ASPHALT EQUIPMENT GOES HIGH-TECH
BUILDING SAFE & INCLUSIVE WORKPLACES
TREATING CRACKS IN CONCRETE
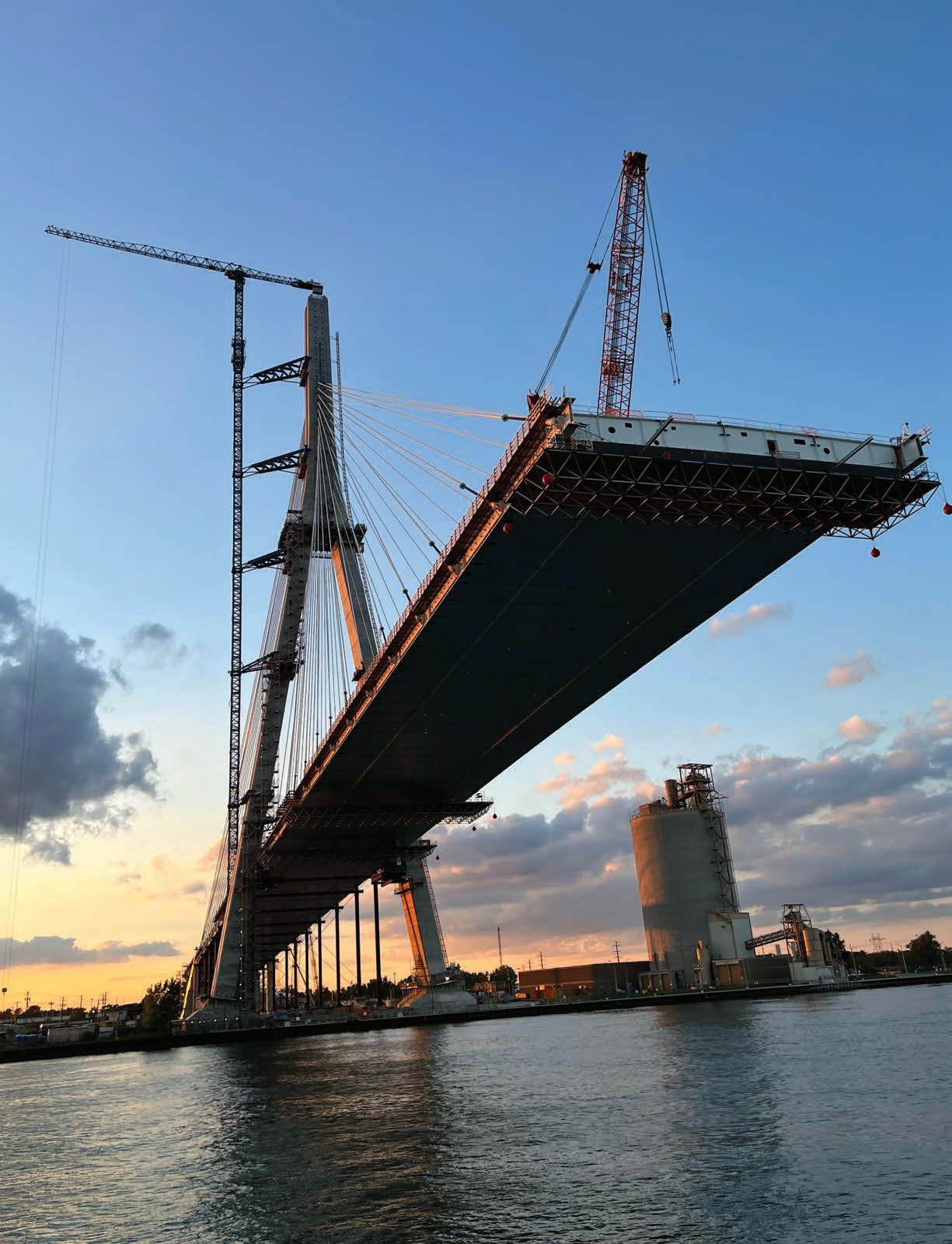
> INSIDE < CONCRETE ON-SITE PG.33
ASPHALT EQUIPMENT GOES HIGH-TECH
BUILDING SAFE & INCLUSIVE WORKPLACES
TREATING CRACKS IN CONCRETE
> INSIDE < CONCRETE ON-SITE PG.33
PUTTING A FOCUS ON ROAD AND TRANSIT PROJECTS
Since 1953 we’ve believed in keeping things simple. The Power Curber 5700-D, the world’s #1 selling curb machine, is a reliable, simple, and versatile solution for curb and gutter, safety barrier, bridge parapet, sidewalk, and more. We stand behind our equipment with world-class support and unmatched commitment.
Over the past several weeks, I’ve spent a fair bit of time immersed in the concrete segment of On-Site’s areas of coverage. Not unlike many sectors of Canada’s construction industry, it too is undergoing some significant challenges and changes, which is why I am grateful for events like the recent Concrete Paving Seminar, presented by Concrete Ontario and the Cement Association of Canada (page 40 in this edition), as well as major shows like the Canadian Concrete Expo (page 34) and World of Concrete (page 36).
These events help keep the industry on top of new technologies and tools, as well as regulatory and best practice issues that are constantly evolving.
While listening to discussions about new approaches to concrete mixes at the paving seminar – changes to materials that are becoming more of a focus as the industry seeks to reduce its carbon footprint – a comment from years ago come back into my head.
When the refrigeration sector was moving away from R-22 gas, the industry was hit with a wide array of replacement options, and more complexity. It prompted an industry veteran I knew to quip, “It is time to rethink your old rules of thumb.”
Hearing about cement alternatives and the need to focus on the performance of the finished product brought back a flood of memories.
It is never a bad thing to re-examine our processes. And this rethinking of our old rules of thumb is not just for the cement and concrete sector. The words, “That’s how we’ve always done it,” are killers of evolution and efficiency, after all.
www.on-sitemag.com
READER SERVICE
Print and digital subscription inquiries or changes, please contact
Angelita Potal
Email: apotal@annexbusinessmedia.com
Tel: (416) 510-5113
Fax: (416) 510-6875
Mail: 111 Gordon Baker Road, Suite 400, Toronto, ON M2H 3R1
PUBLISHER | Peter Leonard (416) 510-6847 pLeonard@on-sitemag.com
EDITOR | Adam Freill (416) 996-2391 afreill@annexbusinessmedia.com
MEDIA DESIGNER | Lisa Zambri lzambri@annexbusinessmedia.com
ASSOCIATE PUBLISHER | David Skene (416) 510-6884 dskene@on-sitemag.com
ACCOUNT COORDINATOR | Kim Rossiter (416) 510-6794 krossiter@on-sitemag.com
AUDIENCE DEVELOPMENT MANAGER | Urszula Grzyb (416) 510-5180 ugrzyb@annexbusinessmedia.com
PRESIDENT/COO | Scott Jamieson sjamieson@annexbusinessmedia.com
Established in 1957, On-Site is published by Annex Business Media 111 Gordon Baker Road, Suite 400, Toronto, ON M2H 3R1 Publications Mail Agreement No. 40065710
ISSN: 1910-118X (Print)
ISSN 2371-8544 (Online)
SUBSCRIPTION RATES Canada $50.49 CAD per year, United States $115.26 CAD per year, Other foreign $139.23 CAD, Single Copy Canada $13.50 CAD. On-Site is published 5 times per year except for occasional combined, expanded or premium issues, which count as two subscription issues. Occasionally, On-Site will mail information on behalf of industry-related groups whose products and services we believe may be of interest to you. If you prefer not to receive this information, please contact our circulation department in any of the four ways listed above.
Annex Business Media Privacy Officer privacy@annexbusinessmedia.com
Tel: 800-668-2374
Content copyright ©2024 by Annex Business Media may not be reprinted without permission.
Follow us on @OnSiteMag
As technology advances throughout the construction industry, we would be well served to re-examine the assumptions that many of us use in our daily activities.
Apps are changing our task lists and new building materials are impacting everything from cost expectations to labour needs and timeframes.
It’s not a bad thing to recalibrate our tools every now and then, and the best tool any of us brings to our worksites is the one between our ears.
Until next time, stay safe and do good work.
Adam Freill / Editorafreill@annexbusinessmedia.com
On-Site receives unsolicited materials (including letters to the editor, press releases, promotional items and images) from time to time. On-Site, its affiliates and assignees may use, reproduce, publish, re-publish, distribute, store and archive such unsolicited submissions in whole or in part in any form or medium whatsoever, without compensation of any sort.
DISCLAIMER This publication is for informational purposes only The content and “expert” advice presented are not intended as a substitute for informed professional engineering advice. You should not act on information contained in this publication without seeking specific advice from qualified engineering professionals.
The heavy equipment industry is set to gather once again for Canada’s largest trade event for the industry, the biennial National Heavy Equipment Show.
Scheduled to take place on April 11 and 12 at the International Centre in Mississauga, Ont., the show will span across four halls of the facility offering industry professionals a unique glimpse into the innovations and products available on the market.
“Hard to believe another edition of this incredible event is just around the corner,” stated national show manager, Mark Cusack. “Exhibitors and visitors alike are sharing in our excitement to be back on the show floor.”
The last edition of the event, held in 2022, attracted more than 9,000 industry professionals, including many key decision makers and purchasers, which had many exhibitors making favourable comments about the event. This year’s show has added an additional hall, which has Cusack looking forward to seeing more exhibitors on the show floor than ever before. A full list of exhibitors is available on the show’s website.
The main market segments served by the show include heavy equipment, road building, construction, snow removal, crushing and screening, and infrastructure, with products for these sectors represented on the exhibition floor. Visitors will have a chance to network, compare machines, see the latest and most innovative gear, and stay on top of industry trends in this ever-changing market. Show hours are 9 a.m. to 5 p.m. on the Thursday, and 9 to 4 on the Friday.
Registration is now open online, where those looking to attend can pre-register for free using promo code NHES2115. Registration is $30 at the door. For more information, visit www.nhes.ca.
The two newest additions to Toronto’s Port Lands Bridges are now open to the public. The bridges, says structural engineering consultancy Entuitive, signify a major step in the redevelopment of 500 acres of once underutilized land. The Cherry Street North and Commissioners Street bridges are modern, eye-catching structures for vehicle, pedestrian, and bicycle traffic.
Waterfront Toronto’s Port Lands Flood Protection Enabling Infrastructure (PLFPEI) project called for innovative and aesthetically stunning bridges to be placed over current and future waterways in the area. The Port Lands Bridges, which are central to the $1.3 billion revitalization and regeneration effort, were designed by Entuitive, schlaich bergermann partner (sbp), and Grimshaw Architects.
“We’re pleased to celebrate the opening of Cherry Street North and Commissioners Street bridges, and to reflect on our rewarding and fruitful collaboration with sbp and Grimshaw, as well as our construction partners at EllisDon,” stated Michael Meschino, principal at Entuitive.
Cherry St. South Bridge with the newly opened Cherry St. North Bridge and roadway in the distance.
Founder and CEO of Freed Developments, Peter Freed, recently announced that the first-ever Freed Hotel and Residences tower will be located at Adelaide and Duncan, in Toronto’s downtown.
The skyscraper project is being designed by Chicago-based Adrian Smith + Gordon Gill Architecture, a firm known for its work on the next world’s tallest skyscraper, Jeddah Tower in Saudi Arabia, as well as Central Park Tower in New York.
The Toronto project will feature 100 five-star luxury hotel rooms and 400 luxury condominiums with a world-class restaurant on the 63rd floor and a boutique spa. In addition, artist Takashi Murakami’s artwork Together with the Flower Parent and Child will be featured prominently in the lobby of the hotel and residences.
“This project is a testament to my profound love for Toronto,” said Freed. “Freed Hotel and Residences represents a ground-breaking moment for Freed Developments with the opportunity to merge art, culture, and sophistication through hotel-style living.”
With the introduction of two new tandem roller compaction machines to the North American market, its CT160 and CT260 models, JCB is once again active in the North American paving market.
“We are re-entering the North American market with a strong, proven product,” said James Gill, product manager for backhoe loaders, site dumper and compaction equipment at JCB North America. “The models have been available in markets outside of North America for some time. They have proven to be a great success, and the durability has been truly tried and tested.”
The machines will be branded “Vibromax,” after the German company JCB acquired in 2005.
The Montreal Port Authority (MPA) has entered into an agreement with Contrecoeur Terminal Constructors General Partnership (CTCGP), formed by firms Pomerleau and Aecon, to assist the MPA in the design of the in-water works for its Contrecœur expansion project. The project to build a new container terminal in the municipality of Contrecœur will take a progressive design-build approach.
With the support of the Canada Infrastructure Bank, the Government of Canada and the Government of Quebec, the Port of Montreal and its partners plan to develop a new state-ofthe-art container terminal able to handle up to 1.15 million containers.
Last October, the MPA stated that it would be using a hybrid approach for the design and construction of the expansion project, with land side works to be carried out by a private partner and in-water works, including dock construction and dredging, to be undertaken by the MPA with partner support.
Under the collaborative
DB approach, CTCGP and the MPA will work closely together throughout the project’s development phase to finalize the design and arrive at an estimated schedule and cost for the project works.
“The close working relationship between these two renowned companies, combined with our innovative progressive design-build approach, strengthens our commitment to the efficiency, coordination and success of this future-oriented project,” said Julie Gascon, president and chief executive officer of the MPA. “We look forward to delivering on this ambitious vision for the future of Canada’s supply chains, and better serving our businesses and our community.”
Project design with CTCGP, along with assessment of cost and schedule, will take place over the next 12 months. At the end of this phase, the MPA aims to award the dock construction and dredging project works based on its procurement processes, and will present an updated implementation schedule.
Investment in building construction edged up 0.3 per cent in December versus November, to reach $19.8 billion on the month, reports Statistics Canada. Contributing to the slight rise were the residential sector’s 0.3 per cent gain, to reach $13.8 billion, and a 0.3 per cent gain in non-residential investment, which reached $6.1 billion.
On a year-over-year basis, the condo and rental apartment segment was the lone residential component to post investment growth, gaining $285 million compared to December of 2022, an increase of 8.3 per cent. December 2023 non-residential sector investment saw a 3.4 per cent gain in the institutional component, which reached $1.7 billion, and a 0.4 per cent nudge higher in the industrial component, but those gains were offset by a decline in commercial investment, which dipped 1.3 per cent to $3.1 billion.
December’s total value of building permits in Canada fell 14 per cent from November, coming in at $9.2 billion, the lowest monthly level since October 2020. According to the figures shared by Statistics Canada, declines were recorded in both the residential and non-residential sectors, however two segments were the key drivers of the dips: multi-family residential and institutional permits in the non-residential sector.
The total value of residential permits fell 17.9 per cent to $5.7 billion in December, driven by a 31 per cent decline in multi-unit construction intentions, the largest monthly drop in the series.
On the whole, non-residential sector permits decreased seven per cent in December, landing at $3.6 billion. A 56 per cent decline in institutional permit values in Quebec, caused by a pair of high-value permits in November, more than offset the 4.1 per cent gain in commercial intentions and 4.7 per cent rise in industrial permits across Canada.
Year over year, the total current dollar value of building permits fell 3.2 per cent to $132.2 billion in 2023. On a constant dollar basis, using 2017dollar values, the total annual value of building permits decreased 8.9 per cent from 2022 to $84.2 billion in 2023.
Investment in non-residential construction, December 2023 (in $Millions)
Newfoundland and Labrador $24.8
Prince Edward Island $18.3
Nova Scotia $88.3
New Brunswick $77.6
Quebec $1,317.1
Ontario $2,565.5
Manitoba $183.1
Saskatchewan $129.9
Alberta $698.6
British Columbia $930.8
Yukon $17.5
Northwest Territories $8.6 Nunavut $4.2 TABLE: STATISTICS CANADA
Despite falling from a summertime peak, on a seasonally adjusted basis Canada’s construction sector posted a gain of just under one per cent in December compared to the same month in 2022. Looking at monthly figures, Statistics Canada reports that construction payroll employment increased for second month in a row in its latest Survey of Employment, Payrolls and Hours. The number of employees receiving pay and benefits from an employer in the construction sector rose by 2,700, or 0.2 per cent. This followed an increase of 1,200 positions in November. Despite these increases, seasonally adjusted payroll employment in construction was down by 8,300, or 0.7 per cent, in December from the employment peak that was recorded in July. Payroll employment in construction of buildings, including non-residential and residential building construction, held steady in December.
Total Employment in Canada
20,237,800 Unemployment Rate
5.8% Construction Employment
1,544,400
On the jobsite you need a truck that’s tough, safe, and smart. So, we built the new Volvo VHD to be the best-looking, most rugged vocational vehicle in the industry, packed with innovative ideas like Volvo Active Driver Assist and the revolutionary Volvo Dynamic Steering. Your toughest jobs just got easier.
Learn more at volvotrucks.ca/en-ca/trucks/vhd/
Demographics, economics, environmental concerns, and technological advances are behind the surging popularity of compact construction equipment, say industry experts.
“Growth drivers include urbanization, upgrading and expansion of infrastructure, commercial and residential development,” says David Caldwell, national product manager with Takeuchi-U.S. “As the world’s population continues to grow, there’s an ongoing need to expand existing infrastructure and create new infrastructure, primarily in urban locations. Compact equipment can work in these confined spaces due to its smaller size and better maneuverability.”
“Yesterday’s compact equipment models were reserved for cut-and-dried utility work,
utilized either for quick, precise tasks when a larger machine didn’t make sense, or one-off jobs that may not necessarily have been lucrative for a contractor,” adds Mike Fitzgerald, Bobcat’s marketing manager. “Thanks to significant advancements in performance and productivity features, however, operators can rely on today’s compact equipment for a wide variety of demanding tasks.”
“The industry for small excavators continues to grow because of their overall versatility. Small excavators can handle many jobs from start to finish, eliminating the need for additional equipment onsite. An example is digging a hole, loading a truck, backfill-
ing, compacting and then final grading, all with just one operator and one machine,” explains Brian Riniker, product manager for small excavators at John Deere.
“Compact construction equipment offers increased maneuverability and allows operators to excavate or load near buildings and structures that traditional construction machinery cannot access. These compact machines can also be used indoors,” adds Taimoor Khan, business development manager for carbon neutral products at Komatsu.
Komatsu’s PC45MR-5 and PC55MR-5 compact hydraulic excavators boast minimal swing radii and are equipped with standard auxiliary hydraulics and My Komatsu digital portals that can analyze telemetric data. Likewise, Bobcat’s new E40 compact excavator offers minimal tail swing, plus fast cycle times, excellent maneuverability, and “an over-the-blade lift capacity and over-the-side lift capacity that competitors can only achieve – or come close to – with conventional tail swing models,” says Fitzgerald.
Tail swing aside, Bobcat’s new L95 compact wheel loader has a tight turning radius, automatic ride control, a powerful transmission, and “exceptional material-handling capabilities with large bucket capacity, high lift height, swift travel speeds and the maneuverability operators need to accomplish more,” he continues.
Compact equipment is also ideal for
From the original compaction brand comes a full line of construction equipment designed to help you get the job done with efficiency, quality and comfort. Whether your challenge is to load, move or place material, compact soil and asphalt, or to provide light, heat, power or pumping on your job site, Wacker Neuson has the machines to get it done right. This includes zero-emission, battery-powered solutions to meet the demands of the construction environment today, as well as tomorrow.
Contact your local Wacker Neuson dealer today.
www.wackerneuson.com
electrification, says Grant Van Tine, electric vehicle product manager at John Deere. “Compact construction machines, especially small excavators, are good candidates for battery electric solutions. The daily runtimes and energy requirements are lower on compact equipment,” he explains.
In addition to requiring fewer and/or smaller batteries that take less time to recharge, the size of compact equipment also brings with it the simple fact that it can be easier to move than larger equipment.
“If it’s under a certain weight you don’t need a special licence to transport it from job site to job site,” explains Jonathan Gardner, project manager for construction equipment at Kubota Canada.
Furthermore, while large equipment has to be moved on trailers to specialized charging stations, operators could take a compact loader “down to the local gas station and use the J1772 plug they have there and top it up,” says Darren Ashton, Volvo Construction Equipment’s North American product manager for compact.
Volvo’s EC18 and ECR18 electric compact excavators take six and five hours respectively, to charge from zero to 100 per cent on a 16A workshop outlet, dropping that to one hour and 15 minutes and one hour to charge from zero to 80 per cent in a fast charger.
Compact electric equipment can provide companies with “green” credibility and
access to areas where traditional equipment might prove problematic, due to emissions. Case’s new CX15EV electrified mini-excavator produces no emissions and minimal noise, so it could be used “at a hospital or retirement community or a fancy urban setting in a neighbourhood that has covenants that you can’t dig before 10 a.m.,” states Brady Lewis, product manager for emerging products and technology at Case Construction Equipment.
In a similar fashion, Takeuchi’s new TB20e battery powered compact excavator operates quietly and gives off zero emissions, “making it useful in more sensitive areas or even in enclosed spaces,” says Caldwell. Electric compact equipment also requires less maintenance, as there’s no engine filters, oil changes, and coolant, much less liquid fuel.
Whether conventional or electric, compact equipment holds a powerful appeal for smaller firms. Some are even viewing compact machines as a way to help them navigate rising labour costs and difficulties associated with finding new skilled workers.
“You’re seeing a pretty clear diversion away from larger machines moving into more compact machines … I think you’re starting to see a migration towards a lower cost option for owner-operators to do more work themselves versus relying on employees and team members,” says Ryan Anderson, product manager for Case Construction Equipment’s sub-compact lineup.
Going forward, it’s highly likely the
compact category will continue to grow, especially as this equipment starts to sport features once reserved for larger machines.
Kubota’s new KX080-5 compact excavator, for instance, offers a standard, factory-fitted rear-view camera with a seven-inch LCD display and the company’s KubotaNOW telematics system. Cab noise has been reduced and cab heating and cooling improved as well.
Based on customer demand, John Deere has been making its compact equipment more powerful and versatile while “adding features found in larger equipment, such as SmartGrade 3D grade control on the 333G compact track loader,” says Emily Pagura, product marketing manager at John Deere.
“Companies are adding features to [compact] machines that will make them more effective, such as 2D/3D machine guidance, machine control,” echoes Diego Butzke, product manager for excavators and motor graders at Case. He says these features “have been part of the heavy equipment world, but I think they will start to come over to compact equipment as well, because the same lack of labour that impacts larger excavators, you also have now on mini-excavators. You need to be more effective with doing more things with less people.”
Nate
With long hours that don’t easily match childcare schedules, gear that is not always available in proper sizing, and even a basic lack of private washrooms, construction is not an easy industry for women.
A recent industry survey indicated that only 42 per cent of women felt welcome when they joined the industry. A similar number felt isolated on their crew because of their gender, and 70 per cent experienced harassment or were actively concerned about their safety while at work.
In today’s economic and labour environment, construction firms need to make changes to address such issues, especially since the industry is expecting the labour shortage to only worsen.
Unfortunately, when they step onto the job site, many women will still find they are the only female around. Statistics Canada suggests that roughly seven per cent of construction workers in Canada are female, but the actual figures are closer to the three to five per cent range.
Despite the challenges, there has never
been a better time for women to enter the construction industry. Government programs and interest groups are actively encouraging women to join an industry that is growing in an economy that seems to be shrinking.
Construction firms that want to recruit and retain enough female workers to combat the labour shortage will need to recognize the critical role that workplace culture plays, and how a poor culture can drive women away from a company, and even the industry. Actively creating an inclusive environment offering equal opportunities for men and women on the job site is a critical component of being an employer of choice.
The good news is that creating an inclusive culture may be easier than you think. It starts with a basic foundation of respect, and is enhanced by meeting each individual employee’s needs.
Personal Protective Equipment (PPE) is not “one-size-fits-all.” Remember that PPE is intended to protect workers from injury and other hazards. Offering men’s PPE to female
workers compromises their safety since the sizing can be all wrong. Even worse, women who make do with the wrong PPE often find it difficult to do their jobs effectively.
PPE based on female anthropometric data is available from a number of suppliers, however. As a best practice, contract with PPE vendors that offer a wide range of equipment for both men and women, and keep a close eye on supply to ensure that appropriate PPE is available as needed.
Women are three times more likely to be injured on the job compared to men, and some of these injuries are linked to women using equipment that wasn’t designed for their bodies. They come to the workplace with a different set of personal risk factors, including medical conditions, personal fitness and even medications that can influence the possibility of ergonomic injury.
Best practice calls for the use of a variety of tactics, from workplace monitoring and body mechanics training, to pre-shift exercises, to prevent ergonomic injuries.
Meet the International ® S13 ® Integrated powertrain. Now available in the HX™ Series.
After revolutionizing highway driving in the LT ® and RH™ Series, the S13 Integrated is now ready for severe duty work in the HX Series. A huge step forward in performance, design, and operating economy, the S13 Integrated is the lightest 13L in North America. But it still brings 515 horsepower, 1,850 lb-ft of torque, and optional factory-installed PTOs. Not to mention simpler serviceability for more uptime. Now all that’s left to do is get to work.
Consider providing female workers with tools that can be adjusted for women’s bodies, and developing safe lifting guidelines that are appropriate for women.
At many small job sites, a single unisex portable washroom is the norm, and it may not be well-maintained. For women working at a site like this, the choice is (at best) an awkward one. Use the facility and risk contact with a contaminated seat, or not use the facility and risk health problems.
Ontario recently announced it will be requiring separate women’s washrooms on job sites. Washrooms must be private, properly lit and include hand sanitizer when running water is not available.
Construction sites are home to a variety of hazards, many of which could impact not only a woman’s health overall but also her reproductive health. Whether it’s ongoing
exposure to chemicals or simply movement that might be too strenuous in a later stage of pregnancy, it’s important to understand the risks, and mitigate them where possible.
Organizations should also note that every situation is different. Women in the construction industry must share information about their workplace hazards and challenges with their family doctor to determine what is right for them, and organizations must be ready to make accommodations, when necessary. This includes for women who may struggle to perform their regular duties during later stages of pregnancy. Keep in mind that properly fitting PPE, while important for everyone, is especially important for women who are expecting.
Women in construction are largely positive about their experience, but they also recognize best practices to make their experience even better: more support, respectful management and more mentorship.
Breaking down a “macho” culture starts with small steps, all related to increasing respect. Women today expect fair and equal treatment, including pay equity. Similarly, female employees should be able to come to work and feel safe. They should be comfortable to report unwanted behaviour or other concerns to their managers, without worry that reporting their concerns will impact their job opportunities. In addition, it should go without saying that sexual harassment must not be permitted.
A safe and inclusive culture is key for any industry to maintain a successful workforce, but it also brings additional benefits, including increased innovation, higher engagement, better decision-making skills, reputational enhancement, and more.
Danielle Fenn is senior vice-president in the construction practice for insurance brokerage Hub International.
POPULATION GROWTH DRIVING ROAD AND TRANSIT PROJECTS
The construction industry stands on the cusp of a significant growth period fuelled by increased government investment in infrastructure projects and the ever-growing demand for resource extraction. Yet, this exciting outlook is tempered by unique challenges. Manufacturing capabilities are experiencing a decline, environmental concerns necessitate an increased focus on sustainability, and supply chain constraints continue to disrupt project timelines and budgets.
Despite these complexities, the Link-Belt brand has a proud legacy spanning 150 years. Throughout our history, we’ve consistently pursued innovative solutions that optimize efficiency across every aspect of construction operations. Today, our commitment to progress continues with the seamless integration of cutting-edge technologies into our machinery. These advancements empower operators with unprecedented levels of customization and automation, keeping them informed, engaged, and in control.
This dedication to innovation is reflected in Link-Belt Excavators’ core purpose: providing reliable and innovative machinery that contributes to the strength and prosperity of the communities we serve. We achieve this by nurturing strong relationships with our dealer network, delivering exceptional products, and fostering a vibrant and dynamic company culture. These core values position us for continued relevance and growth not just in 2024 but well beyond.
Link-Belt Excavators is proud to sponsor On-Site Magazine’s 2024 Canadian Infrastructure Report. Looking ahead, we believe in collaborative solutions, and together with our partners, we can dismantle the barriers hindering construction success. Collectively, we can build essential infrastructure, foster stronger connections, and optimize resource allocation across Canada, ensuring a brighter future for our communities.
Despite lingering uncertainty about the economy and disputes between the provincial and federal governments over governance, it’s pretty much full steam ahead for road and public transit projects across Canada.
In British Columbia this past December, the long-awaited Surrey-Langley SkyTrain extension took a big step towards seeing shovels in the ground when project propo-
nents released the official names for eight new stations.
Green Timbers, 152 Street, Fleetwood, Bakerview-166 Street, Hillcrest-184 Street, Clayton, Willowbrook, and Langley City Centre Stations represent the heart of the $4-billion, 16-kilometre above-ground extension of the Expo Line. If all goes to plan, commuters will be able to travel on rail between Langley and downtown Vancouver in just over an hour.
Port Coquitlam mayor Brad West, chair
of the regional mayors’ council, underscored the extension’s importance to ongoing population growth, predicting 50,000 new residents will continue to move into Metro Vancouver annually.
“By investing in public transit, we are helping make the lives of these new British Columbians easier while simultaneously improving the quality of life and travel for everyone else,” West told journalists when the station names were announced.
The project is being delivered through three separate contracts for the guideway,
stations, and track work and systems. The province has announced the firms selected to respond to the requests for proposals. Contracts are expected to be signed early this year. Some advance work started four years ago, including utility relocations and the now-completed widening of Fraser Highway between 140 and 148 Streets. Proponents say they expect construction of the extension itself to begin by year’s end.
Kelly Scott, president of the B.C. Road Builders and Heavy Construction Association, says the work stands to help the economy and keep his members and others in the construction sector busy.
“It will be fairly active for everybody,” Kelly says, adding it will help ease the housing shortage by enabling growth outside already-dense urban centres. “Rather than driving for an hour and a half, people living in the Surrey area will be able to jump onto a SkyTrain and commute into Vancouver.”
The SkyTrain extension isn’t B.C.’s only major porject. The province is on the cusp of forming a Fraser River Crossing tunnel project team. Projected at $4.15 billion with possible completion by 2030, the eight-lane tunnel will replace the old Massey Tunnel and look to ease commuter and commercial traffic along Highway 99 around Vancouver and south towards Washington State.
The Fraser Valley Highway 1 Corridor Improvement Program also continues, with about $1 billion being spent to improve and widen sections between Langley and Abbotsford, and Sumas Prairie to Chilliwack. Improvements also continue along Highway
1 between Kamloops and Golden, and crews in multiple areas are mitigating impacts on roads from severe weather.
The timing of these works is fortuitous, says Scott, “Site C is coming to an end, the Kicking Horse project is coming to an end, and the pipeline is coming to an end. There’s going to be 5,000 to 15,000 workers in our industry looking for work.”
an 18-kilometre corridor from the downtown southwards.
In Alberta, Calgary’s Green Line LRT continues to move towards construction with utility relocation and design work underway, along with negotiations with the lead contractors chosen to develop the first stretch of the two-phase, $5.5-billion project.
With 29 stations planned, the 46-kilometre line stands to become the largest public infrastructure project in Calgary’s history and the city’s first rail line to operate low-floor trains. The line will be powered through wind generation and will run between Calgary’s north-central and southeastern boundaries, connecting with the Red and Blue lines downtown.
Bow Transit Connectors has been selected as development partner for Phase 1, which will see 13 stations built along
Construction looked set to begin in early 2021, but then-Premier Jason Kenney famously characterized the line as “a train to nowhere” and his government withheld funding for two years. The province eventually supported the project, and PCL Construction was retained to oversee utility relocations. Bow Transit Connectors has since brought in Barnard Constructors of Canada, Flatiron Constructors Canada, WSP Canada, and EllisDon Capital.
With two kilometres of tunnel as well as bridges crossing two rivers and multiple roadways, Phase 1 has its share of complexities, and debate now centres around tunnels, routing, development around stations, and escalating costs. In fact, one founding member of the Ad Hoc Citizens Committee to Rethink the Green Line has publicly described the project as “too big to get wrong.”
Costs are indeed nothing to ignore. The city’s Green Line Board has acknowledged that committed spending has already passed the $1-billion mark, largely going towards design and engineering, preliminary work, land acquisition, utility relocation, and procuring 28 rail cars.
Planning is expected to continue through June, with construction potentially beginning later this year. Proponents say they expect the construction of Phase 1, alone, will generate 20,000 jobs.
“It’s a massive project,” says Ron Glen, CEO of the Alberta Roadbuilders & Heavy Construction Association.
Clearly, the project looks to address growing traffic congestion. The route runs alongside much of the busy Deerfoot Trail, the primary link between north-central and southeast Calgary. “Calgary is a very spreadout city,” Glen says. “This should make the downtown more attractive.”
Phase 2 would run northwards but remains in its earliest planning stages, with some preliminary funding already allocated.
Looking northward in the province, also underway is the Yellowhead Freeway conversion in Edmonton. The largest roadworks program in northern Alberta, it has a valuation of just over $1 billion. Also known as Highway 16, it is a major east-west thoroughfare which the City of Edmonton committed years ago to upgrading.
“The work includes a number of interchanges, reconfigurations and new roadways to accommodate closed roads so that it can become a full freeway,” Glen says. It stands to replace the Calgary and Edmonton Ring Roads as a significant source of jobs.
Bridge projects continue to be a mainstay for construction in Quebec with shovels officially hitting the ground in December for the $2.3-billion Île-aux-Tourtes bridge. The new span will replace a badly aging structure, which was built in 1965 but has experienced ongoing safety closures, frustrating commuters crossing this major access point on Route 40 between Vaudreuil-Dorion and the island of Montreal.
The new six-lane bridge, just north of the existing structure, will offer widened shoulders for bus service and a path for pedestrians and cyclists. Quebec’s Ministère des Transports et de la Mobilité durable plans to open it by 2027, with removal of the original structure expected by 2030.
“This new link will be better adapted to the realities of the region’s citizens, and will ensure a smoother flow of traffic,” Minister Geneviève Guilbault said in a recent public statement.
Other bridge work includes replacing the central slab on the Laviolette Bridge on Route 55 between Trois-Rivières and Bécancour. Pegged at $261 million, it’s slated for completion by mid-2025. And planning is underway to rebuild the Honoré-Mercier bridge on Route 138.
Tunnelling is also active. The current $2.5 billion projected for repairs to the Louis-Hippolyte-La Fontaine bridge-tunnel underneath the Saint Lawrence River near Montreal make that the province’s current biggest-ticket roadworks item, according to the Quebec Construction Commission’s annual economic overview. Completion is expected in 2025. As well, repairs to the Ville-Marie and Viger tunnels, estimated at $2 billion, are forecast to wind up in 2030.
Multiple highway projects in the province include the ongoing $890-million extension of Highway 19 between Highways 440 and 640 in Laval, which is slated for completion in 2027. Phase 3 of some $883.3 million in upgrades
to Route 185 between Saint-Antonin and Bas-Saint-Laurent region near New Brunswick are also scheduled to end late next year. And more than $493 million in improvements are underway along Route 389 between Baie Comeau and Fermont, near the Labrador border.
Public transit projects are also making headlines. In Montreal, an extension of the Metro Blue Line, awarded in 2023, is currently set at $6.4 billion, with substantial completion projected by 2030. One leg of a $6.9-billion undertaking on the Réseau Express Metropolitain (REM) is slated for substantial completion later this year, but further plans remain uncertain.
Xavier Turcotte, spokesperson for the Quebec Road Builders and Heavy Construction Association, says road-related projects, in particular, have been gaining traction, with more work on tap for 2024 than in previous years.
“We’re optimistic,” Turcotte says, adding that a deputy minister from the transport ministry addressed his association’s annual conference and indicated additional infrastructure activity in the years ahead. “We must continue to develop our road network, whether for long distances, the transport of goods, or essential services.”
In Ontario, work continues on the $6.4-billion Gordie Howe International Bridge. Completion is now expected to happen in September of 2025. Crews recently finished the two bridge towers, and tasks now include connecting the two bridge decks over the Detroit River, installing the remainder of 216 stay cables, completing the point-of-entry agency buildings, and concrete work.
Highways are also a high priority. Crews continue to widen Highway 17 from two to four lanes between Kenora and the Manitoba border, and some early works have been underway for more than a year on the 16.3-kilometre Bradford Bypass, which stands to link Highways 400 and 404 north of Toronto. The province retained AECOM Canada to undertake a project-specific
We are up for any challenge. Complex projects are opportunities to demonstrate our unmatched skill, outside-the-box innovations, and unyielding strength. Whether you are looking to replace aging water/ wastewater infrastructure or need a trenchless solution with minimal impact on the surrounding environment, we will exceed your expectations for quality, safety and sustainability.
Partner with Michels Canada and expect more.
environmental assessment for the route itself, and requests for proposals stand to be issued early this year for engineering and design and, later this year, for other contractors for the western section.
Less certain are prospects for Highway 413, which would run 60 kilometres through suburbs north and west of Toronto. Preliminary planning and design are underway, but the project remains designated for a federal environmental assessment.
While the Supreme Court of Canada has ruled aspects of the federal Impact Assessment Act infringe on provincial jurisdiction, jurists reaffirmed federal environmental assessments are appropriate if they respect the constitutional division of powers and address matters clearly within national jurisdiction such as indigenous rights, migratory birds, federally protected species, and federally regulated waters and fisheries.
The federal government hasn’t yet stated how it will apply the decision to transportation projects, and so the province has applied to the Federal Court of Canada for a judicial review of Highway 413.
At the annual convention of the Ontario Road Builders Association in February, Premier Doug Ford reiterated his government’s commitment “to ensure that Ottawa can’t impede or stop desperately needed infrastructure projects like Highway 413.”
Meanwhile, work continues on several large public transit projects. Tunnel boring for a 7.8-kilometre, three-station extension of the Scarborough Subway Line is underway, with a projected 2030 service date and cost projections reaching $5.5 billion. And, early site preparation is underway for the Ontario Line, which is expected to cost up to $19 billion and possibly open by 2031.
Nadia Todorova, executive director of the
Residential and Civil Construction Alliance of Ontario, says the province “has done a good job in terms of prioritizing infrastructure investment for transformational infrastructure projects like the Ontario Line, Highway 413, and the Bradford Bypass, and also providing funding for general maintenance of infrastructure assets.”
Ontario Road Builders Association CEO Walid Abou-Hamde, meanwhile, says ORBA fully supports Premier Ford and the Ontario government in asserting provincial jurisdiction over infrastructure development.
Says Abou-Hamde, “We call on our federal partners to join our effort to get these generational projects built.”
As the backbone of Canadian society, infrastructure plays a critical role in maintaining the quality of life that Canadians have come to enjoy. While, of late, there has been a spike in interest in constructing new roadways, mass transit systems, energy facilities, pipelines, and so forth, there’s also a baseline need to maintain, replace and repair the existing structures that we need to move people and goods, and to stay safe and healthy in our homes and businesses. And despite recent increases in project counts and spending, infrastructure needs seem to always outpace spending.
Government-driven projects, including key infrastructure projects, are providing stability and growth to Canada’s construction sector. To get a better picture of the state of Canada’s infrastructure sector, in February On-Site Magazine welcomed a panel of representatives from key construction organizations to a webinar exploring current infrastructure projects, upcoming projects, and the sector’s prospects going forward.
The panel, moderated by Adam Freill, editor of On-Site Magazine, included Chris
Atchison, president of the B.C. Construction Association, John Casola, chief investment officer at Canada Infrastructure Bank (CIB), Angela Clayton, president of project delivery at Infrastructure Ontario (IO), and Mary Van Buren, president of the Canadian Construction Association (CCA).
“British Columbia’s infrastructure forms the backbone of our provincial economy,” explained Atchison as he introduced his organization and some of its activities. “We never take our eyes off the infrastructure ball. It’s embedded into our mission and our operations as it’s our members in our industry that are building this incredible array of infrastructure that we’re seeing come online.”
Casola explained that Canada Infrastructure Bank was created by the federal government with seed money of $35 billion and a focus on spending across five priority sectors. “Those are public transit, clean power, which involves generation transmission and storage, green infrastructure, which involves carbon capture and low carbon fuels, our building retrofits program, which is very popular and being taken
advantage of, broadband, and trade and transportation, which includes airports, ports, critical minerals, and irrigation infrastructure,” he explained.
Unlike traditional lenders, CIB, he said, is an investor that can afford to take on levels of risk that other lenders would not. “We are a gap filler. We identify what gap is preventing a project from proceeding.” This allows projects to carry forward despite difficulties associated with securing traditional financing, including longer timeframes for investment returns. “We are patient capital; we are created to take more risk than is ordinarily out there.”
His company recently came to the aid of an airport project in Manitoba where the facility was sinking and needed a solution to save an important gateway to the North for many northern Indigenous communities. “Already other businesses are starting to form around that airport, knowing that it’s going to be built,” he said. “So that’s great.”
In Ontario, IO has completed over 100 projects since its inception in 2005, explained Clayton. “Our current program of work is just under $80 billion; 61 projects.”
With a focus on such concerns as risk, market constraints and cost escalations, she explained that the organization has its eyes on project models, the management of available labour, and project costs.
At the CCA, Van Buren says there is a strong desire to establish a national picture and plan for infrastructure.
“Two-thirds of the Canadian economy depends on trade; that trade depends on high quality trade-enabling infrastructure,” she stated. “One of the initiatives that we’re very proud of is the Canada Trade Infrastructure Plan.” That plan calls for a national perspective on infrastructure planning, taking a long-range approach, rather than basing decisions on election cycles. “This plan has received endorsement from premiers across Canada. So that’s something that we’re continuing to champion.”
The association is also focused on workforce capacity, to ensure that Canada has the workers needed, for today and into the future. “A big part of that is working on aligning immigration,” she said. “The way it is, it is not really working to bring in the people that we need.”
All four panellists expressed optimism about upcoming and potential infrastructure projects in the pipeline, although concerns about geographic alignment of workers and staging of projects to match labour availability were raised.
“All across the country, we are seeing unprecedented levels of activity and
deals,” said Casola. “We have closed on almost 60 infrastructure projects worth over $12 billion… along with private capital, we’re close to $35 billion across the country.”
He said that last year CIB closed 26 deals. “This year, we’re on pace to close over 30. And when I look at my pipeline next year, it just keeps growing.”
Infrastructure Ontario’s Clayton painted a robust picture of the segment in Ontario, where the provincial government has made a $185 billion commitment to infrastructure spending over the next decade.
“In terms of projects in construction, we have 29 projects that are in construction, with nine of them reaching substantial completion this year,” she stated, adding that they are among the 61 projects on the organization’s books. “On top of all of that, we have 19 projects that are in the planning stage,” she added. “This government is definitely all-in on infrastructure.”
Van Buren echoed the optimism, adding that government focus on infrastructure extends to other provinces as well. “Premier Kinew, for example, is also quite committed to investing in infrastructure for the Province of Manitoba,” she explained.
There are some concerns about the potential for some softening in the pipeline in British Columbia, however, which Atchison illustrated. “The LNG Canada project, of course, the complementary Coastal GasLink project, our Site C project up in the northeast and Trans Mountain pipeline: Those are four major projects
that have been ongoing in British Columbia for some time, but they are all past peak construction,” he said. “There’s been some concern… as those projects mature and near completion, we need to backfill with new projects in order to retain that workforce.”
Aging infrastructure is also a going concern.
“Unfortunately, we’re not keeping up,” said Van Buren. “We have a significant infrastructure deficit. If you look at the Canadian infrastructure report card, 40 per cent of our roads and bridges are in fair to poor or very poor condition.”
“We need to work on these new infrastructure projects and the existing infrastructure projects in tandem. They’re not mutually exclusive,” added Atchison.
When asked about their view of the next 12 to 24 months, the panel were unified with a significantly positive outlook, however. As Casola summed it up, he is “Very optimistic, despite some of the challenges.”
“We are very optimistic about the next 12 to 24 months,” echoed Atchison. “I think the federal government is listening, they’re paying attention. They’re not kicking the proverbial football down the field any further.”
To view the full webinar session, scan the QR Code, or visit On-Site’s YouTube channel.
The tools of the trade for asphalt paving keep getting tech upgrades.BY NATE HENDLEY
Original equipment manufacturers are continuing their march forward, adding sensors, monitors, automation, and other high-tech features to asphalt equipment. In addition to enhancing efficiency and productivity, these solutions are designed to reduce emissions and bridge a skills gap. Electric power is also becoming more common, and autonomous equipment might soon hit the marketplace. One thing is certain, the paving sector is anything but static.
In late 2021, for example, Volvo Construction Equipment unveiled its CX01, a conceptual single-drum asphalt compactor, at the Utility Expo in Louisville, Kentucky. The CX01 can be operated by remote control or in completely autonomous fashion.
While the CX01 is just a concept for now, “autonomy is definitely a focus we see the industry looking more and more towards,” says Justin Zupanc, head of electromobility and autonomous solutions for road products at Volvo Construction Equipment.
Manufacturers are also “looking for ways to make the machines more productive; more operator friendly—easier for
operators to accomplish the job with less effort,” adds Zupanc.
Given that construction companies are “struggling to find operators” user-friendly software and other solutions can help firms cope with labour shortages and simplify training for new workers, he says.
Another focus is on the quality of the end product. Case Construction Equipment, for example, offers ACE Force Intelligent Compaction technology, which aims to improve compaction quality and reduce the number of passes required to meet target specs. This, in turn, “saves time, fuel costs, and machine maintenance, while avoiding pitfalls related to under or over-compaction,” states Jeremy Dulak, the company’s North American product and marketing manager for dozers and compaction.
With technological change in mind, let’s see what’s new and noteworthy in asphalt equipment.
Volvo introduced the battery electric DD25, the company’s first asphalt electric compactor, at CONEXPO last year. A quiet, low-maintenance, compactor that gives off
zero exhaust emissions the company says its machine can charge from zero to 100 per cent in three hours, depending on the AC power-level.
“We got a lot of feedback from customers that have tested it and said, ‘Wow! This thing is quiet!’ Even when the drums are vibrating—and they typically generate a lot of noise—the customers were still able to identify the reduction in sound,” says Zupanc.
The double roller DD25 Electric can be used near hospitals, schools, residential neigbourhoods, or other areas where noise might be an issue. The lack of emissions also means it can be used indoors without the need for an elaborate ventilation system to siphon off fumes. And no engine means reduced maintenance.
“You no longer have oil changes. You no longer have filters. You have a hydraulics system, but basically you charge the batteries, and you go,” states Zupanc.
The DD25 Electric has an overall height of 104.3 inches (2,650 mm) and a drum width of 39.3 inches (1,000 mm) in narrow format and 47.2 inches (1,200 mm) in wide format. Given these diminutive dimensions, it’s well-suited for “smaller-size parking lots, driveways, limited shoulder work, patching, some sub-base preparation,” says Zupanc.
Volvo asphalt equipment can be fitted with Company Assist, a solution that provides pass mapping and temperature mapping. The latter is an important detail
as “you want to be able to make sure you’re rolling at the right temperature range. Certain temperature ranges are undesirable,” explains Mike Wasielewski, product owner for asphalt compaction at Volvo Construction Equipment.
More advanced versions of Compact Assist compile data and offer real-time Compaction Measurement Value (CMV), which “gives an indication of the stiffness of the material. As operators reach a CMV that has been specified, they can basically determine when they’re done compacting that area,” he says.
The company also offers a version of “Compact Assist with Density Direct—a real-time density measurement of the output of the machine. After you roll over the mat, you get a real-time density reading of what you’ve just completed,” adds Wasielewski.
Case Construction Equipment has announced its DV23E EP and DV26E EP (Efficient Power) compact double-drum rollers as new entries to its asphalt compaction lineup.
At 24.5 hp (18.6 kW), the EP models “have slightly less power” than their non-EP counterparts [the DV23E and DV26E] but offer “similar compaction output,” says Dulak.
The Efficient Power models “do not require any engine emissions technology to meet Tier 4 Final standards, meaning there’s no diesel particulate filter or exhaust gas recirculation to maintain. All other options, features and benefits are the same as the DV23/26E models,” he continues.
Case has also expanded its single drum vibratory roller lineup with the new SV215E and SV217E soil compactors. Each is fitted with a Tier 4 Final 154 hp (115 kW) engine, and can reach 7.9 mph (12.7 kph). The SV215E weighs 33,420 pounds (15,160 kg) and the SV217E weighs 36,500 pounds (16,555 kg). These models can be equipped with ACE Force Intelligent Compaction and Case SiteWatch telematics.
Vögele, a brand of the international Wirtgen Group, exhibited the Super 700i Mini Class
paver, the Super 1703-3i eight-foot paver, and the Super 2000-3i Highway Class paver at CONEXPO 2023 in Las Vegas.
While Vögele pavers and screeds are made in Germany, these particular products are specifically intended for use in North America.
Featuring a liquid cooled four-cylinder diesel engine, the Super 700i paver can pave basic widths ranging from threefeet-11-inches (1.2 metres) to seven-feetthree-inches (2.2 metres) with an AB 220 extending screed.
A compact model, the Super 700i is recommended for paving small areas or doing pavement repairs. It comes with
telematics and an ErgoBasic operating system. This system features status and function indicators, a choice of operational modes, and glare-free backlighting, which helps in nighttime conditions.
The Super 1703-3i eight-foot paver has a four-cylinder, liquid cooled diesel engine, is capable of pave speeds up to 250 feet/minute (76 m/minute), and pave basic widths from eight feet (2.45 metres) to 15-feet-six-inches (4.75 metres) when fitted with a VF 500 front-mounted screed. This paver has an ErgoPlus 3 operating system, Automatic Grade and Slope Control, a RoadScan asphalt temperature measurement system, and is intended for
municipal and commercial applications.
For its part, the Super 2000-3i boasts a six-cylinder, liquid cooled design engine, a maximum laydown rate of 1,540 tons/hour, and has a basic paving width ranging from 9-feet-10-inches (three metres) to 19-feeteight-inches (six metres) when equipped with an AB 600 extending screed. Wellsuited for highway and large-scale commercial work, the Super 2000-3i has ErgoPlus 3, Automatic Grade and Slope Control, telematics, and RoadScan.
Caterpillar has entered into an agreement with Axenox, Inc., a construction solutions provider, to purchase the intellectual properties of an innovative three-dimensional screed plate and accompanying modular screed plate fastening system.
While most screed plates are flat, Axenox uses an angular 3D design to ensure better mat smoothness and higher density, which can reduce the required number of passes, saving time and costs. The 3D cast plates are made from high-strength chromium carbide for durability and longevity. A modular fastening system reduces the time required to change screed plates from days to under four hours.
The plate and fastening system will be available exclusively as options for customers of Caterpillar asphalt paving equipment.
The company also offers Cat Paving Technology solutions for its line of asphalt pavers and screeds. Cat Compact with Compaction Meter Value (CMV) determines material stiffness, while the Cat Grade and Slope system features sensors that detect elevation and makes automatic adjustments. Cat Grade and Slope can be operated and monitored from a paver or screed.
Caterpillar’s Pave Start Assistant is a machine management tool that records paving speed, width, and other metrics to simplify the setup required for repeatable performance.
In the asphalt pavement industry, accurate moisture measurement is vital to producing and laying down a durable, quality surface. Most asphalt mixes contain petroleum additives and water, and the ratio of moisture to solids is critical to the curing process.
To pave roads and parking lots, hot mix asphalt (HMA) is widely used because it hardens quickly and provides good traction. This material is typically mixed at an asphalt plant before transportation to the site by truck or rail car, at which point operators dump the mix into hoppers and then dispense it before heavy rollers compact the surface.
During its journey, the moisture content in the HMA can vary due to environmental conditions or water vapour loss as the HMA mix is heated, stored and dispensed. This variability can be disastrous to the quality, finish, longevity, and even safety of the finished asphalt.
To ensure the moisture content remains consistent, operators would ideally test the moisture content at every step of the way. Unfortunately, moisture measurement tests are rarely or inconsistently conducted. In addition, many moisture meters require calibration, sampling, and time. Many of the tools are not portable or durable enough to be used on heavy construction job sites.
The availability of cost-effective, automated and instant moisture measurement devices is providing the industry with an option, however, and it an option that some
contractors are using to ensure optimal moisture levels from the plant to the paving site.
One traditional approach to test for moisture content involves Loss on Drying testing. This uses a moisture balance to measure the total change in the material weight change of a mixture after drying. However, such tests typically require technicians to prepare a sample to be brought to a lab, and each test takes upward of 15 minutes to several hours to perform. And asphalt samples are not small. Larger samples require a big drying oven, a big pan, and often overnight drying.
To ensure consistent moisture content at HMA plants, the industry now uses Near-Infrared (NIR) light equipment for a highly accurate, non-contact, secondary-measurement method that delivers immediate, laboratory-quality moisture readings.
NIR moisture meters generate accurate instant measurement of solids, slurries and liquids without contact or sample preparation. Available in desktop, handheld portable and inline models, when used with analysis software, inconsistencies can be quickly detected and corrected.
For real-time testing of HMA, either during plant processing or dispensed to and from trucks or rail cars, inline tools can be used for 100 per cent inspection of all mixed materials without having to take samples offline for testing.
Moisture analyzers provide an instant, non-contact, non-destructive measurement
of liquids and solids while the product is moving. For frequent spot checks of materials anywhere in the process, operators can use portable, handheld and instant moisture meters. The user simply points the instrument and the moisture content is instantly shown on a digital display.
Once technicians lay the asphalt, handheld units can also instantly measure not only the road surface but also sublayer moisture to ensure proper curing.
NIR composition analyzers work well for asphalt producers or contractors who want to analyze the composition of the mix as well and, as recycled materials become a larger percentage of the inputs for asphalt production, these analyses will also play a role in documenting the components of the mix.
Some can instantly verify the correct quantity of additives and binders, as well as recycled materials in the mix such as tire rubber, Reclaimed Asphalt Pavement (RAP), Reclaimed Asphalt Shingles (RAS), slags, glass, and even pig manure.
As the asphalt industry strives to improve the quality of its end product, automated instant moisture testing and composition analysis tools are available to play a role in achieving superior quality and performance, which will ultimately translate into greater profitability.
John Bogart is managing director of Kett US, a manufacturer of a full range of moisture meters and other analyzers.
Not even a bit of snow could dampen the spirts of attendees and exhibitors at the 2024 edition of Canada’s national concrete show, the Canadian Concrete Expo (CCE), which returned to the International Centre in Mississauga, Ont., this past February.
The sixth edition of the event, which attracted more than 7,000 members of the concrete, aggregates and construction industries, was the largest yet, growing by some 20 per cent over last year with an expanded show floor, some new attractions, and the return of a fan favourite, all of which garnered positive responses from visitors, exhibitors, and show organizers alike.
“We were 20 per cent bigger this year, and it looks like our attendance has grown in the same capacity,” said Stuart Galloway, president of the Canadian concrete Expo from the show floor on Day 2. “The feedback we’re getting from attendees and exhibitors is excellent.”
In addition to offering more than 40 conference sessions, as well as live demonstrations and stage presentations, organizers brought back a large equipment demonstration area and introduced the 2024 CCE Pump Rodeo, sponsored by CanCrete.
“Everybody seems to kind of embrace this event, and it shows with the increased attendance that we get and with increasing the size of the show each year,” said Galloway. “We brought back the large equipment demonstration area. We haven’t had it since 2020. And the pump rodeo had about 300 people attend it.”
Pitting a pair of experienced pump operators against each other in a test of
speed and precision, the deft touch of Hugo Lacroix of Pompage Industriel saw him navigate his pump through the obstacle course in the fastest time, earning him the title of Pump Truck Rodeo Champion.
Galloway says that the use of the large spaces at the trade centre is something that the show plans to take advantage of going forward. “They have 42-foot ceilings in a couple areas so they can get their booms out there,” he explained. “We’re going to expand in that area for 2025.”
The main attraction for the exhibitors were the attendees, of course, and the show delivered on that front as well.
“I was happy with the attendance over previous years,” said Dave Watson, concrete specialist for Canada at Sunbelt Rentals. His company, which he says will be back for more in 2025, specializes in the rental of machinery like concrete grinders, scarifiers, shavers and shot blasters. He usually expects to see a bit of a lull on the final day of a show, but that was not the case this year. “We seem to have had some traction.”
“The attendance seems like it’s up, and the show seems much bigger than it was last year,” added Troy Steele, regional sales manager at Brokk Sales Canada. He too expects to see his company back again next year. “For us, it’s a perfect show because it’s focused on what we focus on, concrete.”
With the more than 350 booths on the show floor now including over 50 American-based exhibitors, and visitors coming in from all over the globe, Galloway is focused on continuing the event’s growth curve.
“Our goal is to make this a truly national show, and we keep growing
every year in attendance from outside of Ontario,” he said.
Next year’s dates have been set for February 12 to 13, with the event returning to the International Centre for its seventh edition.
“For next year, we’ll probably be expanding again,” said Galloway, who says his team is aiming to hit, or exceed, the 400-exhibitor plateau. “We’re trying to expand the interactiveness of the show with the large equipment demos, and more demonstration-stage presentations and conference sessions to create more value for those that are attending.”
Watch for more information about the 2025 event to be posted on the show’s website, canadianconcreteexpo.com.
50 th anniversary show attracts almost 60,000 construction professionals.BY ADAM FREILL
Texhibitors also made the trek to showcase the tools, resources and tricks fuelling the future of the trade. Regardless of where they were from, exhibitors appeared to be happy with both the quality and quantity of visitors this year.
“Rather than having to push the concepts of enhanced efficiency, data utilization and collaboration across workflows through software, we saw a lot of energetic, inquisitive contractors at World of Concrete who were already aware of, and actively looking for, these opportunities,” said Greg Norris, marketing communications director at B2W Software. “Traffic was steady, and we met with more large concrete contractors focused on civil-type work than at past World of Concrete shows. This was a valuable show.”
he 50th anniversary edition of World of Concrete (WOC) did not disappoint. The largest event dedicated to the concrete construction and masonry industries in North America attracted nearly 60,000 registered professionals from all segments of the industry to Las Vegas for three days of exhibitions and four days of education.
The event, which saw a 23 per cent increase in traffic from its 2023 edition, presented products and services from more than 1,400 companies, along with a record-high 185 education sessions, as it covered more than 700,000 square feet of indoor and outdoor space. Large crowds kept the exhibit halls bustling and training sessions at capacity.
Along with well-known brand names like Caterpillar, Hilti, Husqvarna, John Deere, Makita and Stihl, the event welcomed 325 new, first-time exhibitors, and more than 450 international
In addition to the seasoned and experienced veterans of the industry, event organizers say that new audiences and the incoming next generation of concrete professionals continue to be a focus for increasing visibility in the sector.
“Every year, World of Concrete serves as the cornerstone where concrete and masonry professionals exchange knowledge and hone skills that propel businesses forward,” said Jackie James, vice-president of the show. “We emphasize creating real-world scenarios, hands-on situations to try and test products and share expertise, which is what makes WOC so unique and our community so special. We look forward to continuing to share the latest and greatest in concrete and masonry for another 50 years to come.”
In honour of its 50th anniversary, World of Concrete donated 50 trees to the Las Vegas Tree Initiative. The ongoing program aims to lower the urban heat island effect that currently makes Las Vegas the fastest-warming city in the United States.
World of Concrete will return to the Las Vegas Convention Center again in January, with the trade show running from January 21 to 23, and the education program starting one day earlier. Visit www.worldofconcrete.com for more information on the upcoming exposition.
The 5700-D curb and gutter machine from Power Curbers is a slipform unit designed for such applications as curbing, sidewalks, barrier, ditches, paving, and tunnels. The compact-sized machine can be used with the SlipSmart Control System to interface with 3D, stringless systems. It is equipped with auto-calibration for the radius steer sensor, a vibrator master scaling knob, and a single switch that raises or lowers all crawler posts simultaneously. A canopy with an overhead lamp is also available, in addition to Bimini and umbrella choices.
Gomaco’s Xtreme GT-3600 is available as a hybrid machine powered by a 74-hp engine, a 48-volt generator/motor and between four and six 7-kWh capacity lithium-ion batteries, which provide supplemental power when needed. Features include rotary-sensored slew drives on each of its three tracks, independent hydraulic control to each track, and the ability to slipform a 24-inch radius. The hybrid model is the same size as the non-hybrid version, and is available with Gomaco Remote Diagnostics.
Wirtgen’s SP 15/SP 15i is engineered for paving large poured-inplace concrete profiles at heights of up to 1.3 m or widths of up to 1.8 m. The machine can produce a wide variety of different profile geometries, including curbs and gutters, among others. Changing moulds or switching them from one side of the paver to the other can be accomplished quickly and easily right on site. The company’s AutoPilot 2.0 can be used to assist with the automated paving of offset and inset concrete profiles, such as curbs for traffic islands.
Husqvarna Soff-Cut® is an ideal system for Ultra Early Entry™ sawing of contraction joints one to two hours after pouring a concrete slab. The system is designed to minimize the risk of random cracks - one of the most costly and aggravating problems for contractors. Appreciate high production rates, the ability to pour and cut concrete on the same day, and the tidy end result achieved by only cutting shallow depths. To learn more visit our website.
www.husqvarnaconstruction.com
There are a variety of current methods for treating and healing narrow cracks.BY JENNIFER MIZER
Today’s concrete technology provides several ways to limit the size of cracks, and to prevent them.
Despite available preventative measures, such as a sound subgrade, designs for low-shrinkage concrete that incorporate shrinkage-reducing or shrinkage-compensating admixtures, using concrete with lower water-to-cementitious ratios, adding macro or microfibres, proper curing, using evaporation retarders, and performing joint cutting operations as soon as possible, concrete can still maintain its tendency to crack.
Narrow cracks in concrete slabs, typically in the 0.01 to 0.06-inch width range, are especially troubling when they occur on bridge and parking decks, elevated floor slabs and similar high-use horizontal slab surfaces. Cracking can allow for the penetration of water, sulfates, chlorides and other harmful agents, accelerating surface spalling and the corrosion of steel reinforcement.
This cycle of deterioration can shorten the life of a concrete deck, requiring expensive repairs or full replacement of in the future. There are several common methods for treating cracks, however.
One way to treat narrow cracks in concrete is to use film-forming acrylic waterproofing coatings. Many of these coatings are quite flexible and have crack bridging properties.
Traffic deck coatings based on epoxy or urethane polymers are commonly installed on bridge decks, parking decks, factory floors and loading docks. Many of these systems incorporate an aggregate broadcast to provide skid resistance and have the added benefit of waterproofing the concrete.
Since protective coatings are applied to the concrete surface, exposure to weather, abrasion or other damage will eventually lead to the deterioration of these materials. As such, many acrylic coatings, for example, are primarily used on vertical surfaces and horizontal decks for decorative purposes or exposure to lighter pedestrian traffic.
Penetrating water repellent sealers containing silane, siloxane or a silane/siloxane blend penetrate the crack and coat its sides to provide the substrate with a water-repellent barrier, but do not fill the cracks entirely or fully seal the concrete surface.
Penetrating silane or siloxane sealers soak into the surface of the concrete where they chemically react to form a hydrophobic barrier within the pores that causes water and other liquids to bead off the surface, reducing the absorption of water.
These sealers will not change the appearance or colour of the concrete, and do not leave behind a visible surface film. When properly applied, silane and siloxane sealers can last for up to 10 years before resealing.
Another treatment for narrow cracks is to use a thin, chemically curing polymeric resin to fill the cracks. Penetrating by gravity alone, the resin fills the crack and seals out water, salts and other damaging elements. This method of crack repair is intended to seal cracks that are “static” or “non-moving,” such as shrinkage and settlement cracks that have stabilized.
This method can also be used to protect the entire concrete deck by applying a flood coat of the polymeric resin on the entire surface. This essentially seals the deck while sealing or “healing” the cracks. The term healer/sealer is often used to describe the polymeric resin applied in this process.
Although concrete healer/sealers have been around for decades, their ability to fully fill, seal and heal cracks often yielded mixed results. When healer/sealers were first developed, it was easy to look at the viscosity of the resin as the reason for these mixed outcomes. If the viscosity was too low, it could flow into the crack and out the bottom of the slab. If the viscosity was too high, it didn’t penetrate far enough to fill the crack.
When a new generation of healer/sealers were developed, other factors were considered, including the method used to achieve the desired viscosity, modulus of elasticity and surface tension.
Through laboratory testing and field trials, the best results were found when the crack healer/sealer material was found to be low viscosity. In formulating chemically curing polymeric sealers and coatings, the simplest way to lower the viscosity of a product is to increase solvent content, however increased solvent typically means a higher
volatile organic compound (VOC) content, increased hazards in mixing and handling, and an impact on physical properties.
Formulators can adjust the molecular weight and molecular weight distribution of the healer/sealer, which can have a profound effect on the viscosity of the finished product. Generally, the higher the molecular weight, the higher the viscosity. This is often not desirable for a crack healer/ sealer. Higher molecular weight also results in higher strength and durability of the final product though.
To solve this conundrum, the molecular weight distribution of the healer/sealer is adjusted, resulting in lower viscosity, without affecting the strength properties of the material.
A wide distribution of different sized polymer chains results in a healer/sealer with higher viscosity and therefore less ability to flow and penetrate cracks. Newer generation healer/sealers are formulated with a narrower distribution of polymer sizes, which produces a more flowable material.
Modulus of elasticity is a measure of stiffness, with higher-modulus materials exhibiting less deformation under load compared to low-modulus materials. A low-modulus crack healer/sealer can provide better resistance to mechanical or thermal movement of the concrete deck.
Since many treated cracks found on bridge and parking decks are often subjected to this type of movement, a low modulus of elasticity product is optimal in many instances, as it will withstand a certain amount of movement and help prevent re-cracking. In addition, low surface tension is an important factor in allowing the healer/ sealer to penetrate the crack. Healer/sealer products are formulated using specially designed agents to reduce surface tension, which allows the resin to penetrate the concrete cracks more readily.
A liquid with high surface tension contains molecules that are more attracted to each other than they are to the surface upon which they are applied. Also, the molecules at the surface of a high surface tension liquid have no molecules attracting them
from above, so these surface molecules can only be attracted down and in. This attraction to itself coupled with strong surface tension causes the liquid to bead up instead of spreading out on the surface.
Concrete healer/sealer formulators incorporate surface tension reducing additives called surfactants to ensure the healer/ sealer spreads out onto the concrete surface instead of beading up.
Application of a healer/sealer begins with proper surface preparation. The concrete surface must be structurally sound and free of grease, oil, curing compounds, soil, dust and other contaminants. New concrete and masonry must be at least 28 days old. Surface laitance must be removed. Concrete surfaces must be roughened and made absorptive, preferably by mechanical means, and thoroughly cleaned of dust and debris.
If the surface was prepared by chemical means (acid etching), a water/baking soda or water/ammonia mixture, followed by a clean water rinse, must be used for cleaning to neutralize the substrate. The Concrete Surface Profile (CSP) should be CSP 2-5 in accordance with Guideline 310.2R from the International Concrete Repair Institute.
Following surface preparation, the strength of the surface can be tested if quantitative results are required by project
specifications. A tensile pull-off tester may be used in accordance with ASTM C1583, with a required tensile pull-off strength commonly specified to be at least 250 psi.
The application of the materials includes pretreating large cracks, if necessary, flood coating with the low-viscosity, low-modulus epoxy, distributing the epoxy onto the substrate, removing excess epoxy, broadcasting fine sand onto the wet epoxy, removing the excess sand when the resin has cured, and opening the deck to traffic.
After properly mixing the material, cracks may be pre-treated by gravity feeding the healer/sealer by hand directly on top of the crack or by ponding the material over cracks, permitting it to sink in and seal the crack onto the properly prepared surface in a wave form, and spread uniformly with a squeegee or a short nap roller.
If necessary, allow the epoxy to penetrate the surface, re-applying to cracks and porous areas as needed. Excess epoxy can be removed with a squeegee before it becomes tacky. Broadcast clean, oven-dried silica sand (recommended 16/30 or 20/40 mesh) into the wet epoxy to provide a skid-resistant surface, or where subsequent toppings or coatings will be applied. Before opening to traffic, and when the healer/sealer has cured, remove any loose aggregate.
Despite current concrete technology’s aim to avoid cracks in concrete, and to limit the size of any such cracks, they still happen. Cracking in concrete slabs is especially troubling when it occurs in bridges and parking decks, elevated floor slabs and similar high-use horizontal slab surfaces.
There are methods for treating and healing narrow cracks, however including film-forming coatings, penetrating water repellent sealers, and chemically cured polymeric resin.
Jennifer Mizer is the director of marketing services at Euclid Chemical, a manufacturer of specialty concrete and masonry construction solutions that includes admixtures, fibre reinforcement, concrete repair products, flooring materials and decorative concrete systems.
Second annual Concrete Pavement Seminar was an opportunity to share practical advice about emerging materials and best practices.BY ADAM FREILL
More than 60 industry professionals hit Mississauga, Ont., in February for the second annual Concrete Pavement Seminar, presented by Concrete Ontario and the Cement Association of Canada. The day-long event featured several sessions, ranging from updates on key projects and advances in concrete mixes, to technical applications of concrete as a paving medium.
In his discussion about the next generation of pavement, the Cement Association of Canada’s Tim Smith discussed how an examination of project timelines can impact both the strength and the carbon footprint of the concrete being poured. He said, for example, where the project can provide for a longer curing time, it becomes possible to select a concrete mix that will deliver the prescribed strength, while reducing the carbon impact.
“If we start thinking about the carbon footprint of the material, then we can possibly reduce the amount of cementitious material. We can actually go with a later date on the strength, so that we can minimize that cement content and minimize the carbon footprint of the pavement,” he explained. “Something that we need to start thinking about is when is the project going to be open to traffic… if you don’t need that for a while, then maybe we should start thinking, from a global warming potential, of the 56-day or the 92-day strengths instead of 28 days.”
Also leading a technical discussion during the event was Mark Popik of Thurber Engineering Ltd. He shared insights into the use of lightweight cellular concrete applications, outlining a few projects where the material has made it possible to solve some unique problems, such as those that can be created by trying to build a road foundation on soft organic substrates.
Brian Killingsworth of the National Ready Mixed Concrete Association kicked off the afternoon sessions with a look at his organization’s Pave Ahead program.
“We try to partner with other technical groups with representation from contractors, users, cement suppliers, stone suppliers; we all try to work together to be able to promote a product that we fully believe in,” he explained. His organization has created
a website containing information that the industry can access without fees, to help with their concrete projects.
“Where we want to help is to be able to step in and say here’s some of the best practices; here’s how you can improve your specifications; here’s some of the tools that you may need, and provide those tools,” he said. “We do that through our design assistance program.”
In addition to outlining some of his organization’s activities, Peter Taylor of the National Concrete Pavement Technology Center talked about water and cement ratios, and provided advice about how admixtures are changing the rules of thumb as the constituents of concrete mixes are changing.
“Do your homework. Do your trial batches,” he advised. “You will get the performance you need, but don’t just flip one [mix] out and put another one in and hope it’s all going to go well.”
After a quick look at some research projects conducted over the past few years at the University of Waterloo’s Centre for Pavement and Transportation Technology, the day wrapped up with a networking social.
The dates have been set for next year’s event. The third annual Concrete Pavement Seminar will take place on February 19, 2025. Keep an eye on the Concrete Ontario website for more details.
Hardware and software advances are behind massive improvements, and significant expansion, in drone surveying in construction.
echnologies often really take off when simultaneous developments combine. In construction, developments in drone hardware and BIM/VDC modelling software are fuelling significant expansion of construction use cases.
“We’ve seen huge advances on both the drone side and the VDC/ BIM modelling side,” says Amir Jalali Afshar, integrated construction technology specialist at PCL Construction, and a Transport Canada certified drone pilot. “So, if we can combine those two forces, we can get a lot more value out of drone data.”
Advances in cameras and sensors, the drones that carry them, and the software that manages the data are all contributing to this synergy. The latest drones are faster, more versatile and can carry bigger payloads.
“One thing that’s improved is that some of these drones can carry two payloads,” says Brad North, manager of integrated construction technology at PCL (Saskatoon). “So, you could have a thermal camera plus a zoom lens on some of these drones. You can also have interchangeable lenses, so you could get, for example, close-ups of a bridge without losing quality from digital zoom.”
Drones have become a lot safer as well, allowing them to gather data at close range. “We’re working with drones that have what’s called omni-directional obstacle avoidance,” says North. “It has sensors around the entire drone to make sure it’s not going to hit anything. So, we can use them for scanning a building or a bridge because they’re so much safer.”
Emergency parachutes are another drone feature that’s becoming more common, North notes. Drones so equipped can fly safely and legally over areas where people are present.
More drones are also able to carry LiDAR scanners, which improves ground surveys.
“If you fly a greenfield site in Saskatchewan, there might be vegetation or tall grass on the surface,” says North. “With a regular camera, any vegetation is going to give you an inaccurate image of the ground, so you’d have to clean that up in the model. But with LiDAR, you actually penetrate that and get an accurate image of the surface. So again, additional and different payloads on drones are helping us strive for increased accuracy.”
One of the keys to better ground surveys is Real-Time Kinematic (RTK) technology, which adjusts the data from drones by using base station coordinates to create surveys that are far more accurate than conventional GPS. “With coverage from only a few checkpoints on the ground,” says Afshar, “RTK information allows us to bring that drone data to exactly where our model is, with an accuracy of less than two inches.”
Longer battery life and shutter technology are also impacting the power and efficiency of drones. Not having to change batteries mid-flight reduces downtime, and faster shutters in the cameras enable surveys of large areas to be done in a fraction of the time.
“A mission that used to take us 25 minutes with a couple of battery changes now takes four minutes,” says North. “If you had to map 100 acres with a previous drone, that might have taken two to three hours. Now, that mission would take literally 20 minutes.”
Use cases for drone surveys are expanding throughout the construction cycle.
“I’d say that in the past few years, we’ve seen a tenfold increase in demand,” says Neil Chauhan, director of VDC services at EllisDon. “In pre-construction, it might be for mapping out an area for pursuit or estimating. During construction itself, it could be for in-progress tracking of the project, stockpile analysis, or just to provide data-rich and accurate 3D models in general. Then post construction, it could be used to showcase a project.”
Chauhan believes improvements in technology will lead to further growth. “I would say the software for processing this data that’s captured in the field by a drone is continuing to accelerate in its development,” he says. “So, we’re going to see a lot of new and exciting use cases for drone technologies.”
Mandates for virtual models on major projects will further accelerate the trend.
“We’re pushing for mandates in terms of BIM and VDC adoption, and I see drone surveys going along with that,” says Chauhan.
Jacob Stoller is principal of StollerStrategies. Send comments to editor@on-sitemag.com.
The path forward requires the fostering of diverse, equitable, and inclusive workplaces. Discover the strategic advantages of recruiting and retaining talent from traditionally underrepresented groups, including Indigenous communities and newcomers to Canada.
Industry leaders in the mechanical, electrical, plumbing, and general contracting sectors will lead and participate in crucial discussions, sharing insights on building a workforce that reflects the rich tapestry of Canada’s talent. Explore how embracing inclusivity propels innovation, fosters growth, and positions your organization as an employer of choice, creating a workplace where everyone thrives.
KEYNOTE SPEAKER
Rubiena Duarte
VP of Diversity and Inclusion at Procore NAVIGATING UNCONSCIOUS BIAS
PANEL 1:
BUILDING & MAINTAINING YOUR CULTURE OF INCLUSION
From Intent to Impact: Dive into proven steps to establish an inclusive workplace culture, with practical insights on enforcement for transformative change.
Hosted by Mary Van Buren President
PANEL 2:
PUTTING YOUR CULTURE OF RECRUITMENT INTO PRACTICE
Elevate Your Team: Explore the undeniable business benefits of recruiting from non-traditional talent pools for enhanced innovation, resilience, and sustainable success.
Hosted by Martin Luymes VP Government and Stakeholder Relations
PANEL 3:
LEVERAGING YOUR INCLUSIVE WORKPLACE AND BECOMING AN EMPLOYER OF CHOICE
Inclusive Excellence: Learn the strategic secrets to transform your workplace into a sought-after employer of choice, attracting top talent with a culture of innovation, belonging, and sustained success.
Hosted by Michelle Branigan CEO
roject owners and construction contractors looking to see shovels hit ground need to work closely together to find ways to make their projects stand out, for the right reasons, to those who supply financial capital.
The interest rate environment is at its highest point in years, and this is seeing some projects being cancelled or delayed. A meaningful way project stakeholders can improve project finance terms is through the use of sound risk management strategies and insurance solutions, since these can help satisfy any growing concerns of their debt partners.
Lenders base their pricing on the perceived risk of the endeavour into which they are deploying capital. In the days of low interest rates, the floor cost for debt was so low that project stakeholders didn’t have to expend too much effort communicating their risk management strategies. The risk premium charged
Compliance, Regulatory, Licencing and Permitting
Cost or Schedule Overrun
Construction Contractor Failure
Subcontractor/Supply Chain
Technology (Using New Technology)
Legal review
Project management technology
Natural Catastrophe (Flood, Earthquake, etc.)
Water Damage due to Construction (Roof and/or Mechanical Failure)
Labour Supply and Productivity
didn’t have as much impact on the project’s financial model. With today’s much higher floor cost for debt, project stakeholders should be digging deeper into their project risk management narrative to not only curb growing financing costs, but, in some cases, to make their project bankable/feasible.
Table 1 illustrates the kind of framework project stakeholders can use to improve their project risk management narrative, to bat down any risk concerns their debt partners may have.
This table is only a sample chart, and is by no means an exhaustive list of construction phase risks and associated risk controls and risk finance solutions. In addition to construction phase risks, there are several operations phase risks that lenders will need to assess for adequacy of risk controls and risk finance solutions, with respect to the project being built.
Key areas of focus for manufacturing facilities, for example,
None
Owner procures permitting prior to bid, where possible
Request for qualification
Evidence of financial, business and safety review of contractor
References
Project technologies
Request for qualification
Evidence of financial, business and safety review of contractor
Listing of subcontractors and suppliers
Evidence of financial, business, and safety review of sub/supplier
Evidence of technology success
Third party engineer verification
Reality capture
Mock-ups of key systems
Quality control procedures
Nat Cat zone assessment (latest technology to capture flood, quake data)
IoT technology
Portable flood barrier technologies
Prequalification of subcontractors (Subcontractor prequal technology)
IoT Technologies (water detection, environmental)
Reality capture
Quality control procedures
Mock-up to check for design and workmanship
Prequalification of subcontractors
Labour supply monitoring technology
Reality capture technology
Safety training, inspections and procedure adherence
Quality control procedures
Liquidated damages
Letters of credit
Surety bond
Liquid surety bond
Parental guarantee
Letter of credit
Surety bond
Liquid surety bond
Parental guarantee
Letter of credit
Surety bond
Liquid surety bond
Subcontractor default insurance
Technology performance insurance
Boiler and machinery insurance
Property insurance - pay attention to business interruption and natural catastrophe (nat cat) deductibles and sub-limits
Professional liability (nat cat resiliency design)
Property insurance (pay attention to business interruption and water coverage limitations)
Professional liability
Liability insurance (contractor)
Surety
Subcontractor default insurance
Surety bond
Subcontractor default insurance
Workers compensation insurance
may include: i) supply of inputs; ii) supply chain disruptions; iii) technology and equipment failure; iv) demand for product manufactured; v) quality control and product liability; vi) energy costs and availability; vii) political and economic instability; viii) natural catastrophe risk; ix) environmental risks; and x) safety and health of labour; to name a few. For each, a similar assessment of risk controls and risk finance solutions should be done.
Ultimately a project risk management assessment framework, if properly executed, should be effective at showing sources of capital that you have consider all potential threats and are using the latest and most effective risk control and risk finance solutions to eliminate or minimize the risk of non-payment – your capital partners do expect to see a return on their investment, after all.
In a time of tight credit, driven by higher interest rates, it becomes imperative to have a very strong risk management plan for all phases of your project’s (or asset’s) life.
David Bowcott is the managing director, construction, at NFP Corp. Please send comments to editor@on-sitemag.com.
This past November, the Supreme Court of Canada released its decision in R. v. Greater Sudbury (City), a case about whether the owner of a construction project should be considered an employer under the Occupational Health and Safety Act.
A split decision by the Supreme Court means that a prior decision of the Ontario Court of Appeal, which views the project owner as an employer sharing liability under the OHSA for health and safety on the project, will remain in place.
This has been polarizing across the construction industry in Canada, with many criticizing the decision for being divorced from reality, and others applauding the decision for championing the “belts and braces” approach to workplace safety.
The case stems from the City of Greater Sudbury contracting with Interpaving Limited to act as constructor to repair a watermain. The city also employed inspectors to attend the project site, for quality assurance purposes.
During the project, a pedestrian was tragically struck and killed while crossing an intersection. A Ministry of Labour investigation determined that the project lacked safety measures, such as a fence and signaller, contrary to the OHSA regulations. The ministry charged the city, among others, with breaching its purported obligations as “constructor” and “employer” under the OHSA.
At the lower court levels, the city had successfully argued that it was neither the constructor nor employer. The ministry appealed to the Ontario Court of Appeal, which found the city to be an employer.
The city’s appeal to the Supreme Court arrived at a split decision, resulting in the Court of Appeal decision remaining in place and not providing the clarity project owners were seeking about their health and safety obligations.
The four Supreme Court judges who supported the Court of Appeal decision found that nothing in the OHSA required the ministry to establish that the city had control over the workers or workplace to prove the city breached its OHSA obligations as employer. They found that the city met the definition of employer, having employed quality control inspectors and by hiring Interpaving as constructor.
The other four judges held that it would be absurd to interpret the OHSA in a manner that could arguably obligate every employer at a construction project to ensure compliance with all measures contained in the OHSA regulations.
Notwithstanding the split decision, the majority of the Supreme Court judges noted that the city could avoid conviction if it could show it exercised due diligence under the OHSA, however, the issue of due diligence was not decided by that court, so the case has been sent back to the provincial court for determination.
For now, the viability of the due diligence defence in circumstances where an owner retains a constructor remains uncertain.
Also uncertain is whether the Supreme Court will grant a city motion requestion a re-hearing of the appeal.
In December 2023, Sudbury City Council passed a motion requesting that the province amend the Occupational Health and Safety Act to clarify the definition of employer under the act. It remains to be seen if the Ontario legislature will step in and amend the OHSA to address the potential liability that may arise for project owners as a result of this decision.
For the time being, the practical consequence is that project owners may be found to be an employer under the OHSA by reason of engaging a contractor for a construction project, even though the contractor has the obligations of constructor. This may impose additional risks and create unintended consequences for owners and project developers.
It also raises questions about the scope of owners’ responsibility under the OHSA, the role of the constructor, and the responsibility of contractors.
Owners may want to consider evaluating their current procurement procedures and practices, and include a review of their contractor’s health and safety record, health and safety plan, capacity to ensure compliance with the OHSA, and whether they engage their own health and safety experts to provide reviews and guidance.
It would also be prudent for owners, and contractors taking on projects for owners, to obtain guidance with respect to their own ongoing health and safety obligations and procurement strategies as well.
Richard Yehia, partner, and Mark Borgo, senior associate, are construction lawyers at Borden Ladner Gervais LLP. This article provides an overview and is not intended to be exhaustive of the subject matter contained therein. Although care has been taken to ensure accuracy, this article should not be relied upon as legal advice.
Six all-new models of Manitou skid steers and compact track loaders deliver greater breakout forces, improved operator comfort and control, and numerous exclusive designs such as a new sloped roof and contoured lift arms - plus Manitou exclusives such as the IdealAccess fold-up door and the IdealTrax automatic track tensioning system. Learn more at Manitou.com
See our full range of solutions for your business at Manitou.com.