HOLZ-HER’S EVOLUTION SERIES Complete CNC machining in a COMPACT FORMAT
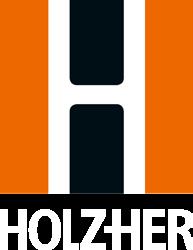
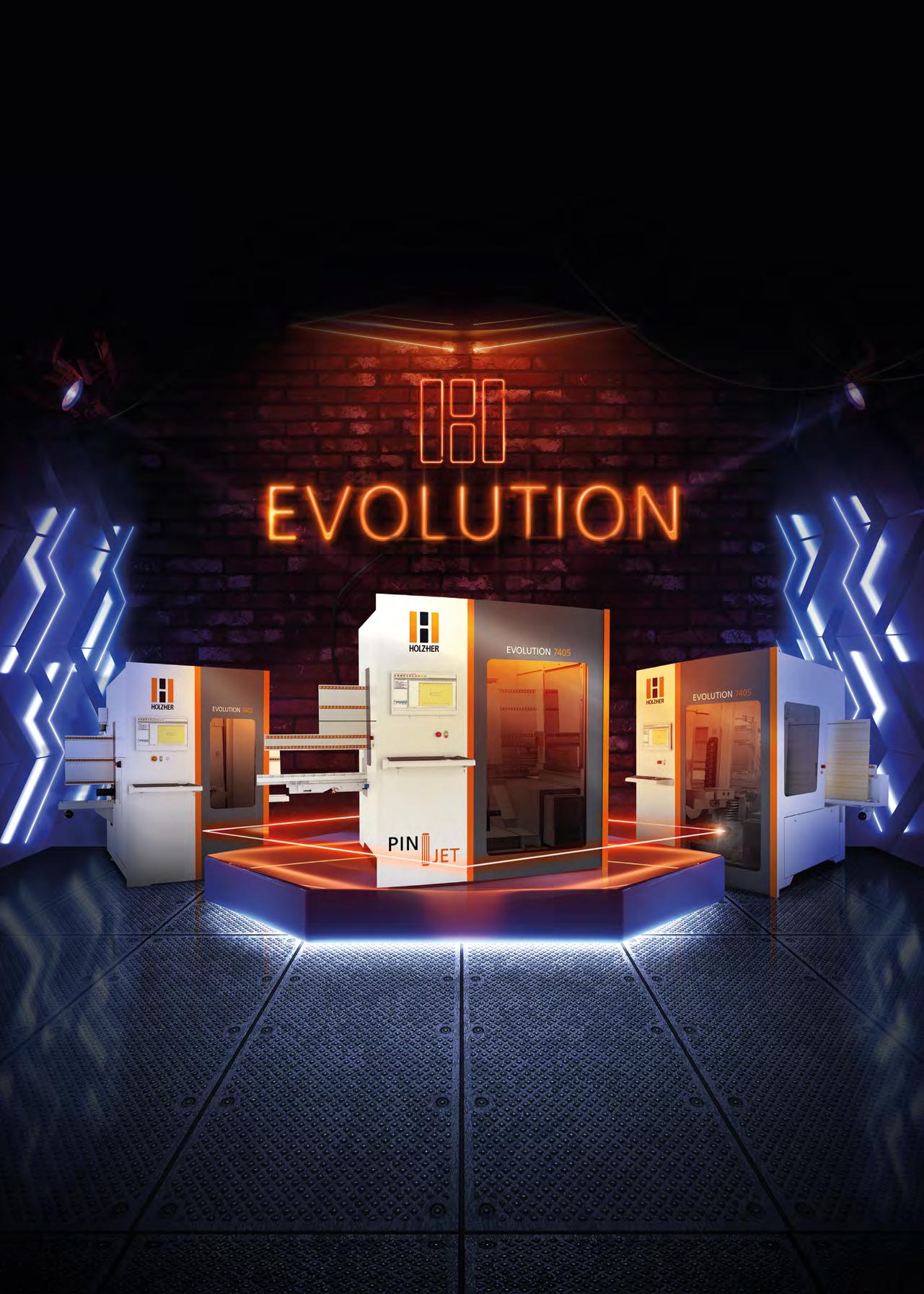
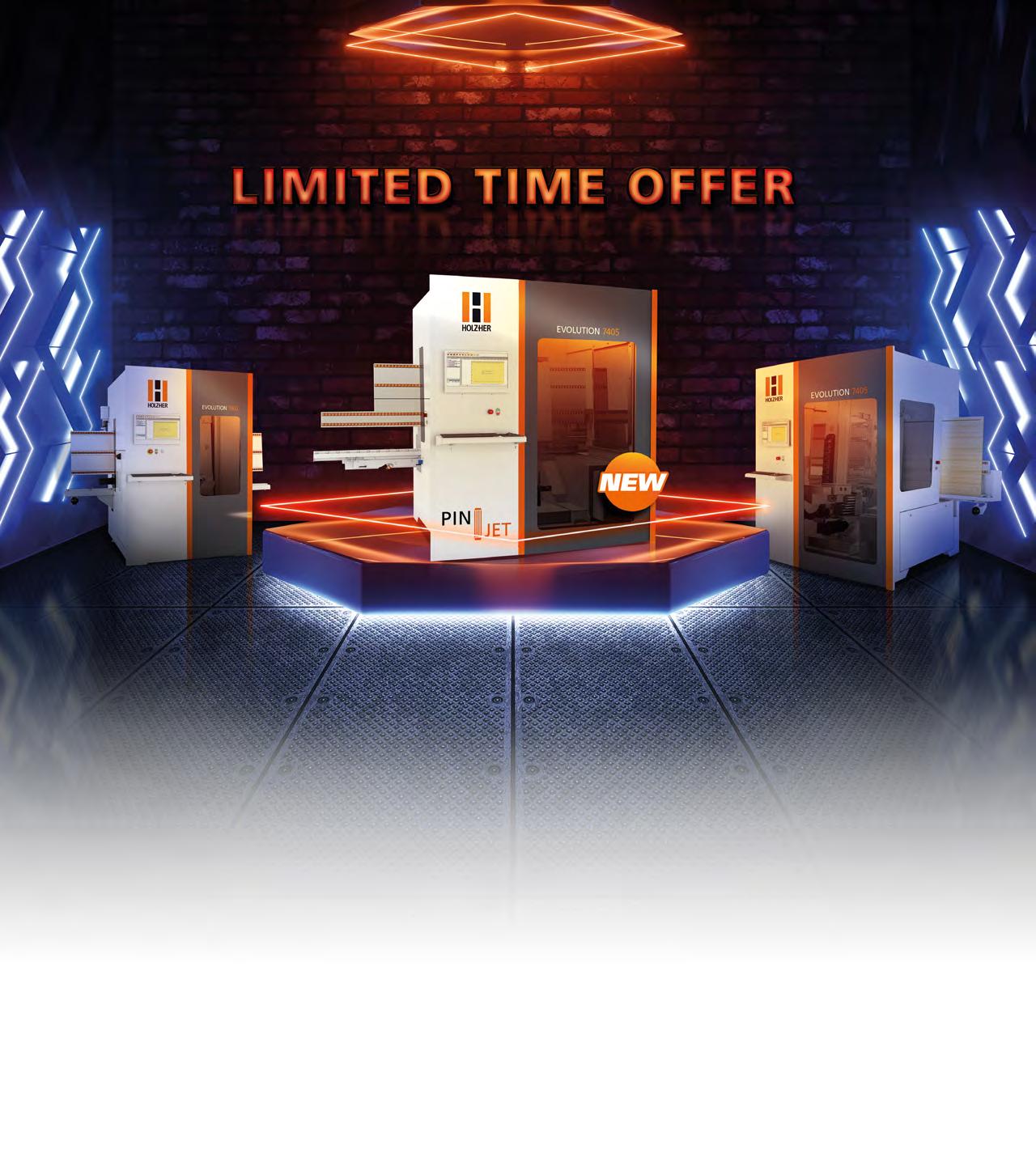
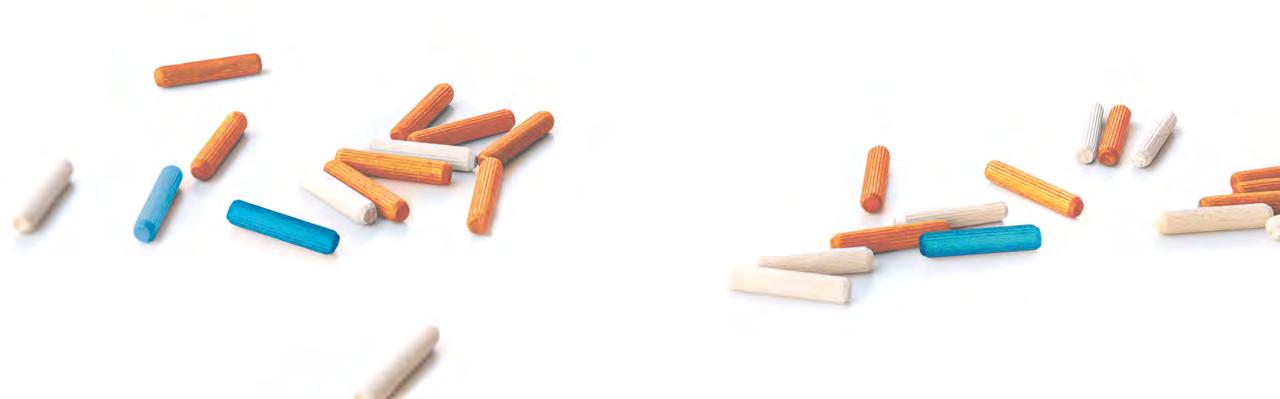
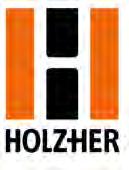
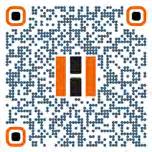
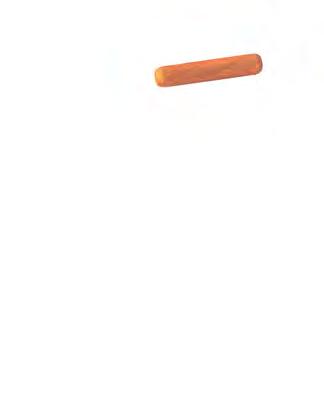
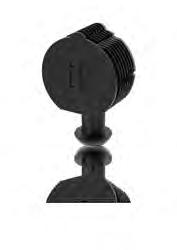
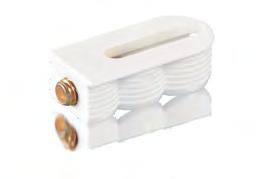
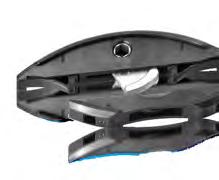
HOLZ-HER’S EVOLUTION SERIES Complete CNC machining in a COMPACT FORMAT
The volume and sheer diversity of CNC machinery and equipment that is available for furniture and joinery manufacturers today is truly astounding. From small-but-mighty hand-held options to behemoth five or more axes machines, the unbridled range of CNC technology in all categories underpins the development of furniture and joinery businesses both large and small – and with the onset of Industry 4.0, the growth of CNC is only going in one direction.
CNC machining is such a wonderful solution to the modern challenge of cost-effective furniture and joinery production so much so that it has become a staple of modern production. The birth of this impactful technology can trace its roots back to the immediate post-war period when researchers began looking into how to improve aircraft control. That research ultimately gave rise to an early, experimental milling machine. At around the same time, a company in the US discovered how to calculate aerofoil coordinates and feed them into a jig borer, this was claimed to be the first ever numerically-controlled machine to produce manufactured parts. Soon after in the 1960s and 1970s, numerous CNC machines were launched which most people would recognise today.
Coming back up to date, the woodworking machinery industry’s global meeting point – Ligna – is looming into view for the first time since the halcyon days(?) of 2019. Surely it is within Hannover
Messe’s hallowed halls that we will find the broadest intersection of the CNC world for the furniture and joinery industry – the great and the good, the weird and the wonderful will be there present their innovations hoping to impress the assembled visitors.
But before then, in this issue, we present a collection of diverse articles on CNC equipment to suit a range of situations. From impressive hand-held solutions to heavy-duty five-axis machines across a range of applications, there is something for all in this supplement – there are also individual product updates and installation articles with companies striding forwards with CNC investment to inspire us all.
I hope you enjoy the issue.
John Legg, editorial directorHOMAG’s CENTATEQ E-310 is a universal CNC processing centre that excels at edge banding on shaped parts. The compact machine offers a high level of performance with an array of impressive machining features as standard.
Using airTec, the powerEdge Pro Duo head achieves the same quality as a laser head for a fraction of the price. This makes invisible joint quality accessible to even more sectors of the industry. With the ability to run EVA, PUR and airTec, the revolutionary powerEdge Pro Duo edge banding unit is powered by the latest woodWOP 8 software making it quick and simple to achieve the perfect edge banding result on shaped panels, time after time. The CENTATEQ E-310 provides the highest edge quality, unbeatable butt joints and total flexibility.
Based in San Francisco with offices in Stuttgart, Germany, Shaper was founded in 2012 with a mission of developing a revolutionary line of computer-augmented power tools, beginning first with a handheld CNC router called Origin. Today, Shaper supports thousands of woodworkers and craftspeople around the globe with the simple approach of developing tools to meet users’ needs, rather than expecting users to conform to the tools.
Being close to the customer is a fundamental idea of Shaper’s company philosophy. In the EU, the company mainly sells products directly via its own online store and can regularly be found at trade shows. This offers the advantage that customers and interested parties can contact the company’s own support team directly and receive advice from experienced specialists.
Since 2022, Axminster has been a dealer for Shaper products in the UK, making it even easier to try out and purchase all Shaper Products locally.
The goal of every product and every further development should be to make advanced technologies usable in a simple and economical way. True to the motto: ‘precision cutting simplified’, Shaper is aimed specifically at the woodworking trade and wants to open up a new
way of routing, combining the advantages of traditional hand tools and familiar processes with the modern possibilities of digital support and CNC technology.
The Shaper System is an integrated system that brings intuitive precision to any cutting operation. At its heart is Origin, the world’s first hand-held CNC router. It resembles a traditional router, but is also equipped with a camera and a touch display. The tool uses computer vision to understand its location relative to a work piece. Its precision motors fine-tune the router spindle’s position in real time using sophisticated sensing and control algorithms that keep the user accurate of your intended path. If you leave the correction area of Origin, the spindle, and with it the router bit, automatically retracts and protects the work piece. Think of Origin as an auto-corrector for your hands.
Origin is designed specifically for woodworkers with a familiar hands-on form factor and slots seamlessly into a traditional workshop. It brings CNC accuracy and efficiency to all cutting operations with an easy-to-use interface. This offers a wide range of possible applications such as fine woodworking, carpentry, flooring,
even boat building, sign making and more. The advantage is that Origin can be used anytime and anywhere, without a lot of preparation, setting up the workplace or CAD knowledge.
After applying ShaperTape to the work piece, it can be scanned with Origin to create a digital image. The user can set a customised zero point, define a grid and thus place a cutting file with absolute precision. Then enter all the necessary cutting parameters and you are ready to go. Simple shapes such as a circle or rectangle with defined dimensions can be created directly ontool, or you just import your own SVG files.
The handy Origin can not only used in the workshop, but is also mobile and therefore ideal for any precision work at the customer’s site.
“With Origin, every job is done to the millimetre,” says Maximilian Messner, Engineer for Interior
Design, who did an incredible detailed medallion inlay in a narrow staircase. “I can use it to cut shapes in any size and level of detail.”
Origin is ideal for solid wood projects and bespoke furniture with sophisticated elements and hand-crafted details such as individual cutouts, perfect hardware fittings or intricate joints like box joints or dovetails. From fine engravings to large scale work and unique inlays, everything is possible.
Carpenter Gary Banks has been convinced of the possibilities of Origin since the beginning and is pleased that, thanks to the flexibility and precision, he can produce bespoke furniture –even in his small workshop. “A lot of people might think Origin is only for small jobs, details or sight lines. However, we often use Origin to make large scale parts or templates, with curves and radii.”
As well as being a way for woodshops to easily streamline their workflow and take a step into the world of digital manufacturing, Origin is also popular in the education sector. In trade schools, universities or training centres, students can learn how to use computer-aided manufacturing and CNC technology in a safe and intuitive way. Origin helps them work independently and develop an understanding of processes. They can build their own prototypes, use it for specific projects, or use Origin to build their journeyman or masterpiece.
“Origin highlights the skills that we’re trying to develop in our students to get them ready for post-secondary life, and to work with industry standards from companies looking to hire.”
— Brian Reed, coordinator of STEM and digital learning for the Rockwood School District
The complete Origin system >>Of course, the complete system consists of more than just Origin. Not to be underestimated are the key elements Workstation and Plate. Workstation is an adaptable and efficient fixturing solution for a huge variety of project types. With its durable ShaperTape surface, a clamping face with t-slots and an adjustable shelf, it can be used to reliably fixture vertical work, index and align unwieldy work pieces and secure small, delicate materials. Combined with Origin it’s perfect for accurate mortise and tenon joinery, as well as box joints and more repetitive cutting operations.
With Plate, the universal template for Origin, it is even easier to install hardware to virtually any work piece, make slab repairs, route System 32 holes, and much more with minimal setup time and maximal adaptability. With multiple Flags, a fence and a reticle, Plate can be easily placed exactly where you want it on your work piece. The build in ShaperTape surface can be scanned with Origin so that multiple digital workspaces can be created and saved for different applications. This allows you to quickly load your pre-designed workspace to install hardware like a connector or door hinge.
The best thing is: Plate combines with the ShaperHub hardware catalogue – a collection of fully annotated and Shaper-approved digital hardware templates from leading manufacturers which can be downloaded for free.
For all those who would like to convert their own idea into a ready to cut design, but do not want to go through the hassle of drawing with CAD software, there is a solution too. With Studio, Shaper has brought out an intuitive, browserbased 2D design tool, with which even more complex designs can be created effortlessly. You can use it on your PC, smartphone or tablet, which means it can be operated anytime and anywhere. It impresses with easy-to-use design and layout tools and allows you to combine basic
shapes to create complex designs, add text, and scale using real-world units.
To round off the product portfolio, the range of own bits and other workshop accessories is also constantly growing. This means that users are ideally equipped if, for example, they are looking for suitable roughing bits or speciality bits like T-Slot or Dovetail.
A lot has happened at Shaper in the last few years. The expansion of the portfolio and the constant improvements have not gone unnoticed in the community. In addition to exciting new innovations, users can always rely on regular free software updates for any Origin. This is an absolute advantage, as it guarantees that the tool’s software will always improve and remain up to date. Who can say that about their other power tools?
Shaper Tools – the name stands not only for innovative products and technologies. It also stands for a highly committed team of carpenters and woodworkers, CAD experts and CNC specialists who will provide you with competent advice and support. To learn more about the product variety and application possibilities, those interested are welcome to join the frequent live sessions from the Shaper Studio in San Francisco or Stuttgart. There are also lots of videos on the YouTube channel and plenty of content on Instagram.
The company provides a list of upcoming events in Europe where people can test the products. An overview of dealers who offer Shaper products can be found on the website at shapertools.com/findus.
www.shapertools.com
Introducing Estel, experts in the production of home and office furnishings since 1937, which entrusted its entire ‘batch 1’ production process to SCM. Thanks to the support from this technological partner, the company has managed to satisfy its need to be flexible and fast, especially with nesting, edgebanding and drilling machining.
A star that has been shining brightly for over eighty years in the Made-In-Italy design sky. It is the bright path of a company that, under the guidance of its founder Alfredo Stella, followed by his son Alberto and grandsons Massimo and Matteo, has performed very well in the home and office furnishings market with elegant, modern and high-tech solutions. It all began with a sliding, folding door patented in the 1950s which managed to become a genuine best-seller in no time at all: “Estensibile Stella”. It is no coincidence, therefore, that this company’s name, Estel, stems from the combination of these two words.
The company has two headquarters, one in Thiene and the other in Arsiero, both in the province of Vicenza. A 100% Made-In-Italy and in-house production, mostly for contract and office furnishings. A turnover in excess of €65 in 2021 with 260 employees, more than half of whom work in the production departments. With these figures, Estel proves itself to be a solid and expanding company operating mainly on the Italian market but is increasingly looking with interest towards countries in central Europe, the Middle East and the United States, with a significant export growth in recent years.
“We offer an extensive and in-depth range of products: management and operations offices, chairs, partitions, cordons, technical areas and new furniture sections dedicated to dynamic, deft and modern work,” explains Massimo Stella, owner of Estel and representative of the third generation of the founding family.
With the expanding market, the company has managed to focus on clearly defined cornerstones: excellent production flexibility, the logistics ability to reach and accompany all its clients with a tailor-made and punctual service, its speed in offering an integrated service ranging from design, sample taking and batch-one production to delivery. Strong points
that have led key brands and important banking and insurance institutions to choose Estel furnishings for their numerous branches and headquarters in Italy and abroad.
“In recent years, the market has changed,” continues Stella, “the volume of work remains the same, but the mix of furniture and components requested has changed considerably. It is essential to create different series of production batches, and ensure that the client has their tailor-made office that meets with the architect, designer and interiordesigner’s instructions... there is a need to be flexible and fast: despite the client’s decisional process being lengthy, the final creation is achieved today for tomorrow.”
Over the decades, Estel has increased its investments in research and development, technical-organisational know-how, logistics and technology with the aim of offering increasingly personal-ised and sophisticated products in terms of design, innovation and multi-functioning, even within the short time frame imposed by the market.
Estel’s long history has been interwoven with that of SCM for several decades.
“Market demands lead you to make the effort – you realise that your technological structure does not meet with client demand, so you need to invest in modernisation that is anything but easy. Everything becomes simpler, however, if you find a partner who manages to stay at your side, providing advice on the right technology at the right time based on your actual needs”. For Massimo Stella this is a matter of … “choosing the partner who best meets your needs and for years, SCM has been dealing with and satisfying those needs for us. Thanks to SCM, we have always managed to find the most suitable solution to the business model in vogue on the market.”
Nowadays, Estel’s entire batch 1 production process is managed by a system of state-of-theart SCM cells with a potential of 800/1000 pieces per shift. Varying elements and different orders end up in the same production loop, from nesting to edgebanding and drilling, and are manually reorganised at the end of the process.
A smart&human choice that provides the operators’ work with a decisive quality control role and one that was shared with SCM which fully comprehended the DNA. There is no excluding the possibility that this cell system may evolve further in the future with solutions that are even more automated.
The latest made in SCM purchases are instantly
visible at the Asiero plant. The entire batch 1 process starts from the Morbidelli X200 nesting cell complete with built-in automatic loading with labelling system. The cell’s cutting speed allows for a previously inconceivable productivity even with highly flexible machining work. “Our aim was to deal with the smaller batches more efficiently and with a qualitative result in line with market demands,” explains Giancarlo Sola, Operations Manager.
But, above all, the nesting cell is part of an integrated production system that sees it operating in synergy with a flexible “Stefani Cell H edgebanding and squaring cell. “Nowadays, we can produce pieces in the most fluid flow possible,” continues Sola, “compared to previous machinery, we manage to continually monitor performance.”
The nesting cell is easy and intuitive. It gives us the opportunity to train the operators quickly
and achieve maximum efficiency in the shortest time possible. Furthermore, for certain kinds of products, we can also route and transform the finished, made-to-measure product and avoid subsequent machining work; this is not possible with a blade panel saw.
In the nesting cell unloading area, an operator performs a first re-organisation of the pieces based on the relative orders. The panels are then introduced into the Stefani cell H edgebanding cell. This is also a highly evolved solution, designed by SCM for a highly flexible batch 1 industrial production. The cell has an automatic loading and Pickfeed recirculation bridge that simplifies the handling of mixed stacks with pieces that differ from one another and a Pickback panel return system complete with automatic unloading.
There is no need to stop production to change the machining parameters of the format, finishing and gluing quality, something that can occur frequently during a shift.
“Our product is highly personalised, so we needed a very flexible machine that can perform numerous different kinds of machining work, with different kinds of edges, radii and glue, routing up, under and to the side...With this cell we can reduce the through time set out in the loading or shipment plan. This solution means we can achieve a better-quality product and improve our efficiency on a daily basis thanks to the
production data collected each day,” says Sola.
The drilling stage completes the process and for this Estel has chosen two very different solutions. The first is a Morbidelli UX200 drilling cell with automatic loading and unloading system.
“Its uniqueness lies in its ability to machine all six sides of the panel and can, if necessary, route with two high-powered electro-spindles” comments Sola. “Another advantage is its high productivity and, in the case of uniform batches, it
is also possible to machine two pieces one on top of the other, cutting times by half.”
At its side we find a compact Morbidelli CX210 drilling machine, another solution designed specifically for batch 1, capable of drilling and routing with a production rate of 350 pieces per shift. High-powered and highly efficient drilling heads, shaped clamping gripers for a significant reduction in the cycle times, a made-to-measure worktable even of the most delicate surfaces.
Numerous advantages encapsulated in such a small size.
The entire process is controlled by supervision software for the edgebanding and drilling cells and SCM’s IoT Maestro connect system for all the machines mentioned, with the chance to remotely collect and analyse all the production, performance and maintenance data in real time. The flow of data is linked to Estel’s MES corporate management system and all the machines are equipped with the same HMI Maestro active.
“The most significant advantage in having contacted SCM to be a single technological partner is the integration - comments the owner Massimo Stella -. Shifting from a traditional production to a batch 1 process managed by computer systems and 4.0 technologies requires a cultural leap and adequate training.”
And the latest new entry to the Arserio factory is also from SCM; a Morbidelli P800 drilling-routing and edge treatment machine.
“As well as for the more traditional machining work, it is particularly useful for the 45° edged pieces that have always been our distinctive trade-mark. Thanks to this machine,” explains Sola, “we can reproduce a typically artisan machining pro-cess with the advantage of achieving constant quality in the product over time, greater efficiency and guaranteed times”.
Towards new objectives
Estel is already focusing on the next objective: achieving precise control and tracking of the entire order progress status. “Not only do we want
to optimise the use of raw materials but we want to have the most accurate delivery date possible”.
Sola adds: “Ours is a production line where the information shared in the batch 1 process for nesting, edgebanding and drilling needs to be accurate and correct. We have rethought our way of de-signing and creating furniture, of simplifying and optimising the machining work that, depending on the requirements of the architect, work site or client, should have highly customised sizes, finishes and drilling. This has been our greatest technological challenge.”
Take your CNC machining to the next level with Kimla. The multi-purpose capabilities of Kimla CNC machines make them suitable for any business working with solid wood, wood-based
3/ 4/ 5 axis machining
Z axis from 200 – 700mm
Customisable working areas
Unlimited software licences
Leading UK support
With a 750 millionturnover, 4.000 employees and 3 largehighly specialised productioncentres, Scm Group isatechnological worldleader inprocessing a wide variety of materials and industrial composites.
The Groupcompanies,operatingthroughout theworld, are reliable partnersof leadingcompanies in various market sectors, including the furniture, construction,automotive, aerospace, ship-building andplasticprocessing industries.
Introducing the new Evolution 7405 PinJet CNC machining centre from Holz-Her. Requiring just 5 sqmt, it offers complete CNC machining in a compact format and features fully automatic dowel insertion. Here’s a closer look…
The Evolution 7405 PinJet comes equipped with fully automatic dowel insertion. Pre-glued dowels with a diameter of 8mm and length of 3040mm can be inserted by the dowel unit into pre-drilled 8mm holes in the +/- X direction from both sides. When insert dowel is selected, the machine automatically drills, cleans and applies a mist to active the preglued dowel before insertion.
Unlike other vertical CNC machines that inherently come with machining exclusion zones created by mechanical clamps, the automatic suction cups offer restriction-free machining and fast, error free setting.
Capable of working with panels measuring 1200mm high and virtually unlimited lengths, it offers complete machining on all four edges of the work piece, making it suitable for machining operations such as construction holes, cut-outs and grooves.
Standard features include an integrated six-position tool-changer for tools up to 110mm, a 10.3 kW electro spindle with HSK-F63 connector and a fullyequipped drilling head, making the vertical CNC suitably equipped for milling, engraving, profiling and door processing applications.
“We don’t want space to dictate your manufacturing processes. At Holz-Her, our vertical CNC machine range offers adaptable machining and requires just 5 sq m of floorspace. Ideally suited to a wide range of applications, the latest model comes equipped with fully automatic dowel insertion, whilst our Door Ready package - designed to make light work of door processing – and X-Cut package - which eliminates the need for a cross-cut saw – can be added to deliver extremely flexible, space saving CNC machining on panels and solid wood.”
01235 557600
www.holzher.co.uk
The Evolution guarantees short cycle times and extreme precision because work pieces with lengths up to 1500 mm can be machined without automatic reclamping .
Consisting of a specially developed angle gear for lock boxes and a lock box cutter, the door package allows complete machining of door leaves up to 70mm thick. This process machines the hinge side and lock side in two clamping operations, making it possible to cut lock boxes with different bolt dimensions. Handle and lock holes can also be drilled precisely using HOPS macros. After turning and re-clamping the door leaf, it is possible to recess hinges for rabating doors as well as install concealed hinges or fittings.
The X-cut package allows you to buy in strips eliminating the need to process full sheets on a cross cut saw or vertical panel saw. This allows for easier handling and streamlined production.
The Evolution’s software package provides the pre-requisites for effective machining and convenient operation. Open architecture software allows for the simple transfer of existing data and connection to a wide range of branch, design and CAD/ CAM software.
Richmond Furniture is a privately owned family business with roots dating back to the mid1940s. Renowned for the quality of its superior kitchens it has established a solid reputation as a supplier to the contract kitchen market. With a turnover for 2023 estimated at around £17m, its 117 strong workforce manufactures specialist ranges for the public housing sector, private developer market and trade merchants. It also offers a small bespoke retail service.
“Our business has been built on providing quality, best value products delivered on time and within budget,” explains Richmond Furniture’s managing director, Gary Tootell. He continues, “To achieve this we have always invested in highly skilled crafts people and technically advanced, dependable woodworking machinery.
“The partnership with HOMAG goes back to the early 1980s when we bought our first edge bander from them. Since then we have acquired numerous HOMAG pieces of kit including a complete assembly line in 2006 with through
feed drilling, insertion, pressing, robot stapling and all the assembly stations.”
Looking for a robust drilling
CNC processing centre
“Our most recent purchase from HOMAG is a DRILLTEQ H-600 CNC processing centre. We bought it to replace an ageing Italian machine and while we evaluated a couple of alternatives, the HOMAG machine came out on top.
“Although there wasn’t a significant difference in the capability of the machines, the HOMAG DRILLTEQ stood out in terms of its build quality, the service support provided by HOMAG UK and the fact that HOMAG machines hold their value extremely well over time.
“HOMAG has a long and well established history of designing and manufacturing robust, cutting edge woodworking machinery. There’s no doubt, buying into this heritage gives you peace of mind and a real confidence that if issues occur they will be fixed very quickly, either remotely or by a visit from a service engineer.”
“Another significant advantage of partnering with HOMAG is the team of people who are on hand to help. From Matt Long, HOMAG’s area sales manager, to the installation engineers, trainers and sales support team, they are all friendly, knowledgeable and helpful. You never get the feeling you are being misled or pressured.
“Specifying the drill blocks and tools for the DRILLTEQ H-600 is fairly straightforward. Matt Long, however, was a real help when it came to specifying details such as sensors and parameters that can be included. He was able to guide us as to what we needed to add and what we needed to change on the machine to get to where we wanted to be.
“The DRILLTEQ has features on it that the
‘Specifying the drill blocks and tools for the DRILLTEQ H-600 is fairly straightforward. Matt Long, however, was a real help when it came to specifying details such as sensors and parameters that can be included’Richmond Furniture’s DRILLTEQ H-600
‘The heaviest use of the machine will come in the summer months when we do a lot of small batch, high volume work for student accommodation. From an investment point of view, therefore, we expect the DRILLTEQ to pay for itself within three years’
machine it replaced didn’t, but that’s not surprising given the age of the previous CNC. It is the service support and machine reliability, however, that make the difference. From our point of view, these are the two most important elements of the package and this is where HOMAG comes into its own.”
“The machine was delivered on a Friday in early September 2022 and was fully operational by the end of the following week. The installation engineers trained our team on the basic operations of the DRILLTEQ and how best to use the parameters.
“More recently, we sent three of our operators to Castle Donington for two days intensive training. Our people found this
very useful; they learned more about the parameters of the machine and how to do certain off-line work. They also discovered a few of the machine’s capabilities that they weren’t aware of, so it was good value all round.”
“The DRILLTEQ H-600 enables us to work directly from barcodes. Each panel is barcoded and from the barcode the machine draws the programme, drilling bespoke holes for that panel. This has enabled us to drill components as orders come through rather than at random and in bulk. It also means that individual units only have the holes drilled in each panel that are necessary; there are no generic holes
which can look unsightly when a cupboard is opened.
“The heaviest use of the machine will come in the summer months when we do a lot of small batch, high volume work for student accommodation. From an investment point of view, therefore, we expect the DRILLTEQ to pay for itself within three years.
“Overall we are extremely happy with the new DRILLTEQ H-600. It is a reliable, robust machine which has added more capacity to the business and improved the quality of our product offering,” concludes Tootell.
For a demonstration or further information on DRILLTEQ models or other HOMAG woodworking machinery and software, contact Adele Hunt at HOMAG UK on 01332 856424. www.homag.com
Daltons Wadkin have been sole distributors for Kimla CNC machines for over ten years. During that time the brand has gone from strength to strength with the continual development of cutting-edge routers, waterjets and fibre lasers.
‘Kimla are unique in the market. They have approached the design of their products from a very different standpoint to the majority of other CNC manufacturers. This is immediately evident in the overall build quality but can also be seen in the software and control system,’ comments Daltons Wadkin Managing Director, Alex Dalton.
Founded by award winning Polish entrepreneur Przemysław Kimla, the company spent its first years developing software and electronics, providing CNC systems for third party manufacturers. This included manufacturing PLC’s, inverters and drives – a complete eco system for computer numerical control. It soon became apparent that in order to exploit the full capabilities of the system, Kimla would need to make their own machines. Twenty-five years on and Kimla have over 250 employees across three locations producing a minimum of one CNC
machine every day.
“I have visited the Kimla factory many times and each time I go there is something new to see,” enthuses Alex. “Year on year growth is over 25% – a key aspect driving this demand is an unwavering commitment to innovation and excellence. Almost every aspect of the machine is manufactured in house; monolithic frame; high precision surface grinding; software; PLC; inverter and more. The result is an uncompromised CNC machine with mechanics and electronics working in harmony’.
Further expansion of Kimla’s manufacturing capability is well underway with a fourth site due for completion later this year. The new purpose built factory will boast a production area of almost 300,000 square feet and will allow Kimla to keep pace with soaring demand.
The Kimla range includes three-, four- and five-axis CNC routers and knife cutting systems, from compact prototyping models through to high production machining centres for processing solid wood, wood-based panels, composites, nonferrous metals, rubber, foam and other advanced materials. Particularly useful is the option for an increased Z axis height up to 2100mm.
Waterjet models are popular for customers
working with glass, stone, granite, marble and ceramics which are among the hardest most brittle materials encountered in industry. Working up to a thickness of 200mm or more, one of the principle advantages of CNC waterjet machines is the width of cut, less than 1mm, allowing cutting out of extremely intricate shapes and precision cutting of tight corners.
New to the Daltons Wadkin portfolio for 2022 is the Kimla range of fibre lasers for processing ferrous and non-ferrous sheet metal. An evolutionary jump from CO2 lasers, fibre lasers deliver uncompromised performance when coupled with Kimla’s unique CNC motion technology. With automatic pallet loading, compact operational footprint and a choice of laser powers up to 12kW, the Kimla’s range of fibre lasers are aimed at manufacturers looking for a dynamic and highly efficient cutting system.
One of Kimla’s key areas of innovation is in their linear drive technology. Again, developed and manufactured in house, linear drives are an option on most models, but standard on each axis on their fibre lasers. High powered electromagnets produce frictionless movement – with no wearable parts, speed, acceleration and accuracy is increased tenfold over traditional rack and pinion systems.
At the heart of every Kimla CNC is their patented Dynamic Vector Analysis (DVA) control system – processing up to 20,000 lines of G-code per second for smooth regulation of the feed
speed resulting in an unrivalled finish across a range of materials.
Regardless of what make or model machine you consider for your own production needs, perhaps the most important aspect to consider is support and back up. This is where the symbiosis of Kimla and Daltons Wadkin create a winning formula.
Daltons Wadkin has developed a specialist core team of CNC engineers within their support services department, dedicated to looking after
Kimla customers across the UK and Ireland. This includes regionally based technicians for on-site support, a technical help desk for telephone and net assistance and extensive spare parts inventory held at their Nottingham facility. To arrange a demonstration or for more information on the Kimla range of products and services contact Daltons Wadkin. 0115 986 5201
info@daltonswadkin.com
www.daltonswadkin.com
‘MyVA acts as a Virtual Assistant to the operator, reducing machine setup time, optimising management of jobs, improving ergonomics and automating manual processes’
As well as taking the complexity out of setting pods on a flat table nesting CNC, MyVA Virtual Assistant simplifies the process of running nesting alongside a pod and rail CNC or executing a secondary process. In this way, it enables furniture manufacturers to extract maximum flexibility and value from their CNC machines.
Broadly speaking, there are two types of CNC machine for machining products such as kitchen cabinets, shelves, door and window frames and hand rails.
On a flat table nesting CNC, a porous spoilboard, sometimes known as a slave board, sits on a flat table bed with a vacuum table underneath. The panel is placed on top of the spoilboard where it is held in position by vacuum to allow accurate machining. This type of machine is suited to flat sheet work – essentially for any routing and drilling tasks that can be executed on the face of the panel.
A pod and rail table consists of carriages with rails that move in an x direction and pods in any direction. Suction cups mounted on these carriages hold the work piece in place via vacuum. Biesse machines also offer a quick change to mechanical clamping systems, for example, when
machining window or door frames. A pod and rail machine has the advantage that it can process the edge of the piece as well as the face within one programme.
In an ideal world, most furniture manufacturers would have both flat table CNC and pod and rail routing capabilities within their factories: the flat table for nested production and for cutting large sheets down to size, and the pod and rail for intricate tasks or work that needs to be performed horizontally such as drilling into the sides of a panel.
However, space and budget constraints do not always allow for both, forcing most companies to opt for one or the other.
It is possible to adapt a pod and rail machine to produce flat table parts, or to add pods to a flat table machine for greater flexibility. However, conversion is time-consuming and creates a disjointed workflow.
Biesse has conceived a solution that integrates hardware and software to make the conversion and subsequent processes seamless, efficient and easy. MyVA acts as a Virtual Assistant to the operator, reducing machine set-up time, optimising management of jobs, improving ergonomics and automating manual processes. The net result of faster conversion and a better organised workflow is improved productivity.
The MyVA system comprises four elements …
Typically, the control panel for the CNC machine and the nesting scheme display are in two separate locations. With MyVA, both are incorporated within a single control station. This ergonomic dual screen configuration means the operator can see the nesting scheme whilst working on the machine and all tasks can be executed from one location. Crucially, this control console can be used to carry out nesting on a pod and rail machine that has been converted into a flat table.
The control console also incorporates a label printer. Linked to the nesting software, this printer produces a label for each nested part.
As well as printing a barcode that makes
each panel easily identifiable, the labeller can apply a QR code that contains information and instructions for secondary processing that needs to be carried out on this part.
Using this smart glove barcode and QR code scanner, the operator can scan the barcode and/ or QR code on the label to automatically add the next programme to the work list, which is displayed on the control panel.
These features really come into their own when a pod and rail machine has been converted into a flat bed for nesting, but conversion back to a pod and rail arrangement is needed for secondary horizontal work such as drilling.
In this scenario, the programme instructs the operator where to position the pods for the secondary process, or, if the machine is equipped with automatic positioning, they move into place automatically.
When the need arises for using pods on a flat table nesting CNC, accurate pod placement is essential to avoid costly collisions with the CNC head. Historically, the operator had to carry out manual measurements to ascertain where the pods should be positioned on the table.
With MyVA, a laser scanner linked to the machine software shows the operator where to place the pods, which is far quicker and far more reliable. The laser projects an LED arrow to mark the location, guiding the operator and speeding up machine set-up.
Together, these MyVA elements give manufacturers the flexibility to perform a nesting process on a pod and rail machine and to allow horizontal work to be carried out on a flat table nesting CNC.
Walsall based Ideal & WRS Saddle Company is one of the world’s largest manufacturers of equestrian saddles which are constructed on a wooden saddle tree (frame). The company’s extensive range of saddles available are suitable for dressage, show jumping, eventing, showing styles or just leisure.
The way the saddles are made has changed little over the last 100 years or more meaning the various manufacturing process are very labour intensive. One of the key elements in the construction involves making the wooden subframe is the variability of different shapes and sizes that need to fit the shape and size of both riders and horses. These parts are made using laminated plywood and are known as the Saddle Tree and Cantle.
The Saddle Tree is pressed and shaped using an aluminium jig, and once this has been done it needs trimming to exact size which usually is done by hand. The Cantle is produced in part on a standard three-axis CNC machine, but certain areas of it still require finishing by hand. This ‘hand working’ is time consuming and requires a highly
skilled person to do it.
As a result around 12 months ago the company started to research how they could produce these parts more efficiently and accurately and came to the conclusion a five-axis CNC Work Centre could be the solution.
After looking on line at several manufacturers they selected Pade as their first port of call as it appeared they had a good knowledge of machining complex shaped parts. Production Director James Hitchens picks up the story “We contacted Pade directly, who in turn put us in touch with their UK agent JJ Smith. Following an initial meeting to discuss our requirements, samples where sent over to Pade to review and test.
The results seemed very favourable and so a site visit to the Pade factory was set up for myself and work shop production managers Phil Parsons and Thomas Lugsdin together with Guy Stanley from JJ Smith.”
In the Pade showroom a demonstration machine was set up to produce various size Cantles and Trees as per the customer’s samples. In particular
‘The Velox was also specified up with a 12-position automatic rotary tool change, and for programming, the machine had the Pade E-LAB simulation and anti-collision software along with Alphacam Advanced 3D’WRS Production managers Tom Lugsdin and Phil Parsons in front of the Pade Velox five-axis CNC
the clamping and precise referencing of the Trees was discussed at length, with the end result being a very simple yet effective clamping set up that Pade designed.
The model of machine that was specified was a Velox Solo ‘gantry style’ five-axis CNC, that due to space restrictions in the customers factory, had to be specially modified to fit.
Although working with just one shuttle table – with the option to use vacuum or mechanical clamping – there was the choice to machine both Cantles and Trees at the same time, or selecting to produce a batch of the same parts.
The Velox was also specified up with a 12-position automatic rotary tool change, and for programming, the machine had the Pade E-LAB simulation and anti-collision software along with Alphacam Advanced 3D.
James comments: “From the moment we arrived at Pade we could tell they where a serious company who new their stuff and had a real can do attitude which was refreshing. The machines we looked at where extremely well engineered and we could tell would be up to the job.”
The Velox is just one of six different models of five-axis CNC machining centre that Pade produce for a wide range of complex shaped parts for furniture, construction, garden products, packaging to name but a few.
Once James and his team returned to the UK an order was placed and the machine was delivered and installed on schedule.
Phil Parsons commented: “The whole delivery and installation process was expertly organised and went without a hitch.
For software training and machine operation this was split into three days at the Pade factory and three days at our factory, and I have to say
the technicians from Pade and JJ Smith did an excellent job”.
Guy Stanley from JJ Smith adds “This was a very interesting project to work on and one that initially had some challenges. But with close dialogue with Pade and the customer, the end result is a machine that will significantly help increase both production output and accuracy. In addition, it has been a real pleasure to work with the Ideal WRS team who from the outset had a very positive outlook and open to new ways of thinking.”
0151 548 9000
sales@jjsmith.co.uk
www.jjsmith.co.uk
‘The clamping and precise referencing of the Trees was discussed at length, with the end result being a very simple yet effective clamping set up that Pade designed’
A look inside a Maka will reveal an exceptional depth of experience and know-how that makes the Maka a high-dynamic five-axis machine centre.
The new M-Series range of customisable platforms builds on their highly respected record for providing uncompromisingly robust heavyduty CNC machines, combined with the latest high performance technology.
The M-400 with single or twin tables, are designed for rapid setting, as well as high speed processing with high precision, delivering:
• Higher capacity
• Shorter cycle times
• Greater flexibility
• Rapid setting
• Less programming
• Lower manning
• Improved safety
• Improved dust extraction
• Lower maintenance
• Greater reliability and resilience
The new models are compatible with robotics and Industry 4.0 ready.
The high dynamic construction makes the MAKA machining centre ideal for both bespoke and high volume production.
The M-400s provides a useful working area of 2500 x 1500 x 650 (or 1000)mm to process large work pieces with ease. Additional devices are available for vacuum and pneumatic clamping, and turning.
The hidden detail inside reveals the source of the Maka’s power, speed, reliability, flexibility and unique strength. Structures are deliberately
oversized, and the entirely arc-welded steel is sized in accordance with FEA processes. This is essential to minimise vibration and torsional stress. The structure provides the necessary stiffness to guarantee precision and repeatability in the very long-term, and allows the machine to reach high speeds with rapid acceleration. This also protects the investment long-term.
Images © Maka The POWER-MAKA five-axis head with integral dust extraction Maka M-400 POWER-MAKAMaka’s new BWO CNC Vektor 921 provides complete control for high-speed five-axis machining, and userfriendly tool-tip programming
The POWER-MAKA head is a prime example of Maka’s uncompromising approach and uniqueness. Their rotary drives have long been supplied with Hollowshaft-type servos with encoders reading directly on the actual shaft.
The Hollowshaft’s employed are well-proven in the field, and highly appreciated by Maka users. They provide protection and security in case of collision. They also eliminate the inherent limitations in speed and precision associated with belt drives, and even geared drives. Dynamic precision is controlled better.
The robust head casting secures and protects the drives to ensure long-term reliability, especially when operating continuously at high speed.
The latest POWER-MAKA five-axis heads features high performance Galaxie® Drives combined with the POWER-MAKA spindles. The combination elevates performance, delivering:
• Higher torsional rigidity (650 Nm/arcmin)
• Zero backlash
• High torque (nominally 750 Nm)
• Higher positioning accuracy
• Improved surface quality
• Faster rotary speeds up to 20,000o/min
• Shorter cycle times
Manufactured in Germany, the POWERMAKA package are designed for operating in the harshest environments (and remain easily accessible for servicing and maintenance) will improve quality and productivity.
As Maka’s Iain Young explains “The Maka M-Series are best suited for the most challenging manufacturing environments. The M-Series are truly flexible multi-axis five-axis machining centres, designed to meet every challenge any timber engineer or furniture manufacturer will face today.”
“We are dedicated to serving and supporting our customers and have improved structures to provide higher quality support. We’re also actively recruiting. Our factory trained CNC engineers are available for rapid response, and for all requirements, including refurbishing and upgrading,” concludes Iain.
01952-607700
info@makauk.com
www.maka.com
‘The Maka M-Series are best suited for the most challenging manufacturing environments. The M-Series are truly flexible multi-axis five-axis machining centres, designed to meet every challenge any timber engineer or furniture manufacturer will face today’Combining 50 years of CNC experience, the new Maka M-400t five-axis machine centre provides flexibility and precision at high speed Maka M-400t illustrated views – from front and rear
Frontline Cabinet Design in Netherfield, Nottingham, have once again returned to their long-term machinery supplier, RW Machines, to purchase their fourth CNC pod and rail machine. For over 30 years Frontline have produced their high quality bedroom and kitchen products, processing their cabinets on various Busellato machines. Their latest purchase was the newly launched Busellato Jet Elite equipped with the ‘Easy to go’ software which RW says is the most comprehensive package currently available on the market.
The machine is equipped with a14kW electro spindle linear tool changer, easy-set pod system and 18 spindle drill blocks for optimum drilling selection, along with automatic height setting of all tooling and space-saving safety bumper protection.
Not only was Frontline’s Production Director, Paul Danby, delighted with the new equipment but also with the total efficiency of the installation, praising both Kelly Spencer, RW’s Service Director, for the way the installation was organised and carried out, and especially Steve Ambler, RW Technician, for his friendly manner and expertise reporting that RW was “probably the best service team within our industry, wonderful service!”
Ian McCall, Frontline’s Managing Director, concurred with Paul’s thoughts and commented that once again, from the start of the process, it had been a pleasure to deal with RW Machines. For further information and a list of the ready-todeliver machines in stock, visit RW Machines’s new website – www.rw-machines.co.uk – or contact the company on 01869 244943 or sales@rwmachines.co.uk
ANDERSON GS710 LINEAR DRIVE
Anderson’s most advanced CNC nesting router, driven by linear motors, routing at 50m/min.
The latest Pod&Rail CNC from one of Italy’s most renowned manufacturers!
3-4-5 axis models.
STEMA
The company that always says YES!
Offering endless options of bespoke CNC equipment for the panel/furniture industry.
FIORENZA
A unique Italian supplier, providing solutions for the manufacturer of 5-piece doors with dedicated standalone machines through to high volume automated lines.
AES have been producing high quality CNC machines for over 30 years. Based in Bursa, Turkey, AES have remained true to traditional engineering standards manufacturing heavy duty machine frames designed to allow high positioning speeds for continual production. This rugged frame is the foundation for all AES machines ensuring long term accuracy, reliability and longevity.
Historically, AES predominantly served their home market becoming the number one CNC machine manufacturer to one of the largest markets in the world, with many machines typically running 24/7.
In the last ten years AES have expanded their activities becoming a global organisation with subsidiaries in Europe and USA. This has seen exponential growth as awareness for the AES products has been recognised resulting in substantial investments in both their manufacturing and assembling capacity, design and support infrastructure.
In 2017, AES entered the UK market initially with the CNC drilling machines and as with other markets the momentum soon grew resulting in
the regular installation of the different models of drilling, nesting, door processing CNCs and beam saws.
Following this success, investments have been made in the support of UK based engineers who are readily available for both installations and after sales care along with direct access to the AES technical service team if required.
Having installed new AES machinery since 2017, there have been several customers who have added to their manufacturing capacity with another AES product typically buying a CNC drilling machine then purchasing a nesting machine. AES also have several customers who have purchased a stand-alone nesting machine and have upgraded to fully automatic line machines with auto-loading, off-loading and auto-labelling.
In short, AES can offer a broad range of manufacturing solutions from entry level through to machines running 24/7 with either three-, fouror five-axis configurations.
The AES Flexa Pro series have proved to be a particular hit for those moving from sliding table panel saws and adopting CNC technology for the
first time.
Whether using existing CAD or supplying Polyboard parametric cabinet CAD, we have several customers with no previous CNC experience where we have delivered, installed and trained resulting in them manufacturing in just one week.
The Vega series of pod and rail style machines have also proved popular whether in compact 1325 version (2500 x 1300mm) or 1360 (1300 x 6000mm) for the production of stairs and again in three-, four- or five-axis configurations.
One of the winning features of the Vega series has been the dedicated, double-sided horizontal router head for cutting the locks and hinges typically when processing fire doors.
AES will be at the Ligna trade show in May this year where they will have a commanding presence and will have on display one of the largest selections of CNC nesting, drilling, joinery and panel processing machines. For anyone in the market for a new CNC or beam saw, a visit to the AES stand is a must.
01704 893109
www.ukwoodworkingmachinery.co.uk
‘In short, AES can offer a broad range of manufacturing solutions from entry level through to machines running 24/7 with either three-, four- or five-axis configurations’Raptor Ultra
Arminius will be at the summer edition of Holz-Handwerk and will be showing their range of CNC brushes – designed to imbue a highly precise structural depth – to visitors at the Nuremberg trade fair.
The Detmold, Germany based company provides brushes of
unique and varied design solutions for rceating brushed surfacing solutions. Due to the typical size of the work pieces, the surface structuring of furniture elements is usually carried out on CNC machines. Users of Arminius CNC-sanding tools benefit from exceptionally fast production times.
Users will generate the desired surfaces using Arminius brushes with utmost precision and always achieve a consistent structure throughout entire production cycles – even working on light veneers is no problem says Arminius.
The individual strips of the brushes can be easily exchanged and variably combined. Through combination with sanding bristles, eg, fibres protruding from the surface due to the structuring, can be removed immediately.
Customers can choose the ratio between plastic and brass bristles according to individual needs.
For further information about Arminius CNC brushes for woodworking using this link: https://www.arminius.de/en/products/ brushes/#walzenbuersten-zylindrische-buersten and https://www. youtube.com/watch?v=1JG53lVA3dY
A long established company with an increasing presence in the CNC tooling market, Wealden Tool Company’s wide range includes traditional solid spiral cutters, replaceable tip cutters and many other items such as chipbreaker spirals for stringless cutting on solid timbers.
There is also a comprehensive range of solid tungsten carbide bodies with PCD (poly-crystalline diamond) tips for increased wear resistance when cutting abrasive materials.
Newly designed for the UK market is an econotip PCD range specifically for fast cutting 18mm MFC in one pass. This high shear compression cutter gives a clean cut on both faces without having to sink the cutter into the spoil-board, good longevity and feed rates better than 10m/minute.
Wealden continue to design innovative cutters to keep up with modern needs. Indicative of their unique approach to tooling is their Bead and Butt cutter (see their YouTube channel), but have a look also at their Surface Trepanning cutter with radius tips for spoilboard skimming on vacuum bed
machines. Recently they have been working on cutters to produce one piece MDF doors in the style of a traditional five-piece raised panel door.
Wealden’s sales team has a great deal of knowledge in CNC
machining as well as spindle and routing techniques. They are always available on the phone to shed new light on any problems you may have.
01580 890500
www.wealdentool.com
A long-established company with an increasing presence in the CNC tooling market, Wealden Tool Company has at least 95% of its range in stock at any time, meaning that orders can be dispatched the same day, offering customers a rapid source of supply.
The wide range features traditional solid spiral cutters including larger sizes and many innovative cutters hard to find elsewhere. Some cutters feature replaceable tips, offering the benefits of constant geometry and easy maintenance. All cutters plus toolholders, collet nuts and collets available online or call Wealden for technical advice or to discuss a particular requirement.
Surface Trepanning Swop-Tip© three wing cutter40 YEARS
Having many years of working in the panel and solid wood industry VWM have built up an enviable reputation for the supply of CNC routers and edgebanders, they have now increased the products in this industry selecting the very best on offer at very competitive prices.
Our Trusted Technos range of CNC routers have now been established for well over 20 years with over 140 machine installations in the UK covering a wide range of products and is now one of the best selling CNC machines around.
Our Lange edgebanders have also been within our stable since 2007 working in many different panel industry sectors and coming with an enviable reputation for quality and reliability.
CAD/CAM
(software included)
(conditions apply)
Two years ago, we introduced our Omaksan holemaster range of through feed CNC boring machines which again have been very successful for us we, have supplied a number of these to different panel market sectors from bedroom and kitchen manufacturers to high production office furniture manufacturers, they offer a fantastic flexible range of machines from a simple 5 sided boring machine to ones capable of 6 sides with twin tool changing routing spindles with many different options of boring heads.
We have now taken on our range of Cuttboss CNC beam saws to compliment our range of panel processing machines, these machines are from one of our trusted suppliers and come with many options available and extremely competitive prices.