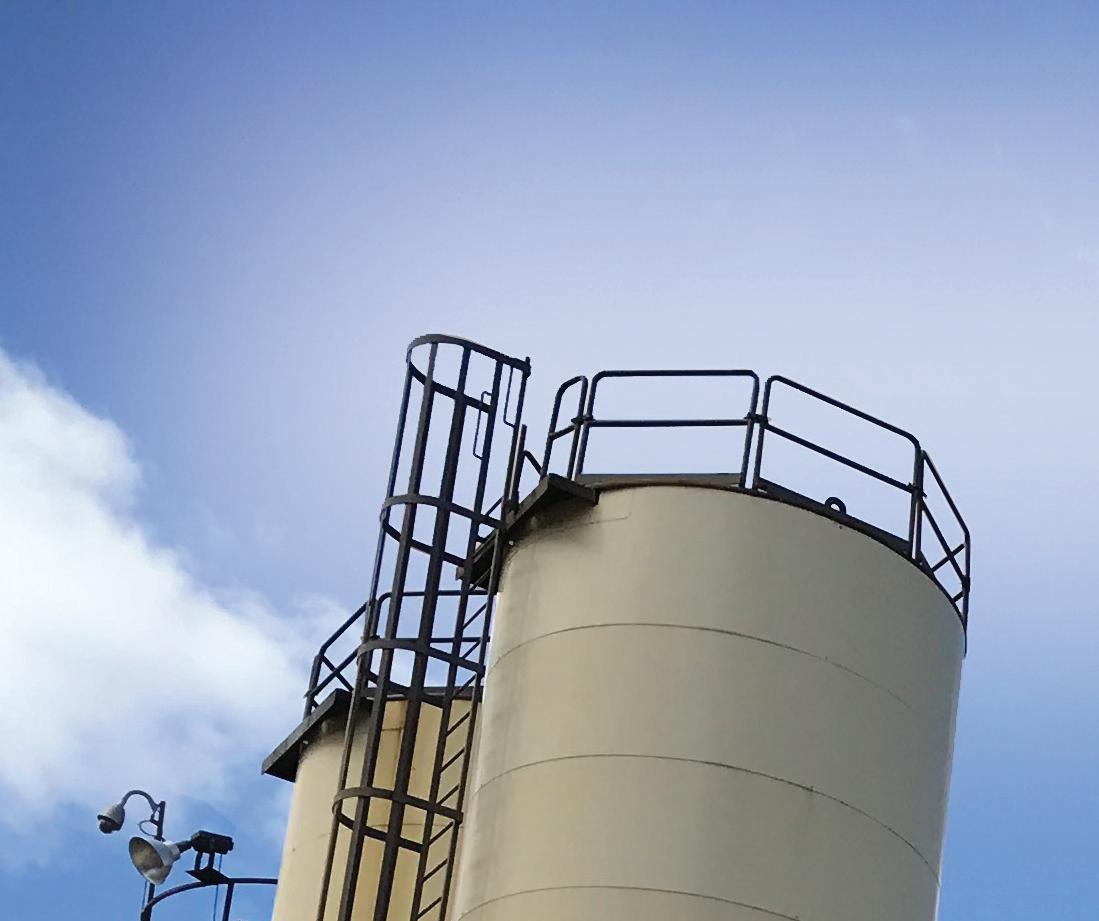

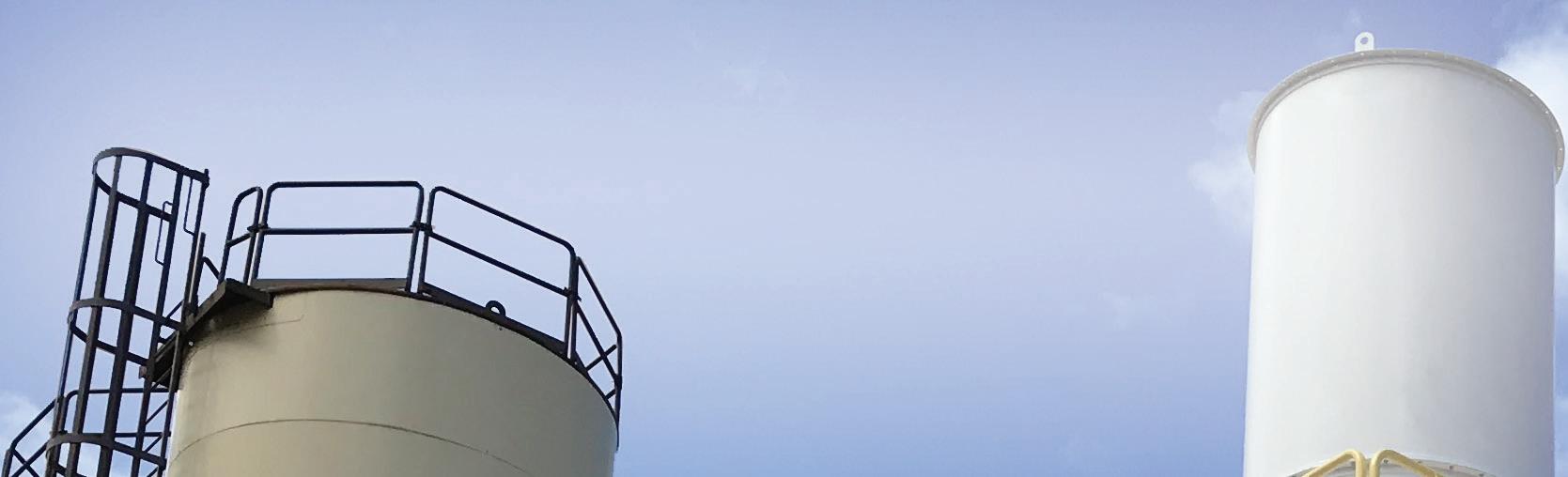



























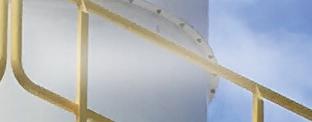

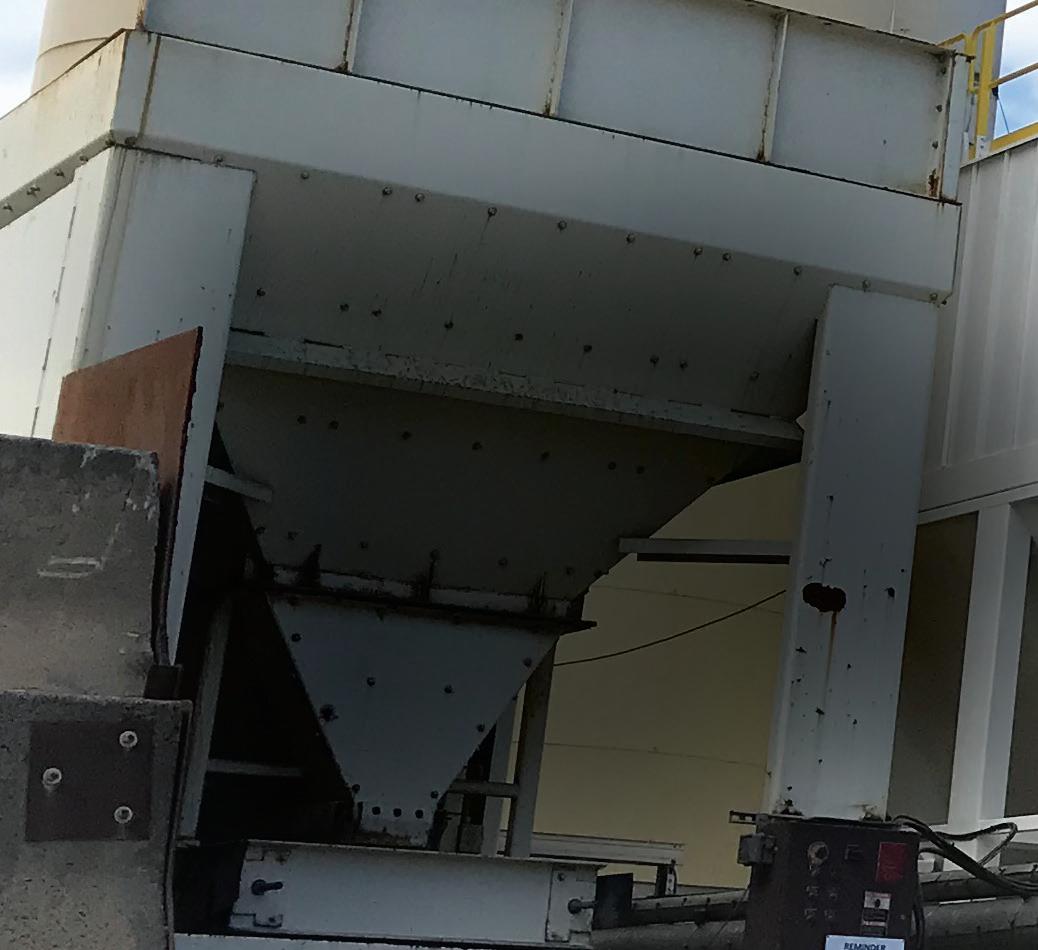

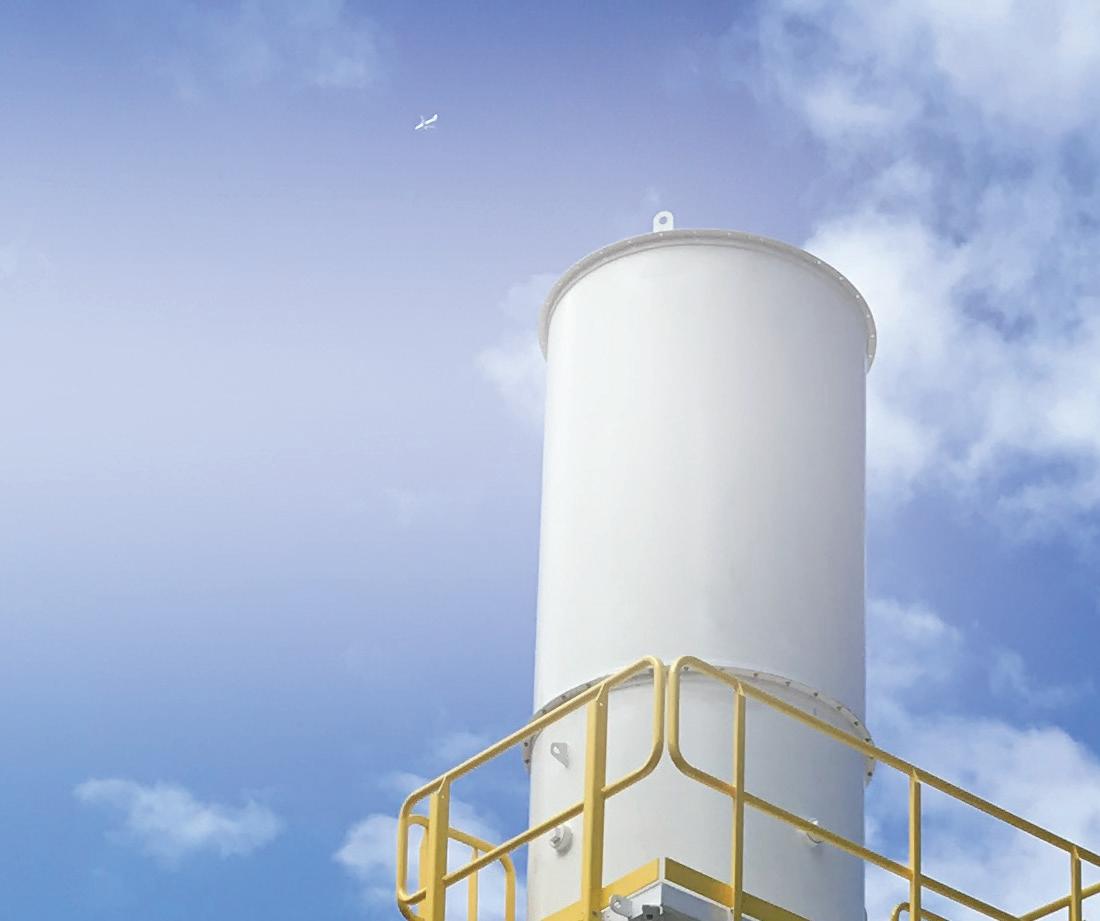

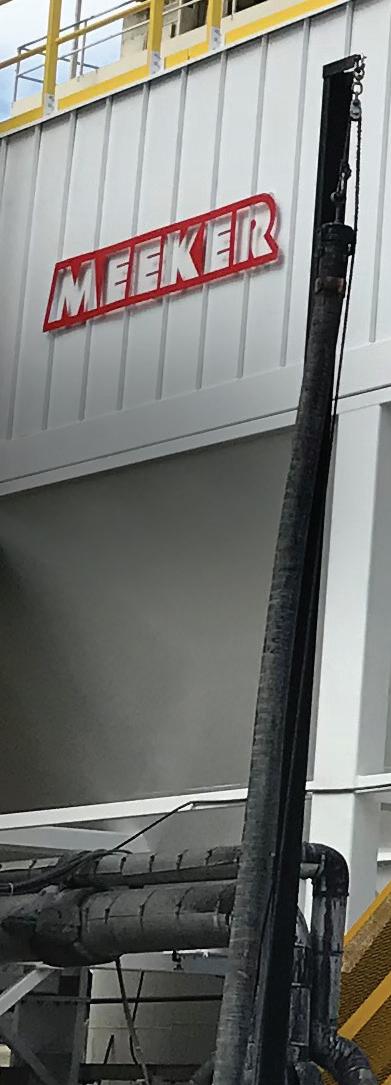
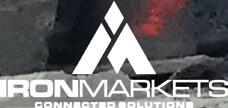
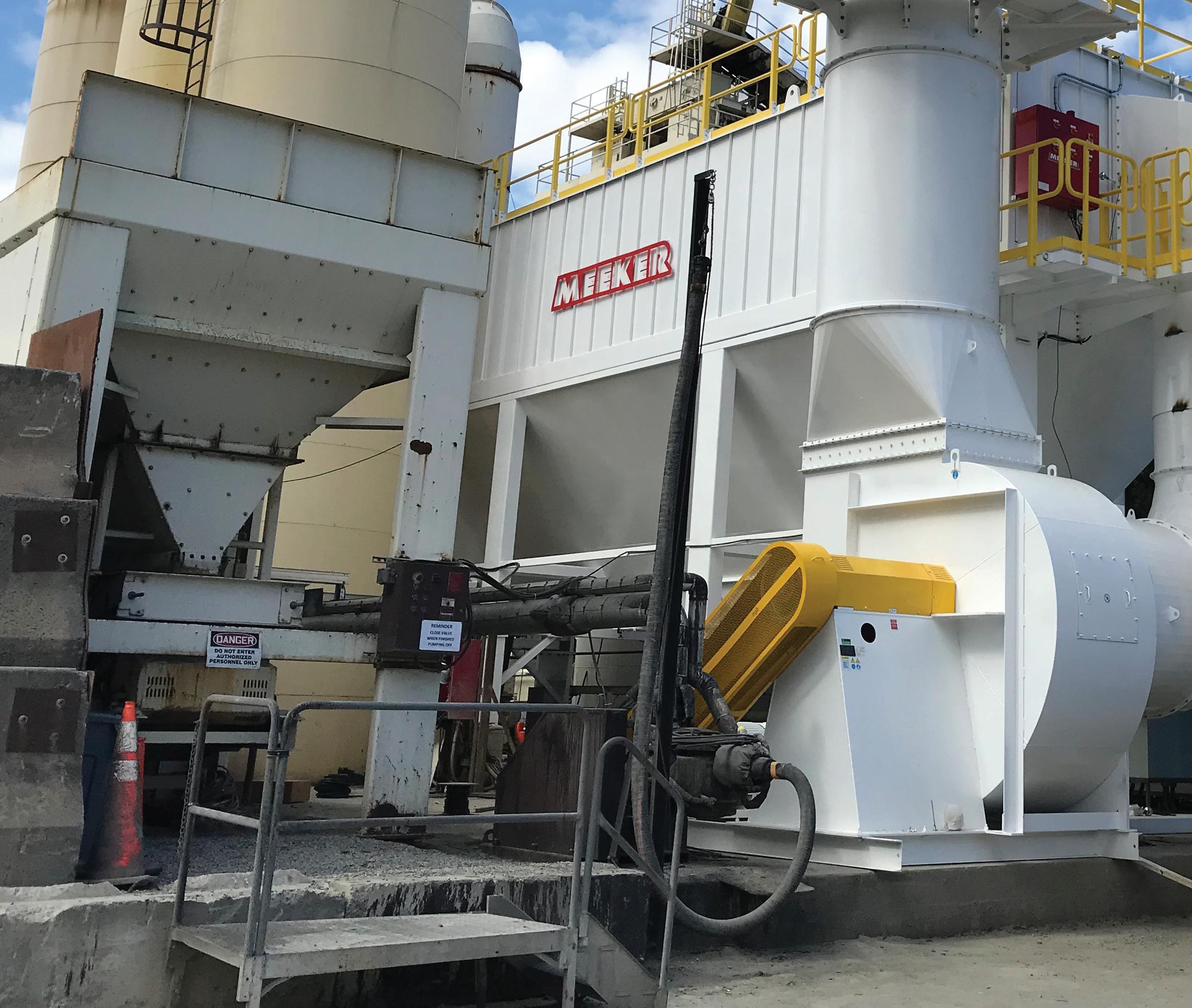
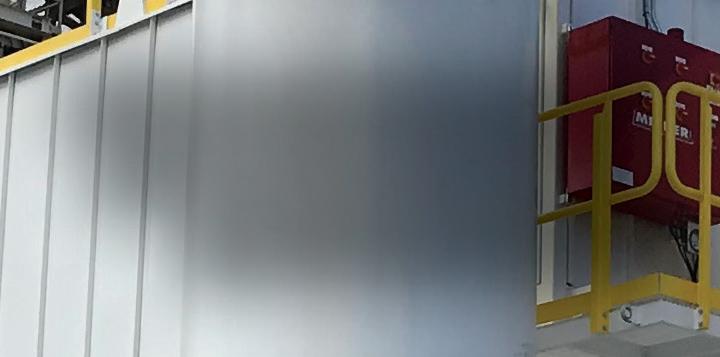


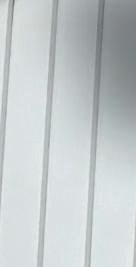


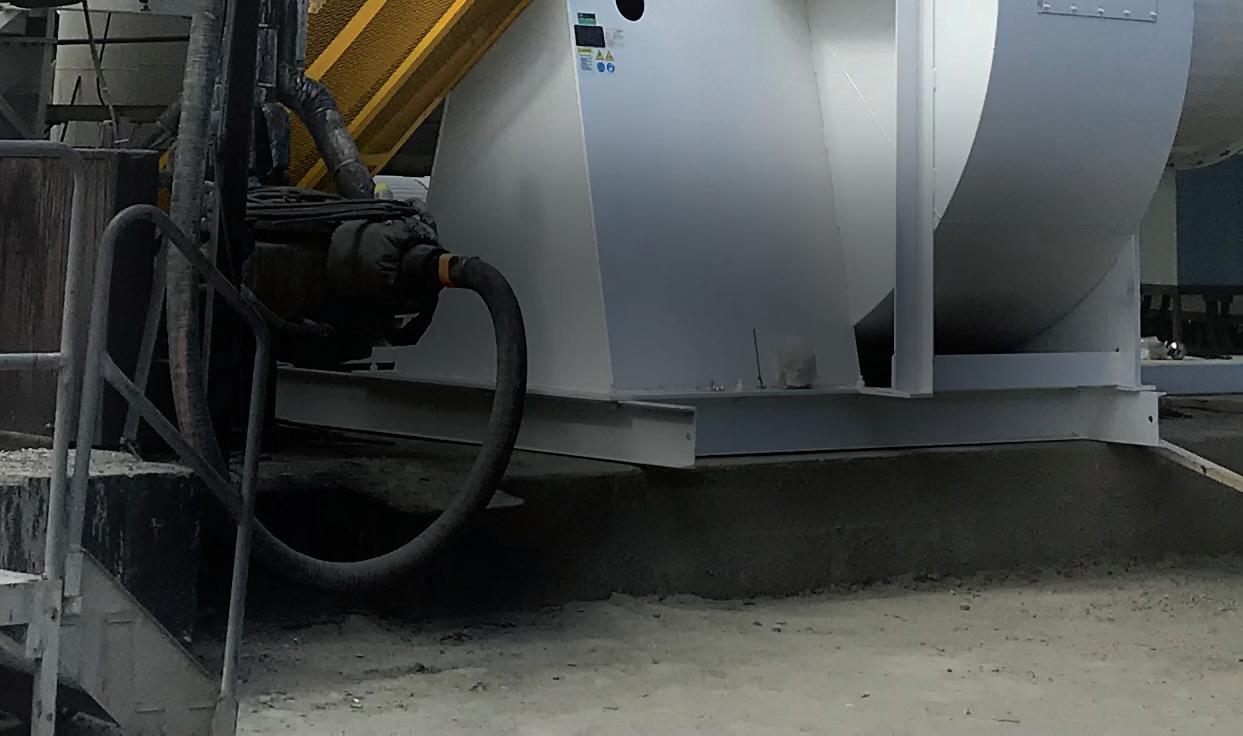
Weiler Material Transfer Vehicles lead the way with proven innovations to provide the lowest cost per ton of operation.
Innovative and reliable operator friendly features such as paver hopper management system with distance to paver, storage hopper management and auto chain tensioning.
Clam shell doors and full width drop down floors provide unmatched access for cleanout and maintenance.
Variable speed elevator and conveyors meet production requirements while minimizing wear.
The multiple, incremental improvements to the 4th generation of chains, sprockets and augers are retrofittable to all machines and provide increased wear life.
14 Decoding The Cloud
The difference between cloud-native and cloudconnected, and what cloud means for your business.
24 Asphalt Industry Annual Training Guide 2024-2025
Adequate training is one of the most important factors when it comes to new employee retention. Checkout the opportunities for the coming season.
32 We Can Do Better
What does making space for women in the asphalt industry really mean? JOBSITE
36 Imperfect Circle: Breaking and Remaking NCAT’s Test Track
Buzz Powell talks about the history of the 1.7 mile NCAT test loop, and how this year’s work was different from years past.
38 Road Resiliency
As our climate-world around us changes, our infrastructure must change too. Year-after-year an increasing number of climate fueled catastrophes damage or destroy roads across the country. At what point do you stop rebuilding it, and just relocate?
Published and copyrighted 2024 by IRONMARKETS. All rights reserved. No part of this publication may be reproduced or transmitted in any form or by any means, electronic or mechanical, including photocopy, recording or any information storage or retrieval system, without written permission from the publisher. Asphalt Contractor (ISSN 1055-9205, USPS 0020-688): is published ten times per year: January, February, March/April, May, June/July, August, September, October, November, December, with an additional Buyer’s Guide issue published in August by IRONMARKETS, 201 N. Main St. Ste 350, Fort Atkinson, Wisconsin 53538. Periodicals postage paid at Fort Atkinson, Wisconsin and additional entry offices.
POSTMASTER: Please send change of address to ASPHALT CONTRACTOR, 201 N. Main St. Ste. 350, Fort Atkinson, WI 53538. Printed in the U.S.A.
SUBSCRIPTION POLICY: Individual subscriptions are available without charge only in the USA. The Publisher reserves the right to reject nonqualifying subscribers. One-year subscription to nonqualifying individuals: U.S. $45.00, Canada & Mexico $65.00, and $95.00 all other countries (payable in U.S.
PAVER OPERATION AND MAINTENANCE
2025 DATES
• January 20 - January 23
• January 27 - January 30
• February 3 - February 6
• February 10 - February 13
REGISTRATION
CLASS SIZE IS LIMITED, register today!
DETAILS
All details can be found at www.blawknox. com/training or contact at (407) 290-6000 ext. 342 or training@blawknox.com
The Blaw-Knox University, is dedicated to training paver operators ad foreman on proper Paver Operation and Maintenance and applied Best Paving Practices through classroom-style and hands-on application courses.
For over a half a decade Blaw-Knox has earned its reputation as the go to source of training and instruction on hot mix paving.
Blaw-Knox provides improved technical and problem-solving skills on a variety of paver operations and maintenance topics. Course instructors share decades of field and teaching experience with attendees, including training on the latest DOT requirements.
Matt Slawson, VP of Special Projects at Atlantic Southern Paving, knows that attending IGNITE is key to helping business owners and leaders grow their operations in 2025 and beyond.
Watch the video at: https://asph. link/04o0b2os
Over the past 50 years, roadbuilding and generalpurpose construction equipment has been manufactured at the Shippensburg factory beginning with compactors, which have remained a focus.
Read more at: https://asph. link/7rywqxtj
What cybersecurity protection truly means and what it entails for your construction business.
How the private and public sectors play a pivotal role in accelerating the transition to a more sustainable construction industry.
Despite considerable risks facing this year’s economy, construction starts are expected to increase at a 10 percent pace in 2024, reaching $1.2 trillion.
Read more at: https://asph. link/aqmaitjy
Read more at: https://asph. link/jv3rmkza
Read more at: https://asph.link/ v6xe7dbw
Signup for the Roadbuilding Update, a free bi-monthly newsletter for the most up-to-date DOT, FHWA, asphalt, and other industry news
Astec paves the way for sustainable, innovative asphalt plants. The new IntelliPac Moisture System is a revolutionary solution that integrates seamlessly with Astec control systems. This provides unparalleled, real-time visibility into virgin aggregate moisture content. IntelliPac empowers operators to optimize mix design, minimize energy consumption, and reduce environmental impact. With Astec, you get superior asphalt production – better for the environment, better for your business.
Brandon Noel, Editor
bNoel@iron.markets
234-600-8983
People talk everywhere about the need for training.
The next time you’re talking to a representative from one of the manufacturers of the equipment you own and use on the jobsite, ask them what their stance on the importance of training is for their machines. The answer will likely be a fairly emphatic and authentic explanation for why proper training is the best way to get the most out of their equipment.
This is even more true with the advent of newer and more high tech bells and whistles that come out with each new machine generation. From excavators to pavers to plants -- they’re smarter and more helpful than they’ve ever been. However, everyone knows that, even when you get yourself a new smartphone, without a decent walk through of how these features work, you’re not going to get all you should out of them.
This is why, each year, the October issue of Asphalt Contractor is dedicated to training. It’s why we compile a list of what offerings are available to contractors from the industry’s top companies, as well as, other educational resources. It’s even part of our mission here at the magazine, to provide insight and resources to our audience about what’s out there, and how to best use it. But I still think, as an industry, we could be doing more for contractors.
I recently had a lengthy conversation with a contractor about a new piece of specialized equipment they purchased.
The contractor got it through their regular dealer, and specifically requested some
training from the manufacturer. They knew that in order to get the most out of their new investment, they needed their crew to know the ins-and-outs of how to best employ it. From the point of view of the contractor, the ball was dropped. They were hoping for something a little more robust, and it wasn’t what they got.
The only way to get what you need, if you don’t see it offered, is to contact your representatives and tell them what you need and don’t let up until you get it. If you’re disappointed, then tell them that, too. Hold them accountable. These machines, software platforms, and high tech products aren’t cheap.
One of the biggest reasons I see people being dissatisfied with a product isn’t because the it can’t do what they need, but that they don’t know how to properly deploy it. If you’re spending that money with a particular brand, then demand better training on how to use their products.
If you don’t know who to talk to, reach out to your dealers and find out who their counterparts are at the supplier and/or manufacturer level. It might take a little leg work, but it’s worth it. You have more leverage in the relationship than you might realize; don’t be afraid to use it.
Believe me when I tell you that these brands want you to be satisfied with your new product. They want to help you.
See you on the road!
EDITORIAL
Editor Brandon Noel bnoel@iron.markets
Content Director, Marketing Services Jessica Lombardo jlombardo@iron.markets
Managing Editor Gigi Wood gwood@iron.markets
Senior Editor, Equipment & Workwear, IRONPROS Michael Cheng mcheng@iron.markets
Junior Editor Merina Shriver mshriver@iron.markets
AUDIENCE
Audience Development Manager Angela Franks
PRODUCTION
Senior Production Manager Cindy Rusch crusch@iron.markets
Art Director April Van Etten
ADVERTISING/SALES
Brand Director Amy Schwandt aschwandt@iron.markets
Brand Manager Megan Perleberg mperleberg@iron.markets
Sales Representative ..................................................Sean Dunphy sdunphy@iron.markets
Sales Representative ................................................... Kris Flitcroft kflitcroft@iron.markets
IRONMARKETS
Chief Executive Officer.................................................. Ron Spink
Chief Revenue Officer Amy Schwandt VP, Finance Greta Teter VP, Marketing & Audience Development ........ Ronda Hughes VP, Operations & IT Nick Raether VP, Demand Generation & Education Jim Bagan
Corporate Director of Sales Jason DeSarle
Brand Director, Construction, OEM & IRONPROS .....................................................Sean Dunphy
Content Director Marina Mayer Director, Online & Marketing Services Bethany Chambers Director, Event Content & Programming Jess Lombardo
CIRCULATION & SUBSCRIPTIONS
201 N. Main St. Ste. 350, Fort Atkinson, WI 53538 (877) 201-3915 | Fax: (847)-291-4816 circ.asphaltcontractor@omeda.com
LIST RENTAL
Sr. Account Manager Bart Piccirillo | Data Axle (518) 339 4511 | bart.piccirillo@infogroup.com
REPRINT SERVICES
Brand Manager Megan Perleberg mperleberg@iron.markets | (800) 538-5544
Published and copyrighted 2024 by IRONMARKETS. All rights reserved. No part of this publication may be reproduced or transmitted in any form or by any means, electronic or mechanical, including photocopy, recording, or any information storage or retrieval system, without written permission from the publisher.
@ASPHALTCONTRACTOR
@ASPHALTCONTRCTR
@ASPHALTCONTRACTOR
@ASPHALT-CONTRACTOR-MAGAZINE
Program ends Dec. 31, 2024
DEDUCT UP TO THE FULL COST OF EQUIPMENT PURCHASED WITH IRS SECTION 179 PROVISION *
ZERO DOWN, NO PAYMENTS FOR 90 DAYS, VARIABLE PAYMENTS BASED ON CASH FLOW FOR QUALIFIED BUYERS
*Consult with your CPA or tax attorney for details on applicable deductibility based on your circumstances
VisionLink Productivity has been upgraded with the introduction of three new features – Cat Grade and Compact, Operator Coaching and E-Ticketing. This unified platform is designed to give managers insights into jobsite performance and equipment utilization. The scalable cloud-based application collects and summarizes data from any subscribed machine equipped with a Cat Product Link device. It simplifies data management with its dashboards. These include jobsite summary and detailed insights with performance indicators (KPIs). The platform analyzes standard telematics data, such as machine location, fuel burn and idle time, providing an overview of machine performance.
Designed for feed capacities up to 350 t/h. A large feed hopper, screening surface of 5.4m² and wide main discharge conveyor provide material guidance. The speed of all conveyor belts is adjustable and a conversion from 2 to 3 final grain sizes is possible. A wide setting range of the screen casing angle (15.4 - 20°) promotes high screening capacity. The selection of screening media also contributes to performance. Whether these are finger decks for clayey excavated earth or square mesh for classifying decorative grit – from a large selection of screen media, the screen decks can be covered to match the required application.
Trimble DA2 GNSS Smart Antenna is available worldwide for civil and building construction applications through Trimble’s subscription program. Combined with Trimble Siteworks or Trimble FieldLink Software, the DA2 can perform a variety of construction surveying tasks and site supervision for both civil and building construction. For civil contractors, this includes pole-mount for checking, truck-mount for site supervision and ATV-mount for progress monitoring, volume calculations, site topos, verifying as-builts, road centerlines and more. For building contractors, this includes underground utility layout, building foundation set out, construction quality assurance and more. The DA2 leverages the Trimble ProPoint GNSS engine for GNSS yield and positioning accuracy when operating near trees and buildings.
• Week 1: January 20 - 23
• Week 2: January 27 - 30
• Week 3: February 3 - 6
• Week 4: February 10 - 13
CLASS SIZE IS LIMITED !
To secure your seat, please register before December 15, 2024
Details can be found at www.gencor.com/training or call us at 407-290-6000 ext. 342.
Improving overall plant production and efficiency are all common concerns for plant owners and operators. Having a well-trained technical crew is vital to maintaining plant performance and efficiency.
Gencor and its training staff represent the biggest concentration of knowledge and expertise in all the sciences and technologies involved in the production of asphalt plants. Customers who attend these seminars benefit by having the support and focused attention of the best specialists in the asphalt industry.
Using Gencor’s state-of-the-art control simulators and actual equipment, our experts take you stepby-step through a comprehensive & intensive concentrated hands-on training program providing the latest techniques on optimizing production efficiency.
The future is connected. That’s why we’ve designed the ALmix Insignia Control System (ICS) around the power of high-speed Ethernet communication. An ethernet-connected facility means our team of programmers have complete visibility into your plant equipment and motor control center for diagnostics and remote troubleshooting. View and control data from your asphalt plants like never before. The Insignia Cloud Platform provides access while you are at the plant, in the office, or on the go. Critical, real-time, plant information is at your fingertips when you need it.
Whether you operate one plant or twenty, the Insignia Cloud Dashboard allows your plant data to be stored off-site and analyzed from any device, anywhere, at any time. Coupled with the ALmix Insignia Control System’s ethernet-connected PLC design and customized by our team of
program engineers, The Insignia Cloud is the most comprehensive plant overview tool on the market.
The difference between cloud-native and cloudconnected, and what the cloud means for your business.
In today’s digital landscape, cloud computing has become integral to how businesses operate and deliver services. However, not all cloud applications are the same. The terms “cloudnative” and “cloud-connected” are often used interchangeably, but they represent fundamentally different approaches to leveraging cloud technology. Understanding the distinctions between these two models is crucial for organizations to make informed decisions that will enhance their operational efficiency, scalability, and performance.
THERE’S A LOT OF “CLOUDY” TERMS OUT THERE, SO WHAT’S THE DIFFERENCE?
The primary distinction between cloudnative and cloud-connected solutions lies in their architectural foundations.
“Cloud-native” applications are designed from the ground up, specifically for cloud environments, employing microservices where each component communicates with others via APIs (Application Programming Interfaces), enabling seamless data exchange and integration across various business functions. This is a modular approach that allows organizations to innovate rapidly, making it easier to respond to fluctuating market demands without overhauling the entire system. This design allows for the decoupling of components, enabling independent updates and deployments without affecting the entire system, further fostering an environment that promotes innovation and rapid iteration.
“Cloud-connected,” on the other hand, involves integrating existing on-premises applications with cloud services. It may even include a hybrid architecture where some components run in the cloud, while others remain on-premises. This approach allows for a gradual transition to the cloud, enabling organizations to adopt cloud capabilities at their own pace.
Companies that utilize cloudconnected tools have the flexibility to leverage cloud services for specific functionalities (data analytics, storage, etc.) while maintaining core systems on-premises.
One well-known advantage of cloudconnected systems – specifically in the heavy building materials industry – is their ability to function even in challenging conditions, such as when reliable internet connectivity is absent or during intermittent outages. With local processing capabilities, these systems continue to operate, ensuring that critical data is still captured, and tasks are executed without interruption. This resilience is paramount in construction environments where downtime can lead to significant financial losses and project delays.
One of the primary advantages of cloud technology is the ability to access realtime data from multiple locations. This capability enables companies to monitor operations, track inventory levels, and manage logistics seamlessly. By utilizing IoT-enabled technologies, cloud solutions encompass enhanced capabilities, including remote management and self-diagnostic features. Having up-to-date information at their fingertips allows businesses to make informed decisions quickly, reducing delays and improving overall productivity.
Another key benefit of cloud solutions is enhanced collaboration among teams. With cloud-based systems, employees can share documents, files, and project updates in real time, regardless of their physical location. This fosters a more connected work environment, where teams can collaborate effectively on projects, share insights, and streamline communication. As a result, the industry can tackle complex projects with greater efficiency and responsiveness to changing conditions.
How often do you get frustrated because you know there’s a kink in your operation, but you just can’t figure out where? How often are you flying by the seat of your pants? Cloud technology supports advanced analytics and reporting that delivers the insights that you need to not only survive, but to optimize and improve. By leveraging cloud-based tools, companies can analyze large volumes of data to identify trends, forecast demand, and optimize resource allocation. This analytical capability allows businesses to refine their operations, minimize costs, and enhance profitability. Access to sophisticated reporting tools also aids in compliance with industry regulations, ensuring that companies meet necessary standards and guidelines.
With the increasing prevalence of cyber threats, having robust security measures in place is crucial for the integrity of business operations. Cloud providers typically offer advanced security features, including encryption, regular backups, and monitoring services. This level of security helps protect sensitive data related to projects, clients, and financial transactions, giving companies peace of mind and allowing them to focus on their core business activities without fear of data breaches.
to harness the full potential of their cloud investments while ensuring that legacy systems can still operate effectively. When applications are unified on a single platform, data sharing becomes more straightforward and efficient. With APIs enabling communication between various components, organizations can break down data silos and gain real-time insights across their operations. This interconnectedness fosters informed decision-making and enhances overall business agility.
Regardless of whether an organization opts for cloud-native or cloud-connected solutions, the value of a unified cloud experience cannot be overstated.
Cost savings represent another significant advantage of adopting cloud solutions. Traditional IT infrastructure can be costly to maintain, requiring investments in hardware, software, and personnel. Cloud solutions operate on a subscription basis, reducing upfront costs and allowing businesses to scale their services as needed. This flexibility enables companies to allocate resources more effectively and invest in other critical areas of their operations.
A unified platform can provide a cohesive environment for managing all applications, data, and services and facilitates seamless integration between cloud-native applications and legacy systems, leading to improved efficiency and collaboration.
Command Alkon’s Command Cloud is an example of a next-generation platform that combines the benefits of cloudnative capabilities with the ability to support existing cloud-connected applications. This approach allows organizations
A unified cloud experience allows organizations to scale their operations seamlessly. Whether they are running cloud-native applications or connecting legacy systems, businesses can adjust resources and capabilities on-demand to meet evolving needs. This flexibility is crucial in a rapidly changing business landscape where organizations must respond quickly to market shifts. By leveraging a unified cloud platform, organizations can optimize their resource usage and reduce operational costs. The ability to manage both cloud-native and cloud-connected applications in one environment minimizes the complexity associated with managing disparate systems. This can ultimately lead to significant savings in infrastructure and maintenance costs.
As organizations continue to embrace digital transformation, the distinction between cloud-native and cloud-connected solutions will become increasingly important. Companies that prioritize cloud-native development will likely gain a competitive edge, as these solutions offer the agility and scalability needed to thrive in the digital era.
However, it is essential to recognize that cloud-connected solutions still hold value, particularly for organizations with existing investments in legacy systems. The key is finding a balance that allows businesses to leverage their current infrastructure while gradually transitioning to more cloud-native architectures.
by Todd McPartlin Vice President, Cloud Platform, Command Alkon
For more information visit https://asph.link/b5xdw5
Thalle Industries shows why investing early and often in your plant upgrades can make all the difference when it counts most.
It’s not uncommon in the northern parts of the country for asphalt plants to perform their regularly scheduled maintenance and upgrades during the colder winter months when road construction and maintenance aren’t active. The work of producing asphalt takes a heavy toll on the various systems and moving parts of a plant, and reinvesting in the replacement of older components while you’re intentionally shut down can make a world of difference in reducing downtime when you’re at the height of the season.
While this might seem like common sense to most, it’s surprising how many people in the industry I talk to who relay various stories about lackluster maintenance programs or only surfacelevel fixes. While it’s not the ideal way to operate, placing the proverbial BandAid on wear-and-tear issues can happen more often in tighter or uncertain economic environments. However, one company’s proactive approach to their plant upgrades shows why playing the waiting game usually backfires in the end, even if it saves on short-term costs.
Joe Klein has been the plant manager at the Thalle Industries in Fishkill, N.Y., for the previous seven years. In that time, he said, it’s been standard practice
to target and take action on plant improvements during their offseason. It’s baked into their annual plans.
Thalle has existed in one form or another since the founding of Thalle Construction in 1947 by Guido Pacchiana, the grandfather of current CEO Glenn Pacchiana. It became Thalle Industries in 1985 under his leadership, and continues today. That kind of longevity doesn’t happen by accident, it’s baked into the way they do things.
“We don’t want to have downtime,” said Klein. “Each winter, everything is planned out in advance. We replace
what needs to be replaced, and we don’t wait around for it to break.
The plant he manages regularly sees up to 350 tons of asphalt per hour head out of its gates, as they produce for a wide variety of contractors and their various needs in the area. Downtime is their biggest enemy, and avoiding preventable breakdowns is what drives their continued investment and careful attention.
“If we have downtime, we won’t be able to provide what someone needs when they need it, so we have to have a plan every winter about what we are going to
fix,” said Klein.
“One of our biggest headaches, believe or not, is that we can sometimes get too busy, and that can become a problem. A plant can only make so much asphalt in a day. It always works out that everybody is scheduled at the same time, you know.”
Ahead of the 2024 season, Thalle decided to make two new upgrades to their plant. The first was to their baghouse system. To do that, they decided to go with the Meeker designed Freedom Reverse Air Baghouse.
This design removes the need for solenoid valves and the need for an air compressor. With a unique control of its turrets, it provides improved control over the return of fines to the drum, extends the overall lifespan.
“It’s a much more consistent product,” explained Klein. “When you think about it, it’s just a way to return dust back into your mix without putting it into the atmosphere, but it makes it more consistent.”
In a press release shared earlier this year, president and CEO Glenn Pacchiana said, “Air quality is one of our top priorities, and the new baghouse ensures that we meet all our obligations.”
The worst case scenario for these extremely busy schedules, is to have a lineup of customers all ready for asphalt, and for a serious breakdown to occur that could have been prevented.
Klein continued, “the [baghouse] we had before worked great too, but these things wear out. We burn fuel, it gets sent through, things rust. It’s part of the plant that is heated to over 280° and then is cooled down in the evening every day. It builds up moisture. The [Meeker] is probably the biggest, most powerful baghouse we could have got. It’s very efficient.”
The second offseason upgrade that Thalle proactively invested in was a
brand new, ultra efficient Astec Heatec hot oil system.
“It’s a much cleaner burning version, that’s why we got it,” said Klein. ‘It’s ultra-low NOX, which is one main reason we got it. It’s much more efficient. Also, another big reason was just the way it works is just a lot simpler [than what it replaced].”
The Heatec heaters are built around a helical coil, an extremely efficient (up to 85% LHV) and reliable design, and they’re also versatile enough to be used for a number of different applications. Increasing efficiency reduces fuel usage, which, in turn reduces costs.
They come in two basic configurations: HCS (single circuit heater) and HC (multi-circuit heater). The HC model has a manifold and side pumps that enable the heater to operate up to four hot oil circuits. The HCS is better suited for situations where are not a lot of components in the circuit.
Andrew Bryson, Product Manager, Fluids Heating and Storage at Astec Inc. explained how the system is more efficient than previous versions of the technology:
This unit was provided with the Heatec Stack Pack exchanger, which pre-heats the return thermal fluid by scavenging heat from the exhaust stack. This boosts the efficiency by of the unit, on natural gas, from 85% to 90%.
The new unit includes a manifold with auxiliary pumps, splitting the flow to the thermal fluid users into multiple circuits, which can improve efficiency in multiple ways:
• Reduced wear and strain on pumps because they will experience less back pressure.
• Zoning of heat demand which allows appropriate flow to higher thermal
fluid users without effecting the remaining users on the thermal fluid system. No part of the circuit is over or under supplied.
• Reduces thermal losses due to the shorter pipe runs and optimized routing.
Klein expressed a high degree of satisfaction working with both companies during and through the installation process.
“Both Astec and Meeker do a phenomenal job,” He said. “They handled everything with the install, and they kept all their deadlines. They both were easy to work with, and had the great ability to say when they were going to be there, and then getting the job done on schedule.”
That’s important for their region, because the weather can be really unpredictable and make things suddenly very difficult to work in.
In the future, Thalle Industries plans to add some more Astec long term storage tanks, like the Heatec ThermoGuard series.
“We have two of those silos already, and we can store material with them up to four days,” said Klein. “When you consider fuel costs, liquid [AC] and starting up and shutting down this plant, the fact that you could fill these silos up and just shut the place off; and you could store the material and come back in the next day without having to worry about it. It’s a big deal. There’s no waste; everything you made is sold.”
“We try to do it where we have everything ordered and ready to go pretty early. We want to be we want to be ready for it, because we only have a couple months to do it,” explained Klein.
“Working in New York, the Upper East Coast, it’s much harder to depend on the weather to cooperate. The biggest thing is having everything set in stone ready to go. We can have cranes ready to go on site, but you know, if it starts snowing, you’re not using a crane. Sometimes it’s not cold enough, so it’ll rain, and that makes it dangerous, so you have to take precautions.”
As improvements and/or replacements are made, however, it’s not just the new component itself that you’re getting with the purchase. While new technology, features, and other bells-and-whistles are all great, there’s another significant reason to consider regularly investing in new equipment.
when there’s a job that might be an emergency, you know, an immediate issue that has to be fixed, like they can depend that we’re going to be able run.”
Such was the case on July 9, 2023, when major storms poured 8 inches of rain overnight, causing significant damages to Bear Mountain State Park and Route 9W in Fort Montgomery and other parts of the Hudson Valley — the region where Thalle Industries has been the go-to supplier for such emergencies for a long time.
In a statement released at the time, Pacchiana commended his employees for their extra efforts.
“Our employees at our Fishkill quarry and asphalt plant [started] their shifts earlier and [worked] later to accommodate orders for rock and asphalt to restore damaged roads,” he said. “We pride ourselves on quick response times for clients, so we are able to respond to emergency requests within a few hours.”
As time progresses, older models and machinery require more and more maintenance as they age, but it can become harder and harder to find the necessary parts for them. As older forms of technology become obsolete, supplanted by newer iterations, the supply of repair materials can become gradually more scarce.
“When you get new equipment, it’s much easier for us to get spare parts or do maintenance, and keep the plant going,” said Klein. “The new equipment keeps us from having downtime. So
Thalle responded to an emergency request for Route 35, where a watermain break damaged and closed the major thoroughfare in Yorktown. With an emergency delivery of 22 tons of asphalt from the Fishkill location, the road reopened in less than a day.
Pacchiana credits the company’s growth and success over the decades to their “rock-star” employees, and Thalle has a reputation for supporting the growth and well being of their workers both in and outside the workplace.
“I’m a big believer in professional and personal development, so Thalle helps employees learn about and develop themselves by providing resources in executive coaching, leadership courses, industry councils/training, computer skills classes, and health and financial wellness initiatives,” said Pacchiana.
Klein echoed these sentiments.
“It’s not some huge [anonymous] corporation, you know, it’s a lot more family friendly. We all work well together, everyone gets along, and nobody is really a stranger.
Experience the industry‘s most comprehensive curriculum, all in one world-class facility.
AT THE WIRTGEN AMERICA CENTER FOR TRAINING AND TECHNOLOGY, we provide an extensive curriculum tailored to the learning needs of technicians, operators, work crews, site managers, service engineers, and service department personnel. From guardrail to guardrail and 20 inches down, our courses cover everything from aggregate production, to paving, compaction, and recycling of road materials. Experience high-quality teaching from industry experts that keeps attendees in step with Wirtgen Group’s cutting edge technology.
CLOSE TO OUR CUSTOMERS
By Brandon Noel, Editor
These dates and schedules were accurate as of press time but are subject to change. Please contact each company directly for the most upto-date information.
Website: https://www.astecindustries. com/service/training
Phone: 423.827.1899
Location: Chattanooga, TN
ASPHALT PLANT CUSTOMER
SCHOOLS:
Registration Opens: Tuesday, Oct. 1, 2024
The Asphalt Plant Customer Schools cover more than any other asphalt industry training school. Expect to enhance your grasp of key aspects of plant maintenance and operation through a unique combination of lectures and extensive hands-on classes. Instructors include asphalt and industrial heating engineers and service technicians with decades of experience. Breaks offer the opportunity to exchange information with fellow students, as well as with Astec service professionals and engineers.
Training Dates:
Week 1: Jan. 6 - 9, 2025
Week 2: Jan. 13 - 16, 2025
Week 3: Jan. 20 - 23, 2025
Week 4: Jan. 27 - 30, 2025
Week 5: Feb. 3 - 6, 2025 (Advanced): Feb. 17 - 20, 2025 (Advanced): Feb. 24 - 27, 2025
During four full days of training, instructors and attendees together will cover topics including: PLC hardware, calibration, segregation and AC
content, diagnostics and troubleshooting, trunnion adjustment, and drum flighting.
Students will have class time at the industrial heating training facility to focus on heating and storage maintenance. Industrial heating topics include: Electrical, drawings, limit devices, burner management, hot oil flow, modulation motors, and pump seals and alignment.
The Paving Professionals Workshops are the industry standard in asphalt paving education. Our structured courses will help your paving operators increase the bottom line and maximize project quality using the Roadtec and Carlson product lines.
Fee: TBD
Required: Basic paving knowledge
Application School: The four-day Level 1 school covers a combination of technical fundamentals for Roadtec and Carlson equipment and an overview of road building applications. Classroom and hands-on opportunities are provided by the technical experts. Topics include the basics of reading schematics, troubleshooting and repair, introduction to paving, best practices and techniques, component location, screed leveling, control panels, and grade control.
Who: Field service technicians, mechanics, operators, shop technicians, supervisors, crew members
When: TBD
Fee: TBD
Required: Complete the Electrical/ Hydraulic Basics Training through Astec University
Dealer Tech School and Certification Events: The four-day Level 2 dealer
technician school is primarily a handson event that ends with the technician’s demonstration of skills to earn the Tech-to-Pro certification. Topics covered include reading schematics, building a troubleshooting plan, safe service and repair of electrical and hydraulic systems, screed leveling, control panels, and grade control.
Who: Field service technicians, mechanics, shop technicians, supervisors
When: TBD
Fee: TBD per person
Required: Complete the Electrical/ Hydraulic Basics Training through Astec University
Astec is offering a 2-day educational course on Asphalt Heaters and Heating Systems at our facility in Chattanooga, TN. This course brings you together with experienced instructors to explore the best practices and techniques for safely operating heating systems at your plant.
When: Oct. 22-23, 2024 | Nov. 12-13, 2024
Fee: $1,650
Website: www.blawknox.com/training/ paver-operation-and-maintenance
Location: Orlando, FL
The Blaw-Knox University is dedicated to training paver operators and foremen on proper paver operation and maintenance as well as applied best paving practices through expertly designed classroom and hands-on application courses. Their expert instructors, who bring decades of invaluable field
experience, are here to enhance technical skills and problem-solving abilities, ensuring professionals stay ahead of the curve with the latest DOT requirements. Blaw-Knox offers multiple dates to satisfy the demand for its popular courses. Don’t miss out.
Training Dates:
Week 1: Jan. 20 - 23, 2025
Week 2: Jan. 27 - 30, 2025
Week 3: Feb. 3 - 6, 2025
Week 4: Feb. 10 - 13, 2025
Cost: $1,300
Who: Any individual interested in, or responsible for the laydown of HMA, WMA, SMA, or Thinlays.
Duration: 4 days
Topics:
• Paving safety on the job site
• Material quality
• Paving principles
• Paver preparation
• Paver and screed operation
• Hands-on paver setup, operation
• Joint construction
• Screed operation and setup
• Troubleshooting mat defects
• Automatic grade, slope operation with Blaw-Kontrol, Topcon or Moba
• Daily maintenance
Phone: 763.315.5510
Email: cat_mpls_training@cat.com
Web: www.cat.com/en_US/by-industry/ paving/real-world-training-solution.html
Cat offers operator and technician training on asphalt pavers, cold planers and rotary mixers. The 2024 - 2025 training schedule will be announced soon.
• Paving Operations Training - This 4-day course is designed for paving supervisors and paving crew members with one or more years of experience with the lay down of hot mix asphalt. training.
Course Fee: $4,200
• Large Asphalt Pavers Service Training
– This 4-day course provides theory and hands-on training. Upon completion,
students will be able to trace the flow of oil through hydraulic systems, test and adjust hydraulic pressures, troubleshoot hydraulic and electrical systems, and explain ECM functions and calibration steps for the Cat asphalt pavers. Course Fee: $4,200
• Cold Planer and Rotary Mixer Technician and Operator Training – On Demand
For the 2025 training season, Caterpillar offers cold planer and rotary mixer technician and operator training on-demand. As an on-demand course, training can be customized to the Cat machines in your fleet and the specific needs of your technicians and/or operators.
• Milling Operations Training –Hands-on training for operation of the Cat PM300, PM600 and PM800 series cold planers. Upon conclusion of this course, attendees will be able to put the machine to work.
Course Length: 2 Days
Min/Max Attendance: 8/10
• PM600 Series and PM800 Series Cold Planer Service Training –Upon completion of the course, students will be able to trace the flow of oil through hydraulic systems, test and adjust hydraulic pressures, troubleshoot hydraulic and electrical systems, explain Electronic Control Module (ECM) functions and calibration steps, and set up automatic grade and slope control.
Course Length: 3 Days
Min/Max Attendance: 8/12
• PM300 Series Cold Planer Service Training – Upon completion of the course, students will be able to trace the flow of oil through hydraulic systems, test and adjust hydraulic pressures, troubleshoot hydraulic and electrical systems, explain ECM functions and calibration steps, and set up automatic grade and slope control.
Course Length: 3 Days
Min/Max Attendance: 8/12
• Paving – Introduction to Rotary Mixers – This rotary mixer operator training course provides theory and
hands-on reclamation training using the Cat RM400, RM500, RM600 and/ or RM800 rotary mixer.
Course Length: 3 Days
Min/Max Attendance: 8/10
• Paving – RM600/RM800 Rotary Mixer Service Training (Course Code: 55408) – Upon completion of the course, students will be able to trace the flow of oil through hydraulic systems, test and adjust hydraulic pressures, troubleshoot hydraulic and electrical systems, and explain Electronic Control Module (ECM) functions and calibration steps.
Course Length: 3 Days
Min/Max Attendance: 8/12
• Paving – RM500 Rotary Mixer Service Training (Course Code: 56274) – Upon completion of the course, students will be able to trace the flow of oil through hydraulic systems, test and adjust hydraulic pressures, troubleshoot hydraulic and electrical systems, and explain Electronic Control Module (ECM) functions and calibration steps.
Course Length: 3 Days
Min/Max Attendance: 8/12
• Paving – RM400 Rotary Mixer Service Training (Course Code: 53595) – Upon completion of the course, students will be able to trace the flow of oil through hydraulic systems, test and adjust hydraulic pressures, troubleshoot hydraulic and electrical systems, and explain Electronic Control Module (ECM) functions and calibration steps.
Course Length: 3 Days
Min/Max Attendance: 8/12
Email: carrie@clarencerichard.com
Phone: 952.939.6000
Web: www.EZFloWeighing.com
Design your own training schedule! Classes fill on first come basis. Choose 1-6 workshop days. Each participant must be individually registered
Silo cone opening is 36” wide for ef cient material ow.
Safety gates on all silos, including long-term and standard options.
Recessed tub liners prevent silo wall wear, avoiding bulging issues.
Silo bin top batchers feature secure long-term seals.
Recessed wireways on silo tops eliminate trip hazards.
Meeker drag conveyors are larger, allowing slower chain speed and reduced wear.
Hydraulic chain adjustment on slats maintains asphalt entry point, minimizing wear.
Visual chain tension indicators on Meeker slat conveyors aid operators.
All silos prewired with top and bottom junction boxes.
Improve: Safety, mix quality, production, energy efficiency and operating costs
Who: New and veteran plant operators, maintenance, management, quality control personnel
Clarence Richard has been using his asphalt plant operation and engineering expertise to train plant operators and personnel throughout the country for more than 30 years.
Virtual classroom and private webinar training options available.
Who: Electricians, mechanics, maintenance
Learn to safely troubleshoot and maintain very complex control systems. Operators learn about electrical safety and basic electricity including troubleshooting procedures and test meter usage.
Safety Director Workshop addresses issues affecting plant operation and maintenance personnel. Plant Safety curriculum includes 2 of 14 modules that plant managers and operators are trained on in the Plant Operation Workshop. This curriculum makes it very easy for a company to implement this program into their existing program.
This Quality Control Workshop addresses issues affected by Plant Operation. The curriculum is made up of 5 of the 14 modules included in the Plant Operation Workshop. The curriculum addresses issues at plants that affect mix quality and provides solutions. These modules are concerned with the proper blending of all materials from the stock piles, tanks, feeder bins and baghouse fines delivery all the way through the silo and into the truck.
Website: https://www.gencor.com/training
Location: Orlando, FL
Gencor adopted the philosophy of “self-help” when it came to plant-downs because they felt no one but the plant personnel could respond fast enough to minimize the costly experience and be able to get up and running quickly even if there was a a serviceman nearby.
Gencor’s expert instructors provide stepby-step comprehensive and concentrated training on their state-of-the-art control simulation and plant equipment. Benefit from their advanced knowledge and expertise in the science and technology of hot mix asphalt production. Then get ready to conquer any challenge. Gencor also offers custom training; contact for more information.
Sales: Sales: 815-732-2116 Sales: Sales: sales@etnyre.com
Gencor Trainings are designed specifically for hot mix asphalt producers who own and operate HMA facilities and are not open to industry vendors, or suppliers.
Duration: 4 days
Training Dates:
Week 1: Jan. 20 - 23, 2025
Week 2: Jan. 27 - 30, 2025
Week 3: Feb. 3 - 6, 2025
Week 4: Feb. 10 - 13, 2025
Website: https://eng.auburn.edu/research/ centers/ncat/education/training-courses/ index.html
Email: slh0037@auburn.edu
NCAT offers training courses for engineers and contractors, including customized and online programs that qualify for CEUs.
This is a 4 1/2-day workshop that provides the attendee with practical classroom sessions and hands-on laboratory testing that will reinforce the experienced technician’s skills and also develop the knowledge and testing ability necessary for new technicians. The course will provide background information on the development of binder grading systems and test procedures and present step-by-step descriptions of test methods used in the performance graded binder system.
When: Oct. 14 -18, 2024
Cost: $1,375
This 2 1/2-day workshop will provide a basic understanding of the balanced mix design process and provide handson training using the laboratory tests
being considered by various agencies to evaluate potential mix performance.
When: Nov. 12 - 14, 2024 | March 18 - 20, 2025
Cost: $900
The purpose of this 3-day workshop is to provide a basic understanding of the advantages of using WMA, high RAP, and RAS.
When: Jan. 28 - 30, 2025
Cost: $1,200
The purpose of this intensive course is to provide a basic understanding of all phases of asphalt technology. Upon completion, the participant will be able to make knowledgeable decisions related to asphalt pavements.
When: Feb. 10 - 14, 2025
Cost: $1,350
From material production to road paving, count on us.
Those who work in construction material production and transportation construction are at the core of what keeps America moving. The companies that are building our infrastructure deserve insurance coverage that’s built for your unique needs. Since 1917, BITCO has provided customized insurance programs across the country, dedicated to protecting you and delivering confidence day-in and day-out.
the service you deserve.
BITCO.com to find a specialist agent near
Phone: (615) 501-0600
Location: Nashville, TN Register: www.wirtgen-group.com/america/en-us/ customer-support/know-how/training-program/
The state-of-the-art training facility is located just outside of Nashville, Tennessee. The 40,000+ sq. ft. facility includes a 5-acre test track, four-bay training shop, multimedia classrooms, a gourmet cafeteria, and a dedicated team of experienced professionals to assist in learning and development.
WIRTGEN - W 100 CFi / W 130 XFi
An in-depth look at the machine and applications will be discussed to better understand Wirtgen cutting technology, operator controls, Level Pro Plus, and daily routine/maintenance.
Cost: $1,000 per person
WIRTGEN - W 100 Fi Series
Level Pro Active, and daily routine/maintenance. Hands on training, as well as assessments will be provided on all objectives during this class.
Cost: $1,000 per person
WIRTGEN - W 100 Fi Series Technical Service for Customers
This two-day course offers an in-depth look at troubleshooting and diagnosing symptoms of the milling machines.
Cost: $1,000 per person
WIRTGEN - W 200 Fi Series Operation
During the course of 2 days, experience an in-depth look at Wirtgen cutting technology and best practices for the cold milling machine.
Cost: $1,000 per person
WIRTGEN - WR 200 i Series Technical Service
3-day course
Cost: $1,500 per person
WIRTGEN - WR 200 i Series Operation
2-day course
Cost: $1,000 per person
KLEEMANN - MSC EVO Series Mobiscreen Classifier Operations - Maintenance - Technical Service
This class provides an in-depth look at daily operation of the Kleemann MSC EVO Series Mobiscreen classifier screening systems by teaching factory recommended best practices for machine operation and maintenance.
Cost: $1,000 per person
KLEEMANN - MSS EVO Series Mobiscreen Scalper Operations - Maintenance - Technical Service
During this two-day course, you will be given an in-depth look at daily operation of the Kleemann MSS EVO Series Mobiscreen scalper screening systems.
Cost: $1,000 per person
KLEEMANN - MC 110 EVO2 Jaw Crusher Operations & Maintenance
2-day course
Cost: $1,000 per person
VÖGELE - 8ft SUPER 3i Technical Service
4-day course
Cost: $2,000 per person
VÖGELE - 10ft SUPER 3i Technical Service
4-day course
Cost: $2,000 per person
VÖGELE - Paver Operations & Application
2-day course
Cost: $1,000 per person
For even more training info visit https://asph.link/lj2hak
The Must-Attend Immersive Trade Show Environment Helping Contractors & Business Owners Propel Their Business & Expertise Forward
Featuring a robust educational program that is unlike any other learning experience in the market with education covering business management, paving, sealcoating, preservation, sweeping, striping and more.
Over the three-day event, there will be an incredible amount of opportunities for next-level networking that will create and strengthen the relationships that are vital to the success of business owners working to grow.
Seeing equipment in action is incredibly important in any equipment buying decision and PAVE/X brings a fast-paced demonstration showcase for attendees to watch equipment at work and ask questions to help ease the decision-making process for them.
What does making space for women in the asphalt industry really mean?
We recently started a branch of Women of Asphalt (WofA) in Pennsylvania (PA). So, this idea of how we make space for women in our industry has been running through my mind on repeat. WofA has been growing over the past few years, with branches being established across the country. I think if you are sitting back watching this unfold, you may think the approach to making our industry inviting to women is to pinkwash everything. “Paint it pink and the women will come!”
No. That is not the solution. And no, that is not what WofA is doing, they are doing so much more, albeit they are doing it in style.
First, let me acknowledge how fortunate I have been in my career. I have worked with a lot of wonderful people who have been supportive and
unconcerned with my gender. I am grateful for my time in academia and the unwavering support of my graduate school advisor and colleagues at NCAT at Auburn University, as well as my colleagues at Ohio University.
I recently transitioned to a new role in the industry. I have never felt more joy in my work or felt more welcome than when I joined the Pennsylvania Asphalt Pavement Association. I see the best in our industry day-in and day-out. I am respected and supported by our board, our members, and our partners, and as far as I am aware, my abilities or inabilities have never been tied to my gender.
Over the course of my career, I have also had some dumb, gross comments made to my face or behind my back. But nothing brazen or harmful. If someone felt my gender kept me from
doing my job, I never heard about it, and it never impeded my growth. So, in many ways I’ve had my head buried in the sand, blind to how sexist or misogynistic people in our industry can be.
It stings even just to write that.
I love the asphalt industry. I love this industry so much that I want to leave it better than when I started.
I want those in this industry to be successful, and those joining it to find it welcoming and find their work worthy and joyful, just as I do.
I believe in my heart those in our industry who are intentionally sexist or misogynistic are the exception rather than the rule. This article will not change their mindset. What I hope is those who are unintentional in their actions will recognize the small changes they can make.
Keeping the Peace Between Management & Labor, Contractors & Quality Control.
In my ignorance, I honestly believed that in 2024, women were no longer being shut out of the workforce because they are female. I thought that was something our grandmothers faced. This is not 1950 any more, right? A recent encounter I had with a family friend who makes equipment for the asphalt industry proved me wrong. I noted the company he works for needed more females working for them.
I said, “I don’t fault your company; I am sure they do not have policies to prevent women from working there.”
Before I could finish my thought (Maybe there needs to be more grassroots efforts to draw women starting at the high school level ) he said so matter of factly, “Oh, I would never hire a woman.” Those words cut me and set me ablaze! I didn’t ask for an explanation. In my opinion, there is no reason that is acceptable. How in 2024 do we shut out 50% of the workforce because they do not check the “M” box? You could argue that company is not really in the industry by saying, “They just make equipment for our industry.” But I would argue back, if it is happening there, it is happening at our asphalt mix plants, on our laydown crews, at the aggregate quarries, at the asphalt binder terminals, in our labs, and even at the inspection companies, consulting firms, and public agencies.
My advice to those reading this is to check in with your hiring managers. While your company may not have policies that would prevent women from being hired, there are individuals who may have opinions or perspectives that are contrary to your company’s policies. If you have an area that is all men, ask yourself why that is the case. I am not asking you to develop a quota or tell someone they must hire women. Hire the person who is right for the job. But do not put up barriers based on gender.
The work requires heavy lifting? Okay. Put it in the job description. Make sure the candidate can do the work. But don’t toss all the female
applications in the trash. Look at their qualifications, just as you would if they had a male-sounding name. If you or someone in your company is worried about the conflict that could occur with a woman in an all-male workplace, I think you will have to ask deeper questions, but more than likely it comes down to Step No. Two.
celebrating their performance with the double-tap. That is really all it takes: respecting people enough to not make dirty, nasty, or stupid jokes at their expense.
As a coworker, as a manager, as an owner, whatever your role is: show respect. Think about the jokes and the comments before you say them. It is not censorship. It is respect. We could all practice the Golden Rule more. Would you want someone to make comments about your gender or your body? Ask yourself what makes you feel valued. I bet it isn’t a “your mom” joke.
Later this summer I came across a video from an asphalt contractor on Instagram. The video was hyping their “quality” paving job on a cul-de-sac. It noted the tight curves and challenges of the situation, they felt it was a good use of a “your mom” joke. I was furious and disappointed at the same time.
“Your mom” jokes have been around since I was in middle school; its not new to me. I just stopped finding them funny two decades ago (but were they ever funny?). Maybe it’s because I am a mom? Most likely, because I am a female and it’s objectifying. It is just totally unnecessary. I wanted to write a comment, but I decided to just ignore and unfollow, but it still gnaws at me because it is a perfect example of the little things we do in our industry that prevent women from feeling comfortable here.
Had they left that dumb joke out, I’d still be following their account and
There are other things that can be done to make space for women. Our equipment could be made for our bodies. It is about impossible for me to find work pants, or a hard hat that fits. We could do more outreach to schools to show girls that women exist and thrive in the asphalt industry, and they can, too. We know representation matters. If a child sees someone who looks like them in a position, they, too, can see themselves in that position. We can and should be doing those things. But the first thing we need to do is make sure the door is open, and when a person walks through it, they are shown the respect they deserve.
We aren’t asking for pink balloons, or streamers, we are asking for an opportunity and the respect any human deserves. Nothing more, nothing less. The balloons and streamers are optional and can come in any color.
I will leave you with a little information on WofA. The mission statement of WofA is simple: Empowering women in asphalt industry careers. You do not have to be a woman to be a member of WofA and membership is free. I suggest you take a look at www.womenofasphalt.org and decide if it is right for you.
by Mary Robbins, Director of Technical Services, Pennsylvania Asphalt Pavement Association
For more information visit https://asph.link/uf44sz
1. A TWIST ON TYPICAL NETWORKING - Engage in Conversations with your peers, while participating in daily networking receptions, and our inaugural golf outing. This event includes corn hole, golf, signature drinks and more!
2. A STAY AT AN AWARD-WINNING PROPERTY - Staying at the Renaissance Esmeralda Resort & Spa will allow the perfect mix of relaxation, fun, and education!
3. EDUCATION LASER-FOCUSED FOR THE FUTURE - Gain access to information and tactics that you can put to use as soon as you get back to the office. Hear from industry experts and receive the resources you need to succeed.
Brandon Noel, Editor
Buzz Powell talks about the history of the 1.7mile NCAT test loop, now in its ninth cycle of being replaced, and how this year’s work was different from years past.
One of the most important places regarding the future of asphalt is in Lee County, Ala., at the National Center for Asphalt Technology (NCAT) test track. It’s a 1.7-mile loop of asphalt road that is specially designed and maintained through a partnership between the National Asphalt Pavement Association (NAPA) and Auburn University.
According to the NCAT website, “[It] was created to ensure this industry’s ability to provide pavements that are
durable, sustainable, quiet, safe and economical. We work with state highway agencies, the Federal Highway Administration and the highway construction industry to develop and evaluate new products, design technologies and construction methods that quickly lead to pavement improvements.
The test track is broken up into 46 sections, which can be individually or group sponsored by various transportation industry collectives or by the industry’s major manufacturers like Astec Inc. Since its completion in 2000, it’s been essential in testing out experimental pavement designs in a safe research environment, and no one has had more direct involvement than Buzz Powell, who has been managing the test track since its construction 1999, and currently serves as the Technical Director for the Asphalt Pavement Alliance (APA).
“I retired last October, but NCAT hired me back part-time to support the transition to the young-bucks
that are taking it over. I’m working a lot of hours, yeah,” Powell explained. “I do have a full-time job. I’m the Technical Director of the APA. When I accepted that position, they actually wanted me to continue with NCAT, so that I can be a liaison between NCAT and APA. I’m not very good at being retired.”
Powell continued, “We’ve been in operation and finished the first track in 2000. The whole objective is to build test pavements and then run a fleet of trucks over it and tear the pavements up so we can help the Department of Transportations (DOTs), make better decisions, better designs, and better materials.”
NCAT also partnered with the Minnesota Department of Transportation’s (MnDOT) MnROAD facility to focus on two important issues that have an effect on all DOTs nationwide: the preservation of pavements and quantifying the impact of both recycled (RAP) and premium mix additives. Long-term data on these areas are deeply important when it comes to the future decisions made by our industry.
• 46 sections on the track
• 11,138,634 total miles driven
• 5 trucks simultaneously driven
• 156,995 lb. average truck weight in the fleet
• 1.7 miles test track length
• 10,052,142 ESALs applied in current research cycle
Every three years, the track is rebuilt, and this year marks the beginning of the ninth research cycle. Just like on
public roadways, the milling work is phased into sections so that others may stay open for use.
“We usually rebuild about a third of it and then do traffic continuation on the other two thirds,” explained Powell. “This cycle, however, it was a little bit more than a third, so it was quite a bit of work. Usually, the thickness of the milling varies between an inch and a half, down to as shallow as three quarters of an inch.”
But this year, the milling work went far beyond those typical ranges, digging down to layers as deep as 5 feet, as well as milling 21 of the track’s 46 sections.
“They removed a tremendous amount of material,” said Powell, referring to the team at Astec Inc. and their RX-700. “What was different about this milling work this time, was that we asked [Astsec] if they would mill it to an average depth of an inch and a half, but mill it as smooth as possible. That would help us to build smoother test sections when we start paving.”
The Astec milling team knew just how to give Powell and the NCAT test track exactly what they wanted.
“Not every test track section was getting milled at the same depth, but they were all focused on rideability,” said Tom Lenger, Product Manager, Road Recycling at Astec. “In order to achieve that, we decided to use the Dual Averaging Sensors (DAS).”
While traditional milling end-gates only monitor about an 8-foot length of work, the DAS can expand that monitoring window up to 30 feet long. The grading system then averages the grade depth over that much longer span, generating an incredibly smooth foundation for the pavements above it.
“Normally, if you hit a bump in the road, your mill is going to immediately correct because you’re within that 8-foot window, whereas with this system you’re looking at the front of the machine, the middle of the machine, and the rear of the machine all at once,” explained Lenger. “You’re not going to have as drastic changes in elevation on your road.”
The DAS system averages the cutting depth over the entire length of the ski, which translates into fewer and less abrupt changes in the mat. Any profile corrections made in this manner are done so no only with more precision, but at a more gradual rate of change. This, in turn, makes the eventual work of the paving team much easier.
“The grade control system and the milling quality were both outstanding,” said Powell. “It was just good work all the way around. It was a step up. If you can mill smooth, it’s easier to pave smooth.”
The performance data is something the APA and NCAT are starting to track and measure. And employing technology like the Dual Averaging Sensor system can have a direct impact on the final result.
“Up until now, the data for environmental product declarations (EPDs) has stopped at the gate, but we’re now working to push that out to the jobsite,” said Powell. “When you run a milling machine and hit your target on the very first pass, because of the precision control systems, instead of having to make multiple passes to correct deficiencies or do extra work to correct imperfect grade, the less diesel fuel it’s going to take. So, you end up with a lower embodied carbon roadway.”
However, there were some sections that needed to go much deeper, getting down far enough into the subgrade material, so that NCAT could run it out with a bulldozer for a special new experiment.
“The purpose was that we have kind of our standard subgrade that we build on top of the test track. And it’s a good quality subgrade and we like to use it if the experiment accommodates it, because it won’t confound the research that you’re trying to do on the surface of the track,” said Powell. “In the case of the deep test sections that we milled this time, it was necessary, because we were pulling out our good subgrade and putting back in a bad subgrade.”
Why would the NCAT test track facility want to pull out the good material and replace it with sub-standard sub grade? The state of Mississippi wanted to run a comparison test on the type of subgrade, versus a new material modified with Portland cement.
“We have a new technology that we’re evaluating at the track that allows you to slash the cement content and stabilize layers through the use of an environmentally sustainable enzyme,” said Powell. “It’s a low embodied carbon approach to doing stabilization. That was the reason for milling the deep section.”
Even at depths in excess of 30 inches, the RX-700 took care of business. For these depths, the DAS ski system was removed, and the team removed material in three different 10 inch lifts. It wasn’t all asphalt either, a sub layer was removed, as well.
The whole job took about a week to complete, with many different working conditions, the likes of which normal contractors in normal circumstances might only come across occasionally. Out on the test track, it was business as usual.
“It was a really unique experience,” said Lenger. “In our industry, there’s academia, there’s manufacturers, there’s producers and customers, and we really value what NCAT does for the industry. That’s why we wanted to be involved in helping them rebuild their test track.”
“It was just good work all the way around,” concluded Powell.
For more information visit http://asphalt.com/kk3fi1
Year-after-year, an increasing number of climate fueled catastrophes damage or destroy roads across the country. At what point do you stop rebuilding it, and just relocate?
Climate change impacts Americans’ lives daily and has increasingly caused the nation’s transportation infrastructure to face more frequent and unpredictable damage from severe weather events, noted Nancy Singer, a spokesperson from the Federal Highway Administration’s (FHWA) Office of Pavements.
Consider Skagit County, Wash., where in July, concrete panels under an asphalt road surface buckled due to searing temperatures.
The Alaska Department of Transportation and Public Facilities noted when dealing with ice-rich silty permafrost, ice wedges, or ice lenses, problems begin when the thawing causes differential settlement, which causes the ground – including roads – to settle, sink or move unevenly.
Its four strategies to manage the effects of permafrost thaw on infrastructure include:
• Avoiding building on permafrost
• Removing it by digging out the frozen material under the ground, replacing it with stable material
• Using techniques to keep the ground frozen
• Acknowledging the challenges inherent in those three options is to build over permafrost using traditional construction methods and accept the consequences
The American Society of Civil Engineers (ASCE) gave America’s roads a ‘D’ grade in its 2021 report card, with report cards issued every four years.
Among the many challenges noted was the impact on an increase in severe weather events, with rising temperatures estimated to add $19 billion to pavement costs each year by 2040.
It’s important to create dedicated federal investments to build resilience into the nation’s road and bridge infrastructure and integrate resilience planning into State Transportation Asset Management Plans, the ASCE noted.
A decade ago, “resilience wasn’t really talked about,” noted Richard Willis, Vice President, Engineering, Research & Technology for the National Asphalt Pavement Association (NAPA).
“It was fringe engineering, especially in the pavement space. NAPA really started putting resources into helping the industry understand it in 2019 and continues to try to help owners and contractors better understand the topic,” he said.
“From a roadway pavement perspective, there has been increasing awareness that there is a need to quantify the impact of climate change in engineering design and management processes,” said Singer.
FHWA’s Transportation Engineering Approaches to Climate Resiliency project includes case studies at the project level utilizing vulnerability assessments to showcase innovations for building climate resilience through engineering analysis of adaptation options.
FHWA noted federal statute does not limit the number of times funding can be provided for an area impacted by a disaster, provided the disaster is declared in accordance with federal agency program requirements.
State departments of transportation are required to consider alternatives when highways and bridges are repeatedly subject to repairs and
reconstruction due to emergency events, particularly when developing transportation plans and programs.
FHWA’s Emergency Relief Program supports the department’s priority of addressing climate change by providing funding to help states perform repairs following major natural disasters and extreme weather events, which increasingly are influenced by climate change.
A listing of fiscal year 2024 allocations for each state, the District of Columbia and Puerto Rico can be on the agency’s Federal-aid Programs and Special Funding site.
The Bipartisan Infrastructure Law also provides new programs and funding opportunities to help the U.S. transportation system be more resilient to climate change.
There is no specific threshold to evaluate the number of times or the cost to rebuild a roadway, said Singer.
“If the roadway meets Emergency Relief (ER) program criteria, then it is eligible for ER funding,” she added. “FHWA encourages state DOTs to consider incorporating resilience betterments into facilities that have been damaged multiple times.”
“Coastal areas are very concerned with sea level rise,” noted Willis. “If you are in Colorado, its resilience program also includes events like rockslides. California considers wildfires. Hawaii even considers impact of lava.”
Climate change impacts are geographically widespread due to differences in the nature of the hazard – hurricanes, flooding, mudslides, wildfires, and other catastrophic weather events – as well as topography and climate, said Singer, adding FHWA’s emergency relief allocations reflect that.
“For example, Hurricane Beryl, which has caused so much damage in Jamaica, Mexico and Texas, is thought to have been made worse by higher sea surface temperatures caused by climate change,” she noted.
As part of developing their federally required Hazard Mitigation Plans, states, some regional and local entities
identify and rank their specific natural hazard risks. Several federal government agencies, state governments, some local governments, and private entities also maintain data for natural hazards risks of interest.
“Building more resilient transportation infrastructure can help our nation better withstand these impacts in the years to come,” noted Singer. “While FHWA’s Emergency Relief program reimburses states for the cost of repairs to roads and bridges damaged by natural disasters or catastrophic events, the PROTECT program funds projects designed to help states make transportation more resilient to withstand future events by making funds available for planning activities, as well as construction projects.”
to alert them. A crew of 14 worked around the clock to haul out the rubble, bring in asphalt, then repave and paint the roads.
Another way affected areas can respond is by following the FHWA Vulnerability Assessment and Adaptation Framework (FHWA 2017a).
“This approach provides agency owners a mechanism for assessing vulnerability of roadways from disaster hazards and identifying adaptation options for building resilience,” said Singer.
Owners and contractors need to have a relationship and have a plan in place ahead of time, noted Willis.
He cites a road restoration project that was completed in seven days after a 7.0 magnitude earthquake hit Anchorage, Alaska on Nov. 30, 2018.
Among the roads damaged by rockslides and aftershocks was the northbound off-ramp of Minnesota Boulevard near Ted Stevens Anchorage International Airport.
The FHWA approved a quick release of $5 million in emergency relief funds to get the $7 million project into place to restore essential travel.
Obtaining the amount of asphalt needed to fix the earthquake-damaged roads against the backdrop of an already tight construction schedule and limited roads proved to be a challenge for the Alaska Department of Transportation & Public Facilities.
Agency staff called asphalt plant owners the day after the earthquake
The department credited planning and training protocols for highway crews as a driving factor toward the rapid response and repair time.
A May 2023 ‘Pave it Black’ podcast Willis and Brett Williams, senior director, engineering & technical services for the NAPA recorded with Andy DeCreane, vice president of Ajax Paving Industries of Florida discussed the company’s task to rebuild the Sanibel Causeway weeks after Hurricane Ian hit Florida in 2022.
“Some people define resilience as the capacity to withstand or to recover quickly from difficulties, or toughness,” Willis noted. “Other definitions talk about adaptation and hardening and looking at recovery from a massive or traumatic event. In the world of pavements, we have to think about resilience, as well. There are times when catastrophic events hit communities and they impact our roads and our abilities to connect people with each other.”
Ajax Paving Industries has a disaster recovery plan in place prior to the storm, establishing meeting places poststorm and assessing employees’ needs.
Everything at the asphalt facilities is strapped down. Silos are filled with aggregate for the weight so the wind doesn’t blow them over. Preparations include having enough generators, chainsaws, and diesel fuel on hand.
DeCreane said most Florida communities are prepared for hurricanes, adding the state’s transportation department “does a fantastic job of getting emergency contracts out early before the storms.
“It’s a matter of getting the roads open. You’re not fixing the roads –you’re just cutting branches. You’re getting everything out of the way. This allows people to get to where they need to be – emergency response.”
After that comes emergency road repair contracts.
Regarding the Sanibel Island Causeway destruction, “This particular area was cut off completely because the road was completely washed out,” said DeCreane. “With the DOT and the designers, we were able to do a complete reconstruct kind of bridge abutment. The designer we hired had it done within two weeks. That was a big feat.”
With the DOT’s roadway section washouts, “we could do more of a typical section with stabilized subgrade base and a lot of asphalt base,” DeCreane said.
DeCreane said among lessons learned from past severe weather events is the importance of design work. Designers are taking a deeper look at Mechanically Stabilized Earth walls for bridge abutments, he added.
nationwide is a lack of a long-term and consistent funding mechanism.
“It may sound silly, but agencies can’t look at their system and make long-term plans when they don’t know how much money they are getting for more than five years out,” he said. “Preparing for and responding to disasters takes funds, and we need to be sure all agencies can strengthen what they have.”
“Climate change is a substantial threat to roadway resilience nationwide, affecting the reliability and capacity of our nation’s transportation system,” said Singer. “Typically, roadway pavement infrastructure is designed and managed assuming a stationary climate. We know this is not the case.
stressors (heat, flooding, etc.) through “engineering-informed adaptation studies” (FHWA 2017c).
Willis noted it’s important to start local.
“Understand the threats, the materials, the design procedures, and then work in partnership with industry to make it happen,” he said. “Agencies also need to better understand how to leverage local materials. Especially when rapid response is needed, agencies cannot wait on long hauls to get materials in place.”
FHWA and its partner agencies are joining together to address the issue of the impact of severe weather events on road repair costs, as well as the economic impact from disrupted travel.
Road builders could build future resilience using the approaches and examples summarized in FHWA’s Synthesis of Approaches for Addressing Resilience in Project Development and the Adaptation Decision-Making Assessment Process.
“These methods allow road builders to account for climate change and resilience in engineering design by generating alternatives, assessing how they would fare under future climate conditions, and considering costs and benefits,” said Singer.
Willis noted the biggest threat to infrastructure/roadway resiliency
“Assuming climate stationarity in the design and management of pavements and other infrastructure could result in pavements that are under-designed for the environmental conditions they may experience over their service lives—such as heavy precipitation, flooding, heat waves, wildfires, sea level rise and storm surge—and lead to failure.”
Funding provided under FHWA’s Emergency Relief program at a national scale continues to be significant, representing the magnitude of the impacts of climate change, noted Singer.
Singer said going forward, “our nation will have to learn to build projects that strengthen the country’s surface transportation system, including roads, bridges, and highways, against extreme weather events.
“FHWA has a range of reports, tools, and case studies focusing on the negative impacts of extreme weather and climate change on transportation, methods to assess vulnerability to these threats, and strategies to address in developing highway projects,” she added.
“By increasing the resilience of these assets, investments will reduce shortand long-term costs by minimizing future needs for maintenance and reconstruction.”
Roadway impacts caused by extreme weather events exacerbated by climate change merit changes in design and management processes to offset their vulnerability, Singer noted.
FHWA’s Vulnerability Assessment and Adaptation Framework (FHWA 2017a) presents a process for conducting vulnerability assessments and developing adaptation options.
FHWA’s Synthesis of Approaches for Addressing Resilience in Project Development provides specific examples of how to incorporate resilience in the project development process for a range of assets (pavements, bridges, ports) and
Addressing the financial toll climate change takes on the nation’s road networks, Willis points to a 2021 article in Climatic Change, ‘Climate effects on U.S. infrastructure: the economics of adaptation for rail, roads, and coastal development.’
In ‘Leveraging SETS Resilience Capabilities for Safe-to-Fail Infrastructure under Climate Change,’ the authors noted safe-to-fail approaches for infrastructure planning and design improve the capacity of cities to adapt for uncertain climate futures by identifying social, ecological, and technological systems (SETS) capabilities to prepare for potential failure scenarios.
by Carol Brzozowski, a freelance writer for Asphalt Contractor.
While you can’t eliminate risk entirely, you can take steps to help reduce it, avoid it and protect against it.
Over the past few years, the cost of doing business has risen significantly. In the wake of the pandemic, owners have had to contend with persistent inflation, continued supply chain issues, and widespread skilled labor shortages.
All of these factors can make it more difficult to finish projects on time and on budget — a critical quality for the industry. While inflation is easing, it’s still important to stay diligent about protecting your business’s financial future.
Fires. Tornadoes. Water damage. All of these disasters, and other unexpected events, often lead to large property losses that can devastate businesses.
It’s more expensive than ever to replace equipment and materials — and it often takes longer now than before to repair or replace damaged items. That’s why it’s important to make sure you have the right types — and amount — of financial protection for your business.
My top recommendation is to get an updated valuation on your property. If it’s out of date, you run the risk of being underinsured, and you may find that the cost to repair or replace building supplies or equipment is much more than you expect. That leaves you vulnerable to large, unexpected expenses—and the safety net insurance can provide will be smaller.
You might be surprised at how much your coverage needs have shifted since
your last renewal due to inflation and supply chain trends.
After completing an updated assessment, you may have several insurance coverages that have been affected. Your agent or insurer can help review your policy to account for recent changes:
• Builder’s risk insurance: Covers property losses that occur during the course of your construction project. This includes building materials, equipment, scaffolding, and storage containers. High inflation during the last few years probably drove up the costs of these items quite significantly, which means your current coverage may be inadequate compared to the cost of repairing or replacing damaged items if losses were to occur today.
• Installation floater coverage: Insures property and materials that you plan to install on a jobsite. Protection can range from damaged items due to fire, weather, and theft. Similar to builder’s risk insurance, you’ll want to confirm your policy has kept up with inflation to avoid underinsuring your materials.
• Contractor’s equipment insurance: Helps protect your equipment and tools on jobsites, in transit, or in storage. Verify that your policy limits are high enough to cover the cost of repairing and replacing the tools and equipment needed to operate your business if they are damaged or lost.
• Business income insurance: Also known as business interruption insurance—can help you stay afloat if your business needs to pause operations after a major property loss. It can help replace lost income and profits, along with payroll and other operating expenses needed while you recover.
In 2023 alone, there were 28 natural disasters in the U.S. that each exceeded more than $1 billion in damage—a new record. In total, they left nearly $93 billion worth of damage in their wake. This is in addition to the wintry weather events at the end of 2022 which also incurred a significant amount of property losses across the country.
While insurance is necessary—and can help you in the aftermath of an incident—it’s more cost-effective to avoid damage and claims altogether.
That’s why you should have a robust safety, inspection, and maintenance program in place. Your project sites change from time to time. Each of those changes could alter your risk.
A formal safety program can help ensure that you’re regularly checking your property, jobsites, equipment, and materials for any sign of damage, wear, or malfunction that could lead to larger issues later. Routine inspections can also help you address the physical security of your supplies and make sure high-value items are secured against weather events, fire, theft, and other perils.
When you make safety a priority and take the time to review your insurance policy, you make your business more resilient to today’s risks. The tips I’ve shared here can serve as a helpful starting point, but it’s best to talk with your agent or local experts for a plan specific to your business.
by Michael Teng, Assistant Vice President of Regional Products, Pricing, and Underwriting for Sentry Insurance.
Astec revolutionized the paving industry with the introduction of the Shuttle Buggy, and now the SB-3000 sets a new standard in material transfer vehicles. Effortless maintenance, unmatched performance, and four steering modes for ultimate agility keep paving seamless. Experience groundbreaking innovation with the patented Ground Crew Control Station for the ultimate user experience and protection. The SB-3000 isn’t a machine, it’s a revolution in material transfer, built on Astec’s legacy of industry firsts.