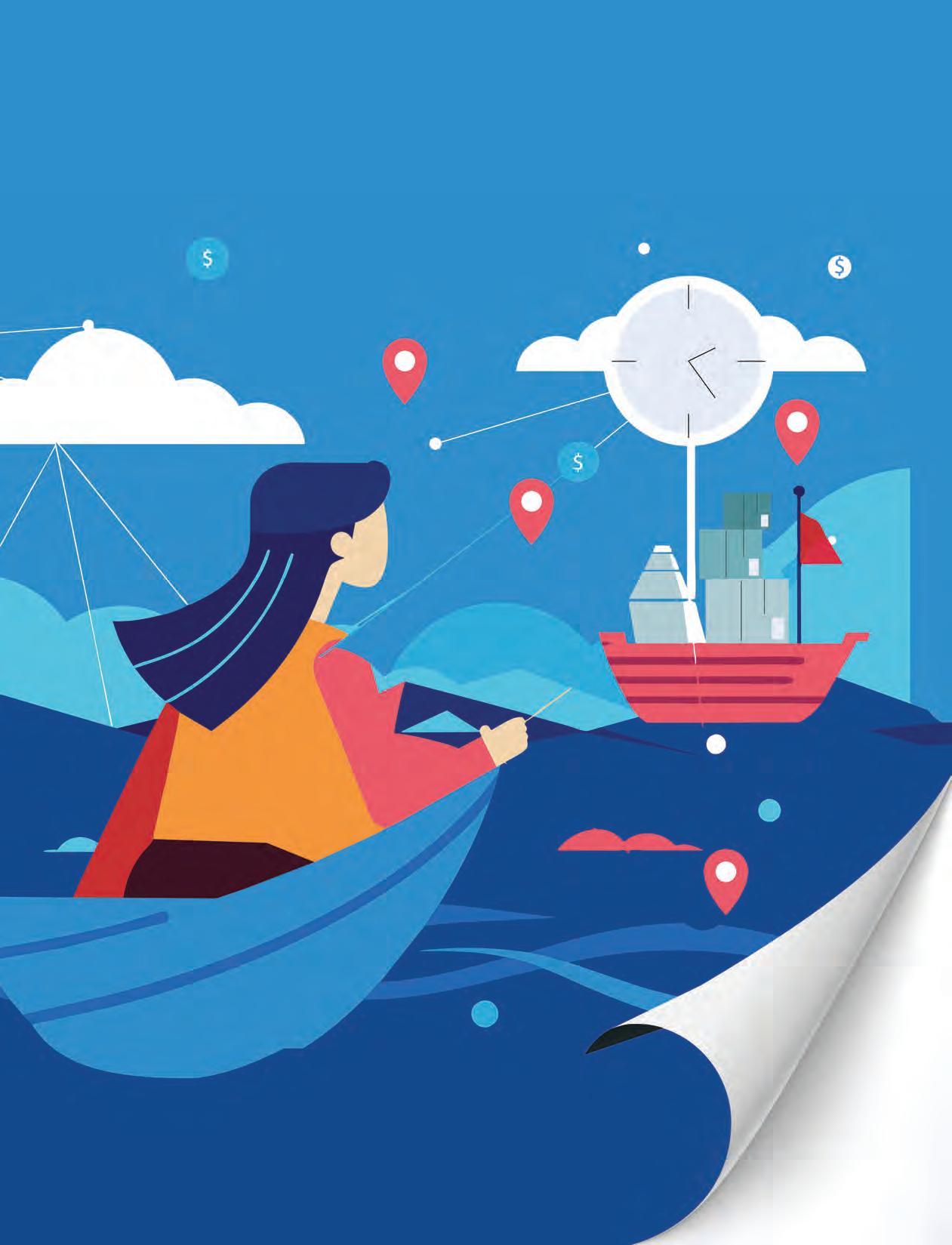
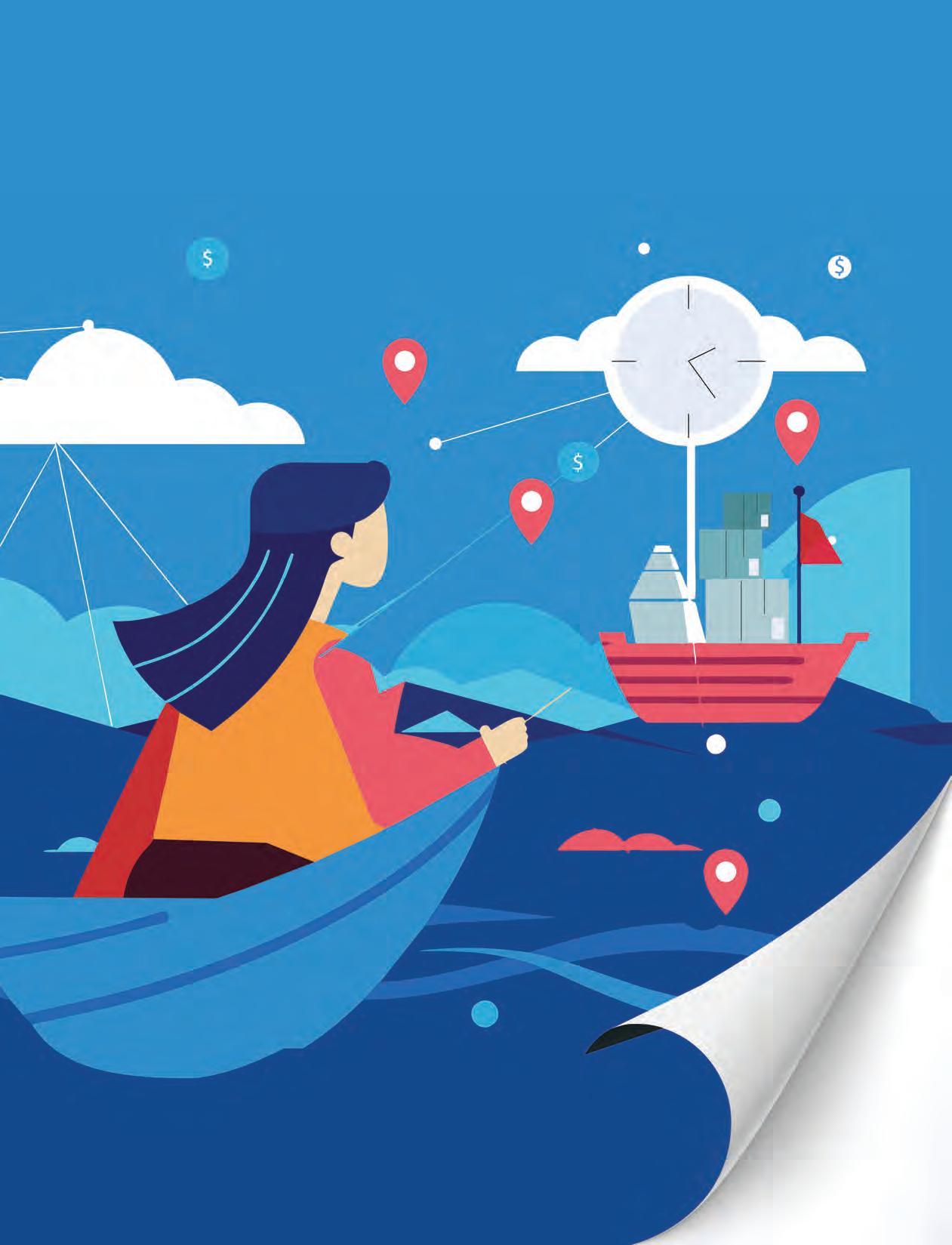
GEOPOLITICAL TURBULENCE
Shipping times, pricing and adaptability has been tested due to Baltimore and Red Sea disruptions
› Technology investments
› Warehouse safety
› Orchestration software
TAKEOFF CLEARED
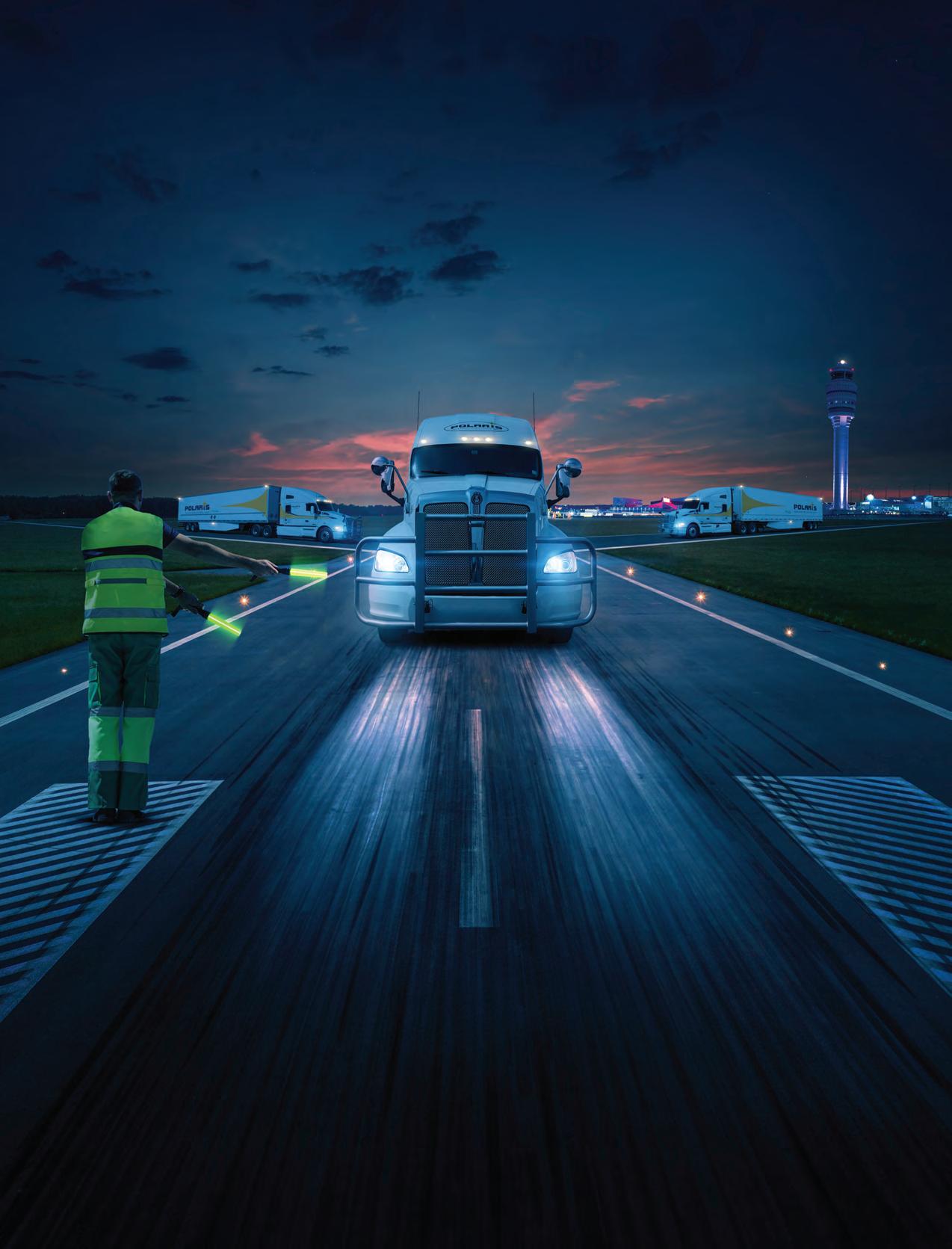
• Travelling to and from Canada & the USA every day
• Simplified cross border processes providing seamless experiences
• Expert ground control ensuring total compliance & limited wait times
• Regulated, certified carrier active in all border security programs
• Strong, longstanding relationships with the CBSA & CBP
• 100% digital customs clearance & instant notifications
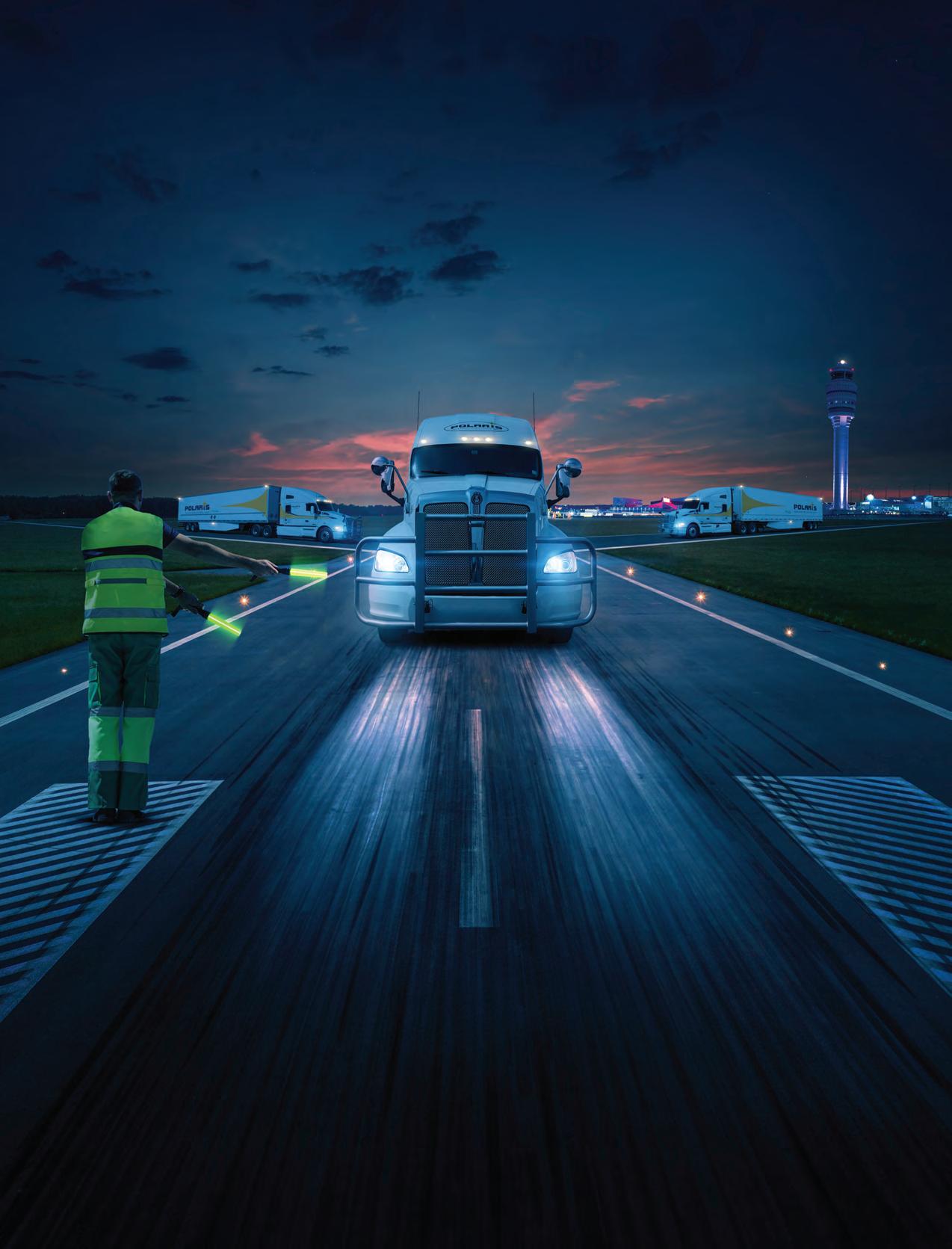
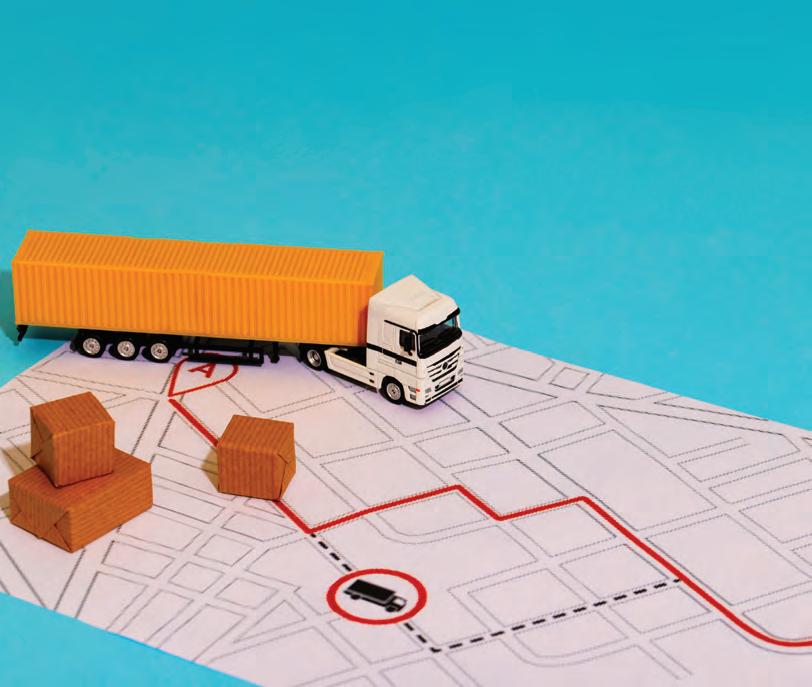
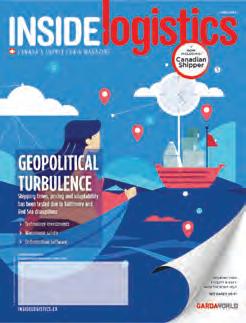
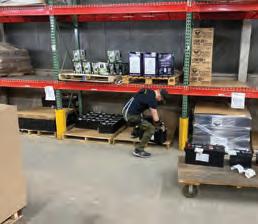
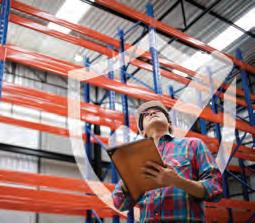
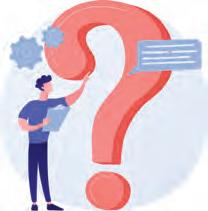
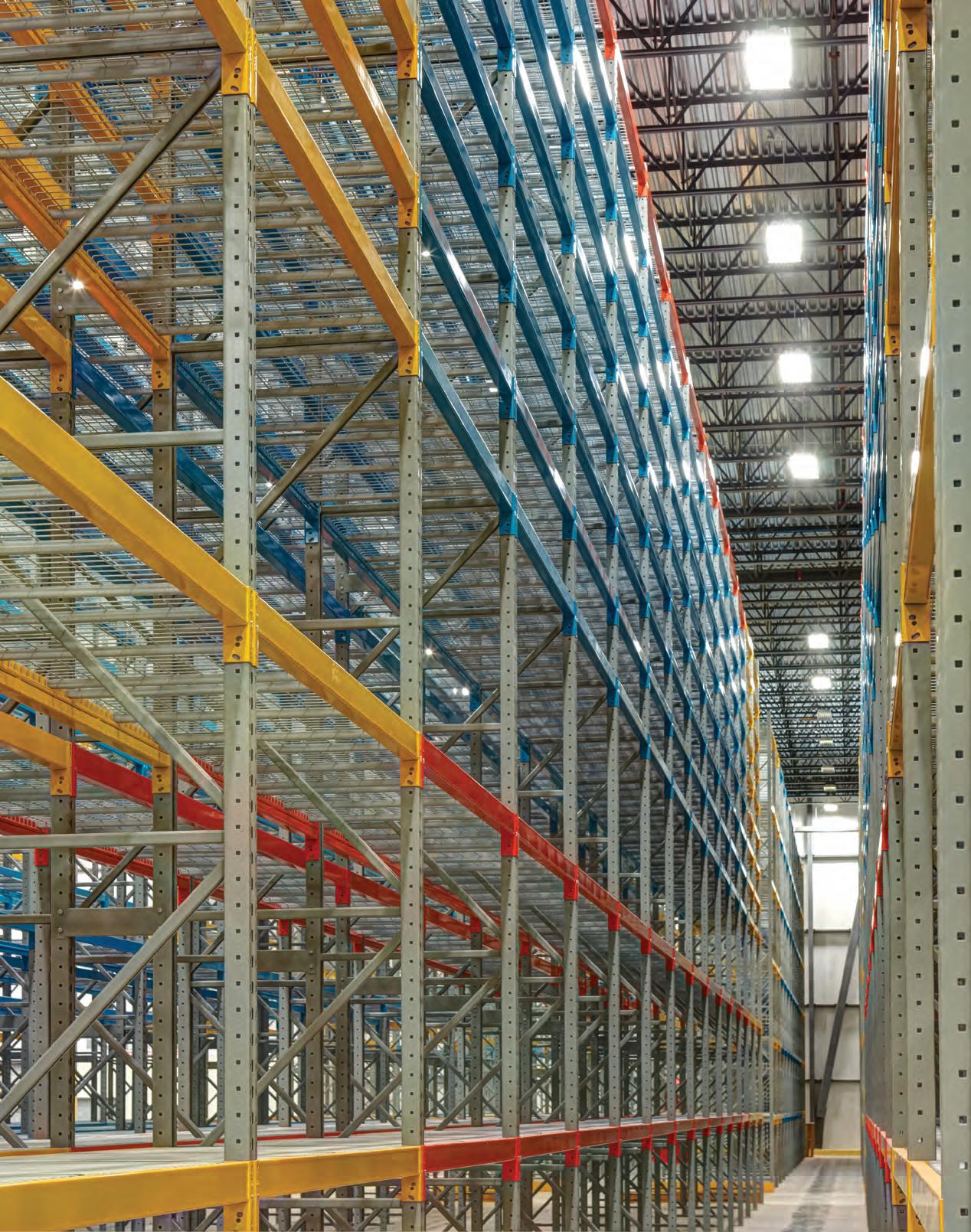
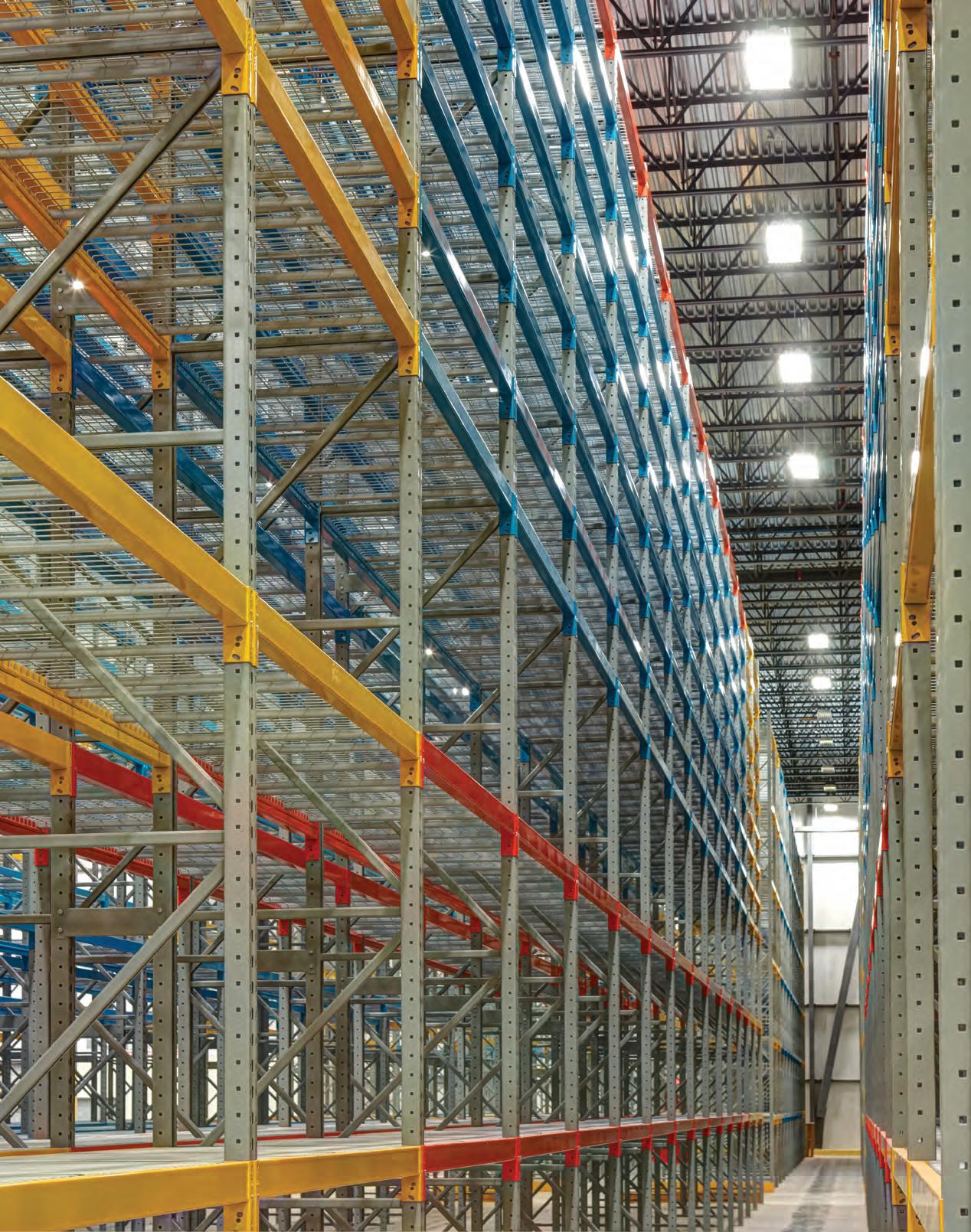
Publisher | Delon Rashid (416) 459-0063 delon@turnkey.media
Editor | Emily Atkins (416) 262-4106 emily@turnkey.media
Editor | Derek Clouthier (403) 899-8793 derek@turnkey.media
Contributing Writers | Norm Kramer, Christian Sivière, Keith Moore, Oana Jinga, Lauren Mollencupp, Shash Anand, Paul Nicholson, Victoria Jones
Creative Director | Samantha Jackson
Video / Audio Engineer | Ashley Mikalauskas, Nicholas Paddison
Sales | Delon Rashid, (416) 459-0063 delon@turnkey.media
Peter Bulmer, (585) 653-6768 peter@turnkey.media
Production and Ad-ops | Tracy Stone tracy@turnkey.media
Inside Logistics magazine is published by Turnkey Media Solutions Inc. All rights reserved. Printed in Canada. The contents of this publication may not be reproduced or transmitted in any form, either in part or full, including photocopying and recording, without the written consent of the copyright owner. Nor may any part of this publication be stored in a retrieval system of any nature without prior consent.
Canada Post Canadian Publications Mail Sales Product Agreement No. 43734062
“Return Postage Guaranteed” Send change of address notices, undeliverable copies and subscription orders to: Circulation Dept., Inside Logistics magazine, 48 Lumsden Crescent, Whitby, ON, L1R 1G5
Inside Logistics magazine (ISSN No.: 0025-5343 (Print); 1929-6460 (Digital) is published six times per year by Turnkey Media Solutions Inc., 48 Lumsden Crescent, Whitby, ON, L1R 1G5
From time to time we make our subscription list available to select companies and organizations whose product or service may interest you. If you do not wish your contact information to be made available, please contact us.

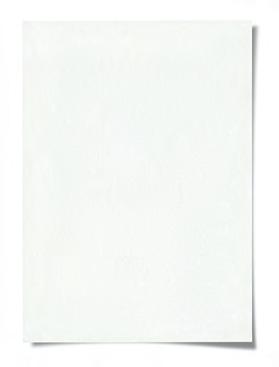
Twenty-two years in 400 words
THE TIME HAS COME, my friends. I’m hanging up my editor’s visor and handing over the reins of Inside Logistics.
It’s been an amazing, fascinating, fun and endlessly educational 22 years at the helm of this magazine. I’ve survived through recessions, a brand change and four owners, all the while jokingly referring to myself as the unsinkable editor.
In the early days, coming from a freight transportation trade paper in Hong Kong, the learning curve was steep. I knew close to nothing about warehousing, and I’m pretty sure it showed at the beginning.
Now I know a little more. Enough to ask good questions most of the time, at least.
From the RFID hype bubble to current advances in artificial intelligence and robotics, this business never stops advancing. And that’s why I’ve maintained my enthusiasm and curiosity about how things work in the huge supply chain world. It’s also why I’ll be keeping my hand in as a writer for hire after I leave this magazine – if you need opinion pieces, blogs, whitepapers, or other copy written about supply chain topics, please look me up on LinkedIn (Emily Atkins Group).
There are many people I want to thank: Warren Patterson, who hired me back in 2002, took a chance and (I think) didn’t regret it. Mary Sanchez, the assistant editor when I took over, helped me learn the industry as well as making me look good. Deb Aarts was the fastest learner and best assistant editor in the world. Tim Dimopoulos gave me chances to expand outside the editor’s role and into the automotive world, which I love. Joe Glionna trusted me first to work from home, then let me to go freelance. John G. Smith always had my back and provided wise counsel.
And to all the wonderful people in the industry who I’ve met, interviewed or consulted – a massive and enduring thank-you. You make this industry the best!
President & Managing Partner | Delon Rashid Head of Sales & Managing Partner | Peter Bulmer
Corporate Office
48 Lumsden Crescent, Whitby, ON, L1R 1G5

ISSN 0025-5343 Online 1929-6460
And now it’s time to introduce my successor: Derek Clouthier is an experienced trade magazine editor. We worked together briefly at Newcom, and I know he’ll do a great job here. Please give him a warm welcome.
A la prochaine, my friends. See you on LinkedIn!
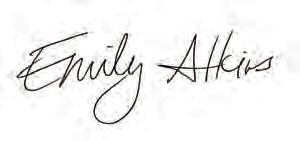
We Fit What Your World Needs
Selecting a box that is the wrong size wastes space, costs more and is not sustainable. Don’t be a wrong sizer, right size with Packsize.
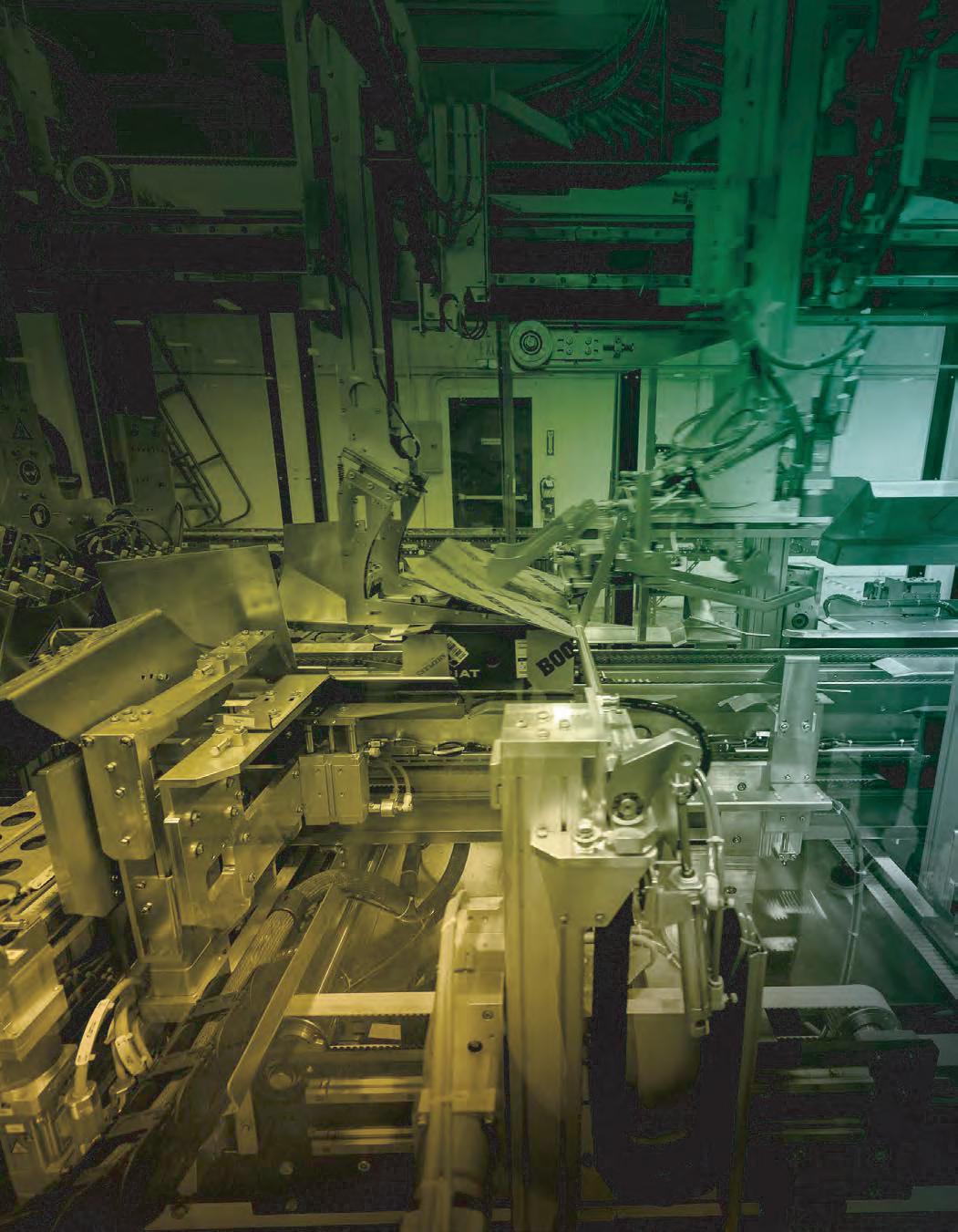
The box is just the beginning. At Packsize, we tailor packaging solutions across your entire packaging process that are better for the planet, better for business, and better for your customers. This is packaging reimagined
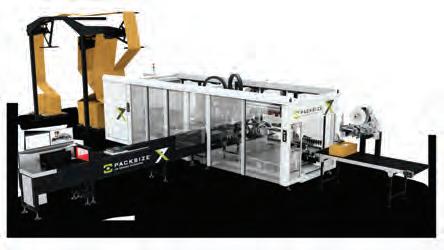
Take the next step, reimagine your packaging when you right size with Packsize.
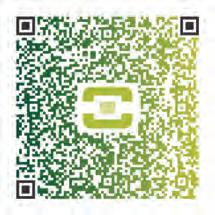
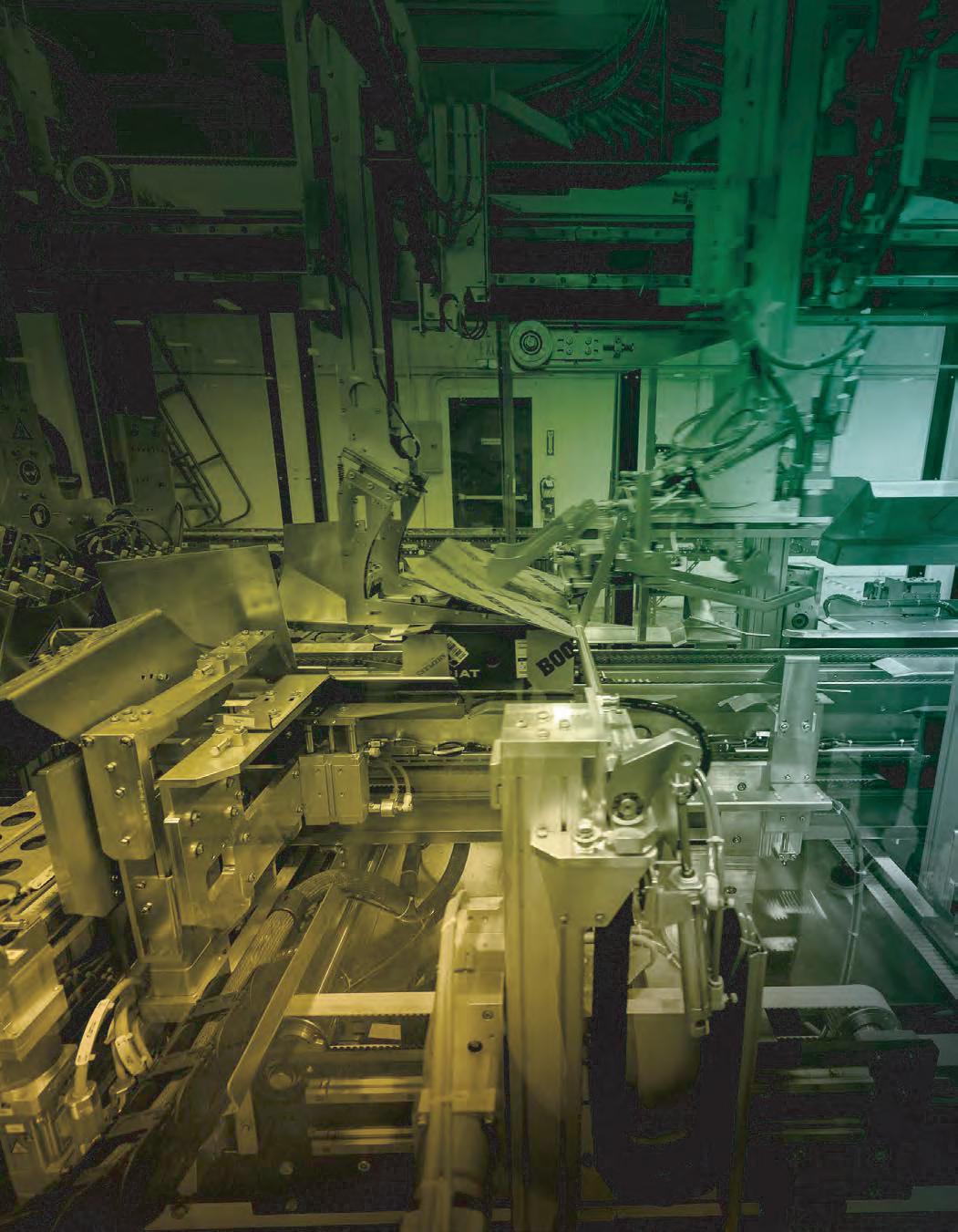
SCMAO rebrands as National Institute of Supply Chain Leaders
By Derek ClouthierCTA
INPUT
CTA offers suggestions to improve supply chain 9
THE SUPPLY CHAIN Management Association Ontario (SCMAO), one of Canada's largest communities of supply chain professionals along with its western counterpart SCMABC, has rebranded itself to the National Institute of Supply Chain Leaders (NISCL).
In a release, NISCL says the change is triggered by the need to reflect the organization's Canada-wide operations and also to amplify the critical role played by the supply chain profession in building a thriving economy, a sustainable future and an inclusive society.
RAIL STRIKE
Feds seek review of potential rail strike
With this new rebrand, NISCL not only aims to empower supply chain professionals with functional excellence but also leadership excellence in order to influence critical enterprise decisions.
MOVERS + SHAKERS Appointments and promotions
"Supply chain professionals have led the Canadian economy with courage and commitment in the past five years – what is clearly marked as one of the most challenging times in the history of Canada's economy,” says Al-Azhar Khalfan, president and CEO of NISCL. “Supply chain professionals have been the frontrunners of Canadian economy during most challenging and disruptive times. They have demonstrated true leadership through their ability to think ahead, solve problems and pivot towards innovative solutions. This rebrand is to ensure that supply chain professionals continue to be recognized for the leadership attributes they demonstrate in driving strategic enterprise success and to ensure that the next generation of supply chain leaders are prepared to meet the expectation of employers.”
The change is also reflected in the rebrand of the Certified Supply Chain Management Professional (CSCMP) Designation, Canada's designation for supply chain professionals, which is bestowed by SCMAO. With the rebrand, this designation will transition to the NISCL, Certified Supply Chain Leader (CSCL) Designation to reflect its new curriculum, which is benchmarked against global standards and is emblematic of NISCL's brand attributes.
New brand attributes include strategic thinking, a sense of responsibility, self-confidence and self-knowledge, integrity and professional pride, ability to influence by providing purpose, direction and motivation.
“Supply chain professionals are critical team members working in a wide range of industries, helping to solve complex problems during emergencies and sus-
taining daily operations,” says Patrick Shannon, president of NISCL B.C., (formerly SCMABC). “SCMABC joining forces with SCMAO in the creation of our new national NISCL and a new NISCL, Certified Supply Chain Leader Designation, is significant and will propel our profession to new levels. At NISCL, we are committed to bringing heightened awareness of the role supply chain professionals play in the global economy; on procurement and distribution of consumer goods; in helping to provide solutions during the climate emergency; in helping to improve our country’s health care system and so much more.
“In terms of membership benefits at NISCL, we are delivering unique education offerings and networking events for our community. At the same time, we are building public awareness to further elevate recognition that supply chain leaders, with the NISCL, Certified Supply Chain Leader Designation (CSCL) are being recognized as an integral part of any company, organization, or institution’s success.”
Recognizing that the scope of the global supply chain community has expanded exponentially, and that change is imperative, NISCL's focus on benchmarking against global standards is also reflected in its recent partnership with CIPS – one of world's largest supply chain and procurement associations. NISCL is now the exclusive Canadian partner of CIPS. By virtue of this partnership, NISCL designation holders will be offered a pathway toward the MCIPS designation offered by CIPS. This is the first step towards a broader partnership between the two organizations.
A quarter of Trade Confidence Index respondents experience supply chain issues
EXPORTER CONFIDENCE HAS surged by nearly five points, as per Export Development Canada (EDC)'s most recent biannual Trade Confidence Index (TCI). The TCI climbed to 70.1 index points in mid-year 2024, marking a rise from 65.7 points recorded at the end of 2023. Nonetheless, it remains below the historical average of 72.7.
Despite the rise in trade confidence, most respondents reported that inflation and elevated interest rates continue to negatively impact their business. Three-quarters of survey respondents reported being impacted by inflation and 72 per cent by higher interest rates. When it comes to trade barriers, on top are shipping costs experienced by 39 per cent of respondents and economic conditions experienced by one-third. About one-quarter of respondents also
reported experiencing supply chain issues. Top supply chain issues included supplier challenges, faced by 67 per cent of respondents, and transportation hurdles such as shipping and logistics, faced by 52 per cent of respondents.
The TCI, which surveyed more than 1,500 Canadian exporters this round, revealed that exporter confidence has increased across all regions and all business sizes. Ontario-based businesses reported the highest confidence with an index score of 70.9 and large businesses reported the highest confidence with a score of 74.4. With an increase of 7.57 index points, businesses in the transportation sector experienced the largest jump (to 70.13 points), followed by those in the information and communications technology sector, which saw an increase of 5.41 index points (to 70.48 points).
Survey results show that 71 per cent of respondents plan on exporting to new destinations in the next two years. Moreover, for those with operations abroad, two-thirds of respondents (64 per cent) expect sales by their foreign affiliates to increase in the next six months and 47 per cent expect their direct investments abroad to increase in the next six months.
The mid-year survey also assessed exporters’ views on the impact of global elections on their business and export activities. Results show 20 per cent of respondents expect the next U.S. election to have a significant impact on their business. Other top-of-mind elections include the European Union (37 per cent), United Kingdom (31 per cent), Mexico (24 per cent) and India (19 per cent).
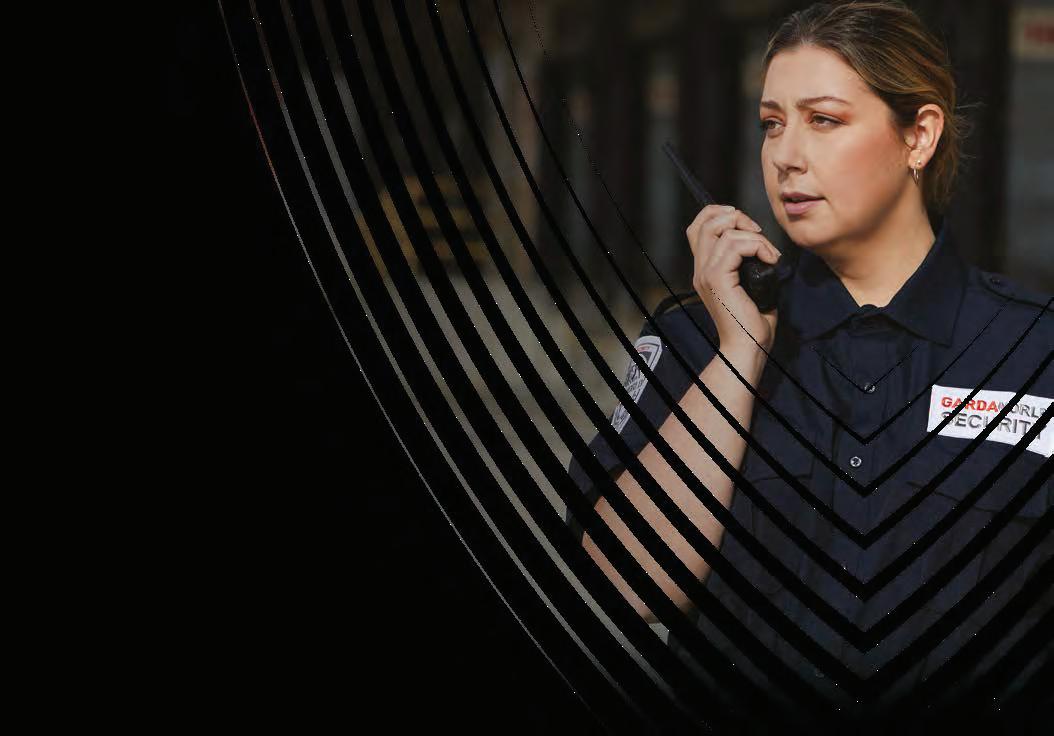
CTA offers suggestions to improve supply chain
THE CANADIAN TRUCKING ALLIANCE (CTA) collaborated with five other organizations to present before the House of Commons Standing Committee on International Trade, which is concentrating on the condition of the international and domestic supply chain and potential improvements.
CTA used this chance to summarize its supply chain proposal, which included recommendations for how the Canadian and United States governments could enhance transportation policies to strengthen the trucking supply chain.
The committee members showed interest in trucking issues like the need to provide the Canada Border Services Agency (CBSA) with support to maintain and increase the presence of sufferance warehouses, address hours of operation at the border for food and agriculture inspections, the Peace Bridge pre-arrival readiness evaluation (PARE), importance of Gordie Howe bridge investment, truck driver rest areas, and aligning winter road maintenance standards.
“CTA is asking the Standing Committee members from all parties to support and champion investments in the trucking supply chain,” said CTA president Stephen Laskowski. “These investments will help spur growth for the overall economy, which helps pay for the
“CTA is asking the Standing Committee members from all parties to support and champion investments in the trucking supply chain.”
– Stephen Laskowski, president of CTA
social network Canadians expect. A healthy Canadian trucking supply chain creates a bright future for all Canadians.”
CTA also championed with Minister Anita Anand, in her capacity as co-chair of the US-Canada Regulatory Cooperation Council, the return of in-transit moves for Canadian carriers and empty trailer moves in Canada and the United States.
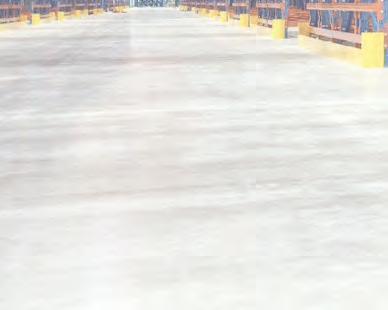
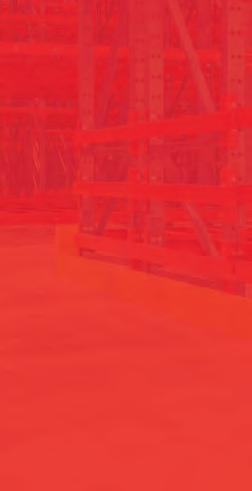
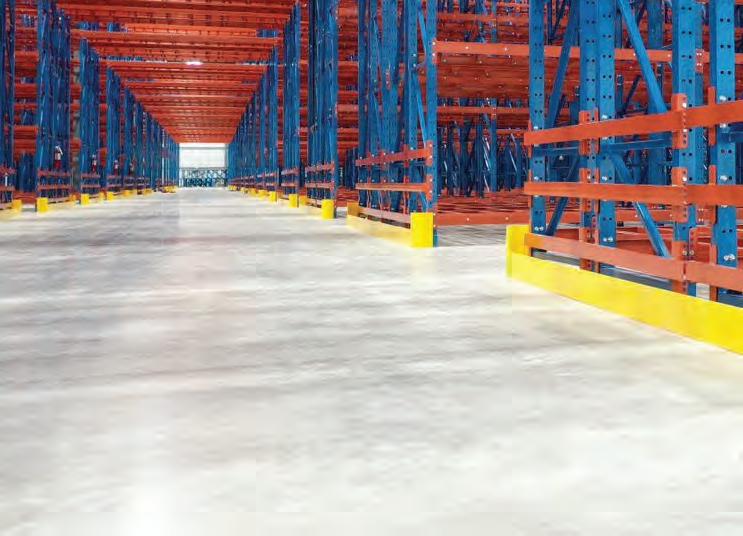
Feds ask Canada Industrial Relations Board to review potential rail strike
THE MINISTRY OF LABOUR has requested that the Canada Industrial Relations Board (CIRB) investigate the potential rail workers' strike and its possible effects on the health and safety of Canadians.
On May 9, Minister of Labour Seamus O’Regan Jr. addressed the issue on social media, stating, "Today, I asked the Canada Industrial Relations Board to look into maintenance of activities
agreements between @TeamstersRail, @CNRailway & @CPKCrail. Serious concerns have been raised about potential impacts to the health and safety of Canadians. It’s our duty to look into this."
Inside Logistics reported May 2 that the Teamsters Canada Rail Conference (TCRC) announced that close to 10,000 workers at CN and CPKC had voted to authorize strikes at both companies.
John Corey, president of the Freight Management Association of Canada (FMA), says a strike would “break the Canadian supply chain” as there are no rail alternatives.
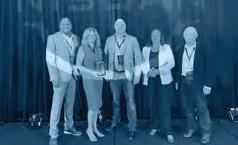
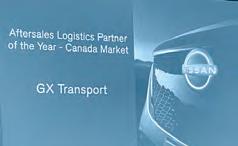
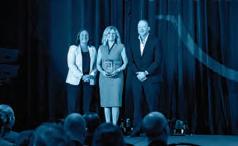
PROUD RECIPIENT OF
SIXTH NISSAN PARTNER OF THE YEAR AWARD
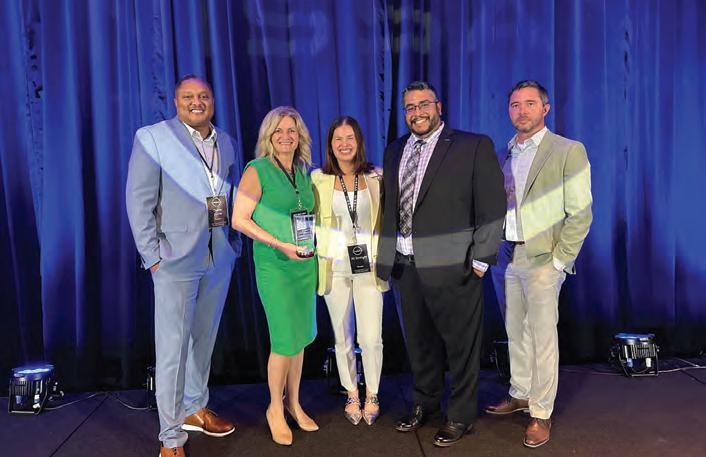
“A rail strike will quickly shut down all major Canadian ports. All imports and exports would be affected. As current inventory is used up, shortages of food, chemicals, fuel, and consumer durables will occur,” says Corey. “Exports of lumber, potash, coal, iron ore, and other minerals will stop. Mines and plants will shut down. Workers will be laid off. Canada’s reputation as a reliable trading partner will be hurt, especially with our U.S. neighbour which receives 75 per cent of all Canadian exports.”
Everstream Analytics also looked at the impact of a rail strike, and says more than 900,000 tons of cargo is moved daily on Canada’s railways.
“About 70 per cent of freight between metro areas in Canada moves by rail and half of Canada’s exports get to the ports by rail,” says Scott Shannon, vice-president of C.H. Robinson, a U.S. supply chain solutions company. “Even freight traveling between Mexico and Canada, which is the case for many automotive manufacturers, would get caught up in a potential strike.”
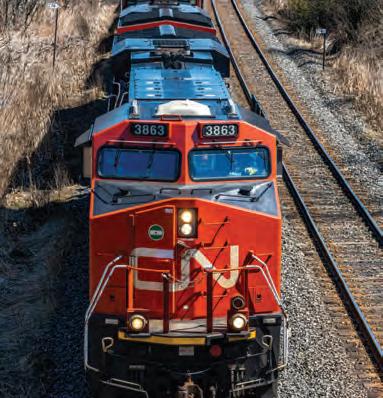
movers + shakers
Manish Arora
Drone Delivery Canada
Manish Arora has resigned as Drone Delivery Canada‘s chief financial officer, effective May 30, 2024. Arora is leaving in order to pursue other opportunities. The company intends to provide an update in due course on his replacement.
CIFFA
CIFFA elected six new board members at its Annual General Meeting. The new board members are: Chris Bachinski, co-CEO and resident at GHY International, Winnipeg; Tim Drake, vice-president, logistics at The Seaboard Transport Group, Toronto; Gary Nicholson, general manager, Polaris Global Logistics, Toronto; Diane Sirois, owner, NOVA Containers Ltd., Montreal; Anna Vitasovic, vice-president international freight, Omnitrans Inc, Montreal; and Anne Waldes, CEO/president Trade Link International Ltd., Toronto.
The Jacques Cartier and Champlain Bridges Incorporated (JCCBI)
The federal government has made appointments to the board of directors of The Jacques Cartier and Champlain Bridges Incorporated (JCCBI), the Crown corporation responsible for the operation of five federal transportation corridors in the Montreal area. Sandra Martel is reappointed as JCCBI’s chief executive officer for a five-year term. The position of chair of the board will be held on an interim basis by Sylvain Villiard for the coming year, or until a new chair is appointed. Lesley Antoun and Henri-Jean Bonnis have been reappointed as directors to the board for another four-year term.
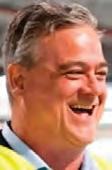
Patrick Kelleher
DHL Supply Chain
Patrick Kelleher will assume the role of CEO of DHL Supply Chain North America effective July 1. Currently serving as global chief development officer, Kelleher will continue reporting directly to Oscar de Bok. With a tenure at DHL Group since 1992, he brings a wealth of experience from various management roles. Kelleher will succeed Scott Sureddin.
Mark Taggart
Toyota Material Handling North America
Mark Taggart, former Toyota Industries Commercial Finance (TICF) president and CEO, assumed the role of chief financial officer (CFO) for Toyota
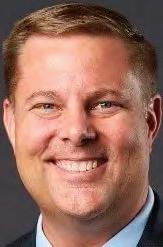
Material Handling North America (TMHNA) on April 1. Taggart will continue his role as chairman of Toyota Industries Global Commercial Finance, overseeing TICF. Taggart joined the Toyota group of companies in 1996. During an assignment in Japan in 2012, Taggart
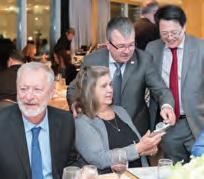
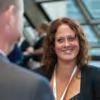
assumed key leadership roles at Toyota Financial Services Corporation (TFSC), culminating in his promotion to vice-president. Before his most recent role at TICF, Taggart was president and CEO of Toyota Financial Savings Bank (TFSB). John Crews, TICF general counsel, secretary and chief compliance officer, will succeed Taggart as TICF president.
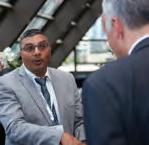
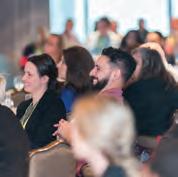

Become a Logistics Insider
Enjoy the benefits of affiliate membership with Canada’s Logistics Association
CITT is Canada’s Logistics Association and the home of Canada’s Logistics Community. If you’re involved in the business of logistics in Canada, you officially join your national community of practice today!
As an affiliate of CITT:
Be well-connected. Join Canada’s most interactive logistics community for networking events, online idea-sharing, exclusive job opportunities and more.
Be informed. Access industry reports, free webinars, and priority registration to professional development opportunities.
Be recognized. You’ll get a fully verified digital credential identifying you as part of Canada’s most respected logistics organization.
Amazon opens robotics fulfillment facility in Calgary
AMAZON HAS LAUNCHED its newest robotics fulfillment center, YYC4, in Calgary, Alta., marking it as only the second facility of this type in Canada.
Spanning 2.8 million square feet and employing over 1,500 workers, the state-ofthe-art center will provide skills training and career advancement opportunities, leveraging advanced technology to expedite customer order fulfillment.
Sushant Jha, general manager of YYC4, says from a technology standpoint, the only other Amazon facility in the country that measures up to this new Calgary warehouse is the London, Ont., location, which opened last year.
“Robotics increases productivity quite significantly,” says Jha. “What it allows us to do is make the environment safer for our associates, which means they want to work with us and grow with us. It also makes [productivity] more efficient.”

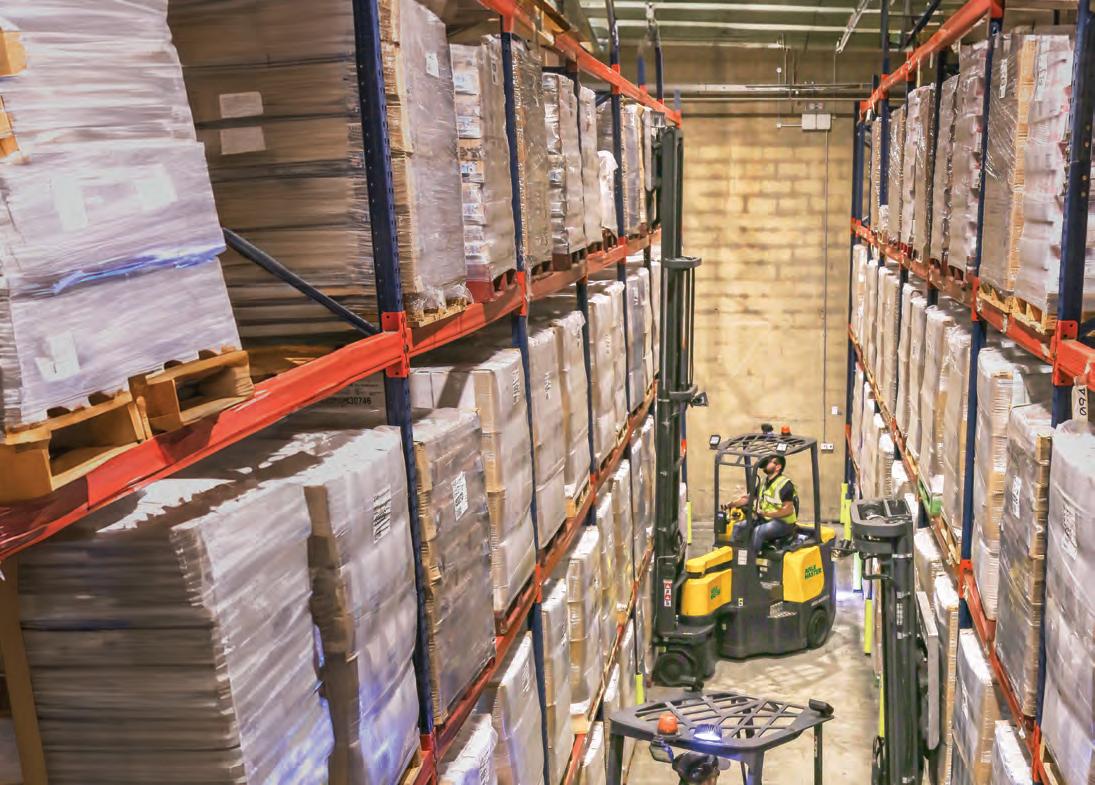
Jha says robotics used at the facility are not fully autonomous and need human assistance, but instead of an Amazon associate having to perform a manual skill, the robot provides greater skilled labour.
“That allows us to make that process more efficient for our customers and to expand overall,” says Jha. “As that consumer base in Canada, Alberta and Calgary grows, it allows us to inject a more efficient system to work.”
Calgary was chosen for its geographic proximity to the Canadian Prairies, where Jha says Amazon is looking to increase its footprint, as well as the neighbouring province to the west.
“With the future demand that the country is seeing overall, we are well geographically located to serve customers in B.C. right now,” says Jha. “This is a great place to set that foundation and expand into B.C. and into Saskatoon. There is excellent logistics with the [Calgary] airport being right here and allows us to do national fulfillment, not just Edmonton or B.C., but also to Toronto.”
Alberta Premier Danielle Smith was present during the grand opening, saying Amazon is a welcome addition to the province, adding to the growth of the economy.
“YYC4 Robotics Fulfillment Centre is the eleventh operations site Amazon has opened in Alberta, and it’s cutting edge to say the least,” Smith said during the ceremony. “This facility shows the confidence that companies have here in Alberta, as a hub of innovation and place where businesses can grow and thrive.”
Calgary mayor Jyoti Gondek said Amazon’s decision to open
WAREHOUSE LABELING SOLUTIONS
the new facility sent a clear signal to the city’s growing prominence on the global stage.
“Calgary has long been a very well-connected city. In fact, 68 per cent of Alberta’s air cargo shipments are transported through the Calgary International Airport, and we can reach 50 million people each day in one day’s drive,” said Gondek. “Cargo can be transported anywhere within 48 hours of leaving Calgary, making us one of the most connected mid-sized cities in North America.”
At Amazon Robotics fulfillment centres, employees work alongside automated systems and robots to pick, pack, and ship customer orders. Amazon's innovative robotics technology creates a safer, more efficient workplace while providing employees with hands-on training to develop new, in-demand career skills. Amazon Robotics technology used at YYC4 includes RWC4, a large robotic arm that sorts totes by destination and builds pallets for shipping, and Kermit, a trolley that focuses on towing empty totes throughout the facility and can adjust its speed and route as needed.
"I've learned a lot working with Amazon Robotics. The goal isn't just to master new technology, but to chart a whole new career path," says Danielle Olliviere, learning trainer at YYC4. "Seeing my colleagues embrace this innovation has been really inspiring for me as a learning trainer. We're not just keeping up with the times; we're shaping the future."
With the launch of YYC4, Amazon now operates five fulfillment centres, one sortation centre, three delivery stations and two AMXL delivery stations in Alberta.
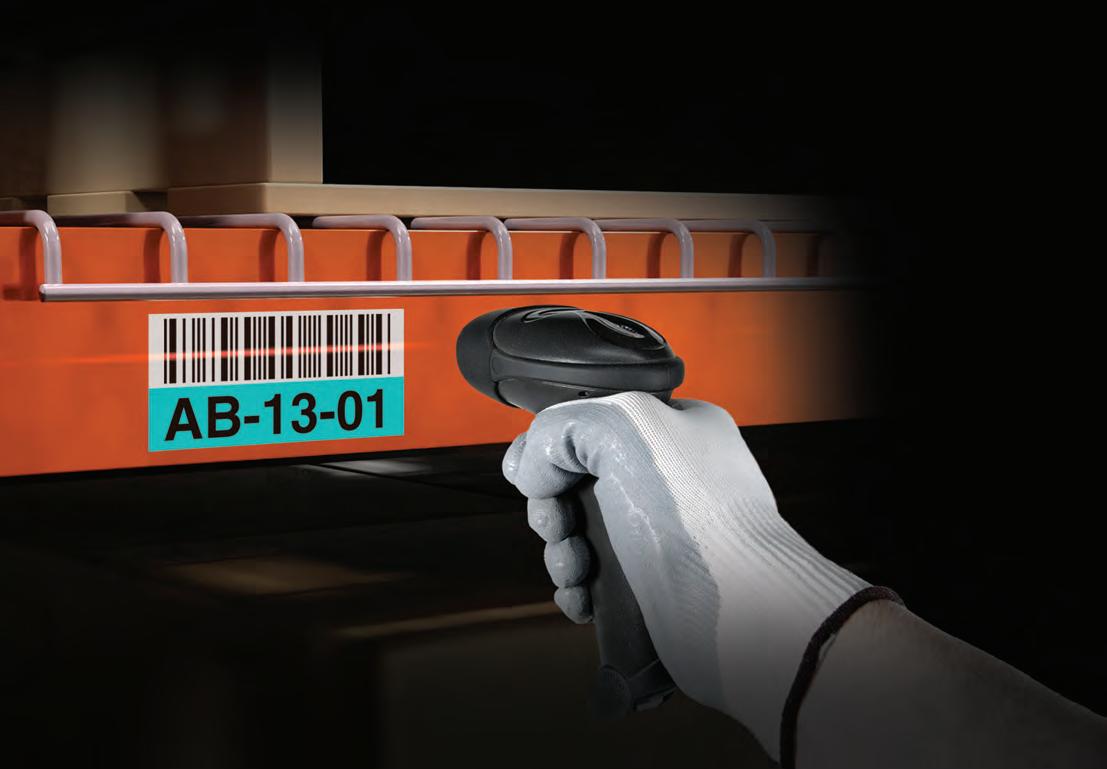
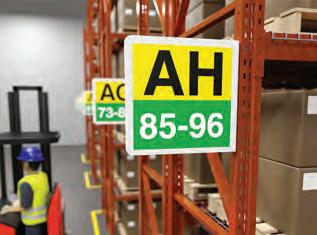
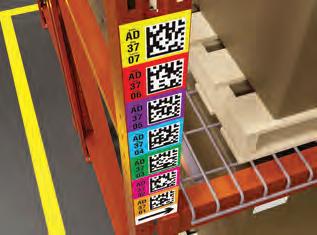
Rail operations ‘severe concern’ due to potential Canadian strike
ALL RAIL OPERATIONS across North America are facing significant concerns due to the potential labor disruption in Canada and inland port intermodal (IPI) congestion at the ports of Los Angeles and Long Beach, as indicated by the U.S. Port/Rail Ramp Freight Index from ITS Logistics.
A strike in Canada would adversely affect ramps in the U.S. Midwest and Toronto since most of these containers enter North America through Canadian ports. ITS suggests the optimal strategy to mitigate these issues is to terminate imports at the port of entry and utilize drayage, transloading and one-way trucking to transport freight to distribution centre networks.
Barry Kukkuk, CTO of Netstock, says if the strike takes place, the impact will continue to be seen across the North American supply chain.
“It could result in delivery delays for inventory, thus negatively impacting inventory levels for many companies across the Canadian and
U.S. supply chain,” says Kukkuk. “This could be particularly devastating for businesses moving high volumes of inventory that are often rail-dependent or can’t be transported via truck. Industries like agriculture and coal could be impacted.”
Kukkuk says these inevitable disruptions in the supply chain should spur businesses to prepare for longer lead times on shipments.
“With the help of accurate data and supply chain technology, businesses can become more agile and responsive," he says, "ensuring they can make the right decisions to meet demands and remain nimble amid future disruptions."
Maersk is also weighing its options in the face of a potential Canadian rail workers’ strike.
“In light of concerns for our customers’ supply chains, Maersk has been reviewing contingency actions,” the company said in a release to its customers. “We continue to explore limited truck options for West/East – East/
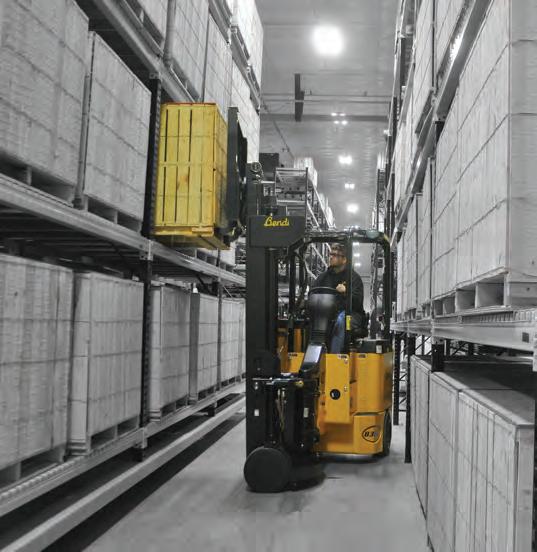
West intra-Canadian transport in the event of a work stoppage.”
On the ocean side, Maersk re-evaluated inducements to Tacoma, Wash., on its TP1 service due to recent developments. Two vessels will induce Tacoma to accommodate U.S. import/export rail cargo, including:
Maria Y – voyages 419N 422S, arriving in Tacoma May 30
Santa Barbara – voyages 420N 423S, arriving in Tacoma June 5
However, the inducements of the following vessels are now under review. Unless otherwise communicated, these vessels will resume their standard scheduled callings:
MSC Domna X – voyages 421N 424S
GSL Effie – voyages 422N 425S
There are no changes to Maersk’s CAE or MCX scheduled sailings calling East Coast Canada at this time.
All contingency sailings have been updated on the company’s online platforms.

Supply chain salaries up eight per cent
AVERAGE SUPPLY CHAIN salaries rose by eight per cent this year.
The Association for Supply Chain Management (ASCM) published its 2024 Supply Chain Salary and Career Report, revealing supply chain professionals are thriving in a robust job market, as evidenced by another year of notable salary growth.
“It’s encouraging to see salaries in the supply chain sector continue their upward trend,” said ASCM CEO Abe Eshkenazi. “The role of talent in fostering a resilient and efficient supply chain cannot be overstated.”
The report found that the median compensation for supply chain professionals reached a major milestone, hitting a record-breaking US$103,000. Additionally, supply chain professionals with degrees reported a significant salary premium of $25,000 above the national average, and individuals with at least one supply chain
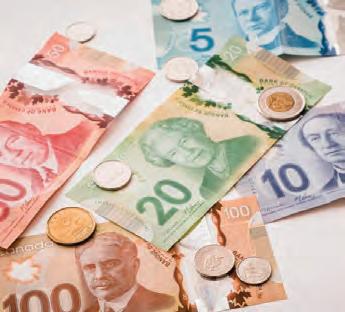
credential earned a median salary 10 per cent higher than their non-credentialed colleagues. Supply chain professionals across the globe report high levels of job satisfaction. Sixty per cent of respondents rated their careers an eight or higher on a 10-point
scale. This enthusiasm is further underscored by the fact that 81 per cent plan to remain in the supply chain field for at least the next five years.
Additionally, a strong sense of professional worth was observed, with 85 per cent taking pride in their work.
This past year, AI and other emerging technologies and tools permeated the workplace and advanced at an unprecedented rate. Results from the research showed that to navigate the ever-evolving supply chain field, a blend of technical and emotional intelligence skills is crucial.
Cloud computing remains the most commonly used technology, followed by AI chatbots, machine learning and robotics. On the soft skills side, critical thinking, collaboration and problem-solving are the key emotional intelligence strengths for success in today’s supply chain landscape.
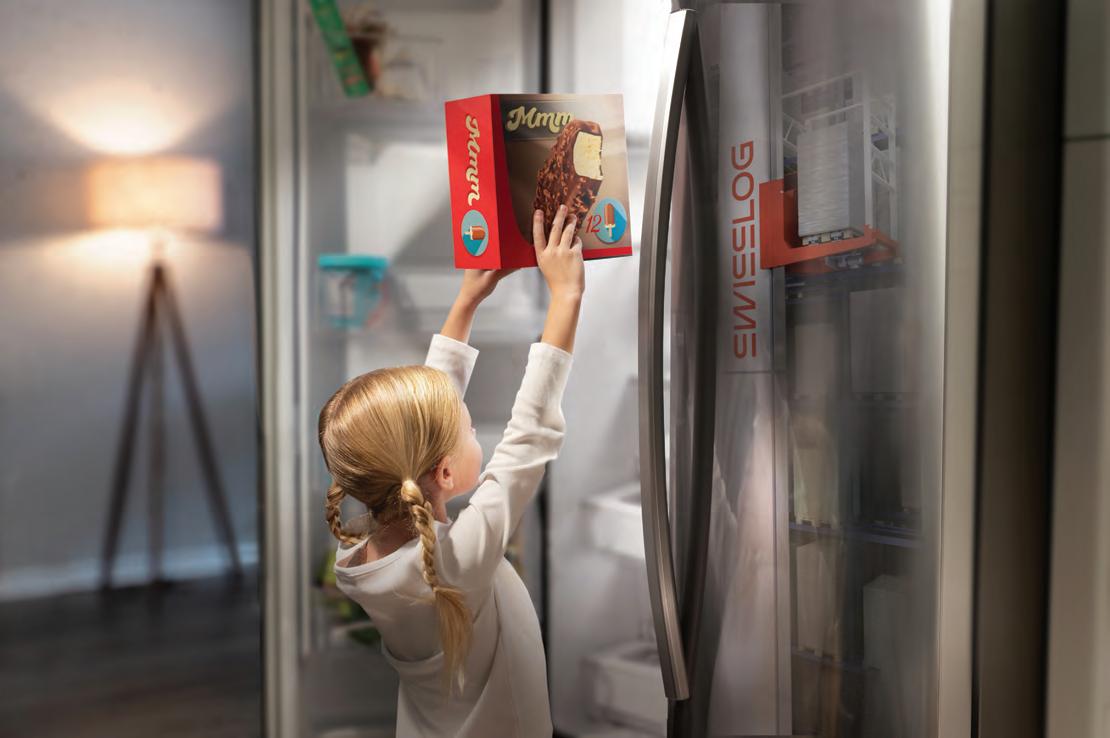
Swisslog’s automated intralogistics solutions for ambient and frozen food are designed to increase speed, accuracy, and e iciency even in demanding temperature-controlled environments.

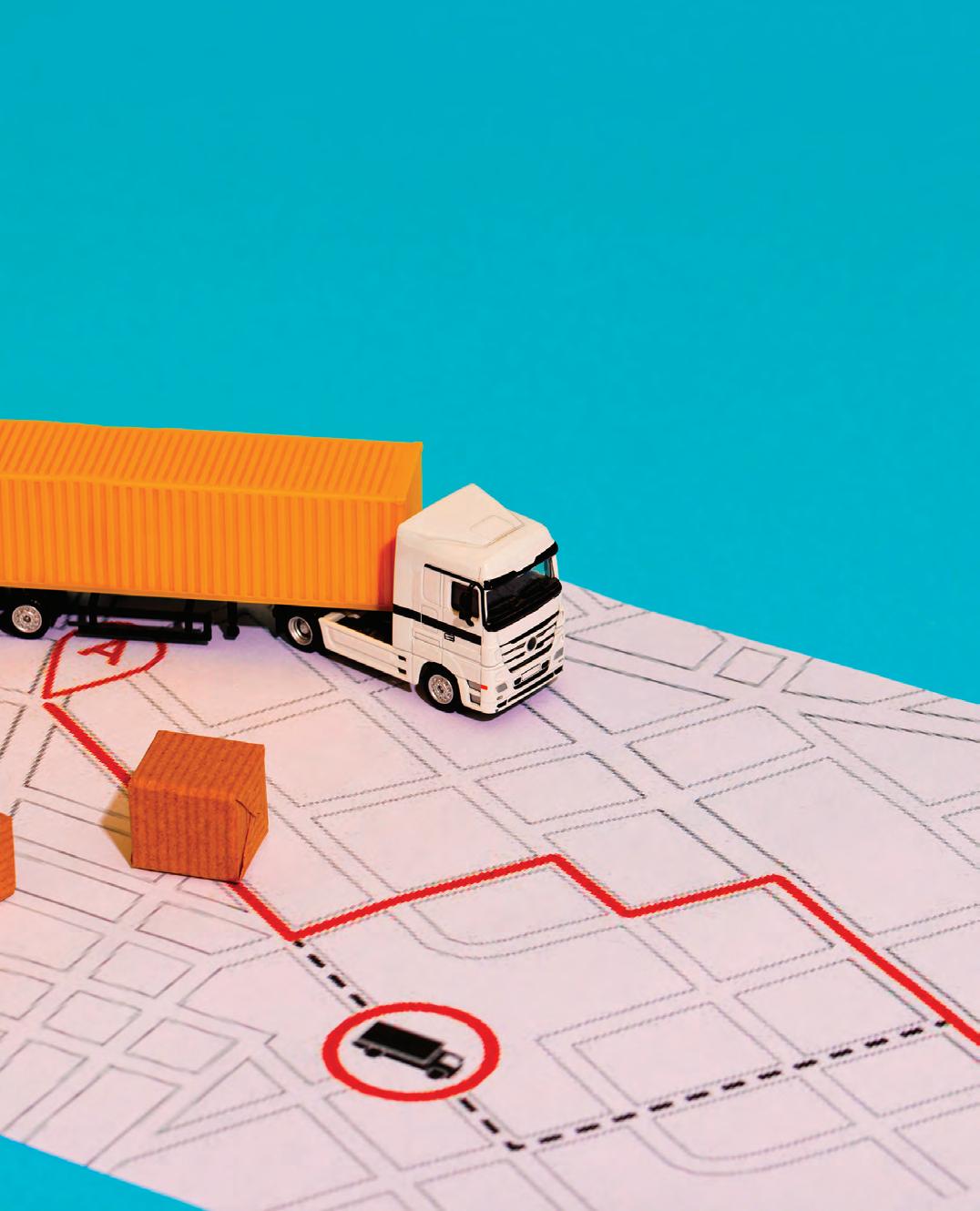
Geopolitical disruptions are nothing new to the global supply chain sector over the past decade. Whether it’s the COVID-19 pandemic, Brexit, trade wars, or a natural disaster, logistics and supply chain companies need to be prepared for the inevitable.
Current tensions and events in the global supply chain are perfect examples of how industry, companies and consumers can be impacted, and how the resilience of logistics companies and shippers has become common.
With tensions high in the Red Sea due to Houthi militants in Yemen targeting commercial ships, and the ongoing impact of Baltimore’s Key Bridge collapse – which was recently destroyed in a controlled demolition – those in the supply chain have had to pivot to minimize the effect on delivery times and pricing.
Rerouting
Ports along the U.S. East Coast have made room for shippers unable to access the Port of Baltimore, but as Jena Santoro, senior manager of global risk intelligence for Everstream Analytics, highlights, this adds time, costs, and challenges to shippers.
“Added transit times both for shipping carriers and truck companies have unsurprisingly increased logistics costs,” says Santoro. “Vehicles typically transported from the Port of Baltimore to Dubai, for example, are now subject to an additional $1,050 fee for the transfer to the Port of Newark. Transporters have to choose to absorb these added costs or pass them on to customers and risk losing future business.”
Brendan Heegan, founder and CEO of 3PL company Boxzooka, agrees, pointing out that space has become a premium along the East Coast, and that comes at a higher cost, particularly on landside and air transport in the Mid-Atlantic region.
“With these operators functioning as a ‘band-aid’ while fulfilling their already committed obligations,” explains Heegan, “it means the cost of this transportation is higher, in some cases much higher, compounded by higher costs for the longer workaround routes that are being used to get around the Port of Baltimore.”
Logistics companies have also needed to navigate the situation in the Red Sea, rerouting shippers to avoid conflict with Houthi militants.
“Their need to reroute is requiring operators to use more container ships adding both to their fuel costs and emissions, which are expected to increase by an estimated 42 per cent per ship for a typical Asia to North Europe weekly liner service,” says Matt Goker, CEO of ATA, a logistics and freight forwarding service provider.
In addition to alternative routes adding to costs, Goker says operators are now delaying plans to replace aging fleets with more fuel-efficient ships.
“While freight rates are currently remaining relatively stable, there is the anticipation that they could increase as more manufacturers elect to use air cargo instead of shipping, which is 10 to 20 per cent higher in costs than shipping,” he says.
And pricing continues to elevate. A recent report from Container XChange indicates that container leasing rates from China to North America surged in the first quarter of the year, including to Canada.
February and March saw a significant spike on the China to Canadian ports, with Yantian to Toronto rates increasing by 68 per cent, Ningbo to Toronto up 35 per cent, Shenzhen to Toronto 26 per cent, Tianjin to Toronto 23 per cent and Qingdao to Vancouver up 64 per cent. The highest container lease rate increase was the Ningbo to Oakland, Calif., route, which saw a 92 per cent bump from February to March.
“China to North America one-way container leasing rates have increased particularly in 2024, with the rise mostly driven by a widening container price delta between China and the U.S.,” commented Christian Roeloffs, cofounder and CEO of Container XChange, an online container trading and leasing platform, in a release. “China becoming ‘more expensive’ up until March versus U.S. container prices stagnating or decreasing.”
Delivery times have also increased, with traffic through the Suez Canal, which connects the Mediterranean and Red Sea, instead being sent around the Cape of Good Hope in South Africa.
“The freight data firm Xeneta reported an estimated 90 percent of the usual container ship capacity passing through the Red Sea and Suez Canal was rerouted around the southern tip of Africa,” says Goker. “This rerouting added on average 10 days to normal delivery times.”
Lisa Osorio, chief strategy officer at Quloi, a cloud-based supply chain solutions provider, says rerouting from the Suez Canal has resulted in shipping costs increasing by as much as five times, impacting imported goods.
She also says this could add to inflation. “Research from Morgan Stanley estimated the disruptions could add 0.7 percentage points to global core goods inflation,” says Osorio. “Container ship operators are now having to use more vessels and incur related increased costs.”
Keep on truckin’
Trucking was hit especially hard by the Key Bridge collapse, as carriers struggled to get their loads to destinations on time.
“Though alternate East Coast ports have been able to absorb the diverted cargo volumes from Baltimore, the trucking sector has struggled to meet the new demands,” says Santoro. “Truck driver shortages have made it difficult to get diverted cargo loads to their now further-away destinations in a timely manner without losing
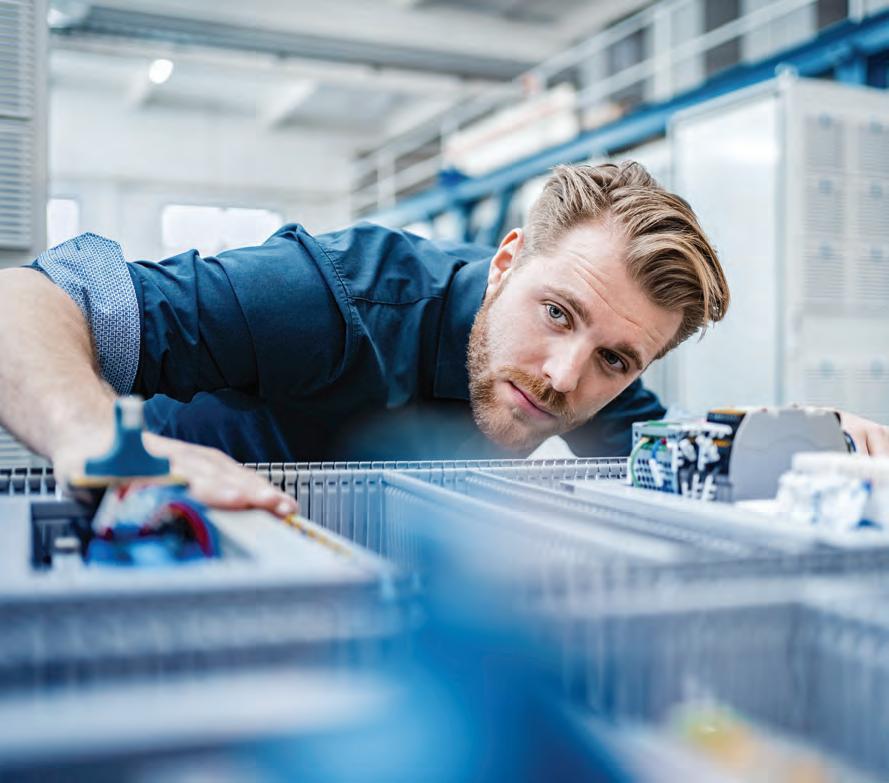
THE FUTURE OF INTRALOGISTICS IS INTEGRATED
Build smart. Stay agile. Now is the time to take a broader look at your overall intralogistics strategy and optimize. Making adjustments to combat today’s challenges will prepare you for a strong and sustainable future. And we can help.
Together, we’ll analyze the strategy and systems you’ve built to move, manage, store and protect goods and bring forward new ideas to enhance or secure the investments you’ve already made. Let’s get started.
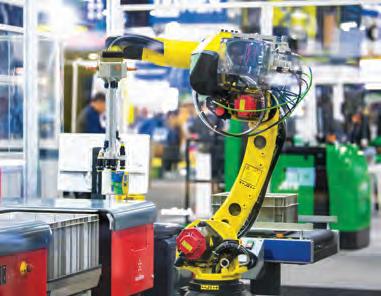
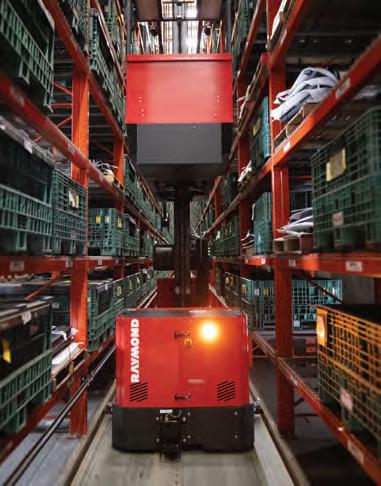
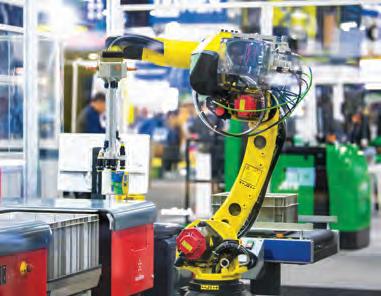
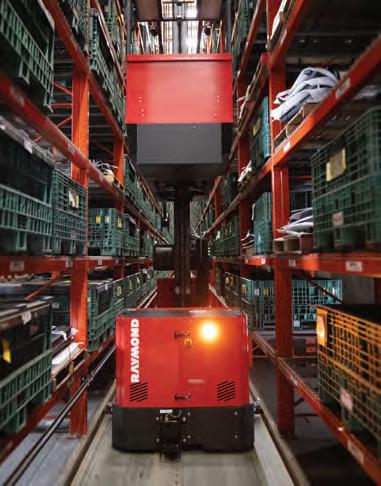
“Though alternate East Coast ports have been able to absorb diverted cargo volumes from Baltimore, the trucking sector has struggled to meet the new demands.”
– Jena Santoro, senior manager of global risk intelligence, Everstream Analyticsmoney or passing on the added transit costs to customers.”
Heegan adds that on top of the impact on the trucking sector, it’s costing more to store goods at alternate ports.
“The more this particular sector is under strain, even as an end may be in sight, this would be where we could still see the most impact,” says Heegan.
Positive outlook
Heegan, who grew up in the Baltimore area and is familiar with the local logistics industry, says things could have been a lot worse following the collapse of the Key Bridge.
Though he points out the event caused approximately 5,000 truckloads to be diverted each day, a significant impact on the local economy, larger supply chains have done their best to minimize the effect on their operations.
“It’s hurting the local communities that relied on that bridge for thousands of jobs and local commerce,” Heegan says of the loss of the Key Bridge. “For the larger supply chains, it absolutely could have been a lot worse. And let me be clear about this; even all of these weeks later, it’s still hard to predict with any high degree of confidence, so even what I say here today, could easily change tomorrow.”
Alternative modes of transportation have helped alleviate some of the backlog with the loss of the port, such as trains, planes, and trucks.
“But now, most of these other transport methods have maxed out and it’s very possible that, the longer this situation continues, the more we are going to witness more direct effects,” says Heegan.
The importance of preparation
There is often a silver lining with any challenging time, and with the Baltimore and Red Sea situations, logistics companies will not only adapt, but will implement a contingency plan for similar future events.
Today’s digital technology is helping companies wade through the complexities of geopolitical disruptions, as is artificial intelligence (AI).
“Those who have experience and the necessary capabilities have been deploying new digital platforms powered by artificial intelligence and machine learning,” says Goker. “This is giving them end-to-end supply chain visibility enabling real-time decision making to best address disruptions and unexpected contingences, while facilitating optimum collaboration between all stakeholders from manufacturers, shippers and suppliers to forwarders and logistics service providers.”
Ensuring collaboration between all stakeholders will be key to implementing a successful strategic plan, and, as Osorio underscores, embracing a real-time, digital freight-forwarding business model will be vital.
“From it, they gain supply-chain visibility for efficient, real-time order tracking, more expedient quoting capabilities and analytics that help improve their performance and customer relationships,” she says.
Keegan also cautions carriers and logistics companies when it comes to liability.
“Contracts between forwarders, cargo carriers, ports, and their customers are almost certainly going under the microscope after the incident in Baltimore,” he says. “Expect to see new verbiage in those agreements on liability and the limits of liability. It also means we could see higher insurance premiums as a result on a move forward basis, which could drive up the costs associated with cargo and shipping.”
AUTO SHIPMENTS DIVERTED FROM BALTIMORE
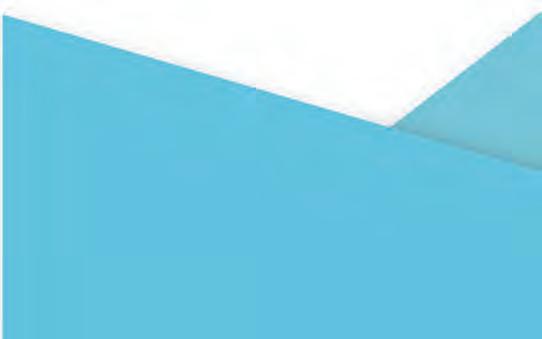
Like various other products that were heading through the Port of Baltimore, automotive shippers are now using alternative ports further south – Mercedes Benz and Stellantis to Georgia or further north and GM and Ford to Newark, N.J.
“Though the Sparrows Point terminal at Baltimore has remained open and accessible to deep-sea car carriers,” says Santoro, “its handling capacity is about 10,000 finished vehicles every two weeks, compared with normal monthly vehicle imports at Baltimore of between 60,000-70,000.”
Heegan again points out that the impact the Key Bridge collapse has had on the trucking industry is trickling down to the automotive sector.
“Much of the burden since the collapse has been placed on the trucking industry to shuffle these vehicles around this closure,” says Heegan. “We’re seeing this play out though with other product sectors too, but not on the scale as automotive. Construction materials, salt, coal, sugar, farm equipment, all of these are major sectors that move through Baltimore, but the strain there has largely been mitigated.”
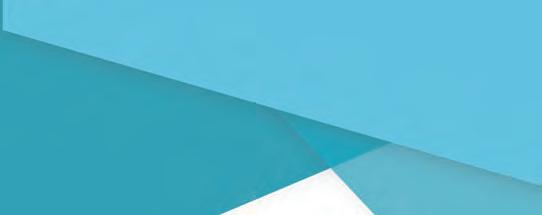
Stop the losses
Securing your facility is easy, with the right help
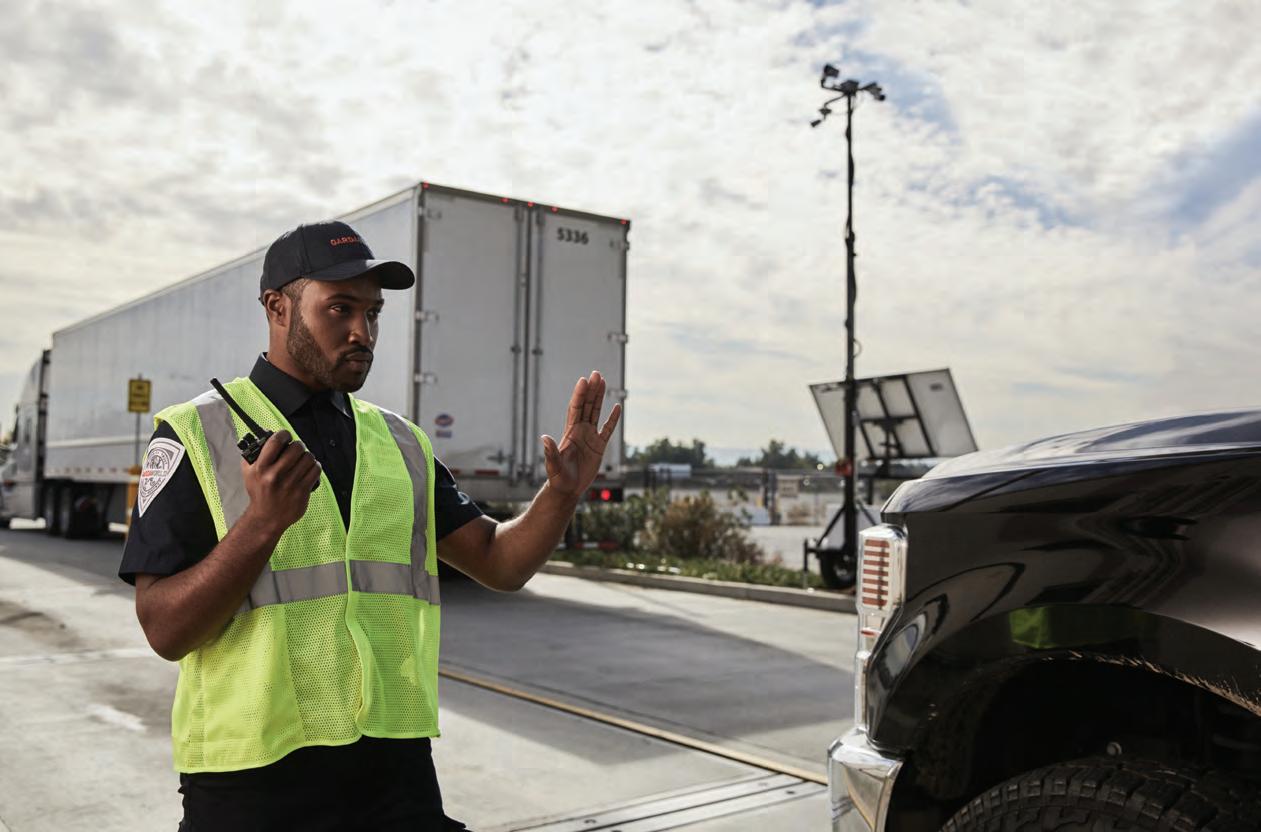
THEFT OF GOODS FROM warehouses is a major source of losses for third-party logistics operators, retailers and manufacturers. Whether it stems from break-and-enter incidents or an inside job by employees with sticky fingers, stolen property poses a substantial risk, leading to considerable losses and operational headaches for warehouse and distribution centre operators.
“That’s why it is critically important to prevent losses by ensuring your facility is secure”, says Neal Kearney, national director of business development at security provider GardaWorld Security Canada.
The first step is to perform a physical audit of the facility and surroundings. Kearney outlines the audit process, where an auditor will visit the site to conduct a comprehensive review of security measures. This includes scrutinizing gate and door access, monitoring fob usage, assessing personnel presence and movement, evaluating alarm systems and surveillance cameras and examining the technological infrastructure in use.
The auditor will do a Crime Prevention Through Environmental Design (CPTED) review, this enables the auditor to assess the facility’s surroundings. This entails assessing its proximity to other entities, whether it’s gated, nighttime access availability, the quality of lighting and the presence of vegetation that could provide cover for potential intruders. Essentially, these factors contribute to
categorizing the facility in terms of security vulnerability.
“Basically, it will determine if you are a hard or soft target,” Kearney says.
RECOMMENDATIONS
After the audit, you receive a report that recommends actions to improve security, to transform your facility into a hard target, Kearney explains. “It lays everything out for you, and you can pick and choose what you want. The good thing about it is that it covers all aspects comprehensively, offering recommendations for everything.”
“Think of a huge warehouse, and your goal is rendering it to be a hard target: you have to push everything away so that when the bad guys roll in, they say, ‘No, it’s too much work to get in here and there’s too much risk, we’re going to go somewhere else.’ We can’t prevent individuals with malicious intent from existing but we can stop them from robbing the site,” Kearney says.
THE BASICS
While every audit will uncover different priorities, there are a few basics Kearney recommends warehouse operators consider. A patrol or guard onsite after hours is one of those table stakes, he suggests.
And if your operation runs 24/7, don’t think you’re safe just because there are people around all the time.
“The people are working. They’re not always paying attention to security. If I’m operating a forklift from midnight to 8 a.m., my job is operating a forklift, it’s not to be a security guard,” he notes. Fortunately, it’s pretty easy to implement measures like security guards and patrols, Kearney says.
From there you want to make sure your systems are up to date and working. This includes everything from access control, to gates, to parking, to cameras, to monitoring, and even mobile surveillance units, which are portable units with pole-mounted cameras that can be monitored remotely.
For access control, he says it is very important to ensure employees only have access to the areas they need to be in. Keycards should be coded so the employee can only open doors to the areas they work or must access, like lunchrooms and washrooms. “Bringing temporary workers into warehouses is nothing new. It’s a part of many companies’ business models. We want to make sure those folks don’t have access to more than they should,” says Kearney.
Employee training is equally important. They should be taught to observe their surroundings and question things like an open door that’s usually shut. “If something doesn’t look secure, you should speak up as well. We want to educate the staff in the facility on that as well. We want our staff to be a part of our security program,” Kearney stresses.
DEALING WITH SERIOUS ISSUES
If your facility is facing a serious security issue of inside theft or cargo theft on your yard, Kearney suggests enlisting the services of an investigation team. GardaWorld employs former police detectives to perform these specialized investigations.
They can immerse themselves within a facility, Kearney says, to get a thorough understanding of what is taking place when you have a recurring or serious issue. “They can come in and be undercover forklift drivers. They can set up an operation where they’re watching the facility, they can follow trucks, they can do all kinds of things. They operate the same way as they did when they were police officers, relentlessly pursuing the targets.”
THE EVOLUTION OF SECURITY
“The security business is taking advantage of rapid developments in technology that are making detection simpler and faster,” Kearney notes. AI, for example, in cameras not only detects motion, but now tells you what kind of motion it is, whether it’s human or an animal. And it allows you to track that person and communicate with them in real-time. However, Kearney warns against the idea that “you won’t need people anymore because your security will be so robust. You’re still going to need people, whether it is to monitor the technology or to engage at some point with trespassers and so on.”
What enhanced security achieves is cost effectiveness. It minimizes the need to deploy human resources every time an alarm triggers, as the nature of the alert is readily discernible.
ALWAYS A GOOD TIME FOR SECURITY
You don’t need to wait until your facility has a break-in or any other security problem to request an audit. Making your warehouse into a hard target is a project that can, and should, be undertaken from the start. “Planning for security from the ground up will make it easier, less costly and quicker,” Kearney says. A GardaWorld audit can be done at any time.
ABOUT GARDAWORLD
CONTACT INFO:
Neal Kearney
National Director, Business Development neal.kearney@garda.com
647-298-3289
COMPANY SIZE:
132,000 + employees around the globe
LOCATIONS:
43 countries
145 + branches in North America
Canadian And World Headquarters / Montreal, Que.
AGE/HISTORY:
Founded in 1995 by Stephan Cretier
SCOPE OF SERVICES:
GardaWorld is a global champion in security services, integrated risk management and cash management solutions, employing more than 132,000 highly skilled and dedicated professionals. Driven by a relentless entrepreneurial culture and core values of integrity, vigilance, trust and respect, GardaWorld offers sophisticated and tailored security and technology solutions through high-touch partnerships and consistently superior service delivery. With a deep understanding that security is critical to conducting business and keeping communities safe, GardaWorld is committed to impeccable governance, professional care and the well-being of everyone. Thanks to a well-earned reputation, GardaWorld is proud to be the long-standing security partner of choice to some of the most prominent brands, Fortune 500 corporations and governments.
CRISIS24 – THE BIG PICTURE
Crisis24, a GardaWorld company, is widely regarded as the leading integrated risk management, crisis response, consulting and global protective solutions firm, serving the world’s most influential people, disruptive brands and prominent organizations. We operate global operation centres across the world, and have highly skilled teams of intelligence analysts, security and consulting professionals and medical experts to respond to client needs anywhere and anytime. Our specialized services include 24/7 security and crisis consulting, protective services, global medical support and proprietary technology platforms enabling us to deliver comprehensive, integrated risk management solutions. From protecting people, organizations and assets to advanced cybersecurity solutions, Crisis24 empowers clients to operate with confidence at home and abroad.
THE EXOSUIT EXPERIMENT
Assessing returns from technology investments
AS PRESSURE FOR innovation increases, organizations are feeling equal pressure to evaluate those innovations before committing to major projects with a high cost in effort and capital. I can speak firsthand to the challenge: no one wants to miss out on potential benefits from new technology, but we can’t constantly burn resources and the focus of our teams on major changes, especially if they don’t pan out.
I’ve learned to look for technologies with multiple potential benefits (including sources of ROI). This increases the odds of seeing real benefits and gives me confidence that the results from small tests will turn into broader rollouts with positive results.
For a growing number of companies, one such multi-pronged ROI technology is exoskeletons. Exoskeletons are a type of assistive technology developed with the goal of improving the physical capacity of users. While this technology may seem relatively new, the idea of assistive wearable devices goes back more than 150 years.
Since then, many variations have been introduced to the market. Exoskeletons can be categorized three ways, by looking at body parts or type of movements they assist, the source of assistance (ei-
ther batteries and motors or elastics and springs) and the nature of the frame and structure (either rigid or soft and textile-based).
As more and more organizations consider implementing these technologies for their workers, the need to understand the potential ROI of the assistive technology has also increased.
ROI calculator
Understanding what products are worth the investment is key to efficient operations. By establishing the ROI of a technology, an organization can ensure it’s investing in an effective product that will consistently deliver results. A Deloitte study indicated that 86 per cent of surveyed manufacturing executives believe smart factory solutions will be the primary drivers of competitiveness in the next five years. These results indicate a wave of technological changes in the manufacturing industry, requiring executives to be extremely decisive when selecting new products to implement. Being able to determine the ROI of these technologies could make these difficult decisions a lot easier. That is why our team created an ROI calculator for evaluating potential return on exosuits.
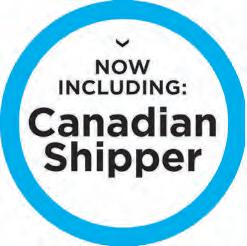
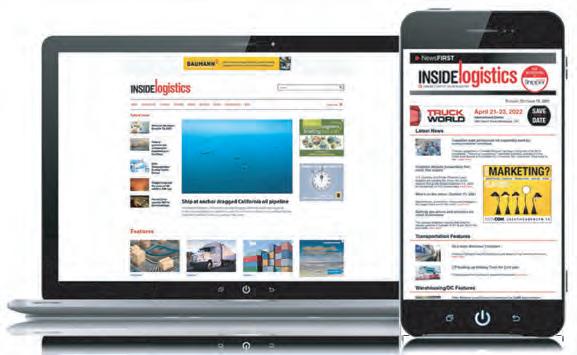
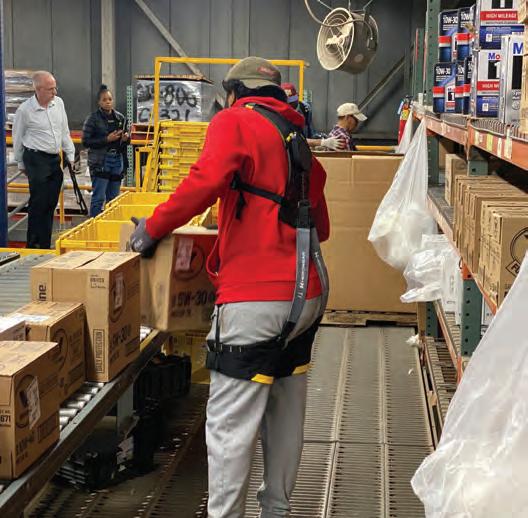
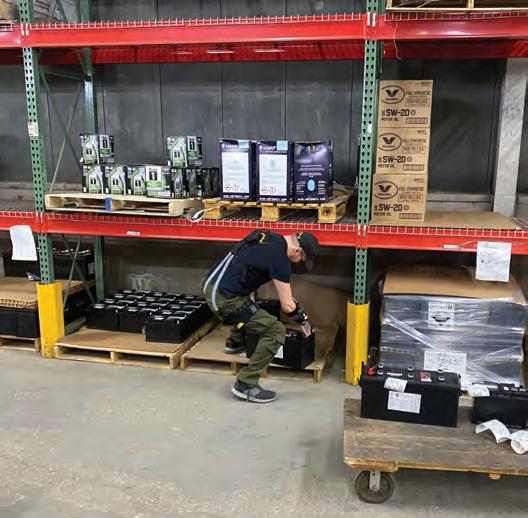
Factors to consider
Establishing the ROI of manufacturing technology requires a tailored approach depending on the aspects of business that the innovation affects. The basic formula for calculating ROI is (net benefitscosts) costs x 100 per cent, however, this is a very high-level approach and isn’t applicable for all types of manufacturing innovations. When determining the ROI of assistive technology, there are three main factors to consider, including the product’s effect on productivity, reduction of injury risk and effect on turnover.
Effect on productivity
In manufacturing, even small savings can make a big impact. When a technology can improve worker productivity, it lowers the cost per unit of work.
How can you determine if assistive technology has an effect on productivity? Our team did a study for an international grocery retailer by evaluating the average number of cases picked per hour before, during and after implementation of an exosuit.
Tracking these numbers gives you long-term insights into how the employees are adapting to the assistive technology. It can also show you how effective implementation was and how long the process took.
The exciting detail here is that increasing productivity didn’t come at a cost to either. Employees actually reported an improvement in work-related discomfort and fatigue. This left workers feeling supported by the organization, knowing the company is providing the technology to make their job easier, and leaving them feeling better at the end of their day.
Reduction of injury risk
If a technology can reduce the risk of injury, it can save your organization a lot of money. Workplace injuries cost U.S. businesses $1 billion a week, with overexertion alone costing an estimated $12.84 billion a year. Indirect costs, including training employee replace-
ment costs, implementation of corrective measures, repairs to damaged equipment and lower employee morale, can add to the costs.
Evaluating a technology’s effect on the reduction of injury risk is essential to the overall ROI calculation. Tools such as ExoLiFFT, developed by teams at Auburn and Vanderbilt universities, can help estimate injury reductions expected from exoskeleton implementations based on the tasks being performed.
Effect on turnover
It’s no secret that improving employee retention can decrease organizational costs. To understand how much a new hire could cost, the Manufacturing Institute suggests considering the salary, recruiting and hiring costs, benefits, training and possible overtime costs. This means the overall hiring cost could be three times the actual salary of a team member.
It’s important to keep employees around. Not only should the direct costs be considered, but social effects in the workforce also add indirect costs. One study found worker turnover impedes coordination between assembly line coworkers by weakening knowledge sharing and relationships. By adopting technology that improves worker’s day-to-day experience, employees feel supported and able to do a potentially physically demanding job for longer.
As organizations navigate the landscape of technological innovation, assessing ROI and lowering the risk associated with innovation becomes paramount. Technologies like exoskeletons offer opportunities to enhance productivity, reduce injury risks and improve employee retention.
Implementing an ROI calculator tailored to these factors enables informed decision-making, ensuring that investments yield sustainable benefits. As the manufacturing industry embraces technological advancements, understanding and quantifying the ROI of such innovations will be integral to maintaining competitiveness and driving success.
Paul Nicholson, VP of Growth at HeroWear.ENHANCING WAREHOUSE SAFETY WITH THIRD-PARTY LOGISTICS PARTNERSHIPS

IN TODAY'S FAST-PACED and competitive business landscape, efficient warehouse operations are critical to the success of any supply chain. As businesses continue to rely on third-party logistics (3PL) providers to manage their warehousing operations, it’s essential to understand the specific roles 3PLs should play in enhancing warehouse safety.
Overall safety
Ensuring the safety of employees, protecting products and maintaining equipment within a warehouse environment is of paramount importance. With warehouse safety concerns hitting news headlines, this topic is a regular conversation among organizations. 3PLs bring significant value to warehouse operations by promoting a safe working environment through implementing key safety strategies and practices.
Expertise and compliance
One of the primary advantages of partnering with a 3PL provider for warehouse operations is gaining their expertise in compliance with safety regulations and industry standards. 3PLs have a deep understanding of local, provincial and federal regulations governing workplace safety. They possess the knowledge to implement best practices and ensure compliance, reducing the risk of accidents and injuries. By staying up to date with evolving safety regulations, 3PLs help warehouse operators avoid costly penalties and maintain a safe working environment.
Employee training and safety culture
A safety-conscious culture is integral to maintaining a secure warehouse environment. 3PL companies prioritize employee training and actively promote safety awareness and compli-
ance among their staff. They invest in comprehensive training programs that provide warehouse workers with the necessary knowledge and skills to perform their tasks safely. Whether the focus is on hazard identification, proper equipment handling or emergency response protocols, 3PLs foster a culture of safety that permeates throughout the entire warehouse facility, mitigating risks and preventing accidents.
Technology and automation
Modern warehouses are embracing cutting-edge technologies and automation systems to streamline operations and enhance safety. 3PLs should possess the resources and expertise to implement these technologies effectively. Automation reduces the need for manual labour in hazardous tasks, such as heavy lifting or working in high-risk areas. Robotics and conveyors minimize physical strain on employees, lowering the likelihood of injuries. Additionally, advanced monitoring systems, such as video su rveillance and sensors, enable real-time identification of potential safety hazards, allowing swift action to be taken.
3PL s have gained significant expertise in utilizing warehouse management systems (WMS) to optimize supply chain operations and enhance overall efficiency. A WMS is a critical component of modern logistics management, providing real-time
v isibility, control and coordination of warehouse activities. As supply chains have become increasingly complex, 3PLs have adapted to leverage WMS to meet the evolving demands of their clients and gain a competitive edge. 3PLs excel in utilizing WMS technology in a variety of ways, including:
Inventory management: WMS allows 3PLs to maintain accurate, up-to-date records of inventory levels and locations. Advanced WMS systems utilize barcode scanning and radio frequency identification (RFID) technology to enable precise tracking of goods from receipt to dispatch. This capability helps 3PLs optimize inventory levels, reduce carrying costs, prevent stockouts a nd improve order fulfillment rates, leading to higher customer satisfaction.
Order processing and fulfillment: 3PLs with robust WMS platforms can efficiently manage and prioritize order picking, packing and shipping processes. WMS platforms optimize the order fulfillment process by determining the most efficient picking routes, reducing the time and effort required to fulfill orders accurately and on time. This efficiency translates into faster delivery times, reduced lead times and increased customer satisfaction and loyalty.
24_003870_Inside_Logistics_JUN_CN Mod: April 30, 2024 2:37 PM Print: 05/20/24 page 1 v2.5
KEEP ON TRUCKIN'
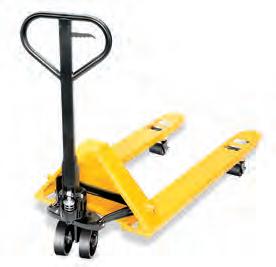
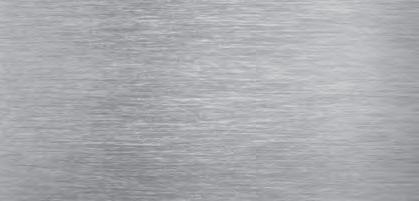
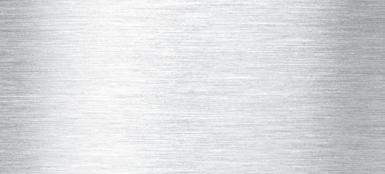

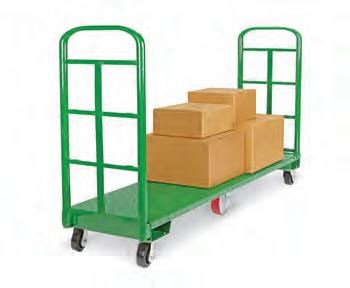





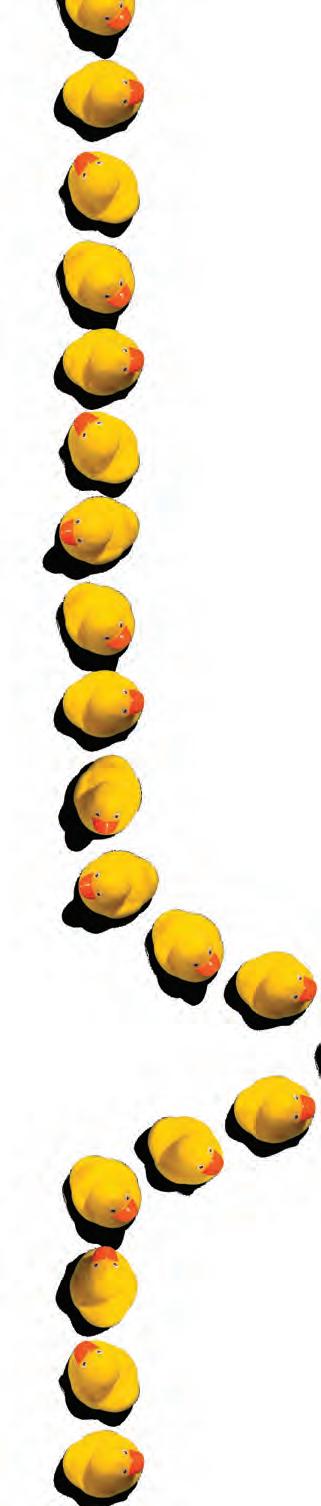
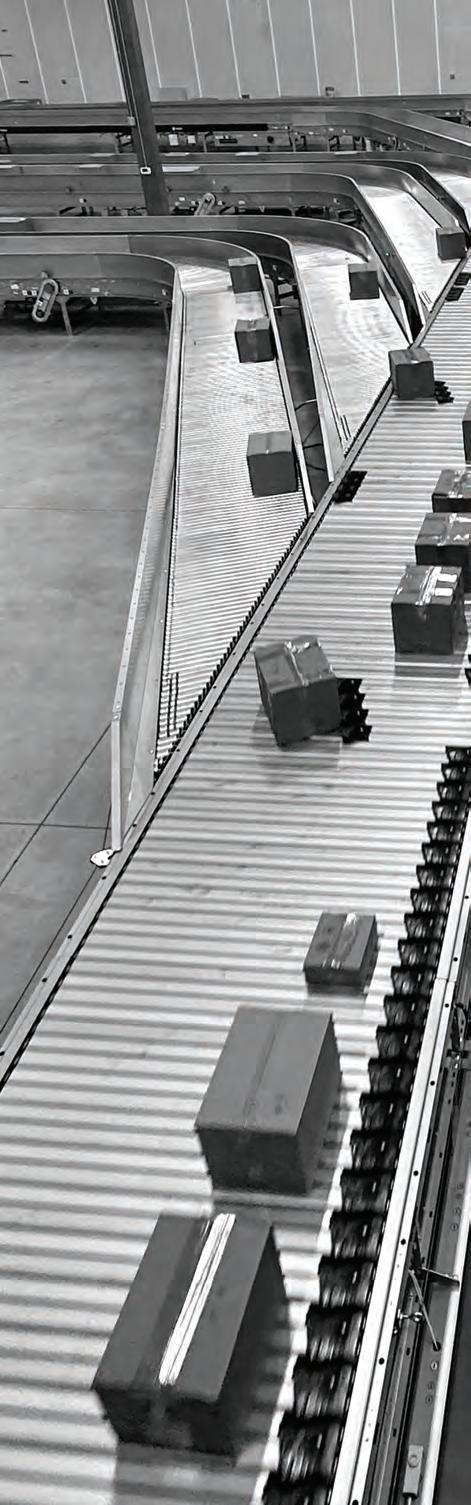
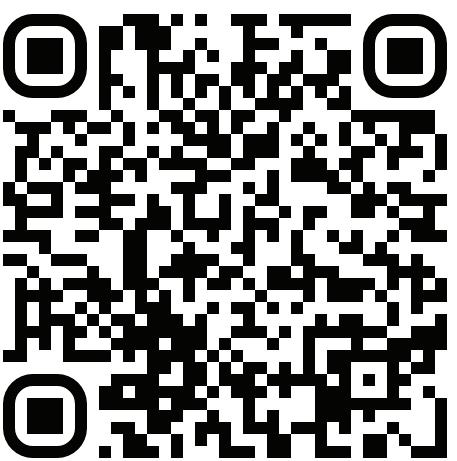
Ready to get your fulfillment operations in a row?
Discover automation and software solutions aligned with your business goals at TREWautomation.com. FOLLOW US!
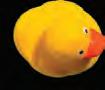
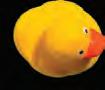

Productivity and labour management: WMS provides real-time data on warehouse performance metrics, such as pick rates, packing accuracy and order cycle times. Armed with this data, 3PLs c a n identify areas of improvement and implement strategies to streamline operations, allocate resources effectively and enhance workforce productivity.
Full visibility: Shippers can access real-time data through web portals or customized reports, allowing them to make informed decisions and collaborate seamlessly with the 3PL.
3PL s have honed their expertise in using WMS to navigate the challenges of modern supply chain management successfully.
Warehouse layout and design
The layout and design of a warehouse significantly impacts safety. 3PLs excel in optimizing warehouse space and flow, ensuring a safer working environment. They meticulously plan the layout, considering factors such as efficient traffic management, ergonomic workstations and clear signage. By reducing congestion, improving visibility and implementing proper storage techniques, 3PLs g reatly minimize the risk of accidents caused by collisions, falls or improper handling of goods while optimizing the flow of materials to and from the warehouse.
Risk assessment and mitigation
Effective risk assessment and mitigation strategies are crucial for warehouse safety. 3PLs conduct thorough risk assessments, identifying potential hazards and implementing measures to minimize t heir impact. They analyze workflow processes, storage methods and equipment usage to identify areas of vulnerability. Through proactive measures such as regular safety audits, incident reporting systems and continuous improvement initiatives, 3PLs ensure potential risks are promptly addressed, reducing the likelihood of accidents and product damages, and promoting an overall safer warehouse environment.
Emergency preparedness
Regardless of how well prepared a warehouse is, emergencies can still occur. 3PLs excel in developing robust emergency response plans and implementing safety protocols. They conduct regular drills and simulations to familiarize employees with emergency procedures, ensuring a swift and coordinated response in case of accidents, fires or natural disasters. By providing adequate training, emergency exits, fire suppression systems and first aid resources, 3PLs enhance warehouse safety and minimize the potential impact of unforeseen events.
I n the dynamic world of logistics and warehousing, prioritizing safety is crucial to protect employees and assets, maintain operational efficiency and safeguard business reputation. With robust expertise in compliance, a commitment to employee training, utilization of technology, emphasis on efficient warehouse design, focus on risk assessment and robust emergency preparedness, 3PLs contribute significantly to creating a secure working environment.
3PL s play a pivotal role in enhancing warehouse safety for shippers. By partnering with a reputable 3PL that prioritizes a "people fir st" philosophy, shippers can benefit from their knowledge and experience to optimize safety practices and promote a culture of well-being within their warehouses.

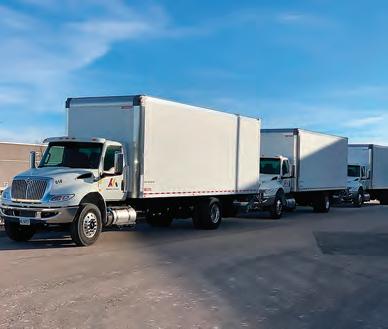

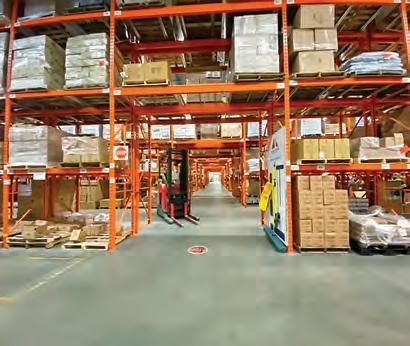
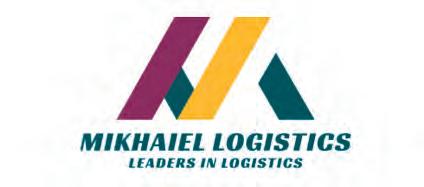
BEING ABLE TO FULFILL orders quickly and accurately is the primary goal of any warehouse. Companies must automate all operational warehouse decision-making in a capacity-considerate way, freeing people to fight the fires that pop up, while m itigating risk. Many companies employ specialized software to assist with warehouse operational efforts.
In today's complex logistics environment, efficiency and precision are paramount. There is a pioneering approach to warehouse management, which offers a centralized orchestration s olution that optimizes processes, labour, and space within warehouses and distribution centres.
These systems function atop existing warehouse management systems (WMS), streamlining operations and significantly boosting efficiency and throughput in facilities. By enhancing labour planning, facilitating seamless human-robotic i nteractions, managing inventory flow more effectively, and optimizing the utilization of space, this software not only improves operational efficiency but also elevates the overall productivity of warehouse operations.
Tribal knowledge
Even with all of the positives of orchestration, one of the most impactful features of this type of software is its ability to capture and utilize tribal knowledge – those invaluable insights a nd practices developed by experienced warehouse coordinators. This is crucial, especially considering that over 80 per cent of warehouse coordinators have been in their roles for less than four years.
By preserving this knowledge within the system, vital operational insights are retained and accessible, even amid high staff t u rnover. This retention not only secures operational continuity but also strengthens the organization's risk management f r amework.
Consider a scenario where a seasoned coordinator's nuanced approach to handling peak season logistics is retained in t he software. This allows even the most novice team members to handle complex operations confidently, seriously reducing risks and supporting continuity.
Centralized orchestration
To operate effectively, project teams learn from the best site leaders on how to optimally run every site. This configuration is then stored in the system, which learns from behavior over time, based on actions taken to capture how sites run effectively. These optimized sites with centralized warehouse orchestration provide unparalleled visibility into warehouse operations, enabling companies to monitor and manage potential r i sks proactively.
This visibility is critical for identifying and addressing issues such as stock outs, over-utilization of space, and upstream logistical bottlenecks before they escalate into more significant problems. By providing a holistic view of warehouse dynamics, the software allows managers to benefit from early detection of disruptions. This, in turn, facilitates the development of targeted risk mitigation strategies that minimize downtime.
Reducing customer service risk
Centralizing warehouse orchestration opens up the potential to provide visibility to customer service teams. Days before orders are picked, staff can be made aware of potential order-fill or shipment-time service issues at a site, and then can proactively work w ith customers to reduce overall risk. For customers like Walmart, this can significantly reduce chargebacks and maximize top-line revenue by ensuring that customer service teams are equipped with the insights needed to manage expectations and resolve issues before they impact the customer experience.
With centralized warehouse orchestration, companies gain better visibility into what is happening within warehouse processes. This visibility helps to monitor potential risks, such as stockouts, overstocking, or bottlenecks in the supply chain. Companies can also assess the impact of disruptions and create risk mitigation strategies that minimize downtime.
Centralized warehouse orchestration leads to indirect labour savings, increased fill rate, increased load on time, and productivity improvements across direct labour by optimizing the work historically released and executed by warehouse operators.
Augmenting workflows with artificial intelligence (AI), machine learning (ML) and digital twins, helps distribution operations to become more agile and responsive to changing market conditions and better adapt to customers' needs. These technologies can help distributors make more informed decisions, reduce costs and improve operational efficiency, improving customer satisfaction and profitability.
With centralized warehouse orchestration, multi-site data is aggregated. Using predictive analytics with the data, orchestration enables top supply chain officers to rank multiple sites, quickly see which areas across the network are out-of-tolerance or at risk and take corrective action to mitigate risk before chaos happens.
Most organizations struggle to quantify tribal knowledge, which often leads to gaps in formal risk management processes. However, frameworks within analytics allow companies to c apture, quantify and operationalize these insights effectively. Incorporating tribal knowledge into the supply chain complements formal risk management processes, providing organizations with a nuanced understanding of their operations.
T h is comprehensive perspective is essential for effectively anticipating, mitigating, and responding to risks. Companies can t r ansform anecdotal experience into actionable data, enhancing their ability to navigate the complexities of supply chain ma nagement with greater agility and informed confidence.
Risk management
By centralizing warehouse orchestration and enhancing risk management through the strategic use of tribal and operational data, companies can equip themselves to thrive in an i ncreasingly complex and demanding logistics landscape. As companies look to the future, embracing such advanced technologies will be crucial for staying ahead in a competitive market and achieving sustained operational excellence.
Keith Moore, CEO, AutoScheduler.AI.THE BIGGEST CHALLENGE FOR LOGISTICS COMPANIES IS VISIBILITY
IN THE PAST FOUR years, we have seen an unprecedented change being driven in the supply chain and warehouse industry. Global events like the pandemic shifted people’s shopping habits to online, causing excess demand for suppliers, coupled with geopolitical issues and conflicts that have meant supply chains are no longer built for efficiency, but rather for resilience.
The modern warehouse is a hub for consistent, around-the-clock action with goods moving in and out at an ever-increasing speed. Inconsistencies and gaps in the level of goods in the warehouse can lead to dissatisfied customers and staff attrition if they are sent on a wild goose chase to look for an item that’s not in the right location. Due to the number of challenges relating to demand forecasting, supplier relationship management, production efficiency, inventory management and technology integration, there is a need for seamless collaboration among different systems.
The role of visibility in supply chains
The warehouse management system (WMS) is typically seen as the single source of truth in the warehouse, but often goods can be misplaced, or available stock has been counted wrong, often through
manual processes or because the space in the warehouse has not been optimally utilized. This, in turn, leads to gaps in visibility within the warehouse and can often lead to inaccurate information being available to operators.
Moreover, in the modern business environment, competition is tighter, and having accurate information available can make or break a business. Therefore, visibility plays a crucial role in achieving resilience within operations.
Visibility refers to the ability to track and monitor the movement of goods, information and resources across various stages in real-time. It is about gaining a comprehensive view that extends from suppliers to end customers. This in turn will give businesses a competitive edge. However, only six per cent of logistics companies can claim full visibility over their operations.
To achieve full visibility of warehouse operations, businesses need to be able to track and monitor each stage of goods moving in and out in real-time. This helps to build resiliency into operations, by providing insights, enabling proactive decision making and fostering collaboration among supply chain partners. Achieving this provides a holistic view, allowing organizations to identify bottlenecks, optimize
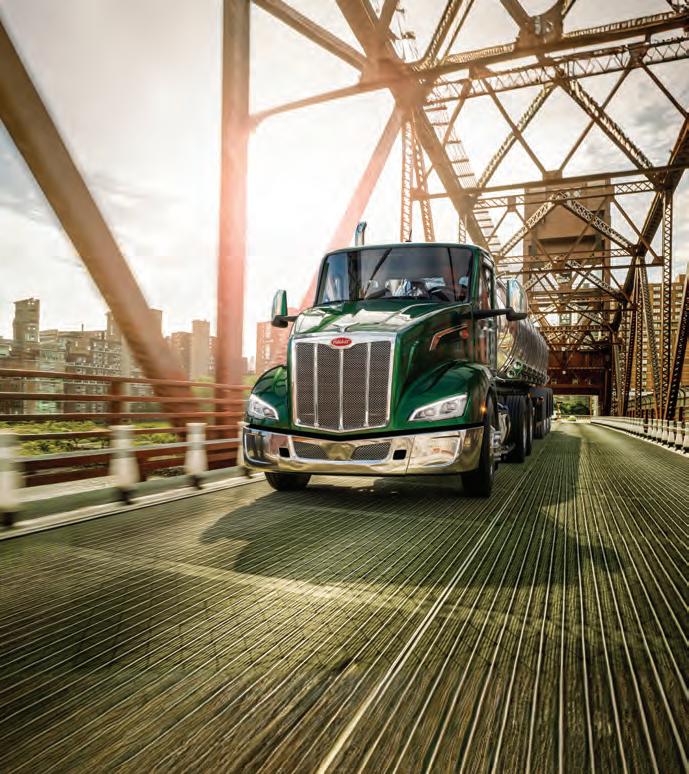
Get a Peterbilt 579 from Brandt with the easiest walk-away lease around! Save now & down the road on a contract that works for you.
• CHOOSE THE DURATION
• FIXED LOW RATES
• OPTION TO BUY WHEN CONTRACT ENDS

Scan here to secure your savings or contact your Brandt Peterbilt dealership today.
processes and enhance overall efficiency. In logistics and warehousing, the ability to track inventory in real-time, monitor shipments and manage warehouse operations with precision is a testament to the power of visibility.
Identifying blind spots
The visibility gap affects the entire supply chain, and we often find the warehouse becomes the focal point when visibility falters. Warehouses are ultimately busy hubs of activity where people, processes, machinery and customers share the same space.
They are often susceptible to visibility issues, especially concerning accurate inventory tracking, stock levels and potential discrepancies between recorded and actual stock. The complexity of warehouse operations underscores the importance of enhanced visibility solutions to address these challenges and ensure a seamless flow of information throughout the supply chain.
One of the fundamental challenges in addressing these blind spots lies in understanding what data needs to be collected. In modern business, vast amounts of data are generated daily from different sources, making it complex to identify and gather the most relevant and valuable information.
Acquiring data is just the first step in identifying blind spots. The real value of data lies in translating it into insights and actionable strategies to help move the business forward.
Understanding the visibility gap
Modern logistics operations are intricate and involve a vast number of stakeholders from transportation providers to distribution, which means gaining and maintaining full visibility is challenging. Many businesses also operate with fragmented and legacy systems where data lives in silos and across different platforms. Usually, these different systems don’t talk to each other, which leads to difficulties in tracking and monitoring operations in real-time. To obtain full visibility, businesses need to ensure a seamless flow of data.
The root cause of the visibility gap is related to data. Several factors cause the fragmentation of data, but three main reasons are:
1. Fragmented systems: Many organizations operate with disjointed systems, creating data silos that hinder the seamless flow of information across the supply chain.
2 Inefficient communication and human error: When critical information isn’t shared promptly or accurately, it creates gaps in visibility and exacerbates operational challenges. Similarly, human error can cause issues through something simple such as a misplaced box in the wrong pallet location or entering it incorrectly in the WMS.
3. Legacy technologies: Outdated or incompatible technologies can impact the real-time exchange of data. Legacy systems often lack the capabilities needed to keep up with the dynamic nature of modern supply chains.
Implications of the visibility gap
Now that we understand where the visibility gap comes in, we need to understand its implications for the business. As outlined, visibility is the fundamental pillar for achieving and maintaining operational effectiveness. Lack of visibility can lead to many risks and inefficiencies.
These inefficiencies have real-world business implications that include, but are not limited to:
1 Increased operating costs: Without a clear view of the supply chain, businesses may face increased operational costs due to inefficiencies, excess inventory and disruptions. This, in turn, affects the overall profitability of the organization.
2. Customer dissatisfaction: In today's consumer-driven market, cus-
tomers expect timely and accurate deliveries. The visibility gap can result in delayed shipments or stockouts, leading to dissatisfied customers and potential damage to a company's reputation.
3. Risk exposure: Lack of visibility makes it challenging to identify and mitigate risks effectively. Whether it's geopolitical issues, natural disasters, or disruptions in the supply chain, organizations with limited visibility are more susceptible to unforeseen challenges.
Closing the visibility gap
In warehouse management, an average of 6,500 hours are dedicated annually to seemingly straightforward tasks such as cycle counts and stock checking. Even though the number of hours is staggering, it isn’t enough. Data is only gathered in partial fragments at any one time and due to the dynamic nature of warehouses or the supply chain, the fragmented data snapshots become outdated quickly. This usually leads to many businesses thinking that their accuracy is better than it is in reality.
But how do companies close the visibility gap? Below are some recommendations for closing this gap in the supply chain.
1 Real-time data: Gathering real-time data allows businesses to gain a holistic view of all their operations and ensure that the data matches the WMS to quickly point out any discrepancies in the system. Organizations must invest in integrated systems that provide instant updates on inventory levels, order status and shipment tracking.
2 Advanced analytics and predictive monitoring: Leverage advanced analytics and predictive modelling to anticipate demand fluctuations, optimize inventory levels and identify potential bottlenecks in the warehouse. By utilizing AI-powered solutions for analytics, businesses can generate more insights and visibility with more data. This is particularly important as it allows businesses to make the decisions on operations as they are, not how they thought they were.
3. Invest in technology infrastructure: Allocate resources to upgrade and integrate technology infrastructure within the warehouse. This includes implementing WMS, Internet of Things (IoT) devices and cloud-based solutions to streamline operations and enhance real-time visibility.
4. Prioritize collaboration: Foster collaboration with suppliers, manufacturers and distributors. Implement shared platforms and standardized data exchange protocols to ensure seamless communication and information flow throughout the supply chain.
5. Employee training and change management: Recognize the importance of employee training to optimize the use of new technologies. Implement change management strategies to ensure a smooth transition and acceptance of new processes, minimizing resistance and maximizing efficiency gains.
6. Continuous improvement: Establish a culture of continuous improvement within the warehouse. Regularly assess and refine processes based on data analytics and feedback loops, ensuring adaptability to evolving market conditions.
The visibility gap poses challenges to businesses in a complex environment. Supply chain professionals need to embrace innovations that allow them to close this visibility gap through a continuous stream of real-time data.
To overcome the challenges of data collection and address warehouse complexities, businesses need to look into deploying advanced technologies that allow them to enhance operational efficiency. Similarly, there is a need to also emphasize end-to-end visibility and data accuracy that will ensure continuity and resilience, while also serving as a strategic tool for proactive decision-making.
Oana Jinga, chief commercial and product officer and co-founder at Dexory.
Manitou offers gas/diesel models with multiple mast options and attachments to meet all industrial material handling needs.
Manitou means forklifts. Manitou means industrial.
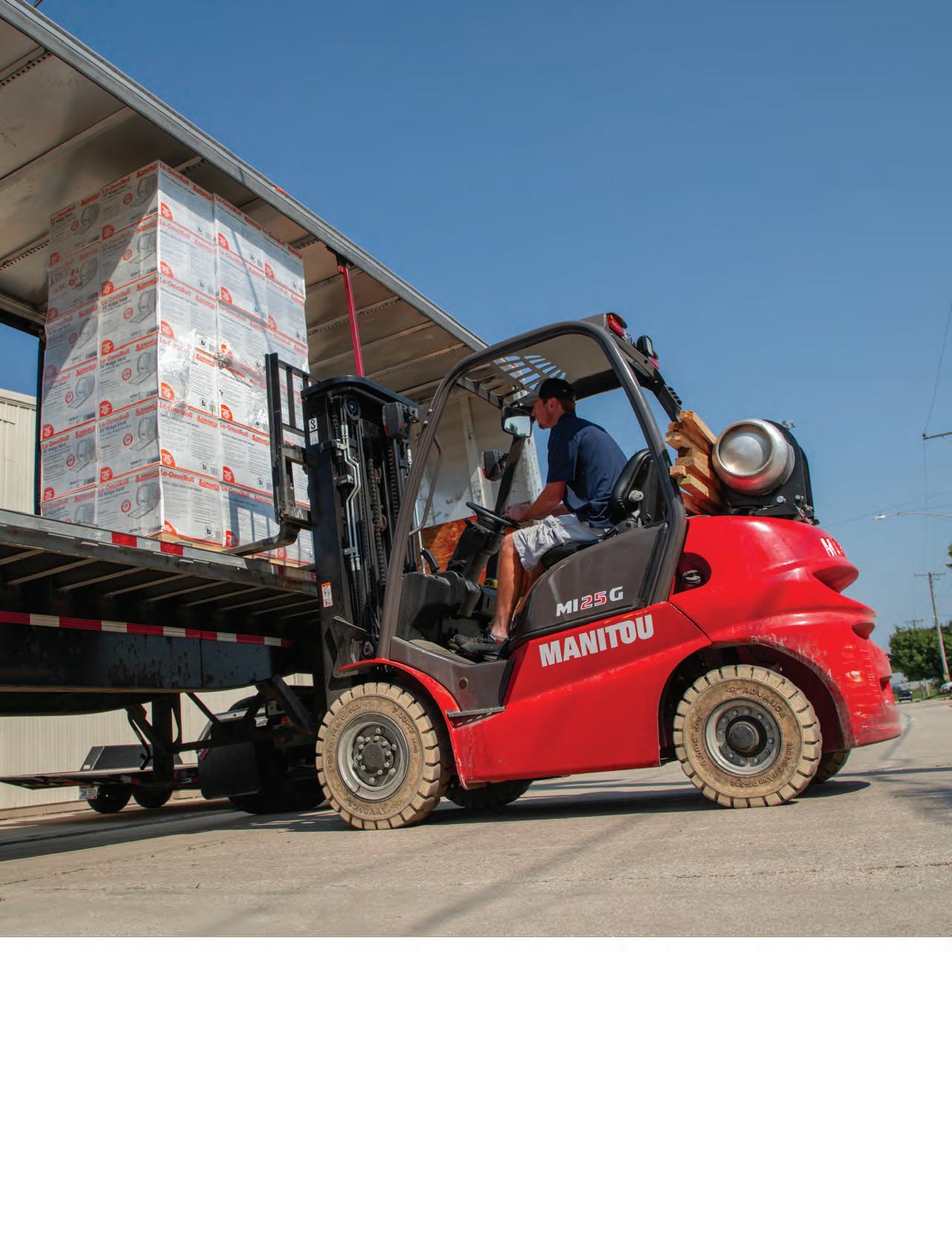
See our full range of solutions for your business at Manitou.com.
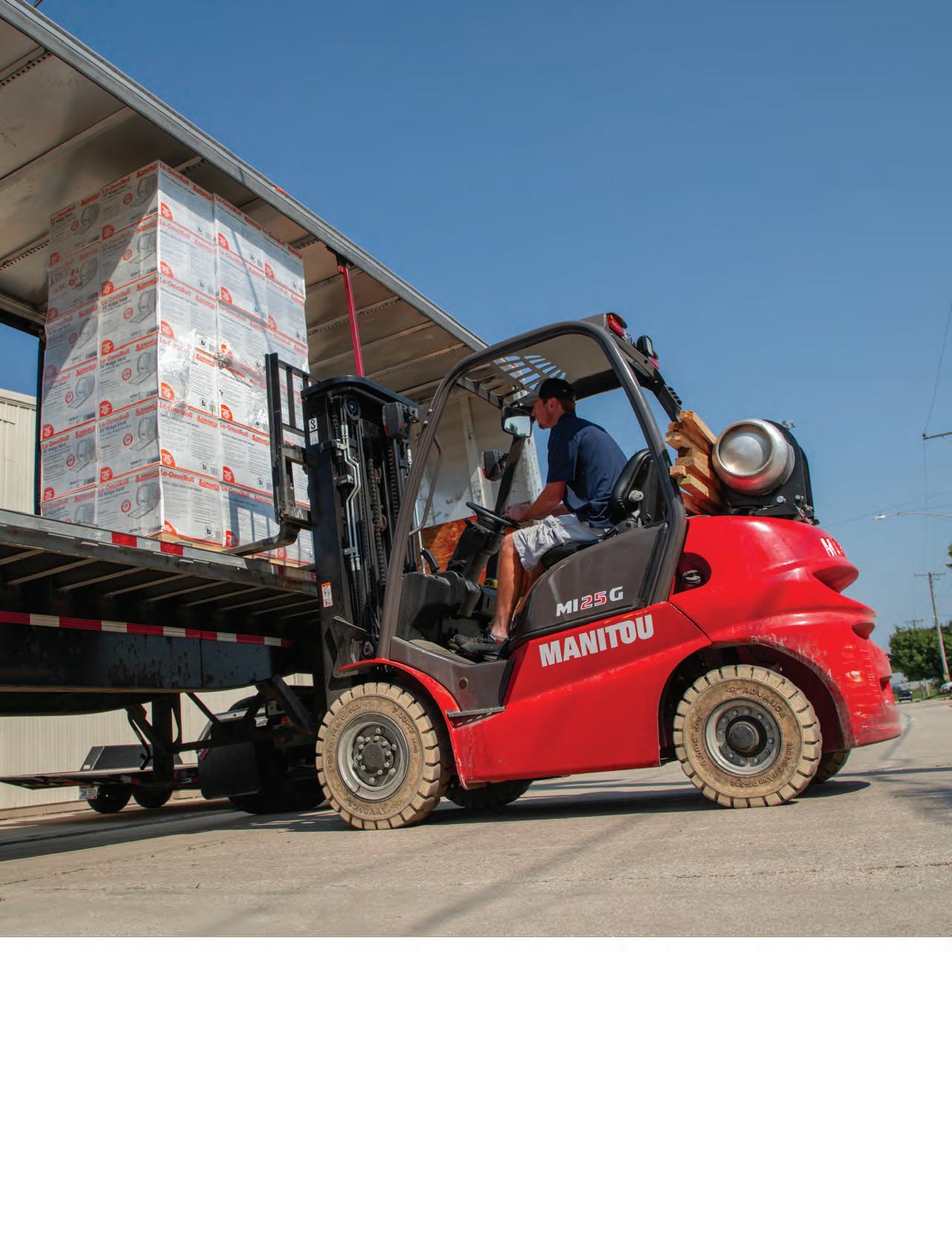
USING TECHNOLOGY TO TACKLE CANADA’S CARGO THEFT CRISIS
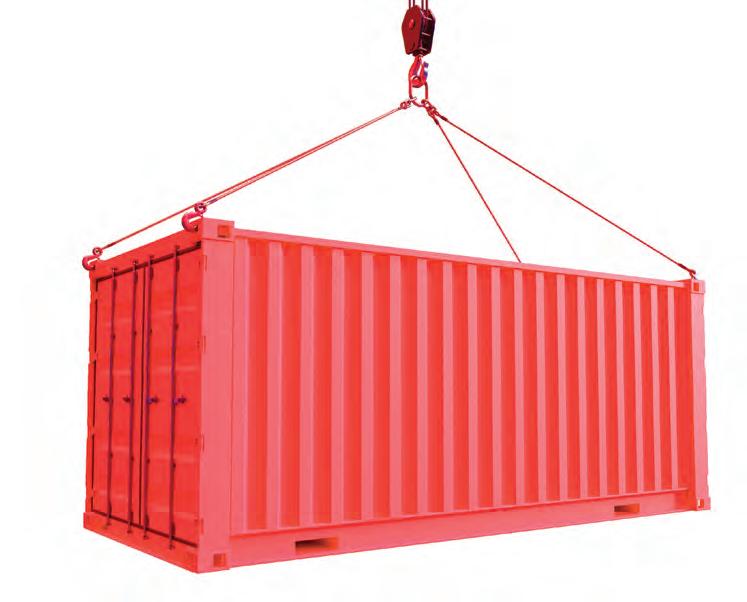
CANADA’S TRANSPORTATION AND logistics (T&L) sector has been grappling with a surge in cargo theft incidents. CargoNet recently reported that cargo theft in Canada and the U.S. increased by 59 per cent compared to last year, with a substantial 692 recorded thefts that cost the industry more than US$31 million.
Strategic cargo theft rings have intensified their activity, particularly around holiday periods. Moreover, these groups have expanded their preferred targets to include truckload shipments of valuable metals such as copper, brass and aluminum, as well as high-demand items such as officially licensed sports apparel and personal care products.
Such crimes not only result in significant financial losses for logistics companies but also pose threats to public safety and national security. Traditionally, investigating such incidents has been difficult to prevent. Can technology help?
With emerging technology, there is newfound hope in the battle against such nefarious activities. One such technological advancement is the use of an enterprise mobility management (EMM) solution to enhance cargo security. Organizations and investigators can access live views of shipments and historical data in real time when mobile devices, such as cell phones and tablets, are stolen alongside the cargo. This capability empowers swift pinpointing of the crime’s location and provides valuable insights into the trajectory of stolen goods.
With real-time access to shipment status and comprehensive historical data, investigators can effectively track stolen goods and identify patterns, with the end goal of apprehending perpetrators. This proactive approach increases the likelihood of recovering stolen cargo and serves as a deterrent to would-be criminals.
Add itionally, the ability to manage, monitor and update the security of mobile devices remotely from a centralized location is a game-changer in combating cargo theft. By leveraging this technology, T&L organizations can significantly enhance their defenses against cyber threats, which have become a favoured tactic among cargo thieves. Cybersecurity threats pose risks to sensitive information and facilitate identity theft, enabling criminals to orchestrate sophisticated schemes to seize cargo largely undetected.
Furthermore, integrating technology into freight security
measures offers additional benefits beyond crime prevention. It enhances operational efficiency, streamlines logistics processes and improves overall visibility within supply chains. By digitizing and automating various aspects of cargo management, T&L companies can optimize resource allocation, minimize risks and respond more effectively to potential threats.
Notably, implementing technology-driven solutions fosters collaboration between key stakeholders within the T&L ecosystem. From carriers and shippers to law enforcement agencies a nd regulatory bodies, leveraging technology creates a unified approach to combating cargo theft. Real-time communication and data sharing enable swift coordination between stakeholders during incidents, facilitating faster response times and leading to more successful law enforcement resolutions.
While technology holds immense promise in the fight against cargo theft, its efficacy relies heavily on proactive measures and continuous innovation from all stakeholders. T&L companies must invest in robust cybersecurity protocols, ample employee training and regular system updates to stay ahead of rapidly evolving threats. Additionally, collaboration between technology providers and industry partners is essential to identify emerging risks and develop solutions tailored to the rise in cargo theft.
Regulatory frameworks must also adapt to accommodate the integration of technology into freight security practices. Policymakers play a crucial role in fostering an environment conducive to innovation while ensuring compliance with data protection and privacy regulations.
Cargo theft poses a significant challenge to the T&L sector in Canada, but technology offers an attainable solution in the quest for enhanced security. By leveraging mobile management technology and fostering collaboration among stakeholders, organizations can fortify their defenses and safeguard supply chains against the alarming rise of cargo-related crime in Canada and beyond.
Shash Anand is senior vice-president of strategy at SOTI and oversees the company’s evolution from a single product centred around mobile device management to an integrated platform that solves many of the challenges around enterprise mobility management.
RENEW YOUR COMPLIMENTARY SUBSCRIPTION! Simply complete this form today and Email to delon@turnkey.media Or Visit
(Email Required
YES, I WISH TO RECEIVE INSIDE LOGISTICS MAGAZINE FREE!
YES, I WISH TO RECEIVE INSIDE LOGISTICS E-newsletter FREE!
Choose your Edition: Print Digital Print & Digital
Signature:
Date:
PLEASE ANSWER THE FOLLOWING QUESTIONS TO QUALIFY FOR YOUR FREE SUBSCRIPTION:
1. Do you purchase, or influence the purchase, of goods and/or services related to distribution logistics, including warehousing operations (receiving, storage or shipping) or inventory control or materials handling? Yes No
2. If Yes, do you have plans to buy any of the following in the foreseeable future? (Check as many as apply)
(A) Forklifts and mobile materials handling equipment
(B) Racking, shelving and storage equipment
(C) Software, eg WMS, TMS, YMS, WES, etc
(D) Automated materials handling systems
(Z) None of the above
TRANSPORTATION SERVICES:
3. What is your company's PRIMARY business?
MANUFACTURING (Check one only)
(01) Food & Beverage
(02) Consumer Durables
(03) Paper & Print
(04) Automotive Parts
(05) Clothing, Apparel & Textile Products
(06) Chemicals, Petroleum & Hazardous Waste
(E) Third-party logistics services
(F) Transportation services
(G) Real estate, warehouses, existing or new building
(H) Data capture and inventory control equipment
(07) Pharmaceuticals
(09) Computers & Electronics
(10) Transportation Equipment
(11) Lumber & Building Materials
(12) Manufactured Industrial Inputs
(98) Other Manufacturing (please specify)________________________________________________________________________
NON-MANUFACTURING (Check one only)
(13) Agriculture, Forestry, Fishing & Mining
(14) Transportation Services
(15) Storage & Warehousing Distributor
(16) Distributor
(17) Construction
(18) Retail Trade
(99) Others Allied to the Field (please specify)____________________________________________________________________
4. Which of the following categories best describes your PRIMARY function? (Check one only)
(A) Executive Management
(B) Purchasing / Procurement
(C) Engineering / Design Engineering / Research & Development
(D) Storage & Warehousing
(E) Financial / Administrative Management
(F) Plant Production / Operations / Maintenance Management
(G) Transportation & Distribution
(H) Materials Management
(Z) Other (please specify)____________ _
5. What is the approximate number of employees at this location?
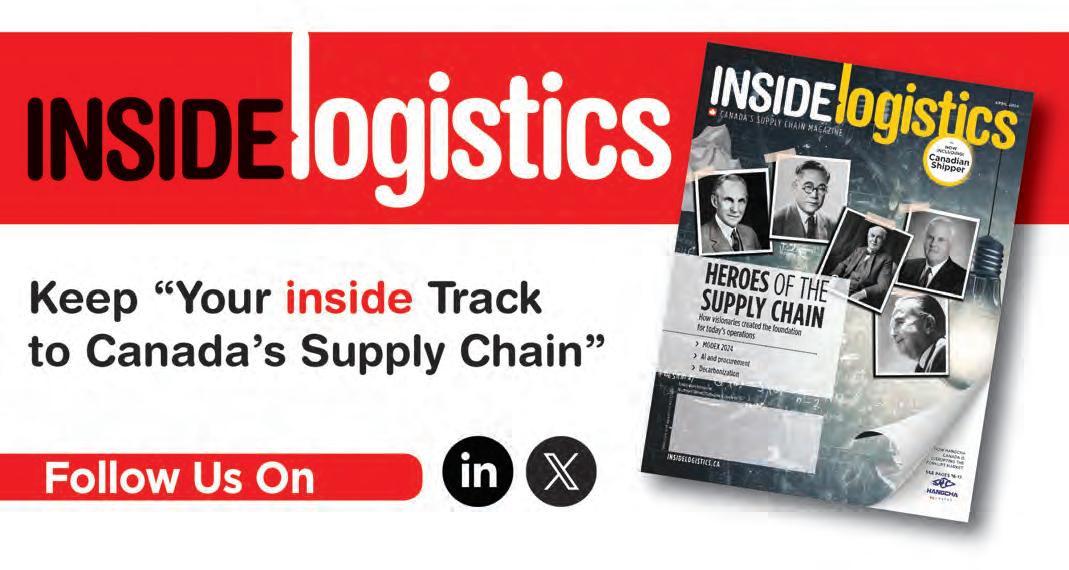
PORT SAFETY IN CANADA
Could Baltimore happen here?
WITH THE RECENT Baltimore Key Bridge catastrophe that the world watched unfold, one wonders how our ports in Canada are preparing for and preventing incidents of this magnitude in our own waters.
“We always have to be prepared,” said Port Saint John (PSJ) CEO Craig Bell Estabrooks. Port Saint John has invested a quarter of a billion dollars into their infrastructure surrounding risk and disruption over the last year, focusing on implementing a risk and compliance committee, as well as changing discourse and talking more about risk. Port Authorities in Canada operate under the arm of Transport Canada and the Canada Marine Act but operate independently across the 17 port authorities. “From a landside perspective we need to account for physical, cyber and infrastructure security,” Estabrooks explained.
Part of the risk overhaul that Port Saint John has been implementing includes a number of people with new skill sets such as the former chief of police who is now the vice-president of risk and compliance for PSJ. Estabrooks explains that while there is always the possibility of a disaster or unknown event, the ships in PSJ do not go anywhere near the Saint John Harbour Bridge, a three-span crossing of Saint John Harbour at the mouth of the Saint John River.
“In my time in this role I have seen nothing like the Baltimore bridge disaster. You will have the odd scenario where a vessel hits a pier or another ship but nothing like this. To see the bridge collapse was unprecedented,” Estabrooks said.
Over the past 10 years, risk plans, heat maps and emergency response plans have been put in place at most Canadian ports to prevent and respond to situations similar to what we saw in Baltimore said Anne Waldes, board chair for the Hamilton Oshawa Por t Authority. A heatmap is used to show relationships between two variables plotted on each axis. This takes into consideration the planning of processes and systems and
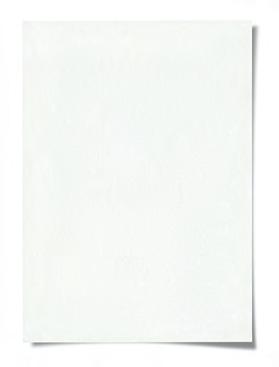
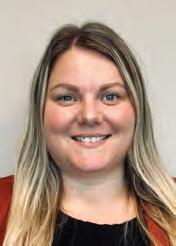
translates that into a guideline which tells you your risk levels.
“Once you have your heat map and your risk level from one to five you go through and plan emergency responses and whatif scenarios. In a heat map you have your knowns or possible risks. And you also have your unknown unknowns, which are risks like a hurricane, or like the ship running into the Baltimore bridge, those things usually don’t happen, and you just can’t predict them. They are also the most difficult to predict because you just don’t know what you don’t know,” said Waldes.
An essential part of the port response plan would also include a control tower, Waldes says there are multiple factors and groups in a crisis response situation using their own heat maps, sometimes they can be redundant and sometimes they can be essential and someone has to be the control tower operating it all smoothly.
The Transportation Safety Board (TSB) and the National Transportation Safety Board (NTSB) are organizations entrusted with the investigation of transportation accidents to decipher their underlying causes and offer recommendations for safety en-
hancements. Both the Canadian and American governments rely extensively on their expertise to formulate regulations and uphold safety standards across diverse modes of transportation, including air, sea, rail, and pipelines, according to Brett Gustavsen, who is a logistics advisor with Rite Route Supply Chain Solutions and a former marine policy analyst for Transport Canada.
“As large commercial vessels approach ports, it is customary for the ship’s captain to yield control to a licensed pilot. These pilots are selected for their knowledge of local waterways, encompassing intricate details such as narrow passages, shallow areas, and prevailing currents,” Gustavsen said.
“Their expertise lies in maneuvering ships through confined spaces, ensuring not only safe but also efficient passage, thereby safeguarding the interests of individuals, the economy, and the environment.”
Canada is currently in the midst of implementing marine safety management systems onto vessels of this type for situations such as power failure which we saw in the striking of the Baltimore bridge.
The safety in harbours across North America has greatly progressed over the last 25 years with new technological advances, communication methods and standard operating procedures. It is because of these innovations that the vessel that hit the Baltimore Key Bridge was able to provide advanced warning and avoid even further devastation.
Of the 241 Canadian marine accidents reported in 2022, The Transportation Safety Board reported that the most frequent shipping accidents were caused by collision (32 per cent), grounding (25 per cent) and fire and explosion (17 per cent). Marine regulations and advancements will only get stronger as we to learn f rom tragedies like what we witnessed in Baltimore and Gustavsen leaves us with this important realization, “At the end of the day, vessels and structures can be replaced, people cannot.”
IS CETA UNDER THREAT?
CETA, CANADA’S COMPREHENSIVE Economic and Trade Agreement with the European Union, provisionally in effect since September 2017 and functioning well, may be under threat due to a surprising rejection by the French Senate.
On March 21, France’s upper chamber rejected the French government’s bill to approve CETA by 211 votes against versus 44 in favour. The agreement had already been narrowly accepted by France’s lower chamber in July 2019, and a vote in the upper chamber had been delayed until now.
Negotiations for this FTA began in Prague, Czech Republic, in May 2009 and were concluded in October 2016 in Brussels, followed by the assent of the European Parliament in February 2017. On the Canadian side, Parliament’s Bill C-30, implementing CETA, received Royal Assent in May 2017, leading to its provisional implementation in September 2017.
Full implementation requires ratification by all 27 EU countries because CETA is a “mixed agreement,” containing new types of provisions on investment falling under the shared competence of both the EU and its member states. The investment provisions refer to an investor protection mechanism, market access for portfolio investment and an investment court system; they are narrow and highly technical.
The other “classic” provisions on trade in goods, services, government procurement and mobility of professionals do not require individual member states’ approval and have been in full force for importers and exporters on both sides of the Atlantic since 2017.
Seven years later, only 17 out of the 27 EU countries’ individual parliaments have ratified it, and the other 10 have dragged down the process, perhaps for fear of rejection by their legislators. In Cyprus, for example, Parliament rejected CETA in 2020. In Italy, the government opposes CETA on principle, even though the agreement has been beneficial to Italian agriculture and food exporters.
The French rejection defies common sense, especially given bilateral trade in goods increased by 51 per cent between 2017 and 2023. Farmers’ protests in France earlier this year have polarized public opinion and politicians
French Senate rejects deal
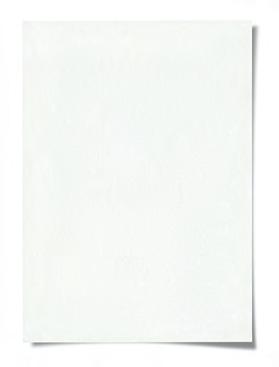

against FTAs, and the negative vote is mostly a result of that, as well as political maneuvers ahead of European Parliament elections in June.
The predicted “flood” of Canadian products in Europe has not materialized. In fact, the opposite has happened. In 2023, Canada exported 1.4 million tonnes of beef to Europe, barely two per cent of the CETA-allocated volume. For France, the figures are insignificant: 29 tonnes of Canadian beef were imported in 2023. Conversely, European livestock producers increased their beef exports to Canada from two to 14 million tonnes in seven years. Similarly, European cheese producers, many of whom are French, have fully utilized their export quota of 19 million tonnes.
Europeans have become skeptical about FTAs, influenced in part by environmentalists and anti-globalization movements. Disinformation on social media has fed populism, with both far-right and far-left political parties pushing for nationalist agendas, not unlike in other parts of the world.
Several years ago, the EU pursued an FTA with the United States, but negotiations were abandoned as Europeans grew afraid of cheaper U.S. agricultural products. Something similar
happened with the EU-FTA with Mercosur countries (Argentina, Brazil, Paraguay and Uruguay), signed several years ago but not implemented so far due to concern over Brazilian meat and agricultural products.
In the past, when free trade agreements were negotiated and implemented, we lived in a different world. We are now living in the era of populism and post-truth, a world where false information can be disseminated with impunity and can greatly influence public perception as a result. Previously, politicians who blatantly lied to the public were shamed; today, politicians who lie through their teeth gain popularity. It has therefore become more difficult to “sell” reasonable agreements to the public, as demonstrated by the CETA saga.
There is no danger of Canadian products invading Europe – we are a modest player. Canada is not the U.S. or Brazil. CETA is a great tool for Canadian exporters to diversify their export markets and sources of supply away from the U.S., lessening our dependence on our southern neighbours. This is especially important ahead of the U.S. elections in November, where one of the incumbents has a protectionist agenda that would be detrimental to Canada.
As geopolitics increasingly influence world trade (geopolitics have been identified as the primary concern of surveyed businesses worldwide in the Allianz Global Survey 2024), it is essential that like-minded countries like Canada and the European Union continue to work closely, promoting the rule of law, fundamental freedoms, equality, democracy and fair trade. At a time when international organizations like the United Nations are dominated by despotic countries, it is vital for democracies to work closely together and preserve their special relationship.
As to CETA, let us hope that common sense will prevail in Europe and that the countries that have not yet ratified it will promptly come to their senses. In the meantime, as far as the trade in goods and services is concerned, CETA is in full force and Canadian companies should consider Europe a primary target market.
SEVEN STEPS FOR EFFECTIVE CONTRACTOR MANAGEMENT IN YOUR WAREHOUSE
Ensuring the health and safety of contracted workers is a shared duty between the contractor and employer
WITH SHIPMENTS CONSTANTLY coming in and going out, warehouses and distribution centres need to have solid systems in place to keep everything running safely. Those systems need to be communicated to any outside contractors they bring in to ensure new hazards are not introduced into the workplace and safe work procedures are followed.
Warehouses and distribution centres have contractors in their facility to perform a variety of necessary work, which may include installing a new pallet wrapper or replacing damaged racking. Other contractors may be onsite for shorter periods of time to refill vending machines or drop off packages. Contractors are any third-party worker who comes into the facility to complete a task and are not classified as a temporary worker. At times, there is confusion about who is responsible for the health and safety of contract workers -- the warehouse manager or the contractor’s employer? The answer is both, so there needs to be coordination between the two to keep contract workers safe. The contractor is required to follow their employer’s safety programs as well as the applicable safety expectations of the workplace they are visiting.
Here are the steps to fulfill the responsibilities under occupational health and safety legislation across Canada prior to the contractor’s arrival at the facility:
Seven steps for effective contractor management
1. Ask the contractor for insurance documentation. Workers’ compensation and general liability. (Workers’ compensation records may be accessible online by visiting the applicable website.) Check the expiry date of both documents carefully to
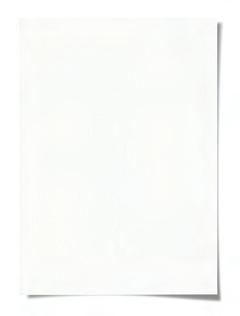

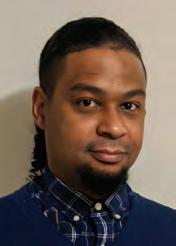
NORM KR AMER, CRSP, P.MM, provides expert, in-depth health and safety consulting services for Workplace Safety & Prevention Services (WSPS) as a Warehouse Specialist in the Greater Toronto region.
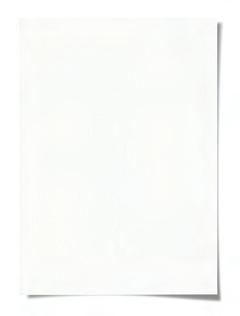
TROY NEL, CHSO, is a Health and Safety Consultant with Workplace Safety & Prevention Services (WSPS).
ensure they cover the duration of the project. Confirm the amount of coverage is appropriate based on risks to your facility, equipment, and the public.
2. Create a contractor health and safety package. Among other things, it should include:
your health and safety expectations for contract workers
everyone’s roles and responsibilities so there is no confusion or grey areas
a copy of your health and safety policy
your hazards, controls, and safe work procedures
incident reporting requirements
entry and exit procedures, which may include sign in and out Send the package to the contractor before they come to your workplace so they can review it and ask questions.
3. Ask for a hazard assessment. Before work starts, both parties must have a clear understanding of exactly what work the contractor is doing and how they are going to do it. Ask for a hazard assessment that identifies the hazards associated with each phase of the work and the controls that will be used to mitigate them. Emergency response or rescue plans should also be provided if the work requires them.
4. Collect proof of training and certifications. The hazard
assessment will indicate if specific certifications are required, depending on the type of work being done. For example, if electrical work is going to be completed, ask for a copy of the electrician’s certificate of qualification. If workers will be on a roof or working at heights, ask for copies of the required training certificates.
5. Complete a health and safety orientation. Whether it’s a single contract worker or a crew, a health and safety orientation must be completed before they start working. If it’s a group, identify the supervisor or the person who will act as the lead. Provide a tour of the facility, particularly the area where they will be working.
Don’t neglect the details – discuss specific hazards workers may be exposed to and corresponding controls. When dealing with a recurring service or regularly scheduled maintenance, make sure new contract workers also receive orientation training. Don’t assume they have received this training from their coworkers.
6. Monitor the work. While you can’t stand beside contract workers the entire time they are working, you do have to periodically check in. Ensure the work is being done according to the hazard assessment and that all health and safety requirements are being followed.
7. Evaluate the job. Once completed, assess the quality of the work. Consider whether health and safety rules were followed or if you had to keep reminding the workers of the expectations. Document your experience with each contractor to refer to when hiring in the future.
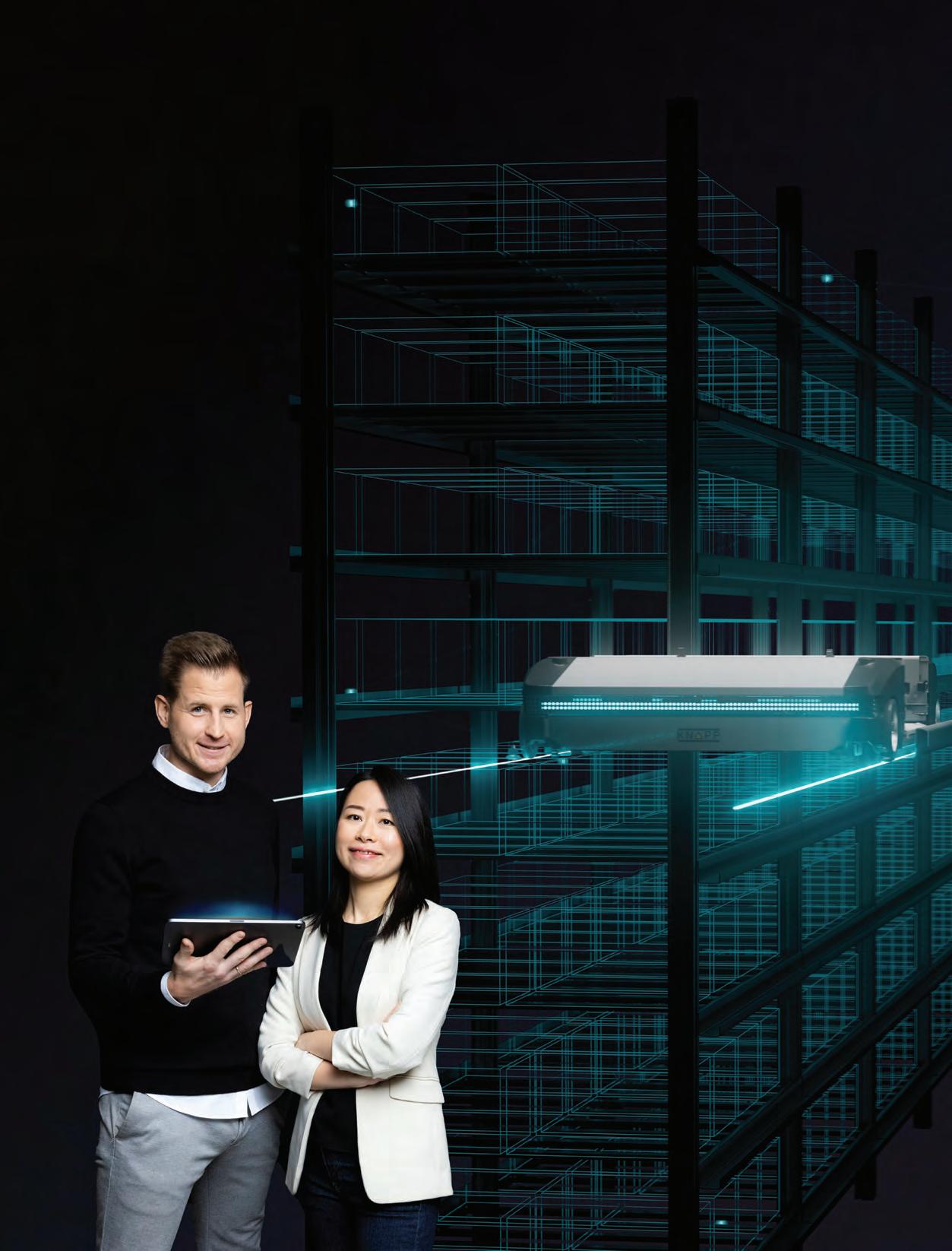
knapp.com
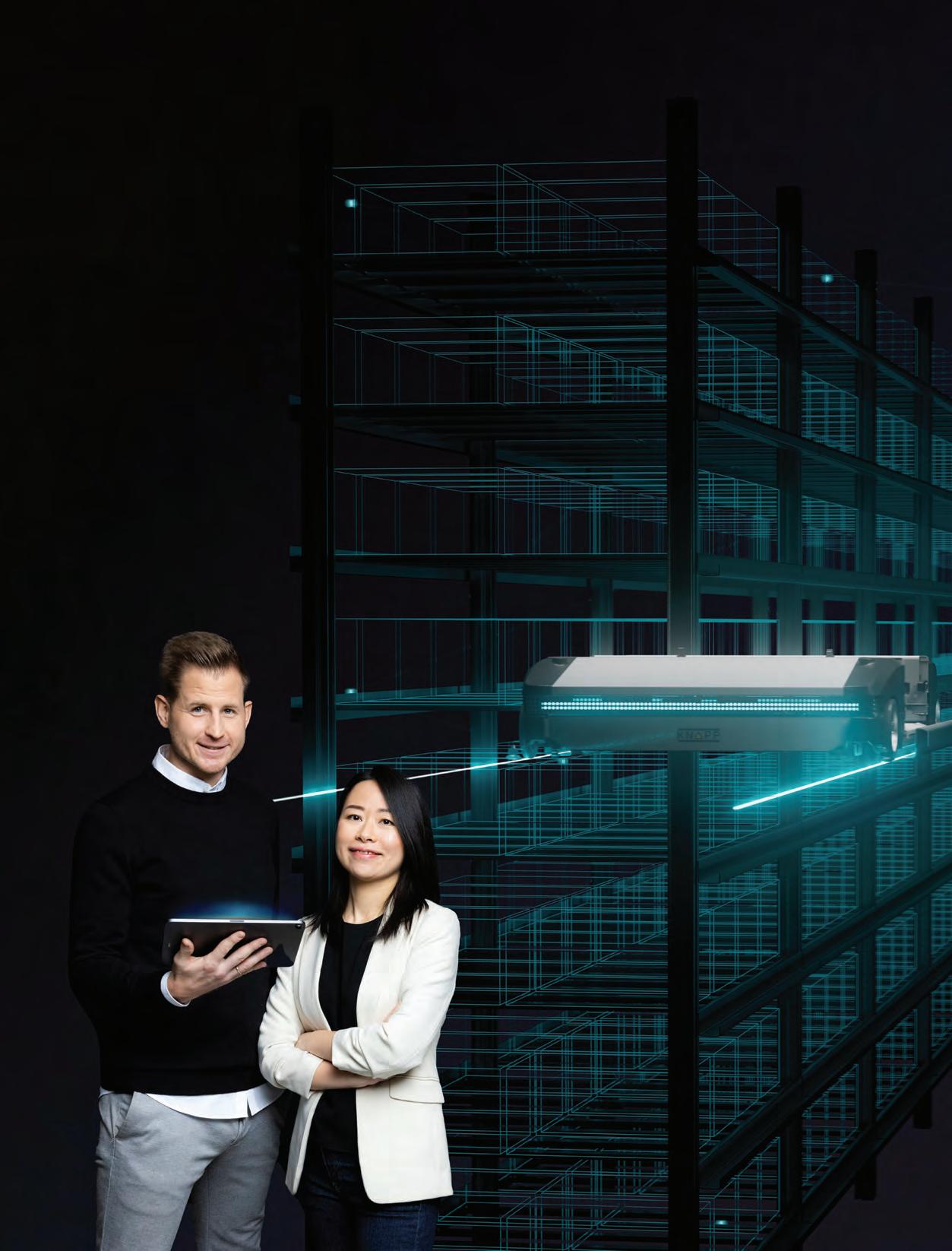
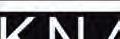
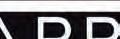


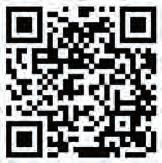


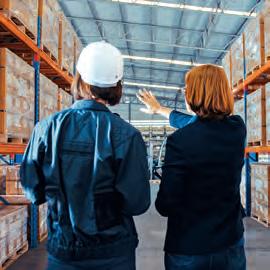
Your partner in facilities evolution
Strong foundations. Smart evolution.
To stay competitive and get ahead, you need innovative, scalable and safe solutions. These solutions can help with better storage, distribution, fulfillment or any combination that can grow with your business as it adapts to change.
As your partner in facilities evolution, you can count on Konstant to transform your facilities. Collaborate with our team to optimize your facility today and evolve, anticipate, adapt and imagine the facility of your future.
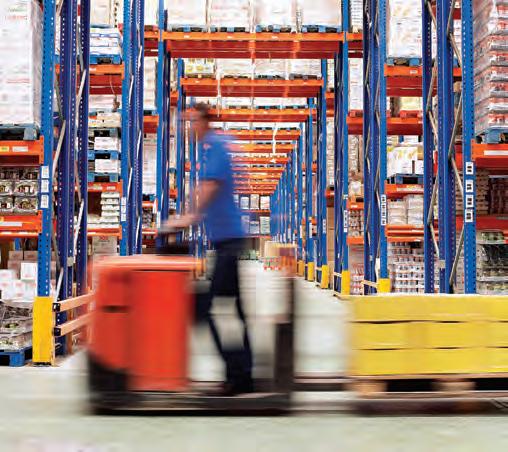
ECOSYSTEM
Get integrated logistics solutions: racks, shelving, trucks and robotics from our partners including Johnston Equipment and GNJ Automation.
EXPERTISE
Access comprehensive services for your project lifecycle, from planning to ongoing management with a skilled team ensuring quality at every step.
EXPERIENCE
For more than 50 years, Konstant has served businesses across Canada, adapting our services to evolving facility management needs.