
4 minute read
MILL STORIES
Dryden Mill conducts safe maintenance outage during pandemic
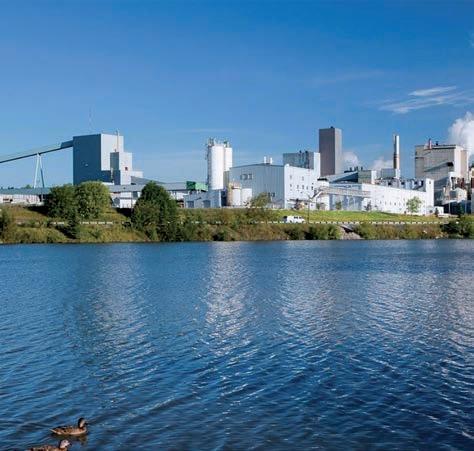
Advertisement
Article by Domtar Newsroom and S. Richard
Maintenance operations Ascheduled maintenance outage is a critical part of any are a challenge for mill managers and mill’s operation. The downtime gives employees an opportunity to complete necessary maintenance that isn’t possible during normal operations, and it ensures the mill continues their teams during the to run safely and efficiently. t s also important to the community. pandemic. While some Vendors and contractors who travel to the site to assist with the have delayed their outage support the local economy by staying in hotels, eating in outage, others have restaurants and shopping at local businesses. decided to maintain Earlier this year, everything was proceeding according to plan their original schedule for the Dryden Mill’s spring maintenance outage. The small comto preserve the industrial assets as well munity of about 8,000 people located in Northwestern Ontario, anada, as also preparing for an in u of about vendors and contractors. as the local economy. hen the pandemic started, and ryden ill anaThe experience of ger Marie Cyr and her team had some tough decisions to make. Domtar’s Dryden pulp hould they proceed ith the maintenance outage f so, could mill in Northwestern they ensure the health and safety of employees and contractors? Ontario, Canada, is Could they maintain proper social distancing? Could the facility quite inspiring in that manage outside visitors in accordance with public health regurespect. lations ould the in u of outside or ers affect the health of people living in Dryden?
COLLABORATION ENABLES SAFE MAINTENANCE OUTAGE
With support from Domtar’s corporate leadership, the team decided to proceed with the maintenance outage, but it designed a reduced work scope that focused only on tasks deemed essential for the mill s safe and efficient operation. ore or ould be performed by mill employees, reducing
the need for outside service providers by 80 percent. n addition, the ma ority of the outside providers who were required would come from within Northwestern Ontario, eliminating the need for travel from outside the region. The change in scope also meant the outage would ta e days instead of days. The team knew the plan couldn’t proceed without support and guidance from local health and safety authorities and Dryden community leaders. “As we developed our plans, we worked closely with community partners to build understanding and get their guidance,” says Marilyn Findlay, Dryden Mill’s health and safety manager. “We wanted to cooperate and assure them that we could safely execute our plan.”
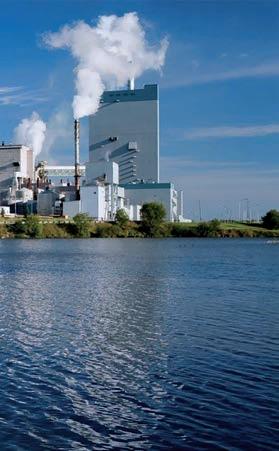
Dryden Mill leaders worked with members of the Northwestern Health Unit, the Dryden Regional Health Centre, the City of Dryden and the Ontario Ministry of Labour, Training and Skills Development to create a detailed health and safety plan that could follo related guidelines and allow the maintenance outage to occur. Naturally, health and safety are always priorities for the mill, but they’re even more critical during a pandemic — especially in Dryden, a small, remote community with limited medical facilities, located roughly ilometers miles from the nearest large city. Dryden Mayor Greg Wilson commended the mill’s efforts to anticipate and quickly respond to local uestions about the in u of contractors by providing facts and figures, as ell as open access to many third-party and internal processes.
“Thank you for putting so much time and effort into communicating your shutdown plans with us over the past few months,” he said. “Your commitment to the safety and wellbeing of our town over the years has only served to enhance an already strong relationship.” n addition to the rigorous measures already in place to address ris s, the mill adopted enhanced protocols for facility use, cleanliness, traffic o and personal protective e uipment . he largest consideration during the maintenance outage was coordinating and caring for visiting contractors to ensure everyone’s protection during the maintenance outage. A key factor in doing this successfully was the strong partnership established with a local hotel where the contractors stayed. Contractors were screened prior to arrival. The hotel staff graciously provided all meals as well as accommodations that were adequately spaced and thoroughly cleaned. Contractors had daily health monitoring and temperature checks before leaving the hotel. To ensure they met proper isolation and social distancing requirements throughout their stay, contractors remained on hotel property when not at the mill, and they were accounted for with each arrival and departure. The maintenance outage happened between ay and une , and everything ent according to plan. he process as e tremely efficient and successful, but most of all, it was safe.
Lindsay Gannon is a superintendent for Venshore Mechanical Ltd., one of the contractors helping with the maintenance outage. She thanked the mill team for their planning efforts. “Everything, from our accommodations, site access, issuing permits and maintaining social distancing in common areas, was well thought out. It really made our job much easier.”
DRYDEN MILL SETS INDUSTRY EXAMPLE
The Dryden maintenance outage’s success in the midst of the pandemic has garnered national attention in Canada at a time when many other pulp and paper operations are considering cancelling, or have already cancelled, similar maintenance outages. The mill shared its story through Canadian industry trade associations, and it’s now considered a best management practice for other mills to consider.
“2020 has brought along many new challenges and uncertainties to overcome,” says Domtar Pulp Vice President Steve Makris. “The challenge presented to the Dryden team to address safe and critical operations during a pandemic was not an easy one. But I’m proud of the process they followed to achieve a positive outcome. It truly embodies Domtar’s core principles of being agile, caring and innovative.”