


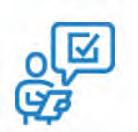



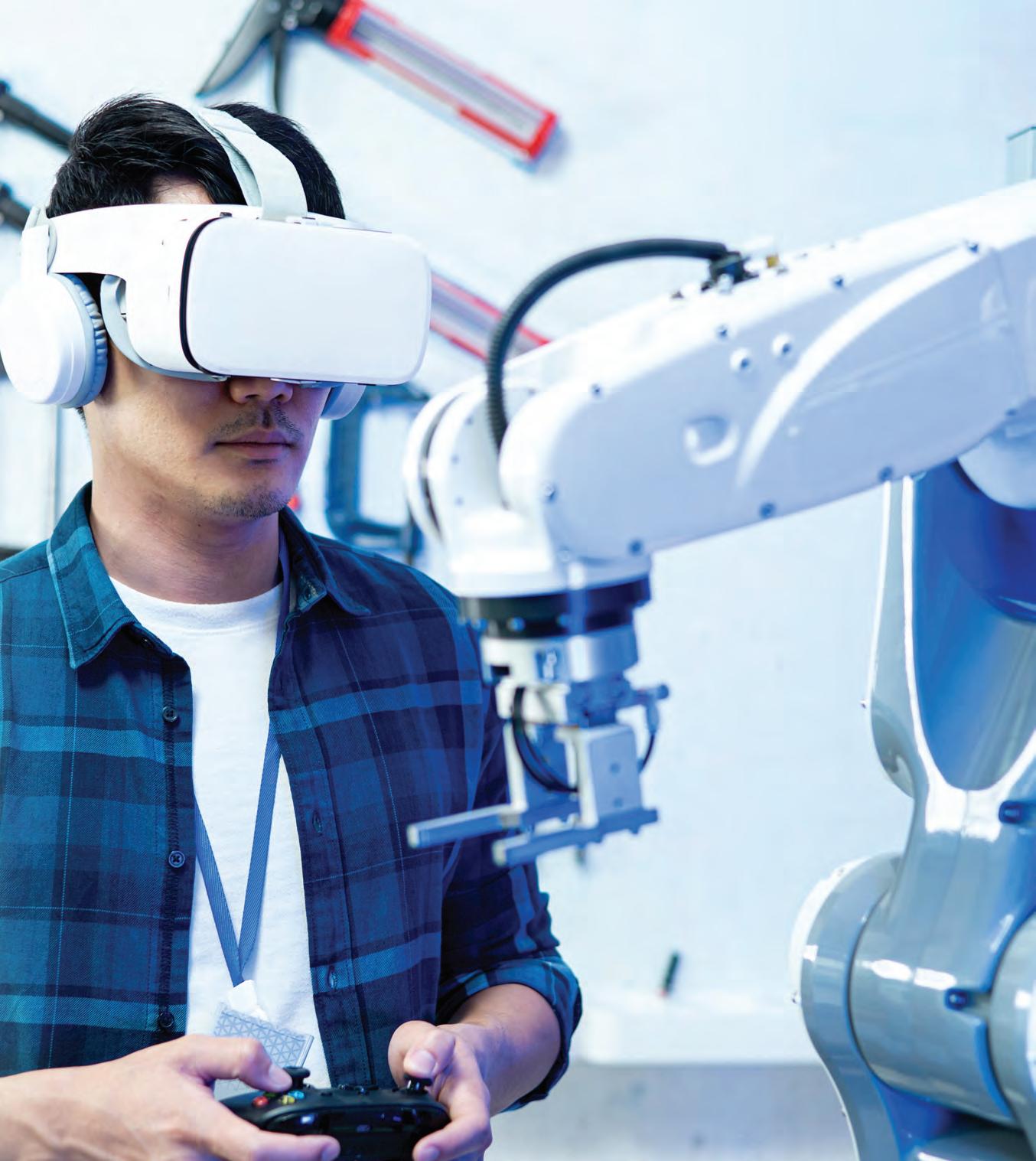
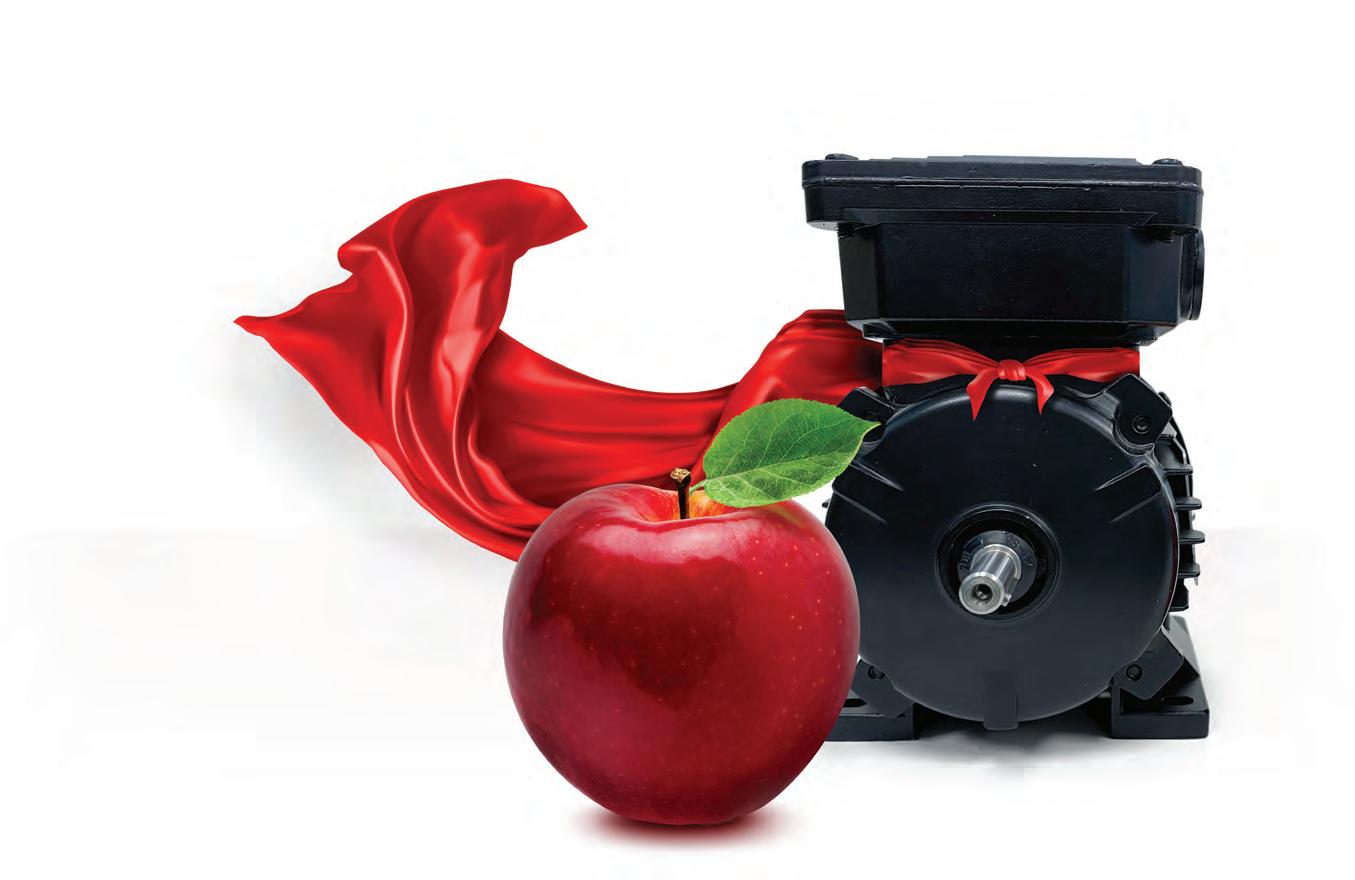
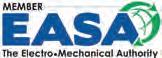


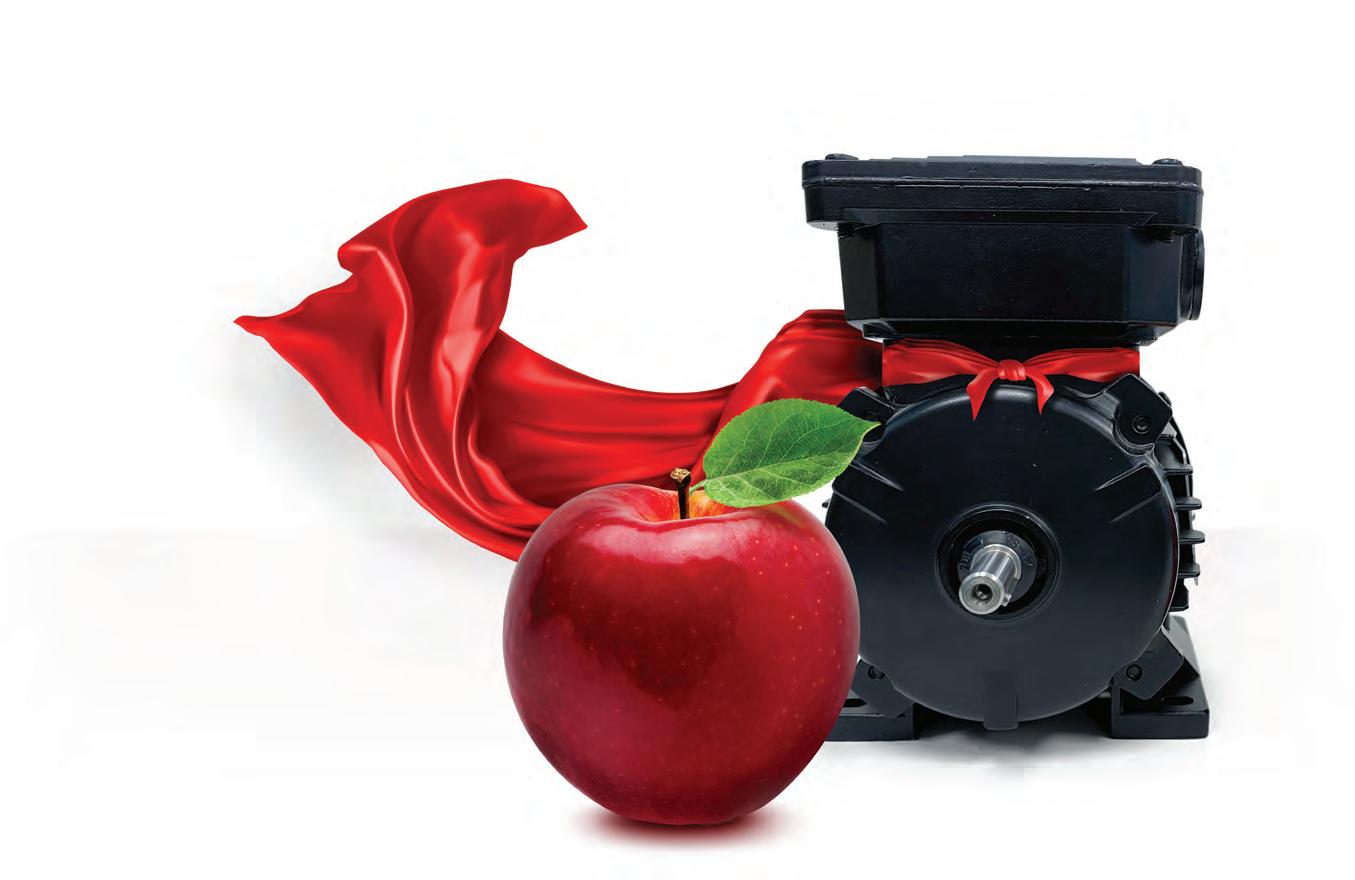
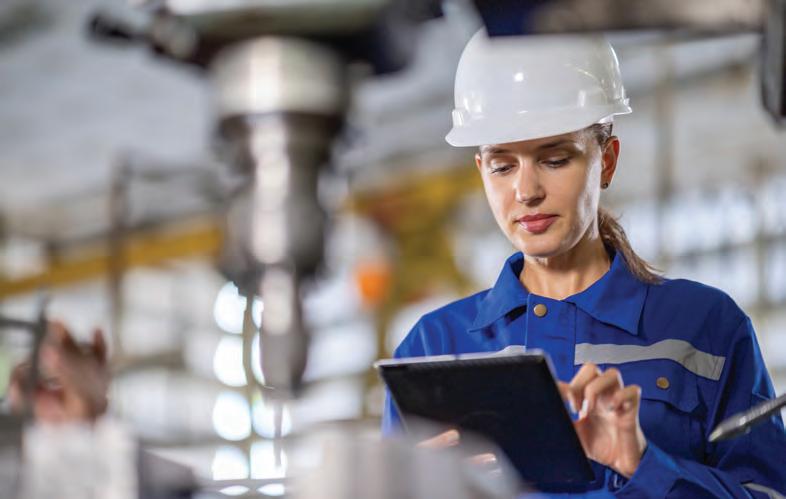
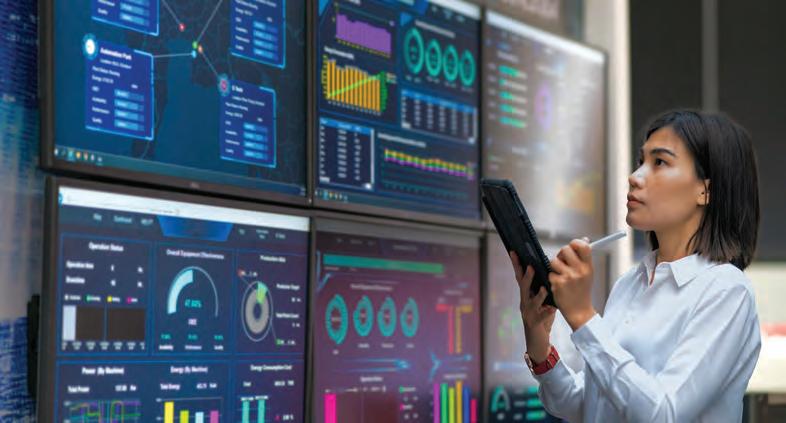
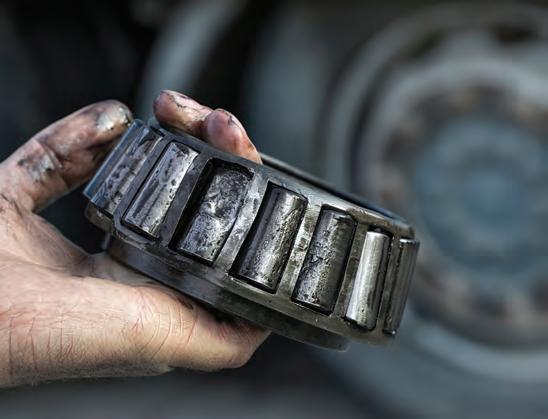
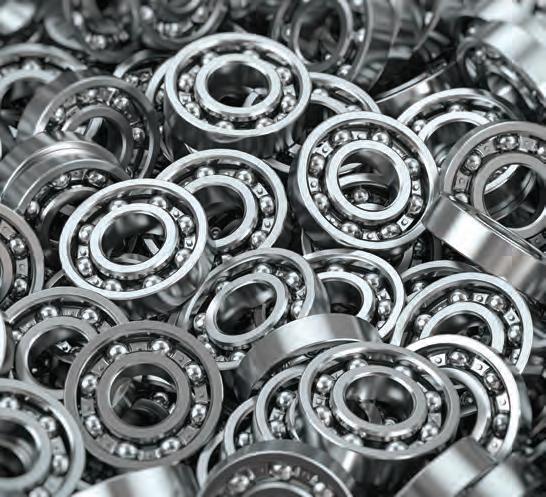
MRO was first published in 1985. What maintenance was then, is not what it is now. Traditionally MRO stood for maintenance, repair, and overhaul. Today, for us, that acronym represents maintenance, reliability, and operations. What was once an industry that mainly used tools to manually fix problems, is now access ing digital tools to do the same tasks, if not more than manual duties.
Since I joined the MRO team four years ago, almost nothing is the same with this B2B media brand. However, as once I was the only constant, we have now had the same core team, along with Publisher Paul Burton, together for nearly three years.
As discussed in the last issue, MRO’s print edition, web site, logo, and largely anything else has been altered.We have added many new products, including the MRO podcast, virtual events, en hanced social media presence, MFO - the French version of MRO, and much more.
The most recent change involves this publication moving to become a quarterly periodical in 2023. As a result, this will be our last print issue of 2022. The December edition will not be published.
To ensure that we cover important topics such as the future of mainte nance, we have decided to cover it along with the originally planned environment and maintenance topic.
These decisions did not come light ly. Many external factors, which have plagued almost every industry, have come knocking at our door as well. With paper costs at sky-high levels, and the continued push to the digital world, something had to be done to make sure that we continue to provide the content that our readers expect.
You will see more exclusive content posted online, as we have an unlimited amount of space on our web site, and
we’re not dealing with paper costs in the digital world. This will include more in-depth features, case studies, industry roundtables, an increased emphasis on video, and more event coverage. This will be in addition to the content that is already a part of our news coverage, product writeups, and more.
What this means for the print edi tion is we will concentrate our efforts to ensure the most important topics are covered within the pages of MRO. Our goal is to make sure that each is sue is strong with useful, informative, and timely content.
For 2023, we will focus our issues on four main themes: the spring is sue will focus on software solutions (CMMS), summer on safety, fall on maintenance and the environment, and winter on the future of mainte nance.
Don’t worry, all the other focus areas will be covered within one of the four issues. Each issue will be jam packed with content.
All that being said, we want reader feedback – as we need to know what you want to see within the pages of the magazine. We’d also like to know what type of industry coverage interests you within all our digital platforms. Don’t hesitate to send either myself or Mon ica your ideas.
Also, we just launched our redesign last issue, and we would love to know what you think of it, so be sure to let us know.
Thank you,
MARIO CYWINSKI Editormcywinskiw@mro.ca Connect
1985
NOVEMBER 2022
Volume 38, Number 5
READER SERVICE
Print and digital subscription inquiries or changes, please contact Customer Service Angelita Potal, Customer Service Administrator Tel: 416-510-5113 email: apotal@annexbusinessmedia.com Mail: 111 Gordon Baker Rd., Suite 400 Toronto, ON M2H 3R1
EDITOR Mario Cywinski 226-931-4194 mcywinski@annexbusinessmedia.com
SENIOR PUBLISHER Paul Burton 416-510-6756 pburton@annexbusinessmedia.com
ASSOCIATE EDITOR Monica Ferguson 416-510-5206 mferguson@annexbusinessmedia.com
NATIONAL ACCOUNT MANAGER Ilana Fawcett 416-829-1221 ifawcett@annexbusinessmedia.com
BRAND SALES MANAGER Chander Verma 437-218-0941 CVerma@annexbusinessmedia.com
AUDIENCE DEVELOPMENT MANAGER Beata Olechnowicz bolechnowicz@annexbusinessmedia.com 416-510-5182
MEDIA DESIGNER Brooke Shaw
ACCOUNT CO-ORDINATOR Catherine Giles 416-510-5232 cgiles@annexbusinessmedia.com COO Scott Jamieson sjamieson@annexbusinessmedia.com
Machinery and Equipment MRO is published by Annex Business Media, 111 Gordon Baker Rd., Suite 400, Toronto ON M2H 3R1; Tel. 416-442-5600, Fax 416-510-5140. Toll-free: 1-800-268-7742 in Canada, 1-800-387-0273 in the USA.
Printed in Canada ISSN 0831-8603 (print); ISSN 1923-3698 (digital)
PUBLICATION MAIL AGREEMENT #40065710
Subscription rates. Canada: 1 year $65, 2 years $110. United States: 1 year $110. Elsewhere: 1 year $126. Single copies $10 (Canada), $16.50 (U.S.), $21.50 (other). Add applicable taxes to all rates.
On occasion, our subscription list is made available to organizations whose products or services may be of interest to our readers. If you would prefer not to receive such information, please contact our circulation department in any of the four ways listed above.
Annex Privacy Officer
Privacy@annexbusinessmedia.com 1-800-668-2374
No part of the editorial content of this publication may be reprinted without the publisher’s written permission © 2022 Annex Business Media. All rights reserved. Opinions expressed in this magazine are not necessarily those of the editor or the publisher. No liability is assumed for errors or omissions.
Harting and TTI, Inc. announced that the two companies are entering into a partnership in the Americas. TTI will be an authorized distributor of Harting’s broad portfolio of indus trial connectivity solutions.
TTI and its subsidiaries, including Mouser Electronics, Sager Electronics, and Exponential Technology Group, employ over 8,000 people at more than 136 locations throughout the Americas, Europe, Asia, and Africa.
Sims Limited named Philip Bainbridge as an independent non-executive director. Bainbridge has experience in the oil and gas sector across explo ration, development, and production.
He has worked in jurisdictions, including North America, Europe, Asia, and Australia. Bainbridge’s most recent role was executive GM LNG for Oil Search Limited.
health monitoring of motor-driven in dustrial equipment as it does not rely on mounting sensors in the field. This means that SAM4 can be deployed on machines in harsh and submerged environments.
Samotics has established SAM4 as a robust and scalable system. It is already being implemented across the wastewater and water, steel, and chemical sectors and has established a fast-growing base with thousands of assets monitored.
Caplugs now has a Canadian hub in in Brampton, Ontario. Formerly Caps’n Plugs, the Brampton facility has a full team of Caplugs product experts, sales support specialists and a warehouse of inventory for shipment nationwide.
This change is part of Caplugs’ global expansion efforts and allows for increased access to product protection, hose protection, mask ing solutions and Caplugs’ custom moulding capabilities.
At the Brampton headquarters, the facilities and team continue to operate as regular, offering the same
service and quality. With the transi tion, Caplugs now serves as a one-stop solution provider.
ABB and Samotics entered a longterm partnership to provide condition monitoring services. As a first step, ABB will integrate Samotics’ plugand-play monitoring solution into its digital portfolio.
Samotics’ SAM4 technology, based on electrical signature analysis, will expand ABB’s application of asset
Research conducted by Tork, reveals that 44 per cent of machine opera tors are interrupted at least 20 times during their workday by having to fetch or dispose of wiping and clean ing products. The study reveals that operators often take more wipers than needed to avoid these interruptions.
The study shows that 69 per cent of machine operators state that they get stressed if they are interrupted in their work when having to divert from their task. Furthermore, 90 per cent of machine operators say that if they were provided with professional industrial wipers close-by, it would help their workplace organization and
Caplugs operations expand to Canada.
Indigo Drive, a software eco-system that enables any mining vehicle to be automated.
The Mining Association of Canada estimates that 10,000 new workers are required annually for the next de cade to fill new positions and replace current ones. Likewise, the Australian Minerals Council predicts a shortfall of 86,000 workers.
According to a Frost and Sullivan’s analysis, Commercial Aircraft Tire Industry Growth Opportunities, the market is expected to reach $8.84 billion by 2032 from $2.31 billion in 2021, registering a compound annual growth rate (CAGR) of 13 per cent.
According to the report, to reap the benefits of the growing global com mercial aircraft tire industry, market participants should:
• Leverage digital technologies and incorporate next-generation tech nologies to develop new revenue streams.
• Deploy IIoT and focus on indus trial automation to streamline manufacturing processes, lower manufacturing costs, and reduce equipment downtime.
• Source renewable materials for manufacturing and adopt envi ronmentally friendly recycling processes to achieve sustainability goals and gain the upper hand over competitors.
The XR1600E, the world’s largest ro tary drilling rig developed by XCMG has rolled off the assembly line. It was designed and put into produc tion especially for large-scale bridge pile construction and offshore wind power piling projects.
The model has set several world records with a maximum drilling di ameter of 7.5 meters and maximum drilling depth of 190 meters, and the output torque of its power head is 1600kNm.
The rotary drilling rig has a height of 42 meters and a weight of 520 tons. The XR1600E is developed with dual power source cooperative control and modular combination technology of super-large tonnage rotary drilling rigs. The drill pile features visualized anti-banding rod technology that re duces the risk of smashing rods by 95 per cent to ensure the safety of piling and foundation operations.
Columbia Okura celebrates shipping its 1000th robotic palletizer. Over the past 26 years, the team has gathered for every one-hundred robot sold milestone, celebrating with lunch and a team photo with the robot.
The 1000th system will be sent to a customer in North Carolina, Cher ry Farms Seed Co., with a unique crest on the arm to denote it is the 1000th robot. The system includes the Ai1800 robot, sheet presenter, pallet dispenser, bag end-effector, bag infeed, station conveyor, and a gravity pickup conveyor.
GE will invest up to $5 million over the next two years to add a second manufacturing location. The plant will be for GE’s aeroderivative units for the Americas region in its existing Global Technology Center in Green ville, South Carolina.
GE’s Global Technology Center in Greenville will increase manufactur ing capability to support deliveries in the Americans region, but also the global aeroderivative growth.
The site, expected to add up to 25 employees, will adopt lean method ologies to drive its transformation: two new lean lines will be created to start manufacturing aero-derivative units.
After two years of going virtual, the Maintrain conference was hosted in-person at the Four Points by Sheraton Toronto Airport, for the first time since 2019. The 2022 event was a hybrid model, so in addition to the 172 attendees at the venue, 79 others joined from the comforts of their home or office.
“Beyond the numeric success, it was so great to be able to connect and learn once again in person. The quality of the content and the high spirit of connection was just phenomenal, and it was great that through a hybrid for mat we were able to extend the opportunity to access the conference content online to people across the country and around the world,” said Cindy Snedden, Executive Director, PEMAC.
The conference allowed attendees to participate in work shops, sessions, panel discussions, keynote speeches and an exhibition showcase. Also, the hybrid model allowed for seven pre-conference online only sessions to be avail able before the conference started. In all, 48 presenters and panelists were a part of the conference.
“Maintrain 2022 was an opportunity to reconnect and net work with asset management, maintenance and reliability colleagues in person while participating in informative and interactive workshops. Everyone was so approachable and willing to share their experiences,” said Susan Lubell, Principal Consultant, Steppe Consulting Inc.
Workshops and sessions were presented by industry ex perts and allowed for attendees to learn from those who are experts on the topics they are discussing. Workshops included: Maintainability and Reliability Best Practice Metrics Workshop by Michael Raible; Demystifying the Digital Twin and Achieving Whole Life Asset Intelligence for Sustainable Operations by David Armstrong; and
(Left) Just one of many presentations that were available during the conference.
(Right) Coco, the robot dog from Cohesive, was at the conference.
Each morning, a breakfast keynote started the day. This year the three keynote speakers included: Ron Bettin who presented Executive Decisions – What Does Your Boss’s Boss Think of Your Asset Management Strategy?; Jeremy Sylvain presented Strategic Investment Into our Greatest Asset – Our People, Maintenance Supervisor & Coordinator; and Danaka Porter presented Maintaining Reliability in Unreliable Times.
Many sessions were also offered to attendees, they were grouped into four categories, asset management, reliability, maintenance, and technology. Speakers included JeanPierre Pascoll, Doc Palmer, Edith Mackenzie, Melissa Schmidt, Cliff Williams, among many others.
A tour is part of each Maintrain conference, this year attendees had the opportunity to visit Capital Power’s Goreway Power Station. The tour included a presentation about the plant, and a look at the main equipment used.
A big part of the conference was the exhibitor showcase, which allowed those in attendance to network with indus try professionals and find out about the latest and greatest products that were available. Those exhibitors in atten dance included: Cohesive, Northern Lakes College, UE Systems, Benchmark PDM, Cameco, ARMS Reliability, and others.
Maintrain will go west next year as the 2022 Maintrain conference will take place in Winnipeg, Manitoba.
PEMAC’s 2022 awards ceremony took place during the Maintrain Hybrid Conference in Toronto recently.
The annual awards program was created to encourage excel lence in maintenance, reliability, and asset management across various industries.
The awards are divided into maintenance management, asset management and mem ber awards and are limited to PEMAC members. Corporate awards are for corporate or allied members and individual awards for individual members.
PEMAC introduced a new award this year: the Maintenance Management Leadership Award, recognizing an individual who has contributed significantly to advancing maintenance man agement in their organization(s) or within Canada.
“Congratulations to all the 2022 PEMAC Award recip ients and thank you to every one who participated in the
nomination and review pro cess this year,” said Alan Cox, chair of the awards committee, PEMAC. “The exceptional contributions that PEMAC members are making towards
Ahmad
next awards, and we encourage everyone to consider recogniz ing the great strides their teams are making, as well as individ uals who have contributed towards improvement.”
Chances are, you’re already aware of the maintenance worker skills gap. This isn’t a new problem – it’s been around for at least 10 years. But every year, the problem seems to get worse.
Fewer young people are getting the training they need to diagnose and repair machine faults.
Maintenance managers and reli ability engineers are seeing the pool of skilled workers get smaller and small er. Meanwhile, qualified workers are hitting retirement age and leaving the workforce.
More and more plants are turning to technology to bolster their main tenance programs. This begs the question – can digital solutions and vibration sensors fill the maintenance skills gap?
The answer isn’t simple. It’s im portant to maintain some perspective and stay realistic about what technol ogy can do. Today’s best tools can’t re place a human workforce. Even with the best technology, you’ll still need human know-how and experience to keep your operation up and running smoothly.
But at the same time, the right connected tools and sensors, coupled with a solid computerized mainte nance management system (CMMS), can help you to shift to a predictive maintenance strategy, so that you can identify and diagnose machine faults early. In the not-too-distant future, AI-enabled analysis software will push these capabilities even further. This means that you will be able to keep your machines up and running for longer, even if you’re operating with a lean maintenance team. If you manage this process correctly, the results can be revolutionary.
Predictive maintenance is a proactive strategy for keeping your assets up and running. It’s premised on the idea that you should only perform the maintenance work on an as-needed basis. Instead of routinely servicing your assets, your maintenance team will monitor them for signs that they need repair.
Predictive maintenance uses a net work of vibration sensors that mon itor the vibrations emitted by your equipment. They collect and store this data so that it can be analyzed for signs of fault.
Data collection isn’t new, of course. Maintenance teams have always col lected data, simply by observing the machines in their plants and keeping track of how they operated.
As plants get bigger and take on more equipment it’s almost impossi ble for a maintenance team to directly monitor every single asset. That’s why sensors are so important, especially as the pool of skilled workers is shrinking.
Here’s how a plant can use vibra tion monitoring sensors, CMMS, and analysis software to make the most of a lean maintenance team.
On its own, data doesn’t add value to your maintenance team. Raw data needs to be organized and analyzed so that your maintenance teams can start to spot patterns. CMMS soft ware can integrate with sensors and software tools so you can organize and analyze your vibration data and put it to use.
The first step is simply identifying any change in vibration emissions. Once a machine shifts from its
baseline vibration signature, that’s a sign that it needs to be examined more closely.
This stage of proactive mainte nance – looking for changes from the baseline – fills the same function as the triage process in a doctor’s office.
In a doctor’s office, nurses perform the first level of triage. They collect data on patients’ weight, blood pres sure, and temperature. That’s usually enough to tell them whether a patient is healthy or not and in need of care.
In the same way, your CMMS software uses the vibration data to perform triage on your assets. It scans for signs of anything unusu al which could indicate a new or developing fault.
Triage saves your team time, en ergy, and funds by allowing you to focus your energy on the machines that actually need to be repaired. You won’t need to waste labour or time on the equipment that’s already running smoothly.
Vibration analysis software can per form diagnostic tests to identify many common machine faults.
To date, vibration analysis software can diagnose the four most common faults in rotating machinery, namely, imbalance, shaft misalignment, loose ness, and bearing faults.
To continue the hospital analo gy, the vibration analysis software is like the primary care physicians who can diagnose patients with common ailments.
And, just as the primary care doctors need to be “called in” by the nurse on duty, the algorithms also need to be called in to start their diagnostic process.
That’s where your CMMS comes in. You can set up your CMMS to automatically generate a work order once vibration levels deviate from the norm. That work order will trigger
software to assess and diagnose the machine in question.
Once the software has diagnosed the machine fault, your CMMS can automatically generate a work order to review recommended repairs based on that diagnosis.
The CMMS lets teams review the recommendation, then schedule the work based on when your mainte nance teams are available, or when it’s convenient to shut down your equipment for repairs.
Most of the time, vibration moni toring and analysis software will alert you to machine faults long before the problems become serious.This means that you will have plenty of time to schedule maintenance at a convenient point for you.
Shifting to a proactive maintenance strategy doesn’t mean that you won’t need maintenance workers any longer.
Instead, it means that you’ll be able to re-configure your workforce so that you get the best possible work out of everyone on your small maintenance team. Building a tech-centered approach means con sidering what you’ll still need from your maintenance team.
In most cases, you will need a group of maintenance experts who have the ability to implement a proactive main tenance strategy. That means knowing which machines vibration analysis software is capable of diagnosing, and which machines are too complex. In the future, it will require a similar un derstand of the limits of AI-enabled vibration analysis software.
If we go back to the hospital analo gy, it’s helpful to think of maintenance experts as the specialists in various medical fields. They can diagnose problems that a primary care physi cian might not know enough about. They can also recommend treatment for these problems.
So, if your machinery has complex faults that AI cannot diagnose, your maintenance experts are on-hand to identify the issues and figure out how to address them.
Bear in mind that you can also outsource the expert level, as need ed. If you’re operating with a small maintenance crew, then it’s worth spending some time looking for a trusted partner to advise you on your maintenance needs.
A successful tech transformation should happen gradually. Too many businesses try to overhaul their whole operation at once. This can lead to chaos and, eventually, disillusionment in the process.
Instead, it’s a good idea to start with a pilot program. Choose 10 or 15 sim ple rotating machines that are prone to breakdowns. Test your proactive maintenance program on those ma chines alone. Chances are, these are the machines that have already cost your operation a good deal of time and money. You have the potential to show a major change by introducing technology here.
Building a tech-centered mainte nance approach takes an investment of time and money. This can raise challenges when it comes to getting your key decision makers on board.
That’s another reason that it makes sense to introduce the new approach gradually as wins happen and prove results.
Start with a pilot program and then gradually add more machines to your program; it’s a good idea to stick with introducing 10 or 15 new machines at a time in phases. As your programs suc ceed, it will be easier to get your decision makers excited about expanding it.
CMMS can also help you here. By keeping track of your work orders, CMMS documents reductions in breakdowns and in maintenance work orders.
If your company has a change in leadership, you’ll be able to use those work orders to show your new boss how successful the new maintenance approach has been. They’ll be able to see that you are keeping your equip ment up and running and that you’ve cut back on routine maintenance costs.
Because ultimately, that’s the goal – decreasing downtime, increasing productivity, and making sure that you’re not overspending on unneces sary maintenance. And that’s what a carefully designed predictive mainte nance program can deliver.
Building this framework of con nected sensors and software now will prepare your organization for the day that AI-enabled maintenance soft ware is ready to take operations to yet another level.
Article provided by Fluke.
Since their inception as a standardized, mass-pro duced product in the late 1800s, rolling element bearings have reduced the friction and thus energy consumption of rotating equipment. For the first 50 years, focus was on converting existing ap plications using sliding bearings into using rolling element bearings; how ever, for the past 75 years, it is a given that most rotating assemblies will be supported by some type of rolling element bearing.
Here are some examples of how today, rolling element bearings and their maintenance can affect the environment.
A pulp mill was having poor reliabil ity of an ID fan. Each time the fan went down, the facility had to report to the Ministry of the Environment (MOE) as certain unwanted gasses were released. At one point the MOE determined that the frequency of fan failures was excessive, and the facility had to take corrective actions. The solution was to bring in some bearing experts to ensure best practices were being used for installation and opera tion of the fan.
The first step was to inspect the bearings removed from service to understand the reasons for the shortened life. The second step was to ensure that the millwrights were using the proper techniques for bear ing installation. The third step was to carefully monitor the operation of the fan. This was achieved by the installation of a continuous vibration monitoring system.
Observations of the bearing sug gested that there were several in stallation issues, which ended in the bearings bearing axially preloaded. Also, there were several checks that were missed, both during the install
and in monitoring while in operation.
Corrective actions were taken to en sure that the oil levels were correct and monitored, the level of vibration in the assembly was kept low and the oper ating temperatures were monitored. As a result, reliability was improved, eliminating the environmental impact of the fan failures.
While conducting a lubrication survey at a steel mill, I was inspecting an area of slow rotating conveyor rolls. They were supported by unit block ball bearings rotating at a speed of less than 10 rpm in a relatively clean part of the mill. Under each bearing was a pile of grease purged from the bear ings as they were being re-lubricating once a week.
What was odd was that electric motors used ‘sealed for life’ bearings that last five to 10 years at 1500rpm without lubrication; however, when the same sized bearings are put in unit blocks and are rotating at 10 rpm, somehow, they need to be greased every week.
In working with the facility, the appropriate re-lubricating frequency was calculated based on speed, tem perature, and degree of contamina tion, and determined that the bearings could run maintenance free; without any additional grease.
Many bearings of this type do not need to be re-lubricated ever in their life, and a proper calculation of the lube requirement would end up with a reduction in the amount of lubrica tion that is added without purpose to the bearing, thus ending up getting scooped up and sent off to a landfill.
Traditional lubricants based on mineral and synthetic oils are ulti mately biodegradable through the slow rate of decomposition. Under
some conditions, they can exist as a contaminant in groundwater for close to a century. However, in terms of a lubricating oil, it is difficult to find an oil that can provide adequate lubrica tion and be biodegradable. As such, there is not many choices for users who want a ‘green’ grease.
Considering the cost and difficulty in sourcing a good cost-effective biode gradable grease, a sealed bearing is a worthwhile consideration, especially now that sealed spherical roller bear ings are more readily available. With a sealed SRBs, the bearing itself can be feed a high-quality bearing grease and the cavity either side of the sealed bearing can be filled with an inexpen sive environmentally friendly grease. Since the bearing needs significantly less grease for lubrication than for sealing, the assembly will not be purg ing out excessive amounts of a grease that may not biodegrade quickly.
To protect the bearing against dirty, wet environments, a ‘green’ biodegradable grease can be used for sealing and purging of the housing cavity without the concern about an accumulation of less earth friendly grease.
There is lots of ‘anti-EV’ discussion about the use of lithium in EV bat teries. What is true is that lithium based grease is the most popular grease for use in bearings, and it just passes though the bearings and then gets disposed of without a chance of being recycled.
However, recently there has been an increase in popularity of calcium sulfonate greases, which in many cases, can provide similar or better performance in bearings. This is an example of how alternate greases are available that can be more earth friendly in ways other than related to disposal.
A world class rebuild shop will have the appropriate procedures for dis posal of recyclables as the machine is disassembled. There should be spe cific disposal bins for expected waste materials, such as excess grease, oil, solvents (contaminated) and grease or oil filled rags. In addition, the recyclable metals can be collected or segregated into aluminum, steel, and yellow metals. Other than seals and grease, bearings are 100 per cent recyclable.
In one particularly difficult applica tion, a compressor draws sour natural gas out of wells, and a hybrid bearing was developed that can withstand the difficult conditions that occurred due to the condensation of the hydrogen sulphide and other gasses into the bearing lubricating oil.
Using a high nitrogen stainless steel and ceramic rolling elements, a bearing was able to withstand these conditions. This was important as every time the compressor was tak en out of service the poisonous gas was vented into the atmosphere. As the time between compressor shut downs, lengthened from months to years, a significant reduction of pol lutants was realized, and the greater reliability of the compressor allowed planned maintenance more often than unplanned downtime.
In both this case and the fan case, the motivation to fix the problem was a financial penalty for the gas release. Perhaps if companies could keep score on their own of pollution abatement, progress could be made without loss of dollars from fines.
Douglas Martin is a heavy-duty machinery engineer based in Vancouver. He specializes in the design of rotating equipment, failure analysis, and lubrication. Reach him at mro. whats.up.doug@gmail.com.
LOGIC: rolling element bearing life expectancy is directly related to the number of revolutions performed by the bearing, the magnitude of the load and the lubrication and cleanliness of the lubricant; assuming correct initial bearing selection and proper installation. Fatigue is the result of shear stresses, referred to as elastic deformation, cyclically appearing immediately below the load-carrying surface, as the rollers or balls pass over the raceway.
BY L. (TEX) LEUGNERAfter many revolutions, these stresses between the rolling element and raceway surfaces will cause subsurface cracks to appear that will gradually extend to the surface of the rolling element, raceway, or both. These cracks may cause surface frag ments of bearing material to break away. This condition is referred to as flaking or spalling that continues until the bearing has reached its life limit as illustrated below.
Troubleshooting of rolling element bearing problems and recognizing their root cause of failure is often dif ficult, because many failure types look very similar. This is because bearing failures are almost always precipitat ed by spalling or flaking conditions of the bearing component surfaces. Spalling occurs when a bearing has reached its fatigue life limit, but also when premature failures occur. For this reason, it is important for the troubleshooter to be aware of and able to recognize all the common failures of rolling element bearings. This ability to correctly troubleshoot and recognize the root cause of bear ing failures will lead the analyst to the
right conclusions.
We often hear the comment, even by knowledgeable and well-meaning engineers and technicians, “this bear ing failed prematurely because it was defective.” Manufacturing defects in rolling element bearings make up less than one per cent of the millions of bearings in use today around the world and this small defect percent age is being reduced continually by improvements in manufacturing techniques and bearing materials.
Only a small fraction of all the bearings in use fail because they have reached their material fatigue limit. Most bearings outlive the ma chinery or component in which they are installed.
LOGIC: the frosted or smeared appearance of this bearing race illustrates what happens when the oil viscosity is too low (thin), and metalto-metal contact occurs. This type of premature failure often occurs during initial start-up of heavily loaded bearings. This damage occurred after only 15 seconds of operation.
Assuming proper design, application, and lubrication, rolling element bearings will fail sooner or later due to their natural material fatigue life limit, but all bearings will fail prematurely from abuse or neglect.
Q | Does the maintenance group understand what constitutes bearing fatigue life limits?
Q | Can the failure investigator explain the cause of the bearing failure illustrated below?
Q | Can the failure investigator recognize and explain the cause of the bearing failure illustrated below?
LOGIC: this bearing has failed due to continual welding contact between asperities on the metal surfaces, eventually causing metal to be ‘pulled out’ as the surfaces adhered to each other during rotation. This condition may have been caused by oil of the wrong viscosity, excessive load, speed, temperature, incorrect internal clearances, trapped contaminants or a combination of these conditions.
Even an increase of as little as 4° or 5° in temperature may contribute to these failures, due to unacceptable thin ning of the lubricant’s viscosity. When analyzing the root cause of a failure, all the possible contributing causes must be considered.
troubleshooter must consider not only the possibility of excessive lubricant, but that the correct lubricant for the application is in use.
LOGIC: the rusting and white colouration on the outer race of the first bearing show a combination of several possible conditions; including small vibrations causing oscillation of the outer race, reddish discolouration of moisture in the bearing caused by poor sealing, poor fits between the outer raceway and housing, lack of lubrication or improper installation.The second bearing shows serious dark corrosion on the inner raceway equidistant between the rolling elements that occurred while the bearing was stationary.
LOGIC: bearings are not safe from potential electrostatic discharge or stray currents generated by electromagnetic forces. In these bearing applications, it is recommended that the bearing be grounded using grounding brushes. For users of fan and electric motor belts and convey ors, the industry standards that define minimum con ductivity are RMA IP-3-3, ISO 1813, and ISO 9563. In addition, drive belt manufacturers recommend the use of static conductive belts of six megohms or less. This bearing’s inner ring shows clear evidence of corrugated surface damage caused by electric pitting.
LOGIC: over lubrication is frequently the cause of grease lubricated bearing failure causing higher than normal bearing operating temperatures. Excessive grease quantities cause internal friction within the lubricant, which in turn promotes excessive temperatures causing oxidation and premature lubricant and bearing failure. Excessive quantities of grease cause a churning action within the rotating components and the result will always be an increase in temperature. Oil of too high viscosity or grease with a too high consistency will also increase operating temperatures. Care must be taken when investigating high temperatures, that the
The challenge for troubleshooters is to learn to recognize the difference between the tiny per cent of bearings that display material fatigue spalling that confirms their end of life and most bearings that display premature failures described above, because in many instances they look like the untrained eye.
It should come as no surprise to experienced equipment troubleshooters that assuming proper design, application, and lubrication, rolling element bearings will fail sooner or later due to their natural material fatigue life limit, but all bearings will fail prematurely from abuse or neglect.
L. (Tex) Leugner, author of Practical Handbook of Machinery Lubrication, is a 15-year veteran of the Royal Canadian Electrical Mechanical Engineers, where he served as a technical specialist. He was the founder and operations manager of Maintenance Technology International Inc. for 30 years. Tex holds an STLE lubricant specialist certification and is a millwright and heavy-duty mechanic. He can be reached at texleug@shaw.ca.
Q | Can the failure analyst recognize and explain the cause of the two bearing failures illustrated below?
If you have conveyor car rying materials, be assured that some gets lost. Col lectively, these materials on the loose that end up where they shouldn’t, are referred to as fugitive materials. This material loss can occur in many forms, including leakage, spillage, or carryback, which is mate rial that adheres to the belting after the discharge point and is deposited along the conveyor return. Fugitive materials can be coarse, heavy, or even light airborne particles that escape the conveyor and settle as abrasive or dan gerous dust. However, why should we
Some industry estimates place the loss from such escapees into billions of dollars, annually. If you have con veyors, the sobering question you might ask is, “What is my share of those losses, and what can I do?”
First, let’s consider where and how these losses occur. When the material that costs so much to produce ends up on the ground or in some other unrecoverable area, it directly affects your bottom line.
Additionally, fugitive materials have serious consequences that may not be as obvious. Lost materials
can degrade the reliability of your conveyor components (e.g., bearings and rollers) and cause excessive wear to the structure. Fugitive materials can also cause workplace hazards. This results in unplanned downtime, constant cleaning work, and even regulatory scrutiny and action.
Can we eliminate the fugitive ma terial problem? No, but with some new practical improvements, we can mitigate it and make life and profits better for your plant. Let’s focus on improving a few key areas that can of fer the greatest return on investment. In recent years, leading manufacturers have engineered innovative solutions that don’t require significant conveyor alteration. Unfortunately, we seldom see these innovations on even new OEM conveyors in some industry segments. Therefore, you can signifi cantly improve your plant’s fugitive material problem with these solutions.
The most obvious solution to the fu gitive material problem is to contain it. Keep those fugitive materials where they belong. A belt skirting system can drastically reduce spillage and dust; the skirting fastens to the conveyor near the loading points or load zone area. Skirting is designed to make light contact near the top edges of the conveyor belt, forming a seal. Con veyor belt skirting isn’t new, but the advancements are worth considering. Choose a system that is simple to install and allows for skirting adjustment and replacement. There are many skirting choices, including styrene-butadiene rubber (SBR), natural gum, and even high-end flexible urethane. In addition, many shapes, including dual lip, create a larger contact surface for the skirting to make a strong seal contact with the belt.
Without a primary belt cleaning solution, fugitive materials will stick to return rolls and build up below the conveyor, creating problems such as belt tracking issues. Belt scrapers re move bulk material product carryback and prevent it from being deposited at points along the conveyor return side of the belt. These primary belt clean ers, sometimes called pre-cleaners, are mounted directly against the head pulley below the typical trajectory of the material.
A scraper has two main com ponents: a blade that contacts the belt and a mechanism that keeps it in the proper contact position. The blades are installed at an angle that peels away anything stuck to the belt surface. Many commonly available cleaners use blades made of polyure thane—effective due to its flexible, chemical-resistant nature—allowing the blade to endure harsh conditions.
The blades are available in dif ferent hardness levels measured in durometer, depending on the application requirements. If you are conveying slurry material, you will want a blade that acts as more of a wiper that essentially squeegees it off the belt. Wiper blades generally have a softer durometer (70A), allowing for flexibility as they perform like a squeegee pushing liquid away.
A secondary cleaner is installed on the return side of the belt after the point where the belt leaves the discharge pulley. Secondary cleaners are very effective at removing fines and significantly increase cleaning efficiency. A two-scraper arrangement with primary and secondary cleaners effectively removes nearly all material.
Installing a ceramic lagged conveyor pulley is one standard improvement to reduce carryback on your belt. Ceramic has many advantages, including shedding water and dirt faster than conventional lagging. However, a key reason for upgrading to a ceramic lagged pulley is to vastly improve traction on the belt, reducing slippage. This upgrade is vital because a slipping belt causes tracking issues and excessive material buildup in the loading zones, resulting in fugitive materials falling off the sides of the belt. But ceramic lagging may not be enough to control the situation.
In some applications, you can in stall a wing pulley. These reduce the risk of belt damage from lumps of material trapped between the belt and the pulley surface. They are effective at self-cleaning since the only surface where material can accumulate is at the edge of the wings, and the rotation of the pulley slings the material away.
The original wing pulleys looked like the paddle wheel on a steamboat, but their designs have improved in the last decade. Look for one with a spiral or herringbone twist to the wings, which performs better for belt tracking and repelling any incoming fugitive materials.
If any material makes it through your fugitive material defenses by wind or control system failure, it can accu mulate over time. Often, this buildup is located on the return side of your conveyor. It is especially problem atic in climates where wet and cold weather makes the fugitive material viscous, bonding to surfaces and then hardening. Like sticky dough on a rolling pin, this material clings to the pulleys, belts, and rollers after the cleaner. The accumulation can cause significant problems with belt tracking and premature failures.
The best option is to replace your standard flat face rollers with disc return rollers, which use rubber or urethane discs spaced along the shaft. By reducing the surface area and belt contact, the discs drastically mini mize material buildup on the roller.
Rubber is a standard selection for disc return rollers; however, polyurethane is a top choice for material due to its natural resistance to adhesion and abrasion. Urethane rollers are also available in spiral form, resulting in a point of contact constantly moving on the conveyor belt surface, creating a smooth cleaning action.
When material escapes the conveyor, it will accumulate anywhere it can settle, covering your conveyor compo nents and equipment. Eventually, you have pulley bearing, idler and gearbox failures. All your moving parts on the conveyors have bearings, which must stay clean to run. In the mining indus try, these pulley shafts glowed red hot as they bored their way through what was left of a failed bearing as it melted, and the housing that once supported it was chewed away. Often, all this bearing carnage starts with dust—tiny
particles of fugitive material that find their way through the bear ing seal. A contaminated bearing is doomed, and bearing failures are dangerous. Entire conveyors and plants have burned down from bearing failures on con veyor pulleys.
Idlers, although using much smaller bearings than pulleys, can cause great damage when bearings fail. Failed idlers can seize, and the belt will continue to scrape across the stationary idler, drawing more motor pow er until the belt grinds its way through the idler. The resulting idler damage produces sharp edges that will slice up the belt, creating another expensive and dangerous failure situation.
Many kinds of bearing seal systems are available and choos ing the right one could be the solution to preventing prema ture bearing, pulley, idler, and belt failures. One significant im provement is installing a quality taconite-duty seal. These robust seals were developed to seal out one of the most notorious fugitive materials in industry history: taconite, an abrasive iron-bearing mineral. These seals comprise two rings (one stationary and one rotating), forming a very narrow labyrinth between the rings.
A v-ring seal on the rotating ring creates a seal against the labyrinth ring, which remains stationary. The v-ring seal guards against contaminants entering the bearing housing and helps purge contamination and old grease when the seal is re-greased. Taconite seals con stitute a significant improve ment, but if you’re serious about keeping those fugitive materials out of your bearings, select the complete triple barrier solution. Barrier one is the taconite con tact seal on the housing, barrier two is the housing cavity filled with grease, and barrier three is the new, factory-sealed for-life spherical roller bearing. These are now available and can be installed in your existing hous ings. With that barrier trio, fugi tive materials must penetrate a highly advanced labyrinth seal, a layer of cavity grease (which can be purged) and another seal on the bearing itself.
Many available options can mit igate the carryback of fugitive materials; these are just a few of the best. With the best bearing seals, a belt cleaner, upgraded pulleys, and disc return rollers all working together, you will make your conveyor more economical, safer, and more reliable.
Your conveyor carries your profits. Simple changes can significantly impact downtime, safety, and productivity gains.
Even if an overhaul is not in the budget, keep in mind that preventing material loss, workplace injuries, unplanned downtime and extra cleaning will start paying back imme diately. Rather than viewing these optimizations as one big project, pick an area of your conveyor that needs the most attention and begin there. Small changes over time yield massive results. Contact a local, qualified distributor
representative/expert and ask them to show you some options and guide you through the se lections that will control your fugitive material problem.
Wyatt Phillips is Motion’s Prince George branch manager in British Columbia. A technical account representative for 10 years before his last three as branch manager, Phillips’ continued interest is reliability-focused solutions for customers in the mining, energy, and pulp sectors.
Simply, maintenance is an important facet of keeping operations running reliably. To achieve that, we need to be smarter ourselves and work leaner, making greater use of technology deployed more strategically than we are today.
No engineer or inventor has ever designed an unbreakable system or equipment. Those who design our systems don’t see it that way, but for those of us in maintenance who do, it means job security. What we maintain and how we do it will change, but since we will be needed to maintain, is im mutable. We already have much of the knowledge we need to do better, so a big change in future will be to leverage that knowledge. Rather than focus on developing even more complex and sophisticated systems, we will focus on using what we already have and what is already being developed.
We know preventing failures are good, and we know all failures cannot be prevented. We also know many
failures (including some preventable ones) can be predicted if we monitor the right conditions. We can monitor equipment conditions (vibration, temperature) or observe system per formance (fuel consumption, flows, valve positions, product quality). As maintainers we tend to do more of the former, rely less on the latter, and distrust operators when they complain about performance issues. We are sub-consciously filtering out valuable information.
Some conditions can be monitored by our human senses (low tech, high touch). Those tend to be inconsistent from person to person, but they can work if we watch for them consistent ly. Other conditions are monitored by instruments and equipment. Both require that we act when we find a problem.
Failures of condition monitoring programs are not usually failures of a sensor (human or otherwise), rather they are failures to be consistent in monitoring, and failures to do the
needed follow up a problem is found. We already know this is a problem, with companies putting more empha sis on leveraging what it learns from its own operational information to better manage failure consequences than we are doing today. That requires some enhancement in planning and supervisory skills so that action is taken in a timely manner.
Ever since we have had computers, we have been experiencing massive growth in technology that enables better monitoring of equipment con ditions. Today, it is becoming more sensitive, wireless, and in turn, sensor prices are dropping. The IIoT is en abling us even more, so our ability to observe is getting better all the time. Some systems are programmed to tell us what to do about those observa tions. It’s no different from predictive maintenance, except that it removes the human from the decision process. As machine learning improves that will grow.
For those who are willing to invest in monitoring, the future will bring us growth in what can be monitored, how we can monitor, and expand on remote monitoring. The use of robot ics will expand along with the need to maintain those robots. That will come in the form of drones both flying and ‘walking’ through our plants and along our linear assets. Those drones will be bristling with sensors and readers to record what sensors installed on the assets are sending out.
Robots doing monitoring could po tentially replace operators and main tainers who today are walking rounds. The robots will be more consistent, and likely more accurate. Readings will be recorded automatically, and more accurately than by humans. Warnings, and needed actions will be produced in some form of notifi cation for action on our management systems. This exists today and there is a lot of growth potential here.
However, it will be incumbent on the maintainers to act on those no tifications in a timely manner, or all that investment in technology will be a waste.
The knowledge needed to use con dition monitoring technologies will become more embedded in the realm of AI and that specialized knowledge will reside only with the providers of those technologies. That will free maintenance workforce from the need to have that expertise.We will still need a maintenance workforce equipped and trained to replace components
This change in future is outside of maintenance. It resides in the education systems that feed our industries with maintainers and business leaders.
when they are failed and to perform troubleshooting that goes beyond what the sensors tell us, and to confirm what the sensors are telling us. Maintainers will become better trouble-shooters, or the parts inventories needed to supply guesswork parts replacements will become very expensive.
Taking full advantage of that re quires the knowhow of what can go wrong and what to look for to monitor effectively. It requires a deeper knowl edge of what is happening inside our assets – the sort of knowledge gener ated when we do reliability centered maintenance (RCM) analysis. The future will bring more of that. Since it is so sensitive to operating context, we will learn that one size doesn’t fit all and resistance to investing will fall. All this means that we will find failures sooner, minimizing business
There is an emerging awareness that we can leverage RCM results that tells us what can happen, how often, and what we can do about it, to en able better material needs forecasting. Without that, we will continue to suf fer materials shortages and deferred or delayed repair work. One solution is to build a more robustness and more redundancy into our assets, but that is very capital intensive. A better solution is to get smarter and leverage what we know works well.
There will be continual introduc tion of new technologies into our physical assets – plants, and mobile equipment. As we introduce those, we will need to learn how they work (so we can operate them) and how they fail (so we can maintain them). Some will dictate new maintenance meth ods that will also need to be taught.
likely continue to be poor communi cators of needs and business benefits, and companies will continue to lag in their investments in the training needed to leverage technologies most effectively.
Technical people need to improve communication skills and business knowledge. Business leaders need a better understanding of the assets they depend on – they can meet in the middle and communication chal lenges will be less. Eventually business schools and technical education pro grams will dedicate some of their cur riculum to these important subjects that today are largely ignored. This change in future is outside of main tenance. It resides in the education systems that feed our industries with maintainers and business leaders.
Last October, Hexagon purchased Infor for $2.7 billion. Included in the purchase was Infor’s flag ship enterprise asset management (EAM) and their CMMS, MP2. This past spring Hexagon announced they would no longer sell the MP2 soft ware and invited MP2 customers to upgrade to EAM.
MP2 along with other maintenance software, have been the industry stan dard for CMMS programs for the past 30 years. As the pioneers of mainte nance software, they determined what companies required and pro vided the industry with a simple, easy to use CMMS software to track their equipment maintenance and spare parts inventory.
Since the 1990s, MP2 has been a long-time favourite of industries ranging from universities, hospitals,
public works, and the manufacturing sector; with approximately 15,000 worldwide installations with 800 in Canada.
This is the second time in its his tory that MP2 has been on the chop ping block. Datastream, the creator of MP2 announced they would be stopping the sale of MP2 in favour of thseir new EAM, called 7i. Shortly af ter that announcement, Datastream was purchased by Infor in 2006. Infor reversed the decision to shelf MP2 and assured users and prospective purchasers that they had no inten tion of discontinuing MP2. To show their commitment, Infor updated MP2 with new features and add-ons and again MP2 became one of the industry favourites.
With Hexagon’s latest decision this is the end of the road for anyone want ing to purchase MP2. To Hexagons’
credit, they are continuing to support MP2 customers for the immediate fu ture. The 2020 MP2 program release provides support for 2019 SQL Server and Windows 10 platforms. The new MP2 build will support the program on these platforms for the near future. The question MP2 users are asking is where do all these changes leave them in the future when Hexagon decides to stop supporting MP2 with software updates? Let’s look at some options.
1. MP2 clients wanting a more sophis ticated version of a CMMS may opt for Hexagon’s offer to upgrade to EAM. However, EAMs in general are more complicated when com pared to programs like MP2. If you are a medium to large facility, an upgrade to EAM could be the best route. An EAM has a more rigor ous maintenance system to meet the needs of larger maintenance departments. They have advanced features, built in KPIs and dash boards to provide the user with key information on maintenance performance and costs. They also offer cloud-based solutions and work order mobility. For smaller companies that have fewer assets and maintenance activities, an EAM may be more than required, and the cost of the EAM may not fit the budget. In this case a better solution could be option two.
2. Move to another brand of CMMS that is like programs like MP2. These latest programs offer the basic maintenance elements but also offer advanced features that MP2 did not offer. New systems are cloud-based to allow access from nearly anywhere without the need of having the CMMS appli cation loaded on your computer. They offer mobility solutions, so technicians can carry and process
For the second time in its history, MP2 is on the chopping block.
MP2 has been a work horse for maintenance departments for a long time, and it is sad to see it go; however, new CMMS and EAM programs are exciting and offer the functionality that MP2 lacked.
their workorders on
and cell phones. There are hundreds of CMMS systems to choose from, it is a matter of matching the needs of the maintenance department and the features they require.
3. There is one more option, keep MP2. Although new software patches may not be available in the future, MP2 has proved itself as a reliable and stable product. Com panies that choose this option can talk to their IT department about keeping MP2 on a separate server with Windows and SQL server operating systems MP2 requires, effectively keeping MP2 alive in definitely. Most facilities already have MP2 configured in this fash ion. It has been a standard practice to keep the MP2 database separate from other corporate processing and financial data.
MP2 has been a work horse for maintenance departments for a long time, and it is sad to see it go; however, new CMMS and EAM programs are exciting and offer the
functionality that MP2 lacked. Cer tainly, there will be adjustments to be made and new software to learn.
The whole implementation pro cess of new software is a challenge. However, proper planning that in cludes data cleansing and organizing of master data during the software implementation will give mainte nance departments a clean slate to build a new maintenance system that
will last another 30 years.
Peter Phillips is the owner of Trailwalk Holdings Ltd., a Nova Scotia-based maintenance consulting and training company. Peter has over 40 years of industrial maintenance experience. He travels throughout North America working with maintenance departments and speaking at conferences. Reach him at 902-798-3601 or peter@trailwalk.ca.
Although automation can create jobs, the present-day myth is that the devel opment and adoption of automation creates as many jobs as it reduces. There is also a direct-link between automation’s reduction in labour and income inequality.
Automation has two aspects:
• The use of technology to reduce the requirement for human interven tion in a process, i.e., the adoption of technology that can assist labour, and;
• The development and adoption of new technologies that enable capi tal to be substituted for labour over a range of tasks.
The first aspect of automation is helpful. There are many tasks that people do not want to do or cannot do: spray paint a car, work with dangerous chemicals and do high precision work.
The second aspect improves produc tivity: automated welding, data entry, and computer tools to assist informa tion analysis. For both aspects, the present economy favours automation over labour.
The common wisdom is that the cre ation and adoption of automation, in addition to reducing the need for people to do jobs, produces as many jobs as the jobs that are lost. Jobs are created due to the use of automation: the design of machines, the mainte nance and repair of these machines, and the design of new processes to use the adopted automation. Jobs are also created by merging new technologies for automation with new applications: plastic forming for containers and toys, 3D printing, and
analytics. Nevertheless, over the past 30 years job creation has not kept up with job losses due to automation. In addition, the rate of the adop tion of automation has accelerated, especially over the past two years to compensate for the effects of the COVID-19 pandemic, and the rate of job losses due to automation has similarly accelerated.
Researchers at Ball State University studied the effect of automation on operations in the U.S. In 2015, they published a report that showed the reduction in jobs in manufacturing and other fields was 88 per cent due to the use of automation and informa tion technology, and that only 12 per cent was due to the transfer of jobs to low wage countries.1 This conclu sion is important. The present-day narrative suggests that jobs have been lost mostly due to the movement of jobs to other countries with low wage labour and that they can be reimport ed. However, in the Ball State study, the lion’s share of jobs was lost due to the adoption of automation, not due to foreign workers taking jobs due to their lower wages.
Over the past several years, Daron Acemoglu (MIT) and Pascual Re strepo (Boston University) have com pared the sources of change in labour demand in the U.S. during the periods of 1947-1987 and 1987-2017.2 They specifically studied the amount of labour used in companies for produc tion and noted the amount of job dis placement due to automation relative to the creation of new work content that led to job replacement.
The greatly reduced job reinstate ment during 1987-2017 was due to the negative 10 per cent change in task content that resulted in a 10 per cent reduction in labour demand over the period. By comparison, task content
changed very little during 1947-1987. The results also show an acceleration of automation and job loss over the 1987-2017 period.
During 1947-1987, it was found that the wage bill increased by about 100 per cent, growing at 2.5 per cent per year, which was mostly due to a productivity increase of 2.4 per cent per year. By comparison, from 1987 to 2017, the wage bill grew 40 per cent over the period at only 1.3 per cent per year with very little gain after 2000. The rate of productivity growth during the period was only 1.5 per cent per year compared to the 2.4 per cent per year during 1947-1987, resulting in a lower wage bill.
From this analysis, Acemoglu and Restrepo concluded that “The com bination of adverse shifts in the task content of production - driven by ac celerated automation and decelerat ing reinstatement of task content - and weak productivity growth account for the sluggish growth of labour demand over the last three decades, and espe cially, since 2000.”3
The adoption of automation leads directly to reduced work content and the loss of jobs.
• The tax code subsidizes the use of equipment through tax credits and accelerated amortization whereas it taxes the employment of labour through various payroll taxes. The present balance is very much in fa vour of automation at the expense of labour.
• The use of automation is acceler ating and used by more businesses due to a tendency towards evolu tionary or incremental improve ment. Conventional automation tends to be revolutionary, i.e., large projects with new, targeted outcomes that greatly increase pro ductivity. Moreover, revolutionary innovation tends to create new jobs elsewhere in the economy. Although incremental automation improves existing tasks, productivity is only improved marginally, and there is little job creation.
• Most companies are shying away from innovation with long time
horizons. Although long term inno vation delivers results more slowly than incremental automation, it cre ates more innovation, more new task content, and results in more new jobs.
Acemoglu and Restrepo have recently studied the relationship between the adoption of automation and wage in equality. They conclude that “a signif icant portion of the rise in U.S. wage inequality over the last four decades has been driven by automation.” They showed that “between 50 per cent and 70 per cent of the changes in US wage structure between 1980 and 2016 are accounted for by the relative wage declines of worker groups specialized in routine tasks in industries experi encing rapid automation.”
During the last 30 years, the devel opment and adoption of automation has displaced labour and there has not been the creation of as many jobs as have been displaced. Due to the strong
take-up of incremental automation, the increase in productivity during the same period was much lower than during previous decades.
Studies used were of businesses in the U.S.; however, since the econom ic environment in Canada was very similar during the periods studied, the results apply equally to Canada. In terms of outcomes, Canada suffers from the same job losses due to auto mation, Canada suffers the same low productivity, in effect even lower than the U.S., and Canada has the same issues regarding income inequality.
The use of automation is increasing and the type of automation that is being used the most is incremental improvement such as the development of specialized software and artificial in telligence for the tasks of white-collar workers in accounting, sales, logistics, trading, and management. These task improvements do not replace people immediately, but over time many jobs are lost. Incremental automation is not highly visible and not easily measured, but it is pervasive in all businesses. It is leading inevitably to job loss. There fore, there is an urgency to address the causes of poor productivity, and mostly, the lack of job creation.
• Governments must change the tax structure that subsidizes automa tion and taxes employment such that newer jobs are created.
• Businesses, especially in new sec tors, need to stress more innovation to create more, new work content alongside automation such that newer jobs are created.
• The industry needs to do more longterm innovation to greatly improve productivity and to create new work content that results in new jobs.
• Governments must structure the economy such that businesses are motivated to innovate and create new work content.
Of these items, changing the tax structure is the most immediate. Governments have unknowingly fa voured automation over labour and have reduced the creation of jobs. It is time to reverse the trend.
1. M Hicks, S Devaraj. The myth and the reality of manufacturing in America. Ball State University, June 2015.
2. D Acemoglu, P Restrepo. Automation and new tasks: How technology displaces and reinstates labor, Journal of Economic Perspectives, 2019, 33(2) 3:30.
3. D Acemoglu, P Restrepo. Tasks, automation, and the rise in US wage inequality. Working Paper 28920, National Bureau of Economic Research, Cambridge, MA, USA, June 2021.
Why has automation affected the demand for labour in such a way?
including a high-efficiency ultra-wideband radio transmitter. This helps to position Wiegand technology (which collects energy from movements of an external magnetic field) beside established energy harvesting techniques such as solar, piezo, or thermo-electrics as an energy source for sensor nodes in IoT.
www.ubito.com/en/
Brass Knuckle’s SmartFlex Full Coat Liquid Resistant Gloves (BK350) are light and provide all over protection from liquid exposure, sealing out liquids and keeping hands dry, to make them less prone to skin diseases.
Work-related skin diseases account for approximately 50 per cent of occupational illnesses and 25 per cent of all lost workdays. Protecting the skin from prolonged exposure to liquids (even clean water) is critical to fighting skin disease.
SmartFlex BK350 are long-wearing with nothing to rub or chafe. The natural latex coating covers the full front and back of the hand to seal out moisture.
Protection from liquids may not be enough if a glove’s lack of grip prevents the wearer from using the necessary tools for the job. SmartFlex 350 has an additional double dip of latex foam on the palm that provides grip, abrasion resistance, and tear resistance. Although not recommend ed for oily applications, this glove is ideal for dry or wet environments. www.brassknuckleprotection. com
Endress+Hauser launched Cerabar and Deltabar pressure gauges with a Bluetooth interface to operate and maintain in safety-critical systems. Their level of safety combined with productivity enhancing features is an application of Endress+Hauser’s smart safety approach.
Cerabar and Deltabar operate via the SmartBlue app, which includes guided operating sequences for parameter ization and commissioning. The inclusion of an additional Bluetooth interface bridges distances of up to 15 meters. The employee does not have to open the housing or connect a cable. Real-time pressure data is available at any time.
internal combustion pneumatic tire lift trucks are built for challenging environments. These forklifts are ideal for the metal industry, lumber yards, industrial machinery, and distribution centre. Including a Kubota V3800 engine, the turbocharged, electronically controlled engine pours out torque at low rpm, producing low emissions. The lift truck has a four-cylinder common rail turbo diesel EPA Tier four engine that produces high power, even in hard-wearing applications. www.logisnextamericas.com
technology is suitable for manufactur ing rubber bladders and other elastomeric products that expand and contract.
https://c3dmaterials.com
Ubito announced its development of Wiegand technology as an energy source for smart sensors. After more than two years, a research team has demonstrated a prototype of a wireless sensor powered by Wiegand technology that could participate in an IoT network.
The project involved the development of a Wiegand Harvester capable of capturing enough energy to power the sensor’s electronics package,
The devices’ functionality can be verified without process interruption – usually in less than three minutes, via Bluetooth using the SmartBlue app. A verification protocol, which provides detailed test information, is generated automatically, based on the continuous self-diagnostic function of the pressure transmitters. It achieves a diagnostic coverage rate of over 95 per cent.
www.endress.com/en
Mitsubishi Logisnext Americas announced the launch of its Cat DP60HP-DP100CP forklift series. The 13,000-to-22,000-pound capacity
Chromatic 3D Materials developed Smooth-Mode technology for 3D printing of durable rubber parts with ultra-smooth surfaces at commercial volumes. With this technology, industrial manufacturers can 3D print smooth polyurethane parts, such as seals, gaskets, grommets, bladders and other elastomeric products, with no post-processing or surface finishing.
Parts printed with Smooth-Mode technology have finer dimensional accuracy. For example, products can be printed with precise uniform thickness at submillimeter scale. The
Blackline Safety launched the G6 personal gas detector, featuring long-lasting connectivity.
Industrial organizations can harness real-time safety data for the first time in scenarios where disposable, traditional beep-and-flash detectors are commonly used.
The solution leverages IoT cellular connectivity, G6 offers longer battery life, lower cost of ownership and fewer false alarms. It gives safety profes sionals access to the data needed to manage safety protocols, processes, and ongoing compliance.
www.blacklinesafety.com
Pfannenberg announces the Intense BR50 series stacklight, which is the brightest stacklight available as it outshines previous Pfannenberg LEDs by 10,000per cent.
The stacklight features an online configuration tool that make it easier to design a simple stack light and provide a manufacturer’s suggested retail price and the resulting bill of materials.
The line of stacklights results in improved safety and productivity from increased levels of ambient light. Whether installed on cabinets, machinery frames, or junction boxes, Intense BR50 stacklights adds to facility safety, productivity, and style. They are available in a variety of mounting options, including
direct-to-base, tube-and-bracket, and tube-and-stand. www.pfannenbergusa.com
Chemline’s floating ball design and cushioned PTFE seats. The valve is bidirectional for precise flow control in both directions. A positioning electric actuator makes the SM Series a cost-effective control valve. www.chemline.com
H2” option and retrofittable for most of the installed Type 3 fleet. The Jenbacher Type 3F is available for applications in 50 Hz countries and will be available in 60 Hz countries in 2024. www.innio.com/en
Kaman Precision Products announced its Air Gap Tool, offering accurate measuring and data storage for hydro electric turbines. The Air Gap Tool is designed for static alignment of rotor / stator in large scale hydro genera tors. It is ideal for measuring air gaps in the field and can be used for initial installation and during re-assembly after maintenance procedures. The tool can measure and store data with the tap of a finger. It can be positioned at predetermined locations between the stator core and rotor poles. Air gap distance is accurately measured and transmitted wirelessly to handheld Android or iPhone devices using the included app and stored on command. www.kamansensors.com
Newtek Sensor Solutions new line of Hazardous Location LVDTs (Linear Variable Differential Transformers) operate safely and accurately in hazardous and explosive environ ments with the presence of flammable or ignitable gases and liquids such as those found in refining and petro chemical plants, pipelines, and oil and storage tanks.
Approved for used in Class 1, Zone 0 and Zone 2 locations, the NT-HL-750 series of LVDT Position Sensors are ideal for pipeline and LNG storage tank structuring monitoring and real-time position sensing of different valves in oil and gas fields, chemical process plants, gas turbines and oil refinery platforms and rigs. These AC-operated sensors are Intertek approved and hold an ETL mark that certifies its use in hazardous locations throughout North America. www.newteksensors.com
Rittal introduces Hygienic Design Pushbutton Enclosures and Accesso ries designed for hygiene zones in food and beverage facilities. Five sizes are available in the hygienic design (HD) pushbutton enclosure line including one-, two-, three-, four-, and six-hole enclosure options that fit standard 22.5 mm pushbuttons and switches.
To meet food safety regulations, the HD pushbutton enclosures feature: 3° slope on all sides to prevent accumu lation of liquids, 304 brushed grain, stainless steel, zinc-plated sheet steel mounting bracket, IP 66 and IP 69 rated and UL Type 4X rated. www.rittal.com/ca-en/
HN Series operates without external power, using centrifugal force. Solids settle into attached bleed tank, which may be flushed using supplied ball valve. Applications include prefiltration on membrane water treatment systems.
The HN Series is offered in three sizes. The one-inch cone is made of glass filled polyamide (PAG), while the two- and three-inch cones are made of glass filled polypropylene (PPG).
Other highlights: ends are alfa rapid grooved, MNPT, or MNPT Union; o-rings are nitrile; and bleed tank and flush valve are included.
www.chemline.com/hydro-cyclones-hn
Chemline Plastics introduced the SM Series Metering Ball Valve, designed for fine linear flow control of chemi cals or clean fluids such as water. The ball is solid with a graduated V-groove cut on the outside surface. Precise linear flow control is accom plished through the 0° to 180° rotation of the handle in 5° increments. The fine flow-control applications include pressure washing systems, aquatic life support and fisheries research. The SM Series includes ball valve features such as: full blocking design, double stem O-rings for safety, and 230 psi rating for PVC. Low stem torques are achieved through
Innio launched the improved Jenbacher Type 3F engine, which offers up to two percentage points of an efficiency boost, the engine line’s highest efficiency.
Delivering efficiency as high as 43 per cent when operating on pipeline gas, the Type 3F engine is optimized for reduced total hydrocarbon emissions and future-proofed fuel flexibility. The new model is offered with a “Ready for
FDB Panel Fittings offer quarter turn locks offer a wide range of standard bodies at their online store.
Panel Fittings have Rocfast lock assembly and logistics service which matches lock bodies in black or chrome, selected from the online range together with lock cylinders or inserts and cams, plus back nuts to deliver as a complete assembly. www.fdb.co.uk
Chemline Plastics HN Series Hydro Cyclones, designed to separate sand and other solids from surface or ground water. The design is construct ed of abrasion-resistant solid plastic.
Quabbin signal cables are available in shielded or unshielded versions, with conductor sizes from 24AWG to 16AWG, and with various conductor counts ranging from two to 25 conductors depending on cable size. Twisted pair or twisted triad options are also available. Individual conductors are stranded tinned copper with colour-coded insulation; all cables include a PVC chrome gray jacket.
These 150-, 300- or 600-volt rated cables are ideal for low-voltage control signals and audio applications. Quabbin control and signal cables are UL and CSA approved, and can be ordered cut to your specified lengths in one-foot increments with a 30-ft minimum.
www.automationdirect.com/ control-signal-cable
Visit mromagazine.com/products for more industry news and events.
Too many times when people or organizations set out to make im provements to their maintenance and reliability programs or want to update their strategic asset management plans to match the new company direction, there is a tendency to focus on being perfect. This results in waiting to start the improvement initiative until all the detailed information is available and decisions have been made.
That famous quote “perfection is the enemy of progress” comes to mind. The world around us is con stantly changing and we can never anticipate all future scenarios.
Just get started – pick a key asset and focus on improving its value to the organization by revising its main tenance and reliability program. Identify what maintenance activi ties need an update and implement those changes.
It won’t be perfect; however, it will be a step in the right direction and further enhancements can be made over time.
A rolling pilot approach where improvements are made to one as set’s maintenance program or a new PdM technique is applied before rolling out to the rest of the plant or fleet enables improved performance to be measured quickly, builds the case for change, and allows flexibil ity in the face of an uncertain and ever-changing business context.
Listen to the podcast here: www. mromagazine. com/podcasts/
Work identification provides a better way to measure maintenance maturity and performance by describing where the work originated rather than the typical proactive to corrective (PM/CM) maintenance ratio.
Was the work identified through proactive, structured, and deliberate means where we are managing our assets? This Proactive element should form about 80 per cent of the total work consisting of preventive (PM) 15 per cent, pre dictive (PdM) 15 per cent, from-PM 15 per cent, from-PdM 35 per cent, and continuous improvement work categories.
Or was the work identified in an unstructured ad-hoc and requested means where our assets are managing us? The reactive element should form about 20 per cent of the total work consisting of breakdown work 10 per cent, and all other requested work not identified through deliberate means 10 per cent.
These percentages are reliability heuristics or rules of thumb reflecting op timal maintenance type mix and are measured in hours.
View all the tips at mromagazine. com/mr-os-tips/ Or scan the QR code!
The challenge is influencing the source of work coming into the maintenance hopper.Work execution management processes (prioritize, plan, schedule, exe cute, record and analyze) have limited influence on the type of work coming in. Our objective is to displace low-value reactive work with high-value proactive work to deliver business value to the organization by achieving the lowest sus tainable cost of service.
Work identification can be the one metric to drive the right behaviors to provide deliberate management of our assets.