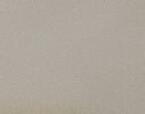

SMART MANUFACTURING
LAMIPAK IN ASEPTIC PACKAGING
OPPPORTUNITIES IN AFRICAN MEAT INDUSTRY
SUSTAINABLE ANIMAL WELFARE
CEO Arnold Prinsloo on the company's contributions to a stable and sustainable pork industry in South Africa
My Company Profile: Eskort
107 years and counting in producing and processing South Africa's pork and meat products. ON THE COVER - Arnold Prinsloo, CEO, Eskort
Packaging & Processing: Lamipak's role in Beverage Packaging
Ajas Shaikh on Lamipak’s Role in Supporting the Growth of the Beverage Industry in the Middle East and Africa
FOUNDER & PUBLISHER
Francis Juma
SENIOR EDITOR
Abel Ndeda
EDITOR
Francis Watari
EDITOR
Nicholas Ng'ang'a
EDITOR
Victor Atsali
BUSINESS DEVELOPMENT DIRECTOR
Virginia Nyoro
BUSINESS DEVELOPMENT ASSOCIATE
Vivian Kebabe
HEAD OF DESIGN
Clare Ngode
ACCOUNTS
Jonah Sambai
Published By: FW Africa
P.O. Box 1874-00621, Nairobi Kenya
Tel: +254725 343932
Email: info@fwafrica.net
Company Website: www.fwafrica.net
Food Business Africa (ISSN 2307-3535) is published
6 times a year by FW Africa. Reproduction of the whole or any part of the contents without written permission from the editor is prohibited. All information is published in good faith. While care is taken to prevent inaccuracies, the publishers accept no liability for any errors or omissions or for the consequences of any action taken on the basis of information published.
www.dairybusinessafrica.com
Reflecting on a year of growth: Africa's food industry milestones and the future ahead
As 2024 draws to a close, we want to congratulate you on your remarkable resilience. December serves as a time to reflect, celebrate our achievements, and recognize how far we’ve come—from January to December. The end of the year is often marked by moments of reflection on the journey we’ve taken, from the joyous to the challenging, and even the quiet moments in between. While this issue wasn’t originally designed as a call to reflect, it offers a valuable perspective on the remarkable developments within Africa’s food industry landscape over the past year.
This year, we celebrated a highly successful AFMASS Food Expo Eastern Africa Edition 2024, and we are thrilled to announce that the 2025 edition will be held in Uganda. Join us from February 11-13, 2025, at Africana Hotel in Kampala, Uganda, as we continue to bring the best of the African food industry together.
The Great Lakes region of Africa continues to offer some of the most promising emerging opportunities in the food sector. The region’s impressive growth in the agricultural production of key commodities, including milk, maize, meat, poultry, fish, coffee, tea, and oilseeds such as soybeans, nuts, and palm oil, positions it as a vital player in Africa's food industry.
Our cover feature in this issue celebrates Eskort Foods, South Africa’s leading pork processor, which has remained dedicated to producing high-quality, antibiotic-free pork for over 107 years. From its humble origins as a farmers' cooperative, Eskort has grown into a leading company with advanced retail stores and state-of-the-art facilities.
The Meat and Poultry section takes a closer look at Africa’s
rapidly expanding meat industry, driven by urbanization and changing diets. While the sector faces challenges, there are abundant growth opportunities through investment in modern farming techniques, cultured meat technologies, and market diversification.
In our technology-focused feature, we delve into the smart manufacturing revolution within the beverage industry, where innovations such as smart factories are enhancing efficiency, reducing labor costs, improving quality control, and boosting transparency and traceability across the value chain.
Additionally, we highlight significant investments in Africa’s beverage industry in 2024. With its youthful and increasingly affluent population, the African beverage market remains poised for continued growth and transformation.
In the food safety standards and practices segment, we bring you an article on comprehensive approach that prioritizes the well-being of animals, enhances food security, and mitigates environmental impacts. This paradigm shift not only addresses pressing concerns but also lays the foundation for achieving long-term goals, such as net-zero greenhouse gas emissions, creating a balanced and thriving ecosystem for all life on Earth.
As we bid farewell to 2024, we extend our warmest wishes for a Merry Christmas and a wonderful New Year. We look forward to seeing you in Uganda!
Abel Ndeda Senior Editor FW Africa
AFMASS Food Manufacturing Expo Uganda Edition
February 11-13, 2025
Africana Hotel, Kampala, Uganda www.ug.afmass.com
Gulfood
February 17-21, 2025 Dubai World Trade Centre www.gulfood.com
IAOM MEA Regional Milling Forum
Feb 18-20, 2025 Rwanda www.iaom-mea.com
Food Pack East Africa Tanzania 2025
Jan 23 – 25, 2025
Diamond Jubilee Hall, Dar-EsSalaam, Tanzania www.mxmexhibitions.com/ foodpackTanzania
East Africa Food & Beverages Expo
Jan 29 - 31, 2025
Old Kampala Sec. Platy Grounds, Kampala, Uganda. www.eafoodbeveragesexpo.com
Kenya International Trade show 2025 – 16th Edition
Jan 31- Feb 2, 2025
Sarit Expo Centre in Nairobi, Kenya www.growexh.com/ kenyatradeshow
Future Food Tech
March 13-14, San Francisco, USA www.futurefoodtechsf.com/
Annual Meat Conference March 24-26, 2025 Orlando, Florida, USA. www.meatconference.com
Sign up today to receive our bi-weekly food, beverage and milling plus packaging industry email newsletters. Never miss breaking news from Africa and the World, twice a week www.foodbusinessafrica.com/signup
IFFA 2025
May 3–8, 2025
Messe Frankfurt, Frankfurt, Germany www.iffa.messefrankfurt.com/ frankfurt
Food Safety Summit
May 12-15, 2025
Donald E. Stephens Convention Centre, Rosemont, Illinois, USA www.food-safety.com/food-safetysummit
AFMASS Food Manufacturing Expo Kenya & Eastern Africa Edition
July 2-4, 2025
Sarit Expo Centre, Nairobi, Kenya www.afmass.com
Africa Future Food Summit
July 2-4, 2025
Sarit Expo Centre, Nairobi, Kenya www.africafuturefoodsummit.com
RWANDA – Luxmi Tea Co. Pvt. Ltd, a global leader in the tea industry, has announced the acquisition of Sorwathe Ltd, one of Rwanda’s oldest and most prominent tea companies for undisclosed amount.
According to the companies, this acquisition marks the beginning of a new era for Sorwathe, renowned for its 50 years of pioneering contributions to Rwanda’s tea sector under the leadership of the Wertheim family.
Meanwhile, Luxmi Tea, led by the Chatterjee family, brings over a century of experience and a heritage of sustainability and quality that aligns with Sorwathe’s values.
Dipankar Chatterjee, Chairman of Luxmi Tea Co.,
expressed his vision for elevating Sorwathe’s reputation to new heights. He highlighted the global shortage of highquality tea, positioning Sorwathe as a key player in addressing this demand.
Chatterjee reaffirmed Luxmi’s commitment to producing world-class teas while building on Sorwathe’s legacy.
In 2019, Luxmi invested US$30 million in expanding the Rugabano Tea Factory in Rwanda’s Karongi District.
The factory, which cultivates 438 hectares and processes green leaf from 4,000 hectares of smallholder farms, is set to reach a processing capacity of 4,000 metric tons annually by 2029.
Rwanda's tea industry has grown steadily, with production increasing from 5,910 tonnes in 1980 to 40,003 tonnes by the financial year ending June 2024.
The sector remains a vital contributor to Rwanda's economy, with exports bringing in significant revenue and creating jobs for thousands of Rwandans.
According to the National Agricultural Export Development Board (NAEB), the sector has supported over 659 community projects since 2005.
These projects include schools, health centers, and water supply systems, underscoring the sector's role in improving livelihoods.
Tanzania’s beverage industry sees robust growth, surpasses US$3B in sales
TANZANIA – Tanzania’s beverage industry has experienced significant growth, generating US$3 billion in total sales in 2023, up from US$2.5 billion in 2022, according to the Tanzania Investment Centre (TIC).
This impressive surge is attributed to increased market demand and proactive government initiatives to foster a conducive business environment.
TIC Executive Director Gilead Teri highlighted the government’s efforts to improve the business and investment climate, which have attracted both local and foreign investments.
“The growth in sales revenue in the beverage industry is contributed by the continued efforts made by the government to create a favourable business and investment environment in the country,” he stated.
The spirits sector alone contributed US$731 million to the overall sales, reflecting a steady recovery and expansion driven by rising consumer demand for both alcoholic and nonalcoholic beverages.
Teri emphasized that government incentives, such as reducing the minimum investment threshold from US$100,000 to US$50,000 in 2022, have facilitated easier market access and bolstered investor confidence.
During an October 2024 address, Vice President Philip Isdor Mpango reaffirmed the government’s commitment to infrastructure development, including upgrading road and port facilities.
These improvements aim to streamline import and export processes, which are critical to supporting the beverage industry’s growth.
Teri further noted that nearly 70% to 80% of beverages available in the Tanzanian market are already produced locally.
He projected that in the next two to three years, the majority of imported beverages would also be manufactured domestically, thanks to sustained investments in local production capacities.
By November 2024, the TIC had registered 800 investment projects, indicating a promising trajectory for the year.
Cape Food Ingredients (CFI) has doubled its factory and office space in Kenya, reflecting continued solid growth in sales and manufacturing volumes.
CFI East Africa (also known as CAPEL Food Ingredients) has been manufacturing flavours and ingredient specialties for over 7 years in Kenya.
The factory also maintained its FSSC/ISO status in its recent 2024 audit, showing a clear commitment to quality production for East Africa.
As part of the expansion of production powder blending facilities have doubled in capacity. For manufacturing of liquids such as flavours, additional blending room has been commissioned.
Product development for customers in East Africa has been enhanced by a new Tasting Evaluation Center. Customers are encouraged to come and work with the New Product
Development team to achieve their goals, whether in beverages, dairy, confectionery, snacks and sauces.
The facilities also boast a full test bakery for breads, cakes, muffins and similar.
The expanded production and product development facilities work together with CFI's other regional factories and NPD Centers inWest Africa (Accra) and Southern Africa (Cape Town). By sharing formulations which are appropriate for Africa, cost for customers are lowered while maintaining quality. CFI has numerous unique products for lowering product costs.
In addition, with its regional centers in full operation, customers benefit from low MOQs, much faster delivery/ transit times, local currency invoicing and also avoid the headaches and high cost of importing flavours and other ingredients.
FEBRUARY 11-13, 2025 | KAMPALA, UGANDA
No.1 Trade Shows for Food Service, Hospitality & Travel Industry in Africa
INDIA – Hindustan Coca-Cola Beverages (HCCB), the bottling subsidiary of Coca-Cola in India, has opened a new Greenfield manufacturing plant in Banda Thimmapur, Siddipet, Telangana.
Spanning 49 acres, the facility represents a planned investment of ₹2,091 crore (approximately US$246.89m), with ₹1,409 crore (US$166.4m) already allocated for the first phase.
The cutting-edge factory features seven advanced production lines and integrates modern manufacturing technologies with sustainable practices.
It is anticipated to generate employment opportunities for 410 individuals, both directly and indirectly.
“This state-of-the-art factory merges advanced manufacturing technologies with sustainability, setting a new standard in the industry. The government’s proactive support has been instrumental in overcoming challenges and ensuring the successful start of operations,” noted Juan Pablo Rodriguez, CEO of HCCB.
This marks HCCB’s second facility in Telangana,
complementing its existing plant in Ameenpur, Sangareddy District.
Together, the two facilities represent a combined investment of ₹3,798 crore (US$448.4m) and provide over 1,000 jobs.
Telangana Chief Minister A Reventh Reddy highlighted the significance of this development, stating, “HCCB’s investment in Banda Thimmapur reinforces Telangana’s position as a key destination for global industrial investments. Their comprehensive approach will not only create jobs but also uplift communities and drive regional development.”
HCCB has been involved in community initiatives in Telangana, positively impacting more than 173,000 individuals. These programs include skill development for youth, financial and digital literacy for women, and installations of Water ATMs and smartboards in schools.
With a robust retail presence of nearly 180,000 outlets in Telangana, HCCB continues to contribute significantly to the state’s economy and the FMCG sector in India.
MAURITIUS – Phoenix Beverages Limited (PBL), the leading brewery in Mauritius, reported a 7.1% rise in group sales volume, reaching MUR 12.17 billion (US$262.87m) for the financial year ending June 30, 2024, compared to MUR 10.61 billion (US$227.42m) the previous year.
Group net profit increased significantly by 49.1% to MUR 1.09 billion (US$23.56m), driven by strong performance in Mauritius and favorable exchange rate movements in its foreign operations.
Operations in Réunion Island notably supported profitability, contributing MUR 172 million (US$3.7m), an increase from MUR 135 million (US$2.9m) in 2023.
The growth was further fueled by the full-year impact of PBL's distribution partnership with Pernod Ricard in Réunion and an increase in export volumes.
Group EBITDA climbed by 35.9% to MUR 1.95 billion (US$42.1m), while company-level EBITDA rose by 44.9% to MUR 1.65 million (US$35.55m).
The company highlighted that its group EBITDA achieved a compound annual growth rate (CAGR) of 15.2% between 2020 and 2024.
Acknowledging the challenges of the current business environment, PBL CEO Bernard Theys cited supply chain disruptions, rising energy costs, high interest rates, and foreign currency shortages as significant hurdles.
Despite these challenges, PBL invested MUR 417 million (US$9m) in FY2024 for capital expenditure, focusing on
bottles, crates, and machinery upgrades.
Looking ahead, PBL intends to continue investing in equipment over the next two years to enhance production capacity and efficiency.
Plans include modernizing production lines, optimizing energy consumption, and improving sustainability practices.
The company is also focusing on strengthening its market position through regional expansion and product innovation.
As part of its growth strategy, PBL acquired a 28.15% stake in African Originals Limited in October 2023.
African Originals, based in the UK, owns 100% of Savannah Brands Limited, a fast-growing Kenyan beverage company. PBL affirmed its commitment to increasing its stake to support Savannah Brands’ growth in East Africa.
PepsiCo launches US$41M new potato chip production
SOUTH AFRICA – PepsiCo South Africa has launched a cutting-edge potato chip production line at its Isando plant in Johannesburg, backed by a significant R746 million (US$41.2 million) investment.
This initiative is designed to enhance the company’s potato chip manufacturing capacity, address increasing local demand, and streamline supply chain operations by minimizing longdistance distribution.
Operating within the competitive savory snack industry, PepsiCo South Africa holds a strong position, competing with key players like AVI Limited.
Companies in this sector are adopting innovative strategies such as product launches, expansions, collaborations, and acquisitions to maintain growth and expand their market presence.
The savory snack market in South Africa is poised for remarkable growth, estimated at US$1.78 billion in 2024 and projected to reach US$2.58 billion by 2029, growing at a CAGR of 7.74%.
This expansion is fueled by evolving consumer behaviors, including the rise of “snackification,” driven by cultural, economic, and demographic changes.
Rising disposable income and increasing demand for convenient snacks further contribute to this trend.
Ingredients
Industrial & Butchers Equipment
Bandsaw Blades
Sausage Casings
Bandsaw Blades Sausage Casings
Home Meal Replacement (HMR)
& Butchers Equipment Home Meal Replacement (HMR)
Technical innovation and customer experience is at the heart of the Freddy Hirsch Group.
PepsiCo’s operations in South Africa began in 1997 with its investment in Simba, and the company has consistently worked to diversify and expand its product offerings.
Technical innovation and customer experience is at the heart of the Freddy Hirsch Group.
Our team is dedicated to developing robust processing systems and quality products to deliver effective solutions to our customers.
Recently, it sold its Marmite and Bovril spreads business, along with its Savoury Food Ingredients division, to Lallemand Inc. via Rymco Pty Ltd., trading as Anchor Yeast.
In the beverage segment, competition has intensified following the acquisition of Beverage Company (BevCo) and its subsidiaries by Varun Beverages Ltd, PepsiCo’s largest franchise bottler.
This acquisition, finalized on March 26, 2024, after obtaining approvals from PepsiCo Inc. and the Competition Commission South Africa, made BevCo a subsidiary of Varun Beverages.
Our team is dedicated to developing robust processing systems and quality products to deliver effective solutions to our customers
Our team is dedicated to developing robust processing systems and quality products to deliver effective solutions to our customers.
+254 113 003483 www freddyhirsch co za info@freddyhirsch co za
Freddy Hirsch Group Kenya Limited
www.freddyhirsch.co.za
info@freddyhirsch.co.za
UAE – Dubai plans to reintroduce a 30 percent tax on alcohol sales starting January 1, 2025, reversing a suspension implemented in late 2022 to boost tourism.
The announcement, conveyed to restaurants and bars by major distributors MMI and African+Eastern, stated that the Dubai government had mandated the reinstatement of the tax on all alcohol purchases invoiced from January 1, 2025. Businesses were instructed to ensure compliance with the new regulation.
Originally, the tax suspension was set to last one year, from January to December 2023, but was extended through 2024.
This initiative allowed restaurants, bars, and hotels to save significantly on alcohol purchases, with consumers benefiting from a 30 percent price reduction at MMI and African+Eastern outlets.
However, these savings were not fully passed on to customers due to operational costs such as rent, labor, and
overheads.
Naim Maadad, founder of Gates Hospitality, noted that the tax's reinstatement might increase the cost of city offerings, potentially affecting Dubai’s competitiveness as a global tourist destination.
This development coincides with significant advancements in Dubai’s alcohol industry. Dutch brewer Heineken, through its joint venture Sirocco, has announced plans for the city’s first large-scale commercial brewery, which will produce globally renowned brands such as Heineken, Amstel, Kingfisher, and Birra Moretti. Construction is expected to begin in late 2025, with completion targeted for 2027.
Meanwhile, Abu Dhabi granted Side Hustle Brews a license in December 2023 to produce and sell beer on-site, making it the first legal alcohol producer in the region.
Prior to this, the company had been distributing imported beer and spirits through various liquor outlets in the UAE.
SWITZERLAND – Migros, Givaudan, and Bühler Group have unveiled The Cultured Hub, a cutting-edge biotechnology facility that aims to advance the production of cellular agriculture products.
Located in Kemptthal, Switzerland, the facility focuses on creating innovative food solutions, including lab-grown meat, dairy substitutes, and cell-based chocolate.
This launch marks the fruition of a collaboration initiated three years ago, with the three companies combining their expertise to establish a platform for scaling up cellular agriculture.
The Cultured Hub is dedicated to streamlining the
development and commercialization of alternative proteins, offering significant support to the rapidly growing industry.
“The Cultured Hub signifies a transformative step in food production,” said Matthew Robin, CEO of Elsa Group, a Migros Industries subsidiary. “This partnership highlights the collaborative spirit of Switzerland’s food ecosystem.”
Yannick Gächter, CEO of The Cultured Hub, highlighted the facility’s mission to assist startups in reaching the market faster by providing advanced production capabilities and leveraging decades of expertise in food technology and commercialization.
The facility features specialized laboratories for cell culture and fermentation, supporting the development of products ranging from cultivated meat and dairy alternatives to pet food, fish, and materials for cosmetics and pharmaceuticals.
Startups can access these resources without significant upfront investment in equipment or sacrificing equity, a crucial advantage in a challenging funding environment for alternative protein ventures.
For instance, investments in cultivated meat startups dropped by 75% last year, with only US$3 million raised in the third quarter of this year.
The Cultured Hub bridges the gap between small-scale experiments and large-scale pilot operations, reducing the time and costs needed for market-ready product development. It also acts as a center for knowledge exchange, promoting sustainability within the food industry.
USA – Mondelez International, the owner of Cadbury, has revealed its plans to acquire U.S.-based confectionery giant Hershey, according to Bloomberg News.
According to the report, if the deal materializes, it could create one of the world’s largest confectionery companies.
Bloomberg reports that Mondelez has made an initial proposal for a potential merger valued at around US$84 billion. However, sources familiar with the discussions indicate that the talks are still in the early stages, with no certainty of an agreement being reached.
A critical factor in any potential transaction is the Hershey Trust Company, which controls voting shares of The Hershey Company. The trust, a charitable organization supporting the Milton Hershey School, must approve any deal involving the Pennsylvania-based chocolate maker.
This is not Mondelez’s first attempt to acquire Hershey. In 2016, it withdrew a US$23 billion bid after Hershey rejected the offer, with sources at the time suggesting Hershey would only entertain offers exceeding US$125 per share.
The proposed merger comes at a challenging time for the confectionery industry, as rising input costs, especially for cocoa and sugar, have led to higher product prices, weakening consumer demand.
Hershey recently reported a decline in quarterly sales, falling to nearly US$3 billion due to subdued consumer spending. In contrast, Mondelez achieved a slight increase in sales, rising nearly 2% to reach US$9.2 billion.
The industry is also grappling with global sugar shortages caused by climate issues, including droughts in Thailand and dry spells in India, which have driven up sugar prices.
In response, Mondelez announced further price hikes earlier this year. CEO Dirk Van de Put stressed the importance of straightforward price adjustments to combat inflation, ruling out shrinkflation as an option.
This potential acquisition follows other notable deals in the sector, such as Mars’ US$36 billion purchase of Cheez-It maker Kellanova, which united brands like M&M’s and Pringles.
WEST AFRICA – Switzerland-based shipping company MSC has unveiled a new direct shipping service to strengthen trade between Europe and West Africa.
This marks the company’s first direct route connecting Northern Europe to Angola, Congo, and DR Congo, aimed at expediting the transport of dry goods, refrigerated cargo, and project materials.
The new MSC NWC-Morocco to West Africa service features a direct route to Pointe Noire, with transit times of 23 days from Rotterdam, 21 days from Antwerp, and 19 days from Le Havre.
It also includes a direct route to Luanda, with transit times of 25 days from Rotterdam, 23 days from Antwerp, and 21 days from Le Havre. Expanded access to Matadi in DR Congo will be facilitated through a feeder service from Pointe Noire.
MSC highlighted that the service will integrate intermodal solutions, enabling the transport of goods from Pointe Noire to key cities like Kinshasa and Brazzaville. In Angola, intermodal services will ensure seamless delivery from Luanda to inland regions.
The service launched on November 25, 2024, during week 48, with the MSC SUEZ voyage WM448A. Its rotation includes ports such as Rotterdam, Antwerp, Le Havre, Casablanca, Las Palmas, Dakar, Conakry, Lomé, Pointe Noire, and Luanda.
West Africa remains the EU’s largest trading partner in sub-Saharan Africa, according to the European Commission.
The EU serves as the primary market for West African exports, including fuels and food products, while West Africa imports fuels, machinery, food, and chemicals from the EU.
This initiative complements MSC’s existing NWC to WAF service. Earlier in January 2024, MSC announced enhancements to its Europe-South Africa route, adding Bremerhaven as a direct stop beginning in March 2024.
The updated route includes London Gateway, Rotterdam, Antwerp, Hamburg, Bremerhaven, Le Havre, Sines, Las Palmas, Coega, Durban, Cape Town, and back to London Gateway.
KENYA – Kenya’s coffee sector stakeholders have voiced strong opposition over a new directive by the Ministry of Cooperatives, requiring farmers to be paid directly for their produce.
The directive, issued by Cabinet Secretary for MSMEs Wycliffe Oparanya, instructs the Nairobi Coffee Exchange (NCE) to implement a direct sale settlement system.
This system will credit coffee sale proceeds directly into farmers’ accounts or through M-Pesa.
While the government argues the move will enhance transparency and ensure farmers receive timely payments, stakeholders warned it could undermine cooperative movements and rural savings and credit cooperatives (saccos).
The directive is one of ten reform measures introduced by Oparanya to improve profitability and competitiveness in the coffee sector.
These measures include capping cooperative societies’ administrative and operational costs at 20% of gross coffee earnings, separating operational funds from farmer payments, and requiring service contracts to be lodged with commercial banks for settlement through the Direct Settlement System.
In addition, cooperative societies must digitize coffee weighing scales and stock cards, centralize data access for growers by 2024/2025, and insure coffee against loss or damage.
Societies and associations are also required to seek member-approved loans and ensure these are sanctioned during annual general meetings.
Officials holding roles in both primary cooperative societies and saccos have been ordered to relinquish one of the roles immediately.
These reforms are part of the Crops (Coffee) (General) Regulations 2019, established under the Crops Act of 2013.
NIGERIA – Dangote Sugar Refinery Plc (DSR) has announced plans to raise N50 billion (US$32.28M) from the debt capital market through the issuance of Series 6 and Series 7 commercial papers under its N150 billion debt programme.
According to Market Watch, the Series 6 commercial paper, which has a 180-day tenor, is offered at a 24.9889 percent discount rate, translating to an implied yield of 28.5 percent.
The Series 7 commercial paper, with a 270-day tenor, is priced at a 24.5524 percent discount rate, providing an implied yield of 30 percent.
Investment banking firms have confirmed that the offering will remain open to investors until December 12, 2024. The proceeds from the issuance are earmarked to support the company’s working capital and other operational funding needs.
A subsidiary of Dangote Industries Limited (DIL), Dangote Sugar Refinery is a leading player in Sub-Saharan Africa’s sugar industry, refining and distributing granulated sugar to wholesalers as well as the skincare, food and beverage, and pharmaceutical industries.
With an installed refining capacity of 1.49 million metric tonnes per annum, DSR is Sub-Saharan Africa’s largest sugar refinery.
The company is also advancing its backward integration program, aiming to produce an additional 1.5 million metric tonnes of refined sugar from locally grown sugarcane in the medium term. This initiative seeks to position DSR as a globally integrated sugar producer.
The decline is largely attributed to a 176 percent surge in finance costs, which rose from N108.7 billion (US$70.3M) to N300.2 billion(US$194.2M), coupled with disruptions in the supply chain and fluctuating sugar prices.
– GNT Group has launched GNT Ventures, a separate investment firm aimed at collaborating with startups to advance plant-based coloring technologies.
This move aligns with the growing emphasis in the food and beverage industry on sustainability and the use of natural ingredients.
GNT Ventures will concentrate on investing in early-stage companies focused on developing innovations in areas such as raw material sourcing, fermentation, processing methods, ingredient development, and upcycling.
The firm plans to fund rounds ranging from pre-seed to Series A, with investments of up to US$1.1 million per venture.
One of its early collaborations is with Plume Biotechnology to enhance Exberry color solutions through fermentationbased processes.
Finn Rieken, managing director of GNT Ventures, emphasized the company’s commitment to supporting startups that are creating sustainable industry solutions, a strategy in line with the broader trend of established companies partnering with emerging firms to foster innovation.
To support its partners, GNT Ventures offers access to a food-grade pilot plant for process testing and development, as well as R&D support.
In addition to launching GNT Ventures, GNT Group has expanded its Exberry range with a new paprika emulsion, Exberry Shade Vivid Orange, which delivers clean-label orange hues for various products, including confectionery, dairy, baked goods, and plant-based meats.
Made from non-GMO paprika, this water-dispersible color provides intense vibrancy with smaller quantities, offering a natural alternative to additives like paprika oleoresin emulsion (E 160c) and Sunset Yellow (E 110).
Produced using physical methods without chemical solvents, it can be classified as a food ingredient in many regions.
GNT Ventures' combined focus on investment and innovation underscores the industry’s shift towards sustainable, natural food solutions that meet consumer demands.
ETHIOPIA – Neumann Kaffee Gruppe (NKG), a global leader in green coffee services, has entered a bilateral coffee marketing partnership with MIDROC Investment Group, a prominent Ethiopian conglomerate owning some of the largest coffee plantations in the world through Horizon Plantations and Ethio Agri-CEFT.
The agreement encompasses coffee processing and storage facilities in Addis Ababa, aiming to boost coffee productivity and enhance Ethiopian coffee’s global competitiveness.
The collaboration also focuses on advancing coffee science and fostering sustainable development in the industry.
David M. Neumann, CEO of NKG, expressed his enthusiasm for the partnership, describing it as a venture rooted in trust, mutual respect, and a shared commitment to strengthening Ethiopia's critical role in the global coffee market.
He highlighted the collaboration as an opportunity to celebrate Ethiopian coffee’s rich heritage while expanding its international reach.
MIDROC Investment Group, renowned for its dedication to high-quality coffee production, manages six major coffee farms—Bebeka, Limu, Ayehu, Gemadro, Duyena, and Beha
The group’s CEO, Jamal Ahmed, praised David Neumann for his unwavering efforts to promote Ethiopian coffee worldwide.
Recently, MIDROC executives announced that their brand name would remain unchanged in Ethiopia, even after adopting the "Granitor" name in Sweden.
However, reports suggest that a rebranding in Ethiopia could eventually follow, a move speculated to stem from the impact of Sheikh Al-Amoudi’s detention in Saudi Arabia, which affected the company's reputation in Europe.
This partnership marks a significant milestone for NKG, which established a representative office in Ethiopia in 2007 to support its group companies in the region.
Ethiopia, recognized as the birthplace of Coffea arabica, is the top coffee producer in Africa and the fifth-largest globally.
Coffee remains Ethiopia's leading export, contributing roughly 30–35% of total export earnings and supporting millions of small-scale farmers.
ZIMBABWE – Choppies Enterprises Limited, a leading grocery retailer, has announced plans to exit the Zimbabwean market, citing intense competition from the informal sector.
The company operates 30 retail stores in Zimbabwe through its wholly owned subsidiary, Nanavac (Pty) Ltd.
While details of the potential buyer and sale price remain undisclosed, analysts speculate that local players may seize the opportunity to expand their presence in Zimbabwe’s retail sector.
Choppies stated that the potential sale, subject to regulatory approval, aligns with its strategy to focus on profitable markets.
“The board of directors of Choppies (“Board”) hereby advises all shareholders that the Company has entered into discussions regarding a possible sale of the business operations of Nanavac (ty) Ltd trading as Choppies Zimbabwe for cash (“Possible Sale”), which, if successfully concluded, could have an impact on the Company’s share price,” said the company in
a statement.
Although the company remains optimistic about Zimbabwe's economic potential, it acknowledged that sustaining operations would require significant additional capital.
Formal retailers face stringent regulations and penalties, whereas informal shops and vendors operate with fewer restrictions, often selling goods in hard currency.
In related developments, Choppies Supermarket Namibia has settled a case with the Namibian Competition Commission (NaCC) over an unapproved merger. The settlement includes a N$2.2 million fine and a mandatory compliance program.
The NaCC found that Choppies had violated competition laws by acquiring control of Grootfontein Supermarket and Bottle Store without notifying the Commission, as required under the Competition Act.
Dina //Gowases, NCC spokesperson, emphasized that compliance measures are now in place to prevent future violations.
GHANA – International buyers of Ghana's cocoa have provided substantial upfront payments to the state marketing board, Cocobod, to secure supplies and mitigate heavy losses experienced in the previous season.
By mid-November, with season-to-date arrivals reaching 183,000 tons, these advance payments amounted to approximately US$550 million, although much of this cocoa is yet to be shipped.
Cocobod asserts that the system is functioning effectively, and farmers confirm they are receiving payments.
However, opinions within the industry remain divided.
According to Reuters, traders are still awaiting up to 350,000 metric tons of cocoa from contracts that Cocobod failed to deliver last season, resulting in losses of at least US$1 billion on corresponding futures market hedges.
While Cocobod disputes this figure, it has acknowledged rolling over contracts and assured traders that they will be fulfilled this season.
Reuters estimates suggest that companies could face additional losses of US$2,500 per ton for undelivered contracts from last season at current prices.
Analysts, including Tedd George, a commodities expert, estimate that around 900,000 tons of cocoa would be needed to cover these roll-overs.
This target exceeds Cocobod’s production estimate by 250,000 tons, which some industry players already view as overly optimistic. George noted that this shortfall might leave certain traders and local processors without beans this season.
To protect farmer incomes and mitigate losses, Cocobod is reportedly requiring traders to purchase additional contracts at near-record high spot prices to offset the price differences. Cocobod now demands that companies pay at least 60% of contract values upfront and pre-finance Licensed Buying Companies (LBCs), having moved away from using banks for financing.
Historically, Cocobod relied on bank loans to purchase cocoa from farmers, selling forward contracts to international companies. However, declining production and management decisions led the regulator to forgo syndicated financing for this season—the first time since 1992. Instead, Cocobod shifted to company financing, aiming to save US$150 million in interest payments.
USA – International Flavors & Fragrances Inc. (IFF) has introduced Texstar, an innovative enzymatic solution designed to enhance the texture of both dairy and plant-based fermented products.
The enzyme aims to provide a unique solution for manufacturers seeking to improve product consistency while eliminating the need for added stabilizers.
Texstar’s formula creates the necessary viscosity in fresh fermented products through fermentation, eliminating the requirement for traditional texturants such as starch-based additives.
By converting sucrose into poly- and oligosaccharides, Texstar reduces sugar content, improving product texture with smoother consistency and increased shine.
This also results in better taste profiles, particularly in plant-based dairy alternatives, where it helps to neutralize
off-putting flavors like the “beany” taste commonly associated with plant proteins.
The enzyme’s benefits extend beyond texture and taste. IFF highlights that Texstar can contribute to a more sustainable production process by reducing the carbon footprint of fermented products.
Texstar can help decrease Scope 3 greenhouse gas emissions by up to 90% when used as a partial replacement for milk proteins.
This is achieved due to the enzyme’s low usage rate, significantly lowering the need for texturants and reducing the associated environmental impact.
The new enzyme solution is expected to offer manufacturers a more stable and sustainable alternative to conventional texturants, potentially transforming the production of fermented dairy and plant-based products.
GLOBAL – Kerry, a global leader in taste and nutrition, has announced its 2025 Taste Trends, offering a forward-looking perspective on the future of food and beverage innovation.
Developed by Kerry’s taste experts and validated through its global insights team, the report delves into consumers' evolving preferences, highlighting the “why” and “how” behind emerging flavors.
The 2025 Taste Trends aims to equip Kerry’s customers with the insights to create innovative solutions that align with consumer demands.
A central theme of this year’s report is balancing fun with functionality, ensuring products taste great and deliver
tangible health benefits, and maximizing the value of fewer ingredients.
The report emphasizes combining technology, creativity, and culinary arts to redefine food and beverage experiences in 2025.
Six key trends were highlighted: Imagination Infused: This trend combines digital advancements, societal shifts, and artificial intelligence to inspire groundbreaking product innovations, blending creativity with data-driven insights.
Roots Redefined: It focuses on reimagining traditional cuisines, blending time-honored culinary techniques with modern creativity to make classic flavors more accessible and appealing.
Little Luxuries: In an era of increased cost awareness, this trend highlights the importance of small, everyday indulgences that bring sophistication and moments of joy to daily life.
Fun with Functional: This trend reflects growing consumer demand for health-forward foods. It incorporates fun, novel flavors into products with functional benefits, making wellness more engaging.
Clean & Simple: This trend celebrates natural ingredients, emphasizing their intrinsic benefits and employing innovative cooking methods to enhance flavor and nutrition.
Chain Reaction: Addressing global supply challenges, this trend encourages the creative use of alternative ingredients and resource efficiency to turn limitations into opportunities.
GLOBAL – Tate & Lyle, a global leader in ingredient solutions, has published a report titled The Future of Mouthfeel. The report identifies nine emerging trends shaping the food and beverage industry.
The report provides key insights to help brands and manufacturers innovate and reformulate products while addressing changing consumer demands.
Mouthfeel, a critical sensory element encompassing texture, taste, and overall sensation, is pivotal in consumer food preferences.
According to the report, achieving the right mouthfeel is essential for unlocking taste, which remains the primary driver of consumer choice.
The report emphasizes the evolving drivers of innovation, including affordability, clean labels, healthier options, and sustainability, all of which influence the texture and mouthfeel of food products.
Tate & Lyle highlight formulators' challenges in three areas: retaining mouthfeel during cost optimization, regaining mouthfeel when reformulating products for cleaner labels or healthier profiles, and innovating with new textures to create engaging sensory experiences.
In collaboration with research firm Kantar, Tate & Lyle identified nine mouthfeel trends, including hyper-crunch, mouthfeel mimicry, convenience and shelf-proof mouthfeel, next-gen naturality, multi-layered mouthfeel, and climateproof food.
These trends reflect shifts in consumer behaviour driven by factors such as busier lifestyles, climate change, and the demand for healthier alternatives.
The publication of The Future of Mouthfeel follows Tate & Lyle’s acquisition of CP Kelco, a global supplier of pectin and specialty gums.
This acquisition will enhance Tate & Lyle’s sweetening, mouthfeel, and fortification capabilities, aligning with the growing demand for healthier and more sustainable products.
CHINA – German systems supplier KHS Group has partnered with Carlsberg Asia to build a cutting-edge brewery in Foshan, South China, marking a major milestone in their decade-long collaboration.
The Foshan brewery, Carlsberg’s 27th facility in China, spans 16 hectares and represents a €191 million (US$200.49m) investment. With a planned annual output of 14 million hectoliters, it is one of the region’s largest and most advanced brewing facilities.
This project builds on a successful partnership history, including delivering high-capacity canning lines in Dali and Yibin during the COVID-19 pandemic.
“We achieved line efficiencies of 99% and 100%—ahead of schedule,” noted Norman Gras, KHS’s global key account manager.
Paul Kime, Carlsberg Asia’s senior director for assets, projects, and utilities, emphasized trust-driven collaboration, “Our teams work as one, enabling streamlined processes and exceptional outcomes.”
Designed with Carlsberg’s Together Towards Net Zero initiative in mind, the brewery integrates eco-friendly practices. The Sponge Brewery Concept includes rainwater harvesting and wastewater treatment systems, conserving water resources.
Construction materials meet China’s 3-star ecological standards, while a rooftop photovoltaic system supplies 30% of the brewery’s electricity. An intelligent energy management system further reduces energy consumption and environmental impact.
KHS equipped the brewery with advanced filling and packaging technology, including:
Keg Line: Processes 90 kegs per hour with the Innokeg CombiKeg and Innopal RK robot.
Glass Bottle Lines: Two lines handle 48,000 bottles per hour and feature the Innofill Glass DRS ECO filler for reduced CO2 use.
Canning Line: This line handles 90,000 cans per hour with patented CO2 purging technology, cutting oxygen levels by 90% and minimizing CO2 consumption.
USA – Archer Daniels Midland (ADM) has introduced a new interactive platform to provide insights into global consumer behavior concerning sugar reduction.
The tool, which analyzes data gathered from 13,900 individuals across 15 countries, reveals significant trends in how people worldwide manage their sugar intake.
The findings show that 83% of global consumers actively limit or avoid sugar in their diets, with varying concerns depending on the region.
In North America, 69% of shoppers check the sugar content of pancake syrup bottles, a concern not seen in other regions.
While non-alcoholic beverages are a global focus for sugar monitoring, preferences for what to avoid differ across markets.
North Americans are focused on milk alternatives, while Europeans prioritize chocolates and pastries.
In Latin America and Asia Pacific, snacks and specialized nutrition products are the most scrutinized.
The new tool gives manufacturers a comprehensive view of sugar-related consumer behaviors and highlights regional variations.
For example, in Poland, consumers are more likely to buy nutrition bars and sports drinks because they are driven by health and fitness goals.
Australians favor sugar-free products, while Mexicans are drawn to plant-based options and alternative sweeteners like stevia and agave.
Brazilians, on the other hand, show a strong preference for sustainably sourced products.
This launch comes amid financial challenges for ADM, which reported a 28% drop in operating profit to US$1.04 billion in the third quarter of 2024.
The company’s Ag Services & Oilseeds segment experienced a 43% profit decline, while other divisions, including Carbohydrate Solutions and Nutrition, also saw decreases.
As a result, ADM has revised its 2024 adjusted earnings per share forecast to US$4–US$5, down from an earlier estimate of US$5.25–US$6.25.
FRANCE – Sidel, a leader in liquid packaging equipment, has launched the Hydra Ultrasonic bottle washer. This washer combines chemical and ultrasonic technology to optimize performance, reduce costs, and lower environmental impact.
The innovation comes as demand for refillable returnable glass bottles rises, driven by sustainability goals and legislative reuse targets.
This washer addresses the industry's need for efficient, hygienic cleaning by enhancing the mechanical cleaning effect with ultrasonic waves.
It significantly reduces washing time, temperature, and detergent use while improving cleaning performance for both interior and exterior bottle surfaces.
The Hydra Ultrasonic delivers multiple benefits, including lower rejection rates and up to a 15% increase in production rates. It's ultrasonic cleaning also handles caustic-resistant dirt and ensures thorough cleaning of carrier beams.
By integrating this advanced technology, Sidel achieves notable sustainability gains: a 20% reduction in steam consumption, 15% less water usage, and CO2 savings via 100% electrification using a heat pump.
This replaces steam with hot water, cutting plant heating needs by up to 50%.
The washer also reduces manufacturers' total cost of ownership (TCO) by requiring fewer components, such as motors and chains, and enabling shorter washing cycles.
Its compact design decreases the machine's footprint by 20% compared to traditional solutions and simplifies maintenance requirements.
Andrea Solfa, Product Manager at Sidel, explained, “Real progress means doing more with less. With Hydra Ultrasonic, we aimed to increase washing capacity while reducing consumption and the carbon footprint.”
KENYA - Farmers Choice has appointed Felisters Gitau Mutugu as its new Chief Executive Officer,succeeding James Taylor.
Mrs. Gitau has been with Farmers Choice for a decade and has held several key positions within the company, including Deputy Managing Director for Commercial Operations, Director of Sales and Marketing, Head of Sales and Operations, and Sales Administration Manager.
She brings over ten years of global experience in the fast-moving consumer goods (FMCG) sector. Her educational background includes a Senior Executive Program for Africa (SEPA) from Harvard Business School, a Postgraduate Diploma in Marketing from the Chartered Institute of Marketing, a Master’s degree in Strategic Management from the University of Nairobi, and a Bachelor of Commerce in Finance from Jomo Kenyatta University of Agriculture and Technology.
Under her leadership, Farmers Choice aims to enhance its operations and continue producing 21,000 tons of meat annually.
KENYA – Jude Chesire, the Acting CEO of the Kenya Sugar Board (KSB), has been elected as the Vice Chairman of the International Sugar Organization (ISO), a historic first for both Kenya and Africa since the organization’s establishment in 1968.
Chesire’s extensive experience and leadership in Kenya’s sugar sector played a pivotal role in his nomination.
Over the past 12 years, he has held senior positions in statutory agencies, including serving as the Director and Head of the Sugar Directorate and Deputy Director of Legal Services at the Agriculture and Food Authority (AFA).
Chesire also contributed to drafting Kenya’s National Sugar Policy and served as a member of the Presidential Task Force on the Sugar Industry.
Additionally, Chesire has represented Kenya in the negotiation of sugar safeguards at the COMESA Council since 2014, demonstrating his expertise in regulatory affairs and international collaboration.
Consequently, Edgar Herrera, Executive Director of LAICA in Costa Rica, was elected as the Chairman of the ISO Council.
TOGO – BB Lomé, Togo’s leading brewer and part of the French Castel group, has announced the appointment of Diogo Victoria as the new Director General. Victoria takes over from Thierry Feraud, who held the position for the past eight years.
Diogo Victoria brings over 15 years of experience in the fast-moving consumer goods (FMCG) industry, particularly in Africa and the Middle East.
Before joining BB Lomé, he worked at Saudi Dairy & Foodstuff Company (SADAFCO), where he held several roles, including Director of Commercial Operations and Sales Director. He also worked with Lactalis Group as Director of Business Development for the Middle East and Africa.
BB Lomé’s diverse product portfolio includes popular beer brands like Pils, Lager, Awooyo, and Flag Spéciale, alongside non-alcoholic beverages such as Cocktail de fruits, Pom Pom, Youki Pamplemousse, and Malta Tonic.
The company operates two production sites, one in Lomé and the other one Kara, dedicated for production of beers and soft drinks.
SOUTH AFRICA – Poultry producer
Astral Foods has announced that its current Chief Operating Officer (COO), Gary Arnold, will step into the role of Chief Executive Officer (CEO) on February 1, 2025.
Arnold will take over from Chris Schutte, who is set to retire following the company’s annual general meeting on January 30.Having served as COO and an executive director since 2012, Arnold brings 28 years of experience with Astral Foods.
He started his career in 1997 as animal nutritionist for Meadow Feeds Delmas and Meadow Feeds Welkom. Effective 1 October 2021, Gary was appointed as Group COO of Astral. This position was introduced with a specific mandate to optimise expansion opportunities and continuous improvement initiatives, whilst effectively allocating capital and human resources across all Astral divisions.
Schutte has been the CEO of Astral Foods since 2009, after having been with the company for seven years.
In 2023, Astral Foods slaughtered 290 million broilers, making it Africa’s largest poultry producer. Globally, Astral Foods ranks as the 33rd largest poultry producer and the 100th largest feed producer.
ECOWAS – Promasidor Group, one of the leading supplier of quality food products in more than 30 African countries, has appointed its current CEO of Ghana, Festus Tettey as the CEO of ECOWAS excluding Nigeria with immediate effect.
In the new role, Mr. Tettey will oversee its operations across the rest of West Africa excluding Nigeria, that is Benin, Burkina Faso, Cape Verde, Cote D’Ivoire, Gambia, Ghana, Guinea, Guinea-Bissau, Liberia, Mali, Mauritania, Niger, Senegal, Sierra Leone and Togo.
The Group commended Festus Tettey for his immense contribution to the robust and solid growth of Promasidor Ghana, having held numerous leadership roles including Sales and Marketing Director, Ghana, Commercial Director of Promasidor Nigeria and recently, CEO Promasidor Ghana for 6 years.
In the same strategic reshuffle, the Group also appointed Samir Sadaoui as its new CEO for Ghana effective January 6, 2025 reporting to the CEO of ECOWAS excluding Nigeria.
Samir Sadaoui assumes his new role with extensive experience from his past roles as the Commercial Director of Promasidor Algeria, as well as Ghana, during which period he delivered outstanding results and achievements.
PepsiCo appoints Felix Enwemadu
NIGERIA – PepsiCo has appointed Felix Nnamdi Enwemadu as the new General Manager of its Foods business in Nigeria as the company aims to strengthen its presence in the region.
Enwemadu, who brings over 25 years of experience in the fast-moving consumer goods (FMCG) sector, has held senior roles, including Vice President of Customer Development and Executive Director at Unilever and General Manager at Diageo Brands Limited.
His deep understanding of the Nigerian consumer landscape, coupled with strong leadership skills, will be instrumental in driving the company’s continued growth and success in the market.
This leadership transition in Nigeria comes as PepsiCo navigates challenges in other markets, recently adjusting its sales growth forecast for fiscal 2024.
PepsiCo Foods Nigeria Limited (PFNL) has developed a strong foothold in Nigeria’s local market, particularly under Enwemadu’s leadership, which will focus on delivering high-quality products for Nigerian consumers.
Tanzania’s Mega Beverages Limited (MBL) is marking its 20th anniversary with the launch of a special-edition K-Vant Premium Spirit, a unique, locally crafted spirit aged in oak barrels.
The K-Vant Premium Spirit Special Edition, the first of its kind in Tanzania, is presented in elegant packaging and boasts a distinctive golden-amber liquid.
www.megabeverages.net
Brookside Dairy, a leading dairy producer in Kenya, has introduced a new line of fruit jams under its Delamere brand, featuring refreshed packaging designed to enhance co nsumer appeal.
The new fruit jam offerings are expected to provide consumers with a variety of flavors, complementing Brookside Dairy's existing product lineup.
The refreshed packaging enhances visual appeal and underscores the company's focus on environmental responsibility.
www.brookside.co.ke
Unilever Kenya has officially introduced the Royco Chilli Cube, a product designed to enhance the flavor of beans, responding to growing consumer demand for chili-based seasonings.
In addition to the spice range, Royco also launched wet and dry fry spices and nyama choma seasoning variants, which are processed and packaged locally at Njoro Canning.
www.unilever.com
Almarai, Saudi Arabia's largest dairy producer, has introduced its Vegetable Fat Feta Cheese to the Egyptian market. This product is tailored for diverse culinary applications, offering a creamy texture and easy spreadability.
It is produced in Egypt under Almarai's stringent quality standards, reflecting the company's investment in local cheese production lines to cater to regional consumer preferences.
www.almarai.com
Markis Food has introduced Aris Jus Ananas, a pineapple juice product, to the Tunisian market.
This refreshing beverage is crafted to meet local preferences, offering a natural and vibrant pineapple flavor.
Aris Jus Ananas reflects Markis Food's commitment to quality and innovation in beverages, providing a delightful option for fruit juice enthusiasts in Tunisia.
www.arisdrinks.com
Juhayna Food Industries has launched a new range of Greek yoghurt to meet the evolving needs and preferences of its customers.
This creamy, protein-rich yoghurt is made from natural ingredients, gluten-free, and provides 30% of the recommended daily protein intake. The range features four different fat levels, catering to various dietary preferences.
It is a vailable in an array of delicious flavors such as pineapple, mixed berries, French vanilla, and peach.
www.juhayna.com
Lamipak has been supporting the growth of the beverage industry in the Middle East and Africa for over a decade. Ajas Shaikh, Head of the Middle East and Africa Cluster, discusses the company’s well-established presence as the region’s first-choice aseptic packaging solutions partner, its ongoing support for the food and beverage industry, and new innovations aimed at supporting the transition to a circular economy.
Could you share a brief introduction to Lamipak and its journey into the Middle East and Africa region?
Lamipak is a global leader in aseptic packaging. From our two sites in Kunshan, China, and Indonesia, we supply high-quality liquid beverage cartons to leading food and beverage brands in over 87 countries worldwide. In 2023, we delivered over 13 billion packages to more than 430 dairy and juice customers globally.
Our journey into the Middle East and Africa region began in 2014 when we first started exporting our packaging materials to the region. We have earned the trust and confidence of our customers through our quality and dedicated service, which has helped us expand across the region and become a reliable supplier during challenging times.
Over the years, we have listened to our customers' pain points and needs, which has allowed us to evolve from being just a packaging material supplier to a complete business solution provider. Today, in addition to our packaging, we offer our customers technical support services, which have been crucial in ensuring that many plants across the region operate at optimal capacities. What is truly unique about this service is that it is custom-tailored to meet our customers’ needs, ensuring both effectiveness and cost minimization.
What prompted Lamipak to expand its presence in this market, and what specific opportunities do you see here? We expanded into the region because it presented immense potential for aseptic packaging. In 2023, the region consumed about 13 billion liters of white and flavored milk and around 7.6 billion liters of juice and juice drinks, according to GlobalData. This represents a significant market opportunity for aseptic packaging, as it is the most suitable solution for the region, given that ambient beverages are preferred due to limited refrigeration infrastructure. Additionally, our entry provided a reputable alternative aseptic packaging solutions supplier that customers had been seeking. We have not only filled this gap but have also comprehensively met our customers’ needs, growing alongside them.
Opportunities for growth are further amplified by the fact that the Middle East and Africa have one of the fastestgrowing populations in the world. The World Bank estimates that Africa's working-age population will grow by 450 million people—nearly 70%—by 2035. This trend is expected to further increase milk and juice consumption in the region,
with volumes projected to grow by 600 million liters and 1.2 billion liters, respectively, over the next five years.
As suppliers of aseptic packaging solutions, we aim to be present and support industry players in meeting this growing demand for dairy and juice products.
What unique packaging products and solutions does Lamipak offer to cater to the specific needs of the Middle East and Africa market?
Given the vast and diverse nature of the Middle East and Africa, we have seen different markets favoring various packaging formats. For example, our pillow pack, which performs well in tough terrains, is highly favored in markets like Kenya, Egypt, and Nigeria, while markets in South Africa tend to lean toward the brick slim format for milk. The same trend is seen with juice, with many players across the region preferring our brick slim format, and brands seeking to differentiate themselves on the shelf are pivoting to more premium formats such as LamiDiamond, LamiEdge, LamiGemina, and LamiSlim Leaf.
The diversity in packaging preferences is evident as you move from country to country, but as Lamipak, we pride ourselves on having one of the most extensive portfolios of pack formats in the industry. With over 65 pack formats across 14 pack designs, we are uniquely positioned to offer packaging solutions suited to the distinct needs of different markets in the region.
Additionally, as a customer-focused company, we respond quickly to unique customer requirements for new pack designs or formats, especially when they are committed to building a long-term partnership with Lamipak.
Are there any recent innovations or products that Lamipak has launched?
We have an exciting lineup of new innovations, including LamiNatural, our very first eco-friendly product; LamiPure, an aluminum-free aseptic carton; and Lamisleeve, our first foray into sleeve-fed filling technology.
LamiNatural is made from bio-based polyethylene (bioPE) and unbleached paperboard. The unbleached paperboard minimizes chemical consumption, while the bioPE layer increases renewable content to 85% compared to the standard aseptic carton. Its unique structure results in a 10% reduction in carbon footprint compared to standard packs.
With Lamisleeve, we offer a solution that caters to a broad spectrum of liquid foods, including those containing
particulates, offering unprecedented flexibility to manufacturers. This technology also aligns with consumer preferences for products with enhanced texture experiences, such as drinking yogurts containing real fruit or juices with pulp.
LamiPure represents a significant step forward in sustainable packaging. Its proprietary polyethylene barrier structure makes it easier to recycle compared to existing aseptic cartons, aligning perfectly with the global push toward a circular economy.
Lamipak recently attended the Gulfood Manufacturing exhibition. What were the key highlights of your participation?
Gulfood Manufacturing is one of the most influential and comprehensive trade events for the food and beverage manufacturing industry in the Middle East. As an exhibitor, it provided a unique opportunity to connect with key industry players, establish new partnerships, and gain valuable insights into emerging trends and technologies in food manufacturing. Our participation in Gulfood Manufacturing strengthened our brand reputation, positioning Lamipak as a key player in the aseptic packaging industry as we continue to move forward with the vision of becoming the world’s secondlargest supplier of aseptic packaging solutions.
What can we expect from Lamipak in the coming years in terms of product development, partnerships, or regional initiatives?
Lamipak is a dynamic company, continuously adapting to everchanging market conditions and customer demands. Moving forward, our growth will be driven by a customer-first vision and highly customized solutions designed to meet the evolving needs of our clients.
In the coming years, we plan to expand our premium pack portfolio with additional roll and sleeve-fed options. LamiSleeve, which we recently launched, will be available in 4 shapes and 19 formats once production reaches full capacity.
As a leader in sustainable packaging, we also plan to expand our support for recycling activities in the region, collaborating with extended producer responsibility organizations in markets where we have a presence.
We see tremendous potential in the region and are committed to allocating more resources to ensure we continue to meet the needs of our customers. FBA
By Francis Watari
We are currently in the middle of a substantial transformation regarding the way we produce products. With increasing pressure to meet sustainability goals, improve efficiency, and adapt to changing consumer demands, beverage producers are investing in cutting-edge technologies to modernize production, resulting in the development of smart factories.
Smart manufacturing, also known as Industry 4.0 (Fourth Industrial Revolution), combines automation, Internet of Things (IoT) devices, artificial intelligence (AI), and other digital tools to create a seamless, data-driven approach to beverage production. The evolution from Industry
1.0 to Industry 4.0 includes the use of steam in the First Industrial Revolution, electricity in the Second, basic automation and computing power in the Third, and cyber-physical systems and intelligent technologies in the Fourth.
The term Smart Manufacturing was coined in 2006 at a National Science Foundation workshop on Cyberinfrastructure. Initially called Smart Process Manufacturing, it was quickly shortened to Smart Manufacturing as the concept evolved and was applied to other sectors. Smart manufacturing has led to improved end-to-end production processes, helping machine operators, line supervisors, engineers, company executives, and others make better decisions.
Coca-Cola Beverages Africa (CCBA) recently unveiled East Africa’s fastest plastic bottle production line, with a capacity of 67,000 bottles per hour, equipped with state-of-the-art technology such as robotic arms and automated fillers. Robotic arms handle bottle filling, capping, labeling, and packing, boosting consistency and speed of production. CCBA’s automation extends to warehouse logistics, where autonomous robots handle storage and shipment preparation, improving logistics and reducing downtime.
This technology takes over repetitive and labor-intensive tasks, allowing companies to streamline operations and focus on quality and innovation. The use of robots reduces errors in production caused by human mistakes and decreases instances of human injuries, especially in tasks involving heavy equipment.
Fanuc Robotics, a manufacturer of robotic systems, has developed specialized robots for food packaging. These robots handle tasks ranging from filling and sealing packages to palletizing finished products. In partnership with Nestlé, Fanuc’s robotic arms package a range of products with precision and speed, ensuring each package meets strict quality standards.
Automation and robotics have become essential in beverage production, achieving desired production levels within short time intervals and at lower labor costs. Austin-based Briggo introduced robotic baristas capable of making a wide range of coffee beverages. These robotic coffee kiosks, known as ‘Coffee Hauses,’ allow customers to order and customize their drinks via a mobile app. The robots operate 24/7, serving high-quality coffee quickly and efficiently without human intervention.
IoT-enabled devices allow beverage companies to monitor every aspect of the production line in real time. Sensors collect data on parameters like temperature, pH levels, and pressure, providing valuable insights that help prevent issues before they arise and enable predictive maintenance. A 2019 Deloitte study found that companies in the food manufacturing sector experienced a 20% reduction in operational costs and a 15% increase in production capacity after implementing IoT technology. Additionally, a study by IoT Analytics found that
companies implementing IoT technology in their supply chain management saw an average ROI of 15.6%.
Sensors on production lines collect data on temperature, moisture, and fermentation levels, helping maintain consistent quality and efficiency. Beverage companies use real-time data to optimize energy and water consumption, aligning with sustainability goals.
A 15% INCREASE IN PRODUCTION
IMPLEMENTING IOT TECHNOLOGY.
Celli Group, a global company based in Italy, leveraged Microsoft Azure IoT and PTC ThingWorx to create IntelliDraught, a connected beverage distribution system that turns manufactured or already-installed equipment into smart devices. This system improves quality, sales, service, and inventory management for their beverage customers. At Acqua Alma Point refill stations, consumers can craft recipes with personalized flavors, minerals, and carbonation profiles without wasting plastic bottles. The system recognizes users and remembers their preferences, no matter which station they use.
AI and machine learning are transforming how beverage companies maintain quality control and predict consumer demand. Machine learning algorithms analyze vast amounts of data to detect patterns and make real-time adjustments, ensuring product consistency and optimizing inventory levels.
PepsiCo employs AI for demand forecasting, analyzing
consumer trends, weather patterns, and sales data to predict optimal production levels for each region. By leveraging AI, PepsiCo organizes customer data and predicts future spot trends. “AI has changed how we interact with almost every company,” said Athina Kanioura, PepsiCo Chief Strategy and Transformation Officer. “And now businesses have systems
MARKET VALUED AT US$2.31T IN 2023 IS PROJECTED TO GROW TO US$5.71T BY 2032, ACCORDING TO FORTUNE BUSINESS INSIGHTS
with intelligence behind them that have transformed the way we solve problems, engage with consumers, and make products.”
PepsiCo’s quality control systems use machine learning to detect potential defects on production lines, allowing for immediate correction before products reach the market. In combination with sensors, machine learning technology helps brewers precisely monitor fermentation and adjust the process in real time, ensuring consistent quality across batches.
Blockchain technology provides a secure, transparent, and traceable record of every step in the production process, from sourcing raw materials to final product distribution. This level of traceability is particularly valuable in the beverage industry, where consumers demand transparency regarding sourcing
and production practices. BanQu and Anheuser-Busch InBev partnered in 2018 to launch the Chembe cassava online-buying project in Zambia, using blockchain technology to improve supply chain transparency and traceability. BanQu’s solution uses GPS technology to locate farmers, and trained agents use this data to streamline and authenticate transactions. Geotags, farmer profiles, and other relevant information are securely recorded on the blockchain.
With a market size valued at US$2.31 trillion in 2023 and projected to grow to US$5.71 trillion by 2032, according to Fortune Business Insights, a significant portion of this market comprises illicit production, especially in regions like Africa and China. The rampant production of counterfeit and illegal alcoholic beverages poses severe health risks and undermines consumer trust. Blockchain traceability helps beverage companies offer reliable and authentic products while ensuring regulatory compliance and ethical practices.
Smart packaging technologies have revolutionized the food and beverage industry by integrating sensors and indicators that monitor parameters like temperature, humidity, and gas composition. These sensors are embedded within packaging materials or incorporated into labels, caps, or seals, allowing for real-time data collection throughout the product's lifecycle.
Interactive packaging elements, including augmented reality (AR) labels and smart QR codes, have transformed consumer engagement. These technologies create opportunities for personalized interactions between brands and consumers, enhancing brand experiences, increasing customer loyalty, and providing valuable insights for targeted marketing strategies. AR labels overlay digital content onto physical packaging surfaces, accessible by scanning with smartphones or tablets.
Aditi Basu, marketing head at Dubai-based Future Market Insights, notes that intelligent packaging is taking trends to new heights. “Consumers nowadays prefer smart, active, interactive, connected, user-friendly, and eco-friendly
packaging solutions,” she says. “Beverage-makers need to focus on these trends as they impact the industry overall.”
Importance of Smart Manufacturing in the Beverage Industry
Smart manufacturing plays a crucial role in meeting the demands of modern beverage production. Here are key reasons why it is essential for the industry:
1. Enhanced Efficiency and Cost Savings: Integrating automation and IoT reduces operational costs and minimizes waste. Predictive maintenance ensures equipment is serviced before breakdowns occur, saving time and reducing costly downtime.
2. Quality Control and Consistency: AI-driven quality control helps ensure each product meets consistent quality standards. Maintaining consistency across large batches is vital for brand reputation and consumer satisfaction.
4. Sustainability and Resource Management: The beverage industry is resource-intensive, especially in water and energy use. Smart manufacturing enables real-time monitoring and optimization of resource consumption, reducing waste, lowering emissions, and meeting sustainability goals.
5. Agility and Adaptability: With changing consumer preferences, such as a shift towards healthier and sustainable products, smart manufacturing provides the flexibility to adapt quickly to new trends. Companies can efficiently introduce new products, adjust formulations, and respond to market demand.
6. Transparency and Consumer Trust: Consumers increasingly demand transparency regarding product sourcing and manufacturing practices. Smart manufacturing, particularly through blockchain and smart packaging, allows companies to provide traceability and build trust with consumers.
Smart manufacturing is reshaping the beverage industry, helping companies meet growing demands for efficiency, quality, and sustainability. From digital twins to IoT-enabled processes, these technologies revolutionize how beverages are produced, packaged, and delivered. The importance of smart manufacturing extends beyond operational efficiency to include consumer trust, adaptability, and environmental responsibility. As the industry continues to adopt AI, blockchain, and other cutting-edge solutions, the future of beverage production will be marked by further innovation, enhanced sustainability, and a stronger focus on meeting the evolving needs of consumers. Smart manufacturing represents not just a technological upgrade, but a holistic approach to transforming beverage production. Companies that embrace these advancements will achieve operational excellence and pave the way for a more sustainable and consumer-centric industry. FBA
BUSINESS AFRICAAFRICA’S NO.1 FOOD & BEVERAGE INDUSTRY
MAGAZINE
• Reach the food, beverage and milling industry in sub-Saharan Africa (East, West, South and Central Africa) and beyond using one publication and website
• Use the first magazine of its kind in the region available in a digital format, providing our advertisers with a worldwide audience
• Advertizing with us opens the door to key decision makers in the food industry
• Gain access to the best read and visited food industry website in sub-Saharan Africa.
By CP Foods
In an era marked by environmental challenges and growing demand for sustainable food, the agriculture and livestock industries are undergoing a critical transformation. At the heart of this evolution is the concept of sustainable animal welfare—a comprehensive approach that prioritizes the well-being of animals, enhances food security, and mitigates environmental impacts. This paradigm shift not only addresses pressing concerns but also lays the foundation for achieving long-term goals, such as net-zero greenhouse gas emissions, creating a balanced and thriving ecosystem for all life on Earth.
The livestock industry is grappling with a host of issues, including climate change, a rising global population, and growing consumer expectations around ethical and sustainable food production. These interconnected challenges necessitate a careful balance between productivity, environmental preservation, and the well-being of animals. Sustainable animal welfare has emerged as a transformative solution, addressing these priorities while fostering a resilient food system.
Veterinarian Payungsak Somyanontanakul, Deputy Director of Farm Standards and Customer Requirements at Charoen Pokphand Foods Public Company Limited (CP Foods), explains, “Animal husbandry is currently facing increasing challenges, including climate change, the need for sustainable food production, and animal welfare pressures to strike a balance between increasing productivity, preserving the environment, and caring for animals to have a good quality of life.”
Central to sustainable animal welfare are the Five Freedoms of Animal Welfare, which serve as guiding principles for ethical livestock management:
1. Freedom from hunger and thirst – Ensuring access to adequate and clean food and water.
2. Freedom from discomfort – Providing suitable shelter and living conditions.
3. Freedom from pain, injury, and disease – Promoting health and reducing suffering through preventive
measures and proper medical care.
4. Freedom to express normal behavior – Allowing animals to live naturally, in ways that align with their instincts.
5. Freedom from fear and distress – Creating environments that minimize stress and promote psychological well-being.
As Dr. Payungsak notes, “The application of the concept of sustainable animal welfare, which emphasizes caring for animals to be comfortable, stress-free, live naturally, reduce the chances of disease, and reduce the use of antibiotics with the Five Freedoms of Animal Welfare principles, not only helps improve the quality of animals’ lives and improve the quality of their meat, but also helps reduce environmental impacts.”
The integration of cutting-edge technologies is accelerating the transition from traditional livestock practices to Smart Farming systems. Industry leaders like CP Foods are spearheading this movement, leveraging modern tools to revolutionize animal husbandry.
IoT technology enables continuous monitoring of animal health, feeding habits, and living conditions. Real-time data allows for swift interventions, reducing the risk of disease outbreaks and ensuring optimal conditions for animals.
AI-powered systems analyze vast datasets to predict trends and identify potential issues. This supports informed decision-making and enhances long-term sustainability in
farm operations.
Automated sensors track key environmental factors, such as temperature and humidity, ensuring ideal conditions within animal shelters. These advancements minimize stress, improve growth rates, and elevate animal welfare standards.
Dr. Payungsak emphasizes, “Changing the traditional mindset to a new mindset by introducing smart technologies such as the Internet of Things (IoT), artificial intelligence (AI), and automatic sensors in the Smart Farm management process will help monitor animal health, feed management, and create a good environment in the animal shed, reducing stress and preventing epidemics.”
Big Data and cloud-based systems play a critical role in modern Smart Farming practices. By collecting and analyzing large volumes of information, these technologies facilitate efficient farm operations, resource allocation, and supply chain management. Predictive analytics derived from these systems allow farms to remain adaptable to changing conditions and market demands.
Sustainability in animal welfare also encompasses responsible sourcing of raw materials. CP Foods has committed to achieving a Zero Deforestation target by 2025, ensuring that materials such as feed-grade corn, soybeans, and palm oil are legally produced, traceable, and deforestation-free.
THE INTEGRATION OF CUTTINGEDGE TECHNOLOGIES IS ACCELERATING THE TRANSITION FROM TRADITIONAL LIVESTOCK PRACTICES TO SMART FARMING SYSTEMS.
According to Dr. Payungsak, “Food-importing countries have additional import conditions, such as responsible raw material sourcing. CPF has announced a goal to drive sustainable raw material sourcing, including animal feed corn, palm oil, soybeans, and cassava, which must come from legal, traceable, and zero deforestation sources by 2025.”
The benefits of sustainable animal welfare extend beyond improved animal health and productivity. By reducing reliance on antibiotics, cutting greenhouse gas emissions, and conserving resources like water and land, these practices contribute to global environmental goals. Farmers who adopt sustainable methods also enjoy significant cost savings and increased production efficiency, creating long-term stability for their families.
As consumer awareness of ethical and sustainable food production grows, companies must adapt to meet these evolving expectations. CP Foods and other industry leaders are demonstrating that sustainable practices can enhance not only animal welfare but also the quality and safety of food products.
“Leading agro-industrial companies around the world are well aware of the links between animal welfare, quality, food safety, and environmental sustainability. The transition from traditional animal husbandry to modern smart farming with digital technology will help create a better future for animals, humans, and the environment of this planet,”Dr. Payungsak concludes.
Sustainable animal welfare is more than a strategy; it is a vision for a future where progress does not come at the expense of others. By fostering a balance between productivity, environmental preservation, and animal well-being, this approach paves the way for a truly sustainable food system.
Embracing these practices ensures that humanity can thrive alongside nature, creating a legacy of sustainability and ethical responsibility for generations to come. Through collaboration and innovation, the livestock industry can contribute to a harmonious coexistence, where animals, humans, and the environment prosper together. FBA
By Francis Watari
Africa’s beverage industry has emerged as a dynamic and lucrative sector in 2024, attracting substantial investments from global corporations and regional players. With a rapidly growing population, rising urbanization, and shifting consumer preferences, the continent offers a wealth of opportunities for innovation and expansion. From soft drinks to alcoholic beverages and functional wellness drinks, manufacturers are investing heavily to cater to the evolving demands of Africa’s diverse markets.
The year has seen strategic acquisitions, facility expansions, and the introduction of new product lines, underpinned by a strong focus on sustainability, affordability, and premiumization. Leading companies are leveraging Africa's unique market conditions to not only expand their footprints but also address challenges such as infrastructure gaps and fragmented distribution networks.
In addition to the traditional focus on increasing production and improving supply chains, manufacturers are placing emphasis on health-conscious offerings, sustainable packaging, and localization of flavors to resonate with African consumers.
This article recaps the significant investments made in the African beverage industry throughout 2024, highlighting the strategies manufacturers are adopting to stay competitive in a rapidly evolving landscape.
The year 2024 has seen a year of large-scale investments in Africa’s soft beverages industry. Companies such as Coca-Cola and PepsiCo are leading the charge, with a focus on expanding their production capabilities and distribution networks. CocaCola, currently ranked the world’s most valuable brand, has been at the core in revamping the soft drink industry.
In September, Coca-Cola Beverages Africa (CCBA) the soft drink giant announced a major expansion of its Nigerian operations, committing US$1 billion over the next five years. According to the company, this investment will go towards building new production facilities, improving supply chain logistics, and enhancing the company’s retail presence across the country. Additionally, CCBA plans to invest US$175 million in Kenya over the next five years aiming to accelerate the company’s systems expansion in the region.
Not only has the company invested in expanding operations
but also boosted its production capacity. Recently, it invested US$50 million in a new bottling line in Namibia, set to produce 27 000 bottles an hour, boosting production capacity by 30%. “We’ve ensured that this production line goes beyond output numbers. It’s about creating shared opportunities across the value chain. The increased production also provides a boost to local businesses that supply us with raw materials and services,” said CCBA Namibia GM Pottie de Bruyn.
During the year, the beverage company also launched a US$27 million production line in Uganda with a capacity of 67,000 bottles per hour, reinforcing its commitment to the African market.
Coca-Cola HBC, one of the largest CocaCola bottlers, secured a US$130 million loan from the EBRD to support sustainable business practices and people development. Additionally, a US$750,000 grant from the GEF will promote advanced wastewater treatment and water management systems.
Meanwhile, industry competitor PepsiCo has not been left out in boosting its operations in the African market. The Pepsi producer has invested in expanding its production capabilities. In October, the PepsiCo producer announced a US$50 million investment in a production facility in Kiswishi City, Democratic Republic of the Congo (DRC), marking the one of the largest consumer-focused foreign direct investments (FDI) in the country’s history.
The investment cemented its commitment to the country following the opening of a bottling plant in Kinshasa in September 2024, with a capacity to produce 1.2 million bottles per day.
Another key player taking on dominance of the two American soft drinks manufacturers is an Indian multinational company Varun Beverages Ltd (VBL) that has made strategic acquisitions seeking to regain its once popularity in Africa. VBL, also one of the largest franchisees of PepsiCo in the world (outside USA), started the year on a high note completing the acquisition of South Africa-based Beverage Company BevCo and its subsidiaries.
The acquisition valued at US$158.28M saw VBL secure BevCo’s holding franchise and distribution rights for PepsiCo products in South Africa, Lesotho, Eswatini, Namibia, and Botswana. Recently, the company expanded its footprint with the full acquisition of SBC Beverages Tanzania Ltd. (SBCT) and SBC Beverages Ghana Ltd. (SBCG), with investments amounting to
US$154.5M and US$15M respectively.
In the alcoholic beverage industry, the drive to premiumization has attracted global beverage giants to cement their operations in the region. In December 2023, Kenya Breweries Ltd, part of East African Breweries Ltd commissioned production at its US$7.85 million microbrewery. The microbrewery, featuring a tasting room, positioned KBL at the forefront of innovation, solidifying its commitment to delivering topnotch beverages to the Kenyan market and beyond.
In its sustainability efforts, the company through its subsidiary in Uganda, Uganda Breweries Ltd (UBL) commissioned a US$9.66M state-of-the-art biomass plant to help reduce its carbon footprint and promote sustainable manufacturing practices.
IN NUMBERS AMOUNT CCBA TO INVEST IN NIGERIA IN THE NEXT 5 YEARS 1B US$
which has gained significant market traction in Ethiopia.
Additionally, in Tanzania, the company expanded its offerings with the introduction of Namibian-brewed lager, Windhoek beer.
The African alcoholic beverage market also witnessed investment from the world’s largest brewer by both volume and revenue, AB InBev, through its subsidiary in Zambia, Zambian Breweries, invested US$80 million upgrading the production plant in the country. The new plant aims to foster sustainable economic growth and create employment in the region. The company also boosted its operation in Nigeria, helping its subsidiary International Breweries Plc, to repay an outstanding US$379.9 million loan.
The independent local alcoholic beverage companies have not been left behind in chasing a higher competitive advantage in the industry. Ethiopian-owned Kegna Beverages nears completion of the first phase of its 109.075-hectare brewery project in the West Shoa Zone of Oromia State. The company, which started with an initial capital of US$13.5 million has since expanded its investment to US$45.0 million.
The new brewery will be used to brew beer and other beverages like juice and bottled water. Additionally, Kerry also unveiled a new 1000m2 manufacturing facility in Uganda to support local food and beverage manufacturers.
Looking ahead, the African beverage industry shows strong potential for continued growth. With a young and increasingly affluent population, coupled with changing consumption habits, the market is poised for further innovation.
According to 6Wresearch, the Africa Alcoholic Beverage Market is expected to grow at a CAGR of 7.1% during the forecast period 20242030 while Statista projects the Non-Alcoholic Drinks market to grow by 11.92% (2024-2029) resulting in a market volume of US$188.40bn in 2029.
Manufacturers will continue to focus on health-conscious products, sustainability, and local relevance, ensuring that Africa remains an attractive destination for investment. FBA
Eskort, the leading producer of pork products in aims to be one of South Africa’s top five food brands. In an exclusive interview with Marcelle Pienaar, the Marketing Director at the company, we profile the contribution of the company to the development of a stable and sustainable pork industry in South Africa, as it celebrates its 107 years of operation.
By Abel Ndeda
For over 107 years, Eskort has stood as a beacon of innovation and quality in South Africa’s pork industry.
What started with humble beginnings as a bacon cooperative in 1917 has transformed over the years to a multi-faceted operation with Eskort stores and a strong manufacturing presence in two provinces – despite surviving two pandemics: the Spanish flu in 1918 and Covid-19 in 2020.
With over 2,200 employees and an expanding retail footprint, the company is poised to redefine consumer engagement in the pork market while staying true to its heritage and commitment to excellence – as it aims to be one of South Africa’s top five food brands.
Founded in the small town of Estcourt in KwaZulu Natal province of South Africa, Eskort’s journey exemplifies resilience and adaptability. The company prides itself in still having had operations at Estcourt from its founding, to date.
In 1917, a group of nine farmers, including J.W. Moor, gathered at the Plough Hotel in Estcourt, KwaZulu-Natal, to discuss the establishment of a cooperative bacon factory in the area.
By August 1917, the Farmer’s Co-operative Bacon Factory Limited was founded, and building commenced on the banks of the Bushman’s River in Estcourt. When the plant opened
its doors in June 1918, it was inaugurated by Prime Minister General Louis Botha. One year later, the factory produced its first exports to the United Kingdom.
After a fire in 1925 caused significant damage to the factory, production was relocated to Nel’s Rust Dairy Limited in Braamfontein, Johannesburg, while renovations were being done at the plant.
In 1954, the company expanded its operations beyond Estcourt, opening a factory in another small town, Heidelberg in Gauteng province.
What started as a cooperative of farmers has grown into a major player in the South African food industry.
Under CEO Arnold Prinsloo, Eskort has enjoyed sustainable double-digit annual growth and unlocked its potential as an iconic brand. With a tenure of 17 years as CEO, Arnold is an experienced and visionary leader who prioritises quality, value for money and integrity, as he navigates the company for more growth and impact within the pork industry.
According to the CEO, the company’s longevity in the industry is rooted in its strong family values, brave leadership, and a commitment to adaptability and growth, with the qualities of resilience, visionary leadership, and the ability to meet challenges head-on with bravery and adaptability keeping them going.
“For brands that stand the test of time, it’s not just about surviving but thriving with uncompromised quality. Our 107year journey is a testament to that,” he emphasized, reflecting
on the 107-year journey.
THE COMPANY’S LONGEVITY IN THE INDUSTRY IS ROOTED IN ITS STRONG FAMILY VALUES, BRAVE LEADERSHIP, AND A COMMITMENT TO ADAPTABILITY AND GROWTH.
with increasingly health-conscious consumers. This dedication to quality has cultivated a loyal customer base and positioned Eskort as a trusted brand in a competitive market.
The company has utilized the 107-year anniversary as a moment to reflect on its impact and history as South Africa’s leading pork producer, and to celebrate this milestone came up with a number of interesting activities, centred on the number 107.
With dedication to quality remaining unwavering, after more than a century of operations, the company prides itself on producing antibiotic-free pork, a feature that resonates
A key highlight was the introduction of 107 reasons why the company’s products and brand can be trusted by consumers across the country. The reasons were drizzled with informative, history-laden facts and figures, plus sometimes, funny and playful information about the
company’s past, present and future; its people, its impact on the community and sustainable production focus.
Furthermore, the company showcased 107 cakes made entirely from sausages and bacon and hosted a 107-minute instore event that took place at its Meadowdale store. The cakes were donated to SA Harvest and Salt River High School in Cape Town.
It also made 107 exclusive gift drops to iconic South Africans who resonate with the their story of legacy and longevity; and made a sizzling 107-second Bacon ASMR video and a social media competition where fans shared their first memory of Eskort in up to 107 characters , with a chance to win one of 107 Eskort store vouchers.
The company also celebrated its employees in a video by showcasing 107 voices of memorable moments during its annual choir competition – which originated from the company staff’s habit of singing while working, which spawned an annual company choir competition.
A year-long LinkedIn series this year emphasises the firm’s heritage by telling stories about the company’s 107-year history.
Eskort prides itself in producing the widest range of pork products in South Africa.
“Our products range from high-end braai-ready pork cuts to ready-to-cook meals and staples like polony. Our consumers can cook, fry, braai, bake and roast our products. By analysing market trends and consumer behaviour, our product developers are always ahead of the curve,” explains Ms. Pienaar.
The company is always on the look-out to ensure its customers are satisfied with its range of products. “We deliver deliciousness in every pack and provide families with products and easy-to-prepare recipes that make their lives easier. Our
107 cakes representing 107 years in operation
than 400 pork recipes, with many prioritising healthy eating.”
The Marketing Director has introduced a rebrand and a cultural shift that has powered Eskort’s growth, centred around the fact that pork is a great source of high-quality protein.
“We keep moving with the times, innovating technologies to improve productivity and quality, and never stop setting the standard. We have no fewer than 23 sausages and vienna products, ranging from cheese grillers and chicken viennas to German bockwurst and smoked russians. We move fluidly through supply, product development, manufacturing, brandbuilding and retail impact. Our Eskort antibiotic-free pork ensures healthier and safer products for consumers.”
She adds that the company’s new range of air fryer products make it easier for consumers to choose more convenient and healthier alternatives from the hundreds at their disposal.
Some of the standout new products include Eskort Sticky Asian Pork Belly Cubes with sweet soy and ginger glaze; Sage-infused Sausages with caramelised onion sauce; Mini Frikkadels with arrabiata sauce; and Cheesy Pork Schnitzels with mature cheddar cheese sauce, that have been a big hit with consumers since their launch last year.
“We have consumers looking for value propositions and convenient options. . It's truly about understanding what the consumer needs. Furthermore, we are laser-focused on the retail experience, which includes the way our stores and staff look, as well as excellent service. All our products bear the Gold Medal badge. It’s our promise to customers that we value the trust we’ve earned over more than a century.”
Eskort’s strategy is a cornerstone of its success, now and into the future. For many meat processors, stores do not always become an area of focus, but Eskort is different.
The company operates 30 Eskort stores across eight provinces across the country. Twenty-five of the stores are Eskort-owned and five are owned and operated by franchisees.
The retail expansion allows Eskort to offer a diverse range of over 300 products, far beyond the 40 stock-keeping units (SKUs) available in national retail chains, according to the Marketing Director.
Each of our stores has a braai kiosk where customers can buy items like boerewors rolls, russian rolls, prego steak rolls and our amazing rib burgers.
“This strategy helps us balance and meet consumer demand for products they can’t find elsewhere, and that's essentially why we opened our first Eskort stores next to our factories. Subsequently, we saw that there is a big demand for other pork products that consumers don't necessarily find frequently in the retail environment, a value offering that other retailers don't have. It made sense for us to open these Eskortstores.”
In terms of retail expansion scope, the company has a vision of expanding its store footprint with five stores every fiscal year, but takes it cautiously, not to do it too quickly. “We just want to make sure that we do it in a sustainable way. So, five stores per year is our goal,” she noted.
The stores also play a crucial role in educating consumers about pork, addressing misconceptions, and showcasing its versatility. “We tried to understand, from a communication perspective, how to connect with our consumers emotionally, so that our communication is as effective as possible,” she explained.
Sticking to one type of product for 107 years is not an easy feat, especially with constant changes in consumer preferences. To keep up with consumer trends while maintaining its focus on a single product, Eskort says it understands and analyzes consumer behavior to see what products are in demand and
THE COMPANY’S FOOD SAFETY ASSURANCE MOVES BEYOND THE FARMS, STRETCHING THROUGH ITS PLANT OPERATIONS, TO ITS STORES AND THROUGHOUT THE SUPPLY CHAIN
gathers feedback from consumers.
Eskort puts strong emphasis on its mantra: Quality you can trust since 1917, which has been at the core of the business since its founding last century.
The company believes that the success of its business is based on its thorough food safety protocols. It also assures that its value chain is fully traceable from where the pig was reared to the retail point.
The company believes that it all begins from the farms. “Our farmers are our shareholders, and that makes us the custodians of the land, and partnering with them has been key to our success. The farms that supply us are regularly audited and certified by the animal health directorate at the Department of Agriculture, Land Reform & Rural Development.”
The company’s food safety assurance moves beyond the farms, stretching through its plant operations, to its stores and throughout the supply chain, including the large retailers that it supplies with sumptuous pork product delicacies.
“Our food safety system assists with a world-class approach to quality premium products and helps us set a standard for food safety in South Africa. Every ingredient in our 300-plus products meets stringent food safety standards.”
Eskort’s quality assurance programme is called S.A.F.E, and it stands for Sustainable – environmental sustainability, sowfriendly practices, pig welfare, and biosecurity; Accountable – traceability, uncompromised hygiene practices, and rigid quality control measures; Farm-to-fork – responsibility across the entire value chain.
This Farm-to-Fork quality control programme addresses the entire value chain – including processing and manufacturing. Suppliers, manufacturers, and processors are graded and held accountable for complying with how they maintain their facilities, as well as how they look after the pigs’ welfare once they are delivered into those facilities.
The suppliers are trained on biosecurity, sustainability, safety protocols, and animal welfare for sustainable pork production. Ms. Pienaar explained that in achieving a fully traceable and quality value chain, the company relies on stringent farming principles that comply with all safety protocols and standards, and full biosecurity in its factories, through deep cleansing every single night, and they get audited on a regular basis.
She adds that each of their suppliers follow the South African Pork Producers Organisation (SAPPO) ‘Pork 360’ protocols which address biosecurity, food safety, traceability, animal welfare and environmental stewardship.
Eskort is not content to rest on its laurels. Recognising shifting consumer trends, the company has embraced conveniencefocused innovations, such as air fryer-ready products and ready-to-eat options.
“We aim to make life easier for busy parents and those on the go,” Ms. Pienaar shared. Products like pulled pork pies and pork schnitzels exemplify this approach, offering quick, tasty solutions for time-strapped consumers.
Value is another key driver. With the rising cost of other proteins like beef and lamb, pork offers a more affordable option, with the company noting a substantial move by consumers to pork purchases, from the more costly beef, lamb and chicken. Eskort’s ability to provide high-quality, costeffective products has positioned it favourably in a challenging economic landscape.
According to Ms. Pienaar sales figures from Eskort indicated that hard-hit consumers have increasingly turned to cost-effective options such as viennas and polonies, as well as liver or bacon spread for their choice of protein. By the end of March 2022, demand for its viennas and spreads had spiked by 11.4% and 15.2% year on year, respectively, as households sought more affordable meat alternatives.
Despite rapid growth over the past decade, to be the most consumed meat on the planet, accounting for over 36 percent of the world’s meat intake, according to the United Nations Food and Agriculture Organisation, pork consumption in South Africa remains low in the global context.
In South Africa, it constitutes less than 10% of the total meat consumption basket, according to BFAP Data Driven Insight. With a per capita consumption of pork and pork products standing at 4.3 kg per person per year in South Africa, Ms. Pienaar believes that there is a lot of future demand to be realised, considering that the world’s largest consumer, China, leads with 15 kg per person per year.
Despite its success, Eskort acknowledges the barriers to processing and pork consumption, including religious restrictions and health misconceptions. The company has invested in consumer education to dispel myths and promote safe cooking practices.
“There’s a misconception that pork is unsafe or causes health issues, but when cooked properly, it’s a delicious and healthy option.” Eskort’s commitment to transparency and quality assurance, from farm to shelf, helps build consumer trust.
In addition, in the face of challenges such as load shedding and water scarcity, Eskort has implemented robust sustainability measures. To maintain the quality of its products,
the company invested in renewable energy by installing solar panels, backed up by large generators at its factories.
Eskort has also built its own water purification plant at the Heidelberg factory to purify all the water it uses, in addition to reserve water tanks.
The Heidelberg factory, launched in mid-February 2024. The 10,000m² development in Heidelberg – the small town where the company has produced world-class pork products for 70 years – allows Eskort to increase production capacity by 50% to meet retail needs.
The enlarged factory is equipped with the largest continuous box freezer in Africa, capable of freezing 120 metric tonnes of products to minus 18°C every 24 hours. Boxes move on a conveyor belt through the freezing chamber where the air is kept at minus 41°C – a temperature that occurs naturally only in polar regions.
Freezer management at our the factory is automated, datadriven and reliant on robotics.
Chilled and frozen warehouses in Heidelberg now have multi-level picking mezzanine floor systems, the first of their kind in the food industry in South Africa. These systems maximize vertical space by including mezzanine floors that create additional levels for storage and picking, allowing Eskort to handle a high volume of orders quickly and efficiently.
“A big part of this expansion includes the addition of carcass chillers as well as the installation of a huge box freezer to accommodate the influx of raw material,” said Arnold Prinsloo, Eskort's chief executive officer for the past 17 years, noting that the core objective of the factory extension is to create efficiencies.
Eskort’s vision for the future includes continued expansion and innovation. Plans are underway for a new abattoir to increase processing capacity and efficiency.
Ms. Pienaar explained that apart from the Eskort store expansion, the company also focuses on building an additional abattoir, increasing processing capability, and speed. In the next year or two, Eskort plans to build a new abattoir but has not disclosed any potential location.
The company also aims to open five new Eskort stores each fiscal year, balancing growth with sustainability. “Our goal is to become a top-five food company in South Africa,” Ms. Pienaar shares.
She adds that achieving this will require a deep understanding of consumer needs and a relentless focus on quality and innovation.
As Eskort moves forward, it carries with it a rich legacy built on love, dedication, and an unwavering commitment to quality. Each product, each store, and each interaction reflects the heart of a company that sees its customers not just as consumers but as family.
“This isn’t just business,” Ms Pienaar concludes. “It’s a journey we are honored to share with every South African who brings Eskort into their home.” FBA
By Nicholas Ng'ang'a
For years, Africa has seen an increase in the demand for animal products, primarily due to urbanization, which has a considerable impact on food consumption patterns in general and specifically on the demand for meat. As one of the continent's critical sectors, it plays a vital role in economic development, food security, and job creation.
According to the CISAO, the top five African countries producing meat from farmed species are South Africa, Egypt, Nigeria, Morocco, and Sudan. Together, they contribute about 50% of the continent’s total meat production in terms of volume.
Data from The Regional Strategic Analysis and Knowledge Support System (ReSAKSS) indicate that since 2000, Africa's meat production has experienced significant growth, nearly doubling from 11.59 million metric tons to 19.88 million metric tons by 2020. The continent now contributes approximately 6 percent to global meat production, a notable increase from 4.5 percent two decades ago.
Even though there has been a stable increase in meat production, statistics from market research firm, Statista, show that one person consumed on average 9.6 kilograms of meat per year in Africa in the period between 2021 and 2023, the lowest meat consumption per capita in the world. Chicken meat was the most consumed on the continent, at 3.8 kilograms per capita yearly. By 2033, the demand is expected to reach around 9.8 kilograms per capita.
Other market research projects that by 2050, beef and poultry consumption will increase tenfold compared to today, reaching 13.5 million and 11.8 million tons, respectively.
While many African countries have traditionally relied on farming methods, there has been a noticeable shift towards more modern practices in recent years. This change is becoming increasingly important as urban populations expand and dietary habits change. It is approximated that the farmed species include chickens (1.9 billion), goats (374 million), sheep (350 million), cattle (320 million), pigs (35 million), dromedaries (23 million), and equids (donkeys, horses, and mules 2.6 million).
Meat production across Africa varies from region to region.
Records from ReSAKSS show that South Africa leads in beef and poultry production, with outputs of 1 million and 1.9 million metric tons, respectively. It is also the second-largest producer of pork, with 0.3 million metric tons. The country also has the highest productivity in cattle farming, with an average yield of 231 kilograms per animal, and also leads in pig meat production with 86 kilograms per animal. In poultry, it stands out with a yield of 1.94 kilograms per bird.
Other than South Africa, Egypt and Kenya are major cattle producers, each producing approximately 0.5 million metric tons. Egypt boasts an impressive yield of 314.6 kilograms per animal, while Kenya's average is 108.5 kilograms. For poultry, Egypt is the second-largest producer in Africa, with 1.5 million metric tons and a yield of 1.4 kilograms per bird. Morocco also contributes significantly with 0.9 million metric tons, maintaining the same yield per bird as Egypt.
When it comes to pork, a recent ILRI study has shown that Uganda is now producing nearly as much or even more pork than South Africa.The Ugandan livestock census revealed a rise in the number of pigs from one million to 7.1 million with 1.1million households rearing pigs.
The people of Uganda have also been named as the biggest pork consumers in Africa and second globally after China. Uganda’s big appetite for pork was disclosed by the International Livestock Research Institute (ILRI), consuming an average of 3.5 Kgs of pork annually. Although the demand and supply of pigs is huge and growing the pigs in Uganda have poor weight gain and growth due to potential feed according to the research.
Nigeria and South Africa are also among the leading producers, each with around 0.3 million metric tons. South Africa's pig meat production is more intensive, achieving a higher yield of 86 kilograms per animal. In contrast, Nigeria
focuses on larger-scale production, managing a herd of 8 million pigs, though its yield per animal is lower at 45 kilograms. In addition to production, Africa is becoming an increasingly immense importer of meat, especially beef, from international markets, but its role as an exporter remains relatively limited. Historically, the continent’s meat exports have been focused on live animals, such as cattle from the Sahel to West African coastal markets, and sheep and goats from the Horn of Africa
AFRICA'S MEAT PRODUCTION HAS EXPERIENCED SIGNIFICANT GROWTH, NEARLY DOUBLING FROM 11.59 MILLION METRIC TONS
IN 2000 TO 19.88 MILLION METRIC TONS BY 2020.
to the Middle East. The only meat category where an African country ranks as a major global exporter is sheep and goat meat, with Namibia standing as the 10th largest exporter worldwide.
Infrastructure deficiencies
One of the most significant obstacles to the meat industry in Africa is inadequate infrastructure. Many regions lack
efficient cold chain logistics, which are essential for maintaining meat quality from production to consumption. For instance, in Kenya, poor road networks and insufficient refrigerated transport facilities lead to high post-harvest losses. According to Livestock Principal Secretary Jonathan Mueke, these infrastructural issues result in low-value addition and poor processing skills, crippling the sector's performance, especially in export markets.
Access to finance is another challenge for the meat industry, particularly for smallholder farmers who form a large part of the sector. In countries like Tanzania and Ethiopia, although livestock numbers are high, low productivity persists due to the lack of financial services and support for small-scale producers. Similarly, in South Africa, the industry faces tough conditions with farmers operating on razor-thin profit margins.
beef, which was between US$3.16 and US$3.42 per kilogram two years ago, now struggles to reach US$2.94 per kilogram.
Animal diseases pose another threat to the meat industry across Africa. Outbreaks of diseases such as foot-and-mouth disease (FMD) can lead to devastating consequences for livestock populations and halt exports entirely. For instance, Botswana faced a culling process due to an FMD outbreak that disrupted its beef exports to the European Union (EU) in 2022. Although shipments resumed later that year after rigorous health checks, such incidents are proof of the fragility of animal health management systems in place.
In 2024, Nigeria faced a resurgence of highly pathogenic avian influenza (HPAI), specifically the H5N1 serotype, which severely impacted the poultry industry. The outbreak, confirmed in January, marked the first detection of HPAI in the country since August 2023. According to a report by LiveGAPS, this led to the culling of approximately 10,000 birds from affected flocks in Kebbe, a northwestern state. Since the onset of this outbreak wave in December 2020, Nigeria has reported over 454 outbreaks across 31 of its 37 states, directly affecting more than 2.4 million birds.
The economic repercussions have been substantial; the country has seen prices for poultry products rise sharply. For instance, reports indicate that chicken prices increased by nearly 25% in early 2024 compared to the previous year, exacerbating food insecurity in a nation where poultry serves as a primary protein source for many households.
Investment potential
2.5B
AMOUNT JBS TO INVEST IN NIGERIAN MEAT PROCESSING FACILITIES
Paul Makube, a senior agricultural economist at FNB, South Africa, believes that recovery could be possible, provided certain economic and environmental conditions improve. Adding to the challenges, meat prices have stagnated. Economic pressures on consumers have limited spending, preventing prices from rising. For instance, in South Africa, the price of Class A
Investment in modern farming techniques can significantly enhance productivity within the African meat sector. Brazil-based meat producer JBS is allocating US$2.5 billion to establish six meat-processing facilities in fiveyear in Nigeria. This will make Nigeria a meat powerhouse, considering that JBS is the largest meatpacker in the world. In South Africa , Eskort Food, the leading pork manufacturer, plans for more expansion. This year, it has expanded its Gauteng production capacity by 50% with a factory extension that will be used to create more
efficiencies.
In another instance, the African Chicken Genetic Gains (ACGG) program was launched 1n 2014 to improve poultry farming by introducing more productive chicken breeds suited to the specific conditions of smallholder farmers in Africa. Initially focused on Ethiopia, Nigeria, and Tanzania, the program aimed to enhance productivity through collaborations with farmers, private sector entities, and policymakers.
Due to the program's success, it attracted further investment and expanded beyond Africa, incorporating countries like Kenya, Ghana, Zimbabwe, Cambodia, Myanmar, and Vietnam. As a result of its global reach, the program was renamed Tropical Poultry Genetic Solutions (TPGS). Research conducted through the program has shown impressive results, with on-station and on-farm trials revealing up to a 200% increase in egg production and a 300% increase in body weight in tropically adapted chicken breeds compared to indigenous breeds in Ethiopia, Tanzania, and Nigeria.
Such programs can be adopted more into the industry, which will surely translate into the production and quality.
The adoption of cultured meat has made strides in various parts of the world, with countries like the United States, Singapore, and the Netherlands leading the way. In these regions, cultured meat has gained traction as a sustainable alternative to conventional meat production, driven by increasing consumer demand for environmentally friendly food sources.
However, Africa has been relatively slow to embrace this innovative technology due to several factors, including limited consumer awareness, regulatory challenges, and a lack of investment in biotechnology.
In South Africa, while there is a growing interest in alternative proteins—evidenced by a 2021 study showing that 60% of South Africans were highly likely to try cultivated meat—regulatory hurdles have hindered progress. The South
African Department of Agriculture imposed restrictions on labeling plant-based and cultured meat products, which has created confusion among consumers and discouraged investment from international companies.
This regulatory environment contrasts sharply with regions that have successfully integrated cultured meat into their markets. For example, in the Netherlands, investment in cultured meat startups has surged, with companies like Mosa Meat and Meatable receiving millions in funding to scale production. By 2023, Mosa Meat had successfully launched its first cultivated beef burger in restaurants across Europe, demonstrating the viability of this technology.
While other parts of the world have made significant strides in diversifying their meat markets, Africa has been relatively slow to embrace these changes. Countries like Brazil and Australia have successfully expanded their meat exports by tapping into high-value markets and adopting innovative production techniques. For instance, Brazil has become one of the world's largest exporters of beef, with exports reaching over $7 billion in 2021, largely due to its ability to meet international quality standards and effectively market its products globally.
Regions that have diversified their markets have seen significant growth. Namibia, for instance, has established itself as a top exporter of premium game meat. According to reports by the Ministry of Environment and Tourism Namibia, In 2022, the country produced 7,110 tonnes of game meat, a slight 0.636% increase compared to the previous year. The highest production occurred in 2015, with 7,126 tonnes, while the lowest was 1,600 tonnes in 1961. In 2024, Namibia's meat market is projected to generate $345.50 million in revenue, with an annual growth rate of 8.47% expected from 2024 to 2029. By 2029, the market is anticipated to reach 57.01 million kg in volume, with a 4.7% growth forecast for 2025. FBA
KENYA - Kenya is intensifying efforts to boost its meat exports to Europe under the Economic Partnership Agreement (EPA) with the European Union (EU), which became operational on July 1.
The initiative, involving the government and private sector collaboration, aims to capitalize on the EU’s vast market of over 448 million consumers.
According to the Kenya Association of Manufacturers (KAM), the country's meat exports were valued at US$135.23 million (KES 17.5 billion) in 2023, as per the United Nations COMTRADE database.
Trade Principal Secretary Alfred K’Ombudo noted that the EU imports approximately US$50 billion worth of meat and edible meat offal annually, along with US$11 billion in live animals. Despite these figures, Kenya’s market share remains negligible, highlighting the need for targeted strategies to tap into this lucrative market.
To bridge this gap, the State Department for Trade and KAM hosted a sensitization program in Isiolo. Organized in partnership with the European Union in Kenya, the program engaged stakeholders from the livestock sector, emphasizing export opportunities under the EPA.
KAM underscored the economic potential of Northern Kenya, home to robust livestock activities. The EPA, which builds on the East African Community-European Union trade framework, includes provisions to support Kenya’s development, such as agricultural safeguards and protections for local industries. Under the agreement, Kenya will gradually liberalize 82.6% of imports from the EU over 25 years, starting in the seventh year of implementation.
The country’s meat production is already on an upward trajectory. According to the Economic Survey 2024, Kenya’s production of meat and meat products grew by 10.1% in 2023, while fish processing and preservation increased by 2.8%. Meanwhile, total exports to the EU climbed by 12.7%, reaching US$1.16 billion (KES 150.1 billion) last year, driven by higher shipments of flowers, avocados, and beans.
ABU DHABI - Al Ghurair Foods has commenced construction of a cutting-edge hatchery and poultry processing facility in KEZAD Al Ma’mourah, Abu Dhabi.
Spanning 15.5 hectares, the facility will feature a hatchery, processing plant, rendering plant, and effluent treatment plant. The hatchery is set to produce 10 million day-old chicks annually, while the processing unit will generate 10,000 tonnes of finished poultry products per year to meet local demand in the UAE.
The rendering plant, among the largest privately owned in the country, will process 1,600 tonnes of protein meals and 400 tonnes of oil and fat from poultry by-products. These outputs will be repurposed as aquaculture feed or alternative fuels, supporting sustainability goals.
Aligned with the UAE’s National Strategy for Food Security 2051, the project aims to reduce dependence on imported poultry and address rising local demand. Strategically located within KEZAD, the facility will create 180 jobs once operational. This initiative stems from a 50-year land lease agreement signed in April 2023 between Al Ghurair Foods and KEZAD.
The US$272 million investment includes other food projects, such as a corn starch manufacturing plant, a 60-hectare broiler farm, and a liquid eggs facility launched in 2023. These developments seek to capitalize on the Middle East's growing poultry market, where consumption varies widely. Kuwait leads with 57 kg per capita annually, while Sudan records 0.8 kg. Saudi Arabia dominates regional production, producing 71% of the total and achieving over 60% self-sufficiency in 2022. Despite producing 56,000 metric tons of poultry in 2022, the UAE faces challenges scaling production due to high input costs and fresh chicken price controls. The project partners include SDV Consulting Engineers, Al Qanater Al Thahbia General Contracting, and equipment providers like Baader and Petersime.
USA - Tyson Foods, a leading meat processing company, has announced the permanent closure of its beef and pork processing plant in Emporia, Kansas, affecting 804 employees.
The closure is scheduled for February 14, 2025, with an additional five laboratory workers set to lose their jobs on January 31. This marks the latest in a series of reductions by Tyson, which has shuttered multiple facilities since early 2023, including six chicken plants and a pork facility in Iowa.
The Emporia plant, located in a city of 24,000 residents, produced items like marinated meats and ground beef. It stopped slaughtering cattle in 2008 due to limited livestock supplies. Tyson attributes the closure to operational efficiency efforts
and broader strategic adjustments.
While Tyson’s beef division generated US$20.5 billion in revenue in fiscal year 2024, it recorded an adjusted operating loss of US$291 million, a steep drop from the US$233 million profit in 2023. Persistent drought has significantly reduced cattle supplies, exacerbating the division's struggles. The company anticipates further operating losses in the range of US$200 million to US$400 million in fiscal year 2025.
During a recent conference call, Brady Stewart, Tyson’s chief supply chain officer and president of its beef and pork division, highlighted the challenging market conditions, citing external pressures like weather-driven cattle shortages.
Tyson is collaborating with local and state officials to support displaced workers and has encouraged employees to seek alternative roles within the company.
NIGERIA - Brazilian meat giant JBS has announced a US$2.5 billion investment to build six meat-processing facilities in Nigeria, marking a significant step in its global expansion strategy.
This initiative, formalized through a memorandum of understanding with the Nigerian government, will span five years and focus on enhancing the country’s protein production capacity and supply chain.
The investment plan includes feasibility studies, budget preparation, and action plans to develop sustainable food production systems. In return, the Nigerian government has committed to ensuring supportive economic, sanitary, and regulatory conditions for the project's success. JBS also plans to support Nigeria’s National Food Security Plan by sharing its expertise in agro-industrial development and sustainable practices.
Highlighting the urgency of the initiative, JBS cited data from the World Food Programme, revealing that 24.8 million Nigerians face severe food insecurity. Furthermore, the World Bank notes that 76% of sub-Saharan Africa’s extreme poor depend on agriculture for their livelihood. Currently, Nigeria’s protein production accounts for 10% of GDP but satisfies only 40% of domestic demand.
Nigeria, with its population of over 220 million, consumes approximately 1.5 million metric tonnes of meat annually. Despite per capita meat consumption being just 7.3 kg—below the global average—it is steadily increasing due to rising
incomes and urbanization. Beef and poultry are the most popular meats, accounting for 760,000 metric tonnes annually.
Market projections indicate Nigeria’s meat production will grow modestly, reaching nearly 1.6 million metric tonnes by 2028, reflecting an annual growth rate of 0.8%. JBS’s investment is expected to help bridge the supply-demand gap while tapping into this growing market.
This project adds to JBS’s global ventures, including recent investments in Saudi Arabia, Australia, and Canada, as the company seeks to strengthen its position as a leader in global protein production.
MOROCCO - Morocco is ramping up efforts to ensure the safety and quality of imported red meat under stringent regulations led by the National Office for Food Safety (ONSSA).
The measures align with national and international standards to protect public health, covering both fresh and frozen meat imports.
According to ONSSA, imported red meat must originate from countries approved by ONSSA following rigorous risk assessments. These evaluations examine the sanitary conditions of slaughterhouses and the qualifications of veterinary inspectors in exporting nations. Currently, the United States, Australia, and EU countries supply goat and sheep meat, while beef imports come from countries like Brazil, Paraguay, and Ukraine.
Once at Moroccan borders, all shipments undergo meticulous inspections. ONSSA requires health certificates from the exporting nations, ensuring compliance with cold storage, transportation, and labeling standards. Imported meat must also meet Islamic slaughter requirements, verified through certifications from accredited religious bodies. Random laboratory testing further checks for chemical contaminants and veterinary drug residues, guaranteeing consumer safety.
The intensified import protocols coincide with efforts to modernize Morocco's red meat industry. Recent discussions in Rabat with Spanish business leaders addressed rising prices, regulatory challenges, and supply chain improvements. Diversifying supply sources and regulating prices are crucial as droughts have significantly impacted Morocco’s livestock. The national herd consists of 3.5 million cattle, 20.6 million sheep, and 6.5 million goats, with meat production projected to slightly increase to 330,000 metric tons.
Despite these measures, Morocco’s red meat production has sharply declined from 1.39 million metric tons in 2019 to just 541,000 metric tons, placing the country 41st globally.
Tönnies Group rebrands as Premium Food Group to reflect broader focus
GERMANY - German meat processing leader Tönnies Group will rebrand as Premium Food Group (PFG) in 2024, signaling its transformation from a traditional meat producer to a diversified food manufacturing giant.
While the Tönnies name will remain exclusive to its meat division, the rebranding reflects a broader strategy to expand its portfolio and strengthen its position in the global food market.
The move follows a “structural transformation process” initiated several years ago, according to shareholder Maximilian Tönnies. This shift aims to provide greater decision-making autonomy to individual business units, enhancing operational agility and innovation. The change will be visible at the company’s Rheda-Wiedenbrück headquarters, where the Tönnies signage will be replaced with the Premium Food Group logo.
Founded in 1971 as a small butcher shop, Tönnies has grown into one of Europe’s largest meat producers, employing over 15,000 people. The company serves millions of customers daily with a product range extending beyond traditional meat and sausage items. Its offerings now include plant-based alternatives, convenience foods, sauces, soups, and animal feed. Additionally, Tönnies supplies by-products like proteins, fats, and flours to industries such as pharmaceuticals and biofuels.
The rebranding aligns with the company’s recent diversification efforts. In September, Tönnies acquired the German beef operations of Dutch food company Vion, enhancing its position in the beef market. In August, it invested in Nosh, a startup specializing in fermentation technology for sustainable food production. Earlier this year, the group restructured its export packaging division for Asian markets, resulting in its closure and affecting 140 employees.
Sales/Marketing Purchasing/Supply
Others