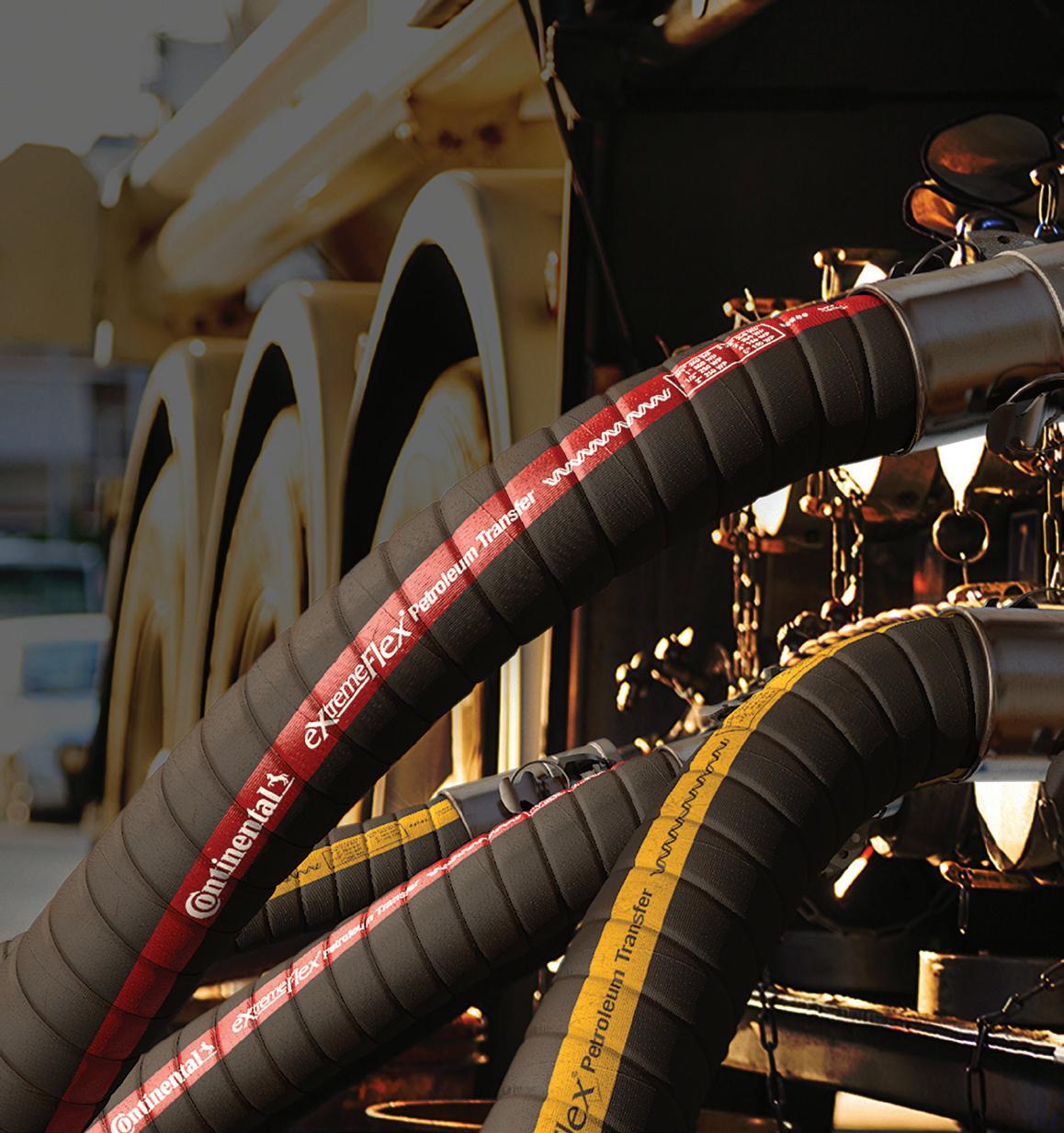
Solares’ STAR Distributor recognition indicates our team meets rigorous fabrication standards when coupling Continental hose assemblies, including Underwriters Laboratories, LLC verification. Our clients trust our premium oil & gas hose assemblies to deliver maximum efficiency, reliability, and safety to their operations.
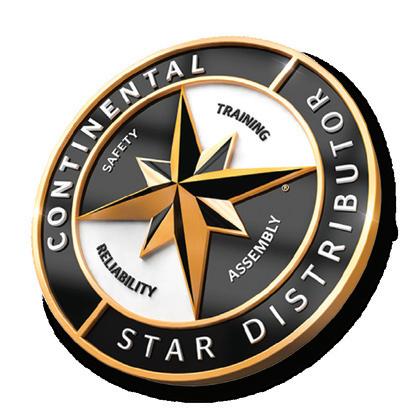
www.solaresflorida.com
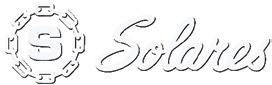
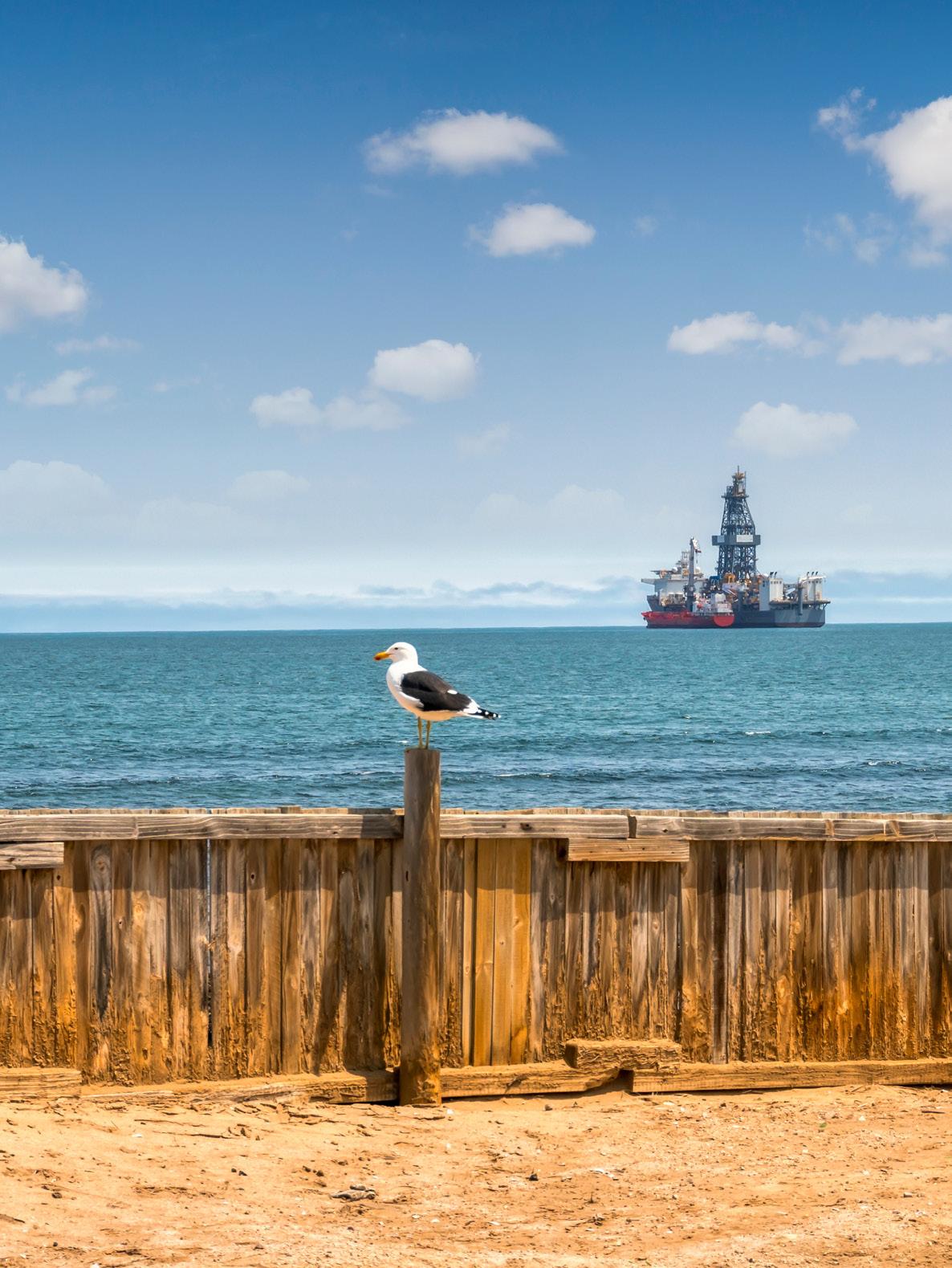
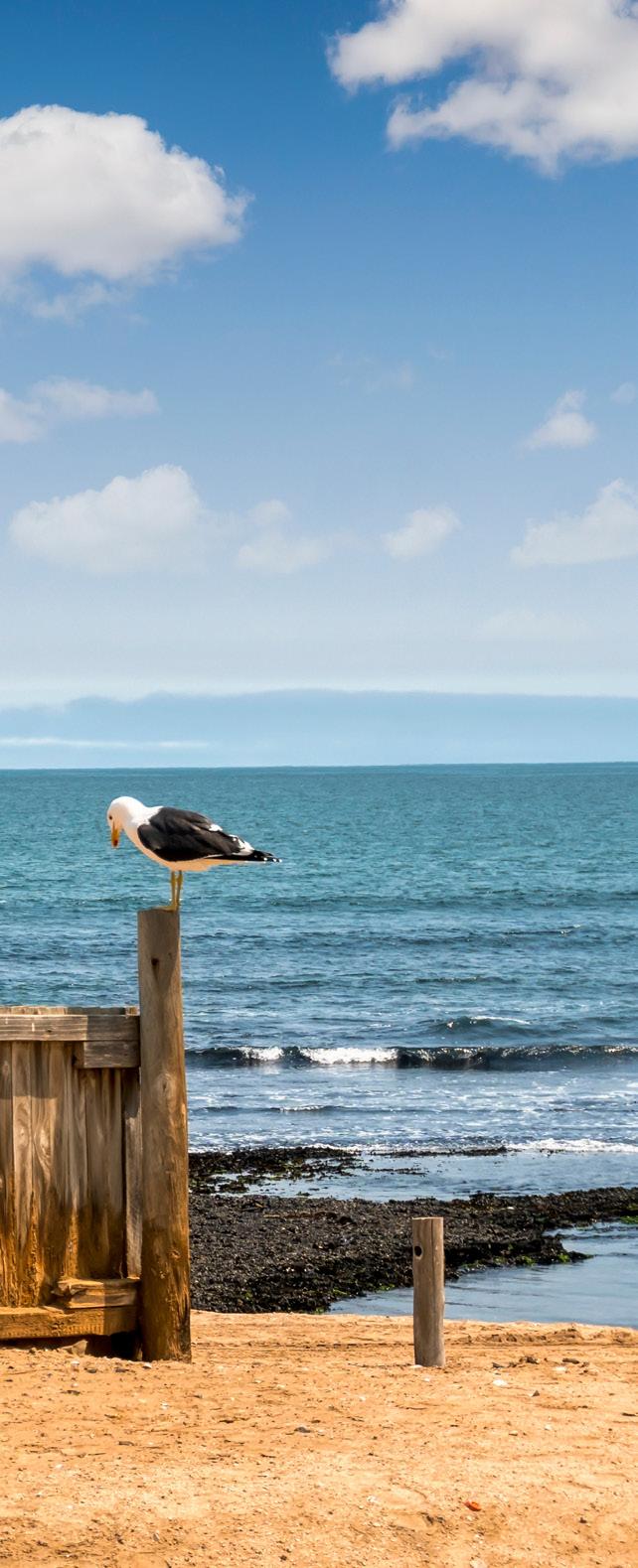
Together with PETROSEN, Société Mauritanienne des Hydrocarbures (SMH) and Kosmos Energy, BP has been working on developing an offshore liquified natural gas (LNG) project on the maritime border of Mauritania and Senegal. The project was signed by Mauritania and Senegal as an intergovernment cooperation agreement (ICA) in early 2018, which outlined the development of a cross-border gas project for which the resources and revenues produced will be split between the sharing countries on a 50/50 basis. The Greater Tortue Ahmeyim LNG project is estimated to contain up to 15 trillion cubic feet (Tcf) of recoverable gas resources to benefit the development of both countries and their role in global LNG markets.
Following the discovery of The Tortue Gas Field in 2015 through the drilling of the Tortue-1 Exploration Well and subsequent Guembeul-1 and Ahmeyim-2 Wells in 2016, the Greater Tortue Ahmeyim (GTA) Field Complex is expected to produce 2-3 million tonnes per annum (mtpa) of LNG in the first phase of its development. The first phase of the development includes an ultra-deep subsea system with four gas production wells, a mid-water floating production, storage, and offloading (FPSO) vessel, and a nearshore floating liquified natural gas (FLNG) facility.
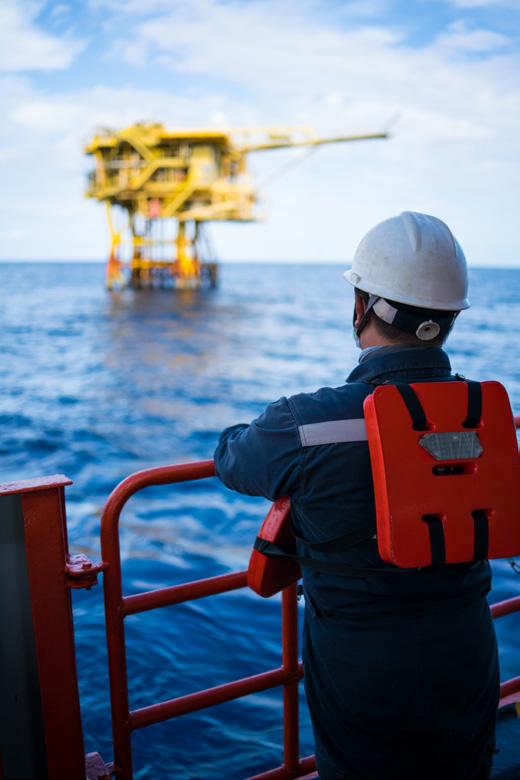
The four wells are expected to produce up to 200 million metric standard cubic feet per day (Mmscfd) of gas. This gas will then be transported via an 80-kilometre (km) subsea tieback to the FPSO facility for processing. The FPSO facility will separate the condensate from the gas, and the gas will be offloaded from the FPSO to the FLNG facility. The LNG output produced will therefore be exported across international markets by tankers, whilst a portion will be allocated to Mauritania and Senegal. The final investment decision (FID) came for phase one of the development of the project in December 2018 and is expected to start production in the final quarter of this year.
The FPSO used in the project set sail from the COSCO Shipyard in China and is set to arrive at the project site in the second quarter of 2023. It will be moored 80km offshore and accommodate up to 140 onboard during normal operations. The vessel is made up of 81,000 tonnes of steel, 37km of pipe spools and 1,520 km of cable, and is equipped with 8 processing and production modules to process up to 5000Mmscfd of gas. Consequently, the FPSO plays a crucial role in removing condensate, water, and other impurities from the field’s gas stream, so high-quality and pure LNG can be transported to the FLNG facility for international and local distribution. The project is set to take place over a period of 30 years, which will help to establish Mauritania and Senegal as key players in the global LNG field. This crucial development is set to bring continued prosperity on both a national and local level by establishing the GTA LNG Project as a new energy hub in Africa. Therefore, BP through its crucial partnerships, is delivering a bright energy future for Mauritania and Senegal, as well as positioning
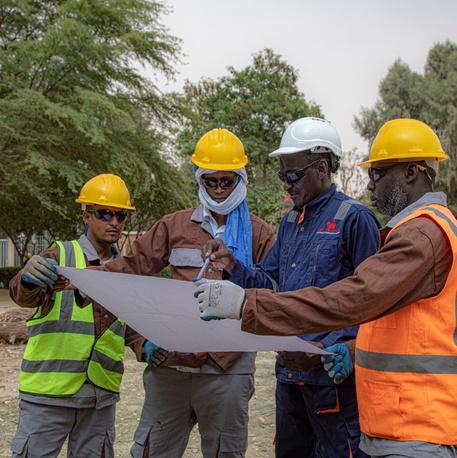
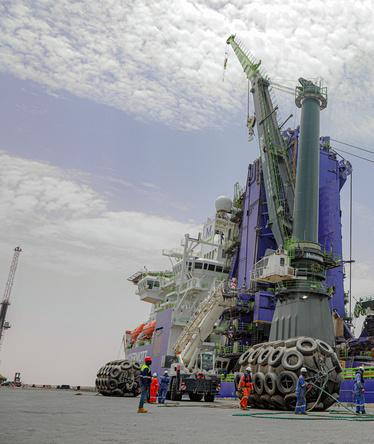
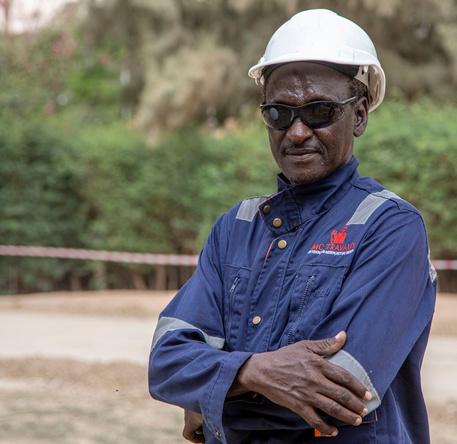

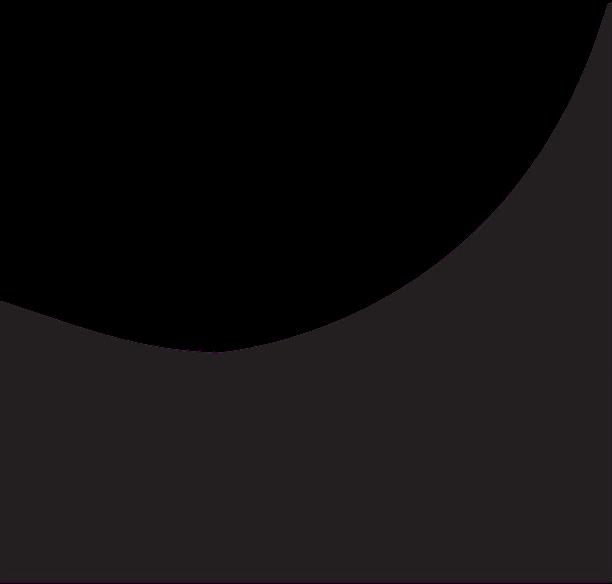

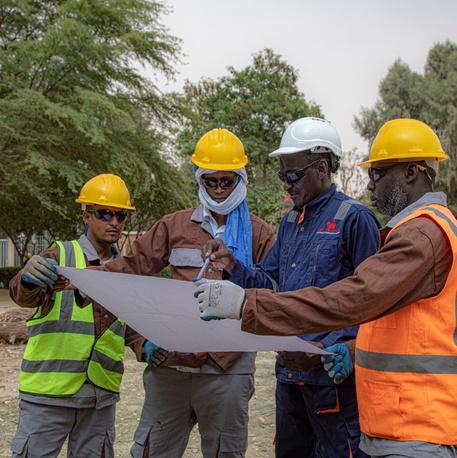
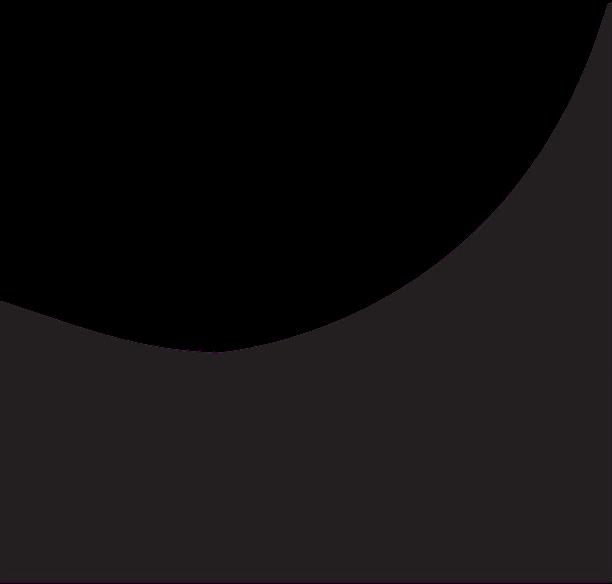
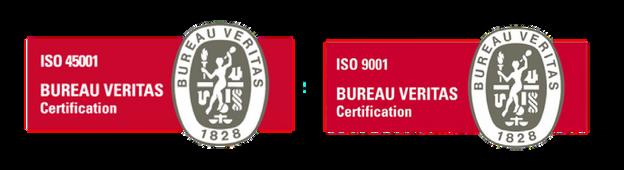

the continent as a key player in the future of energy facilitation. The Executive Vice President for Operations and Production of the GTA LNG project outlined in the press release for the second phase of the project that, it aims “to build on our strong collaboration with our partners, and the Governments of Mauritania and Senegal, to further develop a long-term, successful energy hub in West Africa. GTA continues to underpin our strategy to develop the most resilient hydrocarbons to help provide energy security today.”
The second phase of the BP-operated GTA LNG project was recently announced to have been taken forward to the next stage of the development, as evaluations are beginning for a gravity-based structure (GBS) which will form the basis for the GTA Phase 2 expansion project. The GBS LNG structure development will have a static connection to the seabed and will serve as a key foundation for the liquefication facilities, whilst also providing crucial LNG storage. The second phase of the project will also include the development of new wells and subsea equipment which will develop the existing GTA infrastructures. BP and its partners are currently working with contractors to progress the second phase towards the pre-FEED stage.
Furthermore, as the project continues to make great strides towards future developments of the LNG facilities in the GTA fields, BP and its partner companies involved in the project are crucially concerned with ensuring that safety, sustainability, and respect are maintained throughout its development both within the partnership’s operations and with the local communities. The partnerships have implemented a rigorous process of informed consultation, which is working with local communities to understand and mitigate concerns about the project’s activities.
For BP, it is committed throughout its projects to making a positive impact on surrounding communities through its key operations to establish crucial energy infrastructure. Therefore, whilst the project is set to bring crucial change to the energy sector of Mauritania and Senegal, it is also keenly concerned with ensuring its impact is positive and sustains local communities for generations to come.
Overall, the Greater Tortue Ahmeyin LNG Project is implementing crucial energy infrastructure that is expected to positively impact both Mauritania and Senegal. With its wells, subsurface and subsea developments, pre-treatment FPSO, LNG Hub terminal, FLNG facility, and LNG offtake facilities –the project is an expansive development which is set to put the region on the map for many years to come. For the next 30 years, the project is set to bring economic and energy development across the region and allow them to serve as a crucial hub not just to local countries but to the developing world of energy infrastructure.
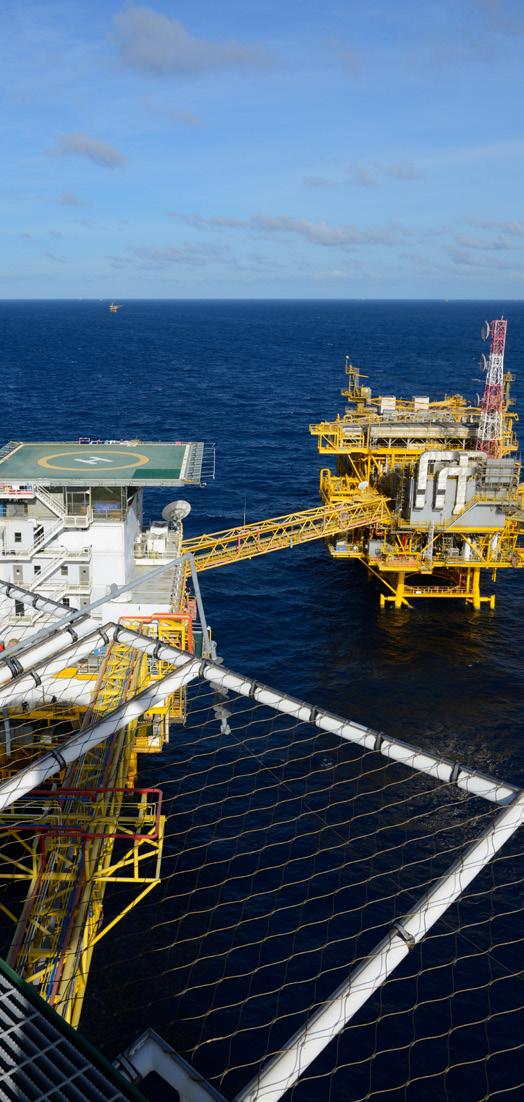
EB MARITIME GROUP


CARGO MANAGEMENT SOLUTIONS
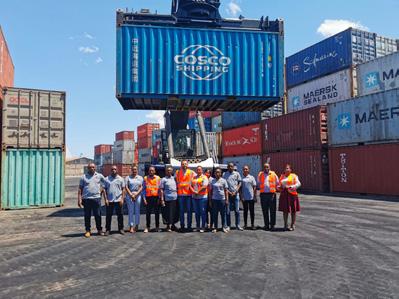
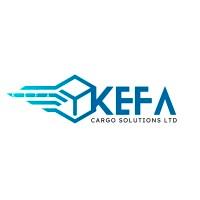

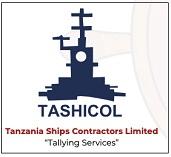
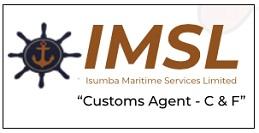

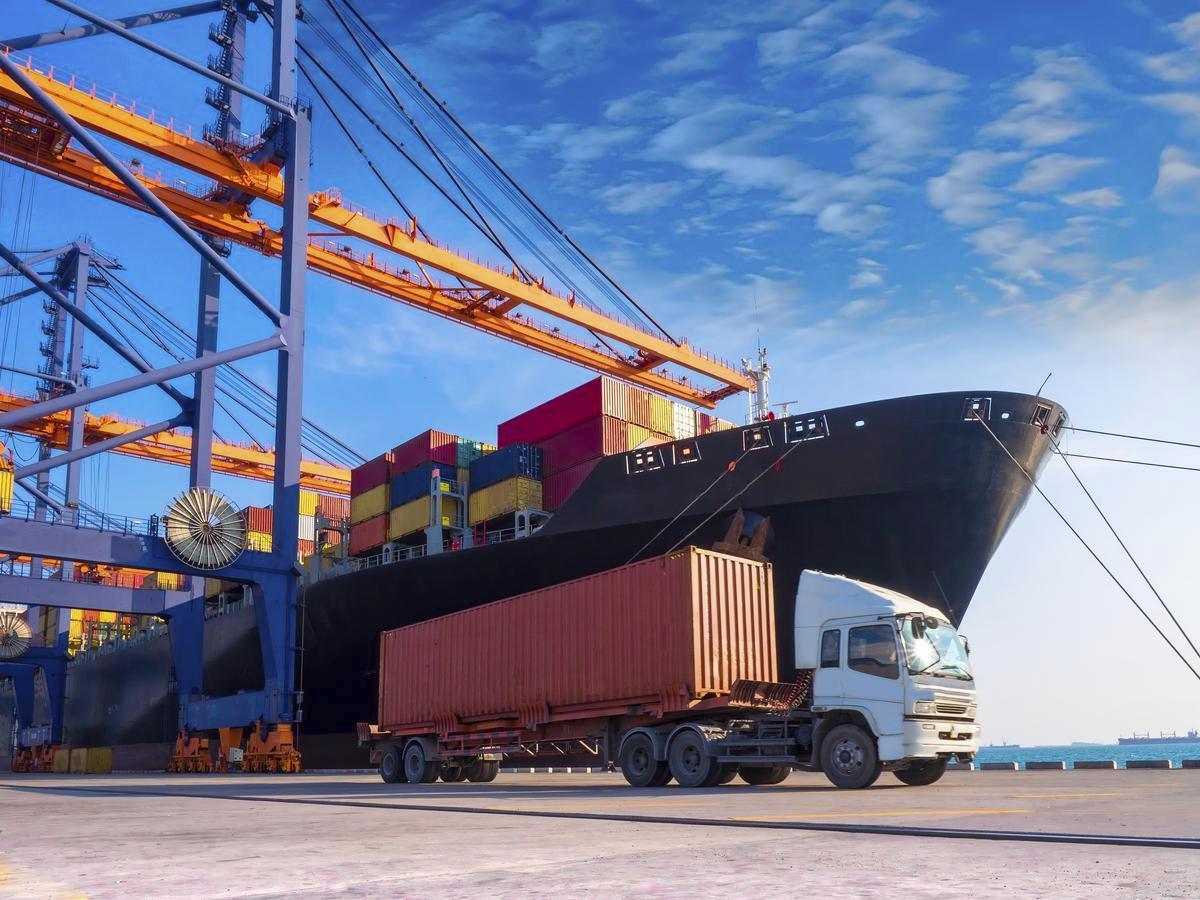
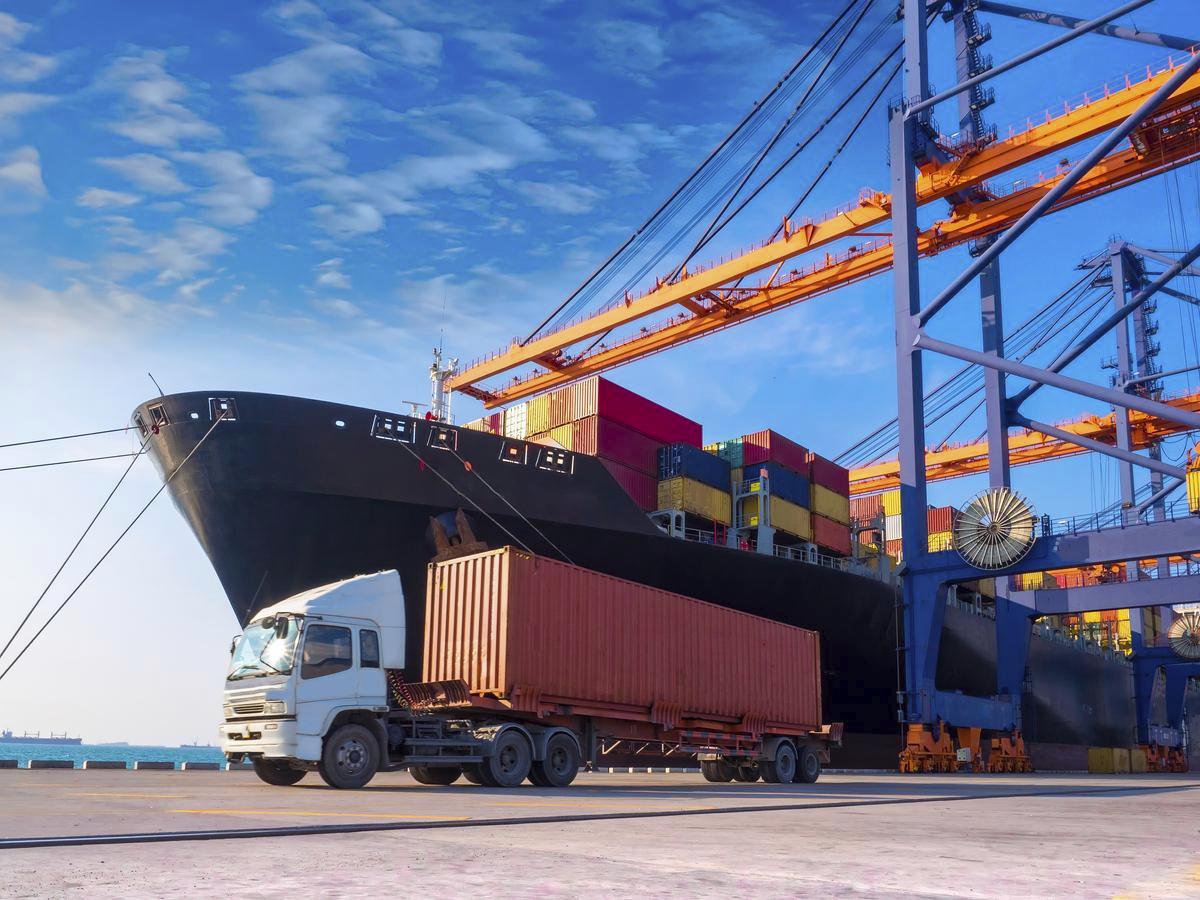
BUSINESS ASSOCIATES
JEFAG Group LTD

Specialized in:
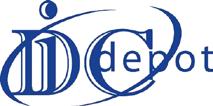
Inland Clearance Depots
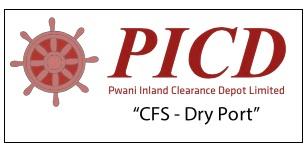
Empty container Depots Cargo Freight Station

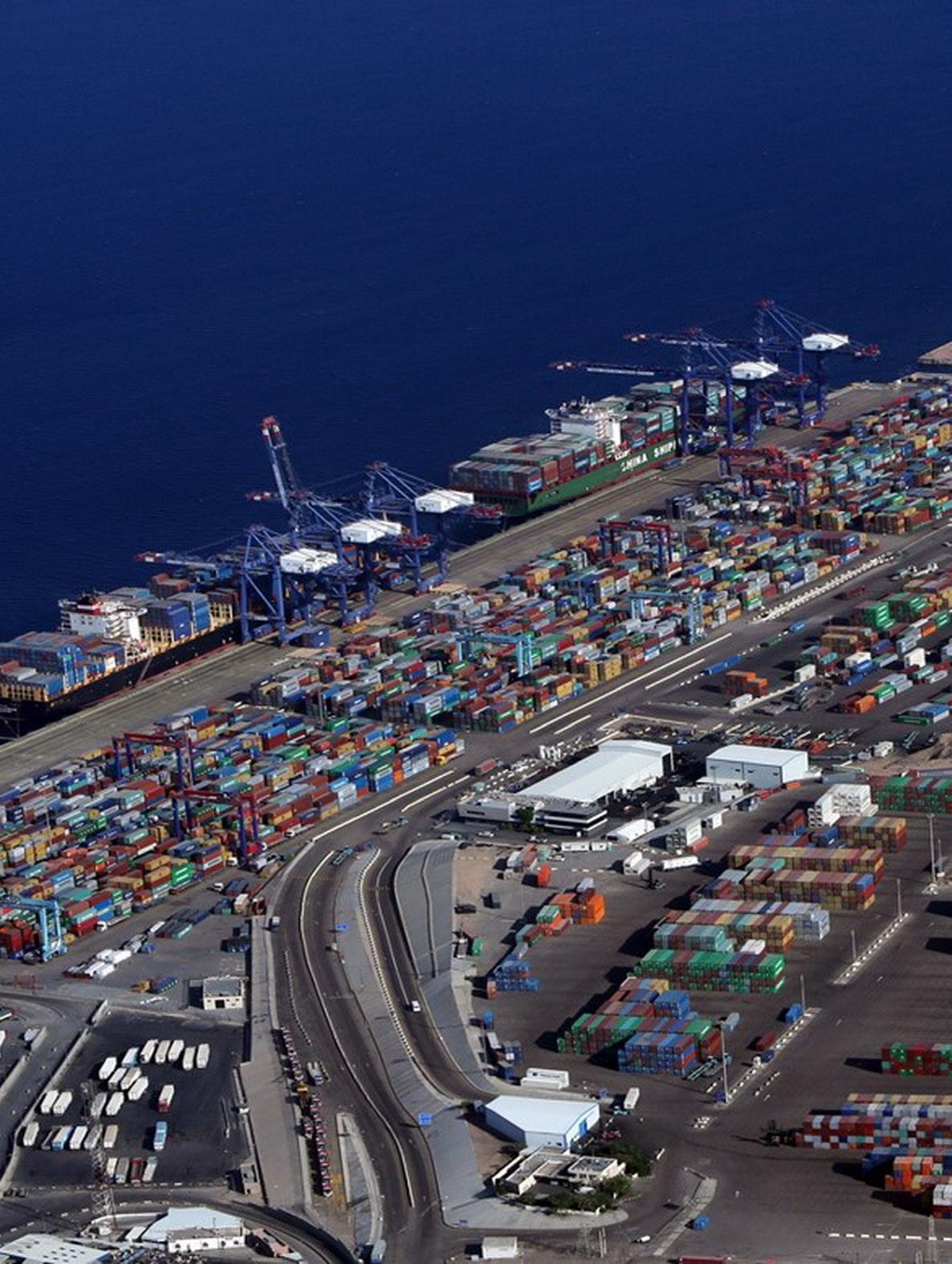
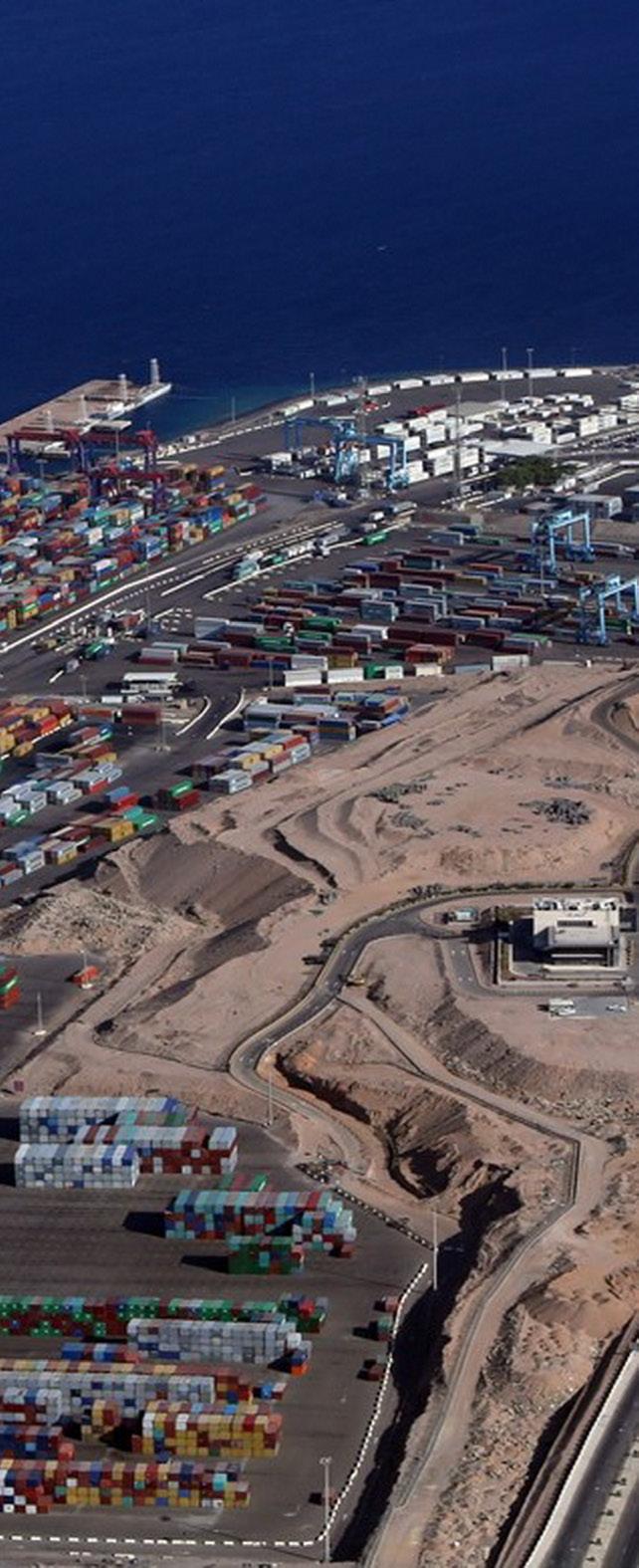
Terminal
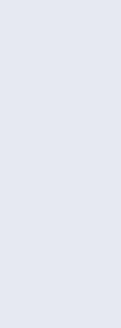
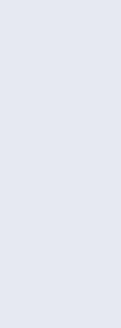
As Jordan’s only container terminal, the Aqaba Container Terminal (ACT) has played a vital role in supporting the national and regional economy of the country through its crucial services in importing and exporting goods. Under the joint ownership of APM Terminals Group and the Aqaba Development Company (ADC), it has provided seamless movement across its operations to regulate operations across the port whilst providing vital services to benefit the container terminal.
The development in ACT by ADC comes as part of a crucial project taken out in 2004 to unlock the potential of the Aqaba Special Economic Zone (ASEZA) by accelerating its economic growth and development. Now in 2023, ACT has seen new changes which has seen a new Chief Executive Officer appointed to bring his breadth of expertise across the global maritime industry to ACT.
Located in the city of Aqaba in Jordan, at the meeting point of three continents and four countries, the services that ACT provides for the movement of cargo across these regions benefit both global and local markets, all whilst developing the economy of Jordan. ACT provides key logistical and economic operations across the ASEZA, as it is the chosen entry point for many active markets around the world due to Jordan’s political stability. Acting as a key corridor for trade, ACT works to provide world-class services powered by advanced technology and equipment across its terminal facilities. Consequently, ACT has developed a reputation for efficiency and proficiency as it is dedicated to establishing the container terminal as a crucial player in global markets through its promise of speed, safety, security, and transparency across all its services.
The container terminal provides a range of container services to seamlessly move cargo from vessels and through to land transport links. These services include providing berths, ship-to-shore operations, stacking and unstacking containers, transferring containers, carrying out temperature checks on reefer containers and technical conditions on containers. Additionally, ACT provides storage container facilities, equipment interchange reports, executes documentary controls, supplies vessels with portable water, weighs containers, provides value-added services, as well as facilitating labour and equipment hiring needs. Marine services are provided through AMPSCo, and include anchorage, pilotage, towage, and berthing whilst working with ACT to facilitate the easy movement of cargo from vessels from the port and into the container terminal.

Furthermore, as part of ACT’s vision to be the sustainable gateway for Jordan and beyond it is constantly looking for ways to develop and upgrade its services towards a more sustainable, modern,
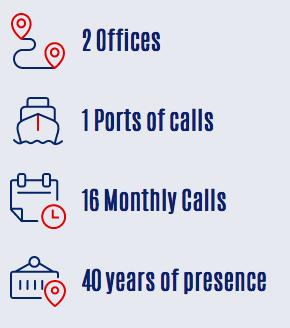
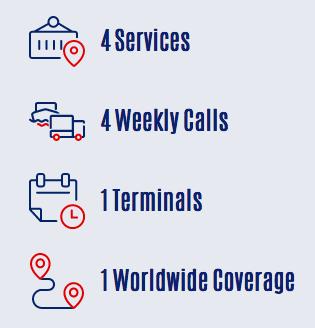
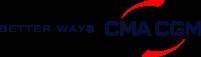
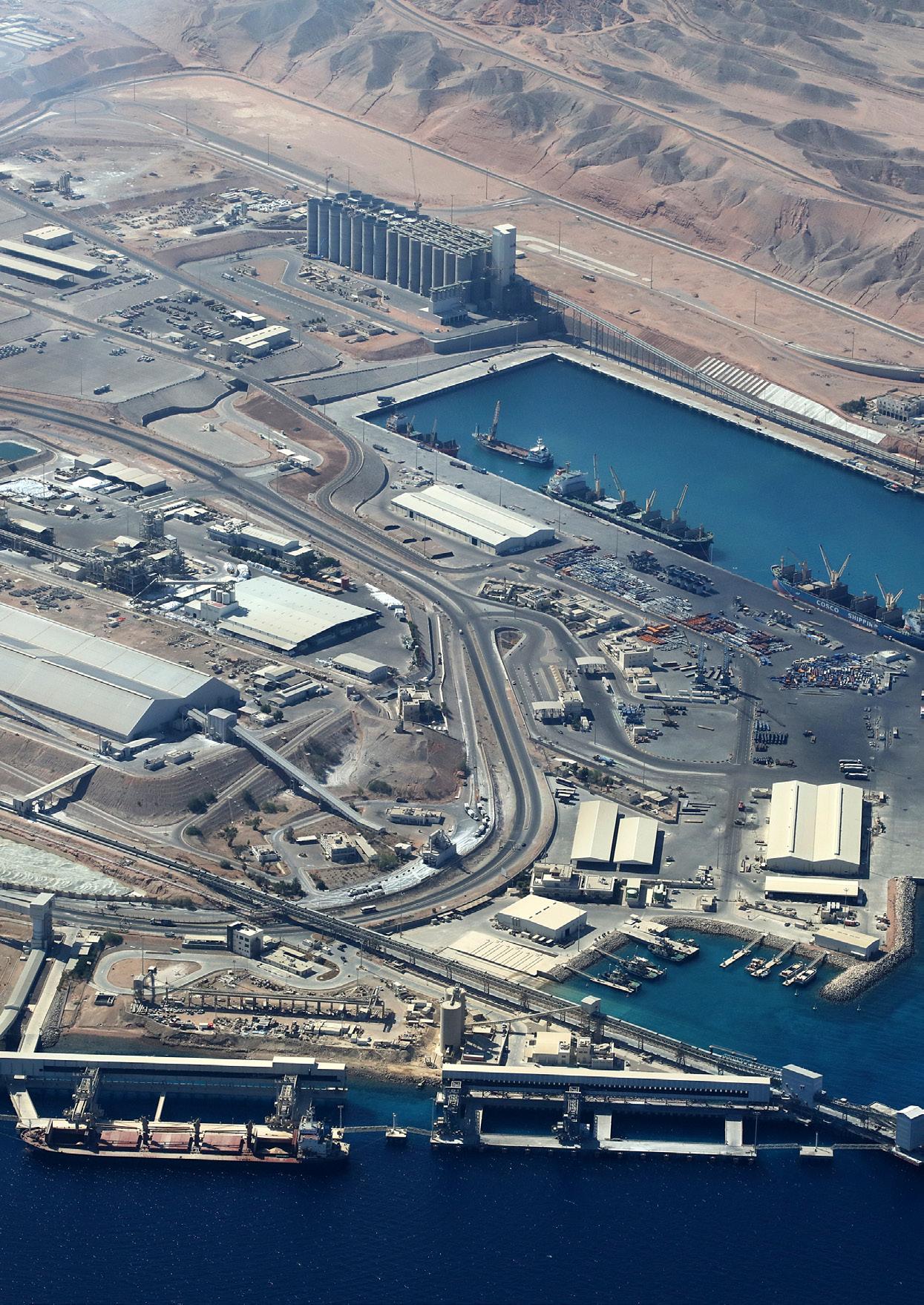
Aqaba Container Terminal
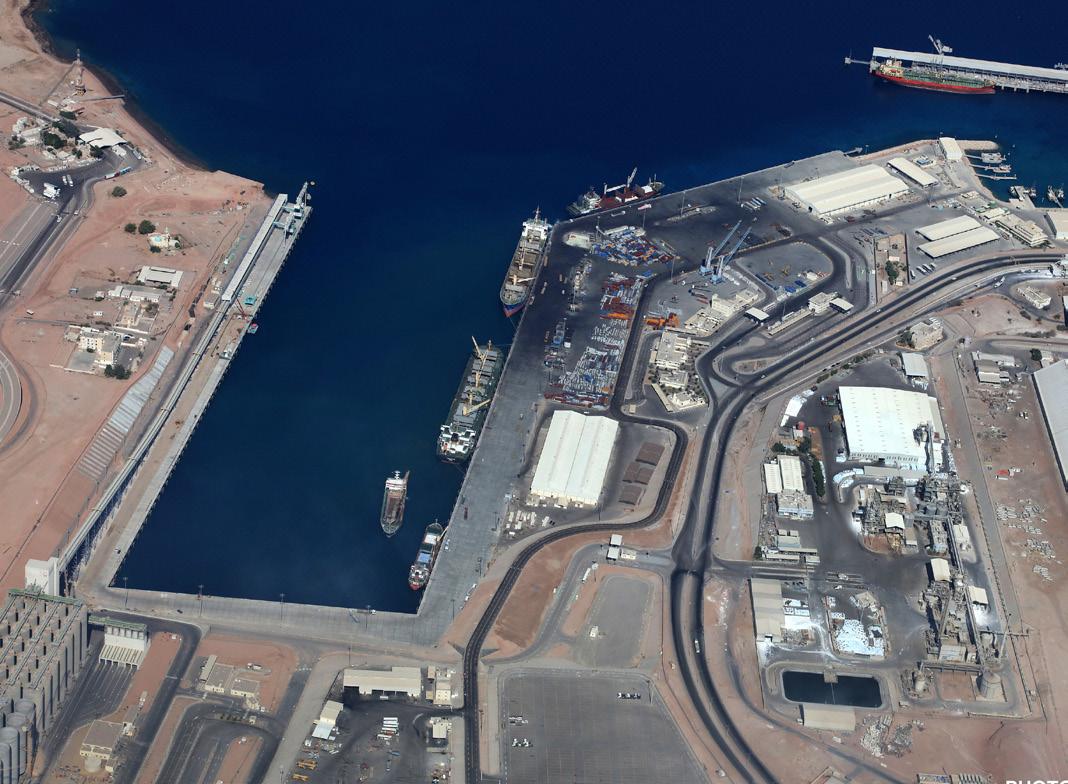
transparent, competitive, reliable, and profitable supply chain. These are commitments that ACT is working towards to continually develop the company’s value chain.
ACT announced in July that a new CEO has been appointed to take on the crucial role of overseeing the company’s operations. APM Terminals Group named Harald Nijhof as its new chief executive officer. Nijhof has had an impressive career across the maritime industry and brings over 30 years of experience to the role having worked in the UK, India, Denmark, Spain, Singapore, and South Africa.
Having joined APM Terminals in 2020 as Head of Operations Execution globally, his expertise was seen across the overarching company’s operations which now is being adopted across ACT. In the press release announcing Nijhof’s position at ACT, he stated “I am truly honoured to assume the CEO role at Aqaba Container Terminal. Leading this exceptional team, continuing ACT’s growth and development, and contributing to Aqaba’s future vision is a privilege. Together, we will strive to achieve new milestones in our aspirations of becoming a green trade hub for Jordan. We will focus on delivering an unparalleled
port experience, fostering community prosperity in Aqaba and its surroundings, and further solidifying ACT’s position as the leading trade hub in the Levant region and beyond. I am extremely confident that our team will achieve great things.”
It is clear to see that under Nijhof’s management, ACT is setting itself up for even greater achievement as it works to strategically place Aqaba’s container terminal as a vital access point for importing and exporting cargo not just for the prosperity of Jordan, but for the added benefit of its surrounding countries.
Furthermore, ACT has implemented a range of projects that are working to care for the wellbeing of the citizens of Aqaba and its surrounding communities. Act believes that focusing on the community is a fundamental way that it aspires to the container terminal’s business operations. ACT has an established broad portfolio of community investments that directly support a number of the United Nation’s sustainable development goals. These investments in Jordan are focused on
education, healthcare, and the environment. ACT’s role in the community of Jordan is therefore crucial as it provides key donations, sponsorships, and community engagement projects all with the united goal of benefitting the local community outside of the terminal. Consequently, ACT is working to develop both its container terminal and beyond, to bring a myriad of benefits to Jordan and beyond.
Overall, the Aqaba Container Terminal has established itself as a sustainable gateway for Jordan and its surrounding countries. The container terminal has been developed over the years to provide modern, transparent, competitive, reliable, and profitable supply chain operations. Furthermore, with the appointment of a new Chief Executive Officer, we look forward to seeing how he brings his experience across the maritime industry to this role as he continues to help develop ACT’s position as a world-class provider of cargo handling across the industry.

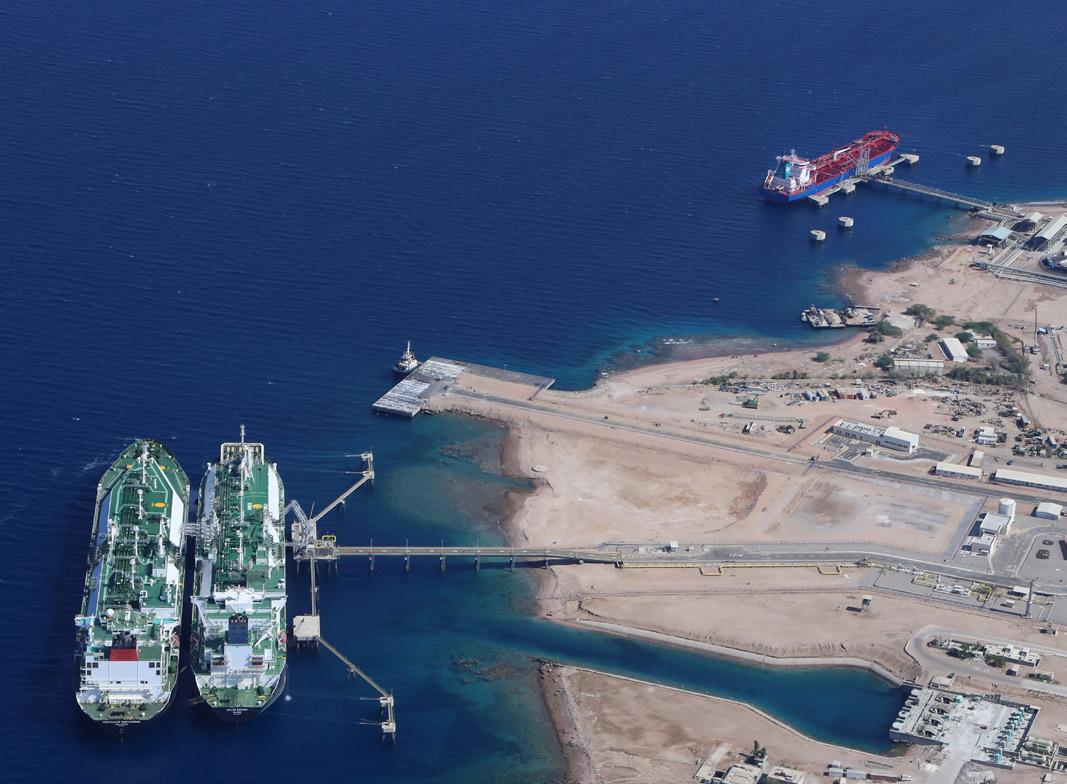


Throughout every industry, the logistical movement of goods between suppliers, manufacturers and customers is one of the most crucial aspects of every business. Therefore, the organisation of logistics is essential for making sure that the customer and supplier relationship is supported by a trusted and reliable supply chain across the industry. Therefore, businesses rely on companies such as Industrial Logistic Systems (ILS) to develop, implement and help facilitate seamless supply chains across all aspects of a company’s business operations. Consequently, ILS prides itself on being a locally and internationally recognised expert in the distribution centre and distribution operations design sector.
ILS is primarily understood as a logistics and supply chain consulting firm that specialises in the design and development of warehousing and distribution facilities across all industries, seeing developments all the way from strategy to execution. With over 600 distribution facilities, the South African company provides awardwinning and proven results through its design and development of supply chains, logistic facilities, and infrastructure to give customers a competitive edge in the strength of supply chain solutions. However, ILS’ role in customers’ supply chain does not end at the implementation of trusted logistical systems, instead, it acts as an extension of its client’s businesses as a specialist logistics department which is always looking for ways to improve the existing system to continue to benefit the customer for many years to come.
ILS approach logistical operations by first evaluating a business’s operations and getting to know how the company works on a firsthand basis. This assessment makes a detailed data-driven analysis of the company and uses information related to sales, inventory, and business trends. Then, using projected growth and expected challenges to the businesses’ capacity, it can assess exactly the best system to implement to get the most out of the logistical development of the company.
Once the capacity and strategy components are known, ILS then develops unique solutions to meet the specific requirements of each business. This personalised touch allows ILS to develop operational and materials handling systems and concepts to best suit your business. These include computer-aided designs (CAD) and 3D models, as well as assessing the budgeting requirements of each system. Once the designs are layout out and fine-tuned to a business’s needs, they then can be drawn up with detailed specifications for the building requirements.
ILS focuses on every single detail of its designs down to floor slab thickness and recommended lighting levels to ensure the smooth running of logistical departments. The complete designs ILS provide are based entirely on each business’s specific operational needs, space and budget requirements. Then, once these plans have been completed ILS works to assist in the implementation of the project. This includes liaising tender and

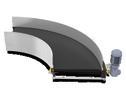
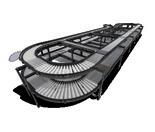

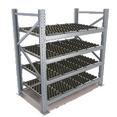

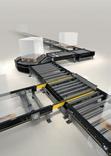
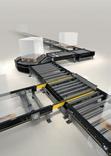
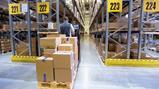
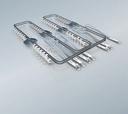
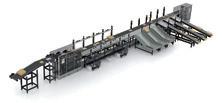

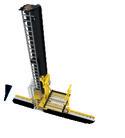
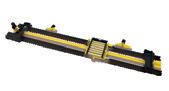


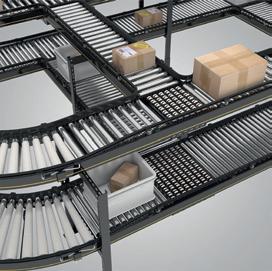

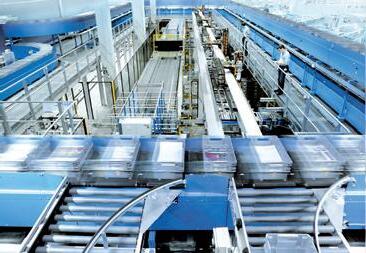
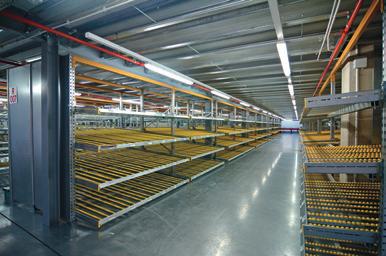
Industrial Logistic Systems
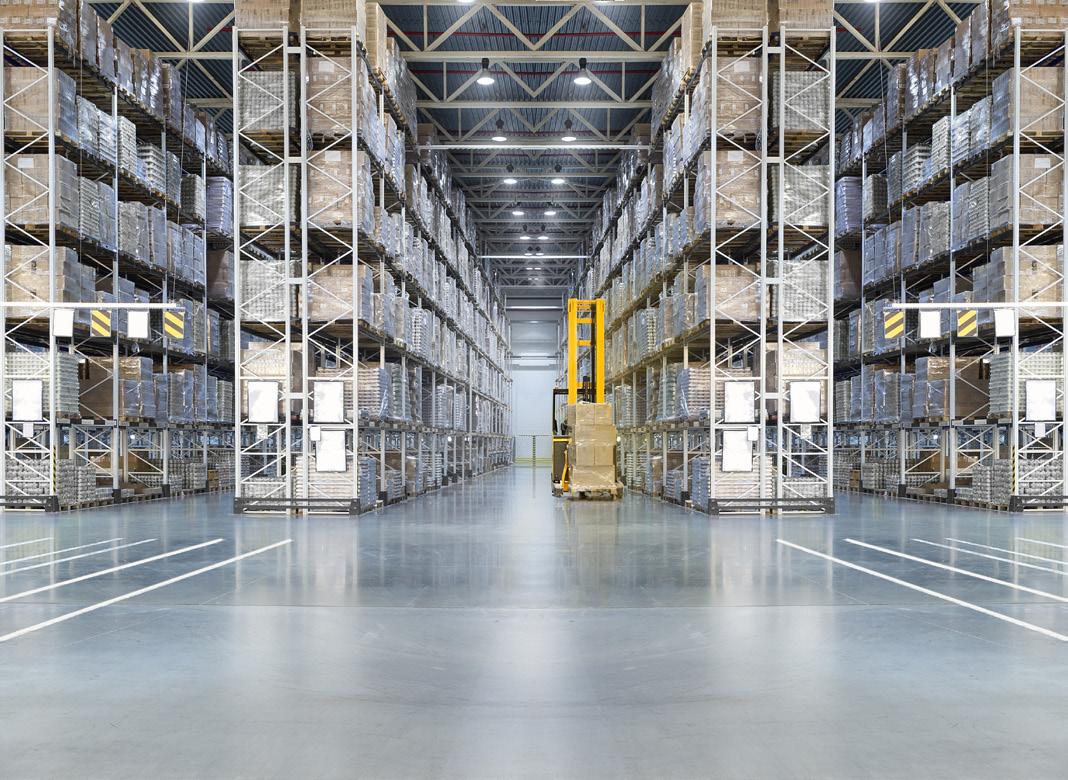
pricing enquiries for all required equipment, whilst also overseeing the purchasing of equipment and ensuring it all meets the project specifications.
ILS’ central role in the project management and systems commissioning of logistical systems. Consequently, ILS take key responsibility for projects from conceptual design and strategic planning and sees them out into fully-fledged operations. However, as mentioned, once the projects are implemented and successful, customers continue to benefit from ILS’ logistics expertise throughout their operations to continue to develop logistics offerings to remain in line with the company’s development and logistical needs. By implementing industry-leading logistical systems, ILS enables its clients to meet a high standard of excellence among peers and competitors.
One of the crucial parts of ILS’ operations is the implementation of world-class infrastructure from concept to actualisation. Its role takes both greenfield and brownfield sites from development
and into functional buildings that facilitate the careful and productive movement of products through a streamlined and personalised system suited to each business. This is one of the crucial parts of ILS’s operations that you can really sense how the customer and helping them to develop their logistical operations towards a more productive but seamless future is the company’s main focus. ILS believes that “Your Success is a Measure of Our Success”, which exemplifies the exact sentiment that ILS provides for its customers.
Every logistical system is planned out and executed as if it were its own business, to ensure that each customer is receiving top-quality logistical support from a company that has established itself across South Africa as a leading provider of logistical excellence. There is no doubt that when using ILS, businesses are receiving topquality logistics systems which will continue to benefit them for many years to come. Therefore, it is through ILS that customers can be sure that their supply chains are protected, supported and developed towards a future of seamless logistical movement.

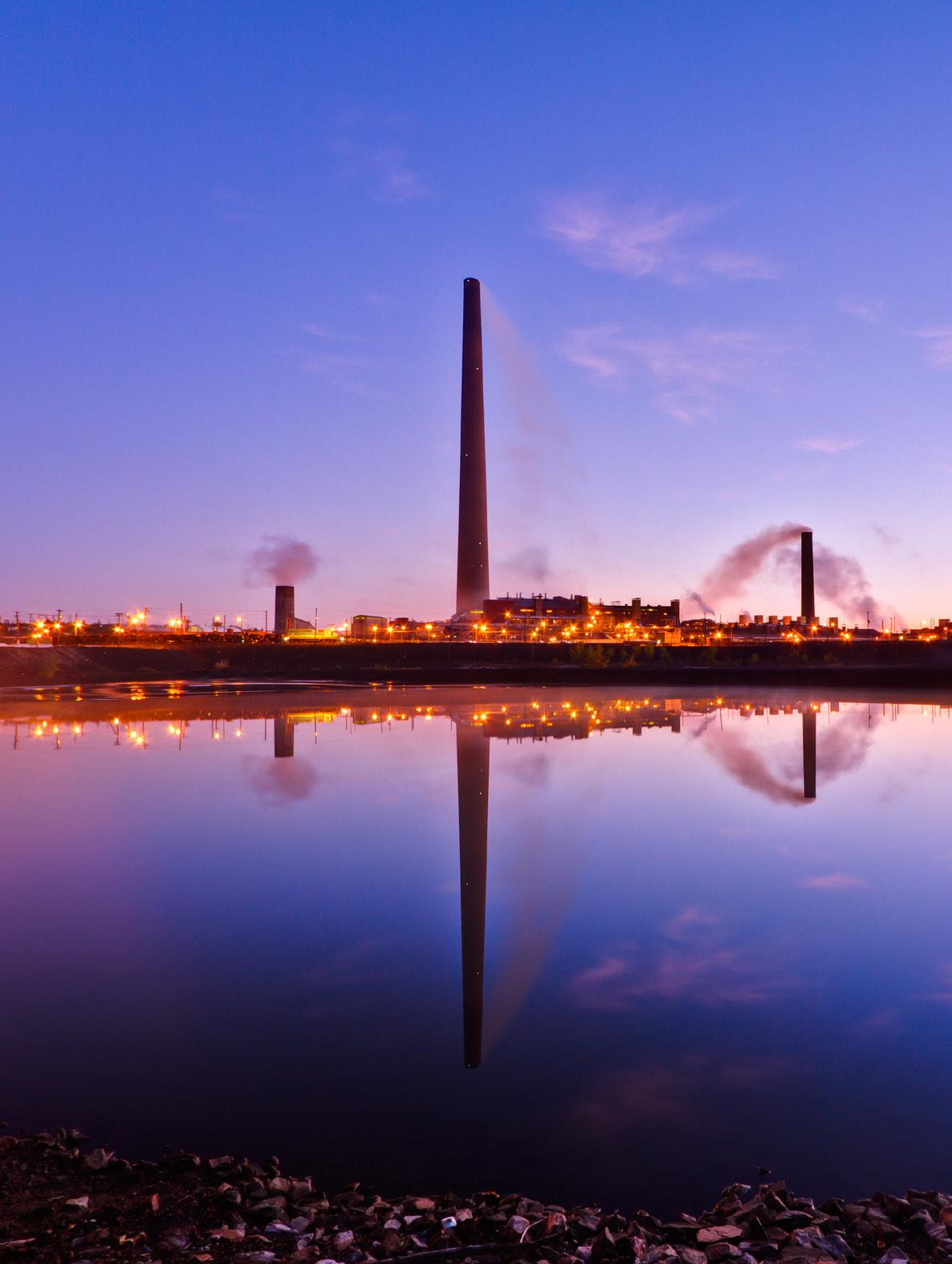
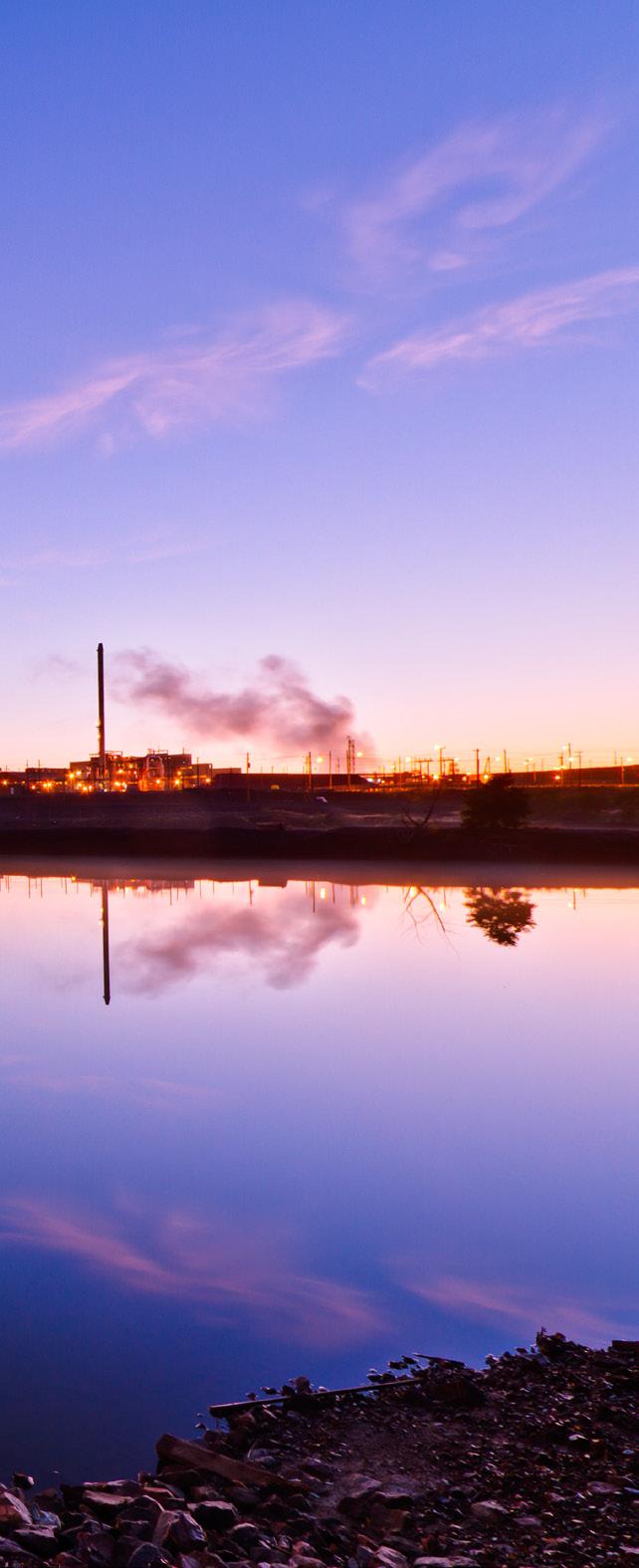
As one of the world’s foremost platinum group metals (PGMs) producers, Impala Platinum Holdings Limited (Implats) is a South African company with key ownership of a range of mines across South Africa, Zimbabwe, and Canada. PGMs are some of the most crucial metals used in essential medical, electronic, and industrial markets today, whilst playing a vital role in moving the world towards a cleaner and more sustainable future. Therefore, as Implats continues to provide a better future for its stakeholders, it is striving to be the most valued and responsible metal producer across the industry on a global sustainability scale.
The Implats Group is a fully integrated PGM producer, which has structured its current operations around 6 key mining operations across the globe, as well as its refining business Impala Refining Services (IRS). These metals serve vast markets from Japan, China, the US, and Europe as the use of PGMs are used across industries to manufacture things such as hard disks, mobile phones, aircraft, turbines, anti-cancer drugs, dental implants, industrial catalysts, and ceramic glazes – to name just a few uses. Therefore, the demand for these metals is ever-increasing, especially for their predominant use in the environmental field in autocatalytic converters, which reduce outdoor air pollution by being fitted to cars, trucks, motorcycles, and other mobile machinery. Consequently, the demand for PGMs in today’s world is ever evolving as we strive towards a more sustainable future across every industry.
Implats owns two of the most significant PGM-bearing ore bodies in the world located at its Bushveld Complex in South Africa and the Great Dyke in Zimbabwe. The Bushveld Comlpex in South Africa comprises 3 operations: Impala Rustenburg, Two Rivers, and Impala Refining Services.
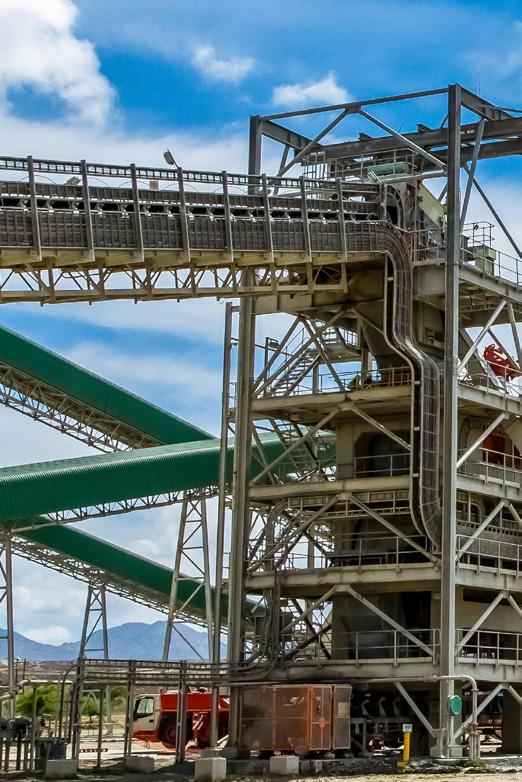
Impala Rustenburg is a 96% owned primary subsidiary mining operation of Implats which is situated on the Western limb of the Bushveld Complex in South Africa. The complex comprises a concentrating and smelting plant servicing its nine-shaft-mining complex which is mined predominately through conventional breast mining. The Two Rivers mining operation, however, is a joint venture with African Rainbow Minerals who own 54% of the operation, with Implats owning 46%. This mining operation comprises two on-reef decline shafts and a concentrator plant. Located on the Dwarsrivier farm in the southern eastern limb of the Bushveld Complex. The Two Rivers complex has a life of mine off-take agreement with Impala Refining Services (IRS) and sees its entire mining operation fully mechanised with the bord and pillar method employed.
The final mining operation across the Bushveld Complex in South Africa includes the Marula mining operation which is one of the first operations developed on the relatively under-explored eastern limb of the Bushveld Complex. Marula holds two contiguous mining rights covering 5494 hectares
(ha) across the farms Winaarshoek and Clapham, and portions of the farms Driekop and Forest Hill. The operations there use hybrid and conventional mining methods operating in the Limpopo province, northwest of Burgersfort.
As a result of Implats’ success across South Africa, they announced in 2021 the approval of the Two Rivers Merensky project, as well as two additional mining projects which were approved during 2022 for the Marula Phase II UG2 project and the North Hill project at Mimosa. These projects result in a significant increase in the Mineral Reserve position at both operations and it will have an overall significant positive impact across the Group’s portfolio level.
Furthermore, the Bushveld Complex also includes its Impala Refining Services (IRS) which is a division dedicated to vehicle housing toll-refining and metal concentrate purchases built up by Implats. IRS provides smelting and refining services
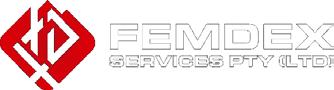
PGMs: The Metals of the Future
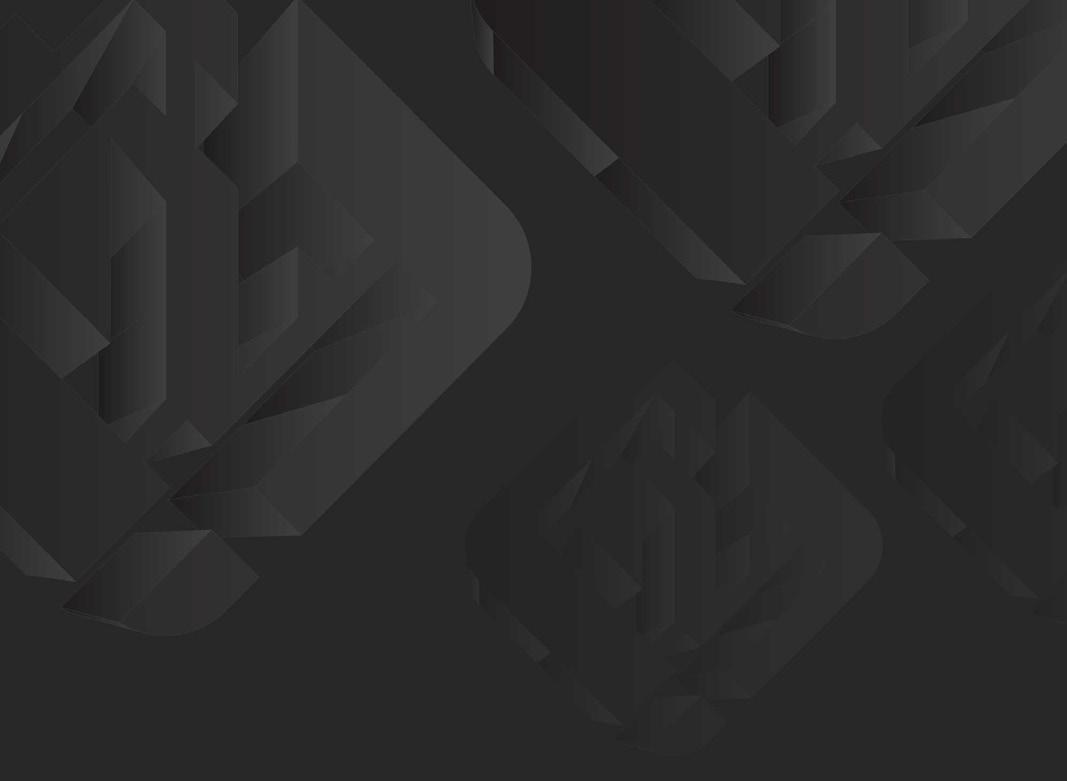
through offtake agreements with Group companies (except Impala) and third parties. Consequently, the Bushveld Complex highlights how Implats has structured its operations to establish and maintain close relationships with its stakeholders while operating within a Group-wide framework that is striving towards managing the economic, social, and environmental implications of its operations in terms of sustainability.
In Zimbabwe, Zimplats is an 87% owned operation by Implats and is located on the Hartley Geological Complex on the Zimbabwean Great Dyke southwest of Harare. The Hartley Geological Complex is one of the largest PGM resources containing 80% of the known PGM in Zimbabwe, of which two-thirds is held by Zimplats. The Zimplats operation contains four shallow mechanised underground mines, as well as one open-pit and two concentrators at Ngezi. Furthermore, the Selous Metallurgical Complex (SMC), is located north of its underground operations and contains a smelter and concentrator.
The other key operation in Zimbabwe is the Implats’ 50/50 jointly held venture with Sibanye
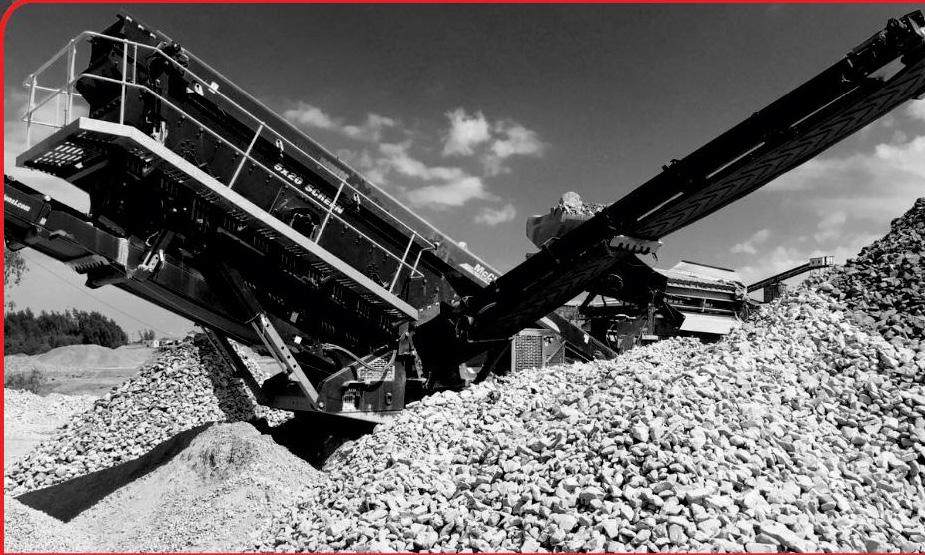
Stillwater secured over years of key acquisitions by each company. Located on the Wedza Geological Complex on the Zimbabwean Great Dyke, the operation includes a shallow underground mine, accessed by a decline shaft and a concentrator. The Mimosa operation holds contiguous mining rights over 6,594 hectares on the North Hill, South Hill, Mtshingwe Block and Far South Hill orebody areas. Consequently, Implats operations across Zimbabwe exemplify the vital role of Zimbabwe in contributing to global PGM production, whilst also establishing Implats as a global company that is working across these key resource areas to deliver this metal towards a sustainable future.
The final operation under Implats is in its wholly owned subsidiary of The Lac des Iles Mine (LDI), which is Impala’s single operating asset located in the Canadian province of Ontario. Implats acquired the mine in 2019, having previously been owned by North American Palladium. The operation comprises underground and surface mining operations, as well as a concentrator. Employing long-hole open stope and sub-level shrinkage mining methods, the mine life is set to span 10 years which currently has an average depth developing to 1080km. Therefore, as we have seen Implats’ role across the PGM industry is vast, recognising the major role that PGM innovation and development with play for the future of the planet.
Consequently, its operations across South Africa, Canada, and Zimbabwe access some of the most crucial PGM deposits in the world and highlight the cooperative approach that must be taken through joint ownership and strategic acquisitions to develop the industry towards prolonged economic success.
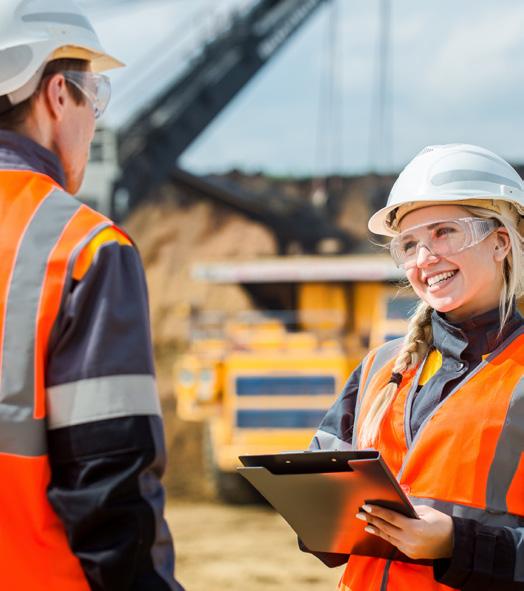
Furthermore, in developing the company towards the future, Implats announced in May this year that Implats has secured a 9.26% shareholding in Royal Batokeng Platinum (RBPlat), which together with previous acquisitions sees Implats take majority control over RBPlat at 55.46%. This acquisition secures Implats’ commitment to implementing broad-based equity ownership in the South African PGM sector. Nico Miller, CEO of Impala Platinum Holdings Ltd., outlined in the press release for this acquisition that “Implats is strongly committed to growing and securing the competitiveness and sustainability of the southern African PGM sector. Through our significant investments in life-of-mine extensions, growth and beneficiations, and with our
ongoing support and facilitation of socio-economic development in our mine-host communities, we are dedicated to creating a better future and delivering enduring benefits for all stakeholders.”
Miller continues that, “Our capital investment programme, together with our acquisitions of a controlling stake in RBPlat, will position southern Africa more competitively as a stable and responsible global mine-to-market PGM producer. We believe in strong and sustainable PGM industry is in the national and regional interest.” As we can see from Miller’s comments Implats is on a mission to be the most valued and responsible metals producer, which is crucially conscious of the vital role it must play in building a better future for its stakeholders and importantly the communities in which they operate.
Overall, Implats is leading the PGM industry towards an ever evolving future. As the demand for PGM’s increases, as we move in global industries towards more sustainable futures, companies such as Implats have already begun to expand its operations to strategically place the company as a key facilitator to these vast and expanding industries, especially those which are contributing towards a more sustainable. Furthermore, as the company announced in June 2023, Patrick Morutlwa took over as Group Operating Officer (COO), and Mark Munroe has been appointed Group Chief Technical Officer (CTO) which will oversee the company for the coming years as the demand for PGM’s globally continues to skyrocket.
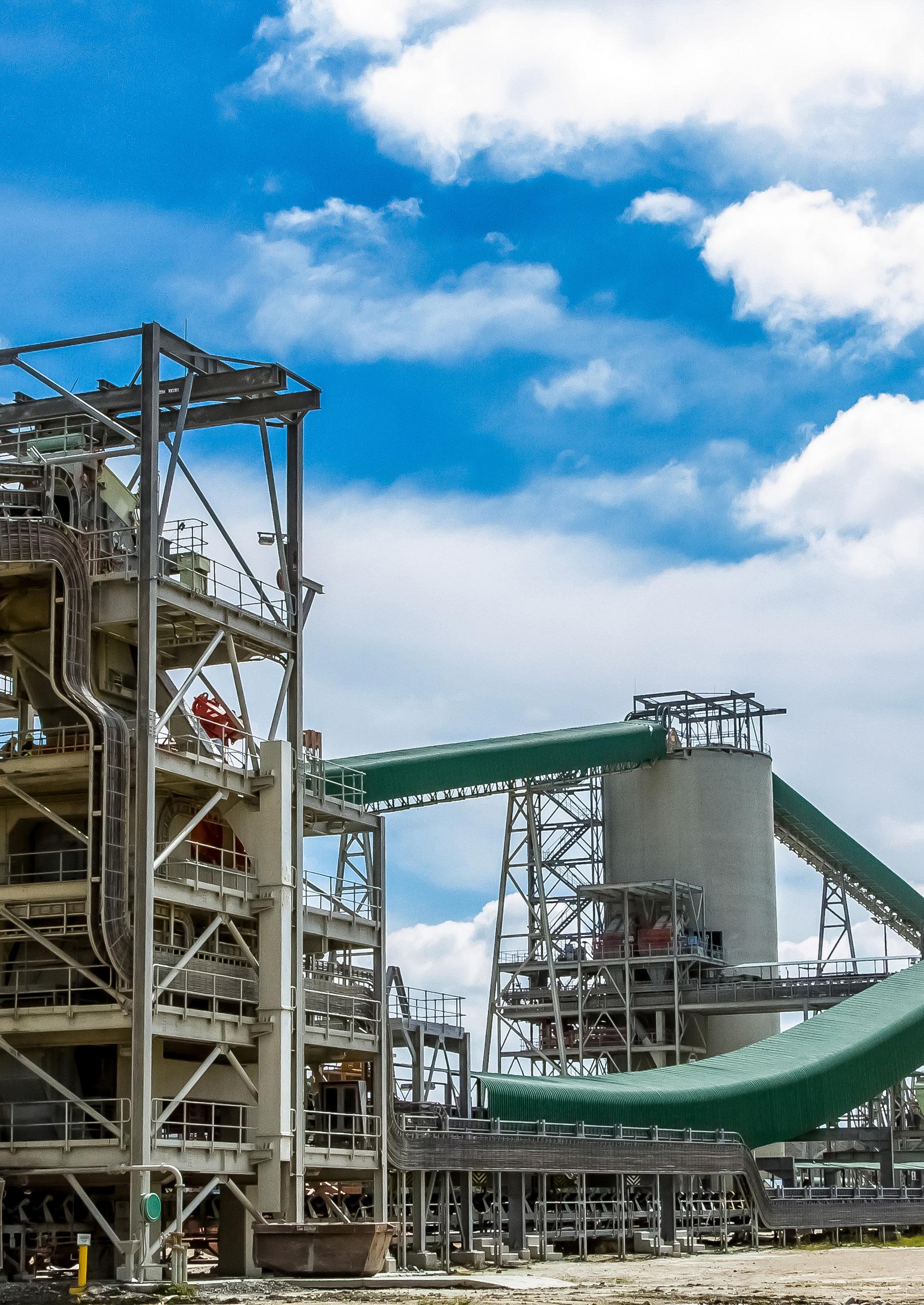
HASHIMA: Ghost Island
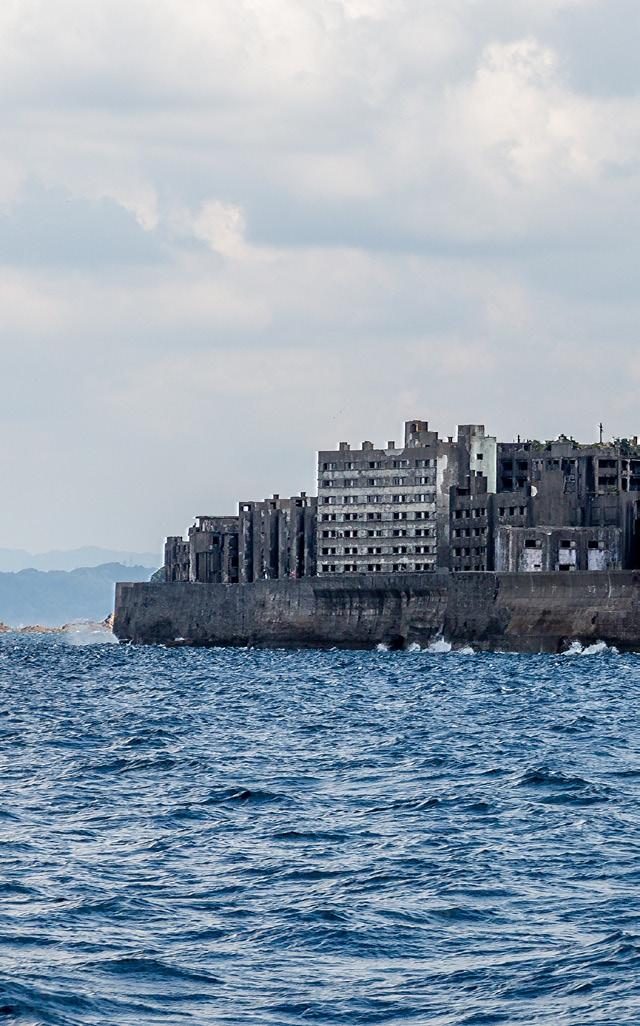
15 miles off the South Coast of Japan, just a short boat ride from the city of Nagasaki, Battleship Island floats eerily and alone, surrounded by the ocean. Now left in ruins, this island holds the remains of Hashima, a manmade structure of just 16 acres that was built at the beginning of the Japanese Industrial Revolution in 1887.
Various aliases are associated with the island; the sea walls create a silhouette that is similar to a battleship, hence the name. It is also renowned for being constructed entirely of concrete buildings, and was therefore referred to by locals as “the island with no green”. However, due to the passing of the time, and the shocking events that happened in the time that Hashima was populated, it is now best known by another name: Ghost Island.
The Island of Hashima was once a thriving metropolis, housing employees of a coal mine (once owned by Mitsubishi) that was situated directly under the island structure.
Citizens of Japan were extremely keen to live there at the beginning of the 20th Century: the concrete building were revolutionary, as not only did they protect people the people living there
from the harsh conditions out at sea, but they also boasted a higher standard of living than the rest of the country. Even for today’s standards, the residents in Hashima were very well off. The island boasted a kindergarten, school, temple, town hall, post office and community centre. For leisure, they enjoyed a club house, cinema, swimming pool, rooftop gardens, shops, a pachinko parlour (a form of Japanese slot machine gambling), and even a brothel! At the end of the 1950’s, Hashima Island was one of the most densely populated areas on the planet, with more than 5000 inhabitants living in the 16 acres. To put this into context, that’s 50 times smaller than Central Park in New York.
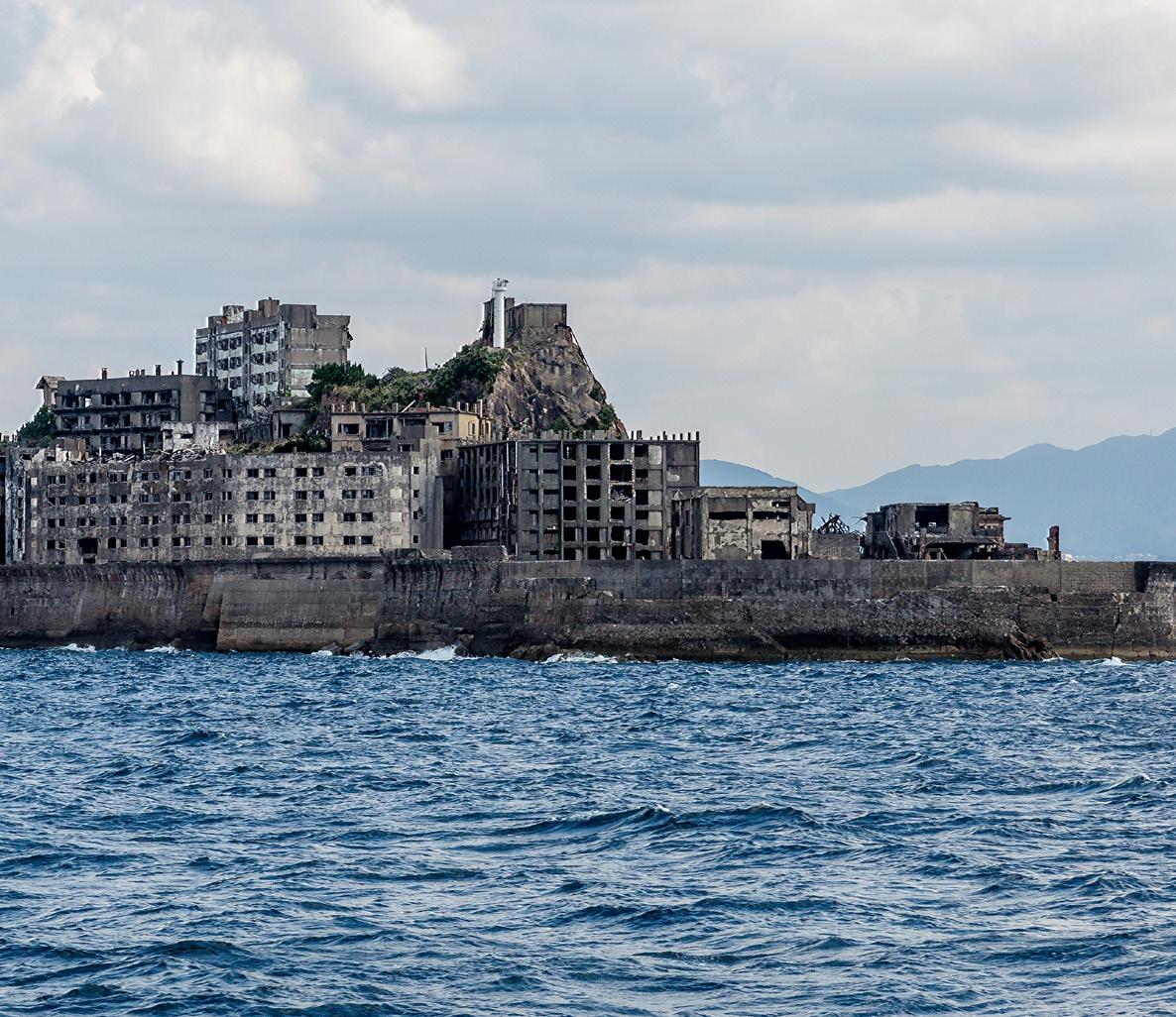
Unfortunately, not everybody was so lucky on the Island. During the 1930’s and 1940’s, in the period surrounding World War II, forced labourers from Korea and China were sent to Hashima and ordered to work the coal mine. Unlike the Japanese citizens’ spacious apartments, the Korean workers were made to live in cramped and unhygienic
areas; many slept in closets. Approximately 500800 people were relocated to the island for forced labour, and due to the poor conditions, being poorly fed, and working shifts of up to 12 hours a day in the coal mine that was 200m below the surface of island, many tried to escape, and any trying. Local records declare that 123 of the Korean workers and 15 of the Chinese workers died due to the hardships that were inflicted on them in their time on the island. It is believed that many more died but went unrecorded.
In the early 1970’s, the mine’s life span was close to expiry, as coal was depleting.
Additionally, petroleum was becoming the main source of energy in Japan. Due to this, in 1974, the mine shut. There was no longer a purpose for the workers on the island to live there, and jobs back on the mainland weren’t plentiful, so everyone had to rush back to Nagasaki to secure an income and a
home for themselves and their families. Within the space of a week, nobody was left.
What remains is a creepy sight. Concrete blocks were left in ruins, but the hardy material means enough still stands to give you a true sense of what it must have been like to live on the island. Many years later, relics of past lives are still scattered throughout the buildings: an intact mosaic remains on the wall of the school, and a slide once frequented by the children in the playground of the school now stands alone.
Amongst the abandoned apartment blocks, TV sets still sit in the corner of living rooms, unfinished bottles of sake are stacked on shelves, and washing up still left in kitchen sinks reminds us of how quickly people left the island. It is as if they were desperate to get away.
In 2009, after being untouched for 35 years, the island was reopened, and tourists are now able to take tours of a small section of the remains; it was even given UNESCO World Heritage recognition in 2015. Many locals and foreign neighbours alike are
not keen on this – Korean nationals disputed this recognition, due to the horrors and human rights violations that occurred there, and voices from China, South and North Korea agreed. There are even those who believe that the island is haunted by the workers who unlawfully died in the depths of the mine.
However tragic, Hashima Island certainly possesses a unique and strange story. The coal mine below the surface once reaped the land of resources, but despite being known as the “island with no green”, Hashima is now taking back what it lost and is beginning to be reclaimed by nature.
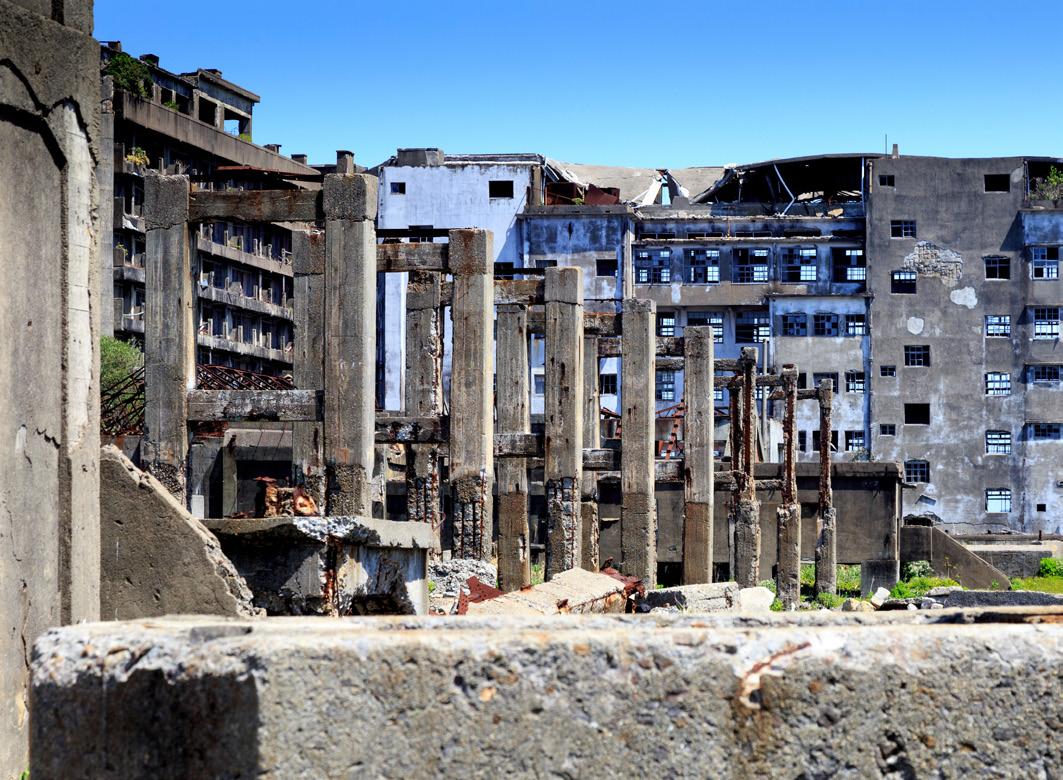
Whether or not it is truly haunted and whilst the physical reminders of the island may completely disappear, the memories of the inhumane treatment of forced workers will forever remain on ‘Ghost Island’.
www.thelittlehouseofhorrors.com/hashima-island
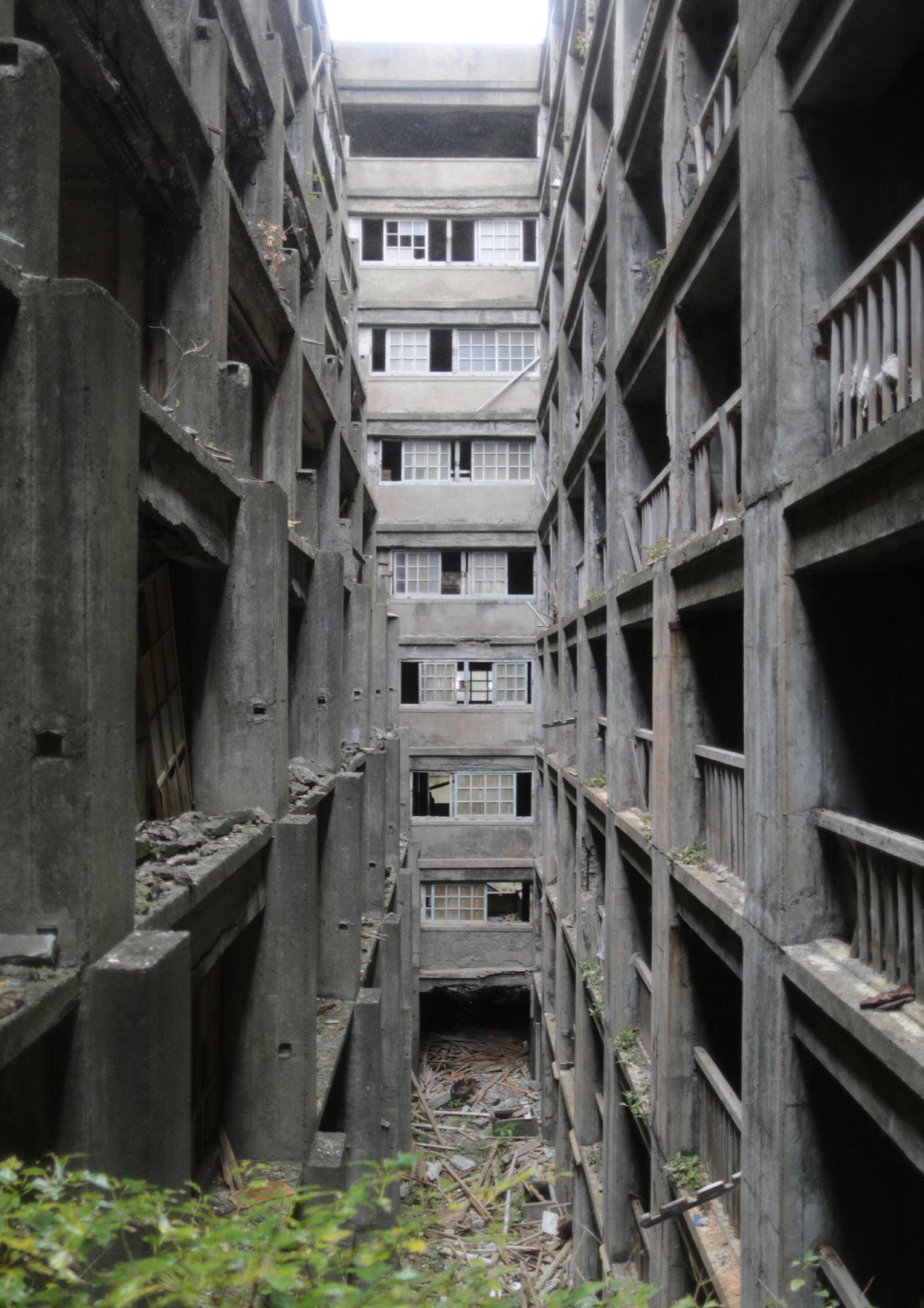

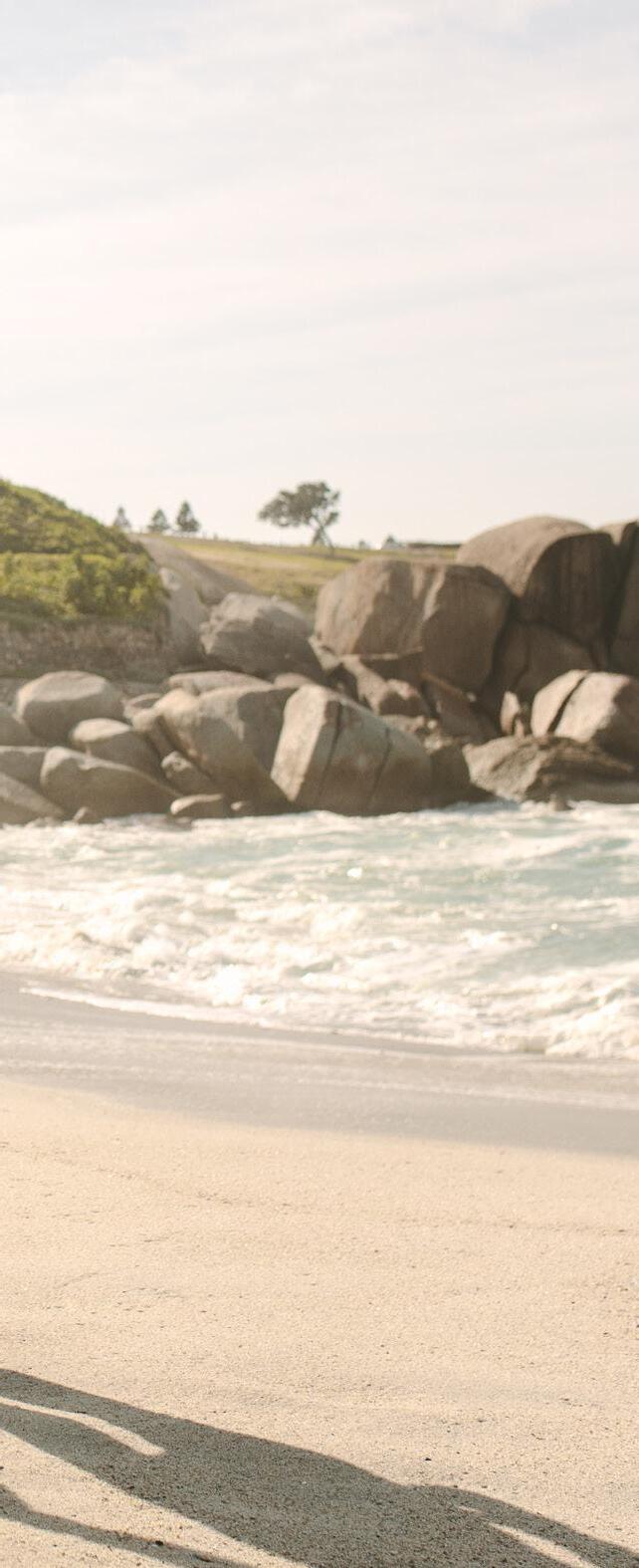
Over the past few years, we have become increasingly aware of the key role hospitals and medical services play in keeping us all safe and cared for. The Covid-19 pandemic exemplified the heroic role that many healthcare professionals and facilities play in ensuring our health is the top priority. With the focus of its operations in Gauteng, Eastern Cape, KwaZuluNatal, Limpopo and Western Cape, the Intercare Group is leading the healthcare sector in South Africa to provide patients with top-quality medical services across a range of routine and specialised medical, dental and rehabilitation services.
Founded in 2000, Intercare was established by Dr. Hendrick Hanekon and Dr. George Veliotes with the simple purpose of striving to make people feel better. The Intercare Group was the first medical and dental centre to open in the country and has now grown exponentially to over 27 multidisciplinary medical and dental centres, 4 day hospitals, 4 sub-acute and rehabilitation hospitals, and 1 Intercare Medfem hospital across South Africa. The medical group is a people-focused organisation that structures its services around the health status and needs of its patients. This patient-focused approach ensures that they can deliver the best and most unique care possible to help people across the country feel better faster.
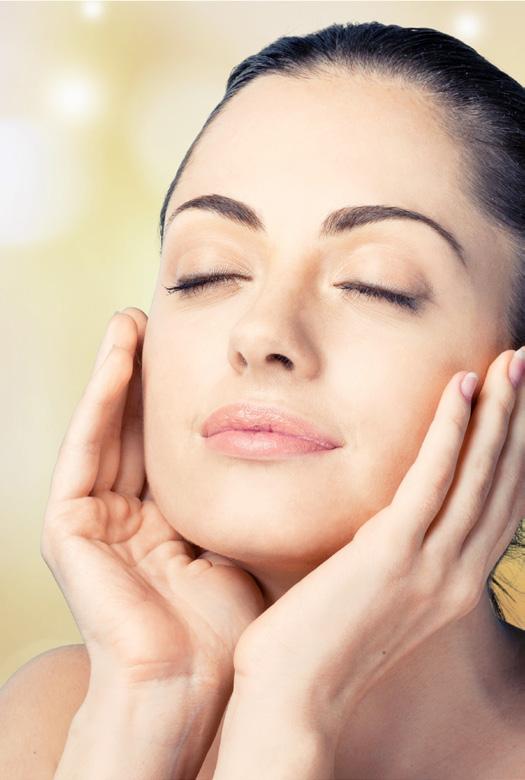
Intercare offers a range of medical services that centers accessibility and convenience at the heart of its care delivery model. A key focus of the company is that gaining access to treatment should not be difficult, therefore, it has carefully located its facilities, implemented extended operating times, and attempted to reduce the physical fragmentation of the location of medical services by bringing multiple services under one roof to make treatment easier to receive. These changes ensure that patients across South Africa have quick and convenient access to general practitioners, dentists, radiologists, pathologists, physiotherapists, psychologists, dieticians, optometrists, audiologists, and pharmacies all under the same Intercare facilities.
An impressive element of Intercare’s treatment is its virtual consultation offerings. Patients can access care virtually through remote video calls with healthcare professionals. This system allows patients who find it difficult to get to the facilities the chance to still receive top-quality and professional care. Whilst this does not replace face-to-face appointments it provides a crucial option for those with disabilities or other illnesses which may prevent them from accessing treatment as easily. However, Intercare goes one step further and focuses on continuity of care. This means that patients can receive in-person and virtual consultations with the same healthcare professional, therefore they continue to receive care from the healthcare professional who best understands their treatment history. This focus on

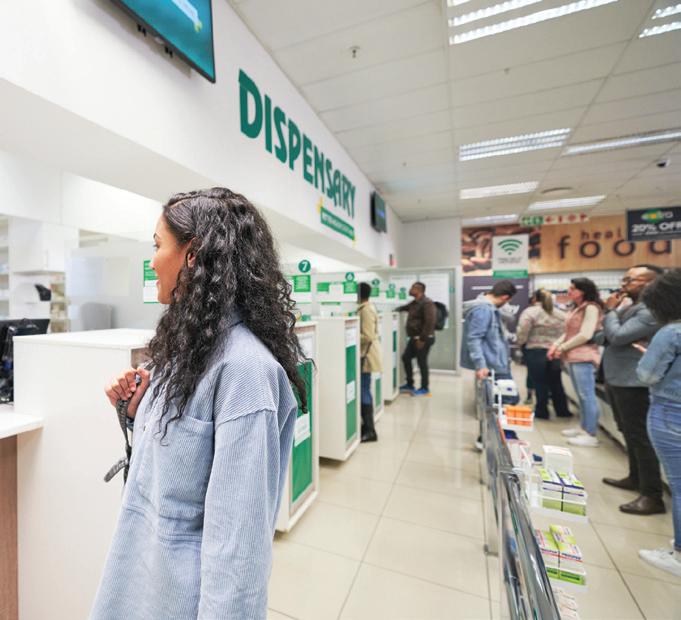
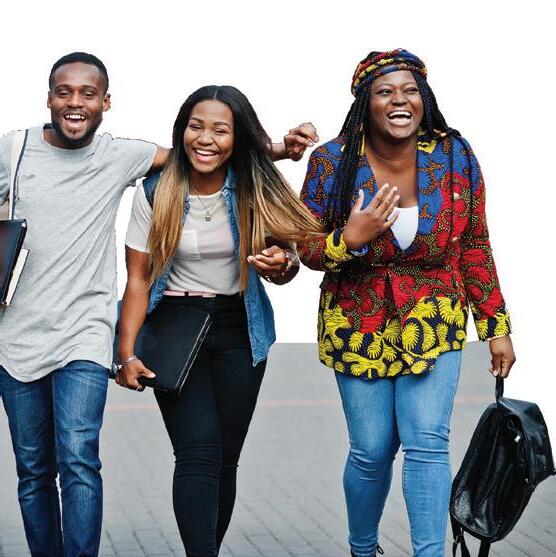
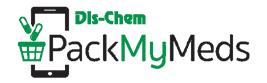
continuity ensures that patients’ personalised care is paramount compared to other virtual services which may prioritize speed and accessibility over quality.
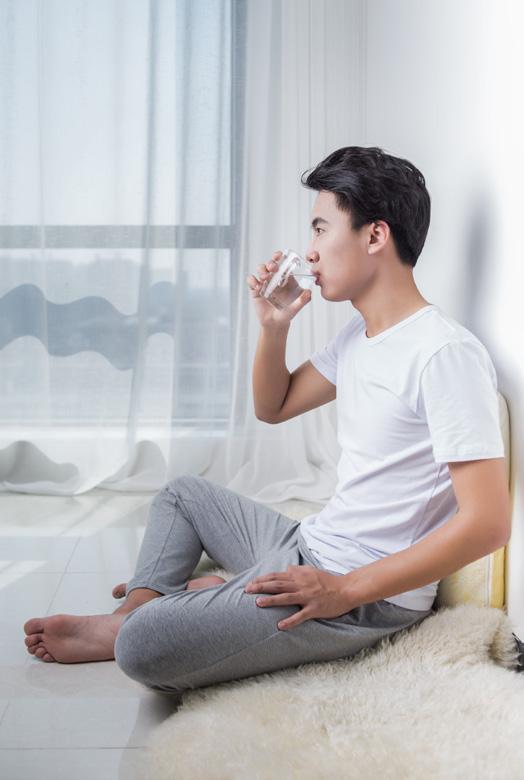
A key division of Intercare’s facilities is in its dental centres which feature fully-fledged dental departments that are filled with topquality dentists and oral hygienists all of whom are well-equipped to provide a full range of dental services to its patients. These services include routine detailed care, to specialised dental services including teeth whitening, porcelain crowns, veneers, inlays, implants, and periodontal screening – to name just a few. The care provided through Intercare’s dental centres ranges from specialised, routine, and oral hygiene care and so patients can receive full dental treatment options from routine to cosmetic across the group’s services.
Another crucial service provided by Intercare is rehabilitation services through its Sub-Acute Rehabilitation Hospitals. These facilities provide services to patients who no longer require intensive diagnostics or invasive procedures but require some medical attention to help promote rehabilitation following surgery, injury, or disease. With access to general practitioners, nurses, case managers, physiotherapists, speech therapists, occupational therapists, psychologists, dieticians and social workers, patients are put in the best conditions to help ensure the maximum restoration of mobility and quality of life possible is achieved. Intercare was the first group to develop this model of rehabilitation care, and its resulting figures show that readmissions were reduced after patients were discharged by 33%, with preventable admissions reduced by 50%. Therefore, the Sub-Acute Rehabilitation Hospitals under Intercare provide crucial care outside of intensive and in-patient units to ensure that quality of life is promoted, and patients are set up in the best conditions to live their lives to prevent them from needing to return to hospital care following their discharge.
Intercare of course also offers day hospitals, or outpatient surgery centres, which carry out procedures that don’t require an overnight stay. These services prioritize patient safety and comfort whilst utilizing the best procedure techniques and technology to speed up patient care. These facilities quickly and efficiently work to provide crucial care to patients but allow them to
rest in the comfort of their own homes. Therefore, they are convenient to patients’ needs, whilst never compromising on quality clinical care. Within these facilities, Intercare has 3 modern operating theatres, 20-24 patient beds, procedure-relevant equipment technology, as well as pathology and child-friendly units.
The final key operation of Intercare is its Medfem Hospital located in Gauteng which specialises in women’s health. The hospital provides gynaecological, fertility and cosmetic surgery. Working alongside reproduction specialists, the facility is focused on providing a caring, convenient, and holistic approach to patients undergoing fertility treatment. In 2021, the Discovery Health Medical Scheme (DHMS) introduced the Infertility and Assisted Reproductive Therapy (ART) benefit which provides cover for assisted reproductive technology such as In-Vitro fertilisation (IVF), IntraUterine Insemination (IUI), Frozen Embryo Transfers (FET), and Intra-Cytoplasm Sperm Injections (ICSI). This program means that female members between the ages of 25 and 42 who are on executive and comprehensive insurance plans, and who have also been members for two years, will have access to
up to 2 cycles of ART. Therefore, through Intercare women’s healthcare is given crucial and sensitive development through Intercare’s top-quality care facility.
Intercare is focused on helping its patients feel better, and so has created an informative online Health Hub that provides patients with essential information on a range of medical and dental concerns they may have. The site also provides a range of family, recipes, and wellness options to give patients a wellrounded approach to healthcare. Furthermore, this service also makes it easy for patients to find a general practitioner, dentist, specialist, or facility nearby. Therefore, Intercare’s online Health Hub is yet another way that it is helping to bring peace of mind through easy access to services and healthcare professionals across the country.
Overall, across Intercare’s range of operations, they are placing the patient and their needs at the centre. By providing a range of facilities that work cohesively with more intensive sectors of the
medical sector they can provide vital rehabilitation, dental, outpatient and female health-focused healthcare that is promoting the betterment of people across South Africa. Intercare focuses on a range of health care concerns so you can be sure that no matter who you are or what you are dealing with, Intercare will be there for you and will provide you with the vital treatment you need in the most efficient, caring and supported way possible. Therefore, in choosing the Intercare Group you are choosing healthcare which is committed to excellence.
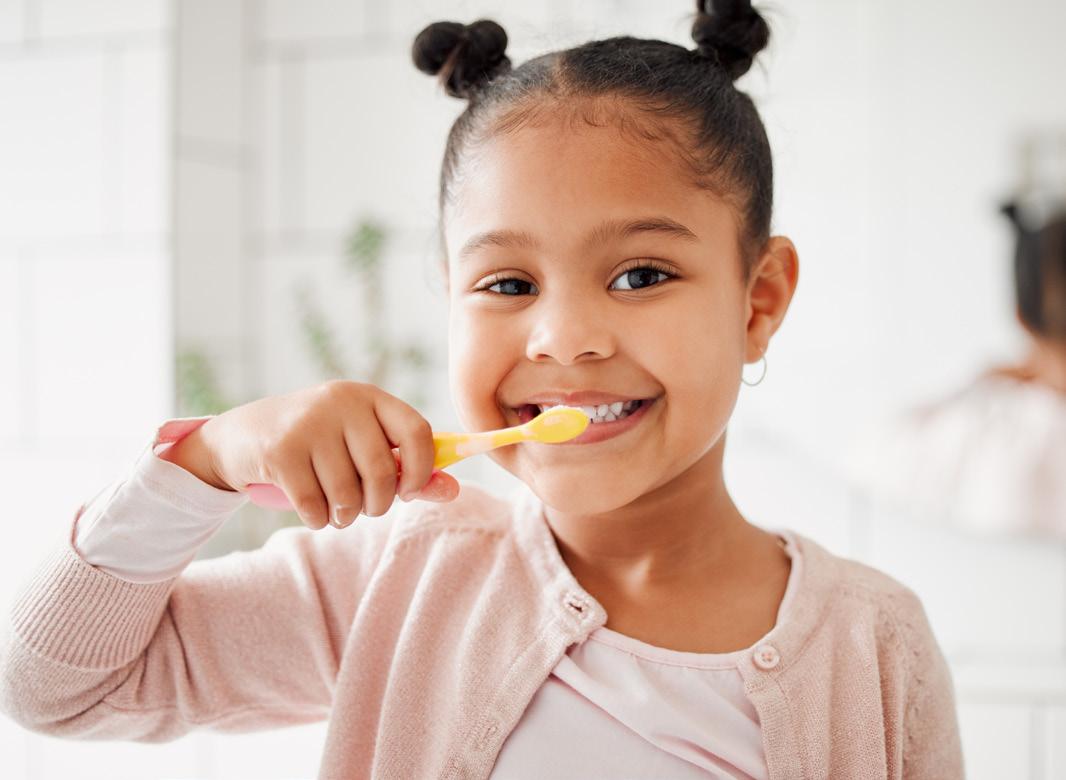
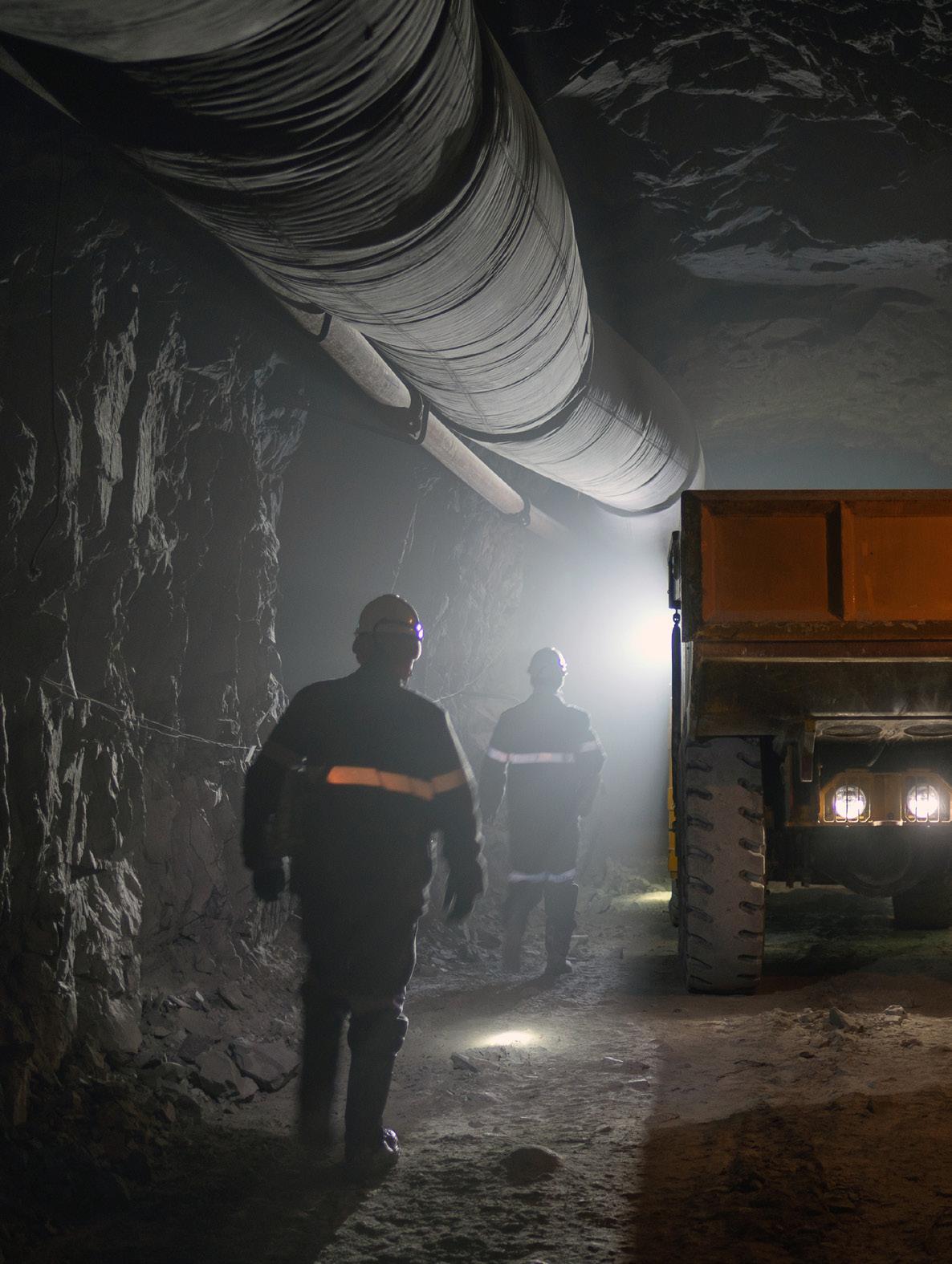
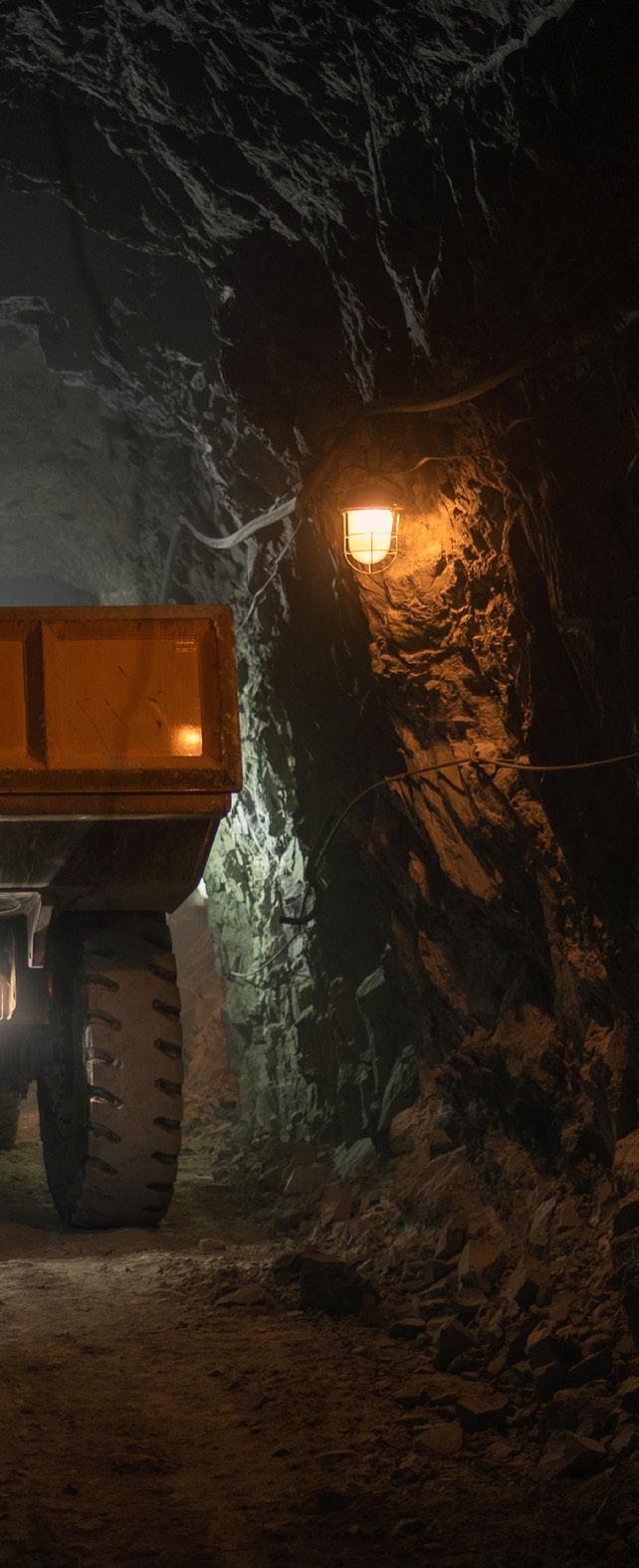
Globally Barrick Gold Corporation spans 13 countries, with 16 sites of operation producing gold and copper. Consequently, its portfolio extends across the globe and is focused on attaining the most prolific gold and copper districts, which are high-margin and long-life assets. With the goal of being one of the world’s most valued gold and copper companies with the best returns and benefits for its stakeholders, Barrick continues to invest in the industry, whilst building its operations towards more sustainable growth. Therefore, its development across its Loulo-Gounkoto Mine Complex is a key milestone for the company positioning itself as a leading global gold supplier.
As one of the largest gold-producing companies in the world, Barrick, which is headquartered in North America, produced 547,00 ounces of gold in 2022 from The LouloGounkoto Project in Mali. This key mine complex is crucial to the company’s gold production and comprises two distinct mining permits: Loulo and Gounkoto. Situated in the west of Mali, bordering Senegal and adjacent to the Falémé River, Barrick has 80% ownership over the two mines, with the State of Mali holding 20% ownership. Production at the Loulo mine site began in 2005 and comprises of an open-pit operation and the development of two underground mines.
Meanwhile, Barrick’s Gounkoto mine is an open-pit operation as well as a number of satellite deposits. Gounkoto poured its first gold in 2011 and began developments in 2020 on a new underground mine which delivered its first ore in 2021. The combined sites make up The Loulo-Gounkoto Complex which as of 2022 had 6.7 million ounces of proven probable gold reserves and combined positions Barrick Gold as one of the top 10 gold producers in the world and the biggest in terms of enterprise value in the whole of Africa. Therefore, when combined with the production at another of Barrick’s gold operations in Mali, the Morila Mine, the two projects collectively contributed $9.3 billion to the Malian economy and accounted for 5-10% of the country’s GDP over the past 10 years, which highlights the significant economic impact of Barrick’s operations across the region.

Barrick announced in January that over 2022 its Loulo-Gounkoto mining complex maintained its historically consistent performance by meeting its production guidance and solidifying its long-term outlook. The complex is predicting 510,000-560,000 ounces of gold in 2023 and has been developing a third underground mine at Gunkoto which is on track to start ore production shortly. Consequently, the mine complex is set to maintain and continue to expand its output, to continue to establish the overarching company as a leader in the mining industry that has positioned its operation towards a future of sustainable growth.
However, a crucial element of Barrick’s operations in Mali is its commitment to partnering with the local community to transform the natural
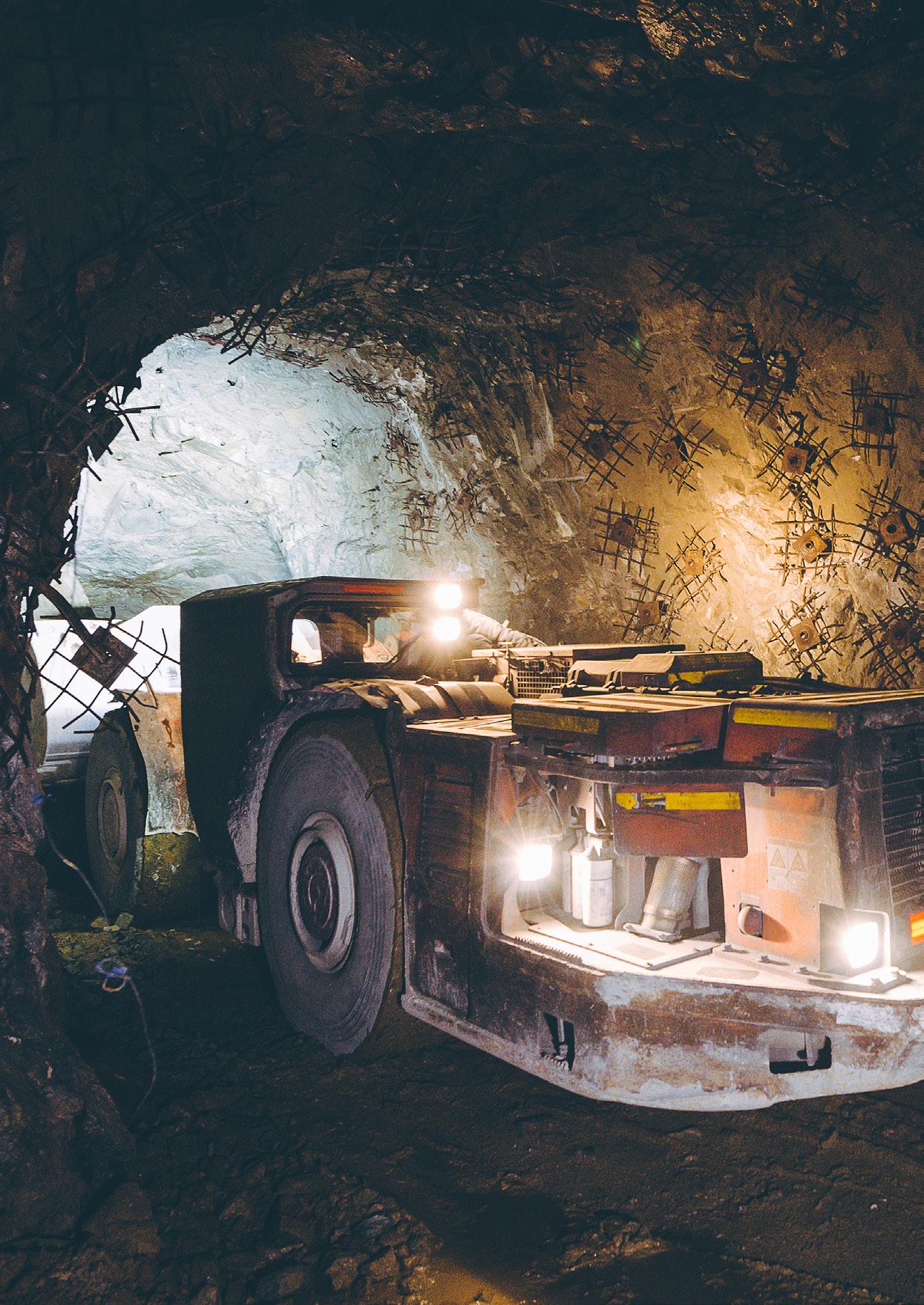
Barrick Gold Corporation: The Loulo-Gounkoto Complex
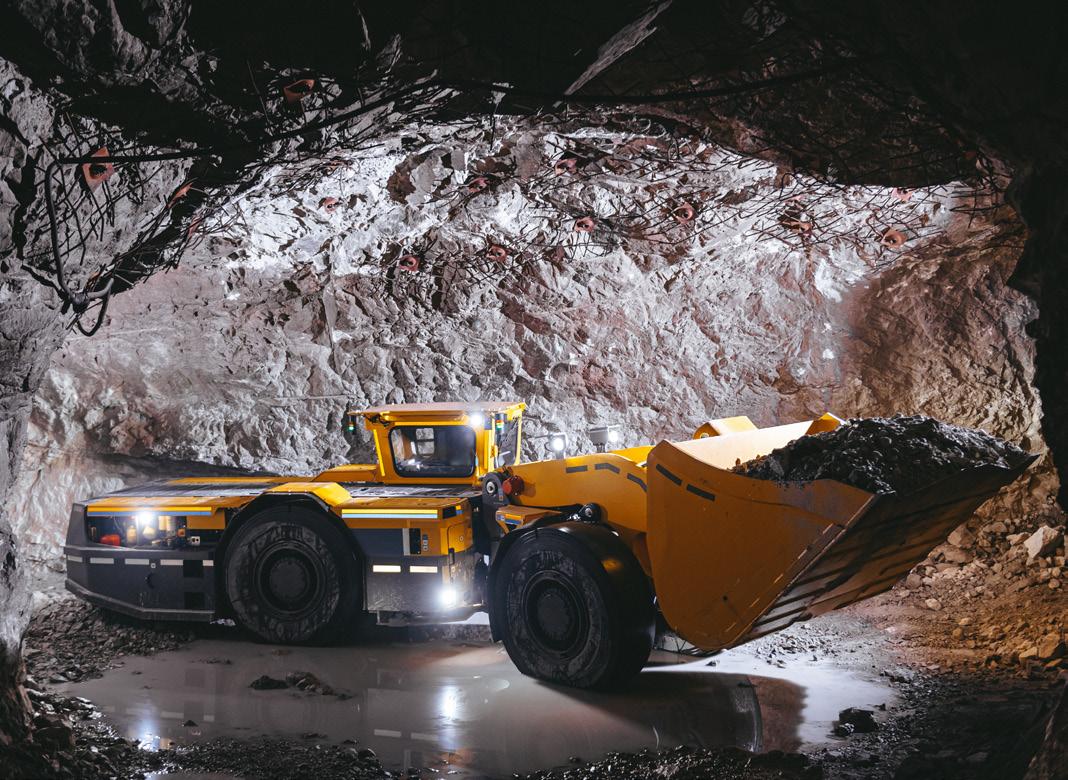
resources of the land into tangible benefits and mutual prosperity. One way that Barrick is doing this is through employment, which sees the complex hire almost its entire workforce from local communities. By employing roughly 700 locals across the company, Barrick is ensuring that its operations are having a positive effect on the communities through employment which encourages the financial development of the region for a more economically diverse future. Additionally, over the entire life of the Loulo-Gounkoto Complex, the state has received more than 70% of the economic benefits that the mining venture has created.
President and Chief Executive of Barrick
Gold, Mark Bristow, has announced in a recent press release that “Host community investment is making a significant difference in the surrounding areas through the ongoing development of infrastructure, agriculture, education, and healthcare. Malian nationals account for 100% of the complex’s management team and 96% of its workforce”.
He also outlines that the company’s “strong partnership network has been a significant factor in enabling Loulo-Gounkoto to maintain an exemplary performance in the face of the many challenges recently experienced by Mali”. Bristow’s comments highlight how their work to employ people from the local community and work with local stakeholders is a key factor in the success of Barrick’s operations. By working alongside people and businesses from the region, Barrick benefits from both the country’s economy and the global notoriety of Malian gold. Furthermore, Barrick is equally concerned with the movement towards a more sustainable future. Barrick has implemented a global green energy strategy across its operations, which has seen The Loulo-Gounkoto complex implement a solar power plant. The company announced in January that since the plant was commissioned in August 2020 it has cut its emissions by 57 kilotons (kt). Then in June, Barrick announced that it was further extending the complex’ solar power installation and battery storage system by 40 megawatts (MW). The project was previously feeding 10MW into the mine’s microgrid and it is expected that its second phase will be commissioned ahead of its planned 2024 timelines.
Overall, Barrick Gold Corporation has established itself as a key player in the global gold and copper fields. Specifically with its sites of operation in Mali, Barrick is leading the way as a gold producer across Africa which is developing the industry towards localised and global economic benefits. However, the company is equally concerned with ensuring that while it is mining finite resources, it is implementing measures to reduce the company’s carbon emissions significantly. Therefore, through Barrick’s partnership with the State of Mali, it has established itself as yet again a sector-leading gold producer, which has a diverse portfolio of highmargin, long-life assets.

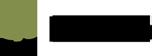
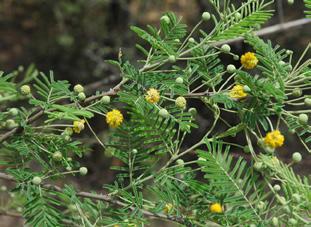
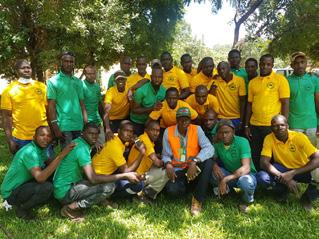
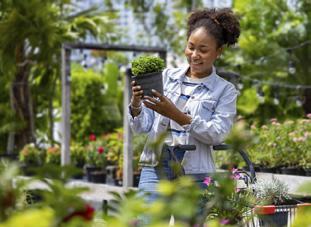
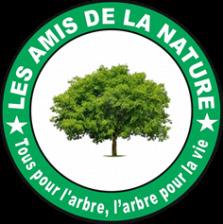
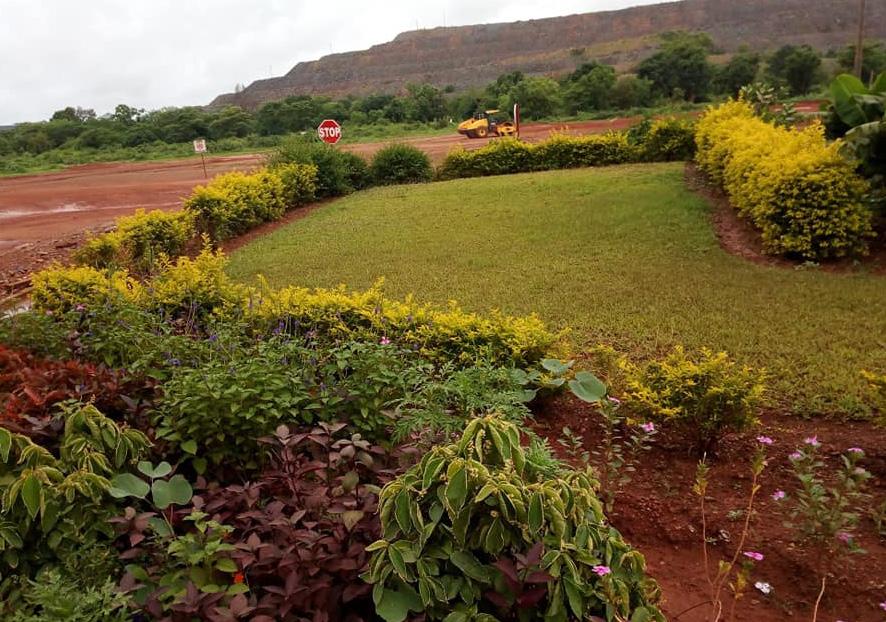
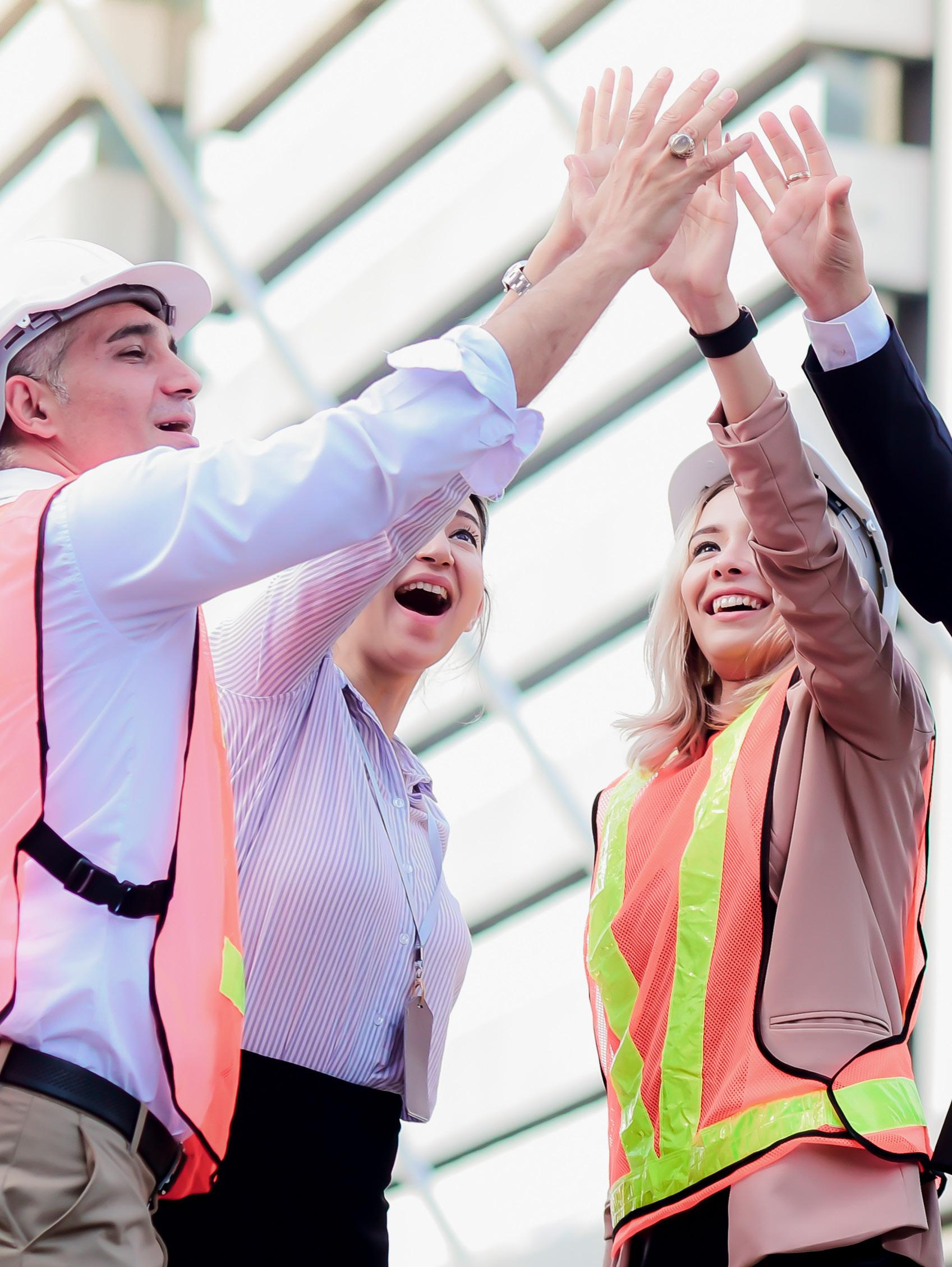
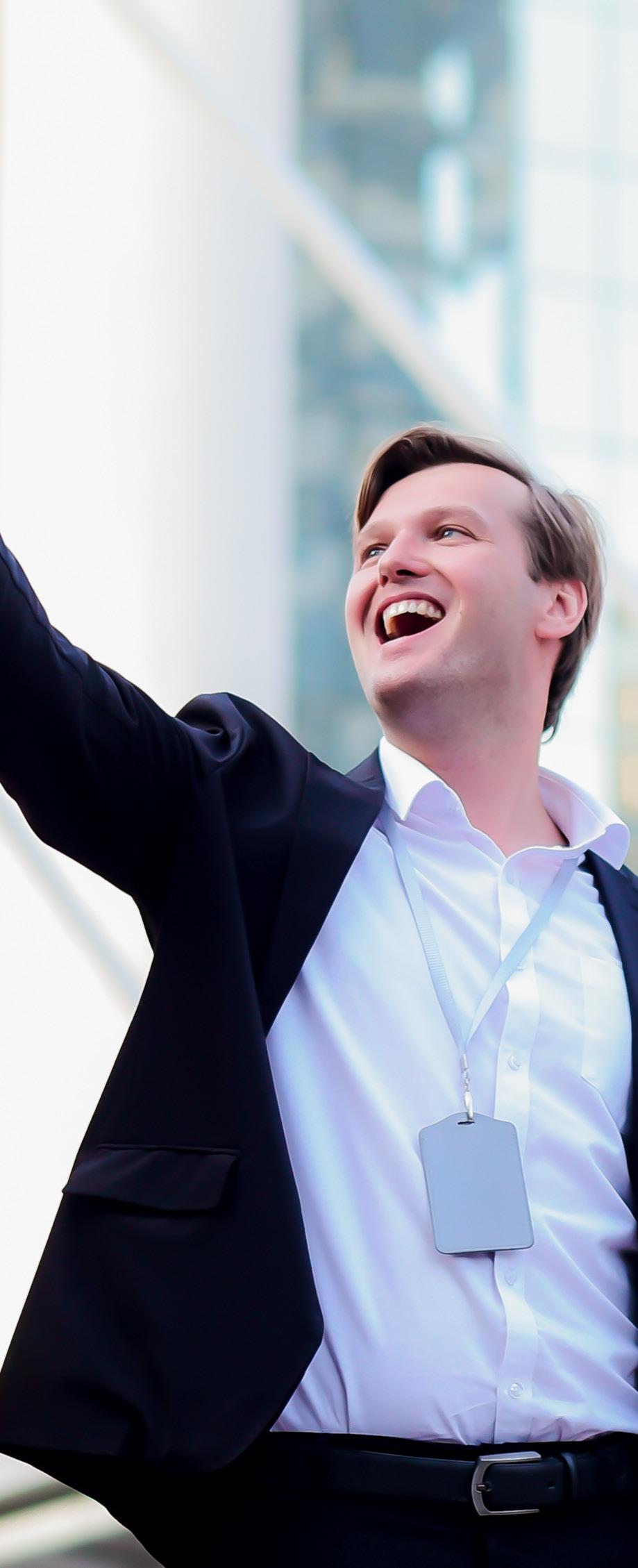
Providing a range of brownfield and greenfield services to its clients, Massy Would Group Ltd. is a leading consultation and engineering solution provider across the energy and built environment sectors. Massy Groups is a joint venture company owned by the Energy division of the overarching company Massy Holdings Ltd. With solutions across the oil and gas, petrochemical, LNG, infrastructure, utilities, and clean energy sectors, it has strategically positioned itself to be the first-choice partner to deliver integrated and sustainable energy solutions across the Caribbean.
Incorporated in 2003, Massy Wood initially began as a 50/50 joint venture between Neal and Massy, and the international energy services company Wood Group, working together under the name NM Wood Group. However, over the last 20 years, the venture has broadened and undergone several amendments to its legal name, whilst achieving several significant milestones which established Massy Wood Group Ltd. in 2014. The development and resilience of the company over the last 20 years, represents the continued investment and success of the company which is now a leading global facilitator across the energy sector.
Massy Wood is focused on using creativity to secure a more sustainable and secure energy future. Therefore, it works with its customers to drive for continued improvement across the energy secure to reduce risks, minimise costs and improve the overall performance and integrity of its client’s assets. The company focuses on providing expertise solutions in engineering, procurement, construction, fabric maintenance services, warehousing, and logistics.
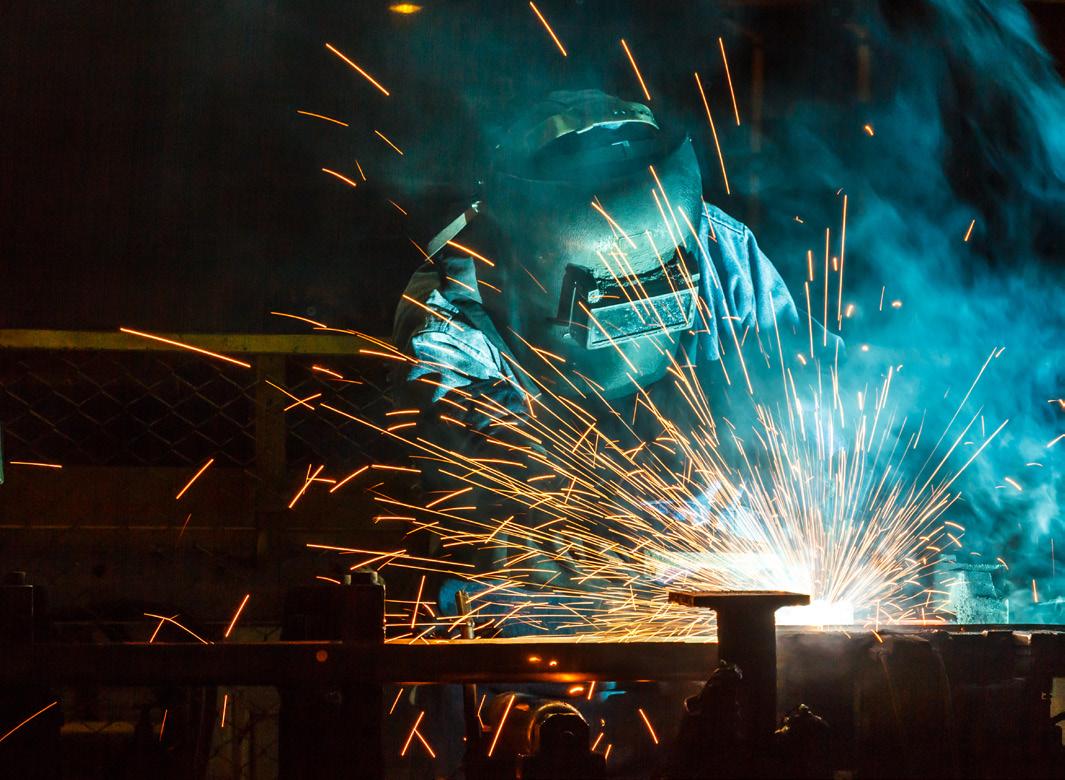
Global Consulting and Engineering Solutions
Massy Wood is therefore able to deliver an integrated suite of services to support its clients across the complete life cycle of their assets from conceptual design to decommissioning. It takes pride in the safety and execution of its projects, which is working to continually improve its strategies to maximise the profitability of its client’s assets.
However, Massy Wood is also concerned with providing consulting solutions and support as part of its role in the global energy sector network. As a facilitator of services and as a consultant it holds a unique perspective that understands both sides of the investment cycle, so can use its expertise to deliver high-quality consultancy services across the design and development, expansion, and upgrading of new and existing assets. Furthermore, they also provide a range of core and specialist services for operations in asset divestment and acquisition. As part of this work, Massy Wood provides environment, clean energy,
concept, pre-feed studies, commissioning, asset integrity management, digital solutions, subsea, automation and decarbonisation solutions – to name just a few!
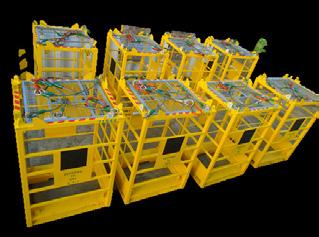
Therefore, its value-added approach to delivery, with the rich heritage of its joint venture companies, has established Massy Wood as a respected global presence in industrial markets. Consequently, in 2022 Massy Wood highlighted 6 projects which it has been working on to move the energy sector across the Caribbean towards a more integrated and sustainable future.
Across the Clifton Hill coastline, Massy Wood is working for BP Trinidad and Tobago to reinforce coastlines by installing 165 metres of rock armour revetment. The coastal protection is aimed to protect the existing NGC, ALNG and PPGP2 pipelines, whilst also preventing shoreline failure along Clifton Hill. The upgrade will improve the site’s conditions and protect BP’s existing pipelines and is expected to span 14 months.
IWES has sustained the reputation as a globally recognized manufacturer of certified DNV standard 271 CCUs as well as the supply of customized portable offshore units to DNV standard 273. IWES has been supplying specialized solutions in the form of portable offshore units and CCUs to the oil and gas industry for the past twenty years. Additionally, with expert resources for design engineering, manufacturing, and field services, IWES is fully capable of mobilizing on very short notice, to facilitate most any situation related to CCUs, including but not limited to, sea fastening, repair, refurbishment, annual recertification, inspection and testing of CCUs.
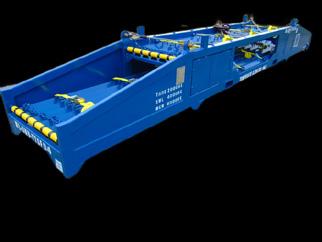
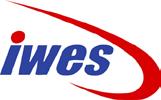
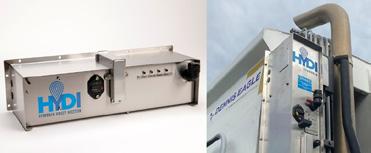
IWES has been delegated the regional agent for Prior Power. Carbon Reduction Solutions.

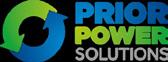
Introducing the hydrogen-on-demand generation system!
• Transform your diesel engine/machinery into an eco-friendly solution with this proven modularized retrofit unit.
• Experience up to 80% reduction in diesel particulate matter.
• Up to 14% reduction in fuel consumption.
• Generate up to 10% more power while supplementing diesel with water.
• Embrace green technology.
Compliment of Carbon Reduction Solution Available on Demand:
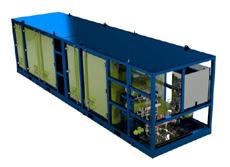
• Electric Nitrogen Pumps (Economic Advantages).
• Single Engine 360K Nitrogen Pump (Conserve 280 Litres of Diesel Daily).
Furthermore, Massy Wood has been engaged by BP Trinidad and Tobago to provide Define Engineering services to the Nitrogen (N2) Generator Installation project on its Mango Offshore Facility. The project is set to span 5 months, providing a variety of services including the FEED engineering of electrical, instrumentation, mechanical, process, structural, etc. These projects with BP Trinidad and Tobago exemplify how Massy Wood has established itself as a leading facilitator of energy solutions across the Caribbean’s energy sector by working with key energy providers in the region.
Additionally, as part of Massy Wood’s work to continually improve its operations and the services it can provide, it has been training its construction departments in Agile methodologies, which has adopted tools such as ADO Boards and Spirit Planning – all to effectively manage construction readiness across its workforce. Consequently, Massy Wood has shown over the last year its dedication to promoting the energy sector towards global stability, by implementing and facilitating
reliable and sustainable energy solutions across the Caribbean region, whilst employing a range of consultancy services to develop Massy Wood’s reach across the global energy sector.
Overall, Massy Wood is a leading global provider of construction, engineering and consulting services across the energy and built environment industry. The company is always striving for success, providing crucial knowledge across all aspects of the industry, and working with its customers to see projects all the way from its conceptual design to end commissioning. Therefore, Massy Wood is continuing to transform lives by implementing value across the industry and its customers’ assets, by prioritising safety, people, quality, ethics and its passion for energy development.

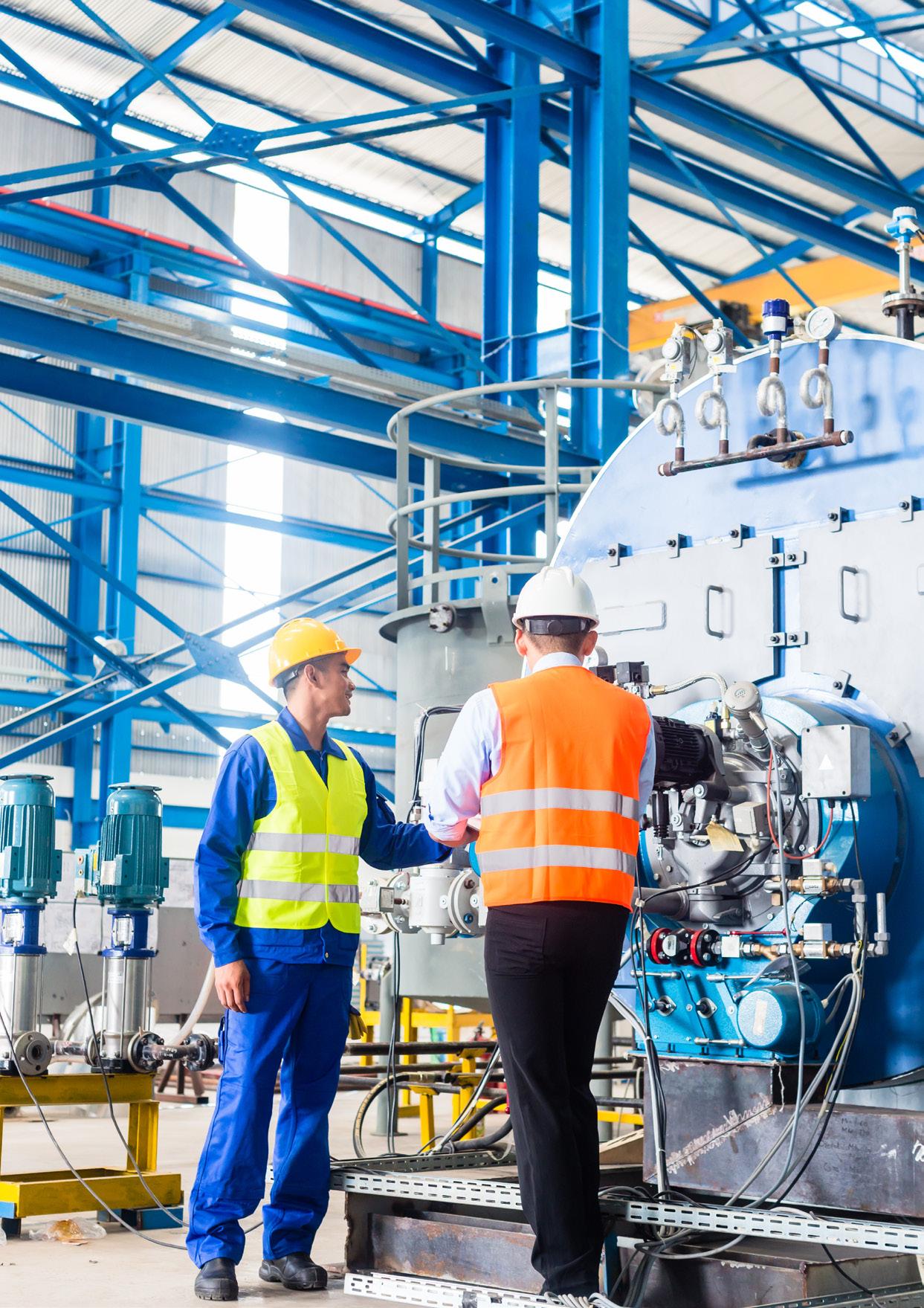
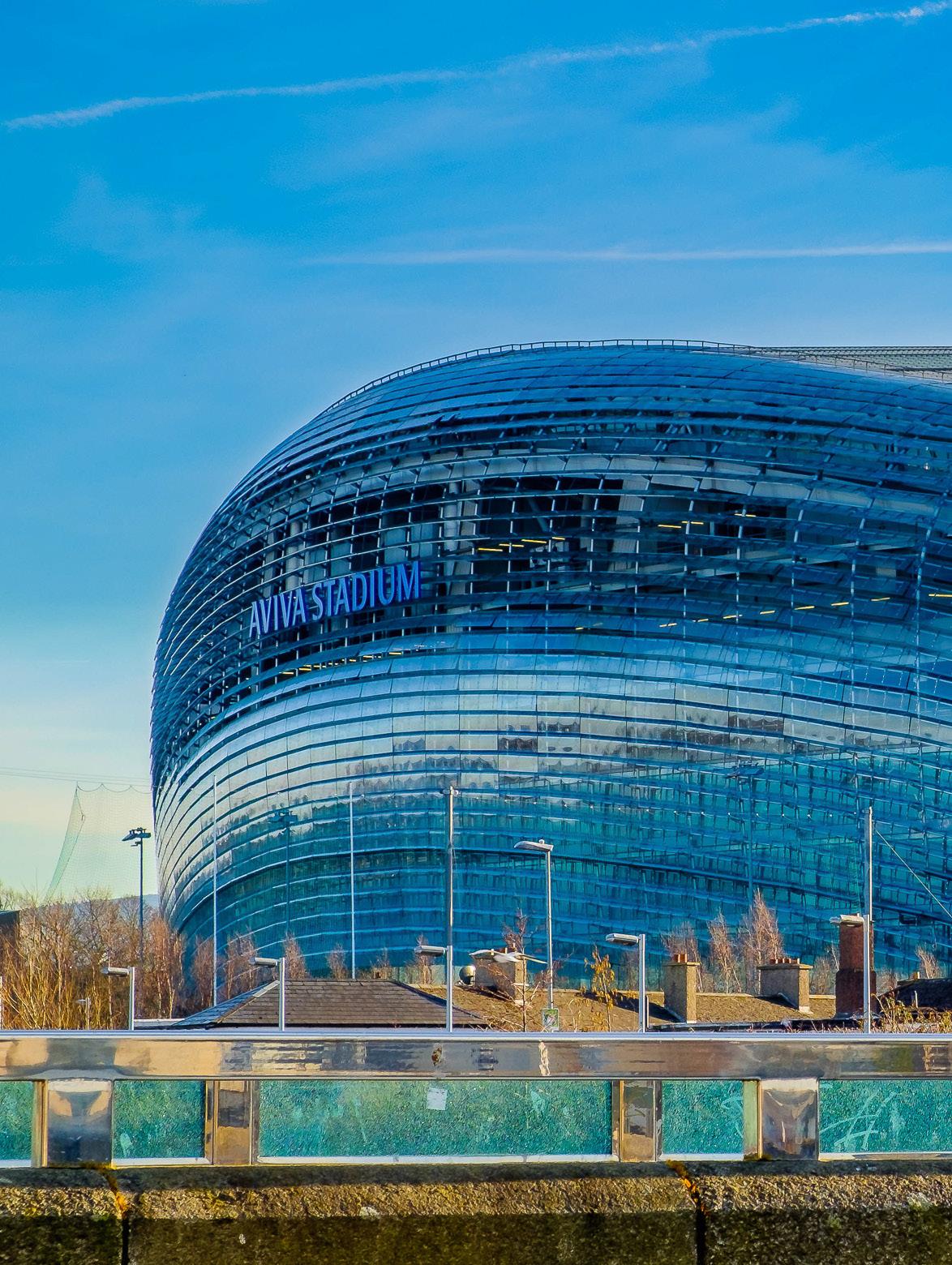
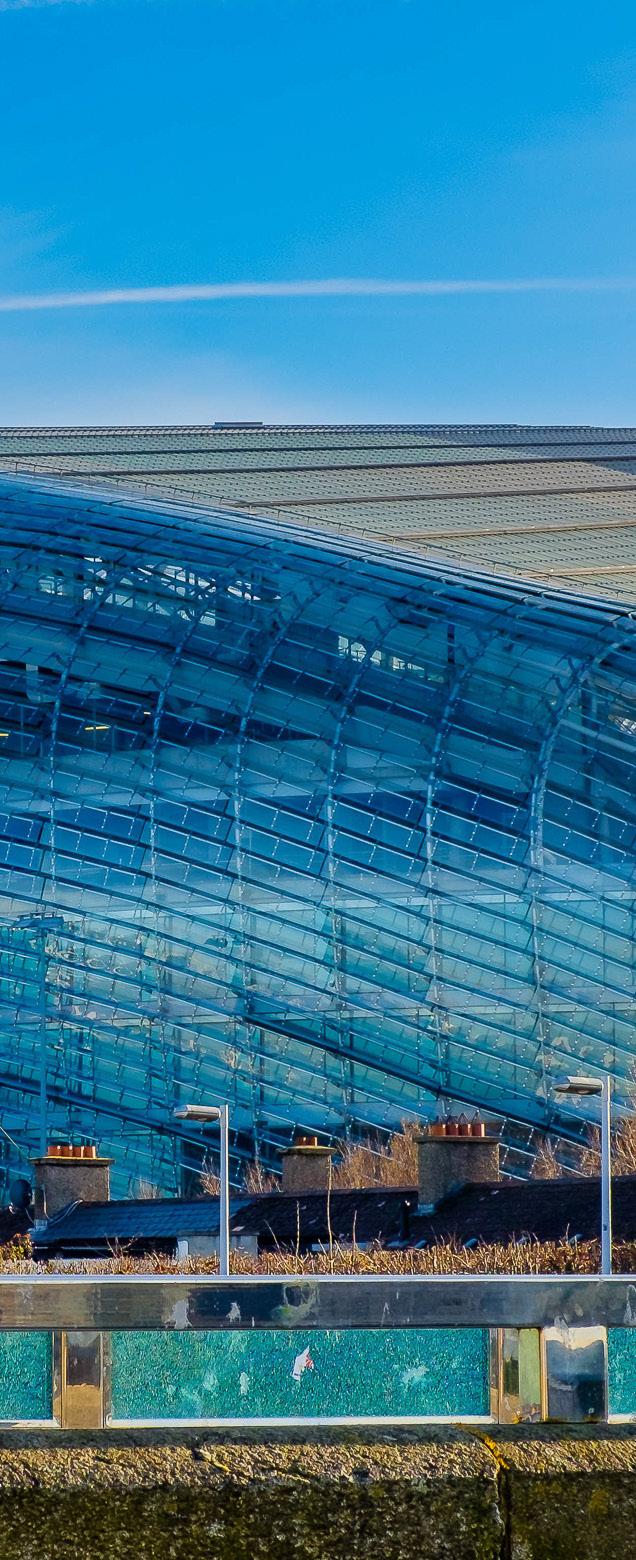
Leading the way across the international manufacturing industry, Palram Industries Ltd. has established itself as a leading producer of semifinished polycarbonate and PVC solutions. With applications across a range of industries, Palram has spent the last 60 years expanding its operations across all aspects of the industry to see its products and service markets across the globe.
Established in Israel in 1963, Palram is an industry leader and multinational conglomerate that provides a vast array of polycarbonate and PVC applications across a range of market segments. Palram’s operations span international audiences through its nine production sites and dozens of worldwide sales and distribution offices, which together provide its customers across the globe with unrivalled support throughout every aspect of their polycarbonate and PVC solution needs. Palram’s portfolio is vast offering a large range of products across the DIY, construction, architectural projects, advertising, agricultural glazing, and fabrication industries. Palram offers a wide range of PVC, polycarbonate, and acrylic sheets, as well as a range of panel systems solutions suitable for every need from manufacturers to professionals and even to “do-it-yourself” individuals.
Solutions provided by Palram include PVC and polycarbonate windows and wall claddings, skylights for commercial buildings, warehouses, greenhouses, impact-resistant and bulletproof material for security forces banks, industrial machinery, hygienic wall claddings, as well as outdoor and indoor signage. Palram’s product offerings are vast, but this is because the company is committed to ensuring that every customer’s unique needs are constantly met and exceeded.
Therefore, in choosing Palram, you can be sure you are choosing a company that fosters innovations throughout its manufacturing and solution facilitations as it continues to deliver excellence across the global marketplace whilst through its offices, providing professional support and service to its customers on a local and regional level.
Products under Palram include corrugated sheets, flat sheets, multiwall sheets, and panel systems, as well as a range of ready-to-assemble solutions for outdoor structures – including greenhouses, carports, patio covers, door awnings, garden sheds and chalets. Furthermore, Palram provides a range of commercial and residential solutions that exemplify their vast product line. Commercial uses are seen throughout construction and architecture, agriculture, signs and displays, safety and security, industrial fabrication as well as home and outdoor living purposes. However, what is crucial about every single one of Palram’s solutions,
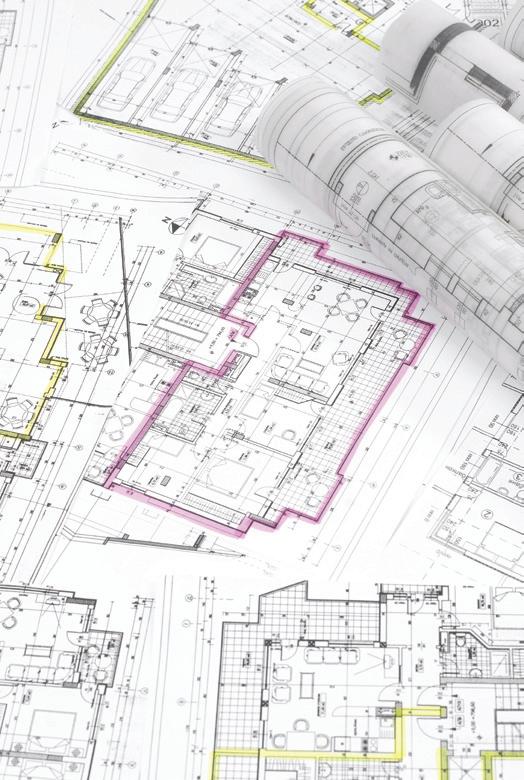
products or services is that innovations are a key driving force, especially in terms of technology.

Consequently, Palram is committed to always being at the forefront of technology. Palram is aware of the challenges that come with manufacturing and often needs fast or adjustable solutions to meet a range of circumstances that each project’s environment might subject to installation and longevity of products. Therefore, through Palram’s implementation of technology throughout its operations, it can identify customers’ needs and communicate with them to come up with the most effective and affordable solutions for its clients. These technologies include Palram Metal Match PC Profile Technology™ which provides fast, economical custom-matching for any metal corrugations. Palram also has SolarSmart™ which controls the light transmittance, indoor heat, and radiation of its products, as well as HYG Technology™ which is used as an active antimicrobial protection across its applications.
Additionally, a crucial technology for Palram is Palram BioBase™ which is part of the company’s
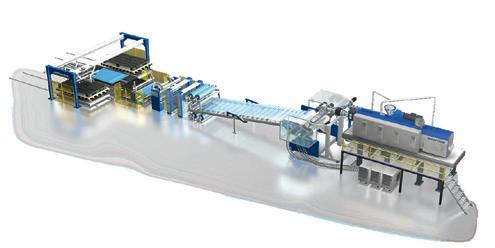
Visions become true.
sustainability initiative to produce plastics that are derived from renewable resources. All of these solutions are often used in large-scale projects that require unique solutions to address the specific needs of every project’s design requirement, engineering constraints, as well as logistical issues. Therefore, we can see that throughout Palram’s service offers and manufacturing options, they have produced a range of products and services that are designed to ensure customer satisfaction and show the leading role that Palram plays across the polycarbonate and PVC industry.
Furthermore, a crucial step of Palram’s operations is working towards a more sustainable future. As a manufacturer of plastic-based solutions, Palram has been working to find solutions that develop both the company and the industry towards a greener, cleaner world for future generations.
Therefore, Palram is a committed member of VinylPlus, a voluntary sustainable development
program that is part of the European PVC industry. Members of this program guarantee that its products are recyclable and maintain a green production process. Additionally, it ensures that all PVC products are produced using regrind vinyl, all in an effort towards a path of carbon-plastic neutrality across the industry.
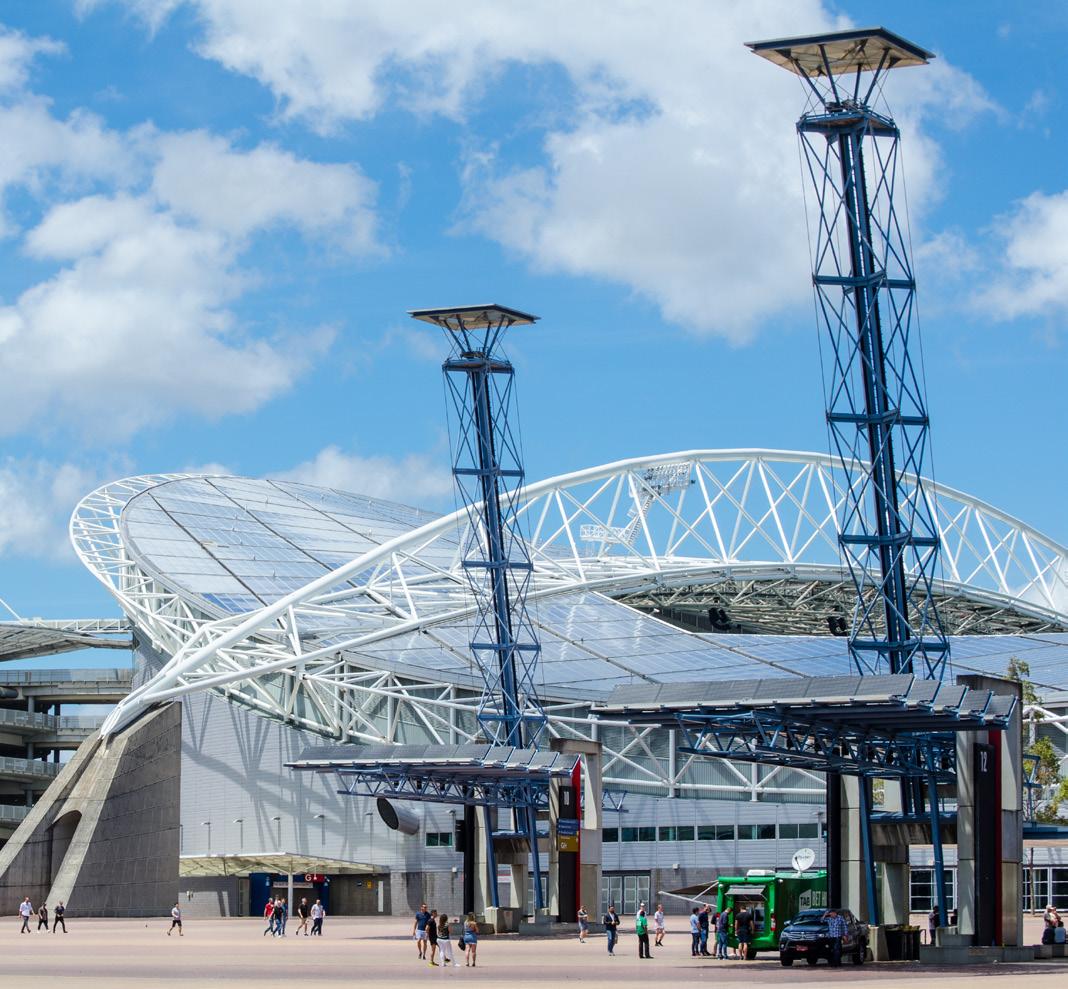
It is working to reduce waste through closedloop manufacturing, as the production of its plastic sheet plants operate with an internal recycling process where scraps and ground-up and repurposed plastics are reused. Therefore, its manufacturing process produces less than 1% waste, and recycles more than 13,000 tons of polycarbonate and PVC every year.
Additionally, it produces climate-friendly thermoplastic sheets – which are constructed by replacing fossil fuel-based materials with biobased feedstock which moves the company’s whole manufacturing process towards a greener future. The production process of durable end-products on recycled materials contributes to the efficient use of resources and increases the material value in a world that is constantly looking for new ways to be more sustainable.
In a further movement towards sustainability across the industry, Palram has continued to produce innovative materials including thermoplastic sheets to become more climatefriendly, whilst also implementing energy-efficient daylight building products that comply with green building regulations. Consequently, as part of its commitment to environmental and energy
sustainability, Palram ensures that it complies with international standards and regulations across the entire company. Overall, by contributing toward facilitating more sustainable practices and solutions for buildings on a global scale using sustainable resources, it plays a crucial role in the construction of energy-efficient buildings which are building the future for sustainability within the construction industry.

Palram is such a giant company that is exemplifying how focusing on sustainability whilst providing essential solutions to meet its customer’s need is possible, especially as the demand for polycarbonate and PVC use across industries is increasing. Therefore, the company serves as a crucial single resource for polycarbonate, PVC and acrylic sheets in all their forms across the industry, which has only expanded over the last 60 years to place them as a key player across vast industries from its humble beginnings in Israel. Consequently, Palram Industries Ltd. now leads the way in providing innovative PVC and polycarbonate solutions that are made to stand the test of time by a manufacturer that seeks to find a perfect solution to every customer’s need.
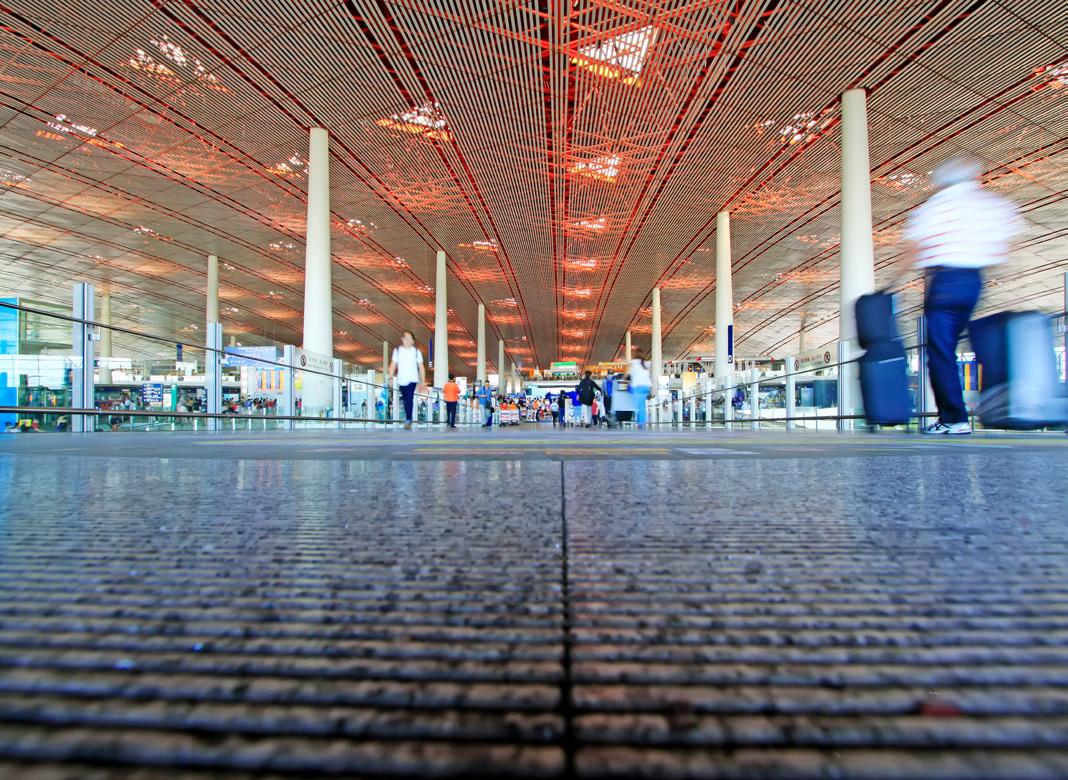
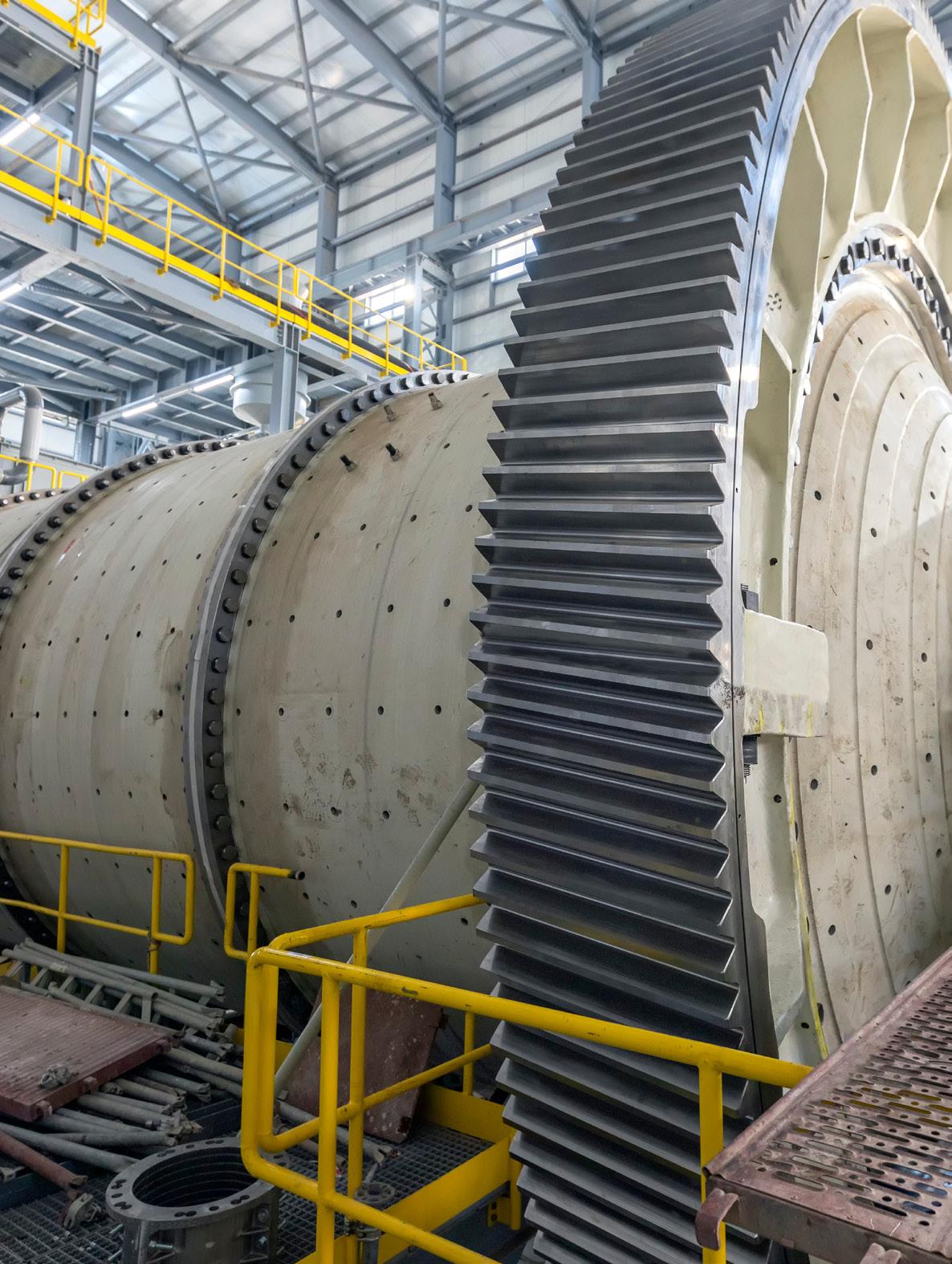
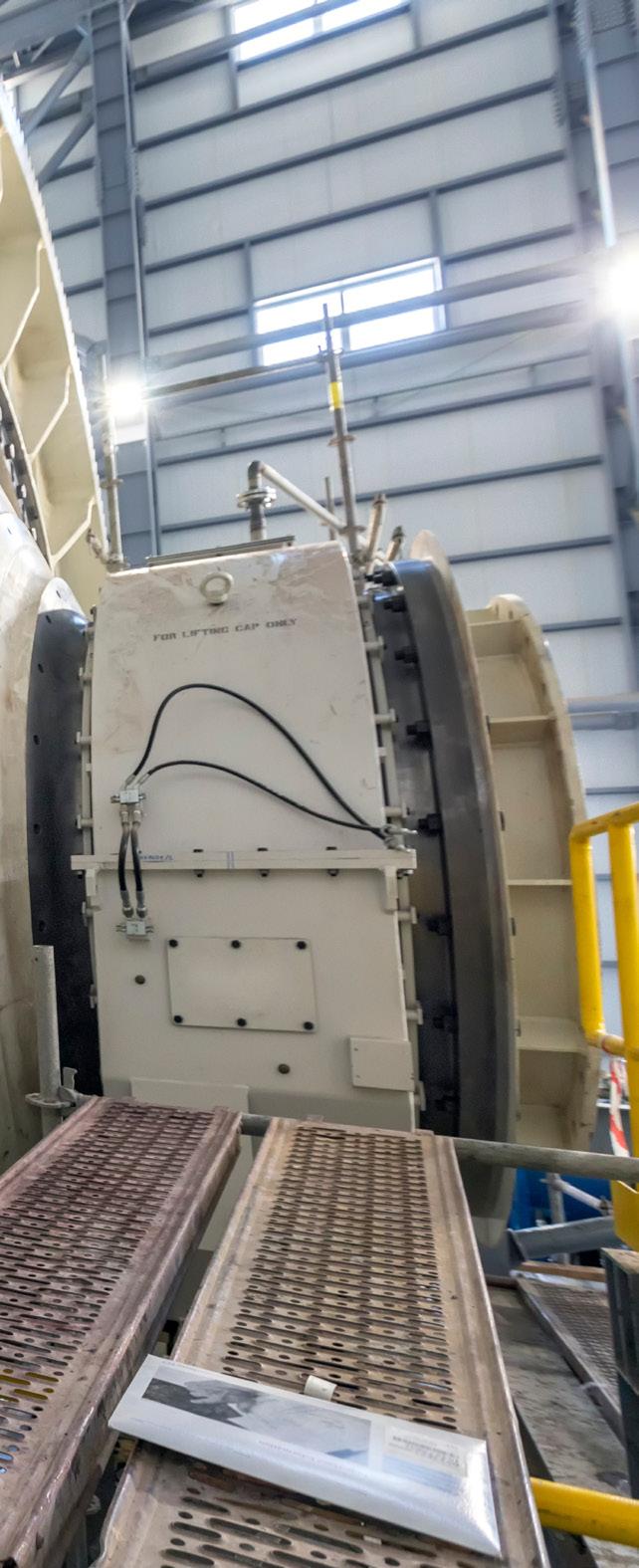
Having built a strong reputation for its outstanding service, industry knowledge and trusted supply, Molycop has established itself as a market leader in the manufacturing and supply of grinding media, mining chemicals and rail consumables. Known for producing high-quality products with maximum durability, designed to resist wear and deliver exceptional performance to mining assets, Molycop serves a diverse range of businesses which are direct suppliers to mining companies and manufacturing suppliers in the mining industry. Having expanded its operations since 1917, Molycop today serves the increasing demand being generated by a diverse range of mining consumables products and associated services that will shape the future of the mining industry for generations to come.
With 12 grinding media operations located strategically across the global mining industry, Molycop works across copper, gold, and iron ore sectors throughout Chile, Peru, Mexico, USA, Canada, Indonesia, Spain and Australia. The overarching company started in 1917, with The Commonwealth Steel Company (Comsteel), which established its original facility on the Waratah Site in Newcastle, Australia. On this site, Molycop first pioneered the Electric Arc Furnace (EAF) steelmaking with the installations marking the first EAF in the southern hemisphere. From here the company expanded from manufacturing parts for the rail industry, including wheels, axles, etc., to shells and other munitions during the Second World War. By 1960, Molycop had built its first grinding ball operation outside of the USA, in Chile with its owner Armco. It was from this point that the company began to grow exponentially, and saw it open grinding plants all across the globe over the next 40 years.
Molycop has seen a range of different ownerships across its operation time, which have all worked to establish Molycop as a respected brand for industry-leading products made available through its unique international footprint. However, the company is now setting up for the future and plans to expand its current capacities to facilitate the growing demand being generated by a diverse range of mining operations worldwide. Therefore, Molycop is working towards facilitating the future of innovative mining consumables products and the associated services that will shape the mining industry toward improvement for many generations to come.
Molycop provides SAG milling, with a product range which has been specifically designed to meet today’s high-impact SAG million environments. These products are built with innovation in mind throughout the manufacturing process and so the resulting products are built with high-impact resistance and superior wear. They also produce Ball and Rod milling, which is designed for maximum grind abrasion resistance using high carbon content and high hardness levels. Therefore, the Molycop Ball Milling range is manufactured to deliver its internationally recognised outstanding performance across the globe. Furthermore,

Molycop manufactures and distributes a wide range of flotation chemicals and related auxiliary products that can be individually tailored to suit your requirements and maximise your recovery.
In terms of service, Molycop provides topnotch technical experience, software, service, and support across its operations, to bring customers personalised services suitable for both start-up and established mining operations. Therefore, with Molycop they are determined to be a leading provider and manufacturer for its customer’s projects throughout their operations from beginning to well-established mining operations. Included in this is Molycop Tools, a software that incorporates a full set of digital simulators to help engineers characterize and evaluate the operating efficiency of any given grinding circuit following Molycop’s software standardized evaluation criteria.
Furthermore, Molycop facilitates a range of Comsteel product ranges including forged and rolled railway wheels, forged railway axles and fully assembled wheelsets for all classes of the international rail and heavy haul industry. Finally, it
also offers a range of Ball and Rod milling products included in its range of Cast High Chrome grinding media. These are suitable for a wide range of sizes and chrome levels that can be adjusted to fit the customer’s specific needs and particularly have been designed for fine and dry grinding applications which can perform in a wide range of milling environments and applications.
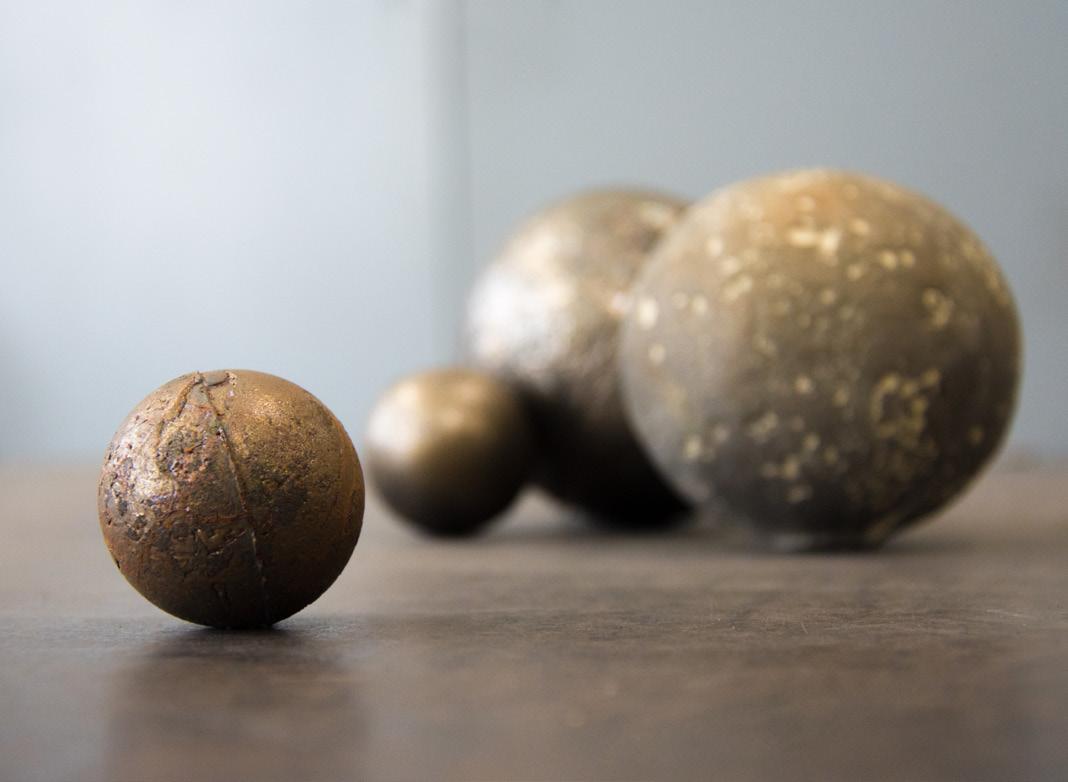
Consequently, Molycop has established itself as one of the largest and most experienced suppliers of mining consumables and associated services worldwide. The thing that Molycop is most known for is its industry-leading standard, which is recognised across the industry for providing innovative products and services that work for you. This is why Molycop believes that innovation is in its DNA, as it continues to focus on the future and how its operations can be improved whilst maintaining a commitment to meeting a greater output never stops increasing.
Part of this commitment to innovation was seen late last year with Molycop expanding its digital solutions and process optimization
capabilities with the introduction of its Process IQ acquisition. The Process IQ technology is a leading mining technology provider of proprietary data analytics and visualisation, instrumentation, and advanced process control solutions. It marks an important step in Molycops digital transformation, to complement its existing MillSlicer technology platform and expands its product and service capabilities across leaching, milling (comminution) and flotation.
Process IQ has a reputation for being a trusted technology partner of metallurgists and miner processing engineers. It has specialised in bringing technology to its full potential for its mineral processing customers, by combining specialist instrumentation with advanced process control, data analytics and visualisation.
Therefore, Molycop with Process IQ helps to build solutions that deliver step-change improvements for its customers, and so has established a strong market presence and reputation for delivering topquality differentiated technology offerings focused
MITSUBISHI FORKLIFTS
• Australian Exclusive Supplier
• Comprehensive National Coverage
• Products include: Rental, Sales, Service, Parts

on improving customer throughput, recovery, and efficiency.
Overall, Molycop is a global company that is seeking to develop the manufacturing and supply of grinding media, mining chemicals and rail consumables using innovative design and forwardthinking technology to lead the industry towards continuous expansive success. By manufacturing and supplying products with a reputation for durability, Molycop products are a favourite across the industry, as they are designed throughout their manufacturing for continued deliverance of highquality results. Therefore, Molycop provides valuable assurance of high-quality mining consumables accompanied by on-time, flexible supply, and personalised technical support to lead the industry towards a future of continued success.
• An Extensive Range of Material Handling Solutions
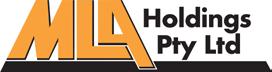
The core business of Mitsubishi Lift trucks Australia, MLA, is the sale, hire and service support of materials handling equipment. We are the exclusive Australian distributor of three complementary brands – Mitsubishi Forklift Trucks, Nichiyu Electric Forklifts and MLA Vulcan Equipment.
www.mlaholdings.com.au
We operate our business nationally through seven MLA owned branches and an extensive regional authorised dealer network.
MLA is widely regarded as a leader in a competitive market thanks to our strong focus on customer needs, and ongoing commitment to delivering quality, cost-effective materials handling solutions. Our customers know their requirements will be satisfied through our comprehensive equipment range – from the largest Container Handlers and Reach Stackers, to every type and size of industrial forklift or warehousing piece of equipment.
Through more than four decades, MLA has built a reputation for excellence in customer service, safety, operational reliability, engineering and equipment maintenance.
Tough Smart Green
MITSUBISHI FORKLIFTS
MITSUBISHI FORKLIFTS
MITSUBISHI FORKLIFTS
MITSUBISHI FORKLIFTS
www.mlaholdings.com.au
WHEN RELIABILITY IS EVERYTHING...
WHEN RELIABILITY IS EVERYTHING...
WHEN RELIABILITY IS EVERYTHING...
www.mlaholdings.com.au
WHEN RELIABILITY IS EVERYTHING...
• Australian Exclusive Supplier
• Australian Exclusive Supplier
• Australian Exclusive Supplier
• Australian Exclusive Supplier
• Comprehensive National Coverage
• Comprehensive National Coverage
• Comprehensive National Coverage
• Comprehensive National Coverage
• Products include:

• Products include: Rental, Sales, Service, Parts
Rental, Sales, Service, Parts

• Products include: Rental, Sales, Service, Parts
• Products include: Rental, Sales, Service, Parts
MITSUBISHI FORKLIFTS
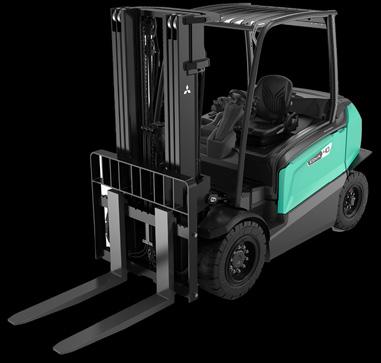
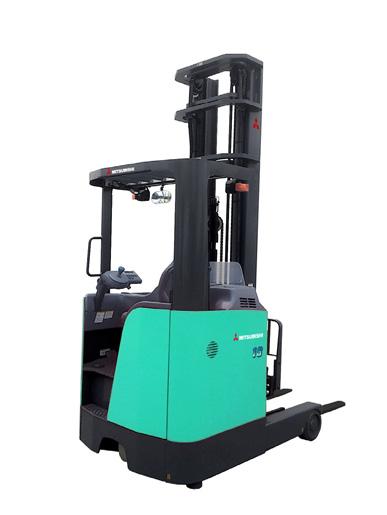
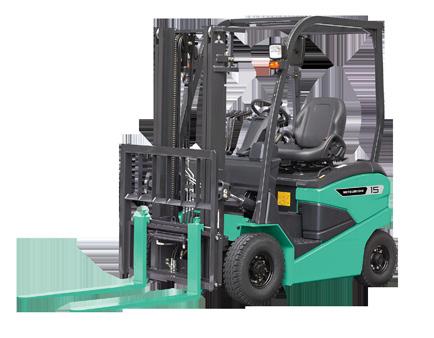


• An Extensive Range of Material Handling Solutions
• An Extensive Range of Material Handling Solutions
• An Extensive Range of Material Handling Solutions
• An Extensive Range of Material Handling Solutions
• Australian Exclusive Supplier
• Renewed Long Term Supply Partnership with Molycop in 2022
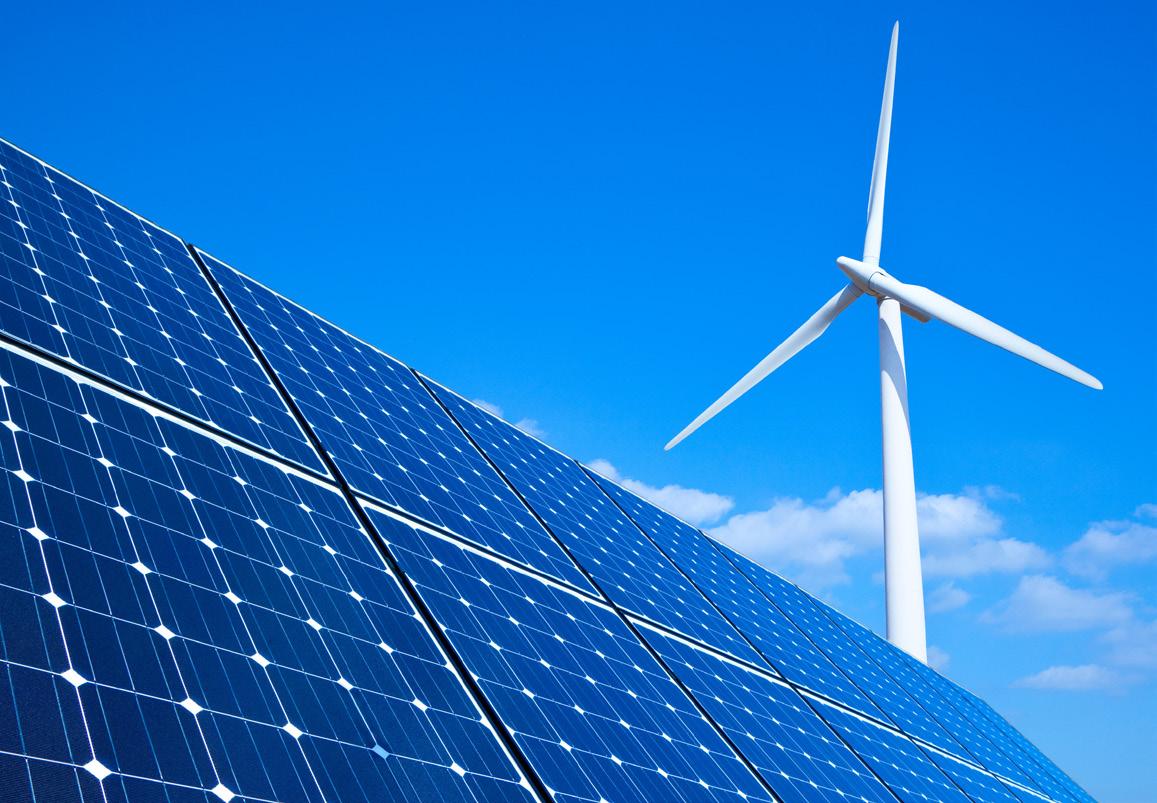
www.mlaholdings.com.au
www.mlaholdings.com.au
• Comprehensive National Coverage
www.mlaholdings.com.au
• Products include: Rental, Sales, Service, Parts



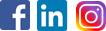






• An Extensive Range of Material Handling Solutions
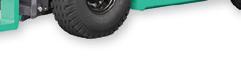
www.mlaholdings.com.au
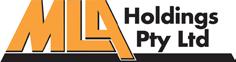
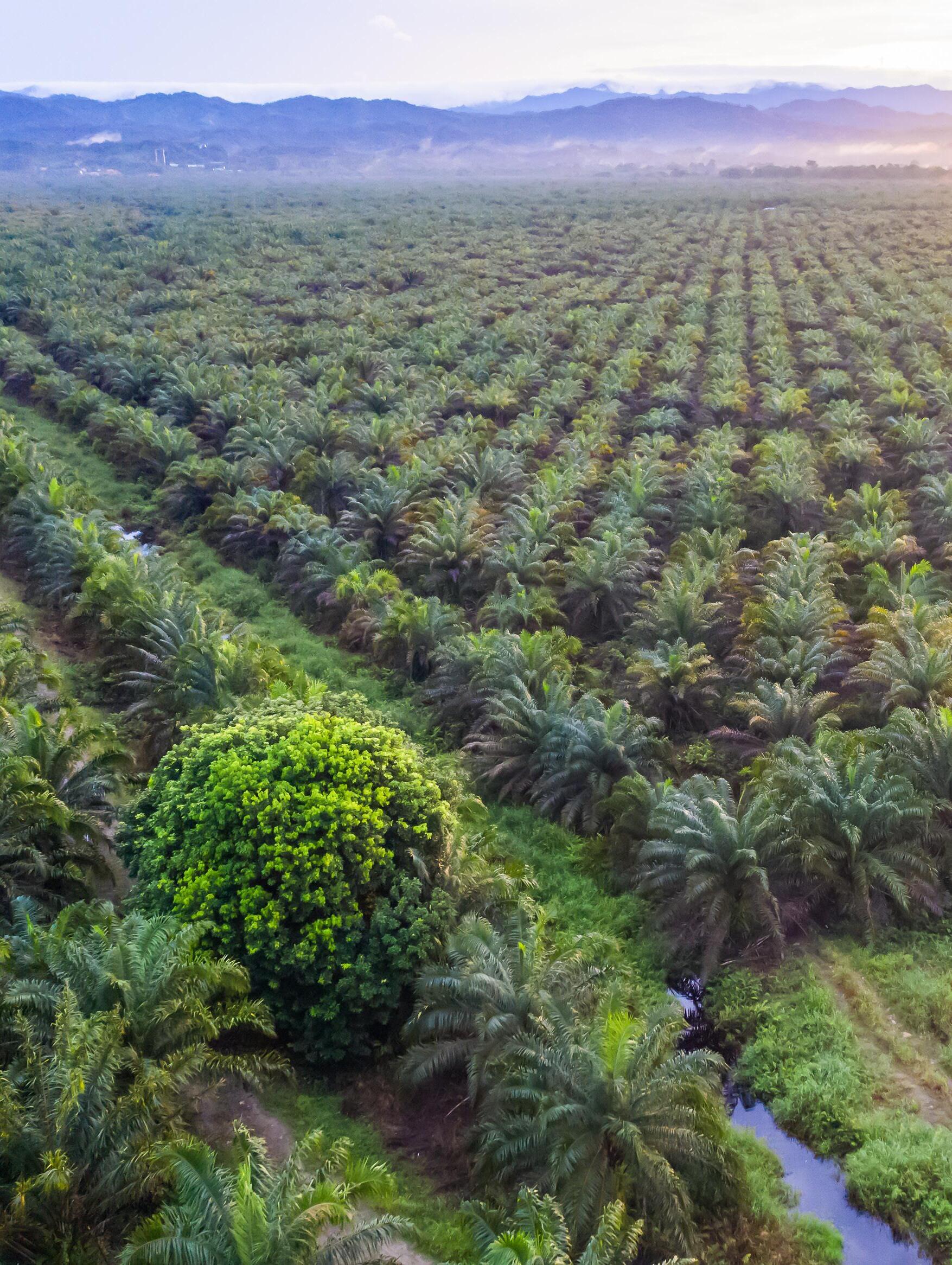
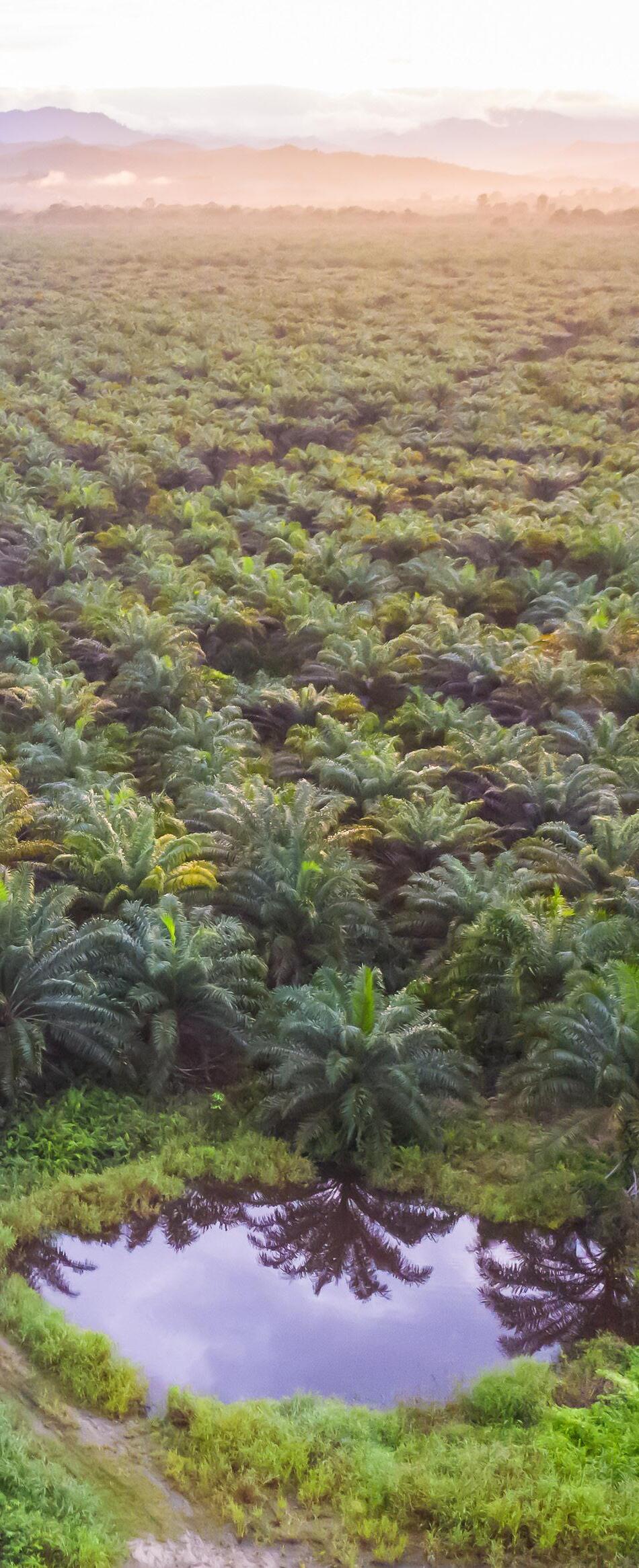
As a leading agribusiness group across Asia, Wilmar International Limited’s span of the industry is vast and diverse. Working across the entire supply chain of the agricultural commodity business, it deals with the cultivation of oil palm, oil seed crushing, edible oils refining, sugar milling, sugar refining, and the manufacturing of consumer products. Wilmar’s business operations span from cultivation and milling, all the way to the branding, processing, and distribution of food products to international markets. Consequently, as a leading agri-business, the company has positioned itself to facilitate a range of markets, whilst it develops the company through key investments and acquisitions across the industry.
Headquartered in Singapore, Wilmar operates 500 manufacturing plants across its extensive distribution network spanning China, India, Indonesia, and some 50 other countries and regions. Having implemented a key strategic agribusiness model that encompasses the entire value chain of the agricultural commodity business, Wilmar oversees every aspect of the supply chain’s operations.
The first stage of the model involves the cultivation and milling of palm oil and sugar cane which is then processed by Wilmar into feed and industrial products. Then the model includes the processing, merchandising and distribution of animal feeds, non-edible palm and lauric products, agricultural commodities, oleochemicals, gas oil and biodiesel. The next stage of Wilmar’s business model takes processed products and delivers them toward trading markets through merchandising and distribution.
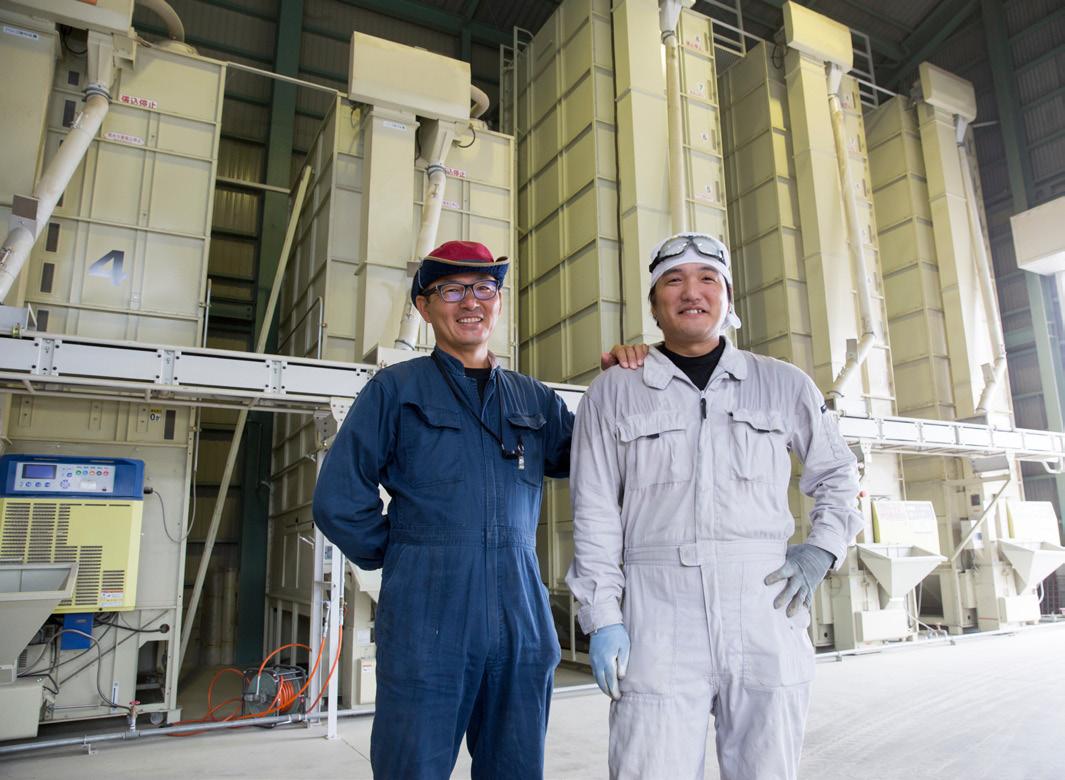
This process includes processing, branding, and distributing a range of edible food products – for example, vegetable oils from palm and oil seeds, sugar, flour, rice, noodles, speciality fats, snacks, bakery, and dairy products. These products are sold in either consumer, medium or bulk packaging options depending on the requirements of the consumer.
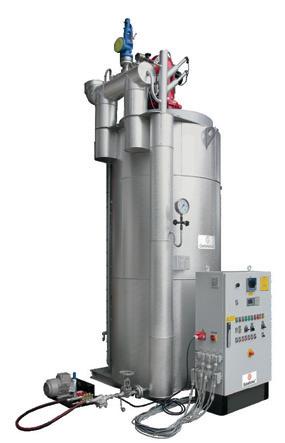
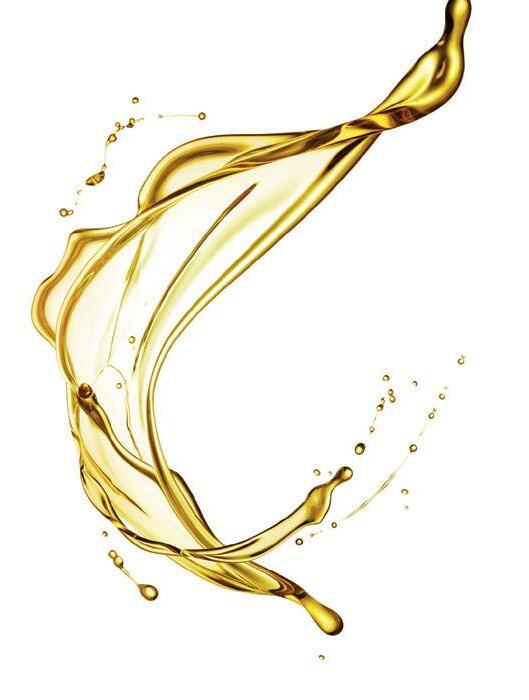
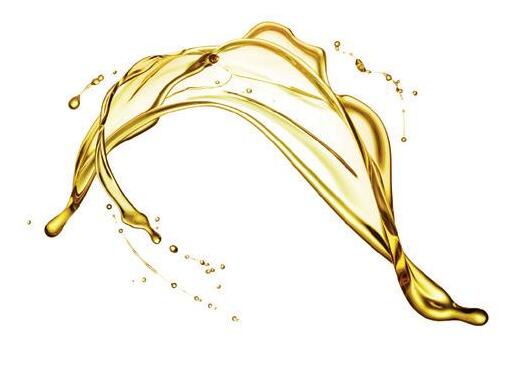
The final step in Wilmar’s all-encompassing operation is logistics to deliver its products to customers. To facilitate the logistical movement of its products, Wilmar owns a fleet of liquid bulk and dry bulk carriers which provide greater flexibility and efficiency of its logistical operations, along with help from a third-party shipping company. Wilmar operations span 38 liquid bulk vessels, 16 dry bulk vessels, 9 ports in Indonesia, 7 ports in China and 1 port in Myanmar. Consequently, as of the end of 2022, Wilmar owned and operated tankers and dry bulk vessels with a combined total tonnage of roughly 2.6 million metric tonnes (MT). As Wilmar’s vertically integrated business model outlines, it has strategically built the company into a leading
A Leading Agri-Business Across Asia
business across the agriculture commodity sector, by working throughout every aspect of its value chain to ensure that not only are the highest standards and regulations followed, but it can maintain a close but diverse network across the agri-business industry.
Consequently, in July we saw Wilmar refiguring its stakes across the sector, which saw them sell their 30% minority interest in Consumar, a Moroccan sugar processor, to be purchased by investors in Morocco. The sale is set to cost Dh5.9 billion ($600 million) and the deal is set to close in the fourth quarter of 2023. Furthermore, in the same press release, Wilmar announced that they are engaged in talks with a Moroccan production and processing business of vegetable fats and byproducts.
This deal is set to cost Dh85 million and would become a wholly owned subsidiary of Wilmar International if the sale is to go through. The sale
would coincide with Wilmar taking a 43.3% interest in Durah Advanced Development by taking Consumar’s stake in the company. Wilmar already owned 5% of Durah Advanced Development, whilst the final 51.7% is held by Investors in Saudia Arabia. Whilst these deals are not expected to be finalised until the end of September, they exemplify the strategic positioning of Wilmar across the industry as it buys and sells shares to expand its global reach.
These potential sales come a month after Wilmar announced its syndicated loan facility which it initially announced in April totalling USD 1,200 million. However, due to strong interest from lenders during syndication, the facility has been upsized to totalling USD 1,700 million to partially accommodate the oversubscription. The facility will comprise of a 5-year revolving credit facility of USD 702.5 million and a 5-year term loan facility of USD 997.5 million. Supported by a total of 37 lenders including all 6 original mandated lead arrangers and bookrunners (OMLAB) and 31 participating lenders. The facility was granted to Wii Ptd Ltd, which is a whollyowned subsidiary of Wilmar.
In 2022 Wilmar saw great achievements with a record of USD 2.40 billion in net profit – a 27.1% increase from the previous financial year – which Wilmar credits to the combined ability to do well by placing
sustainability at the core of its business. For Wilmar, sustainable operations are crucial to creating shared value for its customers, shareholders, and stakeholders. Therefore, it is striving towards a palm oil supply chain that is responsible, sustainable and provides livelihood opportunities for rural communities. Wilmar, therefore, has a strict no deforestation, no peat, and no exploitation policy throughout all its operations internationally. Furthermore, as announced in Wilmar’s 2022 sustainability report, 81% of its plantation areas are responsibly certified and produced 1,654,399 MT of RSPO-certified palm oil and kernels last year. In 2022, Wilmar reported that 89.9% of palm oil and lauric product volumes to its supply chain are from suppliers that have group-level commitments and action plans that address no deforestation. Consequently, throughout its operations, Wilmar is ensuring that every division and subdivision of its operations are working towards a combined goal of sustainable development.
Overall, Wilmar has created expansive networks across the agri-business industry which sees it facilitate every aspect of its supply chains to ensure quality and sustainability measures are maintained throughout. However, through strategic investments and acquisitions, Wilmar has established itself over the years as a clear global leader, which supported by its 100,00 multi-national workforce, focuses on embracing sustainability in its global operations, supply chain and communities across the industry.

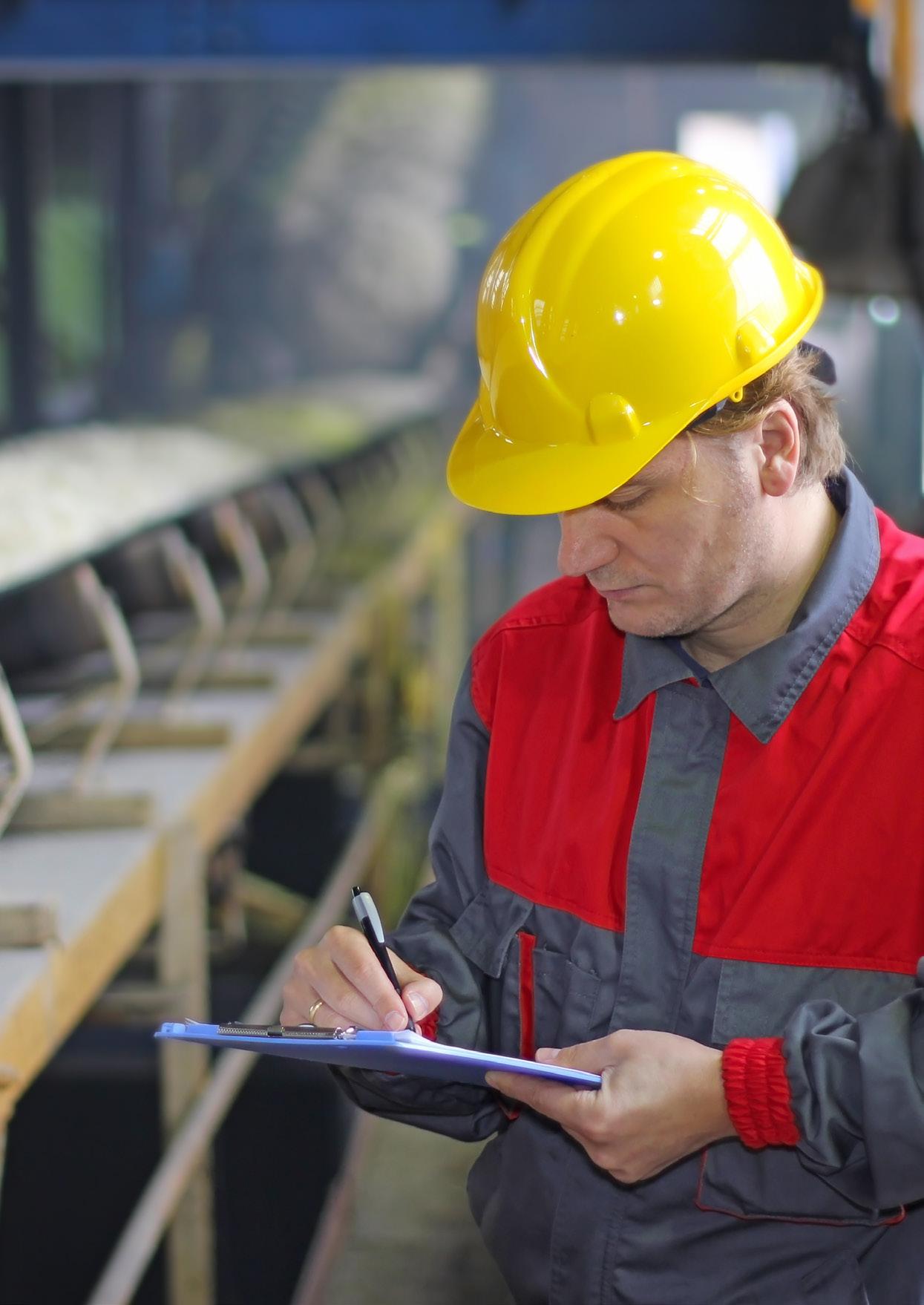
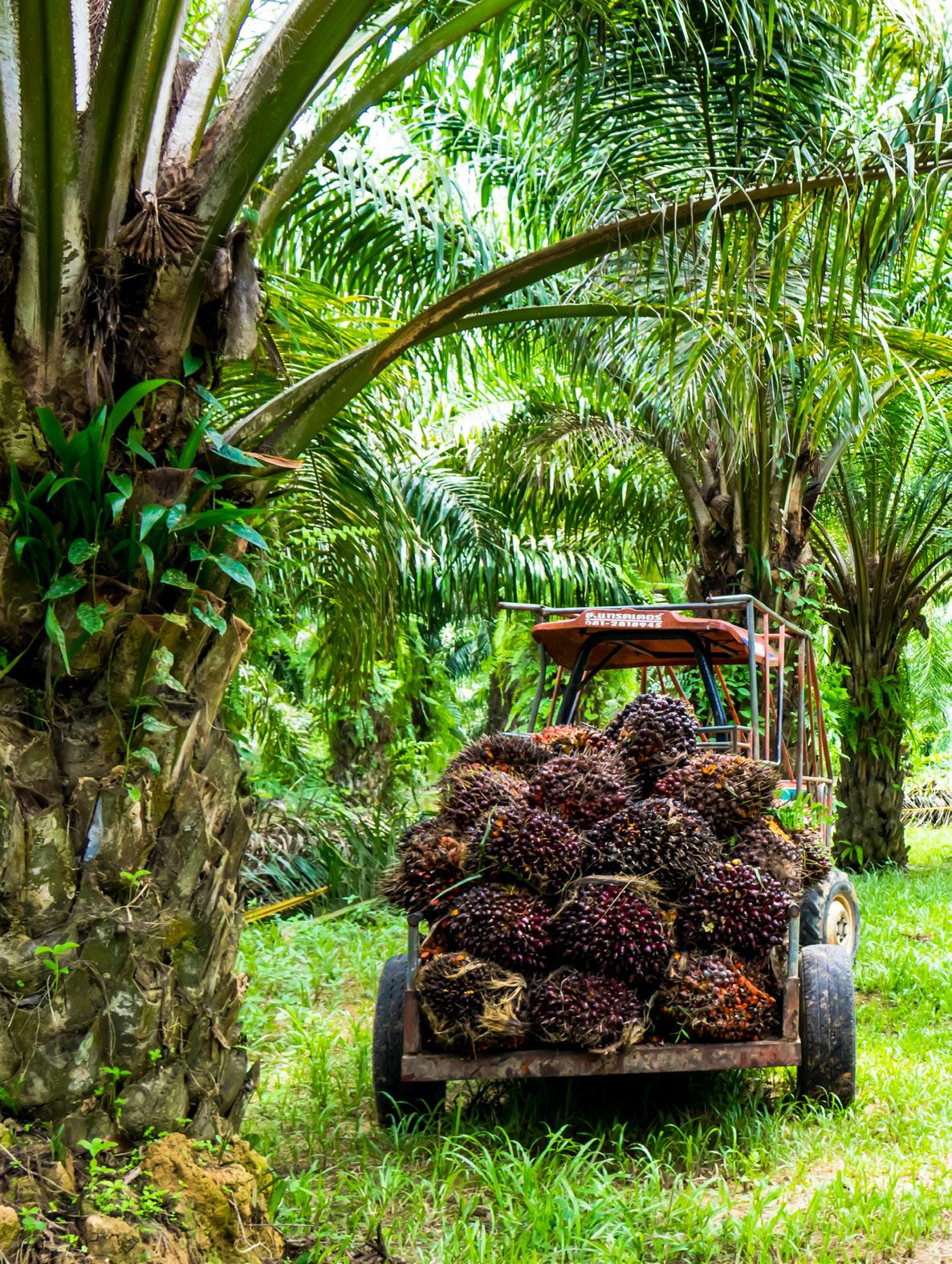
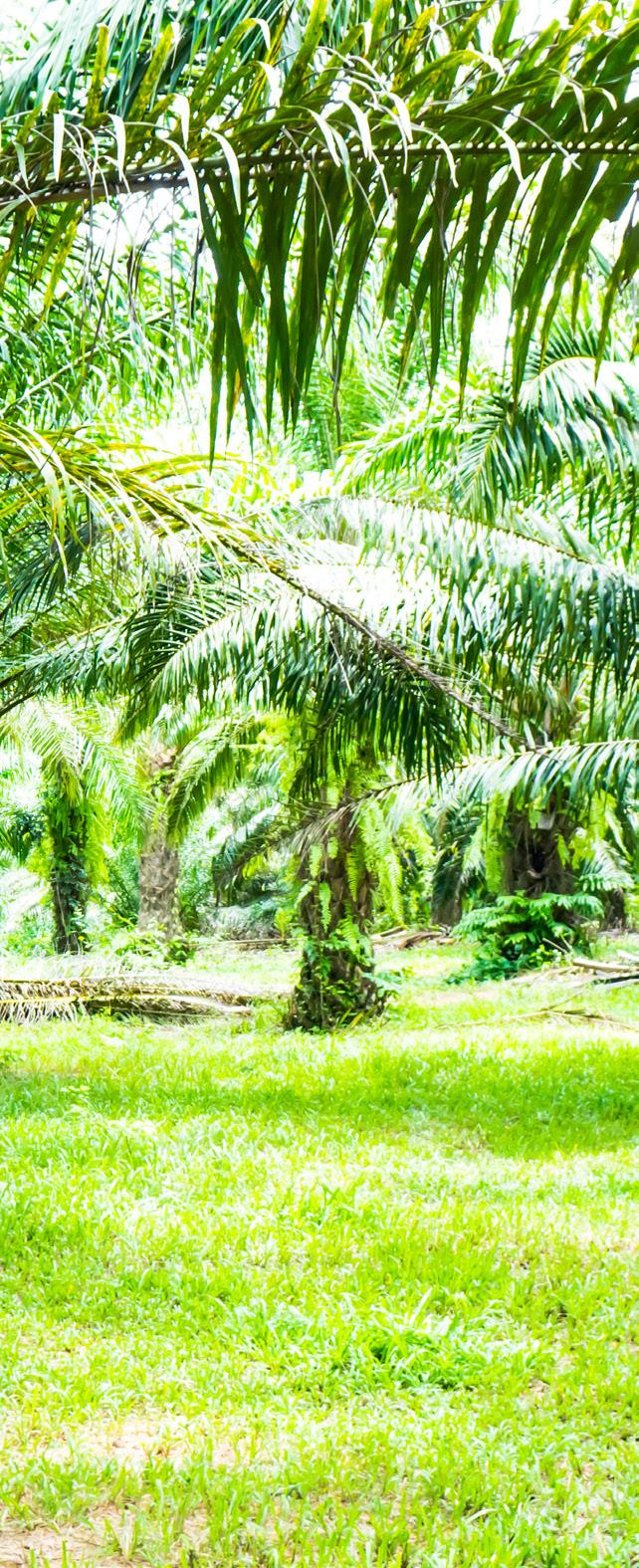
Emerging from Malaysia’s industrial scene in 1975, palm oil evolved into a key industry for the country, which now over 40 years later sees the export of refined and processed palm oil accounting for roughly 90% of Malaysia’s total palm oil production. Prior to the emergence of palm oil refining in Malaysia, only 10% of the country’s crude palm oil was refined in just a handful of factories.
NEW CHALLENGES NEW PERSPECTIVES
Kunak Refinery Sdn Bhd (KRSB) is a wholly owned company of Sawit Kinabalu Sdn Bhd Group, a Sabah State-owned government linked company (GLC).
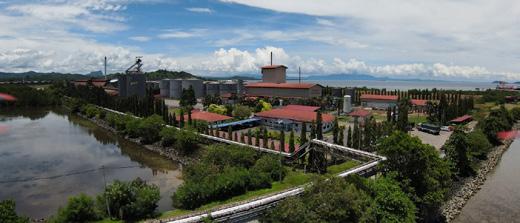
Daily production capacity of 1500 mt for Crude Palm Oil (CPO) refining and 400 mt for Palm Kernel (PK) crushing
+6088-235 811
+6088-247 358
cc@sawitkinabalu.com.my
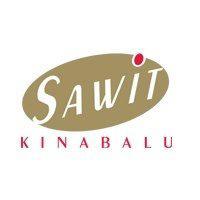
cc.sawitkinabalu@gmail.com
With the rapidly increasing demand for palm and palm kernel oil refining and fractionation today, Malaysia has established itself as not only a leading producer but also as a major marketing force in international oil and fats markets. Consequently, with the development of palm oil refining, the Palm Oil Refiner Association of Malaysia (PORAM) was established to bring stringent observance of quality and capacity to local refiners. The Association, therefore, helps Malaysia to continue to meet the high standard demands of world markets.
PORAM is home to almost all palm and palm kernel oil refiners in Malaysia and works with its members to produce a wide range of processed oil products from fully refined products such as speciality fats and oils. These products can then be shipped across local and international markets to meet global demands for palm oil, whilst establishing Malaysia as a key exporting country for highquality palm oil. With membership open to any company or corporation involved in the processing of palm oil and palm kernel oil, and any activities related to the oils and fats business across Malaysia, PORAM takes on a key governing role across the industry to promote Malaysia’s palm oil refiners towards international recognition.
The key objective of PORAM is to provide an organisation that supports and promotes the interests of palm oil refiners, with the goal that the palm oil refining industry and its products across Malaysia are well established in the global sector. PORAM is working on establishing the industry, and by consequence shows the vital role oil refiners play in developing Malaysia’s economic development. Therefore, through PORAM’s stringent observance of quality control and the capacity of local refineries to meet the ever-increasing demand for palm oil in world markets, it has seen great success across all aspects of the industry due to its breakthroughs into markets that were once dominated by other vegetable oils and fats.
PORAM provides a continual flow of valuable info to its members, to keep them informed on the palm oil trade, whilst working with the government across local and international regulations. Furthermore, PORAM provides guidance to its members across every aspect of the palm oil industry to ensure that
its members have access to key trading markets, and a valuable network of key players across the industry all whilst upholding strict regulations to ensure that Malaysian palm oil is top quality. The trade aspect of PORAM’s operations is crucial as they are working to establish key business contacts to promote its members’ exports by meeting trade delegations and visitors, channelling trade engines to members, organizing trade missions and arranging for members’ participation in government-led missions, making recommendations/proposals to the Government - all aimed at facilitating the export of processed palm oil products from Malaysia and across international markets.
Palm oil and palm kernel oil refineries produce a range of products used in both food and non-food products. These include shortenings, margarine, cooking oils, vanaspati, confectionery or speciality fats. Additionally, palm oil is often incorporated into many food products such as hot beverages, ice cream, coffee creamers, and bakery products. Furthermore, due to the excellent stability of palm oil, it is a first choice for many to fry food. Therefore,
Uniting Malaysia’s Palm Oil Refiners
palm oil is often seen being used to fry instant noodles, french fries, potato crisps, doughnuts, fried meats, and snacks across the globe.
Additionally, a key draw of palm oil is in the production of trans-free products, as approximately 50% of saturated fat and 50% of unsaturated fat make up palm oil. Therefore, this unique characteristic means that these two can be separated using controlled thermal conditions into a solid form (stearin) and a liquid form (olein), which are used to make trans-free products. Stearin is used to form solid fats without the need for hydrogenation making it trans-free, which is why it is often a go-to frying oil.
Non-food uses of palm oil and palm kernel oil include soaps, biofuels, candles, cosmetic products, rubber, processing, lubricants, printing ink, and the washing and cleaning of raw materials. Therefore, the use of palm oil is vast across several industries from food and beverage all the way to
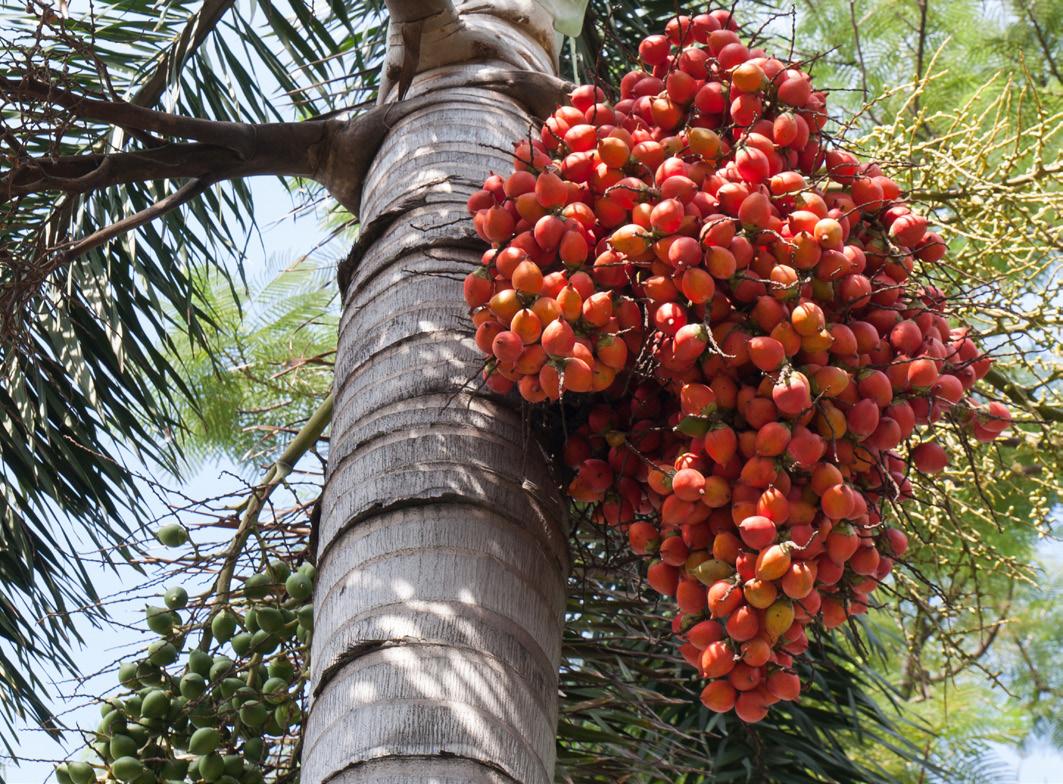
Palm Oil Refiners Association of Malaysia
construction and cleaning products. Consequently, the role that palm oil plays in the daily lives of many of us is clear, and so PORAM has established its association to highlight and promote the role that oil refineries play in such expansive markets, and so its role as a major contributor to the economic development of the country.
PORAM works alongside many key players across Malaysia’s palm oil industry, including the Malaysian Palm Oil Association (MPOA), Malayan Edible Oil Manufacturers Association (MEOMA), and the Federation of Oils, Seeds and Fats Association (FOSFA International). Collectively these organisations have implemented contracts that are recognized worldwide as trading rules and standards for the trade of palm oil and palm kernel oil across the global industry.
The implementation of these rules ensures that all palm oil purchased from Malaysia is guaranteed to be of high quality and from reputable sources that PORAM and its fellow companies are working to unite. By uniting the industry, these companies and
associations can all work as a cohesive movement to develop the use of Malaysian palm oil across the globe to serve even more diverse markets.
Overall, PORAM is providing unrivalled support to enhance and unite the status of palm oil refining industries across Malaysia. As we have seen here palm oil plays such a crucial role in a number of industries across the globe, and therefore the regulation and standardisation of operations across palm oil refineries is essential to be able to meet the growing demand for this type of oil globally. Consequently, by establishing the role of palm oil refineries in Malaysia, PORAM is bringing much-needed attention and recognition from government agencies on the vital role they play in fuelling the Malaysian economy.
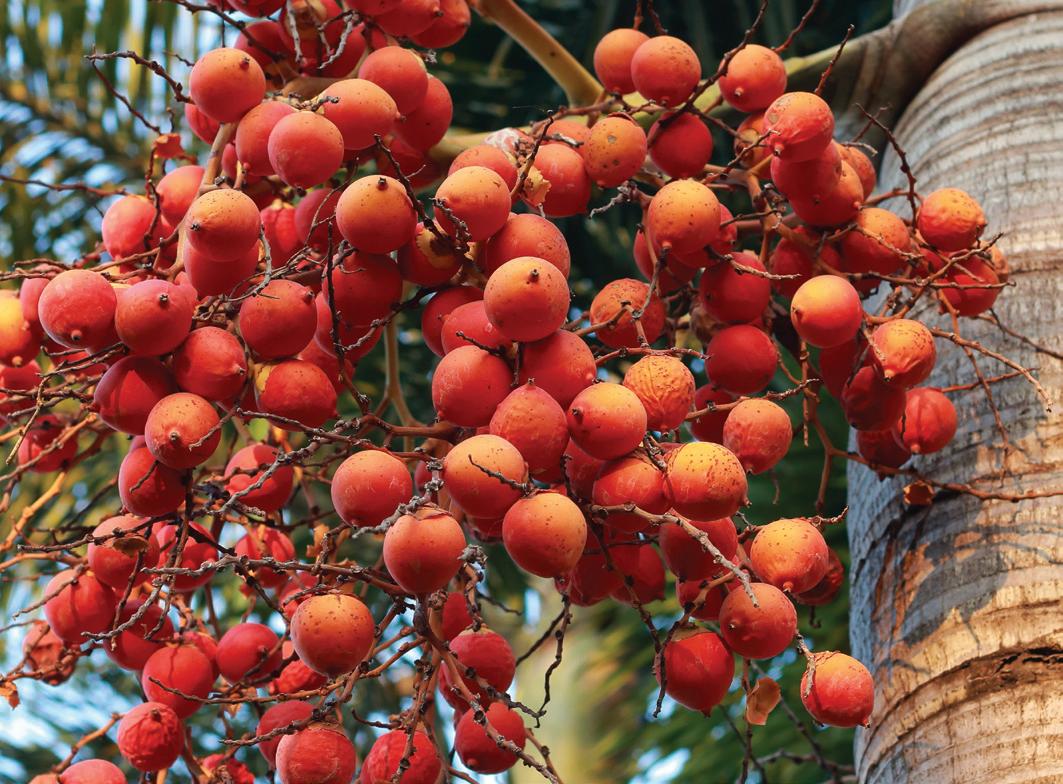

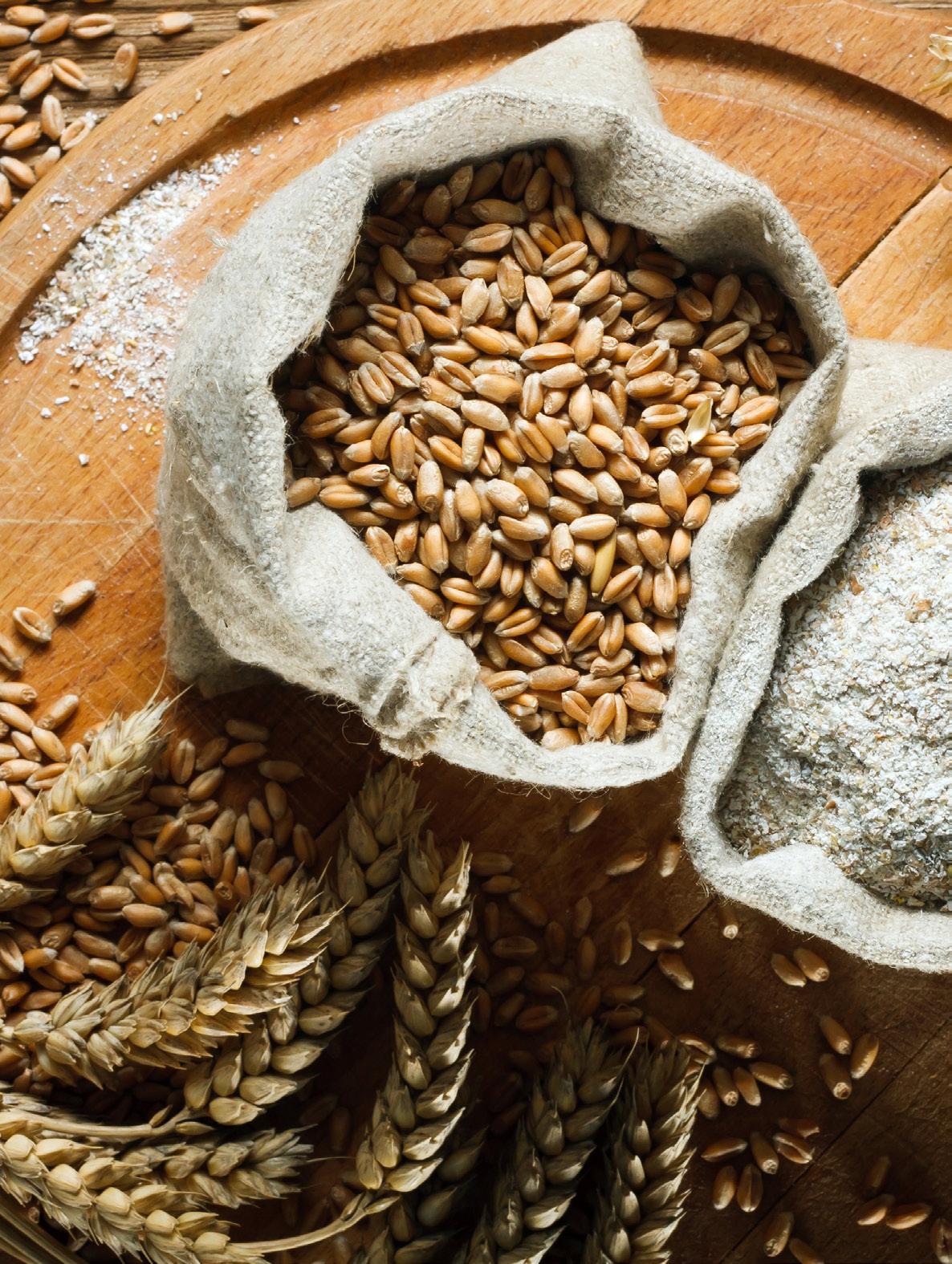

As a provider of exceptional quality flour and plant-based ingredients, Bay State Milling has developed its network of suppliers to facilitate every step of the process from grain to end packaged products. Supplying their high-quality ingredients to retail and wholesale bakeries, food service operators, distributors and food manufacturers, Bay State Milling has a wide reach across the industry in the United States with an expansive and reliable nationwide distribution network. However, the basis of Bay State Milling’s operations is family, as it has been passed down over the last 175 years through five generations of one family, who have remained committed to providing access to healthy, delicious, responsibly sourced and produced food ingredients.
Established in 1899, Bay State Milling started as a company that predominantly milled wheat flour for bread and snacks. However, over the years the way people eat has changed; not only are allergens such as gluten catered for in a more diverse way, but people are more conscious of the ingredients used in products for health reasons. Therefore, Bay State Milling has adapted over the years to diversify its product offerings in line with consumer demands. Now they produce wheat and rye flour, oats, seeds, spices, and unique varietals all with varying options including gluten-free, high protein or high-fibre diets. As the food system and the way we eat continues to change, Bay State Milling is prepared to evolve to always stay ahead of its customers’ needs to provide a variety of options, which taste great and are affordable. All whilst maintaining the trust that the company has built with customers and across its supply chains for generations.
For Bay State Milling a trusted and reliable supply chain is crucial, as the company works across every aspect of their ingredients’ lives from seed to end products. All products are responsibly sourced from its dedicated supplier and grower partners, which are expertly processed and milled to meet the exact specifications for its product uses. Consequently, the company has an expansive network of research and development teams, commercial teams, as well as state-of-the-art milling and production facilities across North America and Canada.
Bay State Milling has strategically placed its milling and production facilities across North America to ensure that it minimises freight costs to deliver competitive ingredients that seamlessly integrate into its customers’ operations. Bay State Milling operations have therefore perfectly positioned themselves to supply expansive markets geographically, whilst also ensuring that the products it does supply are constantly evolving with consumer needs.
A key focus for Bay State Milling is innovation, as the company has established a dedicated team of food and cereal scientists, culinary experts, nutritionists, and sensory experts to ensure its products are always high in quality. These teams are working to improve the quality of all ingredients produced and milled across the company’s network.
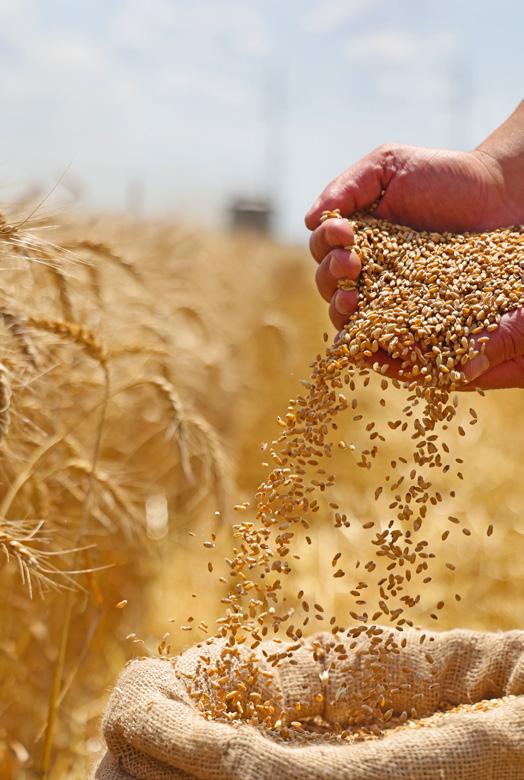
The Bolivian Reference in the Production and Export of Chia Seeds
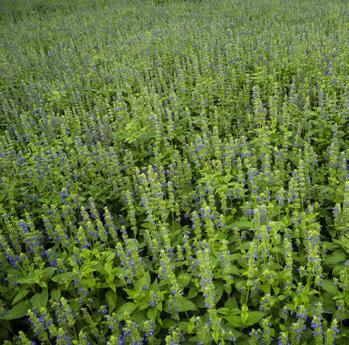
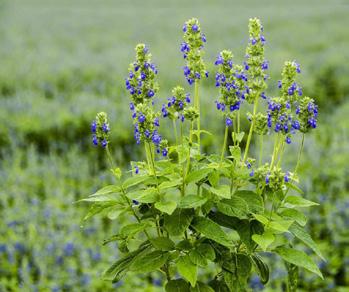
and Other Non-Conventional Products
Semear Group is a family farming production company of 3 generations that is totally involved with the delivery of the best quality products. Our experience is focused on Chia and Quinoa.
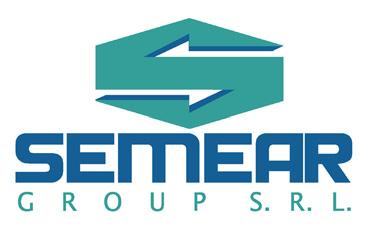
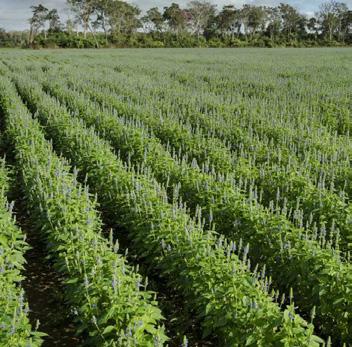
We are a company with a lot of experience in the international market. Located in Santa Cruz de la Sierra, Bolivia economic and industrial center of the country. Our production has a strict quality control plan in all its stages, from sowing to the time of export. Semear sows, harvests, processes and exports organic chia seeds of the highest quality to the world.
Our mission is to produce food in strict compliance with the quality standards agreed with the client in the committed deadlines, but also in a responsible way with the Society and the Environment, watching over the conditions of our collaborators, assuring sustainable markets for our associated products.
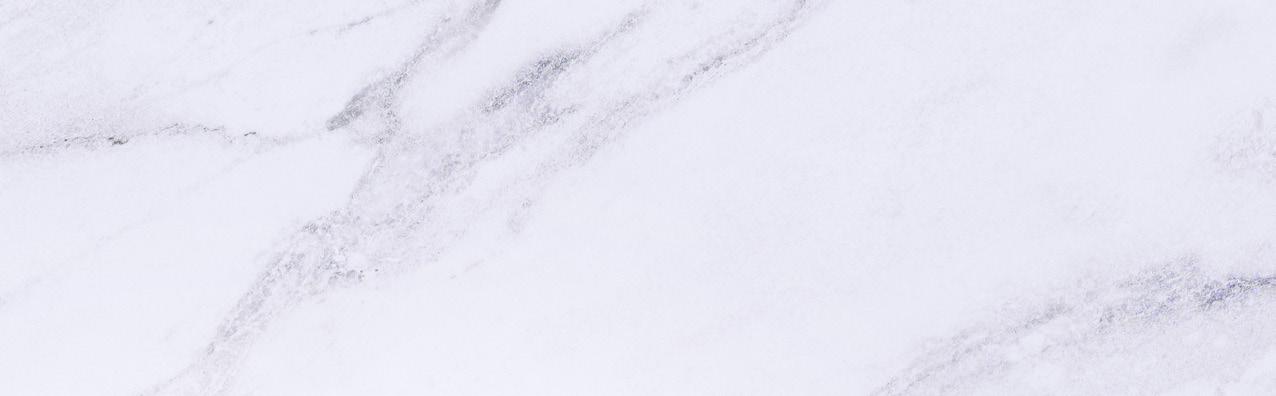
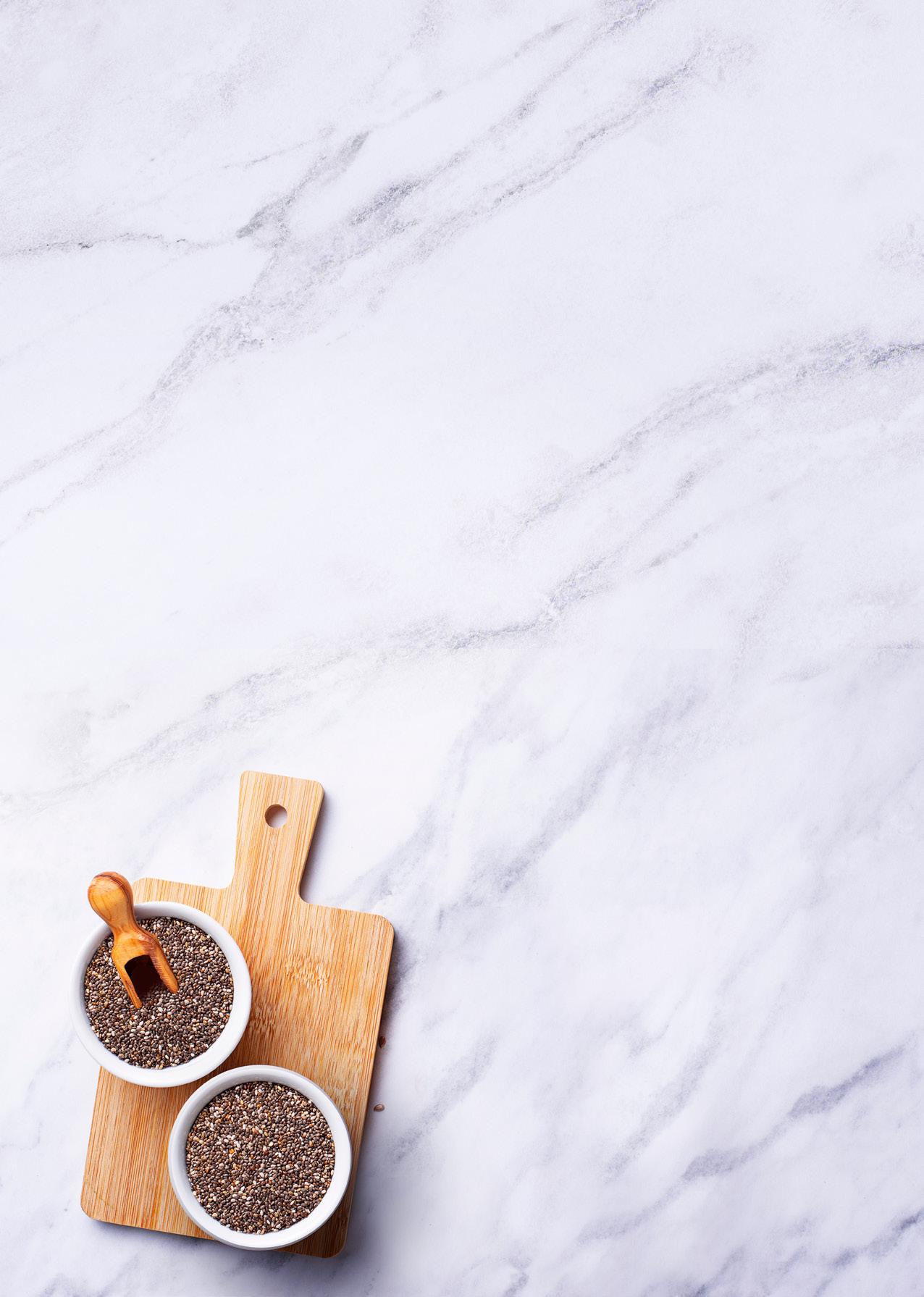
This has provided the company with a proven track record of formulating top-quality products and commercialized ingredients that are used in many of today’s leading brands. A lot of this work is being facilitated in the company’s Rothwell Grain Essentials Center to develop its ingredients, whilst working directly with its partners and customers.
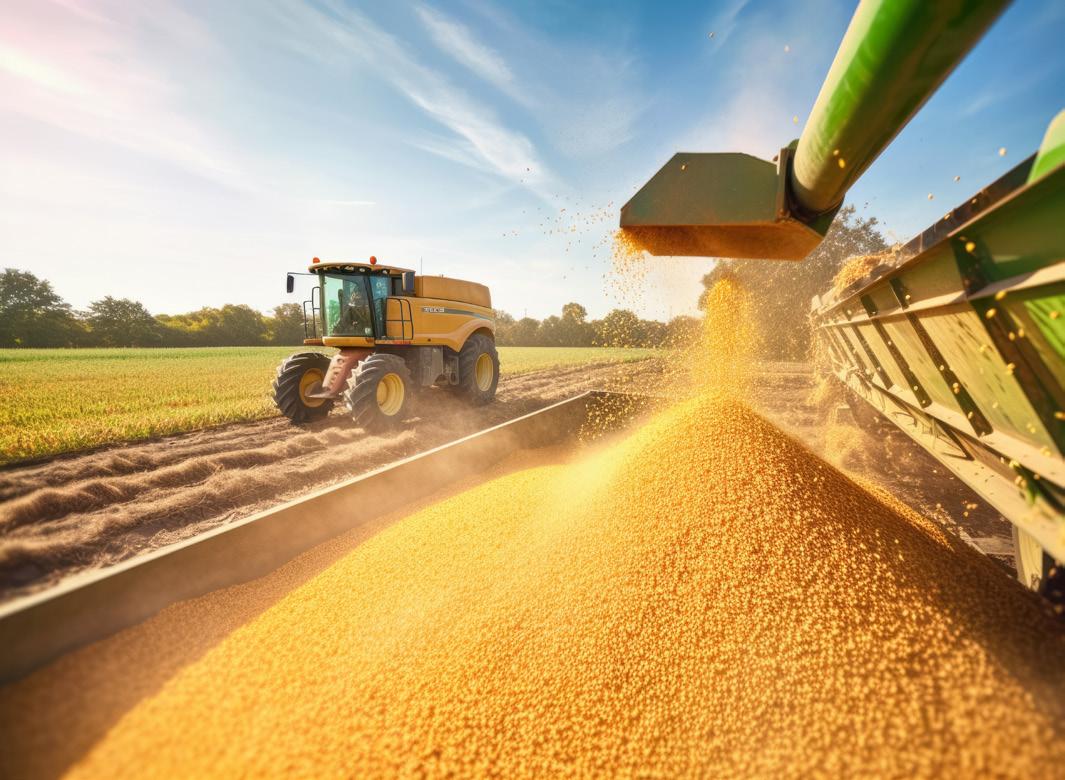
By working with its customers, the company can use its real-time feedback to continue to develop its ingredients and keep tabs on the changing eating habits across the nation to better supply them for the future through this direct communication. The Rothwell Grain Essential Center takes product development from concept to commercialisation, whilst ensuring that throughout every stage of a product’s life from seed to end product is critically managed with the most advanced technology and agricultural knowledge. This is what ensures the trusted quality throughout its production that Bay State Milling is known for.
One product development that sets Bay State Milling ahead of its competitors is its HealthSense® line which has disrupted the market to allow consumers to enjoy their favourite foods such as pizza, pasta and bread whilst also meeting their dietary requirements for healthy fibre. The HealthSense® Wheat Flour allows people to be more engaged with their food, to know what is included and where it came from. The range is aimed to help the consumer to feel more in control of their food. Consequently, the Bay State Milling Company announced the launch of Wingold® Wellness multipurpose flour in May 2023, which is marketed as a better-for-you blend with three times the guthealthy fibre of traditional refined wheat flour. The new blend has the same taste, functionality, and quality that customers know and love from Bay State Milling, but it has been innovatively developed to provide a more gut-friendly option. This announcement highlights the company’s commitment to evolving in line with consumer preferences, to ensure it remains ahead of the game across the industry.
Overall, Bay State Milling provides its diverse and growing array of customers with innovative,
distinctive, and high-quality grain-based ingredients. These ingredients have established the company as changing the game for the grainbased ingredient industry as they are remaining in touch with its consumer base to ensure that its products are serving both their needs and dietary requirements. However, it is the familyowned quality that really makes this company stand out as throughout its operation the company’s sense of care and ownership is the foundation for every product’s expansion and development. Consequently, Bay State Milling continues to evolve with the changing tide of customers’ food requirements, and so remains ahead of the industry by actively working throughout supply chains for the benefit of its customers.
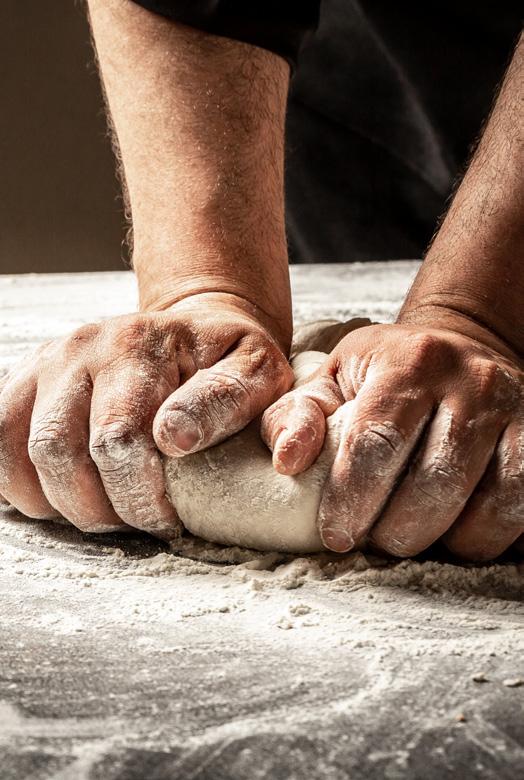

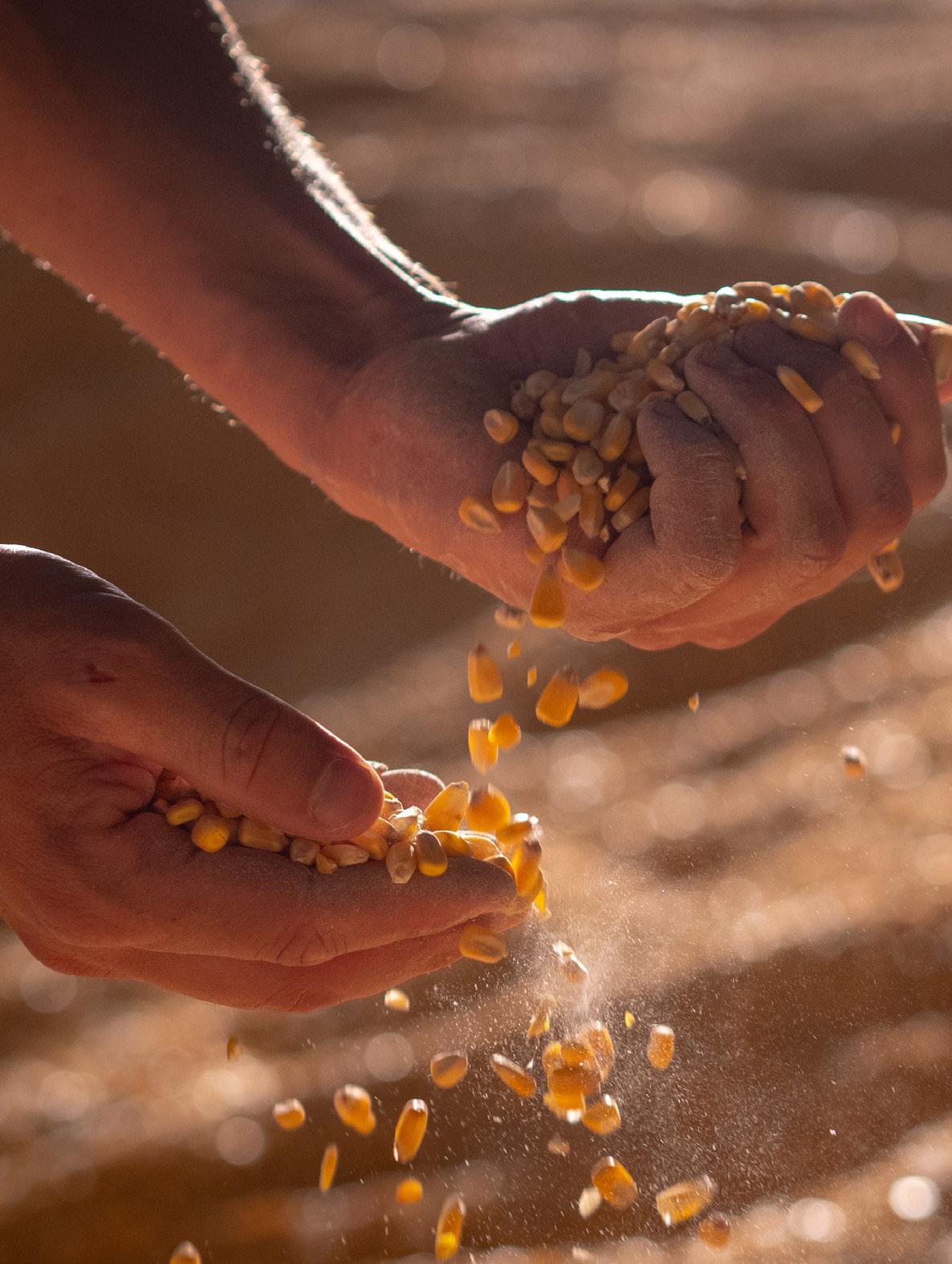
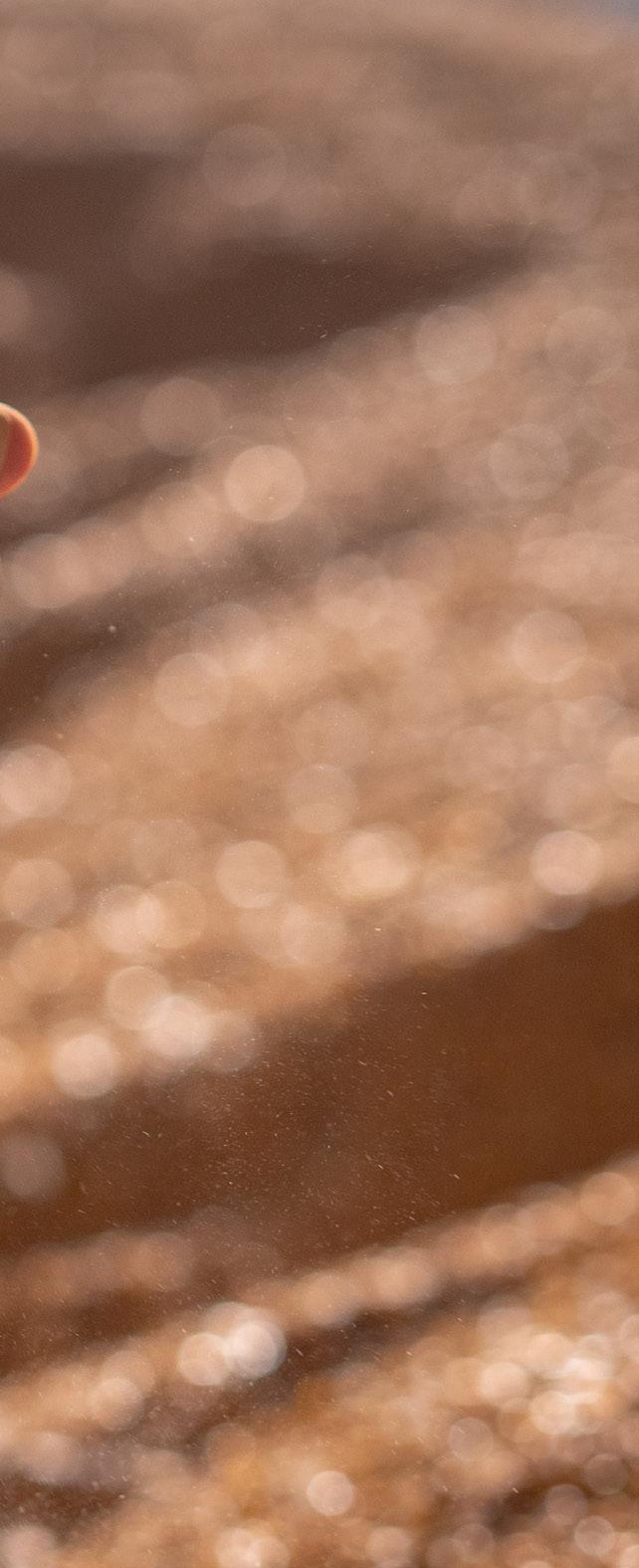
South African National Seed Organisations
The seed industry in South Africa has evolved over the past 100 years and now plays a crucial role in the highly competitive and dynamic industry across the country. Consequently, the South African National Seed Organisation (SANSOR) has spent the last 30 years facilitating the uninterrupted movement of highquality seed across South Africa by positioning itself as a key player in local and international seed industries.
Established in 1989, SANSOR provides local seed enterprises with a formal and strategic body to advocate and protect the interests of the seed trade across South Africa. To facilitate this, SANSOR has established strict certification regulations, legislation, training, phytosanitary support, and liaison across the industry to proudly play a significant role in today’s global seed industry. Therefore, SANSOR today is the nationally designated authority for seed certification throughout South Africa and continues to provide crucial support, communication, access, and research into the seed industry to benefit its member companies. SANSOR’s vision is to be the foremost authority on all seed matters and hopes that through its work across the industry, it can proactively shape the seed industry environment and continue to meet the growing demands of the population.
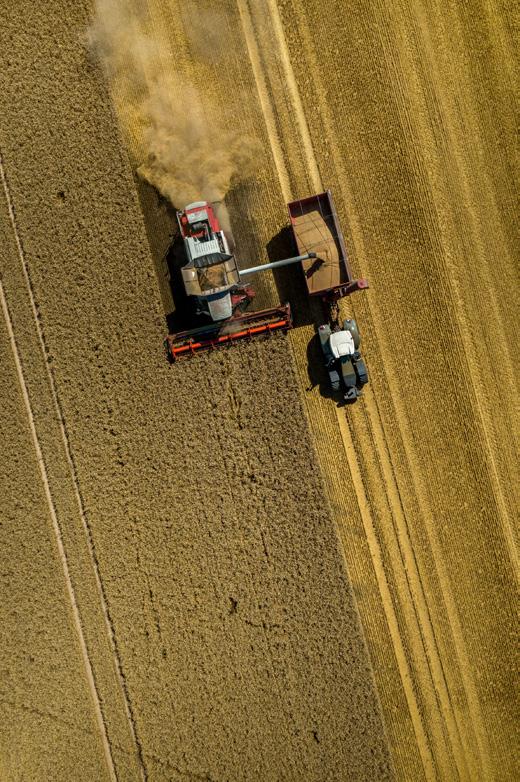
SANSOR has 79 full members which include seed trade companies and cooperatives across the industry. SANSOR also has 18 associate members which include those that provide its products and services to full members and 3 affiliate members which are trade and technical associations. Additionally, SANSOR includes 4 international members, 2 thirdparty members, 8 research initiatives and 12 honorary members. Collectively these members work together with SANSOR to develop the industry across South Africa towards continued success.
SANSOR provides its members with services including certification, phytosanitary support, trading links, development and training programs, global and local promotion, negotiation, and advocacy with government bodies, and conducting research to develop the industry in line with evolving population demands and climate needs. Furthermore, SANSOR itself is also a member of the International Seed Federation (ISF) and the African Seed Trade Association (AFSTA), which allows it to represent its members on various national and international platforms, whilst benefitting from the adoption of industry-wide recognised strategies and regulations. Consequently, SANSOR’s role across the seed industry is vast and works in conjunction with all the members, international seed organisations and government bodies to establish South African seed as a key facilitator to global markets.
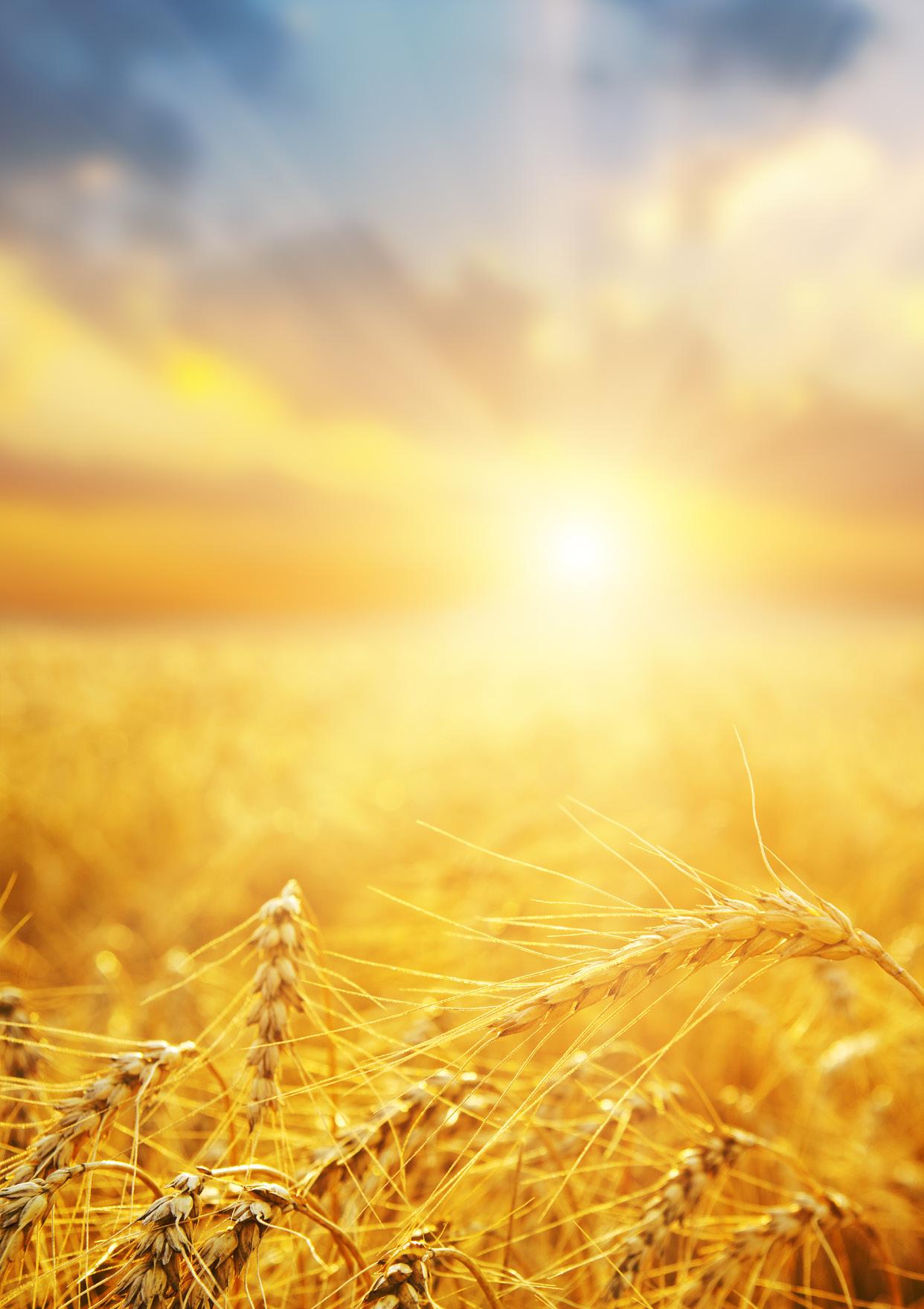
South African National Seed Organisations
The major function of SANSOR however is its role in the certification of seed across the industry. SANSOR provides a legally sanctioned system for quality control of seed production, to ensure that every pack, box, bag, or tin received with the SANSOR quality stamp is ensured to contain exactly what it says it will. By establishing a set of regulations and standards for seed quality across its members, the Association is promoting seed liability, physical purity, varietal purity, and varietal identity of seeds for a stronger seed future for South Africa’s seed trade industry.
SANSOR’s certification process involves more than 320 trained and authorized private seed inspectors and samplers who verify more than 50,00 hectares of seed crops annually. They analyse and establish the sources of seeds from breeder seeds, through to pre-basic to basic and certified seeds. Furthermore, SANSOR has more than 90 control and checkpoints to ensure that all seed that passes its certification is high quality and pure.
The resulting certification ensures that all seed meets the demanding South African Seed
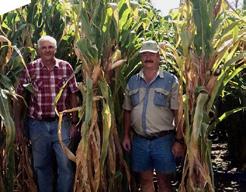

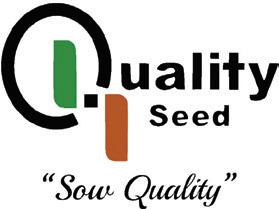
Certification Scheme, which requires seeds to be certified as varietally pure both in terms of identity and physical appearance. By controlling the complete system from the release of a variety to the eventual release of seeds to a producer, SANSOR can ensure that all seeds produced across South Africa with the SANSOR certification logo can be trusted for its quality and purity.
At present seed comprises only around 12% of grain farmers’ total input costs, but it plays a vital role in the resulting yield obtained at the end of the season. Therefore, through SANSOR’s quality assurance farmers can be sure seeds with the SANSOR certification stamp will help to produce uniform and disease-resistant crops, as without the certification poor seeds would lack the same yield potential even with the highest quality of soil and technology available. Consequently, SANSOR’s certification assurance allows farmers to purchase seeds with peace of mind knowing they are not compromising on quality, yield, and subsequent income.
Furthermore, as seeds play such a key part in food production and hunger alleviation globally, the increase in seed quality through certifications
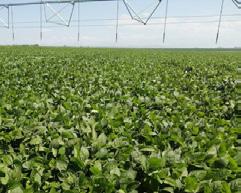

such as those that SANSOR offers is evermore essential. Additionally, pest introductions and outbreaks can have disastrous effects across food production, and cost farmers, governments, and consumers millions every year. To prevent this loss, certification and regulations across seed industries are essential to keep a free-flowing state of seed in local, national, and international markets. To ensure the development of a viable and sustainable global seed market, prevention remains the best policy.
Therefore, it is imperative for countries and governments to establish effective regulations to control and manage these risks. Ultimately, we can see that the role SANSOR plays in the global seed market is essential to ensure that the South African food and agriculture sector is supported and regulated for its continued seed prosperity.

Overall, SANSOR continues to establish a consistent supply of high-quality seed across the industry in South Africa to establish a competitive and productive seed industry. By implementing regulations, working with its
members, and government bodies and providing a leading certification to all seed produced in the country, SANSOR has created a predictable trading environment by eliminating trade barriers and promoting a consistent supply of high-quality seed. Therefore, SANSOR continues to lead the seed industry across South Africa and into global markets as a governing body which unites an everevolving industry toward the secure future of seed delivery and subsequent crop production.
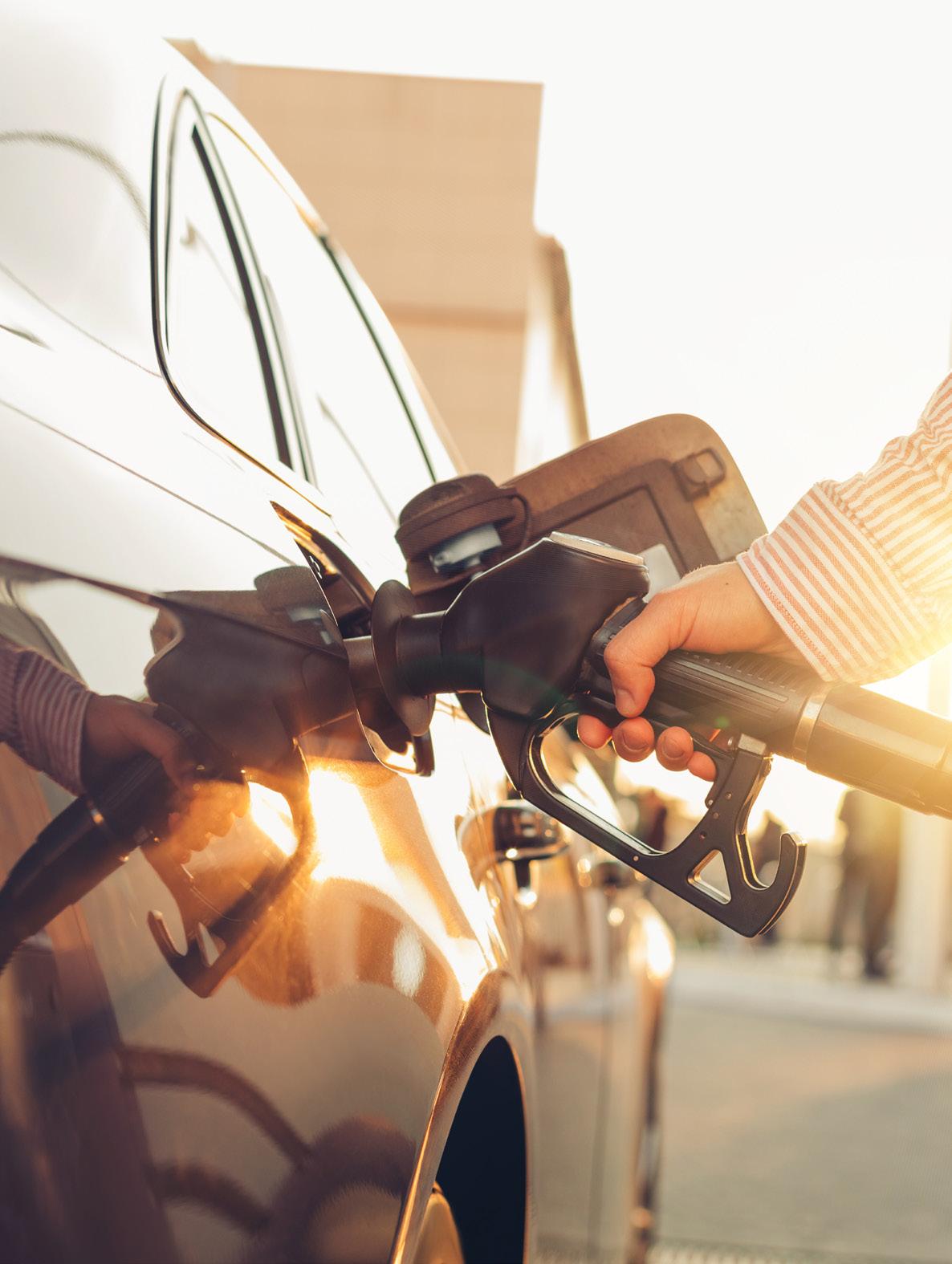
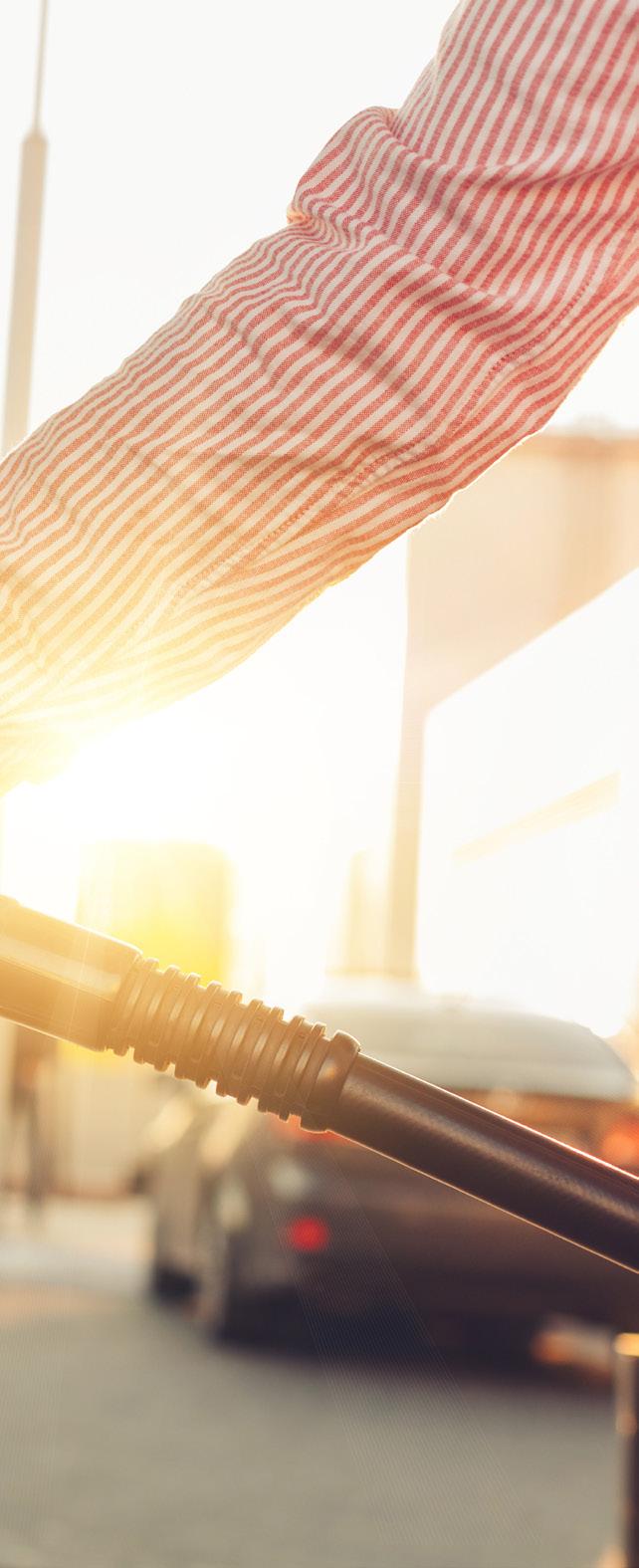
With a mission to provide quality petroleum products and ancillary services across the petroleum industry of Trinidad and Tobago, the National Petroleum Marketing Company Ltd. (NP) has marked itself as the most diversified petroleum marketing company across the English-speaking Caribbean. NP, motivated by a relentless drive to deliver results for its customers, markets a range of products including petroleum fuels, lubricants, and grease, liquified petroleum gas (LPG), and compressed natural gas. However, NP strives not just to lead the industry with its vast array of petroleum businesses, but instead to play a vital role in the daily lives of those across Trinidad and Tobago through its operations.
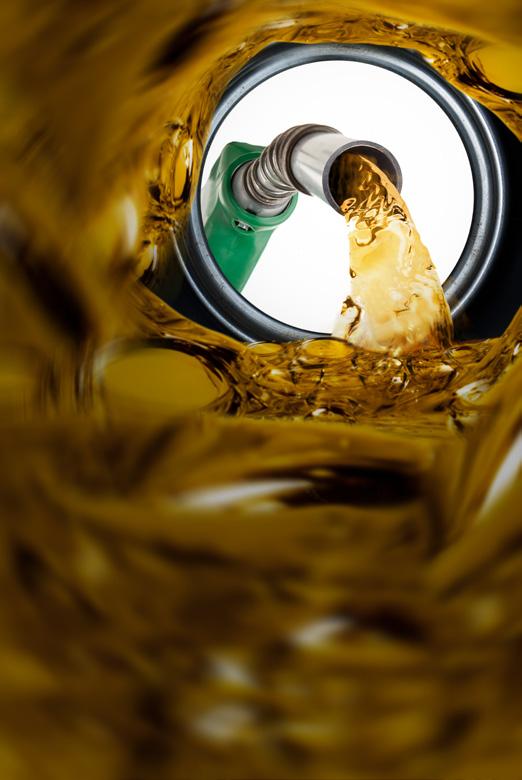
In 1969, The National Petroleum Company was established by law due to new petroleum legislation that was enacted across the region. The Trinidad and Tobago National Petroleum Marketing Company was established following the government’s purchase of assets from the previously owned BP Caribbean Ltd which was the local marketing arm for BP across the region. Over the next few years, NP consolidated its role across the region and by 1976 was the sole distributor of petroleum fuels in Trinidad and Tobago through key acquisitions of Trinidad and Tobago Oil Company (formerly Shell Trinidad Ltd.) and TEXACO Trinidad Ltd. Now in 2023, NP is the most diverse petroleum marketing company in the region playing a vital role in the fuel industry. Furthermore, as a regional enterprise, it is seeking to establish itself as a trusted brand of world-class fuels and lubricants backed by a reputation for excellence.
NP’s operations are working to produce profitable revenue growth and maintain its market share by challenging conventional thinking across the petroleum industry and providing innovative ways of expanding its offerings to both local and regional markets. Furthermore, NP wants to be a brand that is ever present across the industry for its domestic and international customers through its excellent standards of service at service station forecourts to its work supplying fuel to the aviation and shipping industries.
The most prominent way that NP is present in local communities is through its QuikShoppe and QuikShoppe Plus service stations. The QuikShop stores provide people from across the region with access to petrol to fuel their cars and other vehicles of transportation. It also provides a selection of convenience products and groceries ranging from everyday essentials to beverages and snacks. These service stations are one of the most prominent ways that local customers interact with NP on an everyday basis.
However, in an effort to expand this relationship between customer and NP, it has implemented a range of QuickShoppe Plus stations across the country, which not only provide the standard everyday essentials people may expect from NP, but also include a range of ‘read-to-go’ food and meal options. NP’s implementation of a wide variety of offerings across their service stations aside
from the basic convenience products and petrol filling facilities, recognises the growing demand internationally for convenience stores to raise the bar in food-service offerings by providing easy and convenient meal services nationwide. Consequently, across the region, the QuickShoppe brand, whether that be their standard stations, ‘Plus’, or mini stores, plays a vital role in the daily lives of those in Trinidad and Tobago who are likely familiar with the brand across its 30+ current stores nationwide.

NP, however, fulfils an even broader range of services across Trinidad and Tobago. At NP’s core is its hub where a large majority of its petroleum businesses take place through its 22-acre bulk storage facility and head office located at Sea Lots, at the Port of Spain in Trinidad. NP provides a range of motor fuels, aviation fuels, marine bunkering, ultra lubricants, and LPG services.

The company’s LPG cylinder assets exceed 1 million for 20lb cylinders and has over 350,000 for 100lb cylinders. Consequently, as the leading supplier of LPG for homes and businesses across Trinidad and Tobago its role in the everyday lives of many is crucial.


Under NP is NATPET Investments Company Limited, a wholly owned subsidiary of NP, that operates a filling, testing and refurbishment plant which has earned a reputation of being a reliable producer of efficient energy and fuel solutions. Since its origins in 2004, NATPET has transformed the LPG sector for Trinidad and Tobago and remains a leading player providing a range of services. These services include the walk-in refilling service in which customers have the option to wait whilst their cylinders are refilled. Additional functions of NATPET include bulk transportation of LPG from refineries to its filling plant, inspection, testing and refurbishment of all cylinders entering and exiting the filling plant, filling LPG cylinders for domestic markets, sales of LPG cylinders to authorized distributors, as well as

National Petroleum Marketing Company Limited
ensuring that there is an adequate, reliable, and safe supply of LPG available for domestic markets.
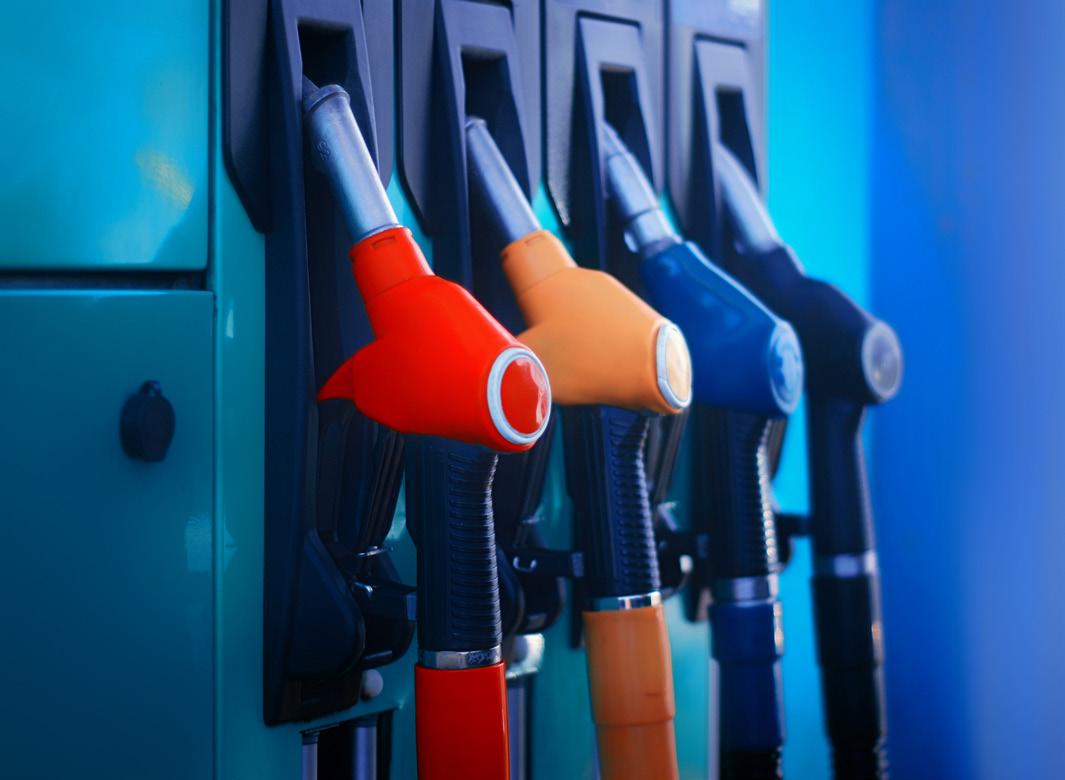
Alongside its LPG cylinder offerings, NP provides a range of internationally accredited motor oils for all classes of diesel and gasoline engines, as well as a range of automotive products. These products include ultra lubricants that adhere to internationally recognised quality standards, as determined by the American Petroleum Institute (API). Furthermore, NP has a Grease Plant which was first commissioned in 1986 and has a design capacity of 500 tonnes per annum. NP manufactures a wide range of engine, gear, and hydraulic oils through this plant and so can market both industrial and automatic lubricants which sees its products serve a diverse industry with engine oils, gear transmission and power steering fluids, and even coolants.
The final key aspect of NP’s operations is in its bunkering services which works to secure competitive rates and receive customised solutions for its customer’s bunkering needs. NP provides seamless operations with over 45 years of experience across the bunkering supply industry. Therefore, it is focused on providing the highest standards of marine fuels with reliability and
stability. Consequently, NP Bunkering is one of the most respected marine fuel and lubricant trading companies in Trinidad and Tobago. The company has a proven heritage and currently services three categories of bunkering customers, providing them with flexible solutions and an exceptional quality of products through its superior value-added bunkering services.
National Petroleum Marketing Company is one that has heart and is focused on playing a key role in developing Trinidad and Tobago’s petroleum industry towards both local and international success. Through its operations across the industry including its service stations, Grease Plant and bunkering services, NP is building stronger relationships across markets as it reconfigures its strategy to improve the brand’s presence across the industry. As a purpose-led, state-affiliated agency it is striving to make a difference, which it seems to do successfully as it continues to make crucial decisions to pursue initiatives that maximise the positive benefits of the industry for the people of Trinidad and Tobago. Therefore, with NP, they are with you for all of life’s journeys!

WITH LFS WAREHOUSE MANAGEMENT SYSTEM BY EPG: UNION COOP HANDPICKS LFS FOR DUBAI WAREHOUSE
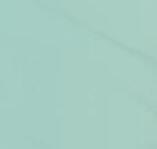

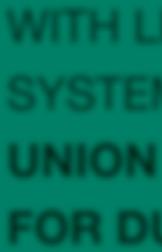
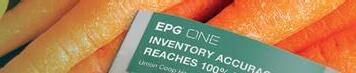
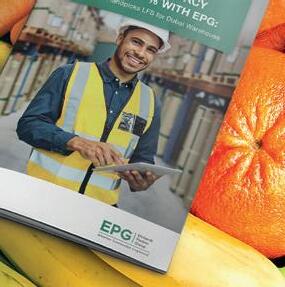

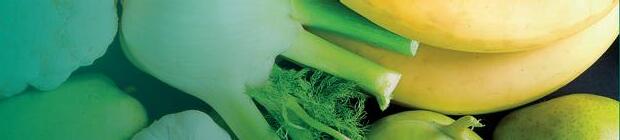
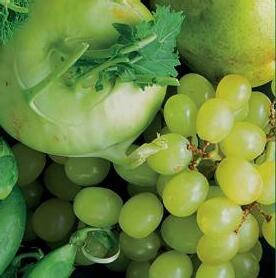
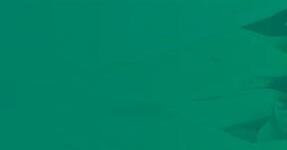





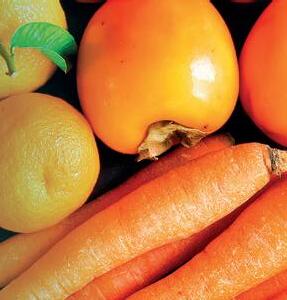
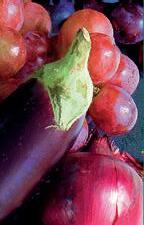
“LFS provides detailed, real-time WMS data that we can use to make critical inventory management decisions.”
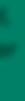
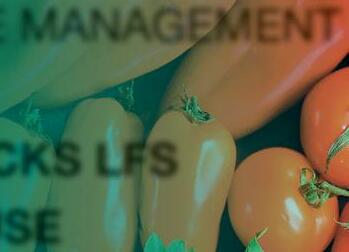
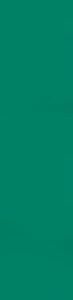

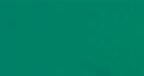
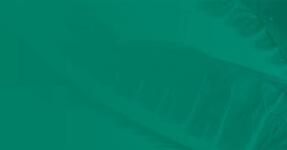
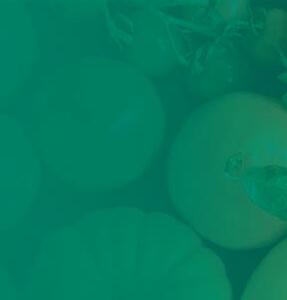
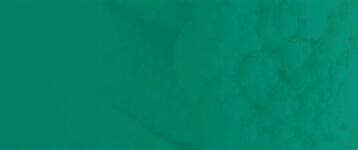
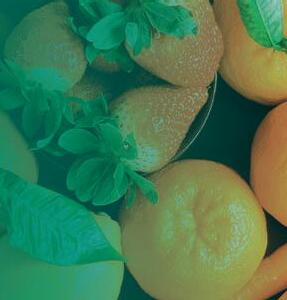
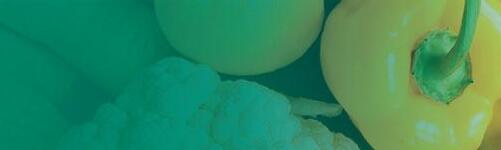
Kashif Rasheed, Project Manager at Union Coop
95% increase of pick-up times
Up to 90% error reduction
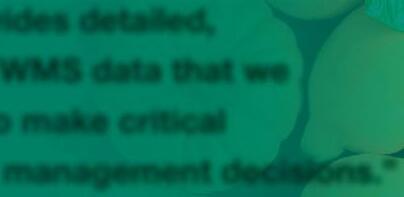

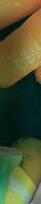
95% improvement in storage location allocation


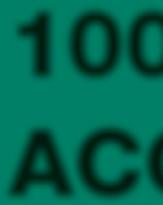



www.epg.com
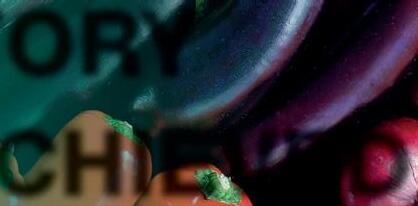
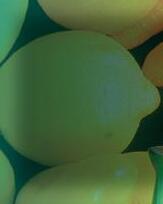
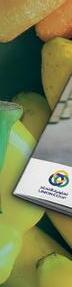

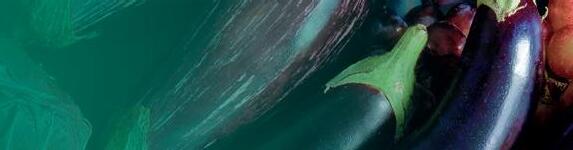
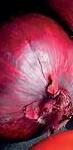
