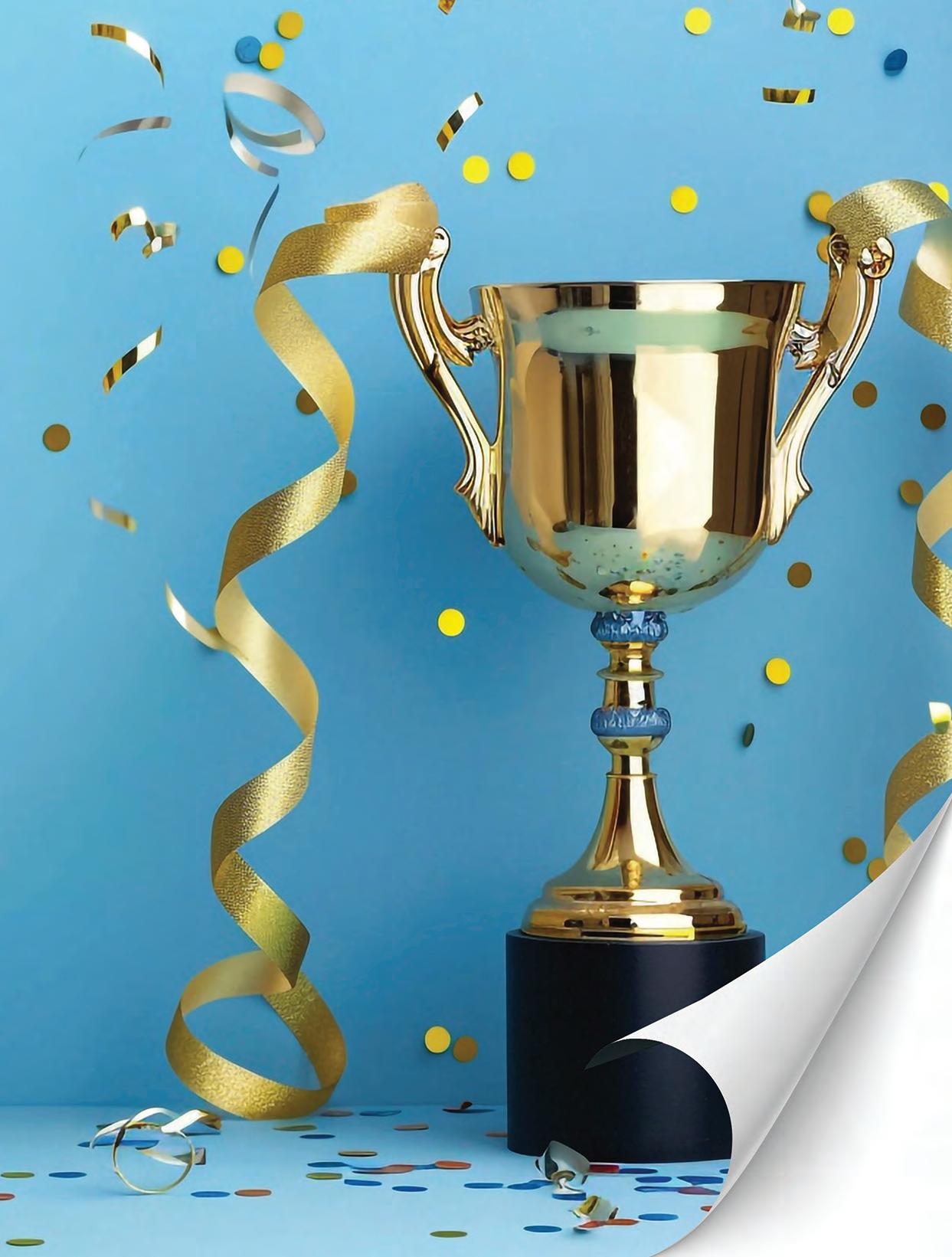
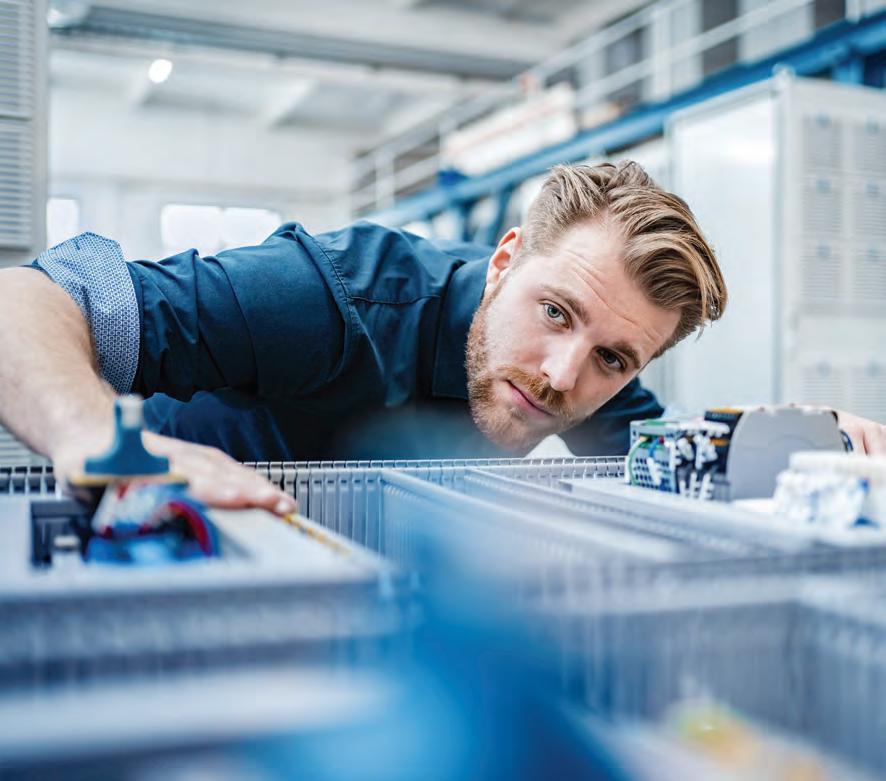
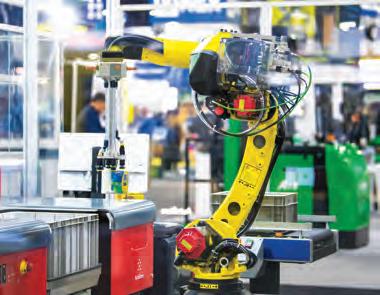
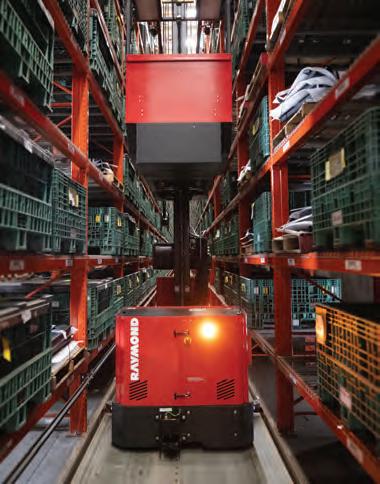
Build smart. Stay agile. Now is the time to take a broader look at your overall intralogistics strategy and optimize. Making adjustments to combat today’s challenges will prepare you for a strong and sustainable future. And we can help.
Together, we’ll analyze the strategy and systems you’ve built to move, manage, store and protect goods and bring forward new ideas to enhance or secure the investments you’ve already made. Let’s get started.
RUN BETTER. MANAGE SMARTER.™
Discover how Johnston Equipment can help optimize your facility.
Publisher | Delon Rashid (416) 459-0063 delon@turnkey.media
Editor | Derek Clouthier (403) 899-8793 derek@turnkey.media
Contributing Writers | Emily Atkins, Victoria Jones, Norm Kramer, Stephanie Smith, Christian Sivière, Keith Moore
Creative Director | Samantha Jackson
Video / Audio Engineer | Ashley Mikalauskas, Nicholas Paddison
Sales |
Delon Rashid, (416) 459-0063 delon@turnkey.media
Peter Bulmer, (585) 653-6768 peter@turnkey.media
Production and Ad-ops | Tracy Stone tracy@turnkey.media
Inside Logistics magazine is published by Turnkey Media Solutions Inc. All rights reserved. Printed in Canada. The contents of this publication may not be reproduced or transmitted in any form, either in part or full, including photocopying and recording, without the written consent of the copyright owner. Nor may any part of this publication be stored in a retrieval system of any nature without prior consent.
Canada Post Canadian Publications Mail Sales Product Agreement No. 43734062
“Return Postage Guaranteed” Send change of address notices, undeliverable copies and subscription orders to: Circulation Dept., Inside Logistics magazine, 48 Lumsden Crescent, Whitby, ON, L1R 1G5
Inside Logistics magazine (ISSN No.: 0025-5343 (Print); 1929-6460 (Digital) is published six times per year by Turnkey Media Solutions Inc., 48 Lumsden Crescent, Whitby, ON, L1R 1G5
From time to time we make our subscription list available to select companies and organizations whose product or service may interest you. If you do not wish your contact information to be made available, please contact us.
I AM CERTAINLY COMING into this industry during an interesting time. Whether it’s disruption, technology or sustainability, there is no shortage of content. The supply chain and logistics sector, as you know, is a broad industry that comprises many industries, from the various modes of transportation and warehousing to robotics, artificial intelligence, manufacturing, and operations. Some of these industries I am quite familiar with, while others I have already learned so much about in my short time as editor of this publication.
To provide some background, I come into this position with experience as an editor with several B2B magazines, including five years covering the commercial trucking industry throughout Western Canada and the U.S., which is the most applicable to the supply chain sector. I have also covered western Canadian agriculture, the potato industry (fairly niche, as you might imagine), commercial real estate, insurance, financial services, and cancer research, to name a few.
My first assignment since joining Inside Logistics was to cover the CITT’s annual Canada’s Logistics Conference in Halifax, N.S., this past June. I ran into some familiar faces at the event from my days on the trucking side and was able to meet several more. The first thing that struck me was that this broad supply chain sector is filled with talented, genuine people – much like what I experienced in the trucking industry – who are not only willing to help out an editor like me but want to help, as they are proud of the industry they call home.
You will see some of my coverage of the CITT conference in this magazine. It was fascinating to learn about the work being done at Canada’s ports – and also the efforts of the Port of Detroit to reduce its emissions (a story you can find on our website). I also provided a modal update, outlining what is happening in the air, on land, and on rail.
You will also see this is our annual Shipper’s Choice Awards issue, which is a source of pride for everyone who works on this publication, as well as those who are recognized by their peers and customers as the best in their respective categories.
Moving forward, I hope to continue covering the supply chain sector with the same insight and quality as my predecessor, Emily Atkins, who, after more than two decades, has embarked on a new venture, still within the industry, and still, from time to time, contributing to Inside Logistics. Don’t miss her feature on a behindthe-scenes look at the logistics of the Formula 1 Grand Prix du Montreal.
President & Managing Partner | Delon Rashid Head of Sales & Managing Partner | Peter Bulmer
Corporate Office
48 Lumsden Crescent, Whitby, ON, L1R 1G5
ISSN 0025-5343 Online 1929-6460
Please don’t be shy to reach out to me; I am one of the most approachable people you will meet. Much like I did during my time in the trucking industry, over time, I hope to become a recognizable face in the supply chain sector. We will be working on some great projects in the near future, and I hope you will be excited to come along for the ride.
HOW INNOVATION AND ADAPTABILITY CAN RACK UP SUCCESS – PAGE 18.
Rail capacity to increase at Port of Vancouver
By Inside Logistics Staff
+
Appointments and promotions
THE TRANSPORTATION SAFETY BOARD OF CANADA (TSB) says there are deficiencies in Canada's ability to handle marine emergencies that surpass the response capabilities of a vessel's crew, creating risks for vessels, the environment and public health and safety.
The findings come following TSB’s investigation of the 2021 loss of containers and fire on board the container vessel ZIM Kingston, off Vancouver Island, B.C., which spurred two safety concerns.
The first safety concern relates to the risk of a phenomenon called parametric rolling, which led to the loss of containers, and the second concern addresses gaps in Canada’s preparedness to respond to marine emergencies.
On Oct. 21, 2021, while waiting for an anchorage to become available, the ZIM Kingston was drifting outside the Juan de Fuca Strait, with 21 crew members on board, when it experienced a series of severe side-to-side rolls, resulting in the loss of 109 containers overboard and damage to others. Approximately 36 hours later, while the vessel was anchored off Victoria,
B.C., a fire broke out in a damaged container that held dangerous goods. The fire then spread to nearby containers and lasted for five days before it was declared extinguished.
Model testing conducted during TSB’s investigation determined the ZIM Kingston experienced parametric rolling – which occurs when sea conditions converge with vessel-specific factors in a precise way, resulting in dangerous side-to-side rolling motions. The forces created by the vessel’s extreme motions were the precipitating factor for the container loss.
The investigation found the risk of parametric rolling could have been identified using guidance material that is generally available to industry; however, this material was not on board the ZIM Kingston. This investigation and several other investigations into container loss occurrences that involved parametric rolling have revealed inconsistencies and inadequacies with respect to bridge crew training and the adoption of procedures and tools to support them in managing the risk of parametric rolling. The
“We know from past experience that developing regulations could take substantially longer than anticipated, but there’s no need for that. It’s a matter of priorities, and surely it can be done much quicker”
– Kathy Fox, chair, TSB.
International Maritime Organization is taking steps to update industry guidance; however, this will take time.
In the meantime, TSB says it is concerned that the absence of up-to-date comprehensive industry guidance for the management of parametric rolling may cause company policies, procedures, tools and training to be inconsistent, ineffective or absent altogether.
This occurrence also brought to the forefront the challenges that Canada faces when dealing with marine emergencies that go beyond the response capacity of the vessel’s crew. Unlike the United States, Canada does not require pre-arranged plans for emergency
response or marine salvage. In addition, the Canadian Coast Guard does not directly participate in marine fire response, nor does it have fire suppression capabilities to directly respond to a vessel fire. In this occurrence, it was fortunate that the vessel’s manager had made pre-arrangements for emergency response and that only by happenstance were there two suitably equipped vessels nearby.
“The emergency response that followed was initiated mainly due to incidental, but fortunate, circumstances. It is important not to mistake this luck for emergency preparedness, as the next time, we might not be as lucky,” said TSB chair Kathy Fox. “There needs to be more urgent and effective action to address marine emergencies in Canadian waters.”
Following amendments to the Canada Shipping Act, 2001, the Governor in Council now has the ability to make regulations regarding emergency arrangements for vessels. Transport Canada is developing regulations to require emergency response arrangements, which are not projected to be in place until 2028.
“We know from past experience that developing regulations could take substantially longer than anticipated, but there’s no need for that,” said Fox. “It’s a matter of priorities, and surely it can be done much quicker.”
Get a Peterbilt 579 from Brandt with the easiest walk-away lease around! Save now & down the road on a contract that works for you.
• CHOOSE THE DURATION
• FIXED LOW RATES
• OPTION TO BUY WHEN CONTRACT ENDS
KEURIG CANADA INC., operating as Keurig Dr Pepper Canada (KDP Canada), has revealed an enhancement of its distribution network by signing a lease agreement with XTL Group for a 100,000 square foot area in its new Balzac, Alta., warehouse.
This strategic expansion is designed to significantly enhance the company’s ability to service its customer base in Western Canada and, in part, supports the creation of 50 new jobs for Albertans. By strengthening its supply chain network and improving operational productivity, KDP Canada aims to support the increasing demand for its products and growth.
“In addition to expanding our already significant distribution footprint in Canada, the decision to establish our operations in this new distribution centre in the Calgary region marks a major milestone in our growth and innovation journey,” said Carl Saba, vice-president of supply chain and operations, Keurig Dr Pepper Canada. “This multi-million-dollar investment over the next five years underscores our unwavering commitment to providing exceptional service to our customers in Western Canada. This new collaboration with the XTL team will also enable us to improve the flexibility and responsiveness of our
operations from the Port of Vancouver.”
Covering 474,000 square feet, this state-of-the-art facility, managed and operated by XTL Group, includes 40-foot clearance, 16,000 racking positions, over 400,000 sq. ft of bulk storage, 112 loading dock doors, 120 trailer parking spots and is C-TPAT certified, making it the ideal choice for preserving bottled beverages, coffee products and small appliances.
“XTL Group has made a significant investment in Alberta’s economic sector with the creation of over 200 jobs since we first began operating here in 2008,” said Luc Francoeur, vice-president of sales, XTL Group. “The construction of this infrastructure will lead to an additional 50 jobs in handling, logistics management, and delivery services to serve tenant businesses. Our team is proud to provide world-class infrastructure to support the operations and initiatives of companies like Keurig Dr Pepper Canada that wish to establish a foothold in the Calgary region.”
Keurig Dr Pepper Canada’s operations from the new XTL distribution centre will begin in July 2024. Other terms of the agreement have not been disclosed
Swisslog’s automated intralogistics solutions for ambient and frozen food are designed to increase speed, accuracy, and e iciency even in demanding temperature-controlled environments.
swisslog.com/vectura
THE VANCOUVER FRASER Port Authority announced that a new four-lane overpass at Holdom Avenue in Burnaby, B.C., will enhance rail capacity for Port of Vancouver terminals, ensuring the dependable movement of goods throughout the region.
Construction the overpass crossing the rail lines at Holdom Ave. in Burnaby will begin later this year. The Vancouver Fraser Port Authority is delivering the Holdom Overpass project in partnership with the City of Burnaby, CN and the Government of Canada.
“We are pleased to partner with the City of Burnaby, CN and the Government of Canada to begin construction on the Holdom Overpass in Burnaby,” said Peter Xotta, president and CEO, Vancouver Fraser Port Authority. “The new overpass will create critical capacity and resiliency in the gateway, ensuring we can enable Canada’s trade more reliably and efficiently, while also delivering tremendous benefits to the local community in Burnaby.”
The overpass will extend Holdom Ave. south over the rail corridor and Still Creek, connecting it with Douglas Road.
The rail corridor through Burnaby is the only rail connection to transport goods and commodities to and from port terminals located in North Vancouver, a vital link in the national supply chain that connects Canadian products like grain and fertilizer to global markets. The rail corridor moves more than 40 million metric tonnes of export cargo, accounting for more than 40 per cent of the port’s total international exports in 2023.
Canada’s trade through the region is growing, and the project is designed to mitigate the impacts of trade on those who live, work and commute in Burnaby. It will provide significant community benefits, including improved safety and traffic flows, reduced greenhouse gas emissions from less idling traffic at the existing crossing, better community access by creating more reliable travel times and better
emergency response options.
The project will add to the rail improvements completed by CN in 2022, which included updates to the Thornton Tunnel to reduce the time between trains travelling through the tunnel and a new rail siding track running from Willingdon Ave. to Piper Ave.
The port authority has previously completed two phases of public engagement and continuous First Nations consultation, and input from these efforts has helped shape the overpass design.
The road enhancements are part of the Burnaby Rail Corridor Improvements Project, a series of road and rail improvements to increase transportation efficiency and trade capacity through Port of Vancouver terminals on the North Shore. The Burnaby Rail Corridor Improvements Project is funded by the Government of Canada, through its National Trade Corridors Fund, the port authority and CN.
CN
CN has named Matt McClaren as its new vice-president of safety. McClaren joined CN as a conductor in 1999 and over the years, he has been a driving force in enhancing CN’s safety programs and fostering a culture of safety. CN said it is excited to see his continued impact as McClaren leads its efforts to uphold the highest safety standards and drive innovative solutions for a safer future.
The board of directors of Supply Chain Canada, announced the retirement of its president and CEO, Martin Montanti, which will be effective as of October 2024. Montanti served as the CEO of Supply Chain Canada for more than two years. Montanti has a 40-year history within the supply chain industry, as an SCMP designation holder since 1985 and is a former assistant deputy minister for the Government of Manitoba.
UPS announced the appointment of Brian Dykes as its new executive vice-president and CFO. Dykes will be responsible for UPS’s financial strategies and will lead the global finance organization, including planning, treasury, tax, financial reporting, financial operations and investor relations.
The Erb Group announced the appointment of Greg Tuckwell as president and COO. Tuckwell joined The Erb Group in 2018 as vice-president of operations and was promoted to COO in 2023. He brings experience in both family-owned enterprises and large corporate transportation entities. His understanding of the industry and commitment to operational excellence have been instrumental in navigating Erb through transformative periods and driving sustainable growth.
RONA Inc. has appointed J. P. Towner to the role of president and CEO.
Towner joined RONA in October 2023 as CFO. He is a seasoned executive with more than 15 years of experience in corporate strategy, financial management and leadership, whose extensive
of driving profitable growth will support RONA’s ambition of becoming the best home improve ment retailer in Canada.
The Prince Rupert Port Authority (PRPA) appointed Rod Graham tors. Graham is the president of Velocity Truck Centres and has experience as a senior corpo rate executive in various sectors. Based in Cal gary, Graham has served on more than two dozen public, private and not-for-profit boards in Western Canada, including the board of gov ernors of the Business Council of British Colum bia and Alberta Indigenous Opportunities Corporation.
For 65 years, elite logistics professionals have set themselves apart with the CCLP
Take your first step to join them this fall. Start online September 9
We are incredibly grateful
like to extend our heartfelt thanks to everyone who voted for us. We will continue to provide you with exceptional service and retain your trust in our incredible team. for being selected for this award and would
Apex Motor Express has connected Canada with quality LTL service since 1948. With 13 terminals across Ontario and Quebec, along with a network of 43 terminals across Canada, you can depend on Apex to meet scheduled appointments and prioritize time-sensitive freight. Contact us today to discuss your supply chain needs.
1.800.895.2739www.
No matter the size of your business, enjoy all the perks of premium LTL service.
Offering an expansive network of 13 Regional terminals and 43 Cross-Canada terminals.
DIRECT REGIONAL SERVICE CANADA WIDE COVERAGE PREMIUM LTL SERVICE
Our strategically located terminals allow us to offer direct services to 90% of the region by noon the next day.
An update on the current status of Canadian rail, air and road transportation modes was one of the highlights of the CITT’s Canada’s Logistics Conference, this year held in Halifax, N.S.
On the rail side, Jordan Kajfasz, assistant vice-president, international intermodal and autos for Canadian Pacific Kansas City (CPKC), said CP’s acquisition of KC just over a year ago has not only transformed the company but also the Canadian rail network.
“It was a transformational acquisition and combination for the North American rail network, making CPKC the first and only railroad to connect Canada, the U.S., and Mexico on a single rail line,” said Kajfasz.
He went on to highlight the importance of Canadian trade with Mexico, saying the North American partner can be a supplement to China, particularly when considering what happened to global supply chains during the COVID-19 pandemic.
“The Mexico business environment,” said Kajfasz, “not a day goes by where you don’t hear about near-shoring and manufacturing being built in Mexico and really with the goal of Mexico becoming maybe not necessarily the replacement for China, but certainly a supplement to what comes out of Asia.”
Since the merger, CPKC has also been able to run a single-line, four-day service from Mexico to Chicago that competes with single-driver trucks and has been moving reefers from Mexico into Canada and the U.S. The railroad has also started construction on a second rail span across the Rio Grande River in Laredo.
“We believe that trade lane is going to grow every year and we’re going to need the infrastructure to support it,” said Kajfasz.
Frank Figliomeni, chief commercial officer with Fastfrate Group, echoed Kajfasz’s sentiments on the emergence of Mexico, saying the country is now the largest importer, based on its location and ability to get products to market quicker.
“Customers are trying to get their product closer to market just to avoid some of the challenges in the supply chain,” he said.
Fastfrate, which has a long-term partnership with CP as its largest drayage supplier, has invested in approximately 400 containers, around 100 of which are in the Mexican market.
“We had to learn about Mexico, it’s not an easy market,” said Figliomeni. “There are a lot more manual processes to get containers from Mexico into Canada.
“Part of our future initiatives is opening up an office in Mexico, as well, and replicating what we have in Canada from a drayage perspective.”
Corrine Kostyshyn, assistant vice-president, international intermodal for CN Rail, said there are several options her company utilizes to help improve the efficiency of moving goods from Mexico into the North American market.
“We have what we’ve had for years,” she said. “Access to a rail ferry that gets you from the Coatzacoalcos Coast into the Gulf and then connects with our rail network that way. And that’s carload shipments. So, for carload shipments, a product can move up into the North American network that way.”
CN also has a short-sea shipping option and its Falcon Premium service, which is a partnership with Union Pacific and Ferromex to reach into the Mexican market north and southbound.
Since the pandemic, Janet Wallace, managing director, cargo operations and transformation for Air Canada, said the air cargo business has completely changed for the airline.
“At the end of 2019, we were competing for space on all of the passenger aircraft to move cargo,” said Wallace. “And then during the pandemic, we took control of over 50 wide-body aircraft and we were travelling internationally and creating new relationships with suppliers in terms of how we would import into Canada or move commodities to and through Canada.”
Over the last two years, Air Canada made the case to operate its own freighters and now has eight Boeing 767s with the plan to ship over an ocean soon.
“Oftentimes in the passenger world we think it’s the last customer who boards the aircraft who makes the route viable,” said Wallace. “We’ve now proven it’s really the last kilo that gets boarded onto these aircraft that makes the routes viable.”
Wallace said Air Canada cargo saw really good business to Latin America and the Middle East between 2020-24, but moderate business within North America during that time.
“But overall, Air Canada cargo remains very optimistic in terms
of what we can bring through air, through the country,” she said.
Wallace said the future of air freight will remain strong, particularly with the rise of e-commerce.
“As long as we all continue to buy everything online on our phones, as long as we want to have everything with the speed of now,” she said. “If you look back, 80-something years ago, we weren’t happy with mail arriving in a couple of days. And I’m still not happy with mail arriving in a couple of days. It’s an indicator of what’s going to be going forward. I think things are just going to be sped up really fast.”
Pierre-Yves Fouillen, business development, North America, for Flying Whales, a French aeronautic start-up that develops environmentally friendly airships to transport large, heavy loads, said his company will be in operation within a five-year timeline.
Flying Whales is in its last phase of engineering and by the end of 2024 plans to start construction of its first factory in France.
And, by 2026, the first machine is scheduled to take flight and the certification process in the EU and Canada will commence.
“Once we are certified, we will start the production in France, and in Quebec to deliver in the Americas, to have the first commercial operations in the second quarter of 2028 in Quebec and then have all the airships delivered to various regions in Canada and in the Americas,” said Fouillen.
Over the past few years, there has been a slight shift toward the use of electric and hydrogen electric truck options to help maximize efficiency and reduce emissions.
“The electric vehicle is definitely starting to be more prevalent, but, unfortunately, when you look at the overall infrastructure and at long-haul, it’s not something in Atlantic Canada that is supported 100 per cent,” said Maryse Doucet, vice-president, LTL and terminal operations at Armour Transportation.
Doucet said the use of advanced telematics is another area where companies are investing to help reduce miles per gallon, as well as idling time.
Shelley Walker, CEO of the Women’s Trucking Federation of Canada, said in order for carriers to reap the advantages of all the new technologies available to trucking companies, training is key.
“People often assume that drivers are scared of new technology, and actually in this case, drivers are embracing it,” said Walker. “A key piece of advice is making sure your drivers get the proper training on that equipment because that is one of the big fallbacks.”
From a competitive landscape, Benoit Poirier, vice-president and industrial products analyst at Desjardins Securities, has confidence in what Canada has to offer.
“Canada is pretty attractive. We’ve made very sizable investments at the ports,” he said, pointing to recent labour issues as a potential hurdle to overcome. “I’m sensitive about Canada’s reputation. I hope those labour issues will get resolved to make sure that Canada is not losing a competitive advantage over the country south of the border.”
Poirier also believes Canada must continue to invest in new technologies to remain competitive in the global supply chain market.
“We’ve seen a lot of investment toward EV, toward technologies and labour skills,” he said. “I think we need to continue to look forward and sustain those investments in order to keep up our productivity and improve productivity.”
Investment and improving efficiencies keys to maximizing port productivity
Alain Berard says that in the face of continued disruption in the global supply chain, what the Port de Montréal needs is “EVI.”
“Not an electric vehicle. We needed visibility, elasticity, and investment, and that’s how we’ve been dealing with the disruptions.” Berard, who is in charge of new business development and international affairs at the Port de Montréal, explained during the CITT’s Canada’s Logistics Conference that when it comes to elasticity, ports must be able to clear excess containers from loading and unloading areas quickly to avoid congestion when volumes go back up.
“We worked with our third-party storage partners in that area and we have a plan for when volumes spike so we can clearly decongest the
offer a dock to dock service second to none with visibility through integrated GPS on all our trucks and trailers. Along with: Pick & Pack, Inventory control, Kitting,
In terms of visibility, Berard said ports need to be able to determine which containers take priority.
“Instead of having three or four or 5,000 containers, a comfortable number, you have 10,000 containers,” he said. “They’re not all the same priority. You have to figure out which ones need to exit the port quickly.”
The Port de Montréal invested in and developed an AI system called Cargo Two AI that helps prioritize urgent cargo, which Berard said came in handy during the pandemic.
Captain Allan Gray, president and CEO of the Halifax Port Authority, said although people may see recent supply chain disruptions as something new, they are not.
“I was at sea on container ships in the early ‘80s and these same sorts of disruptors existed in the early ‘80s,” said Gray. “So there hasn’t been a sudden change that we had a norm and we’ve gone to disruptors.”
Instead, Gray says there has been a closing of the capacity gap, with a lot of waste available across the supply chain.
“We could all be a little bit lax in what we did because we had capacity in the system that allowed us to be inefficient,” Gray said of times past. “And what we’re seeing now is those same disruptors that are kicking in the system, there isn’t this space anymore in the system to cope. And the first cry we hear out there is more capacity. We need to build more capacity.”
At the Port of Halifax, Gray said they are leaning more toward optimizing their current capacity.
“Pre-COVID, we were at 75 per cent on-time performance from
shipping lines. Post-COVID, we’re at 23 per cent,” said Gray. “So that means berth that I used to operate at 75 per cent berth utilization, I now operate at 45 per cent. So the first cry is to build another $300 million berth rather than getting ourselves back to on-time performance.”
At the Port of Prince Rupert, Jeff Stromdahl, manager of trade development for the Prince Rupert Port Authority, said there has been heavy investment to improve the offerings at the port.
One of those investments included the expansion of DP World’s terminal during the pandemic, increasing capacity from 1.35 million TEUs to 1.6 million.
“The benefit of that timing was there was a lot of cargo that was being backed up inland,” said Stromdahl. “There was a tremendous amount of congestion that was backing it up all the way out to the ports. When we were able to bring that capacity online, quite literally the next day we filled up all of that physical space at the port, but it did help to build somewhat of a relief valve.”
The Prince Rupert Port Authority also invested in the Fairview-Ridley connector corridor, which Stromdahl said is a critical piece of infrastructure for the port’s overall intermodal ecosystem. The corridor is a private haul road from the terminal to Ridley Island, where the container examination facility and import/export facilities are located.
“This took our drayage down from approximately 21 kilometres roundtrip that went through the city on municipal roads, provincial roads, on the highway out to Ridley Island down to five-and-a-half kilometres,” said Stromdahl.
24_006372_Inside_Logistics_AUG_CN Mod: June 25, 2024 3:52 PM Print: 07/12/24 page 1 v2.5
CITT’s annual Toronto Area Council Golf Tournament took place at Pipers Health Golf Club in Milton, Ont. July 18. In addition to playing a best-ball format, the event included various prizes and a barbecue lunch and dinner. Proceeds from the event were donated to Daily Bread, which supports vulnerable youth through community engagement programs.
Over the years, the material handling industry has evolved with ever-changing technologies and innovations to better meet customer needs. Since 1972, North American Steel (NAS) has been at the forefront of the Canadian racking industry, empowering growth and efficiency in industrial shelving and warehouse rack systems.
To continue building on partnerships with its customers, NAS has invested in research and development to best adapt to a changing industry, including the design, engineering and implementation of automated storage and retrieval systems (AS/RS).
“These systems automate the placement and retrieval of products from specific storage locations while significantly reducing labour costs and improving throughput,” says Mike Tripp, vice-president of operations at NAS. “By utilizing robotics and advanced software, AS/RS ensures precise inventory management and fast order processing, a trend where the modern supply chain industry is heading in Canada.”
Another key innovation spearheading NAS’s success is the integration of 3D design and warehouse layout generation in collaboration with leading software providers. For several years, NAS has been automating warehouse design processes, which generates fast, accurate layout renderings and estimates.
“This automation significantly reduces quoting and response times for customers and dealers across North America, enhancing overall efficiency and customer satisfaction,” says Tripp. This kind of efficiency is vital for any company looking to minimize costs and meet increasing demand for industrial storage space.
Offering a range of high-density storage solutions, including manual, automated and semi-automated systems, NAS ensures that each of its clients’ specific requirements are met.
“Automated systems, in particular, have revolutionized warehouse operations by significantly reducing the need for manual labour and
downtime,” says Tripp. “This leads to faster order fulfillment with fewer errors, enhancing overall efficiency and accuracy.”
Focusing on these innovative solutions has helped NAS build reliable partnerships with its customers, something Tripp says leads to future growth and innovation in the racking industry.
“This approach ensures that customers view NAS not just as a supplier, but as a strategic partner dedicated to their long-term success,” he says. “NAS is committed to building longterm relationships with customers, offering ongoing support and adapting to their evolving needs. This partnership approach ensures that customers receive not only high-quality products but also expert guidance and support throughout their project lifecycle.”
As part of that guidance, NAS is committed to ongoing maintenance, training, adaptability and customer support. While regular maintenance and prompt customer support address operational issues, minimize downtime and extend the lifespan of implemented racking systems, NAS’s training and education programs are proactive.
“As customer needs evolve, NAS offers upgrade and expansion options, ensuring that the racking systems remain relevant and effective,” says Tripp. “This adaptability allows businesses to scale their storage solutions in line with their future growth.”
NAS’s in-house design and engineering team also provides consulting services to clients, offering access to industry experts to help optimize storage solutions.
“This level of expertise and support distinguishes North American Steel from mere suppliers, positioning them as a trusted advisor and partner in their customers’ success,” says Tripp. “Our commitment to forming partnerships ensures that customers can rely on NAS for continuous improvement and innovation, rather than just a one-time transaction.”
To ensure a high level of expertise, NAS engineers and designers partake in regular training to help them adapt to emerging trends and technologies. They also attend weekly sessions to review new design tools that can be used to maximize the efficiency of storage systems.
“This in-house expertise allows NAS to develop customized systems that maximize storage capacity and operational efficiency,” says Tripp. “Our consultants work closely with customers to design efficient layouts, helping businesses make the most of their available warehouse space and enhancing productivity.”
There are several advantages to shopping locally, one of which is quality control and assurance.
“Domestic manufacturing ensures adherence to stringent standards and regulations as set by North American codes and standards, providing reliable and durable products,” says Tripp. “Customers can trust that their racking systems will meet the highest safety and performance criteria.”
Getting your product faster is another key advantage of working with a domestic racking system provider like NAS, as close proximity reduces lead times for production and delivery. Local support is also a major advantage.
“Customers can rely on NAS’s support services, which include prompt responses to the availability of spare parts and quick-ship services,” says Tripp. “The local presence ensures that any challenges can be addressed quickly, minimizing downtime and maintaining operational continuity.”
Keeping its customers’ needs in mind and maintaining a principled approach to its business practices, sustainability does not fall by the wayside at NAS. With its commitment to eco-friendly practices in its manufacturing plants and operations, NAS aims to fully automate its facilities using the latest robotic and IT solutions.
“The goal is to streamline the entire production process – from raw coil to roll forming, followed by welding, painting, packaging and producing ready-to-ship components – by spring 2025,” says Tripp. “North American Steel is committed to sustainable manufacturing and adopting environmentally responsible practices. The company not only meets regulatory requirements but also appeals to a growing customer base that values sustainability.”
By focusing on quality and durability, excellence in innovation and exceptional customer service, NAS continues to lead the way in the Canadian racking industry.
“By focusing on these innovative solutions, North American Steel not only meets current market demands but also positions itself as a reliable partner for future growth and innovation in the racking industry,” says Tripp. “This approach ensures that customers view NAS not just as a supplier, but as a strategic partner dedicated to their long-term success.”
Unlock the NAS advantage and start building a partnership by visiting naseco.ca, where nothing stacks up like North American Steel.
COMPANY CONTACTS AND LOCATIONS:
North American Steel
300 Hopkins St., Whitby, Ont., L1N 2B9 905-668-3300
sales@naseco.ca
North American Storage - Calgary 105-7850 66th Street SE, Calgary, Alta., T2C 5V1
587-327-8944
sales@naseco.com
North American Storage - Nisku 2103 - 7th Street, Nisku, Alta., T9E 7Y3 780-955-2444
sales@naseco.com
Company Size: Approx. 250 employees, 50+ authorized dealers across Canada and U.S.
SERVICES:
Manufacturing
Design & Engineering
Permitting
Project Management
Rack Inspections & Maintenance/ Repairs
Upgrades & Relocations
Installation
Custom Powder Coating
North American Steel was originally founded in 1898 as a subsidiary of Steel Equipment of England, incorporated as North American Steel in 1952, and acquired by the Fabricius Family in 1972, who remain owners of the company to this day.
IN A RECENT STUDY of 1,000 supply chain and logistics leaders in Europe and North America to better understand the challenges associated with the current workforce, 56 per cent of respondents said warehouse operations suffer from the most resource shortages.
The study also revealed that 37 per cent of respondents are experiencing high workforce shortages and 58 per cent believe these shortages have impacted customer service.
Many industry experts blame these shortages on the pandemic when millions left the workforce during the “Great Resignation.”
According to Statistics Canada, the Great Resignation left close to one million job vacancies in Canada, 80 per cent more than in 2019. In 2024, more employees are eyeing job switches than in 2022. T he Financial Post reported that a quarter of Canadian employees say they are very or extremely likely to quit their jobs and find new employment. Warehousing jobs for skilled professionals in Canada are in high demand due to the expanding e-commerce industry.
South of the border, close to 100 million Americans quit their jobs during 2021 and 2022. Since then, a ripple effect on the workforce continues to impact companies today. Labour shortages are especially significant in warehouses and distribution centres.
Technology, ranging from warehouse automation to labour management systems, is used to address these labour shortages. However, a new breed of technology has been introduced that is available to help enhance the productivity and efficiency of warehouse labour: warehouse orchestration systems.
Warehouse orchestration systems intelligently allocate tasks to workers based on real-time data and predefined rules to ensure tasks are assigned to the right employees, considering their skills, availability and
KEITH MOORE CEO, AutoScheduler.AI, www.autoscheduler.ai
current workload. If there are any bottlenecks or delays in the schedule, the system can automatically adjust task assignments to ensure smooth operations. This agility is helpful for maintaining high levels of efficiency, especially during peak periods.
Wa rehouse orchestration systems integrate with other enterprise systems, such as warehouse management systems (WMS), enterprise resource planning (ERP) systems and transportation management systems. This integration ensures a ll parts of the supply chain are aligned, leading to more efficient labour management and operations.
Ma nagers can make informed decisions on labour management based on data collected from these systems. For example, they can identify patterns in labour demand, optimize scheduling and predict future labour needs. This proactive approach helps in preventing labour shortages and overstaffing.
Wa rehouse orchestration systems that utilize AI-enhanced algorithms and predictive analytics can look into the future
to see what orders are coming in and when they need to be fulfilled. These algorithms aim to optimize labour capacity, inventory availability and demand to ensure the proper labour is at the right place to fulfill the correct orders.
Warehouse orchestration systems enhance workforce utilization by balancing workloads, ensuring employees are neither overburdened nor underutilized. A centralized system allows companies to balance labour across all sites.
A centralized warehouse orchestration platform offers a bird’s-eye view of multisite data for centralized command and control. These platforms aggregate data and use predictive analytics to rank sites, highlighting areas at risk. Excess workers at one location can be reallocated to sites needing additional labour.
Often, warehouse managers lack awareness of daily orders, leading to labour imbalances across locations, which i s costly and affects customer service. A centralized warehouse orchestration platform monitors labour distribution, compares site performance with varying labour levels, and forecasts labour demand using historical data and predictive a nalytics. This helps improve efficient labour use, enhanced productivity and reduced overstaffing costs. For example, in a wa rehouse with three shifts and varying truck arrivals, the challenge is to match available labour with demand, which is usually higher at the start of the day. Effective orchestration ensures capacity meets demand, keeping the supply chain flowing smoothly.
This is where warehouse orchestration systems can be beneficial. By better utilizing the workforce to meet demand with available capacity, warehouse operations can work more efficiently and effectively. By leveraging these systems, warehouses can achieve higher worker productivity, lower costs and improved employee satisfaction.
The 2024 Shipper’s Choice Awards are presented to the carriers who surpass the industry’s benchmarks of excellence according to our annual survey of transportation buyers.
The annual Shipper’s Choice Awards measure how well carriers perform against our Benchmarks of Excellence. In our annual survey, the scores are estab lished by shippers, 3PL service providers and freight forwarders from across Canada.
These transportation buyers rate each of their top three carriers on a five-point scale against six key per formance indicators, and use another five-point scale to rate the importance of the key performance indica tors themselves. The weighted rankings are determined by multiplying the two numbers together.
These weighted rankings are then compared to the Benchmarks of Excellence, which represent averages of the weighted scores for each category’s key performance indicators.
Twenty-two carriers met or exceeded the benchmarks established for the 2024 awards. Four companies earned the coveted Carrier of Choice designations because they have scored above the benchmarks for at least five years in a row (see page 31).
respondents answered the survey
This year 419 respondents – buyers of transportation services, and those who manage shipments handled by freight forwarders or 3PL providers – completed our survey.
To qualify, carriers need to receive a minimum number of evaluations. To prevent tampering, we watch for multiple submissions by known respondents; look for similar IP addresses; and if carriers have invited customers to submit scores, we compare those email addresses to our own database.
The Shipper’s Choice Awards survey is undertaken through a continuing partnership with CITT and the Freight Management Association of Canada (FMA), and conducted by an independent research firm.
The TL mode has historically been the toughest for carriers to score above the Benchmark of Excellence. The TL mode had the highest benchmarks in four of the six KPIs tracked by this year’s Shipper’s Choice survey: on-time performance, competitive pricing, customer service and leadership in problem solving. Six TL carriers surpassed the Benchmark of Excellence this year.
Managing so many different shipments, sharing space on one trailer and touchpoints between terminals makes the LTL business complicated. The demands from buyers of LTL services are high and carriers have to navigate a tightrope between providing excellent customer service while keeping prices competitive.
This year’s survey found LTL carriers had the second highest benchmark for on-time performance, competitive pricing and customer service. Seven LTL carriers surpassed the Benchmark of Excellence.
For the 16th consecutive year, Cardinal has been recognized for the Shipper’s Choice Award and 11 consecutive years for Carrier of Choice. We want to thank our loyal customers for your appreciation and ranking us as a top carrier in 2024. Your success is our success.
uyers of ocean freight services have traditionally been very price sensitive and this year’s Shipper’s Choice survey found little difference. Competitive pricing had the second highest benchmark among the ocean carrier KPIs, with customer service edging it out for top spot. Three ocean carriers surpassed the Benchmark of Excellence this year.
ir carriers have the highest overall Benchmark of Excellence this year. Buyers of air freight services have particularly high expectations when it comes to on-time performance, setting the highest individual benchmark in the air category this year. For air carriers, quality of equipment and operations was also deemed important, receiving the highest score across the modes. Three air freight carriers surpassed the Benchmark of Excellence this year.
Rail freight service buyers place an emphasis on competitive pricing, with it being the highest level of importance in the survey. Buyers also looked for on-time performance. Two rail companies made the benchmark this year.
Buyers of courier services have high expectations when it comes to on-time performance, so it’s no surprise this area had the highest benchmark for the mode. Buyers also look for competitive pricing and customer service. Four courier companies made the benchmark this year.
Carriers are presented with this prestigious award if they have demonstrated the consistency necessary to attain the highest levels of service by surpassing the industry Benchmarks of Excellence for a minimum of five consecutive years. This is a particularly difficult task. Aside from having to maintain consistent excellence in their operations, carriers have to meet a standard that rises every year, while also responding to changing priorities. To remain part of this exclusive fraternity, carriers must requalify each year.
For over 100 years, Oceanex has been providing efficient and reliable intermodal transportation services safely and with environmental leadership. With our fleet of 3 vessels and the largest dedicated fleet of containers and trailers servicing the province of Newfoundland and Labrador, we keep retail shelves stocked and deliver the materials that build and support our communities, keeping the economic engines of the province running.
A custom fleet to meet any requirement
Automotive
Purpose built vessels LTL
Project Cargo
Experienced professionals, dedicated technology
To and From Anywhere. Oceanex can help you move what matters.
www.oceanex.com
No load is too small for Oceanex International Cargo
Global Logistics
THE PORT OF HALIFAX has long been of historical significance. From the rescue mission deployed after the sinking of the Titanic in 1912, recovering 190 bodies to be buried in Halifax, to the Halifax Explosion of 1917, which killed 2,000 people, injured 9,000 others and destroyed 325 acres of land, the port has always been active. The opening of Pier 21 in 1928 allowed more than one million immigrants to find new beginnings in Canada, including the grandfather of this columnist. Today, it remains a bustling hub for import and export on Canada’s eastern shores.
The Halifax Port Authority began containerized cargo operations in 1969 and today oversees the movement of almost 600,000 TEUs annually. Halifax is the only eastern Canadian port able to handle 14,000 TEUs plus vessels.
In 2022, the total impact of the Port of Halifax, including Nova Scotia exporters, on the province of Nova Scotia was $4.87 billion in economic output, with the direct portion being $3 billion. This level of activity generated direct and spin-off positive impacts of $2.5 billion in GDP, $1.6 billion in labour income and over 25,300 jobs, according to the Port of Halifax.
The world’s largest shipping lines call on the Port of Halifax, connecting it to more than 150 countries.
In a recent publication in the Journal of Commerce, Paul MacIsaac, senior vice-president at the Port of Halifax, said, “Unlike many ports where ships often wait in harbour for a berth, our congestion-free berths allow us to service ships promptly upon arrival. Our container dwell time is among the lowest in North America. Import boxes discharged in Halifax bound for inland destinations such as Toronto, Chicago and Detroit typically arrive three days earlier, leading to savings in transit inventory expenses for importers and quicker sales revenue. Our newly established Port Operations Centre, managed by our team at the Halifax
Port Authority, seamlessly coordinates ship movements from arrival in the harbour to terminal handling and further onward connections by truck or rail.”
The Port of Halifax has come a long way. What started in 1752 as a saltwater ferry service port turned dockyard, which opened in 1758, has evolved into a behemoth that regularly welcomes some of the largest container vessels on the water, including the CMA CGM Marco Polo at 396 metres long with over 16,000 TEU capacity. The Port of Halifax has seen its share of change and recently welcomed members from CITT’s Canadian Logistics Conference in June with a container terminal tour to see firsthand how operations have improved.
As the first-inbound, last-outbound port in eastern North America, the Port of Halifax and PSA Halifax (the operator of both terminals at the port) continue to develop the infrastructure and acquire new equipment required to accommodate additional container ship traffic, larger vessels and efficient intermodal connections. In 2023, this included the addition of two mega cranes, bringing the total to seven at PSA Halifax’s Atlantic Hub. These cranes are the
largest in Eastern Canada and measure 52 metres high and can reach 24 containers across, making them capable of serving the increasing number of ultra-class vessels calling on Halifax. To support PSA operations, the Port of Halifax is also working on infilling at the ocean terminals to expand PSA’s Atlantic Hub, increasing container capacity from 1.2 million TEUs to 1.36 million. The Port of Halifax and PSA are also advancing the inter-terminal rail solution project to improve downtown Halifax truck traffic and expand the ondock rail to 14,000 feet by 2026, optimizing trade flows through the port.
One of the greatest historical impacts the Port of Halifax has had is the operation of Pier 21 from 1928 to 1971, which welcomed over one million immigrants to Canada’s eastern shore. It was here where passengers escaping the turmoil of war in Europe and in search of a better life came through the brick walkway at Pier 21 to start their new lives. During the Second World War, Pier 21 also acted as the key embarkation facility for soldiers and military personnel destined for Europe, many of whom would never return. Today, it is an immersive museum that showcases what it was like for immigrants coming to Canada.
While the view of the shoreline of Halifax has changed from one of freedom and new beginnings from passenger vessels coming in from overseas, the Port of Halifax still welcomes tourists and cruise liners for disembarkation on Canada’s east coast. In 2023, the Port of Halifax reached historic levels with 178 vessel calls and 434,000 passengers and crew, reportedly injecting $130 million into the local economy.
With its strategic location on the east coast, its historical impact in the Maritimes and throughout the rest of Canada and the infrastructure developments that are just setting sail at the container terminal, it is clear to see the Port of Halifax is no sinking ship.
THE CIRCUS CAME to town in June. Not the actual circus, but a much bigger show landed in Montreal the weekend of June 7–9: the Formula 1 Grand Prix du Montreal.
Instead of animals and clowns, this event features cars, drivers and their teams, media, volunteers, thousands of spectators and tons of equipment. In Montreal, with the event taking place on the Circuit Gilles Villeneuve on Île Notre-Dame, all that gear and all those people are jammed onto a tiny island with only two bridges for access.
Getting the freight in place falls to DHL. As the ground-handling agent for the race, the global forwarding company manages up to 1,400 tons of freight, including race cars, tires, fuel, hospitality for all 10 teams and broadcasting equipment.
This is no easy feat, as the gear is brought in from disparate locations by multiple modes and must all arrive within a very tight timeframe. The Montreal race was the second of four North American races on the 2024 schedule. After Canada, DHL transported Formula 1 back to Europe for five more races before the summer break, which started with the Spanish GP June 23.
DHL invited Inside Logistics for a behind-the-scenes tour of operations and a chat with the two logistics brains who make it happen. Mathieu Levasseur is the motorsports event manager at DHL Global Forwarding, and Christian Pollhammer is the senior event logistics coordinator with F1. It was the Wednesday before the race, and Île Notre-Dame
was an anthill of activity, with thousands of workers in constant motion setting up concessions, grandstands and fencing. Dozens of forklifts – every single one that could be rented within hundreds of miles –buzzed back and forth along pit lane, delivering crates of freight and maneuvering equipment into place for each of the teams.
The race cars had arrived days before, and the teams were hard at work, mostly behind screens in their pit stalls reassembling and tweaking their setups. Meanwhile, the drivers were over at Montreal Olympic Stadium doing promotional stunts for Red Bull.
But before all that could happen, DHL got to work. After the Miami GP in early May, equipment that stays in North America was loaded onto 100 trucks and driven north. DHL stored it until it was required onsite in Montreal. Meanwhile, the teams and cars returned to Europe, where they contested the Italian and Monaco GPs. Equipment for these races is moved around Europe and held at the teams’ own headquarters or storage sites when not in use.
“Right after the race in Monaco concluded, that gear was packed up and sent back to the team HQs for sorting and repacking,” Pollhammer explained. It was then delivered to DHL for air freighting to Canada. At the same time, other gear that had been used at the Japan GP in April was making its way to Montreal via ocean freight, landing in Vancouver before being trucked cross-country to Montreal.
“Every team has four, five or six kits, and it’s always moving, even in
the off-season,” Levasseur said. “We ship the cargo for the first race of the next season. The air freight is always going to fly to the race, which is predictable. So that will never be late. Ocean freight: they always plan ahead, like a good month and a half before. The Japan race was in early April, so that’s the time they took from April to get here.”
Last-minute items are called “late freight” and can arrive right up to the Saturday of race weekend. This typically includes parts for the cars that have been refined in the teams’ home workshops. DHL airfreights these shipments on commercial flights and facilitates their transport to the race location the same day.
Remarkably, the DHL team that makes this all happen onsite is small. Levasseur and Pollhammer are joined by another eight people on the admin side, while the crew on the ground who load and unload trucks and move the gear to the right location is about 10 people. “They’re efficient,” Pollhammer said.
After the checkered flag
While F1 setup is a week-long affair, getting out of town after the race is a bit of a panic. “For us to get out of here, there is enormous time pressure because two weeks later we race in Spain. So, the teams need to go back, wait for the freight to arrive back in the factories, need to transfer it back onto their trucks and then have to travel up to 1,500 kilometres to reach Spain. So that is a very tight turnaround for us,” Pollhammer said.
He explained they often give teams nine or 10 hours to get packed up after a race. “We tell them six o’clock in the morning, seven o’clock. But because we need to move quick, the timeframe is much shorter. Six to seven hours is the minimum they need to pack up. Much less than that we can’t do.”
“I would say because I’m a logistics geek, I would prefer almost watching the team packing up, which is a race after the race,” Pollhammer added. “It’s ridiculous how fast they operate just to repack
it. Everybody knows which part goes in which kit.”
With all the tight turnarounds and airfreight being used, both F1 and DHL are aware of the significant carbon footprint of the event’s logistics. F1 has set a target of carbon neutrality by 2030. DHL uses multimodal logistics solutions, including air, sea and road transport, to minimize its impact. Rail is only an option when there is a lot of time to work with, Levasseur said, because if it gets stopped for some reason, there’s no way to retrieve the cargo. That’s why the gear that arrived by sea from Asia was trucked from Vancouver, he explained.
For air freight, DHL employs fuel-efficient Boeing 777 aircraft, achieving a 17 per cent reduction in emissions compared to older planes. In Europe last year, DHL introduced a fleet of biofuel-powered trucks, with each truck reducing emissions by an average of 83 per cent compared to conventional diesel trucks. This season, the number of biofuel-driven trucks has more than doubled, reaching a total of 37.
In addition, the waste generated by the teams on site is removed. “Nothing stays in the country as garbage,” Levasseur said. That includes the used tires, of which there are seven or eight container loads for each race. They get shipped back to Pirelli in Romania or Italy for recycling, while teams pull a few that are labelled for testing, also at Pirelli’s facilities.
“The partnership between DHL and Formula 1 is strong not only because of our logistics expertise but also due to our shared commitment to sustainability. Both organizations prioritize eco-friendly practices and continually seek innovative sustainable logistics solutions for upcoming seasons,” Levasseur noted.
Clearly, with 20 years of experience moving Formula 1 around the world, DHL is on its game. Proof positive is that the two organizations have just inked a new nine-year contract that will see DHL continuing to maintain the pace.
to get your fulfillment operations in a row? Discover automation and software solutions aligned with your business goals at TREWautomation.com.
IT’S HARD TO imagine a warehouse and distribution center without conveyor systems. Boxes can be quickly moved from one end of the warehouse to the other, from ceiling to floor or wall to wall, without any manual material handling effort. While conveyor systems can help reduce the risk of repetitive strain injuries, they come with other, often deadly, hazards.
Worker’s hair or clothing can be drawn into equipment, belts moving over the head and tail pulleys can create an in-running nip hazard, rotating pulleys with raised edges can cause entanglement, and access to drive system belts or chains can also cause serious injury.
When these hazards are overlooked, there can be disastrous consequences. In a recent incident, an employee working alone tried to fix a conveyor belt that was slipping off its pulley by applying belt dressing between the belt and the pulley while the conveyor belt was still moving. Hours later, the worker was found deceased. The company was convicted of violating health and safety laws and fined $200,000.
Preventing incidents like this one comes down to appropriate lockout and tagout procedures, machine guarding, greater awareness, safe work procedures and effective training. Here are five steps your workplace can take to better protect workers who work around conveyor belts.
Five steps to preventing injuries on conveyors
1) Understand the legislative requirements for conveyor systems (and other machines) in your jurisdiction. Also, CSA Z460:20, Control of Hazardous Energy, Lockout & Other Methods, reviews hazardous energy control methodology.
2) Carry out a risk assessment. Look at the equipment, identify hazards and understand how people will interact with the machine (what tasks are being done on or around the equipment?) Many warehouses have a layout that causes order pickers to be near moving conveyors. Ask questions to help determine your control measures, such as:
What type of conveyors are you using, and what are their unique hazards?
Where are the in-running nip/pinch points? A nip/pinch point is a place where it is possible for a body part, article of clothing or an object to be caught between moving parts or between moving and stationary machine parts.
Where else can workers be entangled, drawn in or crushed?
Can the product fall off the sides of a floor conveyor or overhead conveyor and strike a worker?
Are e-stops within easy reach of where operators are working (loading and unloading areas, inspection areas, etc.?)
What steps need to be taken if the conveyor becomes jammed? Or when maintenance or cleaning occurs? Do you have a lockout/tagout system in place for conveyors?
Do employees need to move from one side of the conveyor to another? Or across a room full of conveyors? How will they do that safely?
Is misuse possible – removal of guards, or climbing onto or going under conveyors?
3) Control hazards using the hierarchy of controls: eliminate, substitute, engineering controls, administrative controls, and personal protective equip-
ment. Engineering controls include fixed guards and safeguarding devices such as light curtains or interlocks. Ensure guards are in place for all moving parts of the drive system and where hazards such as in-running nip, drawing-in, trapping and crushing are present. Don’t forget about portable, expandable conveyors moved into trailers to unload floor loaded boxes; fingers can easily get caught when expanding or collapsing equipment.
Administrative controls include warning signs, startup signals and safe work practices. Safe work practices can include:
pre-shift inspections and preventative maintenance
reporting missing or damaged guards
de-energizing the conveyor and locking out before removing jams or debris, or performing maintenance
operating at correct speed and belt tension, and not overloading
never walking on, climbing on or ducking under the conveyors
never wearing loose clothing, jewelry or long hair around conveyors
4) Train supervisors, workers and maintenance staff. Make sure information is getting across. Don’t just talk to people, show them what you mean and get them to show you. Augment classroom training with visual images. When people can visually make connections, their understanding increases. Also, think about the message you are delivering when it comes to productivity and safety. Today’s fast paced warehousing and distribution centers place a high value on productivity. Workers may think it is better to keep conveyors running when performing seemingly minor repairs, with the worker paying the ultimate price. Prioritize safety over productivity.
5) Inspect the conveyor on a daily basis. Make sure all guards and safeguards are in place. Are guards still functional? Have people made adjustments that would make the guards ineffective? Do the belts have enough tension so they won’t slip, and are they in good condition?
NORM KR AMER, CRSP, P.MM, provides expert, in-depth health and safety consulting services for Workplace Safety & Prevention Services (WSPS) as a Warehouse Specialist in the Greater Toronto region.
SMITH, provides in depth health and safety consulting services in a variety of areas as Senior Consultant for Workplace Safety & Prevention Services.
While it may be easy for warehouse workplaces to focus on seemingly more prominent hazards such as lift truck speed, storing pallets at high elevations, working at heights, to name a few, don’t take your conveyor systems for granted. Conveyor safety is not just for maintenance workers who must lockout equipment for repairs.
CANADIAN SUPPLY CHAIN professionals face a new challenge this year: the Fighting Against Forced Labour and Child Labour in Supply Chains Act. Known as Bill S-211, it came into effect on Jan. 1, bringing new reporting obligations for entities meeting two of the following conditions: at least $20 million in assets, at least $40 million in revenue, and/or an average of at least 250 employees. Canadian entities are defined as those producing, selling, or distributing goods in Canada or elsewhere, importing goods into Canada, or controlling an entity engaged in these activities. The same obligations apply to government institutions involved in these activities.
The first yearly report was due May 31 and needed to identify any risks of modern slavery within an entity’s supply chain and the steps taken to mitigate them. For smaller companies falling below the above thresholds, it is still essential to be familiar with the Act’s requirements and to prevent any products derived from forced or child labour in their supply chains—not just for ethical reasons, but also because large customers are likely to request such assurances. In a nutshell, companies need to validate their inputs with their upstream suppliers, all the way up to the first extraction and processing of raw materials. This is the new reality of compliance.
“Forced labour” is defined as labour provided by a person under circumstances that could reasonably be expected to cause the person to believe their safety would be threatened if they failed to provide the labour, or constitute forced labour as defined in the Geneva Forced Labour Convention of 1930. “Child labour” is defined as labour by persons under the age of 18 that is provided in Canada under circumstances that are against Canadian law, or under circumstances that are mentally, physically, socially, or morally dangerous to them. It is also defined as anything that interferes with their schooling by depriving them of the opportunity to attend school, obliging them to leave school prematurely, or requiring them to combine school attendance with excessively long and heavy work, as defined in the Geneva
CHRISTIAN
SIVIÈRE runs Solimpex, and is an international trade consultant and lecturer. christian.siviere@videotron.ca
Child Labour Convention of 1999.
Now that the reports have been filed, it is a good time for reflection. There was some confusion around the applicability of the Act and the entities required to file. This is relatively normal for new regulations, although this one topped many, as its language was not always precise and left room for interpretation. Also, since the Act came into effect just five months before the first reporting deadline, many companies had a hard time figuring out whether it applied to them. No doubt, this kept lawyers busy. As a result, it’s possible that more entities than required decided to file a report, just in case. Originally, the government indicated that thousands of companies could potentially be captured by the Act, so that could mean a lot of reading for the civil servants assigned to this.
With the reporting deadline passed, Public Safety Canada will continue to accept late submissions and publish reports received past the May 31 deadline. Companies and government institutions can also submit a revised version of a previously submitted report by completing the online questionnaire a second time. Moving forward, some questions are pending and will hopefully be answered in time for the next filing deadline in May 2025. Regarding
the thresholds, the Act refers to consolidated financial statements and a firm’s total or global assets, revenues, and employees, but what about subsidiaries? Regarding covered activities, the Act refers to companies that distribute and sell goods, but what about importing and producing? And how about transport and warehousing companies? Despite the confusion surrounding the introduction of the Act, it has raised awareness around the important issues of forced and child labour in our supply chains. This is a positive development, with so many imports coming from low-wage countries that have little protection for workers.
The U.S., our most important trading partner, has taken a different approach to this topic with its Uyghur Forced Labor Prevention Act (UFLPA), specifically targeting China. Under the UFLPA, U.S. Customs and Border Protection (CBP) can detain or seize any goods made, in whole or in part, with inputs from China’s Xinjiang Uyghur region, presuming that such goods were made using forced labour. Since this applies to goods made in whole or in part, U.S. importers who source products anywhere in the world are at risk, as inputs from Xinjiang can be used to manufacture goods outside China. This also applies to non-resident importers, i.e., Canadian exporters selling in the U.S. delivery duty paid. CBP publishes a dashboard with relevant shipment statistics, as well as a list of targeted Chinese entities, which is updated regularly.
Did the arrival of your new Porsche or Bentley get delayed? This could be why: A few months ago, CBP held hundreds of these new vehicles at several U.S. ports, as they found they contained a small part that had originated from one of the named Chinese entities targeted by the UFLPA. The brand owner, Volkswagen, had no other choice but to replace that part in all these vehicles, so they could be released and sold in the U.S.
This is a good hint for Canadian companies doing business in the U.S. Make sure you’re compliant with both Canadian and U.S. laws. Even a large and well-organized company like Volkswagen can run into issues.
To stay competitive and get ahead, you need innovative, scalable and safe solutions. These solutions can help with better storage, distribution, fulfillment or any combination that can grow with your business as it adapts to change.
As your partner in facilities evolution, you can count on Konstant to transform your facilities. Collaborate with our team to optimize your facility today and evolve, anticipate, adapt and imagine the facility of your future.
Get integrated logistics solutions: racks, shelving, trucks and robotics from our partners including Johnston Equipment and GNJ Automation.
Access comprehensive services for your project lifecycle, from planning to ongoing management with a skilled team ensuring quality at every step.
For more than 50 years, Konstant has served businesses across Canada, adapting our services to evolving facility management needs.