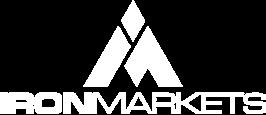
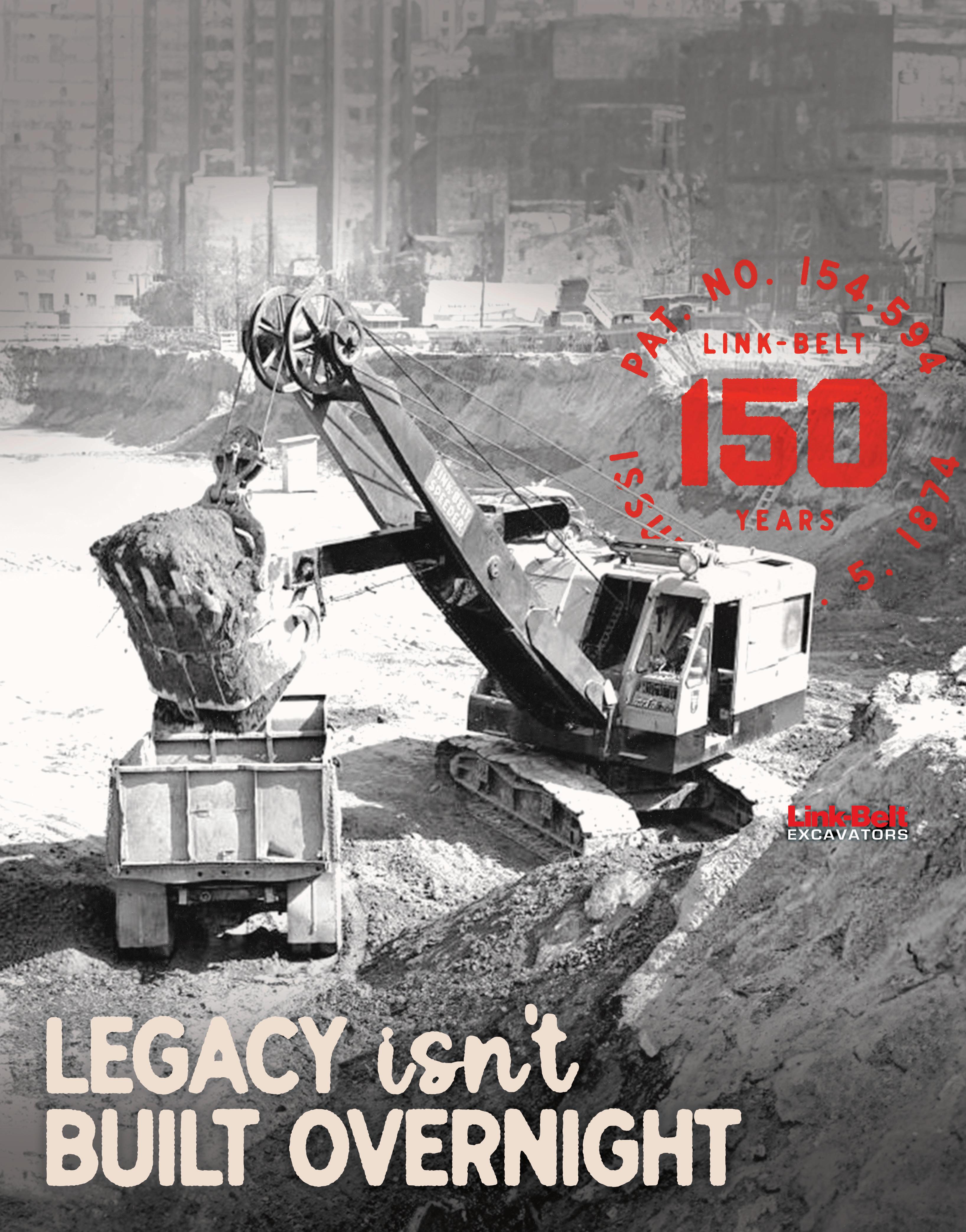
Helping you optimize ROI on your construction equipment
JUNE 2024Helping you optimize ROI on your construction equipment
CHECK OUT THE LATEST MODELS IN THIS YEAR’S INSTALLMENT.
The new DEVELON DX100W-7 mini wheel excavator does big work in small spaces. Multiple steering and power modes, plus 360-degree swing capability, give you more control no matter the application. It all adds up to a job well done. The
During
Komatsu Demo Days: Seeing and operating equipment help our team learn more about the machines in the dirt.
Visiting sites and manufacturers’ proving grounds and customer centers helps our team get close to the equipment and technology we write about every day. A recent visit to the Komatsu customer center in Cartersville, Georgia, allowed me to learn more about the company’s goals and to operate a dozer for the first time.
Before going into the field to see and operate equipment, the Komatsu team gave us a safety review and talked about the company’s goals and industry trends.
Solutions and trends discussed included:
˜ Technology: Predictability with digital solutions including smart construction, intelligent machine control and 3D machine guidance are some of the trends around tech.
˜ Sustainability goals: Power source options and options for your current fleet should be considered. Komatsu to be carbon neutral by 2050. Power options include electric, hydrogen, hybrid and renewable biodiesel.
˜ Labor challenges: Contractors should upskill and retain talent.
˜ Komatsu has the Komatsu Academy to help with education.
Several wheel loaders were available to operate.
˜ Other factors that can help with workforce issues are digitalization and automation.
Operating the Dozer
I have operated construction equipment but never a dozer. I was a little intimidated because the D71PXi-24 is the largest Komatsu hydrostatic transmission dozer. However, with the help of the Komatsu experts and the fully integrated automation, the process was simple.
After moving dirt into a pile, I was able to get everything back to grade automatically with grade control. It also has tilt assist, allowing for 80% less operator input, and track mapping.
Time in a Hybrid Excavator
Several excavators were available to operate including the PC900LC-11, Komatsu’s largest construction excavator. However, I decided to try the HB365LC-3 hybrid excavator because I’d never been in a hybrid machine.
The all-electric swing system has four components:
˜ Electric swing motor
˜ Capacitor—similar to a battery
˜ Inverter (DC to AC)
˜ Motor generator coupled to the engine
The bucket and boom (hydraulic functions) are 15% more productive than a diesel-only excavator and fuel consumption is 20% lower, and the excavator produces fewer emissions.
Smart Construction Solutions
The Komatsu team shared its technology solutions, too. The jobsite management system includes:
˜ Logistics materials in the right place
˜ Drones, terrain mapping
˜ Timecards
˜ A scheduling solution (no lost time)
˜ Cycles for equipment
Other Equipment at the Demo Days
In addition to the dozers and excavators, Komatsu had wheel loaders, including the WA475-10 with auto idle and new lift equipment.
Reader Survey
We want to hear from you. Please take a couple minutes and answer this brief survey. Use the link or QR code.
Read more at: eqtoday.co/ReaderSurvey
Subscribe to Our Newsletter Don’t miss our informative content. Sign up for the Breaking Ground newsletter. Don’t delay. Subscribe today!
Read more at: eqtoday.co/BGSubscribe
These pages feature some of the latest equipment available. For more information on these products, scan the QR code shown
The AT1050 has a Tier 4 Final 75-hp (55.4-kW) engine with a DOC emissions control system. This means that there is no DPF or DEF fluid to manage, helping mitigate de-rates and engine issues related to bypassed regeneration cycles or compromised DEF systems. Equipped with loading forks, the machine has a lifting height of up to 15 ft., 2 in. (4.66 m) and reach of up to 9 ft., 9 in. (3 m). This working range is paired with a lifting force of more than 3 tons at 6,305 lbs. (2,860 kg).
The monoboom design offers a clear view of the work tool, and the lifting kinematics combine the strength and breakout force of a loader and the reach of a telehandler. The panoramic roof and large, tinted windows offer operators visibility of the worksite.
The XL Knight 80 MFG has an updated mechanical, full-width gooseneck trailer design. The 48-ft. long detachable gooseneck lowboy has an overall capacity of 80,000 lbs. and a concentrated capacity of 70,000 lbs. in 16 ft.
The trailer offers 29 ft. of main deck loading space and a loaded deck height of 18 in. The detachable gooseneck features front connection plates with three height settings. The front of the main deck can go up or down 1.5 in., for a total of a 3-in. variance. The raise and lower valve in the rear allows for an adjustment of 1.5 in.
The Ram Heavy Duty offers a towing capacity of up to 37,090 lbs. and a payload capacity of 7,680 lbs. Ram was the first to achieve the 1,000 lb.-ft. of torque milestone with the Cummins I-6 Turbo Diesel, now rated at 1,075 lb.-ft. of torque.
Class-leading ride and handling is accomplished by a class-exclusive link-coil rear (2500) suspension system with optional rear air
suspension (2500 and 3500). The 2024 Ram Heavy Duty now includes a Tailgate Ajar warning lamp standard. The Ram 2500 offers two segmentexclusive rear suspensions: a five-link coil system and an air suspension system. The Ram 3500 continues to use the rear Hotchkiss leaf spring system and offers an exclusive supplemental air suspension system.
Featuring a 24-in. cutting wheel, the model is designed for use with low-flow skid steers and excavators. Similar to the original Stump Ax for higher flow power units, the 24SG has a rigid mount, allowing operators to work by repositioning the power unit, rather than articulating the attachment. Powered by a 110-cc, high-torque radial piston motor, the new Stump Ax is compatible with 17-gpm to 35.9-gpm flow ranges and requires 30 hydraulic hp to 80 hydraulic hp. Read
Bridgestone Americas will debuted its new V-STEEL Z TRACTION (VZT) construction tire. The 25-in. tire is for loader and grader applications and tread compounds are engineered to help improve heat, cut and tear and increase total tire life by up to 15% compared to previous generation product, based on internal estimation related to tread design elements. The new tire includes a tread pattern design with 9% improved traction.
Every construction site is di erent. That’s why Wacker Neuson o ers both mini and compact excavators to handle the many challenges you face. Both rugged and reliable, these machines o er excellent breakout force for the toughest conditions. From conventional and zero-tail tracked models to versatile wheeled excavators, Wacker Neuson provides the power, comfort, visibility and intuitive operation to help you dig into your next job. For more information, please contact your local Wacker Neuson dealer or visit us online.
These pages feature some of the latest equipment available. For more information on these products, scan the QR code shown
Designed for Class-5 chassis applications, the PAL Pro 58 and PSC 8600 TEC Service Crane are engineered to deliver reach, weight reduction and performance on jobsites. Manufactured with 12-gauge all A-60 galvanneal steel and a hybrid torsion box, the PAL Pro 58 eliminates frame and side pack deflection.
It also features a 12-step e-coat process for corrosion protection. Available in 11-ft. body configurations, the PAL Pro 58 includes bolt-on mounting locations for accessories.
Read More at eqtoday.co/83ecrjvm
With a 990-gal. capacity and additional compartments for tools, DEF, grease and more, these DOT compliant fuel trailers allow construction contractors to refuel and service equipment. The rugged chassis is constructed from 6-in. C-channel for durability.
The tank features 7-gauge steel double seam welded for strength. Each tank is equipped with internal fuel surge baffles and cross bracing, a fuel shutoff valve, a lockable vented fill cap, a tank pressure relief vent, and an at-a-glance fuel gauge.
A self-priming industrial grade pump rated at up to 25 gpm is standard and runs on a deep cycle 12-V marine battery.
New Holland Construction introduced three new compact wheel loaders: W60C, W70C and W80C LR. The W60C shares the same frame as the W50C but with enhanced horsepower to elevate output. Upgrades to horsepower and the Z-Bar boom design tailor the W60C for applications like material handling.
With a light operating weight of 12,000 lbs. and 74 hp, the W70C is designed for range of tasks. The W80C LR model is a high-speed option that has a lift capacity of 10,600 lbs. and an operating weight of 13,000 lbs.
The ZW310-7 wheel loader will be offered in a base model and a premium model. Both include a standard fully adjustable, heated air ride seat that incorporates a seatmounted armrest with electric over hydraulic controls.
The armrest and controls adjust forward or reverse to accommodate operators of varying sizes. Both models have Approach Speed Control which gives the operator control of the top speed selected during v-loading. A Payload Checker allows the operator to weigh and log material moved, and a power up feature anticipates power requirements.
Volvo CE launched updated versions of the L30 and L35 compact wheel loaders, designed to meet the needs of contractors looking for 1.3-yd3 to 1.6-yd3 (1-m3 to 1.2-m3) bucket capacity or 2.4-t to 2.6-t fork payload. In addition to their visibility, these updated loaders provide a great range of sight to the front and sides, thanks to a slimmer dashboard.
Operators can access intuitive functions with a larger display that’s navigated via a jog wheel and a multifunction joystick. A new feature available in this size class is a boom kick-out and bucket leveler option with boundary limits that can automatically lift and tilt the bucket to preprogrammed positions.
The fuel delivery system includes a 1-in. hose with auto-trip nozzle, available in 18-ft., 30-ft. or 50-ft. lengths.
Read More at eqtoday.co/8ij6tusb
Not only does this help experienced operators with repetitive movements, but it also helps less experienced operators carry out loading cycles. An electro-hydraulic main control valve supports flow sharing among the hydraulic functions. The adjustable boom and tilt function (optional), allows the operator to set the flow of these functions using the jog wheel and display.
Hitachi Construction Machinery Americas excavators range from 3,790-pound compacts to 1,856,292-pound mining excavators. The latest ZAXIS-7 models feature large, comfortable cabs with ergonomic joysticks and operation levers that travel with the operator seat. The ZX210LC-7 to ZX350LC-7 features a TRIAS III hydraulic system to increase fuel efficiency while optimizing performance.
The KATO compact excavator line offers versatile and durable mini excavators designed for power and precision. Known for reliability, these compact machines excel in landscaping, construction and any project. Featuring technology, maneuverability and performance, the KATO mini excavators are engineered for precision and optimal operation.
*Horsepower and force measured per ISO
Note: Shovel configurations can be found in the online spec guide
Optional around-view monitor (AVM) camera systems on DEVELON crawler excavators display a full view of the machine’s surroundings, giving operators greater confidence when working in tight conditions. AVM systems offer up to 360 degrees of visibility through the monitor inside the cab, allowing operators to better identify potential hazards.
Hyundai’s HX series of compact to large crawler excavators offer power and versatile construction equipment performance with fuel-efficient, fast cycle speeds; impressive hydraulic power; and precision control. Sizes range from 4,080 pounds to 221,280 pounds with the launch of their largest model, the HX1000AL in 2024.
The 350 P-Tier excavator with available SmartGrade technology features improvements including a serviceable arm tip bushing and hardened pin for longer life; electronic, on-demand cooling fans; and an undercarriage design with durability improvements. The 350 P-Tier hydraulic-coupler-ready option integrates coupler controls from the factory, and the grade management path allows customers to choose their grade control solution.
JCB’s large excavators include designs to handle tough environments; CommandPlus cabs; easy-to-use hydraulic pipework diverters, easy coupler override for larger attachment removal and advanced tool select; extended service intervals; and safety features like standard backup cameras and aluminum studded steps. The company’s mid-range and compact models give operators excellent visibility and boosted power and lift with many zero-tail swing models.
No matter what type of work you do—excavation, trenching or truck loading—Cat excavators
The Bobcat E88 comes equipped with dual-flange track rollers, integrated counterweight and a long arm. The E88 offers fast cycle times and excellent lift capacity allowing operators to dig with confidence. Operators can enhance their machine with available options such as add-on counterweight; the Bobcat depth-check system; a Machine IQ subscription; rearview camera; widescreen touch display;
Komatsu’s PC130LC-11 excavator with an 8% longer undercarriage, increases lifting capacity by up to 20% and uses up to 12% less fuel. Easily transportable, this 97.2-horsepower, small, conventional-tail-swing excavator offers a unique combination of lightweight power and agility. Durable steel castings help spread working loads away from high-stress areas for improved durability.
Generation 8 of Liebherr crawler excavators is a leap into the future. The Gen-8 series is completely redesigned to offer customers improved performance and more operator comfort. This next generation includes higher engine power and options for a heavier counterweight and offers minimal fuel consumption. Liebherr offers technologies in the Generation 8 series such as “Modetronics,” which could assist in adapting the machine to the operator’s speed.
Kubota’s compact excavators combine maneuverability, power and reliability with economy to help operators haul away more pay dirt on every job. Consisting of the KX Series and U Series, Kubota’s compact excavator lineup features machines in the 1-ton to 8-ton
The Equipment Today and ForConstructionPros.com teams travel everywhere to gain information for their readers and website visitors. These travels provide videos, images and other content that shares how manufacturers are developing equipment to improve productivity and decrease emissions. This includes trends in excavators, including excavators with alternative power options.
Excavators are one of the most-used and versatile machines on a site. This spec guide shares the excavators offered by manufacturers. One of these is Volvo Construction Equipment (CE). During a ribbon cutting ceremony last year, I had the honor of learning more about the company’s machines, including excavators, and its new training center.
Taking two years to build, the new technical training center in Shippensburg, Pennsylvania, is for Volvo CE dealer service technicians on diesel and electric heavy equipment, machine control technology, connectivity and productivity services, and more. It includes in-person classrooms, virtual labs and three service bays that can accommodate the company’s largest machines. The facility will be a training hub conducting about 500 classes every year.
“I’m proud to work for a company that invests in not only the equipment and technology of the construction industry’s future, but also the North American workforce,” said Scott Young, head of sales region North America, Volvo CE. “The technicians who come through this training center will be prepared for a more climate-friendly and connected future, supporting our customers in this fast-changing industry.”
Volvo CE offers training to dealer service and sales teams from the U.S. and Canada. The new center doubles the number of students that can be trained in a year. It will also provide hands-on and virtual training to Volvo employees globally. The Customer and Training Center received a 100% certified landfill-free certification by Volvo Group North America.
Federal, state, and local legislators and members from area business and education communities took part in the ribbon-cutting ceremony.
Tim Watters, CEO of Hoffman Equipment and Volvo CE dealer advisory council president, underlined the center’s impact. “The need for expertly trained service techs cannot be overstated, as they are the critical link to ensure maximum customer uptime. This new center has the capacity and knowledge bank to keep our teams at the leading edge of equipment service technology,” he said.
Volvo is also exploring collaboration with local high school and career and
technology centers to provide heavyequipment technology training and mentorship opportunities.
Dr. Ray Gallant, vice president — sustainability and productivity solutions, North America, Volvo CE, and I discussed the capabilities of electric
power and what the industry must do with equipment that ideally cannot be electrified. The use of alternative fuels like hydrotreated vegetable oil and hydrogen will be the future of larger equipment that need more power than electricity can provide. We also discussed the new Volvo EC230 fully electric excavator, which is not tiny and
provides the same operation and power of its diesel counterpart.
Read more at: eqtoday.co/VCERibbon
Lori Ditoro is editor-in-chief of Equipment Today
LiuGong uses well-accepted componentry, such as Cummins engines and Kawasaki hydraulics, and integrates them into chassis across its excavator line. LiuGong North America also has a parts support hub near Houston, Texas, and an active and growing dealer network to support and grow contractors’ businesses.
Takeuchi manufactures 18 compact excavators for distribution throughout North America, ranging from the TB210R (just 2,535 pounds.) to the TB2150R (34,435 pounds when equipped with a cab). Takeuchi introduced its first electric model, the TB20e, in 2022. Other newer models include two short-tail-swing excavators, the TB335R (3.5-ton class) and the TB350R (5-ton class).
SANY America’s swing boom excavators operate well in confined spaces. Offered in different machine configurations, these mini and small excavators perform well in many applications like landscaping, utilities, general construction, sewer and land management. All models feature standard auxiliary lines to operate powered attachments. When you need a smaller footprint, SANY’s small, fixed boom excavators are the ideal solution.
KOBELCO Construction Machinery USA offers a full line of crawler excavators that include zero-tail-swing, compact, standard, long-reach and demolition models to meet every challenge. KOBELCO provides engine efficiency and productivity, plus operator controls and comfort. KOBELCO excavators bring more features as standard and are built to bring performance to help get the job done.
Yanmar’s current mini excavator line features nine models. The lineup includes zeroand ultra-tight-tail-swing excavators that have either no protrusion beyond the track or minimal protrusion. Yanmar backs its mini excavators with a four-year/4,000-hour warranty. Additionally, Yanmar’s SmartAssist remote telematics system comes standard on all excavators free for the first five years.
Major trends at the 2024 American Rental Association Show included focusing on operators and their comfort; listening to the customer; and providing flexible equipment and options such as attachment packages and extra batteries. At the show, many manufacturers featured excavators.
Link-Belt Excavators exhibited the 170-X4S. It has faster cycle times by up to 5% and up to 8% increased lift capacities. Other benefits include:
• New heavy counterweight options
• Increased fuel efficiency
• New ECO mode with 10 different engine rpm settings
• Customizable hydraulic flow balance
• Improved cab spacing
• Large 10-inch vertical LCD monitor
Compact excavators are popular rental equipment because they are used on virtually any jobsite and for many applications. HX-A Series compact excavators’ versatility fits the needs of a vast demographic of applications.
The HX40A and HX48AZ offer standard load-sensing hydraulics, while the HX35AZ and HX48AZ incorporate zero-tail swing for operation in confined spaces. All three models include adjustable auxiliary flow; a 5-inch, full-color LCD monitor; and a new auto-safety-lock function preventing unintended use of a machine.
The John Deere team featured the 85-P excavator, popular rental equipment. It has a larger cab and more auxiliary hydraulic and engine power with multiple attachments. While rubber tracks are most popular, it can be equipped with steel tracks.
Kubota exhibited the 8-ton KX080-5 Compact Excavator. It includes:
• A roomy and quieter cab
• Tech in the cab: Full-color 7-in. LCD monitor with jog dial, standard telematics and standard keyless start
• Lots of power and reach
• LED work lights
• Kubota engine
• Angled and fixed blade options
• Standard rubber tracks with steel as an option
The Takeuchi team discussed the minimal tail swing TB350R Compact
Excavator. It was designed because of the voice of the customer to improve serviceability and make it user friendly.
It has an oversized cooling package; steel sealed compartments; double-wrapped hydraulic hoses; and double-wall, rolled-steel backfill blades. The team also featured the fully electric TB20e compact excavator.
The Wacker Neuson team discussed the new EZ17e mini excavator. It is a fully electric, zero-tail mini excavator without rear projection. Because the operator is not exposed to any exhaust emissions or noise, the excavator is ideal for trenches, tunnels and work indoors. Charging options include intelligent charge management. Read more at:
Lori Ditoro is editor-in-chief of Equipment Today
JCB has built and tested a hydrogen-powered backhoe and telehandler.
Our industry hesitates to change, especially moving away from diesel internal combustion engines. Diesel gets the work done. Also, diesel engine manufacturers are improving efficiency and decreasing emissions. While these improvements to diesel engines are important to decrease emissions today, the Environmental Protection Agency’s emission regulations are forcing the issue for contractors, who must reduce their carbon footprint. What can help with the transition, and what power sources are ideal?
Any reduction in emissions made today is a viable option. We will not just flip a switch and move all existing and new equipment to a zero-emission fuel. Diesel will be an option for years. However, looking at different engines for your equipment can help decrease your company’s carbon output immediately.
“Diesel engine technology has advanced significantly with emissions reductions, optimized engine componentry, combustion technology improvements and improved low-carbon renewable fuels,” Joel Honeyman, vice president of global innovation, Doosan Bobcat, said. “What is particularly exciting about diesel engine advancements is we expect to see continued investments and improvements with this technology.”
Daniel Kakareka, product portfolio
manager – construction products for New Holland Construction, agrees that optimized diesel power remains a short-term answer. “While not as environmentally friendly as the electric or hydrogen power sources, advancements in diesel engine technology continue to improve fuel efficiency and emissions performance. Features like selective catalytic reduction and diesel particulate filters help reduce nitrogen oxide and particulate matter emissions ...”
Optimized engines also use less fuel and require less maintenance while being capable of burning fuels other than diesel.
“The high power and torque capabilities mean that they can be used to replace engines of higher displacement, improving efficiency and reducing overall running costs without impacting productivity,” Jeremy Harsin, off-highway marketing director – EBU – for Cummins said. “[They require] less fuel, less servicing with lower emissions with more reliability and more capability. Operators of these engines can also adopt [HVO] as a drop-in substitute for traditional diesel fuel.”
For small and mid-size machines, battery-electric power has a foothold. According to Ray Gallant, vice president of sustainability and productivity for Volvo Construction Equipment North America (Volvo CE), “in the short-term … I think all the focus right now is on batteries and electrification.”
“Batteries and related component costs are dropping, while charging times are increasing and will provide
more options to customers in the future,” Honeyman said.
This decrease makes battery-electric equipment more cost-effective. The decreased maintenance for battery-electric equipment also reduces these machines’ cost of ownership.
“We have [many] grid-connected machines and applications that are starting to appear on the market or starting to be more prolific on the market. We’ve had grid-connected machines for years, but they’ve been restricted to very few applications. Now you’re starting to see them going [into] more … applications out there.”
With grid-connected equipment, “you connect it directly to a power source. You plug it in, essentially, and run off the electricity of the grid,” Gallant said. He added that these machines can have a battery or even combine a grid connection and diesel, offering hybrid flexibility.
A grid-connected asset must be primarily stationary with the current technology, such as an excavator performing material handling. However, Volvo is looking at options for overhead wire or track on the ground.
Hydrogen & Biodiesels
With larger equipment, electric power may not be the solution. Manufacturers are designing drivetrains that use hydrogen and other fuels that produce zero or markedly fewer emissions.
“We are working on new engine projects focused on hydrogen, methanol and other non-diesel fuels to support our customers,” Paul Muller, senior engineering manager for Caterpillar Industrial Power Systems, said.
JCB is all-in on hydrogen combustion engines.
“Research that JCB has done in England has found that battery electric systems work well in excavators up to 4 tons or 5 tons, but for machines bigger than that, batteries are too expensive, too impractical or too heavy,” Lee Tice, JCB product manager, said. “To power heavier equipment, JCB is developing hydrogen engines and has built and tested a hydrogenpowered backhoe and telehandler.”
Other manufacturers have engines that can burn several alternative fuels, including hydrogen, HVO, methanol and other biodiesels
With new fuels, infrastructure is a priority. Planning for delivery of these sources must occur as the technology is implemented.
“The technologies aren’t all mature yet,” Gallant said. “We have a lot of work to do, so it’s not reasonable to expect everybody to jump to the end state today.”
Another priority is buy-in from operators. Your team must want to use the equipment, feel safe and have the power and functionality for the job.
“As the industry evolves, electric and alternative fueled machines will need to coexist alongside today’s diesel-powered machines as diesel power [will likely continue as] the predominant power source, although some may switch from fossil-based fuels to using increased usage of renewable diesel,” Muller said.
Read more at: eqtoday.co/AltPowerContractors
In the dynamic world of building and construction, ensuring operational safety and efficiency while minimizing disruption is paramount. Often, the optimization of project ROI is not just about labor, material and equipment costs but also the strategic planning and execution of traffic management strategies.
Especially for construction projects intersecting with or on roadways or heavily trafficked areas, proficient traffic management is essential. It involves planning work schedules around peak traffic times; providing clear and timely information; and the strategic deployment of signage, barriers, and pathways and detours.
Work disruptions invite delays, cost overruns and a negative public perception. Implementing best practices helps maximize the return on investment (ROI) through efficient work zone management:
˜ Always plan—Identify potential challenges early in the planning process for swift development of strategies to tackle them.
˜ Seek stakeholder alignment— Collaboration with local authorities, agencies and the public helps ensure that plans are realistic and minimally disruptive.
˜ Take a safety-first approach— Emphasize safety by integrating optimal methods for barrier positioning, signage deployment and pedestrian route design.
˜ Maintain clear communication— Keep the public informed about schedules and traffic changes requires a combination of signage and public announcements.
˜ Conduct regular reviews— Continually assess the effectiveness of work zone measures and remain adaptable to evolving conditions.
The planning phase lays the foundation for smooth integration
For construction projects intersecting with or on roadways or heavily trafficked areas, proficient traffic management is essential.
between construction activities and traffic flow. A carefully crafted plan considers project duration, anticipated traffic volume and site-specific needs determined by a analysis of traffic impact and associated risks. Factors to be included in the plan are:
˜ Traffic impact analysis—This thorough analysis offers insights into potential bottlenecks, detour requirements and the best scheduling of construction phases during peak traffic hours. Advanced modeling tools also predict how activities will impact traffic flow, including forecasting potential congestion locations.
˜ Risk assessment—A detailed risk assessment identifies the hazards associated with different phases of construction including the interface between machinery and vehicular/ pedestrian traffic. This will extend
to considerations for emergency access and environmental factors including terrain, vegetation weather conditions and more.
˜ Collectively these efforts help avert accidents and injuries. Allocating resources toward thorough traffic management planning isn’t merely an expenditure. It is a strategic investment that helps safeguard the project’s financial stability.
The success of traffic management strategies hinges on the knowledge and competence of the workforce. Comprehensive training programs for workers and management are essential to ensure that all personnel are familiar with safety protocols.
At the very least, robust training programs should instruct participants on comprehending traffic control
strategies, using personal protective equipment correctly, following appropriate emergency response procedures and safely performing duties within work zones including operating vehicles and machinery. When assessing training programs, give priority to three criteria. The first is a customized curriculum. Tailoring programs to address the needs and risks of individual construction projects is crucial. For example, urban settings can present different challenges, such as higher congestion and intricate road networks with multiple lanes and crossings. On the other hand, rural roads see less pedestrian activity and feature narrower lanes, limited shoulders and fewer traffic control devices. Training should acknowledge these distinctions. Engagement and interaction are also important. Active engagement
and interactive training methods, such as hands-on simulations, role-playing and group discussions, have been shown to improve retention rates and understanding of complex concepts.
Safety is not a one-time event but a continuous process. Regular refresher courses, updates on new regulations and post-incident reviews are essential.
Management’s involvement in safety training is pivotal. Leaders should participate in comprehensive training themselves and advocate for safety initiatives. Management can reinforce safety in the following ways:
˜ Leading by example—When management actively participates in safety training and adheres to best practices, it sets a powerful example for the entire workforce.
˜ Resource allocation—The adequate allocation of resources for comprehensive training programs encompasses time, financial support and access to high-quality training materials and expertise.
˜ Policy development and enforcement—Management must be diligent in enforcing safety standards and holding all team members accountable for compliance.
Maintaining safety within work zones requires a combination of physical and procedural measures. Best practices include the regular inspection and maintenance of barriers and signage to ensure their effectiveness, the implementation of speed reduction measures within the work zone, and the provision of clear communication to personnel and motorists.
To help ensure the success of traffic management efforts, construction professionals should adhere to several best practices:
˜ Display clear signage—Ensure the use of clear signs to indicate restricted areas, speed limits, detours and other important information along the route.
˜ Have an emergency plan— Developing and disseminating clear emergency response plans, including evacuation routes, assembly points and procedures for dealing with different dangers, are imperative to safeguard workers.
˜ Daily safety briefings—Start each shift with a toolbox talk to address potential hazards, reinforce emergency protocols and share experiences.
˜ First aid and medical access— Ensure the availability of first-aid supplies and trained personnel onsite, along with clear protocols for accessing medical facilities in case of serious injuries.
˜ Evaluation and feedback— Regularly evaluate the effectiveness of traffic
management strategies and seek feedback from workers, stakeholders and the public.
˜ Continuing education—Arrange for the team to participate in safety workshops and seminars.
˜ Companies embarking on projects should integrate professional traffic management services. Expert traffic control providers are well-versed in local regulations
and top-tier work zone practices, firms can avoid legal pitfalls and community backlash.
Enhancing the ROI for construction activities requires a plan for effective traffic management.
By reducing risks, companies safeguard their teams and the public and stand to boost productivity.
This investment contributes to project success and can bolster a
Komatsu introduced the new GD955-7 motor grader to the North American market. The GD955-7 provides operators with the ability to build and maintain haul roads for truck fleets of 100 tons and up. This new machine generates blade downforce pressure for grading performance. With faster working travel speeds compared to the previous model, Komatsu engineered the GD955-7 to increase grading performance while helping reduce maintenance requirements.
The horsepower is 426 hp at 1,900 rpm (313 kW at 1,900 rpm); operating weight: 104,323 lbs. (47,320 kg); moldboard: 18-ft. (5.5 m) standard; and a 20-ft. (6.1 m) moldboard optional. Despite its large size, the GD955-7 offers maneuverability. It can execute tight U-turns on a standard 100-t class haul road without the need to fully cut the wheel or course.
Husqvarna expanded its range of battery-powered machines with the launch of a compact power cutter, the K 540i, and a plate compactor, the LF 60i LAT. Both are part of the company’s BLi-X 36-V battery offering for hardscaping and construction applications.
The K 540i is a new 10-in. battery power cutter with an adjustable blade guard and cutting depth up to 4 in. (100 mm). For performance, the K 540i power cutter is supplied with Husqvarna diamond blades. The LF 60i LAT is the newest product to run on the BLi-X battery system. In addition to the new power cutter and plate compactor, the BLi-X battery system also features the DM 540i core drill, the DE 110i dust extractor, the BV 30i screed for concrete placement, the WT 15i water tank and the WL 8i work light.
While the HD+ 120i V-VIO 12-t tandem roller features a vibrating roller drum (50 Hz or 3,000 vpm) at the front and a VIO drum at the rear, the HD+ 120i VIO-2 HF provides additional application options with two VIO drums. An automatic control feature on the HD+ 120i VIO-2 HF keeps the front drum (in relation to the direction of travel) always working in vibration mode, while oscillation or static compaction is used on the rear drum.
The HD+ 120i VIO-2 HF was also designed as a high-frequency (HF) machine, offering a vibration frequency of 67 Hz or 4,020 vpm (front and rear). Both models are powered by a 115-kW (154-hp) Deutz engine. The tandem rollers also have the ability to switch between vibration and oscillation or, in the case of the HD+ 120i VIO-2 HF, combine two vibration and oscillation drums together, removing the need to switch machines or deploy an additional machine and another operator on the construction site.
Caterpillar announced updates to the mid-sized asphalt compactor line. The Cat CB7, CB8 and CB10 Asphalt Compactors are equipped with edge-management options, optional cab, optional split drums and a new mapping display. Features like AM and FM Bluetooth radio and the heated seat combine with seating and legroom, wide sight lines and climate control functions that can help with performance on the jobsite.
Proper management of unconfined edges can help optimize density. The vertical edge helps provide a stable vertical face for joint matching on the next paving pass.
Trimble Roadworks Paving Control
Platform for Mills & Cold Planers
Trimble announced the availability of the Roadworks Paving Control Platform for Mills and Cold Planers, extending the functionality of Trimble’s nextgeneration, 3D paving control system. Trimble Roadworks for Mills and Cold Planers runs on an Android operating system and allows operators to control the cutting depth of the mill or cold planer, according to project design.
The intuitive system allows operators to meet demanding specs for complex projects, minimizing over-cutting and creating a smooth surface on airport runways, highways, racetracks and other projects that require smoothness. The 3D design is displayed to the machine operator showing areas that are on, above or below grade, comparing the actual drum position and slope with the digital design. The platform automatically guides the milling drum to cut the depth and slope without string lines or manual adjustments.
Bobcat super-flow planers are high-powered attachments capable of milling concrete and asphalt up to 7 in. thick. The super-flow planers are available in 24-in. and 48-in. cutting widths. These versatile attachments use the extra hydraulic power available in the Bobcat T86 compact track loader and S86 skid-steer loader equipped with super flow generating up to 42 gpm and 4,061 psi.
Bobcat also offers a 40-in. planer compatible with super-flow and high-flow hydraulics. In all, Bobcat offers six planer attachments that accommodate standard, high-flow and super-flow hydraulics. The attachment is capable of oscillating up to +/- 15 degrees.
With the right mix of attachments, contractors can turn their compact equipment into a veritable Swiss Army knife for the jobsite. However, stocking an attachment toolbox can get expensive quickly, especially for construction and landscaping outfits with a wide service offering and multiple carriers (and possibly carrier brands). The trick is finding the right balance of dependability, versatility and price. Here are three considerations that can help maximize return on investment (ROI) when it comes to compact equipment attachments.
1. Are You Investing in the Right Duty Level for Your Application?
Most attachment manufacturers offer attachments at several duty levels. These are generally classified as light, standard or heavy/severe based on construction and intended use.
Light-duty attachments typically have a lighter overall weight. They might be manufactured with lowergrade steel or lack the weighty reinforcements.
Standard-duty attachments are more middle-of-the-road. They’re designed for more demanding applications and regular use.
Heavy- or severe-duty is often thought of as the professional grade. These are the most robust offerings, designed for long service life in the toughest jobs.
terms of durability and longevity, this isn’t always the case. All that extra durability usually comes with more weight; the heavier the attachment, the fewer materials the carrier can handle.
While it might seem that a heavy/severeduty attachment would offer the best value in
For example, if a severe-duty bucket weighs 470 pounds and the carrier has a capacity of 2,200 pounds, the maximum weight of the load can only be 1,730 pounds. Depending on the application, the reduced capacity and increased price might not provide the best ROI for the contractor.
Continuing with the bucket example, a contractor or landscaper that’s mostly hauling dirt or gravel
Grapples can offer contractors many benefits if they have machines powerful enough to operate them. A grapple maximizes material handling by allowing the operator to hold materials within the bucket.
can probably get a much better ROI from a standard-duty bucket. On the other hand, if demolition and debris removal are a frequent task, a severe duty bucket is the way to go.
Regardless of duty level, look for high-quality, laser-cut steel and robotwelded construction for long-lasting
dependability. Additional features like flat-faced, connectunder-pressure couplers and full nylon hose sleeves can provide added ease and protection for better ROI.
2. Is Your Attachment Designed to Optimize Your Carrier? Let’s go back to carrier capacity. This is probably the most important spec when determining an attachment’s potential ROI. In the example above, it’s clear that the carrier has a maximum capacity. The weight of any attachment must be subtracted from this number to ensure safe operation.
With a simple attachment like a bucket, the math might be easy enough. However, start adding additional components, like a grapple, and it’s worth taking a closer look at the exact weight breakdown.
Some manufacturers use advanced testing to determine exactly where reinforcements are needed. Finite element assessment testing uses a computer simulation to put potential attachments through the wringer. It identifies weak points in the design, allowing engineers to add reinforcements only in these spots, resulting in maximum durability and minimum weight.
By reserving more of the carrier’s rated operating capacity for lifting and transporting heavy materials, operators can lift more and do more. This approach to design can also enable the use of certain types of attachments with compact machines.
Grapples are a good example. A lot these tools can offer contractors and landscapers many benefits if they have machines powerful enough to operate them. A grapple maximizes material handling capabilities by allowing the operator to hold materials within the bucket. Now imagine how many more
pounds of debris an operator could safely transport in a single load.
It’s not as simple as “lighter is better,” though. Again, it’s important to consider the application. When it comes to augers, for example, heavier tools help provide the necessary power and downforce to get the job done.
Augers with a classic-drive system provide productive torque ratios at any rpm. This simple design provides fast, deep holes in tough soil conditions including clay, small rocks and frozen ground. Fewer moving parts and easy maintenance combine for a low total cost of ownership.
For more challenging digging conditions, including shale, rocky soil, layers of frost and heavy clay, a planetary drive that maximizes torque and power will be a better long-term investment. This drive type will add extra weight overall, but in this case, the extra pounds make more of an impact. It’s similar with breakers.
More contractors are renting. Rentals may reduce overhead costs. Key considerations include:
˜ How often will the attachment be used?
˜ What maintenance is required? More moving parts typically mean more maintenance. Downtime and replacement parts can quickly reduce an attachment’s ROI.
˜ Are there potential new revenue opportunities provided by the attachment? For example, would adding an auger allow a landscape company to take on more hardscape jobs?
˜ Asking these important questions can help determine if renting or buying will provide the best ROI.
the Numbers
The right tools can make or break a project, whether that’s a simple
Phillips head screwdriver or something much larger—like a grapple, auger or breaker.
By answering a few simple questions, professionals can quickly determine if the ROI on an attachment justifies the upfront cost.
Keep in mind that it still pays to shop around. Some aftermarket attachment manufacturers provide the same quality and dependability as traditional equipment brands but at a lower cost. For value-minded professionals, a quick online search might turn up new opportunities for high-quality, cost-effective attachments.
Read more at: eqtoday.co/AttachROI
Darin Gronwold is senior product specialist for Ignite Attachments.
The Terminator Tree and Stump Remover attachment for skid steers and compact track loaders has enough clamping power to uproot trees up to 12-in. in diameter and remove stumps.
The dual 3.5-in. x 4-in. bore cylinders have a clamping force of 29,000 lbs., allowing for the removal of shrubs and trees along with their roots to prevent regrowth. The Terminator has 66 total AR400 teeth, 32 of which are horizontal and 34 are vertical, and a replaceable 1- x 8-in. cutting edge.
Using the 5/8-in. vertical teeth to saw upward through the roots allows an operator to sever the root ball.
The new Batwing BW15 series by Woods Equipment is a redesigned flex-wing rotary cutter line for land-clearing, site-preparation and landscaping applications. The 15-ft. Batwing is available in two models: the BW15.52 for 45-hp to 200-hp tractors and the heavy-duty BW15.72 for 65-hp to 300-hp tractors. Level Lock Technology keeps the wings level across rugged terrain and doesn’t require re-leveling while a 13-in. cutting deck with high-lift blades gives a clean cut.
Maintenance is simple with the shimless EZ-Change blade system which allows blade changes with only a ¾-in. wrench. The BW15 series includes aligned grease points, magnetic wing driveline shields and a metal thumbscrew dipstick. The SmartLift system does the heavy lifting by holding the 80-lb. driveline while users are attaching to the tractor PTO shaft.
Direct Forestry Mulcher Head
Attachment
SEPPI M. introduced the new E20 direct for excavators. weighing from 12 tons to 21 tons.
E20 Direct represents the first model of a new family of forestry mulchers for excavators.
The heart of E20 direct is the rotor with fixed tools featuring the CUT CONTROL system, driven by the DIRECT DRIVE hydraulic transmission. The machine can mulch vegetation up to 20 cm in diameter.
Skid Steer
Attachment
The EZ Patcher skid steer attachment is for pavement repairs. Designed by Crafco’s Equipment Engineering department from the ground up, this patented technology offers safe application of repair material.
The EZ Patcher provides roadwork
agencies and contractors with a method for repairing long, linear cracks, such as deteriorated longitudinal joints or utility cuts, using a repair material known as mastic—a binder and aggregate mix that is heated and applied to distressed pavement for a durable, weight-bearing repair without extended road closures.
Vermeer SC48TX
Stump Cutter
The new Vermeer SC48TX stump cutter provides a solution to access residential jobsites with a narrow footprint and low ground pressure to remove larger stumps. Powered by a 48-hp (36-kW), 1.7-L Cat diesel engine certified to Tier 4 Final/Stage V emissions regulations, the Vermeer SC48TX can cut up to 28 in. (71.1 cm) above grade and 16 in. (40.6 cm) below the surface.
It features a straightline cutting width of 65 in. (170.2 cm). The retractable tracks transform the machine to only 35 in. (89 cm) for navigating narrow jobsites and standard 36-in. (91-cm) gates. Tracks can be extended to 49 in. (140 cm) for stability.
John Deere
Mulcher & Brush Cutter
Excavator
Attachments
The ME36 and ME50 Mulchers and the RE40 and RE50 Rotary Brush Cutters are equipped with knifestyle cutting teeth on a split ring rotor.
The spiral, double helix tool pattern and tool shape allow for efficient cutting for mulch up to 5-in. material. A controlled and metered cutting depth allows the operator to maintain high rotor rpm and a productive mulching rate.
The teeth may be sharpened and flipped for a fresh cutting edge, extending the tool’s life. Three swinging blades mounted to a blade carrier can fell and cut material up to a 6-in. diameter. A heavy-duty, hinged debris shield retracts when the head is engaged with trees and brush, exposing the blades, and allowing for aggressive cuts.
The FX26 Forestry Mulcher is a forestry mulcher for excavators from 8,000 to 16,000 lbs., with a direct coupled motor which provides power during use. A heavy wall 14-in. rotor is fitted with 21 fixed knives to shred brush, limbs and standing trees to 6 in. in diameter.
The bite-limiting tooth design maintains drum speed and prevents stalling. Material is passed through two breaker bars to create fine mulch. The FX26 weighs 785 lbs. and requires 15-35 gpm of hydraulic flow to power the gear motor but features a 26-in. working width for production. With two grease points and no additional drive components, this simple design can be maintained on jobsites.
For more modern engines, oils have been engineered following environmental regulations that did not exist 50 years ago.
Diesel engines have been around for more than half a century. They have been described as the workhorses of the industry, and they provide users with the power they need. Diesel engines are everywhere.
Diesel engines have evolved, and a diesel engine today may not exactly line up with the diesel engines of the past. However, their evolution has been slower than that of the gasoline engine. For instance, many diesel engines today still use a 40-weight oil (albeit multigrade or semi-synthetic), which can tell us about the changes in the viscosity requirements over the years.
This column explores how the specifications changed to get a better idea of:
˜ The evolution of diesel engine oils
˜ Some reasons behind its degradation
˜ Ways that degradation sources can be identified through oil analysis
As per the American Petroleum Institute (API), the standards governing Diesel Engine oils began with the CA spec which became obsolete in 1959.
The latest diesel engine oil standards were upgraded to CK4 and FA4 in December 2016. However, the gasoline spec entered its standard, the SP spec, which includes 0w16 and 5w16, in May 2020.
Most API standards are backward compatible. This means that an engine that requires a CJ4 spec oil can still use a CK4 spec oil, but the reverse is not true.
For today’s engines, oils follow environmental regulations that did not exist 50 years ago. Also, newer engines have more demand compared to older engines. The oil is under more duress and must perform under these conditions. Modern oils are formulated with this in mind.
CK4 oils provide enhanced protection against oil oxidation and viscosity loss caused by shear and oil aeration, catalyst poisoning, particulate filter blocking, engine wear, piston deposits, degradation of low- and high-temperature properties, and soot-related viscosity increase compared to the CJ4 oils (API, 2024). FA4 oils are not backward compatible with the CJ4 oils nor are
sustaining emission control system durability if particulate filters and other aftertreatment systems are used. Like CK4 oils, they provide enhanced protection against oil oxidation and viscosity loss caused by shear and oil aeration. They also protect against catalyst poisoning, particulate filter blocking, engine wear, piston deposits, degradation of low and high-temperature properties, and sootrelated viscosity increase.
What’s the Difference Between CK4 & FA4 oils?
CK4 oils are specifically designed for use in high-speed, four-stroke-cycle diesel engines designed to meet the 2017 model year, on-highway and tier 4, non-road exhaust emission standards and for previous model year diesel engines. However, they are also formulated for diesel engines using diesel fuel with sulfur content up to 500 parts per million (ppm) (0.05% by weight). Diesel fuels that contain more than 15 ppm (0.0015%) may impact the exhaust aftertreatment system’s durability and/or the oil drain interval.
On the other hand, FA4 oils are xW30 oils specifically designed for use in select high-speed, four-stroke-cycle diesel engines designed to meet 2017
model year, on-highway greenhouse gas emission standards. These are formulated for diesel fuels with a sulfur content up to 15 ppm (0.0015% by weight).
API FA-4 oils are not interchangeable or backward compatible with API CK-4, CJ-4, CI-4, CI-4+ and CH-4 oils. Additionally, these oils cannot be used with diesel fuel containing between 500 ppm to 15 ppm of sulfur.
Figure 1 shows the API donut for both specifications (API, 2016). This API donut typically appears on every diesel engine oil that is sold (those that are original and not counterfeit).
Why Does My Diesel Engine Oil Degrade?
All oils degrade. They can be considered consumable because they must be replaced. Diesel engine oils are no different except that they may be susceptible to certain mechanisms that turbine oils are not. The diesel engine is often placed under a lot of pressure to deliver power while keeping cool and managing emissions.
The critical areas for lubricant performance include:
˜ Viscosity control
˜ Alkalinity retention, base number (BN)
˜ Engine cleanliness control
˜ Insoluble control
˜ Wear protection
˜ Oxidation stability
˜ Nitration
Typically, these factors are monitored to ensure that they remain in a healthy condition.
Several factors affect oil degradation. According to The International Council on Combustion Engines (The International Council on Combustion Engines, 2004), these include specific lube oil consumption; specific lube oil capacity; system oil circulation speed; NOx content in the crankcase atmosphere; and influence on the lubricant, fuel contamination in trunk piston engines, deposition
tendency on the cylinder liner wall, metals in lubricant systems, and oil top-up intervals. These can further be divided into systemic conditions (which cannot be easily altered) and environmental conditions because of processes occurring within or to the system (see Figure 2).
Conditions
While lubricant degradation can be caused by environmental strains, sometime the operating design of the system also encourages degradation. Three such cases are specific lube oil consumption, specific lube oil capacity and system oil circulation speed.
Specific lube oil consumption (SLOC, g/kWh) is defined as the oil consumption in grams per hour per unit of output in kilowatts (kW) of the engine (The International Council on Combustion Engines, 2004). Over the years, a reduction in the SLOC for engines with special rings inset into the upper part of the cylinder liner has occurred. These reduce the rubbing of the crown land against the cylinder liner surface.
With reduced oil consumption, oil top-ups, which would have introduced fresh oil into the system, are reduced. This fresh oil would have increased the presence of additives and helped maintain the required viscosity of the current oil. However, since the SLOC is reduced, the oil does not get a “boost” during its lifespan and will continue to degrade at its current rate. Hence, a lower SLOC may encourage the degradation of diesel engine oil.
Specific lube oil capacity, also known as the sump size, which is the nominal quantity in kilograms (kg) of lubricant circulated in the engine per unit of output in kW. According to The International Council on Combustion Engines, the specific oil capacity does not directly affect the equilibrium level of degradation. However, it can influence the rate at which
deterioration occurs because smaller sump sizes can increase the rate at which degradation achieves an equilibrium level. Typically for dry sump designs, the specific oil capacity is around 0.5 kg/kW to 1.5 kg/kW. These values are closer to 0.1 kg/kW to 1.0 kg/kW for wet sumps.
System oil circulation speed refers to the time taken for one circulation of the total bulk oil. In diesel engines, lubricants are usually subjected to blow-by gas (including soot and NOx) during their time in the crankcase. If the lubricant spends a longer time in the crankcase, it can become degraded quicker. Typically, the time required for one circulation of bulk oil averages between 1.5 minutes to 6 minutes. However, a trend toward smaller sump sizes and, by extension, shorter circulation times, should reduce the degradation rate.
The environmental conditions that lubricants must endure also influence their degradation. These conditions can either be enforced through the system, its operating conditions or from conditions outside the system. A few environmental conditions must be addressed (The International Council on Combustion Engines, 2004).
NOx content in the crankcase atmosphere and influence on the lubricant has more applicability to gasoline engines than diesel engines, but they should not be fully ruled out. Diesel engines are more susceptible to sulfur-derived acids. However, NOx can be produced by the oxidation of atmospheric nitrogen during combustion, affecting degradation.
Field studies show a correlation between nitration levels, an increase in viscosity and an increase in acid in the oil. NOx can also behave as a precursor
catalyst that promotes oxidation by forming free radicals in the lubricant. On the other hand, there can be direct nitration of the lubricant and its oxidation products to produce soluble nitrates and nitro compounds. These can eventually polymerize to form similar by-products of oxidation, which can lead to increased acidity (lowering the BN) and increased viscosity of the lubricant.
Fuel contamination in trunk piston engines happens often in diesel engines. If the fuel injectors are defective or the seals do not effectively seal, fuel enters the oil. When fuel is in the oil, oil can become degraded quickly, often causing the viscosity to reduce to a value that compromises the oil’s ability to form a protective layer. The fuel dilution test can quantify the content of fuel in the oil. Depending on the type of engine, the tolerance levels differ.
Deposition tendency on the cylinder liner wall is usually caused by unburned fuel or excess oil in this area or the chamber. Typically, the piston rings scrape these deposits back into the oil, leading to an increase in the volume of insolubles. This also increases the viscosity of the oil, and it appears darker.
Reducing the SLOC also decreases the deposits on the liner wall because special rings (near the top of the liner) are installed to have controlled clearance of the piston crown. This reduces the crown land deposit, which can minimize bore polish and hot carbon wiping.
In addition, with a reduction in SLOC, the number of oil top ups is also reduced. As such, the replenishment rate of additives (in particular the BN) is not as frequent. Therefore, the degradation of the oil will advance at
a slightly faster rate due to the lower SLOC which affects the rate of top ups.
Metals in lubricant systems may also act as a catalyst for the oil degradation. During oxidation, copper is one of the most common catalysts in addition to other wear metals (such as iron) that can increase oxidation rates. As such, the presence of these metals increases the degradation rate.
Oil top-up intervals must be managed so that they do not disturb the balance of the system. Typically, when the sump level falls below 90% to 95% (depending on the manufacturer), a top-up is needed. When fresh oil enters the system, it replenishes some additives and breathes new life into the oil. However, with this change in temperature of new oil coming into the system (especially in large quantities of about 15%), the deposits held in suspension tend to precipitate.
Additionally, foaming (caused by the increased concentration of some additives) can occur if too much fresh oil is added at once. As such, oil topup intervals must be managed to avoid further degradation.
Understanding Your Oil Analysis Results
Having the information above is great to understand how your diesel engine oil degrades, but how will you know that it is degrading? One of the most reputable ways is to submit your oil for testing in the lab. Depending on the type of diesel engine, different tests will be involved. However, you should be familiar with some basic ones.
When determining the health of your diesel engine oil, the first thing to check is the oil’s viscosity, total base number (TBN), whether all the additives are at the correct levels, if there are any wear metals or contaminants present and finally the presence of water or fuel dilution (see Figure 3).
Viscosity (American Society for Testing and Materials D445) – The viscosity levels should fall within ±5% of the original value. If they exceed ±10% of the original value, then the levels will fall out of the classification for that grade of oil. For instance, Mobil Delvac 15w40’s kinematic viscosity, at 100°C, is 15.6 millimeters squared per second (mm2/s), according to its data sheet. If this value drops below 14.04 mm2/s or above 17.16 mm2/s then it can no longer be classed as a 15w40 oil and will not be able to properly lubricate the engine. These values vary depending on the manufacturer, application of the oil and the lab being used. These are a guideline in this example.
TBN – This is the amount of alkalinity remaining in the oil. The oil’s alkalinity helps neutralize the acids formed in a diesel engine. This value is always depleting because acids are continuously forming in an engine. However, if the TBN drops below 40% to 50%, then there isn’t much reserve left to continue to protect the oil. This is the threshold limit, which can vary
depending on the application, but this is a good guide to follow.
Additives – All finished lubricants have additive packages. These will vary depending on the oil producer. However, a few additives should be on your radar when trending their depletion in diesel engine oils. These include zinc, phosphorus, magnesium and calcium. They typically form parts of the dispersant, corrosion and antiwear additives that protect the oil. Ideally trending the decline of these may be helpful but your lab would have reference values (based on the type of oil) and can advise on concerning levels.
Wear metals – During the engine’s lifetime, components will wear. Depending on the engine’s manufacturer, the warning limits will also vary (this also differs depending on the application). Iron, aluminum, chromium, copper, lead, molybdenum and tin are some metals to trend. If other special metals are in your engine, then you can ask your lab to include them. Typically, if there is an upward trend, this indicates wear/damage of specific components.
Operators can perform a simple test to determine if metal filings are in their oil (indicating some form of wear). They can place the oil in a shallow container and then place a magnet below the container or place the magnet in a sealed plastic bag and immerse it into the container. If metal filings are on the magnet when it’s removed, then this indicates the presence of wear metals, and the mechanic should begin investigating for damaged components.
material that is foreign to the lubricant. Typically, labs test for the presence of sodium and silicon. Depending on the application’s environment, these values can increase, indicating that they are entering the system somehow. Usually, this can occur during lubricant top-ups or improper storage and handling. Presence of water – This is never a good sign because water can affect the lubricant by changing its overall viscosity, bleaching out some of the additives and even acting as a catalyst. Many labs perform a crackle test (where the oil is heated and if it produces a “pop” sound, then that confirms water in the lubricant). In certain instances, it is obvious that water is present because it settles out in the sump/container. Labs can also perform a test to quantify the volume of water present. Typically, 2,000 ppm to 5,000 ppm is too much for most applications, but this varies depending on the manufacturer.
Operators can perform their version of the crackle test by placing some of the oil in a metal spoon and heating it with a flame. If it produces a pop, then they can confirm that the oil has too much water in it before sending it off to the lab. Note: This should not be done in a highly flammable environment!
Fuel dilution – This occurs because of the nature of the diesel engine. However, limits need to be adhered to because too much fuel in the oil can lead to drastic changes in its viscosity. Usually, this value should not exceed
drop of the oil on a coffee filter and leave it to dry. The oil will spread out in concentric rings. If fuel is present, there will be a rainbow ring. This means that the mechanics need to figure out if any injectors or seals in the diesel engine have an issue. The main idea with oil analysis is to develop equipment trends and understand how the values align over time. This can help operators spot if an inaccurate sample was taken (possibly after a top-up, directly after an oil change or even from the bottom of the sump). An analysis also assists in planning component maintenance. For instance, if the value of iron in the oil report keeps increasing, then some iron component may be wearing. This can give the mechanic time to investigate the engine and replace the component before it causes unscheduled downtime.
References
• American Petroleum Institute (November 18, 2016). New API Certified CK-4 and FA-4 Diesel Engine Oils are Available Beginning December 1. https:// eqtoday.co/Ref1
• American Petroleum Institute (February 19, 2024). API’s Motor Oil Guide. Retrieved from API: https://eqtoday.co/Ref2
• The International Council on Combustion Engines. (2004). Guidelines for diesel engines lubrication - Oil Degradation | Number 22. CIMAC.
Doug Holmes has built a successful business by investing in state-of-the-art equipment and technology that gives his company an edge over the competition.
As a company grows, your equipment fleet’s preventive maintenance and refueling needs to evolve. To keep up, you need to monitor the effectiveness of your current approach and rightsize your service tools. Take Doug Holmes Construction, a Texas-based company that updated its service equipment to meet the fueling and maintenance demands of an expanding fleet for example.
Company President and Owner Doug Holmes grew up in the construction, working for his father’s paving and grading business. In 2011, he ventured to Lubbock, Texas, to help a friend adopt automated grade control when the advanced technology was still in its infancy in the region. After realizing the demand for advanced grading services, he launched Doug Holmes Construction in 2013.
Today, this heavy construction contractor specializes in dirt work, concrete and asphalt jobs using cutting-edge technology and late-model equipment that helps streamline project costs. The company’s equipment fleet quickly grew to 75 pieces to meet local demand, creating a maintenance and refueling challenge.
“When we started, we serviced most of our equipment out of a pickup with a diesel tank in the back,” said Holmes.
Having the right fuel and lube solution helps drive overall fleet efficiency.
With no onesize-fits-all lube truck, Holmes weighed needs like product capacity and maneuverability to find the right solution.
“As our needs grew, we added more pickups. Finally, we got to the point that we just could not keep up.”
When three crew members struggled manage the fleet’s maintenance schedule, Holmes realized he needed a different approach. In every other part of the business, Holmes and his crew were using state-of-the-art equipment and technology. It was time to bring fuel and maintenance up to speed.
During the 2020 CONEXPO-CON/AGG trade show, Doug and his son, who works in the family business, began researching a solution to break the maintenance bottleneck.
The challenge was to find a solution tailored to Holmes’s unique situation. With no one-size-fits-all lube truck, Holmes weighed needs like product capacity and maneuverability to find the right solution. After careful deliberation and consultation, they
determined that a Class 7 FL1270S fuel/lube body fit their needs. Upon delivery, Holmes quickly saw impressive efficiency gains.
“When it showed up, it was every bit as good as we’d hoped it would be,” he said.
Replacing a fleet of pickup trucks with a dedicated Class 7 fuel and lube truck allowed one person to maintain all 75 machines in the fleet, freeing up two employees for other critical tasks.
“I service all of the equipment in the field [with the Class 7 truck],” said Nick Balderama, service technician for Doug Holmes Construction. “There’s never a minute that I’m not busy throughout the day working here. This truck really makes my job easier because the size helps me get in and get out.”
Class 7 Truck Hits the Sweet Spot
On jobsites, a larger Class 8 truck could make accessing equipment a challenge, but the single-rear-axle Class 7 truck provides enhanced maneuverability for efficient service. For instance, the truck features a short, 187-inch wheelbase. This enhances the turning radius so the truck can get in and out of tight spaces.
“[With the Class 7 truck] I can roll right up to wherever I need to service a piece of equipment ... if it were a little bit larger, sometimes I would have to just post up somewhere and let that equipment come to me,” said Balderama.
Having the right fuel and lube solution helps drive overall fleet efficiency. Doug Holmes’ Class 7 truck is outfitted with a 1,000-gallon diesel tank and five product tanks, allowing it to handle everything from diesel exhaust fluid to hydraulic oil.
Having all the fluids needed in the right quantities helps Balderama be more productive without frequent trips to the shop—even during the busy season.
“This truck really helps me get a lot more done each day because it has all of the fluids that I could possibly need,” said he. “On our heavier days, we can run as much as 800 gallons of fuel through this truck in one day.”
Keeping Things Clean
Oil spills remain a big concern in equipment management. The Doug Holmes Construction equipment in the fleet hold large quantities of oil that must be safely contained during fluid exchanges.
Preventing spills with the antiquated practice of pulling drain plugs and draining oil into buckets is challenging. Fluid exchanges enter into the modern age with lube exchange systems. Vacuuming the used oil out of the engine helps reduce the chance of spills, guards the jobsite against contamination and keeps the technician clean. Holmes has seen the difference the technology has made first-hand.
“It’s a very clean operation, where it used to be extremely filthy,” said Holmes.
In addition to peace of mind and cleanliness, the fuel and lube truck has enhanced overall productivity. The system uses compressed air to build vacuum pressure and remove hot oil from products at 6 gallons per minute (gpm) to 8 gpm. This allows the technician to safely complete more fluid changes per day compared to traditional pumpbased systems.
Replacing multiple trucks with a single fuel and lube truck makes the Class 7 truck a critical piece of equipment. Doug Holmes Construction cannot afford unplanned downtime, so support is essential.
“[The service truck company] knows that we’re running one big truck that services a whole lot of equipment, and [that team has] been able to keep our uptime running, and they’ve made life very smooth and easy for us for the last two years,” says Holmes. “They have been extremely easy to work with ...”
Holmes has built a successful business by investing in state-of-theart equipment and technology that gives his company an edge. Now the company has invested in a fuel and lube truck that increases the efficiency of servicing this fleet.
However, every fleet faces unique demands. When selecting the right preventive maintenance solution, fleet size, the distance between jobsites, and fluid types and quantities must be considered. You want to be able to carry all the fluids, filters and components necessary to perform service without multiple trips back to the shop.
Fluid exchange speed is another important consideration for many preventive maintenance programs. There are many trade-offs, and it is advisable to seek expert advice.
Read more at:
eqtoday.co/ServTruck
Chance Castillo is the corporate sales manager for Sage Oil Vac.
In addition to peace of mind and cleanliness, the fuel and lube truck has enhanced overall productivity.
During the Atlantic hurricane season and beyond, contractors
must be prepared for the
unexpected.
June begins the Atlantic hurricane season, which runs through Nov. 30. Natural disasters present challenges for construction equipment and operators in such a way that calls for planning and preparation (tips can be found in “4 Natural Disaster Preparedness Tips for Construction Contractors” on ForConstructionPros.com).
Disaster Preparedness for Equipment
Disaster response has an immediate mobilization timeline, so a fleet must be ready to respond to the affected area quickly, noted Tyler Havens, Stellar Industries product manager.
Case in point: Team Rubicon (TR) is a veteran-led humanitarian organization serving global communities before, during and after disasters and crises. Its primary scope in heavy equipment disaster response includes route clearance, debris management and sawyer support.
“Our primary uses for the equipment are for route clearance, debris removal and vegetative debris removal,” said Jeremy Moore, TR operations manager. “We typically use the equipment in concert with our chainsaw crews to move the larger and heavier tree debris. Typically, we use [the] CASE TR310A/B for our heavy equipment needs.”
Fleet Management
Before a natural disaster strikes, ensuring that the right equipment is in a fleet and ready to perform vital tasks is a top priority, Havens said.
“Don’t delay purchasing the equipment you need ahead of the storm,” he added. “Once you have the right equipment in place, allow yourself enough time to get the tools you need incorporated, including filling the fuel tanks in your fuel trailer.”
During a natural disaster, proper disaster preparedness for equipment will ensure that necessary repairs can be conducted at the point of need during the response, reducing the likelihood of major breakdowns and subsequent disruption, said Havens.
“Sourcing items from local vendors will take more time in the recovery
phase, so it’s essential to plan … and stock extra supplies,” he added.
When monitoring natural disaster seasons, such as the hurricane season, “knowing [the] typical areas that are hit the most and having a position where your equipment is in those areas is a critical step towards being ready,” said Ted Polzer, CASE North America director, product, and customer support.
Also, have solid tires to prevent flats leading to downtime because of sharp objects and debris on the ground, he said.
According to Justin Steger, John Deere product marketing manager, John Deere recommends that, for fleet management in known disasters, operators should plan and know how much fuel and diesel exhaust fluid are available and where they are located. Stock up on lubricants, grease and other needed fluids and parts, added Matt Costello, John Deere product marketing manager. Greasing machines will often play a significant role in keeping them operating especially if an operator is working in wet conditions, noted Costello, adding that it helps keep the joints clear and moving freely.
Eric Mayfield, Caterpillar product consultant, echoed the importance of properly inflated tires and noted that batteries should be fully charged. He advised contractors to stock up as much as reasonably possible on items such as clean fuel, grease, fuel filters and parts.
Polzer said having a fuel supply in the event of a natural disaster is important, adding that, in some areas, “fuel can be a challenge to get because the roads are either treacherous or they’re jammed.”
Contractors using electric equipment should consider having a good generator and accompanying supplies, said Polzer.
“It goes back to having your own power source and not depending on anyone else,” he said. “That way, you can control your own destiny.”
“If equipment is not used daily or weekly, make sure everything works as designed,” said Mayfield. “Not only do you want to make sure [that]
TR is a veteran-led humanitarian organization serving global communities before, during and after disasters and crises. Its primary scope in heavy equipment disaster response includes route clearance, debris management and sawyer support.
the machine is ready to go, but the method of transportation is as well. Ensure [that] the trailer/truck is ready and that you have the proper tie-down equipment to secure the machine.”
Construction companies should perform routine maintenance and machine upkeep to ensure that fleets are fully prepared to support disaster clean-up, noted Steger.
“All machines should be properly greased; any underlying maintenance should be performed, and all issues should be fixed ahead of time, especially before forecasted hurricanes or snowstorms,” he said.
If the contracting company and its equipment are in an area prone to natural disasters, identify special machine attachments such as grapples, mulchers and forks that will assist in disaster recovery, Mayfield noted. Grapple attachments are best to have on hand for gripping fallen trees, debris and other items needing to be loaded and moved, Polzer said.
Polzer concurred, adding that grapples “are an extremely effective tool not only for disasters but many other jobs. It’s an attachment that somebody can invest in and [be used] no matter what.”
Costello said that brushes and mulching heads may prove effective in clean up.
“You can mulch up overburden like trees and branches,” Polzer said. “That might be a good investment because then you’re not having to haul away wood chips and other debris, especially on roads that might be covered with debris, trees and powerlines. It makes it … difficult. You want to be as self-sufficient as you can be.”
If contractors don’t own the recommended attachments, they should rent attachments ahead of time for a machine, Mayfield said.
Polzer said he tells people to prepare themselves with the right equipment, “because what’s also going to happen locally is that everybody in need of those attachments or tires is going to already be seeking them out, which drives up the price.”
It can be harder to get in the lead times because tires may have to be shipped from a greater distance “because somebody’s already beaten them to the punch,” he added.
Fuel trailers and mechanic trucks are essential pieces of equipment. They can help businesses and communities affected by natural disasters with clean-up, equipment repairs and refueling needs, said Havens.
He added that they should be ready at a moment’s notice.
Taking care of the equipment that takes care of everything else can sometimes be overlooked, Havens said, adding that regular maintenance is crucial to ensuring a work truck is prepared at all times, especially during a disaster response mobilization. Adhering to the manufacturer’s recommended preventive maintenance and inspection schedules—including oil changes and filter checks—and performing daily maintenance extends a work truck’s lifespan and ensures that it’s running at peak performance, according to Havens.
“A simple daily walk-around can identify and address potential issues before they escalate, providing the reassurance [that] a truck is operating at its full potential at all times,” he added.
To be prepared for natural disasters, TR volunteers perform monthly and quarterly maintenance.
“During these quarterly maintenance events, we ensure [that] we operate the equipment for 15 minutes to 30 minutes,” said Moore.
In situations such as wildfires, Polzer advises to follow firefighters’ guidelines to have the right protection gear in kits if a contractor is stranded.
“There’s a lot of good government guidance programs out there to support and drive an initiative to put in more firebreaks to try to reduce some of the risk,” Polzer said.
“Winch Optimization on New Fire Dozer Packages” on ForConstructionPros.com illustrates how winch optimization on new fire dozer packages developed based on input from the U.S. Bureau of Land Management, U.S. Fish and Wildlife Service, U.S. Forest Service, the Georgia Forestry Commission, and CAL FIRE for the Caterpillar D5 and its predecessor, the D6N. This optimization helps in the effort to save human lives, property and timber.
Dust and debris are often significant in areas affected by a natural disaster, noted Havens. He added that, after disaster strikes, inspecting the equipment exterior and tires for any punctures, wear or damage is important.
“Scheduled maintenance to check air filters and clean components will improve operator comfort and safety while also extending the longevity of the [vehicle or equipment],” he added.
Before disaster strikes, “be mindful of where equipment is parked [because] potential falling hazards could damage equipment,” Steger said. “Additionally, move equipment
to higher ground in instances of major flooding.”
Mayfield noted that machines moved away from the disaster area or to higher ground before disaster strikes should be secured to a trailer to be ready at a moment’s notice.
“Make sure you have all the proper personal protective equipment such as a hard hat, safety vests, steel-toe boots, communication tools, water and food ready to go,” he added.
“I can tell you from living in Kansas with tornadoes that, typically, we always used to park our equipment in low places—areas that had indentions in the ground,” Polzer noted. “Even
though it would be full of debris, it wouldn’t take direct shots from highspeed debris.”
Polzer said he’s seen contractors stage equipment just outside of an area that they believe will be hit.
“It won’t take that frontline type of wind gusts and damage because they’re just outside that area,” he added. “A lot of contractors will have fleets of machines already loaded on trucks and trailers and ready. As soon as they’re cleared to be able to start coming in to respond, they’re immediately in action.”
Contractors are encouraged to think of what other possible uses
machines can have for cleanup or relief efforts, he added.
“We’ve seen wheel loaders carrying sandbags through flooded areas, articulated dump trucks being used as rescue vehicles in deep water conditions, and machines with grapple attachments moving debris,” Costello said.
In a route clearance role, TR will stage equipment outside the projected path of the storm but close enough to quickly respond, noted Patrick Wright, Sr., TR heavy equipment associate.
Fleet Management During Natural Disasters
When operating in a disaster environment, it is paramount that detailed site surveys are conducted to identify existing and potential hazards, said Wright.
“Each piece of equipment requires both an operator and a spotter,” said Wright. “Spotters provide additional site awareness, operating assistance and crowd control. Pre- and postoperational inspections are conducted daily to identify equipment issues and provide preventive maintenance.”
Before a predicted natural disaster occurs, operators should ensure that all cab doors and windows are closed before leaving the jobsite, Steger said.
If a machine has vandal covers, they should be installed beforehand, if possible, to help save cab glass from damage from falling objects or debris, Steger said, adding that operators should also consider covering exhaust stacks to avoid unnecessary damage.
Costello noted that, when possible, a quick machine wash is helpful following a natural disaster to protect the machine’s components.
Operator Concerns
“Truck Manufacturers Pivot Designs, Embrace Change in Face of Natural Disasters, COVID 19” on ForConstructionPros.com illustrates how the challenges of natural disasters, the COVID 19 pandemic, supply chain and labor shortages
amplified the importance of increased cab comfort for operators and how safety and technology updates serve to recruit and retain drivers.
Still, there are evergreen considerations. Operators should also be conscious of underfoot conditions as well as any compromised structures or fall hazards surrounding where they’ll be working, Steger said.
Other concerns include downed powerlines and natural gas leaks, Mayfield said.
“In disaster situations, it is very important to take a step back and think through every action and assess the situation, finding any safety concerns,” said Mayfield. “Perform a jobsite safety analysis and walk through it with everyone you are working around.”
Operators should prioritize rest and hydration “just so they have their wits about them,” Polzer said.
“Typically, they’re in an area that also has been hit. They’re already tired. They’ve got their own family on their minds.”
Proficiency is the largest operator concern, said Wright.
“Heavy equipment operation is a perishable skill and as a volunteer organization our challenge is to stay current on our skills and operational responsibilities,” he added.
“Operators must recognize that operating in a disaster zone is very different than in a controlled construction environment,” Wright noted. “Conditions and hazards are constantly changing. Many responders are not familiar with working around heavy equipment. Clear communication, safety briefs and site vigilance are paramount.”
Wright points out that the volunteers spend many hours in the seat when deployed.
“Self-awareness and self-care are extremely important,” he noted. “Having two operators alternating throughout the operational period decreases fatigue and increases risk management effectiveness.”
Mayfield concurs that it’s important to be trained on each piece of equipment, whether it be for normal duty or in a natural disaster recovery situation.
Caterpillar’s Equipment Training Solutions offers e-learning modules and instructor-led programs for operators.
Also, many CASE contractors specialize in demolition.
“They’re used to looking for buried utilities in certain places, power lines and gas leaks. Not everyone has that experience level. That’s where you have to be aware of and understand exactly what those dangers are,” Polzer said.
“We’ve seen that in the Midwest, where a big tornado comes through and inexperienced operators might be in a heavy piece of machinery on a wooden floor going over a basement,” Polzer added. “A typical demolition person is accustomed to understanding that can be a problem.”
Protecting Equipment Post-Disaster
Following a disaster in which flooding is an issue, “depending on the extent of the flooding, you may need to change oils in the [different] compartments, such as axles and the transmission if it was submerged,” said Mayfield of fleet management during natural disasters. “Grease the machine more frequently when operating in water as well.”
Because machines will likely be used for tasks such as pulling trees, and moving debris, “as an operator, make sure you work within your experience level and think through recovery efforts as there are always safety issues present that you may not see,” Mayfield advises. “Ensure [that] no downed powerlines are active in the area where you are working.”
“If you’re operating your machine in water over half of the track or the tire height right where there’s water out to the axles or the drive train components, there’s an opportunity for the machine to take on water
within the hydraulic system, which can create a lot of expense and downtime because of a failure,” said Polzer. He added that there needs to be a change in the typical maintenance pattern to an increased frequency.
Inspection procedures in a situation where there is a lot of debris call for looking for hoses that are chafed or fresh fluid leaks because debris fell on some hoses or tugged on them.
TR long-term recovery includes structure demolition with compact track loaders and excavators.
For those contractors who toggle between a regular project and helping in post-disaster cleanup, Polzer noted that one CASE client who focuses on road and bridge projects with their newer machines. Rather than trading in older machines, they keep them as backups for jobs such as post-disaster clean-up.
“As long as they have enough labor on the site, it doesn’t really slow down their other projects,” he said. “If this is their only equipment and they are on a road and bridge project, they do need to consider if they don’t have solid tires, grapples and things like that if they are going to be less productive in that environment than other contractors equipped differently.
“You have to be prepared that you won’t be as efficient and it’s possibly a challenge to get your equipment out. Clean-ups take longer than ever anticipated. It’s hard to forecast exactly what the commitment might be.” Read more at:
Carol Brzozowski is a freelance writer for Equipment Today
The market for synthetic lubricants is only expected to grow. Here are the main benefits, costs and considerations to know before making a switch.
In November 2023, Chevron Products Company, a division of Chevron, U.S.A. Inc., announced plans to transition its Delo Heavy Duty Engine Oil (HDEO) product line into a simplified line of synthetic blends and full synthetic products. The move came after the company began facing supply chain challenges amidst the pandemic.
While components used as building blocks for lubricants were harder to come by, the company reflected on its portfolio and focused on what was best for its customers.
“We found synthetics and synthetic blends to be best aligned with what customers are demanding,” said Shawn Whitacre, principal engineer for Chevron. “Those are things like better efficiency, longer oil change intervals, better oil consumption characteristics, lower emissions and lower viscosities.”
Chevron hasn’t been the only manufacturer prioritizing synthetics and synthetic blends in recent
years. More original equipment manufacturers (OEMs) are requiring synthetics for heavy-duty equipment because they can better keep pace with advancing engine technology and a wider range of operating environments.
This is by design. While conventional lubricants are made with standard mineral base oils, synthetic lubricants are made with artificially synthesized base oils. Synthetic blends are made from synthetic and mineralbased oils.
“Synthetic base oils are produced in a variety of ways and often in the same types of refineries as conventional base oils, but they’re more highly processed,” said Whitacre. “So, they’ve got characteristics that lend themselves more favorably to the demands of today’s products.”
Synthetic Lubricant Benefits
What are the qualities of synthetics that make them so popular?
Construction and maintenance service
contractors can expect the following benefits from most synthetics.
One of the most significant qualities of a lubricant is its response to temperature. This is especially key for engine oils, which can be impacted by the climate outside and the environment inside the engine.
“We’re looking for characteristics like improved thermal stability, which can certainly be enhanced through the use of synthetic base oils but also a good viscosity index,” said Whitacre.
A high viscosity index is one of the defining features of synthetic base oils, which makes synthetics and synthetic blends uniquely suited for more operating temperatures.
Increased Protection & Resiliency
Synthetic lubricants can provide greater protection against equipment wear. The lubricant leaves a thin coated layer of oil on the equipment,
reducing friction and the amount of work needed for parts to move.
“Heavy-duty equipment is designed to be rugged and used in extreme conditions. As such, the lubricants should be able to withstand these conditions and still perform their regular functions,” said Sanya Mathura, managing director of Strategic Reliability Solutions.
“Mineral oils have lower tolerances compared to synthetic oils, which may cause the equipment to break down during an important job.”
This protective quality can extend equipment lifespan.
“If you’re using a mineral oil, the gears of your machine will be grinding down constantly. You may have to replace that in five years or so, whereas with synthetic, you may have to replace it in about 10 years,” said Mathura.
Synthetics and synthetic blends can offer a longer oil drain interval (ODI)
than conventional oils. In many cases, major OEMs will recommend engine ODIs at 500 hours or as high as 1,000 hours, when synthetics are used, rather than the traditional standard maintenance interval of 250 hours.
This can be encouraging to contractors who are concerned about the cost of synthetic oils.
“While there is a larger initial cost to purchase synthetic oils, their value greatly benefits the customer in the long run,” said Mathura. “By doubling the ODI, an equipment owner in the construction industry can potentially save thousands of dollars at the end of [the] year.”
Some synthetics may improve fuel efficiency, which can result in significant savings for contractors using the lubricants in multiple machines. This benefit is typically due to the additives that are blended with the synthetic base oils, rather than a quality inherent to synthetics.
“Improved fuel efficiency is not limited to synthetic oils, but synthetics started introducing it with the development of a 0w16 engine oil,” said Mathura. “They have led the way in the drive towards fuel efficiency.”
According to Whitacre, synthetic lubricants’ response to temperature also makes it a more sustainable option. Conventional lubricants can be more volatile and evaporate more readily than synthetic lubricants, especially when exposed to heat. Synthetic lubricants’ improved thermal stability means that they will release fewer emissions overall.
Additionally, synthetic lubricants emit fewer greenhouse gases.
“[With] synthetics’ thinner base oils, you improve the efficiency of the engine itself, so the engine has to do less work to push that engine oil around,” Whitacre said. “It inherently burns less fuel and emits less carbon dioxide and some of the other greenhouse gases associated with internal combustion engines.”
Many factors should be considered when faced with a choice between a fully synthetic, synthetic blend or conventional lubricant.
For starters, it’s helpful to have a proper understanding of synthetic blends, which are also referred to as semi-synthetics. While synthetic blends are made with a combination of synthetic and mineral base oils, the percentage of each can vary.
“Semi usually alludes to the fact that it’s half, but that may not be the case for each synthetic blend,” said Mathura. “Even if a manufacturer has 1% of synthetic in the base oil, they could get [call] it a synthetic blend.”
While synthetic blends may have
some properties of fully synthetic lubricants, it can be hard to know just how much synthetic oil is in the product. Fortunately, consumers have several criteria to evaluate when determining the ideal lubricant to use—whether full synthetic, synthetic blend, or conventional. These include: ˜ OEM SPECIFICATIONS – First, ask your OEM for guidelines on the proper lubricant for your machine. For those in North America, guidance on engine oils will start with compliance with the performance specifications outlined by the American Petroleum Institute. Your OEM may require a specific lubricant or recommend a range of lubricants
˜ VISCOSITY GRADE – OEMs will typically recommend a range of ambient operating temperatures appropriate for your machine, which provide a selection of viscosity grades to choose from, according to Karin Haumann, OEM technical services manager for Shell Lubricants. This is where synthetic lubricants with a high viscosity index can be an asset.
“These synthetic oils are really great in extreme temperature situations,” said Haumann. “For example, if you’re in Canada and it’s extremely cold, you’ve got the superior low-temperature pumpability and protection at startup. If you’re in a desert climate in Arizona with really high temperatures, it prevents the oil from [becoming] too thin.”
˜ COMPATIBILITY – If you’re switching to a new lubricant, you’ll want to ensure that the lubricant is compatible with the fluids you currently have left in your machine, said Mathura. Incompatibility issues can cause problems, which “can lead to downtime for your equipment, which nobody wants.”
You can’t make a purchase decision without factoring in cost. When selecting a lubricant, Whitacre, Mathura, and Haumann all stressed the importance of conducting a costbenefit analysis.
“Especially in the heavy-duty engine oil world, a ... majority of our customers are running a business,” said Whitacre. “Their primary objective is to make money or save money. Often, oil selection plays into that second part of the equation more than anything else.”
While synthetic lubricants may often have a higher initial purchase price, their potential to help reduce expenses could make the investment worthwhile. Whitacre suggested three criteria to help evaluate the financial impact of lubricants: ˜ LUBRICANT’S ABILITY TO IMPROVE DURABILITY – The cost of equipment, maintenance
and replacement parts adds up. The longer equipment remains operational, the more money you can save.
“The lubricant can certainly play a role in protecting against wear and keeping the emission control system clean and maintenance requirements low,” said Whitacre. ˜ LUBRICANT LIFESPAN – This includes factors like ODIs.
Lubricants that withstand operating conditions across a longer period require less frequent oil changes, reducing the cost of labor, filters and downtime for maintenance.
˜ LUBRICANT EFFICIENCY – The lubricant’s ability to affect fuel consumption should also be considered. Whitacre explained, “In today’s fuel price environment, anything businesses can do to reduce fuel burn has a significant impact on their overall fuel spend and, of course, their overall operational cost.”
However, the characteristics of the lubricant alone shouldn’t drive your decision. Mathura stressed that a synthetic lubricant needs to make sense for the scope of your operation and your equipment.
“If a synthetic can offer fuel efficiency, you will see more of it if you apply it across a fleet compared to just one piece of equipment,” she said. “Ask yourself, ‘How much can this save me? What is the investment up front? How long will it take to show that impact?’”
The Future of Synthetics Synthetics and synthetic blends
have been used commercially in construction for several decades. However, the global market for synthetic lubricants is projected to grow at a higher rate than conventional lubricants through 2027, according to a 2023 report by MarketsandMarkets. While this rapid growth can primarily be attributed to construction and maintenance firms in North America and Europe, companies in Africa, Asia and Latin America may be slower to adopt synthetics.
“We must remember there are pieces of equipment out there which do require mineral oil,” said Mathura. “Depending on the country that you live in, the age of construction equipment may vary. I have seen people with 20- or 30-year-old machines because they’ve kept them in good condition and can’t afford to replace them.”
Haumann anticipates the trend toward synthetics can only continue as technology advances.
“As equipment advances and our manufacturing capabilities for these synthetic base oils improve, they’ll become more prevalent in the market,” she added. “And we’ll be able to take advantage of those performance benefits.”
Grace Rybak is a freelance writer for Equipment Today
Trackunit launched the TU700, its newgeneration IoT device for the construction industry. The product is the latest version of its Raw device, harnessing the power of IoT to deliver technical capability and longevity.
TU700 will also enable fleets to move toward 100% coverage offering global roaming, long-range Bluetooth support and Wi-Fi ready capabilities with new selfservice CAN configuration for equipment manufacturers that collects machine data and translates them into insights on Iris.
The launch of TU700 coincides with the introduction of the Trackunit Pass K300 keypad.
Electric Vehicles
Lincoln Electric offers the Velion DC Fast Charger for electric vehicles, a Level 3 DC fastcharger platform.
Western Global announced upgrades to its FuelCube onsite fuel tank. The FuelCube now offers four-way forklift pockets that allow it to be moved around the work area with a forklift when empty.
The new design uses less metal than the previous model, making the 250-gal. and 500-gal. versions light enough to be relocated with a pallet jack. The upgraded FuelCube comes in 250-gal., 500-gal., 1,000-gal. and 1,800-gal. sizes.
Its 110% double-walled containment eliminates the need for a secondary basin.
The FuelCube also offers a removable inner tank for cleaning and inspection.
It features corner brackets to save space on the jobsite by stacking it up to two-high when empty. Additionally, a lockable equipment cabinet increases security for the fuel supply.
DC output voltage is 200 VDC to 1,000 VDC. DC output current is up to 150 A. DC output power is up to 150 kW, and input voltage is 460 VAC +/-10% (60 Hz), 3-phase, Protective Earth (UL model).
The 150-kW Velion DC fast charger exceeds 75% domestic content and is engineered to exceed 97% uptime with an output of up to 1,000 V at 150 A and 500 V at 300 A. It operates within the temperature range of -31°F to 122°F (-35°C to 50°C). It is backed by Lincoln Electric’s multi-point service network.
The products include the Kabgard Headache Rack System, extended ladder rack and Universal Class-5 Hitch Receiver for both Ford- and GM-mounted service bodies.
The Kabgard, offered in a black or white powder coat finish, is bundled with the mounting brackets and fasteners for installation and mounting to the service body. Built-in, tie-down points secure cargo.
Thunder Creek Class 5 Isuzu NRR
Chassis
Thunder Creek Equipment announced the expansion of its truck upfit line of fuel and service solutions with the addition of the Class 5 Isuzu NRR truck chassis. This expansion
includes both the No HAZMAT Fuel and Service Upfit (MTU) model and the Service and Lube Truck Upfit (SLU) for daily fluids and preventive maintenance.
The Isuzu NRR truck chassis features a GVWR of 19,500 lbs. and is built sturdy to handle bulk fluid delivery to jobsites. Thunder Creek upfit platforms offer the ability to get in and out of more compact or crowded sites, minimized disturbance and low ground pressure, and the ability to deliver critical fluids to each site without requiring a HAZMAT endorsement or a CDL.
that will be integrated into the body of a Mack MD Electric truck for Class 6 to Class 8 vehicles.
The mobile
be used for a limited time by customers wanting to
vehicle demos. The off-grid charging
by renewable propane and 120-kW charger. The system will be mounted on the back of the MD Electric truck transporting it. The Mack MD Electric can be configured to be a Class 6 or Class 7 vehicle.
This dual-facing, heavy-equipment dash camera is integrated with TennaCANbus, which allows it to deliver ECU data alongside video telematics. Paired with a monitor and additional auxiliary cameras around the sides and rear of the machine, this product provides footage and live visibility around the operation and surrounding area.
The intent is for contractors to see how well the operator is performing, giving them with a view of the jobsite from the cab to reduce blind spots all while seeing the machine’s real-time telematics data from the TennaCANbus tracker.
The rack, designed to protect the cab’s rear window from damage, is available in two sizes to accommodate either a single-rear-wheel or a dual-rear-wheel service body. The service body ladder rack has built-in tie-down points for cargo, along with built-in grab handles for stability when climbing into and out of the truck bed. The over-cab design allows for a capacity up to 1,000 lbs.
Enerpac Cube Jack Lifting System
Based on Enerpac SCJSeries Cube Jacks, it enables lifting and holding of the entire cab, boom and arm, allowing the undercarriage to be safely removed.
During maintenance of the excavator’s swing drive and bearings, the undercarriage unit must be separated from the upper body cab and arm to give access to the swing motor and multiple sets of planetary gears.
The Enerpac cube jack lifting system offers a safe, CE-certified approach to removing the undercarriage. It comprises two pairs of cube jacks providing coordinated hydraulic lifting of loads up to 25-t per jack to a height of 6.5 ft.
This column offers advice about adjusting to higher sticker prices on most types of equipment.
Whether you’re browsing construction equipment on the lot or food in your local grocery store, there’s a good chance you’ve done a double-take at prices within the last year. Unfortunately, construction equipment has not been immune to the heavy toll of inflation. Overall, equipment prices are up as much as 30% when compared to 2020 according to Associated Builders and Contractors.
With prices across the U.S. increasing, the risk of sticker shock is running rampant. Industry veterans like me have experienced price increases but nothing like this. We are accustomed to the ups and downs of the market, and in times like this, we need to lean on tried-and-true tactics to pad against the sting of higher prices.
Before we go on the defensive against rising prices, keep in mind that there’s a silver lining in all of this. According to the Association of General Contractors, construction demand continues to be strong in infrastructure and power projects. Other private sector construction is rising with more new homes and large commercial buildings like hospitals and data centers being built. However, more demand and increasing equipment and input costs can still make for a balance sheet full of snarls. Contractors and equipment professionals must remove their rosecolored glasses and return to basic practices to protect profit and keep their business in the black. One of your biggest allies with things getting
tricky is always going to be your equipment dealer. This installment of “Dennis in the Dirt” examines a few ways you and they can partner to navigate this season’s higher prices.
Extend Existing Equipment’s Lifespan
It’s simple: a regular service schedule protects investments. Fleet managers need to understand each machine’s average number of production hours daily. This is the simplest reflection of wear and tear on a machine. To make it easy, many managers connect machines to fleet management software (FMS) to sync their fleet’s usage reports, which can include idle time and fuel usage, and better understand the work’s exertion on a particular machine. Understanding your machine’s production hour limit and monitoring its efficiency daily is a must.
When fleet managers see their team’s work in real-time, they can share that information with their trusted service partner to optimize
preventive maintenance plans. With preplanned appointments, fleet managers ensure that each machine working on a jobsite is in the best possible condition.
Efficiency is key to equipment longevity, so fleet managers are wise to reduce the likelihood of excessive wear and tear with machine control technology. Machine control can help boost productivity and efficiency even for less experienced operators, meaning it’s not just your veteran employees who can help you get the most out of your fleet. Through automated machine control technology, fleet managers safeguard the machine and the operator from unnecessary work.
With prices up, you’ll realize that if you traditionally prefer that shiny, new model straight off the lot, you may need to be open to considering different acquisition options from your dealer. Because suddenly, a
Technicians evaluate equipment, giving contractors a full picture of their machine’s longevity.
machine once priced at $100,000 might now be priced at $130,000 or more. You’ll need to ask yourself if you’re willing to buy the machine at that price or if you have a hard line that you and your accountant will not cross. If it’s the latter, your equipment partner can help you understand other acquisition strategies to consider.
An easy first option is to investigate used equipment in your market. To prepare for that, determine your threshold of machine production hours for a used piece of equipment. The number of acceptable hours for used machinery is subjective based on personal preference, machine type, machine history and more. For example, excavators that have been on an optimized maintenance schedule can last up to 10,000 hours, meaning you can probably still get a great amount of production out of a used one that’s been taken care of. Take into account these factors and the work you’ll need to accomplish in the
next six months as you explore used equipment options.
Talk to your dealer about your fleet’s budget. When you can’t budge on the machine type, and you know you prefer the newest model, that partner may be able to offer rental purchase options that allow you to ease into an equipment investment with few strings attached before you know it’s the right fit.
Speaking of rental, most equipment inventories have returned to prepandemic health, so machines with low production hours are readily available in most rental fleets. At times, renting equipment is the right decision. If you find yourself needing a machine for just a few months or a specialized machine for a one-off job, you may want to fill the gap by renting from a familiar equipment expert.
Most of a dealer’s rental equipment fleet will also be under warranty, which is beneficial to you because you can rest assured that, should that machine stop working, your rental team will be able to source a backup from the manufacturer.
In addition to the peace of mind that a rental machine under warranty provides, some dealers connect their rental fleet to an FMS where they have a connected support team to monitor and dispatch a field technician if a machine requires parts or services.
With this rental partnership, as well as the right machine for the job, a fleet manager acquires the service expertise to keep that machine operating with as little downtime as possible.
Need a Warranty? You Bet
Warranties provide peace of mind for rental fleets, and the same is true if you’re purchasing that machine. At a high level, warranties are an essential business tactic to consider to protect equipment investments, but they come in many different levels and options.
Your equipment partner can help you understand if a warranty makes sense for your business. If so, they can also help you understand the right level of coverage to pursue. Simply put, warranties protect against unforeseen hazards, and that’s important because, even with today’s incredible machine monitoring capabilities, equipment sometimes goes down for one reason or another. Your equipment partner should be able to share warranty options— whether based on production hours, years or both—to cover your back.
Before buying or renting a machine, complete an equipment inspection.
When considering used equipment, consult with a trusted technician to inspect the machinery’s undercarriage.
Technicians inspect the hydraulics used in the excavator. This year’s high equipment prices push more contractors to consider buying used equipment.
Guidance When Managing Pricing Sticker shock happens. As I work with contractors to update outstanding bids for projects they have been planning for months, we are all taken aback as we realize the way increased prices can drain the budget compared to last year’s bids. When talking with contractors, I encourage revising bids to consider inflation’s effects to protect profitability.
Despite the sometimes sudden and piercing sting of increasing prices, contractors can still win by following established guidelines.
With this information and the partnership of an experienced equipment dealer, any contractor can find opportunities to take advantage
and expert guidance.
How these technologies provide precision and finesse, even for novice operators responsible for moving earth and materials to exact design specifications
The lack of young talent entering the construction industry and an exodus of veteran operators retiring or moving to a different career have created a shortage of experienced, skilled labor. Quality and productivity must be maintained, shifting the focus toward technology as a way of closing the skills gap.
Contractors who have not updated their machines or fleets with autonomous controls may have struggled to compete because basic, traditional equipment requires dead reckoning and an escort of grade checkers and surveyors to minimize the multiple passes required to get a surface xamaterial, inability to adjust to changing conditions on the fly and added rework are forcing old-guard operators to modernize.
Meanwhile, machine and grade control technology only gets more sophisticated, cheaper and easier to install. It’s not unusual for owners of older equipment to install a simple 2D control unit on a machine and suddenly inject new life into an aging investment.
“It’s easier than ever to get into the game,” said Cameron Clark, earthmoving industry director for Trimble. “Tiered solutions exist that can take you from entry-level technology add-ons for basic bucket and blade control up to laser, global positioning system (GPS), onboard diagnostics and full 3D control, all installed on an existing piece of equipment.”
Original equipment manufacturers (OEMs) have been designing different levels of machine and grade control automation into their earthmoving equipment since the late 1990s, when research and development teams began experimenting with smart technology for construction applications. Early solutions evolved from basic hydraulic valve controllers and lasers to onboard hardware sensors and software that automatically read a machine’s position in relation to a surface and adjust to match the design—a science
A new operator can get onboard equipment with machine control and nail a plan to spec in a minimum number of passes.
that has gotten more precise with every passing year.
These days, you’ll find diggers that automatically grade, machines that automatically detect nearby objects, and trucks that automatically drive featured at every industry event. Most of the new equipment comes with special harnesses and brackets built in that make it easy to upgrade an earth mover to the latest technology on demand.
As Oscar Cantu, construction content manager at Topcon Positioning Systems, puts it, “There’s no sacrifice involved in putting control technology on an existing machine. You simply bring the vehicle into the shop for a day; the sensors get mounted, calibrated, and tied to the electronics; and the surgery is complete. [It is] ready to roll and
start producing at a higher degree of accuracy immediately.”
Machine control is widely viewed as the first step in the automation trajectory, leading from 2D grading and earth moving to 3D trenching, sloping, digging, and other complex project applications. At its core, machine control relies on the GPS and global navigation satellite system to position a tractor extension to cut a stretch of earth to a prescribed height and level according to a triangulated digital map. Often, an external base station is used to read the satellite signals, then relay the reference points to receivers on the machine that automatically control the equipment in relation to the earth,
guiding the tractor along the correct path and plane.
Where 2D control tells the operator the position of his equipment relative to the desired plan—high, low, or on a slope—3D control is better for more complex designs, adding depth and angles to the modeling data and grading scheme.
“While OEMs are working hard to bring next-generation machines to the market, it’s difficult to foresee changing needs in the field that may require different functionalities not already designed into the equipment,” said Joe Baldi, director of new business ventures at Moog Inc. “Fortunately, it’s easy enough to equip these machines with controls that manage grade, payload weight, material conditions and other
“Trenching for utility infrastructure, curbing and certain landscaping projects come to mind. This is where 3D machine control can really pay off.”
variable factors just by adjusting the onboard software.”
Mark Colvin, senior product manager for grade management at John Deere, agrees. “You can get a lot of productivity out of a tractor equipped with advanced sensors and GFSS heads alone,” he said. “A new operator can get onboard one of these machines and nail a plan to spec in a minimum number of passes, eliminating rework, saving material and finishing the job in less time.”
A basic system will read a 2D site plan and control grade to within onetenth of a foot. Add-ons can include:
˜ External base stations for more precise digital mapping
˜ Rover components that pick up signals and collect data
˜ Inertial measurement units to finesse position changes
˜ Other technology to enhance safety, improve accuracy and minimize waste
3D control offers more precision and accuracy, reading terrain variations through a combination of GPS data, sensors and modeling software that account for X, Y, and Z axes. With 3D machine control, operators can excavate, grade and pave to within millimeters of any given site plan.
Fine-Tuning the Grade for
If 2D control is considered entry-level technology for machine automation, 3D grade control would be a significant step up. Concerned most often with excavating equipment used in trenching and digging operations, applications may include digging ponds, waterways, drainage features or other complex surfaces where control over a blade, bucket or auger
is required to satisfy a plan. Even rock drills and rock saws can be precisely controlled using the technology.
In most cases, an operator will be in the cab. However, in some cases, such as in mining operations where human safety is a concern, remote joystick controls may be used to achieve the design without an operator in the cab.
“Some projects call for added flexibility in tight spaces, where a tilt bucket, rotator or boom needs to perform some complex excavation,” said Sean Mairet, group product manager for grade management for John Deere. “Trenching for utility infrastructure, curbing and certain landscaping projects come to mind. This is where 3D machine control can really pay off.”
The very nature of 3D grading involves multi-axis control, calling for an added dimension of automation and visibility. For instance, 3D software onboard a backhoe enabled with GPS capabilities will display a site plan in 3D, showing the exact dozer blade position as it carves or moves the required surface material to spec. The result is a more accurate pass on the first attempt.
2D technology can also perform some level of 3D work using GPSenabled sonic tracers or lasers with the right software but without the same level of precision. Projects may include rough cutting a trench to a specified depth or grading areas in tight spaces using a compact track loader equipped with the technology.
Connecting Operator to Machine & Machine to Design Joe Baldi likens the “automation upgrade concept” to adding an app
on a smartphone. His company offers the all-electric TerraTech ecosystem for intelligent vehicle control, among other integrated technologies. “Once the central control system is set up on a vehicle, it’s as easy as downloading a new program to gain new capabilities without adding new hardware.”
Selectable settings on most control systems allow different users to save their configurations, so the same machine can quickly accommodate a new operator. Likewise, different applications set for different seasons of the year can be saved for future reference, allowing contractors to build a custom library of settings, for example, cold-weather paving or heavy payloads.
“You’re … looking at a twostep connection, either way,” said Cantu, whose company designs, manufactures and distributes precision measurement and workflow solutions. “The solution connects the operator to the machine so that in turn, the machine can connect to the surface and design [that] it’s targeted to prep.”
Getting Results Regardless of the Application or Materials Used
Whether equipped with 2D or 3D technology, automated machine and grade control can achieve project results. Clark’s company provides field solutions, from semiautonomous machine control to virtual reality. With more than 20 years in the business, he’s seen grade control used on simple residential driveways and car parks to large-scale projects, such as airports and golf courses.
“There’s nothing cookie-cutter about it,” says Clark. “You can program a machine to grade a golf course fairway exactly to spec, causing a ball to roll to an exact spot, just as the course architect intended.”
Rail construction; solar pad preparation; oil and gas platforms; mining operations; and more common applications, such as building pads and road construction can all be prepared artfully and accurately using autonomous equipment.
In addition, different materials can be manipulated accurately by adding sensors to detect stiffness, helping determine the exact level of compactness required for a job. Or sensors can be added to read the temperature of asphalt, for instance,
ensuring that the grade is paved at the right setting, without having to remove it and start again.
John Deere’s Mairet assures that even a 2D system without a base station or rover can produce some amazing results.
“Cutting a ditch around a house so that water slopes away from the structure is a good example,” he says. “Add a laser app to the system and you can accurately grade areas in wooded areas, working around tree cover, or finesse a surface inside a building before the concrete gets poured.”
The benefits are clear. Autonomous machine and grade control can eliminate the need for bulky survey staking and other manual gradechecking tasks, saving time and money, while also reducing errors and rework. Without a traditional ground crew escorting the machine, not only is labor reduced, but safety is improved.
Last-minute adjustments can be made on the fly using onboard software, without re-staking the job, easily accommodating unplanned changes. The fact that rookie operators can perform all this work with minimal training is an advantage, especially in a tight labor market. Most important, the design plan is met precisely, often on the first pass, creating customer satisfaction and boosting contractor reputation in the process.
Adding control technology on an existing machine is simple. You simply bring the vehicle into the shop for a day. The sensors get mounted, calibrated. and tied to the electronics. Then the process is is complete.
The way to autonomous machine and grade control is straightforward. Expert advice suggests that you ask around, see what your peers have experienced and get a few recommendations before you jump in. Remember, everyone has their preferences, skill level, working style and familiarity with the equipment.
Most technology can be used in diverse ways, so learn what the options are and plan accordingly. Avoid buying more technology than you need.
It’s a good idea to make a list of questions to ask in advance. Dealers and machine and grade control technology companies know their capabilities and are adept at explaining them. Once you feel comfortable with a purchase, request a demo, and try the equipment for yourself before you buy.
Lastly, make sure that your chosen supplier offers adequate support and training on the technology. Schedule a day for your operators to learn the system. Designate a super user, if possible, to serve as your internal trainer. And be sure that your technology vendor can answer technical questions by phone or in the field.
A good, dedicated, tech support team is critical to ensuring that you get the most out of your investment. If something isn’t working right, a
quick call to the support desk can be all it takes to remedy the situation.
There’s no reason to delay adopting machine and grade control technology for your business. The technology has been around for decades and has been developed into
a fine art. Even novice operators can achieve amazing results.
Using machine and grade control technology can immediately open the door to improved safety, savings, profitability, productivity and a marked competitive edge. Make precision and finesse your best practice. Connect and control your machinery, and experience the
benefits of autonomous technology today. Talk to a dealer about the best way to start.
Read more at: eqtoday.co/MachineGradeCont
Joe Zagorsky is a freelance writer for Equipment Today.
Adopting technology, finding ways to retain talent and shoring up finances are among the steps to help your business succeed.
Looking at the success of your construction business through the remainder of 2024 and 205, it seems everything is moving ahead at breakneck speed. I recently watched “Squawk Box,” where Jim Cramer interviewed the CEO of Nvidia, who said that almost all technology will need to be replaced to keep up with the latest chips and AI adoption. I sat there with my mouth hanging open imagining what the world would look like in five years.
What was most interesting was how the Nvidia chips are being allocated to different industry segments. Nvidia sponsored a user conference, and thousands showed up representing their area of expertise, wanting to know how they could get Nivida products working with their systems. I learned that Nivida chips are designed so that users can keep their current
systems and integrate to increase speed and efficiency.
And guess what? Constructionrelated companies attended to find out how to adopt this new technology.
Step 1: Know How to Apply the Tech
How does this new technology apply to your business? All contractors can benefit in terms of time, cost, cash flow and efficiency. If you think you will avoid these changes, you cannot!
For example, a recent Forbes article featured a large national contractor who wanted the following:
˜ To be faster
˜ Use fewer people with robots to help do work
˜ Have better bargaining power with vendors and better access to capital along with lower interest rates
If you do nothing, you will find yourself in a competitive market requiring you to shave more profit out of your bids.
Step 2:
Contractors must work faster while spending less. At the same time, you should find out what others are doing regarding system changes and project turnaround time.
I would be talking to my banker (who should be familiar with the construction industry) to find out what other contractors are doing.
The same goes for the other professionals you work with, including your accountant and attorney. They
should be construction experts who can help improve profitability.
Do not forget your system providers. They should provide industry-specific data and comparison numbers relative to sales per employee, gross profit per employee, gross margin percentage and operating expense comparisons to industry data.
Find folks who can provide industry data that you can compare to your numbers so you can see when you start falling behind the curve.
Review your hiring practices and all employee-related programs to keep people on your payroll. You need to be flexible in terms of pay and benefits.
I also suggest that you work to make your employees feel like partners. You can take many steps that will not cost much but will be appreciated by your employees’ families.
Everybody wants to feel appreciated, have a chance for advancement, be trained on the latest equipment being used, and have a profit-sharing plan or other 401K type plans available with some discussion and training on how to use them.
A big benefit that keeps folks around is a high-end health insurance program covering hospital, doctor visits, medicine, eye and dental requirements. This type of plan with a minimal employee contribution keeps people on the payroll.
When putting the cash flow plan together, investigate each cost line item to see if there are price adjustments to ask for now that inflation is slowing down.
Step 4: Organize Your Finances
Make sure you understand your bank arrangements, covenants, interest rates and ability to cover your work in 2024. A detailed cash flow statement is mandatory to share with the bank.
Step 5: Optimize Your Insurance Policies
The insurance market is difficult right now. The cost of coverage has increased dramatically. Ask your agent, who should also have significant expertise regarding the construction industry, to review your coverage and policies.
Also, ask if your coverage was sent to different companies for a quote. If so, what were the results? In addition, inquire if insurance certificates are required from subcontractors or for equipment rentals and if you are complying with the terms.
Step 6: Evaluate Your Tax Position
Evaluate your tax position for 2023 and know what to expect in 2024. Be aware that there was a change regarding bonus depreciation. It was supposed to be phased out, but that has been reversed and 100% is available for 2023 purchases.
Read more at:
eqtoday.co/RuntheBus0424
Garry Bartecki is managing member of GB Financial Services LLP and a consultant to the Independent Equipment Dealers Association.
When integrating AI into their business models, construction companies should carefully weigh the costs and benefits of this technology.
“ Hey Chat GPT, finish this building.” This dare, written on a billboard that went viral last year, captures a truth and a stereotype about the world of construction. The truth is that the construction industry will, for the foreseeable future, rely primarily on human intelligence and manpower to convert raw material into buildings and highways.
Despite recent advances in artificial intelligence (AI) that have outperformed Moore’s Law, no one expects robots and algorithms to build the next Burj Khalifa. The stereotype is that the construction industry is hidebound, ever the domain of manual labor and diesel-powered hydraulics instead of cutting-edge technology. But AI is starting to transform the industry, which accounts for more than $1 trillion in annual GDP and employs more than 8 million people.
Despite the industry’s tendency to move slowly when adopting new technologies, construction companies are increasingly integrating advanced AI systems into their operational blueprint. Indeed, AI is now used in every phase of a project including design and planning, supply chain and project management, and quality control. Some upsides of AI in an industry experiencing hefty spending and long delays are cost efficiency and sped-up timetables for
project completion. For construction workers, AI offers advantages such as improved on-the-job training, new jobs to facilitate the use of AI, and tools that will aid workers in their performance and decision-making. AI also promises to improve worker safety and accessibility for workers with disabilities.
Construction work is hazardous. In the U.S., more than 1,000 constructionrelated fatalities occurred annually from 2019 to 2022. The Occupational Safety and Health Administration (OSHA) and the U.S. Department of Labor classifies the four major construction hazards as falls, caught in or between hazards, struck-by hazards, and electrocution. Under the federal Occupational Safety and Health Act (OSH Act), employers have a duty to monitor worksites and prevent hazardous conditions.
As it does with other major industry sectors, OSHA issues specific regulations targeting construction safety risks. Despite regulatory oversight and employers’ efforts to minimize hazards, a combination of human error, noncompliance (whether willful or negligent), and other factors open the door for costly and tragic mishaps resulting in injury, death and legal action against employers.
AI helps mitigate some risks, which have long been part of construction sites, reducing the likelihood that workers will be harmed on the job. As employees enter a worksite, control systems, armed with computer vision and image analysis algorithms, can determine whether workers are authorized to be on the site and scan their attire for compliance with personal protective equipment
standards set by OSHA. Safety professionals used to rely solely on walkarounds and inspections to perform spot checks, but AI-powered cameras placed around a worksite can continually monitor conditions, searching for hazards and detecting noncompliance. If a violation is detected, these systems alert safety managers to take remedial measures. In addition to AI’s role in ensuring that workers comply with safety standards,
people working in construction report having a disability. AI stands to broaden employment opportunities for construction workers with disabilities by allowing them to assume functions they could not have performed before or permit them to enter the trade in the first place. The ability of some wearable technologies, such as exoskeleton suits and robotic arms, to supplement mobility and muscle function may lower employment
AI is also used to ensure that heavy machinery functions properly. For instance, predictive maintenance systems assess the condition of equipment and gauge the need for maintenance, preventing failures that can cause worker injury.
AI wearable safety devices can help prevent falls, assess fatigue, monitor workers’ mental status, and mitigate musculoskeletal issues. Wearables include smart hard hats, proximity sensors and smart monitors.
The industry can also benefit from AI-enabled advances that assist workers with disabilities. When it enacted the Americans with Disabilities Act (ADA) in 1990, Congress intended to open everyday commercial, economic and social opportunities to disabled persons. Under certain circumstances, the ADA requires employers to provide a reasonable accommodation to applicants and employees with disabilities.
Because of its often-strenuous, physical demands, construction work presents challenges for workers covered by the ADA. About 6% of
Under the federal OSH Act, employers have a duty to monitor worksites and prevent hazardous conditions from developing. As it does with other major industry sectors, OSHA issues specific regulations targeting the safety risks unique to the construction sector.
barriers for those with physical impairments.
Digital applications such as building information modeling software, virtual and augmented reality tools and voice user interfaces, may help expand opportunities for disabled persons. However, employers are excused from providing a reasonable accommodation if they can demonstrate that it would impose an undue hardship on the business. AI’s cost is relevant in determining whether employers are legally obligated to offer it. The high costs associated with robotics, for instance, may limit AI’s short-term impact on efforts to increase accessibility. Construction companies should weigh AI’s costs and benefits. However, its promise to enhance safety and lower barriers points the way to the future.
Read more at: eqtoday.co/AIWork
James McGehee is an associate for Littler Mendelson, and Bradford Kelley is a shareholder for Littler Mendelson.
• Trailer Weight: 8,380 lbs.
• Overall Width: 102", Length: 31'4"
• Deck Length: 21’ Flat (model shown)
• 6’ Beavertail
• Deck Height: 34"
• Tires: Eight 215/75R17.5 (H)
• Brakes: Air (Full ABS System)
• Ramps: 72" Long x 22” Wide
Range: 102" Max. 29" Min.
• Lighting: 100% Sealed Wiring harness
Versatile and environmentally friendly special tire designed for the needs of modern farming and machine contracting
VERSATILE PROFESSIONAL CONTRACTING TIRE FOR YEARROUND USE
Nokian Tyres TRI 2 excels in a wide variety of tasks from job sites to highways, from snowy winters to hot tarmac. Its durability, economy and comfortable driving response make it a reliable choice for versatile contracting work.
Excellent grip, high loadbearing capacity and a pleasant driving response
Sturdy and fast also on the road (max. 65 km/h / 40 mph)
WINTER TIRE FOR WHEEL LOADERS
• Open block design creates excellent selfcleaning
• Aggressive tread design creates reference level lateral and traction grip
• New compound and more rubber in the tread creates better grip and increased lifetime
• Re-designed carcass structure gives more lifetime and better stability
• Siped non-directional thread design with premarked stud position
EXTEND THE ALL-SEASON CAPABILITIES OF YOUR MACHINE
The versatile Nokian Tyres Hakkapeliitta TRI brings the most winter grip to your work. Tough enough for years of extensive use, this specialist tire has excellent braking, accelerating and steering properties.
Precise control and great efficiency
Driving comfort on class on its own Superior traction and lateral grip
Nokian Tyres Hakkapeliitta TRI has made my job safer, faster and more efficient.” “