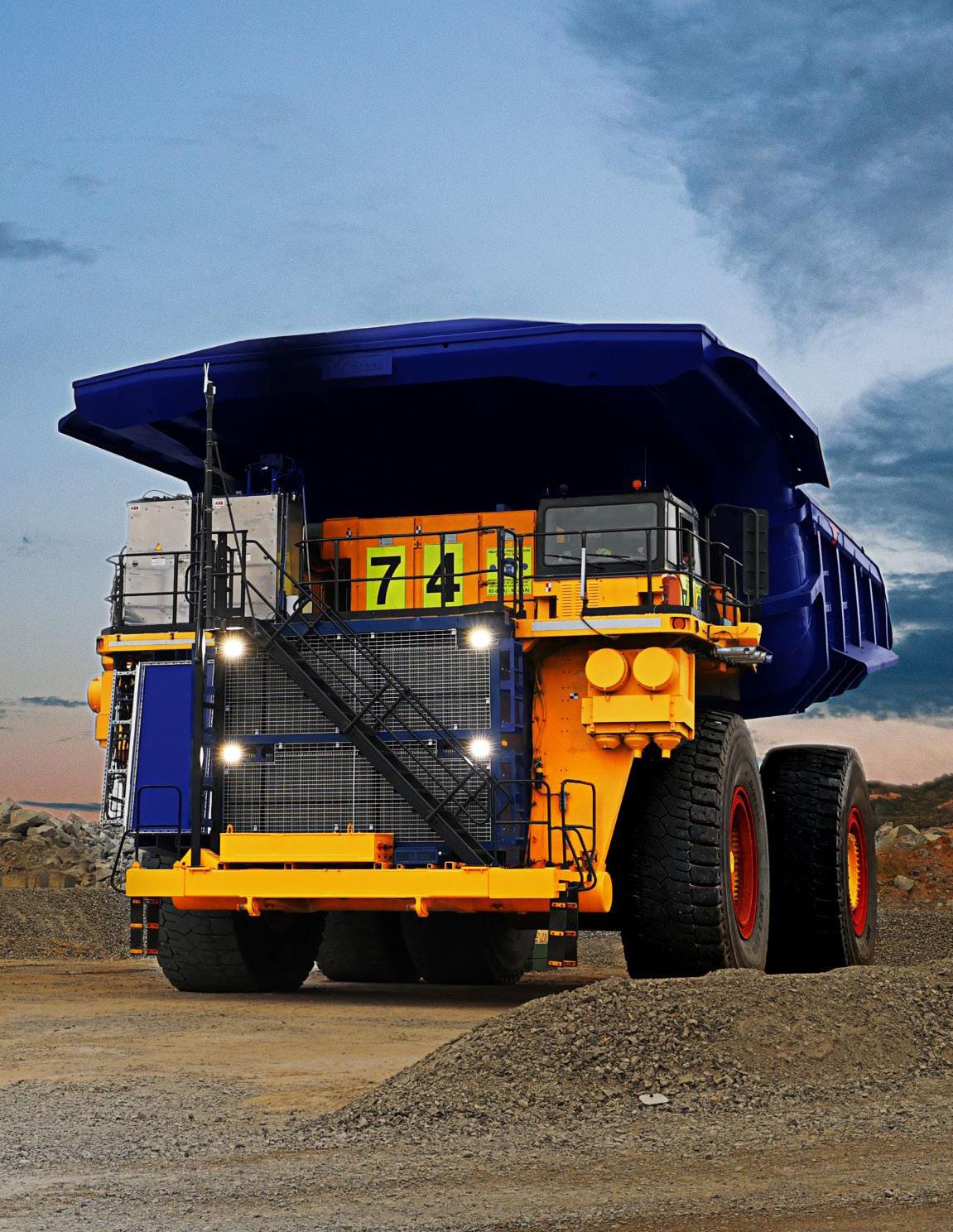
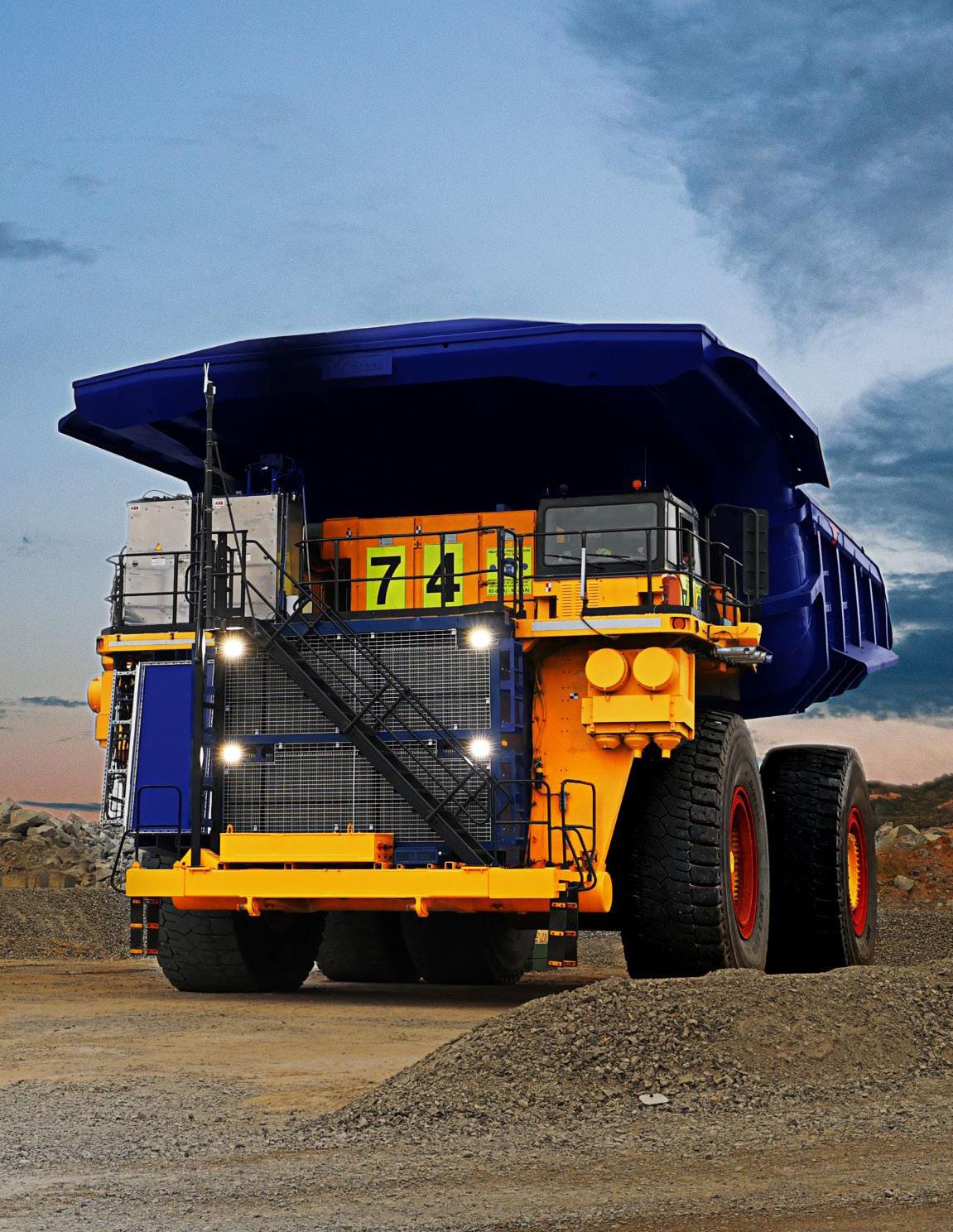
DECARBONISATION, ELECTRIFICATION, RENEWABLES, HYDROGEN AND ESG FOR MINES
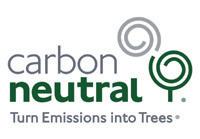
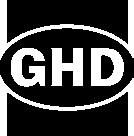
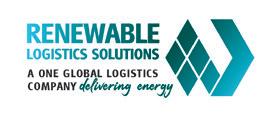
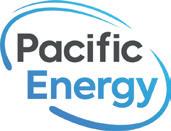
TITLE SPONSOR:
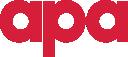
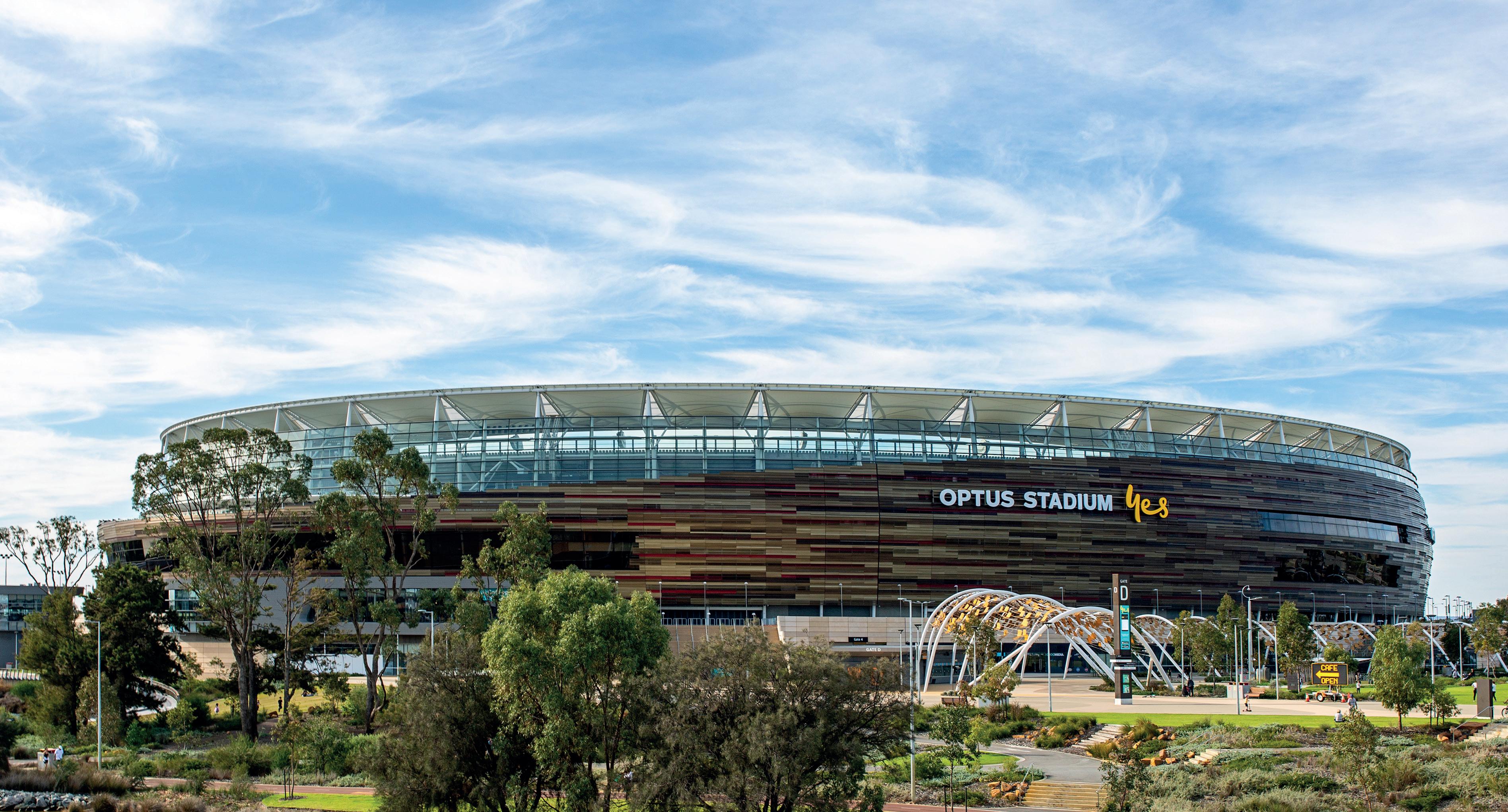
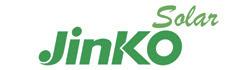
PREMIER SPONSOR:


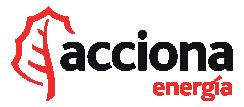
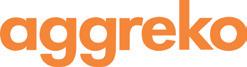
THOUGHT-LEADER SPONSOR:
DINNER SPONSOR: LUNCH SPONSOR:
LANYARD SPONSOR:
SESSION LEADERS:
BAR SPONSOR:
HYDROGEN
LEAD SPONSORS:
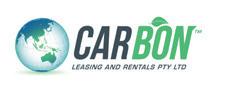
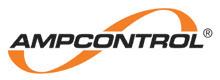
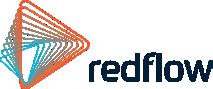
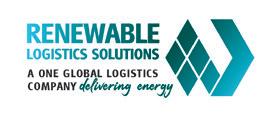
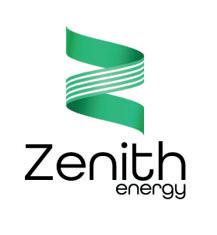

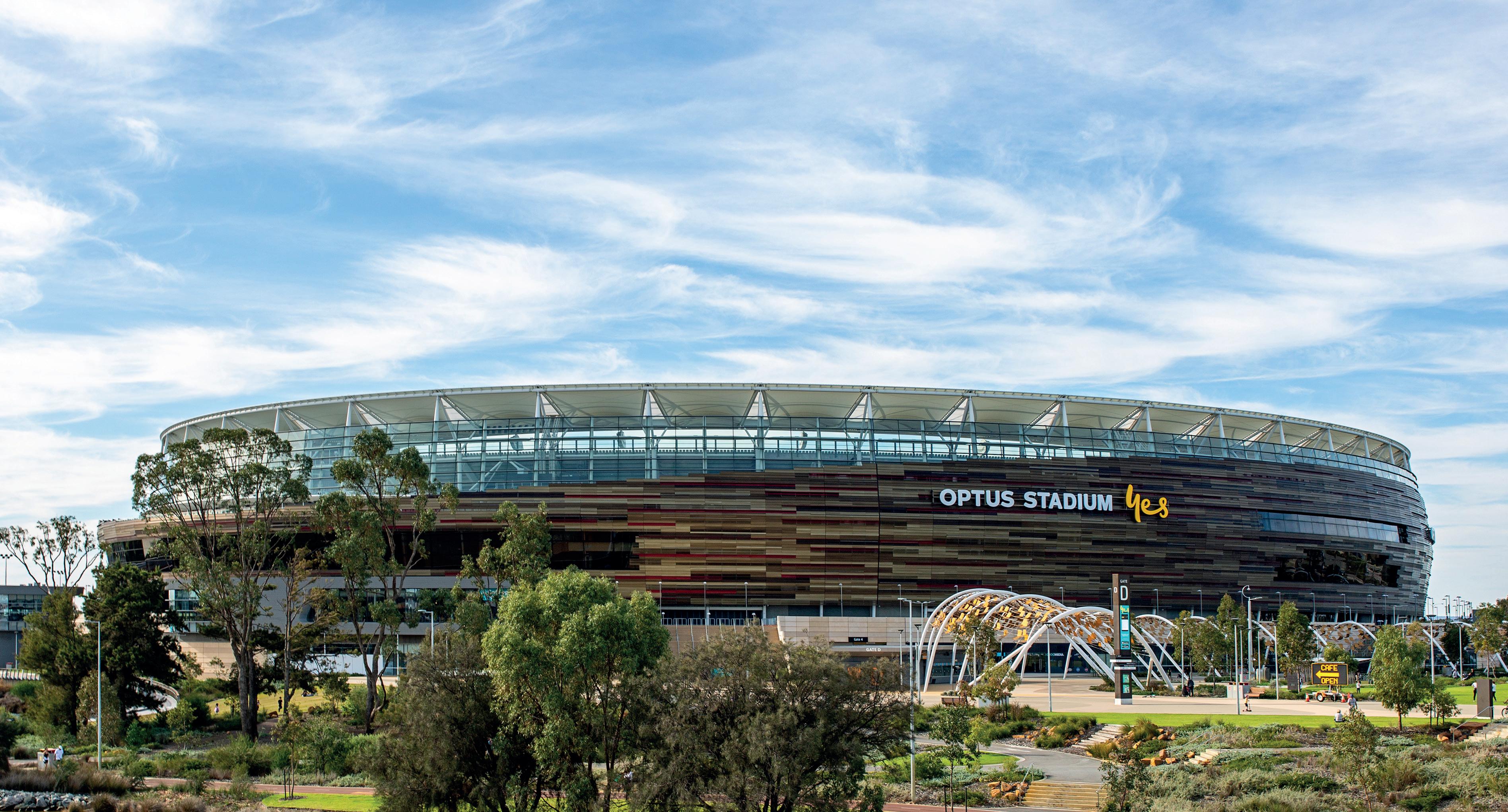
BREAKFAST BRIEFING SPONSORS:
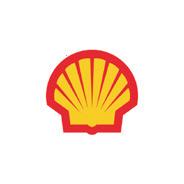
NETWORKING DRINKS PARTNER: BARISTA SPONSORS:
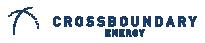
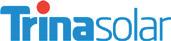





SUPPORTING SPONSORS:
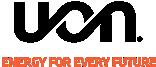

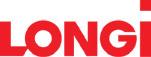
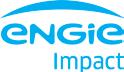
EXHIBITORS:
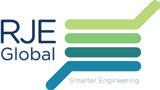
Transitioning Australia’s Energy
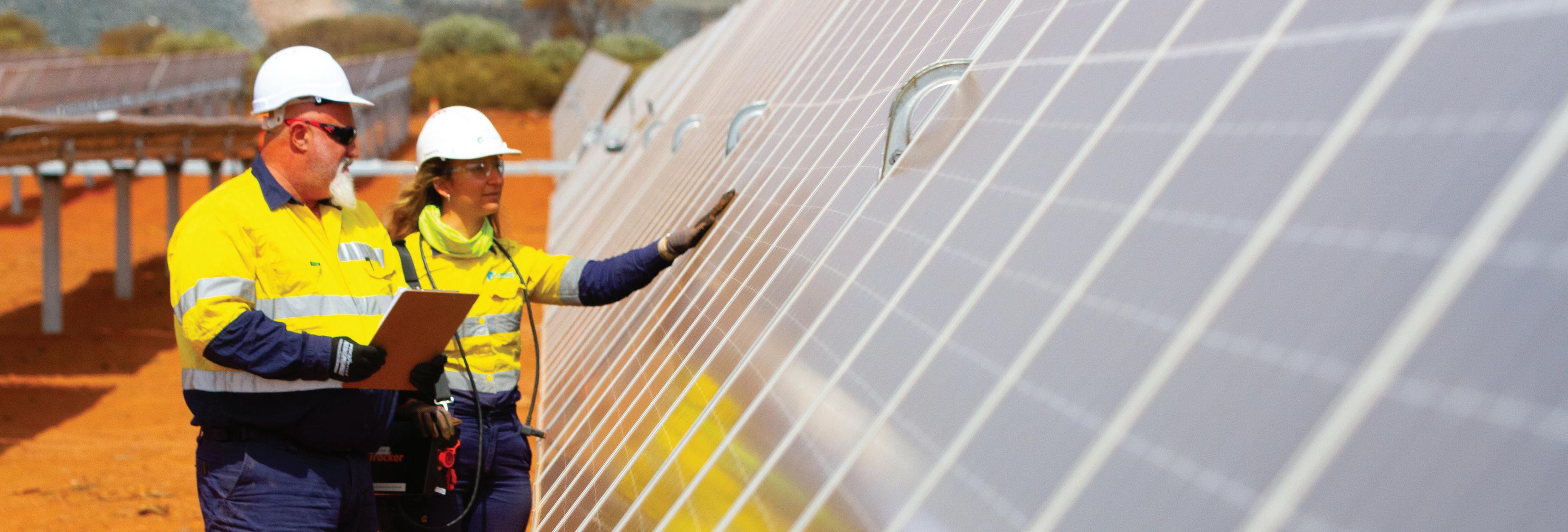
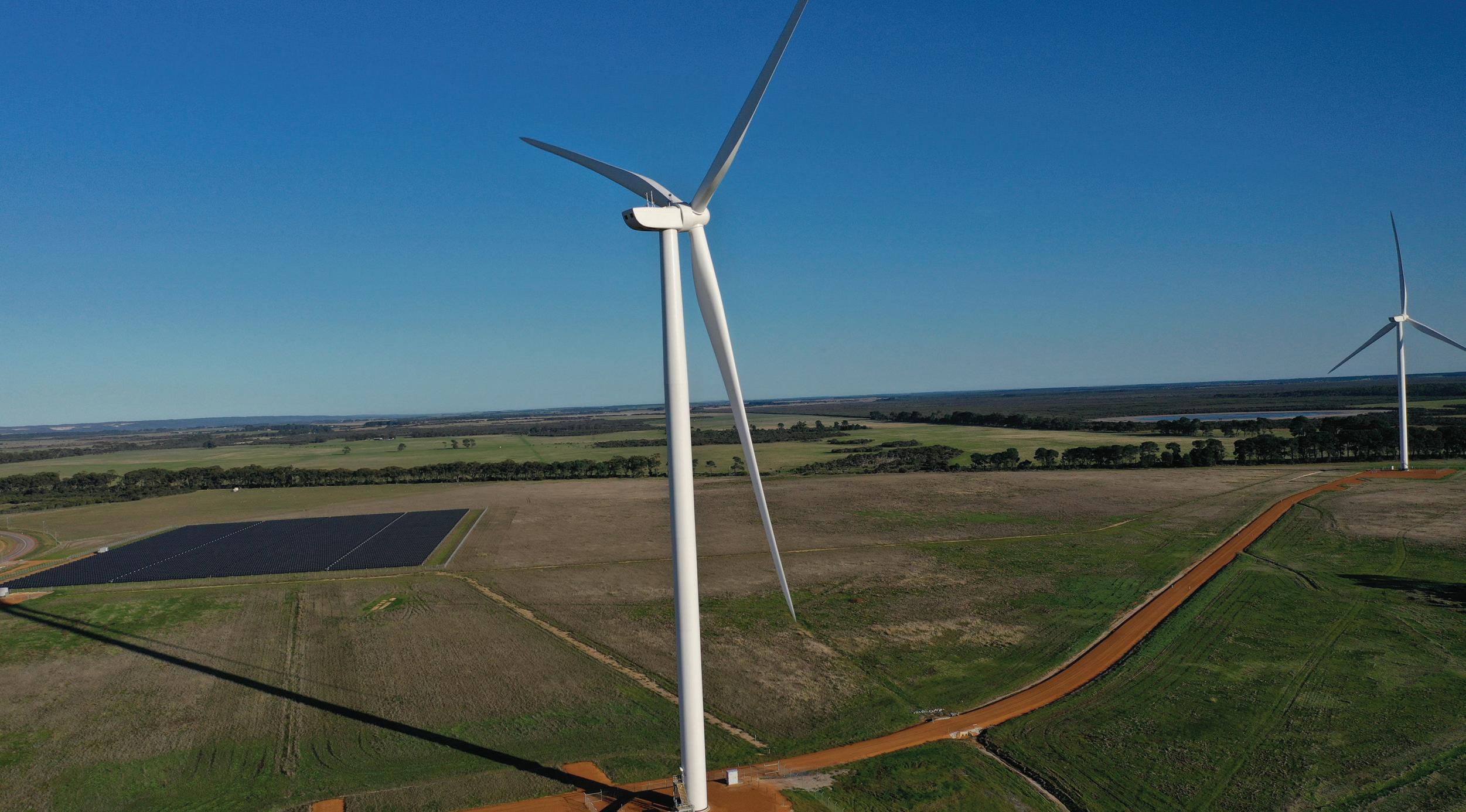
Leaders in sustainable distributed energy, and the only one with in-house capability to design and deliver integrated energy solutions using solar, wind, battery storage, green hydrogen, LNG and diesel technologies.
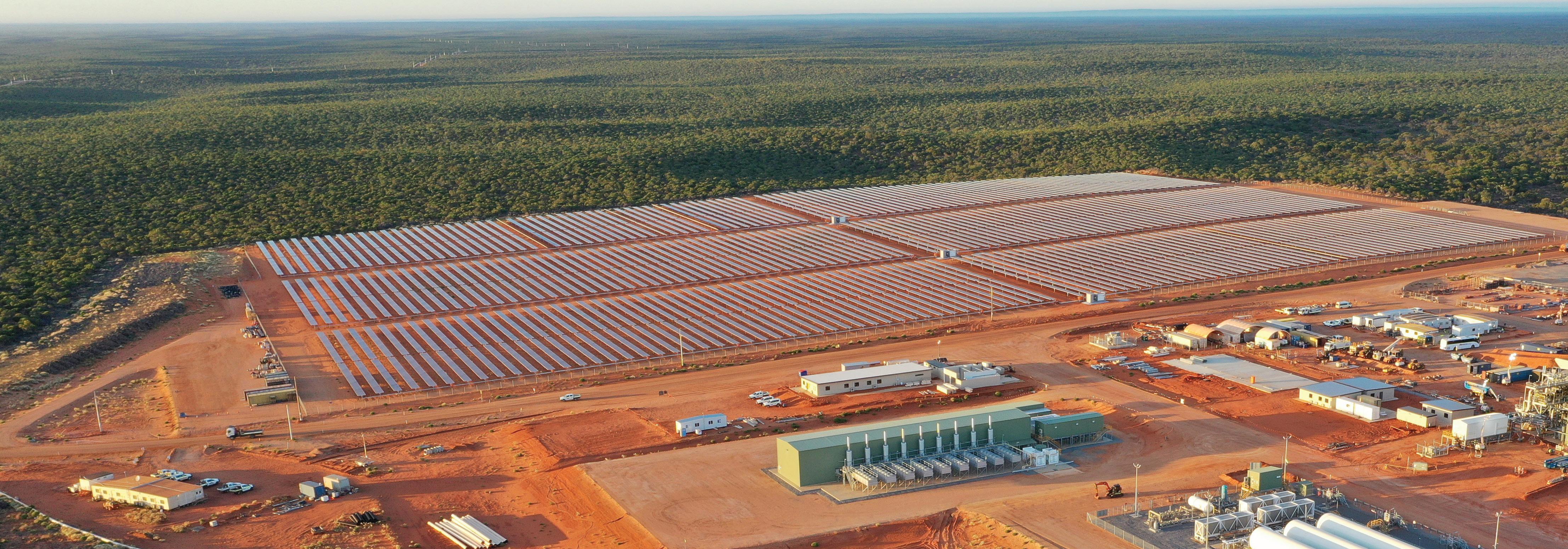
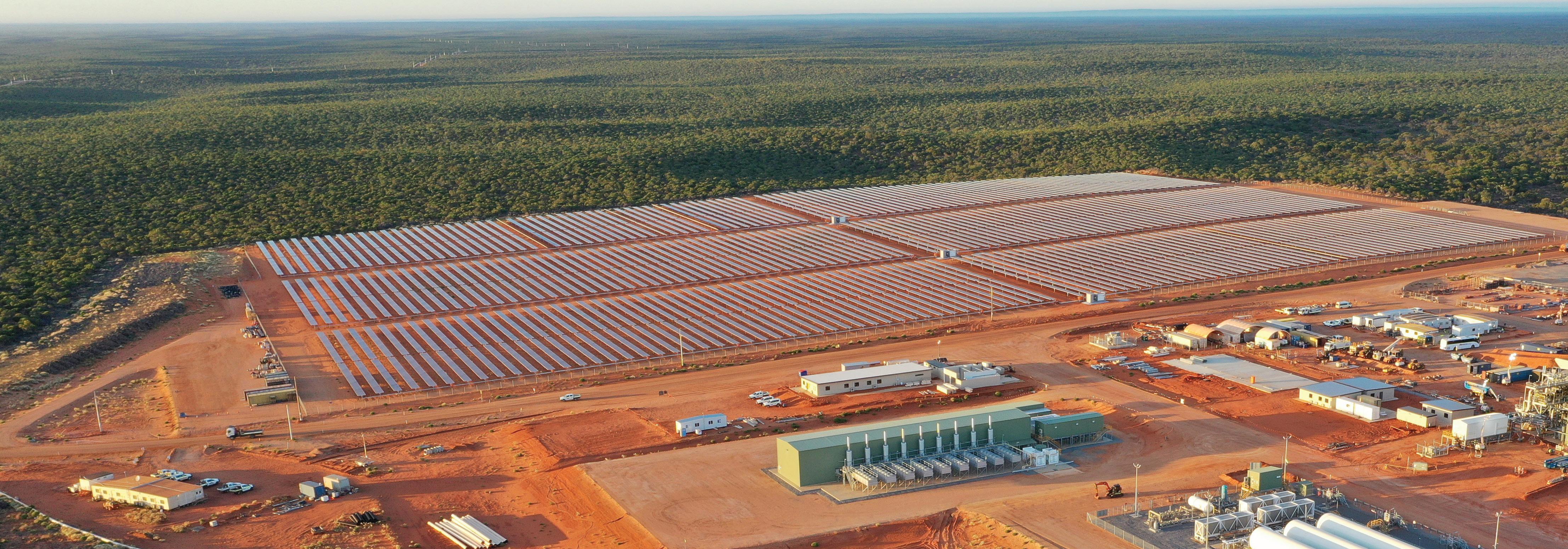
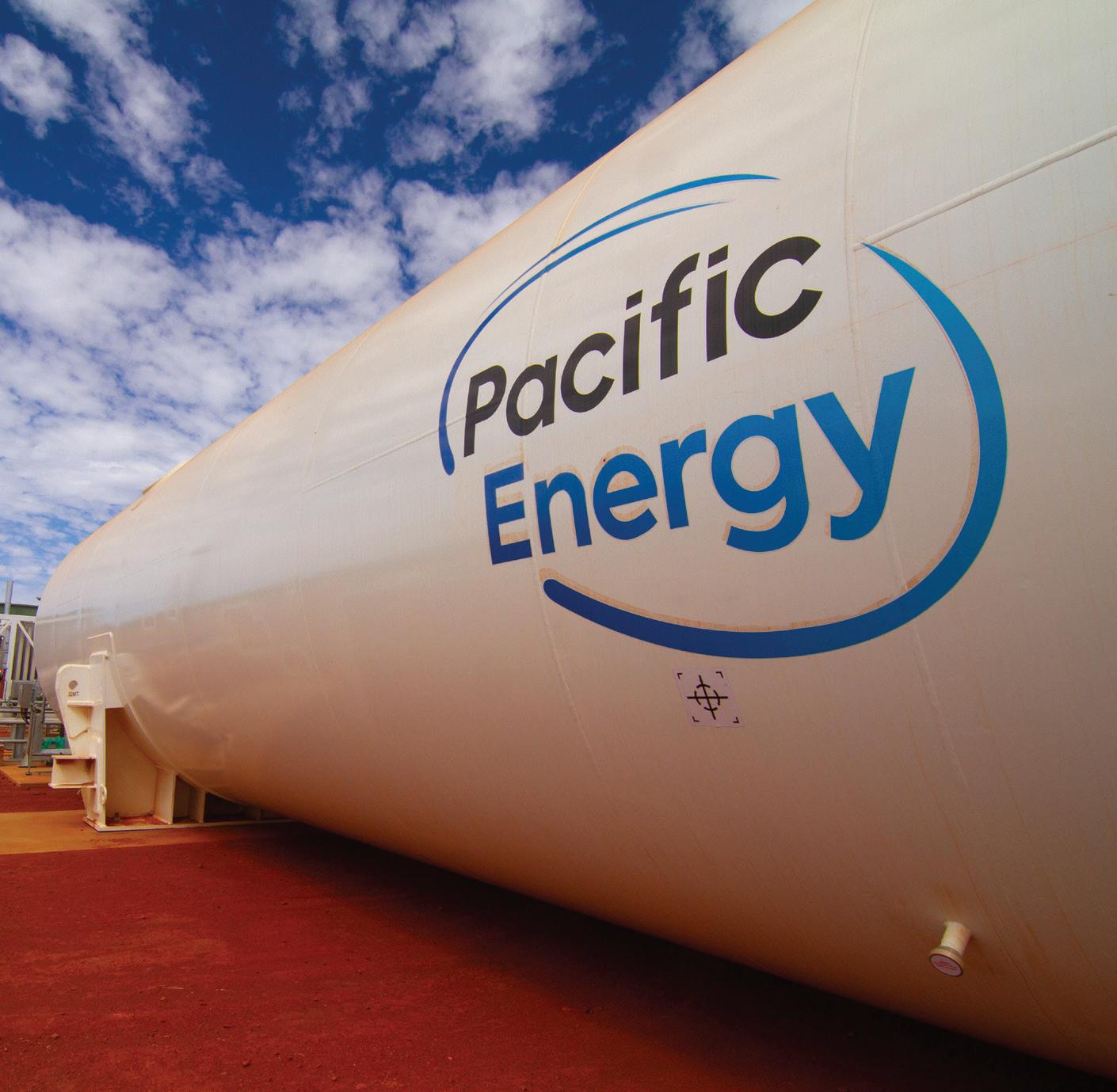
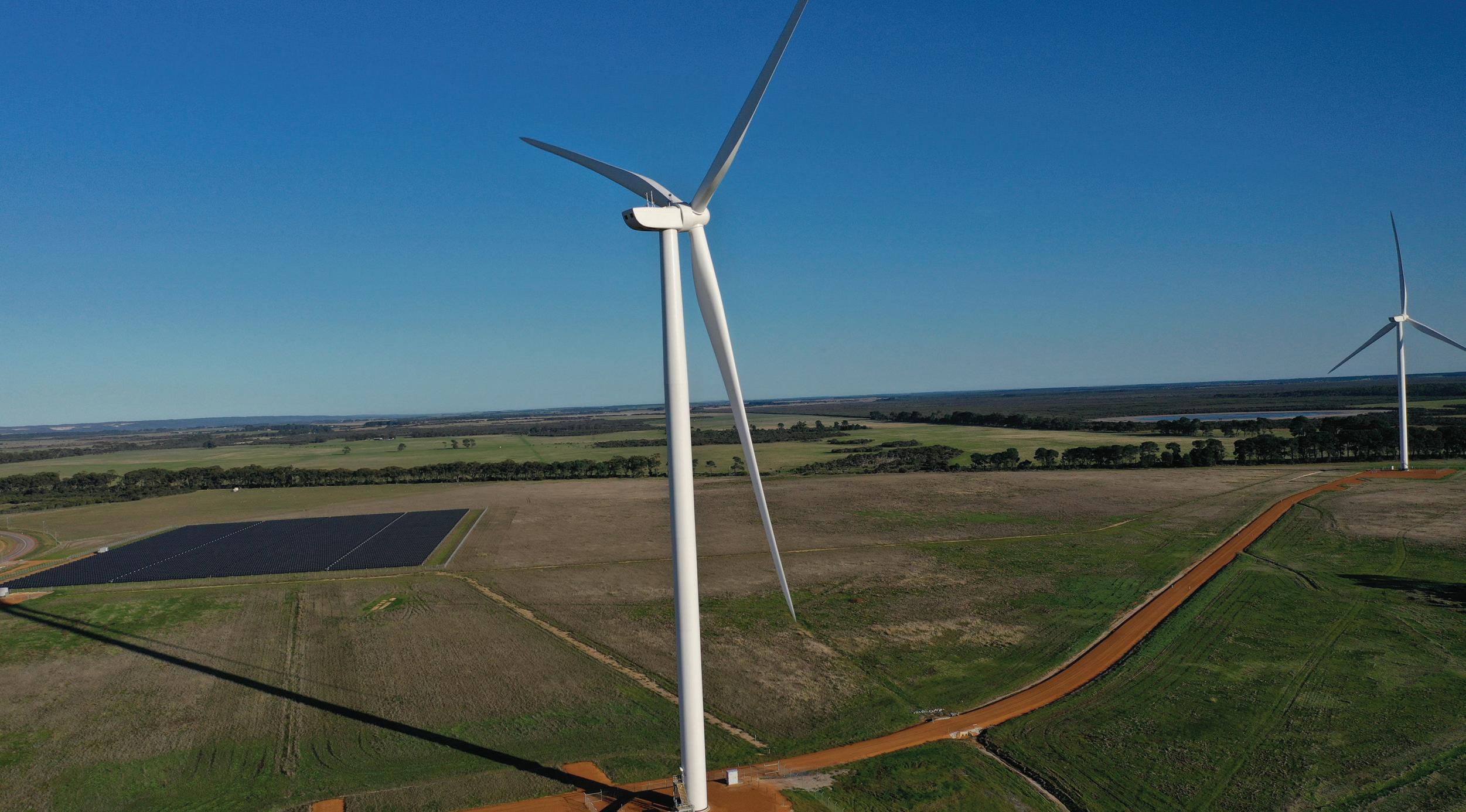
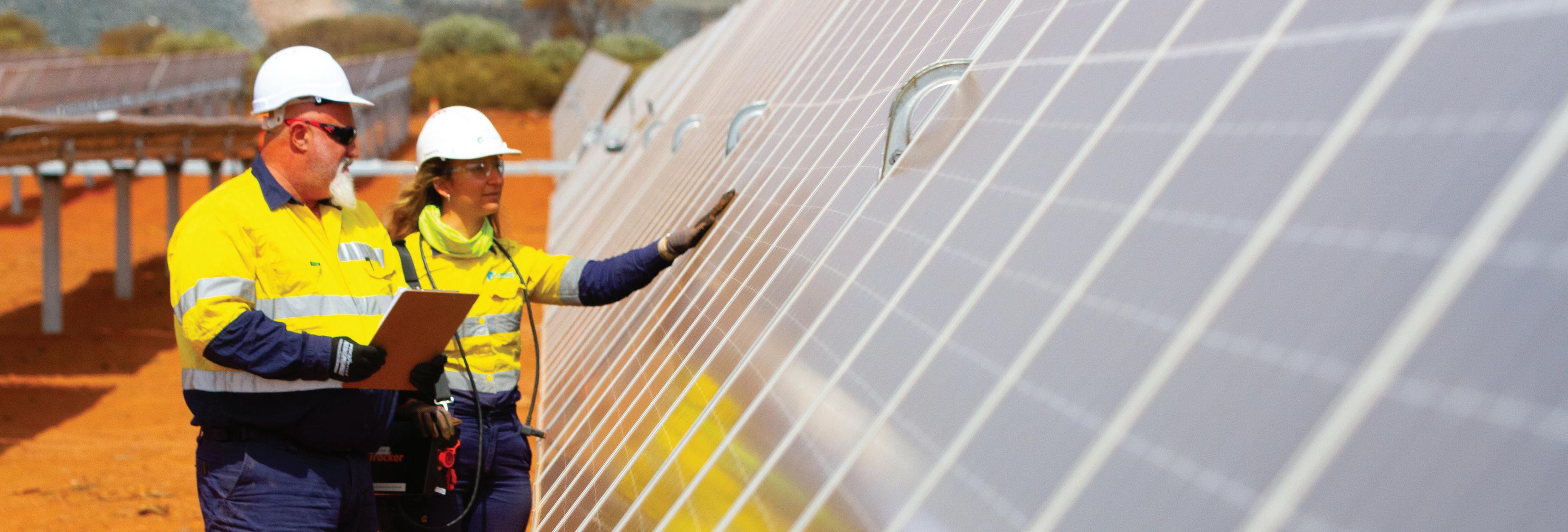
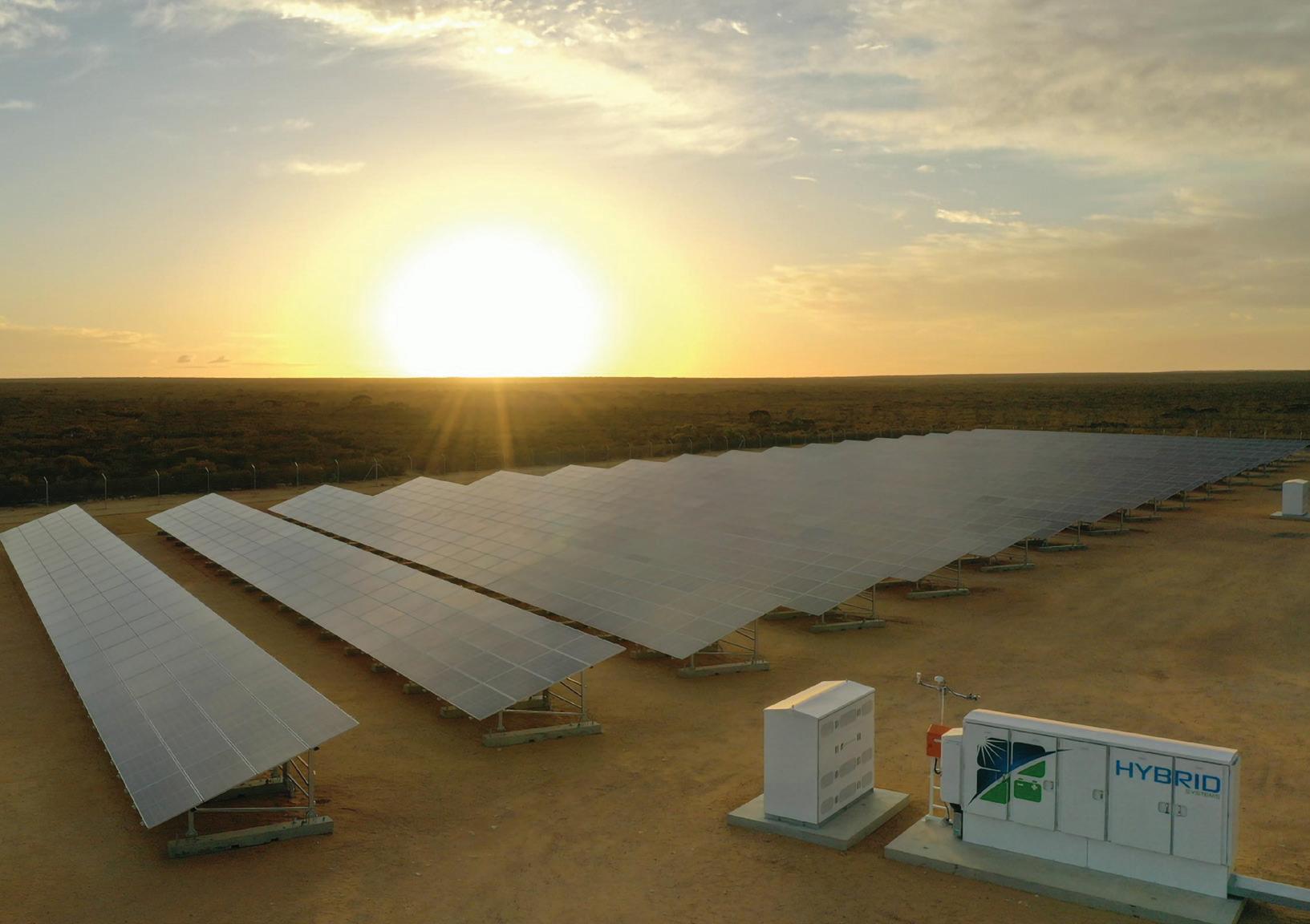
Electrified mine fleets: Off the starting blocks

Four years after Newmont Goldcorp made history with the world’s first all-electric gold mine at the Borden site in Ontario, Canada, fleet electrification has gathered a lot of pace. Almost all tier 1 mining companies are currently trialling electric equipment, from small ancillary vehicles to massive hauling trucks — the holy grail of carbon-free mining.
In Australia alone, BHP has begun operating 16 battery-electric Epiroc Jumbos at Olympic Dam; Rio Tinto is testing the Caterpillar battery electric 793 mining truck at its new Gudai Darri iron ore mine; AngloGold Ashanti is trialling a 65-ton Sandvik electric underground mining truck at the Sunrise Dam site; and Fortescue is preparing to deploy a 240-ton electric mining haul truck developed in partnership with Liebherr.
While the race to full fleet electrification is still very much in its first few laps, the experience gained by first movers is already providing some insights about what this transformation means for the mining industry.
NO ONE SIZE FITS ALL
The first thing that has become clear through the development and testing of electric equipment is that even when the sector matures, no one technology will have monopoly. Among the most popular low and zero-carbon technologies that are currently being developed are standalone and trolley-assisted batteryelectric vehicles, hydrogen fuel cell engines, and diesel substitutes. Based on existing pilots, battery-

electric equipment appears to be the primary technology miners are betting on.
“We chose the battery-electric approach rather than hydrogen because a lot of our projects are very close to renewable energy sources so it doesn’t make sense to incur the additional cost of transferring those photons through an electrolysis program into hydrogen and then deal with the cost of storing hydrogen prior
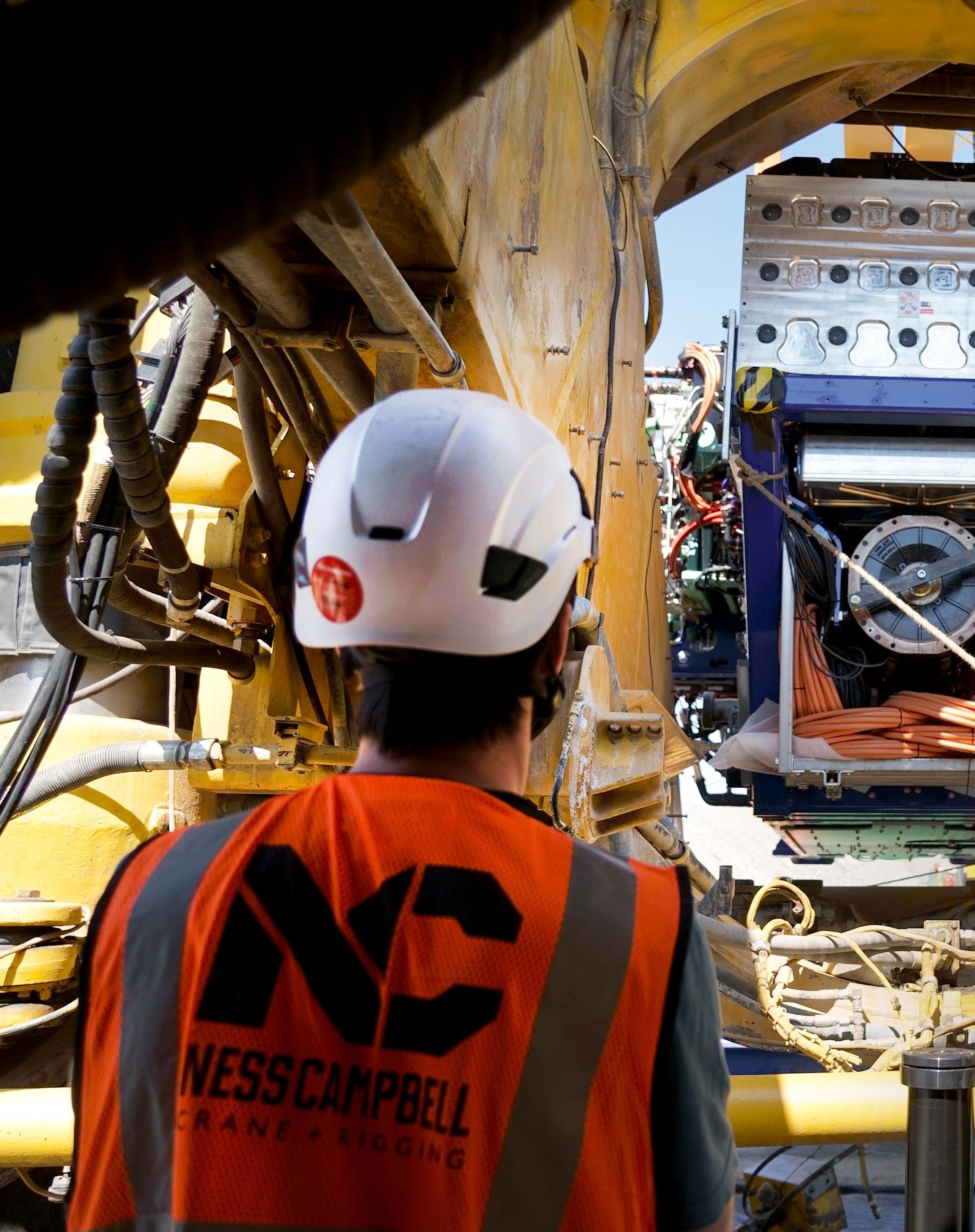
to filling up your truck, explained Shane Clark, General Manager of Strategy and Growth at MACA. “It makes a lot more sense to use the energy at the source to charge an electric vehicle, and that stationary storage could help firm the grid,” he said, adding that even the players that began their journey with a stronger focus on hydrogen seem to have pivoted towards BEVs, “given how impressive the current battery-electric prototypes are”.
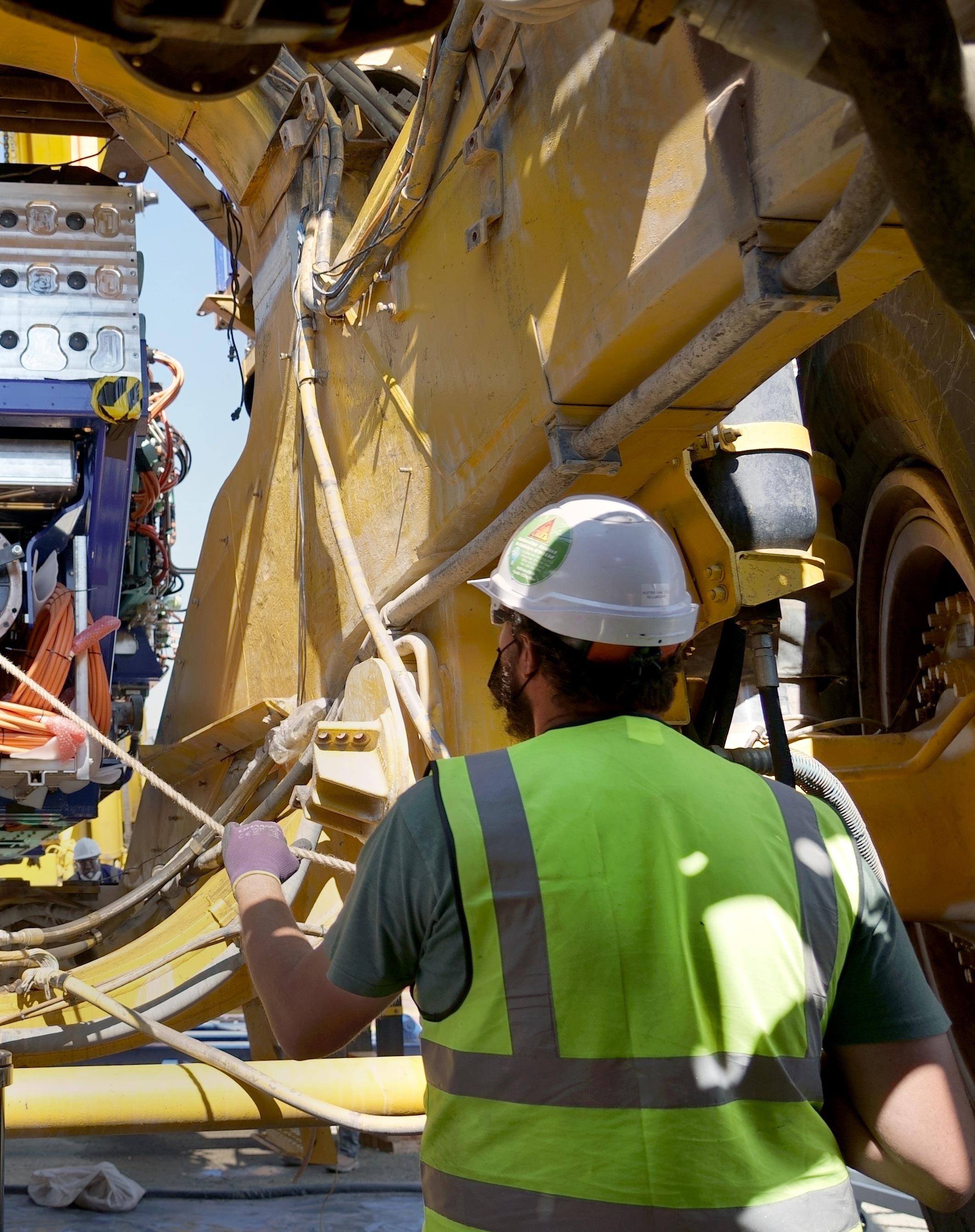
Still, hydrogen will likely have a role to play in the transition, and some equipment manufacturers are working on combining the two technologies. As a case in point, First Mode’s hybrid hydrogen and battery-powered nuGen engine should be available on the market in 2025 following a successful one-year trial at Anglo American’s platinum group metals mine in Mogalakwena, South Africa.
Since each mine presents different needs and characteristics, from location, type of pit, mine life and metal extracted to grid connection and availability of renewable resources, experts recommend evaluating and trialling the most suitable technology at the site before implementing a specific solution at a larger scale.
“There is no one solution that fits every mine or every piece of equipment at the mine or even every application scenario at every mine. The solution will also vary regionally due to the availability of green energy,” explained Michael Lewis, Technical Director at Komatsu. “For example: a deep pit mine with a long life may be best suited for battery/trolley whereas a more shallow pit may be better suited for battery with static charging or hydrogen fuel cell.”
To meet clients’ requirements, Komatsu has adopted a poweragnostic approach to truck development, allowing a mine to purchase a diesel power truck and later retrofit it with one of the company’s decarbonized solutions, such as battery or hydrogen.
DEEPENING RELATIONSHIPS BETWEEN MINERS AND OEMS
Because of this broad diversity in both mine profiles and electrification solutions, finding the right technology for a specific site requires strong collaboration between miners and
their OEMs.
For miners, it involves an adjustment from purely transactional relationships, and a willingness to share longer-term plans with their OEMs.
Industry-wide initiatives like the Electric Mine Consortium and the BluVein Consortium are promoting the type of open cooperation needed to accelerate the sector’s transition, but certain OEMs have also launched their own platforms to gather feedback from a variety of potential mining customers. That’s

the case of Caterpillar’s Early Learner Program, launched in 2021 with BHP, Freeport-McMoRan, Newmont, Rio Tinto and Teck Resources, or Komatsu’s Greenhouse Gas Alliance, started the same year with Rio Tinto, BHP, Codelco and Boliden.
OEMs are also having to expand the scope of their operations to offer unique solutions aligned with miners’ ambitions and requirements. According to Julian Soles, CEO of First Mode: “OEMs are starting to realise that they need to go much further beyond their traditional boundaries to support miners in this transition, as the change extends beyond the platform itself.”
Overall, OEMs are slowly shifting their focus from the traditional product level to the systems level, and this is going to have an impact on their business models. “We may see OEMs having to provide different payment options, such as leases for batteries or bundling of system elements so miners only need to make monthly payments to smooth out those higher costs,” added Soles.
There is another reason why OEMs might make adjustments to their business models in the future: as the electrification of global transportation progresses, the competition to obtain the materials to manufacture battery-electric vehicles is set to heat up.
“The size and scale of the automotive sector is a challenge for the comparatively small mining sector. The mining industry may have to leverage its position as the primary producer of the key ingredients in the battery supply chain to secure certainty of supply,” explained Paul Murphy, Executive General Manager, Future Industries Project at Liebherr.
Some OEMs are accelerating their development processes in order to lower their waiting times for battery components. Others are choosing slightly different battery chemistries to avoid
direct competition with the automotive sector. “Lithium titanate oxide is a power-optimised, long-life chemistry that does not provide the energy density nor cost competitiveness required in automotive applications. For us, the safety, power optimization and higher lifetime contribute to a safer, lower overall total cost of ownership of our solution. Automotive companies have historically used NMC, NCA and some are now looking at LFP, which compete for many of the same raw materials, but have different manufacturing and supply chains to deliver a completed
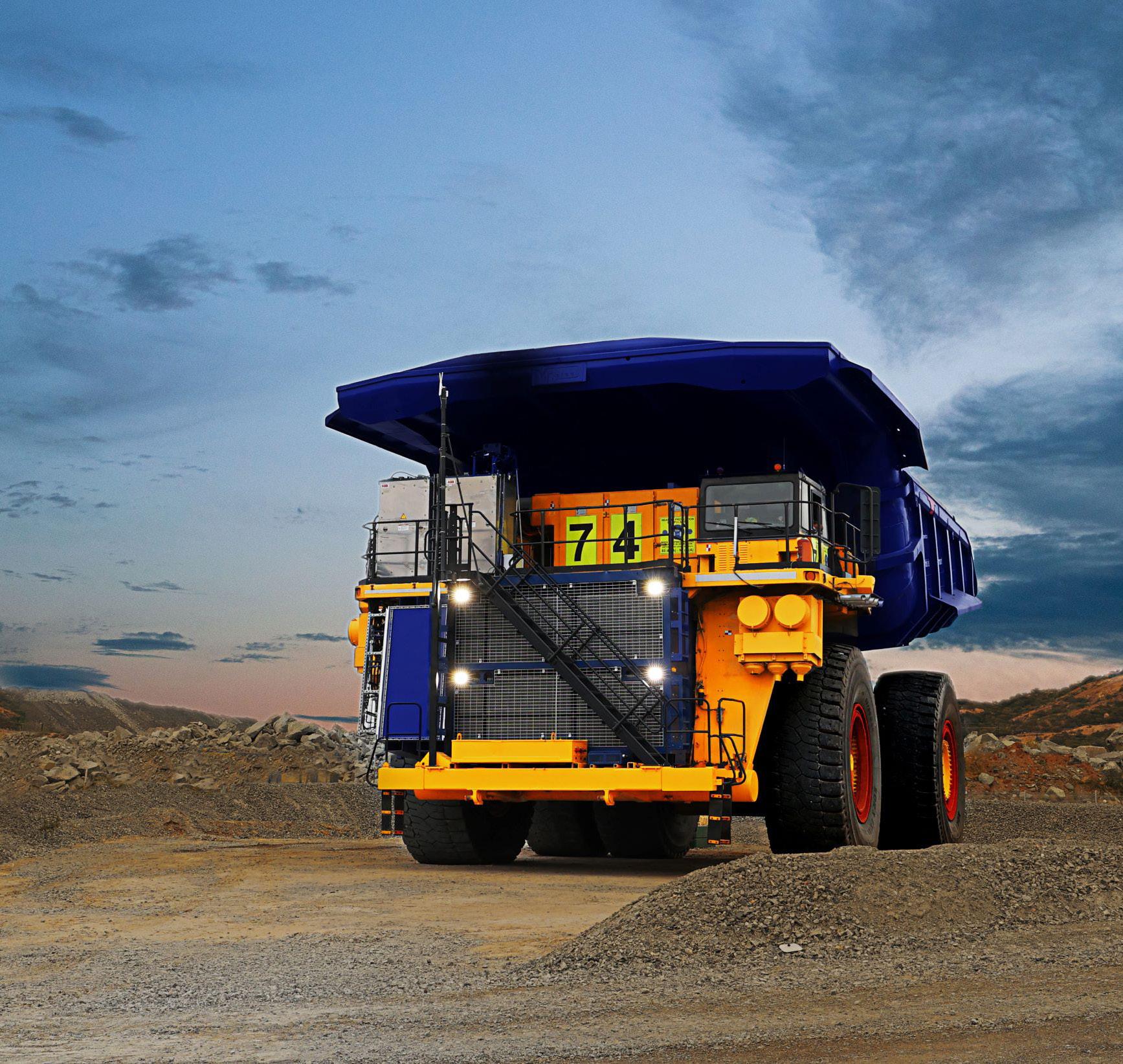
battery cell,” said Soles at First Mode.
The sector is also likely to become more vertically integrated as OEMs seek to secure the supply of battery minerals they need to build electric fleets.
FILLING TECHNOLOGY AND SUPPLY GAPS
While we are all watching the development of new types of battery or hydrogen-powered mining vehicles very closely, it’s important
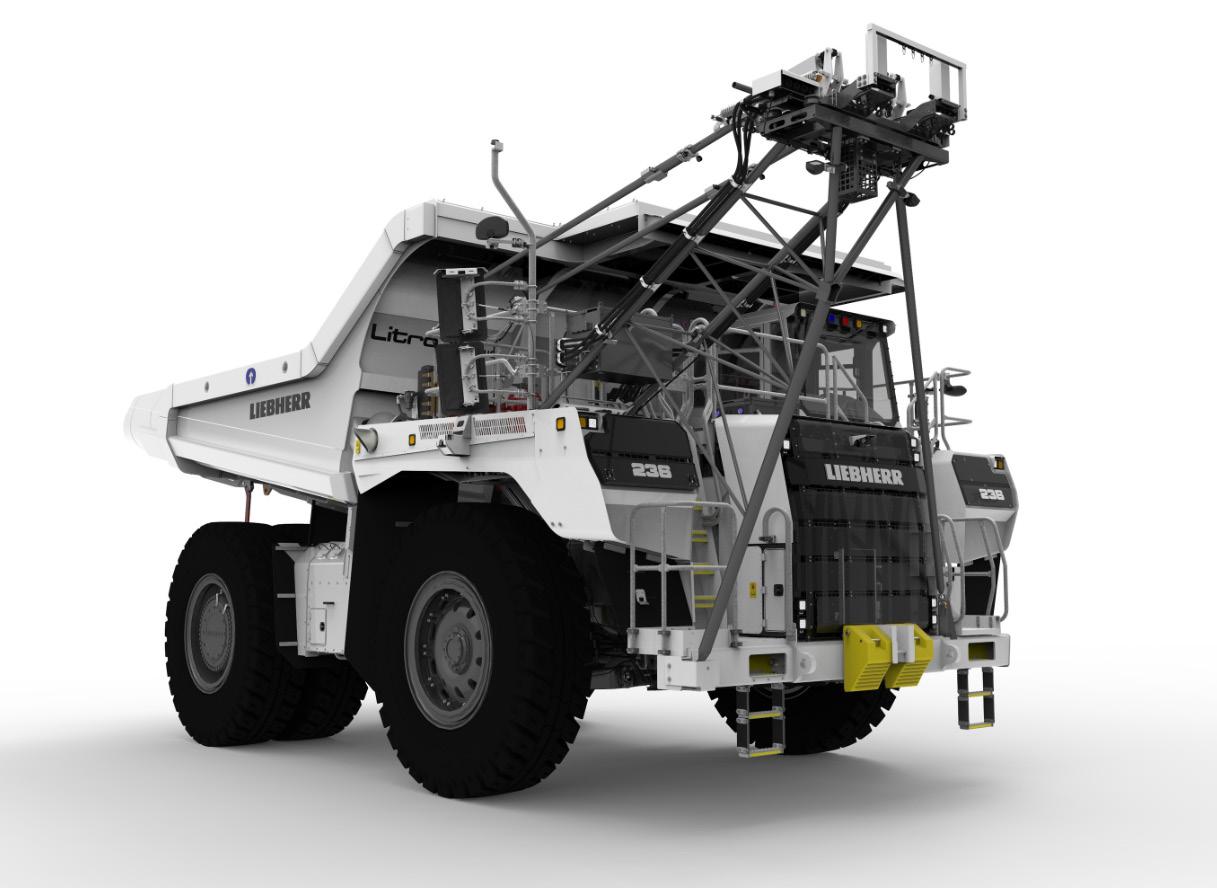
to remember that interim solutions, such as hybrid diesel-electric vehicles or truck retrofits, are already available today to help miners achieve decarbonisation targets.
Of course, switching from diesel to electric vehicles will reduce miners’ carbon footprint — but let’s not forget that manufacturing the tens of thousands of vehicles currently in operation also generated significant emissions. Retrofit solutions offer a relevant alternative to brand new equipment and ensure that operational vehicles are not wasted.
“OEMs transitioning from their current production runs to full BEV is going to be very difficult. They’re going to need robust supply chains out on very long horizons, so more dynamic manufacturers who can work both with the OEMs and battery packaging companies will be out to fill that niche with retrofit solutions,” said Clark at MACA.
But whatever technology they end up choosing, it’s important for miners to begin preparing now for the transition. “The OEMs,distributors and customers need to work together to ensure that their timeline for decarbonisation aligns with the ability to both procure the equipment and technology and enabling infrastructure but also prepare the mine for any process changes required. There will be capacity limitations but effective collaboration between the OEMs and the operators will minimise any mismatch,” advised Lewis at Komatsu.
Decarbonised fleets may still be gathering momentum, but it’s time for miners to begin the journey if they haven’t already. Considering supply chain pressures, starting a transparent conversation and setting expectations with OEMs now could determine whether or not climate goals are met within established deadlines.
The future of mining is Net Zero
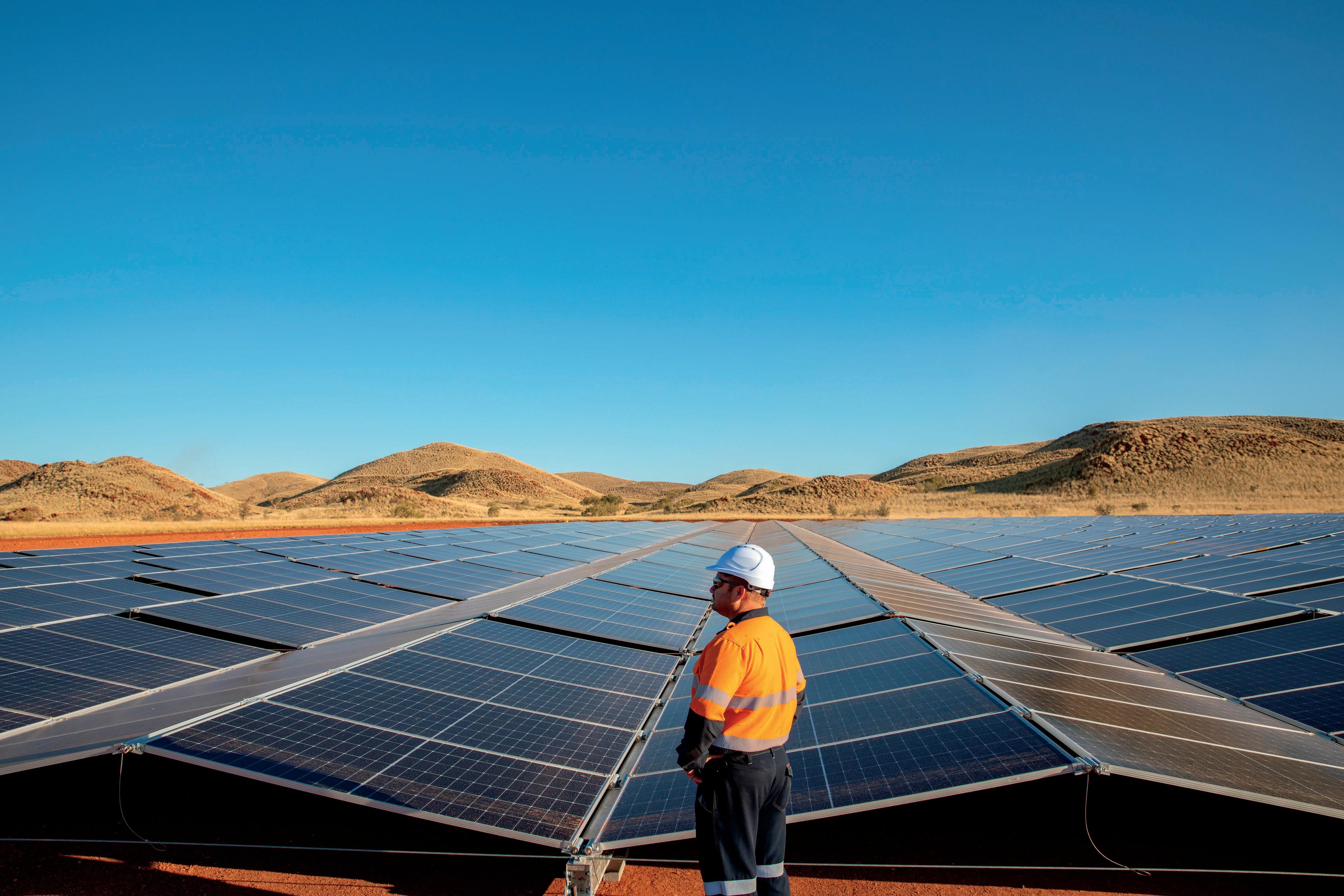
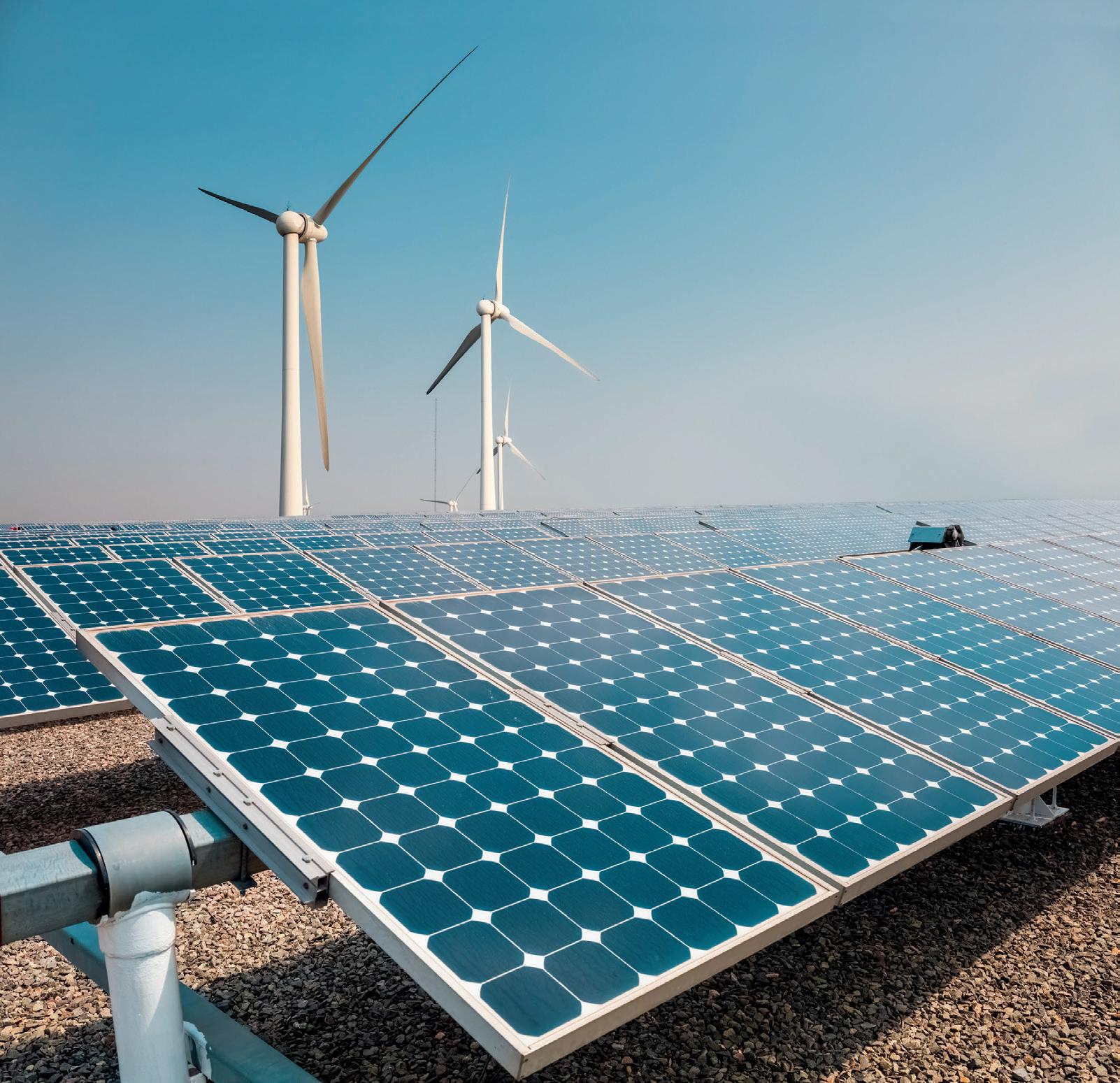
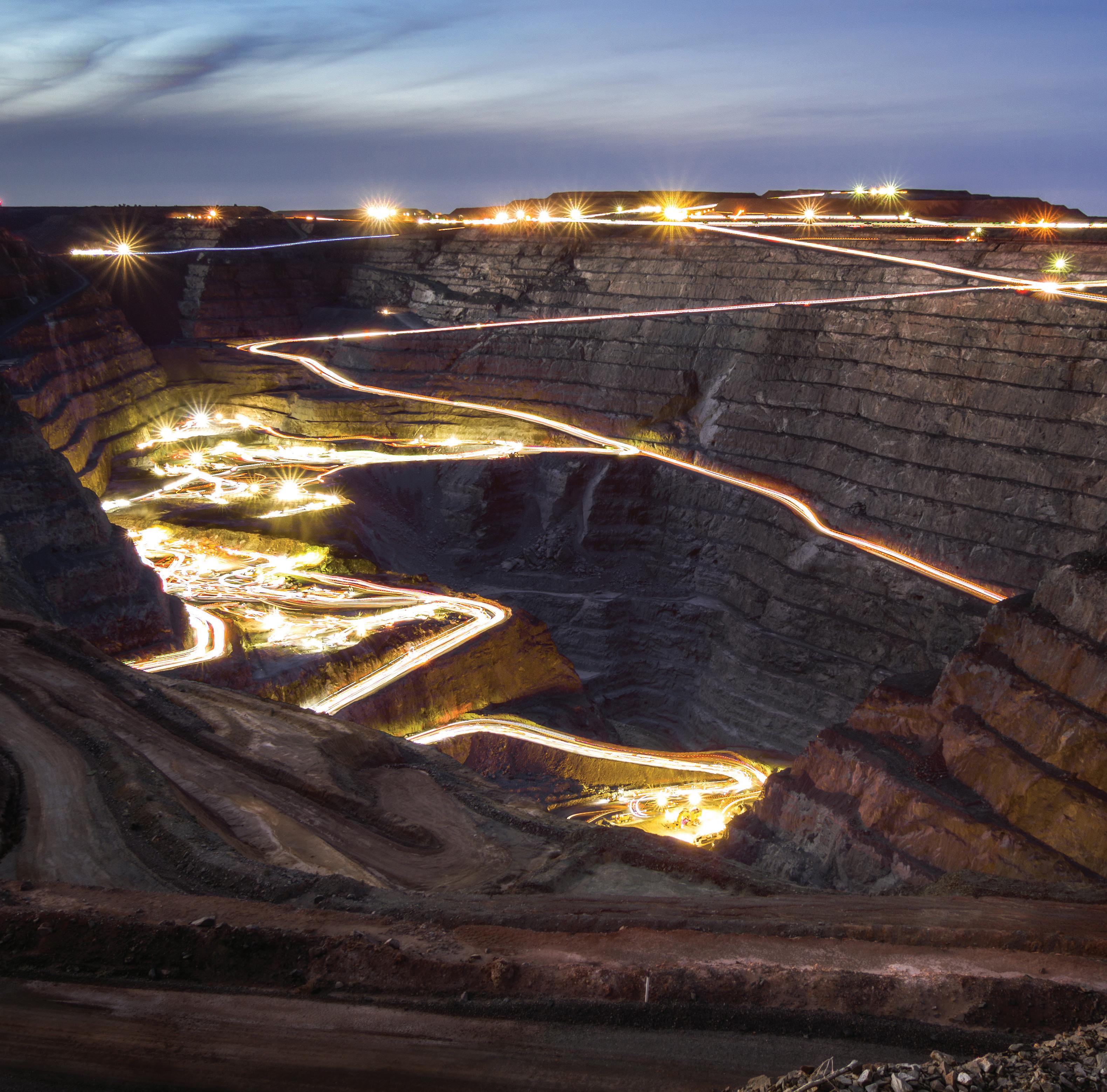
Towards the all-electric mine

Mine electrification is a necessary step in achieving a net zero mining sector, but technological, infrastructure and cost hurdles remain. Bernard Norton, Country Managing Director, Hitachi Energy in Australia, shares the lessons learned from the company’s recent work in Australian mines.
Energy and Mines: What are the main challenges with managing the transition to electrification?
Bernard Norton: If we look at the specific challenges of the energy transition from an “on the ground” perspective several issues need to be considered. First, the current infrastructure may not be sufficient to support electrification, which will bring significant new load onto the network with battery electric dump trucks, electric excavators, etc. Additionally, a stable network where generation and load are matched with the necessary connectivity to ensure availability is a major consideration. Integrating new power generation assets, managing intermittency, maintaining power quality and ensuring energy availability as and when needed whilst maintaining operational efficiencies is key, and sustainable energy and digitalisation are inextricably linked. OT & IT will need to work seamlessly to optimize the operation and maintenance of the interconnected network. New skills will be required to operate and maintain a complex, interconnected energy network.
Miners are competing with other market sectors and global economies in the drive to transition to a sustainable energy future. Efforts to build a robust and resilient supply chain, recover from the
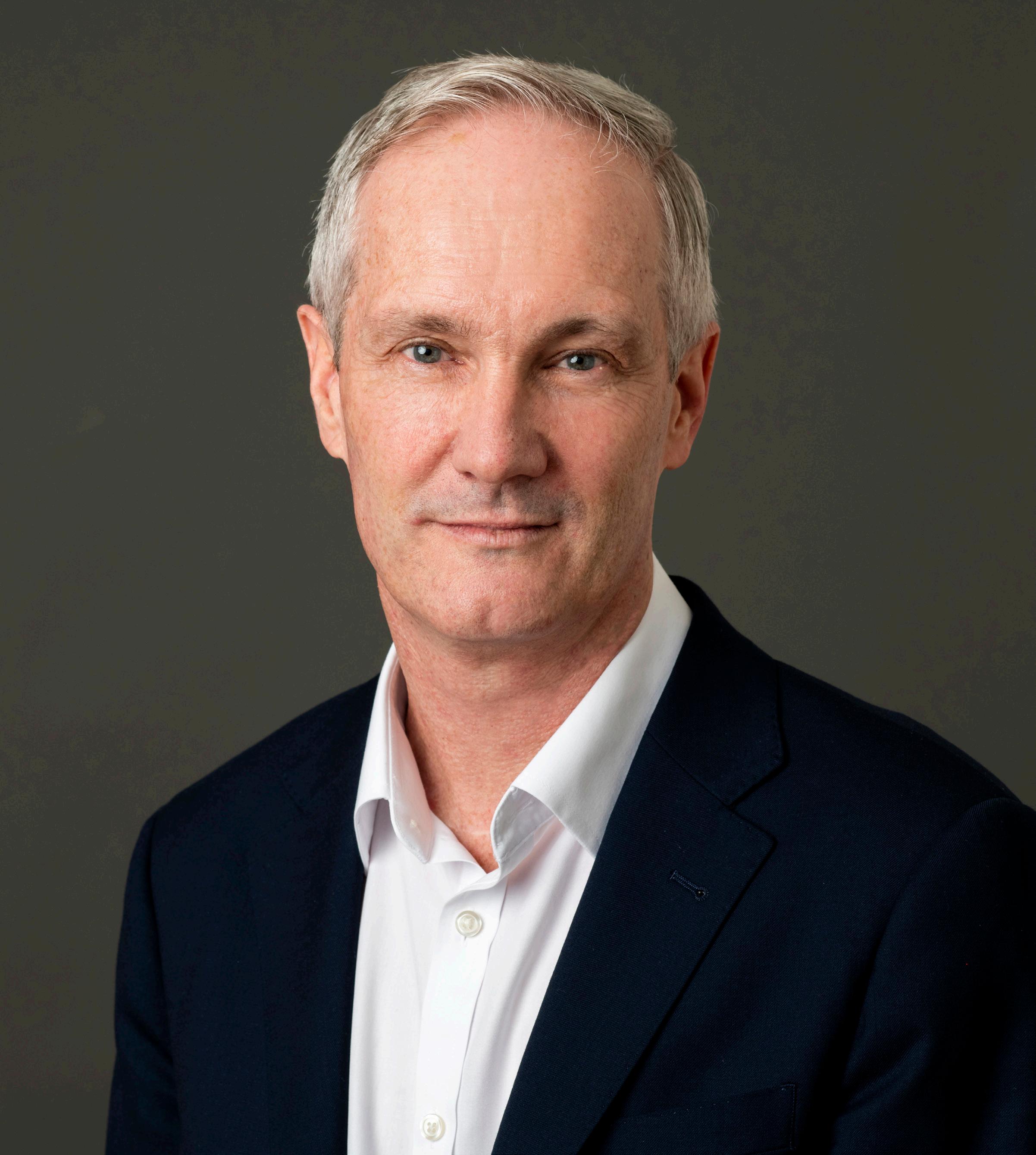
pandemic, and rebuild logistics capacities are needed. Taking a collaborative approach which engages all stakeholders and focuses on an overall program of works rather than individual projects will be a key to the successful transition to electrification. Finally, governments need to implement supportive policies and regulations to encourage, support and drive the energy transition.
E&M: How can miners choose which electrification options are best suited for a site?
BN: Assuming the driver for electrification is the decarbonisation of operations, the most important factor to consider is an understanding of what parts of the operation contribute the most to the mine’s emissions profile. For example, in a large open cut iron ore mine, digging and in mine hauling of ore contributes between 50% and 70% of total emissions. The work Hitachi is doing as part of the Charge On Innovation Challenge has strong prospects of delivering a cost-effective battery electric dump truck that charges in minutes and minimizes impact on mine operational efficiency.
Depending on whether the mine operates its own generation assets or buys in electricity, another significant contributor to emissions is energy generation. BESS operating as Virtual Spinning Reserve such as Alinta’s Mt Newman project has continued to ensure supply reliability, reduced emissions and has already recouped the initial investment since being in operation from 2017.
Other factors that miners should consider when selecting electrification options include energy needs, resource availability, operational requirements, infrastructure and cost.
E&M: Greenfield vs. brownfield electrification - how do the approaches differ?
BN: With greenfield sites, mining engineers can be more proactive and design the power system and processes with the end goal in mind. Because they are starting with a “clean sheet of paper”, fleet electrification, microgrids, digitalisation, BESS and integration with other operational features such as autonomous haul can be addressed and implemented in an optimal way.
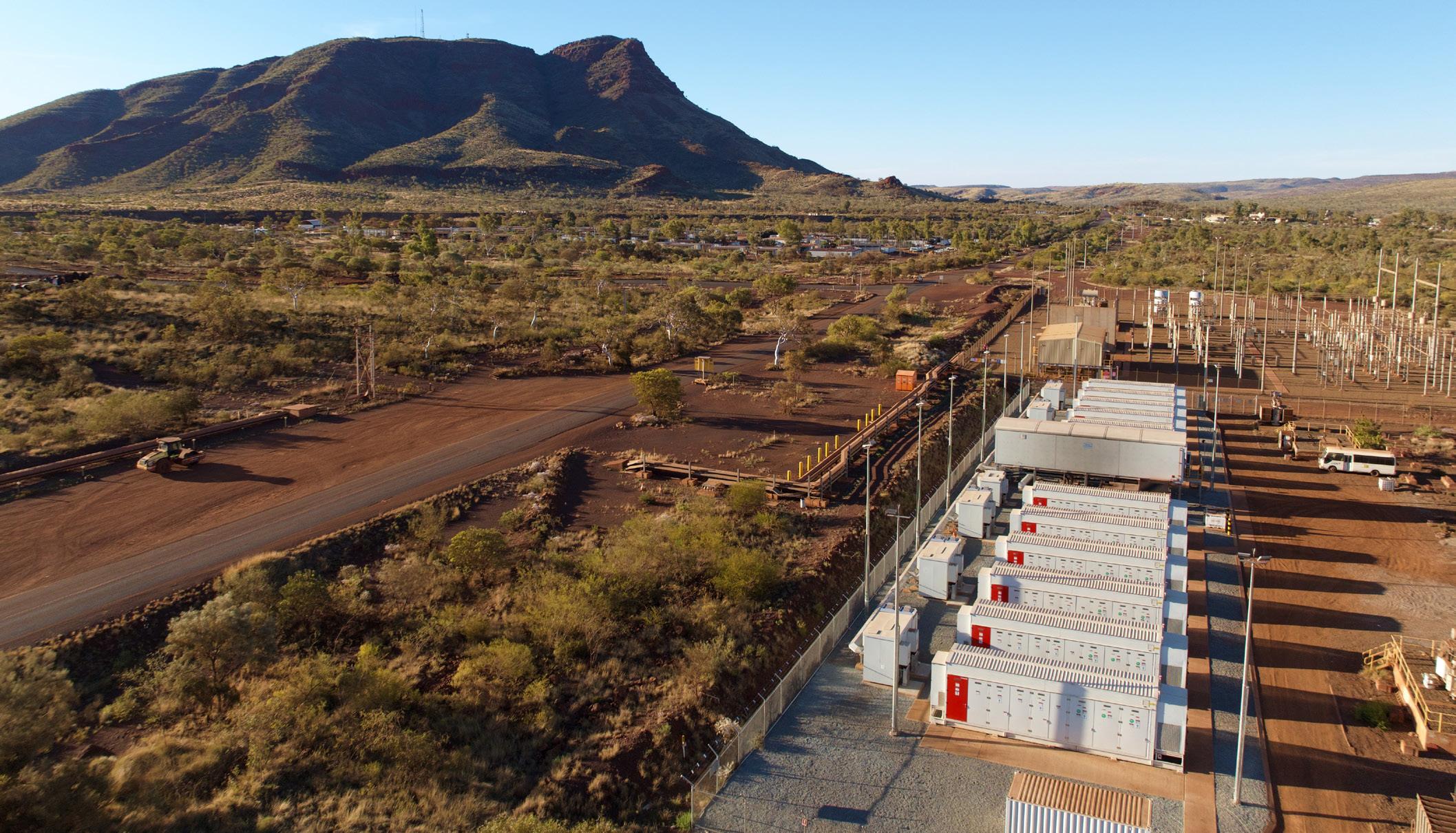
Brownfield mines, on the other hand, often have legacy systems and require more staging and management of constraints through automation and scheduling. For brownfield sites, Hitachi Energy recommends incremental mine hybridisation, where projects are staged to build toward the transition while some benefits can still be realized early. For example, we have supported off-grid mines such as Roy Hill, Tom Price, Soloman, Northstar, and many others with virtual synchronous machines and battery energy storage for virtual spinning reserve. This typically provides a sub-fiveyear payback and lays a strong foundation to connect high levels of renewables over time while ensuring power system stability.
For both brownfield and greenfield sites the starting point of the electrification journey needs to be a clear understanding of the current and future energy needs of the mine, the level of automation and digitization that will be implemented, and sustainable energy resource availability for the site. Hitachi
Energy’s consulting team can assist with establishing this baseline for both greenfield and brownfield locations.
E&M: What is the best strategy for combining automation with electrification?
BN: It’s important to understand that digitalisation and automation of the energy network are fundamental to the shift to sustainable energy. Supply, distribution and consumption systems must be integrated to ensure a reliable and resilient energy system. Data is key to successful integration of these systems, and availability of quality data enables the opportunity to further automate operations.
Key issues to consider include:
• Determine which automation and electrification technologies are best suited for your mine’s needs and operations by evaluating the scalability, interoperability, and costeffectiveness of various options.
• Develop a phased implementation plan by identifying priority areas or operations for automation and electrification and building a timeline and budget for implementation.
• Prioritize data management by investing in systems and infrastructure to collect, store, and analyze data.
• Ensure system stability by implementing measures to maintain frequency and voltage levels, manage power quality and prevent power outages.
• Invest in training and upskilling employees to operate and maintain new technologies.
• Seek partnerships with experienced providers who can provide guidance and support for the implementation of new technologies.
E&M: How can mines estimate and prepare the energy system to make the leap to all-electric?
BN: The investment required to electrify is an investment in medium and long-term assets. As with any investment of this nature careful planning and assessment of future needs is required. In the case of the transition to all electric operations, a careful assessment of the adequacy and availability of generation, transmission and distribution assets is required as part of overall mine planning.
To enable this, a techno-economic assessment is needed, which requires collaboration between technology and mining experts. And this means bringing together and working collaboratively with the right industry partners with the requisite knowledge and experience is key. This team needs to focus on balancing technology solutions with customer needs and risks to achieve the optimal techno-economic outcome for the mining operation.
The pace of change is rapid, and traditional engineer-procureconstruct models that focus solely on lowest cost CAPEX investment can leave customers with stranded or obsolete infrastructure. An optimized outcome therefore needs to consider whole-of-life and systems / solutions that enable and support enhancements and innovations that adapt the system over time.
Along with our deep domain expertise in hardware and software, Hitachi Energy has significant expertise in energy consulting. We can support miners in their electrification journey from feasibility and planning right through to execution and ongoing maintenance.
Mission
A mining industry

built on zero-emissions renewable energy, hydrogen and future fuels.
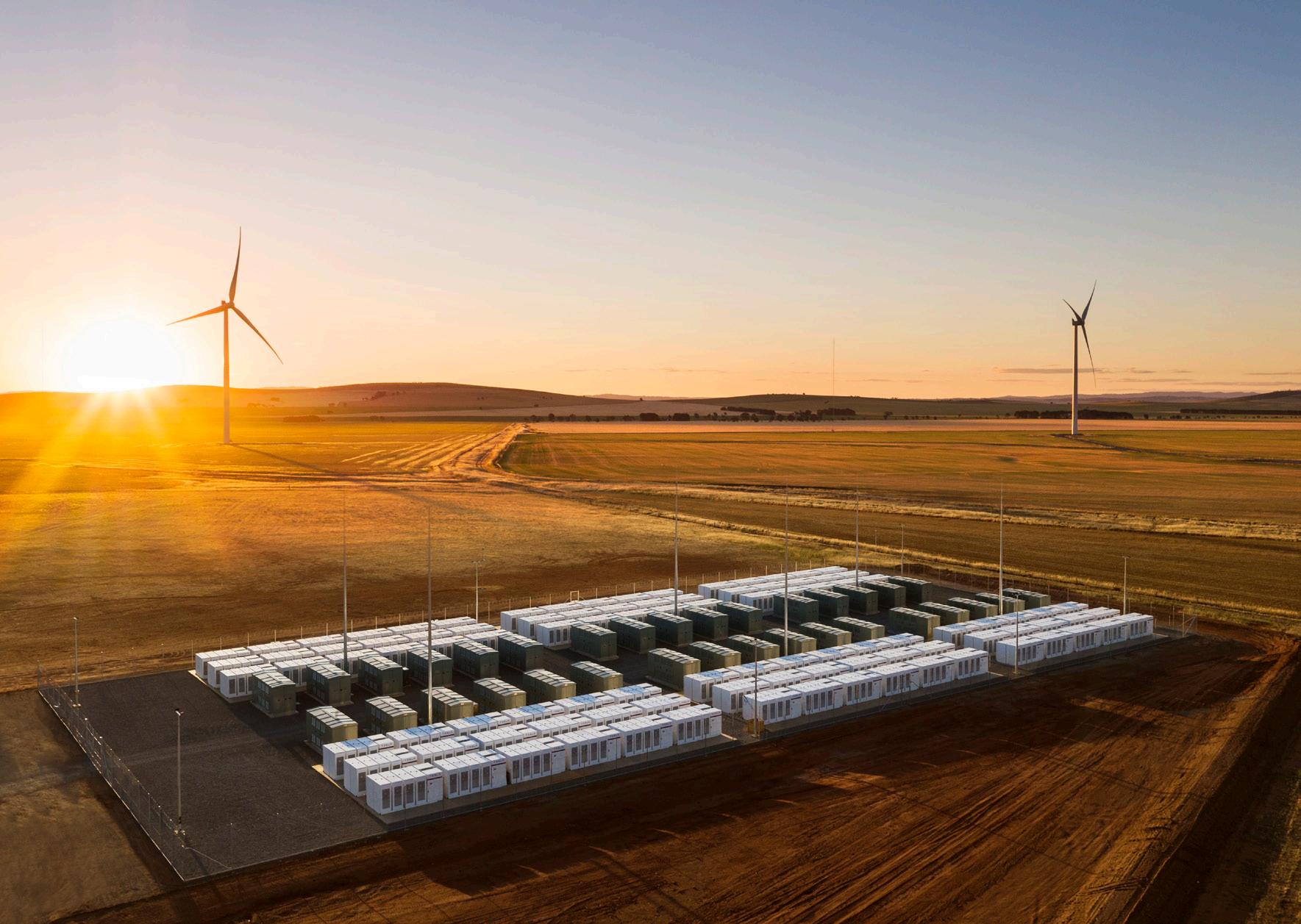
The global energy sector is transforming at pace. The way we make, move, store and use energy is quicklyand irrevocably - changing.
Discover how we’re enabling the energy transition at ghd.com/futureenergy
We are a world-leader in hybrid renewables.

As the first to deliver megawatt-scale, 100% renewable capable, off-grid hybrid power systems, we know what it takes to achieve reliable power from renewables.
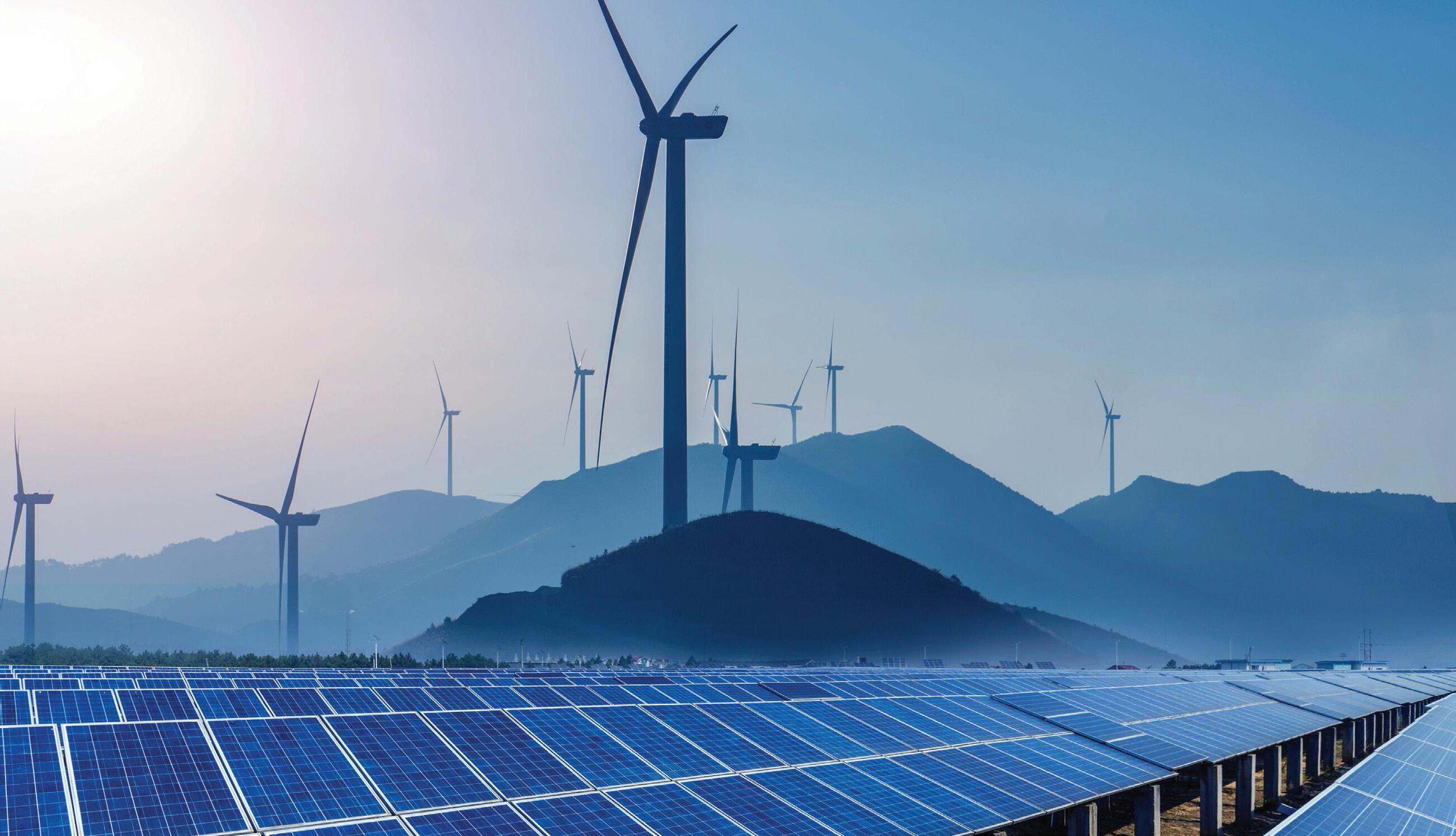
We can work with you as an advisor or system integration partner through all phases of your hybrid project from concept, feasibility and detailed design through the hybrid control deployment and commissioning.
Being independent of any manufacturer, Entura delivers the best solutions for your specific project. We’ll work closely with you to successfully manage risks where there are technical and environmental challenges.
If you would like to connect and learn more about our capabilities, please phone Greg Koppens on +61 417 393 546 or email enquiry@entura.com.au
entura.com.au
Navigating the complexity of mine decarbonisation
When it comes to powering mines, renewables are clearly the future — but they come with a steep learning curve. Andrew Drager, Business Development Manager, Energy Solutions Power at APA, shares his advice on how to leverage bundled energy solutions to achieve decarbonisation goals without compromising on reliability.
Energy and Mines: What is the ideal mix of large-scale renewable solutions that miners should consider to help achieve their decarbonisation ambitions?
Andrew Drager: There is no question renewable energy generation is stepping up at ever-increasing rates.
Wind and solar are clearly the primary technologies but the optimum mix will be site-specific, depending on factors such as site wind speeds, solar irradiance, location, mine life and existing conventional firming capacity.
However, renewables are intermittent with wind generation capacity factors typically 40% to 50% and solar around 20% to 30%. That’s why a mix of wind and solar with gas firming is essential to provide the most affordable, reliable and lowemissions energy.
E&M: What are some of the challenges of developing largescale renewables and how can miners best navigate the enormous complexities of decarbonising their operations?
AD: There are a number of challenges facing miners in decarbonising their operations, including the cost of deploying high-penetration renewable energy, the complexity of firming
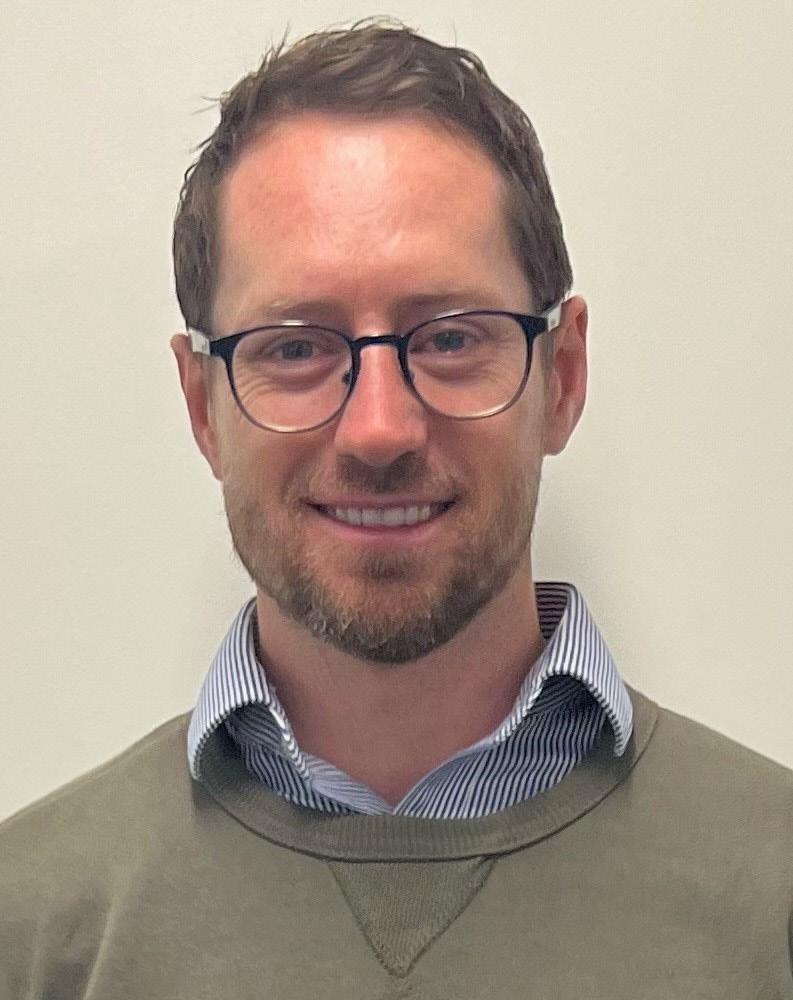
intermittent renewables, and price certainty with current supply chain and resource constraints, especially given the rest of the world is aggressively competing for these very same resources.
Large-scale renewables such as wind and solar are an excellent tool for meeting decarbonisation targets but often come with a few lessons along the way.
Partnering with industry experts is a great way to avoid an otherwise steep learning curve – long-term owners and operators of renewables and energy infrastructure can provide guidance and modelling on different solutions and help determine the optimal decision.
A flexible, data-centred approach is beneficial, looking for the optimum level of renewables penetration to match each site and budget.
Navigating the challenges of decarbonising the mining sector today, will determine success of their transition to a lower emissions future in 2030 and beyond.
E&M: How can hybrid or bundled energy solutions help miners achieve ambitions to deliver energy that is reliable, affordable and low emissions?
AD: Put simply, bundled energy solutions will help the mining sector achieve three outcomes – energy that is reliable, affordable and low emissions.
There is no doubt that reliability is key to introducing renewables. And from an operational perspective, bundled solutions can deliver simplicity and accountability.
E&M: What experience does APA have in developing largescale renewables?
AD: APA is a leading Australian energy infrastructure business with $22 billion of renewables and electricity and gas transmission assets. This includes a number of utility-scale wind farms and solar farms connected to the grids in Western Australia and on the East Coast within the National Electricity Market.
APA also owns and operates a number of microgrids including at the Gruyere mine where APA integrated a 13MWp solar farm and a 4.4MW/4.4MWh battery energy storage system (BESS), as well as the Mount Isa combined cycle power station where APA is integrating a 100MWp solar farm.
These microgrids leverage the existing gas supply infrastructure to manage the variability associated with renewable energy and ensure the reliable supply of electricity to the mine. The microgrids have reduced the cost of energy and reduced associated emissions.
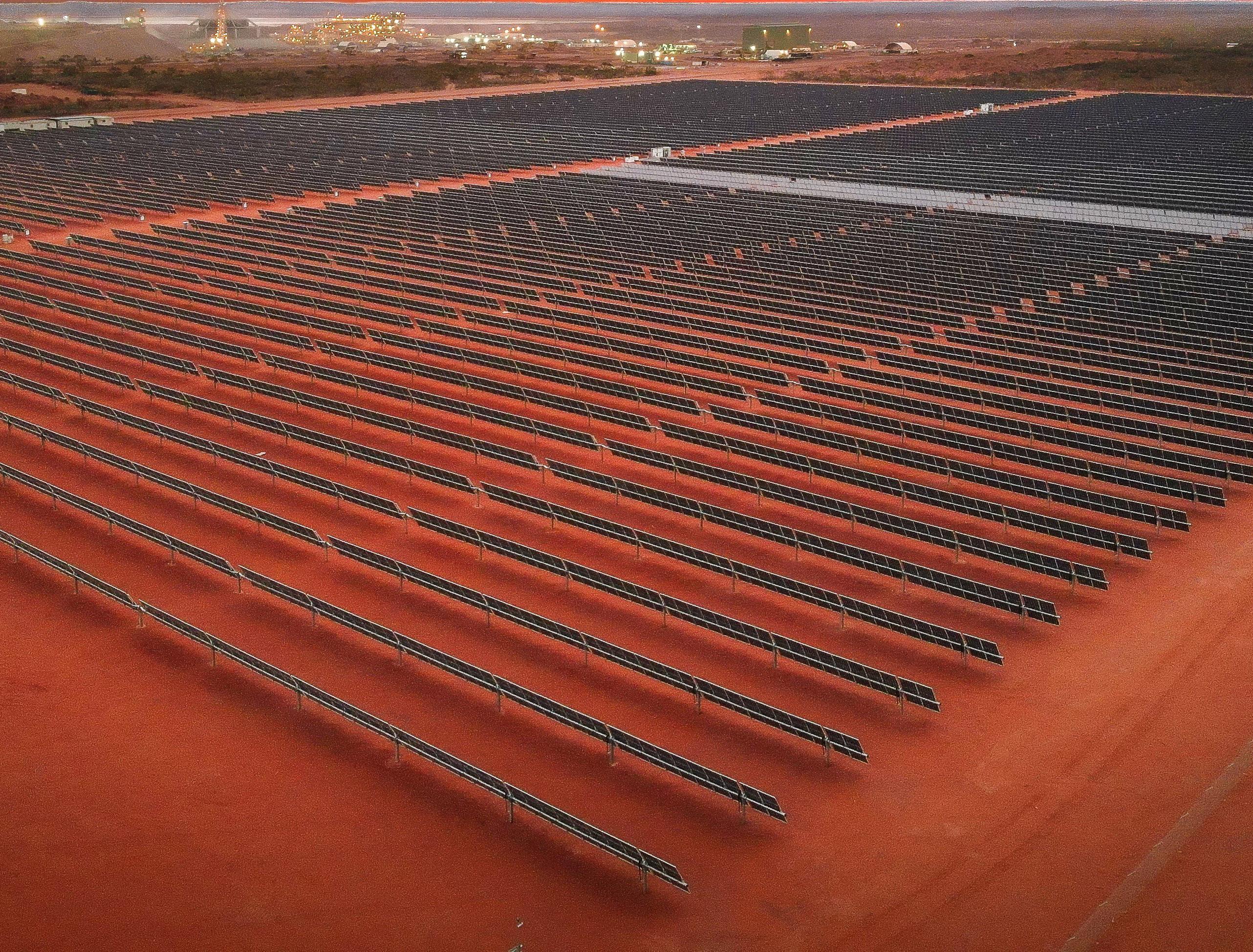
E&M: What are some of the challenges and complexities you have overcome in partnering with your mining customers to deliver bundled renewable energy solutions?
AD: Gruyere is supplied power from a natural gas power station and pipeline owned by APA and was expanded to include solar PV and BESS.
A collaborative and transparent approach with the customer overcame complexity and allowed for the lowest cost and shortest delivery timeline, particularly considering the challenges of the COVID lockdown period.
At the 100MWp solar farm in Mount Isa, APA undertook all development activities, contracting the output to three different
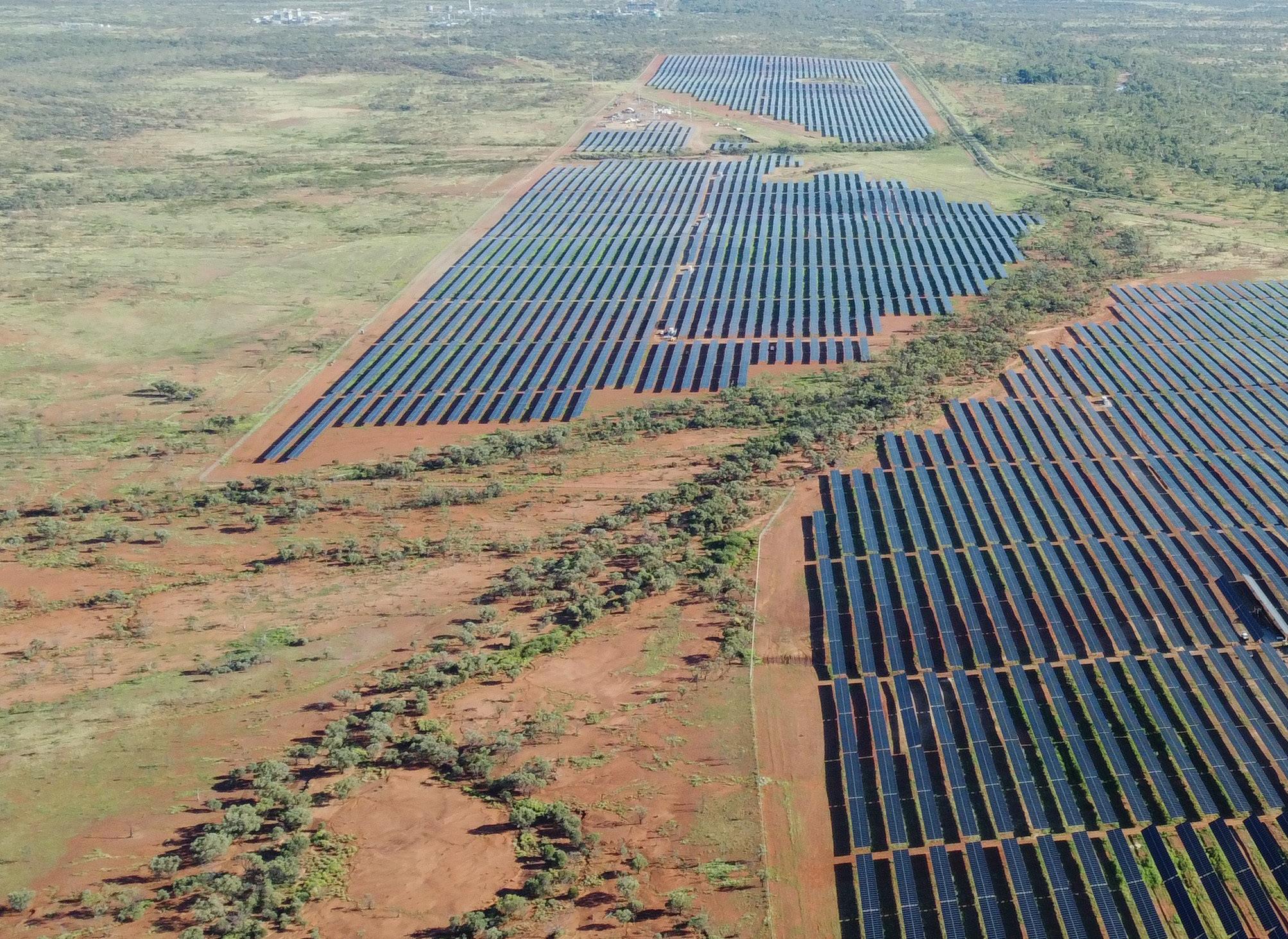
mining companies in conjunction with firming from APA’s gas power station as a single bundled service. This ensured economies of scale while providing the customers with the simplest and lowest cost solution.
The success of these projects was built on a collaborative and transparent approach with a good alignment of interests among all parties.
APA brings the skills and capability in infrastructure development and operation. And as a listed-Australian business, we’re playing an active role in supporting our customers to decarbonise their operations and achieve their net zero ambitions.
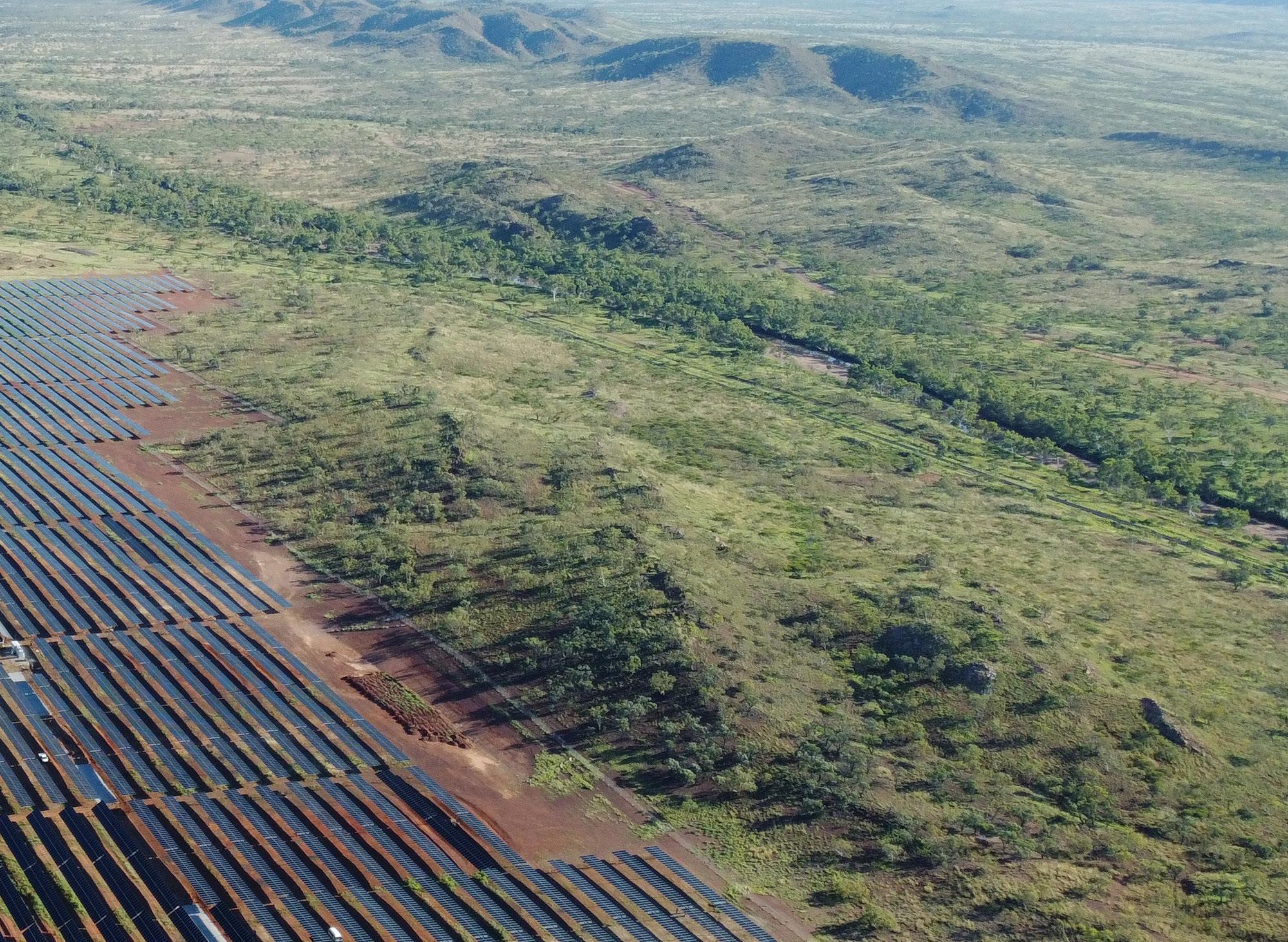