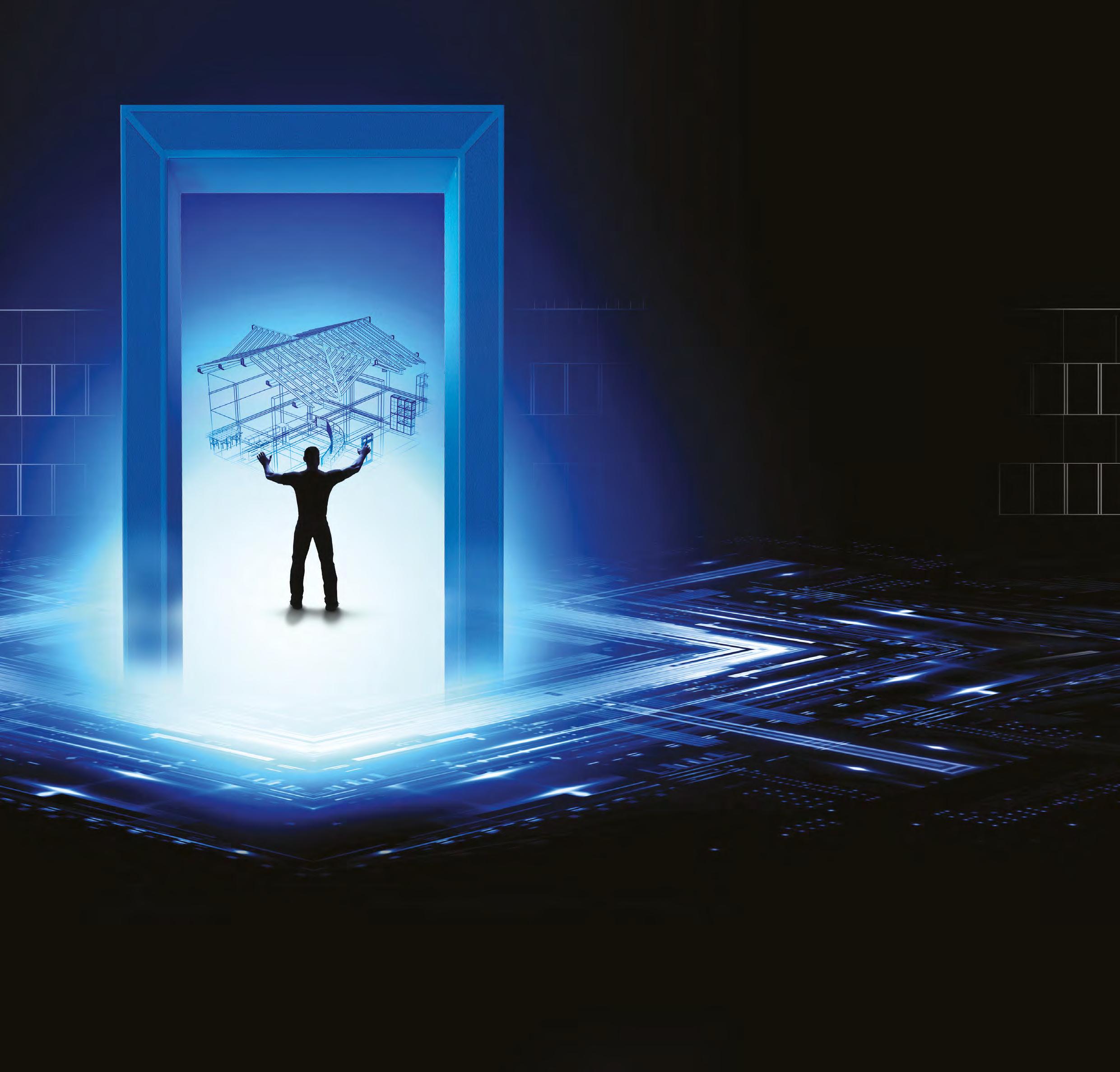
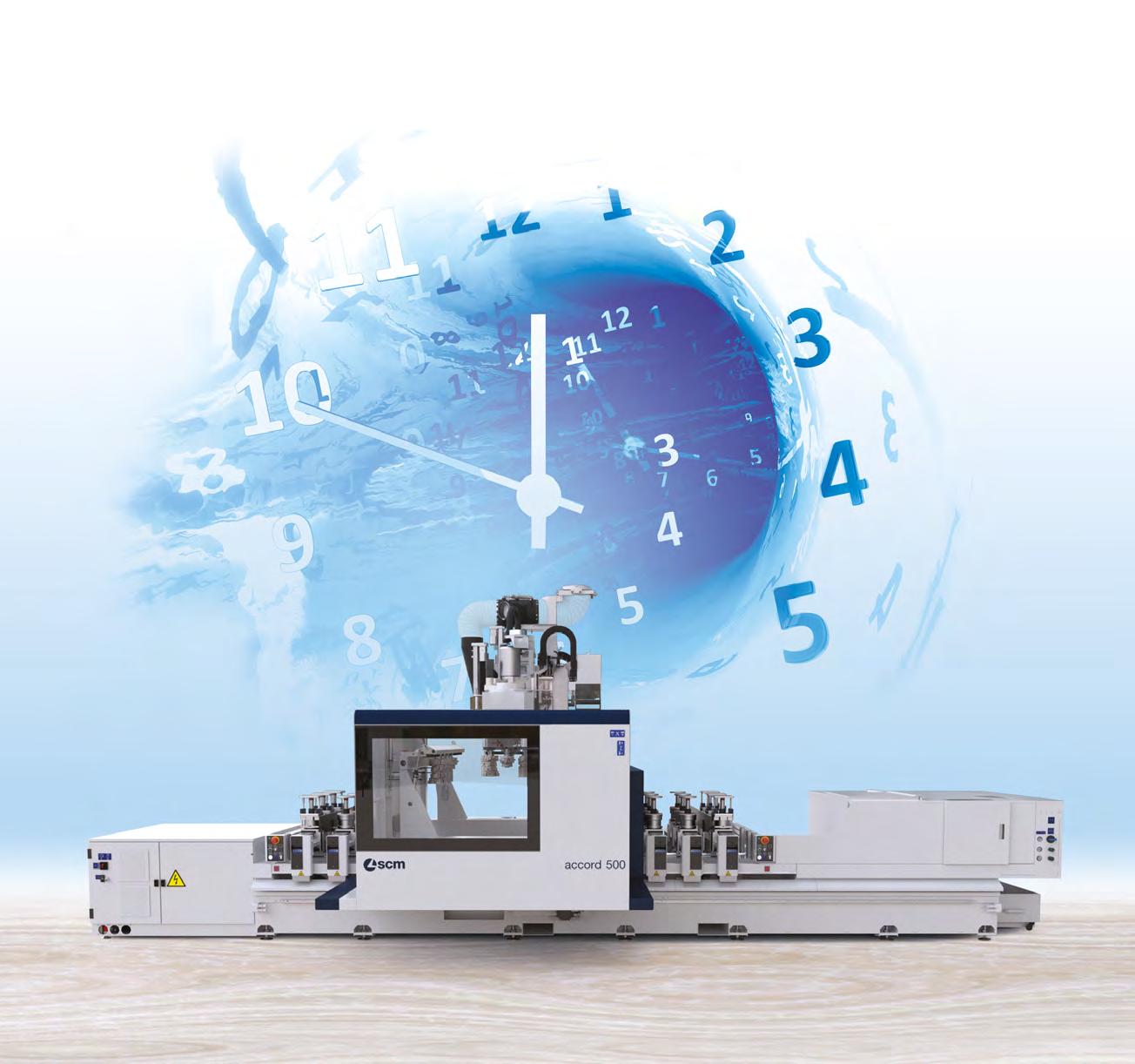
If ever we needed reminding that our planet is changing because of our actions and inactions, the current extraordinary weather situations across Europe – and the world for that matter –provide a stark reminder that plans and actions need to be taken by governments, businesses, councils and individuals to try and maintain an equilibrium of sorts. In terms of what the UK furniture and joinery manufacturers can do to offset the carbon footprint of their manufacturing operations and move towards, and perhaps beyond, net zero production is a major issue of our time and one which we should all have a very keen interest in.
Most would agree I’m sure that furniture and joinery manufacturers are under pressure to adopt eco-friendly production processes, to use sustainable materials and reduce waste. It seems clear to me that companies that fail to align with these values will probably face reputational damage and a decline in customer loyalty. It’s seems obvious to say that long-term success in furniture and joinery manufacturing is not just about being good at designing, producing and marketing a product, sustainable manufacturing is intrinsically linked to the success of business.
I feel confident in saying that sustainability is nowadays generally seen as an important consideration for all manufacturers – and thankfully, several companies in our industry stand out as impressive examples of how to draft and execute a plan towards net zero production. Along with the October issue, we will be publishing our first Sustainability Manufacturing supplement, so please do reach out and get involved if you have a story to tell or an interesting perspective –I’d welcome input from all quarters.
Looking at this issue, we have features including edgebanding materials and technology; dust extraction and wood waste management; joinery, window and door manufacturing; storage and materials handing along with the usual roster of content.
I hope you enjoy the issue.
John Legg, editorial directorTCM Living Group has joined The Furniture Makers’ Company, the City of London livery company and charity to the furnishing industry, as a corporate member.
TCM Living Group, the parent company of recognised upholstery brands Alstons, Ashley Manor, AMX-Design and Alexander and James, was formally welcomed as a corporate member on Tuesday 20 June 2023 at Furniture Makers’ Hall, London. Andy Kennaugh, Managing Director of Alstons; Gareth Mayhew, Director of ESG
and Compliance of TCM Living Group; and Jonathan Fearn, CEO of TCM Living Group, were admitted as corporate liverymen and personally welcomed by the Master of The Furniture Makers’ Company during an admission ceremony. Corporate membership provides opportunities for leading businesses to support the Company’s charitable activities, attend civic events and network with other members.
Amanda Waring, Master of The Furniture Makers’ Company, said:
“We are delighted that TCM Living Group has joined The Furniture Makers’ Company as a corporate member and we welcome Andy, Gareth and Jonathan. Our corporate members are of the greatest importance to us. We are delighted that so many different companies from the wider furnishing industry understand the importance of joining as members and supporting our charitable endeavours. All members, individual or corporate, are invited to participate in the many events in
the City livery calendar, which are great for networking, entertaining, as well as having fun.”
Jonathan Fearn, CEO of TCM Living, said: “Andy, Gareth and I are delighted to represent TCM Living as a corporate member of The Furniture Makers’ Company. We believe strongly in the need to work together as an industry to support and develop the UK’s future furniture makers, and to increase awareness of the skills and value in each piece of furniture produced every day.”
Effective immediately, IMA Schelling is taking over the specialist companies Carmet Automazioni and Blumenbecker Engineering System Technology, enabling it to offer its customers an even broader range of automation, handling and transport solutions. With the acquisition of an Italian and a Polish specialist company, the IMA Schelling Group is now adding even more to this range for its customers. The company is continuing to strengthen its strategic goal of becoming the number one contact for automation solutions in the furniture industry.
Carmet Automazioni, from the north Italian town of Treviso, has been developing, producing and distributing technologies for industrial automation and handling for over 50 years. The company’s range of products, for example, for cutting with a multi-blade saw, perfectly complements the IMA Schelling portfolio. The company with its talented team of 30 is now part of the IMA Schelling
Group, but will continue to operate under its established name and Carmet will also continue as the brand name.
Previously operating as a business unit of the international Blumenbecker Group, Blumenbecker Engineering System Technology, based in Katowice, Poland, specialises in consulting, project planning, design, software development, system integration and switchgear construction. The company has established itself as a leading expert in automation and robotics solutions in Poland and has a remarkable record in terms of product innovation and customer satisfaction. Plus, thanks to a partly identical customer base, it harmonises perfectly with IMA Schelling. Blumenbecker Engineering System Technology, with its team of around 60 employees, remains an independent company and will operate under the name IMA Schelling Polska Automation in the future.
At the AGM of Moralt AG in June, the Bavarian manufacturer of door blanks and licensed systems for functional interior and exterior doors board member and majority shareholder Klaus Feile announced a sales upturn of 15.5% for the 2022 trading year.
“Despite great challenges, Moralt successfully mastered the year 2022,” exclaimed Klaus. There was consensus on this conclusion at the AGM of Moralt AG where all 15 shareholders were present.
“With the acquisition of both highly specialised providers, we are continuing the development that began in 2016 with the merger of IMA Klessmann and Schelling Anlagenbau to form the IMA Schelling Group,” explains Managing Director Maximilian Lehner. “The yardstick for our strategic decisions is always the benefit we can offer our customers. And we are looking forward to now being able to provide our customers with an even wider product range and even more in-depth knowledge with our new partners.”
www.imaschelling.com
At the post-AGM meeting, Klaus gave an insight into the business development and the strategic orientation of the traditional company, which has had an impressive success story with many international case study projects since it focused on doorrelated business in 2013.
The export quota of Moralt AG was 68% in 2022. One of the most prestigious projects in 2022 was the Mandarin-Oriental Hotel in Muscat, Oman, on the famous
Shatti-Al-Qurum seafront.
Compared to the previous year, sales increased by 15.5% and a clearly positive result was reported. The increase in equity and thus also the increase in value of the Moralt share is 12.4%. Equity is a remarkable 66%. Tax advisor, Ms Gabriele Witte, explained the approved annual financial statements, the most important business figures and the positive development of the past few years.
www.moralt-ag.de
This year’s Wood & Panel Machinery Show will give visitors the opportunity to discuss their sawing, sanding, planing, moulding and profiling requirements with our expert team. Focusing on multi-material processing, our extensive machine portfolio covers equipment for working with solid wood, wood-based panels, composites, plastics, foam, rubber, metal and more.
Visitors are kindly asked to book ahead where possible for specific demonstrations.
→ Salvador automatic crosscut saws
→ Kimla CNC router and fiber laser
→ Elcon vertical panel saws
→ SCM and Altendorf sliding table panel saws
→ Stenner band resaws
→ Houfek and SCM wide belt sanders
→ Classical equipment from Wadkin and SCM
Made Smarter has launched a whitepaper to help SME manufacturers in the furniture industry accelerate their net zero plans.
‘Decarbonisation through Digitalisation: manufacturing made smarter and greener with technology’ is a practical guide to industry’s biggest challenge and opportunity.
The free-to-download document from the government-backed and industry-led technology adoption programme, aims to simplify a complex and fast-evolving topic by demystifying some of the terminology and analysing the latest research.
Crucially, the whitepaper offers insights about how a variety of technologies enable manufacturing and engineering businesses to make things smarter and greener,
while powering growth and creating new highly skilled jobs.
The whitepaper showcases makers who have started their decarbonisation journeys with Made Smarter including Crystal Doors In Rochdale.
It also signposts manufacturers to other initiatives including, Race to Zero, a campaign led by the United Nations, and the SME Climate Hub, a non-profit global initiative that empowers companies with tips and tools, including its Business Carbon Calculator.
Donna Edwards, Director of Made Smarter’s North West Adoption Programme, said: “Manufacturing is vital to the UK economy and our daily lives. But it also has a colossal impact on our environment.
“The pressure and scrutiny on the sector to be more sustainable is ramping up, and coming from all directions. It is our biggest challenge, but it is also a significant opportunity.
“Decarbonisation is not a distraction. It is an imperative. Talk needs to stop and make way for action and a concerted commitment to change. UK manufacturing must get behind the mantra that the future is decarbonised and digital.
“Made Smarter is committed to help small and medium sized makers get there with vision,
technology, leadership and collaboration. Our hope is that our ‘Decarbonisation through Digitalisation’ whitepaper will become a valuable part of any manufacturer’s toolkit to support their net zero journey.”
Over the last four years, Made Smarter has provided impartial, tailored and expert advice to thousands of manufacturers of every size and shape, and from every sector.
Digital transformation workshops offer practical steps towards digitisation and a clear digital roadmap to follow. There is also funding to help SMEs invest in technology and a variety of support to enable businesses to adapt to the green skills and digital leadership a net zero future demands.
Donna Edwards added: “In recent years we’ve seen technology play an incredibly important part in tackling disruptive and emerging challenges. It has helped businesses navigate the Covid-19 pandemic and recover, negotiate supply chain disruption
and labour shortages, as well as focus on solutions to mitigate the energy crisis.
“For the climate emergency, digitalisation offers manufacturers a huge opportunity to deliver operational efficiencies, decarbonise heat and power, optimise design and materials, and improve logistics and transport, benefitting their business, their bottom line and the environment. Then there is the reputational gain which helps secure customer loyalty, as well as attract new talent and investment.
“While decarbonisation might feel overwhelming, and it is by no means a simple task, it is vital manufacturers recognise they are not alone. Combating climate change demands collaboration, and that is exactly what Made Smarter is here for.”
To download the whitepaper visit: https://www.madesmarter.uk/ resources/decarbonisation-throughdigitalisation www.madesmarter.uk
New research from the British Woodworking Federation (BWF) reveals signs that timber windows and doors are viewed positively by homeowners, but that misunderstandings over their performance persist.
The survey of 1500 homeowners unearthed the main factors guiding product choice. It found that, aside from cost, for both windows and doors energy efficiency was the main priority for homeowners when selecting products (50% for
windows and 39% for doors).
When it came to windows, cost and energy efficiency weren’t the only significant factors for homeowners. Aesthetic appeal was most important to almost a third (32%), while the source and sustainability of timber was an important consideration for almost half (48%) of all homeowners, and almost three quarters (73%) of period property owners.
For doors, aesthetic appeal was also a prominent factor, a
top priority for 32%, with product lifespan (31%) and security features (24%) also important.
Encouragingly, 59% of homeowners felt that timber windows offered a wider opportunity for design and style options than alternatives, and 56% thought timber windows were more sustainable.
Helen Hewitt, CEO at the BWF, said: “The beautiful aesthetic of timber has always been its enduring appeal, whatever the
property type. And with timber products being designed to be repaired rather than replaced, they are a naturally sustainable choice. It’s hugely encouraging that the benefits of timber are recognised by those who may be considering replacing windows or doors in their homes or buying properties in need of renovation.”
www.bwf.org.uk
Research says homeowners positive over timber in the home, but misconceptions remainDonna Edwards Richard Hagan from Crystal Doors in Rochdale
It was in 1958 when Striebig founder, Ludwig Striebig constructed his first vertical panel saw from a small joinery workshop in Lucerne, Switzerland. Fast forward 65 years and the global vertical panel saw specialist –which has become synonymous with quality, precision and longevity – has completed the build of its 50,000th vertical panel saw.
To mark this impressive milestone, the Striebig Control vertical panel saw – which has already been earmarked for a furniture manufacturing company in Ireland – features a certificate of uniqueness that has been signed by Striebig AG’s management team and employees.
“The personal gesture is a resounding nod to the many people that have helped the company to grow and become a leader in its field,” says Daniel Bucher, Striebig’s CEO. “On their retirement, Ludwig and Ida Striebig left the company
The Hausham, Bavaria based specialist in door blanks and door systems for timber performance door products, has again won a TOP 100 award.
Moralt is well established in this segment and internationally successful. Focus centres around the technical characteristics of doors, such as fire, smoke, sound and thermal insulation or security.
Numerous case studies impressively show the possibilities of processing companies as contractual partners of Moralt. In order to promote a
positive innovation climate, the Management Board and Supervisory Board issue shares to employees.
This promotes personal identification and strengthens motivation. Every employee has the freedom to pursue new ideas. This is how market innovations keep emerging, which are also reflected in some patents.
“Innovation within ever more rapidly changing markets is a very important factor for us,” emphasises CEO Klaus Feile. The long-standing network with
the following recipe for success: ‘If you want to be successful in the market, you need a healthy company that is perfectly positioned at all times. Committed and satisfied employees are essential.’ These words have shaped the company you see today and continue to influence the paths we take to grow and diversify. The completion of our 50,000 machine is the result of a combined effort and could not have been achieved single-handedly.” www.tmmachinery.co.uk
cooperation partners facilitates the innovation work. A short reaction time is important: current developments are discussed daily
The East Anglian Golf Day, a charity event organised by independent furniture retailer John Doe of Diss in aid of The Furniture Makers’ Company, has raised a tremendous £5000.
Around 70 golfers from companies including Abingdon, Belfield Home & Leisure, Brockway Carpets, Clifford Floors, David Gundry, Elite Interiors, Glasswells, Harrison Spinks, Kaymed, Square Trade, Ulster Carpets and Westex Carpets, took part in the tournament in June at Diss Golf Club in Suffolk. The event was generously sponsored by Fama, Karndean, Kettle Interiors,
Lebus, Sherborne, Square Trade, Stressless, Victoria Carpets, Vida, and Wiemann.
After a great day of play, competitors enjoyed a buffet lunch which was followed by a prize giving ceremony and raffle.The winners of the competition were: President’s Cup: Daniel Donnelly; Kingsbury Cup: first prize: Charles Doe, second prize: Nathan Doe; Albro Cup - first prize: Joe King, second prize: Liam Riley.
Edward Doe, director of John Doe of Diss, organiser of the event, said: “I would like to take this opportunity to express my sincere thanks and appreciation to everyone that
supported the charity golf day we hosted last week at Diss Golf Club in aid of The Furniture Makers’ Company, the furnishing industry’s charity.
“I’m sure everyone will agree that it was a brilliant day, which seemed to be very much enjoyed by all. I am proud and delighted to officially announce that thanks to everyone’s generous support, we managed to raise the magnificent grand total of £5020! Every penny of which will help The Furniture Makers’ Company continue their amazing work.”
Jonny Westbrooke, CEO of The Furniture Makers’ Company, said: “I
and suggestions from employees are implemented promptly.
www.moralt-ag.de
www.top100-germany.com
would like to say a huge thank you to Edward and the team at John Doe of Diss for organising such a successful event. We are delighted that £5,000 has been raised for the charity. The money raised will go a long way to supporting more people in the UK furnishing industry who have fallen on hard times.”
Kölnmesse announces a new biennial event for the furniture production and interior design industry with interzum forum italy. The interzum forum italy presents an inspiring congress format with an accompanying exhibition area specifically tailored to Italy and its neighbouring countries, but also to other major European markets. The innovative format will be hosted on 6-7th June 2024 at the Fiera di Bergamo trade fair grounds in Bergamo, Italy.
The event’s concept focuses on a rich two-day programme of high-calibre lectures, which will offer deep insights into the latest trends, the most interesting innovations and current market developments. The congress format will be accompanied by an exhibition focusing on the interzum product segments such as offices, upholstery and textile machinery as well as surfaces and fittings.
“The interzum forum is an ideal platform for the Italian market, one of the most important markets in the industry. Many of the central questions of the industry considering the requirements of the Italian market can and will find new solutions here in the competition of ideas and innovations”, says Matthias Pollmann, Vice President of Kölnmesse.
“This broad set of lectures, networking and business opportunities, combined with workshops and matchmaking, will make interzum forum italy the ideal place to discuss
current industry trends. The event will provide the perfect forum for shaping the innovations that are driving rapid transformation in the markets and having a significant impact on production chains and the skills required for the furniture production and interior design sectors”, says Thomas Rosolia, Managing Director of Kölnmesse Italia.
Responding to industry’s needs “interzum 2023 in Cologne has demonstrated the importance of being closer to companies by creating opportunities for discussion and providing an in-depth analysis of key topics for the industry”, adds Rosalia. “We are now responding to the industry’s need for a streamlined and visitor-friendly format in Italy as one of the major furniture-producing countries in Europe. In the years when interzum is not hosted in Cologne, we will offer industry professionals a mix of a congress with current, high-level topics and an exhibition section.”
interzum forum italy has chosen the Fiera di Bergamo trade fair grounds, as it is an already well-established exhibition complex, strategically located in the heart of Lombardy with excellent infrastructure connections. Travelling to and from the fair grounds is easy and convenient, allowing attendees to get the most out of the two days of the event and to focus their energies on the business opportunities that will be generated.
interzum forum italy is designed for all the sectors linked to furniture production and interior design. It is aimed at a broad spectrum of manufacturers, specialist retailers, architects, interior designers, decorators, contractors and consultants. The event will offer them outstanding content and an innovative format that enhances the congress element. It will be held in even years starting from June 2024, in synergy with interzum in Cologne, which is hosted on a regular schedule in odd years. www.interzum.com
Preparations for the next Xylexpo, the biennial international exhibition of woodworking and furniture industry technology, are underway. The timeline of the next edition, scheduled from 21st- 24th May next year at FieraMilanoRho in Milan is approaching fast, so it is is now launching the registration campaign for the exhibitors who do not want to miss the opportunity to be in Milan.
The communication campaign for early bird exhibitor registrations has started offering attractive opportunities for those who submit their application before 30th October.
The campaign is also presenting some of the key topics of Xylexpo 2024 – primarily Xylepxo will reaffirm its strong focus on digital. The Xylexpo Arena will be the epicentre hosting meetings, presentations, round-
table discussions and seminars, that will be broadcast in different areas inside the show ground, and following the success of this initiative in 2022 it will be streamed live via the Xylexpo Digital platform. Insodoing, also those who cannot attend the exhibition will have the opportunity to experience the Xylexpo 2024 atmosphere.
Xylexpo will offer its online visitors a one-ofa-kind opportunity to walk through the booths, joining issue-specific ‘tech-tours, listening to interviews and following the itineraries organised by our shooting crews and broadcast live. All this content will be available and accessible after the event via the Xylexpo digital platform.
Xylexpo, in collaboration with FieramilanoRho, will offer innovative tools and services for promotion inside and outside the fairgrounds: from digital signage from a new video promotion system installed all over the expo centre to the new exhibition app, to the interactive digital platform Expo Plaza where exhibitors can present their offer, collect contacts, and arrange meetings and video chats.
www.xylexpo.com
Daltons Wadkin is pleased to announce that this year’s Wood & Panel Machinery Show will be held in Nottingham on 3rd-5th October 2023. The event offers a fantastic opportunity to see live demonstrations of the latest machinery for processing multiple materials, from solid timber and wood-based panels to plastics, composites and metal.
“Our in-house exhibitions have proved a great success with attendees increasing year on year,” enthuses sales director, Andy Walsh. “We are excited to showcase our leading brands and give customers the chance to witness first-hand what sets us apart from the competition. Our customers can expect the highest quality equipment backed by professional, reliable aftercare. We welcome the industry to visit, discuss and plan their future machinery investments.”
There will be a big emphasis on crosscutting, with automatic and manual models on show along with a range of tables and
stop systems. The full range of Salvador optimising crosscut saws – including the ever-popular SuperPush 200, high capacity SuperPush 250 and versatile SuperAngle 600 – will showcase the huge production benefits these machines can deliver.
Kimla CNC routers and fibre lasers will be showing the multi-material processing capabilities of the range. These are ideally suited to those working with sheet metal, panels, rubber or foam, for example.
A range of optional cutting heads including high speed spindles (up to 60,000 rpm), oscillating knife and creasing wheel can be configured to suit almost any production requirement.
Kimla’s unique operating system and superior build quality deliver significant advantages and need to be seen to be believed.
Daltons Wadkin is proud to claim that it offers the largest range
of panel saws in the UK and Ireland. Working with leading manufacturers including SCM, Elcon and Altendorf, the company can call upon any one of over 40 models of sliding table panel saw, vertical panel saw, or beam saw to solve customers’ sawing requirements.
On show will be the latest Elcon wall saws with patented dust extraction technology, SCM dimension saws with the new Eye-S touch screen control, along with further models to be confirmed.
Key models from SCM and Houfek will highlight the many benefits modern wide belt sanders can bring to almost any workshop. Save time, improve calibrating accuracy and surface finish while protecting operators from exposure to harmful sanding dust. A choice of head configurations and working widths are available to satisfy solid wood and panel finishing demands.
It wouldn’t be a show without the impressive Stenner band resaws. The latest ST100R model will be on demonstration with pitless installation, powerful feed mechanism, advanced operator safety features and modern guarding. Customers are increasingly trading in their old style resaws or more modern but light weight “equivalents” for this heavyduty workhorse. Come and see why.
Classical machinery from Wadkin and SCM, including planer moulders, thicknessers, spindle moulders, lathes and more will also be on show. Full details of makes and models will be confirmed soon.
For the latest show news follow Daltons Wadkin on Instagram, Twitter, Facebook, LinkedIn, YouTube and TikTok. Or, contact a member of the Daltons Wadkin team. 0115 986 5201
The grand opening of the new Technology Centre in Rimini will take place from 2830th September. The opening will offer an opportunity to discover how SCM’s latest technological and digital innovations can assist clients with developing their business.
These include the innovative automated Cargo system for machining centres, the new Maestro Lab software and the advisory services enabled by Maestro Connect for a new standard of relationship with the client.
SCM is a well-established brand which continues to grow and innovate, investing in its industrial sites in Italy to increase its production capacity and further enhance its relationship with its clientele.
The new Technology Centre has been created as part of this expansion and modernisation programme at SCM’s headquarters in Rimini. Its opening is aimed at companies and stakeholders from the entire woodworking industry at a global level.
Housed within a 4,000m2 space which, for all intents and purposes, is the new digital home for woodworking innovation, every detail of the technology centre has been planned to offer the client the widest range of technologies and services possible and to provide integrated, connected, flexible, more sustainable and
optimised processes at each stage of secondary wood processing.
The event will be an opportunity to discover the latest solutions developed by the Group, which combine strong technological skill for the production of solutions for furniture, doors and windows, timber construction and artisan joinery, with the development of software and services, to accompany the client at each stage of their production process.
Some of the main new entries include those applied to machining centres, which will be the subject of a specific training event: Cargo, innovative automatic system for loading and unloading doors and panels, and the new CADCAM Maestro lab programming software. Cargo will be presented integrated with the morbidelli m200 pods and rails machining centre. It is a fully automated cell that requires no operator supervision, and is unique in the market for its ability to continuously load and unload pieces in masked time while the machine performs drilling and routing operations. This exclusive solution allows for maximum efficiency by avoiding manual work phases and their associated costs and unproductive time. In addition to an unprecedented ease of use, both the machining centre and Cargo are directly managed with the Maestro active HMI interface.
Though technology remains at the heart of the SCM experience, its software and services offering is an increasingly crucial element of the business’ continuous and shared relationship with the client.
Maestro lab is the new state-of-the-art CAD/ CAM programming software for both office and machine use. Intuitive and dynamic, it allows you to easily transform an idea into a finished product, thanks to intelligent and technologically advanced programming functions and more than 150 already integrated apps. So, from the office to the factory in a flash via an enjoyable and fast user experience.
The contextualised and continuous exchange of information from the machine to the cloud thanks to the IoT Maestro Connect platform means SCM can provide clients with rapid access to answers, as well as specific advice which will support the operators and maintenance workers with their challenges and needs for autonomy when using, carrying out maintenance and programming the machine and software.
On this topic, a specific area has been created inside the Technology Centre which will demonstrate how the data is transformed into bespoke assistance and advisory services of a proactive and predictive nature – all with a view to guaranteeing the client operational continuity thanks to the most evolved digital technologies and constant attention by the SCM service team. SCM continues to invest in the excellence of its customer service and, for the event, will open the doors to its new automatic storage for spare parts – Autostore. This innovation has allowed SCM to increase the pick-up speed of the codes fivefold and increase the number of orders handled within 24h by 26%. All this with an energy consumption of less than 0.1 kWh per robot, confirming the Group’s focus on sustainability.
Sustainability, which also means ergonomics and ease of use, is made available to operators of all the SCM machines by the renewed eye-M control panel, which makes the operator’s work easier and offers a modular programming and a higher calculation power.
The new SCM Technology Centre will see flexible cells integrated with the unmanned AMR shuttles: for beam saw, gabbiani gt2 with robot for loading and unloading; for edgebanding, stefani cell E with gantry panel return system;
“Though technology remains at the heart of the SCM experience, its software and services offering is an increasingly crucial element of the business’ continuous and shared relationship with the client”
for drilling and dowelling, morbidelli cx220 which can be used either with just the robot or partially manned.
Also highlighted is a beam saw and nesting cell for batch 1 with flexstore hp automatic storage and robot to unload the finished pieces, small pieces and waste, a gabbiani p80 panel saw and a morbidelli x200 nesting machining centre integrated into the same storage.
Worth highlighting for edgebanding is the new olimpic 500plus. It can achieve even higher productivity to machine edges in solid wood up to 12mm and glue plastic edging using hot-air technology for a line of invisible glue.
In terms of assembly, action e is particularly notable. Its new loading and unloading system greatly helps the work of the operator. Meanwhile, the action p loading and unloading electromechanical clamp with new HMI allows work programs, production data and general database to be imported and exported.
The latest in the dmc eurosystem will be present for sanding and calibration for machining work on unfinished and painted panels. This includes the new 15” eye-S control panel to handle all the functions directly from the touch screen; the new HMI Maestro active sand for ideal handling of the tool storage; and the new planetary unit for an accurate finish on any surface.
Also on display will be the new dmc sd 90 functions – a highly customisable solution, available in 12 versions, to guarantee the best results on solid, lacquered and painted wood.
It will be possible to request a specific demo at the Surface Lab at Villa Verucchio (Rimini) on the new dmc system with laser unit, for exclusive productions and three-dimensional scorings on parquet, wooden elements, mdf panels to be
veneered, fibre cement panels and solid surfaces of any length.
In a link up with Superfici’s Technology Centre, there will also be demos of the latest new entries for painting and finishing, such as the compact xl sprayer for high capacity productions and a more efficient paint recovery system; the innovative UV LED polymerisation system for performances on a par with conventional UV polymerisation, while keeping the advantages of LED; Excimatt, the Superfici excimer technology for the finishing on different finished products and materials, capable of providing extra-opaque effects that are surprisingly smooth with no more compromising on the surface resistance. In addition, don’t miss the Cartesian and articulated robots for painting windows and doors and panels, designed to guarantee production speed and continuity together with a very high level of precision and machining quality.
During the Grand Opening, visitors will have a chance to discover, in a world preview at the expanded production site in Rimini, the new system 9 integrated range for the production of windows and doors with a brand-new entry – the celaschi action bilateral tenoner.
The SCM range stands out for the high speed at which it changes configuration and the extreme flexibility in handling the piece lengths. This makes it possible to produce up to 200 complete windows per shift, even with mediumsmall batches. The new celaschi action, in particular, allows for two elements of differing lengths to be machined simultaneously, making the most of the principle of machining with the transfer of the motors when the pieces are stopped. Some of the advantages include the presence of four electro-spindles, each one
subjugated by an eight-position tool change. Windorflex – the new automatic cell for complete windows and doors which optimises productivity by keeping a high flexibility and machining quality – will also be on show at the plant in Rimini.
The automatic superset nt throughfeed moulder will be on show at the Technology Centre for the first time, complete with SCM’s Maestro connect IoT platform, for an intelligent and connect production of profiles for windows, doors, staircases, matchboards and furniture parts.
The new entries also include Connexus fj – a tenoner-mortiser that meets all the machining demands for different kinds of solid wood or coated MDF, including complex joins such as miter doors, face frames and French joints on cabinet doors and shutters.
Those SCM machines that are best suited to artisan work will also be on show. This will include stand-alone as well as integrated solutions, such as those for the beam saw, edgebanding and drilling of the Smart&Human Factory integrated cell. This is dedicated to flexible and bespoke production from raw materials to finished furniture, and is enhanced by the integration with MES software.
Other new entries will include: “blade off”, SCM’s innovative safety system applied to circular saws which, thanks to the smart sensors, prevents accidental contact between the human body and the blade; as well as startech cn k – a compact three-axis machining centre for routing of any kind, decorations, engravings, production of signs and 3D model prototyping.
A good price-performance ratio and design are among the decisive criteria for buyers of brand kitchens when selecting their kitchen. Nolte Kitchens meets these needs with a wellthought-out variety of colours and appealing surface concepts. For this purpose, Venjakob was asked to supply a spray coating system with drying, which also works economically with small batch sizes and saves resources.
For 60 years, Nolte Küchen from Löhne in East Westphalia has been producing high-quality fitted kitchens that focus on people. For this reason, the company was named Germany’s most popular kitchen brand for the third time in a row. Consumers give the brand very good ratings for design and a good price-performance ratio. The award was presented by the German Institute for Service Quality.
The need for individuality is increasing. “Kitchen fronts shape the look of a kitchen. Styleconscious and design-oriented consumers want an ever-greater selection of colours and colour combinations,” says Raphael Gottschalk,
project manager at Nolte Küchen. This variety has to be produced in the shortest possible time and in a wide variety of quantities – from batch size one – in a customer-oriented manner. In order to meet these criteria in the future, the kitchen manufacturer is continuously investing. In this case, in a spray coating line with drying technology, which was projected together with Venjakob, the mechanical engineering specialist for surface processing.
The project objectives included cost optimization, quality aspects, reduction of throughput times, and greater flexibility in the production process,” explains Raphael Gottschalk. Before deciding to finish the surrounding materials (side panels, visible sides, plinths, etc.) internally, Nolte Küchen resorted to external partners. As general contractor, Venjakob took over the complete implementation of the finishing line for coating
and drying matt surfaces. With the exception of the sanding machine, all system components and the conveyor technology were designed, produced and installed by Venjakob. The external sanding machine was integrated into the plant control system. The plant was to be designed in such a way that kitchen furniture components of smallest sizes up to max. 2,800 mm length and 1,300 mm width can be coated automatically in a continuous process.
Colour management system shortens set-up times
Nolte Küchen defined specific requirements for the performance of the system. Only waterbased coatings are used. The challenge was the variety of colours. “The system had to be able to run economically in small batches and allow up to 20 colour changes,” says Reinhard Prus, head of the Surface Department in Löhne. Since each colour change takes time, a colour management system was used.
This keeps set-up times as short as possible. The coating process is carried out by four
spray guns in high-performance linear mode. The gun speed is infinitely adjustable and fully automatically controlled. A scanner in front of the spray booth determines the workpiece shape, number and position. The guns are switched on and off precisely above the workpiece. Each individual workpiece is detected separately. Workpiece measurement takes place automatically and is largely parameterisable. All relevant adjustable parameters can be preset in any quantity at a central operating point in front of the spray booth via a touch-screen computer and called up as a spray program. The individual programs can be easily changed by the operator and can be stored in the system. “All relevant process parameters are stored in the recipes,” explains Christian Schulze, sales engineer at Venjakob.
Another customer requirement: short through feed times so that the kitchen fronts are completely dry after the finishing process and the rear sides can be coated directly afterwards. The drying process was coordinated with the manufacturer of the two-component waterbased UV coating material used. In addition, several test series were run in Venjakobs’ own technical center. Drying is carried out with rising air temperatures: After coating, the workpieces first pass through a leveling zone for two minutes.
Then follows a flash-off channel with an air temperature of 30-35°C. The components are continuously conveyed on closed belt conveyors. Now they pass into jet drying channel with a temperature of 40-50 °C. Following drying,
‘This variety has to be produced in the shortest possible time and in a wide variety of quantities –from batch size one – in a customer-oriented manner’Pump stations for paint supply
the coated surface is cured with UV light. The UV curing oven has its own electrical control cabinet, but is controlled via the control system of the overall production line. A built-in real power control compensates voltage fluctuations that occur in overloaded or unstable power grids, ensuring consistent high-quality results.
Best finishing results due to special air supply
The required process air is supplemented by two central supply air systems, which were projectplanned by Venjakob and integrated into the overall concept. In the area of spray coating, the supply air system works with humidification. Before it leaves the unit, the supplied air is heated, cleaned and humidified to ensure optimum air quality for the best coating results. A second supply air system without humidification supplies the areas of the sanding machine, the dust removal system and the drying section.
Sanding machine can be used separately
There was a special feature in the conveyor technology. The sanding machine integrated in the finishing line was supposed to be used separately. For this purpose, a movable belt
conveyor on flanged rollers was installed between the sanding and the spray coating machine. When rolled aside, this allows the sanding machine and the spray coating machine to be used separately. For combined operation (sanding + coating), the belt is in line and allows line operation.
Production at the Löhne site started immediately after the in-house training in July 2021. The output of the finishing line has been continuously expanded using a two-shift operation to date. With Nolte Küchen, Venjakob has another good reference. “Our requirements were fully met according to the specified parameters. The support and service after the final acceptance were also very flexible and top in every respect!”, Reinhard Prus and Raphael Gottschalk confirm the good performance of the Venjakob team.
www.venjakob.de
Mirka’s innovative Galaxy abrasive combines effectiveness with long life, thanks to a new self-sharpening ceramic grain, a clog resistant coating and the new Multifit™ hole configuration.
For further information or to arrange a demonstration, please contact Customer Services on 01908 866100.
Based in Greenford, West London, Claris Housewares & Stationery Solutions Limited trades as Highdecora, and specialises in custom fitted furniture in the home and office sectors. Product categories include fitted bespoke kitchens, wardrobes, media walls, bed frames and other bespoke home and office furniture.
“Each and every product sold on our website is designed and produced by us in our 15,000ft2 facility,” explains managing director, Sanjay Bajariya. He continues, “Recently, our manufacturing capacity has been restricted because of the manual machinery we were using. We realised that to achieve our growth potential we needed to invest in more advanced machinery.
“When we analysed the bottlenecks. It was clear that our panel dividing and drilling operations had to be improved. Consequently, we researched the market looking for a suitable beam saw and CNC drilling centre. We narrowed our shortlist down to a couple of brands and carried out a more thorough investigation which included seeing the machines in operation at other companies.”
“HOMAG began to emerge as the best option on the market. Not only are its products robust and technically advanced, but also the intuitive control software makes them extremely easy to operate. The fact that they are designed and engineered in Germany gave us confidence that they would be reliable over the lifetime of the machines.
“Taking our short and long-term requirements into account, we decided to place orders for a HOMAG SAWTEQ B-130 entry level beam
saw and the highly rated DRILLTEQ V-200 CNC processing centre.
“As you’d expect from a German company, the preparation, scheduling and installation of the machines was precise and organised. Both the saw and the drilling CNC were installed by HOMAG engineers on time and inside five days.
“Our operators were given a day’s training on both machines. This was carried out by one of the HOMAG installation engineers who did an excellent job getting each team member fully up to speed on the saw and the CNC.”
Both machines are very easy to operate; the SAWTEQ uses the Magicut software whilst the DRILLTEQ is controlled by HOMAG’s market leading software, woodWOP.
“From day one, the new machines have transformed our production,” says Sanjay. “When we relied on the manual saw and drilling machine it could take up to a week to get a job processed. Now, we can easily process four or five jobs a day. What’s more, the accuracy and finish quality are superb.
“These are the first machines we have bought from HOMAG, but I’m sure they won’t be the last. From the moment we first showed interest, through the sales process, installation and aftersales support, each HOMAG person we have come in contact with has been responsive, helpful and extremely knowledgeable. We can’t fault them,” concludes Sanjay.
For a demonstration or further information on HOMAG woodworking machinery or software, contact Adele Hunt at HOMAG UK on 01332 856424 or email: info-uk@homag.com
www.homag.com
www.clarisworld.co.uk
“Taking our short and long-term requirements into account, we decided to place orders for a HOMAG SAWTEQ B-130 entry level beam saw and the highly rated DRILLTEQ V-200 CNC processing centre”HOMAG SAWTEQ B-130 entry level beam saw DRILLTEQ V-200
Whether you are a designer or a producer of interior furniture and fittings, floorings, outdoor facades, windows or doors, we have the right finish for you. At Sherwin-Williams we have a coating solution to meet virtually every need. As the leading provider of customized finishing solutions we can offer you the latest industry innovations at the highest quality to add value to your process and your everyday life. If you require a finishing solution, and you want the optimal one for your operations then look no further.
Forbo has just introduced three new colours to its furniture linoleum line. Launched at Salone del Mobile 2023, Clay, Walnut and Leather are timelessly elegant additions to its ‘Furniture Linoleum Desktop’ collection, and are already available from Ostermann in rolls (from 1 metre), cut to size or as ready-to-install fronts or furniture parts.
According to Forbo, the three light, sand brown earth tones are designed to blend in best with the natural materials found in a classic interior. The result is three calming creations with an exceptionally matt look.
When carefully merged into a balanced colour scheme, the new surfaces will bring nature inside and create a harmonious atmosphere.
Alternatively, individual furniture pieces in earth tones combine well with all furniture in matt plain colours, for example in dark blue, claret, or green.
New colours, new options
Furniture linoleum is a truly sustainable surface. Made from renewable raw materials, the material’s matt apperance and soft feel bring a timeless elegance. The flexibly mouldable and antistatic material is easy to process and equally suitable for horizontal and vertical applications.
For linoleum surface bonding, Ostermann’s experts recommend the REDOCOL Kombicoll Super-N D3 white glue. One option is to press the linoleum onto multiplex boards. If chipboard is preferred as a substrate, multiplex wood veneer edgings are a good alternative to create the high-quality look. If the edging is to be colour-matched, an ABS edging in the exact same colour can be found under the respective linoleum product in the Ostermann online shop.
www.ostermann.eu
“Made from renewable raw materials, the material’s matt apperance and soft feel bring a timeless elegance”At Ostermann, furniture linoleum is now available in three new, warm natural shades
“The Curve” is a multi-layered thick veneer edging so flexible that it opens up new dimensions in the processing around tight radii.
It differs from conventional thick veneer edgings by way of its special setup. This feature enables a processor to run a thick veneer edging around even the tightest radii (e.g., radius 20) in just one pass on a processing centre. This ensures significant time savings and is thus also clearly beneficial in terms of economy and efficiency.
It can be used on standard processing centres with hotmelt or dispersion adhesives. Users should observe the instruction manual of their machine and the material safety and data sheet of their glue supplier.
The edgings should be stored horizontal. Ideal conditions are approximately 20°C and a relative humidity between 50% and 60%. Under this condition the moisture content of the edgings should establish at ~ 10%. A climate-controlled storage is essential to preserve the flexible properties of the edging.
In summary: “The Curve” unfolds its special qualities when it comes to cover edges of workpieces with small radii on processing centres. This is what makes this thick veneer edging so attractive for the discerning user.
info@h-heitz.de
www.h-heitz.de
“This feature enables a processor to run a thick veneer edging around even the tightest radii (e.g., radius 20) in just one pass on a processing centre”
We offer an extensive selection of different hotmelt, PUR, contact and special adhesives, white and wood veneer glues, plus the appropriate application devices and cleaners for your project. In addition, you will also nd practical user tips from our experts.
For further information, go to www.ostermann.eu and type in
#adhesives
SERVICE, DIVERSITY AND SPEED - THAT IS OSTERMANN.
Having established the business in Malvern, Worcestershire in 2018, Kal Sandhu and Derrick Gray decided their successful Edging Supplies business needed a more practical, larger facility.
Having twice outgrown its original premises thanks to ongoing success, Edging Supplies has recently relocated taking an alternative and more substantial part of the same building yielding a 11,000 sq ft warehouse, workshop and offices to enable the company’s next phase of development.
Since it was established in 2018, Edging Supplies has been the official UK distributor for the impressive Tece edging manufacturer. Since then, the company has grown to become an important and reliable supplier of a comprehensive range of in-stock edgings and ancillary products from numerous suppliers and this growth has created a wider cross-section of customers across the country.
EDGING SUPPLIES LTD, ARE A STOCKIST OF EDGE BANDING MATERIAL FOR SOME OF THE LARGEST FURNITURE MANUFACTURING MAKERS IN THE UK
Edging Supplies Ltd
����� ������
enquiries@edgingsuppliesltd.co.uk www.edgingsuppliesltd.co.uk
Derrick Gray - ����������� / Kal Sandhu - ����������� Unit � /11 Advantage Business Park, Spring Lane South, Malvern, WR�� �ATWith more than 30 years of experience under their belt, Kal and Derrick and their team have developed a strong and varied customer base and continue to build on the company’s reputation for high-quality, responsive service. Being responsive in this market is a crucial advantage – smaller orders received by Edging Supplies before 1pm are processed the same day for delivery the following day by DHL; and for larger pallet-based orders, they use a courier or pallet-carrier – again with the next-day delivery service scenario. A shining example of the owners’ commitment to their customers is that both Kal and Derrick will always answer messages and telephone calls seven days a week where required.
This recent move, although geographically not far from where they were previously, has allowed the business to increase its stock-holding further to more than five million metres of edgings and a comprehensive range of accessories. Edging Supplies company is well set with a strategy for growth and continues to attract new clients with quality products and outstanding service ethos – to “Edging Supplies is well-set with a strategy for growth and continues to attract new clients with its quality products and outstanding service ethos www.edgingsupplies.com
Here at VWM we have complete edgebander solutions to suit all pockets and di erent production needs our Lange series of edgebander o er something for all types of furniture manufacturing.
The B85 series o ers a compact edgebander for the Medium sized workshop, but gives you options of pre-milling, corner rounding, panel cleaning, radius, glue scraping and bu ng.
The B80 series o ers a compact edgebander for the smaller workshop, but gives you options of pre-milling, panel cleaning and options of radius or glue scraping stations.
The B90 series o ers a compact edgebander for the Larger sized workshop, but gives you options of pre-milling, corner rounding, faster feed rates, panel cleaning and options of radius, glue scraping and bu ng, it can also give options of dual glue pots for PUR and EVA.
The B92 L-Motion series o ers a compact edgebander for the high production manufacturing unit it gives CNC position for all movements saving set up times when changing tape sizes which is a time saver for “just in time” production runs.
The machine has options of pre-milling, corner rounding, faster feed rates, panel cleaning and options of radius, glue scraping and bu ng, it can also give options of dual glue pots for PUR and EVA.
Industry-wide changes regarding the usage of PUR adhesives are just around the corner. The legislation according to REACH regarding the handling of diisocyanates will change on 24th August 2023.
In light of this, Kenyon Group is heralding the manifold benefits of Technomelt Micro Emissions (ME) PUR adhesives. Henkel ME PUR adhesives contain less than 0.1% monomeric diisocyanate, which therefore reduces the hazardous isocyanate-containing vapours by up to 90% .
Technomelt Micro Emissions (ME) PUR adhesives have no hazardous labels and do not require the specific professional training for operators which will be required when the legislation changes for standard PUR adhesives. Technomelt (ME) PUR adhesives offer easy and safe handling in production. Nobody likes
warning labels and the fact that these can now be eliminated brings huge benefits. Mindful of health and safety, companies are now assessing which options within the sphere of PUR adhesives will allow them to improve their operating procedures, whilst at the same time reducing risk. The solution, for Kenyon Group, is simple – Technomelt Micro Emissions (ME) PUR adhesives.
These adhesives offer the same performance benefits that come with PUR technologies – low coat weight, tight joints, invisible glue lines, exceptional high performance combined with excellent heat and water resistance – but without the hazardous labelling, making it more environmentally friendly and safer for operators to handle.
Henkel Technomelt Micro Emission (ME) PUR adhesives are available for flat lamination, edgebanding and profile wrapping applications. Available in two kilo blocks, 20 kilo drums, 200 kilo drums and shortly in the ever-popular granules – Kenyon Group has your application covered and the environmental impact reduced.
To discuss the positive impact Technomelt Micro Emission (ME) PUR adhesives can have upon both the climate and a company’s working environment, or to arrange a trial, call the Kenyon Group team on 0161 627 1001.
www.kenyon-group.co.uk
“Henkel ME PUR adhesives contain less than 0.1% monomeric diisocyanate, which therefore reduces the hazardous isocyanatecontaining vapours by up to 90%”
Cantisa, the Spanish edgebanding manufacturer, has reached its 38th anniversary. The company would like to express its gratitude to everyone who has contributed to its continuous improvement over the years.
For 38 years, Cantisa has focused on innovation, learning, and growth, all with the aim of providing its customers with the best possible service. In Cantisa’s own words: “Thanks to your support, we have come this far, and there is much more to come!”
On this occasion, the company would like to highlight the achievements that have shaped its history – “We won’t go into the details of our 38-year journey, but here’s a summary of the key milestones that have shaped this family-owned company and brought us to where we are today:”
2014, Venturing into Export
Cantisa explored new markets outside Spain and subsequently established an Export Department. The name Cantisa became recognised in countries across Europe, Africa, America, and Asia. Today, it exports to over 50 countries.
2017, Selling +1m meters per day
The demand for Cantisa’s products continued to grow. Thanks to its commitment to maximum quality, the company surpassed the milestone of selling one million metres of edgebanding per day, and the numbers continued to rise.
2019, Winning an Interzum Award
improve and innovate with the same enthusiasm as on the first day.
Cantisa takes pride in having built a great team over the years. “Our team is now organised into various departments: production, quality, sales, export, marketing, IT, administration ... all working harmoniously with the clear objective of offering the best edges in the market, with fast and high-quality service.”
1931, Our Beginnings: Wood Veneers
The Rico family established a company dedicated to wood veneer production, which still exists today.
1985, Creation of Cantisa
They expanded their wood-related activities by establishing Cantisa S.A., specialising in the manufacture of edgebanding and trim covering products.
1993, Melamine and PVC Edgebanding
Cantisa anticipated market trends and began selling melamine and PVC edgebanding, which were relatively unknown in Spain at that time, but soon gained significant demand.
2010, Custom Textures and Prints
The company started printing and applying textures on PVC. Custom prints for each customer became highly successful in the market. Over the following years, Cantisa expanded its production capacity with multiple printing lines.
The company introduced the innovative “Décor Programme” collection, aiming to showcase edgebands as decorative elements rather than mere accessories. One of its products, the “Grid Effect Edgeband,” received an Interzum Award.
2023, Digital Printing: First in Spain
Cantisa is proud to claim that it became the first edgebanding manufacturer in Spain to incorporate digital printing technology. This innovation enables it to create exact reproductions of new digital melamines entering the market.
“Today, we look towards the future without forgetting our roots,” it shares. “We continue to
The company reveals its recipe for success, with specialisation as the main ingredient, followed by attention and service, continuous innovations, and its commitment to quality: “We have a team of professionals dedicated to guaranteeing the quality of our products, ensuring that our references perfectly reproduce the surface of the board for which they are homologated.”
All these ingredients, based on experience gained after 38 years of specialising in manufacturing PVC and veneer edgebands in all their finishes, have positioned Cantisa as a leading company and a reference in the industry.
(+34) 961 597 242 www.cantisa.es
“We continue to improve and innovate with the same enthusiasm as on the first day”
• SERVING THE WOODWORKING INDUSTRY FOR 30 YEARS
CAMCO ARE ONE OF THE LARGEST SUPPLIERS OF EDGE BANDING MATERIAL IN THE COUNTRY, WE HAVE OVER 3 MILLION METERS IN STOCK MATCHING ALL MAIN BOARD SUPPLIERS AND WE CAN SHIP ON A NEXT DAY BASIS NATIONWIDE.
• ANY WIDTH SPLIT TO ORDER
We have probably the largest selection of veneer edgebanding from stock, here in the picture you see Tom preparing an order of 30,000 meters of 2mm Ash from stock on a next day service to one of our valued customers.
• NO MINIMUM ORDER QUANTITY
• NEXT DAY DELIVERY
Our edgebanding can be slit to any width required in any thickness and all our edgebanding is full FSC certified.
• PERFECT MATCH TO COLOUR AND SHEEN
We can handle large volume orders as well as single rolls, so if you use ABS, PVC, Melamine or Veneer edge banding material why not add value to your supply chain by adding Camco to your preferred list of trusted suppliers?
• COLOUR MATCHING TOOL ON WEBSITE
High Seat Ltd (HSL) is an award-winning manufacturer of ergonomically-designed feel good furniture with a heritage stretching back over half a century. The family-owned business now employs over 500 people, with stores throughout the UK, and today operates from a modern manufacturing plant on a 10,000m2 site in Batley, West Yorkshire – just a short distance from where the company began trading back in 1968.
“HSL’s business and reputation has been built on the quality of the handcrafted chairs, sofas and beds that we continue to manufacture here in West Yorkshire,” says Rob Spurr, who has responsibility for the company’s woodworking machinery and CNC equipment. “It’s fair to say
that our high-speed CNC machines now handle a great deal of the cutting and profiling work which used to be carried out using more traditional machinery, but there are still numerous operations necessary for the production of our traditional furniture that are regularly undertaken using machinery we have maintained here for many years.”
Although still in regular use, these ‘vintage’ machines are generally operating intermittently during the working day, and in relatively short bursts of activity depending on production requirements. “Extractly look after LEV testing for HSL,” Rob explains, “as well as all the ongoing service and maintenance of our extraction system, and their engineers have often commented on how beneficial an Ecogate installation could be for our factory.”
Sales engineer Tom Firth comments: “To exert some control over extraction usage, ductwork connections to each of the traditional machines had previously been fitted with individual, manually-operated dampers but, with the best will in the world, manual operation could never match the efficiency of Ecogate’s computer-controlled,
The system also collects waste dust from the company’s four CNC machines, and the surging cost of electricity required to power the three 30kW extraction fans ultimately accelerated the decision to go ahead with the capital investment.
To maintain clean air in the factory, the main extraction fans were previously required to operate on full power, throughout the working day – even when machines were stopped for loading and offloading, or during operators’ break times. But now, with Ecogate installed, the system operates using only the minimum power required to exactly match the demand for extraction at any given time. Effectively, whenever an individual machine is stopped, and not creating dust, the relevant fan will be slowed automatically and electricity consumption reduced.
The system also recognises when there is no production taking place on one or more of the three extraction lines; the appropriate fan is then either slowed or shut down completely. To ensure employees’ safety, minimal airflow is managed across the entire ductwork system to reduce the risk of fire or explosion.
“with Ecogate installed, the system operates using only the minimum power required to exactly match the demand for extraction at any given time”
Ecogate is proud to claim that it has the only system in the world that continuously monitors pressure, air velocity, and air volume in the main duct and at each individual gate, and the Ecogate greenBOX controller uses this data to regulate the system and ensure correct transport velocities are always maintained throughout the ductwork system.
The Ecogate installation at HSL was the first in the UK to feature the latest “greenBOX Nxt” controller. As well as controlling the extraction system, a large colour touchscreen displays real-time performance data; showing how much energy the fan motor is consuming and providing an insight to machine utilisation and energy savings being achieved across the factory.
The highly-intelligent, user-friendly Ecogate greenBOX Nxt has the capacity to efficiently control the operation of an extraction system with multiple main fans and up to 72 individual workstations. The Nxt can also be programmed to stop and start an extraction system automatically at both ends of the working day; system performance is checked at start-up, and confirmed by text or email, and at the end of the day the greenBOX Nxt will message again to confirm successful system shutdown.
Ben Waters, group operations director at HSL, comments: “Although our furniture has been handcrafted in Yorkshire for 55 years, using traditional skills and time-proven machinery, we still embrace change and innovation at HSL, and we are delighted to be the first manufacturer in the UK to benefit from Ecogate’s latest advances in energy-saving technology.”
Extractly has predicted that the Ecogate installation at HSL will achieve cost savings of over 45% and is expected to pay for itself through savings realised over the next 12 to 24 months – and after that, it will effectively be
using half price electricity.
Extractly is the master UK distributor and installer of the Ecogate® energy-saving system, and an authorised dealer and installer of Nordfab Quick-Fit® ductwork, providing extraction system design & installation, maintenance and a nationwide LEV testing service for customers in the woodworking industry.
Extractly Limited
01924 520462
info@extractly.co.uk
www.extractly.co.uk
“The highly-intelligent userfriendly Ecogate greenBOX Nxt has the capacity to efficiently control the operation of an extraction system with multiple main fans and up to 72 individual workstations”Installation and programming of the highly-intelligent greenBOX Nxt controller Final checks on a 560mm diameter automatic Ecogate damper fitted to a ‘vintage’ Rye Rotary Shaper “Polite Request” notice is no longer needed at HSL –the old manual gates are now left permanently open as Ecogate dampers do the job automatically
Chris Franklin, MD at Ranheat Engineering – a leading UK manufacturer of wood combustion equipment – continues his series of exclusive articles for Furniture and Joinery Production.
Most purchasers of modern wood-waste burning equipment want one supplier to provide a “turn- key” solution. For Ranheat, that includes making every aspect of the installation, from the heating equipment and fuel storage to often even the building to house the investment in. This issue, he looks at some of the range of products made “in-house” by Ranheat. Many customers want us to undertake the complete project, from getting planning consent for the chimney, to chimney height approval and local authority permits.
Most of our equipment is purpose made to order, which gives our design engineers greater flexibility when coming up with creative answers to customer’s needs. We use standard components configured to a unique layout. Ranheat produce inventive solutions to overcome installation problems. Sometimes it is not possible to have the storage silo adjacent to the boiler. So Ranheat produce remote silos, blowing the material via a closed loop over to the boiler/heater location where the heat is needed. In addition to all of the mechanicals, Ranheat
also make all their control panels in their purpose-built electrical department.
As well as the control panel, Ranheat also undertake the complete mechanical and electrical installation on site.
Ranheat use flanged and welded pipework that is fabricated off-site at the factory in Northampton. This avoids the need for any “hot work” on site. Heaters are delivered mounted on a frame, pre-wired and pre-plumbed and generally attached to the steel portal frame. The buildings are surveyed often using a 3-D optical scanner that produces an accurate 3-D drawing of the factory to avoid clashes with other services such as extraction ducting, lighting, and compressed air.
Ranheat also make spares and service and repair other makes of woodburning boilers and heaters.
For further information on all types and sizes of industrial woodburning equipment from 150 kW upwards, contact Ranheat on 01604 750005 sales@ranheat.com or visit www.ranheat.com
“Most of our equipment is purpose made to order, which gives our design engineers greater flexibility when coming up with creative answers to customer’s needs”
In many manufacturing facilities, extraction fans operate continuously, at full power, throughout the working day.
Even when some machines are not in use, and often during factory breaks, the powerful, energy-consuming fans continue to run at full speed – wasting valuable energy... and money!
With ECOGATE, the extraction system responds in real-time to variations in machine use. When a production machine is switched on, the greenBOX Controller opens a motorised damper to provide extraction for that particular machine.
With ECOGATE technology installed, an extraction fan will consume the minimum power required to provide optimum extraction – reducing electricity bills by 68% on average. www.ecogate.co.uk
Many businesses that produce raw materials, such as wood manufacturing, now depend heavily on dust collection. In addition, employers must follow COAHH health and safety regulations for dust procedures, so it’s essential to maintain effective dust collection to prevent dangerous incidents. Here, Nordfab explores the importance of dust collection, and why your joinery needs a dust collection system.
Some business owners may not consider dust a problem, but a lot can go wrong without an effective dust collecting system. COSHH defines dust as tiny particles that, when suspended in the air under specific circumstances, pose a risk of exploding. During operations, dust that collects in the materials generated can ignite and explode accidentally.
Dust is naturally explosive, making an excessive amount of it a serious safety risk in workplaces. Making it a priority to invest in a dust management system can help to keep workplace fires and explosions from happening unintentionally.
Dust from wood can cause coughing fits, wheezing, and tightness in the chest. Some dust is worse than others. Breathing issues brough on by excessive dust exposure can develop into possibly deadly respiratory disorders. While pneumonia brought on by a build-up of dust and infection in the lungs can be lethal, occupational asthma is a crippling condition.
Despite the alarming facts about dust, the good news is that you can control dust with various dust extraction systems. The type of dust and debris you’re dealing with, the size of the joinery, and the job’s nature will all influence your choice. But one thing is certain, your workers, your finished product, and your operational equipment all benefit when an efficient dust collecting system is installed at your place of business.
By working in a joinery, you are constantly exposing yourself to dangerous dust, particles, and pollutants in the air. However, with an effective dust extraction and dust control system in use, you and your team can work safely without worrying about getting sick from dust particles. The improved health and safety for the workers are, by far, the greatest achievements of having a dust collector and extractor on worksite!
Due to their small size and near invisibility, dust may appear harmless, but you’d be shocked at how much it can impact your work’s quality. Dust particles can easily combine with chemicals, liquids, and other mixed materials, impacting the product’s quality when used. Those who work in floor preparation know that dust can harm completed floors and reduce quality.
“One thing is certain, your workers, your finished product, and your operational equipment all benefit when an efficient dust collecting system is installed at your place of business”
Your completed surfaces can remain spotless, and the quality of your chemicals and mixed materials may be ensured with the correct dust management system.
3. It increases productivity
Machines and equipment are quickly clogged by dust and other tiny particles, which can reduce their performance or prevent them from operating. You can reduce the dust and debris collected on tools and machines by practicing effective dust control. This frees up more time for you to use your equipment rather than cleaning it.
In addition, the expensive tools and equipment may require fewer repairs and last longer if there is less dust on the job site.
4. It saves time
Every joinery involves some clean-up. Dust sticks to nearly any surface and spreads everywhere, including your clothing, equipment, and even the walls and floors. By installing an effective dust extraction system, time can be saved and as a result, you can complete tasks more quickly and on time.
5. It helps meet safety guidelines
Effective dust extraction is necessary for many projects and construction work due to the negative impacts of dust, small debris, and small toxins. You can meet compliance requirements and ensure the safety of your team throughout the project with the help of the appropriate dust control and dust extraction equipment.
For safety concerns, it is advised to employ appropriate dust extraction devices even if they are not necessary for your projects.
For more information on how to create a dust-free environment for your joinery, contact Nordfab on +44 11 32 739 400 or email sales@ nordfab.co.uk.
Office and educational furniture manufacturer, West Sussex Office Furniture, has invested in a new waste extraction system from Wood Waste Control which is instantly paying dividends in improved factory cleanliness, reduced waste and clear financial savings.
The company designs and manufactures ranges of ‘white label’ office and educational furniture. These are sold exclusively to a network of dealerships which apply their own branding. It has grown steadily since being formed in 2004 and last year reported its “best ever trading year”.
WSOF employs 54 people at its 18,000ft2 factory at Birdham Business Park, near Chichester in West Sussex, and the production machinery in its woodworking plant includes two CNC machines, a flatbed saw, and two edgebanders. There is a separate metalworking plant.
“We use only large sheets of chipboard in our woodworking plant and all items of machinery require dust extraction,” explains WSOF MD, Ian Hamlett. “We had a longstanding extraction system with wood burner but the main burning chamber on the burner had rust holes in it causing it to smoke excessively. Everywhere was covered in dust and we desperately needed a cleaner working environment.”
The company turned to Wood Waste Control (Engineering), which has hundreds of successful waste extraction, processing and heating equipment installations across the UK, in Europe, Russia and Africa.
Wood Waste Control specified a much larger extraction system utilising its WFS 13-2J modular filter unit. The collected waste is discharged through the filter unit via a rotary valve unit and dropped pressure-free directly into a silo feeding its WWH 25 automatic warm air heater. In addition, a Reinbold Azr 600 18.5kW shredder chops chipboard offcuts into small pieces ready for burning in the heater.
“They also added a separate small filter exclusively to extract the small plastic clippings cut off by the edgebander into separate dust bags so they can go off to landfill,” Ian adds.
“The installation went very well and Wood Waste Control’s installation team was tremendously knowledgeable and helpful. The extraction is much more efficient, and the factory is now cleaner and tidier, creating a better place to work which means happy staff and so a happy company. The new system demonstrates our professional approach to working and is also more environmentally friendly.
“Our investment in the new system, including various extras, was £150,000. We are now saving well over £30,000 each year on the cost of skips to landfill and forecast a three-to-fiveyear payback on our investment, as well as the improvement in working conditions and
environmental benefits.
“We are delighted with the end result and with the work of Wood Waste Control, who did everything they said they would. I would recommend them to anyone.”
Wood Waste Control is based in Bourne End near High Wycombe. The family company manufactures its wide range of filters in the UK and supplies shredders, briquette presses, biomass heaters/boilers, plus quick-assemble and spiral ductwork to enable it to offer solutions from simple stand-alone bagging units through to complex integrated systems.
01628 525290
“The extraction is much more efficient, and the factory is now cleaner and tidier, creating a better place to work which means happy staff and so a happy company”Dropping into place: the new Wood Waste Control dust extraction filter is hoisted onto site at West Sussex Office Furniture
Fercell is a leading supplier of industrial ventilation and recycling systems. With over 40 years’ experience, thousands of its solutions are in use every day in the woodworking industry. Continuously looking to improve and expand its product range, Fercell presents the COIMA MPT-Series.
Step into the future of dust extraction with the WhisperFlow+ technology – “the ultimate solution for a quieter, cleaner workspace”. Combining a compact modular design with whisper-quiet operation and inbuilt dust collection storage, this innovative series of dust extraction filter units sets new standards for efficiency and convenience.
The MPT-Series is designed to adapt to customers’ unique needs. Its modular system allows you to configure and expand the unit effortlessly, catering to the demands of a company’s evolving projects, and seamlessly integrating and delivering unparalleled performance wherever it’s needed. Featuring a negative pressure filter, it’s designed to run in constant operation.
The MPT’s sturdy construction guarantees long-lasting performance, while its space-saving design maximises workspace without sacrificing performance.
Its sleek and streamlined structure seamlessly integrates all proprietary parts into a single tower, freeing up valuable room. Customers’ facilities can be kept organised and clutter-free, while they enjoy the benefits of optimum dust extraction.
Experience the power of quiet efficiency with WhisperFlow+ technology. Equipped with innovative noise reduction engineering, it operates at a very low sound output, eliminating noise pollution.
The MPT-Series puts you in control with its user-friendly interface, where the system performance can be quickly viewed, and settings can be easily adjusted.
The fan speed is automatically adjusted based upon system load, ramping up and down as and when machine tools come on and offline. Fan duty is seamlessly and automatically adjusted to minimise energy consumption, noise and maximise filter life.
Don’t let its compact design fool you – the MPTSeries packs a punch when it comes to dust extraction. Equipped with powerful centrifugal fans, it’s designed for the transport of clean air at high pressures.
Each fan is equipped with a highly efficient self-cleaning backward bladed impeller and aerodynamically designed inlet.
The impellers are both statically and dynamically balanced to ensure very stable and vibration free performance.
Its advanced filtration system effectively captures both fine dust particles and larger chip. Removing airborne contaminants, it helps to establish a healthier, cleaner atmosphere.
The filter service lift is extended due to the inlet design, utilising the downflow principle to pre-treat contaminated air, promoting heavier particles to fall into the collection facility while the finest particles are directed to the filter elements.
The MPT is fitted with approved explosion membranes, positioned to vent explosion pressure to a safe area, according to EN 14491. It has been designed and constructed in
harmony with EN 1127-1, both UKCA and CE marked to have an internal, dirty, zone 21 and zone 22, for the clean air side.
The MPT features convenient inbuilt dust collection storage capacity, alleviating issues around secondary waste collection arrangements such as skips and trailers. The storage facility eliminates the hassle of frequent emptying. This means you can work for longer periods without interruption, boosting productivity and saving valuable time.
Each MPT module uses a left-sprung scraper bottom with material discharge to a maximum of three discharge points, providing options for various downstream material handling (trailer loading or biomass silo loading).
Setting up the MPT-Series is a breeze. With userfriendly instructions, it can be up and running in no time. Maintenance is equally straightforward, with accessible filters and quick-release couplings, ensuring a seamless experience from start to finish.
Embrace the quiet revolution of dust extraction with the MPT-series and WhisperFlow+ technology. With the perfect blend of modularity, quiet operation, and inbuilt collection capacity, the MPT-Series is designed to elevate customers’ production to new heights of performance.
For further information, contact Fercell on 01622 791414 or email info@fercell.com www.fercell.com
Those within the furniture manufacturing industry will be no stranger to the varied and important legislation and regulations surrounding everything from processing wood, to using waste wood as a fuel to produce energy.
ECS (Environmental Compliance Solutions) a Staffordshire-based consultancy business, offers nationwide services dedicated to companies involved in the manufacture of woodbased products. The business also has expert knowledge regarding the use of waste wood or biomass for heating, along with ensuring compliance to the non-domestic renewable heat incentive.
Biomass boiler and waste wood to energy installations that have been accredited to the Non-Domestic Renewable Heat Incentive Scheme (NDRHI) continue to have potential to make a vital contribution towards the UK’s obligations for renewable energy production and carbon emission reduction. To ensure that this can be achieved, ongoing compliance to the NDRHI and local environmental permitting requirements must be met. Those who are not participants of the NDRHI scheme or want to upgrade their current technology, may want to explore acquiring RHI Tariffs during this pivotal time.
The NDRHI scheme can be a confusing area to navigate due to continual updates to regulations, whether to improve the sustainability of fuel sources or the need to ensure that applicants have genuine carbon reduction projects. As such, ECS are well-placed to help, with decades of experience in the deployment of biomass and waste wood projects from conception to post completion. Director and founder of ECS, Amy Fielding, has collaborated with a wide range of Government Agencies to help develop both national and international markets. She is currently part of the Renewable Energy Association (REA) Wood Heat Forum Steering group committee and the Hetas/ Woodsure (BSL) Fuel Quality and Waste Advisory Panel. This means that she is kept abreast of any changes in RHI and Environmental policy, along with any new incentives that are on the horizon. ECS also welcomed to the team a masters graduate in Environmental Law last year.
ECS can offer ongoing support subscriptions or one-off compliance works. As part of the subscription service, it will help to ensure that a company is maintaining and providing all the correct record keeping which is required as part of meeting ongoing obligations, both from an RHI perspective and Environmental compliance point of view.
Bespoke and one-off works can include Hetas Accreditations, Clean Air Act Exemptions and Testing, RHI Emissions Certificate Drafting, Part B/Medium Combustion Directive Permit Applications, Environmental Management Systems implementation, Lawful Development Certificate Application Support, along with NDRHI ongoing obligation and NDRHI Tariff Trading Guidance.
ECS adopts a pragmatic approach and is always on hand to answer customer queries. Its overriding aim is to take the pressure off and allow companies to focus on the day-to-day operation of their businesses.
For further information, contact the team on info@envirocompliant.co.uk and quote ‘FP August 2023’.
www.envirocompliant.co.uk
“ECS are well-placed to help, with decades of experience in the deployment of biomass and waste wood projects from conception to post completion”
Amy Fielding, firector and founder of Environmental Compliance Solutions
According to NESTRO® Lufttechnik GmbH the world-renowned extraction and filter technology specialists, the development of their new generation type – NE J – sets a new standard for the industry, citing that is the first series of clean air dedusters equipped with IE5 reluctance motors and frequency converters (both made by ABB).
Nestro says that users can save up to 22% energy costs compared to those using IE3 motors in workplaces with a variety of
processing machines. In this way, the German company makes a significant contribution to climate protection.
The new range features the well-established performance classes 250, 300 and 350 with an operating air volume of up to 9500m³/h and is based on decades of company experience in woodworking, in device technology and in the technology of high efficient fans. The use of these dedusters for the extraction of various materials pays off cost-wise for companies in
many industries. Nestro says the NE J verifiably saves:
• investment costs through indoor installation close to the machine using short pipeline routes only with overall low line resistances,
• operating costs thanks to the frequency controlled IE5 reluctance motor (efficiency above 90%),
• heating costs through circulating air operation with a guaranteed residual dust content of <0.1 mg/m³,
• maintenance costs through an intelligent, certified automatic fire extinguishing system – no water or dry chemicals needed – and
• installation and base costs as a mobile plug-and-play device (requires only power and compressed-air connection plus junction of the pipeline).
The new state-of-the-art design offers four different disposal options: mobile dust bins, 800l norm container, separator lock or briquetting press. The NESTRO-LOGIC control for automatic fan start recognises up to ten processing machines and controls the associated gate valves via potential-free contacts or spools. A wired control terminal gives the user optimal freedom of movement in terms of operation and data analysis. The deduster can be parameterized and operated in 16 languages via the 7 in colour touch panel. Thanks to WLAN, commissioning can even take place directly at the processing machines.
A Northwest furniture manufacturer has purchased a wood waste heater from Wood Waste Technology to continue to save money on heating and waste disposal costs.
Established in 1999, Dalewood Furniture Frames manufactures furniture frames from its workshop in Bolton, Lancashire.
Having acquired an old wood waste heater many years ago, the management team at Dalewood needed a replacement, so started to do some research on alternative models. They read the highly recommended reviews of the wood waste heaters manufactured in the UK by Wood Waste Technology, and decided to contact the business to find out more.
Dalewood Furniture Frames has benefited from free heating and waste disposal by owning a wood
waste heater, so was keen not to be without one for long. The heating is required for the company’s 5,000ft2 workshop, which has a glass roof and can be a cold place to work in the winter months, especially with the ever opening and closing roller shutter door. From a waste disposal angle, the business generates an enormous amount of waste wood that needs to be regularly disposed of.
“As we work with waney and straight edge beech timber, which can generate 30% waste, we have a lot of wood waste to dispose of,” explains MD at Dalewood Furniture Frames, Michael Doran. “It just makes sense to burn the waste wood to transform it into free heating, rather than pay for skips to take it away to landfill.”
Following a site survey and quote, Dalewood Furniture Frames
purchased a WT15 complete with a heat dump, in order to be able to continue to use the wood waste heater to burn wood without generating heat during the summer.
Michael says: “We’re delighted with our purchase. It does everything we were promised in terms of helping us reduce our heating and waste bills. The staff at Wood Waste Technology have been immensely helpful at every stage, from placing the order to installing the heater. We can see how the company has got such a great reputation and comes so highly recommended – we’d definitely recommend them to others.”
Wood Waste Technology’s years of expertise in wood waste solutions have helped many companies reduce their waste disposal and heating costs. As well as offering site survey, design, manufacture, installation and ongoing maintenance for new units, the company also services all types of wood waste heaters and supplies
genuine spares that it proudly claims are up to 60% cheaper than other suppliers.
In addition, Wood Waste Technology is the UK official distributor for Gross Apparatebau GmbH, a German manufacturer of dependable, precision engineered shredders and briquetters, available in various size and specifications to suit all business applications.
www.woodwastetechnology.com www.grossuk.co.uk
“It just makes sense to burn the waste wood to convert it into free heating, rather than pay for skips to take it away to landfill”
Introducing the new Power-Pin from Holz-Her. Launched at LIGNA 2023, this state-of-the-art drilling and dowel insertion machine is the perfect complement to nesting. With a horizontal drilling aggregate and a dowel insertion unit as standard, it eliminates the need for manual dowel insertion after CNC machining – presenting huge cost and time-saving benefits. Here’s how …
Suitable for use with workpieces from 602600mm in length, widths of 150mm for both horizontal and vertical machining and thickness of 12-60mm, the Power-Pin offers adaptable workpiece sizing.
Designed to incorporate all aggregates and storage tanks in the machine, the Power-Pin has a footprint of just 4m2 and an overall height of just 1755 mm (2095mm with the machine lid open).
The space on the lid has also been cleverly designed to offer storage space for workpieces and, depending on material flow, the Power-Pin can stand freely in a room or be placed against the wall.
The Power-Pin can drive in both pre-coated dowels and standard wooden dowels measuring 30, 35 and 40mm in length. For standard wooden dowels, glue is injected into the holes prior to insertion. With the optional second step conveyor, the change from 6 to 8mm dowels is done in minutes.
Holz-Her’s Campus NC-HOPS software comes as standard on every Power-Pin. With simple operation at the forefront of its design, the software allows the user to programme individual components and adapt them quickly using simple macros.
Its EasySnaps parametrically programmable feature also guarantees the upmost precision, whilst the complete machining operation is displayed in a 3D format on a 21.5” touch screen display for ease of use. A barcode scanner is also part of the software’s optimisation options.
The large-area support table enables multi-area loading of up to four components at one time. The intuitive clamping concept – which automatically adjusts depending on the material being processed –ensures that longer components up to 2600mm can be loaded and off-loaded quickly and safely. It also makes for simple operation when running large batch and recurring component sizes.
For short machining cycles, the dowelling unit can be variably off-set in 32mm increments up to 192mm, with the software automatically calculating whether simultaneous dowelling and drilling is possible. Depending on the number of holes and dowels, this can result in a 20% reduction in time.
For simple machining on the Power-Pin Dynamic, automatic program selection measures the width of the workpiece via a light barrier. When a pre-programmed workpiece width is detected, the appropriate program is automatically loaded. Additional VISE LED position indicators also simplify operation further. On the Classic, the drilling depths and height can be set manually with two pre-defined drilling depths.
Energy saving credentials
Eco Mode offers a time controlled shutdown to save energy and reduce running costs.
The three-fold drilling unit allows for a variable speed of 2750–4000 rpm and individually presettable drilling spindles in a 32mm grid – ideal for carcass construction.
Paul Nightingale, national sales manager, Holz-Her UK“The new Power-Pin offers vast time savings as the horizontal drilling and dowelling can be done by the nesting CNC operator whilst the next sheet is being nested,” explains Paul Nightingale, national sales manager, Holz-Her UK.
“Thanks to the machine’s low machine height, the operator can easily oversee the nesting process whilst drilling and dowelling in masked time – essentially completing this step without adding any time whatsoever to production.”
www.holzher.co.uk
A cabinet with a beaded face frame immediately conveys a high level of quality and craftsmanship and distinctly sets it apart from other utilitarian overlay-door cabinets. The most common way to manufacture beaded face frames, is to use square profiles and to apply the bead profile separately. The major disadvantage to this system is the time required to produce a complete frame.
Apart from time consumption, mismatched grain and mitre joints, due to inconsistent bead profiles can be a concern. Any of these faults are only highlighted by being painted. A dissatisfied customer or a call-out, will damage not only the cabinetmakers reputation but also the bottom line. Clearly, the most efficient way to produce beaded face frames is to start with pre-beaded profiles. All of the above-mentioned disadvantages are then eliminated from the start. Several systems have been devised, but their set-up and calibration are a timeconsuming process and their cost (over €18K plus tooling) places them out of the reach of most bespoke cabinetmakers.
Hoffmann’s solution
The Hoffmann Beaded Face Frame System offers cabinet makers of all sizes a fast, precise and efficient method to manufacture beaded face frames, whether it is in single or series production. Starting with pre-beaded profiles, stiles are notched in pairs and the rails are coped on a fixed blade, Morso guillotine style notching machine.
These NF series machines are manufactured for Hoffmann by Dan-List (Morso) in Denmark. They cut all kinds of wood, plastic, MDF and plywood and leave the cut surface of the profile perfectly smooth and accurate, requiring no further preparation before joining.
For a standard, stile to rail connection, this operation takes about five seconds with a manual, foot-operated notching machine – and the automatic model is even faster.
The second step takes place on the Hoffmann MU-3 dovetail routing machine equipped with special fixtures for beaded and notched material. Dovetail keyways are routed into all mating parts and the frames are assembled by applying some glue and inserting Hoffmann Dovetail Keys. These keys draw the parts together to form a tight, secure and permanent joint. No large clamping tables or bar clamps are required and the frames can be finished immediately upon assembly.
All dovetail routing machines are set-up with a complete fixture set to process stiles and rails, but can also be used to process regular mitre joints and butt joints. They are also available in Digital and Pneumatic models which increase accuracy and speed.
Below is a brief overview of the Hoffmann MU-3 line-up:
• MU-3 Entry Level version for the quick and precise routing of dovetail slots.
• MU-3 D Digital version, with electronic two-axis display for the adjustable routing depth as well as the positioning of the centre fence for the routed slot location. It is ideal for high precision work.
• MU-3 P Pneumatic version for series production and high throughput. Pneumatic work piece clamping and controlled router feed.
The MU-3 P is operated by foot-pedal control.
• MU-3 PD Pneumatic/Digital version – the top machine with the highest operating comfort for a wide range of requirements. Functional features are similar to MU-3 P with a digital twoaxis display for the adjustable routing depth as well as the positioning of the centre fence for the routed slot location.
The MU-3 and the MU-3 D have a work piece thickness capacity of up to 140mm – in the versions MU-3 P and MU-3 PD this increases to 170mm. Infinitely adjustable routing depths up to 95mm and protection against break-through of the finished surface.
Also new is the two-function hand lever for even faster machine cycles when routing smaller work pieces. The scale tapes in the table and now also in the rear fences assist the quick and precise positioning of the work pieces. All versions of the new MU-3 routing machine are equipped with a motor carriage which has vernier adjustment for the fine setting of the router cutter and hence the tension of the joint. All of the company’s machines, and the full range of products and methods, are detailed on the Hoffmann website.
01524 841500
info@hoffmann-uk.com
www.hoffmann-uk.com
CNC machining centre, Accord 500, puts the customer’s time front and centre by optimising and speeding up production processes, while simultaneously guaranteeing excellent finishing quality.
Each technical feature is designed to save time at the most crucial stages for each industry manufacturer: from machine programming to setup, from the machining process to maintenance.
SCM reports an “increase in productivity by 30% compared to market standards”, thanks to the “gantry” structure with closed frame that, in continuity with the accord project, allows for sturdiness and precision to be achieved even at maximum advancement speed and with the most difficult machining jobs.
The routing speed is further increased and now exceeds 15 metres per minute with the new five-axis KPX machining unit with Hiteco 17 kW electro-spindle, designed to allow the most complex operations to be carried out rapidly and accurately.
Even the production cycle times are dramatically reduced with the exclusive BRC-S unit, which is even more flexible and compact and allows you to complete all the cutting, routing and drilling machinings typical of window components.
Set-up times are also reduced to zero thanks to the MATIC automatic worktable with simultaneous positioning of bars and pods or clamping devices: the ideal solution for
machining pre-finished elements that involve workpiece repositioning within the programme.
Another significant new entry is the quick access to more than 100 tools, easily available and ready for use with the new Caddy 35 storage, unique both for its capacity as well as its structure because it is integrated into the machining centre without increasing the machine’s bulk.
Tool management is further optimised and simplified by the new Maestro Power TMS software, integrated with SCM’s Maestro suite. Thanks to this program that maximises the ability of the storage and optimises
programming, there is no need for the operator to waste time and energy in looking for the most suitable tool: the software will identify and indicate the tool’s exact position in the storage, thus minimising machining times.
Cleaning the surrounding area is another crucial matter when machining solid wood and, in order to deal with the problem, SCM has devised a new shavings conveyor automatically positioned in accordance with the machining program, that can ensure maximum suction efficiency under any conditions.
www.scmgroup.com
“Each technical feature is designed to save time at the most crucial stages for each industry manufacturer: from machine programming to set-up, from the machining process to maintenance”
Masterwood provides outstanding furniture and joinery production CNC machines which it has developed over many years. “Masterwood now offers a full range for the efficient manufacturing of windows of any shape and size, including traditional box windows, along with timber framed doors and solid core doors,” explains sales director, Dave Kennard. “These production methods can also be moved up to automated systems for higher capacities.
“Since woodworking machines were first introduced, one of the major uses has always been the production of windows and doors; timber frame doors and in later years, solid core doors,” adds Dave. “The procedure to make a timber window or door with traditional methods has not changed – once you have your material prepared you need to draw on the timber cut-off lines, mortise and tenon positions etc. A timeconsuming process.
“Then setting and using each machine; the X-Cut, a mortiser, a tenoner, a spindle moulder, and maybe an overhead router. Assembly follows and adjustments to make everything fit together, including cutting out haunches on the band saw and using hand routers for ironmongery.
“As a wood machinist apprentice, I spent many hours drawing lines onto door stiles and then swinging on the old Wadkin chisel mortiser arm to try and cut out all those mortises staring at me on the pallet,” says Dave. “Today, life can be so much easier with just one machine. A CNC can produce the same work more accurately and in a fraction of the time”.
For the past 25 years, Masterwood Spa, the Italian machine manufacturer, has evolved its machines to suit today’s demands for bespoke solid timber joinery. An impressive roster of developments includes: the use of large diameter tooling, allowing full length mortise and tenon joints production; higher powered router motors, allowing stack tooling to be used; heavy duty clamps to ensure components are held rigid on the machine bed; more tooling positions to cover the extra tools required for window and door production; automatic bed positioning to speed up production times and reduce set up times and specialised software, to ensure the minimum time from design to production. Keeping with tradition, Masterwood continues to develop bespoke and dedicated solutions for
the solid timber industry. A recent introduction of the Teknoline, a CNC for high levels of door frame production, bolsters the innovative machining options Masterwood offers. It is available as a standalone machine with manual loading, or as a complete line with infeed and outfeed equipment.
The Teknoline offers a high-quality finished product due to the elimination of mechanical vibrations, thanks to its highly rigid structure. The automatic positioning clamps provide high accuracy with repetitive machining.
Masterwood can supply a full range of solutions to suit any customer’s manufacturing requirements, from an entry level Project 250, through to the top end Project 565 – a five-axis machine with all possible options for multirouters, tooling and clamping.
“We can provide dedicated machines like the 4WIN, a CNC machine with a unique clamping system for windows where the workpiece never moves,” Dave continues. “Each component is firmly held in place while every operation is carried out, even the recesses for all the ironmongery, so once the material leaves the machine it can be put together like a jigsaw and is ready for finishing and glazing.”
‘‘open up new opportunities”
Traditional box windows can be seen in all major towns and cities and are a traditional part of joinery history. They are, however, notorious for being difficult to produce with traditional methods.
“The many varying set-ups and joints are a minefield for costly mistakes,” explains Dave. “Today we have a number of customers who have produced traditional sliding sash windows on their CNCs where the machining time for one complete frame and a pair of sashes is under
two man-hours. This includes the pulley cut outs, frame joints, pocket cut outs and sash horns.
“The parts all then fit together with practically no bench or hand work. Using traditional methods this same job could take a full day with only limited work being possible on traditional woodworking machines.
“We have found that customers with CNC machines can now produce batches, or one-off windows and doors, in a fraction of the time that is needed with traditional woodworking machines.”
Timber frame doors are the same. As opposed to multiple operations using a number of classic machines, Masterwood’s CNC machines allow everything to be done in one big operation, from cutting components to length, through to mortises, haunches, tenons scribes, profiles, and ironmongery housings, and including the after assembly once the door parts have been assembled.
www.masterwood.com
Traditional sliding sash windows Timber frame doors TeknolineInternational Woodworking Machinery Ltd Unit 20, Newark Business Park, 3 Brunel Drive, Newark, NG24 2EG
IWM Falach Briquetting Presses Turning Your Biomass Wood Waste into Renewable Energy Briquettes. Turn Your Biomass Wood Waste including MDF Dust into Renewable Energy Wood Briquettes, eliminating landfill costs or even giving them away. IWM have Five Models Falach 30, 35, 50, 70 & 100 to suit your Production Requirements at very competitive prices. Each machine can be Supplied freestanding our Installed under your existing Dust extraction with 5 Bag Carousel Bagging Units. We have many examples installed in UK, Please ask for details of installations near YOU Bring your waste material for Demonstration
FP32:21 HYDRAULIC FRAME PRESS
3.2M X 2.1M HYDRAULIC WINDOW & DOOR PRESS
FP32:21 HYDRAULIC FRAME PRESS
3.2M X 2.1M HYDRAULIC WINDOW & DOOR PRESS
Mobile 07944 108747 • Email ibrown@iwmachines.co.uk www.iwmachines.co.uk • www.soukup.co.uk
THE VERSA 3 AXIS AUTOMATIC CNC MILLING AND DRILLING MACHINE FOR WINDOW & DOOR COMPONENTS
THE 3 AXIS AND WINDOW
TEMAC THE INTELLIGENT CNC AUTOMATIC SINGLE END TENONER (NO MORE MANUAL PUSH AND PULL)
TEMAC THE INTELLIGENT CNC AUTOMATIC SINGLE END TENONER (NO MORE MANUAL PUSH AND PULL)
International Woodworking Machinery Ltd
Unit 20, Newark Business Park, 3 Brunel Drive, Newark NG24 2EG
Tel 01636918280 / Mobile 07944108747
CRAFTER UK’S BEST SELLING CNC WINDOW & DOOR MACHINING CENTRE DESIGNED FOR THE PRODUCTION OF UP TO 30/50 “A” RATED UK WINDOWS A DAY
CRAFTER UK’S BEST SELLING CNC DOOR MACHINING CENTRE FOR THE PRODUCTION “A” RATED UK WINDOWS
International Woodworking Machinery Ltd Unit 20, Newark Business Park, 3 Brunel Drive, Newark NG24 2EG Tel 01636918280 / Mobile 07944108747
Email ibrown@iwmachines.co.uk
www.iwmachines.co.uk / www.soukup.co.uk
Email ibrown@iwmachines.co.uk www.iwmachines.co.uk / www.soukup.co.uk
Those with woodworking facilities not much bigger than the size of a double garage probably haven’t given much thought to automated storage systems. Well, maybe it’s time to think again. The latest automated storage solutions from global market leader, HOMAG, have changed the game, opening up cost-effective solutions for all sizes of wood processing businesses.
From a carpenter with a small workshop, to a furniture manufacturer producing on an industrial scale, HOMAG’s latest storage solutions solve logistical challenges at the frontend of the production process.
Whether used as a standalone picking storage system, or in combination with a processing machine such as a saw or nesting CNC, these
latest models have many benefits. Not only do they help increase production capacity by enabling orders to be processed more flexibly, faster and more economically, but they also improve health and safety within a production facility, and substantially reduce damage to raw materials caused by mishandling.
New HOMAG STORETEQ F-100 single-axis feeder
This single-axis storage system is an entrylevel automated solution for fully automatic panel handling. It is easy to use, doesn’t take up much floor space and it significantly increases throughput.
Designed to work in combination with a SAWTEQ S-200, the STORETEQ F-100 creates
a complete woodworking panel sizing cell, including convenient offcut management. The integrated all-in-one solution results in considerably higher saw performance due to the accelerated feeding.
The single-axis feeder avoids any material damage during transportation from storage to the saw, thus maintaining the integrity of each and every panel. The feeder is controlled directly at the saw via woodStore 8, making operation intuitive and simple.
Using vacuum suction units, the gantry fetches the required panel from the stacking position adjacent to or behind the saw, turns the panel if needed, and then places it in the saw, all on a just-in-time basis.
The STORETEQ F-100 allows you to determine where the panel stacking stations are located, so you can match the layout to your specific processing requirements. Available in various expansion modules, it can grow with the business. One or more machines, as well as several stacking stations, can be integrated as required.
“The latest developments have not only opened up automated storage systems to small woodworking shops, but also provided some major new space-saving and throughput benefits to large industrial sized manufacturers”
For those businesses which are cutting 20 or more panels a day, it will pay to install an automated storage system to feed the saw. By investing in a STORETEQ S-200, HOMAG claims that productivity increases of up to 40 percent are achievable with no additional personnel required.
Both the STORETEQ S-200 and S-500 systems optimise storage area, saving valuable production space. These sophisticated material management systems guarantee optimal material consumption right down to the offcuts. In addition, the systems only consume energy when they are moving boards.
The standard lifting and movement mechanism, ST61, is designed in an ‘X’ shape with vacuum suction units; this allows the use of a more diverse range of panel sizes and types including 3mm coated panels. The optional ST71 suction traverse is a self-learning unit that generates the data required for panel handling; this ensures dependable process reliability without the operator having to enter information into the machine.
For larger manufacturers, the STORETEQ S-500 unlocks more potential from processing machines. This storage system provides highly efficient logistics for industrial applications and woodworking shops.
The STORETEQ S-500 is a true all-rounder; it handles plastic, plexiglass or laminates, and coated or uncoated panels. It easily deals with panel weights up to 350kg and panel lengths up to 5600mm.
The STORETEQ P-300 and P-500 storage and retrieval systems are designed for larger manufacturing operations. Essentially similar to the STORETEQ S-200 and S-500 systems, the more robust P-300 and P-500 versions can feed
a saw, nesting and CNC processing machines with more than 50 stacking positions.
The span width of the P-300 ranges from 5000mm with the basic machine to a maximum of 12,000mm with optional extras, whilst the frame length is from 10,000 to 50,000mm.
For the P-500, the span width is from 5,000 to 16,000mm and the frame length 10,000 to 100,000mm.
Another major benefit of the P-500 range is the different format options available. The ‘Twin’ version has two bridges side by side to provide simultaneous loading of machines. This enables much faster storage and retrieval times to shorten loading and increase throughput.
The P-500 Dual model has its two bridges one above the other and is able to access any storage location and any processing machine with both cross beams. This provides more flexibility with minimum space requirements.
New models announced at LIGNA include the STORETEQ P-310/P-510 along with the P-320/P-520. These new variants increase the storage capacity in a limited space by essentially adding a second or ‘mezzanine’ floor. The P-310/P-510 feature a new double scissor-lift which enables the use of the space on the second level for the storage of the boards.
The STORETEQ P-320/P-520 can be configured for second-level storage only or double-level storage. With the double-level storage, boards can be stored around the saw and CNC processing machines on the groundlevel, with the remainder of the boards stored on the second level.
“HOMAG has pioneered automated storage and retrieval systems for the woodworking industry and, with the latest models launched at LIGNA, it remains by far and away the market leader,” comments HOMAG UK’s MD, Simon Brooks.
“The latest developments have not only opened up automated storage systems to small woodworking shops, but also provided some major new space-saving and throughput benefits to large industrial sized manufacturers.
“One of the keys to the success of all the STORETEQ systems is the easy-to-use woodStore software. This has been designed to control all aspects of storage and retrieval operations. It has complete integration with standardised interfaces including control via mobile devices connected to the machine’s wi-fi.
“Using intelliStore, all storage movements are monitored continuously and automatically adjusted to current production requirements. The software even controls the return of saw offcuts to storage to ensure maximum use of materials is achieved at all times.
“If you thought storage and retrieval systems were only for the big boys, I’d urge you to reconsider and take a look at what the latest systems can deliver. You’ll be surprised at the production efficiencies your business could be missing out on,” concludes Simon.
For a demonstration or more information on the STORTEQ range of advanced storage solutions or other HOMAG machinery and software solutions, contact Adele Hunt at HOMAG UK on 01332 856424.
www.homag.com
“If you thought storage and retrieval systems were only for the big boys, I’d urge you to reconsider and take a look at what the latest systems can deliver. You’ll be surprised at the production efficiencies your business could be missing out on”
Those in search of a reliable solution for storing long and heavy goods should consider OHRA UK – a company with the potential to revolutionise business’ storage experience with its top-of-the-line cantilever racking systems.
OHRA is one of the leading manufacturers of storage equipment in Europe. Its broad portfolio ranges from small racking systems up to a full, automatic warehouse operation, including storage and retrieval machines and warehouse software.
OHRA provides bespoke products for many applications, customised to the goods to be stored and to the
available handling devices.
In accordance with these requirements, OHRA plans, produces and installs storage systems like cantilever racking for long goods, pallet racking for heavy loads or mezzanine floors for an ideal use of the existing storage space.
All racking systems are made of high-quality solid hot-rolled steel and are available in high-quality powder coating or a hot-dipped galvanized finish for outdoor installation.
With 44 years of experience in warehouse technology and storage solutions, OHRA offers its customers a wealth of advantages.
With a wealth of experience in the industry, OHRA UK is a true pioneer in racking system solutions.
The company understands the challenges businesses face when it comes to storing long and heavy goods, and the company has developed innovative designs to address those specific needs.
OHRA UK understands that every business has unique requirements. Storing furniture and treated wood requires specialist care and attention.
That’s why OHRA offers tailored solutions to fit the customer’s specific needs. Its team of experts work closely with customers to design and implement a cantilever racking system that seamlessly integrates into specific operations, enhancing efficiency and productivity.
OHRA prioritises the safety of its customers’ goods and personnel. Its cantilever racking systems undergo rigorous testing to ensure they meet the highest industry standards. The sturdy construction and integrated safety features provide peace of mind, preventing accidents and damage to customers’ valuable inventory.
When it comes to cantilever racking systems for long and heavy goods, OHRA UK is an industry leader its customers can rely on. The company prides itself on delivering top-notch products, excellent customer service, and unmatched expertise. Countless satisfied customers have chosen OHRA UK for their storage needs. Contact OHRA UK to discover how to transform a storage space with its impressive cantilever racking systems.
“OHRA’s team of experts work closely with customers to design and implement a cantilever racking system that seamlessly integrates into specific operations, enhancing efficiency and productivity”
2 5
The new COMBi-CB70E electric multidirectional forklift is the most compact 7,000kg counterbalance truck on the market. Multidirectional ability enables the handling of both long and bulky loads, maximising the safety, storage & efficiency of your logistics.
The CB70E is loaded with a host of ergonomic features that greatly enhance operator comfort, including excellent all-round visibility, a spacious gas-strut suspension cab, independent electric traction and our newly developed Auto Swivel Seat which intelligently swivels 15 O in the direction of travel.
Contact Us Today
To find out how Combilift can help you unlock every inch of your storage space.
Fresh off the back of Ligna, Furniture & Joinery Production Magazine caught up with Maximilian Schmidt, Director of aggregates specialist, ATEMAG, to find out more about the company’s experience at the show, its recent launches, and plans for the future ...
Did you find Ligna as busy as you anticipated?
At ATEMAG, we were more than enthusiastic about the rush of customers to our booth.
In retrospect, we are rather surprised at the reduced total number of visitors compared to 2019. We were convinced by the quantity and quality of the enquiries. Only the Friday afternoon should be considered by the trade fair organisation.
Could you share any recent innovations?
ATEMAG claims to be the innovator in aggregates. We have decided to shift even more manual work to the machine. Accordingly, we have developed two units together with HolzHer which now automatically insert dowels. One of the units is installed in the HolzHer Evolution PinJet, the other in the new HolzHer PowerPin. We also recently presented the prototype of our LabelPrinter unit, which makes it possible to automatically and subsequently apply labels on a nesting machine, for example. This avoids confusion between labels and provides relief when there is a shortage of skilled workers.
Can you tell me about ATEMAG’s initiatives towards sustainability and the environment?
Sustainability at ATEMAG must be considered from two perspectives. On the one hand, 90% of our work is with regional suppliers within a radius of 50km. This means that our environment is less burdened by the supply chain, and we also create work in our environment socially.
Secondly, ATEMAG is known for highperformance units. With our units, we increase productivity, which saves resources. Not to forget our new packaging for the aggregates which enables us to reduce the use of plastics by 80%.
What sets Atemag products apart from others in the market?
ATEMAG has a clear corporate culture. Innovation, manufacture and quality. We are independent and 100% customer focused. We not only build the right unit, but we also build the optimal unit – even in quantity.
We know our customers and they are often small and medium-sized companies with problems from small and medium-sized companies. This distinguishes us from competitors with large corporate structures. Also, we are focused on our aggregate product, which helps us to respond quickly and efficiently to the market and satisfy the customer.
We have set ourselves the goal of continuing to be an innovator in the market. Accordingly, we will continue our efforts of the last three years and develop aggregates for the future. We force ourselves to develop and recognise the benefits for our customers.
What helps us are the many projects in the composite products market. In recent years, great insights have been gained here, especially in the area of floating aggregates, which we can integrate into specific developments for both markets.
You are welcome to take a look at the new Soft Touch 3D Function Line Aggregate.
www.atemag.de
Häfele has launched its new Bespoke Worktop Service to help customers achieve precise, entirely customisable designs while also saving time during the installation process. Perfect for kitchen, bathroom or utility room projects, users simply select their choice of solid surface worktop from Häfele’s Maia and Minerva ranges, and the products will be manufactured to specification using high quality craftsmanship, using advanced cutting tools and technologies to ensure precision and accuracy, eliminating gaps or unevenness when fitted. Both worktops have been awarded a FIRA gold award for product excellence, meaning they have been rigorously assessed for performance and installation. Maia worksurfaces are available in 15 standard colourways and are resistant to staining and heat. Likewise, Minerva worktops are also stain and heat resistant and are available in a broader range of 19 standard colourways and manufactured to a full 25mm thickness with a square edge.
The Bespoke Worktop Service offers complete customisation, including different shapes, sizes and finishes, to create pieces that blend perfectly with the desired design. Once cut and packaged, the bespoke worktops are delivered direct to site within 14 working days. The service has been developed to save customers valuable time in the installation process, meaning they can complete projects more efficiently. And because of the high quality materials and tools used, customers can be sure of a perfect and durable finish.
“Whether it’s in the kitchen, bathroom or utility room, worktops are so integral to homes
across the UK that we often underappreciate their importance,” comments Jashdip Kaur, product manager for worktops, splashbacks and surfaces at Häfele UK.
“However, an expertly designed, cut and installed worktop has the potential to elevate something we usually take for granted to something impressive – both in terms of functionality and style.
“For the last 100 years we’ve been thinking of ways to make our customers’ lives easier, providing services that shake up the more traditional ways of working. We’ve worked closely with them to understand their pain points when it comes to worktops and have developed this service around their feedback – which centred on accuracy, quality and efficiency.
“By cutting worktops to exact measurements for customers prior to delivery, we can take on the burden of ensuring the products fit perfectly with a customer’s space. This saves joiners and installers huge amounts of time, which they can spend on the other aspects of their project.
“The range of tones, hues and finishes available across the Maia and Minerva ranges means there’s a design to suit every type of aesthetic – with everything from fresh and bright to monotone on offer – while our 14 working day lead time and to-site delivery means customers can utilise this service as and when it suits them, based on the timelines of their project.”
“We’ve worked closely with (our customers) to understand their pain points when it comes to worktops and have developed this service around their feedback – which centred on accuracy, quality and efficiency”
The innovative Quickfit TL5 “Full Metal Jacket” dowels from cabinet hardware expert, TITUS, provide strong, reliable joints in all types of wooden materials, including MDF, chipboard and solid wood. This means that it is no longer necessary to use different dowels for different materials, or to reinforce joints by adding supplementary wooden dowels.
In addition, the new dowels – which are part of the TITUS “Engineered for Your Kitchen” programme – offer fast, tool-free insertion, reducing assembly time by up to 50% for homeassembled furniture. Alternatively, for maximum efficiency in volume production applications, they can be inserted automatically using TITUS FastFit machines.
Quickfit TL5 dowels, which are used in conjunction with TITUS Cam5000 cams, incorporate an expanding steel sleeve that provides high resistance to torsion and pull out. This ensures rigid furniture construction, with
complete freedom from the tendency for joints to loosen over time. Furniture using the dowels can also be disassembled and reassembled repeatedly without compromising joint integrity.
The dowels are designed for insertion into a 5mm hole and, on insertion, they positively and reliably engage with the hole, greatly simplifying subsequent assembly steps. When edge inserted, the dowels immediately engage with the cam and remain securely positioned until the cam is tightened.
A further key feature is that the special design of the dowel head adopted for these
innovative and time-saving products means that the performance of Quickfit TL5 dowels is unaffected by edge-to-hole-centre (ETHC) tolerances of up to ± 1 mm. Therefore, they easily accommodate not only drilling inconsistencies, but also the natural movement of wooden panels.
The dowels can be supplied in versions to suit ETHC dimensions of 24mm and 34mm. The required hole diameter for the face board is 5mm, and for the edge board 8mm. The minimum hole depth in the face board is 12.5mm.
uk.titusplus.com
“It is no longer necessary to use different dowels for different materials, or to reinforce joints by adding supplementary wooden dowels”
Quickfit TL5 dowels combine versatility with performanceTitus’ Quickfit TL5 dowels
Immerse yourself in the combination consisting of smart glass accentuated with a subtle metallic lustre: A new era of exciting uni decors. Honored with the German Design Award.
UKenquiries@REHAU.com
Located in Cookstown, Co Tyrone, for more than 30 years, Cookstown Panel Centre has enjoyed considerable success as specialist suppliers right across the furniture spectrum, from joiners servicing the domestic market to high profile interior fit-out specialists servicing the commercial, education and health sectors.
CPC is widely recognised as a reliable one-stopshop for the trade and boasts a comprehensive offering with everything from sheet materials (MFC, MDF, plywood, laminate, etc) to kitchen sinks, taps, hinges, drawers and much more. The company is aligned major manufacturers such as Egger, Blum and Reginox, to name a few, and with such a broad range of products, in reality there are very few limitations when it comes to meeting the needs of designers and their clients.
With the ability to refine and manufacture products, CPC offer the complete package ranging from bespoke cutting and edging a wide range of materials to postforming and flatbonding.
Investment
The company’s impressive production facility has received much investment over the years with the most recent CNC and heated press installations allowing it to offer a more
comprehensive range of bespoke products, up to 54mm thick, including:
• curved tops
• table tops
• worktops (including breakfast bars, upstands and splashbacks)
• office furniture
• rounded table tops
Location
The size of Cookstown’s fleet and its central position in Mid-Ulster, beside both major motorways, enables CPC to offer not only a province-wide but island-wide coverage with a 48 hour delivery service – although this is dependent on the delivery run cycle.
Since launching the company’s ecommerce website in March 2021, many customers have chosen the website as their primary means of placing orders. They are able to browse the full product range and place orders at a time convenient to them in an easy and efficient manner; once placed, the orders are automatically added to its in-house software and processed as normal.
CPC is focused on high quality products, customer needs and first class service! For those who would like a tour of the company’s facility, or require further information on any of its products/services, contact Cookstown via the following: 028 8676 2685 (Cookstown) 028 8676 3275
info@cookstownpanel.com www.cookstownpanel.com
Progressive panel supplier, ML Panels, now boasts a broader offer with a creative manufacturing service for its customers. Based near Manningtree, Essex, ML Panels is a leading importer of solid and wood-based panels and furniture components and has many years of experience supplying the furniture manufacturing industry in the UK. They have over 20 years’ experience of sourcing worldwide supply maintaining the high and consistent quality they need to keep the customer’s needs fulfilled.
ML’s client base includes small and large furniture and kitchen manufacturers nationwide whose requirements range from a single oak panel to container loads of panels and furniture components.
The furniture panel components consist of items such as solid edge glued drawer fronts, drawer backs and drawer sides as well as solid edge-glued cabinet tops, table tops, table legs and more. ML’s predominant solid hardwood
and softwood species are Oak, Ash, Maple, Knotless Radiata Pine, Tulipwood and American Black Walnut. Recently added to this portfolio is its distinctive End Grain Block Board in various species – in stock and bespoke formats including round.
In terms of a wider range of sheet materials, ML Panels is similarly well set up to provide a comprehensive range of MDF MFC and Plywood, including Finsa Hidrofugo MDF MR. ML have their “Butt & Bead” panel made from Hidrofugo MR and primed white giving a much better finish and less spraying and labour time for the customer. In addition, the company supplies new décor ranges from both Egger and Kronospan. Further new stock lines also include Finsa 12 Twenty 8’x4’ MDF Melamine Decorative range. The company also says it stocks other species and that it can supply ‘practically any requirement’ on a forward basis.
In terms of ML’s manufacturing capability,
an SCM Sigma Prima automatic Beam Saw is complemented by a Biesse Jade 240 single-sided edge bander, enabling the company to provide a highly accurate ‘cut-and-edge’ service to its customers. Further imminent production plans include the installation of a Biesse CNC machine set-up to allow more complex parts fulfilment. The company has also recently invested in an electric forklift truck fuelled by green electricity supply which chimes well with its ethical outlook and circular economy – Last year ML Panels achieved PEFC and FSC certification with a 70% mix. Some of ML Panels’ customers have included members of the British Furniture Manufacturers association – to whom they consistently provide quality products at competitive prices with a 24–72 hour delivery service from stocks.
01206 396725
www.mlpanels.com
sales@mlpanels.com
@mlpanels.com
‘ML Panels has the know-how and facilities opportunity to offer its services to manufacturers and benefit from a mutually beneficial business arrangement’ML Panels’ SCM Sigma Prima automatic beam saw is complemented by a Biesse Jade 240 single-sided edge bander will be joined by a Biesse CNC machine later this year
41 inspiring décors created to inspire designers, architects and craftsmen.
Environmentally friendly, combining uni-colour and authentic woodgrain textures.
Based on Kronospan’s high-quality core boards and are available with matching edge banding.
All décors available as PVC edged doors using HPP’s exclusive Aspects Optima service.
An eclectic mix based on weathered timbers and natural fabric textures for an ethnic and handcrafted look.
Inventive, flexible, creative and adaptable, making it ideal for domestic and business settings.
An impressively realistic range with a rich, opulent and masculine ambience.
Visit hpponline.co.uk/kronospan-trends to view the range
A bright, colourful, design-forward style that is playful, open-minded and with a nostalgic feel ideal for domestic and retail locations.
ORDER ONLINE TODAY AT HPPONLINE.CO.UK
Five new super matt colours have been added to the Avanti Opus off-the-shelf doors collection by Hill’s Panel Products (HPP) as it evolves its stock door range to keep abreast of trending colours and styles.
The new painted additions – Indigo Blue, Monument Grey, Light Grey, Soft Grey and Angora Grey – are all imported from Europe and treated with anti-fingerprint technology relatively new to the UK market.
A High Gloss Graphite has also been added to the collection, while some colours are being phased out to leave the ongoing range with five
super matt and five gloss options.
“We have been re-evaluating the whole of our Avanti stock door offering, with a view to refreshing the range,” explains Vicky Downs, senior buyer for the Oldham-based manufacturer and supplier of board, doors, fittings and accessories for the KBB industry.
“Several of the colours have been in the range for quite a few years and although they have sold well for us, they now need replacing with some of the new modern colours that are emerging into the industry.”
“The new painted additions – Indigo Blue, Monument Grey, Light Grey, Soft Grey and Angora Grey – are all imported from Europe and treated with anti-fingerprint technology relatively new to the UK market”
Keeping HPP’s multiple ranges on-trend is the job of its keen-eyed buyers, led by purchasing manager Gary Kinder, who closely monitor trends all over Europe to spot those they think will transition to the UK market.
By visiting the European trade shows and suppliers they look out for emerging trends and get a feel for what is likely to hit UK in coming months.
Gary and Vicky recently attended the Interzum trade show in Cologne, Germany, for example.
“There was a good vibrancy to the show this year and it really felt like things were getting back the normal following Covid,” says Vicky.
“There continues to be a lot of development on painted oak effect structures and new uni-colours. While many of the exhibitors were showing reeded style frontals in various guises such as glass, painted finishes and foil wrapped products. This is a trend that seems to be gathering momentum.”
Opus - Monument GreyThe Avanti off-the-shelf furniture doors are all available for next day delivery nationwide and, as well as the new Opus colours, HPP has recently added two new super matt additions to its Juno skinny Shaker-style collection – Light Grey and Angora Grey, which join the existing décors in Dust Grey, Black, Indigo Blue and Highland Green.
HPP first introduced the Avanti collection to great customer acclaim in 2011 and has seen it go from strength to strength over the years.
The current range consists of: Opus – available in matt white or a range of high gloss finishes with an integrated J-Pull handle
• Juno: a thin-stiled version of the classic Shaker door, available in five on-trend décors
• Quadro: a classic Shaker-style door with grained painted effect décors
0161 628 1147
www.hpponline.co.uk
“You may already know that we are the main supply route for adhesives from the Henkel and Tuskbond stables covering many applications within woodworking, furniture, and building component markets,” says Kenyon Group MD, Ian Kenyon. “But did you know we are the premium UK distributor for Tec glue guns and Tecbond adhesives used in manufacturing?
“Our products have a host of applications, including woodworking, assembly, furniture, caravan, insulation, mattress, upholstery, foam bonding, granite worktop fitters, V-Groove, knot filling and repair, kitchen manufacturers and installers, window and door manufacturers, coffin and casket manufacturers etc., – with ever-growing possibilities for instant bonding hot melt adhesives.”
“We pride ourselves on supplying proven adhesive technologies which deliver results, delivery on time across the UK from stock, and offering very competitive prices and technical support – the complete adhesive package from one source”
Tecbond glue sticks are manufactured in the UK and based on a range of formulations ranging from EVA, Polyolefin, Polyamide right through to Acrylic, with the aim of meeting the ever-changing and challenging materials used in today’s woodworking, furniture and building component markets.
Tecbond hot melt adhesives are used in assembly, as a holding bond while PVA cures, bonding mitre joints, templates for granite worktops, fixing of moulding to coffins, staircases, trimmings and edgings, drawer assembly, knot filling and repair, picture framing, foam and fabric bonding, V groove bonding, plus many more possibilities.
They are also used by flooring contractors for attaching tack strips (gripper rods) to concrete, wood and tiled floors, as well as attaching door bars, stair nosing and laminate floor trim.
“We have been supplying glue guns and glue sticks since 1979,” explains Ian. “Over the years we have been challenged on a daily basis to find the answer to various adhesive problems and new applications. You will be amazed at what we have been asked to bond and the majority of the time we have surprised ourselves by providing the answer to some very difficult and sticky problems.
“We supply an amazing range of Tec glue guns, supported by over 40 Tecbond glue stick formulations from fast-setting packaging grades for sealing your packaging, right through to high performance grades for bonding difficult materials such as polypropylene bonding.
“Remember, Tecbond glue sticks contain no solvents, no toxic emissions or ozone-depleting chemicals and are supplied in 12, 15, and 43mm and bulk formulations.
“We pride ourselves on supplying proven adhesive technologies which deliver results, delivery on time across the UK from stock, and offering very competitive prices and technical support – the complete adhesive package from one source.
“This leaves only one more thing to say – if you have an adhesion problem, don’t come unstuck, challenge our team, call 0161 627 1001.”
www.gluegunsdirect.com
AXYZ, a leading provider of CNC routing solutions has unveiled the all-new AXYZ WOODWORKER CNC Router. Designed to “revolutionise the woodworking industry”, this powerful all-in-one solution is engineered for fast and effortless high-volume cabinetry and furniture production. With its customised machine configuration and a range of specially developed options, the WOODWORKER offers furniture and cabinet makers a clean and efficient manufacturing process.
Key features of the AXYZ WOODWORKER CNC Router include:
The WOODWORKER boasts a wide variety of process areas that can accommodate all standard sheet sizes, with a notable 10” high gantry clearance. This flexibility makes it easy to use, with accessories such as vacuum pods or a rotary axis device enhancing productivity and precision.
Equipped with powerful direct servo drives and helical racks, the WOODWORKER delivers outstanding performance, highspeed cutting, and impeccable finishes across a wide range of wood types. It excels even with
phenolic-based products like High Pressure Laminate (HPL).
The WOODWORKER offers a choice of a single 5, 10, or 15HP HSD spindle, allowing users to tailor their setup to match specific production requirements. Additionally, a nineposition drill bank can be added to the multi-head configuration for faster and more productive operations.
With a selection of 7, 10, 14, or 21 position automatic tool changers, the WOODWORKER ensures fast and efficient tool changes, minimising downtime and maximising productivity.
The router features a highvolume 4” dust collection system, complemented by an oversized dust boot, high-flow manifold, and hose management system. This comprehensive setup effectively collects both large chips and fine dust, maintaining a clean and safe working environment.
The WOODWORKER offers an optional AXYZ Automated Label Printer (ALP), simplifying the identification of parts during the
final assembly process. This integrated solution streamlines operations and enhanced overall efficiency.
For machining complex parts requiring 360° rotation, the WOODWORKER offers optional rotary axis equipment. This feature expands the router’s capabilities and enables the production of intricate and precise parts.
When it comes to furniture and cabinet making, the AXYZ WOODWORKER is the ultimate CNC
solution. AXYZ has put extensive effort into developing a machine that seamlessly combines power, versatility, and precision to meet the unique needs of woodworking professionals.
AXYZ is confident that the WOODWORKER will revolutionise the industry by delivering exceptional performance and transforming production processes. Contact AXYZ to learn more about this innovative solution, and how it can be customised.
01952 291600
enquiries@axyz.com
www.axyz.com
“AXYZ has put extensive effort into developing a machine that seamlessly combines power, versatility, and precision to meet the unique needs of woodworking professionals”
From the 18th to 23rd of September, the EMO trade fair will take place in Hannover and Biberach-based sharpening specialist, Vollmer, will be showing its latest sharpening machines and services.
In Hall 6 at Stand F32, the machine builder will be presenting automated grinding, eroding and laser machines that can be used to machine tools made of ultra-hard cutting materials such as PCD, CBN or carbide. Vollmer will also be providing information on its maintenance and training services and its digital V@dison solutions. In addition, Vollmer’s subsidiaries, Loroch and ultraTEC Innovation, will be exhibiting their products on the Vollmer EMO stand.
As a world-leading production technology trade fair, EMO is increasingly focusing on the interlinking of products and services. This makes EMO the ideal place for Vollmer to showcase its machines, services and digital solutions. As a full-line supplier, Vollmer covers all production technologies with which rotary tools as well as circular and band saws can be machined –regardless of the cutting material used.
This year’s product highlight at EMO will be the VHybrid 260 grinding and eroding machine, which can grind and erode 100 cutting tools. It features multi-level machining, which is realised via two vertically arranged spindles. Here, the lower spindle is designed for both grinding and EDM. With a new V@dison booster solution, the VHybrid 260 achieves a surface quality of up to 0.05µm Ra (micrometre/centre roughness
value) when eroding PCD tools. Thanks to the digital application, EDM can be integrated as a complete manufacturing process into tool production.
With the Vpulse EDM generator, even the smallest micro tools with diameters of 0.5mm and smaller can be produced with the highest precision, performance and surface quality. High-precision machining is achieved via the integrated ‘Laser Check’ measuring system, which achieves required tolerances of ±2µm in fully automatic closed-loop round machining.
The VGrind 360S tool grinding machine at EMO also features the concept of multi-level machining. At the show, Vollmer will focus on the machining of CBN tools and how tool manufacturers can use the machine to individually configure and equip their production – regardless of whether they manufacture special tools or produce tools in high volumes. With appropriate automation such as the new HP 170 pallet magazine, the HPR 250 free-arm robot or the HC4 chain magazine, the VGrind 360S is suitable for unmanned machining around the clock. With the HP 170, optical detection of the cooling channels is optionally integrated. In addition, up to eight grinding wheel packs including the coolant supply can be changed fully automatically.
The Vollmer laser machine at EMO will be the VLaser 370. It can machine ultra-hard materials directly in the pivot point thanks to patented kinematics that effectively produce tools with high precision thanks to fewer compensating movements.
In addition to its machines, Vollmer will also be presenting the products and services of its subsidiaries, Loroch and ultraTEC Innovation. Loroch manufactures machines for sharpening circular saw blades. UltraTEC Innovation offers ultrasonic deburring systems that can be
used to deburr components made of metal or plastic without contact and in a resource-saving manner.
Services and digital solutions from Vollmer With its services for maintenance, repair, training, financing and digitalisation, Vollmer completes its EMO trade fair presence. These offerings include the digital initiative V@ dison that incorporates the V@ boost solution ‘Performance Package for the VHybrid 260’.
“The positioning of EMO as the world’s leading trade fair for production technologies coincides with our corporate philosophy because we are the world’s full-liner for sharpening technologies to manufacture tools with high precision and automation,” says Jürgen Hauger, MD of the Vollmer Group.
“We don’t just offer a very specific process, but the exact process that customers need. In addition, we flank our machines with individual services and digital solutions to optimally support tool manufacturers and sharpening services in automated and cost-efficient production.”
0115 9491040
admin-uk@vollmer-group.com
www.vollmer-group.com
“This year’s product highlight at EMO will be the VHybrid 260 grinding and eroding machine, which can grind and erode 100 cutting tools”
Boddington is the founder and chairman of Silverlining Furniture, a leading name in furnituremaking, known across the globe for its compelling vision, remarkable skills, and boundless creativity shared by the 62-strong team.
“Silverlining is a hive of activity, a melting pot of dreams and ideas. Under the roof of our workshop, you will find dozens of creatives –from leather artisans to engineers, research and development specialists to the brightest designers.”
“Clients from all over the world come to our workshop and leave it spellbound. They know that whatever they can imagine, we can make. The possibilities are infinite.”
Boddington’s energy is contagious – although he’s been running Silverlining Furniture for over 35 years, there’s a spark of excitement
in his eye at a mention of new ventures.
“As the business grew over the decades, my role within it started to focus more and more on management – from finances to teams, deadlines to supply chain. Then the Covid pandemic came, and it shook up both me and the business. As we had to quickly pivot our operations, systems, supply chains, and ways of working, I had to ask myself what I want for myself and the business in the years and decades to come.”
“The answer is simple – I want to bring together extraordinary creatives, to work with nature’s abundance, centuries of craftsmanship heritage, and the latest technologies, to create the world’s most exceptional objects. Objects that encase this extraordinary moment in time in which we live. I want to see people
grow, think, fail, learn, innovate, test their limits, and together, create.”
To that end, Boddington launched Silverlining Academy of Skills – a paid training and apprenticeship programme, open to people of all ages and from all walks of life, who want a start a design career.
Boddington is pouring his heart into future generations and ethical design too. This autumn sees the launch of Enzo – a new waste and offcut leather accessories brand.
“Whilst delivering bespoke commissions for our international clients, our leather atelier leads started to explore how we can work with the offcuts and waste leathers from these projects and give them a new lease of life. Our craftspeople have completely transformed these materials, with etching, painting, and embossing – each piece done by hand, each unique.” The designs will be available directly to consumers
later this year from Enzo’s website. Research and development are another area that Boddington is focused on. “Our R&D team is working on incredible new finishes and design solutions. A lot of work is done on harnessing materials abundant in nature and turning them into artisan luxury finishes – whether that’s cork with its selfhealing properties or karuun – a durable plastic alternative made out of rattan.”
Boddington’s head is clearly brimming with ideas and he’s making them happen one by one.
“Next on my radar is the opening of our new workshop in 2025 and an on-site gallery in 2027. I like to have my hands full.”
Boddington is shaping Silverlining to expand and grow in the decades to come, setting the gold standard for 21st-century design and craftsmanship.
‘Progressive design has craftsmanship, technology, and ethics at its heart. Remove one of these key elements, and we’re not really moving forward’MARK BODDINGTON Founder and chairman of Silverlining Furniture Photo © Mark Cocksedge
For 50 years, Nordfab ducting has been used around the world in dust collection application in wood shops. From oneperson shops in home garages, to large manufacturing plants.
Let’s take a closer look on why Nordfab ducting is one of the preferred solutions within the woodworking industry.
Easy & Fast to install
Quick-Fit ducting systems clip together. No rivets screws, or welding are needed, cutting installation and downtime by more than 45% compared to flanged ductwork installation.
Quick-Fit ducting is easy to uninstall and relocate as you move machinery or have other changes in work areas, providing one of the lowest life cycle cost of any ducting product.
Fits most applications
Quick-Fit components are adaptable to existing ductwork.
Fast Friendly Reliable
Visit us at www.nordfab.com
2021 Panhans 680/200 Automatic Panel Saw £17,500 +VAT
2020 SCM Olimpic K560R HP Edgebander £38,950 +VAT
2022 SCM Morbidelli n100 CNC 8x4 £58,950 +VAT
2019 SCM Olimpic K560 Edgebander top spec £34,950 +VAT
SCM Sintex NT 4 Sided Planer, Tersa Heads £8950 +VAT
Sedgwick 2 Head Tenoner, 3 Phase, £3950 +VAT
2010 Altendorf ELMO F45 3.4m, Auto Panel Saw £13,950 +VAT
NEW EQUIPMENT
SCM DMC SD10 950 Wide Single Sander £13,750 +VAT
SCM DMC SD30 1100 ‘B Version” Twin Belt Sander £22,750 +VAT
SCM Nova Fs520 ‘P1’ Planer Thicknesser ‘Xylent’ £13,250 +VAT
SCM si400 Nova 3,2m Panel Saw £10,500.00 +VAT
SCM Minimax CU410c combination, 2.6m saw, tersa £10,950 +VAT
Inventair Dust Extraction single, 3 and 4 Bag units in stock