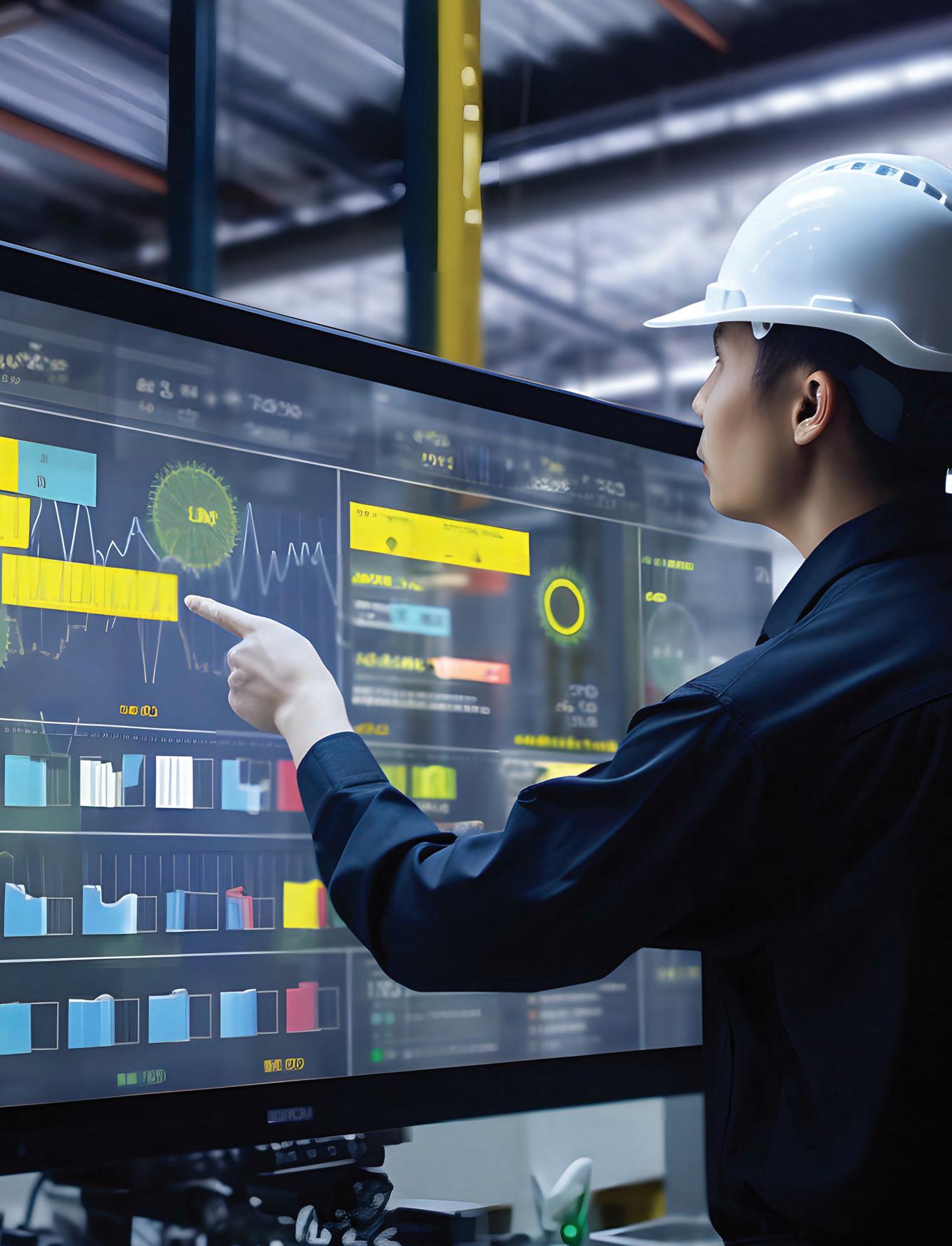
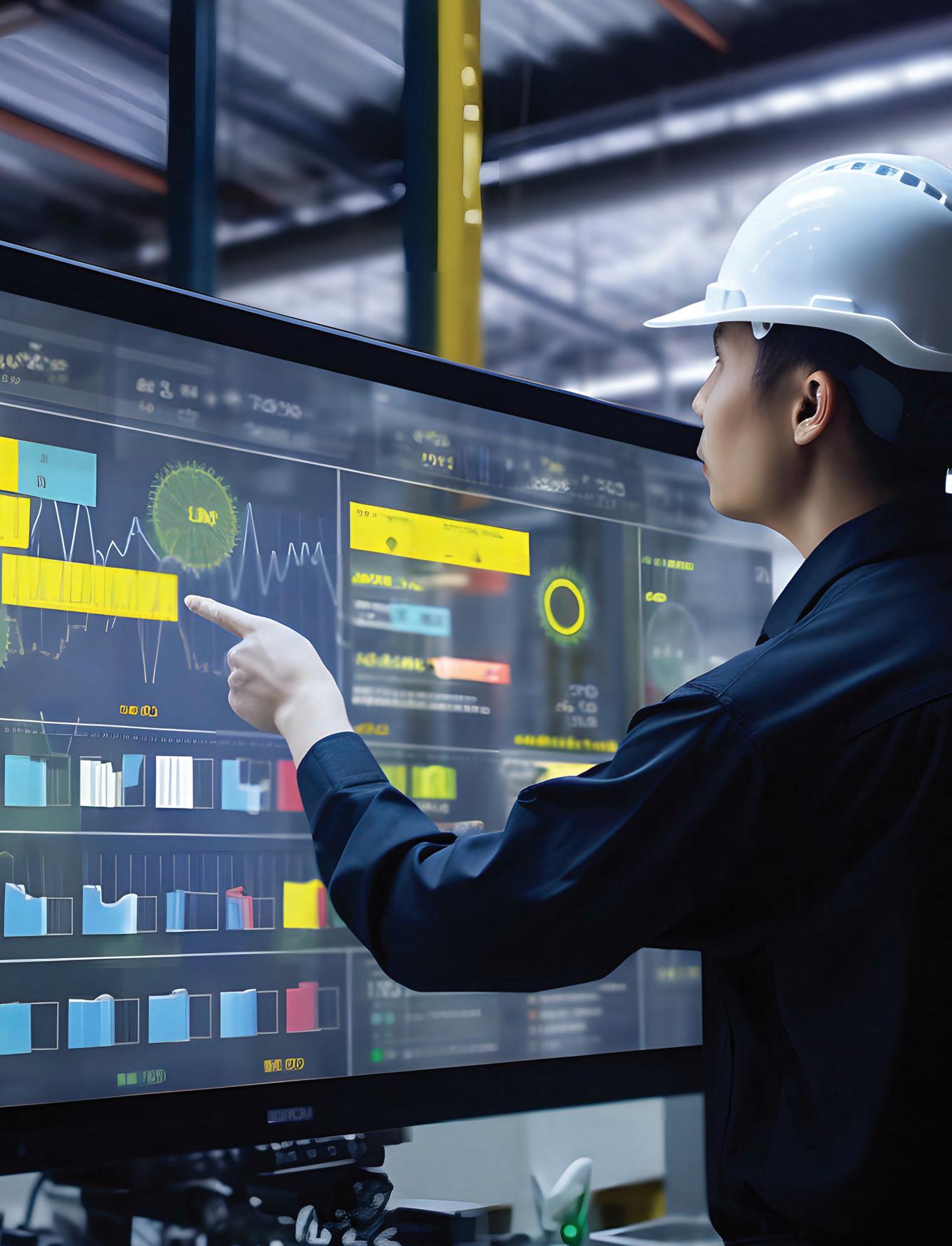
SMART MACHINES
Exploring AI application in functional safety systems
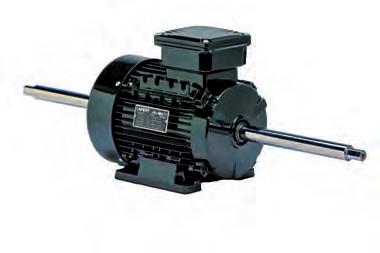



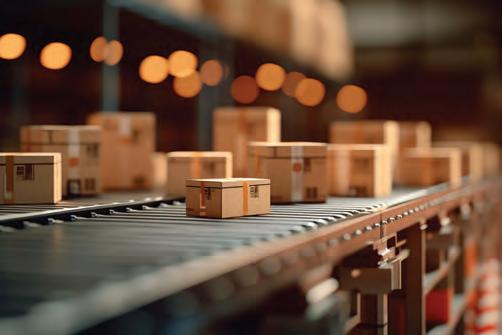


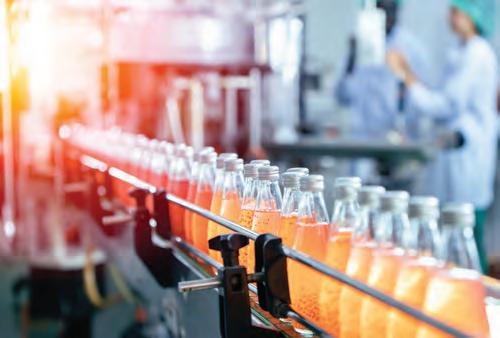
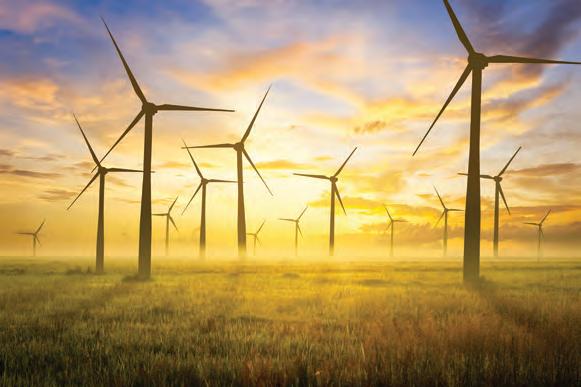
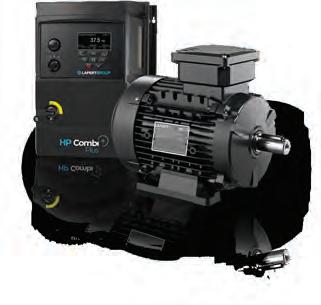

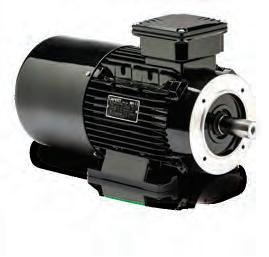


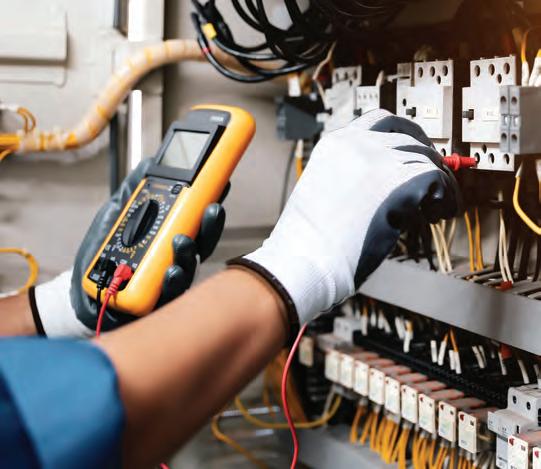
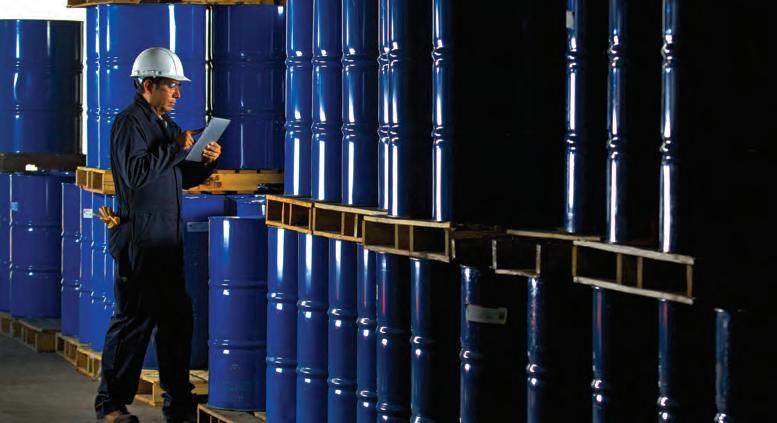
THE ROLE OF CMMS SOFTWARE IN BUSINESS GLOBALIZATION
Asset management provides enterprises with a strategic tool to stay competitive in challenging times.
Selecting and applying appropriate lubricants to industrial machinery components is critical to a machine’s function. 10 8 14 18 22 24
SK SAFETY PROGRAMMING FUNDING IN DISPUTE
The Saskatchewan’s Workers Compensation Board administer funding to safety associations for use in safety programs for manufacturers in the province.
AN ABUNDANCE OF OPPORTUNITY
Jobsite mechanization offers cutting-edge construction and demolition industry solutions.
SMART MACHINES
Researchers at MIT are working on the convergence of artificial intelligence and robotics to bring about what they call “physical intelligence”.
WORKER HEALTH & SAFETY
Enhancing safety and efficiency with the right workwear choices in MRO settings.
DEBUNKING FOUR MISCONCEPTIONS WHEN SELECTING GREASE
Building a safer future
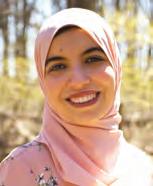
As we delve into another issue of MRO, it’s important to reflect on health and safety within the manufacturing sector.
The manufacturing industry, a cornerstone of economic stability and growth, has always been synonymous with innovation, productivity, and resilience. However, amidst the relentless pursuit of efficiency and output, we must never lose sight of our most valuable asset: our people.
Health and safety in manufacturing are not mere regulatory checkboxes; they are the bedrock upon which sustainable success is built. The well-being of our workforce directly correlates with operational excellence, and it is our collective responsibility to foster an environment where safety is an ingrained culture rather than an afterthought.
Historically, manufacturing has been fraught with hazards. Heavy machinery, high temperatures, chemical exposure, and repetitive motions are just a few of the risks inherent to the industry. Despite significant advancements in technology and safety protocols, workplace injuries and illnesses remain a pressing concer n.
This statistic underscores a critical need for continuous improvement in our health and safety practices. It is essential that manufacturers not only comply with existing regulations but also proactively seek innovative solutions to mitigate risks. This involves a holistic approach that encompasses training, technology, and a robust safety culture.
Training is the cornerstone of any effective safety program.Workers must be equipped with the knowledge and skills to identify and mitigate hazards. Regular training sessions, safety drills, and continuous education are imperative. However, training should not be a one-size-fits-all approach. Tailoring
programs to address the specific risks associated with different roles within the manufacturing process ensures that all employees, from the factory floor to the administrative offices, are well-prepared.
Not to mention that technology plays a pivotal role in enhancing workplace safety. The advent of Industry 4.0 has ushered in a new era of smar t manufacturing, where interconnected systems and data analytics can predict and prevent accidents. Wearable technology, for instance, can monitor workers’ vital signs and environmental conditions in real-time, alerting them to potential dangers. Similarly, the integration of automation and robotics can reduce human exposure to hazardous tasks, significantly lowering the risk of injury.
Yet, the most sophisticated technology and comprehensive training prog rams will fall short without a deeply ingrained safety culture. Safety must be a core value, championed by leadership and embraced by every employee. This cultural shift requires open communication, where workers feel empowered to report hazards without fear of reprisal. Regular safety audits, employee feedback mechanisms, and visible commitment from management are essential in cultivating this environment.
In this issue of MRO Magazine, we delve into the latest trends, technologies, and best practices in health and safety. From expert insights to case studies, our goal is to provide you with the knowledge and tools to enhance your safety protocols and foster a safer, healthier work environment.
Stay safe, stay informed, and let’s build a safer future together.
MARYAM FARAG Editor mfarag@annexbusinessmedia.comESTABLISHED 1985
SUMMER 2024 Volume 40, Number 2
READER SERVICE
Print and digital subscription inquiries or changes, please contact Customer Service
Angelita Potal, Customer Service Administrator Tel: 416-510-5113 email: apotal@annexbusinessmedia.com
Mail: 111 Gordon Baker Rd., Suite 400 Toronto, ON M2H 3R1
EDITOR Maryam Farag 226-931-4194 mfarag@annexbusinessmedia.com
SENIOR PUBLISHER Paul Burton 416-510-6756 pburton@annexbusinessmedia.com
NATIONAL ACCOUNT MANAGER Ilana Fawcett 416-829-1221 ifawcett@annexbusinessmedia.com
BRAND SALES MANAGER Chander Verma 437-218-0941 CVerma@annexbusinessmedia.com
AUDIENCE DEVELOPMENT MANAGER Beata Olechnowicz bolechnowicz@annexbusinessmedia.com 416-510-5182
MEDIA DESIGNER Curtis Martin
ACCOUNT CO-ORDINATOR Debbie Smith 416-510-5107 dsmith@annexbusinessmedia.com
GROUP PUBLISHER Anne Beswick 416-410-5248 abeswick@annexbusinessmedia.com
CEO Scott Jamieson sjamieson@annexbusinessmedia.com
Connect with MRO magazine @mro_maintenance @MROMagazine /company/mro-magazine @mromagazine info@mromagazine.com mromagazine.com @mrocanada
Machinery and Equipment MRO is published by Annex Business Media, 111 Gordon Baker Rd., Suite 400, Toronto ON M2H 3R1; Tel. 416-442-5600, Fax 416-510-5140. Toll-free: 1-800-268-7742 in Canada, 1-800-387-0273 in the USA.
Printed in Canada ISSN 0831-8603 (print); ISSN 1923-3698 (digital)
PUBLICATION MAIL AGREEMENT #40065710
Subscription rates.
Canada: 1 year $66.30, 2 years $105.06. United States: 1 year $145.86. Elsewhere: 1 year $167.28. Single copies $10 (Canada), $16.50 (U.S.), $21.50 (other). Add applicable taxes to all rates.
On occasion, our subscription list is made available to organizations whose products or services may be of interest to our readers. If you would prefer not to receive such information, please contact our circulation department in any of the four ways listed above.
Annex Privacy Officer Privacy@annexbusinessmedia.com 1-800-668-2374
No part of the editorial content of this publication may be reprinted without the publisher’s written permission © 2024 Annex Business Media. All rights reserved. Opinions expressed in this magazine are not necessarily those of the editor or the publisher. No liability is assumed for errors or omissions.

Daemar
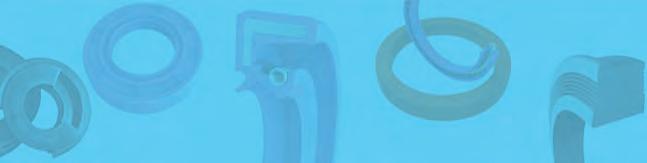
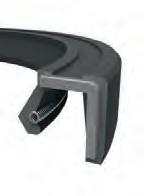




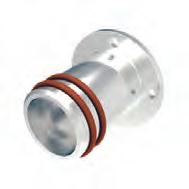
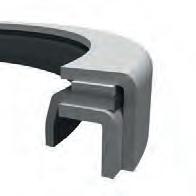
NEWSWATCH
SKILLED TRADES ONTARIO LAUNCHES INDUSTRY RESOURCE HUB
Skilled Trades Ontario (STO) has launched a new online information centre, providing a platform to access insights and information on the skilled trades sector.
The STO Resource Hub features newly published trade reports, a directory of helpful links as well as other skilled trades related resources and research.
“Our mission at Skilled Trades Ontario is to streamline services and make it easier to learn more about how the skilled trades operate in our province. I’m proud to say that we are making progress on that mission,” said Melissa Young, CEO and Registrar of Skilled Trades Ontario.
STO recently published more than 50 Red Seal trade reports offering insights into trade characteristics, educational pathways, workforce demographics and current labour market conditions. In the coming months, additional research and assets will be added to the Hub.
“Skilled Trades Ontario’s new Resource Hub is an excellent source of infor mation on Ontario’s 144 skilled trades,” said David Piccini, Minister of Labour, Immigration, Training and Skills Development. “By helping apprentices and workers learn more about these rewarding, high-paying careers, Ontario continues to lead the way in promoting and opening up pathways into the skilled trades.”
Skilled Trades Ontario has also unveiled a comprehensive inventory of updated training and curriculum standards. The lists outline new standards for Ontario’s skilled trades that have been developed since the agency’s launch.
OSCO SAFETY ACQUIRES PARTNERS WITH BEDFORD REINFORCED PLASTICS
OSCO Safety, a provider of safety solutions, has partnered with Bedford Reinforced Plastics, acquiring the r ights to be the exclusive source for ReadySeries pre-engineered modular composite products.
Adding ReadySeries to OSCO’s suite of top-quality safety solutions marks a significant milestone in
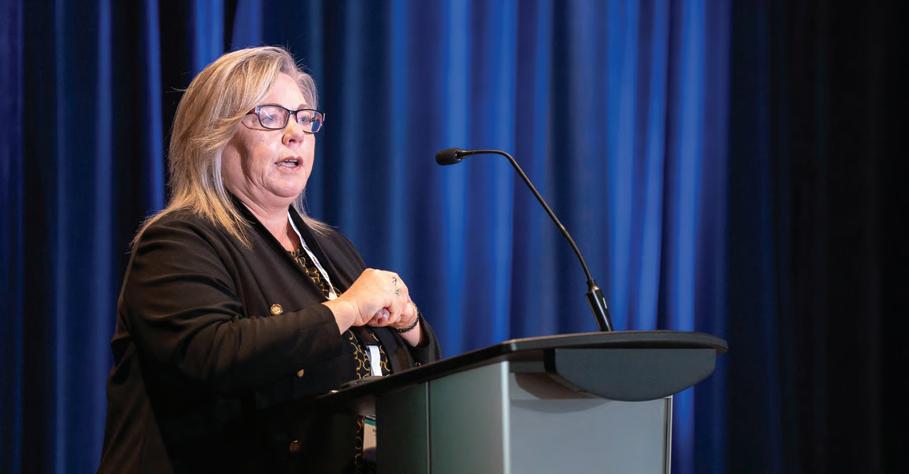
enhancing safety, access and maintenance needs in industrial and utility markets, as well as other critical applications. The ReadySeries system offer s industrial platforms and mezzanines, walkways, fixed ladders, handrails, guardrails, stairs and more. ReadySeries provides configurable options to suit various applications.
“Our relationship with Bedford represents a significant step forward in advancing safety standards across many industries,” said Kyle Pollino, Sales Manager at OSCO Safety. “With ReadySeries now part of our portfolio, we are empowered to deliver comprehensive safety solutions that address the most complex challenges with speed and efficiency.”
Key advantages of the ReadySeries system include its quick-ship capability and ease of installation. These configurable solutions typically align with maintenance fund thresholds, allowing customers to address safety, maintenance and access concerns quickly and easily. With ReadySeries, there’s no need to wait for annual budget renewals to alleviate safety risks — issues can be resolved immediately, minimizing downtime and enhancing workplace safety.
In addition, OSCO’s streamlined project management approach with a dedicated team of project managers ensures a seamless experience for
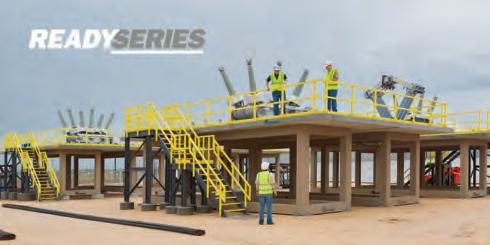
customer s, guiding them through the process from concept to completion.
CANADIAN GOVERNMENT CELEBRATES YOUTH IN THE SKILLED TRADES AT 2024 COMPETITION
Premier Doug Ford, Ontario Ministers, and Toronto Mayor Olivia Chow gathered with approximately 40,000 competitors, volunteers, and the public at the Toronto Congress Centre to witness the future skilled trades and technologies workforce compete at the 2024 Skills Ontario Competition.
Started in 1989, the Skills Ontario Competition is the largest skilled trades competition in Canada and offers a unique opportunity for top students to demonstrate that they are the best of the best in their skilled trade or technology field.
This year, Skills Ontario saw over 2800 young people from across the province competing in over 75 different contests. It is the largest number of youth competing in the competition in the organization’s history.
During the event, Skills Ontario welcomed Premier Doug Ford and Ministers Peter Bethlenfalvy, David Piccini, Jill Dunlop, Stephen Lecce, Lisa Thompson and Charmaine Williams, along with Toronto Mayor Olivia Chow, to the 2024 Skills Ontario Competition to celebrate careers in the skilled trades and technologies.
“This is the largest skills Competition in the country with approximately 2,800 competitors exploring educational and career pathways in much needed and coveted careers,” said Ian Howcroft, CEO of Skills Ontario. “We appreciate the support, contribution and investments the
Ontario government is making to promote skilled trades and build the workforce of the future.”
The event wrapped up with a closing ceremony on the morning of May 8thwith winners receiving gold, silver or bronze medals, and some also receiving monetary awards, along the oppor tunity to compete at the Skills Canada National Competition in Quebec City.
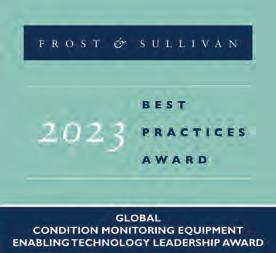
SCHAEFFLER RECEIVES 2023 GLOBAL ENABLING TECHNOLOGY LEADERSHIP AWARD
Frost & Sullivan recently assessed the condition monitoring equipment market and, based on its findings, recognizes Schaeffler Group with the 2023 Global Enabling Technology Leadership Award.
Schaeffler provides solutions tailored to the evolving needs of industrial maintenance and predictive analytics. “The company enhances its existing products, such as OPTIME Ecosystem, with unique designs, the latest technology, and unparalleled capabilities to fill gaps and push the limits in the market.”
“The distinct advantage for Schaeffler that guarantees a positive purchase experience and customers’ absolute satisfaction is that the company offer s user-friendly condition monitoring solutions that customers can easily deploy on their own within the shortest possible timeframe and immediately start monitoring their machine operations within their budgets.” said Krishnan Ramanathan, Research Director, Frost & Sullivan.
Schaeffler’s OPTIME Ecosystem, a condition monitoring and smar t lubrication solution, provides a user-friendly experience that simplifies complex data analysis and machine care. As a smart lubrication solution, OPTIME Ecosystem exemplifies the seamless integration of sensor technology, data analytics, and Internet of Things (IoT) connectivity, as well as digital-embedded access to service experts. The solution suite incor porates multiple monitoring tools to anticipate and address the nuanced demands of predictive maintenance.
“Schaeffler’s renowned brand name in the condition monitoring and predictive maintenance markets is due to its comprehensive portfolio of lifetime solutions, reliable predictive maintenance solutions, expertise in industrial automation, cost-effective solutions, and customer focus. Its proficiency in navigating the complexities of automation has been instrumental in the success of its condition monitoring solutions,” said Ramanathan.
IMPROVED MARGINS FOR CANADIAN FOOD AND BEVERAGE MANUFACTURERS IN 2024
After hitting a record $165 billion in food and beverage manufacturing sales last year, 2024 is expected to see sales moderate in sync with slowing inflation and tighter household budgets.
Despite sector-specific headwinds and changing consumer s hopping habits, the overall outlook is more positive. Population growth and stabilizing input costs are two reasons margin improvement is expected in 2024.
“High inflation and interest rate increases over the past two years have put pressure on household budgets, leading to changes in consumer spending habits,” said FCC chief economist, J.P. Gervais in highlighting the evolving consumer landscape. “As a result, Canadians
spent less on average on food and beverages in 2023.”
“While changing shopping habits may pose challenges, they also present opportunities for food and beverage m anufacturers,” said Gervais. “Taste remains the top consideration for consumers, but pr ice sensitivity has increased, leading processors to innovate and meet evolving consumer demands.”
“FCC Economics is projecting a slight decrease of 1.4 per cent in food and beverage manufacturing sales for 2024. However, we anticipate gross margins to improve by 1.7 per cent on average. One wildcard in our forecasts is the resilience of the U.S. economy, which could lead to growth in exports,”added Gervais.
Many commodity prices have declined which will work their way through the supply chain. These trends are anticipated to continue, boosting marg ins in 2024.
The report forecasts a decrease in the inflation rate for food purchased at g rocery stores, falling below 2.0 per cent this spring and stabilizing around pre-pandemic levels thereafter.
“While challenges persist, 2024 holds promise for Canadian food and beverage manufacturers,” said Gervais. “By adapting to changing consumer preferences and leveraging opportunities presented by population growth, the industry can navigate the year ahead with cautious optimism.”
The annual FCC Food and Beverage Report features insights and analysis on grain and oilseed milling; dairy, meat, sugar, confectionery, bakery and tortilla products; seafood preparation; and fruit, vegetable and specialty foods, as well as soft dr inks and alcoholic beverages.
GOVERNMENT INVESTS OVER $97 MILLION IN CLEAN TECH FOR FARMERS
Lawrence MacAulay, Minister of Agriculture and Agri-Food,
announced more than $97 million under the Agricultural Clean Technology (ACT) Program. This funding will support 162 projects across Canada.
Minister MacAulay made the announcement at Folly River Farms Limited, a 74-year-old family-owned dairy farm in Debert, Nova Scotia. The farm operation received $49,280 under the Adoption Stream of the ACT Program to purchase and install a solar energy system. This project uses solar energy to replace electricity from the grid, significantly reducing the farm’s greenhouse gas (GHG) emissions.
The ACT Program provides farmers and agri-businesses funding to help develop and adopt the latest clean technologies to reduce GHG emissions and boost their long-term competitiveness. The funding is focused on three priority areas: green energy and energy efficiency, precision agriculture; and bioeconomy solutions.
Across Nova Scotia, the ACT Program has supported 24 projects to date, representing a total of more than $6 million. The Government of Canada will continue to support the research, development and adoption of clean technology to help the sector adapt to climate change, so Canadian farmers can continue feeding our country, and the world.
“Canadian farmers fully understand the need to take care of the environment and they are constantly innovating to find new solutions to reduce their emissions. Our investment in the Agricultural Clean Technology Program will help keep our farmers and ranchers on the cutting edge, so they can make their operations more resilient today and for generations to come.” said MacAulay. 414 projects hav e been announced to date under the ACT Program, totalling up to nearly $196.9 million. These projects complement the work already underway to help farmers reduce carbon emissions and develop technology to adapt to climate change.
The role of CMMS software in business globalization
BY NAVIN KULKARNIAsset management provides enterprises with a strategic tool to stay competitive in challenging times. Labor and expertise shortages, broken supply chains, and a new focus on sustainability are just a few of the hurdles modern organizations face. Not to mention the cost of downtime: automotive manufacturers, for example, lose on average $22,000 per minute when production shuts down. Managing business globalization effectively is key to survival and growth in this environment. How does an organization connect international teams? Work across languages, time zones, and currencies? Discover a winning maintenance strategy, and standardize it to scale business success?
Enterprise Asset Management (EAM) or Computerized Maintenance Management System (CMMS) software are proven solutions that can not only help extend the lifecycle of your critical assets across the entire enterprise but also can empower the maintenance technicians to maximize wrench time.
Unlocking the power of CMMS software for globalization
A capable CMMS can serve as a command center for managing asset lifecycle, deploying the right mix of maintenance strategies, planning, scheduling and tracking work, as well as optimizing spare parts inventory.With these software systems, businesses can apply organization-wide maintenance practices and support localization needs (language, currency etc.) levering a single platform. Gaining enterprise-wide asset ecosystem visibility can help drive several
strategic decisions ranging from improved budgeting and planning of capital expenses to cross-pollination of maintenance best-practices across the organization.
In addition to greater organizational control, a CMMS can also improve collaboration across maintenance teams (whether on desktop or mobile) as they manage work, apply safety procedures, or even track parts usage.
Recently, organizations are also leveraging their CMMS platform to combat a greying of the workforce and exodus of proprietary knowledge. Solutions like digital work instructions, Artificial Intelligence (AI), predictive maintenance technologies, and automation of regulatory compliance reporting are some effective ways to combat labor shortages and accelerate onboarding of new talent.
Embracing CMMS or EAM software gives you the power to drive key metrics like uptime, OEE, and MTTR. Your team reduces costs and drives production. Beyond near-term successes, though, a CMMS also prepares you for tomorrow, an era in which smart manufacturing, AI, and Industrial Internet of Things (IIoT) technology will become the norm.
A CMMS is a strategic investment in building a global organization that thrives, lasts, and evolves –futureproofing your business.
Talk to industry leaders, and you can hear the excitement in their voices when it comes to smart factory innovations, from AI to SCADA/ BMS integration. A recent study from Deloitte revealed that that 86% of manufacturing executives believe smart factory solutions will be the key factor in competitiveness over the
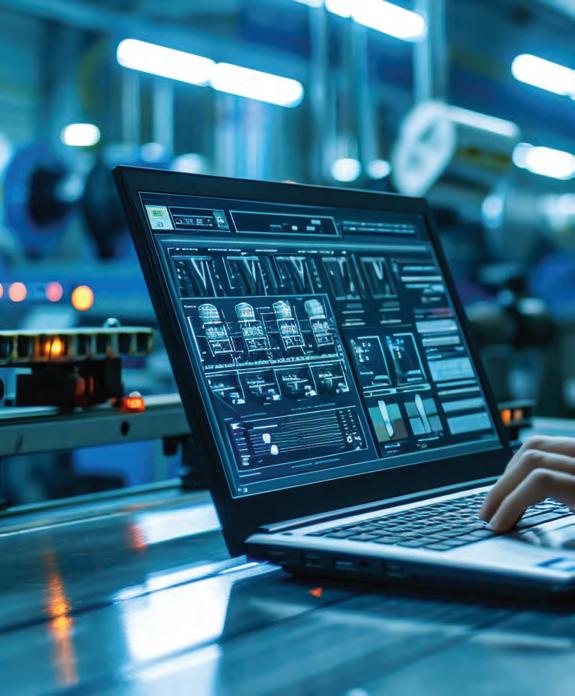
next five years. CMMS empowers organizations to harness all these technologies and more.
You may be asking, though, what are the key elements that make CMMS software a strategic, enterprise-level investment for globalization?
Let’s start with the heart of a CMMS: asset management.
Global asset management and maintenance
In the realm of global business operations, maintaining asset integrity and reliability across diverse locations is paramount. CMMS software emerges as a cornerstone technology, facilitating the centralized management of maintenance activities, asset tracking, and simplified work order management on an international scale. It enables businesses to implement consistent maintenance practices across all sites, helping them ensure that high standards of asset performance are uniformly maintained.
This is essential for minimizing downtime and optimizing operational efficiency. As businesses grow and expand into new markets, the challenges of managing assets across multiple sites, time zones, languages, and currencies intensify. Here, the role of a CMMS evolves from a maintenance tool to a global operational platform.
Enhanced inventory and supply chain management
Global operations often struggle with managing inventory and spare parts
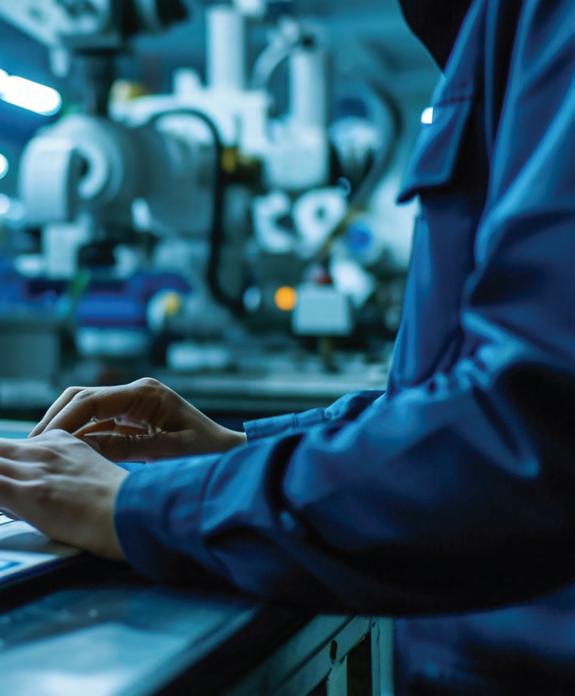
across multiple locations, especially in times of stagnant supply chains.
A Deloitte survey showed that 76% of manufacturers are utilizing digital solutions for supply chain issues, gaining visibility and strengthening their resilience across the value chain.
CMMS software addresses this challenge by providing a global view of parts inventory, allowing for the optimization of stock levels and the sharing of critical spares between sites. This global parts inventory management tool helps minimize downtime and improve the Mean Time to Repair (MTTR) for critical assets.
A CMMS offers a range of sophisticated inventory management features, including tracking of parts usage, automated reordering, and optimization of spare parts inventory. This capability ensures that critical parts are available when needed, reducing the risk of operational delays and improving the efficiency of the supply chain.
By providing a comprehensive view of inventory needs and movements across all locations, CMMS software can help businesses make informed decisions on inventory optimization and cost reduction.
Breaking down barriers: Multilingual and multicurrency support
A critical feature of modern CMMS software is its multilingual capabilities and support for multiple currencies. This functionality eliminates the language and financial barriers
that often complicate international operations. By providing a platform that can operate in the native language of each location and handle local currencies, CMMS software ensures that maintenance strategies are effectively communicated and implemented across all sites.
Maintenance success doesn’t get lost in translation. Teams don’t suffer delays waiting on coworkers living on the other side of the world. And those hours saved can be worth millions in production revenue in critical industries.
Standardizing maintenance strategies across borders
Global businesses face the challenge of ensuring consistent maintenance practices across all operations. CMMS software enables the standardization of maintenance strategies, workflows, and procedures, ensuring that best practices are shared and applied uniformly.
Work order procedures, mandatory approval flows, real-time reporting – a CMMS gives powerful tools for control and performance visibility.
A CMMS solution provides a framework for deploying standardized maintenance protocols across all operational sites, facilitating the sharing of best practices and enhancing the overall quality of maintenance work. This harmonization not only improves operational efficiency but also improves asset reliability and longevity, which are crucial for maintaining competitive advantage in the global market.
CMMS software simplifies the monumental challenge of scaling innovation across the entire enterprise.
Facilitating enterprise reporting and data analytics
In a global operation, the ability to quickly generate insightful reports and analytics across all sites is a major competitive advantage. Global production and maintenance leaders need enterprise-level reporting that gives them complete visibility into maintenance operations worldwide.
A CMMS serves as a critical data hub, collecting detailed and accurate information on maintenance activities, asset performance, and operational costs. This wealth of data supports advanced analytics and reporting capabilities, enabling businesses to more effectively identify trends, optimize maintenance schedules, and
allocate resources.
The insights gained from CMMS data analytics help drive strategic decision-making, enhancing the agility and responsiveness of global operations.
Regulatory Compliance and Audit Readiness
Compliance with international standards and regulations is a significant challenge for global businesses. A National Association of Manufacturers (NAM) survey found that 63% of manufacturers report spending over 2000 hours a year on federal regulation compliance.
CMMS software helps organizations standardize compliance processes and maintain detailed records for audit purposes by automating compliancerelated tasks and providing complete audit trails. This helps businesses ensure they meet regulatory requirements across different regions, minimizing the risk of penalties and reputational damage.
Managing compliance with a CMMS also allows you to automate the documentation and reporting processes required by various regulatory bodies.
And the system’s ability to monitor and report on environmental, health, and safety (EHS) metrics supports comprehensive risk management strategies, safeguarding both your personnel and assets.
Growing your global business success with CMMS software
A CMMS revolutionizes asset management by enabling predictive maintenance strategies, enhancing asset lifecycle management, and improving operational efficiency.
Maintenance and reliability industry best practices are evolving at a startling pace. To keep up, it’s vital to invest in tools like CMMS and EAM software, which can help you simultaneously focus on operational excellence, scale global expansion, and prepare for the future of asset management.
Navin Kulkarni oversees the next generation enterprise software product management solutions for Fluke Reliability. With more than 15 years of expertise in enterprise software, spanning EAM, CMMS, manufacturing execution & warehouse management, Navin is helping customers accelerate their reliability and maintenance journey with innovative connected reliability solutions. He is based in Atlanta, GA.
SK safety programming funding in dispute
BY MATT JONESThe Saskatchewan’s Workers Compensation Board (WCB) administer funding to safety associations for use in safety programs for manufacturers in the province. While the WCB have finalized funding agreements for the programs with six of the safety associations, a deal with the seventh – the Safety Association of Saskatchewan Manufacturers (SASM) – was unable to be finalized and as a result, $1.4 million in funding was withheld.The WCB are pursuing legal action against the SASM.
“The Saskatchewan Workers’ Compensation Board believes there is great value in well-run safety associations that are focused on the needs of their members,” reads a statement provided via e-mail by a WCB spokesperson. “As the entity facilitating the funding of such safety associations, the WCB has a legal responsibility to ensure the funds collected and distributed to safety associations, including the Safety Association of Saskatchewan Manufacturers (SASM), are used for their intended purposes.”
The good news, according to SASM Chief Executive Officer Desira Rostad is that the delivery of safety programs by the association has largely been unaffected. But the association did drastically reduce overhead to compensate.
“We downsized our staff considerably,” says Rostad. “We’re continuing to still work with the members within the four rate codes, we’re still providing services, just on a smaller scale. We had to give up our offices, we’ve relocated to our homes to work out of. But we’ve been able to maintain it. We’ve just been really, really busy. Longer days.”
Rostad says the crucial issue in the negotiations with the WCB has been rate codes. The previous funding agreements saw the WCB provide funding, and having oversight over the implementation of programming, specific to four manufacturing rate codes – M41 (dairy products or soft drinks), M72 (processing meat, poultry and fish), M91 (agricultural equipment) and M94 (iron and steel fabrication). However, the SASM also allows companies to buy memberships outside of those four rate codes.
“Our funding agreement doesn’t permit the WCB access to that side,” says Rostad.

“That side is to be audited by an external third party and the WCB cannot have access to that auditor to ask any questions. However, when our contract expired in September, the WCB tried to renegotiate to get access to everything.”
Rostad states that many of their members were upset at a lack of transparency over the issue – she claims that no letters were sent or any other communications to indicate that the WCB were looking to access the SASM’s entire ledger.
“[Our members] told us very clearly that if they would have known this, they would not use any of those services,” says Rostad. “The problem we have is that if members aren’t going to trust us with that information to use us, then we’re not going to be able to impact injury prevention the way we have been over the past few years, so that’s a huge problem.”
Several firms informed the SASM that they could no longer trust the association if it acquiesced to the WCB’s demands, says Rostad. One firm specifically threatened legal action, arguing that providing the information to the WCB would be violating non-disclosure agreements (NDA) that the SASM often has to sign to protect a firm’s proprietary secrets.
“A lot of manufacturers won’t let you into their plants [without one],” says Rostad. “We take pictures for ergonomic assessments,
and we do safeguarding engineer reports and bring in an actual engineer to do those reports. So you sign off on certain things when you walk in the door. Not every firm has that, but some do. The one that was looking at potentially going after us legally, we have quite a few NDAs signed with that firm.”
Rostad says that offers to have an independent auditor review that side of SASM’s work, or to provide a redacted version of the SASM’s general ledger with names removed, were declined by the WCB.
“That was not what the WCB wanted,” says Rostad. “They wanted access to the entire general ledger and our members were clear that the answer was no.”
The first court date in the WCB case against the SASM is set for late May. The WCB spokesperson declined to answer any follow-up questions about the conflict with the SASM, referring MRO back to their original statement. That statement continues to say that the WCB are committed to protecting Saskatchewan workers and businesses through innovative and effective programs and services and would continue to work with industry partners to ensure they have access to the work of a safety association in whatever form that might take.
Matt Jones is s a freelance writer and journalist with a specialization in trade publications.

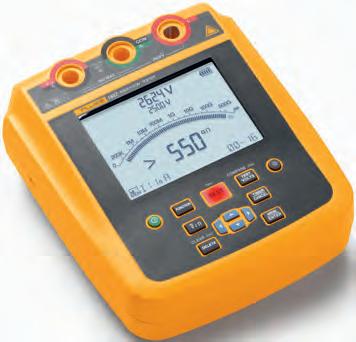
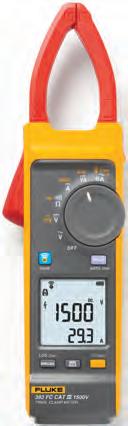
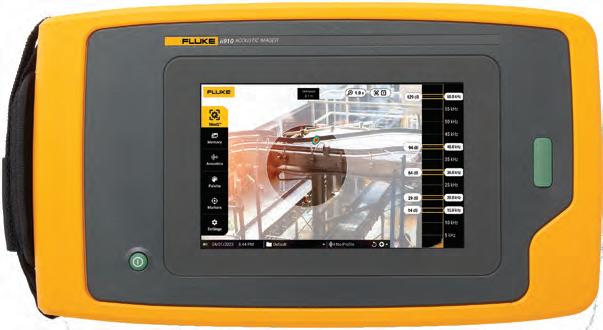
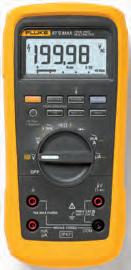
Avoiding downtime is what we do.

Maintenance teams trust Fluke products for their reliability, safe operation, ease of use, ruggedness, and rigid standards of quality. They can depend on their Fluke tools. Fluke has been in the forefront of helping maintenance professionals keep their plants and processes up and running for over 75 years.
Find out more at: https://www.fluke.com/en-ca
The care and maintenance of electrical transformers
Any plant has the potential to have a successful maintenance team providing focused equipment.BY L. (TEX) LEUGNER

Electrical transformers are used to transform or step down a high voltage to a lower utilization level. Power transformers are defined as those larger than 500 kVA, while distribution transformers are those 500 kVA or smaller. They are vital links in electrical power systems and are among the most reliable components in any industrial electrical system. If they are not overloaded or abused, they will provide long, trouble free years of service.
As a result of their reliable performance, coupled with lack of movement, noise, or any obvious sign of problems, transformers are often treated with disregard and neglect. Do you maintain your transformers on a routine basis or simply ignore them? A transformer failure can be a serious problem requiring extensive
repair, lengthy downtime and even cause serious injury if any overheating conditions cause one to explode. R egular maintenance will ensure continued and ongoing high reliability. Transformers are categorized by their insulating medium and construction; dry type or liquid filled.
1. Do you know what type of transformers are used in your facility?
Dr y type transformers operate in either air or gas, rather than a liquid. They may be ventilated or sealed tank types. Ventilated are usually varnish impregnated or cast coil construction. Sealed type dry transformers are cooled and insulated with a high dielectric inert gas, such as nitrogen, sulfur hexafluoride or perfluoropropane. Liquid filled transformers are those in which the core and coils are immersed in a liquid, such as askarel or mineral oil. (Note; Askarel is
made up of polychlorinated biphenals and are strictly regulated as a toxic substance. When testing a transformer that shows 50 PPM of chlorobyphenals, it confirms an older liquid filled transformer that has not been converted to oil or hydrocarbon fluids). The liquid is an insulator and serves to transfer heat away from the windings to be dissipated by the cooling fins, tank surface or radiator. Other types of liquids in these transformers are less flammable such as silicone or stabilized hydrocarbon fluids.
2. How often do you carry out transformer inspections?
The frequency of inspections should be based on the criticality of the unit, the severity of the loading conditions and the operating environment, but should be done at least once every year. Whether it’s a liquid filled or dry transformer, the inspection should include insulation testing, load current, voltage, ground and coil resistance, liquid level and temperature, winding hot-spot temperature, ambient temperature, leaks, general cleanliness and condition.
3. How does your organization manage the testing of transformers?
The current, voltage and temperature readings should be taken at the time of peak load, while the liquid level reading taken at the end of a low load period with permanent records maintained. In general, insulation tests are the major maintenance requirements for all transformers, while liquid filled transformers should be tested regularly to determine the quality and condition of the insulating liquid.
4. What fluid analyses testing does your organization carry out when analyzing transformer fluid?
Insulating liquids in most newer transformers are napthenic base oil stocks, non-conductors of electricity, have good solvency and a low natural pour point, all of which makes these fluids attractive for transformer operation most of which are located outside and subject to ambient temperatures. Critical tests for these transformer fluids are neutralization number, water content (by Karl Fischer test), power factor and dielectric strength (that measures even small amounts of dust, water, acidic compounds, cellulose fibres and metallic particulate), all of which can lead to the reduction of
cooling, potential fires and in severe cases, transformer explosions.
5. Is your maintenance group aware of the acceptable transformer fluid analyses results based on ASTM tests?
Insulating liquid analysis should be based in accordance with ASTM D 923 while acceptable individual standard test results are as follows; Acceptable dielectric breakdown based on D887 is 35 kVA. Neutralization number based on D974 is .04. Specific gravity test result based on D1298 should not exceed 890 kg/m at 15 degrees C. Water content must not exceed 25 PPM and power factor % @ 25 degrees C must not exceed 1.8 max.
6. Is your organization aware that percentages of combustible gases in the nitrogen cap of oil filled transformers can provide information on incipient f aults?
The gases analyzed by ASTM D3612 are nitrogen, oxygen, CO2, CO, methane, ethane, ethylene, hydrogen and acetylene. Ordinarily, the nitrogen cap will have less than 1 per cent of combustible content.
As problems develop, any increase in combustible gasses of 2 per cent suggests a potential problem. The transformer should taken out of service when combustible content is 5 per cent or more.
7. Does your organization understand that routine maintenance depends on whether a transformer is energized or de-energized?
For safety reasons, visual checks for cracks in porcelain bushings, the temperature of joints, bushings and leaks should only be carried out while a transformer is energized. When low insulation resistance is experienced, it is usually caused by humidity on winding surfaces and drying is necessary, while the tightening, cleaning and correction of leaking bushings and gaskets, welding of leaking joints can only be safely carried out when de-energized. Monitoring temperature of transformers is critically important as excessive temperature always indicates overloading or interference with cooling. High temperatures accelerate the deterioration of liquid and dramatically reduce the life of insulation. Some
transformers have temperature gauges and readings should be monitored and recorded regularly.
In conclusion, regular transformer care and maintenance with the recommended addition of an annual application use of infrared inspections can add years to the useful and long life of your transformers; in fact it is recommended today that infrared inspection can be applied to every piece of critical equipment in your plant. For those who desire more information, a sound and very informative reference is the National Fire Protection Association 70B, an Inter national Codes and Standards Organization.
L. (Tex) Leugner, author of Practical Handbook of Machinery Lubrication, is a 15-year veteran of the Royal Canadian Electrical Mechanical Engineers, where he served as a technical specialist. He was the founder and operations manager of Maintenance Technology International Inc. for 30 years. Tex holds an STLE lubricant specialist certification and is a millwright and heavy-duty mechanic. He can be reached at texleug@shaw.ca.
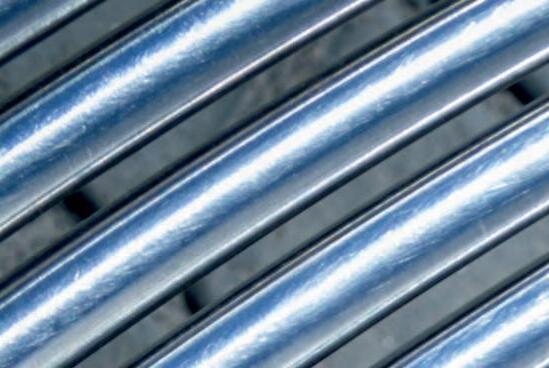
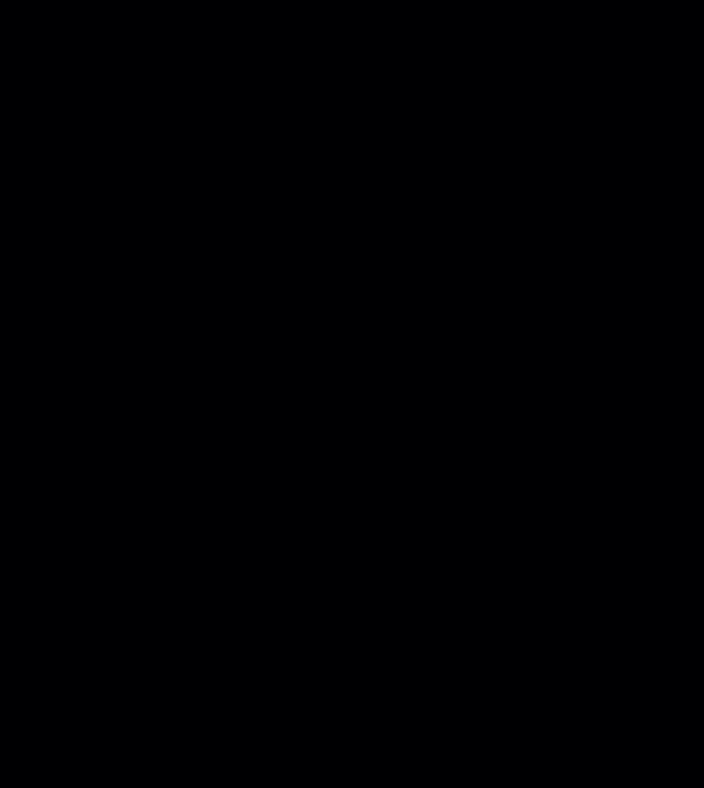
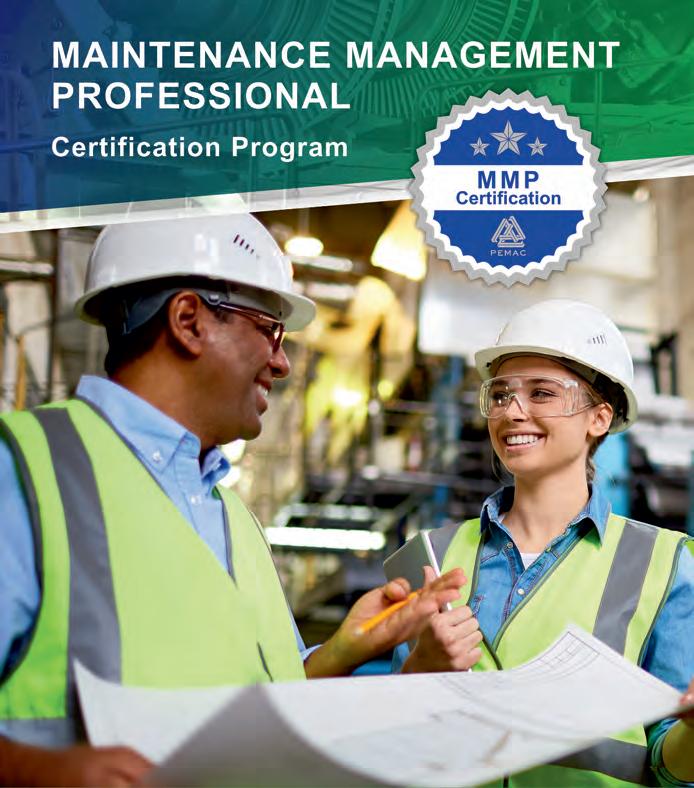






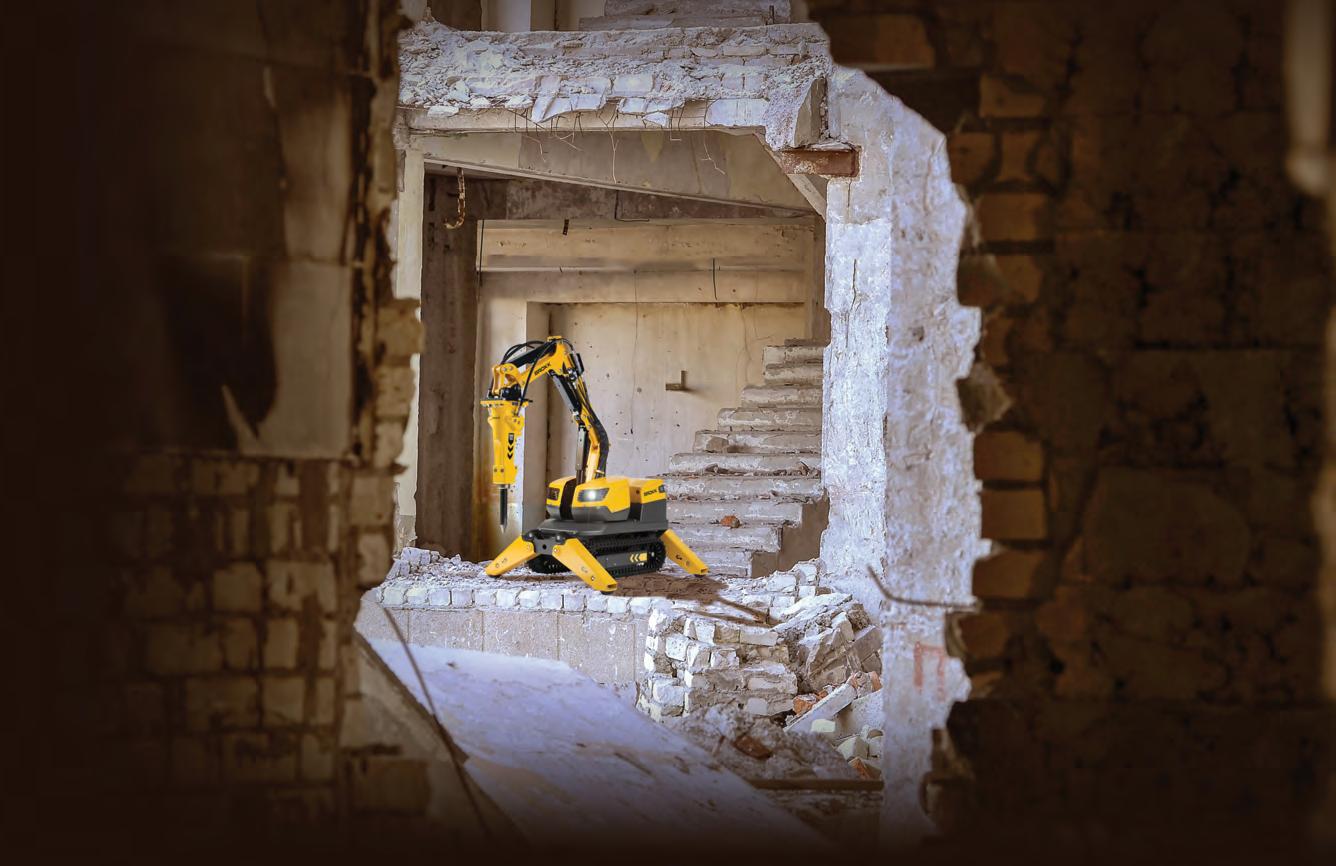
An abundance of opportunity Jobsite mechanization offers cutting-edge construction and demolition industry solutions.
BY JEFF KEELINGThe construction and demolition industries continue to see steady change. Contractors, labourers and project managers are pushing for safer and more productive solutions to transform modern jobsites while facing an ever-growing backlog of projects fueled by the $1.2 trillion Infrastructure Investment and Jobs Act. At the same time, “The Great Resignation” and Baby Boomer mass retirements contribute to labor shortages across the board.
With all these factors at play, relying on manual labor is simply unsustainable — in terms of worker recruitment and retention, safety, productivity and overall cost-effectiveness. As a result, successful contractors work to think outside the box and supplement experienced crew members with technologically advanced equipment
like robotic demolition machines to increase efficiency and reduce the physical strain on labourers. Additional mechanization options help contractors take advantage of current opportunities while accommodating industry trends.
Productivity boost
Handheld pneumatic breakers and other highly physical methods have been commonplace on jobsites for decades. However, increased jobsite mechanization has allowed contractors to revolutionize productivity.
A demolition robot paired with a hydraulic breaker, for example, improves upon previous productivity goals with an impressive hitting power, on par with excavators three times their size, and offer industry-leading power to weight ratios.These compact machines access
some of the most confined and restrictive jobsites — including those with dust, vibration and noise restrictions as well as low floor loads. At 31 inches (79 centimeters) wide and weighing 1,235 pounds (560 kilograms), the most compact units are small enough to fit through standard doorways and light enough to be transported on passenger elevators, making them ideal for confined spaces and interior demolition projects. Larger models are available with higher power ratios for more challenging applications. By employing these heavy-hitting machines, contractors can greatly increase efficiency in applications previously limited to large crews with handheld equipment. For example, one contractor was able to cut their demolition crew by a third during the nearly 1-millionsquare-foot (92,903-square-meter), multi-level tear out. The two 2,183-pound
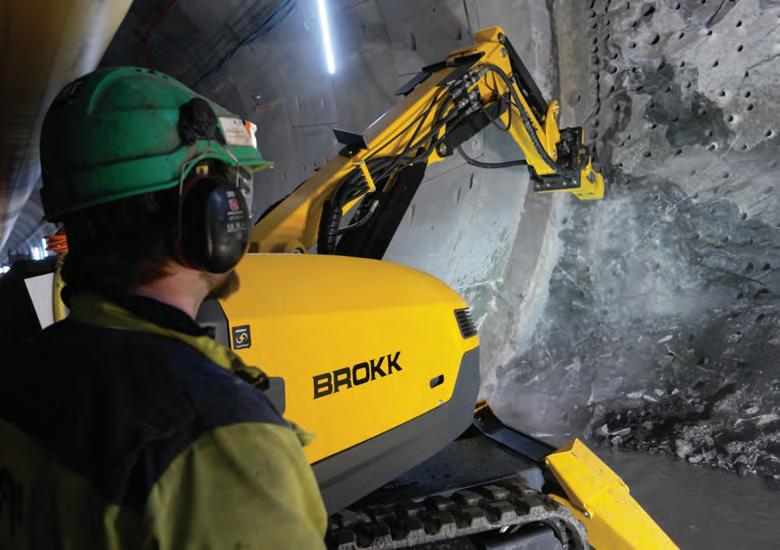
(990-kilogram) demolition robots were able to access floors where even skid steers were deemed too heavy. With each robot only requiring a single operator, the contractor was able to better utilize remaining employees across simultaneous jobsites while increasing productivity and lowering overall labor costs.
Safety benefits
For many in construction and demolition, increased safety is one of the biggest benefits
of mechanization. Remote-controlled demolition equipment addresses some of the most pressing safety concerns these industries face.
With an operating distance of up to 984 feet (300 meters), remote-controlled units physically distance employees from harmful silica dust, as well as the strong vibrations of handheld equipment such as breakers, rivet busters and chipping guns. Long-term use of these common demolition tools is linked
Contractors who invest in mechanization reduce the amount of dangerous and hard manual labor workers must perform, which is a powerful benefit to young and experienced workers alike. A young employee may consequently see construction as a long-term profession while an experienced worker may see it as more realistic to remain in the industry for the duration of their career.
to a number of chronic injuries, including carpel tunnel syndrome, nerve damage and hand-arm vibration syndrome.
Additionally, remote-controlled demolition machines help prevent one of the most common causes of serious work-related injury and death in construction — falls. A remote-controlled unit allows operators to remain a safe distance from ledges and other fall hazards. This provides peace of mind for workers and project managers, but also increases productivity by minimizing the need for erecting fall protections.
For contractors using remote-controlled machines, these safety benefits can quickly
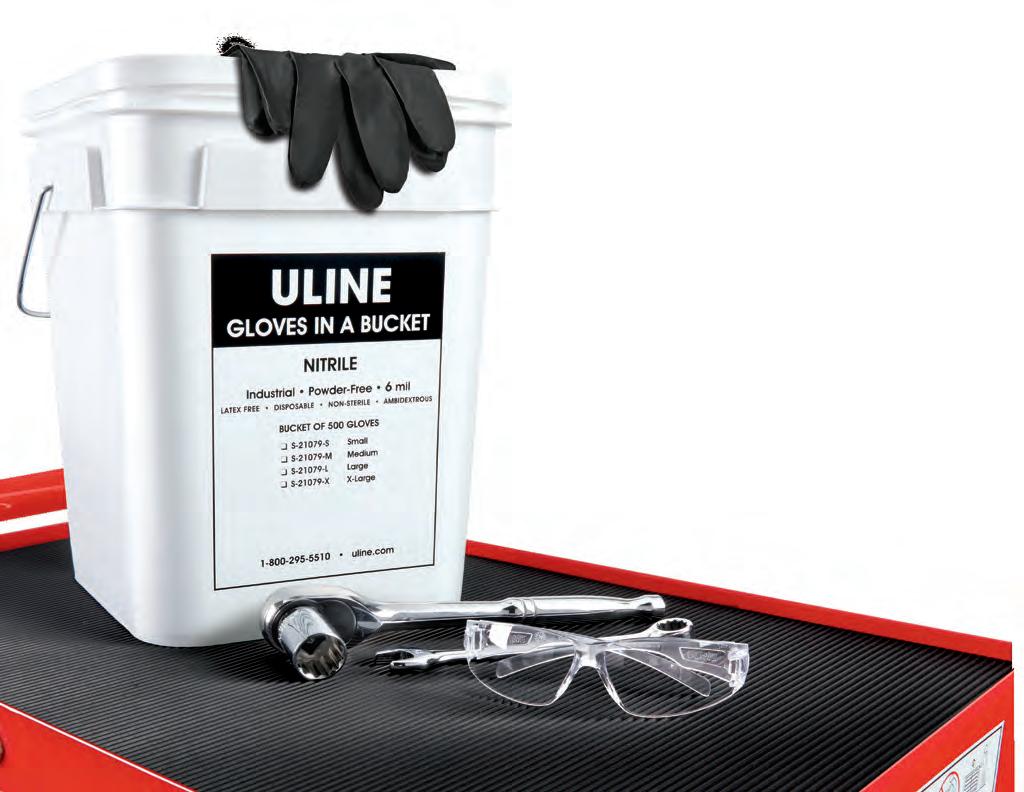


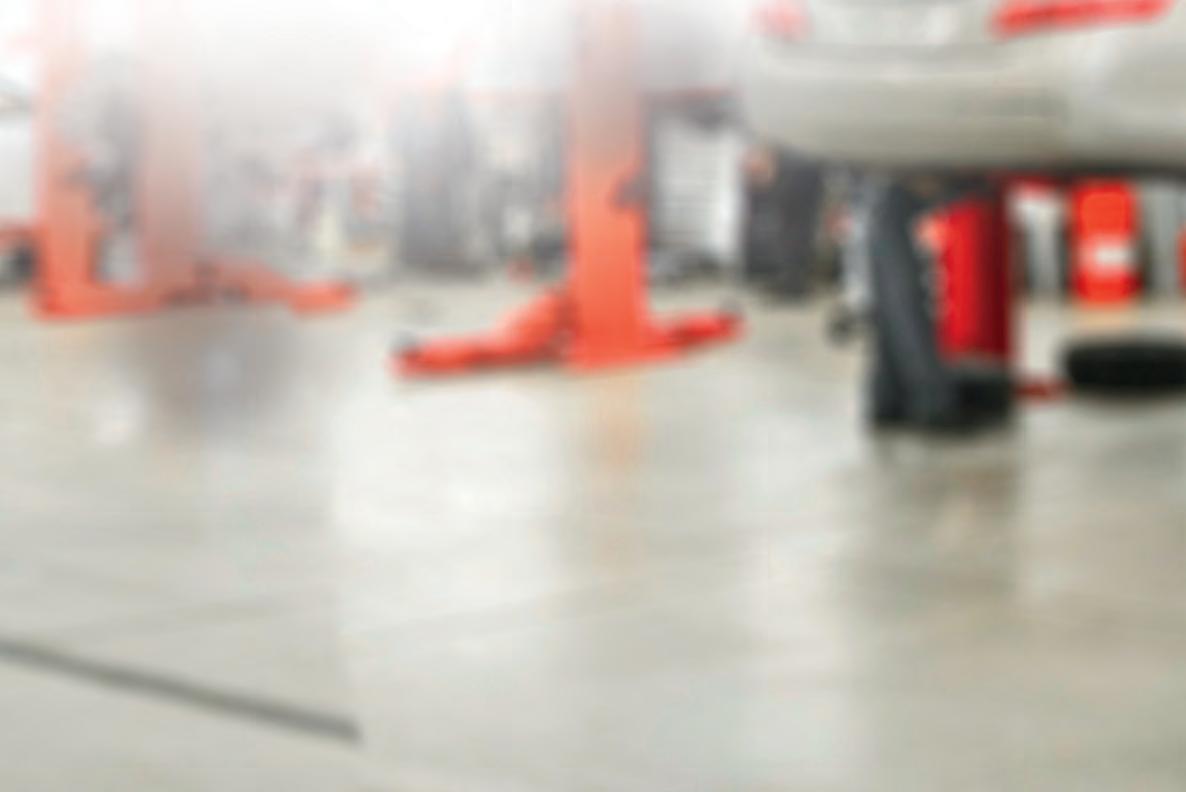
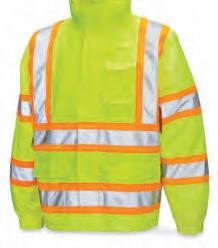
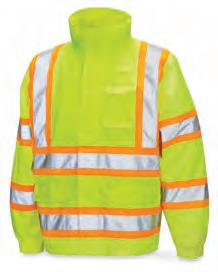

Technological advances, such as robotic demolition, can help change the way contractors work and make it possible to thrive in today’s environment while preparing for the future.
add up to significant savings on workman’s comp and insurance premiums. Remote operation paired with smaller crew size can significantly lower worker liability costs by limiting personnel in confined spaces or hazardous operations. One concrete cutting contractor who made the switch to demolition robots has seen a decrease in annual workers compensation claims by about 50%. The company has also seen a 25% decrease, or about $40,000 - $50,000 savings, in injury costs per year. Another concrete cutting operation reduced its experience modification rate (EMR) by adding demolition robots to their equipment fleet. Insurance companies calculate EMR based on a company’s safety record. Higher EMRs result in higher insurance premiums.
Recruitment and retention
Implementing cutting-edge technology also offers some powerful recruitment and retention tools. When it comes to safety, for example, the workforce is well-aware that quality of life and length of career can
be significantly affected by injuries and silica dust exposure. At this time, the median age of a construction worker is 42.3 years. Contractors who invest in mechanization reduce the amount of dangerous and hard manual labor workers must perform, which is a powerful benefit to young and experienced workers alike. A young employee may consequently see construction as a long-term profession while an experienced worker may see it as more realistic to remain in the industry for the duration of their career.
Cutting edge technology also attracts younger workers. For one concrete cutting company, including advanced robotic technology in their fleet helped reduce the median age of their 300-strong workforce to just 25 years old and cut turnover 10%. The machines also allowed the contractor to do more work with fewer people, increasing productivity 17% over three years.
The mechanization advantage It’s both an exciting and challenging time for construction and demolition.
Opportunities abound for contractors, especially those who find creative ways to recruit, retain and best use the skills of their workers. Technological advances, such as robotic demolition, can help change the way contractors work and make it possible to thrive in today’s environment while preparing for the future. Mechanization allows companies to quickly adapt to changes in labor, process or regulation, keeping them ahead of the curve — and the competition.
Jeff Keeling is the vice president of sales & marketing for Brokk Inc. He works closely with regional sales managers to develop and grow the Brokk brand in key segments across the United States and Canada. He is also responsible for educational initiatives aimed at helping customers maximize their Brokk machines’ potential..
When it comes to safety, for example, the workforce is well-aware that quality of life and length of career can be significantly affected by injuries and silica dust exposure.
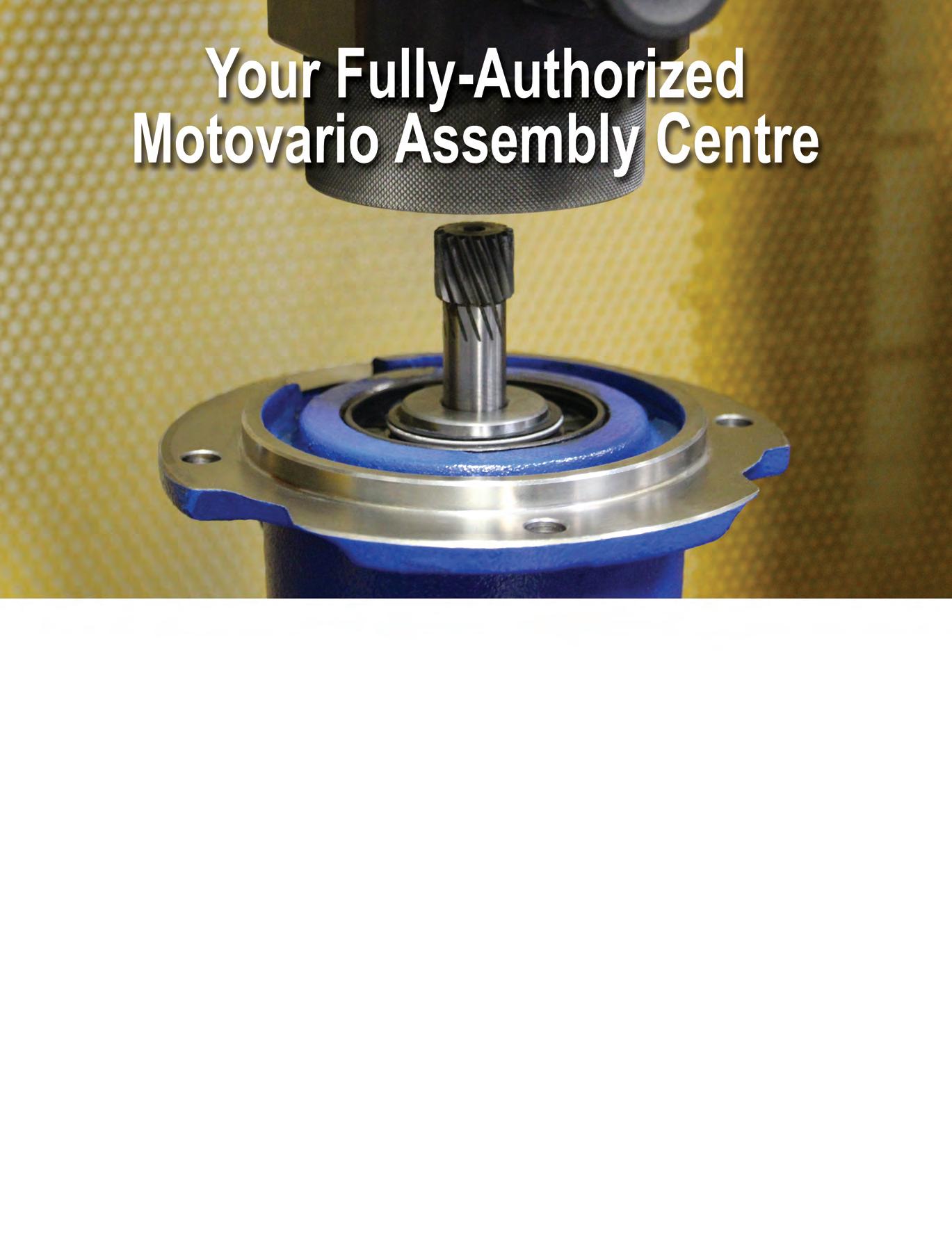

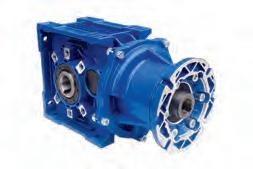
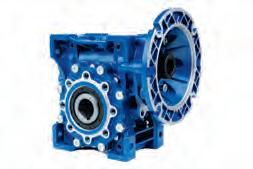
Smart machines
Exploring AI in functional safety systems.
BY MARI-LEN DE GUZMAN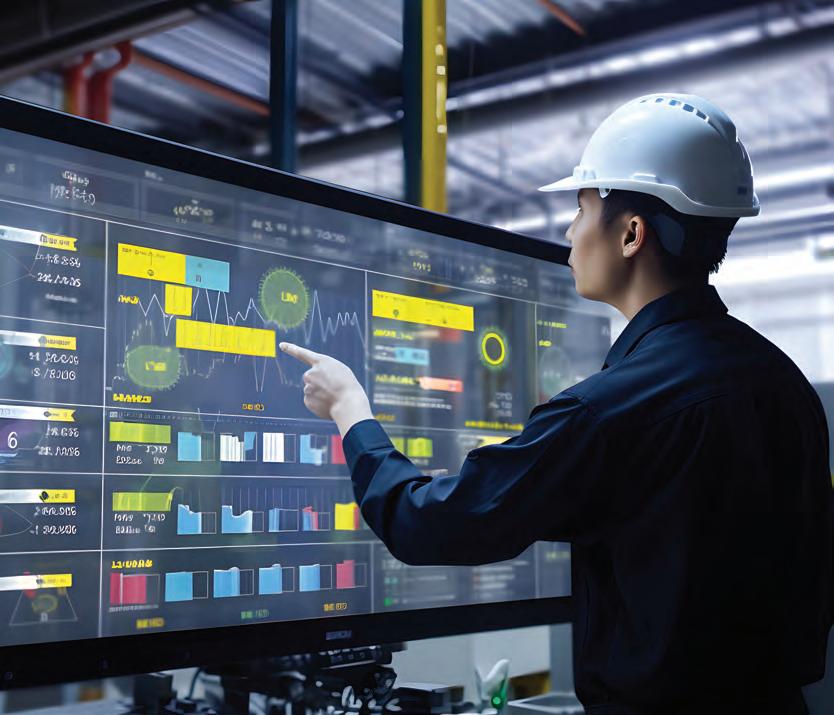
In her April 2024 TED Talk, Daniela Rus, director of the MIT computer science and ar tificial intelligence laboratory, spoke about the convergence of artificial intelligence and robotics to bring about what she calls “physical intelligence.”
Researchers at MIT are already working on this development, according to Rus. Combining robotics with AI can help intelligent machines process data more efficiently and allow AI to move beyond the digital world into the physical realm.
It’s the stuff of science fiction coming to life. Realistically, however, most companies and business leaders are not in a hurry to jump on the AI bandwagon just yet - particularly where worker safety is concerned.
“The safety industry is notably conservative,” says Doug Nix,
managing director of Compliance InSight, an industrial machinery safety consulting fir m based in Kitchener. Ont. “And we’re conservative for good reason, because we are expected to protect people’s lives.”
Although there are numerous applications of AI in a variety of industries and for a variety of purposes - improving efficiencies, reducing or eliminating human errors, reducing injuries, streamlining processes - autonomous machines may be one of the technology’s biggest potentials. We see a glimpse of this on some streets today with autonomous vehicles (AVs).
Proponents of these self-driving cars are pointing to their potential to reduce car crashes caused by human error. In 2021, for example, the annual vehicular fatality rate in the US was 42,915, and 94 percent of
these crashes are due to human error. Reducing incidents of crashes by 90 percent through AVs would mean potential savings of about $190 billion per year, according to a fact sheet from the University of Michigan’s Center for Sustainable Systems.
Despite its many perceived benefits, regulators in Canada are putting the brakes on fully autonomous vehicles - those that don’t require a human operator. These types of AVs are largely prohibited from roaming the streets, except in vehicle testing or pilot program situations. And likely for good reason. South of the border, legislation pertaining to AVs vary by state.
The U.S. National Highway Traffic Safety Administration reports AVs are more than twice as likely as traditional vehicles to be involved in an accident. In 2015, there were 9.1 crashes related to driverless vehicles per million miles driven, compared to 4.2 crashes in conventional vehicles per million miles driven.
Clearly, the technology requires more finetuning, which includes much better data processing. After all, data is key when it comes to AI functionality and decision-making capabilities.
Functional safety
AI-enabled autonomous machines, capable of making accurate and correct decisions based on a set of parameters, are the future of work. How far or how close we are from that future is still unknown, but it has already led to the development of new standards and technical reports to create guidelines and frameworks for integrating AI in machinery.
“When we start to talk about safety systems for machinery or any kind of electromechanical system… functional safety is the branch of engineering that focuses on the ability of the control system to function correctly under difficult situations, let’s say. We’re looking at making sure that the safety systems can always function when they’re needed,” explains Nix, who is part of a technical committee that recently developed a technical report on functional safety and AI systems (ISO/IEC TR 5469:2024) for the International Organization for Standardization (ISO).
Functional safety systems are embedded in machinery or equipment to provide automatic safeguards or protections against risk or harm.
Safety systems have traditionally been hardwired to machines, but software evolution over the last decade has enabled the development of programmable safety modules and programmable logic controllers (PLC), explains Nix.
The possibility of incorporating AI into these programmable systems has given rise to more safety-related concerns. Safety systems are expected to be deterministic, which prescribes a set of inputs to get an exact set of outputs, Nix says. A set of inputs programmed on a piece of machinery that defines a dangerous condition will result in the machine going to a safety state, i.e. shutting down, when this programmed dangerous condition is present.
These PLCs are what’s commonly used in factory automation, which are specially engineered for safety applications. The possibility of using AI in some conjunction with those prog rammable systems raises many questions that are yet to be answered.
“The problem with some kinds of AI, not all kinds, but especially with generative AI tools, is that because they’re based on statistics normally, then you only get an estimate of what the correct answer should be, you don’t get a specific correct answer every time. And that’s why they can hallucinate,” Nix says. AI hallucinations refer to incorrect or misleading results generated by AI, usually caused by insufficient or biased training data, or incorrect modeling assumptions.
Deterministic AI, as opposed to generative AI, may be more adoptable with machine safety applications.
“You need to understand what the risk is. And then based on the risk, you can decide what level of involvement you want your AI to have. And then based on that, you can come up with a safety system that’s likely to be acceptable,” Nix says.
Devil in the data
The biggest driver for AI effectiveness and accuracy is data. Integrating AI into systems and processes requires vast amounts of data to make correct calculations and decisions. For most organizations, therein lies the problem.
“AI needs data to make decisions... So it really comes down to how good the data is and what does that look like? And so the better the data, the better the decisions can be made, the better decisions that are made, then the better results you get,” says Dylan Short, managing director of The Redlands Group, an Oakville, Ont.-based health, safety and risk management consulting firm.
Proper and consistent data collection and management is not always black-and-white in many organizations, particularly when it
comes to workplace safety data. Data analysis is a significant part of a health and safety r isk assessment, and when reviewing a company’s incident or injury reports, Short says the data often f all short.
Entering incident reports and other health and safety data often falls under the purview of supervisors, whose day-to-day challenges and responsibilities may not always allow them to become masterful keepers of data, leading to inconsistent unreliable data,
Short says.
It’s a challenge, but also an opportunity where AI can be a useful tool.
“If organizations have the ability to control that data a little better, either through an administrator, through highly trained individuals that are specialists on taking the information out of something like an investigation and putting it into a data set. That’s where I think AI could have a huge advantage,” Short says.
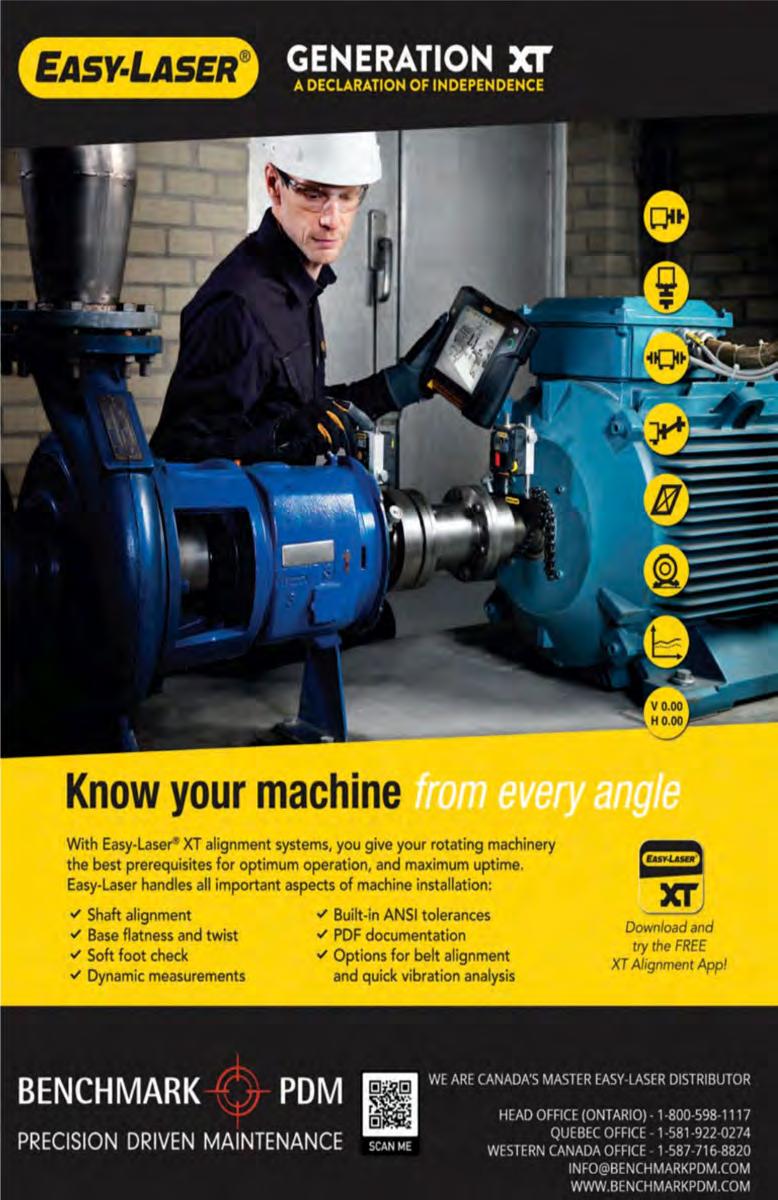

“It takes away things like my team sitting down and literally reading the 80-odd investigation reports and trying to connect the dots. AI is way better at those kinds of things, when it’s given the right data to look at.”
Predictive maintenance
One of the widely used applications of AI in industrial settings is in preventive maintenance systems, and this is where machine learning comes into play.
AI modeling can measure a piece of machinery’s operational profile, like normal vibrations, temperatures and other parameters, until it has learned and accumulated enough data to gain an understanding of the machine. With a vast database of knowledge collected overtime about the equipment, AI can predict when to do preventative maintenance based on changes in the normal condition of the machine.
“The great thing with systems like that is that if you have machinery that has to be up all the time and running all the time… you can watch the way the equipment is performing, and decide how you’re going to schedule maintenance in the future so that you can keep that machinery available when It needs to be available,” says Nix.
AI-enabled preventative maintenance systems are not new, and many of the early adopters are large
organizations that require continuous processes, such as public utilities and other infrastructure facilities.
Predictive maintenance data can also offer valuable insights for companies in terms of optimizing systems and machiner y.
“I think that’s the place where AI can really potentially help organizations not just get better at predicting but optimizing; are we doing our maintenance often enough, or too often? Should we be looking and saying, this piece of equipment has this type of f ailure on a regular basis and we need to do something about that differently,” Short says.
New and emerging applications
Some of the new and emerging applications of AI in workplace safety are not always machine-related. AI-enabled risk assessment systems can provide significant benefits to an organization.
“One of the challenges about risk assessments is when you do a risk assessment about every job task in an organization, that becomes this really big data set. But really, big datasets are what AI does really, really well,” Short says.
Risk assessments with huge amounts of company data can be accomplished by generative AI so much better than a human can, he adds.
Vision-based safety systems, driven
by AI, is another emerging approach to safeguarding machines. It uses video cameras to watch the area around a piece of equipment, which effectively eliminates perimeter fences around machiner ies. The camera system is programmed to know what things are supposed to be in that space - which is the “safe condition.”
“Then if a person comes in, the system has to be able to track the person as they walk into the danger zone, determine how quickly they’re moving, and what their angle is in relation to the dangerous things that are inside that space. And then it has to make a decision about should this system shut down or not? Or maybe we just slow it down?” Nix says.
Despite the growing interest and the various levels of AI applications and adoptions aimed to enhance workplace safety and reduce or eliminate risks, both Nix and Short believe adoption will not likely be swift particularly when it involves worker safety.
“At the moment, you’re gonna get a lot of skepticism in terms of how available systems like that are, and how useful they are, and so on, because we have a lot of tools already that are already doing a really good job for us. So why would we want to bring in something new, that is an unknown and kind of unproven thing?” Nix says, adding this is particularly true for the safety market.
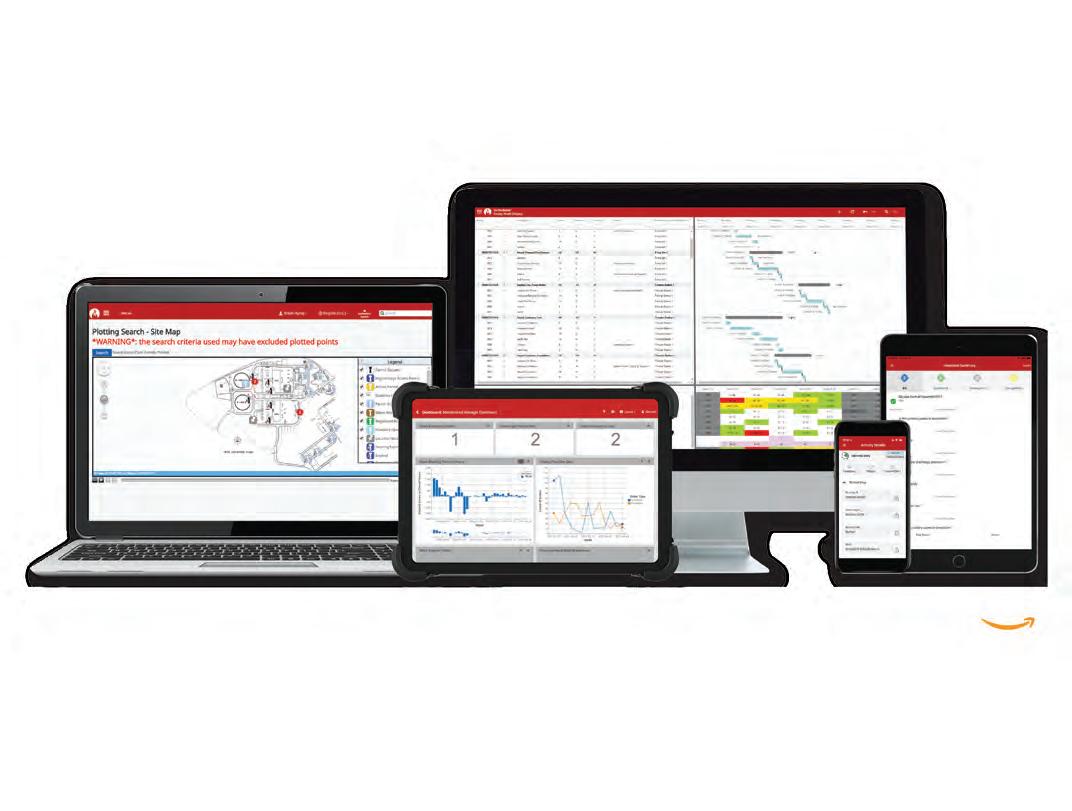
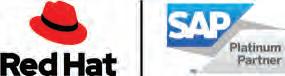
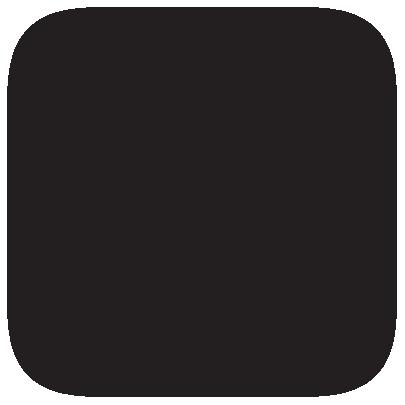
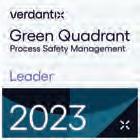
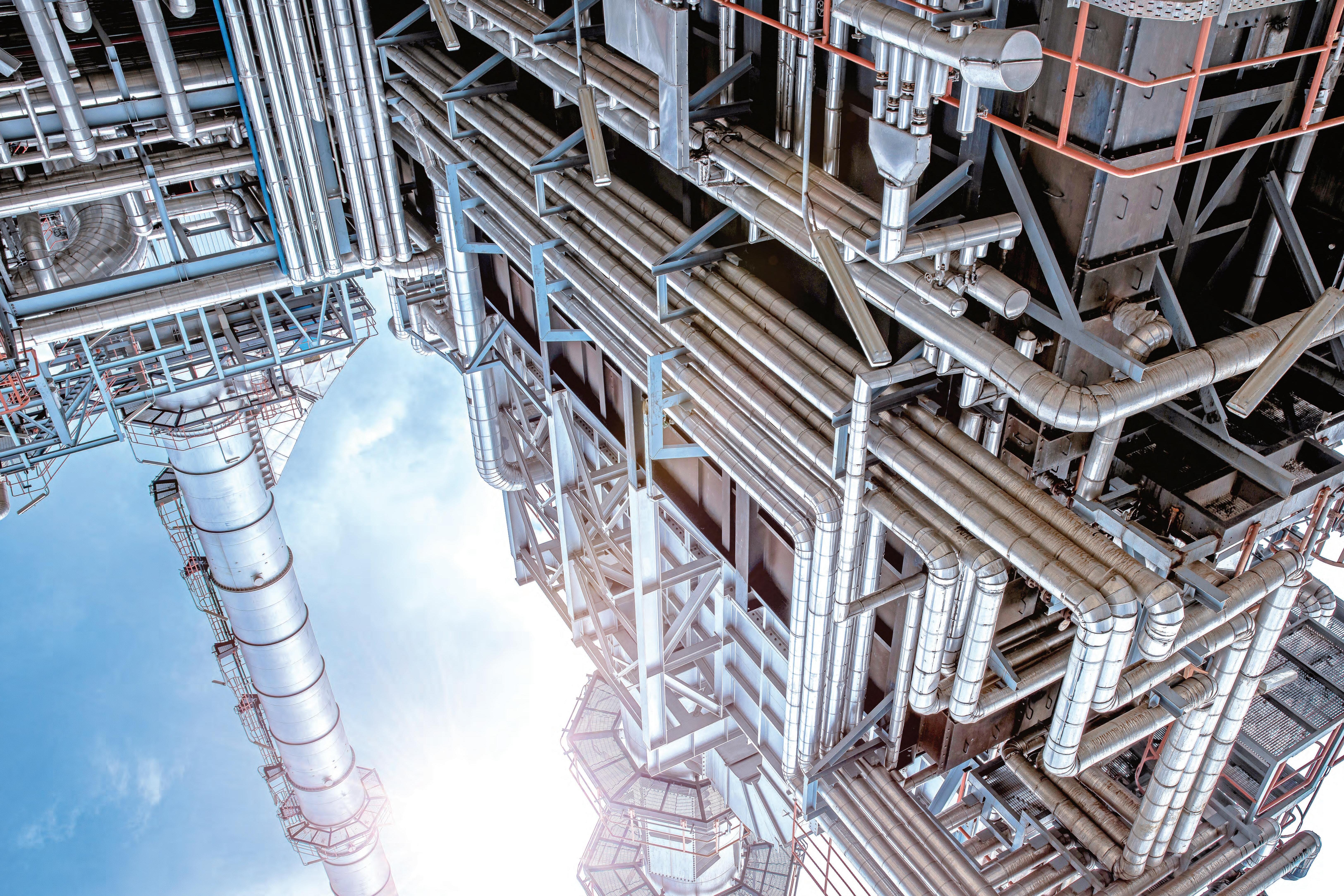
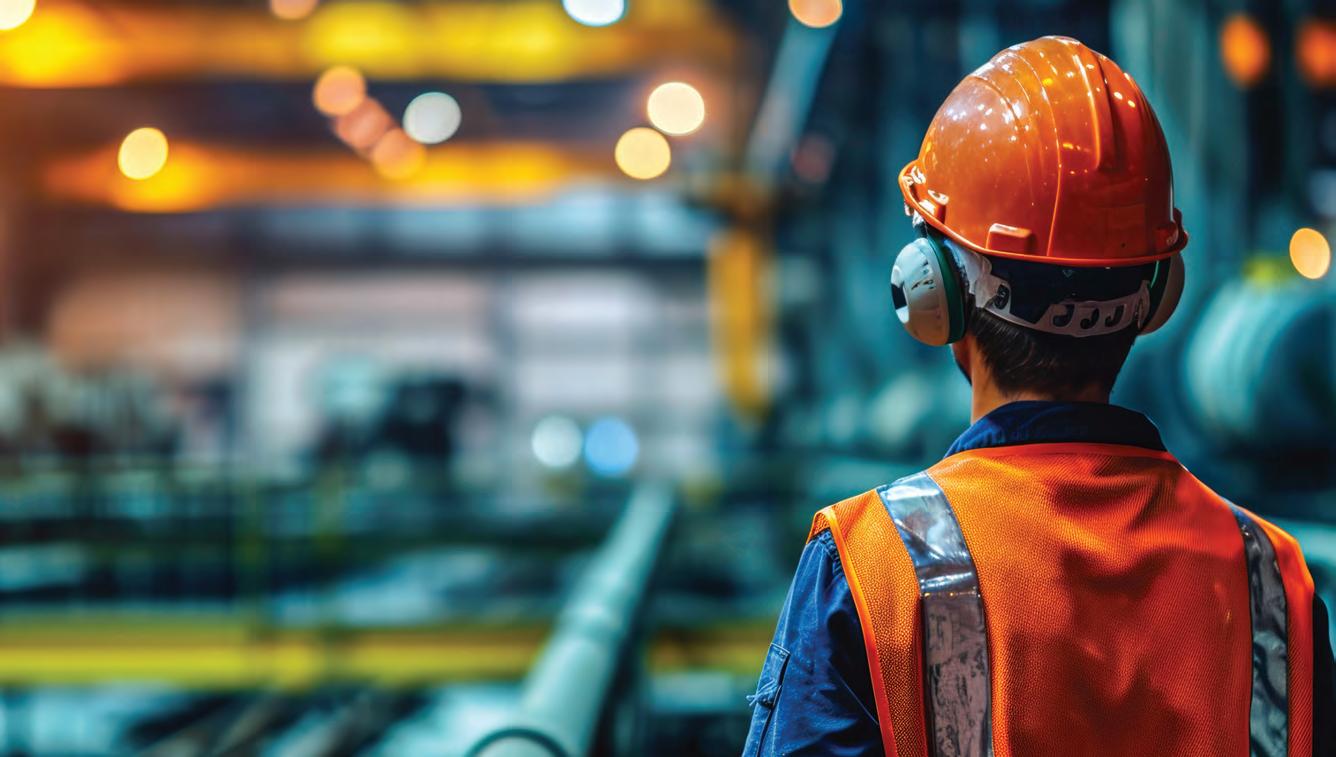
Safety in maintenance
Enhancing safety and efficiency with the right workwear choices in MRO settings.
BY NICK WARRICKMRO refers to the activities and processes involved in maintaining, repairing, and managing the facilities, equipment, and assets of a company or organization. This includes everything from routine maintenance tasks to emergency repairs and the procurement of supplies needed to keep operations running smoothly. MRO is essential for ensuring that equipment and facilities remain in optimal condition, minimizing downtime, and ensuring safety and efficiency in the workplace.
When it comes to enhancing safety and efficiency in MRO settings, choosing the appropriate workwear goes beyond mere style, although a professional image is often important. Dressing for personal safety and enhancing performance is much more important, especially for maintenance or repair jobs and operations tasks. The correct workwear can safeguard against cuts, burns, and other workplace hazards while ensuring your visibility to others. Choosing the right workwear will ensure you adhere to regulations and establish a safe and effective work environment.
The Role of Workwear in MRO Environments for Enhancing Safety and Efficiency
Employers have a legal responsibility to ensure the safety and well-being of their workers. Providing the correct protective workwear can significantly reduce the risk of exposure to hazardous substances and workplace accidents. In addition, safety workwear can enhance productivity by making employees feel secure and safe in their working environment. Mandating protective workwear is also vital in ensuring adherence to health and safety regulations, thereby minimizing the potential for penalties or legal issues.
Types of Workwear for Different MRO Environments
Choosing suitable workwear for the right environment is crucial for worker safety and high productivity. Different work settings often require specific gear to protect workers effectively. For instance, industries dealing with hazardous materials and chemicals necessitate specialized clothing made of chemical-resistant materials to safeguard workers from exposure that could cause
chemical burns, skin irritation, and longterm health problems.
Warehouse workers usually require steeltoed boots to prevent injuries, whereas those working in a manufacturing setting must avoid loose-fitting work clothing to avoid getting tangled in machinery. A risk assessment needs to be made for each location to ensure the correct workwear is available.
Key Considerations for Selecting Workwear in MRO Environments
When selecting workwear for safety, the management team should conduct a thorough hazard assessment of the work environment to identify potential risks and hazards. Employers should consider factors such as exposure to chemicals, sharp objects, extreme temperatures, naked flames, and moving machinery.
Compliance with relevant industry standards and regulatory requirements is the bare minimum expected of an employer to ensure protective workwear and adequate protection for workers. Prioritizing workwear that not only meets minimum safety standards but also offers a comfortable fit that allows for
ease of movement without being too loose is crucial. Restrictive clothing can impede productivity and reduce morale, whereas workwear that is too loose can increase the risk of accidents.
High-visibility workwear enhances visibility and safety and makes sense in almost any maintenance or repair role. However, choosing workwear with the right features tailored to the specific work environment is essential. For example, flame-resistant clothing is crucial for workers in settings where fire or electrical hazards are a danger.
Comfort is another issue to consider, as in some work environments, workwear that provides adequate breathability and moisture management is essential to prevent overheating, so moisture-wicking fabrics and ventilation panels can help keep workers cool and dry during prolonged wear in hot or humid conditions.
Ensuring that workwear is compatible with other personal protective equipment is crucial. If gloves, safety helmets, goggles, or respiratory protection are required, the workwear must integrate with PPE to enhance overall protection.
Durability is essential, too, as robust workwear will last longer, reducing the need for frequent replacements and minimizing costs.
Dangers of Long Hair and Loose Clothing
Workwear should be comfortable but not baggy or loose-fitting. When not adequately secured, long hair and loose clothing in an MRO environment can become entangled in unguarded moving or spinning parts of plant equipment, machinery, or power tools. Entanglement injuries are common in the workplace with over 30,000 per year in the USA alone. These injuries typically result from clothing, hair, or jewelry getting caught in movable or spinning parts. These injuries can include amputation of body parts, degloving of fingers, strangulation, and even partial or complete scalping if hair becomes entangled. Entanglement injuries can even be fatal due to severe blood loss and shock.
It is crucial to ensure all employees are aware of entanglement dangers and to identify the potential for these hazardous situations. Employers should prominently display warning information on safety posters throughout the area and on any equipment with moving parts. When entering a work area with equipment that could potentially cause entanglement injury:
• All loose-fitting clothing needs to be secured or removed.
• If required, long hair must be securely restrained behind the head using a hair net/cover.
• Long beards should also be netted and kept close to the face.
How Does Compliance with Safety Regulations Impact MRO Workwear Choices?
In MRO settings, safety is paramount; selecting the right workwear goes beyond mere style and branding. It’s about ensuring the workforce’s well-being and adhering to industry regulations. Workplace safety begins with choosing the correct workwear. Maintenance and repair professionals often work in hazardous environments, making it imperative to invest in the correct workwear and PPE to provide robust protection. Compliance with industry regulations is not just a minimum legal requirement; it’s a moral and ethical obligation to workforce safety. Choosing workwear that meets or exceeds safety standards is a proactive approach to minimizing employee risks by creating a safe working environment. It also demonstrates a commitment to the
well-being of employees and improves morale and productivity within the organization.
Maximizing Safety and Efficiency with the Right Workwear
Choosing the correct workwear for safety and compliance is a decision that extends beyond aesthetics or company branding. It’s about prioritizing the protection of the workforce, ensuring adherence to industry regulations, and fostering a positive work setting with a culture of responsibility. Choosing suitable workwear in MRO settings can enhance a company’s reputation. By prioritizing safety with workwear, companies can project a professional image to customers while boosting productivity and keeping employees happy. Investing in the proper workwear shows employees that their safety is taken seriously.
Nick Warrick is the Sales Manager at All Seasons Uniforms. With over 15 years of experience in the work uniform business, he has worked with over 100 clients across 20 different industries. Holding bachelor’s degrees in both Business Administration and Information Technology, Warrick revamped the company’s online presence, offering its customers a new uniform shopping experience.
NEED A HELPING HAND TO CHOOSE
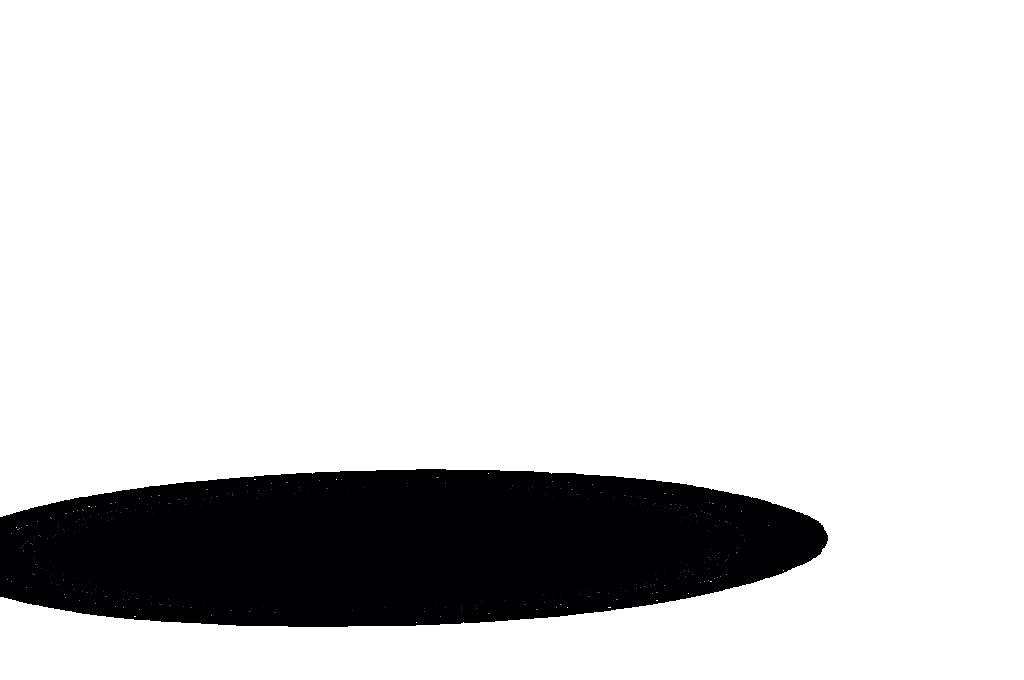
• All jewelry should be removed, especially necklaces, rings, bracelets, and dangly earrings.
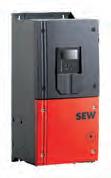
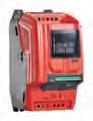

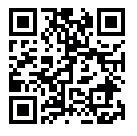
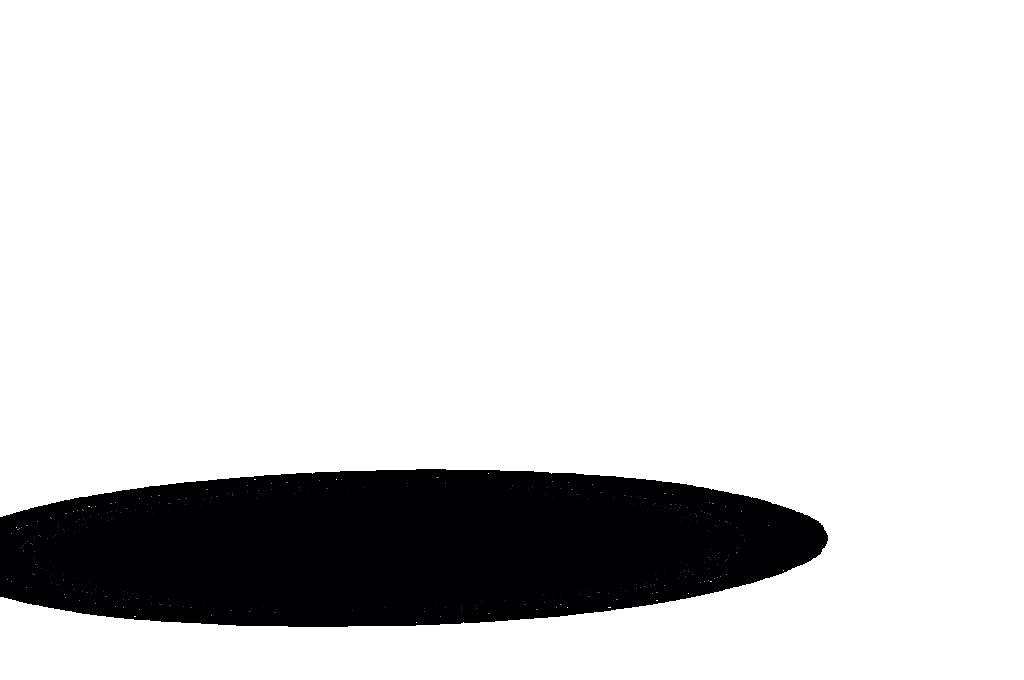
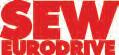
Debunking four misconceptions when selecting grease
BY ZACH SUTTONSelecting and applying appropriate lubricants to industrial machinery components is critical to a machine’s function.
Beyond making sure the wheels of machinery run smoothly, lubricant selection has an impact on equipment performance, reliability, productivity, longevity, and ultimately, profitability. This means maintenance and lubrication engineers have a big task on their hands to make the right lubricant decision for each application.
Proper lubrication of machinery is an often overlooked, yet critical aspect of ensuring an operation is running efficiently. Selecting the optimal lubricant for equipment has become a highly specialized process, with more choices than ever before.
Equipment manufacturers continue to refine designs to take advantage of new technologies, as well as to improve efficiency and long-term performance.
Newer, more compact machinery tends to run at higher speeds and under more severe pressure, with tighter clearances between moving parts than just a decade ago. These engineering trends, combined with constantly evolving environmental, energy and safety regulations have led to the proliferation of lubricant formulations in the marketplace. This makes the process for choosing the optimal lubricant more challenging and requires a bit of homework.
Maintenance managers generally know the type of grease they want, but they may be misinformed on the different categories and types of greases as well as their functions. With that in mind, here are four of the most
common misconceptions users have when selecting a grease for industrial machinery applications.
Four misconceptions of selecting a grease:
• Misconception 1: Any grease will do
Many in the field do not understand that not every thickener is compatible with every machine. Suppliers in the industry have tried implementing a color designation for greases of various categories to help with selection, but there is no one standard, meaning different colors of grease can mean different things. So for example, you might buy a lithium complex grease versus a simple lithium product grease, and both could be compatible with your machine and similar in color. However, a lithium complex product will typically outperform a simple lithium by providing added protection in various operating conditions.
While coloring greases is designed to help with identification, color is not a measure of performance or always an identifier of the thickener in the product. Meaning that coloring can be helpful in narrowing down products, however if a user selects and applies a product not ideal for the pressure and temperature requirements of a given machine, they could be jeopardizing or outright breaking an industrial machine that costs hundreds of thousands of dollars.
• Misconception 2: I can only use the brand of grease my OEM recommended

The Original Equipment Manufacturer’s (OEM) recommendation should be the starting point for any grease selection process, because they built the machine and know best what the pressure requirements are for a grease in that machine. The manufacturer will typically specify the viscosity grade, performance properties, and fluid cleanliness levels required to protect the components in a specific application. Keep in mind, viscosity is the single most important property that you have to get right when selecting a grease. OEM recommendations will lead you to a grease with the right viscosity requirements, but may stop short of recommending a specific oil. If the lubricant viscosity is incorrect, you run a very high risk of premature equipment failure.
Some OEMs have begun to engage with lubricant suppliers to ensure they offer the recommended product for their machine--under most circumstances, an OEM
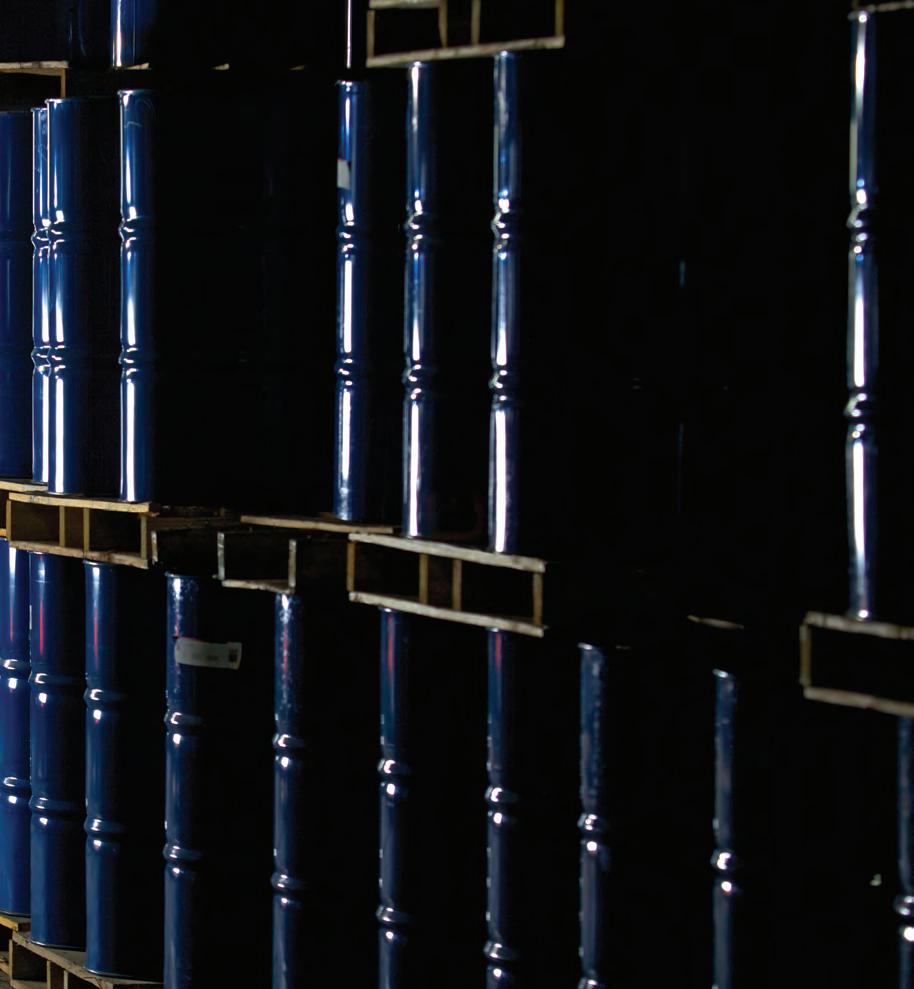
cannot require users to only buy one specific lubricant brand or product. Even if the OEM manual calls out a specific lubricant by name, that does not pigeonhole you out of other options. Work with your supplier and ask for evidence that its products meet the OEM specifications for a particular application. This can also help consolidate the number of vendors with whom you need to work.
• Misconception 3: Greases function in any environmental conditions
Both the equipment operating temperature and the temperature of the surrounding environment have a direct impact on the performance of a lubricant. All lubricants have a specific temperature range for optimal performance, and in some cases that range may be fairly broad. However, some lubricants are better suited for extremely cold or hot operating and environmental temperatures. As mentioned,
• Misconception 4: Grease is just an expense with no ROI
While greases are a maintenance expense, the cost of improperly maintaining equipment is far greater. That means maintaining equipment with lubricants is a mechanism for cost savings rather than an additional expense. According to research from Polaris Labs, lubrication represents an investment rate as high as 45:1, meaning that for each $1,000 spent on quality lubricants and lubrication practices, a yield of $45,000 of savings is possible.
viscosity is critical for a lubricant, so when volatile temperature either makes lubricants too thick or thin, you risk increased wear or system damage.Therefore, the temperature range and the environment in which the equipment operates is critical.
Operators must also ensure they apply greases with clean handling of the product to reduce the potential to pump unnecessary contamination into a component. Greases and grease guns should be stored in clean, cool and dry locations to prevent contamination and oxidation.
If machinery functions outdoors, both cleanliness and temperature are even more important to monitor and can cause lasting damage or outright break a system. In these situations, engineers should take every precaution when selecting a grease to ensure contamination is minimized and the suggested temperature range for the grease is not threatened with a severe dip or spike in temperature.
Lubrication is an investment that achieves returns in the form of higher performance and efficiency, reduced downtime, and longer equipment life. For optimal performance, many believe that the most expensive grease is inherently the best solution for their machine – which is also incorrect. Rather, the best lubricant is the one that best fits a machine’s needs and provides overall wear protection that aligns with the site’s maintenance workmanship. Operators should also maintain a record of bearing life so they can effectively monitor for wear and review the components as they come out of service. This type of proactive monitoring for damage can lead to corrective actions and maintenance during downtime to prevent shutting down a machine or system.
All of these considerations underscore the fact that choosing an optimal grease is a complex process. Even with a wealth of information about available solutions, separating fact from fiction when it comes to selecting a grease is critical, which is why maintenance managers should keep in close contact with their OEMs and lubricant providers. Suppliers are constantly aiming to understand customer needs as they evolve and guide them toward making an informed decision for their specific application.
With knowledge of all of the factors that can lead to choosing the right lubricant, maintenance managers and engineers can focus on developing timelines for effective equipment maintenance to ensure they are saving money and avoiding malfunctions in their systems.
Zach Sutton is an industrial, grease, coolants sector manager at Chevron Lubricants.
WHAT’S NEW IN PRODUCTS

TECHNIDRIVE BOOSTS EFFICIENCY AND CUTS COSTS IN CONVEYOR APPLICATIONS
Technidrive, an electric motor and gearbox provider, has developed a drive solution for heavy-duty conveyors that minimises costs while maximising efficiency and uptime.
The Drum Drive reduces the total cost of ownership by up to a third compared to conventional bevel helical gearbox units for quarrying and recycling applications.
Industries like quarrying and recycling are evolving in response to climate change and soaring energy costs. McKinsey estimates that the mining sector needs to reduce emissions by 85 per cent by 2050. Switching to mobile electrified equipment like conveyors while optimising energy efficiency is core to this transition.
The Drum Drive is a compact track drive gearbox with 53 per cent less mass than a typical bevel helical gearbox unit with the same power, torque and speed.
The Drum Drive can be installed directly inside a conveyor head drum. As the unit acts as a bearing, it eliminates the need for shaft and bearings requiring regular lubrication. Fewer parts translate into lower upfront costs, reduced maintenance and extended lifespan.
The Drum Drive achieves a 20 per cent higher service factor and 60 per cent higher shaft radial load ratings.
With its high-efficiency motor technology from WEG, the drive can be fitted with the latest permanent magnet (PM) motors or hybrid motors integrating PM, ferrite, or neodymium magnets, along with synchronous reluctance (SynRM) technologies.
Initially developed for low-speed, high-torque feeders, the Drum Drive range has been expanded to suit high-speed, low-torque conveyors with higher power ratio requirements.
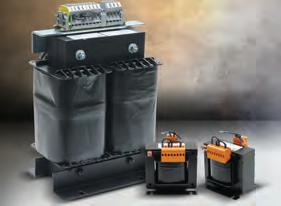
MURRELEKTRONIK OPEN CORE CONTROL TRANSFORMERS FROM AUTOMATIONDIRECT
AutomationDirect has added Murrelektronik open core control transformers that provide a flexible solution for stepping down a variety of primary voltages ranging from 208 to 550 VAC.
The universal input on these transformers provides eleven different voltage options that are easily configurable using simple quick-connect jumpers.
The primary side can be configured for 208, 230, 380, 400, 420, 440, 460, 480, 500, 525, or 550 VAC with 115/230 VAC on the secondary. Rated at 50/60 Hz, they offer an electrostatic shield for noise reduction and IP20 finger-safe terminal connections.
These open-style transformers are available in ratings from 100 to 6300 VA and provide valuable time and cost savings by allowing OEMs and system integrators to standardize on a single model for a variety of applications.
The new Murrelektronik open core control transformers are UL recognized, RoHS compliant, and CE and DNV-GL marked.
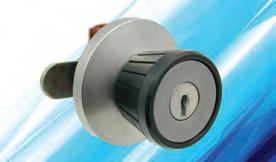
LOWE & FLETCHER
KNOB LOCK FROM FDB PANEL FITTINGS
The Online Store at FDB Panel Fittings now offers an ex-stock 1605 Knob lock from sales partner Lowe & Fletcher for the twist-and-go operation of cabinet doors to suit various applications, including metal office furniture and doors for industrial workspaces and
elsewhere.
Knob locks present a compact option with simple rotary action that is convenient and stylecompatible with many existing installations.
They feature rear mounting for security and a clean appearance achieved with a satin chrome body and black plastic handle. Spindle length and cam may be customer specified.
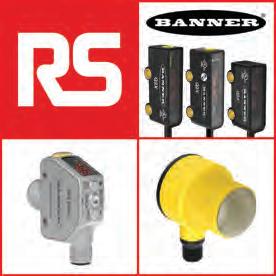
RS OFFERS BANNER ENGINEERING’S PORTFOLIO OF SENSOR PRODUCTS
RS now offers Banner Engineering’s extensive portfolio of sensor products, which spans a wide variety of sensor technologies — including photoelectric, laser, and radar — and can satisfy the needs of almost any industrial automation application.
Banner’s photoelectric sensors emit a beam of light that detects the presence or absence of items and targets made of most materials — including shiny, dark, clear, and multicolored ones — as well as changes in surface conditions.
When the emitted light is interrupted or reflected by the item, the change in light patterns is measured by a receiver, and the target is recognized.
These sensors are available with an extensive selection of styles (e.g., self-contained, long-range, heavy-duty, and compact), housings, mounting options, sensing modes, and detection ranges.
They perform a wide variety of tasks, exhibit very fast response times, and are widely used in industrial manufacturing, material handling, and packaging applications in markets spanning
food and beverage to medical.
The Q2X Series miniature photoelectric sensors, for example, provide unparalleled versatility and performance with five different sensing modes engineered to accurately detect even the most challenging targets over short- and long-range distances.
They also offer compact housings optimized for today’s increasingly space-constrained industrial automation applications. Banner recently added two new sensing modes, laser measurement and fixed-field, to the original three: adjustable-field, polarized retroreflective, and opposed.

NEW SIEMENS SOFTWARE IDENTIFIES VULNERABLE PRODUCTION ASSETS
To address the need to identify cybersecurity vulnerabilities on the shop floor as quickly as possible, Siemens has launched a new cybersecurity software-as-aservice.
The cloud-based SINEC Security Guard offers automated vulnerability mapping and security management optimized for industrial operators in OT environments.
The software can automatically assign known cybersecurity vulnerabilities to the production assets of industrial companies. This allows industrial operators and automation experts who don’t have dedicated cybersecurity expertise to identify cybersecurity risks among their OT assets on the shop floor and receive a riskbased threat analysis.
The software then recommends and prioritizes mitigation measures. Defined mitigation measures can also be planned and tracked by the tool’s integrated task management.


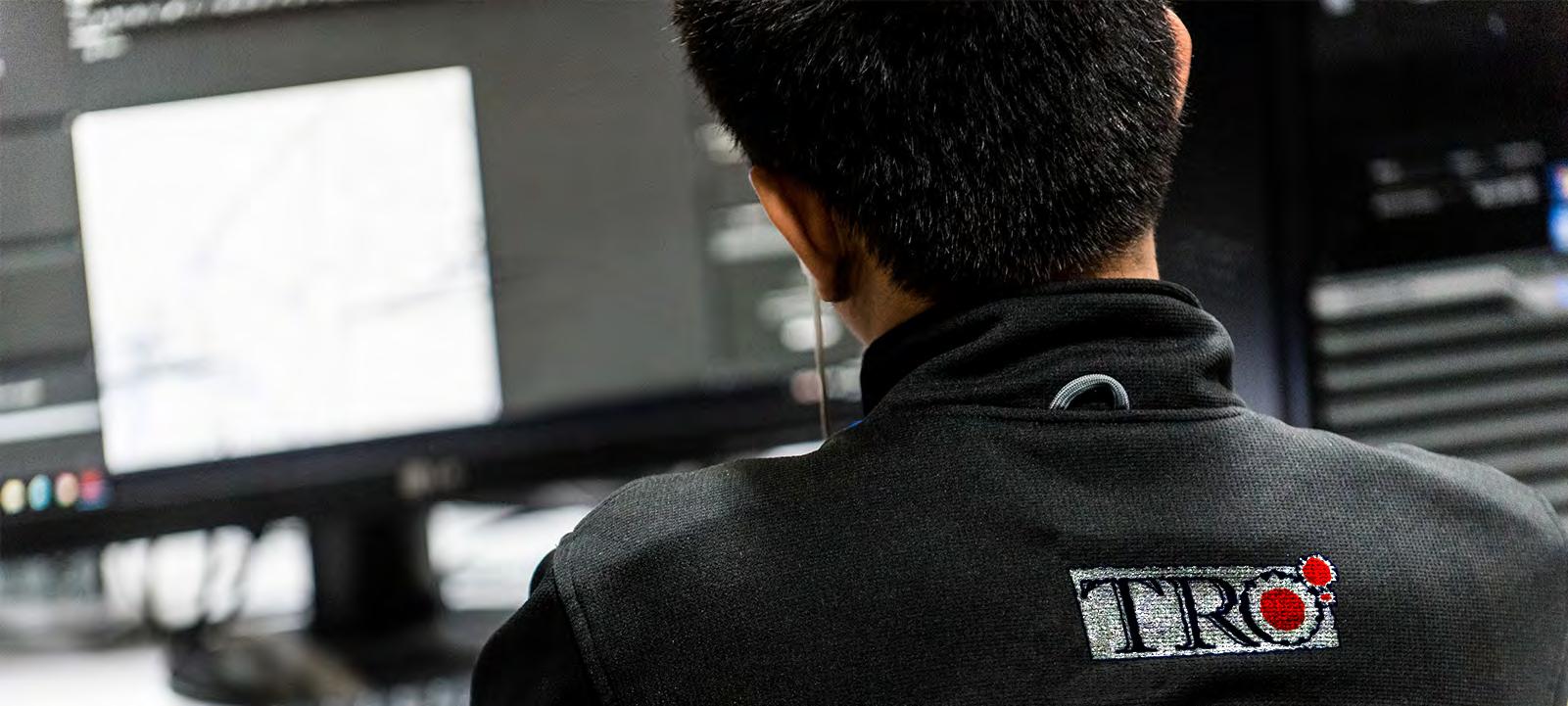
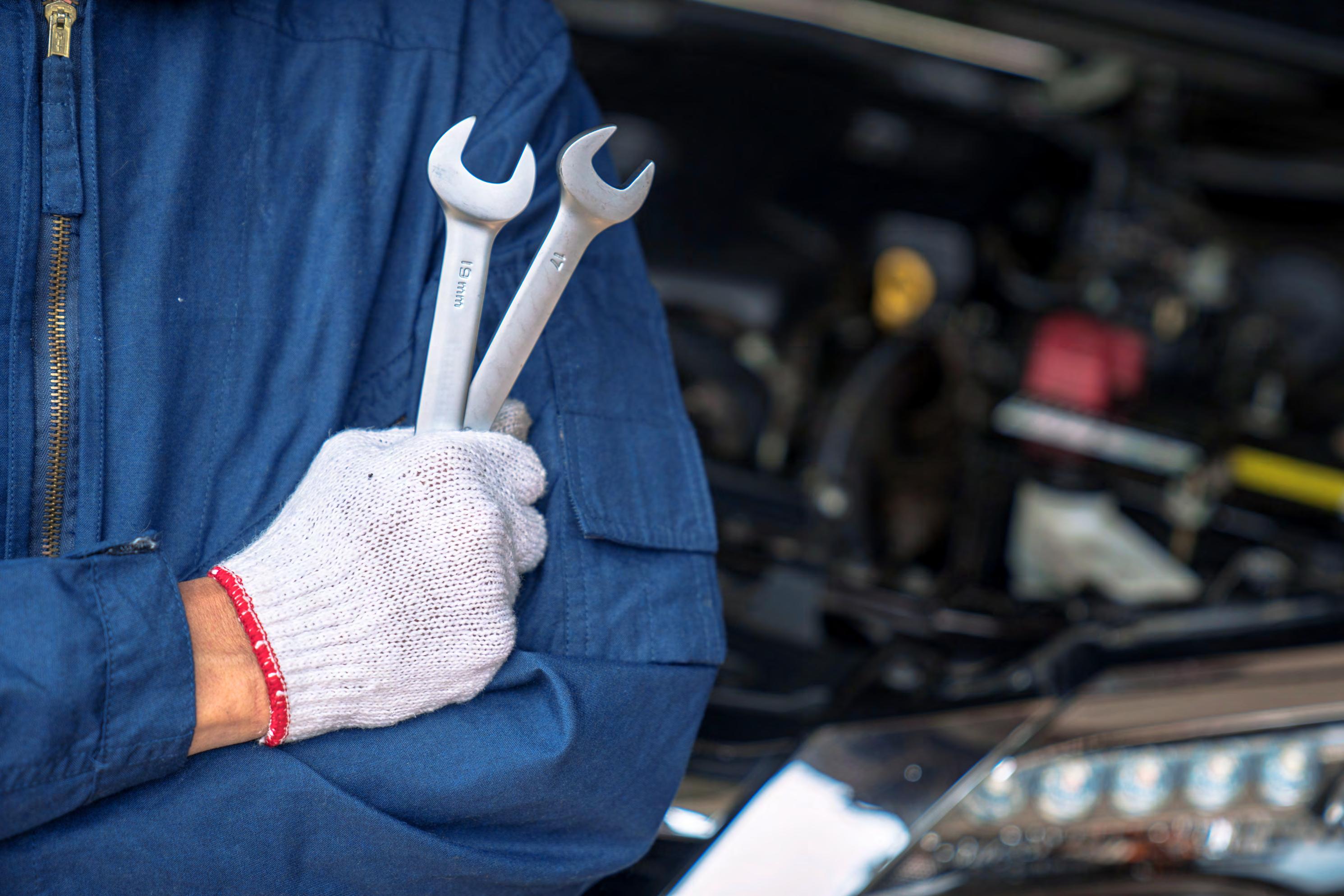
WHAT’S NEW IN PRODUCTS

DANFOSS RELEASES ANTISTATIC HOSES
Danfoss Power Solutions has launched its Boston by Danfoss EHP530 and EHP531 antistatic hoses. Designed for oil, fuel, and gas transfer applications, the hoses increase safety, reliability, and ease of use.
Suitable for suction and discharge applications, EHP530 and EHP531 antistatic hoses enhance safety by protecting against static buildup and discharge. The inner tube is constructed of a specialized antistatic rubber compound, ensuring 100% antistatic performance. The hoses feature
high-tensile textile reinforcement with copper wire for grounding and steel helix wire to prevent collapse during suction, enhancing performance and reliability. An NVC blend rubber cover offers ozone and oil resistance.
EHP530 hose has a pressure rating of 10.5 bar (150 psi) and is available in sizes ranging from -12 to -192. EHP531 hose features a pressure rating of 20.7 bar (300 psi) and is available in sizes ranging from -16 to -128. All hoses within each product line maintain these pressure ratings, offering consistent performance regardless of size. With a 3:1 safety factor, the hoses offer durability and reliability in demanding applications.
EHP530 and EHP531 hoses offer great flexibility, as with dual ink and embossed laylines, the hose is easier to identify — even after a long service life — which improves traceability and simplifies hose replacement.
EHP530 and EHP531 hoses are compatible with various oil types and petroleum, including petroleum products with aromatic content up to 50 per cent.
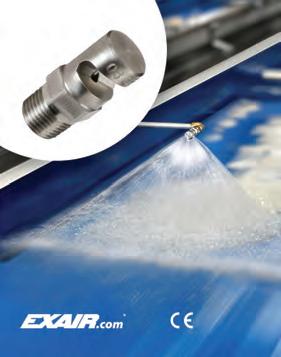
EXAIR’S LAUNCHES FLOODSTREAM LIQUID NOZZLE
For spraying processes where space is at a premium, Exair offers the new 1/8 NPT FloodStream liquid
atomizing spray nozzle.
Producing a deflected flat fan pattern, the FloodStream provides a consistent and proficient spray for precise coverage in close quarters. Manufactured from 303 stainless steel, common applications include washing/wetting, dust suppression, lubrication, part cooling and more.
With a maximum operating pressure up to 250 PSI, the nozzle channels liquids through the body and against a precision-tuned, angled surface. This creates a wide-angle, flat fan spray pattern at 75° from nozzle orientation. Its compact build allows it to be effective in tight spaces while still providing coverage with precision. The stainless-steel construction also provides durability and corrosion resistance, and works well with water, light oils, rust inhibitors, chemicals, paints, dyes and other common liquids.
The World of Bearings and Power Transmission...
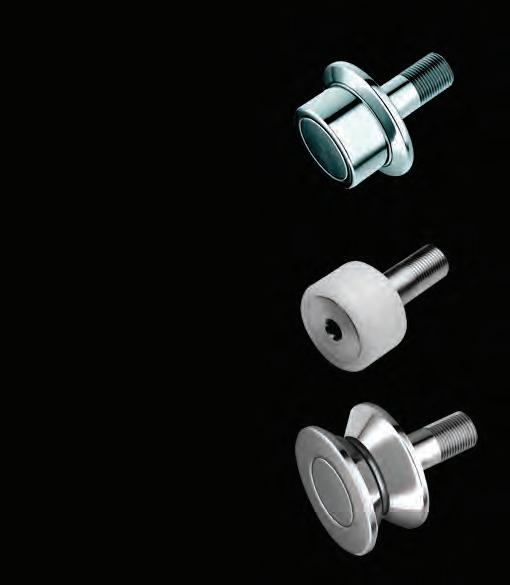

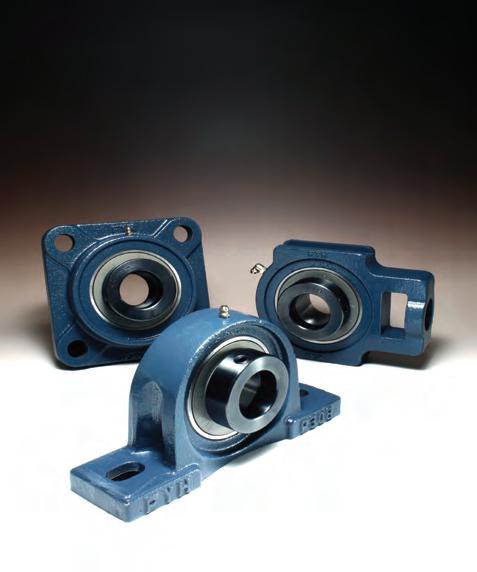
The Maintenance Corner

In this summer’s edition of MRO, we are launching the first column of the Maintenance Corner. We want to give our readers a chance to ask specific maintenance questions regarding maintenance challenges they are facing. In turn the maintenance corner will give advice on the question supported maintenance best practices. We also want to encourage maintenance departments to share their stories about maintenance challenges they have experienced and how they solved them.
The idea for this column came to me for a couple of reasons.
1. I wanted to share my experiences after my thirty plus years of consulting with hundreds of maintenance dep artments throughout North America and Europe. I was fortunate enough to work with maintenance managers and supervisors and I soon realized people f aced remarkably similar challenges.
Regardless of the industry or facility I worked with, the same topics came up over and over and the solutions were often very common with slight variations to fit specific circumstances. We would like this column to serve as a conduit for maintenance departments to ask questions and receive helpful advice through this publication.
2. The second reason I pitched this column to our editor, was to provide an avenue for maintenance people to share their maintenance experiences. There are people who have come to retirement age and have a wealth of knowledge from their years of working in maintenance. When they retire that wealth of experience and wisdom is most often lost. I am sixty-eight years old and in semi-retirement mode. I have been fortunate to have been writing for MRO for the
past 20 years and have shared my experiences with the MRO readers. There are maintenance people with a mountain of technical skills and knowledge that need to be shared. I hope this column will give maintenance people a chance to share their stor ies, challenges, and successes.
Our editor will explain how to submit your questions, stories, and comments to share in the next editions of the Maintenance Corner
The solutions and best maintenance practices shared in the column will not only come from my experiences but also from the companies and maintenance personnel I have worked with that developed creative solutions to their problems. Sharing maintenance knowledge is immensely powerful, as I said earlier most maintenance departments share the same challenges therefore sharing solutions is a powerful tool.



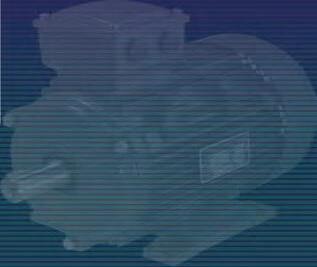
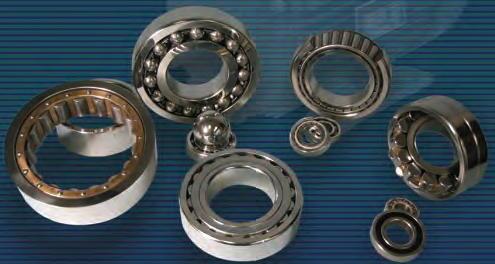
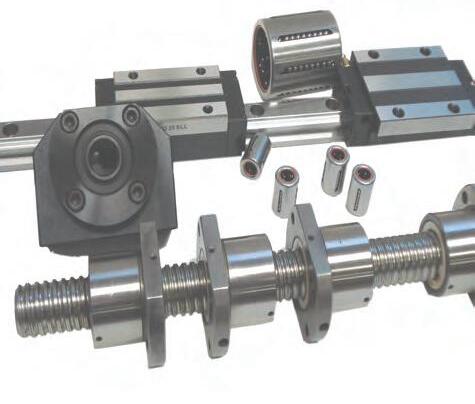
The last 6 years of my working life, I was the Maintenace Support Manager for CertainTeed Gypsum where I was responsible for implementing best maintenance practices. During those 6 years my team organized quarterly maintenance meetings with the fourteen gypsum facilities to discuss common problems within the gypsum plants. Plant maintenance departments made presentations to the rest of the attendees about maintenance issues they experienced and how they solved them. There were presentations on innovative technology and how it helped improve reliability.
In addition, all the maintenance support managers from other divisions of the Cer tainTeed Manufacturing groups meet regularly to share challenges and solutions between the divisions. This committee had the responsibility of implementing solutions that would help solve common maintenance issues. The committee also spearheaded technological solutions to make the maintenance department’s activities more efficient and to increase equipment reliability.
The column will do its best to give advice and guidance to help maintenance departments with their challenges.
I know there are lots of questions out there and maintenance staff are looking for solutions that will work in their industry.
The questions cover a wide variety of topics that include:
• What is the best CMMS solution?
• How to implement new maintenance software.
• Should I go with a Work Order Mobile solution for my technicians?
• What solutions will help reduce the amount of equipment downtime we need to complete all the preventive maintenance.
• How to get our maintenance spare parts organized into a functional stockroom.
The column will not only give helpful information to address our readers’ questions but will also cover the topics just mentioned.
To get this first Maintenance Corner column started, I am going to talk about one of the most frequent question I get asked.What is the best CMMS solution?
There is a large selection maintenance solutions on the market.They all offer remarkably similar solutions and almost all use a cloudbased system. Cloud based systems reduce the amount of hardware and support that on-site solutions require. Instead of buying the software, cloud-based solutions charge a fee to host the maintenance data and provide access to the software through the web. Some offer a basic CMMS system while others offer a full ERP (Enterprise Resource Planning).
Each solution carries administration and user fees based on the type of system, its’ functionality, and the number of users accessing the program. There are other fees for advanced functionality that can be added to the maintenance solution.
My advice is to find a maintenance software solution that meets your current and future needs. Do not buy something you will never use, no sense in paying for functionality that is not needed now or in the future. Here is an example, many research laboratories and hospitals do not carry much in the way of spare parts. Most of their maintenance is carried out by contractors, therefore an elaborate inventory and purchasing module is not needed?
The best way to determine the current and future maintenance software requirements is to list the current needs to be satisfied by the maintenance solution. Then develop a 1–5 year plan that details the goals and objectives
of the department. For example, within 2 years, the plan is to have maintenance technicians check parts out from the storeroom and record them on work orders in the maintenance solution. That would mean the CMMS system will need to have an inventory system and maintenance personnel will need access to the software through a computer to record the parts on work orders. These elements in the future plan may not currently be available and will need to be implemented. There needs to be thought and planning before the purchase of a maintenance system. Considerations need to include:
• Is the system simple and easy to use, remember the technicians will be the primary users. Sometimes extra bells and whistles are nice to have but add extra steps and clicks for the technician to navigate the software.
• Does the software have the ability to create the maintenance reports needed to manage the department, IE, Work order completion, asset cost, inventory reports etc.,
There we have it, the first issue of the Maintenance Corner. I hope you will submit your questions and experiences in future editions.
Peter Phillips is a maintenance consultant with over 45 years of industrial experience. Peter’s career started with Michelin Tire where he led preventive, proactive and reliability centered maintenance for over 20 years. For the past 25 years Peter has travelled throughout North America and Great Britain consulting and training with a wide spectrum of industries. Peter’s company, Trailwalk Holdings Ltd., focuses on helping companies and organizations with maintenance issues and introduces them to world class maintenance practices. His experience in maintenance management provides companies with down-to-earth practical maintenance solutions that are fresh off the plant floor.
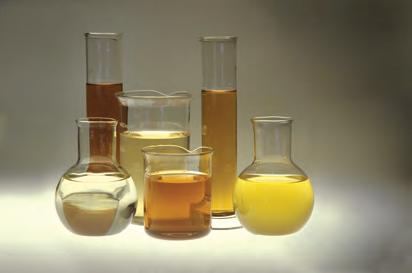

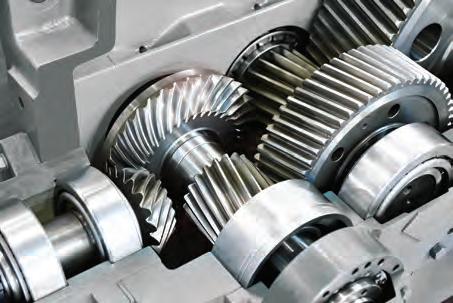
Lubriplate’s ultra-high-performance, 100% synthetic lubricants have been engineered to provide unsurpassed performance in the most demanding plant environments. They provide a wide range of benefits designed to make your plant run better. Benefits include: extended lubrication intervals, lubrication consolidation through multiple application capability, reduced friction, extended machinery life and reduced downtime. Products include...
HIGH-PERFORMANCE SYNTHETIC GEAR OILS
SYNTHETIC AIR COMPRESSOR FLUIDS
SYNTHETIC HYDRAULIC FLUIDS
HIGH-PERFORMANCE SYNTHETIC GREASES
NSF H1 REGISTERED FOOD GRADE LUBRICANTS
ECO-FRIENDLY SYNTHETIC LUBRICANTS
SPECIALTY LUBRICANTS Scan the QR Code for More Information About Lubriplate’s Products and Services.

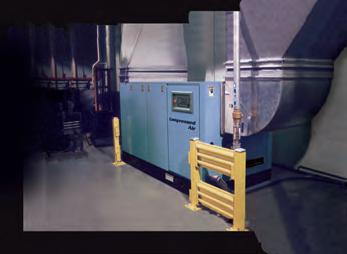

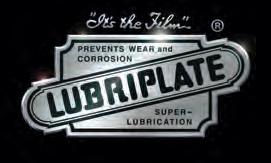
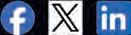
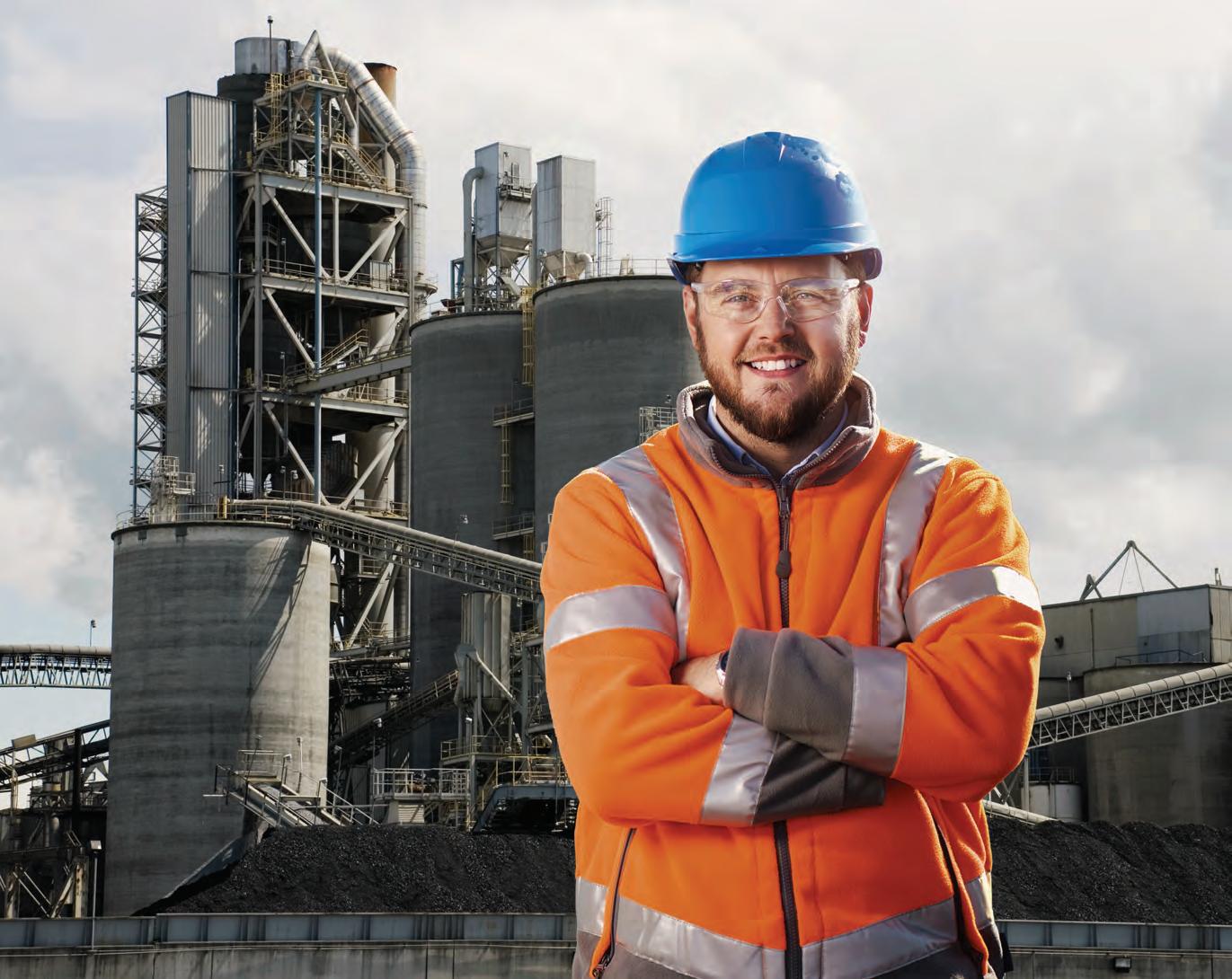
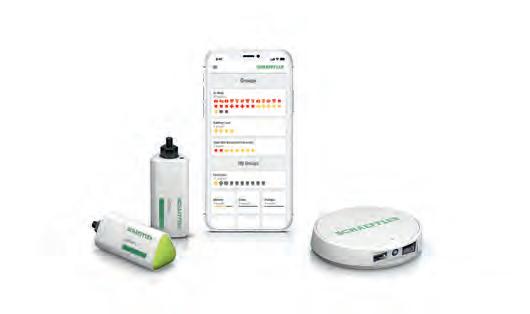