
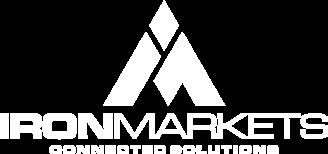
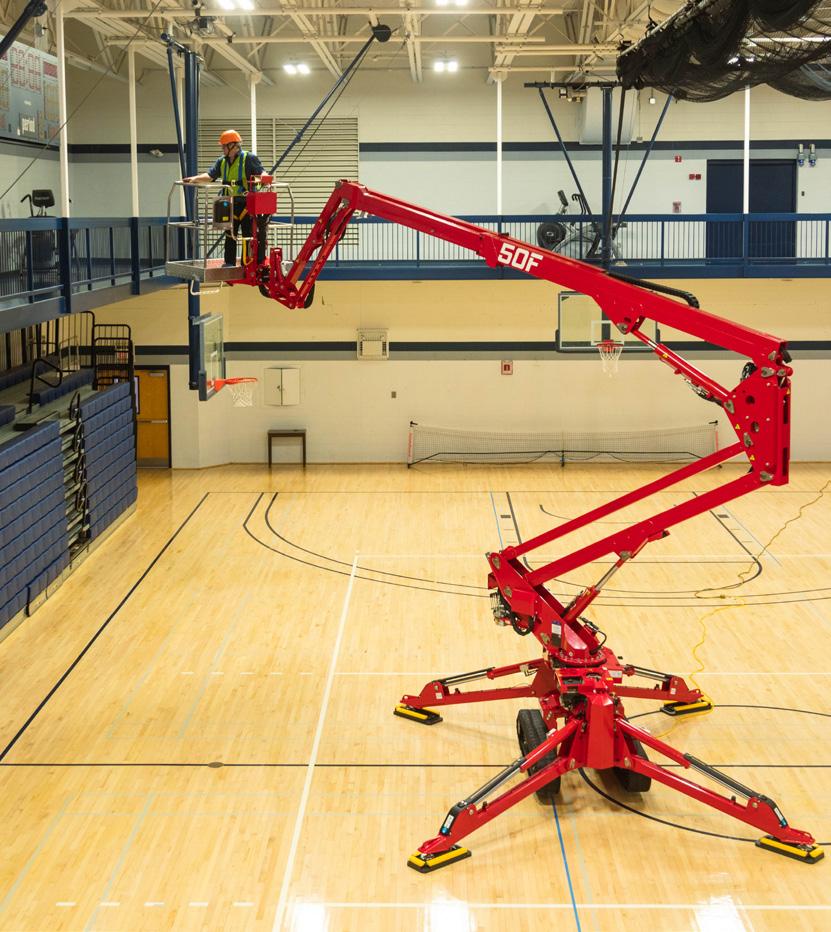
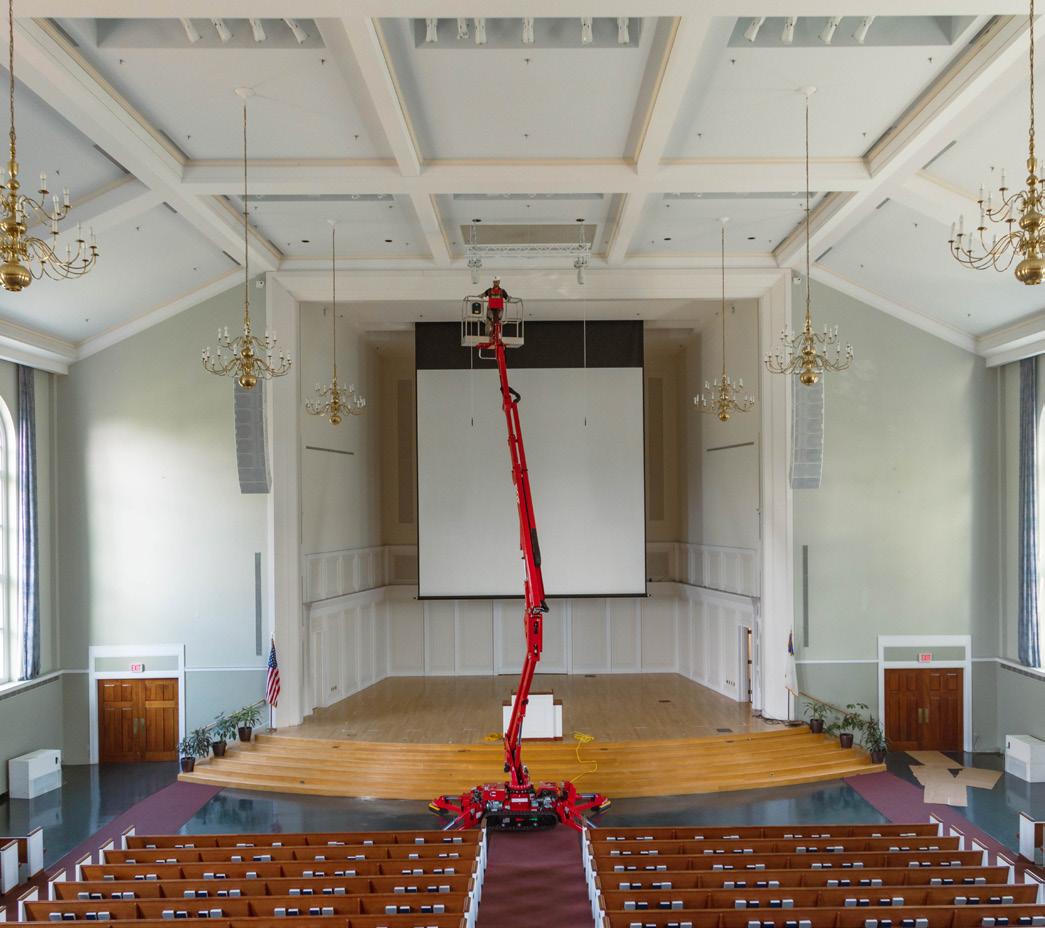

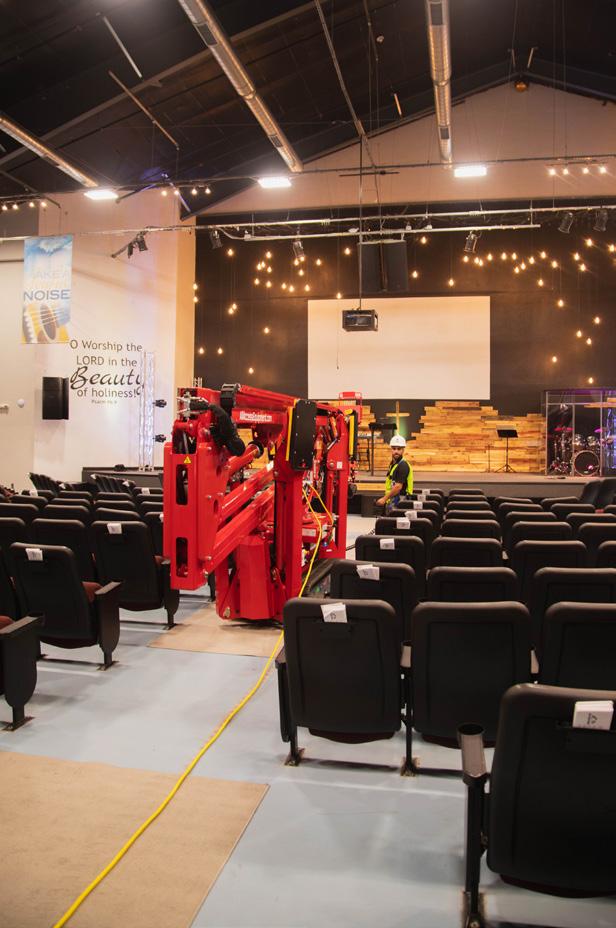
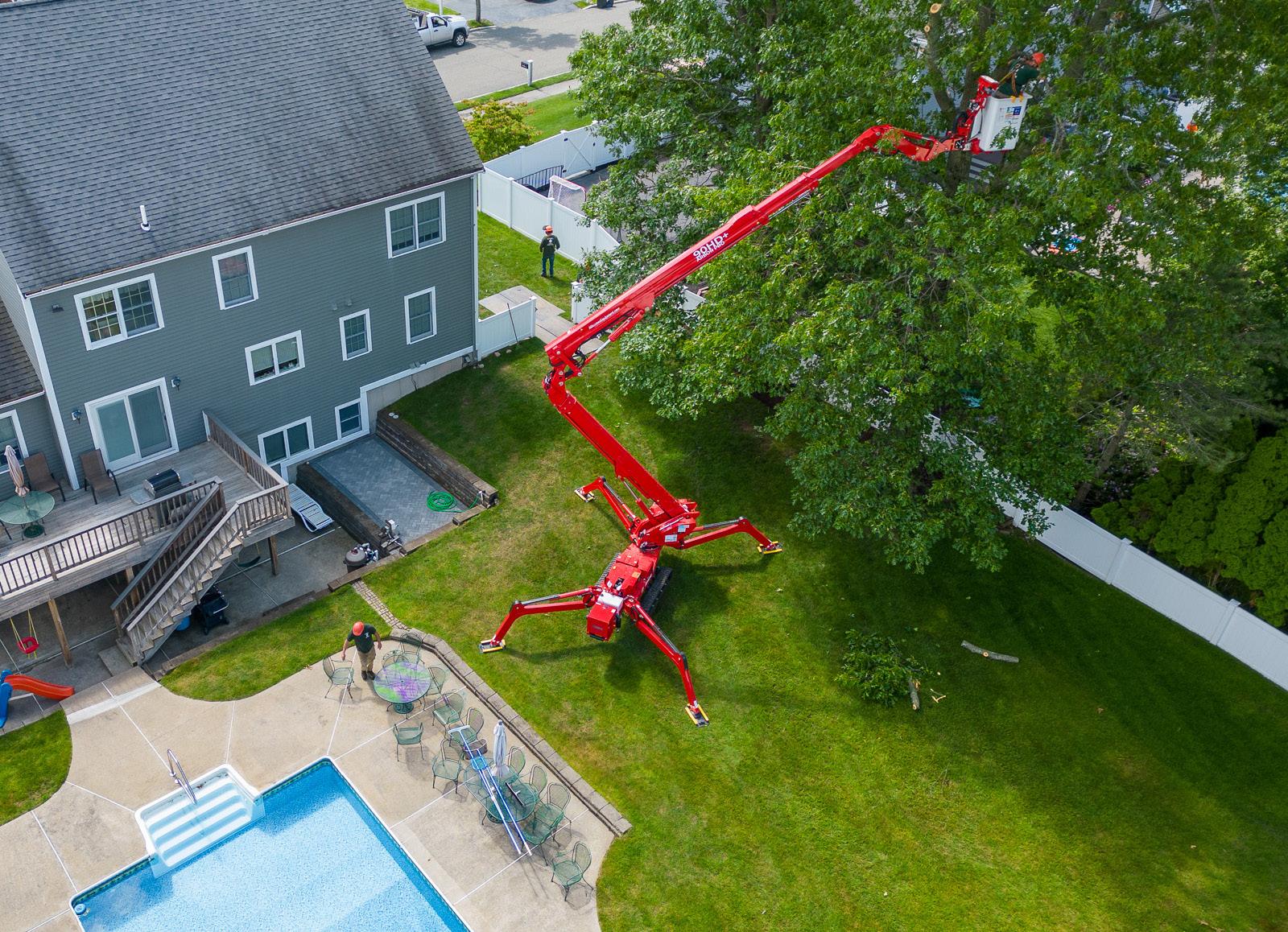
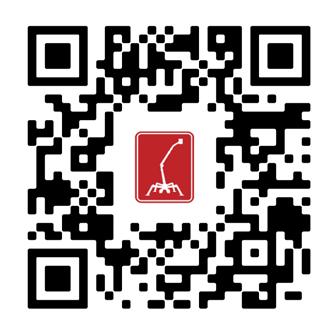
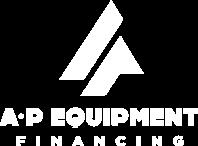
Eye on
Rental (ISSN 2375-9925, Print | ISSN 2471-7657, online USPS 686-370) is published eight times per year: January/February, March, April, May, June/July, August/September, October/November and December by IRONMARKETS, 201 N. Main Street, Ste 350., Fort Atkinson, WI 53538. Periodicals postage paid at Fort Atkinson, WI and additional entry offices. POSTMASTER: Please send change of address to Rental, PO Box 3605, Northbrook, IL 60065-3605. Printed in the USA.
SUBSCRIPTION POLICY: Individual subscriptions are available without charge in the U.S. to rental centers, equipment distributors, and other businesses with rental departments. To subscribe please visit www.ForConstructionPros.com. Publisher reserves the right to reject nonqualified subscribers.
One year subscriptions for nonqualified individuals: U.S. $ 35.00; Canada and Mexico $60.00; and $85.00 all other countries (payable in U.S. funds, drawn on U.S. bank). Single issues available (prepaid only) $10.00 each.
Published and copyrighted 2024 by IRONMARKETS. All rights reserved. No part of this publication may be reproduced or transmitted in any form or by any means, electronic or mechanical, including photocopy, recording or any information storage or retrieval system, without written permission from the publisher.
8
Let’s take a look at electrics, generators, energy storage units, and the latest on the scene: hybrid.
12
MANAGEMENT Organizational Leadership in Action
The first key to effective organizational leadership is harnessing inspiration.
20
CONSTRUCTION
Evolution of Construction Tire Innovations
The factors behind how tires adjust to new conditions without diminishing performance.
26
SECTOR REPORT: TRUCKS & VANS EV Limitations Addressed at Work Truck Week
The electrification journey continues for many OEMs in the commercial vehicle market.
29
SECTOR REPORT: DISASTER RECOVERY
Construction Supply Chain & the Baltimore Bridge Collapse
How much will construction and other supply chains be impacted by the collapse.
In preparing this issue, let me tell you a bit about one of the interviews.
Not too long ago, I spoke with Alex Meek, co-founder and president at Moxion. If you’re not aware, they are a manufacturer of mobile energy storage products. As I always do, we spoke about the company’s background and some explanation regarding different aspects of the power generation industry. Turns out they have a second factory scheduled to open this summer right across from their headquarters (California) allowing them to grow their production capacity. He says that outside of the automotive sector, they will be “one of the largest module manufacturers in the country just by scale.”
With this issue featuring Rental’s Power Generation Report, I also asked about the major issues in the mobile power generation industry. Aside from the evergreen issues that have been around since the invention of the engine and diesel generator, being in California he quickly brought up policy, regulation, and permitting. He explains that there are strict operating requirements that “adds layers of complexity for the OEMs” where these regulations can very well slowly trickle down across the country.
As I’m sure you can guess, dear reader, these regulations likely deal with the big three: noise, emissions (air quality), and efficiency. If you consider the litmus test that is the annual ARA Show, there were more battery energy storage solutions on the floor than five or six years previous, which tells an observer like myself that the concept of a hybrid system is a continuing trend
that could very well indicate growth.
Let me be reinforce myself here, I’m no analyst—but the drive to lower carbon emissions across the construction industry isn’t going away. But rest assured that it’s not changing overnight.
We spoke on hybrid solutions where Meek explained that placing a battery unit in front of the load and allowing the generator to recharge the battery can very well reduce the fuel consumption on the generator by significant percentages. The idea is written on a lot, but telematics here might provide the perfect insight into reality and the actual loads customers are putting on your generators. You can guess how that can benefit you to provide a most efficient power unit vs something that might be an overkill of power.
Thank you for reading.
Stay safe out there.
EDITORIAL
Editor Jonathan Kozlowski jkozlowski@iron.markets
Managing Editor Gigi Wood gwood@iron.markets
Junior Editor Merina Shriver mshriver@iron.markets
AUDIENCE
Audience Development Manager ..................... Angela Franks
PRODUCTION
Senior Production Manager Cindy Rusch crusch@iron.markets
Art Director Marcy Murphy
ADVERTISING/SALES
Brand Manager, OEM & Construction Nikki Lawson nlawson@iron.markets
Sales Representative Patty Maroder pmaroder@iron.markets
IRONMARKETS
Chief Executive Officer Ron Spink
Chief Revenue Officer ....................................... Amy Schwandt VP, Finance Greta Teter VP, Audience Development Ronda Hughes VP, Operations & IT Nick Raether VP, Demand Generation & Education Jim Bagan
Corporate Director of Sales Jason DeSarle
Brand Director, Construction, OEM & IronPros Sean Dunphy
Content Director Marina Mayer Director, Online & Marketing Services ......... Bethany Chambers Director, Event Content & Programming Jess Lombardo
CIRCULATION & SUBSCRIPTIONS
P.O. Box 3605, Northbrook, IL 60065-3605 (877) 201-3915 | Fax: (847)-291-4816 circ.ConcreteContractor@omeda.com
LIST RENTAL
Sr. Account Manager Bart Piccirillo | Data Axle (518) 339 4511 | bart.piccirillo@infogroup.com
REPRINT SERVICES
Brand Manager, OEM & Construction Nikki Lawson nlawson@iron.markets
With Protect+ Warranty, Hatz offers the ability to extend coverage up to 60 months or 3,000 operating hours for Air-Cooled engines and up to 60 months or 5,000 hours for the H-Series. After the Standard 2-Year Warranty, the Protect+ Warranty offers multiple year or hour options, providing extended coverage to reduce the risk of unexpected expense for covered components and repairs.
Protect+ conditions include*:
- engine registration when the machine is new
- all maintenance only at authorized Hatz service partners
- perform all maintenance according to Hatz published intervals
- only genuine Hatz parts used during standard warranty and extended coverage
*Some requirements and exclusions apply
For more information contact a Hatz distributor. network.hatz-diesel.com/main-map/?L=3
Months up to 36 up to 48 up to 60
Hours up to 3,000 up to 4,000 up to 5,000
Months up to 36 up to 48 up to 60
Hours up to 3,000 up to 4,000 up to 5,000
Would you like to stay up to date on the latest happenings across the rental industry but can’t wait for the next print issue of Rental magazine to come out? Be sure to subscribe to our e-newsletters— including Rental Watch, Rental Market Watch, Power Rental, and IPAF Elevating Safety. Use the QR code, so you can stay informed on what’s going on around the industry.
Do you have an interesting story that you’d like to talk about on our podcast? Or, maybe you’re an industry expert and you’d like to share some of the best practices that can help fellow rental companies grow their business?
Email your ideas to Rental Editor Jonathan Kozlowski, jkozlowski@Iron.Markets.
To stay up to date on the latest happenings around the rental industry, be sure to follow Rental’s social media channels:
A verified 15,790 industry professionals from 29 countries and all 50 U.S. states gathered March 5-8 at Indiana Convention Center in Indianapolis, breaking last year’s attendance record of 14,885. Exhibit space was sold out with 536 companies filling the exhibit hall and New Exhibitor Pavilion with the latest commercial vehicles, equipment and technology.
Produced annually by NTEA–The Work Truck Association, it encompasses The Work Truck Show, Green Truck Summit, NTEA Annual Meeting, Work Truck Week Ride & Drive, educational sessions and more. The event was held virtually in 2021 and has been growing steadily since returning to Indianapolis in 2022.
“Work Truck Week 2024 was more than a trade show–it was a complete commercial vehicle experience,” says Steve Carey, NTEA president & CEO. “You could feel the energy throughout the exhibit hall, educational sessions, Ride & Drive and even just walking from place to place. The commercial vehicle industry has taken ownership of the week and has made it the epicenter for showing off the best the industry has to offer every year. The dedication and passion of our exhibitors and attendees has driven the continued expansion of Work Truck Week.”
Work Truck Week 2024 kicked off with Green Truck Summit, NTEA’s full-day advanced vehicle and fuel technology conference on March 5. A verified 883 participants attended sessions focused on the commercial vehicle industry’s drive toward greater sustainability, productivity and efficiency. Also starting on March 5, the educational program included a range of sessions focused on ideas and strategies to help improve efficiency, implement best practices and enhance operational growth.
Attendees had plenty of opportunities to get hands-on with many of the new vehicles and equipment. Work Truck Week Ride & Drive let participants drive, ride in and explore 19 vehicles, including all-electric vans, trucks and chassis, as well as internal combustion vehicles featuring advanced technology.
If networking was the goal, Work Truck Week offered plenty of opportunities to score, from listening to retired NFL running backs at NTEA Annual Meeting to playing amateur quarterback on the Lucas Oil Stadium field during Opening Reception.
HTTPS://RNT.NEWS/MED3SLOK
Bringing 40+ years of experience in sales and account management, Rick Penkert has joined MEC Aerial Work Platforms as National Account Manager. Penkert will be responsible for overseeing and nurturing relationships with key accounts across North America. Penkert brings a wealth of leadership skills, knowledge, and a proven track record of success. Delivering the highest quality of customer service while building partnerships for growth will be an invaluable contribution as MEC continues to expand its better solutions in the industry.
HTTPS://RNT.NEWS/D7N2DBPY
Several truck trailer outlets are reporting a reduction in trailer orders from February 2024 to March 2024, as well as a year-over-year decrease. While not unexpected, orders are expected to be in flux the remainder of the year. At 13,600 units, orders also were lower compared to last March, down 24% y/y. Seasonal adjustment at this point in the cycle leaves March’s tally essentially unchanged at 13,800 units.
HTTPS://RNT.NEWS/9DONYQVS
CNH Industrial, the umbrella construction heavy equipment producer for CASE Construction and New Holland Construction, has announced new leadership. Gerrit Marx was named CEO, effective July 1. He has previously worked for CNH, initially joining in 2019. He has also worked for McKinsey, Daimler Trucks, and Bain Capital, living in Brazil, China, Europe and Japan.
HTTPS://RNT.NEWS/BZPFEHPN
Club Car has opened a new factory in the state of Georgia that will be used for producing popular utility task vehicles (UTVs) that are powered electrically. UTVs have become popular in numerous industries because they are easy to operate and drivers don’t need a commercial driver’s license (CDL), which is particularly helpful as construction, landscaping and other industries continue to grapple with a worker shortage. The UTV is a great starter vehicle for workers new to those industries.
HTTPS://RNT.NEWS/7TNVHDE9
Let’s take a look at electrics, generators, energy storage units, and the latest on the scene: hybrid.
As construction equipment manufacturers continue to innovate the construction industry, the source of power and recharging the tools and equipment (both light and heavy) will be crucial to the jobsite. These sources of power always have been, but now changing market needs and policies are having their effect on the manufacturing and rental market.
“Overall, the market continues to demand increasingly high volumes of power both on grid and off,” says Ben Froland, product manager of power generation at Hatz Americas. “Emerging technologies such as efficient solar and improved lithium batteries present great opportunities to organically complement existing solutions like clean coal powerplants and low emissions diesel-powered mobile generators.”
Construction customers are now having to pay more attention to their environmental impact. “Companies are now required to report on the ESG (Environmental, Social, and
Governance) scores of their portfolio companies and carbon emissions,” says Madison McCormick, marketing manager at ANA Inc.
As companies actively seek more sustainable solutions like hybrid energy systems or solar options, Anne Nelson, director of marketing for Powr2 sees a growing push toward green initiatives in the rental industry. Adding that generators and energy storage systems will likely play even more of a pivotal role in a rental company’s fleet, having a fleet of sustainable rental equipment unlocks new revenue streams and growth opportunities by tackling a wider range of customer challenges.
In the past, explains McCormick, changes in the industry have been driven by technology and cost. The emphasis has shifted toward sustainability with more focus now on reducing the carbon footprint of operations and improving efficiency. This shift will require investment not only in the technology and the supporting infrastructure but a shift in mindset and culture.
While this emphasis on green initiatives isn’t new for 2024, the drive continues. However, Froland notes that the approaches have scaled back from the “flashy and radical” concepts of pure battery applications to more pragmatic solutions like hybridization and traditional movers like diesel.
As the industry addresses needs, Erin Brown, product manager at Doosan Bobcat, recommends that rental business owners and fleet managers alike should understand several key aspects of modern portable generators to ensure efficient operation and customer satisfaction: power output and capacity, fuel type and efficiency, noise levels, portability and mobility, and maintenance requirements. Adding to that, Brown suggests that rental houses should understand the unique features and benefits of their generator lineup. Diesel is still the dominant fuel source for general rental. Despite the requirements to move forward with green initiatives, the transition to sustainable practices can be tough for
power generation industry players. Any stakeholders who aren’t fully convinced of the benefits behind sustainability efforts will likely be reluctant to change any established processes.
It’s hard to beat the return on investment of a solid, diesel generator, notes Froland. He adds, “Modern diesel generators are very clean and reliable, and they should be considered as part of a practical, green fleet. The last round of emissions (Tier 4 Final) reduced NOx and particulate emissions by 90%. Diesel generators powered by engines up to 74hp are simple and reliable with no SCR (selective catalytic reduction) and no DPF (diesel particulate filter).”
Meanwhile, hybrid solutions pairing a mobile energy storage unit to a generator are staking claim to their own space within the power generation arena. McCormick forecasts that energy storage and hybrid systems will have the highest growth in the power generation industry.
“We are transitioning away from a traditional industry where you have a power generation that comes from a traditional diesel or other gas generator,” says Alex Meek, co-founder and president at Moxion Power Co. “Our products and our commitment is rethinking how that energy and power is delivered to customers in a different, more efficient way.”
Nelson explains that the adoption of hybrid energy systems is being driven by factors such as regulatory requirements and pressure to reduce CO2 emissions— equipment rental companies are seeing the value in integrating these solutions into their fleets. However, hybrid energy systems tend to have a higher upfront cost. Recognizing this and that many of the rental industry are still catching up with the newest technological developments,
McCormick recommends looking at the long-term to find the cost savings. She’s optimistic. “Hybrid energy systems can revolutionize the rental industry by providing a more sustainable and cost-effective power solution,” says McCormick.
Considering current emission standards, she says that Tier4 Final engines are a challenge for light and variable loads resulting in service and possible dependability issues. While a Loadbank may help address these issues on-site, this may burn additional fuel. “A proper hybrid system,” adds McCormick, “can solve these issues with the added benefits of reducing emission, reduced fuel use, less maintenance, reduced generator run time, and with a higher level of dependability.”
Both Nelson and Froland state that battery energy storage solutions (BESS) have gained traction within today’s rental fleets. The primary application, explains Nelson, “is often the optimization of diesel generator usage to drastically reduce generator runtime, reduce fuel costs, and cut CO2 emissions.”
She looks back at ARA 2024 where there were several more BESS manufacturers on the floor as compared to the pre-pandemic years.
‘how can we bring in new technologies to reduce [carbon emissions].’ Once you start getting into the equipment side, you quickly get to generators as being a primary contributor to the emissions profile. That has really sparked the demand. The GCs are turning around to the rental companies and saying, ‘We’re looking for this.’ Rental companies that are adopting it are able to have an edge.
“Their ability to win business, as a result of during an RFI over a bid, they can provide what is electrified or green equipment. We have found that—with a lot of the activity here but also across the country, those very large GCs are those big early adopters where there’s a lot of success happening.”
“Customers are specifically asking for BESS,” adds Nelson. “End-user demand is driving adoption. We increasingly find individuals and teams within client organizations devoted to sustainability, as indicated by titles like Sustainability Manager
“What we’re really seeing is the initial pull into adopting electric construction equipment and in our instance, mobile energy storage.,” says Meek. “You have very large customers that have very aggressive carbon emissions reduction goals. They look to their general contractors saying,
or ESG Team. These stakeholders are eager for effective means to lessen the organization’s environmental footprint. This conscientious transformation extends far beyond construction. Large-scale events, from music festivals to international sporting competitions, are increasingly adopting sustainability policies and innovative solutions.”
Take advantage of ANA's wide range of power solutions to maximize the efficiency and performance of your fleet. With prime power models ranging from 13 kVA to 400 kVA, ANA has a generator to meet your power demands. All our S-Series generators feature 24-hour runtime fuel tanks and include auxiliary fuel tank connections for extended runtimes. Our generators have the industry’s best automatic voltage regulation (±0.5%) with the widest range of voltage selection and best-in-class motor starting capability.
“With prime power models ranging from 13 kVA to 400 kVA, ANA has a generator to meet your power demands.”
When integrating the hybrid energy system, Energy Boss, you can monitor in real-time and get advanced analytics to identify hazards and prevent or minimize downtime. Ensure crew and fleet safety, minimize costs, and maintain operational efficiency all while improving your fleet's carbon footprint.Delivering prime power outputs of 30 kVA/24kW and 70 kVA/56 kW, these units boast optimization, performance, and maximum efficiency. Your first step to Zero Emissions starts with ANA's EBOSS™ Hybrid Energy Systems.
By employing the SDG25SV ,Pump and Power is made easy. With an integrated VFD inverter which allows the V-Pump 20kW generator the ability to start a 20hp pump or motor that would normally require a 50-55kW generator. The VFD also gives full control over your motor and pump speeds and can help with possible light loading issues on the generator. ANA is here for you.
Whether you are currently managing a team of a dozen or less, or leading a force of a 1,000+ people, the first key to effective organizational leadership is harnessing the remarkable power of inspiration.
Whether you are currently managing a team of a dozen or less, or leading a force of a 1,000+ people, the first key to effective organizational leadership is harnessing the remarkable power of inspiration.
It’s been said that the greatest creation Thomas Edison ever invented was Menlo Park. This 34-acre parcel of land just outside of Newark, New Jersey of course became the home to the world’s first research and development laboratory where the ‘Wizard’ himself oversaw the near daily creation of modern miracles, including that undeniable symbol of creative thought: the light bulb.
While Edison was indeed a prolific innovator in his own right, many argue that his real genius was in his ability to manage and influence others. Some say the actual magic being performed within the walls of Menlo Park was Edison’s leadership. Over time, Edison grew increasingly motivated by the freedom earned through commercial success and how it allowed him to pursue more of his ideas that would positively impact the lives of his customers. He became less an inventor and more a leader responsible for recognizing and recruiting exceptional intelligence, marshalling the collective creativity of some of history’s greatest minds, aligning their efforts and unique talents toward a singular goal, and ultimately bringing his vision to life.
With so many obvious parallels in the lore of our company culture, it’s no wonder the contemporaries of our founder Sakichi Toyoda, dubbed him “Japan’s Thomas Edison.”
When Sakichi Toyoda (1867-1930), founder of the Toyota Motor Corporation was laying the foundation for what would become one of the most renowned global brands, he encouraged his associates to:
• Always be faithful to your duties, there-by contributing to the company and to the overall good.
• Always be studious and creative, striving to stay ahead of the times.
• Always be practical and avoid frivolousness.
• Always strive to build a homelike atmosphere at work that is warm and friendly.
• Always have respect for spiritual matters, and remember to be grateful at all times.
Hopefully, you have a group of lifelong learners at your company who are always eager to learn new things. The next step is to align them with a good teacher, somebody who can help them grow and improve.
One mistake leaders often make is introducing a philosophy under which they intend to operate, but then stopping short of actually supporting or enforcing it. If they had followed through, they may have enjoyed the enduring benefits of a sound, robust company culture.
Failing to support or enforce your operational philosophy has a potent effect on organizational culture. In the absence of proactive leadership, follow through may begin to decrease, employee expectations may begin to hollow, and a general apathy can begin to crystallize as the foundation for the company’s culture. Three strategies we use at Toyota to help foster positive cultural awareness include:
• Reciprocal communication through recognition and feedback loops;
• Empowerment through well-defined decision-making abilities; and
• Encouraging innovation through continuous improvement.
At Toyota, we address these strategies a few different ways. For instance, Toyota associates are empowered to call out and actively participate in solving problems as they occur—a process referred to as Jidoka. Once an associate has called attention to an issue, it is incumbent upon managers and associates alike to practice what we call Genchi Genbutsu—or go and see—where they can observe first hand what the issue is, why it’s occurring, and how it is being fixed. This places the responsibility of correcting the issue in everyone’s hands.
Nemawashi is another exercise we use to solve problems, by taking our time to consider all options and making inclusive consensus-based decisions, then rapidly implementing the fix that’s been decided upon. Nemawashi roughly translates to “laying the foundation for proposed change” and is one of the first, critical steps in the decision-making process. Finally, we end with kaizen, or continuous improvement. Kaizen prompts discussions and considerations for how we might improve what we’re doing moving forward. This helps ensure we maintain a level of innovative thinking at all times. The idea behind reflection meetings— even during successful times—is to manage the collection, vetting, and appropriate implementation of all incoming ideas and feedback for improving our products, services, and processes. We can always be better. Taking the time to discuss the specific ways in which we can improve – often immediately after a project is completed—brings clarity to that premise. Assigning this responsibility helps ensure these observations are given the attention they deserve and are never lost or overlooked. Consider integrating a similar practice within your organization to help drive continuous improvement in your operation.
Like Edison, Toyoda was innovative and let his inventions guide the way. He was responsible for the invention of the automatic loom which then led to the Toyota Motor Corporation. I find this transition fascinating, taking a company from textile looms to automotives, and beyond that—the industry’s most complete lineup of material handling products and solutions.
Whether you are currently managing a team of a dozen or less or leading a large corporate force of a 1,000+ people, the first key to effective organizational leadership is harnessing the remarkable power of inspiration.
The article preceding this one (“Strengthening Your Rental Business the Toyota Way” by Brett Wood, President & CEO, Toyota Material Handling North America, published in Rental January/February 2024) in this 4-part series introduces the foundational principles and philosophies on which our company is built—what we call The Toyota Way. What is most unique to this set of principles is the focus on people. “Respect for people” forms the first of two pillars upon which The Toyota Way is built—the other being “Continuous Improvement” or “Kaizen.” This humancentric pillar is echoed repeatedly throughout the tenets of The Toyota Way.
A core philosophy held by the company insists that “building things is about building people”.
The Toyota Way mandates that an organization creates value by developing its people. The management tenets encompass principles that charge leaders with equipping their people with the tools they need to continuously improve their work. In summary, team building is the cornerstone to achieving successful organizational leadership. Like the conductor of an orchestra, in your role as a leader in your organization, you are responsible for assembling the best team possible, and empowering their unique and diverse skillsets.
But just because you have all the instruments and musicians needed to
BI Rental Mechanx150 2023.psd @ 66.7% (The BOSS MECHANX 150 is the perfect match for that the Mr. do-i, RGB/8) *
perform the symphony—that doesn’t mean the music will be delivered as it’s been envisioned. You, the conductor, are responsible for bringing all the players together, orchestrating their delivery, and bring the music to life. This is achieved through masterful and effective communication of your vision to your team. Done properly, your team will be motivated, inspired and empowered to
work in concert and bring your vision into reality.
At Toyota, we define our primary purpose as contributing to the sustainable development of society. This is pointed to in Principle #1 of The Toyota Way: “Base your management decisions on a long-term philosophy, even at the expense of short-term financial goals.”
The philosophy under which Toyota associates operate harkens back to 5 precepts coined by Sakichi Toyoda. When he was laying the foundation for what would become one of the most renowned global brands, he encouraged his associates to:
■ Always be faithful to your duties, thereby contributing to the company and to the overall good.
■ Always be studious and creative, striving to stay ahead of the times.
■ Always be practical and avoid frivolousness.
■ Always strive to build a homelike atmosphere at work that is warm and friendly.
■ Always have respect for spiritual matters, and remember to be grateful at all times.
Today, we still work to instill these same values in our associates. As time has tested and proven, people who share common values become a community, and when a community or company shares a mission and a clear vision—great things can happen. As you build and develop your team, you can build a solid foundation by clearly identifying and sharing your mission and vision.
Set the tone and communicate your expectations for your team by instilling enduring values that are important to you. In doing so, you create a system of accountability for yourself and your team.
Edison’s ability to influence people was perhaps the foremost element to his particular genius. Through this influence he was able to achieve great things for society at large—and also himself. Ultimately, we must acknowledge that as leaders, the direction and culture of our organization is in our hands. Depending on who is at the helm, an organization can appear to be serving the interests of the organization and its stakeholders, or, without a strong ethical compass, can seem as if the focus is more on serving the interests of the leaders.
As leaders, it’s important that we create a continuous process flow to bring problems to the surface. Work processes are redesigned to eliminate muda— or waste—such as overproduction and waiting times through the kaizen process. At Toyota, we’ve built a culture where production can be stopped to identify out-of-standard conditions and build in quality.
Hansei represents our identity as a learning company that relies on our people and relentless reflection to continuously improve. We know from 100+ years of The Toyota Way that an organization creates value by developing its people first. As a leader, your success can hinge on your ability to establish and support a core set of organizational and personal ethical values that contribute to a strong culture. Strong cultures ultimately translate to success. Take a moment to consider your company’s culture, mission and values and your own leadership ethics. Can your team clearly articulate those values and mission?
Editor’s Note: Part 3 in this series on exceptional cultures and leadership will explore building value for your organization by creating engagement opportunities and events that sustain a people-focused culture.
›› Isn’t it time a Jenny was hiding on your customer’s jobsite?
The only time people notice an air compressor is when it’s not working. That’s why Jenny has basically gone unnoticed since 1927. It’s the hazard of offering the most reliable compressors on the market, but we wouldn’t have it any other way…nor would our customers.
A quality diagnostic and repair tool is essential for businesses that maintain various types of heavy-duty equipment or vehicles. Reliable tools with the latest features and coverage help companies turnover their tasks quicker, leading to increased uptime and improved profits. To ensure you make the best purchase, consider our three tips below.
Choose a diagnostic and repair solution that covers the makes and models of equipment you service, quickly connects to all components/modules, and features an easy-to-use interface. Your application should help manage everything from triage to completed repair and include built-in troubleshooting assistance and repair information integration to maximize
technician efficiency. It’s important to buy from a reputable dealer to avoid purchasing pirated software, which can be illegal, outdated, and lack free updates and support options. Pirated software can also expose your device to cybersecurity threats that can render your devices worthless.
Unfortunately, buyer’s remorse is a common occurrence after purchasing inadequate diagnostic and repair solutions. With the best tool, you will feel like you made an investment; with the worst tool, you will feel like you wasted your business’s hard-earned money. You are making a significant investment that is supposed to drive profits for your business, so we highly recommend performing research before you make a buying decision. Products like JPRO Professional allow you to test drive the solution before buying with a free demo mode; this empowers customers to ensure the software performs as expected before spending any money.
When it comes to buying diagnostic and repair solutions, it’s important to make the right investment to expedite the process and improve efficiency. Research the product, test it out, and ask for the opinion of experienced users. Consider if it’s user-friendly, covers the models you service, fits the needs of your employees, and has consistent updates. Don’t hesitate to ask around with colleagues or industry partners for honest opinions.
The factors behind how tires adjust to new conditions without diminishing performance so your customers can overcome obstacles and stay on schedule.
Let’s begin with two obvious facts: One, heavy-duty vehicles are vital to completing any construction, and two, the tires on those vehicles are the most important piece of equipment on any jobsite. The heavy-duty vehicles required for off-theroad work are unlike any other machines found in the field and make the rugged and challenging work possible. These vehicles require tires that can keep up with demanding work and operate flawlessly under extreme pressure because if they can’t, jobsites would be at a standstill.
With the advancement of technology, tire manufacturers have designed products that not only handle the pressure but thrive in it. Using years of data acquired through tire monitoring and simulation tools, engineers have the power to see what design tweaks need to be made to improve tire performance and operator comfort. The insights gained from these technologies have paved the way for tires to become “smarter,” expanding the options at the disposal of engineers to bring more efficiency, safety, and productivity to construction sites.
Before you dive into manufacturing a new tire, it is important to answer this question: what is at stake if a piece of equipment gets a flat tire? Construction teams work on tight deadlines and rely heavily on equipment to maintain schedules. If a wheel loader experiences a problem and needs to be shut down for inspection, the project is likely to get behind schedule and new costs may arise. To ensure neither problem surfaces, reliable tires are key.
There are numerous ways to address reliability through tire design and a lot of designs are determined by the type of equipment and the type of work. However, with every new tire product brought to market, you will find common characteristics such as durability, traction, and versatility at the center of it all. It is through these themes that engineers are dreaming up new ideas to bring elevated levels of tire reliability to construction sites.
Tire durability is obviously needed on a construction site because of what heavy-duty equipment is required to do. Yet, the emphasis on this characteristic should never be understated. As machines have evolved to provide operators with more comfort, efficiency, and productivity, tires have needed to evolve as well. A construction tire has become so much more complex than just rubber and air. With the help of technology, engineers have developed layer after layer of materials, each with a dedicated purpose to bring strength and durability to the tire.
For example, construction tires are manufactured with a more durable, specially compounded rubber to create an outer tread with enhanced cut and chip resistance. Underneath the tread, multiple belts are layered on top of one another to add more protection near the exterior against cuts and punctures. Depending on the tire, these belts are made from rubber-coated steel or fabric. Modern premium construction tires have also leaned into the use of steel wire
and cords to help create a sturdy foundation for the outer tread and strong anchor points for the tire’s casing.
A tire with excellent traction is critical for any construction site because of the uncertain ground typically encountered by these fleets. Traction innovation has been introduced to the construction industry through the abundance of tire options manufacturers have brought to market to fit each application. There is no one-size-fitsall solution and tire manufacturers have focused efforts into creating tires for exactly what the vehicle needs. To understand a tire’s traction, you need to look at the tread pattern design and casing structure. For example, a dump truck may want a direction tread pattern to assist with fuel efficiency because of the miles driven to remove debris from jobsites, whereas a loader may want a non-directional tread pattern to help drive over uneven surfaces. In both cases, the tread pattern enhances the traction the vehicle will receive based on its function.
With the help of modern technologies, engineers have been able to take durability a step further and develop protection features in a tire’s tread that help meet the specific needs of on-site equipment. Take a loader, for example—loaders are among the most common pieces of machinery used in construction worldwide. The tires being developed for loaders need wide shoulder grooves to allow operators to move with confidence on wet, muddy, and challenging terrain. Like the use of durable rubber, these design choices help minimize damage and fight against tears and cuts. The tread for loader tires must also be deep to drive over all types of landscapes. To ensure nothing gets stuck within the deep tread, engineers utilize stone rejector platforms for the gaps to prohibit materials from being lodged within the tread. All five of these innovative design features allow loaders to drive over any surface comfortably with ease and play integral roles in protecting the health of the tire.
Versatility is the final characteristic of construction tires that tire manufacturers have worked hard to advance. Over time, construction equipment has become more streamlined and designed to bring more convenience to jobsites. The same goes for tires. With many new tires brought to market, it is becoming known that the tires are compatible with multiple applications. For example, it is common for loaders and graders to use the same tire due to similar operating conditions. This may not seem like a major benefit, but for construction fleets that perform a lot
IT IS COMMON FOR LOADERS AND GRADERS TO USE THE SAME TIRE… THIS MAY NOT SEEM LIKE A MAJOR BENEFIT, BUT FOR CONSTRUCTION FLEETS THAT PERFORM A LOT OF WORK WITH THESE TWO TYPES OF MACHINES, BUYING ONE TYPE OF TIRE THAT PROVIDES OPTIMAL PERFORMANCE ON BOTH IS APPEALING.
of work with these two types of machines, buying one type of tire that provides optimal performance on both is appealing. It offers additional flexibility at jobsites if a tire on one vehicle must be retired and it allows customers to minimize their tire inventory.
A tire’s versatility also relies on its adaptability. Construction sites are challenging and unpredictable at times, throwing new elements at construction crews constantly. Having tires that can adjust to new conditions without diminishing the quality of performance is crucial to overcoming obstacles and staying on schedule. With the help of modern technologies such as tire sensors, engineers can acquire real-time data from tires when in service on a job site. The constant delivery of up-to-date insights helps better understand what is needed out of tires in certain elements. By combining real-time historical and simulation insights into one place, engineers can make better-informed decisions and design better tires that remove unpredictable situations from job sites.
The construction industry is constantly striving for better efficiency, productivity, and safety with the help of advanced equipment—particularly tires. Tire engineers have been able to harness the available data to design tires that are more durable, versatile, and have optimized traction. This has been possible due to their innovative work. The construction industry confidently relies on technology to fuel its growth. This reliance will certainly lead to a continuous stream of innovations in the future.
Cummins Performance Series are the latest industrial engines for rental construction equipment and are US Tier 4 Final and EU Stage V certified.
The six-cylinder Cummins B6.7 engine is available from 116-243 kW (155-326 horsepower) with a high peak torque of 1375 Nm. With a low weight and compact size, it delivers a high-power density that enables it to replace engines of higher displacement with no impact on machine operation. This supports machines needing higherspeed power delivery, with low-end torque capability for transient performance benefits. Equipment manufacturers can use the B6.7 to improve machine capability and offer more value to their customers.
The B6.7 engine is combined with the Cummins Single Module™ after-treatment system to meet and exceed the ultra-low emissions levels demanded by Stage V. The efficient SCR technology means cooled exhaust gas recirculation (EGR) is not needed on the engine. Having no EGR means the engine is lower weight and has a simpler design, allowing for easier installation into equipment; together with lower cooling requirements. The simpler configurations also mean better reliability, reducing the total cost of operation and boosting availability.
This product is ideal for use in a range of off-road equipment including crushers, screeners, wheel loaders, excavators, fork-lift trucks, terminal tractors, and empty container handlers. It can be tailored by Cummins engineers mechanically and electronically to each machine type. This powertrain integration capability delivers the best all-around performance and running costs to match the required operating cycle.
More power with less complexity and less weight. The Cummins B6.7 engine delivers the productivity you need to keep your equipment running. The power increases up to 326 hp / 243 kW and peak torque up to 1014 lb-ft / 1375 Nm, enabling replacement of engines with higher displacement with no impact on productivity.
Work Truck Week’s Ride & Drive features the industry’s latest advanced technology and fuel, sustainability offerings and propulsion systems.
Trends point to more power in partnerships as the electrification journey continues for many OEMs in the commercial vehicle market.
Work Truck Week 2024, was held March 5-8 at the Indiana Convention Center in Indianapolis, Ind. The annual event, produced by NTEA – The Work Truck Association, encompasses The Work Truck Show, Green Truck Summit, NTEA Annual Meeting and Work Truck Week Ride & Drive, along with many educational sessions and networking opportunities.
Breaking recent attendance records, this year’s event hosted 15,790 industry professionals from 29 countries and all 50 U.S. states. With 536 exhibiting companies, the week offered a look at the latest in commercial vehicles, equipment and technology.
Green Truck Summit, the event’s
advanced vehicle and fuel technology conference, brought together 883 participants for sessions centered on the drive toward greater sustainability, productivity and efficiency in commercial vehicle industry.
“While most of Work Truck Week is focused on commercial vehicles, equipment and technology available now, Green Truck Summit is all about what’s happening in the future, exploring where the industry is moving and
how we are getting there,” explains Nikki Wilson, NTEA senior director of member services.
Throughout the week, commercial
vehicle OEMs and experts outlined their goals for sustainability and emission reduction, supported by the launches of several new electric vehicle (EV) offerings and technologies.
Similar to the recent uptick in EV technologies in the consumer environment, the commercial truck market is taking strides to encourage the adoption of EVs in commercial fleet operations. However, commercial truck applications face some of the same electrification challenges many offhighway OEMs face, including building and rightsizing the proper charging infrastructure required to support the needs of a more electric future. As OEMs continue to develop strategies to overcome some of these challenges, speakers throughout Green Truck Summit addressed the issues and laid out resources and insights to pave a path forward.
Opening the Green Truck Summit was keynote Mary Aufdemberg, general manager, product strategy and market development at Daimler Trucks North America. Aufdemberg discussed the challenges and opportunities facing the work truck industry in terms of sustainability and the ongoing transformation of the transportation industry, highlighting the shift toward electric and hydrogen fuel cell technology and the importance of infrastructure development, partnerships with dealerships, and ecosystem challenges. She emphasized the need for collective action through partnerships, highlighted the importance of increasing access to information on various fueling options, and stressed the urgency of taking action to shape the future of transportation.
The discussion highlighted the challenges, particularly the importance of sustainable transportation infrastructure and ensuring that dealerships
are prepared for zero-emission vehicles. Noting that partnership acceleration is the way forward, she recognized the recent formation of Powering America’s Commercial Transportation (PACT), the partnership of Daimler Truck North America, Navistar, Inc. and Volvo Group North America, established in January 2024 as the unified voice for medium- and heavy-duty zero-emission vehicle infrastructure.
Other Green Truck Summit sessions covered the challenges and opportunities of electrifying work trucks, including the need for costeffective and reliable solutions and understanding customer needs, and addressed technical and safety challenges along with energy requirements.
In addition, speakers addressed strategies for future-proofing battery electric vehicles, including life cycle planning, serviceability, safety, recycling, and educating end users about battery performance.
Weaved throughout the week was an emphasized message of the importance of building partnerships to bridge infrastructure gaps and address EV range anxiety by way of options for different battery capacities.
Tim Campbell, managing director at Campbells Electric Vehicle Consultancy, discussed the challenges of decarbonizing the transportation industry, emphasizing the need for clear policies and guidelines. Campbell echoed the need for partnerships to propel the industry forward, citing again that infrastructure is a major sticking point for the widespread adoption of electrified fleets.
Following the Summit’s exploration of sustainable transportation practices, The Work Truck Show opened
“ACROSS THE GLOBE, IT’S PRETTY MUCH THE SAME. WHETHER YOU GO TO INDIA, CHINA, EUROPE OR THE UK, EVERYONE’S IN THE SAME BOAT. WE’RE ALL IN IT TOGETHER AS A TEAM. THAT’S A REALLY IMPORTANT THING. WE’VE NEVER EVER HAD THIS, WHERE EVERYBODY’S LEARNING FROM EACH OTHER. WE ARE ALL GOING THAT DIRECTION…EVERYBODY IS REALLY INTO LOW EMISSION OR ZERO EMISSION.”
—TIM CAMPBELL, MANAGING DIRECTOR, CAMPBELLS ELECTRIC VEHICLE
its exhibition space to showcase new offerings and technologies. With partnership acceleration and electric offerings seemingly paving the road ahead, many exhibiting companies launched new releases and announced new collaborations throughout the show, which is on track for continued success in 2025 as these trends and technologies continue to unfold.
“The commercial vehicle industry has taken ownership of the week and has made it the epicenter for
Spanning the course of 24 press conferences in two days, exhibitors and manufacturers shared their latest announcements and product launches:
• Ram Professional’s new commercial vehicle division
• Ford Pro’s new extended range capability for E-Transit
• Mack Trucks’ Mack MD Electric battery-electric truck
• GreenPower Motor Company Inc.’s GP Truck Body
• Morgan Olson and EAVX’s new Proxima step van on a Freightliner Custom Chassis Corp. chassis
• REE Automotive Ltd. and Knapheide’s new electric vehicle on the REE P7-C chassis cab (upfit with a Knapheide KUV body)
Along with several equipment and technology debuts:
showing off the best the industry has to offer every year,” said Steve Carey, NTEA president and CEO. “The dedication and passion of our exhibitors and attendees has driven the continued expansion of Work Truck Week.”
The event’s Ride & Drive arena gave attendees and operators the opportunity to drive, ride in and check out 19 vehicles, including several all-electric vans, trucks and chassis, as well as internal combustion vehicles featuring advanced technology. All vehicles featured in this section of the event incorporated advancements that promote reduction of fuel use, greenhouse gases or particulate matter, helping both OEMs and end users meet their sustainability goals.
As vocational trucks, OEMs and end users continue to travel on the path toward the more electric future
of fleets, one thing is becoming more apparent: No one can do it alone. Alongside the evolving challenges of infrastructure, charging capabilities, regulations and standards, and sustainability goals, OEMs are also faced with meeting the efficiency and productivity requirements of electrified fleets across various industries and applications. Looking ahead, the industry seems to have adopted a team mentality, with the aim of working together and learning from each other’s successes and failures to reach the common goal of a more electrified future.
Work Truck Week returns to Indianapolis March 4-7, 2025.
• APSCO’s dump truck display and control system
• DEL Hydraulics Inc.’s DEL Interlock System
• Shyft Group’s Utilimaster Rapid Driver Cooling System
• Ranger Design’s prototype pick-up truck utility system
• Palfinger’s PAL Pro 58 mechanics truck and PSC 8600 TEC service crane
• Vanair’s PTO shaft-driven underdeck all-in-one power system
• Lincoln Electric’s Ranger Air 260MPX multifunction engine drive
• Ketchel Axle Systems eRhino electrified axle system for Class 3–8 vehicles
How much will construction and other supply chains be impacted by the collapse of the Baltimore Bridge and the suspension of traffic through the Port of Baltimore?
End users may temporarily face delays and increases. The dramatic collapse of the Francis Scott Key Bridge in Baltimore, Maryland, has raised significant questions about the robustness of supply chains operating in and out of the Port of Baltimore. The port is a major roll-on roll-off (ro-ro) port for construction and agricultural machinery, and the incident—which caused loss of life—is likely to have an impact on imports and exports for the off-highway vehicles industry. However, the question is what alternatives exist and how significant will the impact be?
Following the collision of a container ship with one of the support columns, the collapse of the 1.6-mile long Baltimore Bridge into the Patapsco River has featured in headlines around the world. In addition to the tragic loss of life, news reports have covered the potential impact on global supply chains, with all traffic through the port currently suspended until further notice. The Port of Baltimore handled more than 47 million tonnes of foreign cargo last year and U.S. Secretary of Transportation Pete Buttigieg has stated, “There is no question that this will be a major and protracted impact to supply chains.”
In general, Baltimore is the No. 1 U.S. port for ro-ro cargo. A U.S. census reveals the Port of Baltimore was No. 1 in the country for farm machinery imports and exports ($5 billion) in 2023 and third for construction machinery ($6.6 billion). Imports of construction machinery exceeded exports by a factor of more than five, with the port serving as a key port for imports of vehicles from Europe and China. The figure below details some of the major manufacturers of construction and agricultural machinery that use the Port of Baltimore for exports.
A container ship, the Dali, struck the 47-year-old bridge after losing power. The Dali made a distress call and dropped anchor to slow the vessel, causing authorities to shut the bridge to traffic and likely savings lives. The victims of the disaster were six construction workers fixing potholes on the
bridge when the collision occurred in the early hours of March 26, 2024.
The Port of Baltimore is used by many of the largest construction machinery manufacturers. A short-term slowdown in sales is expected, with positive growth forecast going forward.
In the wake of the collapse, two temporary channels around the wreckage have been established in and out of the port to provide access for some shallow-draft vessels and a third channel is planned over the coming days. However, this does not mean the Port of Baltimore is back up and running, a process that could take considerably longer. There are also a number of large commercial ships, including the Dali, unable to leave the port because of debris remaining in the channel and the process of removing it is a difficult and hazardous one for the authorities.
Maryland Gov. Wes Moore has stated it is likely to take more than a month before the port reopens. Replacing the bridge itself—which was named after the man who wrote the poem behind “The Star-Spangled Banner”—could take years.
Interact Analysis, has identified the following short-term effects of the Francis Scott Key Bridge on the off-highway vehicle supply chain:
■ Longer delivery times for imports: For construction machinery orders from outside the U.S., different ports
will need to be used if Baltimore is the main entry point. This could cause delays, with additional warehouse space for temporary storage required and changes made to on-road transportation routes.
■ Delays or increased costs for specific equipment types and models: In some cases there may be no easy alternative to the Port of Baltimore and end users could face delays or increased costs as a result. However, the effect may be minimal, depending on the equipment type, with ample supply between domestic construction machinery production in the U.S. and dealer inventory. In these instances, it is unlikely contractors or dealers will face equipment shortages.
■ Price increases: Short-term price increases are anticipated for certain models because of the points raised above, with additional costs incurred by changes to the logistics network potentially passed onto customers. However, any impact on the off-highway vehicles supply chain in the U.S. is expected to be short term and we expect that things will return to normal relatively soon. According to estimates for the bridge repairs, the port should reopen towards the end of May (although setbacks could well push this to the end of June). In the meantime, the Port of Savannah in Georgia (No. 1 in 2023 for imports and exports of construction equipment) and other ports along the East Coast—many of which are considerably larger than Baltimore—should be capable of handling any additional traffic.
The Port Act, emergency legislation designed to help workers and businesses affected by the collapse of the Francis Scott Key Bridge, has been approved by lawmakers. It allows Moore to access funds to provide support for those workers who rely on the port for their livelihoods and businesses impacted by the collapse. It can also be used to provide incentives for companies to use the port again when it is fully reopened. This could provide the impetus needed for the Port of Baltimore to return to its previous levels of operation relatively swiftly.
As the chart below shows, Interact Analysis expects the agriculture vehicle market in North America to contract by around 6% in 2024 and the road building vehicle market to drop by around 4%. Although, it does not predict the collapse of the Baltimore Bridge having a substantial impact on these forecasts and sales of both agriculture and construction machines are anticipated to return to a growth trajectory from 2025 through to the end of the decade.
Fecon’s Fusion is a telematics platform that uses dynamic features such as automatic machine calibration, location services and performance tracking, for mulching operations. Fusion automatically calibrates the attachment to the carrier in real-time to optimize performance, minimize downtime and expand the machine’s lifespan. Initially available on high-flow Bull Hog and Blackhawk attachments, Fecon brings intelligent control technology to a new level in the mulching industry. It automates mulcher set up through its Plug n’ Play design that eliminates manual setup and tuning. With this feature, customers can attach their mulcher to any compatible carrier and run the machine. The mulcher is optimized to the carrier and working conditions at all times.
https://RNT.news/74lmloqb
Manitou’s High-strength Demolition Bucket for compact machines is a very strong bucket for severe application: demolition, ship trimming, etc. It is constructed with reinforced structure, including the sides, upper part etc. It includes a 400 HB wear plate and side plates. It’s a low-profile bucket designed for good material penetration and cab access. Heaped capacity of 48-230 gal., width of 43 in. to 48 in.
https://RNT.news/bd0q9r0f
EZG Manufacturing has introduced the Hog Guard, a solution designed for safety on scaffolding assemblies during typical masonry and block jobs. The Hog Guard is engineered to block off openings in scaffolding assemblies, such as door frames, window allowances or any large opening that may pose a potential fall risk. This innovative accessory provides a safety measure for workers, addressing common challenges in the construction industry. Inter-changeable components are sold separately to custom fit site needs for added safety. Ready-fit design for simple assembly and break down.
https://RNT.news/4nco2zr6
Serving as a new addition in Kubota’s excavator lineup the KX080-5 compact excavator replaces the KX080-4 with performance, utility and various upgrades. Equipped with a 66.6-hp (SAE J1995 gross) Kubota engine, the KX080-5 features a digging depth of 15 ft., 1.1 in., a maximum dumping height of 17 ft., 2.7 in., and a bucket breakout force of 14,660 lbs. The two-pump load-sensing system supports the use of attachments, letting operators perform simultaneous tasks. The auto-shift system enables automatic travel shift from high to low depending on traction effort and terrain, providing simultaneous operations when dozing and turning.
https://RNT.news/5ca732bf
Coast is an ultra-secure fuel and fleet card that helps you control, monitor, and manage your fleet and business expenses. Spend less at every fillup by eliminating card misuse, and optimizing fuel spend. Coast runs on the Visa network, so you can focus on finding the cheapest, most convenient station. Coast cards and software are designed to be easy to use, so you can order cards or update your spending rules with just a few clicks. Should you run into any issues, the Coast U.S.-based customer service is committed to finding a solution by the time you hang up. Coast integrates with top telematics and fleet management providers so you can supercharge your fleet operations.
https://RNT.news/4cz6dqdc
Designed for power management of generators on construction sites, this solution enables operators to activate and deactivate generators from a different location, as well as receive real-time alerts related to performance and utilization. With remote generator monitoring and control, it is possible to track generator percent load, outputs, phase status and fault codes. Machine communication is facilitated by dual-channel J1939 CANbus and Modbus data. Operators can access generator utilization metrics.
https://RNT.news/pgr7twgy
The Flex Battery Tracker is designed for connected vehicles. With a battery life of five years, the Flex Battery Tracker facilitates continuous and reliable operation over an extended period. Built to withstand various environmental conditions, this tracker also offers multiple mounting options and compatibility with various types of vehicles and assets. In addition, multiple reporting options are available based on desired frequency of updates for in-motion or stationary assets. Equipped with tamper detection technology, the Flex Battery Tracker alerts users to any unauthorized interference or tampering.
https://RNT.news/qkbcp3s9
JLG’s ES4046 Electric Scissor Lift has a platform height of 39 ft. (indoors) and a zero turning radius, which provides access to narrow aisles and tight overhead spaces. This model offers over 50% more duty cycles than the previous R4045 Electric Scissor Lift, as well as uses fewer hoses and fittings and a single lift cylinder. Equipped with fold-down rails, ClearSky Smart Fleet comes standard on the ES4046 Electric Scissor Lift to allow for fleet tracking. Operators also can add optional features such as CleanGuard leak containment system for working on sensitive flooring, a 900-watt inverter to charge tools and SkySense detection system that helps protect workers and property.
https://RNT.news/wav5iwx6
Haulotte has released its next-generation HA61 RTJ PRO rough terrain articulating boom, redesigned to meet the challenges of working at heights up to 61 ft. Its articulated arm has 39-ft. horizontal outreach. Haulotte Dual Reach increases the load capacity of the basket up to 770 lbs. and enables working on sloping ground up to 6 degrees. Once Dual Reach is activated on the upper control box, the machine continues to elevate, limiting the number of back-and-forth movements between the ground and the working area. When Dual Reach is activated, the machine’s working envelope is automatically adapted for stability. Equipped with standard 4-wheel drive and four-wheel steering, the HA61 RTJ PRO moves over various types of terrain.
https://RNT.news/7uan16ke
Genie’s next generation TraX system has been redesigned to simplify maintenance while delivering performance on the jobsite. TraX is available as a factory-installed option on four boom lifts — two with standard lifting capacity (Z-62/40 and S-80 J) and two with Xtra Capacity lifting capacity (S-45 XC and S-65 XC). By allowing the XC machines to maintain their dual capacity, TraX increases the flexibility of the lifts, because it can be used on jobsites that require both additional lifting capacity and work on sensitive surfaces. Four independent tracks support smooth break-over on rough terrain. Oscillating axles and the ability to swivel up and down by 22 degrees enable the tracks to grip and climb over obstacles in extreme working conditions. The redesigned TraX system comes in two sizes: a small frame (for S-45 XC machines) and a large frame (for S-65 XC, Z-62/40 and S-80 J lifts).
https://RNT.news/yo0uvptz
Designed with toughness and flexibility, the portable NM series is built to withstand harsh conditions like extreme heat and dust. The units offer start-up and commissioning between sites, as well as an integrated feed air manifold for connecting diverse compressed air sources. Each model is equipped with an integrated feed air filtration system and membrane technology for a consistent supply of high-purity nitrogen. By design, the new series also works with other products in Atlas Copco’s portfolio.
https://RNT.news/aisxfraq
Engineered for construction applications, from concrete to steelwork, the RTH 10.37 rotating telehandler facilitates lifting operations with power, versatility and safety. The RTH 10.37 has a lifting height of 120 ft., 5 in. and a maximum lift capacity of 22,700 lbs. for handling heavy loads. At its maximum height, the telehandler maintains a capacity of 17,600 lbs. The RTH 10.37 features Magni’s patented outrigger system for stabilization. From 0% to 100%, this system adapts to a variety of terrain or confined space. Once positioned, the telehandler features an automatic leveling function accessible through the digital display. This technology adjusts the load chart based on outrigger configuration, allowing individuals to operate within safe limits during rotation and lifting tasks. The digital Load Moment Indicator system utilizes RFID-tagged attachments to update the load chart digitally for load management.
https://RNT.news/lfex2lud
Richard Vasquez, regional rental manager of Sonsray Rentals,
shares some of the challenges he’s faced and what he believes makes a company stand out.
n this month’s Rental Snapshot, we speak to Richard Vasquez, regional rental manager of Sonsray Rentals. With an impressive background in customer service. Vasquez shares some of the challenges he’s faced and what he believes makes a company stand out.
Rental: How did you first get your start in the rental industry?
I started as an equipment delivery driver in the industry. Within a few months, I was helping with dispatching trucks and learning the meaning of customer service.
Rental: Can you give us some insight into your current company?
In 2010, we saw a need for a highquality rental and leasing option for
refrigerated transport customers, so Sonsray Rental & Leasing was founded. In 2012, the company expanded to include the construction equipment industry. Sonsray Machinery stretches the length of the West Coast, serving customers from Washington to Arizona. By 2014, Sonsray Inc., was established to house all the company’s divisions under one corporate roof.
Finally, Sonsray Rentals joined the family in 2019 to better serve customers interested in machinery rentals. Sonsray Rentals is now the largest CASE CE distributor on the West Coast with seven locations for sales, parts and service, and seven locations for rentals in California, Nevada, Oregon and Washington.
Rental: What have been some of the challenges and successes you’ve had since you’ve been in business?
One of the biggest challenges I’ve faced has been keeping up with the demands of our customers. Making sure they have the right equipment for the job is a 24/7 task. But customer service is key in this industry. Without it, you’ll struggle to be successful.
A lot of the success I’ve had has centered around the honor and privilege of working for two good companies. It’s so important being a part of a company that looks and treats you like family.
Speaking of can-do attitudes, Sonsray Rentals has a special page on their website called “Sonsray Superpowers.” They start with the question, “How do you move a mountain?” and answer with, “Probably superpowers.” They share videos from various employees describing what their superpower is, such as multitasking, communication and teamwork. It’s a great tribute to the employees and wonderful insight into the team’s strengths.
Rental: What is one business tool that you recommend every rental business owner have, and why?
This may be untraditional, but one business tool I recommend every rental business owner have is a “can-do attitude.” You have to believe that there’s nothing you and your team can’t do. Hustle hard. It’s a mindset.
Rental: What do you think is most important for a business to do in order to foster success?
In my opinion, an important thing for a business to do in order to foster success is to employ people who have the same mindset and goals—people who want to succeed and aren’t just working for the bare minimum. People who care and are contributors to the
• Air Hose
• Water Hose
• Suction Hose
• Discharge Hose
• Hydraulic Hose
• Pressure Washer Hose
• Plaster/Grout Hose
• Sand Blast Hose
business! That’s why our slogan is, “Together, We Move Mountains.”
Sonsray also encourages employees to take a day off and volunteer for a charity organization of their choosing. Doing good for others feels good inside, and it’s nice to have a company that recognizes and prioritizes that.
Rental: If you won the lottery, what’s the first thing you do with your winnings?
The first thing I would do with my lottery winnings is to invest in Sonsray! That’s what family does for family; it believes in it.
Rental companies can learn a lot from the great salespeople at companies that supply their products to rental companies. Let’s focus on the relationship building between your staff and your customers.
The sales personnel for the suppliers of rental equipment and related products can make a huge difference in deciding which supplier company gets the order. In fact, some of them are so great at all the tangible and intangible ways they can help you to become more successful with their products that a wise rental business operator often doesn’t entertain the thought of working with a competing supplier. These salesmen and saleswomen certainly deserve applause for their exceptional work and are excellent role models for rental company employees.
There are so many lessons that can be learned from great salespeople at companies that supply their products to rental companies. Additional lessons can also be learned from their parts and service personnel. They play an indispensable role in their company’s success. Great suppliers know the importance of their parts, service, office, and shipping personnel. These skilled professionals help make the rental products they provide to rental companies even more rentable, and profitable. One can tell by their attention to detail and their shared sense of urgency that these individuals care. They are often the unsung heroes behind the scenes and certainly deserve recognition for their contribution to the effort as well.
Here are some additional thoughts
and opinions concerning relationship building between your staff and your customers.
Certainly, part of the recipe for even greater success is having a strong culture of relationship building that differentiates your company in your market area. To a large degree, some of the main ingredients include having great product knowledge, being a great teacher, and having sincere empathy for your customers.
Stress that every team member is involved in growing the company, and therefore everyone is a salesperson. Certain positions require far more intensive rental salesmanship training of course. When I train rental company counter personnel, for example, I always stress the importance of using proper and helpful closing and building the order techniques that I have developed—and to not be a “pushy” salesperson. Also, your team should be trained to stress the “benefits” not just the “features” of equipment. Done properly, the sales training can greatly increase rental income and at the same time build the customer relationship— which leads to more repeat business.
The strong, positive relationships your staff develop with customers are a key reason why customers should be doing business with your company instead of going to a competitor. I believe that having a well-scripted and powerful mission statement that accurately describes your company’s
mission can be helpful. Also, I believe you should consider having a written list of your company’s core values posted in your lunchroom. These statements, many dealing with building and maintaining super-positive relationships with your customers, focus your team’s attention even more in the direction that will lead to greater success. They help to identify and promote the distinguishing characteristics between your company and the others in your market area. It can also be a valuable addition to your website and other marketing tools.
Don’t just say “customer service” as your company’s distinguishing characteristic. This should be better defined not only for potential customer consideration but also for use in promoting the ultra-service culture to your staff.
Customers certainly have choices of where to rent so it’s wise to place additional focus on what could be one of the most visible and memorable advantages of doing business with your company. Don’t rest on your laurels— make your company’s customer relationship strength even stronger. Maintain this competitive edge with appropriate reinforcement of your team’s training. Finally, instead of assuming that your customers and potential customers are well aware of this distinguishing advantage of doing business with you, have your team continuously demonstrate it.
We’re continually updating your favorite workhorses to meet the demands of today’s most demanding worksites. And the newly remastered 8042 SkyTrak® Telehandler is built to deliver. Its redesigned build bears the same SkyTrak-strong reliability but is now more cost-efficient to transport. Enhanced tech options and improved cab styling heighten focus and productivity. All this and more without an ounce of compromise to its 8,000–lb capacity. In other words, you can work with confidence in a machine just as driven as you.