FOCUS ON:
Ways to use condition-based predicitve maintenance
ALSO: Case study: optimizing operations and tracking progress
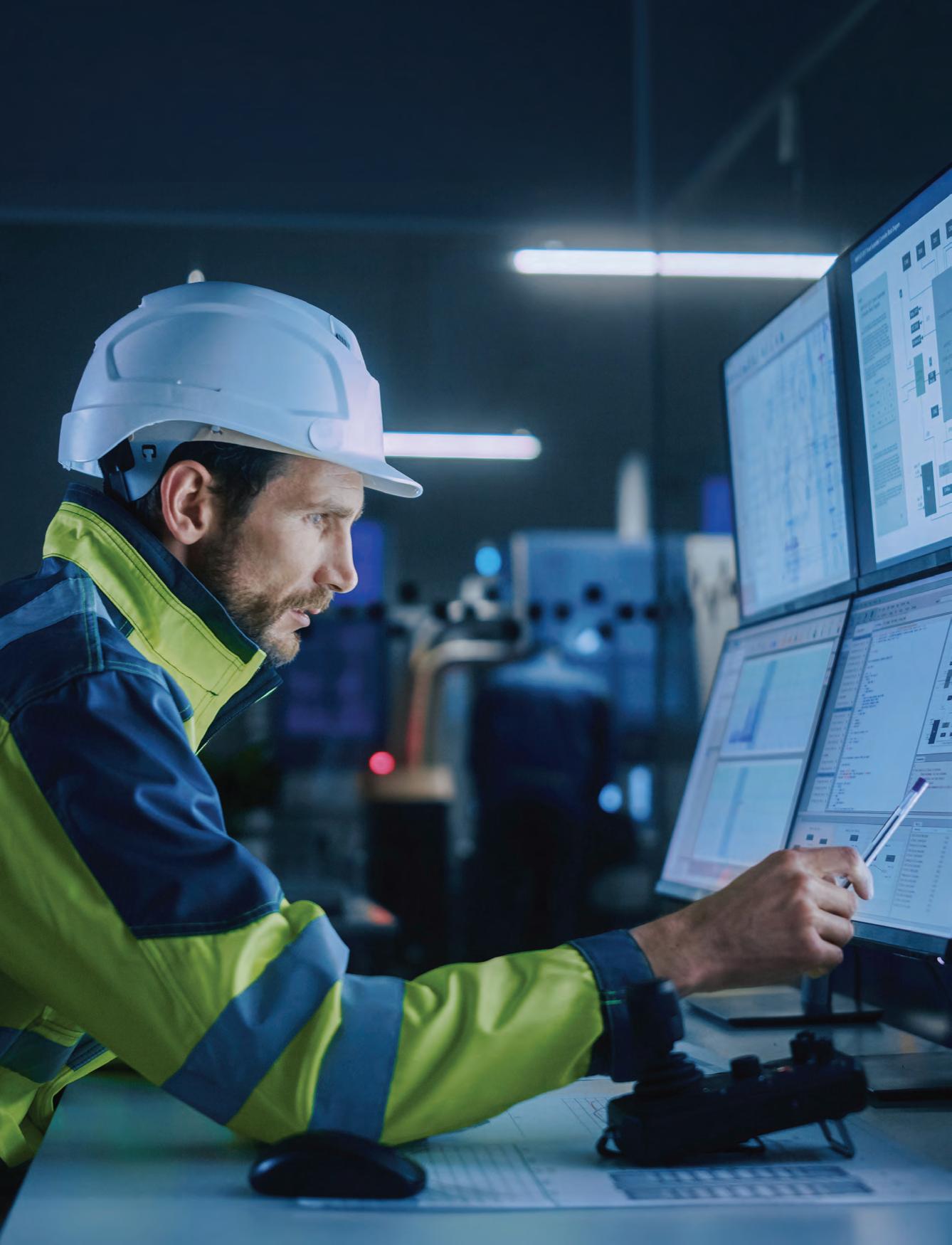
FOCUS ON:
Ways to use condition-based predicitve maintenance
ALSO: Case study: optimizing operations and tracking progress
4
20
6 NEWSWATCH
24
ORIENTATION FOR NEW AND YOUNG WORKERS
While young workers are busy thinking about starting their new summer jobs and others are re-joining the worforce, they may not realize that their “newness” could affect their safety and health.
MAINTENANCE STRATEGIES: HOW ADVANCED IS YOUR PROGRAM?
While AI-powered solutions and predictive data analytics tend to dominate the conversation, these technologies are just one component of the ongoing evolution of maintenance.
HOW MAINTENANCE 4.0 TECHNOLOGY WILL HELP BRIDGE THE SKILLS GAP
Chances are, you’re already highly aware of the maintenance worker skills gap.
CASE STUDY: OPTIMIZING OPERATIONS AND TRACKING PROGRESS
Cameo corporation explores different solutions to create efficiences among maintenance groups.
HOW 3D DIGITAL TWINS ARE USHERING IN A NEW ERA OF MANUFACTURING
Enhancing visibility and strengthening decision-making across production facilities
This issue is indeed a special one, celebrating my first issue as the editor of MRO magazine. And let me say, this industry is also a very special one.
In the realm of maintenance, repair, and operations, we find ourselves at the intersection of innovation and necessity.
The machiner y that keeps our industries running smoothly demands meticulous care and attention, and it is the dedication and exper tise of MRO professionals that ensure seamless operations day in and day out.
As the new editor of MRO Magazine, I am honoured to be in a team dedicated to bringing you the latest insights, trends, and best practices in the field. Our mission is clear: to be your trusted companion on the journey towards excellence in maintenance, repair, and operations.
Within the pages of this magazine, you will find a valuable collection of knowledge, from expert interviews and case studies to technology spotlights and industry analyses. We aim not only to inform but also to inspire, fostering a community of collaboration and innovation among MRO professionals in Canada.
However, MRO Magazine is more than just a publication—it’s a platform for dialogue and exchange. We encourage you, our valued readers, to actively participate in this conversation. Share your experiences, insights, and challenges with us, for it is through this platform that we can truly advance the field of MRO.
I extend my deepest gratitude to our contributors, whose expertise and passion is our number one reason this magazine is valued to all our audience. And to you, our readers, thank you for embarking on this journey with us. Together, let us elevate the standards of maintenance, repair, and operations, shaping a future of efficiency, reliability, and excellence.
Many great topics and conversations are covered, and we hope to cover many more as we go. For that reason, I welcome suggestions, comments, or bringing our attention to innovations and development happening in the industry. Reach me at mfarag@annexbusinessmedia.com.
From all of us at MRO magazine, stay safe and well.
MARYAM FARAG Editor mfarag@annexbusinessmedia.comESTABLISHED 1985
SPRING 2024
Volume 40, Number 1
READER SERVICE
Print and digital subscription inquiries or changes, please contact Customer Service
Angelita Potal, Customer Service Administrator
Tel: 416-510-5113
email: apotal@annexbusinessmedia.com
Mail: 111 Gordon Baker Rd., Suite 400 Toronto, ON M2H 3R1
EDITOR Maryam Farag 226-931-4194 mfarag@annexbusinessmedia.com
SENIOR PUBLISHER Paul Burton 416-510-6756 pburton@annexbusinessmedia.com
NATIONAL ACCOUNT MANAGER Ilana Fawcett 416-829-1221 ifawcett@annexbusinessmedia.com
BRAND SALES MANAGER Chander Verma 437-218-0941 CVerma@annexbusinessmedia.com
AUDIENCE DEVELOPMENT MANAGER Beata Olechnowicz bolechnowicz@annexbusinessmedia.com 416-510-5182
MEDIA DESIGNER Svetlana Avrutin
ACCOUNT CO-ORDINATOR Debbie Smith 416-510-5107 dsmith@annexbusinessmedia.com
GROUP PUBLISHER Anne Beswick 416-410-5248 abeswick@annexbusinessmedia.com
PRESIDENT/COO Scott Jamieson sjamieson@annexbusinessmedia.com
Machinery and Equipment MRO is published by Annex Business Media, 111 Gordon Baker Rd., Suite 400, Toronto ON M2H 3R1; Tel. 416-442-5600, Fax 416-510-5140. Toll-free: 1-800-268-7742 in Canada, 1-800-387-0273 in the USA.
Printed in Canada ISSN 0831-8603 (print); ISSN 1923-3698 (digital)
PUBLICATION MAIL AGREEMENT #40065710
Subscription rates.
Canada: 1 year $66.30, 2 years $105.06. United States: 1 year $145.86. Elsewhere: 1 year $167.28. Single copies $10 (Canada), $16.50 (U.S.), $21.50 (other). Add applicable taxes to all rates. On occasion, our subscription list is made available to organizations whose products or services may be of interest to our readers. If you would prefer not to receive such information, please contact our circulation department in any of the four ways listed above.
Annex Privacy Officer Privacy@annexbusinessmedia.com 1-800-668-2374
No part of the editorial content of this publication may be reprinted without the publisher’s written permission © 2024 Annex Business Media. All rights reserved. Opinions expressed in this magazine are not necessarily those of the editor or the publisher. No liability is assumed for errors or omissions.
Walter Surface Technologies has appointed Jean-Marie Maayoufi as safety sales director of its safety division, leading sales for the Allegro Industr ies brand.
In this role, Maayoufi will lead Allegro’s safety specialists in North America towards growth. He will be working closely with both the WALTER and Allegro sales teams as Walter continues its mission to promote the Allegro brand across North Amer ica. Maayoufi will support sales team through enhanced training and marketing programs in addition to continue to help customers work better by keeping them safe.
“Jean-Marie brings with him over 30 years of sales experience growing the Walter brand in both Canada and the United States.We are thrilled to see him
take on this new challenge to replicate success for our safety division,” said Mark Wilcox, President, U.S. sales, Walter Surface Technologies.
Jean-Marie Maayoufi joined Walter Surface Technologies in 1991 and has contributed to the brand’s growth for over three decades. He has held several sales leadership positions in both Canada and the U.S. and has contributed to the growth of Walter’s family of brands.
Blackline Safety Corp., a company that specializes in connected safety technology, announced a four-year contract valued at $2.7 million with a major U.S. upstream energy company headquartered in Houston, Texas.
The company selected Blackline to provide over 800 G7c cloud-connected wearable safety devices, 40 EXO
cloud-connected area monitor s, and 75 G7 Docks.
The decision to upgrade was driven by the company’s dedication to safety and need to better protect their workers — especially those working alone — by ensuring consistent, reliable cellular coverage across a vast geographic area. The features include SOS latch, fall and no motion detection, push-totalk, and real-time connectivity.
“The customer evaluated Blackline’s connected safety devices in comparison to products from their long-term supplier. It took less than a week for G7c to stand out for its broad connectivity range, and the ability to see where their lone workers might be in imminent danger so they can make sure their people are safe,” said Sean Stinson, President and Chief Growth Officer, Blackline Safety. “The company was also impressed with the EXO area monitor’s ability to monitor rigs, tank batteries, and wellsites during repair and maintenance operations.”
G7 Dock is Blackline’s simple solution to calibrating, bump testing
and charging G7 devices without any complicated ethernet or Wi-Fi connection requirements. This new deal provides protection for over 800 workers so they have the confidence to do their job and get home safe at the end of their day.
“We unseat the competition because Blackline products set the standard for the safest lone worker solution on the market,” Stinson said. “We’ve innovated a stagnant industry and elevated the bar to keep workers safer than they have ever been.”
All Material Handling (AMH) has added the Cartec series of lifting points and rotating hoist rings to its product portfolio, “ensuring that riggers have easy access to the right tools for the job when it’s a non-standard load.”
Peter Brettner, CEO of ‘below the hook’ equipment supplier All Material Handling, said, “Whether on a construction site, in a machine shop, or at a manufacturing facility, there are two primary goals: move the load without damaging it; and make it home safely at the end of your shift.
“We’re still seeing a lot of incorrect use of eye bolts in particular.Traditional eyebolts are best used for straight in-line lifts only, or they incur a significant reduction in the working load limit. The old school alternative was often to wrap a round sling around the load and see how it went, but frankly both can be an accident waiting to happen.”
While a sling and some hooks are usually suitable for a standard lift with easy connections such as a shackle and welded eye or plate, a non-traditional lift like a largae motor or a flat gear can be much more challenging. In these cases, AMH recommends rotating hoist rings, as they are specifically designed to lift from the focal point and keep the load centered – traditional eyebolts can tend to sideload.
“Using the right swivel hoist ring and rotating eyebolt means there is no more second-guessing the reduced working load limit of a standard eyebolt because it is not an inline pull. The load limit is easily checked as it’s forged into the product and doesn’t change,” added Peter.
“There is also no more shimming the shoulder to get a proper lift angle, which can happen with traditional eyebolts – or worse, risk having lousy positioning and causing a failure. Contractors are increasingly focused on enhancing safety. While a swivel eyebolt has a slightly higher price than a standard eyebolt, this is nothing compared to the human and financial cost of an incident that causes injury or even death.”
Trivium Packaging has retained its Platinum status for its third consecutive year, the highest ranking in the 2024 EcoVadis sustainability ratings.
EcoVadis’ platinum award reflects demonstrated improvements and contributions towards sustainable growth in the past year, with high scores in the Environment, Labour & Human Rights, Ethics, and Sustainable Procurement categories, including a rating of “outstanding” in the Environment category.
EcoVadis, a provider of business sustainability ratings, awards the Platinum honour to the top one per cent of over 100,000 participating companies assessed globally, spanning over 175 countries and 200 industr ies.
“We are honoured to receive the prestigious ‘Platinum’ sustainability rating from EcoVadis for a third consecutive year. It is a testament to Trivium Packaging’s unwavering commitment to our Environmental, Social, and Governance (ESG) responsibility in packag ing and all levels of our business,” said Michael Mapes, CEO, Trivium’s. “This recognition underscores our dedication to dr iving positive change in the packaging industry and reinforces our belief that sustainable practices are integral to our business success.”
“Now more than ever, the bar has been raised,” said Jenny Wassenaar,
Chief Sustainability Officer, Trivium. “This achievement, awarded by EcoVadis, is a testament to the work we’ve sought to achieve at Trivium and the long-term investment we’ve put into sustainable practices. Through our dedication to driving a positive and transparent sustainability impact, we aim to inspire others to join the continuous improvement processes that suppor t our customers, our plant, and our people.”
The EcoVadis rating system scales from Bronze to Silver, Gold, and ultimately Platinum – which recognizes the top one per cent of all companies assessed over the last 12 months who are leading the way in ESG standards.
LEADERSHIP
Daedong-USA Inc., the U.S. subsidiary of Daedong Corporation, appoints Chiwhan Yoon as executive vice -president and deputy CEO to its North American machinery brand, KIOTI Tractor.
“The equipment sector continues to rapidly evolve, and as we look to the future, we have aligned our vision to ensure Daedong and KIOTI Tractor are leading the industry. The organizational changes reflect this shift in strategy and our commitment to long-term growth,” said Peter DongKyun Kim, president and CEO of Daedong-USA Inc. KIOTI Tractor Division. “Chiwhan will be integral in bringing this vision to life, and we are excited to have his expertise helping guide the future of KIOTI Tractor.”
Yoon boasts more than 28 years of international success across a range of industries, including automotive,
financial services, and consulting. He held roles at notable international companies, including Hyundai Motor Group, Kearney, PwC Consulting, and LG Uplus Corp.
As executive vice-president and deputy CEO, Chiwhan Yoon is responsible for strategic planning, operational oversight, business growth, product & par ts service support, captive finance development, and profitability.
“I am excited to join KIOTI during this important moment in the brand’s history,” said Yoon. “As we move toward this vision as a total solution provider, I look forward to driving new products, platforms, parts service transformation, and financing solutions that address the top challenges our dealers and customers face.”
FedDev Ontario invests nearly $2.4 million to help three innovative food companies scale up and create 56 skilled jobs
Filomena Tassi, Minister responsible for the Federal Economic Development Agency for Southern Ontario (FedDev Ontario), along with Iqwinder Gaheer, Member of Parliament for Mississauga–Malton, visited Coco Bakery, a Mississauga-based French pastries manufacturer, where they met with employees and announced an investment of nearly $2.4 million towards the growth of three southern Ontario food manufacturing companies: Coco Bakery, Metzger Meats and Al-Shamas Food Products.
Ontario’s food and beverage manufacturing sector is vital to the Canadian economy. The sector is the third largest in Nor th America with annual revenues of more than $48 billion and employing over 104,000 people. This investment will help these three companies adopt new equipment, increase their manufacturing capacity and create 56 jobs across southern Ontario.
The Government of Canada supports the diverse, hardworking manufacturers in the food industry so they can g row, scale up and reach their full potential. Today’s announcement is part of the Government of Canada’s plan to work with Canada’s largest grocery chains, food processors and other industry actors—both domestic and international—to stabilize food prices in Canada. The Government of Canada is continuing its work to stabilize grocery prices, build more homes and make life more affordable for Canadians.
“Investing in southern Ontario’s food manufacturers and the businesses that support them is integral to ensuring that high-quality food reaches grocery store shelves and families across the country.Today’s investment of nearly $2.4 million will support three businesses as they showcase the abilities of our local food manufacturers, while also creating good jobs, and contributing to a strong southern Ontario economy.” said Filomena Tassi, Minister responsible for the Federal Economic Development Agency for Southern Ontario.
“Our food manufacturing sector is critical to the well-being of our residents and communities. This announcement will support our local businesses as they grow and strengthen their manufacturing capacities and compete in global markets, while creating valuable jobs.” said Iqwinder Gaheer, Member of Parliament for Mississauga–Malton.
The NGen-supported project will enable the integration of CarbiCrete’s decarbonized concrete technology into a masonry plant in Port Colborne.
CarbiCrete, a firm in the decarbonization of concrete has announced that NGen – Canada’s Global Innovation Cluster for Advanced Manufacturing
– will provide funding for the integration of CarbiCrete’s cement-free concrete technology into a masonry plant in Port Colborne, Ontario that is owned and operated by project partner Canal Block.
NGen will contribute $3 million toward an $8 million project to design, build and install a system that incorporates CarbiCrete’s latest curing technologies into Canal Block’s concrete block-making operations
CarbiCrete’s patented process for making concrete products replaces cement in the concrete mix with a steel-making by-product, avoiding cement-related emissions. CarbiCrete products are then cured with carbon dioxide, which is mineralized and permanently removed from the atmosphere. The technology is currently being deployed commercially in Quebec by hardscape manufacturer Patio Drummond, after two successful NGen-funded projects.
“Consumers in Quebec can buy cement-free concrete blocks made with our technology today,” says Chris Stern, CarbiCrete’s CEO. “And so, I’m very excited that through our partnership with Canal Block, we will be able to offer the same to builders in Ontario. We are tremendously grateful for NGen’s continued support, which is helping Canada position itself as the undisputed world leader in low carbon concrete.”
“Canal Block has had a long history of developing sustainable products for the masonry industry,” says Durk Bylsma, Canal Block’s president. “We are excited to partner with CarbiCrete to bring this truly revolutionary technology to market and further our commitment to be an ecologically and socially responsible manufacturer.”
Last Fall, CarbiCrete attained a number of key milestones, announcing
that it received third-party validation that its process is carbon-negative, that CarbiCrete products available on the market meet ASTM C-90 performance requirements, and that it had entered into an agreement with Lafarge Canada, for the processing of steel slag, its alternative concrete binder.
In total, improvements will boost the airport’s cargo capacity by 160,000 tonnes, representing a $22 billion increase to Canada’s trade potential annually.
The Government of Canada is investing up to $74.3 million under the National Trade Corridors Fund for an expansion at the Vancouver International Airport. This will equip the air port to handle more cargo, as well as improve its facilities and efficiency, and reduce pollution.
This project will enable the movement of larger aircraft between cargo f acilities and the runway. It will:
• increase parking space capacity to accommodate four additional widebody freighter aircraft;
• upg rade an access road; and
• prepare the site for the construction of a new air cargo warehouse.
“We’re improving our supply chains through this project by increasing capacity to handle higher air cargo volumes and improve efficiency at the Vancouver International Airport, while reducing pollution,” said Pablo Rodriguez, Minister of Transport.
This project will support business growth of Canadian carriers, including Air Canada, WestJet and Cargojet.
It is estimated that the project will reduce truck travel by up to 229 million kilometres over 30 years because local exporters will not need to transport their products to an airport further away. This will improve highway safety and reduce GHG emissions.
The goods exported through Vancouver International Airport support key economic growth in sectors such as advanced manufacturing and pharmaceuticals. In addition, traditional sectors such as agriculture and fisheries need reliable air cargo export shipments to ensure perishable items can reach global markets in a timely manner.
Air Canada have announced an agreement with seven colleges across Canada to provide financial assistance to students who self-identify as women or visible minorities who are looking at a career as an Aircraft Maintenance Engineer (AME).
“Air Canada is committed to fostering the next generation of AMEs and we are proud to collaborate with these schools from across Canada,” said Joshua Vanderveen, Vice President of Maintenance at Air Canada. “This scholarship is in addition to other programs we have in place, such as workplace integrated learning, and will help traditionally under-represented students move forward with their education in this exciting, professional STEM field.”
The seven schools are the British Columbia Institute of Technology and BC’s Northern Lights College, École Nationale d›Aérotechnique in Quebec, and Centennial College, Fanshawe College, Canadore College, Mohawk College and Northern Lights College, all of which are in Ontario. One student from each school will receive a $1,500 scholarship to assist with education costs. Those awarded the scholarship will also be offered an opportunity for a work placement with Air Canada Maintenance.
“Today’s AMEs are highly skilled people who require technical expertise, critical thinking skills, effective, collaborative problem-solving abilities in working with some of the most complex and advanced commercial aircraft,” said Vanderveen. “Through initiatives like this, Air Canada is working to help the Canadian aviation industry continue developing skilled AMEs to support commercial flights.”
Women and minorities are typically underrepresented in the aircraft maintenance field – in 2022, Transport Canada noted that only 2% of licensed AME are women. The US Bureau of Labor Statistics reported that 89.3% of aircraft mechanics and service technician were Caucasian in 2021. Air Canada’s agreement with the colleges lasts three years, there is no word on whether they intend to continue the scholarship beyond that.
– by Matt JonesKelowna-based KF Aerospace have won the maintenance contract for the Royal Canadian Air Force (RCAF)’s new surveillance planes. The federal government announced
Air Canada will provide $1,500 to AME students at seven Canadian
plans in late November to replace the Lockheed CP-140 with the Boeing P8-A Poseidon. The cost for the planes runs just shy of $6 billion, part of an over $10 billion deal being negotiated with Boeing.
It is said that the deal will create an estimated 3,000 new jobs, though with many of the details not yet finalized, it is unclear where those jobs would be located or what specific maintenance services will be provided.
“The jobs we will be adding will be highly skilled labour jobs,” says KF Aerospace spokesperson Matt Stone. “Mostly aircraft maintenance engineers that are the backbone of our workforce. They are high quality jobs.”
The P8-A will be used for “anti-submarine and intelligence, surveillance, and reconnaissance,” according to the Department of National Defense. The first plane is due to be delivered in 2026, at which point KF Aerospace’s work will begin. KF Aerospace have decades of experience working on civilian Boeing models, though never before for military applications.
“KF Aerospace’s growing relationship with the Boeing Company has led to more high-quality jobs at our company and increased economic benefits around our operations in British Columbia and Ontario,” said company CEO Tracy Medve in a media release. “This partnership empowers us to increase the skills of our workforce while continuing to establish our company as a leading Canadian aerospace firm and extend our global reach.”
With this agreement, Canada becomes the final member of the Five Eyes Intelligence alliance to adopt the Boeing P8-A, following the United States, the United Kingdom, Australia and New Zealand. Defense Minister Bill Blair noted in a news conference that the P8-A is ‘not only the right choice, but frankly, the only choice.’
– by Matt JonesThe governments of Alaska and Yukon have come to an agreement on highway maintenance. During Alaskan Governor Mike Dunleavy’s February visit to Yukon – his first official visit since becoming governor five years ago – a memorandum of understanding was signed between Dunleavy and Yukon Premier Ranj Pillai.
“By working cooperatively with our neighbors in the Yukon, we can help ensure that people traveling to or from Alaska on the road are able to do more safely with fewer road hazards,” Governor Dunleavy stated to media during the visit.
The result is the Alaska Highway Yukon Territory Permafrost Repairs Project (wisely refer red to simply as ‘the Project’ in the MOU, side-stepping the unwieldy AHYTPRP acronym), which will see Alaska provide the funding for road repairs that will be car ried out by Yukon on the stretch of highway on the Canadian side leading to the Alaskan border. The vast majority of cars that use that highway are Americans driving to and from Alaska.
Since 1977, repairs and maintenance of the Alcan (Alaska-Canadian) Highway have been funded through a US-Canadian highway construction funding accord called the Shakwak Agreement. However, with road conditions on the highway deteriorating due to thawing permafrost and other impacts, a new agreement was required.
‘The Project’ will be included in Alaska’s 2024-2027 Statewide Transportation Improvement Program, supported by Alaska’s appor tionment funding. The funding will be
made available on a reimbursement basis.
“By working together and pursuing common goals, we aim to shape a future of shared opportunities for our region,” said Premier Pillai. “This visit signifies a key milestone in strengthening our relationship, fostering a collaborative path towards a more interconnected future for both Alaskans and Yukoners.”
An Intergovernmental Relations Accord, aimed at information sharing and fostering further cooperation, was also signed.
– by Matt JonesABB and CERN, the European laboratory for particle physics, have identified significant energy-saving potential through a research partnership focused on the cooling and ventilation system.
The study included energy efficiency audits which have helped to identify a savings potential of 17.4 percent across a fleet of 800 motors.
The research, conducted between 2022 and 2023, followed an agreement between ABB and CERN. This saw the partners developing a roadmap for reducing the energy consumption of the site’s cooling and ventilation system via data-driven energy efficiency audits. It has identified potential annual energy savings of up to 31 gigawatt-hours (GWh). If achieved, these savings could be enough to power more than 18,000 European households and could avoid four kilotons of CO2 emissions, the same as planting over 420,000 trees.
Energy efficiency audits work by evaluating the performance and efficiency of motors based on their operational data. Audits help large f acilities like CERN to identify the most significant energy saving opportunities across whole fleets of motors. CERN and ABB experts assessed a wide variety of data from motors in various cooling and ventilation applications. They combined data from multiple sources, including digitally-connected motors, CERN’s SCADA system and data gathered directly from their pumps, piping, and instrumentation. The experts analyzed the efficiency of the whole system to provide insights to pinpoint the motors with the best business case for energy efficiency upgrades.
“We are proud to cooperate with CERN and support its ambition to conduct physics research with a low-carbon footprint, by helping them to achieve more energy-efficient operations of their cooling and ventilation
systems,” said Erich Labuda, President of the Motion Services division at ABB. “This research project represents another step in CERN’s energy efficiency journey. As an institution with a large installed base of motors, working with CERN is a great example of how we can support in making a big impact in improving energy efficiency.”
Giovanni Anelli, Head of the Knowledge Transfer group at CERN said, “The collaboration with ABB was set up with the aim
of optimizing the laboratory’s cooling and ventilation infrastructure to reduce its energy consumption and is in line with CERN’s commitment to minimize its environmental footprint.”
CERN’s next step is to create a roadmap for the upgrade of the first motors to the solutions recommended as part of the energy efficiency audit: IE5-rated Synchronous Reluctance Motor s operating with variable speed drives.
While young workers are busy thinking about starting their new summer jobs and others are re-joining the workforce, they may not realize that their “newness” could affect their safety and health. As an employer, you have the responsibility to create and foster a safe and healthy work environment to protect all your workers. Make sure you have a comprehensive orientation program in place and communicate the importance of health and safety roles and responsibilities to your new workers. Providing the right orientation sets the tone for the workplace and ensures that your workers are starting on safe footing.
New workers are different from young workers in that they are not necessarily entering the workforce for the first time. They could be returning to work after an absence such as a health-related leave or an injury, and it’s possible that conditions and procedures have changed. Or they could be working for the same company, but in a new role or location. As a result, they may be facing new hazards for which they are not prepared or adequately trained. These workers should also participate in the orientation program
Providing training and extra assistance during the initial period of employment is critical, regardless of age, as they are not familiar with the hazards of the job or the workplace.
and have an opportunity to review and discuss their work, ask any questions, and receive appropriate training.
Get started with an orientation
Health and safety education starts with orientation when a person joins the organization or is transferred to a new job. Orientation sessions typically introduce workers to the function of the work unit, organizational relationships, administrative arrangements. They should also introduce your workplace’s health and safety policies and rules, what to do in an emergency, and who workers can contact if they have questions or concerns, such as their supervisor and health and safety representative or committee. You must also cover the occupational health and safety laws that apply to the worker and the work being done, as well as the rights and responsibilities of the employer, manager, and workers.
Timely and effective training is also essential when starting a new job. Arrange for handson or simulation training before starting the actual task, mentoring by experienced workers, or apprentice programs. Provide written safe work procedures that are clear, concise, and written in an active voice. Allow practice time and opportunity for workers to ask questions and obtain feedback. Don’t forget to clearly and frequently communicate with the worker about their job tasks and repeat and confir m this training over the first few weeks of work and as needed.
Include both physical and psychosocial hazards in your training. For example, show and allow workers to practice how to safely operate equipment and tools such as fryers or mixers, how to conduct safe lifts, how to work safely with cleaning chemicals or other products, the affects of a noisy work environment, as well as how to respond to harassment, or threats while ensuring their own safety.
Providing training and extra assistance during the initial period of employment is critical, regardless of age, as they are not familiar with the hazards of the job or the workplace. During this period, workers develop the knowledge, skills, and abilities that are necessary to work safely. While training for new workers is always important, it should also be provided when they are transferred to jobs or work areas, they are unfamiliar with, or returning from an extended period away from work.
Not all training can or should be held on the first day. Time sessions to best match the needs of the workplace, the information being shared, and the tasks being done, but be sure all relevant areas and topics are covered before the worker is asked to perform a task.
Employers have an important role in helping any new worker – regardless of age – stay safe on the job. Making time for training that is specific and relevant and keeping the training dialogue open and ongoing will go a long way to protecting your workers from harm.
The Canadian Centre for Occupational Health and Safety (CCOHS) promotes the total well-being — physical, psychosocial, and mental health — of workers in Canada by providing information, advice, education, and management systems and solutions that support the prevention of injury and illness. Visit www.ccohs.ca for more safety tips.
While AI-powered solutions and predictive data analytics tend to dominate the conversation, these technologies are just one component of the ongoing evolution of maintenance. In addition, many organizations are just beginning to build maintenance strategies and aren’t currently prepared to deploy these solutions. Other s have built robust maintenance functions and learned that they don’t need to adopt the latest technology to meet their goals and serve their organizations. Still others have reached the point where integrating new solutions into their existing systems is exactly what they need to g row more proactive and reach their full potential.
A holistic assessment of a maintenance department’s program takes into account its cur rent needs, its performance against goals, and its readiness to embrace innovation. Organizations differ in what they ask of their maintenance depar tments. Ultimately, success is best measured in ter ms of the function’s role within the
45.7%
of all machine maintenance is reactive.
organization. As capabilities evolve, maintenance should shift to a prominent advisory position and be recognized as a critical function supporting the company’s bottom line.
Which maintenance strategies are right for your organization?
Picking the right maintenance strategy isn’t all about striving for predictive capabilities. Different approaches work better for different assets. As such, each organization requires a mix of strategies to manage its assets as cost effectively as possible. Though a purely reactive strategy often means dealing with unexpected breakdowns and excess costs, carrying out proactive maintenance or investing in monitoring tools doesn’t always make sense for every piece of equipment. The decision to invest in more advanced maintenance tools and processes will depend on factors including the cost and business criticality of your assets, the size of your team, and the number of facilities you manage.
The reactive approach to maintenance sees technicians respond to breakdowns as they occur. While more proactive approaches present up-front costs and complications, reactive maintenance proves 30 to 40% more expensive over time due to excess downtime and emergency expenses.
Research from the National Institute of Standards and Technology (NIST) confir ms that 45.7% of all machine maintenance is reactive. That doesn’t mean nearly half of maintenance teams are struggling to keep their assets operational. Corrective work can play a role in an effective maintenance program. For some inexpensive, low-criticality assets it is the most cost effective approach.
Conducting a criticality assessment is an important early step in building and refining a maintenance program. The process offers a data-backed approach for determining which assets demand proactive attention and which ones would cost more to repair than to replace altogether.
PEOPLE: Organizations may opt for reactive maintenance as a result of staffing shortages or skills gaps.
TECHNOLOGY: Reactive maintenance teams typically are not using any dedicated tools for assessing equipment health and performance. It’s possible they’re managing maintenance entirely on pen and paper or spreadsheets. If they’ve invested in advanced technologies without any maintenance management tools in place, they likely aren’t seeing a return on their investments.
PROCESSES & POLICIES: True to the ad hoc nature of their maintenance work, reactive teams may not have standard operating procedures or clear guidelines for safely and efficiently completing repairs.Without SOPs for everyday procedures like issuing work orders and no system for monitoring asset health, reactive teams risk shorter asset lifespans and less productive maintenance functions.
MAINTENANCE’S ROLE: Stakeholders and decision makers across the organization lack the visibility to recognize how maintenance can support their goals. They may view the maintenance function as a cost center rather than a value driver unless they have insights into its potential impact on equipment health, production volume, and overall revenue. As a result, maintenance teams may f ace challenges in advocating for buy-in and additional resources.
Preventive maintenance is the first step in addressing common challenges. A recent survey by Limble found that almost 80% of maintenance professionals are currently leveraging plans and schedules to mitigate unplanned downtime and its costs.
Access to equipment performance data and maintenance work history enables teams to improve PM schedules and implement a highly effective preventive maintenance strategy. A whopping 91% of manufacturers surveyed are looking to evolve their capabilities with tools for data collection and analysis. For many, this means centralizing asset and maintenance management with a CMMS.
PEOPLE: Effective preventive programs include training and on-boarding procedures for introducing employees to new processes and solutions. To make preventive maintenance a reality, managers should strive to introduce a culture of continuous improvement.
TECHNOLOGY: Technology like Computerized Maintenance Management Systems (CMMS) simplify processes like issuing planned work orders, completing preventive
Conducting a criticality assessment is an important early step in building and refining a maintenance program. The process offers a data-backed approach for determining which assets demand proactive attention and which ones would cost more to repair than to replace altogether.
maintenance tasks, and tracking asset health to make preventive maintenance possible. Maintenance teams can automate PM scheduling, create PM templates with SOPs, checklists, parts, and tools, and easily track completion rates in real-time to reduce costly unplanned downtime.
PROCESSES & POLICIES: At the most basic level, preventive maintenance involves proactively planning and scheduling maintenance tasks. Leveraging a CMMS to manage preventive maintenance, empowers teams to optimize PM schedules and standard processes across their assets. The more data a maintenance team has at their disposal, the better their chances are of avoiding unplanned breakdowns.
MAINTENANCE’S ROLE: Through improvements to metrics like Mean Time Between Failures (MTBF), maintenance teams can make a bottom-line impact and begin to build their reputation as a strategic value driver. As the maintenance function builds more and more clout with stakeholders, teams will have an easier time securing buy-in to invest in resources like monitoring technology, new equipment, and additional staff.
Not all maintenance departments are aiming for predictive capabilities. Though a majority of Limble’s survey respondents leverage preventive maintenance, productivity tracking and condition monitoring are f ar less common. Just under a third of maintenance pros reported leveraging IoT sensors to monitor their equipment.
Even in industrial industries, where keeping downtime to a minimum is everything, many organizations have yet to embrace the
most advanced tools. When asked about the new technologies they plan to pursue in 2024, only 33% of manufacturing professionals expressed interest in IoT technology. Fewer than half (45%) of manufacturers are hoping to enhance their maintenance operations with sensors for condition-based planning and scheduling in the next year. As the world of maintenance evolves, these tools will likely become increasingly prevalent.
PEOPLE: As maintenance programs evolve, their talent needs change alongside their solution portfolio. New tools don’t eliminate the need for skilled employees. They should, however, empower your teams to perform more efficiently.
TECHNOLOGY: At this level, maintenance teams are familiar with the impressive timeand money-saving capabilities of CMMS platforms.They’ve leveraged their platform’s data analytics tools to drive improvements and integrated the tools with condition-monitoring sensors and IoT technology.
PROCESSES & POLICIES: Maintenance has integrated its processes with predictive technologies to promote a just-in-time response and keep the cost of their work to a minimum.
MAINTENANCE’S ROLE: Data-backed insights have made maintenance an increasingly valuable business function. Thanks to its impact both inter nally and across the supply chain, it continues to bolster its reputation.
Prescriptive programs not only promote timely maintenance but offer technicians and operators instructions for reducing wear and tear on equipment to avoid breakdowns and maximize each critical asset’s lifetime value.
Though it will be years before AI-powered, predictive tools become common in most organizations, interest in new solutions is high among maintenance teams at all stages. Some of the businesses that are just now seeing the benefits of their CMMS or IoT sensors will evolve into the next generation of early adopters, pursuing more powerful technologies and setting a new standard for maintenance.
PEOPLE: Prescriptive tools can take many data interpretation responsibilities off your plate, but they still require operators with specialized training. Expecting technology to do too much on its own is a common pitfall that leaves professionals struggling to justify their investments.
TECHNOLOGY: Solutions for prescriptive maintenance use advanced algorithms to outline proactive processes for keeping
business assets as productive as possible. This technology augments the capabilities of maintenance teams rather than automating them into irrelevance. The best AI-enabled solutions empower human operators to perform more effectively and spend more time on value-adding processes.
PROCESSES & POLICIES: A wealth of data and prescriptive analytics make it possible to continually refine maintenance’s processes. Maintenance tasks are carefully planned and scheduled to ensure the most critical assets remain as productive as possible for as long as possible.
MAINTENANCE’S ROLE: By mastering prescriptive strategies, maintenance assumes a role as a cross-functional advisor capable of making a significant bottom-line impact.
Asking the right questions about each component of your maintenance program can help you assess your current strategies, identify opportunities for improvement, and start distinguishing the function as an essential strategic ally.
PEOPLE:
• Are team members trained to effectively follow standard processes and leverage the department’s tools?
• Does our culture encourage feedback to drive continuous improvement?
TECHNOLOGY:
• Which tools are the maintenance team leveraging to improve asset management and resource allocation?
• Are we using solutions to their full potential and getting everything possible from our vendor relationships?
PROCESSES & POLICIES:
• What percentage of your maintenance work is planned and scheduled ahead of time?
• How does real-time tracking and historical data help your team maintain each asset in the most cost effective way possible?
MAINTENANCE’S ROLE:
• Do you have KPIs in place for measuring maintenance’s performance?
• Are maintenance’s goals tied to broader organizational objectives?
Maintenance professionals are poised to continue empowering their organizations while serving as a model for labor efficiency and tech-enabled innovation. It all starts
with a more proactive approach to asset management. Here’s a simple guide for beginning to preempt breakdowns and keep equipment operational.
• Set prog ram goals
• Appoint project leader s
• Analyze the criticality of your assets
• Tailor maintenance strategies to each asset
• Implement the right tools
• Develop standard procedures and processes
• Implement your program
• Analyze and improve your program over time
Bryan Christiansen is the Founder and CEP of Limble CMMS, a mobile CMMS software company. He can be reached at bryan@limblecmms.com.
Chances are, you’re already highly aware of the maintenance worker skills gap.
This isn’t a new problem – it’s been around for at least 10 years. But every year, the problem seems to get worse.
Fewer young people are getting the training they need to diagnose and repair machine faults.
Maintenance managers and reliability engineers are seeing the pool of skilled workers get smaller and smaller. Meanwhile, qualified workers are hitting retirement age and leaving the workforce.
More and more plants are turning to technology to bolster their maintenance programs. This begs the question – can digital solutions and vibration sensors fill the maintenance skills gap?
The answer isn’t simple. It’s important to maintain some perspective and stay realistic about what technology
can do. Today’s best tools can’t replace a human workforce. Even with the best technology, you’ll still need human know-how and experience to keep your operation up and running smoothly.
But at the same time, the right connected tools and sensors, coupled with a solid Computerized Maintenance Management System (CMMS), can help you to shift to a predictive maintenance strategy, so that you can identify and diagnose machine faults early. In the not-toodistant future, AI-enabled analysis software will push these capabilities even further. This means that you’ll be able to keep your machines up and running for longer, even if you’re operating with a lean maintenance team. If you manage this process cor rectly, the results can be revolutionary.
Predictive maintenance is a proactive strategy for keeping your assets up and running. It’s premised on the idea that you should only perform the maintenance work on an as-needed basis. Instead of routinely servicing your assets, your maintenance team will monitor them for signs that they need repair.
Predictive maintenance uses a network of vibration sensors that monitor the vibrations emitted by your equipment. They collect and store this data so that it can be analyzed for signs of fault.
Data collection isn’t new, of course. Maintenance teams have always collected data, simply by observing the machines in their plants and keeping track of how they operated.
As plants get bigger and take on more equipment, though, it’s almost impossible for a maintenance team to directly monitor every single asset. That’s why sensors are so important, especially as the pool of skilled workers is shrinking in front of our eyes.
Here’s how a plant can use vibration monitoring sensors, CMMS, and analysis software to make the most of a lean maintenance team.
Step one: Performing triage
On its own, data doesn’t add value to your maintenance team. Raw data needs to be organized and analyzed so that your maintenance teams can start to spot patterns.
CMMS software can integrate with sensors and software tools so you can organize and analyze your vibration data and put it to use.
The first step is simply identifying any change in vibration emissions. Once a machine shifts from its baseline vibration signature, that’s a sign that it needs to be examined more closely.
This stage of proactive maintenance – looking for changes from the baseline – fills the same function as the triage process in a doctor’s office.
In a doctor’s office, nurses perform the first level of triage. They collect data on patients’ weight, blood pressure, and temperature. That’s usually enough to tell them whether a patient is healthy and not in need of care or is in fact ill.
In the same way, your CMMS software uses the vibration data to perform triage on your assets. It scans for signs of anything unusual which could indicate a new or developing fault.
Triage saves your team time, energy, and funds by allowing you to
focus your energy on the machines that actually need to be repaired. You won’t need to waste labor or time on the equipment that’s already running smoothly.
Step two: CMMS, analysis software, and work orders
Vibration analysis software can perform diagnostic tests to identify many common machine f aults.
To date, vibration analysis software can diagnose the four most common faults in rotating machinery, namely, imbalance, shaft misalignment, looseness, and bearing faults.
To continue the hospital analogy, the vibration analysis software is like the primary care physicians who can diagnose patients with common ailments.
And, just as the primary care doctors need to be “called in” by the nurse on duty, the algorithms also need to be called in to start their diagnostic process.
That’s where your CMMS comes in.
You can set up your CMMS to automatically generate a work order once vibration levels deviate from the norm. That work order will trigger software to assess and diagnose the machine in question.
Step Three: Scheduling repairs
Once the software has diagnosed the machine fault, your CMMS can automatically generate a work order to review recommended repair s based on that diagnosis.
The CMMS lets teams review the recommendation, then schedule the work based on when your maintenance teams are available, or when it’s convenient to shut down your equipment for repairs.
Most of the time, vibration monitoring and analysis software will alert you to machine faults long before the problems become serious.
This means that you’ll have plenty of time to schedule maintenance at a convenient point for you.
Shifting to a proactive maintenance strategy doesn’t mean that you won’t need maintenance workers any longer.
Instead, it means that you’ll be able to re-configure your workforce so that you get the best possible work out of everyone on your small maintenance team.
Building a tech-centered approach means considering what you’ll still need from your maintenance team.
In most cases, you’ll need a group of maintenance experts who have the ability to implement a proactive maintenance strategy.That means knowing which machines vibration analysis software is capable of diagnosing, and which machines are too complex. In the future, it will require a similar understand of the limits of AI-enabled vibration analysis software.
If we go back again to our hospital analogy, it’s helpful to think of maintenance experts as the specialists in various medical fields. They can diagnose problems that a primary care physician might not know enough
It’s important to maintain some perspective and stay realistic about what technology can do. Today’s best tools can’t replace a human workforce. Even with the best technology, you’ll still need human know-how and experience to keep your operation up and running smoothly.
about. They can also recommend treatment for these problems.
So, if your machinery has complex faults that AI cannot diagnose, your maintenance experts are on-hand to identify the issues and figure out how to address them.
Bear in mind that you can also outsource the expert level, as needed. If you’re operating with a small maintenance crew, then it’s worth spending some time looking for a trusted partner to advise you on your maintenance needs.
A successful tech transformation should happen gradually.
Too many businesses try to overhaul their whole operation at once. This can lead to chaos and, eventually, disillusionment in the process.
Building this framework of connected sensors and software now will prepare your organization for the day that AI-enabled maintenance software is ready to take these to yet another level.
Instead, it’s a good idea to start with a pilot program.
Choose 10 or 15 simple rotating machines that are prone to breakdowns. Test your proactive maintenance program on those machines alone.
Chances are, these are the machines that have already cost your operation a good deal of time and money. You have the potential to show a major change by introducing technology here.
Building a tech-centered maintenance approach takes an investment of time and money. This can raise challenges when it comes to getting your key decision makers on board.
That’s another reason that it makes sense to introduce the new approach gradually as wins happen and prove results.
Start with a pilot program and then gradually add more machines to your program; it’s a good idea to stick with introducing 10 or 15 new machines at a time in phases.
As your programs succeed, it’ll be easier to get your decision makers excited about expanding it.
CMMS can also help you here. By keeping track of your work orders, CMMS documents reductions in
breakdowns and in maintenance work orders.
If your company has a change in leadership, you’ll be able to use those work orders to show your new boss how successful the new maintenance approach has been. They’ll be able to see that you’re keeping your equipment up and running and that you’ve cut back on routine maintenance costs.
Because ultimately, that’s the goal – decreasing downtime, increasing productivity, and making sure that you’re not overspending on unnecessary maintenance. And that’s what a carefully designed predictive maintenance program can deliver.
Building this framework of connected sensors and software now will p repare your organization for the day that AI-enabled maintenance software is ready to take these to yet another level.
As a mechanical application and product specialist with Fluke Reliability, home to eMaint CMMS, John Bernet works with customers from all industries to successfully implement their reliability programs. He has more than 30 years of experience in the maintenance and operation of commercial machinery and as a nuclear power plant electrician in the U.S. Navy. He holds a Category II Vibration Analyst certification and is a Certified Maintenance Reliability Professional (CMRP).
There are two fundamental methods that can be used to carry out this practice; the first is to establish routes through the plant where technicians can monitor critical equipment by obtaining oil samples, monitoring ultrasound, vibration and temperatures. The second method is to install transducers or other data collection technologies to monitor equipment condition automatically on an ongoing basis. The data collection transducers are mounted near or on critical equipment components such as bearings and data is collected continually where maintenance specialists or operators trained in the interpretation of the conditions can monitor critical machinery or it’s components on a regular basis.
In either case the plant or organization can use the P-F Curve principle to respond to any machine or condition that requires attention. The P-F Curve illustration below highlights condition monitoring technologies and as the curve from point “P” to point “F” illustrates, each technology used might indicate a problem is occurring and corrective action should be taken based on the priority in the curve.
Let’s consider the actions one might use based on the P-F Curve.
Q | How does your maintenance group respond to a problem where ultrasonic energy is detected?
LOGIC: ultrasonic energy detects liquid or gas leaks moving from high pressure. The intensity of the ultrasound measured in decibels (dB), will be loudest at or near the leak
site. Ultrasonic leak detection can be used to detect internal hydraulic leaks, such as oil passing through a closed control valve, engine manifold vacuum leaks, steam traps, air brakes, leaks in seals, heat exchangers, boilers, chillers, vacuum systems, compressor valve operation and warning of bearing failure. An 8 dB increase over the baseline indicates a lack of bearing lubrication or a tiny crack or spall. A 12dB increase indicates potential failure. A 16 dB increase indicates an advanced failure, while a 35–50 dB gain indicates a potentially catastrophic failure. A base line ultrasound level must be established for each bearing, if comparative ultrasonic readings are to be effective. Arcing, tracking and corona discharge of cer tain electrical systems do not generate heat and ultrasonic testing can be more effective than thermographic imaging. Ultrasonic devices can be connected to a grease gun and used to determine when a sufficient amount of grease has been applied to the bearing.
Q | How does your maintenance group respond when a machine vibration is detected?
LOGIC: every piece of equipment contains moving parts, each of which will vibrate at certain frequencies. These frequencies are generated by the vibration sources and will vary across a wide spectrum. Common sources of vibration are unbalance, misalignment, bent shafts, defective bearings or gears, mechanical looseness and electrically induced problems. Technically defined, vibration is the oscillation of an object about its position of rest and the number of these
oscillations (or cycles) in a given length of time, is referred to as the frequency of vibration measured in cycles per minute (CPM), or cycles per second hertz (HZ). The amplitude of vibration is measured in displacement (distance or movement), velocity (speed) and/or acceleration (force), of the source of the frequency. Using an FFT (fast Fourier transform) analyzer, vibrations can be measured and displayed in either a time waveform, indicating vibration severity, or a spectrum analysis, illustrating the frequencies of the various sources of vibration.
Q | Does the maintenance group include a lubrication specialist who understands oil analysis report interpretation?
LOGIC: oil analysis should be carried out on every piece of lubricated critical equipment on a regularly scheduled basis when the oil is hot and well-circulated, either by obtaining samples physically or using monitoring devices mounted on lubricated components. Benefits include monitoring component wear rates, viscosity, alkalinity, acidity, additive levels, contaminant types and their sources, including determining optimum drain intervals and remaining lubricant quality. Oil viscosity is reported in CST at 40 and 100 degrees C respectively for multi-grade oils that have a tendency to shear and viscosity changes of 15 per cent or more should be investigated immediately. Water must be monitored carefully depending on the type of equipment. A “trace” of water is about 0.1-0.2 per cent or 1000-2000 PPM. It is a mistake to ignore this much water in certain recirculating systems with high oil flow rates and turbulence that may experience foaming problems with as little as 100 PPM of water. In systems that contain bronze components, too much water can cause severe corrosion. In systems that use biodegradable oils, control of water is critical to the life of the oil. The Karl Fischer water test must be part of any effective oil analysis program.
Oil degradation conditions can also be measured by infrared scan. This test reports soot levels, nitration, oxidation, additive levels and other conditions that affect the oil’s ability to properly lubricate. Oxidation stability can be tested using the RULER “remaining useful life test” to assess the remaining life of turbine and hydraulic oils. Acid number (AN)
is a measure of acidity based on ASTM D664 and should be monitored in critical hydraulic, gear drive, turbine, compressor and natural gas engine oils. Accepted recommendation is to replace the oil when the AN “doubles” that of new oil specifications. Base number (BN) is a measure of the reserve alkalinity remaining in diesel engine oils and is related to the detergent/dispersant ability to counteract acids based on ASTM D2896, providing accurate results of BN that decreases as oil nears the end of service life. The oil should be changed when the BN is reduced by ½ that of new oil. (Oxidation rates increase as temperatures increase, while nitration rates increase as temperatures decrease).
Q | Does the lubrication specialist know the metallurgical makeup of the equipment components and the purpose of the additives in the oils that are in use?
LOGIC: In order to avoid confusion and unnecessary reaction it is critical that someone in the maintenance organization is aware of these considerations to ensure proper interpretation of oil analysis reports.
How does the maintenance group monitor dirt and dust contamination to determine filter quality? Effective contamination monitoring requires the use of particle counts as par t of ISO 4406 standards.
Q | Does the maintenance group use preventive maintenance tasking to effectively cover priorities two and three?
LOGIC : Sound , well planed preventive maintenance is used for machine problems in these categories and equipment not critical to the operation can be run to failure, depending on replacement cost
Using condition monitoring ultrasonic and vibration analysis combined with the most effective oil analyses, in combination with temperature monitoring , will effectively provide downtime scheduling , avoidance of unnecessary repairs , shorter repair times , improved planning for operations and maintenance activities, consistently provide accurate equipment condition trending , improved monitoring of maintenance tasks , while offering guidance for continuous equipment reliability improvement.
In summary; to properly establish an effective condition monitoring program it is first necessary to determine the critical machines to which the program is applied. The next step in the process is to apply all of those condition monitor ing technologies that will be most effective at providing the best and most complete condition information that applies to specific critical machines. For example, ultrasound and vibration analyses must be applied to rotating equipment, while both oil and vibration analyses and ultrasound should be applied to all critical rotating machines that use lubricants of any quantity Infrared thermography and oil analyses should always be applied to equipment like transformers that contain oil
L. (Tex) Leugner, author of Practical Handbook of Machinery Lubrication, is a 15-year veteran of the Royal Canadian Electrical Mechanical Engineers, where he served as a technical specialist. He was the founder and operations manager of Maintenance Technology International Inc. for 30 years. Tex holds an STLE lubricant specialist certification and is a millwright and heavy-duty mechanic. He can be reached at texleug@shaw.ca.
Founded in 1988, Cameco Corporation, headquartered in Saskatchewan, Canada, is the world’s largest publicly traded uranium company — and one of the global leaders in uranium production. Cameco produces uranium to fuel nuclear reactors in Canada and internationally. It owns mines, mills, and fuel production facilities in Canada, the United States, and Kazakhstan. The Cigar Lake Mine site, located in northern Saskatchewan, began commercial operation in 2015. It employs some 530 staff and contractors and has repeatedly received safety awards.
Initially, the Cigar Lake Mine site was looking for one solution to a fundamental problem: a fast and easy way to pull multiple documents from multiple sources and have them all printed out with the work order from SAP. Collating these documents ensured maintenance teams were best prepared before commencing maintenance work.
However, after implementing Prometheus planning and scheduling for their enterprise resource planning (ERP) system, SAP, they quickly realized they could use the solutions to overcome other challenges. For instance,
they were managing the status of materials and components or producing compliance reports to regulatory bodies.
Overall, Prometheus Group unlocked new ways to create efficiencies while maintaining or exceeding their already high standards for safety, environmental protection, quality, and accuracy.
• Collecting maintenance documents from various sources to print with the work orders to better equip their maintenance crews
• Gaining visibility into the interdependencies between jobs on and off the cr itical path
• Simplifying and streamlining daily tasks with user-friendly dashboards, tools, and functions that put an end to repetitive data entry work
• Forecasting planned outages as well as regular maintenance activities
The Cigar Lake site has used Prometheus planning and scheduling for SAP since 2012. They fully leverage the powerful Navigator
[now Dashboard] and enjoy how it drastically simplifies SAP for work management. Now, all the maintenance supervisors have their own configured Navigator that acts as their cockpit for business management.
It has become so popular that it has extended outside of the maintenance team and into many operations groups.The operations teams leverage [Dashboard] for work request approvals, backlog reviews on their assets, and even auto-generating regulator y inspection reports.
Another area where Cameco has found time-saving efficiencies and improved accuracy is by leveraging material shopping cart. Floor-level and front-level supervisors use it to locate materials and components, see in real-time what is and is not in stock, and add materials to work orders while continuing to execute work.
“You don’t have to use wildcards.You don’t have to get your search terms in the exact right order or the perfect wording,” said Kris Halland, senior planner of maintenance at Cameco. “Material Shopping Cart saves you time and frustration by consolidating SAP searches into one function. It’s about as close to a Google search as you can get.”
Most recently, they have started working with Prometheus Group’s Extended Functionalities (XF) package to track, manage, and forecast maintenance shutdowns and turnarounds. Previously, it was a challenge to identify and monitor the maintenance tasks along the critical path, as well as “float” work that could potentially interfere with completing the shutdown on time.
When Cameco adopted the Prometheus Group solutions, they had a small scope of goals they wanted to achieve. Since implementing the tools, they’ve achieved a range of process improvements, created numerous efficiencies, and enhanced what their planners and schedulers can do.
Cameco staff are saving many hours in the day by streamlining planning and scheduling processes – without sacrificing the quality of work. Prometheus Planning & Scheduling is designed to take labor-intensive, repetitive tasks and automate them.
“It can be time-consuming to do tasks such as entering selection criteria for SAP variants,” said Halland.“But now we can do that in just one click. Or for example, scheduling 200 work orders. Where that used to take 20 minutes, now I can do that in under 30 seconds with the mass change function. And all these small-time savings add up to a lot of hours re-gained that we can spend more productively.”
The various teams now have clear visibility into maintenance work on and off the critical path. This means supervisors can proactively anticipate issues before timelines are derailed. As Halland noted, “We can keep track of the forest and the trees.” Teams have the visibility they need to monitor schedules and individual jobs in their own context but quickly and easily see how they fit into the bigger picture of next week, next month, and so on.
The visual way that planning and scheduling presents data enables planners, schedulers, supervisors, and even maintenance technicians to understand the working relationships between various jobs – rather than seeing jobs in isolation. Understanding these interdependencies means they can coordinate, sequence, and execute work effectively so that work is always done in the right order at the right time.
Maintenance supervisors use the solutions to do work assignments and dispatching, using the drag-and-drop functionality. “It’s possible to do some of this work in other tools, but it isn’t always fast or intuitive. The Prometheus Group solutions opened up new avenues for us,” said Halland.
Cameco has big goals, and Kris and his team are committed to continuous improvement. They continue exploring new ways to improve their processes and leverage every feature of planning and scheduling for SAP.
And when they have questions, they know help is just a phone call away.
“Prometheus Group has ‘old-fashioned’ customer relations — in a good way,” said Halland. “When we need something, we don’t have to submit a ticket and wait through a long, drawn-out process to solve a simple problem. I pick up the phone, and there’s someone to help. The Prometheus
Group team is there, ready to have those conversations.”
“We’ve seen a massive number of small improvements across all areas that add up to huge time savings. For instance, with one-click scheduling, what used to take 20 minutes now takes 30 seconds. Suddenly, you have more time to get more done and to do an even better job.” said Halland.
Are you a tech employee helping a manufacturing plant adopt a 3D digital twin? Learn about some fascinating ways these offerings can enhance visibility and strengthen decision-making across production facilities of all sizes and types.
Software engineers and other tech professionals are increasingly in demand due to the exper tise they can offer manufacturing clients regarding 3D digital twins. Operating a successful manufacturing business requires dealing with times of uncertainty. Although a 3D digital twin can’t eliminate that reality, it can give users more visibility, allowing them to try specific options before committing to them in real life.
Making confident manufacturingrelated construction investments
Manufacturers occasionally must make decisions about expanding their factories or moving to new, larger sites. Both those changes are often vital for enabling producers to meet new marketplace demands, especially if some plans involve making more products or lengthening assembly lines.
As a 2024 manufacturing industry outlook found, spending for construction-related needs has risen significantly over the past several years. That trend has often occurred while legislators have introduced packages
to decrease inflation’s strain or encourage manufacturers to build new factories to combat shortages of essential products, such as semiconductors.
Some companies offer 3D digital twin tools that can make models ranging in specificity from entire cities to single properties. User s can study factors such as local infrastructure suitability, ease of access to factory facilities and proximity to universities, residential communities or other amenities that could affect the manufacturing plant’s ability to attract employees.
Suppose a manufacturing leader intends to open a new facility or expand an existing one. In that case, they may need to operate according to limitations associated with local waterways, protected nature areas, public parks and other local aspects. A 3D digital twin can aid them in meeting such requirements, greatly reducing the chances of mandated rework, denied permits or other complications.
Many manufacturing leaders are increasingly considering how worsening climate change could affect their businesses, such as by making storms and temperature extremes happen more frequently. However, a 3D digital twin makes approving proactive options in a new or expanded manufacturing building much easier, helping manufacturers mitigate environmental effects.
Changing consumer tastes and rising living costs are a few of the societal trends that can cause slumps, even if manufacturers recently went through comparatively profitable periods. New marketplace entrants can also cause competitive shakeups. People may be curious about an unfamiliar brand that seems better or comparable to something already in the market.
These realities mean manufacturers must continually explore ways to innovate, whether by improving existing products or launching new ones. Sometimes, manufacturing effor ts in these areas directly respond to consumer needs. When people in the target market feel understood, valued and catered for, they’ll be more likely to stick with the manufacturers and brands they know well — even when new options become available.
Some consumers expect brands to frequently push the boundaries, too. Many tech companies are excellent examples. When the newest laptop or smartphone gets released, loyal customers eagerly scan the specifications, looking to see how those models compare to previous options.
Some entire product categories demand innovation, too. For example, electric vehicle makers rely on digital twins to predict how their creations will perform in real-world
environments. In addition to helping determine a model’s range, safety, aerodynamics and other f actors, digital twins can optimize manufacturing processes and design m eetings. When those outcomes occur, automakers are well-positioned to release high-performing, visually enticing cars faster than competitors can.
A 3D digital twin can also reduce waste that happens once products leave factories. People have used digital twins to monitor temperature changes for perishable products, determining which factors make the goods spoil faster. Better resource usage through loss prevention supports competitiveness.
Using 3D digital twins to improve factory layouts
3D digital twins also aid manufacturers in creating or enhancing factories to make them meet current and future needs. Factories are perpetually busy places, so traffic bottlenecks, poorly placed equipment or overly narrow aisles can all make those environments fall short of their productivity potential.
Some technology solutions turn 2D and 3D sensing data into three-dimensional
digital twins. The highly detailed models facilitate manufacturers in proceeding with robotic path planning, the placement of new connected machinery or the addition of new internal storage areas.
Well-planned factory layouts give manufacturers more flexibility to accommodate changing needs. They might need to hire more team members, install a production line for a new product or launch an on-site repair service as a customer perk. Conversely, when people rush layout planning or hardly consider it, the environment could contribute to injuries, wasted time and frustration for everyone working in it.
A 2023 study found dig ital twins could shorten the time to design industrial floor plans and create more effective factories. One important conclusion related to accurately mapping physical assets to digital mo dels, ensuring the two closely reflect each other.
The researchers envisioned cases whereby the digital twin updates as the real-world environment changes. When that happens, leaders have pertinent information to shape decision-making and optimize internal processes. The digital twin’s data could also
aid in answering challenging questions. For example, what impact would moving an assembly line a few feet to the right have in promoting smoother movement of pedestrians and vehicles around the factory?
A dig ital twin can also identify the root causes of identified problems. For example, is the current facility really too small? Might strategic layout changes make it feasible to keep operating in the space for the foreseeable future?
Setting aside ample time for learning how to use 3D digital twins and become familiar with their primary features will also help manufacturers succeed. Although these offerings are relatively new, many vendors offer in-depth support, ensuring customers can maximize their investments.
Finally, people involved in designing or otherwise working with digital twins must think about the barriers these technologies will help a manufacturing plant overcome. When a facility operates smoothly and accommodates changing needs, the company will likely thrive in a challenging marketplace.
As the world’s largest retailer, Walmart Stores is on a mission to determine the social and environmental impact of every item it puts on its shelves. And it has recruited scholars, suppliers, and environmental groups to help it create an electronic indexing system to do that.
The idea is to create a universal rating system that scores products based on how environmentally and socially sustainable they are over the course of their lives. Consider it the green equivalent to nutrition labels
Walmart plans to begin by asking its more than 100,000 suppliers around the world to answer the following 15 simple questions about the sustainable practices of their companies. Here is an opportunity to see if you answer them about your organization.
Reduce energy costs and greenhouse gas emissions
1. Have you measured your corporate greenhouse gas emissions?
2. Have you opted to report your greenhouse gas emissions to the Carbon Disclosure Project (CDP)?
3. What are your total greenhouse gas emissions reported in your most recently completed report? (Enter total metric tons CO2e, e.g. CDP6 Questionnaire, Section 2b – Scope 1 and 2 emissions)
4. Have you set publicly available greenhouse gas reduction targets? If yes, what are those targets? (Enter total metric tons and target date; 2 fields or leave blank)
Scores will be automatically calculated based on your participation in the packaging scorecard in addition to the following:
5. If measured, please report total amount of solid waste generated from the facilities that produce your product(s) for Walmart Inc. for the most recent year measured. (Enter total lbs)
Have you established publicly available sustainability purchasing guidelines for your direct suppliers that address issues such as environmental compliance, employment practices, and product/ ingredient safety?
6. Have you set publicly available solid waste reduction targets? If yes, what are those targets? (Enter total lbs and target date; 2 fields or leave blank)
7. If measured, please report total water use from the facilities that produce your product(s) for Walmart Inc. for the most recent year measured. (Enter total gallons)
8. Have you set publicly available water use reduction targets? If yes, what are those targets? (Enter total gallons and target date; 2 fields or leave blank)
Natural Resources
High quality, responsibly sourced raw materials
9. Have you established publicly available sustainability purchasing guidelines for your direct suppliers that address issues such as environmental compliance, employment practices, and product/ing redient safety?
13. Do you have a process for managing social compliance at the manufacturing level?
14. Do you work with your supply base to resolve issues found during social compliance evaluations and also document specific corrections and improvements?
15. Do you invest in community development activities in the markets you source from and/or operate within?
In conclusion, Whether you are designing a Process or purchasing a product or service you should factor in these questions as part of your review and decision analysis.
10. Have you obtained 3rd party certifications for any of the products that you sell to Walmart? If so, from the list of certifications below, please select those for which any of your products are, or utilize materials that are, currently certified.
11. Do you know the location of 100% of the facilities that produce your product(s)?
12. Before beginning a business relationship with a manufacturing facility, do you evaluate their quality of production and capacity for production?
Flexicon has released a twin tilt-down flexible screw conveyor system with dual hoppers on a common mobile base, constructed and finished to 3-A sanitary standards.
Ready to plug-in and run, the self-contained system can fill two vessels with the same material simultaneously, or convey two different materials. Mounted on a frame with locking casters for in-plant mobility, it can be utilized in multiple locations, and rolled to a wash-down booth.
Each four cubic foot (113 litre) hopper is equipped with grates capable of supporting a 250 lb (115 kg) bag of material, level sensors, and mechanical agitator assemblies to promote flow into the conveyor inlets.
The two BEV-CON conveyors are engineered to move dry bulk solids efficiently without product degradation, especially non-free-flowing materials that pack, cake, smear, fluidize, compress, or are otherwise problematic to convey.
The screws are the only moving parts contacting material, and are driven beyond the point at which material is discharged, eliminating wear and contamination related to product contacting seals and bearings.
Discharge housings of the conveyors are supported by dual motorized booms that cantilever from the mobile base, allowing discharge of
material into processing equipment or storage vessels. The support boom and conveyor assembly can be tilted down to maneuver through standard doorways and aisles, and around corners for use anywhere in the plant.
The system is constructed to 3-A standards, and features sanitary quick-release clean out caps, quick-disconnect discharge box access covers, and wash-down motors. The stainless NEMA 4X control panel allows operation of either or both conveyors. HMI controls allow manual and automatic start/stop, reverse and variable speed adjustment.
Movu Robotics, a provider of warehouse automation solutions, has announced a partnership with supply chain integration partner PeakLogix, an Alta Material Handling company.
This partnership means Movu Robotics and PeakLogix can offer the benefits of Movu’s plug-and-play robotics portfolio as part of their solutions for customers in the North American market.
PeakLogix helps businesses maximize efficiency and productivity in their warehouse operations through tailored solutions based on their specific needs and requirements.
With a philosophy of ‘no warehouse left behind’, Movu Robotics tackles automation with easier, modular, scalable, flexible and efficient solutions that customers need and helps them to upgrade their warehouses.
The Movu portfolio is built around a range of innovative sub-systems designed to provide easier, scalable, flexible and energy efficient solutions accessible for all kinds of warehouses and quick to roll out. These include the Movu atlas, a pallet shuttle system for multiple deep lane storage; Movu escala the robotized 3D storage and fulfilment system; Movu ifollow Autonomous Mobile Robots (AMRs) for collaborative picking or transport of load carriers such as pallets; and the Movu eligo picking arm robot; as well as the appropriate supporting software.
“ This partnership opens up a world of possibilities for us and our clients. By combining our cutting-edge technology and proven solutions with PeakLogix expertise, we are excited to deliver even greater value and efficiency in warehouse operations,” said Stefan Pieters, CEO of Movu Robotics.
“Movu Robotics sub-systems are designed with seamless integration in mind and I am glad that our strategic partnership with PeakLogix will bring automated solutions to more customers globally, helping them to meet their challenges and boost their performance, resilience and service levels.”
“Because our mission centers on solving current and emerging business challenges for our clients, the partnership with MOVU enables PeakLogix to provide a new portfolio of powerful solutions that solve operational problems.” said Mike Holler, executive vice-president of PeakLogix.
Fairlane Products, a North American supplier of workholding technologies and machine tool components, makes available a wide range of rectangular and square bumpers, all designed to protect parts ranging from those that are delicate or fragile to those that are heavy or unusually shaped.
Rubber and urethane bumpers are designed to guard, stop, align, and protect a machine or work piece during the manufacturing process. They are available in square and rectangular shapes (standard and custom sizes available) with a variety of different styles that integrate well into an industrial application or commercial end product. These bumpers are available in “off-the-shelf” sizes, as well as special cut to custom requirements. Bumpers are most often used in material handling, assembly and manufacturing operations to guide, stop and support parts as they are moved and transferred. Fairlane Products maintains a large inventory of products and they are an economical alternative in many applications to eliminate the need for custom engineered molded components. The square and rectangular bumpers are available in black neoprene, white nitrile and colored urethane in 60 and 80 durometers with sizes of ¾” square to sizes of ½” x 4”. Heights from 3/8 to 2”. Special cut bumpers are available in black neoprene, 80-durometer, with thickness from 3/8 to 2”. The bumpers can be counterbored and can come with washers molded inside for added reinforcement. The black neoprene bumpers are flame resistant, while also resisting gasoline, oil and high temperatures. The white nitrile is resistant to gasoline, oil, alcohol and abrasion. The urethane bumpers offer high abrasion resistance, strength and load bearing and provide high elongation hardness with a resistance to ozone and oxygen degradation.
AutomationDirect adds new ReeR Micron series light grids, available in detecting or measuring versions, that use multi-beam photoeye arrays to detect the presence of objects anywhere within the controlled height of the sensor array.
They are used for detecting, measuring, and counting various sized and shaped objects at random positions as they pass through the target area.
Detection light grids with discrete complementary outputs provide object detection signals and are available with detection heights up to 740mm. Measuring light grids with analog outputs or IO-Link compatibility are available with detection heights up to 1490mm and provide both object detection and height measurements.
All series offer 10 or 30mm beam resolution options, a 0-10m operating distance, and rugged anodized aluminum housings with IP65/67 protection ratings.
ReeR Micron light grids are sold in sender/receiver pairs, are CE marked, UL listed, and offer a 2-year warranty.
Emerson announced the new PACSystems IPC 2010 Compact Industrial PC (IPC ), an industrial computer designed to handle a
wide range of machine and discrete part manufacturing automation applications.
The solution is designed to serve manufacturing sites and OEM machine builders who need a compact, durable IPC to support their Industrial Internet of Things (IIoT) and other digital transformation initiatives.
The IPC 2010 addresses this by pre-loading the PACEdge industrial edge platform and elements of Movicon.NExT SCADA software, helping users run applications quickly using browser-based configuration.
Provisions are included for keeping the software platform current and passively maintained, minimizing user effort, while maximizing reliability.
Running an industrial version of Linux, and including serial and Ethernet connectivity, the IPC 2010 can be used as a communications gateway in a variety of topologies, and simultaneously or separately as an edge computing device. Users can implement the IPC 2010 as a flexible protocol converter—and for many other computing functions— in many IIoT, edge, OT/IT convergence, HMI visualization, SCADA connectivity, and digital transformation roles.
cooled IPC, with a low power consumption of just four watts, and tough packaging so it can be installed virtually anywhere.
The IPC 2010 offers an advantageous price/performance ratio, with no ongoing annual licensing costs, or charges for general and cybersecurity updates. Additional features,
such as Movicon Connext or WebHMI, can be activated or added at any time.
“Many customers undergoing a digital transformation want to start small and earn trust as they seek out value from edge-enabled applications,” said William Paczkowski, product manager for the IPC 2010 for Emerson’s discrete automation business. “The IPC 2010 is specifically designed as a pre-packaged and economical solution so they can get running quickly and cost effectively.” to get the latest news affecting your
Both the hardware and software are designed to be adaptable, universal, and scalable, providing a standardized and unified user experience that is easy-to-use, powerful, and supported by Emerson’s lifecycle services. The compact form factor IPC 2010 features the widest operating temperature range of any passively
ControlAir LLC, manufacturer of precision pneumatic and electro-pneumatic control products, has introduced the new Type 410 High Precision Pressure Regulator.
The Type 410 provides a high level of regulation accuracy and repeatability during variable operating conditions.
Type 410 consistently meets control requirements, even amidst fluctuating operating conditions.
Built to withstand the harshest industrial environments, the Type 410 features die-cast housings protected with a chromate finish and epoxy paint, ensuring long-lasting durability and performance.
Every regulator undergoes rigorous pressure, leak, and flow tests at the factory before shipment, guaranteeing exceptional quality and reliability straight out of the box.
The Type 410’s combination of stability, reliability, and precision makes it well-suited for a wide range of industrial applications where precise air pressure regulation is critical to performance and productivity.
Applications include pneumatic control systems, pressure testing equipment, HVAC systems, laboratory instrumentation, and packaging machinery.
The Type 410 High Precision Air Pressure Regulator is available in 1/4” porting. Output ranges include 0-2 psig (0-0.15 bar), 0-10 psig (0-0.7 bar), 0-30 psig (0-2 bar), 0-60 psig (0-4 bar), and 0-100 psig (0-7 bar).
Exhaust capacity is 0.1 scfm (2.8 Nl/ min) downstream pressure 5 psig (0.3 bar) above set point. Sensitivity is 1
inch (25.4 mm). Air consumption is less than 6 scfh (170 Nl/min). A wide temperature range of 0º to 160º F (-18º to 71º C).
IDEC Corporation has expanded its SmartAXIS touch family with the new FT2J Series combined PLC+HMI.
A compact all-in-one form factor combines built-in full function controller features and functions, both onboard and expandable I/O, and an advanced technology 7” touchscreen display, providing many advantages for a wide variety of industries.
An all-in-one PLC+HMI consumes less panel space than separate units. Because the PLC and HMI are internally connected, require only one power supply, and share the same network connection, installation is simplified.
The FT2J is ready to use and communicate right out of the box, and end users perform configuration with an intuitive and easy-touse integrated development environment for both PLC and HMI functions, cutting configuration and programming time.
The integrated PLC and HMI each have their own dedicated CPU and user memory for optimized scan time performance, and they communicate natively with each other. Built-in I/O includes 14 points of DC discrete inputs (5 of them configurable as high-speed counters), and 4 points of analog inputs (configurable as 0-10VDC or 4-20mA).
A relay version provides 8 points of relay outputs, while transistor versions provide 6 points sinking or 6 points sourcing of discrete outputs (4 of them configurable as pulse outputs) and 2 points of 0-10VDC or 4-20mA analog outputs.
FDB Panel Fittings has announced the launch of full stock of easy to fit traditional L and T style lock handles for all types of generic industrial applications, from production line to office, specialist vehicles to marine, offshore to hangers, control rooms to distribution centres.
These high-quality L and T handles with sealing to IP65 and IP67 are intuitive in operation with or without inserts or lock cylinders. With sophisticated ergonomic design they typically come easily to hand and are comfortable to use. Their leverage allows operation of internal rod systems for multi-point gasket sealing and added security, which is increasingly important for the protection of sophisticated digital process controls.
Also, the Panel Fittings Online store now carries wing-knob inserts which function as smaller variants for wall mounted enclosures. Likewise standard “spanner lock” style inserts for standard quarter turns enable the use of an extended handle key, which offers enhanced leverage in situations where a larger fixed handle is not appropriate.
Well suited to office and industrial applications, these modern variants of a proven traditional L and T designs are convenient and natural in feeling during operation, excellent in larger spaces, suit floor standing cabinets and large enclosures. They are available in polyamide, zinc die chrome and black powder coat, plus in polished stainless steel with a wide selection carried in stock for urgent delivery to customers production facility or project site.
Emerson announced the new PACSystems IPC 2010 Compact Industrial PC (IPC ), a rugged industrial computer designed to handle a wide range of machine and discrete part manufacturing automation applications. The new solution is designed to serve manufacturing sites and OEM machine builders who need a ruggedized, compact, durable IPC to cost-effectively support their Industrial Internet of Things (IIoT) and other digital transformation initiatives.
The IPC 2010 addresses this by pre-loading the PACEdge industrial edge platform and elements of Movicon.NExT™ SCADA software, helping users run applications quickly using browser-based configuration. Provisions are included for keeping the software platform current and passively maintained, minimizing user effort, while maximizing reliability.
Running an industrial version of Linux, and including serial and Ethernet connectivity, the IPC 2010 can be used as a communications gateway in a variety of topologies, and simultaneously or separately as an edge computing device. Users can implement the IPC 2010 as a flexible protocol converter—and for many other computing functions— in many IIoT, edge, OT/IT convergence, HMI visualization, SCADA connectivity, and digital transformation roles.
The compact form factor IPC 2010 features the widest operating temperature range of any passively cooled IPC, with a low power consumption of just four watts, and tough packaging so it can be installed virtually anywhere.
The IPC 2010 offers an advantageous price/performance ratio, with no ongoing annual licensing costs, or charges for general and cybersecurity updates. Additional features, such as Movicon Connext© or WebHMI, can be activated or added at any time.
Emerson is already building the IPC 2010 into a range of larger offerings for leak detection, compressed air monitoring, batching systems, cloud enablement services, and other packaged solutions.
We pioneer motion
OPTIME ™
enables me to keep an eye on hundreds of machines in just a few hours – which makes OPTIME a quick, easy and economical condition monitoring solution.
www.schaeffler.ca/optime