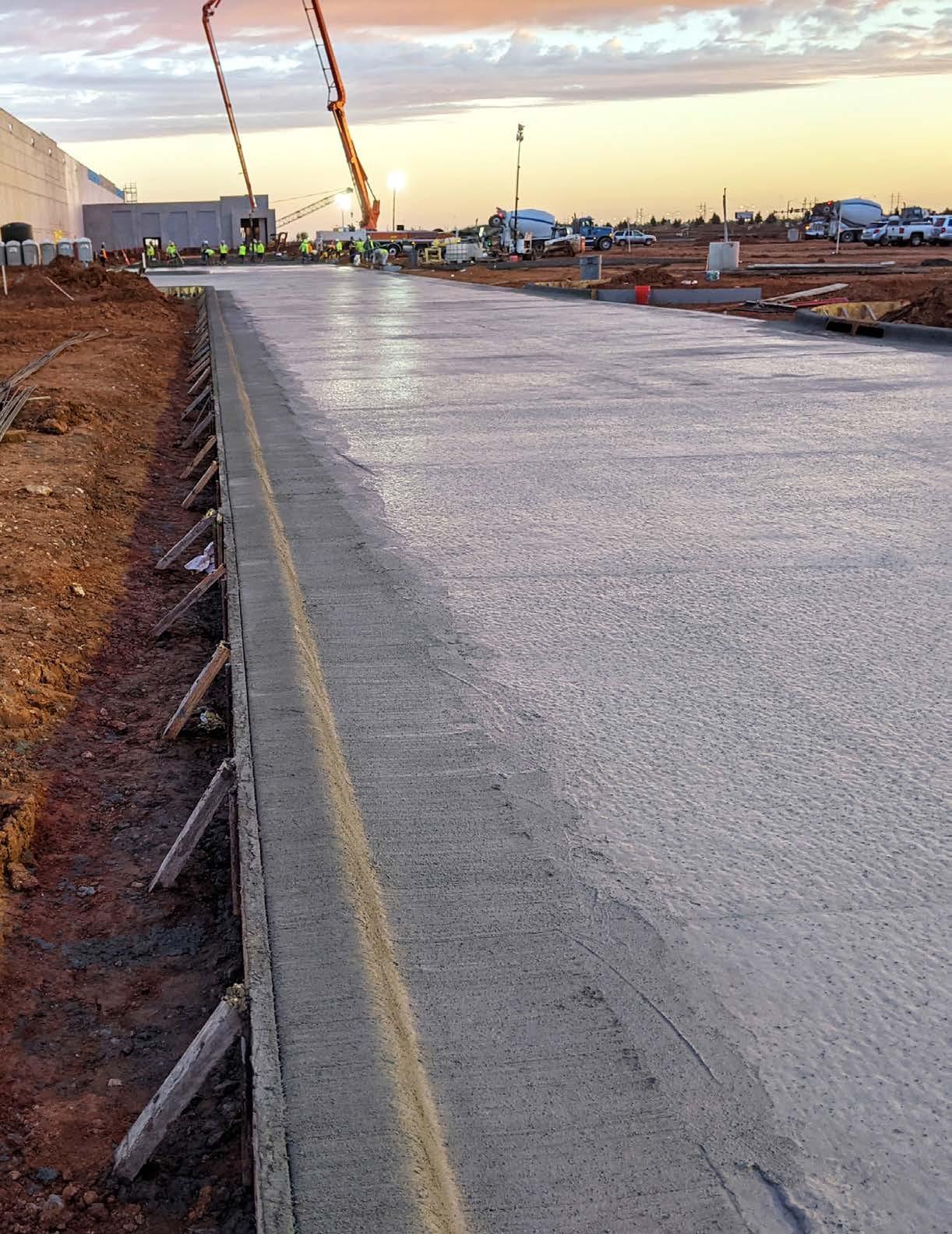
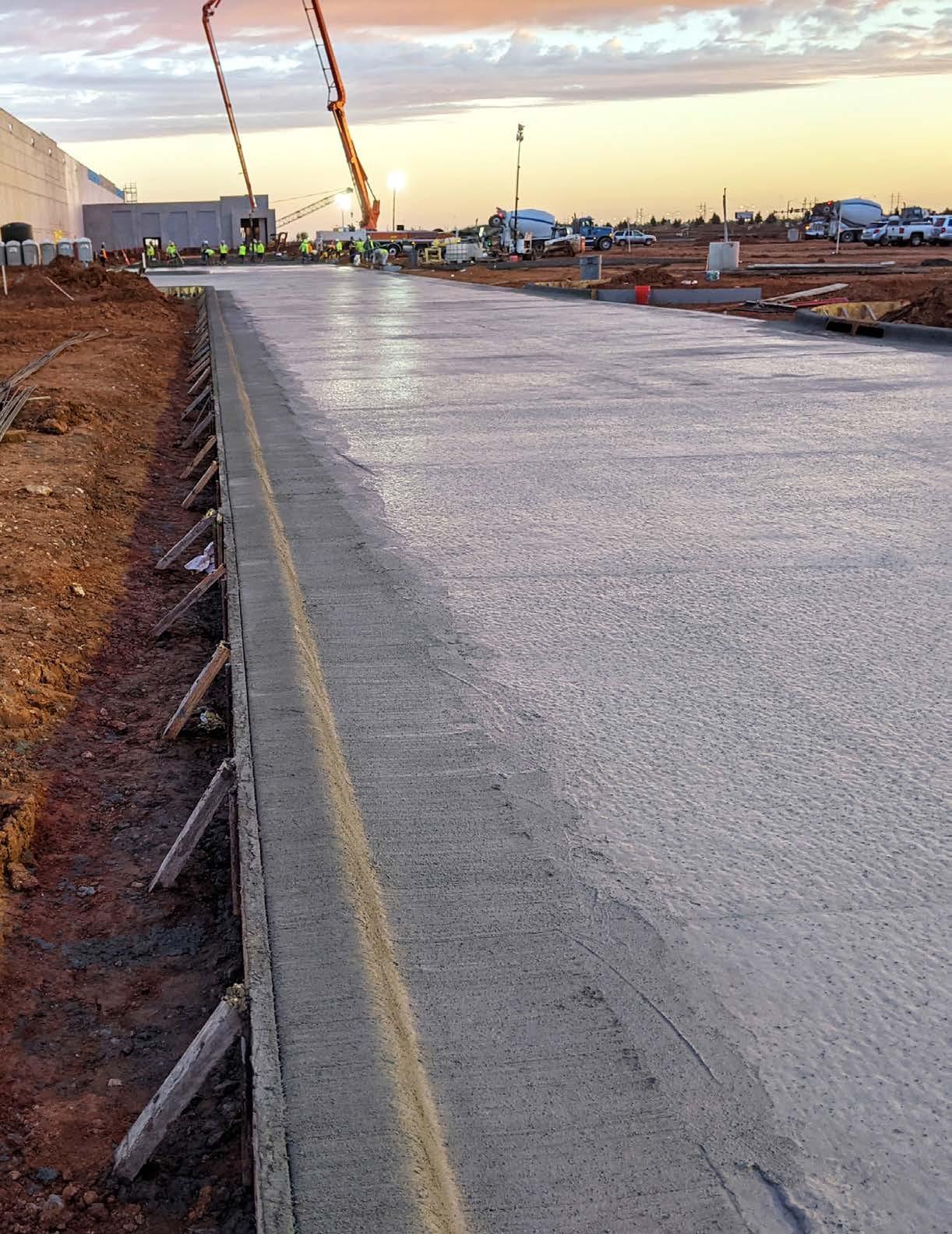
CCE 2023 POSTS RECORD ATTENDANCE
BY ADAM FREILLWith attendees showing genuine interest in the products and technologies on display, exhibitors were happy with the flow on the floor, and the discussions they were able to have with current and potential customers.
“Traffic has been amazing. I am very surprised and impressed on the amount of traffic from open to close on both days. And it’s been engaging. So, there’s been both a quantity and quality engagement with attendees,” stated Carl Seleem senior manager, marketing, at Brafasco, National Concrete Accessories and Brock White. “We’ve spoken to people that are in flat work, as well as in mid-rise and high-rise commercial… everywhere from small to large commercial to multi-family to residential. It’s just nice to see a good mix and everybody ready to just hammer out a good year.”
Over 6,000 members of the concrete, aggregates and construction industries made the fifth edition of the Canadian Concrete Expo (CCE), Canada’s national trade show for the concrete construction industry, the busiest one yet.
The show, held at the International Centre in Mississauga, Ont., on February 16 and 17, had aisles that were filled and booths that were buzzing. In addition to displays from more than 300 exhibitors, the show offered a mix of conference sessions, technology demonstrations, and even a special appearance by mixed martial arts legend Georges St. Pierre, who delivered a message of finding strength and using focus to build forward, both on and off the job.
“We hit record attendance yesterday. And it was by far the best day we’ve ever had at the Canadian concrete Expo,” stated show president, Stuart Galloway, from the show floor on Day 2. “It’s nice to see the trade show industry back on his feet. We weren’t 100 per cent certain where it was going to go after COVID. Were we going to get everybody to come back? Were the sellers going to want to exhibit? It looks like the demand is there for face-to-face.”
“The show attracted a good number of local contractors and crew members… we always enjoy the opportunity to meet and discuss Hydrodemolition with them,” stated Keith Armishaw, Aquajet’s business development manager for North America. “Many of the trade shows I attend are in the U.S., so as a Canadian resident, it was also exciting to attend a show in Canada dedicated to the concrete industry. We hope Canadian Concrete Expo continues to have a solid turnout.”
“It was nice to get face-to-face with some of our existing and bigger customers,” added Sean McElroy, head of marketing and IT at Plastruct Polyzone. “We definitely have had some more traffic compared to last year.”
And if exhibitor feedback is correct, attendees were using the show to research and plan for their upcoming construction season.
“Overall, show attendees were very optimistic about the year ahead,” said Seth Ulmer, sales manager at Curb Roller Manufacturing. “We spoke with many contractors who are either already fully booked or expect to be soon. The Canadian Concrete Expo was an excellent venue for them to prepare for the working season.”
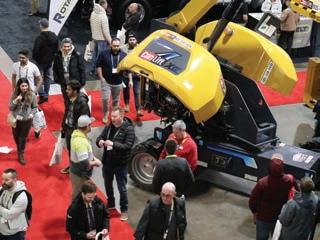
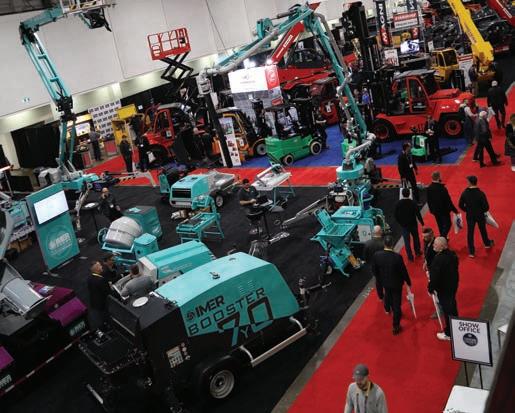
“If Canadian Concrete Expo was an indication of what this year’s trade shows will be like, I believe we’re in for a busy and successful year at the events we attend,” said Troy Steele, Brokk’s regional sales manager for Western Canada.
Plans are already underway for the 2024 edition of the show, which will once again take place at the International Centre. Show dates will be February 14 and 15.
The 2023 edition of Canada’s national concrete show returned to February, and the crowds came out to see all that is new, and to get some advice from MMA legend GSP.
The Worldwide Leader in Concrete Paving Technology
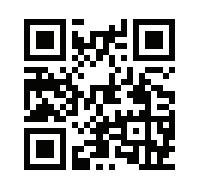
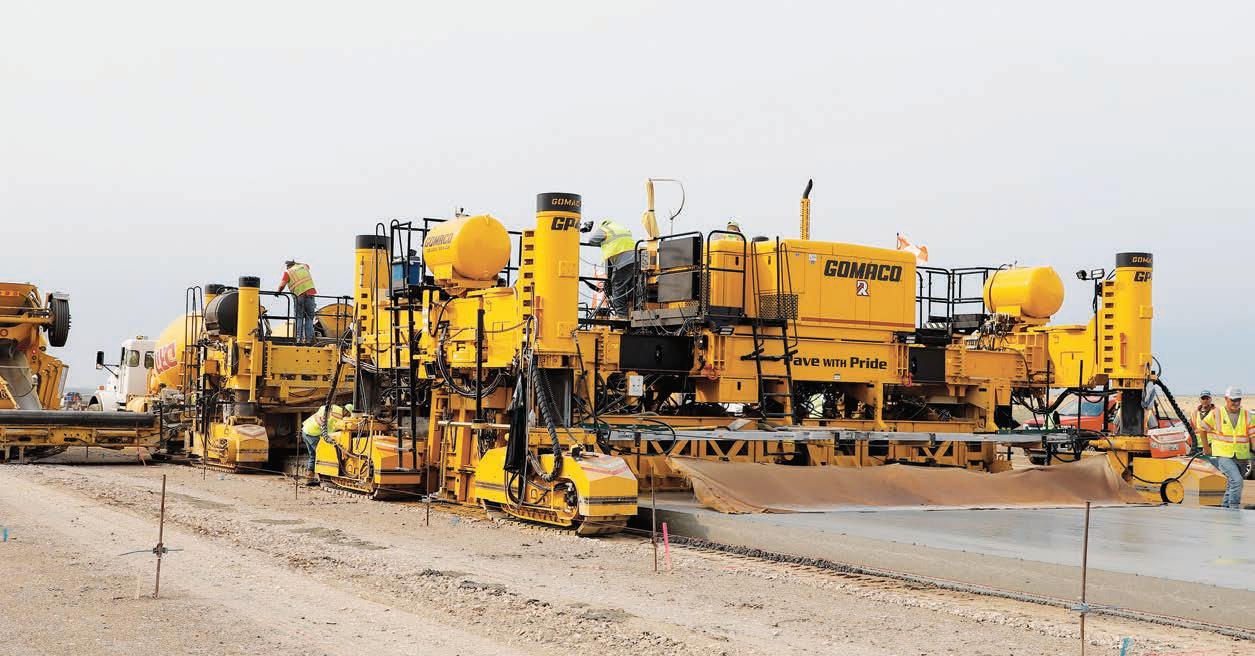
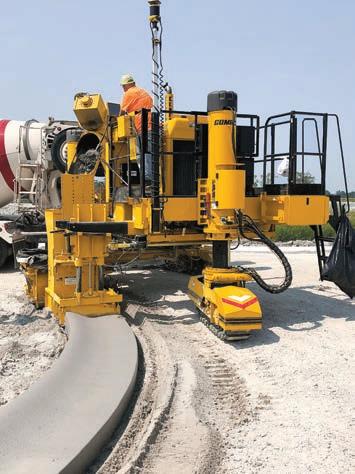
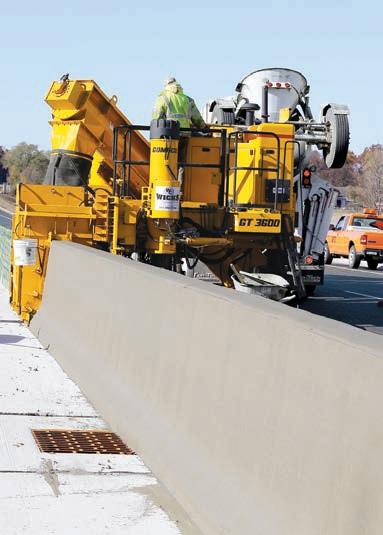
GOMACO offers the full range of concrete slipform pavers, curb and gutter machines, trimmers, placer/spreaders, texture/ cure machines and bridge/canal finishing equipment. GOMACO equipment features our exclusive and proprietary G+® control system, created in-house by our software engineers from the wants and needs of contractors paving in the field. At the heart of GOMACO equipment is our passion for concrete and our commitment to our customers. We look forward to visiting with you about your upcoming paving projects and your concrete paving equipment needs. Our worldwide distributor network and our corporate team always stand ready to serve and assist you.
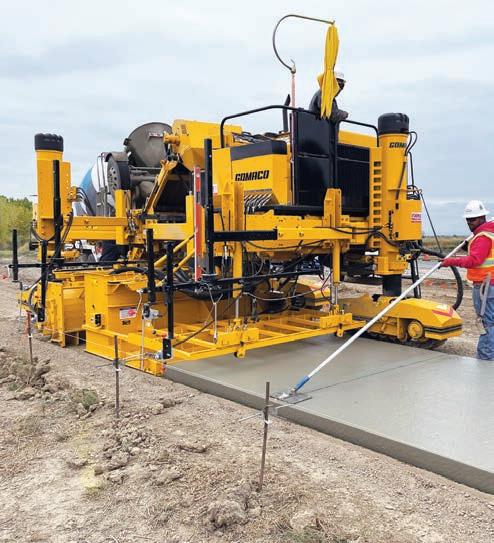
monolithic Going
Driving efficiency with monolithic pours.
BY SETH ULMERThroughout history, new processes have come along to improve how people achieve end results. Innovations, even those that eliminate just one step, often lead to dramatic increases in productivity and efficiency.
Developing film is a good example. When digital cameras entered the market, they cut out the step of going to the store to develop a roll of film, accelerating the process of viewing family photos.
When it comes to concrete, monolithic pours are one process that contractors can use to drive efficiency. Monolithic pours streamline concrete work by pouring curb and gutter simultaneously with flatwork, instead of completing these pours one at a time. If completed with the right equipment and considerations, contractors can reap the benefits without sacrificing quality.
SAVING TIME
A traditional pour most often requires curb and gutter work to be poured, finished and cured to outline the pavement area. Then, the crew returns at another time to pour and complete the flatwork. A monolithic pour, or an all-in-one pour, improves efficiency by completing curb and gutter at the same time as flatwork, saving a considerable amount of time.
Driven to continually seek new ways to keep up with ever-growing demand, more contractors are seeing the benefits of monolithic pours, especially for parking lots and streets. Contractors who streamline the most time-consuming aspects, such as hand-shaping curb and gutter, experience
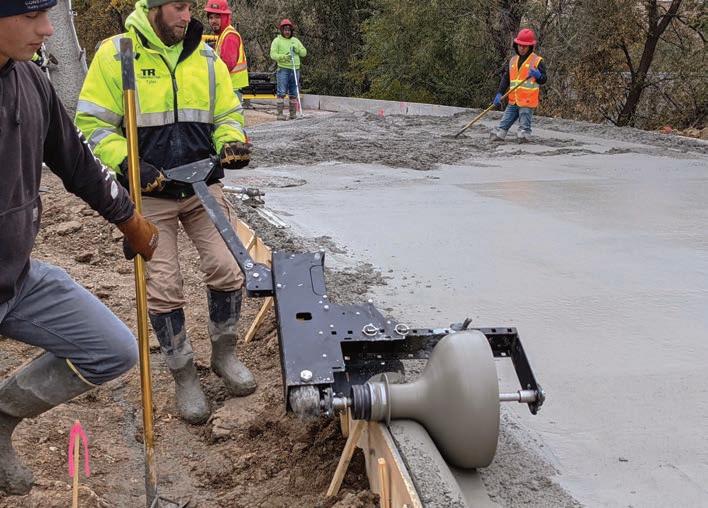
the most significant spike in efficiency and often double production. Just as the digital camera created a more productive photo development process, monolithic pours can drive up efficiency for contractors.
PUSHING THE PACE
As contractors look for ways to maximize efficiency, many turn to laser screeds to boost flatwork capabilities. Their ever-wider adoption in the market has significantly sped up the process of screeding large areas of flatwork. But contractors lose the efficiency gained with a laser screed if the curbing work falls behind during a monolithic pour.
Crews that are responsible to shape and
finish the curb by hand typically operate at a slower pace than a laser screed. This can slow the whole operation as they wait for the curb to be completed before moving to the next section. While slipform pavers can be an option, their size may complicate a busy jobsite and they may not be ideal for relatively complex areas of curbing associated with monolithic pours.
Walk-behind curbing machines are able to maintain the production pace of laser screeds while eliminating the physical labour and need for large machinery for curbs. These machines consist of a handle attached to a metal drum that is connected to a hydraulic power source.
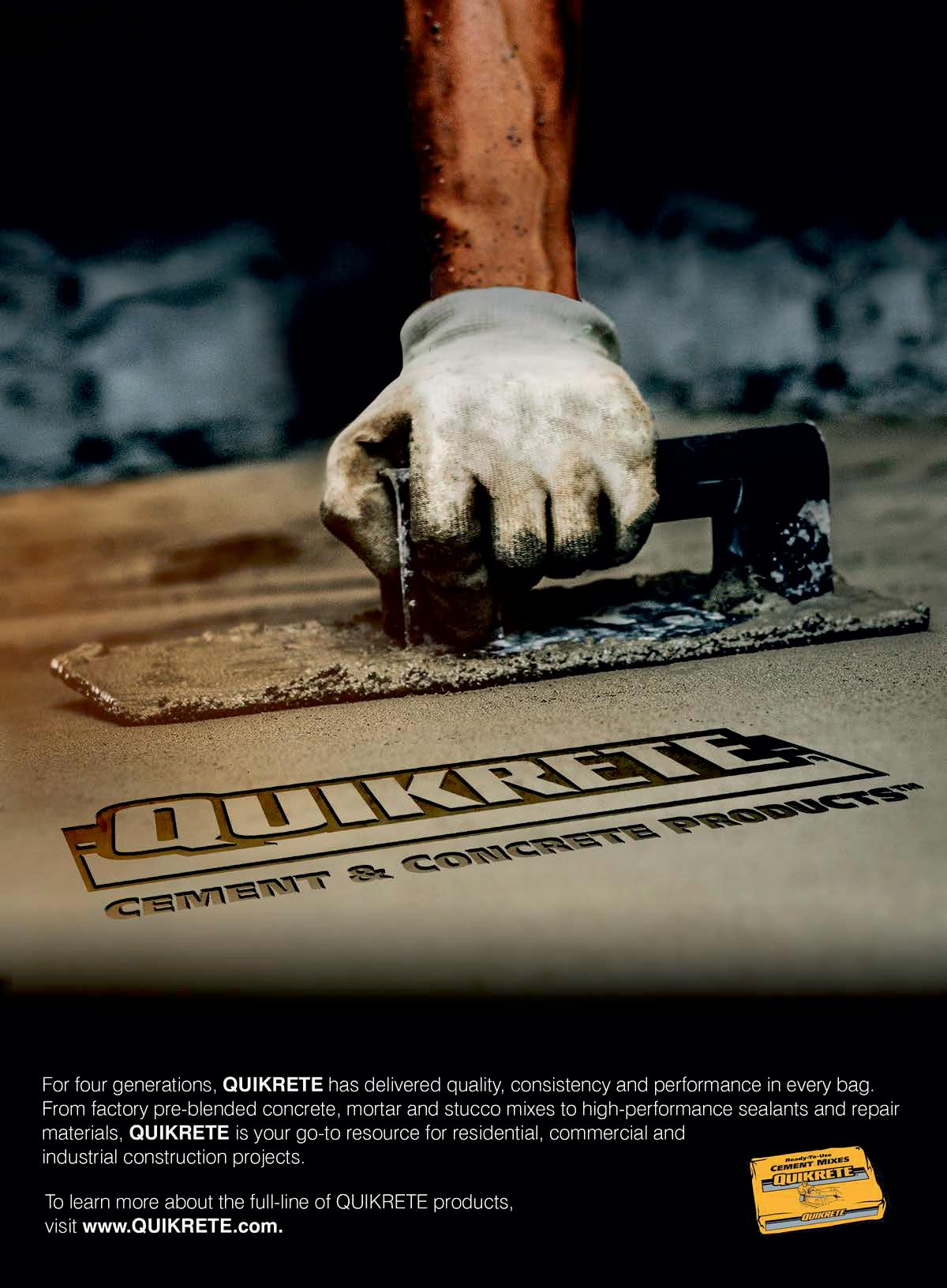
The single-operator machines reduce the manual labour needed when shaping the curb and gutter while producing a consistent result, even for operators with minimal experience. While these machines were originally developed for completing curb and gutter work on traditional pours, most can be modified to adapt them for use during monolithic pours.
Newer entries to this class of equipment incorporate battery power and a design specifically created for monolithic pours. These machines combine the benefits of traditional walk-behind curbing equipment with lightweight portability to quickly move throughout the jobsite.
A concrete contractor hired to install a large parking lot for a private company used a laser screed due to the sheer size of the project. Working during the night to limit traffic interference, they were able to pour about 2,000 yards of pavement per night. The operation was limited by the finite amount of curb the crew could shape by hand, however: only 300 to 400 feet
per night. When the contractor invested in a battery-powered walk-behind curbing machine, the crew doubled productivity, shaping closer to 700 linear feet per shift and achieving their target efficiency.

TAKING TO THE STREET
Laser screeds and walk-behind curbing machines are ideal for projects like parking lots — jobs with large amounts of flatwork and multiple areas of curb. However, a single machine that can shape curb and gutter simultaneously with flatwork is more ideal for certain monolithic pour applications like street construction or replacement.
Traditionally, large slipform machines have been the most efficient solution if the project matches the machine design parameters and has enough volume to justify their operation and overhead costs, but new equipment offerings are expanding the options for these jobs.
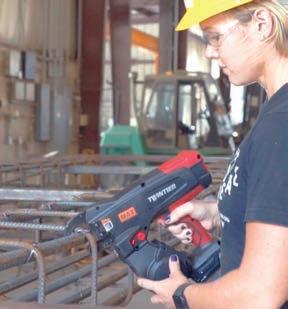
Some manufacturers offer custom drum options for hydraulic screeds. These
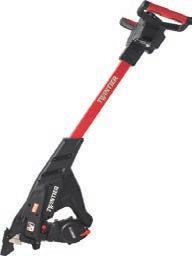


drums, typically up to 16 feet long, are designed to match a specific shape, like half of a street, including the curb and gutter. Custom drums replace the pipe on a hydraulic roller screed and use a spinning motion to shape the concrete.
This monolithic pour method is ideal for streets due to the long stretches of pavement that are the same shape, and it can be convenient for replacing existing streets because it allows one lane of traffic to remain open.
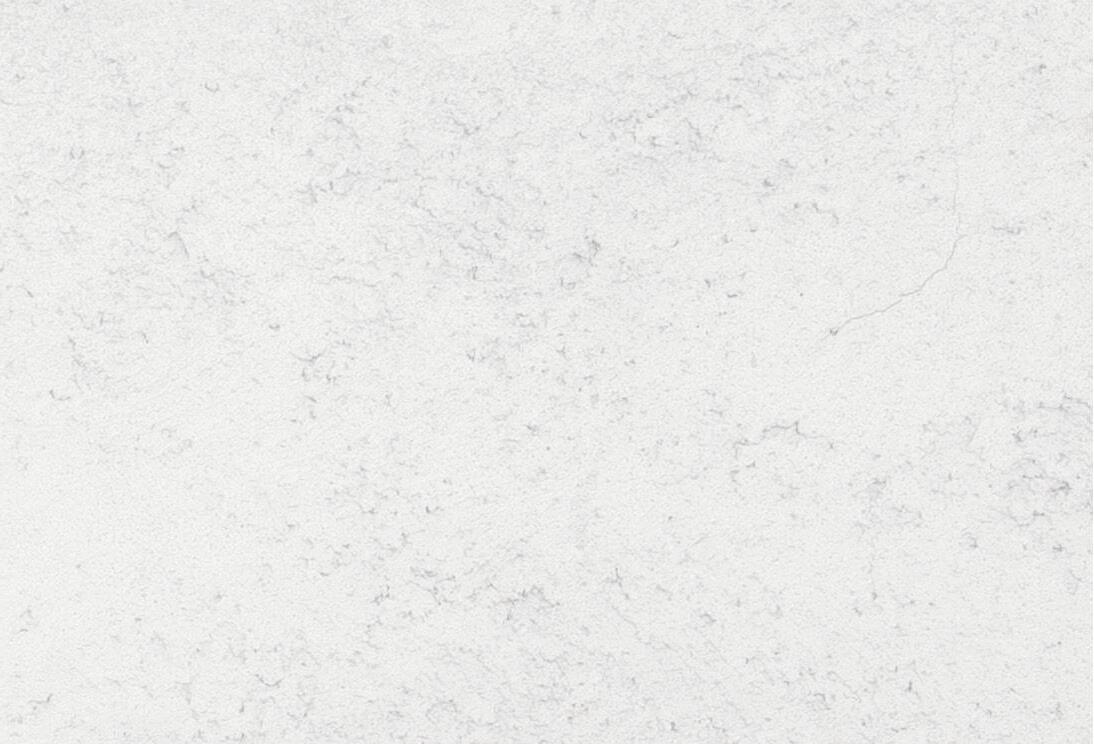
In the past, this was only possible with large, slipform pavers or through manual labour, but a custom drum with a hydraulic screed now provides an additional method to complete the work.
DRIVING CONSISTENCY AND QUALITY

A common misconception is that monolithic pours produce low-quality curb work. This may be true if the crew has little experience in curb and gutter work and is hand shaping the curb while being primarily focused on flatwork, which is the larger
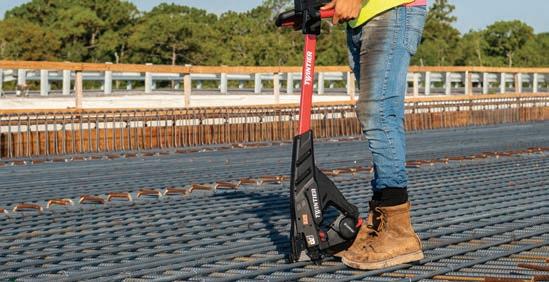
portion of the job. But properly equipped, a key advantage to a monolithic pour is increased all-around quality — if contractors use the proper equipment.
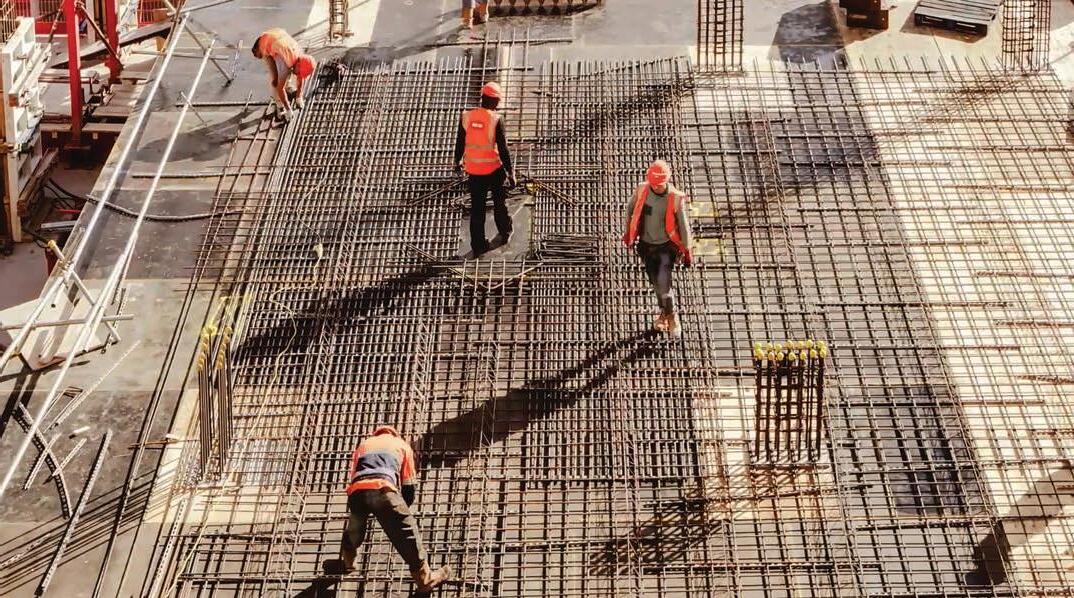
Replacing manual curb work with a mechanized system makes it easy to achieve consistent, spec-matching results, even with an inexperienced crew. The equipment is user friendly and enables contractors to accomplish more with less labour, a key advantage in a difficult employment environment.
FACTORING IN THE WEATHER
A key consideration when determining whether a monolithic pour is the right solution is the weather. Monolithic pours really shine in tough weather conditions. As seasoned concrete workers know, the weather dictates when and how efficiently they can pour. Dealing with a small pour window becomes less of an issue with a smaller number of pours.
With the right equipment, monolithic pours can double or even triple production
and help crews maximize the work they can complete before that window closes.
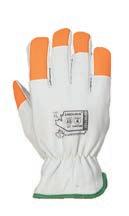
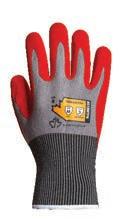
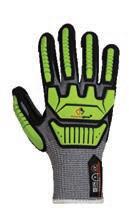
Despite all the advantages, there are some cases where a monolithic pour is not the best solution. These situations will come into play in colder climates.
If a job uses asphalt for the pavement, the concrete curb and gutter must be poured separately. Additionally, the monolithic pour method is not ideal if the curb and gutter or flatwork may need to be replaced separately. In some regions, freeze and thaw cycles can lead to a shorter life for the curb and gutter than the pavement.
BEYOND THE MONOLITH
Contractors can maximize their investment in concrete equipment by purchasing machines that increase productivity for a variety of applications. Beyond custom drums for monolithic pours, hydraulic screeds also pair with standard pipes to screed flatwork for jobs such as streets and sidewalks.
Walk-behind curbing machines have multiple drum options and can also complete curb and gutter for traditional pours. Additionally, battery-powered walk-behind curbing machines effectively complete patch and repair work and complement slipform machines to complete corners and tight radii.
The demands of the construction industry are shifting rapidly. There is a high demand for work, and contractors can capitalize on these opportunities by finding innovative solutions that improve their processes and increase their capacity. Monolithic pours are not the answer for every concrete project, but with the right equipment and the right application, a monolithic pour may be what drives an operation to peak efficiency.
RENOVATIONS
FAN EXPERIENCE BUILDING THE
Major renovation aims to enhance the ballpark experience for Toronto Blue Jays fans.
BY ADAM FREILLAt the crack of the bat at the Toronto Blue Jays’ home opener in April, the fan experience at Rogers Centre will be elevated, thanks to some impressive off-season work by PCL Constructors for Rogers Stadium Limited Partnership.
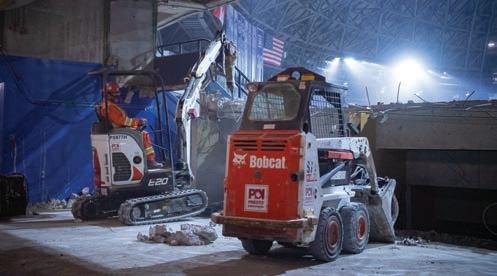

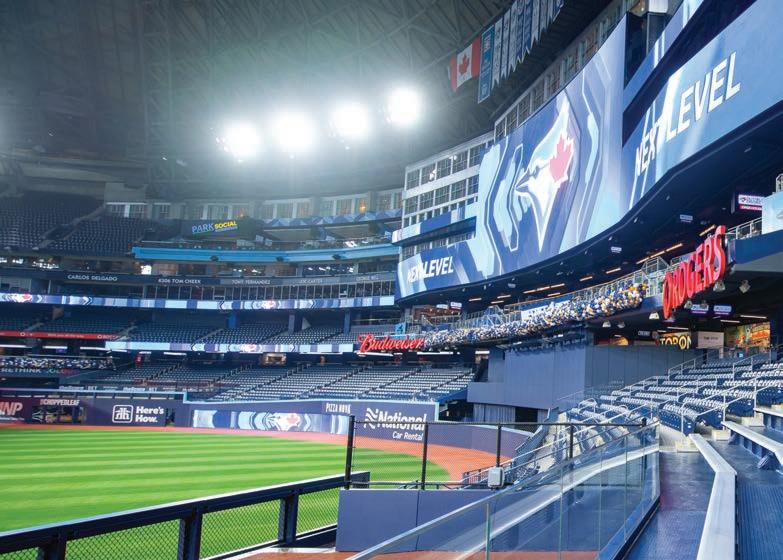
The stadium now features four brandnew outfield neighbourhoods plus a redesigned WestJet Flight Deck, all completed during the first phase of a $300-million multi-year renovation aiming to transform the facility into a ballpark with a modernized fan experience, as well as world-class player facilities.
“PCL and our partners are passionate about bringing the Toronto Blue Jays’ reimagined vision for Rogers Centre to life,” says Monique Buckberger, vice-president and district manager, PCL Toronto. “Following months of preconstruction planning, our team hit the ground running on the first phase of renovations to give the home of Canada’s major league baseball team a new look for the 2023 home opener.”
The first phase began shortly after the final pitch of the 2022 season, starting on October 14 with 35 days of demolition work. Construction of the new areas started on November 14 as work continued six days a week until shortly before the scheduled first pitch on home turf for 2023.
“As soon as our last game was played, we were able to roll up the playing field and remove our outfield walls to use that area as a staging space,” says Sanj Perera, senior manager of project management with the Toronto Blue Jays.
A 200-tonne crane was used for heavy structural removal, while small machinery was used to break up concrete. In total, 2.2 million pounds of materials were recycled from the stadium, including 1.3 million pounds of concrete and 900,000 pounds of steel and metal.
The size of the stadium allowed for multiple projects to progress at the same time, so while demolition was being completed, building was able to start during the second week of November with concrete
being poured in the 500 level and new structural steel installation.
“We were able to bring in pump trucks,” says Perera about the concrete work on the project. “For areas which we could not reach with a crane in this renovation, we used buggies to move concrete. In total, we poured approximately 500 cubic metres of concrete in 160 locations.”
Changes to the stadium include a players’ family room, 5,000 sq. ft. weight room and staff locker rooms at field level; multiple new social spaces, like The Stop bar behind the batter’s eye in centre field and The Catch Bar perched above the visitor’s bullpen; raised bullpens; and two new social decks on the 500 level, the Corona Rooftop Patio in right field and Park Social in left field. Additionally, seats have been brought forward to new outfield walls that will bring fans closer to the game, and every 500-level seat, which dated back to the building’s opening, has now been replaced.
“Creating the new social spaces was the most intensive component of the renovation,
from an engineering perspective,” states Perera. “Key challenges included the cutting of the existing bowl and rakers to open up the concourse sightlines and accommodate new steel structure to support the new social decks, as well as the coordination and installation of steel beams.”
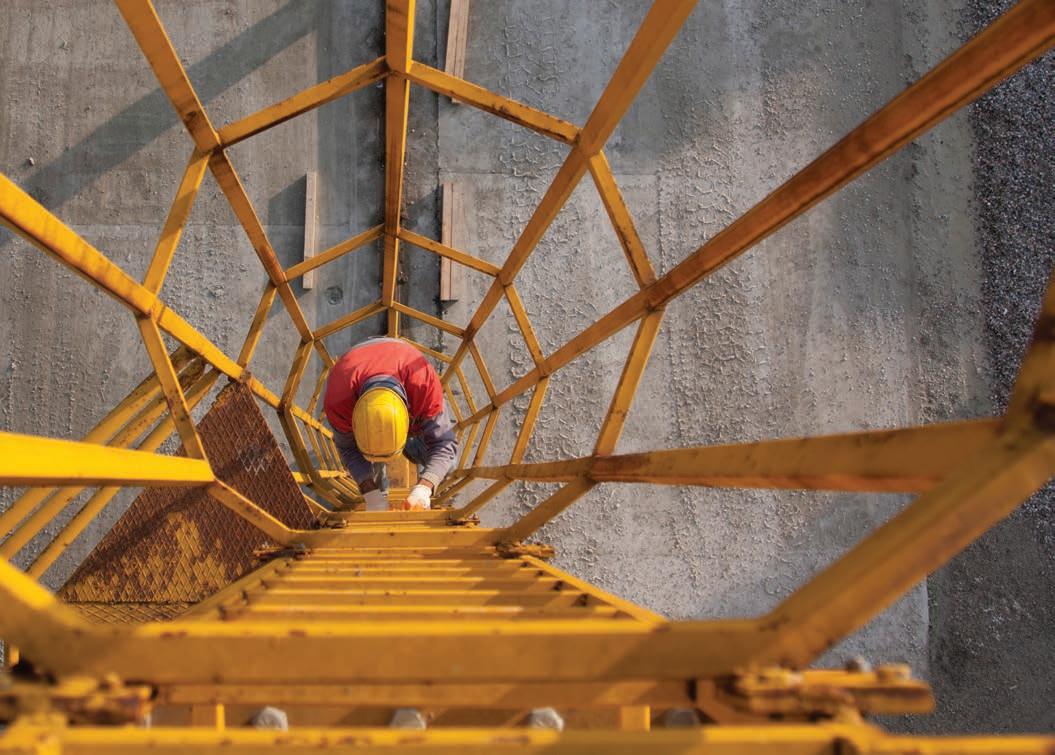
One challenge that did not exist, given that Rogers could keep the roof closed through the winter months, was the weather.
“We were fortunate to be working within an enclosed facility and did not have to accommodate for weather delays,” says Perera. “Having a secure facility also allowed us to procure long-lead items and have them staged on site, which was needed as the construction industry is still experiencing delays on material due to the global pandemic.”
Workers, many of whom could been seen sporting Blue Jays hats, T-shirts and sweaters, were also able to make use of the stadium’s lighting system, allowing them to work into the night, which was a big plus during the shorter days of winter.
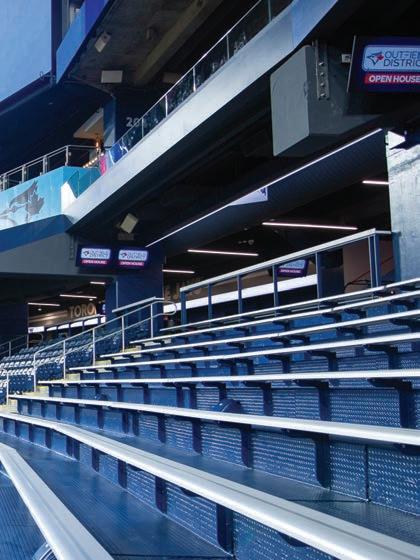
With an average of 110 workers on the site in a given day of construction, the Blue Jays fostered the sense of community and pride of a job well done by supporting their efforts with a few extras along the way, like water bottles, hats, and Blue Jays and Rogers Centre stickers to recognize workers’
efforts to create a great fan experience for the coming season.

“We know many construction workers wear that sticker on their hardhat as a badge of honour,” says Perera. “They take that hardhat to subsequent jobs and are able to say they were a part of this amazing project.”
Rogers Centre was conceptualized as a multi-purpose stadium when it opened in 1989 and has not undergone a largescale renovation in its 33-year history. The next phase of the current renovation plan is expected to take place in the 20232024 offseason, with a focus on field level premium clubs and social spaces as well as the clubhouses and player facilities.
Stated Mark Shapiro, president and CEO of the Toronto Blue Jays as he unveiled the renovation plans, “We are committed to building a sustainable championship organization for years to come, and this renovation to Rogers Centre will give new and lifelong Blue Jays fans a ballpark where they can proudly cheer on their team.”
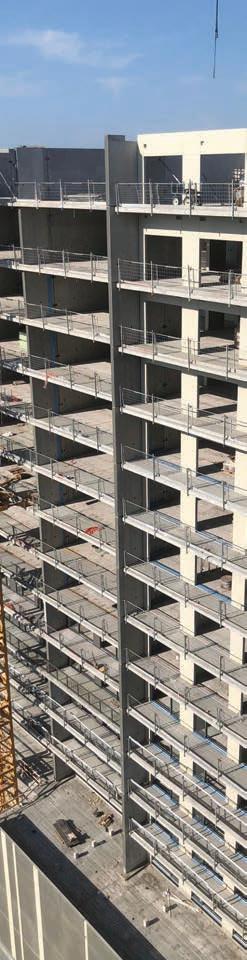
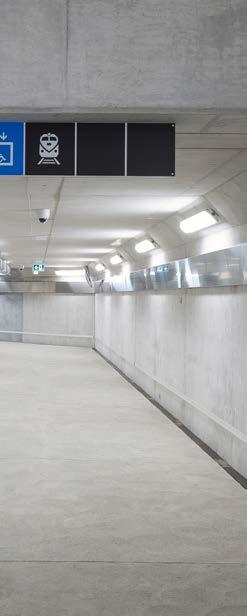
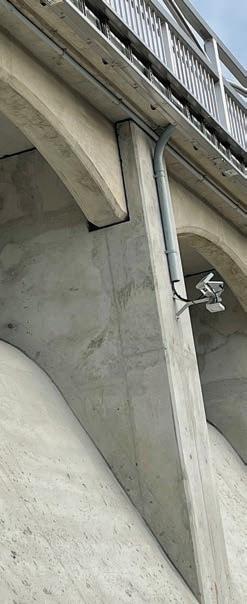
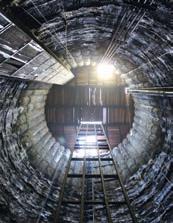
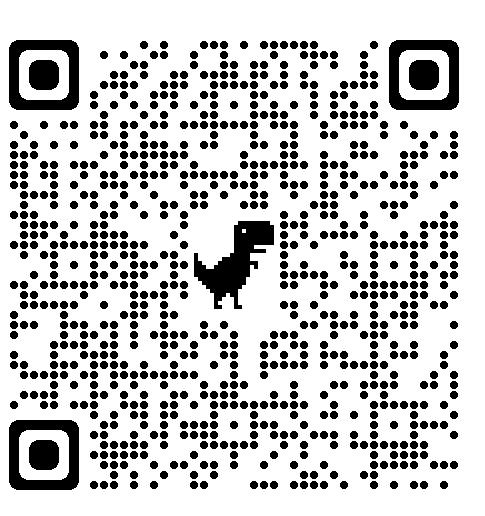