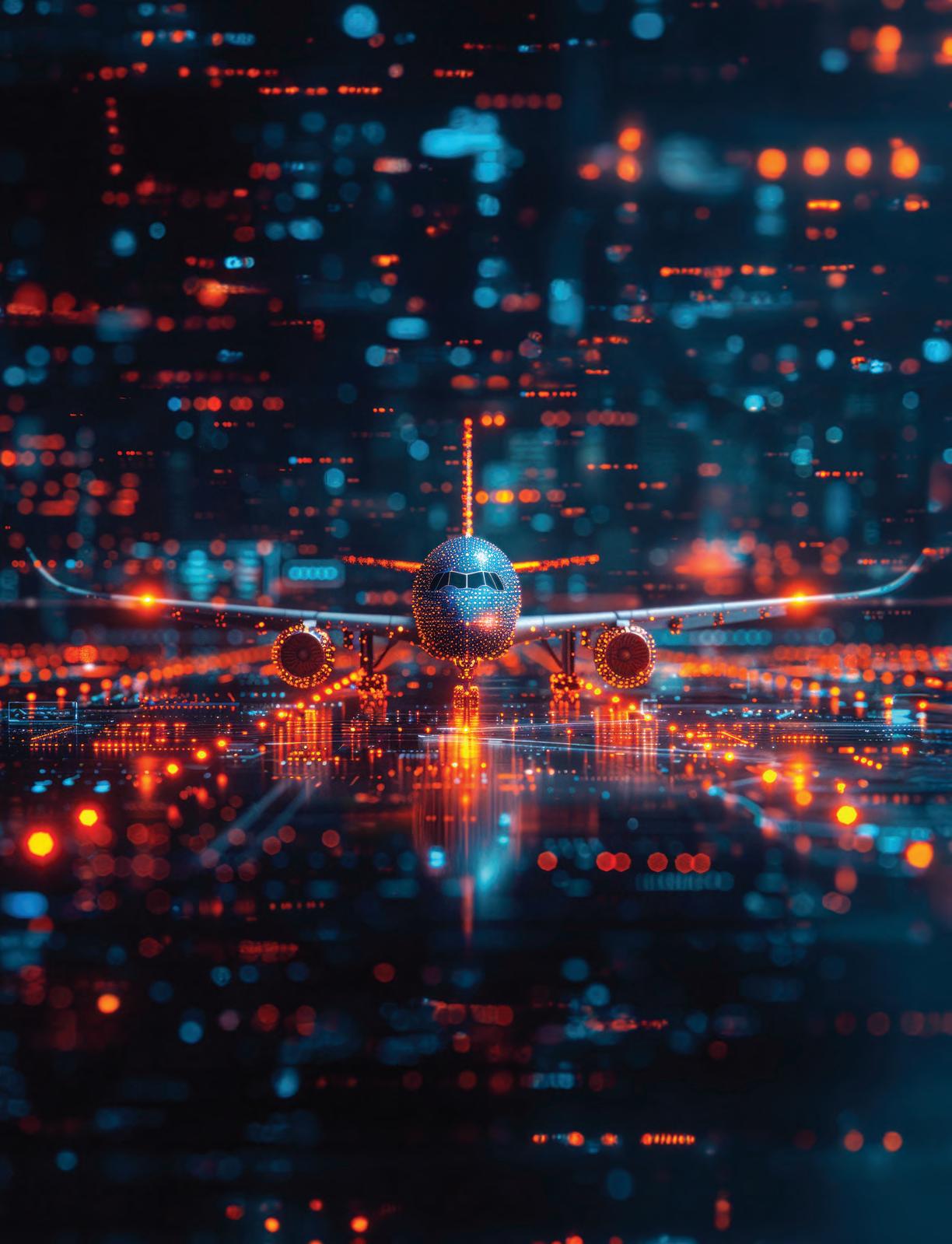
3D SCANNING
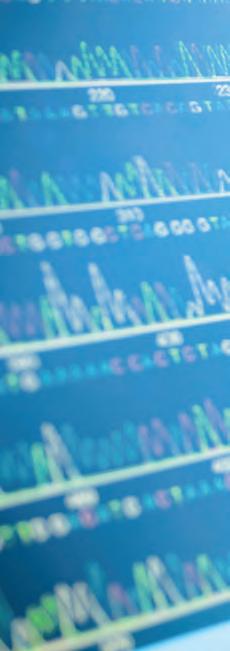
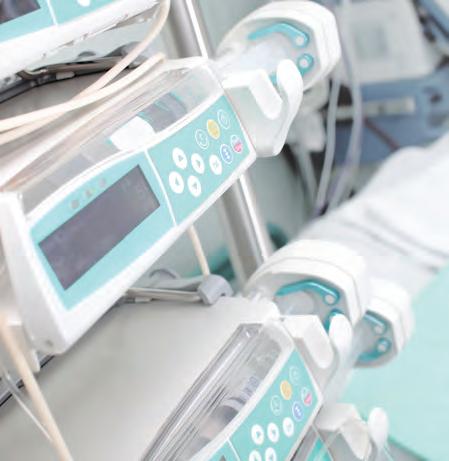

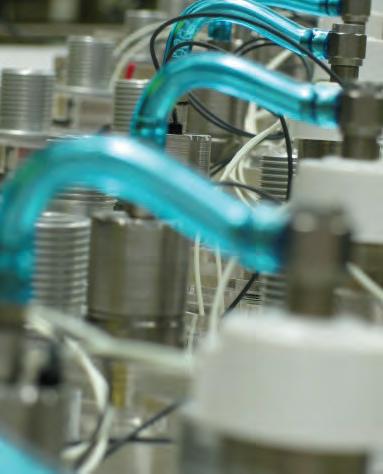

Designing efficient systems involves much more than simply understanding a few basic principles. There is a true art to balancing the specific requirements of an application in order to achieve the desired goals in the best possible way. Help us understand the unique needs of your application and together, we’ll develop something that surpasses what any of us could have done alone.
Contact your distributor to learn more, or clippard.com to request a free catalog and capabilities brochure.
I urge you to dive into our Top 10 Under 40 honourees, starting on page 10. This awards program has been a fantastic way to introduce myself to the engineering talent we have in our country. It has also been a great way to spotlight an often-overlooked segment of the profession: those emerging in their careers. Their passion and accomplishments are inspir ing—and their profiles only scratch the surface.
These up-and-comers are leading across all sectors, including a pair of innovations in health: from revolutionizing menstrual products to be more sustainable (page 10) to revolutionizing communication accessibility for the Deaf community (page 12). As well, their accomplishments span nearly every elevation on Earth— from under the ocean (page 10) to up in the air (page 14).
There are many positives to be found.
But as we celebrate their exceptional talent, it’s clear that diversity remains a pressing challenge in engineering. Despite our best efforts to attract a range of nominees, I couldn’t help but notice that female-identifying honourees were underrepresented—as they are in the profession as a whole, where women also make up a slim percentage of the engineering workforce.
Engineers Canada’s 30 by 30 initiative, launched a decade ago, set an ambitious goal: by 2030, 30 per cent of newly licensed engineers should be women. The initiative has made strides, with the percentage of newly licensed female engineers rising from 17.1 in 2014 to 20.2 in 2022. 30 by 30 invites employers to join the collaborative effort to change organizational cultures, be intolerant to harassment and discrimination, promote policies that enable work-life balance, and create more welcoming workplace environments. (Visit engineerscanada.ca, where Engineers Canada lays out what employers can do to promote diversity in their organizations.)
Awards programs like Top 10 Under 40 have a responsibility to not just reflect the world we live in but to also shine a light on the stories that aren’t being told. I see it as an opportunity for growth—and one area where Design Engineering can always do better.
Moving forward, I urge you to consider the talented people in your teams of all gender expressions. Who stands out? Who is making an impact?
Please reach out to me if you have someone who deserves recognition. I am committed to making sure our year-round editorial coverage and future Top 10 honourees are fully representative of the diverse talent within our industry.
ANDRÉ VOSHART
Editor avoshart@annexbusinessmedia.com
Editorial Board
DR. ALAIN AUBERTIN
Special Advisor, Canada Consortium for Aerospace Research and Innovation in Canada (CARIC)
DR. MARY WELLS, P.ENG
Dean, Faculty of Engineering / Professor, Mechanical and Mechatronics Engineering; University of Waterloo
AJAY BAJAJ, P.ENG
President and CEO, Rotator Products Limited; Past President and Board Member, Power Transmission Distributors Association (PTDA)
DR. ISHWAR PURI, P.ENG
Vice President of Research; Engineering Professor, University of Southern California
SEPTEMBER 2024
Volume 69, No.4 design-engineering.com
READER SERVICE
Print and digital subsciption inquiries or changes, please contact Angelita Potal Tel: (416) 510-5113 Fax: (416) 510-6875
Email: apotal@annexbusinessmedia.com
Mail: 111 Gordon Baker Rd., Suite 400, Toronto ON M2H 3R1
SENIOR PUBLISHER Paul Burton (416) 510-6756 • pburton@annexbusinessmedia.com
ASSOCIATE PUBLISHER Kathryn Swan (416) 510-6757 • kswan@annexbusinessmedia.com
EDITOR André Voshart (416) 510-5244 • avoshart@annexbusinessmedia.com
NATIONAL ACCOUNT MANAGER Ilana Fawcett (416) 829-1221 • ifawcett@annexbusinessmedia.com
ACCOUNT COORDINATOR Cheryl Fisher (416) 510-5194 • cfisher@annexbusinessmedia.com
GROUP PUBLISHER Anne Beswick (416) 510-5248 • abeswick@annexbusinessmedia.com
AUDIENCE DEVELOPMENT MANAGER
Beata Olechnowicz (416) 510-5182 • bolechnowicz@annexbusinessmedia.com
CEO Scott Jamieson sjamieson@annexbusinessmedia.com
Design Engineering, established in 1955, is published by Annex Business Media, 5 times per year except for occasional combined, expanded or premium issues, which count as two subscription issues.
Printed in Canada
Publications Mail Agreement #40065710
ISSN: 0011-9342 (Print), 1929-6452 (Online)
Subscriber Services: Canada: $58.65 for 1 year; $94.35 for 2 years;
Outside Canada: USA - $143.31; Overseas - $154.02; $10.00 for single copy.
All prices in CAD funds.
Add applicable taxes to Canadian rates.
From time to time we make our subscription list available to select companies and organizations whose product or service may interest you. If you prefer not to receive this information, please contact our circulation department in any of the four ways listed above.
Annex Business Media Privacy Officer: privacy@annexbusinessmedia.com Tel: 800-668-2374
No part of the editorial content of this publication may be reprinted without the publisher’s written permission.
©2024 Annex Business Media. All rights reserved. DE receives unsolicited features and materials (including letters to the editor) from time to time. DE, its affiliates and assignees may use, reproduce, publish, re-publish, distribute, store and archive such submissions in whole or in part in any form or medium whatsoever, without compensation of any sort. DE accepts no responsibility or liability for claims made for any product or service reported or advertised in this issue. DE is indexed in the Canadian Business Index by Micromedia Ltd., Toronto, and is available on-line in the Canadian Business & Current Affairs Database.
The Engineers Canada-sponsored Financial Security Program offers a range of plans with Canada Life to help you grow your savings then turn your savings into income for your retirement years.
Personalized guidance to help you reach new heights
As an engineer or geoscientist, you know that nothing should be built without a solid foundation. That’s where your personal health and wealth consultant comes in. They’re licensed professionals who can:
Meet with you online – when it’s convenient for you
Help guide you through all stages of your financial journey
Talk to you in more than 10 languages
Plus, being part of a group plan means you get to enjoy lower-than-retail fees* – which means more money for you!
Take it from those** who have met with a health and wealth consultant:
97% said they felt valued
98%
felt they were spoken to in a way that was easy to understand
said all their questions were answered on their personal needs
Brampton, Ont.’s MDA Space has landed a $1-billion contract with the Canadian Space Agency for the next phases of the Canadarm3 robotics system.
The contract includes funding for Phase C (final design) and Phase D (construction, system assembly, integration and test) of the full robotics system, composed of a large arm, a smaller dexterous ar m, specialized tools for performing maintenance and science tasks, as well as a ground segment for command and control.
Canadarm3 will be used aboard Gateway, a collaboration led by NASA to establish a space station in lunar orbit. Gateway is a key part of NASA’s Ar temis program to return astronauts to the moon.
Engineers Canada appointed Philip Rizcallah, P.Eng., as the organization’s next CEO, succeeding Gerard McDonald, who retired after six years of service. Rizcallah has been a transformative voice in the public service for more than three decades, most recently serving as CEO and deputy head of Accessibility Standards Canada and, prior to that, led teams at the National Research Council of Canada as both program director and director for the Building Regulations Resource Unit.
Canadian researchers have developed a new 3D printing method called blurred tomography that can rapidly produce microlenses with commercial-level optical quality. The new method may make it easier and faster to design and fabricate a variety of optical devices.
“We purposely added optical blurring to the beams of light used for this 3D printing method to manufacture precision optical components,” says Daniel Webber from the National Research Council of Canada. “This enables production of optically smooth surfaces.”
In the Optica journal, Webber and the other article authors demonstrated the new method by using it to make a millimeter-sized plano-convex optical lens with an imaging performance similar to a commercially available glass lens. They also show that the method can produce optical components that are ready to use in just 30 minutes.
“We anticipate this method to be valuable for cost-effective and swift prototyping of optical components due to the affordability of the tomographic 3D printer and the materials used,” Webber says. “Also, the inherent freeform nature of tomographic 3D printing could enable optical designers to simplify designs by replacing multiple standard optics with
printed optics that have complex shapes.”
Tomographic volumetric additive manufacturing is a relatively new manufacturing approach that uses projected light to solidify a light-sensitive resin in specific areas. It allows an entire part to be printed at once without any support structures. But existing tomographic methods cannot directly print imaging-quality lenses because the pencil-like beams used cause striations that lead to small ridges on the component’s surface.
The new technique uses a custom projection lens to blur the laser beams used to solidify a light-sensitive resin, which produces an optically smooth surface. Researchers are now working to improve component accuracy by optimizing the light patterning method and by incorporating material parameters into the printing process.
“Tomographic 3D printing is a rapidly maturing field that is finding use in many application areas,” Webber says. “Here, we leverage the intrinsic advantages of this 3D printing method to fabricate millimeter-sized optical components. In doing so, we have added to the repertoire of optical manufacturing techniques a rapid and low-cost alternative that could potentially have an impact in future technologies.” |DE
Daemar’s
Radially Assembled Rings
Axially Assembled Rings
We present our inaugural lineup of honourees. BY ANDRÉ VOSHART
This year, Design Engineering launched its inaugural effort to recognize up-and-coming leaders across the country— those who exemplify the spirit of innovation and are driving progress in their fields. This year’s winners are spread across Canada, with five in Ontario, three in British Columbia, one in Quebec and one in Nova Scotia.
Steve Bergen, P.Eng., 33, is the manager of project engineering and director of cor porate services at Lauren Services. Based in Vancouver, he joined the company eight years ago and has excelled in various roles over his tenure, always curious and learning more about different operating practices, engineering disciplines and processes.
Reflecting on his career, Bergen considers his involvement in Lauren Services’ growth as his most significant achievement. “I was lucky enough to join Lauren when it was about a third of its current size,” he says. Being part of the company’s dynamic growth allowed him to take on diverse roles, including pipeline engineer, project engineer and project manager, across a range of increasingly large projects. These include expansion and
maintenance of large diameter gas and liquids pipelines, meter stations and district gate stations in British Columbia and Alberta. “It’s been a very rewarding journey to see Lauren grow and continue to earn the reputation we have today.”
He has also developed as a leader, learning the value of truly listening to others. “Leading by example only goes so far,” he explains, and in building something better together, it’s cr ucial to more deeply understand the thoughts and motivations of your team. “I’ve also learned that teaching, training and empowering others requires you to step back. Be available, b ut don’t over-teach or over-contribute. When people feel supported, tr usted, and have the space to bring in their ideas, they can do great things, and can take ownership.”
Bergen’s interest in engineering was sparked by spending time with his father—a welder—who restored old cars and trucks, including rebuilding engines, drivetrains and suspensions. “I spent a lot of time around it as a kid and it sparked my curiosity around how things worked.”
His advice to aspiring professionals is to follow their strengths rather than just passion. “Some people say to follow your passion because you’ll never work a day in your life. I think that’s a bit naïve. But if you follow your strengths in areas that interest you, you’ll get more of those small wins that keep you motivated and building the skills to excel in that field. And when you excel, doors open for you, and you can find yourself with the ability to choose roles you truly enjoy.”
Vitaliy Maladyka, 36, serves as the field technical support specialist at ifm efector Canada in Mississauga, Ont. Over the past eight years, he has become known for his expertise in designing and implementing innovative solutions that set new industry standards. A graduate of the University of Toronto, specializing in system controls, his passion for integ rating electrical, controls and hydraulic systems has driven his career forward.
Reflecting on his journey, he says, “In my career, I had the chance to work on many individual and team projects. It is always rewarding to watch something that started as an idea materialize and come to life.” One of his most notable achievements is the development of a semi-autonomous core drill system. This modular drill system, capable of being transported to remote locations by helicopter, exemplifies his technical proficiency and his commitment to pushing the boundaries of industrial automation.
In his current role, Maladyka emphasizes three significant lessons that have shaped his approach to leadership and innovation: “First, you can never have too many tools in your toolbox. Continuous learning and acquiring new skills is the key to success. Second, communication skills are just as
24_006378_Design_Engineering_SEP_CN
impor tant as technical proficiency. And third, efficient teamwork is crucial for any project’s success. Working in a team environment, it is important to leverage the strong suits of all members of the team.”
He actively engages with the engineering team at ifm efector, sharing his exper ience and providing invaluable training sessions to colleagues and customer s alike. His dedication to empowering others to achieve their goals in system design and engineering fosters a culture of innovation within his organization.
Maladyka’s initial draw to engineering stemmed from his love of problem-solving. “For me, engineering has to do pr imarily with problem-solving. This is something that I always enjoyed, so it only made sense to follow this career path. I would tell young professionals to always maintain an inquisitive approach and not be intimidated by challenges. Putting yourself out there and not being afraid of failure is the only way to gain valuable experience.”
Rashmi Prakash
Rashmi Prakash, 29, is the co-founder and CEO of Aruna Revolution Health in Dartmouth, N.S. With a background in biomedical engineering, she has made a profound impact globally through her innovative work in assistive technologies and medical devices.
Her career is distinguished by her commitment to improving health and sustainability. Her contributions span from developing assistive technologies for individuals with disabilities to enhancing the safety of surgical devices and pioneer ing surgical robots for MRI-guided breast biopsies. Currently, she’s focused on revolutionizing menstrual products to be more sustainable, functional and safe. Along with running her own company, she teaches biomedical engineering students, imparting knowledge on creating medical innovations with an eye on future sustainability and health implications
Prakash’s proudest accomplishments are rooted in being able to see her work helping people. “One of my most memorable moments was developing a modified gaming controller for Timothy, a 10-year-old who had lost fine motor control due to hypoxia,” she says. “This controller allowed him to enjoy video games just like any other kid, something he had never been able to do before.” Another significant achievement was seeing a sensor she developed
for medical diagnostics being used in the treatment of her best friend’s son, Oliver, who was diagnosed with medulloblastoma. She also takes pride in empowering a team of female engineers, contributing to gender diversity in the tech industry.
In her role as CEO, she has learned the importance of resilience and adaptability in the face of challenges. “Leading a startup in the sustainable product space has taught me to navigate complexities in manufacturing, regulatory compliance and market penetration without compromising our core values of sustainability, responsibility and inclusivity,” she says. She has gained valuable insights into aligning business operations with broader environmental and social goals and recognizes that significant change is a collaborative effort.
Witnessing the adverse effects of traditional menstrual products on women’s health and the environment motivated Prakash to innovate in this field. “The opportunity to lead a company that could make a tangible difference in these critical areas was a compelling draw, aligning with my values and professional aspirations.”
Keegan McCallum
Keegan McCallum, 32, is the hardware engineering manager at Waterloo, Ont.based Voyis, which specializes in creating 3D laser scanners, lighting systems and cameras for underwater ROVs
(remotely operated vehicles) and AUVs (autonomous underwater vehicles).
With more than eight years of experience at Voyis, he has become an integ ral part of the company, significantly contributing to the design and development of deep-sea technologies illuminating the unknown.
His expertise spans from designing titanium housings and optical assemblies to laser mapping and systems integ ration. These skills have been crucial in tackling the challenges of harsh subsea environments and optical inspection. Since joining Voyis in 2016, Keegan has played a pivotal role as mechanical designer, systems engineering lead and more, ensuring the successful completion of numerous complex projects.
One of McCallum’s most notable accomplishments is the development of a new underwater camera product equipped with advanced optics, which was instrumental in documenting the historic shipwrecks of Ernest Shackleton’s Endurance and the Titanic.
“The Endurance was particularly cool because it was the first time anyone had laid eyes on it since it had sunk in 1915,” he says. “The amount of detail we were able to capture with the camera was incredible, down to the grain in the wood, nails, rivets and riggings. And then the Titanic was also just cool to see because of how massive and bold it was.”
In his current role, he has learned the importance of effective communication and a collaborative approach to leader ship. “Really making sure that you understand what others are trying to communicate and making them feel heard [is crucial],” he says, adding that approaching both people and technical challenges with curiosity, openness and the desire to learn is key.
McCallum’s passion for engineering is deeply rooted in his upbringing, where engineering projects at home sparked his interest. Reflecting on his career path, he advises young professionals to remain curious and humble.
“You never stop learning. More experienced people may know more than you, but they don’t know it all. The ones that do the best are those who stay humble and crave new information and knowledge.”
Thomas Zuiderveen
Thomas Zuiderveen, P.Eng., 30, is a product engineer – design specialist at IFD Technologies in Vancouver. He joined IFD in 2017 as a mechanical engineering graduate and quickly made a significant impact on the company’s product line.
“My proudest accomplishments have always been seeing my designs in real life,” he says. “Having been part of designing multiple safety products for distribution transformers, including one sold across North America, it’s powerful to look up wherever I go and see my product working out in the field.” His innovative redesign of the company’s flagship mechanical sensor for detecting transformer faults improved the device’s sensitivity without compromising its strength. This redesign involved a clever linkage design and the development of a mathematical model for various mechanical components, which accelerated the iterative design process. These innovations resulted in a new patent and the launch of a product that has sold over a million units since August 2020.
Zuiderveen’s work extends beyond these efforts. He is currently the lead mechanical designer for a mechanical temperature sensor project. His unique approach to solving a critical problem related to the creep properties of the thermal sensing element led to another patent. “When I am designing new products, I focus on using the fewest parts in the simplest ways,” he explains. “This is especially important when designing for
molding/manufacturing and assembly.”
His self-starting nature and commitment to continuous learning have made him a key mentor within the team, where he helps develop mechanical design skills among his colleagues. His proactive approach includes traveling to customers, tradeshows and manufacturers to gather insights that further refine his expertise.
For young professionals looking to achieve similar success, Zuiderveen
advises, “Try new things even if you don’t know if you’ll like them. Work at companies where you get to see a wide variety of work even if it’s not your dream job or field.” His contributions have not only advanced the company’s product offerings but have also had a tangible impact on safety and reliability in the field. “Knowing I am a part of that inspires me to keep growing my skills and continuously improve my designs.”
Brendan Klassen
Brendan Klassen, P.Eng., 29, is the lead electrical engineer at RAM Consulting in Vancouver. He joined RAM in 2018 as an electrical engineer-in-training, bringing with him a solid backg round from a co-op term at BC Hydro and a bachelor’s degree in applied science in electrical engineering with distinction from the University of British Columbia (UBC).
Dur ing his time at UBC, his capstone project earned him the Industry Award and Faculty Award at the UBC Applied Science Design and Innovation Day in 2018. This early recognition set the stage for his career at RAM, where he quickly began leading BC Hydro design projects.
One of Klassen’s most notable projects involved converting BC Hydro’s electr ical distribution infrastructure from overhead to underground in Vancouver’s Chinatown, Gastown and Yaletown areas. His innovative solution to temporarily offload an underground transformer vault allowed it to be safely decommissioned.
About theYaletown project, he says, “It was an exciting project which improved the safety and reliability of the electrical infrastructure for future generations in my hometown. Although designing around existing utilities in congested urban streets made the design challenging, I was able to implement innovative design solutions to simplify the design
and reduce construction costs.”
Other significant projects include designing power distribution for new 5G infrastructure in Edmonton and designing electric service connections for electric vehicles chargers across British Columbia.
He emphasizes the importance of clear and concise communication, especially when explaining complex engineering concepts to colleagues, clients and contractors, and believes that the times when he faced the toughest challenges at work were also when he learned the most valuable skills. “Because of this,” he says, “I try to give challenging tasks to my team, with assurance that myself and other team members will be available to help.”
Klassen was initially drawn to electrical engineering due to his enjoyment of mathematics and interest in the mathematical aspects of the profession. To young professionals aspiring to achieve similar success, he advises, “Strive for a comprehensive understanding of electrical systems. Instead of memorizing mathematical for mulas, seek to understand what the formulas mean. There isn’t a formula to solve every problem, so it takes attentiveness to overcome a design obstacle. When clients see your diligence in solving the problem, it builds trust.”
Mehdi Masoumi
Mehdi Masoumi, 34, is the CEO of Deaf AI based in Toronto. His leadership has propelled Deaf AI to the forefront of assistive technology, revolutionizing communication accessibility for the Deaf community.
The rapidly growing digital world often excludes those with hearing loss due to insufficient accessibility, leaving them behind in technology use. Under his guidance, Deaf AI has made significant strides in integrating AI technology with sign language inter pretation, creating innovative solutions that enhance communication in public spaces
One of Masoumi’s proudest achievements is founding Deaf AI, where they developed an AI-based sign language interpreter that enhances accessibility for the Deaf community in public spaces. “This innovation not only addresses a significant accessibility gap but also empowers Deaf individuals
by integrating cutting-edge technology into their daily lives in public spaces,” he says. This innovation has not only improved accessibility but also fostered greater inclusivity, positively impacting thousands of lives globally.
In his role as CEO, he has learned valuable lessons about the importance of empathy, user-centric design and connecting the dots between technology and societal needs. “Understanding the unique needs of the Deaf community has shaped my approach to leadership and innovation, emphasizing the value of inclusive solutions that bridge communication gaps and foster a more equitable and Deaf-friendly society,” he says.
Masoumi’s career path was driven by a desire to merge technology with social impact. “My advice to young professionals is to remain curious, seek out diverse perspectives and never lose sight of the potential for technology to create positive change,” he says. “Perseverance, collaboration and a commitment to inclusivity can drive meaningful innovation and generate value beyond money. Don’t underestimate the power working with like-minded people.”
As a leader in the tech industry, he exemplifies the power of combining technological advancements with a strong social mission. His work with Deaf AI stands as a testament to his dedication to improving accessibility and inclusivity.
Arvindsunil Thisai
Arvindsunil Thisai, P.Eng., M.Eng., 38, serves as the manufacturing interface manager at Accelera by Cummins in Mississauga, Ont. He has been at the forefront of developing cutting-edge hydrogen fuel cell projects, a field that holds significant promise for the electricity and transportation sectors, as well as for environmental sustainability.
His journey with Cummins began in 2019, and since then, he has distinguished himself through his hands-on approach and leadership. Visiting the facility where he works, one can see him actively engaging on the floor, guiding and mentoring his team while being deeply involved in solving technical issues.
Thisai’s fascination with mechanical design engineering was sparked by a childhood curiosity about how things work and a passion for problem-solving. This curiosity, combined with a love for math and science, naturally led him to pursue a career in mechanical engineering. “Throughout my journey, I’ve been
inspired by the impact that innovative design can have on people’s lives,” he says. “From developing medical devices that improve patient outcomes to creating sustainable solutions that reduce environmental footprints, I’ve seen firsthand the power of mechanical design engineering to drive positive change.”
Reflecting on his career, he considers his involvement in the development of his company’s hydrogen fuel cell engines as his proudest accomplishment.
He recalls the early brainstorming sessions, numerous design iterations and r igorous testing phases that culminated in a zero-emission solution for the railway industry. “Seeing the railway hydrogen fuel cell engine evolve from a sketch to a tangible product that improves lives was incredibly fulfilling,” he says. “This accomplishment stands out to me because it showcased the impact that mechanical design engineers can have on society.”
Thisai’s approach to leadership and innovation has evolved significantly in his current role. He emphasizes the importance of empathy and understanding in driving innovation.
“Early in my career, I focused primarily on technical excellence, often prioritizing design perfection over user needs and team dynamics,” he explains. But he has learned that true innovation requires a deep understanding of stakeholders’ needs, constraints and motivations. “This shift enabled our team to develop more intuitive, user-centered designs that met real needs.”
Matthew Bailey, P.Eng., 39, is the vice-president of engineering at Design 1st in Ottawa. With 14 years at the company, he has been a pivotal force in establishing the standards and design concepts that define its success.
His career at Design 1st has been marked by his innovative approach to complex mechanical design and engineering. Specializing in intricate projects such as autonomous robots, drone garages, combat robots, connected medical devices and rugged mechanical systems, he has demonstrated problem-solving skills and a commitment to delivering high-quality, cost-effective solutions. His training as a Project Management Professional allows him to excel in setting new product architectures and leading challenging projects.
One of Bailey’s notable accomplishments includes his integral role in Design 1st’s success, contributing to the company’s impressive tally of over 75 awards. His client-centric approach has been crucial in securing contracts and fostering strong relationships, showcasing his ability to balance technical exper tise with business acumen.
His leadership philosophy emphasizes the importance of hard work, patience and collaboration. He has learned that while relentless effort can drive significant progress, sometimes allowing time for solutions to evolve is more effective. Building a great team requires time and repeated collaboration, and maintaining openness and
humility often leads to better outcomes.
His childhood was marked by a fascination with dismantling and reassembling objects, from toys to household items, which fuelled his love for tinker ing and problem-solving. As a young adult, he further honed his skills through First Robotics Mentorship, where he gained valuable experience in machine and motion design.
This experience proved foundational as he took on complex projects at Design 1st, including autonomous robots and connected medical devices. His role as the lead mechanical engineer for Lucky, the only Canadian robot to compete in the Battlebots World Championships, highlights his expertise and dedication.
He encourages young professionals to find a community of like-minded individuals and embrace opportunities to showcase their skills. His advice includes staying curious, engaging in continuous learning, and seeking out experiences that push boundaries and enhance personal growth.
Sébastien Duval, P.Eng., 36, is the commercial program deputy chief engineer at Bell Textron Canada in Mirabel, Que. Since joining Bell in 2012 as a design engineer, he has been a driving force behind groundbreaking
innovations in aerospace engineering. With a bachelor’s degree in mechanical engineering from Polytechnique Montreal, he began his career working on cutting-edge projects such as the Bell EDAT (Electrically Distributed Anti-Torque) concept before transitioning to the commercial team.
One of his most notable achievements is leading the development and cer tification of the Single Pilot Instrument Flight Rules solution for the Bell 407, which earned FAA certification in August 2019. This milestone marked the first time in three decades that a single-engine helicopter achieved this level of cer tification, significantly enhancing safety and operational efficiency for helicopter operators.
“Bringing this solution to the market means that owners and operator can maximize their uptime and accept more flights knowing that they will be completed safely,” he says.
Duval has obtained 11 patents in the past three years and has been instrumental in developing the world’s first electr ically driven anti-torque system for helicopters and the integration of equipment on various Bell airframes. His ability to blend creativity with technical expertise has led to innovative designs and solutions.
In his current role, he has learned that effective leadership is about focusing on the success of others rather than oneself. “In my opinion, a good leader abides to the moto, ‘It’s not about me but about them,’” he says. “People are smart; they will figure out how to resolve the issue you have in timely manner if they believe they are part of the team success. This multiplier effects allows for you to build advocate that will echo your vision throughout the business sphere.”
Duval’s career path was driven by his innate curiosity and a desire to find better solutions. His advice to young professionals is to emphasize consistency over intensity. “Great leaders exhibit lots of g rit that provide the perseverance required to reach their long-term goal,” he says. “Leaders must be able to anchor their passion and find the ‘why’ they are doing it as there are days harder than others, but over the course of time, you realize that you are growing as a leader.” |DE
BY ANDRÉ VOSHART
Artificial intelligence (AI) influences nearly every aspect of our day-to-day lives. It helps us generate communications, summarize documents, e ngineer code, translates languages—and much more. It’s difficult to overestimate the widespread impact AI has had, and it’s hard to find areas of life untouched by this disruption—including manufacturing.
As resistant as some people may be, generative AI (Gen AI) is reshaping the way people and software interact—and companies that fail to adapt may risk f alling behind their competition.
Emerging Gen AI and copilot tools are enhancing engineering tasks from design to manufacturing. In design, generative capabilities in CAD systems are evolving, while on the shop floor, AI is improving robotics and machine building. The most exciting development is AI driven by deep learning algorithms and neural networks, capable of synthesizing complex data into useful engineering information.
And the industry has been eager to show off its advances.
Innovations in Gen AI for manufacturers and engineers were a key trend at this year’s Hannover Messe, where providers showed off their new copilots and AI assistants integrated into new and existing technolog ies to support the role of the engineer.
According to a recent report
from ABI Research, the added revenue from Gen AI use cases in manufacturing will be US$10.5 billion by 2034. As well, ABI found that the overall sentiment toward deploying Gen AI solutions in manufacturing is to take a slow-and-steady approach. To achieve this goal of steady progression, Gen AI suppliers are listening to the day-to-day problems faced by manufacturers and are working backward on how AI can be a solution.
“The current focus of vendors is to make Gen AI available and useful to as many employees as possible, regardless of job title or function,” explains James Iversen, industrial and manufacturing industry Analyst at ABI Research.
“This holistic approach is supported by the industry trend of free or freemium Gen AI models.
Vendors are more focused on garnering users than profitability at this moment.”
In early 2024, IT consulting provider SoftServe commissioned a global study to evaluate the effectiveness of organizations’ current Gen AI adoption strategies. The study revealed that while organizations continue to invest and pursue many use cases in search of ones that will deliver the biggest impact, they struggle with internal data readiness, governance and skill development.
Of the many insights in the survey, only 42 per cent of organizations have the capabilities to train Gen AI models—and a staggering
89 per cent face difficulties preparing data for Gen AI use.
It’s an artificial intelligence system designed to support users by automating tasks and offering suggestions.
In engineering, they can help with design processes, code generation, data analysis and problem-solving.
While organizations are trying to keep up with emerging AI tools, many are struggling to find the right use cases and build up the foundation of data necessary to leverage AI effectively. Design Engineering spoke with four organization to uncover pragmatic use cases for AI in manufacturing— and to look ahead at the potential that AI has to revolutionize the role of the engineer.
Andy Burleigh, engineering manager at Beckhoff Canada, highlighted that many AI-focused technology showcases and product announcements are still in the early stages
“AI-assisted tools in automation are in their infancy,” he says. “But we do see that our customers are already using tools like ChatGPT to assist them in many aspects of their work to become more efficient—from research, to design and even code
development. I would say the current use-cases are explorative, and it is typically younger engineers that are rushing to embrace this technology.”
Burleigh detailed TwinCAT Chat, a large language model (LLM) integrated with the TwinCAT XAE engineering environment. “TwinCAT Chat is trained on automation generally, and Beckhoff products specifically,” he explains. This tool, accessible within the TwinCAT IDE, suppor ts engineers by providing instant answers and generating code, HMI configurations and hardware setups. “Code objects created by TwinCAT Chat can be reviewed in the Chat window and added to the project with a click.”
“The response has been very positive,” he noted, referencing the interest generated since Beckhoff’s technology showcase in early 2023. Engineers appreciate AI tools that are easily accessible and contextually sensitive within familiar development environments. “Code generation is a
89% of global companies face difficulties preparing business data for Gen AI use
pr imary theme in the feedback we’ve received.”
Discussing AI’s complement to engineering, Burleigh emphasizes productivity enhancements. “At a basic level, AI-driven documentation searches will simplify access to infor mation and increase the pace of learning. But beyond that, tools which create and optimize automation solutions—whether that is hardware configurations, algorithms or code—will increase the output and quality of that output, of individual engineers.”
He notes how engineering is really an ideal use case for AI technologies because engineering is an act of creation. “AI tools can be used very effectively to allow a creator to achieve their vision more quickly.” But he says one key challenge will be in validating the results of AI-assisted engineering. “Can the results be tested using existing methods, or will new ones be required?” Additionally, security and privacy concerns need addressing, similar to other technology sectors.
Looking ahead, Burleigh expects rapid improvements in LLM training. “Every automation software developer will benefit from virtual assistants creating code, HMI layouts or performing research,” he predicts. Future LLMs will recognize efficient design patter ns, reducing development time and producing more robust solutions, thus continuously optimizing automation systems.
Incorporating AI into the product development processes may be a complicated endeavour—but it’s an inevitable one.
InfinitForm founder and CEO Michael Bogomolny has jumped into the market, eager to shake up the design engineering process. “The CAD industry hasn’t really had any real innovation for decades,” he says. “Most of them do all the same things.” Current CAD systems still rely heavily on manual drafting—and a lot of trial and error when it comes to manufacturability. What’s more, the existing design-for-manufacturing process is challenged by silos, intricate workflows and time-intensive procedures. This process can take weeks to months, involve a multitude of expensive software tools, workflows, and require highly skilled personnel with cumbersome coordination.
The current design engineering process involves creating shapes while considering manufacturing constraints, often without knowing all the details in the early stages.
Design engineers draft initial shapes, iterating between simulation and design before undergoing a manufacturing review. T his process typically involves three to four engineers and can take weeks or months, depending on the complexity. CAD and modeling tools are used manually to create these shapes, making it challeng ing for engineers to
InfinitForm supports CNC part design, assuming the above five-axis machining directions and tool diameters. The ghosted part is the allowable design space.
design optimal parts right away, especially when applying the right manufacturing constraints and materials from the start.
“It’s difficult for a human to design an optimal part right away, to be able to apply the right manufacturing constrains and materials right away,” Bogomolny says. The iterative nature of this process highlights the need for more efficient solutions to streamline design and manufacturing integration.
According to Bogomolny, it’s time to integrate assistance and automation into the design process, leveraging Gen AI to enhance efficiency and innovation. His company, InfinitForm, conducted market research, identifying manufacturers’ top three pr iorities as speed of innovation, part cost and manufacturing cost. He envisioned a platform that integrated all these elements effectively.
With tools like InfinitForm, the goal is also to integrate its AI copilot seamlessly into existing software environments, allowing engineers to work smoothly
without needing to switch platforms. From concept to production, users benefit from advanced Gen AI design, simulation and optimization tools, streamlined collaboration features, and an intuitive user interface.
Integrating Gen AI into the design process can reduce the tedious parts of design work. AI can help in designing better assemblies of different parts, enabling eng ineers to create concepts without getting bogged down in detailed work or other lower-level design tasks.
Bogomolny details how AI offers two primary layers of assistance.
Fir stly, AI can help set up the problem correctly, ensuring that initial design parameters are accurately defined. And secondly, dur ing the design generation process, AI can produce machinable and editable products. This a pproach helps make sure the final products are conceptually sound and ready for manufacturing. Generative design has the potential to overcome human biases, often creating models that
Hallucinations are errors produced by Gen AI models, typically caused by the quality of data used to train the model. This can be combatted by en suring the training data is relevant and of high quality. “Developing specific use casebased generative AI models can reduce the issue of hallucinations because such models are trained with a narrow scope in mind,” Siemens’ Rekhi says. Along these lines, SoftServe’s Mykhalchuk advocates for “implementing robust data governance frameworks and utilizing data integration tools that unify disparate data sources, ensuring a reliable and comprehensive data foundation for AI applications.”
meet all specifications in unexpected ways—resulting in stronger and lighter parts. Algorithms can ensure manufacturability from the start, taking constraints into account and optimizing designs for production. This automation allows engineers to concentrate on the more innovative aspects of their projects, improving overall productivity and innovation in the design process.
For the design engineering industry to innovate, adopting new technologies is crucial, despite the strict regulations there may be in sectors like aerospace, automotive and defence. Integration into existing platforms is key to ensuring a smooth transition.
Gen AI is revolutionizing various industries, and Siemens is at the forefront with its Siemens Industrial
To successfully implement AI features and functionality, the manufacturing sector will need to upskill their workforce to effectively use the tools, as retaining large teams of data scientists, software engineers, data engineers and busine ss intelligence analysts isn’t always feasible. “Thankfully, external tools and businesses are there to support a nd can take on these roles,” Rekhi says. When it comes to existing employees, upskilling is key. “It can be addressed through training programs and collaborative initiatives that upskill the workforce, ensuring they can effectively leverage AI technologies,” Mykhalchuk says.
Copilot—designed to enhance human-machine collaboration and support the role of engineers. The Siemens Industrial Copilot aims to boost productivity and efficiency by automating specific tasks through Gen AI.
Gorve Rekhi, national business development with Digital Enterprise at Siemens, says their Industrial Copilot currently supports two main domains: engineering and operations. In engineering, its capabilities include PLC code generation, human-machine interface visualization generation and providing answers to automation engineering-related questions.
For operations, the copilot assists with predictive maintenance by generating responses to user questions related to operations and maintenance, which is integrated with their predictive maintenance tool, Senseye. When Senseye triggers a maintenance notice, users
Many industrial processes are built on legacy infrastructure that wasn’t designed to support AI. “To address this, we recommend a phased integration approach,” Mykhalchuk s ays. “This involves gradually incorporating AI technologies, starting with pilot projects demonstrating value and building confidence before scaling up.”
“Many companies cannot justify the significant capital investment into AI infrastructure, but this is where cloud-based offerings can support,” Rekhi says. The other domain to be
addressed is the shopfloor where, today, many plants are operating with a heterogeneous environment—new and old machines from different vendors.
“Companies must ensure there is a pipeline in place that can provide inputs to AI applications and action the outputs,” he adds.
Cybersecurity concerns are critical, as integrating AI can increase vulnerabilities. “[Any new implementation] should prioritize robust security measures, including regular assessments and implementing a dvanced security protocols to protect sensitive data and systems,” Mykhalchuk says.
As AI advances, there will be a stronger focus on security and ethical considerations. “Future AI copilots will incorporate robust security measures to protect sensitive data and ensure compliance with regulations,” SoftServe’s Mykhalchuk says. “Additionally, there will be a greater emphasis on developing ethical AI systems that are transparent, fair and accountable to better address concerns around bias and decision-making.”
Building digital twins of assets— parts, production processes, plants, etc.—can be quite the undertaking as they can take several months and require substantial computing and labour resources. “In the future, with generative AI, large language models may be able to generate the code needed drive the mechanics of a digital twin by accessing available code repositories and software development platforms,” Siemens’ Rekhi says.
Copilots will feature advanced predictive analytics, allowing for even more precise forecasting
can inquire about the root cause, service instructions and required tools.
for industries like aerospace and automotive.
in areas like maintenance, supply chain management and production optimization. “By leveraging more sophisticated machine learning models and real-time data, AI will be able to predict issues before they occur and suggest proactive measures,” Mykhalchuk says.
Today, data privacy and laws prohibit the use of certain datasets, and certain data can also be expensive, difficult and time consuming to collect. “Using AI to generate datasets will help the product development cycle and reduce the time to prototype and commercialize software solutions,” Rekhi says. “Instead of waiting long periods of time to collect clean data, generative AI may be able to produce a high-quality dataset in a fraction of the time.”
Copilots are likely to become more intuitive and collaborative, growing a more symbiotic relationship between humans and AI. “These systems will not only automate routine tasks but also enhance human decision making by providing real-time insights and recommendations based on vast amount of data sources,” Mykhalchuk says.
“In the future, Siemens envisions a suite of generative AI-powered industrial copilots across the entire value chain—design, planning, eng ineering, operations and services,” Rekhi says. “These features will work across multiple industries, including auto motive, infrastructure, transportation and health care.” And as manufacturers accumulate more data, the potential for these copilots to improve and expand their capabilities will grow.
In the realm of design, the Industrial Copilot aims to streamline the design process by assisting with brainstorming and generating mechanical design concepts based on specific criteria like performance, materials and manufacturing methods.
Rekhi explains that the copilot introduces the possibility of generating innovative designs that may not have been considered by humans, aiming to create high-performance, lightweight, sustainable parts that meet critical c riteria on an accelerated timeline. Additionally, it aids in creating initial prototypes and mock-ups, providing design variations for faster iteration and experimentation.
Vasyl Mykhalchuk, senior R&D engineer at SoftServe, emphasizes that AI advancements are not merely hype but practical tools delivering measurable benefits today. He notes, “AI plays a crucial role in optimizing weight, cost and performance designs.” For instance, topology optimization tools refine structures to use less material while maintaining strength, which is essential
Integrated AI assistants in CAD software, such as SolidWorks’ XDesign, automate routine tasks, provide suggestions and detect potential er rors early. This not only enhances productivity but also reduces costly design mistakes. Mykhalchuk highlights real-world applications, mentioning that Airbus uses AI for generative design to develop new aircraft components, reducing weight and improving fuel efficiency. Collaborative robots, or cobots, from companies like Universal Robots, use AI to learn tasks and interact safely with human workers, making manufacturing processes more flexible and efficient. “AI is indispensable in robotics and automation,” he says, “and optimizes supply chains by predicting demand, managing inventory and identifying bottlenecks.”
SoftSer ve’s Gen AI Industrial Copilot, powered by Gen AI technologies and the NVIDIA NeMo framework, offers precise insights into maintenance processes. “It automates equipment health checks and aids in preventing malfunctions by analyzing historical KPIs,” Mykhalchuk explains. The integration of the NeMo framework allows the copilot to process complex queries quickly and accurately, enhancing decision-making in maintenance operations.
At its heart is its extensive knowledge base, built from detailed equipment information such as operation and maintenance manuals This enables meticulous searches and the provision of contextualized, accurate answers based on the retrieval-augmented generation (RA G) approach. “The RAG approach significantly speeds up the search process
and reduces the reliance on manual efforts, providing relevant and actionable insights.”
The Industrial Copilot is a game-changer for troubleshooting and planning by leveraging real-time IoT equipment data. “It continuously collects and analyzes data from sensor s embedded in machinery and
equipment, allowing for immediate detection of anomalies and potential issues,” Mykhalchuk says. Understanding equipment performance patterns and predicting future needs helps schedule maintenance during non-peak times, ensuring resources are used efficiently. The use of dynamic 3D models and digital twins by SoftServe’s Industrial
Farbod Khameneifar,
Ph.D., P.Eng. Department of Mechanical Engineering, Polytechnique Montréal
How can companies position themselves to take advantage of AI?
Khameneifar: To position themselves for future AI integration and other Industry 4.0 capabilities, companies can take several proactive measures. Firstly, investing in a robust information technology infrastructure is crucial. This includes
buil ding high-performance computing environments, edge computing capabilities and advanced IoT networks, all of which support real-time data processing and AI deployment. Secondly, companies should implement a comprehensive data strategy focusing on data quality, integration and metadata management. Leveraging data lakes and data warehouses can facilitate efficient data storage and retrieval.
Initia ting small-scale pilot projects would be an effective strategy. These projects—using AI for predictive maintenance, quality control, manufacturing process optimization and supply chain optimization—can demonstrate value and provide insights into full-scale implementation.
A dditionally, developing specialized training programs in AI, machine learning, data analytics and IoT can help upskill employees. This effort can
Copilot significantly improves production process visualization and problem-solving. Digital twins create precise digital replicas of physical assets, allowing for real-time monitoring and analysis. “To achieve photorealistic visualization of the equipment within the SoftServe’s Industrial Copilot, we utilize the cutting-edge NVIDIA RTX renderer bundled in NVIDIA Omniverse,” he says. “Fur thermore, we harness the power of OpenUSD to seamlessly integrate data and 3D assets from various sources, CAD formats and tools into a cohesive 3D scene.”
When integrated with real-time data, engineers can simulate different scenarios to predict outcomes and test solutions without disr upting actual production. “This capability significantly improves troubleshooting, as potential problems can be identified and addressed before they affect the physical equipment,” Mykhalchuk says. |DE
be bolstered by partnerships with universities for certification programs and continuous professional development.
How do companies manage the significant data requirements for training AI models?
Khameneifar: Managing the significant data requirements for training AI models involves several best practices. Data preprocessing is essential, involving advanced t echniques such as outlier detection, noise filtering, and feature engineering to clean and transform raw data into high-quality inputs for AI models. Accurate data annotation is also critical and can be enhanced using sophisticated tools and techniques, including automated labeling and human-in-the-loop approaches. This en sures the accuracy of training datasets.
Scalable and distributed storage solutions, such as the Hadoop Distributed File System or cloud-based services, are vital for efficiently managing large da ta volumes. Additionally, deploying edge computing can help process data locally at the source, reducing latency, bandwidth usage, and the amount of raw data transmitted to central servers.
Establishing comprehensive data governance frameworks ensures data integrity, consistency and security. This includes data lineage tracking, compliance with data protection regulations, and periodic audits. Continuous data quality monitoring systems are also nece ssary to detect and address issues in real time, ensuring that the data used for AI model training remains relevant and accurate.
BY ANDRÉ VOSHART
In a world where artificial intelligence (AI) is becoming increasingly pervasive, companies must evolve to stay competitive. Montreal-based robotics firm Vention exemplifies this evolution by integrating AI and design automation into the core of its operations.
Vention CEO and founder Etienne Lacroix spoke with Design Engineering about their journey to integrating higher autonomy in industrial robotics and the importance of widening access to industrial automation to small- and medium-sized manufacturers.
Vention provides industrial-grade parts, all compatible within a unified platform. This compatibility ensures that every component fits seamlessly with others, like Lego pieces. Vention’s Manufacturing Automation platform is a rich data environment, going beyond traditional CAD capabilities, allowing for intricate design automation. Each design contributes to a vast pool of data, enabling the extraction of valuable insights and inferences that fuel future innovations.
At the heart of Vention’s design process is the application of generative
design using graph neural networks. This deep understanding stems from analyzing hundreds of thousands of designs, allowing the software to predict and suggest the next components needed to complete a design—much like finishing a sentence. By leveraging graph neural networks instead of traditional large language models, Vention’s system infers relationships not between words but between part types. This sentence-completion capability transforms the design process, making it more intuitive and efficient, reducing the time and effor t required to create sophisticated equipment.
This lets Vention understand the intricate relationships between different components. For example, if a designer creates a table with two legs, program understand where the other legs should be to best fit the machine’s footprint.
“This accelerates the design process, allowing engineers and designers to rapidly create complex assemblies with industrial-grade parts,” Lacroix says. “The system’s ability to predict and suggest the next components needed
in a design reduces the time and effort required.”
Another key benefit of Vention’s approach is the lowered barrier to discovery. By starting with a Lego-style assembly system, designers can experiment and innovate more freely, without the steep lear ning curve associated with traditional CAD systems. “We’ve been accumulating design data since 2016,” Lacroix says, which helps inform their system about how different parts can be connected.
While manufacturing may not yet be at the pinnacle of full autonomy, Vention’s approach is paving the way.
Since 2018, Lacroix says Vention has focused on robot cells, employing deterministic and prescriptive sequences, or mission-based programming, to create automated sequences. This approach is crucial as the industry strives to reach higher levels of abstraction and autonomy.
In the world of robotics, achieving higher autonomy involves making machines capable of more complex, independent actions. Vention’s approach exemplifies this by aiming to enable robots to perform tasks such as identifying and moving parts in an unstructured bin to a precise location. This involves sophisticated mission-based programming where the robot learns from its actions, including mistakes, to improve performance over time. The goal is to develop machines that can be trained in a virtual environment, leveraging cloud capabilities to enhance their autonomous functions.
This vision is not without its challenges, and Lacroix acknowledges “we are still far from creating autonomous machines that deliver precision.” The journey toward full autonomy is complex and multifaceted, requiring continuous innovation and human supervision. There is no single solution to achieve complete autonomy, and Lacroix is realistic about the gradual nature of this progress.
The pathway to full autonomy will see varying levels of precision and adoption rates. Lacroix notes that lower-accuracy applications like parcel picking are already seeing success and will continue to be adopted more
rapidly due to their lower complexity and higher tolerance for minor errors.
Tasks that demand greater mechanical accuracy are significantly harder to implement and will take longer to reach the market. For instance, applications requiring robots to manipulate parts with exact precision, where even the slightest deviation can cause failure, are still a work in progress. These tasks require extensive training and development.
In June, Vention announced its collaboration with NVIDIA, after a year of effor ts to leverage AI to simplify the realization of industrial automation and robotic projects. Combined with Vention’s modular hardware and motion control technology, Lacroix says the collaboration is focused on using AI to create near-accurate digital twins significantly faster and more efficiently. |DE
profitability We pioneer motion
How I optimize equipment availability and maximize plant-wide
OPTIME ™ enables me to keep an eye on hundreds of machines in just a few hours – which makes OPTIME a quick, easy and economical condition monitoring solution.
www.schaeffler.ca/optime
BY ANDRÉ VOSHART
In April, Sanctuary AI announced a strateg ic partnership with mobility technology company Magna to support the development, deployment and s caling of general-purpose robots in automotive manufacturing.
Magna—one of the largest automotive suppliers in the world based in Aurora, Ont., and a significant buyer of industrial robots—aims to leverage Sanctuary robots’ unique capabilities across multiple applications within automotive manufacturing processes. The partnership aims to catalyze the scaling of Sanctuary’s robots while maturing the technology for use in challenging manufacturing environments for Magna and other industr ial and automotive customers.
The Magna collaboration supports Sanctuary’s goal to become the first organization in the world to create the world’s first human-like intelligence in general purpose robots. “World-changing goals like these require world-changing partners,” Sanctuary’s co-founder and CEO Geordie Rose says. “Magna’s position as a world leader in the use of robots today makes this partnership an essential advancement for our mission.”
The partnership features
the development of general-purpose AI robots for deplo yment in Magna’s manufacturing operations; a multi-disciplinary assessment of improving cost and scalability of robots using Magna’s automotive product portfolio, engineering and manufacturing capabilities; and a strategic equity investment by Magna.
Sanctuar y says experts estimate that only 10 per cent of automotive manufacturing is automated. “This is because all the robots currently working within automotive manufacturing are special-purpose tools with a narrowly defined set of tasks they can achieve,” Rose says. “The only way to significantly move the needle on automation in automotive manufacturing is to create ‘general purpose’ robots, which are versatile enough to do anything a person can do.”
This is where Sanctuary’s Phoenix robots come in. “General-purpose technologies can deal with tasks and environments that, by design, can’t be rigidly structured,” he says. For example, one of the hardest tasks to automate is called chaotic picking—or the picking of a variety of parts in an uncontrolled environment—which is what machines like Phoenix are built for.
“For a robot to act as a versatile tool in manufacturing
In April, Sanctuary AI unveiled the seventh generation of its general-purpose robot, Phoenix, one of the most sophisticated human behavioural data capture technologies available today.
processes, it must have human-like intelligence, form, function and senses,” Rose explains. “Adopting general-purpose robots into the workforce is much easier and cost-effective than re-structuring an entire workplace around different, special-purpose tools.”
Early on, Sanctuary realized the key to unlocking useful work is in the hands, with 98 per cent of all work requiring the dexterity of a person’s hand.
“With 19 degrees of freedom and proprietary haptic technology, our Phoenix robots have both the dexterity and sense of touch essential to performing tasks successfully,” Rose says. “Our robots are designed to do any task a person reasonably could, with a focus first on addressing the dirty, dull and dangerous jobs in the
manufacturing space.”
But there is a key challenge in scaling robot technology for wide-spread use in industr ial and automotive settings: data.
“The type of data needed is much less readily available than data you can find on the internet,” Rose says. “This is because the AI models we’re building—large behaviour models—need high-quality, high-fidelity human behavioral data.” Sanctuary collects this by showing the robot how to do a task in a process called teleoperation, which involves pilots carrying out tasks via the robot, with the data from this being collected and used to teach the AI models. “We have been able to speed up that process, reducing the time it takes to automate a task from weeks to less than 24 hours,” he adds. |DE
During the pandemic, the urgent need for a labour solution and the overwhelming demand on our health-care system sparked the creation Codi—Cobionix’s autonomous robotic platform that assists in medical procedures, with an initial focus on diagnostic ultrasounds.
“At that time, my co-founder, Dr. Tim Lasswell, was doing his clinical studies in medical school and saw firsthand how our highly trained health-care workforce was spending a significant amount of time on repetitive, low-complexity tasks, such as administering vaccine shots,” Cobionix co-founder and chief technology officer Nima Zamani says. “We thought, ‘Why don’t we build a robotic platform to handle these procedural tasks, so healthcare professionals can focus on more meaningful work at the bedside?’”
Codi leverages AI to perform tasks like remote ultrasound imaging, offering real-time force feedback and improving accessibility for patients in remote areas. These robots aim to enhance health-care efficiency, improve workplace safety and reduce costs by facilitating remote operations and collaboration among clinicians.
With Zamani’s background in robotics and Lasswell’s engineering and medical expertise, they joined forces with a third co-founder, John Van Leeuwen, a serial entrepreneur dedicated to sustainability through his work in
ANDRÉ VOSHART
sustainable plastics. Cobionix is also part of the University of Waterloo’s Velocity incubator. End-user feedback was critical in Codi’s design and development. “As engineers, our expertise lies in electronics, mechanical and software principles,” Zamani says. “However, this often means we lack a deep understanding of the workflow and nuances of health-care staff in a clinical environment.” To bridge this gap, they sought feedback from health-care professionals. “Their insights were invaluable in ensuring that our robot effectively meets the needs of those who use it while also providing an improved experience for patients.”
At present, Zamani says Cobionix is only one of three medical cobot platfor m manufacturers in the world. “What makes our robot unique from what’s available
Codi can interact with patients, equipment and its environment without user input.
Cobionix’s biggest hurdle in transitioning from the initial design to a fully functional prototype was in ensuring the mechanical, electrical and software design integrated seamlessly.
out there is the fact that we have a seamlessly built robot that is designed to be autonomous and scalable for future applications.” Codi is interoperable with different medical devices thanks to Cobionix’s universal tool connector, and when combined with their trained AI models to process its sensory data, Codi can interact with patients, equipment and its environment without user input.
“Existing solutions today require you to integrate a bunch of different third-party sensors and modify the robot for one specific application,” he says. “What you end up with is a Frankenstein solution and a single-use robot that can easily become obsolete.”
Zamani says Cobionix’s biggest hurdle in transitioning from the initial design concept to a fully functional prototype was in ensuring the mechanical, electrical and software design integrated seamlessly. “It’s one thing to design something conceptually. But in reality, things might not go as well together in the real world, and you have to be able to quickly adapt and iterate.”
When it comes to building Codi to meet medical and operational standards, he says Cobionix’s greatest strength was in having a well-documented and traceable process during assembly and manufacturing.
The company is also working toward obtaining necessary regulatory approvals. “We always ensured within our design pr inciples and philosophies that anything we did from the mechanical, electrical and software standpoint would need to be compliant with the various medical grade product requirements,” Zamani says. |DE
Vancouver’s Novarc automates
pipe
welding
with a real-time vision processing system based on continuous data collection and AI modelling.
BY ANDRÉ VOSHART
For autonomous welding, it’s all about self-improvement.
Novarc Technologies recently launched the second generation of its NovEye Autonomy real-time vision processing system, which constantly improves weld quality based on data collection and model enhancement to fully automate the pipe welding process while maximizing productivity and delivering the highest quality welds. The Vancouver-based robotics company specializes in the design and manufacturing of cobots and computer vision AI for automated welding applications.
Novarc says its newest iteration of NovEye Autonomy is the only AI machine learning real-time vision processing system that constantly improves welds based on data collection and model enhancement.
“This is an accomplishment that has resulted from years of data collected through machine learning, and we are extremely excited to be able to offer this solution to the industry,” Novarc CEO Soroush Karimzadeh says. The NovEye gets smarter as it continuously improves, thanks to a terabyte-scale library of welding videos and data.
The software is embedded in the cobot’s control system and controls the weld pool in the same way a human welder would, allowing the repetitive welds to be delegated to the robot. The autonomous welding process enables uninterrupted welding due to its multi-pass and multi-layer autonomous system, which can handle pipe fitting inconsistencies like hi-lo misalignment and varying root gaps. The NovEye can immediately detect and adapt welding parameters to maintain weld integrity.
Fabricators and contract manufacturers worldwide are held to strict standards to provide sophisticated welds in industries like aerospace, food &
beverage, pharmaceutical, shipbuilding and chemical processing. Karimzadeh says the NovEye Autonomy’s precision, consistency and AI-led self-improvement capabilities “lend itself very well to industries that have even a higher and more strict quality standard.”
This latest NovEye is the result of years of data collected from Novarc’s fleet of Spool Welding Robots at customer sites in North America, Europe, the Middle East and Australia, and has undergone extensive internal and external testing to ensure all the features are perfor ming and the weld quality meets ASME standard to ensure unmatched precision and reliability. As well, it can easily integrate into existing manufacturing processes across a range of industr ies.
Automation is a big milestone for the welding industry, dramatically reducing human exposure to welding hazards as it positions the operator away from the welding arc, dangerous fumes and radiant heat. With the latest NovEye, operators can program the weld, and then observe it away from the arc. As
well, muscle fatigue is reduced as the welding process is fully automated.
Another benefit is it helps fill in the gaps to the global welder shortage. “There aren’t enough welders to meet the demand,” Karimazadeh says. “But on the demand side, the world needs to fabricate more of everything.”
He anticipates that, over the next five to 10 years, we’re going to continue to see tasks that couldn’t be automated being automated. He says that we’re already witnessing this with adoption of cobots in the welding industry.
“This is really ushering in a new era for machine builders and it’s going to adjust expectations from customers moving forward,” Karimazadeh says, adding that equipment that isn’t benefiting from an AI road map or isn’t being optimized over time “is probably going to be a thing in the past.” He notes that this shift in market demand for autonomous, intelligent welding robotics will be g radual.
“It’s important for machine builders to think about what that road map looks like and how AI can improve the performance of their equipment that they’re designing in the future.” |DE
ABB has launched OmniCore, an intelligent automation platform, which delivers robot path accuracy at a level of less than 0.6 mm, with multiple robots running at high speeds of up to 1,600 mm per second. It’s built on a scalable, modular control architecture that offers a wide array of functions to create almost any application imaginable, making it suitable for businesses embracing automation in existing and new segments, such as biotechnology and construction. With more than 1,000 hardware and software features, customers can design, operate, maintain and optimize operations easily.
Mitsubishi Electric Automation has announced its newest RV-35/50/80FR series of robots, designed to allow for an
are difficult to reach with other robots. With their protective IP68 hollow-wrist design, the electrical and auxiliary cabling runs inside the wrist which allows the robots to enjoy greater agility while minimizing the risk of damage. They can be mounted on the floor, wall or ceiling to optimize space.
expanded work envelope and increased opportunity through its increased payload and reach compared to prior series. The series has a maximum reach of 2,100 mm and a maximum payload of 80 kg, making them great solutions for palletizing and machine-tending applications. It’s engineered to work seamlessly in manufacturing environments through a wide range of safety functions, including position and speed monitoring. In addition, pairing with Mitsubishi Electric’s MELFA Smart Plus card simplifies installation and programming.
Comau has debuted its new S-Family of six-axis articulated robots. The first two high-speed robots, with payloads of 13 kg and up to 18 kg, are expressly indicated for assembly, arc welding and handling applications where accuracy, repeatability and speed are necessary. The compact robots can easily access small spaces and tight areas that
Micropsi Industries has announced MIRAI 2, the latest generation of its AI-vision software that enables robots to dynamically respond to varying conditions within their factory environment, including variance in position, shape, colour, lighting and background. Building upon its predecessor, MIRAI 2 comes with five new
features that enhance manufacturers’ ability to reliably solve automation tasks with variance in position, shape, color, lighting or background. Available immediately, the latest release offers users even greater reliability, easier and faster deployment and robot-fleet scalability. What sets MIRAI apart from traditional vision solutions is the ability to operate with real factory data without the need for CAD data, controlled light, visual-feature predefinition or extensive knowledge of computer vision.
BY ANDRÉ VOSHART
The evolution of 3D scanning technology has been a journey from aspiration to reality—driven by the desire for ease of use and detailed accurac y. Early adopters were drawn to the concept of scanning as a means to understand and analyze parts without physical contact, envisioning a future where intricate details could be captured effor tlessly. But the technology initially fell shor t of these ideals, requiring significant manual input and the use of touch probes for many features and details. Scanning started as an alter native to tactile measurement that sparked interest and led to increased demand—yet
it wasn’t always as fluid or user friendly to stand on its own.
Despite these early challenges, the allure of creating precise visual representations of parts has fuelled continuous advancements and development in the field. Today, 3D scanning technology is finally aligning with the ambitious vision set forth decades ago. Moder n scanners have reached a point where they can be operated with minimal expertise, functioning almost like a magic wand that can be waved over a part to produce comprehensive and detailed reports. These devices now provide precise geometric dimensioning and tolerancing (GD&T) data and high-quality
visual representations without the need for an industry veteran at the helm.
This leap means that the dream of accurate and user-friendly 3D scanning is now a reality, empowering design engineers and manuf acturers to integrate this tool into their workflows.
The role of 3D scanning is rapidly evolving from a final quality check to an integral component throughout the entire engineering process. Traditionally, scanning was used predominantly for end-checks, serving as a go/no-go decision point to ensure parts met specifications before they moved to the next stage.
But forward-thinking advancements in 3D scanning technology are shifting this paradigm, enabling the integration of scanning earlier in the design and manufacturing workflow. With the reduction in the barrier to entry and the simplification of the technology, 3D scanning can now be used to gather precise data from the outset, guiding the creation of better par ts and more efficient processes.
Hexagon’s first handheld 3D scanning devices enable engineers and manufacturing personnel to easily scan what they need in a range of environments.
“There’s definitely a motivation on efficiency, operating costs, and time to market being driven by manufacturers,” said Joel Martin, Hexagon’s director of product management in North America. By incor porating scanning data into the generative design phase, engineers can use intelligent technology to refine and optimize designs from the start, rather than waiting for end-stage validations.This ensures higher quality parts and minimizes rework.
The ability to continuously gather and analyze data throughout the engineering process transforms 3D scanning from a simple verification tool into a crucial element of a closed-loop system, ultimately leading to a more efficient manufacturing practices.
For AI—the more data, the better
“The whole concept behind AI is learning,” Martin said. “You have to feed it data,” which enables it to make accurate predictions and decisions. This is where 3D scanning comes into play, enhancing AI’s capabilities
by providing rich, detailed data from the physical world.
3D scanning bridges the gap between the virtual and physical realms. By capturing intricate details of objects, these scans offer a wealth of data that AI systems can utilize to refine their algorithms.
As noted, feeding AI with high-quality, comprehensive data is crucial for driving processes with precision. The better the data input, the more accurate and effective the AI output.
In practical terms, Martin says that 3D scanning is becoming integral throughout various stages of production: pre-, mid- and post-process. “We’re actually starting to drive the additive manufacturing software to build the r ight part. That all comes from feeding it closed-loop data.” Instead of relying on theoretical models, AI can work with real-world data, significantly enhancing the accuracy and quality of the final product.
The speed at which 3D scans can be integrated into processes determines how quickly AI can learn and
Designed for fast-paced assembly, packaging and general handling processes, six-axis GP-series robots deliver optimal speed, accuracy and range of movement.
The superior speed of this robot family is only matched by its nimble performance and simple, streamlined design.
improve. This rapid implementation ensures that AI systems can adapt in real time, continuously improving as more data becomes available.
Advanced software functionalities play a crucial role in helping designers integrate scan data into their workflows. Simon Côté, a product manager with Creaform in Lévis, Que., says improved data processing allows for faster and more efficient integration of scan data into CAD or simulation software. “This advancement not only saves time but also fosters creativity, enabling designers to refine their work to perfection.”
Additionally, 3D scanning supports the shift toward model-based definition, where manufacturing and GD&T information are embedded directly into 3D CAD
models, which Côté says “reduces ambiguities and enhances communication across quality control and design teams.”
Portability in 3D scanning technology is transforming the design p rocess, particularly in fields where large, immovable parts are common. The issue of “transportability” highlights the need for scanner s that function seamlessly across different environments.
It’s not just about the size of the scanner; ease of setup, battery life and wireless connectivity are critical factors.
For industries like automotive, aerospace, heavy equipment and wind turbines, Martin says it’s often impractical to bring large parts into a controlled environment.
“These are parts that when you go from design and manufacture, you don’t always have the ability
Creaform’s HandySCAN captures highly detailed measurements, even under challenging environmental conditions and on complex surfaces.
to bring the part into a physical location. You have to have a piece of equipment that go into the field.”
Hexagon recently introduced two handheld 3D scanners—the ATLASCAN Max and MARVELSCAN—to complement its range of manuf acturing inspection devices. The company’s first handheld 3D scanning devices, they enable engineers and manufacturing personnel to easily scan what they need in a wide range of environments inside and outside factory walls. Both highly portable, the new 3D scanners are ideal for handheld and automated quality inspection applications, and for a wide range of reverse engineering needs.
The portability of 3D scanners empowers manufacturers and designer s by removing the constraints of part location. Designers of next-generation wind turbines, for instance, are no longer limited by their ability to inspect and scan prototypes in situ. Portable scanners enable them to capture detailed data directly from the field, informing and accelerating the design and manufacturing process.
“Recent performance improvements have led to handheld and por table 3D scanners replacing traditional 3D measurement tools,” Côté says. “These scanners enhance various stages of product lifecycle management, from design and manufacturing to quality control and servicing. Their ease of use and versatility have significantly boosted their popularity.”
The portability of 3D scanners empowers manufacturers by removing the constraints of part location.
Creaform recently expanded its flagship HandySCAN 3D lineup with the handheld MAX Series line of industrial 3D scanners. “Measuring large and complex 3D surfaces with a handheld device was previously very challenging or, in certain cases, even impossible,” Côté said at the time. “The MAX Ser ies’ unique capability closes the gap and provides innovative dimensional measurement solutions for many manufacturers we’ve met over the years.”
By ensuring tools are easy to transport, set up and operate, the technology helps dr ive innovation and efficiency in manufacturing next-stage products. The ability to capture accurate data onsite—regardless of the part’s location— represents a significant leap forward in engineering.
Innovative image processing technologies significantly improve data quality, processing time and user experience in 3D scanning. “The integration of artificial intelligence (AI) and machine learning can lead to substantial accuracy and speed enhancements,” Côté says. Furthermore, he says that incorporating augmented and virtual reality can help manuf acturers achieve complex tasks more effectively by combining the physical and virtual worlds.
Automation is essential for OEMs due to labour availability, expertise shortages and the need for consistent throughput—and Côté says quality control processes involving 3D scanning must evolve and adapt to this reality.
“Automated 3D scanners offer great flexibility and efficiency in quality control,” he says. “Increasingly, 3D scanners are being integ rated with collaborative robots (cobots), facilitating a smooth transition to the ongoing digital transformation in manufacturing.”
What’s more, the use of digital twins enables real-time monitoring and simulation of manufacturing processes, allowing for data-driven decision-making.
In the rapidly evolving field of 3D scanning, Martin says to stay focused on solving the core problem rather than getting distracted by the plethora of available technologies. Engineers should seek guidance from companies that can help them identify the right solutions for their specific needs. Too often, designers try to fit all their quality inspection routines into the capabilities of a single machine, which can be highly limiting.
“There are so many tools today—laser trackers, 3D scanning, et cetera—so designer s need to try not to pigeonhole one piece of technology to do everything.”
For instance, Martin says Hexagon provides a comprehensive suite of tools that covers every touchpoint in the design and manufacturing process. When explor ing solutions, it’s beneficial to consider the root of the problem and which technology will most effectively address it, possibly more so than the one initially considered.
The focus should be on understanding the fundamental needs and
exploring how different options meet those needs. “What’s the root of the problem, and what technology will get you to where you need to go better?” Having conversations around the why can help in selecting the best technology for the task, ensuring that engineers don’t get sidetracked by shiny new tools but instead focus on solving the problem at hand with the most suitable solution. |DE
BY RALPH GRABOWSKI
In the early days of the cloud, everything was going to run on it, according to the enthusiastic CEOs of certain CAD companies.Then reality hit. Some users weren’t necessarily keen to transition from desktop to cloud, and some vendors, when they found out rewriting desktop software to work in multi-user, multi-ser ver environments was hard enough, gave up on it.
It’s easier to write new CAD software for the cloud from scratch, partly because user expectations of what desktop programs can do aren’t there. Over the past decade, numerous new ventures received funding to build online CAD programs. After a while, though, as revenues proved insufficient, they waited to be bought by legacy vendors—and many were.
But in the past few months, I came across four newish programs that do CAD—or are CAD adjacent—on and off the cloud.
The last thing we’d expect in a tech environment brimming with 3D, AR and AI is a new CAD program that’s 2D-only. It’s from France, and it’s called Rayon. Although it’s meant for home and office floor plans, it could be used on the mechanical side for tasks like factory-floor planning.
On one hand, Rayon offers a modern user interface, along with most of what we expect from the cloud: multi-user collaboration, commenting and versioning. On the other hand, it should be taking advantage of knowledge accumulated after forty years of 2D CAD but lacks basics like editing dimension text or zooming to extents.
Rayon imports DWG, DXF and PDF files, so we can bring in 2D mechanical drawings for sharing and limited editing. The problem is that vector entities are imported as “path” objects, not native entities like lines or arcs. (Path objects are found in vector editing programs, such as Illustrator.)
The user interface of Rayon with an imported DWG file.
Rayon is free to a maximum of three drawings. This includes a seven-day history and a limited block library. To remove the limits and access more functions, pricing starts at US$29 per user per month.
Siemens’ Zel X offers businesses a convenient, browser-based experience.
We can do some editing like moving, stretching and erasing, while the Properties panel lets us edit with precise values. Editing imported circle and arc paths is awkward, because they don’t have a radius associated with them. Drawings can be exported in DWG, DXF and PDF formats.
Small-scale PLM with Zel X
Zel X is a new offering from Siemens Software. When industry watcher Matt Lombard reviewed it, he called it a “collection of tools that looks and works like a miniaturized PLM platform.” It’s aimed at small- and medium-size businesses (SMBs) who want to track projects.
Zel X runs on most platforms, because it operates in a web browser and operates from the cloud. It handles many of the tasks a small manufacturing business could use: project management, quotations, editing of designs, basic analyses, collaboration and markup, manufacturing processes, and order fulfillment.
Upon star ting Zel X, the dashboard gives us an overview of projects. It has a version of NX
for making edits to CAD drawings, models and sheet metal designs; also for 2.5D CAM paths. We cannot start from scratch, but we can start with included 3D parts and then modify them using interactive modeling commands, like stretch and move.
To start editing, go to All Projects, select a part, and then choose the Edit icon. Once in the CAD environment, a toggle changes modes between Designing, Machining and Simulation. Being cloud-based, it closes out after twenty-five minutes of inactivity.
Pricing starts at US$1,296 per user per year.You (and four others) can try out Zel X for 30 days in a web browser, after registering an account with Siemens.
Running software on virtual machines (VMs) lets us do things ordinarily impossible, such as running non-native applications (say, Linux CAE) on Windows computers. The rest of the computer acts like a viewer, albeit an interactive one.
VMs can run directly on our computers or remotely on servers. Remote ones run the entire CAD program on another computer hundreds of miles away; the high-resolution graphics need to be pushed to us very quickly. DesignAir thinks it has solved the problem by r unning on top of Splashtop at 25 data centers scattered about the world. (Use the one closest to you.) Splashtop specializes in sends optimized graphics over long distances, but more importantly offers an API into which DesignAir was able to hook.
DesignAir feels its service is best for firms that have remote, contract or part-time employees that need access to engineering software but don’t have engineering-grade computers.
For every new employee, a new instance of DesignAir is spun up (this takes about 20 minutes), into which the employee’s DesignAir account is loaded up with all software that will be needed, including CAD, analysis and Office applications. Being a VM, all the programs are desktop versions. The licenses are acquired and paid for by the employer.
The cost for DesignAir starts at US$576 per user per year.
Running CAD software from cloud has its drawbacks, such as having to log in after the software logs you out for toolong inactivity (typically 20 minutes). There can be a lack of clarity of how
and where our data is stored, and in which format. Sometimes, we’re unable to access it due to Internet failure (less common) or cyberattacks (more common). Relentless updates can change how the software works. And then there is the uncertainty over protection of our intellectual property (IP).
The good news is that not all CAD-related software forces us onto remote servers. The collection of EnSuite Impact 360 programs from CCE lets designer s and non-CAD staff view 3D models, communicate with each other and create workflows. It runs on any employee’s computer, because it’s licensed per company. Being inside the firewall means greater IP protection.
EnSuite acts as a hub and starts with four applications: 3D viewer of many MCAD formats, translators between them, meetings, and pack and go. While we can mark up models, we cannot modify them.
The software generates bills of material and technical data packages. It’s possible to add more applications, written by CCE using a macro language, such as the optional SupplierConnect module that allows communication outside the company firewall. |DE
There is no downloadable demo version; users need to request a demo. Price is a custom quote, based on the number of likely seats at a company.
The
answer is key to estimating product development budgets.
BY KEVIN BAILEY
Product development budgets are the Achilles’ heel of most hardware technology projects.
Let’s say you’ve got a brilliant idea for a physical, real-world product. Now, do you know how much it will cost to create a prototype—let alone bring it to market? You’ll need to know if you want to pitch it to potential investors and customers or determine how much money to put on the line.
The answer lies in determining your product’s complexity. Maybe your product works like something currently on the market but is built with newer materials requiring more complex supply chains. Or maybe your supply chain needs are relatively simple, but the product’s success requires inroads to an untapped and unproven market segment. It’s important to consider these factors (and more)
to have a realistic estimate of the return on investment (ROI) when pitching your idea to the people who count.
The good news is that you can draw on the experience of all the product developers who’ve come before you to create an estimate of your own product idea based on real-world data.
A product development budget isn’t just a spreadsheet with numbers; it’s a strategic blueprint that guides you as you turn an idea into a market-ready physical product. Budget analysis starts by examining a product’s complexity, followed by high-level targets for its market plan and product-market fit. It ends with estimating user adoption based on human factors. Many innovators get caught up in the emotions of creating a new
product. There are going to be bumps in every product development. Thinking through the opportunities and technical risks can be done early on, improving your chance at pointing your money in the best direction. A structured analysis enables you to forecast yearly spend, set realistic timelines and provide management, investors or family with a more objective plan—giving them a reason to take a risk on your idea.
The name of the game is making informed budgetary decisions to drive success. Without a well-defined budget plan, you risk overspending, missing deadlines and failing to deliver.
By planning your product development budget effectively from the outset, you avoid costly surprises and ensure every dollar spent brings you closer to a successful launch. A solid data-driven budget is your roadmap, providing clarity and direction so you can navigate the complexities of device product development with confidence and precision.
Aligning your short-term product development efforts with longterm anticipated sales growth is essential. In terms of a planning timeframe, a good rule of thumb is one to two years of development and five years of selling the product in the market. First, you must deter mine if your high-level ROI matches the market opportunity and projected sales growth. Next, are you balancing immediate needs (like creating a prototype) with maximal long-term outcomes like the ability to scale over a multi-year period? Useful high-quality products can have long tail revenues lasting more than 20 years.
With a long-term view, you ensure your product development budget helps you maximize ROI and timelines. Effective budget planning helps you identify potential obstacles early, allowing for adjustments that keep product development on track. By seeing the big picture, you make informed product decisions on target users, buyers, features, quality, and cost, leading to better profitability and growth outcomes.
Whatever framework you decide to use to estimate your product development budget, the best way to ensure accuracy is through a data-driven approach. This helps predict costs and timelines with precision, providing a clear picture of what it takes to bring your idea to market.
At Design 1st, we’ve leveraged 30 years of product development experience across more than a thousand projects to build a free tool for early-stage product innovators. Our Product Development Budget Tool helps designers create accurate and realistic budgets— giving them a clear picture of what it takes to bring their idea to market. It’s about drawing on historical data to predict costs and timelines without relying on guesswork. Even better, it’s a dynamic guide that evolves with each use, adapting to new data and improving accuracy with every new use case. A framework that can accurately map the complexity of your product, relative to the historical context of similar product development projects, is crucial for your success. (See sidebar.) It enables you to make a plan that clearly states
To best predict a ballpark budget for physical product development, Design 1st recommends its BUMPS™ framework built on five critical areas:
1. Business: What are your year-0to-2 development costs and year-3to-7 operating costs?
2. User: A simple and intuitive product drives product adoption and sales volume growth.
3. Market: Reaching target users with a differentiated product is critical.
4. Product: How challenging will it be to develop key product features?
5. Supply: Identify potential challenges in sourcing materials and components to evaluate impact on product costs, quality and profit margins.
This framework considers the major cost drivers and potential risks in historical context, helping keep your team aligned with project and product objectives.
product objectives, target users and differentiating elements. And it better informs development teams as they make trade-off decisions on features, functions and quality levels to align with product cost targets. These early-stage decisions—when aligned with your ROI plan, timelines and life-cycle costs—ensure every dollar is spent wisely.
Whatever your path to market—either through your business organization,
through investors or with your own bank account—innovators like you are the core of our economy. Instead of an Achilles’ heel, turn your physical product development budget into a strategic advantage. Take control of your product development plan and drive your project to success. |DE
Ruland now offers bellows and double disc couplings with bore sizes up to 1-3/4 inches or 45 mm for use in systems with torque up to 1,4000 in-lbs (158 Nm), available through RotoPrecision. High torque applications commonly found in precision semiconductor, solar, conveyor, and factory automation applications often use these shaft sizes. Ruland disc and bellows couplings
accommodate all forms of misalignment, are zero-backlash, and have a balanced design for reduced vibration at speeds up to 10,000 rpm.
PBC Linear has expanded its MTB Series of belt-driven linear actuators line with the MTB 105, specifically designed to integrate into multi-axis medium- to large-sized Cartesian Gantry systems, providing robust support for medium to high payloads. Its fully enclosed design ensures reliability even in contaminant-prone environ-
ments, making it an ideal choice for a wide range of applications. Precision extrusions for each aluminum actuator body ensure all sides and bottom surfaces are flat and perpendicular giving accurate installations.
The NB rotary ball spline can be used for both rotational motion and linear motion. Applications include SCARA robots, the vertical shaft of assembly equipment, automatic tool changers and loaders. The rotary ball spline has a nut that rolls on the ball spline shaft, making it
How AI copilots are helping enhance design and robotics
capable of both linear and rotary motion and provides sub-millimeter accuracy every time. Splines feature arch-shaped grooves on both the shaft and inner portion of the cylinder. These grooves approximate the diameter of the ball bearings, allowing them to carry a high load in a linear motion.
AutomationDirect has added new DURApulse GS30 drives, which support several control modes including sensorless vector control, closed-loop flux vector control and torque control
This webinar will highlight how AI copilots are empowering engineers and machine builders with practical, real-world applications.
Attendees will dive into the current state of generative AI and get practical case studies showcasing how today’s technology can help in the creation of manufacturable designs, machines and robotic cells Gain practical strategies in how to integrate AI into your processes—and to prepare your organization for the reality of Industry 4.0.
modes in a compact package. The GS30 series expands the DURApulse family by adding internal tension control loop expanded parameter sets for greater versatility, as well as optional EtherCAT and single- or dual-port EtherNet/IP communication cards. GS30 drives support up to four independent induction motor parameter sets or control of a single AC permanent magnet motor.
Stratasys has announced the commercial availability of its new SAF Polypropylene (PP) for use on the Stratasys H350 printer. It is designed to provide cost efficiency and part quality in Powder Bed Fusion technologies. SAF PP is engineered for a wide range of applications, catering to industries like automotive, medical, consumer sports and industrial sectors. SAF PP provides durability, chemical resistance and flexibility for automotive components like housings and ducting, as well as orthotic devices and consumer sports gear like shin guards.
Hyperganic has unveiled HyDesign, a new cloud-native design application for creating 3D-printed lattice structures. This tool makes designing lattice-based products easy, fast, and cost-effective for industrial designers, application engineers and OEMs exploring cutting-edge uses of 3D printing.
The Ultrasim 3D Lattice Library by Forward AM is directly embedded into the software, leveraging the full potential of superior lattice structures in a matter of minutes. This integration will replace the standalone version of the Ultrasim 3D Lattice Engine, further streamlining the design process within HyDesign.
Binder has launched an M8 12-pin circular connector. This product complements the existing M8 series and sets new standards for applications in industrial sensor technology, measurement, control, technology, camera technology, and robotics. The circular connector offers significant advantages, particularly in terms of miniaturization, flexibility and performance. Despite the high number of contacts, the M8 12-pin circular connector remains compact, making it ideal for applications with limited space.
Hirose has expanded its miniature connector offering to include a version with blind mating ability. Constructed with self-aligning elements, the HR34P Series panel mount
connector guides itself into the correct mating position. Commonly used for rack-to-panel connectivity in base stations, industrial machinery, medical equipment and more, the blind mating connector is designed for applications where the electrical receptacle is recessed or hidden in a way. Further simplifying assembly, the HR34P Series circular connector features a unique floating screw design that offers a degree of play to absorb misalignment when mating.
LUTZE expanded its DRIVEFLEX VFD cable offering to include a 2,000-V option for electrically demanding applications. The new A219 series expands upon the existing A220 1,000-V series, offering improved electrical values for 2,000-V applications. With a 7.5 OD bending radius, its flexible design saves time and money by improving ease of stripping and handling. The three symmetrical ground design reduces stray currents in the motor shaft and bearings.
Functional design of on the first heavy Polar Icebreaker in Canada in over 60 years is now 80 per cent complete and 3D modelling of the vessel is well advanced, setting the stage for Seaspan to cut steel on the flagship of the Canadian Coast Guard’s icebreaking fleet before the end of the year.
With Canada’s current largest Icebreaker—the CCGS Louis S. St-Laurent— expected to retire at the end of the decade, the new Polar Icebreaker will be one of the world’s largest, most powerful icebreakers. While designed and built before the implementation of the Polar Code, the Louis’ capability is akin to a Polar Class 4. Canada’s operational requirements drive to building a new Polar Class 2 icebreaker that can independently operate anywhere in the Arctic year-round. This capability includes the ability to operate at –50ºC, which introduces considerable complexity to the design and build of the vessel.
Most icebreakers primarily break ice—but the new Polar Icebreaker will also be capable of fulfilling many demanding missions necessary for Canada, including a wide array of Arctic science missions, search and rescue, security, navigation, transportation, and emergency response.
This wide range of capabilities also adds to the design and engineering challenges that are being addressed by the Canadian Coast Guard
Canada’s operational requirements for the new Polar Icebreaker include the ability to operate in the Arctic year-round, which introduces considerable complexity to the design and build of the vessel.
and the Seaspan team.
“Beginning construction on the Polar Icebreaker will be a monumental achievement for Seaspan, Canada and the National Shipbuilding Strategy (NSS),” said Dave Hargreaves, Seaspan Shipyards’ senior vice-president of strategy, business development and communications.
“By reinvesting in our shipyard’s capabilities and continuously driving improvements in efficiency and quality ship over ship, Seaspan has shown that we have the experience, skills, and personnel to build one of the largest and most complex ships ever to be constructed in Canada.”
The Polar Icebreaker will be 158 metres long and 28 metres wide, and able to
accommodate up to 100 personnel. It will be able to operate farther north, in more difficult ice conditions and for longer periods than any icebreaker in Canada to date.
“The Polar Icebreaker presents unique and complex design challenges, and I’m extremely proud of our team and the progress we’ve made to optimize the design of this important vessel for Canada,” said Jessica Fetterman, chief engineer of the Polar Icebreaker for Seaspan. “Thanks in par t to our cross-country supply chain of 750-plus partners, Seaspan has built Canada’s largest marine engineering and design team.”
In preparation for fullrate constr uction, Seaspan successfully completed
construction of a Polar “prototype block” earlier this year to ensure that its production teams are fully prepared to cut steel on the Polar Icebreaker in late 2024. The process of building the prototype block resulted in learnings in three key areas: improvements in design for manufacturing; testing of new equipment, processes and procedures; and validation of first-time quality in manufacturing to form and weld this new, specialized and thicker steel.
Steel needed to construct the Polar Icebreaker is twice as thick in some areas as the steel Seaspan has used for the other ships built under the NSS and is more challenging to work with combined with the tight frame spaces to support icebreaking capabilities. It also takes additional time to weld, and the thicker steel is not as malleable, therefore constructing this extra prototype block prior to starting full rate constr uction was crucial for Seaspan’s preparedness. |DE
Images: Seaspan
Complete Servo Systems starting at: $964.00 (100W)
LS Electric® iX7 & PHOX Servo
Starting at $964.00 (100W system with cables and I/O breakout)
LS Electric iX7 (AC) & PHOX (DC) servo systems offer advanced multi-axis motion control with EtherCAT networking. The EtherCAT protocol provides extremely fast, real-time, deterministic, and synchronized communication for high precision motion.
• 13 standard servo systems from 100W to 3.5kW
• Multiple input power options:
• 24-80 VDC up to 300W (PHOX)
• 230 VAC single-phase up to 2.2kW (iX7)
• 110 VAC single-phase up to 400W (iX7)
• 230 VAC three-phase up to 3.5kW (iX7)
• Use with any CANopen over EtherCAT (CoE) compatible PLC/host controller or one with ModbusTCP capability (iX7 only)
• Fully digital with 1kHz velocity loop response
• Matched gearboxes available for all wattage levels in 5 :1. 10:1, and 20:1 ratios
• 45-day money-back guarantee
• Two-year warranty
EtherCAT® is a registered trademark and patented technology, licensed by Beckhoff Automation GmbH, Germany.
Need an EtherCAT controller?
LS Electric® XGB PLC
CPUs starting at $299.00 (w/FREE soft ware)
The LS Electric XGB PLC controls up to 16 axes of EtherCAT® motion with several positioning methods including linear, circular, helical, and ellipse interpolation. Seven homing routines are also available and the FREE software offers a graphical interface so you can see the motion in action! The XGB series PLC is a perfect control solution for:
• Palletizers
• Pick-and-place applications
• Rotary tables
• Precision machining tools
• Automated welding systems
• and much more
Online LS Electric Servo System Selector Tool www.automationdirect.com/selectors/ls-ser vo
• Flying cutoff systems
Use our LS Electric Servo System Selector Tool to size your system, and to specify all the required and optional accessories for YOUR application. Get ALL the parts you need on the first order!
PLC
PLC systems with a 4-axis EtherCAT positioning module starting at $691.00 (not including servo systems)
Fast free standard shipping* is available for most orders over $49 U.S., and that includes the brokerage fees (when using an AutomationDirect nominated broker). Using our choice of carrier, we can reach most Canadian destinations within 2 to 3 days.
*Free shipping does not apply to items requiring LTL transport, but those shipments can take advantage of our negotiated super-low at rates (based on weight) that include brokerage fees.
See Web site for details and restrictions at: www.automationdirect.com/canada
500 solutions available 95% at less than $18k
Gripper
$1,340
Sensor
$6,899
Cobot
$6,899
Easily combine components from leading manufacturers with
• Find your ideal solution in just 30 minutes
• Free expert consultations and testing
• Affordable, easy-to-integrate automation
• Components from various industry leaders guaranteed compatibility