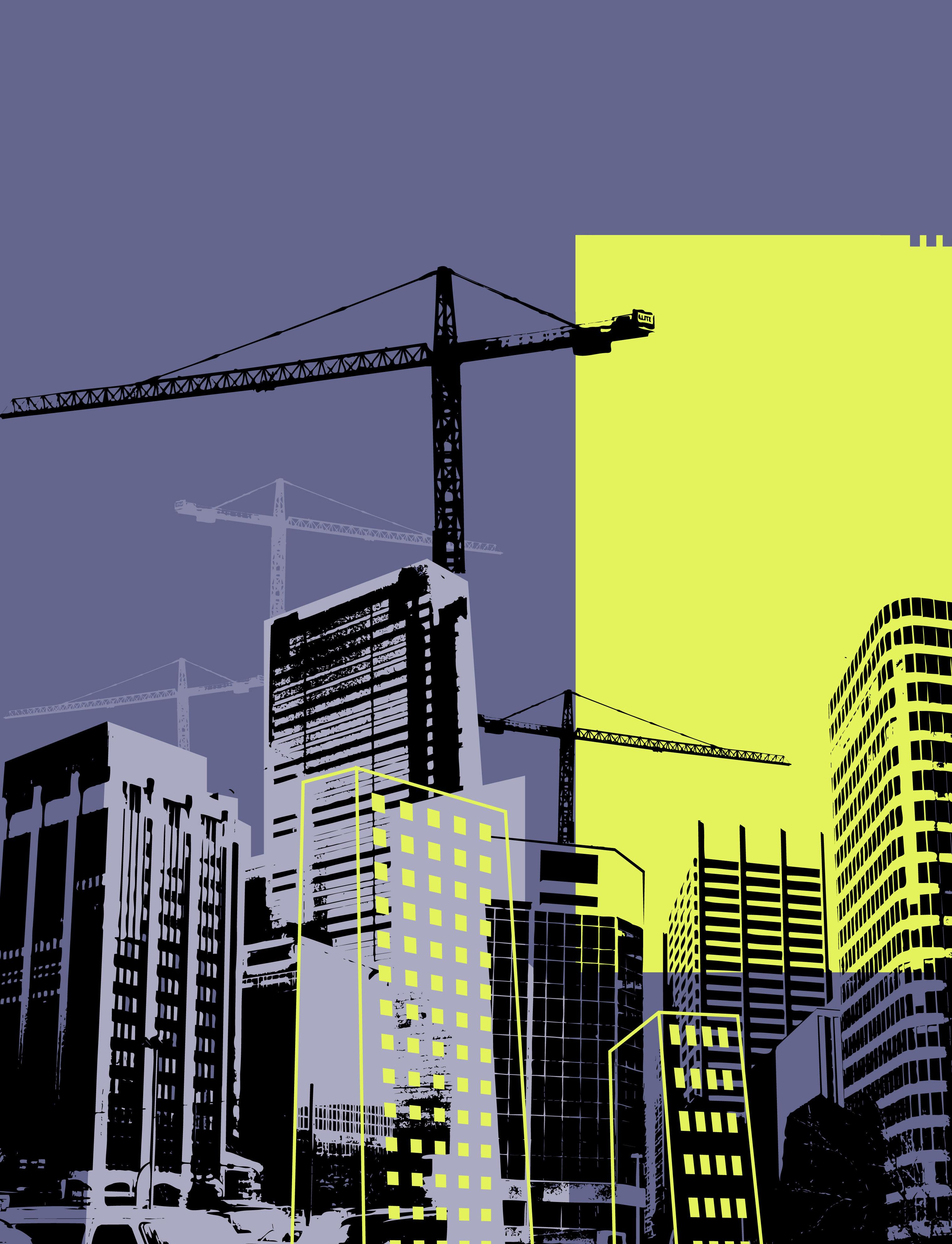
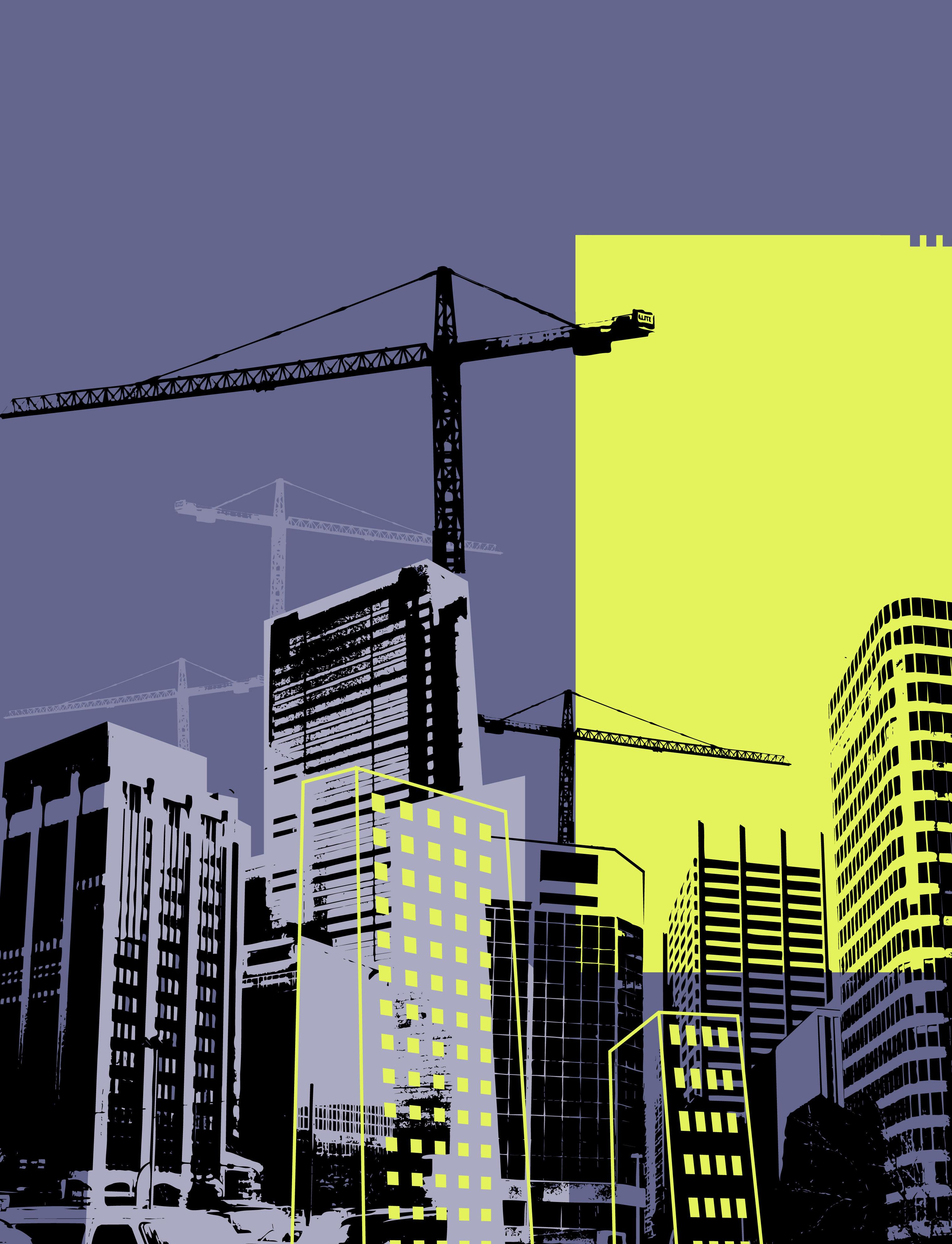
2025 FORECAST
ENOUGH POWER TO GET THE JOB DONE. ALL OF THEM.
P-TIER COMPACT TRACK LOADERS
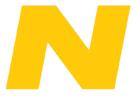
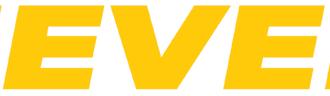


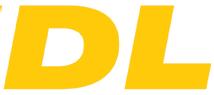
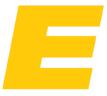
You never know what the work will throw at you. So you need a machine that can catch any of it. Our newest compact machines support over 100 different attachments and have the power to put them to work. Because it’s not enough to be on the jobsite, you have to run it.
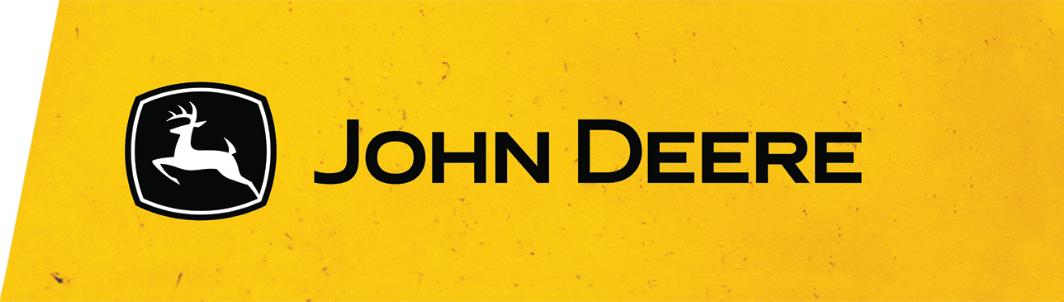
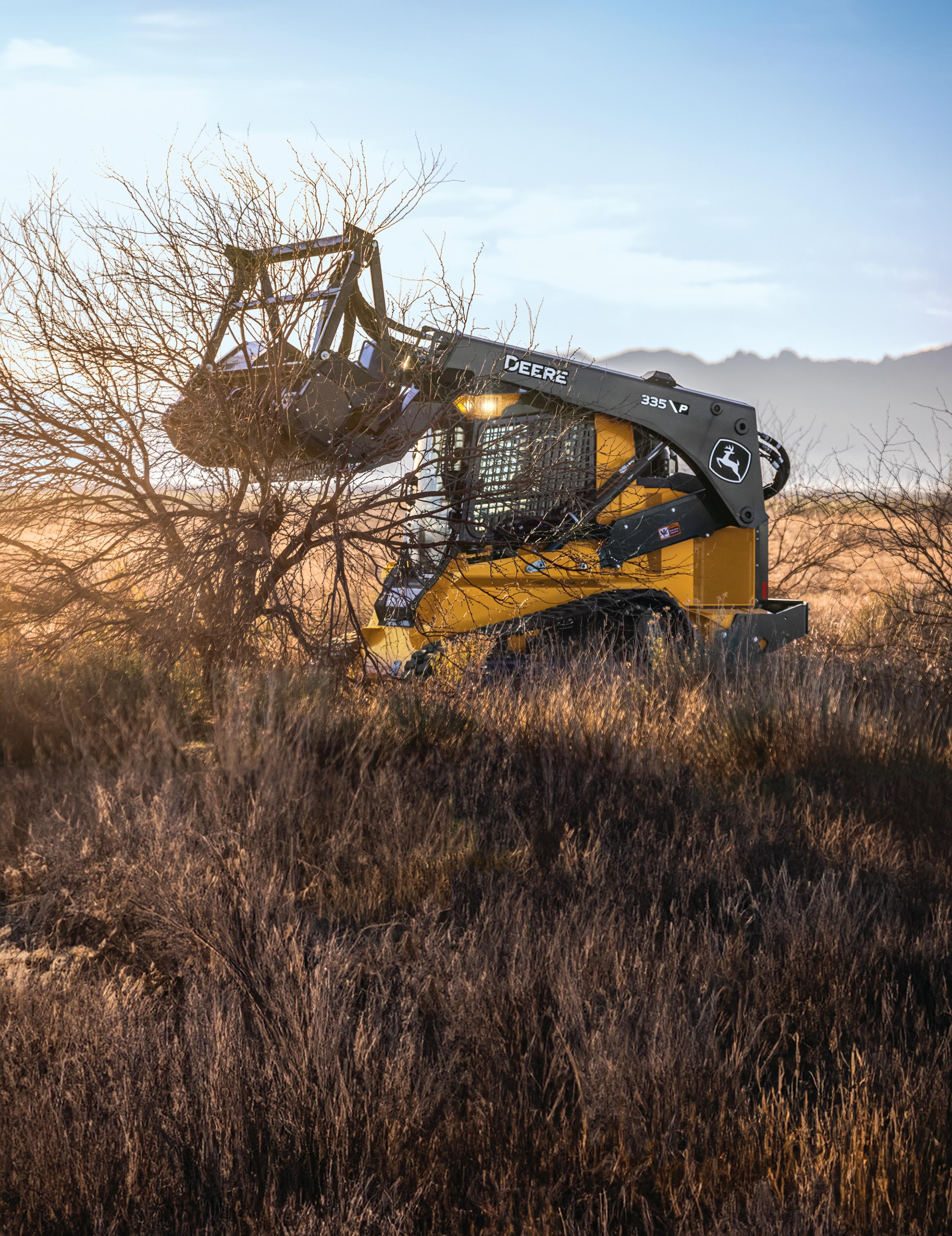
Economic expectations seem to be pointing in a positive direction. That along with existing and planned infrastructure spend, will have shovels hitting the ground, but there is still a level of uncertainty in some regions.
next 12
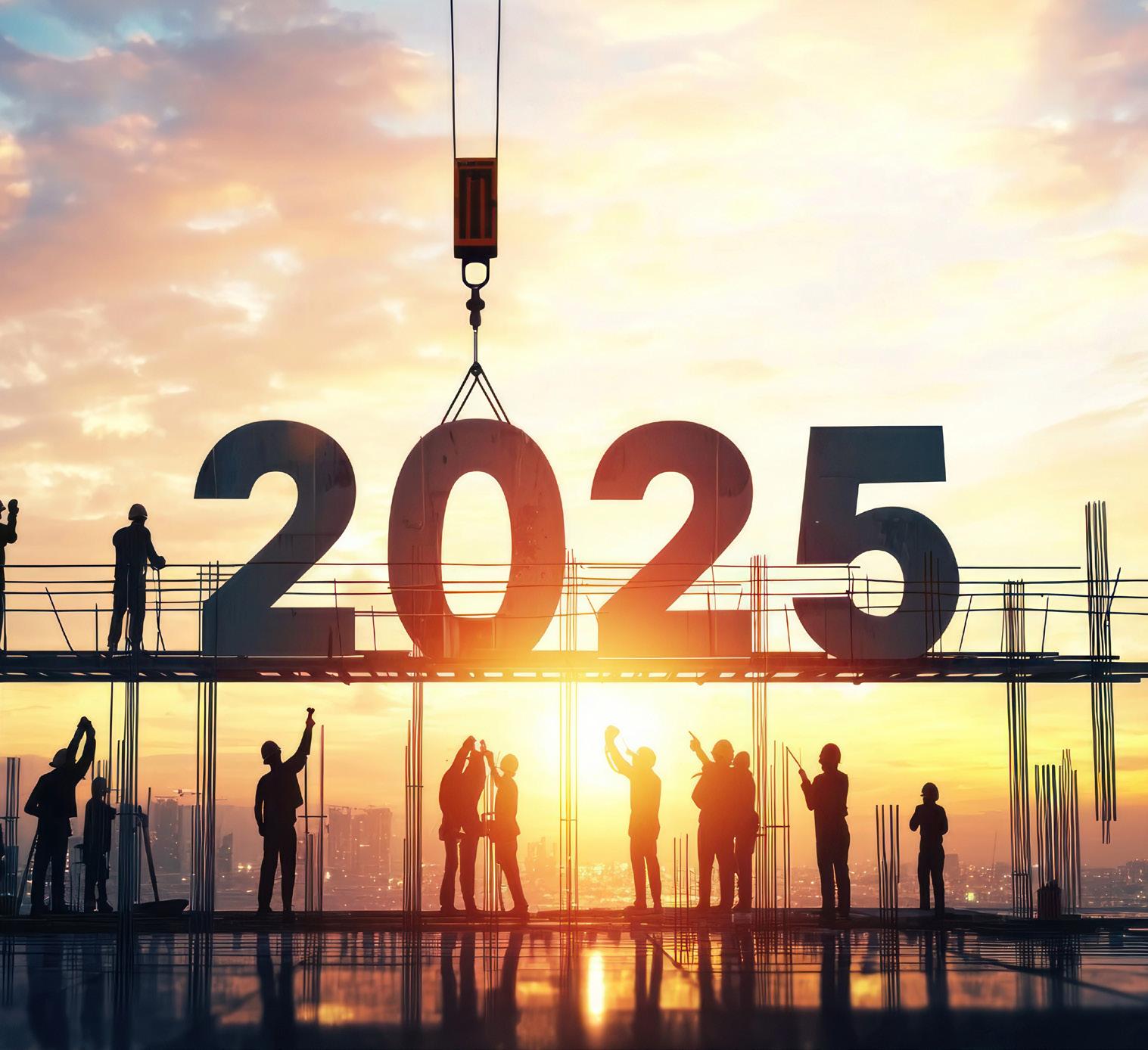
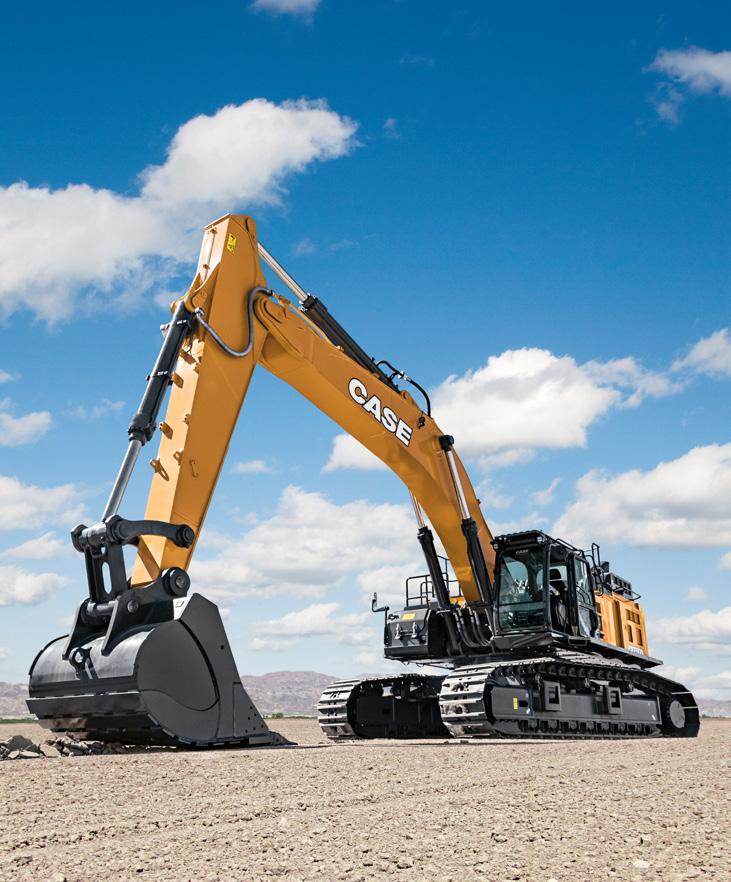
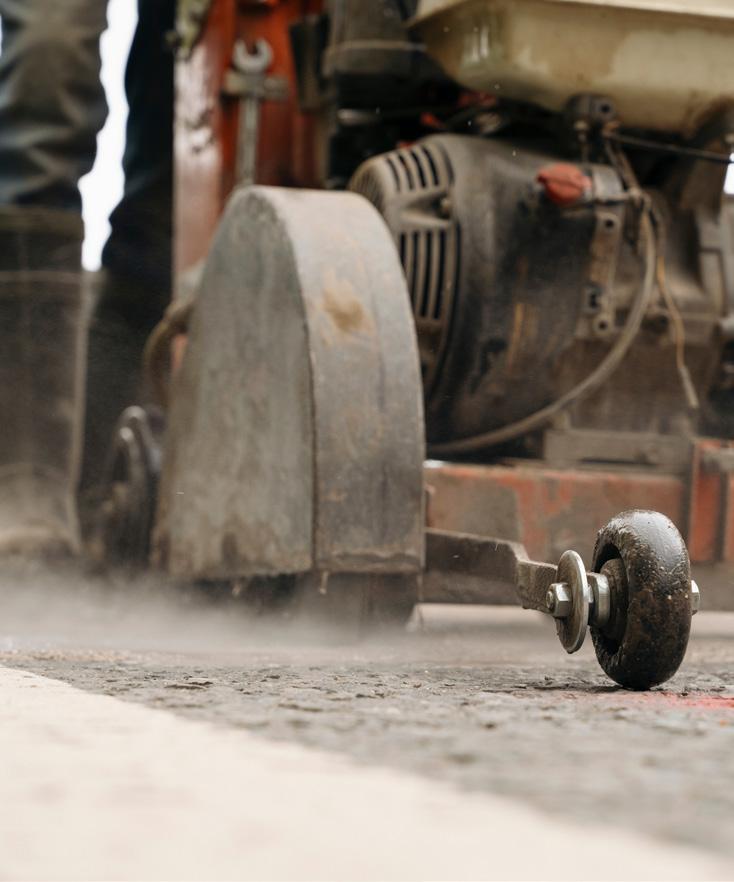

The ongoing labour challenge
Even with efforts to promote careers in the skilled trades, labour remains one of the biggest worry points for the industry. While conducting interviews and reviewing the piles of industry reports to research sector expectations ahead of our annual forecast report (which happens to start on page 17) labour came up as a core challenge time and time again.
Over the past few years, the number of job vacancies in the sector has dropped from almost 95,000 to less than half that this year, but there are still roughly 45,000 open roles waiting for a worker. And the average age of a worker in the sector remains troubling. Current and pending retirements are creating a need for even more workers to enter the field.
This reduction of vacancies has happened at a time when not all segments of the industry have been firing on all cylinders, which mitigated some impact.
The credit crunch has slowed the housing segment, and the non-residential sector has not escaped the realities of available capital either, with some projects slowing their rolls to wait for rate cuts and other economic influencing events to take hold. If the finances had been flowing more freely, the vacancy rate on the labour side could be much greater.
As the industry looks to 2025, with lower borrowing rates and some significant new projects starting up, one has to question whether employment vacancies in the sector could go north of 100,000, especially if the residential segment gets rolling towards the record-high levels of new condos and houses that CHMC says are needed.
www.on-sitemag.com
READER SERVICE
Print and digital subscription inquiries or changes, please contact Angelita Potal
Email: apotal@annexbusinessmedia.com
Tel: (416) 510-5113
Fax: (416) 510-6875
Mail: 111 Gordon Baker Road, Suite 400, Toronto, ON M2H 3R1
PUBLISHER | Peter Leonard (416) 510-6847 pleonard@on-sitemag.com
EDITOR | Adam Freill (416) 996-2391 afreill@on-sitemag.com
MEDIA DESIGNER | Lisa Zambri lzambri@annexbusinessmedia.com
ASSOCIATE PUBLISHER | David Skene (416) 510-6884 dskene@on-sitemag.com
ACCOUNT COORDINATOR | Kim Rossiter (416) 510-6794 krossiter@on-sitemag.com
AUDIENCE DEVELOPMENT MANAGER | Urszula Grzyb (416) 510-5180 ugrzyb@annexbusinessmedia.com
CEO | Scott Jamieson sjamieson@annexbusinessmedia.com
Established in 1957, On-Site is published by Annex Business Media 111 Gordon Baker Road, Suite 400, Toronto, ON M2H 3R1 Publications Mail Agreement No. 40065710 ISSN: 1910-118X (Print) ISSN 2371-8544 (Online)
Get the latest construction news!
Follow us on @OnSiteMag
Higher housing starts, progress on existing non-residential projects, and the start of significant projects like the Ontario Place redevelopment in Toronto all translate into a need for more workers. In addition to finding new entrants to the industry, the rise in work will also generate more competition within the existing labour pool.
As the basic economic theory of supply and demand kicks in, not to mention annual scheduled wage increases for a number of key building trades, changes to the temporary foreign worker program, and a misalignment of immigration credentials to the vacancies within our sector, expect the labour cost line of most budgets to be on the rise in 2025.
On the positive side, the industry should be busy, and busy but coping is better than not busy and laying people off.
Until next time, stay safe and do good work.
Adam Freill / Editor afreill@on-sitemag.com
SUBSCRIPTION RATES Canada $50.49 CAD per year, United States $115.26 CAD per year, Other foreign $139.23 CAD, Single Copy Canada $13.50 CAD. On-Site is published 5 times per year except for occasional combined, expanded or premium issues, which count as two subscription issues. Occasionally, On-Site will mail information on behalf of industry-related groups whose products and services we believe may be of interest to you. If you prefer not to receive this information, please contact our circulation department in any of the four ways listed above.
Annex Business Media Privacy Officer privacy@annexbusinessmedia.com
Tel: 800-668-2374
Content copyright ©2024 by Annex Business Media may not be reprinted without permission.
On-Site receives unsolicited materials (including letters to the editor, press releases, promotional items and images) from time to time. On-Site, its affiliates and assignees may use, reproduce, publish, re-publish, distribute, store and archive such unsolicited submissions in whole or in part in any form or medium whatsoever, without compensation of any sort.
DISCLAIMER This publication is for informational purposes only The content and “expert” advice presented are not intended as a substitute for informed professional engineering advice. You should not act on information contained in this publication without seeking specific advice from qualified engineering professionals.
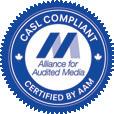
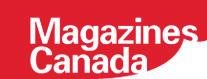
MEMBER OF
INDUSTRY>NEWS
Billions in infrastructure in poor condition
The cost to replace road transportation and water infrastructure in poor or very poor condition in Canada exceeds $350 billion, and that’s just for the assets that have been assessed for condition, reports Statistics Canada.
According to its most recent Core Public Infrastructure Survey, transportation and water infrastructure in Canada had a total replacement value of $2.6 trillion by the end of 2022. The report claims 15 per cent of road transportation assets and 11 per cent of water infrastructure are rated to be in poor or very poor condition, an amount estimated to be $356.7 billion in 2022. Local and regional government

organizations were responsible for almost three-quarters of this infrastructure.
These organizations owned 64 per cent of the replacement value of roads, 76 per cent of the value of public transit assets and 82 per cent of the value of active transportation infrastructure. Bridges and tunnels were an exception, as 69 per cent of these assets are owned by provincial and territorial governments.
The cost to replace all road transportation infrastructure rated as being in poor or very poor condition was estimated to be $250.2 billion, or 15 per cent of the total
Alberta cement plant using low-carbon fuel
Lafarge Canada Inc. has officially commissioned its state-of-the-art Low-Carbon Fuel (LCF) facility at its cement plant in Exshaw, Alta. Working in collaboration with Geocycle Canada, the company, a member of Holcim Group, says the $38 million facility will reduce the plant’s reliance on traditional fuels by replacing up to half of the natural gas used for one of its kilns with alternative thermal energy derived from construction demolition waste, primarily discarded wood that would otherwise end up in landfills.
The plant, which is a key supplier of cement across Canada and the U.S. Pacific Northwest, is projected to divert up to 120,000 tonnes of construction demolition waste from landfills each year, reducing carbon dioxide emissions by as much as 30,000 tonnes annually. Sourced from partners like ECCO Recycling, the company says these materials contribute and align with Canada’s net-zero goals for 2050.
“Our commitment to building a sustainable future is at the core of everything we do,” said Brad Kohl, president and CEO of Lafarge Canada (West). “The LCF project is a prime example of how innovation and collaboration can drive positive change, lowering our environmental footprint through the use of waste biomass materials while closing the material loop to conserve natural resources.”
replacement value. However, 17 per cent of the public transit assets and 42 per cent of active transportation assets were in unknown physical condition, leaving an estimated $45.7 billion of current replacement value, or $141.7 billion when including roads, bridges and tunnels, as unknowns.
The current replacement value of water infrastructure was estimated at $963 billion on December 31, 2022. The share of assets rated as being in poor or very poor physical condition accounted for just over one-tenth (11 per cent) of that amount, or $106.5 billion.

Cutting the ribbon on the LCF facility at the Lafarge Canada cement plant in Exshaw, Alta.
Pair of Canadian projects recognized with ACI awards
Montreal’s Reseau Express Metropolitain (REM) and the Helene Desmarais Building Pavilion at HEC Montreal were among the projects recognized during the 10th annual ACI Excellence in Concrete Construction Awards, showcasing dozens of innovative concrete projects from around the world.
The Overall Excellence award was presented to TSX Broadway – Palace Theater, located in New York City, N.Y. The winning concrete project also received first place in the Repair and Restoration Structures category when the awards were presented during the ACI Concrete Convention in November.
Placing second in the infrastructure category, the Reseau Express Metropolitain (REM) rail network spans more than 67 km (42 miles), connecting major regions in the Montreal area. It includes elevated and underground segments with various concrete structures.
The project required extensive durability planning to ensure a 100-year service life, using a range of concrete mixtures with high supplementary cementitious materials content to reduce heat release and carbon footprint. Two categories of concrete, including seven mixtures and several variants intended for cast-in-place and precast elements, were designed through an extensive laboratory experimental program to meet normative durability requirements based on actual exposure conditions throughout the network route.
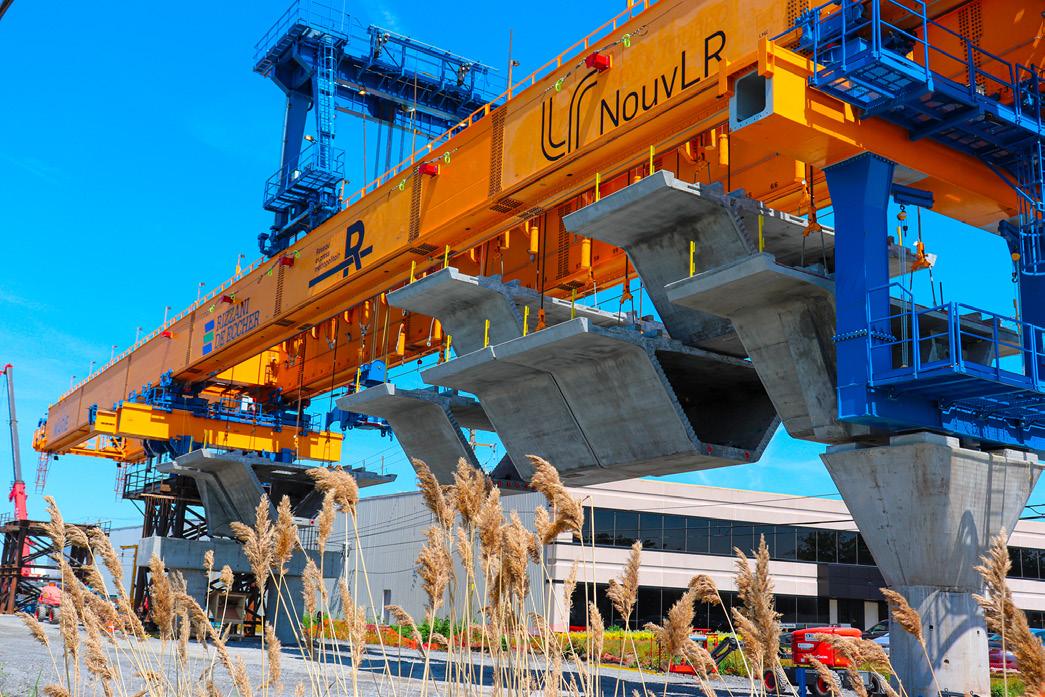
The Helene Desmarais Building Pavilion at HEC Montreal garnered an honourable mention in the Mid-Rise Structures category. The structure opened in August 2023 and is a flagship project featuring reinforced concrete and advanced architectural design to offer top tier learning and study spaces.
Visit www.ACIExcellence.org for the full list of winning projects.

CCPPP reveals P3 winners
Healthcare facilities dominated the 2024 National Awards for Innovation & Excellence in P3s, with projects from Newfoundland and Labrador, Quebec and Ontario earning recognition. The seven award winners also included an all-season highway in the Northwest Territories, a new courthouse in downtown Toronto and a school bundling project now serving 7,000 students in Alberta. Presented by the Canadian Council for Public-Private Partnerships during the P3 2024 conferennce in Toronto in November, the awards put a spotlight on some of the nation’s top project collaborations.
“We had a tremendous group of 10 nominees this year, showcasing the vitality and variety of P3s,” stated said Brad Nicpon, chair of the Awards Selection Committee and partner with McCarthy Tétrault LLP. “In particular, the projects we celebrated this year showcase the long-term nature of P3 agreements.”
Visit www.pppcouncil.ca for a full list of award winners.
Montreal’s REM placed second in the infrastructure category of this year’s ACI awards.
PHOTO:
Gower appointed president at PCL Construction
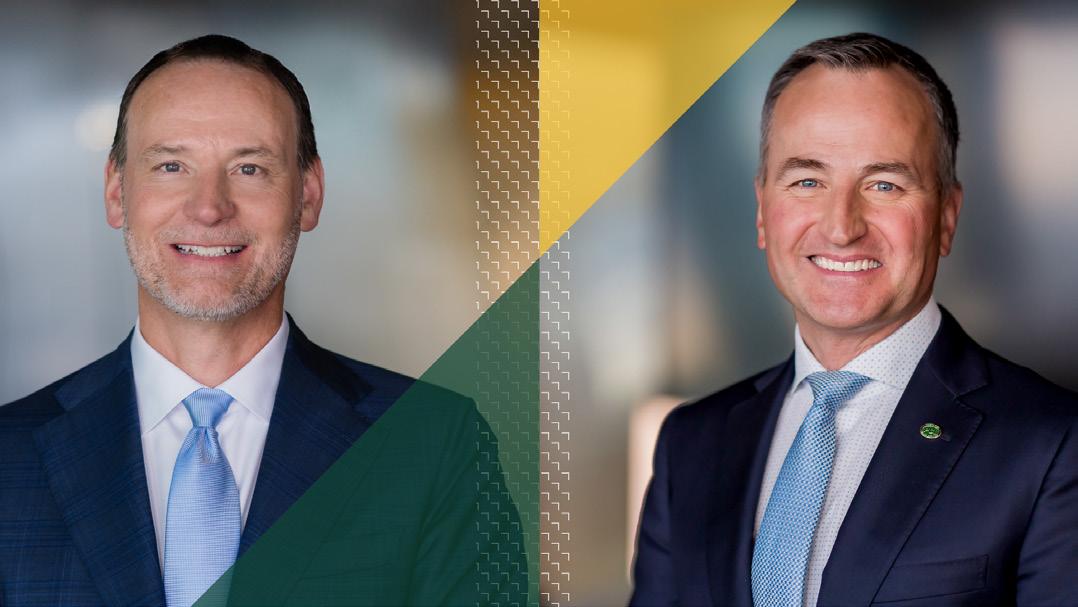
Chris Gower is the new president and chief executive officer of the PCL family of companies, advancing from the role of deputy CEO. He had previously served as the company’s chief operating officer, overseeing PCL’s building operations in Canada, the United States and Australia. Gower is also a CCA Gold Seal certified estimator and project manager and is an alumnus of On-Site Magazine’s 40 Under 40 in Canadian Construction.
“Leading a company with such a
PCL has named Chris Gower (left) president and CEO. Dave Filipchuk (right) is stepping into the role of Board Chair with the company.
rich and successful legacy is a privilege, and I extend my heartfelt thanks to Dave Filipchuk for his leadership over the past eight years,” said Gower. “I also extend my deepest gratitude for his mentorship throughout our transition time together.”
With Gower’s promotion, Filipchuk, the company’s president and CEO for the past eight years, is stepping into the role of chair of PCL Construction’s Board of Directors.
Worries for B.C.’s construction sector
Statistics in the British Columbia Construction Association’s (BCCA) Fall 2024
Construction Industry Stat Pack are setting off alarm bells. While the value of existing projects continues to grow, the threat of declining investments in major projects is an additional challenge for the industry, on top of intense pressure to meet the current demand due to persistent workforce shortages, high labour costs, and lack of payment certainty, says BCCA.
Since the spring of 2024, the value of proposed major infrastructure projects has decreased in value by five per cent and nearly 20 per cent over the past five years.
“British Columbia’s construction industry will be paramount to building our province’s critical infrastructure and alleviating the housing crisis,” said BCCA president Chris Atchison. “We need the government and opposition caucuses to work together to implement policies geared towards payment certainty and workforce development.”
24_011999_On_Site_Magazine_DEC_CN Mod: October 22, 2024 4:57 PM Print: 11/06/24 page 1 v2.5

A tunnel under the highway?
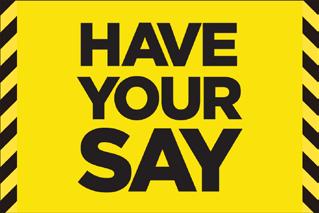
We recently asked for reader’s thoughts on Ontario Premier Doug Ford’s announcement that his government is looking into the possibility of building of a tunnel under Highway 401 to reduce traffic congestion on North America’s busiest freeway. Here is some of what you told us.*
Subterranean is logical
There is no room left to expand the current lanes on the 401. Can’t go in the air. A tunnel is a logical option to be explored. If no action now, what will our traffic look like 10 years from now?
– Michael Mifsud
Arterial nightmares
The cost of such an endeavour is excessive and will not provide the desired benefits in easing traffic congestion through the city. Arterial roads will continue to be a nightmare. The purchase of Hwy 407, redirection of through traffic, and continued investment in efficient public transport would provide a more sustainable future.
– Jim Hamilton
Absolutely
ridiculous! It will take how many years to complete? Reduction in traffic needs to happen now. Make the current 407 highway toll-free and/or have trucks use it for free. This would help a lot of people travelling daily and would cost a fraction of the price.
– Lisa Dosa
Bad idea
Money should be spent on making improvements to existing infrastructure. This would be a mammoth undertaking, and would probably have limited benefit, A better idea would be to negotiate a purchase for Highway 407, which was built with public money and sold by a previous Conservative government for way below value. Big mistake. If we keep building highways, we are soon going to consume much of the available land in Southern Ontario, and pollute the greenspace, much to the detriment of the population. If you build it, they will continue to come.
– Roger Lockie
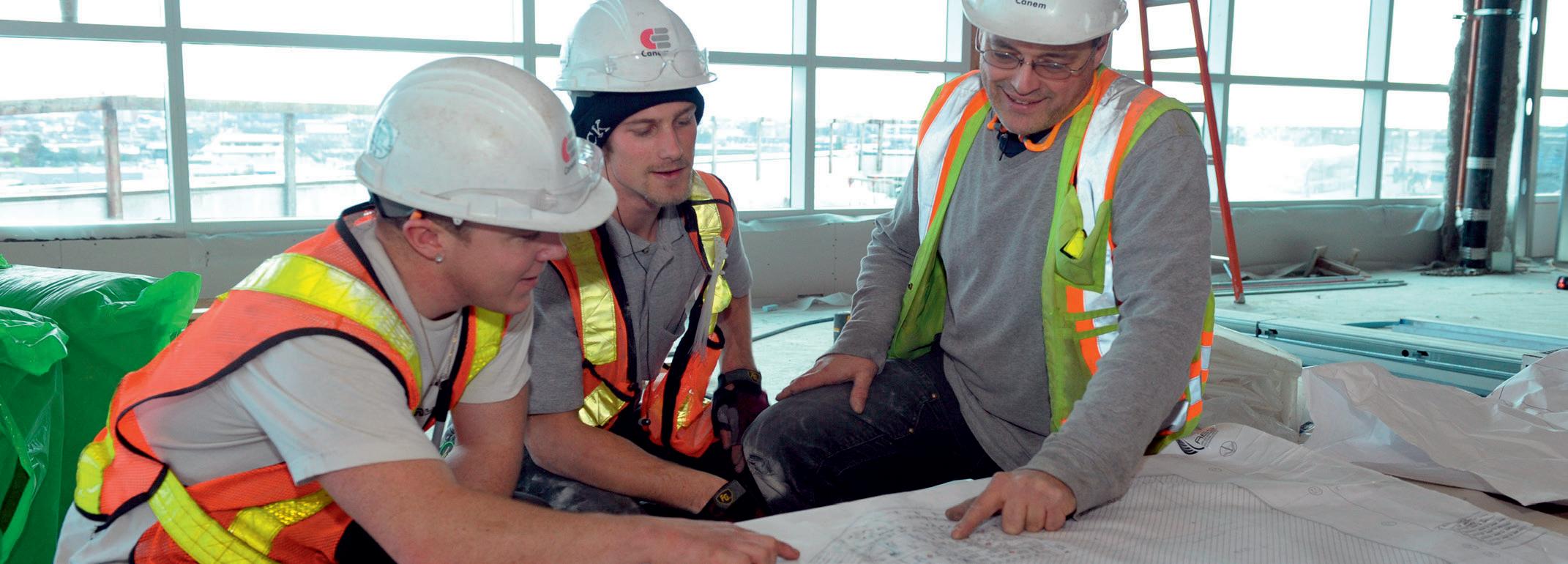

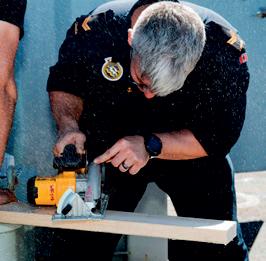
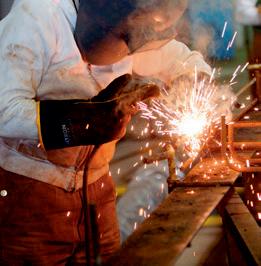
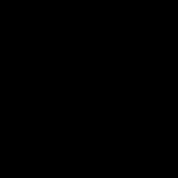
Buy back the 407
Given what’s transpired on the Crosstown link (initially planned to open in 2020 but still not open and without a projected opening date, with massive cost overruns and business inconvenience) the Ford government does not have the ability to undertake a project as complicated as would be required for the described tunnel under the 401. Further, the costs to the taxpayer public would be beyond massive.
Even if they were to go ahead and build the tunnel, that higher volume of cars would have to surface somewhere. I have yet to see any suggestion of how street level traffic will be dealt with. There is no room to expand above ground roads through Toronto to accommodate higher volume.
I suggest the better solution would be, although untasteful, to buy back the 407. It should never have been sold in the first place. We paid to build it, pay to drive on it, now we’ll pay for it again, but that would be a better solution than the proposed 401 tunnel.
– Ivan Cohen
Big Dig 2?
It was done in Boston on a smaller scale. Google “the Big Dig Boston.”
– Thomas Leyes
A crazy idea
Why not utilize the 407 to help move traffic through the city and focus on widening the 401 to three lanes from Cobourg to Kingston. This expansion of the highway is long overdue considering the amount of truck traffic using this stretch. It is clearly unsafe the way it is now.
– Brad Cooney
Terrible idea
Why have they not moved forward or tried any of the ideas previously supported – primarily truck-only lanes on the 401 and 407?
–
Collette Hart
Great idea!
Four lanes inside the tunnel with interchangeable jersey barriers to move to accommodate higher traffic volumes from east to west; a minimum speed of 115, maximum of 120, with heavy fines for infractions; impose a toll on all 400 series highways to help with costs/ maintenance; and use the boring company!
– Jordon Clune
Art of deception
Smoke and mirrors. Takes your mind off Ontario Place fiasco, and the green belt, and other corruption from this government.
– Colin Soucie
*Note: Some responses have been edited for clarity and length.
Sponsored By
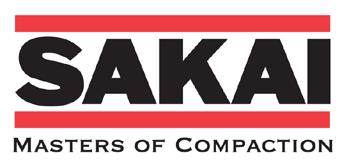
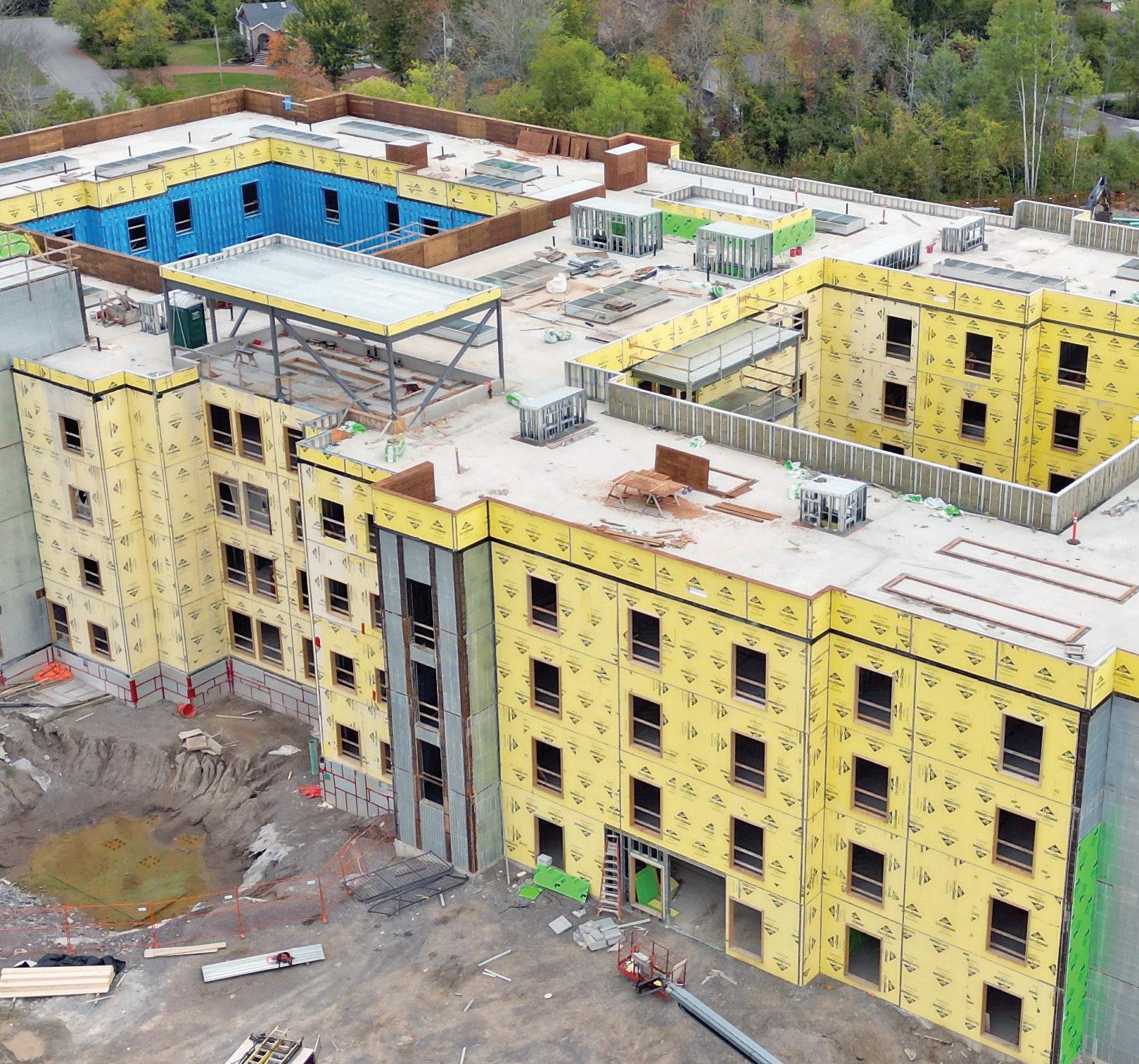
A selection of data reflecting trends in the Canadian construction industry
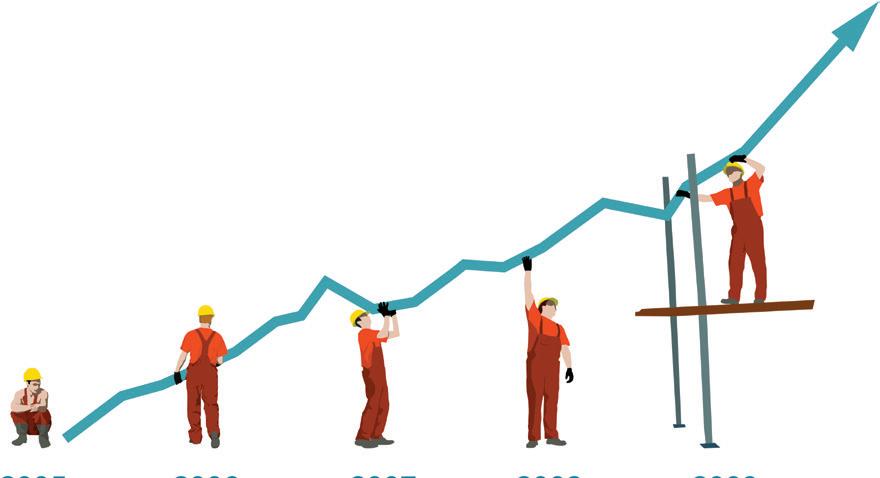
ONTARIO GAINS PACE SEPTEMBER PERMITS HIKE
The total value of building permits in Canada increased by $1.3 billion to $13 billion in September, reports Statistics Canada. The 11.5 per cent jump took values to their second-highest level since the start of the agency’s new data series in January 2017.
Ontario posted the biggest increases amongst the provinces in both the non-residential and residential sectors for the month, as construction intentions in that province grew by $1.2 billion compared to August, to reach $5.9 billion.
On the non-residential side, national permit values increased to $5.2 billion, driven by gains
in the institutional component, which rose by $824.9 million to hit $1.8 billion. Industrial and commercial construction intentions edged down by $17.6 million (1.3 per cent) and $9.9 million (0.5 per cent), respectively. Most of the institutional gains came from a $502.1 million increase in Ontario, generated through permits for long-term care facilities and a hospital.
Nationally, construction intentions for the residential sector rose to $7.7 billion, with Ontario’s multi-unit permits increasing by $812.3 million over the August report.
MODERATE RISE IN CONSTRUCTION INVESTMENT IN AUGUST
INVESTMENT IN NON-RESIDENTIAL CONSTRUCTION, SEASONALLY ADJUSTED, AUGUST 2024 (IN MILLIONS)
Investment in building construction edged up 0.2 per cent to $21 billion in August, after a 1.6 per cent decrease in July. The residential sector edged down by a tenth of a per cent to $14.6 billion, while the non-residential sector was up a full per cent at $6.4 billion. Year over year, investment in building construction grew 7.2 per cent. Investment in multi-unit construction fell by 0.3 per cent from July, which offset the slight growth seen in the single-family component. Quebec posted the largest multi-family drop, coming in $121.9 million shy of July, but Ontario made that back, and more, growing by $125.5 million in the segment. All three non-residential components posted monthly gains, with institutional rising 1.3 per cent to reach a record high of $1.8 billion, the industrial component growing 1.9 per cent to $1.4 billion, and the commercial segment gaining 0.4 per cent to reach $3.2 billion.
Table: Statistics
CONSTRUCTION EMPLOYMENT RISES IN OCTOBER
Canada’s construction sector added 6,300 workers in October, reports Statistics Canada in its Labour Force Survey. Based on seasonally adjusted figures, there were 1,580,900 workers in Canada’s construction industry in October, 0.4 per cent more than in September, and 2,700 more than in October of last year. Canada’s employment rate, or the proportion of the population aged 15 and older who are employed, dipped by 0.1 percentage points to 60.6 per cent in October, while the unemployment rate remained at 6.5 per cent. On a year-over-year basis, the unemployment rate is up 0.8 percentage points.
TOTAL EMPLOYMENT IN CANADA
20,596,900
CONSTRUCTION EMPLOYMENT
1,580,900
UNEMPLOYMENT RATE 6.5%
Sources: Statistics
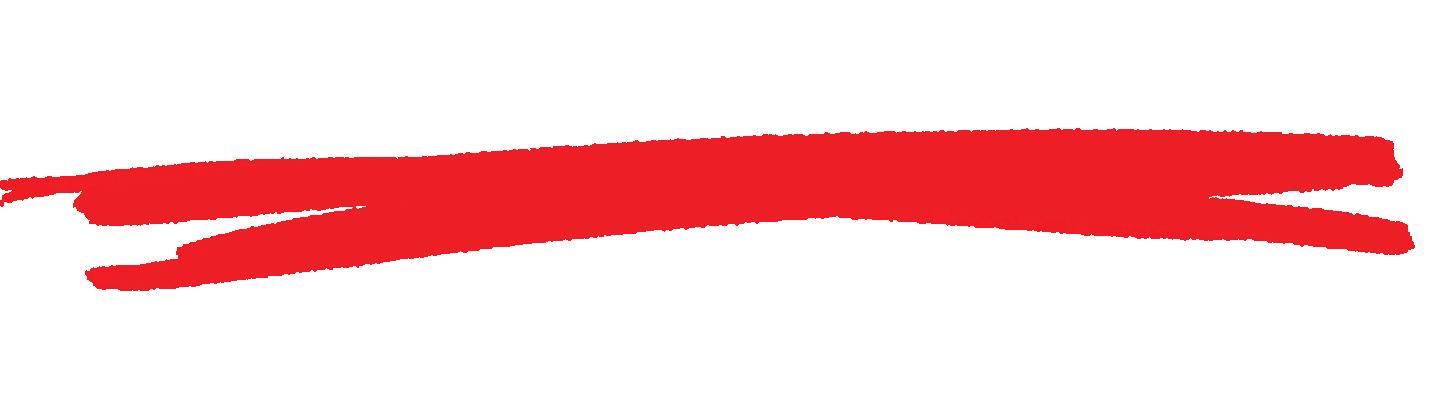
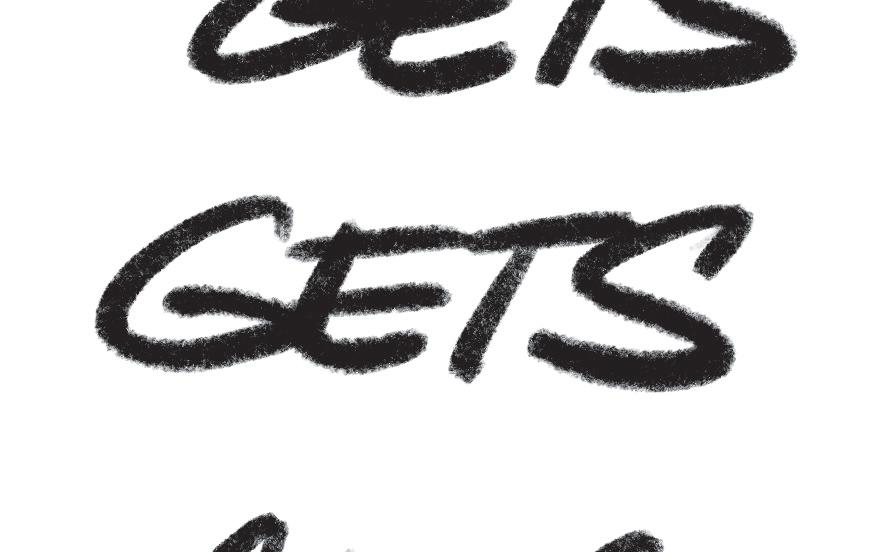
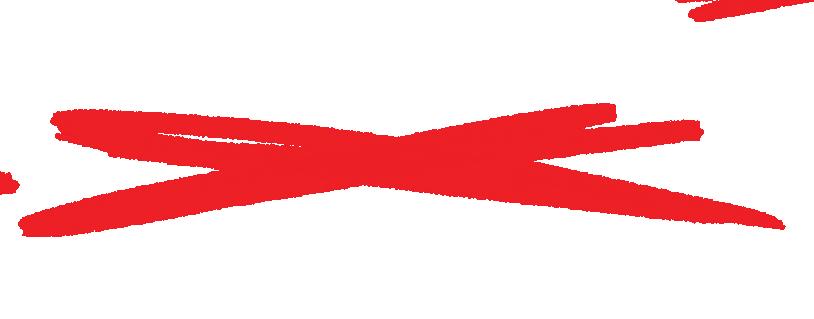
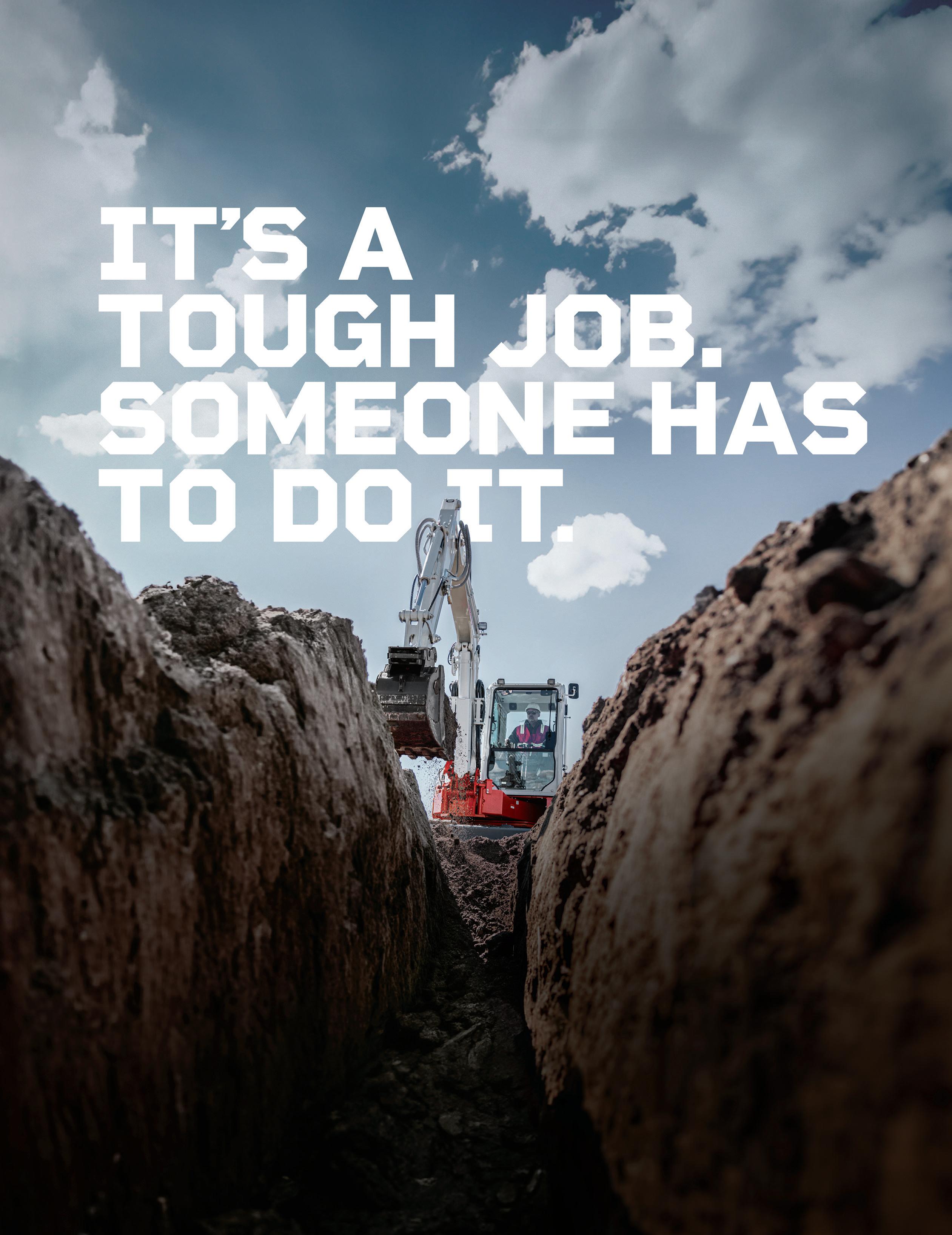
Sized right for tight spaces. Steel-built for heavy-duty work. With groundbreaking power in a nimble package, Takeuchi Compact Excavators are proof positive that it’s not the size of the machine in the work, it’s the size of the work in the machine.
THE MARK OF TOUGHNESS
EXTENSIVE EXCAVATOR LINEUP: INCLUDES CONVENTIONAL TAIL SWING, SHORT TAIL SWING, SIDE-TO-SIDE (STS) OFFSET BOOM, HYBRID AND FULLY ELECTRIC MODELS.


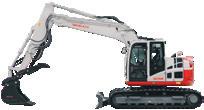
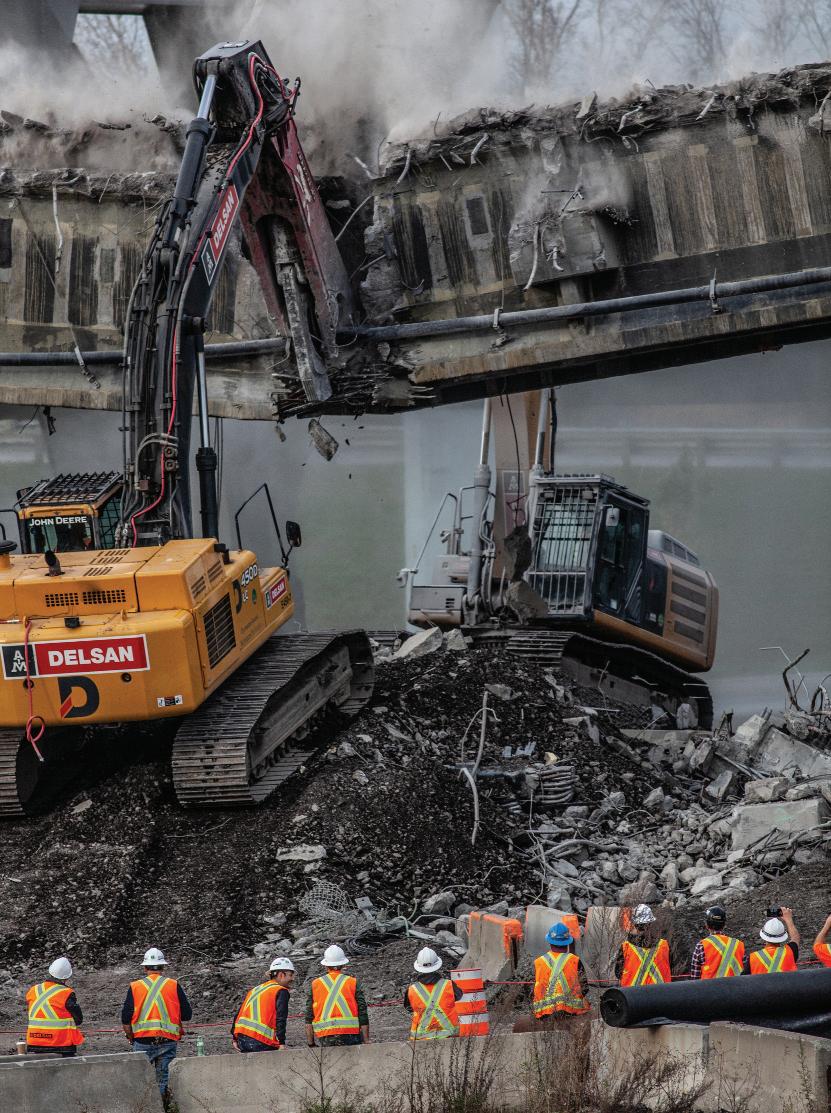
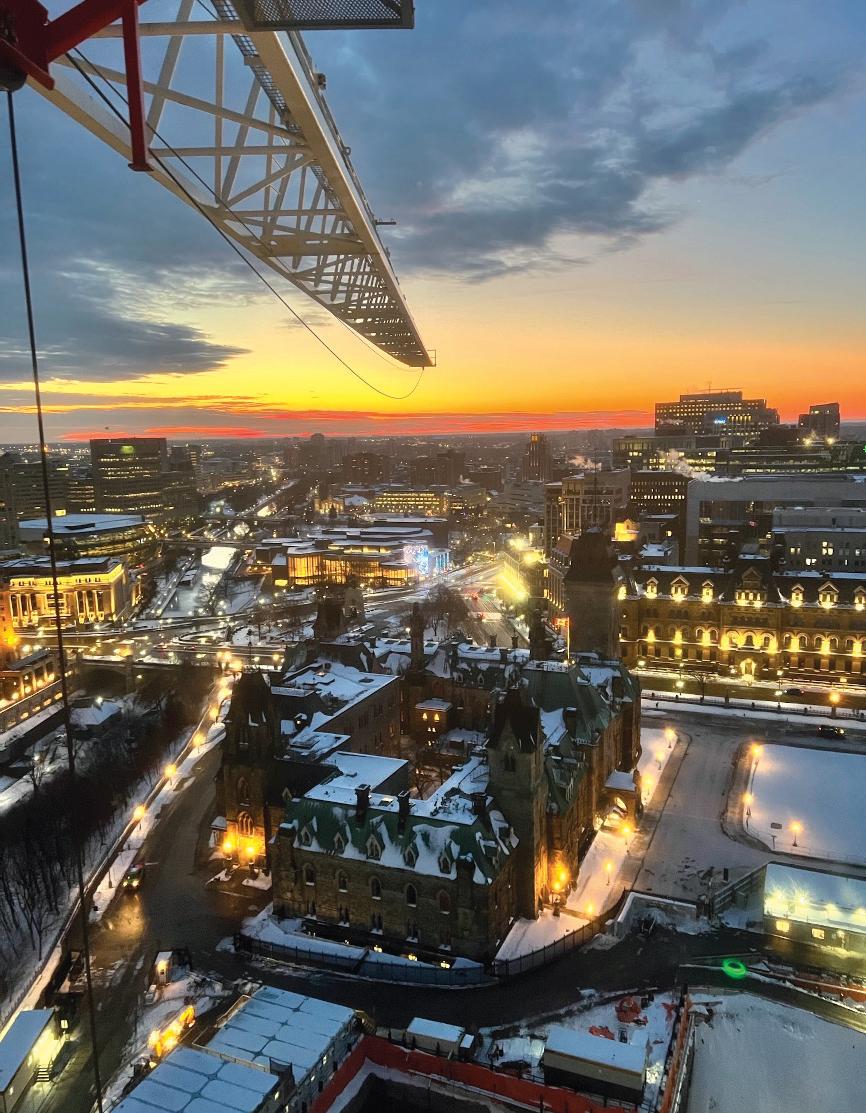
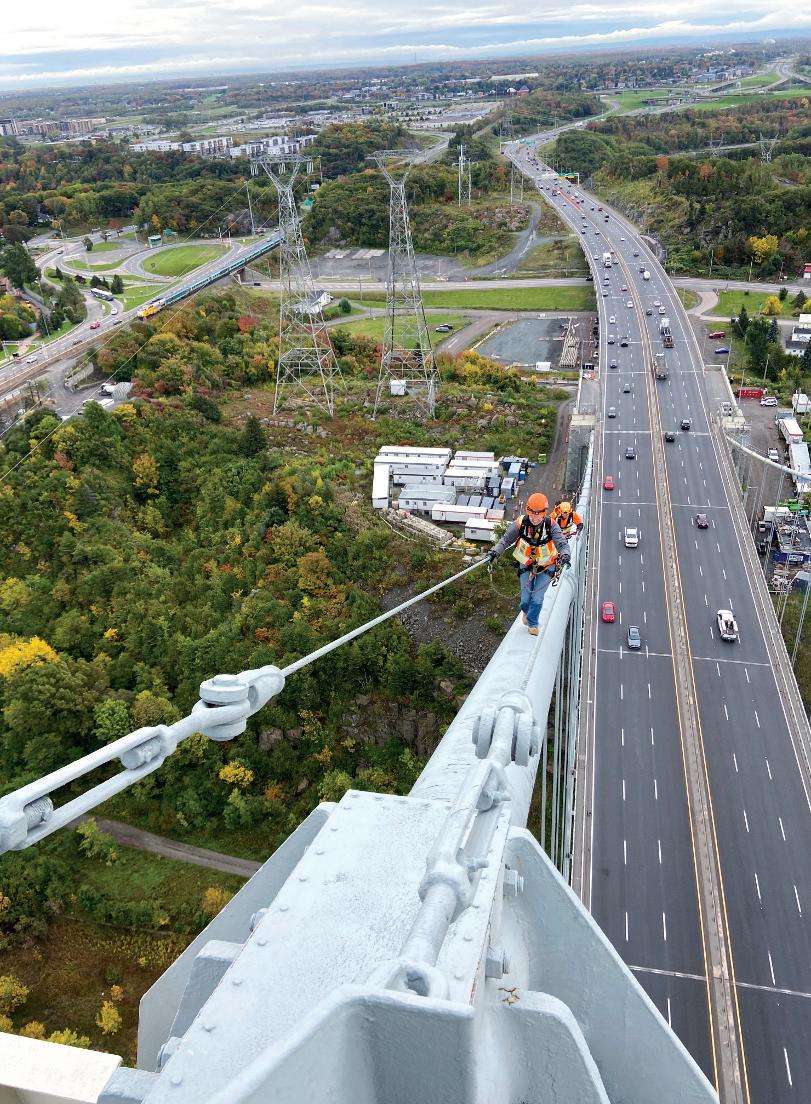


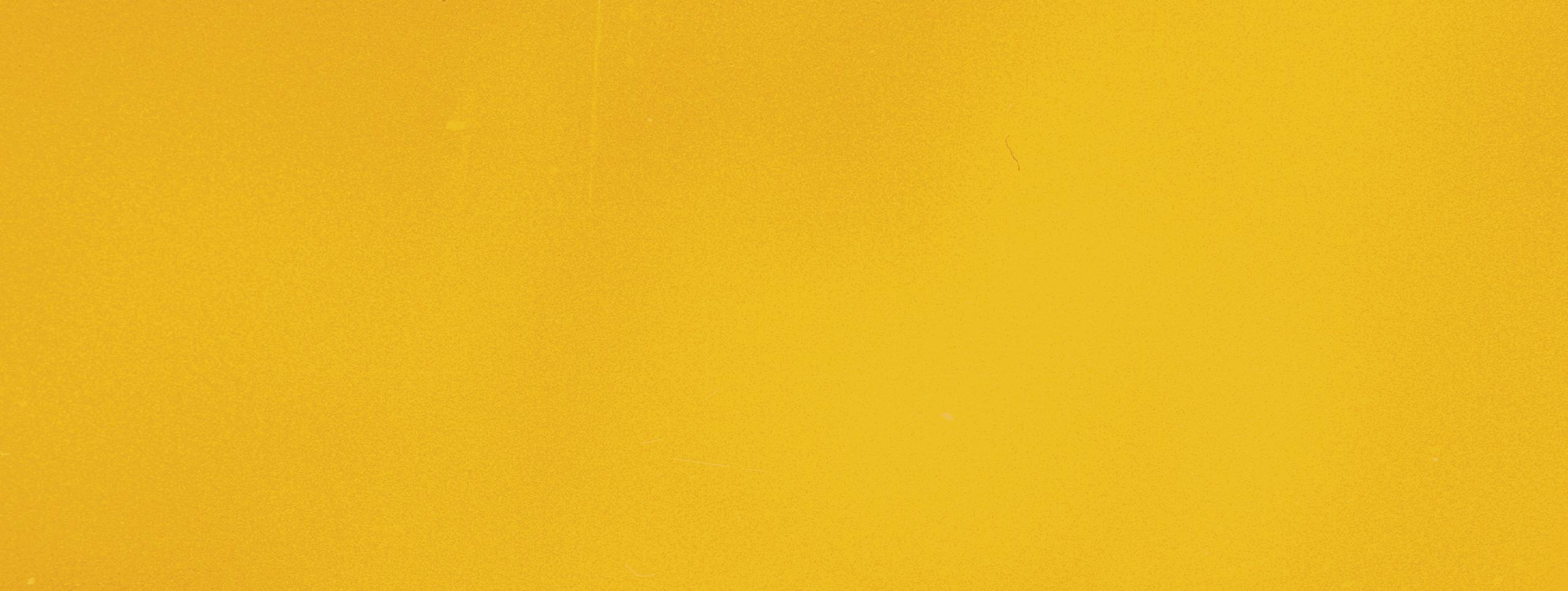
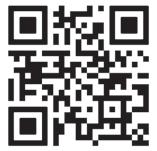
Cybersecurity: Getting a handle on the hackers

On-Site cybersecurity webinar
provides overview of risks associated with doing business in today’s digital world.
BY ADAM FREILL
Much like having a crisis plan for accidents on a site, it pays to have a cybersecurity plan for when hackers come calling. With so much reliance on digital technologies in today’s world of construction, companies of all sizes need to have a solid handle on their cybersecurity risks.
In October, On-Site Magazine presented a webinar featuring Craig Hurst, COO of The Net Effect Contractor Advisors Inc., and chair of the Technology Committee of the Canadian Construction Association, to help assess and mitigate risks in the construction sector. The presentation, sponsored by software company Revizto, provided an overview of strategies that companies can use before, and after, suffering an attack.
“There are really only two types of companies, those that have been hacked and those that will be,” stated Hurst. “And the characters that are out to hack are hiding in the shadows.”
He explained that cybersecurity is becoming a multi-billion-dollar issue, touching companies of all sizes in all sectors of the economy.
“Construction businesses are not exempt from it,” said the security expert. “We tend to think that the companies that are going to be vulnerable are the ones that are issuing credit cards or utilizing credit cards for payment processes, or that have a lot of user identities in their databases. The fact of the matter is every company is as vulnerable as the next. There really is no reprieve. And so construction, just like any other industry, needs to be on top of these issues before these issues get on top of them.”
RISKS ARE EVOLVING
Where once the biggest concerns was the nuisance of viruses taking systems offline, or being used to steal personal information, like credit card numbers and banking details, the world of cybercrimes is evolving.
“In today’s day and age, they are mone-
tizing these attacks and figuring out how to extract hard-earned dollars and cents from the victims that that they’re going after,” he said. “We’re still talking today about malware and viruses, they haven’t gone away, but now there’s ransomware – companies being held hostage, being told to make a payment to retrieve their data and get back into business. That’s probably the biggest concern in the cybersecurity field right now.”
While larger companies tend to be the assumed targets, these contractors usually have digital teams and departments implementing protocols and monitoring for potential intrusions, which is why smaller companies may be more susceptible to the risk than a large enterprise.
“Every business is at risk. Small companies are being attacked as well as the big enterprise contractors,” said Hurst. “Most don’t have effective cybersecurity protections and practices in place, and so the hackers know that they are vulnerable.”
FINANCIAL AND NON-FINANCIAL COSTS
Regardless of corporate headcount, in addition to the potential costs associated with paying a ransom, there are reputational concerns that being hacked brings forward,
On-Site editor Adam Freill, left, and Craig Hurst, COO of The Net Effect Contractor Advisors Inc. and chair of the Technology Committee of the Canadian Construction Association, discuss cybersecurity for the construction industry.
Tougher made smarter
Introducing the new VHD
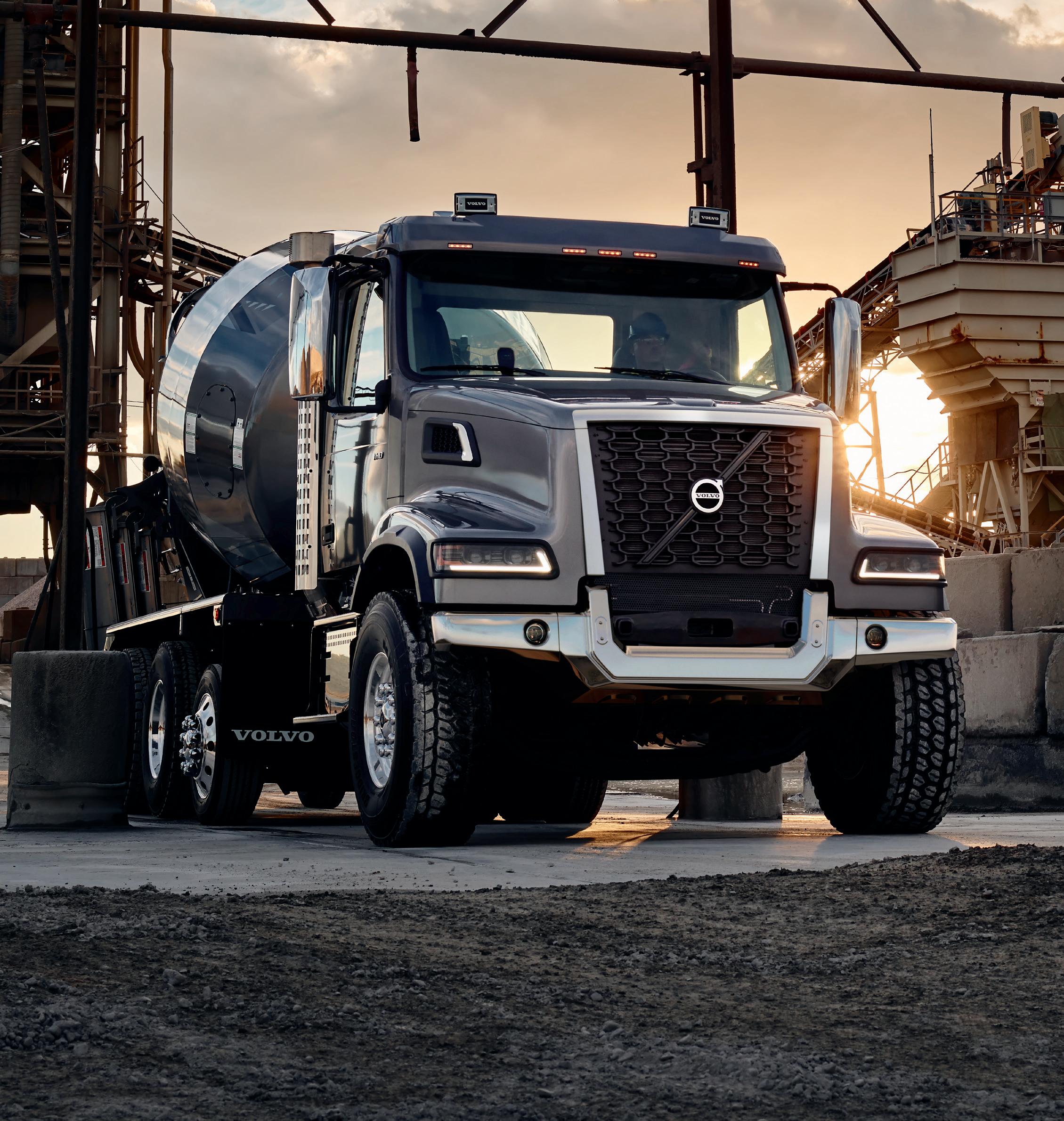
On the jobsite you need a truck that’s tough, safe, and smart. So, we built the new Volvo VHD to be the best-looking, most rugged vocational vehicle in the industry, packed with innovative ideas like Volvo Active Driver Assist and the revolutionary Volvo Dynamic Steering. Your toughest jobs just got easier. Learn more at volvotrucks.ca/en-ca/trucks/vhd/

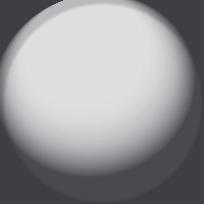
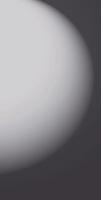
along with a potential loss of income while a company scrambles to get its systems back up and running.
“Does it mean that your projects are going to stop? Maybe not, but there’s no question that there will be a financial impact in terms of number projects going down, getting your systems set back up again, the costs associated with some of the legal impacts that are going to take place, and then there’s reputation damage.”
Navigating the hours and days after an attack is made easier when there is a plan to follow, but what should one include in a cybersecurity manual? While these are generally bespoke documents, tailored to the specific needs of the company and its risk profile, Hurst says that a cyberattack plan should address a number of key points: “Who’s going to be in charge? How does it get identified? Who do we inform? Do we inform the police? Do we inform our insurance company? Do we inform all of our ‘nears and dears’ … our suppliers, our subcontractors, anybody who has a substantial concern about us being hacked… Who are they? And what do we inform them?”
A communication plan is a must, he explained, with designated people who handle specific tasks. And the plan should also address any legal requirements.
“What are our legal responsibilities and compliance responsibilities? Who do we have to inform? What do we need to do with respect to being sued by somebody whose information you let out? What’s our legal responsibility to the owner of the building that we’re working on?”
DEPLOYING THE DOCUMENT
Preventing an attack, or reducing the damage from an attack, is generally easier to achieve through the formation of a plan, but simply having a cybersecurity document in place is not enough – for a plan to be effective, it needs to be understood and followed by a company’s people.
“When we look at what’s happening with cybersecurity attacks, we generally find that it’s because the organization has not taken the time to adequately understand what cybersecurity issues are out there, what their vulnerabilities and risks
are, but more importantly, not taking that kind of information to the next step, which is training staff,” said Hurst.
He also suggested expanding the focus to anyone who may have access to or be impacted by the company’s digital workings.
“If you’re a general contractor, that means you could have vulnerabilities that are being pointed at you because of your subcontractors or your suppliers. It really comes down to understanding who’s involved in your in your digital ecosystem, the kind of vulnerabilities they have as individuals, and how we can batten down the hatches so that those vulnerabilities are less likely to cause us a problem,” he advised.
“The number 1 defense against anything with respect to cybersecurity is multi-factor authentication,” he said, adding that despite how familiar we are with it through online banking and even food delivery services, many companies have yet to fully embrace this relatively simple defensive step.
“We understand it; we accept it; but within our own businesses, we are not demanding it yet,” he said.
Ensuring that the proper defenses are in place, and that everyone in the stakeholder chain is taking the issue seriously, takes repeated focus from the company’s leadership, along with on-going training and support right through to the jobsite. Reframing the topic may help, advised Hurst.
“It’s as much a safety issue for the for a company as making sure that your people are using scaffolding properly, or you’re doing a hazard level assessment on a site location every morning,” he explained.
“We don’t think of it as safety because it’s not like people are getting injured, but in a sense, it is about the protection of the company… Everybody’s got a level responsibility with respect to protecting that safety factor, so reinforce the steps in toolbox talks and put together corporate policies that are included in your onboarding sessions for new employees.”
BUILDING THE BACKUPS
These policies should include regular backing up of data, said Hurst. “Corporately, you want to be doing a backup of everything
that’s created, at minimum, once a day. If you think you’re vulnerable, you may want to be doing it more regularly than that.”
This backup can be stored locally, if a company has appropriate systems in place, but more and more companies are moving their data to the cloud – a solution that he views as a good option for smaller companies in the construction sector.
“If you are a small company without a cybersecurity plan, without an IT department, you are probably more vulnerable than using what’s known as an in-the-cloud or an SaaS application, because the companies that are hosting those applications have extraordinary security in place,” he said. “They have to, or they’d be out of business.”
In the event that an attack does take down a company’s systems, Hurst said it is best to avoid the temptation to automatically reinstall programs and data from a backup. That step may be necessary, but protection comes first.
“You do not run to your backup and plug it in right away,” he said. “You want to make sure that your IT department or your IT consultants are brought in… to make sure that everything is either a new setup of your existing tech stack, or that it is isolated and ensured to be clean before you input your latest backup of your data, otherwise you could be backing your data up into something that is still vulnerable and still exposed to the ransom demanders.”
Hurst shared a number of best practices to follow during the one-hour presentation, but one of the best was also quite simple: “Anytime one of your software vendors sends you a notification that says, ‘Here is the latest update,’ do it… Most of the time they are doing something to improve their system security in those updates and patches,” he stated. “If you are not doing those patches when you find out about them from the software vendors, you are leaving your system vulnerable.”
For more tips and advice, scan the QR code to check out the session on On-Site’s YouTube channel.
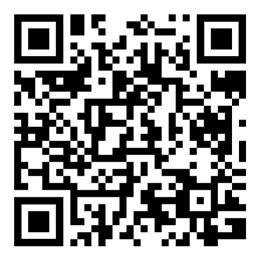
2025 FORECAST
ANTICIPATING GROWTH

POISED FOR GROWTH, BUT WHERE AND WHEN?
PG. 20
REGIONAL PERSPECTIVES
PG. 22
CCA’S TRENDS TO WATCH
PG. 24

PHOTO: © ELENATHEWISE / ADOBE STOCK
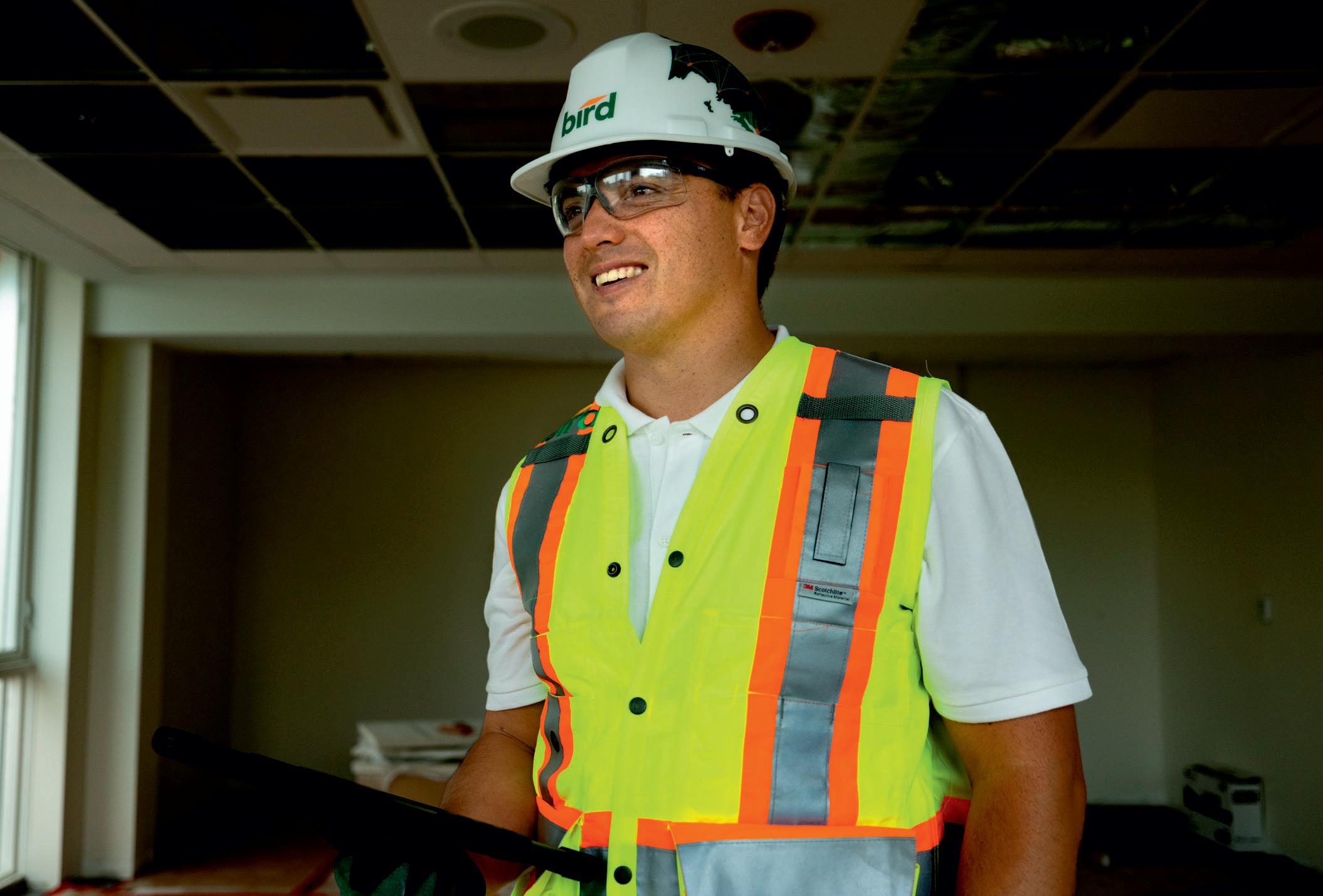

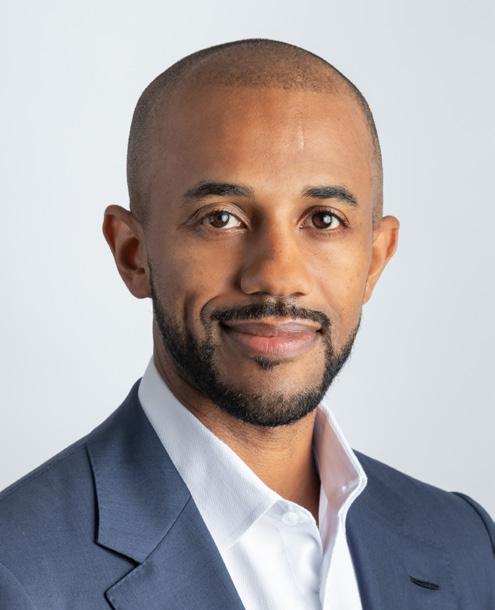
Nolan Frazier Regional Director, Canada Procore
Building a Better Tomorrow
Since its inception more than 20 years ago, Procore’s vision has been to improve the lives of everyone in construction. With the challenges the construction industry continues to face, this vision has never felt more important. Over the past year, we continued to see the impacts of the ongoing labour shortage, economic instability across the industry, and recent declines in productivity growth.
However, we’ve also witnessed innovation, renewed emphasis on problem-solving, and effervescent pride in the industry. It’s the people behind the build who are transforming construction and our communities. Whether it’s learning how to harness data and AI to improve your company’s operations, or understanding the impact culture has on your bottom line, Procore is proud to partner with you to help solve your biggest challenges.
Moving into the next year, we are likely to see Artificial Intelligence (AI) and Large Language Models (LLM) dominate headlines, while consumer technologies, such as wearables, are repurposed in new ways to improve jobsite safety. Regardless of what operational efficiency, technology or equipment arrives in 2025, successful digital transformation remains a long term, methodical and strategic effort. Ongoing innovation and application of the right technology, platform, or solution that meets your needs today, and in the future, is necessary to build better, safer and faster.
Procore is proud to sponsor this year’s Canadian Construction Forecast, which sheds light on the state of our industry and gives us a glimpse into the future. As we move into 2025, we know the industry will face more headwinds, but challenge is what this industry is built on, and every hurdle provides a new opportunity for innovation and success.
Let’s work together to build a better tomorrow.
GROWTH ANTICIPATING
Reductions in the cost of borrowing and continued need for more housing and infrastructure should spell opportunities, if the labour availability can be managed.
BY ADAM FREILL
With lending rates on their way down, paired with a need for additional housing stock and more infrastructure, expectations are for growth in Canada’s construction sector in 2025. The question remains where and when, especially in light of ongoing challenges like the steady rise in material and labour costs, and finding enough workers with skills that align to job openings. Technology may help alleviate some of the pain points, however, and 2025 could be the year where Artificial Intelligence (AI) takes a key role.
“Most projections I’ve seen suggest that we’re going to go through a period of relatively slow economic growth,” stated Keith Reading, senior director of research at Morguard. “Growth is good.”
He, like many who were surveyed for their insights going into next year, expect the two biggest hurdles for the industry to be finding enough skilled labour and navigating rising costs.
“A real driver in terms of economics and costs is the availability of labour and the productivity of that labour,” explained Derron Bain, chief executive officer at Concert Infrastructure. Given the number of workers closing in on retirement, his company is putting a significant amount of support into training programs aimed at building tomorrow’s workforce.
In the more immediate term, Reading
says the industry needs to keep filling the labour funnel via immigration but acknowledges that the system is not without its flaws. “We, as a country, need to refine that process and make sure that we’re bringing in the right workers from other countries to fill the void,” he stated.
And the void is real.
“If we don’t have the people, and they don’t have the proper skillset, projects will have to wait until the labour shortages are closed,” explained Chris Atchison, president of the British Columbia Construction Association, who says the labour crunch is on in his province. “This often means waiting for other projects to finish before the labour pool can move on to other projects.”
TURNING TO TECH
A greater reliance on technology is helping some companies bridge that labour gap.
“The adoption and the practical use of it is really making a huge stride forward, and that’ll lead to boosts in productivity, less rework, more streamlined project execution,” said Kris Lengieza, global technology evangelist at Procore. “When trying to address labour, we have to think about the automation of work… automating the dull, the dirty and the dangerous.”
It’s a sentiment shared by Scott Crozier, vice-president, civil construction at Trimble. “We expect that technology providers will continue innovating with the goal of
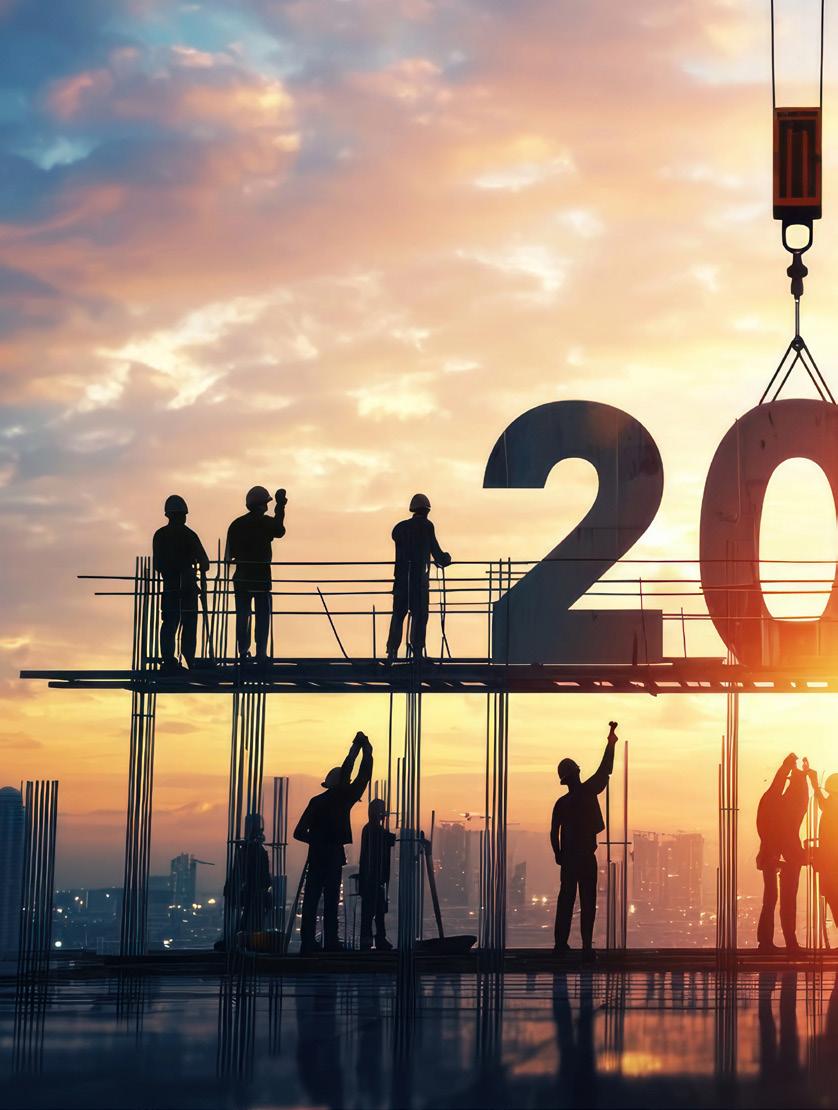
helping offset these challenges,” he said.
“My favourite example of this is a layout robot that helps you lay out information on a slab for the trades to come behind and do the work,” said Lengieza. “That person is still doing that job; they’re just using a different tool to do it. It’s like going from a hammer to a nail gun.”
Labour shortages and safety issues are increasing readiness to invest in technology agreed Troy Steele, regional sales manager for Western Canada at Brokk, who explained, “Many of our customers have started to shift their mindset toward robotics and automation.”
The biggest focus on the tech front will likely remain AI, however.
“Fifty-nine per cent of respondents of a recent Trimble survey said that artificial intelligence and machine learning will be one of the biggest trends in 2025,” stated Aviad Almagor, vice-president of tech innovation at Trimble. “It has, and will continue to, transform the construction industry due to the many efficiencies it brings.”
“AI is really good at parsing through a tremendously large amount of information and then distilling it down into something,” said Lengieza, who added that more focus will have to be put on collection of the data to maximize the technology.
“You cannot deploy AI unless you have
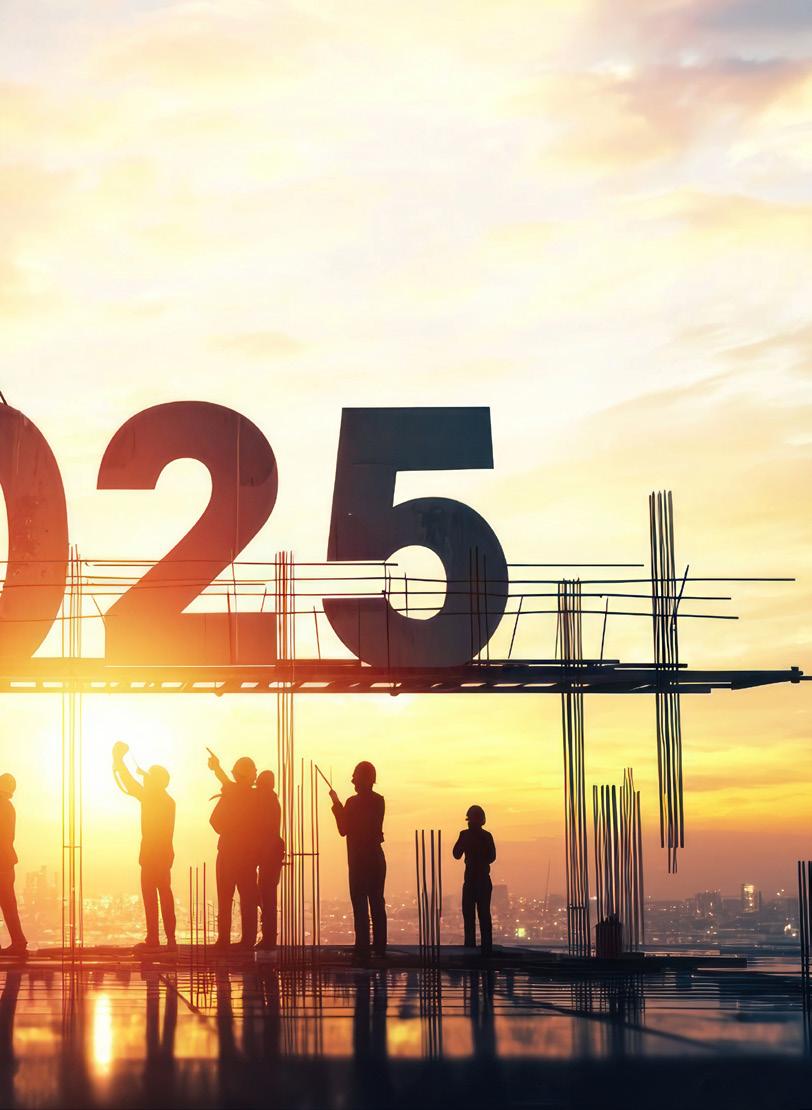
the data first, that’s why everyone in the industry needs to have their path set out and be actively working on it if they want to drive AI in the technology stack,” advised Brandon Milner, senior vice-president and chief information officer at EllisDon. “If you do not have a digital strategy for the next two to three years, then the time is now to begin this.”
INFRASTRUCTURE RENEWAL
Digital strategies will likely be put to work on a number of significant infrastructure projects, a segment expected to remain a strong backbone for the industry ths year.
“It’s pretty well documented that, from an infrastructure standpoint, Canada has some catching up to do, and some pretty significant projects. I don’t see any slowdown in that regard,” stated Reading. “We need more roads. We need better roads. We need more mass transit. The list goes on and on, and a lot of that is population growth driven.”
“Governments across Canada, whether federally or provincially, even into municipalities, are facing historic needs in terms of infrastructure requirements and infrastructure investment,” agreed Bain. “If you look at the state of some of Canada’s infrastructure, it’s not been properly maintained. It’s not been properly lifecycle renewed.
It’s at the end of its useful life, and that requires investment and renewal.”
“We see this continuing into 2025, with public investments in everything from new metro lines and wastewater treatment expansions to road and bridge repairs,” agreed Brokk’s Steele.
THE HOUSING CRISIS
The other major area of focus continues to be the housing crisis.
“Everybody knows that there’s not enough inventory. It needs to get built. I think a lot of people were on the sidelines waiting because interest rates and money was so expensive, we’re starting to see that relax a little bit,” stated Lengieza, who added that growth may not come until late in the year, and into 2026, however.
In the meantime, the desire to turn older, less-optimized properties, into housing developments appears to be gaining some traction.
“There is a growing interest in redeveloping shopping malls into mixed-use communities that integrate residential, commercial and retail spaces,” said Bill Ferreira, executive director at BuildForce Canada. “This approach aims to address aging retail infrastructure and urban housing demand, creating multi-functional spaces with greater density. Many malls, situated on sizable plots with established transit access, offer potential for urban intensification, which could increase housing supply in sought-after locations.”
“Over the past year, I think every owner of a shopping centre, particularly the larger ones, has looked at adding density to their sites, and often that’s residential towers… be it rental apartments or condominiums or the like,” added Reading. “Effectively, you’re building a mini village… you add a new market for your retail stores, and the value of the site typically goes up.”
“While shopping habits may have shifted in recent years, and this was likely exacerbated by the pandemic, shopping malls surrounded by housing will naturally see a boost in activity,” agreed Atchison. “We need to look at where there is usable space in our urban areas to build more multi-unit residential, and some shopping

mall parking lots are underutilized, so they make for a great spot.”
Another market showing strong potential that is expected to continue in 2025 is the purpose-built rental sector.
“Demand for rental housing remains strong. In fact, we have seen impressive growth in apartment starts for the year to-date in 2024 across Atlantic Canada, and in Alberta and Quebec,” shared Ferreira. “Purpose-built rentals remain a promising area for future construction activity as market conditions stabilize and government incentives take further effect.”
Beyond housing and infrastructure, Lengieza is seeing growth in data centre construction. “When you think about the amount of data centre equipment we have to bring online to support the AI revolution that’s happening around us, these big data centre providers can’t build fast enough.”
FINANCIAL FACTORS
The cost of projects, and housing, remains a significant factor in any potential growth, however. And while borrowing costs appear to be coming down, increases in activity may drive material prices higher.
“The reduction in interest rates offered some relief to developers and potential homeowners; however, growth in this segment was constrained by affordability challenges and ongoing tight labour markets,” stated Ferreira, who added that modest growth is expected for 2025.
“I think it will probably be in the spring of next year that we’ll start to see a real impact,” stated Reading. “Over recent history, rates are still relatively high, and depending on the project, you can’t always source financing that easily, particularly in the office sector.”
Waiting on interest rate relief may have some sitting on the sidelines, but that may not ultimately result in any savings on the final bill.
“When I’m speaking to governments and they complain about the cost of projects or budgets, the obvious answer is, ‘Yesterday was the cheapest day to build the project, not tomorrow,’” advised Bain. “That’s just the reality of the world we live in in terms of underlying inflation or cost of capital.”
PHOTO: © GELPI / ADOBE STOCK

A regional look at major projects
Canada’s backlog of significant projects remains robust due to infrastructure and institutional spending.
BRITISH COLUMBIA – Although current construction projects in the province are valued at roughly $170 billion, a decline of proposed project value to $160 billion has BCCA concerned that growth is going in the wrong direction. Work that is underway, or soon to be, includes Phase 2 of the Burnaby Hospital redevelopment, which is expected to start in late 2025. The province is also funding a number of new schools in the province with completion dates in 2025 and 2026. BC Hydro is spending $1.4 billion to construct three new substations, and early works are scheduled for the Fraser River Tunnel Project, as the Cross Fraser Partnership team works towards start of construction.
ALBERTA – Although the Green Line in Calgary is stuck somewhere between cancellation and retooling, the province continues to see significant levels of private and public project investment. For example, the Heidelberg Carbon Capture project, valued at $1.2 billion, is underway and, with record-breaking housing activity in 2024, the province is upgrading roads and building new schools – the province has committed $8.6 billion to complete and open 200,000 new student spaces in the next seven years. Over the summer, Linde also announced a $2-billion clean hydrogen and atmospheric gases facility, and Clark Builders is working
on site preparation for the new patient tower at Red Deer Regional Hospital Centre.
SASKATCHEWAN –
In July, a planning and engineering design work contract for the Westside Irrigation Rehabilitation Project (WIRP) was awarded. Construction timing for the $1.15 billion project is projected for 2026. Highway improvements between Humboldt and Saskatoon are set to continue until mid-year. And a $543-million OSB mill should start construction this year in Prince Albert. That has a 2027 completion target.
MANITOBA
– Manitoba’s 2024 provincial budget earmarked $540 million of capital funding to repair and rebuild Manitoba’s public infrastructure. In addition to rehabilitating the Pembina Highway Overpass at Abinojii Mikanah, as well as rebuilding the Louis Riel Bridge in Ste. Agathe, the province is also putting $47 million towards the rehabilitation of the Rivers Dam to protect against future major flooding events. On the private side, the proposed $650-million redevelopment of Portage Place is gaining momentum.
ONTARIO
– From electric battery and battery component factories to major infrastructure projects, like the Gordie Howe Bridge in Windsor and Toronto’s Ontario Line, work is happening throughout in the
province. Projects like the redevelopment of Ontario Place, construction of the Bradford Bypass, and the long-anticipated Highway 413 are all of interest in the provincial capital. That’s on top of the $15.7 billion Go Expansion, as well as a $13 billion refurbishment of Bruce Power in Tiverton.
QUEBEC – Transportation and energy are key drivers of construction in the province. Work is underway on to replace Île-auxTourtes Bridge. That $2.3 billion project looks to commissioned a new bridge in 2026. Planning is also underway for a new 19-kilometre tramway line linking the Le Gendre, Sainte-Foy, Saint-Roch and Charlesbourg sectors of the Communauté métropolitaine de Québec (CMQ). HydroQuébec has a pair of solar projects in its plans. And work continues on the Champlain Hudson Power Express transmission project.
ATLANTIC CANADA – New Brunswick recently outlined $1.5 billion in planned transportation investments, with two-thirds of that on highways. Bridges will receive another $265 million. In Nova Scotia, work has started on the QEII Halifax Infirmary Expansion Project and a $118 million CIB loan is supporting construction of the Higgins Mountain wind farm. Prince Edward Island is focussed on new schools and expansion of the Charlottetown Airport.

Expect More.
Guided by our past and inspired by the opportunity to create a safer, cleaner, sustainable world, Michels Canada collaborates with our customers to deliver creativity, consistency, quality and an industry-leading safety culture. We leverage experience gained on some of the world’s most complex projects to develop new, better ways to meet evolving energy and infrastructure needs.
Partner with Michels Canada and expect more.
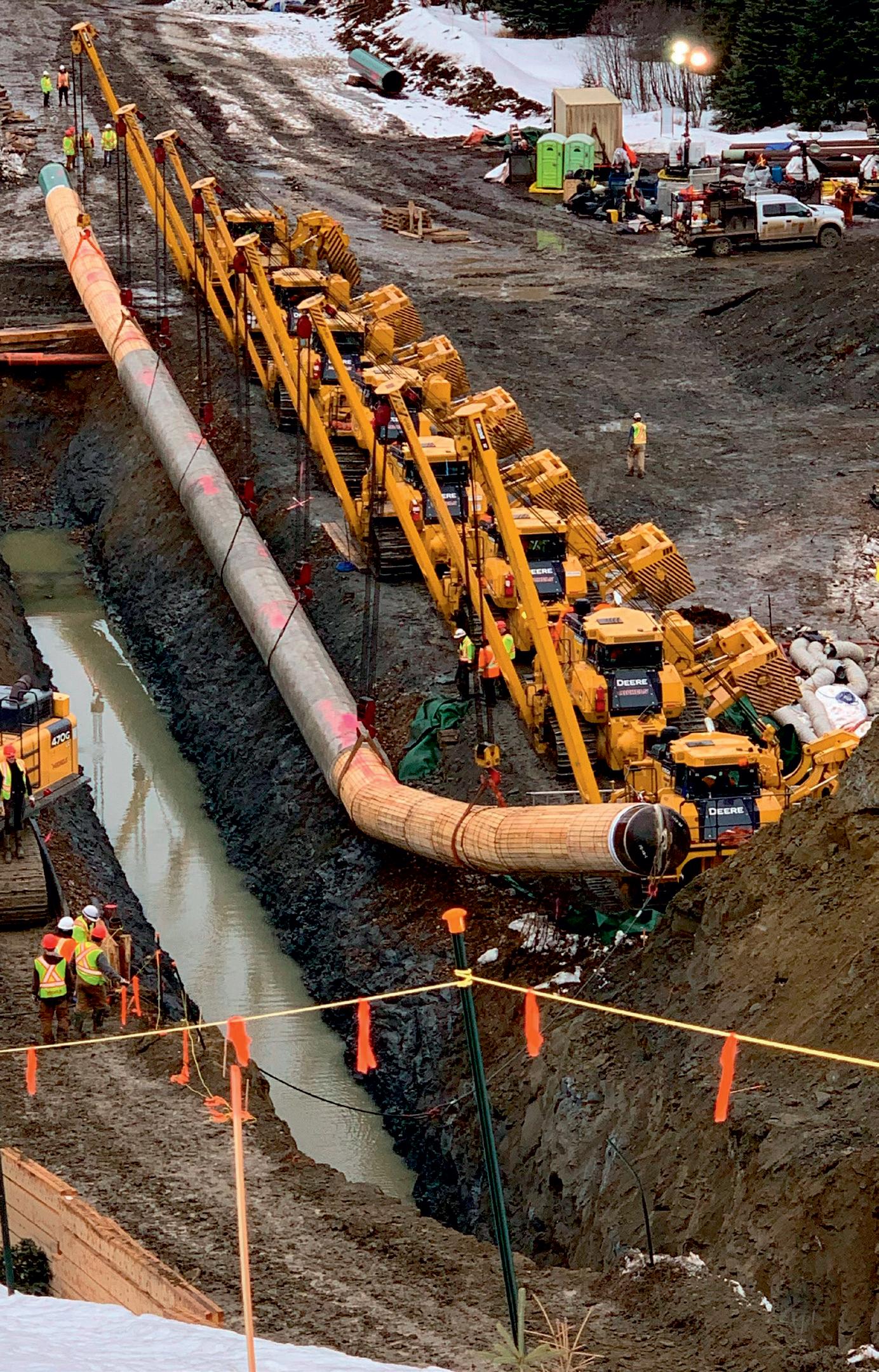
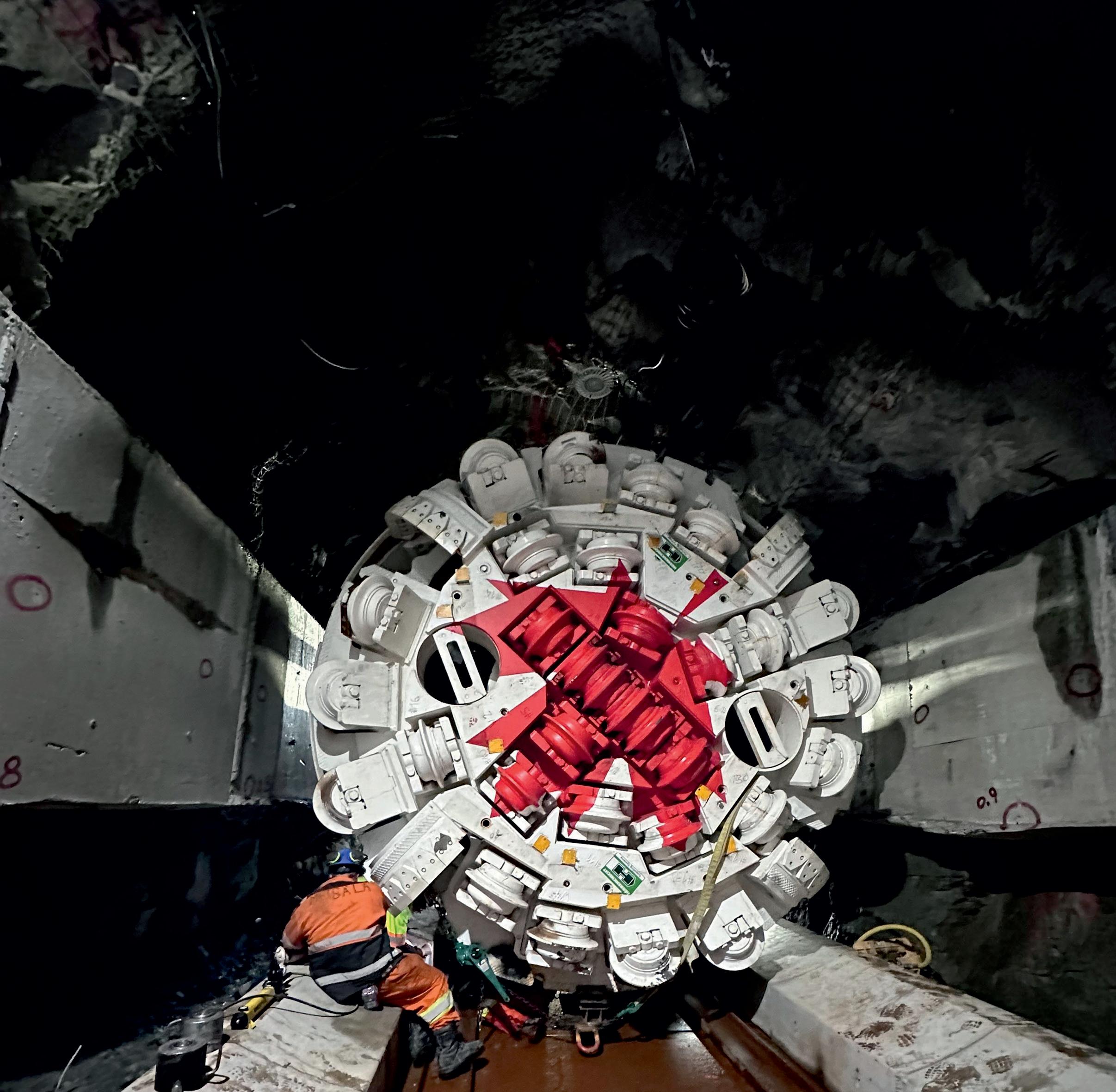
Top 10 Canadian construction trends to watch in 2025
What are some of the continuing and emerging themes to watch for in the coming 12 months? Canadian Construction Association president Rodrigue Gilbert shares some of the items on his radar.
BY RODRIGUE GILBERT
As we approach 2025, the Canadian construction industry is on the cusp of transformative changes driven by advancements in technology, shifting demographics, and evolving policy and regulatory landscapes. Here are the top 10 trends and policy issues that our organization feels will significantly impact the industry in the coming years.
1ELECTION: A PRIME TIME TO SPOTLIGHT CONSTRUCTION
As election season heats up, there is an opportunity for conversations around a national infrastructure strategy to take centre stage. The total investment needed to meet Canada’s housing targets and develop supporting infrastructure could run into the billions of dollars annually.
Canada’s existing, not to mention aging, infrastructure is not prepared for the additional stress. A comprehensive, balanced approach is needed to meet housing targets, repair or replace our aging infrastructure, build for tomorrow, and address labour challenges. With candidates campaigning, now is the time for the industry to work together to elevate infrastructure in national discussions.

PHOTO: IRYNA TOLMACHOVA/GETTY IMAGES

BUILDING GREEN: THE FUTURE IS SUSTAINABLE!
Sustainability is no longer optional. The Canada Green Building Council predicts that green construction will make up 25 per cent of the market by 2025. Construction firms have already been embracing the shift to sustainable practices, adopting green materials, energy-efficient systems, and waste-reduction strategies.
Since 2005, energy emissions in construction have decreased by approximately 16.5 per cent and GHG emissions related to the production of aluminum, cement and steel have seen a drop by 43.5 per cent, 41.6 per cent and 26.5 per cent, respectively. These are huge successes!
Governments can help move the needle further with incentives to help industry comply with new building codes and green standards.
OPTIMIZING DELIVERY AND COST MANAGEMENT: THE POWER OF IPD
Collaboration is key! The trend towards Integrated Project Delivery (IPD) models is gaining momentum, encouraging collaboration among contractors, architects, and owners. Studies have shown that IPD can reduce project delivery times and improve cost predictability. As firms recognize the benefits of shared risks and rewards, this collaborative approach will become more prevalent, fostering innovation and efficiency throughout the industry.
3 4 2 5
BUILDING FOR TOMORROW: RESILIENCE AND CLIMATE ADAPTATION
As extreme weather events become more frequent, the focus on building resilient infrastructure will intensify.
A 2022 report from the Insurance Bureau of Canada found that climate-related damages could cost the country up to $139 billion by 2030. Expect stricter building codes and increased government funding for climate-adaptive projects.
The construction industry has been advocating for these changes for some time to spur innovation and investment in
resilient construction methods – because tomorrow’s infrastructure must withstand the storms of today.
LABOUR SHORTAGES: BOLD GOVERNMENT ACTIONS ARE NEEDED
Canada continues to face a crippling labour crisis across several industries. Without a long-term plan to secure the workforce we need, the construction sector will not be able to meet the needs of Canadians.
With over 30 per cent of construction workers nearing retirement age, industry stakeholders and government agencies will need to work harder to promote careers in construction.
A well-balanced immigration policy that includes a re-evaluation of the current points system and considers the unique needs of our provinces can help ensure that we fill the labour gaps, appropriately, in our sector.
THE DIGITAL REVOLUTION
It’s time to embrace technology. In the fast-paced world of Canadian construction, where deadlines loom and accuracy is paramount, effective document management can make or break a project.
This is why the Canadian Construction Association (CCA) has taken a leap forward by developing a digital contract lifecycle management solution designed specifically for standard construction documents (CCDC and CCA) in Canada.
With SignaSur, all stakeholders, including contractors, consultants and owners, will be able to create, collaborate and seal contracts in one cohesive platform, revolutionizing the way documents are handled in the field.
are also increasingly adopting policies to promote urban density and affordable housing, compelling developers to rethink traditional construction approaches.
8
MODULAR MAGIC: THE RISE OF PREFABRICATION
Modular and prefabricated construction is projected to grow significantly. These methods not only reduce construction time; they also minimize waste, lower labour costs and align with sustainable building goals.
Initiatives such as Canada’s National Housing Strategy are promoting modular construction to address the housing crisis, making this approach more appealing to developers and municipalities. And with our long Canadian winters, building significant portions of a structure within the confines of a factory has the added benefit of mitigating weather delays.
9
10 6 7
POLICY SHIFTS AND REGULATORY FRAMEWORKS
Upcoming changes to building codes and zoning regulations will significantly impact project timelines and costs. The Canadian government is reviewing the National Building Code to improve energy efficiency, which may necessitate additional investments from builders. Municipalities
CYBERSECURITY: BATTLING DIGITAL THREATS
As digital adoption increases, so do cybersecurity risks. A study by the Ponemon Institute revealed that 57 per cent of construction firms have experienced a data breach in the last two years.
As the importance of cybersecurity grows, companies will need to invest in robust systems to protect sensitive project data and client information. Regulatory bodies may also introduce new compliance requirements to safeguard industry data.
BOOSTING EFFICIENCY AND COLLABORATION
Digital tools are revolutionizing project management. A 2020 study by McKinsey & Company found that companies that fully digitize their processes could improve productivity by up to 20 per cent.
Technologies such as Building Information Modeling (BIM) are now being integrated into over 70 per cent of projects, enabling better visualization and collaboration among stakeholders. As more firms adopt digital solutions, the construction landscape will become increasingly interconnected and efficient.
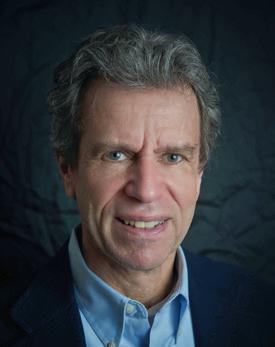
TThe real world of augmented reality
Augmented reality takes a practical turn for the construction industry.
he term “augmented reality” can evoke images of headset-wearing construction workers operating simultaneously in virtual and real-world environments. As the apps mature, however, a less ambitious but more practical set of use cases is emerging.
In August, Meta reportedly cancelled the development of its high-end mixed reality headset, a product that CEO Mark Zuckerberg had frequently boasted about. Analysts pointed to higher-than-expected development costs and disappointing sales of similar devices. That’s not what might have been expected from a tech icon that rebranded itself in 2021 after the word metasphere, or a virtual environment that exists in cyberspace.
The incident reflects a major shift in the direction of augmented reality. In November 2017, the Harvard Business Review published an article declaring that every company must have an augmented reality (AR) strategy. “In the coming months and years, it will transform how we learn, make decisions, and interact with the physical world,” the article boldly predicted.
Today, the direction appears to be less transformative and more practical. This is particularly true in construction.
“Five years ago, the augmented and mixed reality space was extremely bleeding edge,” says Nathan Patton, product marketing manager of construction technology at Trimble Inc. “Only the most innovative early adopters had really picked it up. But as the technology has advanced, we’ve worked really hard to make it easier to use. So, we’re seeing the precipice of early majority adopters starting to apply this on a day-to-day basis.”
A key enabler has been the availability of AR technology on familiar handheld devices. While ordinary compared with headset-enhanced vision, it makes the technology imminently practical.
“Where I see this going is largely around really easy quality assurance and verification inspections where anybody – a superintendent, a foreman, a field engineer – can pull out something as simple as their iPhone or their iPad,” says Patton. “So, it’s these devices you already have that allow you to see the design against the real world. Are the piles located in the right positions? Are we missing a pile? Do we have electrical outlets in the right spots?”
The transition to handheld devices also eases safety concerns.
“A few years ago, there was a lot of talk about putting AR systems directly into glasses and headsets so that you could see the model data in situ,” says Thomas Strong, senior vice-president of technology and innovation in the Construction and Infrastructure group at NFP. “That definitely has a value proposition. But safety is paramount, and you never want to have a scenario where someone’s being distracted by things in their vision that could
As the technology has advanced, we’ve worked really hard to make it easier to use.
affect their awareness of a job site condition.”
Handheld devices, by contrast, don’t encroach on the field of vision. “What we’re seeing is the use of handheld devices where you’re doing something very deliberate,” says Strong. “Using handheld devices, you can register where you are on the job site and then access location-specific data that is current and accurate. And that kind of scenario is obviously much safer because it’s not attached to your vision.”
THE DEMOCRATIZATION OF DATA
While current progress is promising, it’s still early days. Getting the virtual view on a device to match the physical location of the device is often difficult and can be challenging for non-technical people. Leading edge technology is likely to change this.
“I think the best use of AI here is going to be making the workflow easier to adopt,” says Strong.
One of the most promising aspects of the current generation of practical AR construction apps is that it could bring together two worlds: the cyber reality of virtual models seen by people in the office, and the physical reality seen by workers on the jobsite.
“People in the field don’t have access to the same technology that their office counterparts do,” says Patton, “so the strength of the recent technology is that we’re democratizing access to that design information.”
This not only gives site workers access to the virtual model but allows them to improve the value of the model with as-built site details and practical insights. For example, instead of taking a photo to indicate a potential defect, a worker can report the discrepancy against the plan along with practical suggestions about how to resolve it. This more informed approach can eliminate potential finger pointing and streamline the resolution process.
“What you get is a network effect where I’m using my phone to see the design data, and in doing so, I’m capturing data that’s informing progress information back into the model,” says Patton. “I think that’s the future end state that we can be working towards.”
Jacob Stoller is principal of StollerStrategies. Send comments to editor@on-sitemag.com.
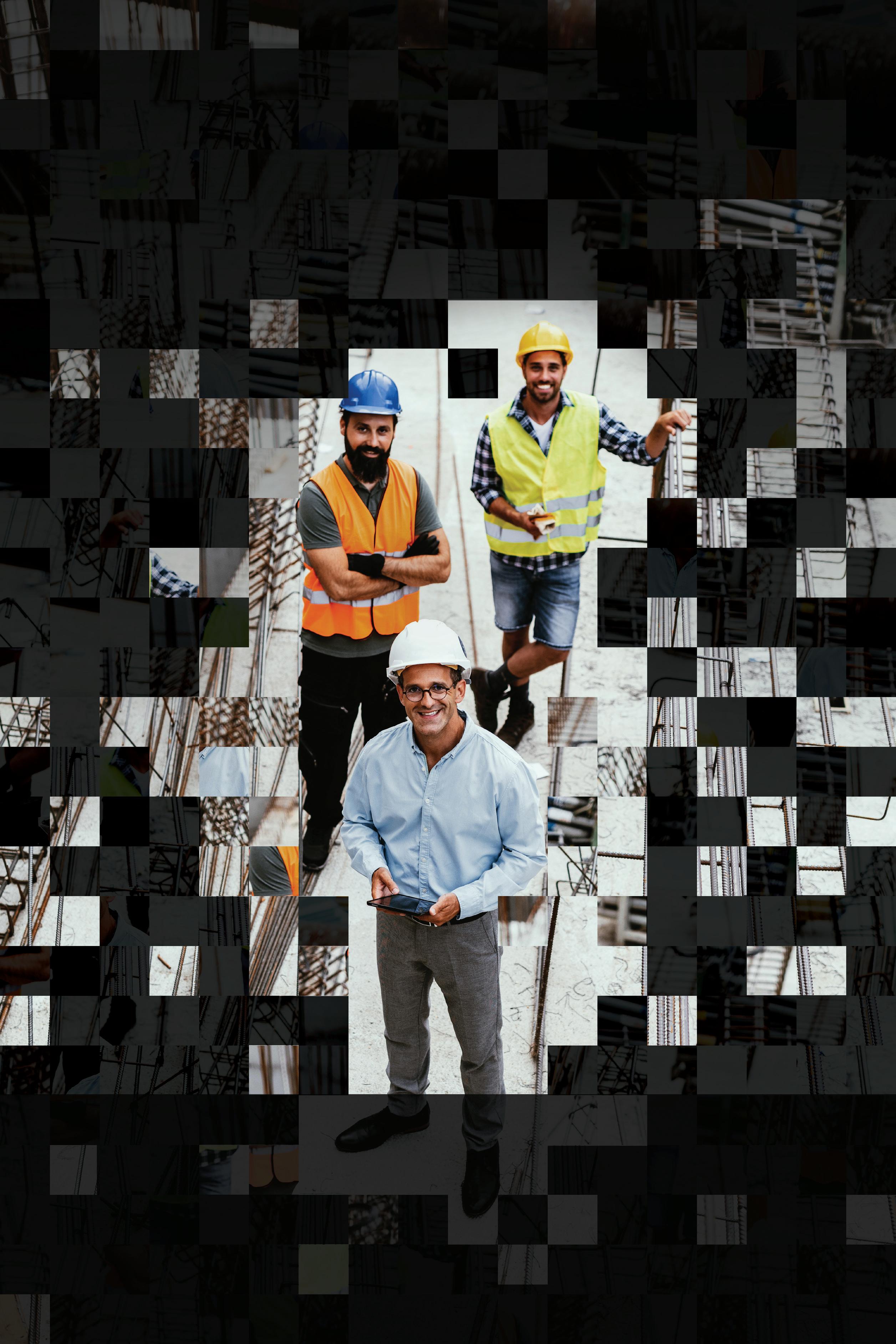
re|CLAIM
BIG MACHINES Big work takes
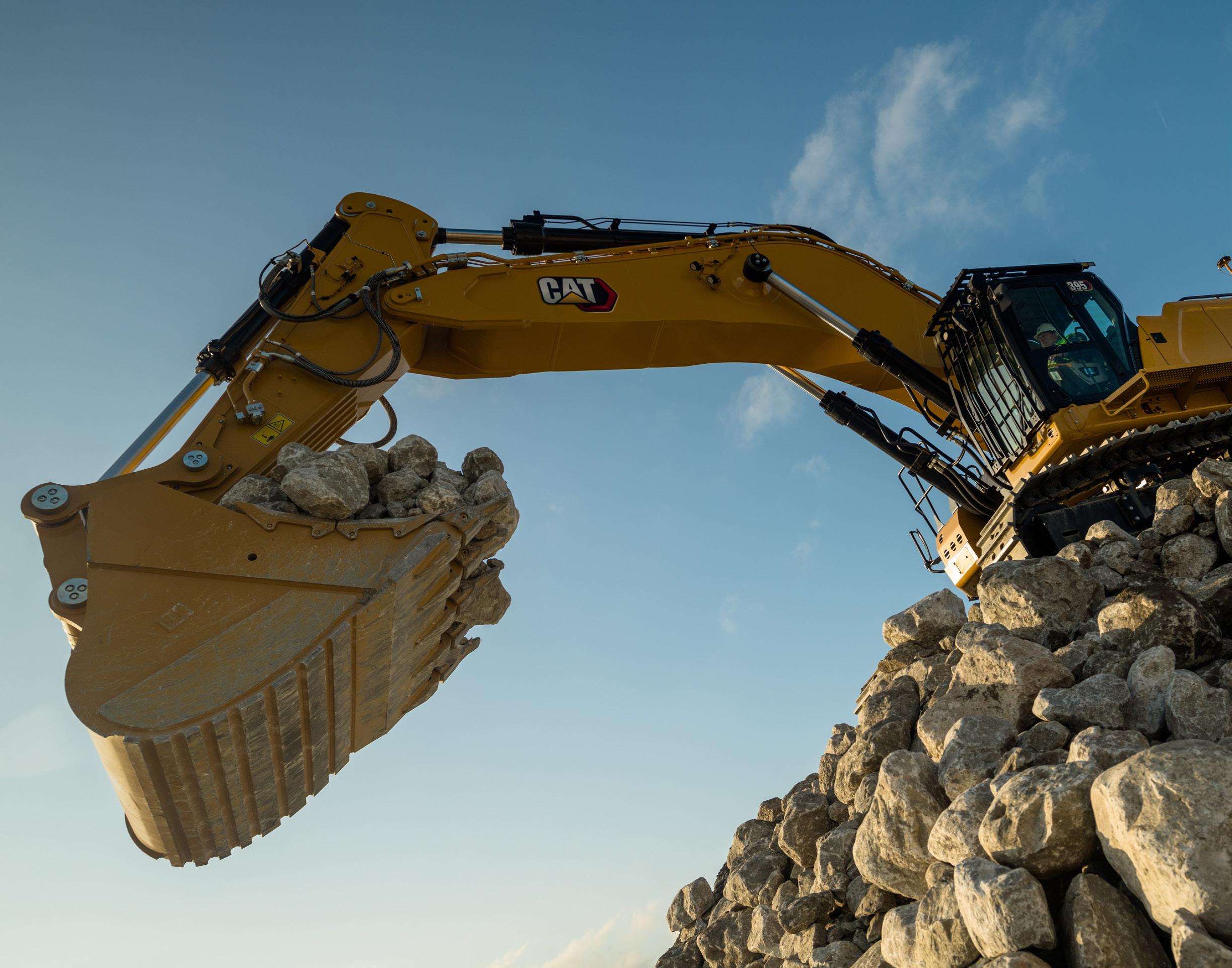
Heavyweight excavators and backhoes proving their worth.
BY NATE HENDLEY
With such a large focus on infrastructure and megaprojects in the construction sector, it may come with little surprise that heavyweight excavators are becoming more common on jobsites.
“We are seeing increased demand for these larger excavators, and I think a big part of it is the need for higher productivity on large-scale projects. Infrastructure development continues to grow globally,” says Brian Kim, heavy excavator product manager at Develon.
“The size class 45 tonnes and [higher] is steady to slightly up. What’s driving that? I think a lot of it is infrastructure spend,”
echoes Justin Steger, product marketing manager for excavators at John Deere.
That said, large excavators pose certain challenges, starting with the fact their bulk makes them difficult to transport. To address this issue, Develon developed a hydraulic removeable counterweight that Kim says makes it easier to load onto a truck without the use of a crane.
Steger says his company is exploring variable gauge undercarriages “so we can retract the tracks to get within a width for transport, minimizing permitting and trailer requirements.”
Visibility due to the number of blind spots on a large excavator is another
concern, notes Ryan Neal, market professional for large excavators at Caterpillar.
His company offers a 360-Degree Camera View system and Cat Detect - People Detection for Excavators, a three-camera aftermarket installation offering 270-degree coverage to spot workers who enter blind spots on an excavator’s left, right and rear. Other OEMs offer similar camera, sensor and/or radar-based visibility-enhancing solutions.
Of course, simply operating a big excavator can be a grueling experience.
“Operator comfort is important at any size, but larger excavators are often used in tougher working conditions, so comfort-re-
MACHINES
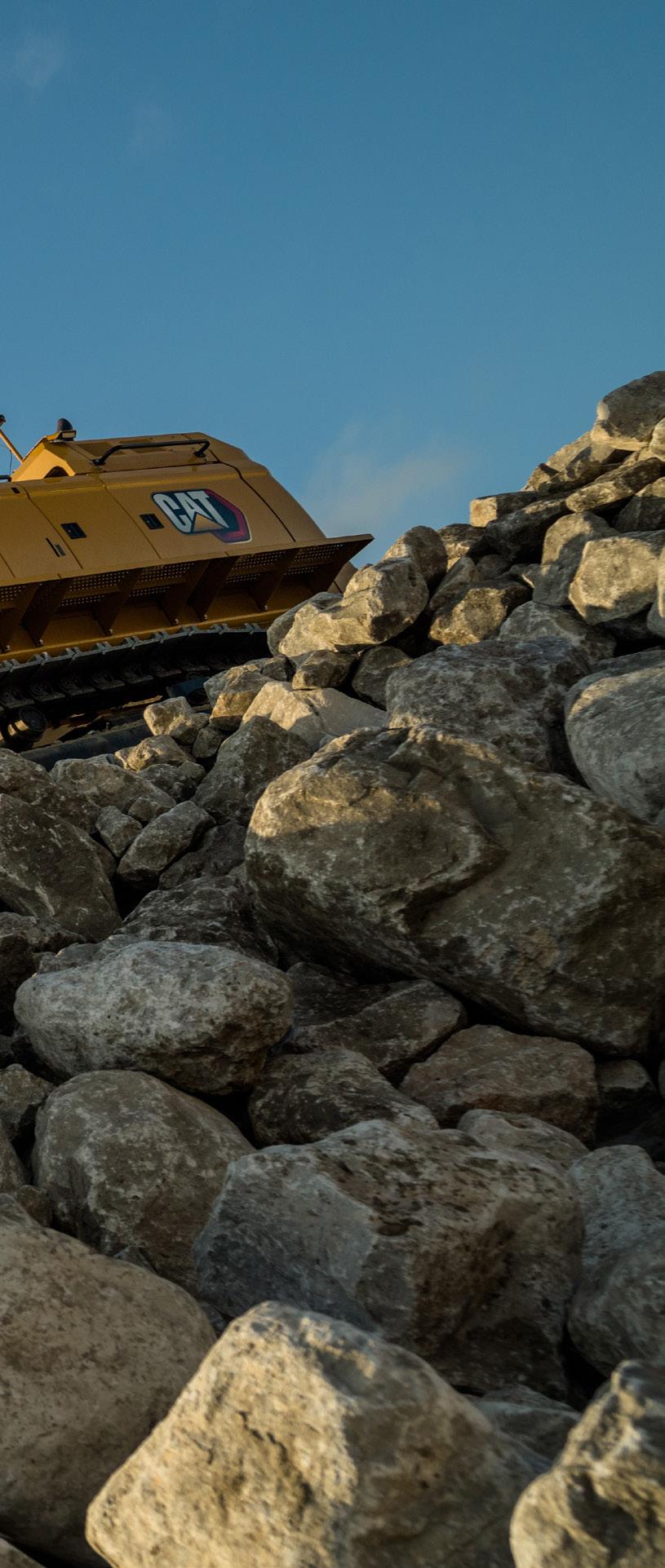
lated features have a bigger [role] on bigger excavators,” says Sejong Ko, product manager for large excavators at Volvo Construction Equipment. “Larger models also work with other machines like trucks more often, so features that support stability and visibility, like adjustable hydraulics or control settings, as well as durability and reliability, are more important.”
While mini and large-sized excavator controls are similar, the consequences of a mishap while filling or dumping buckets are much greater with “a 160,000-pound excavator versus a 16,000-pound one, so extra caution is always recommended,” notes Diego Butzke, product manager for excavators and motor graders at CASE Construction Equipment.
As for what’s coming next, Develon demonstrated an autonomous concept
crawler excavator at CONEXPO 2023.
“Automation and remote control are going to be more and more important because those features can really increase safety and improve precision and also reduce operator fatigue and human error,” states Kim.
Electrification is another trend, although most industry leaders acknowledge that charging infrastructure needs to be more robust before electric excavators will become commonplace. That said, excavator manufacturers are designing conventional machines with fuel economy in mind.
“Future heavy excavators will be more energy-efficient and flexible on energy sources,” says Kim. “And because better productivity can help with this as well, any technologies, features and designs that improve productivity will remain a priority.”
Here’s a look at what’s new and noteworthy in the current large-size excavator and backhoe offerings:
DEVELON
The DX1000LC-7 crawler excavator, the largest machine of its kind in the Develon fleet, is both powerful and smart, claims the manufacturer. The machine’s Perkins 2806J engine produces a massive 629 horsepower.
“The engine and hydraulics work in harmony to give exceptional power to the front working group, the boom, the arm, and the bucket for outstanding breakout forces, and fast cycle times. It also has the highest swing torque in its class,” says Kim.
As for brains, the excavator features Smart Power Control. “In layman’s terms, the pump and engine talk to each other to get the best performance while also increasing fuel efficiency,” explains Kim.
The machine has an operating weight between 219,935 pounds (99,762 kilos) and 221,280 pounds (100,372 kilos) depending on configuration, and boom length of 27 feet, 6.7 inches with a standard front. It comes with four power modes, four work modes, rearview camera, and Auto Idle and Auto Shutdown functions.
A 360-degree All Around View Monitoring (AVM) camera set-up is optional.
Given its size, the DX1000LC-7 is well-suited for large infrastructure projects, demolition work, abrasive environments, and heavy-duty construction, says Kim.
Develon also manufactures wheeled excavators, with its six-cylinder DX210W-7 being the biggest in the lineup. This machine has an operating weight of 50,706 pounds (23,000 kilos) to 51,623 pounds (23,416 kilos), depending on the boom type. The DX210W-7 also features an eight-inch touchscreen cab monitor, and an electronically controlled pump. Rubber tires minimize ground damage, making this excavator a good choice for roadside construction.
Develon excavators also feature telematics systems, which can issue alerts when problems are detected, establish geo-fences to guard against theft, and monitor performance.

PHOTO COURTESY OF CATERPILLAR
EQUIPMENT
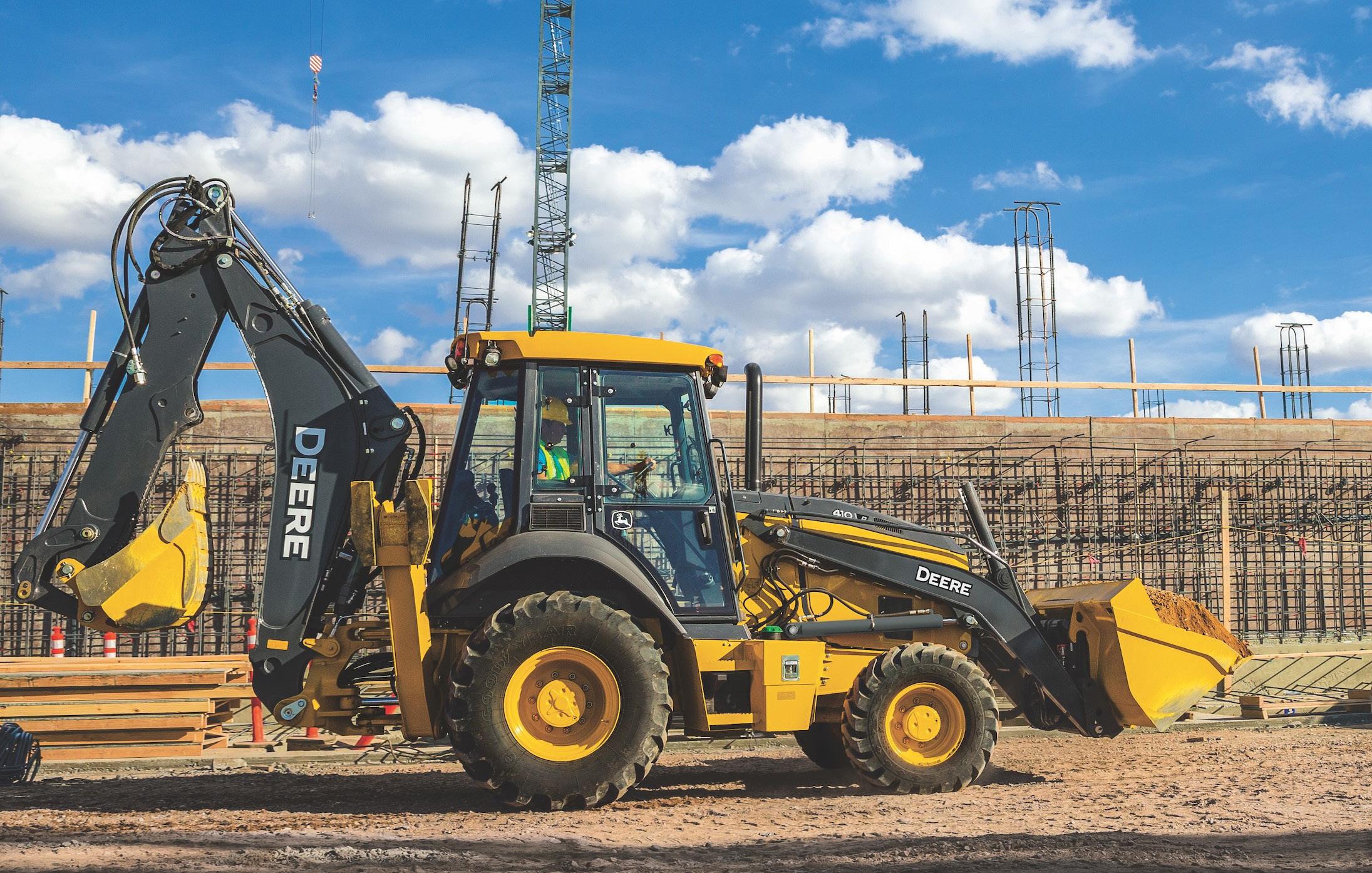
With its ability to lift heavy pipes, manhole covers and trench boxes, John Deere’s largest excavator, the 870 P-Tier, works well in applications involving large-site development and sewer excavation, says Steger.
“The bigger the excavator gets, the more hydraulic digging force that typically comes with it … When you get into tougher digging conditions, you need a little more umph. It may warrant a larger excavator,” he states.
Weighing 188,716 pounds (85,600 kilos), the 512-hp, six-cylinder machine has a maximum digging depth of 23 feet five inches to 36 feet seven inches (7.14 to 11.16 metres). It features JDLink telematics, a new right/rear/left camera system, a selection of engine modes for fuel efficiency or power, an Auto-idle system and a power boost button on the joystick.
At CONEXPO 2023, John Deere introduced another heavy-duty excavator: the 510 P-Tier, which replaces its 470 P-Tier. Weighing 112,436 pounds (51,000 kilos), the 510 has an electronic on-demand cooling system, and Smart Grade, John Deere’s 2 and 3D grade management system. It will be launched commercially in spring 2025.
In the backhoe segment, the 410 P-Tier and 710 P-Tier are “the two largest backhoes we produce,” states Emily Pagura, product marketing manager at John Deere. “They have mechanical front-wheel drive and a limited slip differential resulting in
true four-wheel drive pulling power.”
With an operating weigh of 17,582 pounds (7,975 kilos), the 410 P-Tier backhoe loader offers gross peak power of 118 hp, with a bucket capacity of 1.31 to 1.5 cubic yards (1 to 1.15 cubic metres), depending on the model. The 710 P-Tier backhoe loader weighs 25,790 pounds (11,698 kilos), with gross peak power of 150 hp, and bucket capacity from 1.31 to 1.87 cubic yards (1 to 1.43 cubic metres) depending on model.
CASE
Case Construction Equipment’s biggest excavator, the CX750D, is well-suited for massive infrastructure projects and largesite developments, says Butzke.
At 159,600 pounds (72,400 kilos), the CX750D crawler excavator has a six-cylinder, 512-hp Isuzu engine capable of delivering 1,623 pounds of torque. With a 24-foot, two-inch maximum digging depth, the fuel-efficient CX750D comes with three work modes, comfy cab, and a five-year subscription to Case SiteWatch telematics.
Case also manufactures sturdy backhoes, the biggest being the CASE 695SV side shift backhoe loader. The 695SV features a Tier 4 Final four-cylinder engine capable of 110 gross hp, four-wheel drive, four-wheel steer, and an operating weight of 22,245 pounds (10,090 kilos).
“This machine is especially effective on larger jobsites where materials need to be moved over longer distances. The four-wheel steer feature provides the ability to switch into crab steer or circle steering to better navigate a chaotic jobsite. Circle steering also allows for a much tighter turning radius,” says George MacIntyre, product manager for backhoe and tractor loaders.
The versatile 695SV backhoe can be used in place of a wheel loader and do


JOHN DEERE
PHOTO COURTESY OF JOHN DEERE
BUILT FOR THOSE WHO DO
At Kubota, we build equipment for those who do. No matter the job on the build site, ambitious plans can become reality with the help of tough, versatile equipment and attachments from Kubota. THERE ARE DREAMERS, AND THERE ARE DO-ERS.

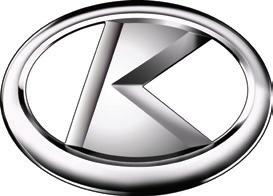
EQUIPMENT
trench digging work that’s usually performed by a mid-sized excavator, he adds.
“The tool carrier loader arms deliver parallel lift for loading operations and can easily handle multiple attachments when paired with a hydraulic coupler,” adds MacIntyre.
VOLVO
Volvo Construction Equipment introduced a new range of medium and large crawler excavators earlier this year, including its EC500, the largest of the manufacturer’s new-gen models launched in North America so far, says Ko.
Weighing between 106,110 and 116,400 pounds (48,130 and 52,800 kilos), the EC500 has a maximum digging reach of 38 feet, nine inches (11,817 mm), and bucket capacity of 1.5 to 4.33 cubic yards (1.15 to 3.31 cubic metres). The fuel-efficient machine boasts an optimized electro-hydraulic system, smart cooling system, an Active Control option for greater accuracy and digging speed, and multiple work modes. Volvo Smart View with Obstacle Detection, a camera/radar solution that offers operators a 360-degree exterior view, is also available.
The Volvo fleet already includes some hefty machines, including the EC950F crawler excavator. The company’s biggest excavator currently in use, that machine weighs between 201,227 and 209,020 pounds with a lifting capacity along the undercarriage of 50,486 pounds, bucket capacity of 5.1 – 10 cubic yards, and a
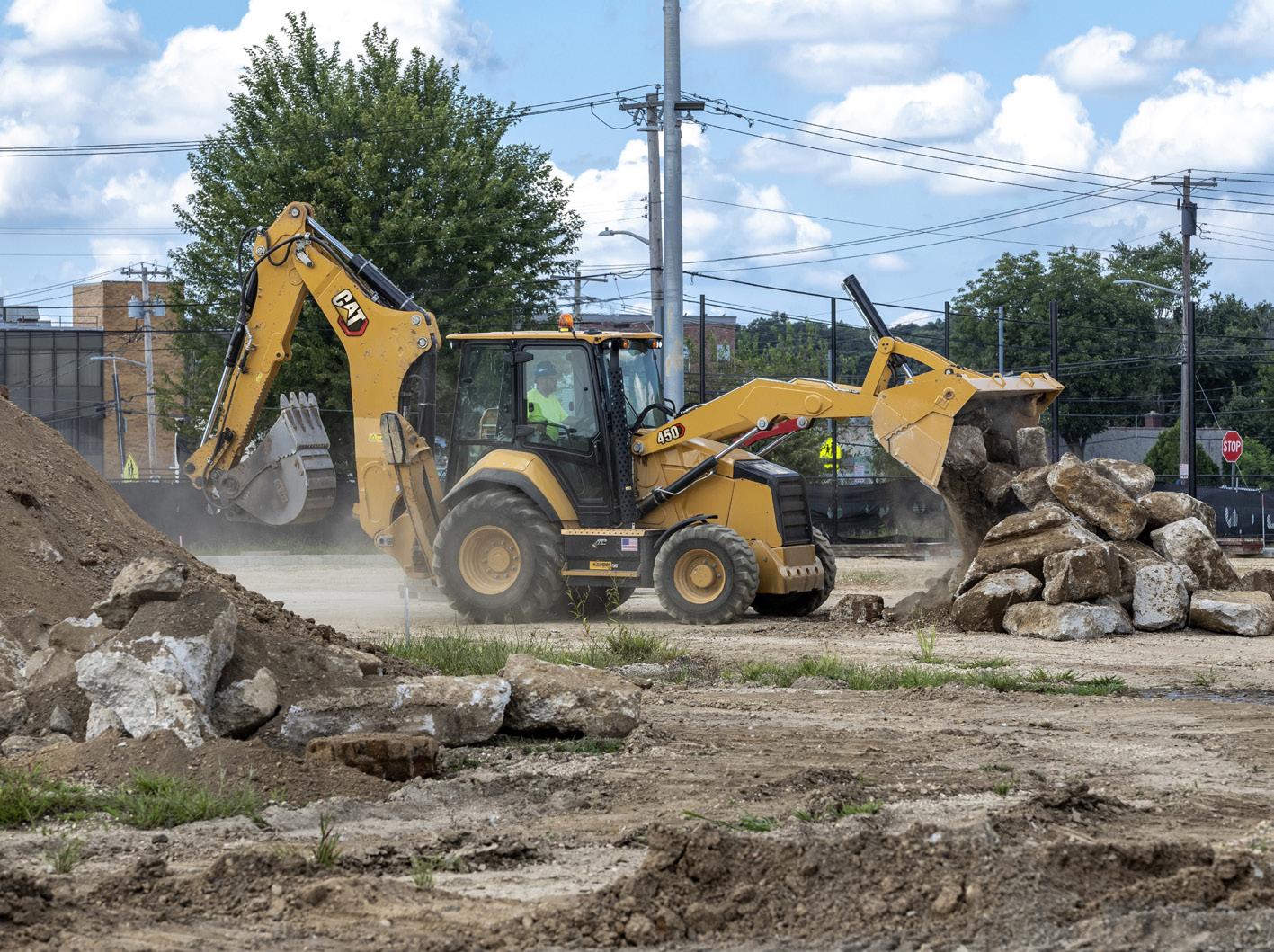
603 hp engine. Well suited to site prep, demolition and road construction, the EC950F’s consistently high hydraulic pressure ensures powerful digging force, states Ko.
“The hydraulic system increases pump power for fast and smooth operation while controlling flow and reducing internal losses in the hydraulic circuit,” he explains.
An automatic idling feature reduces engine speed when levers and pedals aren’t activated to reduce fuel consumption, while an attachment management system contains settings for 20 different attachments. ActiveCare Direct telematics tracks and analyzes machine performance and issues alerts if problems are detected.
The EC950 “can fill a 60-ton truck in four bucket passes with an average cycle time of just over a minute,” adds Ko.
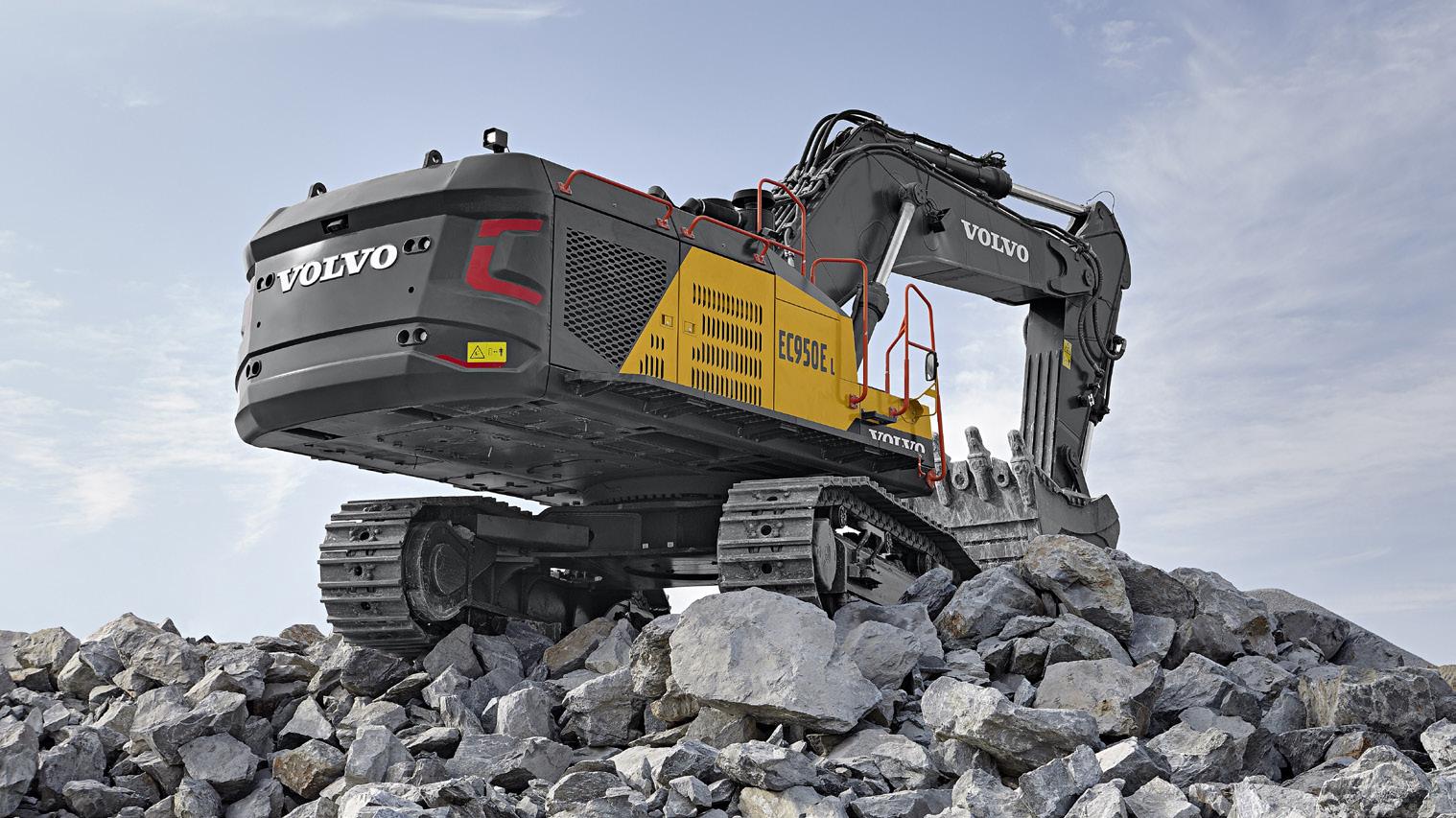
CATERPILLAR
Caterpillar’s largest construction excavator, the 395 is a Tier 4/Stage V hydraulic excavator engineered to excel at mass earth excavation and deep sewer/water work.
“When you’re 30-plus feet deep [the 395] gives you the additional reach and weight to lift large trench boxes, manholes and big pipes,” says Neal.
A complete redesign from the company’s 390F, the newer machine weighs 207,400 pounds, has a maximum digging depth of 31.9 feet and a 542-hp engine. Other standout features include Product Link fleet management and remote monitoring, Cat Grade 2D, and Caterpillar’s 2D E-Fence.
In its backhoes, the largest is its 450 centre-pivot model. “Backhoes are classified in terms of their reach or dig depth. The 450 is capable of over 20 feet of hoe-end reach with an optional e-stick,” explains David Young, product application specialist for the manufacturer.
Weighing 29,321 pounds, the 450 centre-pivot machine has a 131 net horsepower engine, and four same-sized tires. The company says this gives it better ground clearance than a traditional backhoe.
“I think of [the 450] as a wheel loader but with an excavator on the back. It also comes standard with four wheel-drive and all-wheel steering as well,” adds Young.
Nate Hendley is a freelance writer and author, and is a regular contributor to On-Site Magazine.
PHOTO COURTESY OF VOLVO CE
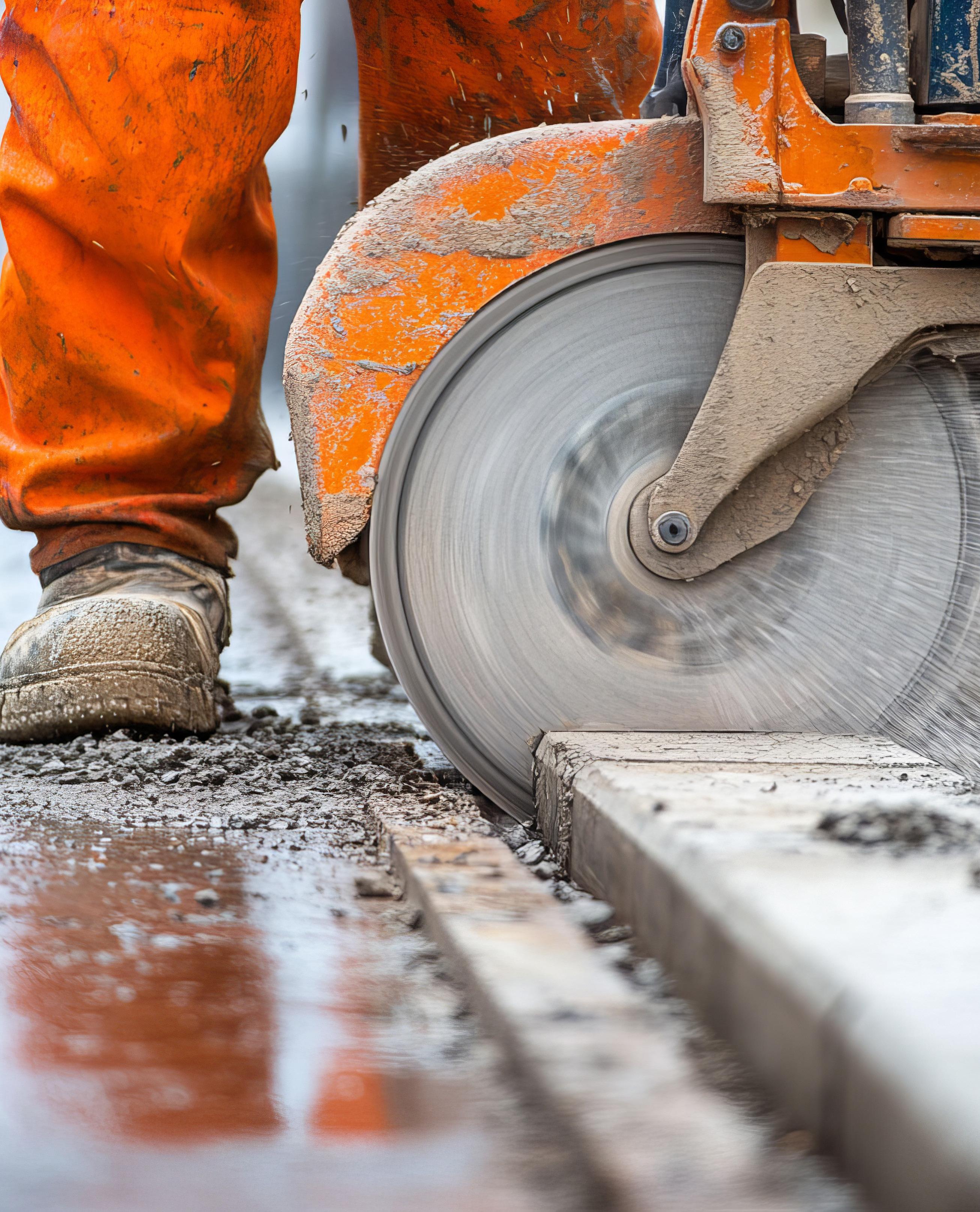
MAKING THE CUT
The Worldwide Leader in Concrete Paving Technology
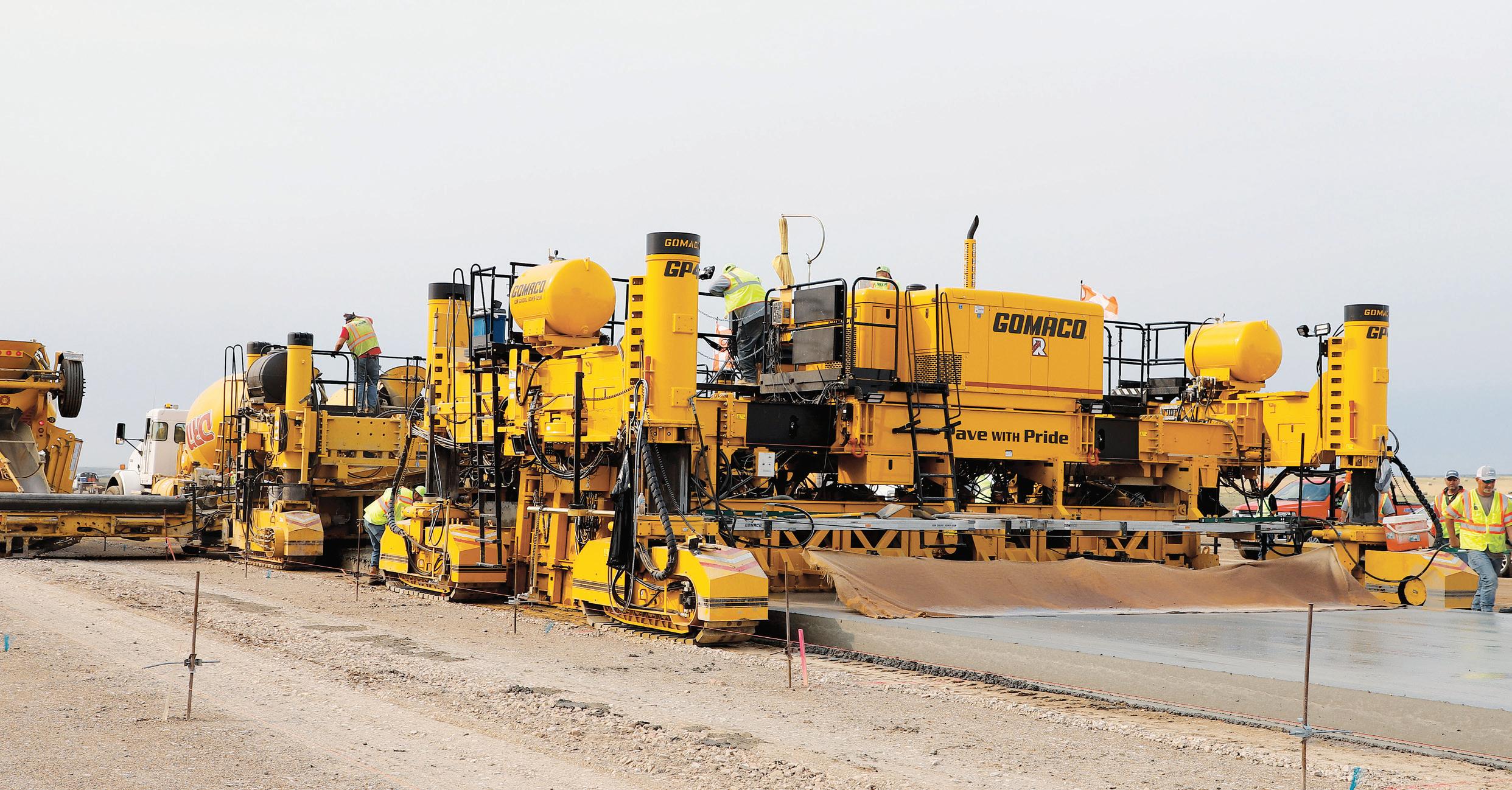

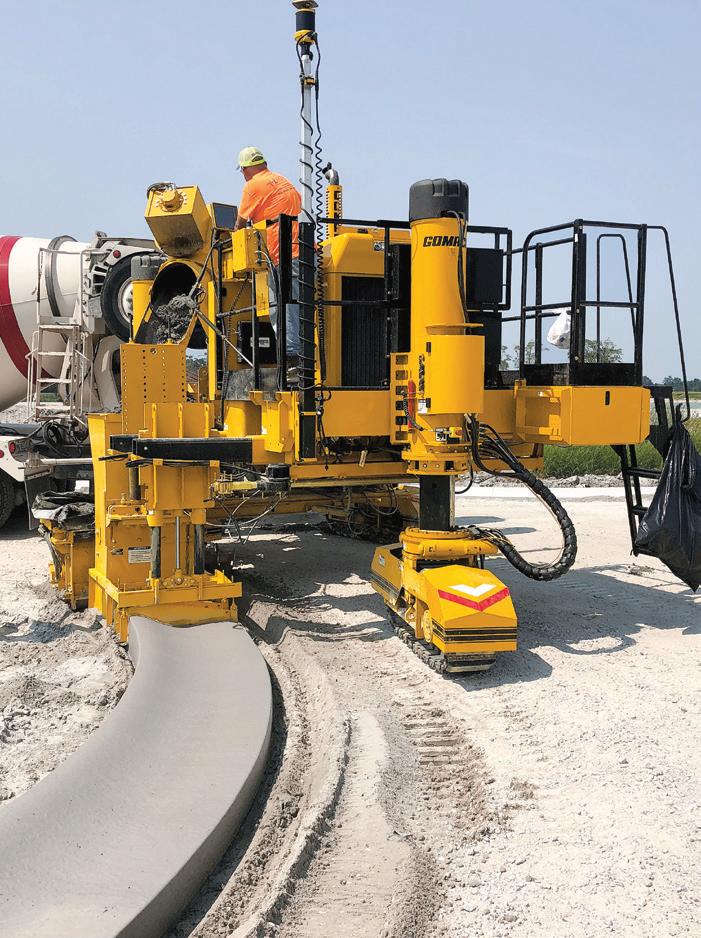
GOMACO offers the full range of concrete slipform pavers, curb and gutter machines, trimmers, placer/spreaders, texture/ cure machines and bridge/canal finishing equipment. GOMACO equipment features our exclusive and proprietary G+® control system, created in-house by our software engineers from the wants and needs of contractors paving in the field. At the heart of GOMACO equipment is our passion for concrete and our commitment to our customers. We look forward to visiting with you about your upcoming paving projects and your concrete paving equipment needs. Our worldwide distributor network and our corporate team always stand ready to serve and assist you.

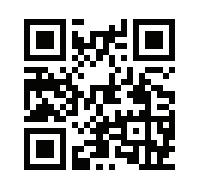

A focus on safety
From a runaway
BY TREENA HEIN
Tsaw blade to exploring best practices when sawing.
his spring in downtown Eugene, Oregon, a four-foot circular saw blade somehow came spiralling away from a concrete slab saw being used to cut a sidewalk for access to a gas main. In the blink of an eye, it spun across a nearby parking and very nearly killed a man.
It was travelling at such high speed that upon striking a nearby convenience store it shook the building and embedded itself two feet deep into the front wall, a few centimetres from the door.
A customer named Shane Reimche had entered the store a moment before, recalling later that as he did, he’d heard a nearby banging sound and a yell. Over his shoulder, he’d also glimpsed a puff of smoke and a worker tumbling into a ditch. Reimche was understandably shaken. “Obviously, it wasn’t my time,” he said to reporters, “but probably the closest I’ve ever experienced.”
The event went viral on social media (scan the QR Code to check it out).
Thankfully, nobody was injured or killed, but
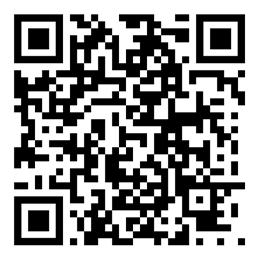
the event serves as an outstanding reminder to adhere to every single safety practice with regard to cutting concrete.
DON’T SKIP THE INSPECTION
The saw in Oregon was a slab model used on a sidewalk, but regardless of the saw type or application, inspection before each use by an experienced person is critical. While details of the incident report are not public, it may well have been that the blade of this slab saw might have been damaged, possibly going unnoted.
Sometimes inspections do not occur, or may not be completely thorough or, at times, damage may occur while using the equipment. Similarly, guards may always get checked to see if they are securely fastened, or perhaps a guard had just come loose.
David Ohashi, and engineer and general manager at Ontario Cutting & Coring, also advises that workers should verify “that all controls are functioning properly, including the throttle, emergency stop button and blade guard” before each use.
When sawing a wall, the mounting housing must be inspected
CONCRETE CUTTING
to ensure it is secure, as should blade alignment to minimize the risk of kickback. Gas-powered saws need their fuel, oil and coolant levels checked, and should also be inspected for fuel leaks. With electric-powered saws, Ohashi says the condition of all connections should be inspected, and they should always be properly grounded using a Ground Fault Circuit Interrupter (GFCI).
When using wire saws, the operator should inspect the wire, pulleys, all other moving parts, the motor, and guards.
“In addition, check and maintain proper wire tension as per the manufacturer’s specifications to prevent breakage or snapping,” says Ohashi. “Never exceed recommended tension levels, and use a wire specifically rated for the job.”
If coring rather than sawing, the bit should be similarly inspected for signs of wear or damage, as should the stand or rig for stability. Ohashi stresses that if drilling overhead, make sure the anchor system is strong enough to support both the drill’s weight and the torque.
NAVIGATING SAFE OPERATION
Working from a stable stance beside the saw and not directly behind it is a best practice that helps avoid injury from sudden saw movement or kickback, and consistent, moderate pressure will allow the blade to cut the concrete efficiently without forcing it. Sudden changes in pressure with a saw or bit can increase the risk of injury from binding or kickback.
One possibility with the accident is that the saw blade could have met with a foreign object or material harder than concrete, causing it to escape its housing.
The Ontario Ministry of Labour, Immigration, Training and Skills Development has a website that shares advice about the use of quick-cut saws. As the site explains, “Saw blades build up tremendous kinetic energy during cutting.” When their speed is suddenly reduced, “the energy must go somewhere.” When they instantly start moving again, they can do so in dangerous ways.
established around a saw in use. The immediate work zone, adds Ohashi, should be marked with safety cones, caution tape or barriers to clearly indicate restricted access. In addition, operators should “carefully mark cutting lines and set up guide rails,” he says, “to ensure precise cuts and reduce the need for on-the-fly adjustments.”
Each concrete saw should have an emergency shutdown mechanism, and all operators should be trained in its use.
“Identify and communicate emergency stops and protocols to all team members working around the equipment,” says Ohashi. “Use radios or hand signals to maintain clear communication with team members, especially when working in areas with high noise levels or restricted visibility.”
Of course, there should also be a Class A/B fire extinguisher nearby and a wellstocked first aid kit on-site, and all personnel should know the locations of these and how to carry out first aid procedures.
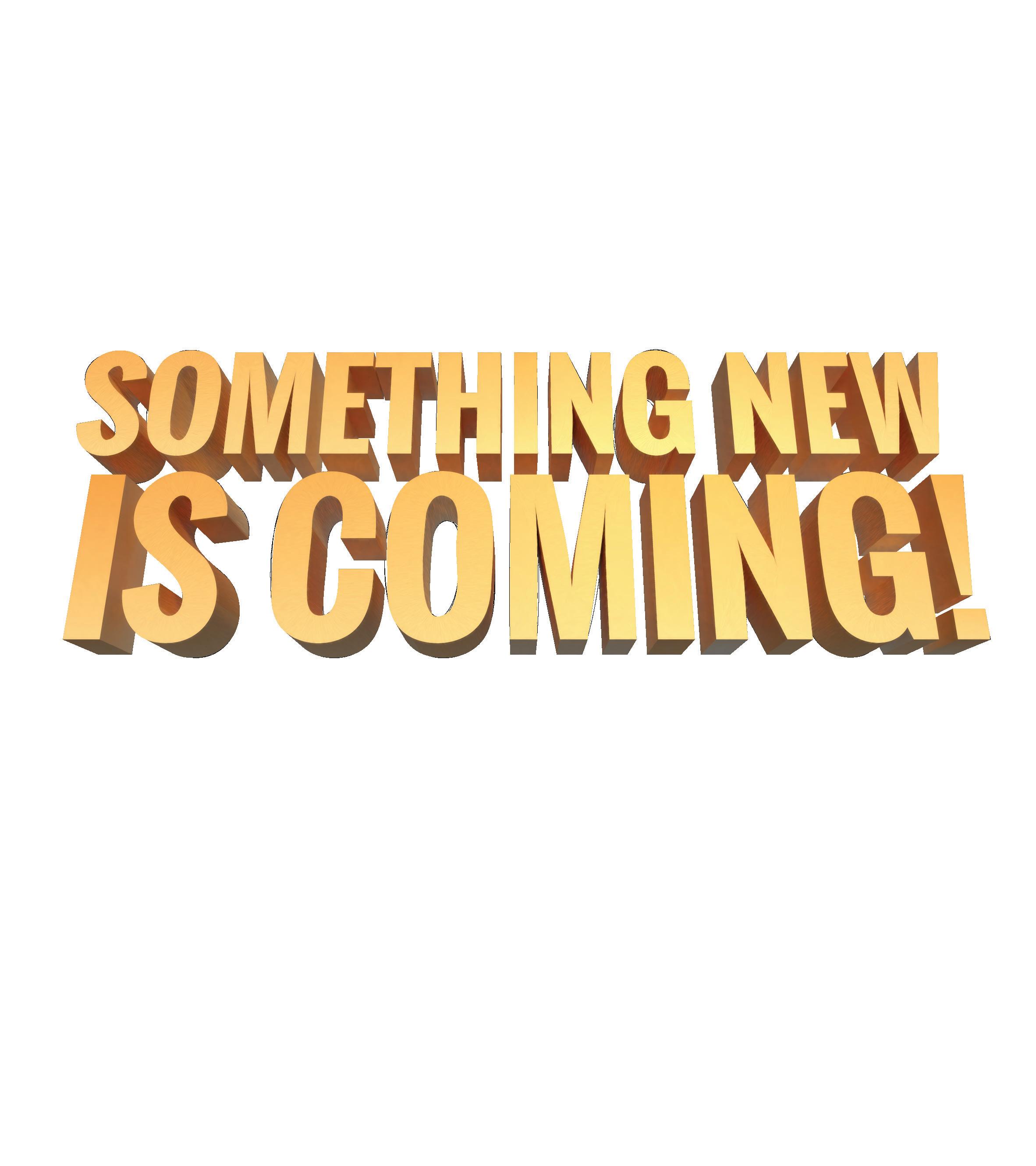
When shutting down the saw, Ohashi explains that the blade should be allowed

OUT: January 21-23, 2025
to come to a complete stop before moving or adjusting it. After use, clean the saw to remove dust and debris, inspect for damage and wear, and store it in a dry location with the blade protected.
HANDLING THE DUST
WorksafeBC notes that cutting concrete without proper dust controls can generate high levels of silica-containing dust.
“Breathing in this fine dust can cause a serious lung disease called silicosis, which is characterized by scarring and thickening of the lungs, and can result in death,” states the organization.
Ohashi advises the use of an N95 or P100 respirator, especially when cutting without water. Using a continuous water supply minimizes dust generation, however, which not only protects the lungs but keeps visibility high and reduces friction and prevent overheating.
“Check the water system for any blockages, and make sure it’s operational before starting,” Ohashi says. “If working indoors, ensure the area is well-ventilated to prevent dust buildup, and consider using additional dust control systems.”
SILICA CONTROL TOOLS
Working with scientists at University of British Columbia, WorksafeBC and industry, the British Columbia Construction Safety Alliance (BCCSA) released its online silica control tool in 2017. BCCSA health and exposure scientist Melanie Gorman says the tool took about three years of development, and that it receives ongoing updates.
Users navigate a series of drop-down menus used to estimate the level of dust from grinding, cutting, drilling, hammering, rock crushing, and other scenarios involving silica dust, to then suggest mitigation options. The tool will also indicate how much each option will reduce dust levels.
An Ontario-compliant version, and one for New Brunswick, were introduced to construction employers in those provinces about a year ago.
PERSONAL PROTECTIVE EQUIPMENT
As with any equipment, it’s crucial to use the right personal protective equipment (PPE). Beyond dust mitigation, we need
to minimize risks associated with flying debris, noise, vibration and potential equipment malfunctions.
Ohashi advises that workers should limit exposure to vibration from the saw by taking frequent breaks and alternating with other tasks if possible.
“Use anti-vibration gloves and maintain good posture to minimize vibration impacts on hands and arms,” he says.
Safety goggles or glasses will protect the
eyes from dust and debris, but a face shield over goggles is recommended to protect the face against flying debris. Hearing protection is a must, for the operator of the saw and for those in close proximity, as well as those in confined spaces with the operator. Cut-resistant gloves with a good grip are recommended, as handling a slab or wall saw can expose hands to sharp edges and abrasive surfaces. Durable, long-sleeve clothing is also a must.
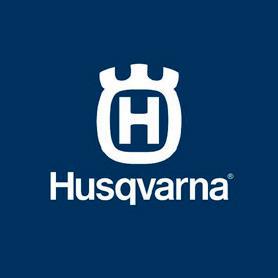

POWERFUL TRENCH COMPACTOR
The Husqvarna LP 9505 is a powerful, easy-to-operate trench compactor essential for demanding compaction jobs. Maintenance is quick and easy with all service points clearly marked under the easy-to-access protective hoods. Featuring smartly designed solutions, the LP 9505 can be used on a wide range of applications. Visit our website to learn more.
CANADIAN CONCRETE EXPO expands its offerings
This year’s CCE is stepping up its game with more exhibitors, specialized pavilions, live demonstrations and more industry educational sessions than ever before.
CANADIAN CONCRETE EXPO
February 12-13, 2025
International Centre
6900 Airport Road, Mississauga, Ont.
Canada’s national trade show dedicated to the concrete, construction and aggregates industries, the Canadian Concrete Expo (CCE) returns to the International Centre in Mississauga, Ont., on February 12 and 13. Building on a highly successful 2024 show, the 2025 event will bring more of almost everything, along with a few new twists that will put attendees in the driver’s seat, or at least at the controls.
In addition to the more than 360 exhibitors across the 300,000-square-foot exhibition floor, the event is ramping up its product demonstrations game, adding a new area with ongoing live equipment and tool demos.
“Attendees can test drive telehandlers, for example, and can operate tools and equipment used in concrete construction,” says CCE president Stuart Galloway, who is looking forward to seeing how the live demonstrations will augment the more traditional equipment displays usually found at an industry show. “This is something new, just to add a little bit more variety, and to give a better user experience for those that are attending.”
In addition to the equipment in the demonstration area, Milwaukee Tool has secured a 10,000-square-foot space to introduce its full line of cordless concrete tools, something the company is calling MX Fuel the Future.
Another new addition is the CCE forming, shoring and scaffolding pavilion.
“We’ve put all the major suppliers and
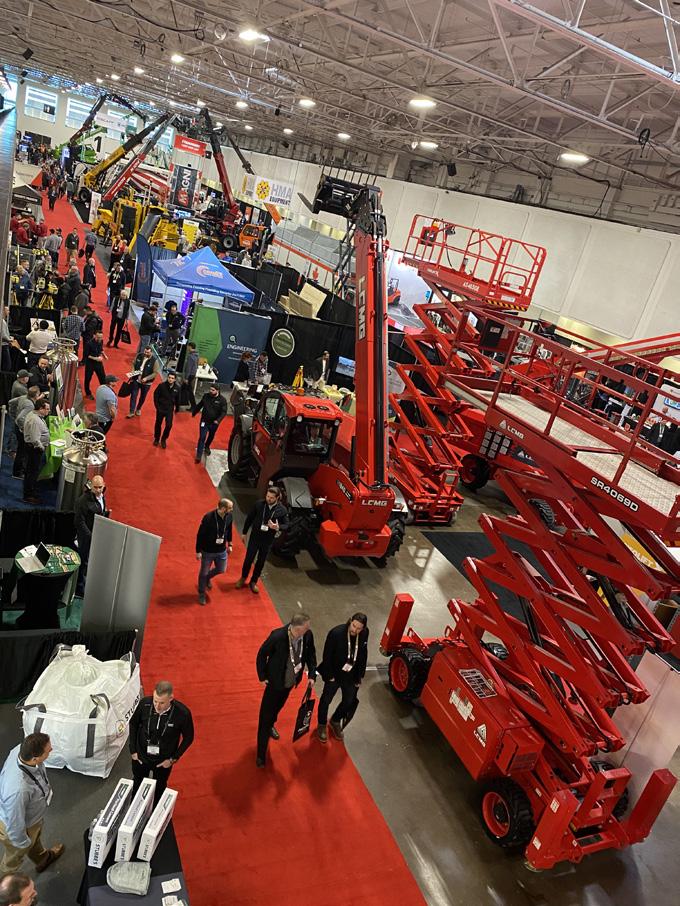
manufacturers in those sectors all in one area, and everybody’s come together and supported it,” says Galloway. “There’s a lot of new things happening this year. We just want to keep evolving and provide value.”
That commitment to value is a big reason for the event’s continued growth.
“We’re probably going to grow by about 15 per cent again for the 2025 show over the 2024 show,” he adds. “The feedback we get is that there are high-quality, targeted attendees that are attending CCE... We’re trying to stay focused in our approach for attendees, and trying to stay focused on concrete construction.”
That sector focus has generated interest from the concrete segment, but the number indicate that the event is also garnering strong interest from general contractors interested in some of the new developments happening in concrete construction as well.
From sourcing new suppliers, reconnecting with industry contacts, or getting hands-on with the latest equipment, the
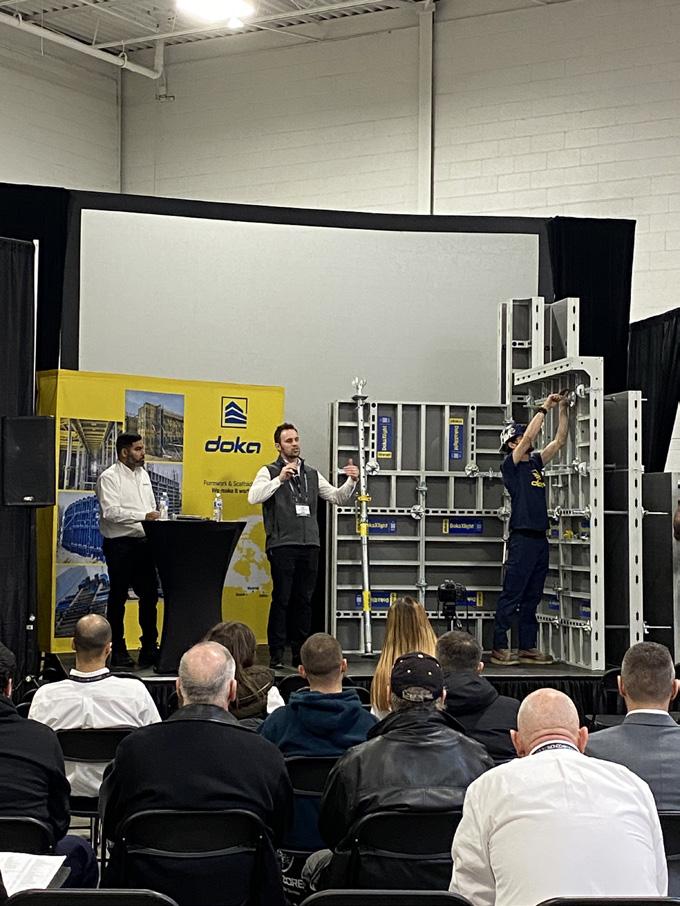
annual CCE show offers lots of opportunity for professionals looking to expand their industry knowledge and skills, including through the 30 educational sessions that are on this year’s agenda.
“We have more sessions than we’ve ever had, and we’ve got a lot of new lot of new speakers,” says Galloway. “We put quite a bit of effort into getting high-quality presentations, and hopefully that pays off.”
Highlights for this year on the education side include new sessions on the concrete pumping industry, as well as a certification program for concrete pump operators.
Set to take place in February, the 2025 edition of CCE will be located at the International Centre in Mississauga, only five minutes from Toronto’s Pearson International Airport. Registration is now open, and pre-registration fees are half of the at-the-door costs.
Visit canadianconcreteexpo.com for more show information, and to register for the event, and for conference sessions.
PHOTOS
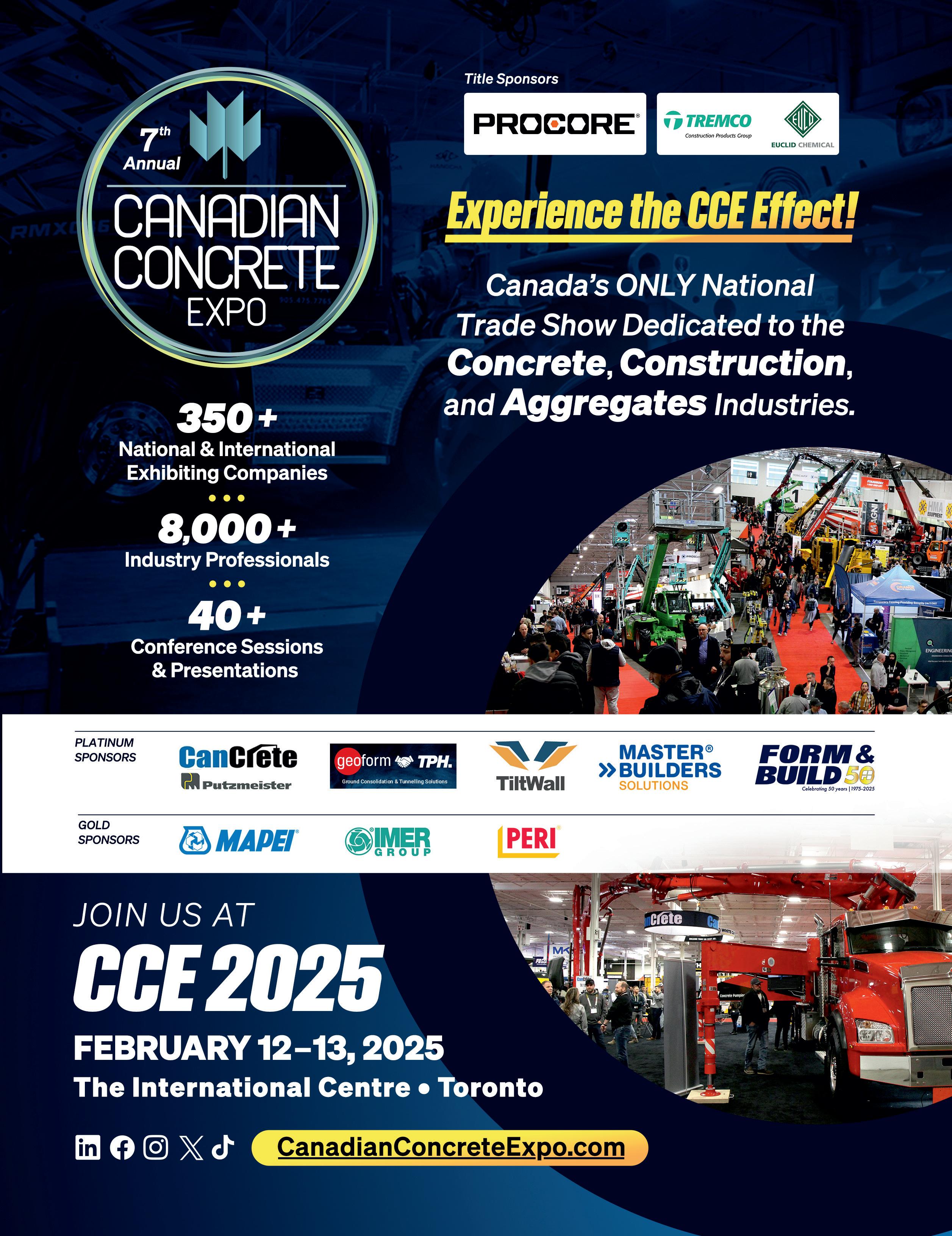
CONCRETE PRODUCT SHOWCASE
CONCRETE REPAIR MORTAR
Designed for horizontal and formed vertical repairs as well as overhead structural repairs, Versaspeed RMC from Euclid Chemical is a fast-setting, one-component, cementitious repair mortar that is shrinkage compensated, pozzolan and microfibre modified, and contains an integral corrosion inhibitor. The product is appropriate for applications where a fast return to service is required. Pre-mixed with pea gravel, the product is ready-to-use, designed to minimize cracking, and offers low permeability with excellent freezethaw resistance.

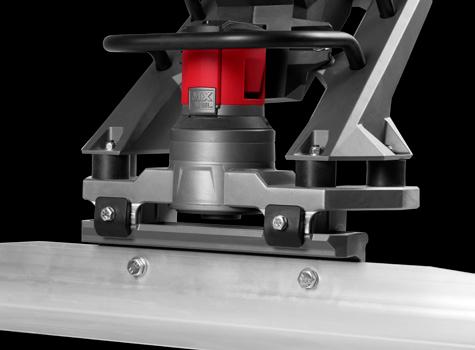
VIBRATORY SCREED
BAR ADAPTER
Milwaukee Tool has expanded its screed accessory offerings with the addition of a Screed Bar Adapter. The adapter allows the MX Fuel Vibratory Screed to accept L-shaped bars, using a clamp-on design for quick attachment and removal, providing concrete professionals greater flexibility and versatility. The adapter accepts four- to 16-foot L-shaped bars.
SMART SENSOR FOR CONCRETE
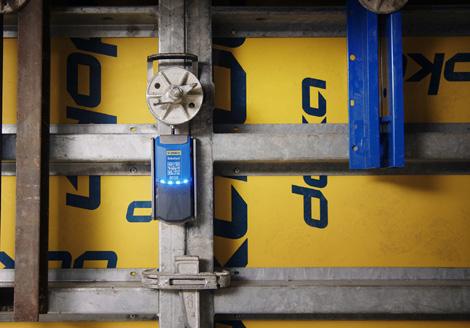
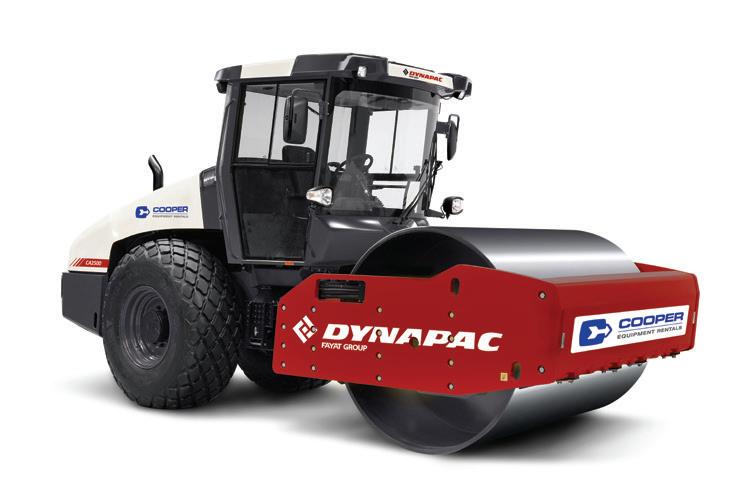

Real-time data from Doka’s wireless DokaXact sensors helps to ensure that concrete is poured as fast as possible while providing the best possible concrete quality. The sensors, which can be used with traditional concrete mixes as well as more climate-friendly CO2-reduced concrete mixes, are designed to be tough, waterproof, dustproof, and easily connected to the user’s smartphone via Bluetooth.
REBAR TYING TOOL
MAX USA has introduced the RB443T, the newest addition to its TwinTier rebar tying tools platform. The tool is designed to streamline operations and maximize productivity with such features as an integrated autoload assist mechanism, to accelerate wire loading and minimize downtime, as well as an easy-pull trigger that requires half the effort compared to its predecessor, the RB441T.
BACKUP SAFETY SYSTEM
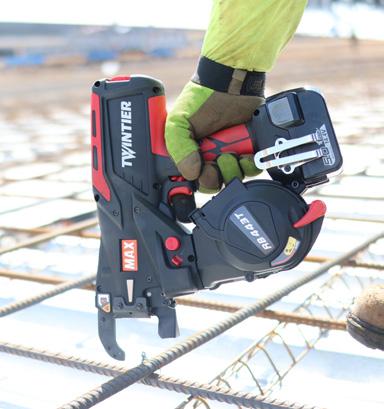

Freightliner Trucks, a division of Daimler Truck North America LLC (DTNA), has introduced the Backup Alert System for its Plus series of trucks. Available as a factory-installed safety option, the passive system includes a seven-inch integrated touchscreen display, backup camera, and reverse proximity sensor to meet the needs of drivers across a multitude of applications, including the construction and utility segments.
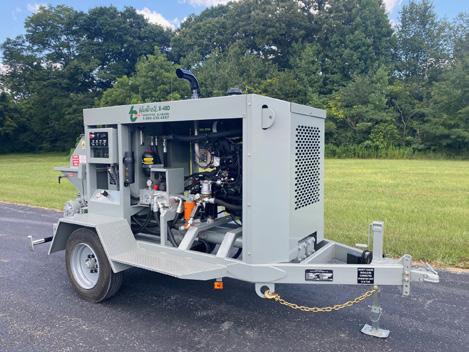
TRAILER-MOUNTED PUMP SYSTEM
The X-40D trailer-mounted concrete pump system from Blastcrete Equipment is engineered to provide high-volume pumping in a compact design for a variety of applications. The versatile pump is capable of handling aggregate mixes up to 1.5 inches, and can be used on projects ranging from residential concrete jobs to highway infrastructure improvements. The system boasts 1,000 psi of piston face pressure, with a five-inch discharge and the ability to put out 40 cubic yards of concrete per hour.
CLIMATE-CONTROLLED CURB AND GUTTER MACHINE
Power Curbers has launched a climate-controlled cabin as an option for the company’s Power Curber 5700-D slipform machine for pouring curb and gutter, sidewalk, barrier, ditches, paving, tunnels, agricultural and specialized applications. The new feature includes a fully enclosed operator’s platform with air conditioning, heating systems, and a unique glass floor insert that is strategically positioned to offer direct visibility of the mould and the finished concrete.
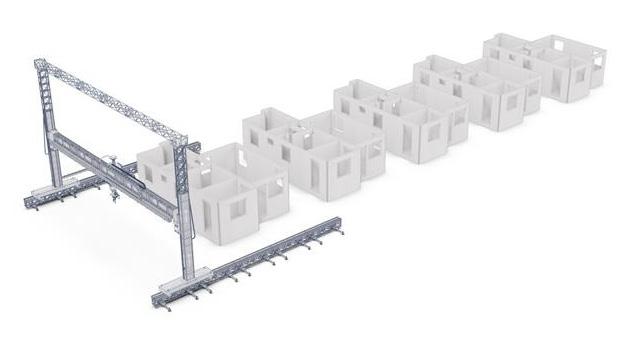
3D CONSTRUCTION PRINTER
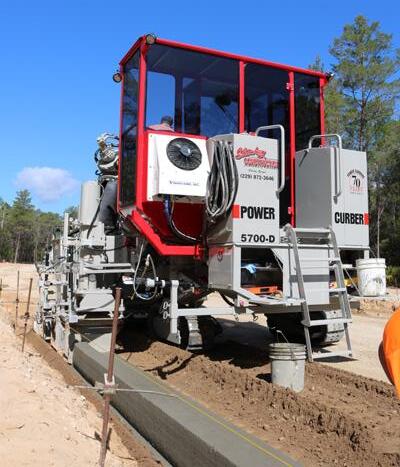
Equipped with an extendable ground-based track system, the BOD3 3D Construction Printer from COBOD International is engineered for 3D printing of real concrete. Designed to be an advanced solution for high-volume low-rise construction, the machine eliminates printer downtime between the printing of multiple buildings on the same site for continuous, linear printing of multiple buildings.
Limitless extension along the Y-axis expands the printable area to cover two or three buildings, reducing setup time to a single installation for multi-building projects.
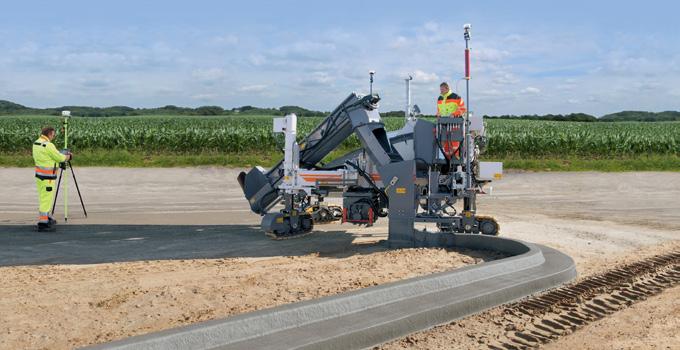
CONCRETE PAVING TRAIN
Wirtgen has a number of machines that can be organized to form a complete concrete paving train. One such example is comprised of a WPS 102i placer/spreader, an SP 124i slipform paver, and a TCM 180i texture curing machine. The company’s SP 15i and SP 25i machines enable flexible positioning of the slipform paving mould, while the SP 15i is equipped with a telescoping extension for a better overview of the paving results, the concrete feeding system, the transfer hopper, and of the inside of the consolidation compartment of the mould.
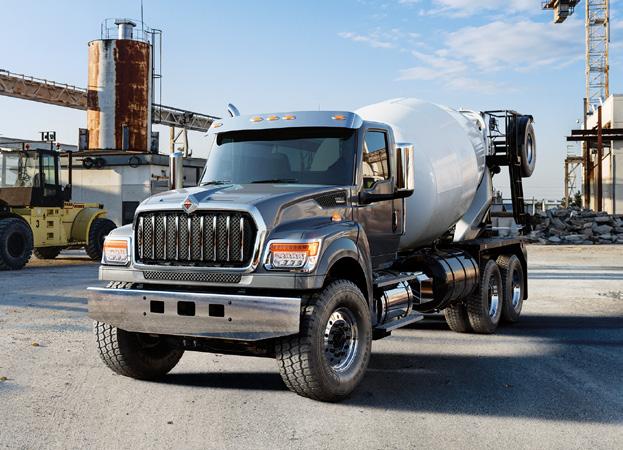
VOCATIONAL WORK TRUCKS
International Truck’s redesigned HV Series equipped with the S13 Integrated Powertrain combines toughness with an advanced integrated powertrain, says the manufacturer. With the S13, workers no longer need to stop work to perform active regens, and the company has simplified maintenance by eliminating components like the exhaust gas recirculation (EGR) cooler and diesel oxidation catalyst. The trucks feature a sloped hood, panoramic windshield, and two smooth and steady crawler gears.
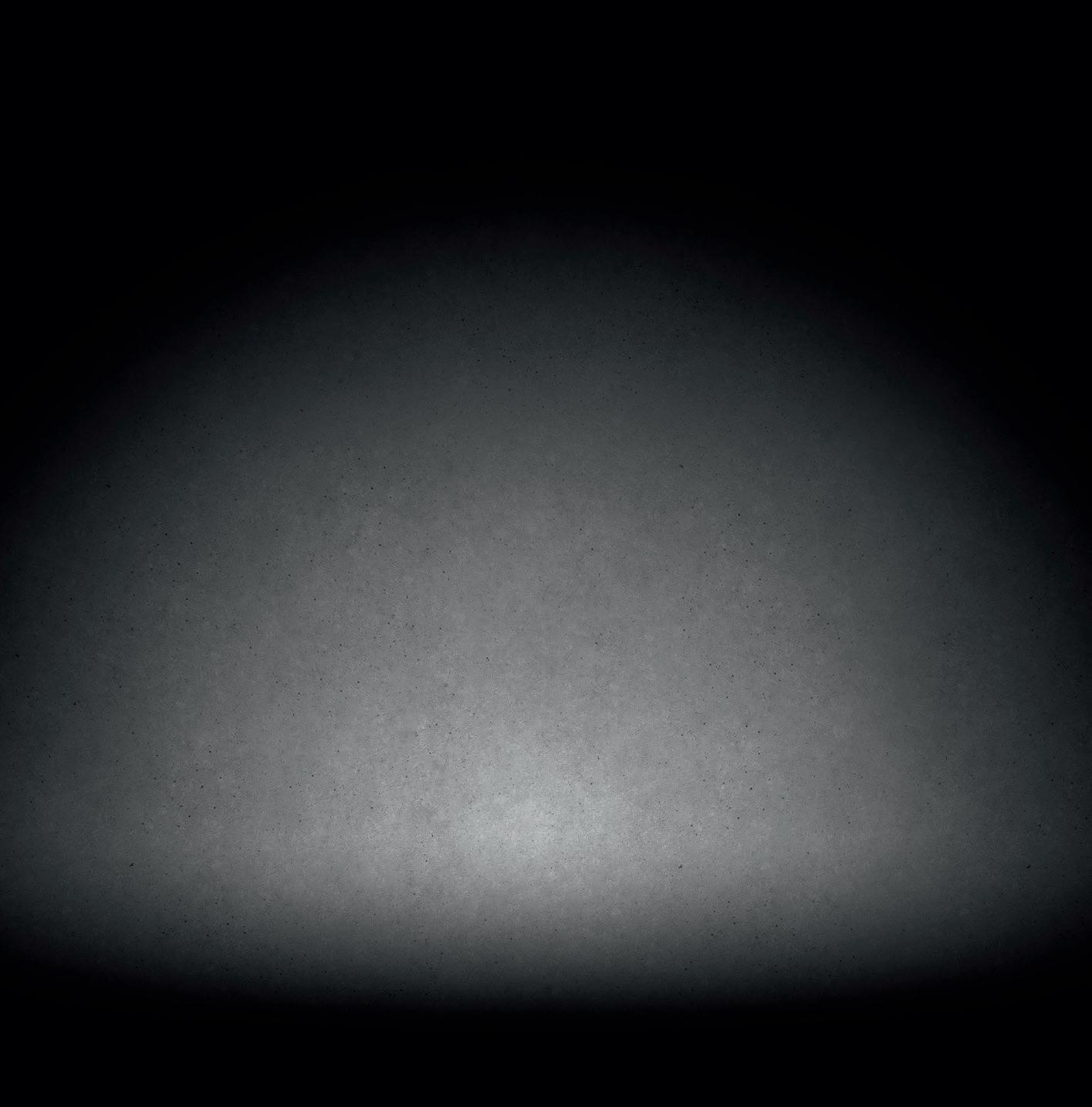
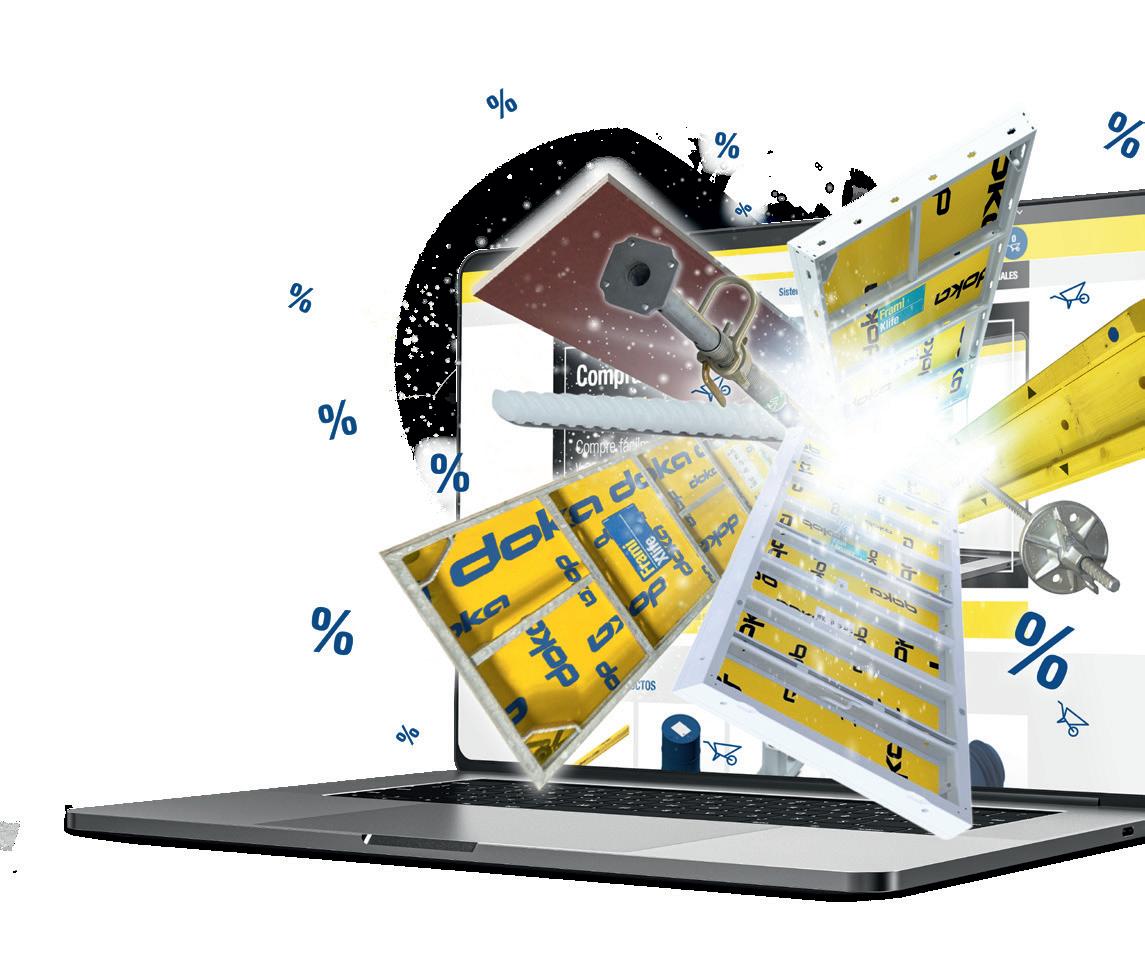
Anticipation building for World of Concrete 2025 in Las Vegas
Returning for its 51st edition, World of Concrete, Informa Markets’ exhibition serving the construction and masonry construction industries, will take place from January 21 to the 23rd at the Las Vegas Convention Center (LVCC). Event organizers are looking forward to building on last year’s 50th Anniversary event, which attracted nearly 60,000 registered professionals from various industry sectors for three days of exhibition and four days of education.
World of Concrete 2025 will have all the newest products, leading-industry suppliers, resources, and educational sessions that concrete and masonry professionals are looking for. This year’s event is expected to have over 1,300 exhibitors putting their newest offerings on display across more than 750,000 square feet of indoor and outdoor exhibit and event space. The show is so large that it will take up the North, Central and South Halls of the LVCC, and will also use the venue’s Silver and Bronze parking lots for outdoor exhibits and events.
“If you’re involved in the commercial concrete or masonry sectors, the World of Concrete is the must-attend international event of the year,” stated the show’s senior marketing manager Steven Pomerantz. “Whether you’re a first-time visitor or a returning attendee, the impressive range of technology, equipment, and new product launches showcased at WOC will inspire you and offer essential insights for success, no matter the size of your business.”
In addition to the ever-popular Spec Mix Bricklayer 500 World Championship and the Mason Contractors Association of America’s Fastest Trowel on the Block, this
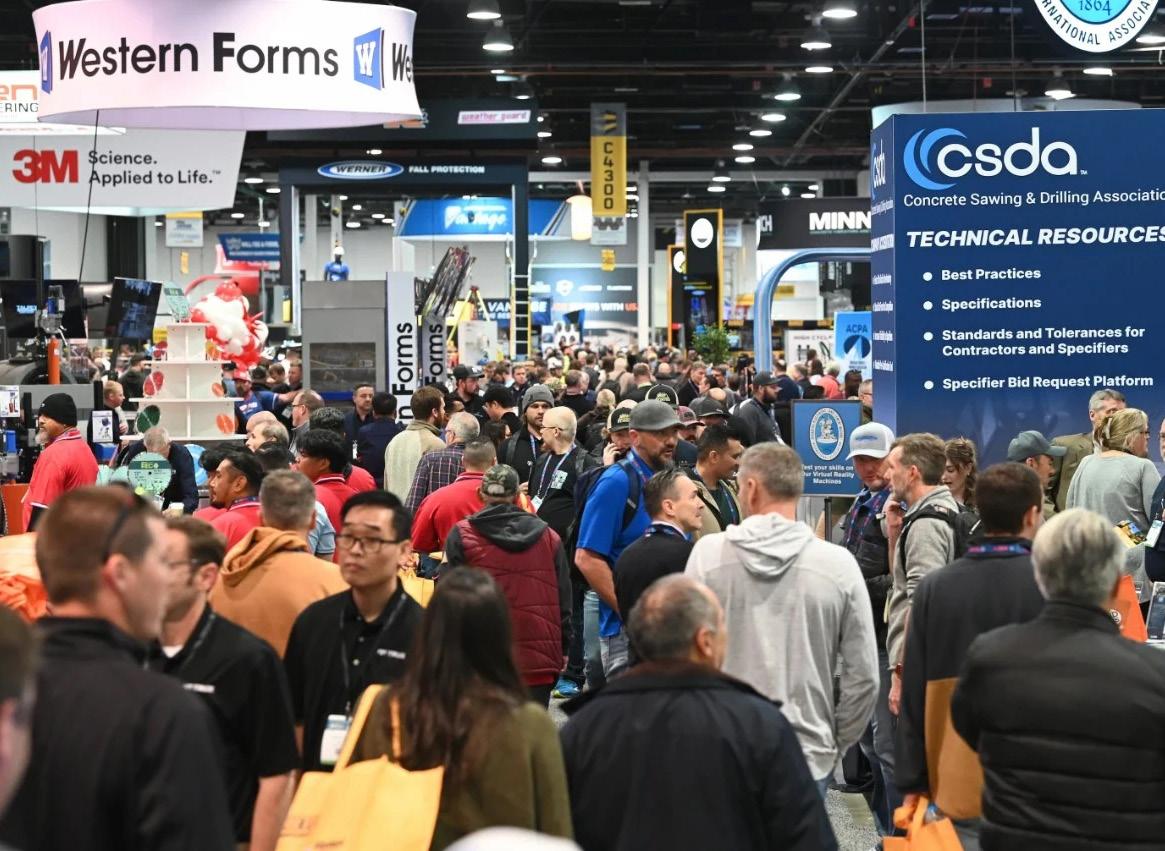
WORLD OF CONCRETE 2025
January 21-23, 2025
Las Vegas Convention Center
year’s special events include the Western Star Trucks Get Tough Challenge, which is open to attendees with a CDL, the Decorative Concrete Experience that features peer-to-peer presentations from industry experts, as well as Work Truck Live, an experiential area designed to showcase the innovations in trucks.
This year’s education program, which gets a one-day head start with first sessions being held the day before exhibits open, will offer more than 180 sessions of in-depth learning options for concrete and masonry professionals, including seminars
exploring technical applications, business best practices, project management, and safety-relevant topics for every skill level and job title from beginner to experienced, and even company owners.
“At World of Concrete 2025, we’re excited to unveil over 40 per cent of brand new educational offerings, featuring more than 180 sessions designed for concrete and masonry professionals at every skill level,” stated Maddie MacLellan, WOC’s senior education manager. “From technical applications to business best practices, our program has something for everyone in the industry.”
The World of Concrete show runs from January 21 to 23, with education sessions available from the 20th to the 23rd. For more information about the show, and to register, visit www.worldofconcrete.com.
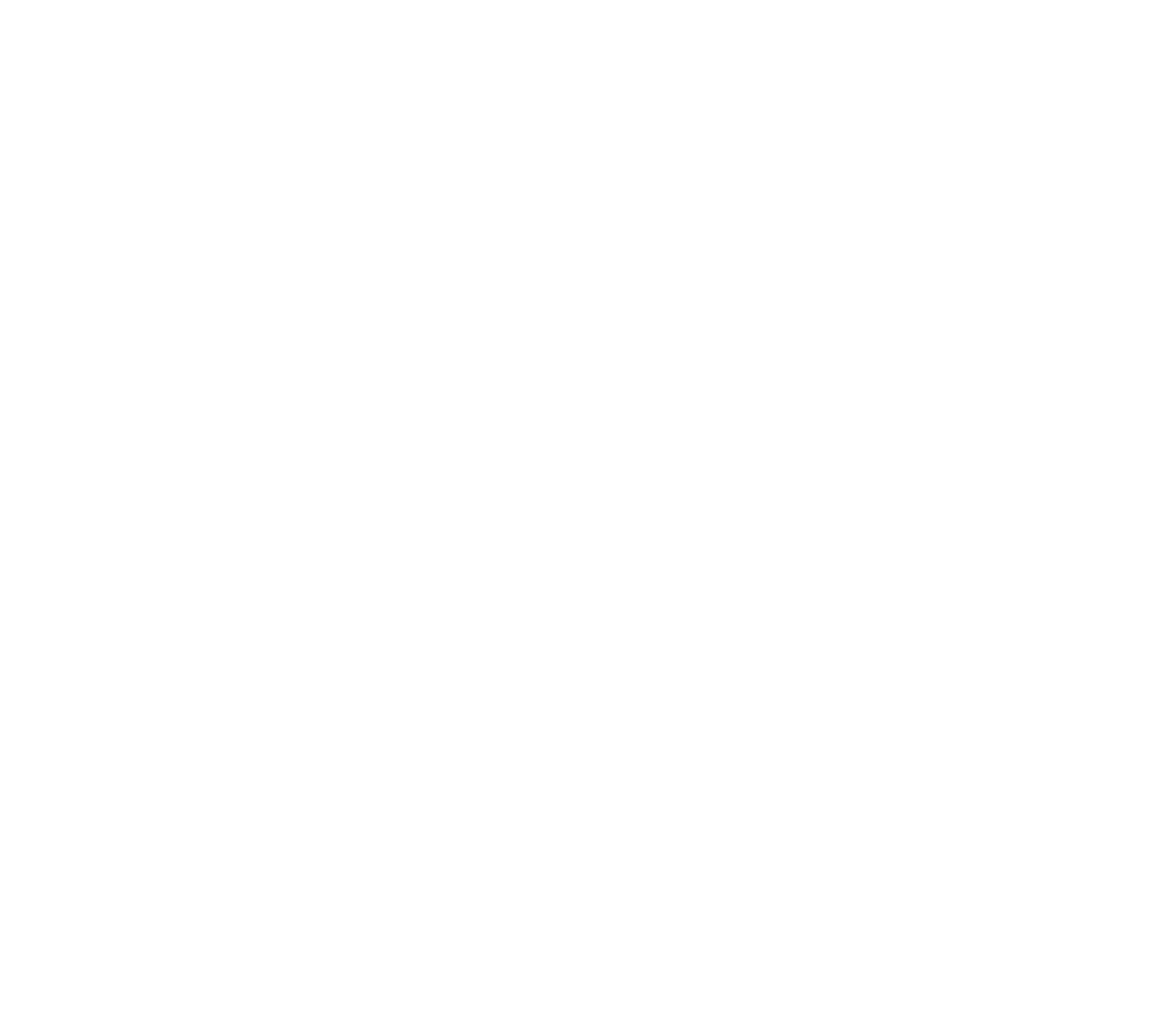
SMOOTH
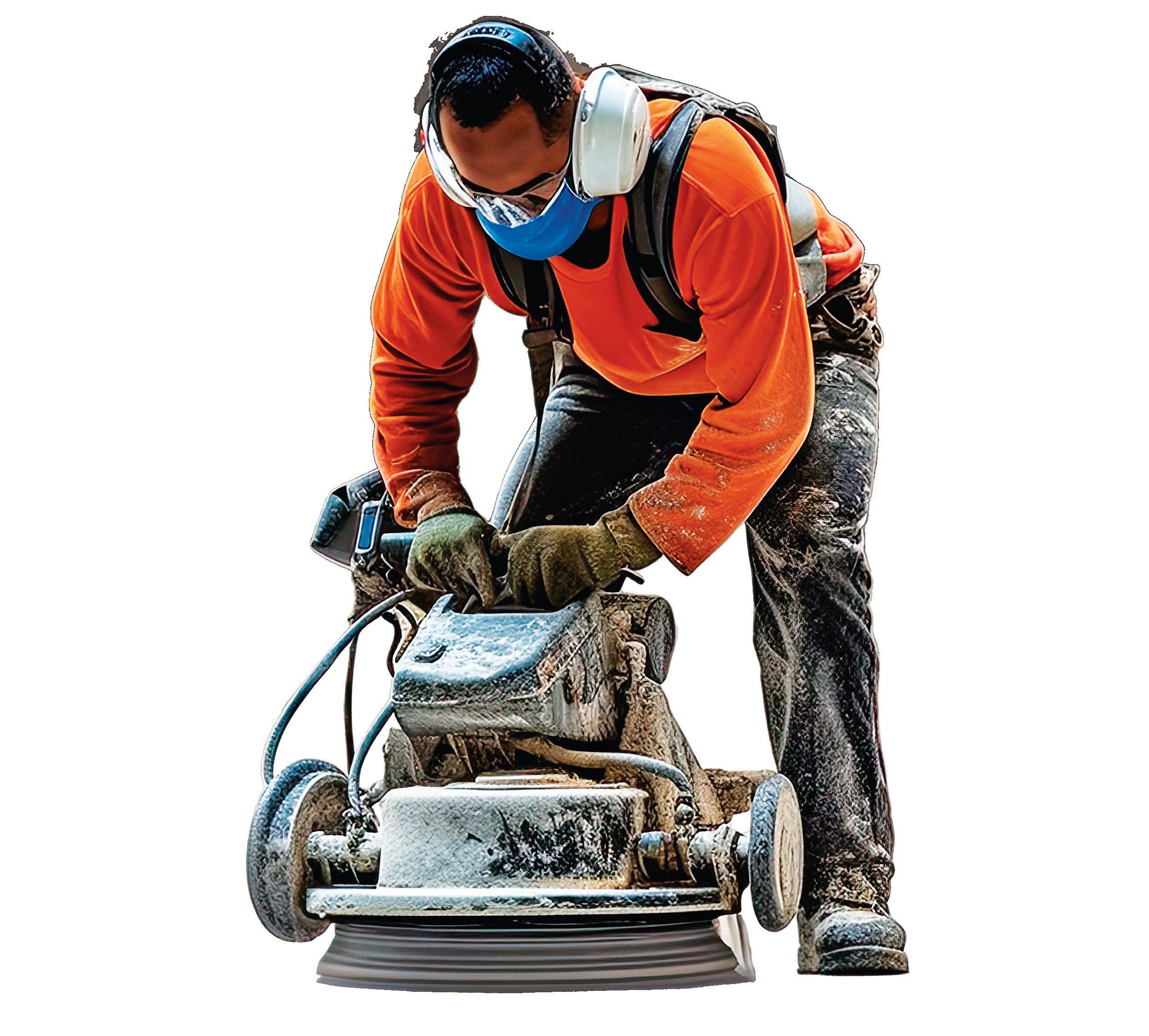
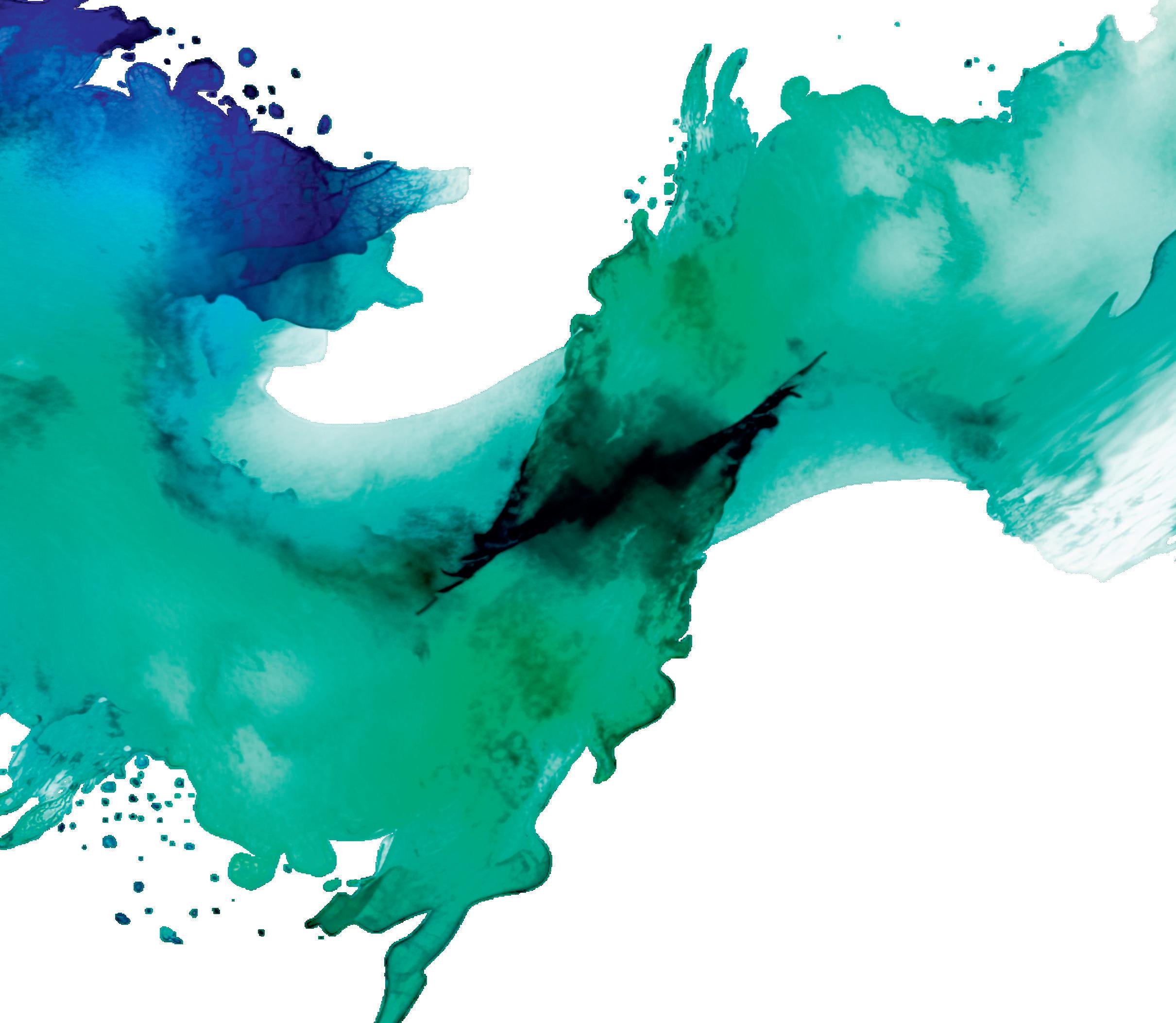
Join the power players of concrete and masonry. OPERATOR
There’s only one place you’ll find the heavy hitters of concrete and masonry this January: Vegas, baby — at World of Concrete 2025, the largest and only annual international event dedicated to your business. Be here to mix with industry giants. Get your hands on the latest technologies revolutionizing safety, performance and speed. And learn what it takes to not only claim a piece of our industry’s massive projected growth but dominate the field.
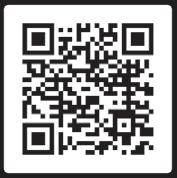
Learn more about WOC

EXHIBITS: JANUARY 21-23, 2025
EDUCATION: JANUARY 20-23
LAS VEGAS CONVENTION CENTER
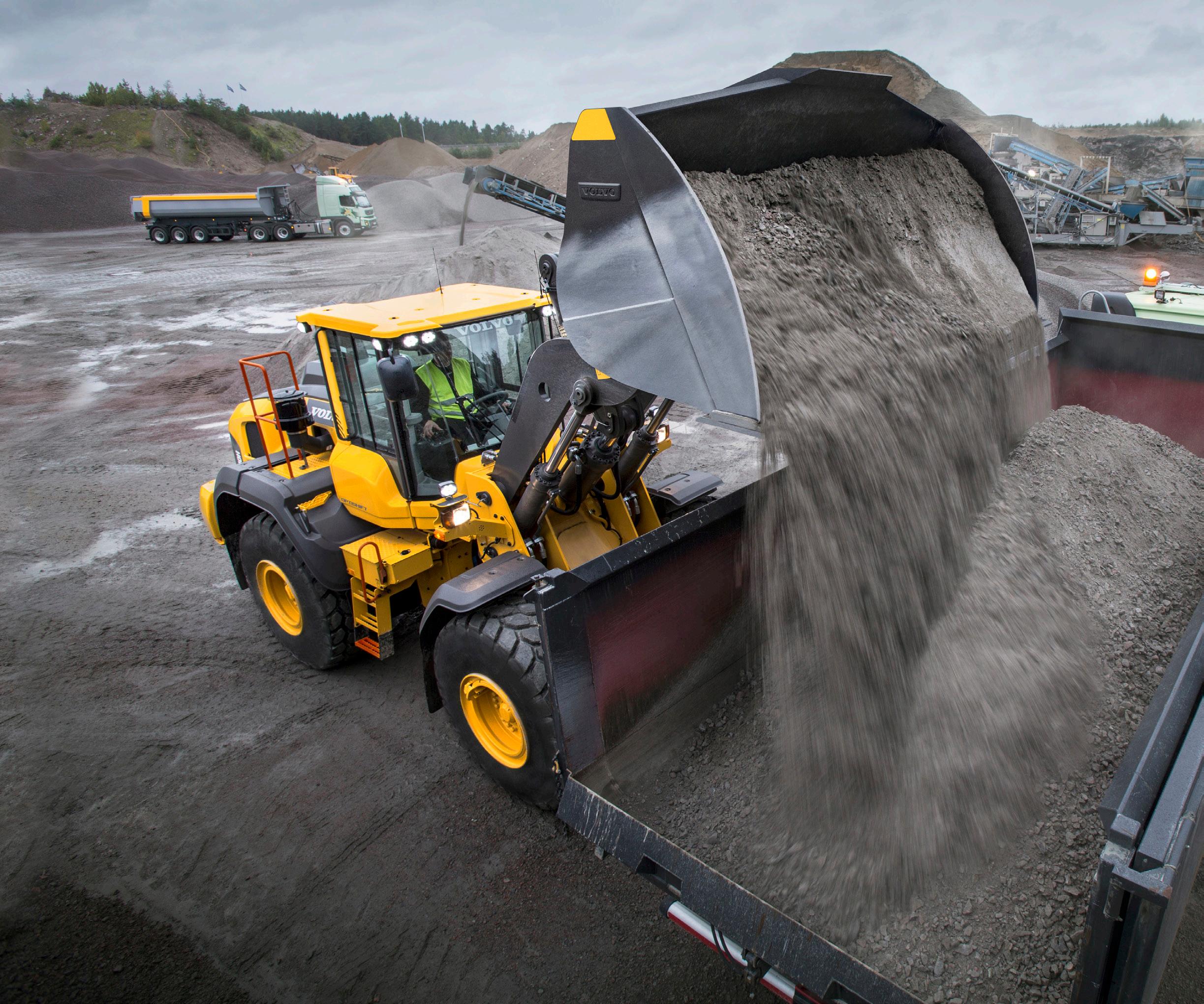
Breaking new ground
Latest bucket technologies bring advanced features to the yard.
BY TREENA HEIN
As loader design continues evolving with a focus on improving efficiency and safety, the bucket is not being left behind. Systems are helping operators align the bucket for maximum loading, ensure loads are balanced, and more.
For example, Case Construction Equip-
ment has engineered new curved-sided buckets that the manufacturer says helps retain more snow and prevent spillage of materials over the sides.
“Ride Control further reduces loss of material and loss of control over rough terrain while reducing shock loads on the machine and operator,” reports Neil Detra, the company’s product manager. “Lift [boom] and tilt [bucket] functions can also be independently set to smooth, moderate or aggressive with our new adjustable electro-hydraulic controls.”
Meanwhile, Develon says a new version of its exclusive “Transparent Bucket” feature is in development. This feature, which is now standard on all of its 7-Series wheel loaders, enables operators to view
otherwise-hidden objects in front of the machine, like large rocks and construction materials. The system involves two cameras mounted on the front of the machine at different heights. Associated software creates a single image from the two camera feeds, making the bucket appear transparent to the operator on the in-cab monitor.
The next version of Transparent Bucket, reports product manager Bill Zak, “will provide an enhanced picture of the area in front of the wheel loader.”
WEIGHING TECH
Bucket weighing systems obviously improve efficiency by preventing additional trips or having to dump excess material.
“Overloading can result in costly fines,
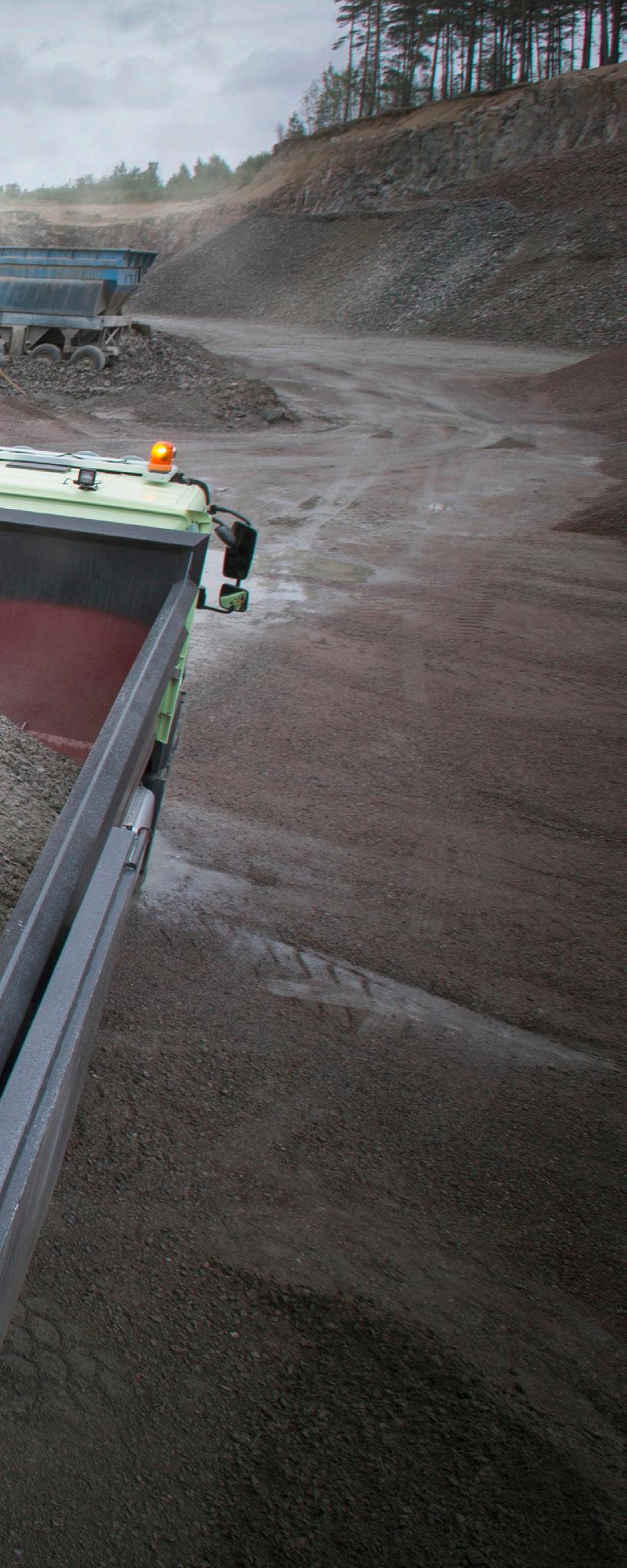
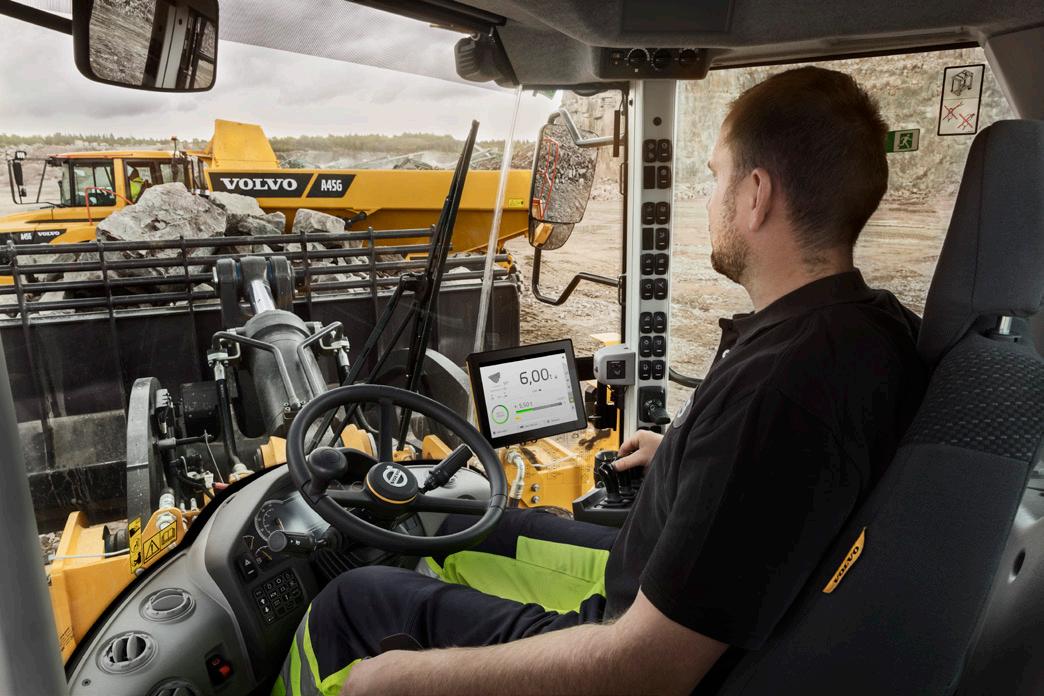
tip-off to truck, tip-off to pile, auto-add and manual-add. These modes allow the system to manage loads according to their application.” In addition, the unit is equipped with a warning function that reacts when the bucket is overloaded.
RE-HANDLING AND AUTO-LEVEL
Earlier this year, Volvo introduced the L180 3-Pass Rehandler. This is the company’s L180 wheel loader, but adapted specifically for rehandling and filling a truck in three passes.
“Its configuration allows for a larger bucket that, combined with On-Board Weighing, provides a great boost in efficiency and productivity,” says Yeomans.
and under-loading increases production costs,” says Eric Yeomans, product manager at Volvo Construction Equipment, which offers On-Board Weighing. “Proper load weight also supports fuel efficiency and helps minimize maintenance costs due to extra wear and tear.”
John Deere’s system, SmartWeigh, provides operators with loading accuracy within 1.5 per cent, says product marketing manager Katie Voelliger. A known weight is not required for calibration. Rather, as Voelliger explains, “the calibration process is in the monitor and takes the operator through the set-up process step-by-step.”
SmartWeigh also has no requirement for the boom to be constantly lowered and raised to get the weight. Bucket capture
height can be set anywhere and captured at any boom speed. To ensure a comfortable purchase decision, John Deere offers a low-cost 250-hour trial period where customers can fully explore the capabilities of the technology.
Develon also offers a highly accurate optional bucket material weighing system, with operators able to enter a target weight for the total truck load through the cab’s touchscreen monitor.
The payload weighing system of Hitachi Construction Machinery Americas uploads productivity information to the company’s ConSite telematic system.
“Operators can check the weight of the load in the bucket from the inside cab monitor and log the material loaded,” explains Hitachi wheel loader product manager Chris Trampush. “The payload weighing system offers four modes —
Meanwhile, Volvo is incorporating auto-leveling into more of its wheel loader models. This function allows the operator to rely on settings that will automatically lift and tilt a bucket to pre-programmed positions, ensuring precise repetitive movement with less fatigue – and helping less-experienced operators carry out faster loading cycles.
Develon also offers a return-to-dig function to align the bucket.
“The customer can set the bucket level, boom lower and upper height through the joystick input,” explains Zak. “The wheel loader arms and bucket will return to the preset positions.”
TECHNIQUE IMPACTS EFFICIENCY
Operator technique has a huge impact on loading efficiency when starting work on a pile, notes Trampush. He advises loading
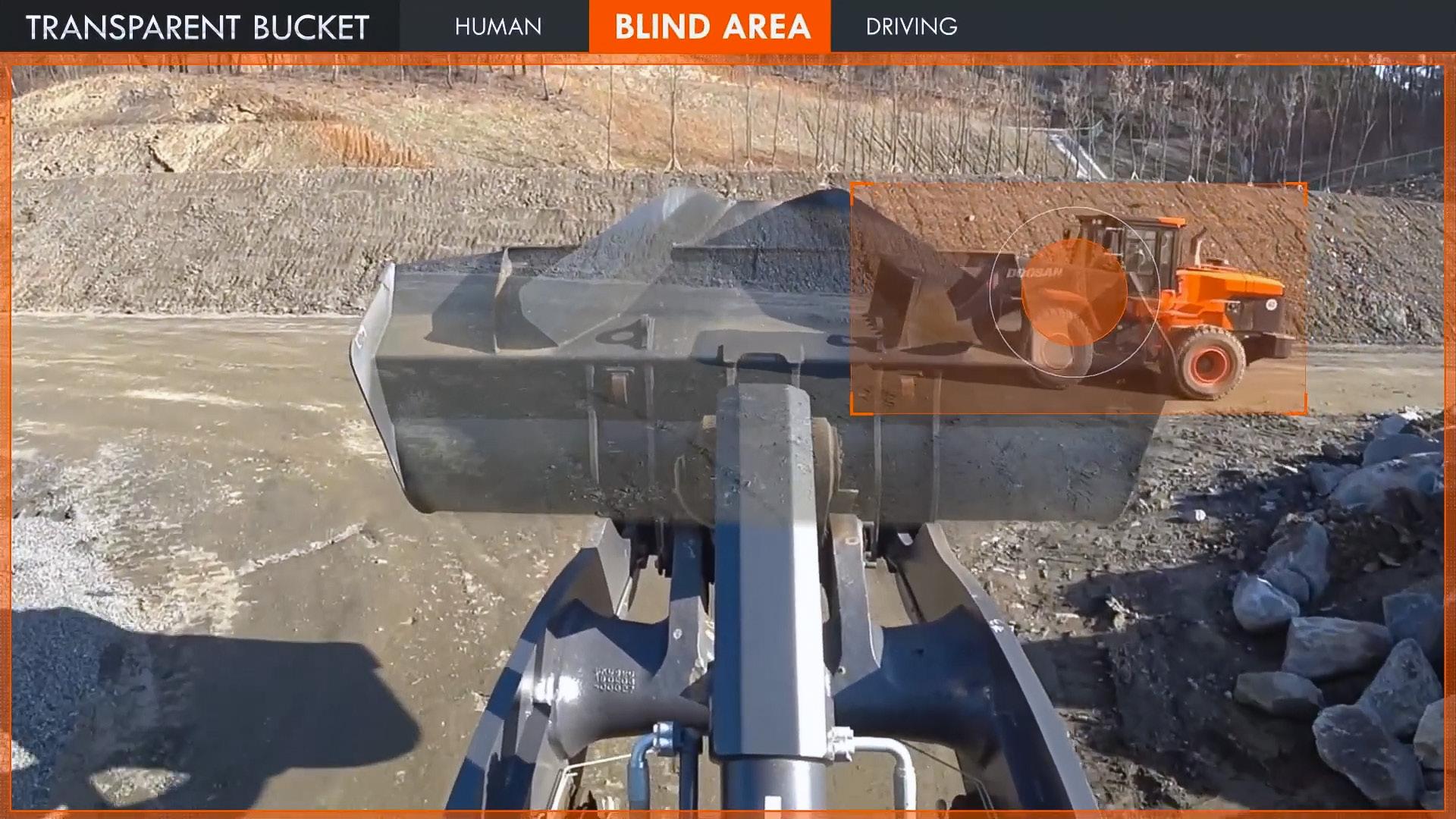
PHOTO: COURTESY OF DEVELON
PHOTO: COURTESY OF VOLVO CE
Develon’s Transparent Bucket technology makes it easier for the operator to see their surroundings.
Volvo’s On-Board Weighing System helps reduce the need for extra trips.
the bucket by engaging material at the bottom and then slowly




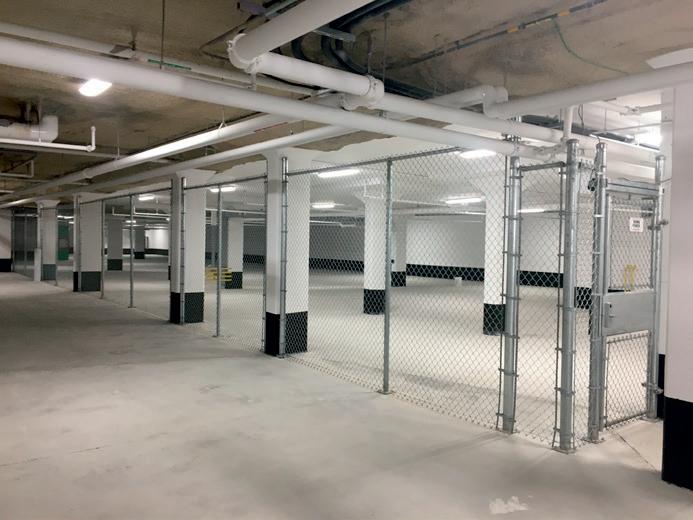

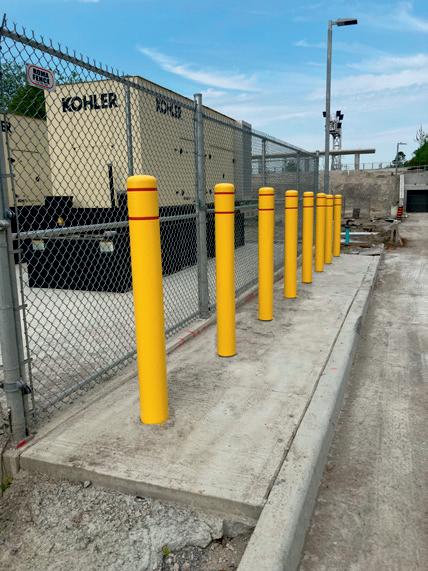
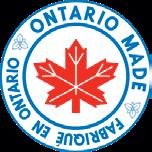
key step is to take advantage of features like Smart Power Mode. Available on Case wheel loaders, Smart Power Mode monitors torque and delivers the high-performance power needed to maintain traction and offers an enhanced operating experience through improved communication between the engine and transmission. This helps achieve smoother shifting, reduced tire wear and up to 10 per cent fuel savings when compared to Max Power Mode.”
MATCHING TOOLS AND TASKS
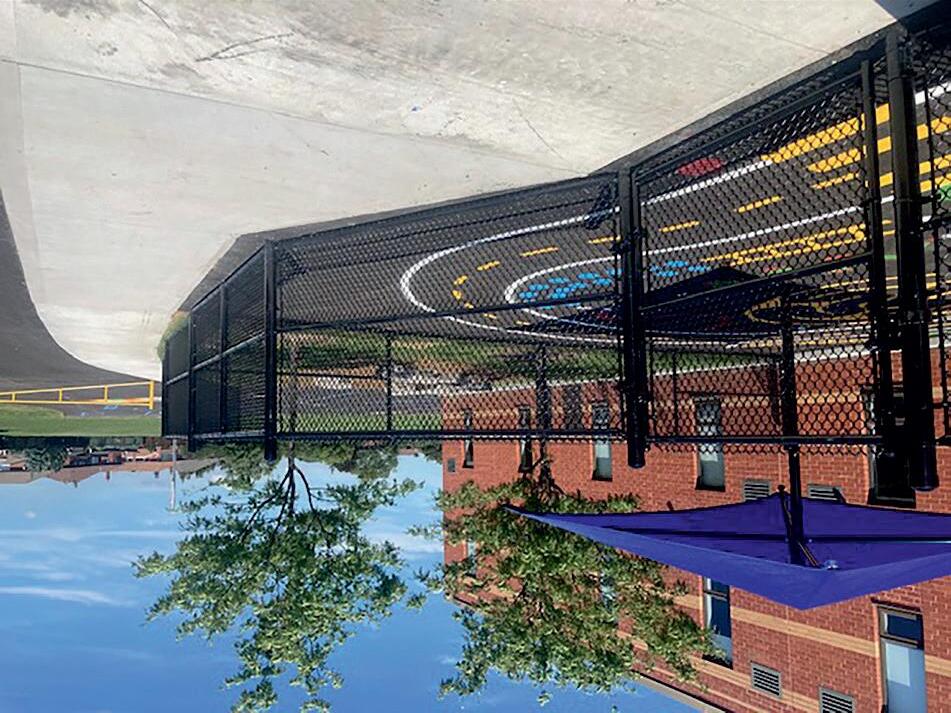
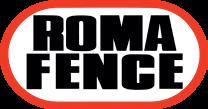
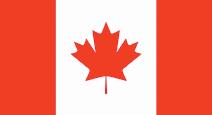
When selecting a wheel loader, Develon’s Zak recommends making sure the machine is equipped with the correct bucket size and type to match the customer’s material type and density.
“A bucket that is too small will lead to operation inefficiencies, and if the bucket is too large for the wheel loader, it may lead to unsafe operating conditions,” he notes. “It’s best to collaborate with a local dealer before selecting the machine and bucket for each customer’s needs.”
Yeomans observes that while it may seem obvious to select whatever fits your wheel loader and has the most volume, volume is not an adequate measure of the loader’s capacity.
“A bigger bucket can actually lower your productivity if it’s more difficult to fill,” he explains. “You have to account for the nature of the material being handled, the condition of the wheel loader, the operator’s skill level and the transport distance. If the transport distance is far, you also want to consider the risk of spillage. The goal is to find the right size and the right shape.”
To help with this, Volvo offers material- and application-specific buckets, including a sand bucket ideal for soft ground conditions where tire traction is compromised, a re-handling bucket for transporting aggregate, and a flat floor bucket for handling, stockpiling and loading processed materials.
“These help reduce cycle times through more efficient material handling and increased material capacity, lowering fuel consumption by up to 10 per cent,” says Yeomans.
Case says curved-sided buckets help prevent spillage of materials over the sides.
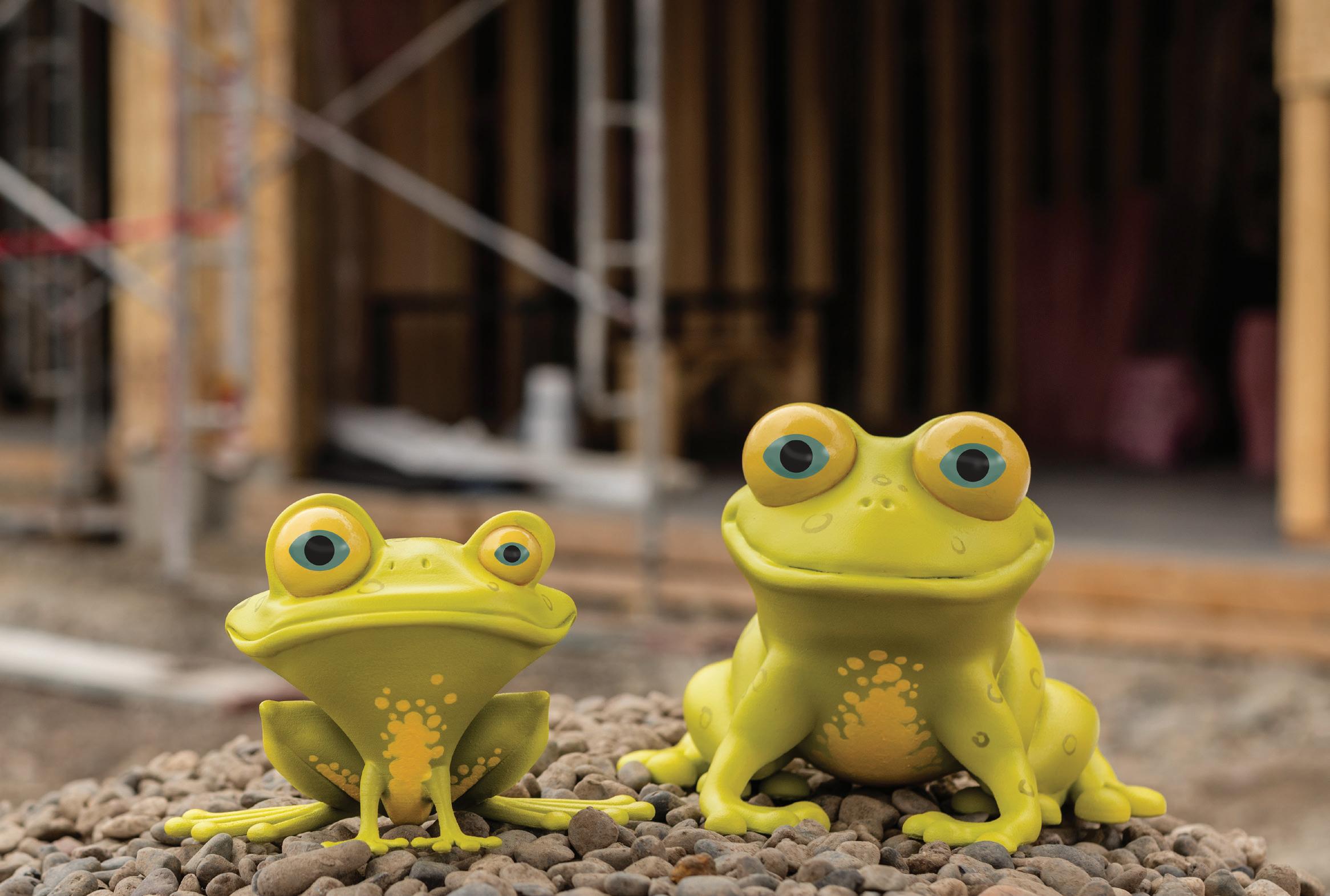
By David Bowcott

IHousing: Are surety bonds part of the solution?
Ontario consultations may allow surety bonds as an alternative to letters of credit.
t is no secret that one of the top issues facing all levels of government in Canada is solving for the housing crisis. Increased population combined with a substantial growth in the cost of housing, driven by a shortage of housing supply and higher financing costs, have pushed the crisis to the top of the agenda when it comes to issues facing Canadians, and the overall Canadian economy.
To address the issue, governments at all levels are introducing solutions to catalyze development in the hopes of driving up supply and alleviate affordability challenges.
In Ontario, the province is exploring the use of pay-on-demand surety bonds to secure homebuilders’ land-use planning obligations under Section 70.3.1 of the Planning Act during the development process. The impact of such a change would allow developers to use less restrictive and potentially more affordable surety bonds as a substitute for the more constraining and often more expensive letters of credit, which often tie up developer capital that could be better used as investment in the development.
By allowing this surety option, the hope is it will encourage greater development activity and accelerate the pace at which new housing comes onto the market. The Ontario Home Builders Association (OHBA) is very much in favour of this optionality when it comes to homebuilder/developer security.
“This is a great step forward for Ontario’s housing industry and the issue of housing affordability,” said Scott Andison, CEO of OHBA. “Allowing builders to access capital held up in letters of credit and reinvest it into new projects is precisely the type of innovative regulatory updates we need to effectively increase our housing supply.”
The use of on-demand surety bonds to secure such obligations isn’t new. Several municipalities across Canada have already allowed developers to put up on-demand surety bonds in lieu of letters of credit. Over 40 major municipalities have allowed this option, with the City of Calgary being the first. What would
SURETY TIPS
BEST FOOT FORWARD
Sureties require information on credit quality, development history, and information specific to individual developments (project economics, schedule, and sources of financing). Ensure you understand the surety underwriting process and have this information presented in the most appealing submission.
be unique about Ontario is that it would mark the first provincial acceptance of surety bonds, representing a top-down versus bottom-up approach.
Typically, to be accepted as part of these housing programs, an on-demand surety bond has to have the following features: demand in nature (seven to 10 days’ payment period); irrevocable; evergreen/continuous; partial drawdowns permitted; partial reductions in amount permitted; reference specific agreement; and notice of cancellation required.
In almost all cases, the issuing surety company must have an acceptable credit rating from one of the following rating entities: DBRS, Fitch, Moody’s, S&P or AM Best. For instance, a rating of A or higher from AM Best would be sufficient to qualify under the Ontario Planning Act, if this change is allowed after the consultation process. Most municipalities require a rating of A-, which broadens the market options.
Developers would be advised to ensure that they have, or will have, an on-demand developer surety facility in place to take advantage of these optional security provisions. A trusted advisor (broker) can help navigate all the requirements that potential surety partners will require, and to secure best terms.
The acceptance of on-demand development bonds as an alternative to letters of credit will, without doubt, stimulate more development and help address the housing crisis. It is crucial that development organizations not only establish an on-demand surety facility, but also ensure that it is secured with the best possible terms.
David Bowcott is the executive vice-president of the Construction Industry Group at Platform Insurance Management. The author would like to thank Scott Andison of the Ontario Home Builders’ Association and Alan Sung and Stephanie Kuntz from Platform for their contributions and input to this column. Please send comments to editor@on-sitemag.com.
RATINGS AND RECORDS
Ensure your advisor identifies sureties that will satisfy any rating entity criteria and ensure the surety options brought forward are willing to write, and have a strong record of writing, on-demand developer instruments.
INDEMNITY AND SECURITY NEGOTIATIONS
Work with your advisor to secure most efficient indemnity and security terms for your on-demand surety facility. Ensure intercreditor issues between your new surety partner and your bank are identified and optimally negotiated to your benefit.
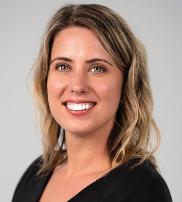


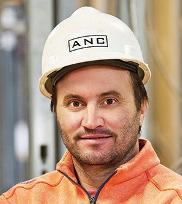
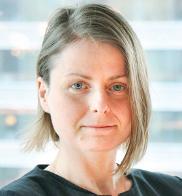
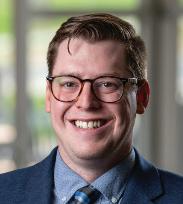
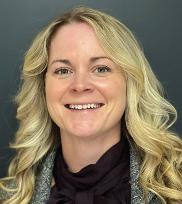
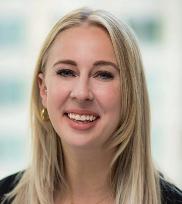


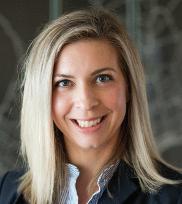
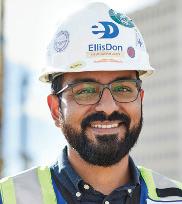
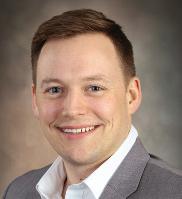
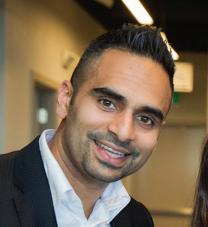
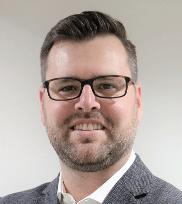

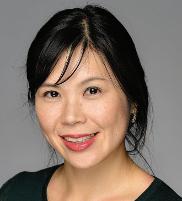

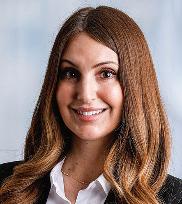
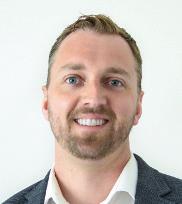
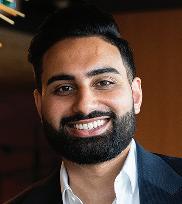
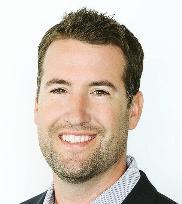

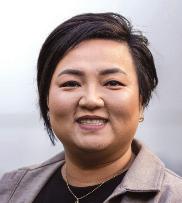
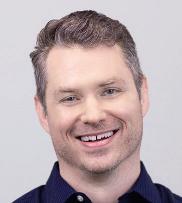
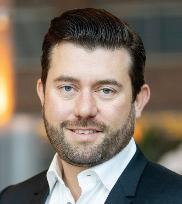
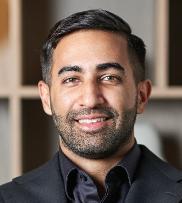
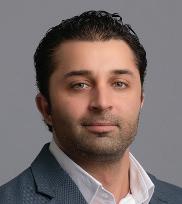
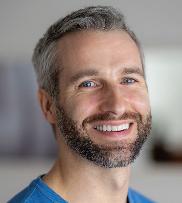
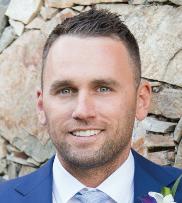
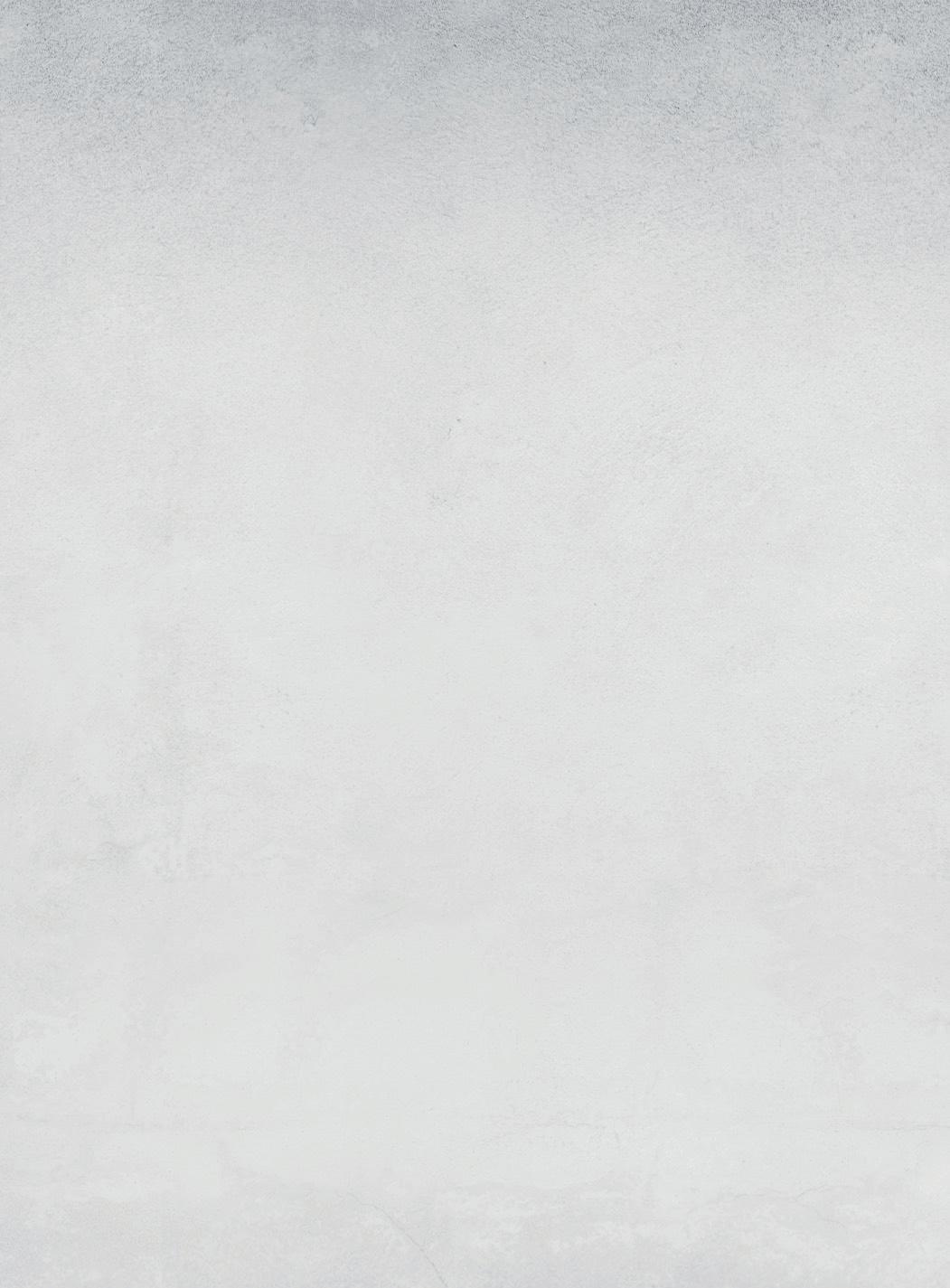
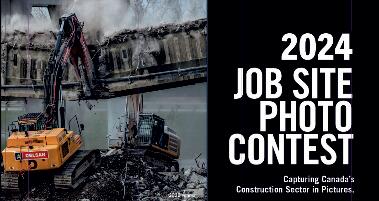
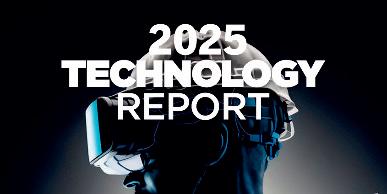
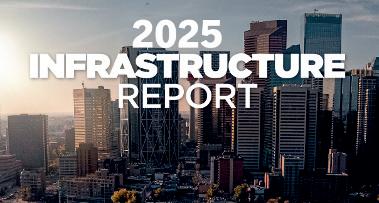
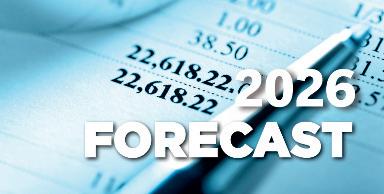
By Erin Cutts and Grace Jiyeon Shory
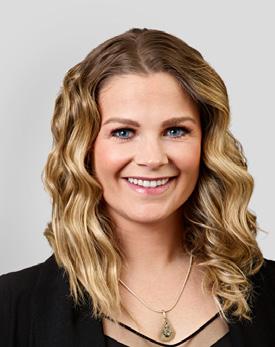
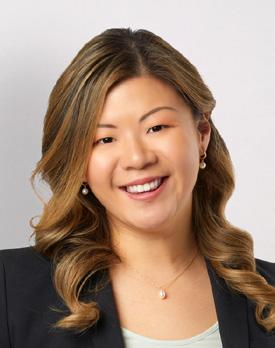
Don’t get caught off guard
It pays to be meticulous in record keeping and timing when managing delay disputes caused by changes in scope.
Changes in scope are common occurrences on large construction projects. Understandably, these changes have the potential to cause delay to the project schedule and increase the costs incurred by all project participants. Responsibility for these delays and additional costs is frequently the subject-matter of dispute among owners, contractors and consultants.
An Alberta decision, Maxim Excavating Ltd v Peace Regional Waste Management Company, 2022 ABQB 351 is a good reminder that contractors and project owners should proactively disclose and diligently document project changes and delays.
Maxim Excavating entered into a contract with Peace Regional Waste Management Company for the construction of a waste management facility. Disputes arose among Maxim, Peace Regional and Peace Regional’s consultant, Omni-McCann Consultants Ltd. over Maxim’s claims for additional payment due to changes in the scope of work and associated delays.
While Maxim alleged that the delays were compensable, being outside its control and scope of the contract, Peace Regional asserted that the delays were ultimately Maxim’s responsibility under the contract. Peace Regional also alleged that Maxim had not provided proper contractual notice for the delays or the additional costs. Peace Regional applied withholdings and backcharges against amounts alleged to be owing and Maxim asserted a claim for damages.
The court awarded $300,000 to Maxim, finding that Peace Regional and the consultant had failed to make payment for additional out of scope work and were unreasonable in refusing to adjust the project schedule.
CREDIBILITY OF CONSULTANTS
While the consultant had been qualified as an expert at trial as a witness with expertise involved in the events underlying the litigation, the court found its testimony to be self-serving and incredible. The court reiterated that consultants who are given discretion over a matter by an owner, have an implied duty to act in good faith when exercising that discretion.
NOTICE REQUIREMENTS
Peace Regional argued that Maxim was not entitled to any additional compensation due to its failure to comply with the notice provisions in the contract. In rejecting Peace River’s allegations regarding notice, the court observed that Peace Regional and its consultant had “routinely failed” to strictly comply with the contract. As such, Peace Regional was prevented from insisting that the notice provisions of the contract be strictly applied to Maxim. The court also reiterated that Canadian courts often reject notice defenses since construction projects often less formal in their nature.
SCOPE CHANGES
The court reviewed the contract terms and ultimately determined that there were changes to the scope of work that justified Maxim’s claims for additional costs. One of the changes was related to excessive unsuitable materials, which were located on-site after the contract award. While Peace Regional argued that the sorting and removal of unsuitable materials was always contemplated as part of the contract’s scope of work, the court found that the volume of unsuitable materials encountered well-exceeded what was anticipated in the contract or its specifications, and thus would have been outside of the commercially reasonable expectations of the parties.
Another change was related to the removal of berms of unsuitable material that were obstructing the project. Peace Regional argued that this removal was not an extra to the contract, as the berms were included in the contract drawings. However, the evidence established that Maxim was, in fact, paid for this removal work on a force account basis, rather than based on the unit rates set out in the contract. The court found that the payments made to Maxim based on something other than the unit rates set out in the contract clearly evidenced Peace River’s agreement that the berm removals were outside of Maxim’s scope of work.
PRACTICAL TIPS
Define the project scope clearly. Ensure that the contract explicitly defines the scope of work, including detailed specifications and responsibilities. Avoid ambiguity to minimize disputes.
Properly document any changes. Clear documentation is critical to avoid disputes. Change orders should be properly documented and approved.
Be proactive and keep diligent records particularizing delays and associated impacts. Documentation of changes, incidents and delays through site or progress reports, daily summaries and detailed communications, can strengthen the validity and provide necessary evidence in support of claims.
Be mindful of notice requirements. While the court in this case commented about the informal approach that is often used by parties on construction projects, it may not always be the case. To minimize disputes, the best practice is to strictly comply with the notice requirements as outlined in the contract. When this is not possible, regular status updates should be provided.
Erin Cutts is a partner and Grace Jiyeon Shory a senior associate, both in the construction group at Borden Ladner Gervais LLP. This article provides an overview and is not intended to be exhaustive of the subject matter contained herein. Although care has been taken to ensure accuracy, this information should not be relied upon as legal advice.
A Wo r ld o f Ex p erie n c e
Perfected for No rth A m eric a
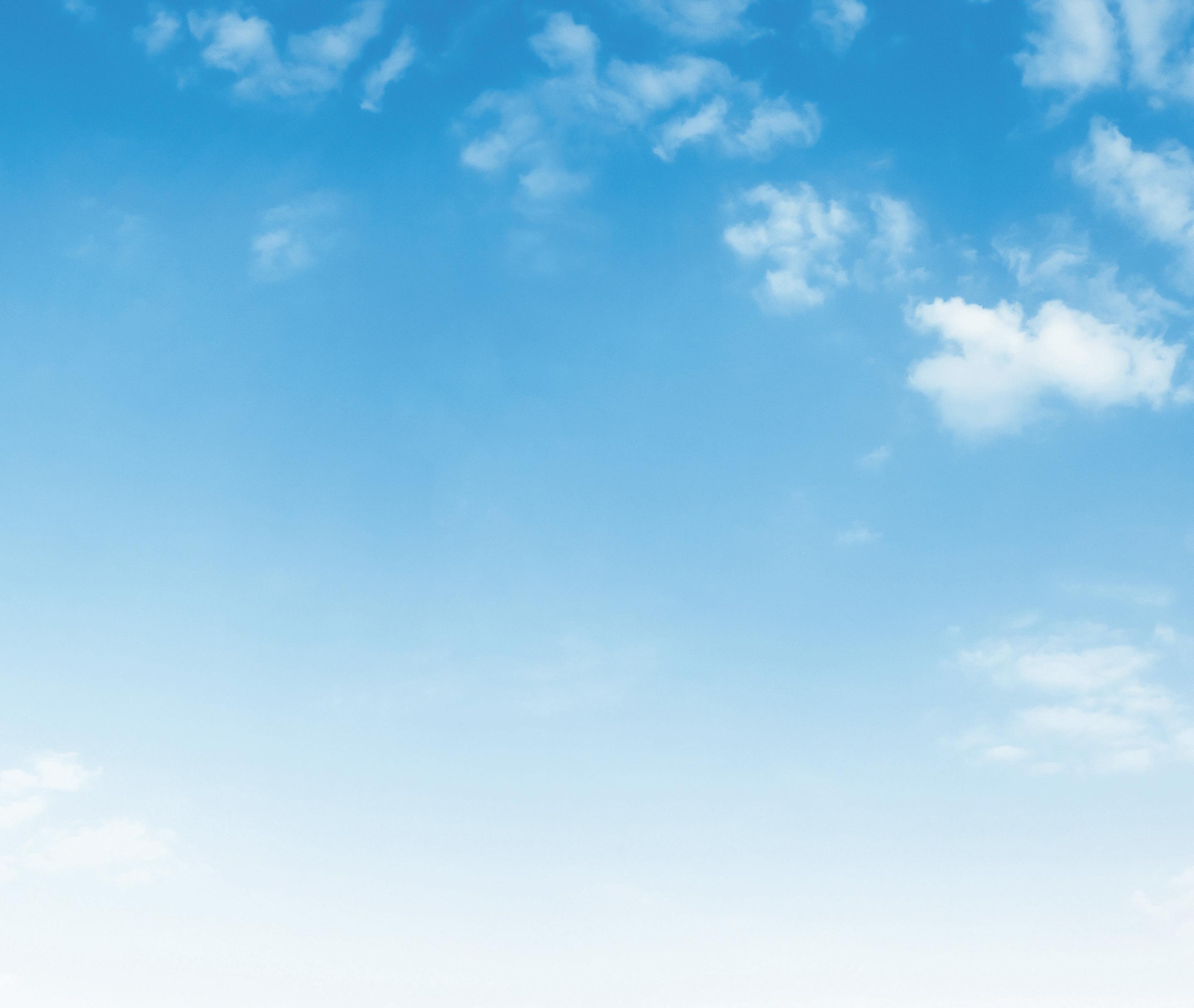

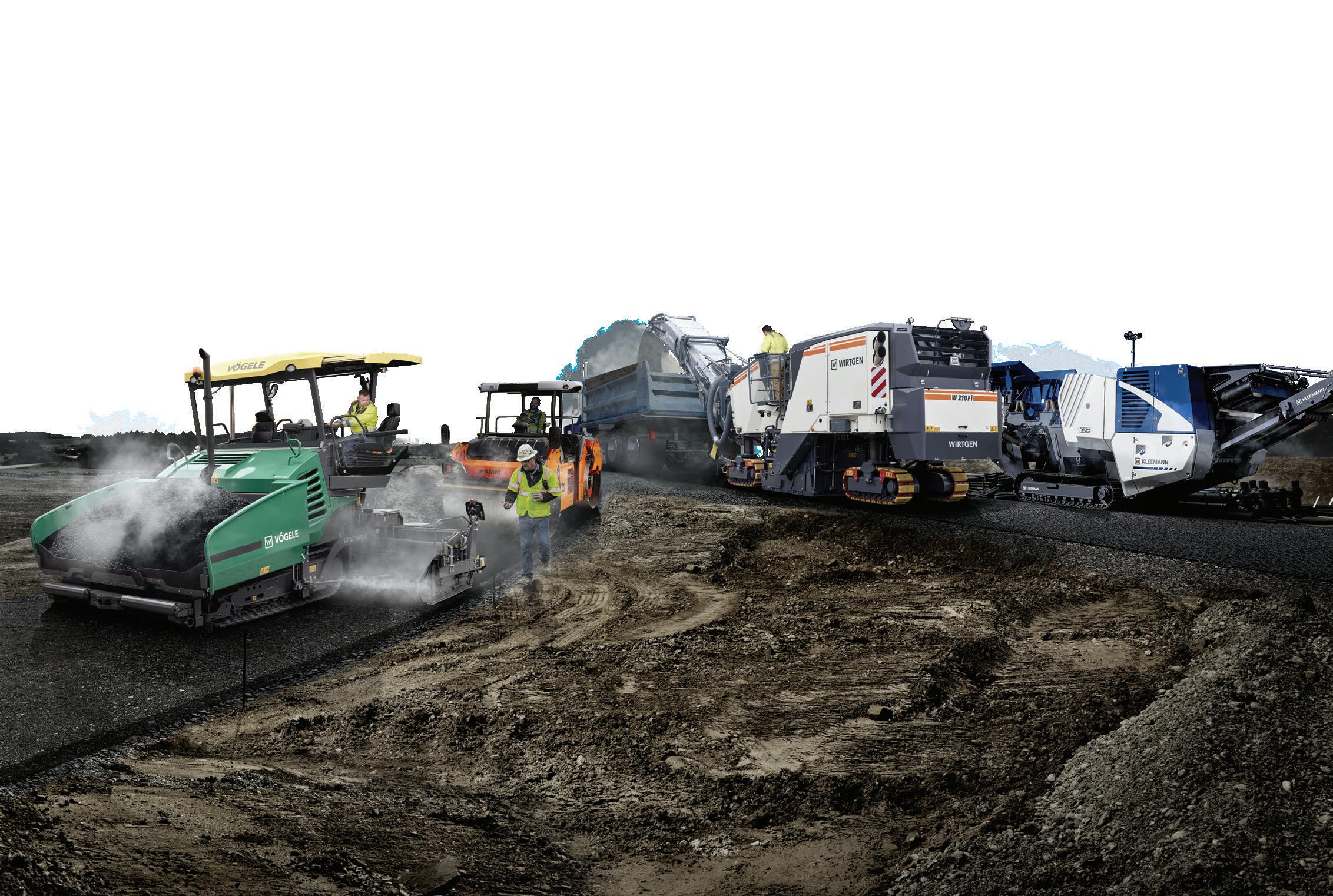
A S THE GLOBAL LE ADER IN ROAD
CONS TRUC TION TECHNOLOGY, the world is our proving ground, in ever y climate, condition, and terrain. From mining and milling, to paving, compac tion and rehabilit ation our machines are smar t, safe, and sus t ainable, consis tently delivering the highes t qualit y and lowes t tot al cos t of owner ship
CLOSE TO OUR CUSTOMERS
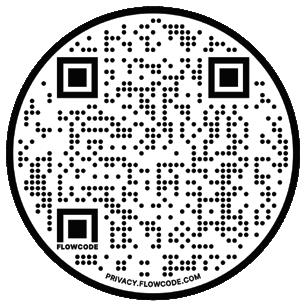
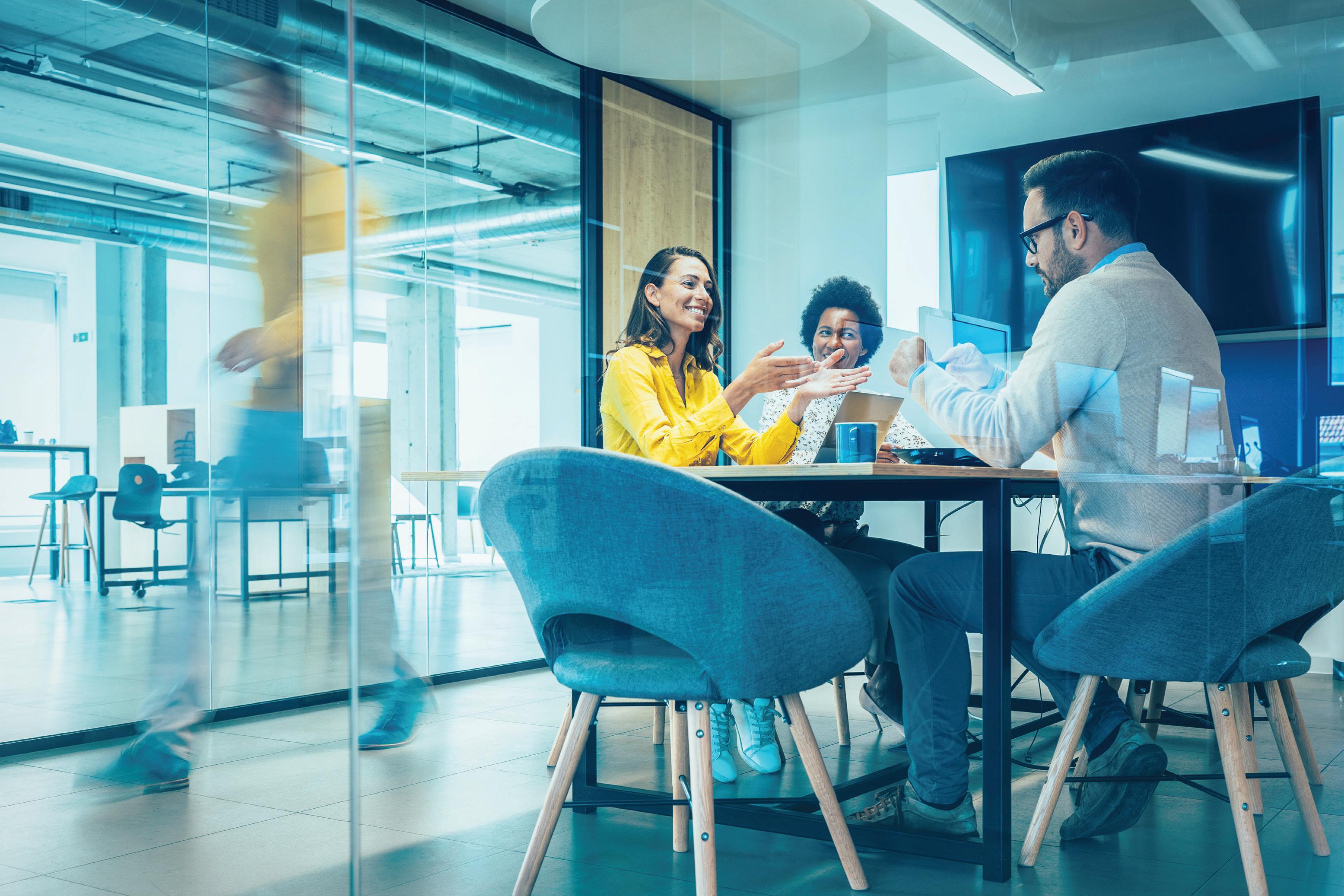