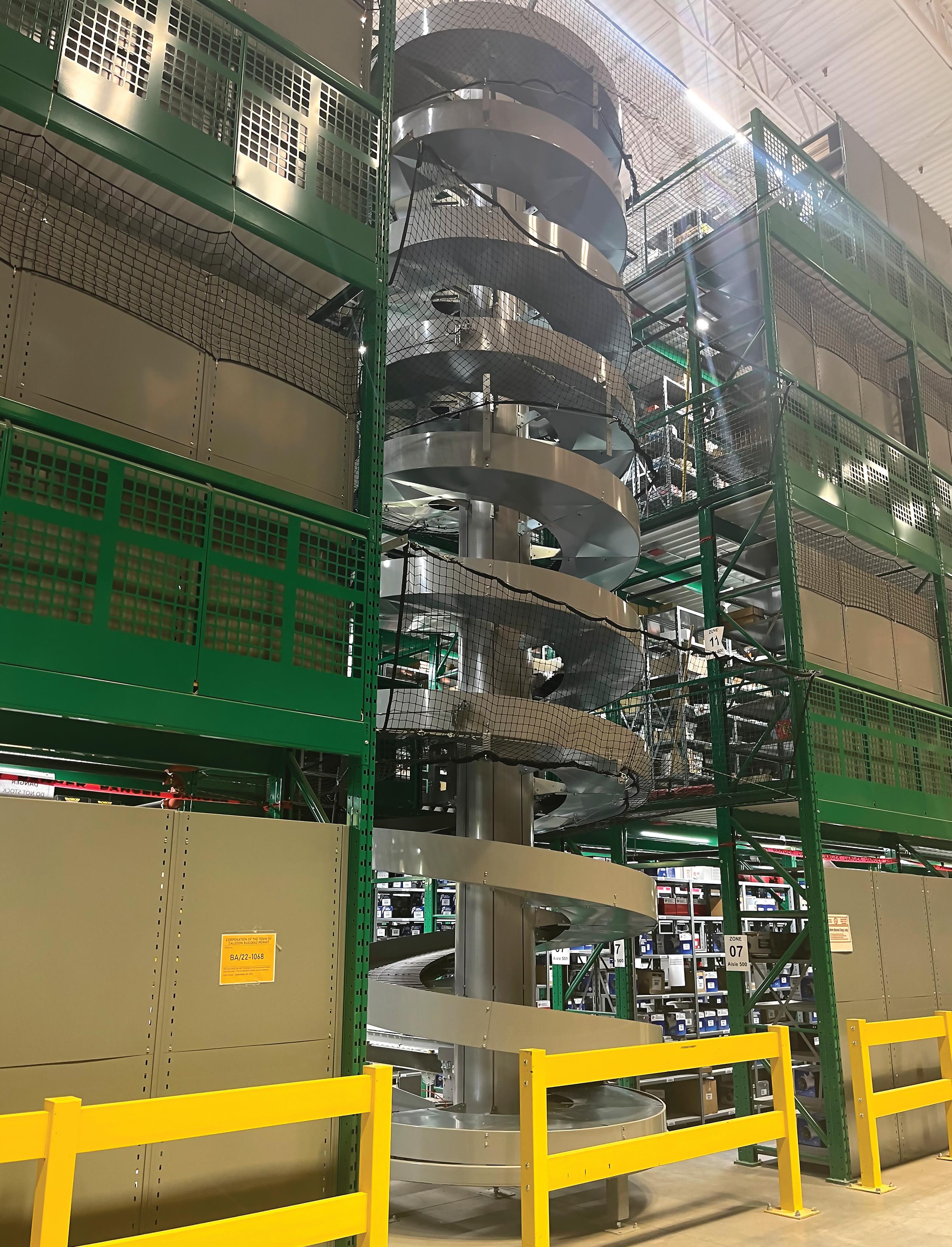
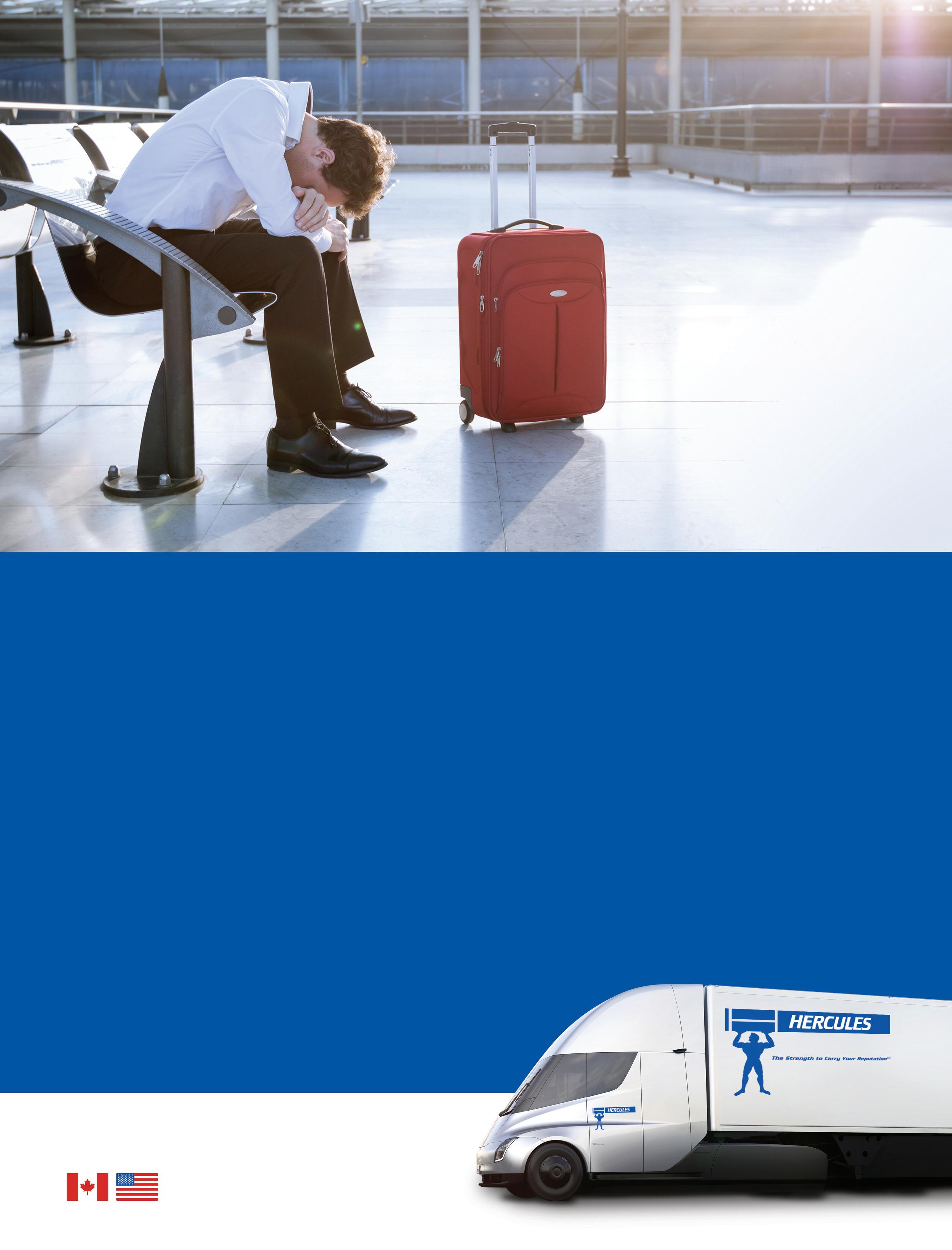



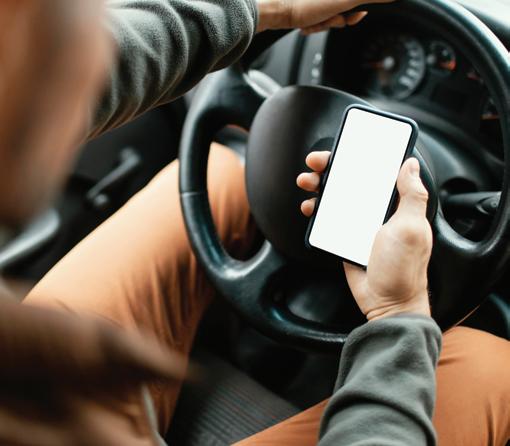
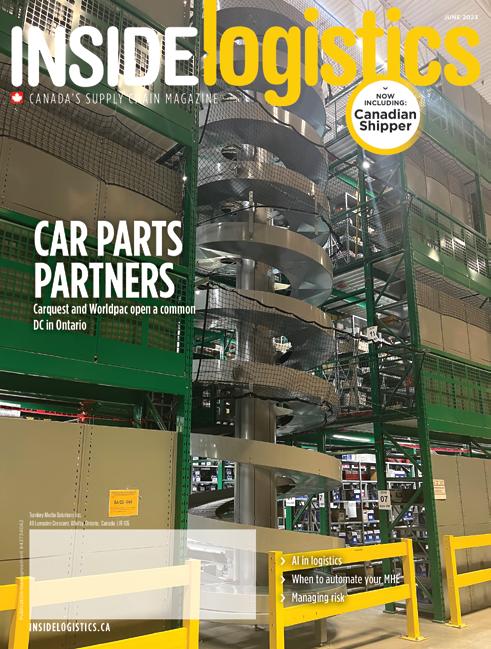
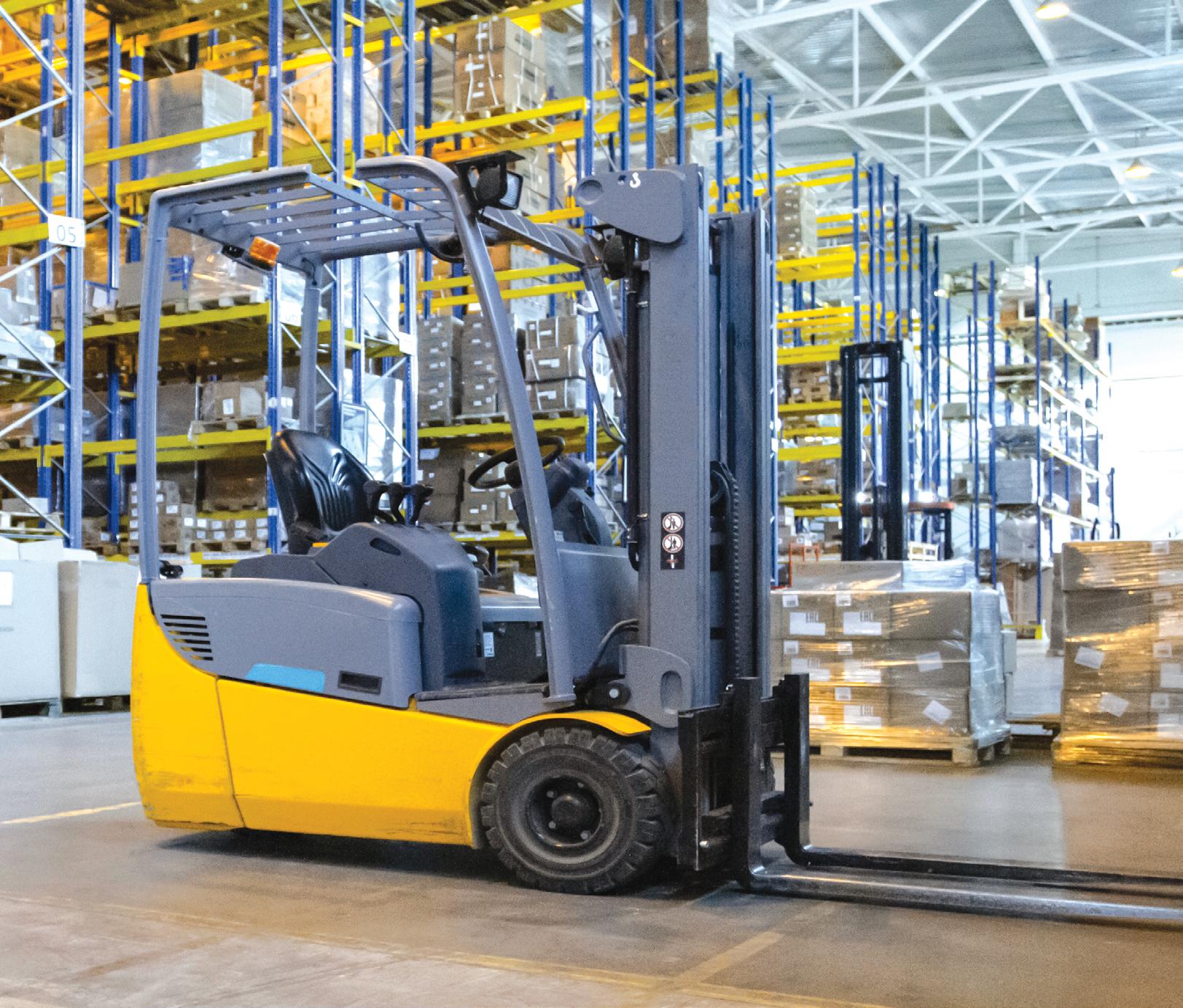
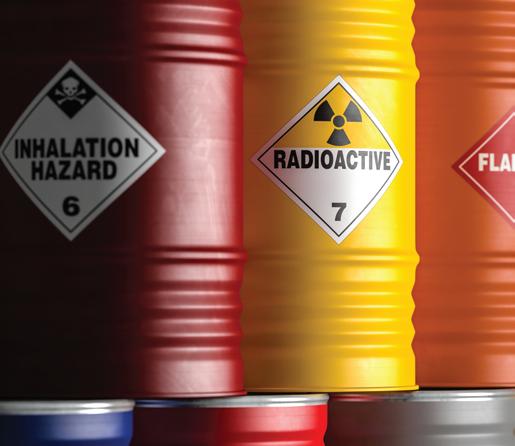
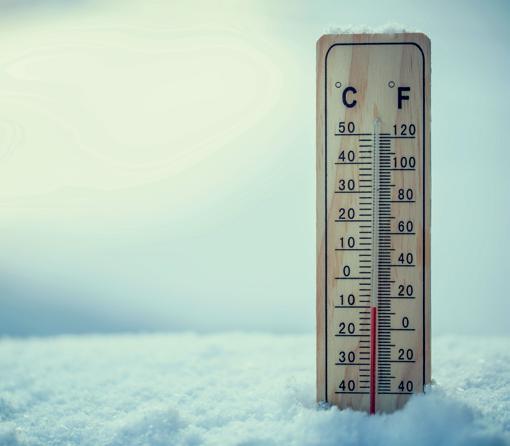
For 65 years, elite logistics professionals have set themselves apart with the CCLP designation. Take your first step to join them this fall, and start online September 5
CCLP (CITT-Certified Logistics Professional) is the one and only professional certification granted by CITT –Canada’s Logistics Association. Created by industry, for industry, CCLP develops and certifies the crucial competencies required of an elite logistics professional.
When you hold the CCLP designation, it tells the industry – from carrier across modes to shippers in all sectors – that you have an expert understanding of the complex business of logistics. And it connects to you an unparalleled network of like-minded professionals who can share expertise and open new doors.
Whether you’re looking to sharpen your abilities, advance in your current organization, unlock new opportunities, or get formal recognition for the expertise you already have, CCLP can help you achieve your career goals.
Get certified via the fully online program or the challenge exam for professionals with deep experience • Access networking events, exclusive job board, topical webinars, and other exclusive resources • Fast-tracks available for previous business education • Recognition of international education and work experience
Publisher | Delon Rashid (416) 459-0063 delon@turnkey.media
Editor | Emily Atkins (416) 262-4106 emily@turnkey.media
Contributing Writers | Norm Kramer, Anar Mammadov, Tyler Mortensen, Bill Pedriana, Mario Sagastume, Christian Sivière, Greg Tuthill, Dale Wales
Creative Director | Samantha Jackson
Video / Audio Engineer | Ashley Mikalauskas, Nicholas Paddison
Sales | Delon Rashid, (416) 459-0063 delon@turnkey.media
Peter Bulmer, (585) 653-6768 peter@turnkey.media
Production and Ad-ops | Tracy Stone tracy@turnkey.media
Inside Logistics magazine is published by Turnkey Media Solutions Inc. All rights reserved. Printed in Canada. The contents of this publication may not be reproduced or transmitted in any form, either in part or full, including photocopying and recording, without the written consent of the copyright owner. Nor may any part of this publication be stored in a retrieval system of any nature without prior consent.
Canada Post Canadian Publications Mail Sales Product Agreement No. 43734062
“Return Postage Guaranteed” Send change of address notices, undeliverable copies and subscription orders to: Circulation Dept., Inside Logistics magazine, 48 Lumsden Crescent, Whitby, ON, L1R 1G5
Inside Logistics magazine (ISSN No.: 0025-5343 (Print); 1929-6460 (Digital) is published six times per year by Turnkey Media Solutions Inc., 48 Lumsden Crescent, Whitby, ON, L1R 1G5
From time to time we make our subscription list available to select companies and organizations whose product or service may interest you. If you do not wish your contact information to be made available, please contact us.
ECONOMIES OF SCALE is a term in economics that refers to a company’s ability to reduce costs by increasing the volume of production.
The term is typically used in reference to manufacturing production, but it can apply in any area where increasing scale of output allows costs to be spread over a larger quantity of goods. This includes the world of logistics and distribution.
Our cover feature this issue (page 12) takes a look at the new master distribution centre that Advance Auto Parts has built in Bolton, Ontario, to handle inventory for two of its brands, Carquest and Worldpak. While the two auto parts distributors share the same parent, they have – until now – managed their own warehousing and distribution.
But when both were outgrowing existing facilities, the parent company had a lightbulb moment and decided to bring the two together under a single roof in a much larger facility. It now has one work force, one building, one set of utilities to manage, and can combine orders for Carquest stores and Worldpac outlets on the same trucks. It only had to install racking, automation, and a pick tower for one new facility, not two.
While the process of integration was not without some challenges – like learning how to operate separately but also together, and pulling down operational silos – the result has management smiling. It’s a formula that seems to be working for the two companies, and they are looking for expansion of the model, both within the new facility and across the country.
The idea is not entirely new, of course. Third-party logistics – which has been around for close to 60 years – takes advantage of these same principles to offer warehousing and distribution services to disparate clients from under the same roof.
But Advance Auto Parts stands to benefit more from this new arrangement than it would by using a third party to manage its distribution operations. Keeping it in house means maintaining control and avoiding the costs of engaging a 3PL, while at the same time enjoying all the benefits noted above.
President & Managing Partner | Delon Rashid Head of Sales & Managing Partner | Peter Bulmer
Corporate Office
48 Lumsden Crescent, Whitby, ON, L1R 1G5
ISSN 0025-5343
Online 1929-6460
From where I stand it feels like a winning combination, and one that I will be watching as the company seeks to build out the model and prepare for future growth.
THE HOUSE OF COMMONS passed Canada’s first supply chain transparency law in May.
The legislation establishes a supply chain reporting obligation for businesses, and expands prohibitions under the Customs Tariff legislation. Bill S-211, also known as Fighting Against Forced Labour and Child Labour in Supply Chains Act and to amend the Customs Tariff, will come into force on January 1, 2024.
The Bill requires Canadian companies to report annually on measures they are taking to identify and address forced labour and child labour risks found in their global supply chains, and creates a public database for consumers to review company submissions. The legislation also amends the Customs Tariff Act to prohibit the import of goods made with child labour.
Companies affected must meet at least two of the following criteria in one of the last two years: have at least $20 million in assets; have generated at least $40 million in revenue; and/or employ an average of at least 250 employees.
"The increased focus on human and labour rights
violations in the context of international trade underscores the need for businesses to pay close attention to their enterprise and supply chains," said Julia Webster, a partner with law firm Baker McKenzie in Toronto.
"While Canada has not yet undertaken robust enforcement of its prohibition on importing goods manufactured with forced labour; with the passage of
“The increased focus on human and labour rights violations in the context of international trade underscores the need for businesses to pay close attention to their enterprise and supply chains.”
– Julia Webster, partner with law firm Baker McKenzie in Toronto.When the weather conditions worsened in Cambodia, Khav was forced to drop out of school and start fishing to earn money.
Bill S-211 and the new USMCA requirements and the growing expectation of consumers, stakeholders and voters, that is sure to change."
Kevin Coon, also a partner at Baker McKenzie, believes Canadian businesses can prepare for the upcoming change in the enforcement landscape. He recommends companies take seven steps to assess the impact on their business.
First, they need to find out if they meet the reporting entity requirements under the Act. Reporting entities’ first annual reports will be due by May 31, 2024.
Second, they need to conduct due diligence on the risk within the enterprise and supply chain for violations of human and labour rights, by producing a risk assessment or matrix.
Third, they must understand the reporting and other obligations in the jurisdictions in which they do business, and determine if those various obligations can be aligned into a single report, and whether compliance can be implemented globally.
Fourth, they should review and align internal policies related to human and labour rights, supply chain, procurement and related issues to ensure they are consistent with corporate values and principles.
Fifth, they will need to train to those in the enterprise who have oversight or responsibility for the implementation of human and labour rights measures.
Sixth, they need to understand their supply chain, evaluating, consolidating where necessary and putting in place commercial measures to define accountability.
And finally, they should review standard operating procedures, including third-party supplier vetting, to ensure that forced labour concerns are addressed by company policies and meet the requirements outlined in the legislation of their home jurisdiction.
"By passing this Bill, Canada is sending an important signal about its commitment to promote human rights and is ensuring that Canadian companies are not contributing to the exploitation of vulnerable workers, especially children," said Michael Messenger, president and CEO of World Vision Canada.
"This Bill provides more transparency to consumers to equip them with the information they need to make ethical purchases, and this legislation serves as an important first step towards ensuring that companies' operations contribute to a more just and sustainable global economy."
For over 100 years, Oceanex has been providing efficient and reliable intermodal transportation services safely and with environmental leadership. With our fleet of 3 vessels and the largest dedicated fleet of containers and trailers servicing the province of Newfoundland and Labrador, we keep retail shelves stocked and deliver the materials that build and support our communities, keeping the economic engines of the province running.
TEAMSTERS CANADA, the Canadian Trucking Alliance (CTA), and the Association du camionnage du Québec (ACQ) have joined forces to call for urgent federal action to put the brakes on the growing Driver Inc. crisis in the country’s trucking sector.
Driver Inc. refers to truck drivers who incorporate, often at the request of dishonest employers who want to pay lower taxes and avoid other payroll deductions. But in reality, these drivers are indistinguishable from regular employees, lacking truck ownership, route choice, or any real independence or financial risk.
Truckers engaged in Driver Inc. are not only missing out on essential protections like workers’ compensation and employment insurance, but are also being duped into believing they’ll have higher earnings, said François Laporte, president of Teamsters Canada.
The trucking industry and labour unions are urging the federal government to increase investment in enforcement and penalties for those involved in the Driver Inc scam. In addition, they call for a coordinated effort between the CRA, the Labour Program, and provincial governments to protect truck drivers and preserve the integrity of the trucking industry.
“None of this is legal, and they could end up losing tens of thousands if they are audited. Because they lack information about rights and obligations in Canada, new Canadians and temporary foreign
• 4,000 lb. (1,814kg) and 5,000 lb. (2,268kg) Capacity at 24” (600mm) Load Center
• Triple and Quad Masts with Lift Heights to 31’ (9.5M)
workers are particularly vulnerable to this scam.”
“The trucking industry is facing an existential crisis due to a labour abuse and tax avoidance scheme. We need the Canada Revenue Agency and the Labour Program to tackle these issues with the enforcement resources this crisis needs,” said Stephen Laskowski, president of the CTA.
“We need substantial audits on carriers involved in the Driver Inc scam. The laws are already in place, they need to be enforced before it’s too late!”
According to Marc Cadieux, president of the ACQ, Driver Inc. is costing governments at least $1 billion annually
• 60” (1.52M) Stacking Aisle with 48” x 40” (1.2M x 1M) Load
• AC Traction and Hydraulic Controllers with Lift Interrupt
• Hydraulic Power Steering by Main Hydraulic Pump (No Separate Power Steering Pump or Motor)
• 110 FPM Lift Speed and 7 MPH Travel Speed
• 90º Rotating Mast and 22” (508mm) Shift for Easy Load Insertion and Retrieval
• Wire Guidance Available for “Steer Free”
Very Narrow Aisle Performance
“We need substantial audits on carriers involved in the Driver Inc scam. The laws are already in place, they need to be enforced before it’s too late!”
– Stephen Laskowski, president of the CTABy Emily
JEREMY WANG IS on a mission to prove that planes no longer require humans in the cockpit.
His ground-breaking work to develop Canada’s first autonomous cargo airline – which is on track to start a commercial pilot project by the middle of next year – has earned Wang an award and $5,000 from Mitacs, an organization which supports Canadian innovation.
In recognition of his efforts to advance self-flying planes through his Toronto-based startup Ribbit, Wang – who earned his PhD in Mechanical Engineering at University of Waterloo and now serves as Ribbit co-founder and COO – was presented with the Mitacs Change Agent Entrepreneur Award on May 18 at a ceremony in Waterloo, Ontario.
“Our goal is to rewire the transportation network to be faster, more efficient and more accessible to remote communities that right now, don’t have reliable air transportation,” said Wang.
Wang, along with Ribbit co-founder and CEO Carl Pigeon, started his career developing drone technology, but soon recognized the need to focus on fullsize aircraft to truly make an impact on transportation at scale.
“We’re not talking about shuttling executives from city to city, we’re talking about providing basic access to reliable transportation so that people living in rural and remote communities can get necessities like food and medicine on time,” he explained.
Working in collaboration with Transport Canada since its inception in 2020, Ribbit completed its first gate-to-gate, hands-free flight in 2021 – marking a first for Canada – and has demonstrated nearly 200 hours of successful autonomous flight since then, always with a human safety pilot on board.
“Our plane taxied out from the hangar, went to the runway, took off, flew around, landed and went back to the hangar, and the safety pilot did nothing but sit in the cockpit,” said Wang, adding that the long-term goal is to equip airlines with fleets of the company’s autonomous planes, which can safely fly using insidelogistics.ca
existing airport infrastructure.
The company’s design is based on retrofitting existing fixed-wing planes with a technology stack that allows them to taxi, take off, fly and land autonomously. By removing the pilot, the planes have more room for cargo and eliminate scheduling barriers, freeing airlines to capitalize on nearly 15,000 under-utilized private airports across North America to provide more direct, non-stop flights between remote destinations, without the need to schedule pilots or travel through major airport hubs.
“When we first got started, we kept hearing from people in northern Canada about how terrible the supply chains were,” said Wang. “Flight schedules were infrequent and unreliable, and they wanted more options.”
Recently, the company signed letters of intent with six leading online wholesaler/ retailers serving the north and is working with Transport Canada to achieve regulatory approval to move forward with commercial flights. The company is already approved for flight testing without a human safety pilot on board and expects to complete its first truly autonomous flight next summer.
“Our technology has been tested, the regulatory framework is in place and there’s a real need for this. It’s time for autonomous air cargo to take flight,” he said.
Wang is one of five winners of the Mitacs Entrepreneur Award who are being recognized for their efforts to turn their research into an innovative business that impacts the lives of Canadians.
ACCORDING TO RESEARCH by market intelligence firm Interact Analysis, the collaborative robot (cobot) market will enjoy growth through 2032, with annual growth rates sitting at around 20 percent.
Collaboration between humans and robots is now widely accepted, so robot manufacturers suggest that the key to future success will be their ability to scale up production and develop new application scenarios. The logistics industry will also play an important role in
this growth trajectory.
As with all industries, the current economic landscape and the Ukraine-Russia war have had an impact on the collaborative robot market. Out to 2027, shipments of collaborative robots in EMEA will decrease from 19.5 percent to 15.9 percent, with a compound annual growth rate (CAGR) of 22.4 percent.
However, the CAGR for the Americas region will sit at 25.8 percent, and at 28.2 percent in APAC. The current year continues to be a difficult period for the US and European collaborative robot market as a result of inflation and ongoing supply chain disruptions.
Interact Analysis forecasts that EMEA will begin to recover in the second half of 2023 and into the first half of 2024, while recovery in the US will take slightly longer, with a US manufacturing downturn expected in 2024.
The majority of collaborative robot vendors are what Interact Analysis refers to as ‘pure-play’ cobot vendors. This means collaborative robots are their main and only product line.
Universal Robots retains its position as market leader, with AUBO, TechMan and JAKA following behind.
Frazier's executive vice-president, Domenick Iellimo died on January 10th, 2023 at the age of 69. In 1977, Iellimo joined Frazier in sales. He was promoted to executive vice-president of sales in 2002. Carlos Oliver, president of Frazier, said “Domenick was a person that really cared about other people; his personality was infectious. Everybody wanted to be around him and part of whatever event he was taking part in. We all have a story (or five) involving Domenick that we will treasure.”
Burak Balki is the new senior director, operations, at DSV - Global Transport and Logistics, in Canada. Previously, Balki was DSV's regional director, operations. He joined DSV in 2017 as manager, engineering, coming from SCI Group, where he was senior manager, supply chain solutions and implementations. He has an MBA and bachelor of business administration degree.
Supply Chain Canada's Alberta Institute has hired Allan To as president and CEO. To is a char-
tered professional accountant. He brings over 20 years of leadership experience across diverse industries, including oil and gas, manufacturing and construction, power utilities, and education. Most recently he was self-employed as an advisor with EnvisionPRO, and previously held positions at Suncor, TransAlta, and Air Canada.
Andres Diez, director of global commercial at Swissport, has been promoted to chief commercial officer for the Americas, including the US, Canada, He joined Swissport in September of 2021, with more than 20 years of experience in business development and financial planning. He most recently worked at GXO Logistics.
Minister of transport Omar Alghabra has made three new federal appointments in the transport sector. Thao Pham of Sainte-Anne-des-Lacs, Québec was appointed chair of the Canadian Air Transport Security Authority for a term of five years. Nancy Di Gregorio from Hamilton, Ontario, was appointed as a part-time director
of the Hamilton-Oshawa Port Authority for a term of three years. Lenore Duff of Ottawa, Ontario, was reappointed as temporary member of the Canadian Transportation Agency for a term of one year.
Canadian Pacific Kansas City Limited announced four new directors on the board of Canadian Pacific Railway. David Garza-Santos, a KCS director since 2016, has been chairman and CEO of Maquinaria Diesel SA de CV (MADISA) since 1994. Antonio Garza, a KCS director since 2010, is currently counsel to the law firm of White & Case in Mexico City. He brings diplomatic, legal and international business skills developed through his experience as an attorney, and as United States’ Ambassador to Mexico (2002-2009). Henry Maier, a KCS director since 2017, served as president and CEO of FedEx Ground, until his retirement in 2021. Janet Kennedy, first appointed a KCS director in 2017, served as vice-president, North America Regions, Google Cloud, and was president of Microsoft Canada.
What happens when you bring distribution operations under one roof for two major players in an industry?
For Advance Auto Parts, which has merged the DCs of its Worldpac and Carquest brands, the results are savings in space and time, along with improved productivity. The two companies are sharing a newly opened distribution centre in Bolton, Ontario. The companies, both vehicle parts distributors, have never collaborated in a DC before, so this is a learning experience for everyone involved.
The 580,000-square-foot greenfield building sits close to Ontario’s Greater Toronto Area (GTA) distribution hub, with easy access to intermodal rail, air and highway transportation. It serves all 112 Carquest retail stores in Ontario and eastern Canada, along with 15 Worldpac locations, and can fill special orders from across the country. These stores and branches serve more than 37,000 professional repair shops and automotive dealerships.
“With more motorists holding onto their vehicles longer, an expanded product offering is required to keep those older vehicles on the road,” said Jason Yurchak, Worldpac senior vice-president, Canadian operations.
“Bringing our Worldpac parts inventory together with Carquest under one roof allows us to carry parts for virtually every type of vehicle on the road today. Our DC team offers nightly replenishment of every Worldpac and Carquest facility with multiple same day deliveries, ensuring customers get the right part at the right time.”
While it’s been operating since last fall, at the grand opening event on May 6, 2023, the facility was not yet at capacity, a state of affairs that is quite intentional. Advance Auto Parts executive vice-president Bob Cushing said at the event that the facility is currently housing about 150,000 active SKUs, with capacity to hold 350,000.
The room for expansion is part of the company’s growth plans in Canada, according to Cushing. “This is another investment in Canada,” he said. “We have high aspirations, basically to double our business here.”
And while he declined to mention the timeline for that
growth, Cushing did mention a new 220,000-square-foot DC that Carquest opened about a year ago in British Columbia. “The market is terrific. Our customers are great. So it’s kind of exciting for us to have both banners in one facility. It’s just beginning, obviously. So we’ll be moving this across Canada, the same way,” he noted.
Before moving to the consolidated building, Carquest and Worldpac operated two separate DCs, both near Pearson airport. According to Cushing, Carquest had run out of space in its Rexdale facility about five years ago. And Worldpac, in nearby Mississauga, had moved three times into larger facilities.
So three years ago Advance Auto Parts decided to build a master DC and bring the two operations under one roof. “That’s different, right? So every banner was independent,” Cushing said. “Take our hats off and throw them away. Say, ‘Hey, we’re actually Canada and that’s all we care about.’ We don’t want to say it’s CarQuest Canada, it’s not Worldpac Canada, it’s Canada.”
With that in mind, Lucien Jurca, Carquest Canada’s director of supply chain, set to work designing a facility that would separately house inventory for both operations, while at the same time allowing for combined distribution and replenishment. What he and his team came up with is simple and elegant.
Under 40-foot-clear ceilings high-bay pallet racking from 3D Storage surrounds a four-storey pick tower that houses small parts inventory. Totes are delivered to pickers in the ‘green monster’ as the team affectionately call it, via a spiral conveyor and exit directly to the loading zones via a conveyor on the opposite side.
All picking is done manually, using a new suite of Motorola RF guns and Gladiator scanners. The companies have been using RF since 2009, Jurca said, but the new equipment has speeded processes up considerably.
The DC can handle up to 190,000 lines per week, at the moment, with a target of 400,000 in time. That will be after the companies bring in additional technology, Jurca said. He pointed out some open areas that could be developed with goods-to-person picking automation, something he and the team recently scoped out while visiting the Promat show in Chicago.
But the initial configuration was chosen for a simple reason: cost effectiveness. They started out considering automation like Autostore, and other goods-to-person systems, Jurca explained.
“We started looking at the numbers,” he said. “What can we do to improve efficiency, what we can do to improve the throughput, the speed and all that. And after a couple of months we realized that step number one was, let’s not overcomplicate things. We wanted a system that’s efficient, a system that is not going to kill us from the investment standpoint. And something that gives us the opportunity to grow.”
So, with the basic principle of keeping it simple, they designed it around a conveyor system that’s able to bring product from A to B through some consolidation points. It also needed to be able to run either totes or product. Being able to convey product directly on the conveyor is new for the companies, Jurca noted. They also wanted a conveyor that was fast.
And this one, that was custom designed for them by Burlington, Ontario-based Mainway Handling Systems, is. It operates at 30 packages per min-
We are expecting a pretty fast return on the investment because productivity is going up,” Jurca said. “We see pieces per hour going up. And we also see the green monster swallowing more and more volume. Today we are pushing 65 percent out of that. That’s high-velocity products.
Location: Bolton, Ontario
Size: 580,000 sq.ft.
ute, which is about 15 times faster than the system at the old Rexdale DC. Picked product takes nine minutes to travel from the green monster to the consolidation points. They also have the option to run it in reverse, if need be, for replenishment.
“We are expecting a pretty fast return on the investment because productivity is going up,” Jurca said. “We see pieces per hour going up. And we also see the green monster swallowing more and more volume. Today we are pushing 65 percent out of that. That’s high-velocity products.”
The system allows the staff to focus on consolidation or picking, depending on the types of order being processed, he noted. The conveyors minimize the distance associates need to walk, which enhance productivity and workers’ job satisfaction.
“It’s technology that we love and technology that really works for us and enables us to grow because we have the insertion points we going to add going forward,” he said. “It’s one of my biggest achievements professionally. I’m very excited and I’m looking forward to, to work on additional opportunities because this is just the beginning.”
Cushing confirms that the building and systems were designed with growth in mind. He noted that there is room for more pick towers if required. “This was the first go around. It’s like proof of concept and then we can basically add more where we need to. It’s a kind of new technology for us,” he said.
“We want to make sure that the capacity of this facility can sustain our business growth over the next 10 years.”
Everybody all in
It was something of a gamble to bring the Carquest and Worldpac DCs under the same roof. As Cushing noted, it required a lot of new thinking and dropping siloed thinking for everyone involved.
“To me, the most fascinating part of it is knowing the change management that you needed to go through. When you think about bringing together two businesses that were both successful, it’s involved,” he said.
“And when you see this place and the work to build something like this, that’s where you build that camaraderie. When you’re working on a major project like this, you need all hands in. There’s no such thing as us and them. That’s gone. And that’s really what happened here. That was what enabled us to really make it one dream, one team.”
Capacity: 350,000 SKUs
Configuration: 40-ft clear, pallet racking, 4-level pick tower, high-speed conveyor
Access: 128 dock doors & 2 drive-ins
Throughput: DC Customer Orders (daytime shuttle deliveries) 19,000 units/week
Replenishment: 5 times/week
Employees: 200 (hiring up to another 30)
MHE: 67 Yale EV pallet jacks, forktrucks etc.
WMS: HighJump
The rapid proliferation of electric vehicles, the growth of e-commerce, and the rise in consumer goods that use lithium batteries have had a profound effect on the dangerous goods (DG) and hazmat market. The DG market is growing. According to SPER Market Research, the global hazardous goods logistics market is expected to reach nearly $432 billion by 2032, with an annual growth rate of 7.25 percent.
The strong growth also brings supply chain challenges. Moving DG is a complex, time-consuming, and challenging process. And in today’s highly competitive environment, organizations that ignore DG compliance put their operational efficiency, competitive agility, reputation, and bottom line at risk.
The regulations that govern DG transport are complex, constantly evolving, and can vary by country and transportation mode, making it challenging to ensure all shipments (including labels, packaging and documentation) are compliant. In fact, in a Labelmaster global survey of DG professionals: 51 percent of respondents found it challenging to keep up with the latest regulations, and 28 percent were not confident, or unsure, that they could ensure DG regulatory compliance across their organization.
Ensuring compliance is especially difficult for organizations with multiple business units or locations, or those where senior leadership views DG management as a “necessary evil” and don’t properly invest in it.
Even though effective DG management technology solutions are available, many companies still rely heavily on manual, inefficient, and error-prone compliance processes. This approach further compounds the challenges of shipping hazmat safely, compliantly, and efficiently, and puts their employees, customers, and business at greater risk.
When a hazmat shipment fails to meet shipping regulations, it ends up stuck until the shipper can find a way to make it compliant. This can cost a business millions of dollars in fees, expenses, and lost customers and revenue. Beyond that, it’s important to understand the far-reaching risks of noncompliance.
Costs resulting from noncompliance can add up – from fees related to stopped shipments, to increased insurance liability following an accident, to the hidden costs of inefficient operations. All told, fees, fines, and other costs can reach into the millions.
Incorrect shipping labels, incomplete documentation, or other compliance-related errors can result in stalled shipments, late deliveries, and frustrated customers. Ultimately, they can also lead to additional penalties levied by the customers themselves.
Incidents with DG that impact public safety or the environment can also harm brand equity. If it involves noncompliance, this can
create a negative sentiment – in the press and, most importantly, from customers, consumers, and other business partners.
Businesses that ship DG effectively have a competitive edge, offering products that other companies cannot, and shipping those products safely and faster than competitors (which may include your company).
The risks of regulatory non-compliance are a constant concern for organizations that move dangerous goods. That’s why many employ DG software to help achieve supply chain goals.
Software can automate and streamline the shipping process by producing documentation and validating shipments, packaging, labels and markings against the latest regulations. These repeatable and reliable processes can then be implemented across all locations, departments, and supply chain partners.
Compliance challenges slow down (or completely stall) processes across the supply chain – from fulfillment to transport. Automating DG shipping processes and ensuring compliance for labels, packaging, documentation, permits and shipping method, helps companies prepare and ship goods faster, and ensure they’re delivered on time.
Automating DG shipment validation helps avoid fines, streamline operations, and identify more cost-effective solutions to ensure they’re not overspending on packaging. They can also ship more goods without having to add personnel.
Shipping technology requires organizations to have complete and accurate master data. This detailed product information not only helps those directly responsible for DG management, but also helps manufacturing and procurement, carriers, 3PLs, customers, and other supply chain partners.
While technology can improve DG shipping operations significantly, it’s important to realize that complete, accurate data and proper employee training are critical to maximizing the potential and value of the solution.
Shipping and handling DG will only become more difficult as supply chains become faster, regulations evolve, and new goods are introduced. Whether a company sends a few DG shipments per month or oversees a complex, global supply chain, ensuring the safe movement of goods is critical.
Compliance is not optional – it is a major risk and success factor. By prioritizing hazmat compliance, investing in technology and training, and implementing better processes, companies can be confident they are fully compliant with the latest rules and regulations. Shipping DG safely and compliantly is simultaneously a strong competitive advantage and risk mitigator.
Mario Sagastume is vice-president of software and customer success for Labelmaster.
Compared to personal drivers, commercial truck drivers are 23 times more likely to cause an accident when texting while driving, seven times more likely when reaching for their phone, and six times more likely when dialing a phone.
With the number of distracted drivers rising, the issue is more prevalent than ever. Along with the worst-case scenario of causing a fatal crash, other significant negative impacts on fleet operators remain, including higher insurance costs, decreased productivity and efficiency, and damage to corporate reputations.
So, how can fleet operators address distracted driving? Telematics, when used as part of fleet technology, helps fleet operators establish policy updates and driver coaching programs to maintain safe driving practices. Here’s how fleet technology can help on and off the road.
Dash cameras can monitor driver behavior, including distractions such as texting, eating, or using a mobile device while driving. Fleet technologies also can be established to send alerts to drivers when they are exhibiting behavior that could lead to distracted driving, such as speeding or weaving within a lane. These alerts help remind drivers to focus on the road and avoid distractions.
By implementing safety solutions, fleet businesses of any size can reduce insurance and collision costs, assist in fleet maintenance management, offset the impact of volatile fuel prices, and provide high-level visibility into how your fleet is running. In addition, these scores help fleet operators identify drivers who need additional coaching and training to improve their driving behavior.
Telematics systems can be used and integrated with in-cab technology such as AI-enabled smart cameras, cell phone usage detection apps, and Bluetooth, to provide drivers with hands-free access to navigation and communication. This can reduce distractions caused by using mobile devices while driving, ensuring safer operation of the vehicle, and leading to lower maintenance costs and reduced risk on the road.
Vehicle telematics gives visibility into critical areas of fleet management. It can help protect people and assets with features like starter disable, remote panic button, and one-touch driver communication. Keeping people safe is priceless, but reducing any preventable costs from distracted driving is also essential.
The accountability that telematics like GPS tracking provides aids in identifying the behaviors that cause high labour and maintenance costs. If a truck is out of commission due to an accident, that’s one less truck a fleet manager has to ensure business continuity.
While many fleets are utilizing GPS tracking, dashcams are gaining popularity to help fleet operators reach their safety goals. Video solutions become reliable witnesses by automatically capturing acci-
If a truck is out of commission due to an accident, that’s one less truck a fleet manager has to ensure business continuity.
dents and unsafe events on the road because the results of distracted driving are not always the fleet driver’s fault.
Businesses can view event videos to understand at-fault crashes, improve coaching measures, and exonerate drivers from false claims. Exonerating drivers from false claims helps reduce insurance and maintenance costs resulting from the collision.
Independent videos are leveraged quite a bit by fleet managers for online driver safety training because they show real-life incidents that can teach drivers how to improve their behaviors on the road. Managers can point to an event, describe what the driver did, review how best to respond and trust that the drivers will make the same decisions if a similar situation happens in the field.
Smart cameras also provide fleet managers with evidence of bad driver habits so they can set them up with coaching sessions to improve the situation moving forward. Drivers should also be able to see the camera footage to help them be more aware of their behaviors and allow drivers to self-coach in real time before a fleet manager is required to step in.
The driver data collected from telematics technologies help by recording safety violations like speed, phone use, or running a red light. They can be used to set measurable safety goals, allowing fleet managers to correct behaviors before an accident occurs.
Safety technologies like GPS tracking and dashcams not only improve driver behavior and reduce incidents, but they also provide proof that the company has safety measures in place, prompting many insurance companies to offer discounts.
Overall, fleet safety technologies are critical to helping prevent distracted driving, improve safety, increase efficiencies in scheduling and delivery, lower costs, and retain talented drivers. By monitoring driver behavior, providing coaching and feedback, and using technology to reduce distractions, high insurance costs can be avoided, and fleet managers can help ensure their drivers stay safe and focused on the road — helping keep the roads clear so drivers can reach their destination safely.
Tyler Mortensen is vice-president of strategy at GPS Insight.
Stakeholders throughout the supply chain understand 2023 is not like any other year – and this is especially true for the cold chain, both in terms of challenges and opportunities.
While a fluid cold chain is critical to feeding the world’s population, cold chain fluidity does not just happen; it relies on investment and innovation. Ocean carriers looking to optimize their refrigerated equipment investment need a strategic roadmap that addresses the ongoing economic and geopolitical challenges, food supply shortages, food waste, and refrigerated equipment capacity – all while working to reach sustainability goals.
Nearly 40 percent of food produced in the world is lost, with seven to 15 percent spoiling during transport. Lost containers contribute to the problem. However, a more significant and preventable problem is related to container temperature or poorly packed containers. This is especially true for fruits and vegetables, which are vulnerable because they are loaded onto containers in corrugated boxes, which offer no protection from spoilage.
Food waste has been a persistent issue, and it will prove to be an even bigger problem in 2023 as experts predict food supply shortages will continue to get worse throughout the year. This elevates the need to take action to reduce food waste by investing in technology that will protect food during transport.
While today’s refrigerated equipment provides superior cold storage, arming reefer fleets with telematics technology allows for greater collaboration to increase transparency, and real-time data, which provides accurate information on the location of the container. Telematics also provide insight into the temperature, humidity, and air flow inside the container, which ensures the quality of the cargo is protected and waste is reduc-
As the world’s population continues to grow, so does the need to move food safely and swiftly throughout the world. The transport journey for this temperature-controlled food can be long, and there is the risk of contamination and damage every step of the way. This elevates the need for state-of-the-art refrigerated equipment that includes telematics to ensure the cargo is handled properly throughout the entire journey.
The reefer market is expected to grow on average five percent year over year through 2025, while breakbulk container demand will drop 15 percent. The movement of fruits and vegetables will be the key driver in the temperature-controlled cargo market as consumers expect off-season perishables to be readily available all year long.
With aggressive sustainability goals, the shipping industry is looking to make changes throughout the supply chain, and there are significant opportunities within the reefer sector.
Carbon dioxide (CO²) is used more as a refrigerant because of its zero depleting characteristics and its global warming potential. CO², as a natural refrigerant, is one of the most environmentally sustainable alternatives for refrigerated marine transport.
Other considerations for reducing greenhouse gas emissions include variable speed drives for compressors, and two-speed evaporator fans, which offer energy efficiency and can elevate even the most optimal operation linked to an energy-efficient fleet. Acting now to limit the damage from climate change is often smarter – and costs less in the long run – than acting later.
Technology and connecting end-to-end Technological advancements, digitization and the digital transformation of businesses
will be a growth driver not just for the reefer market, but for the entire supply chain.
“Smart” containers are equipped with telematics that provide real-time tracking and monitoring. This enables customers to plan their inventory and production accordingly, and lets operators reduce turn-time and improve equipment availability. These containers provide real-time visibility of location and contents.
Telematics also provide preventive measures using algorithms that recognize failures before they happen, notification of erratic driver behavior, potential theft, and safety issues.
The use of telematics in the maritime shipping industry is expected to explode in the coming years. According to data from Allied Market Research, telematics investment is expected to grow in maritime shipping by 21.3 percent by 2026. This shows the supply chain industry’s commitment to investing in technology to address critical cold chain issues.
Challenges and opportunities in 2023
The reefer market represents the most resilient sector within the shipping industry. Even during times of economic and geopolitical uncertainty, food must be transported in equipment that is up to the task. With the growing global population and potential food supply shortages, the industry has a responsibility to take all necessary steps to mitigate food waste – and technology is the key to delivering on that promise.
The pressure to reach very aggressive sustainability goals has the industry looking for a silver bullet. While that may not exist, the current carbon emission-reducing solutions connected to reefers present an opportunity to make a significant impact. The potential solutions on the horizon are very exciting.
Automation is increasingly becoming part of just about every aspect of our lives these days and has found a big opportunity within the material handling industry. To keep up with the high velocity of goods moving across modern supply chains, it’s almost certain that we’ll see warehousing, fulfillment and logistics operations continue to become increasingly automated.
Automation doesn’t need to be complicated or carry a high-tech enterprise-level philosophy; there are many products available today that you can integrate into your operation quickly to deliver a positive return on investment (ROI) from day one without costly or time-consuming integration projects. If you’re wondering if easy-to-deploy automated warehouse equipment is right for your operation, here are five signs you to need to consider.
Do you have employees spending a lot of time moving materials or products around your facility? These tasks may seem simple, but they are non-value-added and monotonous, leading to fatigue, turnover and decreased productivity.
Automated equipment that uses a collaborative approach with staff, such as a cobot or user-directed AMR, can often drop into your warehouse without much of any change and address such issues.
If you are looking to upgrade your warehouse equipment to act as a productivity force multiplier, automation is likely
right for you. Having automated equipment handle non-value-added tasks, like point-topoint travel, frees up workers to focus on higher-value tasks or direct multiple independent workflows concurrently. The promise of doing this with automation is something that many companies have been keenly looking to do for years and now the technology, cost and ease of deployment are at a point to make such solutions accessible for most operations. Autonomous mobile robots are ready to take over repetitive time-consuming tasks and some can be set up and operational in less than one hour.
Manual-driven material handling equipment can be dangerous and can lead to accidents and injuries. Automated vehicles can help reduce such risks as operator distractions, fatigue and operator error during transit are taken out of the loop. Products that come equipped with highly reliable sensors and cam-
eras that detect obstacles and prevent collisions with inventory, equipment and personnel.
3.
As an organization grows and demands increase, the need for automation becomes more apparent. Automated warehouse equipment can help manufacturing and logistics organizations scale up quickly by increasing efficiency and throughput without the need for additional labour, be it for ongoing needs or to supplement a workforce during peak seasons.
4.
Are you experiencing bottlenecks or inefficiencies in your workflows? This could be due to manual processes that are slowing down your manufacturing or logistics operations. Automated vehicles can be programmed to perform missions and move materials between workstations to optimize operations and ensure goods are where they are needed without significant labour requirements or coordination.
With the pace of warehouse operations picking up speed all the time, manufacturers and developers of material handling equipment and software are working hard to keep up. Here’s a roundup of developments in forktrucks and related technologies like fleet management software, safety systems, and charging.
Combining a new, ergonomic cab and electrification with its recently launched 360-degree steering, Combilift has brought a new narrow aisle forktruck to market. Called the CombiCube because the driver is in the middle of the square vehicle. It’s 1.5 metres square, so the vehicle is 1.5m long without forks, and is 1.5m wide. It does not need to stop for forward to sideways direction changes. “In a lot of ways, it’s a forklift truck that’s operating like a hovercraft,” said Martin McVicar, Combilift’s CEO.
The large rear wheel and rubber tires on all three wheels mean that this model is not restricted to super flat floors and is suited for working indoors and out, ensuring that semirough terrain is no impediment to reliable operation. For quick battery changeover during heavy shifts, two new easy-change roll-out batteries are provided.
Are you experiencing quality control issues in your operations? This could be due to inconsistencies in the way products are handled or moved.
Autonomous vehicles can be programmed to handle materials and/or products consistently, ensuring standard operating procedures are met and the product is moved and staged as desired every time.
If repetitive and time-consuming tasks, safety concerns, increased demand, inefficient workflows and inconsistent quality are slowing down your operations, these may be signs that automated equipment is right for you. By investing in even simple autonomous equipment for your operations, it is now possible to attain ROI from day one and unlock more value from your people every day.
Bill Pedriana is CMO at Big Joe Forklifts
Sister companies Hyster and Yale have introduced stability systems to help prevent lift trucks from overbalancing and tipping.
At ProMat, Yale announced the extension of availability for its Yale Reliant operator assist system to electric counterbalanced trucks in the 3,000-12,000-pound capacity ranges and the company’s very narrow aisle (VNA) turret truck and enclosed end rider. These join the five other models available with the operator assistance technology, which first launched in 2021. Reliant was honoured with a 2023 silver Edison award for innovation.
Hyster Company announced the Dynamic Stability System (DSS), which provides automated performance controls and alerts to help reduce forward and sideways forklift tipovers, is standard on all H40-70A models in the recently launched Hyster A Series.
“With OSHA estimating that nearly 100,000 injuries involving forklifts occur annually, warehouses are constantly looking for tools that can help support safety efforts for all types of lift truck equipment, from order pickers and reach trucks to end riders and counterbalanced trucks,” said Nic Temple, director, technology solutions, Yale. “But while we’re already breaking new ground with expanded availability on a broader range of lift truck types, operator assist systems are still a relatively new entry to the market.
Hyster’s DSS sensors are maintenance-free and continually monitor forklift performance such as lift height, hydraulic load, mast tilt, truck speed and steer angle. When the system detects the lift truck exceeding designated stability thresholds, it automatically intervenes with measures to support stable travel. Four different subsystems help to smoothly decelerate the forklift when traveling around corners.
“Safety is critical in materials handling. Fast-paced environments and demanding productivity targets are just another day on the job for forklift operators,” said Jimmy Anderson, product manager, Hyster. “That’s why DSS is engineered to give operators real-time stability support they can count on and learn from. The system is also designed for managers, offering insight to how forklifts are being operated, particularly when integrated with the Hyster Tracker option.”
Yale’s Reliant system monitors truck and load status to prioritize stability as it implements hydraulic and traction controls. It can
provide warnings and assist with operator awareness by proactively reducing truck speed if it detects something in the monitored area, such as obstacles, other trucks or pedestrians.
Vector Security Networks, a division of Vector Security, Inc., has brought a forklift security camera to market. The system uses multisensor video technology feeding into one camera, to create a 360-degree view, recording the actions of both the forklift and its operator. It gives distribution centre operations, safety, risk management and loss prevention teams unprecedented access to video, allowing them to better manage their business and immediately improve both productivity and safety. It was designed to universally fit orderpicker forklifts, and helps warehouses, fulfillment and distribution centres improve operations, manage risk, and mitigate loss in the aisles, the company says.
ELOKON’s sytems are designed to improve forktruck fleet productivity, prevent accidents and collisions involving forklift trucks, AGVs and AMRs, protect pedestrians and ensure a high level of productivity in the warehouse. These solutions use digital technologies such as a cloud-based management system for all material handling assets, the ultra-wideband wireless sensor technology for highly precise indoor location tracking solutions, and off-the-shelf modern smartphones for fleet management and proximity detection solutions.
ELOKON’s cloud-based ELOfleet system incorporates a predictive maintenance feature which complements the existing functionalities such as impact recording, RFID access control, pre-ops checklists and productivity recordings. It can predict when maintenance is next due, and if this falls in a peak period, it can be rescheduled to avoid downtime for uninterrupted availability whenever required.
ELOfleet and ELOshield have been merged onto one hardware platform – a standard off the shelf smartphone. This means that customers can now not only operate a fleet management and a proximity detection system on one, non-proprietary hardware device but also that third-party solutions, such as app-based warehouse management systems, can be operated from this device. In the future the company will be adding expense management, RTLS and digital twin solutions on the cloud portal.
Wireless charging is advancing quickly, and Enersys has upgraded its offering with the NexSys AIR wireless charger. The charger is chemistryindependent and capable of charging flooded lead acid, thin plate pure lead (TPPL) and lithium-ion batteries.
“The new NexSys AIR wireless charger delivers the convenience of a reliable, hands-off charging solution,” said Harold Vanasse, senior director of marketing, motive power global at EnerSys. “Along with charging a range of equipment and battery technologies, our NexSys AIR wireless charger can drive safety and productivity by eliminating the need for extra personnel to physically plug-in automated equipment, something especially important with today’s labour market.”
The wireless charger also offers safety features such as foreign object detection (FOD) and live object detection (LOD) capabilities.
The Raymond Corporation has developed a 48-volt drop-in lithiumion battery (48V LIB), which is available in multiple configurations.
“The 48-volt drop-in lithium-ion battery offers customers a smart alternative energy solution to upgrade existing or new lift trucks,” said Damon Hosmer, senior product marketing manager, energy storage technology and integration, The Raymond Corporation. “This new product solves three of the biggest concerns our customers tend to have when adopting alternative power sources: footprint, power and run-time. This battery delivers higher energy density in a smaller footprint, which creates more power, decreases charging times and increases run-times.”
Designed as a direct, plug-and-play replacement for conventional lead acid batteries, the new 48V LIB fits lift trucks with battery compartments of 13 inches and larger and requires no additional
modifications. The new battery also provides for continuous data exchange between Raymond lift trucks and chargers, giving customers easy access to critical operating data.
The new 48V LIB is suitable for a variety of environments and is designed to deliver a strong business case for alternative energy adoption, including:
Increased productivity from convenient opportunity charging, longer run-times and faster charging;
Reduced maintenance thanks to the sealed design, which eliminates the maintenance requirements of traditional lead acid batteries;
Reduced energy and operating costs due to the decreased need for spare batteries or lift trucks;
Easy installation and implementation thanks to a drop-in design that’s compatible with the entire Raymond fleet of new or existing electric lift trucks;
A UL 2580 listing and a six-year or 5,000-cycle warranty.
Inductive charging
Wiferion, an energy solution supplier powering mobile robots and autonomous industrial vehicles through a wireless charging platform, has entered the North American market.
“A strategic approach to power supply solutions is a natural priority for makers and operators of AMRs and AGVs. Navigation works. Tasks are completed. But current approaches to power supply strategy fall short and remain an area of need to deliver optimal efficiencies for fleets,” said Matthieu Ebert, vice-president of Wiferion
North America Inc. “We are focused on a strategic solution to upgrade charging infrastructure and create a standardized process for automated vehicle power that works for any mobile robot or autonomous truck. Our new home base in the U.S. helps us implement, service and engage with North American companies quickly and effectively.”
Wiferion has sold charging systems in more than 20 countries. The system has been designed into more than 100 different industrial EV, autonomous guided vehicles and mobile robots, with thousands of units sold globally, including installation in several renowned European and U.S. automotive manufacturing facilities.
Wiferion’s inductive charging systems supply energy to entire industrial vehicles fleets automatically, regardless of voltage, current or battery type. The charging innovation increases productivity by up to 32 percent through automated in-process charging.
Wiferion provides a wireless power supply solution for the mobile robotics industry, including:
• a 3kW contactless inductive power supply;
• a 12kW scalable energy wireless battery charging system with an efficiency of 93%;
• lithium iron phosphate and lithium-titanate battery options for AGV, AMR & mobile robots;
• a plug-and-play battery retrofit for forklifts and other industrial trucks;
• and, a charge optimization platform for remote diagnostics to optimize battery life and vehicle performance.
(AI) platforms such as ChatGPT has led to increased interest across all industries in exploring its potential applications. In logistics, for example, AI has shown great potential to increase operational efficiency.
The main reason why many industries, including logistics, have embraced artificial intelligence on such a wide scale is its superior data processing capabilities, as the ultimate goal of the logistics sector is to deliver goods as efficiently as possible. Although “efficiency” is often thought to equate to speed, it also involves cost, maximizing capacity, and other factors.
Human error is one of the biggest detriments to efficiency, as it causes slowdowns, increases costs, and can lead to a reduction in capacity. To combat this, many industries – including logistics – are beginning to embrace artificial intelligence to eliminate potential sources of human error.
One of the most exciting use cases for AI in the logistics industry has been route optimization. There is much more to route optimization than finding the quickest route.
Often, drivers are dealing with multi-stop routes, where they have multiple pick-up or drop-off points that must be reached in a timely manner. AI has the power to optimize a route based on these multiple stops, ensuring the driver will complete the delivery as efficiently as possible.
AI can also automate the dispatch process in logistics. An algorithm can determine what driver can best complete the delivery based on a combination of factors, including proximity to pick-up, distance to drop-off, vehicle capacity, the driver’s performance, and more. The driver is automatically dispatched more quickly than a human dispatcher ever could.
Another application for which AI has shown great potential in logistics – and
perhaps the most interesting consumer-facing use case – is the use of AI-powered chatbots for answering customer service questions and taking orders. The goal is to enhance the customer experience by reducing waiting time, while also improving efficiency by allowing human workers to focus their attention on more demanding tasks and stop wasting time on mundane tasks.
That said, an AI chatbot does not serve as a perfect replacement for a human worker in terms of customer service. For more mundane tasks, such as frequently asked questions, a chatbot can be useful because it can answer the question without delay.
However, for more complex issues, a human worker is necessary for relationship management. When dealing with clients, the human touch can make the difference in maintaining an account.
Additionally, even though artificial intelligence is generally more efficient than a human worker, it is important to remember that these programs are not infallible. AI still makes mistakes, so it is important to have someone in place to check the algorithm’s work and ensure that no mistake is made that will have catastrophic consequences.
For example, if a delivery is perishable or otherwise time-sensitive, and the AI makes a mistake optimizing the route, that could mean the entire delivery is ruined.
Another part of the logistics process unique to human ability is on-the-spot decision-making. Although an AI algorithm can do a fantastic job of optimizing routes and dispatching based on pre-existing data, there is often a delay in its ability to process new data.
For example, if a driver is on a route optimized by AI and there is a wreck ahead, it will take some time for the AI to realize this. On the other hand, a human driver can recognize this potential delay as soon as it happens, allowing them to take immediate action and prevent a delay.
One of the most significant steps companies must take to find an effective balance between artificial intelligence and maintaining a human workforce is embracing retraining and reskilling. Although some jobs might go away in favor of the efficiency of AI – such as dispatching jobs – there will still need to be people to oversee the AI, fix it if something goes wrong, and step in if the AI should stop working. Training workers to complete these jobs can ensure they stay relevant.
The best approach a company can take towards AI – particularly in the logistics sector – is to use it as a tool that can enable humans to do their best work. AI-powered route optimization and automated dispatch allow drivers to do a better job. Chatbots for customer service allow human representatives to pay better attention to customers with more complex issues.
When we stop looking at AI as something that can do our jobs for us, and instead as a tool that can help make our jobs easier, we will begin to empower our workers to be more effective and efficient in nearly everything they do.
Full Name: Company:______________________ Title:___________________
Address:_______________
Phone: ______________ Email:__________________________________ (Email Required
YES, I WISH TO RECEIVE INSIDE LOGISTICS MAGAZINE FREE!
YES, I WISH TO RECEIVE INSIDE LOGISTICS E-newsletter FREE!
Choose your Edition: Print Digital Print & Digital
Signature: Date:
PLEASE ANSWER THE FOLLOWING QUESTIONS TO QUALIFY FOR YOUR FREE SUBSCRIPTION:
1. Do you purchase, or influence the purchase, of goods and/or services related to distribution logistics, including warehousing operations (receiving, storage or shipping) or inventory control or materials handling? Yes No
2. If Yes, do you have plans to buy any of the following in the foreseeable future? (Check as many as apply)
(A) Forklifts and mobile materials handling equipment
(B) Racking, shelving and storage equipment
(C) Software, eg WMS, TMS, YMS, WES, etc
(D) Automated materials handling systems
(Z) None of the above
TRANSPORTATION SERVICES: LTL
3. What is your company's PRIMARY business? MANUFACTURING (Check one only)
(E) Third-party logistics services
(F) Transportation services
(G) Real estate, warehouses, existing or new building
(H) Data capture and inventory control equipment
NON-MANUFACTURING (Check one only)
Others Allied to the Field (please specify)__
4. Which of the following categories best describes your PRIMARY function? (Check one only)
(please specify)____________
5. What is the approximate number of employees at this location?
93 percent of logistics professionals are spending nearly half of their working day solely dedicated to addressing problems. A third of logistics professionals are spending a significant amount of time on manual transactions, with an average of 10 minutes per transaction, highlighting the need for digital adoption for even the simplest operations in the container operations industry.
(Source: Container xChange)
Forwarders and freight brokers see customer demand for real-time visibility as the second biggest challenge they face in 2023 (after price pressure).
This is seen most in e-commerce, where the need for more real-time tracking and automated processes has been the number one impact for the past five years.
(Source: Descartes)
“Investing in technology continues to be the top strategy for brokers and forwarders to address continuous economic and industry changes,” said Chris Jones, EVP industry at Descartes
“Top performing forwarders and brokers are much more aggressive in their IT strategies and investments to help sustain their competitive advantage and enhance profitability.”
(Source: Descartes)
Investing in technology has been the top and dominant overall strategy for the past eight years.
(Descartes)
Top performing forwarders and brokers see digital customer self-service as a key differentiator. 43% of those surveyed by Descartes placed it as the top customer service advantage
(Descartes)
By automating just three processes – online marketplace for equipment and partner sourcing; container tracking, release references of live ETAs; and online chat for negotiating terms and conditions –one could save more than eight hours per week or four full working days per month.
(Container XChange)
Automating processes, with 60 percent saying it’s a strategy they use, has been in the top two choices for forwarders and brokers over the past eight years, along with offering more high-value services (chosen by 63 percent).
(Descartes)
“Digitization is the inevitable evolution for every industry, and the container logistics industry is no different,” said Christian Roeloffs, CEO of Container xChange.
“In today’s difficult times, companies are struggling with innumerable macroeconomic and geopolitical disruptions. With these manual processes, it can become even more difficult to do business. Our research shows that the move to digital tools can save time, increase efficiency and improve profitability. Logistics professionals need to embrace digital transformation to stay ahead in a competitive market.”
(Container xChange)
Digital customer self-service was seen as delivering the highest value, garnering 41% of responses, with automating carrier updates second at 34%.
(Descartes)
AGAINST A BACKDROP of ongoing supply chain challenges caused by the Russian invasion of Ukraine, the tightening of global financial conditions, high interest rates, inflation and the resulting slowdown of economic growth, air cargo continues to encounter headwinds.
In line with weakening global trade, the Purchasing Manager’s Index (PMI), published by S&P Global and measuring new export orders, has remained below the critical line for the last twelve months. The PMI for supplier delivery time and other indexes indicate persisting high inventory levels, and this tends to have a negative impact on air cargo growth. Overall global goods trade declined by 2.6 percent in February, following a one percent decline in January.
Let’s see what the figures say regarding air cargo. The Montreal-headquartered International Air Transport Association’s (IATA) statistics for March show a continuous decline of air cargo performance compared to a year ago. Global air cargo demand measured in cargo tonne-kilometers (CTKs) fell 7.7 percent compared to March 2022. But slightly improved over February’s performance, which stood 9.4 percent below last year’s, and half the decline seen in January and December (down 16.8 percent and 15.6 percent, respectively).
The trend began in early 2022 and continues this year. This brings the March performance 8.1 percent below pre-Covid levels.
Capacity, meantime, was up 9.9 percent, reflecting the addition of belly freight capacity, ahead of the spring/summer travel season, as the passenger side of the airline business continues to recover.
Asia-Pacific airlines saw their air cargo volumes decrease by 7.3 percent in March compared to the same month of 2022, while available capacity was up 23.6 percent. North American carriers posted the weakest performance of all regions, with a 9.4 percent decrease in volume against a modest 0.4 percent capacity increase.
European carriers saw their cargo volumes decrease by 7.8 percent against an 8.8 percent
capacity increase. Middle Eastern airlines experienced a 5.5 percent decrease while capacity increased 9.7 percent. Latin American carriers reported a 5.3 percent decrease in cargo volumes, while capacity was up 12.9 percent. African airlines saw cargo volumes go down 6.2 percent in March.
The outlook for air cargo this year remains mixed, to say the least. IATA economist Bojun Wang, speaking at the World Cargo Symposium at the end of April, predicted that air cargo would decline by four percent this year, compared with 2022 levels, reflecting the ongoing challenging economic environment.
The International Monetary Fund recently downgraded its global GDP growth outlook for the year to 2.8 percent from the previous forecast of 2.9 percent. This figure lags behind the 3.4 percent growth recorded in 2022.
According to Wang, cargo yields, the average rate paid by customers to transport one ton of freight on one cargo revenue kilometre, an indirect but polite way to refer to rates, are expected to decline by around 23 percent this year, following a seven percent increase last year, a 24 percent increase in 2021 and a 50 percent increase in 2020.
In a nutshell, air cargo rates are slowly returning to more normal levels, although they are not there yet. Another interesting development is the increase in supply driven by the return of passenger flights with the corresponding, added belly capacity. Before the pandemic, passenger flights carried around 50 percent of all air cargo and this dropped to 26 percent in 2022 but belly freight now accounts for about 40 percent of total air cargo.
Following this deluge of statistics and percentages, what is happening closer to home with our Canadian airlines? Continuing its expansion into the air cargo business, Air Canada Cargo began a freighter service from Toronto to Liege, Belgium, in March and to Mulhouse/ Basel in April. These followed the recent start of service to Dallas, Atlanta and Bogota. In early May, Air Canada Cargo received two more factory-built Boeing 767 freighters in Toronto, joining its growing freighter fleet.
Cargojet, which operates an extensive air cargo network in Canada for express and e-commerce deliveries, had to take steps to cut costs and preserve cash due to weaker domestic cargo demand. It unloaded a third second-hand Boeing 777-300 intended for conversion into a main-deck freighter and plans to finalized the sale of three of its current 777s.
As we’re getting close to mid-year and with the Russian invasion of Ukraine continuing, given the regrettable but tacit support or neutrality of important countries, like China, India, South Africa and even Brazil, it is hard to imagine a return to growth and stability any time soon.
What’s worse is that this tragedy prevents the world from uniting to work together to fight climate change. Collectively, airlines are committed to net-zero carbon emissions by 2050. There are costs involved, but the climate crisis is real and we have seen early signs of it already this year with fires in Alberta and floods in British Colombia this spring. Only a peaceful world will be able to tackle climate change.
Global economic conditions continue to restrain air freight
NOBODY WAKES UP in the morning thinking, “today my warehouse is going to experience an emergency as the result of an unexpected earthquake, severe storm, or some other outside disaster.” But emergencies like these happen more often than you think. When they do, you don’t have time to think; you need to respond promptly to prevent loss.
Of particular importance are polished and well-practiced shelter-in-place and evacuation plans, and effective communication. Otherwise, complications can arise during the emergency.
For example, during an earthquake, it’s not safe for workers to be under or beside steel storage racks. A shaking structure could result in collapse and/or falling loads. These risks can be reduced by having a competent person install racks, keep your loads within rack capacity, ensure pallets are placed evenly across both beams and consider installing safety accessories such as pallet safety bars or wire mesh decks.
A poorly prepared evacuation plan could result in a disorganized evacuation or response, which could be catastrophic. And poor communication with employees can lead to worry, frustration and people acting on their own, which could put them in more danger.
In a warehouse environment, communication needs to transcend obstacles like the physical distance between people, and noise, which may require visible warning lights, loud and distinct alarms, and a sweep of the area to ensure everyone is out.
14 quick tips
With thorough planning and preparation, workplaces can minimize harm to their employees in the event of an outside emergency. Use these 13 tips to improve your plan.
Shelter in place
1. Choose an area that is well-lit, secure,
NORM
provides expert, in-depth health and safety consulting services for Workplace Safety & Prevention Services (WSPS) as a Warehouse Specialist in the GTA region.
DALE WALES, is a specialized consultant for WSPS in confined space. Whether in an agricultural, industrial, or educational setting, Dale provides confined space expertise with the goal of keeping workers safe.
easy for employees to get to, away from windows, has good cell reception, and a landline. There must be enough room to accommodate all your employees comfortably.
2. People in a warehouse may need to be moved to several smaller rooms, such as a washroom or conference room. Carefully consider optimum locations that provide adequate space, doors that can be locked, sturdy walls and ceilings, tables to crawl under or use as barricades, and no windows.
3. Carry out a head count when all employees have gathered. Make sure you have a system in place to account for the whereabouts of all employees and visitors. This will help focus responders on locating missing individuals.
4. Allow people to notify family and friends they are safe, but don’t allow them to leave the designated area unless you know exactly where they are going and when they are coming back (e.g., bathroom breaks).
5. Wait for direction from authorities to evacuate, or the “all clear” is sounded.
Evacuation
6. Ensure workers who are operating lift trucks and other equipment, such as pallet wrappers and compactors, immediately stop and shut off equipment. An order picker working at an elevation should immediately lower them-
selves to the floor, get off equipment and proceed to the muster point. There should be no delay in leaving the premises quickly and safely.
7. Map out at least two muster points, evacuation routes, and exits to provide an alternate if the main route and muster point are compromised. Consider the risk that truck traffic entering the yard may not know an evacuation is taking place, especially during low light conditions.
8. Assign roles and responsibilities –who’s going to coordinate with outside emergency services? Who’s going to evacuate people? The more employees you have, the more coordinators you will need to help with the evacuation. Specify the chain of command so there is no confusion.
9. Provide copies of the emergency response plan, with diagrams, to all employees in digital format, and also post them in the workplace.
10. Train employees, supervisors and managers on the plan, and hold practice drills on a regular basis using different scenarios. You want everyone to know exactly what to do and where to go.
11. Debrief as soon as possible after each drill, and after a real evacuation, and adjust your plan as needed.
12. Maintain a list of emergency services contacts and determine how you will get notifications about the need to evacuate and the status of an emergency.
13. Determine a fast and reliable way to communicate with workers over the course of the emergency, such as a PA system, group text or runners that provide communication verbally or in written notes.
14. If workers are sheltering in place, provide updates every 15 minutes, whether or not the situation has changed. Encourage everyone to stay calm.
Asset-based, award-winning Canadian LTL carrier
Delivering to & from all points Canada and USA
Canada and USA customs bonded carrier
LTL, TL & global 3PL
Warehousing & distribution within Canada and the USA
Industry-leading transit times & on-time delivery
Expedited next day service between Canada & the USA
Online ordering, rating, transit times & real-time tracking
Cutting-edge technology including AI, robotics, distributed ledger & smart contract process
Intelligent customs document processing for efficient cross border shipping to the USA & Canada
Technology company providing intelligent automation software