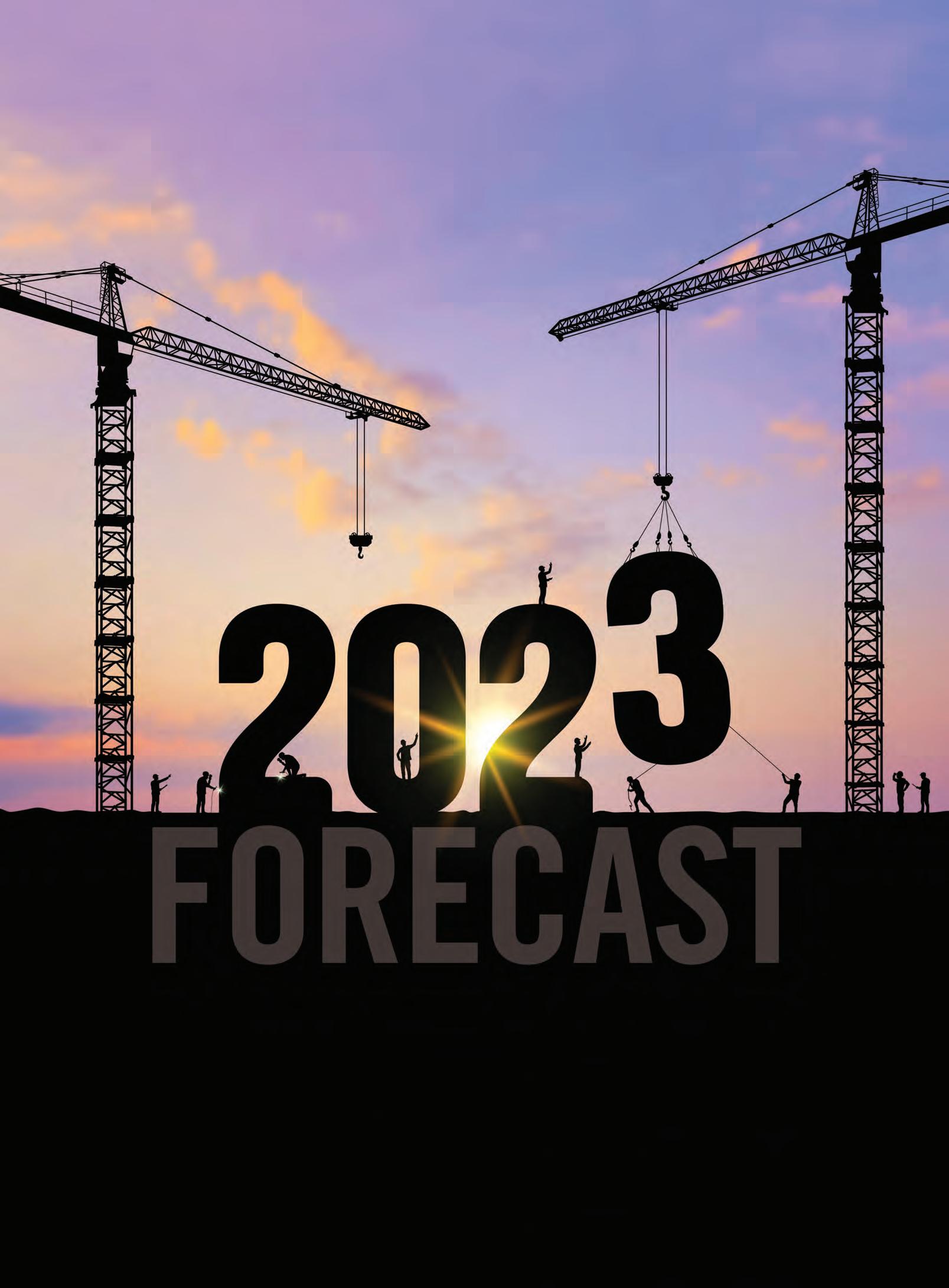
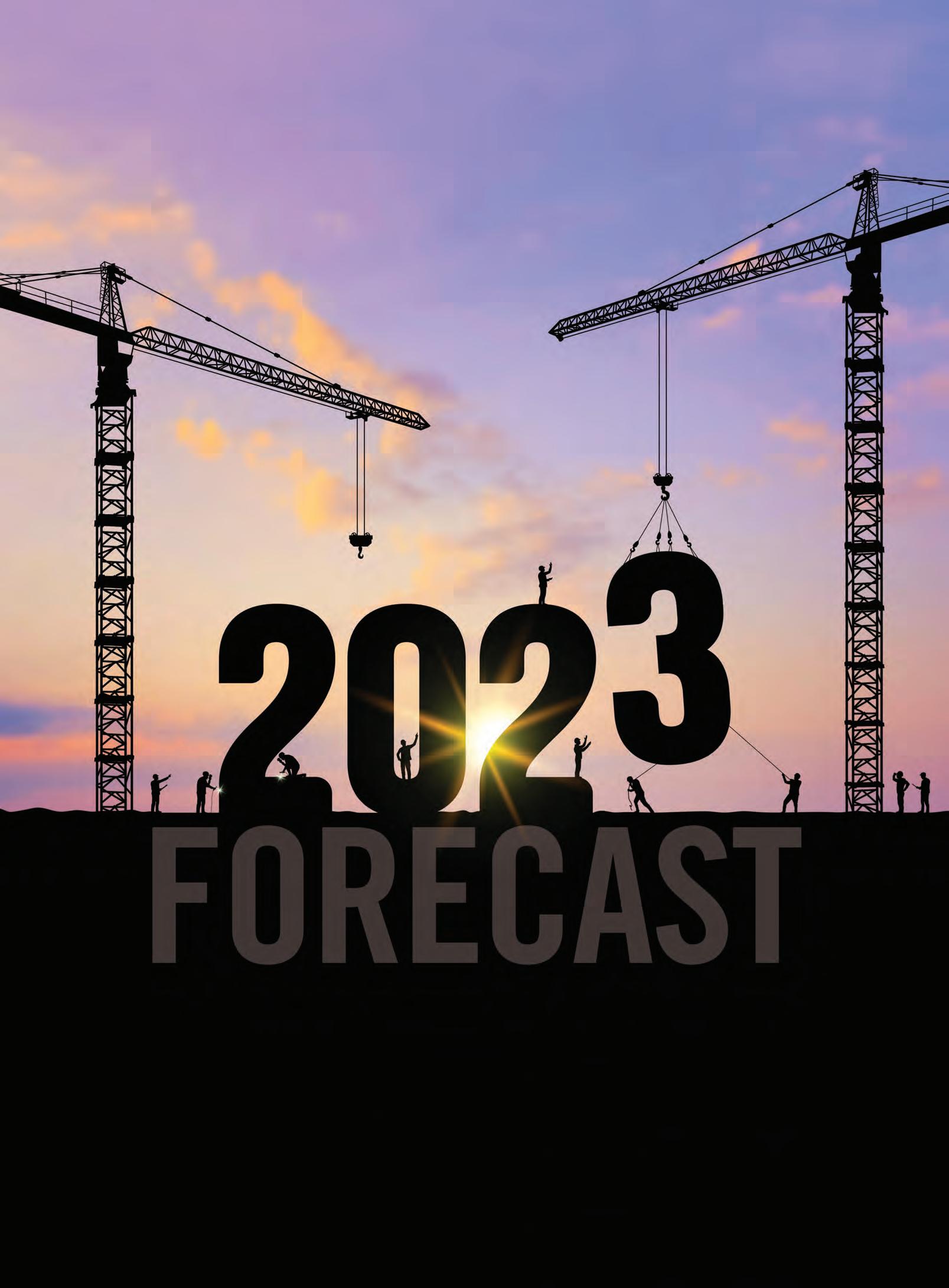
MTWO Construction Cloud, The Next Generation of Construction Software

MTWO is a construction cloud solution that connects all stakeholders, processes, and data in one platform enabling better collaboration,
driven decision making. With applications that address the plan, build, and operate phases of construction, MTWO is the next generation of construction project lifecycle management software.
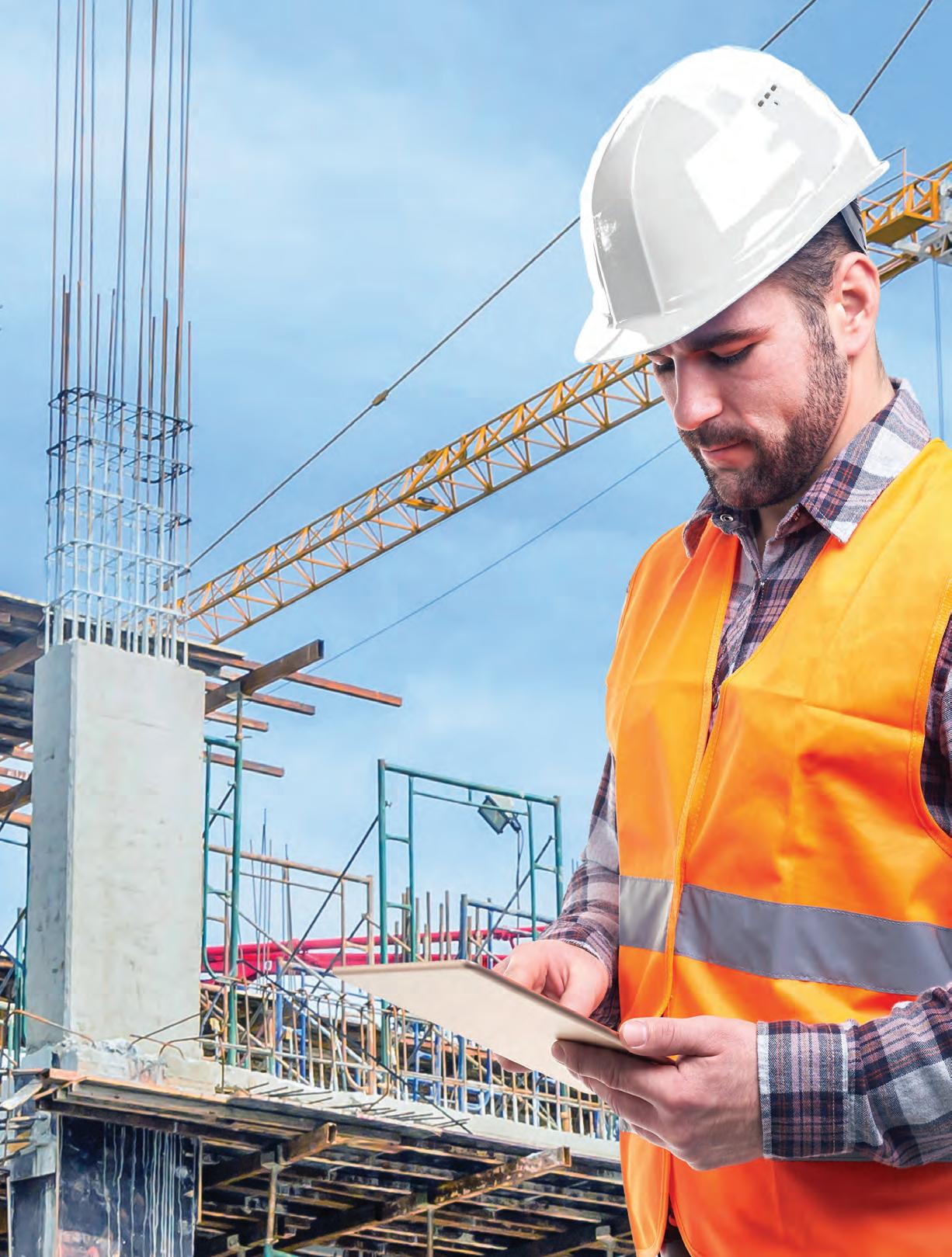

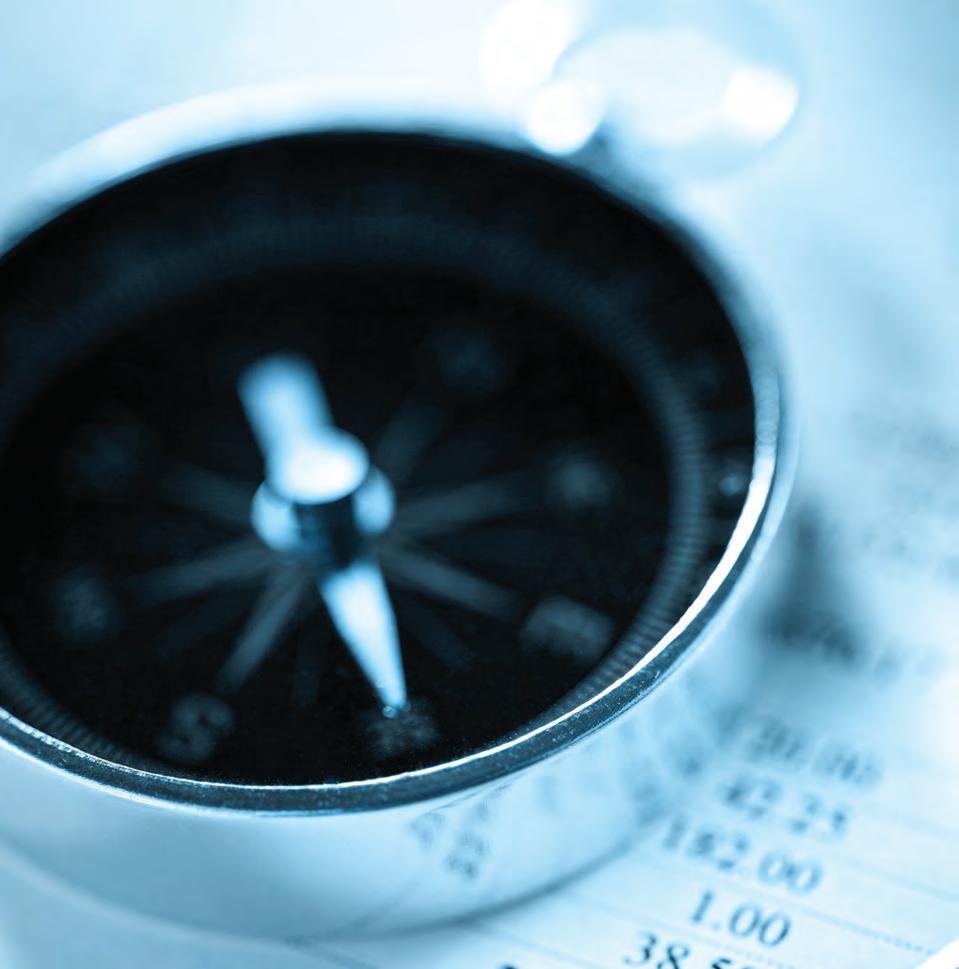
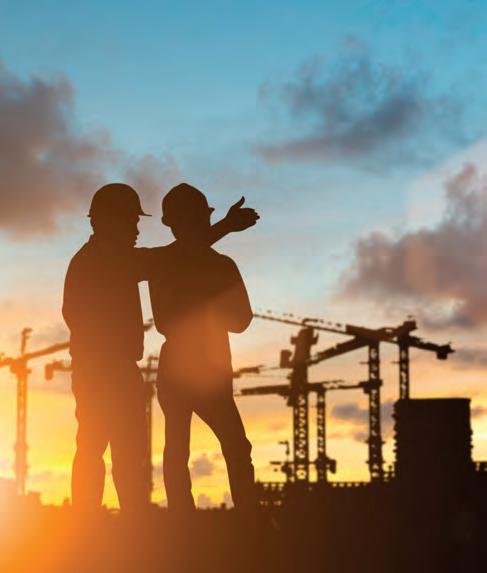
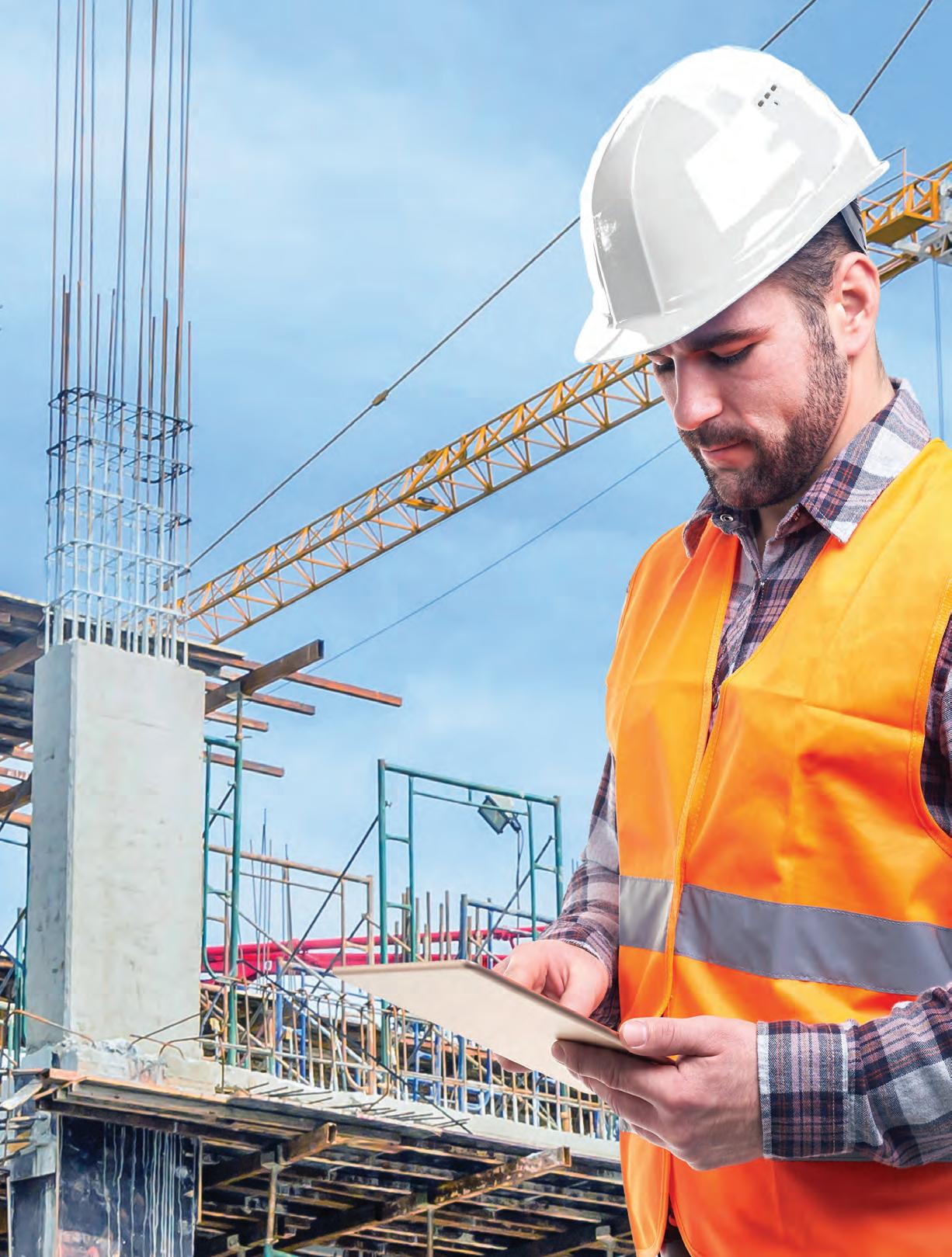
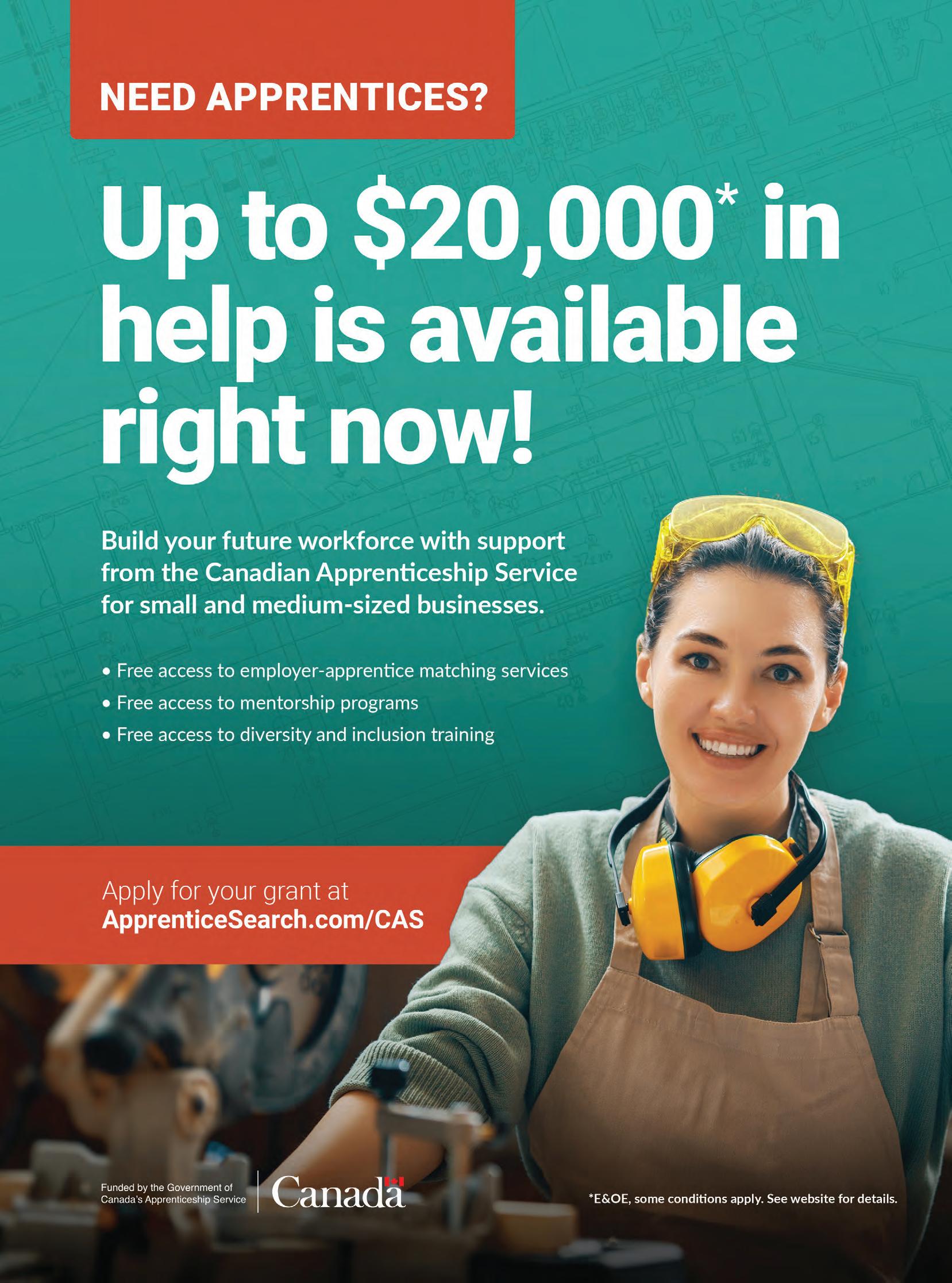
A bounce rather than a break
In the year since I joined On-Site, it has been almost impossible to go more than a day or two without hearing something about labour shortages, material cost increases (and shortages), inflation and lending rates, so it should come as no surprise that those topics take the lead in our 2023 forecast that starts over on page 11. And while I would never advise anyone to not worry about these interwoven individual topics, I’m also very hesitant to suggest that the sky is falling – sorry Chicken Little.
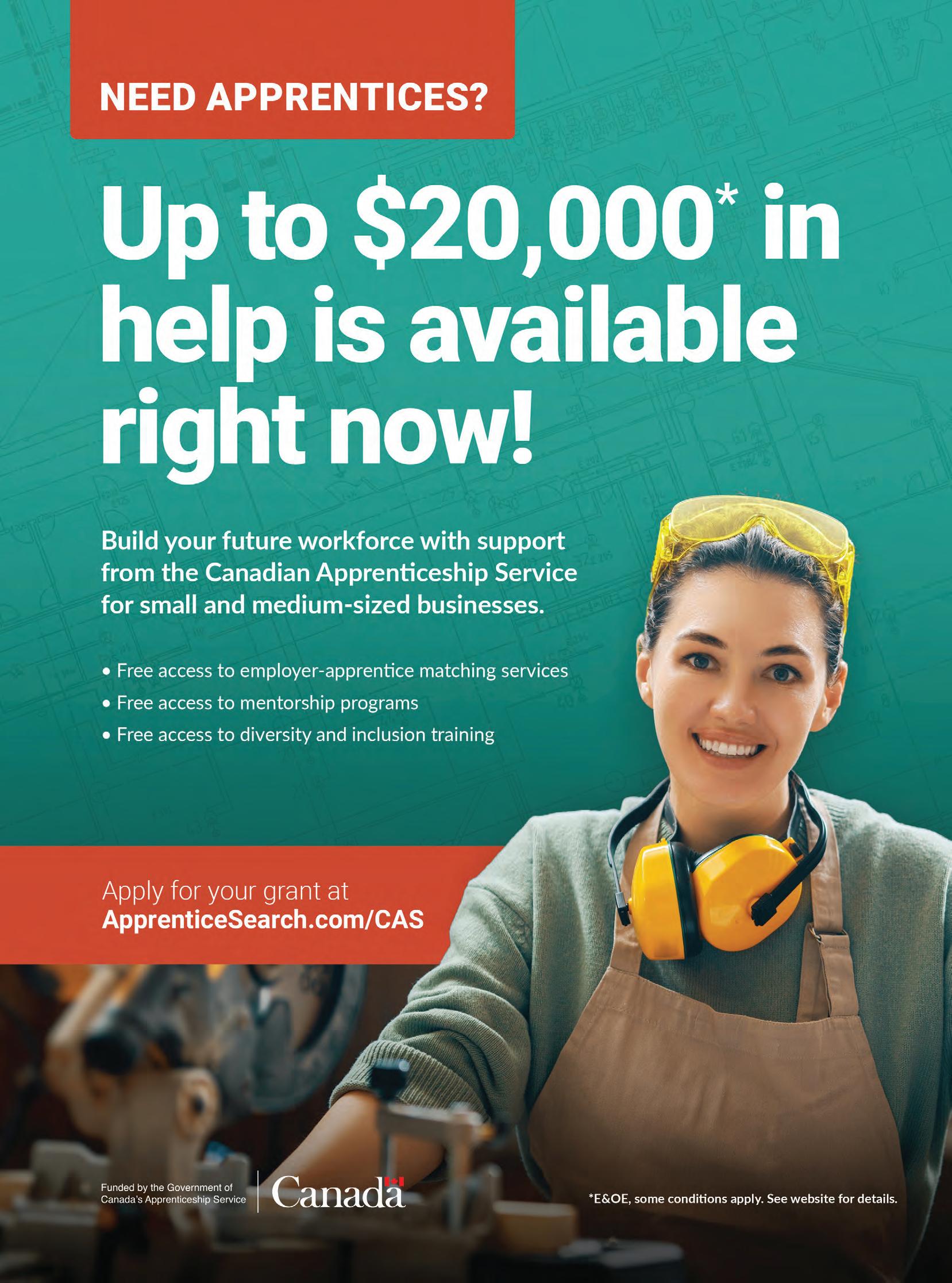
Far too many years ago to count, I sat in on a very interesting lecture that explained the more we examine a topic, the more complex it becomes. It was a lesson that stuck, and has shaped my thinking, especially when analyzing situations and looking for paths forward. I think the lecture is why I am not as worried about the non-residential construction sector, and even the multi-residential high-rise sector, even when faced with dire headlines about prices and lending rates.
Yes, as I write this, inflation is sitting at more than double the 3.14 per cent average rate experienced between 1915 and 2022. Yes, there are still price fluctuations, supply chain issues, and nobody can seem to find enough skilled workers. And yes, project plans are being impacted with some projects cancelled and others delayed or reworked. But that’s not the full story.
While attending the recent Groundbreak event put on by Procore, I heard several comments from companies who were beyond capacity and were thus hesitant to bid on new work. With labour pools stretched thin, delays in having to bid on projects may actually be a blessing in disguise for these contractors. They will now have a chance to work through
some of what’s already in their healthy backlogs without the risk of losing out on those future projects that they either would not have bid on, or would have stretched their resources to the point of possibly breaking.
With fewer concurrent projects, don’t be surprised if you see some catch-up happening in the supply chain as well. With any luck, we might even see some easing of prices for products that are available.
Of course, don’t expect a few delayed projects to derail the bulk of work, or to reduce the amount of spend in the sector. Between the ongoing projects that will continue through 2023, projects that are funded and committed to begin over the next 12 months, and others jobs that will hit the RFQ stage next year, machines will be moving, sites will be active, and more work will be coming. Not only that, but with inflation impacting prices, many companies will likely find themselves posting higher average per-project revenues this year over last year or the year before.
And the RFQ tap won’t get turned completely off any time soon. Between our country’s massive infrastructure deficit –anywhere from $110 billion to $570 billion, depending on whose numbers you choose to believe – and immigration targets that have been recently increased by an additional 25 per cent, we cannot escape the ongoing need for new and renewed buildings and structures. Even in the face of a possible recession, this sector is well positioned for a soft bounce rather than a rough ride.
Until next time, stay safe and do good work.
Adam Freill / Editor afreill@annexbusinessmedia.com
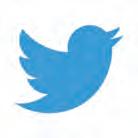
CONTRIBUTORS
MEET OUR CONTRIBUTORS FOR THIS ISSUE
MARY VAN BUREN / President, Canadian Construction Association
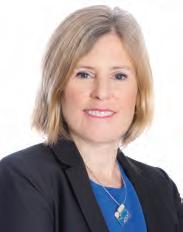
On construction trends to watch over the next 12 months: “New appreciation for skilled trades combined with an infusion of new Canadians will help propel diversity and inclusivity forward, with greater representation from women, new Canadians, Indigenous and other equity-seeking groups.”
JACOB STOLLER / Principal, StollerStrategies
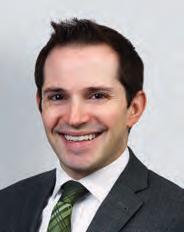
On the use of heavy equipment simulators for training: “As remote control sees wider adoption in construction, a day may come when a simulator-like environment becomes the predominant method for controlling live machinery.”
VOLUME 67, NO.7/December 2022 www.on-sitemag.com
READER SERVICE
Print and digital subscription inquiries or changes, please contact Angelita Potal Email: apotal@annexbusinessmedia.com Tel: (416) 510-5113 Fax: (416) 510-6875 Mail: 111 Gordon Baker Road, Suite 400, Toronto, ON M2H 3R1
PUBLISHER | Peter Leonard (416) 510-6847 pLeonard@on-sitemag.com
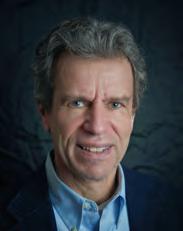
EDITOR | Adam Freill (416) 510-6821 afreill@annexbusinessmedia.com
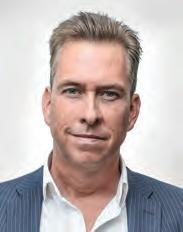
MEDIA DESIGNER | Lisa Zambri lzambri@annexbusinessmedia.com
ASSOCIATE PUBLISHER | David Skene (416) 510-6884 dskene@on-sitemag.com
ACCOUNT COORDINATOR | Kim Rossiter (416) 510-6794 krossiter@on-sitemag.com
AUDIENCE DEVELOPMENT MANAGER | Urszula Grzyb (416) 510-5180 ugrzyb@annexbusinessmedia.com COO | Scott Jamieson sjamieson@annexbusinessmedia.com
Established in 1957, On-Site is published by Annex Business Media 111 Gordon Baker Road, Suite 400, Toronto, ON M2H 3R1 Publications Mail Agreement No. 40065710
DAVID
BOWCOTT/ Managing Director, Construction, at NFP Corp.
On risk reduction and enhanced productivity: “The digital twin is the convergence of all data and technology from all phases of the built environment (design, construction, and operations) delivered through a unified and federated platform, and it can be used to manage risks.”
ERIN CUTTS AND DAVID MAJOR / Borden Ladner Gervais LLP
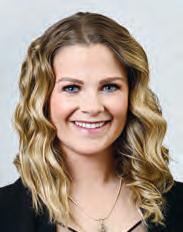
On price escalation clauses for construction: “When drafting supplementary conditions involving material price escalation clauses, parties should also consider whether storage costs may be incurred, and whether the parties are prepared to share costs that allow materials to be purchased at quoted prices at an earlier stage.”
ISSN: 1910-118X (Print) ISSN 2371-8544 (Online)
SUBSCRIPTION RATES Canada $49.50 per year, United States $113.00 per year, Other foreign $136.50, Single Copy Canada $13.50. On-Site is published 7 times per year except for occasional combined, expanded or premium issues, which count as two subscription issues. Occasionally, On-Site will mail information on behalf of industry-related groups whose products and services we believe may be of interest to you. If you prefer not to receive this information, please contact our circulation department in any of the four ways listed above.

Annex Business Media Privacy Officer privacy@annexbusinessmedia.com Tel: 800-668-2374
Content copyright ©2022 by Annex Business Media may not be reprinted without permission.
On-Site receives unsolicited materials (including letters to the editor, press releases, promotional items and images) from time to time. On-Site, its affiliates and assignees may use, reproduce, publish, re-publish, distribute, store and archive such unsolicited submissions in whole or in part in any form or medium whatsoever, without compensation of any sort.
DISCLAIMER This publication is for informational purposes only The content and “expert” advice presented are not intended as a substitute for informed professional engineering advice. You should not act on information contained in this publication without seeking specific advice from qualified engineering professionals.
Thousands of students to benefit from trades scholarship campaign
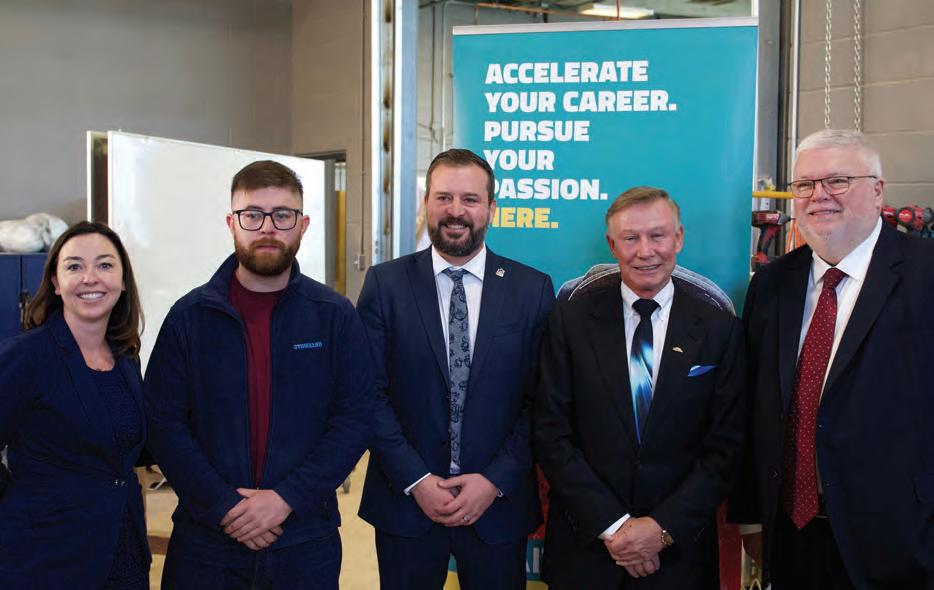
Facing a massive need for skilled tradespeople, an Alberta-based builder has initiated a $15-million campaign to fund trades training at Northern Alberta Institute of Technology (NAIT) and Southern Alberta Institute of Technology (SAIT). Jay Westman, chair and CEO of Jayman BUILT, is spearheading the campaign that will provide scholarships for constructionrelated trades at the two schools.
This fall, Westman challenged industry peers and community leaders to match funds raised to establish the BILD Alberta Scholarships for Construction Careers initiative. Thanks to a $2 million donation from Westman and contributions from other leaders in the building community, that initiative has surpassed its initial $3 million goal, so Westman is upping the ante. With the funds committed now sitting at over $7 million, he recently announced that he will lead a further push aimed at growing the funds to $15 million.
“The shortage of skilled labour is the largest single issue our industry has ever
Left to right: Reva Bond, dean of the SAIT School of Construction; Michael Orr, SAIT carpentry student: Scott Fash, executive director of BILD Alberta; Jay Westman, chair and CEO of Jayman BUILT; and David Ross, SAIT president and CEO.
faced,” stated Westman. “I have chosen to lead by example and lead this investment campaign to make a notable impact in overcoming the financial concerns of students, while also bolstering our industry’s much-needed construction capacity across Alberta. This is an Alberta initiative with an Alberta solution.”
The awards will cover a wide range of construction career-training options, including carpentry, plumbing, sheet metal, electrician, bricklayer, cabinet maker, roofer, drywall, glazier, insulator and painter, for example, and will help workers on a pathway to their journeyperson certifications.
A portion of the funds will also be dedicated to engaging high school students and enhance skilled trades
Fund aims to encourage females to study civil engineering
A $60,000 memorial scholarship fund is being created at the University of Manitoba (UM) in memory of Ruth Eden to support females studying civil engineering. Eden was the first woman hired by the province in 1988 to work as an engineer and was a member of the 30 by 30 Task Force, which works to increase the representation of women within engineering.
She was also the assistant deputy minister of the former Department of Infrastructure’s Technical Services and Opera-
tions division and was widely considered a leader and mentor in the field of civil engineering. The fund is being established by the Manitoba government, with the support of the Eden family.
“Ruth Eden was a dedicated public servant who faithfully served Manitobans for over 30 years. She was an inspiring and keystone leader within the department, and will forever be remembered for her heart, passion and determination,” said Transportation and Infrastructure
development in the province by building awareness of rewarding careers in the skilled trades.
“Careers in skilled trades provide important contributions to our communities and Alberta’s growing economy,” stated David Ross, president and CEO of SAIT. “Through this funding, SAIT students will have access to a scholarship program focused on building equity in the construction trades, and programming to engage with youth will foster an early interest in skilled trades.”
“Supporting student awards not only removes their financial barriers, but also gives them the help and encouragement to succeed and make a real difference in their chosen field,” added Laura Jo Gunter, president and CEO of NAIT.
Minister Doyle Piwniuk. “I am honoured to announce we are establishing three scholarships that pay tribute to Ruth and will support the next generation of civil engineers.”
The scholarships will support individuals that identify as female and who are studying civil engineering full-time at UM’s Price faculty of engineering. Given Eden’s passion for bridges and water, related coursework will be incorporated into the eligibility criteria, the minister noted.
Toronto towers over North American crane index
Even with 8.7 per cent fewer cranes since the previous report in Q1 of this year, Toronto continues to lead Rider Levett Bucknall’s (RLB) Crane Index for North America. Toronto had 230 cranes on sites during the Q3 2022 look at construction activity. With almost as many cranes in the sky as the other 13 key markets combined, RLB data shows that construction activities in Canada’s largest city remain very strong.
Overall, the net figures across the 14 cities surveyed saw a nominal decrease of 0.62 per cent (three cranes) from the Q1 2022 edition of the RLB Crane Index.
Toronto’s dip was attributed to a significant decline in new condo sales and mixeduse projects, along with staffing challenges related to recent strike activity in Ontario’s construction sector. The industrial market continues to be a hub of activity, however, with GTA demand for crane services centred
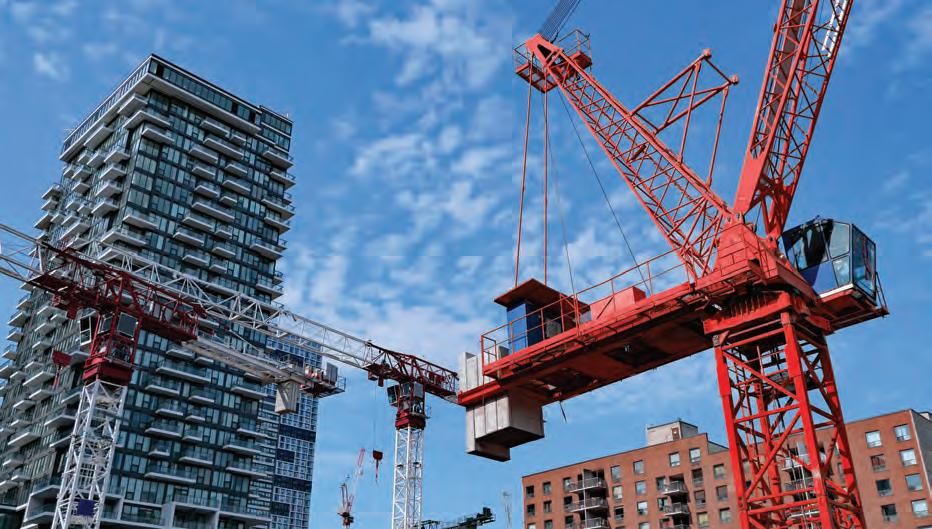
on logistics and distribution, manufacturing, consumer goods and services, and retail/e-commerce businesses.
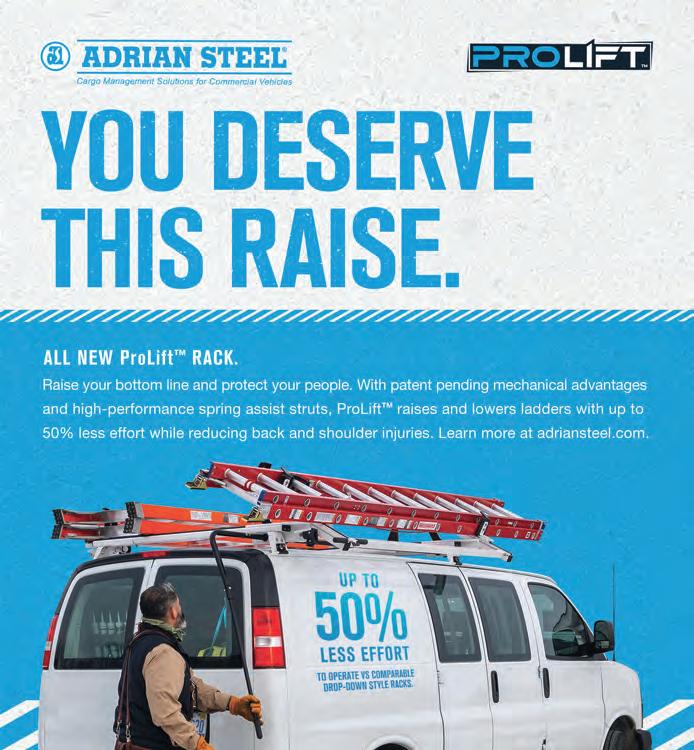
Looking ahead, the report says that promised government investments in transportation infrastructure will benefit the region’s economy.
The only other Canadian city in the index, Calgary, also experienced a drop since the first quarter of the year, but still had 21 cranes dotting its iconic skyline in Q3. The decreases were associated with the completion of many residential and office
building projects in the downtown area. A rebound is anticipated, however, as the city has a variety of new construction projects underway with an estimated value exceeding $7.4 billion.
As the region’s population continues to grow, the city is investing in infrastructure, including highway interchanges, flood mitigation projects, community improvements, bridge work, and transit improvements, including the new Green Line light-rail transit project, the city’s largest infrastructure investment in its history.
highway
Ontario is taking innovative steps to improve traffic flow in Northern Ontario. The province has issued a request for proposals (RFP) for a 2+1 highway pilot on Highway 11 north of North Bay.
A 2+1 highway is a three-lane highway with a centre passing lane that changes direction approximately every two to five kilometres. The province say the model, which is used in other jurisdictions, is more cost efficient than twinning a highway.
“This first of its kind highway pilot in North America will keep people and goods moving safely across Northern Ontario,” said Transportation Minister Caroline Mulroney. “This is a key next step to get shovels in the ground on critical infrastructure projects.”
Two potential locations for the highway pilot have been identified. While both sites will be assessed, the design and environmental assessment for Highway 11 from Sand Dam Road to Ellesmere Road (14 kilometres) will be prioritized.
Ontario to build North America’s first 2+1PHOTO: © SPIROVIEW INC. / ADOBE STOCK
Indigenous-owned hotel opens on Winnipeg reserve
Winnipeg has a new hotel; the first to be on the Madison urban reserve in the city. The Wyndham Garden Winnipeg Airport (Odé Aki) hotel, which celebrated its grand opening this week, is owned by Long Plain First Nation.
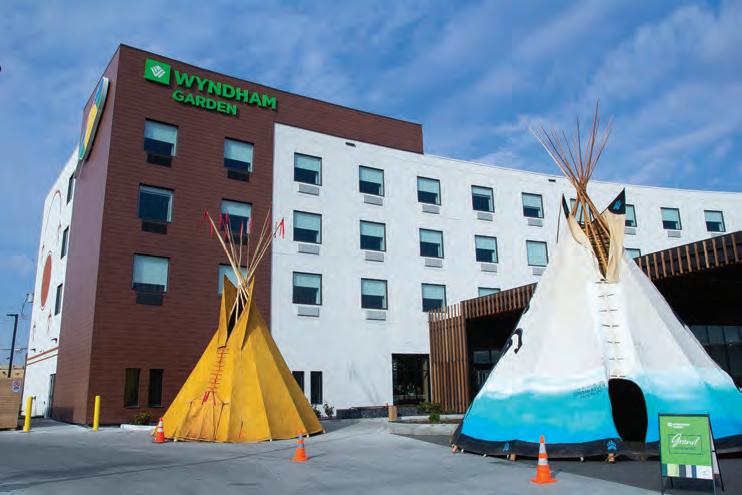
The 132-room facility was a designbuild project built by PCL Construction and designed by f-BLOK architecture inc. It is the first Indigenous-owned hotel in the Wyndham Garden group and is located a short distance from city’s Polo Park shopping centre.
“Long Plain First Nation has succeeded in building a hotel on an urban reserve that both achieves a world-class brand standard and embeds Indigenous cultural meaning throughout,” said Brock Klassen of f-BLOK. “The building serves its guests every need and also immerses visitors in a cultural experience. One cannot miss the fact that they are on Treaty 1 Urban Reserve land when they visit this hotel.”
The Long Plain First Nation purchased the land that would become the Madison urban reserve from Manitoba Hydro in 2006. The three-acre property was set aside as a reserve in 2013 and commercial businesses now provide revenue and employment opportunities.
“We began our discussions with PCL in 2015. With their help we were able to proceed with our custom-built Wyndham Garden Hotel,” stated Cindy Allard of Long Plain First Nation. “This is the largest project our nation has completed. We are grateful to have partnered with PCL and for their commitment to exceeding our expectations.”
The hotel is owned by Long Plain First Nation and will be operated by Sparrow Hotels. It features a large ballroom and a total of 5,800 square feet of flexible meeting space, including Knowledge Keepers meeting space.
“The vision of Long Plain First Nation and Arrowhead Development Corporation is an inspiring model for urban Indigenous development in Winnipeg and across Canada,” said Kelly Wallace, PCL vice-president and district manager. “It represents a step forward for First Nations economies and communities across Canada.”
PHOTO COURTESY OF PCL CONSTRUCTION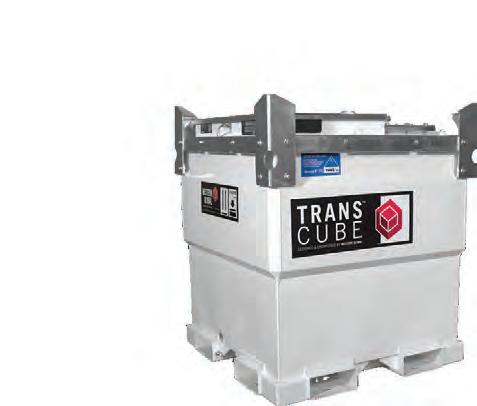
Long Plain First Nation worked with PCL Construction to build the Wyndham Garden Winnipeg Airport (Odé Aki) hotel less than 10 km from downtown.
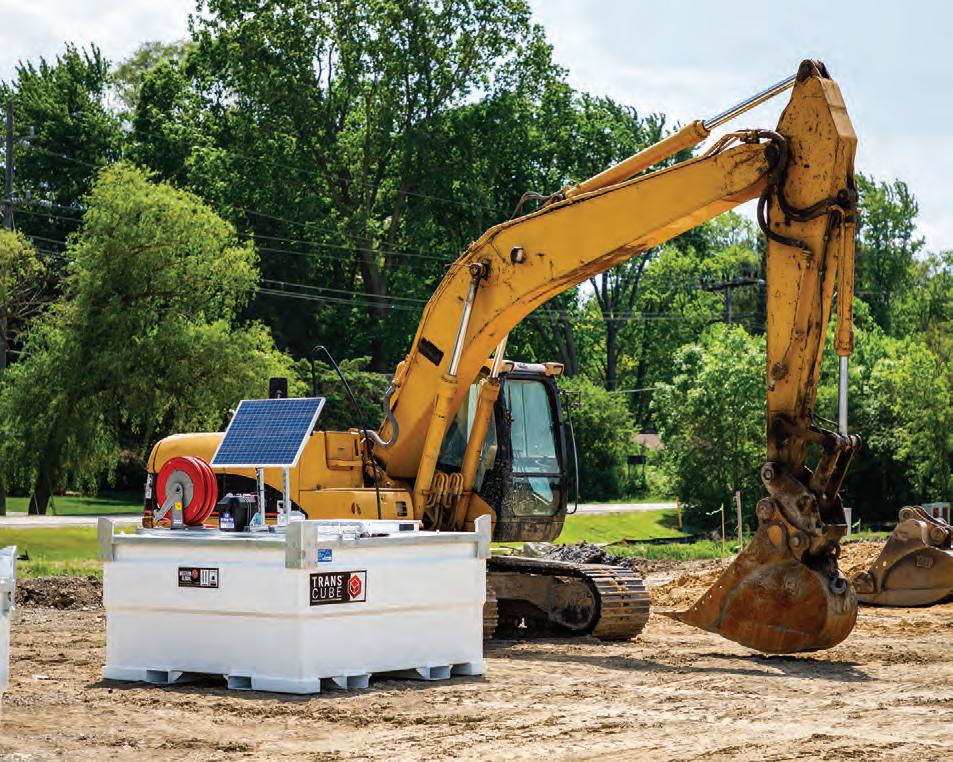
CONSTRUCTION STATS
A selection of data reflecting trends in
construction industry
NON-RESIDENTIAL CONSTRUCTION POSTS MODEST SEPTEMBER GAINS
Overall investment in building construction was on the decline in September, maintaining a downward trend that kicked in from a peak in February, but the non-residential sector showed a bit of life, posting a gain of 1.6 per cent, reaching $5.4 billion for the month. In its latest report, Statistics Canada indicated a loss in September across all sectors of 0.6 per cent, to $20.9 billion. Most of the weakness was attributed to Quebec’s residential sector, where the multi-unit component had a fourth consecutive contraction, this time dropping 5.6 per cent.
Overall, eight provinces reported gains in non-residential construction, with Ontario leading the way in each component and posting a total Industrial, Commercial, Institutional (ICI) gain of two per cent. Nationally, the industrial segment was up almost three per cent for the month and is up 24 per cent year over year, while commercial construction investment rose a little over one per cent, to $3 billion, and institutional construction also felt a small bump, rising 1.6 per cent to reach $1.4 billion for the month.
SEPTEMBER PERMITS COME CRASHING DOWN
September was a slow month in building permit offices across the nation. Statistics Canada reports the total value of building permits in Canada fell 17.5 per cent to $10.2 billion, marking the largest recorded monthly decline and the first time all survey components posted monthly decreases since September 2019. Only the single-family residential segment was spared a double-digit drop, but both the residential and the non-residential sectors posted big drops, falling 15.6 per cent and 21.5 per cent, respectively.
The value of residential permits fell to $7 billion nationally in September. The value of building permits in the multi-family component tumbled 21.2 per cent. Statistics Canada attributed much of the fall to Ontario sinking 40 per cent from a record high that was posted in August. While August saw the submission of four permits valued at over $100 million in that province, including one for $480 million, there were no permits in September that broke the $100-million mark.
Permits were down across the board in the non-residential sector, falling by 21.5 per cent as a group, to $3.2 billion in September. After three consecutive monthly increases, the institutional component dropped 37.2 per cent in the month, while intentions in the commercial component fell 11.5 per cent, and the industrial component declined 23.4 per cent. That was the industrial component’s lowest point since late 2021.
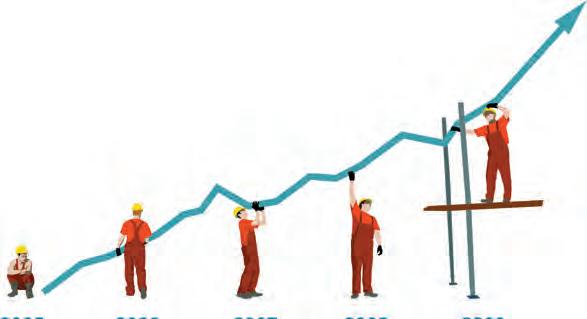
Investment in non-residential construction, September 2022
(in $Millions)
Canada 5,441.3
Newfoundland and Labrador 30.6
Prince Edward Island 21.8 Nova Scotia 61.2 New Brunswick 56.8 Quebec 1,320.8 Ontario 2,136.3 Manitoba 181.9 Saskatchewan 114.4 Alberta 694.8 British Columbia 799.9 Yukon 13.9 Northwest Territories 4.2 Nunavut 4.6
TABLE: STATISTICS CANADA
CLAIMS AND DISPUTES BATTER MAJOR CAPITAL PROJECTS
Changes to a project’s scope and incorrect or incomplete designs result in higher costs and longer timeframes. Those were some of the key findings in the fifth annual CRUX Insight Report, published by risk mitigation and dispute resolution consultancy firm HKA.
Globally, costs claimed in disputes averaged more than a third of a project’s capital expenditure (35.1 per cent of CAPEX) and amounted to US$98.7 million per project. Moreover, projects faced even heavier losses in time, with time extensions averaging 16.5 months, or 68.6 per cent, of original planned project durations.
The Canadian projects included in the analysis fared better than the international averages, however claims still bumped project costs by an average of 22 per cent, or US$53 million, and extended timeframes by an average of 9.5 months.
the Canadian




WELCOME LETTER
Procore is proud to sponsor On-Site Magazine’s 2023 Canadian Construction Forecast, our industry’s go-to resource on what construction leaders are watching for in the upcoming year.
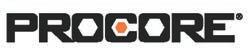
As a leading provider of construction management software, we are aware and mindful of the challenges owners, general contractors, subcontractors continue to face since the last few years. With issues like increasing material costs, a fragmented and unpredictable supply chain, inflationary and interest rate pressure, disconnected teams, project productivity, thinning profit margins, continuing safety concerns, and a labour shortage—now is the time for the construction industry to embrace platform technology in order to do more with less.
It would be unrealistic to expect the industry to be able to continue its rapid growth without innovating operationally and looking at ways to boost productivity. There has never been a better time to embrace change and digitally connect your field and office teams. Ongoing innovation will enable the industry to keep pace with increasing complexity and ensure performance.
It’s not too late to start the journey towards a digital transformation of your business. As industry leaders you care about preserving margins, boosting profitability, and reducing risk in all of its forms. Procore is your partner on this journey.
We can use this report to help us identify specific market signals, and build agile and enduring businesses that can effectively weather whatever challenges 2023 has in store for us.
Sincerely, Jas Saraw Vice-President, Canada Procore Technologies
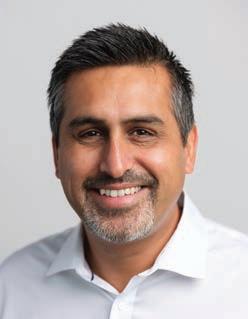
Let’s get to work!
GO ON THE SHOW WILL
BY ADAM FREILLDespite the mix of rising inflation and lending rates, as 2023 approaches few companies are finding the time to slow down.
As contracting firms continue to adjust to ongoing supply chain and labour supply challenges, it may seem like the addition of spiking inflation, rising lending rates, and the threat of project delays and cancellations would be enough to put a bucket of ice water on the industry, but most companies seem to be moving ahead as strong backlogs of work are providing a level of resiliency that is not present in all segments of Canada’s economy.
While whispers about a slowing list of projects to bid on exist, many are viewing the slight reprieve as a blessing in disguise, especially at companies concerned about whether their available labour could be stretched further to allow them to bid on additional projects to add to their backlogs.
“I feel like the pipeline of work is there between public infrastructure, P3 and even some of the residential work,” said Jas Saraw, vice-president, Canada, at Procore. “I think that’s there’s an argument to be made that we’re going into possibly a very good year in 2023.”
Even if recession hits as some are predicting, he says there is a decent likelihood that the ICI and infrastructure segments would be spared the worst, going into a lower level of growth rather than a contraction. Confidence in the industry’s resiliency varies, however.
“We have seen a bearish outlook from the general contractors that I have spoken with,” said Giovanni Cautillo, president of the Ontario General Contractors Association (OGCA), although he was still cautious about looking too far ahead. “There is a reduction in the number of tenders being issued, and that is a definite red flag for ICI construction that should not be ignored.”
Of course, even in light of red flags, there continues to be interest in his province for new institutional and transit infrastructure.
“In the ICI realm, infrastructure projects are needed, and must continue, although increases in interest rates may stave off subsequent phases of building out a project in lieu of a more favourable economic climate,” he explained.
B.C.’s ICI sector is also facing its challenges.
“I think even though the ICI industry

in British Columbia seems very busy right now, that elevated demand is hiding a significant amount of underlying vulnerability,” said Chris Atchison, president of the B.C. Construction Association (BCCA).
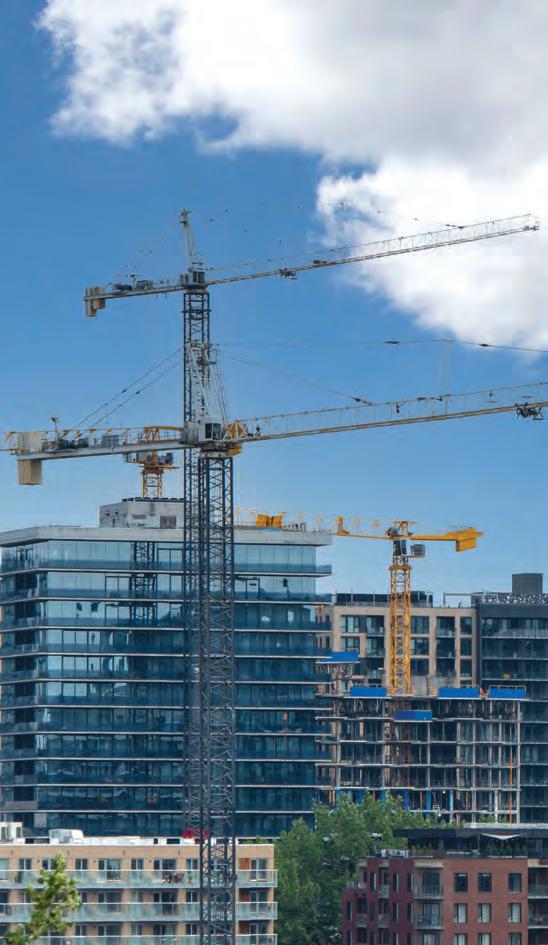
He explained that the post-COVID expansion of work-from-home staff has hit the commercial segment hard. As people are far more willing to work from home, or with some sort of hybrid model, the demand for new office space has suffered.
“There’s not this demand for more commercial construction, and in amongst that we’ve got equipment shortages, material price volatility, the ongoing skilled worker shortages.”
He expressed concern that the combination of material shortages, skilled worker shortages and slowing demand could combine to drive the cost of construction even higher. Despite those worries, there is still a buzz of activity.
“There are so many projects that have secured financing both in the private and public sector,” said Atchison as he pointed out hospital projects, Kitimat’s liquid natural gas terminal, and the rebuilding of roads that became a priority after last year’s flooding. All are strong drivers of
Amid a stack of challenges, 2023 looks likely to illustrate the resiliency of Canada’s construction sector.
activity for the B.C. construction sector. “There will still be economic activity. It’s not going to be a collapse or a shutdown.”
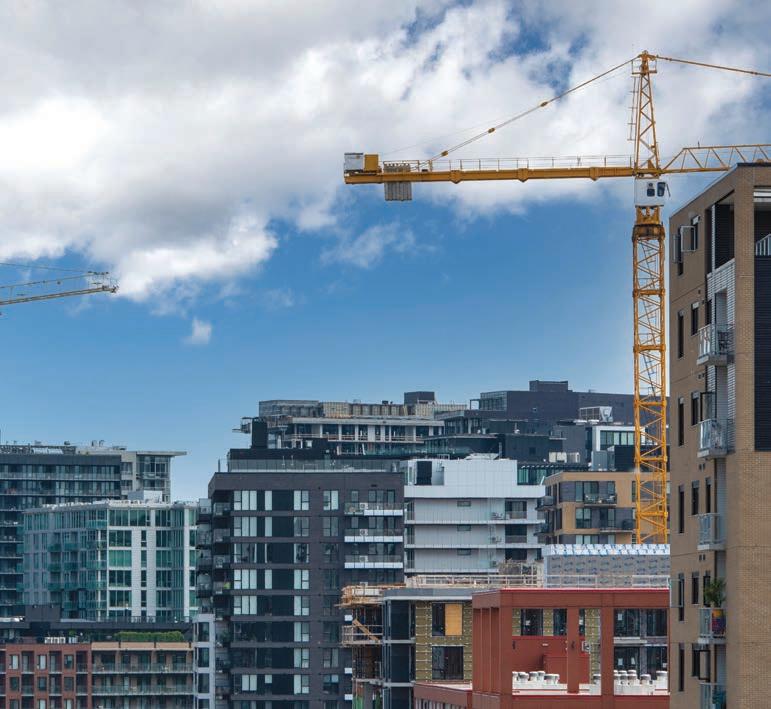
“One thing we’ve seen over the long term is an investment from Canadian governments in public infrastructure, and that seems to be continuing,” added Saraw. “Whether it’s four or five new hospitals getting built in B.C. right now, and some in the Maritimes, and a lot of P3 works being put in the ground – we’ve got subway expansion happening in Ontario – there’s a lot of infrastructure projects that are allowing a lot of contractors to dive into work.”
Once started, major projects like the transit projects in Ontario and Quebec and the building of new highways like Ontario’s Highway 413, are highly unlikely to stop, despite the risk of cost inflation.
“We’ve been in an absolute bubble for the last 10 to 15 years – a real bull market – and I think we’re seeing the benefit of that in terms of the infrastructure we’re building and the projects that we have in the ground, and the reality is that it is difficult to stop those jobs,” explained Saraw.
Labour and supply chain challenges continue to be the major impediments to taking on new work, however.
“When we talk to our specialty contractor and contractor customers, a lot of a lot of them are turning down work right now,” he said, explaining that the labour shortage is making it difficult for these companies to take on more work. And that’s a concern in many parts of the country.
“The construction industry has been trying to attract new entrants into all of the possible construction roles. Existing workers are either retiring or departing from the industry and the workforce required greatly exceeds those entering the field,” stated Cautillo. “This discrepancy translates into a limit on the number of projects any one general contractor can accept due to a physical lack of people to perform said project.”
“There is a significant labour shortage in the industry,” said Saraw. “And that’s not something that is going to get solved anytime soon.”
Training of a next generation of trades professionals is the ideal solution, but it is also a solution that needs a long runway, explained Cautillo. “Government-led campaigns targeting students are a step in the right direction, and may yield results in five to 10 years, but they do not solve our
immediate need,” he said
A shorter-term option is immigration, but it too also has limitations and challenges as immigration policies may not align with the sector’s need for specific skilled trades, and training or retraining is often still needed.
“The OGCA is working with other associations, including the Canadian Construction Association, on reducing the barriers for immigration, especially for skilled workers,” he added.
An additional concept of doing more with less and finding efficiencies in processes is a complementary option that may have a more immediate impact on a company’s ability to tackle additional projects, however.
“In partnership with Dodge Data, Procore published a survey found that 20 per cent of specialty contractors’ time was spent on low-productivity tasks,” explained Saraw. “That’s where a platform like Procore comes in, where we can drive the level of efficiency to take a task that might be hours down to minutes… It allows you to take on more work.”
Creative solutions are also helping contractors manage the uncertainty of the supply chain as well. New contracts with price escalation clauses are becoming more common, as are more collaborative project procurement models. To that end, organizations like the OGCA have crafted escalation clauses that member companies can use to reduce overall exposure in contracts.
“We recommend that contractors ensure that contracts allow for such volatility in the supply chain. Moreover, contractors need to be keeping complete and detailed records of all interactions and communications,” advised Cautillo.
Becoming more efficient, finding new workers and finding ways to manage the unexpected are all key strategies that may help contractors navigate what could be an interesting year ahead, and fewer project commitments may help return balance to material pricing and availability.
“The expectation for the Canadian market over the course of the next nine to 12 months is hopefully a minor blip, and perhaps an opportunity for a bit of a reset,” said Saraw.
Busy in all regions
BRITISH COLUMBIA
By the middle of 2022, the province was tracking a list of more than 350 major projects worth $135 billion that included roadworks, condominium buildings, hospitals and schools – most with completion dates between 2023 and 2025.
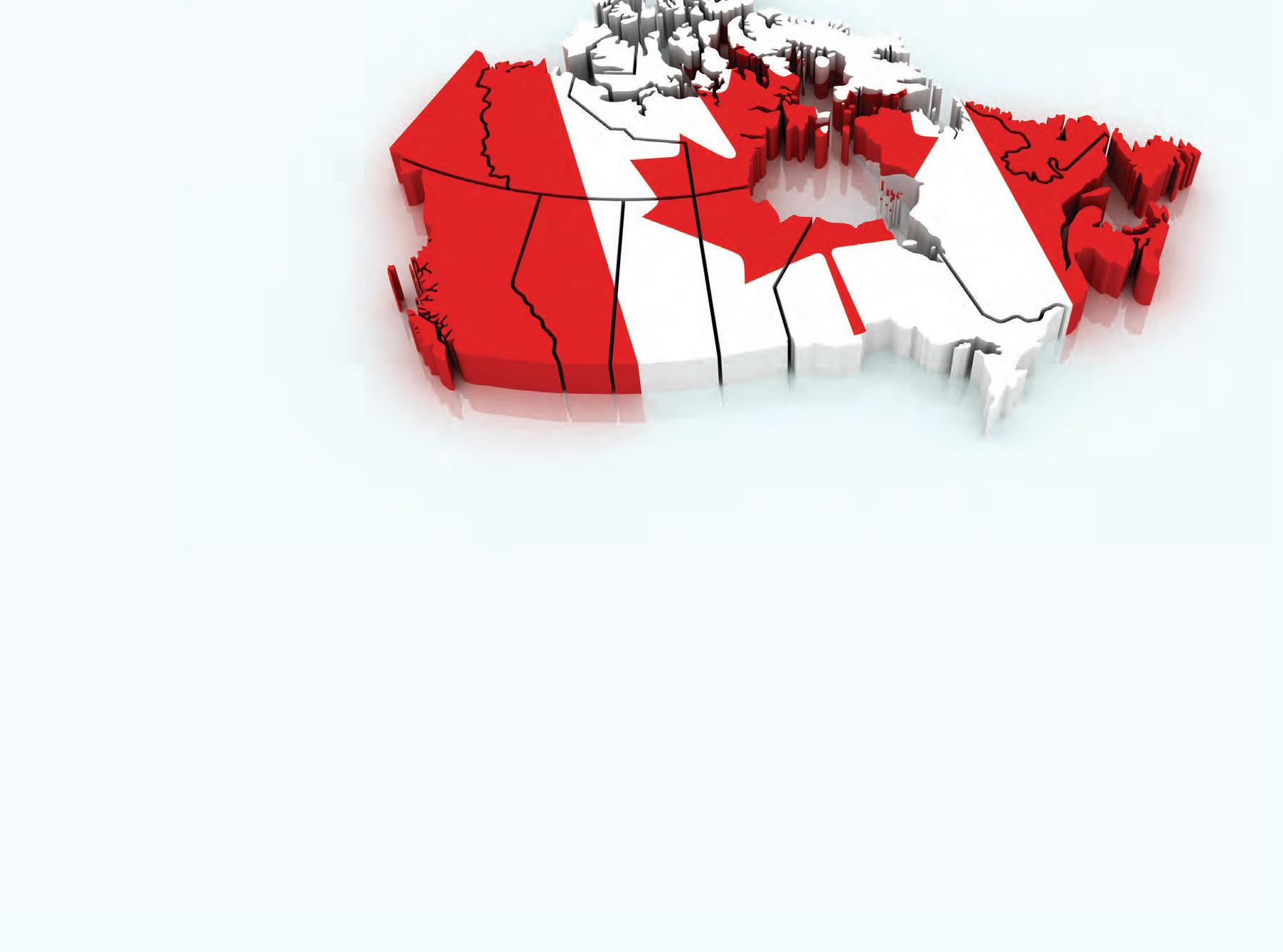
Key projects include the widening of Highway 1 in Langley, the construction of the Gateway Building at UBC in Vancouver, the replacement of Stuart Lake Hospital in Fort St. James, a new hospital and cancer centre in Surrey, and a new transit exchange with 12 bus bays to service communities on Vancouver’s north shore.
ALBERTA
The first nine months of 2022 saw more than $4.6 billion of permits issued by the city of Calgary alone. In Edmonton, the city’s four-year budget plan includes $2.2 billion to maintain existing infrastructure, and another $4.4 billion for such approved construction projects as LRT expansion projects and new recreation centres.
In addition to oilfield and pipeline projects, the province also has a large number of road projects, infrastructure work, institutional builds and commercial projects on the docket for 2023, including $133 million in provincial money to expand and build new operating rooms over the next three years.
SASKATCHEWAN
In its 2022-23 budget, Saskatchewan’s provincial government posted a target to invest $30 billion in infrastructure by

2030. Included in that figure is roughly $1.6 billion in transportation infrastructure over the next four years, with $479.5 million landing in the 2022-23 budget. The province has upgraded more than 1,000 km this year, and 3,500 over the past three years, putting the province about a third of the way through that ongoing plan.
MANITOBA
Flood mitigation and roads are key focal points for Manitoba. The provincial transportation and infrastructure ministries have a three-year capital plan that includes upgrading Winnipeg’s Perimeter Highway to freeway standards, expansion of the grid of highways that can support heavy commercial loading, and improved flood protection for Lake Manitoba and Lake St. Martin. Construction is also expected to soon start on a $64.4 million planned renovation and expansion at Boundary Trails Health Centre in Winkler, one of several healthcare projects in an $812 million planned spend across the province.
ONTARIO
From the Ontario Line subway to new highways and LRT systems and, of course the Gordie Howe Bridge, Ontario is the land of the multi-billion project. The provincial government has a 10-year $61.6 billion plan to improve public transit, and recently broke ground for the Ontario Line, which will provide rapid transit between the exhibition grounds near Ontario Place and the Ontario Science Centre by 2030. The province also has several hospital projects in
various stages, including the Gilgan Family Queensway Health Centre in Etobicoke and a new Mississauga hospital. Also on the docket are Highway 413, a $36 million Confederation GO Station in Hamilton, a $540 million biomanufacturing facility in Hamilton, an $800 million laboratory research centre in Deep River, northwest of Ottawa, and Nokia Canada’s $340 million plan to build a research and development campus in Kanata.
QUEBEC
Along with Montreal’s Metropolitan Express Network light rail system that should open its first station in 2023 (which has a stated completion target of 2024), the province has numerous major projects that will keep construction firms busy next year. Jacques-Bizard bridge is set to be replaced. The Centre Hospitalier Universitaire de Quebec (CHUQ) is redeveloping Enfant-Jesus hospital. And major roadwork is underway, including the widening of Highway Henri-IV (Route 573).
ATLANTIC CANADA
Rebuilding efforts after the floods and hurricanes over the past two storm seasons will continue in Canada’s Atlantic provinces in 2023, but there are also other projects in the works, including the South Shore Regional Hospital Redevelopment Project in Bridgewater, N.S., $1.13 billion over the next three years in New Brunswick for transportation projects, and a new $330 million Adult Mental Health and Addictions Facility in St. John’s.
© MRTIMMI / ADOBE STOCK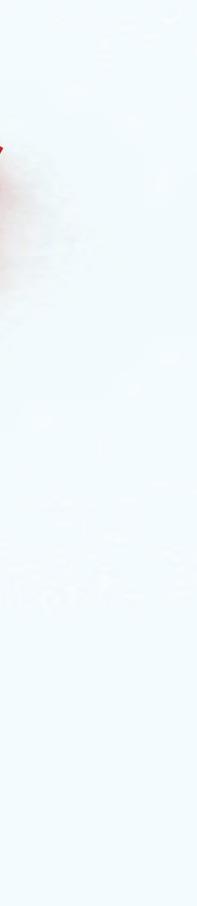
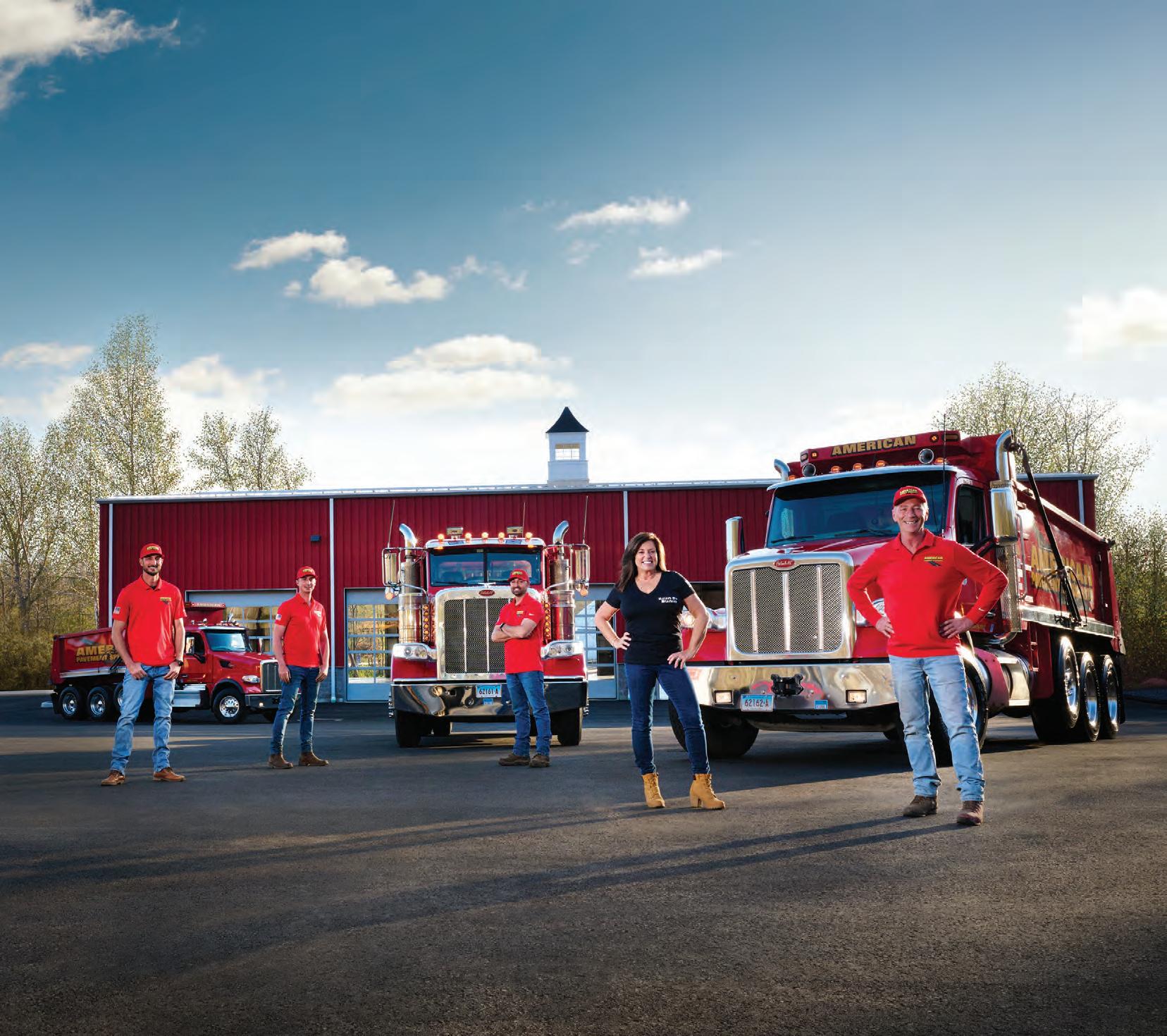
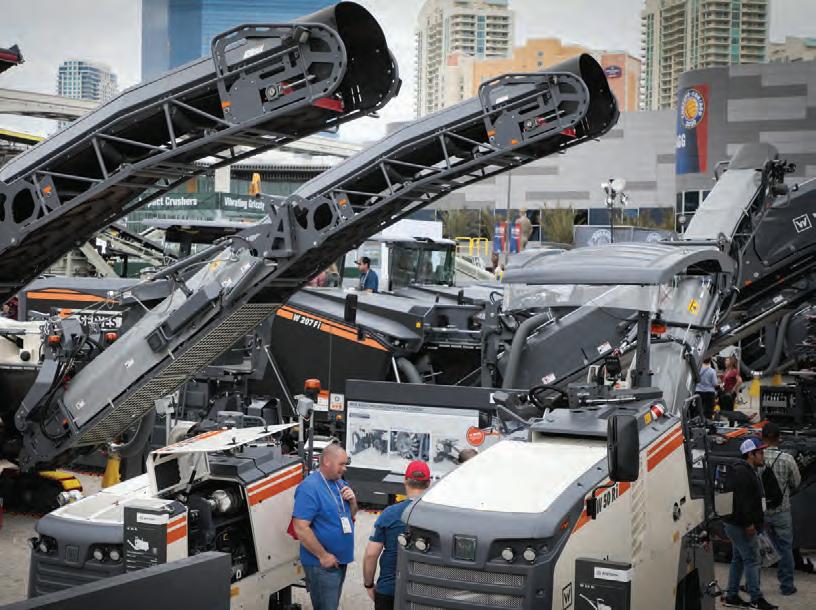
TOP 10
CANADIAN CONSTRUCTION TRENDS TO WATCH IN 2023
Canadian Construction Association president Mary Van Buren shares her insights into what to have on our collective radars as the
BY MARY VAN BUREN1.Recession or ramp up?
The case for investing in infrastructure makes economic and social sense. As Canada and other countries seek to curb inflation, there will be more onus on governments to continue to invest. There are new highway and light rail developments, climate resilience retrofits, and vital maintenance projects underway as part of the nation’s growth plan. Risk can fluctuate in every construction project, but private investors are especially vulnerable in today’s market of escalating prices, supply chain disruptions, rising interest rates on loans, and challenges securing workers.
2.
The federal government’s 2021 invitation to consult on Canada’s National Infrastructure Assessment was highly welcomed by the Canadian Construction Association (CCA) and our industry, but what happened?
We jumped on the opportunity to provide a national vision for infrastructure resilience, recommending a strategy that would identify needs and priorities based on independent expert advice.The consultations appeared to be a step in the right direction yet little concrete action has taken place since.
3.
Rallying around increased investment in trade-enabling infrastructure
Canada’s reputation as a trading nation is in steep decline. In just 10 years, the country has fallen from 10th position to 32nd in terms of its trade transportation infrastructure. This is just below Azerbaijan and ahead of Turkey and Saudi Arabia. We need a massive scale-up in our country’s trade infrastructure.
The 2022 Federal Budget made some modest investments to improve supply chain infrastructure and support the existing National Trade Corridors Fund, but more is needed for Canada to remain globally competitive, expand into new and emerging markets, attract investors, and boost employment.
The industry has recommended a path forward, identifying and investing in Canada’s key trade gateways and corridors across the country that will link resources to industry, people to jobs, and products to market. It’s time to show that Canada can deliver the goods through a strategic trade infrastructure program.
4.
Targeted immigration to build industry workforce capacity
It’s no secret that Canada is facing its most severe labour shortage in over 50 years. The situation is especially
acute for the construction sector and its 81,000 open yet unfilled jobs. Retirements and recruitment challenges will be a heavy blow to Canada’ future economic growth if steps aren’t taken to rebuild Canada’s workforce now.
Training takes time and we need workers now. Immigration and temporary foreign labour can help alleviate the choke points, but to get there we need to modernize Canada’s immigration policy. While the federal government has pledged to increase immigration, it’s not just a numbers game. The current federal immigration point system does not favour the trades. Many newcomers cannot even find work in their field of expertise. We need to put their skills and experience to work and expedite the recognition of their training and credentials.
5.
Renaissance of skilled trades as a valued career path

After years of relegating skilled trades to a career of last resort, governments and educational institutions are reinvested in promoting these careers.

The projected demand for skilled workers is far outweighing the number of people who are choosing to pursue a career in the trades. A report by the Canadian Apprenticeship Forum found that 75,000 new apprentices will need to be hired per year over the next five years to meet the
© TREECHA / ADOBE STOCKWhere is the action on the federal promise to collaborate?
next 12 months unfold.PHOTO:
demand for skilled journeypersons in Red Seal trades.
Smart investments are now being made to support businesses in offering apprenticeship training to Canadians from all backgrounds. The Canadian Apprenticeship Service is one such program that CCA is promoting, and it offers financial incentives to small and medium-sized employers who hire and train new first-year apprentices in 39 Red Seal trades. Schools and local businesses are also doing a better job at exposing youth to potential career paths.
This new appreciation for skilled trades combined with an infusion of new Canadians will help propel diversity and inclusivity forward, with greater representation from women, new Canadians, Indigenous and other equity-seeking groups.
6.
New constraints for projects
Today’s financial climate and supply chain issues are forcing developers to rethink their project plans. Rising interest rates, taxes and debt financing are particular concerns, delaying or slowing down projects. Availability of bonding and insurance may also tighten.
Contractors will continue to face unpredictability in supply availability and costing. The war in Ukraine, the “Buy U.S.” initiative, massive infrastructure investment south of the border, and the
potential for disruptions from climate related events all stand to impact the supply chain. It will be important to influence and monitor policies to secure a more resilient and green supply chain.
7.
Green building takes a strong
forward
step
Over 120 countries, including Canada, are setting targets to limit emissions and decarbonize economies. With buildings representing almost 40 per cent of global greenhouse gas emissions, not to mention the environmental impact of heavy industry, Canada’s Green Building Strategy is looking to the Canadian construction sector to make a real impact on annual carbon dioxide emissions.
This is perhaps a once in a generation opportunity to make a quantum leap in building green. It requires mobilization of both private and public sectors, and all levels of government. Developing a buy clean policy, incenting businesses, mandating change through building code amendments, and deliberately including climate resilience in the project scope at the tender process should be considered. Education and training are also critical pieces of the puzzle, including access to better data, technologies, tools and standards as well as supporting workforce training programs geared towards low-carbon construction.
8.
Uncertainty surrounding hybrid workplaces
COVID-19 significantly disrupted both employer and employee beliefs that the office is the centre of corporate culture and connectedness. Even before the pandemic, the construction industry began adopting digital tools and apps for the job site. With many firms only recently establishing rules of in-office presence, there will continue to be some tension between employers and employees as we navigate new ways of working together.
9.
Automation is becoming essential
As self-checkouts replace traditional cashiers in grocery stores and pharmacies as a response to a lack of workforce, the construction industry will also be turning its attention to increased use of technology. With 81,000 job openings, and despite significant effort to recruit and retain a workforce, the business case for automation is strengthening.
Some companies are looking at robotics and new technologies, like exoskeletons and drones, as tools to increase productivity, growth and safety. As more technology is adopted in the industry, new types of jobs will be added within the sector – attracting new talent that wish to use cutting-edge technologies in the industry.

10. Collaboration gains strength
The value of involving contractors earlier in the project is gaining steam. Owners are recognizing that early engagement and collaboration can produce a more informed project plan, resulting in better pricing for risk and potentially identifying more efficient and effective ways of delivering projects.
This is a step in the right direction to updating Canada’s current procurement system to one that supports fair competition, long-term value and sustainability over low-cost bid, and shared risk. Too often contractors take on the majority risk of project costs and delays due to the shortage of workers, materials and supply chain disruptions.
Almost like the real thing
Heavy equipment simulators look a lot like video games. That said, the cautious behaviour that simulators are designed to instil couldn’t differ more from the aggressive risk-taking that earns high game scores.
Heavy equipment operation requires a precise set of skills that were traditionally developed over thousands of hours in live environments. Seasoned operators claim that it’s the physical feedback – the sounds, smells, impacts and vibrations – that guides them in their everyday work. Accordingly, it’s understandable that many are skeptical about the value of simulator training.
“We’ve had simulators in our program for 13 or 14 years,” says Lawrence Boyd of Nova Scotia Community College (NSCC). “Our faculty is old school, and at first they weren’t sure of the value of simulators. But they’ve proven to be a great way to get the students introduced to the mechanics of how the equipment operates.”
Schools like NSCC use simulators to shorten and augment the training cycle as part of a blended learning approach. Students can learn, for example, how to read the instrumentation panel and get the feel of the controls before taking the seat on a live machine.
“They’re as close to getting out into the real thing as you can get,” says Andrew Coles at Vancouver Island University. “We get the students onto simulators because it really helps with their muscle memory. They’re learning the controls before they actually move the machine around.”
The exercises are much more than driving lessons, however. Simulators can be programmed to present and reinforce a variety of training objectives such as safe operating procedures.
Coles explains that all the same steps are followed in simulator exercises. “This forces them to follow safe operating procedures so that when they get onto the machine, they know those procedures.”
Simulators can also present a student with a wide variety of terrain environments and operating techniques. “You can go from trenching to top loading, bank loading or flat-ground truck loading, whether it’s an excavator or a wheel loader,” says Wade Turlington, at Volvo Construction Equipment.

The simulator experience also reduces the anxiety of the initial experience with a live machine. “Years ago, first getting into that piece of equipment and starting up the engine was a daunting experience,” says Boyd. “Simulation has eliminated that start-up hesitancy.”
Moving seats that provide motion feedback help to reduce that anxiety. In a study conducted by University of North Carolina and Volvo CE, participants operating a live machine for the first time who had previously trained on motion feedback simulators had lower heart rates compared with participants trained on non-motion machines or on no simulator at all.
“The group that had the lower heart rate and was most productive was the one that did the exercise on the simulator with full motion,” says Turlington, adding that simulators can also train operators to avoid costly mistakes. “When an operator drives into a pile, you want to teach the operator not to go in with the machine articulated one way or the other.”
Similarly, the machines can train operators to economize on movement, power, and fuel consumption. “All these things help the operator be more productive, more efficient, and burn less fuel,” he says.
LOOKING AHEAD
Three-dimensional virtual reality platforms, offered by start-ups such as Edmonton-based Serious Labs, could well define the next generation of heavy equipment simulators. “I think people will be able to use their gaming setups at home to do virtual training,” says Turlington.
As remote control sees wider adoption in construction, a day may come when a simulator-like environment becomes the predominant method for controlling live machinery. In that scenario, operating a simulator won’t just resemble the real thing – it will be the real thing. And younger operators are likely to adapt to that without too much trouble.
“With the new generation of students, it’s not that big a stretch to be operating equipment from behind a computer,” says Boyd.
Jacob Stoller is principal of StollerStrategies. Send comments to editor@on-sitemag.com.
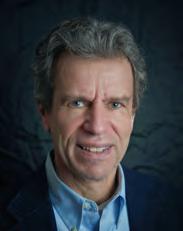
Heavy equipment training simulators provide a more realistic training experience than they did a decade ago. They are not, however, a substitute for live training.PHOTO: COURTESY OF VOLVO CONSTRUCTION EQUIPMENT
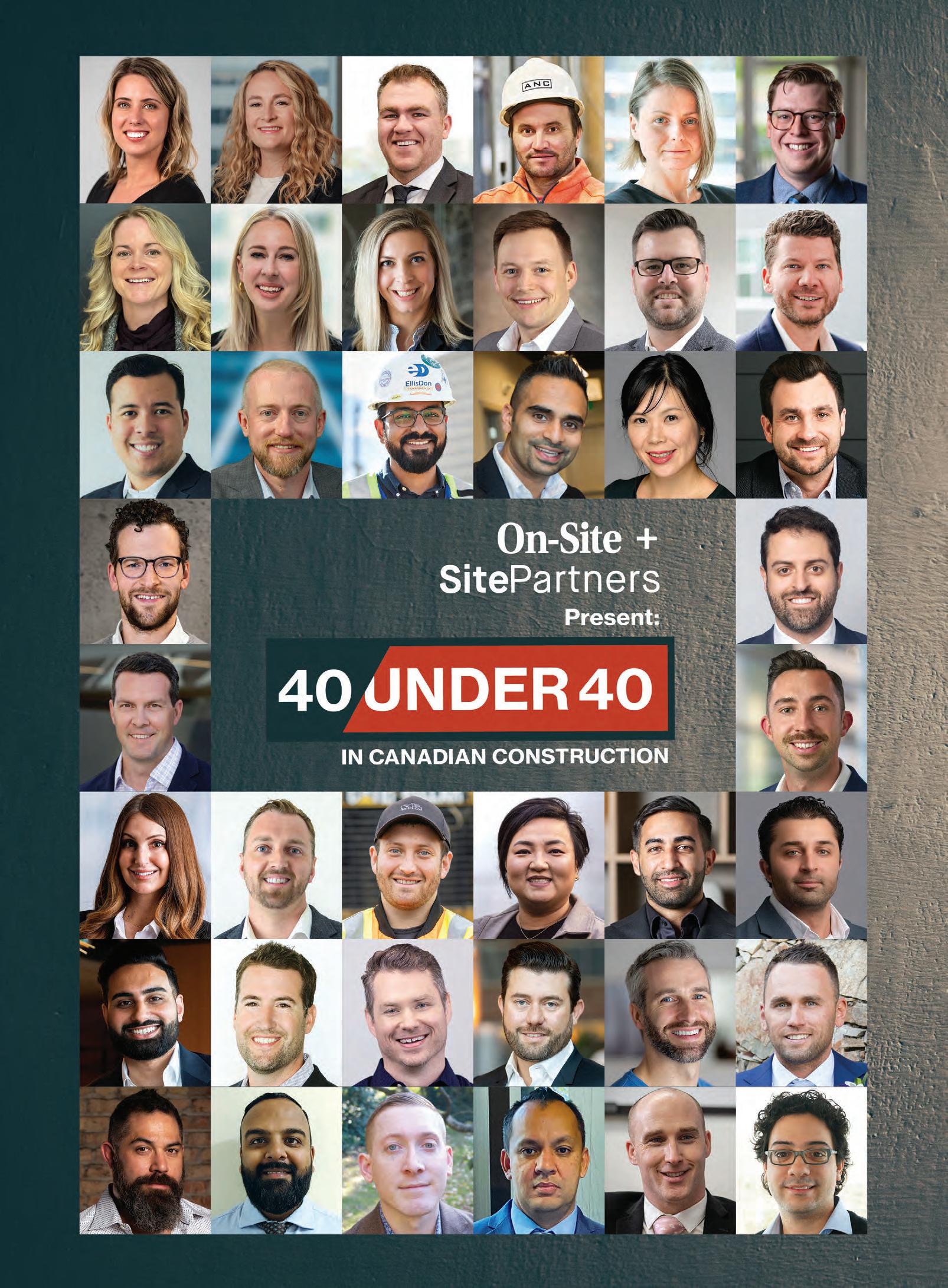
WELCOME LETTER
On behalf of Northbridge Insurance, we are very proud and honoured to be the sponsor of On-Site Magazine’s 2022 Top 40 Under 40 in Canadian Construction celebration.
This year has been a momentous year for the construction industry. Like most industries, it is ever changing and evolving, and it can be tough to keep up with new innovations and growth. However, each of the individuals mentioned in this report are doing just that.
We are excited to recognize this group of exceptional, progressive, and innovative young leaders who are working to elevate the construction industry in Canada. They have been chosen for their commitment to excellence within their firms and for their tremendous contributions to their local communities.
Fostering innovation, operating ethically, and leading by example are just a few of the traits that these nominees share. These individuals are working to advance complex infrastructure projects, implementing or launching powerful software tools to increase on-site safety, and building communities for families to thrive in. This gives us great confidence in the future of our vibrant and diverse industry.
We would also like to share our gratitude and our sincerest appreciation for all the individuals who took the time to recognize and nominate members of their organizations or work communities, along with the firms that give these individuals the opportunity to grow and thrive within their roles.
At Northbridge Insurance, we constantly strive to work with the construction industry to create a safer future and we’re proud to be a trusted insurance partner. We want to offer our wholehearted congratulations to all of the nominees for what they have achieved so far, and what they will achieve in the future. The Canadian construction future is bright!
Sincerely,
Shari Dodsworth Senior Vice-President Northbridge Insurance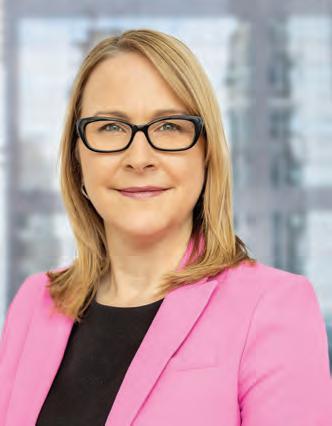
RISING LEADERS IN OUR INDUSTRY
What does it mean to be recognized in this third edition of the Top 40 Under 40 in Canadian Construction, as presented by On-Site Magazine and SitePartners? The 40 individuals in the pages that follow are our industry’s young leaders. They are the innovators and professionals who have vision within their companies, as well as beyond their own walls. They are the top minds who are working to help shape the future of the construction sector in Canada, and they are doing so with purpose.
As you will read, each brings a unique set of experiences and skills to their role, but they all share a common trait regardless of where in the country they work or the specific job they fulfill. Each of these 40 individuals share a motivation that pushes them to aim ever higher. Whether they are a business owner, engineer, executive, trades professional, software developer, legal professional, researcher, or any of the other roles you can find among the 2022 honourees, their ability to execute their vision is what is going to keep the industry moving forward
We are proud to highlight these talented individuals, and we hope that their stories will help influence others in our industry.

President and CEO
QM Environmental Mississauga, Ont.
On a mission to help the environment, in April Agnes Wietrzynski was handpicked by Wes Hall, one of the Dragons on CBC’s “Dragons’ Den,” to run his environmental and industrial services company, QM Environmental.
Building on her leadership and management experience, Wietrzynski has an aim to navigate QM to more than double its size. To that end, she will be leading significant projects in important Canadian sites such as the Port Lands in Toronto.
Wietrzynski holds an MBA from Queen’s University, which she completed while working in the industry, earning the program’s Creativity and Innovation Award. She is also a board member of the Ontario Environment Industry Association (ONEIA) and is highly skilled in the art of team building, cultural integration and inclusivity.
ALEXIS BARR-GUSA Partner Dentons Canada LLP Edmonton, Alta. Environmental, Social and Governance (ESG) is not just a set of vague targets and goals for Alexis BarrGusa. She is dedicated to putting these practices into action.
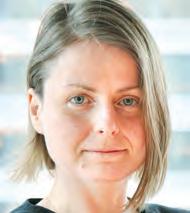
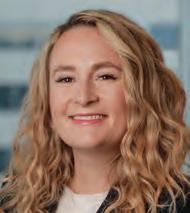
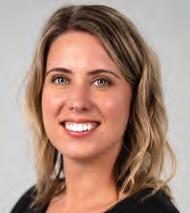
As a partner in Dentons’ Edmonton and Vancouver Construction, Infrastructure and Public Private Partnerships (P3) groups, Barr-Gusa is regularly involved in the negotiation and drafting of project agreements, including complex multiphased engineering, procurement and construction contracts and P3 transactions involving a wide variety of infrastructure projects worth billions of dollars. She also frequently leads presentations to members of the construction industry on relevant and current construction issues.
She is a coach and mentor, and a
member of her firm’s WomenLEAD (Leadership, Entrepreneurism, Advancement, and Development) Canada affinity group, as well as its Indigenous Inclusion Working Group.
She is also passionate about renewable energy and has pursued key opportunities to advise nationally and internationally on renewable projects.
ANDREW KAVANAGH Vice-President, Finance Aecon Group Inc. Toronto, Ont.
Having joined Aecon’s finance team in January 2010 as a co-op student, Andrew Kavanagh quickly demonstrated his potential, resulting in an employment offer upon completion of his studies in May of 2011. He has been on a vertical trajectory ever since.
This past February, he was named vice-president, finance at Aecon Utilities, a subsidiary of Aecon Group Inc., with a scope of accountability that includes finance, procurement, and continuous improvement across the utilities sector.
Committed to continuous improvement initiatives, he has been integral to the success of his company’s utilities team, with continual efforts towards leading edge innovation, lean construction solutions and a highly efficient supply chain. Consistently demonstrating that he cares not only about Aecon’s success, but of the success of the people and projects around him, the CPA also commits time and effort to Aecon’s mentorship program to help support the career advancement of others.
ANDREW NEILL
President and CEO ANC Group of Companies
Brantford, Ont. Andrew Neill started his career in construction at the age of 17, progressing to superintendent at 21, before moving to EllisDon at 27 to become a superintendent and then a project manager.
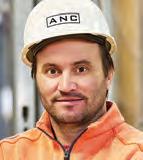
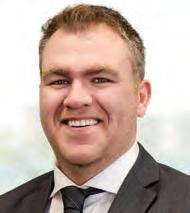
At 31, he started Andrew Neill
Construction (ANC) as a general contractor and construction management firm, building custom homes before growing the business into the industrial, commercial and institutional sectors. A few years later, ANC Modular was incorporated.
After achieving CSA A277 certification for the modular units, ANC Modular Inc. has gone on to successfully manufacture many design-build projects for municipalities and government-funded affordable housing projects, mostly as part of Canada’s Rapid Housing Initiative.
Most recently, Andrew has developed an international patent pending design incorporating a modular volumetric and concrete superstructure.
ANYA BARKAN
Sustainability Manager
Multiplex Construction Canada Ltd. Toronto, Ont.
After eight years working at Toronto Community Housing as an associate construction manager, Anya Barkan joined Multiplex Construction Canada this past January as a sustainability manager.
Since joining the team, she has helped the company earn the 2022 Green Building Pioneer award from the Canadian Green Building Council (CaGBC) and be recognized as a finalist in Procore’s 2022 Groundbreaker awards in the Excellence in Sustainability category.
Experienced in the construction of residential, commercial and life-science buildings as well as infrastructure, she continues to push the envelope when it comes to supporting the environment through her company’s sustainability-driven initiatives, including the aim to reach carbon neutrality.
She is constantly seeking change and improvements for the businesses and communities in which she builds, and has dedicated herself to changing the built environment through environmental, social and governance strategies.
Director, Innovation and Operations

UNB Off-site Construction Research Centre
Fredericton, N.B. Instrumental in the ongoing development of the Off-site Construction Research Centre (OCRC) at University of New Brunswick (UNB), Brandon Searle has been actively growing the centre’s board and partners. The OCRC recently introduced its first executive board of construction leaders from across the country and secured collaborative research projects with more than 20 industry partners.
The centre, which was established in 2019 and includes computational labs with over 14 workstations, a state-of-art collaboration space and seven full-time employees. OCRC also continues to
advance its technical capabilities with a new building envelope testing lab. Based on the significant, and rapid, growth in the OCRC, Searle was promoted from innovation director to director of innovation and operations in late 2021.

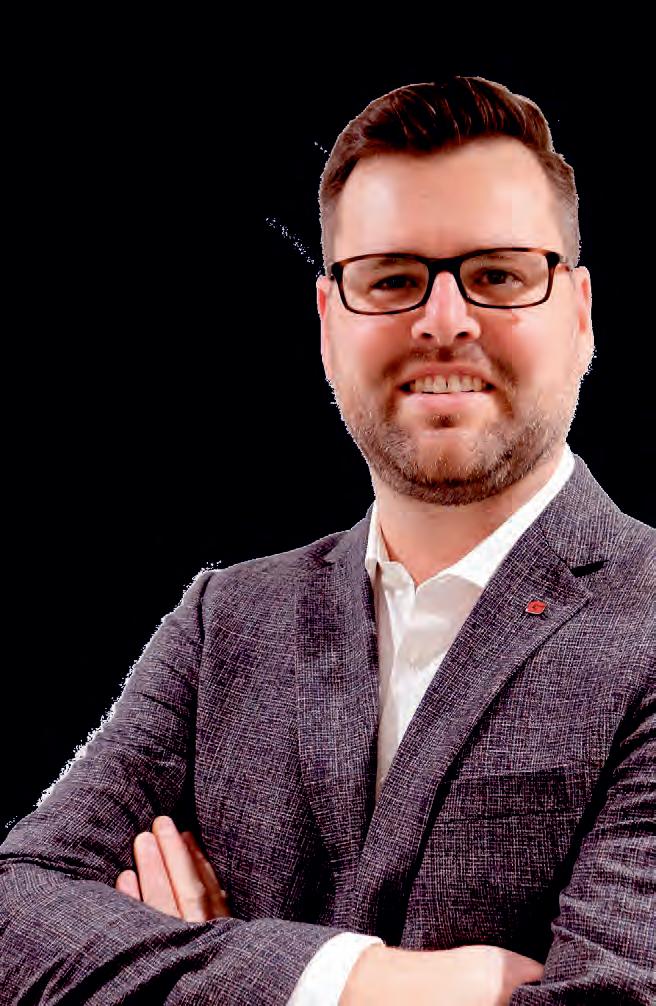
A licenced professional engineer under the Association of Professional Engineers & Geoscientists NB, Searle is also the co-founder and partner at DCA Consulting Inc., sits as a board member and secretary for Building Transformations (formerly CanBIM), and is an active member of the Off-site Construction working group with the International Council for Research and Innovation in Building and Construction.
BRIAR BEERSVice-President
Cutting Edge Consulting Inc. Kamloops, B.C. After earning a degree
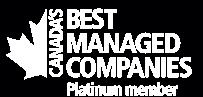
in civil engineering from the University of Waterloo, Briar Beers developed her career as a senior project manager before taking the leap to becoming an owner at Cutting Edge Consulting (CEC), an industrial construction company with a focus on bridge construction and rehabilitation, mobile crane services, pile driving, welding, fabrication, and other such services.
As one of the company’s key leaders, Beers developed its safety program and helped it achieve COR certification. She also developed the company’s project management and estimating programs and fostered its growth over a five-year period from a single employee to a company with more than 60 workers.
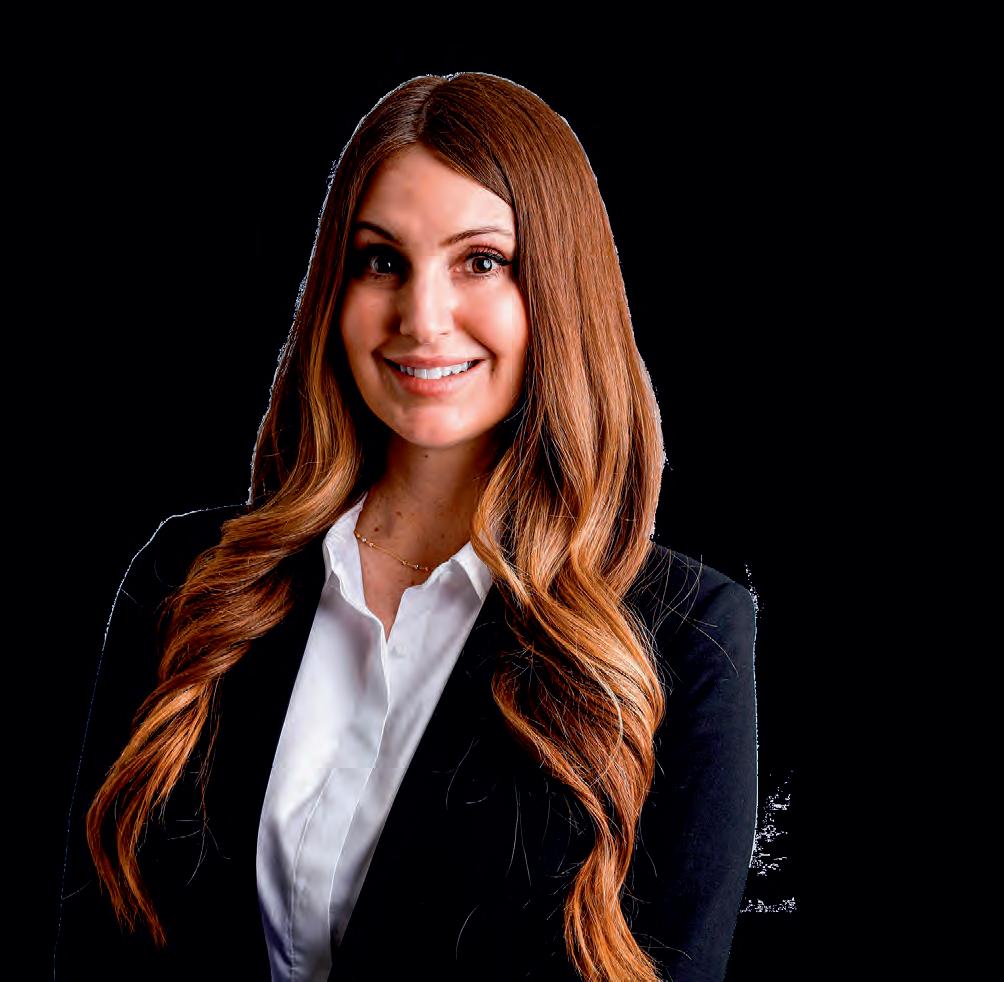
An advocate for women in the construction industry, Beers is a mentor and a teacher. In addition to dedicating time to participate in Chamber of Commerce activities, she also partakes in community events and local shows.
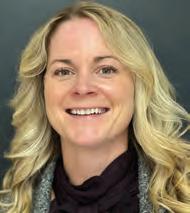
CAYLEY VAN HEMMEN Interiors and Special Projects Division Manager
Canadian Turner Construction Company Vancouver, B.C.
After joining Turner Construction’s Vancouver business unit as an intern in January of 2013, Cayley Van Hemmen has advanced through a number of roles at the company to now find herself as the company’s interiors manager of its Special Projects Division (SPD).
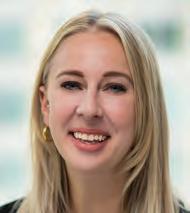
A team player who aims to make those around her better, she played a key role in restructuring the division. She joined Turner when it was a seven-person company in Vancouver and has helped it grow into a business unit with more than 145 people over the past 10 years.
In addition holding a bachelor’s degree in civil engineering from UBC, an MBA from the UBC Sauder School of Business, and a LEED AP Building Design & Construction distinction, she is also the co-chair of the mentorship committee at the Urban Land Institute and is a dedicated proponent for industry equity.
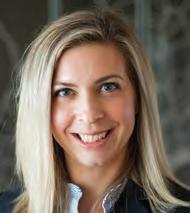
CHEYANNE HAMMELL Special Projects Manager
PCL Construction Toronto, Ont. Promoted to PCL Toronto’s senior operations team as special projects manager in 2022, Cheyanne Hammell has managed several high-profile projects, including the renovation of the observation level at the CN Tower, the implementation of a complex baggage handling and sorting system for the Greater Toronto Airports Authority, and the first long-term care home built under Infrastructure Ontario’s Accelerated Build program, delivered in just 13 months.
Starting at PCL as a student, Hammell completed four work terms before officially joining the company in 2007 as a field engineer. Since then, she has progressed through various roles, including project
manager and senior project manager.
In 2020, Hammell was the Toronto district recipient of PCL’s Robert Stollery Construction Leadership Award, given to one rising project management star per year who models excellence and inspiration. She is also dedicated to encouraging young girls to explore career opportunities in the construction industry.
Graham as a project coordinator in 2010. His in-depth technical knowledge, attention to detail, work ethic and leadership qualities were quickly noticed by his peers and leaders while working on the Key Lake Acid and Steam Facility project.
Always willing to roll up his sleeves when needed and go above and beyond, Chubey was nominated because he cares about the success of others around him.
CLAYTON MACEACHERN
Area Manager, Fort McMurray
Flint, a Division of ClearStream Energy Services
Fort McMurray, Alta.
A passionate and innovative leader, Clayton MacEachern has led his business unit of 1,200 team members for over 3 million exposure hours without a recordable injury.
Joining Flint as a heavy equipment operator in 2010, MacEachern has grown with the company, and now as area manager he oversees its largest corporate business unit. This spring he also became a Harvard Business School alum.
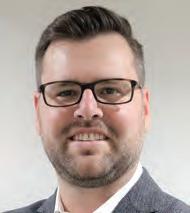
He is an advocate for equality, community, and reconciliation, and was able to successfully build a joint venture partnership with the Fort McMurray #468 First Nation in 2021.
He turned his passion for training, apprenticeship and mentoring into the development of Flint’s Emerald Career Training Program that uses heavy equipment simulators to train high potential candidates. After six years, the program is launching up to 150 careers each year and has added a second training centre in central Alberta.
COLBY CHUBEY Senior Project Manager Graham
Saskatoon, Sask. Currently leading a joint venture submission for a large energy project with two gas turbine facilities in Saskatchewan, Colby Chubey joined
A believer in constant development, Chubey holds several professional certifications and is continually championing innovation to address process efficiency and jobsite challenges at Graham. His work to design and fabricate a temporary IT infrastructure solution to provide internet connectivity on new sites has been shared and used by teams across the business as they move on and off projects.
He also actively participates in student information sessions, awards nights and other industry forums.
DARREN SAUER
Director of Development Wales McLelland Construction Richmond, B.C. Professional and passionate, Darren Sauer started his construction career as a labour right out of high school. After graduating from BCIT, he started working as a project coordinator, then a project manager, managing ever larger and more complex projects for Wales McLelland.
He rejoined the firm three years ago following a five-year period working for a private landowner and developer.
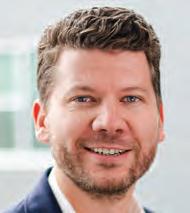
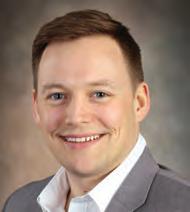
In his newest role at Wales McLelland, he provides leadership and strategic direction for the company, exploring new market opportunities, improving processes and functions, growing the business, while recruiting and developing staff and expanding its services for its clients.
Over the past three years, that has included the creation and growth of a Development Services department with a growing team of four.
CONGRATS TIMES TWO!
PCL Construction would like to congratulate Jordan Clouthier and Cheyanne Hammell on being named to On-Site Magazine’s Top 40 Under 40 in Canadian Construction list. Their leadership and unwavering commitment to excellence ensures PCL’s continued success atop Canada’s construction industry.
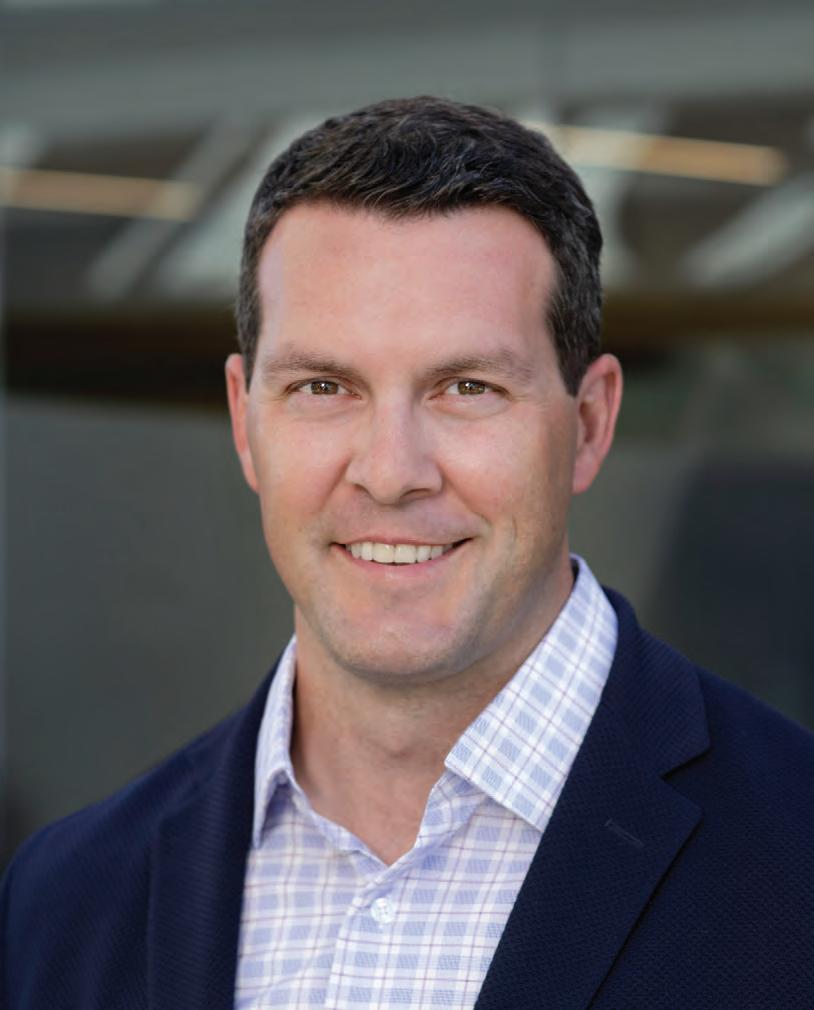
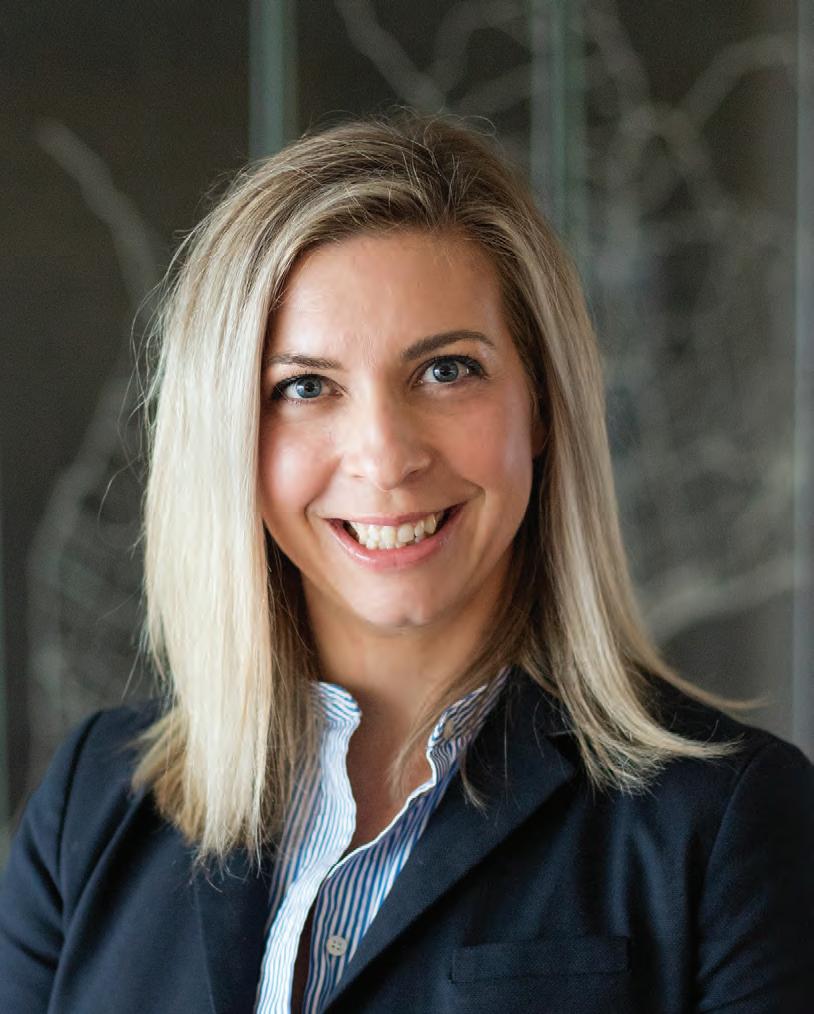
FELIPE SUZUKI Technical ManagerHurontario LRT
John Laing
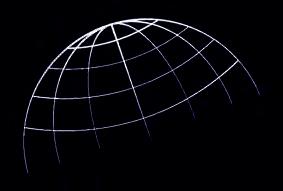
Toronto, Ont.
Felipe Suzuki has contributed to major infrastructure projects in Canada and internationally since 2006. He initially developed his technical skills by working on several designs for transit projects, gaining progressive construction and contract management experience on multibillion-dollar projects, including as a core member of the team that executed the Subway Line 4 in Rio de Janeiro for the 2016 Olympic Games.
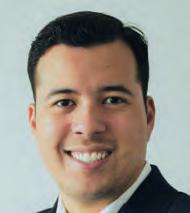
In 2017, he moved to Canada with the goal of helping companies to structure and deliver PPP projects. At the same time, he completed a two-year validation process and successfully obtained his P.Eng.
license for civil engineering in Ontario.

In 2019, he joined John Laing’s asset management team and has been a key member of the Mobilinx management team delivering the Hurontario LRT Project.
GRAHAM CURRIE Regional Manager Ledcor Construction Limited
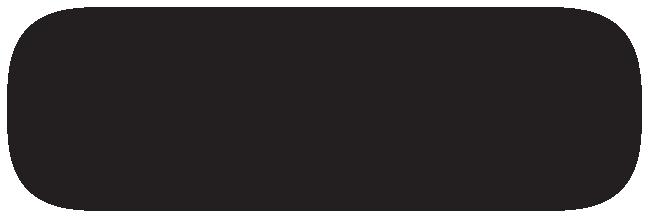
Calgary, Alta.
Graham Currie immigrated from the United
Kingdom in 2010, where he earned a bachelor’s degree in building surveying and a master’s in project management before taking on his first construction role.
In Canada, he got his start at Ledcor as a junior project coordinator on The Bow Project – a $1.6 billion office tower in Calgary.
Since then, he has worked on flagship projects across Western Canada, gaining knowledge in Edmonton and Saskatoon
before returning to Calgary, where he is the regional manager of the Ledcor’s building construction branch.
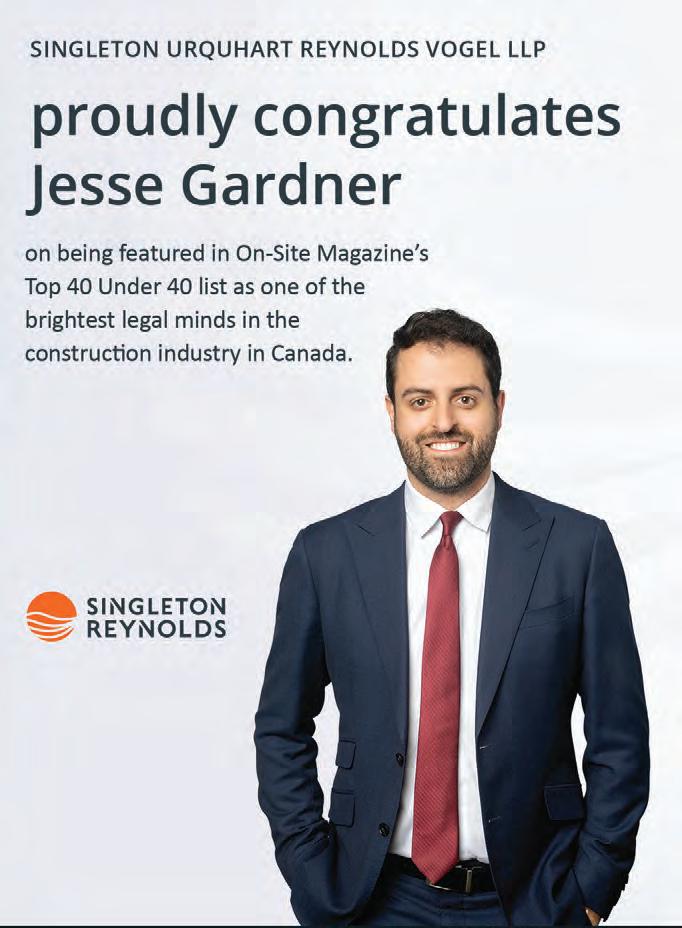
With his leadership and experience, the Calgary Building Construction branch recently opened a new office downtown and is on track for its most successful year yet.
HAMMAD CHAUDHRY National Director, Digital Project Delivery EllisDon Corporation
Calgary, Alta.
Hammad Chaudhry is a pioneer in digital construction technologies in Canada. EllisDon’s national director of digital project delivery overseeing the company’s strategic approach to digital construction, he started his career as an architectural technologist.
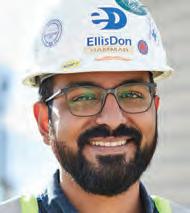

In 2014, he joined EllisDon as the project BIM coordinator for Brookfield Place Calgary, spearheading the project’s
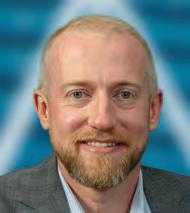

flintcorp-mag-ad-quarter-page-nov-2022-vert.pdf 1 2022-11-17 10:19:55 AM
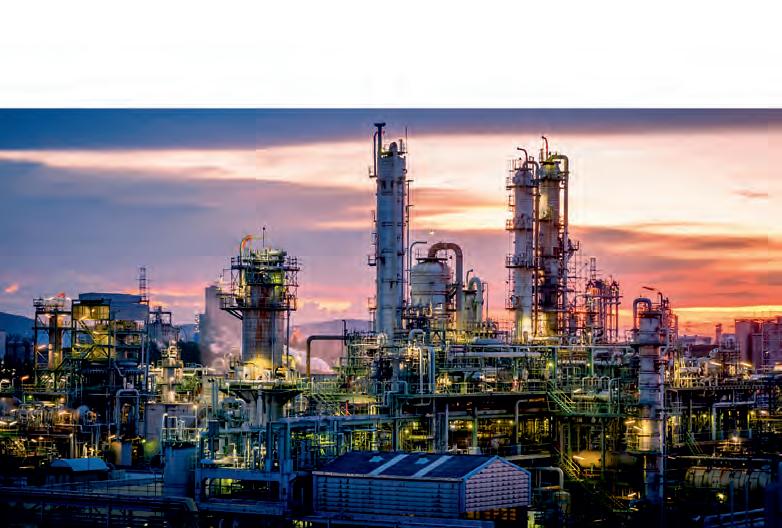
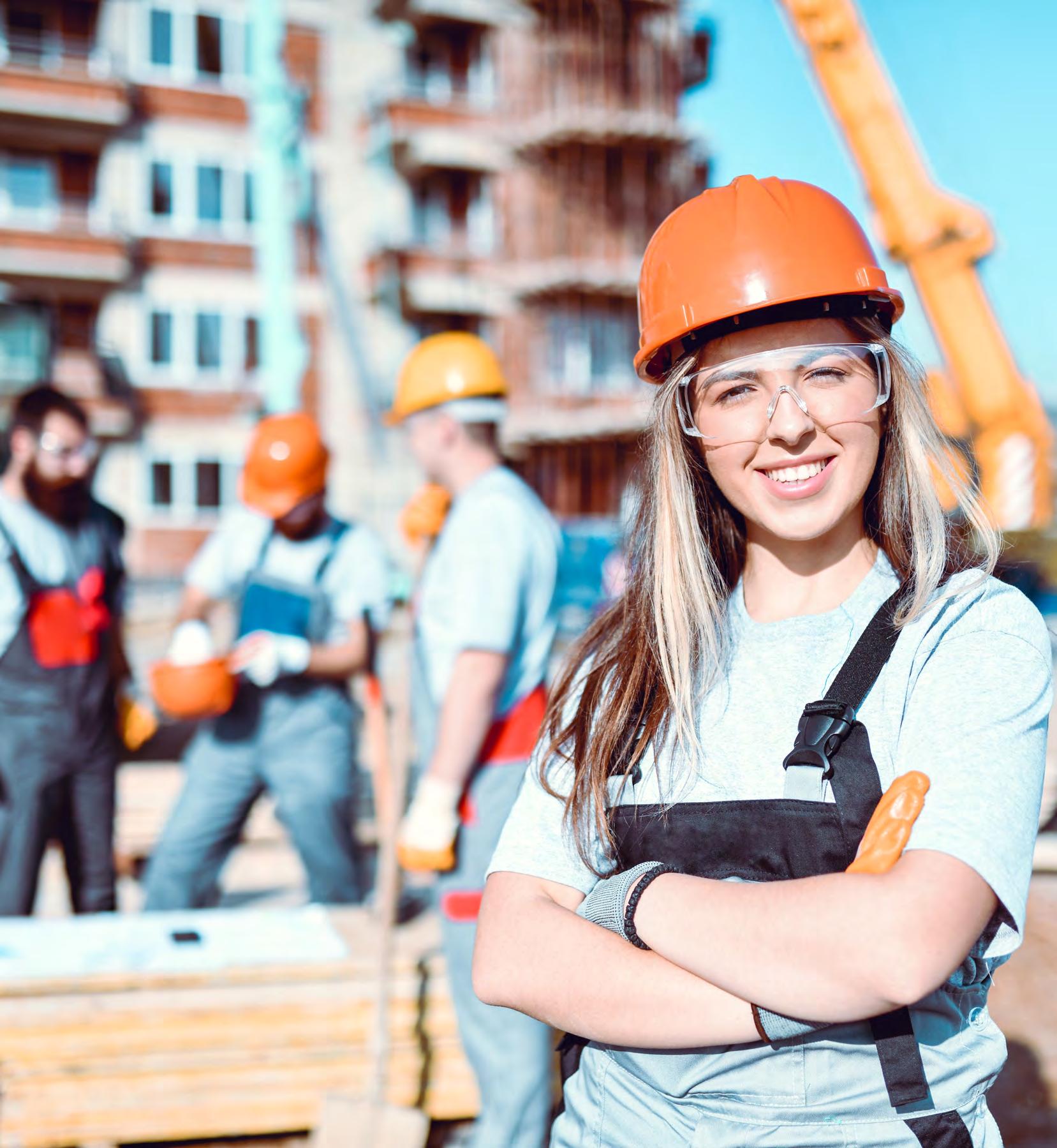
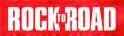
VDC processes, creating and maintaining the BIM requirements, and managing the construction models, field layout strategy, and interference and clash coordination.
In 2017, he was promoted to VDC manager for Western Canada where he managed and executed BIM and VDC on over $3 billion of construction projects. Today, he focusses on advancing EllisDon’s business by integrating and digitizing project delivery using the latest digital tools and solutions.
INDER MANNPresident & CEO
Mann Group Surrey, B.C. Inder Mann has been a driving force at the Mann Group for nearly two decades, growing the company from four people to a 50-person team. Along the way, he has established several vertical integrations and acquisitions, developing a civil services team, acquiring LifeTec Construction Group and developing a mortgage investment corporation known as Aventus Capital Corp.
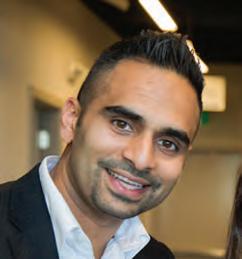
He began his career at Mann Group in 2004 with involvement in every part of the operation. His journey provided him with hands-on experience running and leading every function of the construction and development process, from financing, development planning, permitting, estimating, project management, sales, property management, and more. In 2016, he became president and CEO of the company. Throughout his career, he has demonstrated foresight, making critical business decisions and developing the company through strong vertical integrations.
JANICE CHUANG
Vice-President, Infrastructure Investments
Ledcor Industries Inc. Vancouver, B.C. In 2015, Janice Chuang joined Ledcor as its treasury manager, quickly building a solid understanding of Ledcor’s diverse business lines and successfully deliver-
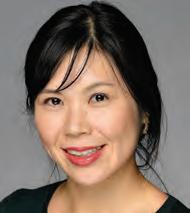
ing enterprise-wide and division-specific financing solutions. In January of 2021, following a succession of expanding roles and responsibilities, Chuang was promoted to vice-president of infrastructure investments at the company, where she leads the financing strategy for Ledcor’s infrastructure pursuits.
Her previous experience provided her with insights into construction financing, including for the construction of the Vancouver Harbour Flight Centre, a float plane terminal project that redeveloped the Coal Harbour area ahead of the Vancouver 2010 Winter Olympic Games.
A member of Ledcor’s Executive Inclusion and Diversity Council, Chuang has also represented the company on the board of Bringing Woman Together, a not-forprofit organization empowering women to network, grow and develop, volunteering as a mentor for others.
JASON HERD CEO/Founder Tradetraks Inc. Hamilton, Ont.
Jason Herd is a disruptor in the construction software space. Starting in the electrical field at 16, Herd was one of the first youths enrolled in the Ontario Youth Apprenticeship Program in its inaugural year and has been on a fast track ever since. He completed the two-year electrical engineering technician program at Mohawk College in 18 months, was licensed at the age of 21, and by the time he was 29 he managed the planning, estimating, and negotiations of the contract for Tim Hortons Field, home of the Hamilton Tiger-Cats.
Under his direction as vice-president and director of business development, Fairway Electrical Services grew from $3.5 million to $20 million, landing it among Canada’s fastest-growing companies list. When he saw gaps in operational processes, he turned to technology, founding Tradetraks, a purpose-built SaaS platform built on the core pillars of running a successful trades business: operations, finance, health and safety, and communication.
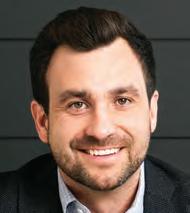
JEAN-FRANÇOIS BERTRANDPELLETIER Vice-President Technologies and Client Experience
CREO Solutions Montreal, Que.
Jean-François Pelletier, one of the co-founders of CREO Solutions, aims to help owners, developers and contractors implement technologies that help them reach operational excellence through data-driven management and continuous improvement.
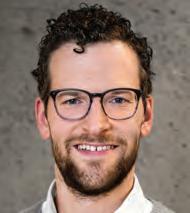
The mechanical engineer has spent the past four years building CREO Solutions to help its clients mitigate risks through the use of technology. Eminently conscient of the challenges faced in change management, he makes use of personalized guidance and education to assist with projects deploying new and innovative technology. He has also collaborated with academic institutions, such as University of Quebec in Montreal, to host conferences and share best practices in data and information management.
To date, Pelletier has implemented project management information systems on such notable projects Montreal’s mega hospital, CHUM, and Quebec City’s tramway system, while also streamlining and optimizing document management procedures for the Montreal airport.
JESSE GARDNER Partner
Singleton Urquhart
Reynolds Vogel LLP
Toronto, Ont.
A partner in the Construction and Infrastructure Practice Group at Singleton Reynolds, Jesse Gardner advises a wide variety of construction and infrastructure clients on dispute management, including court proceedings, mediation and arbitration.
As a member of the Professional Services Committee at the firm, Gardner has taken a lead role in the recruitment of students and associates and was instrumental in developing the firm’s summer
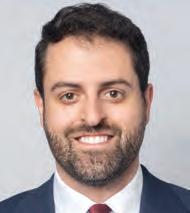
Bow River Bridge Calgary, AB
We Transform Infrastructure

We are proud of Octavio Flores – in 40 under 40 – and all of our outstanding employees. Congratulations to the other recipients of 40 under 40. Our diverse team shares their expertise to build stronger communities where we live and work.
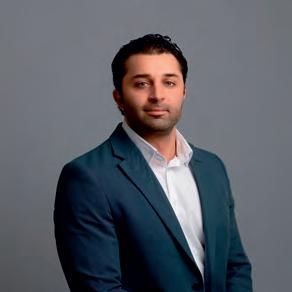
Flatiron partners with clients across Canada to deliver innovative solutions to infrastructure challenges.
student program. He has also led the firm’s harassment committee and has assisted in presentations relating to equity and diversity.
Gardner is a frequent speaker on topics related to the construction law industry at legal and educational events. He has been recognized by Who’s Who Legal and Benchmark Canada as a “litigation star.” He is also featured as a leading construction lawyer in Lexpert Globe and Mail reports, including the special report on infrastructure.
JORDAN CLOUTHIERDistrict Manager
PCL Construction Regina, Sask.
Jordan Clouthier began his PCL career as a field engineer in Ottawa before quickly progressing to project coordinator and then project manager, working on many unique and challenging projects while gaining valuable experience in various sectors, including healthcare, aviation, retail, high security, and commercial and institutional construction.
A civil engineering graduate from Carleton University, he joined PCL in 2008 and has since earned his LEED Green Associate designation.
In addition to working on such major projects as the Bayshore Shopping Centre, Mattawa Plains Compound, and the Ottawa Macdonald Cartier International Airport, he has been recognized at PCL through the company’s High Potential Development Program, which typically selects fewer than 10 participants out of the more than 4,500 employees in PCL’s operations group.
JOSEPH GVILDYS
Cement Industrial Director, Western Canada
Lafarge Calgary, Alta. Passionate about the intersection between manufacturing and sustainability, Joseph Gvildys has illustrated that sustainability and profitability can go hand in hand. In Ontario, Gvildys
led two major sustainability initiatives that both resulted in carbon dioxide reductions: developing and implementing cement kiln dust (CKD) as an addition to cement to lower the CO2 associated with the product; and leading the conversion of an idle ball mill into a slag grinding operation, which replaced a portion of cement.
In his current role as cement industrial director, he is part of a team working to identify creative uses for captured CO2 and illustrating that the possibility of full carbon capture and sequestration is very real.
In 2021, after a series of promotions in cement distribution, including managing all cement terminals in Western Canada and the Pacific Northwest in the U.S., he was promoted to his current role, and is now responsible for all Lafarge cement plants and grinding stations in the region, overseeing a team of 350 people.
KATIE
and Calgary Women in Energy (CWIE), she is an influencer with peers and customers.
KEVIN BRENNAN General Manager
Cavanagh Concrete Ltd. Carleton Place, Ont.
Kevin Brennan started his career in the concrete field at the age of 17, developing experience as a labourer and dispatcher with Lafarge Canada. He rapidly climbed into higher positions within the organization while attending the University of Ottawa fulltime as a student-athlete, completing his honours bachelor of commerce in 2010.
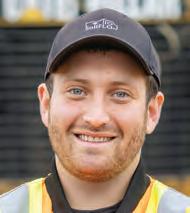
DEMPSTER
Vice-President, Industrial Relations and Development Graham Calgary, Alta.
A key member of Graham’s senior leadership team, Katie Dempster leads the business relations and development function of Graham’s industrial division, with a focus on new business acquisition as well as supporting customer retention and organic growth opportunities.
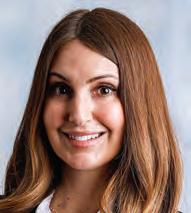
Adept at supporting customers in adopting collaborative contract models, she has helped her division build a backlog of business of over $2 billion while achieving $1.2 billion in annual revenues across operations in Western Canada and Ontario, as well as Ohio and Pennsylvania.
She is a member of Graham’s Sustainability Committee and has brought her unique perspective on how energy producers can be part of Canada’s green future via energy transition and greenhouse gas reduction project development. A participant in various industry forums and networking events, including the Construction Owners Association of Alberta (COAA), Canadian Heavy Oil Association (CHOA),
At Lafarge, he served as the project manager for the MHLH Helicopter Support Facilities in Petawawa, Ont., and concrete project manager for the Lansdowne Park Stadium redevelopment project, followed by the Ottawa Light Rail Transit tunnel.
In 2017, he joined Cavanagh Concrete as operations manager, earning a promotion to general manager in February of 2020, and taking responsibility for all day-today ready-mix operations of the business. In addition to implementing several new supplier partnerships, he has also led the design of a new concrete production facility site, which is entering the construction phase in the coming months.
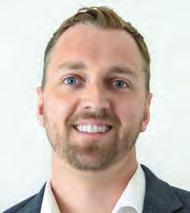
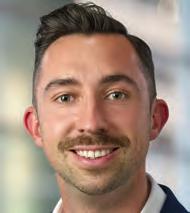
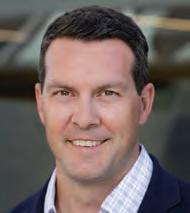
KEVIN GOLDBERG President
SoilFLO
Toronto, Ont.
Kevin Goldberg began his career working for a company handling liquid solidification on subway tunnel spoils. After experiencing the pain of handling disposal paperwork, the Western University environmental engineering grad began exploring a venture to solve this problem. In 2019, he and fellow engineer Adam Matyja started SoilFLO, software that enables users to manage the movement of excess material across construction projects.
The company has since expanded inter-
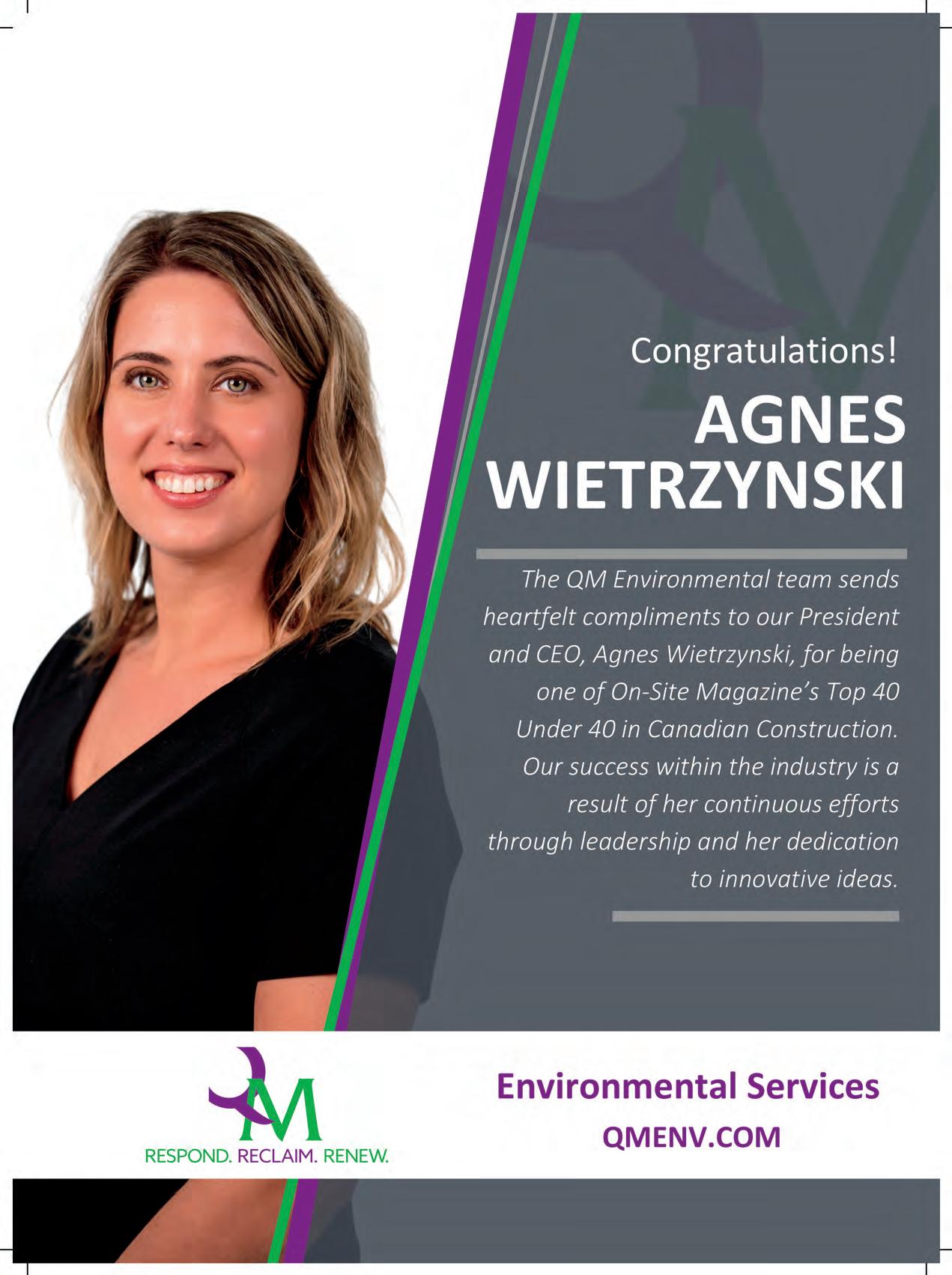
nationally, with customers in the United States, United Kingdom and Australia in addition to more than 100 customers in Canada, including three LRT subway projects in Ontario.
A disruptor in the earthworks industry, Goldberg’s work has brought a new layer of environmental control to an industry that otherwise did not exist. Quarries and other various rehabilitation projects across Canada can now confidently import soil with a lower risk of contamination.
MI KIM Senior Commercial ManagerJacob Bros Construction South Surrey, B.C.
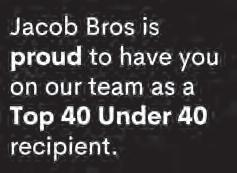
A leader of equity and diversity initiatives and a devoted supporter of women in construction, Mi Kim is working to ensure that programs impart

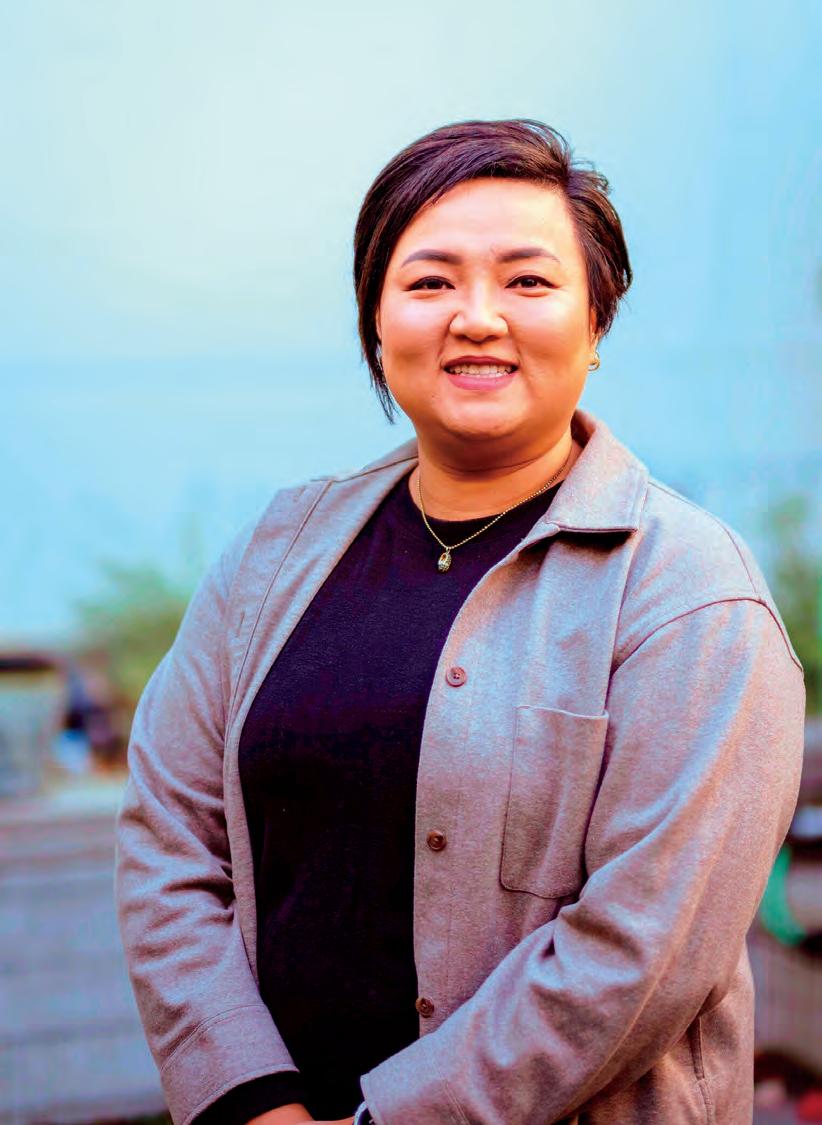
meaningful change at companies and drive lasting impacts on the industry.

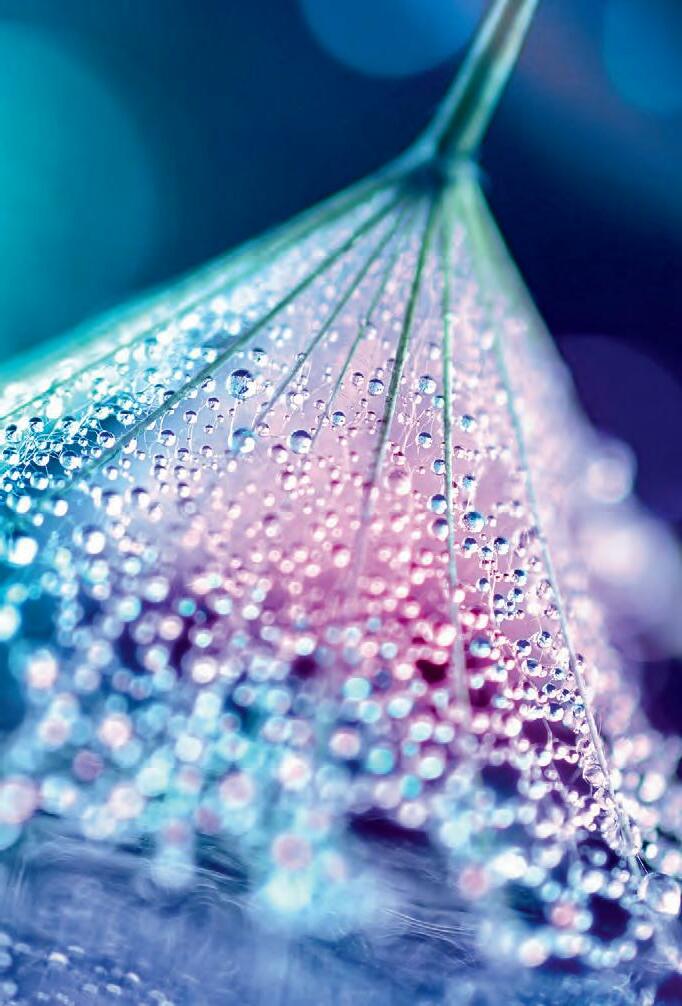
The senior commercial manager for Jacob Bros Construction, a multi-discipline general contractor primarily focussed on heavy civil and building construction, is a people person with the ability to deliver effective and positive change in commercial management, governance and contract management.
In addition to mentoring engineers within her own company, she has spent time facilitating growth of young female engineers through the Women in Engineering group at the University of British Columbia, and earlier in her career, served as an active operations recruiter at university and college career fairs.
MILAN MANNPresident, Real Estate Development and Construction BM Group of Companies
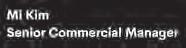
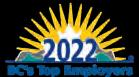
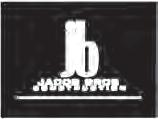
Coquitlam, B.C.
In addition to leading BMG’s real estate division and its current development pipeline of 16 active projects, Milan Mann is also navigating the land redevelopment process at the family-owned firm, from concept through to sales and construction with the company’s general contracting and project management company, Penmat.
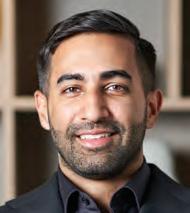
BM Group is a family-owned and operated portfolio of companies based in British Columbia, and Mann has been pivotal to the growth and acquisition strategy which has led to the group now consisting of 16 companies. The company is supported by a team of over 400 and has additional offices in the U.S. and India.
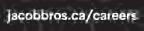
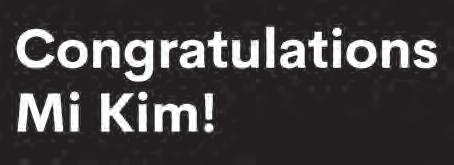
your projects forward, in Canada and everywhere else you do business.
Diversity has long been championed at the minority-owned corporation, providing opportunity for those in need of a first chance, and sometimes even a second, to get a foothold in the construction industry.
OCTAVIO FLORES Area Operations ManagerFlatiron Construction Vancouver, B.C.
Moving to Canada in his youth, Octavio Flores soon developed an interest in the construction industry. At 19, he purchased his own equipment and began working on small commercial and residential projects before rising through the corporate construction ranks, winning numerous awards along the way. Today, Flores holds an executive position with Flatiron where he leads a team of over 30 professional staff and oversees projects across Western Canada.
Flores is recognized for his decades of experience in complex projects (worth up to $17 billion) and management of alternative and traditional delivery contracts. He is most notably accomplished in the construction and management of bridges, light rail and high-speed train systems, hydroelectric dams, highways, freeways, airports, tunnel boring, and open surface mining.
Outside of Flatiron, Flores is actively involved in many industry associations. He speaks at his university, volunteers with humanitarian events, and engages his network to help build affordable housing for families in need.
PARM DHALIWAL CEO

Steelix
creating homes that will make a lasting impression on the neighbourhoods where the company builds. For its Harlo project in Surrey, B.C., he worked with the municipality to increase the density to rezone an initial project of 30 townhomes into 132 much-needed condos. Currently under construction, the project is on track for occupancy by the summer of 2024.
Wanting to get homeowners’ feedback to influence future projects, Dhaliwal has created an online survey to understand their needs better. For every survey response, a tree is planted in B.C. to give back to nature.
Developments
Surrey, B.C.
As the company visionary for Steelix, Parm Dhaliwal is focused on
Using a structured methodology, Dhaliwal creates KPIs for his team to help understand roadblocks and celebrate wins, which he says is fundamentally how the team grows and improves from each challenge.

Graham Currie Regional Manager, Construction
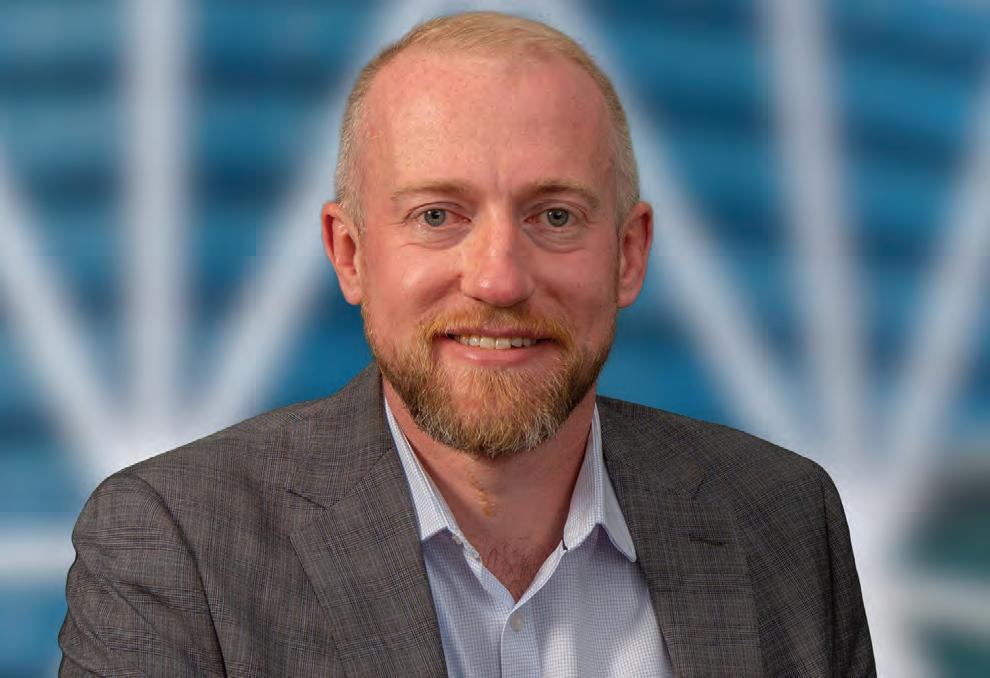
Quattro Constructors
Vancouver, B.C.
Over his 20 years of experience in construction, Rick Morrison has held many roles, including president, area manager, project manager, superintendent, field engineer and estimator, with experience that spans a range of construction projects, including dams, bridges, highways, water and sewer construction, and municipal development.
In the three years since starting Quattro Constructors with only a team of two, the company now numbers more than 100 employees and averages five or more major infrastructure projects a year.
Morrison, a registered professional engineer in B.C. and Alberta, is known as a dedicated and results-oriented manager with an ability to listen, understand and address client needs. Among the key projects that he can count on his resume are the Highway 8 reinstatement, Site C generating station and spillway, Ruskin Dam Generating Station, and the Donald Bridges and Approaches project.
ROB CLIFFORD Co-Founder and Chief Technology Officer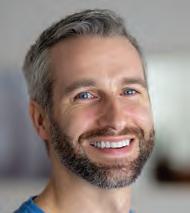
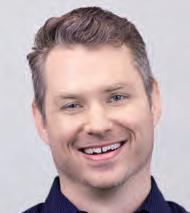
Salus
Vancouver, B.C. Rob Clifford, co-founder and CTO of Salus, has a passion for developing people as well as software. At Salus, he has built and led a team of engineers in bringing to life a health and safety software platform that mirrors industry best-practice workflows with a high degree of usability.
Despite a lack of prior ties to the construction industry, Clifford saw merit in an idea presented by company CEO, Gabe Guetta, who was running a large high-rise window installation company at the time. Facing challenges around managing his own company’s safety, Guetta approached Clifford for a possible solution. Immersing himself into the industry, Clifford went to
work to gain a deep understanding of the regulatory requirements, the processes and the challenges faced by construction companies and their employees when it comes to safety, harnessing that new knowledge into a software platform that solves real challenges for the industry it serves.
ROBERT
talent. After observing Canadian contractors recruit from Ireland and the U.K. and having the first-hand experience of assisting his brother relocate to Canada as a civil engineer, Ruairi set out to build an agency that would specialize in matching global talent with Canadian construction firms.
BARTHPartner and Senior Vice-President, Construction CentreCourt
Toronto, Ont.
Robert Barth has more than 17 years of high-rise residential construction experience, joining CentreCourt in 2014. At CentreCourt, he has played an instrumental role in the creation and growth of CentreCourt Construction, the company’s construction management function, making significant contributions to many of the company’s 19 completed and ongoing developments, bringing deep expertise in the development and oversight of construction budgets, schedules and project teams.
He currently oversees five active construction projects in the Greater Toronto Area, totalling over 2,350 units and $1.5 billion of development value. He is actively involved in the GTA real estate community and is a committee member of the Hold’em for Life Charity Challenge, which is dedicated to raising money for cancer research. The organization has raised more than $42 million since 2006 to be distributed to leading local cancer research centres.
RUAIRI SPILLANE Founder and Managing DirectorOutpost Recruitment and Moving2Canada
Vancouver, B.C. Ruairi Spillane moved to Canada from Ireland in 2008 for an employment opportunity in finance. After the global financial crisis, he identified that Canada was experiencing a labour shortage in construction at a time when his native country was exporting construction
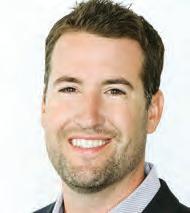
In 2012, he launched his two companies, Outpost Recruitment and Moving2Canada, with the symbiotic goals of recruiting construction talent, both local and international, while enabling newcomers to navigate the immigration and settlement process by themselves.
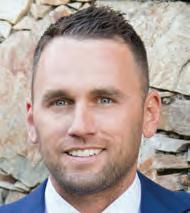
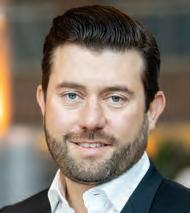
Since its founding, Outpost Recruitment has successfully placed hundreds of workers from around the world on some of Canada’s largest building and infrastructure projects. The award-winning Moving2Canada website provides free online resources to help job seekers, generating more than 500,000 visits monthly.
RYAN JOHNSTON President
West Coast Pile Driving (2013) Ltd.
Maple Ridge, B.C. Ryan Johnston began his career as a general bridgeman/pile driver with various pile driving companies in the Lower Mainland of B.C. He worked his way up through the industry to become a top crane operator and the president of his company, West Coast Pile Driving. Taking on the leadership role in the company, Johnston not only works directly in the field operating the company’s heavy equipment and machinery, but he also handles office tasks including estimating, project management, invoicing, and business development.
His company, which is a certified Aboriginal-owned business, offers a variety of pile driving and shoring services, recently expanding capabilities to include ground-release drilling. Specializing mainly in sheet piling, Johnston’s company is outfitted with top-of-the line sheet pile installation and pipe pile installation equipment featuring several Junttan and ABI Piling Rigs, and has become known their ability to serve, with excellence, large
general contractors and work on large projects around B.C.

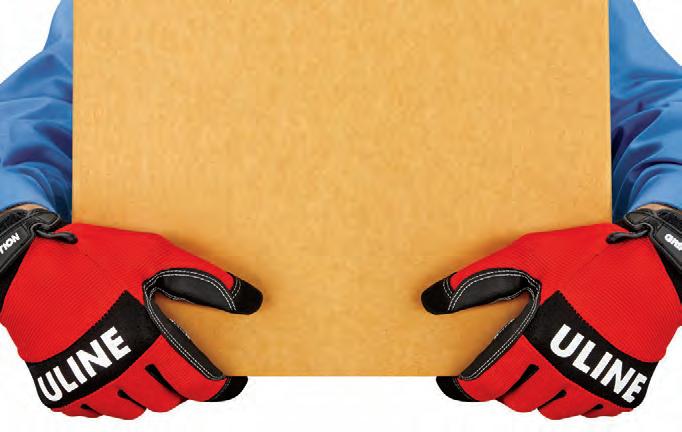


Threeosix Industrial Services Inc. Saskatoon, Sask.
As a civil engineering technologist with an Applied Science Technologist (AScT) designation, Scott Longmuir has over 17 years of hands-on experience in the construction, mining and engineering sectors. His entrepreneurial spirit began in the early 2000s in Alberta where he worked to create, develop and operate business interests in the engineering and construction services space.
In 2016, he launched Threeosix Industrial, a company focussed on being an industry-leading contractor in the industrial, mining and energy sectors with
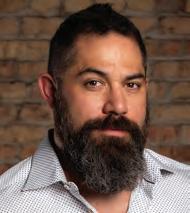

strategic operations and partnerships across Canada. The company, which now has more than 250 employees, has a goal of providing a professionally managed and safety conscious approach to construction, maintenance, fabrication and mining.

Longmuir strongly believes in creating opportunities for community members local to their projects, and this is evidenced by the company’s commitment to diversity, inclusion and capacity-building within the communities in close proximity to the areas in which it operates.
SEAN LAL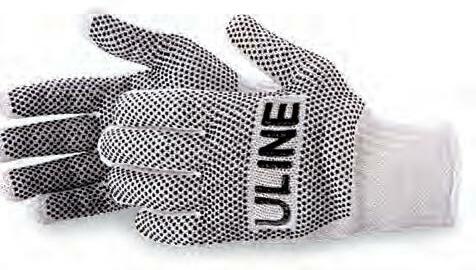
Legal Consultant/Senior Commercial Advisor Systech Infrastructure Inc. Toronto, Ont.
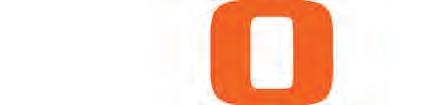
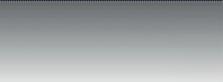
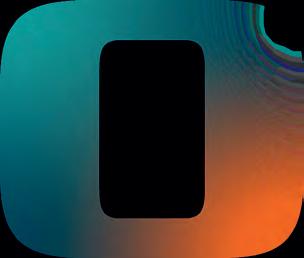
Instrumental in building a collaborative relationship with contractors on major Metrolinx subway projects, Sean
22_003849_OnSite_DEC_CN Mod: October 20, 2022 5:51 PM Print: 11/08/22 8:34:58 AM page 1 v7
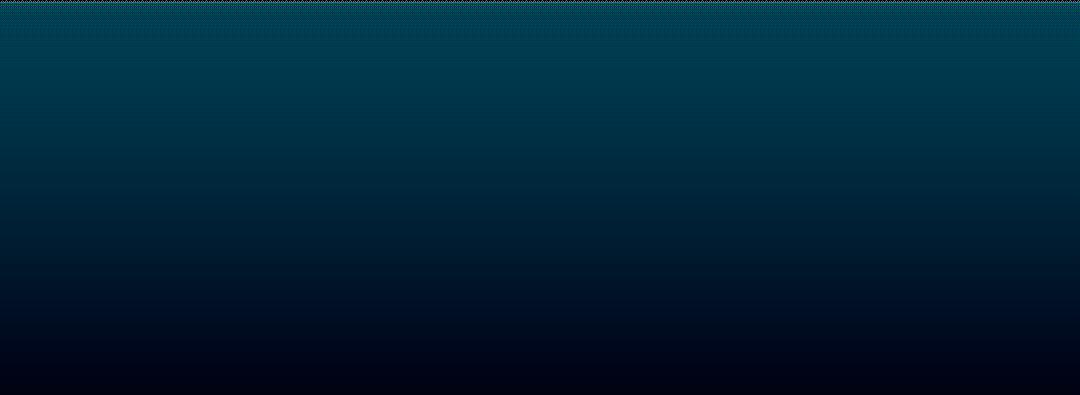
Lal is a qualified solicitor in Ontario and New York State with more than 10 years of experience in legal, construction, commercial and contracts management.
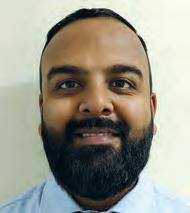
For the past five years, his focus has been on Toronto’s Eglinton Crosstown LRT and Finch West LRT projects with Aecon Construction, and the new Ontario Line subway, new Younge-North subway, and the Scarborough subway extension projects.
Prior to that, he was project counsel on the Waterloo LRT project, another large LRT project that was completed in the Ontario.
Passionate about mentoring new lawyers and engineers in construction, he dedicates time each week to mentoring and discussing the commercial thought process required in the day-to-day activities on large construction projects, including how to take large complex issues and convey them simply and efficiently.
Director of Construction Chard Development Ltd.
Vancouver, B.C. Currently the director of construction for Chard Development, an urban real estate development firm based out of Vancouver, Shane McKernan is a seasoned construction professional with a successful career path as a Red Seal carpenter, project manager and Professional Quantity Surveyor (PQS). He has been working in B.C.’s lower mainland for over 15 years.
Since 2012, as a PQS, he has consulted on over $963 million in construction costs. In his project management capacity in that time, he has worked on commercial office and tilt-up buildings, townhomes, multi-family residential and multi-tower high-rise residential construction projects with combined construction costs in excess of $600 million.
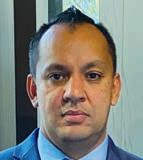
He was the first student member of the CIQS B.C. Chapter, and has held positions as chapter treasurer, vice-president and president. He is also a past observer of the organization’s national board, where he helped cocreate a Young Quantity Surveyor (YQS) community within the CIQS framework.
VENUS GARG Vice-President, Program Management BL AECOM Canada MarkhamOnt.
A collaborative, versatile and innovative leader, Venus Garg has built a wealth of experience in the transportation infrastructure space leading large multi-disciplinary teams of managers, engineers, field coordinators and other staff to deliver world-class transportation solutions. He leads complex infrastructure pursuits on both the advisory side and design-builder side, procured under various delivery models like P3, Alliance, Program Delivery Partner and Progressive Design-Build (PDB).
His work as capture lead at AECOM has significantly improved the company’s use of its global talent, as well as increased its knowledge base and application of collaborating contracting methods which are relatively new to Canada.
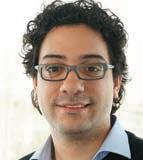
With his strong work ethic and collaborative approach, he has been key to the successful delivery of such critical pursuits as the VIA High Frequency Rail, QEW/ Credit River Bridge, Union Station, GO Expansion delivery partner, Scarborough Subway Extension and the VivaNext bus rapid transit project.
YURI BARTZIS
Innovation Director of Operations, Canadian Building Operations/ Quebec Building Operations
Pomerleau
Mississauga, Ont.
WILLIAM DONNELLAN Principal CEO of Construction
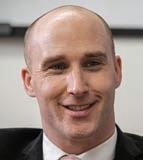
IRL Construction Ltd. Vancouver, B.C. William Donnellan grew up in the building trades. Having qualified as a carpenter in Ireland, and coming from a family of tradespeople, he has spent the past 14 years gaining direct experience in all areas of construction in Canada.
Under his leadership, IRL Group has established a solid reputation for work in concrete, framing and wood tackling commercial and residential projects throughout B.C. This past year, the Independent Contractors and Businesses Association (ICBA) in B.C. recognized him with the 2022 Gord Stewart Workplace Health and Safety Innovation Award for his company’s use of an intelligent illumination safety system that makes workers more visible on a site.
In 2017, the Vancouver Regional Construction Association presented Donnellan with its U40 Excellence in Construction Award in recognition of him growing IRL from its starting point of three employees in 2009 to more than 70 working on projects across Canada.
On a parallel path to his construction company, Donnellan has also built up a hospitality division, which has benefitted from his skills in construction as it developed five Irish pubs in Vancouver.
An advocate for innovation in construction, Yuri Bartzis is a mentor, leader, influencer and strategist. After several years of gaining site experience supporting construction projects and bringing BIM to a national player in the market, Bartzis transitioned to Pomerleau Construction as an innovation manager. Three years later, he became one of the company’s directors of innovation operations, leading a team of over 50 VDC coordinators throughout Canada.
A virtual design and construction specialist himself, he participated in building the innovation team at Pomerleau and continues to be involved in adopting new technologies in construction.
In 2019, Pomerleau, and Bartzis’ team, was recognized by Building Transformations (formerly CanBIM) with its General Contractor’s Award for the development of the Willow Square Continuing Care Centre long-term care facility in Fort McMurray, Alta.
Bartzis is also a sought-after speaker on the topics of BIM and digital construction tools and techniques and sits on several industry think tanks and advisory committees.
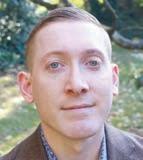
MEET JUDGING PANEL
President, SitePartners
Manager, Innovation and Public Affairs, Ontario General Contractors Association
Executive Director, Residential & Civil Construction Alliance of Ontario
Director of Construction Chard Development Ltd.
Vancouver, B.C. Currently the director of construction for Chard Development, an urban real estate development firm based out of Vancouver, Shane McKernan is a seasoned construction professional with a successful career path as a Red Seal carpenter, project manager and Professional Quantity Surveyor (PQS). He has been working in B.C.’s lower mainland for over 15 years.
Since 2012, as a PQS, he has consulted on over $963 million in construction costs. In his project management capacity in that time, he has worked on commercial office and tilt-up buildings, townhomes, multi-family residential and multi-tower high-rise residential construction projects with combined construction costs in excess of $600 million.
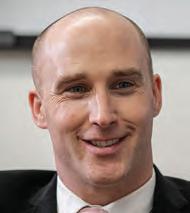

He was the first student member of the CIQS B.C. Chapter, and has held positions as chapter treasurer, vice-president and president. He is also a past observer of the organization’s national board, where he helped cocreate a Young Quantity Surveyor (YQS) community within the CIQS framework.
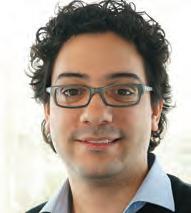
Ont.
A collaborative, versatile and innovative leader, Venus Garg has built a wealth of experience in the transportation infrastructure space leading large multi-disciplinary teams of managers, engineers, field coordinators and other staff to deliver world-class transportation solutions. He leads complex infrastructure pursuits on both the advisory side and design-builder side, procured under various delivery models like P3, Alliance, Program Delivery Partner and Progressive Design-Build (PDB).
His work as capture lead at AECOM has significantly improved the company’s use of its global talent, as well as increased its knowledge base and application of collaborating contracting methods which are relatively new to Canada.
With his strong work ethic and collaborative approach, he has been key to the successful delivery of such critical pursuits as the VIA High Frequency Rail, QEW/ Credit River Bridge, Union Station, GO Expansion delivery partner, Scarborough Subway Extension and the VivaNext bus rapid transit project.
YURI BARTZIS
Innovation Director of Pperations, Canadian Building Pperations/ Quebec Building Operations
Pomerleau
Mississauga, Ont.
WILLIAM DONNELLAN Principal CEO of ConstructionIRL Construction Ltd. Vancouver, B.C. William Donnellan grew up in the building trades. Having qualified as a carpenter in Ireland, and coming from a family of tradespeople, he has spent the past 14 years gaining direct experience in all areas of construction in Canada.
Under his leadership, IRL Group has established a solid reputation for work in concrete, framing and wood tackling commercial and residential projects throughout B.C. This past year, the Independent Contractors and Businesses Association (ICBA) in B.C. recognized him with the 2022 Gord Stewart Workplace Health and Safety Innovation Award for his company’s use of an intelligent illumination safety system that makes workers more visible on a site.
In 2017, the Vancouver Regional Construction Association presented Donnellan with its U40 Excellence in Construction Award in recognition of him growing IRL from its starting point of three employees in 2009 to more than 70 working on projects across Canada.
On a parallel path to his construction company, Donnellan has also built up a hospitality division, which has benefitted from his skills in construction as it developed five Irish pubs in Vancouver.
An advocate for innovation in construction, Yuri Bartzis is a mentor, leader, influencer and strategist. After several years of gaining site experience supporting construction projects and bringing BIM to a national player in the market, Bartzis transitioned to Pomerleau Construction as an innovation manager. Three years later, he became one of the company’s directors of innovation operations, leading a team of over 50 VDC coordinators throughout Canada.
A virtual design and construction specialist himself, he participated in building the innovation team at Pomerleau and continues to be involved in adopting new technologies in construction.
In 2019, Pomerleau, and Bartzis’ team, was recognized by Building Transformations (formerly CanBIM) with its General Contractor’s Award for the development of the Willow Square Continuing Care Centre long-term care facility in Fort McMurray, Alta.
Bartzis is also a sought-after speaker on the topics of BIM and digital construction tools and techniques and sits on several industry think tanks and advisory committees.
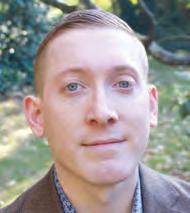
MEET JUDGING PANEL
President, SitePartners
Manager, Innovation and Public Affairs, Ontario General Contractors Association
Executive Director, Residential & Civil Construction Alliance of Ontario
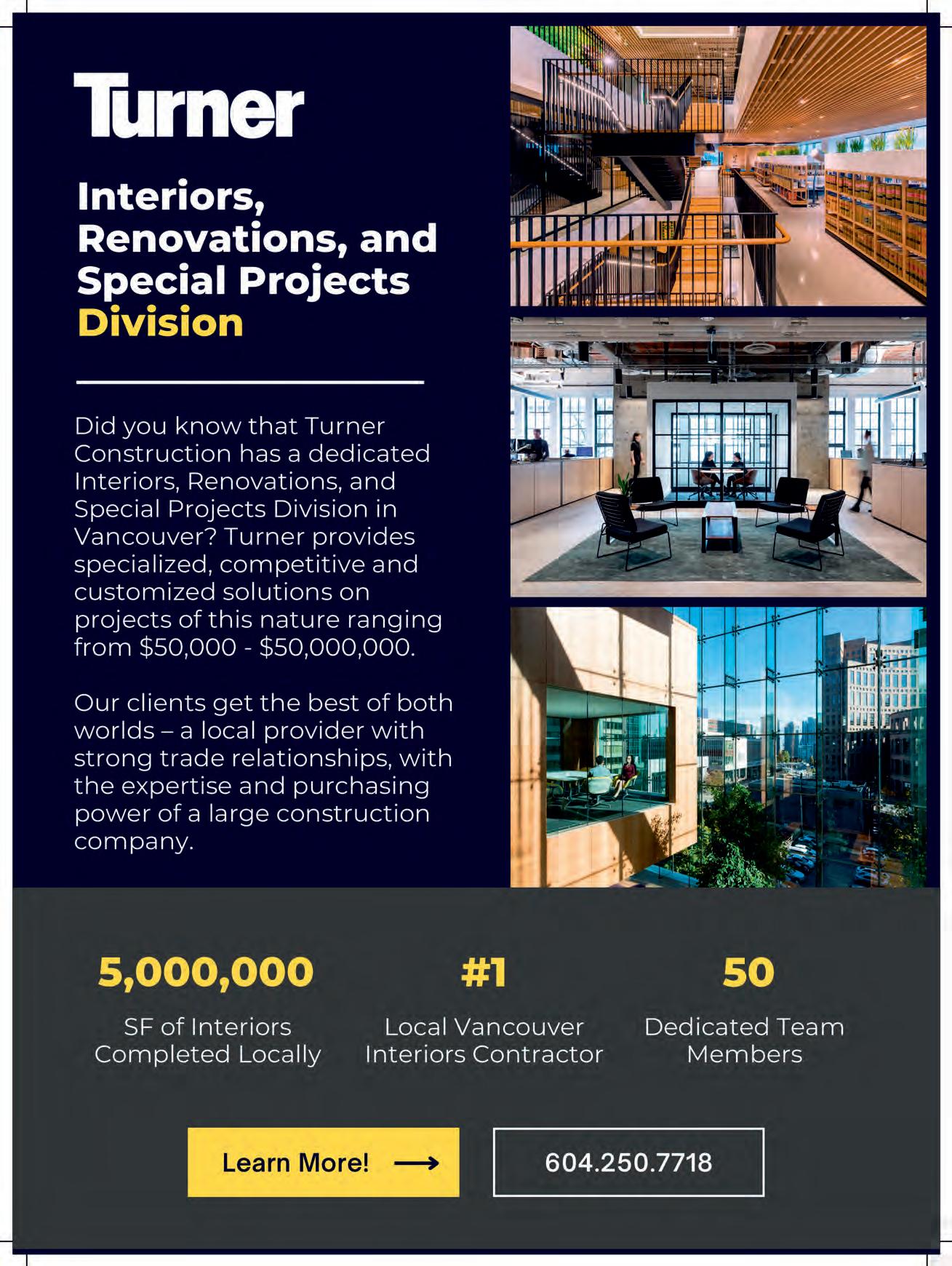

BUILDING BEYOND THE BA SEMENT
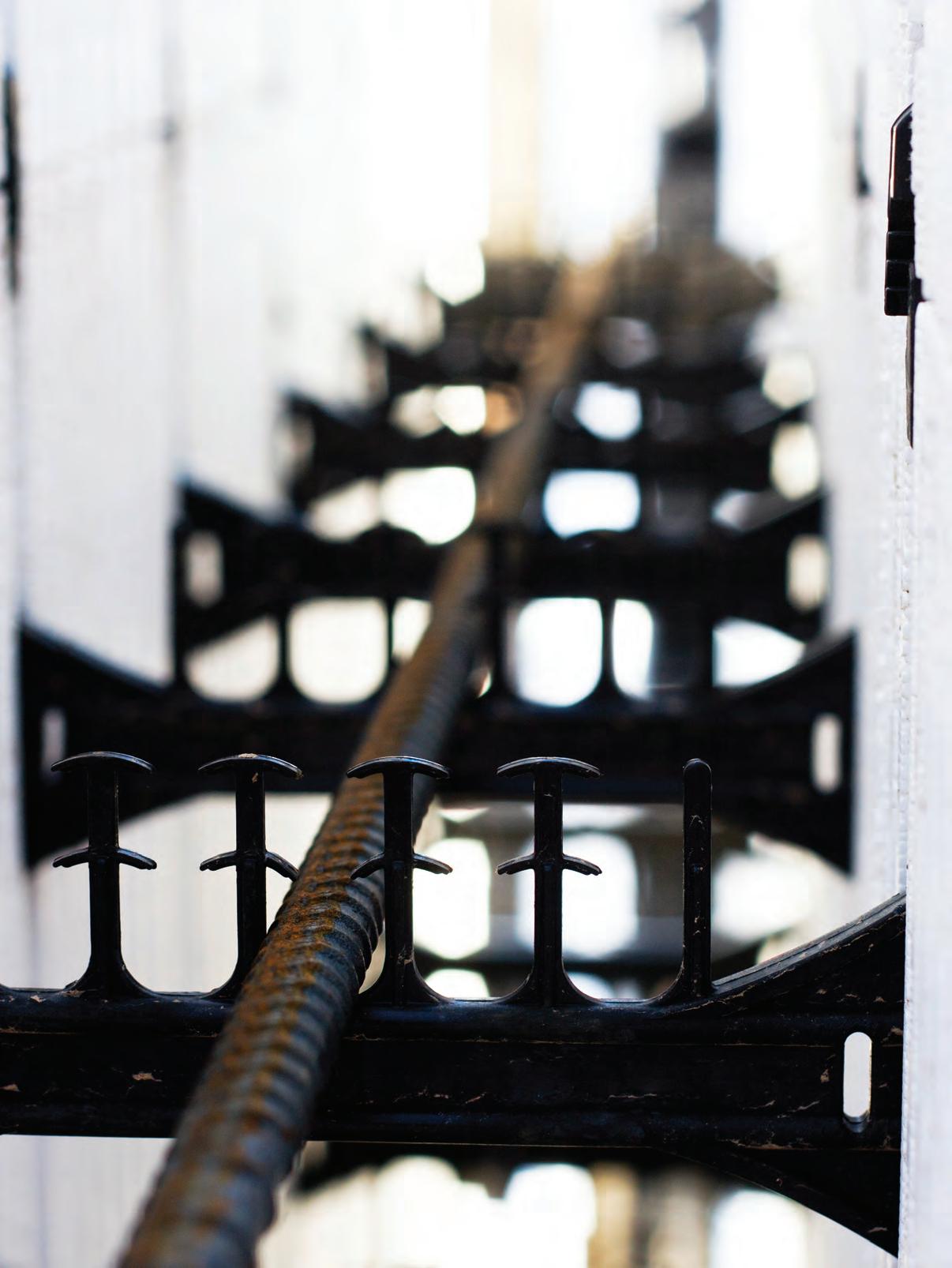

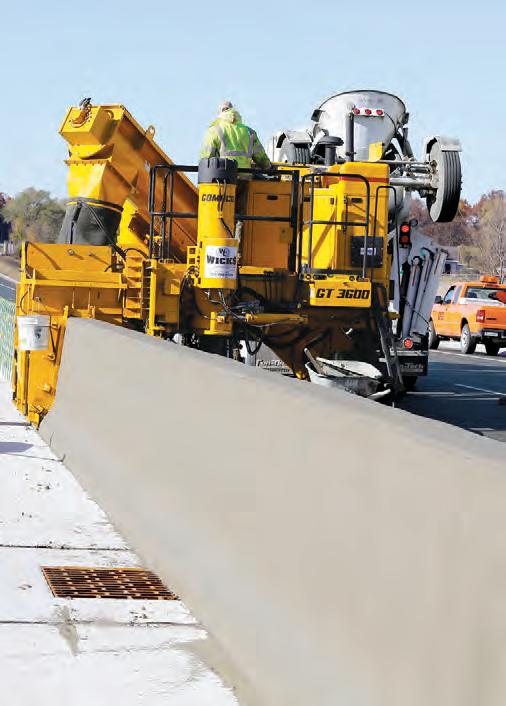
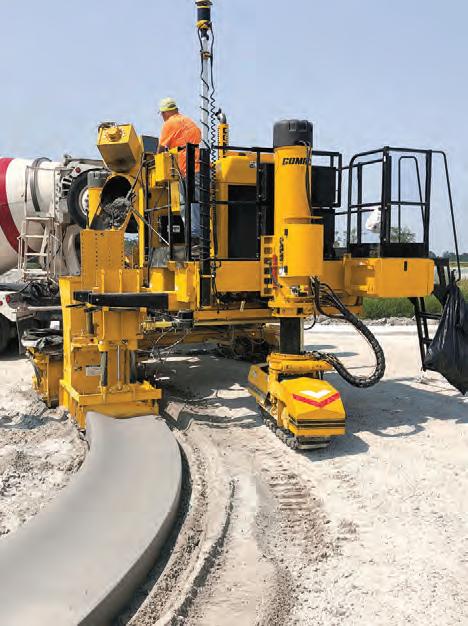
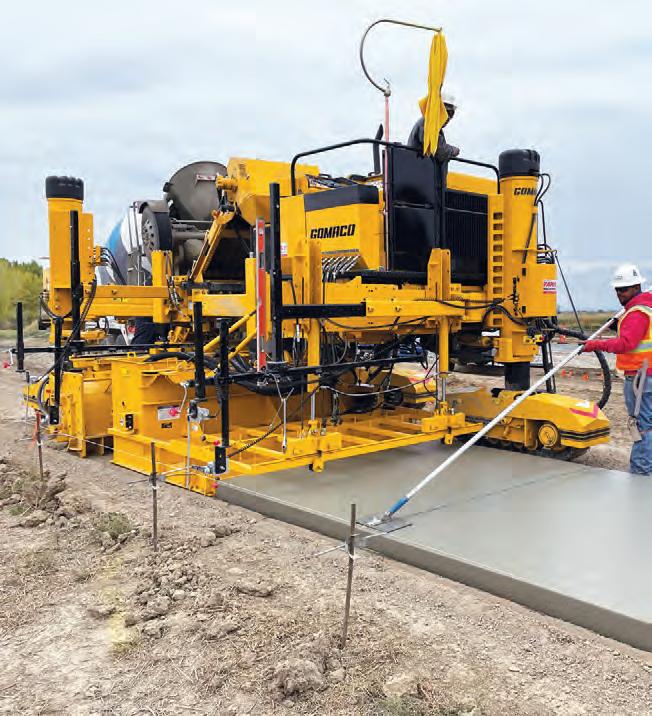


BASEMENT BUILDING BEYOND THE
BY ROSS MONSOURAround for more than 40 years, Insulating Concrete Forms (ICFs) represent a simple solution to achieve many government- and industry-led climate or environmental goals. Among their benefits are air tightness, labour savings, energy efficiency, resiliency, low carbon intensity, and more.
Most ICF systems can be described as two sections of expanded polystyrene insulation connected by a series of plastic ties. These may arrive on a jobsite in block form, or they may be assembled on site. Blocks have interlocking joints on their edges to connect them together to form the structure. Steel rebar is placed horizontally on the webs and then concrete is cast in the form to create a structural wall.
The plastic webs are embedded in the expanded polystyrene insulation and create flanges that the contractor can use to attach exterior and interior finishes. Many ICF companies have specially designed forms for brick ledges and corners.
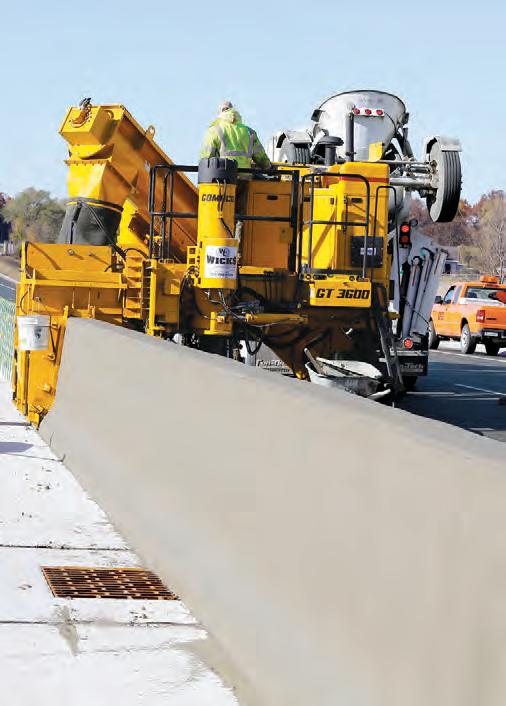
The initial introduction of ICF focussed mainly on residential basements. This was due, in part, to engineering restrictions imposed by building codes. Gradually, the market moved to above-grade residential and commercial construction. As concrete pumping has allowed the ICF universe to expand, today’s ICF industry also serves high-rise buildings, schools, commercial buildings and retirement homes.
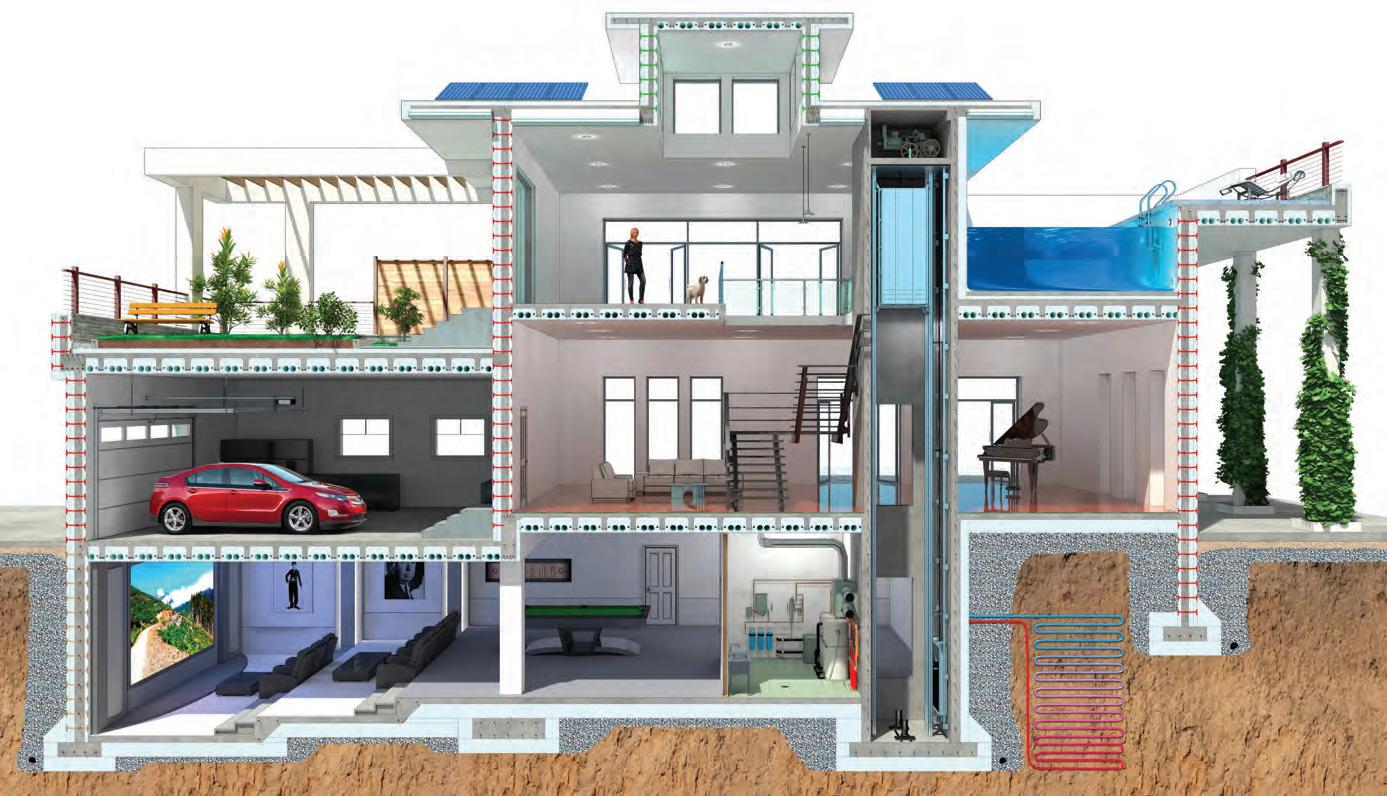
In the Kitchener-Waterloo region of Ontario, more than 80 eight-storey
buildings have been constructed over the past 20 years. The main driver for many of these builds was time. For example, the use of ICF allowed student housing to be constructed and occupied before the next school year. This advantage allowed the owners considerate improvement in obtaining fully occupied residences in a short amount of time.
Another driver is winter construction. Once the ICF shell is constructed, winter heating is often not necessary as the insulated thermal mass often provides sufficient heat to continue the indoor work to complete the building.
The latest edition of the National Building Code (NBC) 2020 has recognized the national standard for ICFs: “ULC

The use of insulating concrete forms has evolved to address many of today’s construction challenges.
S717.1 Standard for Flat Wall Insulating Concrete Form (ICF) Units - Material Properties.” Other relatively recent changes to the NBC allow for interior and exterior attachment to the plastic webs. Tables have been created to outline the type of fasteners and under which wind and seismic conditions they can be used.
Another significant change is that under Part 9, ICF builds will be allowed up to two storeys without additional engineering. Also revised over the past little while is the allowance for the use of 10M rebar rather than 15M, which is lighter and more manageable to use on site.
To support these changes, the Insulating Concrete Form Manufacturers Association (ICFMA) has created a free document, available on its website, that explains the prescriptive designs for residential buildings, and is stamped for all the provinces. All commercial and industrial ICFs must still be designed to Part 4 of the NBC. These requirements are dictated by the “CAN/CSA A23.3 Design of Concrete Structures.”
TALL AND THIN
Reinforced concrete is one of the strongest structural systems for walls, its used in wall that spans vertically between lateral supports allows for a thinner design. Depending on the project design requirements, some multi-storey buildings up to five storeys have been constructed with a 6” (150 mm) concrete core ICF. Other projects, such as box big stores with walls up to 32-foot (9.75 m) in height have been constructed using an 8” (200 mm) ICF. These ICF walls have load bearing capacities that can support any type of floor or roof system.
For large, multi-storey buildings, ICF walls may be designed as shear walls, elevator shafts and interior load-bearing walls. There is a simplicity with the design and installation of an ICF wall system - the insulating form, the reinforcement, and the concrete working together as one in the structural building envelope. Designs can exceed 20 storeys and beyond.
Concrete contractors should treat ICF construction as typical concrete wall
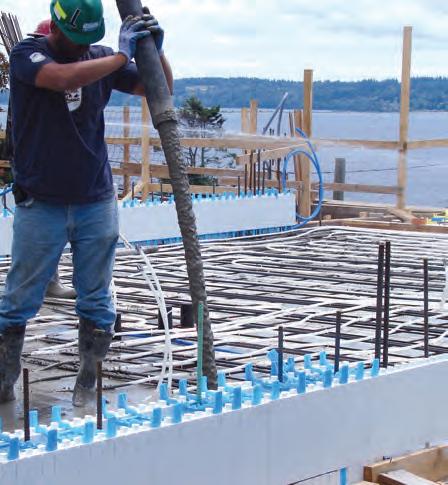
construction for both commercial and residential applications. Vibration, in order to achieve consolidation, is a requirement.
Curing is achieved by the nature of the insulating properties of the ICF form. In cold weather the only concern is the exposed top of the pour, which can be protected by thermal blankets or speciality products recommended by the manufacturer. Since the concrete is never exposed to the weather, it retains a higher moisture content. This slow cure results in a high early strength and longevity. By not being exposed to the weather and having the concrete insulated, the requirement for expansion or control joints is eliminated on most walls.
The responsibility for the concrete mix design should remain with the ready-mix producer. Most producers have a concrete mix design for ICF walls, but they may have to be adjusted due to weather or site conditions. This should always be done in conjunction with your producer.
Concrete specifications for ICFs have two main requirements that are important to the placement and flow of concrete within the forms. The recommended concrete slump for commercial work should be a minimum of 5” to 6” (102 mm to 152 mm), subject to climate and engineering design. This higher slump allows the concrete to flow easily within the forms and prevents damage to the cross-ties during placement. Slump verification by testing upon delivery is recommended. In some instances, higher concentrations of reinforcement may dictate higher slump than this minimum.
Furthermore, a smaller aggregate size is recommended to alleviate congestion in the walls between the reinforcement bars
COURTESY OF ICFMAand the inside face of the ICF. A smaller aggregate also improves the flow rate within the forms. The recommended aggregate size for a 6” (150 mm) ICF core size is either 3/8” to 1/2” (9.5 to 12.5 mm).
For larger ICF forms with 8” (200 mm) and higher core sizes, 1/2” to 3/4” (12.5 to 19 mm) aggregate may be used.
Concrete placement is typically done from a pump truck or line pump with the placement rate controlled and regulated by multiple lift heights, minimizing the hydrostatic pressure within the forms. All ICF wall applications are required to be consolidated by an internal vibrator. Typically, concrete is placed and consolidated in the ICF walls from floor level to floor level as a continuous pour in four-foot (1,220 mm) lifts.
LOOKING AHEAD
In today’s world, low-carbon concrete and embodied energy have become a major part of design criteria, and ICFs can augment the industry’s efforts toward producing high-performing buildings.
Concrete mix designs have improved the reduction in carbon production by making use of supplemental cement materials such as fly ash and slag – waste materials that provide additional qualities to the long-term performance of the concrete. Chemical admixtures such as water reducers and strengtheners may reduce the need for additional cement, which also lowers the carbon footprint of a project. And cement producers are making use of PLC cements, which lower the carbon footprint of the end product.
ICFs take these performance characteristics and add an airtight building envelope, with higher insulation values and thermal mass performance to create a solid base for the construction of Net Zero buildings going forward. And the sector is not standing still. Exciting developments exist, such as the introduction of fibreglass reinforced rebar and polypropylene fibres as replacement for rebar.
Ross Monsour is the director of ICFMA. For additional information on ICF technology, visit www.icf-ma.org.
FIBER SOLUTIONS FOR INDUSTRIAL

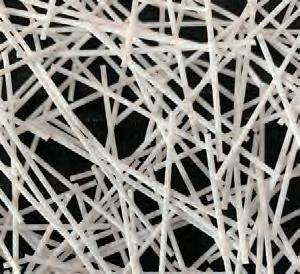


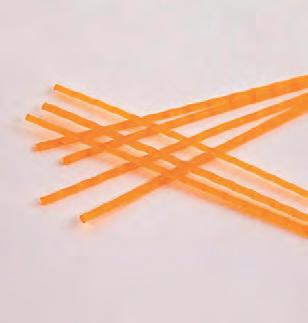
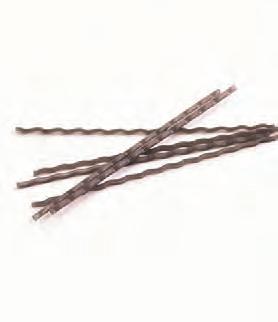
Functionality is the main requirement for concrete flooring in industrial and commercial environments. In addition to a very high aesthetic quality, MAPEI products provide excellent flatness and dimensional stability, partially or completely eliminating the need for traditional metal reinforcement and contraction joints.
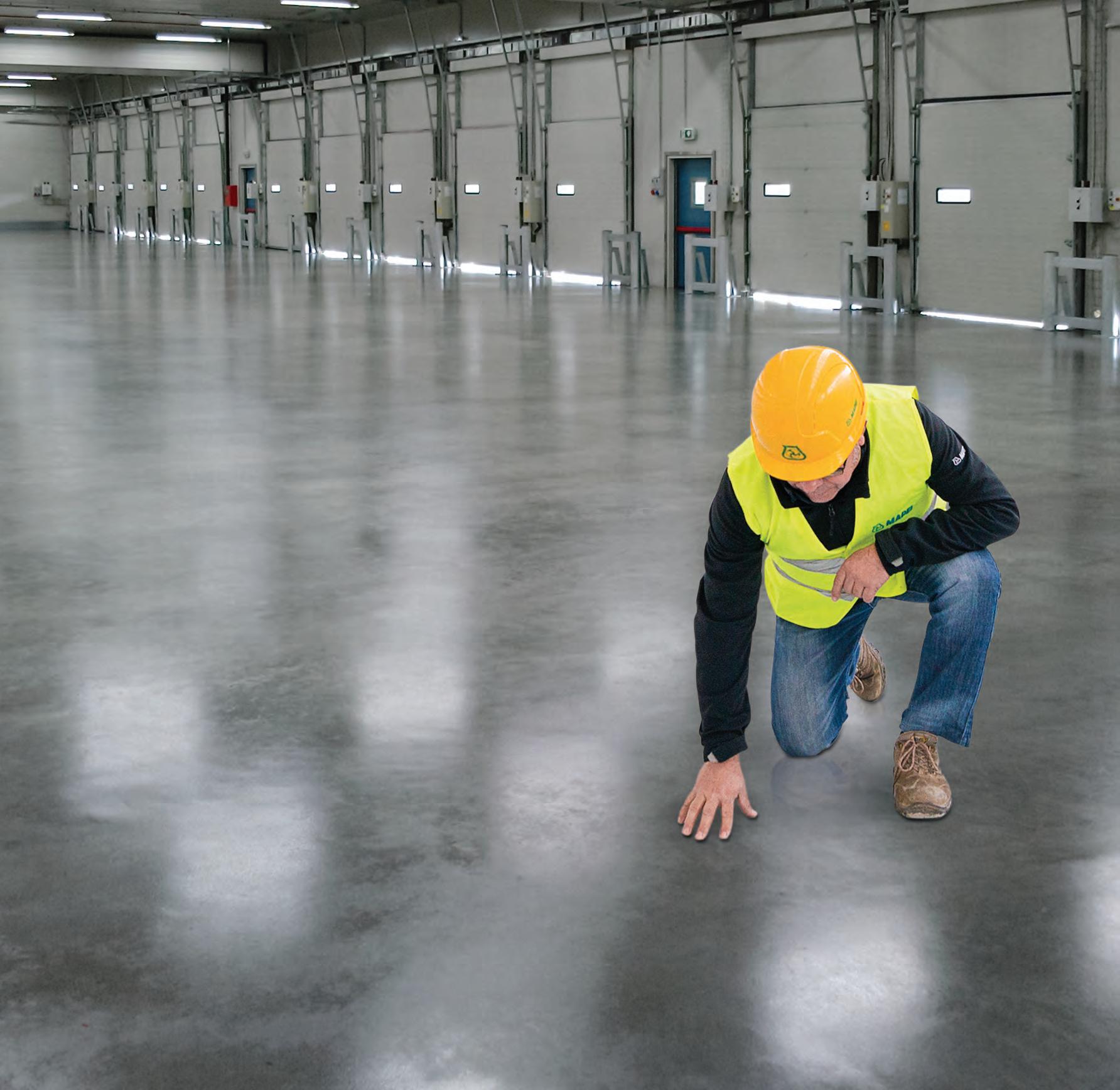
CCE RETURNS TO FEBRUARY
The Canadian Concrete Expo (CCE), Canada’s national trade show for the concrete construction industry, returns to the International Centre in Mississauga, Ont., this February 16 and 17. More than 7,000 people are expected to attend this fifth edition of this national event, where they will have the opportunity to connect with over 300 exhibitors and participate in the event’s 30-plus conference sessions, presentations and demonstrations.
New technology that’s likely to garner significant attention includes the printing of a full-scale 3-D concrete structure – the first to be printed live and indoors in North America – as Nidus3D will have its system in full operation on both days of the show. And don’t forget to stick around after the close of Day 1, as CCE will host a networking event for all exhibitors and attendees featuring food, entertainment and special guests Georges St. Pierre and P.J. Stock.
Stuart Galloway, president of the Canadian Concrete Expo, describes the event as an ideal environment to connect with suppliers, as well as source new suppliers, find business solutions and build partnerships.
“Nearly 4,000 industry professionals attended CCE 2022 despite being in the height of the construction season and weather that was ideal for construction crews and pouring concrete. Business and sales on the show floor were brisk,” he stated. “After three years, we are pleased to have CCE back into its February time slot and are looking forward to providing the best industry event in Canada for the
construction industry. The trade show floor at CCE 2023 will be the largest to date.”
The 2023 show is set to take place at the International Centre, 6900 Airport Rd. in Mississauga, Ont. Show hours are 9 a.m. to 5 p.m. on Thursday, February 16, and 9 a.m. to 3 p.m. on Friday, February 17.
Pre-registration is now open, and anyone registering prior to February 15 will qualify to save half off the door admission prices. For more information about the show, or to register, visit www.canadianconcreteexpo.com.
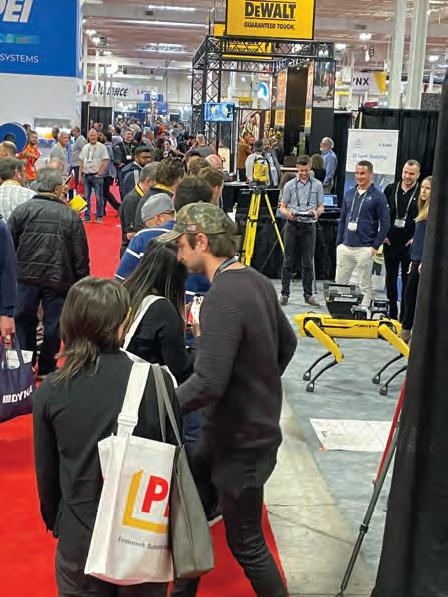
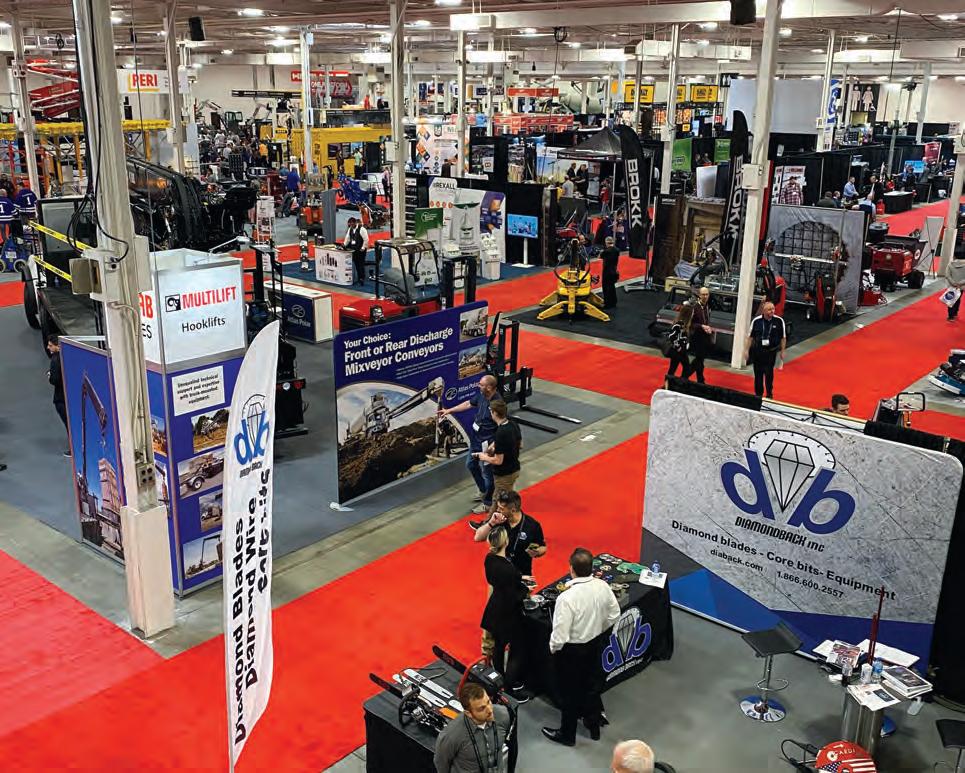

WORLD OF CONCRETE CONTINUES TO BUILD UP VEGAS SHOW
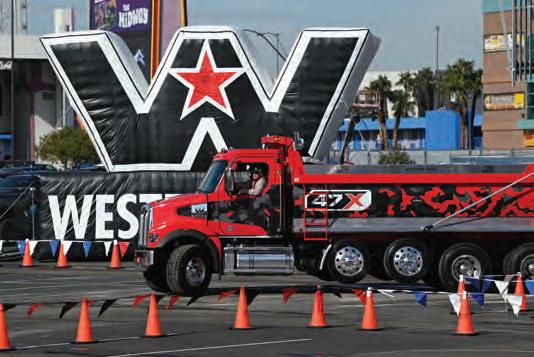
International event for the concrete and masonry industries is adding a work truck feature, awards, and more when it
hits the LVCC in January.
concrete and masonry industries,” stated Kevin Archibald, senior show manager.
Work Truck LIVE! aims to highlight innovations in the design and configuration of work trucks, while showcasing some of the most innovative accessories designed to help contractors increase safety and productivity. It will also include a “Ride and Drive” experience with the opportunity to test drive select Class 1 through 7 vehicles.
The North Hall’s autoclaved aerated concrete area will examine all facets of the building material, from production technology through to typical applications of the product in the construction industry.
World of Concrete (WOC) is growing. Informa Markets’ exhibition for the concrete construction and masonry industries is adding features as it prepares for the 49th edition of the show, set for January 17 to 19 at the Las Vegas Convention Center (LVCC). In 2022, WOC drew close to 37,000 registered professionals.
For 2023, organizers are aiming for bigger and better. Along with more than 1,000 exhibitors, over 600,000 square feet of indoor and outdoor exhibit and event space, and its skills challenges and demos, organizers have announced the launch of “Work Truck LIVE!,” as well as a new area of the show that will focus on autoclaved aerated concrete. New forums have also been added.
“World of Concrete continues to be the annual inaugural exhibition for the materials, tools, and equipment focused on the
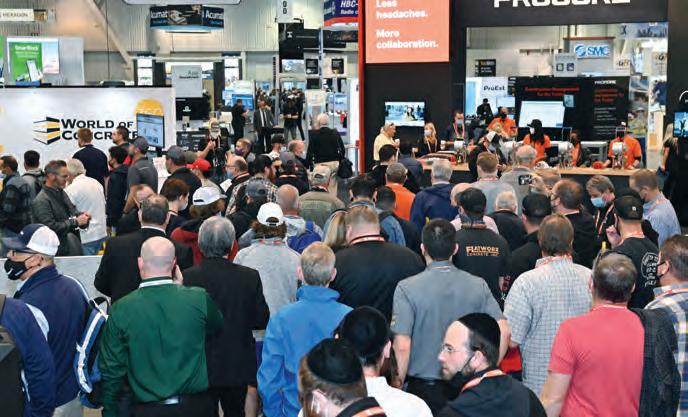
Starting one day earlier than the show floor opening, the education component of the event brings 164 technical, business and safety sessions to attendees of the World of Concrete Education Program. In addition to popular business and project management seminars, industry certifications and interactive workshops, the lineup will also highlight many new technical topics, including petrography, mass concrete, fibre reinforcing, reshoring, superflat floors, repair and restoration, and 3-D printing.
“The 2023 WOC Education Program has scheduled 164 sessions to address the current and anticipated needs of concrete and masonry industry professionals,” said Archibald. “Several technical classes specifically focus on mass concrete placement; pavement design, construction, preservation and repair; commercial/industrial project specifications; 3-D printing in concrete construction; use of high-performance materials; and environmental product declarations.”
Exhibit hall hours for the 2023 edition of WOC are 9:30 a.m. to 5 p.m. from January 17 to 19. For more information, or to register, visit www.worldofconcrete.com.
COURTESY OF WOC/INFORMA MARKETSwww.wirtgen-group.com

Concrete Product Showcase
CONCRETE PRODUCT GUIDE
Concrete Solutions is a digitized product guide from Brafasco that focusses on key commercial concrete markets. The guide introduces the construction sectors, followed by a streamlined, to-the-point fundamental product listing of products used on all common jobsites. Businesses can realize a range of options likely not considered in the past when planning their next project.
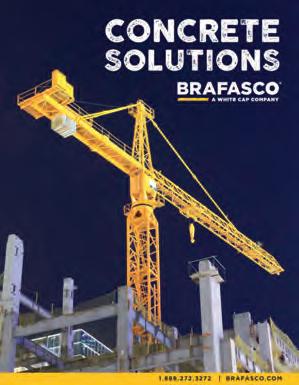
CORDLESS CHIPPING HAMMER
SURFACE PREPARATION PRODUCTS
Husqvarna Construction’s recently rebranded Blastrac and Diamatic surface preparation product range, which includes floor scrapers, shavers, scarifiers and floor grinders, is available in Canada and the United States. The company’s walk-behind concrete floor shaver and ride-on milling machines are well suited to jobs where enhanced depths in a controlled pattern are desired. Scarifiers in the lineup allow for the levelling of large surfaces and the removal of thick coatings. They are designed to quickly and cleanly remove concrete to help level slabs, expose large aggregate before concrete polishing, and for coatings removal in demolition applications.
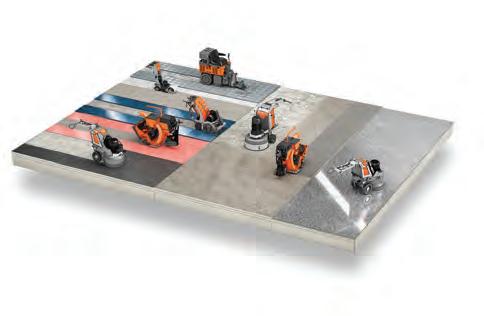
CONCRETE POWER CUTTER
The electric 536-E power cutter from ICS Diamond Tools offers professional-grade cutting capabilities using electric power. Designed to slice through concrete, stone, masonry and ductile iron, the 536-E uses a 4.8 hp motor to deliver industrial cutting capacity while eliminating the need to mix fuel and oil, or maneuver heavy hydraulic hoses. It runs on 220V, making it compatible with most generators.
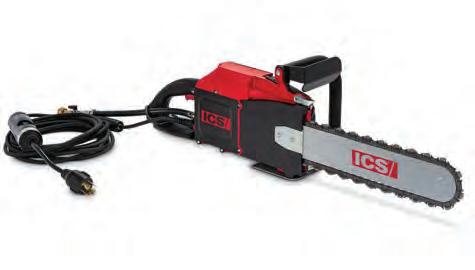
CONCRETE COATINGS
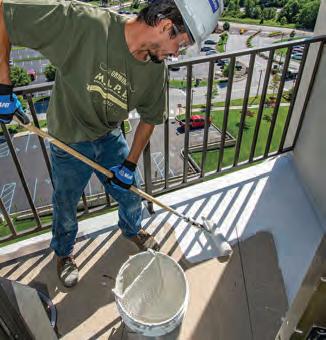
MAPEI’s Mapecoat Deck T is a high-build, textured, slip-resistant, water-based acrylic deck coating designed for use on new and previously coated concrete. Featuring a light sanded texture and UV-resistance, the coating is suitable for slab-on-grade applications and can handle pedestrian and light vehicular traffic. The company’s custom colour-match capabilities allow for enhanced aesthetics over repairs and irregular substrates to restore the appearance of old and/or damaged concrete.
Designed for heavy-duty demolition, concrete, and masonry work, the Dewalt 60V Max 22 lb. cordless SDS Max Chipping Hammer is designed to break down dense concrete with up to 19.4 Joules of impact energy. The hammer can be used to tackle horizontal and downward chipping in mid-to-lower wall and flooring tasks, and is also suited to demanding highway jobs. The company also offers a mid-weight 60V Max 15 lb. cordless SDS Max Chipping Hammer capable of delivering up to 10.5 Joules of impact energy. It can be used for horizontal chipping in upper or lower walls and concrete surface preparation applications.
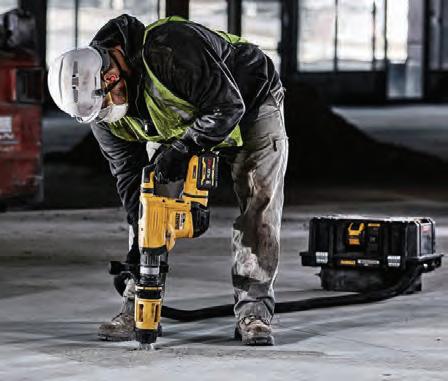
HYDRAULIC HAMMERS
Takeuchi has added seven sound-suppressed hydraulic hammer models to its attachment program, allowing compact track loader and compact excavator owners to break up asphalt, concrete, rocks and other hard materials. Designed to providing noise and vibration insulation, the sound-suppressed design also protects the hammers from dust and debris. The company offers seven models in its lineup.
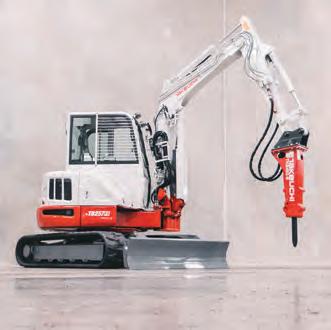
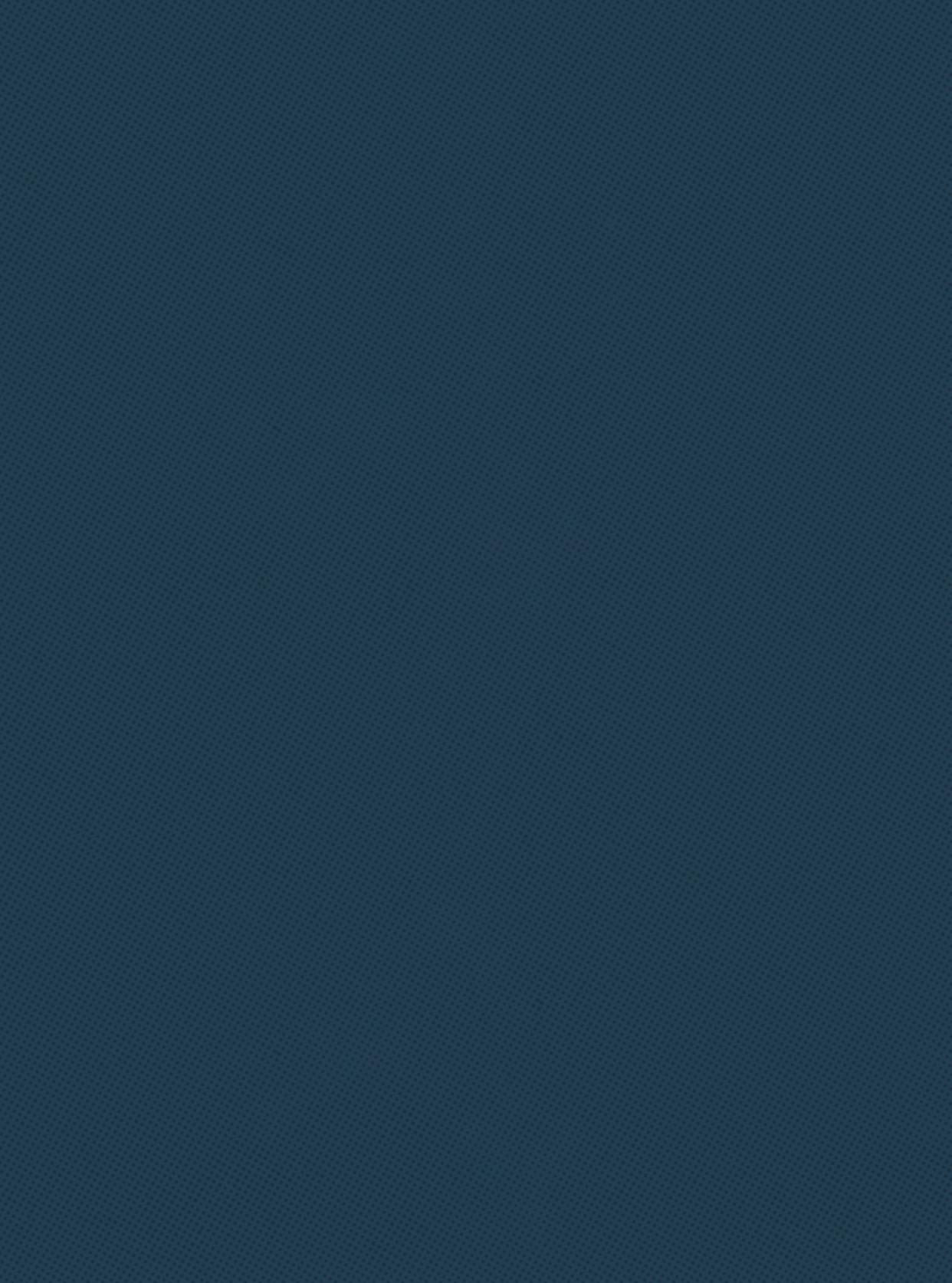
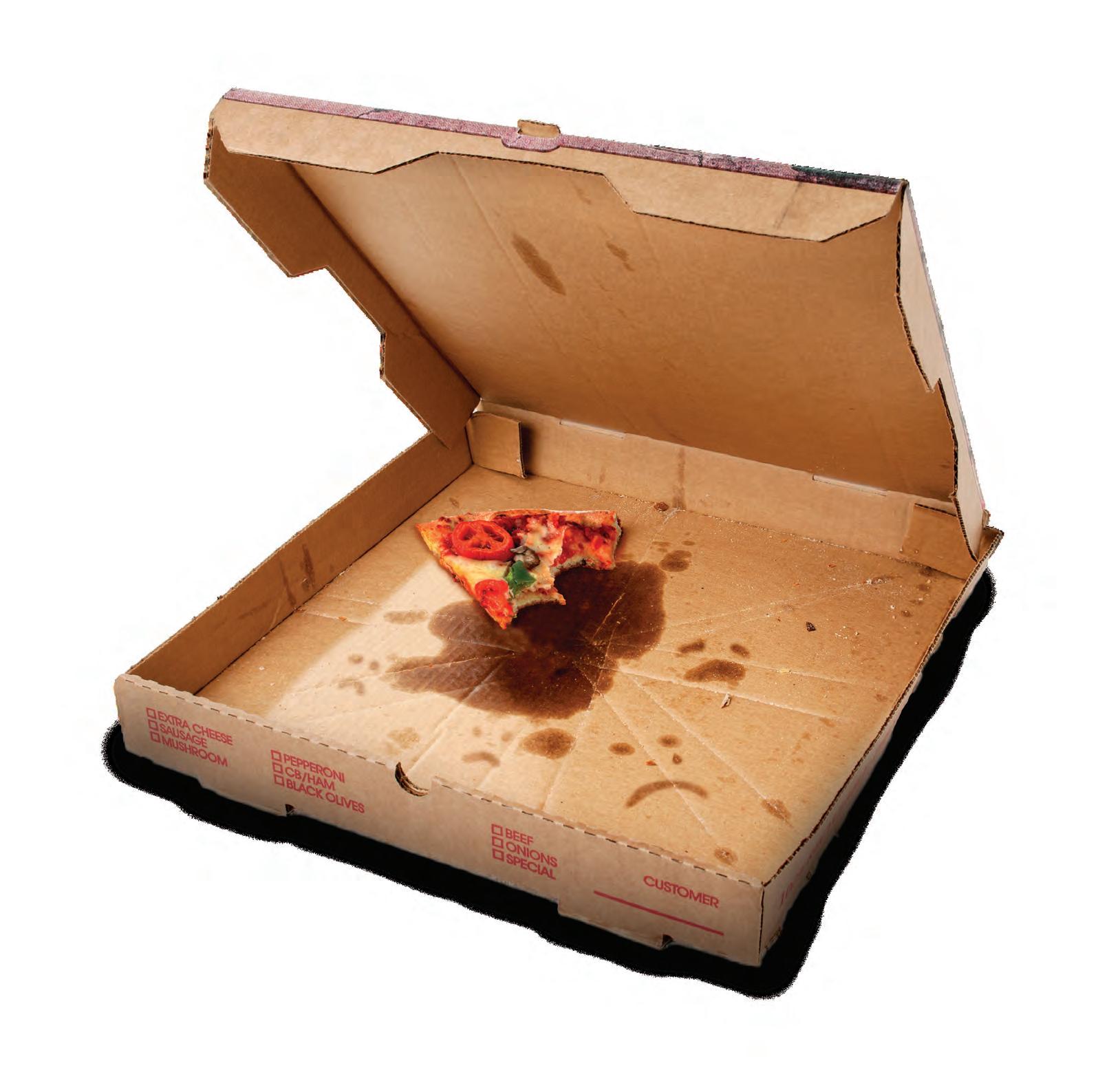
New Year’s resolutions
The past three years have seen massive changes within the construction and infrastructure sectors of the economy. The net impacts have been substantial supply chain disruptions and inflation. We are also seeing strange disruptions to the labour marketplace that are leaving many wondering about the staffing of future project opportunities. The impact of these changes will be felt well into the future.
In a world where the scale of change seems to be accelerating, you need to find ways to harness the power of information flows to make better decisions. In many respects the answer is staring you right in your face – quite literally if you are likely looking at this article on a computer, smartphone or tablet. Whatever device you use, it represents a front-row seat to the emergence of what many consider to be the most powerful tool ever developed for the built environment: the digital twin.
Pre-Construction Technologies: These are technologies like Building Information Modelling, specification technologies and budgeting technologies.
Scheduling Technologies: Initiated in the pre-construction phase, these technologies help schedule the project, confirm the schedule will work, and allow for optimal changes to the schedule.
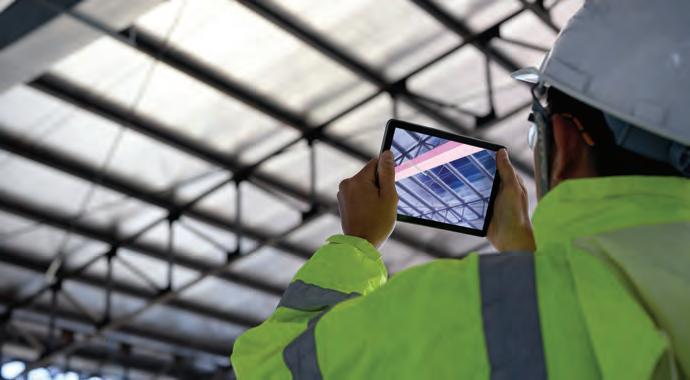
Project Management Technologies: Originally document management platforms, this part of the digital twin represents the most likely vehicle to house all component parts of the digital twin.
Supply Chain Intelligence: This component part allows users to prequalify their partners, suppliers and subcontractors. It also provides real-time information on supply chain pricing and potential events that could disrupt the flow of supply chain.
Reality Capture: The digital capture of reality on a frequent basis can ensure that your project is being executed to plan. These solutions literally allow you to overlay the design onto the reality, which can highlight costly design or workmanship errors before they become substantial.
Construction Phase IoT Backbone: Devices are like nerves. When you join these nerves under a unified platform (the backbone), you have the ability to see events on a jobsite in real-time. It also unlocks the potential to see events before they happen via predictive analytics.
THE DIGITAL TWIN
The digital twin is the convergence of all data and technology from all phases of the built environment (design, construction, and operations) delivered through a unified and federated platform, and it can be used to manage risks.
Do you want to track how external events are disrupting your project’s access to material? Check the digital twin. Do you want to monitor activity on your jobsite remotely during semi-lockdown periods? Check the digital twin. Do you want to do more with less access to skilled labour? You guessed it: check the digital twin.
As the data converges under a common, unified and federated framework, you will be in a better position to reduce the many risks being brought forward from this age of massive change while allowing you to rely on data to also improve productivity.
WHAT’S IN THE DIGITAL TWIN?
The more information that’s available, the more powerful a digital twin platform becomes, but it is still possible to choose what to incorporate. Here’s a primer on a few components to consider.
External Event Monitoring Technology: This component provides joined up monitoring of external events related to your jobsite, either through proximity or through connections to your jobsite’s supply chain. Events like weather, strikes, port shutdowns, and many others can be monitored, which will allow you to make better and faster decisions to avoid risks that could reduce productivity.
Operational Phase Categories: The digital twin’s true value is optimizing total cost of ownership throughout the lifecycle of the built asset. Several of the component parts in the construction phase can be married up with operational phase component parts to unify the digital twin throughout the life of the asset. This is a tremendous opportunity for the industry.
As these, and other, component parts of the digital twin converge, all stakeholders associated with a particular built asset will have greater awareness, transparency, predictive capabilities and, ultimately, better decision-making capabilities. Further, the digital twin can become an ideal playground to test options prior to implementation, aiding the rise of more collaborative procurement models. Quite simply, the digital twin will improve productivity, reduce risk and generate greater societal benefit.
Bowcott is the managing director, construction, at NFP Corp. Please send comments to editor@on-sitemag.com.
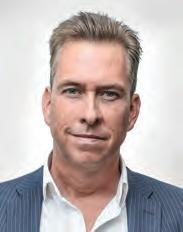
Use more technology to reduce risk and improve productivityPHOTO:
Adrian Steel
www.adriansteel.com 8
Brafasco www.brafasco.com 56
Canadian Concrete Expo www.CanadianConcreteExpo.com 47
Canadian Construction Association www.ApprenticeSearch.com/CAS 4
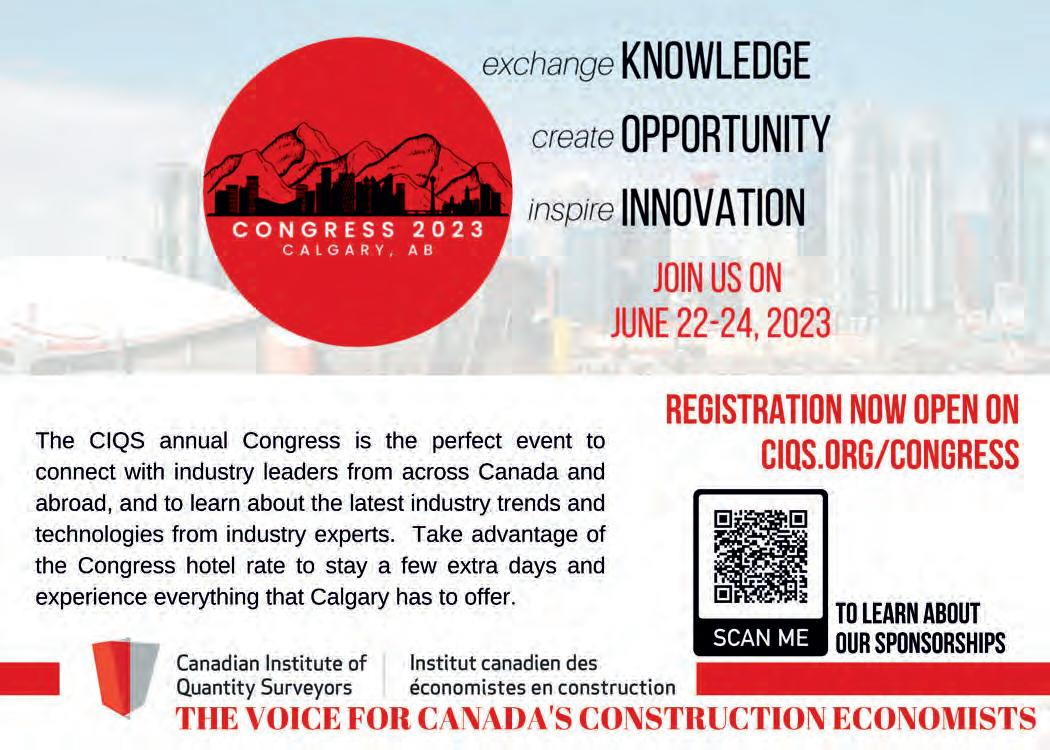
CIQS www.ciqs.org/congress 53
Clearstream Energy Services www.flintcorp.com 28
CONEXPO www.conexpoconagg.com 17
Dentons Canada LLP www.dentons.com 34
Flatiron www.Flatironcorp.com 31
Gomaco www.gomaco.com 42
Graham www.grahambuilds.com 25
Jacob Bros. www.jacobbros.ca/careers 34
Ledcor www.ledcor.com 35
MAPEI www.mapei.ca 45
Northbridge Insurance www.northbridgeinsurance.ca 40
OpenCircle www.opencircle.ca/pizza-party 51
PCL www.pcl.com 27
Procore www.procore.com 12
QM Environmental qmenv.com 33
Raken www.rakenapp.com 55
Singleton Urquhart Reynolds Vogel LLP www.singleton.com 28
SoftwareONE www.softwareone.com/construction 2
Threeosix Industrial www.threeosix.ca 37
Turner Construction www.turnerconstruction.com 39
Uline www.uline.ca 37
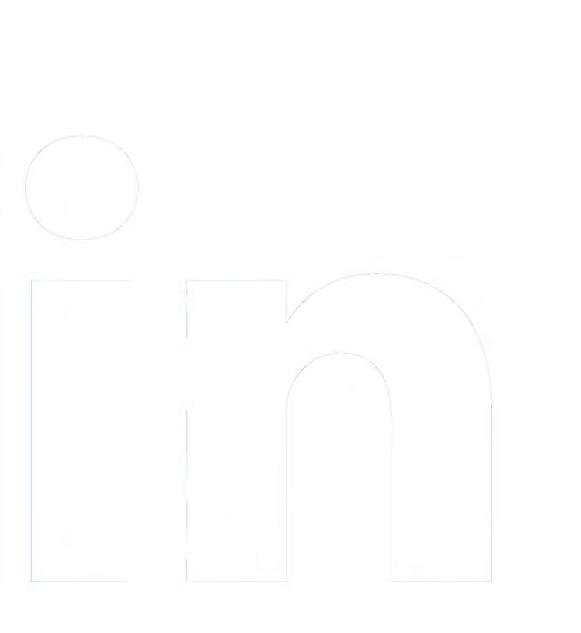
Western Global www.western-global.com 9
Wirtgen www.wirtgen-group.com 49
Navigating and applying price escalation clauses
Following a trend that began in 2020 with the onset of the coronavirus pandemic, and continued due to, among other reasons, the persistence of supply chain and labour shortage issues, construction costs continue to rise. With the uncertainty of these costs, suppliers, subcontractors, contractors or owners entering into a new contract involving the procurement of material should consider how best to manage the risk associated with material price increases. This risk may best be managed by using a material price escalation clause.
These clauses are designed to protect a contractor from increasing job costs by potentially passing the risk of price increases – or the benefit of price decreases – along to the client or owner. However, they have an added benefit of creating some certainty as to who accepts the risk of a price increase by protecting all parties from unnecessary defaults that might shut a project down.
With cost uncertainty and hesitation from contractors to enter into agreements without some reservation of risk, parties appear to be increasingly prepared to cooperate.
None of the project participants benefit if the project is shut down, or if a contractor abandons the project, or if there are significant delays in the delivery of materials that delay the overall project. More and more, parties are being forced to work together to achieve a mutually advantageous result.
DRAFTING A CLAUSE
If using a typical Canadian Construction Documents Committee (CCDC) or Canadian Construction Association (CCA) standard-form fixed-price contract with supplementary conditions, the safest approach is to build in a material price escalation clause to mitigate against rising material costs.
Contracting parties can consider proposing the inclusion of a mutual or bilateral clause where each party stands to accept some of the risk and some of the reward. In that approach, price increase risk shifts to the owner, but a corresponding benefit will also be provided to the owner if material prices drop.
Before a material price escalation clause is chosen for a contract, the contracting parties should have in mind the two preliminary considerations.
First is whether all materials are to be included within the clause. By limiting the clause to a specific product, it increases risk, but may serve as an incentive to a client or owner who would not entertain entering into a broader price escalation clause.
The second is whether the clause should include an adjustment for price decreases as well. If a party is entering into a project that could last three to five years, costs could fluctuate
in both directions. A carrot for the owner or client could involve granting a price de-escalation clause.
Two of the more common triggers used in material escalation clauses are event-based clauses and threshold-based clauses.
In a delay- or event-based clause, the contractor agrees to stand by its material prices for a certain period of time. Sometimes this is as short as the day the contract is signed.
For this type of clause, the parties should consider how the price increase will be verified. If there is no index for the material, what is the material price measured against? Options include the insertion of a formula into the supplementary conditions of the contract. In those circumstances, is a neutral third party assigned to the task of assessing the price, or is the onus on the contractor to provide reasonable proof?
With a threshold- or percentage-based clause, once material prices on the open market increase by a certain pre-agreed percentage beyond the estimated amount, the owner and contractor will agree to adjust the contract to account for the excess in the form of either full or partial additional compensation.
STORAGE AND OTHER CONSIDERATIONS
When drafting supplementary conditions involving material price escalation clauses, parties should also consider whether storage costs may be incurred, and whether the parties are prepared to share costs that allow materials to be purchased at quoted prices at an earlier stage.
The method and timing of notice under the contract should also be well defined, along with an agreed-upon method to illustrate there has been a price escalation – or price decrease – and possibly how to arbitrate such a claim.
Additional considerations include how material cost mitigation may impact a party’s entitlement to obtaining overhead and profit, whether limits should be placed on price escalation clauses, how often cost increases can be sought, and whether there’s a maximum increase that could trigger an entitlement to terminate the contract.
Ultimately, parties will need to be creative when entering contracts aimed at minimizing risks associated with the continued rise in material prices.
Erin Cutts, partner, and David Major, senior associate, are construction lawyers at Borden Ladner Gervais LLP. This article provides an overview and is not intended to be exhaustive of the subject matter contained therein. Although care has been taken to ensure accuracy, this article should not be relied upon as legal advice.
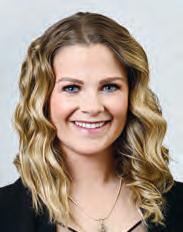
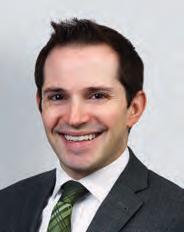
As material prices continue to rise, it may be beneficial to find ways to share risk with clients.


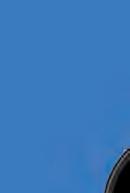
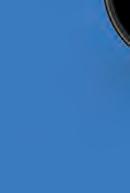
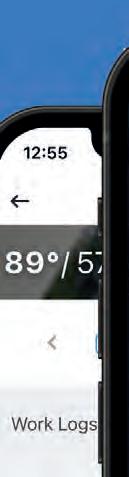
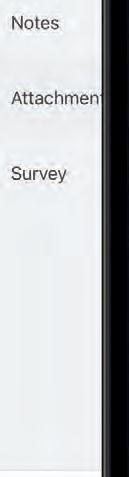
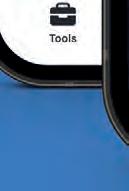


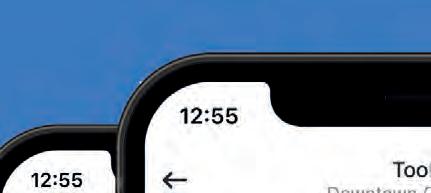

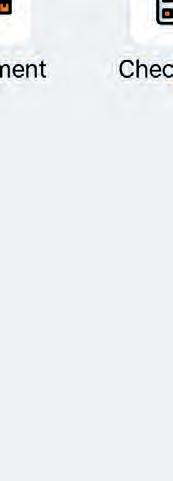

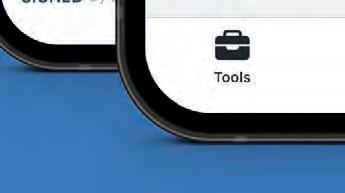




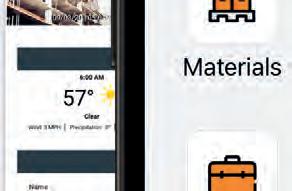
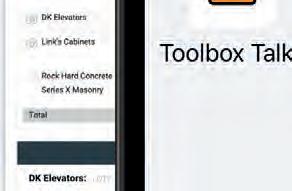
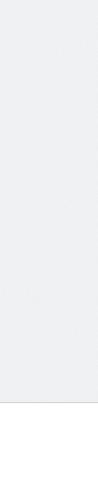
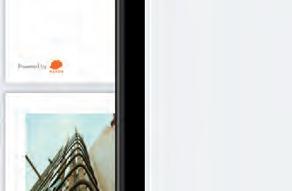
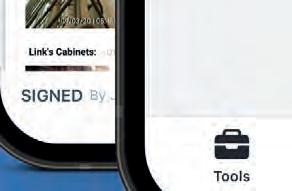










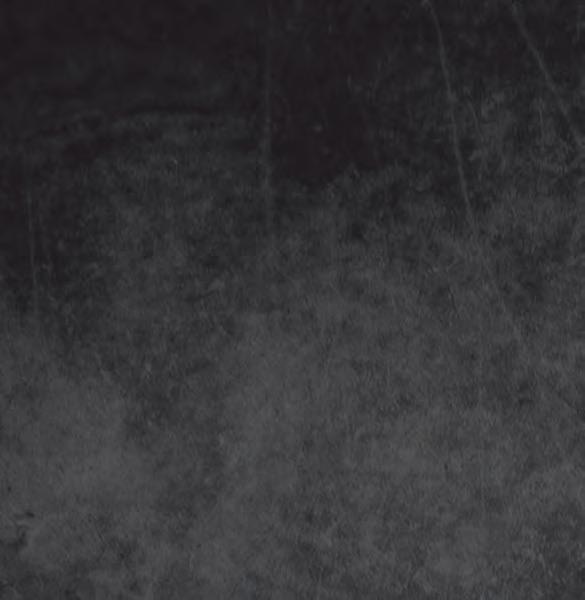
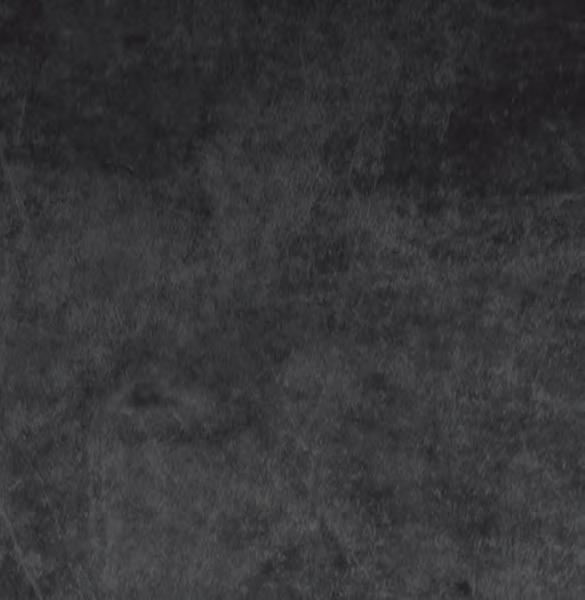
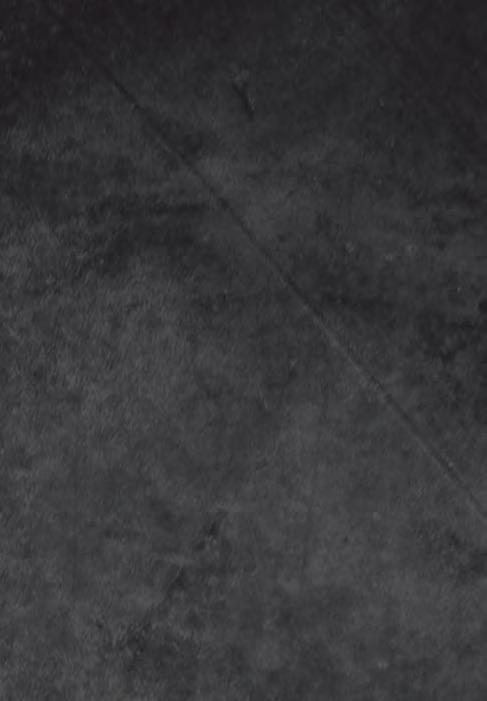
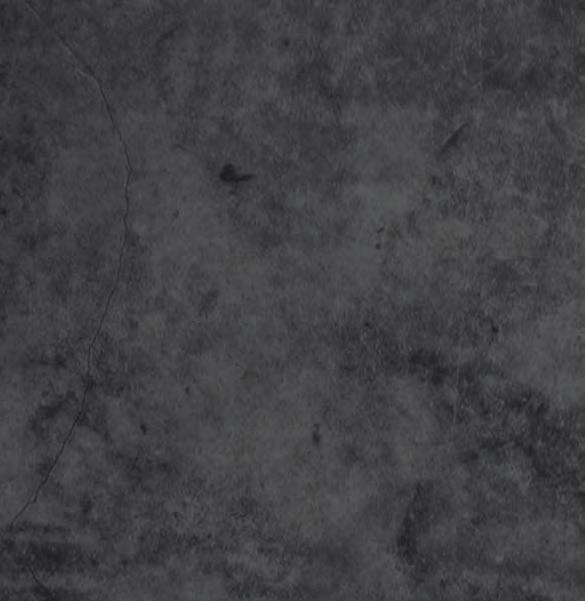
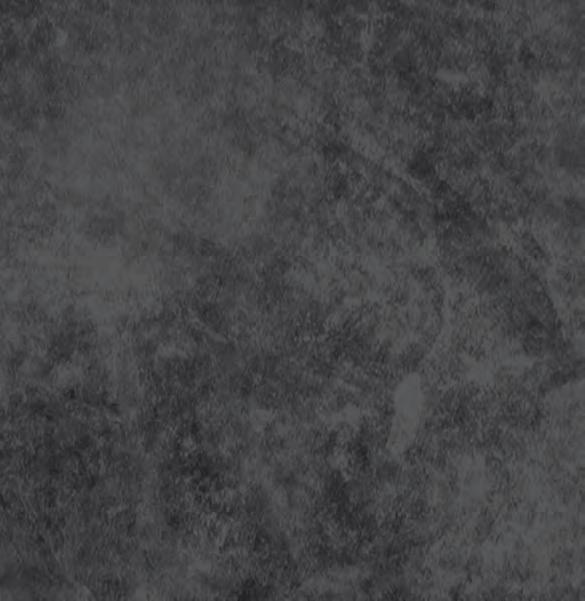
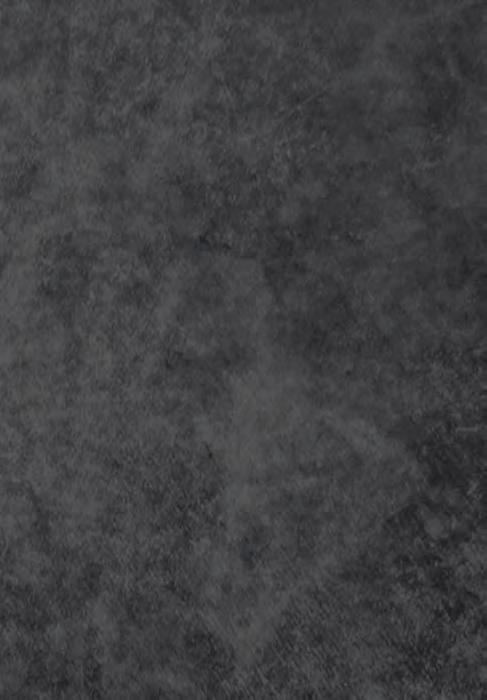
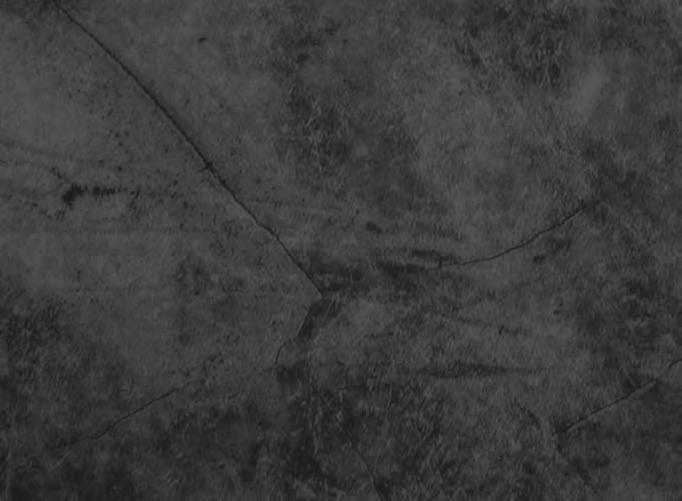
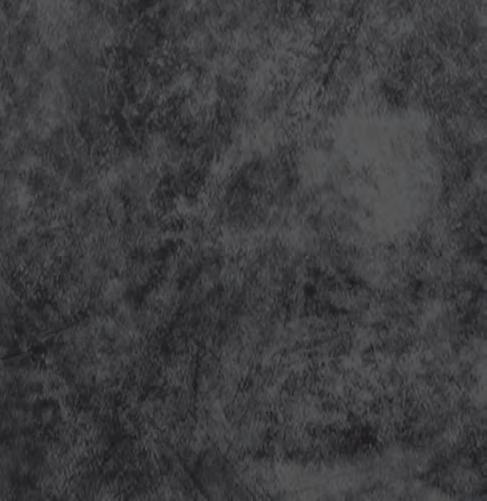
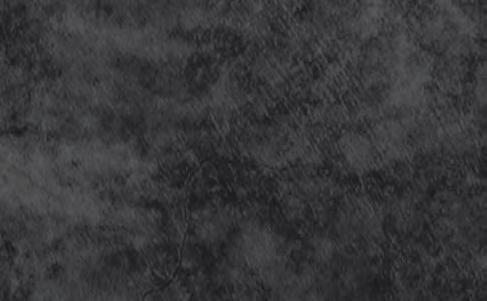
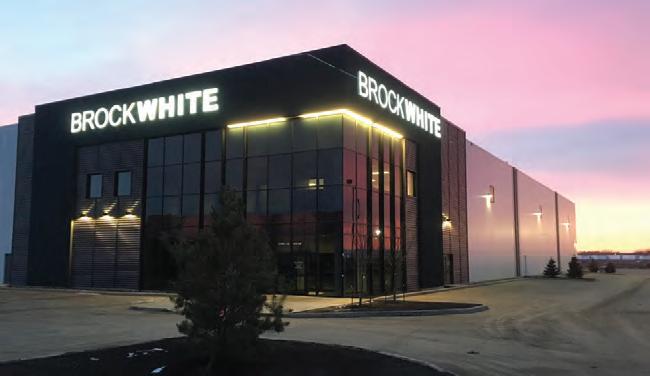
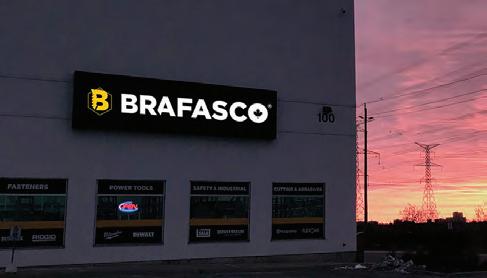
